Risk Management and Supply Chain Analysis: ACC Construction
VerifiedAdded on 2023/04/23
|23
|4765
|416
Case Study
AI Summary
This case study examines risk management and operational challenges within the construction industry, using the Arabian Construction Company (ACC) as a focal point. It delves into various aspects of ACC's operations, including lean management strategies for waste reduction, inventory control methods such as ABC analysis, and the impact of logistical factors like landlocked countries on the supply chain. The study also evaluates the role of third-party logistics firms and the importance of supplier relationship management. Furthermore, it analyzes the effects of inventory levels on liquidity and provides recommendations for improving quality and efficiency within ACC's operations. The analysis underscores the significance of proactive risk management and optimized supply chain practices for construction companies operating in dynamic global markets. Desklib provides access to similar case studies and solved assignments for students.
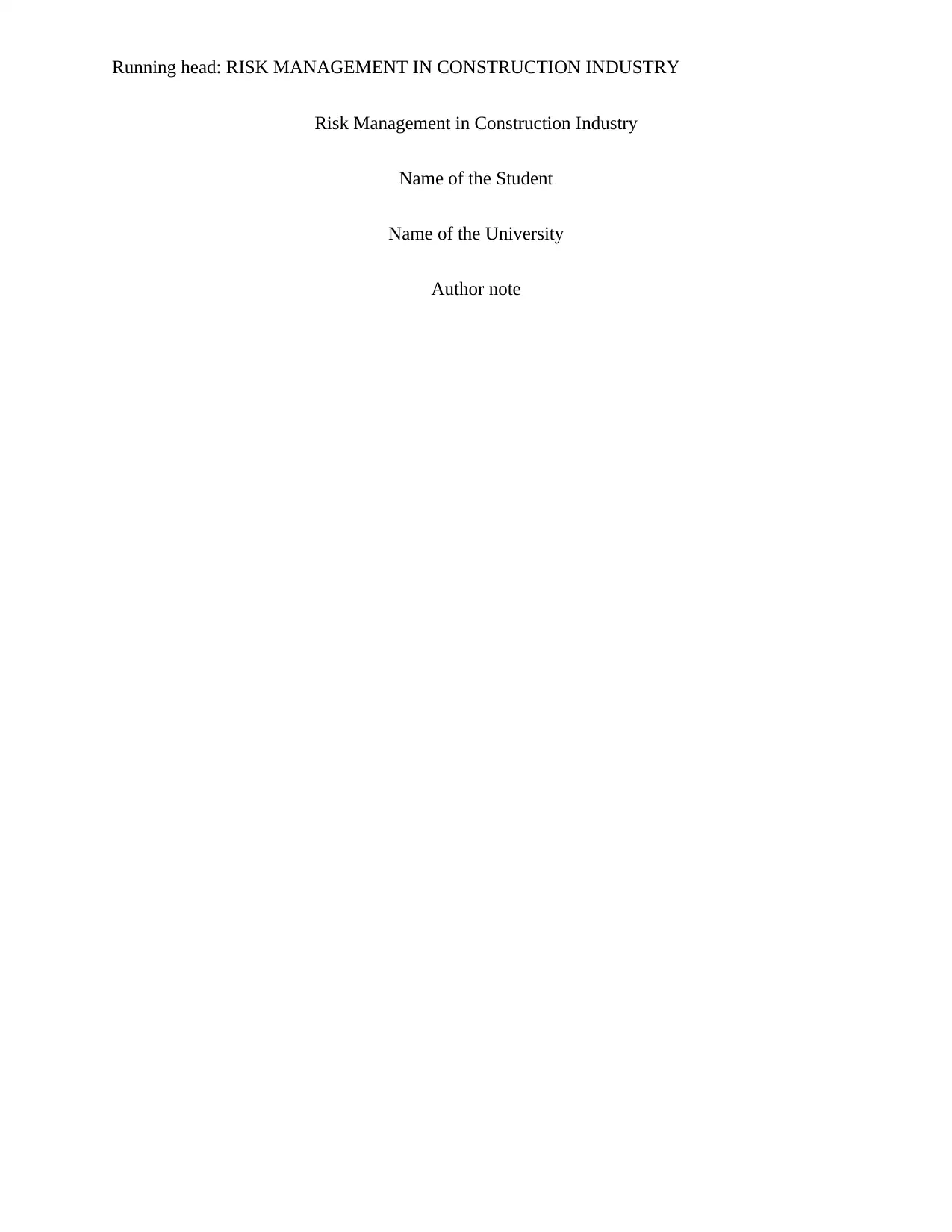
Running head: RISK MANAGEMENT IN CONSTRUCTION INDUSTRY
Risk Management in Construction Industry
Name of the Student
Name of the University
Author note
Risk Management in Construction Industry
Name of the Student
Name of the University
Author note
Paraphrase This Document
Need a fresh take? Get an instant paraphrase of this document with our AI Paraphraser
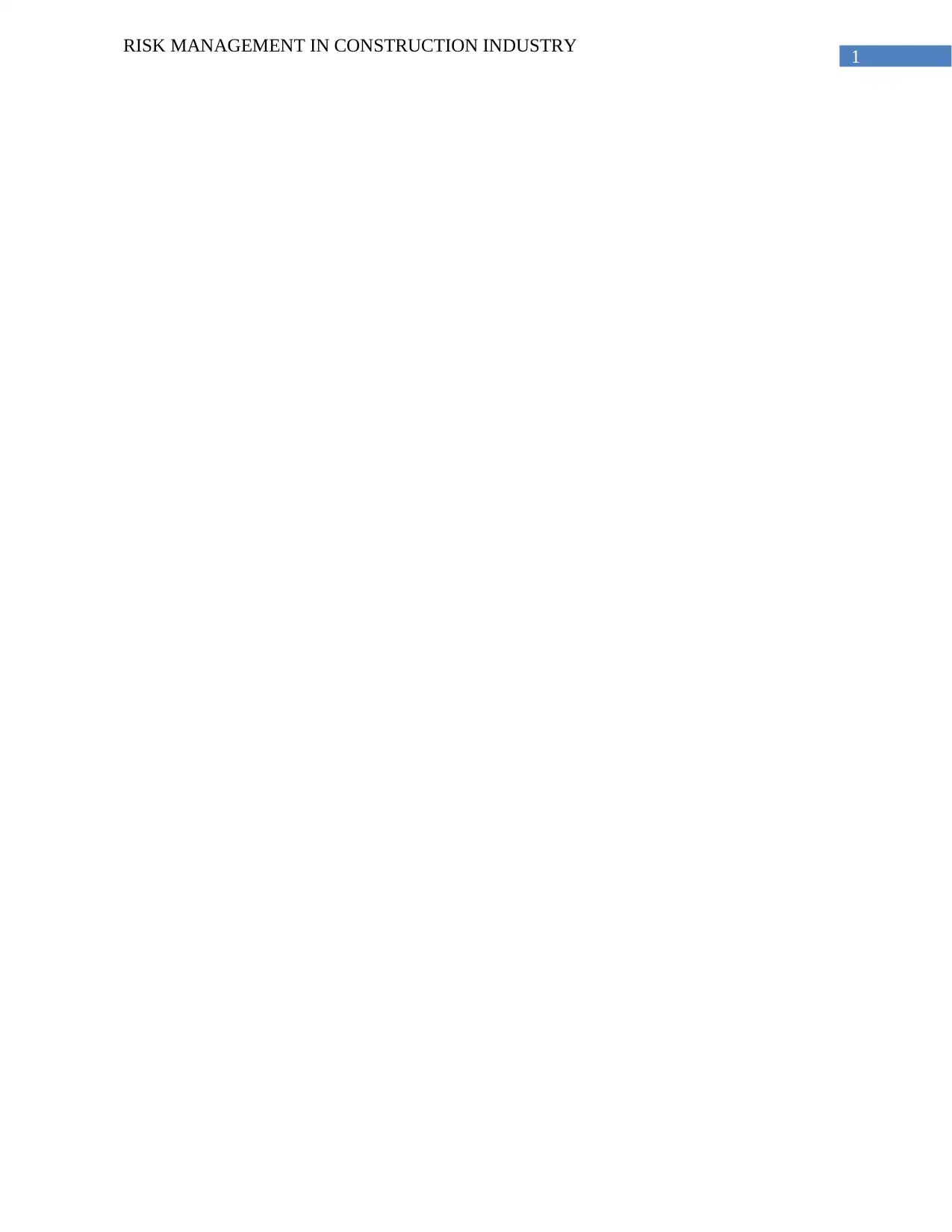
1
RISK MANAGEMENT IN CONSTRUCTION INDUSTRY
RISK MANAGEMENT IN CONSTRUCTION INDUSTRY
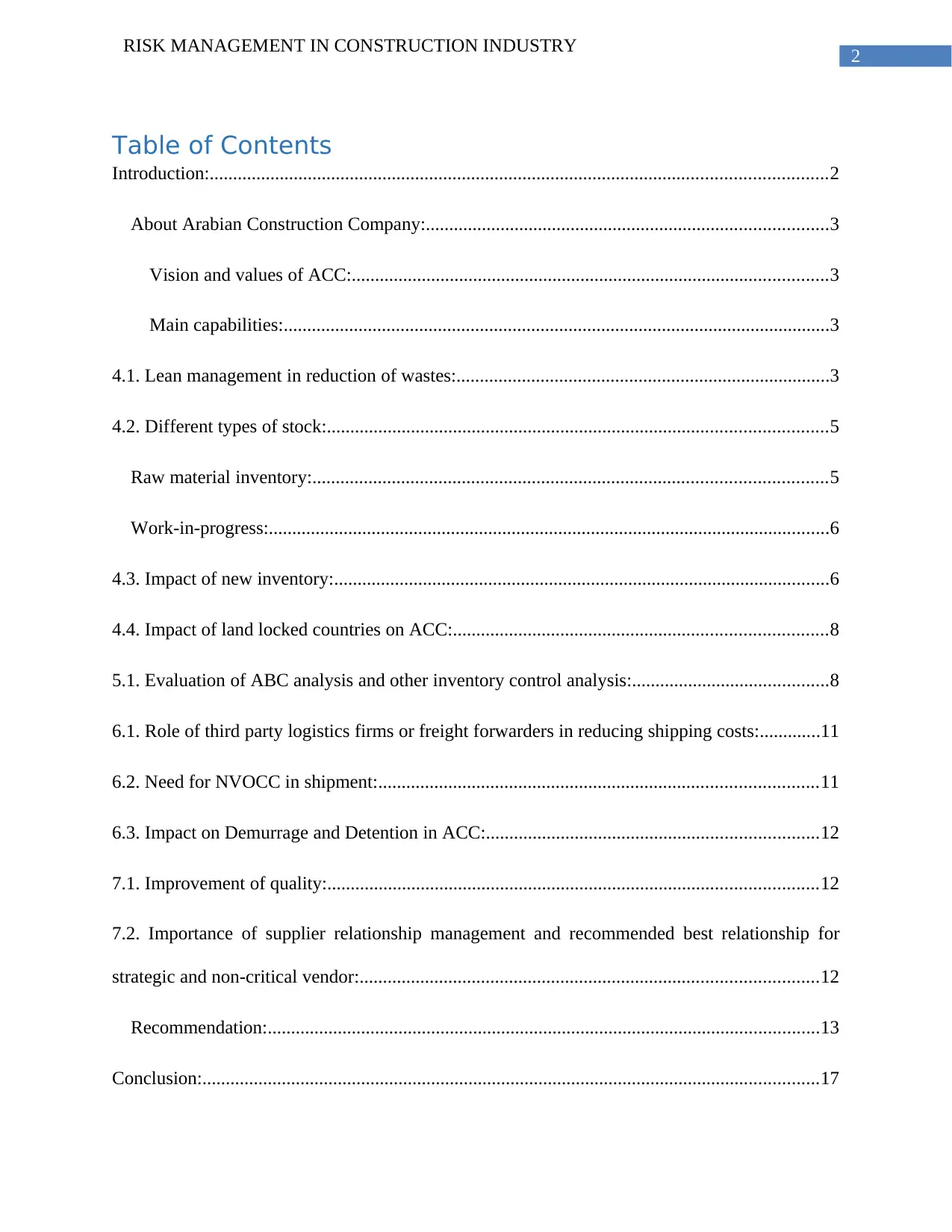
2
RISK MANAGEMENT IN CONSTRUCTION INDUSTRY
Table of Contents
Introduction:....................................................................................................................................2
About Arabian Construction Company:......................................................................................3
Vision and values of ACC:......................................................................................................3
Main capabilities:.....................................................................................................................3
4.1. Lean management in reduction of wastes:................................................................................3
4.2. Different types of stock:...........................................................................................................5
Raw material inventory:..............................................................................................................5
Work-in-progress:........................................................................................................................6
4.3. Impact of new inventory:..........................................................................................................6
4.4. Impact of land locked countries on ACC:................................................................................8
5.1. Evaluation of ABC analysis and other inventory control analysis:..........................................8
6.1. Role of third party logistics firms or freight forwarders in reducing shipping costs:.............11
6.2. Need for NVOCC in shipment:..............................................................................................11
6.3. Impact on Demurrage and Detention in ACC:.......................................................................12
7.1. Improvement of quality:.........................................................................................................12
7.2. Importance of supplier relationship management and recommended best relationship for
strategic and non-critical vendor:..................................................................................................12
Recommendation:......................................................................................................................13
Conclusion:....................................................................................................................................17
RISK MANAGEMENT IN CONSTRUCTION INDUSTRY
Table of Contents
Introduction:....................................................................................................................................2
About Arabian Construction Company:......................................................................................3
Vision and values of ACC:......................................................................................................3
Main capabilities:.....................................................................................................................3
4.1. Lean management in reduction of wastes:................................................................................3
4.2. Different types of stock:...........................................................................................................5
Raw material inventory:..............................................................................................................5
Work-in-progress:........................................................................................................................6
4.3. Impact of new inventory:..........................................................................................................6
4.4. Impact of land locked countries on ACC:................................................................................8
5.1. Evaluation of ABC analysis and other inventory control analysis:..........................................8
6.1. Role of third party logistics firms or freight forwarders in reducing shipping costs:.............11
6.2. Need for NVOCC in shipment:..............................................................................................11
6.3. Impact on Demurrage and Detention in ACC:.......................................................................12
7.1. Improvement of quality:.........................................................................................................12
7.2. Importance of supplier relationship management and recommended best relationship for
strategic and non-critical vendor:..................................................................................................12
Recommendation:......................................................................................................................13
Conclusion:....................................................................................................................................17
You're viewing a preview
Unlock full access by subscribing today!
