Manufacturing of Scuba Tanks: Process and Materials Used
VerifiedAdded on  2023/06/11
|12
|2415
|325
AI Summary
This article discusses the process and materials used in the manufacturing of scuba tanks. It covers the chemical treatments, extrusion press, heat treatment, quenching, drilling, pressure testing, sanding, and painting involved in the process. Aluminium and steel are the main materials used for scuba tanks.
Contribute Materials
Your contribution can guide someone’s learning journey. Share your
documents today.
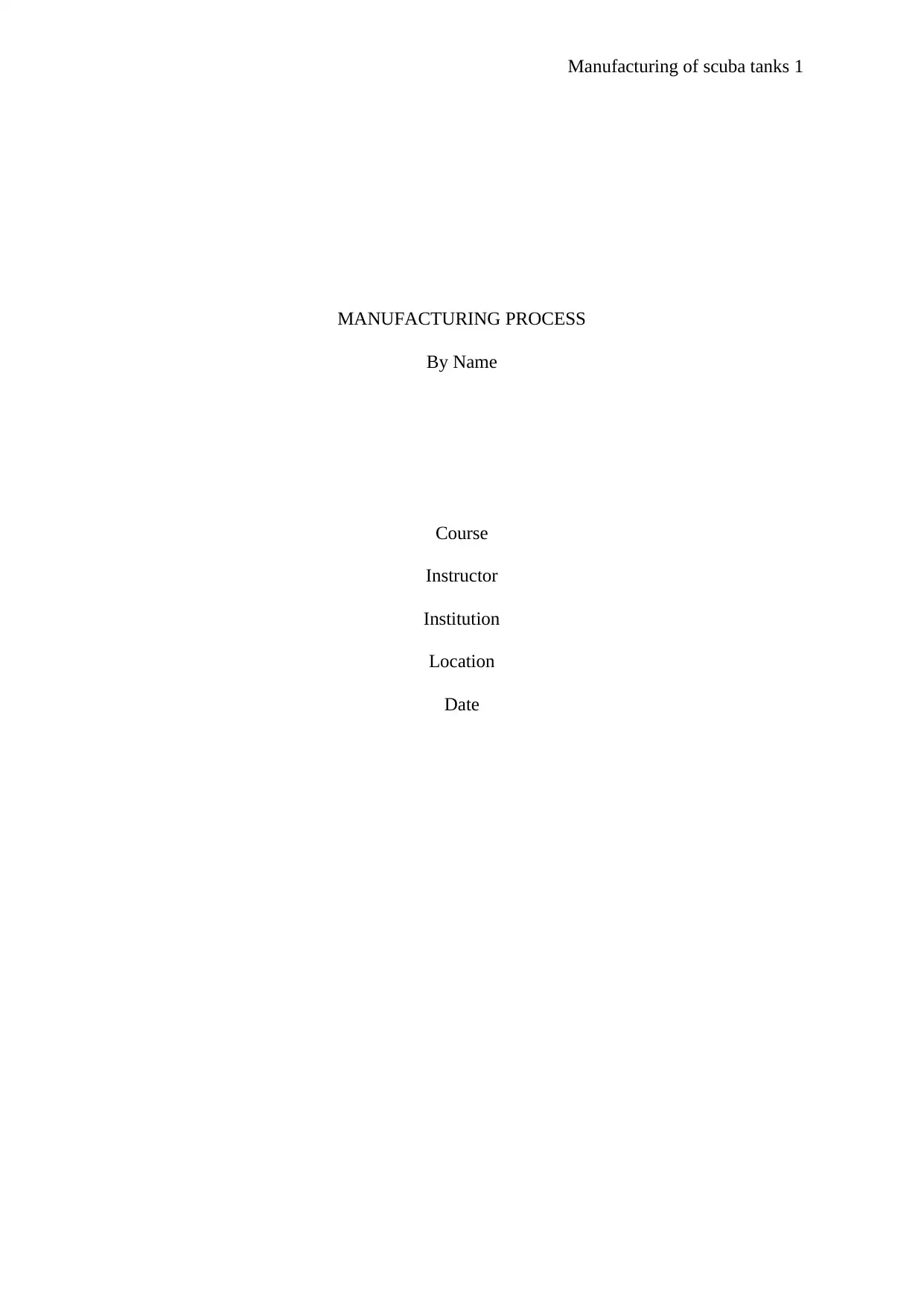
Manufacturing of scuba tanks 1
MANUFACTURING PROCESS
By Name
Course
Instructor
Institution
Location
Date
MANUFACTURING PROCESS
By Name
Course
Instructor
Institution
Location
Date
Secure Best Marks with AI Grader
Need help grading? Try our AI Grader for instant feedback on your assignments.
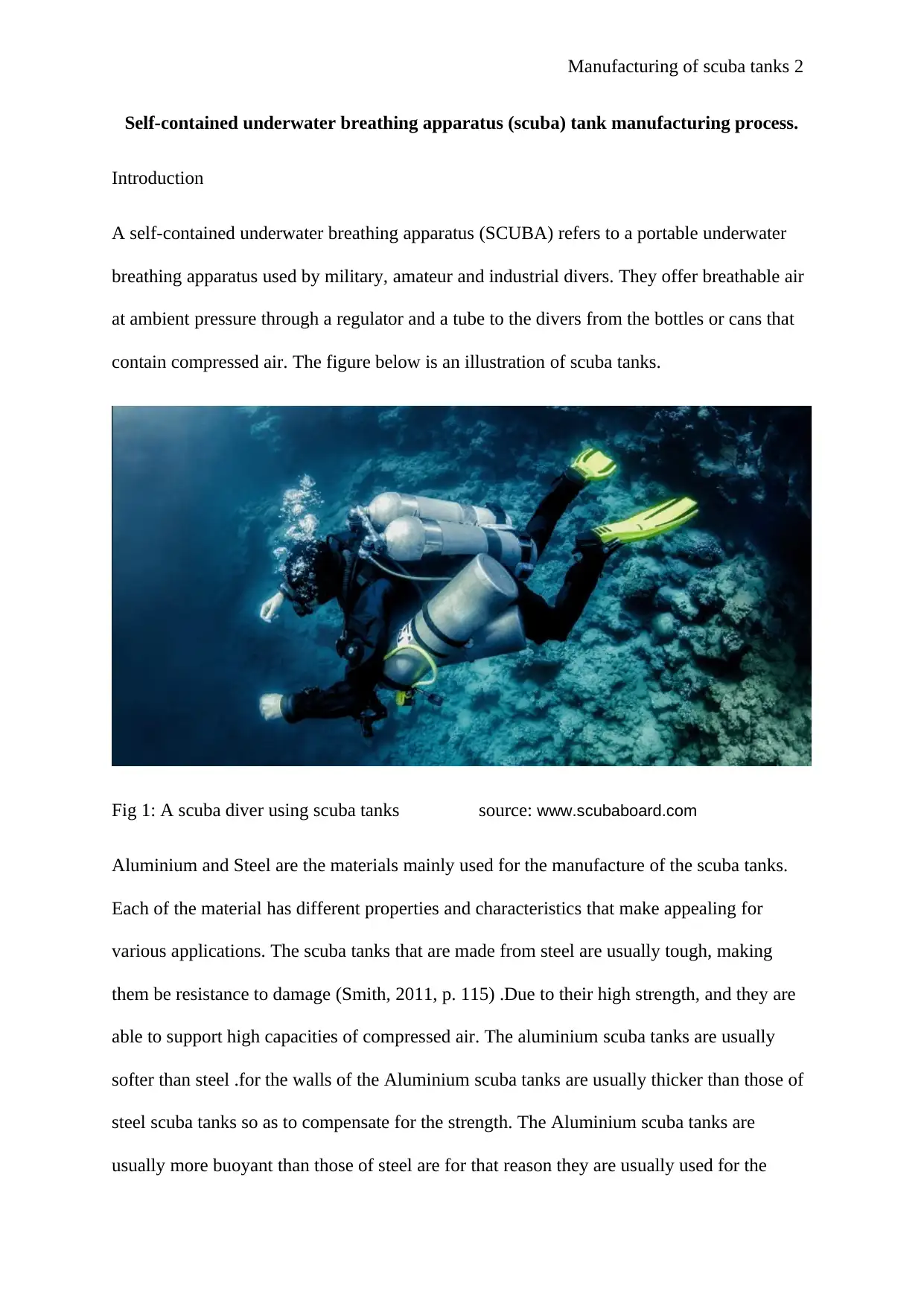
Manufacturing of scuba tanks 2
Self-contained underwater breathing apparatus (scuba) tank manufacturing process.
