Comparative Analysis of Costing Methods: Sewing Easy Ltd. Report
VerifiedAdded on 2023/06/10
|11
|2665
|369
Report
AI Summary
This report provides a detailed analysis of traditional and activity-based costing (ABC) methods. It begins with an introduction to traditional costing, which allocates overhead based on volume, and then delves into a case study of Sewing Easy Ltd. The report includes calculations using both costing methods, comparing per-unit costs for basic and advanced models. It presents profit and loss statements under each method, highlighting how ABC can lead to more accurate product costing and potentially influence pricing strategies. The report also addresses the over- or under-application of manufacturing overhead, explaining the causes and treatments. Finally, it outlines the advantages and disadvantages of ABC, such as improved product cost accuracy and information about cost behavior, while acknowledging its complexity and potential for higher implementation costs. The report concludes with a discussion on the implications of these costing methods for business decisions.
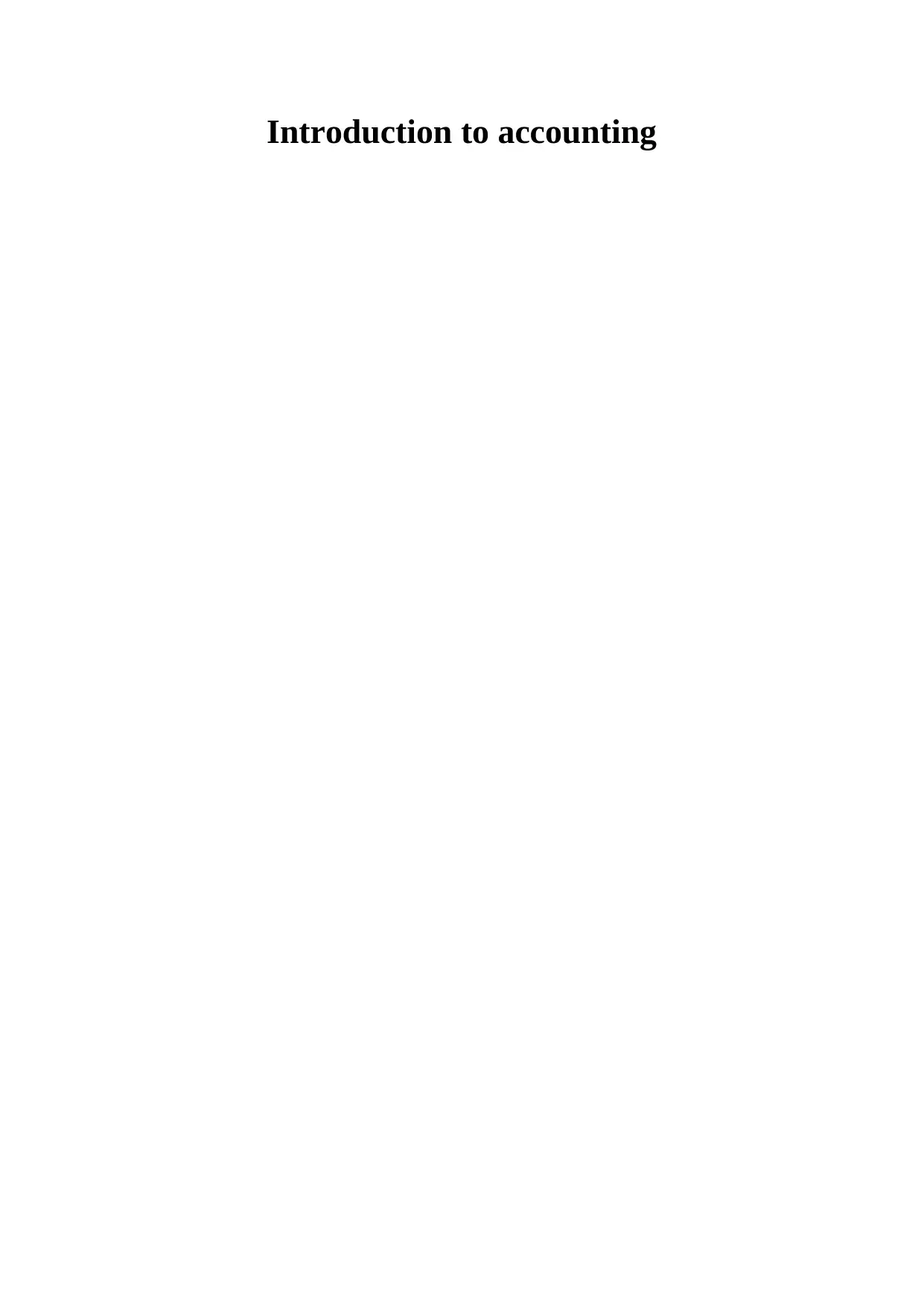
Introduction to accounting
Paraphrase This Document
Need a fresh take? Get an instant paraphrase of this document with our AI Paraphraser

Table of Contents
Introduction................................................................................................................................4
Question 1..................................................................................................................................5
Calculation as per traditional costing method........................................................................5
Question 2..................................................................................................................................5
Calculation as per activity base costing model......................................................................5
Question 3..................................................................................................................................6
Statement of profit and loss as per Traditional method as well as ABC method...................6
Question 4..................................................................................................................................7
Question 5..................................................................................................................................9
Advantages of Activity Based Costing..................................................................................9
Disadvantages of Activity Based Costing............................................................................10
Conclusion................................................................................................................................10
References................................................................................................................................12
Introduction................................................................................................................................4
Question 1..................................................................................................................................5
Calculation as per traditional costing method........................................................................5
Question 2..................................................................................................................................5
Calculation as per activity base costing model......................................................................5
Question 3..................................................................................................................................6
Statement of profit and loss as per Traditional method as well as ABC method...................6
Question 4..................................................................................................................................7
Question 5..................................................................................................................................9
Advantages of Activity Based Costing..................................................................................9
Disadvantages of Activity Based Costing............................................................................10
Conclusion................................................................................................................................10
References................................................................................................................................12
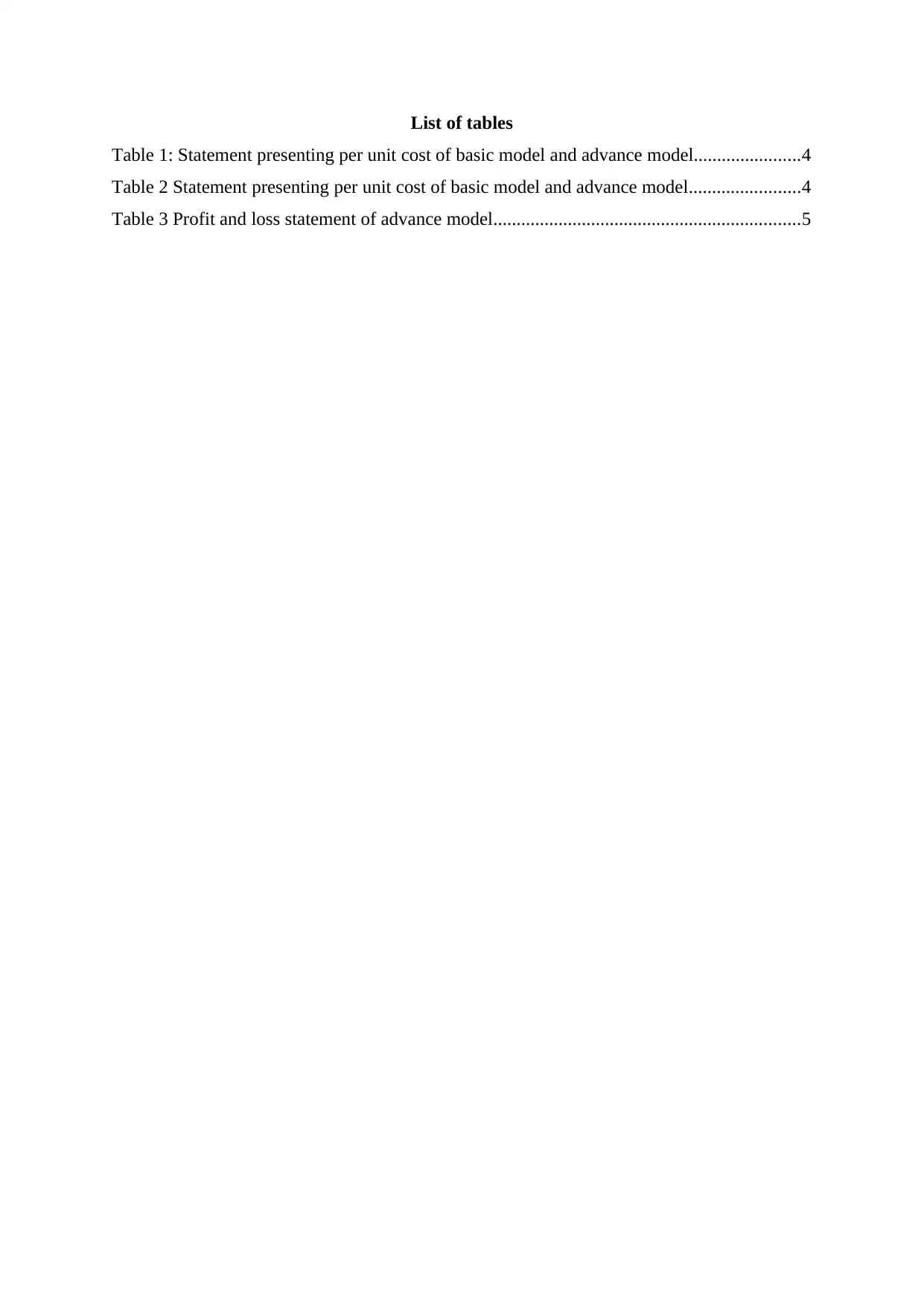
List of tables
Table 1: Statement presenting per unit cost of basic model and advance model.......................4
Table 2 Statement presenting per unit cost of basic model and advance model........................4
Table 3 Profit and loss statement of advance model..................................................................5
Table 1: Statement presenting per unit cost of basic model and advance model.......................4
Table 2 Statement presenting per unit cost of basic model and advance model........................4
Table 3 Profit and loss statement of advance model..................................................................5
⊘ This is a preview!⊘
Do you want full access?
