Probe Microscopy Section (SPM)
VerifiedAdded on 2022/08/25
|25
|5964
|27
AI Summary
Contribute Materials
Your contribution can guide someone’s learning journey. Share your
documents today.
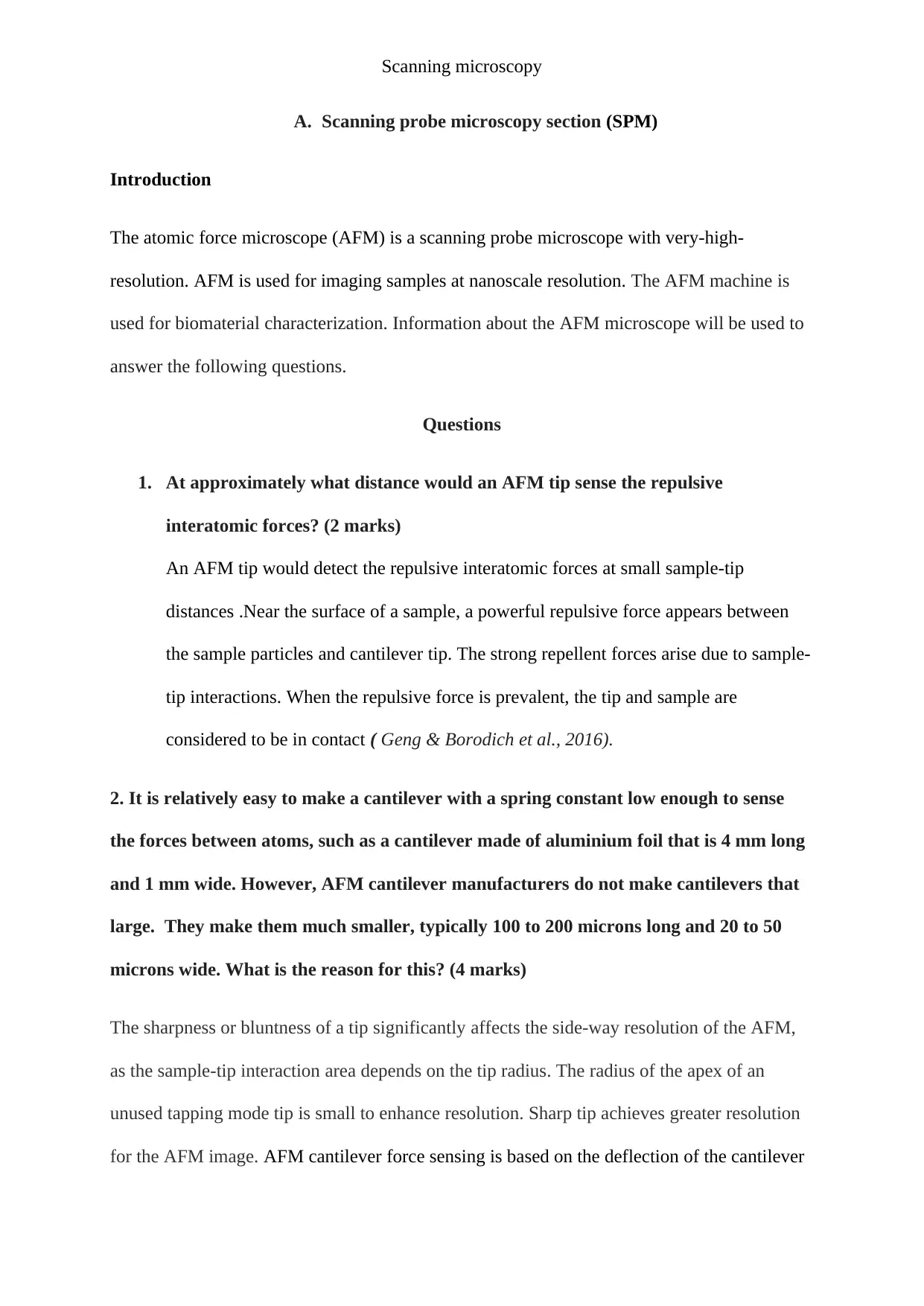
Scanning microscopy
A. Scanning probe microscopy section (SPM)
Introduction
The atomic force microscope (AFM) is a scanning probe microscope with very-high-
resolution. AFM is used for imaging samples at nanoscale resolution. The AFM machine is
used for biomaterial characterization. Information about the AFM microscope will be used to
answer the following questions.
Questions
1. At approximately what distance would an AFM tip sense the repulsive
interatomic forces? (2 marks)
An AFM tip would detect the repulsive interatomic forces at small sample-tip
distances .Near the surface of a sample, a powerful repulsive force appears between
the sample particles and cantilever tip. The strong repellent forces arise due to sample-
tip interactions. When the repulsive force is prevalent, the tip and sample are
considered to be in contact ( Geng & Borodich et al., 2016).
2. It is relatively easy to make a cantilever with a spring constant low enough to sense
the forces between atoms, such as a cantilever made of aluminium foil that is 4 mm long
and 1 mm wide. However, AFM cantilever manufacturers do not make cantilevers that
large. They make them much smaller, typically 100 to 200 microns long and 20 to 50
microns wide. What is the reason for this? (4 marks)
The sharpness or bluntness of a tip significantly affects the side-way resolution of the AFM,
as the sample-tip interaction area depends on the tip radius. The radius of the apex of an
unused tapping mode tip is small to enhance resolution. Sharp tip achieves greater resolution
for the AFM image. AFM cantilever force sensing is based on the deflection of the cantilever
A. Scanning probe microscopy section (SPM)
Introduction
The atomic force microscope (AFM) is a scanning probe microscope with very-high-
resolution. AFM is used for imaging samples at nanoscale resolution. The AFM machine is
used for biomaterial characterization. Information about the AFM microscope will be used to
answer the following questions.
Questions
1. At approximately what distance would an AFM tip sense the repulsive
interatomic forces? (2 marks)
An AFM tip would detect the repulsive interatomic forces at small sample-tip
distances .Near the surface of a sample, a powerful repulsive force appears between
the sample particles and cantilever tip. The strong repellent forces arise due to sample-
tip interactions. When the repulsive force is prevalent, the tip and sample are
considered to be in contact ( Geng & Borodich et al., 2016).
2. It is relatively easy to make a cantilever with a spring constant low enough to sense
the forces between atoms, such as a cantilever made of aluminium foil that is 4 mm long
and 1 mm wide. However, AFM cantilever manufacturers do not make cantilevers that
large. They make them much smaller, typically 100 to 200 microns long and 20 to 50
microns wide. What is the reason for this? (4 marks)
The sharpness or bluntness of a tip significantly affects the side-way resolution of the AFM,
as the sample-tip interaction area depends on the tip radius. The radius of the apex of an
unused tapping mode tip is small to enhance resolution. Sharp tip achieves greater resolution
for the AFM image. AFM cantilever force sensing is based on the deflection of the cantilever
Secure Best Marks with AI Grader
Need help grading? Try our AI Grader for instant feedback on your assignments.
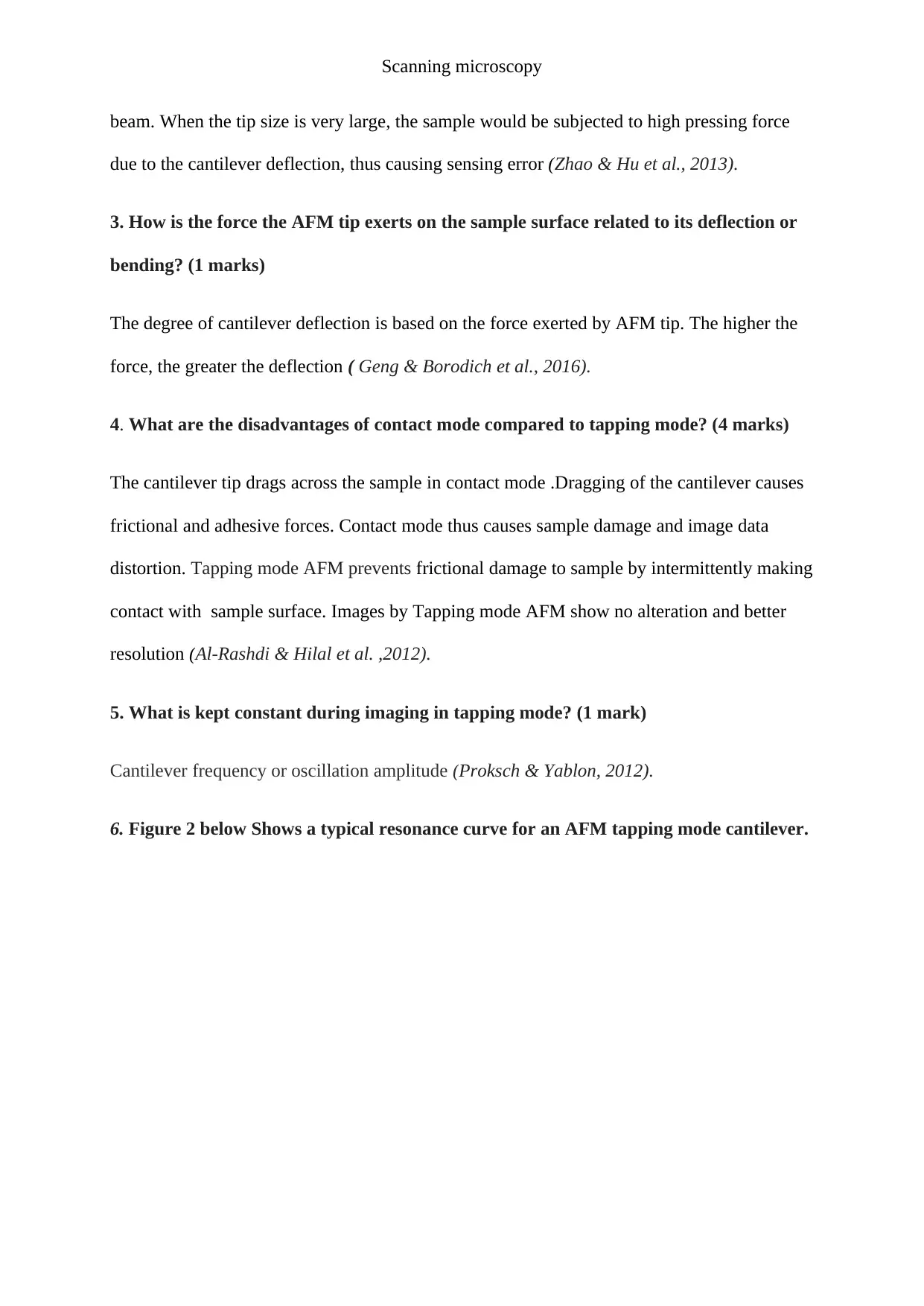
Scanning microscopy
beam. When the tip size is very large, the sample would be subjected to high pressing force
due to the cantilever deflection, thus causing sensing error (Zhao & Hu et al., 2013).
3. How is the force the AFM tip exerts on the sample surface related to its deflection or
bending? (1 marks)
The degree of cantilever deflection is based on the force exerted by AFM tip. The higher the
force, the greater the deflection ( Geng & Borodich et al., 2016).
4. What are the disadvantages of contact mode compared to tapping mode? (4 marks)
The cantilever tip drags across the sample in contact mode .Dragging of the cantilever causes
frictional and adhesive forces. Contact mode thus causes sample damage and image data
distortion. Tapping mode AFM prevents frictional damage to sample by intermittently making
contact with sample surface. Images by Tapping mode AFM show no alteration and better
resolution (Al-Rashdi & Hilal et al. ,2012).
5. What is kept constant during imaging in tapping mode? (1 mark)
Cantilever frequency or oscillation amplitude (Proksch & Yablon, 2012).
6. Figure 2 below Shows a typical resonance curve for an AFM tapping mode cantilever.
beam. When the tip size is very large, the sample would be subjected to high pressing force
due to the cantilever deflection, thus causing sensing error (Zhao & Hu et al., 2013).
3. How is the force the AFM tip exerts on the sample surface related to its deflection or
bending? (1 marks)
The degree of cantilever deflection is based on the force exerted by AFM tip. The higher the
force, the greater the deflection ( Geng & Borodich et al., 2016).
4. What are the disadvantages of contact mode compared to tapping mode? (4 marks)
The cantilever tip drags across the sample in contact mode .Dragging of the cantilever causes
frictional and adhesive forces. Contact mode thus causes sample damage and image data
distortion. Tapping mode AFM prevents frictional damage to sample by intermittently making
contact with sample surface. Images by Tapping mode AFM show no alteration and better
resolution (Al-Rashdi & Hilal et al. ,2012).
5. What is kept constant during imaging in tapping mode? (1 mark)
Cantilever frequency or oscillation amplitude (Proksch & Yablon, 2012).
6. Figure 2 below Shows a typical resonance curve for an AFM tapping mode cantilever.
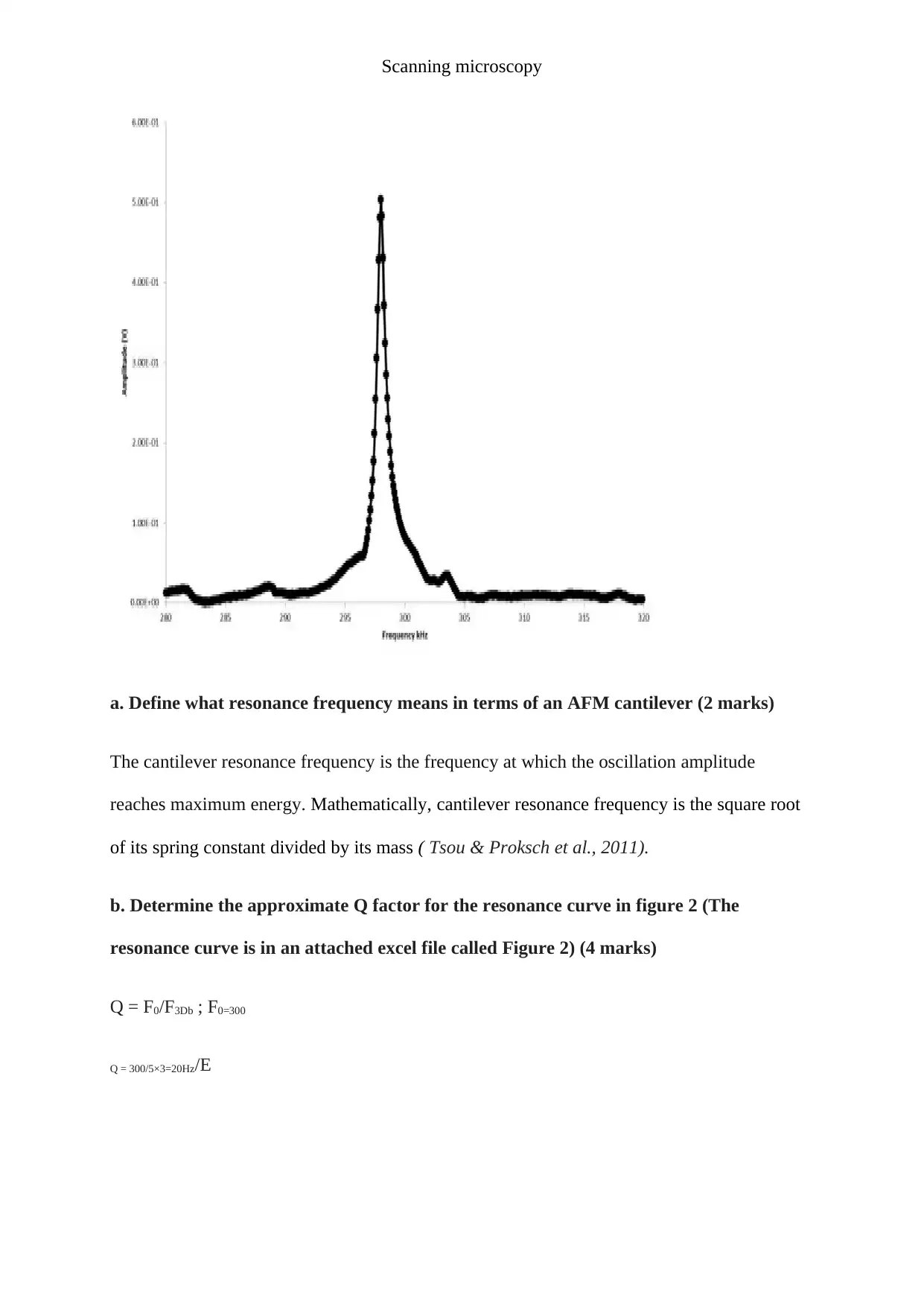
Scanning microscopy
a. Define what resonance frequency means in terms of an AFM cantilever (2 marks)
The cantilever resonance frequency is the frequency at which the oscillation amplitude
reaches maximum energy. Mathematically, cantilever resonance frequency is the square root
of its spring constant divided by its mass ( Tsou & Proksch et al., 2011).
b. Determine the approximate Q factor for the resonance curve in figure 2 (The
resonance curve is in an attached excel file called Figure 2) (4 marks)
Q = F0/F3Db ; F0=300
Q = 300/5×3=20Hz/E
a. Define what resonance frequency means in terms of an AFM cantilever (2 marks)
The cantilever resonance frequency is the frequency at which the oscillation amplitude
reaches maximum energy. Mathematically, cantilever resonance frequency is the square root
of its spring constant divided by its mass ( Tsou & Proksch et al., 2011).
b. Determine the approximate Q factor for the resonance curve in figure 2 (The
resonance curve is in an attached excel file called Figure 2) (4 marks)
Q = F0/F3Db ; F0=300
Q = 300/5×3=20Hz/E
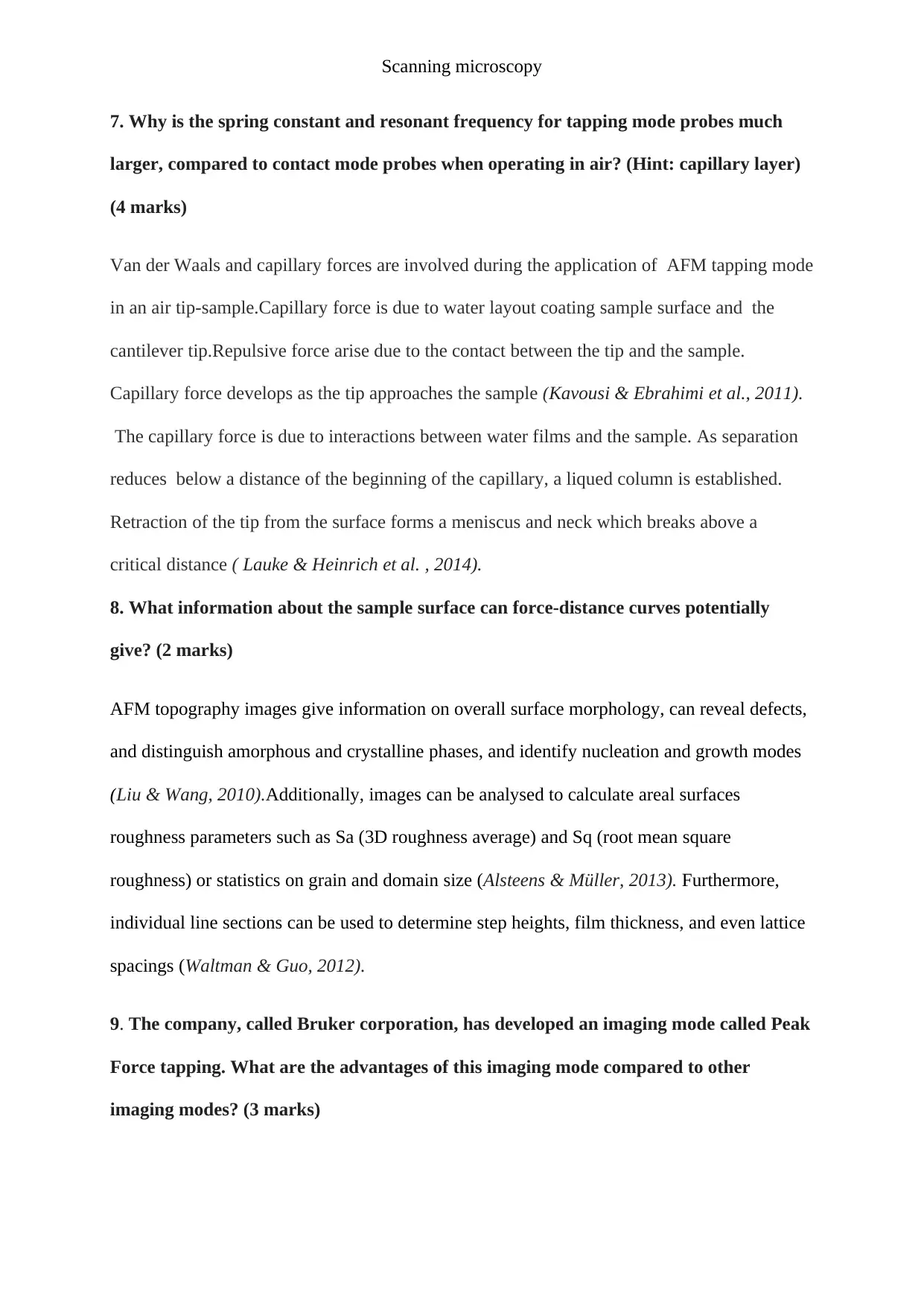
Scanning microscopy
7. Why is the spring constant and resonant frequency for tapping mode probes much
larger, compared to contact mode probes when operating in air? (Hint: capillary layer)
(4 marks)
Van der Waals and capillary forces are involved during the application of AFM tapping mode
in an air tip-sample.Capillary force is due to water layout coating sample surface and the
cantilever tip.Repulsive force arise due to the contact between the tip and the sample.