Introduction
A self-contained underwater breathing apparatus (SCUBA) refers to a portable underwater
breathing apparatus used by military, amateur and industrial divers. They offer breathable air
at ambient pressure through a regulator and a tube to the divers from the bottles or cans that
contain compressed air. The figure below is an illustration of scuba tanks.
Fig 1: A scuba diver using scuba tanks source: www.scubaboard.com
Aluminium and Steel are the materials mainly used for the manufacture of the scuba tanks.
Each of the material has different properties and characteristics that make appealing for
various applications. The scuba tanks that are made from steel are usually tough, making
them be resistance to damage (Smith, 2011, p. 115) .Due to their high strength, and they are
able to support high capacities of compressed air. The aluminium scuba tanks are usually
softer than steel .for the walls of the Aluminium scuba tanks are usually thicker than those of
steel scuba tanks so as to compensate for the strength. The Aluminium scuba tanks are
usually more buoyant than those of steel are for that reason they are usually used for the
Self-contained underwater breathing apparatus (scuba) tank manufacturing process.
Introduction
A self-contained underwater breathing apparatus (SCUBA) refers to a portable underwater
breathing apparatus used by military, amateur and industrial divers. They offer breathable air
at ambient pressure through a regulator and a tube to the divers from the bottles or cans that
contain compressed air. The figure below is an illustration of scuba tanks.
Fig 1: A scuba diver using scuba tanks source: www.scubaboard.com
Aluminium and Steel are the materials mainly used for the manufacture of the scuba tanks.
Each of the material has different properties and characteristics that make appealing for
various applications. The scuba tanks that are made from steel are usually tough, making
them be resistance to damage (Smith, 2011, p. 115) .Due to their high strength, and they are
able to support high capacities of compressed air. The aluminium scuba tanks are usually
softer than steel .for the walls of the Aluminium scuba tanks are usually thicker than those of
steel scuba tanks so as to compensate for the strength. The Aluminium scuba tanks are
usually more buoyant than those of steel are for that reason they are usually used for the
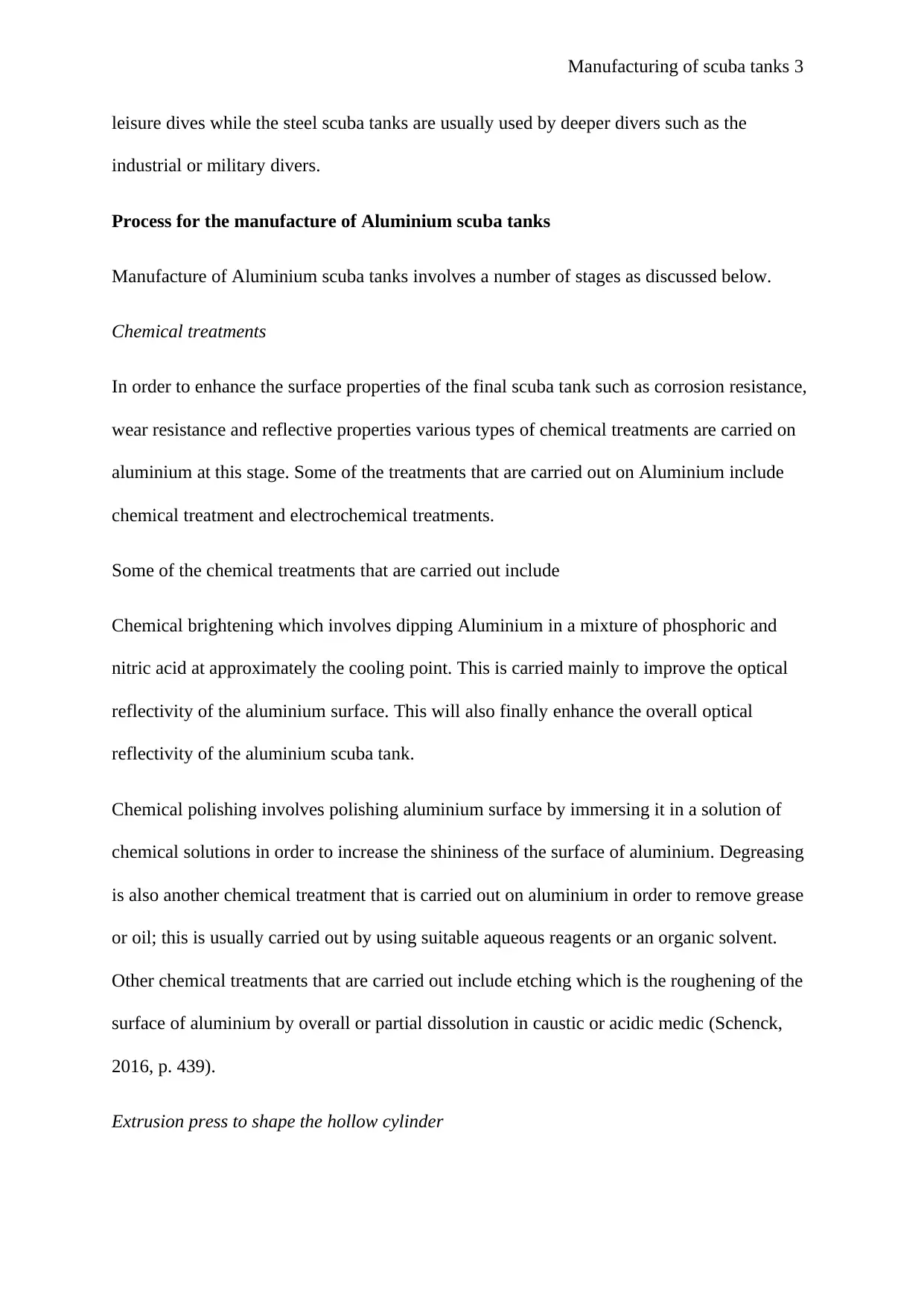
Manufacturing of scuba tanks 3
leisure dives while the steel scuba tanks are usually used by deeper divers such as the
industrial or military divers.
Process for the manufacture of Aluminium scuba tanks
Manufacture of Aluminium scuba tanks involves a number of stages as discussed below.
Chemical treatments
In order to enhance the surface properties of the final scuba tank such as corrosion resistance,
wear resistance and reflective properties various types of chemical treatments are carried on
aluminium at this stage. Some of the treatments that are carried out on Aluminium include
chemical treatment and electrochemical treatments.
Some of the chemical treatments that are carried out include
Chemical brightening which involves dipping Aluminium in a mixture of phosphoric and
nitric acid at approximately the cooling point. This is carried mainly to improve the optical
reflectivity of the aluminium surface. This will also finally enhance the overall optical
reflectivity of the aluminium scuba tank.
Chemical polishing involves polishing aluminium surface by immersing it in a solution of
chemical solutions in order to increase the shininess of the surface of aluminium. Degreasing
is also another chemical treatment that is carried out on aluminium in order to remove grease
or oil; this is usually carried out by using suitable aqueous reagents or an organic solvent.
Other chemical treatments that are carried out include etching which is the roughening of the
surface of aluminium by overall or partial dissolution in caustic or acidic medic (Schenck,
2016, p. 439).
Extrusion press to shape the hollow cylinder
leisure dives while the steel scuba tanks are usually used by deeper divers such as the
industrial or military divers.
Process for the manufacture of Aluminium scuba tanks
Manufacture of Aluminium scuba tanks involves a number of stages as discussed below.
Chemical treatments
In order to enhance the surface properties of the final scuba tank such as corrosion resistance,
wear resistance and reflective properties various types of chemical treatments are carried on
aluminium at this stage. Some of the treatments that are carried out on Aluminium include
chemical treatment and electrochemical treatments.
Some of the chemical treatments that are carried out include
Chemical brightening which involves dipping Aluminium in a mixture of phosphoric and
nitric acid at approximately the cooling point. This is carried mainly to improve the optical
reflectivity of the aluminium surface. This will also finally enhance the overall optical
reflectivity of the aluminium scuba tank.
Chemical polishing involves polishing aluminium surface by immersing it in a solution of
chemical solutions in order to increase the shininess of the surface of aluminium. Degreasing
is also another chemical treatment that is carried out on aluminium in order to remove grease
or oil; this is usually carried out by using suitable aqueous reagents or an organic solvent.
Other chemical treatments that are carried out include etching which is the roughening of the
surface of aluminium by overall or partial dissolution in caustic or acidic medic (Schenck,
2016, p. 439).
