Additive Manufacturing Report 2022
VerifiedAdded on 2022/10/13
|7
|2305
|15
AI Summary
Contribute Materials
Your contribution can guide someone’s learning journey. Share your
documents today.
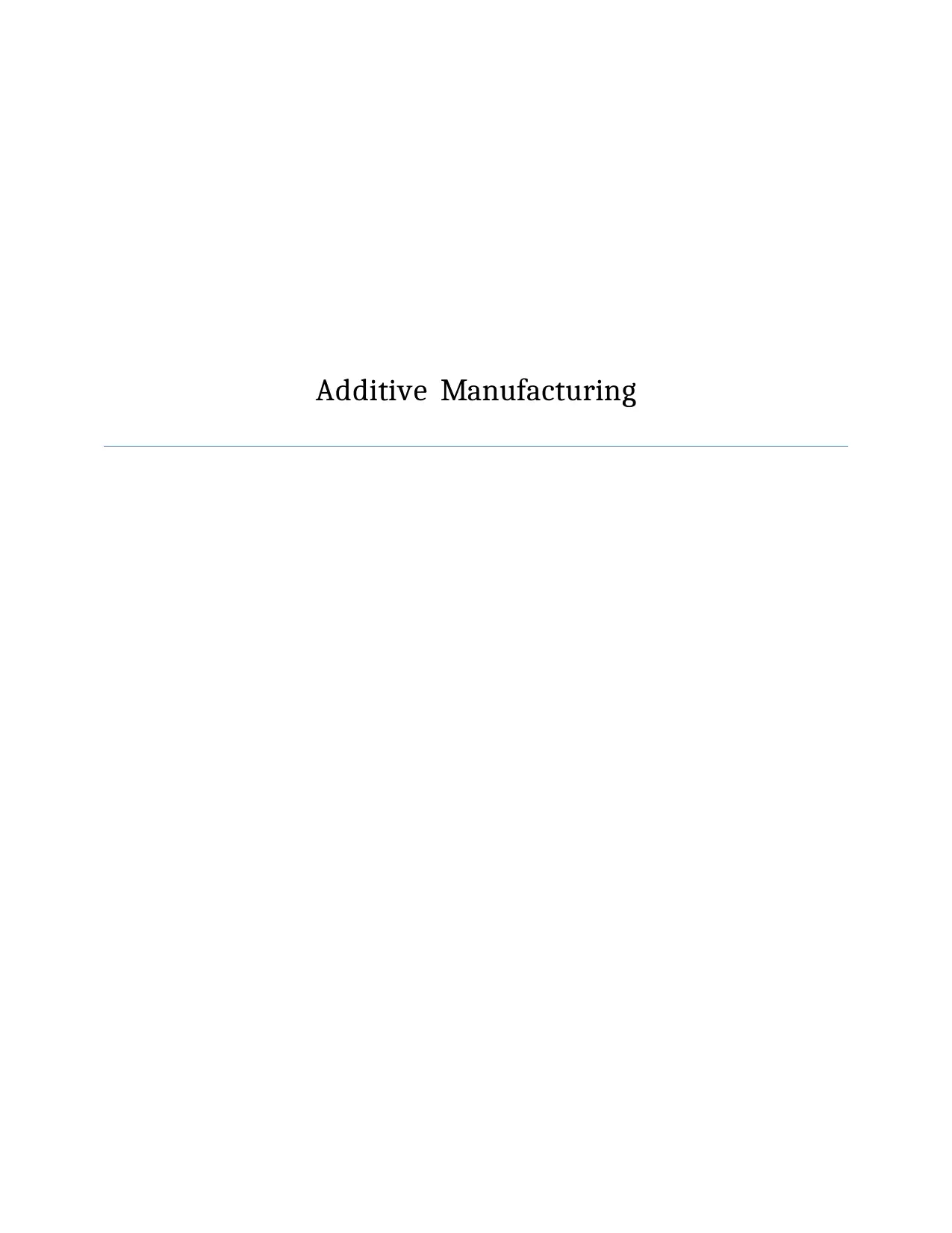
Additive Manufacturing
Secure Best Marks with AI Grader
Need help grading? Try our AI Grader for instant feedback on your assignments.
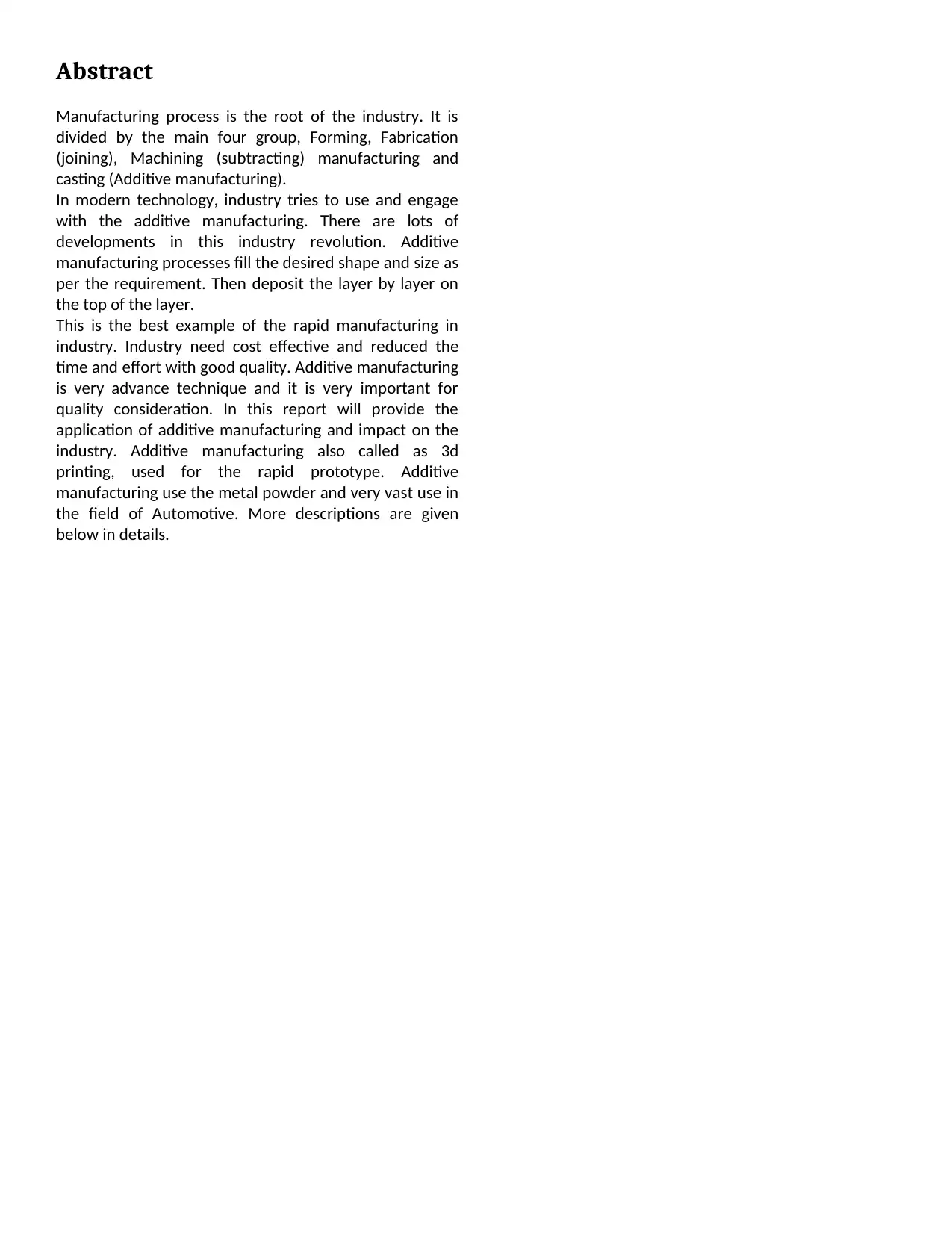
Abstract
Manufacturing process is the root of the industry. It is
divided by the main four group, Forming, Fabrication
(joining), Machining (subtracting) manufacturing and
casting (Additive manufacturing).
In modern technology, industry tries to use and engage
with the additive manufacturing. There are lots of
developments in this industry revolution. Additive
manufacturing processes fill the desired shape and size as
per the requirement. Then deposit the layer by layer on
the top of the layer.
This is the best example of the rapid manufacturing in
industry. Industry need cost effective and reduced the
time and effort with good quality. Additive manufacturing
is very advance technique and it is very important for
quality consideration. In this report will provide the
application of additive manufacturing and impact on the
industry. Additive manufacturing also called as 3d
printing, used for the rapid prototype. Additive
manufacturing use the metal powder and very vast use in
the field of Automotive. More descriptions are given
below in details.
Manufacturing process is the root of the industry. It is
divided by the main four group, Forming, Fabrication
(joining), Machining (subtracting) manufacturing and
casting (Additive manufacturing).
In modern technology, industry tries to use and engage
with the additive manufacturing. There are lots of
developments in this industry revolution. Additive
manufacturing processes fill the desired shape and size as
per the requirement. Then deposit the layer by layer on
the top of the layer.
This is the best example of the rapid manufacturing in
industry. Industry need cost effective and reduced the
time and effort with good quality. Additive manufacturing
is very advance technique and it is very important for
quality consideration. In this report will provide the
application of additive manufacturing and impact on the
industry. Additive manufacturing also called as 3d
printing, used for the rapid prototype. Additive
manufacturing use the metal powder and very vast use in
the field of Automotive. More descriptions are given
below in details.
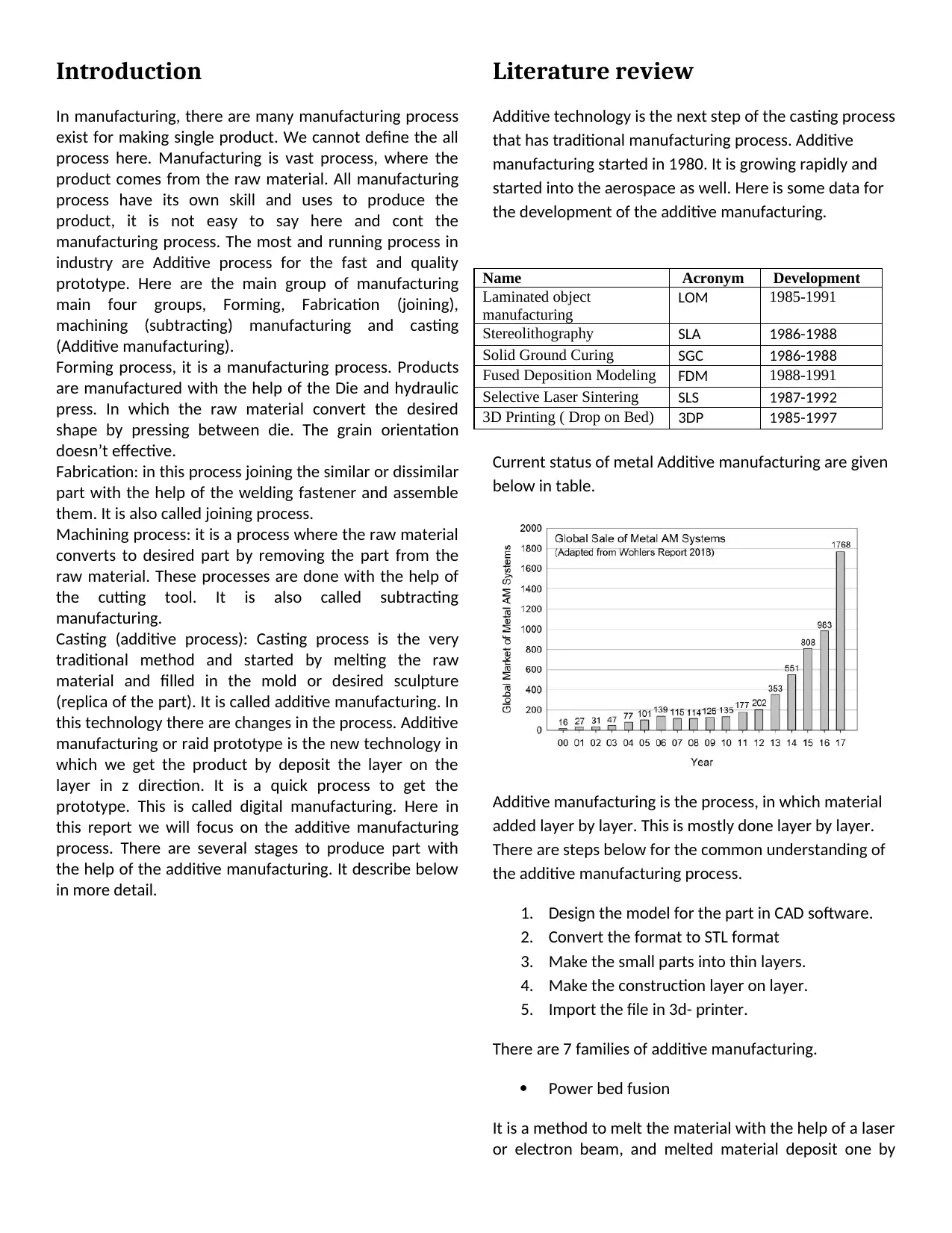
Introduction
In manufacturing, there are many manufacturing process
exist for making single product. We cannot define the all
process here. Manufacturing is vast process, where the
product comes from the raw material. All manufacturing
