Simulation of Plastic Analysis - Study Properties, Material Properties, Loads and Fixtures, Mesh Information, Study Results
VerifiedAdded on  2022/10/02
|11
|619
|163
AI Summary
Get detailed information about the study properties, material properties, loads and fixtures, mesh information, and study results of Plastic Analysis simulation on Desklib. Analyzed with SOLIDWORKS Simulation.
Contribute Materials
Your contribution can guide someone’s learning journey. Share your
documents today.
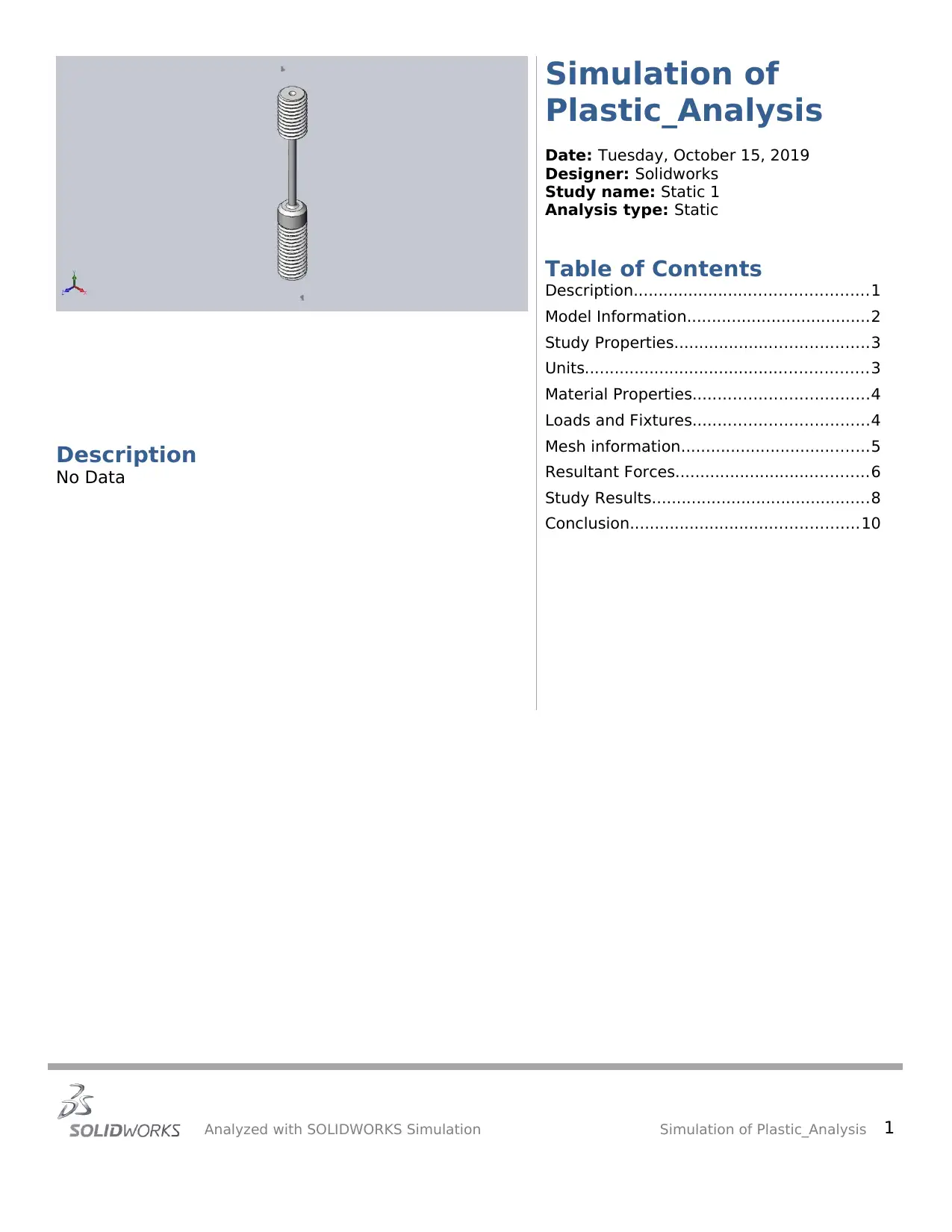
Simulation of
Plastic_Analysis
Date: Tuesday, October 15, 2019
Designer: Solidworks
Study name: Static 1
Analysis type: Static
Table of Contents
Description...............................................1
Model Information.....................................2
Study Properties.......................................3
Units.........................................................3
Material Properties...................................4
Loads and Fixtures...................................4
Mesh information......................................5
Resultant Forces.......................................6
Study Results............................................8
Conclusion..............................................10
Description
No Data
Analyzed with SOLIDWORKS Simulation Simulation of Plastic_Analysis 1
Plastic_Analysis
Date: Tuesday, October 15, 2019
Designer: Solidworks
Study name: Static 1
Analysis type: Static
Table of Contents
Description...............................................1
Model Information.....................................2
Study Properties.......................................3
Units.........................................................3
Material Properties...................................4
Loads and Fixtures...................................4
Mesh information......................................5
Resultant Forces.......................................6
Study Results............................................8
Conclusion..............................................10
Description
No Data
Analyzed with SOLIDWORKS Simulation Simulation of Plastic_Analysis 1
Secure Best Marks with AI Grader
Need help grading? Try our AI Grader for instant feedback on your assignments.
