Analysis of Budgeting and Costing: Management Accounting Report
VerifiedAdded on 2020/01/23
|20
|4773
|101
Report
AI Summary
This report provides a comprehensive analysis of management accounting principles, specifically focusing on budgeting, cost classification, and variance analysis within the context of a cloth manufacturing retailer, Smart Looks. The report begins by exploring different types of cost behavior, categorizing costs as fixed, variable, and semi-variable, and providing examples. It then delves into other cost classifications, including direct and indirect costs, as well as factory, administrative, and marketing costs. The report includes calculations of total and unit costs at different production levels, followed by an analysis of cost data and graphical representations of cost behavior. Furthermore, the report examines inventory valuation methods such as FIFO, LIFO, and average cost methods. It also identifies key performance indicators (KPIs) for measuring customer experience, supplier quality, operational efficiency, and cost reduction. Finally, the report discusses strategies for cost reduction, value enhancement, and quality improvement, along with an overview of different budgeting methods and their purposes.
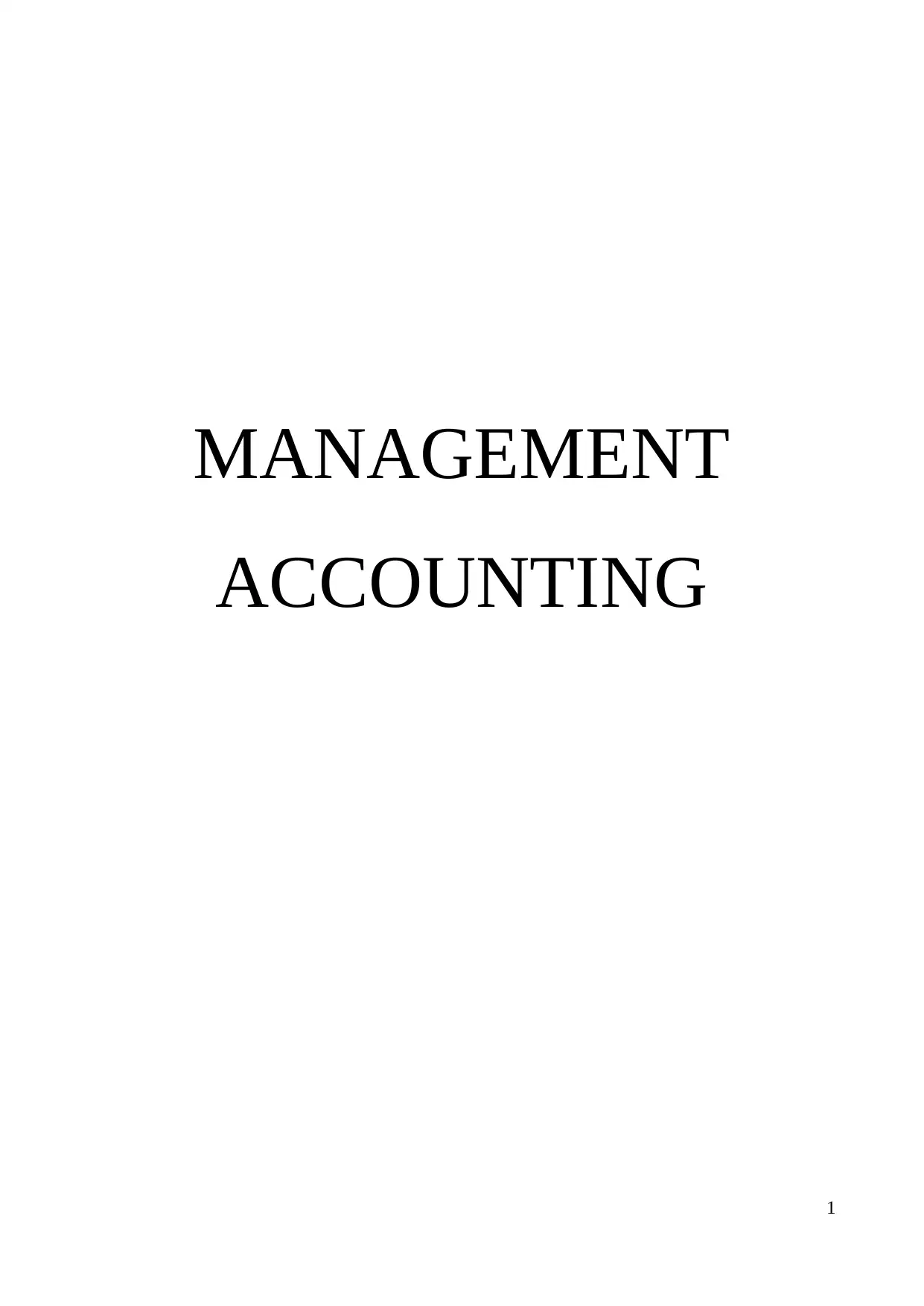
MANAGEMENT
ACCOUNTING
1
ACCOUNTING
1
Paraphrase This Document
Need a fresh take? Get an instant paraphrase of this document with our AI Paraphraser
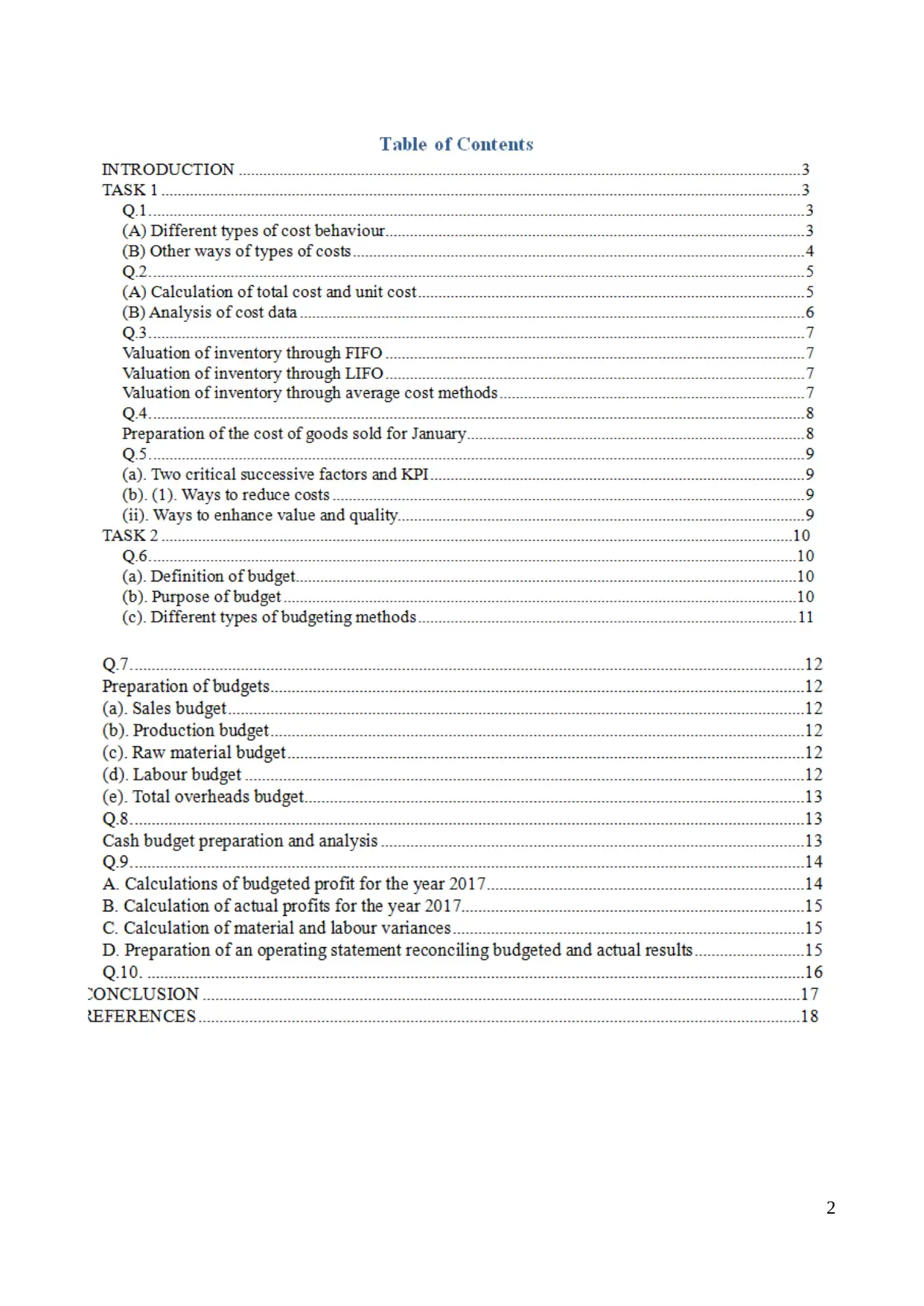
2
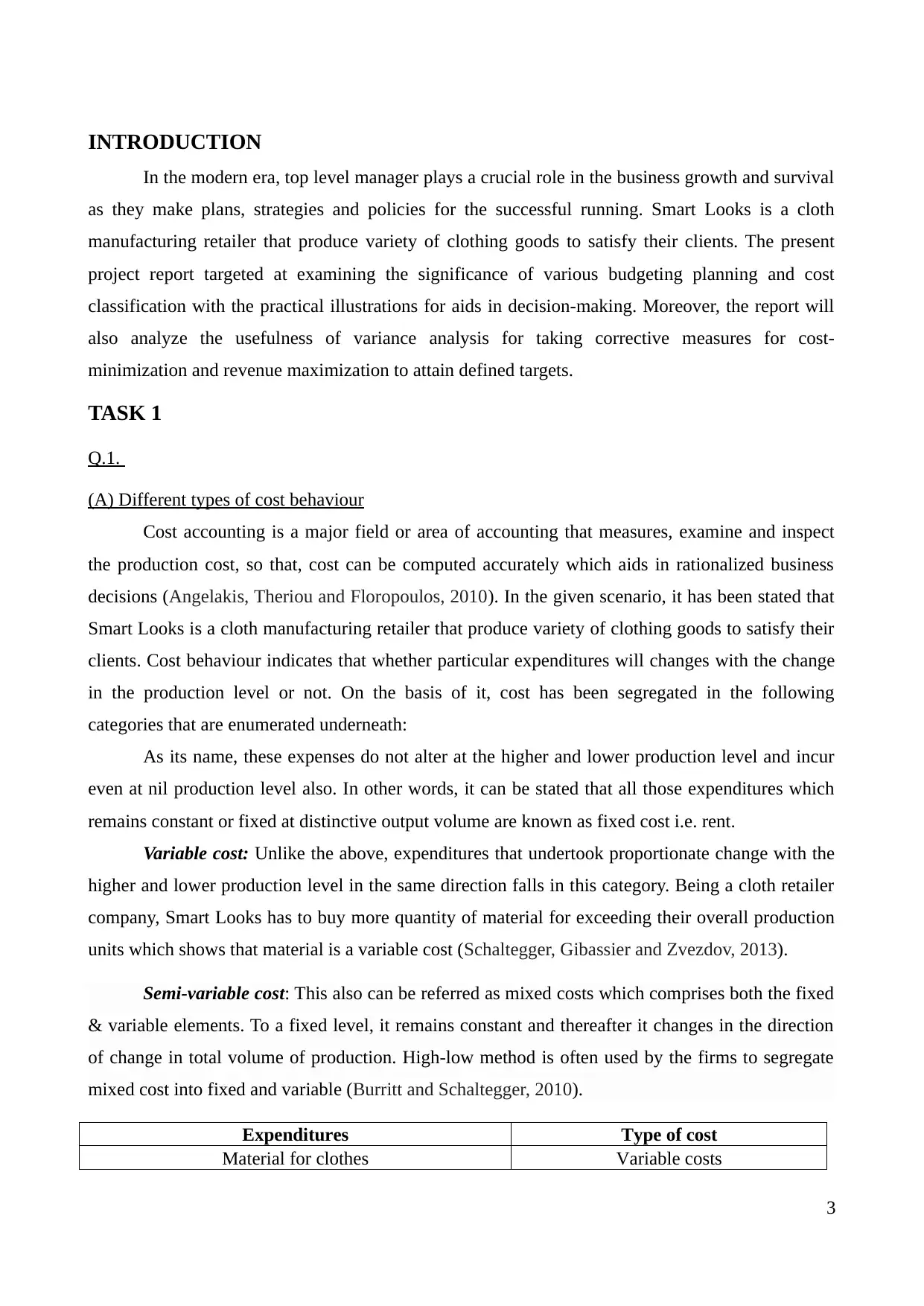
INTRODUCTION
In the modern era, top level manager plays a crucial role in the business growth and survival
as they make plans, strategies and policies for the successful running. Smart Looks is a cloth
manufacturing retailer that produce variety of clothing goods to satisfy their clients. The present
project report targeted at examining the significance of various budgeting planning and cost
classification with the practical illustrations for aids in decision-making. Moreover, the report will
also analyze the usefulness of variance analysis for taking corrective measures for cost-
minimization and revenue maximization to attain defined targets.
TASK 1
Q.1.
(A) Different types of cost behaviour
Cost accounting is a major field or area of accounting that measures, examine and inspect
the production cost, so that, cost can be computed accurately which aids in rationalized business
decisions (Angelakis, Theriou and Floropoulos, 2010). In the given scenario, it has been stated that
Smart Looks is a cloth manufacturing retailer that produce variety of clothing goods to satisfy their
clients. Cost behaviour indicates that whether particular expenditures will changes with the change
in the production level or not. On the basis of it, cost has been segregated in the following
categories that are enumerated underneath:
As its name, these expenses do not alter at the higher and lower production level and incur
even at nil production level also. In other words, it can be stated that all those expenditures which
remains constant or fixed at distinctive output volume are known as fixed cost i.e. rent.
Variable cost: Unlike the above, expenditures that undertook proportionate change with the
higher and lower production level in the same direction falls in this category. Being a cloth retailer
company, Smart Looks has to buy more quantity of material for exceeding their overall production
units which shows that material is a variable cost (Schaltegger, Gibassier and Zvezdov, 2013).
Semi-variable cost: This also can be referred as mixed costs which comprises both the fixed
& variable elements. To a fixed level, it remains constant and thereafter it changes in the direction
of change in total volume of production. High-low method is often used by the firms to segregate
mixed cost into fixed and variable (Burritt and Schaltegger, 2010).
Expenditures Type of cost
Material for clothes Variable costs
3
In the modern era, top level manager plays a crucial role in the business growth and survival
as they make plans, strategies and policies for the successful running. Smart Looks is a cloth
manufacturing retailer that produce variety of clothing goods to satisfy their clients. The present
project report targeted at examining the significance of various budgeting planning and cost
classification with the practical illustrations for aids in decision-making. Moreover, the report will
also analyze the usefulness of variance analysis for taking corrective measures for cost-
minimization and revenue maximization to attain defined targets.
TASK 1
Q.1.
