Warehouse Performance KPIs Analysis
VerifiedAdded on  2020/01/07
|12
|2218
|239
Report
AI Summary
The assignment delves into the critical role of Key Performance Indicators (KPIs) in evaluating warehouse performance for Ready-Mix Concrete (RMC) production. It analyzes various KPIs such as On Time Delivery, Plant Capacity, Rejected Rate, Rework Rate, and Order Booking Accuracy. The report highlights how these KPIs provide valuable insights into operational efficiency, potential areas for improvement, and strategies for maximizing productivity within the RMC warehouse.
Contribute Materials
Your contribution can guide someone’s learning journey. Share your
documents today.
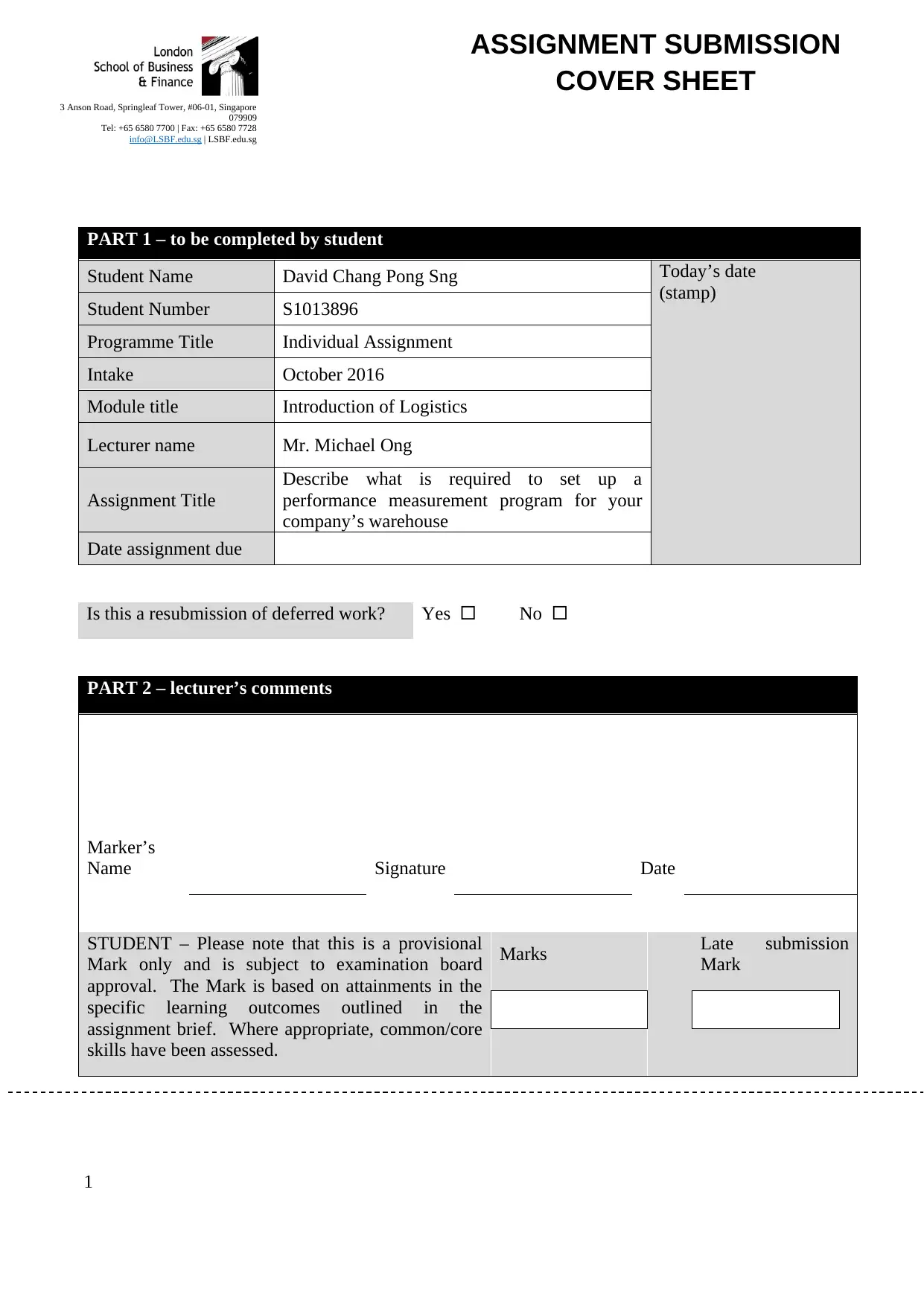
PART 1 – to be completed by student
Student Name David Chang Pong Sng Today’s date
(stamp)
Student Number S1013896
Programme Title Individual Assignment
Intake October 2016
Module title Introduction of Logistics
Lecturer name Mr. Michael Ong
Assignment Title
Describe what is required to set up a
performance measurement program for your
company’s warehouse
Date assignment due
Is this a resubmission of deferred work? Yes  No 
PART 2 – lecturer’s comments
Marker’s
Name Signature Date
STUDENT – Please note that this is a provisional
Mark only and is subject to examination board
approval. The Mark is based on attainments in the
specific learning outcomes outlined in the
assignment brief. Where appropriate, common/core
skills have been assessed.
Marks Late submission
Mark
1
3 Anson Road, Springleaf Tower, #06-01, Singapore
079909
Tel: +65 6580 7700 | Fax: +65 6580 7728
info@LSBF.edu.sg | LSBF.edu.sg
ASSIGNMENT SUBMISSION
COVER SHEET
Student Name David Chang Pong Sng Today’s date
(stamp)
Student Number S1013896
Programme Title Individual Assignment
Intake October 2016
Module title Introduction of Logistics
Lecturer name Mr. Michael Ong
Assignment Title
Describe what is required to set up a
performance measurement program for your
company’s warehouse
Date assignment due
Is this a resubmission of deferred work? Yes  No 
PART 2 – lecturer’s comments
Marker’s
Name Signature Date
STUDENT – Please note that this is a provisional
Mark only and is subject to examination board
approval. The Mark is based on attainments in the
specific learning outcomes outlined in the
assignment brief. Where appropriate, common/core
skills have been assessed.
Marks Late submission
Mark
1
3 Anson Road, Springleaf Tower, #06-01, Singapore
079909
Tel: +65 6580 7700 | Fax: +65 6580 7728
info@LSBF.edu.sg | LSBF.edu.sg
ASSIGNMENT SUBMISSION
COVER SHEET
Secure Best Marks with AI Grader
Need help grading? Try our AI Grader for instant feedback on your assignments.
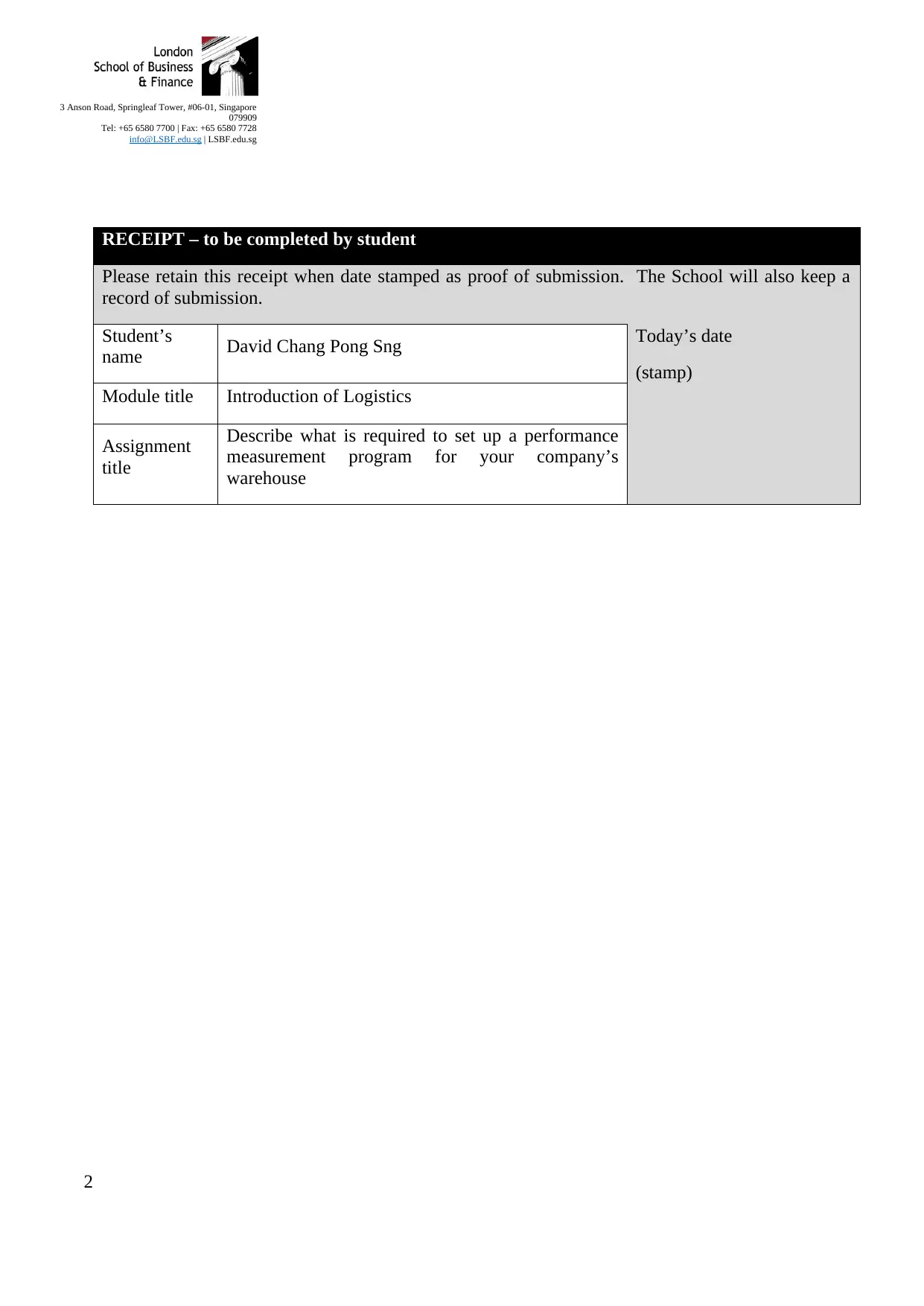
RECEIPT – to be completed by student
Please retain this receipt when date stamped as proof of submission. The School will also keep a
record of submission.
