SCM Globe Simulation Project: Cincinnati Seasonings Analysis Report
VerifiedAdded on 2019/09/30
|15
|3532
|304
Project
AI Summary
This project analyzes a student's experience with an SCM Globe simulation for Cincinnati Seasonings, a company producing seasoning mixes. The simulation involved optimizing the supply chain, including a factory, distribution center, and several stores. The student experimented with truck capacities, ...
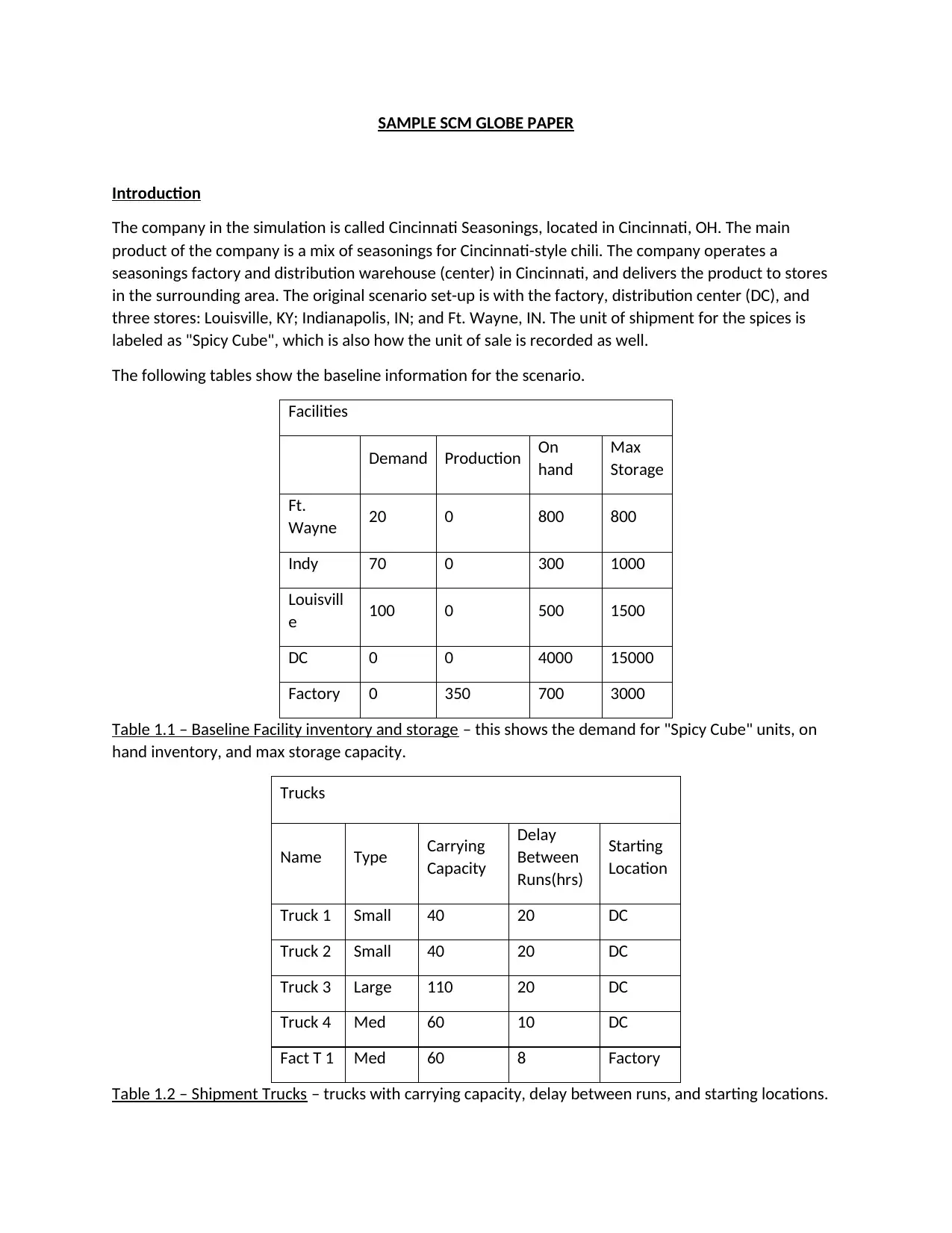
SAMPLE SCM GLOBE PAPER
Introduction
The company in the simulation is called Cincinnati Seasonings, located in Cincinnati, OH. The main
product of the company is a mix of seasonings for Cincinnati-style chili. The company operates a
seasonings factory and distribution warehouse (center) in Cincinnati, and delivers the product to stores
in the surrounding area. The original scenario set-up is with the factory, distribution center (DC), and
three stores: Louisville, KY; Indianapolis, IN; and Ft. Wayne, IN. The unit of shipment for the spices is
labeled as "Spicy Cube", which is also how the unit of sale is recorded as well.
The following tables show the baseline information for the scenario.
Facilities
Demand Production On
hand
Max
Storage
Ft.
Wayne 20 0 800 800
Indy 70 0 300 1000
Louisvill
e 100 0 500 1500
DC 0 0 4000 15000
Factory 0 350 700 3000
Table 1.1 – Baseline Facility inventory and storage – this shows the demand for "Spicy Cube" units, on
hand inventory, and max storage capacity.
Trucks
Name Type Carrying
Capacity
Delay
Between
Runs(hrs)
Starting
Location
Truck 1 Small 40 20 DC
Truck 2 Small 40 20 DC
Truck 3 Large 110 20 DC
Truck 4 Med 60 10 DC
Fact T 1 Med 60 8 Factory
Table 1.2 – Shipment Trucks – trucks with carrying capacity, delay between runs, and starting locations.
Introduction
The company in the simulation is called Cincinnati Seasonings, located in Cincinnati, OH. The main
product of the company is a mix of seasonings for Cincinnati-style chili. The company operates a
seasonings factory and distribution warehouse (center) in Cincinnati, and delivers the product to stores
in the surrounding area. The original scenario set-up is with the factory, distribution center (DC), and
three stores: Louisville, KY; Indianapolis, IN; and Ft. Wayne, IN. The unit of shipment for the spices is
labeled as "Spicy Cube", which is also how the unit of sale is recorded as well.
The following tables show the baseline information for the scenario.
Facilities
Demand Production On
hand
Max
Storage
Ft.
Wayne 20 0 800 800
Indy 70 0 300 1000
Louisvill
e 100 0 500 1500
DC 0 0 4000 15000
Factory 0 350 700 3000
Table 1.1 – Baseline Facility inventory and storage – this shows the demand for "Spicy Cube" units, on
hand inventory, and max storage capacity.
Trucks
Name Type Carrying
Capacity
Delay
Between
Runs(hrs)
Starting
Location
Truck 1 Small 40 20 DC
Truck 2 Small 40 20 DC
Truck 3 Large 110 20 DC
Truck 4 Med 60 10 DC
Fact T 1 Med 60 8 Factory
Table 1.2 – Shipment Trucks – trucks with carrying capacity, delay between runs, and starting locations.
Paraphrase This Document
Need a fresh take? Get an instant paraphrase of this document with our AI Paraphraser
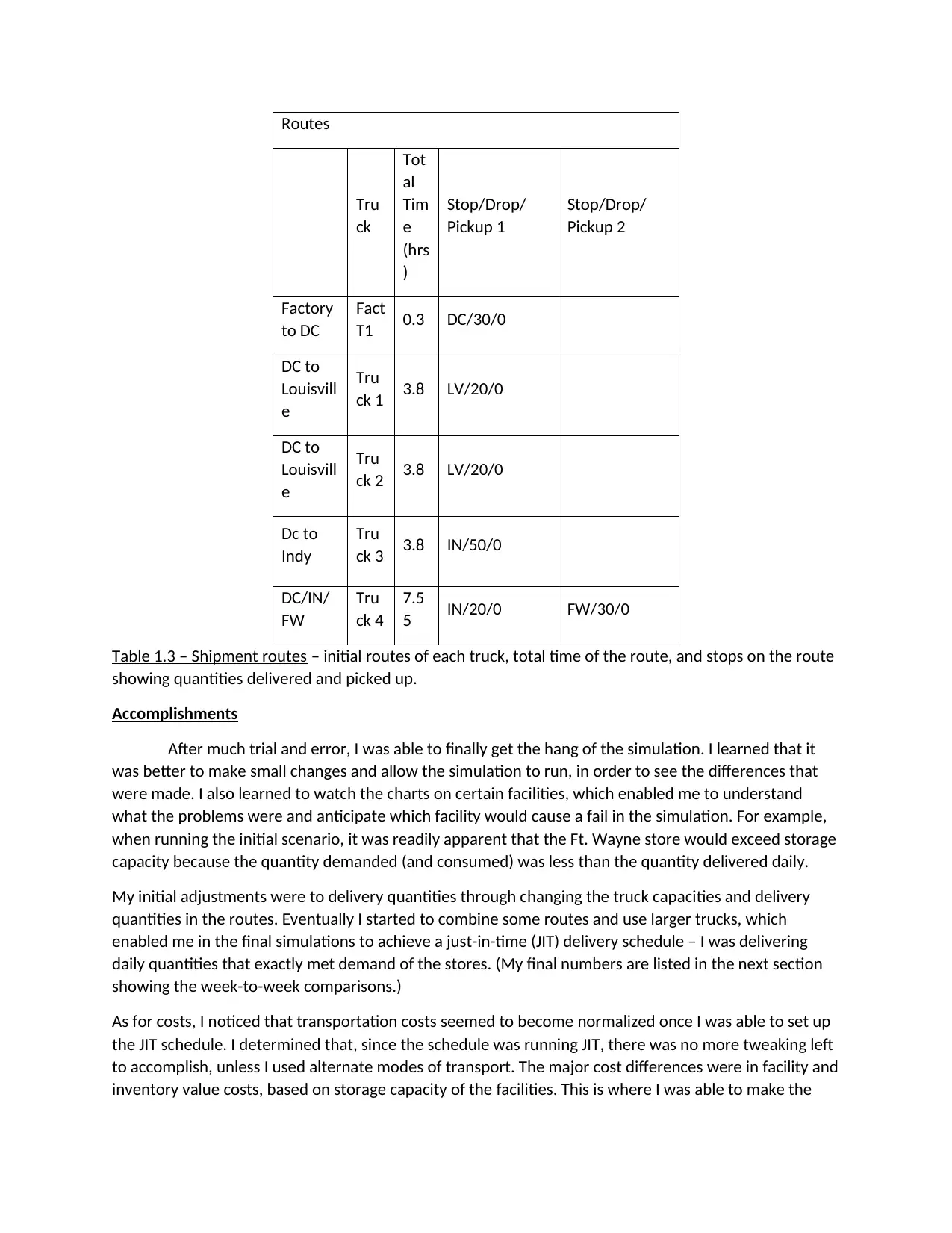
Routes
Tru
ck
Tot
al
Tim
e
(hrs
)
Stop/Drop/
Pickup 1
Stop/Drop/
Pickup 2
Factory
to DC
Fact
T1 0.3 DC/30/0
DC to
Louisvill
e
Tru
ck 1 3.8 LV/20/0
DC to
Louisvill
e
Tru
ck 2 3.8 LV/20/0
Dc to
Indy
Tru
ck 3 3.8 IN/50/0
DC/IN/
FW
Tru
ck 4
7.5
5 IN/20/0 FW/30/0
Table 1.3 – Shipment routes – initial routes of each truck, total time of the route, and stops on the route
showing quantities delivered and picked up.
Accomplishments
After much trial and error, I was able to finally get the hang of the simulation. I learned that it
was better to make small changes and allow the simulation to run, in order to see the differences that
were made. I also learned to watch the charts on certain facilities, which enabled me to understand
what the problems were and anticipate which facility would cause a fail in the simulation. For example,
when running the initial scenario, it was readily apparent that the Ft. Wayne store would exceed storage
capacity because the quantity demanded (and consumed) was less than the quantity delivered daily.
My initial adjustments were to delivery quantities through changing the truck capacities and delivery
quantities in the routes. Eventually I started to combine some routes and use larger trucks, which
enabled me in the final simulations to achieve a just-in-time (JIT) delivery schedule – I was delivering
daily quantities that exactly met demand of the stores. (My final numbers are listed in the next section
showing the week-to-week comparisons.)
