Simulating and Understanding Localised Corrosion Report on Steels
VerifiedAdded on 2023/03/29
|8
|1449
|316
Report
AI Summary
This report details the progress of an experiment simulating and understanding localized corrosion in additively manufactured 316L stainless steels under simulated pipeline mechanical, corrosion, and erosion conditions. The study utilizes SLM processing to create specimens with varying parameter...
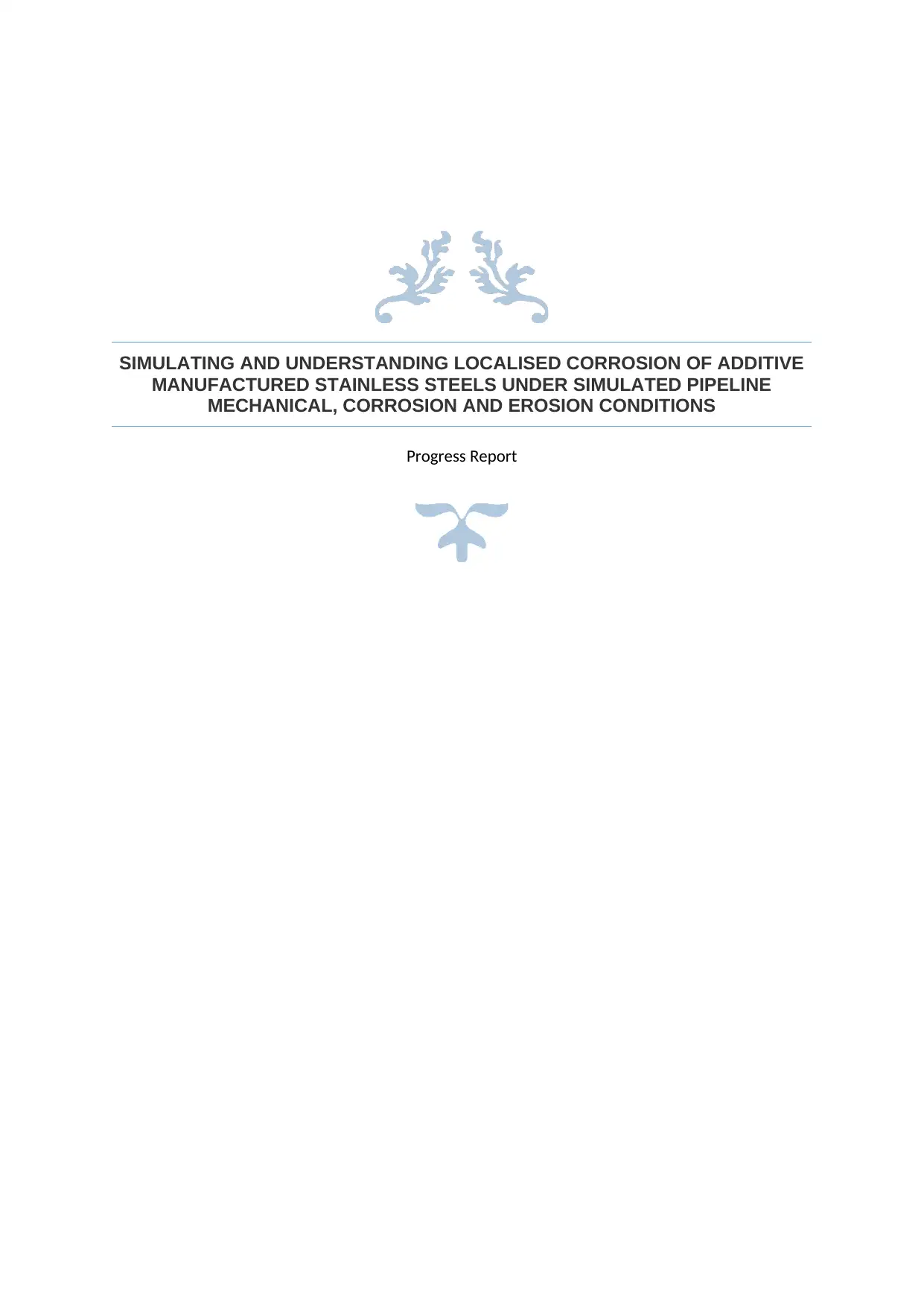
SIMULATING AND UNDERSTANDING LOCALISED CORROSION OF ADDITIVE
MANUFACTURED STAINLESS STEELS UNDER SIMULATED PIPELINE
MECHANICAL, CORROSION AND EROSION CONDITIONS
Progress Report
MANUFACTURED STAINLESS STEELS UNDER SIMULATED PIPELINE
MECHANICAL, CORROSION AND EROSION CONDITIONS
Progress Report
Paraphrase This Document
Need a fresh take? Get an instant paraphrase of this document with our AI Paraphraser
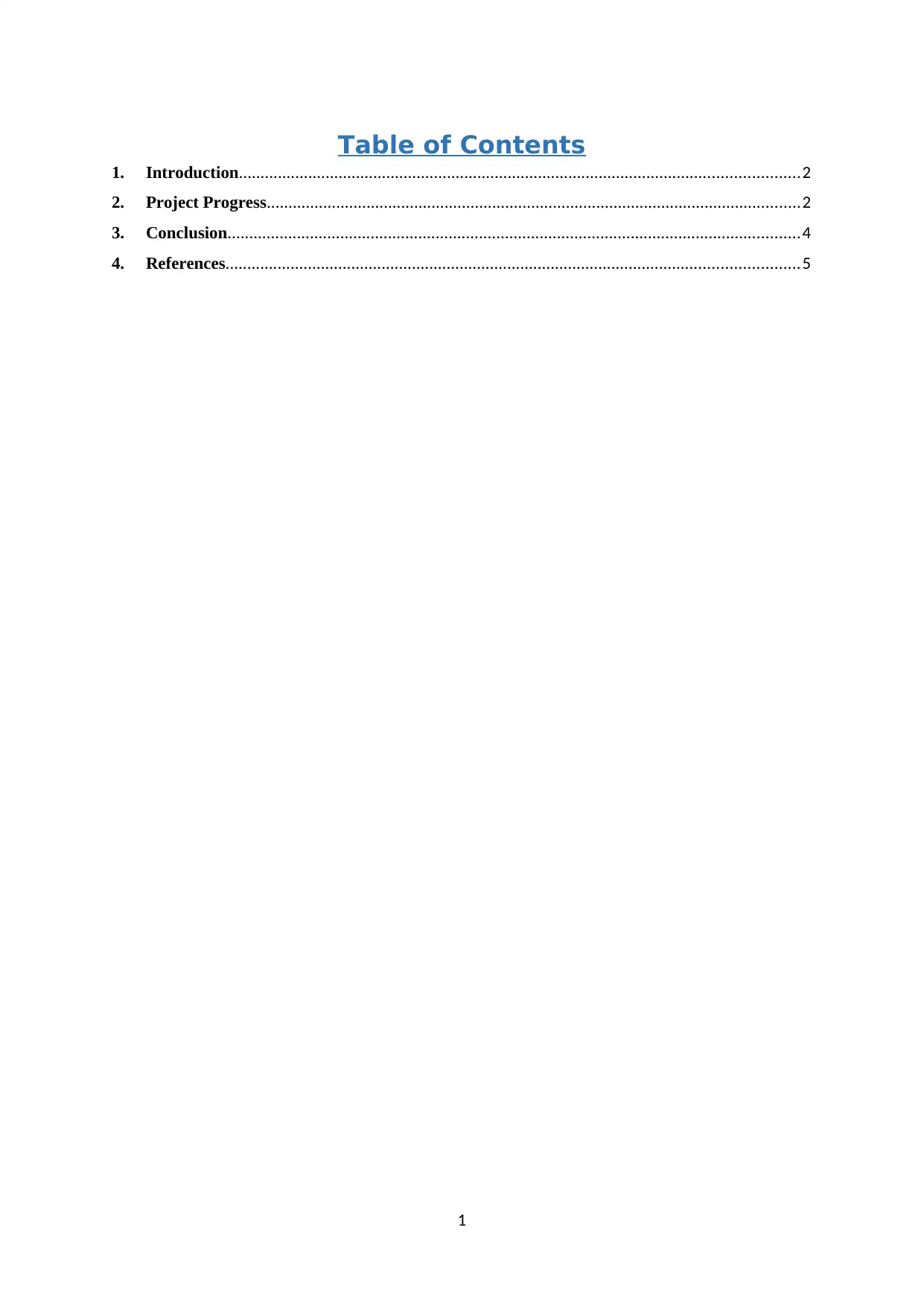
Table of Contents
1. Introduction.................................................................................................................................2
2. Project Progress...........................................................................................................................2
3. Conclusion....................................................................................................................................4