Student’s
name David Chang Pong Sng Today’s date
(stamp)
Module title Introduction of Logistics
Assignment
title
Describe what is required to set up a performance
measurement program for your company’s
warehouse
2
3 Anson Road, Springleaf Tower, #06-01, Singapore
079909
Tel: +65 6580 7700 | Fax: +65 6580 7728
info@LSBF.edu.sg | LSBF.edu.sg
Please retain this receipt when date stamped as proof of submission. The School will also keep a
record of submission.
Student’s
name David Chang Pong Sng Today’s date
(stamp)
Module title Introduction of Logistics
Assignment
title
Describe what is required to set up a performance
measurement program for your company’s
warehouse
2
3 Anson Road, Springleaf Tower, #06-01, Singapore
079909
Tel: +65 6580 7700 | Fax: +65 6580 7728
info@LSBF.edu.sg | LSBF.edu.sg
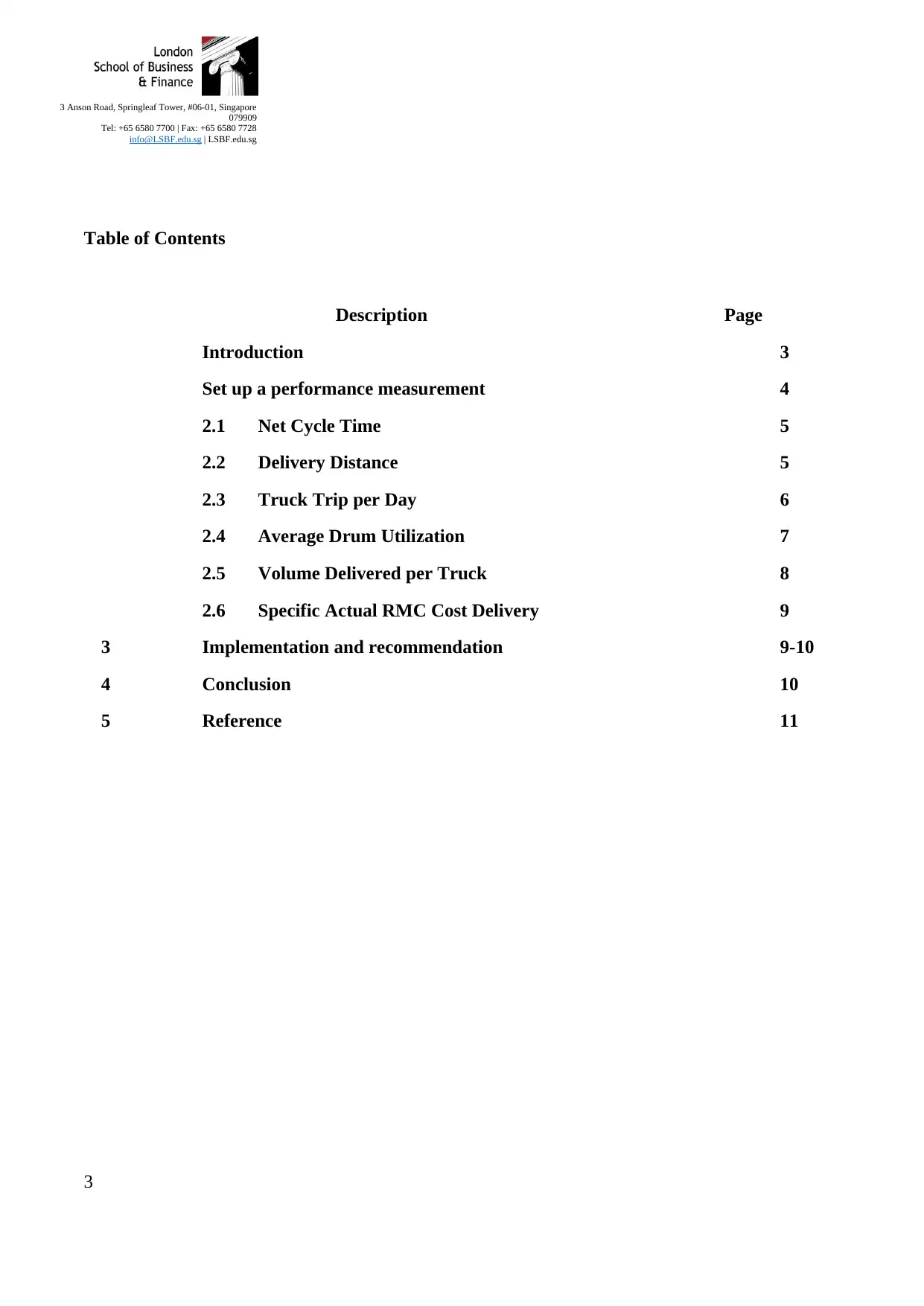
Table of Contents
Description Page
Introduction 3
Set up a performance measurement 4
2.1 Net Cycle Time 5
2.2 Delivery Distance 5
2.3 Truck Trip per Day 6
2.4 Average Drum Utilization 7
2.5 Volume Delivered per Truck 8
2.6 Specific Actual RMC Cost Delivery 9
3 Implementation and recommendation 9-10
4 Conclusion 10
5 Reference 11
3
3 Anson Road, Springleaf Tower, #06-01, Singapore
079909
Tel: +65 6580 7700 | Fax: +65 6580 7728
info@LSBF.edu.sg | LSBF.edu.sg
Description Page
Introduction 3
Set up a performance measurement 4
2.1 Net Cycle Time 5
2.2 Delivery Distance 5
2.3 Truck Trip per Day 6
2.4 Average Drum Utilization 7
2.5 Volume Delivered per Truck 8
2.6 Specific Actual RMC Cost Delivery 9
3 Implementation and recommendation 9-10
4 Conclusion 10
5 Reference 11
3
3 Anson Road, Springleaf Tower, #06-01, Singapore
079909
Tel: +65 6580 7700 | Fax: +65 6580 7728
info@LSBF.edu.sg | LSBF.edu.sg
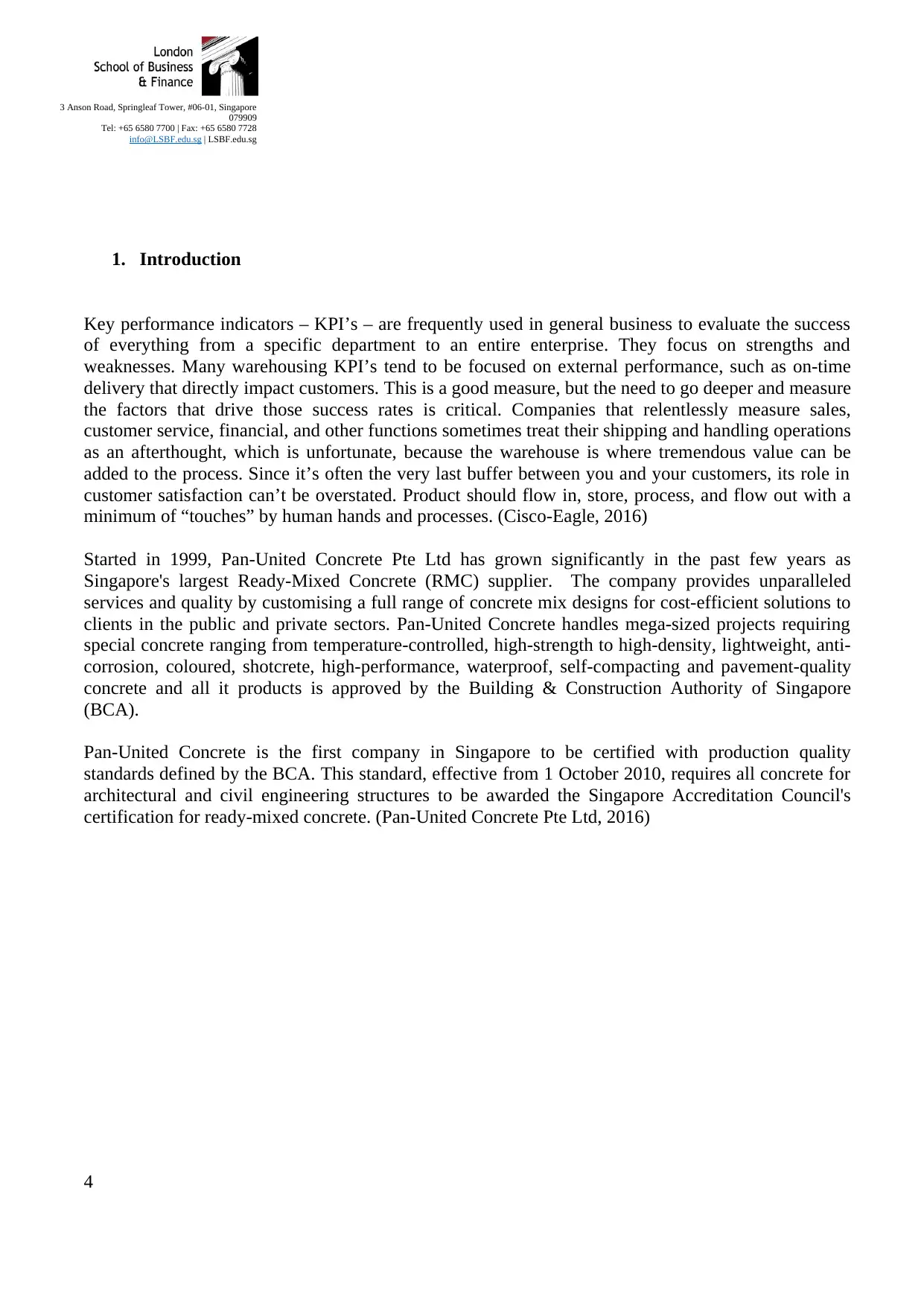
1. Introduction
Key performance indicators – KPI’s – are frequently used in general business to evaluate the success
of everything from a specific department to an entire enterprise. They focus on strengths and
weaknesses. Many warehousing KPI’s tend to be focused on external performance, such as on-time
delivery that directly impact customers. This is a good measure, but the need to go deeper and measure
the factors that drive those success rates is critical. Companies that relentlessly measure sales,
customer service, financial, and other functions sometimes treat their shipping and handling operations
as an afterthought, which is unfortunate, because the warehouse is where tremendous value can be
added to the process. Since it’s often the very last buffer between you and your customers, its role in
customer satisfaction can’t be overstated. Product should flow in, store, process, and flow out with a
minimum of “touches” by human hands and processes. (Cisco-Eagle, 2016)
Started in 1999, Pan-United Concrete Pte Ltd has grown significantly in the past few years as
Singapore's largest Ready-Mixed Concrete (RMC) supplier. The company provides unparalleled
services and quality by customising a full range of concrete mix designs for cost-efficient solutions to
clients in the public and private sectors. Pan-United Concrete handles mega-sized projects requiring
special concrete ranging from temperature-controlled, high-strength to high-density, lightweight, anti-
corrosion, coloured, shotcrete, high-performance, waterproof, self-compacting and pavement-quality
concrete and all it products is approved by the Building & Construction Authority of Singapore
(BCA).