Subscribe today to unlock all pages.

Trusted by 1+ million students worldwide
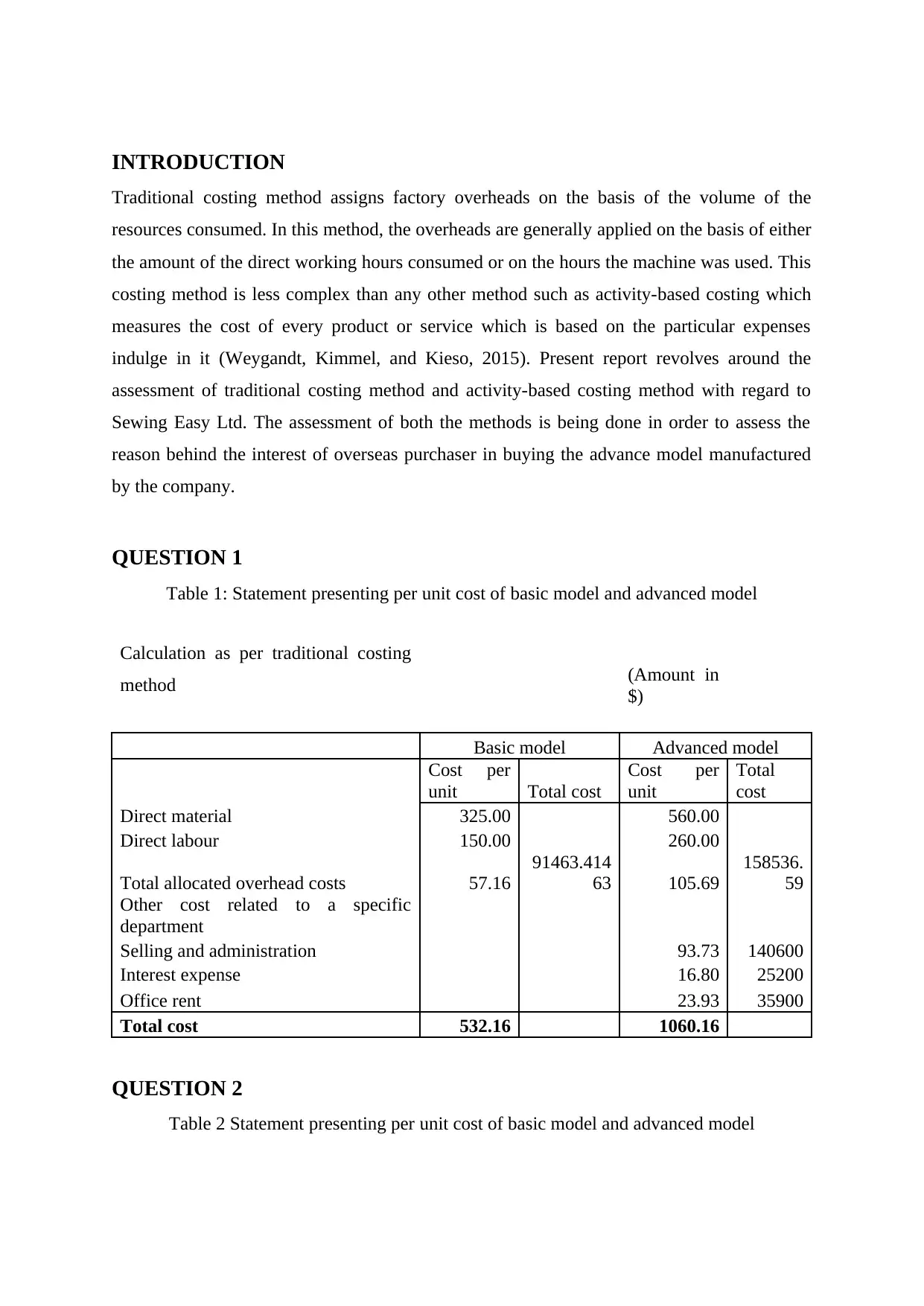
INTRODUCTION
Traditional costing method assigns factory overheads on the basis of the volume of the
resources consumed. In this method, the overheads are generally applied on the basis of either
the amount of the direct working hours consumed or on the hours the machine was used. This
costing method is less complex than any other method such as activity-based costing which
measures the cost of every product or service which is based on the particular expenses
indulge in it (Weygandt, Kimmel, and Kieso, 2015). Present report revolves around the
assessment of traditional costing method and activity-based costing method with regard to
Sewing Easy Ltd. The assessment of both the methods is being done in order to assess the
reason behind the interest of overseas purchaser in buying the advance model manufactured
by the company.
QUESTION 1
Table 1: Statement presenting per unit cost of basic model and advanced model
Calculation as per traditional costing
method (Amount in
$)
Basic model Advanced model
Cost per
unit Total cost
Cost per
unit
Total
cost
Direct material 325.00 560.00
Direct labour 150.00 260.00
Total allocated overhead costs 57.16
91463.414
63 105.69
158536.
59
Other cost related to a specific
department
Selling and administration 93.73 140600
Interest expense 16.80 25200
Office rent 23.93 35900
Total cost 532.16 1060.16
QUESTION 2
Table 2 Statement presenting per unit cost of basic model and advanced model
Traditional costing method assigns factory overheads on the basis of the volume of the
resources consumed. In this method, the overheads are generally applied on the basis of either
the amount of the direct working hours consumed or on the hours the machine was used. This
costing method is less complex than any other method such as activity-based costing which
measures the cost of every product or service which is based on the particular expenses
indulge in it (Weygandt, Kimmel, and Kieso, 2015). Present report revolves around the
assessment of traditional costing method and activity-based costing method with regard to
Sewing Easy Ltd. The assessment of both the methods is being done in order to assess the
reason behind the interest of overseas purchaser in buying the advance model manufactured
by the company.