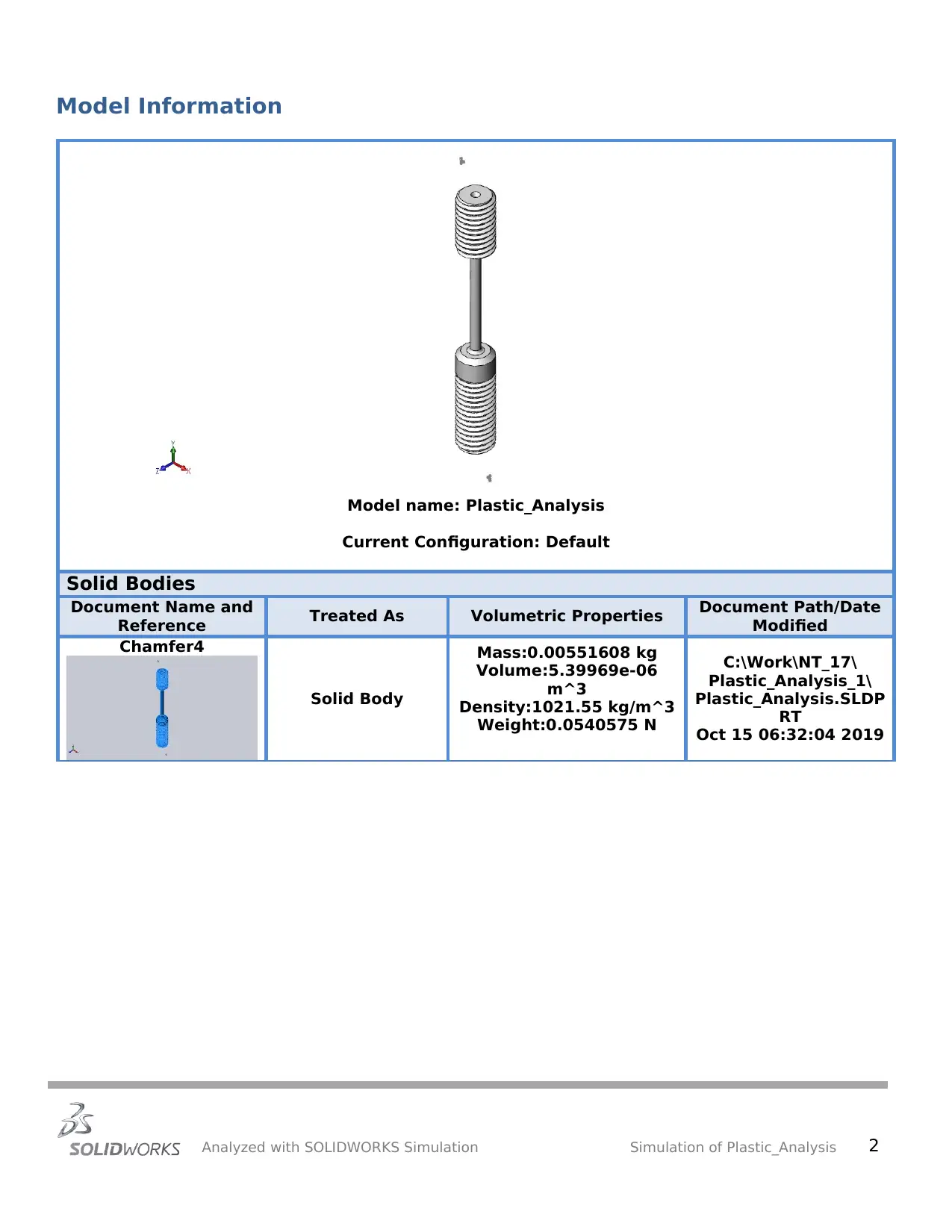
Model Information
Model name: Plastic_Analysis
Current Configuration: Default
Solid Bodies
Document Name and
Reference Treated As Volumetric Properties Document Path/Date
Modified
Chamfer4
Solid Body
Mass:0.00551608 kg
Volume:5.39969e-06
m^3
Density:1021.55 kg/m^3
Weight:0.0540575 N
C:\Work\NT_17\
Plastic_Analysis_1\
Plastic_Analysis.SLDP
RT
Oct 15 06:32:04 2019
Analyzed with SOLIDWORKS Simulation Simulation of Plastic_Analysis 2
Model name: Plastic_Analysis
Current Configuration: Default
Solid Bodies
Document Name and
Reference Treated As Volumetric Properties Document Path/Date
Modified
Chamfer4
Solid Body
Mass:0.00551608 kg
Volume:5.39969e-06
m^3
Density:1021.55 kg/m^3
Weight:0.0540575 N
C:\Work\NT_17\
Plastic_Analysis_1\
Plastic_Analysis.SLDP
RT
Oct 15 06:32:04 2019
Analyzed with SOLIDWORKS Simulation Simulation of Plastic_Analysis 2
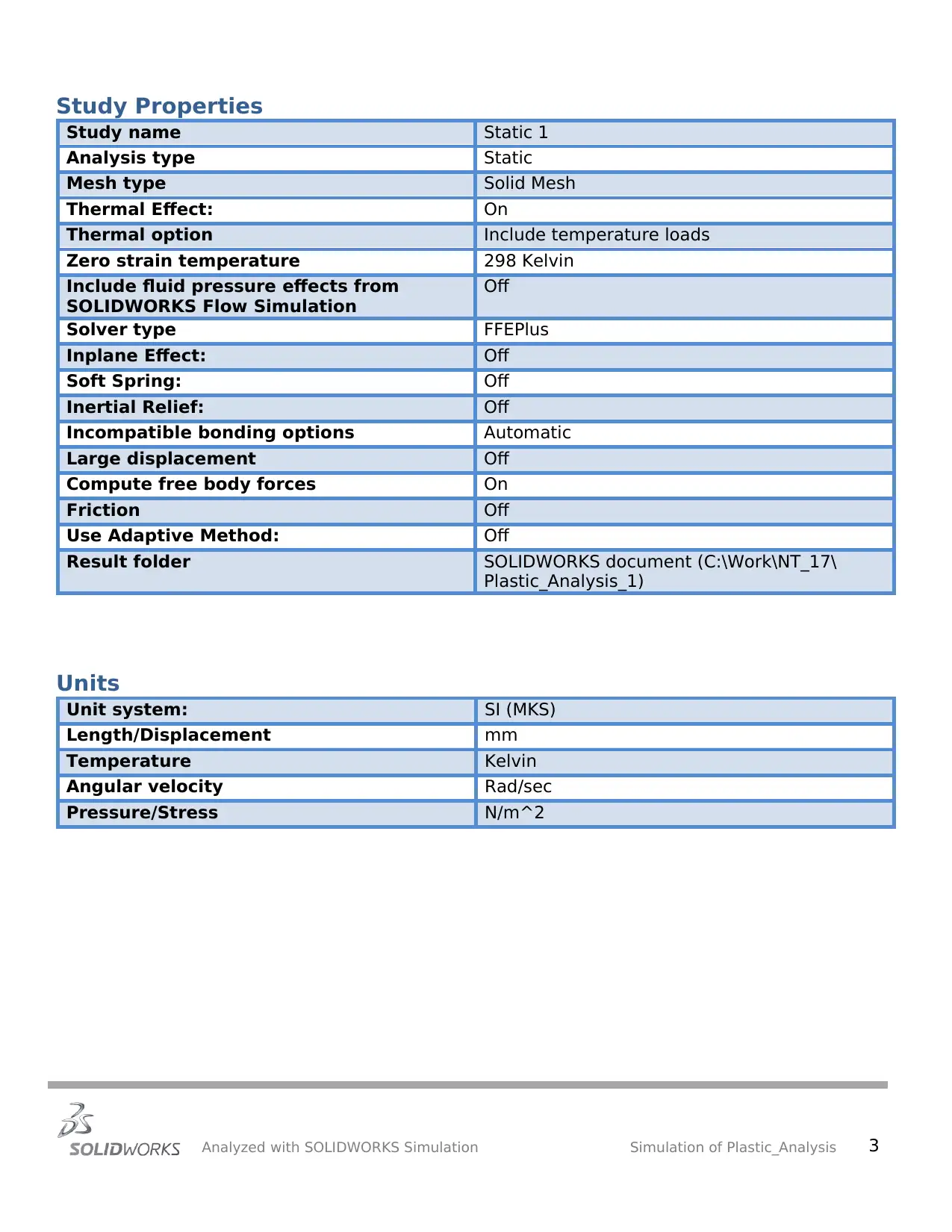
Study Properties
Study name Static 1
Analysis type Static
Mesh type Solid Mesh
Thermal Effect: On
Thermal option Include temperature loads
Zero strain temperature 298 Kelvin
Include fluid pressure effects from
SOLIDWORKS Flow Simulation
Off
Solver type FFEPlus
Inplane Effect: Off
Soft Spring: Off
Inertial Relief: Off
Incompatible bonding options Automatic
Large displacement Off
Compute free body forces On
Friction Off
Use Adaptive Method: Off
Result folder SOLIDWORKS document (C:\Work\NT_17\
Plastic_Analysis_1)
Units
Unit system: SI (MKS)
Length/Displacement mm
Temperature Kelvin
Angular velocity Rad/sec
Pressure/Stress N/m^2
Analyzed with SOLIDWORKS Simulation Simulation of Plastic_Analysis 3
Study name Static 1
Analysis type Static