Extrusion press to shape the hollow cylinder
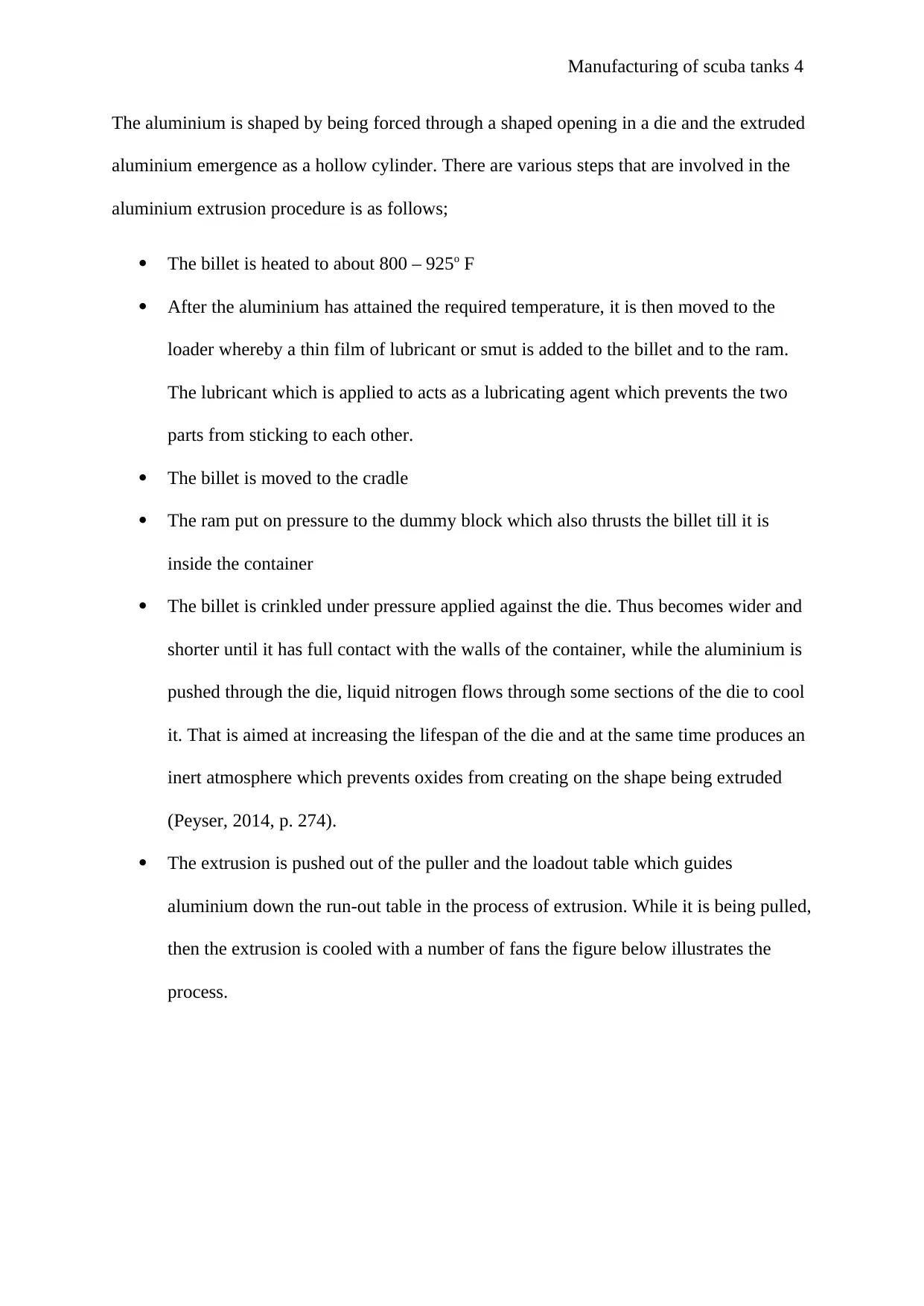
Manufacturing of scuba tanks 4
The aluminium is shaped by being forced through a shaped opening in a die and the extruded
aluminium emergence as a hollow cylinder. There are various steps that are involved in the
aluminium extrusion procedure is as follows;
 The billet is heated to about 800 – 925o F
ï‚· After the aluminium has attained the required temperature, it is then moved to the
loader whereby a thin film of lubricant or smut is added to the billet and to the ram.
The lubricant which is applied to acts as a lubricating agent which prevents the two
parts from sticking to each other.
ï‚· The billet is moved to the cradle
ï‚· The ram put on pressure to the dummy block which also thrusts the billet till it is
inside the container
ï‚· The billet is crinkled under pressure applied against the die. Thus becomes wider and
shorter until it has full contact with the walls of the container, while the aluminium is
pushed through the die, liquid nitrogen flows through some sections of the die to cool
it. That is aimed at increasing the lifespan of the die and at the same time produces an
inert atmosphere which prevents oxides from creating on the shape being extruded
(Peyser, 2014, p. 274).
ï‚· The extrusion is pushed out of the puller and the loadout table which guides
aluminium down the run-out table in the process of extrusion. While it is being pulled,
then the extrusion is cooled with a number of fans the figure below illustrates the
process.
The aluminium is shaped by being forced through a shaped opening in a die and the extruded
aluminium emergence as a hollow cylinder. There are various steps that are involved in the
aluminium extrusion procedure is as follows;
 The billet is heated to about 800 – 925o F
ï‚· After the aluminium has attained the required temperature, it is then moved to the
loader whereby a thin film of lubricant or smut is added to the billet and to the ram.
The lubricant which is applied to acts as a lubricating agent which prevents the two
parts from sticking to each other.
ï‚· The billet is moved to the cradle
ï‚· The ram put on pressure to the dummy block which also thrusts the billet till it is
inside the container
ï‚· The billet is crinkled under pressure applied against the die. Thus becomes wider and
shorter until it has full contact with the walls of the container, while the aluminium is
pushed through the die, liquid nitrogen flows through some sections of the die to cool
it. That is aimed at increasing the lifespan of the die and at the same time produces an
inert atmosphere which prevents oxides from creating on the shape being extruded
(Peyser, 2014, p. 274).
ï‚· The extrusion is pushed out of the puller and the loadout table which guides
aluminium down the run-out table in the process of extrusion. While it is being pulled,
then the extrusion is cooled with a number of fans the figure below illustrates the
process.
Secure Best Marks with AI Grader
Need help grading? Try our AI Grader for instant feedback on your assignments.
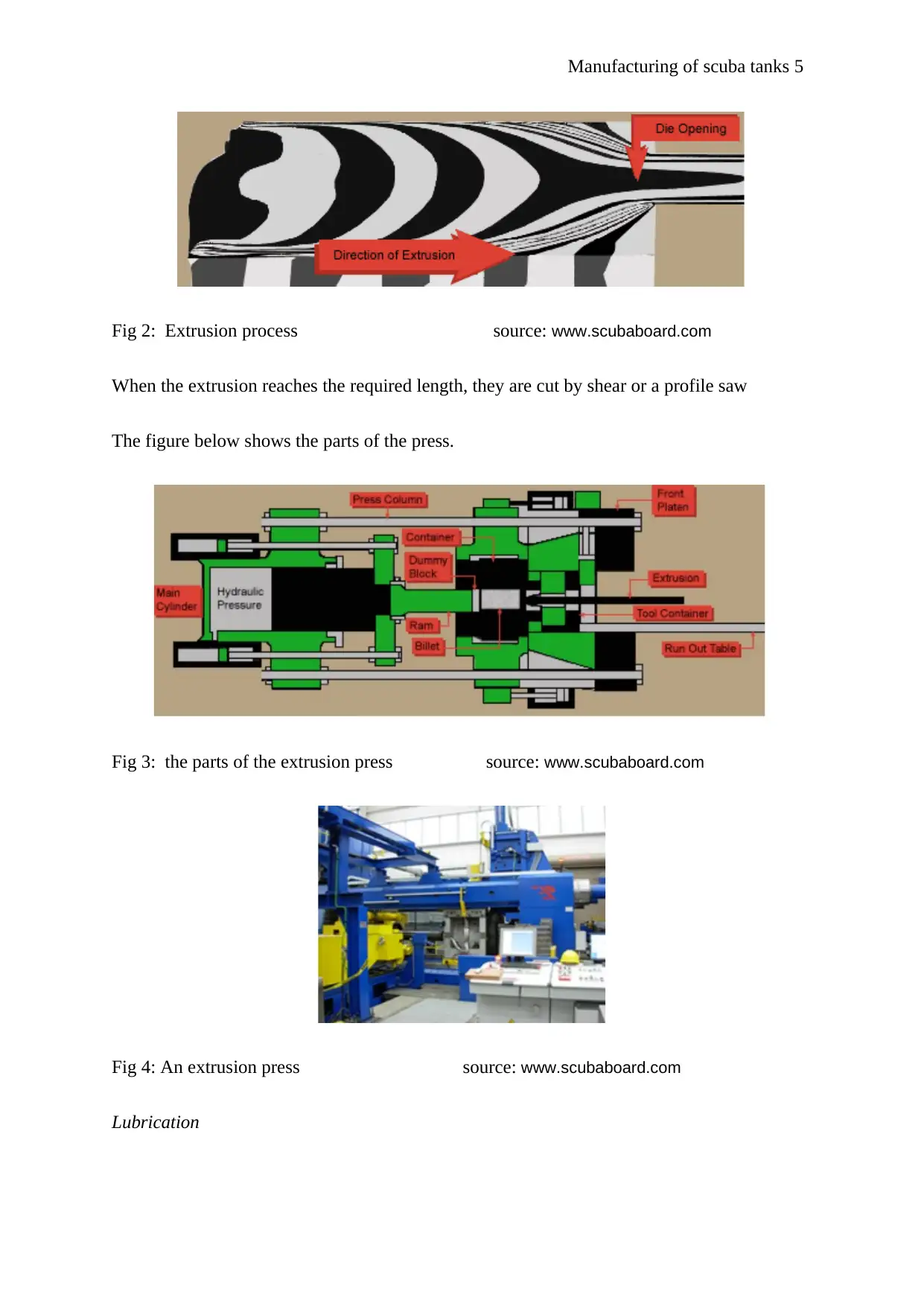
Manufacturing of scuba tanks 5
Fig 2: Extrusion process source: www.scubaboard.com
When the extrusion reaches the required length, they are cut by shear or a profile saw
The figure below shows the parts of the press.
