Resource Planning and Management - Desklib
VerifiedAdded on 2023/06/14
|8
|1144
|331
AI Summary
This document discusses resource planning and management, including inventory management, demand forecasting, and buffer stock strategies. It also includes a Pareto analysis of materials and recommendations for top management. The content is relevant for students studying supply chain management, logistics, and operations management.
Contribute Materials
Your contribution can guide someone’s learning journey. Share your
documents today.
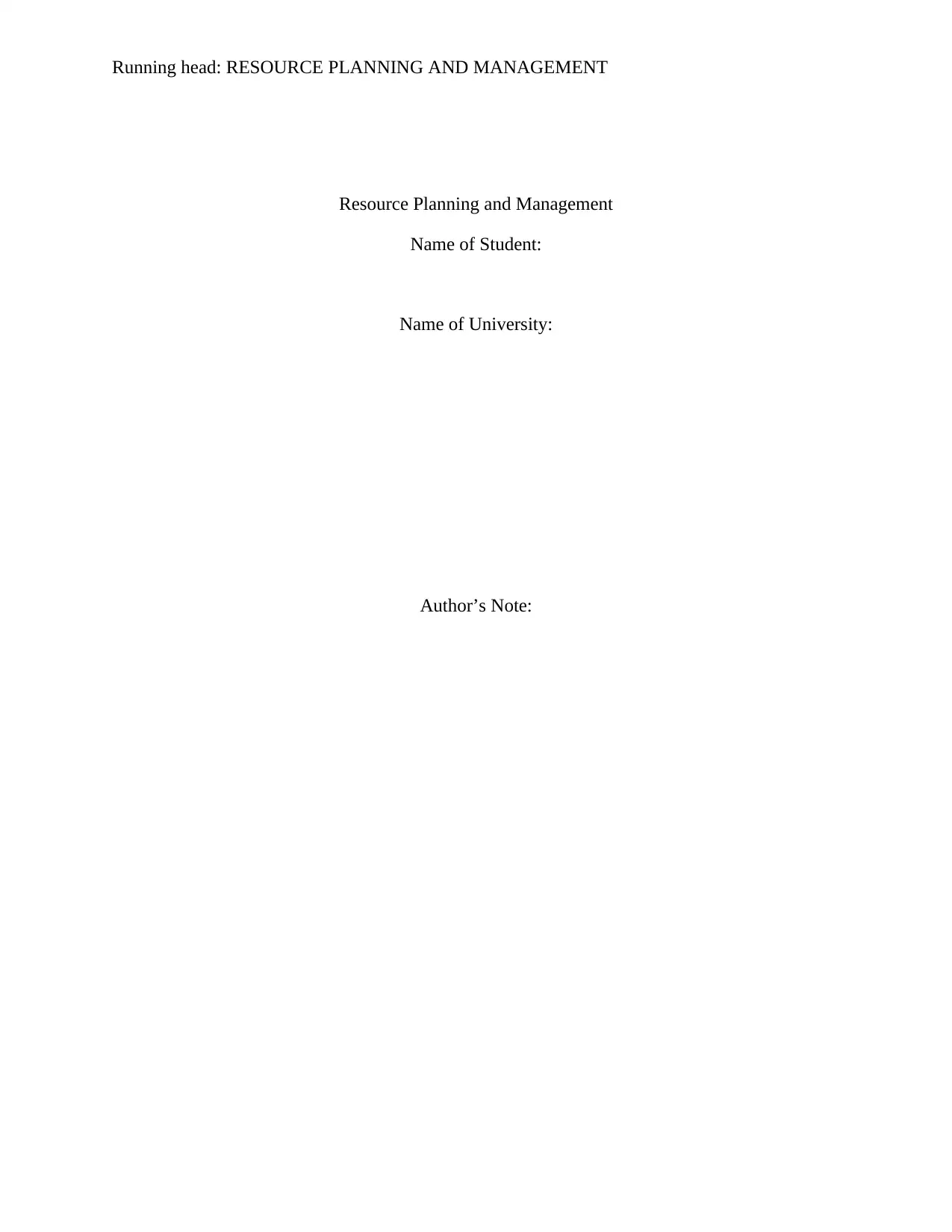
Running head: RESOURCE PLANNING AND MANAGEMENT
Resource Planning and Management
Name of Student:
Name of University:
Author’s Note:
Resource Planning and Management
Name of Student:
Name of University:
Author’s Note:
Secure Best Marks with AI Grader
Need help grading? Try our AI Grader for instant feedback on your assignments.