As for costs, I noticed that transportation costs seemed to become normalized once I was able to set up
the JIT schedule. I determined that, since the schedule was running JIT, there was no more tweaking left
to accomplish, unless I used alternate modes of transport. The major cost differences were in facility and
inventory value costs, based on storage capacity of the facilities. This is where I was able to make the
Tru
ck
Tot
al
Tim
e
(hrs
)
Stop/Drop/
Pickup 1
Stop/Drop/
Pickup 2
Factory
to DC
Fact
T1 0.3 DC/30/0
DC to
Louisvill
e
Tru
ck 1 3.8 LV/20/0
DC to
Louisvill
e
Tru
ck 2 3.8 LV/20/0
Dc to
Indy
Tru
ck 3 3.8 IN/50/0
DC/IN/
FW
Tru
ck 4
7.5
5 IN/20/0 FW/30/0
Table 1.3 – Shipment routes – initial routes of each truck, total time of the route, and stops on the route
showing quantities delivered and picked up.
Accomplishments
After much trial and error, I was able to finally get the hang of the simulation. I learned that it
was better to make small changes and allow the simulation to run, in order to see the differences that
were made. I also learned to watch the charts on certain facilities, which enabled me to understand
what the problems were and anticipate which facility would cause a fail in the simulation. For example,
when running the initial scenario, it was readily apparent that the Ft. Wayne store would exceed storage
capacity because the quantity demanded (and consumed) was less than the quantity delivered daily.
My initial adjustments were to delivery quantities through changing the truck capacities and delivery
quantities in the routes. Eventually I started to combine some routes and use larger trucks, which
enabled me in the final simulations to achieve a just-in-time (JIT) delivery schedule – I was delivering
daily quantities that exactly met demand of the stores. (My final numbers are listed in the next section
showing the week-to-week comparisons.)
As for costs, I noticed that transportation costs seemed to become normalized once I was able to set up
the JIT schedule. I determined that, since the schedule was running JIT, there was no more tweaking left
to accomplish, unless I used alternate modes of transport. The major cost differences were in facility and
inventory value costs, based on storage capacity of the facilities. This is where I was able to make the
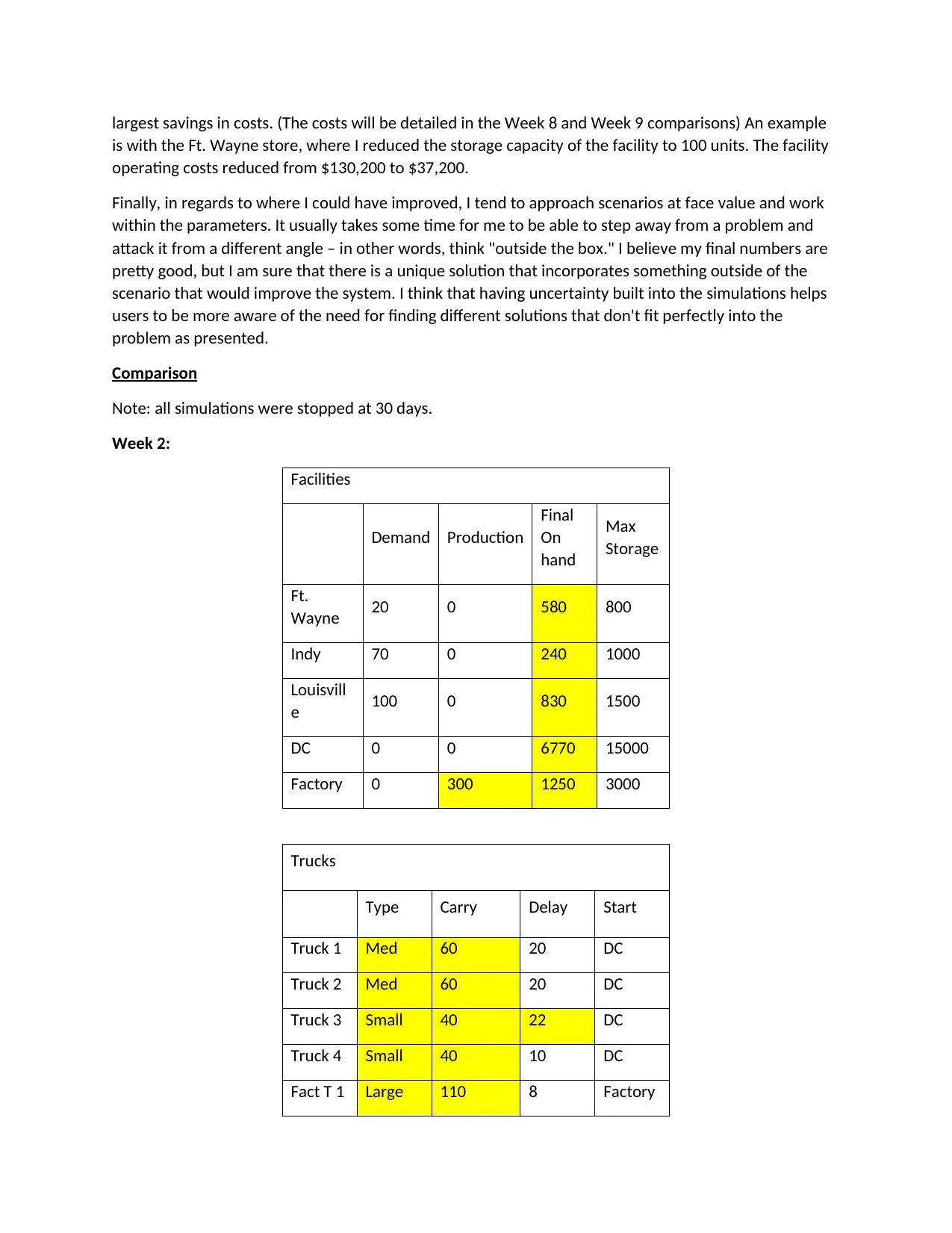
largest savings in costs. (The costs will be detailed in the Week 8 and Week 9 comparisons) An example
is with the Ft. Wayne store, where I reduced the storage capacity of the facility to 100 units. The facility
operating costs reduced from $130,200 to $37,200.
Finally, in regards to where I could have improved, I tend to approach scenarios at face value and work
within the parameters. It usually takes some time for me to be able to step away from a problem and
attack it from a different angle – in other words, think "outside the box." I believe my final numbers are
pretty good, but I am sure that there is a unique solution that incorporates something outside of the
scenario that would improve the system. I think that having uncertainty built into the simulations helps
users to be more aware of the need for finding different solutions that don't fit perfectly into the
problem as presented.
Comparison
Note: all simulations were stopped at 30 days.
Week 2:
Facilities
Demand Production
Final
On
hand
Max
Storage
Ft.
Wayne 20 0 580 800
Indy 70 0 240 1000
Louisvill
e 100 0 830 1500
DC 0 0 6770 15000
Factory 0 300 1250 3000
Trucks
Type Carry Delay Start
Truck 1 Med 60 20 DC
Truck 2 Med 60 20 DC
Truck 3 Small 40 22 DC
Truck 4 Small 40 10 DC
Fact T 1 Large 110 8 Factory
is with the Ft. Wayne store, where I reduced the storage capacity of the facility to 100 units. The facility
operating costs reduced from $130,200 to $37,200.
Finally, in regards to where I could have improved, I tend to approach scenarios at face value and work
within the parameters. It usually takes some time for me to be able to step away from a problem and
attack it from a different angle – in other words, think "outside the box." I believe my final numbers are
pretty good, but I am sure that there is a unique solution that incorporates something outside of the
scenario that would improve the system. I think that having uncertainty built into the simulations helps
users to be more aware of the need for finding different solutions that don't fit perfectly into the
problem as presented.
Comparison
Note: all simulations were stopped at 30 days.
Week 2:
Facilities
Demand Production
Final
On
hand
Max
Storage
Ft.
Wayne 20 0 580 800
Indy 70 0 240 1000
Louisvill
e 100 0 830 1500
DC 0 0 6770 15000
Factory 0 300 1250 3000
Trucks
Type Carry Delay Start
Truck 1 Med 60 20 DC
Truck 2 Med 60 20 DC
Truck 3 Small 40 22 DC
Truck 4 Small 40 10 DC
Fact T 1 Large 110 8 Factory
⊘ This is a preview!⊘
Do you want full access?
Subscribe today to unlock all pages.

Trusted by 1+ million students worldwide
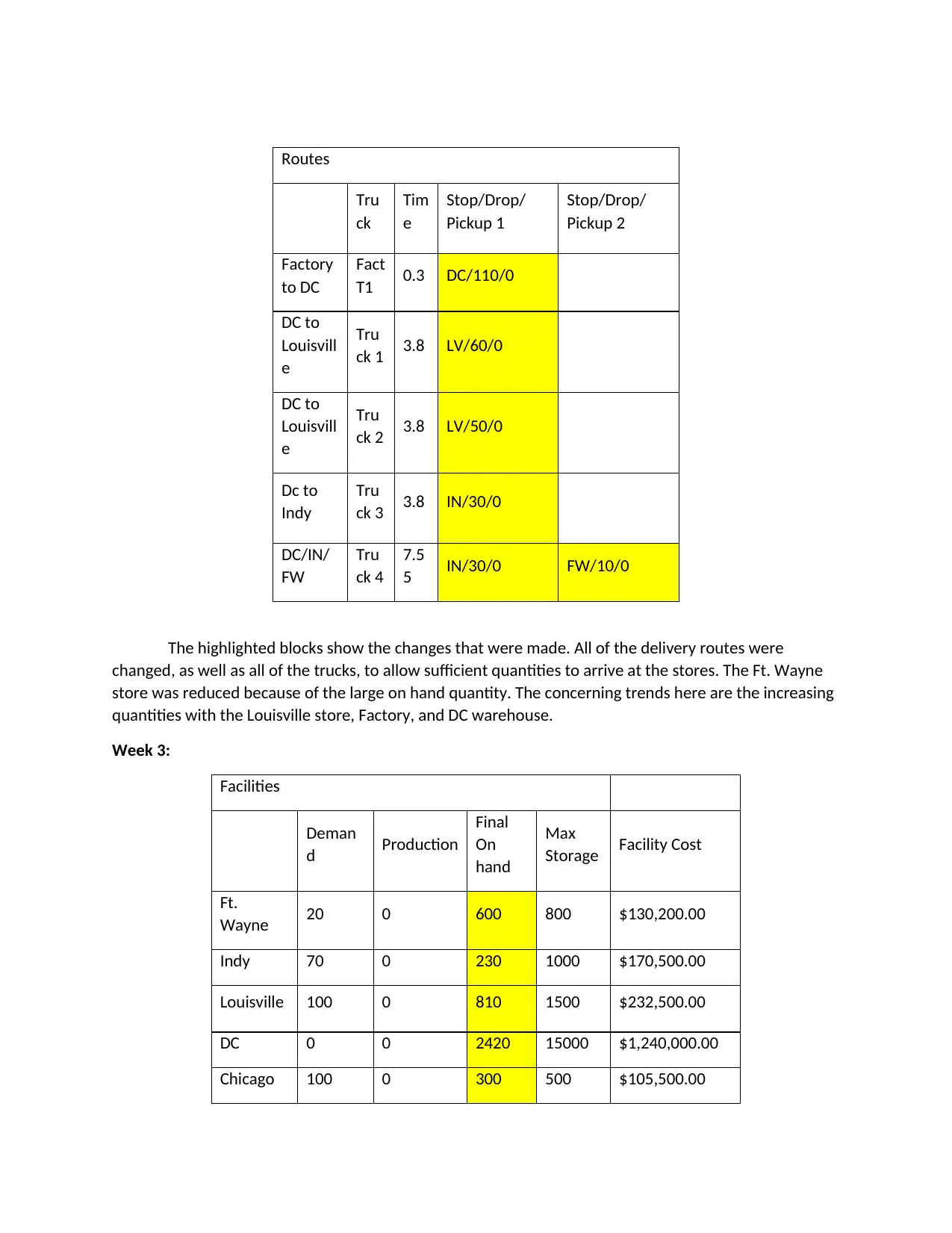
Routes
Tru
ck
Tim
e
Stop/Drop/
Pickup 1
Stop/Drop/
Pickup 2
Factory
to DC
Fact
T1 0.3 DC/110/0
DC to
Louisvill
e
Tru
ck 1 3.8 LV/60/0
DC to
Louisvill
e
Tru
ck 2 3.8 LV/50/0
Dc to
Indy
Tru
ck 3 3.8 IN/30/0
DC/IN/
FW
Tru
ck 4
7.5
5 IN/30/0 FW/10/0
The highlighted blocks show the changes that were made. All of the delivery routes were
changed, as well as all of the trucks, to allow sufficient quantities to arrive at the stores. The Ft. Wayne
store was reduced because of the large on hand quantity. The concerning trends here are the increasing
quantities with the Louisville store, Factory, and DC warehouse.
