Costing Techniques for Real Food: Departmental Costing and Activity Based Costing
VerifiedAdded on 2023/06/05
|6
|1420
|143
AI Summary
Understand the importance of cost classification and the relevance of departmental costing and activity based costing for Real Food's management. Learn about the manufacturing process and the benefits of these techniques for long term sustainability.
Contribute Materials
Your contribution can guide someone’s learning journey. Share your
documents today.
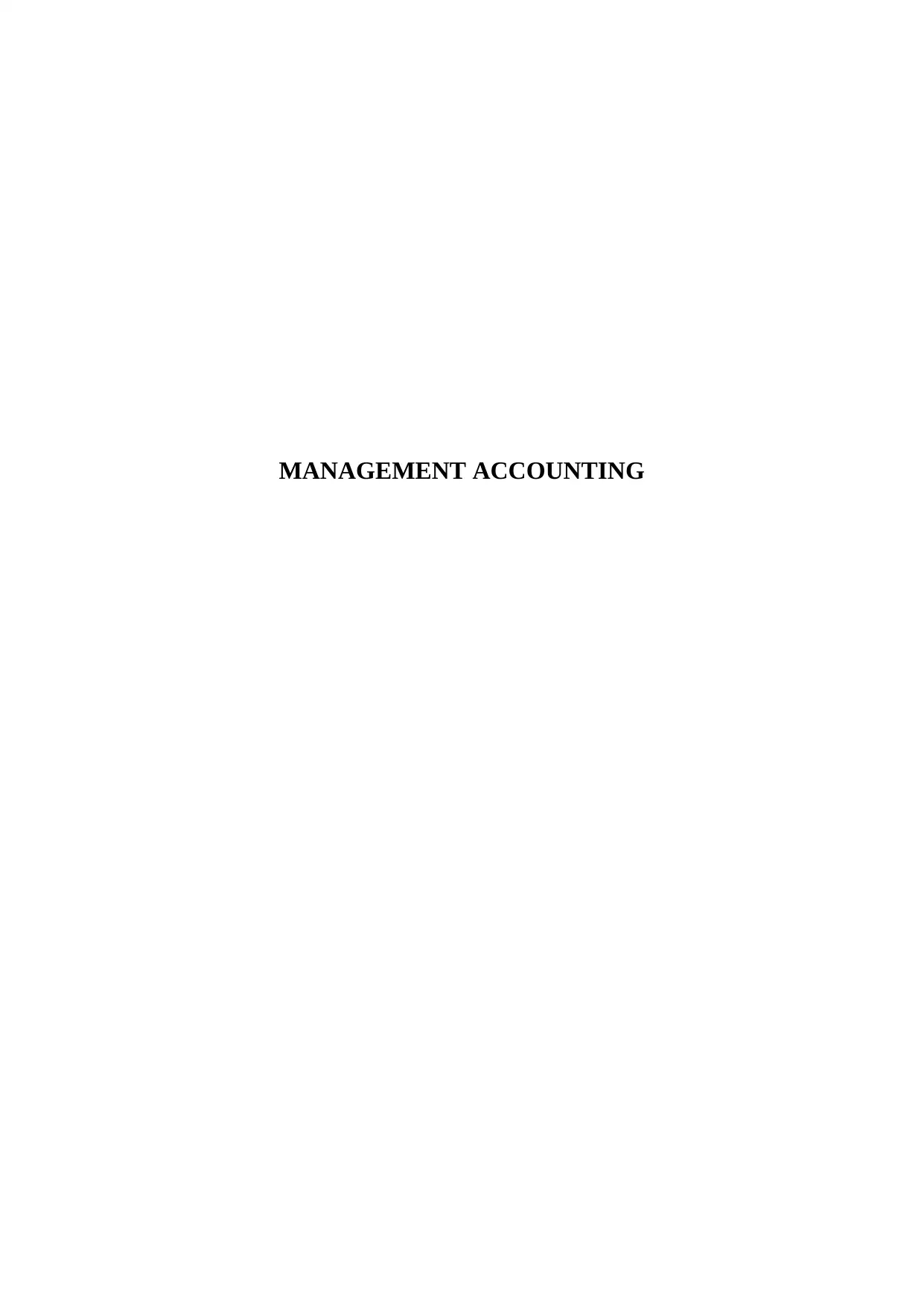
MANAGEMENT ACCOUNTING
Secure Best Marks with AI Grader
Need help grading? Try our AI Grader for instant feedback on your assignments.