Capillary force develops as the tip approaches the sample (Kavousi & Ebrahimi et al., 2011).
The capillary force is due to interactions between water films and the sample. As separation
reduces below a distance of the beginning of the capillary, a liqued column is established.
Retraction of the tip from the surface forms a meniscus and neck which breaks above a
critical distance ( Lauke & Heinrich et al. , 2014).
8. What information about the sample surface can force-distance curves potentially
give? (2 marks)
AFM topography images give information on overall surface morphology, can reveal defects,
and distinguish amorphous and crystalline phases, and identify nucleation and growth modes
(Liu & Wang, 2010).Additionally, images can be analysed to calculate areal surfaces
roughness parameters such as Sa (3D roughness average) and Sq (root mean square
roughness) or statistics on grain and domain size (Alsteens & Müller, 2013). Furthermore,
individual line sections can be used to determine step heights, film thickness, and even lattice
spacings (Waltman & Guo, 2012).
9. The company, called Bruker corporation, has developed an imaging mode called Peak
Force tapping. What are the advantages of this imaging mode compared to other
imaging modes? (3 marks)
7. Why is the spring constant and resonant frequency for tapping mode probes much
larger, compared to contact mode probes when operating in air? (Hint: capillary layer)
(4 marks)
Van der Waals and capillary forces are involved during the application of AFM tapping mode
in an air tip-sample.Capillary force is due to water layout coating sample surface and the
cantilever tip.Repulsive force arise due to the contact between the tip and the sample.
Capillary force develops as the tip approaches the sample (Kavousi & Ebrahimi et al., 2011).
The capillary force is due to interactions between water films and the sample. As separation
reduces below a distance of the beginning of the capillary, a liqued column is established.
Retraction of the tip from the surface forms a meniscus and neck which breaks above a
critical distance ( Lauke & Heinrich et al. , 2014).
8. What information about the sample surface can force-distance curves potentially
give? (2 marks)
AFM topography images give information on overall surface morphology, can reveal defects,
and distinguish amorphous and crystalline phases, and identify nucleation and growth modes
(Liu & Wang, 2010).Additionally, images can be analysed to calculate areal surfaces
roughness parameters such as Sa (3D roughness average) and Sq (root mean square
roughness) or statistics on grain and domain size (Alsteens & Müller, 2013). Furthermore,
individual line sections can be used to determine step heights, film thickness, and even lattice
spacings (Waltman & Guo, 2012).
9. The company, called Bruker corporation, has developed an imaging mode called Peak
Force tapping. What are the advantages of this imaging mode compared to other
imaging modes? (3 marks)
Secure Best Marks with AI Grader
Need help grading? Try our AI Grader for instant feedback on your assignments.
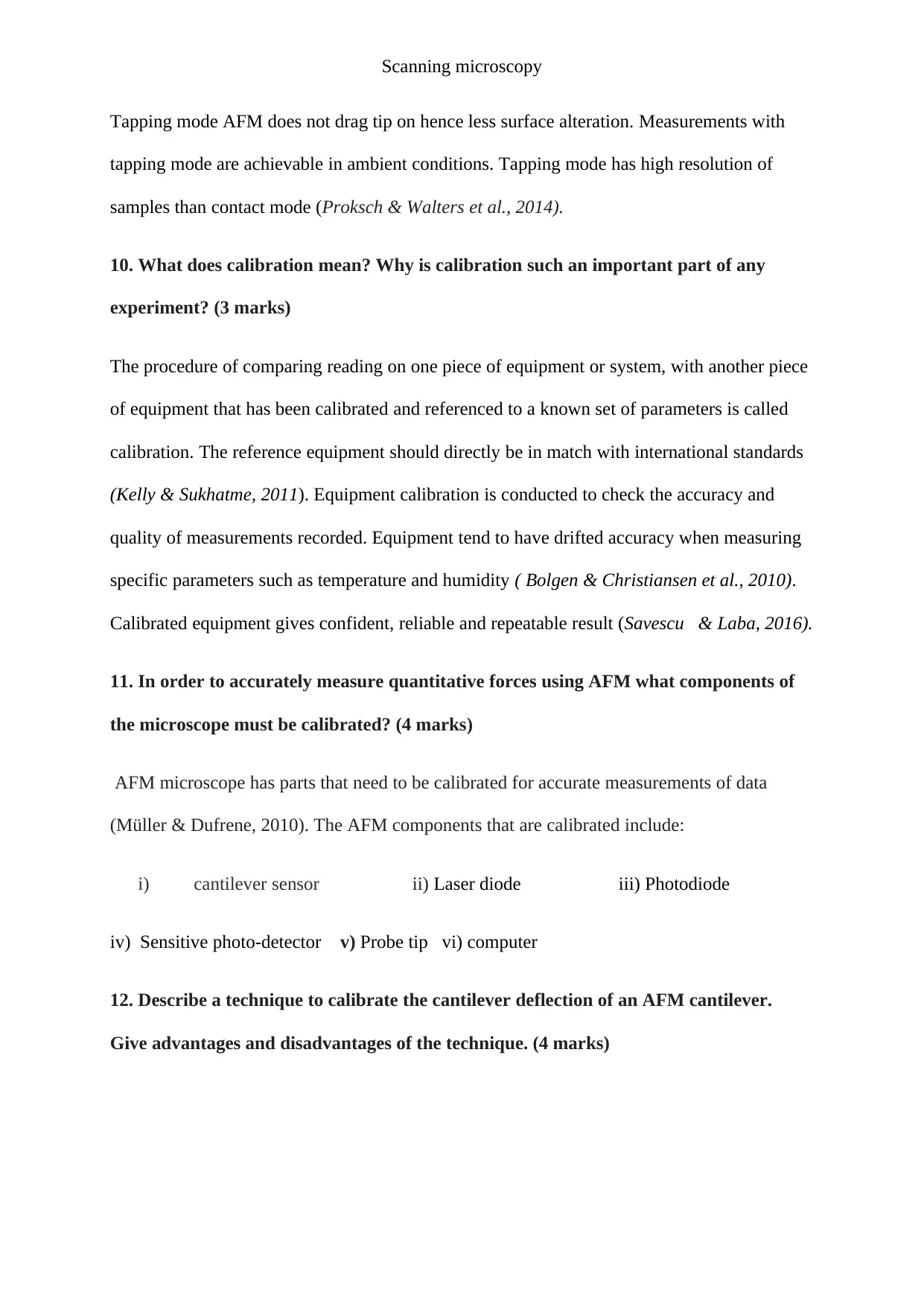
Scanning microscopy
Tapping mode AFM does not drag tip on hence less surface alteration. Measurements with
tapping mode are achievable in ambient conditions. Tapping mode has high resolution of
samples than contact mode (Proksch & Walters et al., 2014).
10. What does calibration mean? Why is calibration such an important part of any
experiment? (3 marks)
The procedure of comparing reading on one piece of equipment or system, with another piece
of equipment that has been calibrated and referenced to a known set of parameters is called
calibration. The reference equipment should directly be in match with international standards
(Kelly & Sukhatme, 2011). Equipment calibration is conducted to check the accuracy and
quality of measurements recorded. Equipment tend to have drifted accuracy when measuring
specific parameters such as temperature and humidity ( Bolgen & Christiansen et al., 2010).
Calibrated equipment gives confident, reliable and repeatable result (Savescu & Laba, 2016).
11. In order to accurately measure quantitative forces using AFM what components of
the microscope must be calibrated? (4 marks)
AFM microscope has parts that need to be calibrated for accurate measurements of data
(Müller & Dufrene, 2010). The AFM components that are calibrated include:
i) cantilever sensor ii) Laser diode iii) Photodiode
iv) Sensitive photo-detector v) Probe tip vi) computer
12. Describe a technique to calibrate the cantilever deflection of an AFM cantilever.
Give advantages and disadvantages of the technique. (4 marks)
Tapping mode AFM does not drag tip on hence less surface alteration. Measurements with
tapping mode are achievable in ambient conditions. Tapping mode has high resolution of
samples than contact mode (Proksch & Walters et al., 2014).
10. What does calibration mean? Why is calibration such an important part of any
experiment? (3 marks)
The procedure of comparing reading on one piece of equipment or system, with another piece
of equipment that has been calibrated and referenced to a known set of parameters is called
calibration. The reference equipment should directly be in match with international standards
(Kelly & Sukhatme, 2011). Equipment calibration is conducted to check the accuracy and
quality of measurements recorded. Equipment tend to have drifted accuracy when measuring
specific parameters such as temperature and humidity ( Bolgen & Christiansen et al., 2010).
Calibrated equipment gives confident, reliable and repeatable result (Savescu & Laba, 2016).
11. In order to accurately measure quantitative forces using AFM what components of
the microscope must be calibrated? (4 marks)
AFM microscope has parts that need to be calibrated for accurate measurements of data
(Müller & Dufrene, 2010). The AFM components that are calibrated include:
i) cantilever sensor ii) Laser diode iii) Photodiode
iv) Sensitive photo-detector v) Probe tip vi) computer
12. Describe a technique to calibrate the cantilever deflection of an AFM cantilever.
Give advantages and disadvantages of the technique. (4 marks)
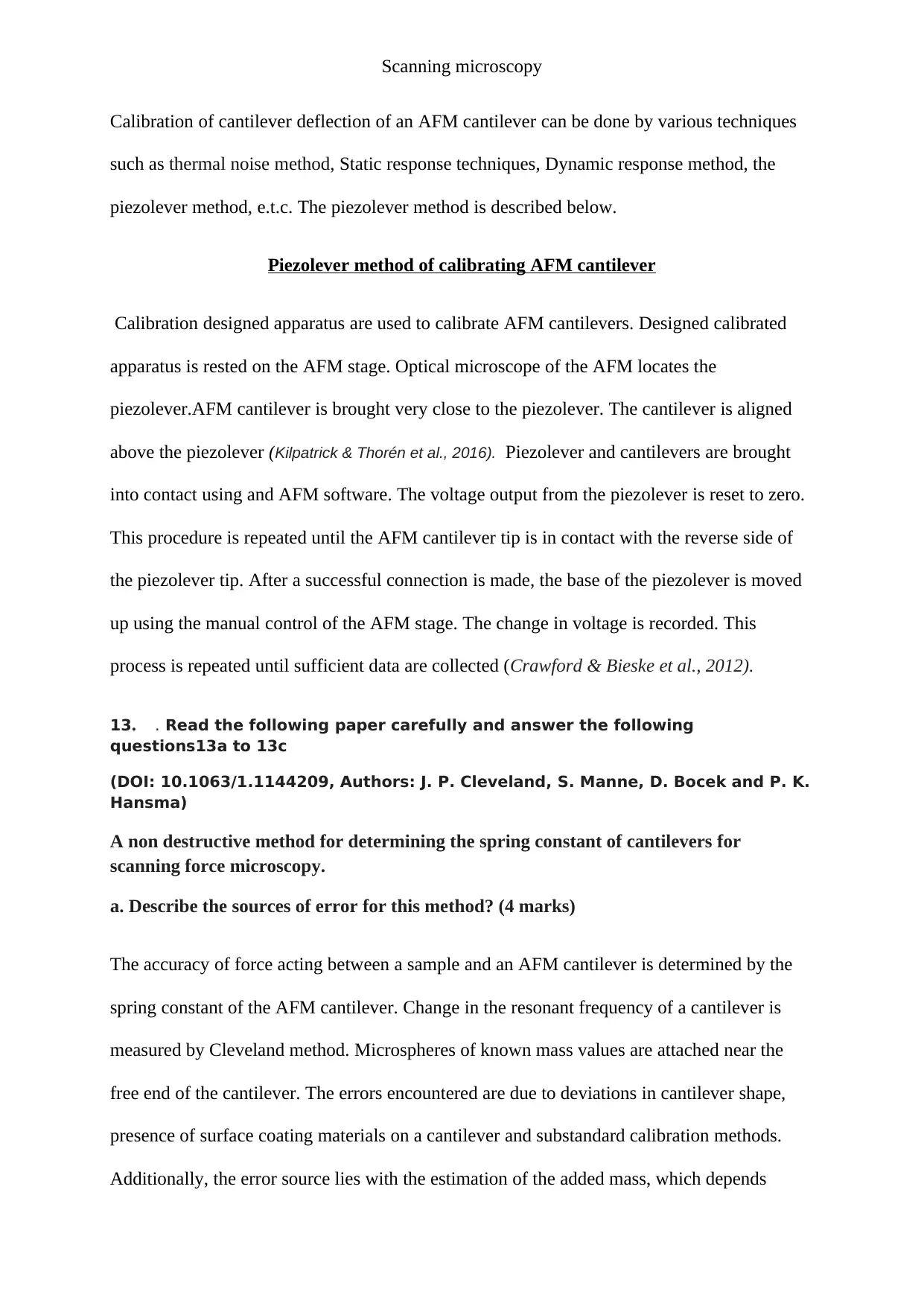
Scanning microscopy
Calibration of cantilever deflection of an AFM cantilever can be done by various techniques
such as thermal noise method, Static response techniques, Dynamic response method, the
piezolever method, e.t.c. The piezolever method is described below.
Piezolever method of calibrating AFM cantilever
Calibration designed apparatus are used to calibrate AFM cantilevers. Designed calibrated
apparatus is rested on the AFM stage. Optical microscope of the AFM locates the
piezolever.AFM cantilever is brought very close to the piezolever. The cantilever is aligned
above the piezolever (Kilpatrick & Thorén et al., 2016). Piezolever and cantilevers are brought
into contact using and AFM software. The voltage output from the piezolever is reset to zero.
This procedure is repeated until the AFM cantilever tip is in contact with the reverse side of
the piezolever tip. After a successful connection is made, the base of the piezolever is moved
up using the manual control of the AFM stage. The change in voltage is recorded. This
process is repeated until sufficient data are collected (Crawford & Bieske et al., 2012).
13. . Read the following paper carefully and answer the following
questions13a to 13c
(DOI: 10.1063/1.1144209, Authors: J. P. Cleveland, S. Manne, D. Bocek and P. K.
Hansma)
A non destructive method for determining the spring constant of cantilevers for
scanning force microscopy.
a. Describe the sources of error for this method? (4 marks)
The accuracy of force acting between a sample and an AFM cantilever is determined by the
spring constant of the AFM cantilever. Change in the resonant frequency of a cantilever is
measured by Cleveland method. Microspheres of known mass values are attached near the
free end of the cantilever. The errors encountered are due to deviations in cantilever shape,
presence of surface coating materials on a cantilever and substandard calibration methods.
Additionally, the error source lies with the estimation of the added mass, which depends
Calibration of cantilever deflection of an AFM cantilever can be done by various techniques
such as thermal noise method, Static response techniques, Dynamic response method, the
piezolever method, e.t.c. The piezolever method is described below.
Piezolever method of calibrating AFM cantilever
Calibration designed apparatus are used to calibrate AFM cantilevers. Designed calibrated
apparatus is rested on the AFM stage. Optical microscope of the AFM locates the
piezolever.AFM cantilever is brought very close to the piezolever. The cantilever is aligned
above the piezolever (Kilpatrick & Thorén et al., 2016). Piezolever and cantilevers are brought
into contact using and AFM software. The voltage output from the piezolever is reset to zero.
This procedure is repeated until the AFM cantilever tip is in contact with the reverse side of
the piezolever tip. After a successful connection is made, the base of the piezolever is moved
up using the manual control of the AFM stage. The change in voltage is recorded. This
process is repeated until sufficient data are collected (Crawford & Bieske et al., 2012).
13. . Read the following paper carefully and answer the following
questions13a to 13c
(DOI: 10.1063/1.1144209, Authors: J. P. Cleveland, S. Manne, D. Bocek and P. K.
Hansma)
A non destructive method for determining the spring constant of cantilevers for
scanning force microscopy.
a. Describe the sources of error for this method? (4 marks)
The accuracy of force acting between a sample and an AFM cantilever is determined by the
spring constant of the AFM cantilever. Change in the resonant frequency of a cantilever is
measured by Cleveland method. Microspheres of known mass values are attached near the
free end of the cantilever. The errors encountered are due to deviations in cantilever shape,
presence of surface coating materials on a cantilever and substandard calibration methods.
