A Study on Load Moment Indicator (LMI System)
VerifiedAdded on 2022/07/28
|8
|1837
|39
AI Summary
Contribute Materials
Your contribution can guide someone’s learning journey. Share your
documents today.
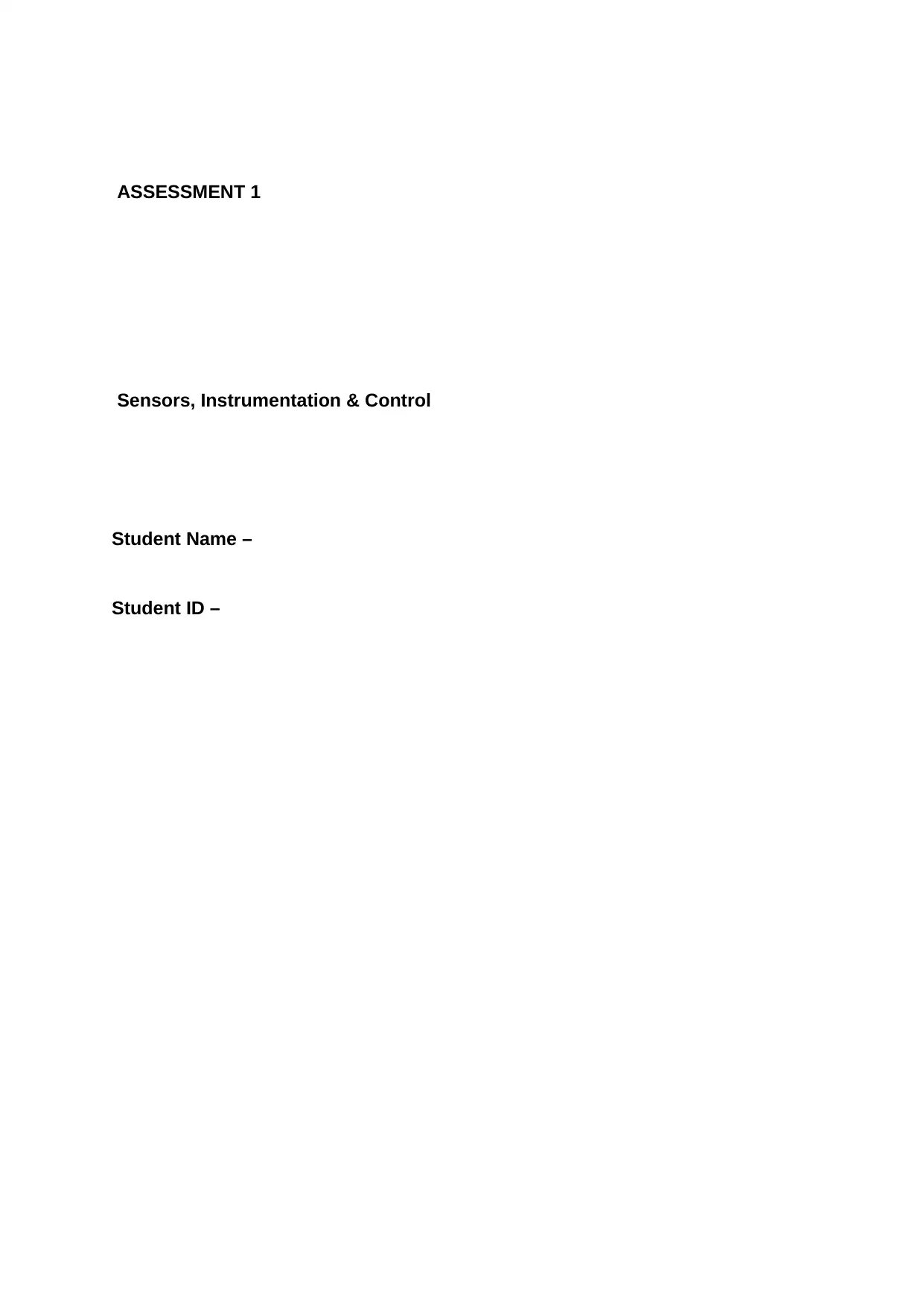
ASSESSMENT 1
Sensors, Instrumentation & Control
Student Name –
Student ID –
Sensors, Instrumentation & Control
Student Name –
Student ID –
Secure Best Marks with AI Grader
Need help grading? Try our AI Grader for instant feedback on your assignments.
