Strategic Supply Chain Management Analysis: ABC Company Case Study
VerifiedAdded on 2022/09/26
|11
|2105
|21
Report
AI Summary
This report presents a comprehensive analysis of ABC Company's supply chain network, focusing on the US distribution system. The report begins by outlining the existing supply network, detailing the flow of goods from China and Taiwan through US ports to distribution centers and warehouses, along with associated costs. It then explores alternative supply chain configurations, including the introduction of a distribution center in Los Angeles, evaluating the potential cost savings and operational efficiencies. The analysis extends to considering quality processing at different distribution centers and examines the impact of adding a distribution center in Seattle. The report concludes by identifying key strategies for optimizing the supply chain network, emphasizing responsiveness, delivery performance, and risk mitigation. The report also provides recommendations for strategic planning and implementation, including establishing a supply chain council, developing a well-staffed supply chain structure, and leveraging technology to improve efficiency and visibility. The report uses Excel-based models to derive the conclusions.
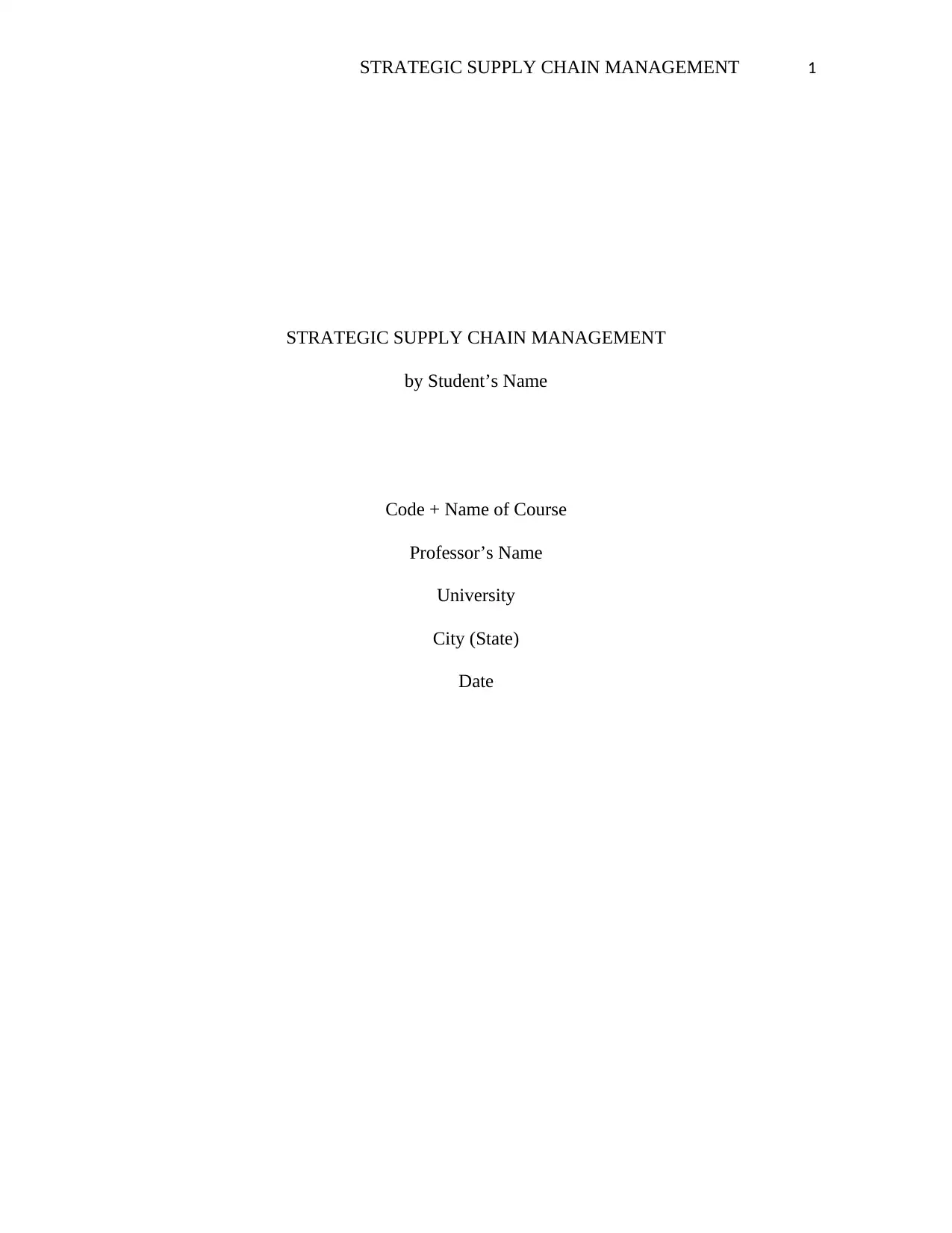
STRATEGIC SUPPLY CHAIN MANAGEMENT 1
STRATEGIC SUPPLY CHAIN MANAGEMENT
by Student’s Name
Code + Name of Course
Professor’s Name
University
City (State)
Date
STRATEGIC SUPPLY CHAIN MANAGEMENT
by Student’s Name
Code + Name of Course
Professor’s Name
University
City (State)
Date
Paraphrase This Document
Need a fresh take? Get an instant paraphrase of this document with our AI Paraphraser
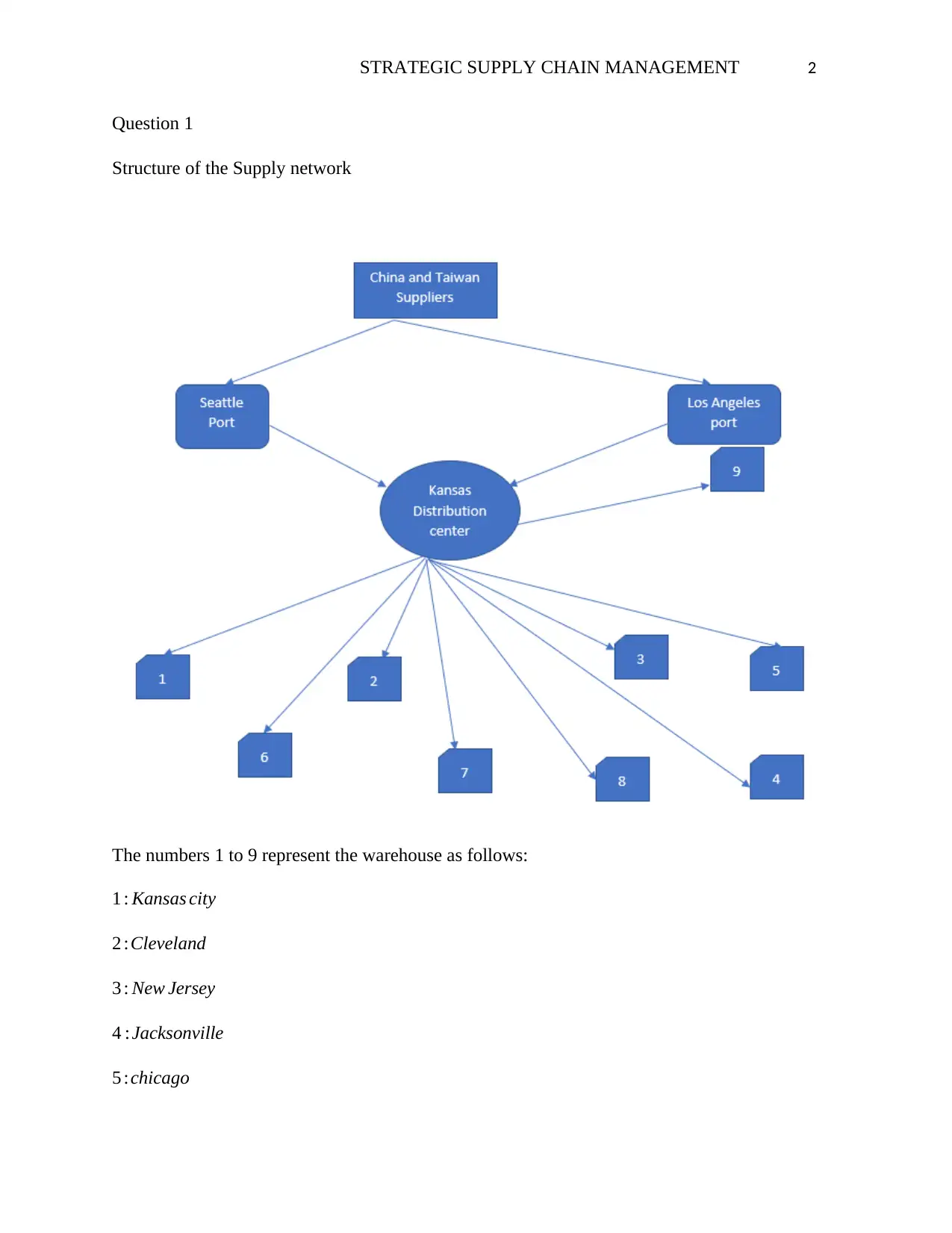
STRATEGIC SUPPLY CHAIN MANAGEMENT 2
Question 1
Structure of the Supply network
The numbers 1 to 9 represent the warehouse as follows:
1 : Kansas city
2 :Cleveland
3 : New Jersey
4 : Jacksonville
5 :chicago
Question 1
Structure of the Supply network
The numbers 1 to 9 represent the warehouse as follows:
1 : Kansas city
2 :Cleveland
3 : New Jersey
4 : Jacksonville
5 :chicago
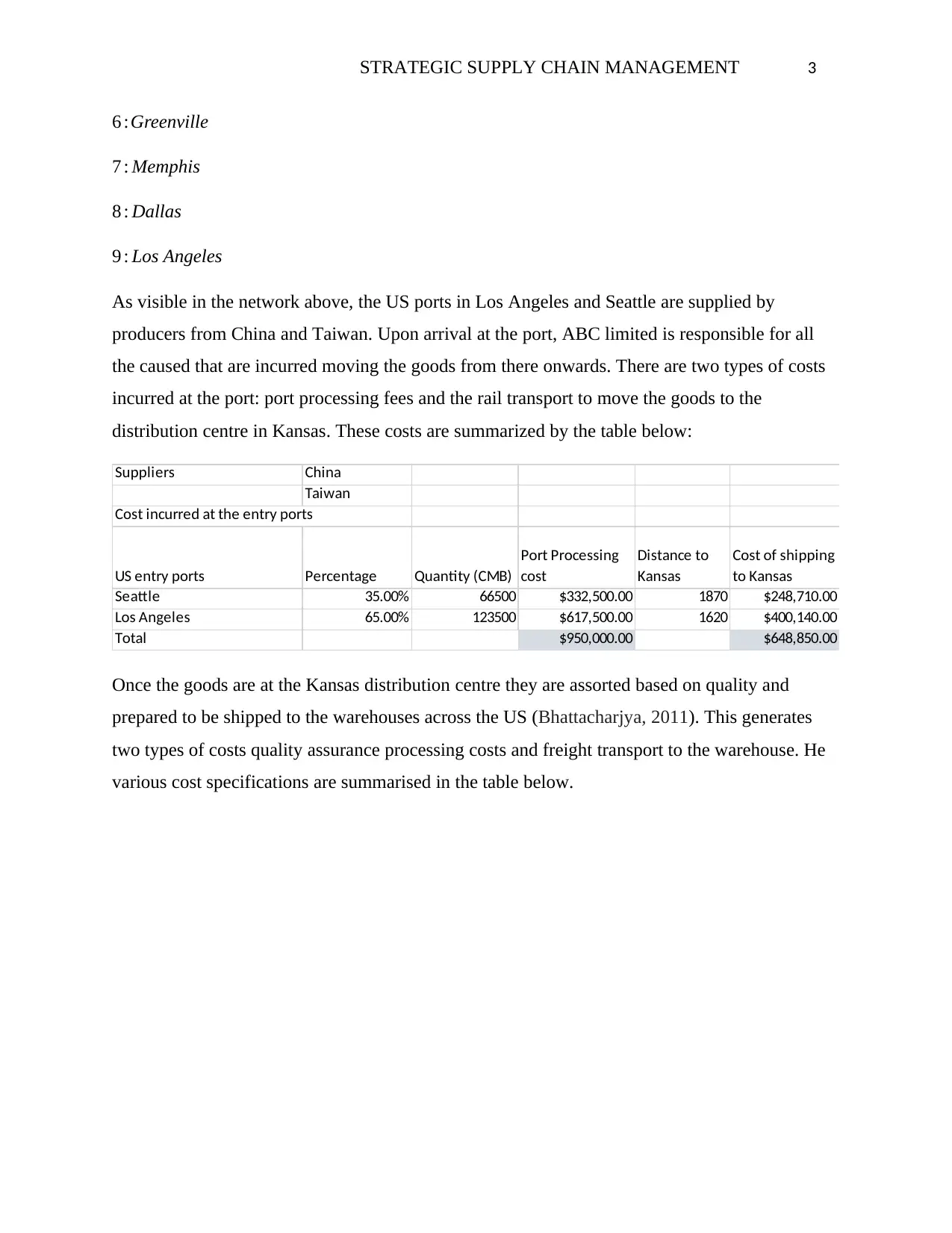
STRATEGIC SUPPLY CHAIN MANAGEMENT 3
6 :Greenville
7 : Memphis
8 : Dallas
9 : Los Angeles