QUESTION 1
Table 1: Statement presenting per unit cost of basic model and advanced model
Calculation as per traditional costing
method (Amount in
$)
Basic model Advanced model
Cost per
unit Total cost
Cost per
unit
Total
cost
Direct material 325.00 560.00
Direct labour 150.00 260.00
Total allocated overhead costs 57.16
91463.414
63 105.69
158536.
59
Other cost related to a specific
department
Selling and administration 93.73 140600
Interest expense 16.80 25200
Office rent 23.93 35900
Total cost 532.16 1060.16
QUESTION 2
Table 2 Statement presenting per unit cost of basic model and advanced model
Paraphrase This Document
Need a fresh take? Get an instant paraphrase of this document with our AI Paraphraser
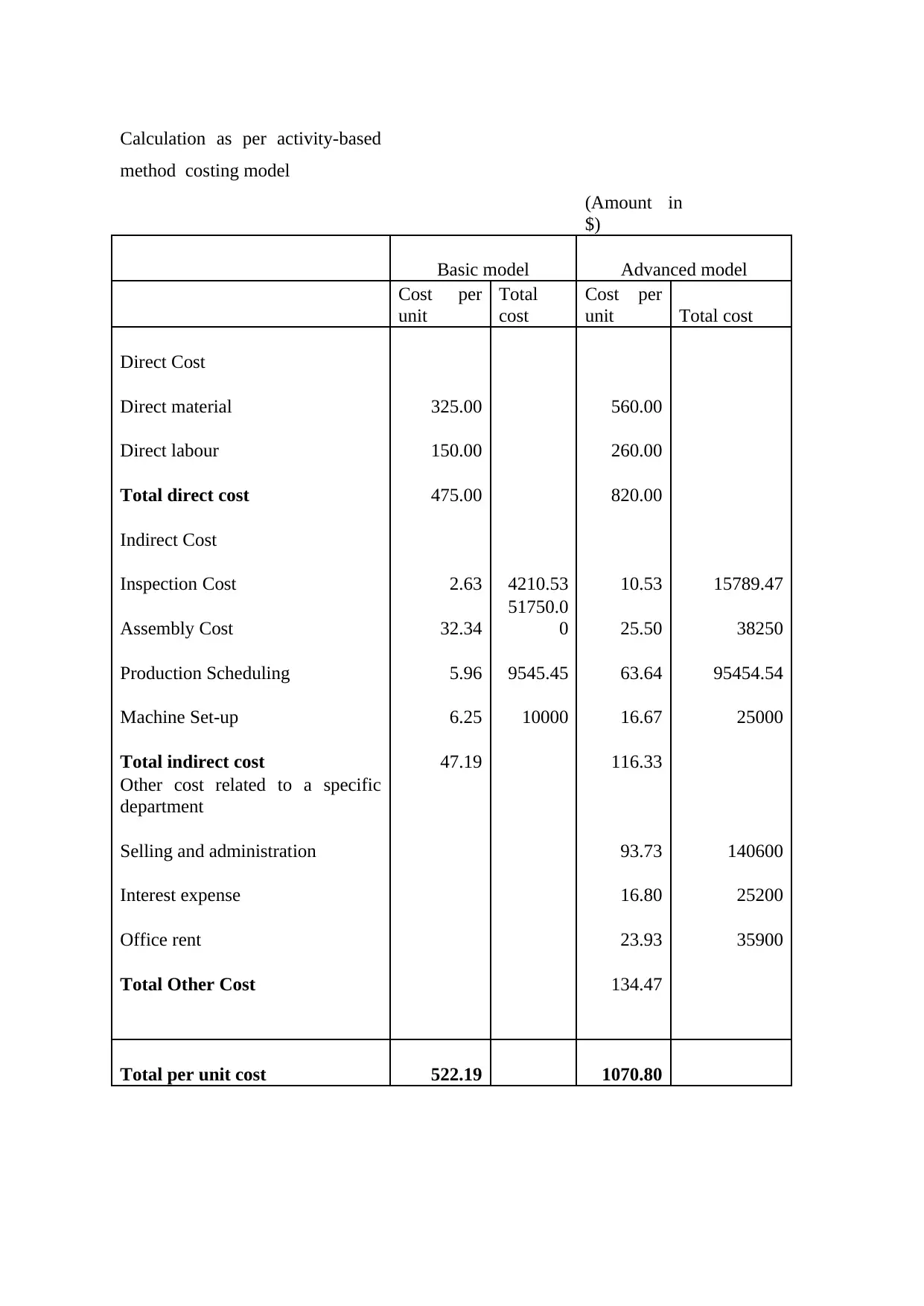
Calculation as per activity-based
method costing model
(Amount in
$)
Basic model Advanced model
Cost per
unit
Total
cost
Cost per
unit Total cost
Direct Cost
Direct material 325.00 560.00
Direct labour 150.00 260.00
Total direct cost 475.00 820.00
Indirect Cost
Inspection Cost 2.63 4210.53 10.53 15789.47
Assembly Cost 32.34
51750.0
0 25.50 38250
Production Scheduling 5.96 9545.45 63.64 95454.54
Machine Set-up 6.25 10000 16.67 25000
Total indirect cost 47.19 116.33
Other cost related to a specific
department
Selling and administration 93.73 140600
Interest expense 16.80 25200
Office rent 23.93 35900
Total Other Cost 134.47
Total per unit cost 522.19 1070.80
method costing model
(Amount in
$)
Basic model Advanced model
Cost per
unit
Total
cost
Cost per
unit Total cost
Direct Cost
Direct material 325.00 560.00
Direct labour 150.00 260.00
Total direct cost 475.00 820.00
Indirect Cost
Inspection Cost 2.63 4210.53 10.53 15789.47
Assembly Cost 32.34
51750.0
0 25.50 38250
Production Scheduling 5.96 9545.45 63.64 95454.54
Machine Set-up 6.25 10000 16.67 25000
Total indirect cost 47.19 116.33
Other cost related to a specific
department
Selling and administration 93.73 140600
Interest expense 16.80 25200
Office rent 23.93 35900
Total Other Cost 134.47
Total per unit cost 522.19 1070.80
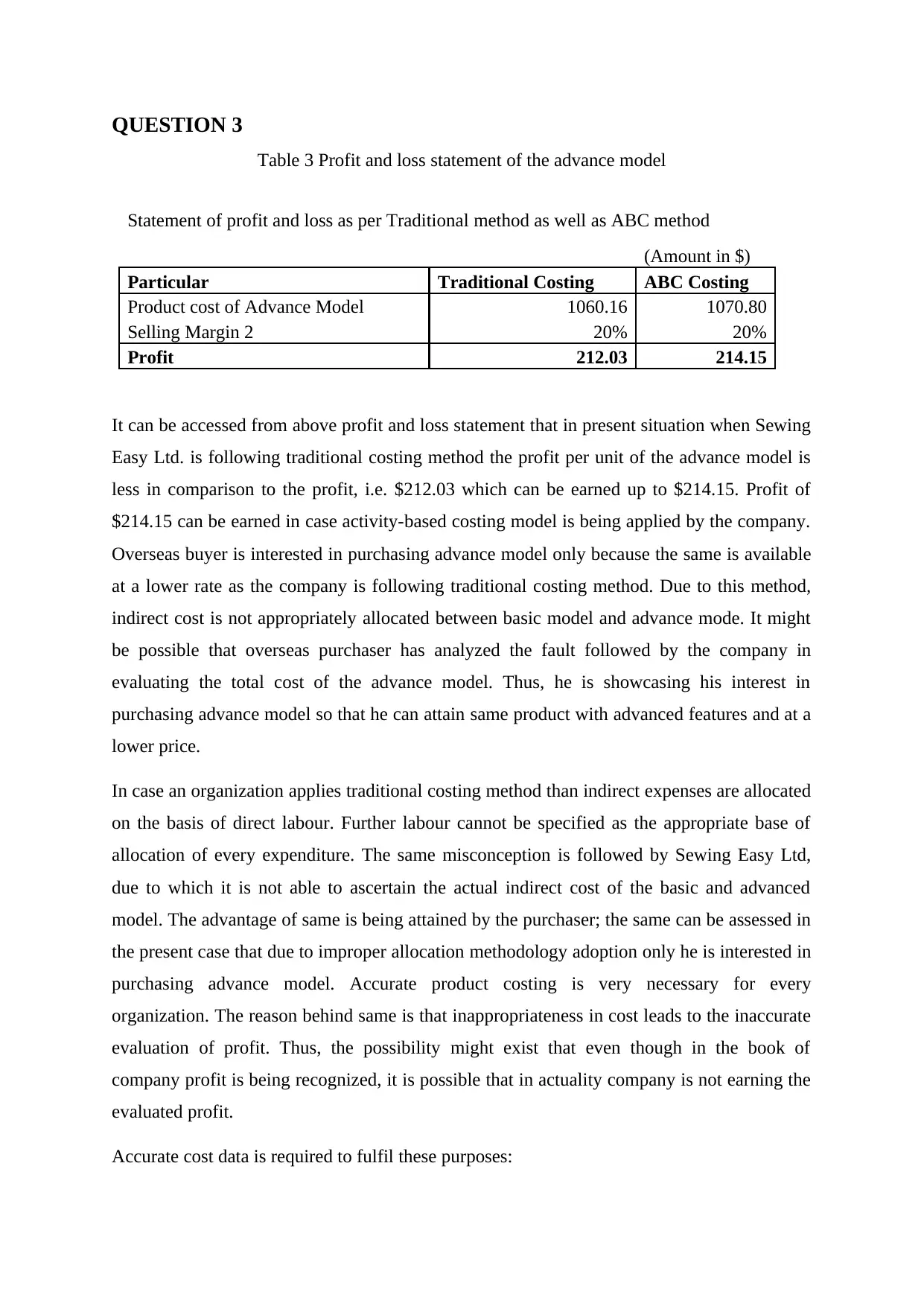
QUESTION 3
Table 3 Profit and loss statement of the advance model
Statement of profit and loss as per Traditional method as well as ABC method
(Amount in $)
Particular Traditional Costing ABC Costing
Product cost of Advance Model 1060.16 1070.80
Selling Margin 2 20% 20%
Profit 212.03 214.15
It can be accessed from above profit and loss statement that in present situation when Sewing
Easy Ltd. is following traditional costing method the profit per unit of the advance model is
less in comparison to the profit, i.e. $212.03 which can be earned up to $214.15. Profit of
$214.15 can be earned in case activity-based costing model is being applied by the company.