process have its own skill and uses to produce the
product, it is not easy to say here and cont the
manufacturing process. The most and running process in
industry are Additive process for the fast and quality
prototype. Here are the main group of manufacturing
main four groups, Forming, Fabrication (joining),
machining (subtracting) manufacturing and casting
(Additive manufacturing).
Forming process, it is a manufacturing process. Products
are manufactured with the help of the Die and hydraulic
press. In which the raw material convert the desired
shape by pressing between die. The grain orientation
doesn’t effective.
Fabrication: in this process joining the similar or dissimilar
part with the help of the welding fastener and assemble
them. It is also called joining process.
Machining process: it is a process where the raw material
converts to desired part by removing the part from the
raw material. These processes are done with the help of
the cutting tool. It is also called subtracting
manufacturing.
Casting (additive process): Casting process is the very
traditional method and started by melting the raw
material and filled in the mold or desired sculpture
(replica of the part). It is called additive manufacturing. In
this technology there are changes in the process. Additive
manufacturing or raid prototype is the new technology in
which we get the product by deposit the layer on the
layer in z direction. It is a quick process to get the
prototype. This is called digital manufacturing. Here in
this report we will focus on the additive manufacturing
process. There are several stages to produce part with
the help of the additive manufacturing. It describe below
in more detail.
Literature review
Additive technology is the next step of the casting process
that has traditional manufacturing process. Additive
manufacturing started in 1980. It is growing rapidly and
started into the aerospace as well. Here is some data for
the development of the additive manufacturing.
Current status of metal Additive manufacturing are given
below in table.
Additive manufacturing is the process, in which material
added layer by layer. This is mostly done layer by layer.
There are steps below for the common understanding of
the additive manufacturing process.
1. Design the model for the part in CAD software.
2. Convert the format to STL format
3. Make the small parts into thin layers.
4. Make the construction layer on layer.
5. Import the file in 3d- printer.
There are 7 families of additive manufacturing.
Power bed fusion
It is a method to melt the material with the help of a laser
or electron beam, and melted material deposit one by
Name Acronym Development
Laminated object
manufacturing
LOM 1985-1991
Stereolithography SLA 1986-1988
Solid Ground Curing SGC 1986-1988
Fused Deposition Modeling FDM 1988-1991