Pan-United Concrete is the first company in Singapore to be certified with production quality
standards defined by the BCA. This standard, effective from 1 October 2010, requires all concrete for
architectural and civil engineering structures to be awarded the Singapore Accreditation Council's
certification for ready-mixed concrete. (Pan-United Concrete Pte Ltd, 2016)
4
3 Anson Road, Springleaf Tower, #06-01, Singapore
079909
Tel: +65 6580 7700 | Fax: +65 6580 7728
info@LSBF.edu.sg | LSBF.edu.sg
Key performance indicators – KPI’s – are frequently used in general business to evaluate the success
of everything from a specific department to an entire enterprise. They focus on strengths and
weaknesses. Many warehousing KPI’s tend to be focused on external performance, such as on-time
delivery that directly impact customers. This is a good measure, but the need to go deeper and measure
the factors that drive those success rates is critical. Companies that relentlessly measure sales,
customer service, financial, and other functions sometimes treat their shipping and handling operations
as an afterthought, which is unfortunate, because the warehouse is where tremendous value can be
added to the process. Since it’s often the very last buffer between you and your customers, its role in
customer satisfaction can’t be overstated. Product should flow in, store, process, and flow out with a
minimum of “touches” by human hands and processes. (Cisco-Eagle, 2016)
Started in 1999, Pan-United Concrete Pte Ltd has grown significantly in the past few years as
Singapore's largest Ready-Mixed Concrete (RMC) supplier. The company provides unparalleled
services and quality by customising a full range of concrete mix designs for cost-efficient solutions to
clients in the public and private sectors. Pan-United Concrete handles mega-sized projects requiring
special concrete ranging from temperature-controlled, high-strength to high-density, lightweight, anti-
corrosion, coloured, shotcrete, high-performance, waterproof, self-compacting and pavement-quality
concrete and all it products is approved by the Building & Construction Authority of Singapore
(BCA).
Pan-United Concrete is the first company in Singapore to be certified with production quality
standards defined by the BCA. This standard, effective from 1 October 2010, requires all concrete for
architectural and civil engineering structures to be awarded the Singapore Accreditation Council's
certification for ready-mixed concrete. (Pan-United Concrete Pte Ltd, 2016)
4
3 Anson Road, Springleaf Tower, #06-01, Singapore
079909
Tel: +65 6580 7700 | Fax: +65 6580 7728
info@LSBF.edu.sg | LSBF.edu.sg
Secure Best Marks with AI Grader
Need help grading? Try our AI Grader for instant feedback on your assignments.
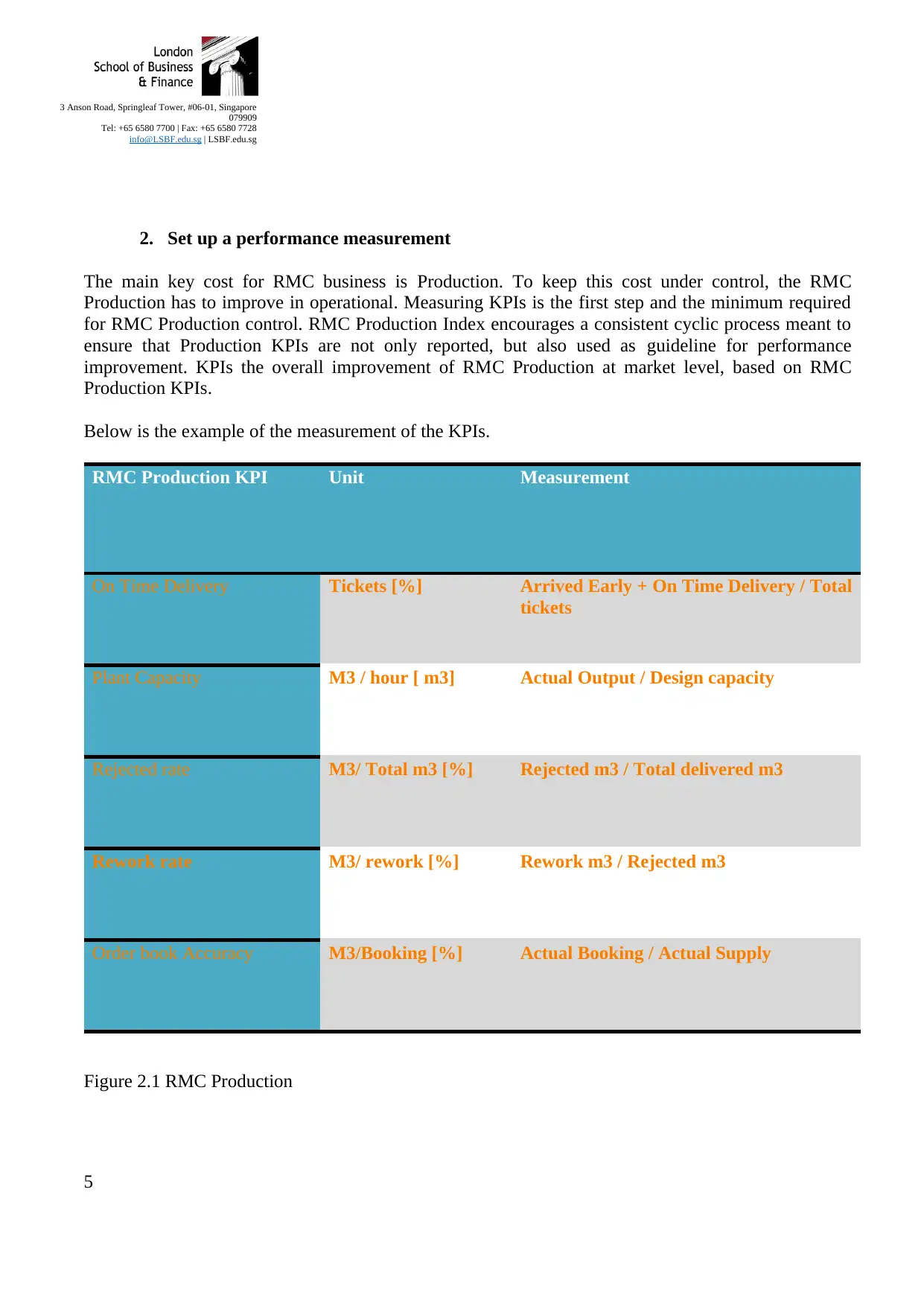
2. Set up a performance measurement
The main key cost for RMC business is Production. To keep this cost under control, the RMC
Production has to improve in operational. Measuring KPIs is the first step and the minimum required
for RMC Production control. RMC Production Index encourages a consistent cyclic process meant to
ensure that Production KPIs are not only reported, but also used as guideline for performance
improvement. KPIs the overall improvement of RMC Production at market level, based on RMC
Production KPIs.
Below is the example of the measurement of the KPIs.
