Process for Manufacturing a SCUBA Tank
VerifiedAdded on 2023/06/15
|7
|2763
|358
AI Summary
This article describes the steps involved in the production of a SCUBA cylinder tank, detailing the various steps involved and what each step achieves/accomplishes. The processes entailed in the manufacture of SCUBA tanks include forming, pressing, spinning, bending, welding, post-weld heat treatments, assembly, and finally, painting. The painting process starts with zinc galvanizing that is finally finished with powder coating to give a colored durable finish.
Contribute Materials
Your contribution can guide someone’s learning journey. Share your
documents today.
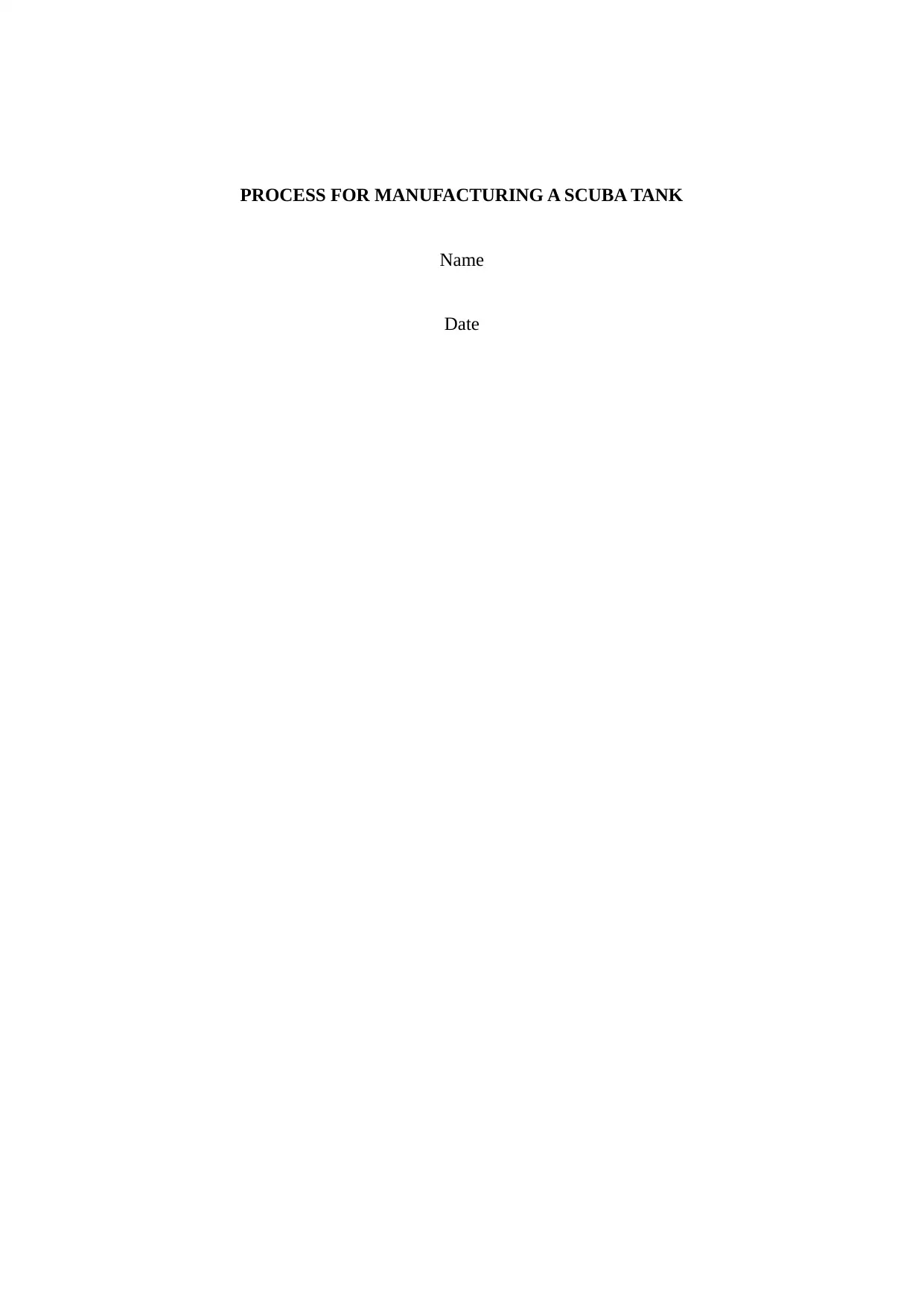
PROCESS FOR MANUFACTURING A SCUBA TANK
Name
Date
Name
Date
Secure Best Marks with AI Grader
Need help grading? Try our AI Grader for instant feedback on your assignments.