As visible in the network above, the US ports in Los Angeles and Seattle are supplied by
producers from China and Taiwan. Upon arrival at the port, ABC limited is responsible for all
the caused that are incurred moving the goods from there onwards. There are two types of costs
incurred at the port: port processing fees and the rail transport to move the goods to the
distribution centre in Kansas. These costs are summarized by the table below:
Suppliers China
Taiwan
Cost incurred at the entry ports
US entry ports Percentage Quantity (CMB)
Port Processing
cost
Distance to
Kansas
Cost of shipping
to Kansas
Seattle 35.00% 66500 $332,500.00 1870 $248,710.00
Los Angeles 65.00% 123500 $617,500.00 1620 $400,140.00
Total $950,000.00 $648,850.00
Once the goods are at the Kansas distribution centre they are assorted based on quality and
prepared to be shipped to the warehouses across the US (Bhattacharjya, 2011). This generates
two types of costs quality assurance processing costs and freight transport to the warehouse. He
various cost specifications are summarised in the table below.
6 :Greenville
7 : Memphis
8 : Dallas
9 : Los Angeles
As visible in the network above, the US ports in Los Angeles and Seattle are supplied by
producers from China and Taiwan. Upon arrival at the port, ABC limited is responsible for all
the caused that are incurred moving the goods from there onwards. There are two types of costs
incurred at the port: port processing fees and the rail transport to move the goods to the
distribution centre in Kansas. These costs are summarized by the table below:
Suppliers China
Taiwan
Cost incurred at the entry ports
US entry ports Percentage Quantity (CMB)
Port Processing
cost
Distance to
Kansas
Cost of shipping
to Kansas
Seattle 35.00% 66500 $332,500.00 1870 $248,710.00
Los Angeles 65.00% 123500 $617,500.00 1620 $400,140.00
Total $950,000.00 $648,850.00
Once the goods are at the Kansas distribution centre they are assorted based on quality and
prepared to be shipped to the warehouses across the US (Bhattacharjya, 2011). This generates
two types of costs quality assurance processing costs and freight transport to the warehouse. He
various cost specifications are summarised in the table below.
⊘ This is a preview!⊘
Do you want full access?
Subscribe today to unlock all pages.