Selective Laser Sintering SLS 1987-1992
3D Printing ( Drop on Bed) 3DP 1985-1997
In manufacturing, there are many manufacturing process
exist for making single product. We cannot define the all
process here. Manufacturing is vast process, where the
product comes from the raw material. All manufacturing
process have its own skill and uses to produce the
product, it is not easy to say here and cont the
manufacturing process. The most and running process in
industry are Additive process for the fast and quality
prototype. Here are the main group of manufacturing
main four groups, Forming, Fabrication (joining),
machining (subtracting) manufacturing and casting
(Additive manufacturing).
Forming process, it is a manufacturing process. Products
are manufactured with the help of the Die and hydraulic
press. In which the raw material convert the desired
shape by pressing between die. The grain orientation
doesn’t effective.
Fabrication: in this process joining the similar or dissimilar
part with the help of the welding fastener and assemble
them. It is also called joining process.
Machining process: it is a process where the raw material
converts to desired part by removing the part from the
raw material. These processes are done with the help of
the cutting tool. It is also called subtracting
manufacturing.
Casting (additive process): Casting process is the very
traditional method and started by melting the raw
material and filled in the mold or desired sculpture
(replica of the part). It is called additive manufacturing. In
this technology there are changes in the process. Additive
manufacturing or raid prototype is the new technology in
which we get the product by deposit the layer on the
layer in z direction. It is a quick process to get the
prototype. This is called digital manufacturing. Here in
this report we will focus on the additive manufacturing
process. There are several stages to produce part with
the help of the additive manufacturing. It describe below
in more detail.
Literature review
Additive technology is the next step of the casting process
that has traditional manufacturing process. Additive
manufacturing started in 1980. It is growing rapidly and
started into the aerospace as well. Here is some data for
the development of the additive manufacturing.
Current status of metal Additive manufacturing are given
below in table.
Additive manufacturing is the process, in which material
added layer by layer. This is mostly done layer by layer.
There are steps below for the common understanding of
the additive manufacturing process.
1. Design the model for the part in CAD software.
2. Convert the format to STL format
3. Make the small parts into thin layers.
4. Make the construction layer on layer.
5. Import the file in 3d- printer.
There are 7 families of additive manufacturing.