Additionally, the error source lies with the estimation of the added mass, which depends
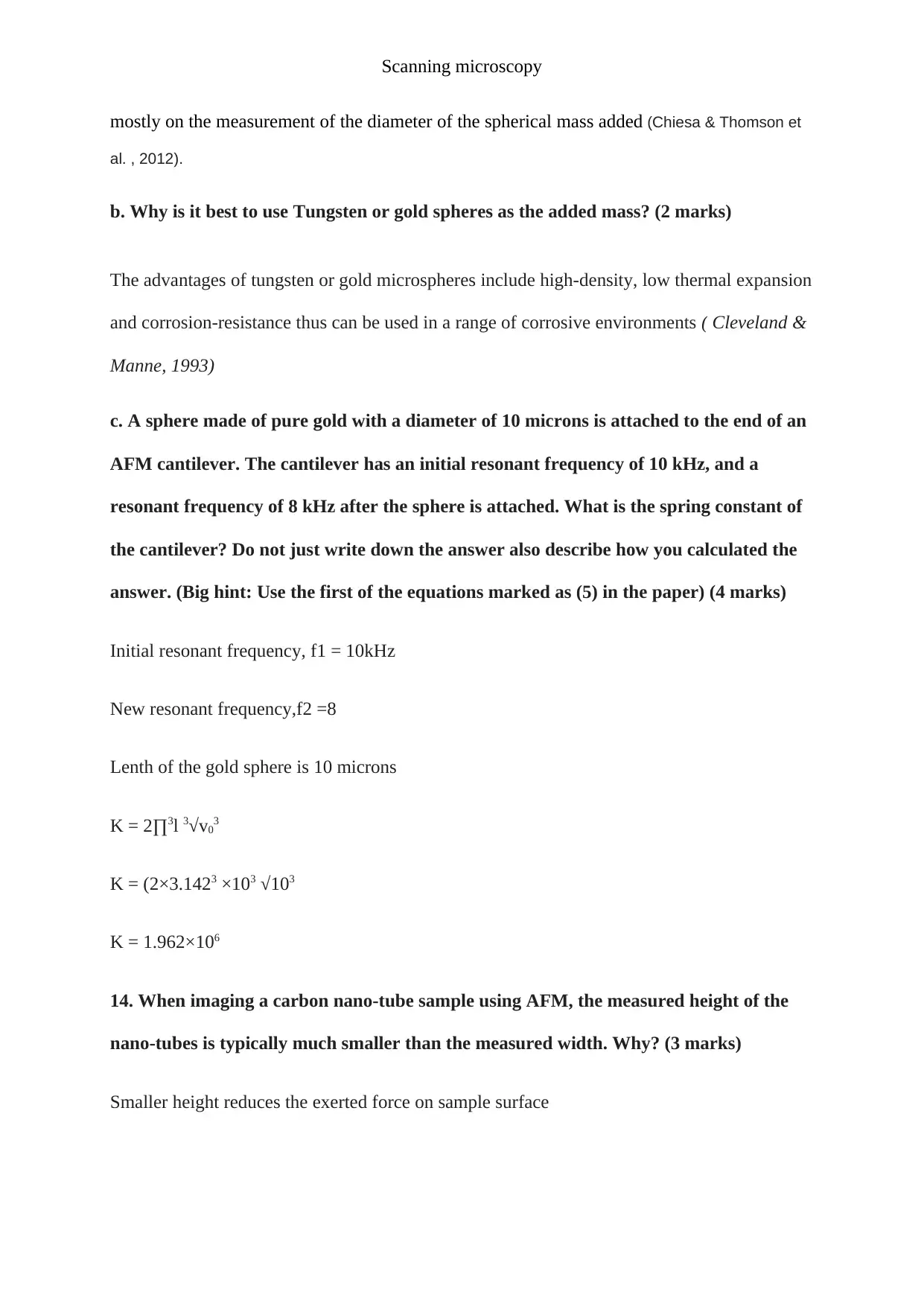
Scanning microscopy
mostly on the measurement of the diameter of the spherical mass added (Chiesa & Thomson et
al. , 2012).
b. Why is it best to use Tungsten or gold spheres as the added mass? (2 marks)
The advantages of tungsten or gold microspheres include high-density, low thermal expansion
and corrosion-resistance thus can be used in a range of corrosive environments ( Cleveland &
Manne, 1993)
c. A sphere made of pure gold with a diameter of 10 microns is attached to the end of an
AFM cantilever. The cantilever has an initial resonant frequency of 10 kHz, and a
resonant frequency of 8 kHz after the sphere is attached. What is the spring constant of
the cantilever? Do not just write down the answer also describe how you calculated the
answer. (Big hint: Use the first of the equations marked as (5) in the paper) (4 marks)
Initial resonant frequency, f1 = 10kHz
New resonant frequency,f2 =8
Lenth of the gold sphere is 10 microns
K = 2∏3l 3√v03
K = (2×3.1423 ×103 √103
K = 1.962×106
14. When imaging a carbon nano-tube sample using AFM, the measured height of the
nano-tubes is typically much smaller than the measured width. Why? (3 marks)
Smaller height reduces the exerted force on sample surface
mostly on the measurement of the diameter of the spherical mass added (Chiesa & Thomson et
al. , 2012).
b. Why is it best to use Tungsten or gold spheres as the added mass? (2 marks)
The advantages of tungsten or gold microspheres include high-density, low thermal expansion
and corrosion-resistance thus can be used in a range of corrosive environments ( Cleveland &
Manne, 1993)
c. A sphere made of pure gold with a diameter of 10 microns is attached to the end of an
AFM cantilever. The cantilever has an initial resonant frequency of 10 kHz, and a
resonant frequency of 8 kHz after the sphere is attached. What is the spring constant of
the cantilever? Do not just write down the answer also describe how you calculated the
answer. (Big hint: Use the first of the equations marked as (5) in the paper) (4 marks)
Initial resonant frequency, f1 = 10kHz
New resonant frequency,f2 =8
Lenth of the gold sphere is 10 microns
K = 2∏3l 3√v03
K = (2×3.1423 ×103 √103
K = 1.962×106
14. When imaging a carbon nano-tube sample using AFM, the measured height of the
nano-tubes is typically much smaller than the measured width. Why? (3 marks)
Smaller height reduces the exerted force on sample surface
Paraphrase This Document
Need a fresh take? Get an instant paraphrase of this document with our AI Paraphraser
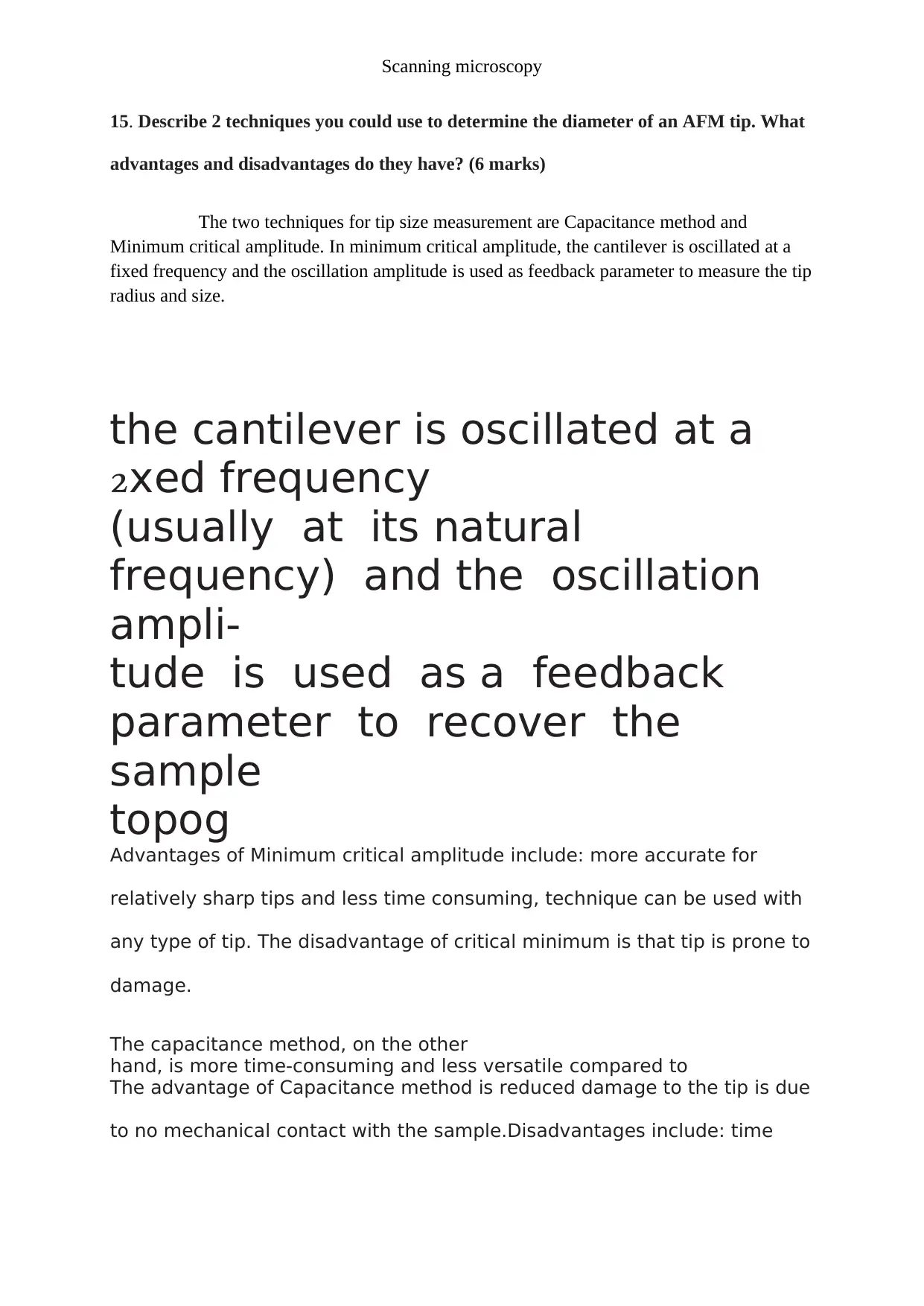
Scanning microscopy
15. Describe 2 techniques you could use to determine the diameter of an AFM tip. What
advantages and disadvantages do they have? (6 marks)
The two techniques for tip size measurement are Capacitance method and
Minimum critical amplitude. In minimum critical amplitude, the cantilever is oscillated at a
fixed frequency and the oscillation amplitude is used as feedback parameter to measure the tip
radius and size.
the cantilever is oscillated at a
xed frequency
(usually at its natural
frequency) and the oscillation
ampli-
tude is used as a feedback
parameter to recover the
sample
topog
Advantages of Minimum critical amplitude include: more accurate for
relatively sharp tips and less time consuming, technique can be used with
any type of tip. The disadvantage of critical minimum is that tip is prone to
damage.
The capacitance method, on the other
hand, is more time-consuming and less versatile compared to
The advantage of Capacitance method is reduced damage to the tip is due
to no mechanical contact with the sample.Disadvantages include: time
15. Describe 2 techniques you could use to determine the diameter of an AFM tip. What
advantages and disadvantages do they have? (6 marks)
The two techniques for tip size measurement are Capacitance method and
Minimum critical amplitude. In minimum critical amplitude, the cantilever is oscillated at a
fixed frequency and the oscillation amplitude is used as feedback parameter to measure the tip
radius and size.
the cantilever is oscillated at a
xed frequency
(usually at its natural
frequency) and the oscillation
ampli-
tude is used as a feedback
parameter to recover the
sample
topog
Advantages of Minimum critical amplitude include: more accurate for
relatively sharp tips and less time consuming, technique can be used with
any type of tip. The disadvantage of critical minimum is that tip is prone to
damage.
The capacitance method, on the other
hand, is more time-consuming and less versatile compared to
The advantage of Capacitance method is reduced damage to the tip is due
to no mechanical contact with the sample.Disadvantages include: time
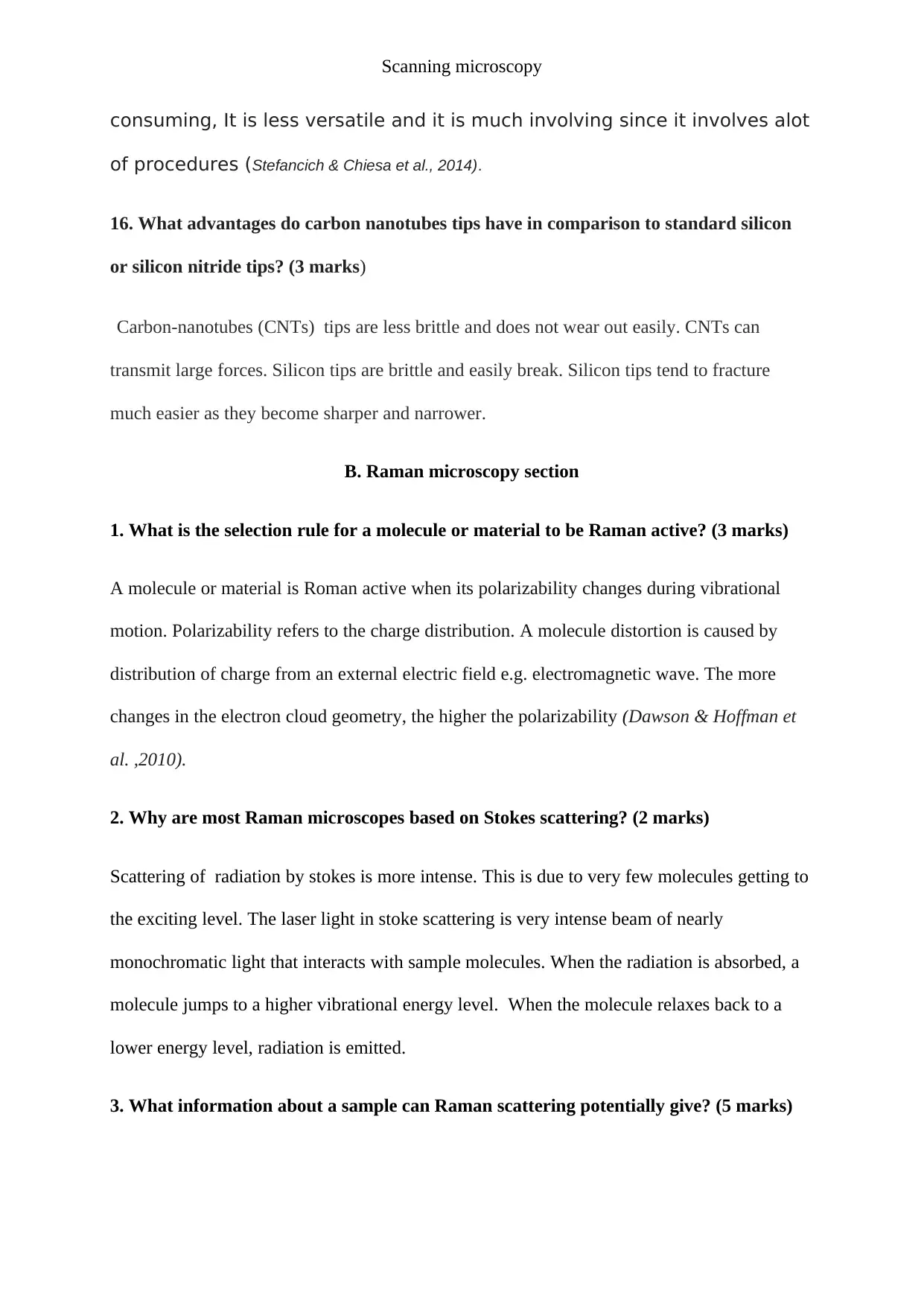
Scanning microscopy
consuming, It is less versatile and it is much involving since it involves alot
of procedures (Stefancich & Chiesa et al., 2014).
16. What advantages do carbon nanotubes tips have in comparison to standard silicon
or silicon nitride tips? (3 marks)
Carbon-nanotubes (CNTs) tips are less brittle and does not wear out easily. CNTs can
transmit large forces. Silicon tips are brittle and easily break. Silicon tips tend to fracture
much easier as they become sharper and narrower.
B. Raman microscopy section
1. What is the selection rule for a molecule or material to be Raman active? (3 marks)
A molecule or material is Roman active when its polarizability changes during vibrational
motion. Polarizability refers to the charge distribution. A molecule distortion is caused by
distribution of charge from an external electric field e.g. electromagnetic wave. The more
changes in the electron cloud geometry, the higher the polarizability (Dawson & Hoffman et
al. ,2010).
2. Why are most Raman microscopes based on Stokes scattering? (2 marks)
Scattering of radiation by stokes is more intense. This is due to very few molecules getting to
the exciting level. The laser light in stoke scattering is very intense beam of nearly
monochromatic light that interacts with sample molecules. When the radiation is absorbed, a
molecule jumps to a higher vibrational energy level. When the molecule relaxes back to a
lower energy level, radiation is emitted.
3. What information about a sample can Raman scattering potentially give? (5 marks)
consuming, It is less versatile and it is much involving since it involves alot
of procedures (Stefancich & Chiesa et al., 2014).
16. What advantages do carbon nanotubes tips have in comparison to standard silicon
or silicon nitride tips? (3 marks)
Carbon-nanotubes (CNTs) tips are less brittle and does not wear out easily. CNTs can
transmit large forces. Silicon tips are brittle and easily break. Silicon tips tend to fracture
much easier as they become sharper and narrower.
B. Raman microscopy section
1. What is the selection rule for a molecule or material to be Raman active? (3 marks)
A molecule or material is Roman active when its polarizability changes during vibrational
motion. Polarizability refers to the charge distribution. A molecule distortion is caused by
distribution of charge from an external electric field e.g. electromagnetic wave. The more
changes in the electron cloud geometry, the higher the polarizability (Dawson & Hoffman et
al. ,2010).
2. Why are most Raman microscopes based on Stokes scattering? (2 marks)
Scattering of radiation by stokes is more intense. This is due to very few molecules getting to
the exciting level. The laser light in stoke scattering is very intense beam of nearly
monochromatic light that interacts with sample molecules. When the radiation is absorbed, a
molecule jumps to a higher vibrational energy level. When the molecule relaxes back to a
lower energy level, radiation is emitted.