(A) Different types of cost behaviour
Cost accounting is a major field or area of accounting that measures, examine and inspect
the production cost, so that, cost can be computed accurately which aids in rationalized business
decisions (Angelakis, Theriou and Floropoulos, 2010). In the given scenario, it has been stated that
Smart Looks is a cloth manufacturing retailer that produce variety of clothing goods to satisfy their
clients. Cost behaviour indicates that whether particular expenditures will changes with the change
in the production level or not. On the basis of it, cost has been segregated in the following
categories that are enumerated underneath:
As its name, these expenses do not alter at the higher and lower production level and incur
even at nil production level also. In other words, it can be stated that all those expenditures which
remains constant or fixed at distinctive output volume are known as fixed cost i.e. rent.
Variable cost: Unlike the above, expenditures that undertook proportionate change with the
higher and lower production level in the same direction falls in this category. Being a cloth retailer
company, Smart Looks has to buy more quantity of material for exceeding their overall production
units which shows that material is a variable cost (Schaltegger, Gibassier and Zvezdov, 2013).
Semi-variable cost: This also can be referred as mixed costs which comprises both the fixed
& variable elements. To a fixed level, it remains constant and thereafter it changes in the direction
of change in total volume of production. High-low method is often used by the firms to segregate
mixed cost into fixed and variable (Burritt and Schaltegger, 2010).
Expenditures Type of cost
Material for clothes Variable costs
3
You're viewing a preview
Unlock full access by subscribing today!
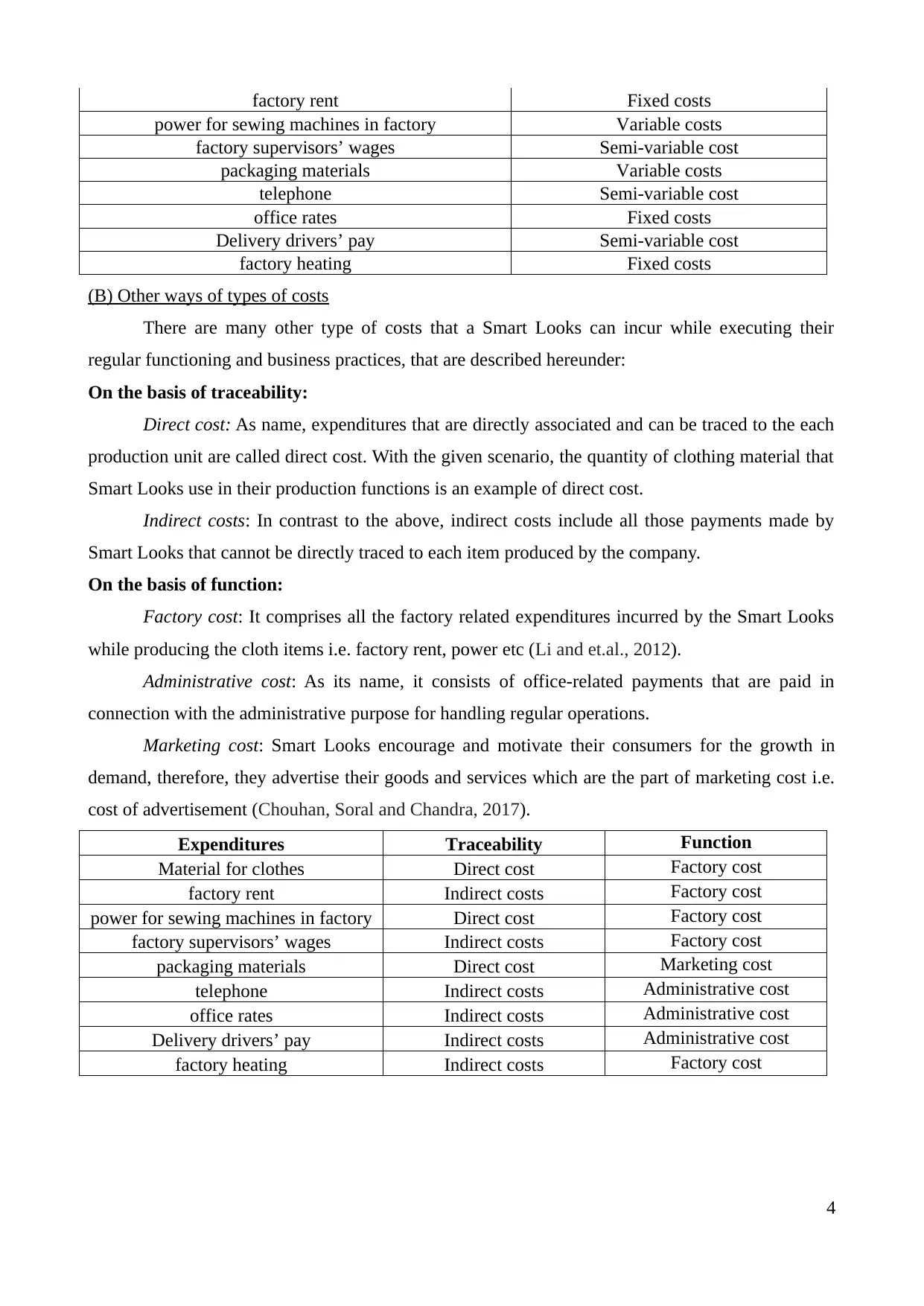
factory rent Fixed costs
power for sewing machines in factory Variable costs
factory supervisors’ wages Semi-variable cost
packaging materials Variable costs
telephone Semi-variable cost
office rates Fixed costs
Delivery drivers’ pay Semi-variable cost
factory heating Fixed costs
(B) Other ways of types of costs
There are many other type of costs that a Smart Looks can incur while executing their
regular functioning and business practices, that are described hereunder:
On the basis of traceability:
Direct cost: As name, expenditures that are directly associated and can be traced to the each
production unit are called direct cost. With the given scenario, the quantity of clothing material that
Smart Looks use in their production functions is an example of direct cost.
Indirect costs: In contrast to the above, indirect costs include all those payments made by
Smart Looks that cannot be directly traced to each item produced by the company.
On the basis of function:
Factory cost: It comprises all the factory related expenditures incurred by the Smart Looks
while producing the cloth items i.e. factory rent, power etc (Li and et.al., 2012).
Administrative cost: As its name, it consists of office-related payments that are paid in
connection with the administrative purpose for handling regular operations.
Marketing cost: Smart Looks encourage and motivate their consumers for the growth in
demand, therefore, they advertise their goods and services which are the part of marketing cost i.e.
cost of advertisement (Chouhan, Soral and Chandra, 2017).
Expenditures Traceability Function
Material for clothes Direct cost Factory cost
factory rent Indirect costs Factory cost
power for sewing machines in factory Direct cost Factory cost
factory supervisors’ wages Indirect costs Factory cost
packaging materials Direct cost Marketing cost
telephone Indirect costs Administrative cost
office rates Indirect costs Administrative cost
Delivery drivers’ pay Indirect costs Administrative cost
factory heating Indirect costs Factory cost
4
power for sewing machines in factory Variable costs
factory supervisors’ wages Semi-variable cost
packaging materials Variable costs
telephone Semi-variable cost
office rates Fixed costs
Delivery drivers’ pay Semi-variable cost
factory heating Fixed costs
(B) Other ways of types of costs
There are many other type of costs that a Smart Looks can incur while executing their
regular functioning and business practices, that are described hereunder:
On the basis of traceability:
Direct cost: As name, expenditures that are directly associated and can be traced to the each
production unit are called direct cost. With the given scenario, the quantity of clothing material that
Smart Looks use in their production functions is an example of direct cost.
Indirect costs: In contrast to the above, indirect costs include all those payments made by
Smart Looks that cannot be directly traced to each item produced by the company.
On the basis of function:
Factory cost: It comprises all the factory related expenditures incurred by the Smart Looks
while producing the cloth items i.e. factory rent, power etc (Li and et.al., 2012).
Administrative cost: As its name, it consists of office-related payments that are paid in
connection with the administrative purpose for handling regular operations.
Marketing cost: Smart Looks encourage and motivate their consumers for the growth in
demand, therefore, they advertise their goods and services which are the part of marketing cost i.e.
cost of advertisement (Chouhan, Soral and Chandra, 2017).
Expenditures Traceability Function
Material for clothes Direct cost Factory cost
factory rent Indirect costs Factory cost
power for sewing machines in factory Direct cost Factory cost
factory supervisors’ wages Indirect costs Factory cost
packaging materials Direct cost Marketing cost
telephone Indirect costs Administrative cost
office rates Indirect costs Administrative cost
Delivery drivers’ pay Indirect costs Administrative cost
factory heating Indirect costs Factory cost
4
Paraphrase This Document
Need a fresh take? Get an instant paraphrase of this document with our AI Paraphraser
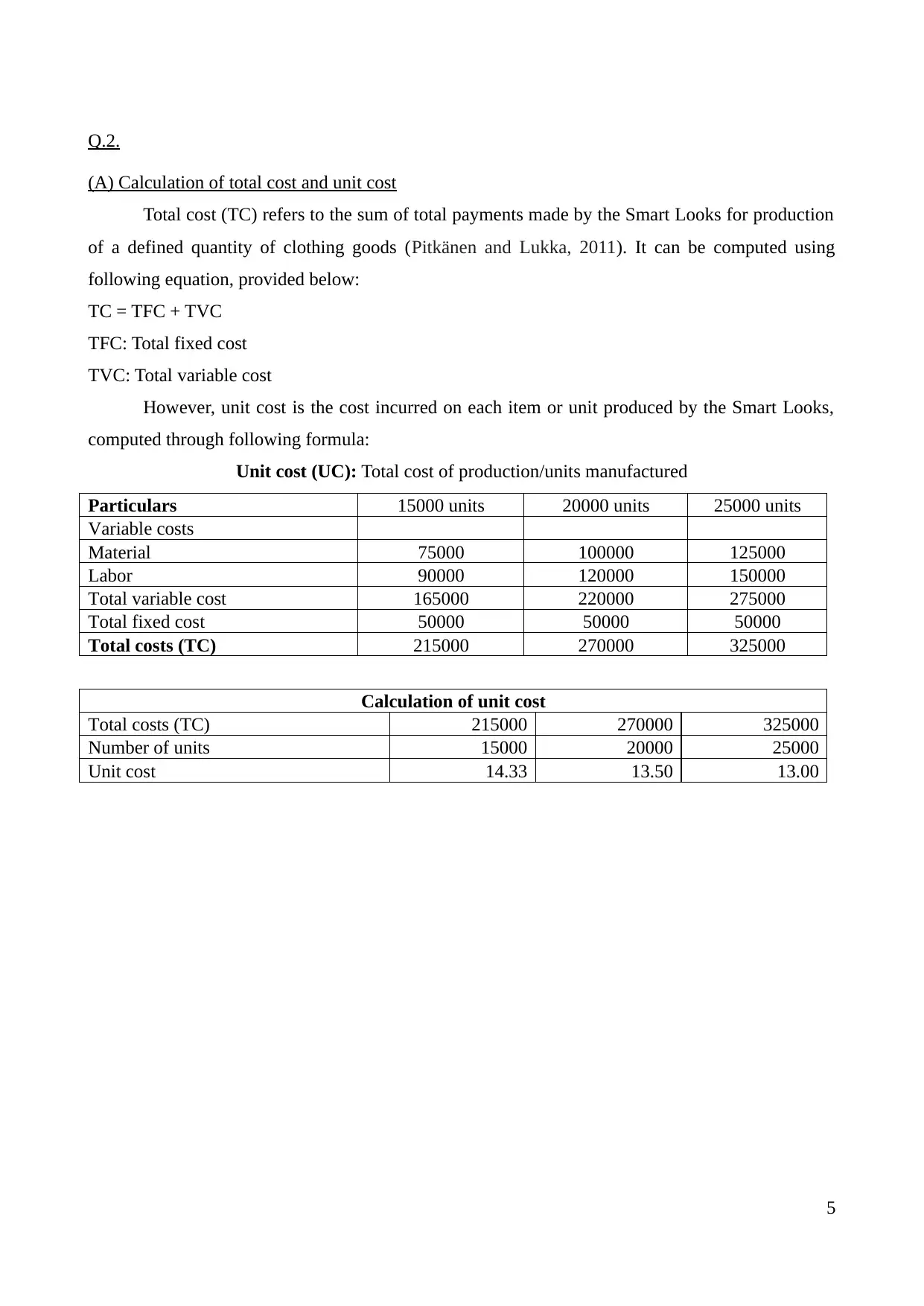
Q.2.
(A) Calculation of total cost and unit cost
Total cost (TC) refers to the sum of total payments made by the Smart Looks for production
of a defined quantity of clothing goods (Pitkänen and Lukka, 2011). It can be computed using
following equation, provided below:
TC = TFC + TVC
TFC: Total fixed cost
TVC: Total variable cost
However, unit cost is the cost incurred on each item or unit produced by the Smart Looks,
computed through following formula:
Unit cost (UC): Total cost of production/units manufactured
Particulars 15000 units 20000 units 25000 units
Variable costs
Material 75000 100000 125000
Labor 90000 120000 150000
Total variable cost 165000 220000 275000
Total fixed cost 50000 50000 50000
Total costs (TC) 215000 270000 325000
Calculation of unit cost
Total costs (TC) 215000 270000 325000
Number of units 15000 20000 25000
Unit cost 14.33 13.50 13.00
5
(A) Calculation of total cost and unit cost
Total cost (TC) refers to the sum of total payments made by the Smart Looks for production
of a defined quantity of clothing goods (Pitkänen and Lukka, 2011). It can be computed using
following equation, provided below:
TC = TFC + TVC
TFC: Total fixed cost
TVC: Total variable cost
However, unit cost is the cost incurred on each item or unit produced by the Smart Looks,
computed through following formula:
Unit cost (UC): Total cost of production/units manufactured
Particulars 15000 units 20000 units 25000 units
Variable costs
Material 75000 100000 125000
Labor 90000 120000 150000
Total variable cost 165000 220000 275000
Total fixed cost 50000 50000 50000
Total costs (TC) 215000 270000 325000
Calculation of unit cost
Total costs (TC) 215000 270000 325000
Number of units 15000 20000 25000
Unit cost 14.33 13.50 13.00
5
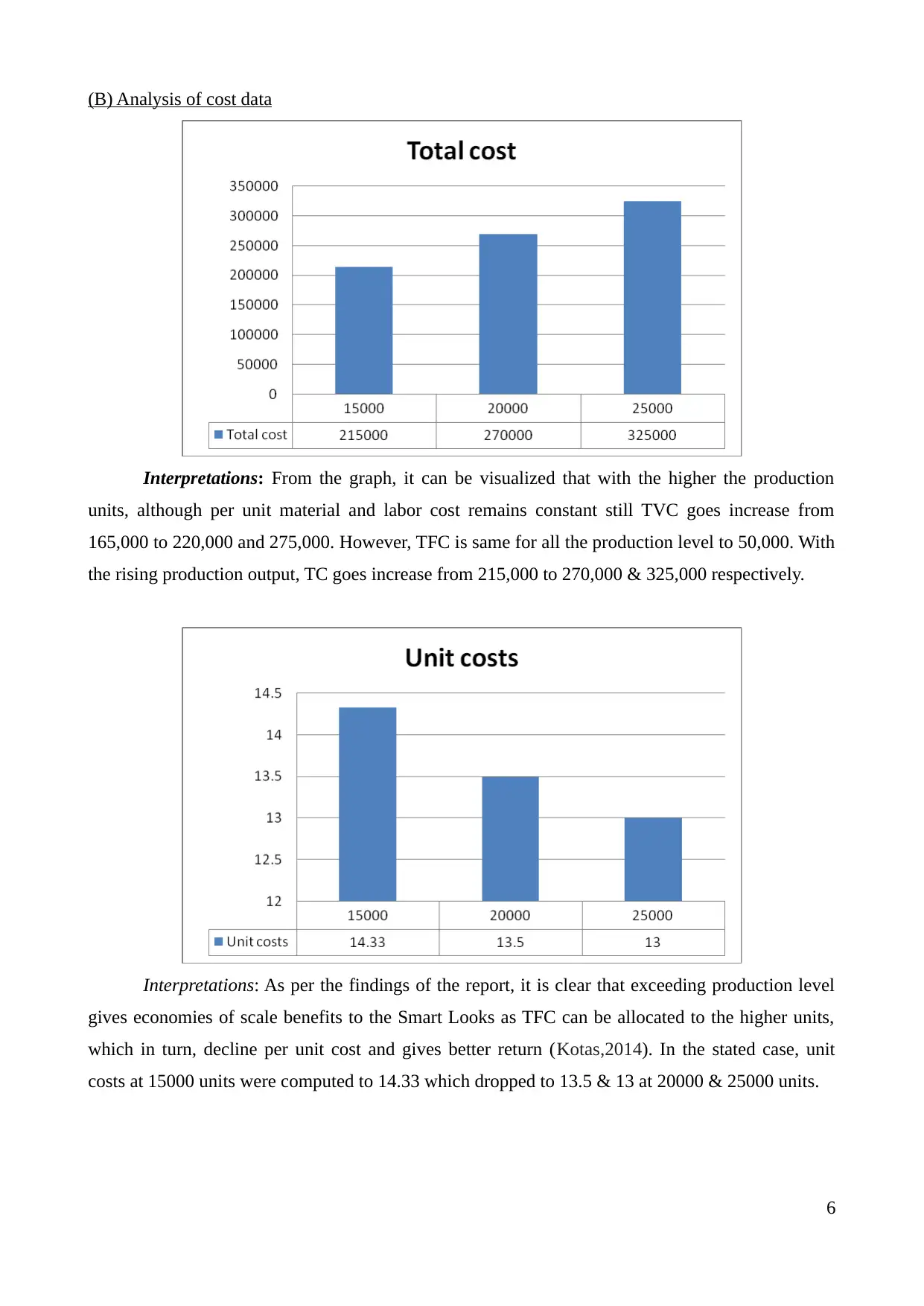
(B) Analysis of cost data
Interpretations: From the graph, it can be visualized that with the higher the production
units, although per unit material and labor cost remains constant still TVC goes increase from
165,000 to 220,000 and 275,000. However, TFC is same for all the production level to 50,000. With
the rising production output, TC goes increase from 215,000 to 270,000 & 325,000 respectively.