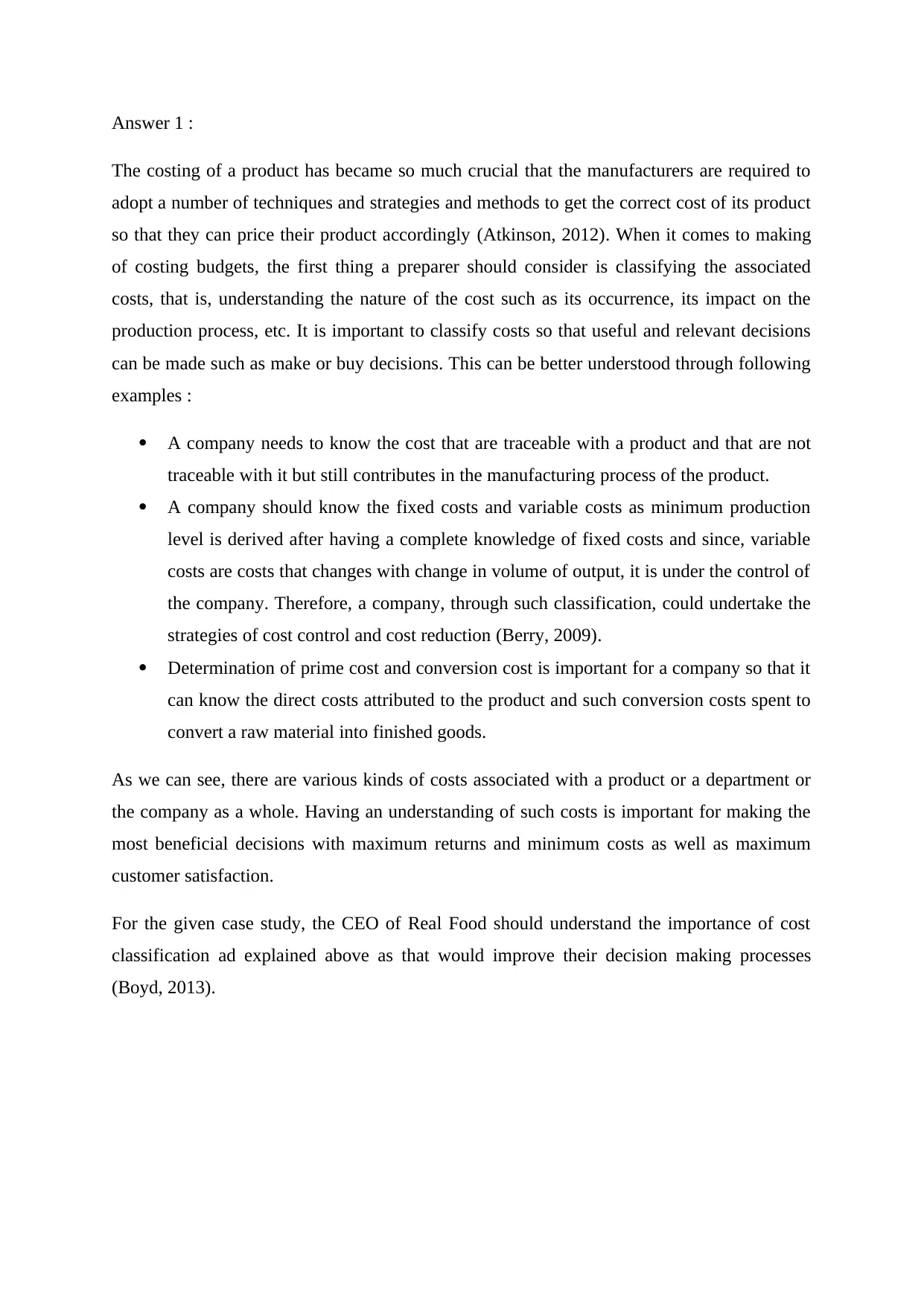
Answer 1 :
The costing of a product has became so much crucial that the manufacturers are required to
adopt a number of techniques and strategies and methods to get the correct cost of its product
so that they can price their product accordingly (Atkinson, 2012). When it comes to making
of costing budgets, the first thing a preparer should consider is classifying the associated
costs, that is, understanding the nature of the cost such as its occurrence, its impact on the
production process, etc. It is important to classify costs so that useful and relevant decisions
can be made such as make or buy decisions. This can be better understood through following
examples :
A company needs to know the cost that are traceable with a product and that are not
traceable with it but still contributes in the manufacturing process of the product.