3. What information about a sample can Raman scattering potentially give? (5 marks)
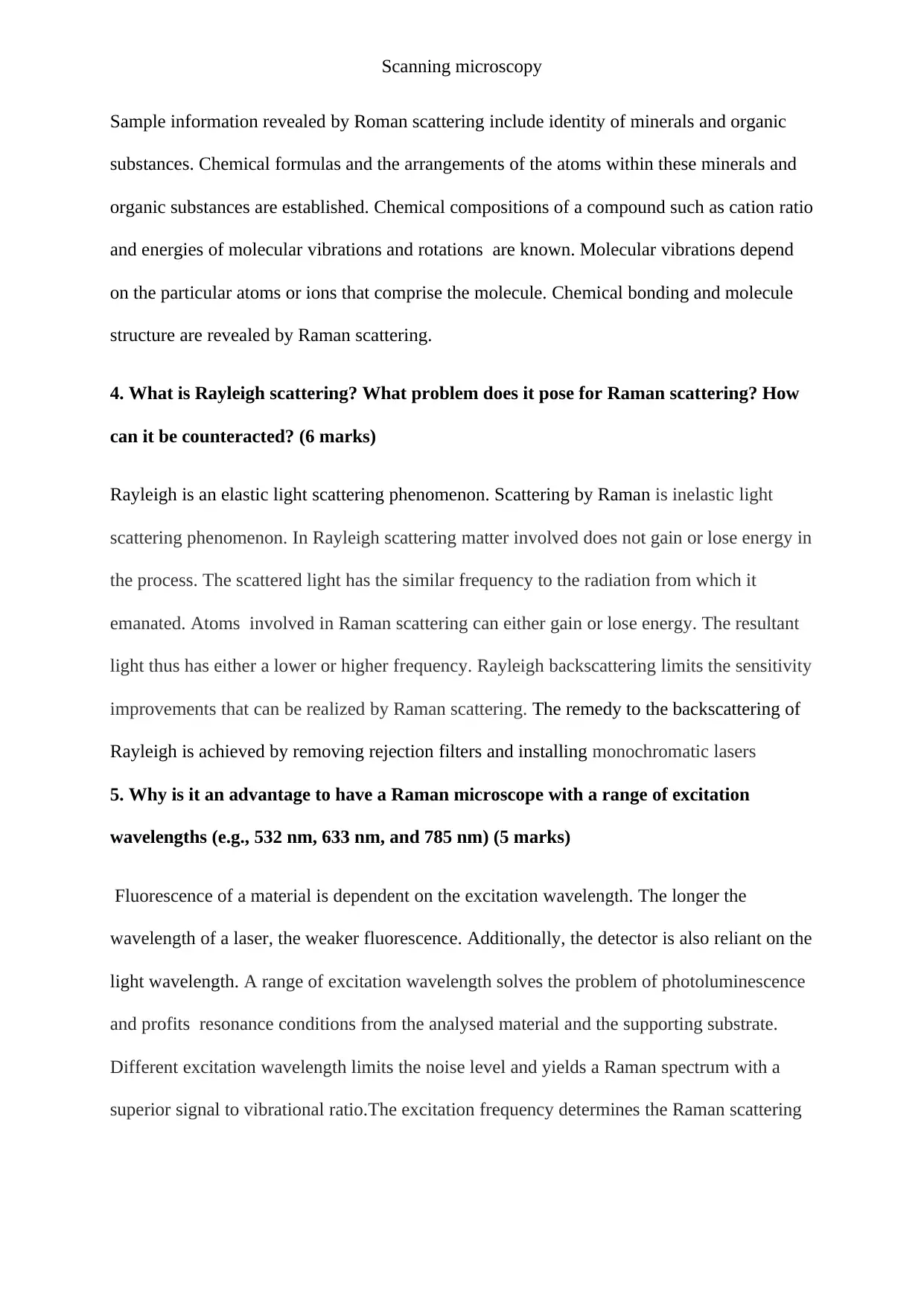
Scanning microscopy
Sample information revealed by Roman scattering include identity of minerals and organic
substances. Chemical formulas and the arrangements of the atoms within these minerals and
organic substances are established. Chemical compositions of a compound such as cation ratio
and energies of molecular vibrations and rotations are known. Molecular vibrations depend
on the particular atoms or ions that comprise the molecule. Chemical bonding and molecule
structure are revealed by Raman scattering.
4. What is Rayleigh scattering? What problem does it pose for Raman scattering? How
can it be counteracted? (6 marks)
Rayleigh is an elastic light scattering phenomenon. Scattering by Raman is inelastic light
scattering phenomenon. In Rayleigh scattering matter involved does not gain or lose energy in
the process. The scattered light has the similar frequency to the radiation from which it
emanated. Atoms involved in Raman scattering can either gain or lose energy. The resultant
light thus has either a lower or higher frequency. Rayleigh backscattering limits the sensitivity
improvements that can be realized by Raman scattering. The remedy to the backscattering of
Rayleigh is achieved by removing rejection filters and installing monochromatic lasers
5. Why is it an advantage to have a Raman microscope with a range of excitation
wavelengths (e.g., 532 nm, 633 nm, and 785 nm) (5 marks)
Fluorescence of a material is dependent on the excitation wavelength. The longer the
wavelength of a laser, the weaker fluorescence. Additionally, the detector is also reliant on the
light wavelength. A range of excitation wavelength solves the problem of photoluminescence
and profits resonance conditions from the analysed material and the supporting substrate.
Different excitation wavelength limits the noise level and yields a Raman spectrum with a
superior signal to vibrational ratio.The excitation frequency determines the Raman scattering
Sample information revealed by Roman scattering include identity of minerals and organic
substances. Chemical formulas and the arrangements of the atoms within these minerals and
organic substances are established. Chemical compositions of a compound such as cation ratio
and energies of molecular vibrations and rotations are known. Molecular vibrations depend
on the particular atoms or ions that comprise the molecule. Chemical bonding and molecule
structure are revealed by Raman scattering.
4. What is Rayleigh scattering? What problem does it pose for Raman scattering? How
can it be counteracted? (6 marks)
Rayleigh is an elastic light scattering phenomenon. Scattering by Raman is inelastic light
scattering phenomenon. In Rayleigh scattering matter involved does not gain or lose energy in
the process. The scattered light has the similar frequency to the radiation from which it
emanated. Atoms involved in Raman scattering can either gain or lose energy. The resultant
light thus has either a lower or higher frequency. Rayleigh backscattering limits the sensitivity
improvements that can be realized by Raman scattering. The remedy to the backscattering of
Rayleigh is achieved by removing rejection filters and installing monochromatic lasers
5. Why is it an advantage to have a Raman microscope with a range of excitation
wavelengths (e.g., 532 nm, 633 nm, and 785 nm) (5 marks)
Fluorescence of a material is dependent on the excitation wavelength. The longer the
wavelength of a laser, the weaker fluorescence. Additionally, the detector is also reliant on the
light wavelength. A range of excitation wavelength solves the problem of photoluminescence
and profits resonance conditions from the analysed material and the supporting substrate.
Different excitation wavelength limits the noise level and yields a Raman spectrum with a
superior signal to vibrational ratio.The excitation frequency determines the Raman scattering
Secure Best Marks with AI Grader
Need help grading? Try our AI Grader for instant feedback on your assignments.
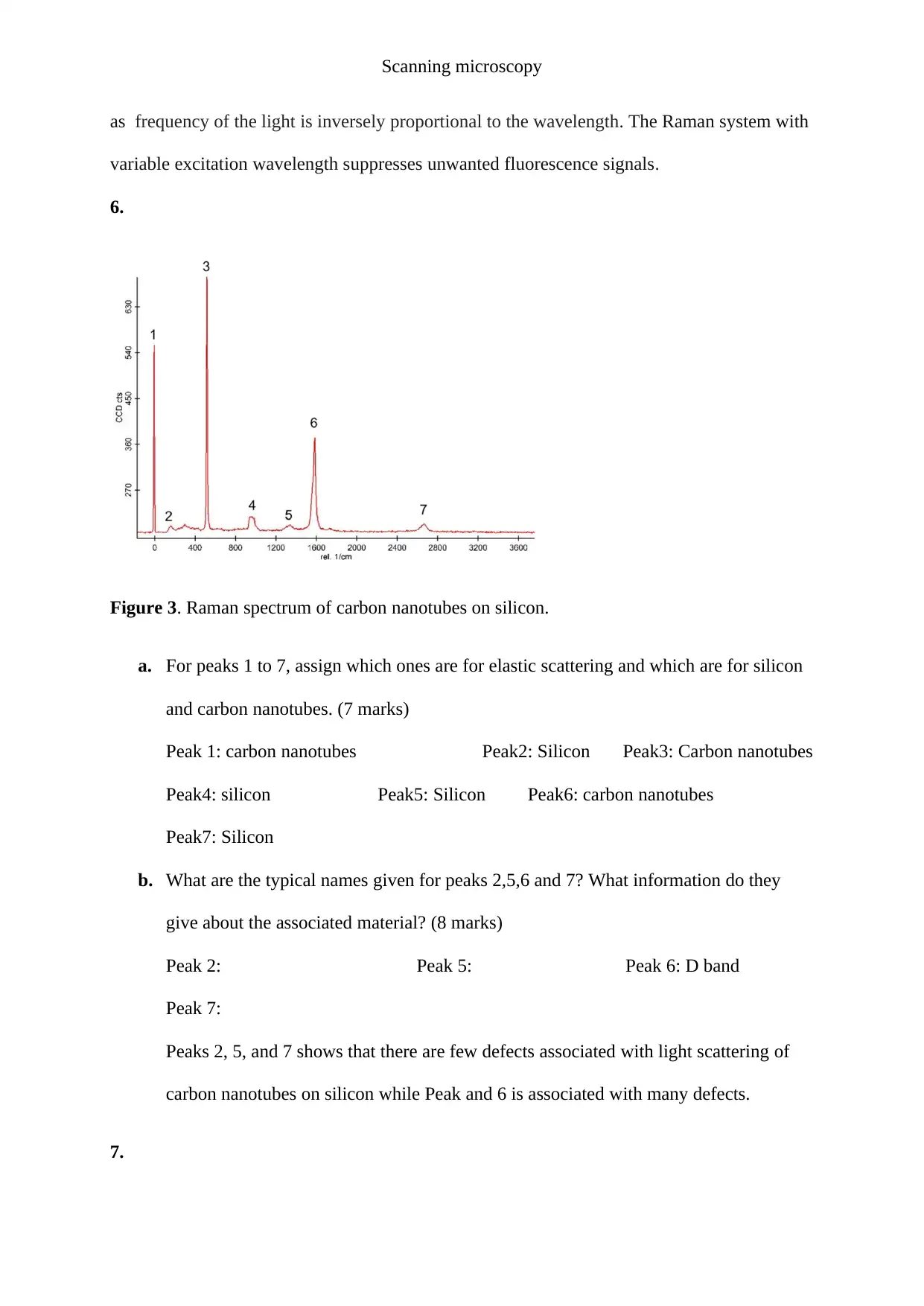
Scanning microscopy
as frequency of the light is inversely proportional to the wavelength. The Raman system with
variable excitation wavelength suppresses unwanted fluorescence signals.
6.
Figure 3. Raman spectrum of carbon nanotubes on silicon.
a. For peaks 1 to 7, assign which ones are for elastic scattering and which are for silicon
and carbon nanotubes. (7 marks)
Peak 1: carbon nanotubes Peak2: Silicon Peak3: Carbon nanotubes
Peak4: silicon Peak5: Silicon Peak6: carbon nanotubes
Peak7: Silicon
b. What are the typical names given for peaks 2,5,6 and 7? What information do they
give about the associated material? (8 marks)
Peak 2: Peak 5: Peak 6: D band
Peak 7:
Peaks 2, 5, and 7 shows that there are few defects associated with light scattering of
carbon nanotubes on silicon while Peak and 6 is associated with many defects.
7.
as frequency of the light is inversely proportional to the wavelength. The Raman system with
variable excitation wavelength suppresses unwanted fluorescence signals.
6.
Figure 3. Raman spectrum of carbon nanotubes on silicon.
a. For peaks 1 to 7, assign which ones are for elastic scattering and which are for silicon
and carbon nanotubes. (7 marks)
Peak 1: carbon nanotubes Peak2: Silicon Peak3: Carbon nanotubes
Peak4: silicon Peak5: Silicon Peak6: carbon nanotubes
Peak7: Silicon
b. What are the typical names given for peaks 2,5,6 and 7? What information do they
give about the associated material? (8 marks)
Peak 2: Peak 5: Peak 6: D band
Peak 7:
Peaks 2, 5, and 7 shows that there are few defects associated with light scattering of
carbon nanotubes on silicon while Peak and 6 is associated with many defects.
7.
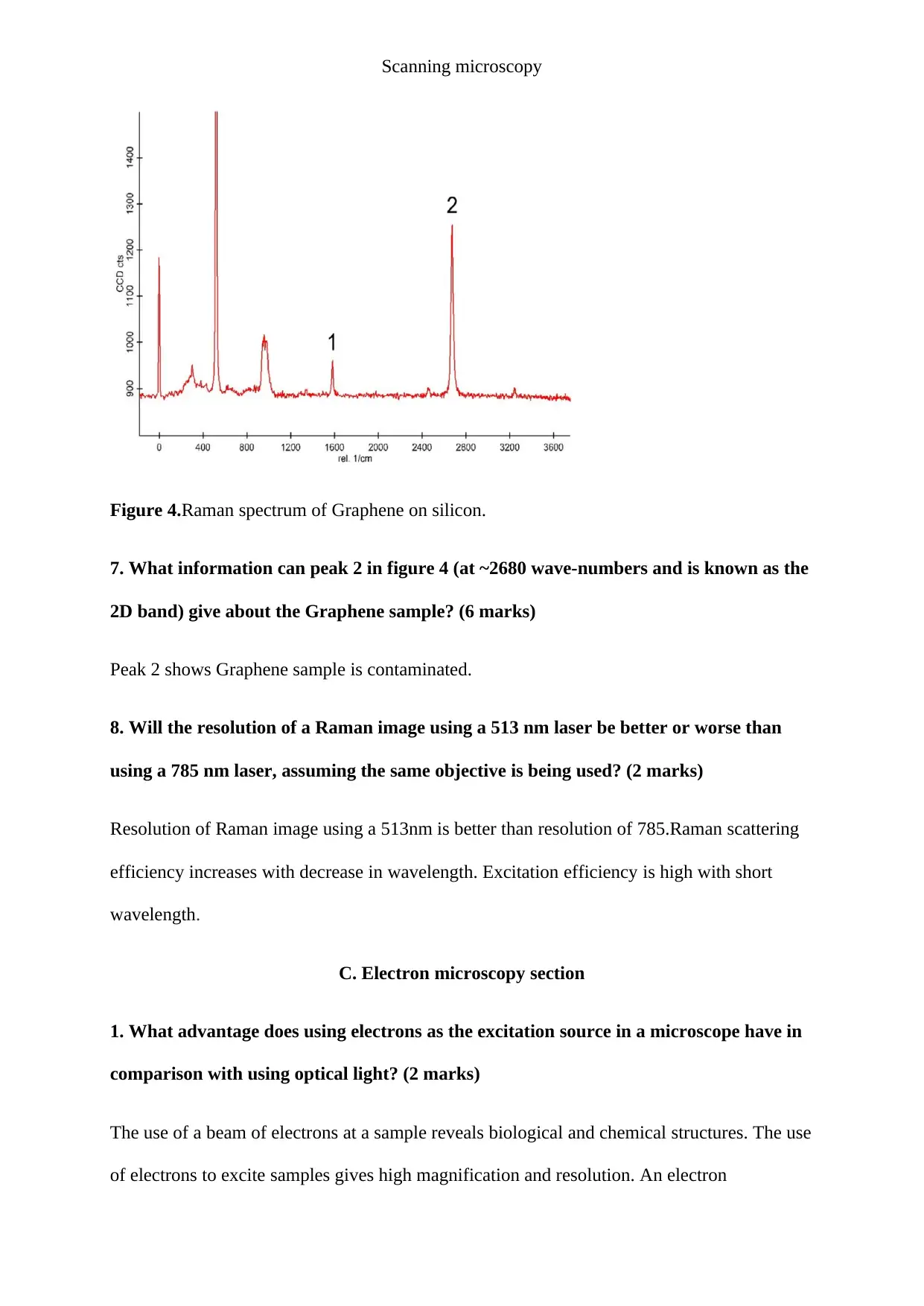
Scanning microscopy
Figure 4.Raman spectrum of Graphene on silicon.
7. What information can peak 2 in figure 4 (at ~2680 wave-numbers and is known as the
2D band) give about the Graphene sample? (6 marks)
Peak 2 shows Graphene sample is contaminated.
8. Will the resolution of a Raman image using a 513 nm laser be better or worse than
using a 785 nm laser, assuming the same objective is being used? (2 marks)
Resolution of Raman image using a 513nm is better than resolution of 785.Raman scattering
efficiency increases with decrease in wavelength. Excitation efficiency is high with short
wavelength.
C. Electron microscopy section
1. What advantage does using electrons as the excitation source in a microscope have in
comparison with using optical light? (2 marks)
The use of a beam of electrons at a sample reveals biological and chemical structures. The use
of electrons to excite samples gives high magnification and resolution. An electron
Figure 4.Raman spectrum of Graphene on silicon.
7. What information can peak 2 in figure 4 (at ~2680 wave-numbers and is known as the
2D band) give about the Graphene sample? (6 marks)
Peak 2 shows Graphene sample is contaminated.
8. Will the resolution of a Raman image using a 513 nm laser be better or worse than
using a 785 nm laser, assuming the same objective is being used? (2 marks)
Resolution of Raman image using a 513nm is better than resolution of 785.Raman scattering
efficiency increases with decrease in wavelength. Excitation efficiency is high with short
wavelength.
C. Electron microscopy section
1. What advantage does using electrons as the excitation source in a microscope have in
comparison with using optical light? (2 marks)
The use of a beam of electrons at a sample reveals biological and chemical structures. The use
of electrons to excite samples gives high magnification and resolution. An electron
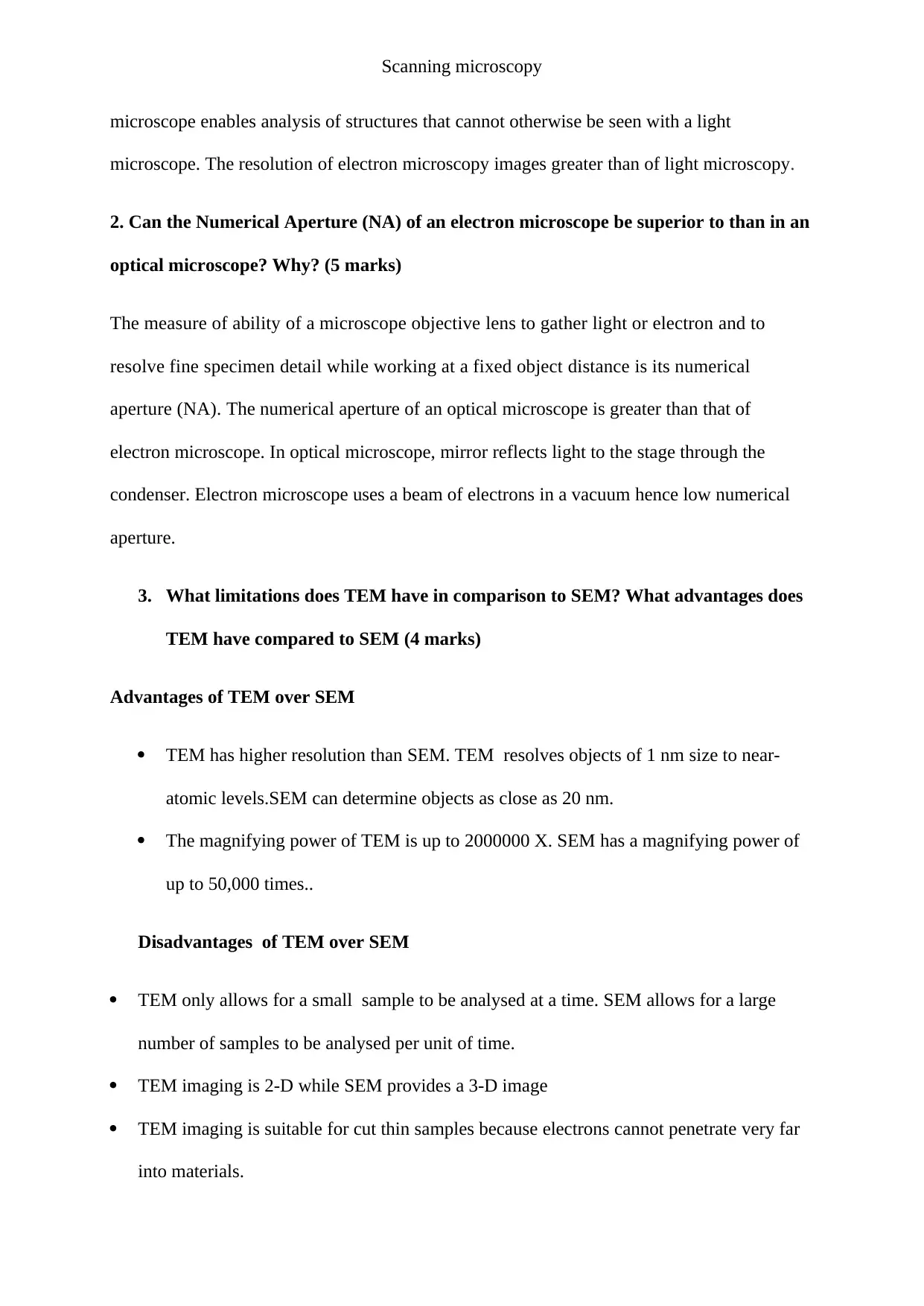
Scanning microscopy
microscope enables analysis of structures that cannot otherwise be seen with a light
microscope. The resolution of electron microscopy images greater than of light microscopy.