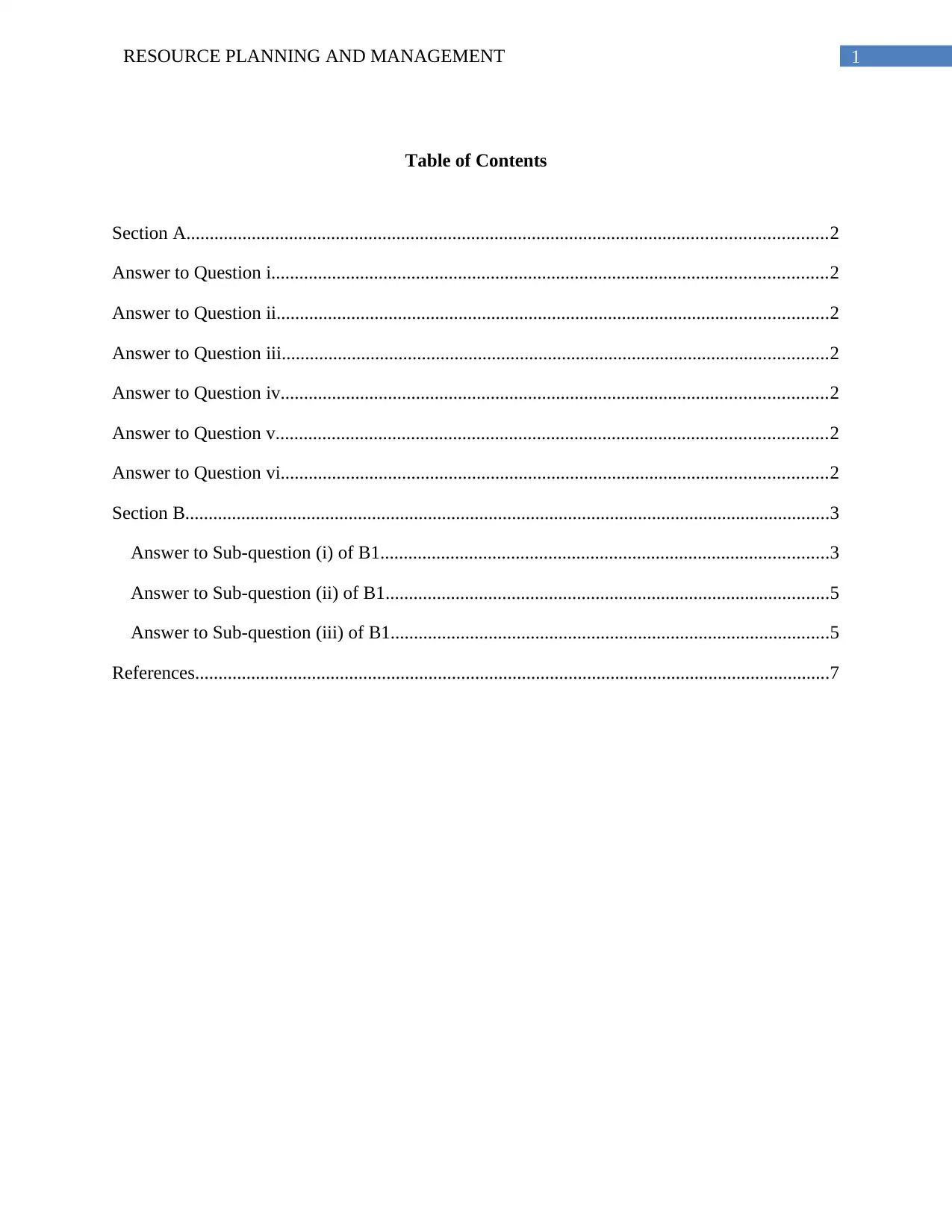
1RESOURCE PLANNING AND MANAGEMENT
Table of Contents
Section A.........................................................................................................................................2
Answer to Question i.......................................................................................................................2
Answer to Question ii......................................................................................................................2
Answer to Question iii.....................................................................................................................2
Answer to Question iv.....................................................................................................................2
Answer to Question v......................................................................................................................2
Answer to Question vi.....................................................................................................................2
Section B..........................................................................................................................................3
Answer to Sub-question (i) of B1................................................................................................3
Answer to Sub-question (ii) of B1...............................................................................................5
Answer to Sub-question (iii) of B1..............................................................................................5
References........................................................................................................................................7
Table of Contents
Section A.........................................................................................................................................2
Answer to Question i.......................................................................................................................2
Answer to Question ii......................................................................................................................2