Week 3:
Facilities
Deman
d Production
Final
On
hand
Max
Storage Facility Cost
Ft.
Wayne 20 0 600 800 $130,200.00
Indy 70 0 230 1000 $170,500.00
Louisville 100 0 810 1500 $232,500.00
DC 0 0 2420 15000 $1,240,000.00
Chicago 100 0 300 500 $105,500.00
Tru
ck
Tim
e
Stop/Drop/
Pickup 1
Stop/Drop/
Pickup 2
Factory
to DC
Fact
T1 0.3 DC/110/0
DC to
Louisvill
e
Tru
ck 1 3.8 LV/60/0
DC to
Louisvill
e
Tru
ck 2 3.8 LV/50/0
Dc to
Indy
Tru
ck 3 3.8 IN/30/0
DC/IN/
FW
Tru
ck 4
7.5
5 IN/30/0 FW/10/0
The highlighted blocks show the changes that were made. All of the delivery routes were
changed, as well as all of the trucks, to allow sufficient quantities to arrive at the stores. The Ft. Wayne
store was reduced because of the large on hand quantity. The concerning trends here are the increasing
quantities with the Louisville store, Factory, and DC warehouse.
Week 3:
Facilities
Deman
d Production
Final
On
hand
Max
Storage Facility Cost
Ft.
Wayne 20 0 600 800 $130,200.00
Indy 70 0 230 1000 $170,500.00
Louisville 100 0 810 1500 $232,500.00
DC 0 0 2420 15000 $1,240,000.00
Chicago 100 0 300 500 $105,500.00
Paraphrase This Document
Need a fresh take? Get an instant paraphrase of this document with our AI Paraphraser
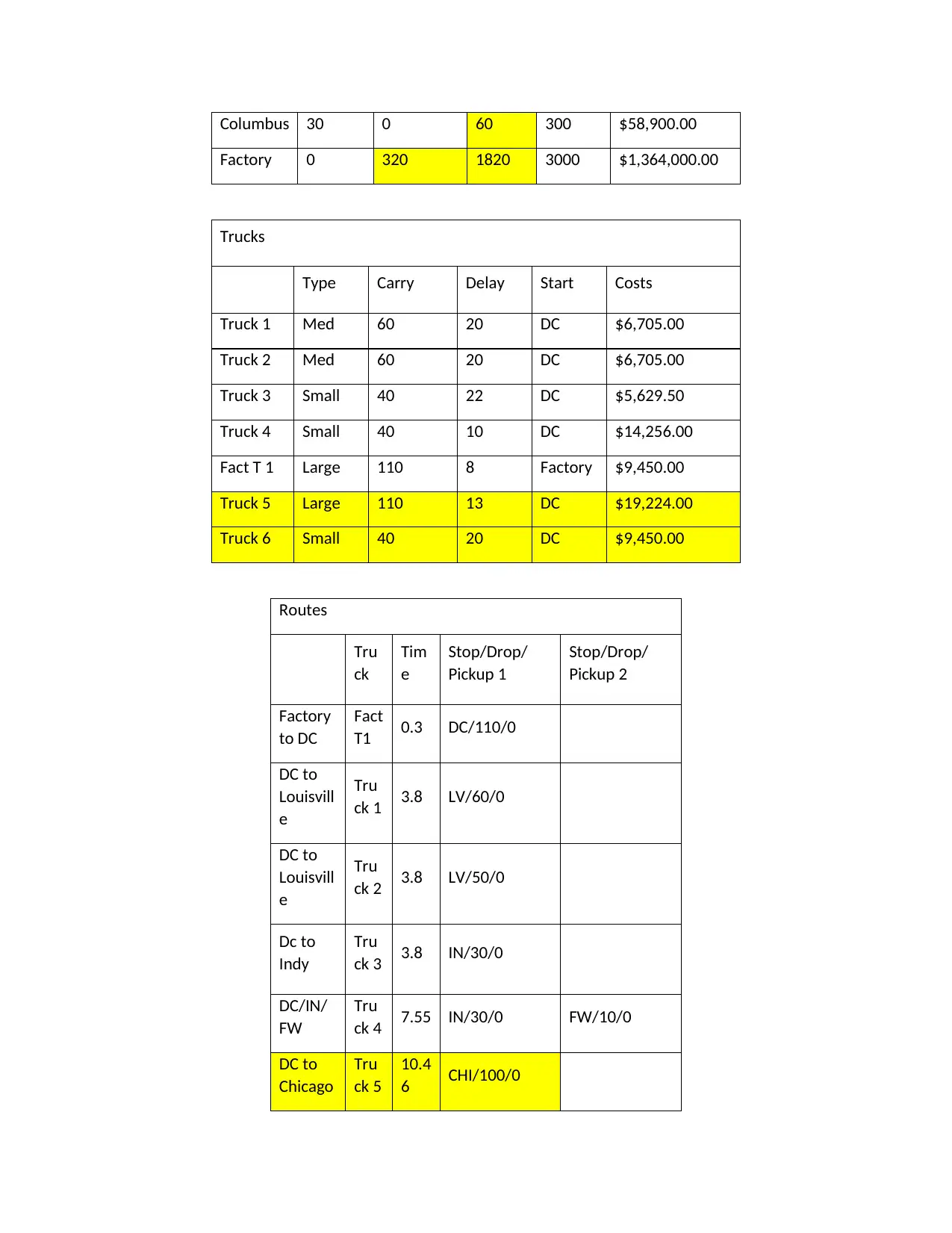
Columbus 30 0 60 300 $58,900.00
Factory 0 320 1820 3000 $1,364,000.00
Trucks
Type Carry Delay Start Costs
Truck 1 Med 60 20 DC $6,705.00
Truck 2 Med 60 20 DC $6,705.00
Truck 3 Small 40 22 DC $5,629.50
Truck 4 Small 40 10 DC $14,256.00
Fact T 1 Large 110 8 Factory $9,450.00
Truck 5 Large 110 13 DC $19,224.00
Truck 6 Small 40 20 DC $9,450.00
Routes
Tru
ck
Tim
e
Stop/Drop/
Pickup 1
Stop/Drop/
Pickup 2
Factory
to DC
Fact
T1 0.3 DC/110/0
DC to
Louisvill
e
Tru
ck 1 3.8 LV/60/0
DC to
Louisvill
e
Tru
ck 2 3.8 LV/50/0
Dc to
Indy
Tru
ck 3 3.8 IN/30/0
DC/IN/
FW
Tru
ck 4 7.55 IN/30/0 FW/10/0
DC to
Chicago
Tru
ck 5
10.4
6 CHI/100/0
Factory 0 320 1820 3000 $1,364,000.00
Trucks
Type Carry Delay Start Costs
Truck 1 Med 60 20 DC $6,705.00
Truck 2 Med 60 20 DC $6,705.00
Truck 3 Small 40 22 DC $5,629.50
Truck 4 Small 40 10 DC $14,256.00
Fact T 1 Large 110 8 Factory $9,450.00
Truck 5 Large 110 13 DC $19,224.00
Truck 6 Small 40 20 DC $9,450.00
Routes
Tru
ck
Tim
e
Stop/Drop/
Pickup 1
Stop/Drop/
Pickup 2
Factory
to DC
Fact
T1 0.3 DC/110/0
DC to
Louisvill
e
Tru
ck 1 3.8 LV/60/0
DC to
Louisvill
e
Tru
ck 2 3.8 LV/50/0
Dc to
Indy
Tru
ck 3 3.8 IN/30/0
DC/IN/
FW
Tru
ck 4 7.55 IN/30/0 FW/10/0
DC to
Chicago
Tru
ck 5
10.4
6 CHI/100/0
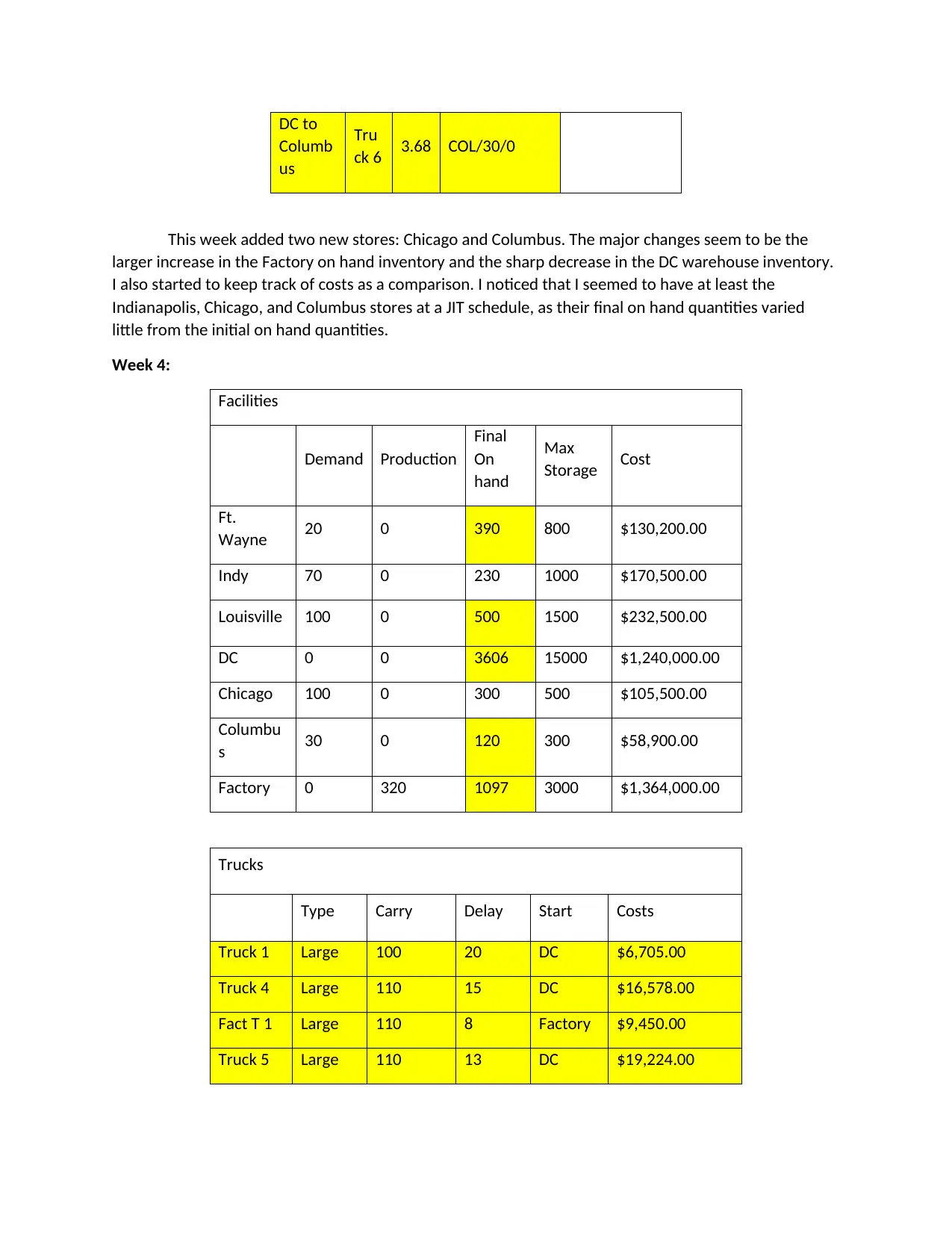
DC to
Columb
us
Tru
ck 6 3.68 COL/30/0
This week added two new stores: Chicago and Columbus. The major changes seem to be the
larger increase in the Factory on hand inventory and the sharp decrease in the DC warehouse inventory.
I also started to keep track of costs as a comparison. I noticed that I seemed to have at least the
Indianapolis, Chicago, and Columbus stores at a JIT schedule, as their final on hand quantities varied
little from the initial on hand quantities.
Week 4:
Facilities
Demand Production
Final
On
hand
Max
Storage Cost
Ft.
Wayne 20 0 390 800 $130,200.00
Indy 70 0 230 1000 $170,500.00
Louisville 100 0 500 1500 $232,500.00
DC 0 0 3606 15000 $1,240,000.00
Chicago 100 0 300 500 $105,500.00
Columbu
s 30 0 120 300 $58,900.00
Factory 0 320 1097 3000 $1,364,000.00
Trucks
Type Carry Delay Start Costs
Truck 1 Large 100 20 DC $6,705.00
Truck 4 Large 110 15 DC $16,578.00
Fact T 1 Large 110 8 Factory $9,450.00
Truck 5 Large 110 13 DC $19,224.00
Columb
us
Tru
ck 6 3.68 COL/30/0
This week added two new stores: Chicago and Columbus. The major changes seem to be the
larger increase in the Factory on hand inventory and the sharp decrease in the DC warehouse inventory.