A company should know the fixed costs and variable costs as minimum production
level is derived after having a complete knowledge of fixed costs and since, variable
costs are costs that changes with change in volume of output, it is under the control of
the company. Therefore, a company, through such classification, could undertake the
strategies of cost control and cost reduction (Berry, 2009).
Determination of prime cost and conversion cost is important for a company so that it
can know the direct costs attributed to the product and such conversion costs spent to
convert a raw material into finished goods.
As we can see, there are various kinds of costs associated with a product or a department or
the company as a whole. Having an understanding of such costs is important for making the
most beneficial decisions with maximum returns and minimum costs as well as maximum
customer satisfaction.
For the given case study, the CEO of Real Food should understand the importance of cost
classification ad explained above as that would improve their decision making processes
(Boyd, 2013).
The costing of a product has became so much crucial that the manufacturers are required to
adopt a number of techniques and strategies and methods to get the correct cost of its product
so that they can price their product accordingly (Atkinson, 2012). When it comes to making
of costing budgets, the first thing a preparer should consider is classifying the associated
costs, that is, understanding the nature of the cost such as its occurrence, its impact on the
production process, etc. It is important to classify costs so that useful and relevant decisions
can be made such as make or buy decisions. This can be better understood through following
examples :
A company needs to know the cost that are traceable with a product and that are not
traceable with it but still contributes in the manufacturing process of the product.
A company should know the fixed costs and variable costs as minimum production
level is derived after having a complete knowledge of fixed costs and since, variable
costs are costs that changes with change in volume of output, it is under the control of
the company. Therefore, a company, through such classification, could undertake the
strategies of cost control and cost reduction (Berry, 2009).
Determination of prime cost and conversion cost is important for a company so that it
can know the direct costs attributed to the product and such conversion costs spent to
convert a raw material into finished goods.
As we can see, there are various kinds of costs associated with a product or a department or
the company as a whole. Having an understanding of such costs is important for making the
most beneficial decisions with maximum returns and minimum costs as well as maximum
customer satisfaction.
For the given case study, the CEO of Real Food should understand the importance of cost
classification ad explained above as that would improve their decision making processes