Trusted by 1+ million students worldwide
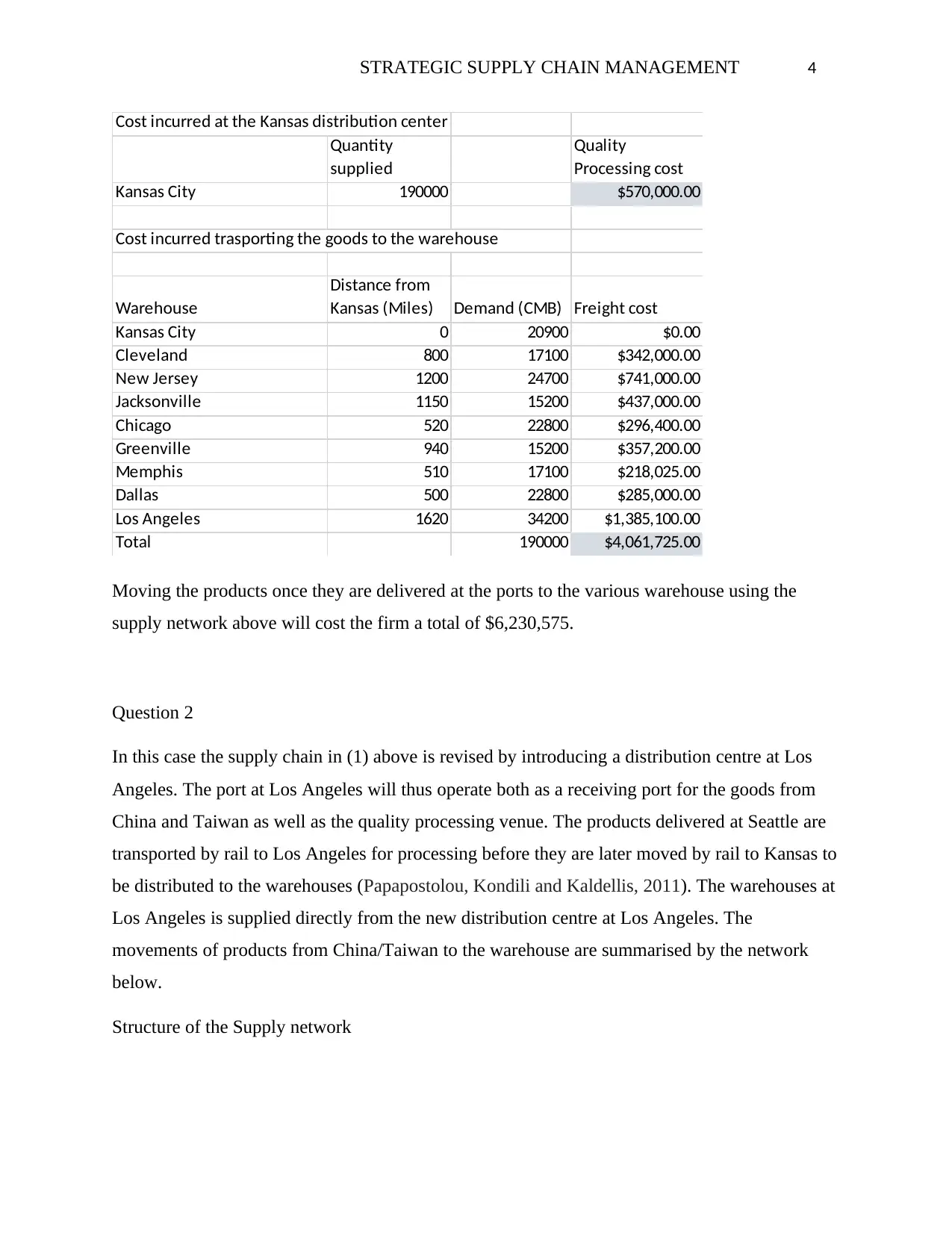
STRATEGIC SUPPLY CHAIN MANAGEMENT 4
Cost incurred at the Kansas distribution center
Quantity
supplied
Quality
Processing cost
Kansas City 190000 $570,000.00
Cost incurred trasporting the goods to the warehouse
Warehouse
Distance from
Kansas (Miles) Demand (CMB) Freight cost
Kansas City 0 20900 $0.00
Cleveland 800 17100 $342,000.00
New Jersey 1200 24700 $741,000.00
Jacksonville 1150 15200 $437,000.00
Chicago 520 22800 $296,400.00
Greenville 940 15200 $357,200.00
Memphis 510 17100 $218,025.00
Dallas 500 22800 $285,000.00
Los Angeles 1620 34200 $1,385,100.00
Total 190000 $4,061,725.00
Moving the products once they are delivered at the ports to the various warehouse using the
supply network above will cost the firm a total of $6,230,575.
Question 2
In this case the supply chain in (1) above is revised by introducing a distribution centre at Los
Angeles. The port at Los Angeles will thus operate both as a receiving port for the goods from
China and Taiwan as well as the quality processing venue. The products delivered at Seattle are
transported by rail to Los Angeles for processing before they are later moved by rail to Kansas to
be distributed to the warehouses (Papapostolou, Kondili and Kaldellis, 2011). The warehouses at
Los Angeles is supplied directly from the new distribution centre at Los Angeles. The
movements of products from China/Taiwan to the warehouse are summarised by the network
below.
Structure of the Supply network
Cost incurred at the Kansas distribution center
Quantity
supplied
Quality
Processing cost
Kansas City 190000 $570,000.00
Cost incurred trasporting the goods to the warehouse
Warehouse
Distance from
Kansas (Miles) Demand (CMB) Freight cost
Kansas City 0 20900 $0.00
Cleveland 800 17100 $342,000.00
New Jersey 1200 24700 $741,000.00
Jacksonville 1150 15200 $437,000.00
Chicago 520 22800 $296,400.00
Greenville 940 15200 $357,200.00
Memphis 510 17100 $218,025.00
Dallas 500 22800 $285,000.00
Los Angeles 1620 34200 $1,385,100.00
Total 190000 $4,061,725.00
Moving the products once they are delivered at the ports to the various warehouse using the
supply network above will cost the firm a total of $6,230,575.
Question 2
In this case the supply chain in (1) above is revised by introducing a distribution centre at Los
Angeles. The port at Los Angeles will thus operate both as a receiving port for the goods from
China and Taiwan as well as the quality processing venue. The products delivered at Seattle are
transported by rail to Los Angeles for processing before they are later moved by rail to Kansas to
be distributed to the warehouses (Papapostolou, Kondili and Kaldellis, 2011). The warehouses at
Los Angeles is supplied directly from the new distribution centre at Los Angeles. The
movements of products from China/Taiwan to the warehouse are summarised by the network
below.
Structure of the Supply network
Paraphrase This Document
Need a fresh take? Get an instant paraphrase of this document with our AI Paraphraser
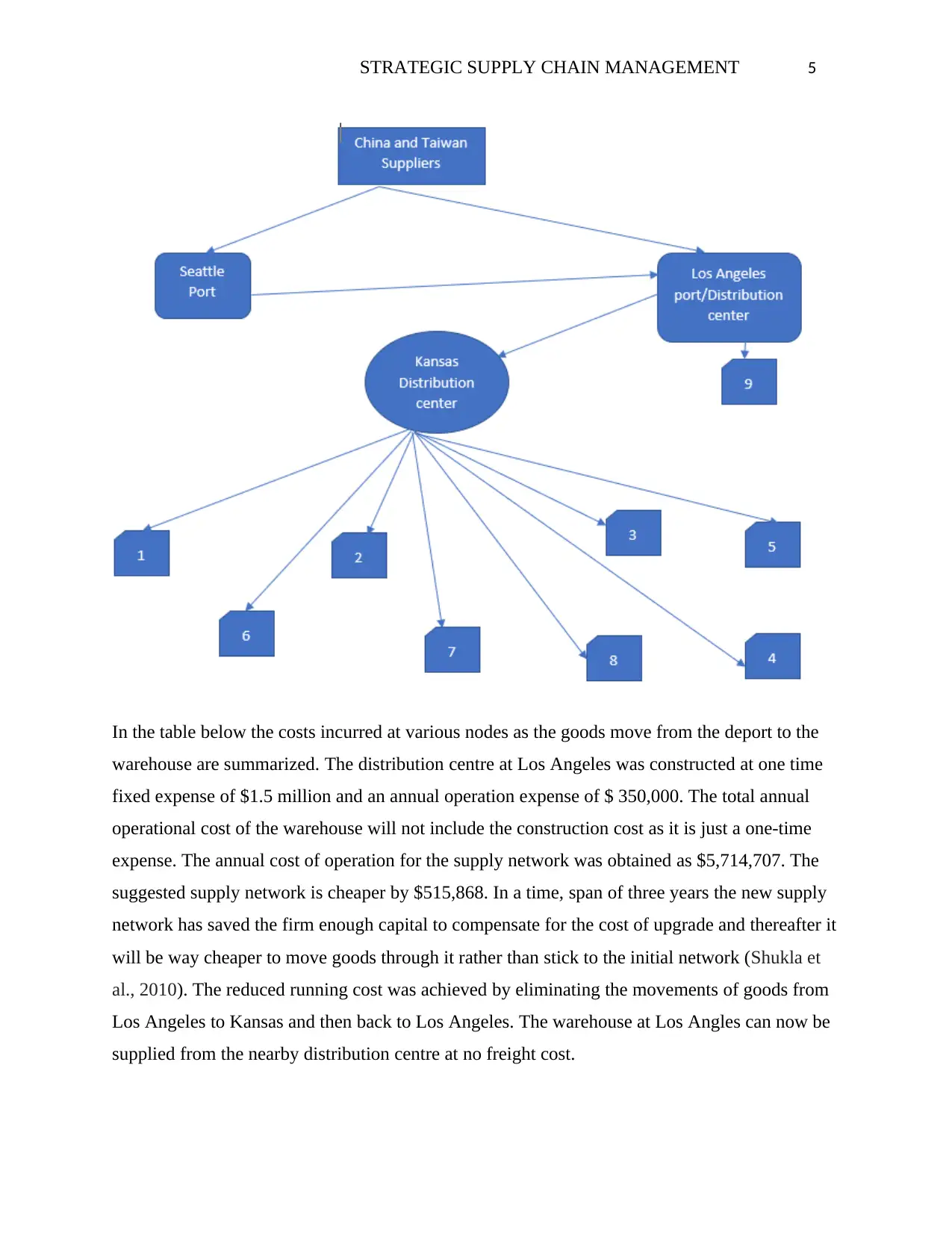
STRATEGIC SUPPLY CHAIN MANAGEMENT 5
In the table below the costs incurred at various nodes as the goods move from the deport to the
warehouse are summarized. The distribution centre at Los Angeles was constructed at one time
fixed expense of $1.5 million and an annual operation expense of $ 350,000. The total annual
operational cost of the warehouse will not include the construction cost as it is just a one-time
expense. The annual cost of operation for the supply network was obtained as $5,714,707. The
suggested supply network is cheaper by $515,868. In a time, span of three years the new supply
network has saved the firm enough capital to compensate for the cost of upgrade and thereafter it
will be way cheaper to move goods through it rather than stick to the initial network (Shukla et
al., 2010). The reduced running cost was achieved by eliminating the movements of goods from
Los Angeles to Kansas and then back to Los Angeles. The warehouse at Los Angles can now be
supplied from the nearby distribution centre at no freight cost.
