GGBS Concrete Strength Development and Durability Analysis Report
VerifiedAdded on 2023/01/12
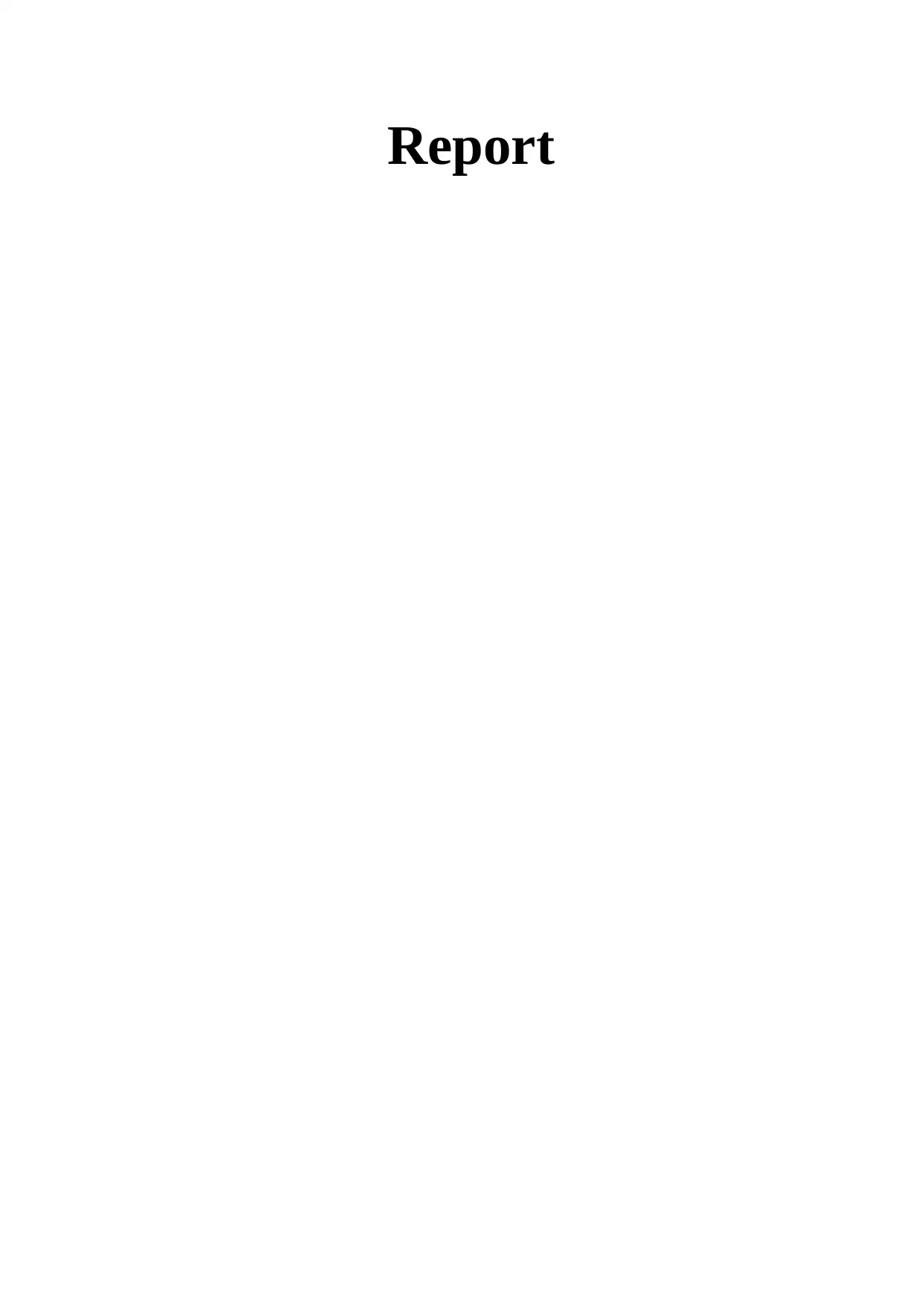
Paraphrase This Document
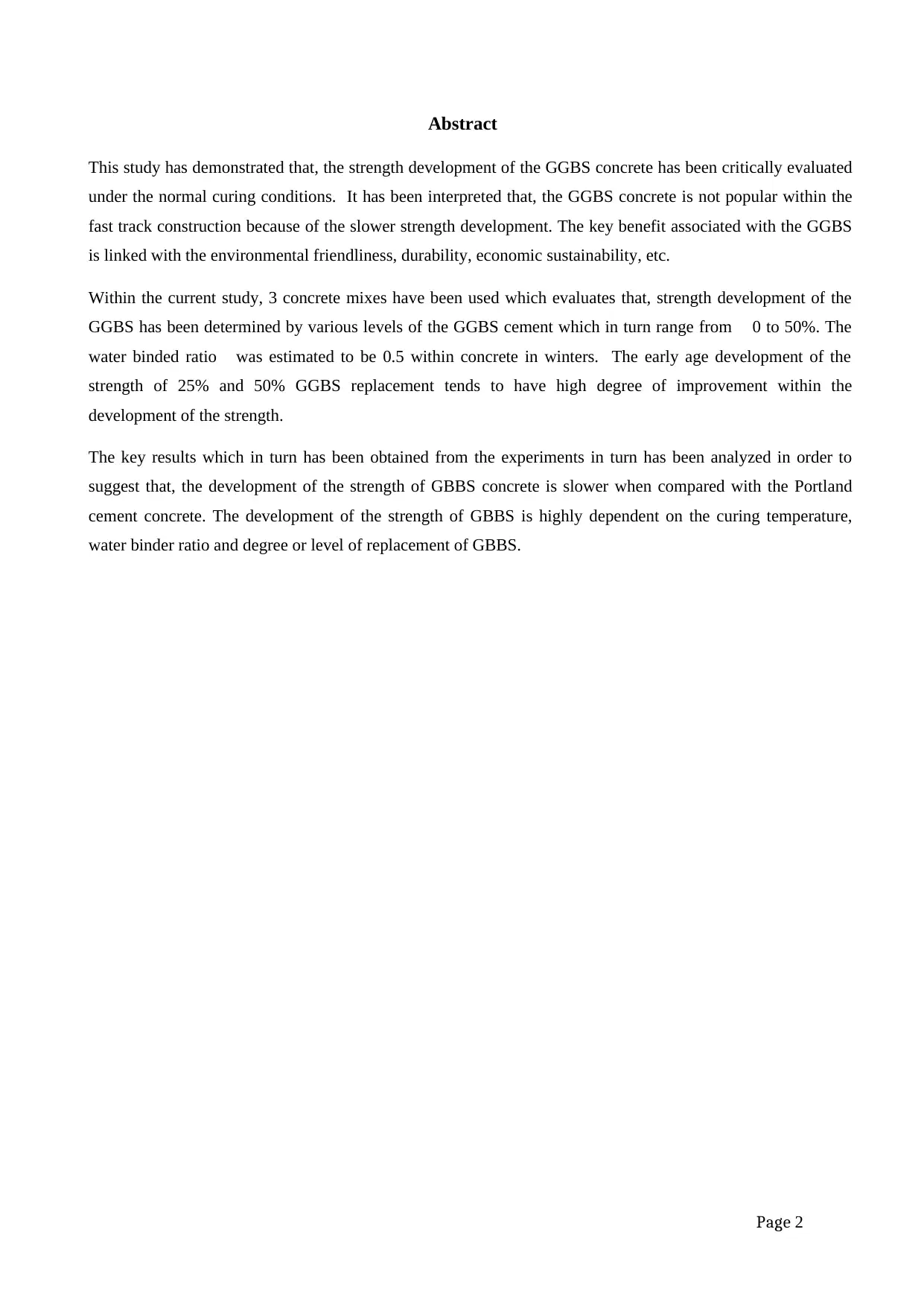
Abstract
This study has demonstrated that, the strength development of the GGBS concrete has been critically evaluated
under the normal curing conditions. It has been interpreted that, the GGBS concrete is not popular within the
fast track construction because of the slower strength development. The key benefit associated with the GGBS
is linked with the environmental friendliness, durability, economic sustainability, etc.
Within the current study, 3 concrete mixes have been used which evaluates that, strength development of the
GGBS has been determined by various levels of the GGBS cement which in turn range from 0 to 50%. The
water binded ratio was estimated to be 0.5 within concrete in winters. The early age development of the
strength of 25% and 50% GGBS replacement tends to have high degree of improvement within the
development of the strength.
The key results which in turn has been obtained from the experiments in turn has been analyzed in order to
suggest that, the development of the strength of GBBS concrete is slower when compared with the Portland
cement concrete. The development of the strength of GBBS is highly dependent on the curing temperature,
water binder ratio and degree or level of replacement of GBBS.
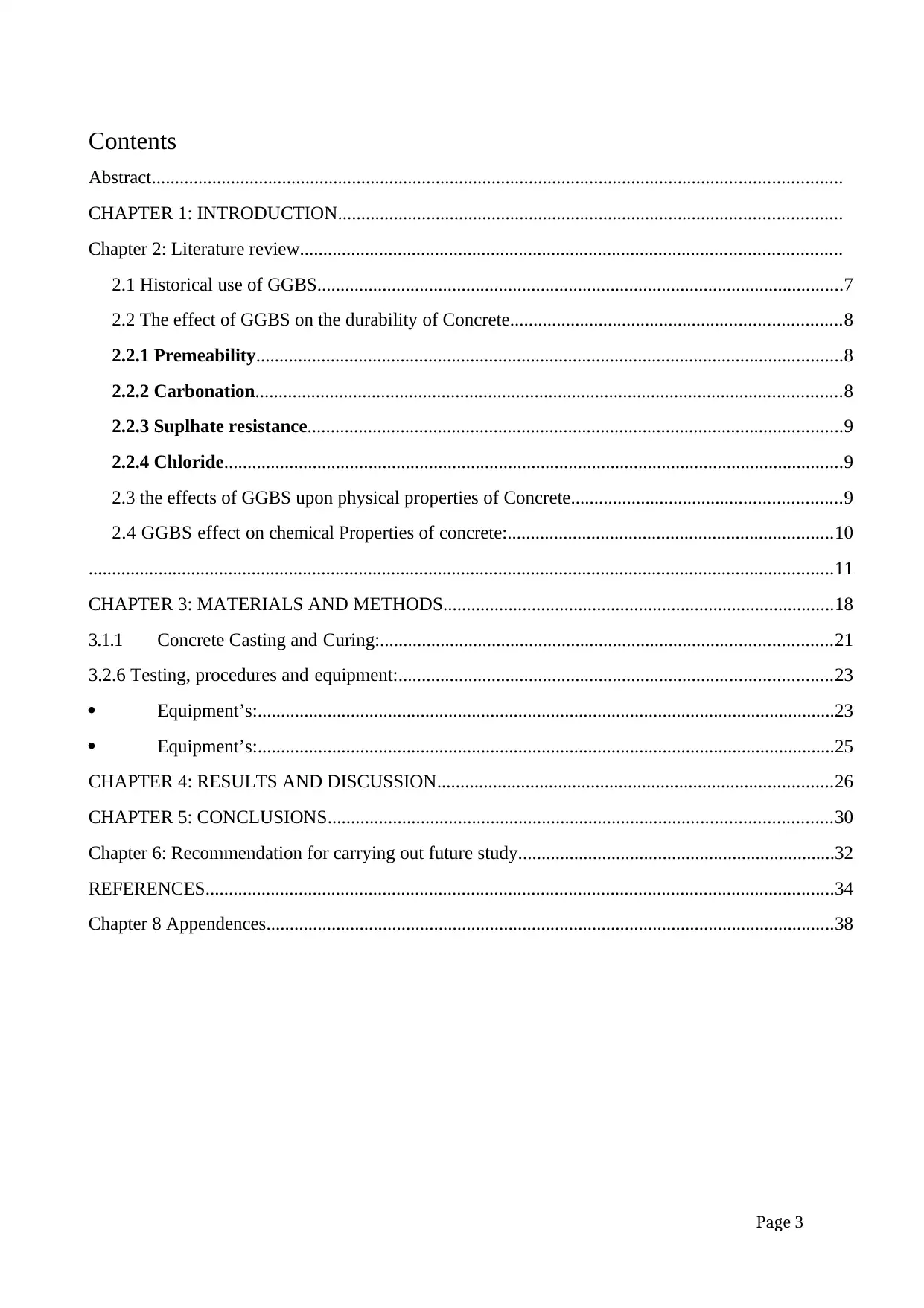
Contents
Abstract....................................................................................................................................................
CHAPTER 1: INTRODUCTION............................................................................................................
Chapter 2: Literature review....................................................................................................................
2.1 Historical use of GGBS.................................................................................................................7
2.2 The effect of GGBS on the durability of Concrete.......................................................................8
2.2.1 Premeability..............................................................................................................................8
2.2.2 Carbonation..............................................................................................................................8
2.2.3 Suplhate resistance...................................................................................................................9
2.2.4 Chloride.....................................................................................................................................9
2.3 the effects of GGBS upon physical properties of Concrete..........................................................9
2.4 GGBS effect on chemical Properties of concrete:......................................................................10
................................................................................................................................................................11
CHAPTER 3: MATERIALS AND METHODS....................................................................................18
3.1.1 Concrete Casting and Curing:.................................................................................................21
3.2.6 Testing, procedures and equipment:.............................................................................................23
Equipment’s:............................................................................................................................23
Equipment’s:............................................................................................................................25
CHAPTER 4: RESULTS AND DISCUSSION.....................................................................................26
CHAPTER 5: CONCLUSIONS............................................................................................................30
Chapter 6: Recommendation for carrying out future study....................................................................32
REFERENCES.......................................................................................................................................34
Chapter 8 Appendences..........................................................................................................................38
⊘ This is a preview!⊘
Do you want full access?
Subscribe today to unlock all pages.

Trusted by 1+ million students worldwide
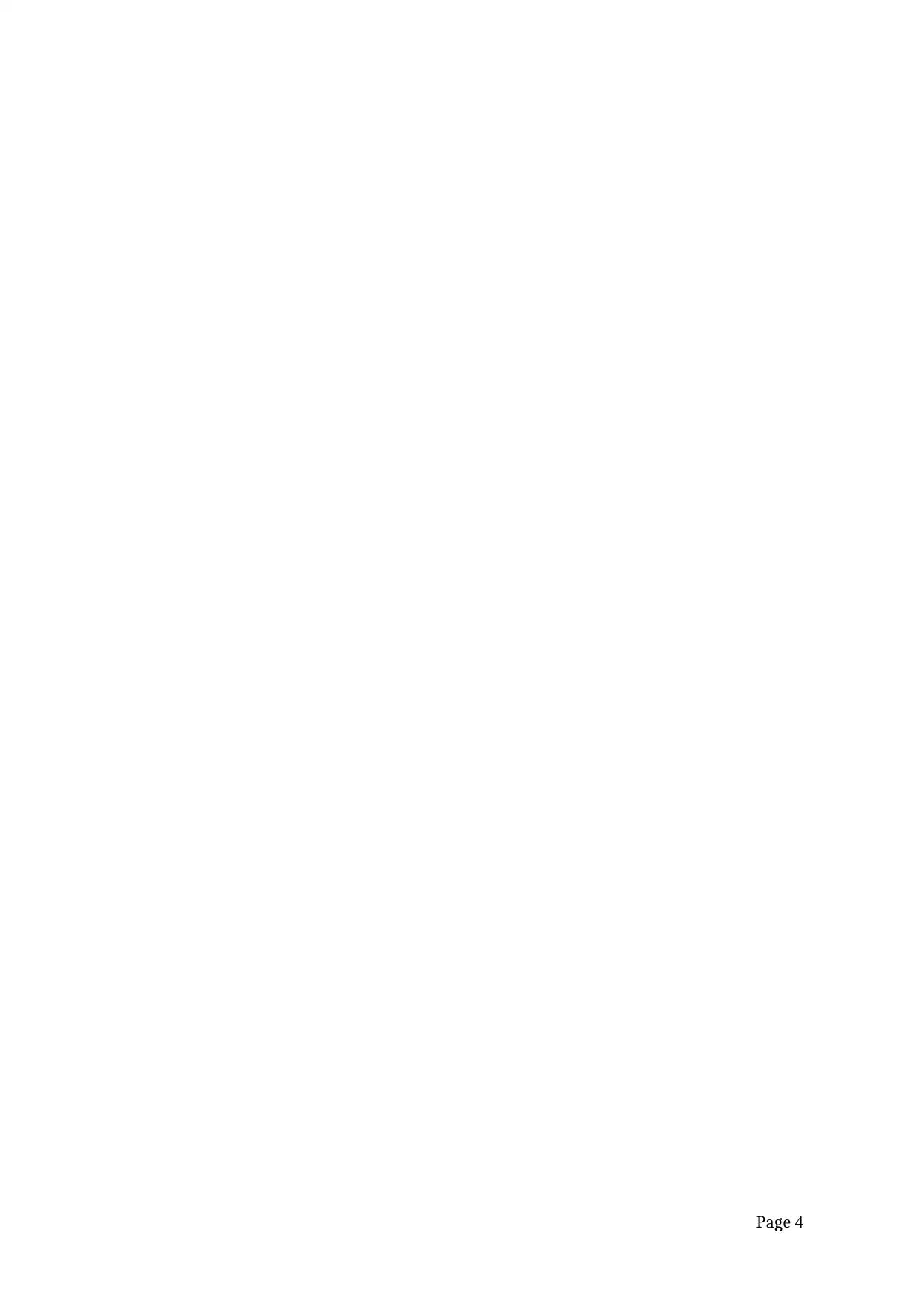
Paraphrase This Document
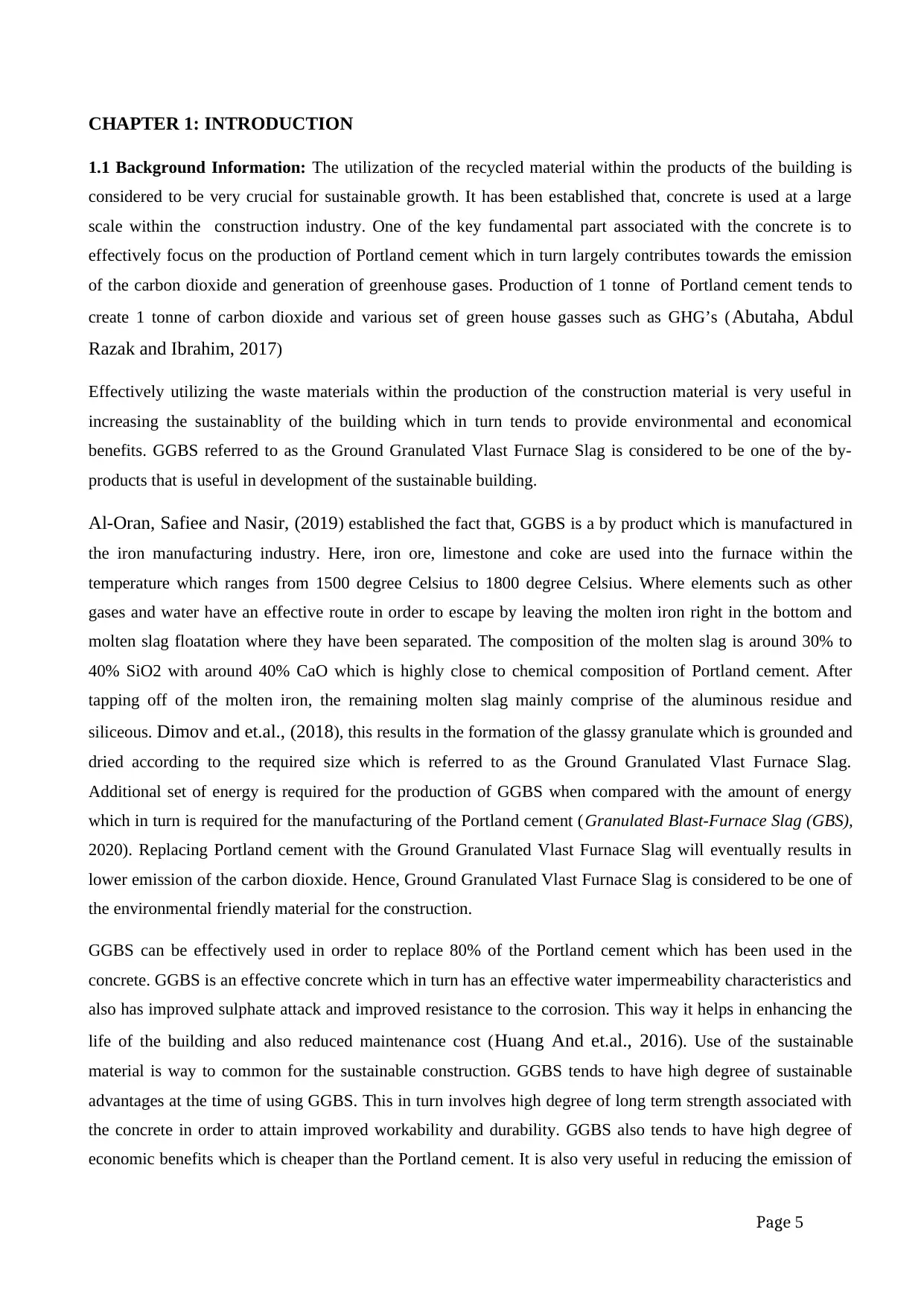
CHAPTER 1: INTRODUCTION
1.1 Background Information: The utilization of the recycled material within the products of the building is
considered to be very crucial for sustainable growth. It has been established that, concrete is used at a large
scale within the construction industry. One of the key fundamental part associated with the concrete is to
effectively focus on the production of Portland cement which in turn largely contributes towards the emission
of the carbon dioxide and generation of greenhouse gases. Production of 1 tonne of Portland cement tends to
create 1 tonne of carbon dioxide and various set of green house gasses such as GHG’s (Abutaha, Abdul
Razak and Ibrahim, 2017)
Effectively utilizing the waste materials within the production of the construction material is very useful in
increasing the sustainablity of the building which in turn tends to provide environmental and economical
benefits. GGBS referred to as the Ground Granulated Vlast Furnace Slag is considered to be one of the by-
products that is useful in development of the sustainable building.
Al-Oran, Safiee and Nasir, (2019) established the fact that, GGBS is a by product which is manufactured in
the iron manufacturing industry. Here, iron ore, limestone and coke are used into the furnace within the
temperature which ranges from 1500 degree Celsius to 1800 degree Celsius. Where elements such as other
gases and water have an effective route in order to escape by leaving the molten iron right in the bottom and
molten slag floatation where they have been separated. The composition of the molten slag is around 30% to
40% SiO2 with around 40% CaO which is highly close to chemical composition of Portland cement. After
tapping off of the molten iron, the remaining molten slag mainly comprise of the aluminous residue and
siliceous. Dimov and et.al., (2018), this results in the formation of the glassy granulate which is grounded and
dried according to the required size which is referred to as the Ground Granulated Vlast Furnace Slag.
Additional set of energy is required for the production of GGBS when compared with the amount of energy
which in turn is required for the manufacturing of the Portland cement (Granulated Blast-Furnace Slag (GBS),
2020). Replacing Portland cement with the Ground Granulated Vlast Furnace Slag will eventually results in
lower emission of the carbon dioxide. Hence, Ground Granulated Vlast Furnace Slag is considered to be one of
the environmental friendly material for the construction.
GGBS can be effectively used in order to replace 80% of the Portland cement which has been used in the
concrete. GGBS is an effective concrete which in turn has an effective water impermeability characteristics and
also has improved sulphate attack and improved resistance to the corrosion. This way it helps in enhancing the
life of the building and also reduced maintenance cost (Huang And et.al., 2016). Use of the sustainable
material is way to common for the sustainable construction. GGBS tends to have high degree of sustainable
advantages at the time of using GGBS. This in turn involves high degree of long term strength associated with
the concrete in order to attain improved workability and durability. GGBS also tends to have high degree of
economic benefits which is cheaper than the Portland cement. It is also very useful in reducing the emission of
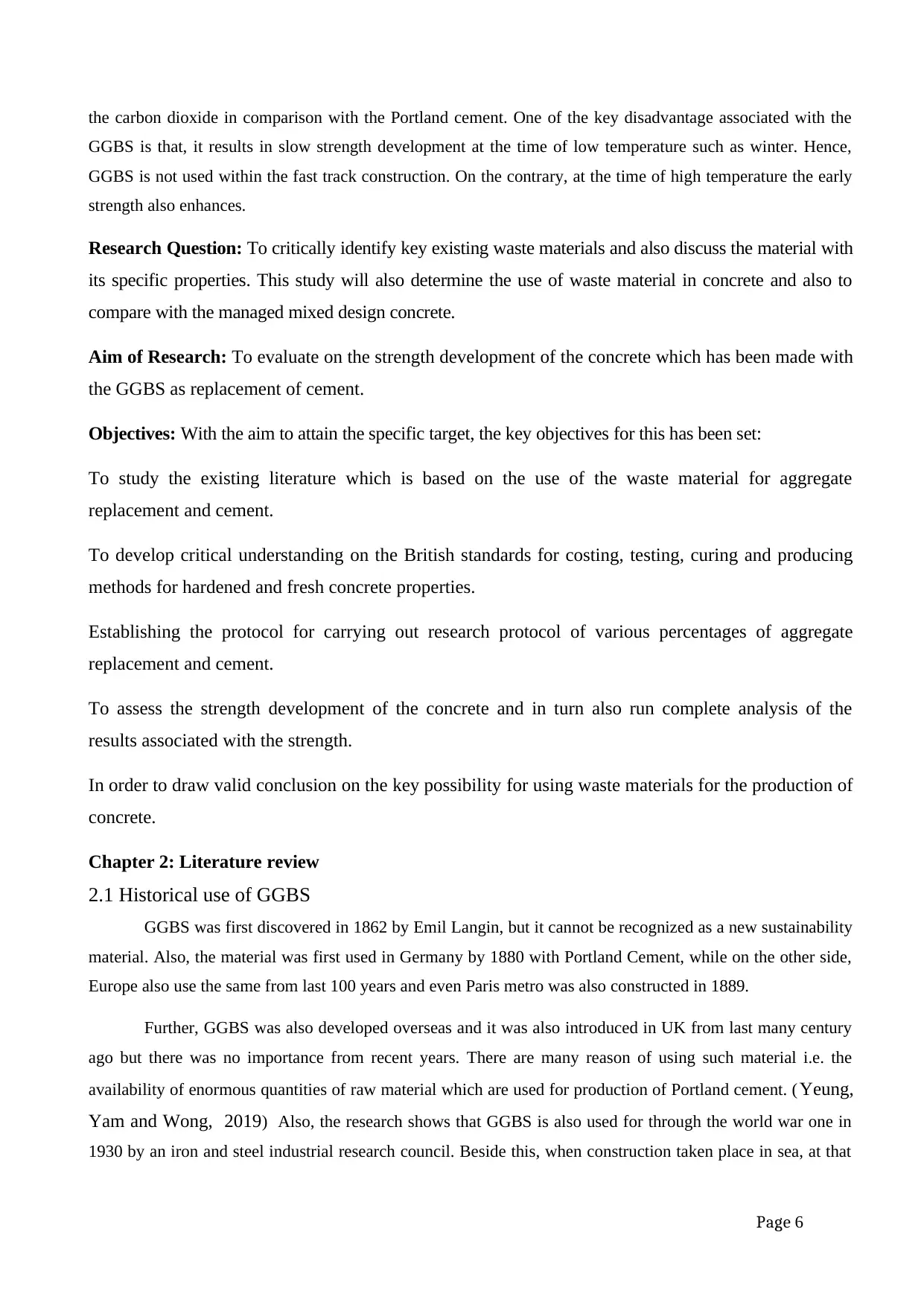
the carbon dioxide in comparison with the Portland cement. One of the key disadvantage associated with the
GGBS is that, it results in slow strength development at the time of low temperature such as winter. Hence,
GGBS is not used within the fast track construction. On the contrary, at the time of high temperature the early
strength also enhances.
Research Question: To critically identify key existing waste materials and also discuss the material with
its specific properties. This study will also determine the use of waste material in concrete and also to
compare with the managed mixed design concrete.
Aim of Research: To evaluate on the strength development of the concrete which has been made with
the GGBS as replacement of cement.
Objectives: With the aim to attain the specific target, the key objectives for this has been set:
To study the existing literature which is based on the use of the waste material for aggregate
replacement and cement.
To develop critical understanding on the British standards for costing, testing, curing and producing
methods for hardened and fresh concrete properties.
Establishing the protocol for carrying out research protocol of various percentages of aggregate
replacement and cement.
To assess the strength development of the concrete and in turn also run complete analysis of the
results associated with the strength.
In order to draw valid conclusion on the key possibility for using waste materials for the production of
concrete.
Chapter 2: Literature review
2.1 Historical use of GGBS
GGBS was first discovered in 1862 by Emil Langin, but it cannot be recognized as a new sustainability
material. Also, the material was first used in Germany by 1880 with Portland Cement, while on the other side,
Europe also use the same from last 100 years and even Paris metro was also constructed in 1889.
Further, GGBS was also developed overseas and it was also introduced in UK from last many century
ago but there was no importance from recent years. There are many reason of using such material i.e. the
availability of enormous quantities of raw material which are used for production of Portland cement. ( Yeung,
Yam and Wong, 2019) Also, the research shows that GGBS is also used for through the world war one in
1930 by an iron and steel industrial research council. Beside this, when construction taken place in sea, at that
⊘ This is a preview!⊘
Do you want full access?
Subscribe today to unlock all pages.