(Boyd, 2013).
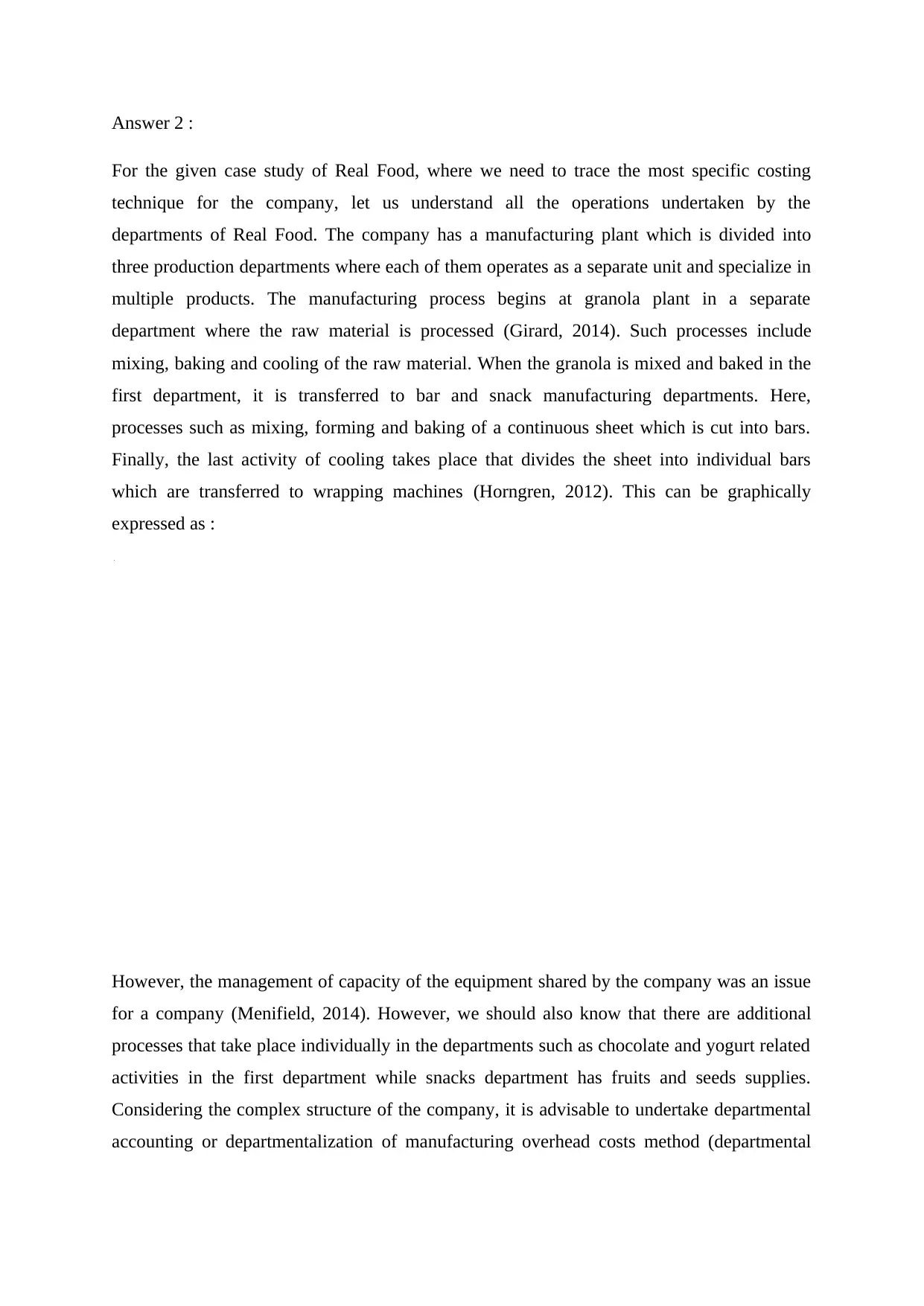
Answer 2 :
For the given case study of Real Food, where we need to trace the most specific costing
technique for the company, let us understand all the operations undertaken by the
departments of Real Food. The company has a manufacturing plant which is divided into
three production departments where each of them operates as a separate unit and specialize in
multiple products. The manufacturing process begins at granola plant in a separate
department where the raw material is processed (Girard, 2014). Such processes include
mixing, baking and cooling of the raw material. When the granola is mixed and baked in the
first department, it is transferred to bar and snack manufacturing departments. Here,
processes such as mixing, forming and baking of a continuous sheet which is cut into bars.
Finally, the last activity of cooling takes place that divides the sheet into individual bars
which are transferred to wrapping machines (Horngren, 2012). This can be graphically
expressed as :
However, the management of capacity of the equipment shared by the company was an issue
for a company (Menifield, 2014). However, we should also know that there are additional
processes that take place individually in the departments such as chocolate and yogurt related
activities in the first department while snacks department has fruits and seeds supplies.
Considering the complex structure of the company, it is advisable to undertake departmental
accounting or departmentalization of manufacturing overhead costs method (departmental
For the given case study of Real Food, where we need to trace the most specific costing
technique for the company, let us understand all the operations undertaken by the
departments of Real Food. The company has a manufacturing plant which is divided into
three production departments where each of them operates as a separate unit and specialize in
multiple products. The manufacturing process begins at granola plant in a separate
department where the raw material is processed (Girard, 2014). Such processes include
mixing, baking and cooling of the raw material. When the granola is mixed and baked in the
first department, it is transferred to bar and snack manufacturing departments. Here,
processes such as mixing, forming and baking of a continuous sheet which is cut into bars.
Finally, the last activity of cooling takes place that divides the sheet into individual bars
which are transferred to wrapping machines (Horngren, 2012). This can be graphically
expressed as :
However, the management of capacity of the equipment shared by the company was an issue
for a company (Menifield, 2014). However, we should also know that there are additional
processes that take place individually in the departments such as chocolate and yogurt related
activities in the first department while snacks department has fruits and seeds supplies.