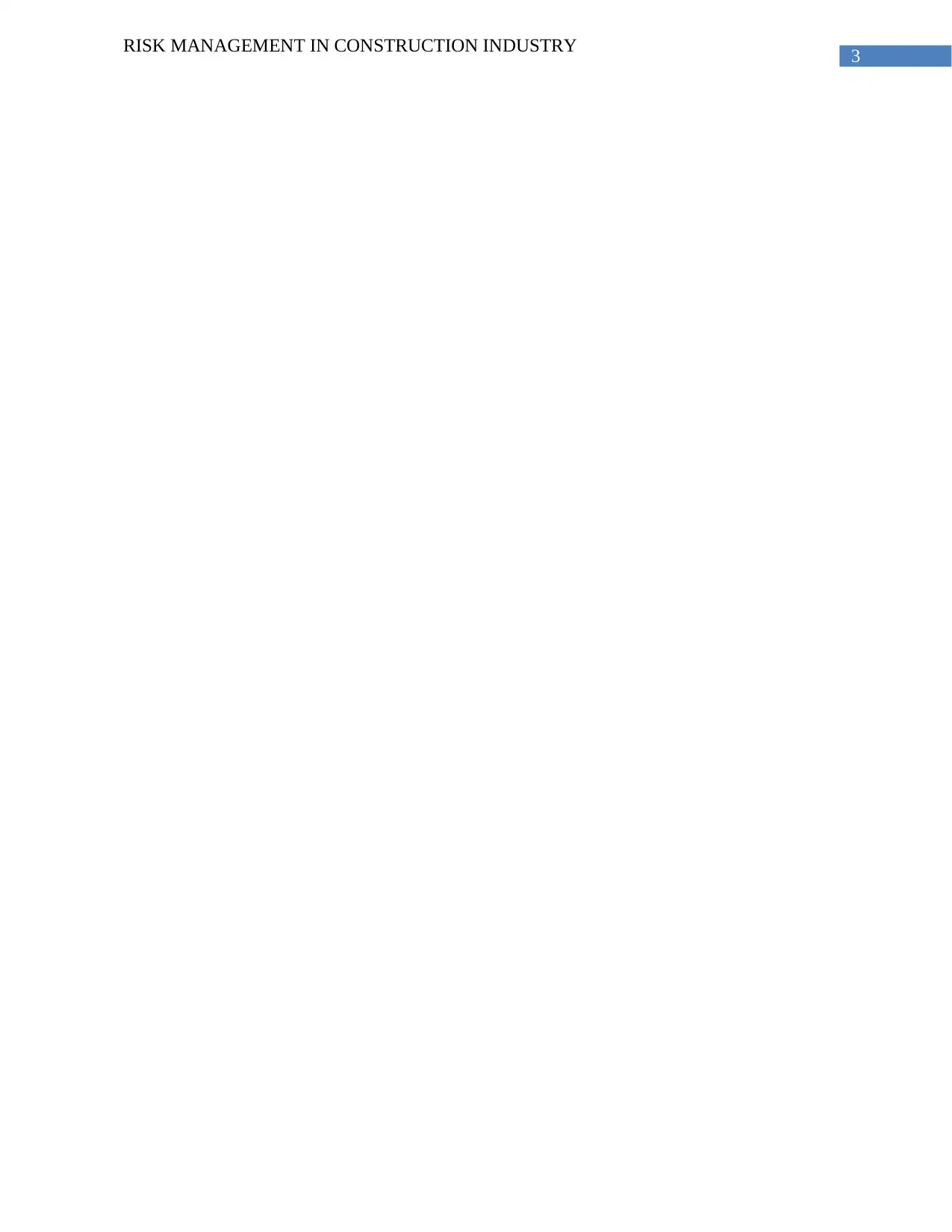
3
RISK MANAGEMENT IN CONSTRUCTION INDUSTRY
RISK MANAGEMENT IN CONSTRUCTION INDUSTRY
Paraphrase This Document
Need a fresh take? Get an instant paraphrase of this document with our AI Paraphraser
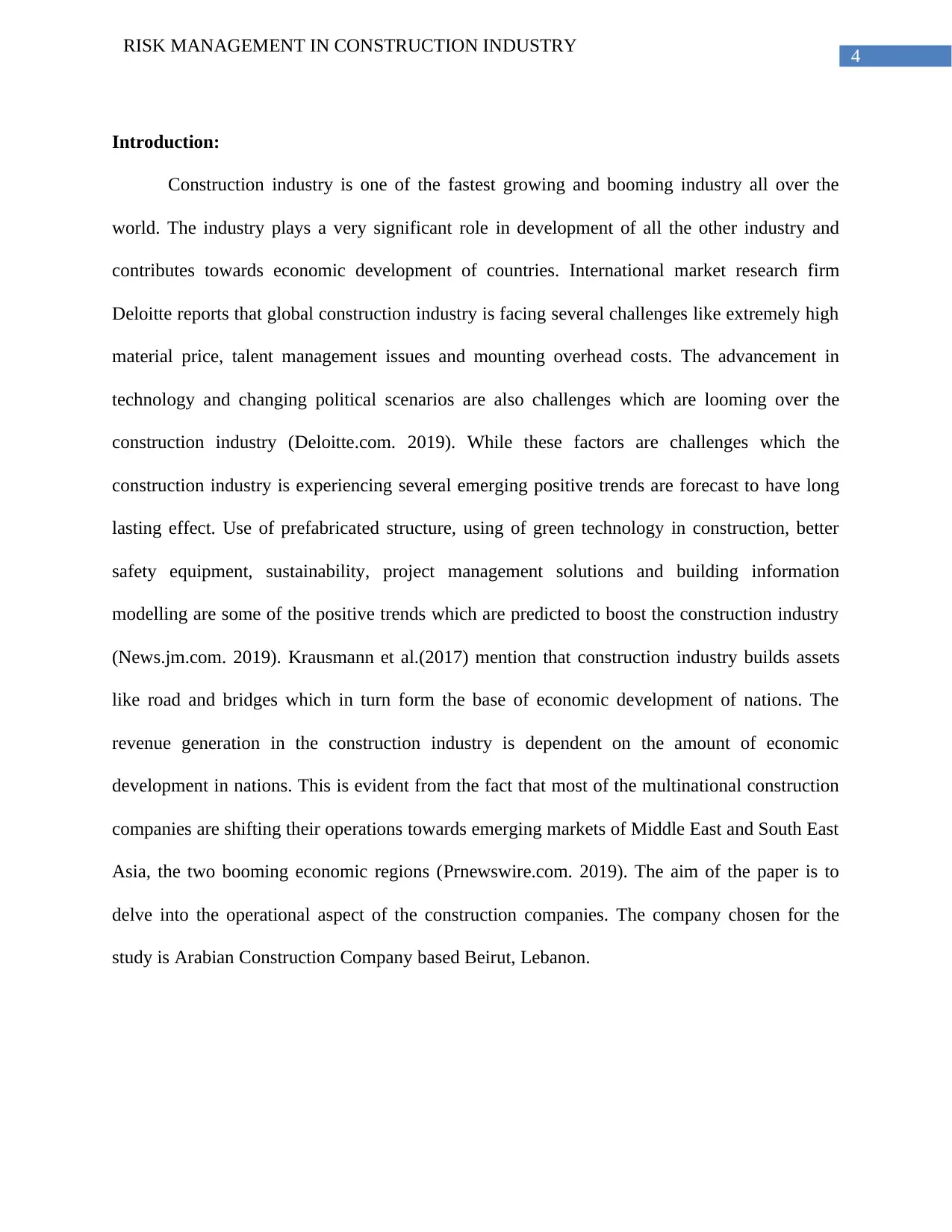
4
RISK MANAGEMENT IN CONSTRUCTION INDUSTRY
Introduction:
Construction industry is one of the fastest growing and booming industry all over the
world. The industry plays a very significant role in development of all the other industry and
contributes towards economic development of countries. International market research firm
Deloitte reports that global construction industry is facing several challenges like extremely high
material price, talent management issues and mounting overhead costs. The advancement in
technology and changing political scenarios are also challenges which are looming over the
construction industry (Deloitte.com. 2019). While these factors are challenges which the
construction industry is experiencing several emerging positive trends are forecast to have long
lasting effect. Use of prefabricated structure, using of green technology in construction, better
safety equipment, sustainability, project management solutions and building information
modelling are some of the positive trends which are predicted to boost the construction industry
(News.jm.com. 2019). Krausmann et al.(2017) mention that construction industry builds assets
like road and bridges which in turn form the base of economic development of nations. The
revenue generation in the construction industry is dependent on the amount of economic
development in nations. This is evident from the fact that most of the multinational construction
companies are shifting their operations towards emerging markets of Middle East and South East
Asia, the two booming economic regions (Prnewswire.com. 2019). The aim of the paper is to
delve into the operational aspect of the construction companies. The company chosen for the
study is Arabian Construction Company based Beirut, Lebanon.
RISK MANAGEMENT IN CONSTRUCTION INDUSTRY
Introduction:
Construction industry is one of the fastest growing and booming industry all over the
world. The industry plays a very significant role in development of all the other industry and
contributes towards economic development of countries. International market research firm
Deloitte reports that global construction industry is facing several challenges like extremely high
material price, talent management issues and mounting overhead costs. The advancement in
technology and changing political scenarios are also challenges which are looming over the
construction industry (Deloitte.com. 2019). While these factors are challenges which the
construction industry is experiencing several emerging positive trends are forecast to have long
lasting effect. Use of prefabricated structure, using of green technology in construction, better
safety equipment, sustainability, project management solutions and building information
modelling are some of the positive trends which are predicted to boost the construction industry
(News.jm.com. 2019). Krausmann et al.(2017) mention that construction industry builds assets
like road and bridges which in turn form the base of economic development of nations. The
revenue generation in the construction industry is dependent on the amount of economic
development in nations. This is evident from the fact that most of the multinational construction
companies are shifting their operations towards emerging markets of Middle East and South East
Asia, the two booming economic regions (Prnewswire.com. 2019). The aim of the paper is to
delve into the operational aspect of the construction companies. The company chosen for the
study is Arabian Construction Company based Beirut, Lebanon.
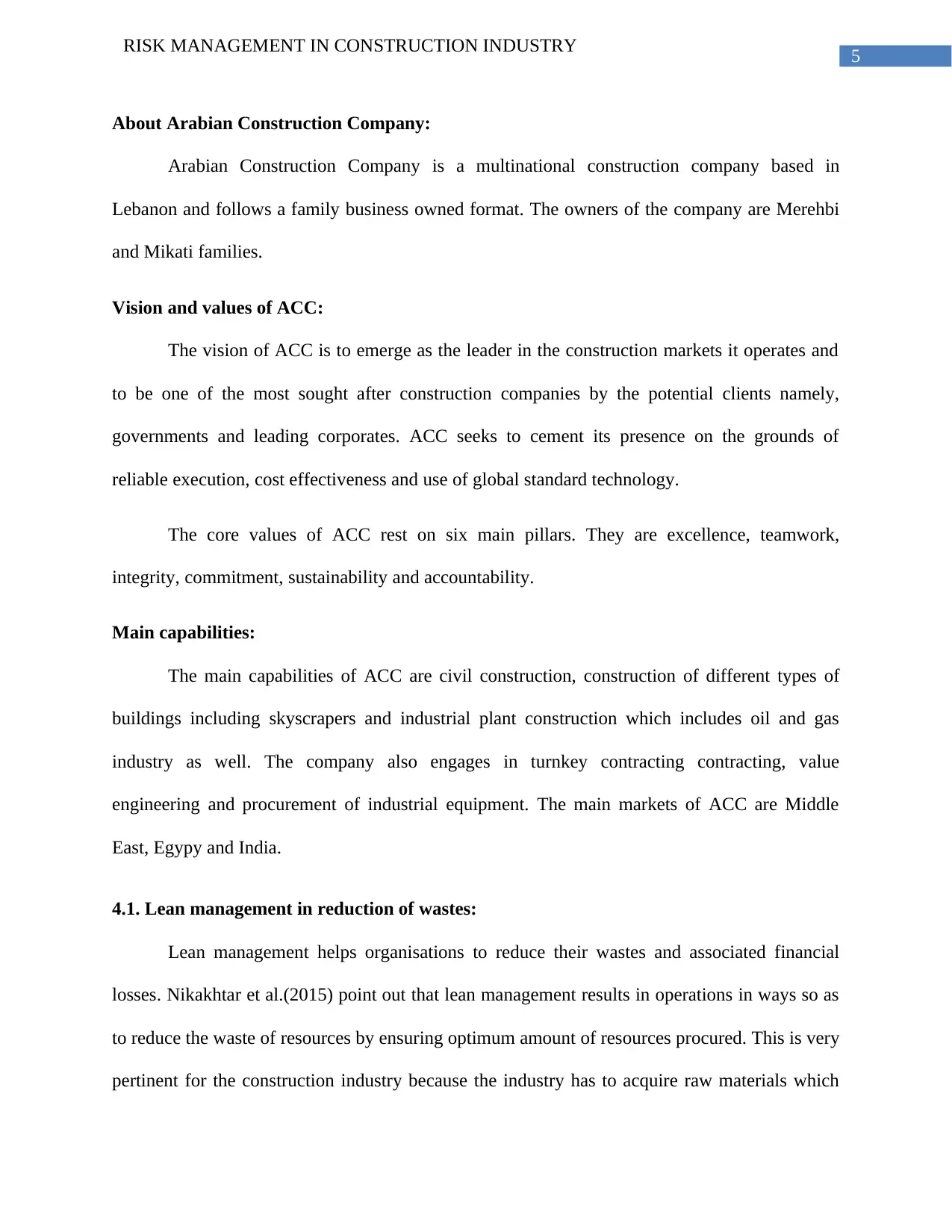
5
RISK MANAGEMENT IN CONSTRUCTION INDUSTRY
About Arabian Construction Company:
Arabian Construction Company is a multinational construction company based in
Lebanon and follows a family business owned format. The owners of the company are Merehbi
and Mikati families.
Vision and values of ACC:
The vision of ACC is to emerge as the leader in the construction markets it operates and
to be one of the most sought after construction companies by the potential clients namely,
governments and leading corporates. ACC seeks to cement its presence on the grounds of
reliable execution, cost effectiveness and use of global standard technology.
The core values of ACC rest on six main pillars. They are excellence, teamwork,
integrity, commitment, sustainability and accountability.
Main capabilities:
The main capabilities of ACC are civil construction, construction of different types of
buildings including skyscrapers and industrial plant construction which includes oil and gas
industry as well. The company also engages in turnkey contracting contracting, value
engineering and procurement of industrial equipment. The main markets of ACC are Middle
East, Egypy and India.
4.1. Lean management in reduction of wastes:
Lean management helps organisations to reduce their wastes and associated financial
losses. Nikakhtar et al.(2015) point out that lean management results in operations in ways so as
to reduce the waste of resources by ensuring optimum amount of resources procured. This is very
pertinent for the construction industry because the industry has to acquire raw materials which
RISK MANAGEMENT IN CONSTRUCTION INDUSTRY
About Arabian Construction Company:
Arabian Construction Company is a multinational construction company based in
Lebanon and follows a family business owned format. The owners of the company are Merehbi
and Mikati families.
Vision and values of ACC:
The vision of ACC is to emerge as the leader in the construction markets it operates and
to be one of the most sought after construction companies by the potential clients namely,
governments and leading corporates. ACC seeks to cement its presence on the grounds of
reliable execution, cost effectiveness and use of global standard technology.
The core values of ACC rest on six main pillars. They are excellence, teamwork,
integrity, commitment, sustainability and accountability.
Main capabilities:
The main capabilities of ACC are civil construction, construction of different types of
buildings including skyscrapers and industrial plant construction which includes oil and gas
industry as well. The company also engages in turnkey contracting contracting, value
engineering and procurement of industrial equipment. The main markets of ACC are Middle
East, Egypy and India.
4.1. Lean management in reduction of wastes:
Lean management helps organisations to reduce their wastes and associated financial
losses. Nikakhtar et al.(2015) point out that lean management results in operations in ways so as
to reduce the waste of resources by ensuring optimum amount of resources procured. This is very
pertinent for the construction industry because the industry has to acquire raw materials which
You're viewing a preview
Unlock full access by subscribing today!