In the table below the costs incurred at various nodes as the goods move from the deport to the
warehouse are summarized. The distribution centre at Los Angeles was constructed at one time
fixed expense of $1.5 million and an annual operation expense of $ 350,000. The total annual
operational cost of the warehouse will not include the construction cost as it is just a one-time
expense. The annual cost of operation for the supply network was obtained as $5,714,707. The
suggested supply network is cheaper by $515,868. In a time, span of three years the new supply
network has saved the firm enough capital to compensate for the cost of upgrade and thereafter it
will be way cheaper to move goods through it rather than stick to the initial network (Shukla et
al., 2010). The reduced running cost was achieved by eliminating the movements of goods from
Los Angeles to Kansas and then back to Los Angeles. The warehouse at Los Angles can now be
supplied from the nearby distribution centre at no freight cost.
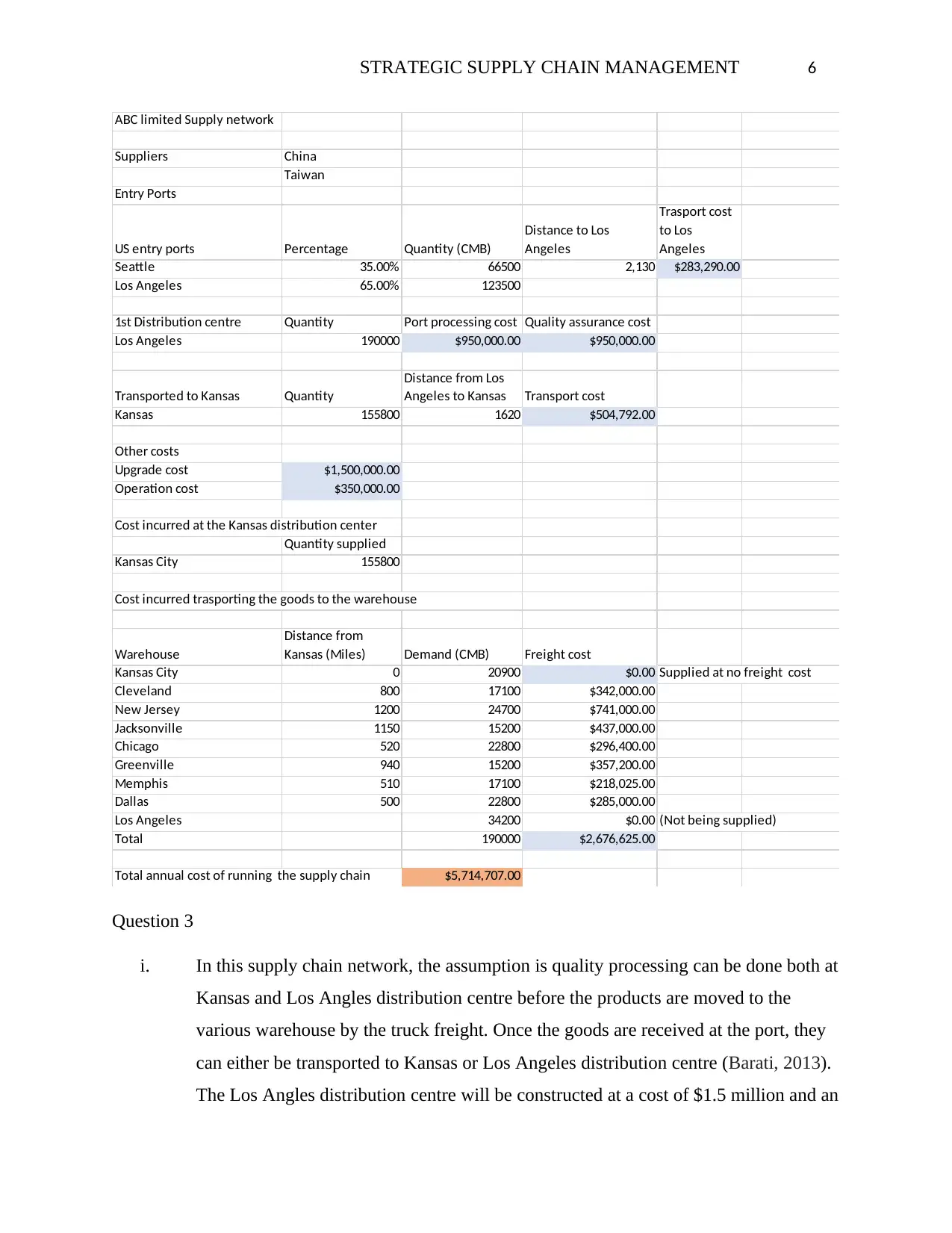
STRATEGIC SUPPLY CHAIN MANAGEMENT 6
ABC limited Supply network
Suppliers China
Taiwan
Entry Ports
US entry ports Percentage Quantity (CMB)
Distance to Los
Angeles
Trasport cost
to Los
Angeles
Seattle 35.00% 66500 2,130 $283,290.00
Los Angeles 65.00% 123500
1st Distribution centre Quantity Port processing cost Quality assurance cost
Los Angeles 190000 $950,000.00 $950,000.00
Transported to Kansas Quantity
Distance from Los
Angeles to Kansas Transport cost
Kansas 155800 1620 $504,792.00
Other costs
Upgrade cost $1,500,000.00
Operation cost $350,000.00
Cost incurred at the Kansas distribution center
Quantity supplied
Kansas City 155800
Cost incurred trasporting the goods to the warehouse
Warehouse
Distance from
Kansas (Miles) Demand (CMB) Freight cost
Kansas City 0 20900 $0.00 Supplied at no freight cost
Cleveland 800 17100 $342,000.00
New Jersey 1200 24700 $741,000.00
Jacksonville 1150 15200 $437,000.00
Chicago 520 22800 $296,400.00
Greenville 940 15200 $357,200.00
Memphis 510 17100 $218,025.00
Dallas 500 22800 $285,000.00
Los Angeles 34200 $0.00 (Not being supplied)
Total 190000 $2,676,625.00
Total annual cost of running the supply chain $5,714,707.00
Question 3
i. In this supply chain network, the assumption is quality processing can be done both at
Kansas and Los Angles distribution centre before the products are moved to the
various warehouse by the truck freight. Once the goods are received at the port, they
can either be transported to Kansas or Los Angeles distribution centre (Barati, 2013).