Considering the complex structure of the company, it is advisable to undertake departmental
accounting or departmentalization of manufacturing overhead costs method (departmental
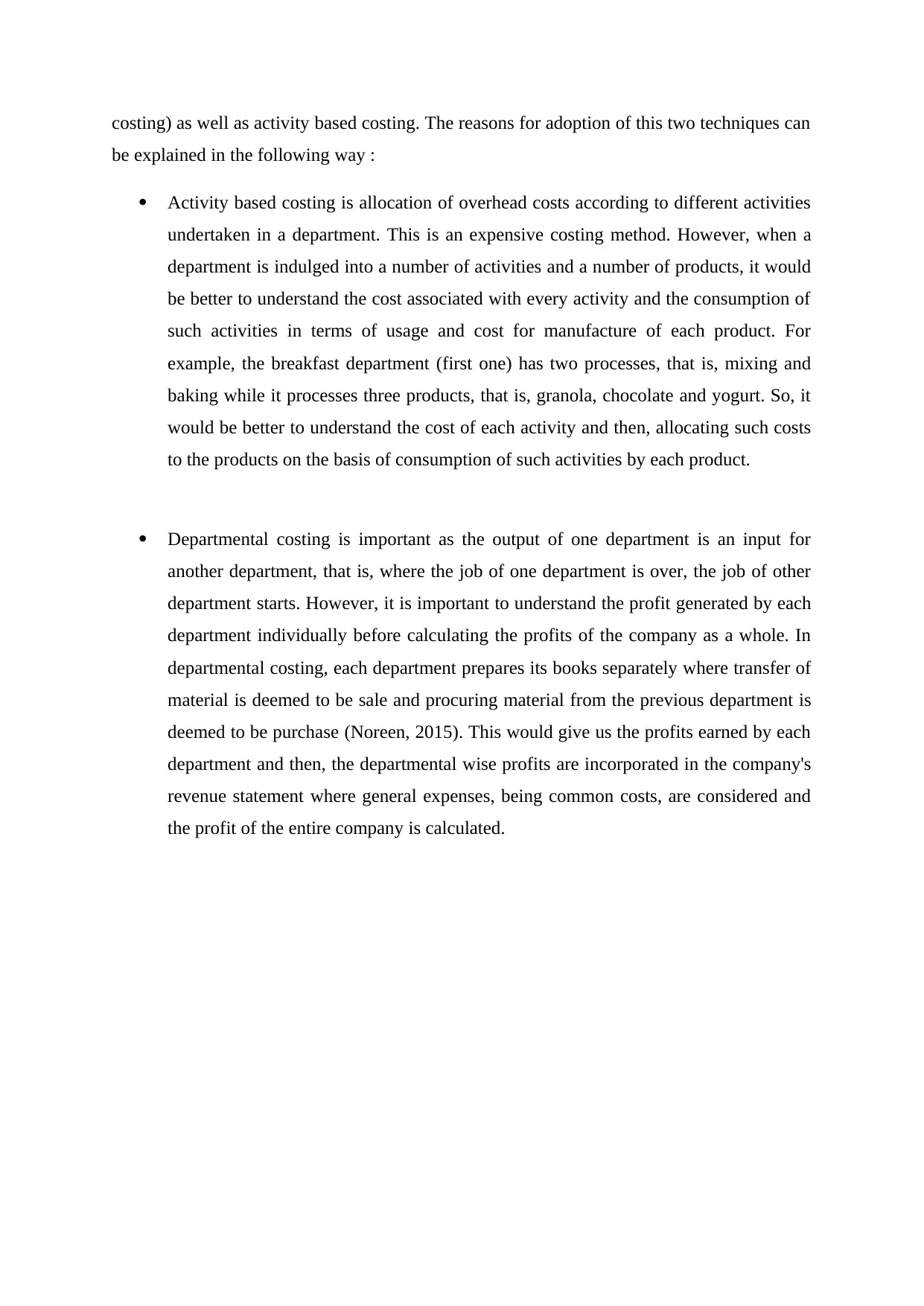
costing) as well as activity based costing. The reasons for adoption of this two techniques can
be explained in the following way :
Activity based costing is allocation of overhead costs according to different activities
undertaken in a department. This is an expensive costing method. However, when a
department is indulged into a number of activities and a number of products, it would
be better to understand the cost associated with every activity and the consumption of
such activities in terms of usage and cost for manufacture of each product. For
example, the breakfast department (first one) has two processes, that is, mixing and
baking while it processes three products, that is, granola, chocolate and yogurt. So, it
would be better to understand the cost of each activity and then, allocating such costs
to the products on the basis of consumption of such activities by each product.
Departmental costing is important as the output of one department is an input for
another department, that is, where the job of one department is over, the job of other
department starts. However, it is important to understand the profit generated by each
department individually before calculating the profits of the company as a whole. In
departmental costing, each department prepares its books separately where transfer of
material is deemed to be sale and procuring material from the previous department is
deemed to be purchase (Noreen, 2015). This would give us the profits earned by each
department and then, the departmental wise profits are incorporated in the company's
revenue statement where general expenses, being common costs, are considered and
the profit of the entire company is calculated.
be explained in the following way :
Activity based costing is allocation of overhead costs according to different activities
undertaken in a department. This is an expensive costing method. However, when a
department is indulged into a number of activities and a number of products, it would
be better to understand the cost associated with every activity and the consumption of
such activities in terms of usage and cost for manufacture of each product. For
example, the breakfast department (first one) has two processes, that is, mixing and
baking while it processes three products, that is, granola, chocolate and yogurt. So, it
would be better to understand the cost of each activity and then, allocating such costs
to the products on the basis of consumption of such activities by each product.