2. Can the Numerical Aperture (NA) of an electron microscope be superior to than in an
optical microscope? Why? (5 marks)
The measure of ability of a microscope objective lens to gather light or electron and to
resolve fine specimen detail while working at a fixed object distance is its numerical
aperture (NA). The numerical aperture of an optical microscope is greater than that of
electron microscope. In optical microscope, mirror reflects light to the stage through the
condenser. Electron microscope uses a beam of electrons in a vacuum hence low numerical
aperture.
3. What limitations does TEM have in comparison to SEM? What advantages does
TEM have compared to SEM (4 marks)
Advantages of TEM over SEM
TEM has higher resolution than SEM. TEM resolves objects of 1 nm size to near-
atomic levels.SEM can determine objects as close as 20 nm.
The magnifying power of TEM is up to 2000000 X. SEM has a magnifying power of
up to 50,000 times..
Disadvantages of TEM over SEM
TEM only allows for a small sample to be analysed at a time. SEM allows for a large
number of samples to be analysed per unit of time.
TEM imaging is 2-D while SEM provides a 3-D image
TEM imaging is suitable for cut thin samples because electrons cannot penetrate very far
into materials.
microscope enables analysis of structures that cannot otherwise be seen with a light
microscope. The resolution of electron microscopy images greater than of light microscopy.
2. Can the Numerical Aperture (NA) of an electron microscope be superior to than in an
optical microscope? Why? (5 marks)
The measure of ability of a microscope objective lens to gather light or electron and to
resolve fine specimen detail while working at a fixed object distance is its numerical
aperture (NA). The numerical aperture of an optical microscope is greater than that of
electron microscope. In optical microscope, mirror reflects light to the stage through the
condenser. Electron microscope uses a beam of electrons in a vacuum hence low numerical
aperture.
3. What limitations does TEM have in comparison to SEM? What advantages does
TEM have compared to SEM (4 marks)
Advantages of TEM over SEM
TEM has higher resolution than SEM. TEM resolves objects of 1 nm size to near-
atomic levels.SEM can determine objects as close as 20 nm.
The magnifying power of TEM is up to 2000000 X. SEM has a magnifying power of
up to 50,000 times..
Disadvantages of TEM over SEM
TEM only allows for a small sample to be analysed at a time. SEM allows for a large
number of samples to be analysed per unit of time.
TEM imaging is 2-D while SEM provides a 3-D image
TEM imaging is suitable for cut thin samples because electrons cannot penetrate very far
into materials.
Paraphrase This Document
Need a fresh take? Get an instant paraphrase of this document with our AI Paraphraser
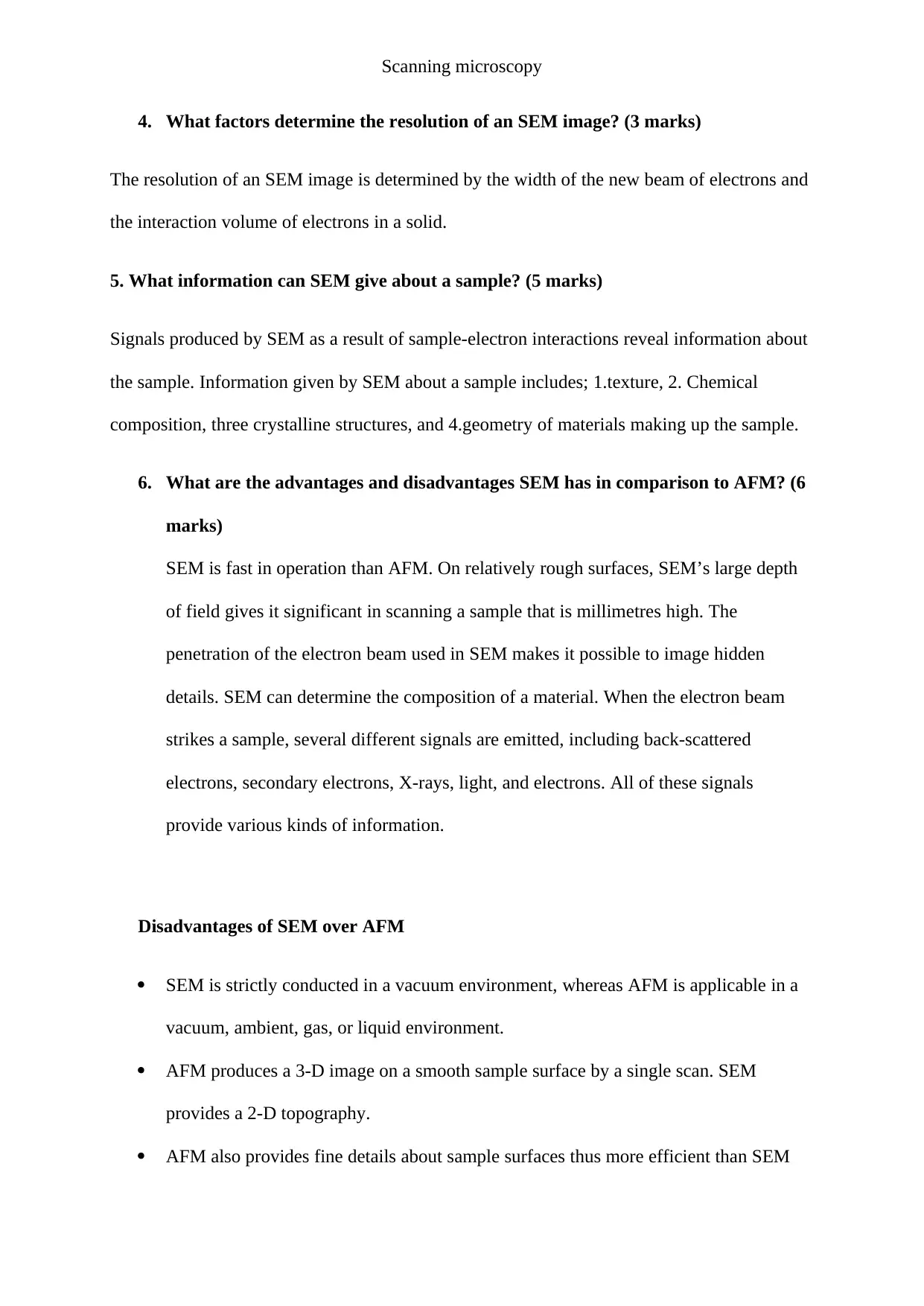
Scanning microscopy
4. What factors determine the resolution of an SEM image? (3 marks)
The resolution of an SEM image is determined by the width of the new beam of electrons and
the interaction volume of electrons in a solid.
5. What information can SEM give about a sample? (5 marks)
Signals produced by SEM as a result of sample-electron interactions reveal information about
the sample. Information given by SEM about a sample includes; 1.texture, 2. Chemical
composition, three crystalline structures, and 4.geometry of materials making up the sample.
6. What are the advantages and disadvantages SEM has in comparison to AFM? (6
marks)
SEM is fast in operation than AFM. On relatively rough surfaces, SEM’s large depth
of field gives it significant in scanning a sample that is millimetres high. The
penetration of the electron beam used in SEM makes it possible to image hidden
details. SEM can determine the composition of a material. When the electron beam
strikes a sample, several different signals are emitted, including back-scattered
electrons, secondary electrons, X-rays, light, and electrons. All of these signals
provide various kinds of information.
Disadvantages of SEM over AFM
SEM is strictly conducted in a vacuum environment, whereas AFM is applicable in a
vacuum, ambient, gas, or liquid environment.
AFM produces a 3-D image on a smooth sample surface by a single scan. SEM
provides a 2-D topography.
AFM also provides fine details about sample surfaces thus more efficient than SEM
4. What factors determine the resolution of an SEM image? (3 marks)
The resolution of an SEM image is determined by the width of the new beam of electrons and
the interaction volume of electrons in a solid.
5. What information can SEM give about a sample? (5 marks)
Signals produced by SEM as a result of sample-electron interactions reveal information about
the sample. Information given by SEM about a sample includes; 1.texture, 2. Chemical
composition, three crystalline structures, and 4.geometry of materials making up the sample.
6. What are the advantages and disadvantages SEM has in comparison to AFM? (6
marks)
SEM is fast in operation than AFM. On relatively rough surfaces, SEM’s large depth
of field gives it significant in scanning a sample that is millimetres high. The
penetration of the electron beam used in SEM makes it possible to image hidden
details. SEM can determine the composition of a material. When the electron beam
strikes a sample, several different signals are emitted, including back-scattered
electrons, secondary electrons, X-rays, light, and electrons. All of these signals
provide various kinds of information.
Disadvantages of SEM over AFM
SEM is strictly conducted in a vacuum environment, whereas AFM is applicable in a
vacuum, ambient, gas, or liquid environment.
AFM produces a 3-D image on a smooth sample surface by a single scan. SEM
provides a 2-D topography.
AFM also provides fine details about sample surfaces thus more efficient than SEM
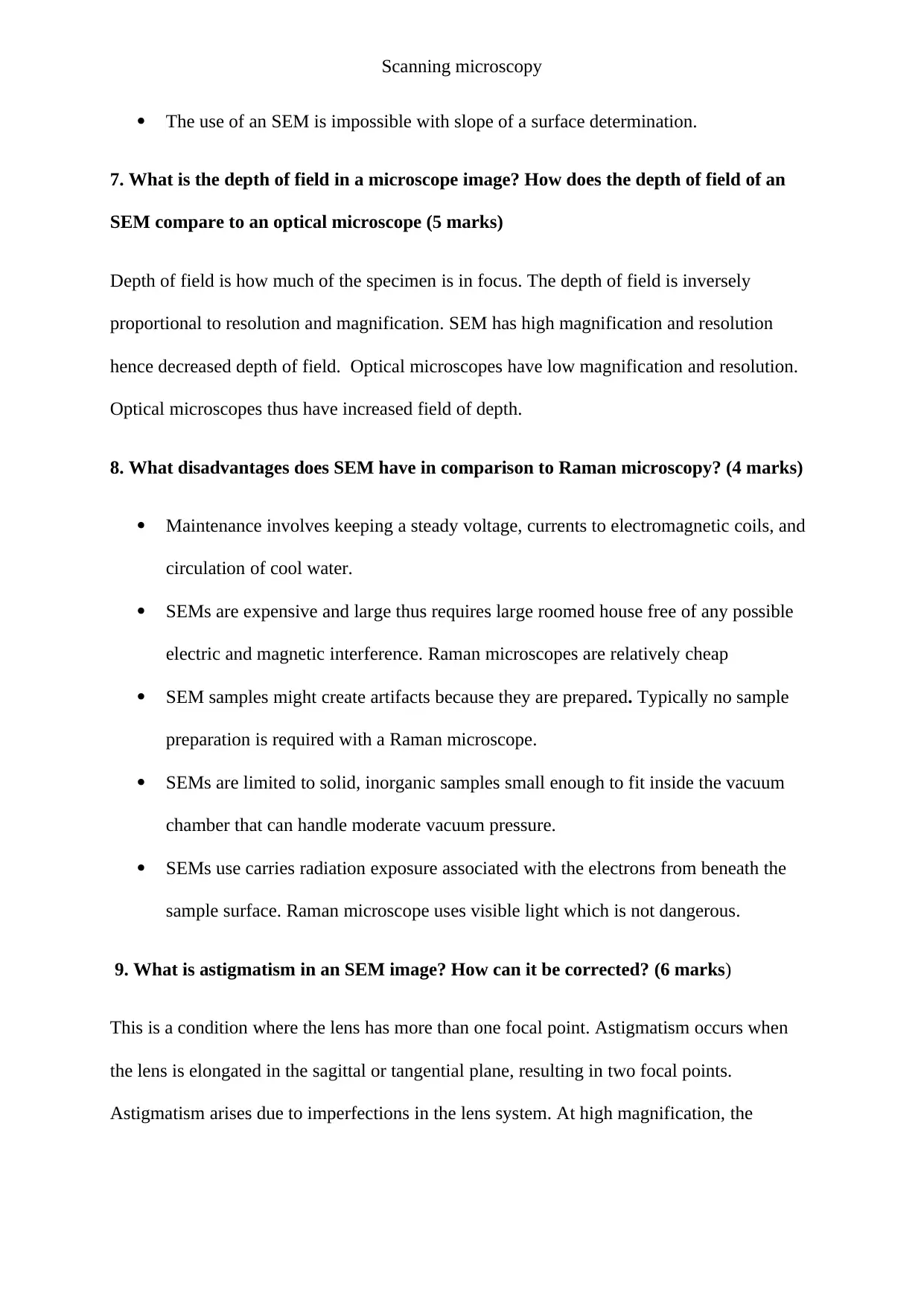
Scanning microscopy
The use of an SEM is impossible with slope of a surface determination.
7. What is the depth of field in a microscope image? How does the depth of field of an
SEM compare to an optical microscope (5 marks)
Depth of field is how much of the specimen is in focus. The depth of field is inversely
proportional to resolution and magnification. SEM has high magnification and resolution
hence decreased depth of field. Optical microscopes have low magnification and resolution.
Optical microscopes thus have increased field of depth.
8. What disadvantages does SEM have in comparison to Raman microscopy? (4 marks)
Maintenance involves keeping a steady voltage, currents to electromagnetic coils, and
circulation of cool water.
SEMs are expensive and large thus requires large roomed house free of any possible
electric and magnetic interference. Raman microscopes are relatively cheap
SEM samples might create artifacts because they are prepared. Typically no sample
preparation is required with a Raman microscope.
SEMs are limited to solid, inorganic samples small enough to fit inside the vacuum
chamber that can handle moderate vacuum pressure.
SEMs use carries radiation exposure associated with the electrons from beneath the
sample surface. Raman microscope uses visible light which is not dangerous.
9. What is astigmatism in an SEM image? How can it be corrected? (6 marks)
This is a condition where the lens has more than one focal point. Astigmatism occurs when
the lens is elongated in the sagittal or tangential plane, resulting in two focal points.
Astigmatism arises due to imperfections in the lens system. At high magnification, the
The use of an SEM is impossible with slope of a surface determination.
7. What is the depth of field in a microscope image? How does the depth of field of an
SEM compare to an optical microscope (5 marks)
Depth of field is how much of the specimen is in focus. The depth of field is inversely
proportional to resolution and magnification. SEM has high magnification and resolution
hence decreased depth of field. Optical microscopes have low magnification and resolution.
Optical microscopes thus have increased field of depth.
8. What disadvantages does SEM have in comparison to Raman microscopy? (4 marks)
Maintenance involves keeping a steady voltage, currents to electromagnetic coils, and
circulation of cool water.
SEMs are expensive and large thus requires large roomed house free of any possible
electric and magnetic interference. Raman microscopes are relatively cheap
SEM samples might create artifacts because they are prepared. Typically no sample
preparation is required with a Raman microscope.
SEMs are limited to solid, inorganic samples small enough to fit inside the vacuum
chamber that can handle moderate vacuum pressure.
SEMs use carries radiation exposure associated with the electrons from beneath the
sample surface. Raman microscope uses visible light which is not dangerous.
9. What is astigmatism in an SEM image? How can it be corrected? (6 marks)
This is a condition where the lens has more than one focal point. Astigmatism occurs when
the lens is elongated in the sagittal or tangential plane, resulting in two focal points.
Astigmatism arises due to imperfections in the lens system. At high magnification, the
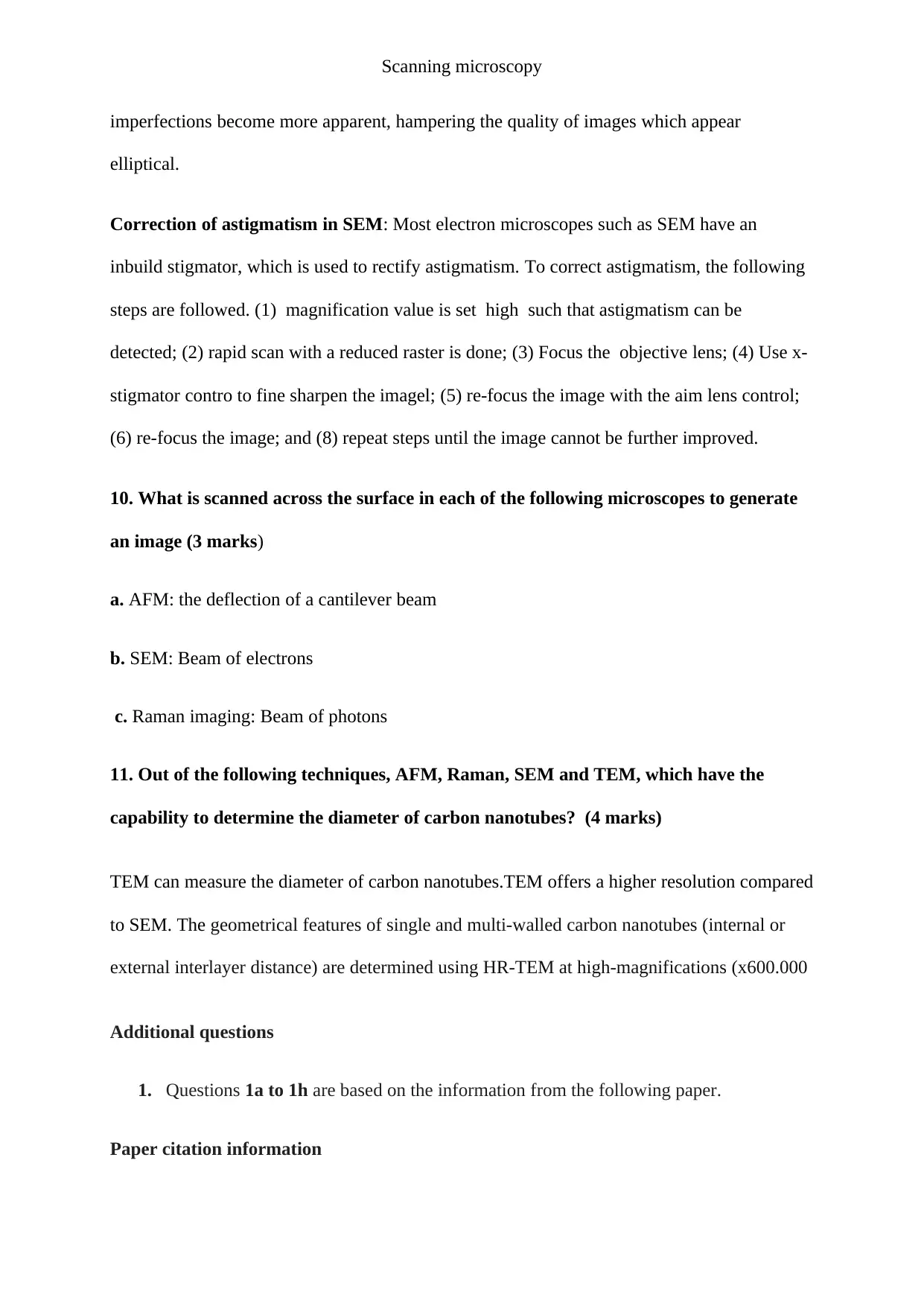
Scanning microscopy
imperfections become more apparent, hampering the quality of images which appear
elliptical.
