Project Execution Planning and Management: Stockyard Hill Analysis
VerifiedAdded on 2022/10/11
|14
|3276
|15
Report
AI Summary
This report provides an in-depth analysis of the Stockyard Hill Wind Farm project, focusing on project execution planning and management. It begins with a background of the project, detailing its scope, objectives, and the involvement of various contractors. The report then explores different project delivery methods, including Design-Bid-Build, Design-Build, and CM@Risk, concluding that the Design-Build model is most suitable for this project. It also examines financial contract types, such as Lump Sum, Guaranteed Maximum Price, and Cost-Plus Fixed Fee, selecting the Lump Sum contract as the most appropriate. Furthermore, the report discusses procurement methods like Competitive, Negotiated, and Best Value, suggesting a negotiated approach. Finally, the report addresses risk management, highlighting the importance of identifying, assessing, and mitigating potential risks to ensure project success. The report concludes with a summary of the key findings and recommendations for the project's successful completion.
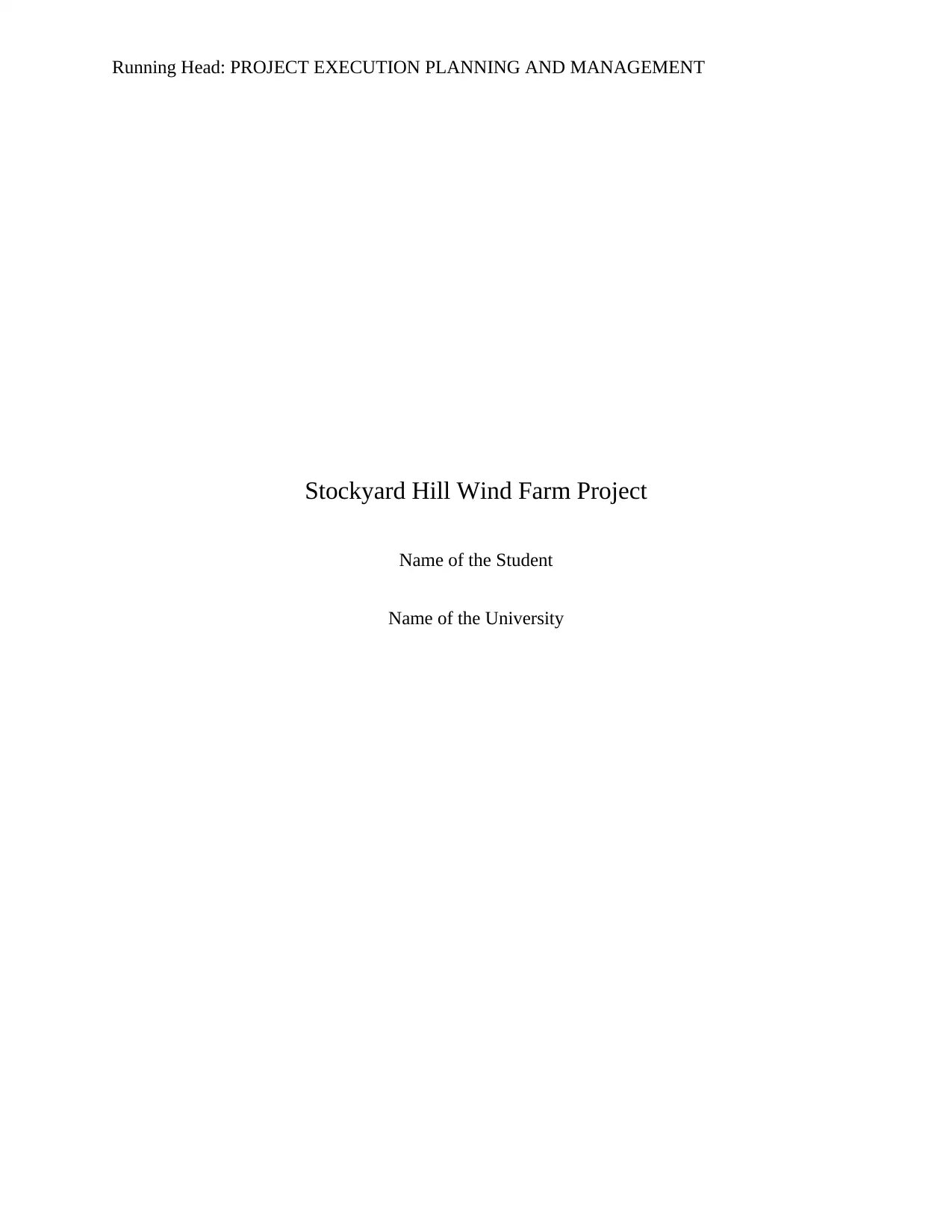
Running Head: PROJECT EXECUTION PLANNING AND MANAGEMENT
Stockyard Hill Wind Farm Project
Name of the Student
Name of the University
Stockyard Hill Wind Farm Project
Name of the Student
Name of the University
Paraphrase This Document
Need a fresh take? Get an instant paraphrase of this document with our AI Paraphraser
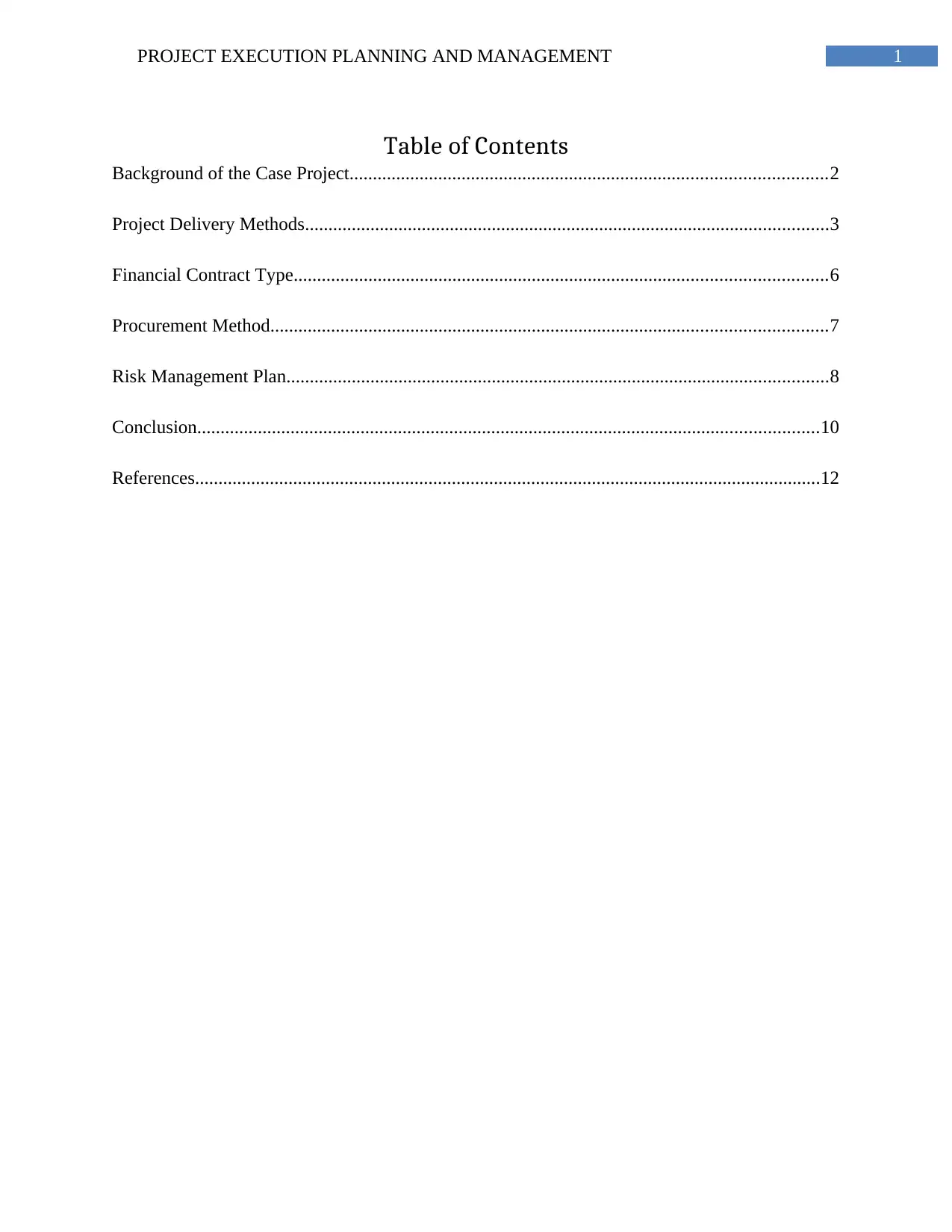
1PROJECT EXECUTION PLANNING AND MANAGEMENT
Table of Contents
Background of the Case Project......................................................................................................2
Project Delivery Methods................................................................................................................3
Financial Contract Type..................................................................................................................6
Procurement Method.......................................................................................................................7
Risk Management Plan....................................................................................................................8
Conclusion.....................................................................................................................................10
References......................................................................................................................................12
Table of Contents
Background of the Case Project......................................................................................................2
Project Delivery Methods................................................................................................................3
Financial Contract Type..................................................................................................................6
Procurement Method.......................................................................................................................7
Risk Management Plan....................................................................................................................8
Conclusion.....................................................................................................................................10
References......................................................................................................................................12
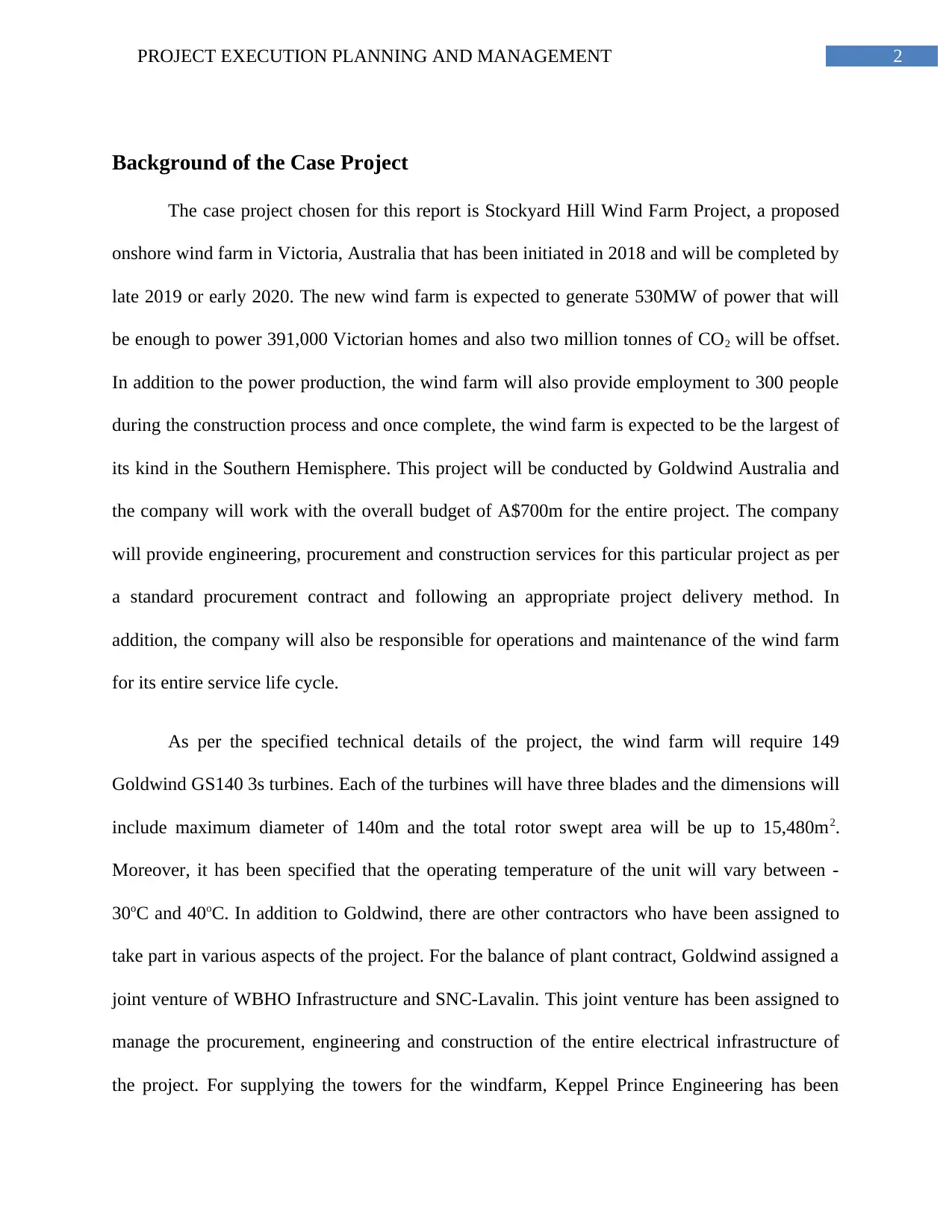
2PROJECT EXECUTION PLANNING AND MANAGEMENT
Background of the Case Project
The case project chosen for this report is Stockyard Hill Wind Farm Project, a proposed
onshore wind farm in Victoria, Australia that has been initiated in 2018 and will be completed by
late 2019 or early 2020. The new wind farm is expected to generate 530MW of power that will
be enough to power 391,000 Victorian homes and also two million tonnes of CO2 will be offset.