I also started to keep track of costs as a comparison. I noticed that I seemed to have at least the
Indianapolis, Chicago, and Columbus stores at a JIT schedule, as their final on hand quantities varied
little from the initial on hand quantities.
Week 4:
Facilities
Demand Production
Final
On
hand
Max
Storage Cost
Ft.
Wayne 20 0 390 800 $130,200.00
Indy 70 0 230 1000 $170,500.00
Louisville 100 0 500 1500 $232,500.00
DC 0 0 3606 15000 $1,240,000.00
Chicago 100 0 300 500 $105,500.00
Columbu
s 30 0 120 300 $58,900.00
Factory 0 320 1097 3000 $1,364,000.00
Trucks
Type Carry Delay Start Costs
Truck 1 Large 100 20 DC $6,705.00
Truck 4 Large 110 15 DC $16,578.00
Fact T 1 Large 110 8 Factory $9,450.00
Truck 5 Large 110 13 DC $19,224.00
⊘ This is a preview!⊘
Do you want full access?
Subscribe today to unlock all pages.

Trusted by 1+ million students worldwide
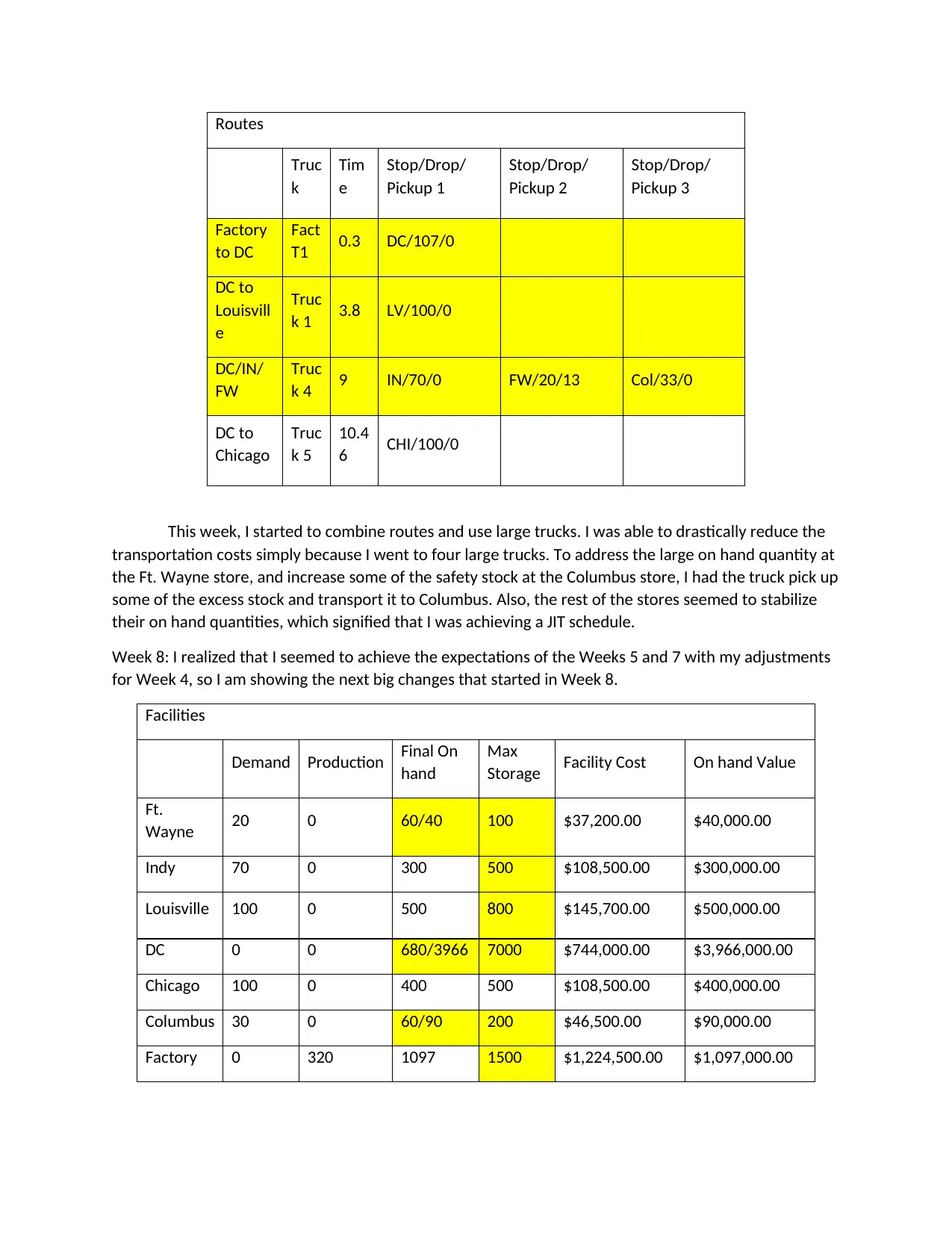
Routes
Truc
k
Tim
e
Stop/Drop/
Pickup 1
Stop/Drop/
Pickup 2
Stop/Drop/
Pickup 3
Factory
to DC
Fact
T1 0.3 DC/107/0
DC to
Louisvill
e
Truc
k 1 3.8 LV/100/0
DC/IN/
FW
Truc
k 4 9 IN/70/0 FW/20/13 Col/33/0
DC to
Chicago
Truc
k 5
10.4
6 CHI/100/0
This week, I started to combine routes and use large trucks. I was able to drastically reduce the
transportation costs simply because I went to four large trucks. To address the large on hand quantity at
the Ft. Wayne store, and increase some of the safety stock at the Columbus store, I had the truck pick up
some of the excess stock and transport it to Columbus. Also, the rest of the stores seemed to stabilize
their on hand quantities, which signified that I was achieving a JIT schedule.
Week 8: I realized that I seemed to achieve the expectations of the Weeks 5 and 7 with my adjustments
for Week 4, so I am showing the next big changes that started in Week 8.
Facilities
Demand Production Final On
hand
Max
Storage Facility Cost On hand Value
Ft.
Wayne 20 0 60/40 100 $37,200.00 $40,000.00
Indy 70 0 300 500 $108,500.00 $300,000.00
Louisville 100 0 500 800 $145,700.00 $500,000.00
DC 0 0 680/3966 7000 $744,000.00 $3,966,000.00
Chicago 100 0 400 500 $108,500.00 $400,000.00
Columbus 30 0 60/90 200 $46,500.00 $90,000.00
Factory 0 320 1097 1500 $1,224,500.00 $1,097,000.00
Truc
k
Tim
e
Stop/Drop/
Pickup 1
Stop/Drop/
Pickup 2
Stop/Drop/
Pickup 3
Factory
to DC
Fact
T1 0.3 DC/107/0
DC to
Louisvill
e
Truc
k 1 3.8 LV/100/0
DC/IN/
FW
Truc
k 4 9 IN/70/0 FW/20/13 Col/33/0
DC to
Chicago
Truc
k 5
10.4
6 CHI/100/0
This week, I started to combine routes and use large trucks. I was able to drastically reduce the
transportation costs simply because I went to four large trucks. To address the large on hand quantity at
the Ft. Wayne store, and increase some of the safety stock at the Columbus store, I had the truck pick up
some of the excess stock and transport it to Columbus. Also, the rest of the stores seemed to stabilize
their on hand quantities, which signified that I was achieving a JIT schedule.
Week 8: I realized that I seemed to achieve the expectations of the Weeks 5 and 7 with my adjustments
for Week 4, so I am showing the next big changes that started in Week 8.
Facilities
Demand Production Final On
hand
Max
Storage Facility Cost On hand Value
Ft.
Wayne 20 0 60/40 100 $37,200.00 $40,000.00
Indy 70 0 300 500 $108,500.00 $300,000.00
Louisville 100 0 500 800 $145,700.00 $500,000.00
DC 0 0 680/3966 7000 $744,000.00 $3,966,000.00
Chicago 100 0 400 500 $108,500.00 $400,000.00
Columbus 30 0 60/90 200 $46,500.00 $90,000.00
Factory 0 320 1097 1500 $1,224,500.00 $1,097,000.00
Paraphrase This Document
Need a fresh take? Get an instant paraphrase of this document with our AI Paraphraser
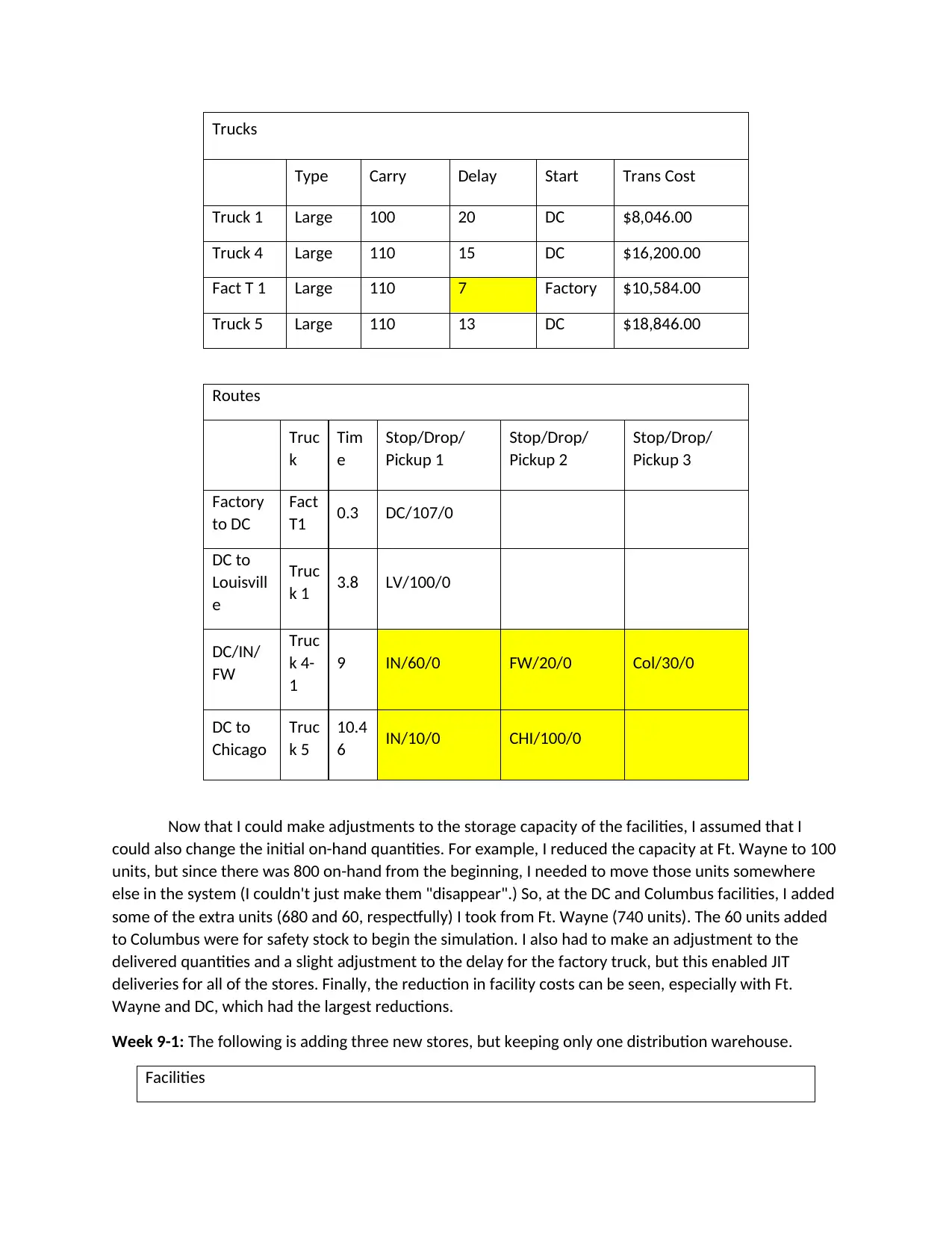
Trucks
Type Carry Delay Start Trans Cost
Truck 1 Large 100 20 DC $8,046.00
Truck 4 Large 110 15 DC $16,200.00
Fact T 1 Large 110 7 Factory $10,584.00
Truck 5 Large 110 13 DC $18,846.00
Routes
Truc
k
Tim
e
Stop/Drop/
Pickup 1
Stop/Drop/
Pickup 2
Stop/Drop/
Pickup 3
Factory
to DC
Fact
T1 0.3 DC/107/0
DC to
Louisvill
e
Truc
k 1 3.8 LV/100/0
DC/IN/
FW
Truc
k 4-
1
9 IN/60/0 FW/20/0 Col/30/0
DC to
Chicago
Truc
k 5
10.4
6 IN/10/0 CHI/100/0
Now that I could make adjustments to the storage capacity of the facilities, I assumed that I
could also change the initial on-hand quantities. For example, I reduced the capacity at Ft. Wayne to 100
units, but since there was 800 on-hand from the beginning, I needed to move those units somewhere
else in the system (I couldn't just make them "disappear".) So, at the DC and Columbus facilities, I added
some of the extra units (680 and 60, respectfully) I took from Ft. Wayne (740 units). The 60 units added
to Columbus were for safety stock to begin the simulation. I also had to make an adjustment to the
delivered quantities and a slight adjustment to the delay for the factory truck, but this enabled JIT
deliveries for all of the stores. Finally, the reduction in facility costs can be seen, especially with Ft.
