Report on Operations Management at Bet-Ker-OY: Analysis and Solutions
VerifiedAdded on 2020/04/07
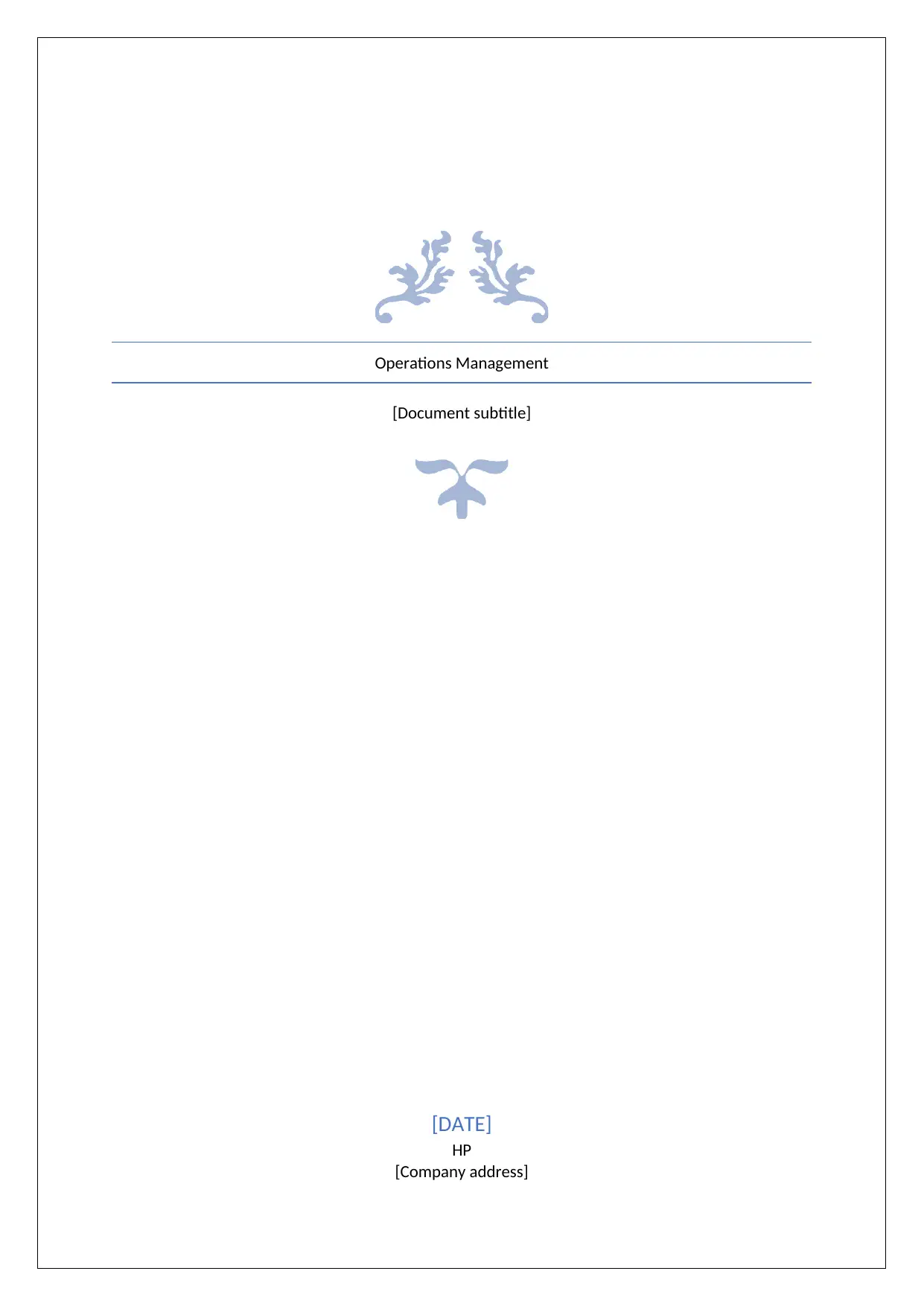
[Document subtitle]
[DATE]
HP
[Company address]
Paraphrase This Document
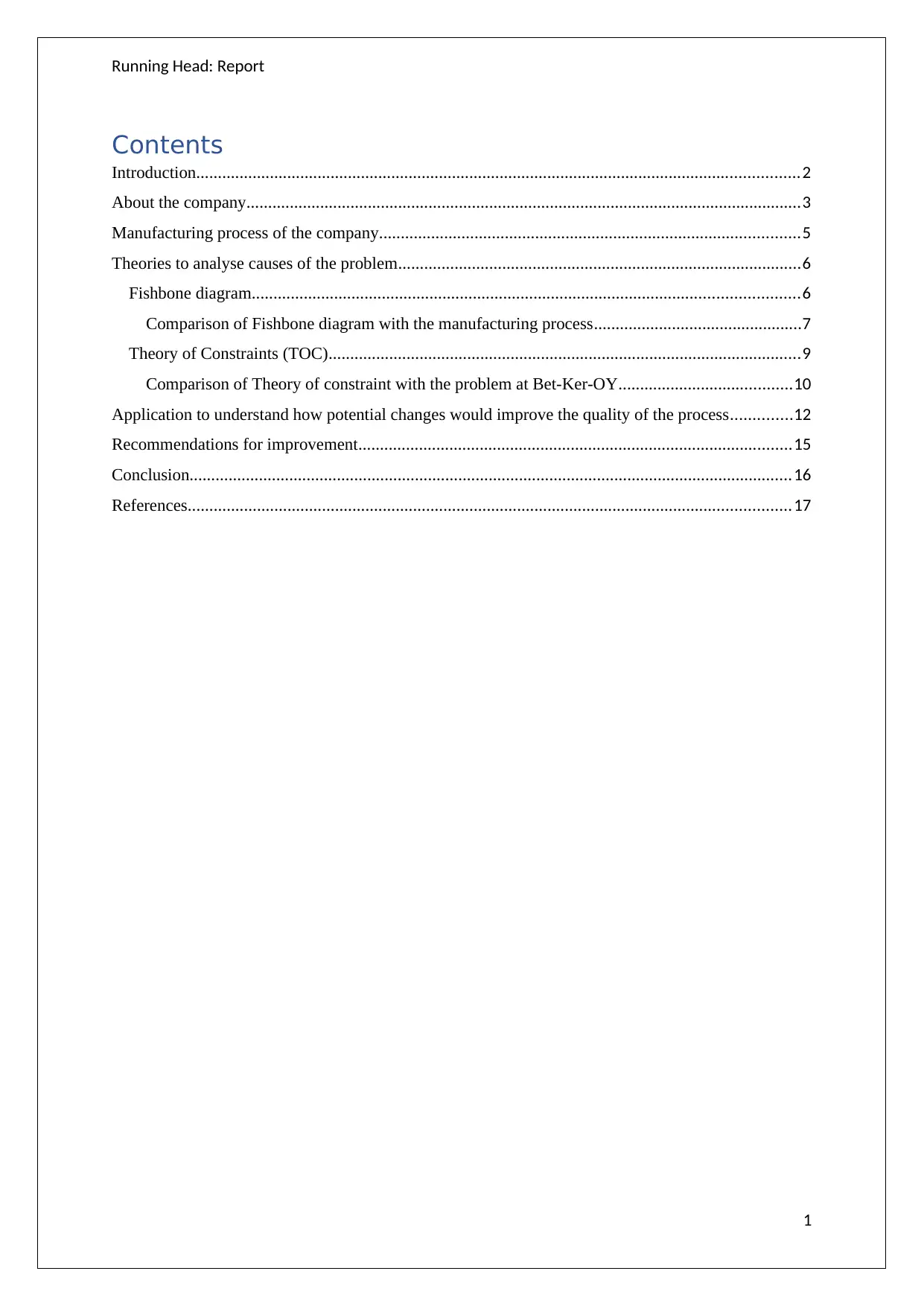
Contents
Introduction...........................................................................................................................................2
About the company................................................................................................................................3
Manufacturing process of the company.................................................................................................5
Theories to analyse causes of the problem.............................................................................................6
Fishbone diagram..............................................................................................................................6
Comparison of Fishbone diagram with the manufacturing process................................................7
Theory of Constraints (TOC).............................................................................................................9
Comparison of Theory of constraint with the problem at Bet-Ker-OY........................................10
Application to understand how potential changes would improve the quality of the process..............12
Recommendations for improvement....................................................................................................15
Conclusion...........................................................................................................................................16
References...........................................................................................................................................17
1
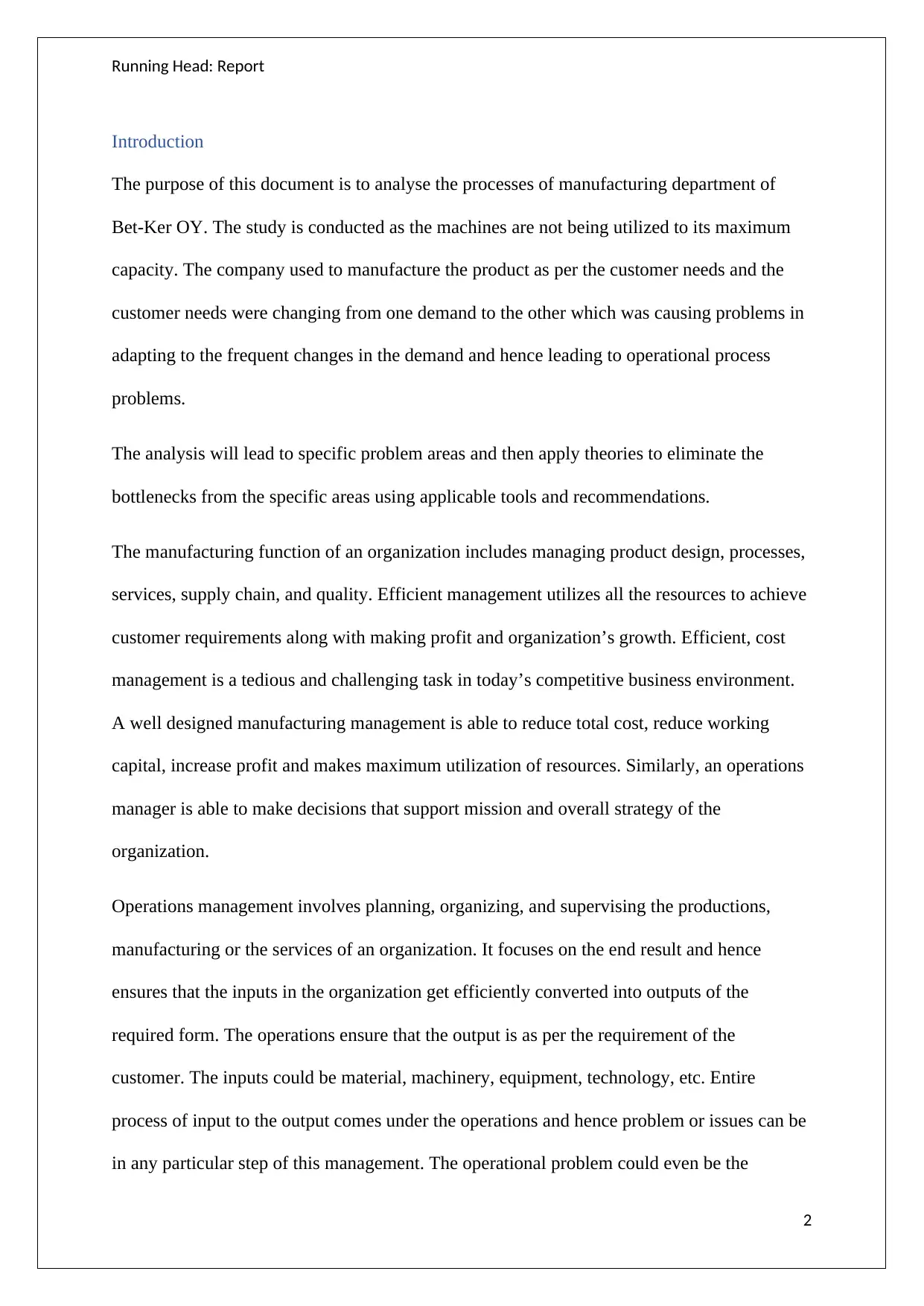
Introduction
The purpose of this document is to analyse the processes of manufacturing department of
Bet-Ker OY. The study is conducted as the machines are not being utilized to its maximum
capacity. The company used to manufacture the product as per the customer needs and the
customer needs were changing from one demand to the other which was causing problems in
adapting to the frequent changes in the demand and hence leading to operational process
problems.