In addition to the power production, the wind farm will also provide employment to 300 people
during the construction process and once complete, the wind farm is expected to be the largest of
its kind in the Southern Hemisphere. This project will be conducted by Goldwind Australia and
the company will work with the overall budget of A$700m for the entire project. The company
will provide engineering, procurement and construction services for this particular project as per
a standard procurement contract and following an appropriate project delivery method. In
addition, the company will also be responsible for operations and maintenance of the wind farm
for its entire service life cycle.
As per the specified technical details of the project, the wind farm will require 149
Goldwind GS140 3s turbines. Each of the turbines will have three blades and the dimensions will
include maximum diameter of 140m and the total rotor swept area will be up to 15,480m2.
Moreover, it has been specified that the operating temperature of the unit will vary between -
30oC and 40oC. In addition to Goldwind, there are other contractors who have been assigned to
take part in various aspects of the project. For the balance of plant contract, Goldwind assigned a
joint venture of WBHO Infrastructure and SNC-Lavalin. This joint venture has been assigned to
manage the procurement, engineering and construction of the entire electrical infrastructure of
the project. For supplying the towers for the windfarm, Keppel Prince Engineering has been
Background of the Case Project
The case project chosen for this report is Stockyard Hill Wind Farm Project, a proposed
onshore wind farm in Victoria, Australia that has been initiated in 2018 and will be completed by
late 2019 or early 2020. The new wind farm is expected to generate 530MW of power that will
be enough to power 391,000 Victorian homes and also two million tonnes of CO2 will be offset.
In addition to the power production, the wind farm will also provide employment to 300 people
during the construction process and once complete, the wind farm is expected to be the largest of
its kind in the Southern Hemisphere. This project will be conducted by Goldwind Australia and
the company will work with the overall budget of A$700m for the entire project. The company
will provide engineering, procurement and construction services for this particular project as per
a standard procurement contract and following an appropriate project delivery method. In
addition, the company will also be responsible for operations and maintenance of the wind farm
for its entire service life cycle.
As per the specified technical details of the project, the wind farm will require 149
Goldwind GS140 3s turbines. Each of the turbines will have three blades and the dimensions will
include maximum diameter of 140m and the total rotor swept area will be up to 15,480m2.
Moreover, it has been specified that the operating temperature of the unit will vary between -
30oC and 40oC. In addition to Goldwind, there are other contractors who have been assigned to
take part in various aspects of the project. For the balance of plant contract, Goldwind assigned a
joint venture of WBHO Infrastructure and SNC-Lavalin. This joint venture has been assigned to
manage the procurement, engineering and construction of the entire electrical infrastructure of
the project. For supplying the towers for the windfarm, Keppel Prince Engineering has been
⊘ This is a preview!⊘
Do you want full access?
Subscribe today to unlock all pages.

Trusted by 1+ million students worldwide
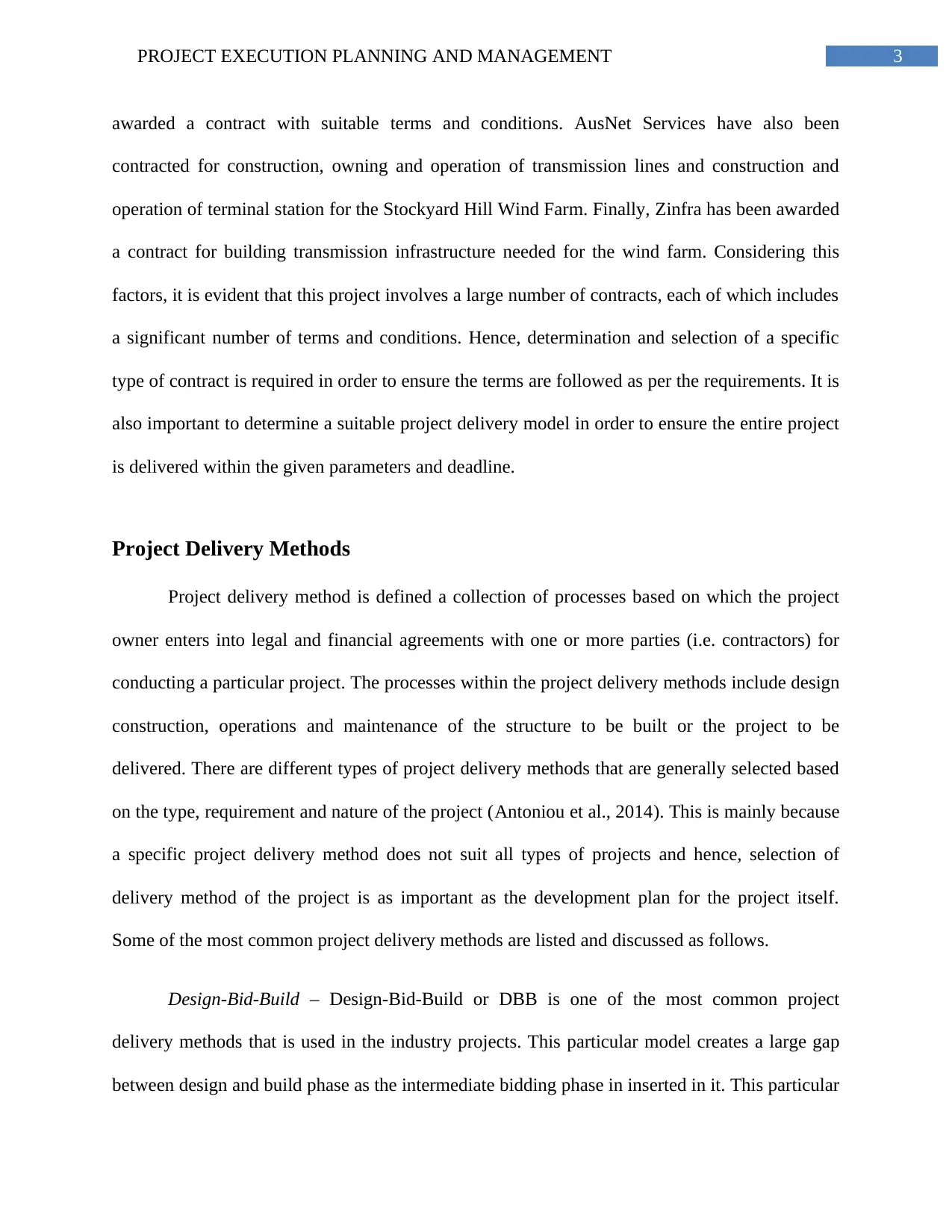
3PROJECT EXECUTION PLANNING AND MANAGEMENT
awarded a contract with suitable terms and conditions. AusNet Services have also been
contracted for construction, owning and operation of transmission lines and construction and
operation of terminal station for the Stockyard Hill Wind Farm. Finally, Zinfra has been awarded
a contract for building transmission infrastructure needed for the wind farm. Considering this
factors, it is evident that this project involves a large number of contracts, each of which includes
a significant number of terms and conditions. Hence, determination and selection of a specific
type of contract is required in order to ensure the terms are followed as per the requirements. It is
also important to determine a suitable project delivery model in order to ensure the entire project
is delivered within the given parameters and deadline.