Power bed fusion
It is a method to melt the material with the help of a laser
or electron beam, and melted material deposit one by
Name Acronym Development
Laminated object
manufacturing
LOM 1985-1991
Stereolithography SLA 1986-1988
Solid Ground Curing SGC 1986-1988
Fused Deposition Modeling FDM 1988-1991
Selective Laser Sintering SLS 1987-1992
3D Printing ( Drop on Bed) 3DP 1985-1997
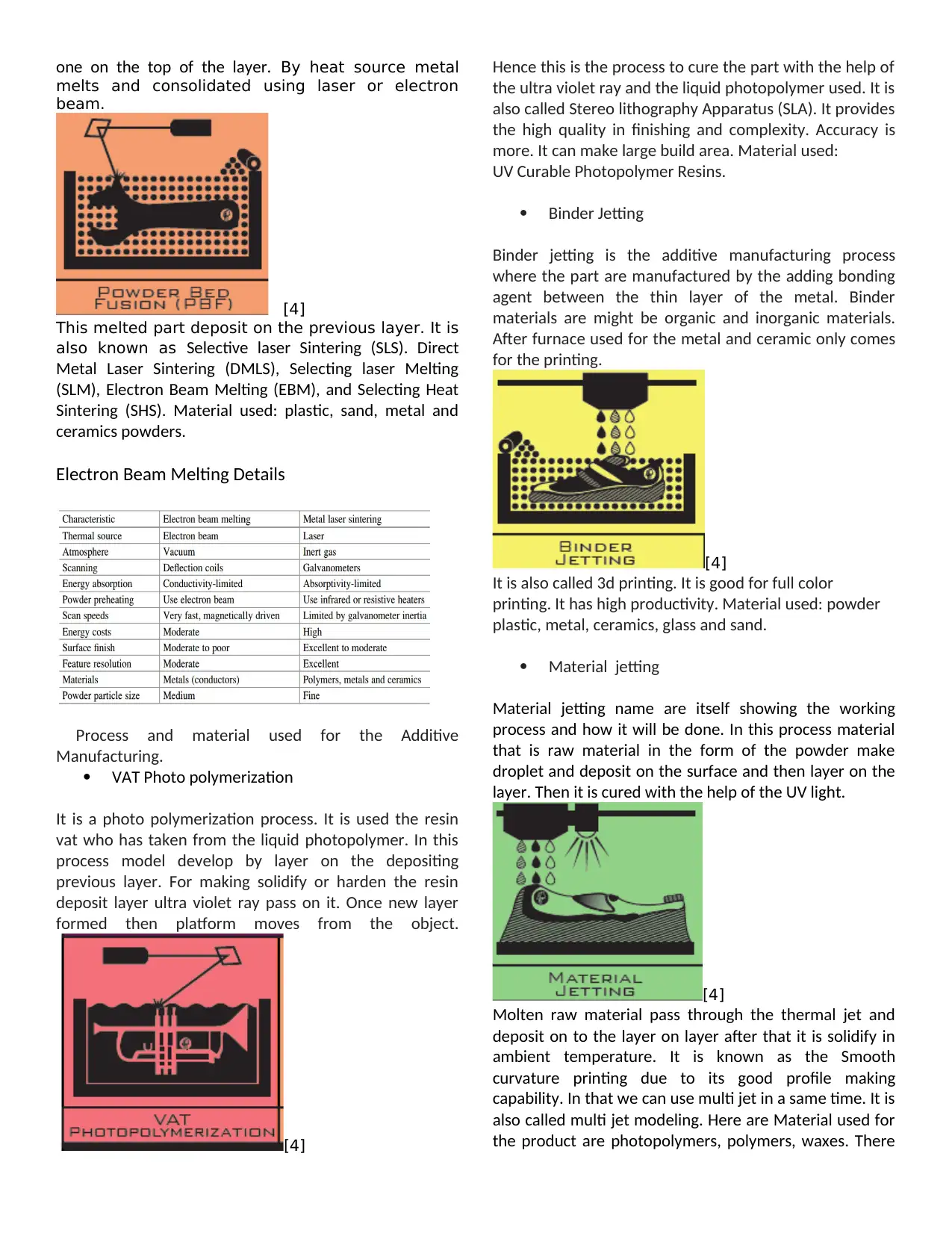
one on the top of the layer. By heat source metal
melts and consolidated using laser or electron
beam.
[4]
This melted part deposit on the previous layer. It is
also known as Selective laser Sintering (SLS). Direct
Metal Laser Sintering (DMLS), Selecting laser Melting
(SLM), Electron Beam Melting (EBM), and Selecting Heat
Sintering (SHS). Material used: plastic, sand, metal and
ceramics powders.
Electron Beam Melting Details
Process and material used for the Additive
Manufacturing.
VAT Photo polymerization
It is a photo polymerization process. It is used the resin
vat who has taken from the liquid photopolymer. In this
process model develop by layer on the depositing
previous layer. For making solidify or harden the resin
deposit layer ultra violet ray pass on it. Once new layer
formed then platform moves from the object.
[4]
Hence this is the process to cure the part with the help of
the ultra violet ray and the liquid photopolymer used. It is
also called Stereo lithography Apparatus (SLA). It provides
the high quality in finishing and complexity. Accuracy is
more. It can make large build area. Material used:
UV Curable Photopolymer Resins.
Binder Jetting
Binder jetting is the additive manufacturing process
where the part are manufactured by the adding bonding
agent between the thin layer of the metal. Binder
materials are might be organic and inorganic materials.
After furnace used for the metal and ceramic only comes
for the printing.
[4]
It is also called 3d printing. It is good for full color
printing. It has high productivity. Material used: powder
plastic, metal, ceramics, glass and sand.
Material jetting
Material jetting name are itself showing the working
process and how it will be done. In this process material
that is raw material in the form of the powder make
droplet and deposit on the surface and then layer on the
layer. Then it is cured with the help of the UV light.