The analysis will lead to specific problem areas and then apply theories to eliminate the
bottlenecks from the specific areas using applicable tools and recommendations.
The manufacturing function of an organization includes managing product design, processes,
services, supply chain, and quality. Efficient management utilizes all the resources to achieve
customer requirements along with making profit and organization’s growth. Efficient, cost
management is a tedious and challenging task in today’s competitive business environment.
A well designed manufacturing management is able to reduce total cost, reduce working
capital, increase profit and makes maximum utilization of resources. Similarly, an operations
manager is able to make decisions that support mission and overall strategy of the
organization.
Operations management involves planning, organizing, and supervising the productions,
manufacturing or the services of an organization. It focuses on the end result and hence
ensures that the inputs in the organization get efficiently converted into outputs of the
required form. The operations ensure that the output is as per the requirement of the
customer. The inputs could be material, machinery, equipment, technology, etc. Entire
process of input to the output comes under the operations and hence problem or issues can be
in any particular step of this management. The operational problem could even be the
2
⊘ This is a preview!⊘
Do you want full access?
Subscribe today to unlock all pages.

Trusted by 1+ million students worldwide
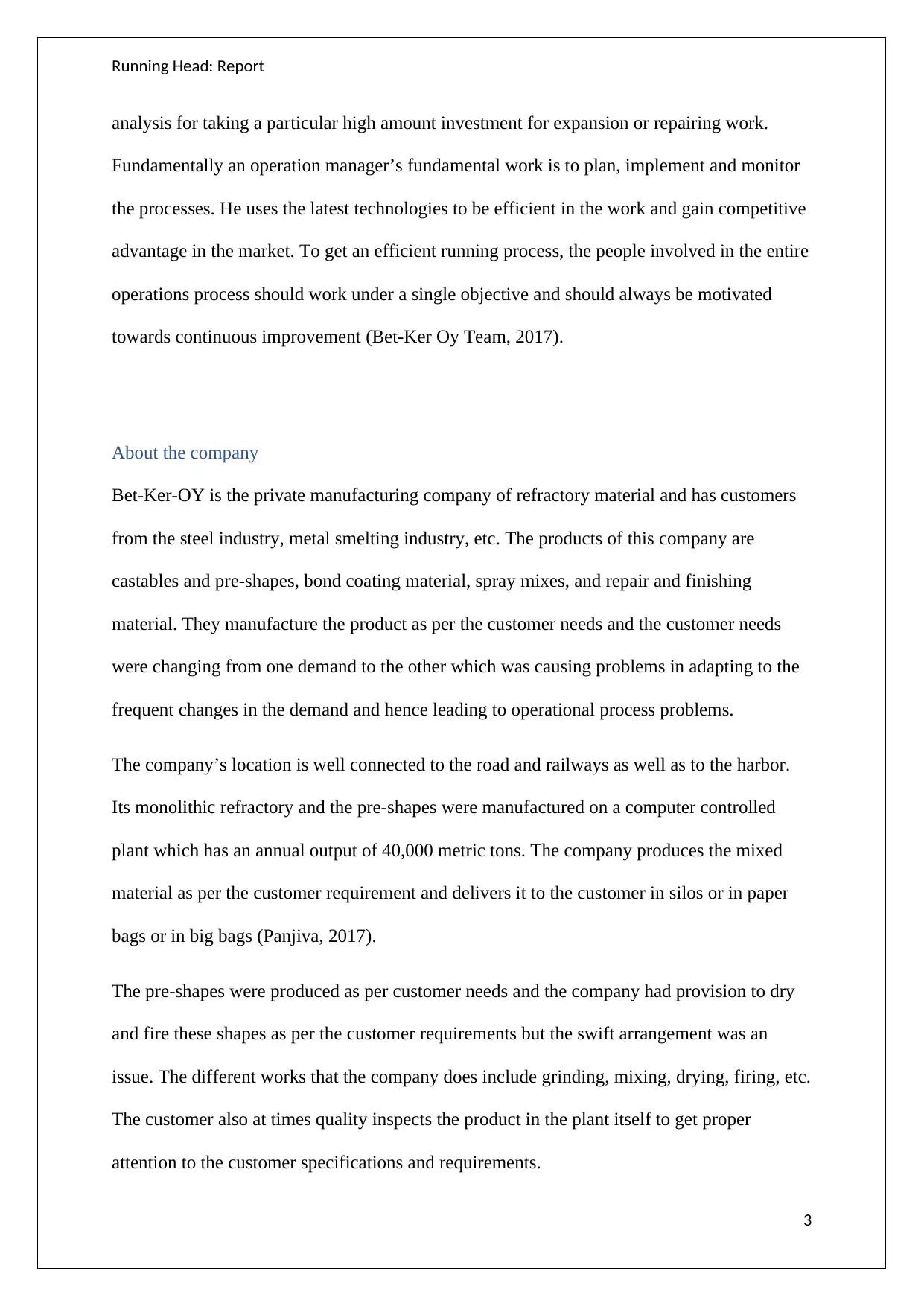
analysis for taking a particular high amount investment for expansion or repairing work.
Fundamentally an operation manager’s fundamental work is to plan, implement and monitor
the processes. He uses the latest technologies to be efficient in the work and gain competitive
advantage in the market. To get an efficient running process, the people involved in the entire
operations process should work under a single objective and should always be motivated
towards continuous improvement (Bet-Ker Oy Team, 2017).
About the company
Bet-Ker-OY is the private manufacturing company of refractory material and has customers
from the steel industry, metal smelting industry, etc. The products of this company are
castables and pre-shapes, bond coating material, spray mixes, and repair and finishing
material. They manufacture the product as per the customer needs and the customer needs
were changing from one demand to the other which was causing problems in adapting to the
frequent changes in the demand and hence leading to operational process problems.
The company’s location is well connected to the road and railways as well as to the harbor.
Its monolithic refractory and the pre-shapes were manufactured on a computer controlled
plant which has an annual output of 40,000 metric tons. The company produces the mixed
material as per the customer requirement and delivers it to the customer in silos or in paper
bags or in big bags (Panjiva, 2017).
The pre-shapes were produced as per customer needs and the company had provision to dry
and fire these shapes as per the customer requirements but the swift arrangement was an
issue. The different works that the company does include grinding, mixing, drying, firing, etc.
The customer also at times quality inspects the product in the plant itself to get proper
attention to the customer specifications and requirements.
3
Paraphrase This Document
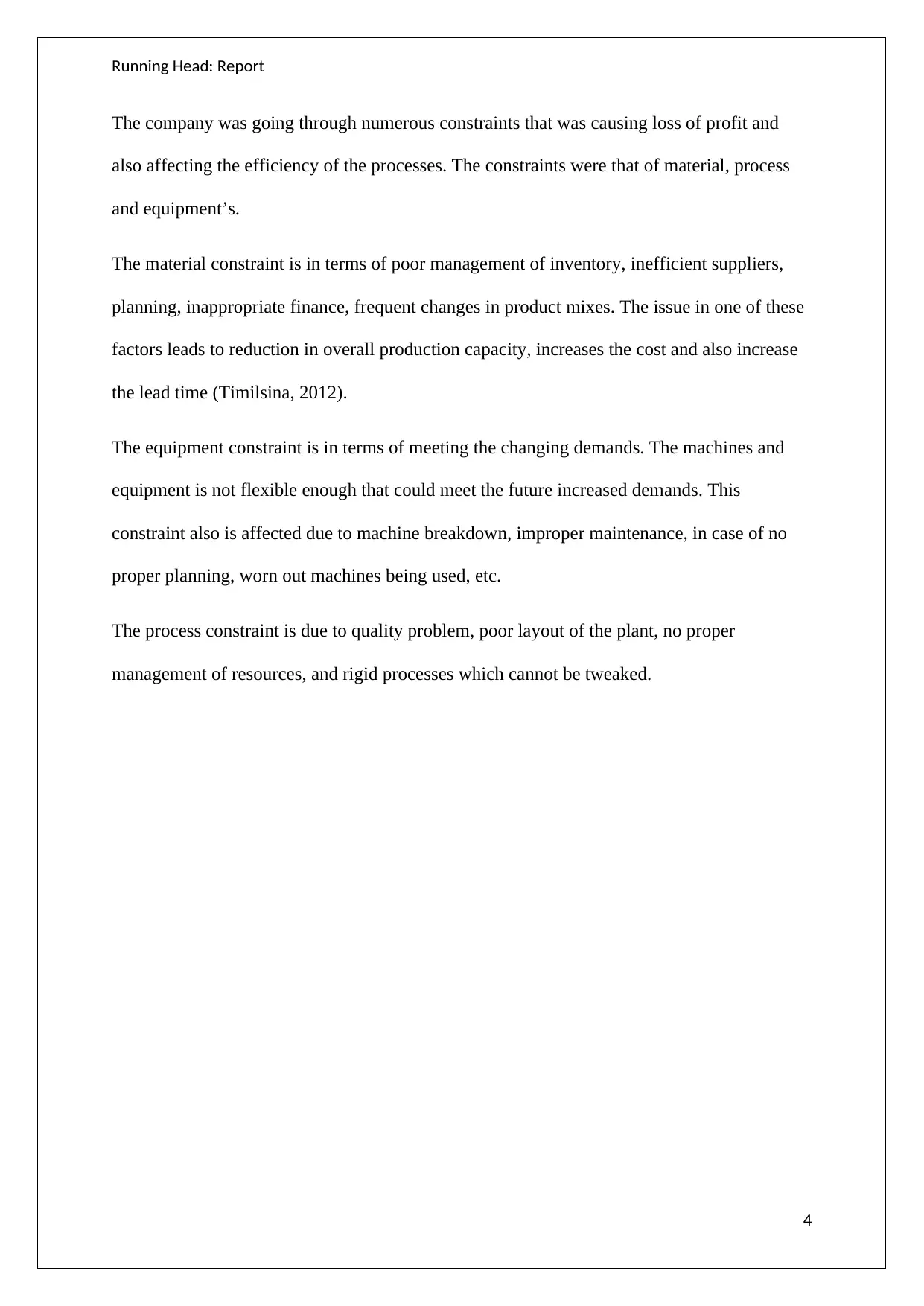
The company was going through numerous constraints that was causing loss of profit and
also affecting the efficiency of the processes. The constraints were that of material, process
and equipment’s.
The material constraint is in terms of poor management of inventory, inefficient suppliers,
planning, inappropriate finance, frequent changes in product mixes. The issue in one of these
factors leads to reduction in overall production capacity, increases the cost and also increase
the lead time (Timilsina, 2012).