Project Delivery Methods
Project delivery method is defined a collection of processes based on which the project
owner enters into legal and financial agreements with one or more parties (i.e. contractors) for
conducting a particular project. The processes within the project delivery methods include design
construction, operations and maintenance of the structure to be built or the project to be
delivered. There are different types of project delivery methods that are generally selected based
on the type, requirement and nature of the project (Antoniou et al., 2014). This is mainly because
a specific project delivery method does not suit all types of projects and hence, selection of
delivery method of the project is as important as the development plan for the project itself.
Some of the most common project delivery methods are listed and discussed as follows.
Design-Bid-Build – Design-Bid-Build or DBB is one of the most common project
delivery methods that is used in the industry projects. This particular model creates a large gap
between design and build phase as the intermediate bidding phase in inserted in it. This particular
awarded a contract with suitable terms and conditions. AusNet Services have also been
contracted for construction, owning and operation of transmission lines and construction and
operation of terminal station for the Stockyard Hill Wind Farm. Finally, Zinfra has been awarded
a contract for building transmission infrastructure needed for the wind farm. Considering this
factors, it is evident that this project involves a large number of contracts, each of which includes
a significant number of terms and conditions. Hence, determination and selection of a specific
type of contract is required in order to ensure the terms are followed as per the requirements. It is
also important to determine a suitable project delivery model in order to ensure the entire project
is delivered within the given parameters and deadline.
Project Delivery Methods
Project delivery method is defined a collection of processes based on which the project
owner enters into legal and financial agreements with one or more parties (i.e. contractors) for
conducting a particular project. The processes within the project delivery methods include design
construction, operations and maintenance of the structure to be built or the project to be
delivered. There are different types of project delivery methods that are generally selected based
on the type, requirement and nature of the project (Antoniou et al., 2014). This is mainly because
a specific project delivery method does not suit all types of projects and hence, selection of
delivery method of the project is as important as the development plan for the project itself.
Some of the most common project delivery methods are listed and discussed as follows.
Design-Bid-Build – Design-Bid-Build or DBB is one of the most common project
delivery methods that is used in the industry projects. This particular model creates a large gap
between design and build phase as the intermediate bidding phase in inserted in it. This particular
Paraphrase This Document
Need a fresh take? Get an instant paraphrase of this document with our AI Paraphraser
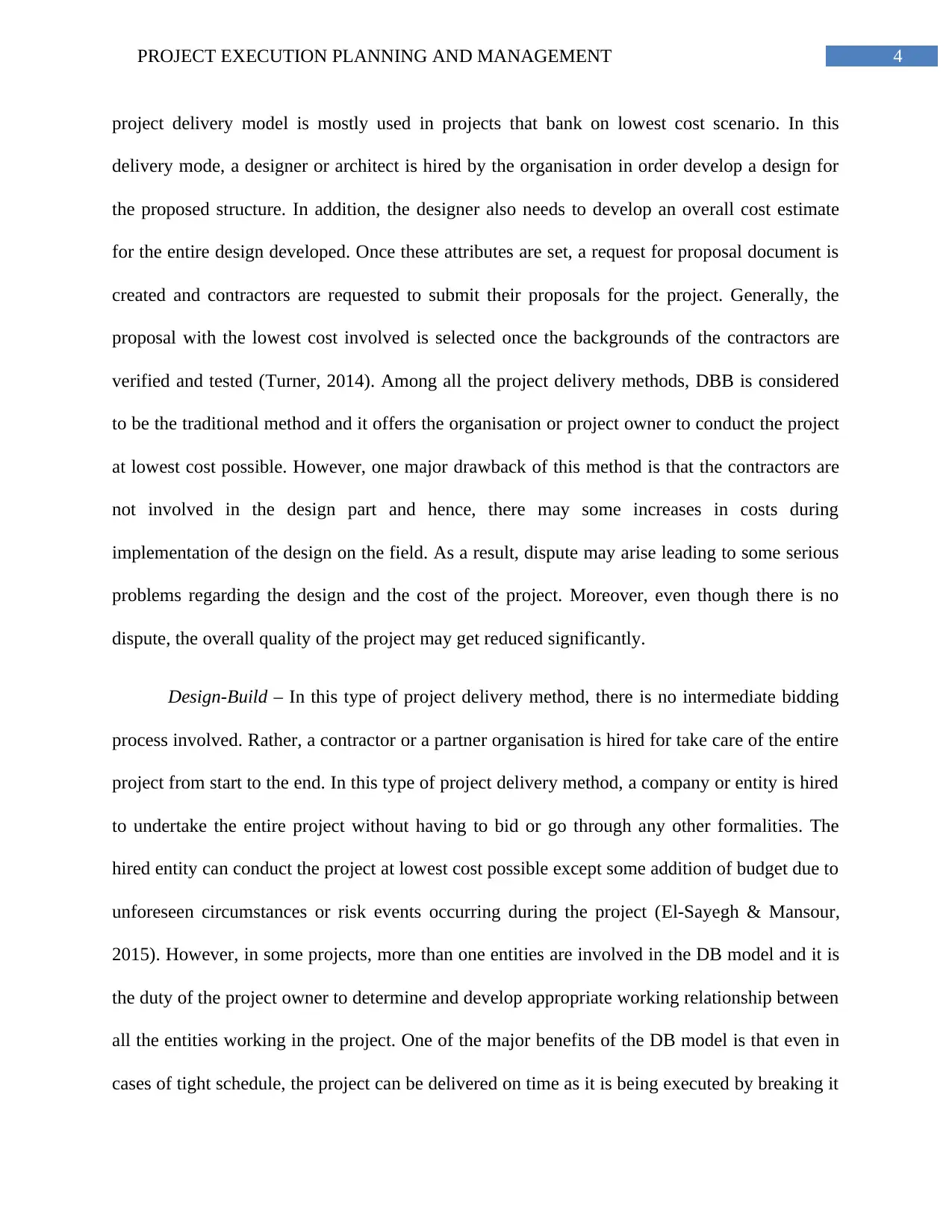
4PROJECT EXECUTION PLANNING AND MANAGEMENT
project delivery model is mostly used in projects that bank on lowest cost scenario. In this
delivery mode, a designer or architect is hired by the organisation in order develop a design for
the proposed structure. In addition, the designer also needs to develop an overall cost estimate
for the entire design developed. Once these attributes are set, a request for proposal document is
created and contractors are requested to submit their proposals for the project. Generally, the
proposal with the lowest cost involved is selected once the backgrounds of the contractors are
verified and tested (Turner, 2014). Among all the project delivery methods, DBB is considered
to be the traditional method and it offers the organisation or project owner to conduct the project
at lowest cost possible. However, one major drawback of this method is that the contractors are
not involved in the design part and hence, there may some increases in costs during
implementation of the design on the field. As a result, dispute may arise leading to some serious
problems regarding the design and the cost of the project. Moreover, even though there is no
dispute, the overall quality of the project may get reduced significantly.
Design-Build – In this type of project delivery method, there is no intermediate bidding
process involved. Rather, a contractor or a partner organisation is hired for take care of the entire
project from start to the end. In this type of project delivery method, a company or entity is hired
to undertake the entire project without having to bid or go through any other formalities. The
hired entity can conduct the project at lowest cost possible except some addition of budget due to
unforeseen circumstances or risk events occurring during the project (El-Sayegh & Mansour,
2015). However, in some projects, more than one entities are involved in the DB model and it is
the duty of the project owner to determine and develop appropriate working relationship between
all the entities working in the project. One of the major benefits of the DB model is that even in
cases of tight schedule, the project can be delivered on time as it is being executed by breaking it
project delivery model is mostly used in projects that bank on lowest cost scenario. In this
delivery mode, a designer or architect is hired by the organisation in order develop a design for
the proposed structure. In addition, the designer also needs to develop an overall cost estimate
for the entire design developed. Once these attributes are set, a request for proposal document is
created and contractors are requested to submit their proposals for the project. Generally, the
proposal with the lowest cost involved is selected once the backgrounds of the contractors are
verified and tested (Turner, 2014). Among all the project delivery methods, DBB is considered
to be the traditional method and it offers the organisation or project owner to conduct the project
at lowest cost possible. However, one major drawback of this method is that the contractors are
not involved in the design part and hence, there may some increases in costs during
implementation of the design on the field. As a result, dispute may arise leading to some serious
problems regarding the design and the cost of the project. Moreover, even though there is no
dispute, the overall quality of the project may get reduced significantly.