The Los Angles distribution centre will be constructed at a cost of $1.5 million and an
ABC limited Supply network
Suppliers China
Taiwan
Entry Ports
US entry ports Percentage Quantity (CMB)
Distance to Los
Angeles
Trasport cost
to Los
Angeles
Seattle 35.00% 66500 2,130 $283,290.00
Los Angeles 65.00% 123500
1st Distribution centre Quantity Port processing cost Quality assurance cost
Los Angeles 190000 $950,000.00 $950,000.00
Transported to Kansas Quantity
Distance from Los
Angeles to Kansas Transport cost
Kansas 155800 1620 $504,792.00
Other costs
Upgrade cost $1,500,000.00
Operation cost $350,000.00
Cost incurred at the Kansas distribution center
Quantity supplied
Kansas City 155800
Cost incurred trasporting the goods to the warehouse
Warehouse
Distance from
Kansas (Miles) Demand (CMB) Freight cost
Kansas City 0 20900 $0.00 Supplied at no freight cost
Cleveland 800 17100 $342,000.00
New Jersey 1200 24700 $741,000.00
Jacksonville 1150 15200 $437,000.00
Chicago 520 22800 $296,400.00
Greenville 940 15200 $357,200.00
Memphis 510 17100 $218,025.00
Dallas 500 22800 $285,000.00
Los Angeles 34200 $0.00 (Not being supplied)
Total 190000 $2,676,625.00
Total annual cost of running the supply chain $5,714,707.00
Question 3
i. In this supply chain network, the assumption is quality processing can be done both at
Kansas and Los Angles distribution centre before the products are moved to the
various warehouse by the truck freight. Once the goods are received at the port, they
can either be transported to Kansas or Los Angeles distribution centre (Barati, 2013).
The Los Angles distribution centre will be constructed at a cost of $1.5 million and an
⊘ This is a preview!⊘
Do you want full access?
Subscribe today to unlock all pages.

Trusted by 1+ million students worldwide

STRATEGIC SUPPLY CHAIN MANAGEMENT 7
additional $350,000 required annually to maintain the operations at the distribution
centre.
Using this information, the supply chain was modelled using excel and the following
information derived;
Once the goods are received at the two ports (Seattle and Los angels) they should be
processed by the custom officers, packed and transported by rail to the distribution
centres as per the table below.
Suppliers China
Taiwan
Entry Ports
US entry ports Percentage Quantity (CMB) Port processing cost
Seattle 35.00% 66500 $332,500.00
Los Angeles 65.00% 123500 $617,500.00
Units moved from the port to the distribution center
Kansas City Los Angeles Total
Seattle 66500 0 66500
Los Angeles 89300 34200 123500
Total 155800 34200
What this mean is that the Seattle port should supply the distribution centre at Kansas.
In addition, 89,300 units from Los Angeles port also transported to Kansas. The units
left at Los Angles should only be enough to supply the warehouse at Los Angeles.
The products movement from the distribution centres to the warehouse should be
according to the presented table.
Distribution center
Warehouse Kansas City Los Angeles
Kansas City 20900 0
Cleveland 17100 0
New Jersey 24700 0
Jacksonville 15200 0
Chicago 22800 0
Greenville 15200 0
Memphis 17100 0
Dallas 22800 0
Los Angeles 0 34200
additional $350,000 required annually to maintain the operations at the distribution
centre.
Using this information, the supply chain was modelled using excel and the following
information derived;
Once the goods are received at the two ports (Seattle and Los angels) they should be
processed by the custom officers, packed and transported by rail to the distribution
centres as per the table below.
Suppliers China
Taiwan
Entry Ports
US entry ports Percentage Quantity (CMB) Port processing cost
Seattle 35.00% 66500 $332,500.00
Los Angeles 65.00% 123500 $617,500.00
Units moved from the port to the distribution center
Kansas City Los Angeles Total
Seattle 66500 0 66500
Los Angeles 89300 34200 123500
Total 155800 34200
What this mean is that the Seattle port should supply the distribution centre at Kansas.
In addition, 89,300 units from Los Angeles port also transported to Kansas. The units
left at Los Angles should only be enough to supply the warehouse at Los Angeles.
The products movement from the distribution centres to the warehouse should be
according to the presented table.
Distribution center
Warehouse Kansas City Los Angeles
Kansas City 20900 0
Cleveland 17100 0
New Jersey 24700 0
Jacksonville 15200 0
Chicago 22800 0
Greenville 15200 0
Memphis 17100 0
Dallas 22800 0
Los Angeles 0 34200
Paraphrase This Document
Need a fresh take? Get an instant paraphrase of this document with our AI Paraphraser
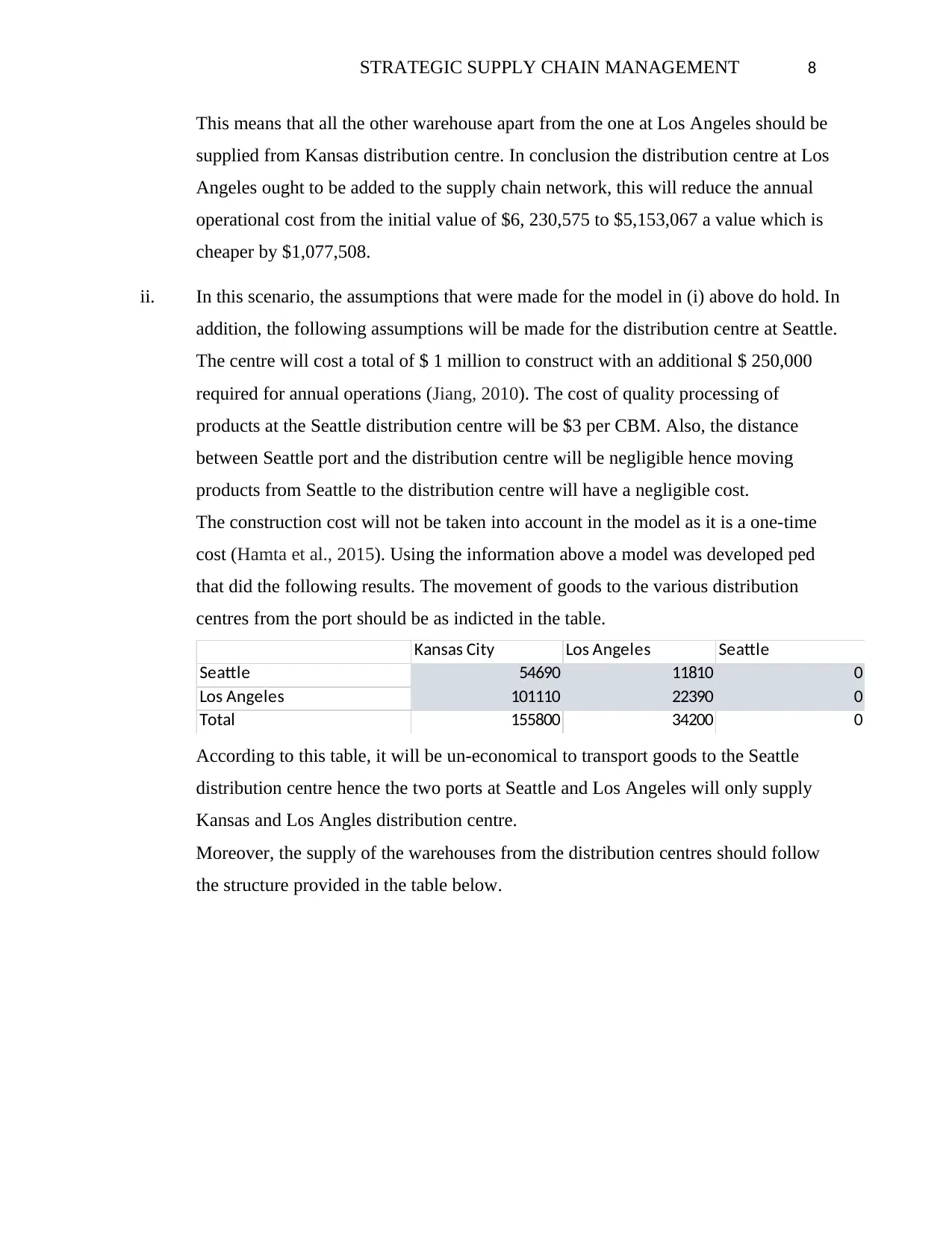
STRATEGIC SUPPLY CHAIN MANAGEMENT 8
This means that all the other warehouse apart from the one at Los Angeles should be
supplied from Kansas distribution centre. In conclusion the distribution centre at Los
Angeles ought to be added to the supply chain network, this will reduce the annual
operational cost from the initial value of $6, 230,575 to $5,153,067 a value which is
cheaper by $1,077,508.
ii. In this scenario, the assumptions that were made for the model in (i) above do hold. In
addition, the following assumptions will be made for the distribution centre at Seattle.