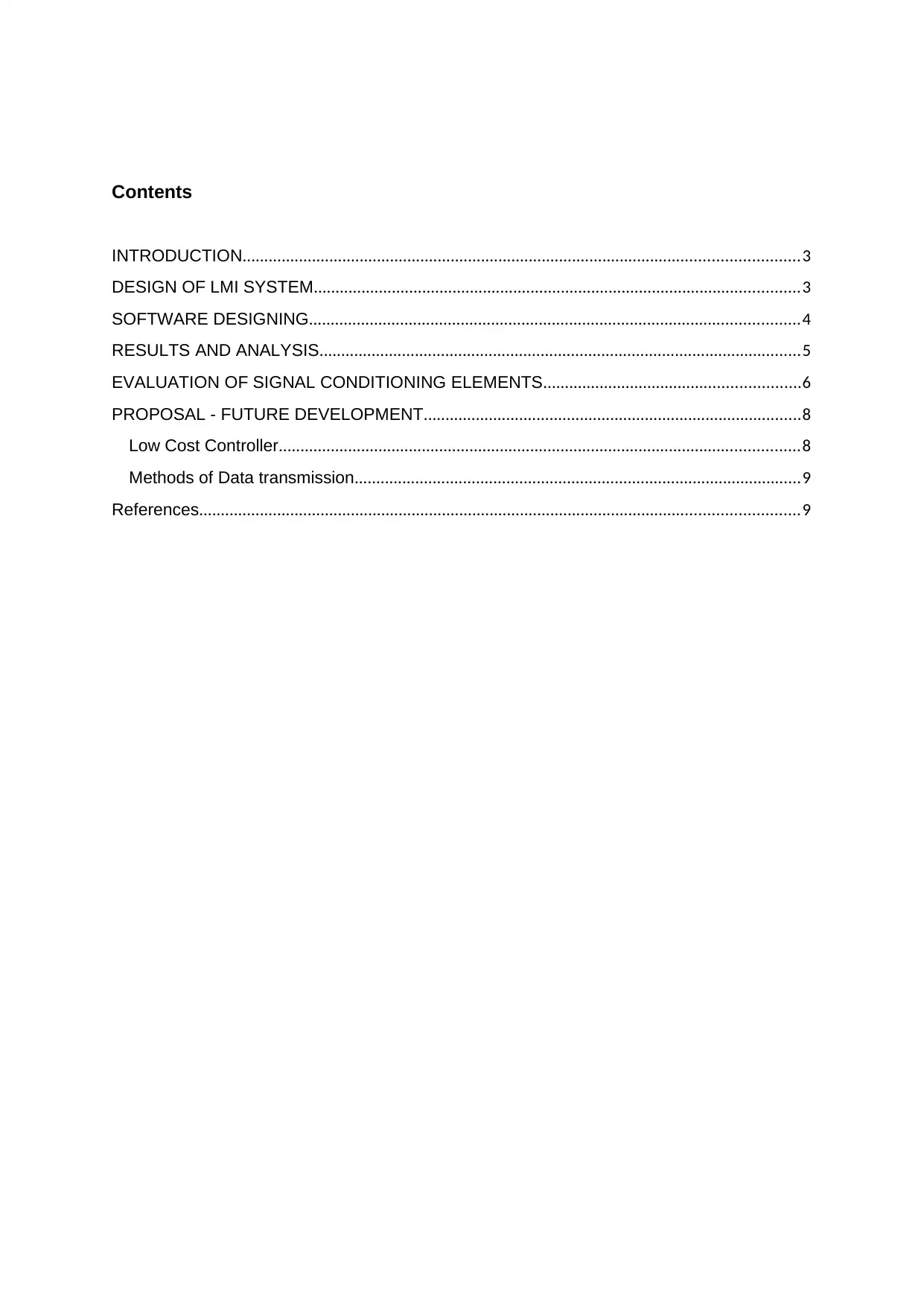
Contents
INTRODUCTION................................................................................................................................3
DESIGN OF LMI SYSTEM................................................................................................................3
SOFTWARE DESIGNING.................................................................................................................4
RESULTS AND ANALYSIS...............................................................................................................5
EVALUATION OF SIGNAL CONDITIONING ELEMENTS...........................................................6
PROPOSAL - FUTURE DEVELOPMENT.......................................................................................8
Low Cost Controller........................................................................................................................8
Methods of Data transmission.......................................................................................................9
References..........................................................................................................................................9
INTRODUCTION................................................................................................................................3
DESIGN OF LMI SYSTEM................................................................................................................3
SOFTWARE DESIGNING.................................................................................................................4
RESULTS AND ANALYSIS...............................................................................................................5
EVALUATION OF SIGNAL CONDITIONING ELEMENTS...........................................................6
PROPOSAL - FUTURE DEVELOPMENT.......................................................................................8
Low Cost Controller........................................................................................................................8
Methods of Data transmission.......................................................................................................9
References..........................................................................................................................................9
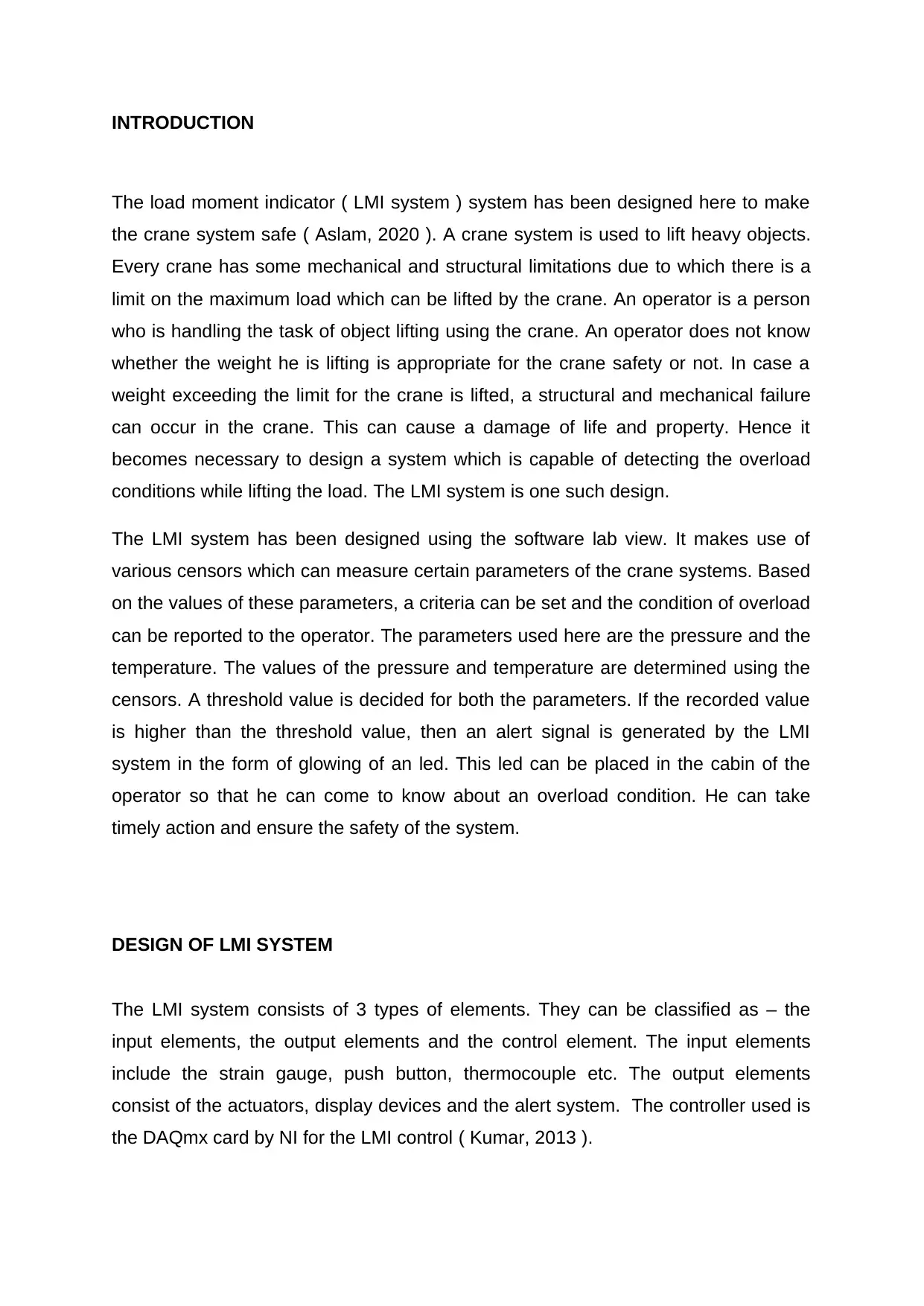
INTRODUCTION
The load moment indicator ( LMI system ) system has been designed here to make
the crane system safe ( Aslam, 2020 ). A crane system is used to lift heavy objects.