Wayne and DC, which had the largest reductions.
Week 9-1: The following is adding three new stores, but keeping only one distribution warehouse.
Facilities
Type Carry Delay Start Trans Cost
Truck 1 Large 100 20 DC $8,046.00
Truck 4 Large 110 15 DC $16,200.00
Fact T 1 Large 110 7 Factory $10,584.00
Truck 5 Large 110 13 DC $18,846.00
Routes
Truc
k
Tim
e
Stop/Drop/
Pickup 1
Stop/Drop/
Pickup 2
Stop/Drop/
Pickup 3
Factory
to DC
Fact
T1 0.3 DC/107/0
DC to
Louisvill
e
Truc
k 1 3.8 LV/100/0
DC/IN/
FW
Truc
k 4-
1
9 IN/60/0 FW/20/0 Col/30/0
DC to
Chicago
Truc
k 5
10.4
6 IN/10/0 CHI/100/0
Now that I could make adjustments to the storage capacity of the facilities, I assumed that I
could also change the initial on-hand quantities. For example, I reduced the capacity at Ft. Wayne to 100
units, but since there was 800 on-hand from the beginning, I needed to move those units somewhere
else in the system (I couldn't just make them "disappear".) So, at the DC and Columbus facilities, I added
some of the extra units (680 and 60, respectfully) I took from Ft. Wayne (740 units). The 60 units added
to Columbus were for safety stock to begin the simulation. I also had to make an adjustment to the
delivered quantities and a slight adjustment to the delay for the factory truck, but this enabled JIT
deliveries for all of the stores. Finally, the reduction in facility costs can be seen, especially with Ft.
Wayne and DC, which had the largest reductions.
Week 9-1: The following is adding three new stores, but keeping only one distribution warehouse.
Facilities
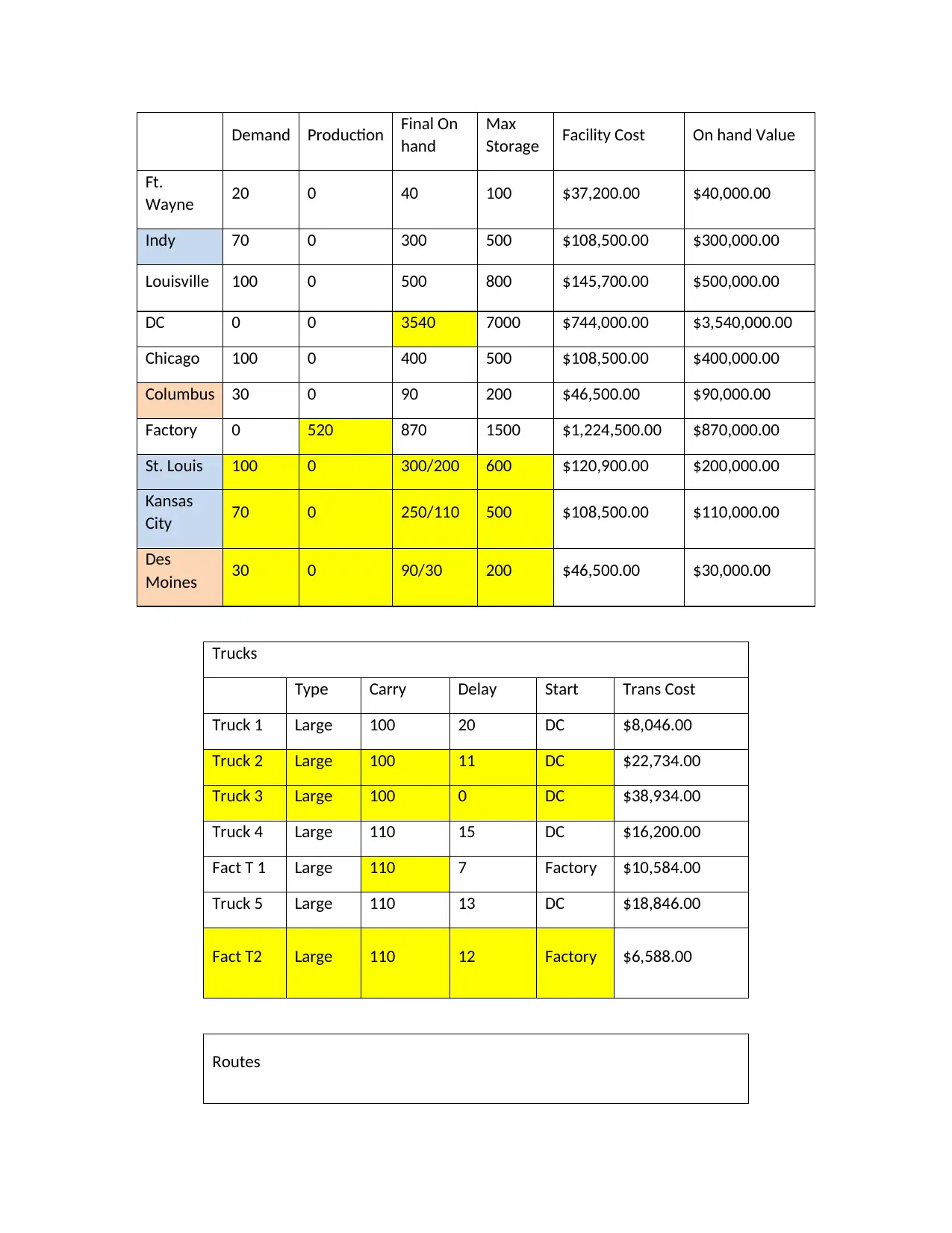
Demand Production Final On
hand
Max
Storage Facility Cost On hand Value
Ft.
Wayne 20 0 40 100 $37,200.00 $40,000.00
Indy 70 0 300 500 $108,500.00 $300,000.00
Louisville 100 0 500 800 $145,700.00 $500,000.00
DC 0 0 3540 7000 $744,000.00 $3,540,000.00
Chicago 100 0 400 500 $108,500.00 $400,000.00
Columbus 30 0 90 200 $46,500.00 $90,000.00
Factory 0 520 870 1500 $1,224,500.00 $870,000.00
St. Louis 100 0 300/200 600 $120,900.00 $200,000.00
Kansas
City 70 0 250/110 500 $108,500.00 $110,000.00
Des
Moines 30 0 90/30 200 $46,500.00 $30,000.00
Trucks
Type Carry Delay Start Trans Cost
Truck 1 Large 100 20 DC $8,046.00
Truck 2 Large 100 11 DC $22,734.00
Truck 3 Large 100 0 DC $38,934.00
Truck 4 Large 110 15 DC $16,200.00
Fact T 1 Large 110 7 Factory $10,584.00
Truck 5 Large 110 13 DC $18,846.00
Fact T2 Large 110 12 Factory $6,588.00
Routes
hand
Max
Storage Facility Cost On hand Value
Ft.
Wayne 20 0 40 100 $37,200.00 $40,000.00
Indy 70 0 300 500 $108,500.00 $300,000.00
Louisville 100 0 500 800 $145,700.00 $500,000.00
DC 0 0 3540 7000 $744,000.00 $3,540,000.00
Chicago 100 0 400 500 $108,500.00 $400,000.00
Columbus 30 0 90 200 $46,500.00 $90,000.00
Factory 0 520 870 1500 $1,224,500.00 $870,000.00
St. Louis 100 0 300/200 600 $120,900.00 $200,000.00
Kansas
City 70 0 250/110 500 $108,500.00 $110,000.00
Des
Moines 30 0 90/30 200 $46,500.00 $30,000.00
Trucks
Type Carry Delay Start Trans Cost
Truck 1 Large 100 20 DC $8,046.00
Truck 2 Large 100 11 DC $22,734.00
Truck 3 Large 100 0 DC $38,934.00
Truck 4 Large 110 15 DC $16,200.00
Fact T 1 Large 110 7 Factory $10,584.00
Truck 5 Large 110 13 DC $18,846.00
Fact T2 Large 110 12 Factory $6,588.00
Routes
⊘ This is a preview!⊘
Do you want full access?
Subscribe today to unlock all pages.

Trusted by 1+ million students worldwide
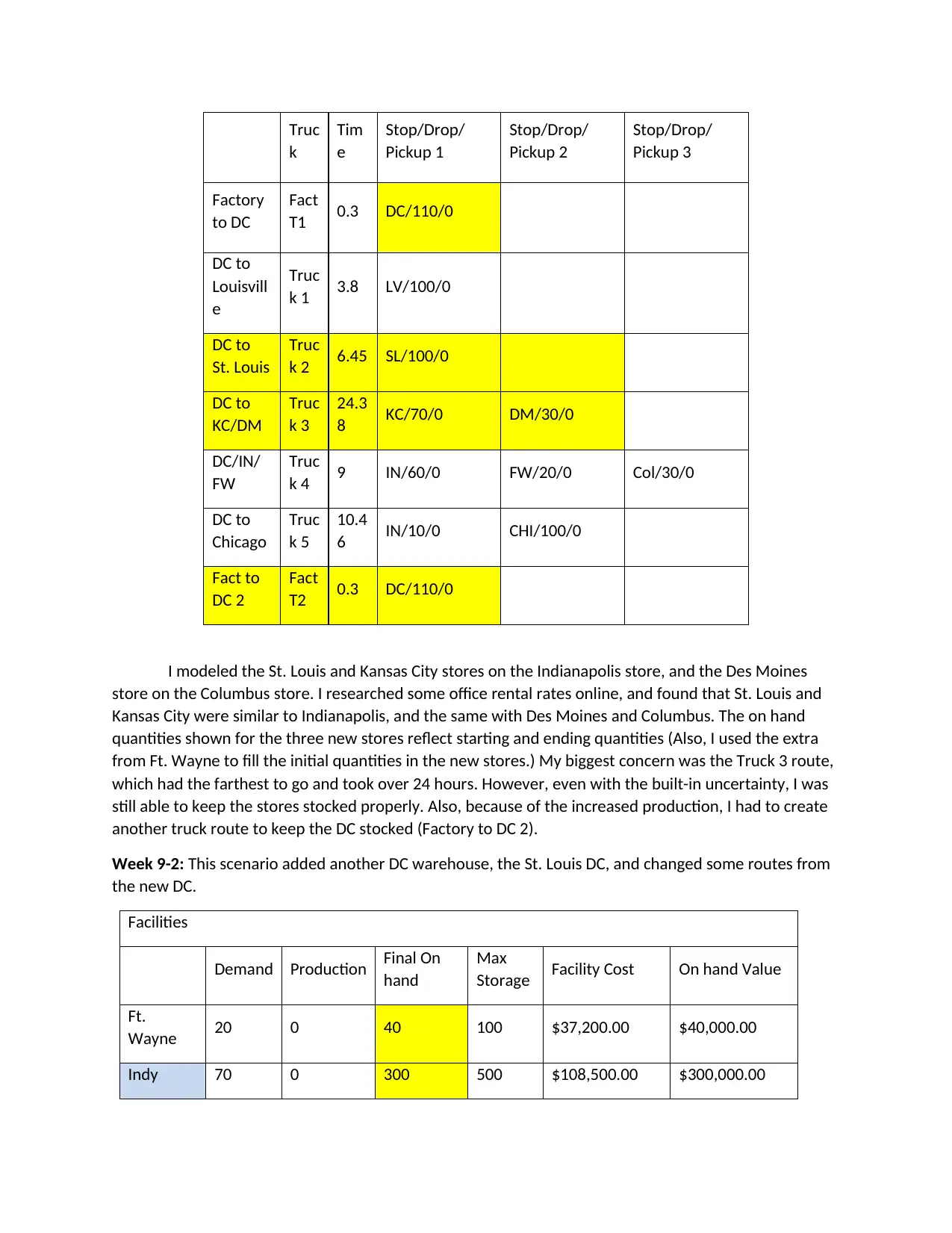
Truc
k
Tim
e
Stop/Drop/
Pickup 1
Stop/Drop/
Pickup 2
Stop/Drop/
Pickup 3
Factory
to DC
Fact
T1 0.3 DC/110/0
DC to
Louisvill
e
Truc
k 1 3.8 LV/100/0
DC to
St. Louis
Truc
k 2 6.45 SL/100/0
DC to
KC/DM
Truc
k 3
24.3
8 KC/70/0 DM/30/0
DC/IN/
FW
Truc
k 4 9 IN/60/0 FW/20/0 Col/30/0
DC to
Chicago
Truc
k 5
10.4
6 IN/10/0 CHI/100/0
Fact to
DC 2
Fact
T2 0.3 DC/110/0
I modeled the St. Louis and Kansas City stores on the Indianapolis store, and the Des Moines
store on the Columbus store. I researched some office rental rates online, and found that St. Louis and
Kansas City were similar to Indianapolis, and the same with Des Moines and Columbus. The on hand
quantities shown for the three new stores reflect starting and ending quantities (Also, I used the extra
from Ft. Wayne to fill the initial quantities in the new stores.) My biggest concern was the Truck 3 route,
which had the farthest to go and took over 24 hours. However, even with the built-in uncertainty, I was
still able to keep the stores stocked properly. Also, because of the increased production, I had to create
another truck route to keep the DC stocked (Factory to DC 2).