RMC Production KPI Unit Measurement
On Time Delivery Tickets [%] Arrived Early + On Time Delivery / Total
tickets
Plant Capacity M3 / hour [ m3] Actual Output / Design capacity
Rejected rate M3/ Total m3 [%] Rejected m3 / Total delivered m3
Rework rate M3/ rework [%] Rework m3 / Rejected m3
Order book Accuracy M3/Booking [%] Actual Booking / Actual Supply
Figure 2.1 RMC Production
5
3 Anson Road, Springleaf Tower, #06-01, Singapore
079909
Tel: +65 6580 7700 | Fax: +65 6580 7728
info@LSBF.edu.sg | LSBF.edu.sg
The main key cost for RMC business is Production. To keep this cost under control, the RMC
Production has to improve in operational. Measuring KPIs is the first step and the minimum required
for RMC Production control. RMC Production Index encourages a consistent cyclic process meant to
ensure that Production KPIs are not only reported, but also used as guideline for performance
improvement. KPIs the overall improvement of RMC Production at market level, based on RMC
Production KPIs.
Below is the example of the measurement of the KPIs.
RMC Production KPI Unit Measurement
On Time Delivery Tickets [%] Arrived Early + On Time Delivery / Total
tickets
Plant Capacity M3 / hour [ m3] Actual Output / Design capacity
Rejected rate M3/ Total m3 [%] Rejected m3 / Total delivered m3
Rework rate M3/ rework [%] Rework m3 / Rejected m3
Order book Accuracy M3/Booking [%] Actual Booking / Actual Supply
Figure 2.1 RMC Production
5
3 Anson Road, Springleaf Tower, #06-01, Singapore
079909
Tel: +65 6580 7700 | Fax: +65 6580 7728
info@LSBF.edu.sg | LSBF.edu.sg
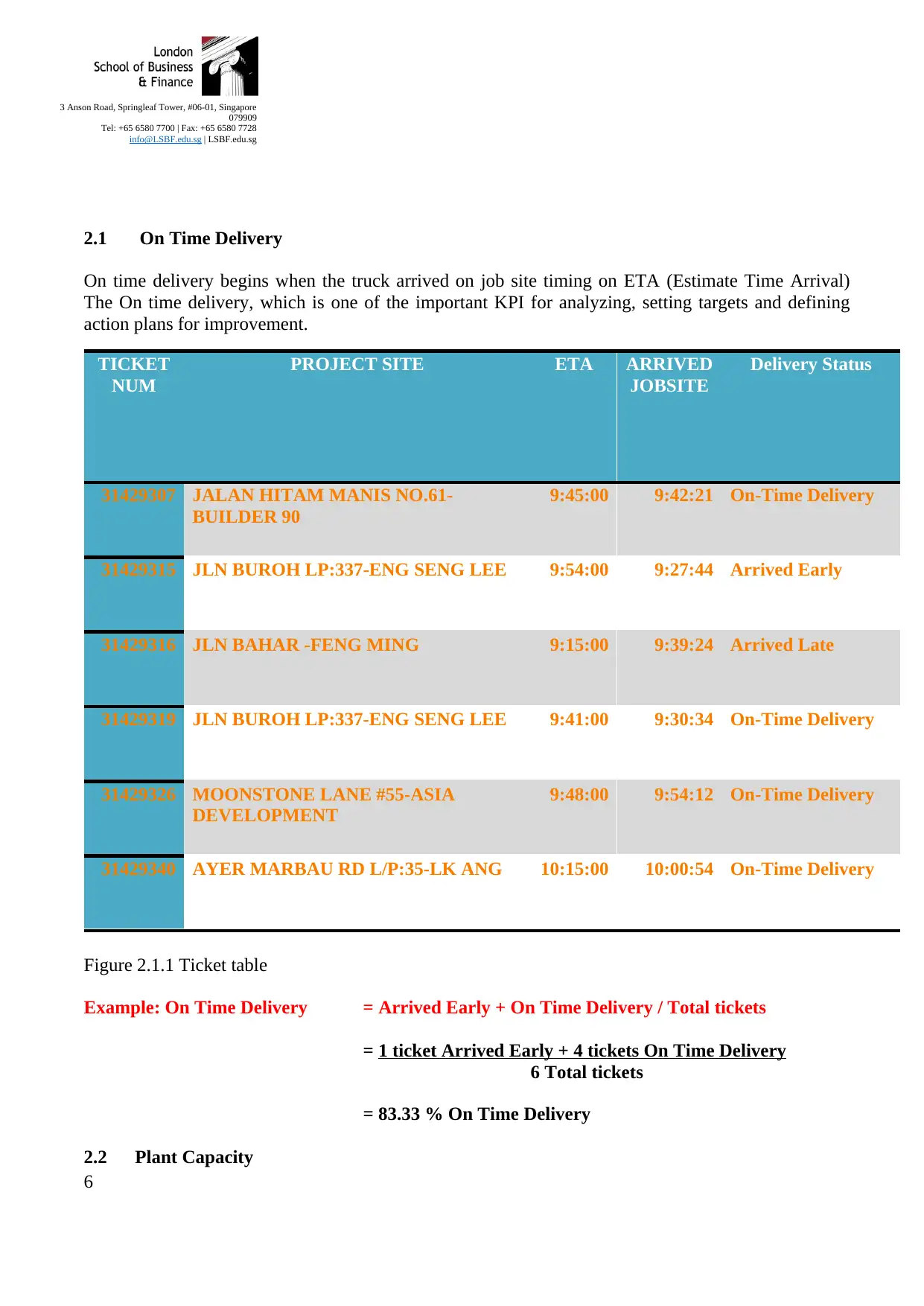
2.1 On Time Delivery
On time delivery begins when the truck arrived on job site timing on ETA (Estimate Time Arrival)
The On time delivery, which is one of the important KPI for analyzing, setting targets and defining
action plans for improvement.
TICKET
NUM
PROJECT SITE ETA ARRIVED
JOBSITE
Delivery Status
31429307 JALAN HITAM MANIS NO.61-
BUILDER 90
9:45:00 9:42:21 On-Time Delivery
31429315 JLN BUROH LP:337-ENG SENG LEE 9:54:00 9:27:44 Arrived Early
31429316 JLN BAHAR -FENG MING 9:15:00 9:39:24 Arrived Late
31429319 JLN BUROH LP:337-ENG SENG LEE 9:41:00 9:30:34 On-Time Delivery
31429326 MOONSTONE LANE #55-ASIA
DEVELOPMENT
9:48:00 9:54:12 On-Time Delivery
31429340 AYER MARBAU RD L/P:35-LK ANG 10:15:00 10:00:54 On-Time Delivery
Figure 2.1.1 Ticket table
Example: On Time Delivery = Arrived Early + On Time Delivery / Total tickets
= 1 ticket Arrived Early + 4 tickets On Time Delivery
6 Total tickets
= 83.33 % On Time Delivery
2.2 Plant Capacity
6
3 Anson Road, Springleaf Tower, #06-01, Singapore
079909
Tel: +65 6580 7700 | Fax: +65 6580 7728
info@LSBF.edu.sg | LSBF.edu.sg
On time delivery begins when the truck arrived on job site timing on ETA (Estimate Time Arrival)
The On time delivery, which is one of the important KPI for analyzing, setting targets and defining
action plans for improvement.