Design-Build – In this type of project delivery method, there is no intermediate bidding
process involved. Rather, a contractor or a partner organisation is hired for take care of the entire
project from start to the end. In this type of project delivery method, a company or entity is hired
to undertake the entire project without having to bid or go through any other formalities. The
hired entity can conduct the project at lowest cost possible except some addition of budget due to
unforeseen circumstances or risk events occurring during the project (El-Sayegh & Mansour,
2015). However, in some projects, more than one entities are involved in the DB model and it is
the duty of the project owner to determine and develop appropriate working relationship between
all the entities working in the project. One of the major benefits of the DB model is that even in
cases of tight schedule, the project can be delivered on time as it is being executed by breaking it
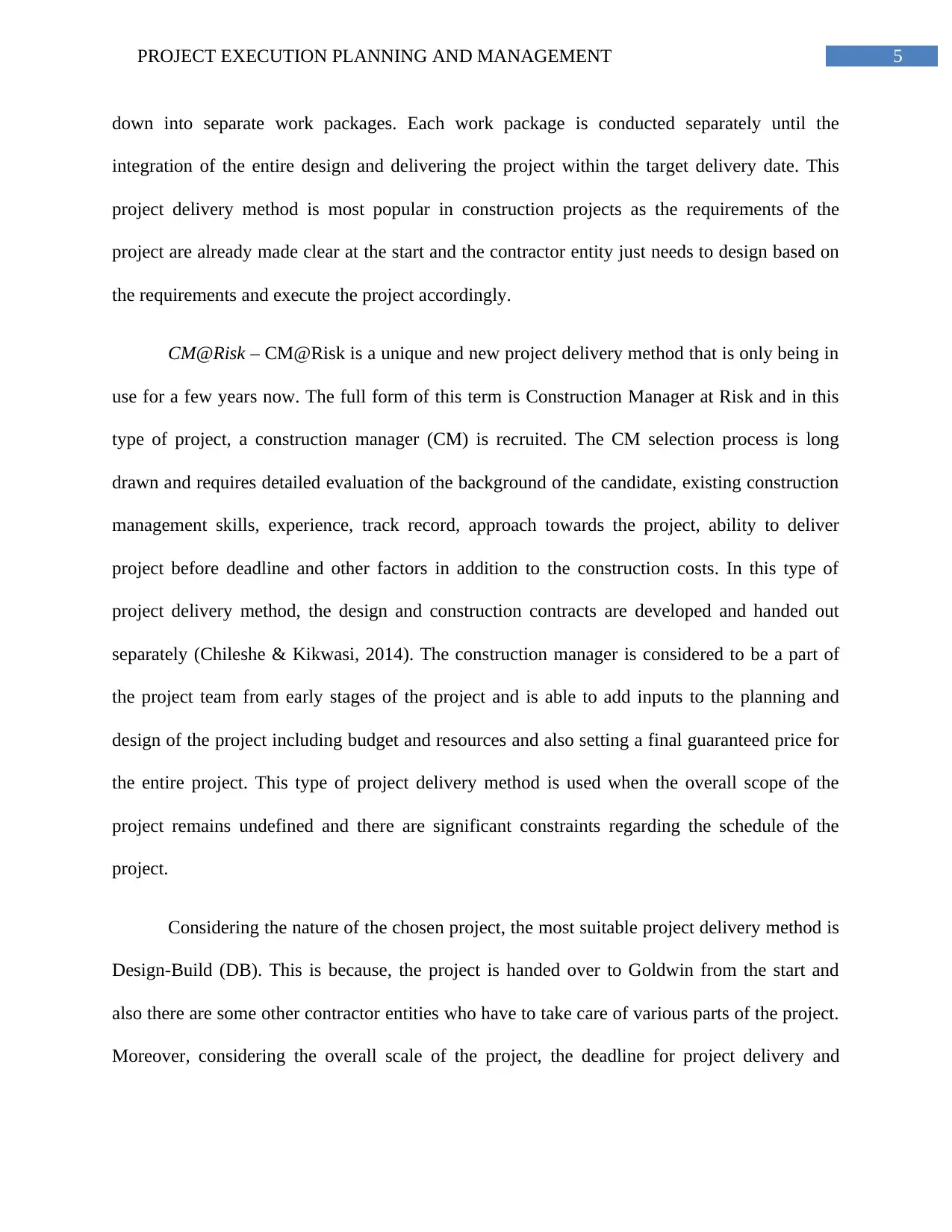
5PROJECT EXECUTION PLANNING AND MANAGEMENT
down into separate work packages. Each work package is conducted separately until the
integration of the entire design and delivering the project within the target delivery date. This
project delivery method is most popular in construction projects as the requirements of the
project are already made clear at the start and the contractor entity just needs to design based on
the requirements and execute the project accordingly.
CM@Risk – CM@Risk is a unique and new project delivery method that is only being in
use for a few years now. The full form of this term is Construction Manager at Risk and in this
type of project, a construction manager (CM) is recruited. The CM selection process is long
drawn and requires detailed evaluation of the background of the candidate, existing construction
management skills, experience, track record, approach towards the project, ability to deliver
project before deadline and other factors in addition to the construction costs. In this type of
project delivery method, the design and construction contracts are developed and handed out
separately (Chileshe & Kikwasi, 2014). The construction manager is considered to be a part of
the project team from early stages of the project and is able to add inputs to the planning and
design of the project including budget and resources and also setting a final guaranteed price for
the entire project. This type of project delivery method is used when the overall scope of the
project remains undefined and there are significant constraints regarding the schedule of the
project.
Considering the nature of the chosen project, the most suitable project delivery method is
Design-Build (DB). This is because, the project is handed over to Goldwin from the start and
also there are some other contractor entities who have to take care of various parts of the project.
Moreover, considering the overall scale of the project, the deadline for project delivery and
down into separate work packages. Each work package is conducted separately until the
integration of the entire design and delivering the project within the target delivery date. This
project delivery method is most popular in construction projects as the requirements of the
project are already made clear at the start and the contractor entity just needs to design based on
the requirements and execute the project accordingly.
CM@Risk – CM@Risk is a unique and new project delivery method that is only being in
use for a few years now. The full form of this term is Construction Manager at Risk and in this
type of project, a construction manager (CM) is recruited. The CM selection process is long
drawn and requires detailed evaluation of the background of the candidate, existing construction
management skills, experience, track record, approach towards the project, ability to deliver
project before deadline and other factors in addition to the construction costs. In this type of
project delivery method, the design and construction contracts are developed and handed out
separately (Chileshe & Kikwasi, 2014). The construction manager is considered to be a part of
the project team from early stages of the project and is able to add inputs to the planning and
design of the project including budget and resources and also setting a final guaranteed price for
the entire project. This type of project delivery method is used when the overall scope of the
project remains undefined and there are significant constraints regarding the schedule of the
project.
Considering the nature of the chosen project, the most suitable project delivery method is
Design-Build (DB). This is because, the project is handed over to Goldwin from the start and
also there are some other contractor entities who have to take care of various parts of the project.
Moreover, considering the overall scale of the project, the deadline for project delivery and
⊘ This is a preview!⊘
Do you want full access?
Subscribe today to unlock all pages.

Trusted by 1+ million students worldwide
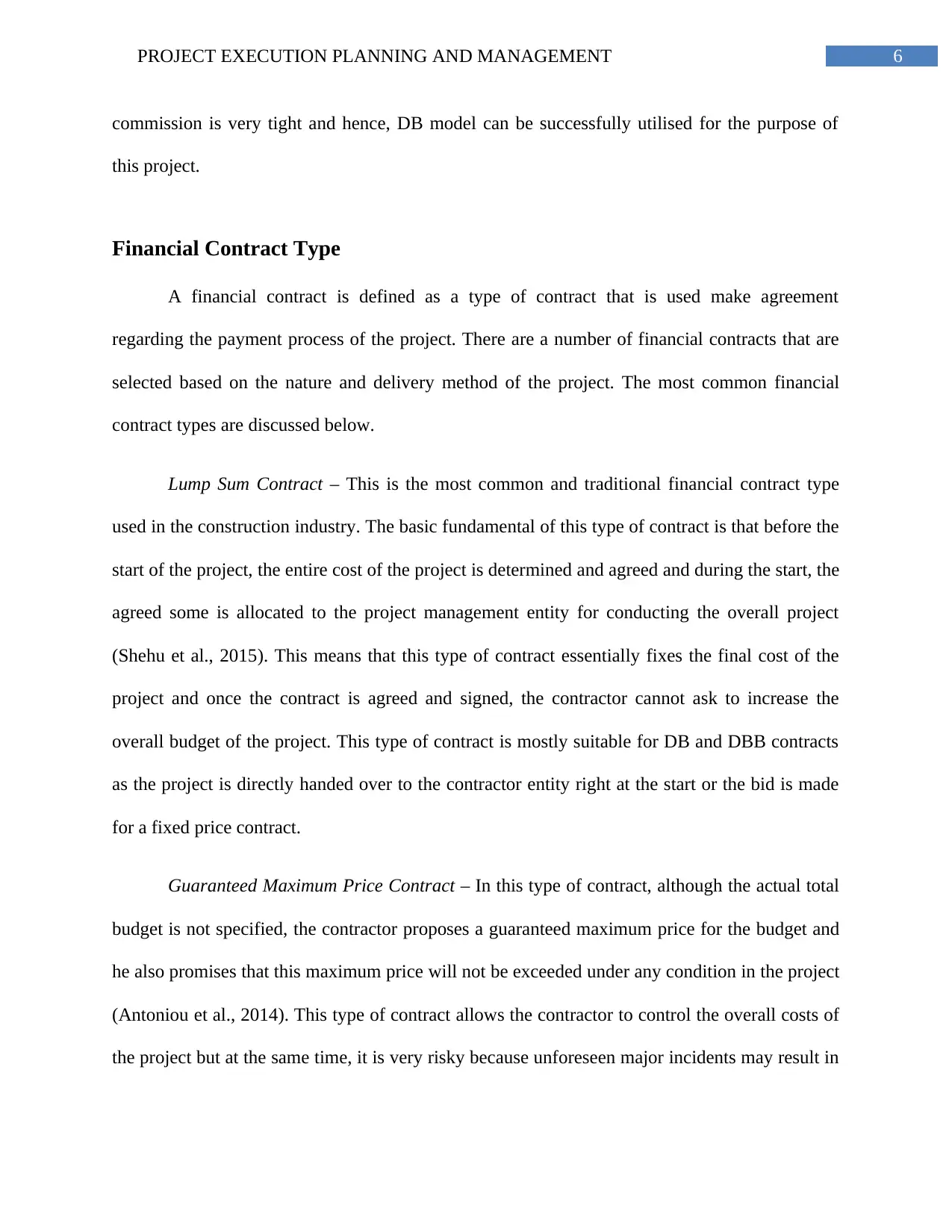
6PROJECT EXECUTION PLANNING AND MANAGEMENT
commission is very tight and hence, DB model can be successfully utilised for the purpose of
this project.
Financial Contract Type
A financial contract is defined as a type of contract that is used make agreement
regarding the payment process of the project. There are a number of financial contracts that are
selected based on the nature and delivery method of the project. The most common financial
contract types are discussed below.
Lump Sum Contract – This is the most common and traditional financial contract type
used in the construction industry. The basic fundamental of this type of contract is that before the
start of the project, the entire cost of the project is determined and agreed and during the start, the
agreed some is allocated to the project management entity for conducting the overall project
(Shehu et al., 2015). This means that this type of contract essentially fixes the final cost of the
project and once the contract is agreed and signed, the contractor cannot ask to increase the
overall budget of the project. This type of contract is mostly suitable for DB and DBB contracts
as the project is directly handed over to the contractor entity right at the start or the bid is made
for a fixed price contract.
Guaranteed Maximum Price Contract – In this type of contract, although the actual total
budget is not specified, the contractor proposes a guaranteed maximum price for the budget and
he also promises that this maximum price will not be exceeded under any condition in the project
(Antoniou et al., 2014). This type of contract allows the contractor to control the overall costs of
the project but at the same time, it is very risky because unforeseen major incidents may result in
commission is very tight and hence, DB model can be successfully utilised for the purpose of
this project.
Financial Contract Type
A financial contract is defined as a type of contract that is used make agreement
regarding the payment process of the project. There are a number of financial contracts that are
selected based on the nature and delivery method of the project. The most common financial
contract types are discussed below.