Fig 3: the parts of the extrusion press source: www.scubaboard.com
Fig 4: An extrusion press source: www.scubaboard.com
Lubrication
Fig 2: Extrusion process source: www.scubaboard.com
When the extrusion reaches the required length, they are cut by shear or a profile saw
The figure below shows the parts of the press.
Fig 3: the parts of the extrusion press source: www.scubaboard.com
Fig 4: An extrusion press source: www.scubaboard.com
Lubrication
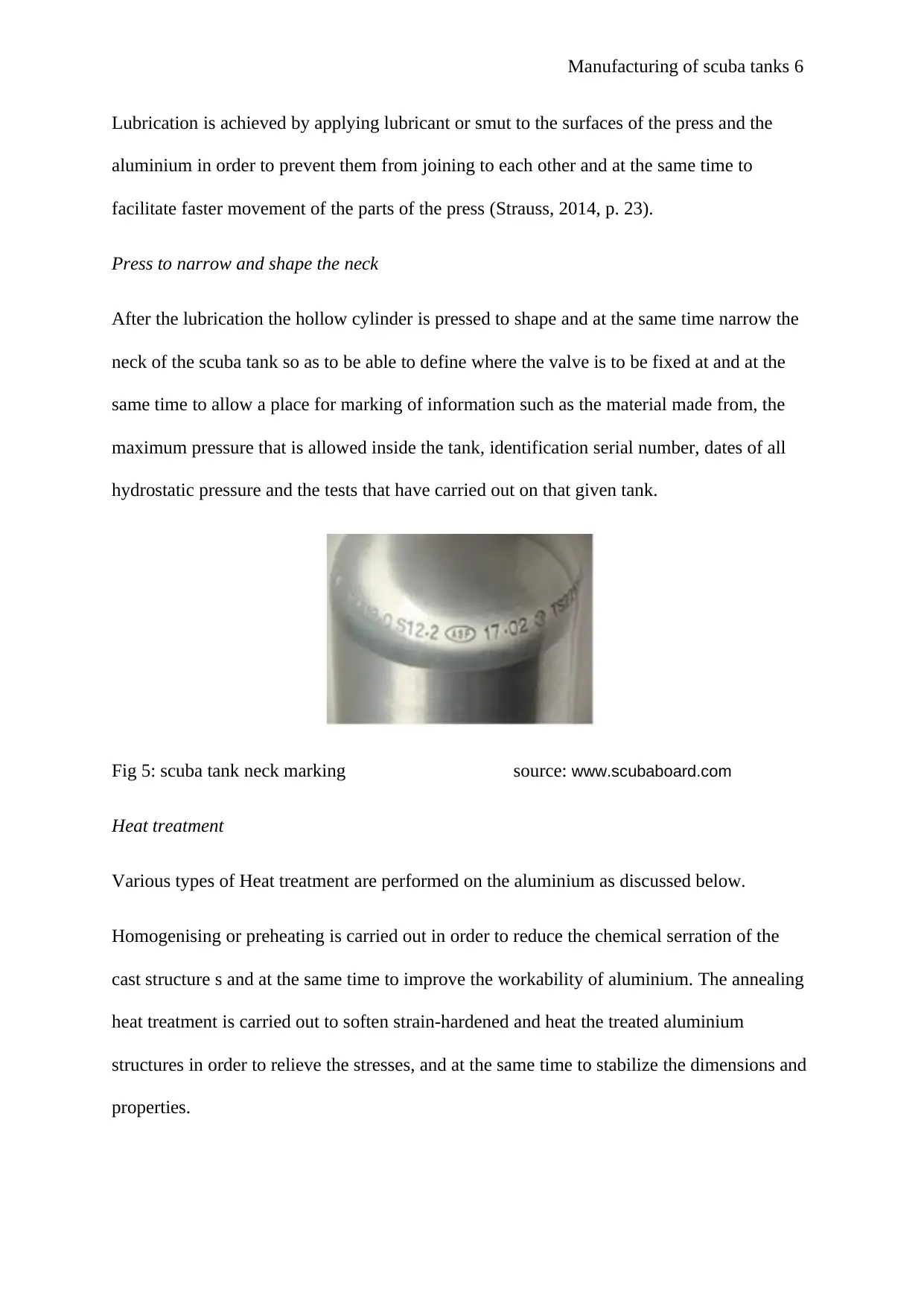
Manufacturing of scuba tanks 6
Lubrication is achieved by applying lubricant or smut to the surfaces of the press and the
aluminium in order to prevent them from joining to each other and at the same time to
facilitate faster movement of the parts of the press (Strauss, 2014, p. 23).
Press to narrow and shape the neck
After the lubrication the hollow cylinder is pressed to shape and at the same time narrow the
neck of the scuba tank so as to be able to define where the valve is to be fixed at and at the
same time to allow a place for marking of information such as the material made from, the
maximum pressure that is allowed inside the tank, identification serial number, dates of all
hydrostatic pressure and the tests that have carried out on that given tank.
Fig 5: scuba tank neck marking source: www.scubaboard.com
Heat treatment
Various types of Heat treatment are performed on the aluminium as discussed below.
Homogenising or preheating is carried out in order to reduce the chemical serration of the
cast structure s and at the same time to improve the workability of aluminium. The annealing
heat treatment is carried out to soften strain-hardened and heat the treated aluminium
structures in order to relieve the stresses, and at the same time to stabilize the dimensions and
properties.
Lubrication is achieved by applying lubricant or smut to the surfaces of the press and the
aluminium in order to prevent them from joining to each other and at the same time to
facilitate faster movement of the parts of the press (Strauss, 2014, p. 23).
Press to narrow and shape the neck
After the lubrication the hollow cylinder is pressed to shape and at the same time narrow the
neck of the scuba tank so as to be able to define where the valve is to be fixed at and at the
same time to allow a place for marking of information such as the material made from, the
maximum pressure that is allowed inside the tank, identification serial number, dates of all
hydrostatic pressure and the tests that have carried out on that given tank.
Fig 5: scuba tank neck marking source: www.scubaboard.com
Heat treatment
Various types of Heat treatment are performed on the aluminium as discussed below.
Homogenising or preheating is carried out in order to reduce the chemical serration of the
cast structure s and at the same time to improve the workability of aluminium. The annealing
heat treatment is carried out to soften strain-hardened and heat the treated aluminium
structures in order to relieve the stresses, and at the same time to stabilize the dimensions and
properties.