Correction of astigmatism in SEM: Most electron microscopes such as SEM have an
inbuild stigmator, which is used to rectify astigmatism. To correct astigmatism, the following
steps are followed. (1) magnification value is set high such that astigmatism can be
detected; (2) rapid scan with a reduced raster is done; (3) Focus the objective lens; (4) Use x-
stigmator contro to fine sharpen the imagel; (5) re-focus the image with the aim lens control;
(6) re-focus the image; and (8) repeat steps until the image cannot be further improved.
10. What is scanned across the surface in each of the following microscopes to generate
an image (3 marks)
a. AFM: the deflection of a cantilever beam
b. SEM: Beam of electrons
c. Raman imaging: Beam of photons
11. Out of the following techniques, AFM, Raman, SEM and TEM, which have the
capability to determine the diameter of carbon nanotubes? (4 marks)
TEM can measure the diameter of carbon nanotubes.TEM offers a higher resolution compared
to SEM. The geometrical features of single and multi-walled carbon nanotubes (internal or
external interlayer distance) are determined using HR-TEM at high-magnifications (x600.000
Additional questions
1. Questions 1a to 1h are based on the information from the following paper.
Paper citation information
imperfections become more apparent, hampering the quality of images which appear
elliptical.
Correction of astigmatism in SEM: Most electron microscopes such as SEM have an
inbuild stigmator, which is used to rectify astigmatism. To correct astigmatism, the following
steps are followed. (1) magnification value is set high such that astigmatism can be
detected; (2) rapid scan with a reduced raster is done; (3) Focus the objective lens; (4) Use x-
stigmator contro to fine sharpen the imagel; (5) re-focus the image with the aim lens control;
(6) re-focus the image; and (8) repeat steps until the image cannot be further improved.
10. What is scanned across the surface in each of the following microscopes to generate
an image (3 marks)
a. AFM: the deflection of a cantilever beam
b. SEM: Beam of electrons
c. Raman imaging: Beam of photons
11. Out of the following techniques, AFM, Raman, SEM and TEM, which have the
capability to determine the diameter of carbon nanotubes? (4 marks)
TEM can measure the diameter of carbon nanotubes.TEM offers a higher resolution compared
to SEM. The geometrical features of single and multi-walled carbon nanotubes (internal or
external interlayer distance) are determined using HR-TEM at high-magnifications (x600.000
Additional questions
1. Questions 1a to 1h are based on the information from the following paper.
Paper citation information
Secure Best Marks with AI Grader
Need help grading? Try our AI Grader for instant feedback on your assignments.
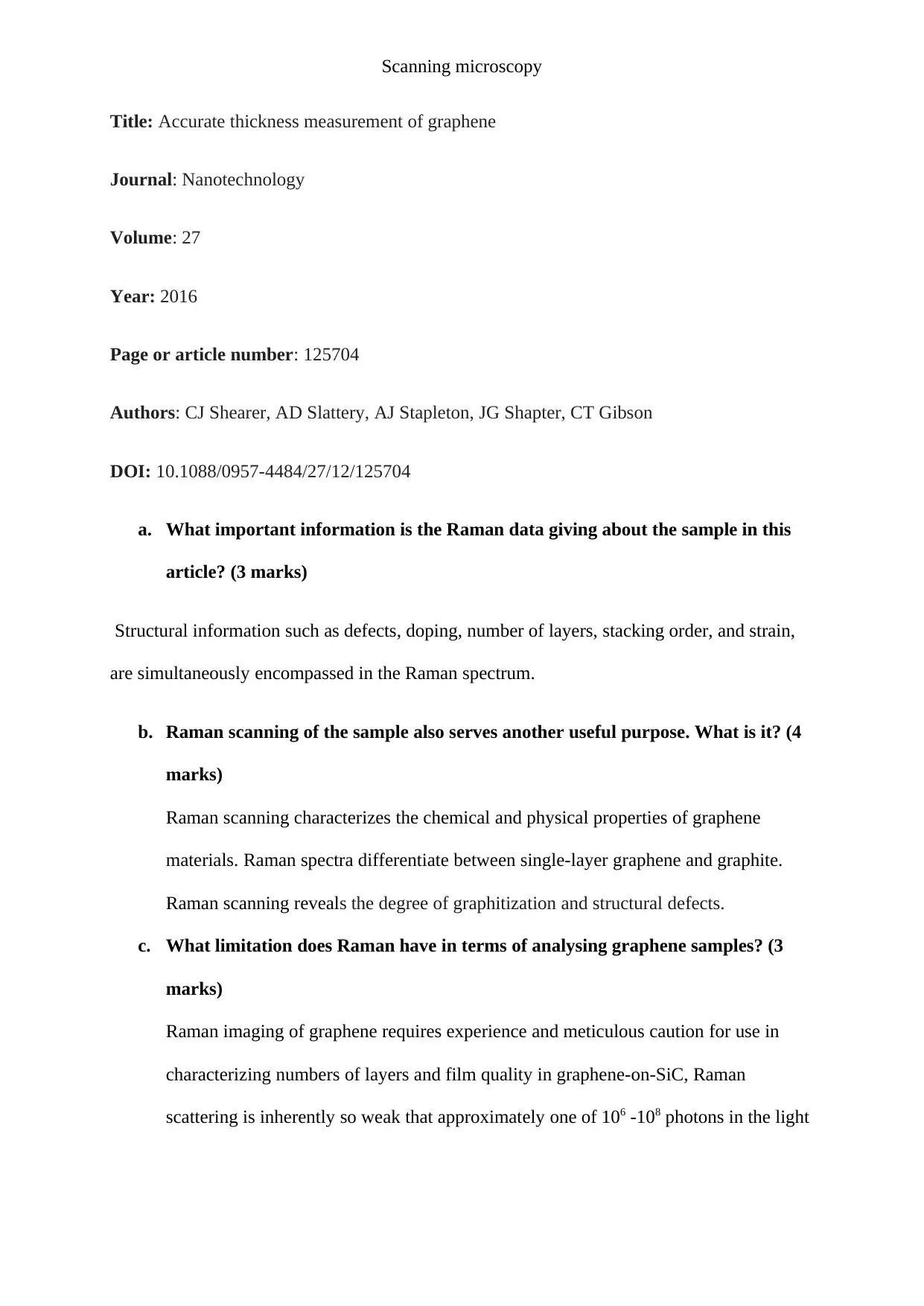
Scanning microscopy
Title: Accurate thickness measurement of graphene
Journal: Nanotechnology
Volume: 27
Year: 2016
Page or article number: 125704
Authors: CJ Shearer, AD Slattery, AJ Stapleton, JG Shapter, CT Gibson
DOI: 10.1088/0957-4484/27/12/125704
a. What important information is the Raman data giving about the sample in this
article? (3 marks)
Structural information such as defects, doping, number of layers, stacking order, and strain,
are simultaneously encompassed in the Raman spectrum.
b. Raman scanning of the sample also serves another useful purpose. What is it? (4
marks)
Raman scanning characterizes the chemical and physical properties of graphene
materials. Raman spectra differentiate between single-layer graphene and graphite.
Raman scanning reveals the degree of graphitization and structural defects.
c. What limitation does Raman have in terms of analysing graphene samples? (3
marks)
Raman imaging of graphene requires experience and meticulous caution for use in
characterizing numbers of layers and film quality in graphene-on-SiC, Raman
scattering is inherently so weak that approximately one of 106 -108 photons in the light
Title: Accurate thickness measurement of graphene
Journal: Nanotechnology
Volume: 27
Year: 2016
Page or article number: 125704
Authors: CJ Shearer, AD Slattery, AJ Stapleton, JG Shapter, CT Gibson
DOI: 10.1088/0957-4484/27/12/125704
a. What important information is the Raman data giving about the sample in this
article? (3 marks)
Structural information such as defects, doping, number of layers, stacking order, and strain,
are simultaneously encompassed in the Raman spectrum.
b. Raman scanning of the sample also serves another useful purpose. What is it? (4
marks)
Raman scanning characterizes the chemical and physical properties of graphene
materials. Raman spectra differentiate between single-layer graphene and graphite.
Raman scanning reveals the degree of graphitization and structural defects.
c. What limitation does Raman have in terms of analysing graphene samples? (3
marks)
Raman imaging of graphene requires experience and meticulous caution for use in
characterizing numbers of layers and film quality in graphene-on-SiC, Raman
scattering is inherently so weak that approximately one of 106 -108 photons in the light
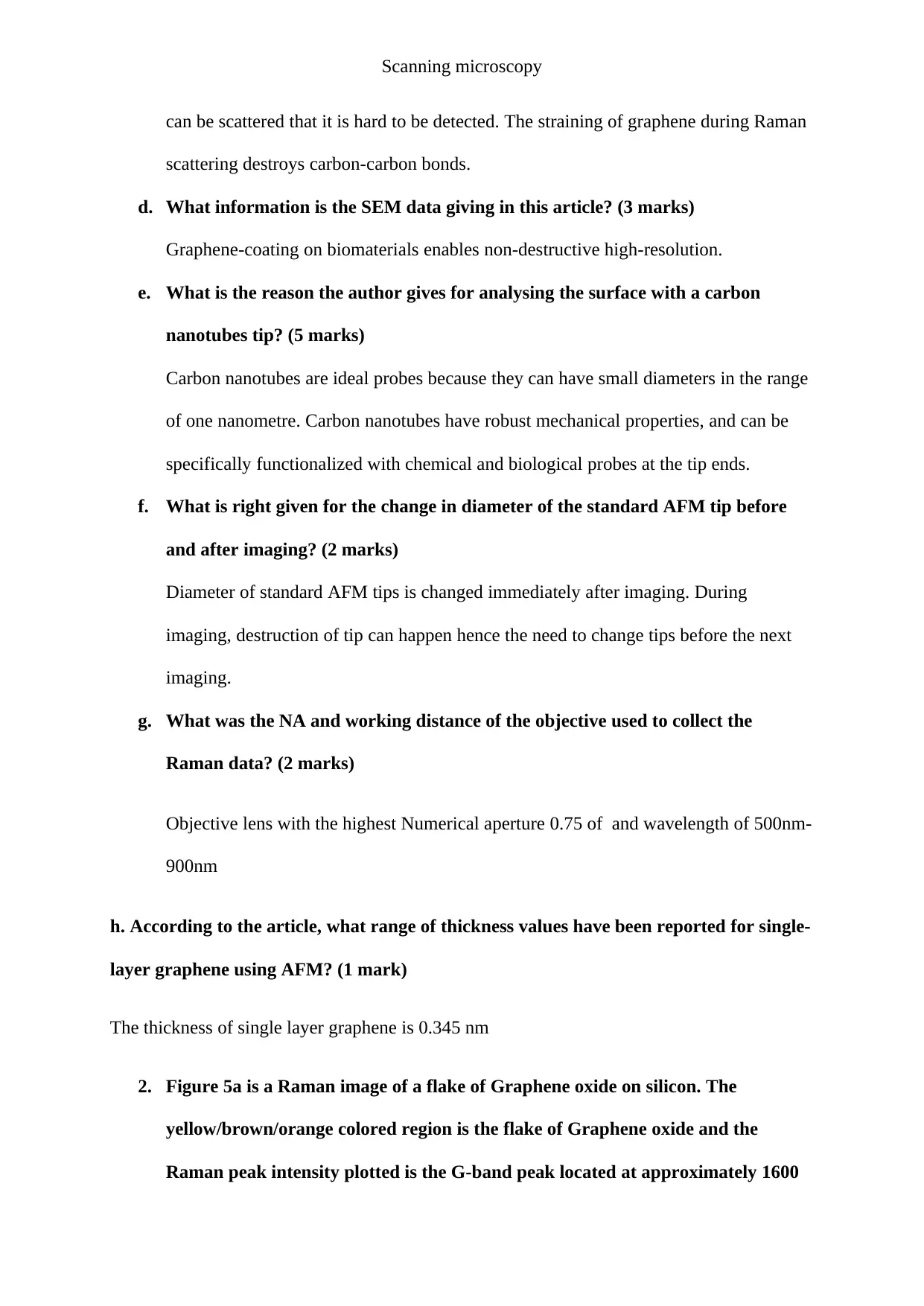
Scanning microscopy
can be scattered that it is hard to be detected. The straining of graphene during Raman
scattering destroys carbon-carbon bonds.
d. What information is the SEM data giving in this article? (3 marks)
Graphene-coating on biomaterials enables non-destructive high-resolution.
e. What is the reason the author gives for analysing the surface with a carbon
nanotubes tip? (5 marks)
Carbon nanotubes are ideal probes because they can have small diameters in the range
of one nanometre. Carbon nanotubes have robust mechanical properties, and can be
specifically functionalized with chemical and biological probes at the tip ends.
f. What is right given for the change in diameter of the standard AFM tip before
and after imaging? (2 marks)
Diameter of standard AFM tips is changed immediately after imaging. During
imaging, destruction of tip can happen hence the need to change tips before the next
imaging.
g. What was the NA and working distance of the objective used to collect the
Raman data? (2 marks)
Objective lens with the highest Numerical aperture 0.75 of and wavelength of 500nm-
900nm
h. According to the article, what range of thickness values have been reported for single-
layer graphene using AFM? (1 mark)
The thickness of single layer graphene is 0.345 nm
2. Figure 5a is a Raman image of a flake of Graphene oxide on silicon. The
yellow/brown/orange colored region is the flake of Graphene oxide and the
Raman peak intensity plotted is the G-band peak located at approximately 1600
can be scattered that it is hard to be detected. The straining of graphene during Raman
scattering destroys carbon-carbon bonds.
d. What information is the SEM data giving in this article? (3 marks)
Graphene-coating on biomaterials enables non-destructive high-resolution.
e. What is the reason the author gives for analysing the surface with a carbon
nanotubes tip? (5 marks)
Carbon nanotubes are ideal probes because they can have small diameters in the range
of one nanometre. Carbon nanotubes have robust mechanical properties, and can be
specifically functionalized with chemical and biological probes at the tip ends.
f. What is right given for the change in diameter of the standard AFM tip before
and after imaging? (2 marks)
Diameter of standard AFM tips is changed immediately after imaging. During
imaging, destruction of tip can happen hence the need to change tips before the next
imaging.
g. What was the NA and working distance of the objective used to collect the
Raman data? (2 marks)
Objective lens with the highest Numerical aperture 0.75 of and wavelength of 500nm-
900nm
h. According to the article, what range of thickness values have been reported for single-
layer graphene using AFM? (1 mark)
The thickness of single layer graphene is 0.345 nm
2. Figure 5a is a Raman image of a flake of Graphene oxide on silicon. The
yellow/brown/orange colored region is the flake of Graphene oxide and the
Raman peak intensity plotted is the G-band peak located at approximately 1600
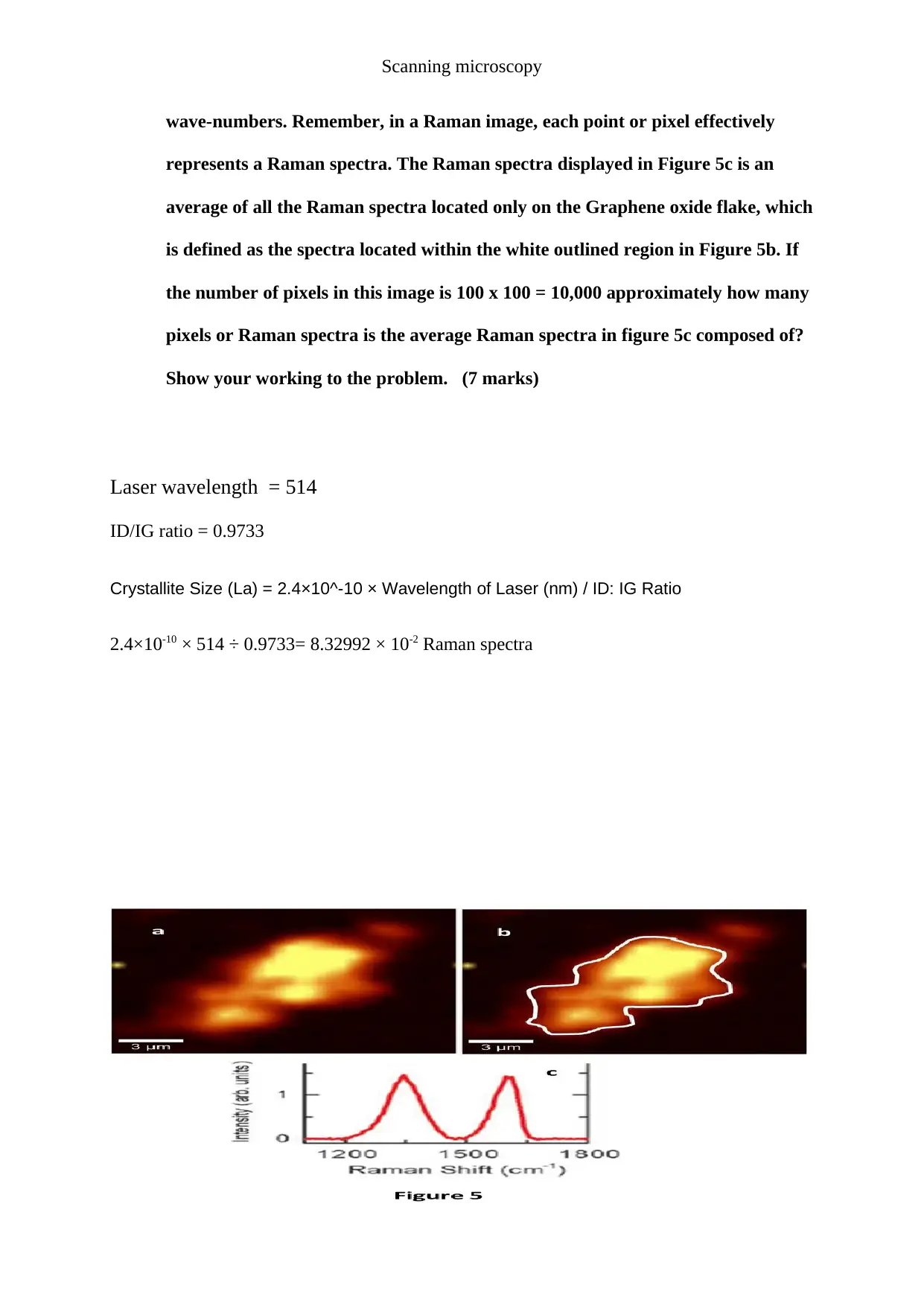
Scanning microscopy
wave-numbers. Remember, in a Raman image, each point or pixel effectively
represents a Raman spectra. The Raman spectra displayed in Figure 5c is an
average of all the Raman spectra located only on the Graphene oxide flake, which
is defined as the spectra located within the white outlined region in Figure 5b. If
the number of pixels in this image is 100 x 100 = 10,000 approximately how many
pixels or Raman spectra is the average Raman spectra in figure 5c composed of?