[4]
Molten raw material pass through the thermal jet and
deposit on to the layer on layer after that it is solidify in
ambient temperature. It is known as the Smooth
curvature printing due to its good profile making
capability. In that we can use multi jet in a same time. It is
also called multi jet modeling. Here are Material used for
the product are photopolymers, polymers, waxes. There
melts and consolidated using laser or electron
beam.
[4]
This melted part deposit on the previous layer. It is
also known as Selective laser Sintering (SLS). Direct
Metal Laser Sintering (DMLS), Selecting laser Melting
(SLM), Electron Beam Melting (EBM), and Selecting Heat
Sintering (SHS). Material used: plastic, sand, metal and
ceramics powders.
Electron Beam Melting Details
Process and material used for the Additive
Manufacturing.
VAT Photo polymerization
It is a photo polymerization process. It is used the resin
vat who has taken from the liquid photopolymer. In this
process model develop by layer on the depositing
previous layer. For making solidify or harden the resin
deposit layer ultra violet ray pass on it. Once new layer
formed then platform moves from the object.
[4]
Hence this is the process to cure the part with the help of
the ultra violet ray and the liquid photopolymer used. It is
also called Stereo lithography Apparatus (SLA). It provides
the high quality in finishing and complexity. Accuracy is
more. It can make large build area. Material used:
UV Curable Photopolymer Resins.
Binder Jetting
Binder jetting is the additive manufacturing process
where the part are manufactured by the adding bonding
agent between the thin layer of the metal. Binder
materials are might be organic and inorganic materials.
After furnace used for the metal and ceramic only comes
for the printing.
[4]
It is also called 3d printing. It is good for full color
printing. It has high productivity. Material used: powder
plastic, metal, ceramics, glass and sand.
Material jetting
Material jetting name are itself showing the working
process and how it will be done. In this process material
that is raw material in the form of the powder make
droplet and deposit on the surface and then layer on the
layer. Then it is cured with the help of the UV light.
[4]
Molten raw material pass through the thermal jet and
deposit on to the layer on layer after that it is solidify in
ambient temperature. It is known as the Smooth
curvature printing due to its good profile making
capability. In that we can use multi jet in a same time. It is
also called multi jet modeling. Here are Material used for
the product are photopolymers, polymers, waxes. There
Secure Best Marks with AI Grader
Need help grading? Try our AI Grader for instant feedback on your assignments.
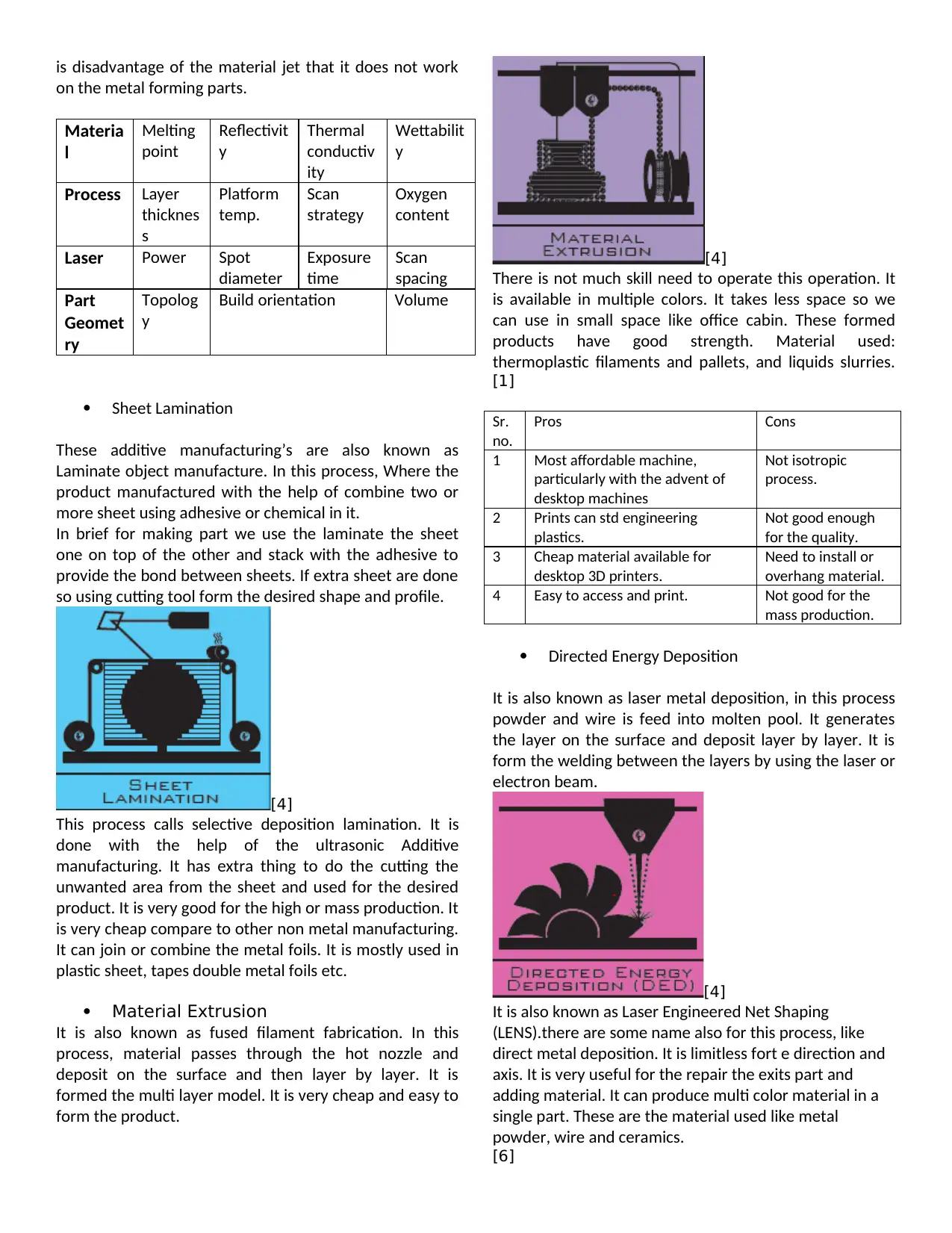
is disadvantage of the material jet that it does not work
on the metal forming parts.