Mesh type Solid Mesh
Thermal Effect: On
Thermal option Include temperature loads
Zero strain temperature 298 Kelvin
Include fluid pressure effects from
SOLIDWORKS Flow Simulation
Off
Solver type FFEPlus
Inplane Effect: Off
Soft Spring: Off
Inertial Relief: Off
Incompatible bonding options Automatic
Large displacement Off
Compute free body forces On
Friction Off
Use Adaptive Method: Off
Result folder SOLIDWORKS document (C:\Work\NT_17\
Plastic_Analysis_1)
Units
Unit system: SI (MKS)
Length/Displacement mm
Temperature Kelvin
Angular velocity Rad/sec
Pressure/Stress N/m^2
Analyzed with SOLIDWORKS Simulation Simulation of Plastic_Analysis 3
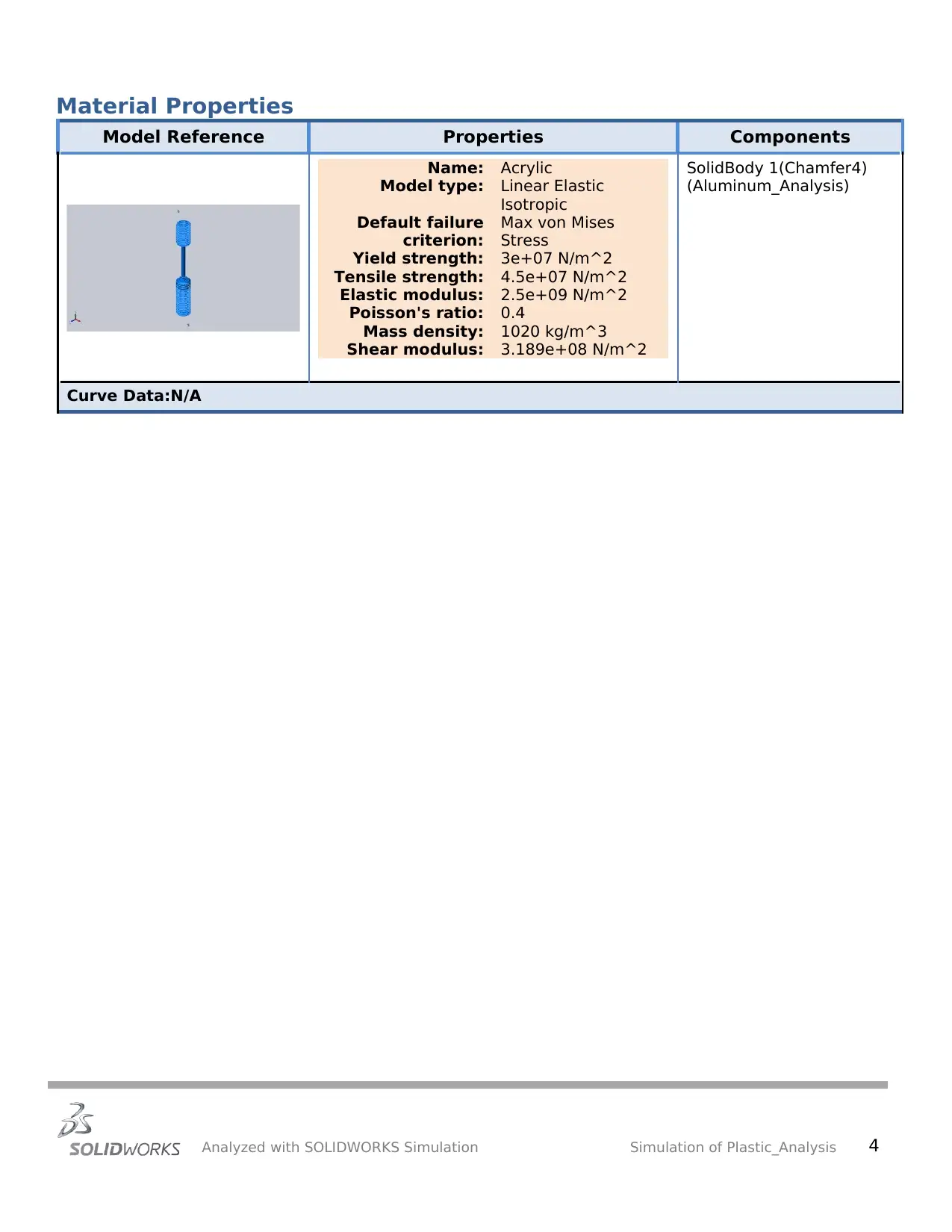
Material Properties
Model Reference Properties Components
Name: Acrylic
Model type: Linear Elastic
Isotropic
Default failure
criterion:
Max von Mises
Stress
Yield strength: 3e+07 N/m^2
Tensile strength: 4.5e+07 N/m^2
Elastic modulus: 2.5e+09 N/m^2
Poisson's ratio: 0.4
Mass density: 1020 kg/m^3
Shear modulus: 3.189e+08 N/m^2
SolidBody 1(Chamfer4)
(Aluminum_Analysis)
Curve Data:N/A
Analyzed with SOLIDWORKS Simulation Simulation of Plastic_Analysis 4
Model Reference Properties Components
Name: Acrylic
Model type: Linear Elastic
Isotropic
Default failure
criterion:
Max von Mises
Stress
Yield strength: 3e+07 N/m^2
Tensile strength: 4.5e+07 N/m^2
Elastic modulus: 2.5e+09 N/m^2
Poisson's ratio: 0.4
Mass density: 1020 kg/m^3
Shear modulus: 3.189e+08 N/m^2
SolidBody 1(Chamfer4)
(Aluminum_Analysis)
Curve Data:N/A
Analyzed with SOLIDWORKS Simulation Simulation of Plastic_Analysis 4
Secure Best Marks with AI Grader
Need help grading? Try our AI Grader for instant feedback on your assignments.