TICKET
NUM
PROJECT SITE ETA ARRIVED
JOBSITE
Delivery Status
31429307 JALAN HITAM MANIS NO.61-
BUILDER 90
9:45:00 9:42:21 On-Time Delivery
31429315 JLN BUROH LP:337-ENG SENG LEE 9:54:00 9:27:44 Arrived Early
31429316 JLN BAHAR -FENG MING 9:15:00 9:39:24 Arrived Late
31429319 JLN BUROH LP:337-ENG SENG LEE 9:41:00 9:30:34 On-Time Delivery
31429326 MOONSTONE LANE #55-ASIA
DEVELOPMENT
9:48:00 9:54:12 On-Time Delivery
31429340 AYER MARBAU RD L/P:35-LK ANG 10:15:00 10:00:54 On-Time Delivery
Figure 2.1.1 Ticket table
Example: On Time Delivery = Arrived Early + On Time Delivery / Total tickets
= 1 ticket Arrived Early + 4 tickets On Time Delivery
6 Total tickets
= 83.33 % On Time Delivery
2.2 Plant Capacity
6
3 Anson Road, Springleaf Tower, #06-01, Singapore
079909
Tel: +65 6580 7700 | Fax: +65 6580 7728
info@LSBF.edu.sg | LSBF.edu.sg
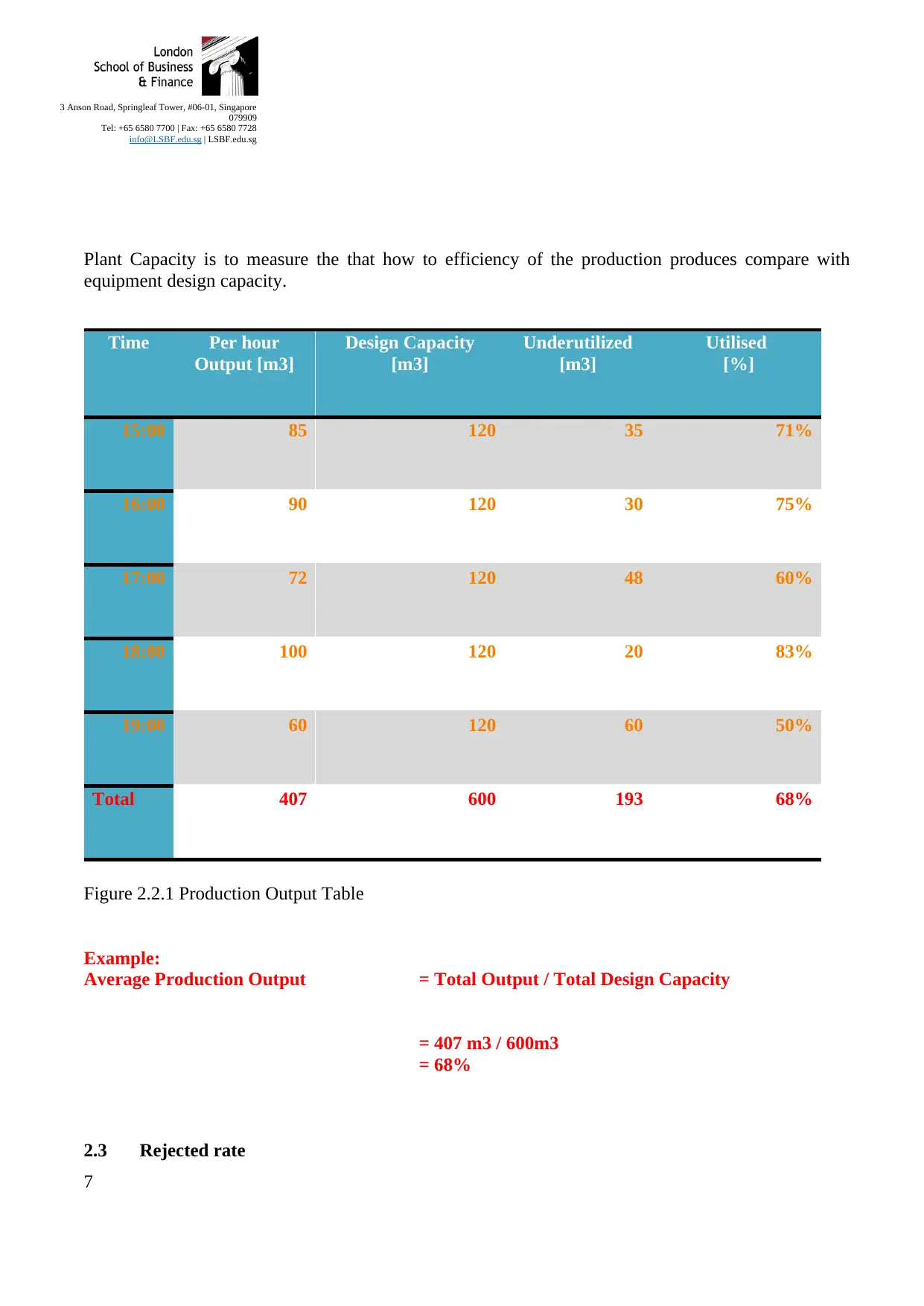
Plant Capacity is to measure the that how to efficiency of the production produces compare with
equipment design capacity.
Time Per hour
Output [m3]
Design Capacity
[m3]
Underutilized
[m3]
Utilised
[%]
15:00 85 120 35 71%
16:00 90 120 30 75%
17:00 72 120 48 60%
18:00 100 120 20 83%
19:00 60 120 60 50%
Total 407 600 193 68%
Figure 2.2.1 Production Output Table
Example:
Average Production Output = Total Output / Total Design Capacity
= 407 m3 / 600m3
= 68%
2.3 Rejected rate
7
3 Anson Road, Springleaf Tower, #06-01, Singapore
079909
Tel: +65 6580 7700 | Fax: +65 6580 7728
info@LSBF.edu.sg | LSBF.edu.sg
equipment design capacity.
Time Per hour
Output [m3]
Design Capacity
[m3]
Underutilized
[m3]
Utilised
[%]
15:00 85 120 35 71%
16:00 90 120 30 75%
17:00 72 120 48 60%
18:00 100 120 20 83%
19:00 60 120 60 50%
Total 407 600 193 68%
Figure 2.2.1 Production Output Table
Example:
Average Production Output = Total Output / Total Design Capacity
= 407 m3 / 600m3
= 68%
2.3 Rejected rate
7
3 Anson Road, Springleaf Tower, #06-01, Singapore
079909
Tel: +65 6580 7700 | Fax: +65 6580 7728
info@LSBF.edu.sg | LSBF.edu.sg
Paraphrase This Document
Need a fresh take? Get an instant paraphrase of this document with our AI Paraphraser
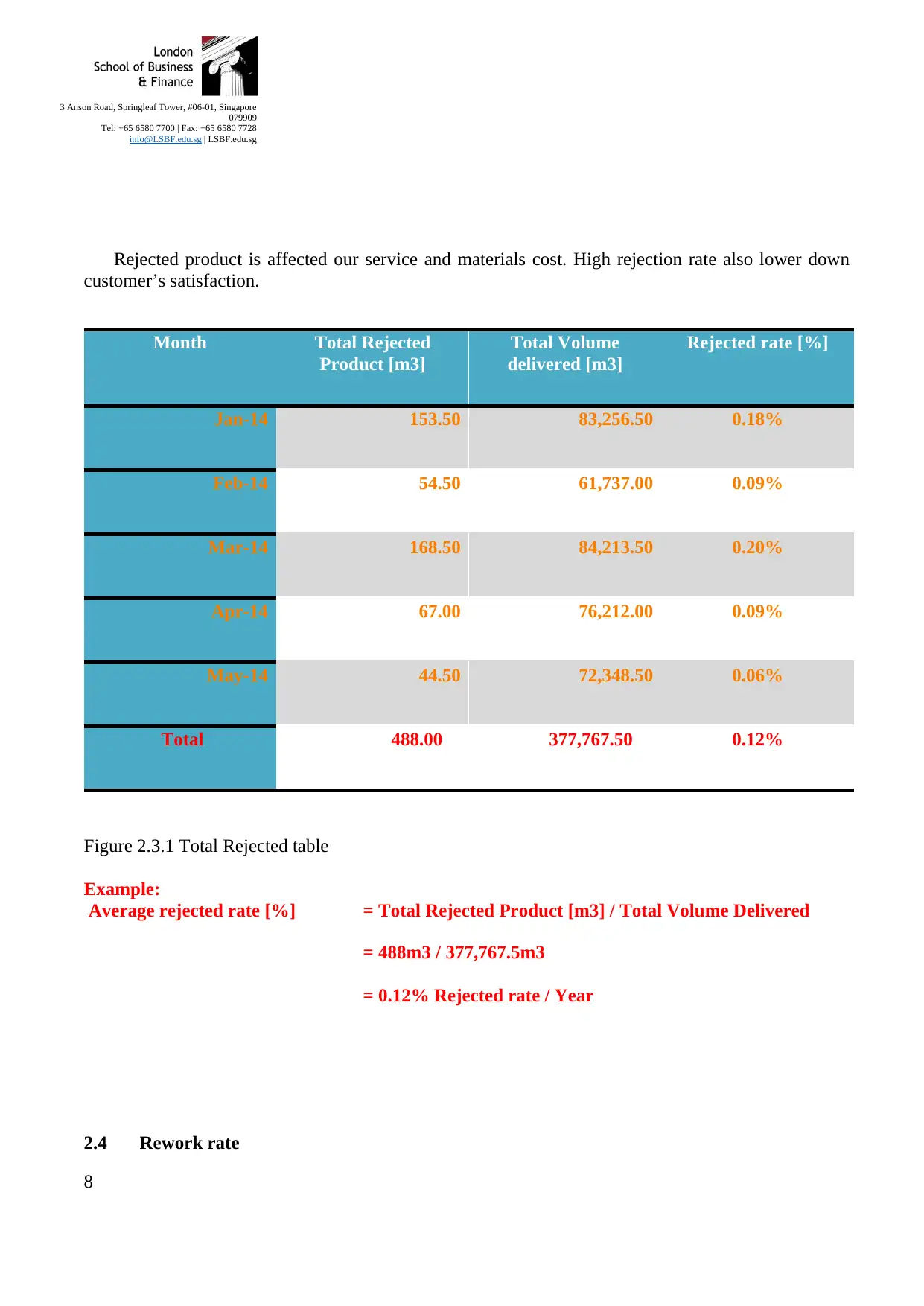
Rejected product is affected our service and materials cost. High rejection rate also lower down
customer’s satisfaction.
Month Total Rejected
Product [m3]
Total Volume
delivered [m3]
Rejected rate [%]
Jan-14 153.50 83,256.50 0.18%
Feb-14 54.50 61,737.00 0.09%
Mar-14 168.50 84,213.50 0.20%
Apr-14 67.00 76,212.00 0.09%
May-14 44.50 72,348.50 0.06%
Total 488.00 377,767.50 0.12%
Figure 2.3.1 Total Rejected table
Example:
Average rejected rate [%] = Total Rejected Product [m3] / Total Volume Delivered
= 488m3 / 377,767.5m3
= 0.12% Rejected rate / Year
2.4 Rework rate
8
3 Anson Road, Springleaf Tower, #06-01, Singapore
079909
Tel: +65 6580 7700 | Fax: +65 6580 7728
info@LSBF.edu.sg | LSBF.edu.sg
customer’s satisfaction.