Week 9-2: This scenario added another DC warehouse, the St. Louis DC, and changed some routes from
the new DC.
Facilities
Demand Production Final On
hand
Max
Storage Facility Cost On hand Value
Ft.
Wayne 20 0 40 100 $37,200.00 $40,000.00
Indy 70 0 300 500 $108,500.00 $300,000.00
k
Tim
e
Stop/Drop/
Pickup 1
Stop/Drop/
Pickup 2
Stop/Drop/
Pickup 3
Factory
to DC
Fact
T1 0.3 DC/110/0
DC to
Louisvill
e
Truc
k 1 3.8 LV/100/0
DC to
St. Louis
Truc
k 2 6.45 SL/100/0
DC to
KC/DM
Truc
k 3
24.3
8 KC/70/0 DM/30/0
DC/IN/
FW
Truc
k 4 9 IN/60/0 FW/20/0 Col/30/0
DC to
Chicago
Truc
k 5
10.4
6 IN/10/0 CHI/100/0
Fact to
DC 2
Fact
T2 0.3 DC/110/0
I modeled the St. Louis and Kansas City stores on the Indianapolis store, and the Des Moines
store on the Columbus store. I researched some office rental rates online, and found that St. Louis and
Kansas City were similar to Indianapolis, and the same with Des Moines and Columbus. The on hand
quantities shown for the three new stores reflect starting and ending quantities (Also, I used the extra
from Ft. Wayne to fill the initial quantities in the new stores.) My biggest concern was the Truck 3 route,
which had the farthest to go and took over 24 hours. However, even with the built-in uncertainty, I was
still able to keep the stores stocked properly. Also, because of the increased production, I had to create
another truck route to keep the DC stocked (Factory to DC 2).
Week 9-2: This scenario added another DC warehouse, the St. Louis DC, and changed some routes from
the new DC.
Facilities
Demand Production Final On
hand
Max
Storage Facility Cost On hand Value
Ft.
Wayne 20 0 40 100 $37,200.00 $40,000.00
Indy 70 0 300 500 $108,500.00 $300,000.00
Paraphrase This Document
Need a fresh take? Get an instant paraphrase of this document with our AI Paraphraser
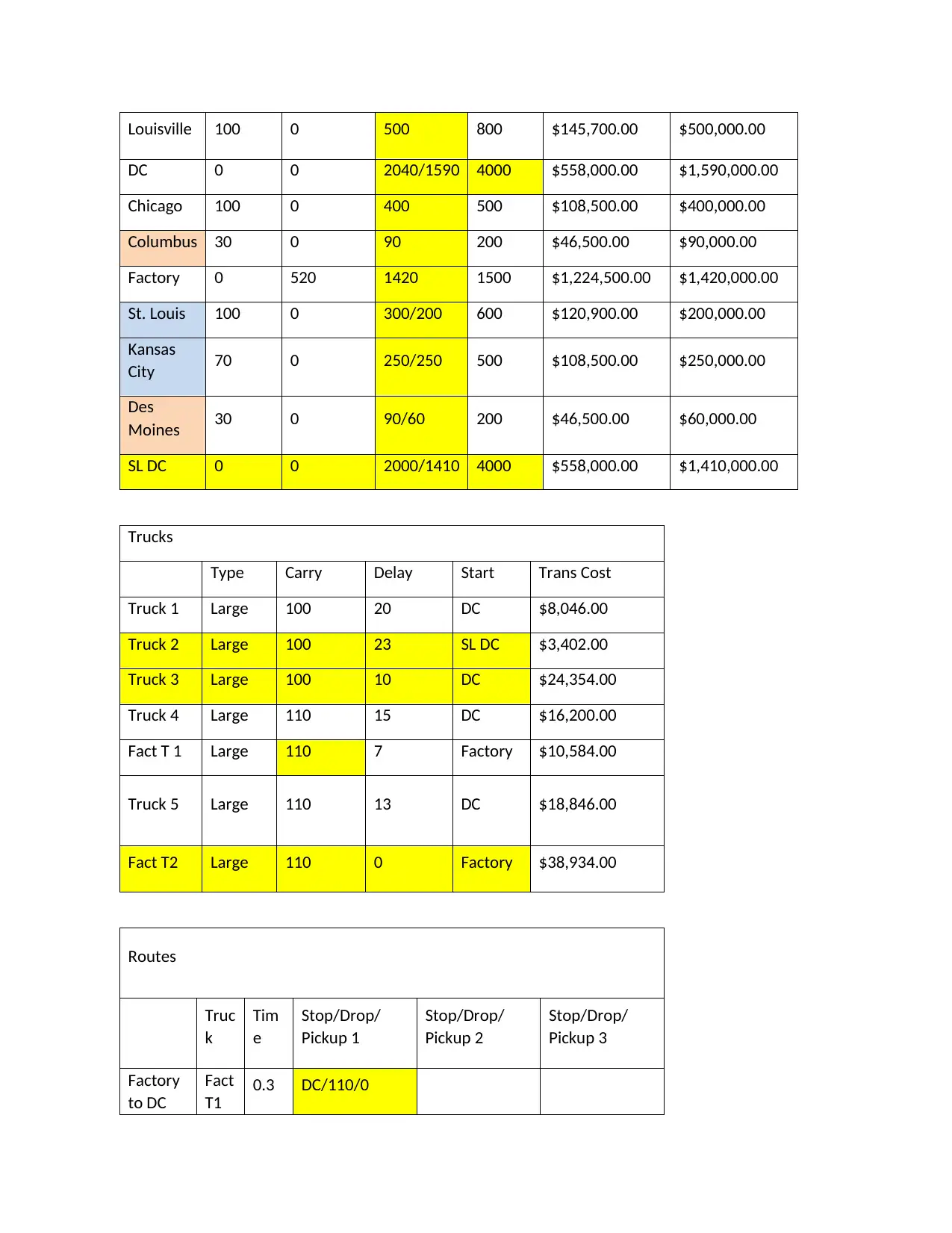
Louisville 100 0 500 800 $145,700.00 $500,000.00
DC 0 0 2040/1590 4000 $558,000.00 $1,590,000.00
Chicago 100 0 400 500 $108,500.00 $400,000.00
Columbus 30 0 90 200 $46,500.00 $90,000.00
Factory 0 520 1420 1500 $1,224,500.00 $1,420,000.00
St. Louis 100 0 300/200 600 $120,900.00 $200,000.00
Kansas
City 70 0 250/250 500 $108,500.00 $250,000.00
Des
Moines 30 0 90/60 200 $46,500.00 $60,000.00
SL DC 0 0 2000/1410 4000 $558,000.00 $1,410,000.00
Trucks
Type Carry Delay Start Trans Cost
Truck 1 Large 100 20 DC $8,046.00
Truck 2 Large 100 23 SL DC $3,402.00
Truck 3 Large 100 10 DC $24,354.00
Truck 4 Large 110 15 DC $16,200.00
Fact T 1 Large 110 7 Factory $10,584.00
Truck 5 Large 110 13 DC $18,846.00
Fact T2 Large 110 0 Factory $38,934.00
Routes
Truc
k
Tim
e
Stop/Drop/
Pickup 1
Stop/Drop/
Pickup 2
Stop/Drop/
Pickup 3
Factory
to DC
Fact
T1
0.3 DC/110/0
DC 0 0 2040/1590 4000 $558,000.00 $1,590,000.00
Chicago 100 0 400 500 $108,500.00 $400,000.00
Columbus 30 0 90 200 $46,500.00 $90,000.00
Factory 0 520 1420 1500 $1,224,500.00 $1,420,000.00
St. Louis 100 0 300/200 600 $120,900.00 $200,000.00
Kansas
City 70 0 250/250 500 $108,500.00 $250,000.00
Des
Moines 30 0 90/60 200 $46,500.00 $60,000.00
SL DC 0 0 2000/1410 4000 $558,000.00 $1,410,000.00
Trucks
Type Carry Delay Start Trans Cost
Truck 1 Large 100 20 DC $8,046.00
Truck 2 Large 100 23 SL DC $3,402.00
Truck 3 Large 100 10 DC $24,354.00
Truck 4 Large 110 15 DC $16,200.00
Fact T 1 Large 110 7 Factory $10,584.00
Truck 5 Large 110 13 DC $18,846.00
Fact T2 Large 110 0 Factory $38,934.00
Routes
Truc
k
Tim
e
Stop/Drop/
Pickup 1
Stop/Drop/
Pickup 2
Stop/Drop/
Pickup 3
Factory
to DC
Fact
T1
0.3 DC/110/0
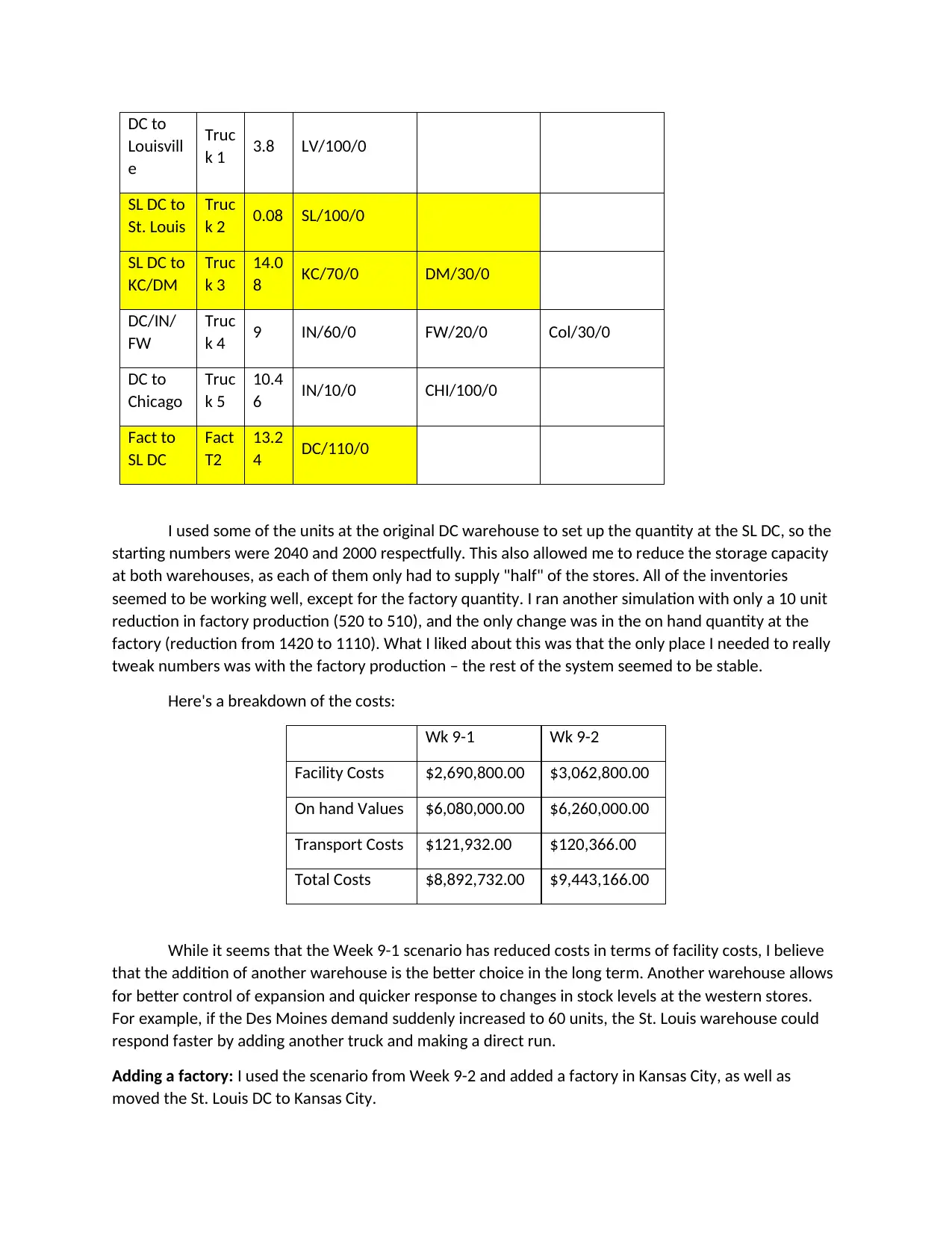
DC to
Louisvill
e
Truc
k 1 3.8 LV/100/0
SL DC to
St. Louis
Truc
k 2 0.08 SL/100/0
SL DC to
KC/DM
Truc
k 3
14.0
8 KC/70/0 DM/30/0
DC/IN/
FW
Truc
k 4 9 IN/60/0 FW/20/0 Col/30/0
DC to
Chicago
Truc
k 5
10.4
6 IN/10/0 CHI/100/0
Fact to
SL DC
Fact
T2
13.2
4 DC/110/0
I used some of the units at the original DC warehouse to set up the quantity at the SL DC, so the
starting numbers were 2040 and 2000 respectfully. This also allowed me to reduce the storage capacity
at both warehouses, as each of them only had to supply "half" of the stores. All of the inventories
seemed to be working well, except for the factory quantity. I ran another simulation with only a 10 unit
reduction in factory production (520 to 510), and the only change was in the on hand quantity at the
factory (reduction from 1420 to 1110). What I liked about this was that the only place I needed to really
tweak numbers was with the factory production – the rest of the system seemed to be stable.