Lump Sum Contract – This is the most common and traditional financial contract type
used in the construction industry. The basic fundamental of this type of contract is that before the
start of the project, the entire cost of the project is determined and agreed and during the start, the
agreed some is allocated to the project management entity for conducting the overall project
(Shehu et al., 2015). This means that this type of contract essentially fixes the final cost of the
project and once the contract is agreed and signed, the contractor cannot ask to increase the
overall budget of the project. This type of contract is mostly suitable for DB and DBB contracts
as the project is directly handed over to the contractor entity right at the start or the bid is made
for a fixed price contract.
Guaranteed Maximum Price Contract – In this type of contract, although the actual total
budget is not specified, the contractor proposes a guaranteed maximum price for the budget and
he also promises that this maximum price will not be exceeded under any condition in the project
(Antoniou et al., 2014). This type of contract allows the contractor to control the overall costs of
the project but at the same time, it is very risky because unforeseen major incidents may result in
Paraphrase This Document
Need a fresh take? Get an instant paraphrase of this document with our AI Paraphraser
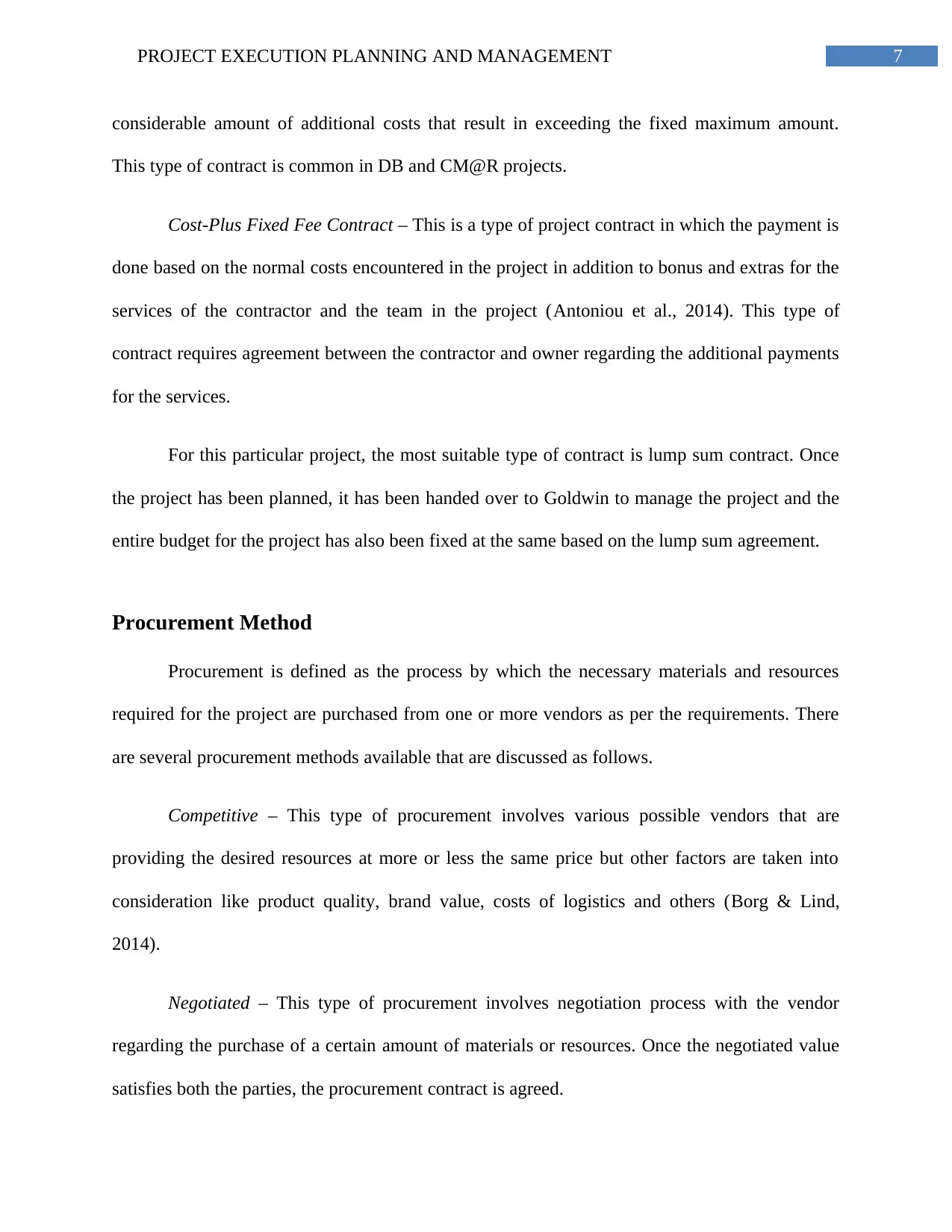
7PROJECT EXECUTION PLANNING AND MANAGEMENT
considerable amount of additional costs that result in exceeding the fixed maximum amount.
This type of contract is common in DB and CM@R projects.
Cost-Plus Fixed Fee Contract – This is a type of project contract in which the payment is
done based on the normal costs encountered in the project in addition to bonus and extras for the
services of the contractor and the team in the project (Antoniou et al., 2014). This type of
contract requires agreement between the contractor and owner regarding the additional payments
for the services.
For this particular project, the most suitable type of contract is lump sum contract. Once
the project has been planned, it has been handed over to Goldwin to manage the project and the
entire budget for the project has also been fixed at the same based on the lump sum agreement.
Procurement Method
Procurement is defined as the process by which the necessary materials and resources
required for the project are purchased from one or more vendors as per the requirements. There
are several procurement methods available that are discussed as follows.
Competitive – This type of procurement involves various possible vendors that are
providing the desired resources at more or less the same price but other factors are taken into
consideration like product quality, brand value, costs of logistics and others (Borg & Lind,
2014).
Negotiated – This type of procurement involves negotiation process with the vendor
regarding the purchase of a certain amount of materials or resources. Once the negotiated value
satisfies both the parties, the procurement contract is agreed.
considerable amount of additional costs that result in exceeding the fixed maximum amount.
This type of contract is common in DB and CM@R projects.
Cost-Plus Fixed Fee Contract – This is a type of project contract in which the payment is
done based on the normal costs encountered in the project in addition to bonus and extras for the
services of the contractor and the team in the project (Antoniou et al., 2014). This type of
contract requires agreement between the contractor and owner regarding the additional payments
for the services.
For this particular project, the most suitable type of contract is lump sum contract. Once
the project has been planned, it has been handed over to Goldwin to manage the project and the
entire budget for the project has also been fixed at the same based on the lump sum agreement.
Procurement Method
Procurement is defined as the process by which the necessary materials and resources
required for the project are purchased from one or more vendors as per the requirements. There
are several procurement methods available that are discussed as follows.
Competitive – This type of procurement involves various possible vendors that are
providing the desired resources at more or less the same price but other factors are taken into
consideration like product quality, brand value, costs of logistics and others (Borg & Lind,
2014).
Negotiated – This type of procurement involves negotiation process with the vendor
regarding the purchase of a certain amount of materials or resources. Once the negotiated value
satisfies both the parties, the procurement contract is agreed.
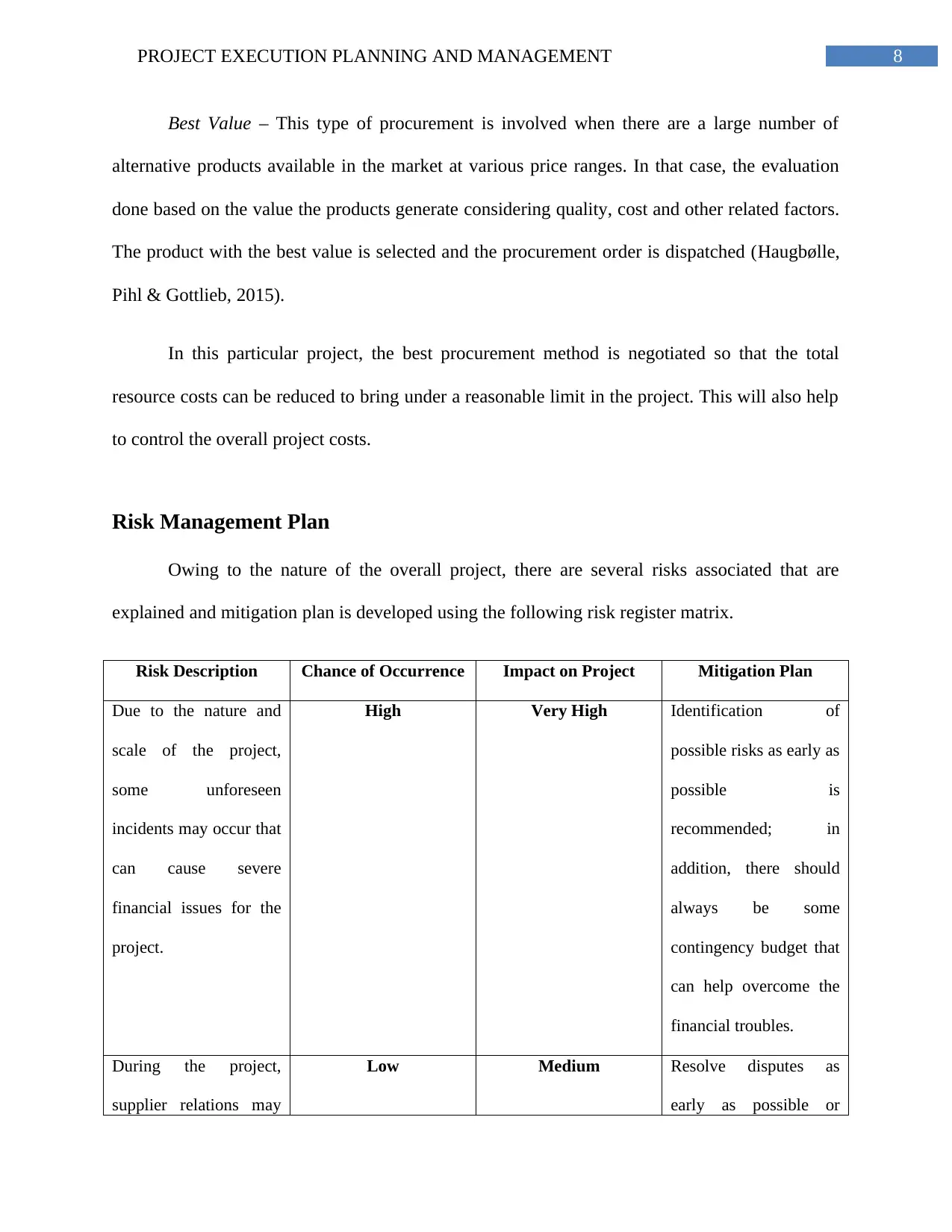
8PROJECT EXECUTION PLANNING AND MANAGEMENT
Best Value – This type of procurement is involved when there are a large number of
alternative products available in the market at various price ranges. In that case, the evaluation
done based on the value the products generate considering quality, cost and other related factors.