Trusted by 1+ million students worldwide
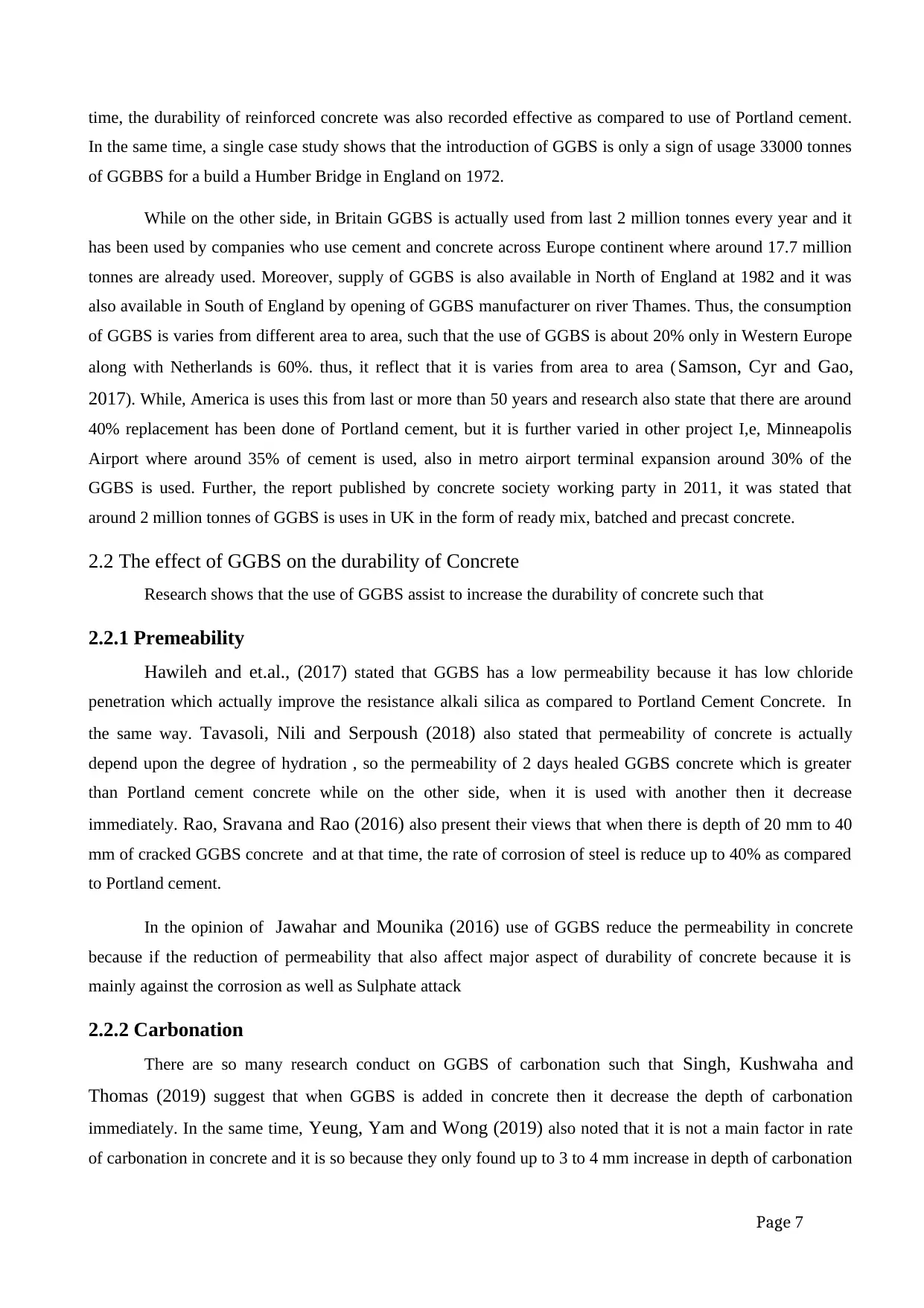
time, the durability of reinforced concrete was also recorded effective as compared to use of Portland cement.
In the same time, a single case study shows that the introduction of GGBS is only a sign of usage 33000 tonnes
of GGBBS for a build a Humber Bridge in England on 1972.
While on the other side, in Britain GGBS is actually used from last 2 million tonnes every year and it
has been used by companies who use cement and concrete across Europe continent where around 17.7 million
tonnes are already used. Moreover, supply of GGBS is also available in North of England at 1982 and it was
also available in South of England by opening of GGBS manufacturer on river Thames. Thus, the consumption
of GGBS is varies from different area to area, such that the use of GGBS is about 20% only in Western Europe
along with Netherlands is 60%. thus, it reflect that it is varies from area to area ( Samson, Cyr and Gao,
2017). While, America is uses this from last or more than 50 years and research also state that there are around
40% replacement has been done of Portland cement, but it is further varied in other project I,e, Minneapolis
Airport where around 35% of cement is used, also in metro airport terminal expansion around 30% of the
GGBS is used. Further, the report published by concrete society working party in 2011, it was stated that
around 2 million tonnes of GGBS is uses in UK in the form of ready mix, batched and precast concrete.
2.2 The effect of GGBS on the durability of Concrete
Research shows that the use of GGBS assist to increase the durability of concrete such that
2.2.1 Premeability
Hawileh and et.al., (2017) stated that GGBS has a low permeability because it has low chloride
penetration which actually improve the resistance alkali silica as compared to Portland Cement Concrete. In
the same way. Tavasoli, Nili and Serpoush (2018) also stated that permeability of concrete is actually
depend upon the degree of hydration , so the permeability of 2 days healed GGBS concrete which is greater
than Portland cement concrete while on the other side, when it is used with another then it decrease
immediately. Rao, Sravana and Rao (2016) also present their views that when there is depth of 20 mm to 40
mm of cracked GGBS concrete and at that time, the rate of corrosion of steel is reduce up to 40% as compared
to Portland cement.
In the opinion of Jawahar and Mounika (2016) use of GGBS reduce the permeability in concrete
because if the reduction of permeability that also affect major aspect of durability of concrete because it is
mainly against the corrosion as well as Sulphate attack
2.2.2 Carbonation
There are so many research conduct on GGBS of carbonation such that Singh, Kushwaha and
Thomas (2019) suggest that when GGBS is added in concrete then it decrease the depth of carbonation
immediately. In the same time, Yeung, Yam and Wong (2019) also noted that it is not a main factor in rate
of carbonation in concrete and it is so because they only found up to 3 to 4 mm increase in depth of carbonation
Paraphrase This Document
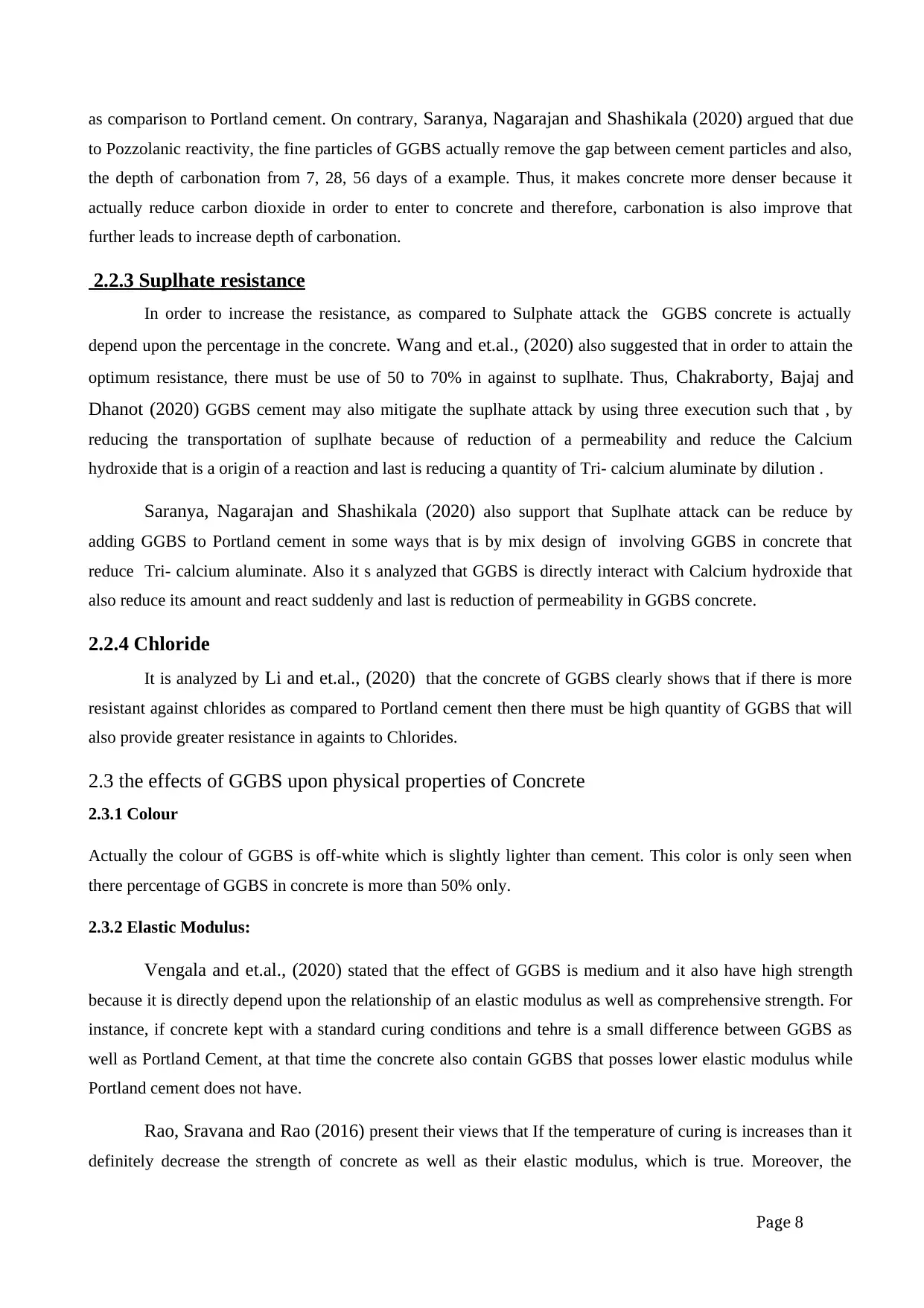
as comparison to Portland cement. On contrary, Saranya, Nagarajan and Shashikala (2020) argued that due
to Pozzolanic reactivity, the fine particles of GGBS actually remove the gap between cement particles and also,
the depth of carbonation from 7, 28, 56 days of a example. Thus, it makes concrete more denser because it
actually reduce carbon dioxide in order to enter to concrete and therefore, carbonation is also improve that
further leads to increase depth of carbonation.
2.2.3 Suplhate resistance
In order to increase the resistance, as compared to Sulphate attack the GGBS concrete is actually
depend upon the percentage in the concrete. Wang and et.al., (2020) also suggested that in order to attain the
optimum resistance, there must be use of 50 to 70% in against to suplhate. Thus, Chakraborty, Bajaj and
Dhanot (2020) GGBS cement may also mitigate the suplhate attack by using three execution such that , by
reducing the transportation of suplhate because of reduction of a permeability and reduce the Calcium
hydroxide that is a origin of a reaction and last is reducing a quantity of Tri- calcium aluminate by dilution .
Saranya, Nagarajan and Shashikala (2020) also support that Suplhate attack can be reduce by
adding GGBS to Portland cement in some ways that is by mix design of involving GGBS in concrete that
reduce Tri- calcium aluminate. Also it s analyzed that GGBS is directly interact with Calcium hydroxide that
also reduce its amount and react suddenly and last is reduction of permeability in GGBS concrete.
2.2.4 Chloride
It is analyzed by Li and et.al., (2020) that the concrete of GGBS clearly shows that if there is more
resistant against chlorides as compared to Portland cement then there must be high quantity of GGBS that will
also provide greater resistance in againts to Chlorides.
2.3 the effects of GGBS upon physical properties of Concrete
2.3.1 Colour
Actually the colour of GGBS is off-white which is slightly lighter than cement. This color is only seen when
there percentage of GGBS in concrete is more than 50% only.
2.3.2 Elastic Modulus:
Vengala and et.al., (2020) stated that the effect of GGBS is medium and it also have high strength
because it is directly depend upon the relationship of an elastic modulus as well as comprehensive strength. For
instance, if concrete kept with a standard curing conditions and tehre is a small difference between GGBS as
well as Portland Cement, at that time the concrete also contain GGBS that posses lower elastic modulus while
Portland cement does not have.
Rao, Sravana and Rao (2016) present their views that If the temperature of curing is increases than it
definitely decrease the strength of concrete as well as their elastic modulus, which is true. Moreover, the
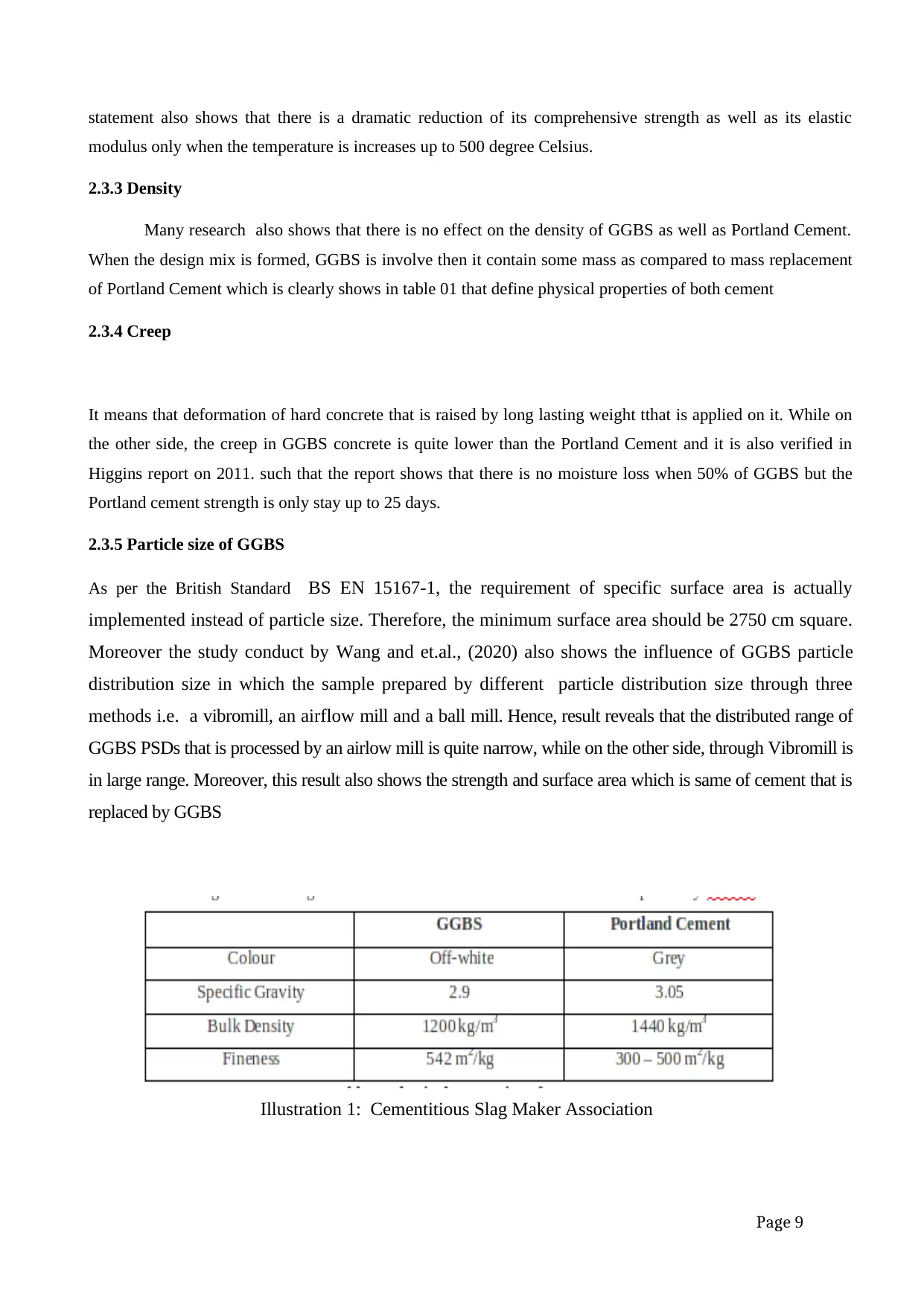
statement also shows that there is a dramatic reduction of its comprehensive strength as well as its elastic
modulus only when the temperature is increases up to 500 degree Celsius.
2.3.3 Density
Many research also shows that there is no effect on the density of GGBS as well as Portland Cement.
When the design mix is formed, GGBS is involve then it contain some mass as compared to mass replacement
of Portland Cement which is clearly shows in table 01 that define physical properties of both cement
2.3.4 Creep
It means that deformation of hard concrete that is raised by long lasting weight tthat is applied on it. While on
the other side, the creep in GGBS concrete is quite lower than the Portland Cement and it is also verified in
Higgins report on 2011. such that the report shows that there is no moisture loss when 50% of GGBS but the
Portland cement strength is only stay up to 25 days.
2.3.5 Particle size of GGBS
As per the British Standard BS EN 15167-1, the requirement of specific surface area is actually
implemented instead of particle size. Therefore, the minimum surface area should be 2750 cm square.
Moreover the study conduct by Wang and et.al., (2020) also shows the influence of GGBS particle
distribution size in which the sample prepared by different particle distribution size through three
methods i.e. a vibromill, an airflow mill and a ball mill. Hence, result reveals that the distributed range of
GGBS PSDs that is processed by an airlow mill is quite narrow, while on the other side, through Vibromill is
in large range. Moreover, this result also shows the strength and surface area which is same of cement that is
replaced by GGBS
Illustration 1: Cementitious Slag Maker Association
⊘ This is a preview!⊘
Do you want full access?
Subscribe today to unlock all pages.