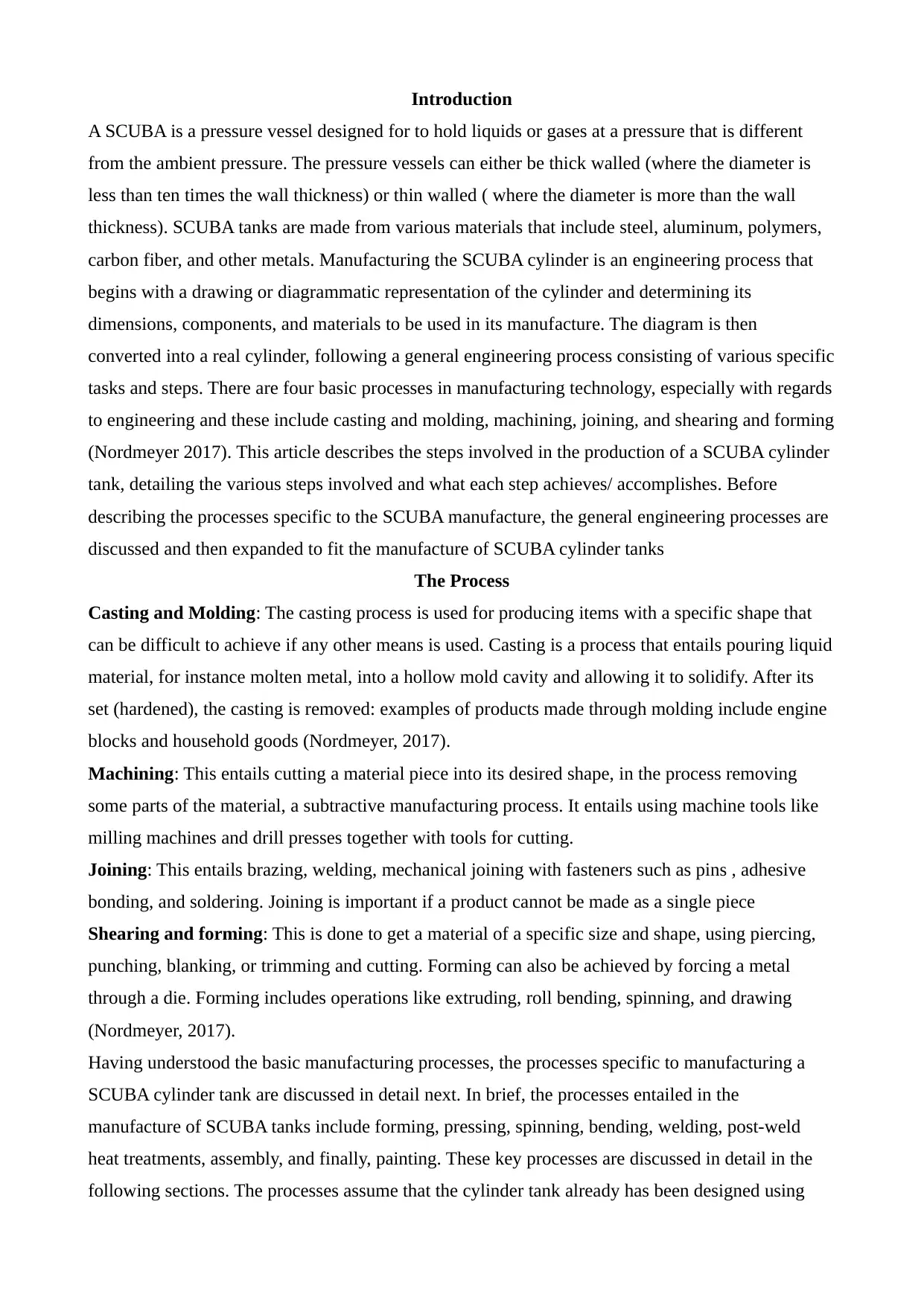
Introduction
A SCUBA is a pressure vessel designed for to hold liquids or gases at a pressure that is different
from the ambient pressure. The pressure vessels can either be thick walled (where the diameter is
less than ten times the wall thickness) or thin walled ( where the diameter is more than the wall
thickness). SCUBA tanks are made from various materials that include steel, aluminum, polymers,
carbon fiber, and other metals. Manufacturing the SCUBA cylinder is an engineering process that
begins with a drawing or diagrammatic representation of the cylinder and determining its
dimensions, components, and materials to be used in its manufacture. The diagram is then
converted into a real cylinder, following a general engineering process consisting of various specific
tasks and steps. There are four basic processes in manufacturing technology, especially with regards
to engineering and these include casting and molding, machining, joining, and shearing and forming
(Nordmeyer 2017). This article describes the steps involved in the production of a SCUBA cylinder
tank, detailing the various steps involved and what each step achieves/ accomplishes. Before
describing the processes specific to the SCUBA manufacture, the general engineering processes are
discussed and then expanded to fit the manufacture of SCUBA cylinder tanks
The Process
Casting and Molding: The casting process is used for producing items with a specific shape that
can be difficult to achieve if any other means is used. Casting is a process that entails pouring liquid
material, for instance molten metal, into a hollow mold cavity and allowing it to solidify. After its
set (hardened), the casting is removed: examples of products made through molding include engine
blocks and household goods (Nordmeyer, 2017).
Machining: This entails cutting a material piece into its desired shape, in the process removing
some parts of the material, a subtractive manufacturing process. It entails using machine tools like
milling machines and drill presses together with tools for cutting.
Joining: This entails brazing, welding, mechanical joining with fasteners such as pins , adhesive
bonding, and soldering. Joining is important if a product cannot be made as a single piece
Shearing and forming: This is done to get a material of a specific size and shape, using piercing,
punching, blanking, or trimming and cutting. Forming can also be achieved by forcing a metal
through a die. Forming includes operations like extruding, roll bending, spinning, and drawing
(Nordmeyer, 2017).
Having understood the basic manufacturing processes, the processes specific to manufacturing a
SCUBA cylinder tank are discussed in detail next. In brief, the processes entailed in the
manufacture of SCUBA tanks include forming, pressing, spinning, bending, welding, post-weld
heat treatments, assembly, and finally, painting. These key processes are discussed in detail in the
following sections. The processes assume that the cylinder tank already has been designed using
A SCUBA is a pressure vessel designed for to hold liquids or gases at a pressure that is different
from the ambient pressure. The pressure vessels can either be thick walled (where the diameter is
less than ten times the wall thickness) or thin walled ( where the diameter is more than the wall
thickness). SCUBA tanks are made from various materials that include steel, aluminum, polymers,
carbon fiber, and other metals. Manufacturing the SCUBA cylinder is an engineering process that
begins with a drawing or diagrammatic representation of the cylinder and determining its
dimensions, components, and materials to be used in its manufacture. The diagram is then
converted into a real cylinder, following a general engineering process consisting of various specific
tasks and steps. There are four basic processes in manufacturing technology, especially with regards
to engineering and these include casting and molding, machining, joining, and shearing and forming
(Nordmeyer 2017). This article describes the steps involved in the production of a SCUBA cylinder
tank, detailing the various steps involved and what each step achieves/ accomplishes. Before
describing the processes specific to the SCUBA manufacture, the general engineering processes are
discussed and then expanded to fit the manufacture of SCUBA cylinder tanks
The Process
Casting and Molding: The casting process is used for producing items with a specific shape that
can be difficult to achieve if any other means is used. Casting is a process that entails pouring liquid
material, for instance molten metal, into a hollow mold cavity and allowing it to solidify. After its
set (hardened), the casting is removed: examples of products made through molding include engine
blocks and household goods (Nordmeyer, 2017).
Machining: This entails cutting a material piece into its desired shape, in the process removing
some parts of the material, a subtractive manufacturing process. It entails using machine tools like
milling machines and drill presses together with tools for cutting.
Joining: This entails brazing, welding, mechanical joining with fasteners such as pins , adhesive
bonding, and soldering. Joining is important if a product cannot be made as a single piece
Shearing and forming: This is done to get a material of a specific size and shape, using piercing,
punching, blanking, or trimming and cutting. Forming can also be achieved by forcing a metal
through a die. Forming includes operations like extruding, roll bending, spinning, and drawing
(Nordmeyer, 2017).