The product with the best value is selected and the procurement order is dispatched (Haugbølle,
Pihl & Gottlieb, 2015).
In this particular project, the best procurement method is negotiated so that the total
resource costs can be reduced to bring under a reasonable limit in the project. This will also help
to control the overall project costs.
Risk Management Plan
Owing to the nature of the overall project, there are several risks associated that are
explained and mitigation plan is developed using the following risk register matrix.
Risk Description Chance of Occurrence Impact on Project Mitigation Plan
Due to the nature and
scale of the project,
some unforeseen
incidents may occur that
can cause severe
financial issues for the
project.
High Very High Identification of
possible risks as early as
possible is
recommended; in
addition, there should
always be some
contingency budget that
can help overcome the
financial troubles.
During the project,
supplier relations may
Low Medium Resolve disputes as
early as possible or
Best Value – This type of procurement is involved when there are a large number of
alternative products available in the market at various price ranges. In that case, the evaluation
done based on the value the products generate considering quality, cost and other related factors.
The product with the best value is selected and the procurement order is dispatched (Haugbølle,
Pihl & Gottlieb, 2015).
In this particular project, the best procurement method is negotiated so that the total
resource costs can be reduced to bring under a reasonable limit in the project. This will also help
to control the overall project costs.
Risk Management Plan
Owing to the nature of the overall project, there are several risks associated that are
explained and mitigation plan is developed using the following risk register matrix.
Risk Description Chance of Occurrence Impact on Project Mitigation Plan
Due to the nature and
scale of the project,
some unforeseen
incidents may occur that
can cause severe
financial issues for the
project.
High Very High Identification of
possible risks as early as
possible is
recommended; in
addition, there should
always be some
contingency budget that
can help overcome the
financial troubles.
During the project,
supplier relations may
Low Medium Resolve disputes as
early as possible or
⊘ This is a preview!⊘
Do you want full access?
Subscribe today to unlock all pages.

Trusted by 1+ million students worldwide
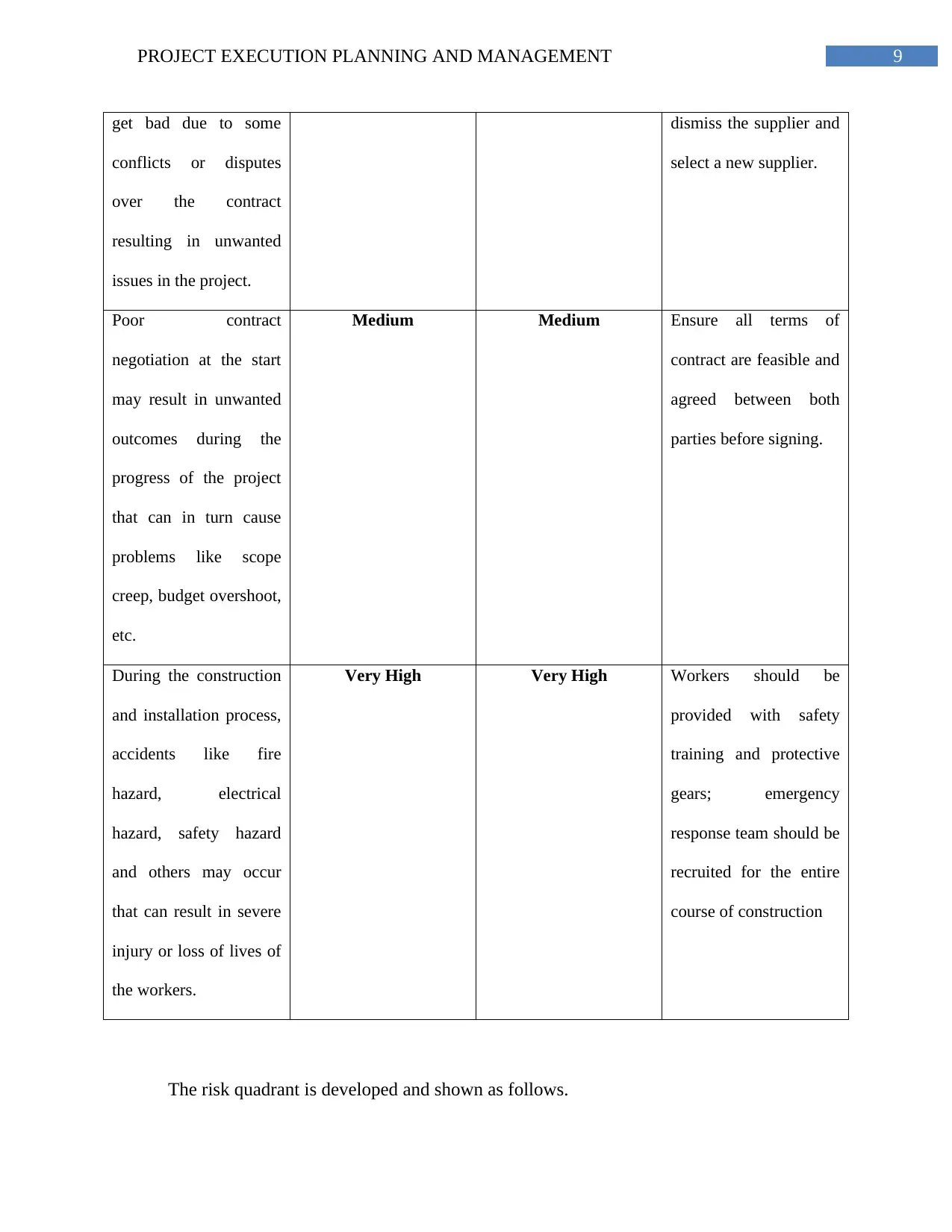
9PROJECT EXECUTION PLANNING AND MANAGEMENT
get bad due to some
conflicts or disputes
over the contract
resulting in unwanted
issues in the project.
dismiss the supplier and
select a new supplier.
Poor contract
negotiation at the start
may result in unwanted
outcomes during the
progress of the project
that can in turn cause
problems like scope
creep, budget overshoot,
etc.
Medium Medium Ensure all terms of
contract are feasible and
agreed between both
parties before signing.
During the construction
and installation process,
accidents like fire
hazard, electrical
hazard, safety hazard
and others may occur
that can result in severe
injury or loss of lives of
the workers.
Very High Very High Workers should be
provided with safety
training and protective
gears; emergency
response team should be
recruited for the entire
course of construction
The risk quadrant is developed and shown as follows.
get bad due to some
conflicts or disputes
over the contract
resulting in unwanted
issues in the project.
dismiss the supplier and
select a new supplier.
Poor contract
negotiation at the start
may result in unwanted
outcomes during the
progress of the project
that can in turn cause
problems like scope
creep, budget overshoot,
etc.
Medium Medium Ensure all terms of
contract are feasible and
agreed between both
parties before signing.
During the construction
and installation process,
accidents like fire
hazard, electrical
hazard, safety hazard
and others may occur
that can result in severe
injury or loss of lives of
the workers.
Very High Very High Workers should be
provided with safety
training and protective
gears; emergency
response team should be
recruited for the entire
course of construction
The risk quadrant is developed and shown as follows.