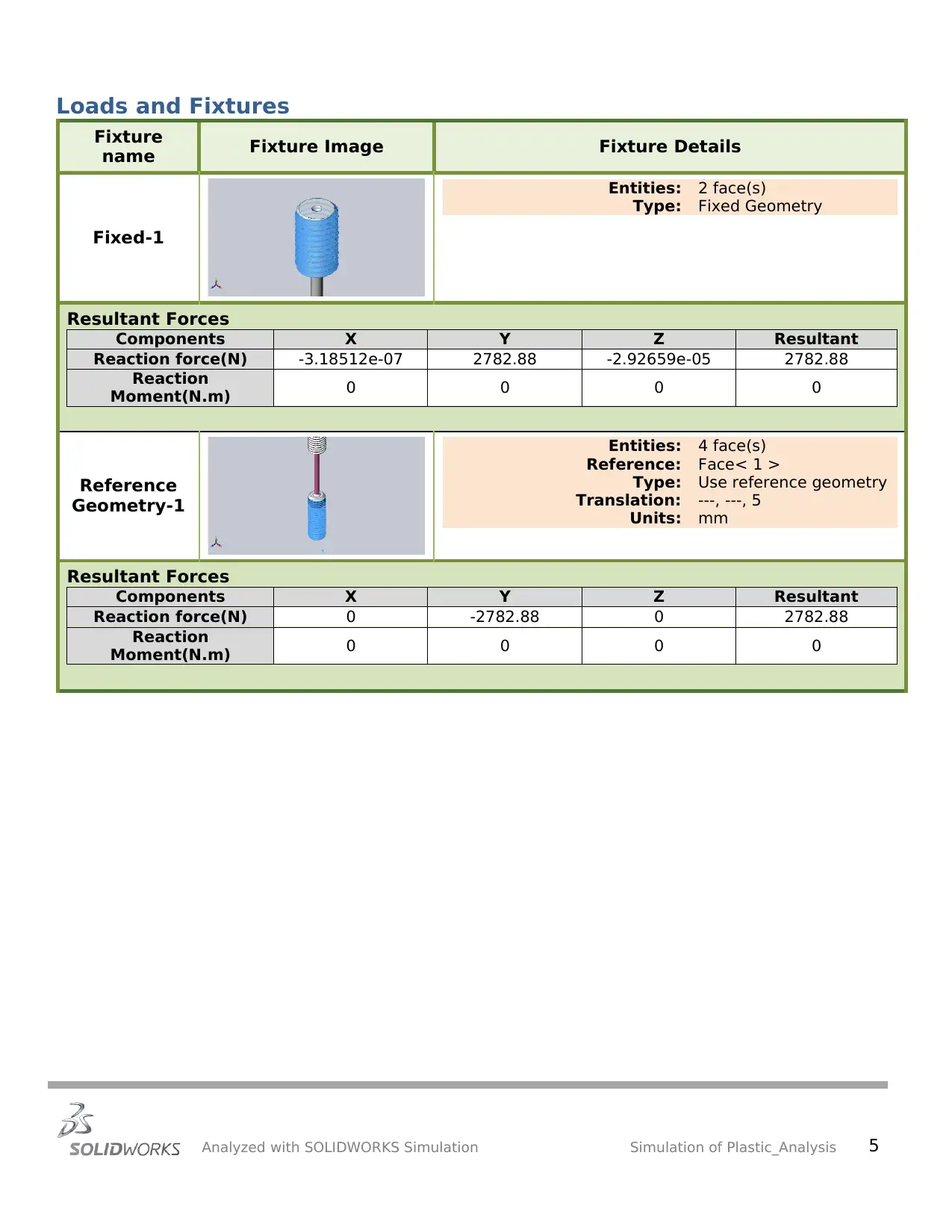
Loads and Fixtures
Fixture
name Fixture Image Fixture Details
Fixed-1
Entities: 2 face(s)
Type: Fixed Geometry
Resultant Forces
Components X Y Z Resultant
Reaction force(N) -3.18512e-07 2782.88 -2.92659e-05 2782.88
Reaction
Moment(N.m) 0 0 0 0
Reference
Geometry-1
Entities: 4 face(s)
Reference: Face< 1 >
Type: Use reference geometry
Translation: ---, ---, 5
Units: mm
Resultant Forces
Components X Y Z Resultant
Reaction force(N) 0 -2782.88 0 2782.88
Reaction
Moment(N.m) 0 0 0 0
Analyzed with SOLIDWORKS Simulation Simulation of Plastic_Analysis 5
Fixture
name Fixture Image Fixture Details
Fixed-1
Entities: 2 face(s)
Type: Fixed Geometry
Resultant Forces
Components X Y Z Resultant
Reaction force(N) -3.18512e-07 2782.88 -2.92659e-05 2782.88
Reaction
Moment(N.m) 0 0 0 0
Reference
Geometry-1
Entities: 4 face(s)
Reference: Face< 1 >
Type: Use reference geometry
Translation: ---, ---, 5
Units: mm
Resultant Forces
Components X Y Z Resultant
Reaction force(N) 0 -2782.88 0 2782.88
Reaction
Moment(N.m) 0 0 0 0
Analyzed with SOLIDWORKS Simulation Simulation of Plastic_Analysis 5