Materia
l
Melting
point
Reflectivit
y
Thermal
conductiv
ity
Wettabilit
y
Process Layer
thicknes
s
Platform
temp.
Scan
strategy
Oxygen
content
Laser Power Spot
diameter
Exposure
time
Scan
spacing
Part
Geomet
ry
Topolog
y
Build orientation Volume
Sheet Lamination
These additive manufacturing’s are also known as
Laminate object manufacture. In this process, Where the
product manufactured with the help of combine two or
more sheet using adhesive or chemical in it.
In brief for making part we use the laminate the sheet
one on top of the other and stack with the adhesive to
provide the bond between sheets. If extra sheet are done
so using cutting tool form the desired shape and profile.
[4]
This process calls selective deposition lamination. It is
done with the help of the ultrasonic Additive
manufacturing. It has extra thing to do the cutting the
unwanted area from the sheet and used for the desired
product. It is very good for the high or mass production. It
is very cheap compare to other non metal manufacturing.
It can join or combine the metal foils. It is mostly used in
plastic sheet, tapes double metal foils etc.
Material Extrusion
It is also known as fused filament fabrication. In this
process, material passes through the hot nozzle and
deposit on the surface and then layer by layer. It is
formed the multi layer model. It is very cheap and easy to
form the product.
[4]
There is not much skill need to operate this operation. It
is available in multiple colors. It takes less space so we
can use in small space like office cabin. These formed
products have good strength. Material used:
thermoplastic filaments and pallets, and liquids slurries.
[1]
Sr.
no.
Pros Cons
1 Most affordable machine,
particularly with the advent of
desktop machines
Not isotropic
process.
2 Prints can std engineering
plastics.
Not good enough
for the quality.
3 Cheap material available for
desktop 3D printers.
Need to install or
overhang material.
4 Easy to access and print. Not good for the
mass production.
Directed Energy Deposition
It is also known as laser metal deposition, in this process
powder and wire is feed into molten pool. It generates
the layer on the surface and deposit layer by layer. It is
form the welding between the layers by using the laser or
electron beam.
[4]
It is also known as Laser Engineered Net Shaping
(LENS).there are some name also for this process, like
direct metal deposition. It is limitless fort e direction and
axis. It is very useful for the repair the exits part and
adding material. It can produce multi color material in a
single part. These are the material used like metal
powder, wire and ceramics.
[6]
on the metal forming parts.
Materia
l
Melting
point
Reflectivit
y
Thermal
conductiv
ity
Wettabilit
y
Process Layer
thicknes
s
Platform
temp.
Scan
strategy
Oxygen
content
Laser Power Spot
diameter
Exposure
time
Scan
spacing
Part
Geomet
ry
Topolog
y
Build orientation Volume
Sheet Lamination
These additive manufacturing’s are also known as
Laminate object manufacture. In this process, Where the
product manufactured with the help of combine two or
more sheet using adhesive or chemical in it.
In brief for making part we use the laminate the sheet
one on top of the other and stack with the adhesive to
provide the bond between sheets. If extra sheet are done
so using cutting tool form the desired shape and profile.
[4]
This process calls selective deposition lamination. It is
done with the help of the ultrasonic Additive
manufacturing. It has extra thing to do the cutting the
unwanted area from the sheet and used for the desired
product. It is very good for the high or mass production. It
is very cheap compare to other non metal manufacturing.
It can join or combine the metal foils. It is mostly used in
plastic sheet, tapes double metal foils etc.
Material Extrusion
It is also known as fused filament fabrication. In this
process, material passes through the hot nozzle and
deposit on the surface and then layer by layer. It is
formed the multi layer model. It is very cheap and easy to
form the product.
[4]
There is not much skill need to operate this operation. It
is available in multiple colors. It takes less space so we
can use in small space like office cabin. These formed
products have good strength. Material used:
thermoplastic filaments and pallets, and liquids slurries.
[1]
Sr.
no.
Pros Cons
1 Most affordable machine,
particularly with the advent of
desktop machines
Not isotropic
process.
2 Prints can std engineering
plastics.
Not good enough
for the quality.
3 Cheap material available for
desktop 3D printers.
Need to install or
overhang material.
4 Easy to access and print. Not good for the
mass production.
Directed Energy Deposition
It is also known as laser metal deposition, in this process
powder and wire is feed into molten pool. It generates
the layer on the surface and deposit layer by layer. It is
form the welding between the layers by using the laser or
electron beam.
[4]
It is also known as Laser Engineered Net Shaping
(LENS).there are some name also for this process, like
direct metal deposition. It is limitless fort e direction and
axis. It is very useful for the repair the exits part and
adding material. It can produce multi color material in a
single part. These are the material used like metal
powder, wire and ceramics.