Having understood the basic manufacturing processes, the processes specific to manufacturing a
SCUBA cylinder tank are discussed in detail next. In brief, the processes entailed in the
manufacture of SCUBA tanks include forming, pressing, spinning, bending, welding, post-weld
heat treatments, assembly, and finally, painting. These key processes are discussed in detail in the
following sections. The processes assume that the cylinder tank already has been designed using
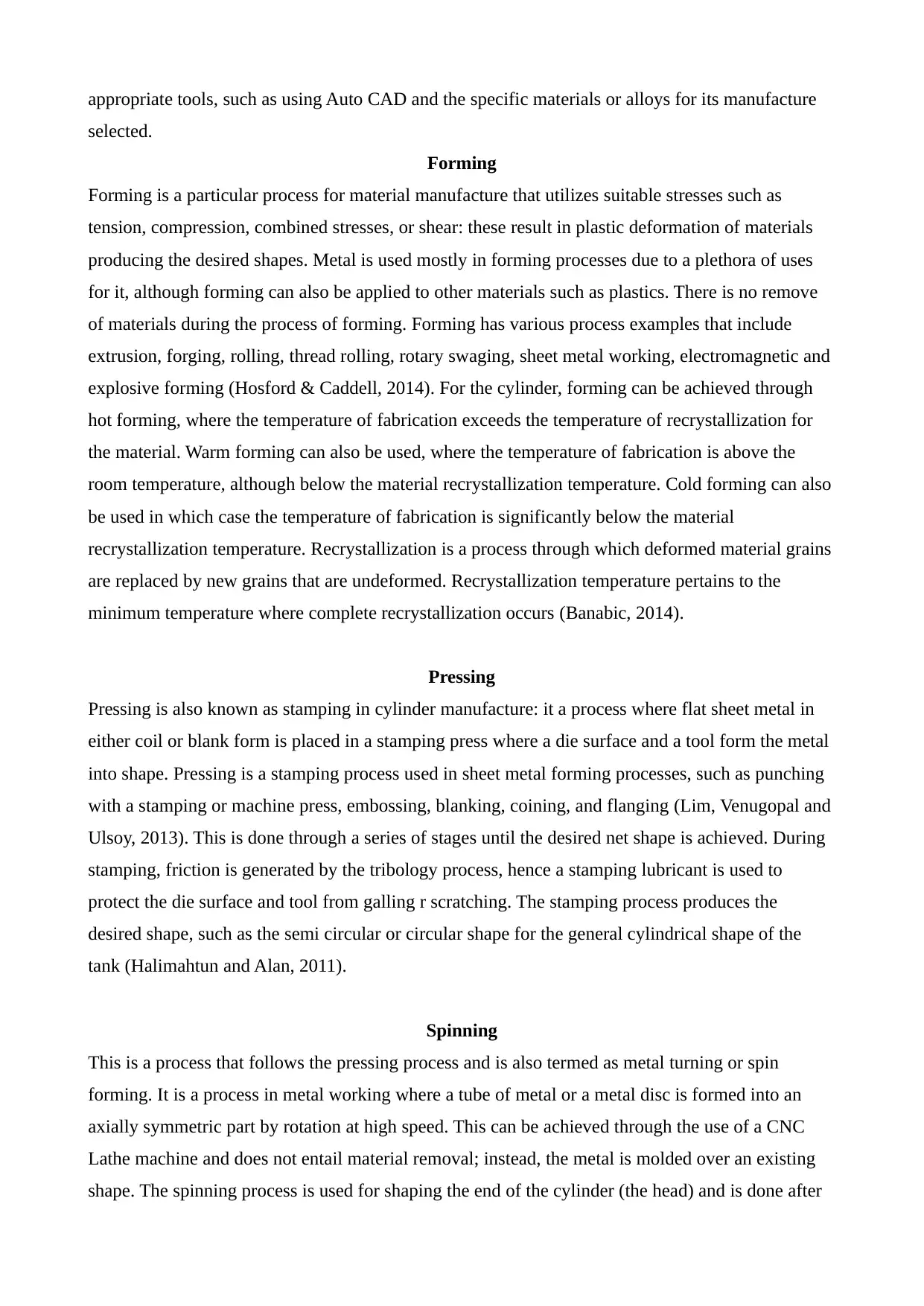
appropriate tools, such as using Auto CAD and the specific materials or alloys for its manufacture
selected.
Forming
Forming is a particular process for material manufacture that utilizes suitable stresses such as
tension, compression, combined stresses, or shear: these result in plastic deformation of materials
producing the desired shapes. Metal is used mostly in forming processes due to a plethora of uses
for it, although forming can also be applied to other materials such as plastics. There is no remove
of materials during the process of forming. Forming has various process examples that include
extrusion, forging, rolling, thread rolling, rotary swaging, sheet metal working, electromagnetic and
explosive forming (Hosford & Caddell, 2014). For the cylinder, forming can be achieved through
hot forming, where the temperature of fabrication exceeds the temperature of recrystallization for
the material. Warm forming can also be used, where the temperature of fabrication is above the
room temperature, although below the material recrystallization temperature. Cold forming can also
be used in which case the temperature of fabrication is significantly below the material
recrystallization temperature. Recrystallization is a process through which deformed material grains
are replaced by new grains that are undeformed. Recrystallization temperature pertains to the
minimum temperature where complete recrystallization occurs (Banabic, 2014).
Pressing
Pressing is also known as stamping in cylinder manufacture: it a process where flat sheet metal in
either coil or blank form is placed in a stamping press where a die surface and a tool form the metal
into shape. Pressing is a stamping process used in sheet metal forming processes, such as punching
with a stamping or machine press, embossing, blanking, coining, and flanging (Lim, Venugopal and
Ulsoy, 2013). This is done through a series of stages until the desired net shape is achieved. During
stamping, friction is generated by the tribology process, hence a stamping lubricant is used to
protect the die surface and tool from galling r scratching. The stamping process produces the
desired shape, such as the semi circular or circular shape for the general cylindrical shape of the
tank (Halimahtun and Alan, 2011).
Spinning
This is a process that follows the pressing process and is also termed as metal turning or spin
forming. It is a process in metal working where a tube of metal or a metal disc is formed into an
axially symmetric part by rotation at high speed. This can be achieved through the use of a CNC
Lathe machine and does not entail material removal; instead, the metal is molded over an existing
shape. The spinning process is used for shaping the end of the cylinder (the head) and is done after
selected.
Forming
Forming is a particular process for material manufacture that utilizes suitable stresses such as
tension, compression, combined stresses, or shear: these result in plastic deformation of materials
producing the desired shapes. Metal is used mostly in forming processes due to a plethora of uses
for it, although forming can also be applied to other materials such as plastics. There is no remove
of materials during the process of forming. Forming has various process examples that include
extrusion, forging, rolling, thread rolling, rotary swaging, sheet metal working, electromagnetic and
explosive forming (Hosford & Caddell, 2014). For the cylinder, forming can be achieved through
hot forming, where the temperature of fabrication exceeds the temperature of recrystallization for
the material. Warm forming can also be used, where the temperature of fabrication is above the
room temperature, although below the material recrystallization temperature. Cold forming can also
be used in which case the temperature of fabrication is significantly below the material
recrystallization temperature. Recrystallization is a process through which deformed material grains
are replaced by new grains that are undeformed. Recrystallization temperature pertains to the
minimum temperature where complete recrystallization occurs (Banabic, 2014).