4. References....................................................................................................................................5
1
1. Introduction.................................................................................................................................2
2. Project Progress...........................................................................................................................2
3. Conclusion....................................................................................................................................4
4. References....................................................................................................................................5
1
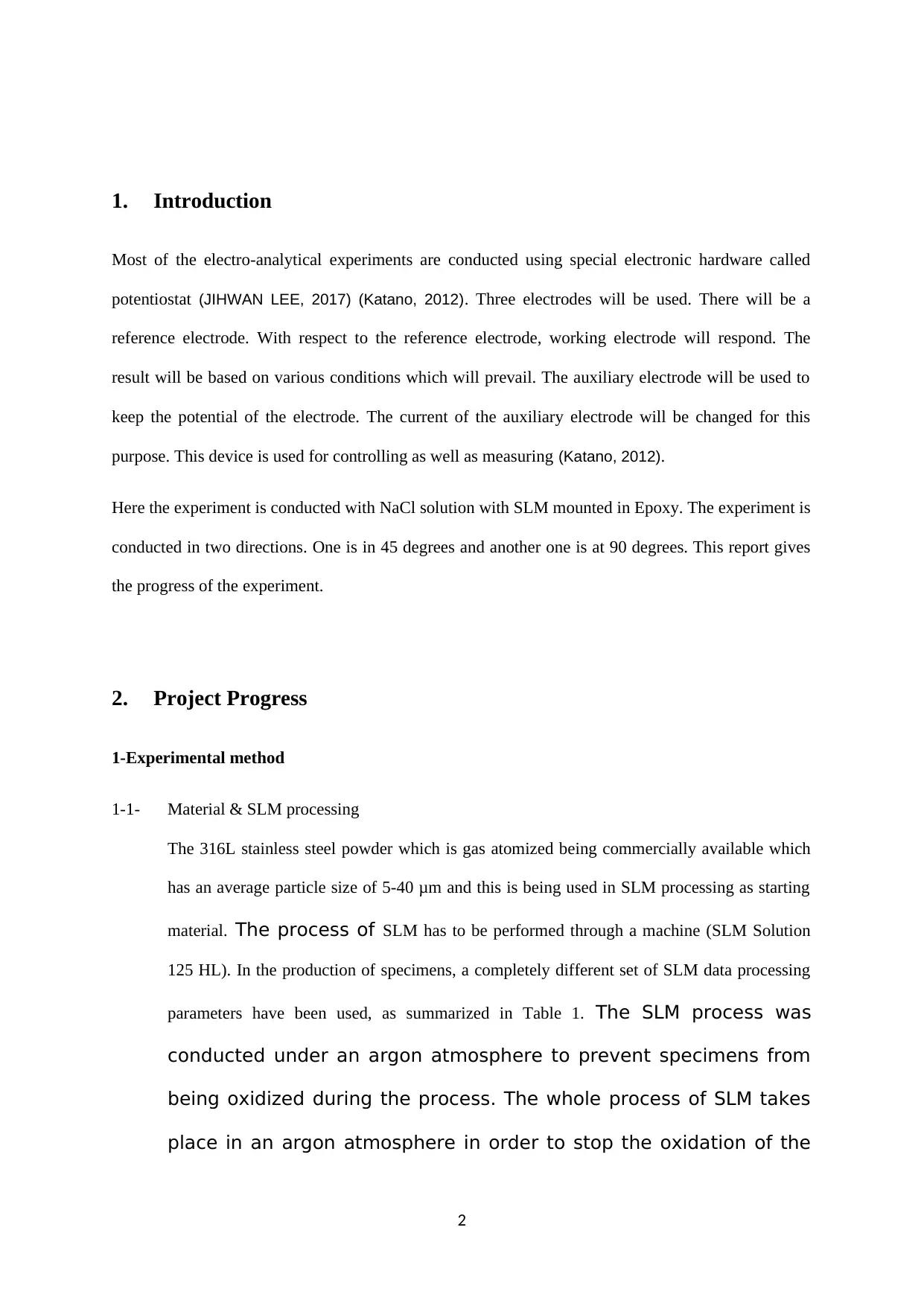
1. Introduction
Most of the electro-analytical experiments are conducted using special electronic hardware called
potentiostat (JIHWAN LEE, 2017) (Katano, 2012). Three electrodes will be used. There will be a
reference electrode. With respect to the reference electrode, working electrode will respond. The
result will be based on various conditions which will prevail. The auxiliary electrode will be used to
keep the potential of the electrode. The current of the auxiliary electrode will be changed for this
purpose. This device is used for controlling as well as measuring (Katano, 2012).