Every crane has some mechanical and structural limitations due to which there is a
limit on the maximum load which can be lifted by the crane. An operator is a person
who is handling the task of object lifting using the crane. An operator does not know
whether the weight he is lifting is appropriate for the crane safety or not. In case a
weight exceeding the limit for the crane is lifted, a structural and mechanical failure
can occur in the crane. This can cause a damage of life and property. Hence it
becomes necessary to design a system which is capable of detecting the overload
conditions while lifting the load. The LMI system is one such design.
The LMI system has been designed using the software lab view. It makes use of
various censors which can measure certain parameters of the crane systems. Based
on the values of these parameters, a criteria can be set and the condition of overload
can be reported to the operator. The parameters used here are the pressure and the
temperature. The values of the pressure and temperature are determined using the
censors. A threshold value is decided for both the parameters. If the recorded value
is higher than the threshold value, then an alert signal is generated by the LMI
system in the form of glowing of an led. This led can be placed in the cabin of the
operator so that he can come to know about an overload condition. He can take
timely action and ensure the safety of the system.
DESIGN OF LMI SYSTEM
The LMI system consists of 3 types of elements. They can be classified as – the
input elements, the output elements and the control element. The input elements
include the strain gauge, push button, thermocouple etc. The output elements
consist of the actuators, display devices and the alert system. The controller used is
the DAQmx card by NI for the LMI control ( Kumar, 2013 ).
The load moment indicator ( LMI system ) system has been designed here to make
the crane system safe ( Aslam, 2020 ). A crane system is used to lift heavy objects.
Every crane has some mechanical and structural limitations due to which there is a
limit on the maximum load which can be lifted by the crane. An operator is a person
who is handling the task of object lifting using the crane. An operator does not know
whether the weight he is lifting is appropriate for the crane safety or not. In case a
weight exceeding the limit for the crane is lifted, a structural and mechanical failure
can occur in the crane. This can cause a damage of life and property. Hence it
becomes necessary to design a system which is capable of detecting the overload
conditions while lifting the load. The LMI system is one such design.