Here's a breakdown of the costs:
Wk 9-1 Wk 9-2
Facility Costs $2,690,800.00 $3,062,800.00
On hand Values $6,080,000.00 $6,260,000.00
Transport Costs $121,932.00 $120,366.00
Total Costs $8,892,732.00 $9,443,166.00
While it seems that the Week 9-1 scenario has reduced costs in terms of facility costs, I believe
that the addition of another warehouse is the better choice in the long term. Another warehouse allows
for better control of expansion and quicker response to changes in stock levels at the western stores.
For example, if the Des Moines demand suddenly increased to 60 units, the St. Louis warehouse could
respond faster by adding another truck and making a direct run.
Adding a factory: I used the scenario from Week 9-2 and added a factory in Kansas City, as well as
moved the St. Louis DC to Kansas City.
Louisvill
e
Truc
k 1 3.8 LV/100/0
SL DC to
St. Louis
Truc
k 2 0.08 SL/100/0
SL DC to
KC/DM
Truc
k 3
14.0
8 KC/70/0 DM/30/0
DC/IN/
FW
Truc
k 4 9 IN/60/0 FW/20/0 Col/30/0
DC to
Chicago
Truc
k 5
10.4
6 IN/10/0 CHI/100/0
Fact to
SL DC
Fact
T2
13.2
4 DC/110/0
I used some of the units at the original DC warehouse to set up the quantity at the SL DC, so the
starting numbers were 2040 and 2000 respectfully. This also allowed me to reduce the storage capacity
at both warehouses, as each of them only had to supply "half" of the stores. All of the inventories
seemed to be working well, except for the factory quantity. I ran another simulation with only a 10 unit
reduction in factory production (520 to 510), and the only change was in the on hand quantity at the
factory (reduction from 1420 to 1110). What I liked about this was that the only place I needed to really
tweak numbers was with the factory production – the rest of the system seemed to be stable.
Here's a breakdown of the costs:
Wk 9-1 Wk 9-2
Facility Costs $2,690,800.00 $3,062,800.00
On hand Values $6,080,000.00 $6,260,000.00
Transport Costs $121,932.00 $120,366.00
Total Costs $8,892,732.00 $9,443,166.00
While it seems that the Week 9-1 scenario has reduced costs in terms of facility costs, I believe
that the addition of another warehouse is the better choice in the long term. Another warehouse allows
for better control of expansion and quicker response to changes in stock levels at the western stores.
For example, if the Des Moines demand suddenly increased to 60 units, the St. Louis warehouse could
respond faster by adding another truck and making a direct run.
Adding a factory: I used the scenario from Week 9-2 and added a factory in Kansas City, as well as
moved the St. Louis DC to Kansas City.
⊘ This is a preview!⊘
Do you want full access?
Subscribe today to unlock all pages.

Trusted by 1+ million students worldwide
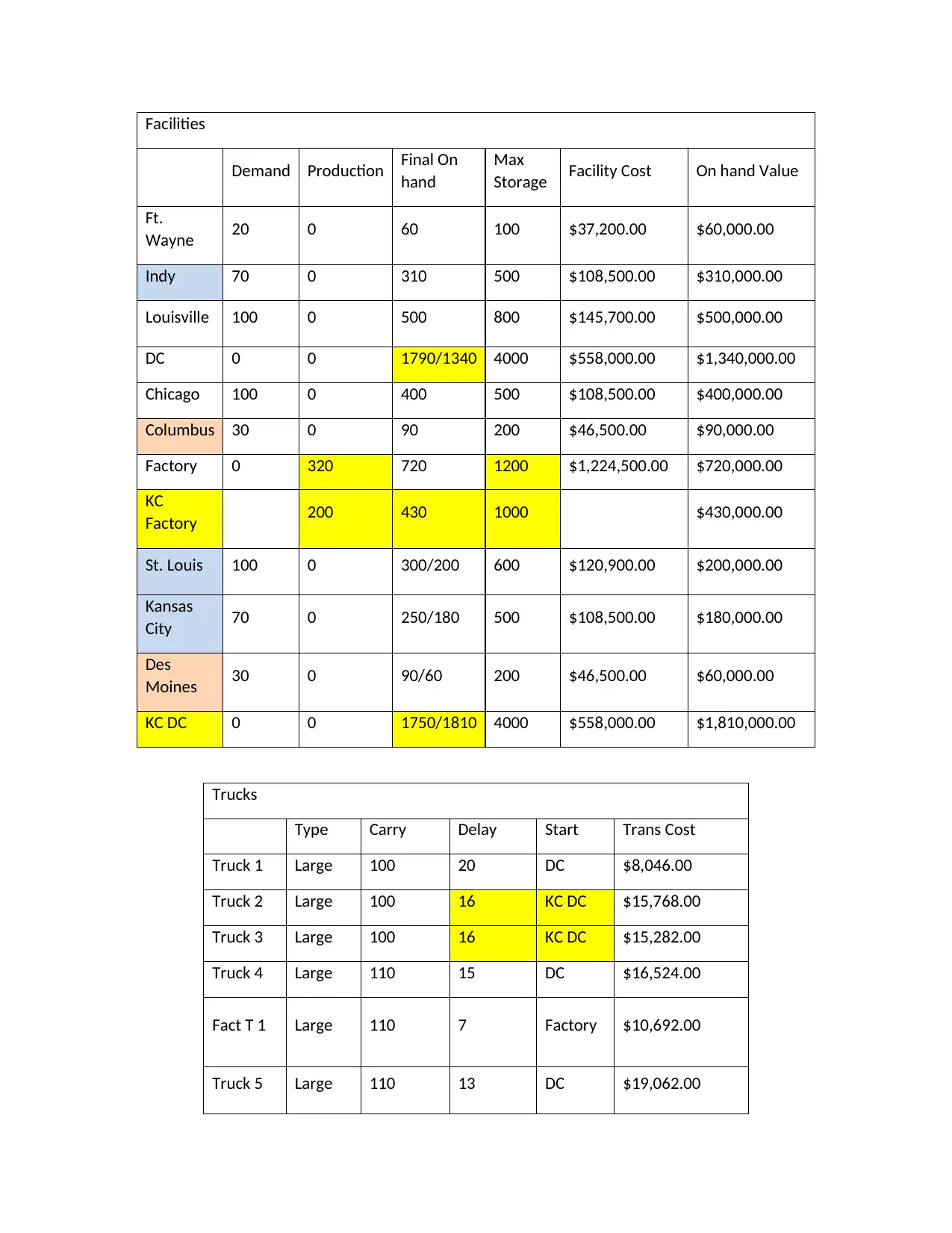
Facilities
Demand Production Final On
hand
Max
Storage Facility Cost On hand Value
Ft.
Wayne 20 0 60 100 $37,200.00 $60,000.00
Indy 70 0 310 500 $108,500.00 $310,000.00
Louisville 100 0 500 800 $145,700.00 $500,000.00
DC 0 0 1790/1340 4000 $558,000.00 $1,340,000.00
Chicago 100 0 400 500 $108,500.00 $400,000.00
Columbus 30 0 90 200 $46,500.00 $90,000.00
Factory 0 320 720 1200 $1,224,500.00 $720,000.00
KC
Factory 200 430 1000 $430,000.00
St. Louis 100 0 300/200 600 $120,900.00 $200,000.00
Kansas
City 70 0 250/180 500 $108,500.00 $180,000.00
Des
Moines 30 0 90/60 200 $46,500.00 $60,000.00
KC DC 0 0 1750/1810 4000 $558,000.00 $1,810,000.00
Trucks
Type Carry Delay Start Trans Cost
Truck 1 Large 100 20 DC $8,046.00
Truck 2 Large 100 16 KC DC $15,768.00
Truck 3 Large 100 16 KC DC $15,282.00
Truck 4 Large 110 15 DC $16,524.00
Fact T 1 Large 110 7 Factory $10,692.00
Truck 5 Large 110 13 DC $19,062.00
Demand Production Final On
hand
Max
Storage Facility Cost On hand Value
Ft.