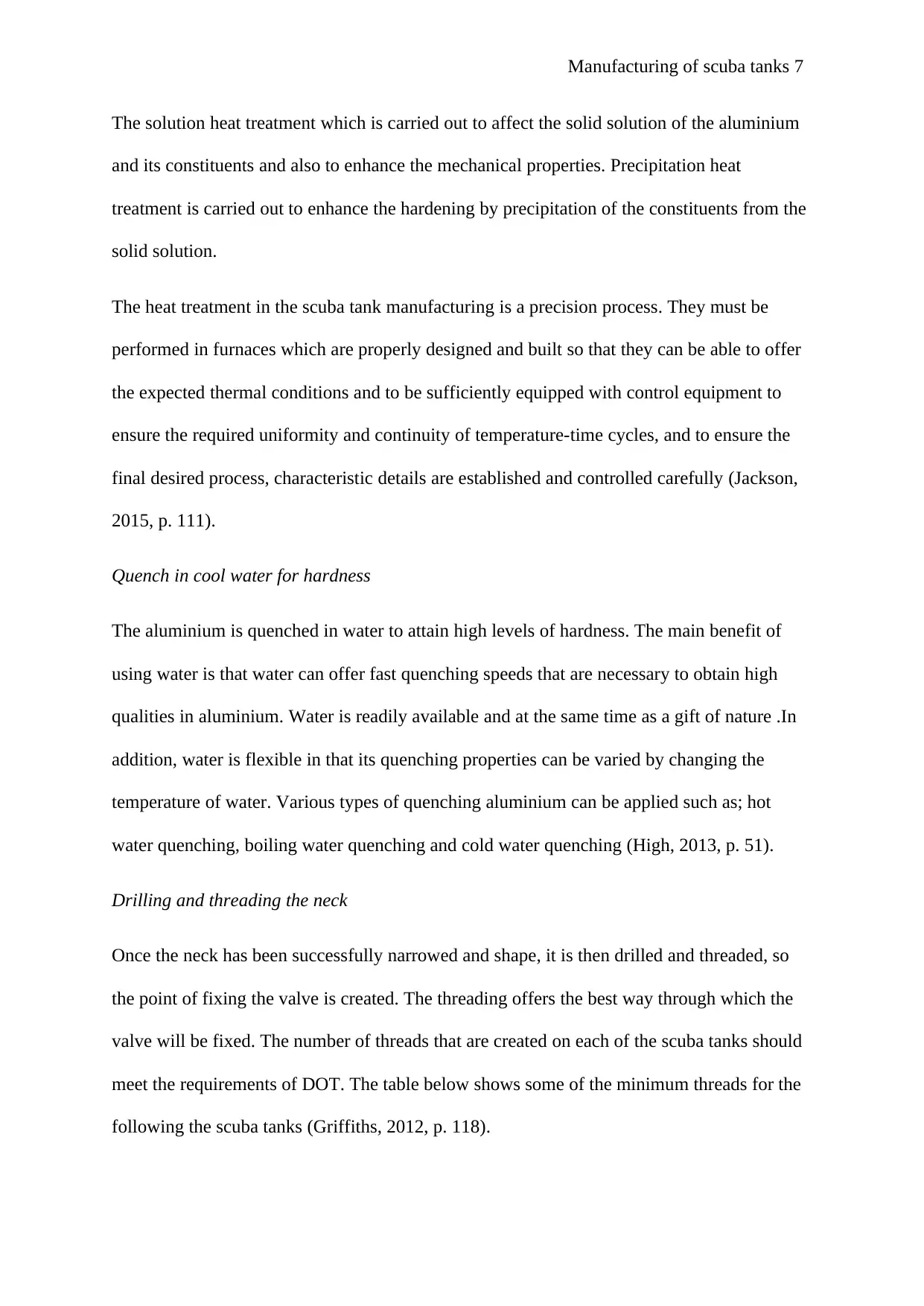
Manufacturing of scuba tanks 7
The solution heat treatment which is carried out to affect the solid solution of the aluminium
and its constituents and also to enhance the mechanical properties. Precipitation heat
treatment is carried out to enhance the hardening by precipitation of the constituents from the
solid solution.
The heat treatment in the scuba tank manufacturing is a precision process. They must be
performed in furnaces which are properly designed and built so that they can be able to offer
the expected thermal conditions and to be sufficiently equipped with control equipment to
ensure the required uniformity and continuity of temperature-time cycles, and to ensure the
final desired process, characteristic details are established and controlled carefully (Jackson,
2015, p. 111).
Quench in cool water for hardness
The aluminium is quenched in water to attain high levels of hardness. The main benefit of
using water is that water can offer fast quenching speeds that are necessary to obtain high
qualities in aluminium. Water is readily available and at the same time as a gift of nature .In
addition, water is flexible in that its quenching properties can be varied by changing the
temperature of water. Various types of quenching aluminium can be applied such as; hot
water quenching, boiling water quenching and cold water quenching (High, 2013, p. 51).
Drilling and threading the neck
Once the neck has been successfully narrowed and shape, it is then drilled and threaded, so
the point of fixing the valve is created. The threading offers the best way through which the
valve will be fixed. The number of threads that are created on each of the scuba tanks should
meet the requirements of DOT. The table below shows some of the minimum threads for the
following the scuba tanks (Griffiths, 2012, p. 118).
The solution heat treatment which is carried out to affect the solid solution of the aluminium
and its constituents and also to enhance the mechanical properties. Precipitation heat
treatment is carried out to enhance the hardening by precipitation of the constituents from the
solid solution.
The heat treatment in the scuba tank manufacturing is a precision process. They must be
performed in furnaces which are properly designed and built so that they can be able to offer
the expected thermal conditions and to be sufficiently equipped with control equipment to
ensure the required uniformity and continuity of temperature-time cycles, and to ensure the
final desired process, characteristic details are established and controlled carefully (Jackson,
2015, p. 111).
Quench in cool water for hardness
The aluminium is quenched in water to attain high levels of hardness. The main benefit of
using water is that water can offer fast quenching speeds that are necessary to obtain high
qualities in aluminium. Water is readily available and at the same time as a gift of nature .In
addition, water is flexible in that its quenching properties can be varied by changing the
temperature of water. Various types of quenching aluminium can be applied such as; hot
water quenching, boiling water quenching and cold water quenching (High, 2013, p. 51).
Drilling and threading the neck
Once the neck has been successfully narrowed and shape, it is then drilled and threaded, so
the point of fixing the valve is created. The threading offers the best way through which the
valve will be fixed. The number of threads that are created on each of the scuba tanks should
meet the requirements of DOT. The table below shows some of the minimum threads for the
following the scuba tanks (Griffiths, 2012, p. 118).
Paraphrase This Document
Need a fresh take? Get an instant paraphrase of this document with our AI Paraphraser
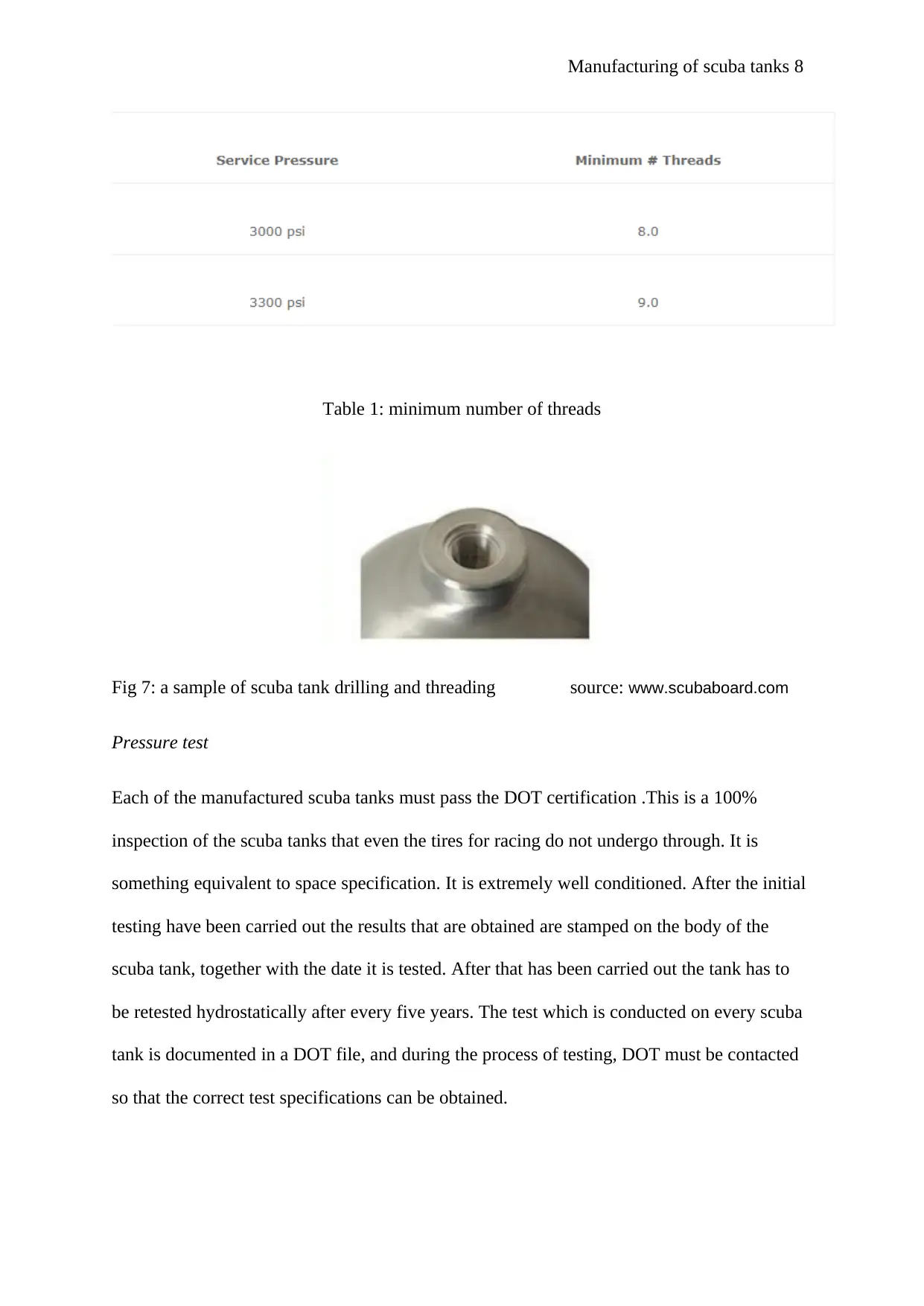
Manufacturing of scuba tanks 8
Table 1: minimum number of threads
Fig 7: a sample of scuba tank drilling and threading source: www.scubaboard.com
Pressure test
Each of the manufactured scuba tanks must pass the DOT certification .This is a 100%
inspection of the scuba tanks that even the tires for racing do not undergo through. It is
something equivalent to space specification. It is extremely well conditioned. After the initial
testing have been carried out the results that are obtained are stamped on the body of the
scuba tank, together with the date it is tested. After that has been carried out the tank has to
be retested hydrostatically after every five years. The test which is conducted on every scuba
tank is documented in a DOT file, and during the process of testing, DOT must be contacted
so that the correct test specifications can be obtained.