Departmental costing is important as the output of one department is an input for
another department, that is, where the job of one department is over, the job of other
department starts. However, it is important to understand the profit generated by each
department individually before calculating the profits of the company as a whole. In
departmental costing, each department prepares its books separately where transfer of
material is deemed to be sale and procuring material from the previous department is
deemed to be purchase (Noreen, 2015). This would give us the profits earned by each
department and then, the departmental wise profits are incorporated in the company's
revenue statement where general expenses, being common costs, are considered and
the profit of the entire company is calculated.
Secure Best Marks with AI Grader
Need help grading? Try our AI Grader for instant feedback on your assignments.
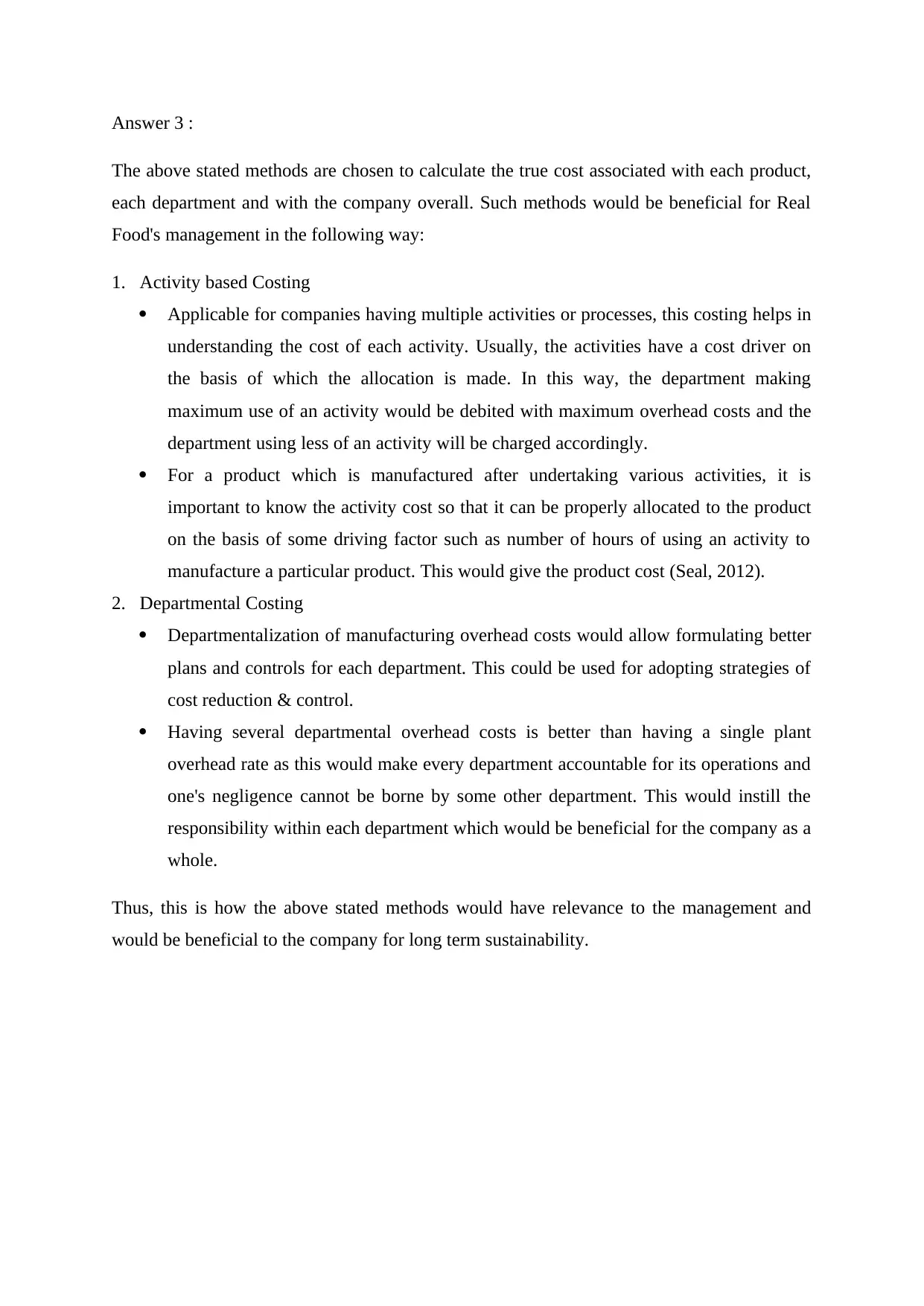
Answer 3 :
The above stated methods are chosen to calculate the true cost associated with each product,
each department and with the company overall. Such methods would be beneficial for Real
Food's management in the following way:
1. Activity based Costing
Applicable for companies having multiple activities or processes, this costing helps in
understanding the cost of each activity. Usually, the activities have a cost driver on
the basis of which the allocation is made. In this way, the department making
maximum use of an activity would be debited with maximum overhead costs and the
department using less of an activity will be charged accordingly.