The equipment constraint is in terms of meeting the changing demands. The machines and
equipment is not flexible enough that could meet the future increased demands. This
constraint also is affected due to machine breakdown, improper maintenance, in case of no
proper planning, worn out machines being used, etc.
The process constraint is due to quality problem, poor layout of the plant, no proper
management of resources, and rigid processes which cannot be tweaked.
4
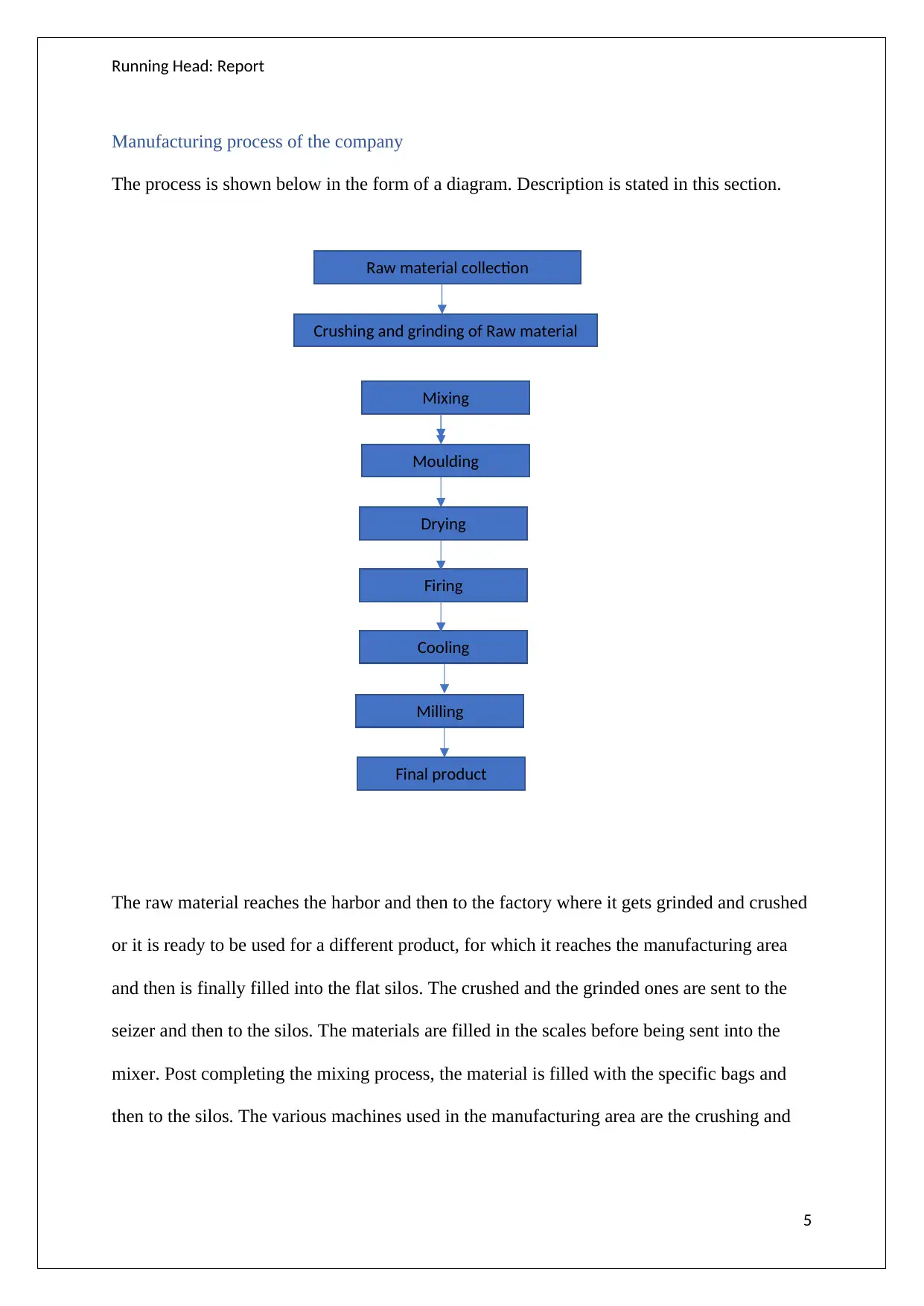
Manufacturing process of the company
The process is shown below in the form of a diagram. Description is stated in this section.
The raw material reaches the harbor and then to the factory where it gets grinded and crushed
or it is ready to be used for a different product, for which it reaches the manufacturing area
and then is finally filled into the flat silos. The crushed and the grinded ones are sent to the
seizer and then to the silos. The materials are filled in the scales before being sent into the
mixer. Post completing the mixing process, the material is filled with the specific bags and
then to the silos. The various machines used in the manufacturing area are the crushing and
5
Final product
Milling
Cooling
Firing
Drying
Moulding
Mixing
Crushing and grinding of Raw material
Raw material collection
⊘ This is a preview!⊘
Do you want full access?
Subscribe today to unlock all pages.

Trusted by 1+ million students worldwide
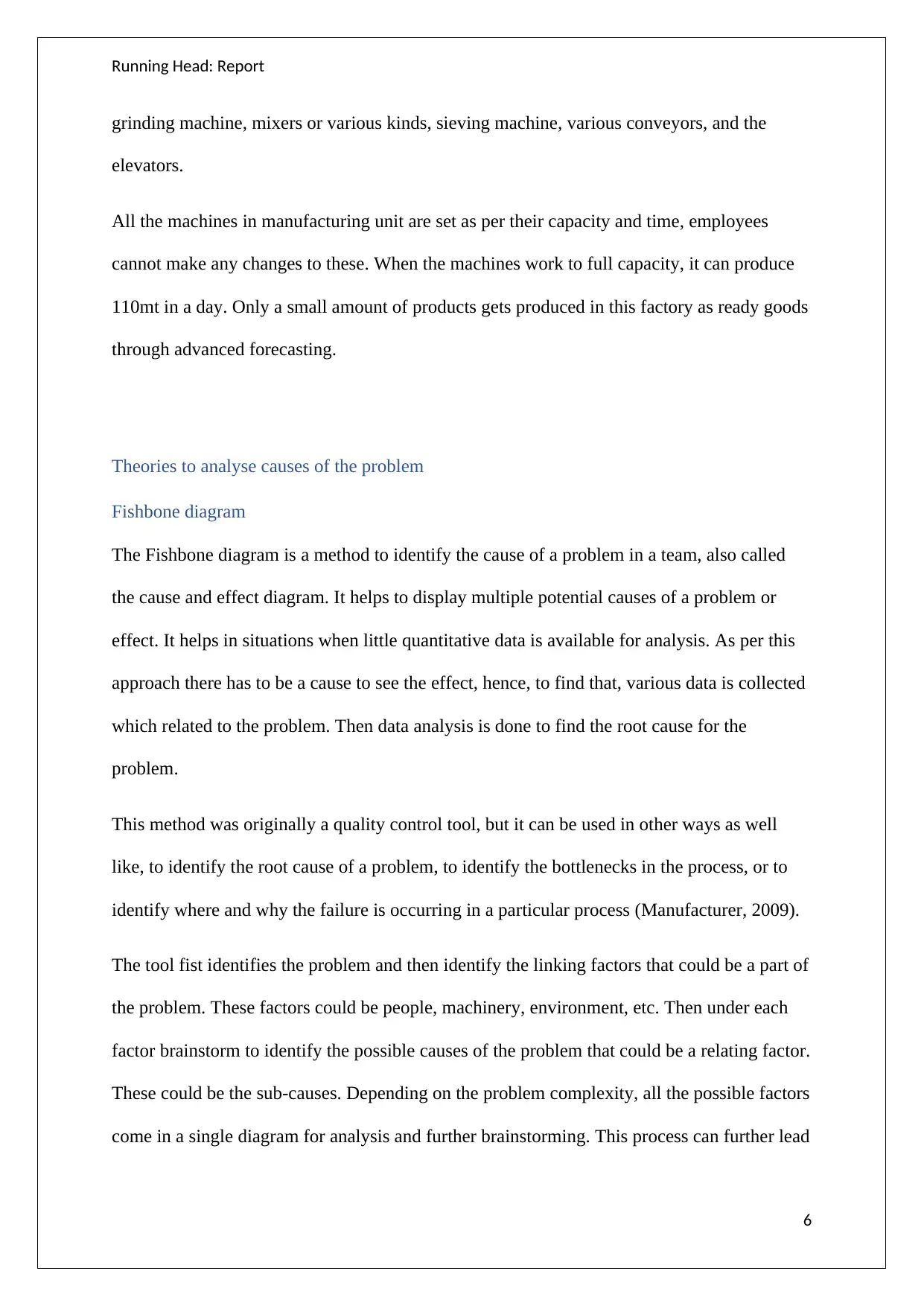
grinding machine, mixers or various kinds, sieving machine, various conveyors, and the
elevators.
All the machines in manufacturing unit are set as per their capacity and time, employees
cannot make any changes to these. When the machines work to full capacity, it can produce
110mt in a day. Only a small amount of products gets produced in this factory as ready goods
through advanced forecasting.
Theories to analyse causes of the problem
Fishbone diagram
The Fishbone diagram is a method to identify the cause of a problem in a team, also called
the cause and effect diagram. It helps to display multiple potential causes of a problem or
effect. It helps in situations when little quantitative data is available for analysis. As per this
approach there has to be a cause to see the effect, hence, to find that, various data is collected
which related to the problem. Then data analysis is done to find the root cause for the
problem.
This method was originally a quality control tool, but it can be used in other ways as well
like, to identify the root cause of a problem, to identify the bottlenecks in the process, or to
identify where and why the failure is occurring in a particular process (Manufacturer, 2009).
The tool fist identifies the problem and then identify the linking factors that could be a part of
the problem. These factors could be people, machinery, environment, etc. Then under each
factor brainstorm to identify the possible causes of the problem that could be a relating factor.