Table 1: minimum number of threads
Fig 7: a sample of scuba tank drilling and threading source: www.scubaboard.com
Pressure test
Each of the manufactured scuba tanks must pass the DOT certification .This is a 100%
inspection of the scuba tanks that even the tires for racing do not undergo through. It is
something equivalent to space specification. It is extremely well conditioned. After the initial
testing have been carried out the results that are obtained are stamped on the body of the
scuba tank, together with the date it is tested. After that has been carried out the tank has to
be retested hydrostatically after every five years. The test which is conducted on every scuba
tank is documented in a DOT file, and during the process of testing, DOT must be contacted
so that the correct test specifications can be obtained.
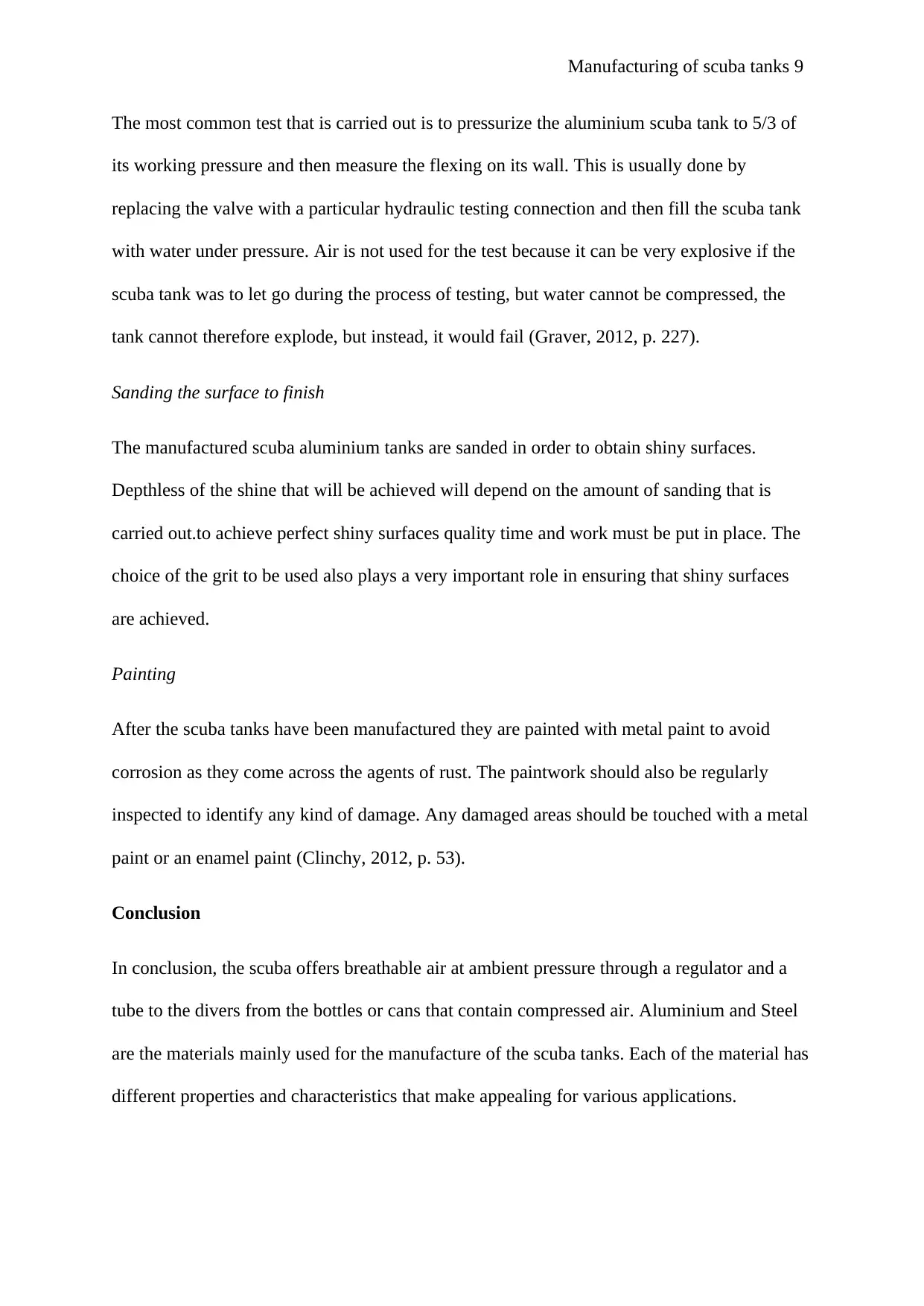
Manufacturing of scuba tanks 9
The most common test that is carried out is to pressurize the aluminium scuba tank to 5/3 of
its working pressure and then measure the flexing on its wall. This is usually done by
replacing the valve with a particular hydraulic testing connection and then fill the scuba tank
with water under pressure. Air is not used for the test because it can be very explosive if the
scuba tank was to let go during the process of testing, but water cannot be compressed, the
tank cannot therefore explode, but instead, it would fail (Graver, 2012, p. 227).
Sanding the surface to finish
The manufactured scuba aluminium tanks are sanded in order to obtain shiny surfaces.
Depthless of the shine that will be achieved will depend on the amount of sanding that is
carried out.to achieve perfect shiny surfaces quality time and work must be put in place. The
choice of the grit to be used also plays a very important role in ensuring that shiny surfaces
are achieved.
Painting
After the scuba tanks have been manufactured they are painted with metal paint to avoid
corrosion as they come across the agents of rust. The paintwork should also be regularly
inspected to identify any kind of damage. Any damaged areas should be touched with a metal
paint or an enamel paint (Clinchy, 2012, p. 53).
Conclusion
In conclusion, the scuba offers breathable air at ambient pressure through a regulator and a
tube to the divers from the bottles or cans that contain compressed air. Aluminium and Steel
are the materials mainly used for the manufacture of the scuba tanks. Each of the material has
different properties and characteristics that make appealing for various applications.
The most common test that is carried out is to pressurize the aluminium scuba tank to 5/3 of
its working pressure and then measure the flexing on its wall. This is usually done by
replacing the valve with a particular hydraulic testing connection and then fill the scuba tank
with water under pressure. Air is not used for the test because it can be very explosive if the
scuba tank was to let go during the process of testing, but water cannot be compressed, the
tank cannot therefore explode, but instead, it would fail (Graver, 2012, p. 227).
Sanding the surface to finish
The manufactured scuba aluminium tanks are sanded in order to obtain shiny surfaces.
Depthless of the shine that will be achieved will depend on the amount of sanding that is
carried out.to achieve perfect shiny surfaces quality time and work must be put in place. The
choice of the grit to be used also plays a very important role in ensuring that shiny surfaces
are achieved.
Painting
After the scuba tanks have been manufactured they are painted with metal paint to avoid
corrosion as they come across the agents of rust. The paintwork should also be regularly
inspected to identify any kind of damage. Any damaged areas should be touched with a metal
paint or an enamel paint (Clinchy, 2012, p. 53).