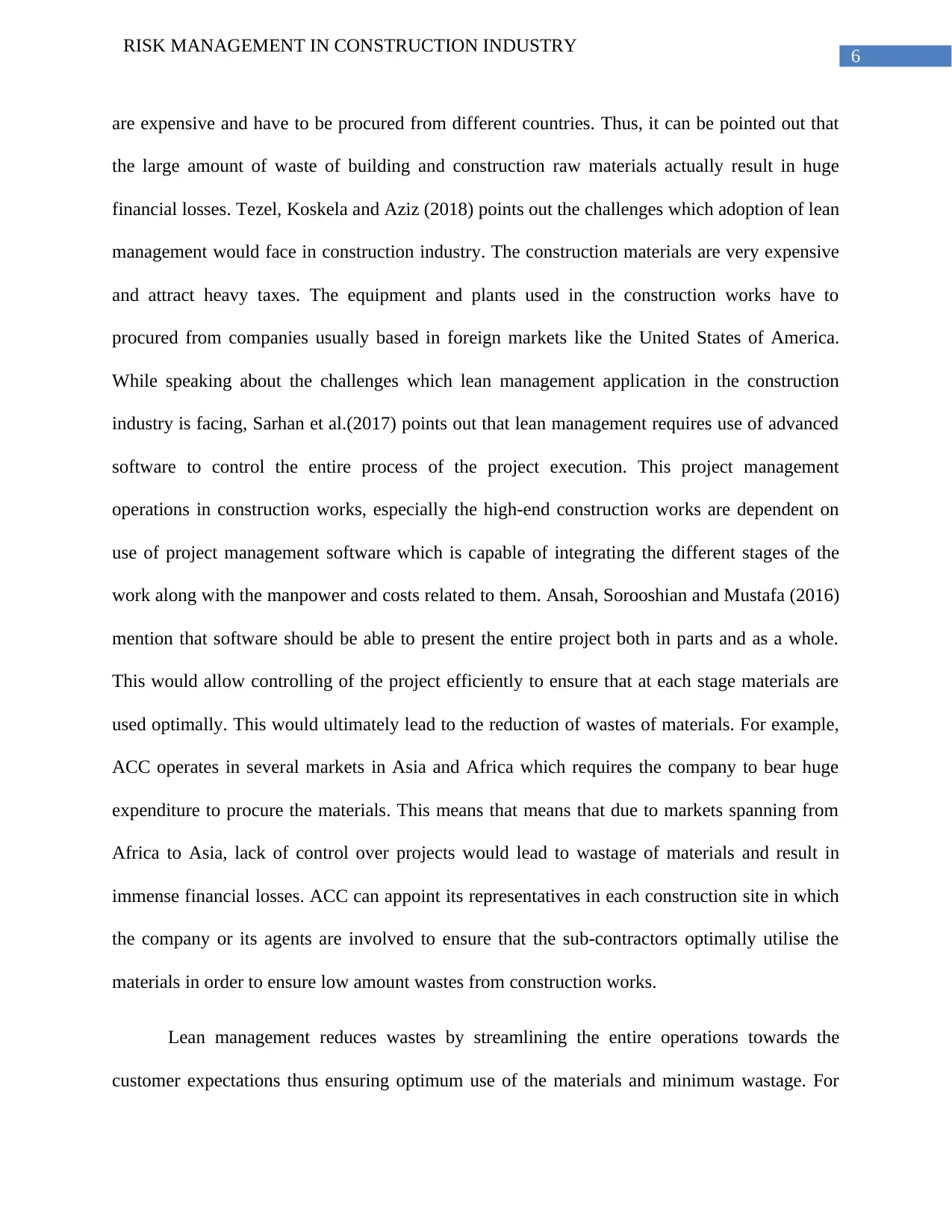
6
RISK MANAGEMENT IN CONSTRUCTION INDUSTRY
are expensive and have to be procured from different countries. Thus, it can be pointed out that
the large amount of waste of building and construction raw materials actually result in huge
financial losses. Tezel, Koskela and Aziz (2018) points out the challenges which adoption of lean
management would face in construction industry. The construction materials are very expensive
and attract heavy taxes. The equipment and plants used in the construction works have to
procured from companies usually based in foreign markets like the United States of America.
While speaking about the challenges which lean management application in the construction
industry is facing, Sarhan et al.(2017) points out that lean management requires use of advanced
software to control the entire process of the project execution. This project management
operations in construction works, especially the high-end construction works are dependent on
use of project management software which is capable of integrating the different stages of the
work along with the manpower and costs related to them. Ansah, Sorooshian and Mustafa (2016)
mention that software should be able to present the entire project both in parts and as a whole.
This would allow controlling of the project efficiently to ensure that at each stage materials are
used optimally. This would ultimately lead to the reduction of wastes of materials. For example,
ACC operates in several markets in Asia and Africa which requires the company to bear huge
expenditure to procure the materials. This means that means that due to markets spanning from
Africa to Asia, lack of control over projects would lead to wastage of materials and result in
immense financial losses. ACC can appoint its representatives in each construction site in which
the company or its agents are involved to ensure that the sub-contractors optimally utilise the
materials in order to ensure low amount wastes from construction works.
Lean management reduces wastes by streamlining the entire operations towards the
customer expectations thus ensuring optimum use of the materials and minimum wastage. For
RISK MANAGEMENT IN CONSTRUCTION INDUSTRY
are expensive and have to be procured from different countries. Thus, it can be pointed out that
the large amount of waste of building and construction raw materials actually result in huge
financial losses. Tezel, Koskela and Aziz (2018) points out the challenges which adoption of lean
management would face in construction industry. The construction materials are very expensive
and attract heavy taxes. The equipment and plants used in the construction works have to
procured from companies usually based in foreign markets like the United States of America.
While speaking about the challenges which lean management application in the construction
industry is facing, Sarhan et al.(2017) points out that lean management requires use of advanced
software to control the entire process of the project execution. This project management
operations in construction works, especially the high-end construction works are dependent on
use of project management software which is capable of integrating the different stages of the
work along with the manpower and costs related to them. Ansah, Sorooshian and Mustafa (2016)
mention that software should be able to present the entire project both in parts and as a whole.
This would allow controlling of the project efficiently to ensure that at each stage materials are
used optimally. This would ultimately lead to the reduction of wastes of materials. For example,
ACC operates in several markets in Asia and Africa which requires the company to bear huge
expenditure to procure the materials. This means that means that due to markets spanning from
Africa to Asia, lack of control over projects would lead to wastage of materials and result in
immense financial losses. ACC can appoint its representatives in each construction site in which
the company or its agents are involved to ensure that the sub-contractors optimally utilise the
materials in order to ensure low amount wastes from construction works.
Lean management reduces wastes by streamlining the entire operations towards the
customer expectations thus ensuring optimum use of the materials and minimum wastage. For
Paraphrase This Document
Need a fresh take? Get an instant paraphrase of this document with our AI Paraphraser

7
RISK MANAGEMENT IN CONSTRUCTION INDUSTRY
example, ACC serves cleints which are either government bodies, international organisations or
body corporates. The company using its advanced project management technology breaks down
the entire scope of the construction works into a number of component like hiring of sub-
contractors and hiring of equipment contractors. The company enters into contracts with all the
suppliers which follow the procurement policy of the company. The contracts provide the firm
the power to inspect the usage of materials and equipment. ACC in order to maintain stronger
vigil on the construction work often builds temporary offices at the sites. The company deploys
specialists like engineers who manage each stage of work and ensure that the sub-contractors use
the materials optimally and do not result in huge wastage. The representatives of the company
maintains communication with the management and the regional offices of ACC to communicate
them about the commencement of the work. The representatives of ACC ensure that the
materials and equipment are stored in appropriate ways which reduces loss due to spilling and
slack material storage system. This way lean management would result in reduction of wastage
of materials and ensure optimum utilisation of materials in the construction work.
4.2. Different types of stock:
The following are the three types of stock which ACC holds:
Raw material inventory:
The raw material inventory consists of raw materials which acquired forusage in the
construction works. As far as ACC is concerned, the raw materials which the firm acquires
consists of bricks, sand, construction materials, cement of different kind and rods. The raw
materials also consist of different types of chemicals which find use in the construction work.
RISK MANAGEMENT IN CONSTRUCTION INDUSTRY
example, ACC serves cleints which are either government bodies, international organisations or
body corporates. The company using its advanced project management technology breaks down
the entire scope of the construction works into a number of component like hiring of sub-
contractors and hiring of equipment contractors. The company enters into contracts with all the
suppliers which follow the procurement policy of the company. The contracts provide the firm
the power to inspect the usage of materials and equipment. ACC in order to maintain stronger
vigil on the construction work often builds temporary offices at the sites. The company deploys
specialists like engineers who manage each stage of work and ensure that the sub-contractors use
the materials optimally and do not result in huge wastage. The representatives of the company
maintains communication with the management and the regional offices of ACC to communicate
them about the commencement of the work. The representatives of ACC ensure that the
materials and equipment are stored in appropriate ways which reduces loss due to spilling and
slack material storage system. This way lean management would result in reduction of wastage
of materials and ensure optimum utilisation of materials in the construction work.
4.2. Different types of stock:
The following are the three types of stock which ACC holds:
Raw material inventory:
The raw material inventory consists of raw materials which acquired forusage in the
construction works. As far as ACC is concerned, the raw materials which the firm acquires
consists of bricks, sand, construction materials, cement of different kind and rods. The raw
materials also consist of different types of chemicals which find use in the construction work.
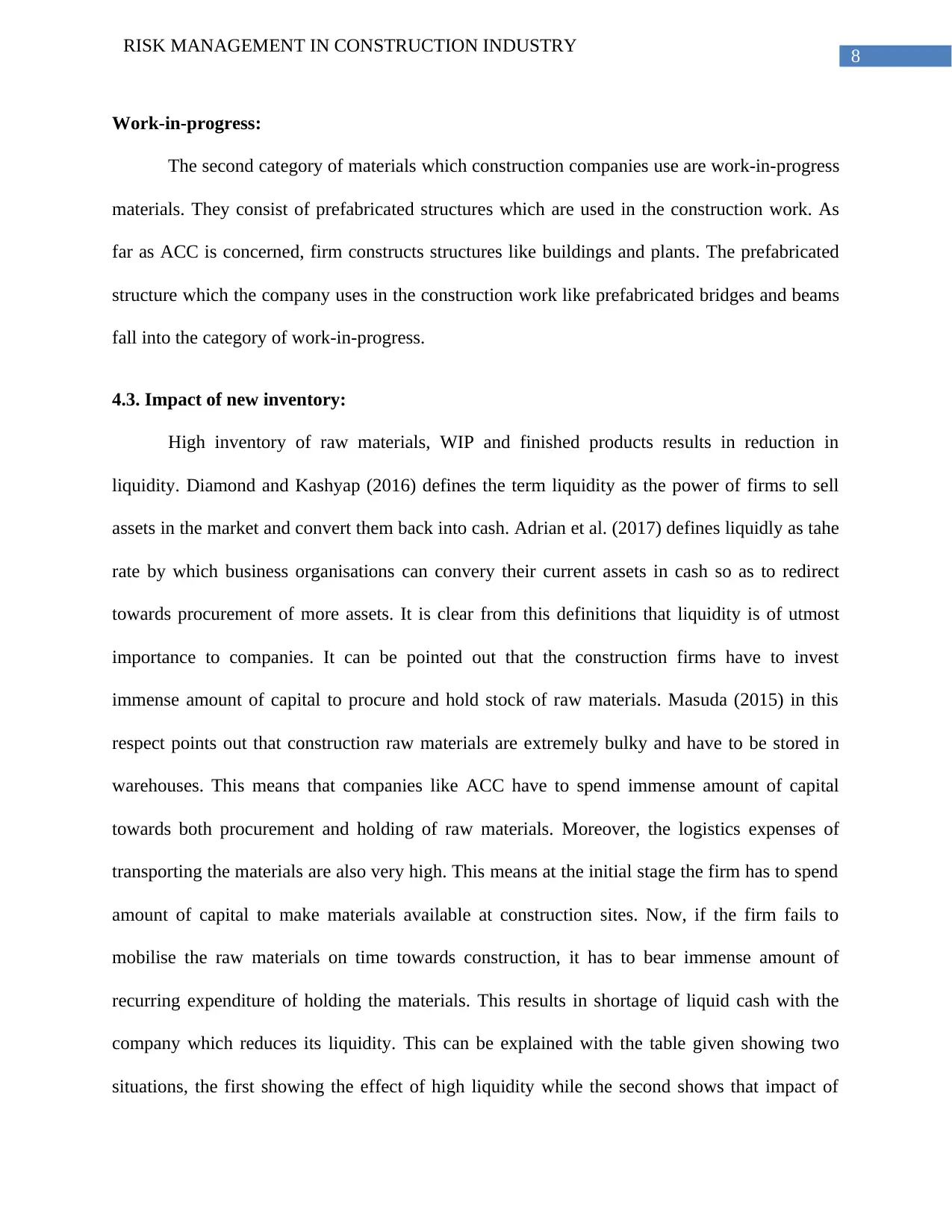
8
RISK MANAGEMENT IN CONSTRUCTION INDUSTRY
Work-in-progress:
The second category of materials which construction companies use are work-in-progress
materials. They consist of prefabricated structures which are used in the construction work. As
far as ACC is concerned, firm constructs structures like buildings and plants. The prefabricated
structure which the company uses in the construction work like prefabricated bridges and beams
fall into the category of work-in-progress.
4.3. Impact of new inventory:
High inventory of raw materials, WIP and finished products results in reduction in
liquidity. Diamond and Kashyap (2016) defines the term liquidity as the power of firms to sell
assets in the market and convert them back into cash. Adrian et al. (2017) defines liquidly as tahe
rate by which business organisations can convery their current assets in cash so as to redirect
towards procurement of more assets. It is clear from this definitions that liquidity is of utmost
importance to companies. It can be pointed out that the construction firms have to invest
immense amount of capital to procure and hold stock of raw materials. Masuda (2015) in this
respect points out that construction raw materials are extremely bulky and have to be stored in
warehouses. This means that companies like ACC have to spend immense amount of capital
towards both procurement and holding of raw materials. Moreover, the logistics expenses of
transporting the materials are also very high. This means at the initial stage the firm has to spend
amount of capital to make materials available at construction sites. Now, if the firm fails to
mobilise the raw materials on time towards construction, it has to bear immense amount of
recurring expenditure of holding the materials. This results in shortage of liquid cash with the
company which reduces its liquidity. This can be explained with the table given showing two
situations, the first showing the effect of high liquidity while the second shows that impact of
RISK MANAGEMENT IN CONSTRUCTION INDUSTRY
Work-in-progress:
The second category of materials which construction companies use are work-in-progress
materials. They consist of prefabricated structures which are used in the construction work. As
far as ACC is concerned, firm constructs structures like buildings and plants. The prefabricated
structure which the company uses in the construction work like prefabricated bridges and beams
fall into the category of work-in-progress.
4.3. Impact of new inventory:
High inventory of raw materials, WIP and finished products results in reduction in
liquidity. Diamond and Kashyap (2016) defines the term liquidity as the power of firms to sell
assets in the market and convert them back into cash. Adrian et al. (2017) defines liquidly as tahe
rate by which business organisations can convery their current assets in cash so as to redirect
towards procurement of more assets. It is clear from this definitions that liquidity is of utmost
importance to companies. It can be pointed out that the construction firms have to invest
immense amount of capital to procure and hold stock of raw materials. Masuda (2015) in this
respect points out that construction raw materials are extremely bulky and have to be stored in
warehouses. This means that companies like ACC have to spend immense amount of capital
towards both procurement and holding of raw materials. Moreover, the logistics expenses of
transporting the materials are also very high. This means at the initial stage the firm has to spend
amount of capital to make materials available at construction sites. Now, if the firm fails to
mobilise the raw materials on time towards construction, it has to bear immense amount of
recurring expenditure of holding the materials. This results in shortage of liquid cash with the
company which reduces its liquidity. This can be explained with the table given showing two
situations, the first showing the effect of high liquidity while the second shows that impact of
You're viewing a preview
Unlock full access by subscribing today!