The centre will cost a total of $ 1 million to construct with an additional $ 250,000
required for annual operations (Jiang, 2010). The cost of quality processing of
products at the Seattle distribution centre will be $3 per CBM. Also, the distance
between Seattle port and the distribution centre will be negligible hence moving
products from Seattle to the distribution centre will have a negligible cost.
The construction cost will not be taken into account in the model as it is a one-time
cost (Hamta et al., 2015). Using the information above a model was developed ped
that did the following results. The movement of goods to the various distribution
centres from the port should be as indicted in the table.
Kansas City Los Angeles Seattle
Seattle 54690 11810 0
Los Angeles 101110 22390 0
Total 155800 34200 0
According to this table, it will be un-economical to transport goods to the Seattle
distribution centre hence the two ports at Seattle and Los Angeles will only supply
Kansas and Los Angles distribution centre.
Moreover, the supply of the warehouses from the distribution centres should follow
the structure provided in the table below.
This means that all the other warehouse apart from the one at Los Angeles should be
supplied from Kansas distribution centre. In conclusion the distribution centre at Los
Angeles ought to be added to the supply chain network, this will reduce the annual
operational cost from the initial value of $6, 230,575 to $5,153,067 a value which is
cheaper by $1,077,508.
ii. In this scenario, the assumptions that were made for the model in (i) above do hold. In
addition, the following assumptions will be made for the distribution centre at Seattle.
The centre will cost a total of $ 1 million to construct with an additional $ 250,000
required for annual operations (Jiang, 2010). The cost of quality processing of
products at the Seattle distribution centre will be $3 per CBM. Also, the distance
between Seattle port and the distribution centre will be negligible hence moving
products from Seattle to the distribution centre will have a negligible cost.
The construction cost will not be taken into account in the model as it is a one-time
cost (Hamta et al., 2015). Using the information above a model was developed ped
that did the following results. The movement of goods to the various distribution
centres from the port should be as indicted in the table.
Kansas City Los Angeles Seattle
Seattle 54690 11810 0
Los Angeles 101110 22390 0
Total 155800 34200 0
According to this table, it will be un-economical to transport goods to the Seattle
distribution centre hence the two ports at Seattle and Los Angeles will only supply
Kansas and Los Angles distribution centre.
Moreover, the supply of the warehouses from the distribution centres should follow
the structure provided in the table below.
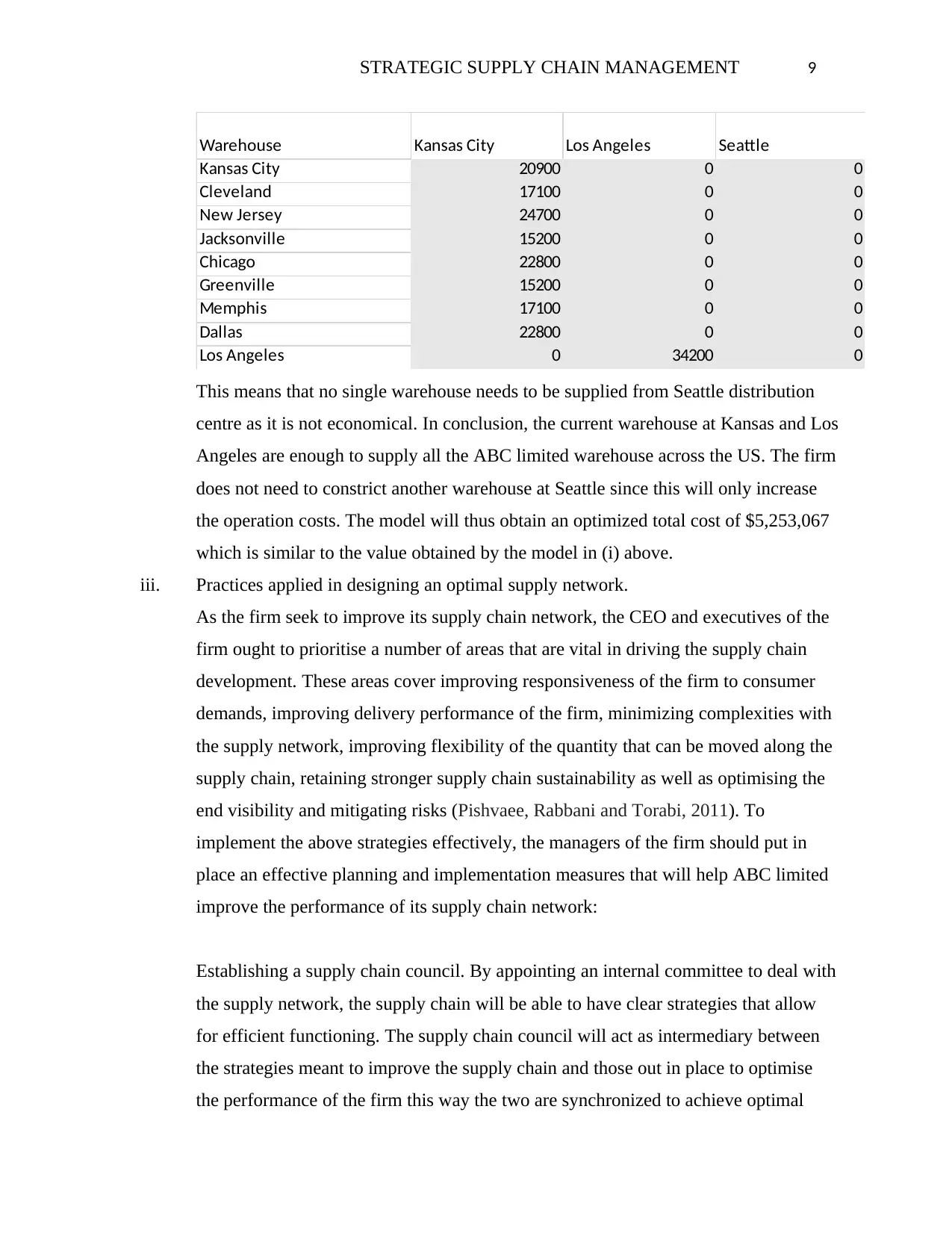
STRATEGIC SUPPLY CHAIN MANAGEMENT 9
Warehouse Kansas City Los Angeles Seattle
Kansas City 20900 0 0
Cleveland 17100 0 0
New Jersey 24700 0 0
Jacksonville 15200 0 0
Chicago 22800 0 0
Greenville 15200 0 0
Memphis 17100 0 0
Dallas 22800 0 0
Los Angeles 0 34200 0
This means that no single warehouse needs to be supplied from Seattle distribution
centre as it is not economical. In conclusion, the current warehouse at Kansas and Los
Angeles are enough to supply all the ABC limited warehouse across the US. The firm
does not need to constrict another warehouse at Seattle since this will only increase
the operation costs. The model will thus obtain an optimized total cost of $5,253,067
which is similar to the value obtained by the model in (i) above.
iii. Practices applied in designing an optimal supply network.
As the firm seek to improve its supply chain network, the CEO and executives of the
firm ought to prioritise a number of areas that are vital in driving the supply chain
development. These areas cover improving responsiveness of the firm to consumer
demands, improving delivery performance of the firm, minimizing complexities with
the supply network, improving flexibility of the quantity that can be moved along the
supply chain, retaining stronger supply chain sustainability as well as optimising the
end visibility and mitigating risks (Pishvaee, Rabbani and Torabi, 2011). To
implement the above strategies effectively, the managers of the firm should put in
place an effective planning and implementation measures that will help ABC limited
improve the performance of its supply chain network:
Establishing a supply chain council. By appointing an internal committee to deal with
the supply network, the supply chain will be able to have clear strategies that allow
for efficient functioning. The supply chain council will act as intermediary between
the strategies meant to improve the supply chain and those out in place to optimise
the performance of the firm this way the two are synchronized to achieve optimal
Warehouse Kansas City Los Angeles Seattle
Kansas City 20900 0 0
Cleveland 17100 0 0
New Jersey 24700 0 0
Jacksonville 15200 0 0
Chicago 22800 0 0
Greenville 15200 0 0
Memphis 17100 0 0
Dallas 22800 0 0
Los Angeles 0 34200 0
This means that no single warehouse needs to be supplied from Seattle distribution
centre as it is not economical. In conclusion, the current warehouse at Kansas and Los
Angeles are enough to supply all the ABC limited warehouse across the US. The firm
does not need to constrict another warehouse at Seattle since this will only increase
the operation costs. The model will thus obtain an optimized total cost of $5,253,067
which is similar to the value obtained by the model in (i) above.
iii. Practices applied in designing an optimal supply network.