Conclusion
In conclusion, the scuba offers breathable air at ambient pressure through a regulator and a
tube to the divers from the bottles or cans that contain compressed air. Aluminium and Steel
are the materials mainly used for the manufacture of the scuba tanks. Each of the material has
different properties and characteristics that make appealing for various applications.
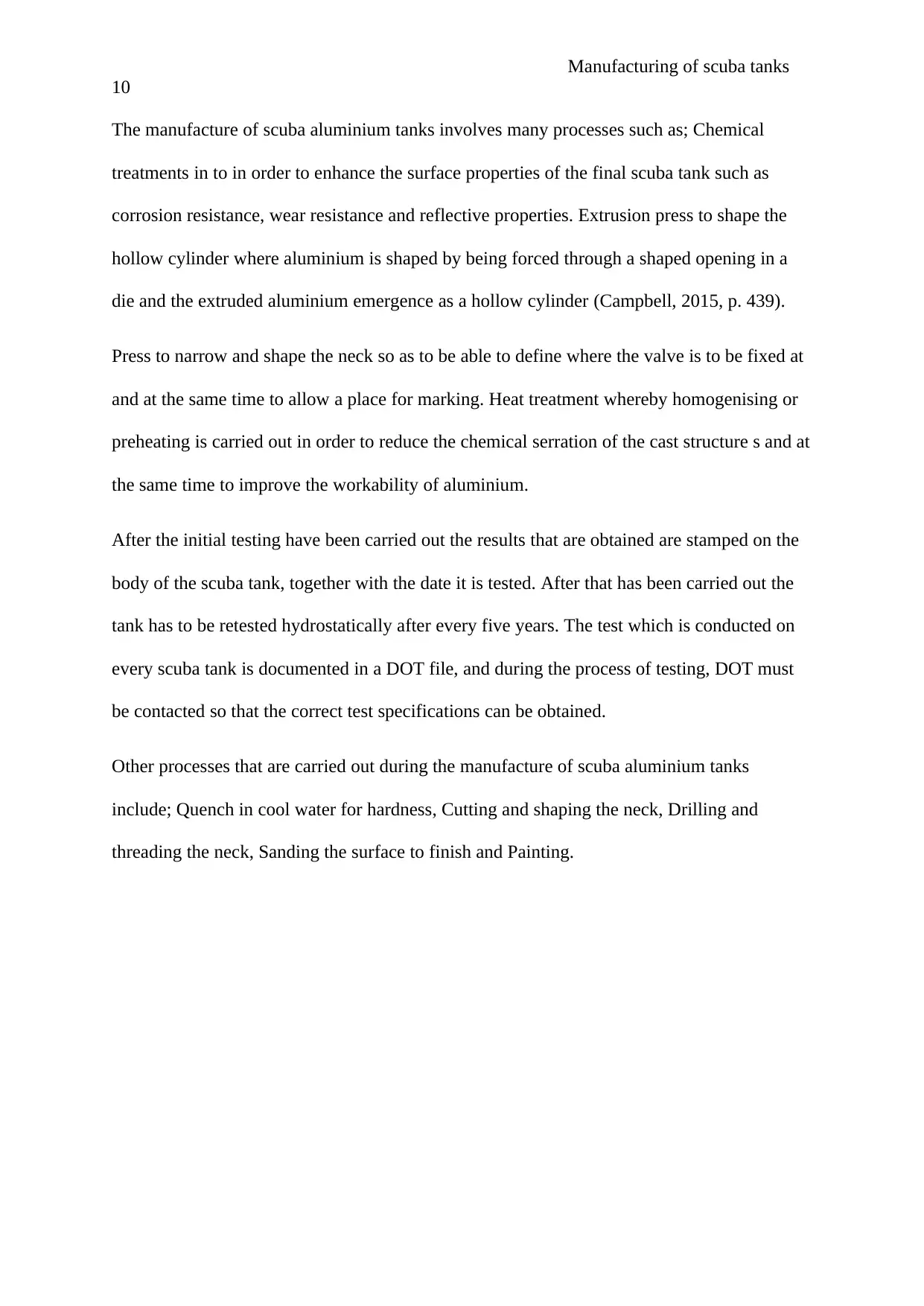
Manufacturing of scuba tanks
10
The manufacture of scuba aluminium tanks involves many processes such as; Chemical
treatments in to in order to enhance the surface properties of the final scuba tank such as
corrosion resistance, wear resistance and reflective properties. Extrusion press to shape the
hollow cylinder where aluminium is shaped by being forced through a shaped opening in a
die and the extruded aluminium emergence as a hollow cylinder (Campbell, 2015, p. 439).
Press to narrow and shape the neck so as to be able to define where the valve is to be fixed at
and at the same time to allow a place for marking. Heat treatment whereby homogenising or
preheating is carried out in order to reduce the chemical serration of the cast structure s and at
the same time to improve the workability of aluminium.
After the initial testing have been carried out the results that are obtained are stamped on the
body of the scuba tank, together with the date it is tested. After that has been carried out the
tank has to be retested hydrostatically after every five years. The test which is conducted on
every scuba tank is documented in a DOT file, and during the process of testing, DOT must
be contacted so that the correct test specifications can be obtained.
Other processes that are carried out during the manufacture of scuba aluminium tanks
include; Quench in cool water for hardness, Cutting and shaping the neck, Drilling and
threading the neck, Sanding the surface to finish and Painting.
10
The manufacture of scuba aluminium tanks involves many processes such as; Chemical
treatments in to in order to enhance the surface properties of the final scuba tank such as
corrosion resistance, wear resistance and reflective properties. Extrusion press to shape the
hollow cylinder where aluminium is shaped by being forced through a shaped opening in a
die and the extruded aluminium emergence as a hollow cylinder (Campbell, 2015, p. 439).
Press to narrow and shape the neck so as to be able to define where the valve is to be fixed at
and at the same time to allow a place for marking. Heat treatment whereby homogenising or
preheating is carried out in order to reduce the chemical serration of the cast structure s and at
the same time to improve the workability of aluminium.
After the initial testing have been carried out the results that are obtained are stamped on the
body of the scuba tank, together with the date it is tested. After that has been carried out the
tank has to be retested hydrostatically after every five years. The test which is conducted on
every scuba tank is documented in a DOT file, and during the process of testing, DOT must
be contacted so that the correct test specifications can be obtained.
Other processes that are carried out during the manufacture of scuba aluminium tanks
include; Quench in cool water for hardness, Cutting and shaping the neck, Drilling and
threading the neck, Sanding the surface to finish and Painting.
Secure Best Marks with AI Grader
Need help grading? Try our AI Grader for instant feedback on your assignments.
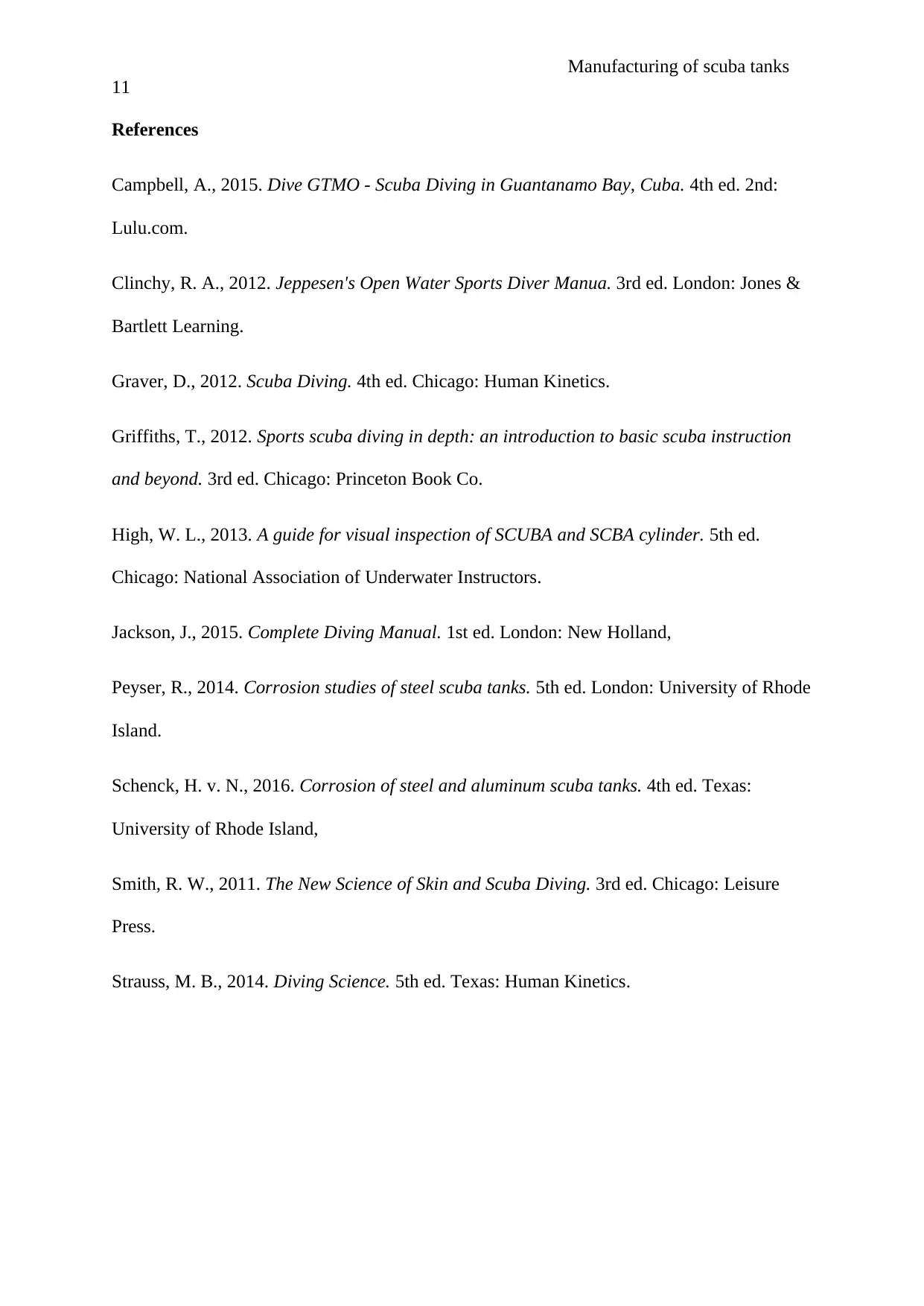
Manufacturing of scuba tanks
11
References
Campbell, A., 2015. Dive GTMO - Scuba Diving in Guantanamo Bay, Cuba. 4th ed. 2nd:
Lulu.com.