Trusted by 1+ million students worldwide
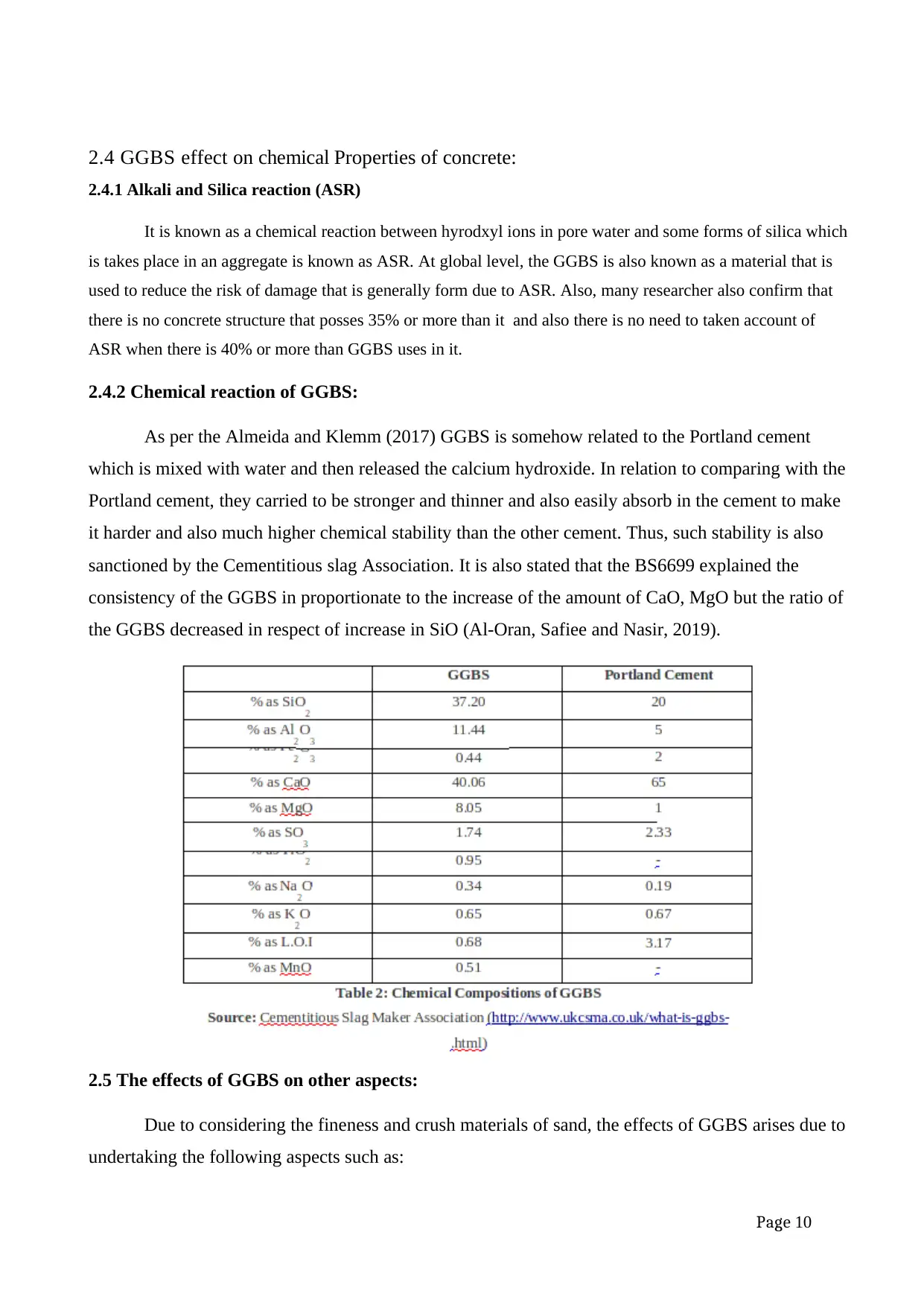
2.4 GGBS effect on chemical Properties of concrete:
2.4.1 Alkali and Silica reaction (ASR)
It is known as a chemical reaction between hyrodxyl ions in pore water and some forms of silica which
is takes place in an aggregate is known as ASR. At global level, the GGBS is also known as a material that is
used to reduce the risk of damage that is generally form due to ASR. Also, many researcher also confirm that
there is no concrete structure that posses 35% or more than it and also there is no need to taken account of
ASR when there is 40% or more than GGBS uses in it.
2.4.2 Chemical reaction of GGBS:
As per the Almeida and Klemm (2017) GGBS is somehow related to the Portland cement
which is mixed with water and then released the calcium hydroxide. In relation to comparing with the
Portland cement, they carried to be stronger and thinner and also easily absorb in the cement to make
it harder and also much higher chemical stability than the other cement. Thus, such stability is also
sanctioned by the Cementitious slag Association. It is also stated that the BS6699 explained the
consistency of the GGBS in proportionate to the increase of the amount of CaO, MgO but the ratio of
the GGBS decreased in respect of increase in SiO (Al-Oran, Safiee and Nasir, 2019).
2.5 The effects of GGBS on other aspects:
Due to considering the fineness and crush materials of sand, the effects of GGBS arises due to
undertaking the following aspects such as:
Paraphrase This Document
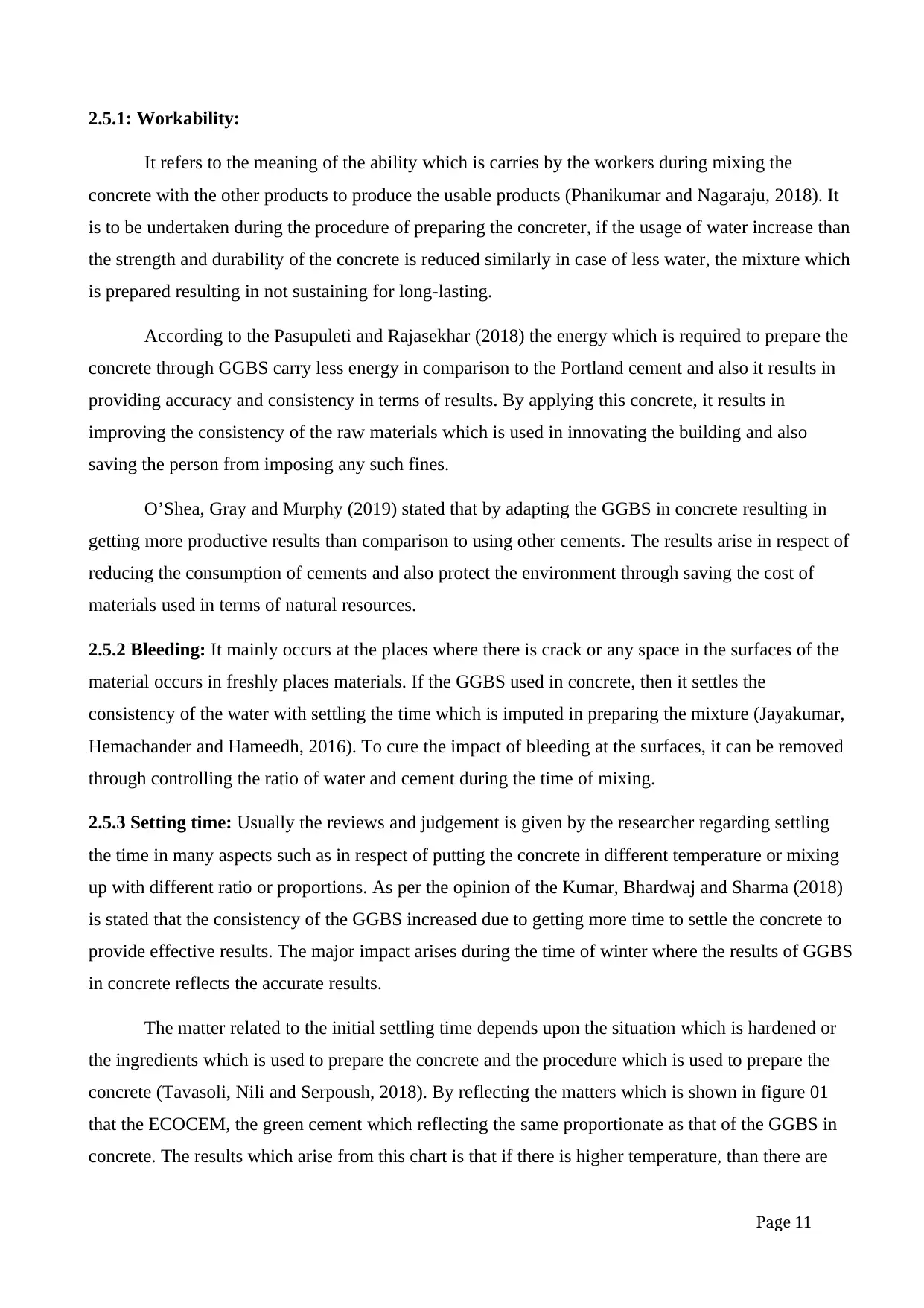
2.5.1: Workability:
It refers to the meaning of the ability which is carries by the workers during mixing the
concrete with the other products to produce the usable products (Phanikumar and Nagaraju, 2018). It
is to be undertaken during the procedure of preparing the concreter, if the usage of water increase than
the strength and durability of the concrete is reduced similarly in case of less water, the mixture which
is prepared resulting in not sustaining for long-lasting.
According to the Pasupuleti and Rajasekhar (2018) the energy which is required to prepare the
concrete through GGBS carry less energy in comparison to the Portland cement and also it results in
providing accuracy and consistency in terms of results. By applying this concrete, it results in
improving the consistency of the raw materials which is used in innovating the building and also
saving the person from imposing any such fines.
O’Shea, Gray and Murphy (2019) stated that by adapting the GGBS in concrete resulting in
getting more productive results than comparison to using other cements. The results arise in respect of
reducing the consumption of cements and also protect the environment through saving the cost of
materials used in terms of natural resources.
2.5.2 Bleeding: It mainly occurs at the places where there is crack or any space in the surfaces of the
material occurs in freshly places materials. If the GGBS used in concrete, then it settles the
consistency of the water with settling the time which is imputed in preparing the mixture (Jayakumar,
Hemachander and Hameedh, 2016). To cure the impact of bleeding at the surfaces, it can be removed
through controlling the ratio of water and cement during the time of mixing.
2.5.3 Setting time: Usually the reviews and judgement is given by the researcher regarding settling
the time in many aspects such as in respect of putting the concrete in different temperature or mixing
up with different ratio or proportions. As per the opinion of the Kumar, Bhardwaj and Sharma (2018)
is stated that the consistency of the GGBS increased due to getting more time to settle the concrete to
provide effective results. The major impact arises during the time of winter where the results of GGBS
in concrete reflects the accurate results.
The matter related to the initial settling time depends upon the situation which is hardened or
the ingredients which is used to prepare the concrete and the procedure which is used to prepare the
concrete (Tavasoli, Nili and Serpoush, 2018). By reflecting the matters which is shown in figure 01
that the ECOCEM, the green cement which reflecting the same proportionate as that of the GGBS in
concrete. The results which arise from this chart is that if there is higher temperature, than there are
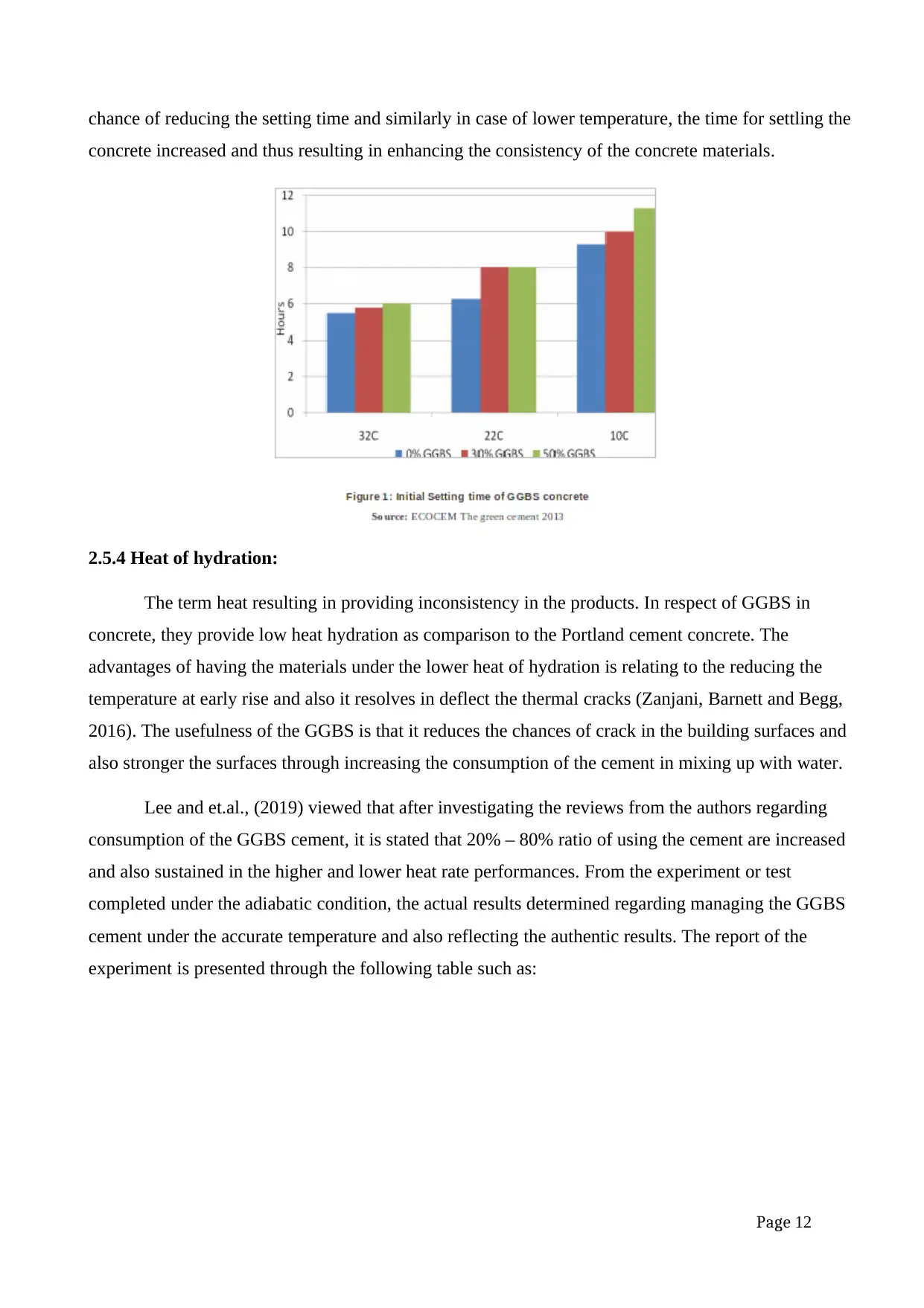
chance of reducing the setting time and similarly in case of lower temperature, the time for settling the
concrete increased and thus resulting in enhancing the consistency of the concrete materials.
2.5.4 Heat of hydration:
The term heat resulting in providing inconsistency in the products. In respect of GGBS in
concrete, they provide low heat hydration as comparison to the Portland cement concrete. The
advantages of having the materials under the lower heat of hydration is relating to the reducing the
temperature at early rise and also it resolves in deflect the thermal cracks (Zanjani, Barnett and Begg,
2016). The usefulness of the GGBS is that it reduces the chances of crack in the building surfaces and
also stronger the surfaces through increasing the consumption of the cement in mixing up with water.
Lee and et.al., (2019) viewed that after investigating the reviews from the authors regarding
consumption of the GGBS cement, it is stated that 20% – 80% ratio of using the cement are increased
and also sustained in the higher and lower heat rate performances. From the experiment or test
completed under the adiabatic condition, the actual results determined regarding managing the GGBS
cement under the accurate temperature and also reflecting the authentic results. The report of the
experiment is presented through the following table such as:
⊘ This is a preview!⊘
Do you want full access?
Subscribe today to unlock all pages.

Trusted by 1+ million students worldwide
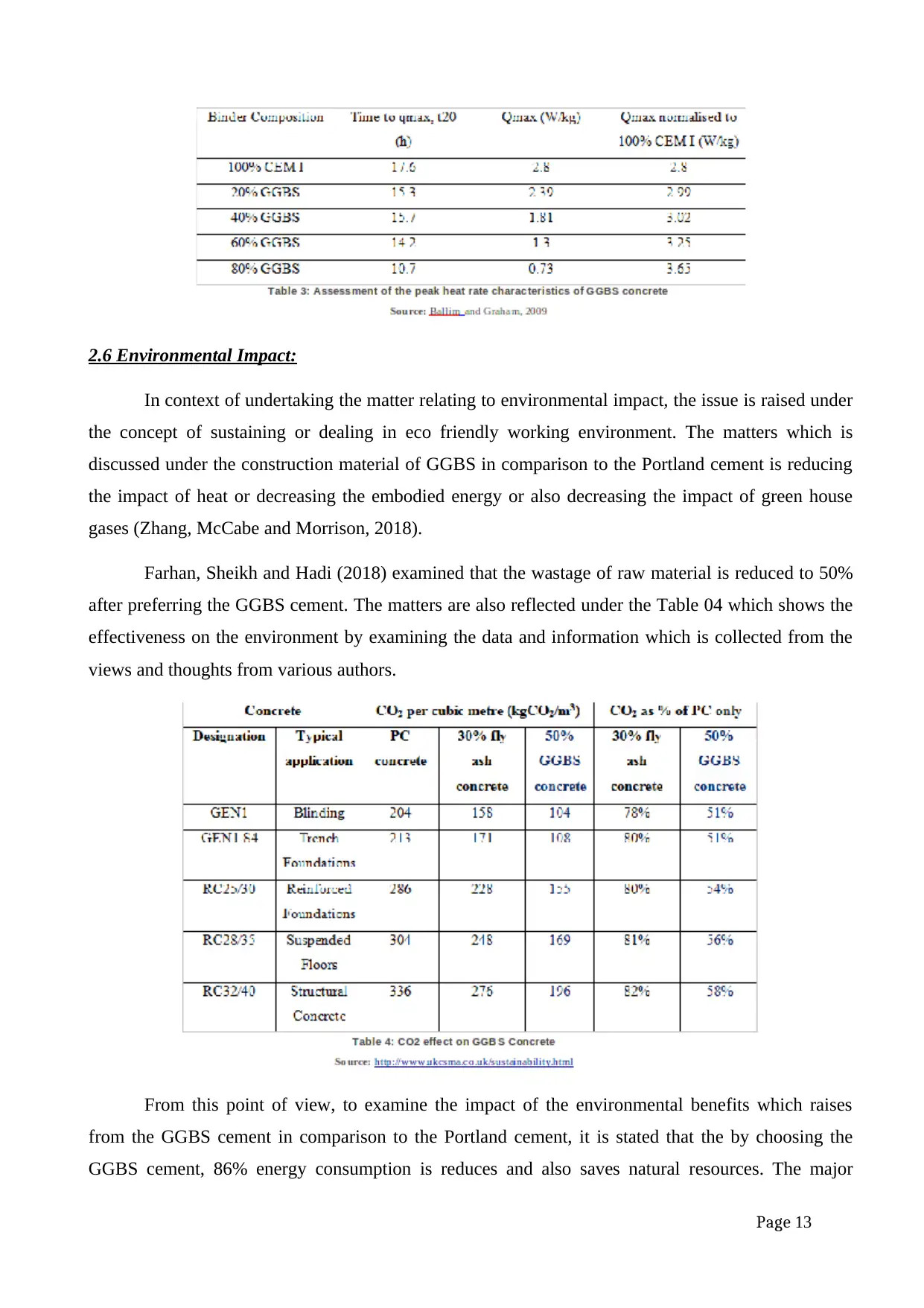
2.6 Environmental Impact:
In context of undertaking the matter relating to environmental impact, the issue is raised under
the concept of sustaining or dealing in eco friendly working environment. The matters which is
discussed under the construction material of GGBS in comparison to the Portland cement is reducing
the impact of heat or decreasing the embodied energy or also decreasing the impact of green house
gases (Zhang, McCabe and Morrison, 2018).
Farhan, Sheikh and Hadi (2018) examined that the wastage of raw material is reduced to 50%
after preferring the GGBS cement. The matters are also reflected under the Table 04 which shows the
effectiveness on the environment by examining the data and information which is collected from the
views and thoughts from various authors.
From this point of view, to examine the impact of the environmental benefits which raises
from the GGBS cement in comparison to the Portland cement, it is stated that the by choosing the
GGBS cement, 86% energy consumption is reduces and also saves natural resources. The major
Paraphrase This Document
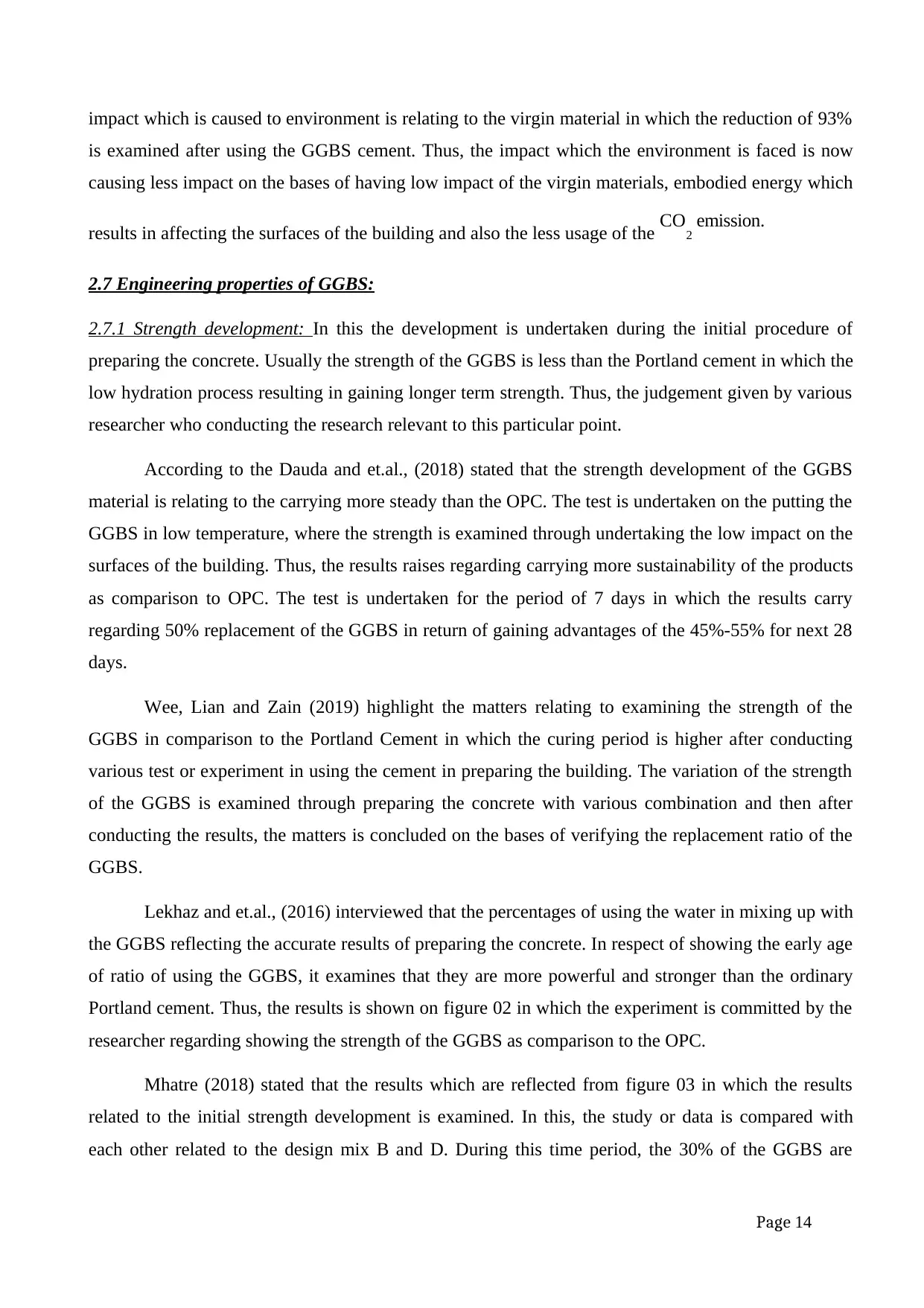
impact which is caused to environment is relating to the virgin material in which the reduction of 93%
is examined after using the GGBS cement. Thus, the impact which the environment is faced is now
causing less impact on the bases of having low impact of the virgin materials, embodied energy which
results in affecting the surfaces of the building and also the less usage of the CO2 emission.
2.7 Engineering properties of GGBS:
2.7.1 Strength development: In this the development is undertaken during the initial procedure of
preparing the concrete. Usually the strength of the GGBS is less than the Portland cement in which the
low hydration process resulting in gaining longer term strength. Thus, the judgement given by various
researcher who conducting the research relevant to this particular point.
According to the Dauda and et.al., (2018) stated that the strength development of the GGBS
material is relating to the carrying more steady than the OPC. The test is undertaken on the putting the
GGBS in low temperature, where the strength is examined through undertaking the low impact on the
surfaces of the building. Thus, the results raises regarding carrying more sustainability of the products
as comparison to OPC. The test is undertaken for the period of 7 days in which the results carry
regarding 50% replacement of the GGBS in return of gaining advantages of the 45%-55% for next 28
days.
Wee, Lian and Zain (2019) highlight the matters relating to examining the strength of the
GGBS in comparison to the Portland Cement in which the curing period is higher after conducting
various test or experiment in using the cement in preparing the building. The variation of the strength
of the GGBS is examined through preparing the concrete with various combination and then after
conducting the results, the matters is concluded on the bases of verifying the replacement ratio of the
GGBS.
Lekhaz and et.al., (2016) interviewed that the percentages of using the water in mixing up with
the GGBS reflecting the accurate results of preparing the concrete. In respect of showing the early age
of ratio of using the GGBS, it examines that they are more powerful and stronger than the ordinary
Portland cement. Thus, the results is shown on figure 02 in which the experiment is committed by the
researcher regarding showing the strength of the GGBS as comparison to the OPC.
Mhatre (2018) stated that the results which are reflected from figure 03 in which the results
related to the initial strength development is examined. In this, the study or data is compared with
each other related to the design mix B and D. During this time period, the 30% of the GGBS are
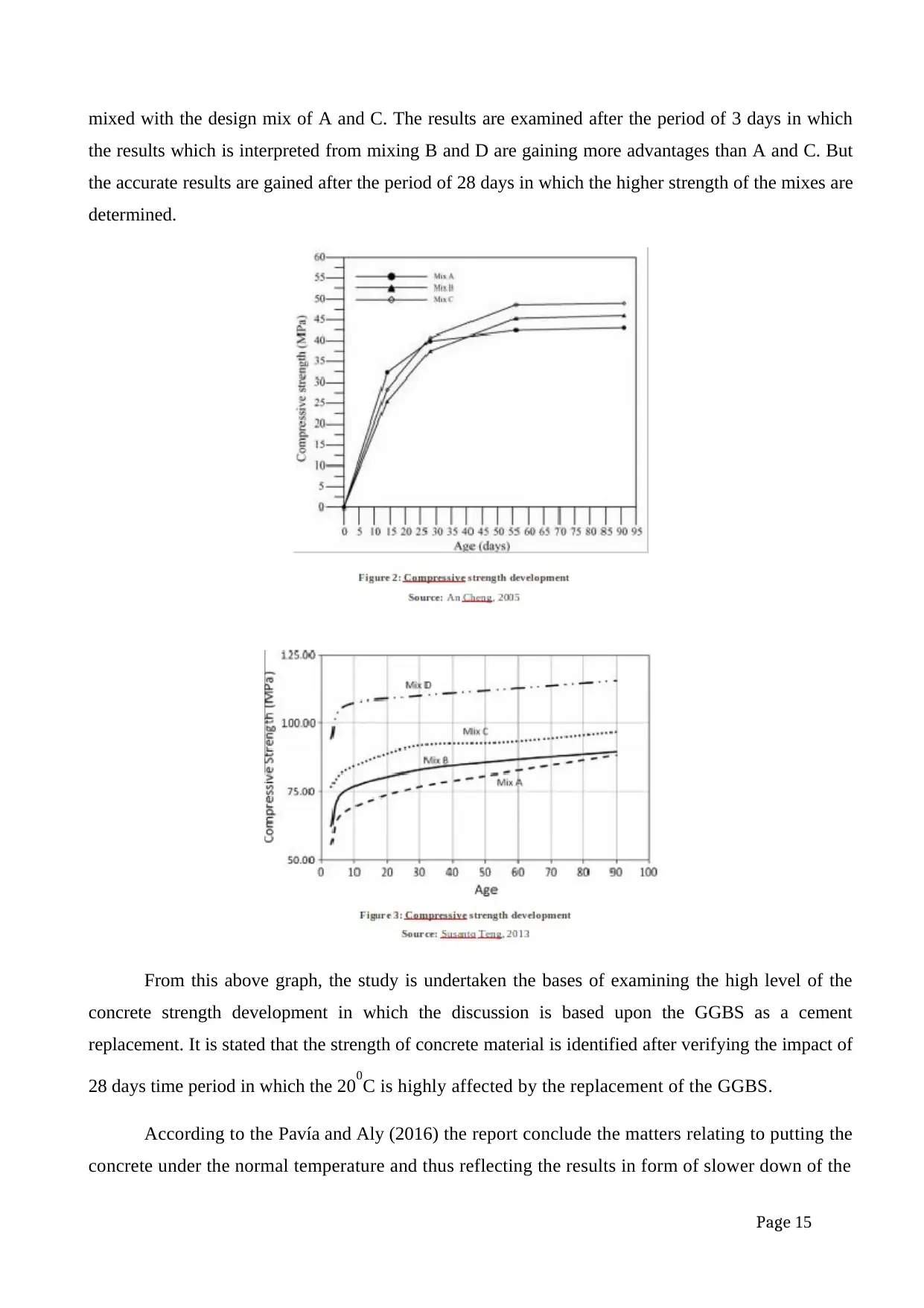
mixed with the design mix of A and C. The results are examined after the period of 3 days in which
the results which is interpreted from mixing B and D are gaining more advantages than A and C. But
the accurate results are gained after the period of 28 days in which the higher strength of the mixes are
determined.
From this above graph, the study is undertaken the bases of examining the high level of the
concrete strength development in which the discussion is based upon the GGBS as a cement
replacement. It is stated that the strength of concrete material is identified after verifying the impact of
28 days time period in which the 200
C is highly affected by the replacement of the GGBS.
According to the Pavía and Aly (2016) the report conclude the matters relating to putting the
concrete under the normal temperature and thus reflecting the results in form of slower down of the
⊘ This is a preview!⊘
Do you want full access?
Subscribe today to unlock all pages.