As the firm seek to improve its supply chain network, the CEO and executives of the
firm ought to prioritise a number of areas that are vital in driving the supply chain
development. These areas cover improving responsiveness of the firm to consumer
demands, improving delivery performance of the firm, minimizing complexities with
the supply network, improving flexibility of the quantity that can be moved along the
supply chain, retaining stronger supply chain sustainability as well as optimising the
end visibility and mitigating risks (Pishvaee, Rabbani and Torabi, 2011). To
implement the above strategies effectively, the managers of the firm should put in
place an effective planning and implementation measures that will help ABC limited
improve the performance of its supply chain network:
Establishing a supply chain council. By appointing an internal committee to deal with
the supply network, the supply chain will be able to have clear strategies that allow
for efficient functioning. The supply chain council will act as intermediary between
the strategies meant to improve the supply chain and those out in place to optimise
the performance of the firm this way the two are synchronized to achieve optimal
⊘ This is a preview!⊘
Do you want full access?
Subscribe today to unlock all pages.

Trusted by 1+ million students worldwide
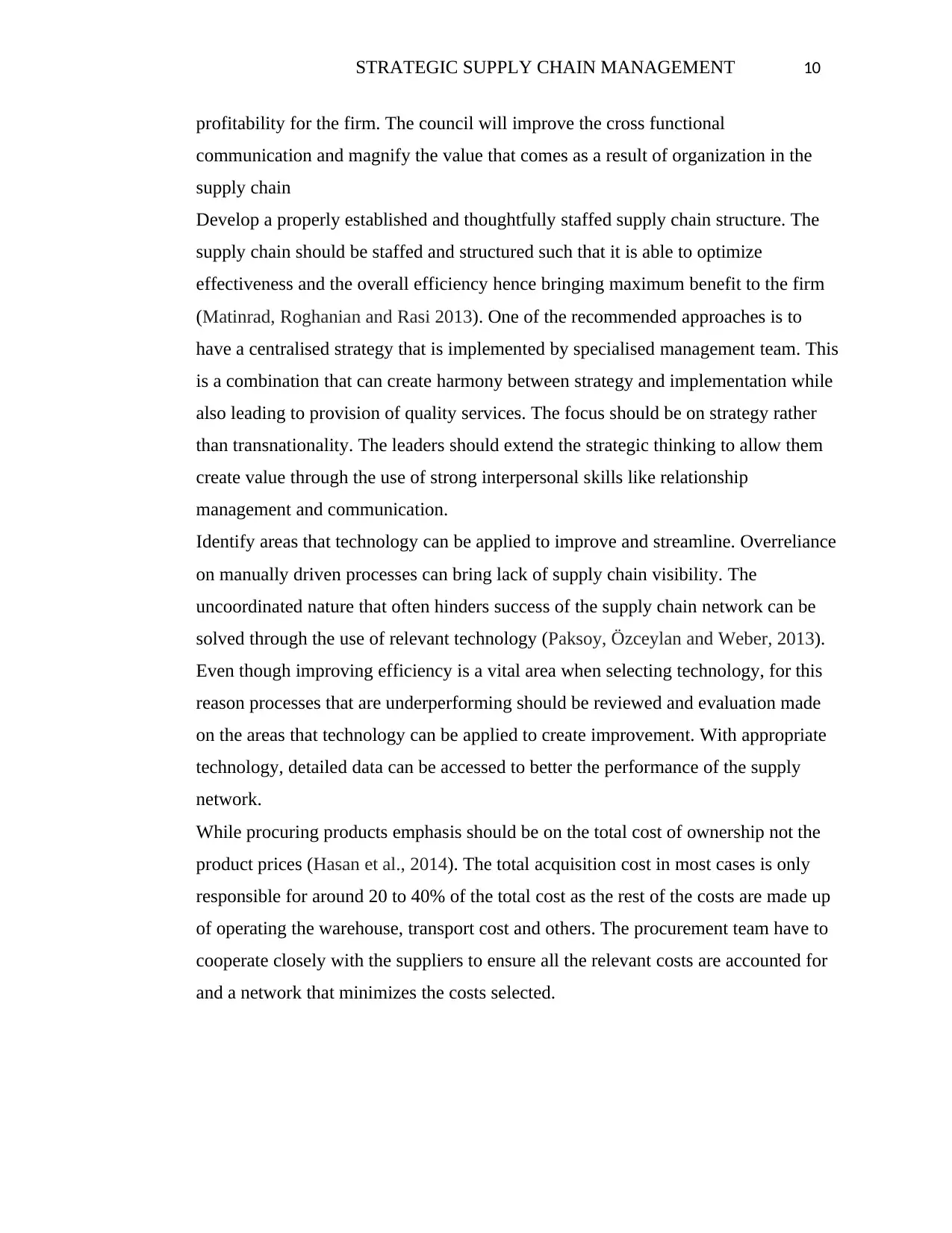
STRATEGIC SUPPLY CHAIN MANAGEMENT 10
profitability for the firm. The council will improve the cross functional
communication and magnify the value that comes as a result of organization in the
supply chain
Develop a properly established and thoughtfully staffed supply chain structure. The
supply chain should be staffed and structured such that it is able to optimize
effectiveness and the overall efficiency hence bringing maximum benefit to the firm
(Matinrad, Roghanian and Rasi 2013). One of the recommended approaches is to
have a centralised strategy that is implemented by specialised management team. This
is a combination that can create harmony between strategy and implementation while
also leading to provision of quality services. The focus should be on strategy rather
than transnationality. The leaders should extend the strategic thinking to allow them
create value through the use of strong interpersonal skills like relationship
management and communication.
Identify areas that technology can be applied to improve and streamline. Overreliance
on manually driven processes can bring lack of supply chain visibility. The
uncoordinated nature that often hinders success of the supply chain network can be
solved through the use of relevant technology (Paksoy, Özceylan and Weber, 2013).
Even though improving efficiency is a vital area when selecting technology, for this
reason processes that are underperforming should be reviewed and evaluation made
on the areas that technology can be applied to create improvement. With appropriate
technology, detailed data can be accessed to better the performance of the supply
network.
While procuring products emphasis should be on the total cost of ownership not the
product prices (Hasan et al., 2014). The total acquisition cost in most cases is only
responsible for around 20 to 40% of the total cost as the rest of the costs are made up
of operating the warehouse, transport cost and others. The procurement team have to
cooperate closely with the suppliers to ensure all the relevant costs are accounted for
and a network that minimizes the costs selected.
profitability for the firm. The council will improve the cross functional
communication and magnify the value that comes as a result of organization in the
supply chain
Develop a properly established and thoughtfully staffed supply chain structure. The
supply chain should be staffed and structured such that it is able to optimize
effectiveness and the overall efficiency hence bringing maximum benefit to the firm
(Matinrad, Roghanian and Rasi 2013). One of the recommended approaches is to
have a centralised strategy that is implemented by specialised management team. This
is a combination that can create harmony between strategy and implementation while
also leading to provision of quality services. The focus should be on strategy rather
than transnationality. The leaders should extend the strategic thinking to allow them
create value through the use of strong interpersonal skills like relationship
management and communication.
Identify areas that technology can be applied to improve and streamline. Overreliance
on manually driven processes can bring lack of supply chain visibility. The
uncoordinated nature that often hinders success of the supply chain network can be
solved through the use of relevant technology (Paksoy, Özceylan and Weber, 2013).
Even though improving efficiency is a vital area when selecting technology, for this
reason processes that are underperforming should be reviewed and evaluation made
on the areas that technology can be applied to create improvement. With appropriate
technology, detailed data can be accessed to better the performance of the supply
network.
While procuring products emphasis should be on the total cost of ownership not the
product prices (Hasan et al., 2014). The total acquisition cost in most cases is only
responsible for around 20 to 40% of the total cost as the rest of the costs are made up
of operating the warehouse, transport cost and others. The procurement team have to
cooperate closely with the suppliers to ensure all the relevant costs are accounted for
and a network that minimizes the costs selected.