Pressing
Pressing is also known as stamping in cylinder manufacture: it a process where flat sheet metal in
either coil or blank form is placed in a stamping press where a die surface and a tool form the metal
into shape. Pressing is a stamping process used in sheet metal forming processes, such as punching
with a stamping or machine press, embossing, blanking, coining, and flanging (Lim, Venugopal and
Ulsoy, 2013). This is done through a series of stages until the desired net shape is achieved. During
stamping, friction is generated by the tribology process, hence a stamping lubricant is used to
protect the die surface and tool from galling r scratching. The stamping process produces the
desired shape, such as the semi circular or circular shape for the general cylindrical shape of the
tank (Halimahtun and Alan, 2011).
Spinning
This is a process that follows the pressing process and is also termed as metal turning or spin
forming. It is a process in metal working where a tube of metal or a metal disc is formed into an
axially symmetric part by rotation at high speed. This can be achieved through the use of a CNC
Lathe machine and does not entail material removal; instead, the metal is molded over an existing
shape. The spinning process is used for shaping the end of the cylinder (the head) and is done after
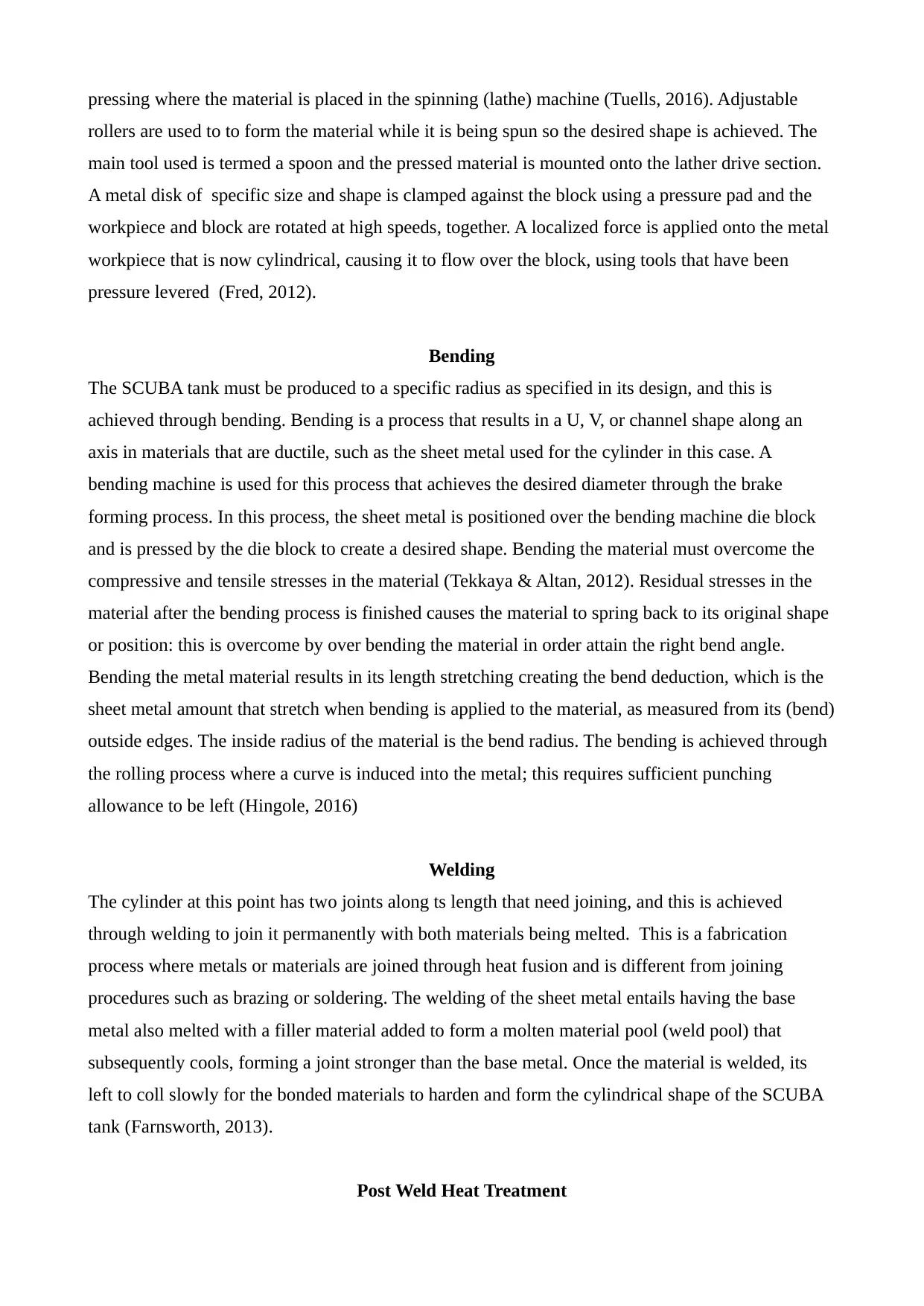
pressing where the material is placed in the spinning (lathe) machine (Tuells, 2016). Adjustable
rollers are used to to form the material while it is being spun so the desired shape is achieved. The
main tool used is termed a spoon and the pressed material is mounted onto the lather drive section.
A metal disk of specific size and shape is clamped against the block using a pressure pad and the
workpiece and block are rotated at high speeds, together. A localized force is applied onto the metal
workpiece that is now cylindrical, causing it to flow over the block, using tools that have been
pressure levered (Fred, 2012).
Bending
The SCUBA tank must be produced to a specific radius as specified in its design, and this is
achieved through bending. Bending is a process that results in a U, V, or channel shape along an
axis in materials that are ductile, such as the sheet metal used for the cylinder in this case. A
bending machine is used for this process that achieves the desired diameter through the brake
forming process. In this process, the sheet metal is positioned over the bending machine die block
and is pressed by the die block to create a desired shape. Bending the material must overcome the
compressive and tensile stresses in the material (Tekkaya & Altan, 2012). Residual stresses in the
material after the bending process is finished causes the material to spring back to its original shape
or position: this is overcome by over bending the material in order attain the right bend angle.