Trusted by 1+ million students worldwide
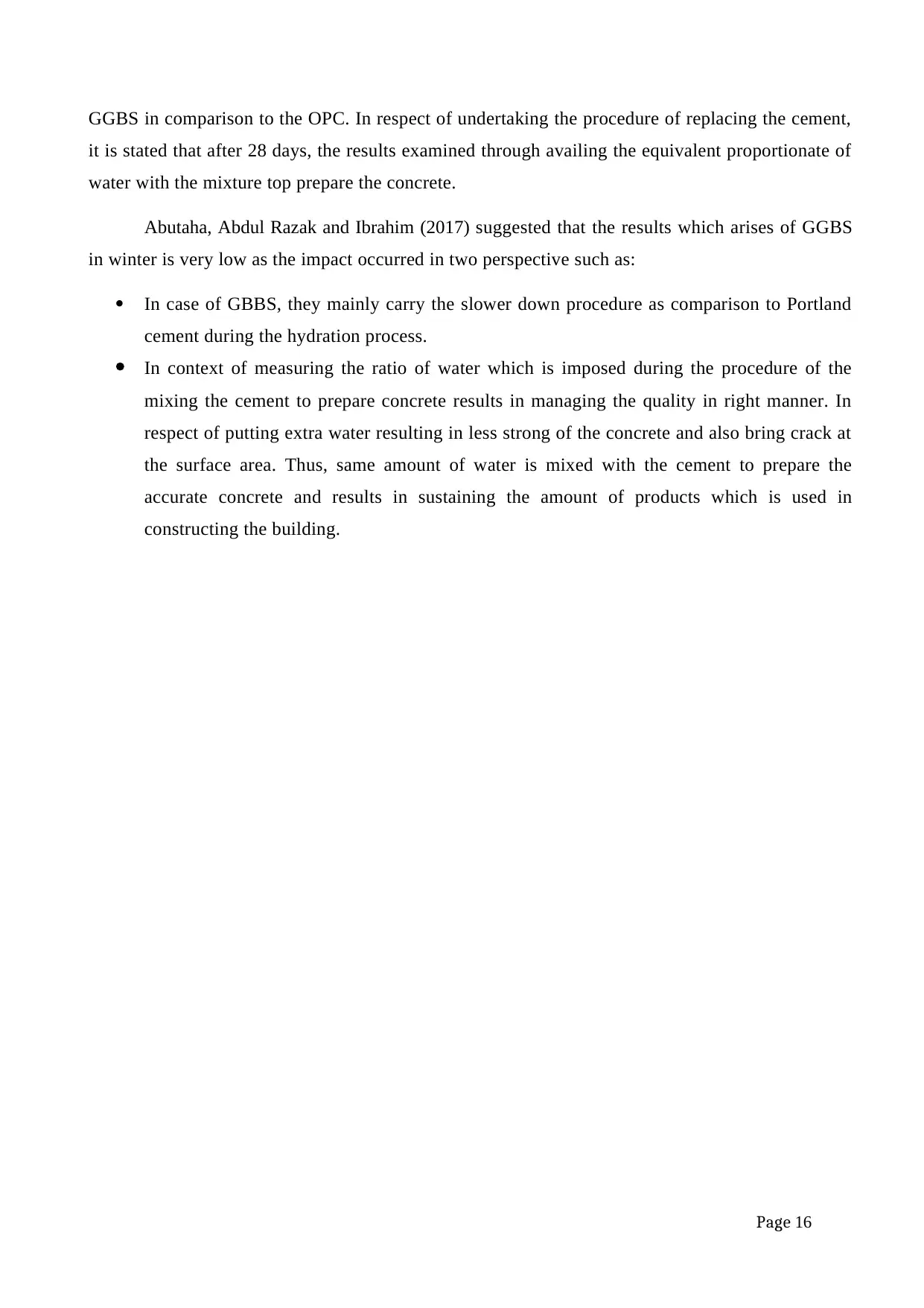
GGBS in comparison to the OPC. In respect of undertaking the procedure of replacing the cement,
it is stated that after 28 days, the results examined through availing the equivalent proportionate of
water with the mixture top prepare the concrete.
Abutaha, Abdul Razak and Ibrahim (2017) suggested that the results which arises of GGBS
in winter is very low as the impact occurred in two perspective such as:
In case of GBBS, they mainly carry the slower down procedure as comparison to Portland
cement during the hydration process.
In context of measuring the ratio of water which is imposed during the procedure of the
mixing the cement to prepare concrete results in managing the quality in right manner. In
respect of putting extra water resulting in less strong of the concrete and also bring crack at
the surface area. Thus, same amount of water is mixed with the cement to prepare the
accurate concrete and results in sustaining the amount of products which is used in
constructing the building.
Paraphrase This Document
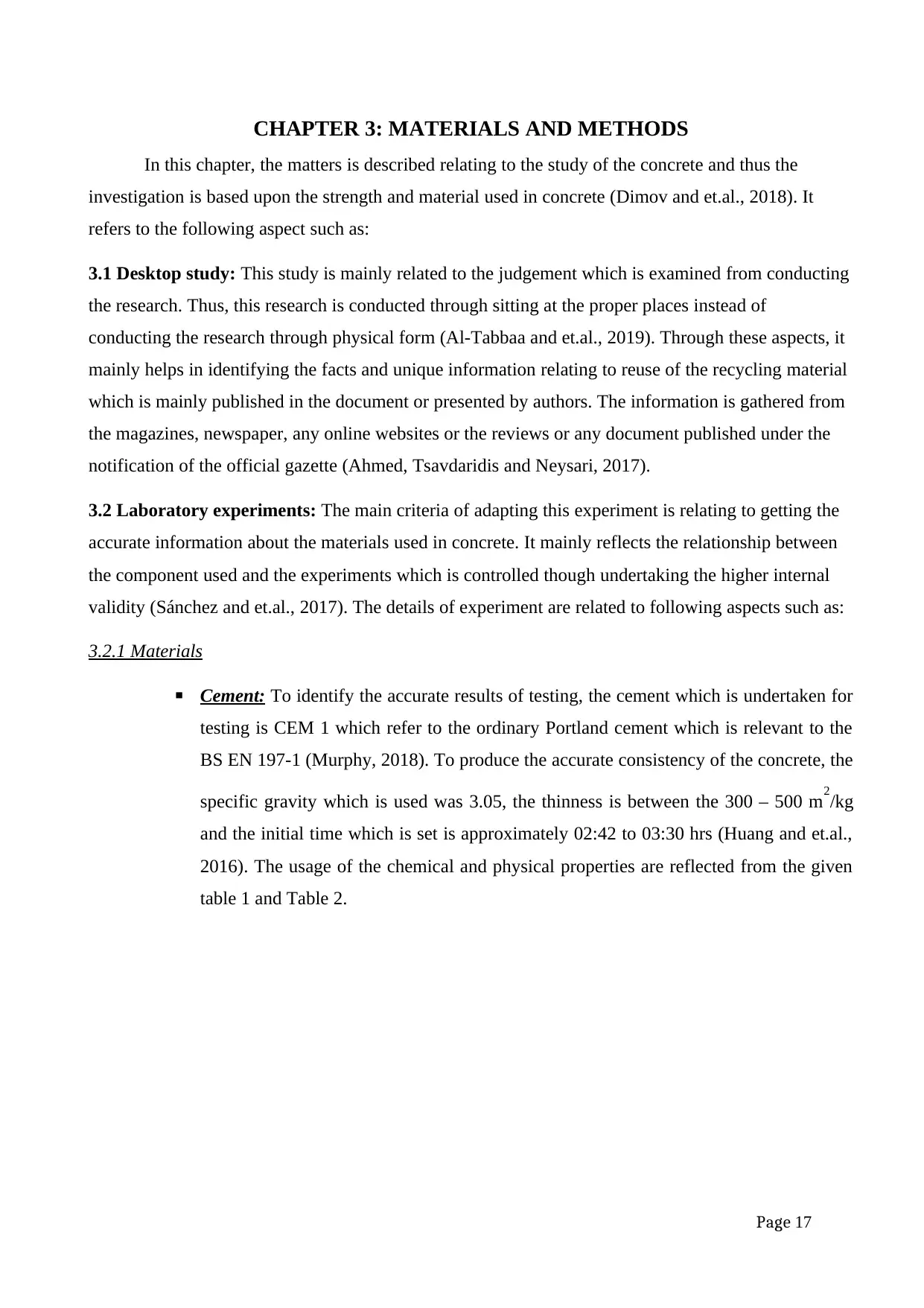
CHAPTER 3: MATERIALS AND METHODS
In this chapter, the matters is described relating to the study of the concrete and thus the
investigation is based upon the strength and material used in concrete (Dimov and et.al., 2018). It
refers to the following aspect such as:
3.1 Desktop study: This study is mainly related to the judgement which is examined from conducting
the research. Thus, this research is conducted through sitting at the proper places instead of
conducting the research through physical form (Al-Tabbaa and et.al., 2019). Through these aspects, it
mainly helps in identifying the facts and unique information relating to reuse of the recycling material
which is mainly published in the document or presented by authors. The information is gathered from
the magazines, newspaper, any online websites or the reviews or any document published under the
notification of the official gazette (Ahmed, Tsavdaridis and Neysari, 2017).
3.2 Laboratory experiments: The main criteria of adapting this experiment is relating to getting the
accurate information about the materials used in concrete. It mainly reflects the relationship between
the component used and the experiments which is controlled though undertaking the higher internal
validity (Sánchez and et.al., 2017). The details of experiment are related to following aspects such as:
3.2.1 Materials
▪ Cement: To identify the accurate results of testing, the cement which is undertaken for
testing is CEM 1 which refer to the ordinary Portland cement which is relevant to the
BS EN 197-1 (Murphy, 2018). To produce the accurate consistency of the concrete, the
specific gravity which is used was 3.05, the thinness is between the 300 – 500 m2
/kg
and the initial time which is set is approximately 02:42 to 03:30 hrs (Huang and et.al.,
2016). The usage of the chemical and physical properties are reflected from the given
table 1 and Table 2.
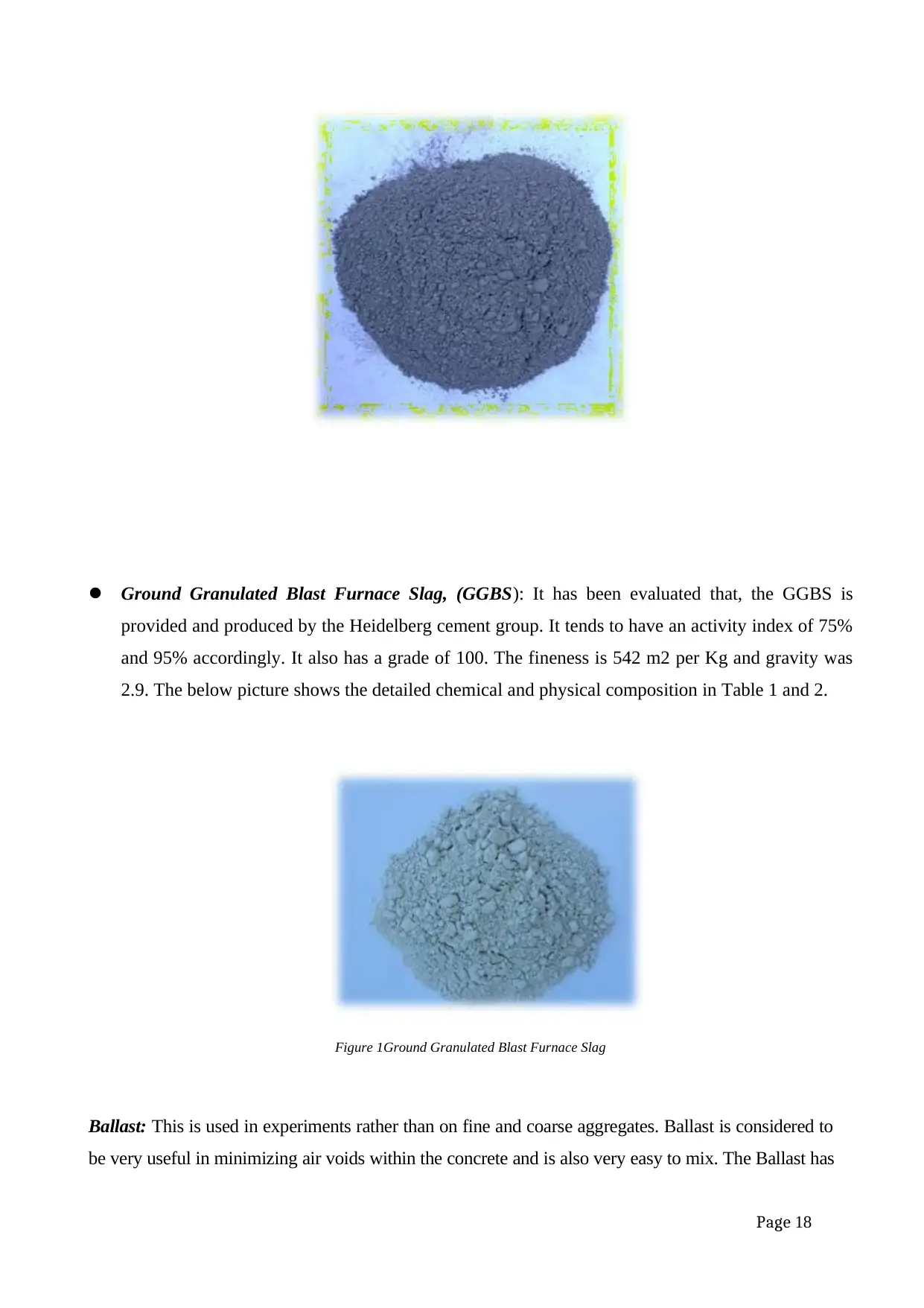
Ground Granulated Blast Furnace Slag, (GGBS): It has been evaluated that, the GGBS is
provided and produced by the Heidelberg cement group. It tends to have an activity index of 75%
and 95% accordingly. It also has a grade of 100. The fineness is 542 m2 per Kg and gravity was
2.9. The below picture shows the detailed chemical and physical composition in Table 1 and 2.
Figure 1Ground Granulated Blast Furnace Slag
Ballast: This is used in experiments rather than on fine and coarse aggregates. Ballast is considered to
be very useful in minimizing air voids within the concrete and is also very easy to mix. The Ballast has
⊘ This is a preview!⊘
Do you want full access?
Subscribe today to unlock all pages.

Trusted by 1+ million students worldwide
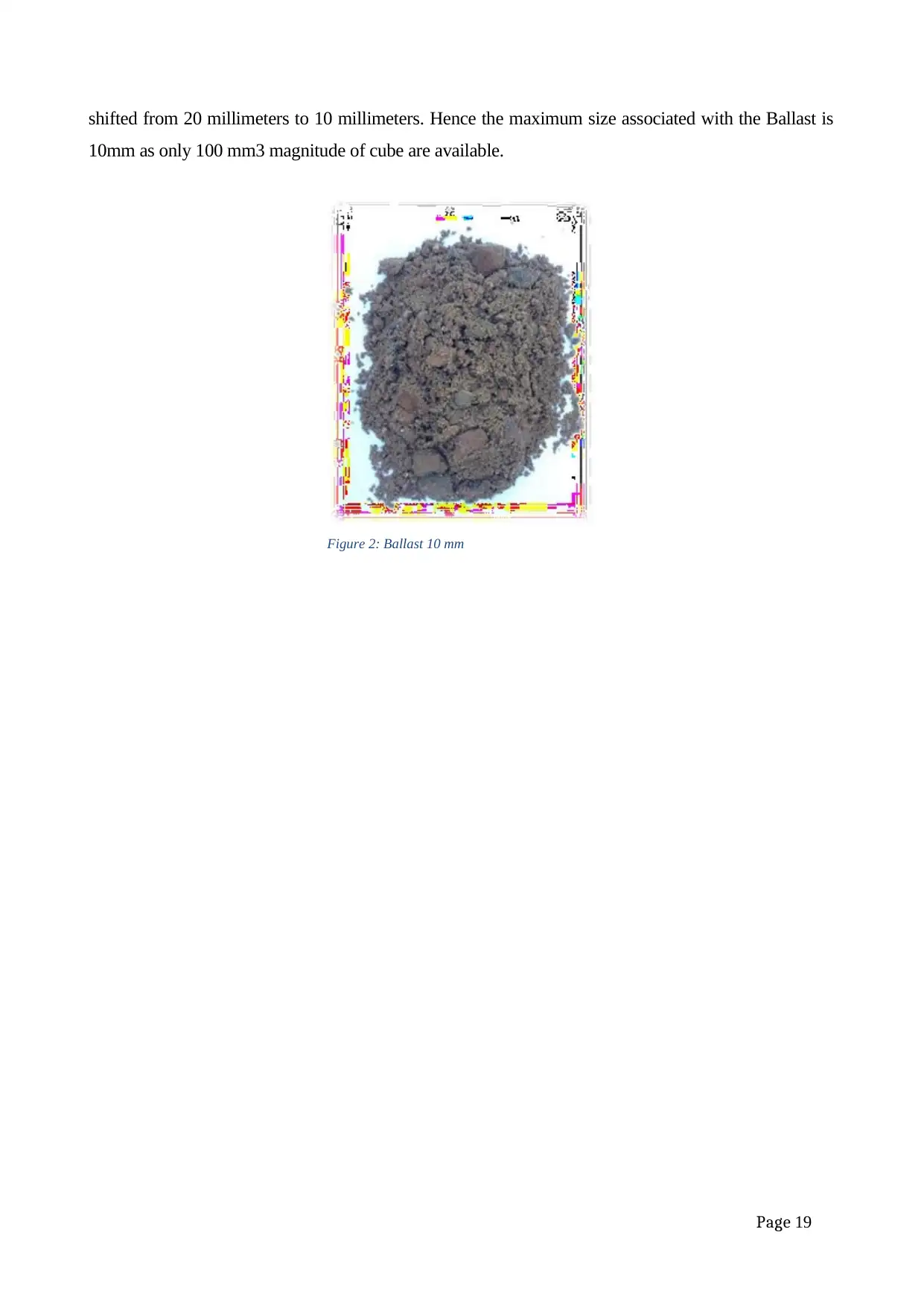
Page 19
shifted from 20 millimeters to 10 millimeters. Hence the maximum size associated with the Ballast is
10mm as only 100 mm3 magnitude of cube are available.
Paraphrase This Document
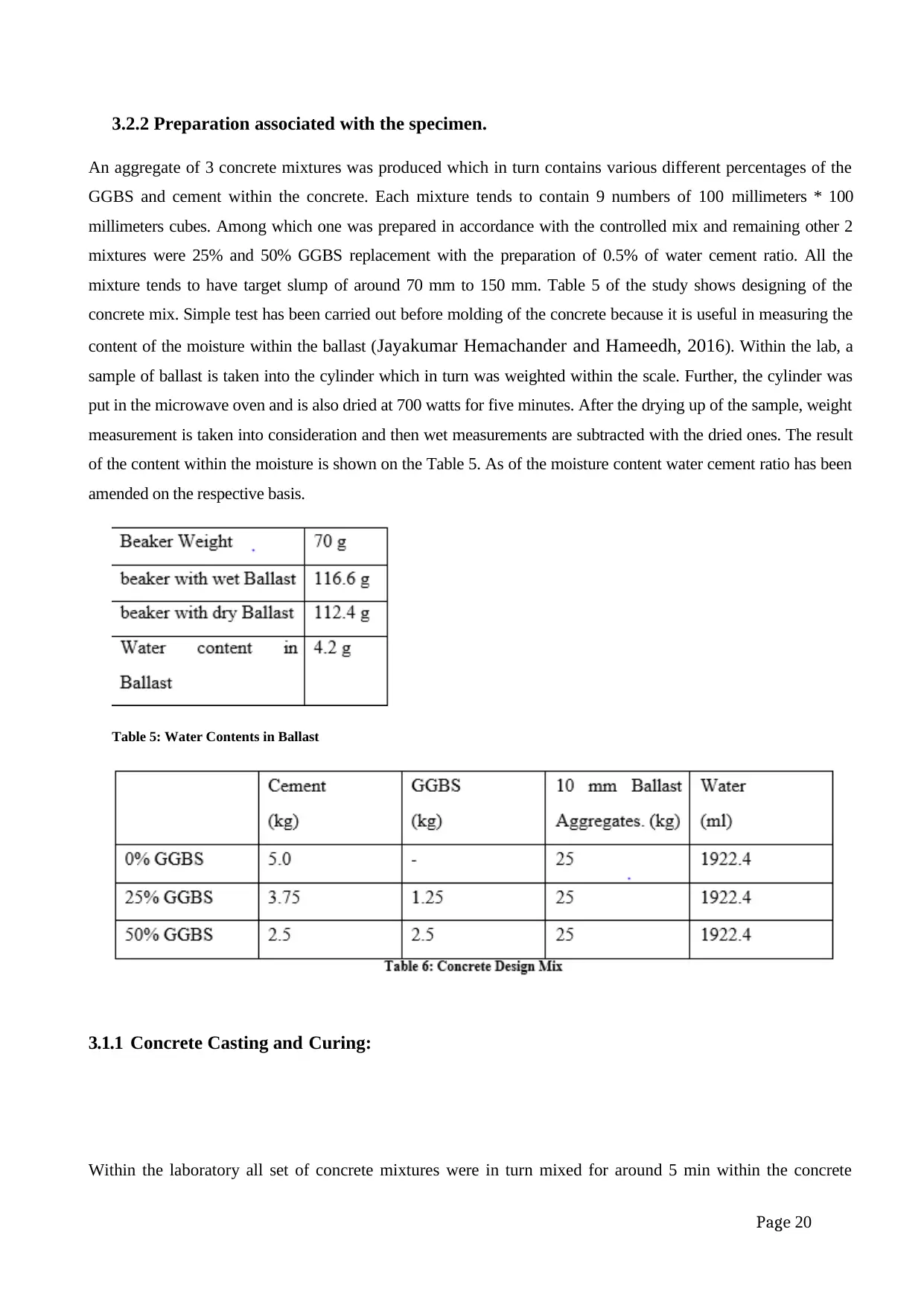
3.2.2 Preparation associated with the specimen.
An aggregate of 3 concrete mixtures was produced which in turn contains various different percentages of the
GGBS and cement within the concrete. Each mixture tends to contain 9 numbers of 100 millimeters * 100
millimeters cubes. Among which one was prepared in accordance with the controlled mix and remaining other 2
mixtures were 25% and 50% GGBS replacement with the preparation of 0.5% of water cement ratio. All the
mixture tends to have target slump of around 70 mm to 150 mm. Table 5 of the study shows designing of the
concrete mix. Simple test has been carried out before molding of the concrete because it is useful in measuring the
content of the moisture within the ballast (Jayakumar Hemachander and Hameedh, 2016). Within the lab, a
sample of ballast is taken into the cylinder which in turn was weighted within the scale. Further, the cylinder was
put in the microwave oven and is also dried at 700 watts for five minutes. After the drying up of the sample, weight
measurement is taken into consideration and then wet measurements are subtracted with the dried ones. The result
of the content within the moisture is shown on the Table 5. As of the moisture content water cement ratio has been
amended on the respective basis.
Table 5: Water Contents in Ballast
3.1.1 Concrete Casting and Curing:
Within the laboratory all set of concrete mixtures were in turn mixed for around 5 min within the concrete
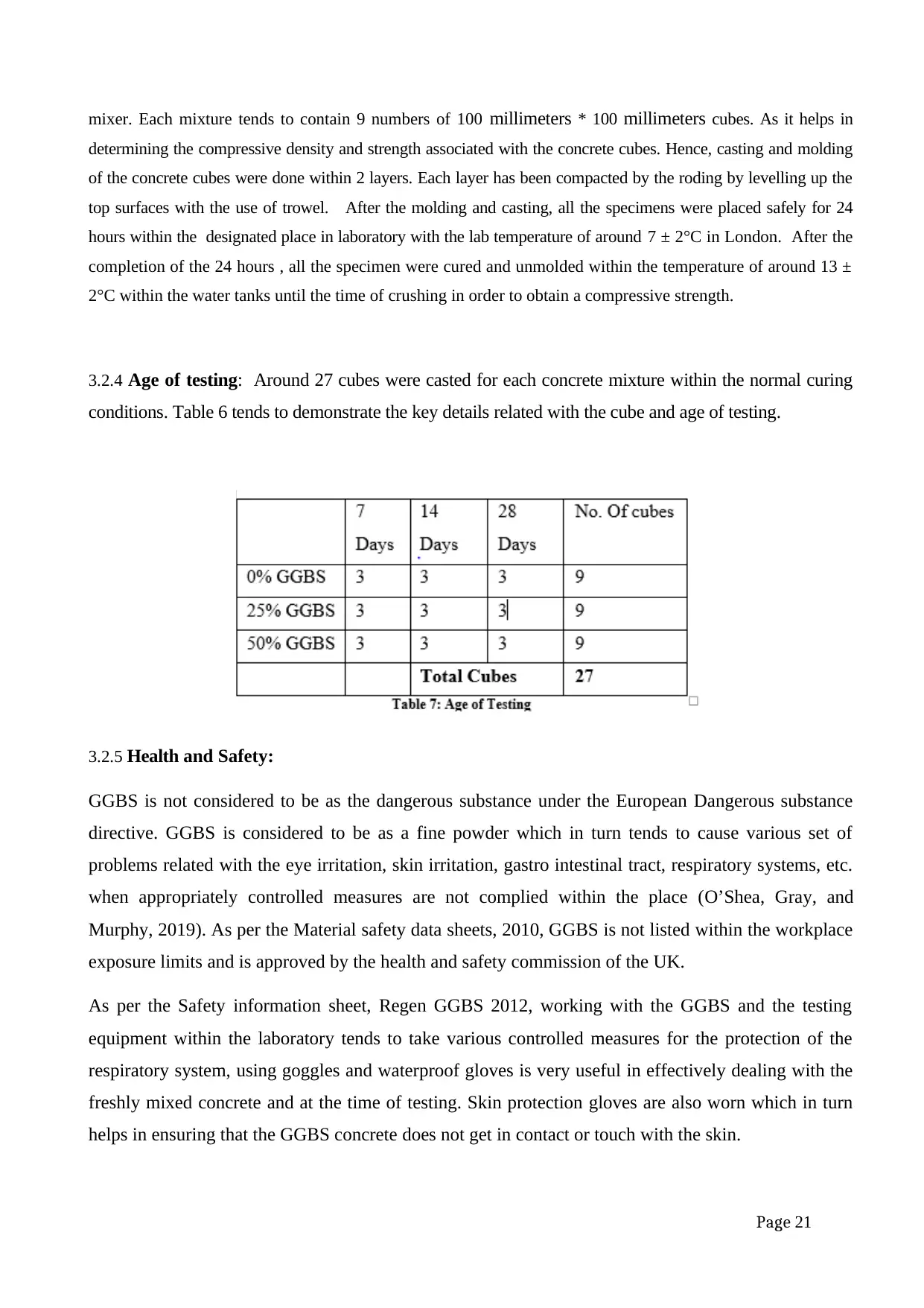
mixer. Each mixture tends to contain 9 numbers of 100 millimeters * 100 millimeters cubes. As it helps in
determining the compressive density and strength associated with the concrete cubes. Hence, casting and molding
of the concrete cubes were done within 2 layers. Each layer has been compacted by the roding by levelling up the
top surfaces with the use of trowel. After the molding and casting, all the specimens were placed safely for 24
hours within the designated place in laboratory with the lab temperature of around 7 ± 2°C in London. After the
completion of the 24 hours , all the specimen were cured and unmolded within the temperature of around 13 ±
2°C within the water tanks until the time of crushing in order to obtain a compressive strength.
3.2.4 Age of testing: Around 27 cubes were casted for each concrete mixture within the normal curing
conditions. Table 6 tends to demonstrate the key details related with the cube and age of testing.
3.2.5 Health and Safety:
GGBS is not considered to be as the dangerous substance under the European Dangerous substance
directive. GGBS is considered to be as a fine powder which in turn tends to cause various set of
problems related with the eye irritation, skin irritation, gastro intestinal tract, respiratory systems, etc.
when appropriately controlled measures are not complied within the place (O’Shea, Gray, and
Murphy, 2019). As per the Material safety data sheets, 2010, GGBS is not listed within the workplace
exposure limits and is approved by the health and safety commission of the UK.
As per the Safety information sheet, Regen GGBS 2012, working with the GGBS and the testing
equipment within the laboratory tends to take various controlled measures for the protection of the
respiratory system, using goggles and waterproof gloves is very useful in effectively dealing with the
freshly mixed concrete and at the time of testing. Skin protection gloves are also worn which in turn
helps in ensuring that the GGBS concrete does not get in contact or touch with the skin.
⊘ This is a preview!⊘
Do you want full access?
Subscribe today to unlock all pages.