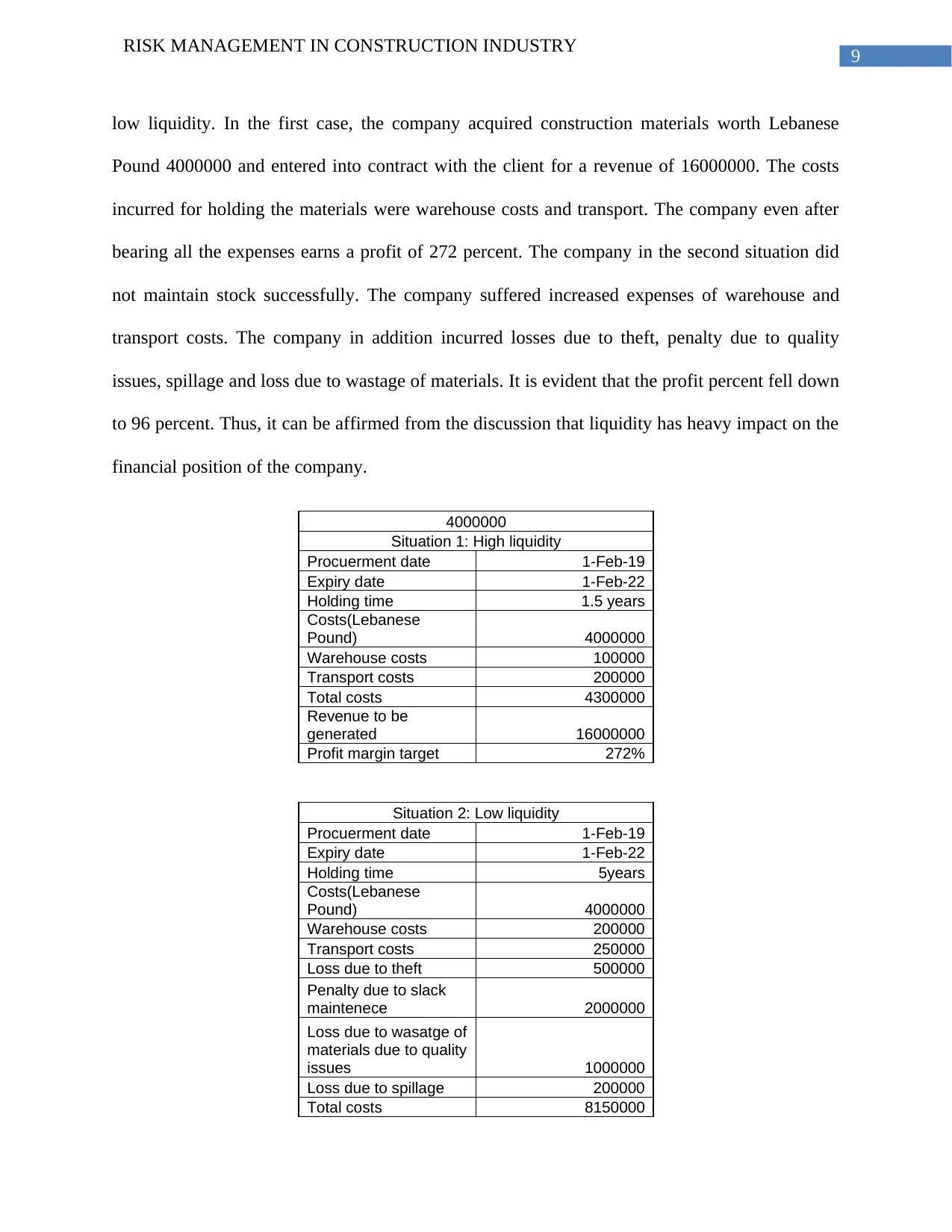
9
RISK MANAGEMENT IN CONSTRUCTION INDUSTRY
low liquidity. In the first case, the company acquired construction materials worth Lebanese
Pound 4000000 and entered into contract with the client for a revenue of 16000000. The costs
incurred for holding the materials were warehouse costs and transport. The company even after
bearing all the expenses earns a profit of 272 percent. The company in the second situation did
not maintain stock successfully. The company suffered increased expenses of warehouse and
transport costs. The company in addition incurred losses due to theft, penalty due to quality
issues, spillage and loss due to wastage of materials. It is evident that the profit percent fell down
to 96 percent. Thus, it can be affirmed from the discussion that liquidity has heavy impact on the
financial position of the company.
4000000
Situation 1: High liquidity
Procuerment date 1-Feb-19
Expiry date 1-Feb-22
Holding time 1.5 years
Costs(Lebanese
Pound) 4000000
Warehouse costs 100000
Transport costs 200000
Total costs 4300000
Revenue to be
generated 16000000
Profit margin target 272%
Situation 2: Low liquidity
Procuerment date 1-Feb-19
Expiry date 1-Feb-22
Holding time 5years
Costs(Lebanese
Pound) 4000000
Warehouse costs 200000
Transport costs 250000
Loss due to theft 500000
Penalty due to slack
maintenece 2000000
Loss due to wasatge of
materials due to quality
issues 1000000
Loss due to spillage 200000
Total costs 8150000
RISK MANAGEMENT IN CONSTRUCTION INDUSTRY
low liquidity. In the first case, the company acquired construction materials worth Lebanese
Pound 4000000 and entered into contract with the client for a revenue of 16000000. The costs
incurred for holding the materials were warehouse costs and transport. The company even after
bearing all the expenses earns a profit of 272 percent. The company in the second situation did
not maintain stock successfully. The company suffered increased expenses of warehouse and
transport costs. The company in addition incurred losses due to theft, penalty due to quality
issues, spillage and loss due to wastage of materials. It is evident that the profit percent fell down
to 96 percent. Thus, it can be affirmed from the discussion that liquidity has heavy impact on the
financial position of the company.
4000000
Situation 1: High liquidity
Procuerment date 1-Feb-19
Expiry date 1-Feb-22
Holding time 1.5 years
Costs(Lebanese
Pound) 4000000
Warehouse costs 100000
Transport costs 200000
Total costs 4300000
Revenue to be
generated 16000000
Profit margin target 272%
Situation 2: Low liquidity
Procuerment date 1-Feb-19
Expiry date 1-Feb-22
Holding time 5years
Costs(Lebanese
Pound) 4000000
Warehouse costs 200000
Transport costs 250000
Loss due to theft 500000
Penalty due to slack
maintenece 2000000
Loss due to wasatge of
materials due to quality
issues 1000000
Loss due to spillage 200000
Total costs 8150000
Paraphrase This Document
Need a fresh take? Get an instant paraphrase of this document with our AI Paraphraser
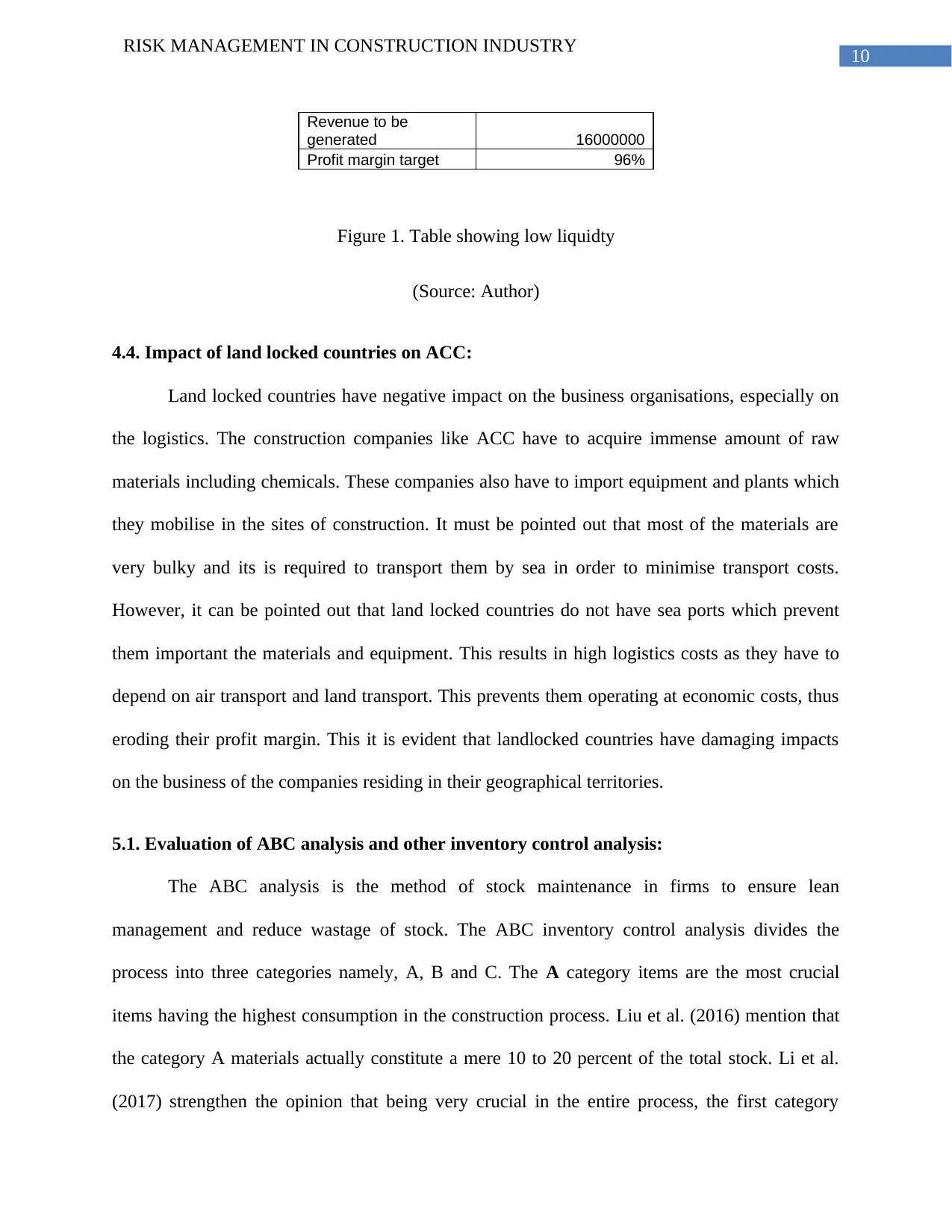
10
RISK MANAGEMENT IN CONSTRUCTION INDUSTRY
Revenue to be
generated 16000000
Profit margin target 96%
Figure 1. Table showing low liquidty
(Source: Author)
4.4. Impact of land locked countries on ACC:
Land locked countries have negative impact on the business organisations, especially on
the logistics. The construction companies like ACC have to acquire immense amount of raw
materials including chemicals. These companies also have to import equipment and plants which
they mobilise in the sites of construction. It must be pointed out that most of the materials are
very bulky and its is required to transport them by sea in order to minimise transport costs.
However, it can be pointed out that land locked countries do not have sea ports which prevent
them important the materials and equipment. This results in high logistics costs as they have to
depend on air transport and land transport. This prevents them operating at economic costs, thus
eroding their profit margin. This it is evident that landlocked countries have damaging impacts
on the business of the companies residing in their geographical territories.
5.1. Evaluation of ABC analysis and other inventory control analysis:
The ABC analysis is the method of stock maintenance in firms to ensure lean
management and reduce wastage of stock. The ABC inventory control analysis divides the
process into three categories namely, A, B and C. The A category items are the most crucial
items having the highest consumption in the construction process. Liu et al. (2016) mention that
the category A materials actually constitute a mere 10 to 20 percent of the total stock. Li et al.
(2017) strengthen the opinion that being very crucial in the entire process, the first category
RISK MANAGEMENT IN CONSTRUCTION INDUSTRY
Revenue to be
generated 16000000
Profit margin target 96%
Figure 1. Table showing low liquidty
(Source: Author)
4.4. Impact of land locked countries on ACC:
Land locked countries have negative impact on the business organisations, especially on
the logistics. The construction companies like ACC have to acquire immense amount of raw
materials including chemicals. These companies also have to import equipment and plants which
they mobilise in the sites of construction. It must be pointed out that most of the materials are
very bulky and its is required to transport them by sea in order to minimise transport costs.
However, it can be pointed out that land locked countries do not have sea ports which prevent
them important the materials and equipment. This results in high logistics costs as they have to
depend on air transport and land transport. This prevents them operating at economic costs, thus
eroding their profit margin. This it is evident that landlocked countries have damaging impacts
on the business of the companies residing in their geographical territories.
5.1. Evaluation of ABC analysis and other inventory control analysis:
The ABC analysis is the method of stock maintenance in firms to ensure lean
management and reduce wastage of stock. The ABC inventory control analysis divides the
process into three categories namely, A, B and C. The A category items are the most crucial
items having the highest consumption in the construction process. Liu et al. (2016) mention that
the category A materials actually constitute a mere 10 to 20 percent of the total stock. Li et al.
(2017) strengthen the opinion that being very crucial in the entire process, the first category
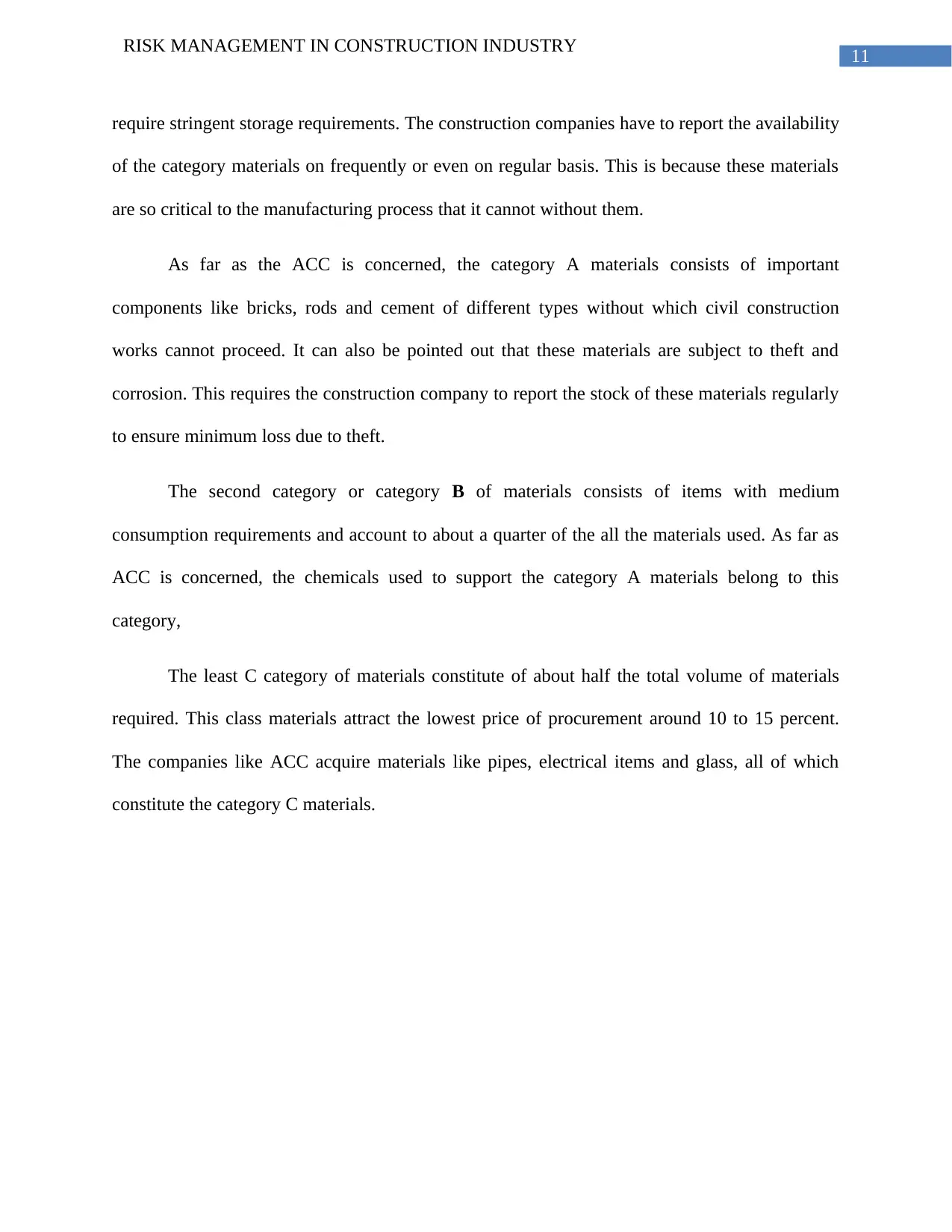
11
RISK MANAGEMENT IN CONSTRUCTION INDUSTRY
require stringent storage requirements. The construction companies have to report the availability
of the category materials on frequently or even on regular basis. This is because these materials
are so critical to the manufacturing process that it cannot without them.