Interpretations: As per the findings of the report, it is clear that exceeding production level
gives economies of scale benefits to the Smart Looks as TFC can be allocated to the higher units,
which in turn, decline per unit cost and gives better return (Kotas,2014). In the stated case, unit
costs at 15000 units were computed to 14.33 which dropped to 13.5 & 13 at 20000 & 25000 units.
6
Interpretations: From the graph, it can be visualized that with the higher the production
units, although per unit material and labor cost remains constant still TVC goes increase from
165,000 to 220,000 and 275,000. However, TFC is same for all the production level to 50,000. With
the rising production output, TC goes increase from 215,000 to 270,000 & 325,000 respectively.
Interpretations: As per the findings of the report, it is clear that exceeding production level
gives economies of scale benefits to the Smart Looks as TFC can be allocated to the higher units,
which in turn, decline per unit cost and gives better return (Kotas,2014). In the stated case, unit
costs at 15000 units were computed to 14.33 which dropped to 13.5 & 13 at 20000 & 25000 units.
6
You're viewing a preview
Unlock full access by subscribing today!
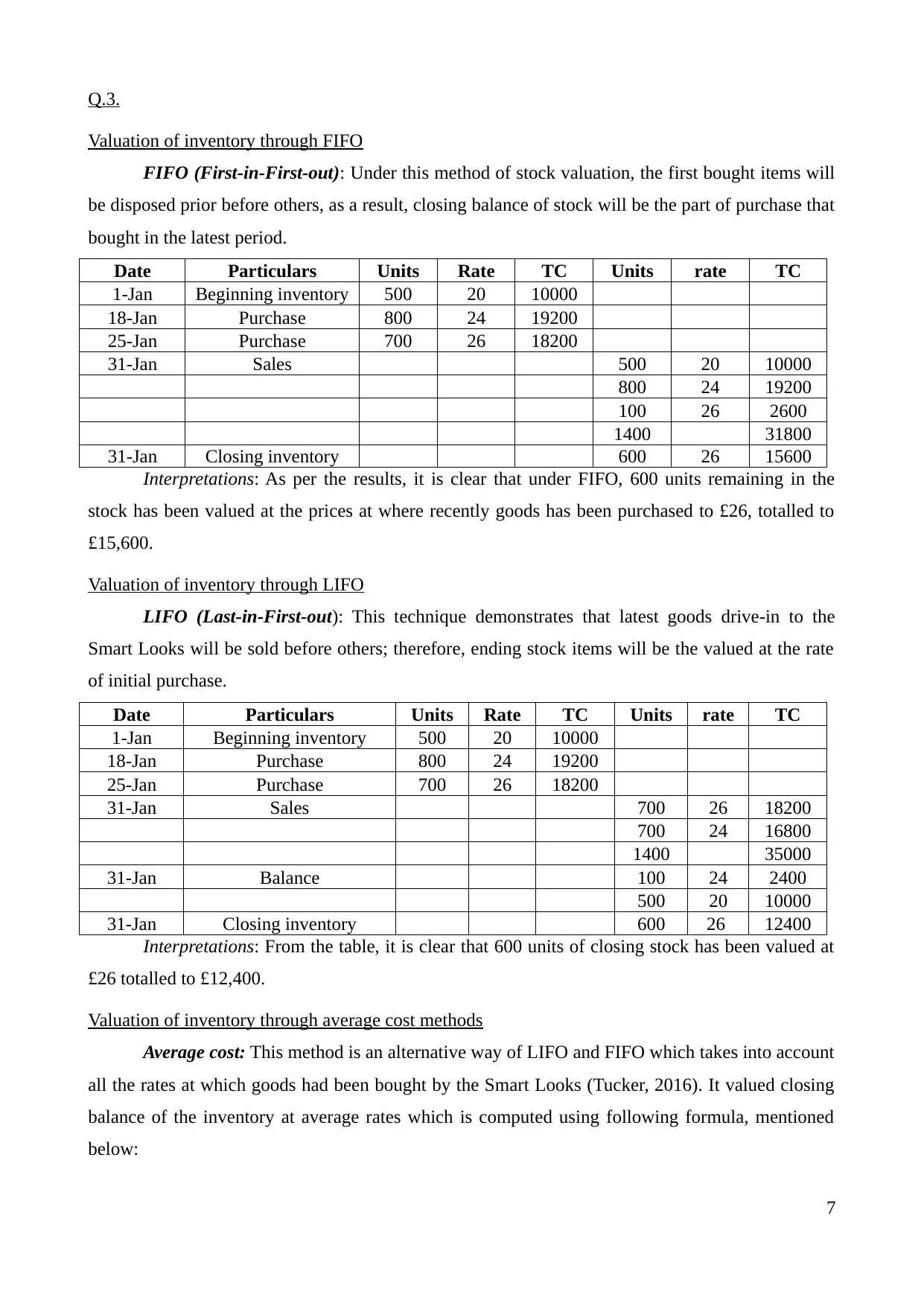
Q.3.
Valuation of inventory through FIFO
FIFO (First-in-First-out): Under this method of stock valuation, the first bought items will
be disposed prior before others, as a result, closing balance of stock will be the part of purchase that
bought in the latest period.
Date Particulars Units Rate TC Units rate TC
1-Jan Beginning inventory 500 20 10000
18-Jan Purchase 800 24 19200
25-Jan Purchase 700 26 18200
31-Jan Sales 500 20 10000
800 24 19200
100 26 2600
1400 31800
31-Jan Closing inventory 600 26 15600
Interpretations: As per the results, it is clear that under FIFO, 600 units remaining in the
stock has been valued at the prices at where recently goods has been purchased to £26, totalled to
£15,600.
Valuation of inventory through LIFO
LIFO (Last-in-First-out): This technique demonstrates that latest goods drive-in to the
Smart Looks will be sold before others; therefore, ending stock items will be the valued at the rate
of initial purchase.
Date Particulars Units Rate TC Units rate TC
1-Jan Beginning inventory 500 20 10000
18-Jan Purchase 800 24 19200
25-Jan Purchase 700 26 18200
31-Jan Sales 700 26 18200
700 24 16800
1400 35000
31-Jan Balance 100 24 2400
500 20 10000
31-Jan Closing inventory 600 26 12400
Interpretations: From the table, it is clear that 600 units of closing stock has been valued at
£26 totalled to £12,400.
Valuation of inventory through average cost methods
Average cost: This method is an alternative way of LIFO and FIFO which takes into account
all the rates at which goods had been bought by the Smart Looks (Tucker, 2016). It valued closing
balance of the inventory at average rates which is computed using following formula, mentioned
below:
7
Valuation of inventory through FIFO
FIFO (First-in-First-out): Under this method of stock valuation, the first bought items will
be disposed prior before others, as a result, closing balance of stock will be the part of purchase that
bought in the latest period.
Date Particulars Units Rate TC Units rate TC
1-Jan Beginning inventory 500 20 10000
18-Jan Purchase 800 24 19200
25-Jan Purchase 700 26 18200
31-Jan Sales 500 20 10000
800 24 19200
100 26 2600
1400 31800
31-Jan Closing inventory 600 26 15600
Interpretations: As per the results, it is clear that under FIFO, 600 units remaining in the
stock has been valued at the prices at where recently goods has been purchased to £26, totalled to
£15,600.
Valuation of inventory through LIFO
LIFO (Last-in-First-out): This technique demonstrates that latest goods drive-in to the
Smart Looks will be sold before others; therefore, ending stock items will be the valued at the rate
of initial purchase.
Date Particulars Units Rate TC Units rate TC
1-Jan Beginning inventory 500 20 10000
18-Jan Purchase 800 24 19200
25-Jan Purchase 700 26 18200
31-Jan Sales 700 26 18200
700 24 16800
1400 35000
31-Jan Balance 100 24 2400
500 20 10000
31-Jan Closing inventory 600 26 12400
Interpretations: From the table, it is clear that 600 units of closing stock has been valued at
£26 totalled to £12,400.
Valuation of inventory through average cost methods
Average cost: This method is an alternative way of LIFO and FIFO which takes into account
all the rates at which goods had been bought by the Smart Looks (Tucker, 2016). It valued closing
balance of the inventory at average rates which is computed using following formula, mentioned
below:
7
Paraphrase This Document
Need a fresh take? Get an instant paraphrase of this document with our AI Paraphraser
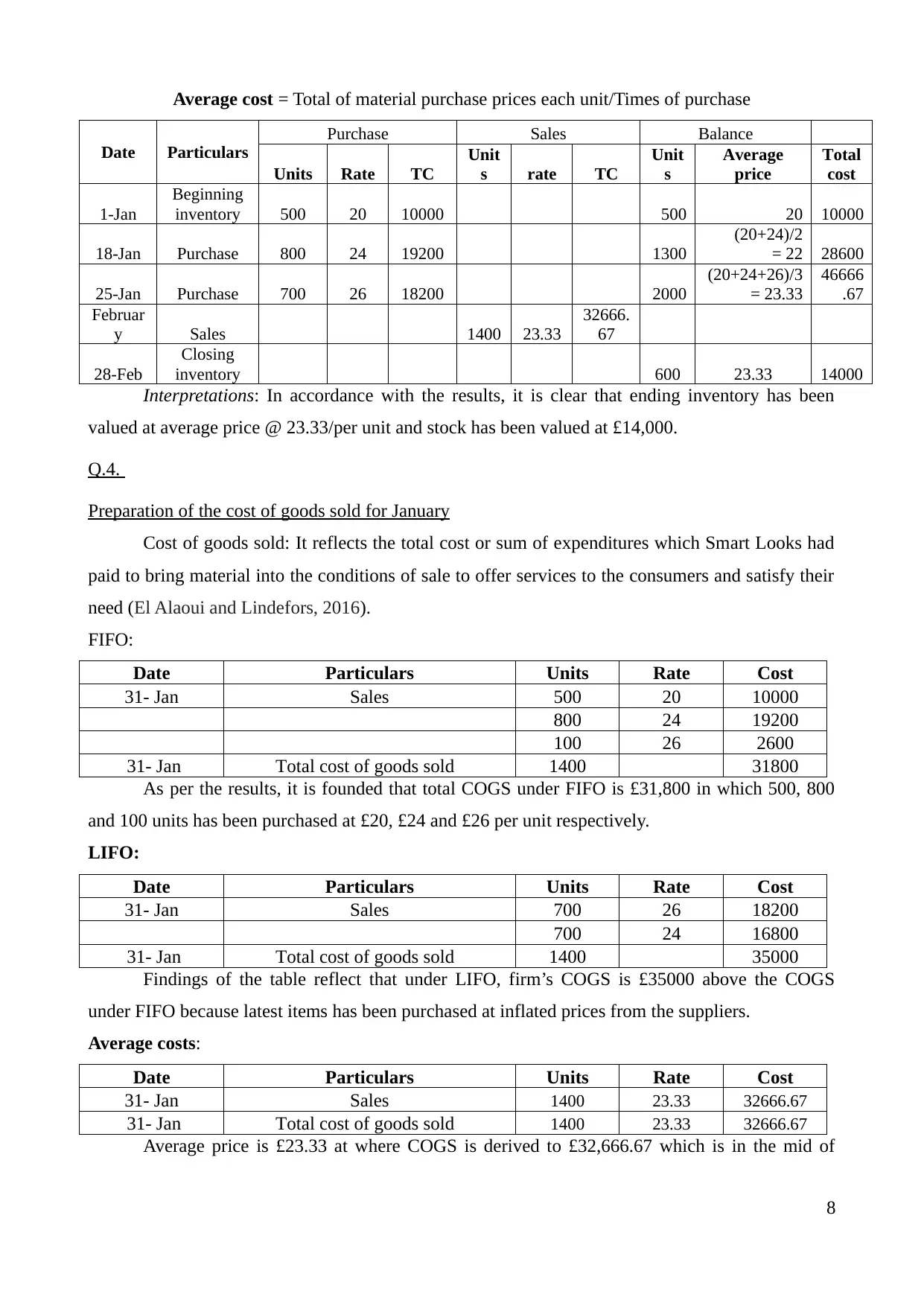
Average cost = Total of material purchase prices each unit/Times of purchase
Date Particulars
Purchase Sales Balance
Units Rate TC
Unit
s rate TC
Unit
s
Average
price
Total
cost
1-Jan
Beginning
inventory 500 20 10000 500 20 10000
18-Jan Purchase 800 24 19200 1300
(20+24)/2
= 22 28600
25-Jan Purchase 700 26 18200 2000
(20+24+26)/3
= 23.33
46666
.67
Februar
y Sales 1400 23.33
32666.