These could be the sub-causes. Depending on the problem complexity, all the possible factors
come in a single diagram for analysis and further brainstorming. This process can further lead
6
Paraphrase This Document
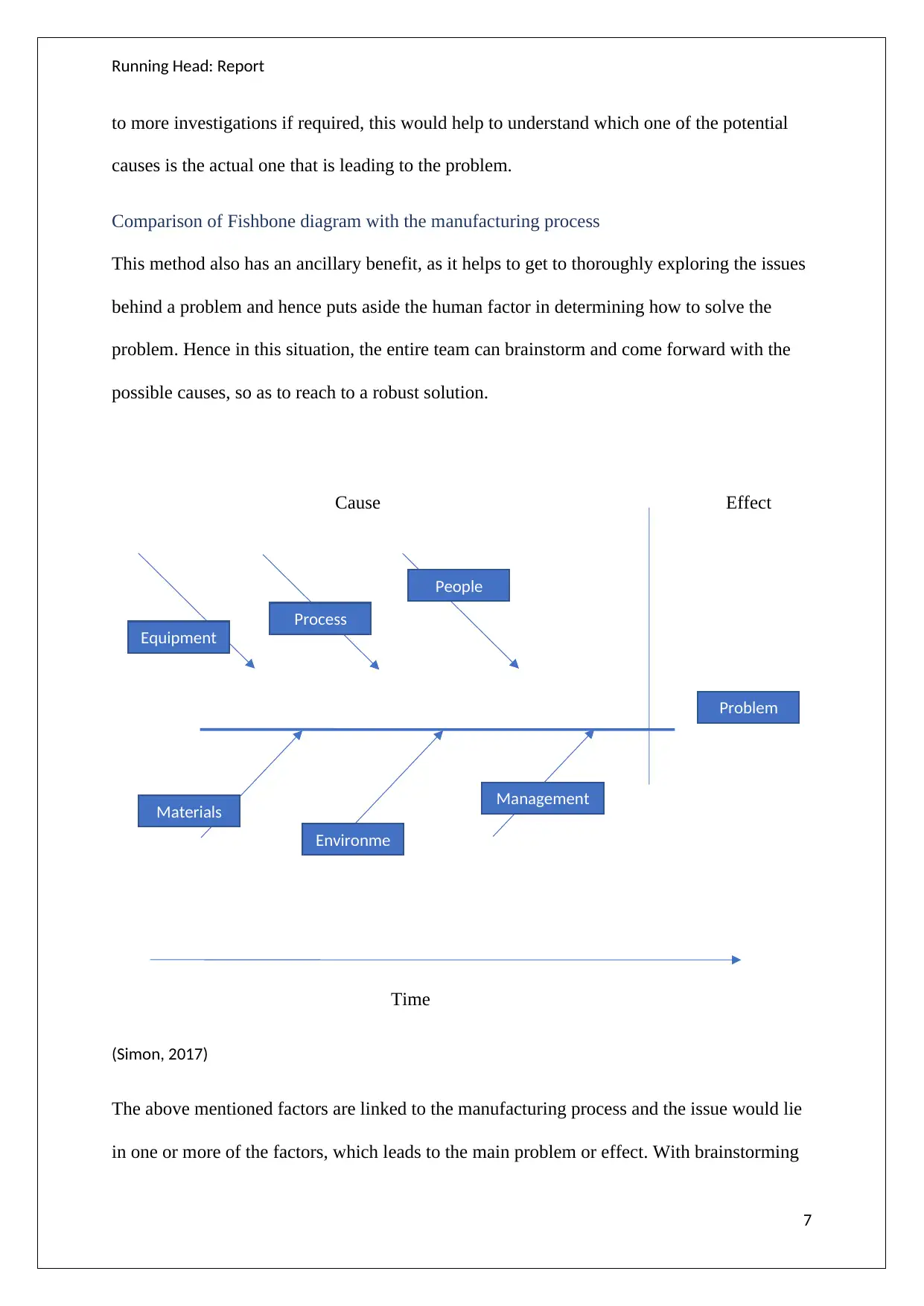
to more investigations if required, this would help to understand which one of the potential
causes is the actual one that is leading to the problem.
Comparison of Fishbone diagram with the manufacturing process
This method also has an ancillary benefit, as it helps to get to thoroughly exploring the issues
behind a problem and hence puts aside the human factor in determining how to solve the
problem. Hence in this situation, the entire team can brainstorm and come forward with the
possible causes, so as to reach to a robust solution.
Cause Effect
Time
(Simon, 2017)
The above mentioned factors are linked to the manufacturing process and the issue would lie
in one or more of the factors, which leads to the main problem or effect. With brainstorming
7
Equipment
People
Process
Materials
Environme
Management
Problem
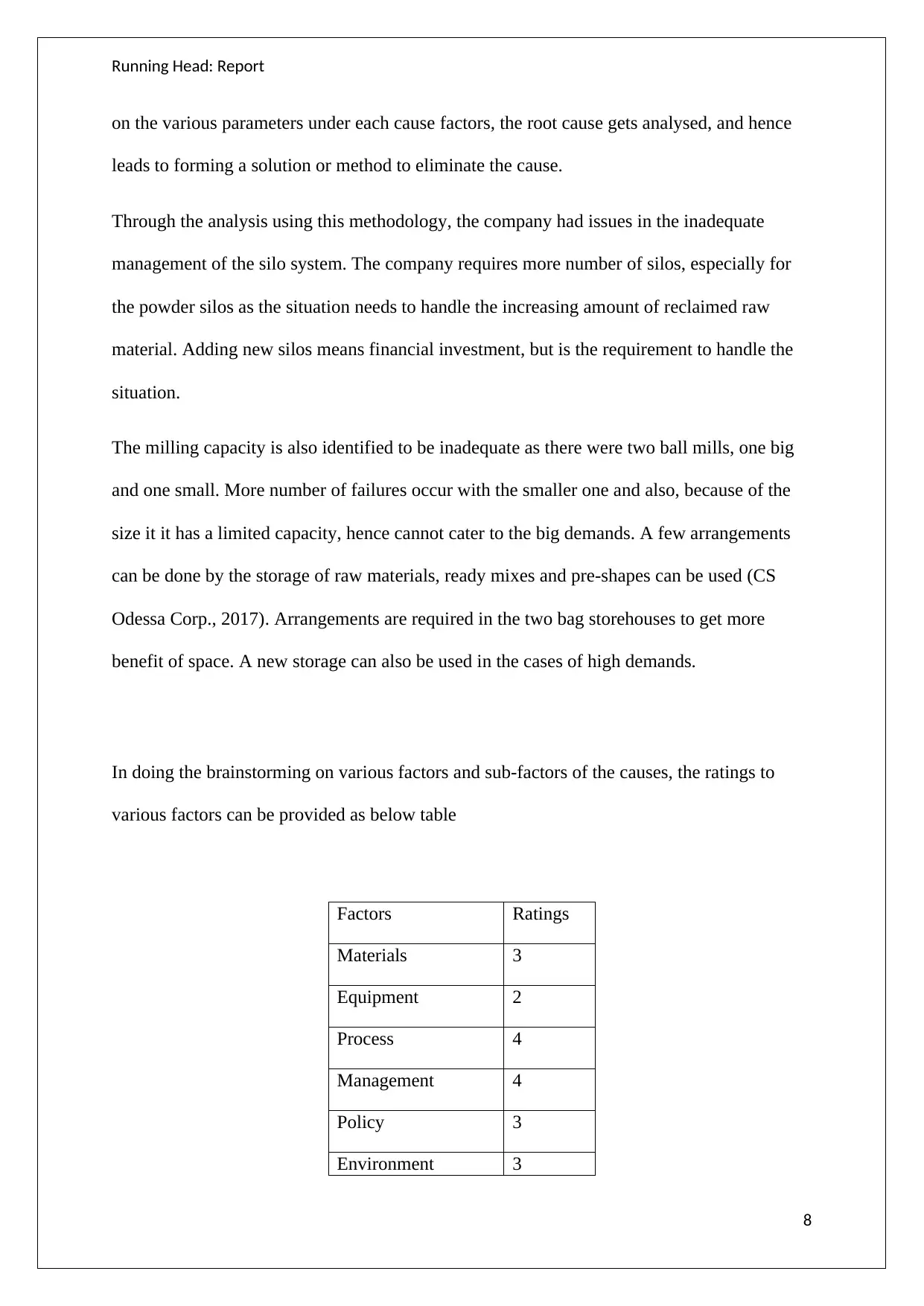
on the various parameters under each cause factors, the root cause gets analysed, and hence
leads to forming a solution or method to eliminate the cause.
Through the analysis using this methodology, the company had issues in the inadequate
management of the silo system. The company requires more number of silos, especially for
the powder silos as the situation needs to handle the increasing amount of reclaimed raw
material. Adding new silos means financial investment, but is the requirement to handle the
situation.
The milling capacity is also identified to be inadequate as there were two ball mills, one big
and one small. More number of failures occur with the smaller one and also, because of the
size it it has a limited capacity, hence cannot cater to the big demands. A few arrangements
can be done by the storage of raw materials, ready mixes and pre-shapes can be used (CS
Odessa Corp., 2017). Arrangements are required in the two bag storehouses to get more
benefit of space. A new storage can also be used in the cases of high demands.
In doing the brainstorming on various factors and sub-factors of the causes, the ratings to
various factors can be provided as below table
Factors Ratings
Materials 3
Equipment 2
Process 4
Management 4
Policy 3
Environment 3
8
⊘ This is a preview!⊘
Do you want full access?
Subscribe today to unlock all pages.

Trusted by 1+ million students worldwide
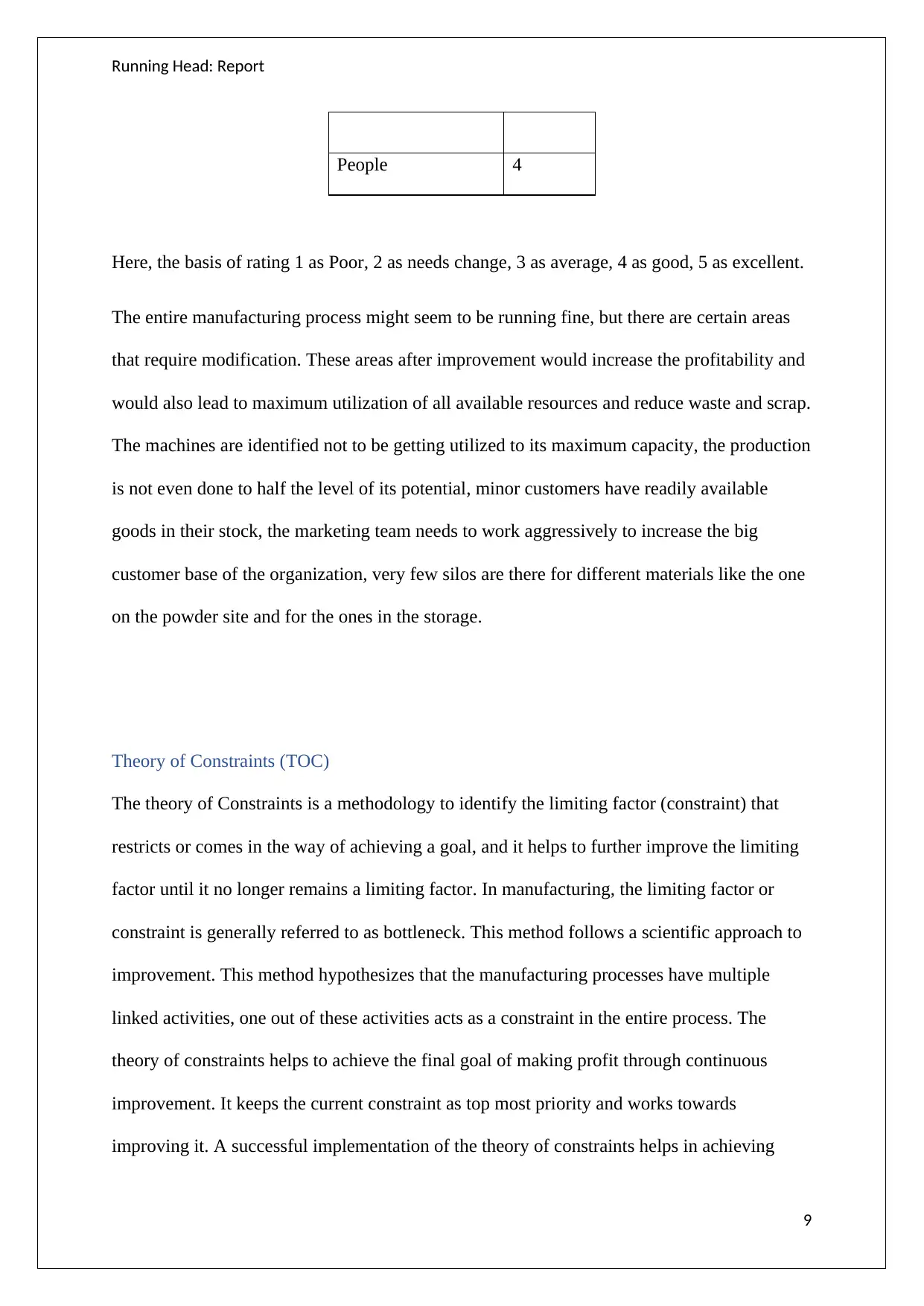
People 4
Here, the basis of rating 1 as Poor, 2 as needs change, 3 as average, 4 as good, 5 as excellent.