Bending the metal material results in its length stretching creating the bend deduction, which is the
sheet metal amount that stretch when bending is applied to the material, as measured from its (bend)
outside edges. The inside radius of the material is the bend radius. The bending is achieved through
the rolling process where a curve is induced into the metal; this requires sufficient punching
allowance to be left (Hingole, 2016)
Welding
The cylinder at this point has two joints along ts length that need joining, and this is achieved
through welding to join it permanently with both materials being melted. This is a fabrication
process where metals or materials are joined through heat fusion and is different from joining
procedures such as brazing or soldering. The welding of the sheet metal entails having the base
metal also melted with a filler material added to form a molten material pool (weld pool) that
subsequently cools, forming a joint stronger than the base metal. Once the material is welded, its
left to coll slowly for the bonded materials to harden and form the cylindrical shape of the SCUBA
tank (Farnsworth, 2013).
Post Weld Heat Treatment
rollers are used to to form the material while it is being spun so the desired shape is achieved. The
main tool used is termed a spoon and the pressed material is mounted onto the lather drive section.
A metal disk of specific size and shape is clamped against the block using a pressure pad and the
workpiece and block are rotated at high speeds, together. A localized force is applied onto the metal
workpiece that is now cylindrical, causing it to flow over the block, using tools that have been
pressure levered (Fred, 2012).
Bending
The SCUBA tank must be produced to a specific radius as specified in its design, and this is
achieved through bending. Bending is a process that results in a U, V, or channel shape along an
axis in materials that are ductile, such as the sheet metal used for the cylinder in this case. A
bending machine is used for this process that achieves the desired diameter through the brake
forming process. In this process, the sheet metal is positioned over the bending machine die block
and is pressed by the die block to create a desired shape. Bending the material must overcome the
compressive and tensile stresses in the material (Tekkaya & Altan, 2012). Residual stresses in the
material after the bending process is finished causes the material to spring back to its original shape
or position: this is overcome by over bending the material in order attain the right bend angle.
Bending the metal material results in its length stretching creating the bend deduction, which is the
sheet metal amount that stretch when bending is applied to the material, as measured from its (bend)
outside edges. The inside radius of the material is the bend radius. The bending is achieved through
the rolling process where a curve is induced into the metal; this requires sufficient punching
allowance to be left (Hingole, 2016)
Welding
The cylinder at this point has two joints along ts length that need joining, and this is achieved
through welding to join it permanently with both materials being melted. This is a fabrication
process where metals or materials are joined through heat fusion and is different from joining
procedures such as brazing or soldering. The welding of the sheet metal entails having the base
metal also melted with a filler material added to form a molten material pool (weld pool) that
subsequently cools, forming a joint stronger than the base metal. Once the material is welded, its
left to coll slowly for the bonded materials to harden and form the cylindrical shape of the SCUBA
tank (Farnsworth, 2013).
Post Weld Heat Treatment
Secure Best Marks with AI Grader
Need help grading? Try our AI Grader for instant feedback on your assignments.
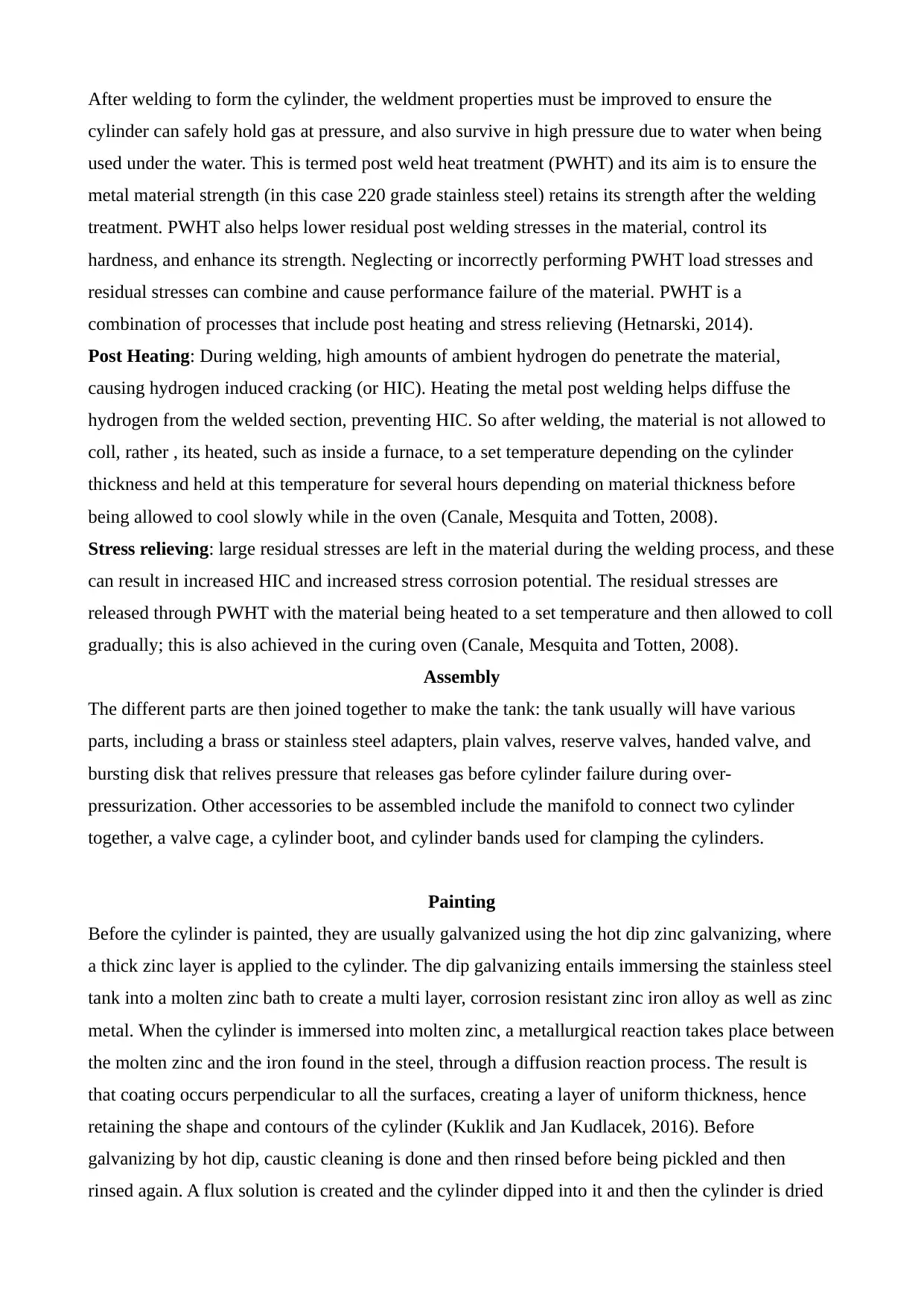
After welding to form the cylinder, the weldment properties must be improved to ensure the
cylinder can safely hold gas at pressure, and also survive in high pressure due to water when being
used under the water. This is termed post weld heat treatment (PWHT) and its aim is to ensure the
metal material strength (in this case 220 grade stainless steel) retains its strength after the welding
treatment. PWHT also helps lower residual post welding stresses in the material, control its
hardness, and enhance its strength. Neglecting or incorrectly performing PWHT load stresses and
residual stresses can combine and cause performance failure of the material. PWHT is a
combination of processes that include post heating and stress relieving (Hetnarski, 2014).