Answer to Question iii.....................................................................................................................2
Answer to Question iv.....................................................................................................................2
Answer to Question v......................................................................................................................2
Answer to Question vi.....................................................................................................................2
Section B..........................................................................................................................................3
Answer to Sub-question (i) of B1................................................................................................3
Answer to Sub-question (ii) of B1...............................................................................................5
Answer to Sub-question (iii) of B1..............................................................................................5
References........................................................................................................................................7
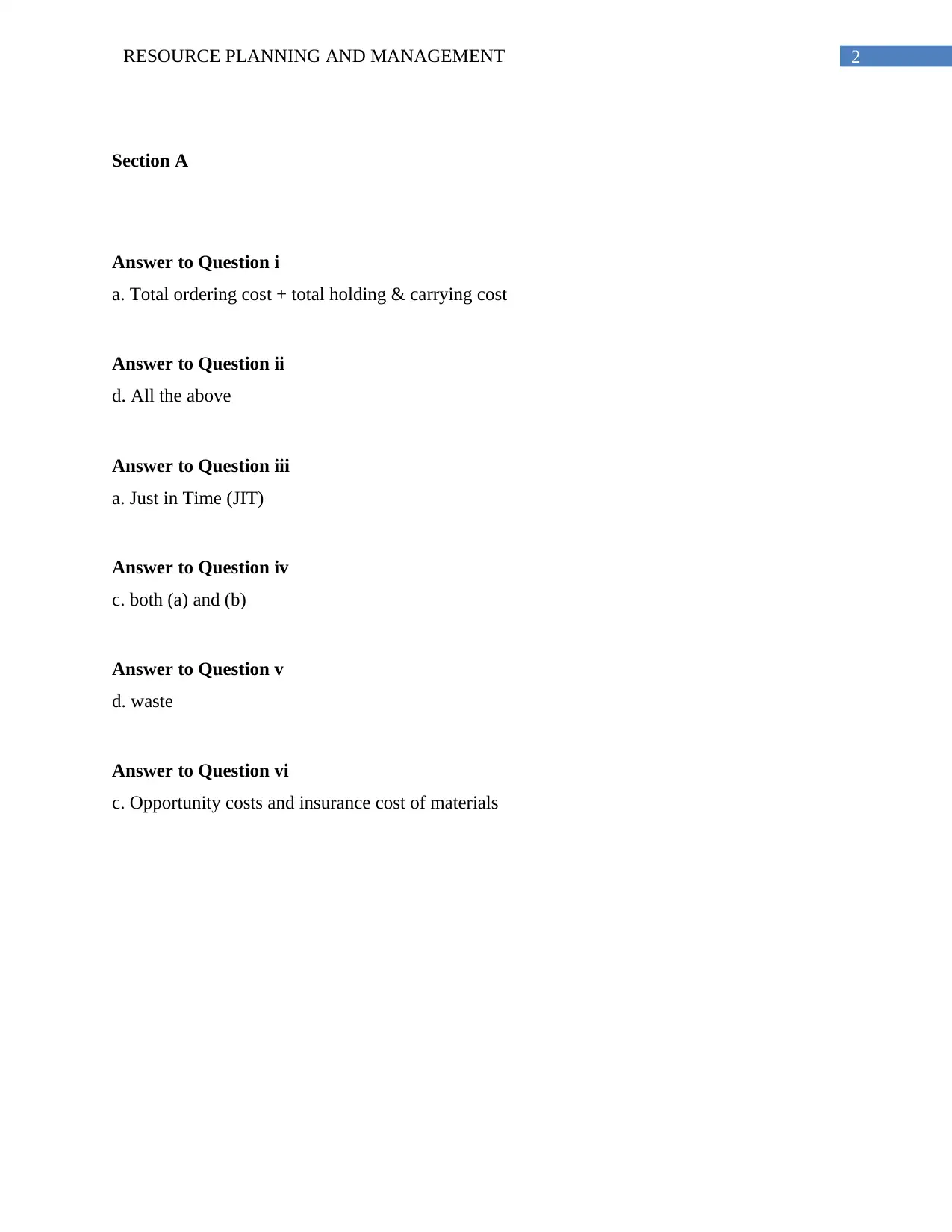
2RESOURCE PLANNING AND MANAGEMENT
Section A
Answer to Question i
a. Total ordering cost + total holding & carrying cost
Answer to Question ii
d. All the above
Answer to Question iii
a. Just in Time (JIT)
Answer to Question iv
c. both (a) and (b)
Answer to Question v
d. waste
Answer to Question vi
c. Opportunity costs and insurance cost of materials
Section A
Answer to Question i
a. Total ordering cost + total holding & carrying cost
Answer to Question ii
d. All the above
Answer to Question iii
a. Just in Time (JIT)
Answer to Question iv
c. both (a) and (b)
Answer to Question v
d. waste
Answer to Question vi
c. Opportunity costs and insurance cost of materials
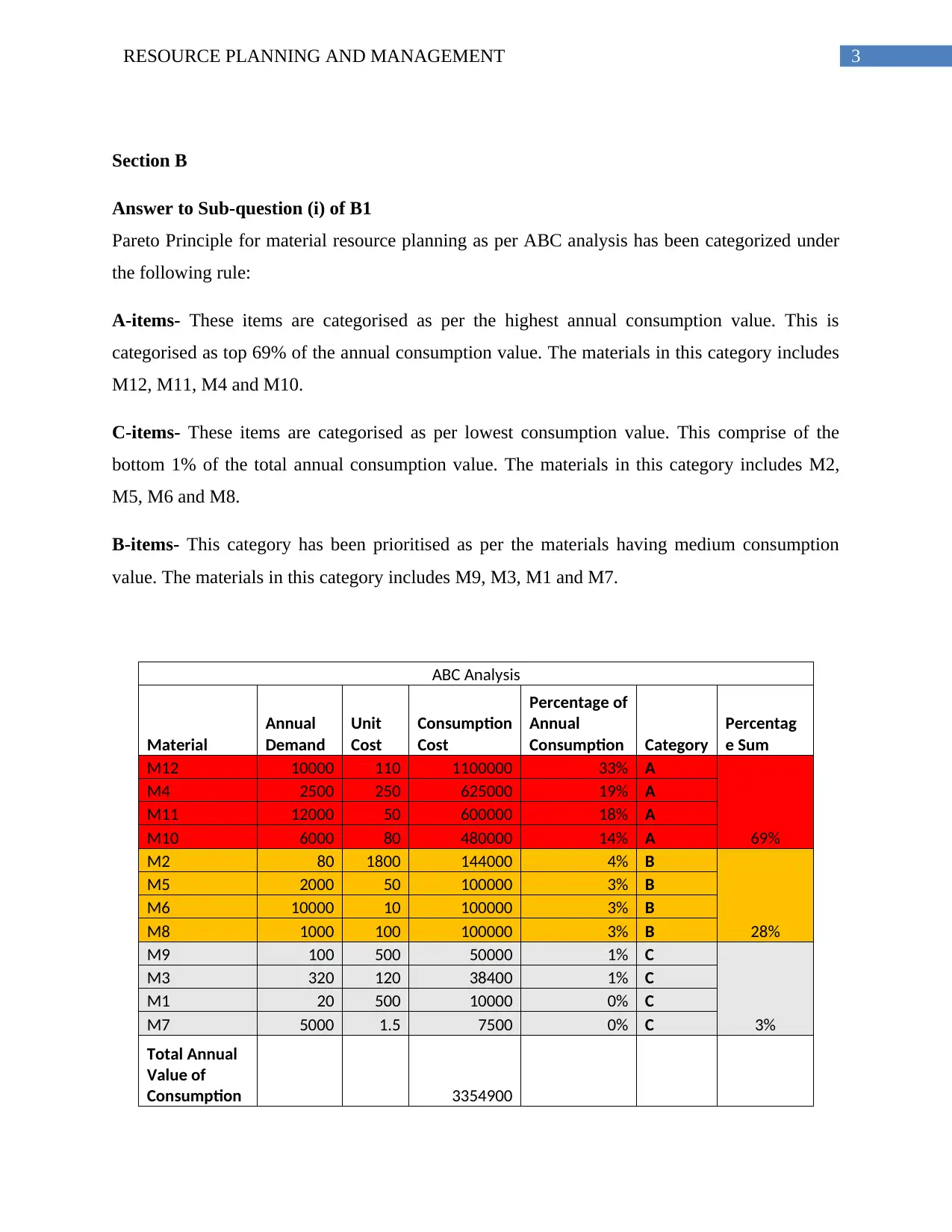
3RESOURCE PLANNING AND MANAGEMENT
Section B
Answer to Sub-question (i) of B1
Pareto Principle for material resource planning as per ABC analysis has been categorized under
the following rule:
A-items- These items are categorised as per the highest annual consumption value. This is