Overseas buyer is interested in purchasing advance model only because the same is available
at a lower rate as the company is following traditional costing method. Due to this method,
indirect cost is not appropriately allocated between basic model and advance mode. It might
be possible that overseas purchaser has analyzed the fault followed by the company in
evaluating the total cost of the advance model. Thus, he is showcasing his interest in
purchasing advance model so that he can attain same product with advanced features and at a
lower price.
In case an organization applies traditional costing method than indirect expenses are allocated
on the basis of direct labour. Further labour cannot be specified as the appropriate base of
allocation of every expenditure. The same misconception is followed by Sewing Easy Ltd,
due to which it is not able to ascertain the actual indirect cost of the basic and advanced
model. The advantage of same is being attained by the purchaser; the same can be assessed in
the present case that due to improper allocation methodology adoption only he is interested in
purchasing advance model. Accurate product costing is very necessary for every
organization. The reason behind same is that inappropriateness in cost leads to the inaccurate
evaluation of profit. Thus, the possibility might exist that even though in the book of
company profit is being recognized, it is possible that in actuality company is not earning the
evaluated profit.
Accurate cost data is required to fulfil these purposes:
Table 3 Profit and loss statement of the advance model
Statement of profit and loss as per Traditional method as well as ABC method
(Amount in $)
Particular Traditional Costing ABC Costing
Product cost of Advance Model 1060.16 1070.80
Selling Margin 2 20% 20%
Profit 212.03 214.15
It can be accessed from above profit and loss statement that in present situation when Sewing
Easy Ltd. is following traditional costing method the profit per unit of the advance model is
less in comparison to the profit, i.e. $212.03 which can be earned up to $214.15. Profit of
$214.15 can be earned in case activity-based costing model is being applied by the company.
Overseas buyer is interested in purchasing advance model only because the same is available
at a lower rate as the company is following traditional costing method. Due to this method,
indirect cost is not appropriately allocated between basic model and advance mode. It might
be possible that overseas purchaser has analyzed the fault followed by the company in
evaluating the total cost of the advance model. Thus, he is showcasing his interest in
purchasing advance model so that he can attain same product with advanced features and at a
lower price.
In case an organization applies traditional costing method than indirect expenses are allocated
on the basis of direct labour. Further labour cannot be specified as the appropriate base of
allocation of every expenditure. The same misconception is followed by Sewing Easy Ltd,
due to which it is not able to ascertain the actual indirect cost of the basic and advanced
model. The advantage of same is being attained by the purchaser; the same can be assessed in
the present case that due to improper allocation methodology adoption only he is interested in
purchasing advance model. Accurate product costing is very necessary for every
organization. The reason behind same is that inappropriateness in cost leads to the inaccurate
evaluation of profit. Thus, the possibility might exist that even though in the book of
company profit is being recognized, it is possible that in actuality company is not earning the
evaluated profit.
Accurate cost data is required to fulfil these purposes:
⊘ This is a preview!⊘
Do you want full access?
Subscribe today to unlock all pages.

Trusted by 1+ million students worldwide
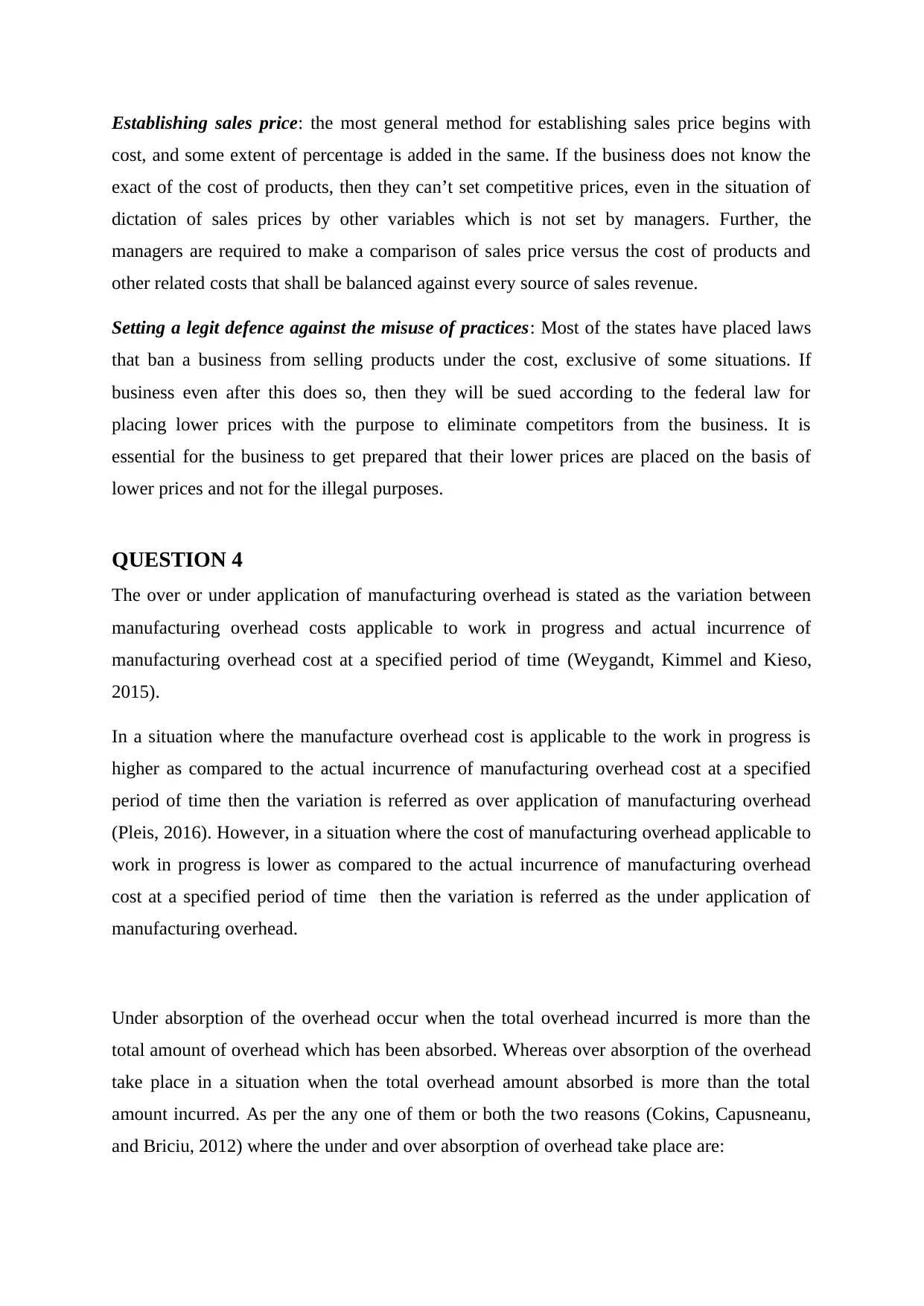
Establishing sales price: the most general method for establishing sales price begins with
cost, and some extent of percentage is added in the same. If the business does not know the
exact of the cost of products, then they can’t set competitive prices, even in the situation of
dictation of sales prices by other variables which is not set by managers. Further, the
managers are required to make a comparison of sales price versus the cost of products and
other related costs that shall be balanced against every source of sales revenue.