The entire manufacturing process might seem to be running fine, but there are certain areas
that require modification. These areas after improvement would increase the profitability and
would also lead to maximum utilization of all available resources and reduce waste and scrap.
The machines are identified not to be getting utilized to its maximum capacity, the production
is not even done to half the level of its potential, minor customers have readily available
goods in their stock, the marketing team needs to work aggressively to increase the big
customer base of the organization, very few silos are there for different materials like the one
on the powder site and for the ones in the storage.
Theory of Constraints (TOC)
The theory of Constraints is a methodology to identify the limiting factor (constraint) that
restricts or comes in the way of achieving a goal, and it helps to further improve the limiting
factor until it no longer remains a limiting factor. In manufacturing, the limiting factor or
constraint is generally referred to as bottleneck. This method follows a scientific approach to
improvement. This method hypothesizes that the manufacturing processes have multiple
linked activities, one out of these activities acts as a constraint in the entire process. The
theory of constraints helps to achieve the final goal of making profit through continuous
improvement. It keeps the current constraint as top most priority and works towards
improving it. A successful implementation of the theory of constraints helps in achieving
9
Paraphrase This Document
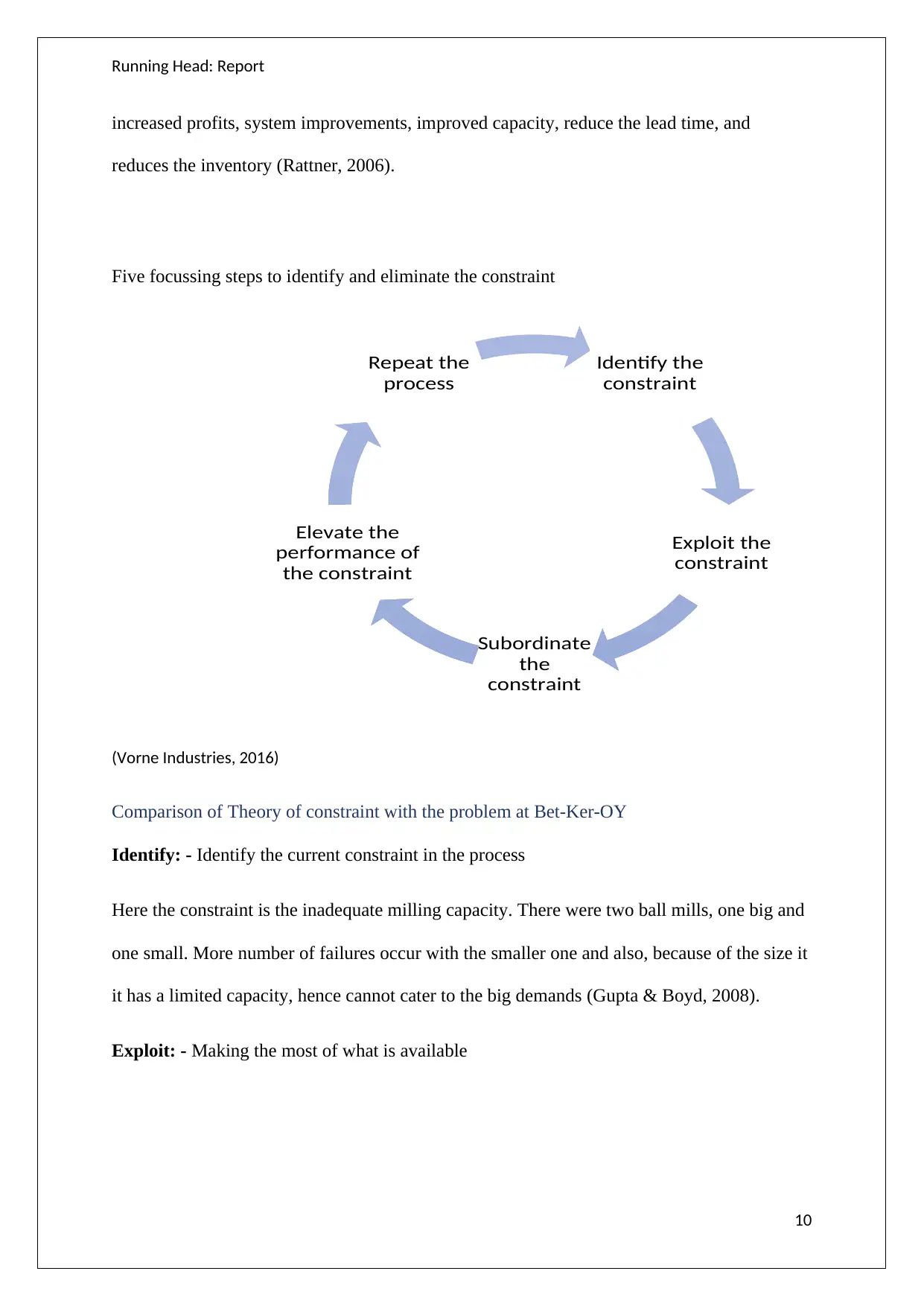
increased profits, system improvements, improved capacity, reduce the lead time, and
reduces the inventory (Rattner, 2006).
Five focussing steps to identify and eliminate the constraint
(Vorne Industries, 2016)
Comparison of Theory of constraint with the problem at Bet-Ker-OY
Identify: - Identify the current constraint in the process
Here the constraint is the inadequate milling capacity. There were two ball mills, one big and
one small. More number of failures occur with the smaller one and also, because of the size it
it has a limited capacity, hence cannot cater to the big demands (Gupta & Boyd, 2008).
Exploit: - Making the most of what is available
10
Identify the
constraint
Exploit the
constraint
Subordinate
the
constraint
Elevate the
performance of
the constraint
Repeat the
process
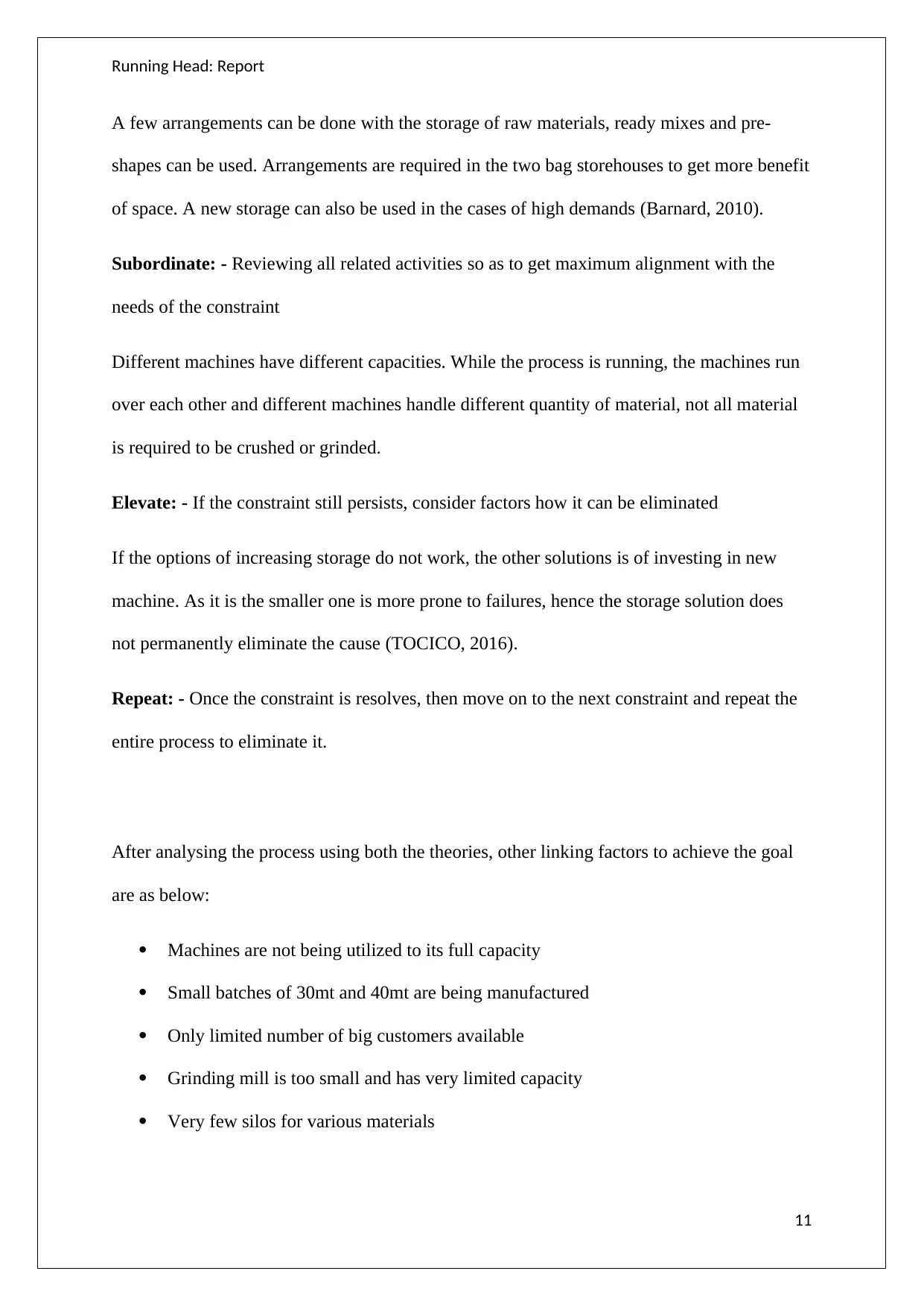
A few arrangements can be done with the storage of raw materials, ready mixes and pre-
shapes can be used. Arrangements are required in the two bag storehouses to get more benefit
of space. A new storage can also be used in the cases of high demands (Barnard, 2010).
Subordinate: - Reviewing all related activities so as to get maximum alignment with the
needs of the constraint
Different machines have different capacities. While the process is running, the machines run
over each other and different machines handle different quantity of material, not all material
is required to be crushed or grinded.
Elevate: - If the constraint still persists, consider factors how it can be eliminated
If the options of increasing storage do not work, the other solutions is of investing in new
machine. As it is the smaller one is more prone to failures, hence the storage solution does
not permanently eliminate the cause (TOCICO, 2016).
Repeat: - Once the constraint is resolves, then move on to the next constraint and repeat the
entire process to eliminate it.
After analysing the process using both the theories, other linking factors to achieve the goal
are as below:
Machines are not being utilized to its full capacity
Small batches of 30mt and 40mt are being manufactured
Only limited number of big customers available
Grinding mill is too small and has very limited capacity
Very few silos for various materials
11
⊘ This is a preview!⊘
Do you want full access?
Subscribe today to unlock all pages.