categorised as top 69% of the annual consumption value. The materials in this category includes
M12, M11, M4 and M10.
C-items- These items are categorised as per lowest consumption value. This comprise of the
bottom 1% of the total annual consumption value. The materials in this category includes M2,
M5, M6 and M8.
B-items- This category has been prioritised as per the materials having medium consumption
value. The materials in this category includes M9, M3, M1 and M7.
ABC Analysis
Material
Annual
Demand
Unit
Cost
Consumption
Cost
Percentage of
Annual
Consumption Category
Percentag
e Sum
M12 10000 110 1100000 33% A
69%
M4 2500 250 625000 19% A
M11 12000 50 600000 18% A
M10 6000 80 480000 14% A
M2 80 1800 144000 4% B
28%
M5 2000 50 100000 3% B
M6 10000 10 100000 3% B
M8 1000 100 100000 3% B
M9 100 500 50000 1% C
3%
M3 320 120 38400 1% C
M1 20 500 10000 0% C
M7 5000 1.5 7500 0% C
Total Annual
Value of
Consumption 3354900
Section B
Answer to Sub-question (i) of B1
Pareto Principle for material resource planning as per ABC analysis has been categorized under
the following rule:
A-items- These items are categorised as per the highest annual consumption value. This is
categorised as top 69% of the annual consumption value. The materials in this category includes
M12, M11, M4 and M10.
C-items- These items are categorised as per lowest consumption value. This comprise of the
bottom 1% of the total annual consumption value. The materials in this category includes M2,
M5, M6 and M8.
B-items- This category has been prioritised as per the materials having medium consumption
value. The materials in this category includes M9, M3, M1 and M7.
ABC Analysis
Material
Annual
Demand
Unit
Cost
Consumption
Cost
Percentage of
Annual
Consumption Category
Percentag
e Sum
M12 10000 110 1100000 33% A
69%
M4 2500 250 625000 19% A
M11 12000 50 600000 18% A
M10 6000 80 480000 14% A
M2 80 1800 144000 4% B
28%
M5 2000 50 100000 3% B
M6 10000 10 100000 3% B
M8 1000 100 100000 3% B
M9 100 500 50000 1% C
3%
M3 320 120 38400 1% C
M1 20 500 10000 0% C
M7 5000 1.5 7500 0% C
Total Annual
Value of
Consumption 3354900
Secure Best Marks with AI Grader
Need help grading? Try our AI Grader for instant feedback on your assignments.