The LMI system has been designed using the software lab view. It makes use of
various censors which can measure certain parameters of the crane systems. Based
on the values of these parameters, a criteria can be set and the condition of overload
can be reported to the operator. The parameters used here are the pressure and the
temperature. The values of the pressure and temperature are determined using the
censors. A threshold value is decided for both the parameters. If the recorded value
is higher than the threshold value, then an alert signal is generated by the LMI
system in the form of glowing of an led. This led can be placed in the cabin of the
operator so that he can come to know about an overload condition. He can take
timely action and ensure the safety of the system.
DESIGN OF LMI SYSTEM
The LMI system consists of 3 types of elements. They can be classified as – the
input elements, the output elements and the control element. The input elements
include the strain gauge, push button, thermocouple etc. The output elements
consist of the actuators, display devices and the alert system. The controller used is
the DAQmx card by NI for the LMI control ( Kumar, 2013 ).
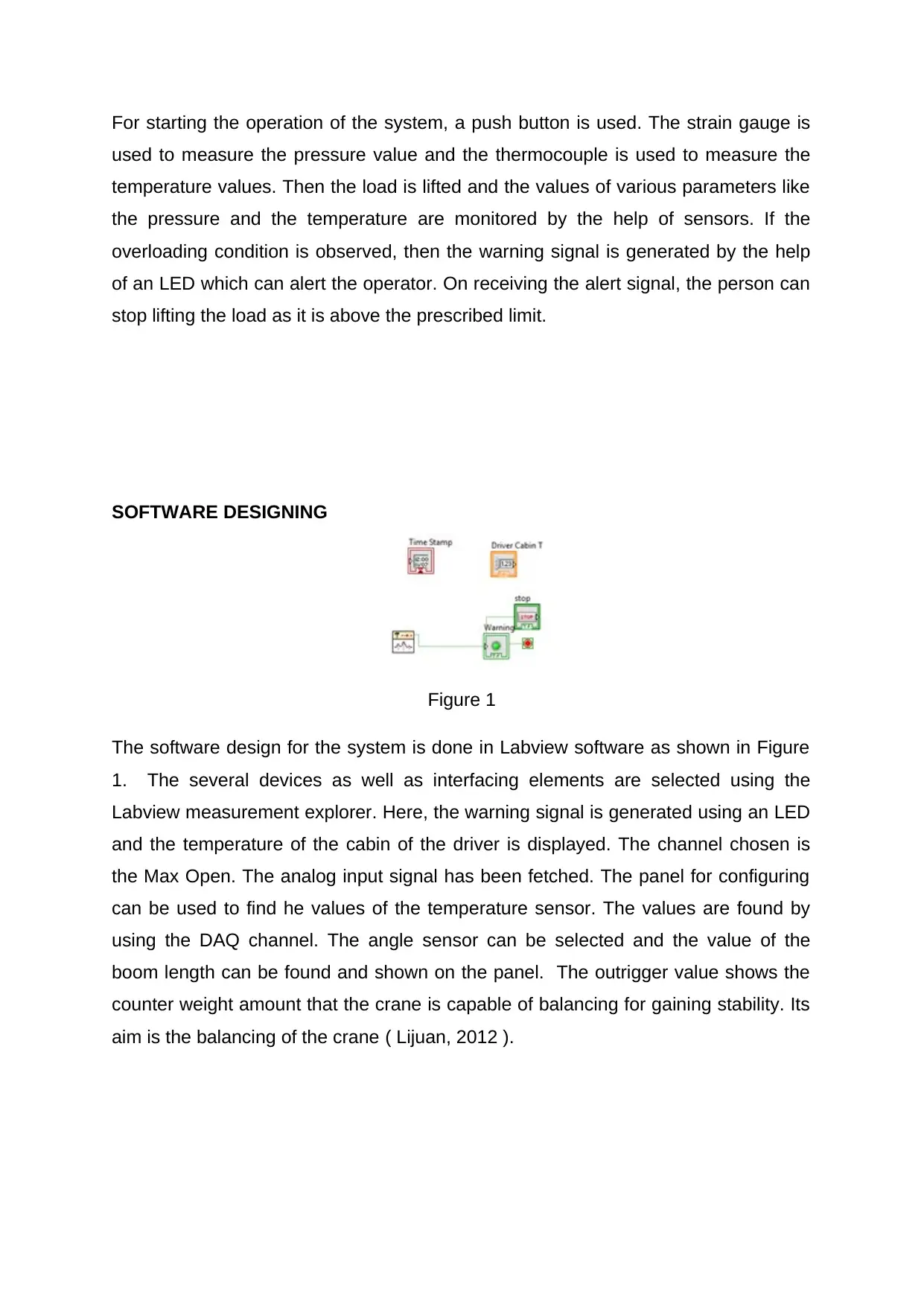
For starting the operation of the system, a push button is used. The strain gauge is
used to measure the pressure value and the thermocouple is used to measure the
temperature values. Then the load is lifted and the values of various parameters like
the pressure and the temperature are monitored by the help of sensors. If the
overloading condition is observed, then the warning signal is generated by the help
of an LED which can alert the operator. On receiving the alert signal, the person can
stop lifting the load as it is above the prescribed limit.