Wayne 20 0 60 100 $37,200.00 $60,000.00
Indy 70 0 310 500 $108,500.00 $310,000.00
Louisville 100 0 500 800 $145,700.00 $500,000.00
DC 0 0 1790/1340 4000 $558,000.00 $1,340,000.00
Chicago 100 0 400 500 $108,500.00 $400,000.00
Columbus 30 0 90 200 $46,500.00 $90,000.00
Factory 0 320 720 1200 $1,224,500.00 $720,000.00
KC
Factory 200 430 1000 $430,000.00
St. Louis 100 0 300/200 600 $120,900.00 $200,000.00
Kansas
City 70 0 250/180 500 $108,500.00 $180,000.00
Des
Moines 30 0 90/60 200 $46,500.00 $60,000.00
KC DC 0 0 1750/1810 4000 $558,000.00 $1,810,000.00
Trucks
Type Carry Delay Start Trans Cost
Truck 1 Large 100 20 DC $8,046.00
Truck 2 Large 100 16 KC DC $15,768.00
Truck 3 Large 100 16 KC DC $15,282.00
Truck 4 Large 110 15 DC $16,524.00
Fact T 1 Large 110 7 Factory $10,692.00
Truck 5 Large 110 13 DC $19,062.00
Paraphrase This Document
Need a fresh take? Get an instant paraphrase of this document with our AI Paraphraser
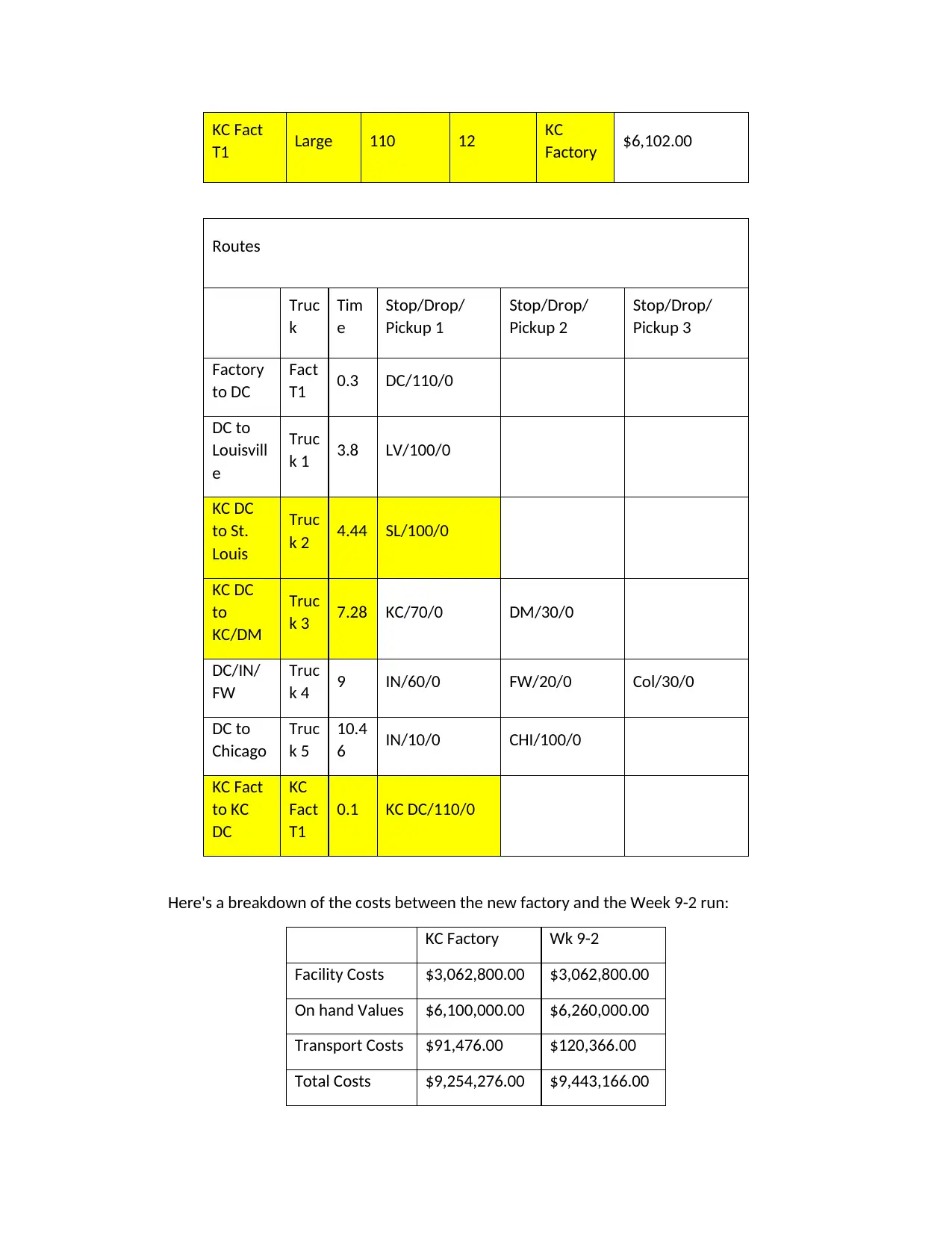
KC Fact
T1 Large 110 12 KC
Factory $6,102.00
Routes
Truc
k
Tim
e
Stop/Drop/
Pickup 1
Stop/Drop/
Pickup 2
Stop/Drop/
Pickup 3
Factory
to DC
Fact
T1 0.3 DC/110/0
DC to
Louisvill
e
Truc
k 1 3.8 LV/100/0
KC DC
to St.
Louis
Truc
k 2 4.44 SL/100/0
KC DC
to
KC/DM
Truc
k 3 7.28 KC/70/0 DM/30/0
DC/IN/
FW
Truc
k 4 9 IN/60/0 FW/20/0 Col/30/0
DC to
Chicago
Truc
k 5
10.4
6 IN/10/0 CHI/100/0
KC Fact
to KC
DC
KC
Fact
T1
0.1 KC DC/110/0
Here's a breakdown of the costs between the new factory and the Week 9-2 run:
KC Factory Wk 9-2
Facility Costs $3,062,800.00 $3,062,800.00
On hand Values $6,100,000.00 $6,260,000.00
Transport Costs $91,476.00 $120,366.00
Total Costs $9,254,276.00 $9,443,166.00
T1 Large 110 12 KC
Factory $6,102.00
Routes
Truc
k
Tim
e
Stop/Drop/
Pickup 1
Stop/Drop/
Pickup 2
Stop/Drop/
Pickup 3
Factory
to DC
Fact
T1 0.3 DC/110/0
DC to
Louisvill
e
Truc
k 1 3.8 LV/100/0
KC DC
to St.
Louis
Truc
k 2 4.44 SL/100/0
KC DC
to
KC/DM
Truc
k 3 7.28 KC/70/0 DM/30/0
DC/IN/
FW
Truc
k 4 9 IN/60/0 FW/20/0 Col/30/0
DC to
Chicago
Truc
k 5
10.4
6 IN/10/0 CHI/100/0
KC Fact
to KC
DC
KC
Fact
T1
0.1 KC DC/110/0
Here's a breakdown of the costs between the new factory and the Week 9-2 run:
KC Factory Wk 9-2
Facility Costs $3,062,800.00 $3,062,800.00
On hand Values $6,100,000.00 $6,260,000.00
Transport Costs $91,476.00 $120,366.00
Total Costs $9,254,276.00 $9,443,166.00
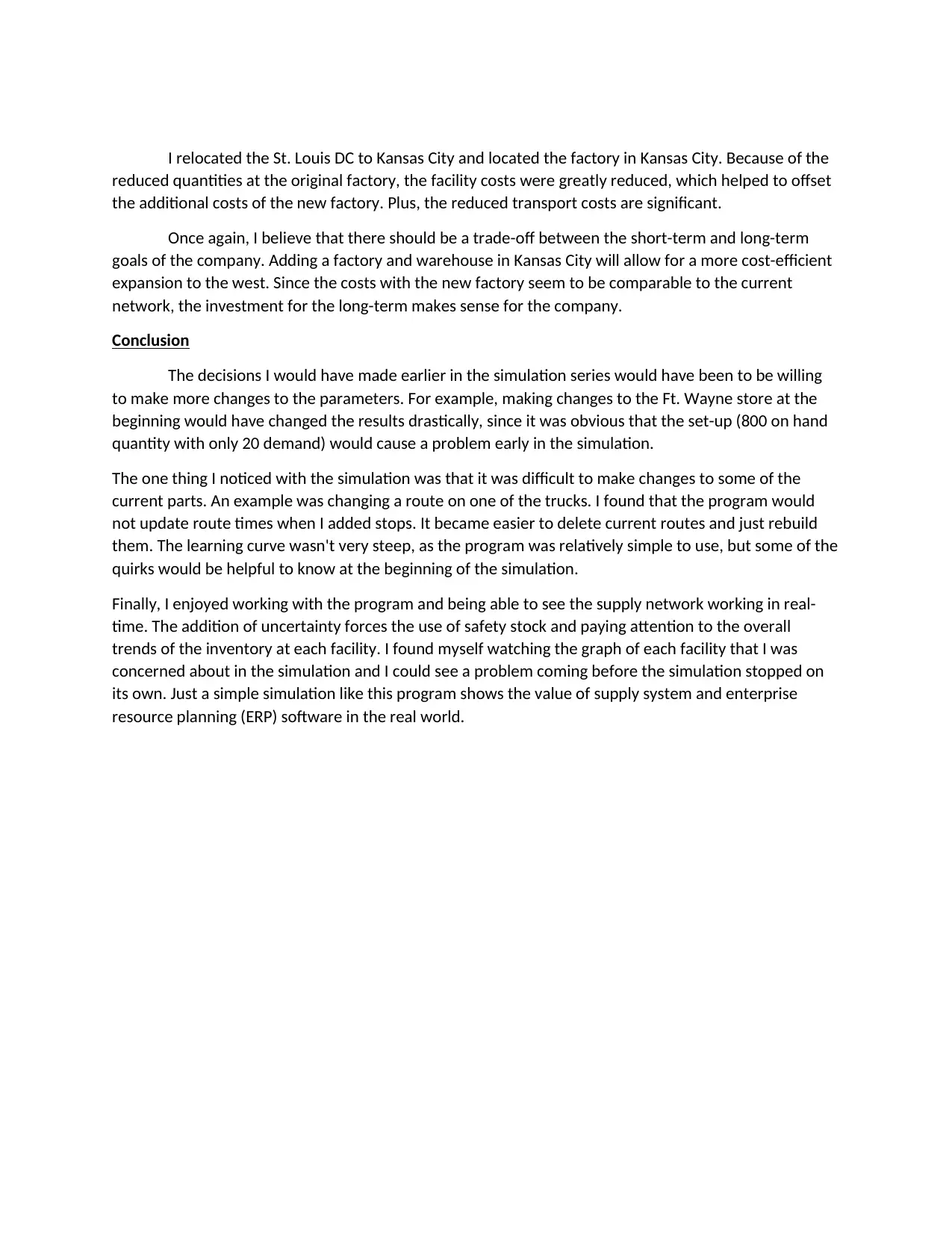
I relocated the St. Louis DC to Kansas City and located the factory in Kansas City. Because of the
reduced quantities at the original factory, the facility costs were greatly reduced, which helped to offset
the additional costs of the new factory. Plus, the reduced transport costs are significant.
Once again, I believe that there should be a trade-off between the short-term and long-term
goals of the company. Adding a factory and warehouse in Kansas City will allow for a more cost-efficient
expansion to the west. Since the costs with the new factory seem to be comparable to the current
network, the investment for the long-term makes sense for the company.
Conclusion
The decisions I would have made earlier in the simulation series would have been to be willing
to make more changes to the parameters. For example, making changes to the Ft. Wayne store at the
beginning would have changed the results drastically, since it was obvious that the set-up (800 on hand
quantity with only 20 demand) would cause a problem early in the simulation.
The one thing I noticed with the simulation was that it was difficult to make changes to some of the
current parts. An example was changing a route on one of the trucks. I found that the program would
not update route times when I added stops. It became easier to delete current routes and just rebuild
them. The learning curve wasn't very steep, as the program was relatively simple to use, but some of the
quirks would be helpful to know at the beginning of the simulation.
Finally, I enjoyed working with the program and being able to see the supply network working in real-
time. The addition of uncertainty forces the use of safety stock and paying attention to the overall
trends of the inventory at each facility. I found myself watching the graph of each facility that I was
concerned about in the simulation and I could see a problem coming before the simulation stopped on
its own. Just a simple simulation like this program shows the value of supply system and enterprise
resource planning (ERP) software in the real world.
reduced quantities at the original factory, the facility costs were greatly reduced, which helped to offset
the additional costs of the new factory. Plus, the reduced transport costs are significant.
Once again, I believe that there should be a trade-off between the short-term and long-term
goals of the company. Adding a factory and warehouse in Kansas City will allow for a more cost-efficient
expansion to the west. Since the costs with the new factory seem to be comparable to the current
network, the investment for the long-term makes sense for the company.
Conclusion
The decisions I would have made earlier in the simulation series would have been to be willing
to make more changes to the parameters. For example, making changes to the Ft. Wayne store at the
beginning would have changed the results drastically, since it was obvious that the set-up (800 on hand
quantity with only 20 demand) would cause a problem early in the simulation.
The one thing I noticed with the simulation was that it was difficult to make changes to some of the
current parts. An example was changing a route on one of the trucks. I found that the program would
not update route times when I added stops. It became easier to delete current routes and just rebuild
them. The learning curve wasn't very steep, as the program was relatively simple to use, but some of the
quirks would be helpful to know at the beginning of the simulation.
Finally, I enjoyed working with the program and being able to see the supply network working in real-
time. The addition of uncertainty forces the use of safety stock and paying attention to the overall
trends of the inventory at each facility. I found myself watching the graph of each facility that I was
concerned about in the simulation and I could see a problem coming before the simulation stopped on
its own. Just a simple simulation like this program shows the value of supply system and enterprise
resource planning (ERP) software in the real world.
⊘ This is a preview!⊘
Do you want full access?
Subscribe today to unlock all pages.

Trusted by 1+ million students worldwide
1 out of 15
Related Documents

Your All-in-One AI-Powered Toolkit for Academic Success.
+13062052269
info@desklib.com
Available 24*7 on WhatsApp / Email
Unlock your academic potential
© 2024 | Zucol Services PVT LTD | All rights reserved.