Here the experiment is conducted with NaCl solution with SLM mounted in Epoxy. The experiment is
conducted in two directions. One is in 45 degrees and another one is at 90 degrees. This report gives
the progress of the experiment.
2. Project Progress
1-Experimental method
1-1- Material & SLM processing
The 316L stainless steel powder which is gas atomized being commercially available which
has an average particle size of 5-40 μm and this is being used in SLM processing as starting
material. The process of SLM has to be performed through a machine (SLM Solution
125 HL). In the production of specimens, a completely different set of SLM data processing
parameters have been used, as summarized in Table 1. The SLM process was
conducted under an argon atmosphere to prevent specimens from
being oxidized during the process. The whole process of SLM takes
place in an argon atmosphere in order to stop the oxidation of the
2
Most of the electro-analytical experiments are conducted using special electronic hardware called
potentiostat (JIHWAN LEE, 2017) (Katano, 2012). Three electrodes will be used. There will be a
reference electrode. With respect to the reference electrode, working electrode will respond. The
result will be based on various conditions which will prevail. The auxiliary electrode will be used to
keep the potential of the electrode. The current of the auxiliary electrode will be changed for this
purpose. This device is used for controlling as well as measuring (Katano, 2012).
Here the experiment is conducted with NaCl solution with SLM mounted in Epoxy. The experiment is
conducted in two directions. One is in 45 degrees and another one is at 90 degrees. This report gives
the progress of the experiment.
2. Project Progress
1-Experimental method
1-1- Material & SLM processing
The 316L stainless steel powder which is gas atomized being commercially available which
has an average particle size of 5-40 μm and this is being used in SLM processing as starting
material. The process of SLM has to be performed through a machine (SLM Solution
125 HL). In the production of specimens, a completely different set of SLM data processing
parameters have been used, as summarized in Table 1. The SLM process was
conducted under an argon atmosphere to prevent specimens from
being oxidized during the process. The whole process of SLM takes
place in an argon atmosphere in order to stop the oxidation of the
2
⊘ This is a preview!⊘
Do you want full access?
Subscribe today to unlock all pages.

Trusted by 1+ million students worldwide
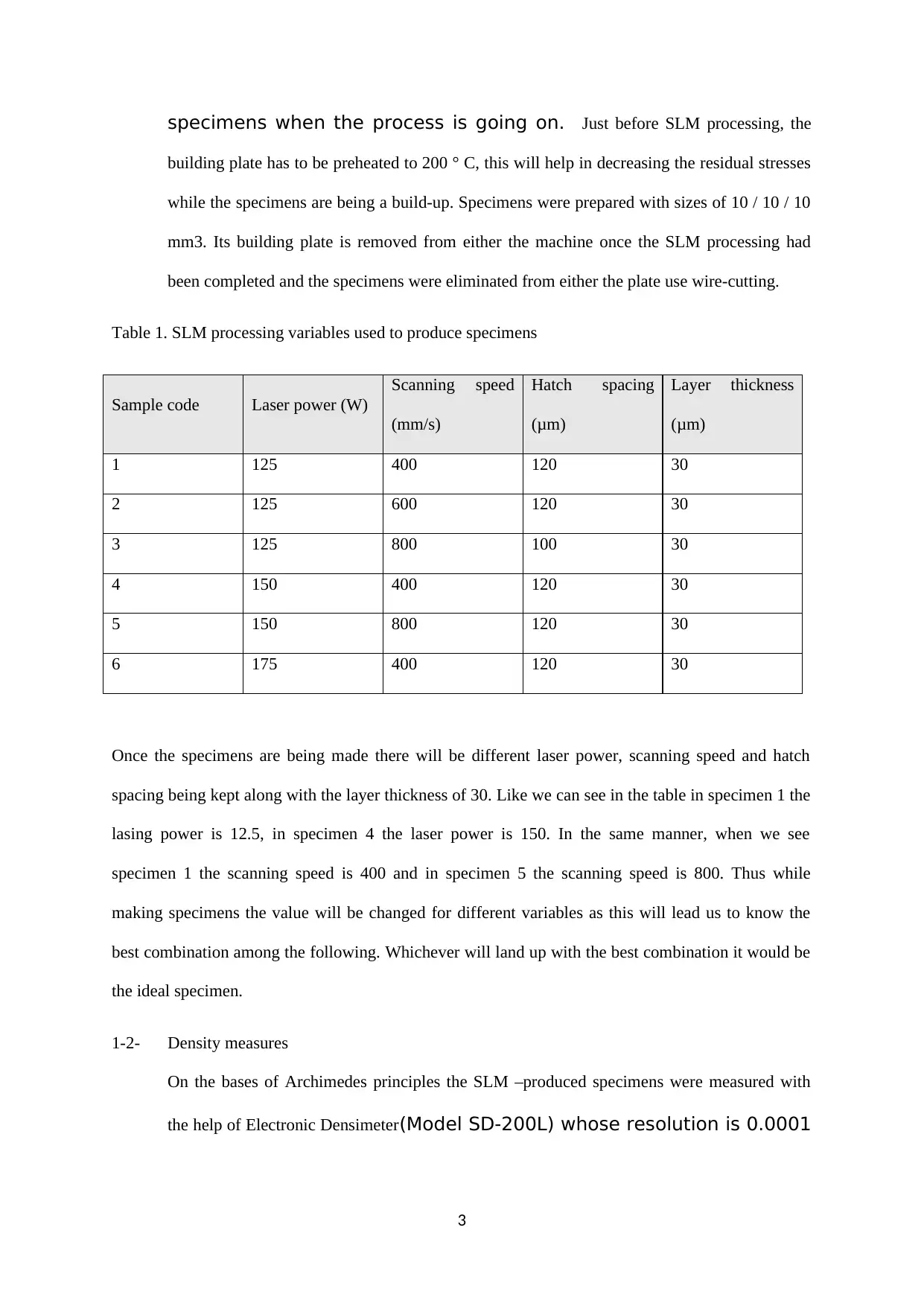
specimens when the process is going on. Just before SLM processing, the
building plate has to be preheated to 200 ° C, this will help in decreasing the residual stresses
while the specimens are being a build-up. Specimens were prepared with sizes of 10 / 10 / 10
mm3. Its building plate is removed from either the machine once the SLM processing had
been completed and the specimens were eliminated from either the plate use wire-cutting.