67
28-Feb
Closing
inventory 600 23.33 14000
Interpretations: In accordance with the results, it is clear that ending inventory has been
valued at average price @ 23.33/per unit and stock has been valued at £14,000.
Q.4.
Preparation of the cost of goods sold for January
Cost of goods sold: It reflects the total cost or sum of expenditures which Smart Looks had
paid to bring material into the conditions of sale to offer services to the consumers and satisfy their
need (El Alaoui and Lindefors, 2016).
FIFO:
Date Particulars Units Rate Cost
31- Jan Sales 500 20 10000
800 24 19200
100 26 2600
31- Jan Total cost of goods sold 1400 31800
As per the results, it is founded that total COGS under FIFO is £31,800 in which 500, 800
and 100 units has been purchased at £20, £24 and £26 per unit respectively.
LIFO:
Date Particulars Units Rate Cost
31- Jan Sales 700 26 18200
700 24 16800
31- Jan Total cost of goods sold 1400 35000
Findings of the table reflect that under LIFO, firm’s COGS is £35000 above the COGS
under FIFO because latest items has been purchased at inflated prices from the suppliers.
Average costs:
Date Particulars Units Rate Cost
31- Jan Sales 1400 23.33 32666.67
31- Jan Total cost of goods sold 1400 23.33 32666.67
Average price is £23.33 at where COGS is derived to £32,666.67 which is in the mid of
8
Date Particulars
Purchase Sales Balance
Units Rate TC
Unit
s rate TC
Unit
s
Average
price
Total
cost
1-Jan
Beginning
inventory 500 20 10000 500 20 10000
18-Jan Purchase 800 24 19200 1300
(20+24)/2
= 22 28600
25-Jan Purchase 700 26 18200 2000
(20+24+26)/3
= 23.33
46666
.67
Februar
y Sales 1400 23.33
32666.
67
28-Feb
Closing
inventory 600 23.33 14000
Interpretations: In accordance with the results, it is clear that ending inventory has been
valued at average price @ 23.33/per unit and stock has been valued at £14,000.
Q.4.
Preparation of the cost of goods sold for January
Cost of goods sold: It reflects the total cost or sum of expenditures which Smart Looks had
paid to bring material into the conditions of sale to offer services to the consumers and satisfy their
need (El Alaoui and Lindefors, 2016).
FIFO:
Date Particulars Units Rate Cost
31- Jan Sales 500 20 10000
800 24 19200
100 26 2600
31- Jan Total cost of goods sold 1400 31800
As per the results, it is founded that total COGS under FIFO is £31,800 in which 500, 800
and 100 units has been purchased at £20, £24 and £26 per unit respectively.
LIFO:
Date Particulars Units Rate Cost
31- Jan Sales 700 26 18200
700 24 16800
31- Jan Total cost of goods sold 1400 35000
Findings of the table reflect that under LIFO, firm’s COGS is £35000 above the COGS
under FIFO because latest items has been purchased at inflated prices from the suppliers.
Average costs:
Date Particulars Units Rate Cost
31- Jan Sales 1400 23.33 32666.67
31- Jan Total cost of goods sold 1400 23.33 32666.67
Average price is £23.33 at where COGS is derived to £32,666.67 which is in the mid of
8

LIFO and FIFO because it considered all the prices by taking into account average rates.
Q.5.
(a). Two critical successive factors and KPI
Customer experience: It can be measured by using key performance indicators like customer
satisfaction scores and compliant rates.
Supplier and Product Quality: Defective percentage and AQL level are the two strong KPIs
for evaluating the quality of goods (Quattrone and Paolo, 2016)
Operations Efficiency: Right First Time & Defect per hundred units (DHU) can be given
preference for the examination of operational efficiency.
Reducing Maintenance Spending: Maintenance expenditures percentage on total turnover
can be measured by Smart Looks to find out that whether it has been reduced or increased.
Cost reduction and profitability increase: Total cost % on sales and profitability ratios like
gross profit ratio, net profit ratio are the factors for measuring cost and profit performance (Yang
and Hao, 2017).
(b). (1). Ways to reduce costs
Budgeting can be used by every departmental manager to exert control over their staff
activities and supervision, which minimizes total cost through taking rationalized cost
measures.
Variance analysis technique can be used for finding out the reasons for poor or adverse
deviations, and thereby right policies and plans can be designed for cost curtailment purpose
(Ismail and King, 2014).
Cost–curtailment strategies can be used to boost saving among staff through creating an
incentive plan for motivating them to minimize wasteful spending. Training also can be
organized for the same purpose.
Technological innovations also reduce paperwork and reduce unnecessary spending, which
in turn, drive higher return.
(ii). Ways to enhance value and quality
High shareholder return: By delivering greater return to the investors, Smart Looks can
maximize value and create a distinctive reputation in the market by having excellent
competitive position (Chenhall and Moers, 2015).
Quality management technique: Total Quality Management (TQM), Six Sigma, Pareto
Analysis and others techniques can also be used for the quality improvement purpose and
9
Q.5.
(a). Two critical successive factors and KPI
Customer experience: It can be measured by using key performance indicators like customer
satisfaction scores and compliant rates.
Supplier and Product Quality: Defective percentage and AQL level are the two strong KPIs
for evaluating the quality of goods (Quattrone and Paolo, 2016)
Operations Efficiency: Right First Time & Defect per hundred units (DHU) can be given
preference for the examination of operational efficiency.
Reducing Maintenance Spending: Maintenance expenditures percentage on total turnover
can be measured by Smart Looks to find out that whether it has been reduced or increased.
Cost reduction and profitability increase: Total cost % on sales and profitability ratios like
gross profit ratio, net profit ratio are the factors for measuring cost and profit performance (Yang
and Hao, 2017).
(b). (1). Ways to reduce costs
Budgeting can be used by every departmental manager to exert control over their staff
activities and supervision, which minimizes total cost through taking rationalized cost
measures.
Variance analysis technique can be used for finding out the reasons for poor or adverse
deviations, and thereby right policies and plans can be designed for cost curtailment purpose
(Ismail and King, 2014).
Cost–curtailment strategies can be used to boost saving among staff through creating an
incentive plan for motivating them to minimize wasteful spending. Training also can be
organized for the same purpose.
Technological innovations also reduce paperwork and reduce unnecessary spending, which
in turn, drive higher return.
(ii). Ways to enhance value and quality
High shareholder return: By delivering greater return to the investors, Smart Looks can
maximize value and create a distinctive reputation in the market by having excellent
competitive position (Chenhall and Moers, 2015).
Quality management technique: Total Quality Management (TQM), Six Sigma, Pareto
Analysis and others techniques can also be used for the quality improvement purpose and
9
You're viewing a preview
Unlock full access by subscribing today!
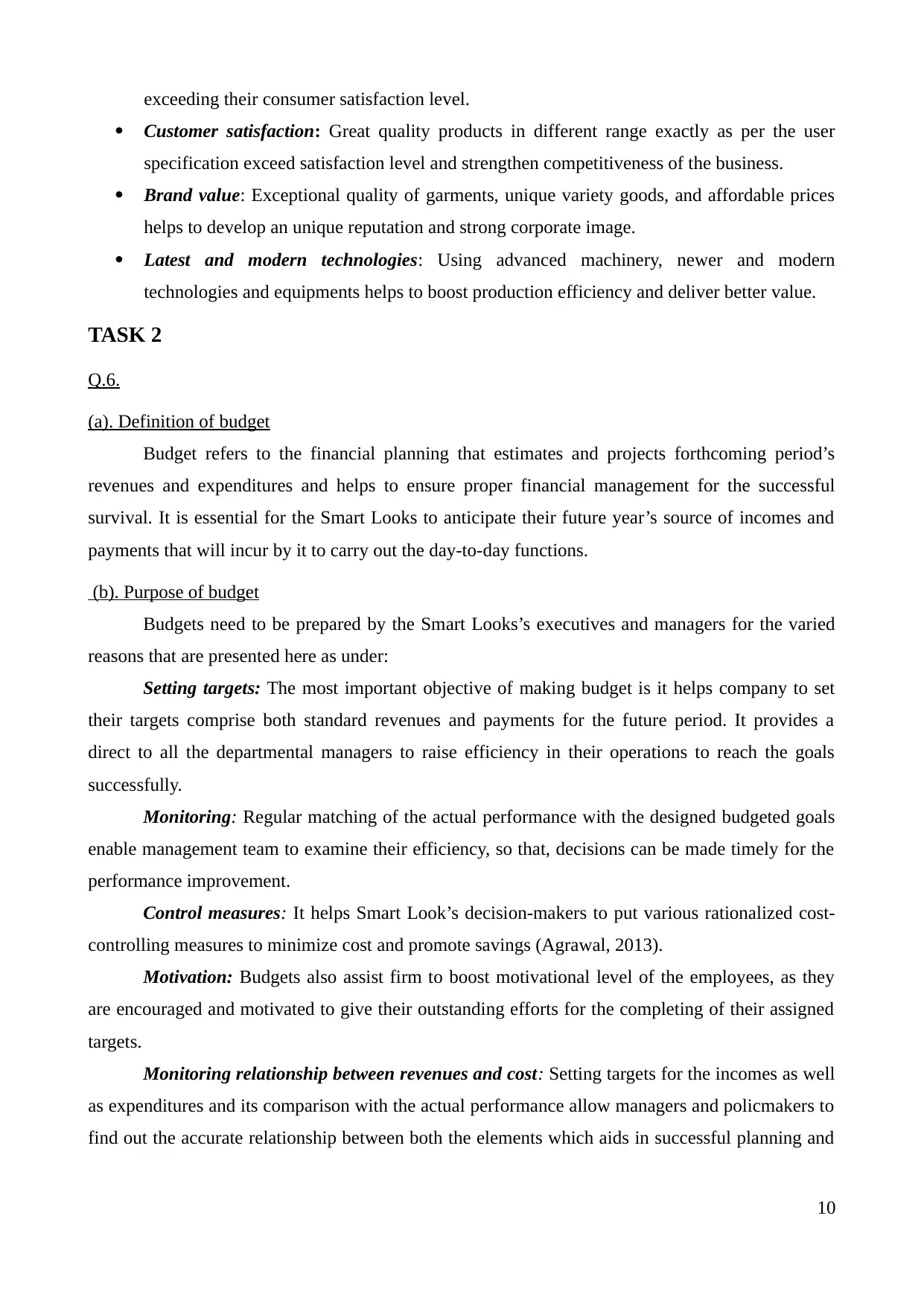
exceeding their consumer satisfaction level.
Customer satisfaction: Great quality products in different range exactly as per the user
specification exceed satisfaction level and strengthen competitiveness of the business.
Brand value: Exceptional quality of garments, unique variety goods, and affordable prices
helps to develop an unique reputation and strong corporate image.
Latest and modern technologies: Using advanced machinery, newer and modern
technologies and equipments helps to boost production efficiency and deliver better value.
TASK 2
Q.6.
(a). Definition of budget
Budget refers to the financial planning that estimates and projects forthcoming period’s
revenues and expenditures and helps to ensure proper financial management for the successful
survival. It is essential for the Smart Looks to anticipate their future year’s source of incomes and
payments that will incur by it to carry out the day-to-day functions.
(b). Purpose of budget
Budgets need to be prepared by the Smart Looks’s executives and managers for the varied
reasons that are presented here as under:
Setting targets: The most important objective of making budget is it helps company to set
their targets comprise both standard revenues and payments for the future period. It provides a
direct to all the departmental managers to raise efficiency in their operations to reach the goals
successfully.
Monitoring: Regular matching of the actual performance with the designed budgeted goals
enable management team to examine their efficiency, so that, decisions can be made timely for the
performance improvement.
Control measures: It helps Smart Look’s decision-makers to put various rationalized cost-
controlling measures to minimize cost and promote savings (Agrawal, 2013).
Motivation: Budgets also assist firm to boost motivational level of the employees, as they
are encouraged and motivated to give their outstanding efforts for the completing of their assigned
targets.
Monitoring relationship between revenues and cost: Setting targets for the incomes as well
as expenditures and its comparison with the actual performance allow managers and policmakers to
find out the accurate relationship between both the elements which aids in successful planning and
10
Customer satisfaction: Great quality products in different range exactly as per the user
specification exceed satisfaction level and strengthen competitiveness of the business.
Brand value: Exceptional quality of garments, unique variety goods, and affordable prices
helps to develop an unique reputation and strong corporate image.
Latest and modern technologies: Using advanced machinery, newer and modern
technologies and equipments helps to boost production efficiency and deliver better value.
TASK 2
Q.6.
(a). Definition of budget
Budget refers to the financial planning that estimates and projects forthcoming period’s
revenues and expenditures and helps to ensure proper financial management for the successful
survival. It is essential for the Smart Looks to anticipate their future year’s source of incomes and
payments that will incur by it to carry out the day-to-day functions.
(b). Purpose of budget
Budgets need to be prepared by the Smart Looks’s executives and managers for the varied
reasons that are presented here as under:
Setting targets: The most important objective of making budget is it helps company to set
their targets comprise both standard revenues and payments for the future period. It provides a
direct to all the departmental managers to raise efficiency in their operations to reach the goals
successfully.
Monitoring: Regular matching of the actual performance with the designed budgeted goals
enable management team to examine their efficiency, so that, decisions can be made timely for the
performance improvement.
Control measures: It helps Smart Look’s decision-makers to put various rationalized cost-
controlling measures to minimize cost and promote savings (Agrawal, 2013).
Motivation: Budgets also assist firm to boost motivational level of the employees, as they
are encouraged and motivated to give their outstanding efforts for the completing of their assigned
targets.