Paraphrase This Document
Need a fresh take? Get an instant paraphrase of this document with our AI Paraphraser
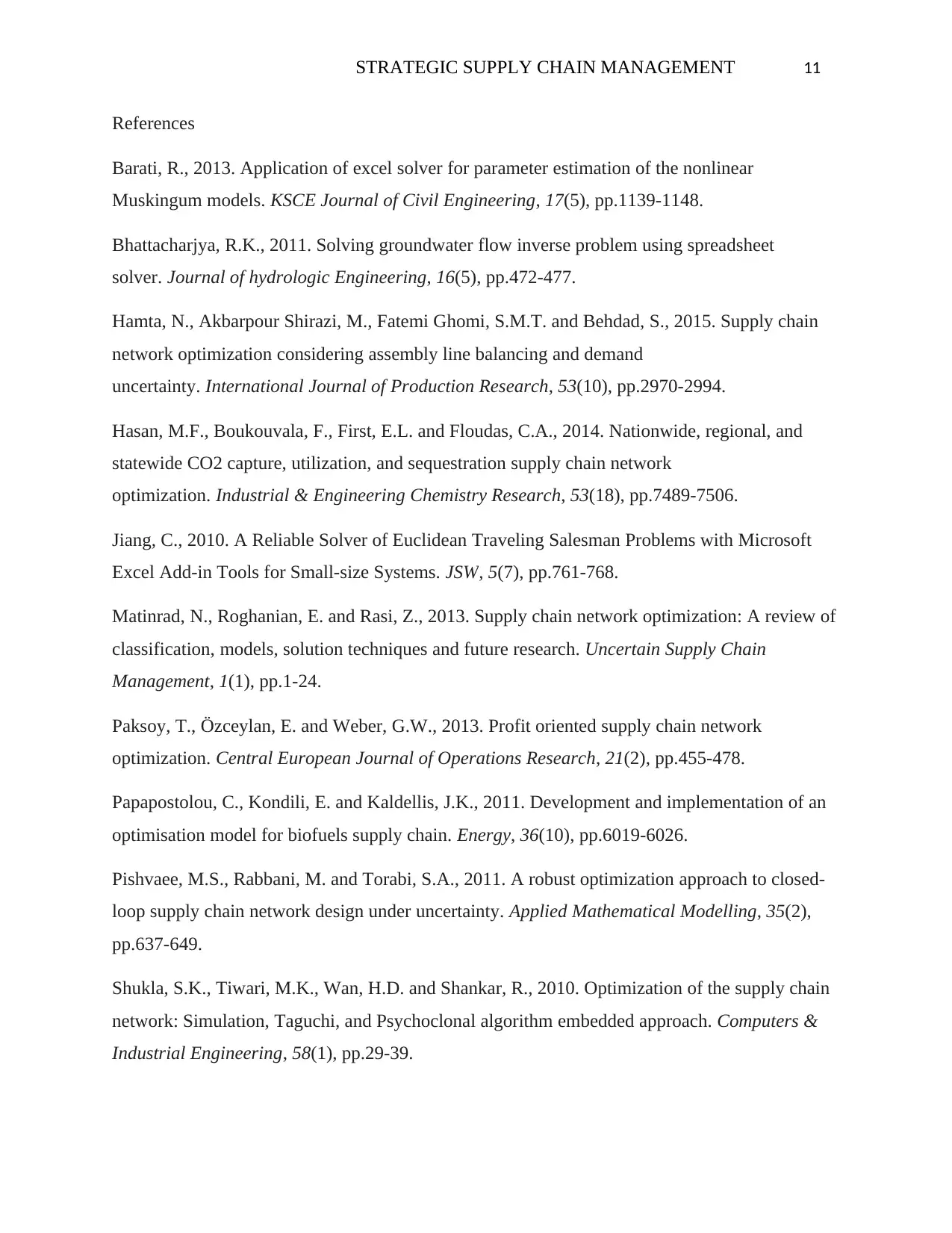
STRATEGIC SUPPLY CHAIN MANAGEMENT 11
References
Barati, R., 2013. Application of excel solver for parameter estimation of the nonlinear
Muskingum models. KSCE Journal of Civil Engineering, 17(5), pp.1139-1148.
Bhattacharjya, R.K., 2011. Solving groundwater flow inverse problem using spreadsheet
solver. Journal of hydrologic Engineering, 16(5), pp.472-477.
Hamta, N., Akbarpour Shirazi, M., Fatemi Ghomi, S.M.T. and Behdad, S., 2015. Supply chain
network optimization considering assembly line balancing and demand
uncertainty. International Journal of Production Research, 53(10), pp.2970-2994.
Hasan, M.F., Boukouvala, F., First, E.L. and Floudas, C.A., 2014. Nationwide, regional, and
statewide CO2 capture, utilization, and sequestration supply chain network
optimization. Industrial & Engineering Chemistry Research, 53(18), pp.7489-7506.
Jiang, C., 2010. A Reliable Solver of Euclidean Traveling Salesman Problems with Microsoft
Excel Add-in Tools for Small-size Systems. JSW, 5(7), pp.761-768.
Matinrad, N., Roghanian, E. and Rasi, Z., 2013. Supply chain network optimization: A review of
classification, models, solution techniques and future research. Uncertain Supply Chain
Management, 1(1), pp.1-24.
Paksoy, T., Özceylan, E. and Weber, G.W., 2013. Profit oriented supply chain network
optimization. Central European Journal of Operations Research, 21(2), pp.455-478.
Papapostolou, C., Kondili, E. and Kaldellis, J.K., 2011. Development and implementation of an
optimisation model for biofuels supply chain. Energy, 36(10), pp.6019-6026.
Pishvaee, M.S., Rabbani, M. and Torabi, S.A., 2011. A robust optimization approach to closed-
loop supply chain network design under uncertainty. Applied Mathematical Modelling, 35(2),
pp.637-649.
Shukla, S.K., Tiwari, M.K., Wan, H.D. and Shankar, R., 2010. Optimization of the supply chain
network: Simulation, Taguchi, and Psychoclonal algorithm embedded approach. Computers &
Industrial Engineering, 58(1), pp.29-39.
References
Barati, R., 2013. Application of excel solver for parameter estimation of the nonlinear
Muskingum models. KSCE Journal of Civil Engineering, 17(5), pp.1139-1148.
Bhattacharjya, R.K., 2011. Solving groundwater flow inverse problem using spreadsheet
solver. Journal of hydrologic Engineering, 16(5), pp.472-477.
Hamta, N., Akbarpour Shirazi, M., Fatemi Ghomi, S.M.T. and Behdad, S., 2015. Supply chain
network optimization considering assembly line balancing and demand
uncertainty. International Journal of Production Research, 53(10), pp.2970-2994.
Hasan, M.F., Boukouvala, F., First, E.L. and Floudas, C.A., 2014. Nationwide, regional, and
statewide CO2 capture, utilization, and sequestration supply chain network
optimization. Industrial & Engineering Chemistry Research, 53(18), pp.7489-7506.
Jiang, C., 2010. A Reliable Solver of Euclidean Traveling Salesman Problems with Microsoft
Excel Add-in Tools for Small-size Systems. JSW, 5(7), pp.761-768.
Matinrad, N., Roghanian, E. and Rasi, Z., 2013. Supply chain network optimization: A review of
classification, models, solution techniques and future research. Uncertain Supply Chain
Management, 1(1), pp.1-24.
Paksoy, T., Özceylan, E. and Weber, G.W., 2013. Profit oriented supply chain network
optimization. Central European Journal of Operations Research, 21(2), pp.455-478.
Papapostolou, C., Kondili, E. and Kaldellis, J.K., 2011. Development and implementation of an
optimisation model for biofuels supply chain. Energy, 36(10), pp.6019-6026.
Pishvaee, M.S., Rabbani, M. and Torabi, S.A., 2011. A robust optimization approach to closed-
loop supply chain network design under uncertainty. Applied Mathematical Modelling, 35(2),
pp.637-649.
Shukla, S.K., Tiwari, M.K., Wan, H.D. and Shankar, R., 2010. Optimization of the supply chain
network: Simulation, Taguchi, and Psychoclonal algorithm embedded approach. Computers &
Industrial Engineering, 58(1), pp.29-39.
1 out of 11