Table 1. SLM processing variables used to produce specimens
Sample code Laser power (W)
Scanning speed
(mm/s)
Hatch spacing
(μm)
Layer thickness
(μm)
1 125 400 120 30
2 125 600 120 30
3 125 800 100 30
4 150 400 120 30
5 150 800 120 30
6 175 400 120 30
Once the specimens are being made there will be different laser power, scanning speed and hatch
spacing being kept along with the layer thickness of 30. Like we can see in the table in specimen 1 the
lasing power is 12.5, in specimen 4 the laser power is 150. In the same manner, when we see
specimen 1 the scanning speed is 400 and in specimen 5 the scanning speed is 800. Thus while
making specimens the value will be changed for different variables as this will lead us to know the
best combination among the following. Whichever will land up with the best combination it would be
the ideal specimen.
1-2- Density measures
On the bases of Archimedes principles the SLM –produced specimens were measured with
the help of Electronic Densimeter(Model SD-200L) whose resolution is 0.0001
3
building plate has to be preheated to 200 ° C, this will help in decreasing the residual stresses
while the specimens are being a build-up. Specimens were prepared with sizes of 10 / 10 / 10
mm3. Its building plate is removed from either the machine once the SLM processing had
been completed and the specimens were eliminated from either the plate use wire-cutting.
Table 1. SLM processing variables used to produce specimens
Sample code Laser power (W)
Scanning speed
(mm/s)
Hatch spacing
(μm)
Layer thickness
(μm)
1 125 400 120 30
2 125 600 120 30
3 125 800 100 30
4 150 400 120 30
5 150 800 120 30
6 175 400 120 30
Once the specimens are being made there will be different laser power, scanning speed and hatch
spacing being kept along with the layer thickness of 30. Like we can see in the table in specimen 1 the
lasing power is 12.5, in specimen 4 the laser power is 150. In the same manner, when we see
specimen 1 the scanning speed is 400 and in specimen 5 the scanning speed is 800. Thus while
making specimens the value will be changed for different variables as this will lead us to know the
best combination among the following. Whichever will land up with the best combination it would be
the ideal specimen.
1-2- Density measures
On the bases of Archimedes principles the SLM –produced specimens were measured with
the help of Electronic Densimeter(Model SD-200L) whose resolution is 0.0001
3
Paraphrase This Document
Need a fresh take? Get an instant paraphrase of this document with our AI Paraphraser
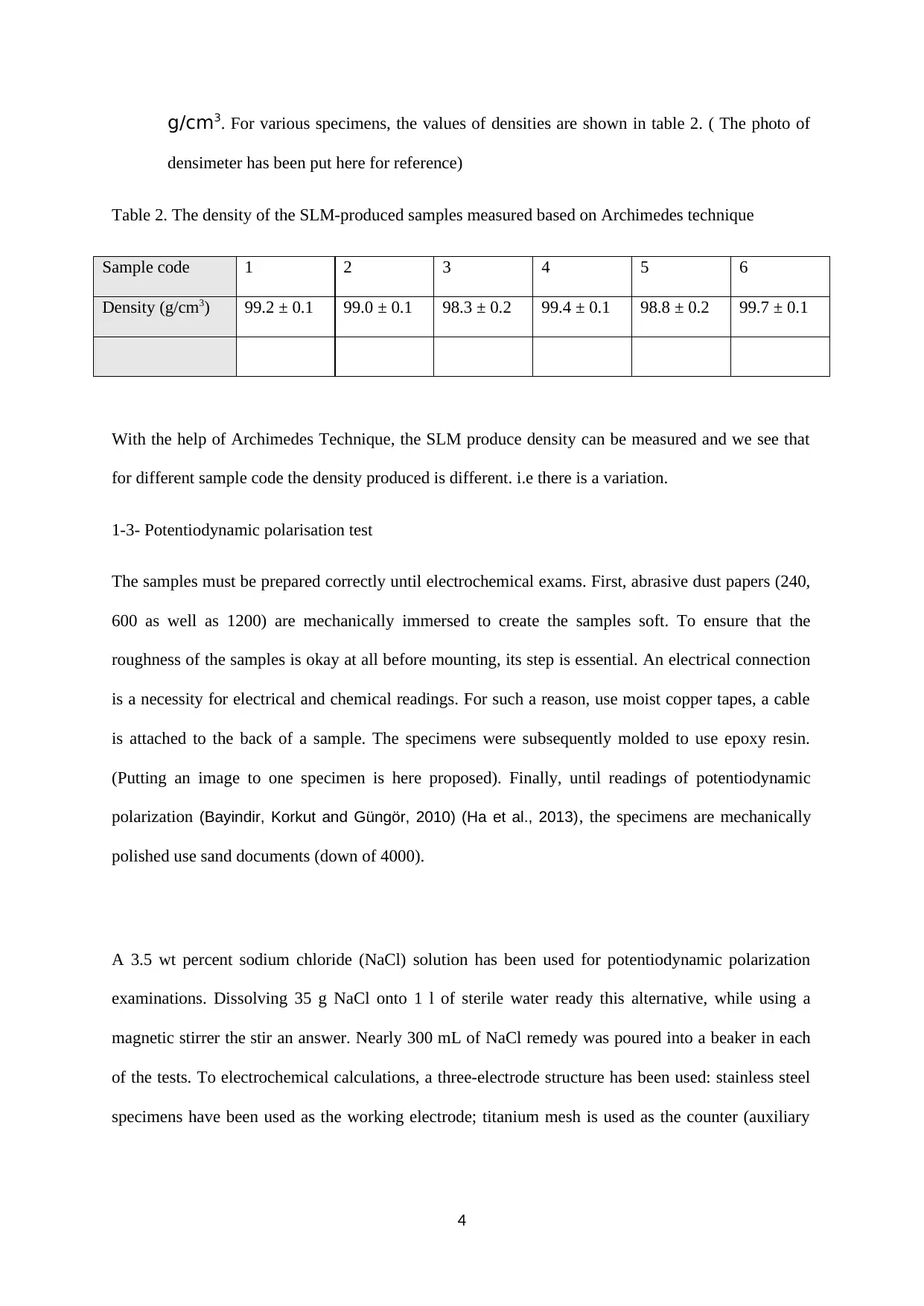
g/cm3. For various specimens, the values of densities are shown in table 2. ( The photo of
densimeter has been put here for reference)
Table 2. The density of the SLM-produced samples measured based on Archimedes technique
Sample code 1 2 3 4 5 6
Density (g/cm3) 99.2 ± 0.1 99.0 ± 0.1 98.3 ± 0.2 99.4 ± 0.1 98.8 ± 0.2 99.7 ± 0.1
With the help of Archimedes Technique, the SLM produce density can be measured and we see that
for different sample code the density produced is different. i.e there is a variation.
1-3- Potentiodynamic polarisation test
The samples must be prepared correctly until electrochemical exams. First, abrasive dust papers (240,
600 as well as 1200) are mechanically immersed to create the samples soft. To ensure that the
roughness of the samples is okay at all before mounting, its step is essential. An electrical connection