Trusted by 1+ million students worldwide
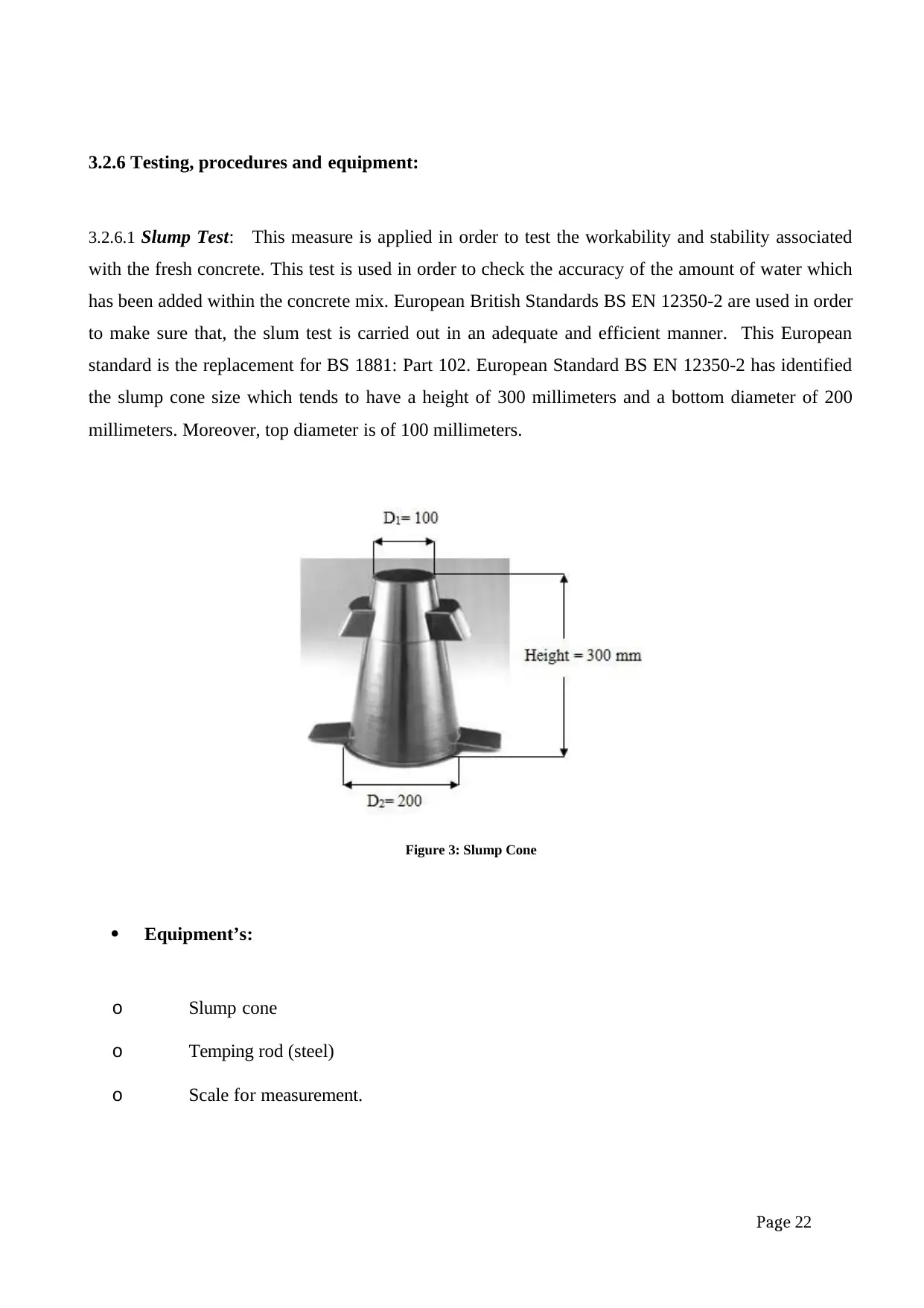
3.2.6 Testing, procedures and equipment:
3.2.6.1 Slump Test: This measure is applied in order to test the workability and stability associated
with the fresh concrete. This test is used in order to check the accuracy of the amount of water which
has been added within the concrete mix. European British Standards BS EN 12350-2 are used in order
to make sure that, the slum test is carried out in an adequate and efficient manner. This European
standard is the replacement for BS 1881: Part 102. European Standard BS EN 12350-2 has identified
the slump cone size which tends to have a height of 300 millimeters and a bottom diameter of 200
millimeters. Moreover, top diameter is of 100 millimeters.
Figure 3: Slump Cone
Equipment’s:
o Slump cone
o Temping rod (steel)
o Scale for measurement.
Paraphrase This Document
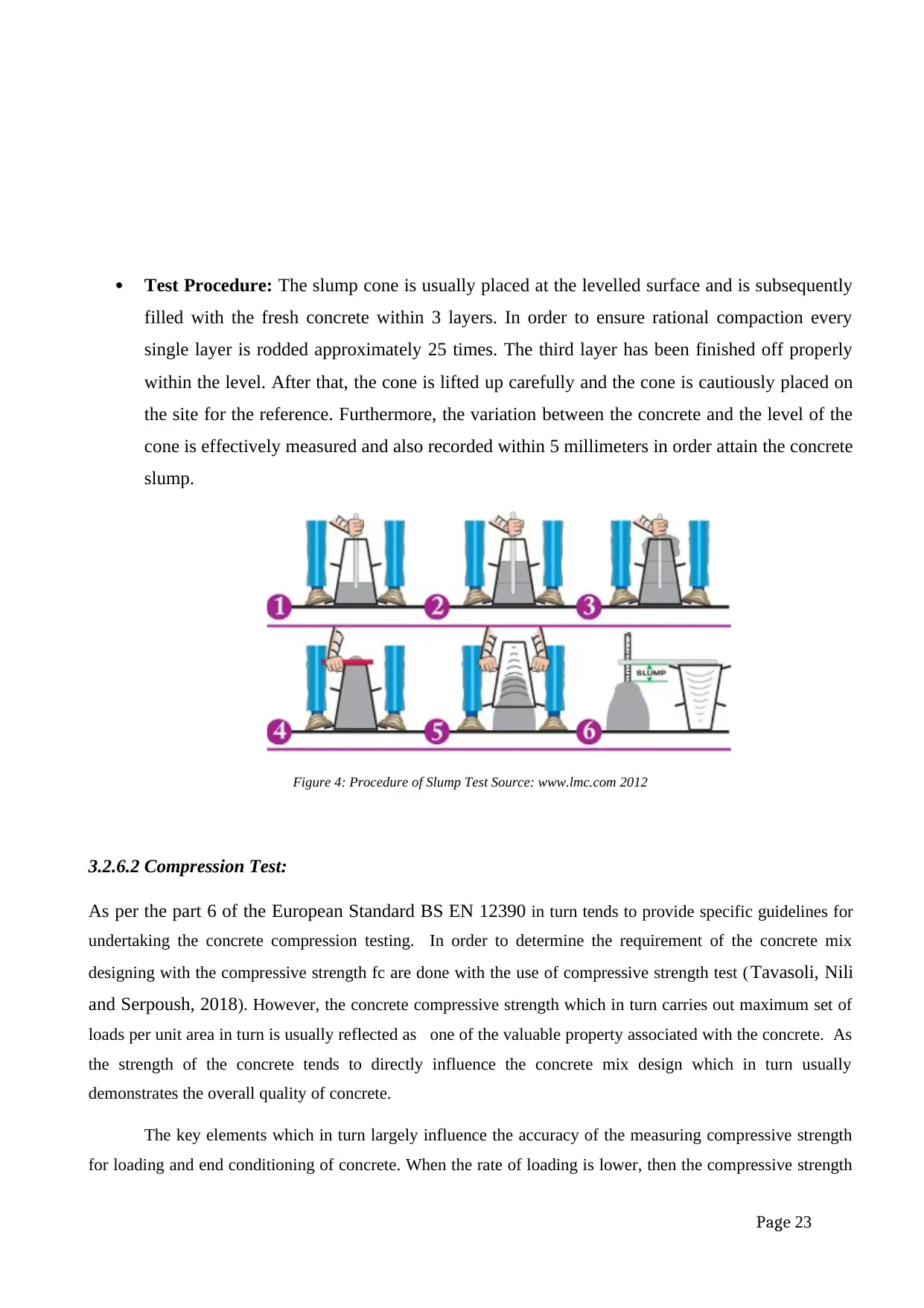
Test Procedure: The slump cone is usually placed at the levelled surface and is subsequently
filled with the fresh concrete within 3 layers. In order to ensure rational compaction every
single layer is rodded approximately 25 times. The third layer has been finished off properly
within the level. After that, the cone is lifted up carefully and the cone is cautiously placed on
the site for the reference. Furthermore, the variation between the concrete and the level of the
cone is effectively measured and also recorded within 5 millimeters in order attain the concrete
slump.
Figure 4: Procedure of Slump Test Source: www.lmc.com 2012
3.2.6.2 Compression Test:
As per the part 6 of the European Standard BS EN 12390 in turn tends to provide specific guidelines for
undertaking the concrete compression testing. In order to determine the requirement of the concrete mix
designing with the compressive strength fc are done with the use of compressive strength test ( Tavasoli, Nili
and Serpoush, 2018). However, the concrete compressive strength which in turn carries out maximum set of
loads per unit area in turn is usually reflected as one of the valuable property associated with the concrete. As
the strength of the concrete tends to directly influence the concrete mix design which in turn usually
demonstrates the overall quality of concrete.
The key elements which in turn largely influence the accuracy of the measuring compressive strength
for loading and end conditioning of concrete. When the rate of loading is lower, then the compressive strength
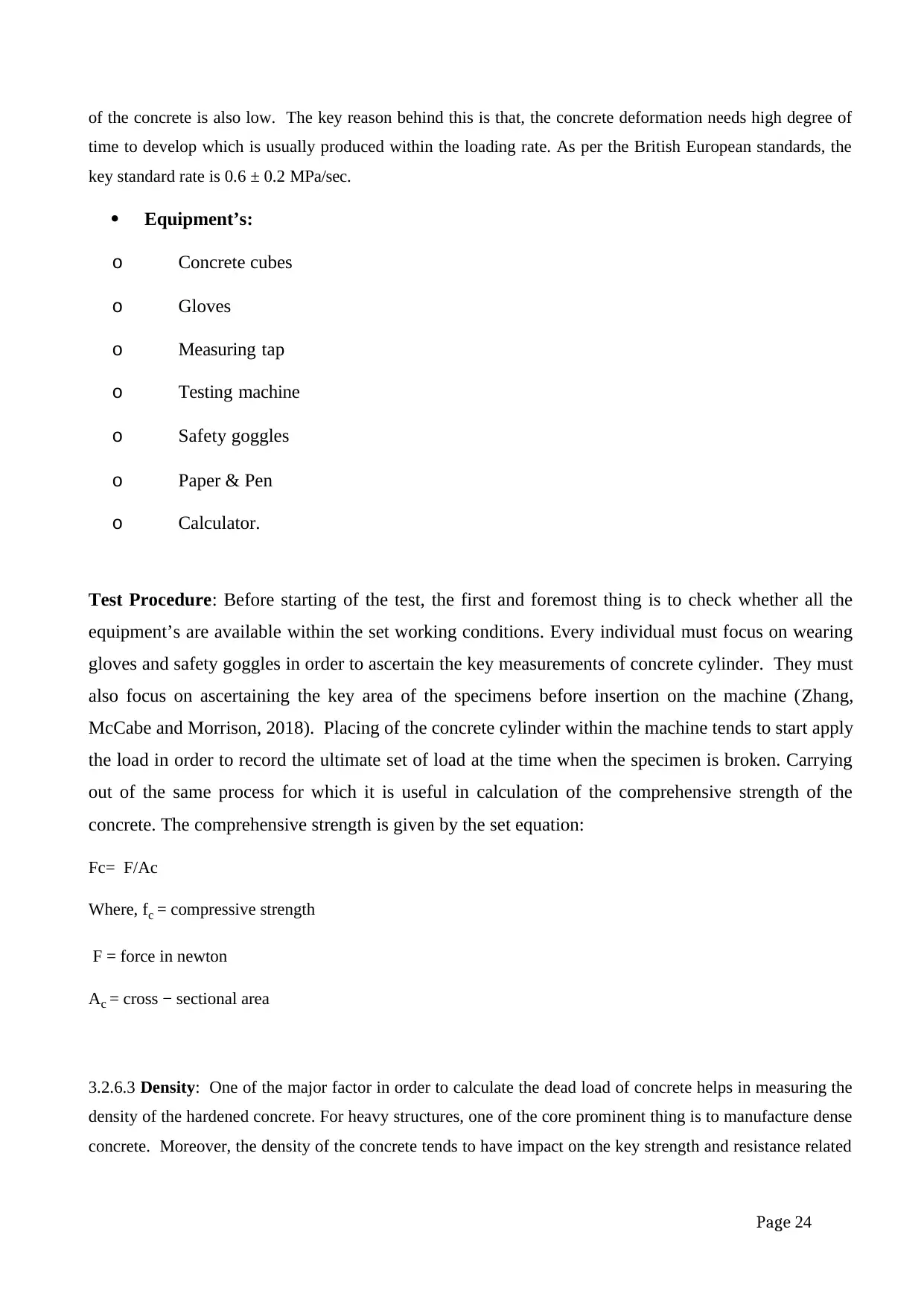
of the concrete is also low. The key reason behind this is that, the concrete deformation needs high degree of
time to develop which is usually produced within the loading rate. As per the British European standards, the
key standard rate is 0.6 ± 0.2 MPa/sec.
Equipment’s:
o Concrete cubes
o Gloves
o Measuring tap
o Testing machine
o Safety goggles
o Paper & Pen
o Calculator.
Test Procedure: Before starting of the test, the first and foremost thing is to check whether all the
equipment’s are available within the set working conditions. Every individual must focus on wearing
gloves and safety goggles in order to ascertain the key measurements of concrete cylinder. They must
also focus on ascertaining the key area of the specimens before insertion on the machine (Zhang,
McCabe and Morrison, 2018). Placing of the concrete cylinder within the machine tends to start apply
the load in order to record the ultimate set of load at the time when the specimen is broken. Carrying
out of the same process for which it is useful in calculation of the comprehensive strength of the
concrete. The comprehensive strength is given by the set equation:
Fc= F/Ac
Where, fc = compressive strength
F = force in newton
Ac = cross − sectional area
3.2.6.3 Density: One of the major factor in order to calculate the dead load of concrete helps in measuring the
density of the hardened concrete. For heavy structures, one of the core prominent thing is to manufacture dense
concrete. Moreover, the density of the concrete tends to have impact on the key strength and resistance related
⊘ This is a preview!⊘
Do you want full access?
Subscribe today to unlock all pages.