SOFTWARE DESIGNING
Figure 1
The software design for the system is done in Labview software as shown in Figure
1. The several devices as well as interfacing elements are selected using the
Labview measurement explorer. Here, the warning signal is generated using an LED
and the temperature of the cabin of the driver is displayed. The channel chosen is
the Max Open. The analog input signal has been fetched. The panel for configuring
can be used to find he values of the temperature sensor. The values are found by
using the DAQ channel. The angle sensor can be selected and the value of the
boom length can be found and shown on the panel. The outrigger value shows the
counter weight amount that the crane is capable of balancing for gaining stability. Its
aim is the balancing of the crane ( Lijuan, 2012 ).
used to measure the pressure value and the thermocouple is used to measure the
temperature values. Then the load is lifted and the values of various parameters like
the pressure and the temperature are monitored by the help of sensors. If the
overloading condition is observed, then the warning signal is generated by the help
of an LED which can alert the operator. On receiving the alert signal, the person can
stop lifting the load as it is above the prescribed limit.
SOFTWARE DESIGNING
Figure 1
The software design for the system is done in Labview software as shown in Figure
1. The several devices as well as interfacing elements are selected using the
Labview measurement explorer. Here, the warning signal is generated using an LED
and the temperature of the cabin of the driver is displayed. The channel chosen is
the Max Open. The analog input signal has been fetched. The panel for configuring
can be used to find he values of the temperature sensor. The values are found by
using the DAQ channel. The angle sensor can be selected and the value of the
boom length can be found and shown on the panel. The outrigger value shows the
counter weight amount that the crane is capable of balancing for gaining stability. Its
aim is the balancing of the crane ( Lijuan, 2012 ).
Secure Best Marks with AI Grader
Need help grading? Try our AI Grader for instant feedback on your assignments.
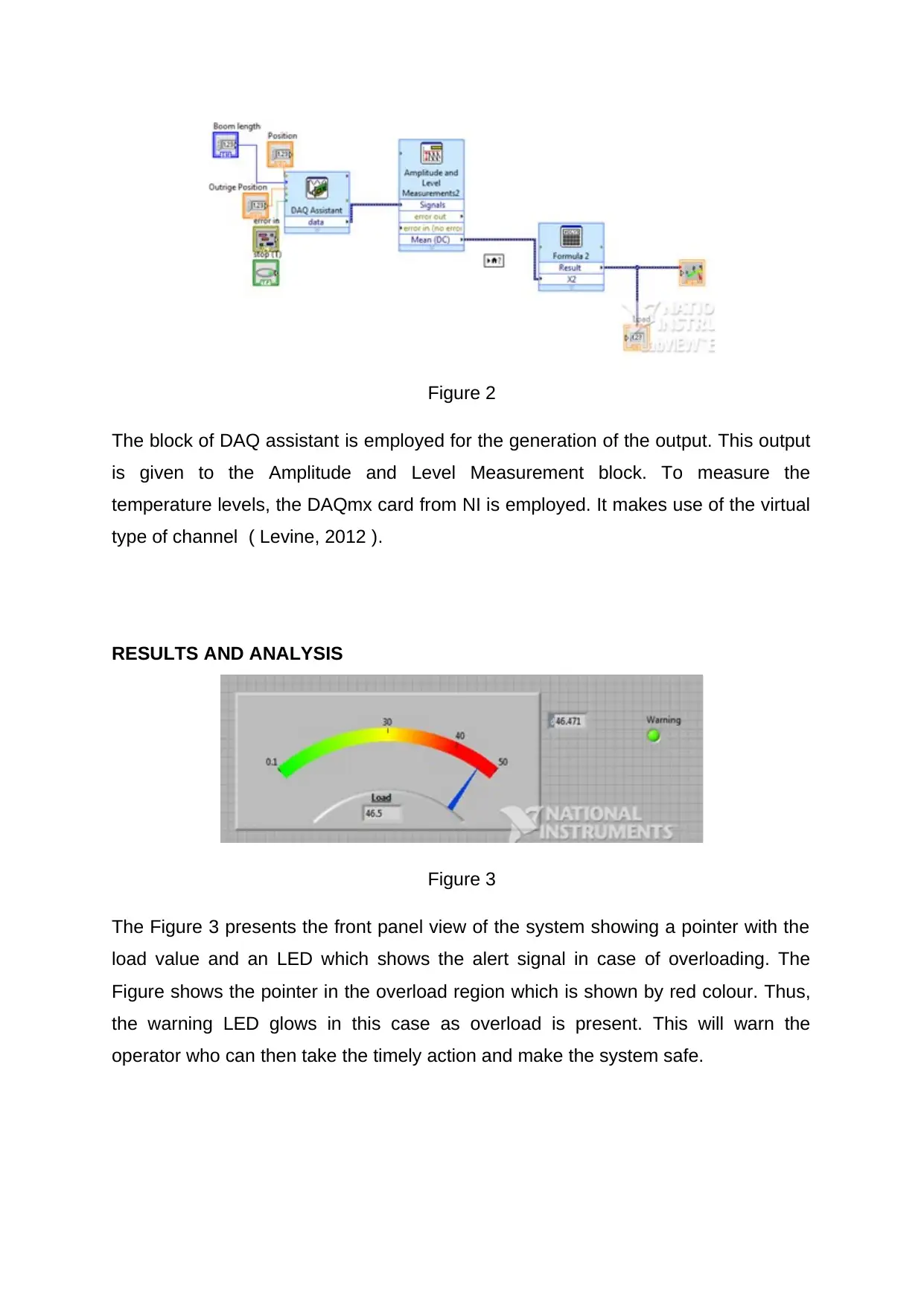
Figure 2
The block of DAQ assistant is employed for the generation of the output. This output
is given to the Amplitude and Level Measurement block. To measure the
temperature levels, the DAQmx card from NI is employed. It makes use of the virtual
type of channel ( Levine, 2012 ).