Setting a legit defence against the misuse of practices: Most of the states have placed laws
that ban a business from selling products under the cost, exclusive of some situations. If
business even after this does so, then they will be sued according to the federal law for
placing lower prices with the purpose to eliminate competitors from the business. It is
essential for the business to get prepared that their lower prices are placed on the basis of
lower prices and not for the illegal purposes.
QUESTION 4
The over or under application of manufacturing overhead is stated as the variation between
manufacturing overhead costs applicable to work in progress and actual incurrence of
manufacturing overhead cost at a specified period of time (Weygandt, Kimmel and Kieso,
2015).
In a situation where the manufacture overhead cost is applicable to the work in progress is
higher as compared to the actual incurrence of manufacturing overhead cost at a specified
period of time then the variation is referred as over application of manufacturing overhead
(Pleis, 2016). However, in a situation where the cost of manufacturing overhead applicable to
work in progress is lower as compared to the actual incurrence of manufacturing overhead
cost at a specified period of time then the variation is referred as the under application of
manufacturing overhead.
Under absorption of the overhead occur when the total overhead incurred is more than the
total amount of overhead which has been absorbed. Whereas over absorption of the overhead
take place in a situation when the total overhead amount absorbed is more than the total
amount incurred. As per the any one of them or both the two reasons (Cokins, Capusneanu,
and Briciu, 2012) where the under and over absorption of overhead take place are:
cost, and some extent of percentage is added in the same. If the business does not know the
exact of the cost of products, then they can’t set competitive prices, even in the situation of
dictation of sales prices by other variables which is not set by managers. Further, the
managers are required to make a comparison of sales price versus the cost of products and
other related costs that shall be balanced against every source of sales revenue.
Setting a legit defence against the misuse of practices: Most of the states have placed laws
that ban a business from selling products under the cost, exclusive of some situations. If
business even after this does so, then they will be sued according to the federal law for
placing lower prices with the purpose to eliminate competitors from the business. It is
essential for the business to get prepared that their lower prices are placed on the basis of
lower prices and not for the illegal purposes.
QUESTION 4
The over or under application of manufacturing overhead is stated as the variation between
manufacturing overhead costs applicable to work in progress and actual incurrence of
manufacturing overhead cost at a specified period of time (Weygandt, Kimmel and Kieso,
2015).
In a situation where the manufacture overhead cost is applicable to the work in progress is
higher as compared to the actual incurrence of manufacturing overhead cost at a specified
period of time then the variation is referred as over application of manufacturing overhead
(Pleis, 2016). However, in a situation where the cost of manufacturing overhead applicable to
work in progress is lower as compared to the actual incurrence of manufacturing overhead
cost at a specified period of time then the variation is referred as the under application of
manufacturing overhead.
Under absorption of the overhead occur when the total overhead incurred is more than the
total amount of overhead which has been absorbed. Whereas over absorption of the overhead
take place in a situation when the total overhead amount absorbed is more than the total
amount incurred. As per the any one of them or both the two reasons (Cokins, Capusneanu,
and Briciu, 2012) where the under and over absorption of overhead take place are:
Paraphrase This Document
Need a fresh take? Get an instant paraphrase of this document with our AI Paraphraser
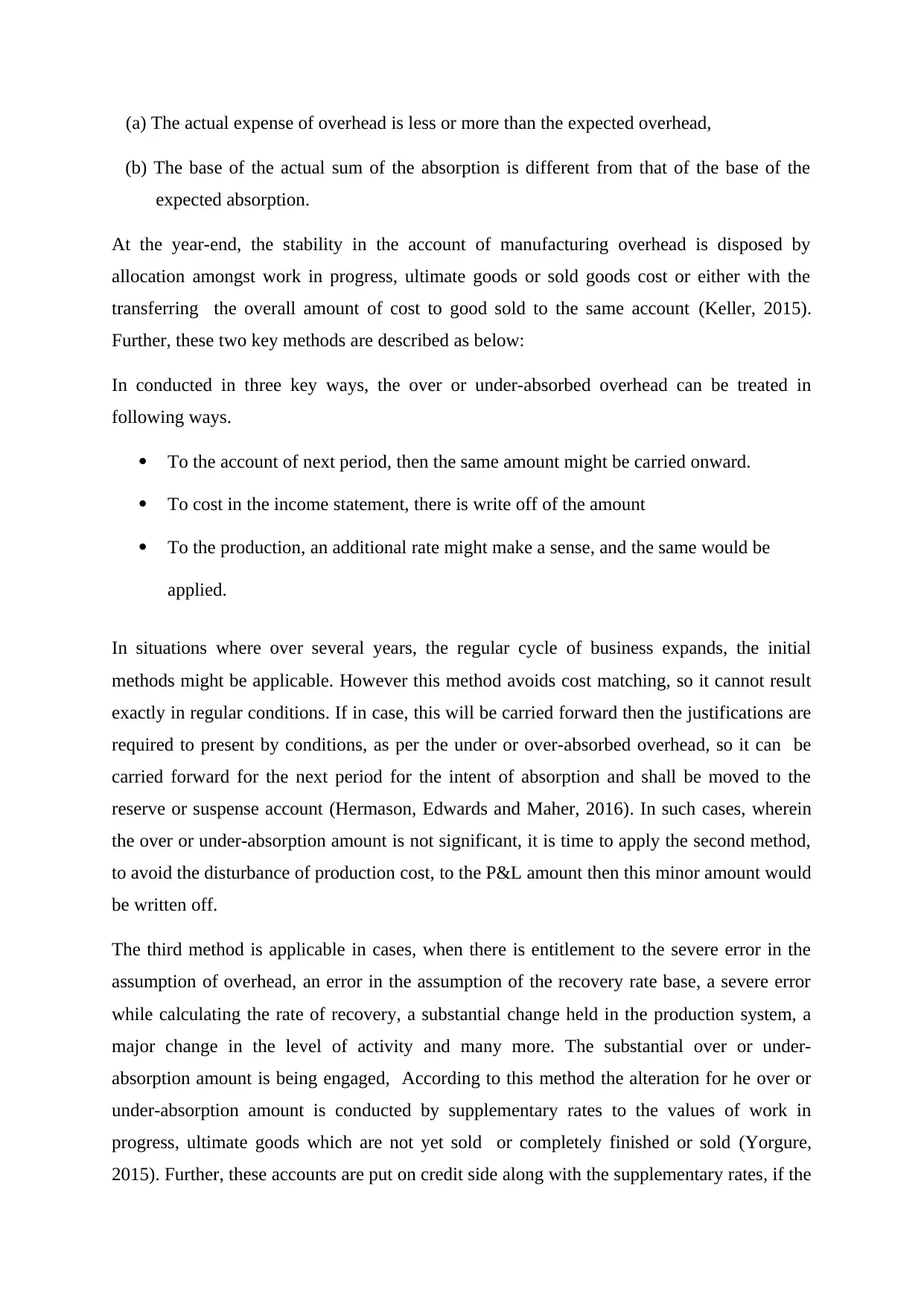
(a) The actual expense of overhead is less or more than the expected overhead,
(b) The base of the actual sum of the absorption is different from that of the base of the
expected absorption.