Month Total Rejected
Product [m3]
Total Volume
delivered [m3]
Rejected rate [%]
Jan-14 153.50 83,256.50 0.18%
Feb-14 54.50 61,737.00 0.09%
Mar-14 168.50 84,213.50 0.20%
Apr-14 67.00 76,212.00 0.09%
May-14 44.50 72,348.50 0.06%
Total 488.00 377,767.50 0.12%
Figure 2.3.1 Total Rejected table
Example:
Average rejected rate [%] = Total Rejected Product [m3] / Total Volume Delivered
= 488m3 / 377,767.5m3
= 0.12% Rejected rate / Year
2.4 Rework rate
8
3 Anson Road, Springleaf Tower, #06-01, Singapore
079909
Tel: +65 6580 7700 | Fax: +65 6580 7728
info@LSBF.edu.sg | LSBF.edu.sg
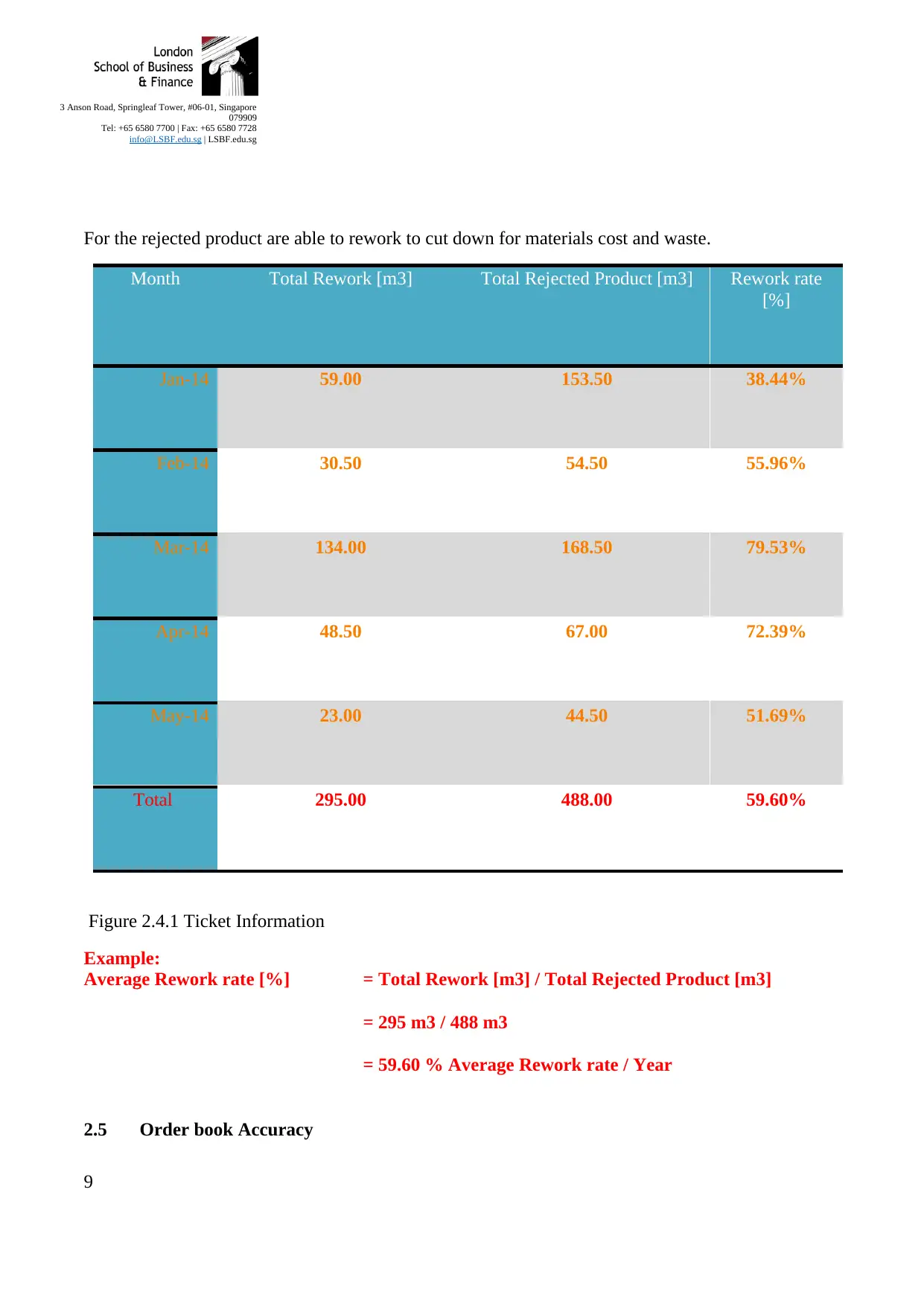
For the rejected product are able to rework to cut down for materials cost and waste.
Month Total Rework [m3] Total Rejected Product [m3] Rework rate
[%]
Jan-14 59.00 153.50 38.44%
Feb-14 30.50 54.50 55.96%
Mar-14 134.00 168.50 79.53%
Apr-14 48.50 67.00 72.39%
May-14 23.00 44.50 51.69%
Total 295.00 488.00 59.60%
Figure 2.4.1 Ticket Information
Example:
Average Rework rate [%] = Total Rework [m3] / Total Rejected Product [m3]
= 295 m3 / 488 m3
= 59.60 % Average Rework rate / Year
2.5 Order book Accuracy
9
3 Anson Road, Springleaf Tower, #06-01, Singapore
079909
Tel: +65 6580 7700 | Fax: +65 6580 7728
info@LSBF.edu.sg | LSBF.edu.sg
Month Total Rework [m3] Total Rejected Product [m3] Rework rate
[%]
Jan-14 59.00 153.50 38.44%
Feb-14 30.50 54.50 55.96%
Mar-14 134.00 168.50 79.53%
Apr-14 48.50 67.00 72.39%
May-14 23.00 44.50 51.69%
Total 295.00 488.00 59.60%
Figure 2.4.1 Ticket Information
Example:
Average Rework rate [%] = Total Rework [m3] / Total Rejected Product [m3]
= 295 m3 / 488 m3
= 59.60 % Average Rework rate / Year
2.5 Order book Accuracy
9
3 Anson Road, Springleaf Tower, #06-01, Singapore
079909
Tel: +65 6580 7700 | Fax: +65 6580 7728
info@LSBF.edu.sg | LSBF.edu.sg
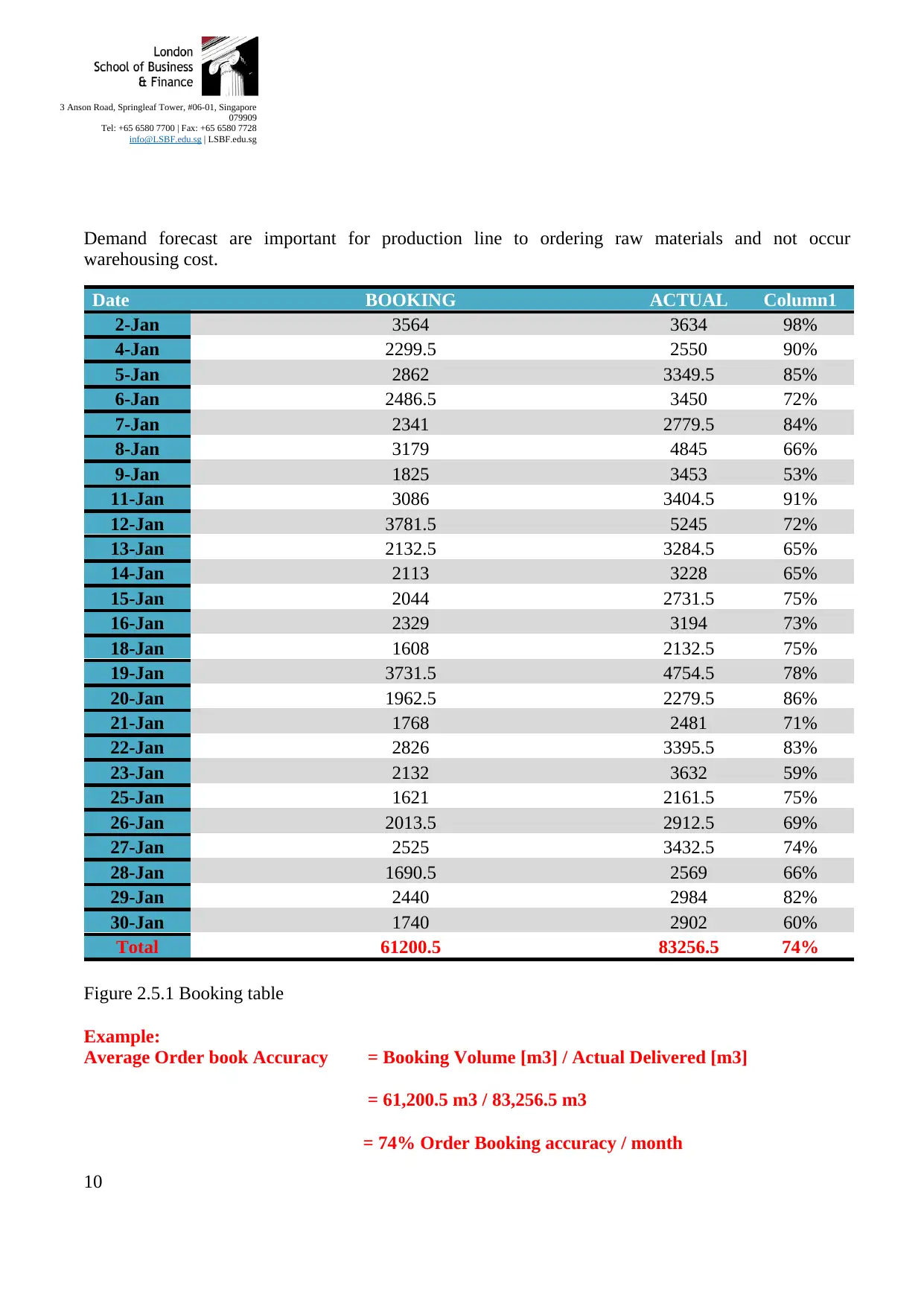
Demand forecast are important for production line to ordering raw materials and not occur
warehousing cost.