RESULTS AND ANALYSIS
Figure 3
The Figure 3 presents the front panel view of the system showing a pointer with the
load value and an LED which shows the alert signal in case of overloading. The
Figure shows the pointer in the overload region which is shown by red colour. Thus,
the warning LED glows in this case as overload is present. This will warn the
operator who can then take the timely action and make the system safe.
The block of DAQ assistant is employed for the generation of the output. This output
is given to the Amplitude and Level Measurement block. To measure the
temperature levels, the DAQmx card from NI is employed. It makes use of the virtual
type of channel ( Levine, 2012 ).
RESULTS AND ANALYSIS
Figure 3
The Figure 3 presents the front panel view of the system showing a pointer with the
load value and an LED which shows the alert signal in case of overloading. The
Figure shows the pointer in the overload region which is shown by red colour. Thus,
the warning LED glows in this case as overload is present. This will warn the
operator who can then take the timely action and make the system safe.
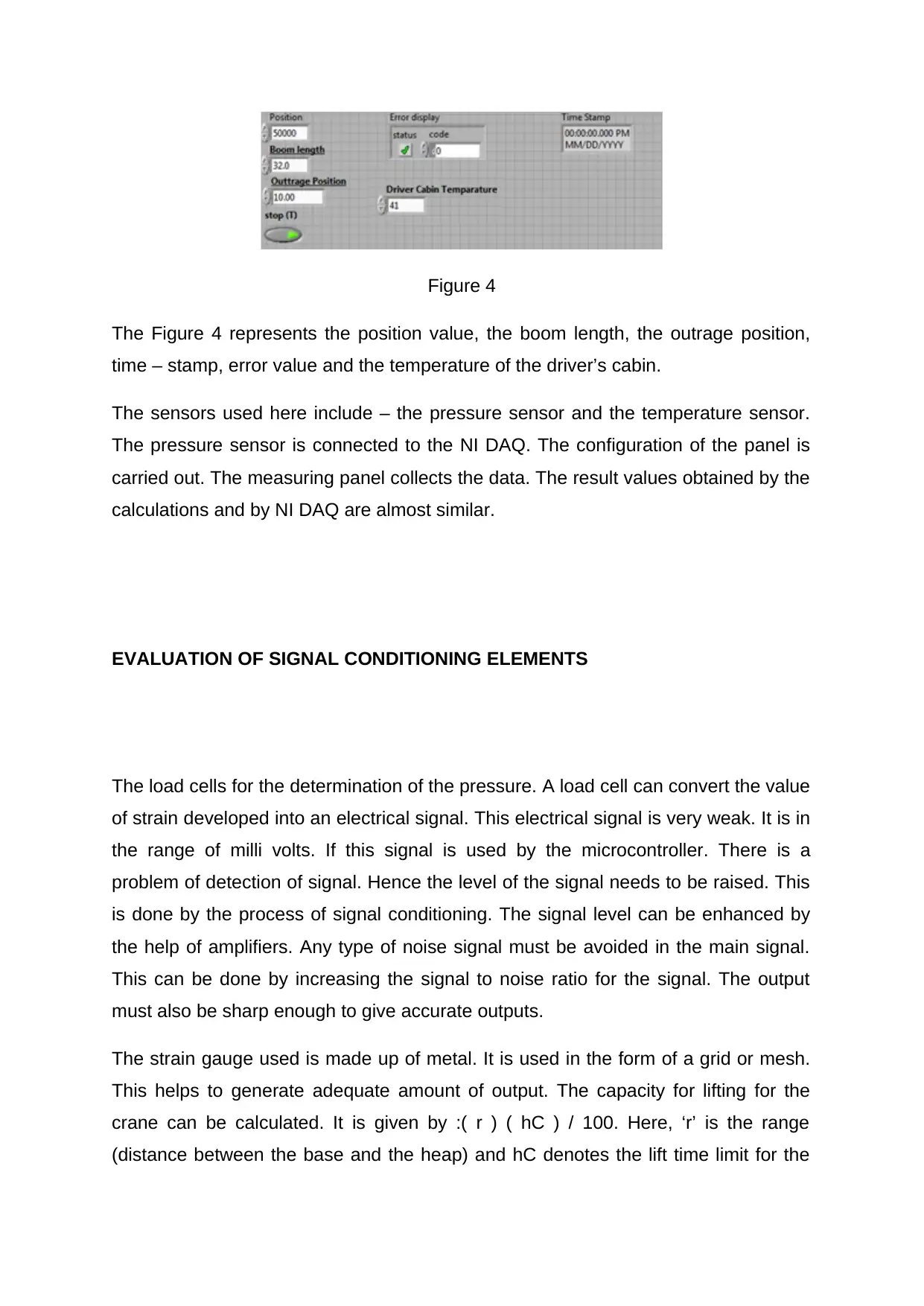
Figure 4
The Figure 4 represents the position value, the boom length, the outrage position,
time – stamp, error value and the temperature of the driver’s cabin.