Post Heating: During welding, high amounts of ambient hydrogen do penetrate the material,
causing hydrogen induced cracking (or HIC). Heating the metal post welding helps diffuse the
hydrogen from the welded section, preventing HIC. So after welding, the material is not allowed to
coll, rather , its heated, such as inside a furnace, to a set temperature depending on the cylinder
thickness and held at this temperature for several hours depending on material thickness before
being allowed to cool slowly while in the oven (Canale, Mesquita and Totten, 2008).
Stress relieving: large residual stresses are left in the material during the welding process, and these
can result in increased HIC and increased stress corrosion potential. The residual stresses are
released through PWHT with the material being heated to a set temperature and then allowed to coll
gradually; this is also achieved in the curing oven (Canale, Mesquita and Totten, 2008).
Assembly
The different parts are then joined together to make the tank: the tank usually will have various
parts, including a brass or stainless steel adapters, plain valves, reserve valves, handed valve, and
bursting disk that relives pressure that releases gas before cylinder failure during over-
pressurization. Other accessories to be assembled include the manifold to connect two cylinder
together, a valve cage, a cylinder boot, and cylinder bands used for clamping the cylinders.
Painting
Before the cylinder is painted, they are usually galvanized using the hot dip zinc galvanizing, where
a thick zinc layer is applied to the cylinder. The dip galvanizing entails immersing the stainless steel
tank into a molten zinc bath to create a multi layer, corrosion resistant zinc iron alloy as well as zinc
metal. When the cylinder is immersed into molten zinc, a metallurgical reaction takes place between
the molten zinc and the iron found in the steel, through a diffusion reaction process. The result is
that coating occurs perpendicular to all the surfaces, creating a layer of uniform thickness, hence
retaining the shape and contours of the cylinder (Kuklik and Jan Kudlacek, 2016). Before
galvanizing by hot dip, caustic cleaning is done and then rinsed before being pickled and then
rinsed again. A flux solution is created and the cylinder dipped into it and then the cylinder is dried
cylinder can safely hold gas at pressure, and also survive in high pressure due to water when being
used under the water. This is termed post weld heat treatment (PWHT) and its aim is to ensure the
metal material strength (in this case 220 grade stainless steel) retains its strength after the welding
treatment. PWHT also helps lower residual post welding stresses in the material, control its
hardness, and enhance its strength. Neglecting or incorrectly performing PWHT load stresses and
residual stresses can combine and cause performance failure of the material. PWHT is a
combination of processes that include post heating and stress relieving (Hetnarski, 2014).
Post Heating: During welding, high amounts of ambient hydrogen do penetrate the material,
causing hydrogen induced cracking (or HIC). Heating the metal post welding helps diffuse the
hydrogen from the welded section, preventing HIC. So after welding, the material is not allowed to
coll, rather , its heated, such as inside a furnace, to a set temperature depending on the cylinder
thickness and held at this temperature for several hours depending on material thickness before
being allowed to cool slowly while in the oven (Canale, Mesquita and Totten, 2008).
Stress relieving: large residual stresses are left in the material during the welding process, and these
can result in increased HIC and increased stress corrosion potential. The residual stresses are
released through PWHT with the material being heated to a set temperature and then allowed to coll
gradually; this is also achieved in the curing oven (Canale, Mesquita and Totten, 2008).
Assembly
The different parts are then joined together to make the tank: the tank usually will have various