is a necessity for electrical and chemical readings. For such a reason, use moist copper tapes, a cable
is attached to the back of a sample. The specimens were subsequently molded to use epoxy resin.
(Putting an image to one specimen is here proposed). Finally, until readings of potentiodynamic
polarization (Bayindir, Korkut and Güngör, 2010) (Ha et al., 2013), the specimens are mechanically
polished use sand documents (down of 4000).
A 3.5 wt percent sodium chloride (NaCl) solution has been used for potentiodynamic polarization
examinations. Dissolving 35 g NaCl onto 1 l of sterile water ready this alternative, while using a
magnetic stirrer the stir an answer. Nearly 300 mL of NaCl remedy was poured into a beaker in each
of the tests. To electrochemical calculations, a three-electrode structure has been used: stainless steel
specimens have been used as the working electrode; titanium mesh is used as the counter (auxiliary
4
densimeter has been put here for reference)
Table 2. The density of the SLM-produced samples measured based on Archimedes technique
Sample code 1 2 3 4 5 6
Density (g/cm3) 99.2 ± 0.1 99.0 ± 0.1 98.3 ± 0.2 99.4 ± 0.1 98.8 ± 0.2 99.7 ± 0.1
With the help of Archimedes Technique, the SLM produce density can be measured and we see that
for different sample code the density produced is different. i.e there is a variation.
1-3- Potentiodynamic polarisation test
The samples must be prepared correctly until electrochemical exams. First, abrasive dust papers (240,
600 as well as 1200) are mechanically immersed to create the samples soft. To ensure that the
roughness of the samples is okay at all before mounting, its step is essential. An electrical connection
is a necessity for electrical and chemical readings. For such a reason, use moist copper tapes, a cable
is attached to the back of a sample. The specimens were subsequently molded to use epoxy resin.
(Putting an image to one specimen is here proposed). Finally, until readings of potentiodynamic
polarization (Bayindir, Korkut and Güngör, 2010) (Ha et al., 2013), the specimens are mechanically
polished use sand documents (down of 4000).
A 3.5 wt percent sodium chloride (NaCl) solution has been used for potentiodynamic polarization
examinations. Dissolving 35 g NaCl onto 1 l of sterile water ready this alternative, while using a
magnetic stirrer the stir an answer. Nearly 300 mL of NaCl remedy was poured into a beaker in each
of the tests. To electrochemical calculations, a three-electrode structure has been used: stainless steel
specimens have been used as the working electrode; titanium mesh is used as the counter (auxiliary
4
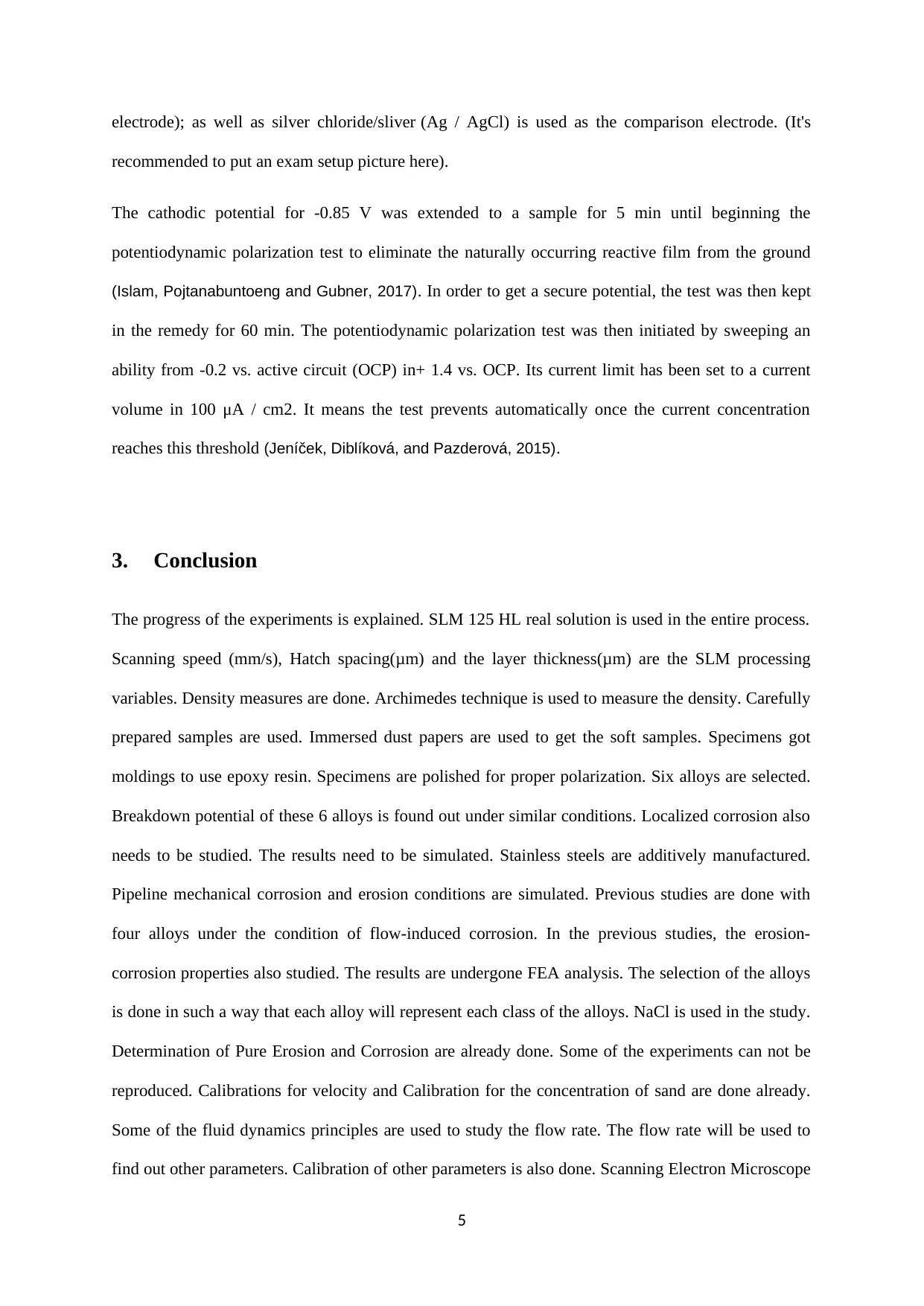
electrode); as well as silver chloride/sliver (Ag / AgCl) is used as the comparison electrode. (It's
recommended to put an exam setup picture here).
The cathodic potential for -0.85 V was extended to a sample for 5 min until beginning the
potentiodynamic polarization test to eliminate the naturally occurring reactive film from the ground
(Islam, Pojtanabuntoeng and Gubner, 2017). In order to get a secure potential, the test was then kept
in the remedy for 60 min. The potentiodynamic polarization test was then initiated by sweeping an
ability from -0.2 vs. active circuit (OCP) in+ 1.4 vs. OCP. Its current limit has been set to a current
volume in 100 μA / cm2. It means the test prevents automatically once the current concentration