As far as the ACC is concerned, the category A materials consists of important
components like bricks, rods and cement of different types without which civil construction
works cannot proceed. It can also be pointed out that these materials are subject to theft and
corrosion. This requires the construction company to report the stock of these materials regularly
to ensure minimum loss due to theft.
The second category or category B of materials consists of items with medium
consumption requirements and account to about a quarter of the all the materials used. As far as
ACC is concerned, the chemicals used to support the category A materials belong to this
category,
The least C category of materials constitute of about half the total volume of materials
required. This class materials attract the lowest price of procurement around 10 to 15 percent.
The companies like ACC acquire materials like pipes, electrical items and glass, all of which
constitute the category C materials.
RISK MANAGEMENT IN CONSTRUCTION INDUSTRY
require stringent storage requirements. The construction companies have to report the availability
of the category materials on frequently or even on regular basis. This is because these materials
are so critical to the manufacturing process that it cannot without them.
As far as the ACC is concerned, the category A materials consists of important
components like bricks, rods and cement of different types without which civil construction
works cannot proceed. It can also be pointed out that these materials are subject to theft and
corrosion. This requires the construction company to report the stock of these materials regularly
to ensure minimum loss due to theft.
The second category or category B of materials consists of items with medium
consumption requirements and account to about a quarter of the all the materials used. As far as
ACC is concerned, the chemicals used to support the category A materials belong to this
category,
The least C category of materials constitute of about half the total volume of materials
required. This class materials attract the lowest price of procurement around 10 to 15 percent.
The companies like ACC acquire materials like pipes, electrical items and glass, all of which
constitute the category C materials.
You're viewing a preview
Unlock full access by subscribing today!
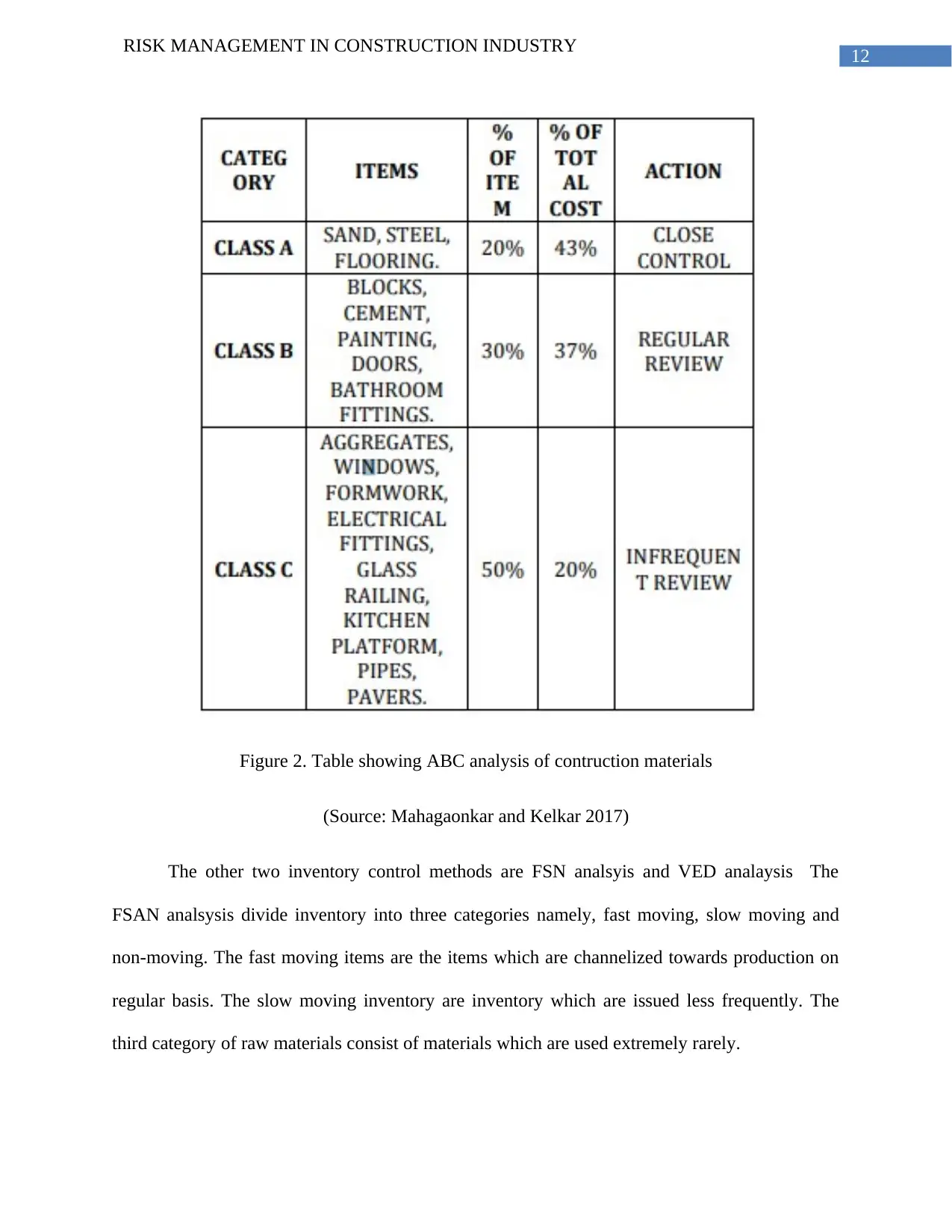
12
RISK MANAGEMENT IN CONSTRUCTION INDUSTRY
Figure 2. Table showing ABC analysis of contruction materials
(Source: Mahagaonkar and Kelkar 2017)
The other two inventory control methods are FSN analsyis and VED analaysis The
FSAN analsysis divide inventory into three categories namely, fast moving, slow moving and
non-moving. The fast moving items are the items which are channelized towards production on
regular basis. The slow moving inventory are inventory which are issued less frequently. The
third category of raw materials consist of materials which are used extremely rarely.
RISK MANAGEMENT IN CONSTRUCTION INDUSTRY
Figure 2. Table showing ABC analysis of contruction materials
(Source: Mahagaonkar and Kelkar 2017)
The other two inventory control methods are FSN analsyis and VED analaysis The
FSAN analsysis divide inventory into three categories namely, fast moving, slow moving and
non-moving. The fast moving items are the items which are channelized towards production on
regular basis. The slow moving inventory are inventory which are issued less frequently. The
third category of raw materials consist of materials which are used extremely rarely.
Paraphrase This Document
Need a fresh take? Get an instant paraphrase of this document with our AI Paraphraser
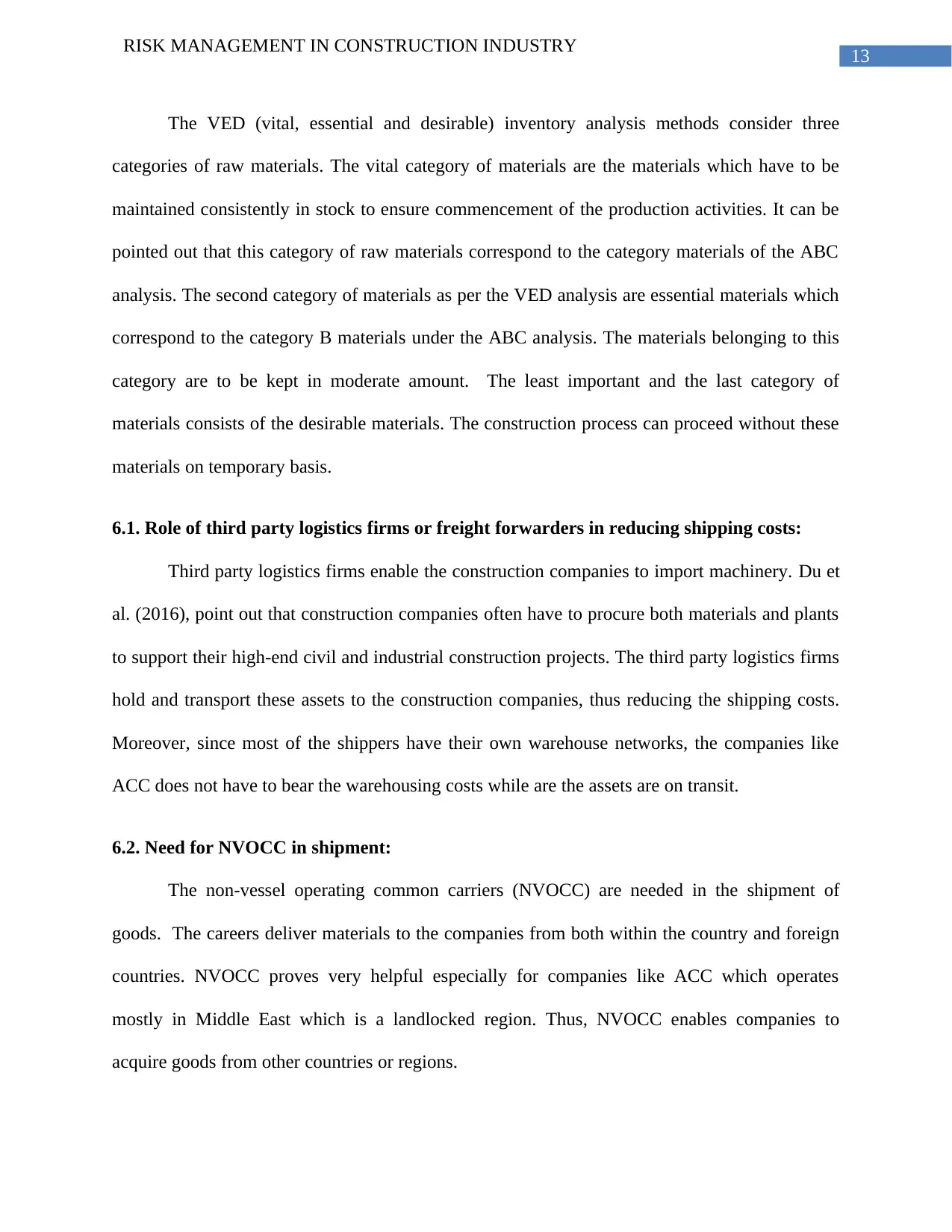
13
RISK MANAGEMENT IN CONSTRUCTION INDUSTRY
The VED (vital, essential and desirable) inventory analysis methods consider three
categories of raw materials. The vital category of materials are the materials which have to be
maintained consistently in stock to ensure commencement of the production activities. It can be
pointed out that this category of raw materials correspond to the category materials of the ABC
analysis. The second category of materials as per the VED analysis are essential materials which
correspond to the category B materials under the ABC analysis. The materials belonging to this
category are to be kept in moderate amount. The least important and the last category of
materials consists of the desirable materials. The construction process can proceed without these
materials on temporary basis.
6.1. Role of third party logistics firms or freight forwarders in reducing shipping costs:
Third party logistics firms enable the construction companies to import machinery. Du et
al. (2016), point out that construction companies often have to procure both materials and plants
to support their high-end civil and industrial construction projects. The third party logistics firms
hold and transport these assets to the construction companies, thus reducing the shipping costs.
Moreover, since most of the shippers have their own warehouse networks, the companies like
ACC does not have to bear the warehousing costs while are the assets are on transit.
6.2. Need for NVOCC in shipment:
The non-vessel operating common carriers (NVOCC) are needed in the shipment of
goods. The careers deliver materials to the companies from both within the country and foreign
countries. NVOCC proves very helpful especially for companies like ACC which operates
mostly in Middle East which is a landlocked region. Thus, NVOCC enables companies to
acquire goods from other countries or regions.
RISK MANAGEMENT IN CONSTRUCTION INDUSTRY
The VED (vital, essential and desirable) inventory analysis methods consider three
categories of raw materials. The vital category of materials are the materials which have to be
maintained consistently in stock to ensure commencement of the production activities. It can be
pointed out that this category of raw materials correspond to the category materials of the ABC
analysis. The second category of materials as per the VED analysis are essential materials which
correspond to the category B materials under the ABC analysis. The materials belonging to this
category are to be kept in moderate amount. The least important and the last category of
materials consists of the desirable materials. The construction process can proceed without these
materials on temporary basis.
6.1. Role of third party logistics firms or freight forwarders in reducing shipping costs:
Third party logistics firms enable the construction companies to import machinery. Du et
al. (2016), point out that construction companies often have to procure both materials and plants
to support their high-end civil and industrial construction projects. The third party logistics firms
hold and transport these assets to the construction companies, thus reducing the shipping costs.
Moreover, since most of the shippers have their own warehouse networks, the companies like
ACC does not have to bear the warehousing costs while are the assets are on transit.
6.2. Need for NVOCC in shipment:
The non-vessel operating common carriers (NVOCC) are needed in the shipment of
goods. The careers deliver materials to the companies from both within the country and foreign
countries. NVOCC proves very helpful especially for companies like ACC which operates
mostly in Middle East which is a landlocked region. Thus, NVOCC enables companies to
acquire goods from other countries or regions.

14
RISK MANAGEMENT IN CONSTRUCTION INDUSTRY
6.3. Impact on Demurrage and Detention in ACC:
Demurrage and detention in Arabian Construction Company have great impact on
the company and its operations. First, demurrage results in detention of assets at the ports which
increases the cost the company incurs to acquire them from foreign nations. Secondly, the
detention of machinery and construction materials delays the flow of the construction projects.
This increases the cost of construction and the clients impose penalty for delay. This further
escalates the costs of constructions and erodes the profit margin of ACC.
7.1. Improvement of quality:
Quality can be used to improve relationship between companies and their suppliers. The
companies involved in construction have to acquire materials from a large number of suppliers
(Wong, San Chan and Wadu, 2016). Derakhshanalavijeh and Teixeira (2017) strengthen the
opinion by mentioning that the suppliers have to deliver the materials within a predetermined
time period. Moreover, since construction works attract immense precision, the companies have
to ensure that the supplies meet their quality parameters. The company can enter into
procurement contracts with suppliers in order to ensure strong and transparent relationship
between the two parties. ACC can also train the suppliers to enhance their quality of supply.
7.2. Importance of supplier relationship management and recommended best relationship
for strategic and non-critical vendor:
Efficient supplier management relationship results in building of strong relationship with
suppliers. Dave et al.(2016) while pointing out the first importance of supplier relationship
management mention that it promotes lean management. Efficient supplier relationship ensure
ready availability of materials. Secondly, this availability of materials relieves ACC from
maintaining huge stock of raw materials. Thus, on the whole it results in more economic
RISK MANAGEMENT IN CONSTRUCTION INDUSTRY
6.3. Impact on Demurrage and Detention in ACC:
Demurrage and detention in Arabian Construction Company have great impact on
the company and its operations. First, demurrage results in detention of assets at the ports which
increases the cost the company incurs to acquire them from foreign nations. Secondly, the
detention of machinery and construction materials delays the flow of the construction projects.