Show your working to the problem. (7 marks)
Laser wavelength = 514
ID/IG ratio = 0.9733
Crystallite Size (La) = 2.4×10^-10 × Wavelength of Laser (nm) / ID: IG Ratio
2.4×10-10 × 514 ÷ 0.9733= 8.32992 × 10-2 Raman spectra
wave-numbers. Remember, in a Raman image, each point or pixel effectively
represents a Raman spectra. The Raman spectra displayed in Figure 5c is an
average of all the Raman spectra located only on the Graphene oxide flake, which
is defined as the spectra located within the white outlined region in Figure 5b. If
the number of pixels in this image is 100 x 100 = 10,000 approximately how many
pixels or Raman spectra is the average Raman spectra in figure 5c composed of?
Show your working to the problem. (7 marks)
Laser wavelength = 514
ID/IG ratio = 0.9733
Crystallite Size (La) = 2.4×10^-10 × Wavelength of Laser (nm) / ID: IG Ratio
2.4×10-10 × 514 ÷ 0.9733= 8.32992 × 10-2 Raman spectra
Paraphrase This Document
Need a fresh take? Get an instant paraphrase of this document with our AI Paraphraser
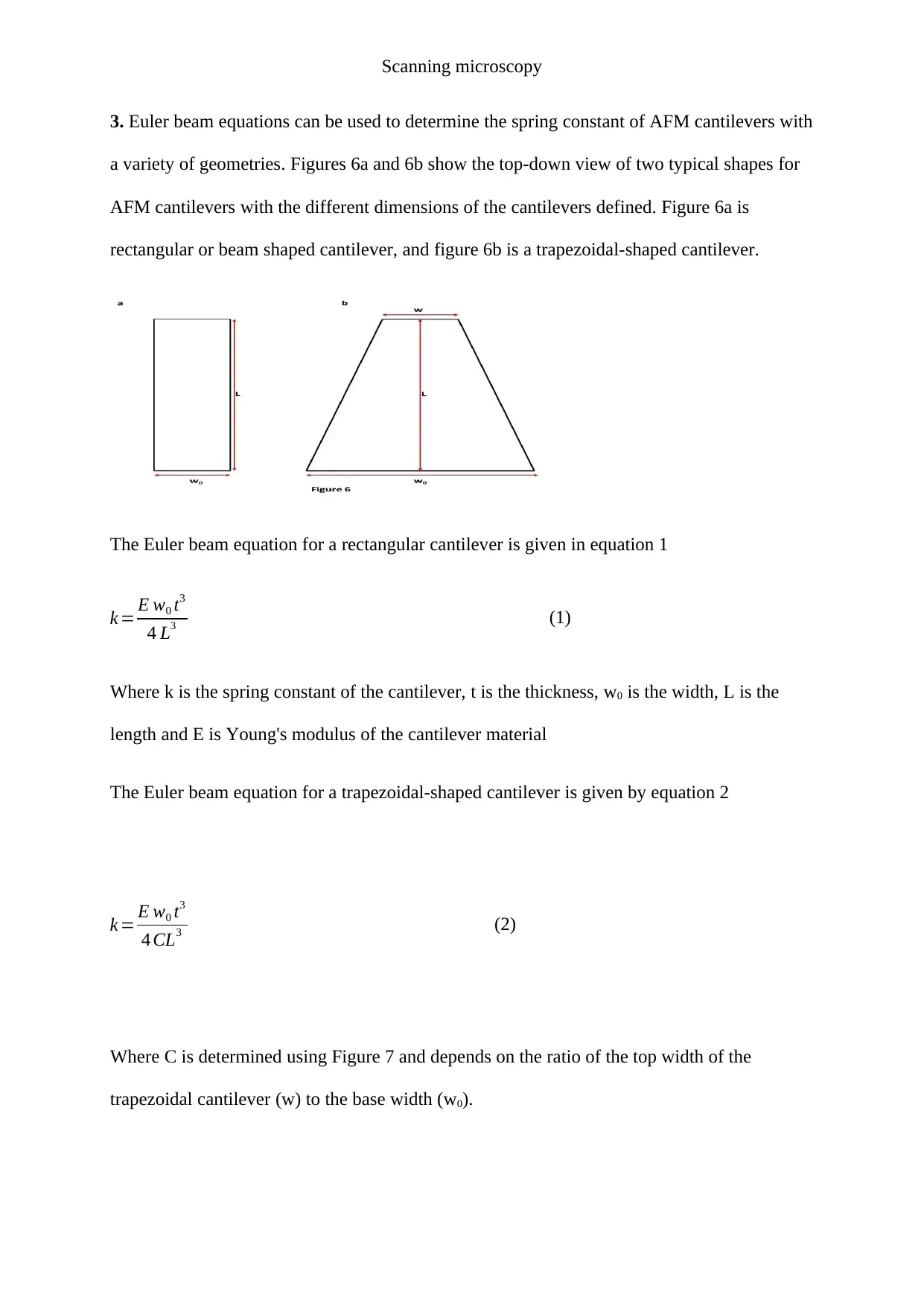
Scanning microscopy
3. Euler beam equations can be used to determine the spring constant of AFM cantilevers with
a variety of geometries. Figures 6a and 6b show the top-down view of two typical shapes for
AFM cantilevers with the different dimensions of the cantilevers defined. Figure 6a is
rectangular or beam shaped cantilever, and figure 6b is a trapezoidal-shaped cantilever.
The Euler beam equation for a rectangular cantilever is given in equation 1
k = E w0 t3
4 L3 (1)
Where k is the spring constant of the cantilever, t is the thickness, w0 is the width, L is the
length and E is Young's modulus of the cantilever material
The Euler beam equation for a trapezoidal-shaped cantilever is given by equation 2
k = E w0 t3
4 CL3 (2)
Where C is determined using Figure 7 and depends on the ratio of the top width of the
trapezoidal cantilever (w) to the base width (w0).
3. Euler beam equations can be used to determine the spring constant of AFM cantilevers with
a variety of geometries. Figures 6a and 6b show the top-down view of two typical shapes for
AFM cantilevers with the different dimensions of the cantilevers defined. Figure 6a is
rectangular or beam shaped cantilever, and figure 6b is a trapezoidal-shaped cantilever.
The Euler beam equation for a rectangular cantilever is given in equation 1
k = E w0 t3
4 L3 (1)
Where k is the spring constant of the cantilever, t is the thickness, w0 is the width, L is the
length and E is Young's modulus of the cantilever material
The Euler beam equation for a trapezoidal-shaped cantilever is given by equation 2
k = E w0 t3
4 CL3 (2)
Where C is determined using Figure 7 and depends on the ratio of the top width of the
trapezoidal cantilever (w) to the base width (w0).
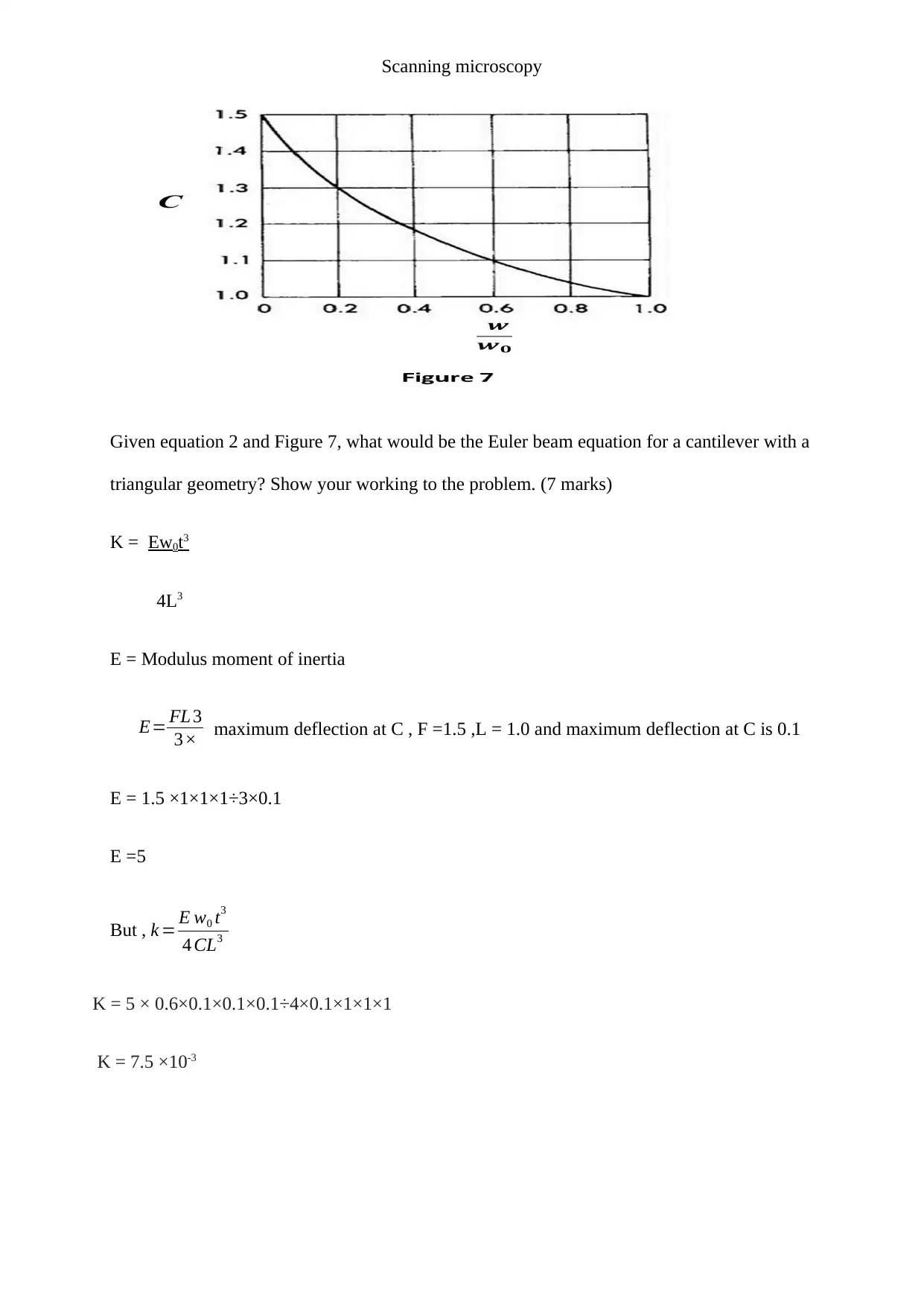
Scanning microscopy
Given equation 2 and Figure 7, what would be the Euler beam equation for a cantilever with a
triangular geometry? Show your working to the problem. (7 marks)
K = Ew0t3
4L3
E = Modulus moment of inertia
E= FL 3
3× maximum deflection at C , F =1.5 ,L = 1.0 and maximum deflection at C is 0.1
E = 1.5 ×1×1×1÷3×0.1
E =5
But , k = E w0 t3
4 CL3
K = 5 × 0.6×0.1×0.1×0.1÷4×0.1×1×1×1
K = 7.5 ×10-3
Given equation 2 and Figure 7, what would be the Euler beam equation for a cantilever with a
triangular geometry? Show your working to the problem. (7 marks)
K = Ew0t3
4L3
E = Modulus moment of inertia
E= FL 3
3× maximum deflection at C , F =1.5 ,L = 1.0 and maximum deflection at C is 0.1
E = 1.5 ×1×1×1÷3×0.1
E =5
But , k = E w0 t3
4 CL3
K = 5 × 0.6×0.1×0.1×0.1÷4×0.1×1×1×1
K = 7.5 ×10-3
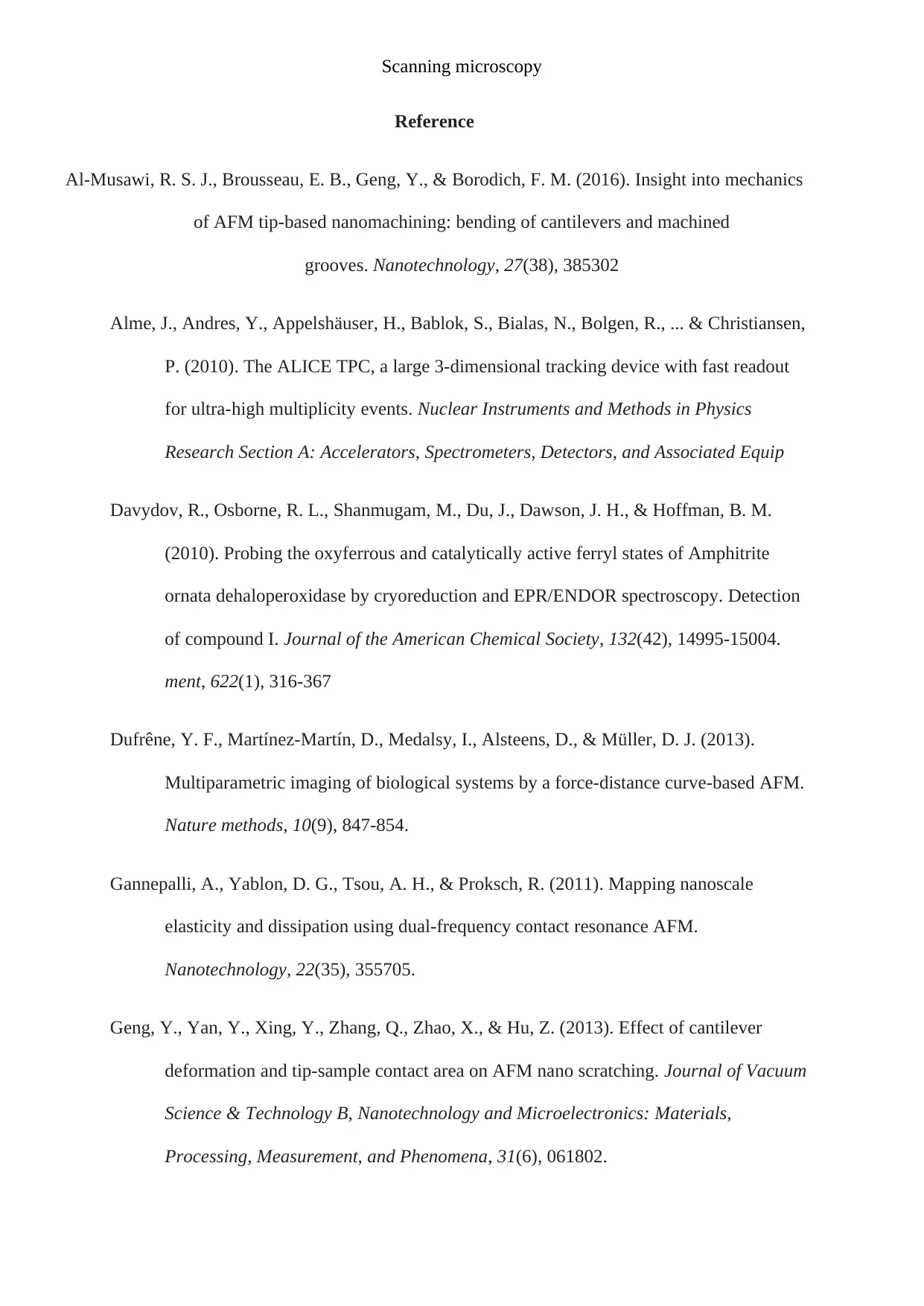
Scanning microscopy
Reference
Al-Musawi, R. S. J., Brousseau, E. B., Geng, Y., & Borodich, F. M. (2016). Insight into mechanics
of AFM tip-based nanomachining: bending of cantilevers and machined
grooves. Nanotechnology, 27(38), 385302
Alme, J., Andres, Y., Appelshäuser, H., Bablok, S., Bialas, N., Bolgen, R., ... & Christiansen,
P. (2010). The ALICE TPC, a large 3-dimensional tracking device with fast readout
for ultra-high multiplicity events. Nuclear Instruments and Methods in Physics
Research Section A: Accelerators, Spectrometers, Detectors, and Associated Equip
Davydov, R., Osborne, R. L., Shanmugam, M., Du, J., Dawson, J. H., & Hoffman, B. M.
(2010). Probing the oxyferrous and catalytically active ferryl states of Amphitrite
ornata dehaloperoxidase by cryoreduction and EPR/ENDOR spectroscopy. Detection
of compound I. Journal of the American Chemical Society, 132(42), 14995-15004.
ment, 622(1), 316-367
Dufrêne, Y. F., Martínez-Martín, D., Medalsy, I., Alsteens, D., & Müller, D. J. (2013).
Multiparametric imaging of biological systems by a force-distance curve-based AFM.
Nature methods, 10(9), 847-854.
Gannepalli, A., Yablon, D. G., Tsou, A. H., & Proksch, R. (2011). Mapping nanoscale
elasticity and dissipation using dual-frequency contact resonance AFM.
Nanotechnology, 22(35), 355705.
Geng, Y., Yan, Y., Xing, Y., Zhang, Q., Zhao, X., & Hu, Z. (2013). Effect of cantilever
deformation and tip-sample contact area on AFM nano scratching. Journal of Vacuum
Science & Technology B, Nanotechnology and Microelectronics: Materials,
Processing, Measurement, and Phenomena, 31(6), 061802.
Reference
Al-Musawi, R. S. J., Brousseau, E. B., Geng, Y., & Borodich, F. M. (2016). Insight into mechanics
of AFM tip-based nanomachining: bending of cantilevers and machined
grooves. Nanotechnology, 27(38), 385302
Alme, J., Andres, Y., Appelshäuser, H., Bablok, S., Bialas, N., Bolgen, R., ... & Christiansen,
P. (2010). The ALICE TPC, a large 3-dimensional tracking device with fast readout
for ultra-high multiplicity events. Nuclear Instruments and Methods in Physics
Research Section A: Accelerators, Spectrometers, Detectors, and Associated Equip
Davydov, R., Osborne, R. L., Shanmugam, M., Du, J., Dawson, J. H., & Hoffman, B. M.
(2010). Probing the oxyferrous and catalytically active ferryl states of Amphitrite
ornata dehaloperoxidase by cryoreduction and EPR/ENDOR spectroscopy. Detection
of compound I. Journal of the American Chemical Society, 132(42), 14995-15004.
ment, 622(1), 316-367
Dufrêne, Y. F., Martínez-Martín, D., Medalsy, I., Alsteens, D., & Müller, D. J. (2013).
Multiparametric imaging of biological systems by a force-distance curve-based AFM.
Nature methods, 10(9), 847-854.
Gannepalli, A., Yablon, D. G., Tsou, A. H., & Proksch, R. (2011). Mapping nanoscale
elasticity and dissipation using dual-frequency contact resonance AFM.
Nanotechnology, 22(35), 355705.