Monitoring relationship between revenues and cost: Setting targets for the incomes as well
as expenditures and its comparison with the actual performance allow managers and policmakers to
find out the accurate relationship between both the elements which aids in successful planning and
10
Paraphrase This Document
Need a fresh take? Get an instant paraphrase of this document with our AI Paraphraser
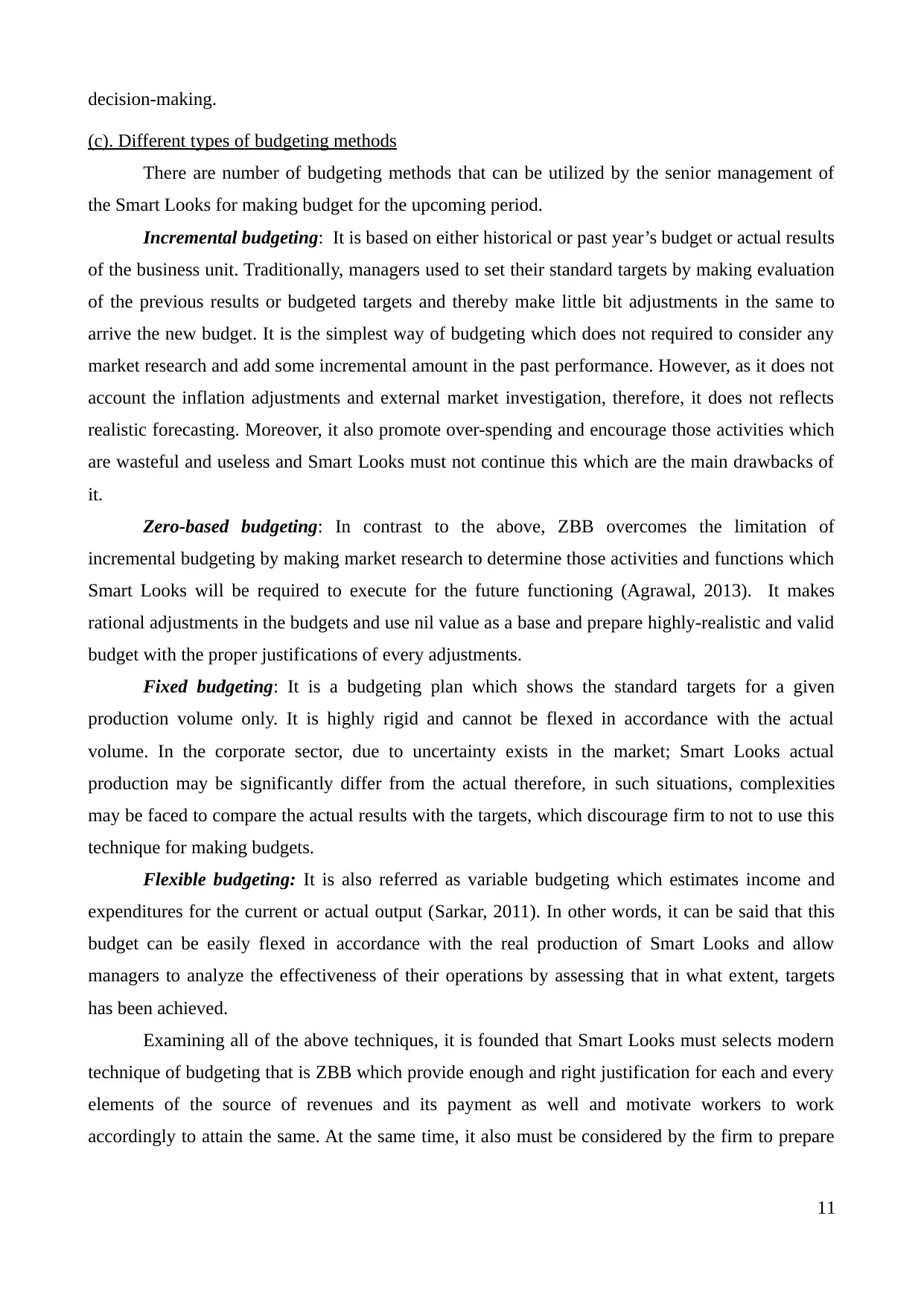
decision-making.
(c). Different types of budgeting methods
There are number of budgeting methods that can be utilized by the senior management of
the Smart Looks for making budget for the upcoming period.
Incremental budgeting: It is based on either historical or past year’s budget or actual results
of the business unit. Traditionally, managers used to set their standard targets by making evaluation
of the previous results or budgeted targets and thereby make little bit adjustments in the same to
arrive the new budget. It is the simplest way of budgeting which does not required to consider any
market research and add some incremental amount in the past performance. However, as it does not
account the inflation adjustments and external market investigation, therefore, it does not reflects
realistic forecasting. Moreover, it also promote over-spending and encourage those activities which
are wasteful and useless and Smart Looks must not continue this which are the main drawbacks of
it.
Zero-based budgeting: In contrast to the above, ZBB overcomes the limitation of
incremental budgeting by making market research to determine those activities and functions which
Smart Looks will be required to execute for the future functioning (Agrawal, 2013). It makes
rational adjustments in the budgets and use nil value as a base and prepare highly-realistic and valid
budget with the proper justifications of every adjustments.
Fixed budgeting: It is a budgeting plan which shows the standard targets for a given
production volume only. It is highly rigid and cannot be flexed in accordance with the actual
volume. In the corporate sector, due to uncertainty exists in the market; Smart Looks actual
production may be significantly differ from the actual therefore, in such situations, complexities
may be faced to compare the actual results with the targets, which discourage firm to not to use this
technique for making budgets.
Flexible budgeting: It is also referred as variable budgeting which estimates income and
expenditures for the current or actual output (Sarkar, 2011). In other words, it can be said that this
budget can be easily flexed in accordance with the real production of Smart Looks and allow
managers to analyze the effectiveness of their operations by assessing that in what extent, targets
has been achieved.
Examining all of the above techniques, it is founded that Smart Looks must selects modern
technique of budgeting that is ZBB which provide enough and right justification for each and every
elements of the source of revenues and its payment as well and motivate workers to work
accordingly to attain the same. At the same time, it also must be considered by the firm to prepare
11
(c). Different types of budgeting methods
There are number of budgeting methods that can be utilized by the senior management of
the Smart Looks for making budget for the upcoming period.
Incremental budgeting: It is based on either historical or past year’s budget or actual results
of the business unit. Traditionally, managers used to set their standard targets by making evaluation
of the previous results or budgeted targets and thereby make little bit adjustments in the same to
arrive the new budget. It is the simplest way of budgeting which does not required to consider any
market research and add some incremental amount in the past performance. However, as it does not
account the inflation adjustments and external market investigation, therefore, it does not reflects
realistic forecasting. Moreover, it also promote over-spending and encourage those activities which
are wasteful and useless and Smart Looks must not continue this which are the main drawbacks of
it.
Zero-based budgeting: In contrast to the above, ZBB overcomes the limitation of
incremental budgeting by making market research to determine those activities and functions which
Smart Looks will be required to execute for the future functioning (Agrawal, 2013). It makes
rational adjustments in the budgets and use nil value as a base and prepare highly-realistic and valid
budget with the proper justifications of every adjustments.
Fixed budgeting: It is a budgeting plan which shows the standard targets for a given
production volume only. It is highly rigid and cannot be flexed in accordance with the actual
volume. In the corporate sector, due to uncertainty exists in the market; Smart Looks actual
production may be significantly differ from the actual therefore, in such situations, complexities
may be faced to compare the actual results with the targets, which discourage firm to not to use this
technique for making budgets.
Flexible budgeting: It is also referred as variable budgeting which estimates income and
expenditures for the current or actual output (Sarkar, 2011). In other words, it can be said that this
budget can be easily flexed in accordance with the real production of Smart Looks and allow
managers to analyze the effectiveness of their operations by assessing that in what extent, targets
has been achieved.
Examining all of the above techniques, it is founded that Smart Looks must selects modern
technique of budgeting that is ZBB which provide enough and right justification for each and every
elements of the source of revenues and its payment as well and motivate workers to work
accordingly to attain the same. At the same time, it also must be considered by the firm to prepare
11
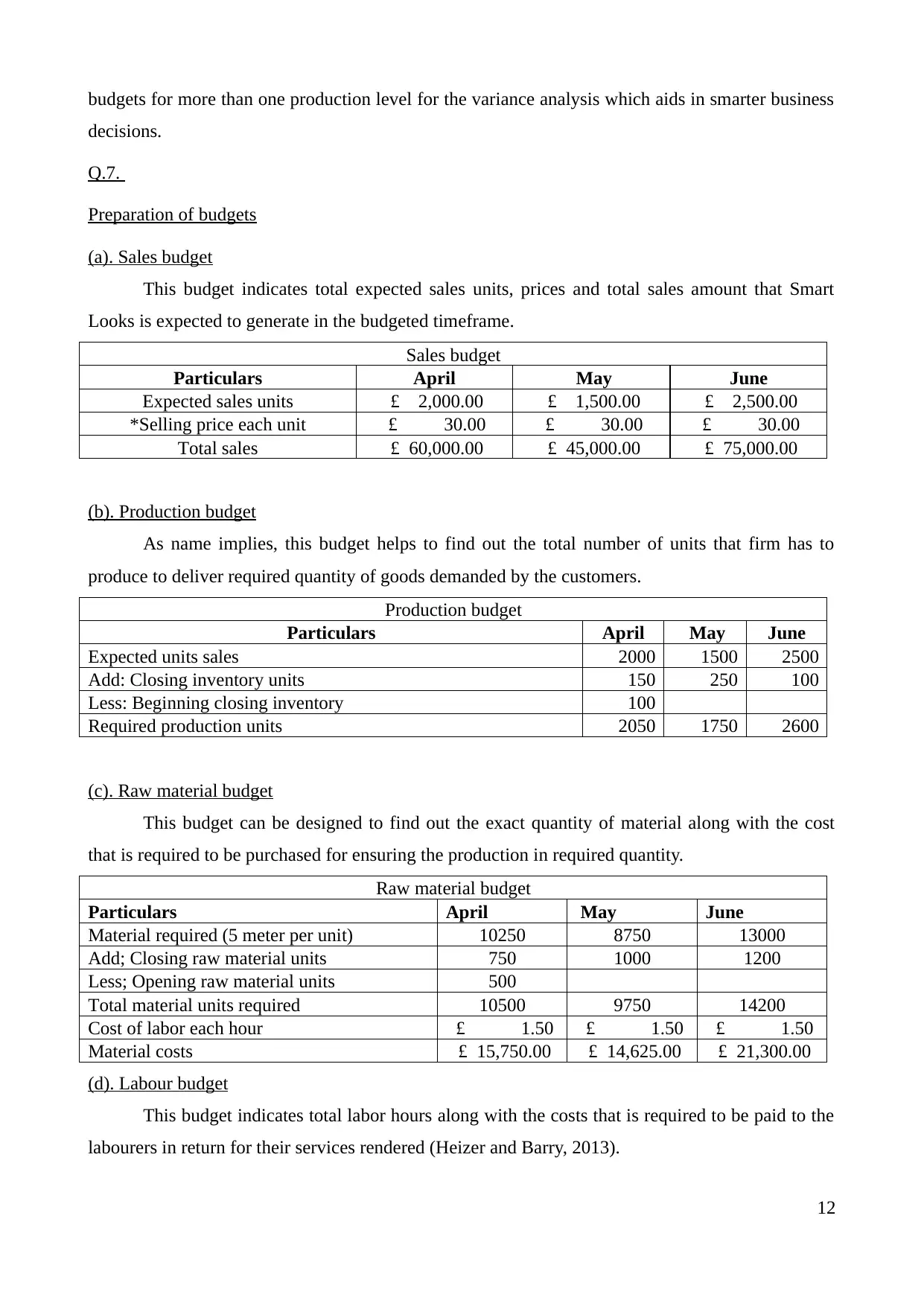
budgets for more than one production level for the variance analysis which aids in smarter business
decisions.
Q.7.
Preparation of budgets
(a). Sales budget
This budget indicates total expected sales units, prices and total sales amount that Smart
Looks is expected to generate in the budgeted timeframe.
Sales budget
Particulars April May June
Expected sales units £ 2,000.00 £ 1,500.00 £ 2,500.00
*Selling price each unit £ 30.00 £ 30.00 £ 30.00
Total sales £ 60,000.00 £ 45,000.00 £ 75,000.00
(b). Production budget
As name implies, this budget helps to find out the total number of units that firm has to
produce to deliver required quantity of goods demanded by the customers.
Production budget
Particulars April May June
Expected units sales 2000 1500 2500
Add: Closing inventory units 150 250 100
Less: Beginning closing inventory 100
Required production units 2050 1750 2600
(c). Raw material budget
This budget can be designed to find out the exact quantity of material along with the cost
that is required to be purchased for ensuring the production in required quantity.
Raw material budget
Particulars April May June
Material required (5 meter per unit) 10250 8750 13000
Add; Closing raw material units 750 1000 1200
Less; Opening raw material units 500
Total material units required 10500 9750 14200
Cost of labor each hour £ 1.50 £ 1.50 £ 1.50
Material costs £ 15,750.00 £ 14,625.00 £ 21,300.00
(d). Labour budget
This budget indicates total labor hours along with the costs that is required to be paid to the
labourers in return for their services rendered (Heizer and Barry, 2013).
12
decisions.
Q.7.
Preparation of budgets
(a). Sales budget
This budget indicates total expected sales units, prices and total sales amount that Smart
Looks is expected to generate in the budgeted timeframe.
Sales budget
Particulars April May June
Expected sales units £ 2,000.00 £ 1,500.00 £ 2,500.00
*Selling price each unit £ 30.00 £ 30.00 £ 30.00
Total sales £ 60,000.00 £ 45,000.00 £ 75,000.00
(b). Production budget
As name implies, this budget helps to find out the total number of units that firm has to
produce to deliver required quantity of goods demanded by the customers.
Production budget
Particulars April May June
Expected units sales 2000 1500 2500
Add: Closing inventory units 150 250 100
Less: Beginning closing inventory 100
Required production units 2050 1750 2600
(c). Raw material budget
This budget can be designed to find out the exact quantity of material along with the cost
that is required to be purchased for ensuring the production in required quantity.
Raw material budget
Particulars April May June
Material required (5 meter per unit) 10250 8750 13000
Add; Closing raw material units 750 1000 1200
Less; Opening raw material units 500
Total material units required 10500 9750 14200
Cost of labor each hour £ 1.50 £ 1.50 £ 1.50
Material costs £ 15,750.00 £ 14,625.00 £ 21,300.00
(d). Labour budget
This budget indicates total labor hours along with the costs that is required to be paid to the
labourers in return for their services rendered (Heizer and Barry, 2013).
12
You're viewing a preview
Unlock full access by subscribing today!