Paraphrase This Document
Need a fresh take? Get an instant paraphrase of this document with our AI Paraphraser
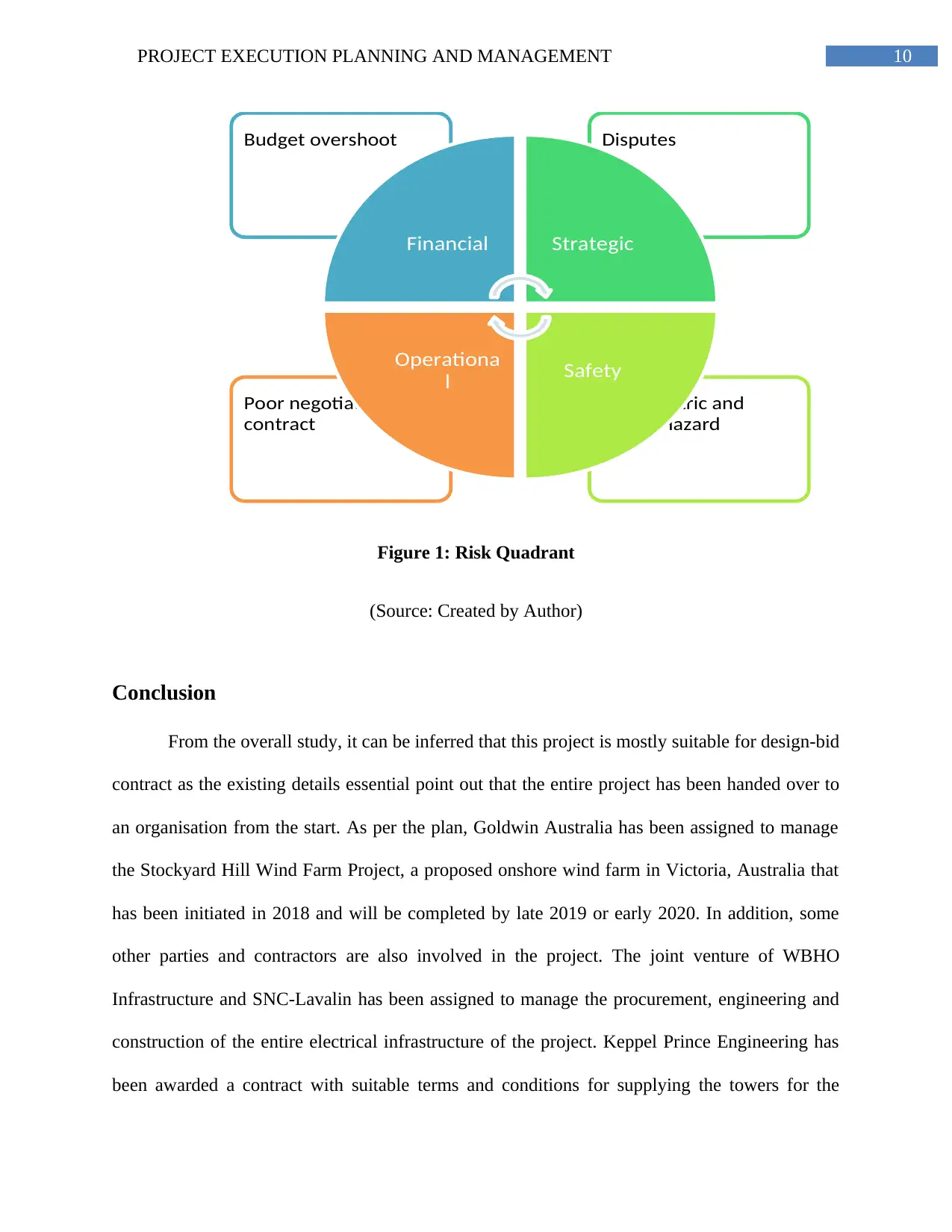
10PROJECT EXECUTION PLANNING AND MANAGEMENT
Figure 1: Risk Quadrant
(Source: Created by Author)
Conclusion
From the overall study, it can be inferred that this project is mostly suitable for design-bid
contract as the existing details essential point out that the entire project has been handed over to
an organisation from the start. As per the plan, Goldwin Australia has been assigned to manage
the Stockyard Hill Wind Farm Project, a proposed onshore wind farm in Victoria, Australia that
has been initiated in 2018 and will be completed by late 2019 or early 2020. In addition, some
other parties and contractors are also involved in the project. The joint venture of WBHO
Infrastructure and SNC-Lavalin has been assigned to manage the procurement, engineering and
construction of the entire electrical infrastructure of the project. Keppel Prince Engineering has
been awarded a contract with suitable terms and conditions for supplying the towers for the
Fire, Electric and
Safety Hazard
Poor negotiation of
contract
DisputesBudget overshoot
Financial Strategic
Safety
Operationa
l
Figure 1: Risk Quadrant
(Source: Created by Author)
Conclusion
From the overall study, it can be inferred that this project is mostly suitable for design-bid
contract as the existing details essential point out that the entire project has been handed over to
an organisation from the start. As per the plan, Goldwin Australia has been assigned to manage
the Stockyard Hill Wind Farm Project, a proposed onshore wind farm in Victoria, Australia that
has been initiated in 2018 and will be completed by late 2019 or early 2020. In addition, some
other parties and contractors are also involved in the project. The joint venture of WBHO
Infrastructure and SNC-Lavalin has been assigned to manage the procurement, engineering and
construction of the entire electrical infrastructure of the project. Keppel Prince Engineering has
been awarded a contract with suitable terms and conditions for supplying the towers for the
Fire, Electric and
Safety Hazard
Poor negotiation of
contract
DisputesBudget overshoot
Financial Strategic
Safety
Operationa
l
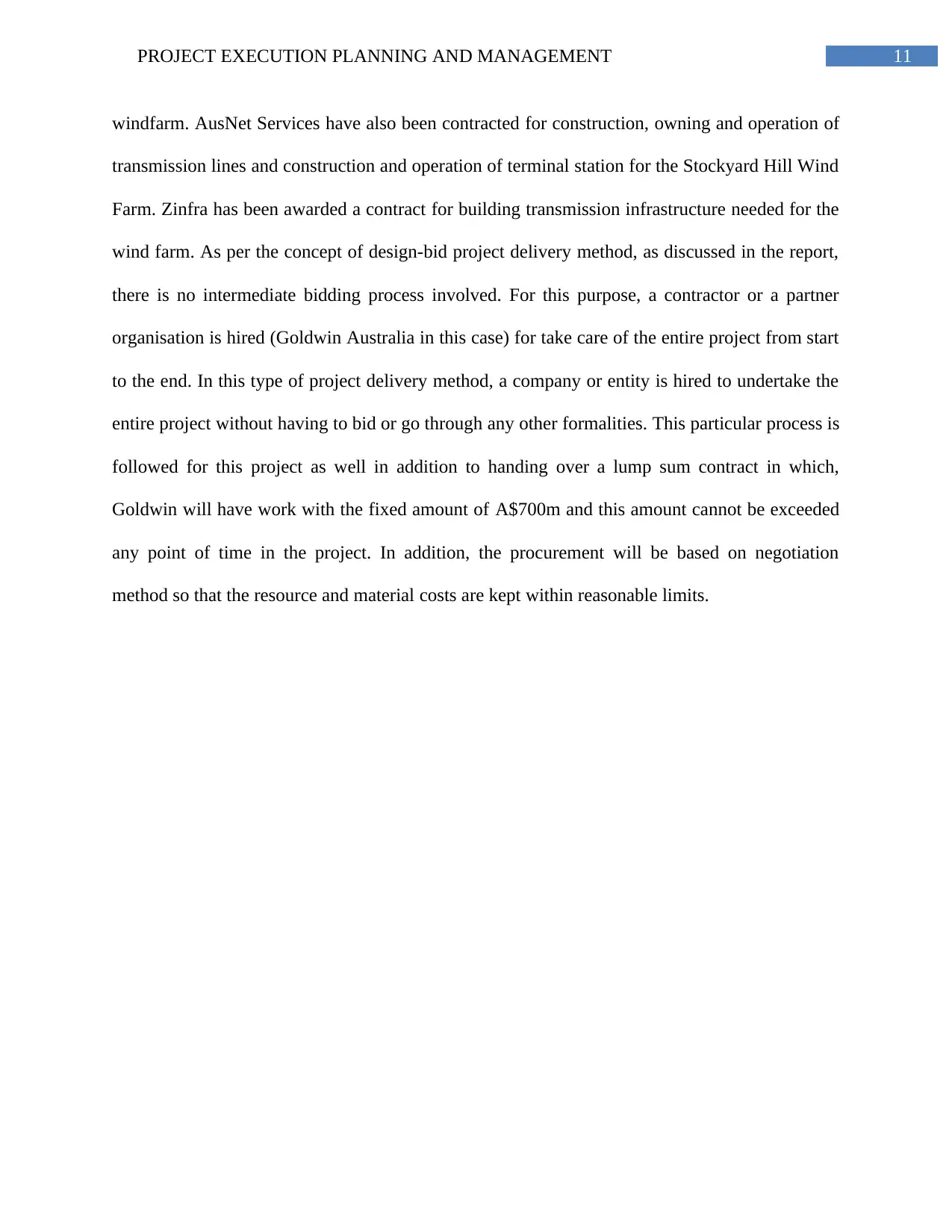
11PROJECT EXECUTION PLANNING AND MANAGEMENT
windfarm. AusNet Services have also been contracted for construction, owning and operation of
transmission lines and construction and operation of terminal station for the Stockyard Hill Wind
Farm. Zinfra has been awarded a contract for building transmission infrastructure needed for the
wind farm. As per the concept of design-bid project delivery method, as discussed in the report,
there is no intermediate bidding process involved. For this purpose, a contractor or a partner
organisation is hired (Goldwin Australia in this case) for take care of the entire project from start
to the end. In this type of project delivery method, a company or entity is hired to undertake the
entire project without having to bid or go through any other formalities. This particular process is
followed for this project as well in addition to handing over a lump sum contract in which,
Goldwin will have work with the fixed amount of A$700m and this amount cannot be exceeded
any point of time in the project. In addition, the procurement will be based on negotiation
method so that the resource and material costs are kept within reasonable limits.
windfarm. AusNet Services have also been contracted for construction, owning and operation of
transmission lines and construction and operation of terminal station for the Stockyard Hill Wind
Farm. Zinfra has been awarded a contract for building transmission infrastructure needed for the
wind farm. As per the concept of design-bid project delivery method, as discussed in the report,
there is no intermediate bidding process involved. For this purpose, a contractor or a partner
organisation is hired (Goldwin Australia in this case) for take care of the entire project from start
to the end. In this type of project delivery method, a company or entity is hired to undertake the
entire project without having to bid or go through any other formalities. This particular process is
followed for this project as well in addition to handing over a lump sum contract in which,
Goldwin will have work with the fixed amount of A$700m and this amount cannot be exceeded
any point of time in the project. In addition, the procurement will be based on negotiation
method so that the resource and material costs are kept within reasonable limits.
⊘ This is a preview!⊘
Do you want full access?
Subscribe today to unlock all pages.