At the year-end, the stability in the account of manufacturing overhead is disposed by
allocation amongst work in progress, ultimate goods or sold goods cost or either with the
transferring the overall amount of cost to good sold to the same account (Keller, 2015).
Further, these two key methods are described as below:
In conducted in three key ways, the over or under-absorbed overhead can be treated in
following ways.
To the account of next period, then the same amount might be carried onward.
To cost in the income statement, there is write off of the amount
To the production, an additional rate might make a sense, and the same would be
applied.
In situations where over several years, the regular cycle of business expands, the initial
methods might be applicable. However this method avoids cost matching, so it cannot result
exactly in regular conditions. If in case, this will be carried forward then the justifications are
required to present by conditions, as per the under or over-absorbed overhead, so it can be
carried forward for the next period for the intent of absorption and shall be moved to the
reserve or suspense account (Hermason, Edwards and Maher, 2016). In such cases, wherein
the over or under-absorption amount is not significant, it is time to apply the second method,
to avoid the disturbance of production cost, to the P&L amount then this minor amount would
be written off.
The third method is applicable in cases, when there is entitlement to the severe error in the
assumption of overhead, an error in the assumption of the recovery rate base, a severe error
while calculating the rate of recovery, a substantial change held in the production system, a
major change in the level of activity and many more. The substantial over or under-
absorption amount is being engaged, According to this method the alteration for he over or
under-absorption amount is conducted by supplementary rates to the values of work in
progress, ultimate goods which are not yet sold or completely finished or sold (Yorgure,
2015). Further, these accounts are put on credit side along with the supplementary rates, if the
(b) The base of the actual sum of the absorption is different from that of the base of the
expected absorption.
At the year-end, the stability in the account of manufacturing overhead is disposed by
allocation amongst work in progress, ultimate goods or sold goods cost or either with the
transferring the overall amount of cost to good sold to the same account (Keller, 2015).
Further, these two key methods are described as below:
In conducted in three key ways, the over or under-absorbed overhead can be treated in
following ways.
To the account of next period, then the same amount might be carried onward.
To cost in the income statement, there is write off of the amount
To the production, an additional rate might make a sense, and the same would be
applied.
In situations where over several years, the regular cycle of business expands, the initial
methods might be applicable. However this method avoids cost matching, so it cannot result
exactly in regular conditions. If in case, this will be carried forward then the justifications are
required to present by conditions, as per the under or over-absorbed overhead, so it can be
carried forward for the next period for the intent of absorption and shall be moved to the
reserve or suspense account (Hermason, Edwards and Maher, 2016). In such cases, wherein
the over or under-absorption amount is not significant, it is time to apply the second method,
to avoid the disturbance of production cost, to the P&L amount then this minor amount would
be written off.
The third method is applicable in cases, when there is entitlement to the severe error in the
assumption of overhead, an error in the assumption of the recovery rate base, a severe error
while calculating the rate of recovery, a substantial change held in the production system, a
major change in the level of activity and many more. The substantial over or under-
absorption amount is being engaged, According to this method the alteration for he over or
under-absorption amount is conducted by supplementary rates to the values of work in
progress, ultimate goods which are not yet sold or completely finished or sold (Yorgure,
2015). Further, these accounts are put on credit side along with the supplementary rates, if the
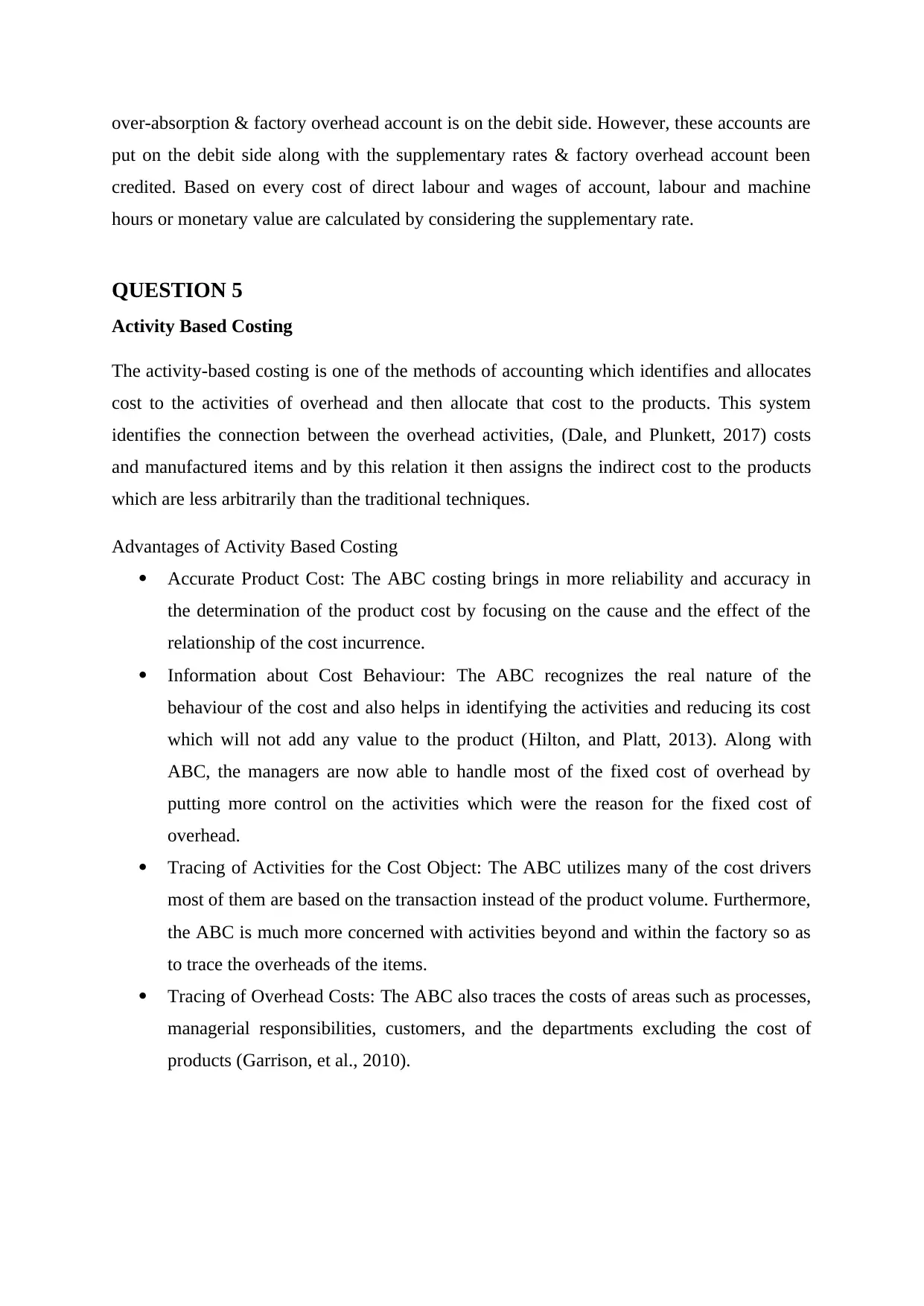
over-absorption & factory overhead account is on the debit side. However, these accounts are
put on the debit side along with the supplementary rates & factory overhead account been
credited. Based on every cost of direct labour and wages of account, labour and machine
hours or monetary value are calculated by considering the supplementary rate.
QUESTION 5
Activity Based Costing
The activity-based costing is one of the methods of accounting which identifies and allocates
cost to the activities of overhead and then allocate that cost to the products. This system
identifies the connection between the overhead activities, (Dale, and Plunkett, 2017) costs
and manufactured items and by this relation it then assigns the indirect cost to the products
which are less arbitrarily than the traditional techniques.