parts, including a brass or stainless steel adapters, plain valves, reserve valves, handed valve, and
bursting disk that relives pressure that releases gas before cylinder failure during over-
pressurization. Other accessories to be assembled include the manifold to connect two cylinder
together, a valve cage, a cylinder boot, and cylinder bands used for clamping the cylinders.
Painting
Before the cylinder is painted, they are usually galvanized using the hot dip zinc galvanizing, where
a thick zinc layer is applied to the cylinder. The dip galvanizing entails immersing the stainless steel
tank into a molten zinc bath to create a multi layer, corrosion resistant zinc iron alloy as well as zinc
metal. When the cylinder is immersed into molten zinc, a metallurgical reaction takes place between
the molten zinc and the iron found in the steel, through a diffusion reaction process. The result is
that coating occurs perpendicular to all the surfaces, creating a layer of uniform thickness, hence
retaining the shape and contours of the cylinder (Kuklik and Jan Kudlacek, 2016). Before
galvanizing by hot dip, caustic cleaning is done and then rinsed before being pickled and then
rinsed again. A flux solution is created and the cylinder dipped into it and then the cylinder is dried
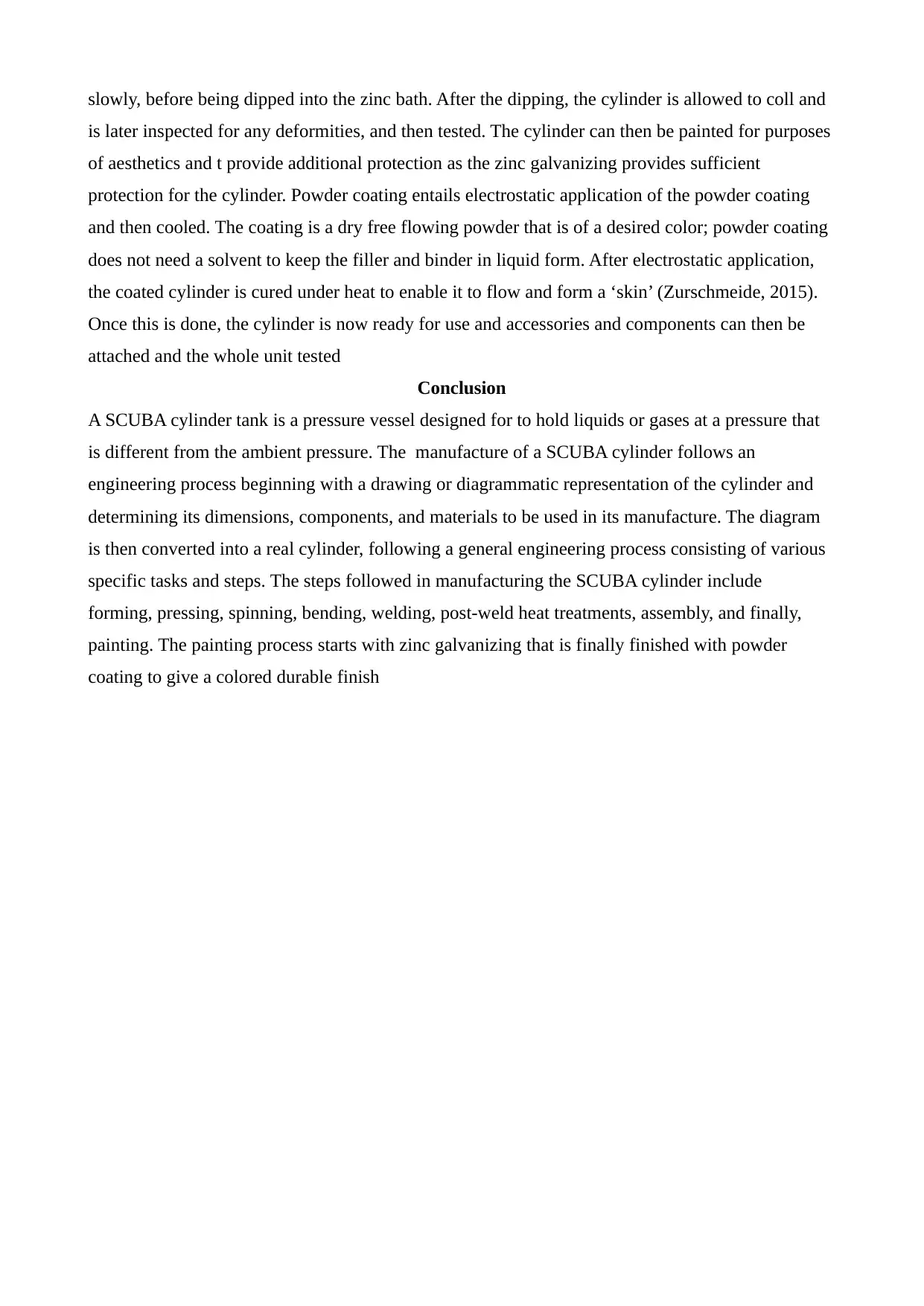
slowly, before being dipped into the zinc bath. After the dipping, the cylinder is allowed to coll and
is later inspected for any deformities, and then tested. The cylinder can then be painted for purposes
of aesthetics and t provide additional protection as the zinc galvanizing provides sufficient
protection for the cylinder. Powder coating entails electrostatic application of the powder coating
and then cooled. The coating is a dry free flowing powder that is of a desired color; powder coating
does not need a solvent to keep the filler and binder in liquid form. After electrostatic application,
the coated cylinder is cured under heat to enable it to flow and form a ‘skin’ (Zurschmeide, 2015).
Once this is done, the cylinder is now ready for use and accessories and components can then be
attached and the whole unit tested
Conclusion
A SCUBA cylinder tank is a pressure vessel designed for to hold liquids or gases at a pressure that
is different from the ambient pressure. The manufacture of a SCUBA cylinder follows an
engineering process beginning with a drawing or diagrammatic representation of the cylinder and
determining its dimensions, components, and materials to be used in its manufacture. The diagram
is then converted into a real cylinder, following a general engineering process consisting of various
specific tasks and steps. The steps followed in manufacturing the SCUBA cylinder include
forming, pressing, spinning, bending, welding, post-weld heat treatments, assembly, and finally,
painting. The painting process starts with zinc galvanizing that is finally finished with powder
coating to give a colored durable finish
is later inspected for any deformities, and then tested. The cylinder can then be painted for purposes
of aesthetics and t provide additional protection as the zinc galvanizing provides sufficient
protection for the cylinder. Powder coating entails electrostatic application of the powder coating
and then cooled. The coating is a dry free flowing powder that is of a desired color; powder coating
does not need a solvent to keep the filler and binder in liquid form. After electrostatic application,
the coated cylinder is cured under heat to enable it to flow and form a ‘skin’ (Zurschmeide, 2015).
Once this is done, the cylinder is now ready for use and accessories and components can then be
attached and the whole unit tested
Conclusion
A SCUBA cylinder tank is a pressure vessel designed for to hold liquids or gases at a pressure that
is different from the ambient pressure. The manufacture of a SCUBA cylinder follows an
engineering process beginning with a drawing or diagrammatic representation of the cylinder and
