Assessing and Optimizing Resource Utilization of a Water Bottling Line Using Simulation
VerifiedAdded on 2023/01/20
|16
|3564
|51
AI Summary
This article discusses the assessment and optimization of resource utilization in a water bottling line using simulation. It explores the factors affecting production process and the implications of simulations and control factors in different production strategies.
Contribute Materials
Your contribution can guide someone’s learning journey. Share your
documents today.
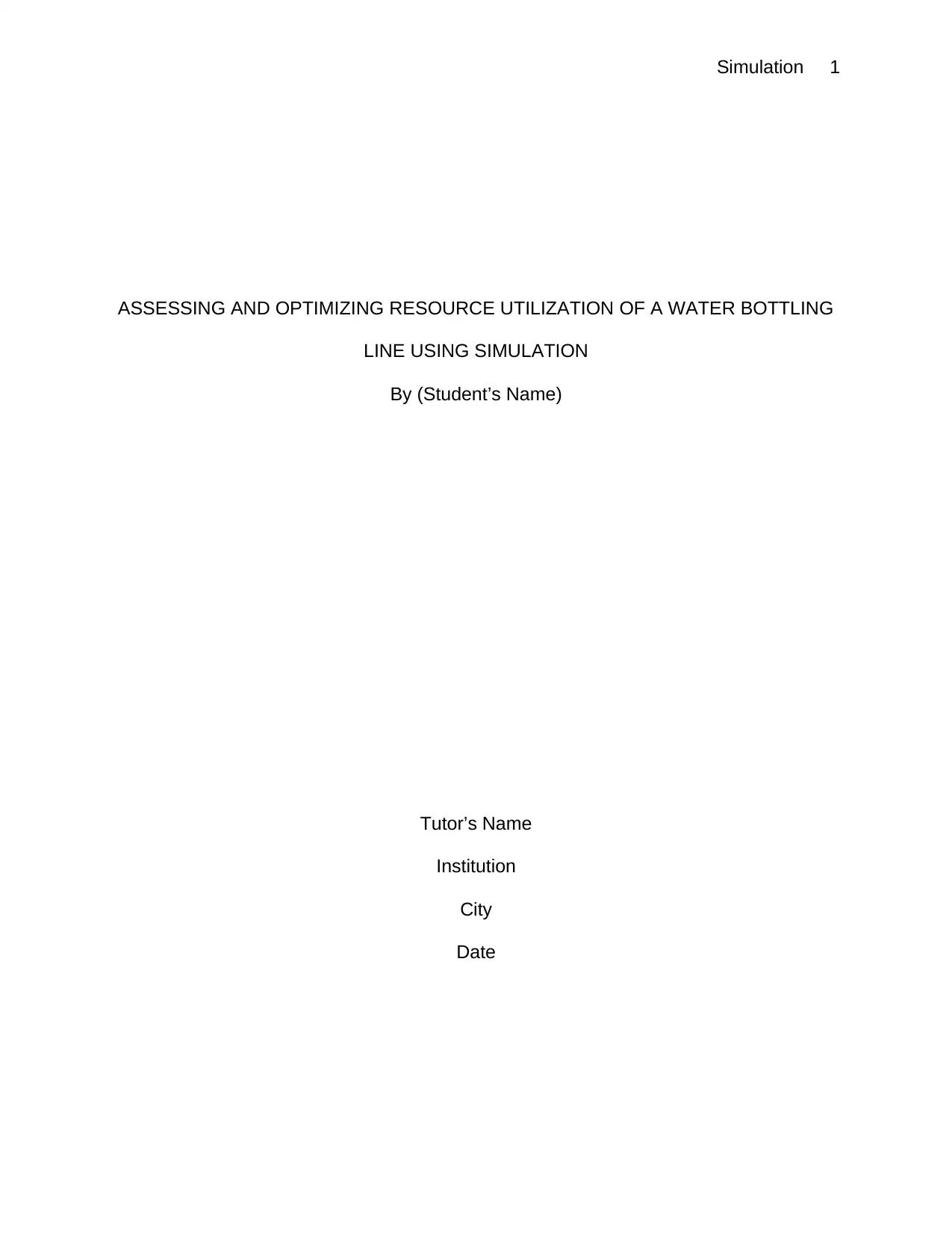
Simulation 1
ASSESSING AND OPTIMIZING RESOURCE UTILIZATION OF A WATER BOTTLING
LINE USING SIMULATION
By (Student’s Name)
Tutor’s Name
Institution
City
Date
ASSESSING AND OPTIMIZING RESOURCE UTILIZATION OF A WATER BOTTLING
LINE USING SIMULATION
By (Student’s Name)
Tutor’s Name
Institution
City
Date
Secure Best Marks with AI Grader
Need help grading? Try our AI Grader for instant feedback on your assignments.
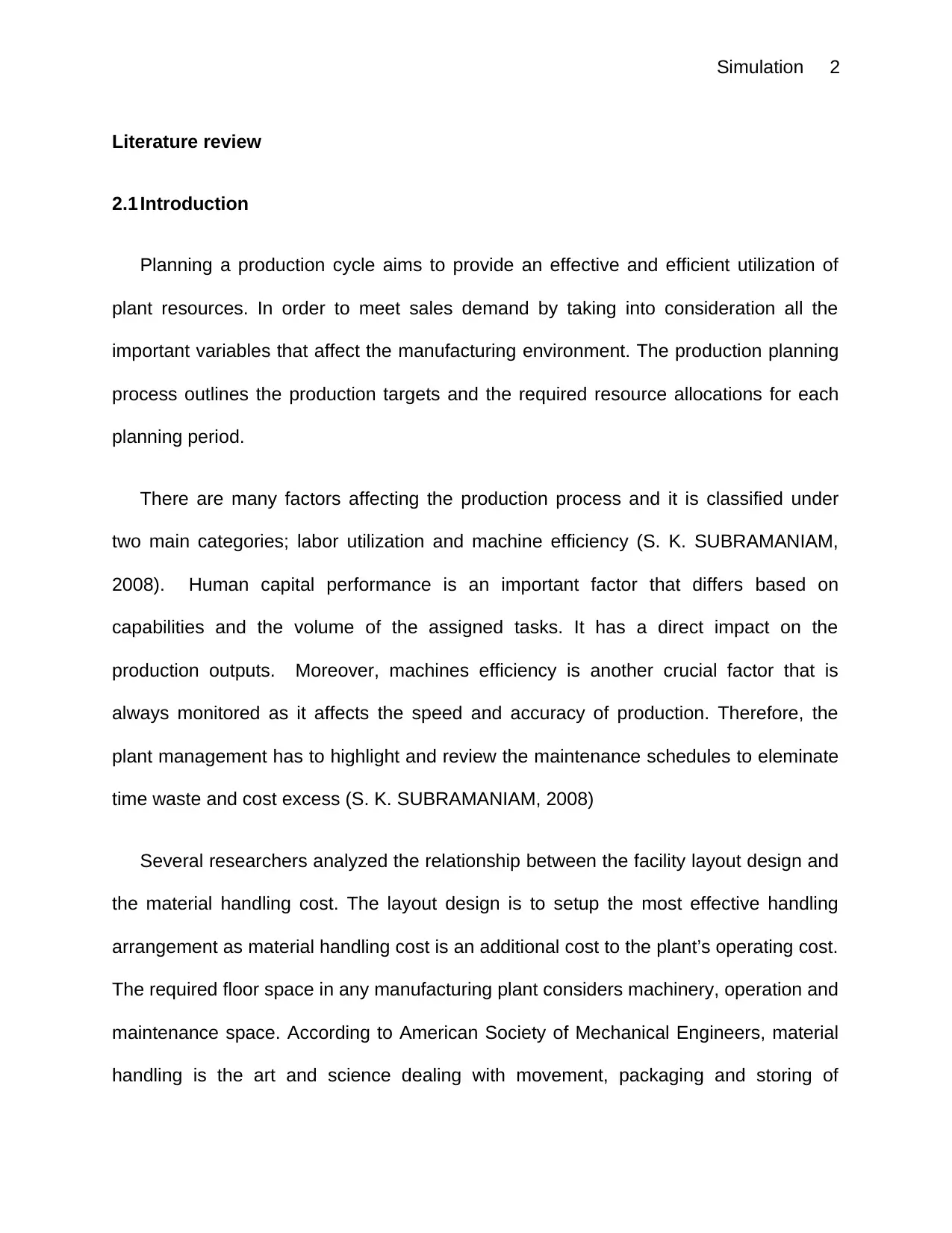
Simulation 2
Literature review
2.1 Introduction
Planning a production cycle aims to provide an effective and efficient utilization of
plant resources. In order to meet sales demand by taking into consideration all the
important variables that affect the manufacturing environment. The production planning
process outlines the production targets and the required resource allocations for each
planning period.
There are many factors affecting the production process and it is classified under
two main categories; labor utilization and machine efficiency (S. K. SUBRAMANIAM,
2008). Human capital performance is an important factor that differs based on
capabilities and the volume of the assigned tasks. It has a direct impact on the
production outputs. Moreover, machines efficiency is another crucial factor that is
always monitored as it affects the speed and accuracy of production. Therefore, the
plant management has to highlight and review the maintenance schedules to eleminate
time waste and cost excess (S. K. SUBRAMANIAM, 2008)
Several researchers analyzed the relationship between the facility layout design and
the material handling cost. The layout design is to setup the most effective handling
arrangement as material handling cost is an additional cost to the plant’s operating cost.
The required floor space in any manufacturing plant considers machinery, operation and
maintenance space. According to American Society of Mechanical Engineers, material
handling is the art and science dealing with movement, packaging and storing of
Literature review
2.1 Introduction
Planning a production cycle aims to provide an effective and efficient utilization of
plant resources. In order to meet sales demand by taking into consideration all the
important variables that affect the manufacturing environment. The production planning
process outlines the production targets and the required resource allocations for each
planning period.