reaches this threshold (Jeníček, Diblíková, and Pazderová, 2015).
3. Conclusion
The progress of the experiments is explained. SLM 125 HL real solution is used in the entire process.
Scanning speed (mm/s), Hatch spacing(μm) and the layer thickness(μm) are the SLM processing
variables. Density measures are done. Archimedes technique is used to measure the density. Carefully
prepared samples are used. Immersed dust papers are used to get the soft samples. Specimens got
moldings to use epoxy resin. Specimens are polished for proper polarization. Six alloys are selected.
Breakdown potential of these 6 alloys is found out under similar conditions. Localized corrosion also
needs to be studied. The results need to be simulated. Stainless steels are additively manufactured.
Pipeline mechanical corrosion and erosion conditions are simulated. Previous studies are done with
four alloys under the condition of flow-induced corrosion. In the previous studies, the erosion-
corrosion properties also studied. The results are undergone FEA analysis. The selection of the alloys
is done in such a way that each alloy will represent each class of the alloys. NaCl is used in the study.
Determination of Pure Erosion and Corrosion are already done. Some of the experiments can not be
reproduced. Calibrations for velocity and Calibration for the concentration of sand are done already.
Some of the fluid dynamics principles are used to study the flow rate. The flow rate will be used to
find out other parameters. Calibration of other parameters is also done. Scanning Electron Microscope
5
recommended to put an exam setup picture here).
The cathodic potential for -0.85 V was extended to a sample for 5 min until beginning the
potentiodynamic polarization test to eliminate the naturally occurring reactive film from the ground
(Islam, Pojtanabuntoeng and Gubner, 2017). In order to get a secure potential, the test was then kept
in the remedy for 60 min. The potentiodynamic polarization test was then initiated by sweeping an
ability from -0.2 vs. active circuit (OCP) in+ 1.4 vs. OCP. Its current limit has been set to a current
volume in 100 μA / cm2. It means the test prevents automatically once the current concentration
reaches this threshold (Jeníček, Diblíková, and Pazderová, 2015).
3. Conclusion
The progress of the experiments is explained. SLM 125 HL real solution is used in the entire process.
Scanning speed (mm/s), Hatch spacing(μm) and the layer thickness(μm) are the SLM processing
variables. Density measures are done. Archimedes technique is used to measure the density. Carefully
prepared samples are used. Immersed dust papers are used to get the soft samples. Specimens got
moldings to use epoxy resin. Specimens are polished for proper polarization. Six alloys are selected.
Breakdown potential of these 6 alloys is found out under similar conditions. Localized corrosion also
needs to be studied. The results need to be simulated. Stainless steels are additively manufactured.
Pipeline mechanical corrosion and erosion conditions are simulated. Previous studies are done with
four alloys under the condition of flow-induced corrosion. In the previous studies, the erosion-
corrosion properties also studied. The results are undergone FEA analysis. The selection of the alloys
is done in such a way that each alloy will represent each class of the alloys. NaCl is used in the study.