Trusted by 1+ million students worldwide
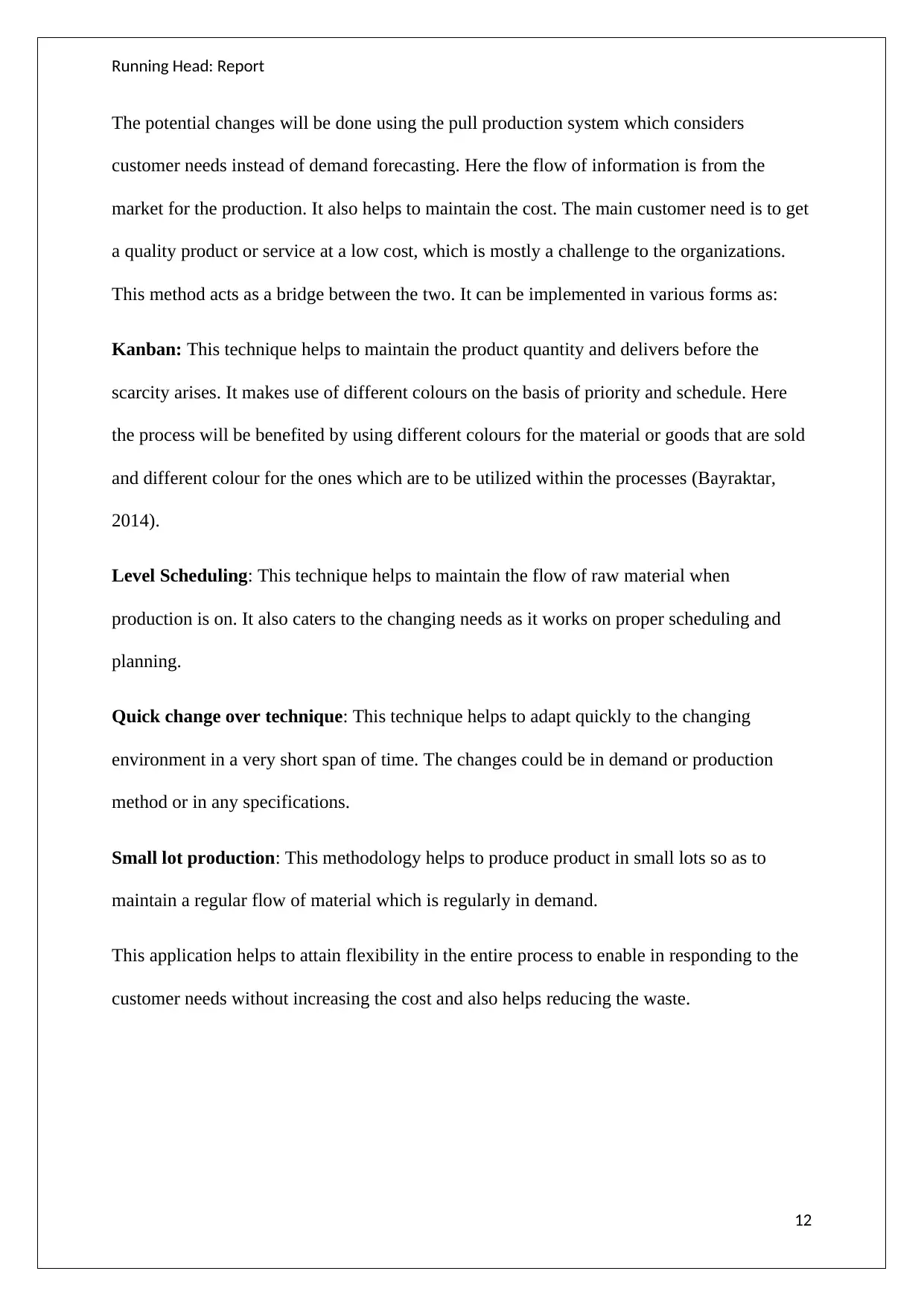
The potential changes will be done using the pull production system which considers
customer needs instead of demand forecasting. Here the flow of information is from the
market for the production. It also helps to maintain the cost. The main customer need is to get
a quality product or service at a low cost, which is mostly a challenge to the organizations.
This method acts as a bridge between the two. It can be implemented in various forms as:
Kanban: This technique helps to maintain the product quantity and delivers before the
scarcity arises. It makes use of different colours on the basis of priority and schedule. Here
the process will be benefited by using different colours for the material or goods that are sold
and different colour for the ones which are to be utilized within the processes (Bayraktar,
2014).
Level Scheduling: This technique helps to maintain the flow of raw material when
production is on. It also caters to the changing needs as it works on proper scheduling and
planning.
Quick change over technique: This technique helps to adapt quickly to the changing
environment in a very short span of time. The changes could be in demand or production
method or in any specifications.
Small lot production: This methodology helps to produce product in small lots so as to
maintain a regular flow of material which is regularly in demand.
This application helps to attain flexibility in the entire process to enable in responding to the
customer needs without increasing the cost and also helps reducing the waste.
12
Paraphrase This Document
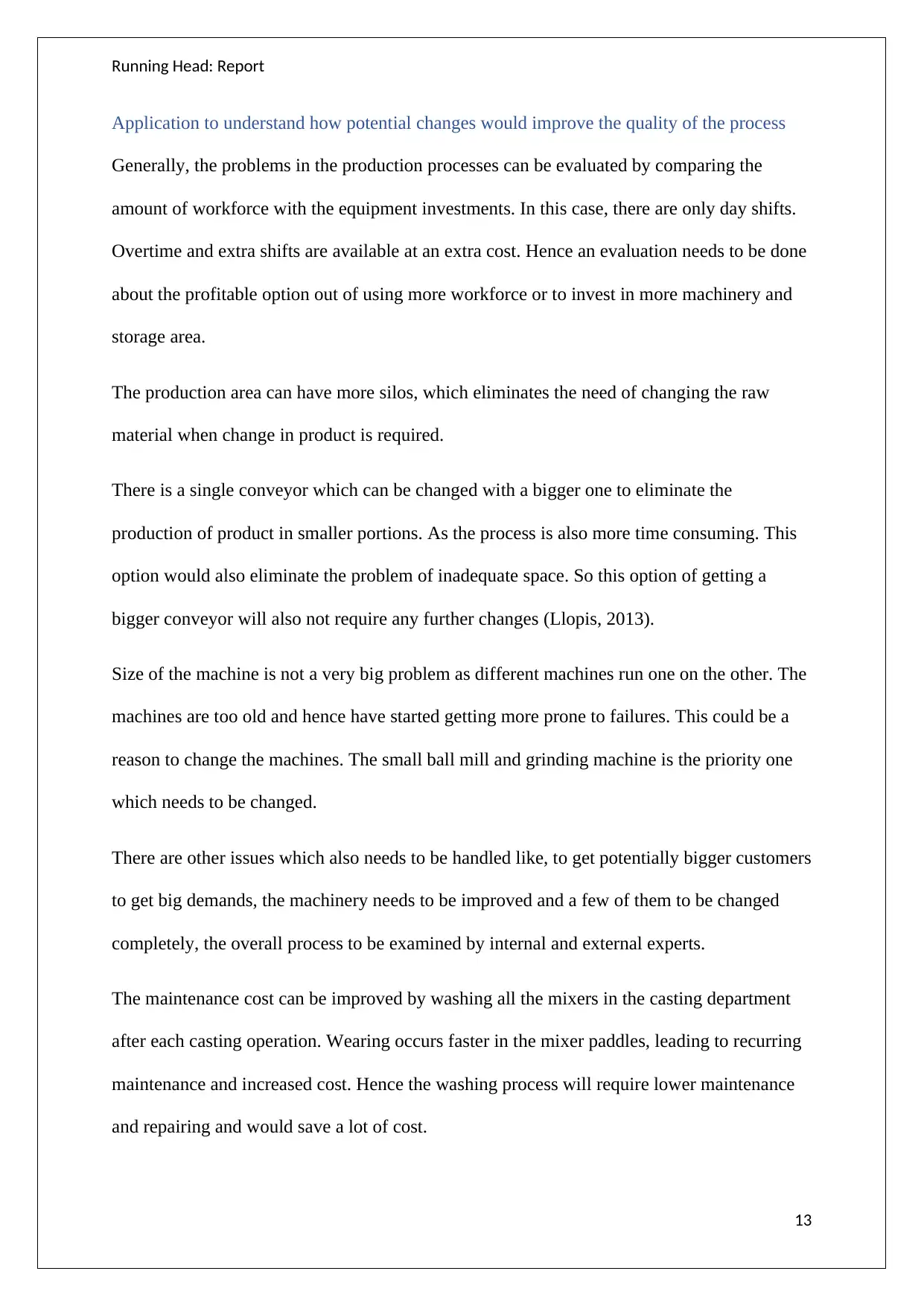
Application to understand how potential changes would improve the quality of the process
Generally, the problems in the production processes can be evaluated by comparing the
amount of workforce with the equipment investments. In this case, there are only day shifts.
Overtime and extra shifts are available at an extra cost. Hence an evaluation needs to be done
about the profitable option out of using more workforce or to invest in more machinery and
storage area.
The production area can have more silos, which eliminates the need of changing the raw
material when change in product is required.
There is a single conveyor which can be changed with a bigger one to eliminate the
production of product in smaller portions. As the process is also more time consuming. This
option would also eliminate the problem of inadequate space. So this option of getting a
bigger conveyor will also not require any further changes (Llopis, 2013).
Size of the machine is not a very big problem as different machines run one on the other. The
machines are too old and hence have started getting more prone to failures. This could be a
reason to change the machines. The small ball mill and grinding machine is the priority one
which needs to be changed.
There are other issues which also needs to be handled like, to get potentially bigger customers
to get big demands, the machinery needs to be improved and a few of them to be changed
completely, the overall process to be examined by internal and external experts.
The maintenance cost can be improved by washing all the mixers in the casting department
after each casting operation. Wearing occurs faster in the mixer paddles, leading to recurring
maintenance and increased cost. Hence the washing process will require lower maintenance
and repairing and would save a lot of cost.
13
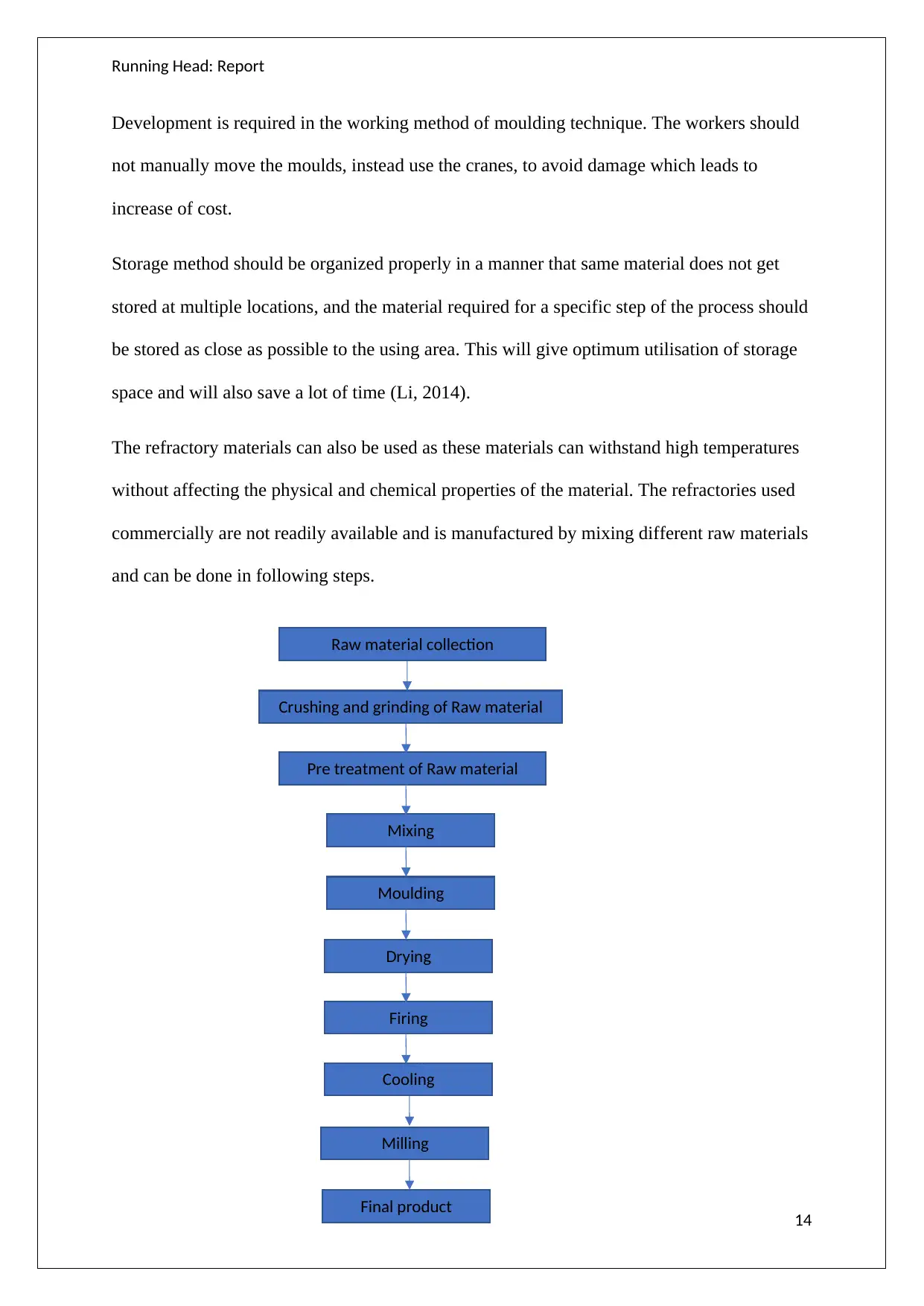
Development is required in the working method of moulding technique. The workers should
not manually move the moulds, instead use the cranes, to avoid damage which leads to
increase of cost.