Clinchy, R. A., 2012. Jeppesen's Open Water Sports Diver Manua. 3rd ed. London: Jones &
Bartlett Learning.
Graver, D., 2012. Scuba Diving. 4th ed. Chicago: Human Kinetics.
Griffiths, T., 2012. Sports scuba diving in depth: an introduction to basic scuba instruction
and beyond. 3rd ed. Chicago: Princeton Book Co.
High, W. L., 2013. A guide for visual inspection of SCUBA and SCBA cylinder. 5th ed.
Chicago: National Association of Underwater Instructors.
Jackson, J., 2015. Complete Diving Manual. 1st ed. London: New Holland,
Peyser, R., 2014. Corrosion studies of steel scuba tanks. 5th ed. London: University of Rhode
Island.
Schenck, H. v. N., 2016. Corrosion of steel and aluminum scuba tanks. 4th ed. Texas:
University of Rhode Island,
Smith, R. W., 2011. The New Science of Skin and Scuba Diving. 3rd ed. Chicago: Leisure
Press.
Strauss, M. B., 2014. Diving Science. 5th ed. Texas: Human Kinetics.
11
References
Campbell, A., 2015. Dive GTMO - Scuba Diving in Guantanamo Bay, Cuba. 4th ed. 2nd:
Lulu.com.
Clinchy, R. A., 2012. Jeppesen's Open Water Sports Diver Manua. 3rd ed. London: Jones &
Bartlett Learning.
Graver, D., 2012. Scuba Diving. 4th ed. Chicago: Human Kinetics.
Griffiths, T., 2012. Sports scuba diving in depth: an introduction to basic scuba instruction
and beyond. 3rd ed. Chicago: Princeton Book Co.
High, W. L., 2013. A guide for visual inspection of SCUBA and SCBA cylinder. 5th ed.
Chicago: National Association of Underwater Instructors.
Jackson, J., 2015. Complete Diving Manual. 1st ed. London: New Holland,
Peyser, R., 2014. Corrosion studies of steel scuba tanks. 5th ed. London: University of Rhode
Island.
Schenck, H. v. N., 2016. Corrosion of steel and aluminum scuba tanks. 4th ed. Texas:
University of Rhode Island,
Smith, R. W., 2011. The New Science of Skin and Scuba Diving. 3rd ed. Chicago: Leisure
Press.
Strauss, M. B., 2014. Diving Science. 5th ed. Texas: Human Kinetics.
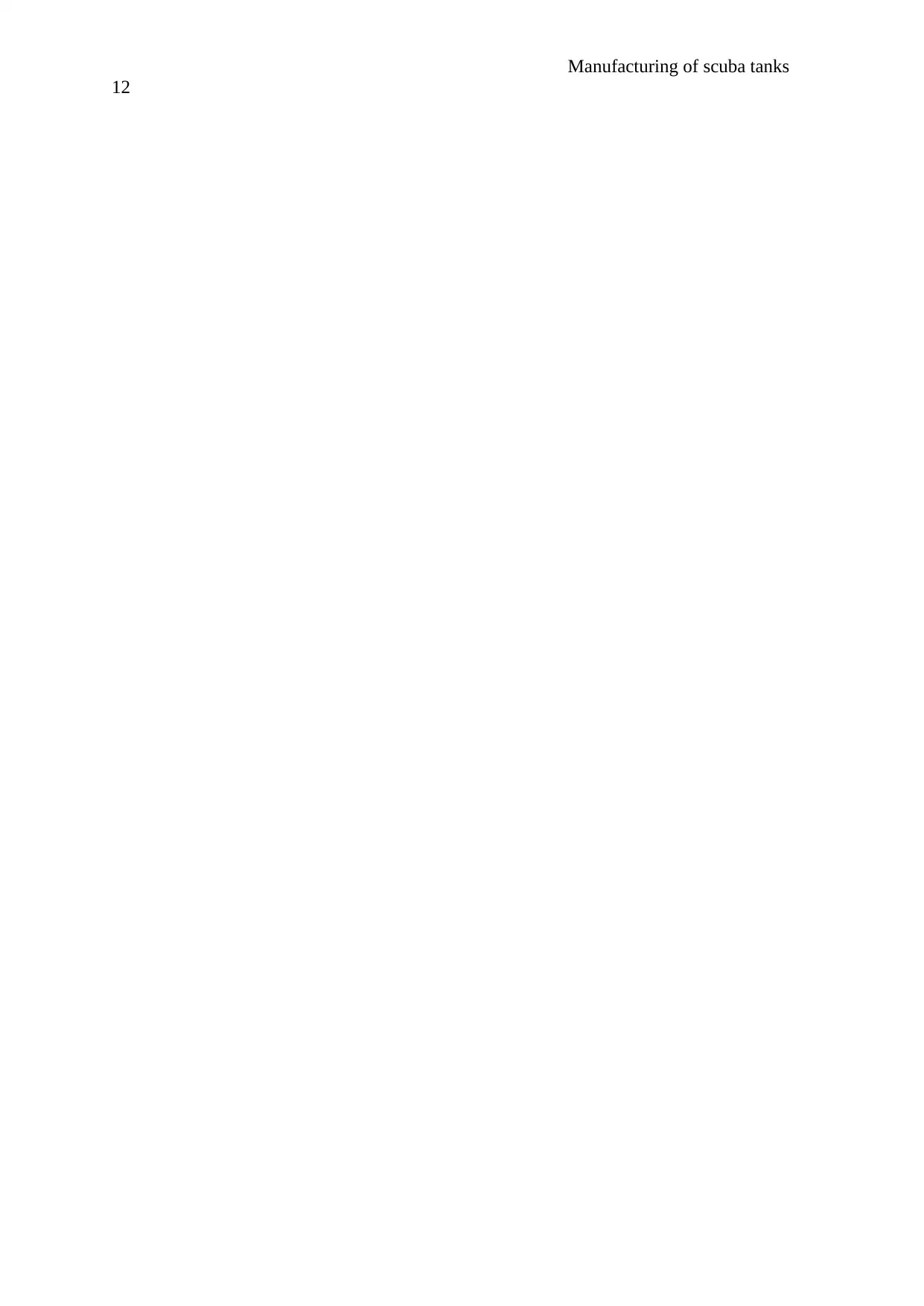
Manufacturing of scuba tanks
12
12
1 out of 12
![[object Object]](/_next/image/?url=%2F_next%2Fstatic%2Fmedia%2Flogo.6d15ce61.png&w=640&q=75)
Your All-in-One AI-Powered Toolkit for Academic Success.
 +13062052269
info@desklib.com
Available 24*7 on WhatsApp / Email
Unlock your academic potential
© 2024  |  Zucol Services PVT LTD  |  All rights reserved.