For a product which is manufactured after undertaking various activities, it is
important to know the activity cost so that it can be properly allocated to the product
on the basis of some driving factor such as number of hours of using an activity to
manufacture a particular product. This would give the product cost (Seal, 2012).
2. Departmental Costing
Departmentalization of manufacturing overhead costs would allow formulating better
plans and controls for each department. This could be used for adopting strategies of
cost reduction & control.
Having several departmental overhead costs is better than having a single plant
overhead rate as this would make every department accountable for its operations and
one's negligence cannot be borne by some other department. This would instill the
responsibility within each department which would be beneficial for the company as a
whole.
Thus, this is how the above stated methods would have relevance to the management and
would be beneficial to the company for long term sustainability.
The above stated methods are chosen to calculate the true cost associated with each product,
each department and with the company overall. Such methods would be beneficial for Real
Food's management in the following way:
1. Activity based Costing
Applicable for companies having multiple activities or processes, this costing helps in
understanding the cost of each activity. Usually, the activities have a cost driver on
the basis of which the allocation is made. In this way, the department making
maximum use of an activity would be debited with maximum overhead costs and the
department using less of an activity will be charged accordingly.
For a product which is manufactured after undertaking various activities, it is
important to know the activity cost so that it can be properly allocated to the product
on the basis of some driving factor such as number of hours of using an activity to
manufacture a particular product. This would give the product cost (Seal, 2012).
2. Departmental Costing
Departmentalization of manufacturing overhead costs would allow formulating better
plans and controls for each department. This could be used for adopting strategies of
cost reduction & control.
Having several departmental overhead costs is better than having a single plant