Advantages of Activity Based Costing
Accurate Product Cost: The ABC costing brings in more reliability and accuracy in
the determination of the product cost by focusing on the cause and the effect of the
relationship of the cost incurrence.
Information about Cost Behaviour: The ABC recognizes the real nature of the
behaviour of the cost and also helps in identifying the activities and reducing its cost
which will not add any value to the product (Hilton, and Platt, 2013). Along with
ABC, the managers are now able to handle most of the fixed cost of overhead by
putting more control on the activities which were the reason for the fixed cost of
overhead.
Tracing of Activities for the Cost Object: The ABC utilizes many of the cost drivers
most of them are based on the transaction instead of the product volume. Furthermore,
the ABC is much more concerned with activities beyond and within the factory so as
to trace the overheads of the items.
Tracing of Overhead Costs: The ABC also traces the costs of areas such as processes,
managerial responsibilities, customers, and the departments excluding the cost of
products (Garrison, et al., 2010).
put on the debit side along with the supplementary rates & factory overhead account been
credited. Based on every cost of direct labour and wages of account, labour and machine
hours or monetary value are calculated by considering the supplementary rate.
QUESTION 5
Activity Based Costing
The activity-based costing is one of the methods of accounting which identifies and allocates
cost to the activities of overhead and then allocate that cost to the products. This system
identifies the connection between the overhead activities, (Dale, and Plunkett, 2017) costs
and manufactured items and by this relation it then assigns the indirect cost to the products
which are less arbitrarily than the traditional techniques.
Advantages of Activity Based Costing
Accurate Product Cost: The ABC costing brings in more reliability and accuracy in
the determination of the product cost by focusing on the cause and the effect of the
relationship of the cost incurrence.
Information about Cost Behaviour: The ABC recognizes the real nature of the
behaviour of the cost and also helps in identifying the activities and reducing its cost
which will not add any value to the product (Hilton, and Platt, 2013). Along with
ABC, the managers are now able to handle most of the fixed cost of overhead by
putting more control on the activities which were the reason for the fixed cost of
overhead.
Tracing of Activities for the Cost Object: The ABC utilizes many of the cost drivers
most of them are based on the transaction instead of the product volume. Furthermore,
the ABC is much more concerned with activities beyond and within the factory so as
to trace the overheads of the items.
Tracing of Overhead Costs: The ABC also traces the costs of areas such as processes,
managerial responsibilities, customers, and the departments excluding the cost of
products (Garrison, et al., 2010).
⊘ This is a preview!⊘
Do you want full access?
Subscribe today to unlock all pages.

Trusted by 1+ million students worldwide
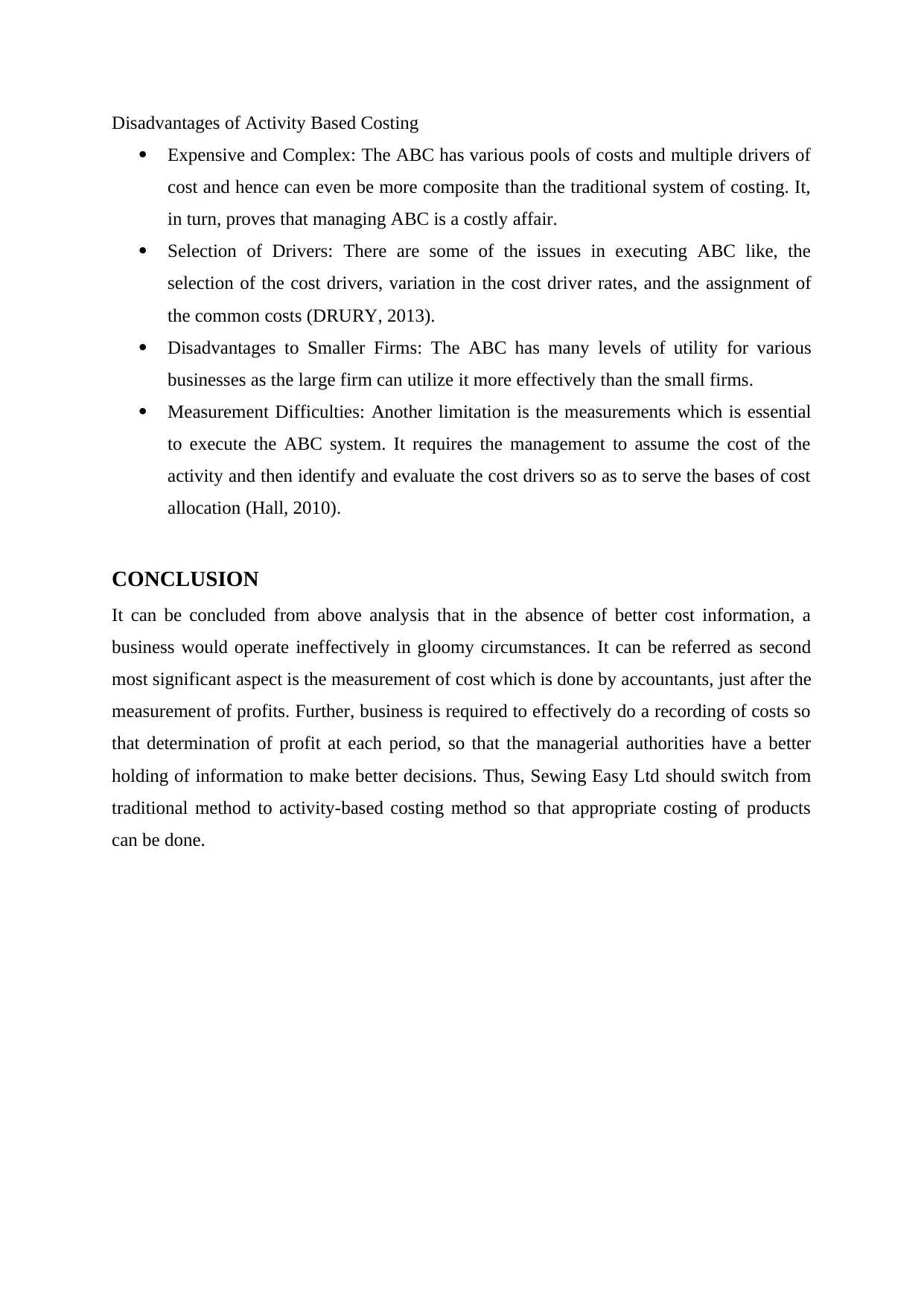
Disadvantages of Activity Based Costing
Expensive and Complex: The ABC has various pools of costs and multiple drivers of
cost and hence can even be more composite than the traditional system of costing. It,
in turn, proves that managing ABC is a costly affair.
Selection of Drivers: There are some of the issues in executing ABC like, the
selection of the cost drivers, variation in the cost driver rates, and the assignment of
the common costs (DRURY, 2013).
Disadvantages to Smaller Firms: The ABC has many levels of utility for various
businesses as the large firm can utilize it more effectively than the small firms.
Measurement Difficulties: Another limitation is the measurements which is essential
to execute the ABC system. It requires the management to assume the cost of the
activity and then identify and evaluate the cost drivers so as to serve the bases of cost
allocation (Hall, 2010).
CONCLUSION
It can be concluded from above analysis that in the absence of better cost information, a
business would operate ineffectively in gloomy circumstances. It can be referred as second
most significant aspect is the measurement of cost which is done by accountants, just after the
measurement of profits. Further, business is required to effectively do a recording of costs so
that determination of profit at each period, so that the managerial authorities have a better
holding of information to make better decisions. Thus, Sewing Easy Ltd should switch from
traditional method to activity-based costing method so that appropriate costing of products
can be done.
Expensive and Complex: The ABC has various pools of costs and multiple drivers of
cost and hence can even be more composite than the traditional system of costing. It,
in turn, proves that managing ABC is a costly affair.
Selection of Drivers: There are some of the issues in executing ABC like, the
selection of the cost drivers, variation in the cost driver rates, and the assignment of
the common costs (DRURY, 2013).