[6]
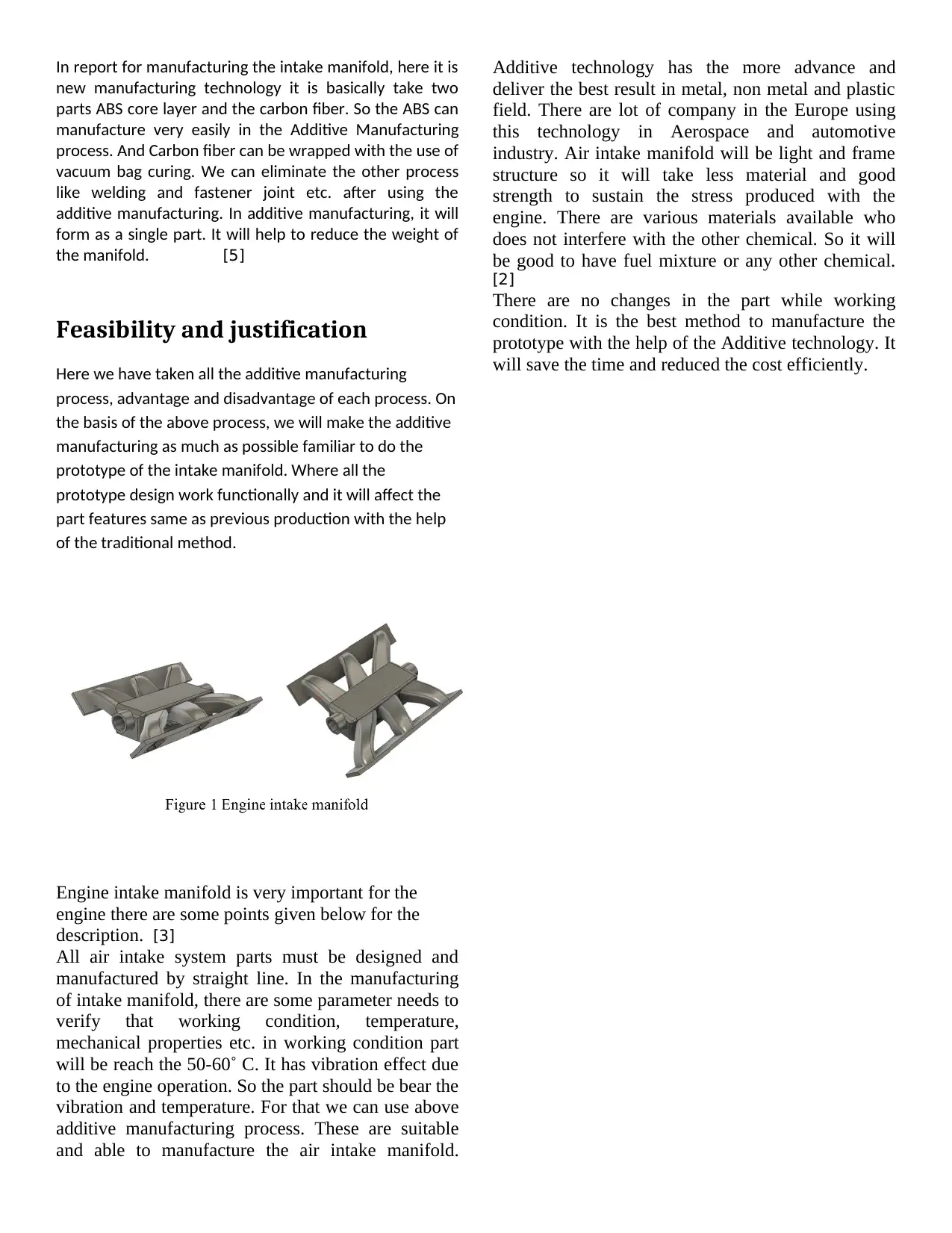
In report for manufacturing the intake manifold, here it is
new manufacturing technology it is basically take two
parts ABS core layer and the carbon fiber. So the ABS can
manufacture very easily in the Additive Manufacturing
process. And Carbon fiber can be wrapped with the use of
vacuum bag curing. We can eliminate the other process
like welding and fastener joint etc. after using the
additive manufacturing. In additive manufacturing, it will
form as a single part. It will help to reduce the weight of
the manifold. [5]
Feasibility and justification
Here we have taken all the additive manufacturing
process, advantage and disadvantage of each process. On
the basis of the above process, we will make the additive
manufacturing as much as possible familiar to do the
prototype of the intake manifold. Where all the
prototype design work functionally and it will affect the
part features same as previous production with the help
of the traditional method.
Engine intake manifold is very important for the
engine there are some points given below for the
description. [3]
All air intake system parts must be designed and
manufactured by straight line. In the manufacturing
of intake manifold, there are some parameter needs to
verify that working condition, temperature,
mechanical properties etc. in working condition part
will be reach the 50-60˚ C. It has vibration effect due
to the engine operation. So the part should be bear the
vibration and temperature. For that we can use above
additive manufacturing process. These are suitable
and able to manufacture the air intake manifold.
Additive technology has the more advance and
deliver the best result in metal, non metal and plastic
field. There are lot of company in the Europe using
this technology in Aerospace and automotive
industry. Air intake manifold will be light and frame
structure so it will take less material and good
strength to sustain the stress produced with the
engine. There are various materials available who
does not interfere with the other chemical. So it will
be good to have fuel mixture or any other chemical.
[2]
There are no changes in the part while working
condition. It is the best method to manufacture the
prototype with the help of the Additive technology. It
will save the time and reduced the cost efficiently.
new manufacturing technology it is basically take two
parts ABS core layer and the carbon fiber. So the ABS can
manufacture very easily in the Additive Manufacturing
process. And Carbon fiber can be wrapped with the use of
vacuum bag curing. We can eliminate the other process
like welding and fastener joint etc. after using the
additive manufacturing. In additive manufacturing, it will
form as a single part. It will help to reduce the weight of
the manifold. [5]
Feasibility and justification
Here we have taken all the additive manufacturing
process, advantage and disadvantage of each process. On
the basis of the above process, we will make the additive
manufacturing as much as possible familiar to do the
prototype of the intake manifold. Where all the
prototype design work functionally and it will affect the
part features same as previous production with the help
of the traditional method.
Engine intake manifold is very important for the
engine there are some points given below for the
description. [3]
All air intake system parts must be designed and
manufactured by straight line. In the manufacturing
of intake manifold, there are some parameter needs to
verify that working condition, temperature,
mechanical properties etc. in working condition part
will be reach the 50-60˚ C. It has vibration effect due
to the engine operation. So the part should be bear the
vibration and temperature. For that we can use above
additive manufacturing process. These are suitable
and able to manufacture the air intake manifold.
Additive technology has the more advance and
deliver the best result in metal, non metal and plastic
field. There are lot of company in the Europe using
this technology in Aerospace and automotive
industry. Air intake manifold will be light and frame
structure so it will take less material and good
strength to sustain the stress produced with the
engine. There are various materials available who
does not interfere with the other chemical. So it will
be good to have fuel mixture or any other chemical.
[2]
There are no changes in the part while working
condition. It is the best method to manufacture the
prototype with the help of the Additive technology. It
will save the time and reduced the cost efficiently.