Storage method should be organized properly in a manner that same material does not get
stored at multiple locations, and the material required for a specific step of the process should
be stored as close as possible to the using area. This will give optimum utilisation of storage
space and will also save a lot of time (Li, 2014).
The refractory materials can also be used as these materials can withstand high temperatures
without affecting the physical and chemical properties of the material. The refractories used
commercially are not readily available and is manufactured by mixing different raw materials
and can be done in following steps.
14
Final product
Milling
Cooling
Firing
Drying
Moulding
Mixing
Pre treatment of Raw material
Crushing and grinding of Raw material
Raw material collection
⊘ This is a preview!⊘
Do you want full access?
Subscribe today to unlock all pages.

Trusted by 1+ million students worldwide
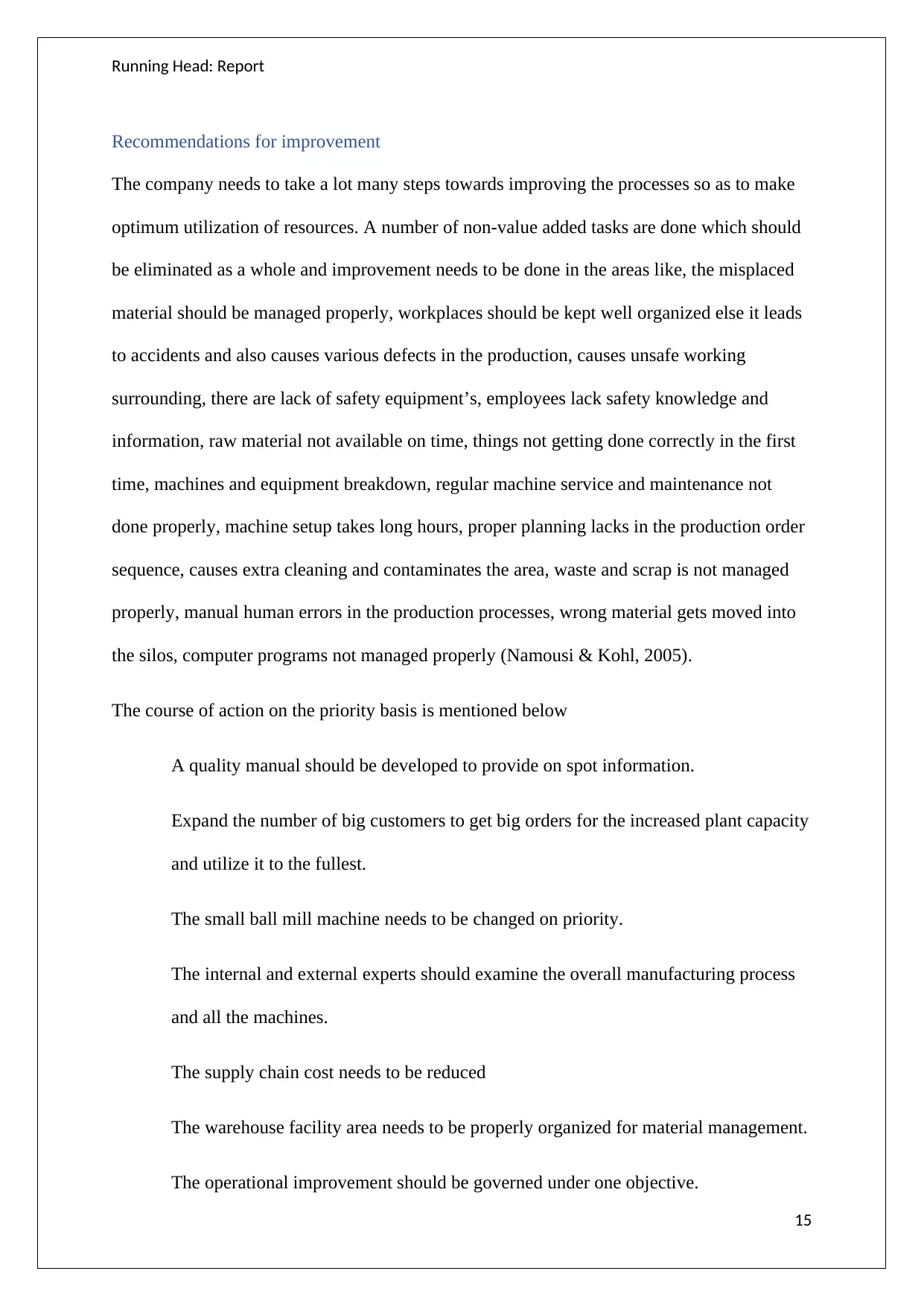
Recommendations for improvement
The company needs to take a lot many steps towards improving the processes so as to make
optimum utilization of resources. A number of non-value added tasks are done which should
be eliminated as a whole and improvement needs to be done in the areas like, the misplaced
material should be managed properly, workplaces should be kept well organized else it leads
to accidents and also causes various defects in the production, causes unsafe working
surrounding, there are lack of safety equipment’s, employees lack safety knowledge and
information, raw material not available on time, things not getting done correctly in the first
time, machines and equipment breakdown, regular machine service and maintenance not
done properly, machine setup takes long hours, proper planning lacks in the production order
sequence, causes extra cleaning and contaminates the area, waste and scrap is not managed
properly, manual human errors in the production processes, wrong material gets moved into
the silos, computer programs not managed properly (Namousi & Kohl, 2005).
The course of action on the priority basis is mentioned below
A quality manual should be developed to provide on spot information.
Expand the number of big customers to get big orders for the increased plant capacity
and utilize it to the fullest.
The small ball mill machine needs to be changed on priority.
The internal and external experts should examine the overall manufacturing process
and all the machines.
The supply chain cost needs to be reduced
The warehouse facility area needs to be properly organized for material management.
The operational improvement should be governed under one objective.
15
Paraphrase This Document
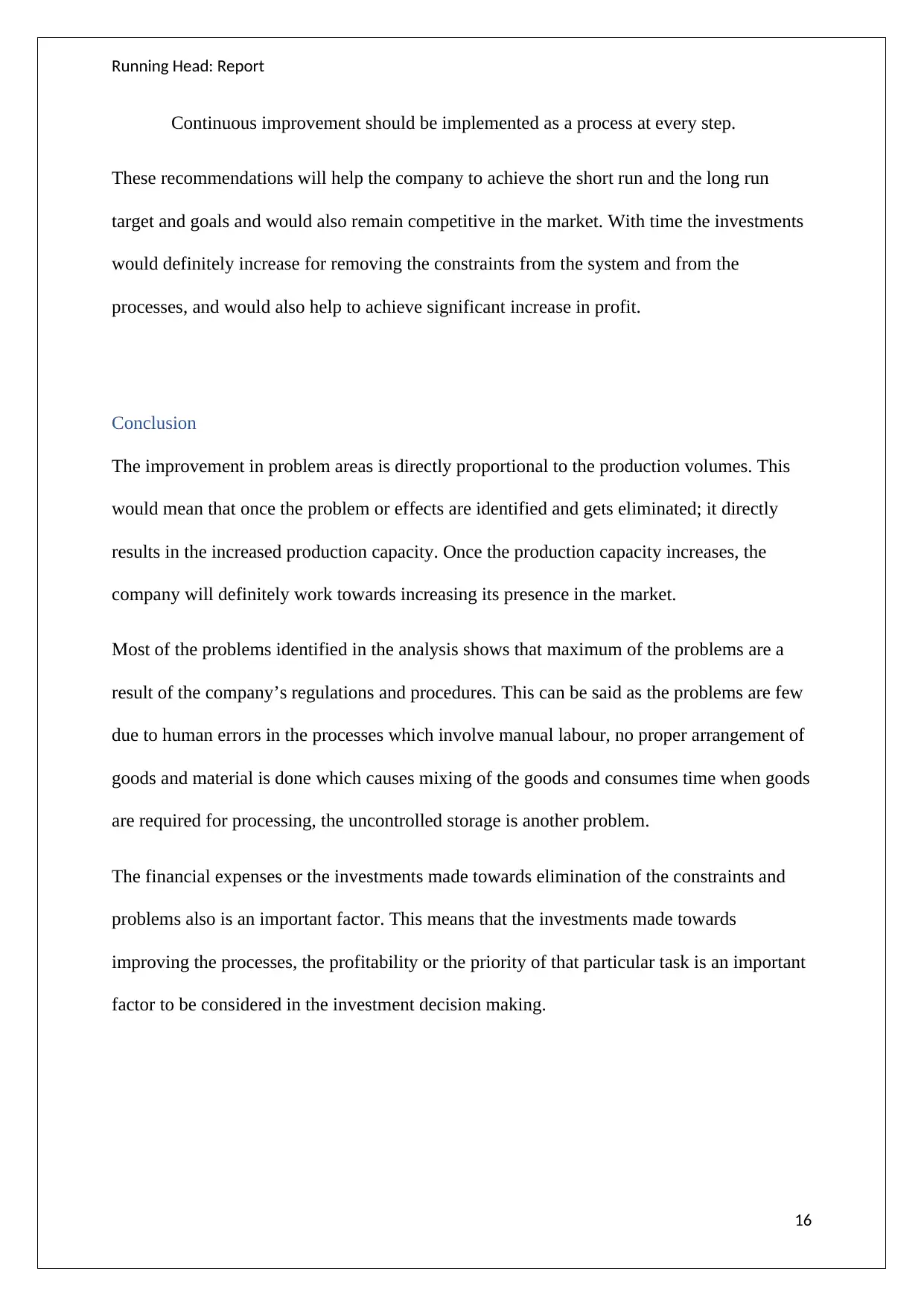
Continuous improvement should be implemented as a process at every step.
These recommendations will help the company to achieve the short run and the long run
target and goals and would also remain competitive in the market. With time the investments
would definitely increase for removing the constraints from the system and from the
processes, and would also help to achieve significant increase in profit.