This increases the cost of construction and the clients impose penalty for delay. This further
escalates the costs of constructions and erodes the profit margin of ACC.
7.1. Improvement of quality:
Quality can be used to improve relationship between companies and their suppliers. The
companies involved in construction have to acquire materials from a large number of suppliers
(Wong, San Chan and Wadu, 2016). Derakhshanalavijeh and Teixeira (2017) strengthen the
opinion by mentioning that the suppliers have to deliver the materials within a predetermined
time period. Moreover, since construction works attract immense precision, the companies have
to ensure that the supplies meet their quality parameters. The company can enter into
procurement contracts with suppliers in order to ensure strong and transparent relationship
between the two parties. ACC can also train the suppliers to enhance their quality of supply.
7.2. Importance of supplier relationship management and recommended best relationship
for strategic and non-critical vendor:
Efficient supplier management relationship results in building of strong relationship with
suppliers. Dave et al.(2016) while pointing out the first importance of supplier relationship
management mention that it promotes lean management. Efficient supplier relationship ensure
ready availability of materials. Secondly, this availability of materials relieves ACC from
maintaining huge stock of raw materials. Thus, on the whole it results in more economic
You're viewing a preview
Unlock full access by subscribing today!
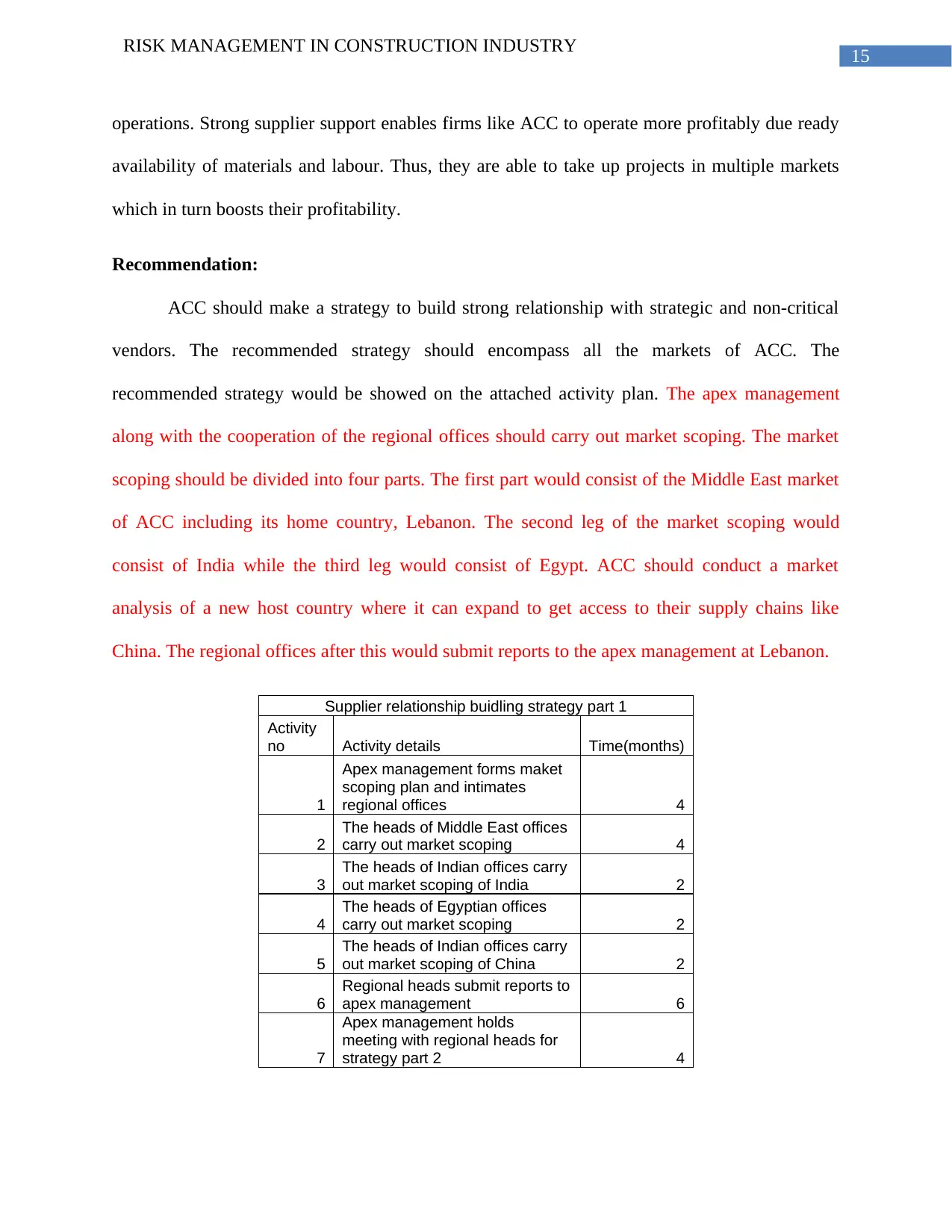
15
RISK MANAGEMENT IN CONSTRUCTION INDUSTRY
operations. Strong supplier support enables firms like ACC to operate more profitably due ready
availability of materials and labour. Thus, they are able to take up projects in multiple markets
which in turn boosts their profitability.
Recommendation:
ACC should make a strategy to build strong relationship with strategic and non-critical
vendors. The recommended strategy should encompass all the markets of ACC. The
recommended strategy would be showed on the attached activity plan. The apex management
along with the cooperation of the regional offices should carry out market scoping. The market
scoping should be divided into four parts. The first part would consist of the Middle East market
of ACC including its home country, Lebanon. The second leg of the market scoping would
consist of India while the third leg would consist of Egypt. ACC should conduct a market
analysis of a new host country where it can expand to get access to their supply chains like
China. The regional offices after this would submit reports to the apex management at Lebanon.
Supplier relationship buidling strategy part 1
Activity
no Activity details Time(months)
1
Apex management forms maket
scoping plan and intimates
regional offices 4
2
The heads of Middle East offices
carry out market scoping 4
3
The heads of Indian offices carry
out market scoping of India 2
4
The heads of Egyptian offices
carry out market scoping 2
5
The heads of Indian offices carry
out market scoping of China 2
6
Regional heads submit reports to
apex management 6
7
Apex management holds
meeting with regional heads for
strategy part 2 4
RISK MANAGEMENT IN CONSTRUCTION INDUSTRY
operations. Strong supplier support enables firms like ACC to operate more profitably due ready
availability of materials and labour. Thus, they are able to take up projects in multiple markets
which in turn boosts their profitability.
Recommendation:
ACC should make a strategy to build strong relationship with strategic and non-critical
vendors. The recommended strategy should encompass all the markets of ACC. The
recommended strategy would be showed on the attached activity plan. The apex management
along with the cooperation of the regional offices should carry out market scoping. The market
scoping should be divided into four parts. The first part would consist of the Middle East market
of ACC including its home country, Lebanon. The second leg of the market scoping would
consist of India while the third leg would consist of Egypt. ACC should conduct a market
analysis of a new host country where it can expand to get access to their supply chains like
China. The regional offices after this would submit reports to the apex management at Lebanon.
Supplier relationship buidling strategy part 1
Activity
no Activity details Time(months)
1
Apex management forms maket
scoping plan and intimates
regional offices 4
2
The heads of Middle East offices
carry out market scoping 4
3
The heads of Indian offices carry
out market scoping of India 2
4
The heads of Egyptian offices
carry out market scoping 2
5
The heads of Indian offices carry
out market scoping of China 2
6
Regional heads submit reports to
apex management 6
7
Apex management holds
meeting with regional heads for
strategy part 2 4
Paraphrase This Document
Need a fresh take? Get an instant paraphrase of this document with our AI Paraphraser
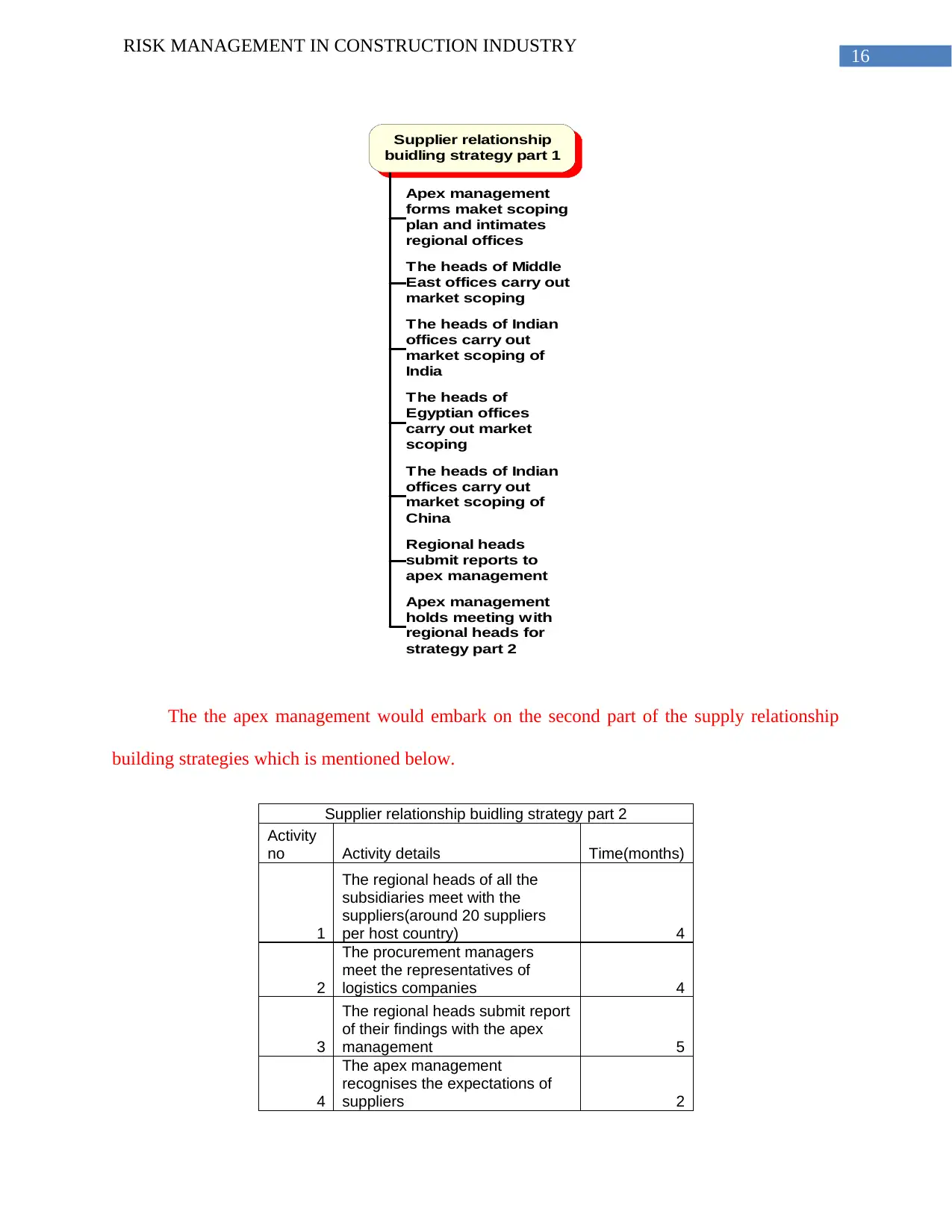
16
RISK MANAGEMENT IN CONSTRUCTION INDUSTRY
Supplier relationship
buidling strategy part 1
Apex management
forms maket scoping
plan and intimates
regional offices
The heads of Middle
East offices carry out
market scoping
The heads of Indian
offices carry out
market scoping of
India
The heads of
Egyptian offices
carry out market
scoping
The heads of Indian
offices carry out
market scoping of
China
Regional heads
submit reports to
apex management
Apex management
holds meeting with
regional heads for
strategy part 2
The the apex management would embark on the second part of the supply relationship
building strategies which is mentioned below.
Supplier relationship buidling strategy part 2
Activity
no Activity details Time(months)
1
The regional heads of all the
subsidiaries meet with the
suppliers(around 20 suppliers
per host country) 4
2
The procurement managers
meet the representatives of
logistics companies 4
3
The regional heads submit report
of their findings with the apex
management 5
4
The apex management
recognises the expectations of
suppliers 2
RISK MANAGEMENT IN CONSTRUCTION INDUSTRY
Supplier relationship
buidling strategy part 1
Apex management
forms maket scoping
plan and intimates
regional offices
The heads of Middle
East offices carry out
market scoping
The heads of Indian
offices carry out
market scoping of
India
The heads of
Egyptian offices
carry out market
scoping
The heads of Indian
offices carry out
market scoping of
China
Regional heads
submit reports to
apex management
Apex management
holds meeting with
regional heads for
strategy part 2
The the apex management would embark on the second part of the supply relationship
building strategies which is mentioned below.
Supplier relationship buidling strategy part 2
Activity
no Activity details Time(months)
1
The regional heads of all the
subsidiaries meet with the
suppliers(around 20 suppliers
per host country) 4
2
The procurement managers
meet the representatives of
logistics companies 4
3
The regional heads submit report
of their findings with the apex
management 5
4
The apex management
recognises the expectations of
suppliers 2
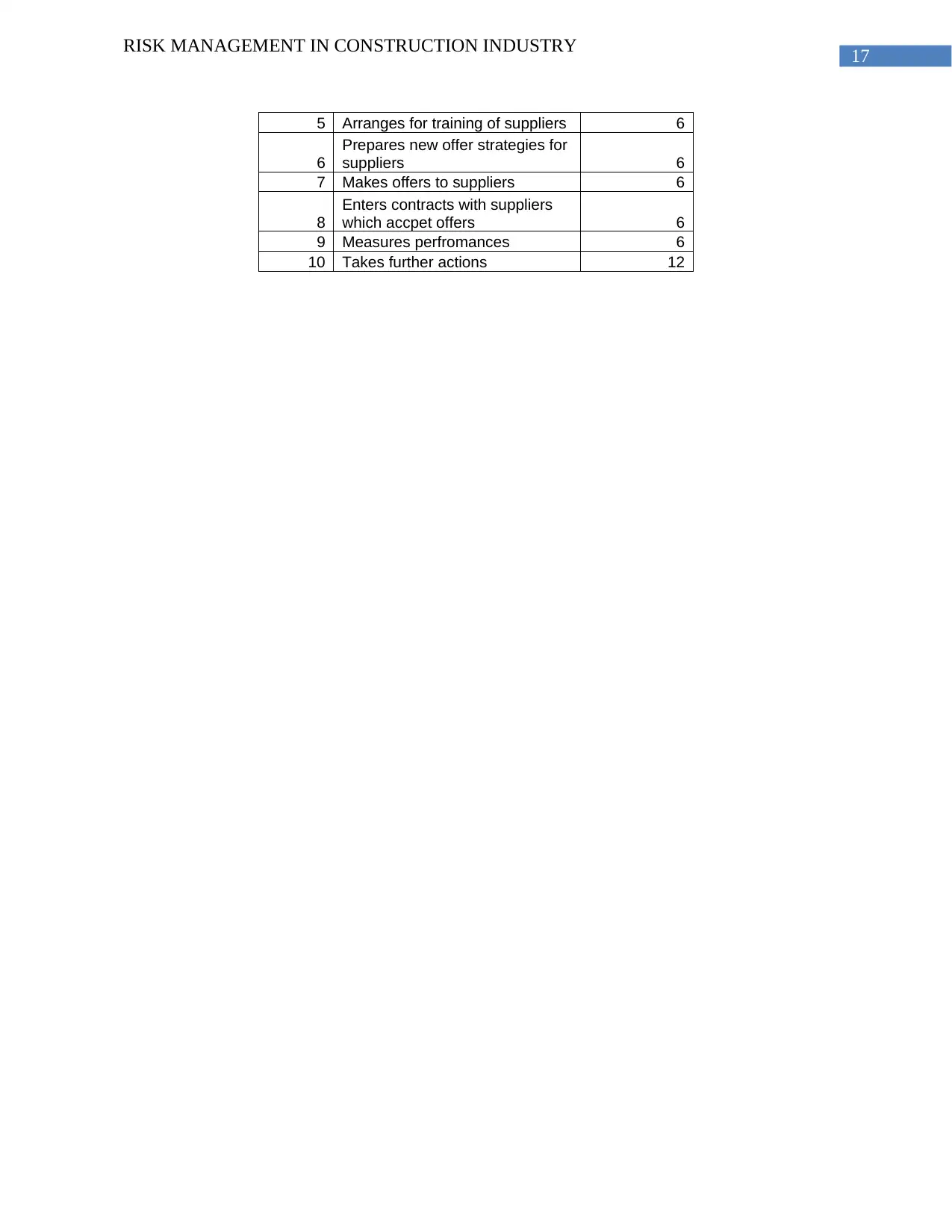
17
RISK MANAGEMENT IN CONSTRUCTION INDUSTRY
5 Arranges for training of suppliers 6
6
Prepares new offer strategies for
suppliers 6
7 Makes offers to suppliers 6
8
Enters contracts with suppliers
which accpet offers 6
9 Measures perfromances 6
10 Takes further actions 12
RISK MANAGEMENT IN CONSTRUCTION INDUSTRY
5 Arranges for training of suppliers 6
6
Prepares new offer strategies for
suppliers 6
7 Makes offers to suppliers 6
8
Enters contracts with suppliers
which accpet offers 6
9 Measures perfromances 6
10 Takes further actions 12
You're viewing a preview
Unlock full access by subscribing today!