Disadvantages to Smaller Firms: The ABC has many levels of utility for various
businesses as the large firm can utilize it more effectively than the small firms.
Measurement Difficulties: Another limitation is the measurements which is essential
to execute the ABC system. It requires the management to assume the cost of the
activity and then identify and evaluate the cost drivers so as to serve the bases of cost
allocation (Hall, 2010).
CONCLUSION
It can be concluded from above analysis that in the absence of better cost information, a
business would operate ineffectively in gloomy circumstances. It can be referred as second
most significant aspect is the measurement of cost which is done by accountants, just after the
measurement of profits. Further, business is required to effectively do a recording of costs so
that determination of profit at each period, so that the managerial authorities have a better
holding of information to make better decisions. Thus, Sewing Easy Ltd should switch from
traditional method to activity-based costing method so that appropriate costing of products
can be done.
Paraphrase This Document
Need a fresh take? Get an instant paraphrase of this document with our AI Paraphraser
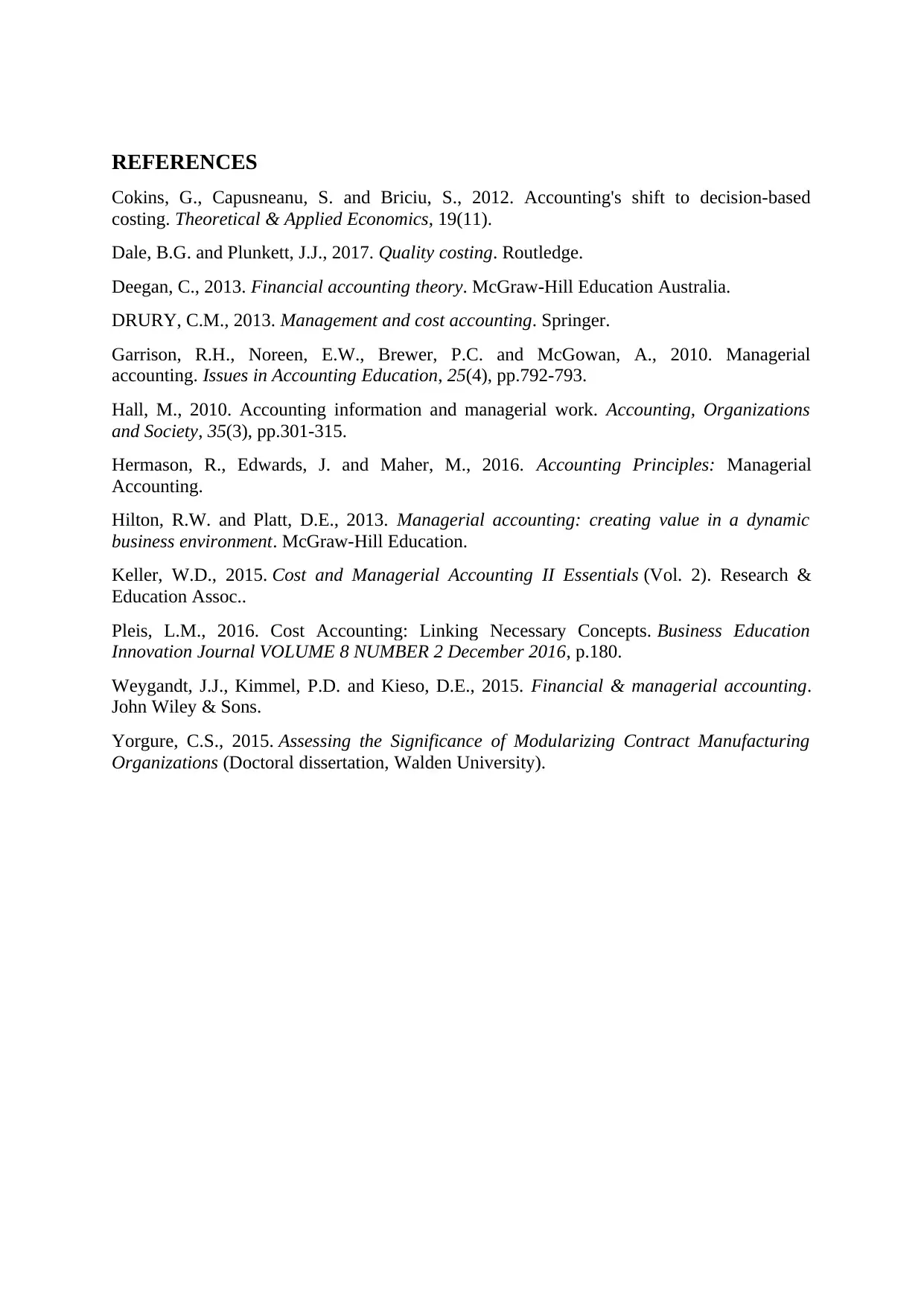
REFERENCES
Cokins, G., Capusneanu, S. and Briciu, S., 2012. Accounting's shift to decision-based
costing. Theoretical & Applied Economics, 19(11).
Dale, B.G. and Plunkett, J.J., 2017. Quality costing. Routledge.
Deegan, C., 2013. Financial accounting theory. McGraw-Hill Education Australia.
DRURY, C.M., 2013. Management and cost accounting. Springer.
Garrison, R.H., Noreen, E.W., Brewer, P.C. and McGowan, A., 2010. Managerial
accounting. Issues in Accounting Education, 25(4), pp.792-793.
Hall, M., 2010. Accounting information and managerial work. Accounting, Organizations
and Society, 35(3), pp.301-315.
Hermason, R., Edwards, J. and Maher, M., 2016. Accounting Principles: Managerial
Accounting.
Hilton, R.W. and Platt, D.E., 2013. Managerial accounting: creating value in a dynamic
business environment. McGraw-Hill Education.
Keller, W.D., 2015. Cost and Managerial Accounting II Essentials (Vol. 2). Research &
Education Assoc..
Pleis, L.M., 2016. Cost Accounting: Linking Necessary Concepts. Business Education
Innovation Journal VOLUME 8 NUMBER 2 December 2016, p.180.
Weygandt, J.J., Kimmel, P.D. and Kieso, D.E., 2015. Financial & managerial accounting.
John Wiley & Sons.
Yorgure, C.S., 2015. Assessing the Significance of Modularizing Contract Manufacturing
Organizations (Doctoral dissertation, Walden University).
Cokins, G., Capusneanu, S. and Briciu, S., 2012. Accounting's shift to decision-based
costing. Theoretical & Applied Economics, 19(11).
Dale, B.G. and Plunkett, J.J., 2017. Quality costing. Routledge.
Deegan, C., 2013. Financial accounting theory. McGraw-Hill Education Australia.
DRURY, C.M., 2013. Management and cost accounting. Springer.
Garrison, R.H., Noreen, E.W., Brewer, P.C. and McGowan, A., 2010. Managerial
accounting. Issues in Accounting Education, 25(4), pp.792-793.
Hall, M., 2010. Accounting information and managerial work. Accounting, Organizations
and Society, 35(3), pp.301-315.
Hermason, R., Edwards, J. and Maher, M., 2016. Accounting Principles: Managerial
Accounting.
Hilton, R.W. and Platt, D.E., 2013. Managerial accounting: creating value in a dynamic
business environment. McGraw-Hill Education.
Keller, W.D., 2015. Cost and Managerial Accounting II Essentials (Vol. 2). Research &
Education Assoc..
Pleis, L.M., 2016. Cost Accounting: Linking Necessary Concepts. Business Education
Innovation Journal VOLUME 8 NUMBER 2 December 2016, p.180.
Weygandt, J.J., Kimmel, P.D. and Kieso, D.E., 2015. Financial & managerial accounting.
John Wiley & Sons.
Yorgure, C.S., 2015. Assessing the Significance of Modularizing Contract Manufacturing
Organizations (Doctoral dissertation, Walden University).
1 out of 11
Related Documents

Your All-in-One AI-Powered Toolkit for Academic Success.
+13062052269
info@desklib.com
Available 24*7 on WhatsApp / Email
Unlock your academic potential
© 2024 | Zucol Services PVT LTD | All rights reserved.