There are many factors affecting the production process and it is classified under
two main categories; labor utilization and machine efficiency (S. K. SUBRAMANIAM,
2008). Human capital performance is an important factor that differs based on
capabilities and the volume of the assigned tasks. It has a direct impact on the
production outputs. Moreover, machines efficiency is another crucial factor that is
always monitored as it affects the speed and accuracy of production. Therefore, the
plant management has to highlight and review the maintenance schedules to eleminate
time waste and cost excess (S. K. SUBRAMANIAM, 2008)
Several researchers analyzed the relationship between the facility layout design and
the material handling cost. The layout design is to setup the most effective handling
arrangement as material handling cost is an additional cost to the plant’s operating cost.
The required floor space in any manufacturing plant considers machinery, operation and
maintenance space. According to American Society of Mechanical Engineers, material
handling is the art and science dealing with movement, packaging and storing of

Simulation 3
substances in a form. The equipment utilized in material handling impacts the plant’s
productivity (Syed Asad Ali Naqvi, 2016)
In a related report, Liz long (2017) discussed factors that affect manufacturing cost
like raw materials, packaging, shipping and labor. Liz discussed an example to minimize
the cost implications in a manufacturing process of a pet clothing line. After seeking the
consultant advice to reduce the production cost, the factory change the fabrics, as it
was slippery. The pervious material was difficult to manage on the cutting machines,
required more time to produce and higher than average defect rate. After the fabrics
change, the factory manages to reduce the production cost to 5% less than the previous
operating plan.
The purpose of this chapter is to discuss several studies that focus on the implications
of simulations and control factors in different productions strategies.
2.2 Facility planning
Facility planning is one of the major success factors in any production plants .It
understand the organization’s culture and analyze in-depth the new or exciting
facilities including capabilities, locations, utilizations and conditions to translate goals
into affordable and achievable plans.
A study has been executed by (Rishi H. Singhania, 2012) to replicate a physical
setup of a manufacturing environment in Arena which is a virtual system to simulate
different production scenarios. The model was subjected to three control points and
one variable response. The control points were batch size, target stock and reorder
point to analyze the response of system outputs.
substances in a form. The equipment utilized in material handling impacts the plant’s
productivity (Syed Asad Ali Naqvi, 2016)
In a related report, Liz long (2017) discussed factors that affect manufacturing cost
like raw materials, packaging, shipping and labor. Liz discussed an example to minimize
the cost implications in a manufacturing process of a pet clothing line. After seeking the
consultant advice to reduce the production cost, the factory change the fabrics, as it
was slippery. The pervious material was difficult to manage on the cutting machines,
required more time to produce and higher than average defect rate. After the fabrics
change, the factory manages to reduce the production cost to 5% less than the previous
operating plan.
The purpose of this chapter is to discuss several studies that focus on the implications
of simulations and control factors in different productions strategies.
2.2 Facility planning
Facility planning is one of the major success factors in any production plants .It
understand the organization’s culture and analyze in-depth the new or exciting
facilities including capabilities, locations, utilizations and conditions to translate goals
into affordable and achievable plans.
A study has been executed by (Rishi H. Singhania, 2012) to replicate a physical
setup of a manufacturing environment in Arena which is a virtual system to simulate
different production scenarios. The model was subjected to three control points and
one variable response. The control points were batch size, target stock and reorder
point to analyze the response of system outputs.
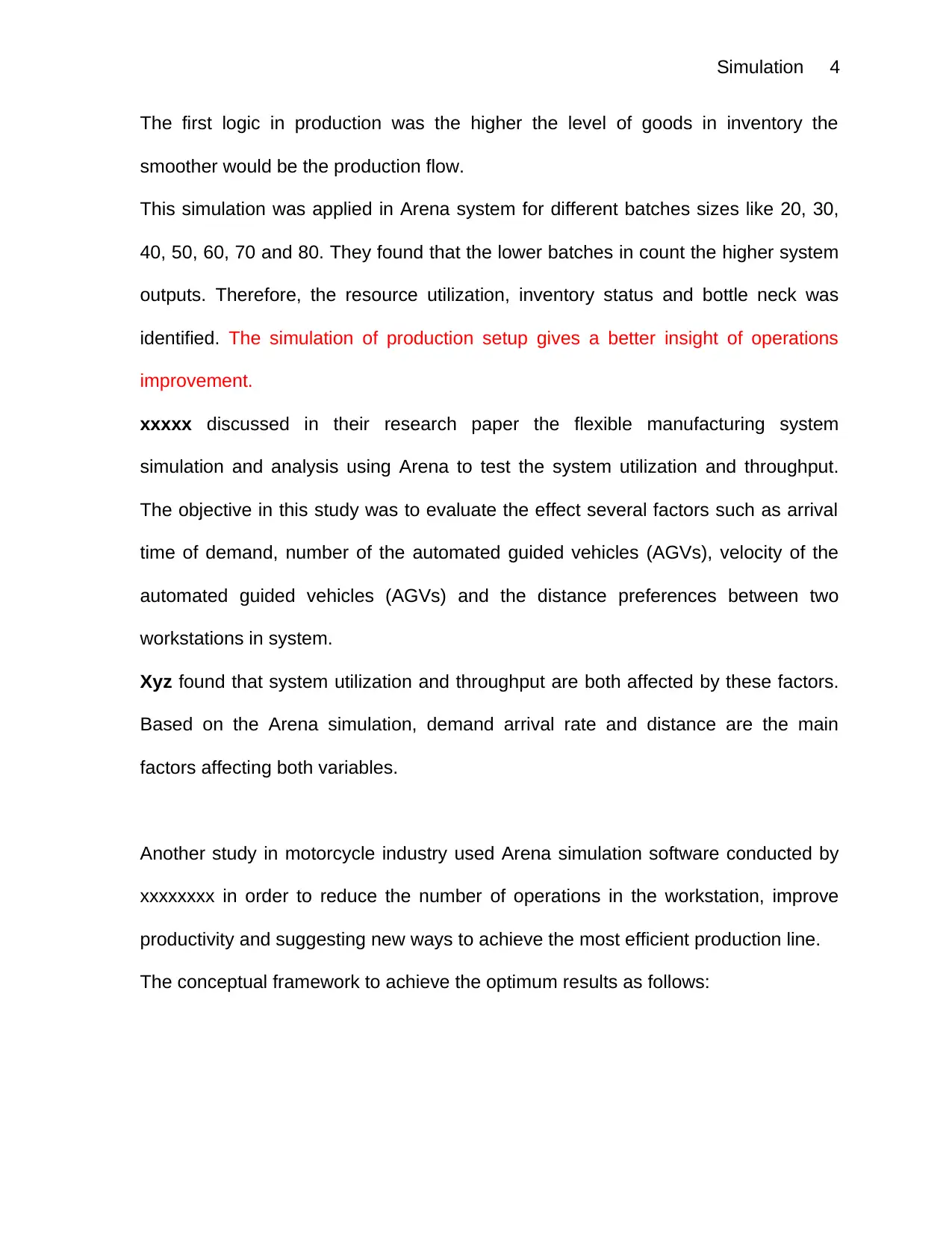
Simulation 4
The first logic in production was the higher the level of goods in inventory the
smoother would be the production flow.
This simulation was applied in Arena system for different batches sizes like 20, 30,
40, 50, 60, 70 and 80. They found that the lower batches in count the higher system
outputs. Therefore, the resource utilization, inventory status and bottle neck was
identified. The simulation of production setup gives a better insight of operations
improvement.
xxxxx discussed in their research paper the flexible manufacturing system
simulation and analysis using Arena to test the system utilization and throughput.
The objective in this study was to evaluate the effect several factors such as arrival
time of demand, number of the automated guided vehicles (AGVs), velocity of the
automated guided vehicles (AGVs) and the distance preferences between two
workstations in system.
Xyz found that system utilization and throughput are both affected by these factors.
Based on the Arena simulation, demand arrival rate and distance are the main
factors affecting both variables.
Another study in motorcycle industry used Arena simulation software conducted by
xxxxxxxx in order to reduce the number of operations in the workstation, improve
productivity and suggesting new ways to achieve the most efficient production line.
The conceptual framework to achieve the optimum results as follows:
The first logic in production was the higher the level of goods in inventory the
smoother would be the production flow.
This simulation was applied in Arena system for different batches sizes like 20, 30,
40, 50, 60, 70 and 80. They found that the lower batches in count the higher system
outputs. Therefore, the resource utilization, inventory status and bottle neck was
identified. The simulation of production setup gives a better insight of operations
improvement.
xxxxx discussed in their research paper the flexible manufacturing system
simulation and analysis using Arena to test the system utilization and throughput.
The objective in this study was to evaluate the effect several factors such as arrival
time of demand, number of the automated guided vehicles (AGVs), velocity of the
automated guided vehicles (AGVs) and the distance preferences between two
workstations in system.
Xyz found that system utilization and throughput are both affected by these factors.
Based on the Arena simulation, demand arrival rate and distance are the main
factors affecting both variables.
Another study in motorcycle industry used Arena simulation software conducted by
xxxxxxxx in order to reduce the number of operations in the workstation, improve
productivity and suggesting new ways to achieve the most efficient production line.
The conceptual framework to achieve the optimum results as follows:
Secure Best Marks with AI Grader
Need help grading? Try our AI Grader for instant feedback on your assignments.