Trusted by 1+ million students worldwide
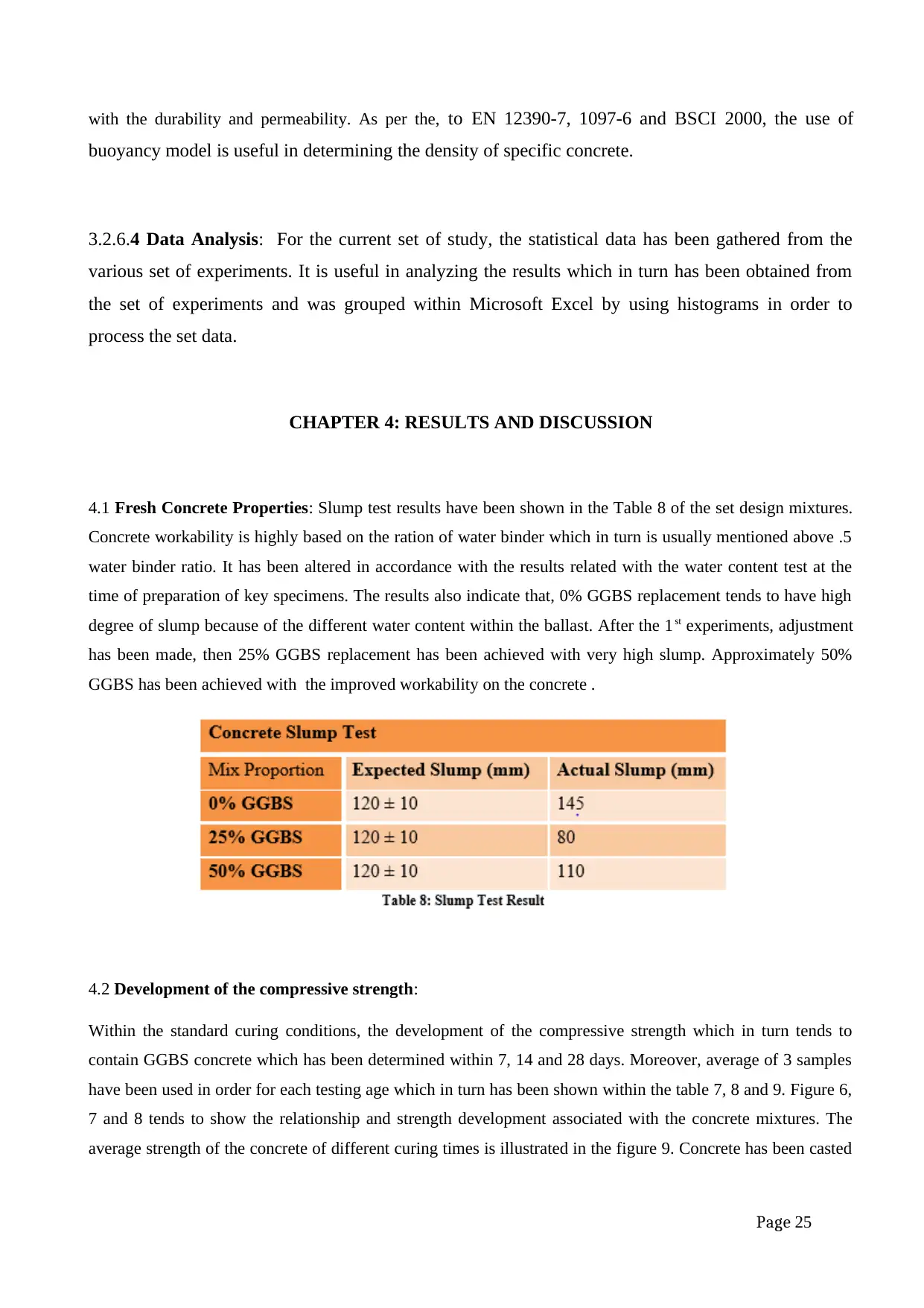
with the durability and permeability. As per the, to EN 12390-7, 1097-6 and BSCI 2000, the use of
buoyancy model is useful in determining the density of specific concrete.
3.2.6.4 Data Analysis: For the current set of study, the statistical data has been gathered from the
various set of experiments. It is useful in analyzing the results which in turn has been obtained from
the set of experiments and was grouped within Microsoft Excel by using histograms in order to
process the set data.
CHAPTER 4: RESULTS AND DISCUSSION
4.1 Fresh Concrete Properties: Slump test results have been shown in the Table 8 of the set design mixtures.
Concrete workability is highly based on the ration of water binder which in turn is usually mentioned above .5
water binder ratio. It has been altered in accordance with the results related with the water content test at the
time of preparation of key specimens. The results also indicate that, 0% GGBS replacement tends to have high
degree of slump because of the different water content within the ballast. After the 1st experiments, adjustment
has been made, then 25% GGBS replacement has been achieved with very high slump. Approximately 50%
GGBS has been achieved with the improved workability on the concrete .
4.2 Development of the compressive strength:
Within the standard curing conditions, the development of the compressive strength which in turn tends to
contain GGBS concrete which has been determined within 7, 14 and 28 days. Moreover, average of 3 samples
have been used in order for each testing age which in turn has been shown within the table 7, 8 and 9. Figure 6,
7 and 8 tends to show the relationship and strength development associated with the concrete mixtures. The
average strength of the concrete of different curing times is illustrated in the figure 9. Concrete has been casted
Paraphrase This Document
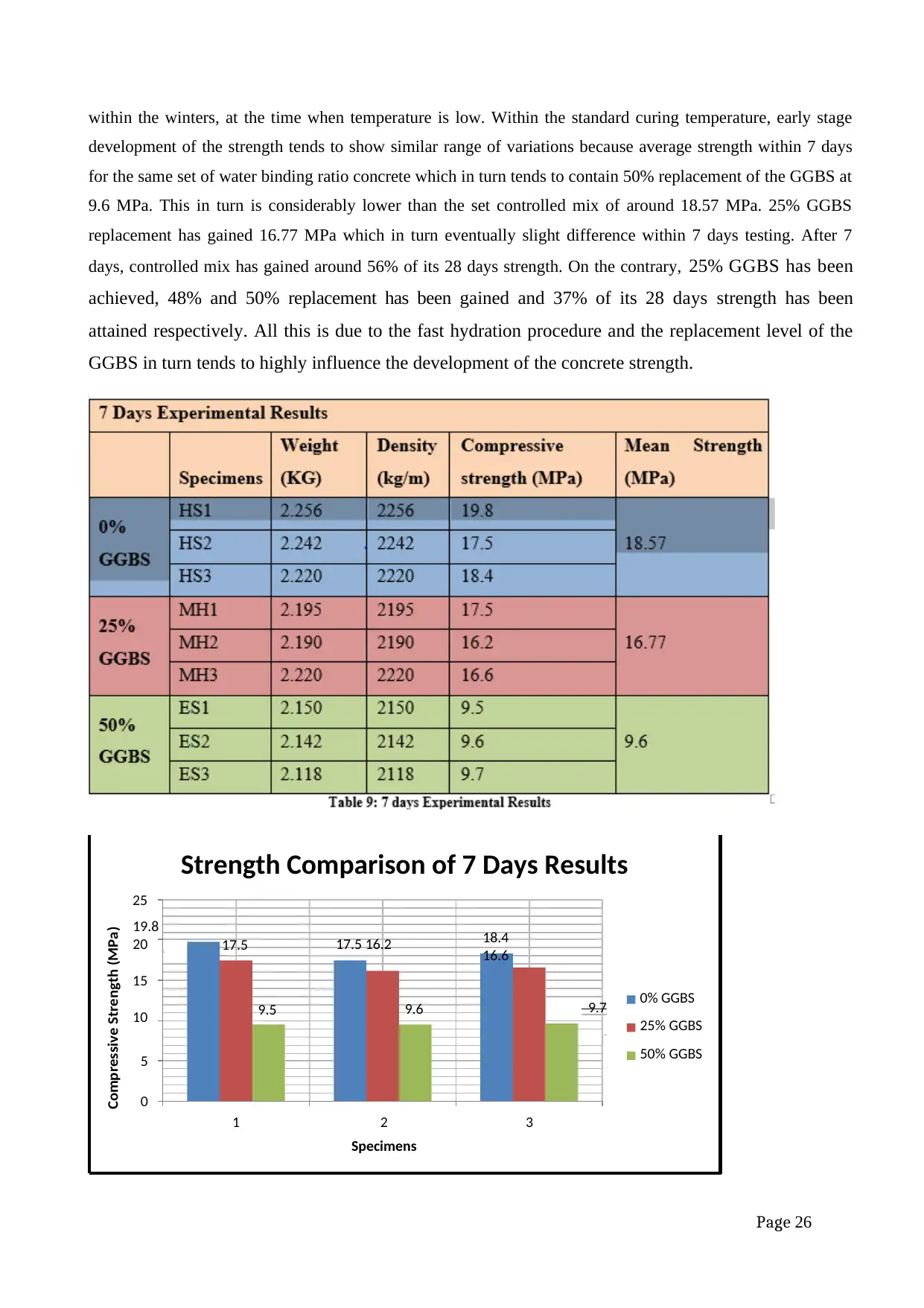
25
19.8
20 17.5 17.5 16.2 18.4
16.6
15
10 9.5 9.6 9.7
5
0% GGBS
25% GGBS
50% GGBS
0
1 2
Specimens
3
Page 26
within the winters, at the time when temperature is low. Within the standard curing temperature, early stage
development of the strength tends to show similar range of variations because average strength within 7 days
for the same set of water binding ratio concrete which in turn tends to contain 50% replacement of the GGBS at
9.6 MPa. This in turn is considerably lower than the set controlled mix of around 18.57 MPa. 25% GGBS
replacement has gained 16.77 MPa which in turn eventually slight difference within 7 days testing. After 7
days, controlled mix has gained around 56% of its 28 days strength. On the contrary, 25% GGBS has been
achieved, 48% and 50% replacement has been gained and 37% of its 28 days strength has been
attained respectively. All this is due to the fast hydration procedure and the replacement level of the
GGBS in turn tends to highly influence the development of the concrete strength.
Compressive Strength (MPa)
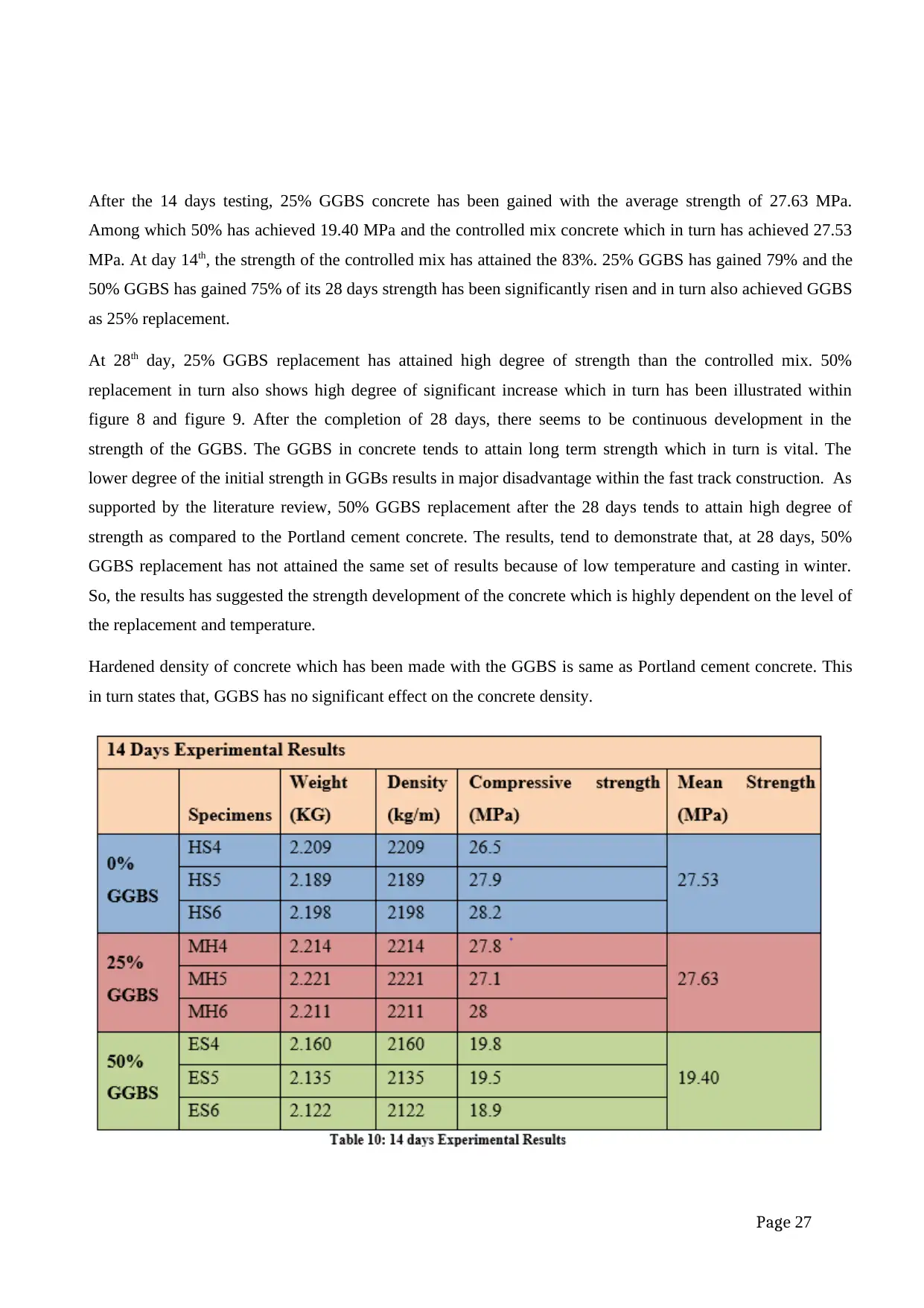
After the 14 days testing, 25% GGBS concrete has been gained with the average strength of 27.63 MPa.
Among which 50% has achieved 19.40 MPa and the controlled mix concrete which in turn has achieved 27.53
MPa. At day 14th, the strength of the controlled mix has attained the 83%. 25% GGBS has gained 79% and the
50% GGBS has gained 75% of its 28 days strength has been significantly risen and in turn also achieved GGBS
as 25% replacement.
At 28th day, 25% GGBS replacement has attained high degree of strength than the controlled mix. 50%
replacement in turn also shows high degree of significant increase which in turn has been illustrated within
figure 8 and figure 9. After the completion of 28 days, there seems to be continuous development in the
strength of the GGBS. The GGBS in concrete tends to attain long term strength which in turn is vital. The
lower degree of the initial strength in GGBs results in major disadvantage within the fast track construction. As
supported by the literature review, 50% GGBS replacement after the 28 days tends to attain high degree of
strength as compared to the Portland cement concrete. The results, tend to demonstrate that, at 28 days, 50%
GGBS replacement has not attained the same set of results because of low temperature and casting in winter.
So, the results has suggested the strength development of the concrete which is highly dependent on the level of
the replacement and temperature.
Hardened density of concrete which has been made with the GGBS is same as Portland cement concrete. This
in turn states that, GGBS has no significant effect on the concrete density.
⊘ This is a preview!⊘
Do you want full access?
Subscribe today to unlock all pages.

Trusted by 1+ million students worldwide
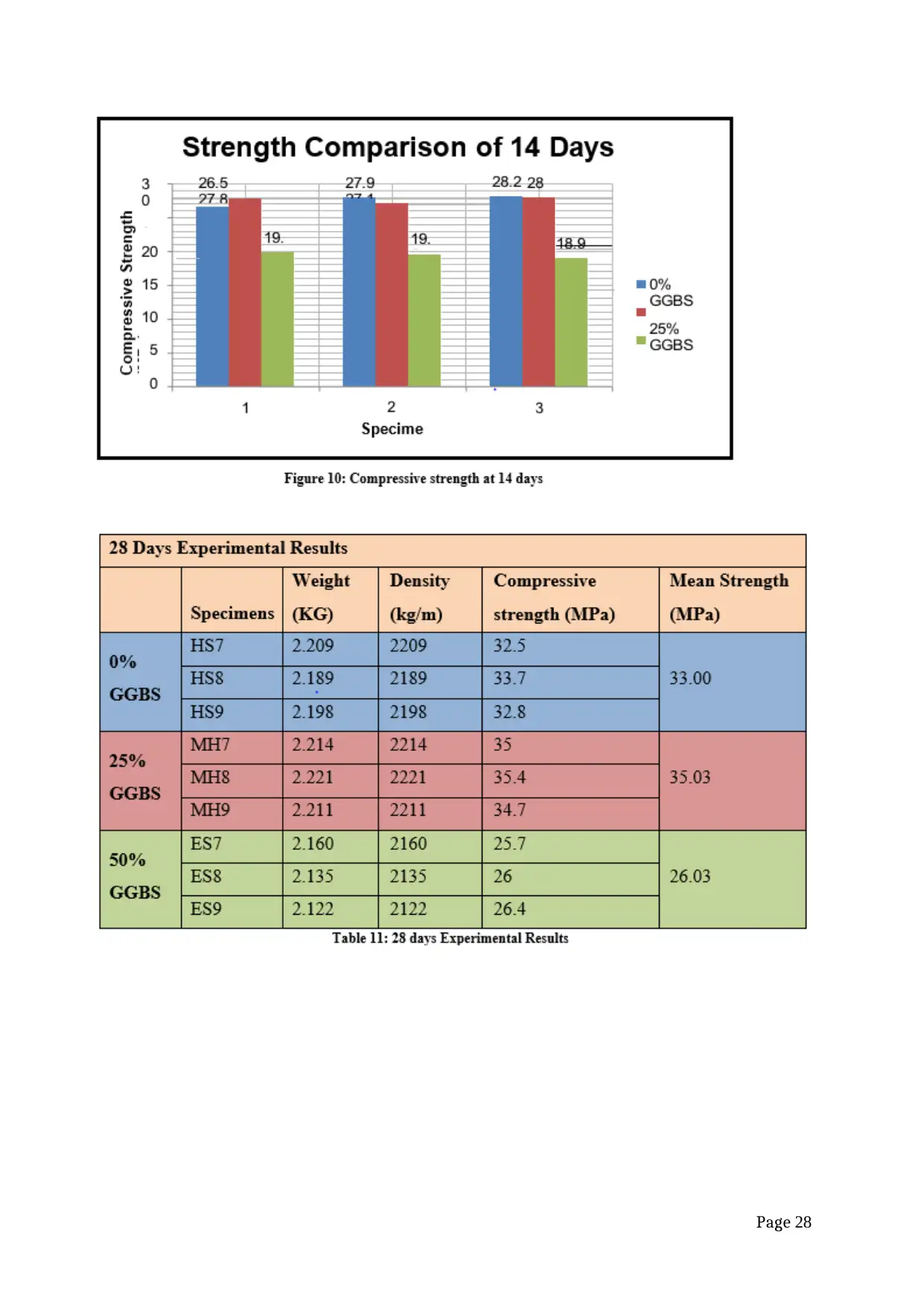
Paraphrase This Document
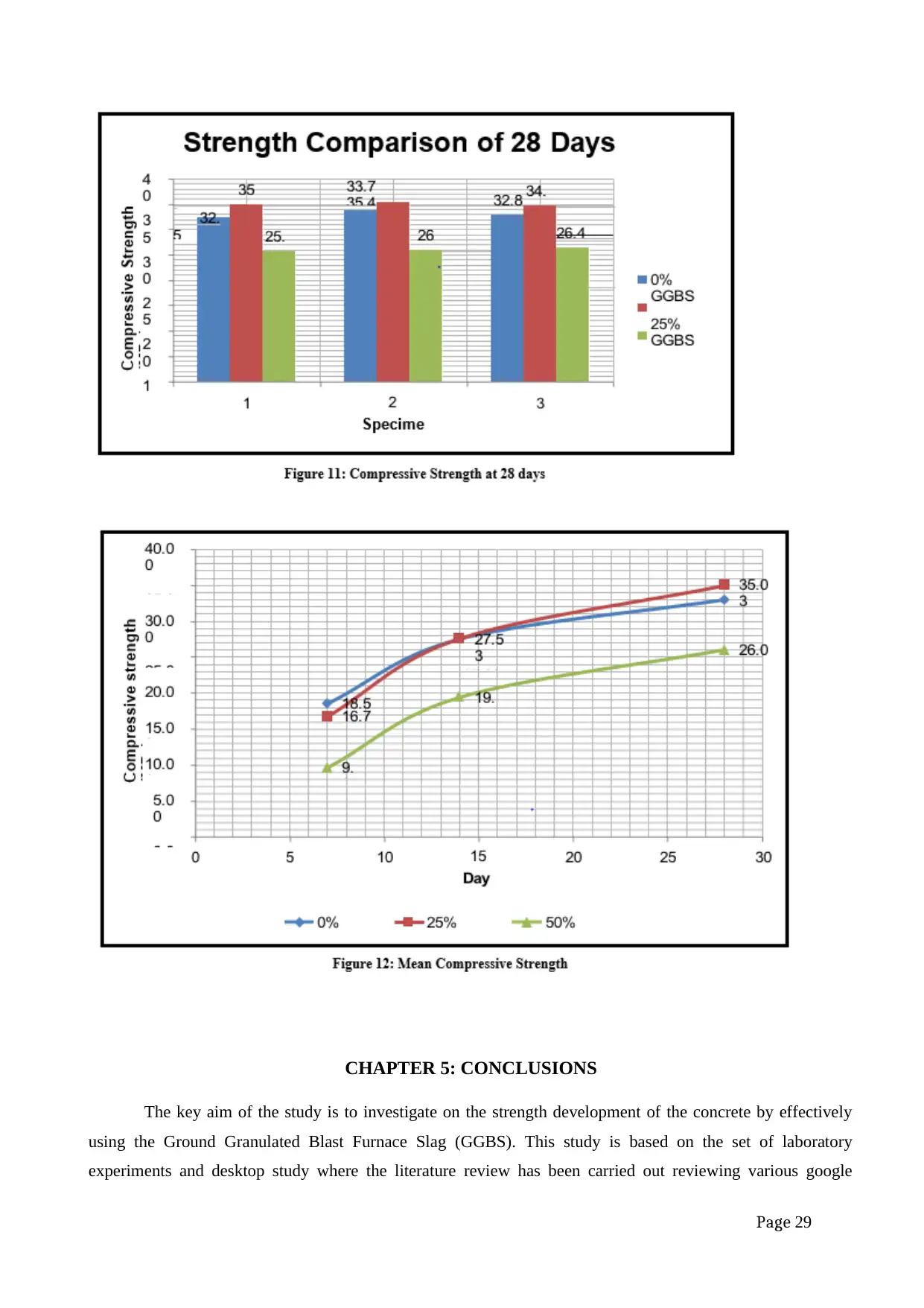
CHAPTER 5: CONCLUSIONS
The key aim of the study is to investigate on the strength development of the concrete by effectively
using the Ground Granulated Blast Furnace Slag (GGBS). This study is based on the set of laboratory
experiments and desktop study where the literature review has been carried out reviewing various google

scholars. Casting of the concrete is also done by the usage of varied percentage of the GGBS and also tends to
compare various sets of results to the Portland cement concrete. Moreover, concrete, has been used widely
across the globe. One of the key necessary element associated with the concrete is mainly linked with the
Portland cement (Saranya, Nagarajan and Shashikala, 2020). It has been examined that, the manufacturing
of the Portland cement tends to require high amount of energy which in turn eventually emits carbon dioxide
within the environment. The production process is also highly expensive. In order to improve the various
environmental impact of the cost and concrete, use of Pozzolonic material is very crucial. This is very vital for
the replacement of the cements which in turn tends to largely reduce the cost and in turn helps in improving the
environmental efficiency of the concrete.
One of the most prominent target of the dissertation, was to effectively measure the development of the
strength of the concrete along with the hardened density and the workability of the concrete. Due to the lack of
resources, durability, chemical properties and physical properties of the GGBS has not been ascertained. The
normal water binder ratio of 0.4 do not have significant influence on the initial setting time related with the
GGBS concrete. It is also very valuable in order to effectively determine the presence of the plasticizer within
GGBS.
Moreover, investigation within the laboratory has been carried out in order to critically measure the
development of the strength within GGBS concrete (Rao, Sravana and Rao, 2016). This study in turn
includes three set of concrete mix within the standard curing conditions. Casting of total 29 specimens have
been done. The following set of conclusion has been drawn which in turn is usually based on the key results of
the three concrete mixes under the specific curing standard conditions. Following set of the conclusion have
been drawn which is usually based on the results of up to 28 days of test age.
a.) GGBS is considered to be one of the most sustainable waste material which in turn is produced by the
iron industry. Inclusion of the GGBS within the concrete helps in reducing the emission of the carbon
dioxide, greenhouse gases, embodied energy. It is also very useful in reducing the effect of the heat
within the process of hydration. According to the Cementitious Slag Maker Associations, 2014,
50% replacement of the GGBS in turn tends to reduce 40% of the emission of carbon dioxide.
b.) Specimens associated with the hardened concrete density is usually prepared by the controlled mix
which in turn is usually based on the GGBS replacement. This in turn tends to have the similar amount
of value associated with the density. This in turn proves that, GGBS and Portland cement does not
influence the density of the concrete.
c.) Development of the early age strength of the GGBS concrete is usually based on the high degree of the
replacement level associated with the GGBS, curing temperature and water binder ratio. The figure 6,
tends to show 50% GGBS replacement tends to gain low degree of strength when compared with the
Portland cement concrete. Whereas, 25% GGBS replacement in turn tends to show small degree of
⊘ This is a preview!⊘
Do you want full access?
Subscribe today to unlock all pages.