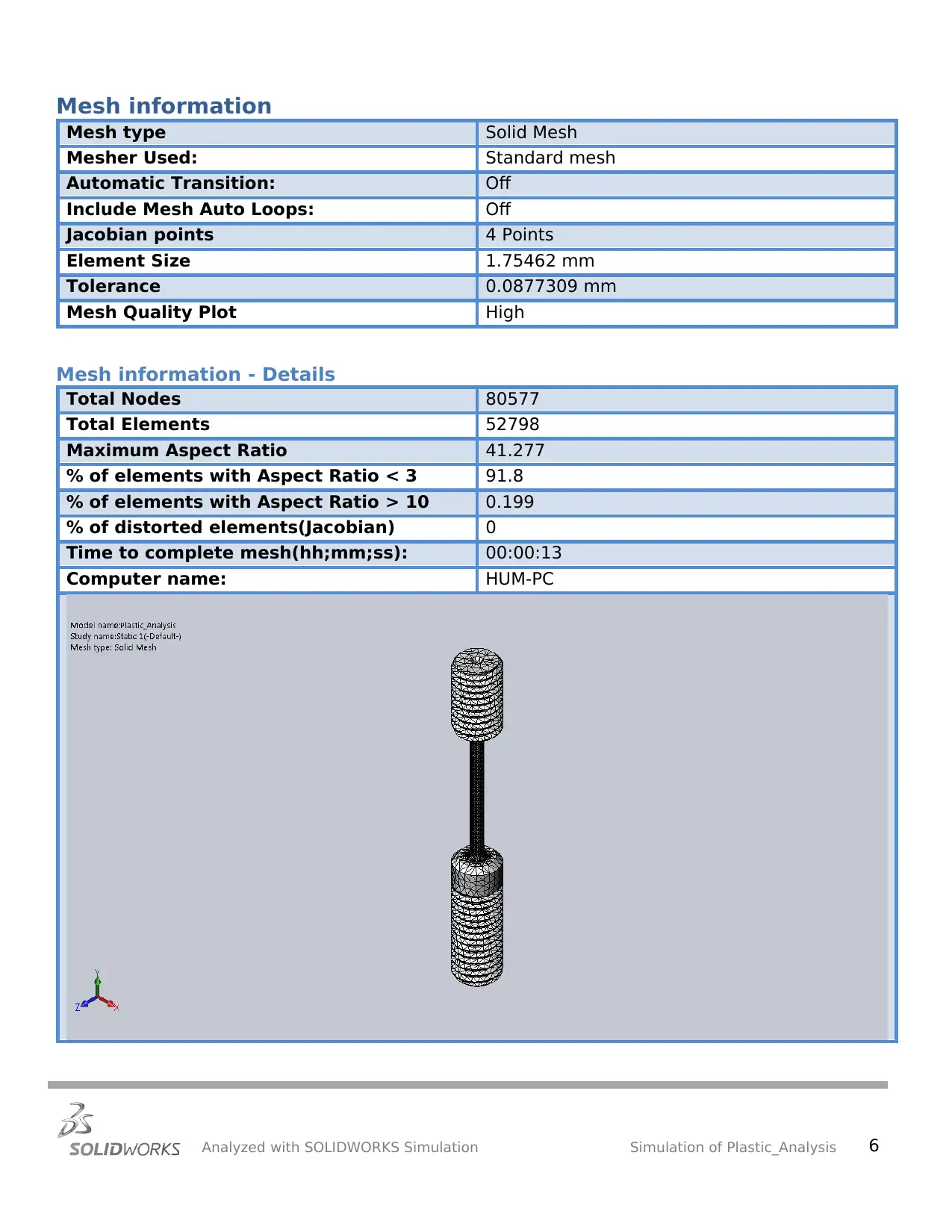
Mesh information
Mesh type Solid Mesh
Mesher Used: Standard mesh
Automatic Transition: Off
Include Mesh Auto Loops: Off
Jacobian points 4 Points
Element Size 1.75462 mm
Tolerance 0.0877309 mm
Mesh Quality Plot High
Mesh information - Details
Total Nodes 80577
Total Elements 52798
Maximum Aspect Ratio 41.277
% of elements with Aspect Ratio < 3 91.8
% of elements with Aspect Ratio > 10 0.199
% of distorted elements(Jacobian) 0
Time to complete mesh(hh;mm;ss): 00:00:13
Computer name: HUM-PC
Analyzed with SOLIDWORKS Simulation Simulation of Plastic_Analysis 6
Mesh type Solid Mesh
Mesher Used: Standard mesh
Automatic Transition: Off
Include Mesh Auto Loops: Off
Jacobian points 4 Points
Element Size 1.75462 mm
Tolerance 0.0877309 mm
Mesh Quality Plot High
Mesh information - Details
Total Nodes 80577
Total Elements 52798
Maximum Aspect Ratio 41.277
% of elements with Aspect Ratio < 3 91.8
% of elements with Aspect Ratio > 10 0.199
% of distorted elements(Jacobian) 0
Time to complete mesh(hh;mm;ss): 00:00:13
Computer name: HUM-PC
Analyzed with SOLIDWORKS Simulation Simulation of Plastic_Analysis 6