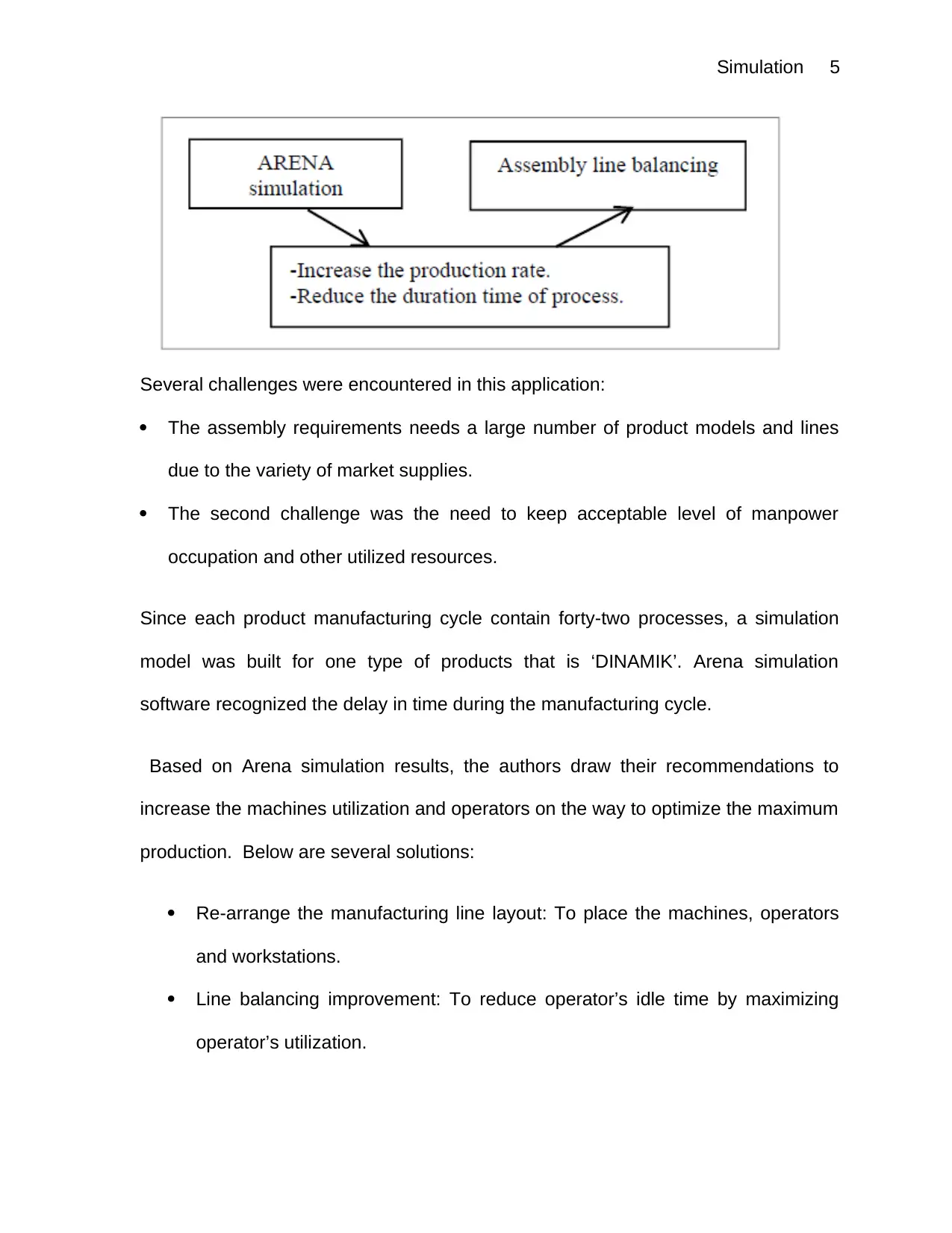
Simulation 5
Several challenges were encountered in this application:
The assembly requirements needs a large number of product models and lines
due to the variety of market supplies.
The second challenge was the need to keep acceptable level of manpower
occupation and other utilized resources.
Since each product manufacturing cycle contain forty-two processes, a simulation
model was built for one type of products that is ‘DINAMIK’. Arena simulation
software recognized the delay in time during the manufacturing cycle.
Based on Arena simulation results, the authors draw their recommendations to
increase the machines utilization and operators on the way to optimize the maximum
production. Below are several solutions:
Re-arrange the manufacturing line layout: To place the machines, operators
and workstations.
Line balancing improvement: To reduce operator’s idle time by maximizing
operator’s utilization.
Several challenges were encountered in this application:
The assembly requirements needs a large number of product models and lines
due to the variety of market supplies.
The second challenge was the need to keep acceptable level of manpower
occupation and other utilized resources.
Since each product manufacturing cycle contain forty-two processes, a simulation
model was built for one type of products that is ‘DINAMIK’. Arena simulation
software recognized the delay in time during the manufacturing cycle.
Based on Arena simulation results, the authors draw their recommendations to
increase the machines utilization and operators on the way to optimize the maximum
production. Below are several solutions:
Re-arrange the manufacturing line layout: To place the machines, operators
and workstations.
Line balancing improvement: To reduce operator’s idle time by maximizing
operator’s utilization.
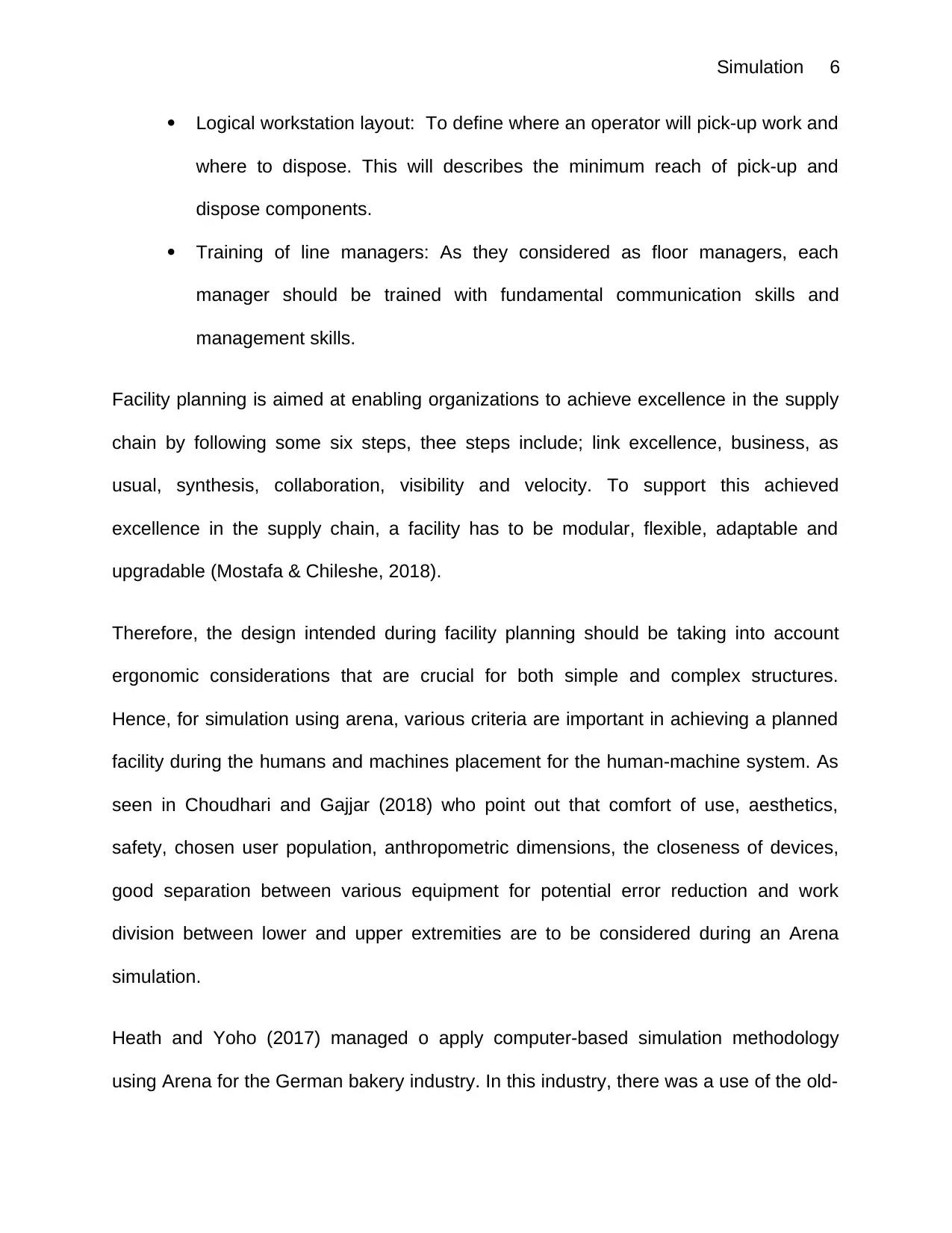
Simulation 6
Logical workstation layout: To define where an operator will pick-up work and
where to dispose. This will describes the minimum reach of pick-up and
dispose components.
Training of line managers: As they considered as floor managers, each
manager should be trained with fundamental communication skills and
management skills.
Facility planning is aimed at enabling organizations to achieve excellence in the supply
chain by following some six steps, thee steps include; link excellence, business, as
usual, synthesis, collaboration, visibility and velocity. To support this achieved
excellence in the supply chain, a facility has to be modular, flexible, adaptable and
upgradable (Mostafa & Chileshe, 2018).
Therefore, the design intended during facility planning should be taking into account
ergonomic considerations that are crucial for both simple and complex structures.
Hence, for simulation using arena, various criteria are important in achieving a planned
facility during the humans and machines placement for the human-machine system. As
seen in Choudhari and Gajjar (2018) who point out that comfort of use, aesthetics,
safety, chosen user population, anthropometric dimensions, the closeness of devices,
good separation between various equipment for potential error reduction and work
division between lower and upper extremities are to be considered during an Arena
simulation.
Heath and Yoho (2017) managed o apply computer-based simulation methodology
using Arena for the German bakery industry. In this industry, there was a use of the old-
Logical workstation layout: To define where an operator will pick-up work and
where to dispose. This will describes the minimum reach of pick-up and
dispose components.