Trusted by 1+ million students worldwide
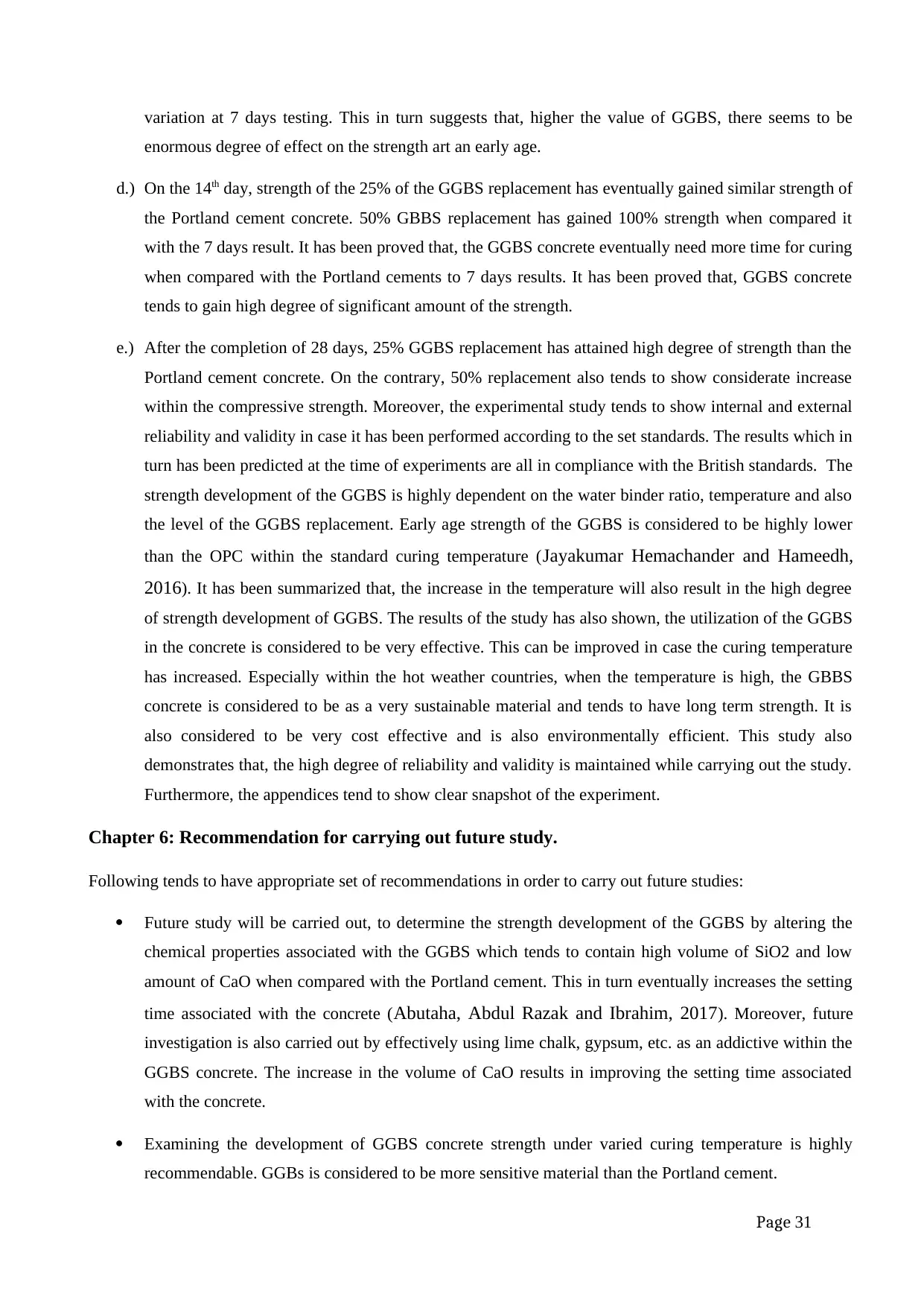
variation at 7 days testing. This in turn suggests that, higher the value of GGBS, there seems to be
enormous degree of effect on the strength art an early age.
d.) On the 14th day, strength of the 25% of the GGBS replacement has eventually gained similar strength of
the Portland cement concrete. 50% GBBS replacement has gained 100% strength when compared it
with the 7 days result. It has been proved that, the GGBS concrete eventually need more time for curing
when compared with the Portland cements to 7 days results. It has been proved that, GGBS concrete
tends to gain high degree of significant amount of the strength.
e.) After the completion of 28 days, 25% GGBS replacement has attained high degree of strength than the
Portland cement concrete. On the contrary, 50% replacement also tends to show considerate increase
within the compressive strength. Moreover, the experimental study tends to show internal and external
reliability and validity in case it has been performed according to the set standards. The results which in
turn has been predicted at the time of experiments are all in compliance with the British standards. The
strength development of the GGBS is highly dependent on the water binder ratio, temperature and also
the level of the GGBS replacement. Early age strength of the GGBS is considered to be highly lower
than the OPC within the standard curing temperature (Jayakumar Hemachander and Hameedh,
2016). It has been summarized that, the increase in the temperature will also result in the high degree
of strength development of GGBS. The results of the study has also shown, the utilization of the GGBS
in the concrete is considered to be very effective. This can be improved in case the curing temperature
has increased. Especially within the hot weather countries, when the temperature is high, the GBBS
concrete is considered to be as a very sustainable material and tends to have long term strength. It is
also considered to be very cost effective and is also environmentally efficient. This study also
demonstrates that, the high degree of reliability and validity is maintained while carrying out the study.
Furthermore, the appendices tend to show clear snapshot of the experiment.
Chapter 6: Recommendation for carrying out future study.
Following tends to have appropriate set of recommendations in order to carry out future studies:
Future study will be carried out, to determine the strength development of the GGBS by altering the
chemical properties associated with the GGBS which tends to contain high volume of SiO2 and low
amount of CaO when compared with the Portland cement. This in turn eventually increases the setting
time associated with the concrete (Abutaha, Abdul Razak and Ibrahim, 2017). Moreover, future
investigation is also carried out by effectively using lime chalk, gypsum, etc. as an addictive within the
GGBS concrete. The increase in the volume of CaO results in improving the setting time associated
with the concrete.
Examining the development of GGBS concrete strength under varied curing temperature is highly
recommendable. GGBs is considered to be more sensitive material than the Portland cement.
Paraphrase This Document
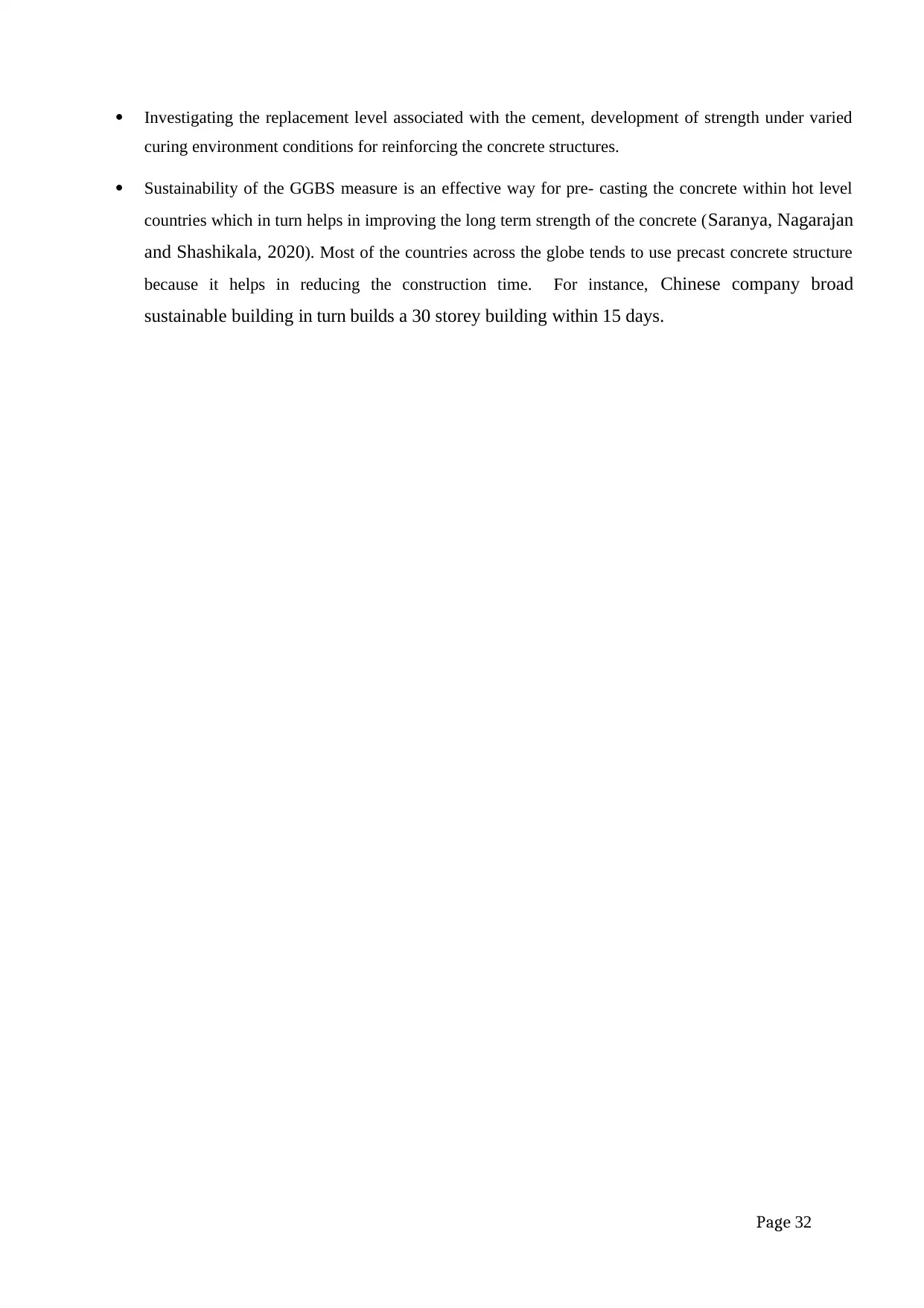
Investigating the replacement level associated with the cement, development of strength under varied
curing environment conditions for reinforcing the concrete structures.
Sustainability of the GGBS measure is an effective way for pre- casting the concrete within hot level
countries which in turn helps in improving the long term strength of the concrete (Saranya, Nagarajan
and Shashikala, 2020). Most of the countries across the globe tends to use precast concrete structure
because it helps in reducing the construction time. For instance, Chinese company broad
sustainable building in turn builds a 30 storey building within 15 days.
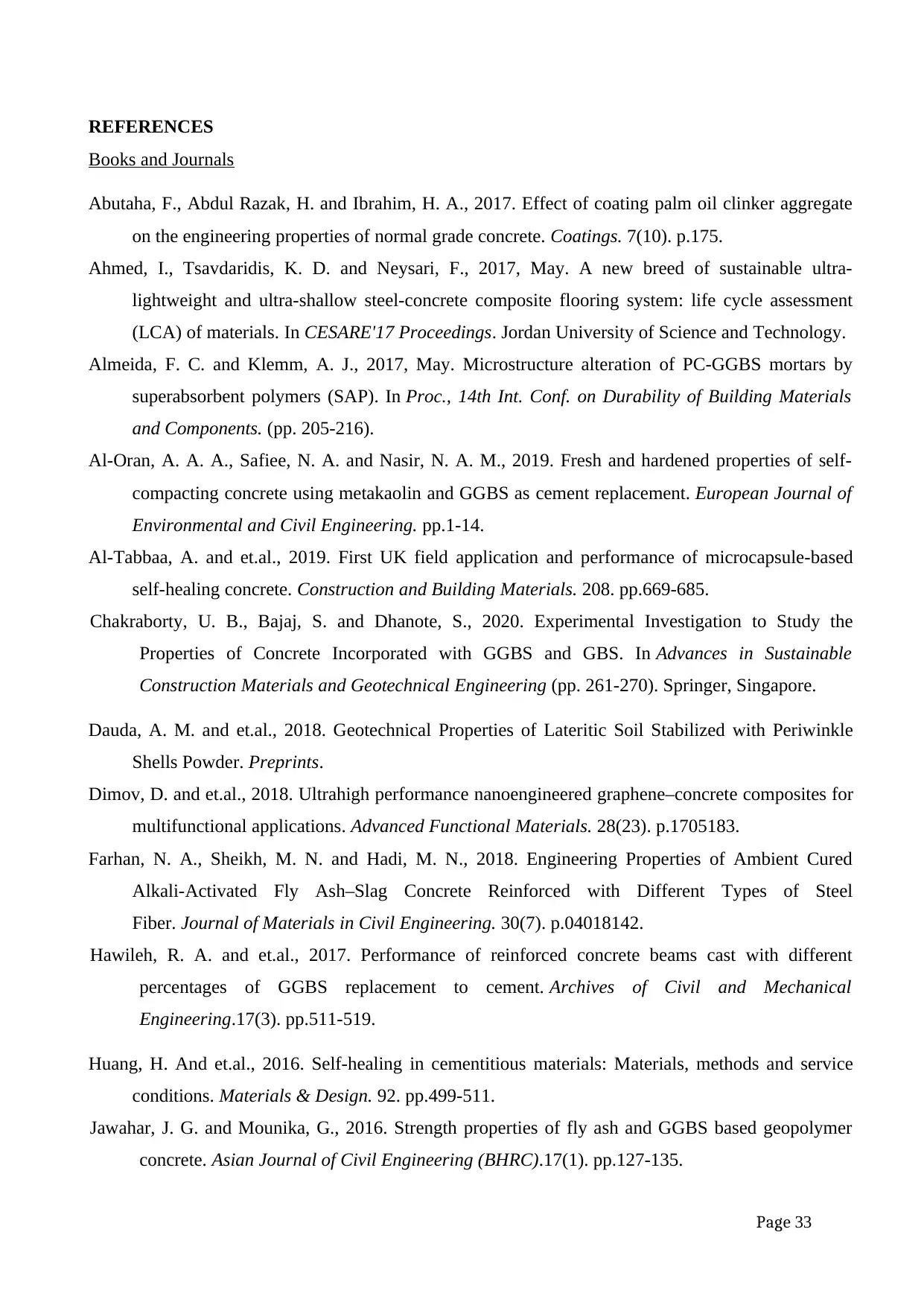
REFERENCES
Books and Journals
Abutaha, F., Abdul Razak, H. and Ibrahim, H. A., 2017. Effect of coating palm oil clinker aggregate
on the engineering properties of normal grade concrete. Coatings. 7(10). p.175.
Ahmed, I., Tsavdaridis, K. D. and Neysari, F., 2017, May. A new breed of sustainable ultra-
lightweight and ultra-shallow steel-concrete composite flooring system: life cycle assessment
(LCA) of materials. In CESARE'17 Proceedings. Jordan University of Science and Technology.
Almeida, F. C. and Klemm, A. J., 2017, May. Microstructure alteration of PC-GGBS mortars by
superabsorbent polymers (SAP). In Proc., 14th Int. Conf. on Durability of Building Materials
and Components. (pp. 205-216).
Al-Oran, A. A. A., Safiee, N. A. and Nasir, N. A. M., 2019. Fresh and hardened properties of self-
compacting concrete using metakaolin and GGBS as cement replacement. European Journal of
Environmental and Civil Engineering. pp.1-14.
Al-Tabbaa, A. and et.al., 2019. First UK field application and performance of microcapsule-based
self-healing concrete. Construction and Building Materials. 208. pp.669-685.
Chakraborty, U. B., Bajaj, S. and Dhanote, S., 2020. Experimental Investigation to Study the
Properties of Concrete Incorporated with GGBS and GBS. In Advances in Sustainable
Construction Materials and Geotechnical Engineering (pp. 261-270). Springer, Singapore.
Dauda, A. M. and et.al., 2018. Geotechnical Properties of Lateritic Soil Stabilized with Periwinkle
Shells Powder. Preprints.
Dimov, D. and et.al., 2018. Ultrahigh performance nanoengineered graphene–concrete composites for
multifunctional applications. Advanced Functional Materials. 28(23). p.1705183.
Farhan, N. A., Sheikh, M. N. and Hadi, M. N., 2018. Engineering Properties of Ambient Cured
Alkali-Activated Fly Ash–Slag Concrete Reinforced with Different Types of Steel
Fiber. Journal of Materials in Civil Engineering. 30(7). p.04018142.
Hawileh, R. A. and et.al., 2017. Performance of reinforced concrete beams cast with different
percentages of GGBS replacement to cement. Archives of Civil and Mechanical
Engineering.17(3). pp.511-519.
Huang, H. And et.al., 2016. Self-healing in cementitious materials: Materials, methods and service
conditions. Materials & Design. 92. pp.499-511.
Jawahar, J. G. and Mounika, G., 2016. Strength properties of fly ash and GGBS based geopolymer
concrete. Asian Journal of Civil Engineering (BHRC).17(1). pp.127-135.
⊘ This is a preview!⊘
Do you want full access?
Subscribe today to unlock all pages.

Trusted by 1+ million students worldwide

Jayakumar, S., Hemachander, J. and Hameedh, J. M., 2016. Experimental study on properties of
rammed earth blended with GGBS and silica flume. IJRET. 5(5). pp.295-297.
Kumar, G. R., Bhardwaj, A. and Sharma, U. K., 2018. Cavitation resistance of concrete containing
different material properties. Advances in concrete construction. 6(1). p.15.
Lee, S. W. and et.al., 2019. Mechanical Performances of Green Engineered Cementitious Composites
Incorporating Various Types of Sand. In Key Engineering Materials (Vol. 821. pp. 512-517).
Trans Tech Publications Ltd.
Lekhaz, D. And et.al., 2016. A Study on Bituminous Concrete Mix with Cement, GGBS, Brick Dust
as a Filler. International Journal of Engineering science and Computing. 6 (10). 2771, 2775.
Li, X. and et.al., 2020. A Comparative Study on the Influence of Supplementary Cementitious
Materials on Marine Concrete. Journal of Testing and Evaluation. 48(3).
Mhatre, D. S., 2018. Effect of partial replacement of GGBS slag as fine aggregate and fly ash as
cement on strength of concrete. International Journal for Emerging Research and
Development. 1(6). pp.26-32.
Murphy, C., 2018. Designing bridges for manufacture and assembly: joining technologies for precast
concrete components. The Structural Engineer: journal of the Institution of Structural
Engineer. 96(11). pp.11-16.
O’Shea, M., Gray, K. and Murphy, J., 2019. An Investigation into the Suitability of GGBS and OPC
as Low Percentage Single-Component Binders for the Stabilisation and Solidification of
Harbour Dredge Material Mildly Contaminated with Metals. Journal of Marine Science and
Engineering. 7(4). p.106.
Pasupuleti, M. K. and Rajasekhar, K., 2018. Experimental Study of Properties of Concrete using
GGBS and M-Sand with Addition of Basalt Fibre. i-Manager's Journal on Structural
Engineering. 7(4). p.15.
Pavía, S. and Aly, M., 2016. Influence of aggregate and supplementary cementitious materials on the
properties of hydrated lime (CL90s) mortars. Materiales de Construcción. 66(324). p.104.
Phanikumar, B. R. and Nagaraju, T. V., 2018. Engineering behaviour of expansive clays blended with
cement and GGBS. Proceedings of the Institution of Civil Engineers-Ground
Improvement. 171(3). pp.167-173.
Rao, S. K., Sravana, P. and Rao, T. C., 2016. Abrasion resistance and mechanical properties of Roller
Compacted Concrete with GGBS. Construction and Building Materials. 114. pp.925-933.
Samson, G., Cyr, M. and Gao, X. X., 2017. Thermomechanical performance of blended metakaolin-
GGBS alkali-activated foam concrete. Construction and Building Materials.157. pp.982-993.
Paraphrase This Document
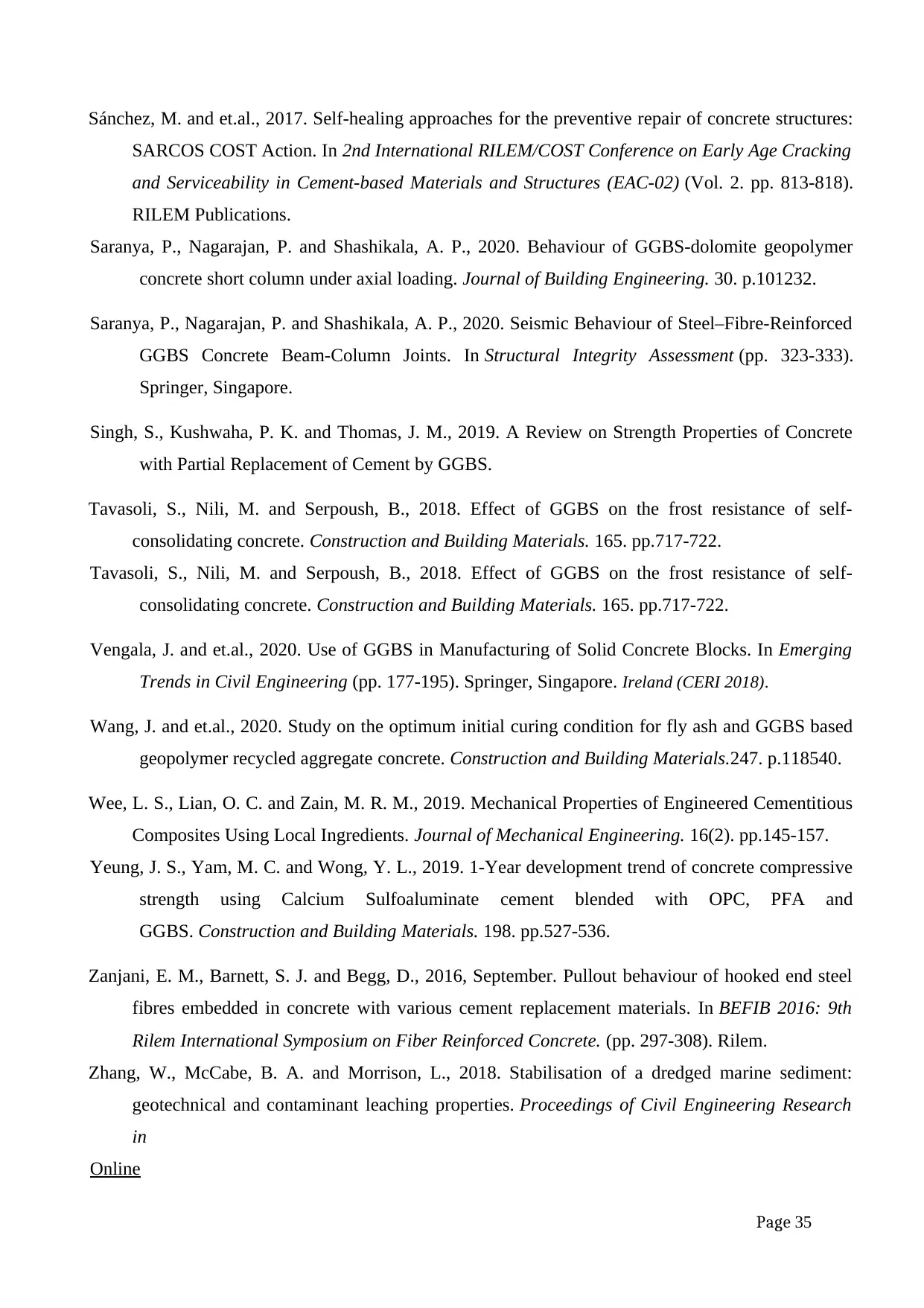
Sánchez, M. and et.al., 2017. Self-healing approaches for the preventive repair of concrete structures:
SARCOS COST Action. In 2nd International RILEM/COST Conference on Early Age Cracking
and Serviceability in Cement-based Materials and Structures (EAC-02) (Vol. 2. pp. 813-818).
RILEM Publications.
Saranya, P., Nagarajan, P. and Shashikala, A. P., 2020. Behaviour of GGBS-dolomite geopolymer
concrete short column under axial loading. Journal of Building Engineering. 30. p.101232.
Saranya, P., Nagarajan, P. and Shashikala, A. P., 2020. Seismic Behaviour of Steel–Fibre-Reinforced
GGBS Concrete Beam-Column Joints. In Structural Integrity Assessment (pp. 323-333).
Springer, Singapore.
Singh, S., Kushwaha, P. K. and Thomas, J. M., 2019. A Review on Strength Properties of Concrete
with Partial Replacement of Cement by GGBS.
Tavasoli, S., Nili, M. and Serpoush, B., 2018. Effect of GGBS on the frost resistance of self-
consolidating concrete. Construction and Building Materials. 165. pp.717-722.
Tavasoli, S., Nili, M. and Serpoush, B., 2018. Effect of GGBS on the frost resistance of self-
consolidating concrete. Construction and Building Materials. 165. pp.717-722.
Vengala, J. and et.al., 2020. Use of GGBS in Manufacturing of Solid Concrete Blocks. In Emerging
Trends in Civil Engineering (pp. 177-195). Springer, Singapore. Ireland (CERI 2018).
Wang, J. and et.al., 2020. Study on the optimum initial curing condition for fly ash and GGBS based
geopolymer recycled aggregate concrete. Construction and Building Materials.247. p.118540.
Wee, L. S., Lian, O. C. and Zain, M. R. M., 2019. Mechanical Properties of Engineered Cementitious
Composites Using Local Ingredients. Journal of Mechanical Engineering. 16(2). pp.145-157.
Yeung, J. S., Yam, M. C. and Wong, Y. L., 2019. 1-Year development trend of concrete compressive
strength using Calcium Sulfoaluminate cement blended with OPC, PFA and
GGBS. Construction and Building Materials. 198. pp.527-536.
Zanjani, E. M., Barnett, S. J. and Begg, D., 2016, September. Pullout behaviour of hooked end steel
fibres embedded in concrete with various cement replacement materials. In BEFIB 2016: 9th
Rilem International Symposium on Fiber Reinforced Concrete. (pp. 297-308). Rilem.
Zhang, W., McCabe, B. A. and Morrison, L., 2018. Stabilisation of a dredged marine sediment:
geotechnical and contaminant leaching properties. Proceedings of Civil Engineering Research
in
Online
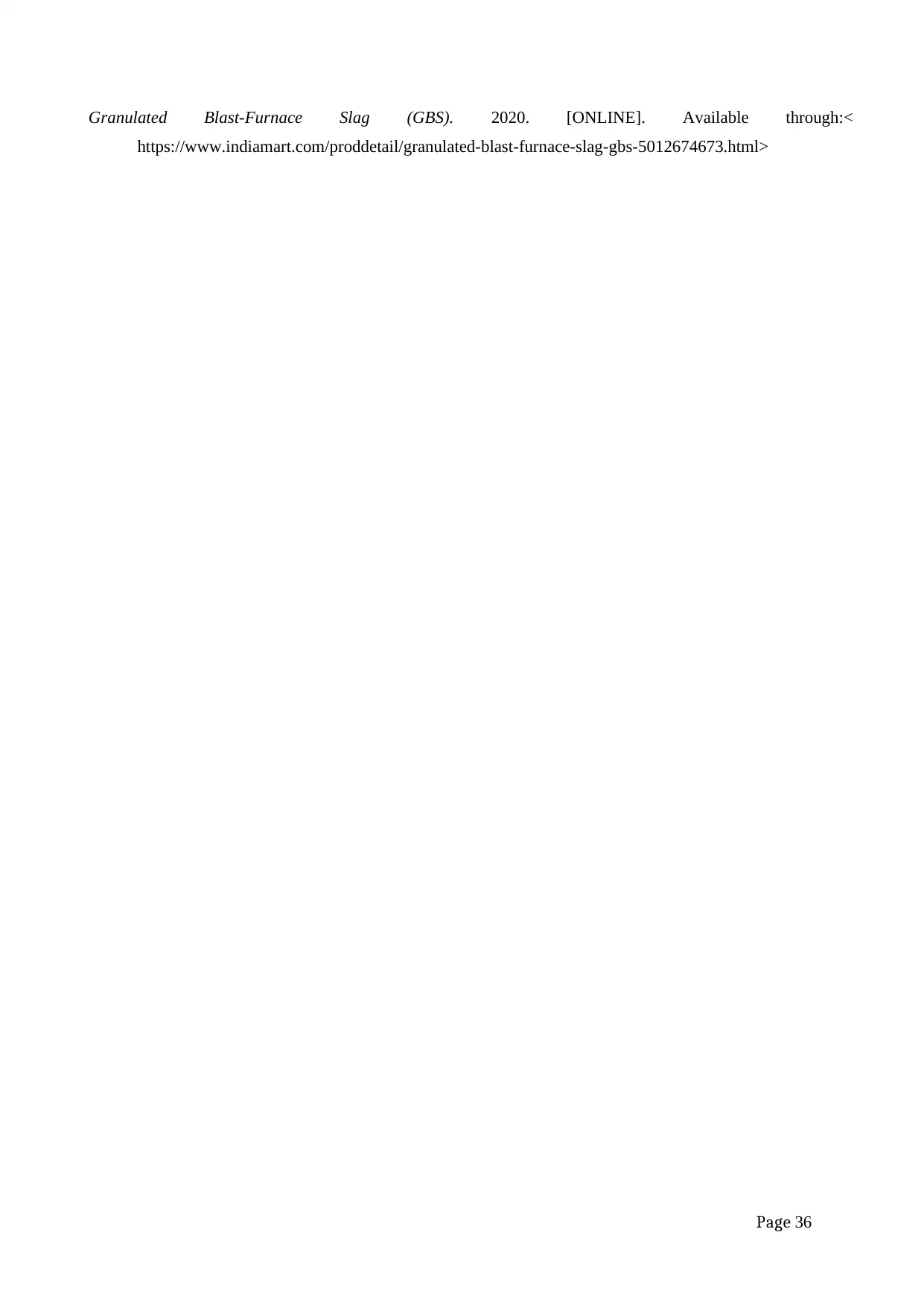
Granulated Blast-Furnace Slag (GBS). 2020. [ONLINE]. Available through:<
https://www.indiamart.com/proddetail/granulated-blast-furnace-slag-gbs-5012674673.html>
⊘ This is a preview!⊘
Do you want full access?
Subscribe today to unlock all pages.