Date BOOKING ACTUAL Column1
2-Jan 3564 3634 98%
4-Jan 2299.5 2550 90%
5-Jan 2862 3349.5 85%
6-Jan 2486.5 3450 72%
7-Jan 2341 2779.5 84%
8-Jan 3179 4845 66%
9-Jan 1825 3453 53%
11-Jan 3086 3404.5 91%
12-Jan 3781.5 5245 72%
13-Jan 2132.5 3284.5 65%
14-Jan 2113 3228 65%
15-Jan 2044 2731.5 75%
16-Jan 2329 3194 73%
18-Jan 1608 2132.5 75%
19-Jan 3731.5 4754.5 78%
20-Jan 1962.5 2279.5 86%
21-Jan 1768 2481 71%
22-Jan 2826 3395.5 83%
23-Jan 2132 3632 59%
25-Jan 1621 2161.5 75%
26-Jan 2013.5 2912.5 69%
27-Jan 2525 3432.5 74%
28-Jan 1690.5 2569 66%
29-Jan 2440 2984 82%
30-Jan 1740 2902 60%
Total 61200.5 83256.5 74%
Figure 2.5.1 Booking table
Example:
Average Order book Accuracy = Booking Volume [m3] / Actual Delivered [m3]
= 61,200.5 m3 / 83,256.5 m3
= 74% Order Booking accuracy / month
10
3 Anson Road, Springleaf Tower, #06-01, Singapore
079909
Tel: +65 6580 7700 | Fax: +65 6580 7728
info@LSBF.edu.sg | LSBF.edu.sg
warehousing cost.
Date BOOKING ACTUAL Column1
2-Jan 3564 3634 98%
4-Jan 2299.5 2550 90%
5-Jan 2862 3349.5 85%
6-Jan 2486.5 3450 72%
7-Jan 2341 2779.5 84%
8-Jan 3179 4845 66%
9-Jan 1825 3453 53%
11-Jan 3086 3404.5 91%
12-Jan 3781.5 5245 72%
13-Jan 2132.5 3284.5 65%
14-Jan 2113 3228 65%
15-Jan 2044 2731.5 75%
16-Jan 2329 3194 73%
18-Jan 1608 2132.5 75%
19-Jan 3731.5 4754.5 78%
20-Jan 1962.5 2279.5 86%
21-Jan 1768 2481 71%
22-Jan 2826 3395.5 83%
23-Jan 2132 3632 59%
25-Jan 1621 2161.5 75%
26-Jan 2013.5 2912.5 69%
27-Jan 2525 3432.5 74%
28-Jan 1690.5 2569 66%
29-Jan 2440 2984 82%
30-Jan 1740 2902 60%
Total 61200.5 83256.5 74%
Figure 2.5.1 Booking table
Example:
Average Order book Accuracy = Booking Volume [m3] / Actual Delivered [m3]
= 61,200.5 m3 / 83,256.5 m3
= 74% Order Booking accuracy / month
10
3 Anson Road, Springleaf Tower, #06-01, Singapore
079909
Tel: +65 6580 7700 | Fax: +65 6580 7728
info@LSBF.edu.sg | LSBF.edu.sg
Secure Best Marks with AI Grader
Need help grading? Try our AI Grader for instant feedback on your assignments.
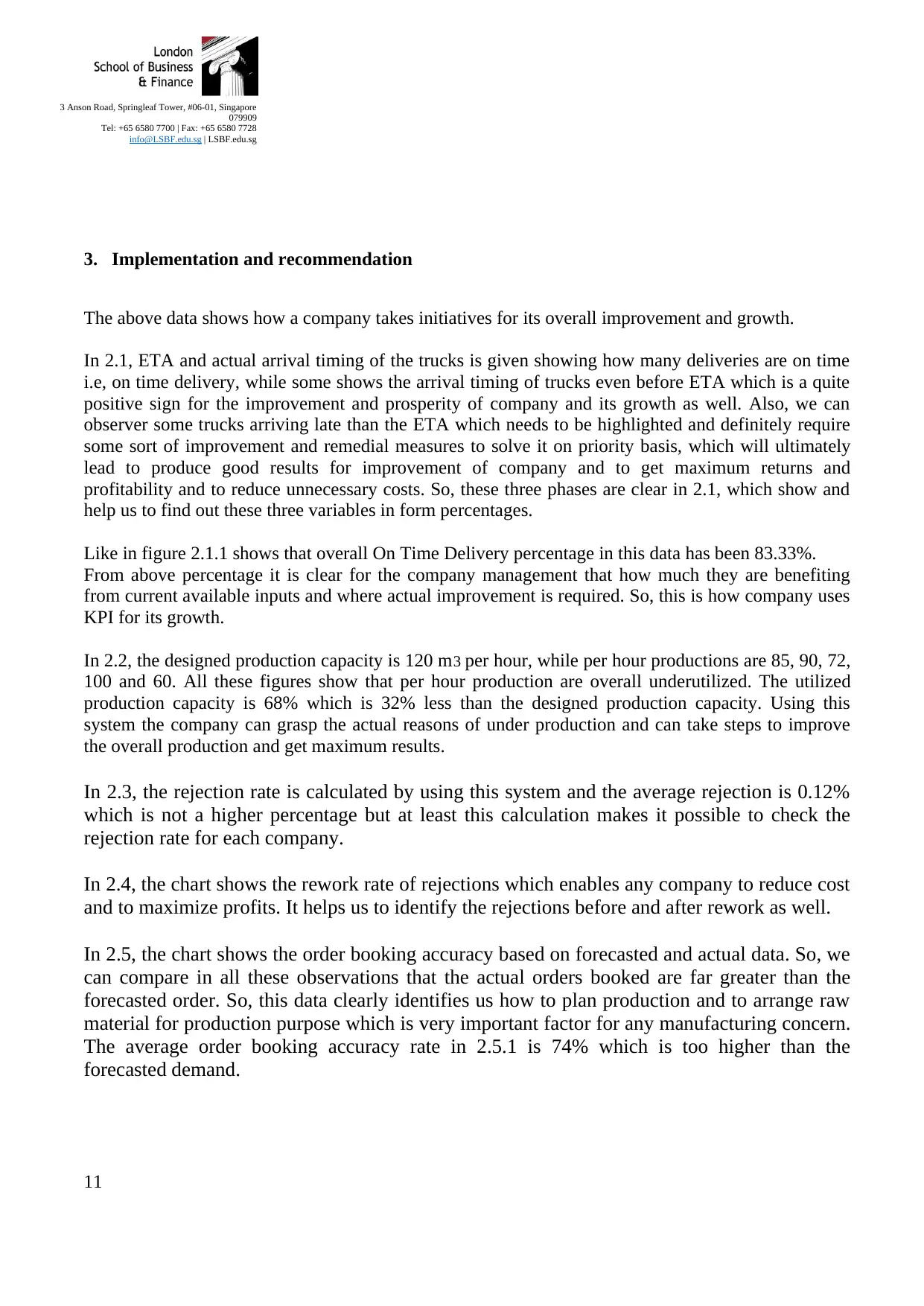
3. Implementation and recommendation
The above data shows how a company takes initiatives for its overall improvement and growth.
In 2.1, ETA and actual arrival timing of the trucks is given showing how many deliveries are on time
i.e, on time delivery, while some shows the arrival timing of trucks even before ETA which is a quite
positive sign for the improvement and prosperity of company and its growth as well. Also, we can
observer some trucks arriving late than the ETA which needs to be highlighted and definitely require
some sort of improvement and remedial measures to solve it on priority basis, which will ultimately
lead to produce good results for improvement of company and to get maximum returns and
profitability and to reduce unnecessary costs. So, these three phases are clear in 2.1, which show and
help us to find out these three variables in form percentages.
Like in figure 2.1.1 shows that overall On Time Delivery percentage in this data has been 83.33%.
From above percentage it is clear for the company management that how much they are benefiting
from current available inputs and where actual improvement is required. So, this is how company uses
KPI for its growth.
In 2.2, the designed production capacity is 120 m3 per hour, while per hour productions are 85, 90, 72,
100 and 60. All these figures show that per hour production are overall underutilized. The utilized
production capacity is 68% which is 32% less than the designed production capacity. Using this
system the company can grasp the actual reasons of under production and can take steps to improve
the overall production and get maximum results.
In 2.3, the rejection rate is calculated by using this system and the average rejection is 0.12%
which is not a higher percentage but at least this calculation makes it possible to check the
rejection rate for each company.
In 2.4, the chart shows the rework rate of rejections which enables any company to reduce cost
and to maximize profits. It helps us to identify the rejections before and after rework as well.
In 2.5, the chart shows the order booking accuracy based on forecasted and actual data. So, we
can compare in all these observations that the actual orders booked are far greater than the
forecasted order. So, this data clearly identifies us how to plan production and to arrange raw
material for production purpose which is very important factor for any manufacturing concern.
The average order booking accuracy rate in 2.5.1 is 74% which is too higher than the
forecasted demand.