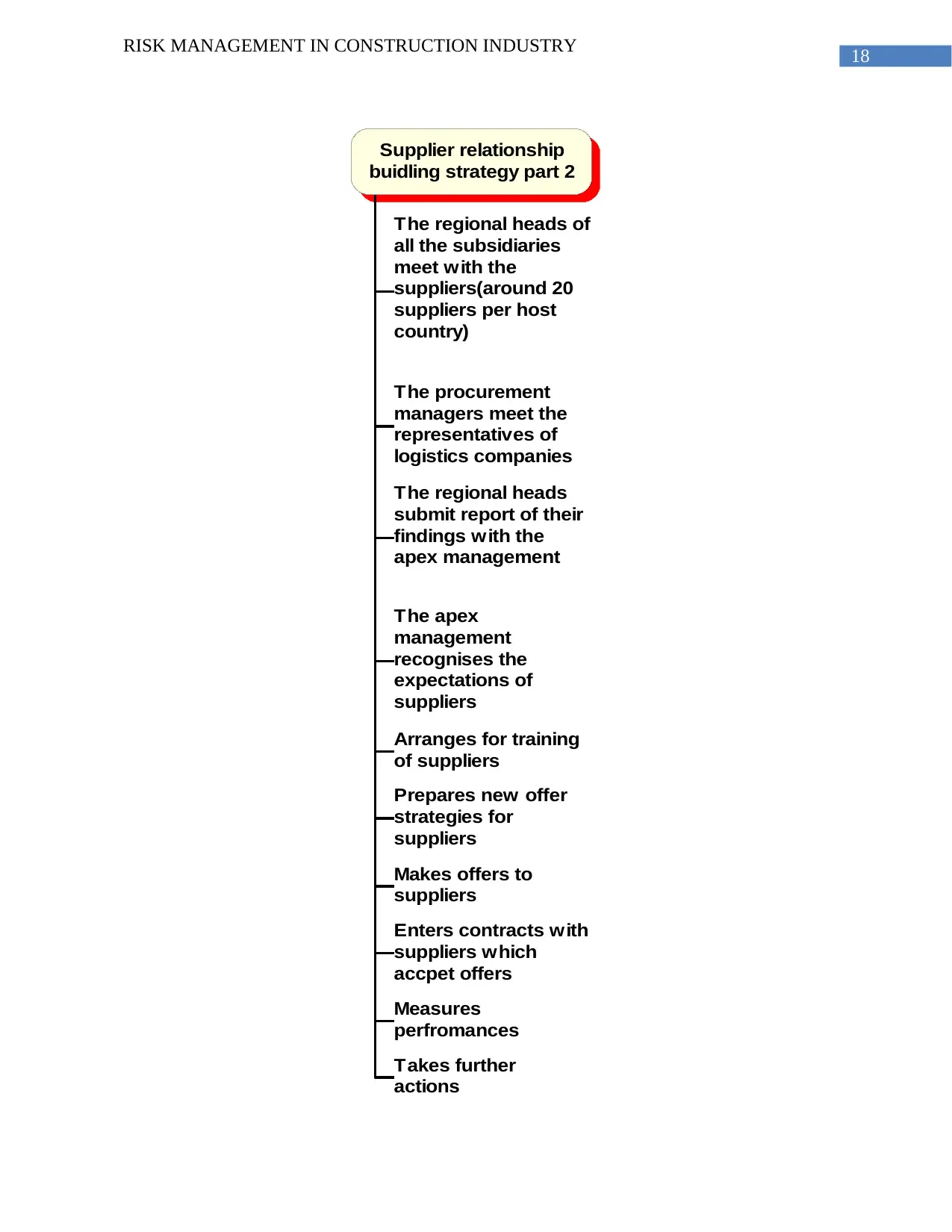
18
RISK MANAGEMENT IN CONSTRUCTION INDUSTRY
Supplier relationship
buidling strategy part 2
The regional heads of
all the subsidiaries
meet with the
suppliers(around 20
suppliers per host
country)
The procurement
managers meet the
representatives of
logistics companies
The regional heads
submit report of their
findings with the
apex management
The apex
management
recognises the
expectations of
suppliers
Arranges for training
of suppliers
Prepares new offer
strategies for
suppliers
Makes offers to
suppliers
Enters contracts with
suppliers which
accpet offers
Measures
perfromances
Takes further
actions
RISK MANAGEMENT IN CONSTRUCTION INDUSTRY
Supplier relationship
buidling strategy part 2
The regional heads of
all the subsidiaries
meet with the
suppliers(around 20
suppliers per host
country)
The procurement
managers meet the
representatives of
logistics companies
The regional heads
submit report of their
findings with the
apex management
The apex
management
recognises the
expectations of
suppliers
Arranges for training
of suppliers
Prepares new offer
strategies for
suppliers
Makes offers to
suppliers
Enters contracts with
suppliers which
accpet offers
Measures
perfromances
Takes further
actions
Paraphrase This Document
Need a fresh take? Get an instant paraphrase of this document with our AI Paraphraser
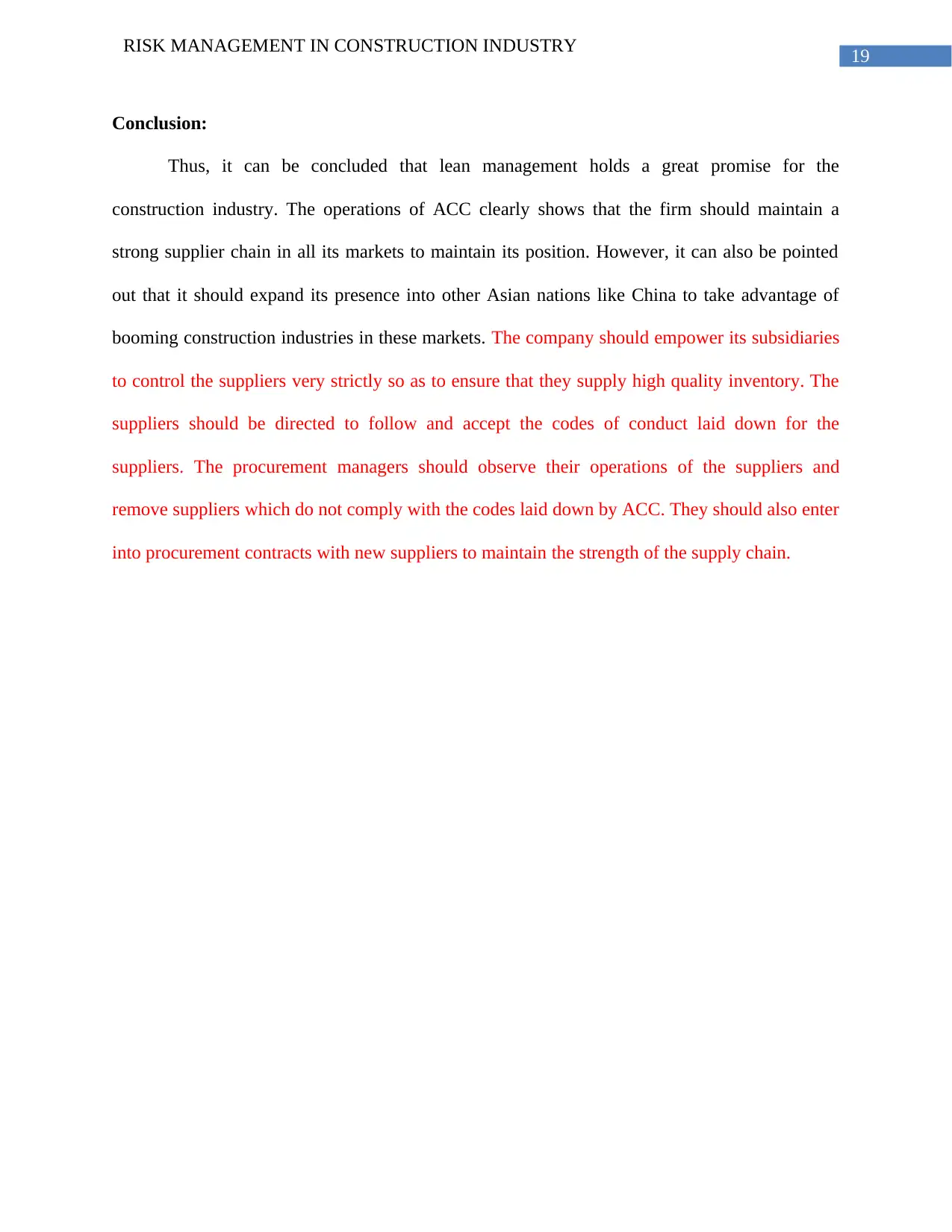
19
RISK MANAGEMENT IN CONSTRUCTION INDUSTRY
Conclusion:
Thus, it can be concluded that lean management holds a great promise for the
construction industry. The operations of ACC clearly shows that the firm should maintain a
strong supplier chain in all its markets to maintain its position. However, it can also be pointed
out that it should expand its presence into other Asian nations like China to take advantage of
booming construction industries in these markets. The company should empower its subsidiaries
to control the suppliers very strictly so as to ensure that they supply high quality inventory. The
suppliers should be directed to follow and accept the codes of conduct laid down for the
suppliers. The procurement managers should observe their operations of the suppliers and
remove suppliers which do not comply with the codes laid down by ACC. They should also enter
into procurement contracts with new suppliers to maintain the strength of the supply chain.
RISK MANAGEMENT IN CONSTRUCTION INDUSTRY
Conclusion:
Thus, it can be concluded that lean management holds a great promise for the
construction industry. The operations of ACC clearly shows that the firm should maintain a
strong supplier chain in all its markets to maintain its position. However, it can also be pointed
out that it should expand its presence into other Asian nations like China to take advantage of
booming construction industries in these markets. The company should empower its subsidiaries
to control the suppliers very strictly so as to ensure that they supply high quality inventory. The
suppliers should be directed to follow and accept the codes of conduct laid down for the
suppliers. The procurement managers should observe their operations of the suppliers and
remove suppliers which do not comply with the codes laid down by ACC. They should also enter
into procurement contracts with new suppliers to maintain the strength of the supply chain.
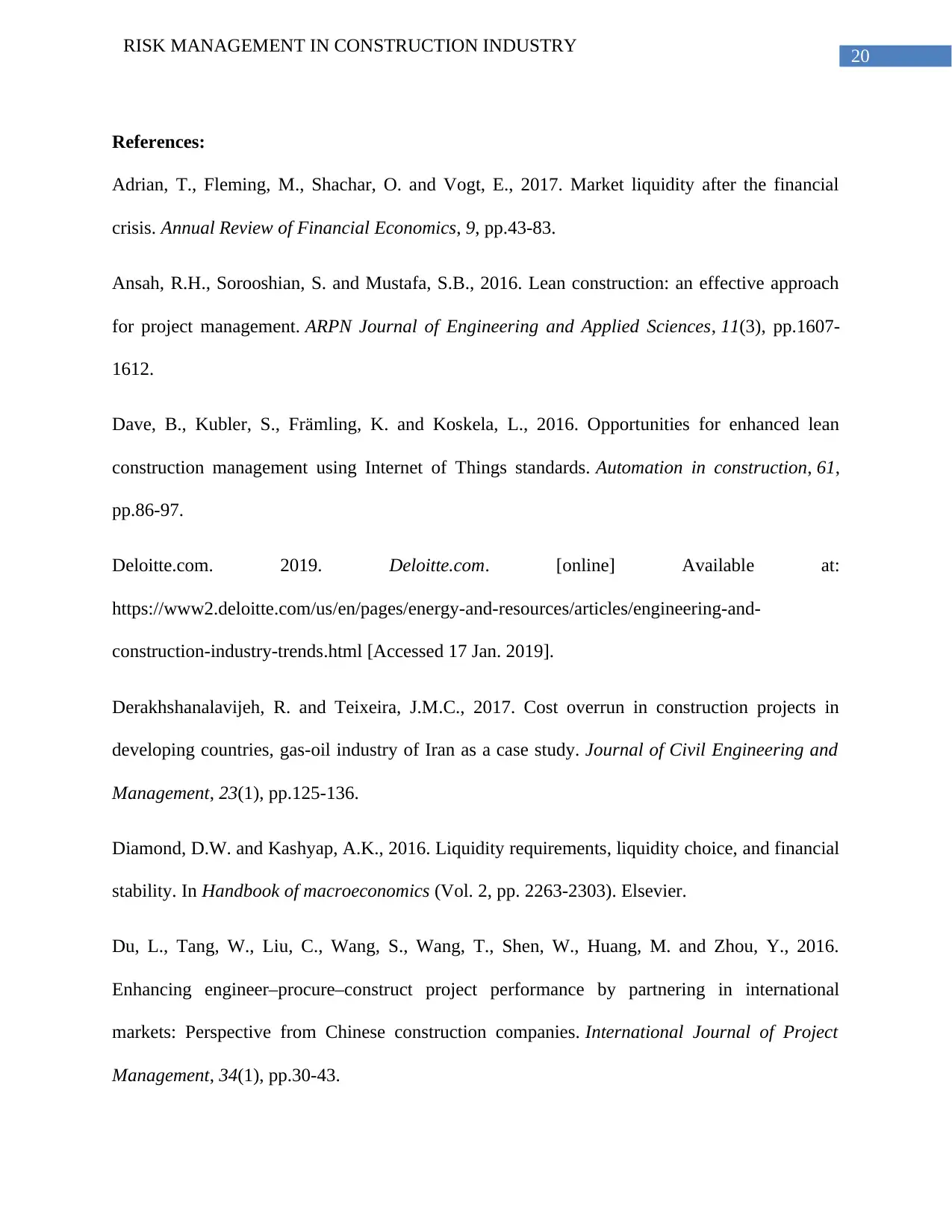
20
RISK MANAGEMENT IN CONSTRUCTION INDUSTRY
References:
Adrian, T., Fleming, M., Shachar, O. and Vogt, E., 2017. Market liquidity after the financial
crisis. Annual Review of Financial Economics, 9, pp.43-83.