The sensors used here include – the pressure sensor and the temperature sensor.
The pressure sensor is connected to the NI DAQ. The configuration of the panel is
carried out. The measuring panel collects the data. The result values obtained by the
calculations and by NI DAQ are almost similar.
EVALUATION OF SIGNAL CONDITIONING ELEMENTS
The load cells for the determination of the pressure. A load cell can convert the value
of strain developed into an electrical signal. This electrical signal is very weak. It is in
the range of milli volts. If this signal is used by the microcontroller. There is a
problem of detection of signal. Hence the level of the signal needs to be raised. This
is done by the process of signal conditioning. The signal level can be enhanced by
the help of amplifiers. Any type of noise signal must be avoided in the main signal.
This can be done by increasing the signal to noise ratio for the signal. The output
must also be sharp enough to give accurate outputs.
The strain gauge used is made up of metal. It is used in the form of a grid or mesh.
This helps to generate adequate amount of output. The capacity for lifting for the
crane can be calculated. It is given by :( r ) ( hC ) / 100. Here, ‘r’ is the range
(distance between the base and the heap) and hC denotes the lift time limit for the
The Figure 4 represents the position value, the boom length, the outrage position,
time – stamp, error value and the temperature of the driver’s cabin.
The sensors used here include – the pressure sensor and the temperature sensor.
The pressure sensor is connected to the NI DAQ. The configuration of the panel is
carried out. The measuring panel collects the data. The result values obtained by the
calculations and by NI DAQ are almost similar.
EVALUATION OF SIGNAL CONDITIONING ELEMENTS
The load cells for the determination of the pressure. A load cell can convert the value
of strain developed into an electrical signal. This electrical signal is very weak. It is in
the range of milli volts. If this signal is used by the microcontroller. There is a
problem of detection of signal. Hence the level of the signal needs to be raised. This
is done by the process of signal conditioning. The signal level can be enhanced by
the help of amplifiers. Any type of noise signal must be avoided in the main signal.
This can be done by increasing the signal to noise ratio for the signal. The output
must also be sharp enough to give accurate outputs.
The strain gauge used is made up of metal. It is used in the form of a grid or mesh.
This helps to generate adequate amount of output. The capacity for lifting for the
crane can be calculated. It is given by :( r ) ( hC ) / 100. Here, ‘r’ is the range
(distance between the base and the heap) and hC denotes the lift time limit for the
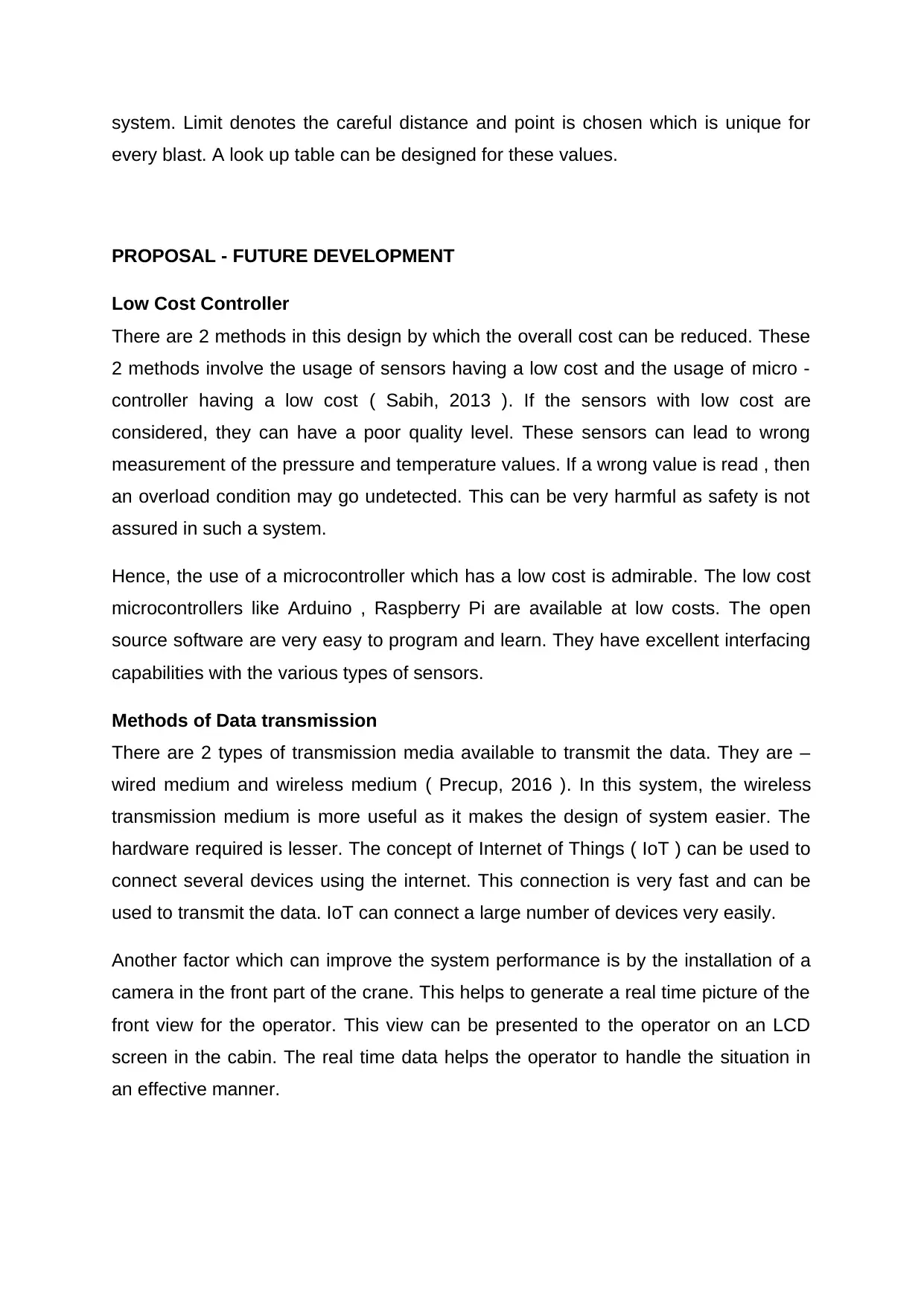
system. Limit denotes the careful distance and point is chosen which is unique for
every blast. A look up table can be designed for these values.
PROPOSAL - FUTURE DEVELOPMENT
Low Cost Controller
There are 2 methods in this design by which the overall cost can be reduced. These
2 methods involve the usage of sensors having a low cost and the usage of micro -
controller having a low cost ( Sabih, 2013 ). If the sensors with low cost are
considered, they can have a poor quality level. These sensors can lead to wrong