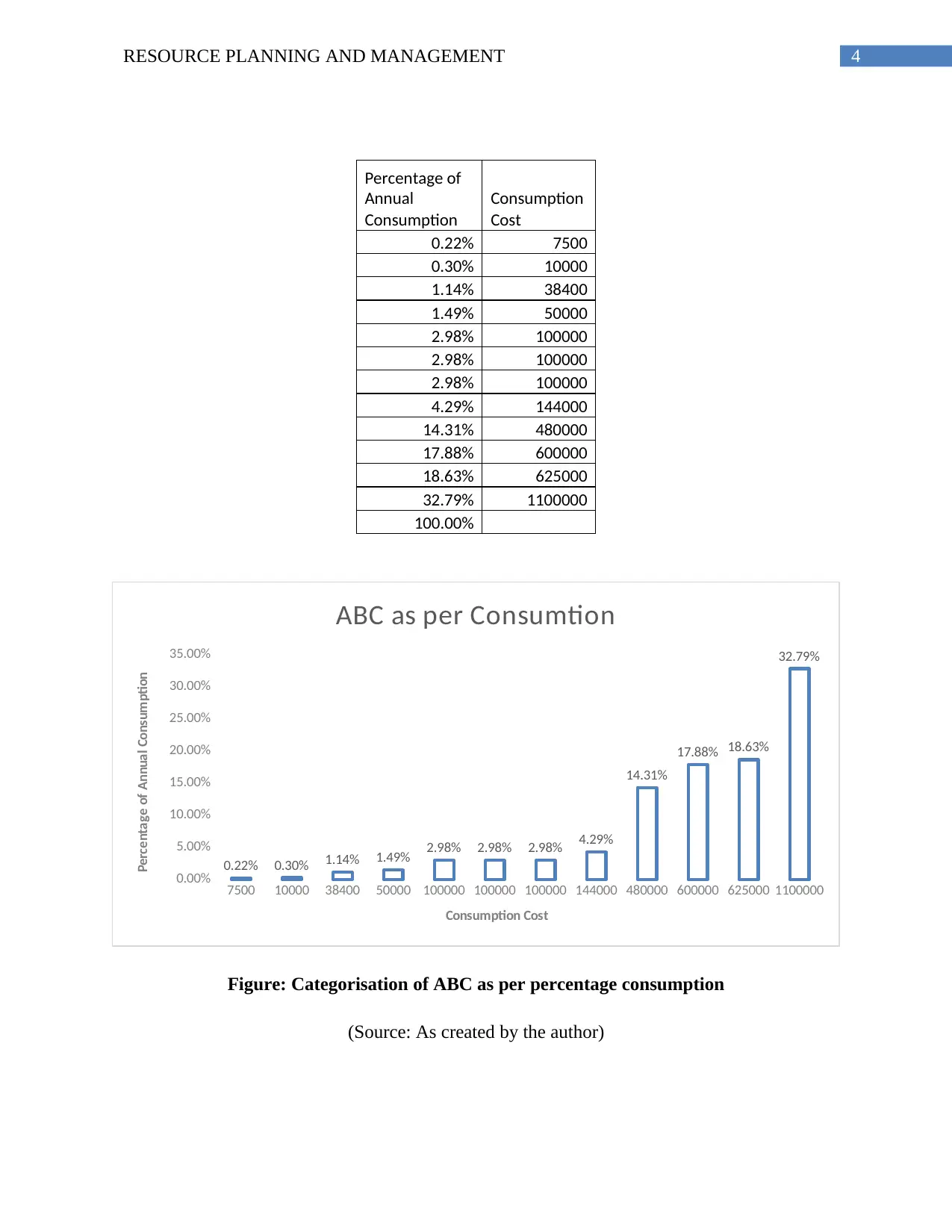
4RESOURCE PLANNING AND MANAGEMENT
Percentage of
Annual
Consumption
Consumption
Cost
0.22% 7500
0.30% 10000
1.14% 38400
1.49% 50000
2.98% 100000
2.98% 100000
2.98% 100000
4.29% 144000
14.31% 480000
17.88% 600000
18.63% 625000
32.79% 1100000
100.00%
7500 10000 38400 50000 100000 100000 100000 144000 480000 600000 625000 1100000
0.00%
5.00%
10.00%
15.00%
20.00%
25.00%
30.00%
35.00%
0.22% 0.30% 1.14% 1.49% 2.98% 2.98% 2.98% 4.29%
14.31%
17.88% 18.63%
32.79%
ABC as per Consumtion
Consumption Cost
Percentage of Annual Consumption
Figure: Categorisation of ABC as per percentage consumption
(Source: As created by the author)
Percentage of
Annual
Consumption
Consumption
Cost
0.22% 7500
0.30% 10000
1.14% 38400
1.49% 50000
2.98% 100000
2.98% 100000
2.98% 100000
4.29% 144000
14.31% 480000
17.88% 600000
18.63% 625000
32.79% 1100000
100.00%
7500 10000 38400 50000 100000 100000 100000 144000 480000 600000 625000 1100000
0.00%
5.00%
10.00%
15.00%
20.00%
25.00%
30.00%
35.00%
0.22% 0.30% 1.14% 1.49% 2.98% 2.98% 2.98% 4.29%
14.31%
17.88% 18.63%
32.79%
ABC as per Consumtion
Consumption Cost
Percentage of Annual Consumption
Figure: Categorisation of ABC as per percentage consumption
(Source: As created by the author)
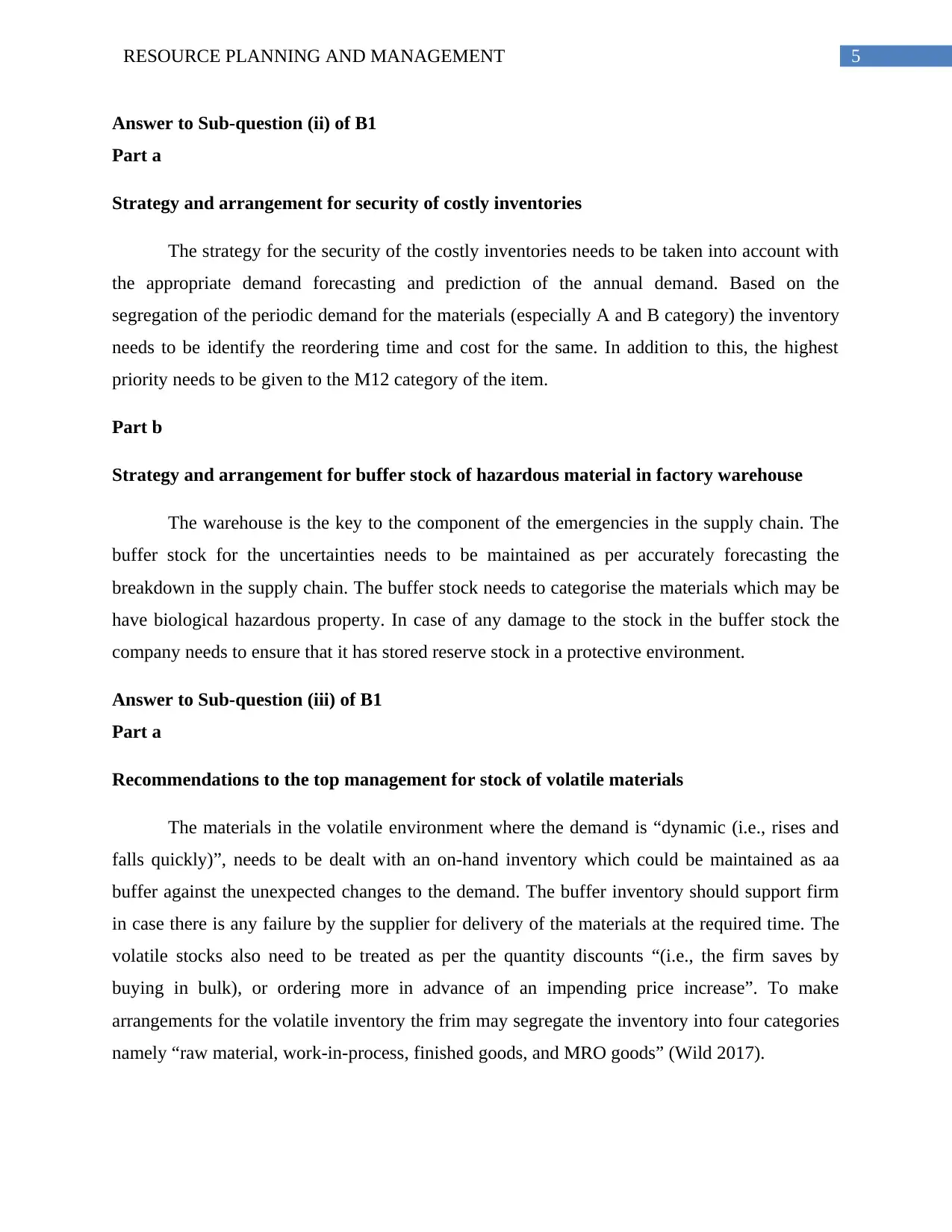
5RESOURCE PLANNING AND MANAGEMENT
Answer to Sub-question (ii) of B1
Part a
Strategy and arrangement for security of costly inventories
The strategy for the security of the costly inventories needs to be taken into account with
the appropriate demand forecasting and prediction of the annual demand. Based on the
segregation of the periodic demand for the materials (especially A and B category) the inventory
needs to be identify the reordering time and cost for the same. In addition to this, the highest
priority needs to be given to the M12 category of the item.
Part b
Strategy and arrangement for buffer stock of hazardous material in factory warehouse
The warehouse is the key to the component of the emergencies in the supply chain. The
buffer stock for the uncertainties needs to be maintained as per accurately forecasting the