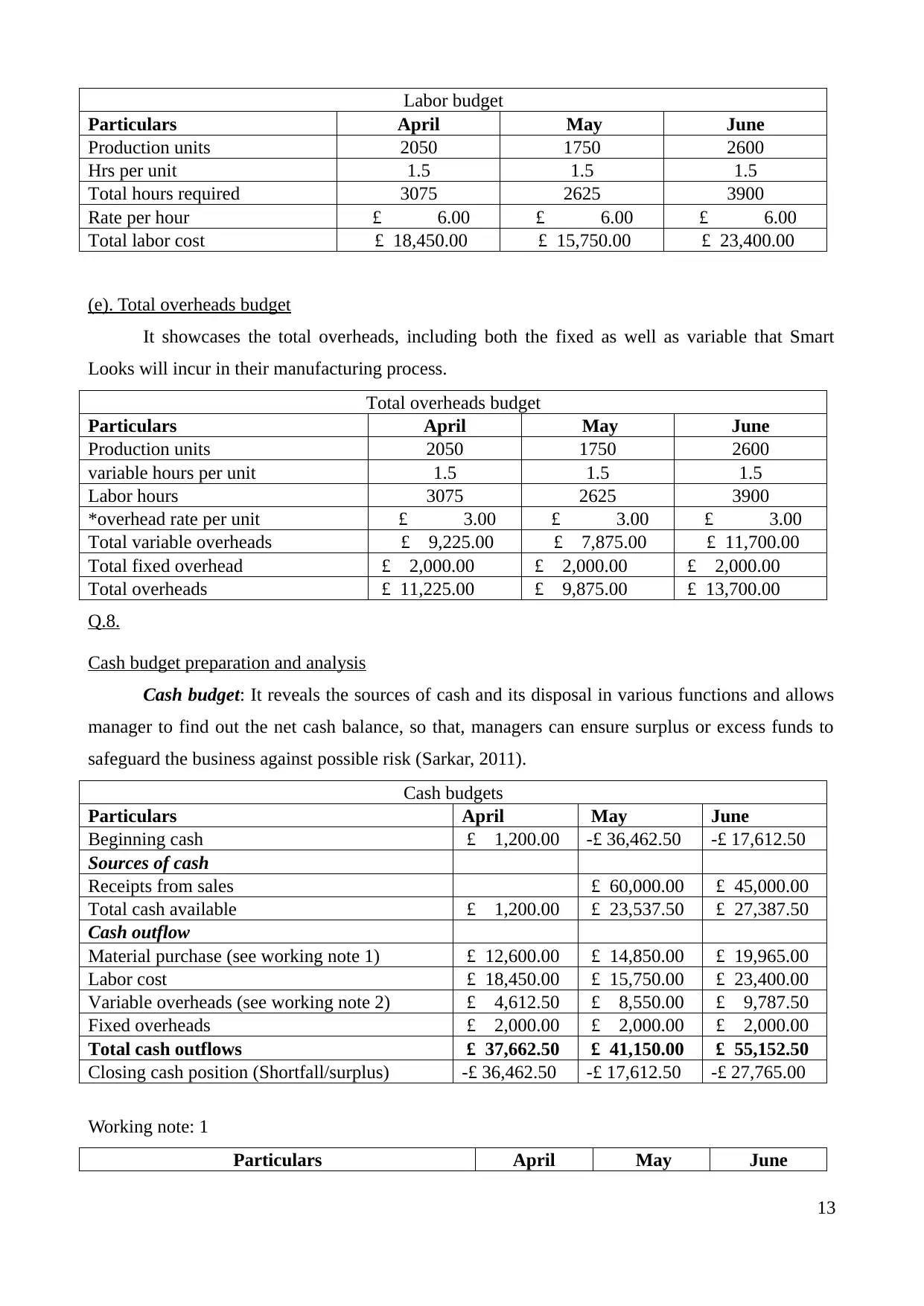
Labor budget
Particulars April May June
Production units 2050 1750 2600
Hrs per unit 1.5 1.5 1.5
Total hours required 3075 2625 3900
Rate per hour £ 6.00 £ 6.00 £ 6.00
Total labor cost £ 18,450.00 £ 15,750.00 £ 23,400.00
(e). Total overheads budget
It showcases the total overheads, including both the fixed as well as variable that Smart
Looks will incur in their manufacturing process.
Total overheads budget
Particulars April May June
Production units 2050 1750 2600
variable hours per unit 1.5 1.5 1.5
Labor hours 3075 2625 3900
*overhead rate per unit £ 3.00 £ 3.00 £ 3.00
Total variable overheads £ 9,225.00 £ 7,875.00 £ 11,700.00
Total fixed overhead £ 2,000.00 £ 2,000.00 £ 2,000.00
Total overheads £ 11,225.00 £ 9,875.00 £ 13,700.00
Q.8.
Cash budget preparation and analysis
Cash budget: It reveals the sources of cash and its disposal in various functions and allows
manager to find out the net cash balance, so that, managers can ensure surplus or excess funds to
safeguard the business against possible risk (Sarkar, 2011).
Cash budgets
Particulars April May June
Beginning cash £ 1,200.00 -£ 36,462.50 -£ 17,612.50
Sources of cash
Receipts from sales £ 60,000.00 £ 45,000.00
Total cash available £ 1,200.00 £ 23,537.50 £ 27,387.50
Cash outflow
Material purchase (see working note 1) £ 12,600.00 £ 14,850.00 £ 19,965.00
Labor cost £ 18,450.00 £ 15,750.00 £ 23,400.00
Variable overheads (see working note 2) £ 4,612.50 £ 8,550.00 £ 9,787.50
Fixed overheads £ 2,000.00 £ 2,000.00 £ 2,000.00
Total cash outflows £ 37,662.50 £ 41,150.00 £ 55,152.50
Closing cash position (Shortfall/surplus) -£ 36,462.50 -£ 17,612.50 -£ 27,765.00
Working note: 1
Particulars April May June
13
Particulars April May June
Production units 2050 1750 2600
Hrs per unit 1.5 1.5 1.5
Total hours required 3075 2625 3900
Rate per hour £ 6.00 £ 6.00 £ 6.00
Total labor cost £ 18,450.00 £ 15,750.00 £ 23,400.00
(e). Total overheads budget
It showcases the total overheads, including both the fixed as well as variable that Smart
Looks will incur in their manufacturing process.
Total overheads budget
Particulars April May June
Production units 2050 1750 2600
variable hours per unit 1.5 1.5 1.5
Labor hours 3075 2625 3900
*overhead rate per unit £ 3.00 £ 3.00 £ 3.00
Total variable overheads £ 9,225.00 £ 7,875.00 £ 11,700.00
Total fixed overhead £ 2,000.00 £ 2,000.00 £ 2,000.00
Total overheads £ 11,225.00 £ 9,875.00 £ 13,700.00
Q.8.
Cash budget preparation and analysis
Cash budget: It reveals the sources of cash and its disposal in various functions and allows
manager to find out the net cash balance, so that, managers can ensure surplus or excess funds to
safeguard the business against possible risk (Sarkar, 2011).
Cash budgets
Particulars April May June
Beginning cash £ 1,200.00 -£ 36,462.50 -£ 17,612.50
Sources of cash
Receipts from sales £ 60,000.00 £ 45,000.00
Total cash available £ 1,200.00 £ 23,537.50 £ 27,387.50
Cash outflow
Material purchase (see working note 1) £ 12,600.00 £ 14,850.00 £ 19,965.00
Labor cost £ 18,450.00 £ 15,750.00 £ 23,400.00
Variable overheads (see working note 2) £ 4,612.50 £ 8,550.00 £ 9,787.50
Fixed overheads £ 2,000.00 £ 2,000.00 £ 2,000.00
Total cash outflows £ 37,662.50 £ 41,150.00 £ 55,152.50
Closing cash position (Shortfall/surplus) -£ 36,462.50 -£ 17,612.50 -£ 27,765.00
Working note: 1
Particulars April May June
13
Paraphrase This Document
Need a fresh take? Get an instant paraphrase of this document with our AI Paraphraser
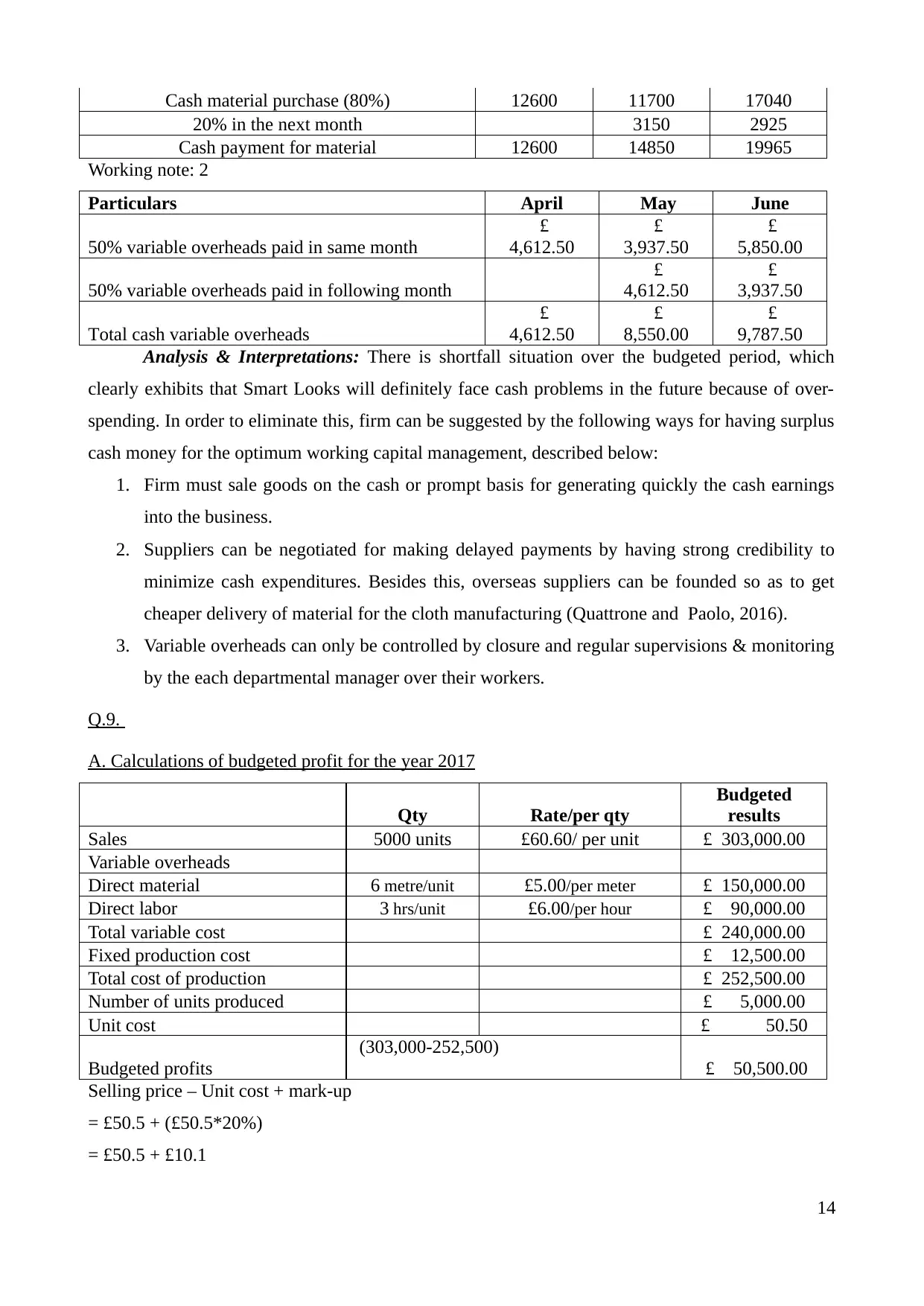
Cash material purchase (80%) 12600 11700 17040
20% in the next month 3150 2925
Cash payment for material 12600 14850 19965
Working note: 2
Particulars April May June
50% variable overheads paid in same month
£
4,612.50
£
3,937.50
£
5,850.00
50% variable overheads paid in following month
£
4,612.50
£
3,937.50
Total cash variable overheads
£
4,612.50
£
8,550.00
£
9,787.50
Analysis & Interpretations: There is shortfall situation over the budgeted period, which
clearly exhibits that Smart Looks will definitely face cash problems in the future because of over-
spending. In order to eliminate this, firm can be suggested by the following ways for having surplus
cash money for the optimum working capital management, described below:
1. Firm must sale goods on the cash or prompt basis for generating quickly the cash earnings
into the business.
2. Suppliers can be negotiated for making delayed payments by having strong credibility to
minimize cash expenditures. Besides this, overseas suppliers can be founded so as to get
cheaper delivery of material for the cloth manufacturing (Quattrone and Paolo, 2016).
3. Variable overheads can only be controlled by closure and regular supervisions & monitoring
by the each departmental manager over their workers.
Q.9.
A. Calculations of budgeted profit for the year 2017
Qty Rate/per qty
Budgeted
results
Sales 5000 units £60.60/ per unit £ 303,000.00
Variable overheads
Direct material 6 metre/unit £5.00/per meter £ 150,000.00
Direct labor 3 hrs/unit £6.00/per hour £ 90,000.00
Total variable cost £ 240,000.00
Fixed production cost £ 12,500.00
Total cost of production £ 252,500.00
Number of units produced £ 5,000.00
Unit cost £ 50.50
Budgeted profits
(303,000-252,500)
£ 50,500.00
Selling price – Unit cost + mark-up
= £50.5 + (£50.5*20%)
= £50.5 + £10.1
14
20% in the next month 3150 2925
Cash payment for material 12600 14850 19965
Working note: 2
Particulars April May June
50% variable overheads paid in same month
£
4,612.50
£
3,937.50
£
5,850.00
50% variable overheads paid in following month
£
4,612.50
£
3,937.50
Total cash variable overheads
£
4,612.50
£
8,550.00
£
9,787.50
Analysis & Interpretations: There is shortfall situation over the budgeted period, which
clearly exhibits that Smart Looks will definitely face cash problems in the future because of over-
spending. In order to eliminate this, firm can be suggested by the following ways for having surplus
cash money for the optimum working capital management, described below:
1. Firm must sale goods on the cash or prompt basis for generating quickly the cash earnings
into the business.
2. Suppliers can be negotiated for making delayed payments by having strong credibility to
minimize cash expenditures. Besides this, overseas suppliers can be founded so as to get
cheaper delivery of material for the cloth manufacturing (Quattrone and Paolo, 2016).
3. Variable overheads can only be controlled by closure and regular supervisions & monitoring
by the each departmental manager over their workers.
Q.9.