overhead rate as this would make every department accountable for its operations and
one's negligence cannot be borne by some other department. This would instill the
responsibility within each department which would be beneficial for the company as a
whole.
Thus, this is how the above stated methods would have relevance to the management and
would be beneficial to the company for long term sustainability.
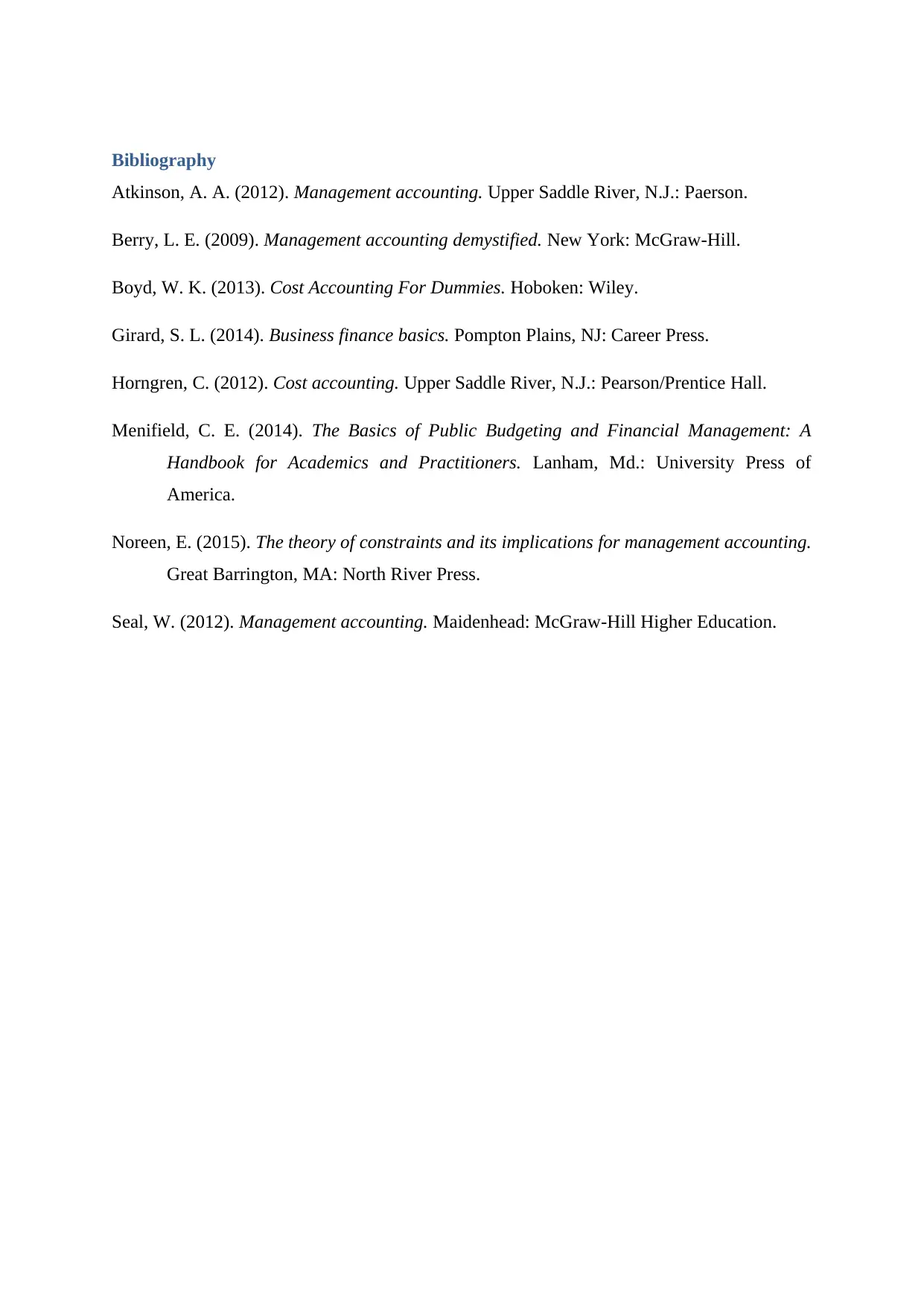
Bibliography
Atkinson, A. A. (2012). Management accounting. Upper Saddle River, N.J.: Paerson.
Berry, L. E. (2009). Management accounting demystified. New York: McGraw-Hill.
Boyd, W. K. (2013). Cost Accounting For Dummies. Hoboken: Wiley.
Girard, S. L. (2014). Business finance basics. Pompton Plains, NJ: Career Press.
Horngren, C. (2012). Cost accounting. Upper Saddle River, N.J.: Pearson/Prentice Hall.
Menifield, C. E. (2014). The Basics of Public Budgeting and Financial Management: A
Handbook for Academics and Practitioners. Lanham, Md.: University Press of
America.
Noreen, E. (2015). The theory of constraints and its implications for management accounting.
Great Barrington, MA: North River Press.
Seal, W. (2012). Management accounting. Maidenhead: McGraw-Hill Higher Education.
Atkinson, A. A. (2012). Management accounting. Upper Saddle River, N.J.: Paerson.
Berry, L. E. (2009). Management accounting demystified. New York: McGraw-Hill.
Boyd, W. K. (2013). Cost Accounting For Dummies. Hoboken: Wiley.
Girard, S. L. (2014). Business finance basics. Pompton Plains, NJ: Career Press.
Horngren, C. (2012). Cost accounting. Upper Saddle River, N.J.: Pearson/Prentice Hall.
Menifield, C. E. (2014). The Basics of Public Budgeting and Financial Management: A
Handbook for Academics and Practitioners. Lanham, Md.: University Press of
America.
Noreen, E. (2015). The theory of constraints and its implications for management accounting.
Great Barrington, MA: North River Press.
Seal, W. (2012). Management accounting. Maidenhead: McGraw-Hill Higher Education.
1 out of 6
![[object Object]](/_next/image/?url=%2F_next%2Fstatic%2Fmedia%2Flogo.6d15ce61.png&w=640&q=75)
Your All-in-One AI-Powered Toolkit for Academic Success.
+13062052269
info@desklib.com
Available 24*7 on WhatsApp / Email
Unlock your academic potential
© 2024 | Zucol Services PVT LTD | All rights reserved.