Determination of Pure Erosion and Corrosion are already done. Some of the experiments can not be
reproduced. Calibrations for velocity and Calibration for the concentration of sand are done already.
Some of the fluid dynamics principles are used to study the flow rate. The flow rate will be used to
find out other parameters. Calibration of other parameters is also done. Scanning Electron Microscope
5
⊘ This is a preview!⊘
Do you want full access?
Subscribe today to unlock all pages.

Trusted by 1+ million students worldwide
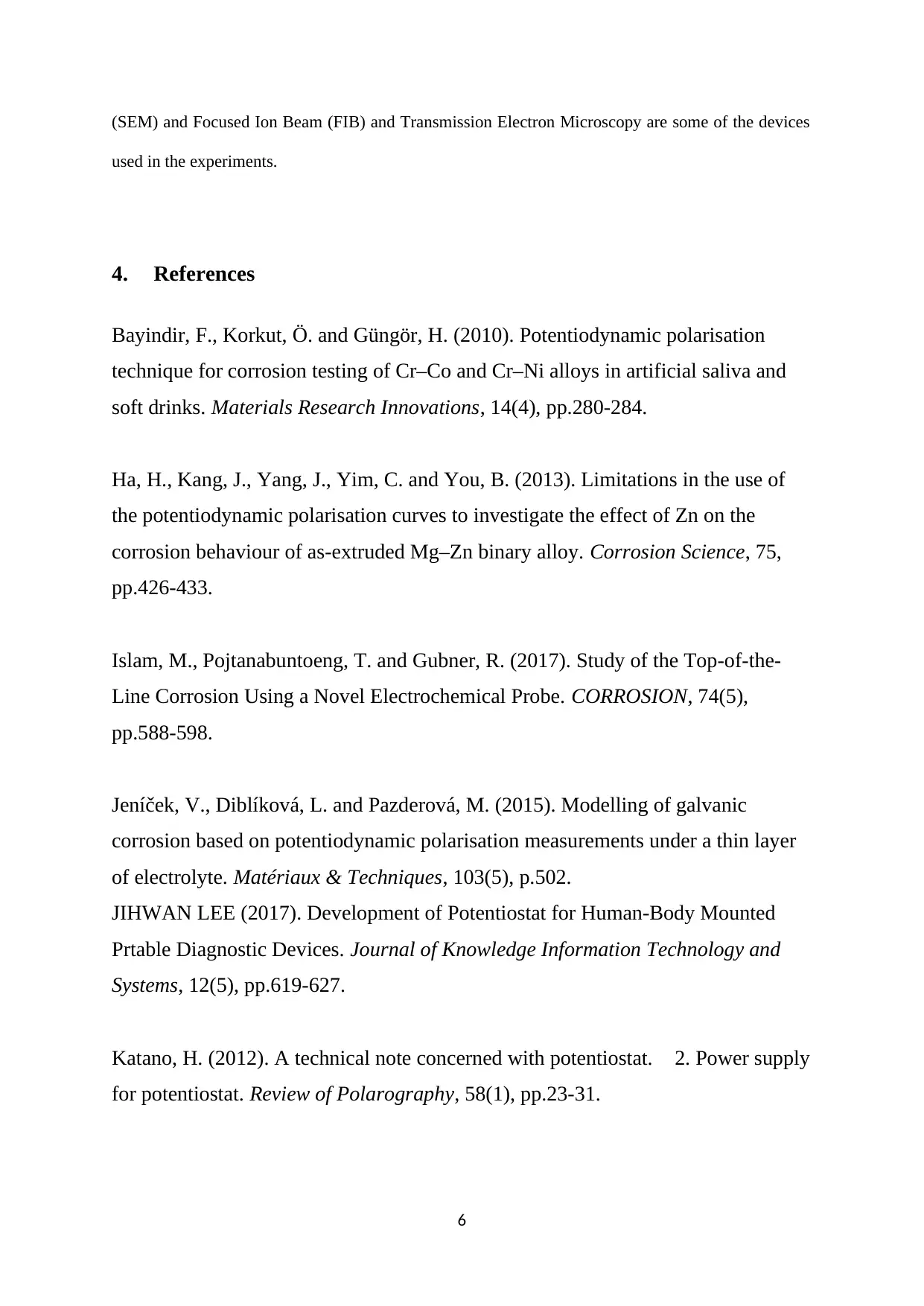
(SEM) and Focused Ion Beam (FIB) and Transmission Electron Microscopy are some of the devices
used in the experiments.
4. References
Bayindir, F., Korkut, Ö. and Güngör, H. (2010). Potentiodynamic polarisation
technique for corrosion testing of Cr–Co and Cr–Ni alloys in artificial saliva and
soft drinks. Materials Research Innovations, 14(4), pp.280-284.
Ha, H., Kang, J., Yang, J., Yim, C. and You, B. (2013). Limitations in the use of
the potentiodynamic polarisation curves to investigate the effect of Zn on the
corrosion behaviour of as-extruded Mg–Zn binary alloy. Corrosion Science, 75,
pp.426-433.
Islam, M., Pojtanabuntoeng, T. and Gubner, R. (2017). Study of the Top-of-the-
Line Corrosion Using a Novel Electrochemical Probe. CORROSION, 74(5),
pp.588-598.
Jeníček, V., Diblíková, L. and Pazderová, M. (2015). Modelling of galvanic
corrosion based on potentiodynamic polarisation measurements under a thin layer
of electrolyte. Matériaux & Techniques, 103(5), p.502.
JIHWAN LEE (2017). Development of Potentiostat for Human-Body Mounted
Prtable Diagnostic Devices. Journal of Knowledge Information Technology and
Systems, 12(5), pp.619-627.
Katano, H. (2012). A technical note concerned with potentiostat. 2. Power supply
for potentiostat. Review of Polarography, 58(1), pp.23-31.
6
used in the experiments.
4. References
Bayindir, F., Korkut, Ö. and Güngör, H. (2010). Potentiodynamic polarisation
technique for corrosion testing of Cr–Co and Cr–Ni alloys in artificial saliva and
soft drinks. Materials Research Innovations, 14(4), pp.280-284.