Training of line managers: As they considered as floor managers, each
manager should be trained with fundamental communication skills and
management skills.
Facility planning is aimed at enabling organizations to achieve excellence in the supply
chain by following some six steps, thee steps include; link excellence, business, as
usual, synthesis, collaboration, visibility and velocity. To support this achieved
excellence in the supply chain, a facility has to be modular, flexible, adaptable and
upgradable (Mostafa & Chileshe, 2018).
Therefore, the design intended during facility planning should be taking into account
ergonomic considerations that are crucial for both simple and complex structures.
Hence, for simulation using arena, various criteria are important in achieving a planned
facility during the humans and machines placement for the human-machine system. As
seen in Choudhari and Gajjar (2018) who point out that comfort of use, aesthetics,
safety, chosen user population, anthropometric dimensions, the closeness of devices,
good separation between various equipment for potential error reduction and work
division between lower and upper extremities are to be considered during an Arena
simulation.
Heath and Yoho (2017) managed o apply computer-based simulation methodology
using Arena for the German bakery industry. In this industry, there was a use of the old-
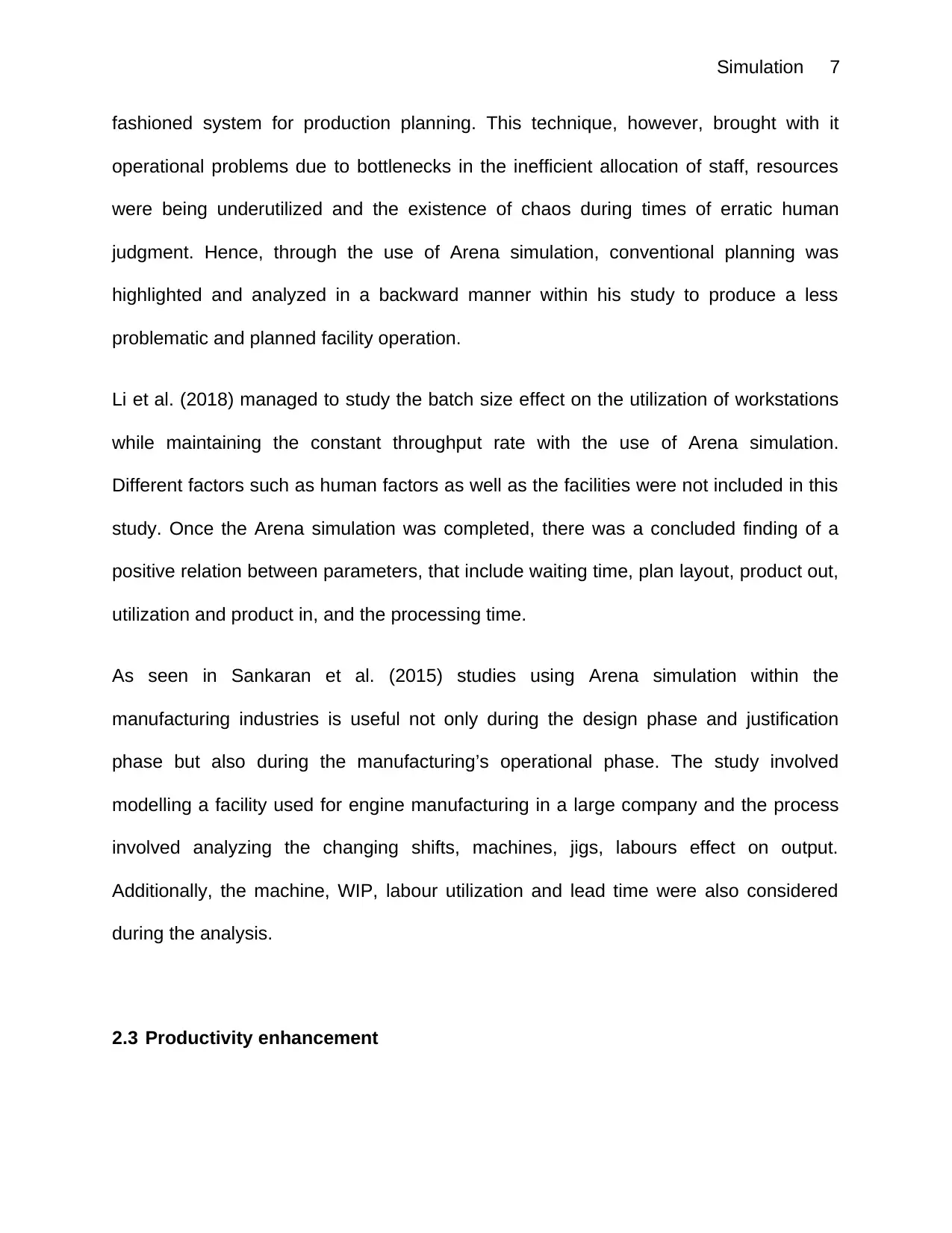
Simulation 7
fashioned system for production planning. This technique, however, brought with it
operational problems due to bottlenecks in the inefficient allocation of staff, resources
were being underutilized and the existence of chaos during times of erratic human
judgment. Hence, through the use of Arena simulation, conventional planning was
highlighted and analyzed in a backward manner within his study to produce a less
problematic and planned facility operation.
Li et al. (2018) managed to study the batch size effect on the utilization of workstations
while maintaining the constant throughput rate with the use of Arena simulation.
Different factors such as human factors as well as the facilities were not included in this
study. Once the Arena simulation was completed, there was a concluded finding of a
positive relation between parameters, that include waiting time, plan layout, product out,
utilization and product in, and the processing time.
As seen in Sankaran et al. (2015) studies using Arena simulation within the
manufacturing industries is useful not only during the design phase and justification
phase but also during the manufacturing’s operational phase. The study involved
modelling a facility used for engine manufacturing in a large company and the process
involved analyzing the changing shifts, machines, jigs, labours effect on output.
Additionally, the machine, WIP, labour utilization and lead time were also considered
during the analysis.
2.3 Productivity enhancement
fashioned system for production planning. This technique, however, brought with it
operational problems due to bottlenecks in the inefficient allocation of staff, resources
were being underutilized and the existence of chaos during times of erratic human
judgment. Hence, through the use of Arena simulation, conventional planning was
highlighted and analyzed in a backward manner within his study to produce a less
problematic and planned facility operation.
Li et al. (2018) managed to study the batch size effect on the utilization of workstations
while maintaining the constant throughput rate with the use of Arena simulation.
Different factors such as human factors as well as the facilities were not included in this
study. Once the Arena simulation was completed, there was a concluded finding of a
positive relation between parameters, that include waiting time, plan layout, product out,
utilization and product in, and the processing time.
As seen in Sankaran et al. (2015) studies using Arena simulation within the
manufacturing industries is useful not only during the design phase and justification
phase but also during the manufacturing’s operational phase. The study involved
modelling a facility used for engine manufacturing in a large company and the process
involved analyzing the changing shifts, machines, jigs, labours effect on output.
Additionally, the machine, WIP, labour utilization and lead time were also considered
during the analysis.
2.3 Productivity enhancement
Paraphrase This Document
Need a fresh take? Get an instant paraphrase of this document with our AI Paraphraser
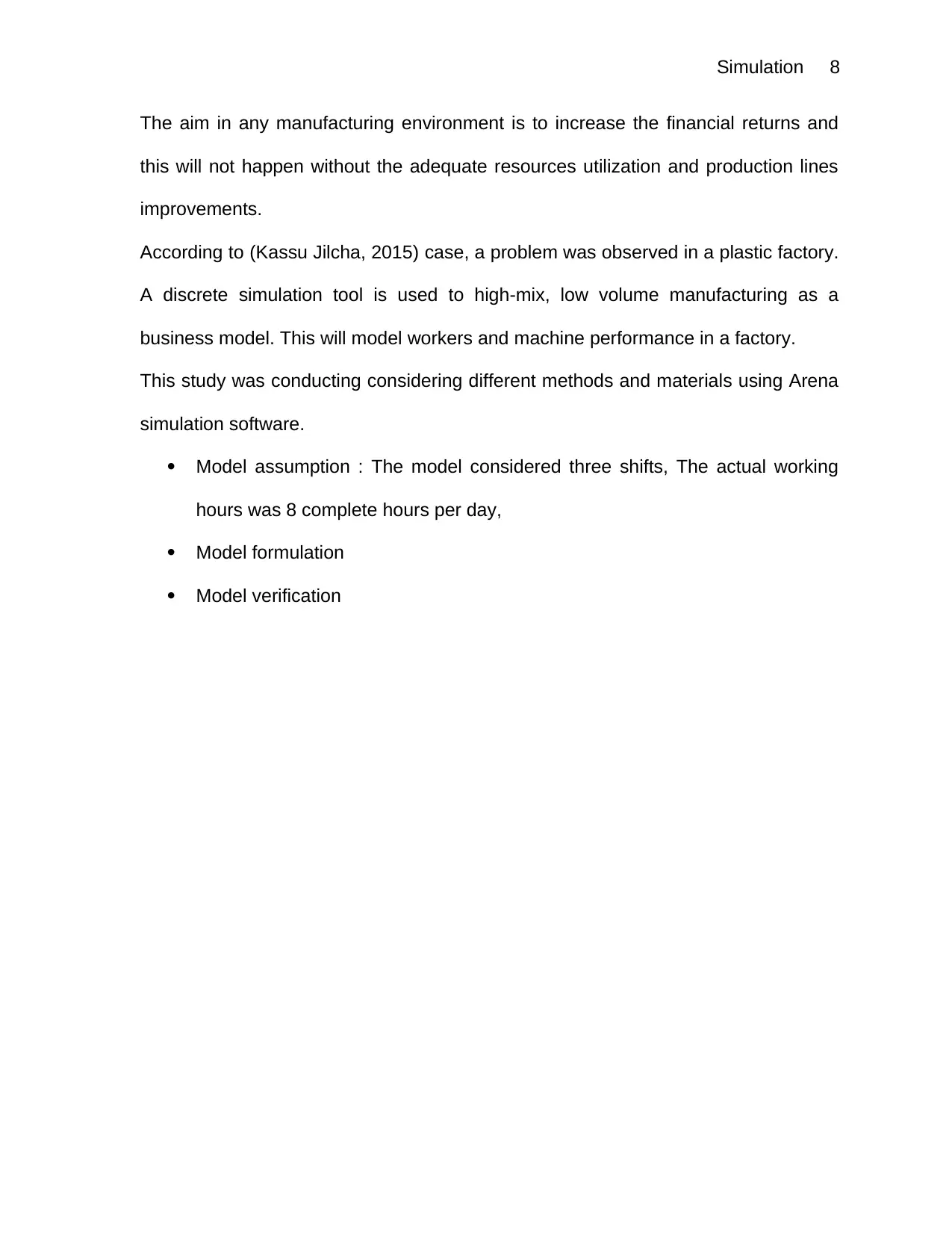
Simulation 8
The aim in any manufacturing environment is to increase the financial returns and
this will not happen without the adequate resources utilization and production lines
improvements.