Geng, Y., Yan, Y., Xing, Y., Zhang, Q., Zhao, X., & Hu, Z. (2013). Effect of cantilever
deformation and tip-sample contact area on AFM nano scratching. Journal of Vacuum
Science & Technology B, Nanotechnology and Microelectronics: Materials,
Processing, Measurement, and Phenomena, 31(6), 061802.
Secure Best Marks with AI Grader
Need help grading? Try our AI Grader for instant feedback on your assignments.
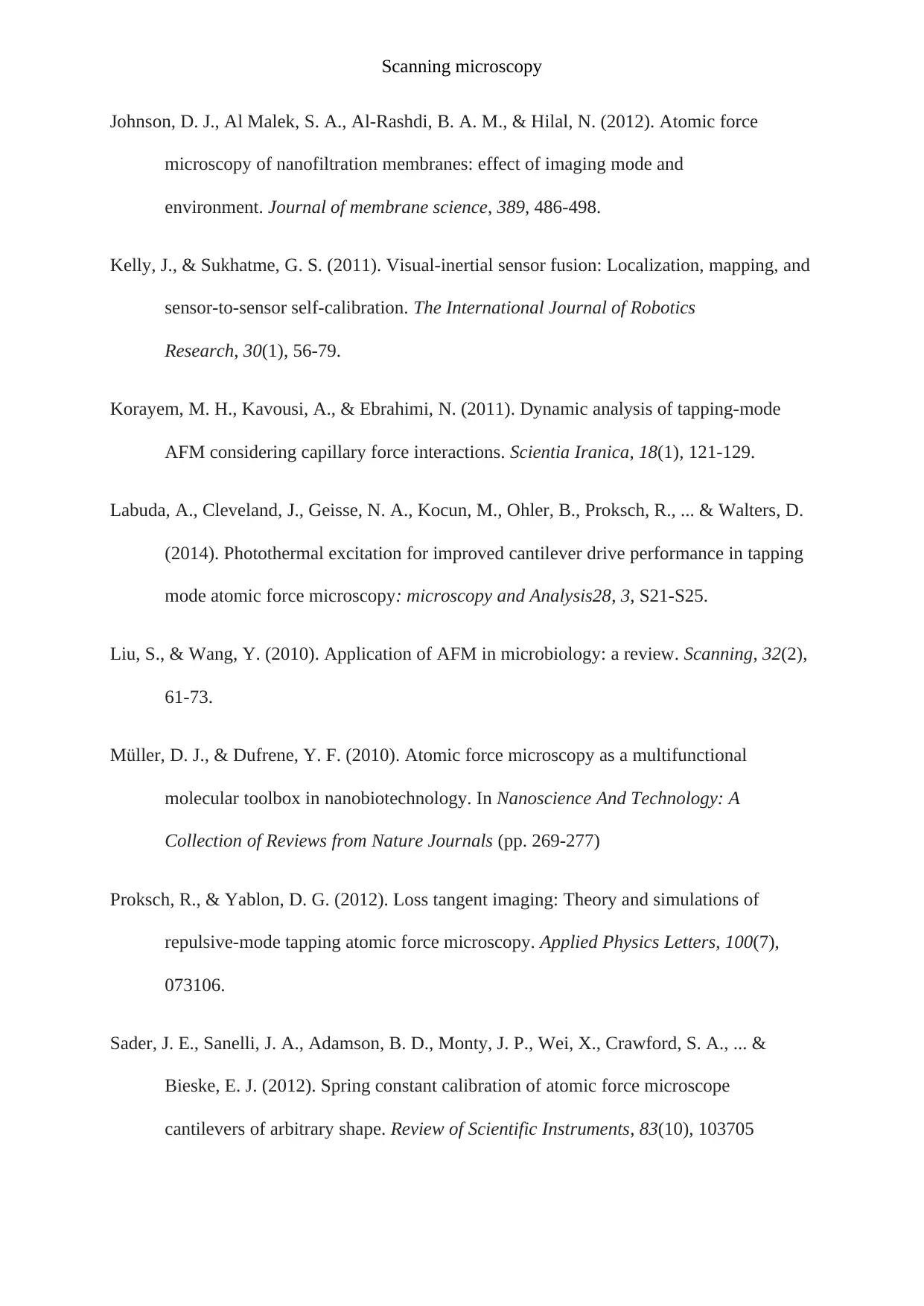
Scanning microscopy
Johnson, D. J., Al Malek, S. A., Al-Rashdi, B. A. M., & Hilal, N. (2012). Atomic force
microscopy of nanofiltration membranes: effect of imaging mode and
environment. Journal of membrane science, 389, 486-498.
Kelly, J., & Sukhatme, G. S. (2011). Visual-inertial sensor fusion: Localization, mapping, and
sensor-to-sensor self-calibration. The International Journal of Robotics
Research, 30(1), 56-79.
Korayem, M. H., Kavousi, A., & Ebrahimi, N. (2011). Dynamic analysis of tapping-mode
AFM considering capillary force interactions. Scientia Iranica, 18(1), 121-129.
Labuda, A., Cleveland, J., Geisse, N. A., Kocun, M., Ohler, B., Proksch, R., ... & Walters, D.
(2014). Photothermal excitation for improved cantilever drive performance in tapping
mode atomic force microscopy: microscopy and Analysis28, 3, S21-S25.
Liu, S., & Wang, Y. (2010). Application of AFM in microbiology: a review. Scanning, 32(2),
61-73.
Müller, D. J., & Dufrene, Y. F. (2010). Atomic force microscopy as a multifunctional
molecular toolbox in nanobiotechnology. In Nanoscience And Technology: A
Collection of Reviews from Nature Journals (pp. 269-277)
Proksch, R., & Yablon, D. G. (2012). Loss tangent imaging: Theory and simulations of
repulsive-mode tapping atomic force microscopy. Applied Physics Letters, 100(7),
073106.
Sader, J. E., Sanelli, J. A., Adamson, B. D., Monty, J. P., Wei, X., Crawford, S. A., ... &
Bieske, E. J. (2012). Spring constant calibration of atomic force microscope
cantilevers of arbitrary shape. Review of Scientific Instruments, 83(10), 103705
Johnson, D. J., Al Malek, S. A., Al-Rashdi, B. A. M., & Hilal, N. (2012). Atomic force
microscopy of nanofiltration membranes: effect of imaging mode and
environment. Journal of membrane science, 389, 486-498.
Kelly, J., & Sukhatme, G. S. (2011). Visual-inertial sensor fusion: Localization, mapping, and
sensor-to-sensor self-calibration. The International Journal of Robotics
Research, 30(1), 56-79.
Korayem, M. H., Kavousi, A., & Ebrahimi, N. (2011). Dynamic analysis of tapping-mode
AFM considering capillary force interactions. Scientia Iranica, 18(1), 121-129.
Labuda, A., Cleveland, J., Geisse, N. A., Kocun, M., Ohler, B., Proksch, R., ... & Walters, D.
(2014). Photothermal excitation for improved cantilever drive performance in tapping
mode atomic force microscopy: microscopy and Analysis28, 3, S21-S25.
Liu, S., & Wang, Y. (2010). Application of AFM in microbiology: a review. Scanning, 32(2),
61-73.
Müller, D. J., & Dufrene, Y. F. (2010). Atomic force microscopy as a multifunctional
molecular toolbox in nanobiotechnology. In Nanoscience And Technology: A
Collection of Reviews from Nature Journals (pp. 269-277)
Proksch, R., & Yablon, D. G. (2012). Loss tangent imaging: Theory and simulations of
repulsive-mode tapping atomic force microscopy. Applied Physics Letters, 100(7),
073106.
Sader, J. E., Sanelli, J. A., Adamson, B. D., Monty, J. P., Wei, X., Crawford, S. A., ... &
Bieske, E. J. (2012). Spring constant calibration of atomic force microscope
cantilevers of arbitrary shape. Review of Scientific Instruments, 83(10), 103705
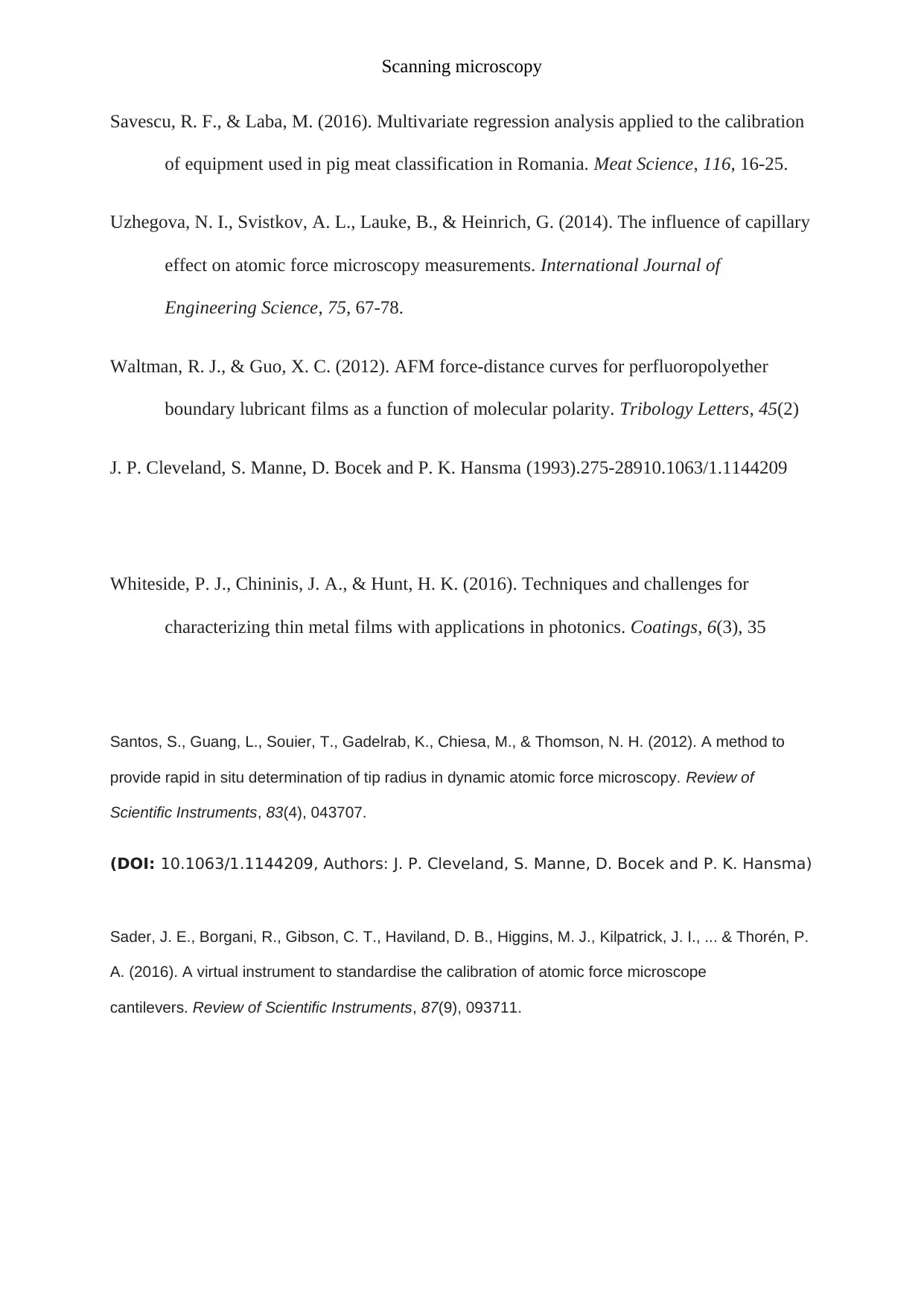
Scanning microscopy
Savescu, R. F., & Laba, M. (2016). Multivariate regression analysis applied to the calibration
of equipment used in pig meat classification in Romania. Meat Science, 116, 16-25.
Uzhegova, N. I., Svistkov, A. L., Lauke, B., & Heinrich, G. (2014). The influence of capillary
effect on atomic force microscopy measurements. International Journal of
Engineering Science, 75, 67-78.
Waltman, R. J., & Guo, X. C. (2012). AFM force-distance curves for perfluoropolyether
boundary lubricant films as a function of molecular polarity. Tribology Letters, 45(2)
J. P. Cleveland, S. Manne, D. Bocek and P. K. Hansma (1993).275-28910.1063/1.1144209
Whiteside, P. J., Chininis, J. A., & Hunt, H. K. (2016). Techniques and challenges for
characterizing thin metal films with applications in photonics. Coatings, 6(3), 35
Santos, S., Guang, L., Souier, T., Gadelrab, K., Chiesa, M., & Thomson, N. H. (2012). A method to
provide rapid in situ determination of tip radius in dynamic atomic force microscopy. Review of
Scientific Instruments, 83(4), 043707.
(DOI: 10.1063/1.1144209, Authors: J. P. Cleveland, S. Manne, D. Bocek and P. K. Hansma)
Sader, J. E., Borgani, R., Gibson, C. T., Haviland, D. B., Higgins, M. J., Kilpatrick, J. I., ... & Thorén, P.
A. (2016). A virtual instrument to standardise the calibration of atomic force microscope
cantilevers. Review of Scientific Instruments, 87(9), 093711.
Savescu, R. F., & Laba, M. (2016). Multivariate regression analysis applied to the calibration
of equipment used in pig meat classification in Romania. Meat Science, 116, 16-25.
Uzhegova, N. I., Svistkov, A. L., Lauke, B., & Heinrich, G. (2014). The influence of capillary
effect on atomic force microscopy measurements. International Journal of
Engineering Science, 75, 67-78.
Waltman, R. J., & Guo, X. C. (2012). AFM force-distance curves for perfluoropolyether
boundary lubricant films as a function of molecular polarity. Tribology Letters, 45(2)
J. P. Cleveland, S. Manne, D. Bocek and P. K. Hansma (1993).275-28910.1063/1.1144209
Whiteside, P. J., Chininis, J. A., & Hunt, H. K. (2016). Techniques and challenges for
characterizing thin metal films with applications in photonics. Coatings, 6(3), 35
Santos, S., Guang, L., Souier, T., Gadelrab, K., Chiesa, M., & Thomson, N. H. (2012). A method to
provide rapid in situ determination of tip radius in dynamic atomic force microscopy. Review of
Scientific Instruments, 83(4), 043707.
(DOI: 10.1063/1.1144209, Authors: J. P. Cleveland, S. Manne, D. Bocek and P. K. Hansma)
Sader, J. E., Borgani, R., Gibson, C. T., Haviland, D. B., Higgins, M. J., Kilpatrick, J. I., ... & Thorén, P.
A. (2016). A virtual instrument to standardise the calibration of atomic force microscope
cantilevers. Review of Scientific Instruments, 87(9), 093711.
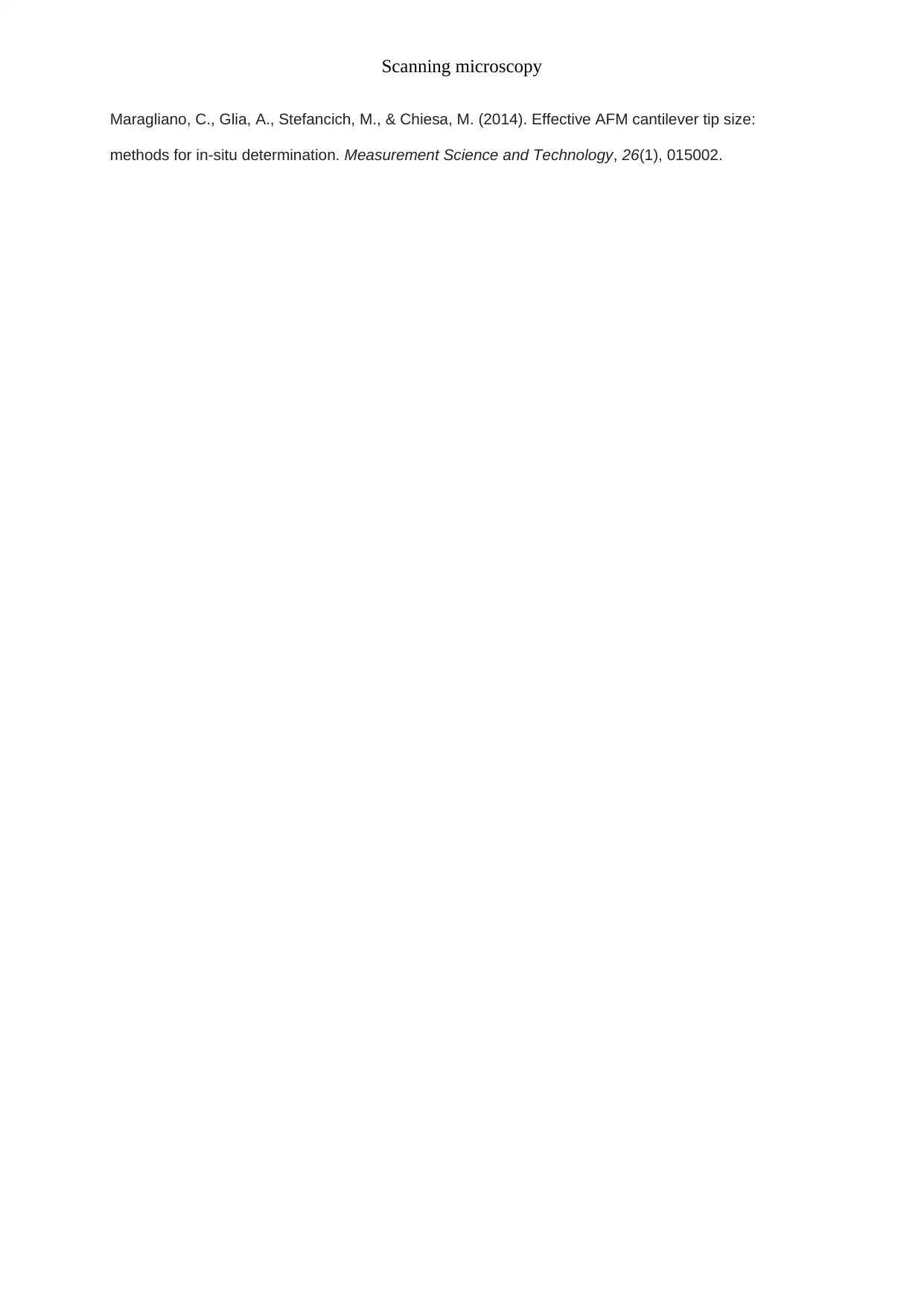
Scanning microscopy
Maragliano, C., Glia, A., Stefancich, M., & Chiesa, M. (2014). Effective AFM cantilever tip size:
methods for in-situ determination. Measurement Science and Technology, 26(1), 015002.
Maragliano, C., Glia, A., Stefancich, M., & Chiesa, M. (2014). Effective AFM cantilever tip size:
methods for in-situ determination. Measurement Science and Technology, 26(1), 015002.
1 out of 25
![[object Object]](/_next/image/?url=%2F_next%2Fstatic%2Fmedia%2Flogo.6d15ce61.png&w=640&q=75)
Your All-in-One AI-Powered Toolkit for Academic Success.
+13062052269
info@desklib.com
Available 24*7 on WhatsApp / Email
Unlock your academic potential
© 2024 | Zucol Services PVT LTD | All rights reserved.