Conclusion
The improvement in problem areas is directly proportional to the production volumes. This
would mean that once the problem or effects are identified and gets eliminated; it directly
results in the increased production capacity. Once the production capacity increases, the
company will definitely work towards increasing its presence in the market.
Most of the problems identified in the analysis shows that maximum of the problems are a
result of the company’s regulations and procedures. This can be said as the problems are few
due to human errors in the processes which involve manual labour, no proper arrangement of
goods and material is done which causes mixing of the goods and consumes time when goods
are required for processing, the uncontrolled storage is another problem.
The financial expenses or the investments made towards elimination of the constraints and
problems also is an important factor. This means that the investments made towards
improving the processes, the profitability or the priority of that particular task is an important
factor to be considered in the investment decision making.
16
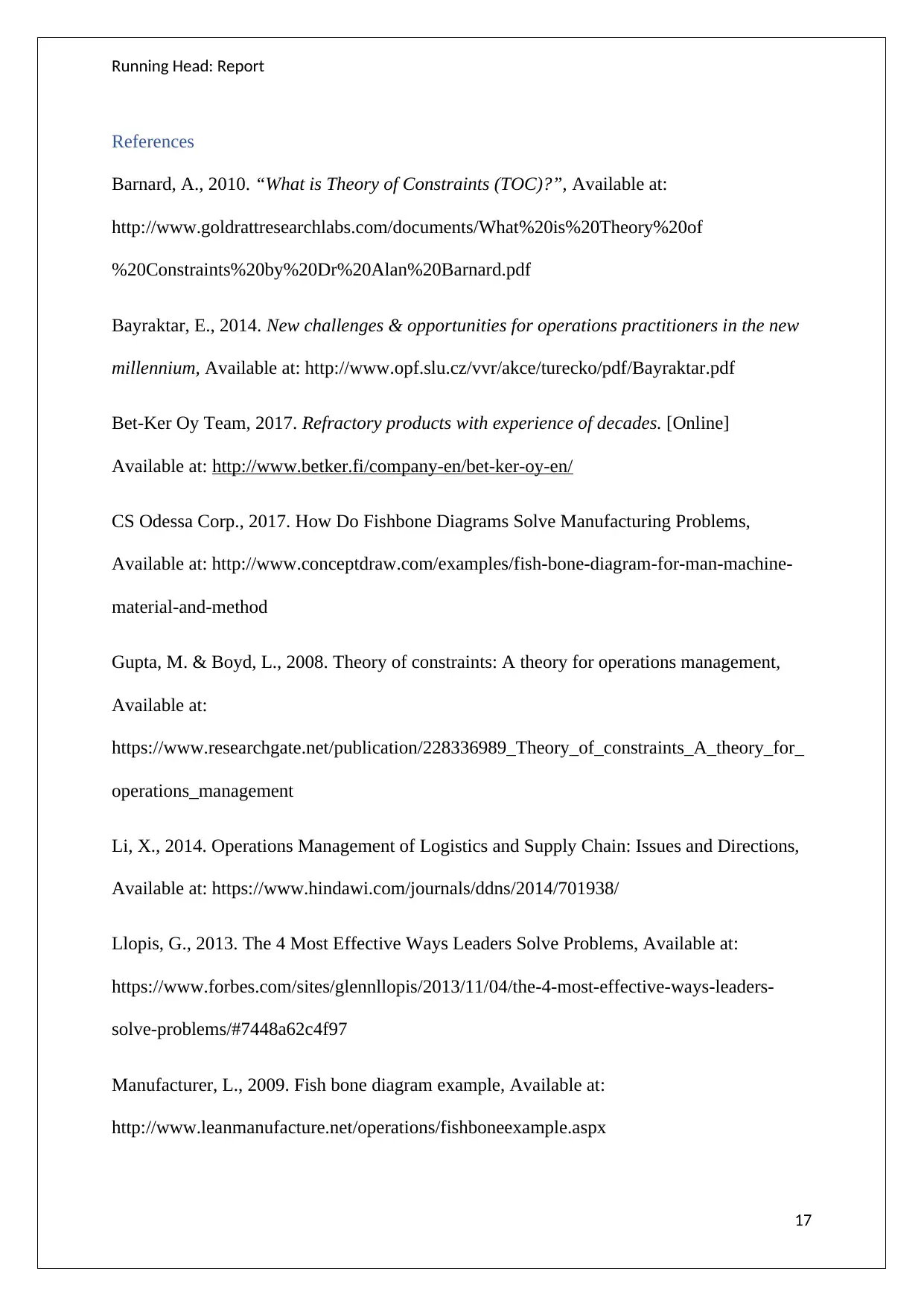
References
Barnard, A., 2010. “What is Theory of Constraints (TOC)?”, Available at:
http://www.goldrattresearchlabs.com/documents/What%20is%20Theory%20of
%20Constraints%20by%20Dr%20Alan%20Barnard.pdf
Bayraktar, E., 2014. New challenges & opportunities for operations practitioners in the new
millennium, Available at: http://www.opf.slu.cz/vvr/akce/turecko/pdf/Bayraktar.pdf
Bet-Ker Oy Team, 2017. Refractory products with experience of decades. [Online]
Available at: http://www.betker.fi/company-en/bet-ker-oy-en/
CS Odessa Corp., 2017. How Do Fishbone Diagrams Solve Manufacturing Problems,
Available at: http://www.conceptdraw.com/examples/fish-bone-diagram-for-man-machine-
material-and-method
Gupta, M. & Boyd, L., 2008. Theory of constraints: A theory for operations management,
Available at:
https://www.researchgate.net/publication/228336989_Theory_of_constraints_A_theory_for_
operations_management
Li, X., 2014. Operations Management of Logistics and Supply Chain: Issues and Directions,
Available at: https://www.hindawi.com/journals/ddns/2014/701938/
Llopis, G., 2013. The 4 Most Effective Ways Leaders Solve Problems, Available at:
https://www.forbes.com/sites/glennllopis/2013/11/04/the-4-most-effective-ways-leaders-
solve-problems/#7448a62c4f97
Manufacturer, L., 2009. Fish bone diagram example, Available at:
http://www.leanmanufacture.net/operations/fishboneexample.aspx
17
⊘ This is a preview!⊘
Do you want full access?
Subscribe today to unlock all pages.

Trusted by 1+ million students worldwide
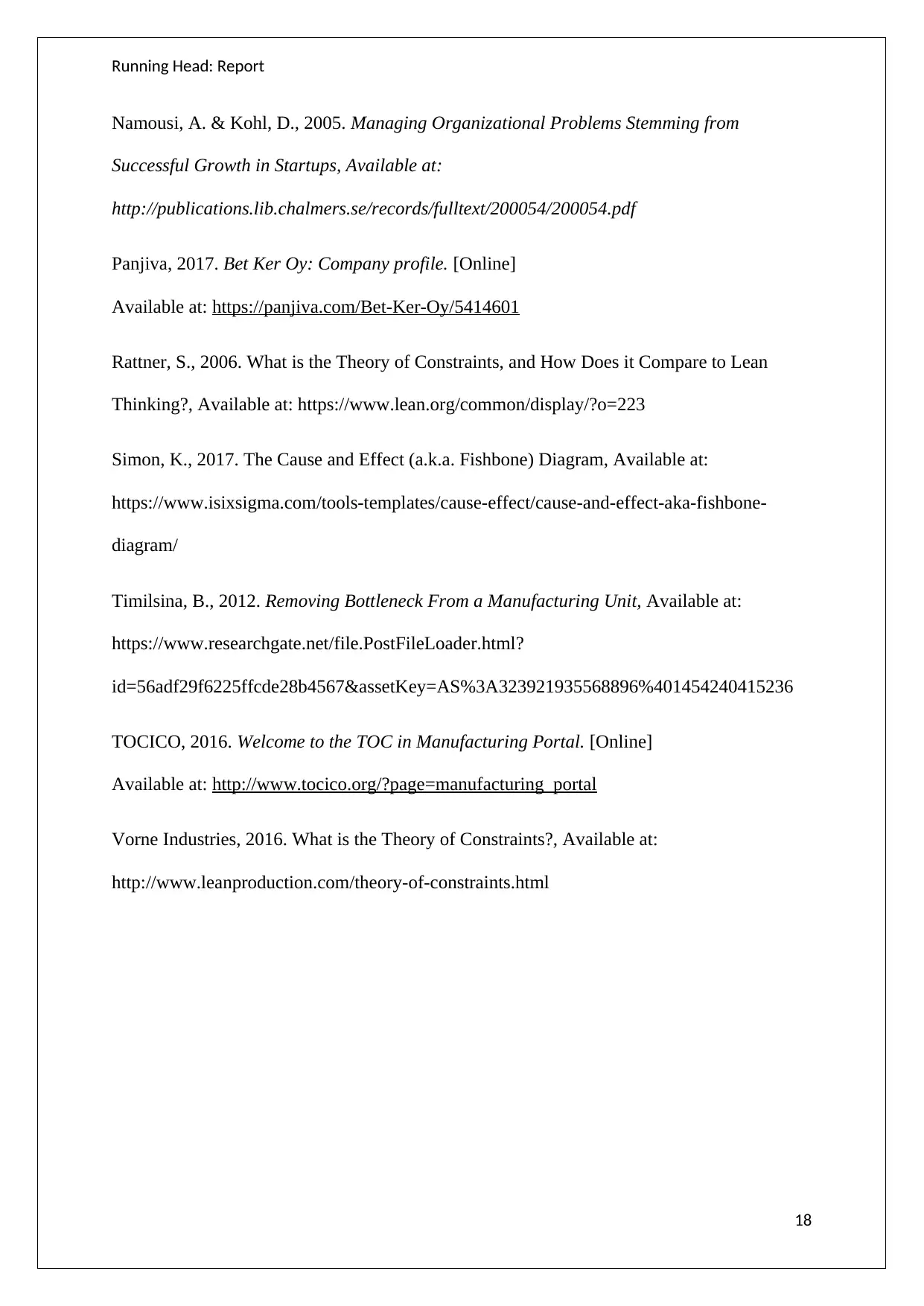
Namousi, A. & Kohl, D., 2005. Managing Organizational Problems Stemming from
Successful Growth in Startups, Available at:
http://publications.lib.chalmers.se/records/fulltext/200054/200054.pdf
Panjiva, 2017. Bet Ker Oy: Company profile. [Online]
Available at: https://panjiva.com/Bet-Ker-Oy/5414601
Rattner, S., 2006. What is the Theory of Constraints, and How Does it Compare to Lean
Thinking?, Available at: https://www.lean.org/common/display/?o=223
Simon, K., 2017. The Cause and Effect (a.k.a. Fishbone) Diagram, Available at:
https://www.isixsigma.com/tools-templates/cause-effect/cause-and-effect-aka-fishbone-
diagram/
Timilsina, B., 2012. Removing Bottleneck From a Manufacturing Unit, Available at:
https://www.researchgate.net/file.PostFileLoader.html?
id=56adf29f6225ffcde28b4567&assetKey=AS%3A323921935568896%401454240415236
TOCICO, 2016. Welcome to the TOC in Manufacturing Portal. [Online]
Available at: http://www.tocico.org/?page=manufacturing_portal
Vorne Industries, 2016. What is the Theory of Constraints?, Available at:
http://www.leanproduction.com/theory-of-constraints.html
18
Related Documents

Your All-in-One AI-Powered Toolkit for Academic Success.
+13062052269
info@desklib.com
Available 24*7 on WhatsApp / Email
© 2024 | Zucol Services PVT LTD | All rights reserved.