According to (Kassu Jilcha, 2015) case, a problem was observed in a plastic factory.
A discrete simulation tool is used to high-mix, low volume manufacturing as a
business model. This will model workers and machine performance in a factory.
This study was conducting considering different methods and materials using Arena
simulation software.
Model assumption : The model considered three shifts, The actual working
hours was 8 complete hours per day,
Model formulation
Model verification
The aim in any manufacturing environment is to increase the financial returns and
this will not happen without the adequate resources utilization and production lines
improvements.
According to (Kassu Jilcha, 2015) case, a problem was observed in a plastic factory.
A discrete simulation tool is used to high-mix, low volume manufacturing as a
business model. This will model workers and machine performance in a factory.
This study was conducting considering different methods and materials using Arena
simulation software.
Model assumption : The model considered three shifts, The actual working
hours was 8 complete hours per day,
Model formulation
Model verification

Simulation 9
The problem observed in this case company is the lack of experts and variation on
processing the PVC pipe in adjusting the heat treatment and low capacity utilization
of the workshop which causes variation to the specified product. During this, the
number of recycled products is higher per days. The industry can fail to achieve the
goal for efficient and economical production. Capacity includes all resources such as
machineries, workers etc. of the factory. Industry Performance improvements arising
from increased manufacturing integration continues to be one of the primary
competitive issues in current days.
In Bianchini, et al. (2018) the study utilizes the Arena simulation as one decision-
making software within a complicated manufacturing setup. The operator fatigue,
conveyor speed as well as the incoming quality of materials were chosen in this
study from a variety of parameters that were seen to affect the line outputs. Working
with the DOE (design of experiments) basis, various experiment s were performed
for capturing the effect of parameter input regarding a line’s output. The results
gotten from the experiment was then further taken for analysis with the use of
analysis of variance as well as the response surface methodology. The output of the
line was determined to have more sensitivity to the operator’s fatigue with an
additional quality of incoming material and the conveyor speed. The study has
therefore provided a structured approach in analyzing a vehicle assembly line for the
automotive industry and describes the Arena simulation as software best for
management analysis during complicated manufacturing system functioning.
Nallusamy et al. (2018) give an explanation of the corrective methods to be used in
the elimination of non-value added activities as seen in most die casting industries
The problem observed in this case company is the lack of experts and variation on
processing the PVC pipe in adjusting the heat treatment and low capacity utilization
of the workshop which causes variation to the specified product. During this, the
number of recycled products is higher per days. The industry can fail to achieve the
goal for efficient and economical production. Capacity includes all resources such as
machineries, workers etc. of the factory. Industry Performance improvements arising
from increased manufacturing integration continues to be one of the primary
competitive issues in current days.
In Bianchini, et al. (2018) the study utilizes the Arena simulation as one decision-
making software within a complicated manufacturing setup. The operator fatigue,
conveyor speed as well as the incoming quality of materials were chosen in this
study from a variety of parameters that were seen to affect the line outputs. Working
with the DOE (design of experiments) basis, various experiment s were performed
for capturing the effect of parameter input regarding a line’s output. The results
gotten from the experiment was then further taken for analysis with the use of
analysis of variance as well as the response surface methodology. The output of the
line was determined to have more sensitivity to the operator’s fatigue with an
additional quality of incoming material and the conveyor speed. The study has
therefore provided a structured approach in analyzing a vehicle assembly line for the
automotive industry and describes the Arena simulation as software best for
management analysis during complicated manufacturing system functioning.
Nallusamy et al. (2018) give an explanation of the corrective methods to be used in
the elimination of non-value added activities as seen in most die casting industries
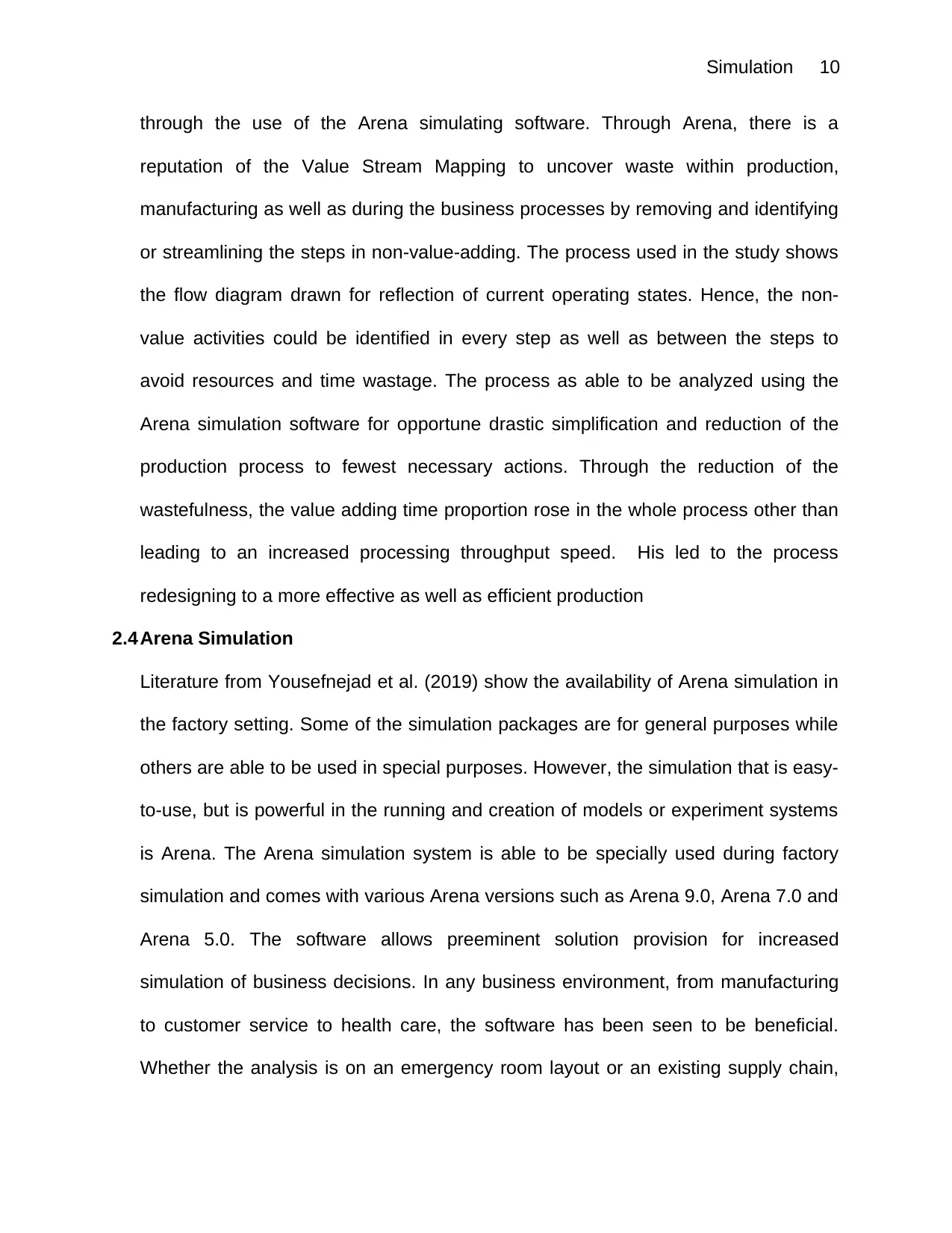
Simulation 10
through the use of the Arena simulating software. Through Arena, there is a
reputation of the Value Stream Mapping to uncover waste within production,
manufacturing as well as during the business processes by removing and identifying
or streamlining the steps in non-value-adding. The process used in the study shows
the flow diagram drawn for reflection of current operating states. Hence, the non-
value activities could be identified in every step as well as between the steps to
avoid resources and time wastage. The process as able to be analyzed using the
Arena simulation software for opportune drastic simplification and reduction of the
production process to fewest necessary actions. Through the reduction of the
wastefulness, the value adding time proportion rose in the whole process other than
leading to an increased processing throughput speed. His led to the process
redesigning to a more effective as well as efficient production
2.4 Arena Simulation
Literature from Yousefnejad et al. (2019) show the availability of Arena simulation in
the factory setting. Some of the simulation packages are for general purposes while
others are able to be used in special purposes. However, the simulation that is easy-
to-use, but is powerful in the running and creation of models or experiment systems
is Arena. The Arena simulation system is able to be specially used during factory
simulation and comes with various Arena versions such as Arena 9.0, Arena 7.0 and
Arena 5.0. The software allows preeminent solution provision for increased
simulation of business decisions. In any business environment, from manufacturing
to customer service to health care, the software has been seen to be beneficial.