11
3 Anson Road, Springleaf Tower, #06-01, Singapore
079909
Tel: +65 6580 7700 | Fax: +65 6580 7728
info@LSBF.edu.sg | LSBF.edu.sg
The above data shows how a company takes initiatives for its overall improvement and growth.
In 2.1, ETA and actual arrival timing of the trucks is given showing how many deliveries are on time
i.e, on time delivery, while some shows the arrival timing of trucks even before ETA which is a quite
positive sign for the improvement and prosperity of company and its growth as well. Also, we can
observer some trucks arriving late than the ETA which needs to be highlighted and definitely require
some sort of improvement and remedial measures to solve it on priority basis, which will ultimately
lead to produce good results for improvement of company and to get maximum returns and
profitability and to reduce unnecessary costs. So, these three phases are clear in 2.1, which show and
help us to find out these three variables in form percentages.
Like in figure 2.1.1 shows that overall On Time Delivery percentage in this data has been 83.33%.
From above percentage it is clear for the company management that how much they are benefiting
from current available inputs and where actual improvement is required. So, this is how company uses
KPI for its growth.
In 2.2, the designed production capacity is 120 m3 per hour, while per hour productions are 85, 90, 72,
100 and 60. All these figures show that per hour production are overall underutilized. The utilized
production capacity is 68% which is 32% less than the designed production capacity. Using this
system the company can grasp the actual reasons of under production and can take steps to improve
the overall production and get maximum results.
In 2.3, the rejection rate is calculated by using this system and the average rejection is 0.12%
which is not a higher percentage but at least this calculation makes it possible to check the
rejection rate for each company.
In 2.4, the chart shows the rework rate of rejections which enables any company to reduce cost
and to maximize profits. It helps us to identify the rejections before and after rework as well.
In 2.5, the chart shows the order booking accuracy based on forecasted and actual data. So, we
can compare in all these observations that the actual orders booked are far greater than the
forecasted order. So, this data clearly identifies us how to plan production and to arrange raw
material for production purpose which is very important factor for any manufacturing concern.
The average order booking accuracy rate in 2.5.1 is 74% which is too higher than the
forecasted demand.
11
3 Anson Road, Springleaf Tower, #06-01, Singapore
079909
Tel: +65 6580 7700 | Fax: +65 6580 7728
info@LSBF.edu.sg | LSBF.edu.sg
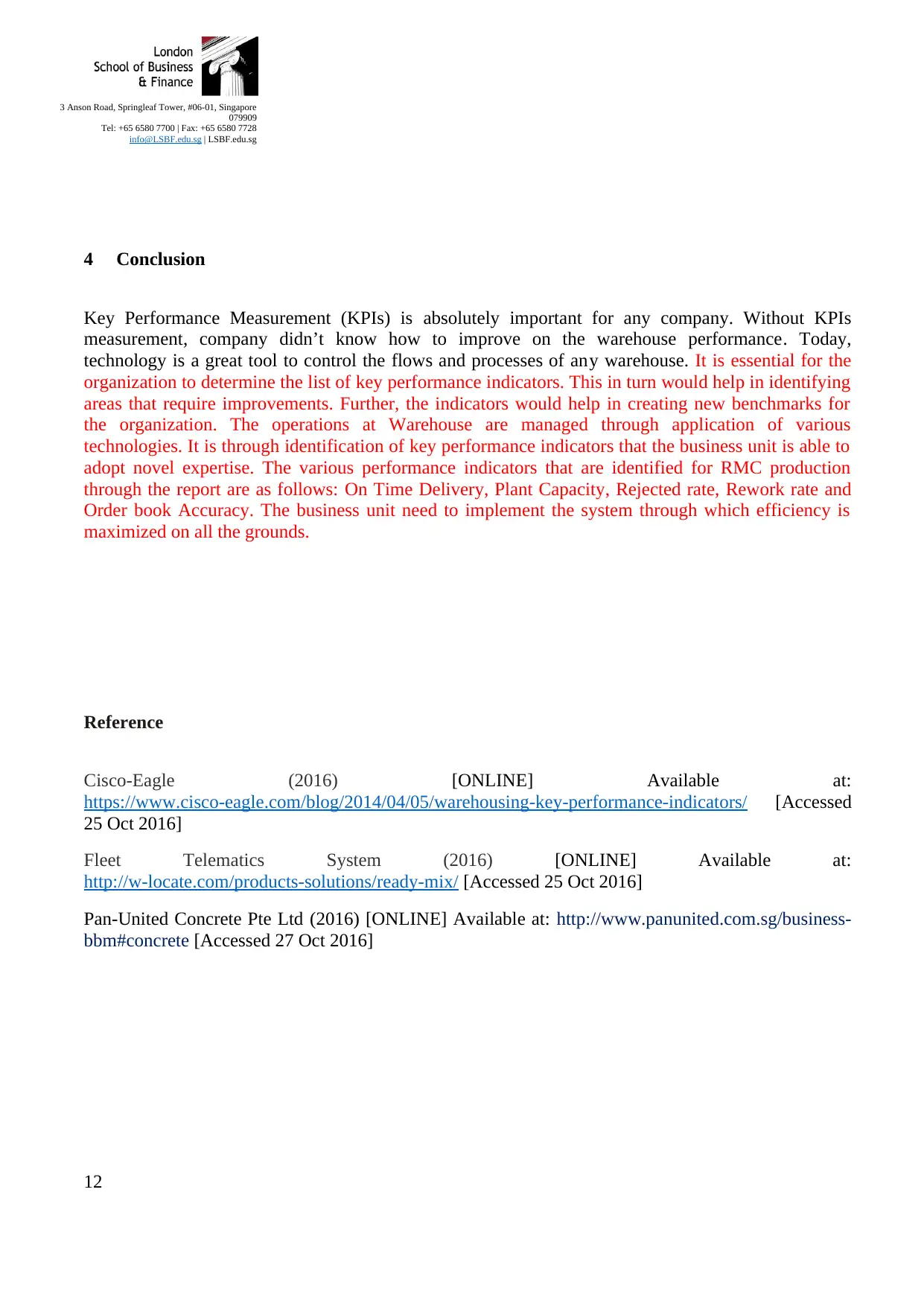
4 Conclusion
Key Performance Measurement (KPIs) is absolutely important for any company. Without KPIs
measurement, company didn’t know how to improve on the warehouse performance. Today,
technology is a great tool to control the flows and processes of any warehouse. It is essential for the
organization to determine the list of key performance indicators. This in turn would help in identifying
areas that require improvements. Further, the indicators would help in creating new benchmarks for
the organization. The operations at Warehouse are managed through application of various
technologies. It is through identification of key performance indicators that the business unit is able to
adopt novel expertise. The various performance indicators that are identified for RMC production
through the report are as follows: On Time Delivery, Plant Capacity, Rejected rate, Rework rate and
Order book Accuracy. The business unit need to implement the system through which efficiency is
maximized on all the grounds.
Reference
Cisco-Eagle (2016) [ONLINE] Available at:
https://www.cisco-eagle.com/blog/2014/04/05/warehousing-key-performance-indicators/ [Accessed
25 Oct 2016]
Fleet Telematics System (2016) [ONLINE] Available at:
http://w-locate.com/products-solutions/ready-mix/ [Accessed 25 Oct 2016]
Pan-United Concrete Pte Ltd (2016) [ONLINE] Available at: http://www.panunited.com.sg/business-
bbm#concrete [Accessed 27 Oct 2016]
12
3 Anson Road, Springleaf Tower, #06-01, Singapore
079909
Tel: +65 6580 7700 | Fax: +65 6580 7728
info@LSBF.edu.sg | LSBF.edu.sg
Key Performance Measurement (KPIs) is absolutely important for any company. Without KPIs
measurement, company didn’t know how to improve on the warehouse performance. Today,
technology is a great tool to control the flows and processes of any warehouse. It is essential for the
organization to determine the list of key performance indicators. This in turn would help in identifying
areas that require improvements. Further, the indicators would help in creating new benchmarks for
the organization. The operations at Warehouse are managed through application of various
technologies. It is through identification of key performance indicators that the business unit is able to
adopt novel expertise. The various performance indicators that are identified for RMC production
through the report are as follows: On Time Delivery, Plant Capacity, Rejected rate, Rework rate and
Order book Accuracy. The business unit need to implement the system through which efficiency is
maximized on all the grounds.
Reference
Cisco-Eagle (2016) [ONLINE] Available at:
https://www.cisco-eagle.com/blog/2014/04/05/warehousing-key-performance-indicators/ [Accessed
25 Oct 2016]
Fleet Telematics System (2016) [ONLINE] Available at:
http://w-locate.com/products-solutions/ready-mix/ [Accessed 25 Oct 2016]
Pan-United Concrete Pte Ltd (2016) [ONLINE] Available at: http://www.panunited.com.sg/business-
bbm#concrete [Accessed 27 Oct 2016]
12
3 Anson Road, Springleaf Tower, #06-01, Singapore
079909
Tel: +65 6580 7700 | Fax: +65 6580 7728
info@LSBF.edu.sg | LSBF.edu.sg
1 out of 12
![[object Object]](/_next/image/?url=%2F_next%2Fstatic%2Fmedia%2Flogo.6d15ce61.png&w=640&q=75)
Your All-in-One AI-Powered Toolkit for Academic Success.
 +13062052269
info@desklib.com
Available 24*7 on WhatsApp / Email
Unlock your academic potential
© 2024  |  Zucol Services PVT LTD  |  All rights reserved.