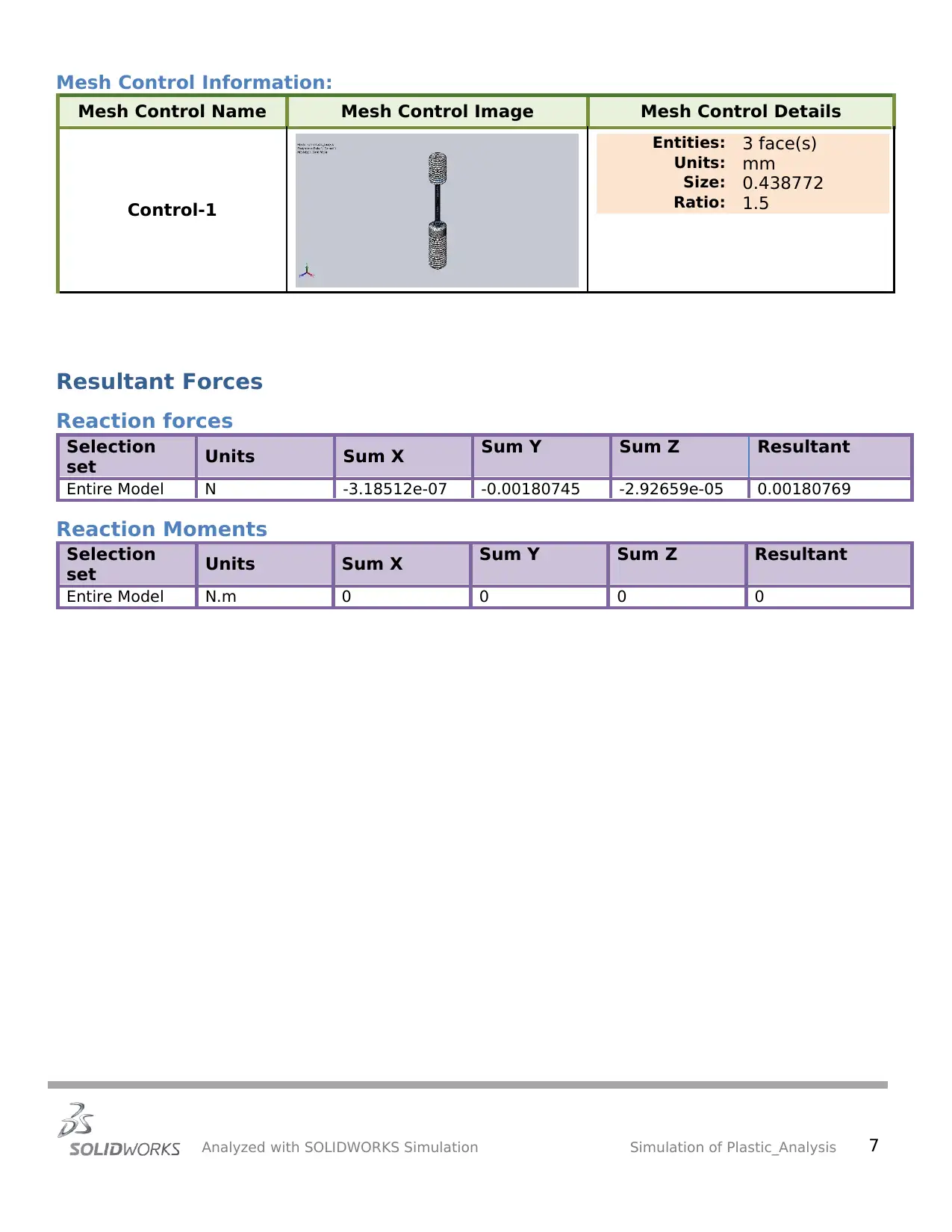
Mesh Control Information:
Mesh Control Name Mesh Control Image Mesh Control Details
Control-1
Entities: 3 face(s)
Units: mm
Size: 0.438772
Ratio: 1.5
Resultant Forces
Reaction forces
Selection
set Units Sum X Sum Y Sum Z Resultant
Entire Model N -3.18512e-07 -0.00180745 -2.92659e-05 0.00180769
Reaction Moments
Selection
set Units Sum X Sum Y Sum Z Resultant
Entire Model N.m 0 0 0 0
Analyzed with SOLIDWORKS Simulation Simulation of Plastic_Analysis 7
Mesh Control Name Mesh Control Image Mesh Control Details
Control-1
Entities: 3 face(s)
Units: mm
Size: 0.438772
Ratio: 1.5
Resultant Forces
Reaction forces
Selection
set Units Sum X Sum Y Sum Z Resultant
Entire Model N -3.18512e-07 -0.00180745 -2.92659e-05 0.00180769
Reaction Moments
Selection
set Units Sum X Sum Y Sum Z Resultant
Entire Model N.m 0 0 0 0
Analyzed with SOLIDWORKS Simulation Simulation of Plastic_Analysis 7
Paraphrase This Document
Need a fresh take? Get an instant paraphrase of this document with our AI Paraphraser
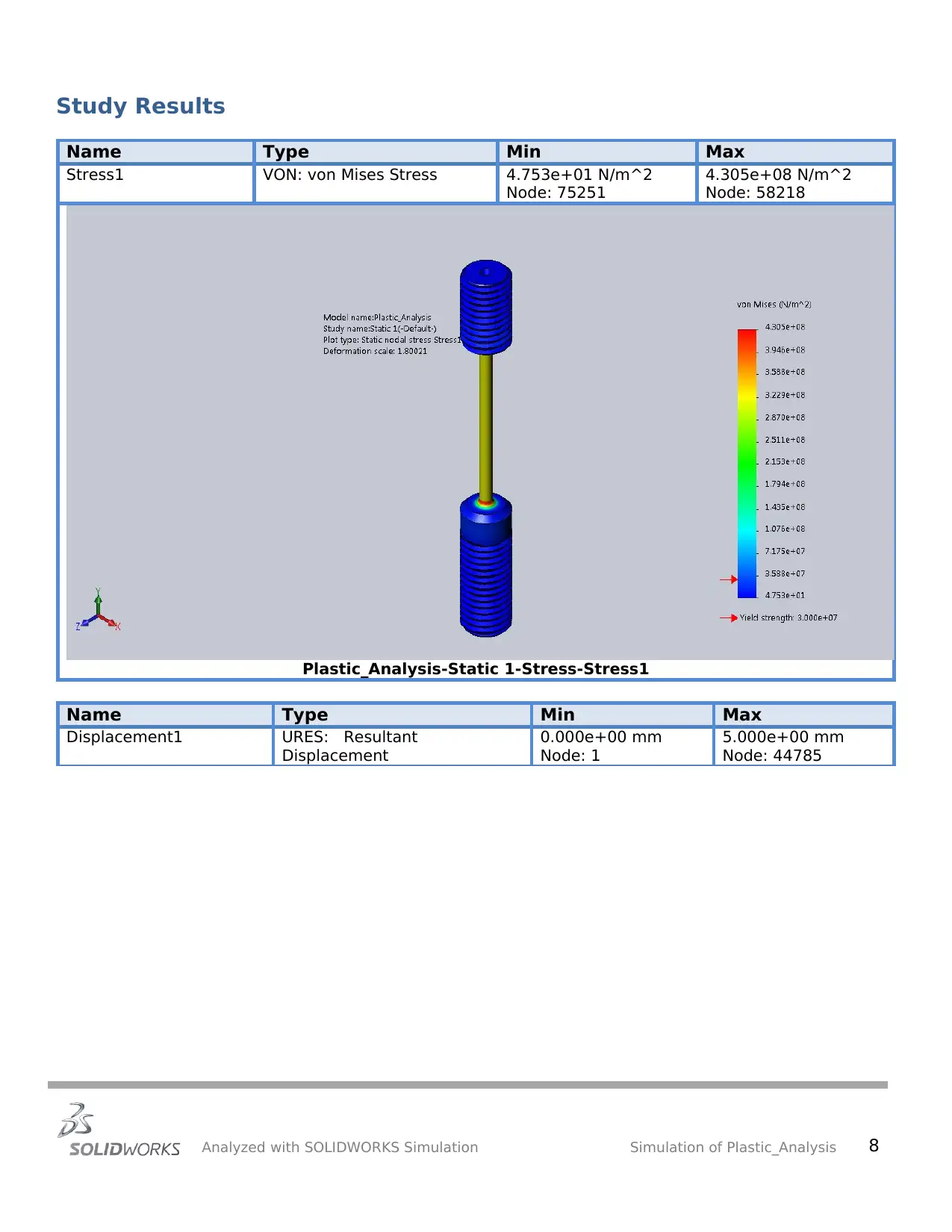
Study Results
Name Type Min Max