Trusted by 1+ million students worldwide
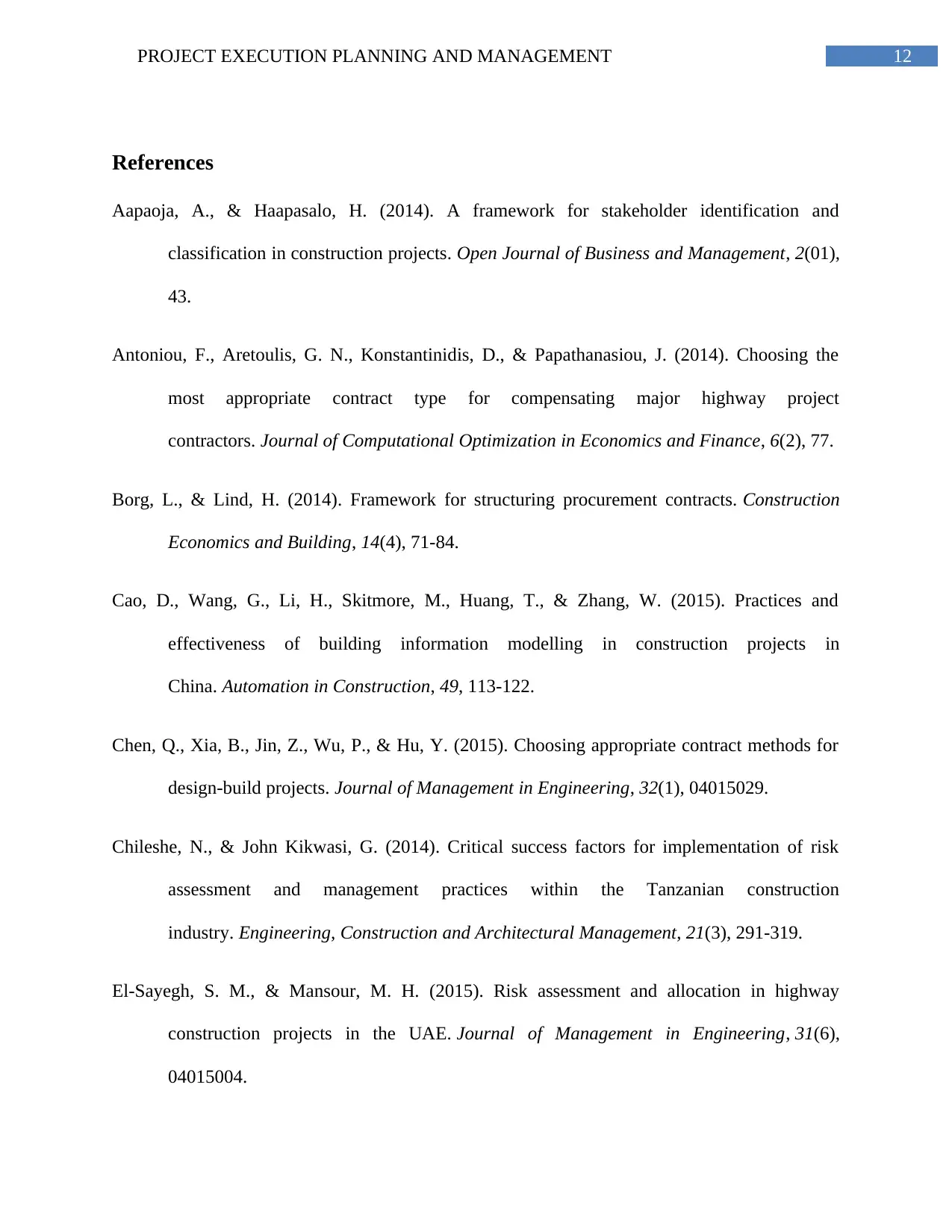
12PROJECT EXECUTION PLANNING AND MANAGEMENT
References
Aapaoja, A., & Haapasalo, H. (2014). A framework for stakeholder identification and
classification in construction projects. Open Journal of Business and Management, 2(01),
43.
Antoniou, F., Aretoulis, G. N., Konstantinidis, D., & Papathanasiou, J. (2014). Choosing the
most appropriate contract type for compensating major highway project
contractors. Journal of Computational Optimization in Economics and Finance, 6(2), 77.
Borg, L., & Lind, H. (2014). Framework for structuring procurement contracts. Construction
Economics and Building, 14(4), 71-84.
Cao, D., Wang, G., Li, H., Skitmore, M., Huang, T., & Zhang, W. (2015). Practices and
effectiveness of building information modelling in construction projects in
China. Automation in Construction, 49, 113-122.
Chen, Q., Xia, B., Jin, Z., Wu, P., & Hu, Y. (2015). Choosing appropriate contract methods for
design-build projects. Journal of Management in Engineering, 32(1), 04015029.
Chileshe, N., & John Kikwasi, G. (2014). Critical success factors for implementation of risk
assessment and management practices within the Tanzanian construction
industry. Engineering, Construction and Architectural Management, 21(3), 291-319.
El-Sayegh, S. M., & Mansour, M. H. (2015). Risk assessment and allocation in highway
construction projects in the UAE. Journal of Management in Engineering, 31(6),
04015004.
References
Aapaoja, A., & Haapasalo, H. (2014). A framework for stakeholder identification and
classification in construction projects. Open Journal of Business and Management, 2(01),
43.
Antoniou, F., Aretoulis, G. N., Konstantinidis, D., & Papathanasiou, J. (2014). Choosing the
most appropriate contract type for compensating major highway project
contractors. Journal of Computational Optimization in Economics and Finance, 6(2), 77.
Borg, L., & Lind, H. (2014). Framework for structuring procurement contracts. Construction
Economics and Building, 14(4), 71-84.
Cao, D., Wang, G., Li, H., Skitmore, M., Huang, T., & Zhang, W. (2015). Practices and
effectiveness of building information modelling in construction projects in
China. Automation in Construction, 49, 113-122.
Chen, Q., Xia, B., Jin, Z., Wu, P., & Hu, Y. (2015). Choosing appropriate contract methods for
design-build projects. Journal of Management in Engineering, 32(1), 04015029.
Chileshe, N., & John Kikwasi, G. (2014). Critical success factors for implementation of risk
assessment and management practices within the Tanzanian construction
industry. Engineering, Construction and Architectural Management, 21(3), 291-319.
El-Sayegh, S. M., & Mansour, M. H. (2015). Risk assessment and allocation in highway
construction projects in the UAE. Journal of Management in Engineering, 31(6),
04015004.
Paraphrase This Document
Need a fresh take? Get an instant paraphrase of this document with our AI Paraphraser
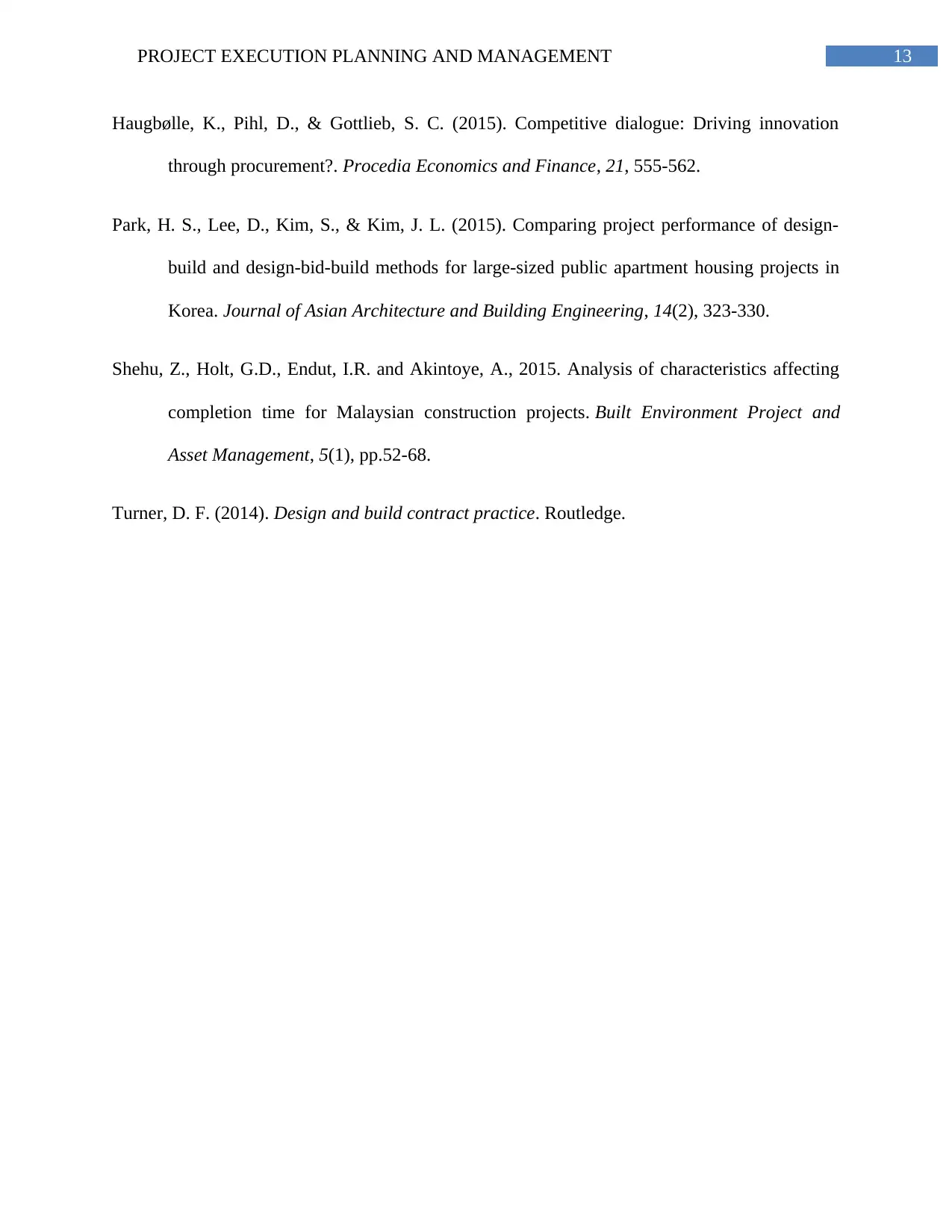
13PROJECT EXECUTION PLANNING AND MANAGEMENT
Haugbølle, K., Pihl, D., & Gottlieb, S. C. (2015). Competitive dialogue: Driving innovation
through procurement?. Procedia Economics and Finance, 21, 555-562.
Park, H. S., Lee, D., Kim, S., & Kim, J. L. (2015). Comparing project performance of design-
build and design-bid-build methods for large-sized public apartment housing projects in
Korea. Journal of Asian Architecture and Building Engineering, 14(2), 323-330.
Shehu, Z., Holt, G.D., Endut, I.R. and Akintoye, A., 2015. Analysis of characteristics affecting
completion time for Malaysian construction projects. Built Environment Project and
Asset Management, 5(1), pp.52-68.
Turner, D. F. (2014). Design and build contract practice. Routledge.
Haugbølle, K., Pihl, D., & Gottlieb, S. C. (2015). Competitive dialogue: Driving innovation
through procurement?. Procedia Economics and Finance, 21, 555-562.
Park, H. S., Lee, D., Kim, S., & Kim, J. L. (2015). Comparing project performance of design-
build and design-bid-build methods for large-sized public apartment housing projects in
Korea. Journal of Asian Architecture and Building Engineering, 14(2), 323-330.
Shehu, Z., Holt, G.D., Endut, I.R. and Akintoye, A., 2015. Analysis of characteristics affecting
completion time for Malaysian construction projects. Built Environment Project and
Asset Management, 5(1), pp.52-68.
Turner, D. F. (2014). Design and build contract practice. Routledge.
1 out of 14
Related Documents

Your All-in-One AI-Powered Toolkit for Academic Success.
+13062052269
info@desklib.com
Available 24*7 on WhatsApp / Email
Unlock your academic potential
© 2024 | Zucol Services PVT LTD | All rights reserved.