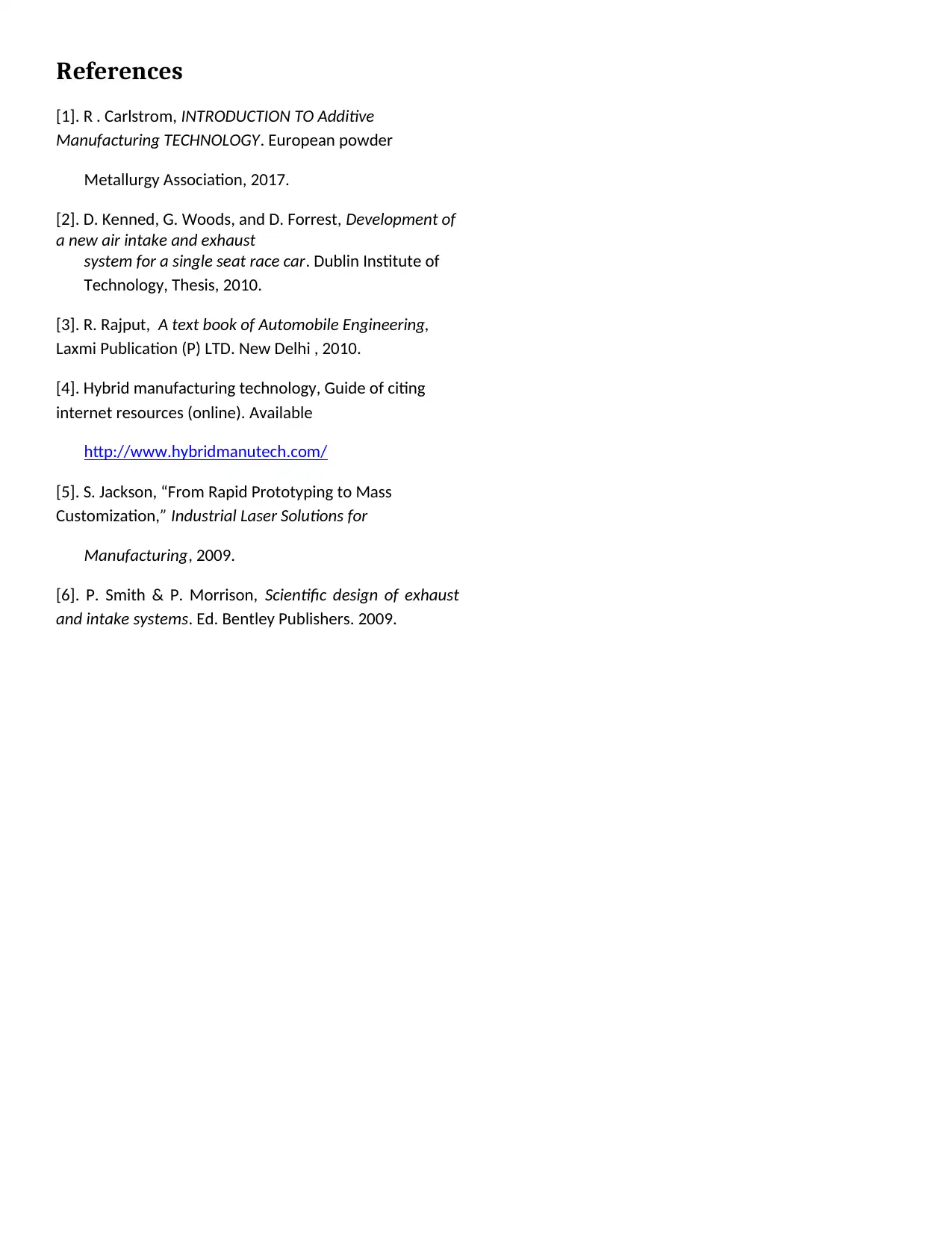
References
[1]. R . Carlstrom, INTRODUCTION TO Additive
Manufacturing TECHNOLOGY. European powder
Metallurgy Association, 2017.
[2]. D. Kenned, G. Woods, and D. Forrest, Development of
a new air intake and exhaust
system for a single seat race car. Dublin Institute of
Technology, Thesis, 2010.
[3]. R. Rajput, A text book of Automobile Engineering,
Laxmi Publication (P) LTD. New Delhi , 2010.
[4]. Hybrid manufacturing technology, Guide of citing
internet resources (online). Available
http://www.hybridmanutech.com/
[5]. S. Jackson, “From Rapid Prototyping to Mass
Customization,” Industrial Laser Solutions for
Manufacturing, 2009.
[6]. P. Smith & P. Morrison, Scientific design of exhaust
and intake systems. Ed. Bentley Publishers. 2009.
[1]. R . Carlstrom, INTRODUCTION TO Additive
Manufacturing TECHNOLOGY. European powder
Metallurgy Association, 2017.
[2]. D. Kenned, G. Woods, and D. Forrest, Development of
a new air intake and exhaust
system for a single seat race car. Dublin Institute of
Technology, Thesis, 2010.
[3]. R. Rajput, A text book of Automobile Engineering,
Laxmi Publication (P) LTD. New Delhi , 2010.
[4]. Hybrid manufacturing technology, Guide of citing
internet resources (online). Available
http://www.hybridmanutech.com/
[5]. S. Jackson, “From Rapid Prototyping to Mass
Customization,” Industrial Laser Solutions for
Manufacturing, 2009.
[6]. P. Smith & P. Morrison, Scientific design of exhaust
and intake systems. Ed. Bentley Publishers. 2009.
1 out of 7
Related Documents
![[object Object]](/_next/image/?url=%2F_next%2Fstatic%2Fmedia%2Flogo.6d15ce61.png&w=640&q=75)
Your All-in-One AI-Powered Toolkit for Academic Success.
+13062052269
info@desklib.com
Available 24*7 on WhatsApp / Email
Unlock your academic potential
© 2024 | Zucol Services PVT LTD | All rights reserved.