Ansah, R.H., Sorooshian, S. and Mustafa, S.B., 2016. Lean construction: an effective approach
for project management. ARPN Journal of Engineering and Applied Sciences, 11(3), pp.1607-
1612.
Dave, B., Kubler, S., Främling, K. and Koskela, L., 2016. Opportunities for enhanced lean
construction management using Internet of Things standards. Automation in construction, 61,
pp.86-97.
Deloitte.com. 2019. Deloitte.com. [online] Available at:
https://www2.deloitte.com/us/en/pages/energy-and-resources/articles/engineering-and-
construction-industry-trends.html [Accessed 17 Jan. 2019].
Derakhshanalavijeh, R. and Teixeira, J.M.C., 2017. Cost overrun in construction projects in
developing countries, gas-oil industry of Iran as a case study. Journal of Civil Engineering and
Management, 23(1), pp.125-136.
Diamond, D.W. and Kashyap, A.K., 2016. Liquidity requirements, liquidity choice, and financial
stability. In Handbook of macroeconomics (Vol. 2, pp. 2263-2303). Elsevier.
Du, L., Tang, W., Liu, C., Wang, S., Wang, T., Shen, W., Huang, M. and Zhou, Y., 2016.
Enhancing engineer–procure–construct project performance by partnering in international
markets: Perspective from Chinese construction companies. International Journal of Project
Management, 34(1), pp.30-43.
RISK MANAGEMENT IN CONSTRUCTION INDUSTRY
References:
Adrian, T., Fleming, M., Shachar, O. and Vogt, E., 2017. Market liquidity after the financial
crisis. Annual Review of Financial Economics, 9, pp.43-83.
Ansah, R.H., Sorooshian, S. and Mustafa, S.B., 2016. Lean construction: an effective approach
for project management. ARPN Journal of Engineering and Applied Sciences, 11(3), pp.1607-
1612.
Dave, B., Kubler, S., Främling, K. and Koskela, L., 2016. Opportunities for enhanced lean
construction management using Internet of Things standards. Automation in construction, 61,
pp.86-97.
Deloitte.com. 2019. Deloitte.com. [online] Available at:
https://www2.deloitte.com/us/en/pages/energy-and-resources/articles/engineering-and-
construction-industry-trends.html [Accessed 17 Jan. 2019].
Derakhshanalavijeh, R. and Teixeira, J.M.C., 2017. Cost overrun in construction projects in
developing countries, gas-oil industry of Iran as a case study. Journal of Civil Engineering and
Management, 23(1), pp.125-136.
Diamond, D.W. and Kashyap, A.K., 2016. Liquidity requirements, liquidity choice, and financial
stability. In Handbook of macroeconomics (Vol. 2, pp. 2263-2303). Elsevier.
Du, L., Tang, W., Liu, C., Wang, S., Wang, T., Shen, W., Huang, M. and Zhou, Y., 2016.
Enhancing engineer–procure–construct project performance by partnering in international
markets: Perspective from Chinese construction companies. International Journal of Project
Management, 34(1), pp.30-43.
You're viewing a preview
Unlock full access by subscribing today!
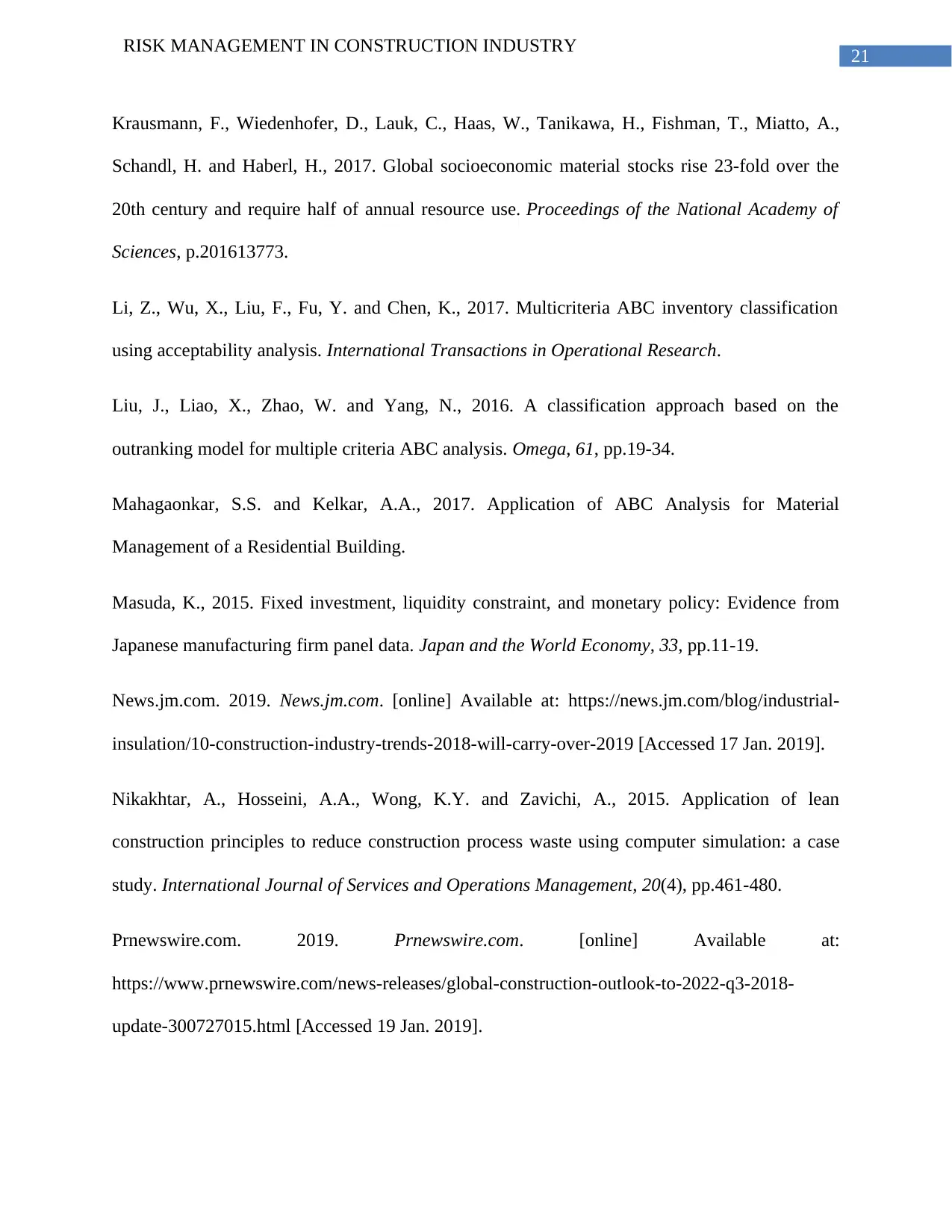
21
RISK MANAGEMENT IN CONSTRUCTION INDUSTRY
Krausmann, F., Wiedenhofer, D., Lauk, C., Haas, W., Tanikawa, H., Fishman, T., Miatto, A.,
Schandl, H. and Haberl, H., 2017. Global socioeconomic material stocks rise 23-fold over the
20th century and require half of annual resource use. Proceedings of the National Academy of
Sciences, p.201613773.
Li, Z., Wu, X., Liu, F., Fu, Y. and Chen, K., 2017. Multicriteria ABC inventory classification
using acceptability analysis. International Transactions in Operational Research.
Liu, J., Liao, X., Zhao, W. and Yang, N., 2016. A classification approach based on the
outranking model for multiple criteria ABC analysis. Omega, 61, pp.19-34.
Mahagaonkar, S.S. and Kelkar, A.A., 2017. Application of ABC Analysis for Material
Management of a Residential Building.
Masuda, K., 2015. Fixed investment, liquidity constraint, and monetary policy: Evidence from
Japanese manufacturing firm panel data. Japan and the World Economy, 33, pp.11-19.
News.jm.com. 2019. News.jm.com. [online] Available at: https://news.jm.com/blog/industrial-
insulation/10-construction-industry-trends-2018-will-carry-over-2019 [Accessed 17 Jan. 2019].
Nikakhtar, A., Hosseini, A.A., Wong, K.Y. and Zavichi, A., 2015. Application of lean
construction principles to reduce construction process waste using computer simulation: a case
study. International Journal of Services and Operations Management, 20(4), pp.461-480.
Prnewswire.com. 2019. Prnewswire.com. [online] Available at:
https://www.prnewswire.com/news-releases/global-construction-outlook-to-2022-q3-2018-
update-300727015.html [Accessed 19 Jan. 2019].
RISK MANAGEMENT IN CONSTRUCTION INDUSTRY
Krausmann, F., Wiedenhofer, D., Lauk, C., Haas, W., Tanikawa, H., Fishman, T., Miatto, A.,
Schandl, H. and Haberl, H., 2017. Global socioeconomic material stocks rise 23-fold over the
20th century and require half of annual resource use. Proceedings of the National Academy of
Sciences, p.201613773.
Li, Z., Wu, X., Liu, F., Fu, Y. and Chen, K., 2017. Multicriteria ABC inventory classification
using acceptability analysis. International Transactions in Operational Research.
Liu, J., Liao, X., Zhao, W. and Yang, N., 2016. A classification approach based on the
outranking model for multiple criteria ABC analysis. Omega, 61, pp.19-34.
Mahagaonkar, S.S. and Kelkar, A.A., 2017. Application of ABC Analysis for Material
Management of a Residential Building.
Masuda, K., 2015. Fixed investment, liquidity constraint, and monetary policy: Evidence from
Japanese manufacturing firm panel data. Japan and the World Economy, 33, pp.11-19.
News.jm.com. 2019. News.jm.com. [online] Available at: https://news.jm.com/blog/industrial-
insulation/10-construction-industry-trends-2018-will-carry-over-2019 [Accessed 17 Jan. 2019].
Nikakhtar, A., Hosseini, A.A., Wong, K.Y. and Zavichi, A., 2015. Application of lean
construction principles to reduce construction process waste using computer simulation: a case
study. International Journal of Services and Operations Management, 20(4), pp.461-480.
Prnewswire.com. 2019. Prnewswire.com. [online] Available at:
https://www.prnewswire.com/news-releases/global-construction-outlook-to-2022-q3-2018-
update-300727015.html [Accessed 19 Jan. 2019].
Paraphrase This Document
Need a fresh take? Get an instant paraphrase of this document with our AI Paraphraser
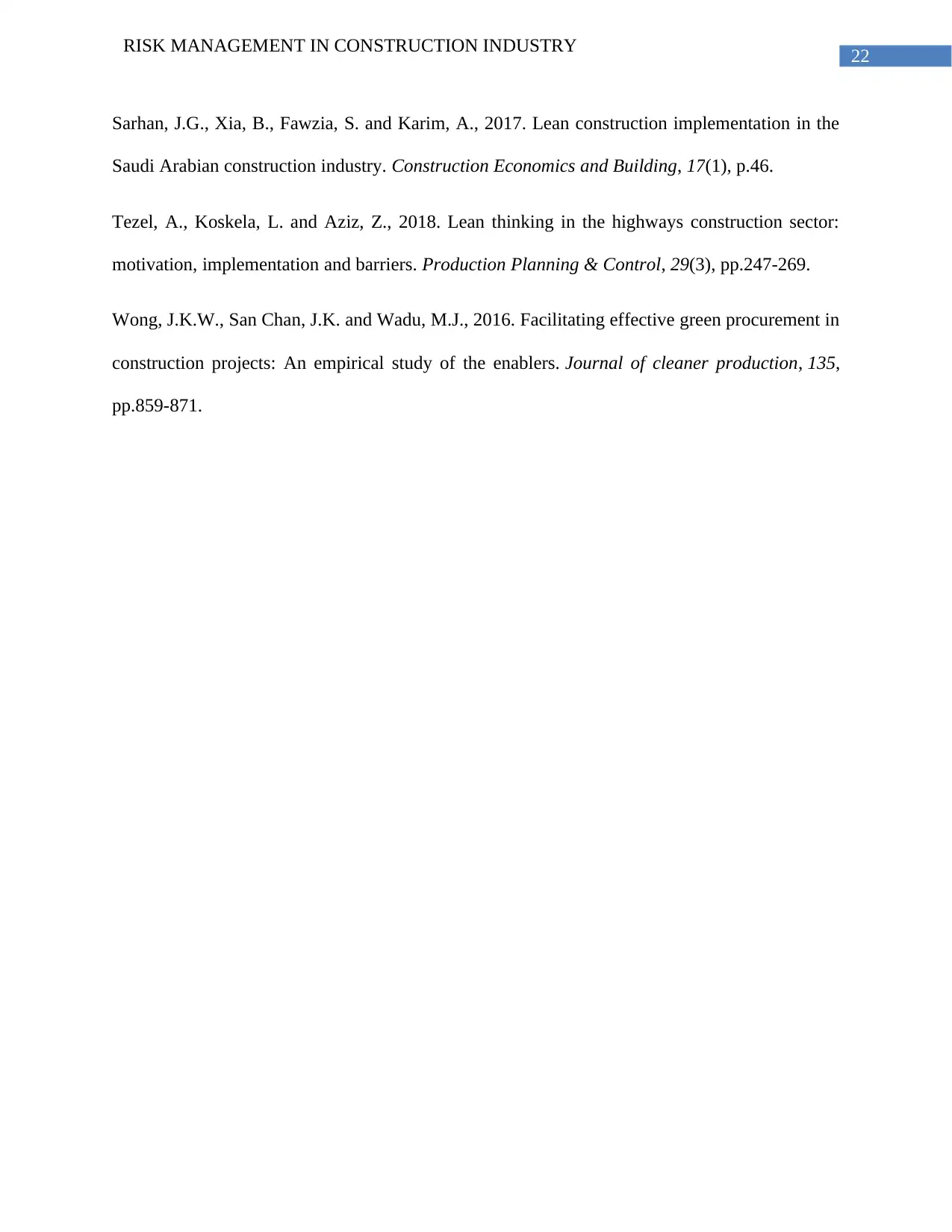
22
RISK MANAGEMENT IN CONSTRUCTION INDUSTRY
Sarhan, J.G., Xia, B., Fawzia, S. and Karim, A., 2017. Lean construction implementation in the
Saudi Arabian construction industry. Construction Economics and Building, 17(1), p.46.
Tezel, A., Koskela, L. and Aziz, Z., 2018. Lean thinking in the highways construction sector:
motivation, implementation and barriers. Production Planning & Control, 29(3), pp.247-269.
Wong, J.K.W., San Chan, J.K. and Wadu, M.J., 2016. Facilitating effective green procurement in
construction projects: An empirical study of the enablers. Journal of cleaner production, 135,
pp.859-871.
RISK MANAGEMENT IN CONSTRUCTION INDUSTRY
Sarhan, J.G., Xia, B., Fawzia, S. and Karim, A., 2017. Lean construction implementation in the
Saudi Arabian construction industry. Construction Economics and Building, 17(1), p.46.
Tezel, A., Koskela, L. and Aziz, Z., 2018. Lean thinking in the highways construction sector:
motivation, implementation and barriers. Production Planning & Control, 29(3), pp.247-269.
Wong, J.K.W., San Chan, J.K. and Wadu, M.J., 2016. Facilitating effective green procurement in
construction projects: An empirical study of the enablers. Journal of cleaner production, 135,
pp.859-871.
1 out of 23
Related Documents

Your All-in-One AI-Powered Toolkit for Academic Success.
+13062052269
info@desklib.com
Available 24*7 on WhatsApp / Email
Unlock your academic potential
© 2024 | Zucol Services PVT LTD | All rights reserved.