breakdown in the supply chain. The buffer stock needs to categorise the materials which may be
have biological hazardous property. In case of any damage to the stock in the buffer stock the
company needs to ensure that it has stored reserve stock in a protective environment.
Answer to Sub-question (iii) of B1
Part a
Recommendations to the top management for stock of volatile materials
The materials in the volatile environment where the demand is “dynamic (i.e., rises and
falls quickly)”, needs to be dealt with an on-hand inventory which could be maintained as aa
buffer against the unexpected changes to the demand. The buffer inventory should support firm
in case there is any failure by the supplier for delivery of the materials at the required time. The
volatile stocks also need to be treated as per the quantity discounts “(i.e., the firm saves by
buying in bulk), or ordering more in advance of an impending price increase”. To make
arrangements for the volatile inventory the frim may segregate the inventory into four categories
namely “raw material, work-in-process, finished goods, and MRO goods” (Wild 2017).
Answer to Sub-question (ii) of B1
Part a
Strategy and arrangement for security of costly inventories
The strategy for the security of the costly inventories needs to be taken into account with
the appropriate demand forecasting and prediction of the annual demand. Based on the
segregation of the periodic demand for the materials (especially A and B category) the inventory
needs to be identify the reordering time and cost for the same. In addition to this, the highest
priority needs to be given to the M12 category of the item.
Part b
Strategy and arrangement for buffer stock of hazardous material in factory warehouse
The warehouse is the key to the component of the emergencies in the supply chain. The
buffer stock for the uncertainties needs to be maintained as per accurately forecasting the
breakdown in the supply chain. The buffer stock needs to categorise the materials which may be
have biological hazardous property. In case of any damage to the stock in the buffer stock the
company needs to ensure that it has stored reserve stock in a protective environment.