determining its dimensions, components, and materials to be used in its manufacture. The diagram
is then converted into a real cylinder, following a general engineering process consisting of various
specific tasks and steps. The steps followed in manufacturing the SCUBA cylinder include
forming, pressing, spinning, bending, welding, post-weld heat treatments, assembly, and finally,
painting. The painting process starts with zinc galvanizing that is finally finished with powder
coating to give a colored durable finish
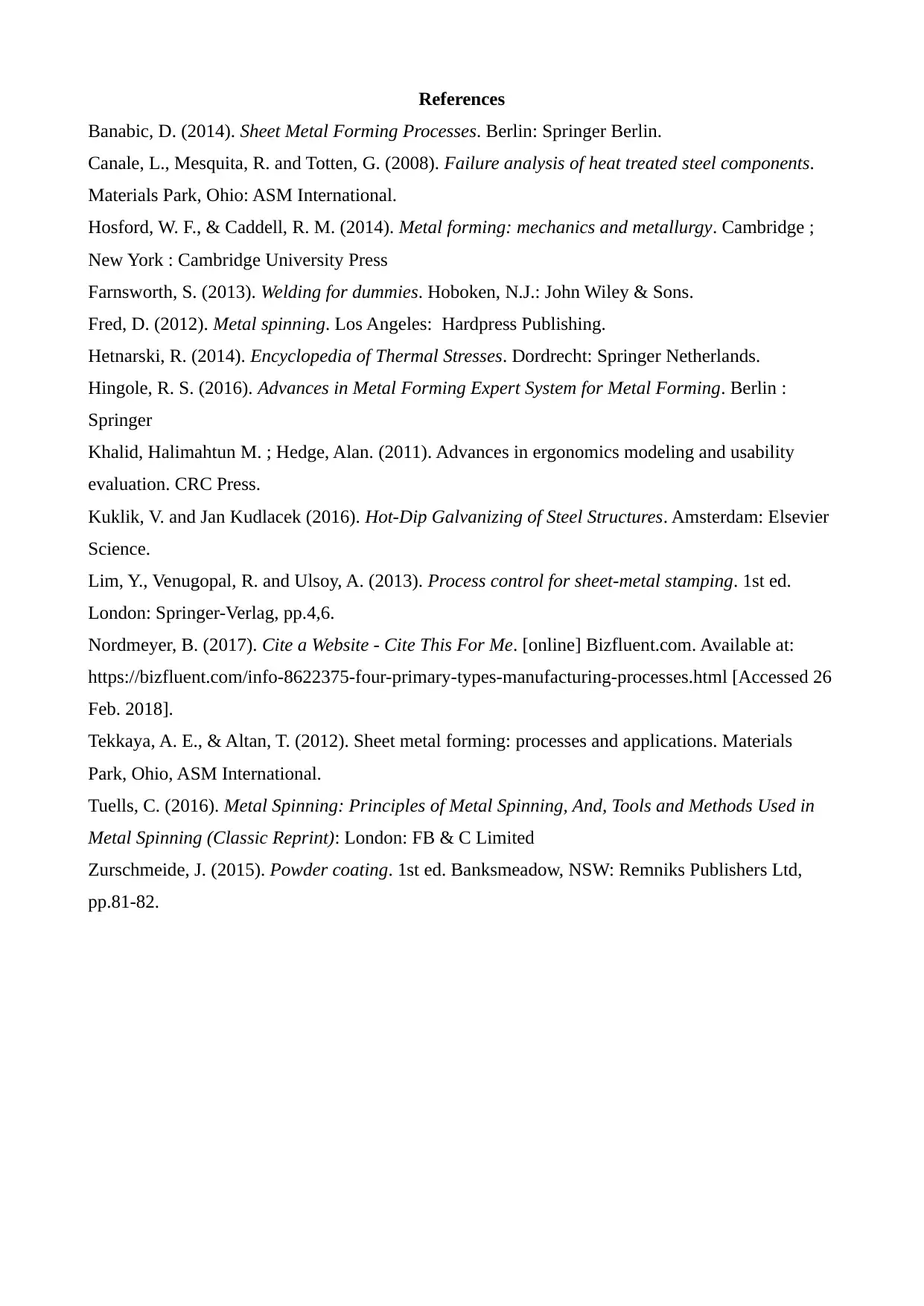
References
Banabic, D. (2014). Sheet Metal Forming Processes. Berlin: Springer Berlin.
Canale, L., Mesquita, R. and Totten, G. (2008). Failure analysis of heat treated steel components.
Materials Park, Ohio: ASM International.
Hosford, W. F., & Caddell, R. M. (2014). Metal forming: mechanics and metallurgy. Cambridge ;
New York : Cambridge University Press
Farnsworth, S. (2013). Welding for dummies. Hoboken, N.J.: John Wiley & Sons.
Fred, D. (2012). Metal spinning. Los Angeles: Hardpress Publishing.
Hetnarski, R. (2014). Encyclopedia of Thermal Stresses. Dordrecht: Springer Netherlands.
Hingole, R. S. (2016). Advances in Metal Forming Expert System for Metal Forming. Berlin :
Springer
Khalid, Halimahtun M. ; Hedge, Alan. (2011). Advances in ergonomics modeling and usability
evaluation. CRC Press.
Kuklik, V. and Jan Kudlacek (2016). Hot-Dip Galvanizing of Steel Structures. Amsterdam: Elsevier
Science.
Lim, Y., Venugopal, R. and Ulsoy, A. (2013). Process control for sheet-metal stamping. 1st ed.
London: Springer-Verlag, pp.4,6.
Nordmeyer, B. (2017). Cite a Website - Cite This For Me. [online] Bizfluent.com. Available at:
https://bizfluent.com/info-8622375-four-primary-types-manufacturing-processes.html [Accessed 26
Feb. 2018].
Tekkaya, A. E., & Altan, T. (2012). Sheet metal forming: processes and applications. Materials
Park, Ohio, ASM International.
Tuells, C. (2016). Metal Spinning: Principles of Metal Spinning, And, Tools and Methods Used in
Metal Spinning (Classic Reprint): London: FB & C Limited
Zurschmeide, J. (2015). Powder coating. 1st ed. Banksmeadow, NSW: Remniks Publishers Ltd,
pp.81-82.
Banabic, D. (2014). Sheet Metal Forming Processes. Berlin: Springer Berlin.
Canale, L., Mesquita, R. and Totten, G. (2008). Failure analysis of heat treated steel components.
Materials Park, Ohio: ASM International.
Hosford, W. F., & Caddell, R. M. (2014). Metal forming: mechanics and metallurgy. Cambridge ;
New York : Cambridge University Press
Farnsworth, S. (2013). Welding for dummies. Hoboken, N.J.: John Wiley & Sons.
Fred, D. (2012). Metal spinning. Los Angeles: Hardpress Publishing.
Hetnarski, R. (2014). Encyclopedia of Thermal Stresses. Dordrecht: Springer Netherlands.
Hingole, R. S. (2016). Advances in Metal Forming Expert System for Metal Forming. Berlin :
Springer
Khalid, Halimahtun M. ; Hedge, Alan. (2011). Advances in ergonomics modeling and usability
evaluation. CRC Press.
Kuklik, V. and Jan Kudlacek (2016). Hot-Dip Galvanizing of Steel Structures. Amsterdam: Elsevier
Science.
Lim, Y., Venugopal, R. and Ulsoy, A. (2013). Process control for sheet-metal stamping. 1st ed.
London: Springer-Verlag, pp.4,6.
Nordmeyer, B. (2017). Cite a Website - Cite This For Me. [online] Bizfluent.com. Available at:
https://bizfluent.com/info-8622375-four-primary-types-manufacturing-processes.html [Accessed 26
Feb. 2018].
Tekkaya, A. E., & Altan, T. (2012). Sheet metal forming: processes and applications. Materials
Park, Ohio, ASM International.
Tuells, C. (2016). Metal Spinning: Principles of Metal Spinning, And, Tools and Methods Used in
Metal Spinning (Classic Reprint): London: FB & C Limited
Zurschmeide, J. (2015). Powder coating. 1st ed. Banksmeadow, NSW: Remniks Publishers Ltd,
pp.81-82.
1 out of 7
![[object Object]](/_next/image/?url=%2F_next%2Fstatic%2Fmedia%2Flogo.6d15ce61.png&w=640&q=75)
Your All-in-One AI-Powered Toolkit for Academic Success.
+13062052269
info@desklib.com
Available 24*7 on WhatsApp / Email
Unlock your academic potential
© 2024 | Zucol Services PVT LTD | All rights reserved.