Trusted by 1+ million students worldwide
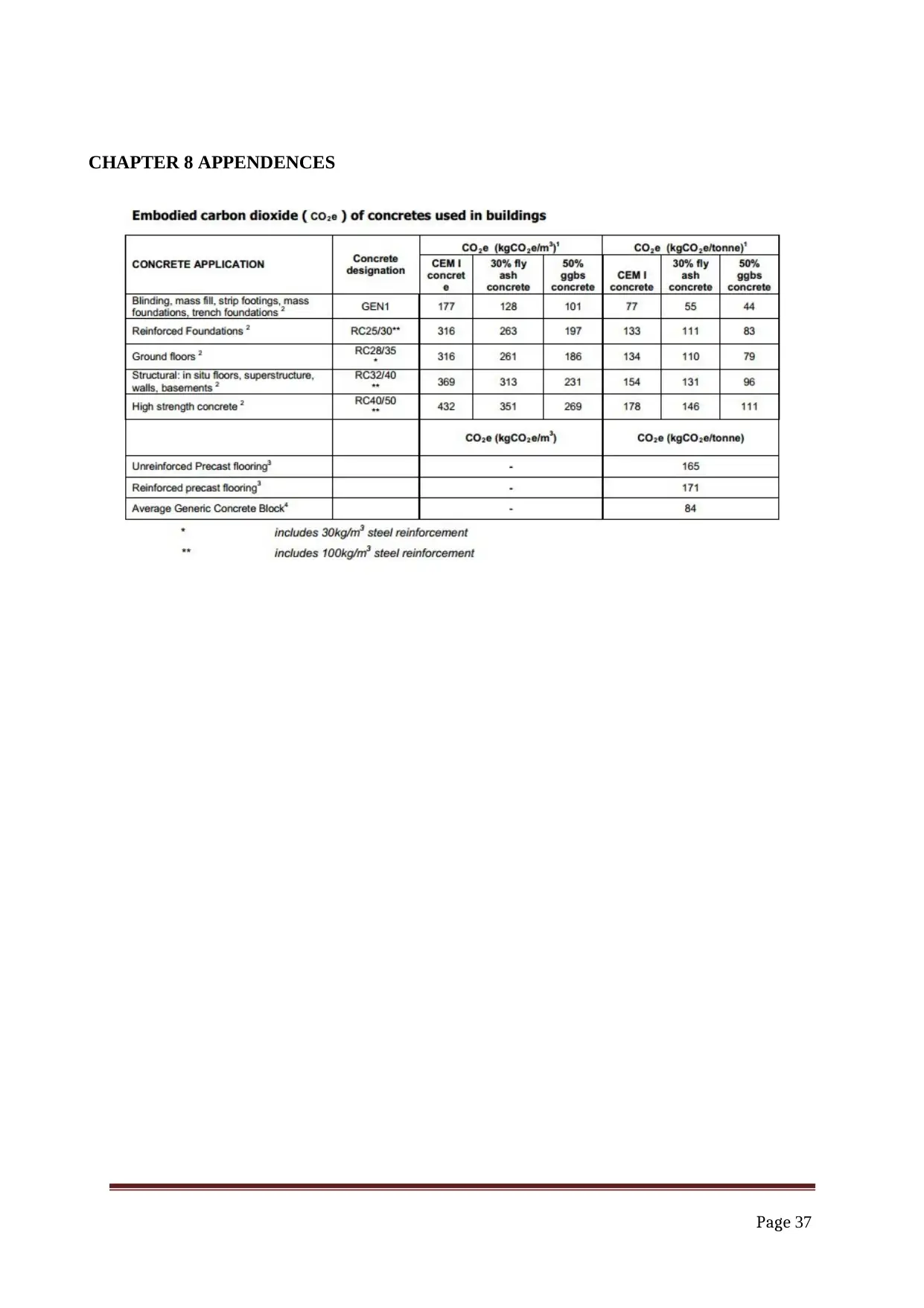
CHAPTER 8 APPENDENCES
Paraphrase This Document
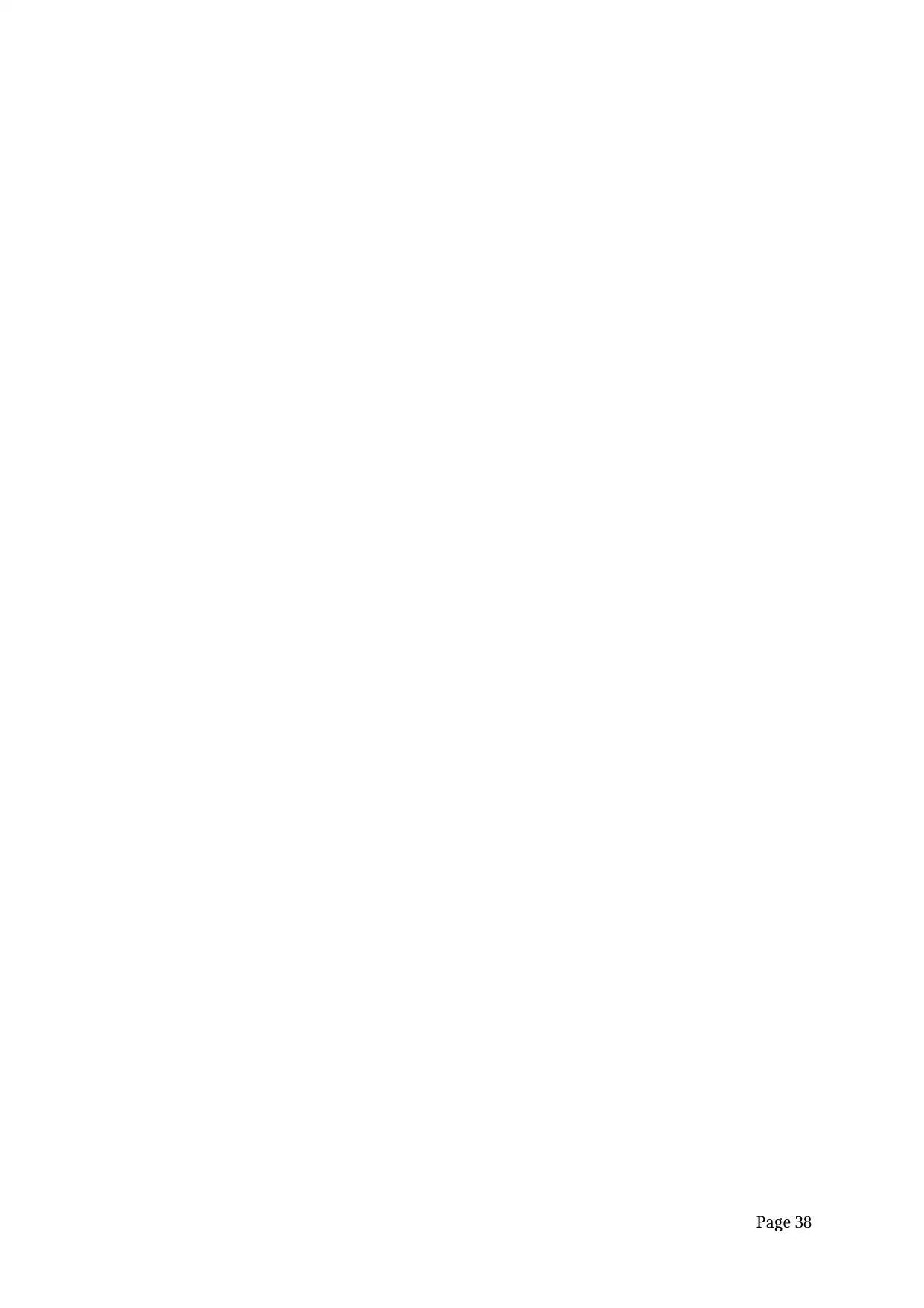

⊘ This is a preview!⊘
Do you want full access?
Subscribe today to unlock all pages.

Trusted by 1+ million students worldwide
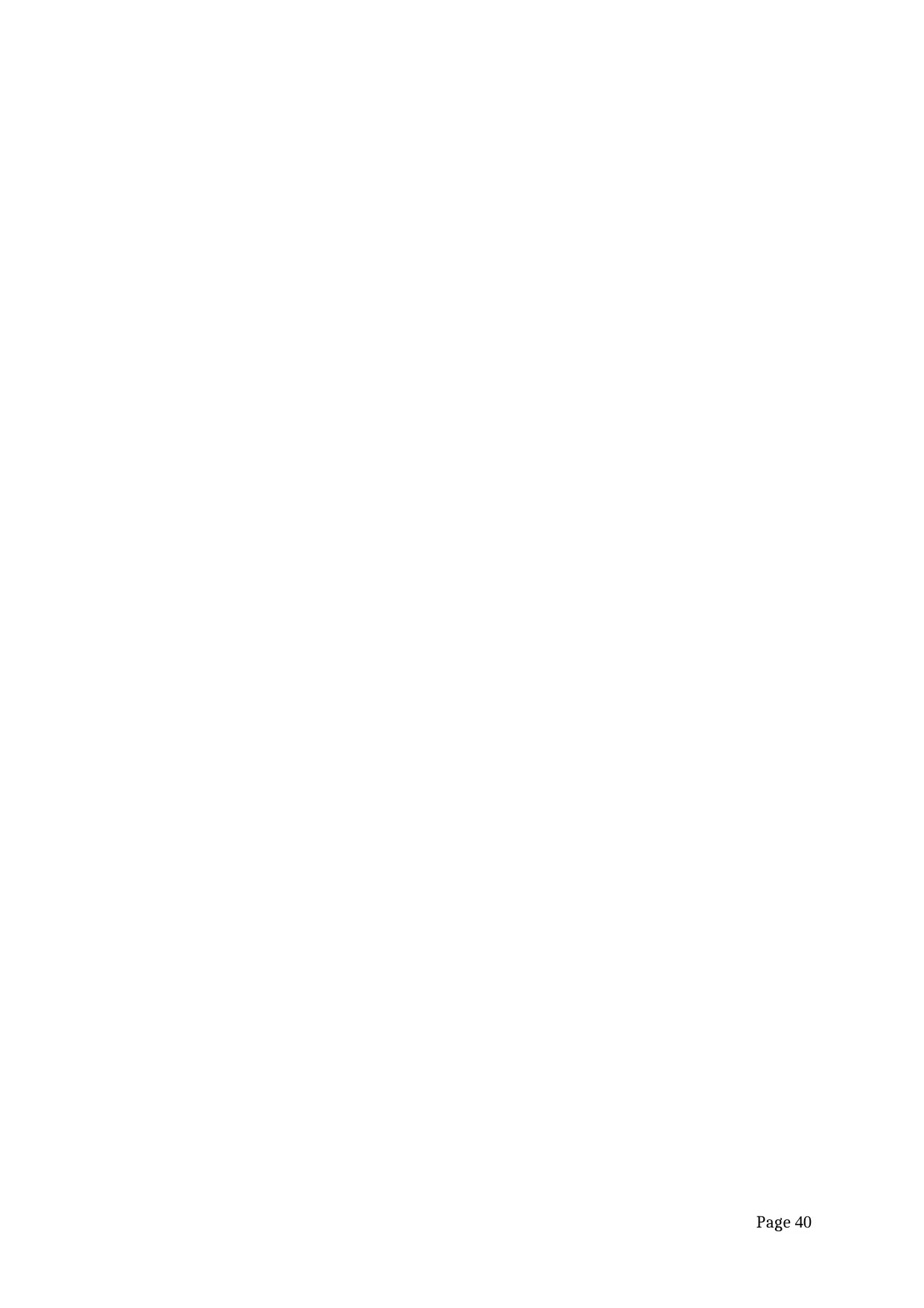
Paraphrase This Document
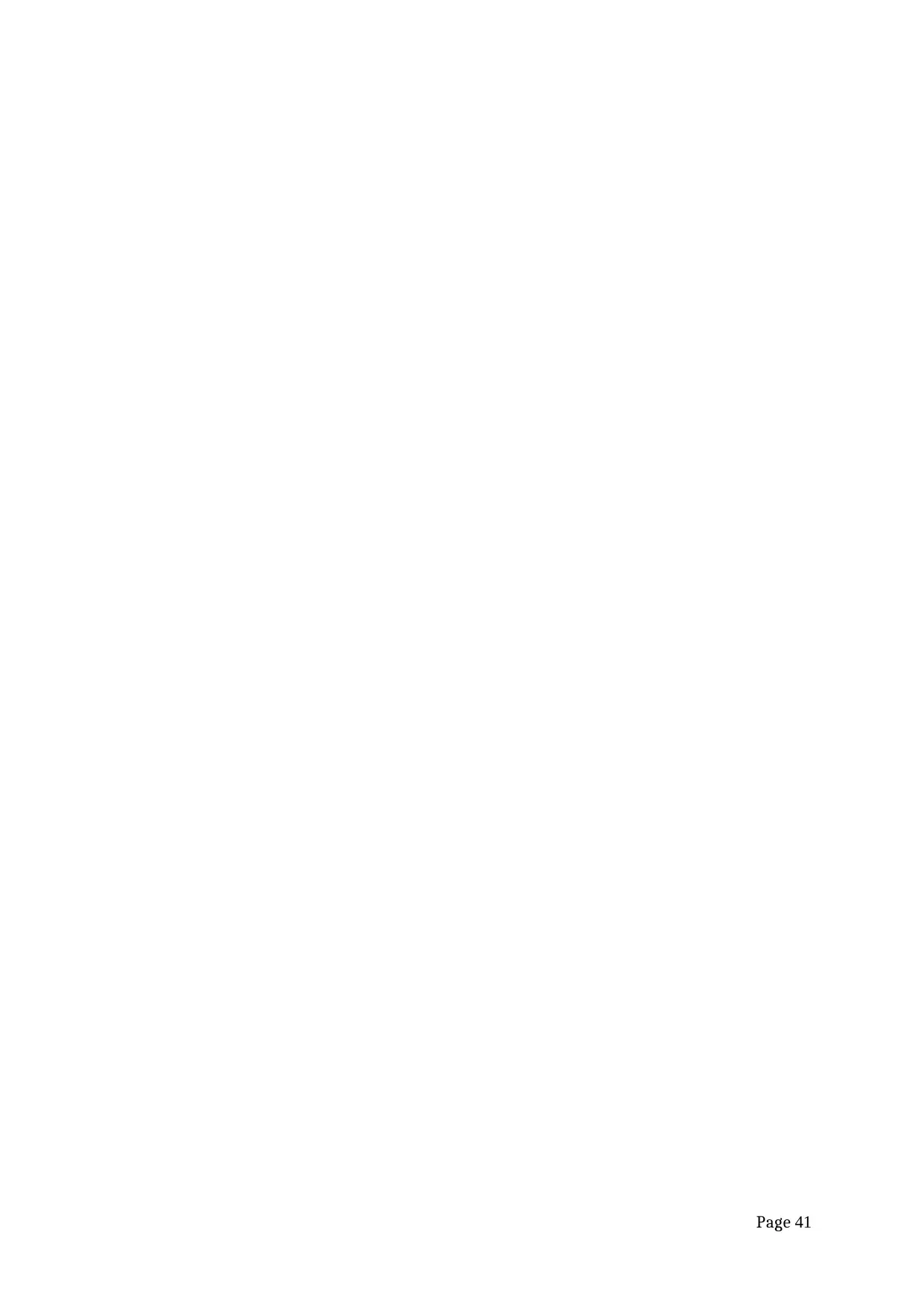
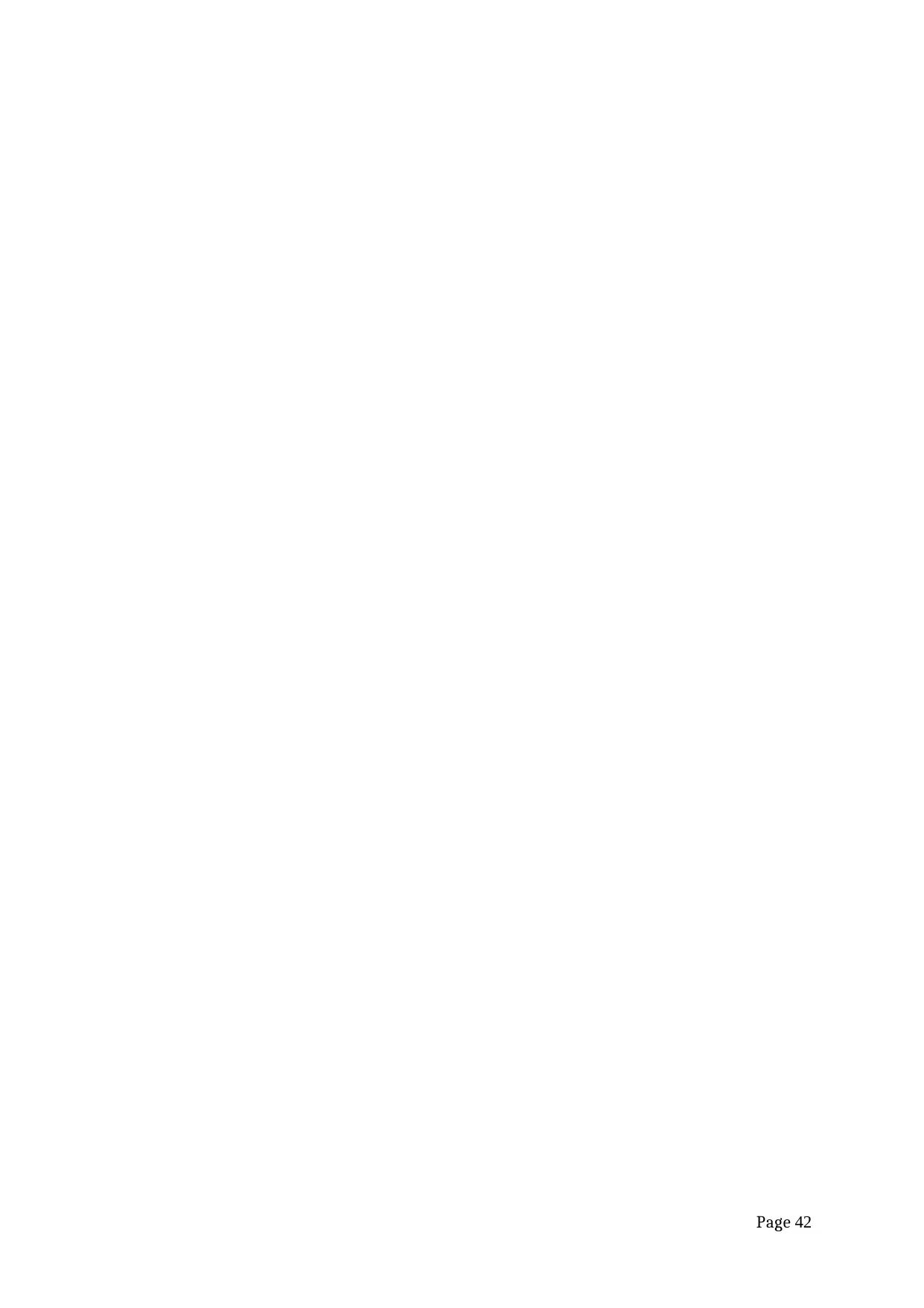
⊘ This is a preview!⊘
Do you want full access?
Subscribe today to unlock all pages.

Trusted by 1+ million students worldwide
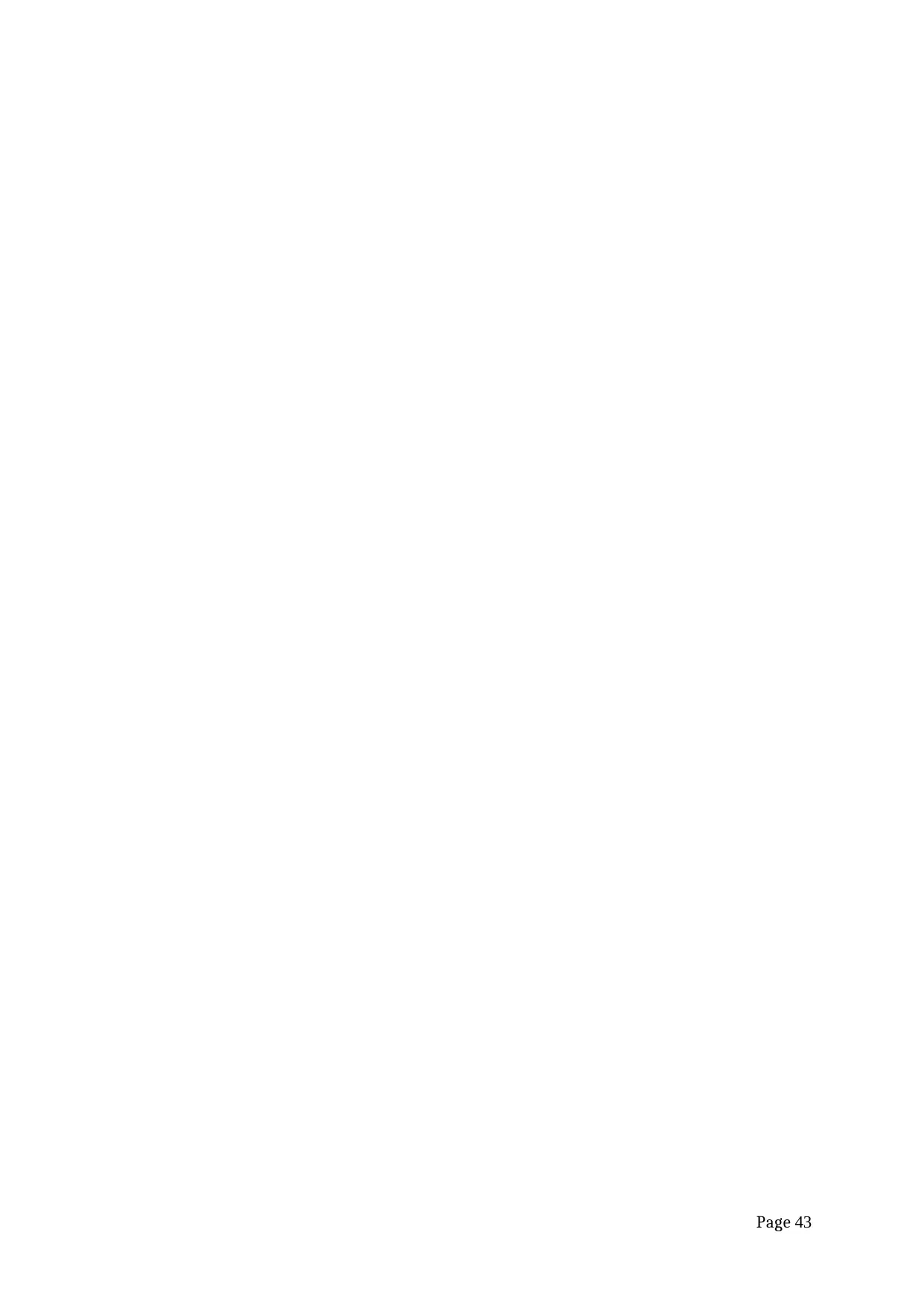
Related Documents

Your All-in-One AI-Powered Toolkit for Academic Success.
+13062052269
info@desklib.com
Available 24*7 on WhatsApp / Email
© 2024 | Zucol Services PVT LTD | All rights reserved.