A. Calculations of budgeted profit for the year 2017
Qty Rate/per qty
Budgeted
results
Sales 5000 units £60.60/ per unit £ 303,000.00
Variable overheads
Direct material 6 metre/unit £5.00/per meter £ 150,000.00
Direct labor 3 hrs/unit £6.00/per hour £ 90,000.00
Total variable cost £ 240,000.00
Fixed production cost £ 12,500.00
Total cost of production £ 252,500.00
Number of units produced £ 5,000.00
Unit cost £ 50.50
Budgeted profits
(303,000-252,500)
£ 50,500.00
Selling price – Unit cost + mark-up
= £50.5 + (£50.5*20%)
= £50.5 + £10.1
14
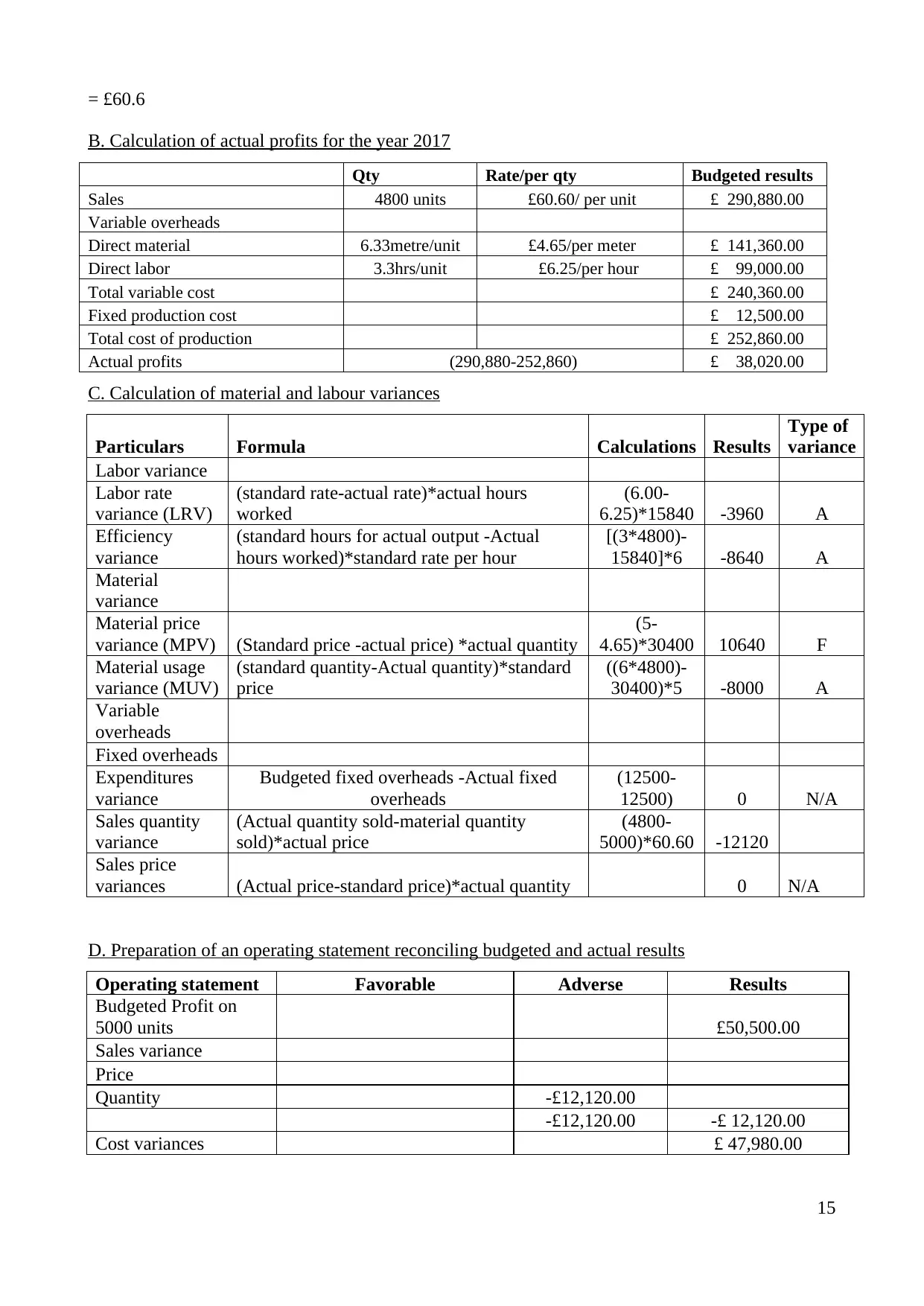
= £60.6
B. Calculation of actual profits for the year 2017
Qty Rate/per qty Budgeted results
Sales 4800 units £60.60/ per unit £ 290,880.00
Variable overheads
Direct material 6.33metre/unit £4.65/per meter £ 141,360.00
Direct labor 3.3hrs/unit £6.25/per hour £ 99,000.00
Total variable cost £ 240,360.00
Fixed production cost £ 12,500.00
Total cost of production £ 252,860.00
Actual profits (290,880-252,860) £ 38,020.00
C. Calculation of material and labour variances
Particulars Formula Calculations Results
Type of
variance
Labor variance
Labor rate
variance (LRV)
(standard rate-actual rate)*actual hours
worked
(6.00-
6.25)*15840 -3960 A
Efficiency
variance
(standard hours for actual output -Actual
hours worked)*standard rate per hour
[(3*4800)-
15840]*6 -8640 A
Material
variance
Material price
variance (MPV) (Standard price -actual price) *actual quantity
(5-
4.65)*30400 10640 F
Material usage
variance (MUV)
(standard quantity-Actual quantity)*standard
price
((6*4800)-
30400)*5 -8000 A
Variable
overheads
Fixed overheads
Expenditures
variance
Budgeted fixed overheads -Actual fixed
overheads
(12500-
12500) 0 N/A
Sales quantity
variance
(Actual quantity sold-material quantity
sold)*actual price
(4800-
5000)*60.60 -12120
Sales price
variances (Actual price-standard price)*actual quantity 0 N/A
D. Preparation of an operating statement reconciling budgeted and actual results
Operating statement Favorable Adverse Results
Budgeted Profit on
5000 units £50,500.00
Sales variance
Price
Quantity -£12,120.00
-£12,120.00 -£ 12,120.00
Cost variances £ 47,980.00
15
B. Calculation of actual profits for the year 2017
Qty Rate/per qty Budgeted results
Sales 4800 units £60.60/ per unit £ 290,880.00
Variable overheads
Direct material 6.33metre/unit £4.65/per meter £ 141,360.00
Direct labor 3.3hrs/unit £6.25/per hour £ 99,000.00
Total variable cost £ 240,360.00
Fixed production cost £ 12,500.00
Total cost of production £ 252,860.00
Actual profits (290,880-252,860) £ 38,020.00
C. Calculation of material and labour variances
Particulars Formula Calculations Results
Type of
variance
Labor variance
Labor rate
variance (LRV)
(standard rate-actual rate)*actual hours
worked
(6.00-
6.25)*15840 -3960 A
Efficiency
variance
(standard hours for actual output -Actual
hours worked)*standard rate per hour
[(3*4800)-
15840]*6 -8640 A
Material
variance
Material price
variance (MPV) (Standard price -actual price) *actual quantity
(5-
4.65)*30400 10640 F
Material usage
variance (MUV)
(standard quantity-Actual quantity)*standard
price
((6*4800)-
30400)*5 -8000 A
Variable
overheads
Fixed overheads
Expenditures
variance
Budgeted fixed overheads -Actual fixed
overheads
(12500-
12500) 0 N/A
Sales quantity
variance
(Actual quantity sold-material quantity
sold)*actual price
(4800-
5000)*60.60 -12120
Sales price
variances (Actual price-standard price)*actual quantity 0 N/A
D. Preparation of an operating statement reconciling budgeted and actual results
Operating statement Favorable Adverse Results
Budgeted Profit on
5000 units £50,500.00
Sales variance
Price
Quantity -£12,120.00
-£12,120.00 -£ 12,120.00
Cost variances £ 47,980.00
15
You're viewing a preview
Unlock full access by subscribing today!
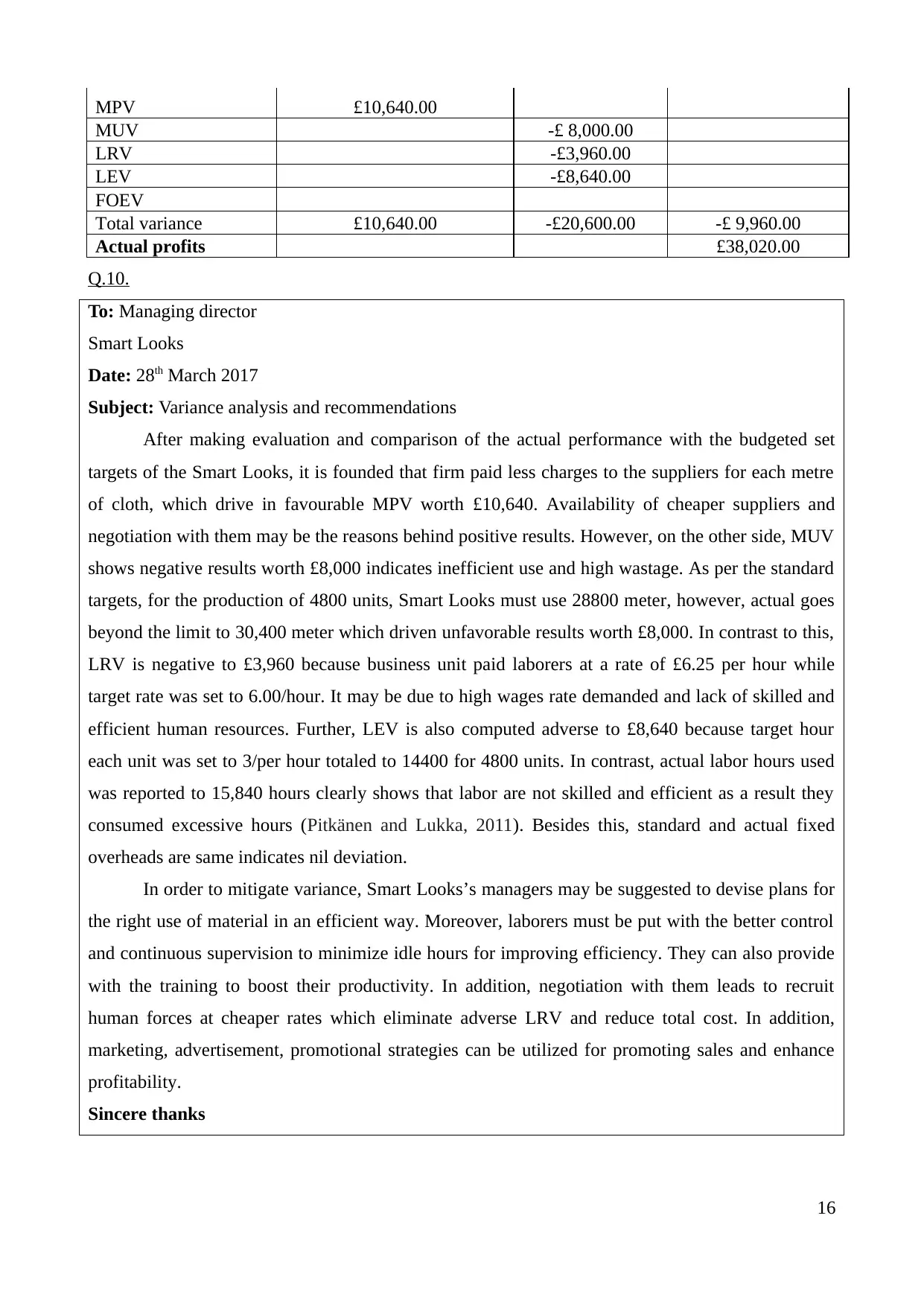
MPV £10,640.00
MUV -£ 8,000.00
LRV -£3,960.00
LEV -£8,640.00
FOEV
Total variance £10,640.00 -£20,600.00 -£ 9,960.00
Actual profits £38,020.00
Q.10.
To: Managing director
Smart Looks
Date: 28th March 2017
Subject: Variance analysis and recommendations
After making evaluation and comparison of the actual performance with the budgeted set
targets of the Smart Looks, it is founded that firm paid less charges to the suppliers for each metre
of cloth, which drive in favourable MPV worth £10,640. Availability of cheaper suppliers and
negotiation with them may be the reasons behind positive results. However, on the other side, MUV
shows negative results worth £8,000 indicates inefficient use and high wastage. As per the standard
targets, for the production of 4800 units, Smart Looks must use 28800 meter, however, actual goes
beyond the limit to 30,400 meter which driven unfavorable results worth £8,000. In contrast to this,
LRV is negative to £3,960 because business unit paid laborers at a rate of £6.25 per hour while
target rate was set to 6.00/hour. It may be due to high wages rate demanded and lack of skilled and
efficient human resources. Further, LEV is also computed adverse to £8,640 because target hour
each unit was set to 3/per hour totaled to 14400 for 4800 units. In contrast, actual labor hours used
was reported to 15,840 hours clearly shows that labor are not skilled and efficient as a result they
consumed excessive hours (Pitkänen and Lukka, 2011). Besides this, standard and actual fixed
overheads are same indicates nil deviation.
In order to mitigate variance, Smart Looks’s managers may be suggested to devise plans for
the right use of material in an efficient way. Moreover, laborers must be put with the better control
and continuous supervision to minimize idle hours for improving efficiency. They can also provide
with the training to boost their productivity. In addition, negotiation with them leads to recruit
human forces at cheaper rates which eliminate adverse LRV and reduce total cost. In addition,
marketing, advertisement, promotional strategies can be utilized for promoting sales and enhance
profitability.
Sincere thanks
16
MUV -£ 8,000.00
LRV -£3,960.00
LEV -£8,640.00
FOEV
Total variance £10,640.00 -£20,600.00 -£ 9,960.00
Actual profits £38,020.00
Q.10.
To: Managing director
Smart Looks
Date: 28th March 2017
Subject: Variance analysis and recommendations
After making evaluation and comparison of the actual performance with the budgeted set
targets of the Smart Looks, it is founded that firm paid less charges to the suppliers for each metre
of cloth, which drive in favourable MPV worth £10,640. Availability of cheaper suppliers and
negotiation with them may be the reasons behind positive results. However, on the other side, MUV
shows negative results worth £8,000 indicates inefficient use and high wastage. As per the standard
targets, for the production of 4800 units, Smart Looks must use 28800 meter, however, actual goes
beyond the limit to 30,400 meter which driven unfavorable results worth £8,000. In contrast to this,
LRV is negative to £3,960 because business unit paid laborers at a rate of £6.25 per hour while
target rate was set to 6.00/hour. It may be due to high wages rate demanded and lack of skilled and
efficient human resources. Further, LEV is also computed adverse to £8,640 because target hour
each unit was set to 3/per hour totaled to 14400 for 4800 units. In contrast, actual labor hours used
was reported to 15,840 hours clearly shows that labor are not skilled and efficient as a result they
consumed excessive hours (Pitkänen and Lukka, 2011). Besides this, standard and actual fixed
overheads are same indicates nil deviation.
In order to mitigate variance, Smart Looks’s managers may be suggested to devise plans for
the right use of material in an efficient way. Moreover, laborers must be put with the better control
and continuous supervision to minimize idle hours for improving efficiency. They can also provide
with the training to boost their productivity. In addition, negotiation with them leads to recruit
human forces at cheaper rates which eliminate adverse LRV and reduce total cost. In addition,
marketing, advertisement, promotional strategies can be utilized for promoting sales and enhance
profitability.