Ha, H., Kang, J., Yang, J., Yim, C. and You, B. (2013). Limitations in the use of
the potentiodynamic polarisation curves to investigate the effect of Zn on the
corrosion behaviour of as-extruded Mg–Zn binary alloy. Corrosion Science, 75,
pp.426-433.
Islam, M., Pojtanabuntoeng, T. and Gubner, R. (2017). Study of the Top-of-the-
Line Corrosion Using a Novel Electrochemical Probe. CORROSION, 74(5),
pp.588-598.
Jeníček, V., Diblíková, L. and Pazderová, M. (2015). Modelling of galvanic
corrosion based on potentiodynamic polarisation measurements under a thin layer
of electrolyte. Matériaux & Techniques, 103(5), p.502.
JIHWAN LEE (2017). Development of Potentiostat for Human-Body Mounted
Prtable Diagnostic Devices. Journal of Knowledge Information Technology and
Systems, 12(5), pp.619-627.
Katano, H. (2012). A technical note concerned with potentiostat. 2. Power supply
for potentiostat. Review of Polarography, 58(1), pp.23-31.
6
Paraphrase This Document
Need a fresh take? Get an instant paraphrase of this document with our AI Paraphraser
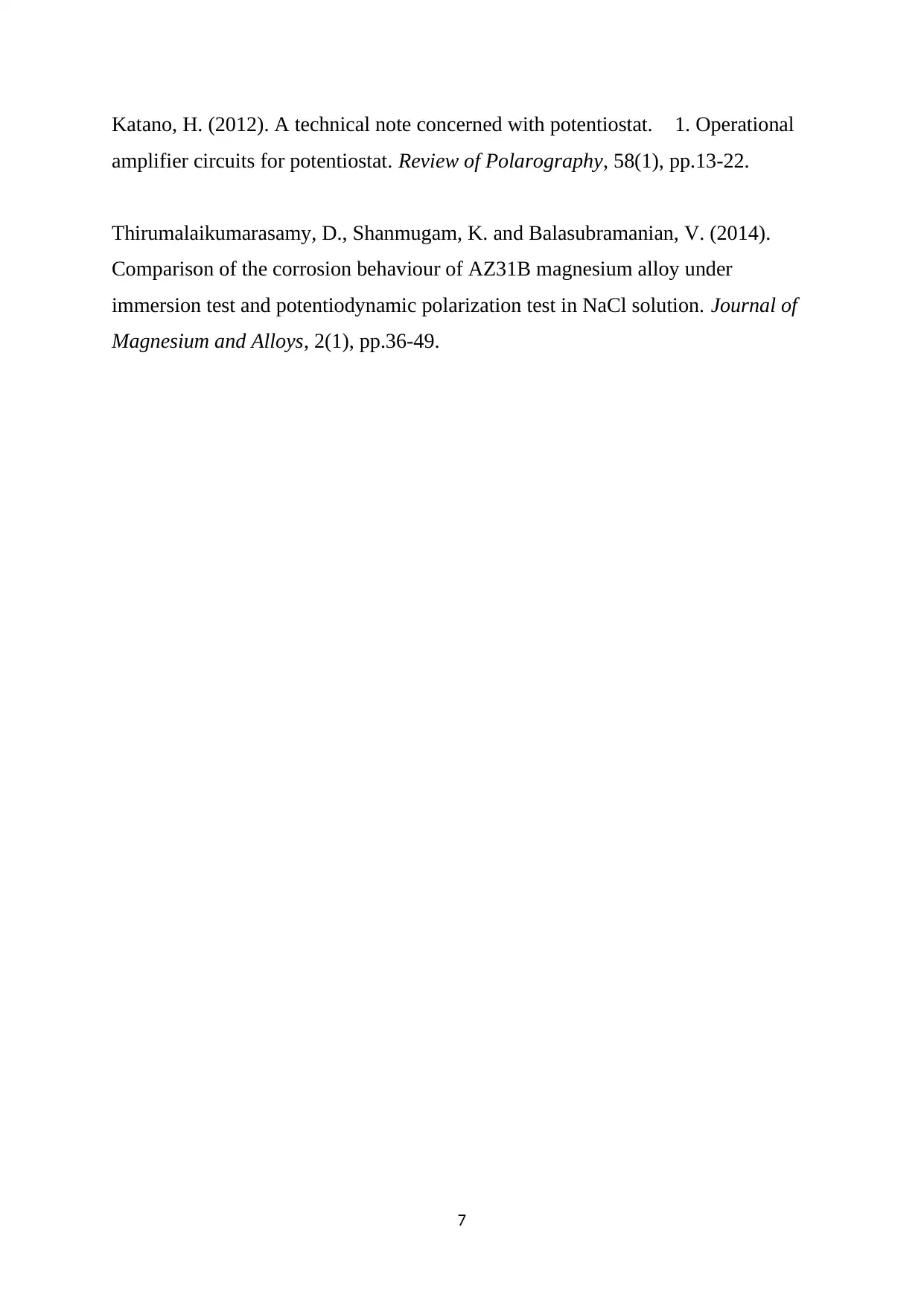
Katano, H. (2012). A technical note concerned with potentiostat. 1. Operational
amplifier circuits for potentiostat. Review of Polarography, 58(1), pp.13-22.
Thirumalaikumarasamy, D., Shanmugam, K. and Balasubramanian, V. (2014).
Comparison of the corrosion behaviour of AZ31B magnesium alloy under
immersion test and potentiodynamic polarization test in NaCl solution. Journal of
Magnesium and Alloys, 2(1), pp.36-49.
7
amplifier circuits for potentiostat. Review of Polarography, 58(1), pp.13-22.
Thirumalaikumarasamy, D., Shanmugam, K. and Balasubramanian, V. (2014).
Comparison of the corrosion behaviour of AZ31B magnesium alloy under
immersion test and potentiodynamic polarization test in NaCl solution. Journal of
Magnesium and Alloys, 2(1), pp.36-49.
7
1 out of 8

Your All-in-One AI-Powered Toolkit for Academic Success.
+13062052269
info@desklib.com
Available 24*7 on WhatsApp / Email
Unlock your academic potential
© 2024 | Zucol Services PVT LTD | All rights reserved.