Whether the analysis is on an emergency room layout or an existing supply chain,
through the use of the Arena simulating software. Through Arena, there is a
reputation of the Value Stream Mapping to uncover waste within production,
manufacturing as well as during the business processes by removing and identifying
or streamlining the steps in non-value-adding. The process used in the study shows
the flow diagram drawn for reflection of current operating states. Hence, the non-
value activities could be identified in every step as well as between the steps to
avoid resources and time wastage. The process as able to be analyzed using the
Arena simulation software for opportune drastic simplification and reduction of the
production process to fewest necessary actions. Through the reduction of the
wastefulness, the value adding time proportion rose in the whole process other than
leading to an increased processing throughput speed. His led to the process
redesigning to a more effective as well as efficient production
2.4 Arena Simulation
Literature from Yousefnejad et al. (2019) show the availability of Arena simulation in
the factory setting. Some of the simulation packages are for general purposes while
others are able to be used in special purposes. However, the simulation that is easy-
to-use, but is powerful in the running and creation of models or experiment systems
is Arena. The Arena simulation system is able to be specially used during factory
simulation and comes with various Arena versions such as Arena 9.0, Arena 7.0 and
Arena 5.0. The software allows preeminent solution provision for increased
simulation of business decisions. In any business environment, from manufacturing
to customer service to health care, the software has been seen to be beneficial.
Whether the analysis is on an emergency room layout or an existing supply chain,
Secure Best Marks with AI Grader
Need help grading? Try our AI Grader for instant feedback on your assignments.

Simulation 11
only a few five steps are to be followed in using Arena. These steps include basic
model creation, model refining, model simulation, simulation result analysis and
selection of the best alternative.
Looking at Altarazi and Ammouri (2018) the advanced Arena simulation is used as
an ancillary tool to allow the mimicking of system designs other than providing a
suitable environment in which the system of the experiment can be done. Various
possibilities are analyzed during the simulation are the produced model is able to
perform higher than previous models due to the advanced scheduling and planning
ability of the software. In this technique, the Arena software looks to provide for all
the production system’s contingencies rates. In excess, the simulation had proved to
be helpful in finding optimal solutions in the event that the cost of production is
reduced and the rate of service level is set to be respected. Therefore, the system’s
utilization with the variety of operation strategies is able to be presented together
with the level of service and the cost of holding in every scenario. The system’s
potential bottlenecks could be analyzed from the reports of the simulation.
Additionally, the optimal solution for the used stock level buffer was set at a current
rate of demand for best satisfaction.
Arena simulation as defined by Ivanov (2018) is providing powerful functions to be
used in modelling. However, the models in use are not too complex during use. The
simulation software has a flexible model capability in building and has an advanced
transfer or process for helping in modelling with the existing strategic decision in
businesses’ supply chain networks. This capability was noticed to improve the
operational planning or add details within the inventory control or production
only a few five steps are to be followed in using Arena. These steps include basic
model creation, model refining, model simulation, simulation result analysis and
selection of the best alternative.
Looking at Altarazi and Ammouri (2018) the advanced Arena simulation is used as
an ancillary tool to allow the mimicking of system designs other than providing a
suitable environment in which the system of the experiment can be done. Various
possibilities are analyzed during the simulation are the produced model is able to
perform higher than previous models due to the advanced scheduling and planning
ability of the software. In this technique, the Arena software looks to provide for all
the production system’s contingencies rates. In excess, the simulation had proved to
be helpful in finding optimal solutions in the event that the cost of production is
reduced and the rate of service level is set to be respected. Therefore, the system’s
utilization with the variety of operation strategies is able to be presented together
with the level of service and the cost of holding in every scenario. The system’s
potential bottlenecks could be analyzed from the reports of the simulation.
Additionally, the optimal solution for the used stock level buffer was set at a current
rate of demand for best satisfaction.
Arena simulation as defined by Ivanov (2018) is providing powerful functions to be
used in modelling. However, the models in use are not too complex during use. The
simulation software has a flexible model capability in building and has an advanced
transfer or process for helping in modelling with the existing strategic decision in
businesses’ supply chain networks. This capability was noticed to improve the
operational planning or add details within the inventory control or production
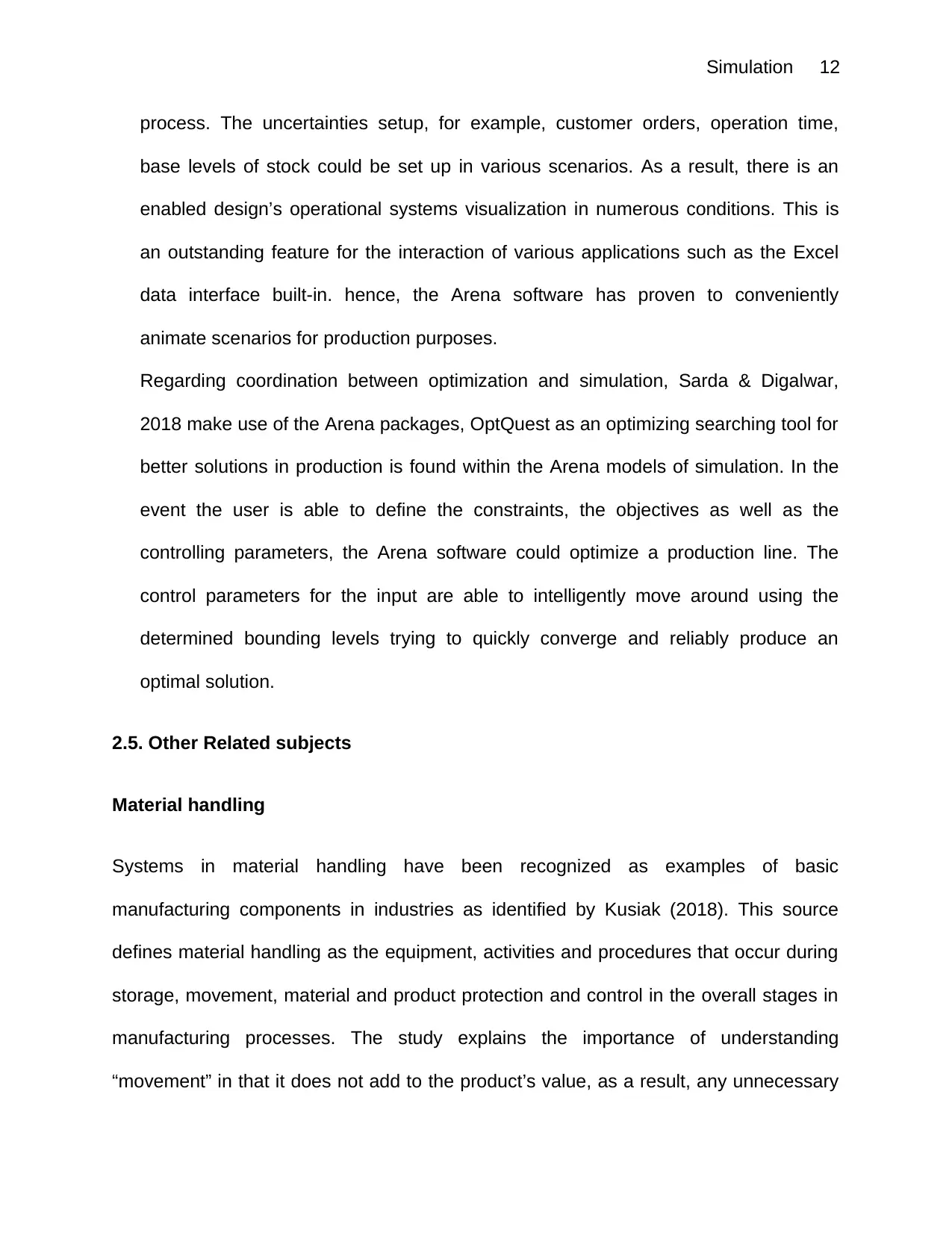
Simulation 12
process. The uncertainties setup, for example, customer orders, operation time,
base levels of stock could be set up in various scenarios. As a result, there is an
enabled design’s operational systems visualization in numerous conditions. This is
an outstanding feature for the interaction of various applications such as the Excel
data interface built-in. hence, the Arena software has proven to conveniently
animate scenarios for production purposes.
Regarding coordination between optimization and simulation, Sarda & Digalwar,
2018 make use of the Arena packages, OptQuest as an optimizing searching tool for
better solutions in production is found within the Arena models of simulation. In the
event the user is able to define the constraints, the objectives as well as the
controlling parameters, the Arena software could optimize a production line. The
control parameters for the input are able to intelligently move around using the
determined bounding levels trying to quickly converge and reliably produce an
optimal solution.
2.5. Other Related subjects
Material handling
Systems in material handling have been recognized as examples of basic
manufacturing components in industries as identified by Kusiak (2018). This source
defines material handling as the equipment, activities and procedures that occur during
storage, movement, material and product protection and control in the overall stages in
manufacturing processes. The study explains the importance of understanding
“movement” in that it does not add to the product’s value, as a result, any unnecessary
process. The uncertainties setup, for example, customer orders, operation time,
base levels of stock could be set up in various scenarios. As a result, there is an
enabled design’s operational systems visualization in numerous conditions. This is
an outstanding feature for the interaction of various applications such as the Excel
data interface built-in. hence, the Arena software has proven to conveniently
animate scenarios for production purposes.
Regarding coordination between optimization and simulation, Sarda & Digalwar,
2018 make use of the Arena packages, OptQuest as an optimizing searching tool for
better solutions in production is found within the Arena models of simulation. In the
event the user is able to define the constraints, the objectives as well as the
controlling parameters, the Arena software could optimize a production line. The
control parameters for the input are able to intelligently move around using the
determined bounding levels trying to quickly converge and reliably produce an
optimal solution.