Answer to Sub-question (iii) of B1
Part a
Recommendations to the top management for stock of volatile materials
The materials in the volatile environment where the demand is “dynamic (i.e., rises and
falls quickly)”, needs to be dealt with an on-hand inventory which could be maintained as aa
buffer against the unexpected changes to the demand. The buffer inventory should support firm
in case there is any failure by the supplier for delivery of the materials at the required time. The
volatile stocks also need to be treated as per the quantity discounts “(i.e., the firm saves by
buying in bulk), or ordering more in advance of an impending price increase”. To make
arrangements for the volatile inventory the frim may segregate the inventory into four categories
namely “raw material, work-in-process, finished goods, and MRO goods” (Wild 2017).
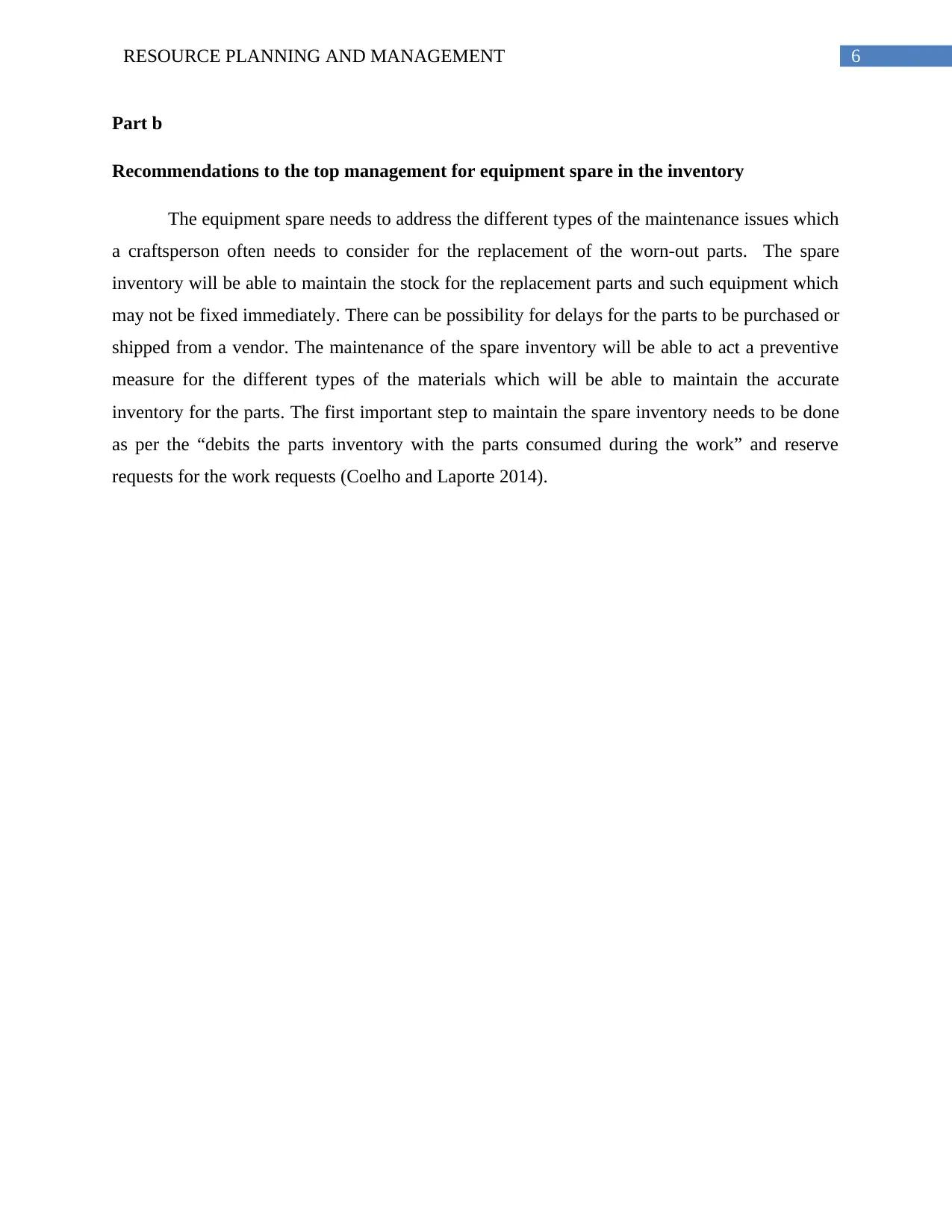
6RESOURCE PLANNING AND MANAGEMENT
Part b
Recommendations to the top management for equipment spare in the inventory
The equipment spare needs to address the different types of the maintenance issues which
a craftsperson often needs to consider for the replacement of the worn-out parts. The spare
inventory will be able to maintain the stock for the replacement parts and such equipment which
may not be fixed immediately. There can be possibility for delays for the parts to be purchased or
shipped from a vendor. The maintenance of the spare inventory will be able to act a preventive
measure for the different types of the materials which will be able to maintain the accurate
inventory for the parts. The first important step to maintain the spare inventory needs to be done
as per the “debits the parts inventory with the parts consumed during the work” and reserve
requests for the work requests (Coelho and Laporte 2014).