Stress1 VON: von Mises Stress 4.753e+01 N/m^2
Node: 75251
4.305e+08 N/m^2
Node: 58218
Plastic_Analysis-Static 1-Stress-Stress1
Name Type Min Max
Displacement1 URES: Resultant
Displacement
0.000e+00 mm
Node: 1
5.000e+00 mm
Node: 44785
Analyzed with SOLIDWORKS Simulation Simulation of Plastic_Analysis 8
Name Type Min Max
Stress1 VON: von Mises Stress 4.753e+01 N/m^2
Node: 75251
4.305e+08 N/m^2
Node: 58218
Plastic_Analysis-Static 1-Stress-Stress1
Name Type Min Max
Displacement1 URES: Resultant
Displacement
0.000e+00 mm
Node: 1
5.000e+00 mm
Node: 44785
Analyzed with SOLIDWORKS Simulation Simulation of Plastic_Analysis 8
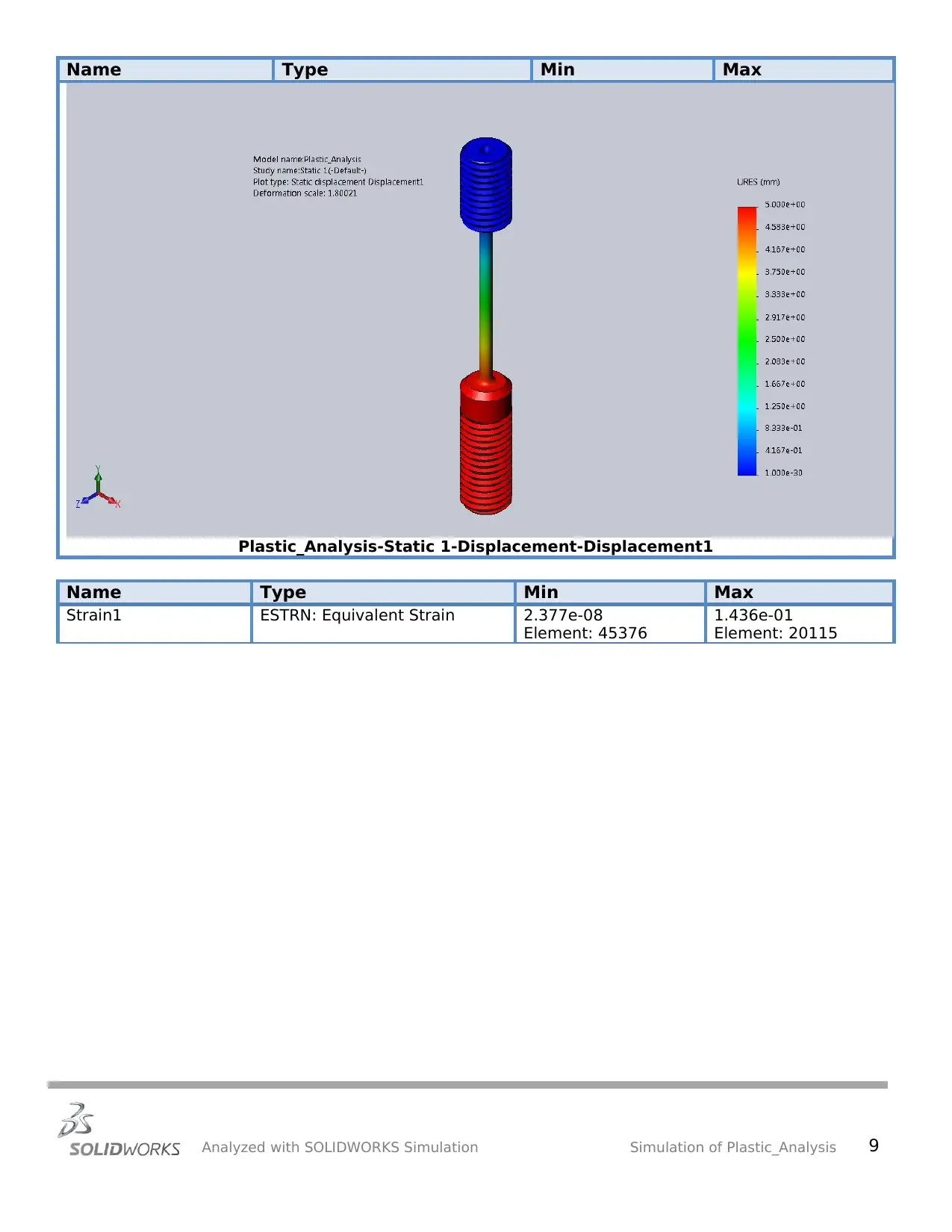
Name Type Min Max
Plastic_Analysis-Static 1-Displacement-Displacement1
Name Type Min Max
Strain1 ESTRN: Equivalent Strain 2.377e-08
Element: 45376
1.436e-01
Element: 20115
Analyzed with SOLIDWORKS Simulation Simulation of Plastic_Analysis 9
Plastic_Analysis-Static 1-Displacement-Displacement1
Name Type Min Max
Strain1 ESTRN: Equivalent Strain 2.377e-08
Element: 45376
1.436e-01
Element: 20115
Analyzed with SOLIDWORKS Simulation Simulation of Plastic_Analysis 9