2.5. Other Related subjects
Material handling
Systems in material handling have been recognized as examples of basic
manufacturing components in industries as identified by Kusiak (2018). This source
defines material handling as the equipment, activities and procedures that occur during
storage, movement, material and product protection and control in the overall stages in
manufacturing processes. The study explains the importance of understanding
“movement” in that it does not add to the product’s value, as a result, any unnecessary
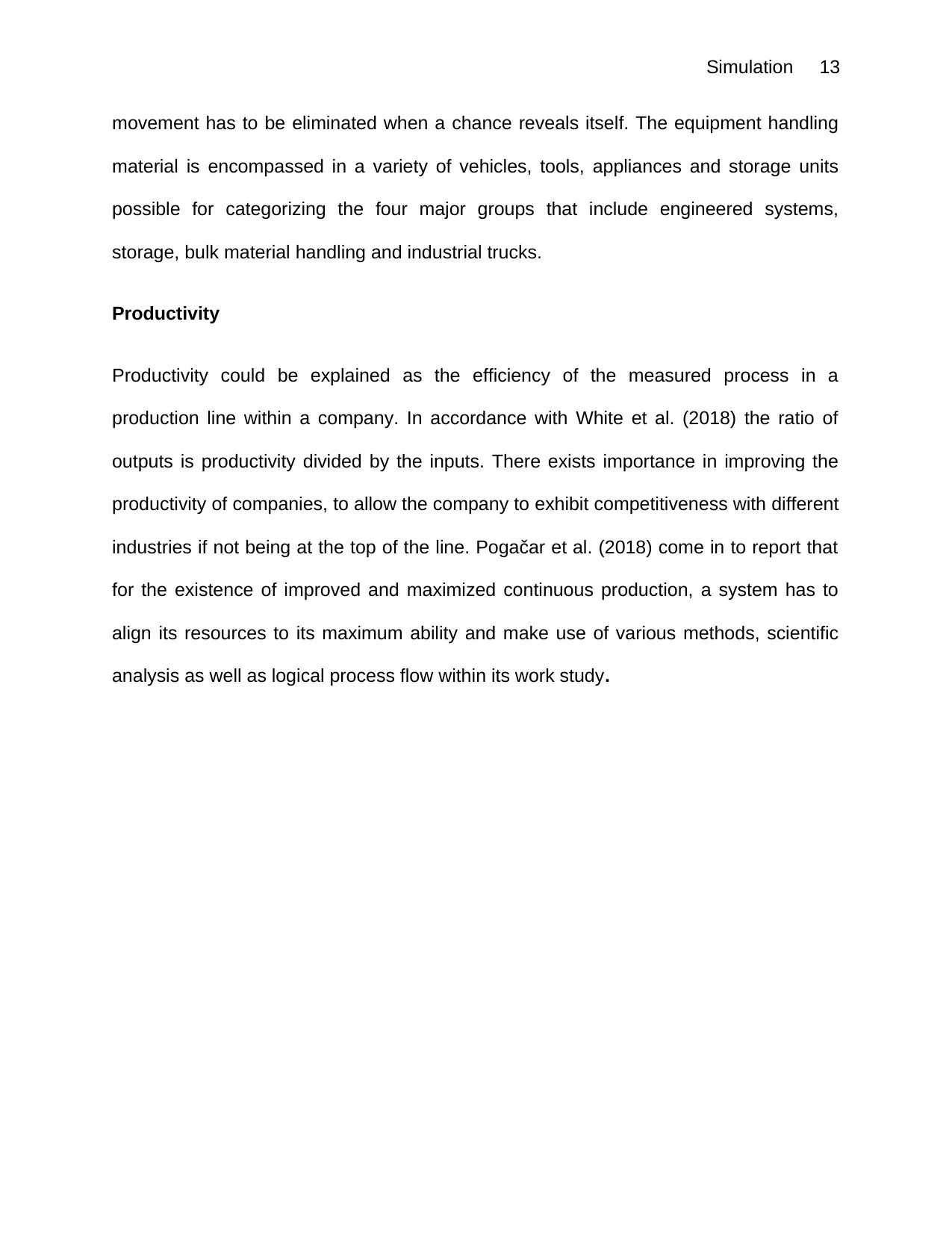
Simulation 13
movement has to be eliminated when a chance reveals itself. The equipment handling
material is encompassed in a variety of vehicles, tools, appliances and storage units
possible for categorizing the four major groups that include engineered systems,
storage, bulk material handling and industrial trucks.
Productivity
Productivity could be explained as the efficiency of the measured process in a
production line within a company. In accordance with White et al. (2018) the ratio of
outputs is productivity divided by the inputs. There exists importance in improving the
productivity of companies, to allow the company to exhibit competitiveness with different
industries if not being at the top of the line. Pogačar et al. (2018) come in to report that
for the existence of improved and maximized continuous production, a system has to
align its resources to its maximum ability and make use of various methods, scientific
analysis as well as logical process flow within its work study.
movement has to be eliminated when a chance reveals itself. The equipment handling
material is encompassed in a variety of vehicles, tools, appliances and storage units
possible for categorizing the four major groups that include engineered systems,
storage, bulk material handling and industrial trucks.
Productivity
Productivity could be explained as the efficiency of the measured process in a
production line within a company. In accordance with White et al. (2018) the ratio of
outputs is productivity divided by the inputs. There exists importance in improving the
productivity of companies, to allow the company to exhibit competitiveness with different
industries if not being at the top of the line. Pogačar et al. (2018) come in to report that
for the existence of improved and maximized continuous production, a system has to
align its resources to its maximum ability and make use of various methods, scientific
analysis as well as logical process flow within its work study.
Paraphrase This Document
Need a fresh take? Get an instant paraphrase of this document with our AI Paraphraser

Simulation 14
References
Altarazi, S. and Ammouri, M. (2018). Concurrent manual-order-picking warehouse
design: a simulation-based design of experiments approach. International Journal of
Production Research, 56(23), pp. 7103-7121.
Bianchini, J., Darú, G. and Berger, S. (2018). Analysis of production planning and
control based on the simulation of a production process using a hybrid MRP and
Kanban model. Journal of Lean Systems, 3(1), pp. 66-86.
Choudhari, S. and Gajjar, H. (2018). Simulation modelling for manpower planning in the
electrical maintenance service facility. Business Process Management Journal, 24(1),
pp. 89-104.
Heath, S. and Yoho, K. (2017). Using simulation to illuminate process improvement
opportunities in a US naval aircraft overhaul facility. Production Planning & Control,
28(14), pp. 1152-1164.
Ivanov, D. (2018). Revealing interfaces of supply chain resilience and sustainability: a
simulation study. International Journal of Production Research, 56(10), pp. 3507-3523.
Kusiak, A. (2018). Smart manufacturing. International Journal of Production Research,
56(2), pp. 508-517.
Li, C., Liu, J. and Li, B. (2018). Performance Prediction and Evaluation Based on the
Variability Theory in Production Lines Using ARENA Simulation. Wireless Personal
Communications, 103(1), pp. 897-920.
References
Altarazi, S. and Ammouri, M. (2018). Concurrent manual-order-picking warehouse
design: a simulation-based design of experiments approach. International Journal of
Production Research, 56(23), pp. 7103-7121.
Bianchini, J., Darú, G. and Berger, S. (2018). Analysis of production planning and
control based on the simulation of a production process using a hybrid MRP and
Kanban model. Journal of Lean Systems, 3(1), pp. 66-86.
Choudhari, S. and Gajjar, H. (2018). Simulation modelling for manpower planning in the
electrical maintenance service facility. Business Process Management Journal, 24(1),
pp. 89-104.
Heath, S. and Yoho, K. (2017). Using simulation to illuminate process improvement
opportunities in a US naval aircraft overhaul facility. Production Planning & Control,
28(14), pp. 1152-1164.
Ivanov, D. (2018). Revealing interfaces of supply chain resilience and sustainability: a
simulation study. International Journal of Production Research, 56(10), pp. 3507-3523.
Kusiak, A. (2018). Smart manufacturing. International Journal of Production Research,
56(2), pp. 508-517.
Li, C., Liu, J. and Li, B. (2018). Performance Prediction and Evaluation Based on the
Variability Theory in Production Lines Using ARENA Simulation. Wireless Personal
Communications, 103(1), pp. 897-920.