Part b
Recommendations to the top management for equipment spare in the inventory
The equipment spare needs to address the different types of the maintenance issues which
a craftsperson often needs to consider for the replacement of the worn-out parts. The spare
inventory will be able to maintain the stock for the replacement parts and such equipment which
may not be fixed immediately. There can be possibility for delays for the parts to be purchased or
shipped from a vendor. The maintenance of the spare inventory will be able to act a preventive
measure for the different types of the materials which will be able to maintain the accurate
inventory for the parts. The first important step to maintain the spare inventory needs to be done
as per the “debits the parts inventory with the parts consumed during the work” and reserve
requests for the work requests (Coelho and Laporte 2014).
Paraphrase This Document
Need a fresh take? Get an instant paraphrase of this document with our AI Paraphraser
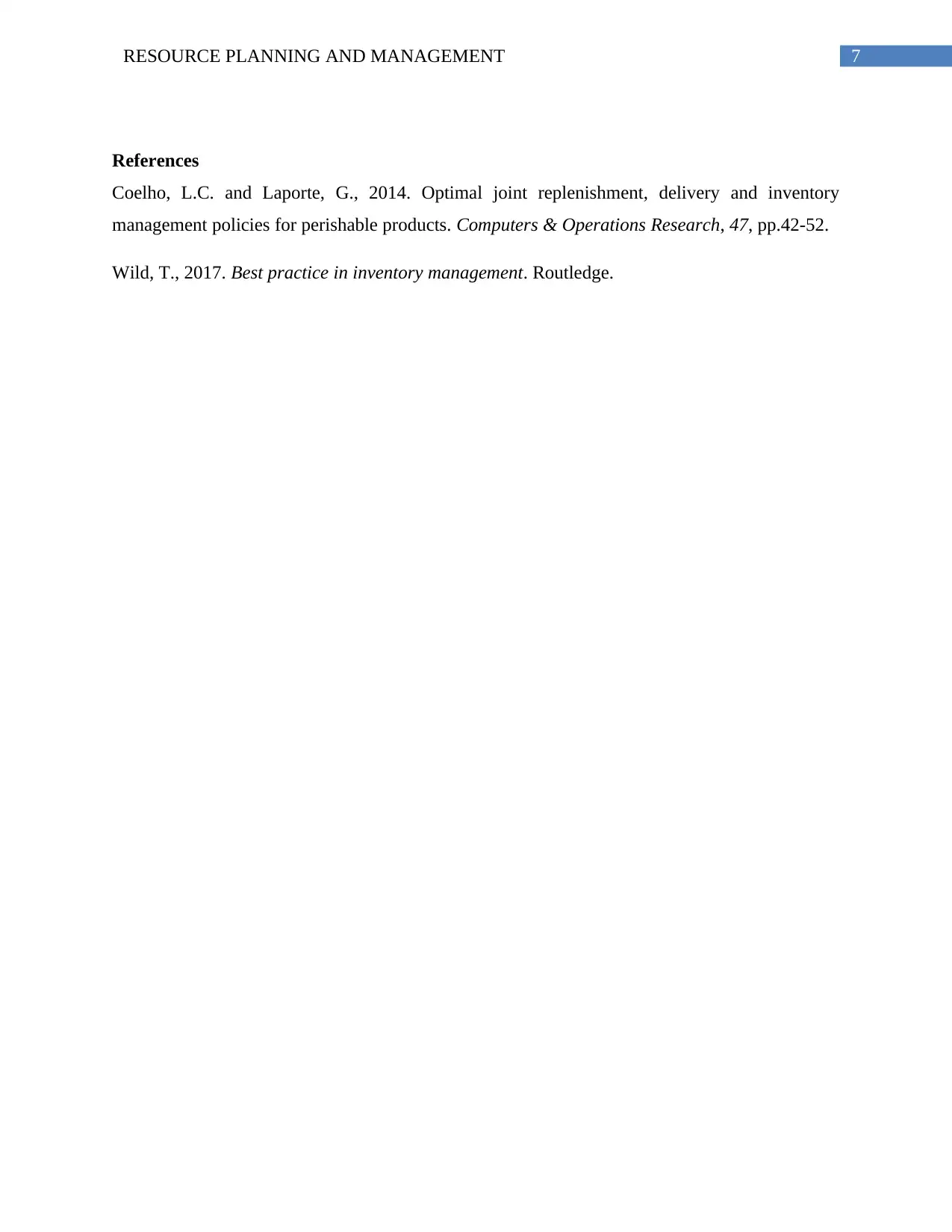
7RESOURCE PLANNING AND MANAGEMENT
References
Coelho, L.C. and Laporte, G., 2014. Optimal joint replenishment, delivery and inventory
management policies for perishable products. Computers & Operations Research, 47, pp.42-52.
Wild, T., 2017. Best practice in inventory management. Routledge.
References
Coelho, L.C. and Laporte, G., 2014. Optimal joint replenishment, delivery and inventory
management policies for perishable products. Computers & Operations Research, 47, pp.42-52.
Wild, T., 2017. Best practice in inventory management. Routledge.
1 out of 8
![[object Object]](/_next/image/?url=%2F_next%2Fstatic%2Fmedia%2Flogo.6d15ce61.png&w=640&q=75)
Your All-in-One AI-Powered Toolkit for Academic Success.
+13062052269
info@desklib.com
Available 24*7 on WhatsApp / Email
Unlock your academic potential
© 2024 | Zucol Services PVT LTD | All rights reserved.