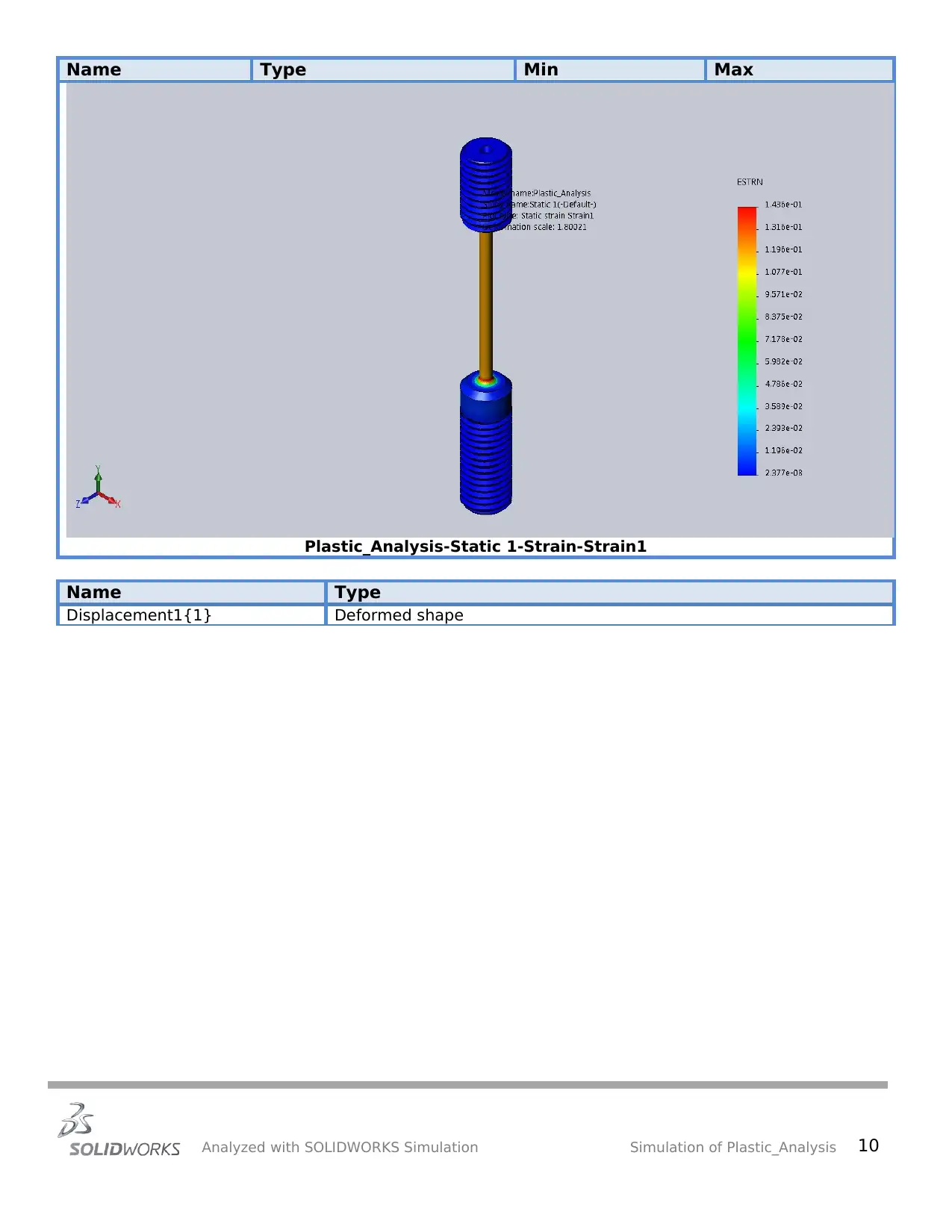
Name Type Min Max
Plastic_Analysis-Static 1-Strain-Strain1
Name Type
Displacement1{1} Deformed shape
Analyzed with SOLIDWORKS Simulation Simulation of Plastic_Analysis 10
Plastic_Analysis-Static 1-Strain-Strain1
Name Type
Displacement1{1} Deformed shape
Analyzed with SOLIDWORKS Simulation Simulation of Plastic_Analysis 10
Secure Best Marks with AI Grader
Need help grading? Try our AI Grader for instant feedback on your assignments.
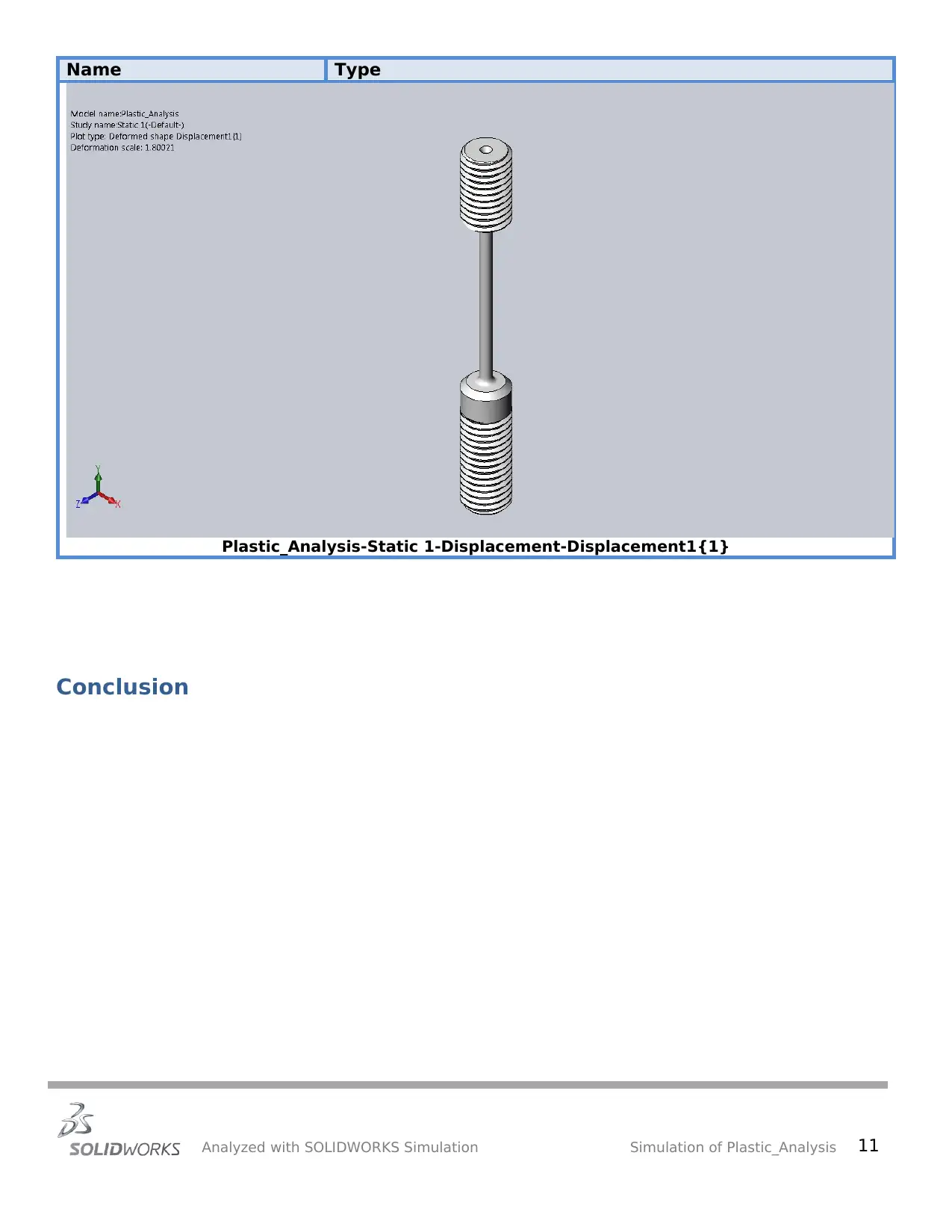
Name Type
Plastic_Analysis-Static 1-Displacement-Displacement1{1}
Conclusion
Analyzed with SOLIDWORKS Simulation Simulation of Plastic_Analysis 11
Plastic_Analysis-Static 1-Displacement-Displacement1{1}
Conclusion
Analyzed with SOLIDWORKS Simulation Simulation of Plastic_Analysis 11
1 out of 11
![[object Object]](/_next/image/?url=%2F_next%2Fstatic%2Fmedia%2Flogo.6d15ce61.png&w=640&q=75)
Your All-in-One AI-Powered Toolkit for Academic Success.
 +13062052269
info@desklib.com
Available 24*7 on WhatsApp / Email
Unlock your academic potential
© 2024  |  Zucol Services PVT LTD  |  All rights reserved.