Sincere thanks
16
Paraphrase This Document
Need a fresh take? Get an instant paraphrase of this document with our AI Paraphraser
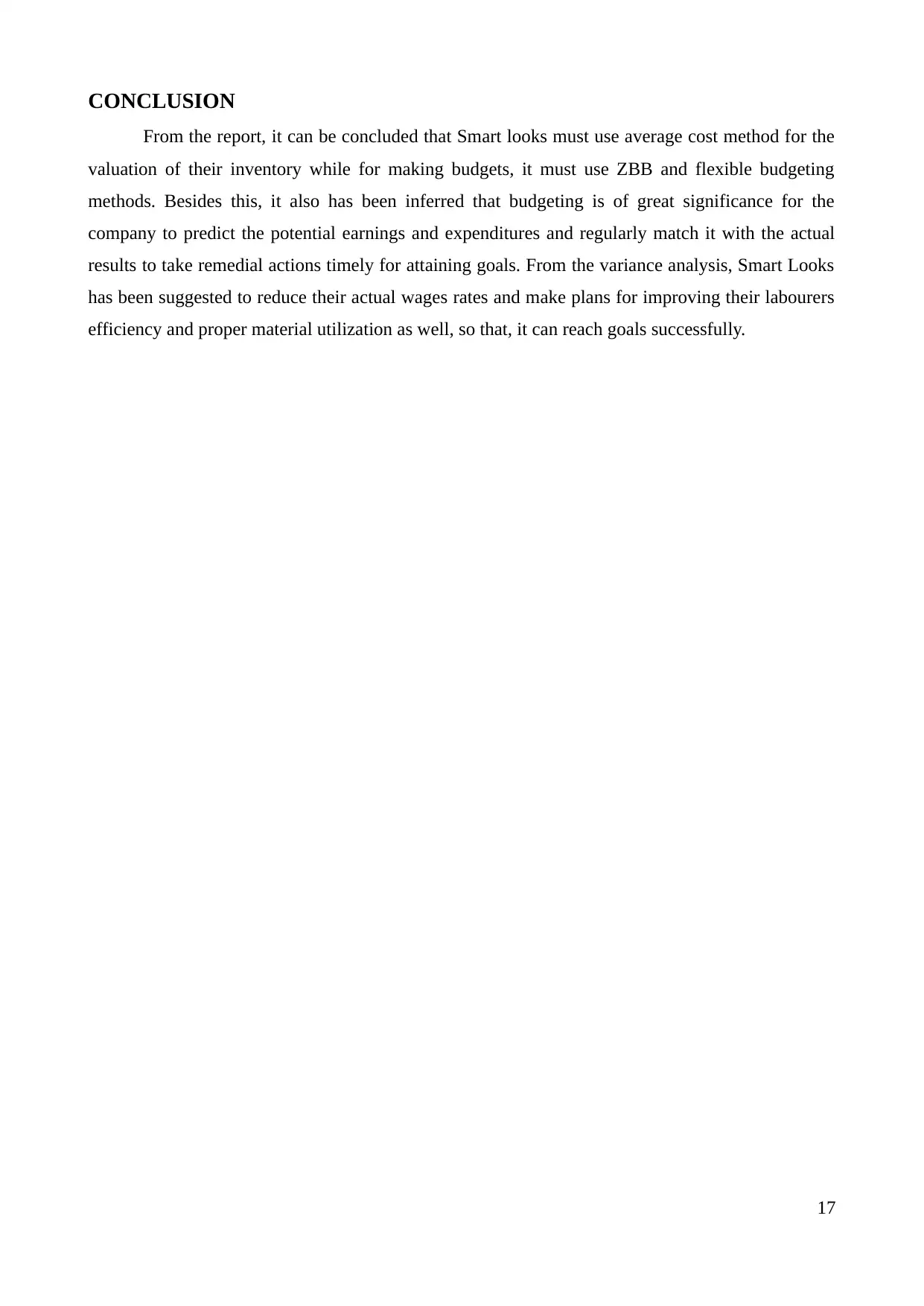
CONCLUSION
From the report, it can be concluded that Smart looks must use average cost method for the
valuation of their inventory while for making budgets, it must use ZBB and flexible budgeting
methods. Besides this, it also has been inferred that budgeting is of great significance for the
company to predict the potential earnings and expenditures and regularly match it with the actual
results to take remedial actions timely for attaining goals. From the variance analysis, Smart Looks
has been suggested to reduce their actual wages rates and make plans for improving their labourers
efficiency and proper material utilization as well, so that, it can reach goals successfully.
17
From the report, it can be concluded that Smart looks must use average cost method for the
valuation of their inventory while for making budgets, it must use ZBB and flexible budgeting
methods. Besides this, it also has been inferred that budgeting is of great significance for the
company to predict the potential earnings and expenditures and regularly match it with the actual
results to take remedial actions timely for attaining goals. From the variance analysis, Smart Looks
has been suggested to reduce their actual wages rates and make plans for improving their labourers
efficiency and proper material utilization as well, so that, it can reach goals successfully.
17
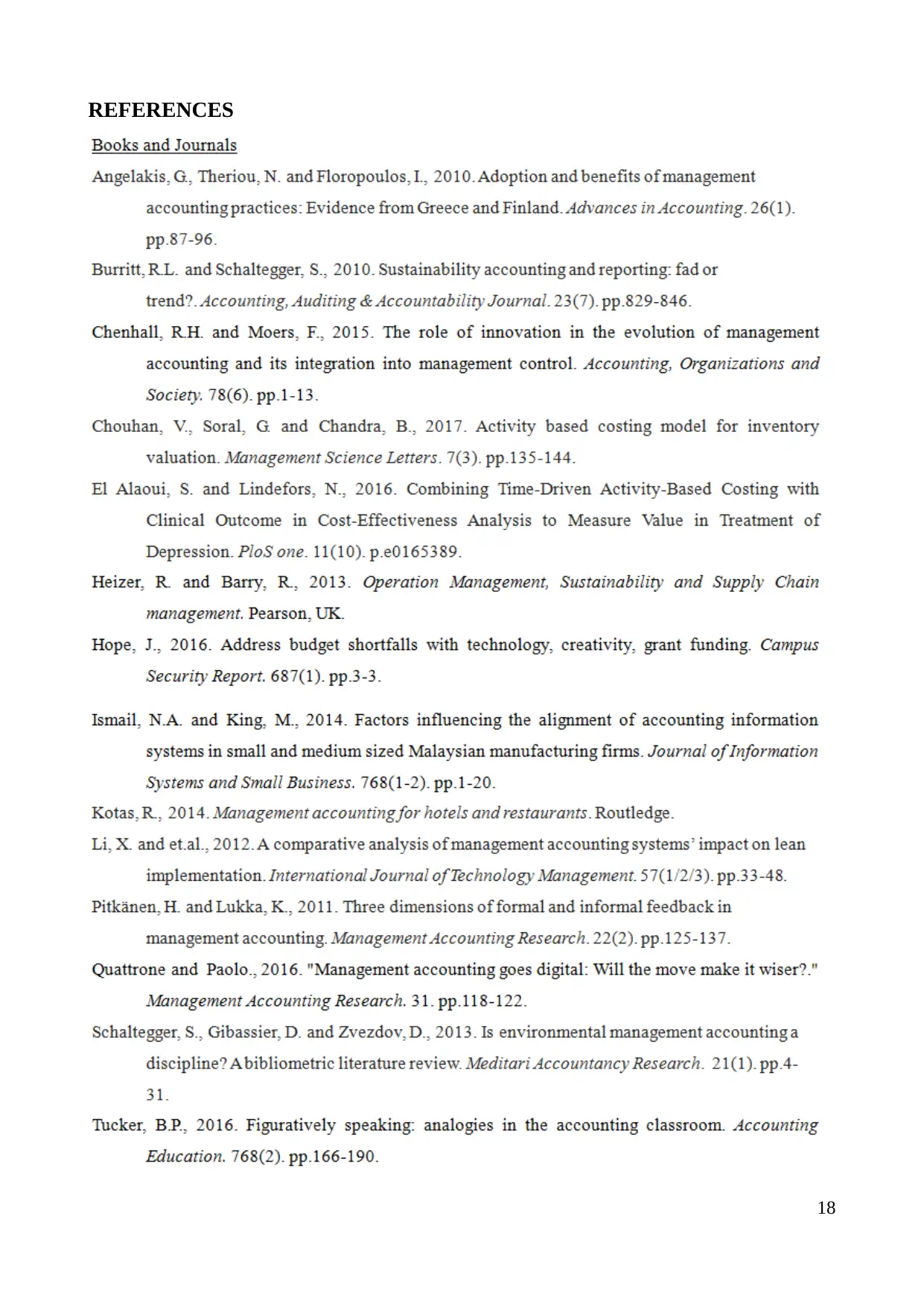
REFERENCES
18
18
You're viewing a preview
Unlock full access by subscribing today!
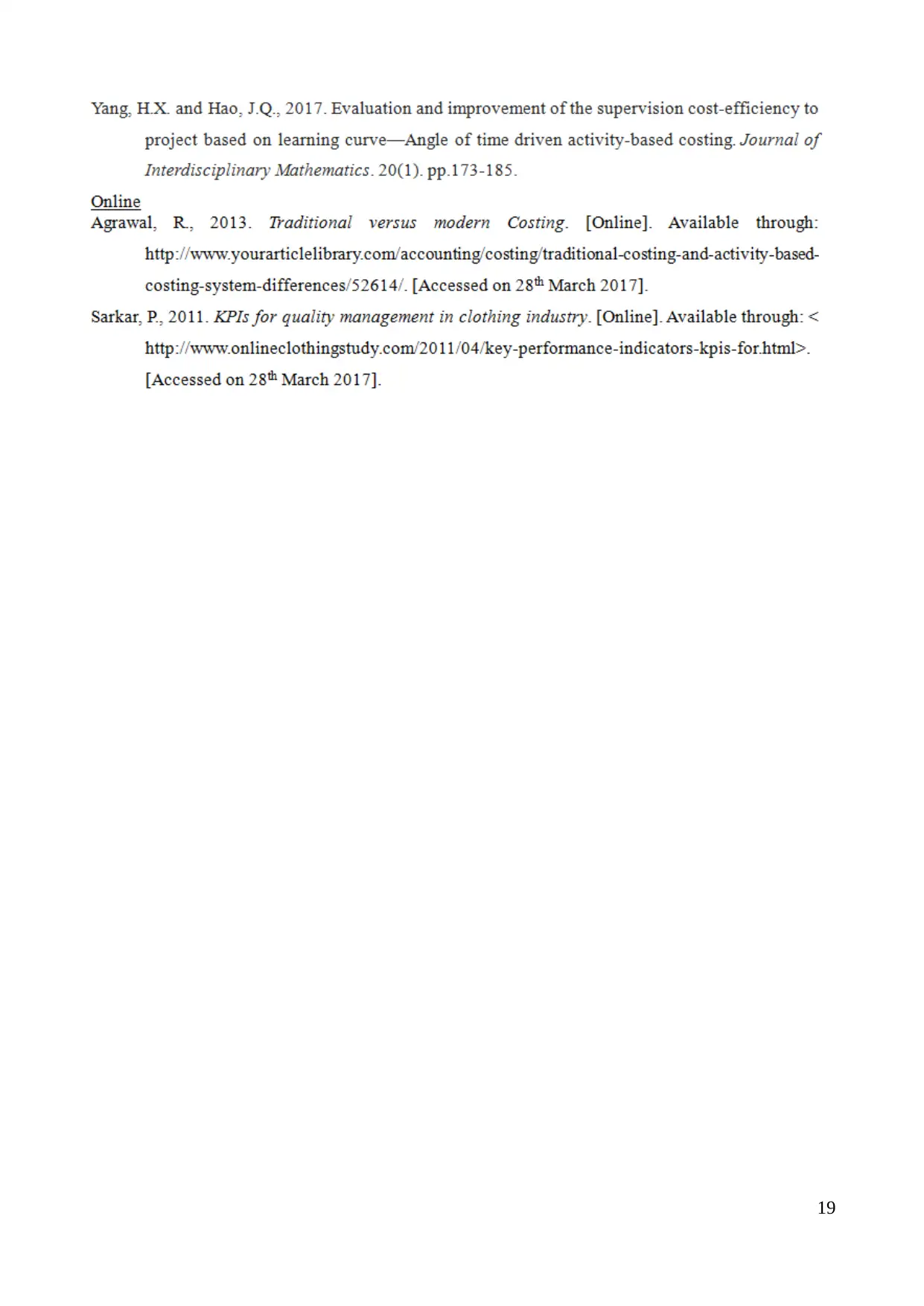
19
Paraphrase This Document
Need a fresh take? Get an instant paraphrase of this document with our AI Paraphraser
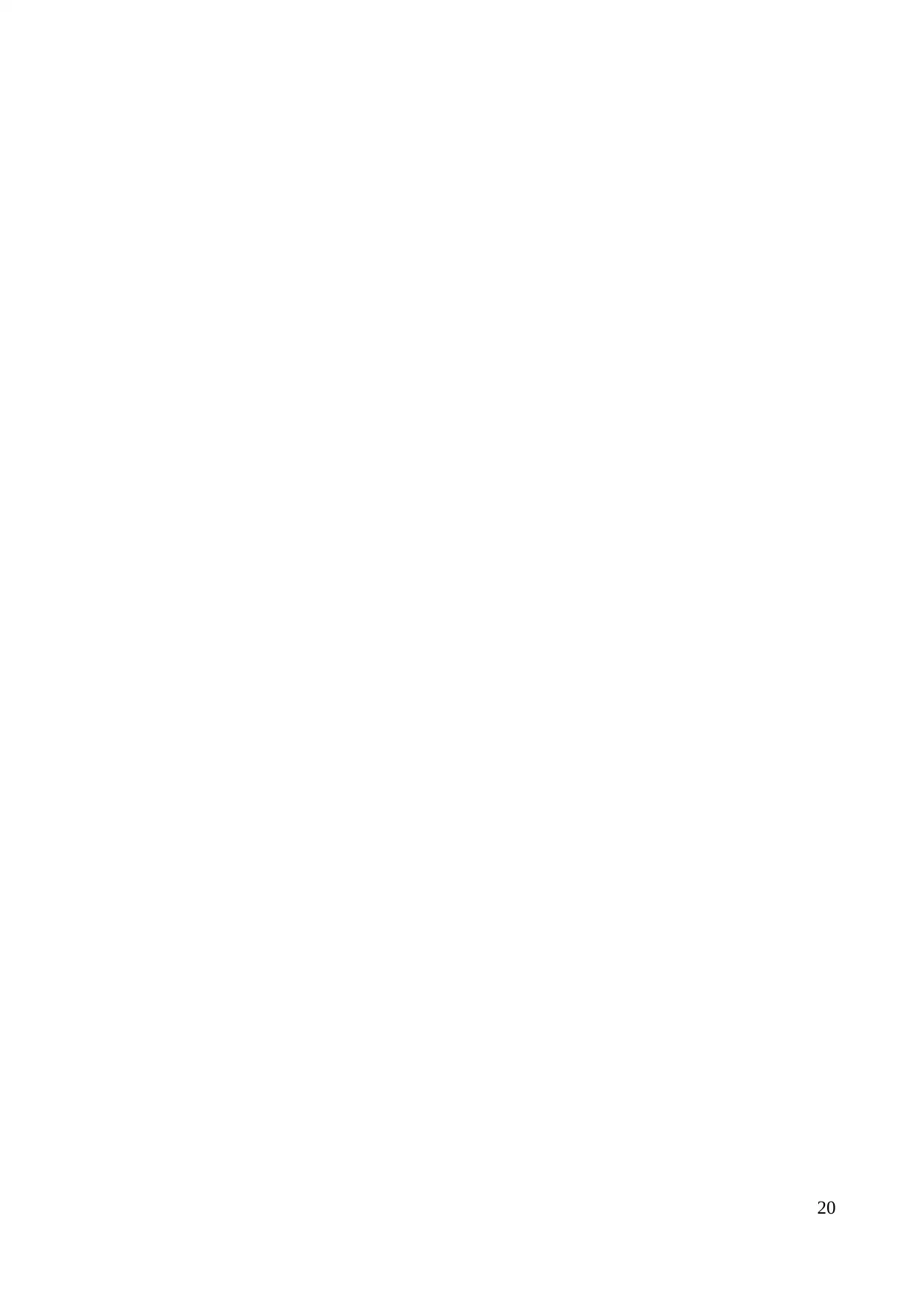
20
1 out of 20
Related Documents

Your All-in-One AI-Powered Toolkit for Academic Success.
+13062052269
info@desklib.com
Available 24*7 on WhatsApp / Email
Unlock your academic potential
© 2024 | Zucol Services PVT LTD | All rights reserved.