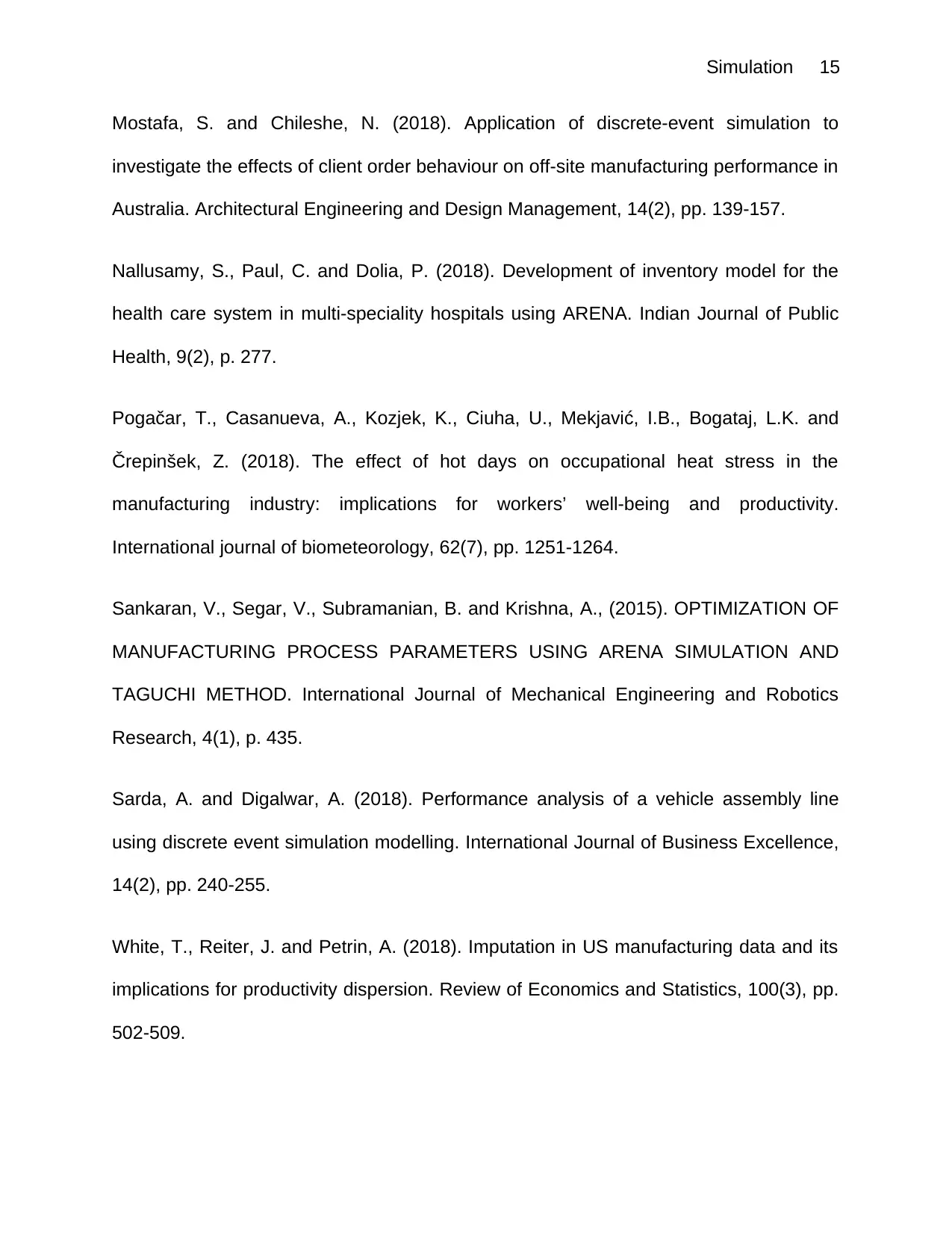
Simulation 15
Mostafa, S. and Chileshe, N. (2018). Application of discrete-event simulation to
investigate the effects of client order behaviour on off-site manufacturing performance in
Australia. Architectural Engineering and Design Management, 14(2), pp. 139-157.
Nallusamy, S., Paul, C. and Dolia, P. (2018). Development of inventory model for the
health care system in multi-speciality hospitals using ARENA. Indian Journal of Public
Health, 9(2), p. 277.
Pogačar, T., Casanueva, A., Kozjek, K., Ciuha, U., Mekjavić, I.B., Bogataj, L.K. and
Črepinšek, Z. (2018). The effect of hot days on occupational heat stress in the
manufacturing industry: implications for workers’ well-being and productivity.
International journal of biometeorology, 62(7), pp. 1251-1264.
Sankaran, V., Segar, V., Subramanian, B. and Krishna, A., (2015). OPTIMIZATION OF
MANUFACTURING PROCESS PARAMETERS USING ARENA SIMULATION AND
TAGUCHI METHOD. International Journal of Mechanical Engineering and Robotics
Research, 4(1), p. 435.
Sarda, A. and Digalwar, A. (2018). Performance analysis of a vehicle assembly line
using discrete event simulation modelling. International Journal of Business Excellence,
14(2), pp. 240-255.
White, T., Reiter, J. and Petrin, A. (2018). Imputation in US manufacturing data and its
implications for productivity dispersion. Review of Economics and Statistics, 100(3), pp.
502-509.
Mostafa, S. and Chileshe, N. (2018). Application of discrete-event simulation to
investigate the effects of client order behaviour on off-site manufacturing performance in
Australia. Architectural Engineering and Design Management, 14(2), pp. 139-157.
Nallusamy, S., Paul, C. and Dolia, P. (2018). Development of inventory model for the
health care system in multi-speciality hospitals using ARENA. Indian Journal of Public
Health, 9(2), p. 277.
Pogačar, T., Casanueva, A., Kozjek, K., Ciuha, U., Mekjavić, I.B., Bogataj, L.K. and
Črepinšek, Z. (2018). The effect of hot days on occupational heat stress in the
manufacturing industry: implications for workers’ well-being and productivity.
International journal of biometeorology, 62(7), pp. 1251-1264.
Sankaran, V., Segar, V., Subramanian, B. and Krishna, A., (2015). OPTIMIZATION OF
MANUFACTURING PROCESS PARAMETERS USING ARENA SIMULATION AND
TAGUCHI METHOD. International Journal of Mechanical Engineering and Robotics
Research, 4(1), p. 435.
Sarda, A. and Digalwar, A. (2018). Performance analysis of a vehicle assembly line
using discrete event simulation modelling. International Journal of Business Excellence,
14(2), pp. 240-255.
White, T., Reiter, J. and Petrin, A. (2018). Imputation in US manufacturing data and its
implications for productivity dispersion. Review of Economics and Statistics, 100(3), pp.
502-509.
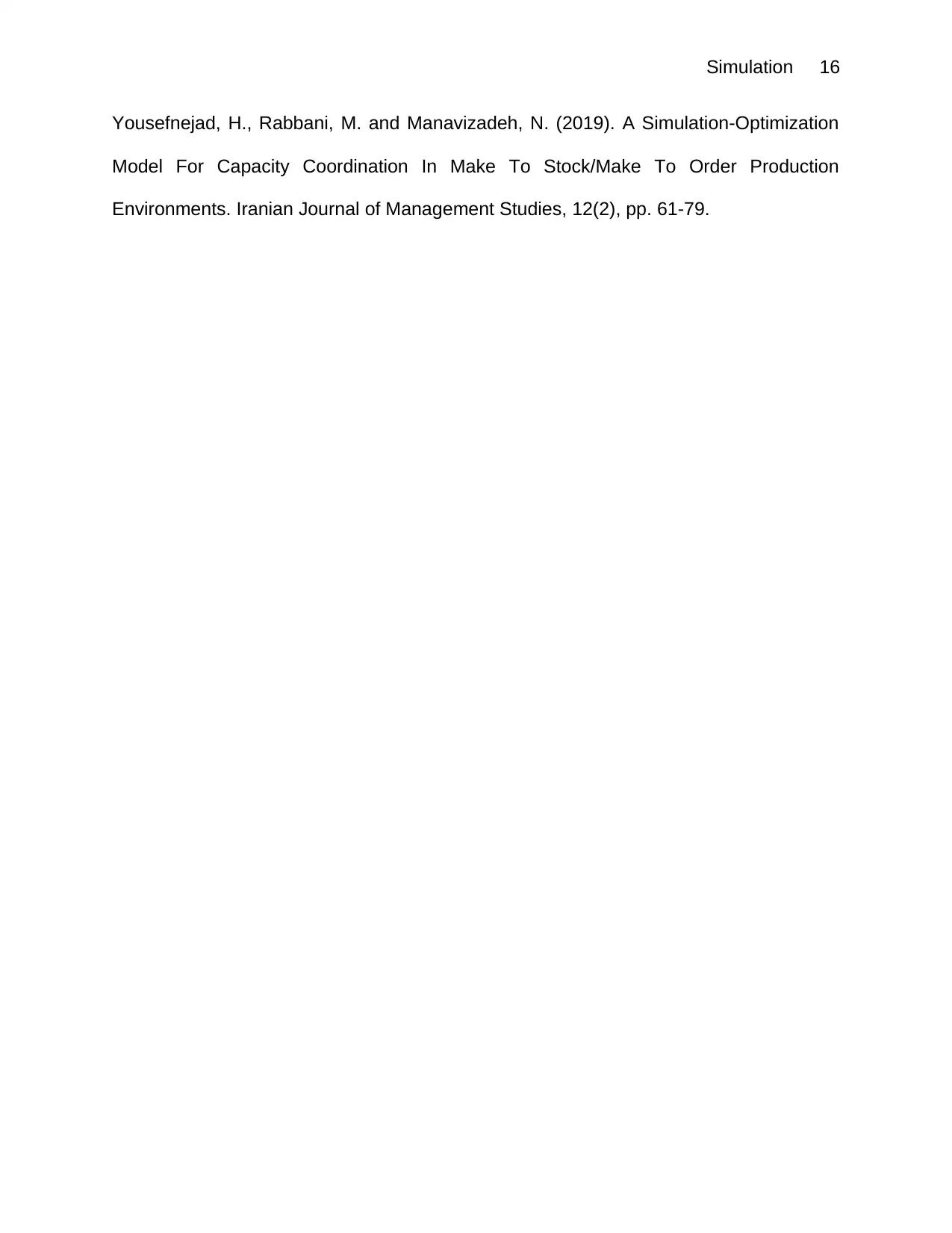
Simulation 16
Yousefnejad, H., Rabbani, M. and Manavizadeh, N. (2019). A Simulation-Optimization
Model For Capacity Coordination In Make To Stock/Make To Order Production
Environments. Iranian Journal of Management Studies, 12(2), pp. 61-79.
Yousefnejad, H., Rabbani, M. and Manavizadeh, N. (2019). A Simulation-Optimization
Model For Capacity Coordination In Make To Stock/Make To Order Production
Environments. Iranian Journal of Management Studies, 12(2), pp. 61-79.
1 out of 16
![[object Object]](/_next/image/?url=%2F_next%2Fstatic%2Fmedia%2Flogo.6d15ce61.png&w=640&q=75)
Your All-in-One AI-Powered Toolkit for Academic Success.
+13062052269
info@desklib.com
Available 24*7 on WhatsApp / Email
Unlock your academic potential
© 2024 | Zucol Services PVT LTD | All rights reserved.