measurement of the pressure and temperature values. If a wrong value is read , then
an overload condition may go undetected. This can be very harmful as safety is not
assured in such a system.
Hence, the use of a microcontroller which has a low cost is admirable. The low cost
microcontrollers like Arduino , Raspberry Pi are available at low costs. The open
source software are very easy to program and learn. They have excellent interfacing
capabilities with the various types of sensors.
Methods of Data transmission
There are 2 types of transmission media available to transmit the data. They are –
wired medium and wireless medium ( Precup, 2016 ). In this system, the wireless
transmission medium is more useful as it makes the design of system easier. The
hardware required is lesser. The concept of Internet of Things ( IoT ) can be used to
connect several devices using the internet. This connection is very fast and can be
used to transmit the data. IoT can connect a large number of devices very easily.
Another factor which can improve the system performance is by the installation of a
camera in the front part of the crane. This helps to generate a real time picture of the
front view for the operator. This view can be presented to the operator on an LCD
screen in the cabin. The real time data helps the operator to handle the situation in
an effective manner.
every blast. A look up table can be designed for these values.
PROPOSAL - FUTURE DEVELOPMENT
Low Cost Controller
There are 2 methods in this design by which the overall cost can be reduced. These
2 methods involve the usage of sensors having a low cost and the usage of micro -
controller having a low cost ( Sabih, 2013 ). If the sensors with low cost are
considered, they can have a poor quality level. These sensors can lead to wrong
measurement of the pressure and temperature values. If a wrong value is read , then
an overload condition may go undetected. This can be very harmful as safety is not
assured in such a system.
Hence, the use of a microcontroller which has a low cost is admirable. The low cost
microcontrollers like Arduino , Raspberry Pi are available at low costs. The open
source software are very easy to program and learn. They have excellent interfacing
capabilities with the various types of sensors.
Methods of Data transmission
There are 2 types of transmission media available to transmit the data. They are –
wired medium and wireless medium ( Precup, 2016 ). In this system, the wireless
transmission medium is more useful as it makes the design of system easier. The
hardware required is lesser. The concept of Internet of Things ( IoT ) can be used to
connect several devices using the internet. This connection is very fast and can be
used to transmit the data. IoT can connect a large number of devices very easily.
Another factor which can improve the system performance is by the installation of a
camera in the front part of the crane. This helps to generate a real time picture of the
front view for the operator. This view can be presented to the operator on an LCD
screen in the cabin. The real time data helps the operator to handle the situation in
an effective manner.
Paraphrase This Document
Need a fresh take? Get an instant paraphrase of this document with our AI Paraphraser
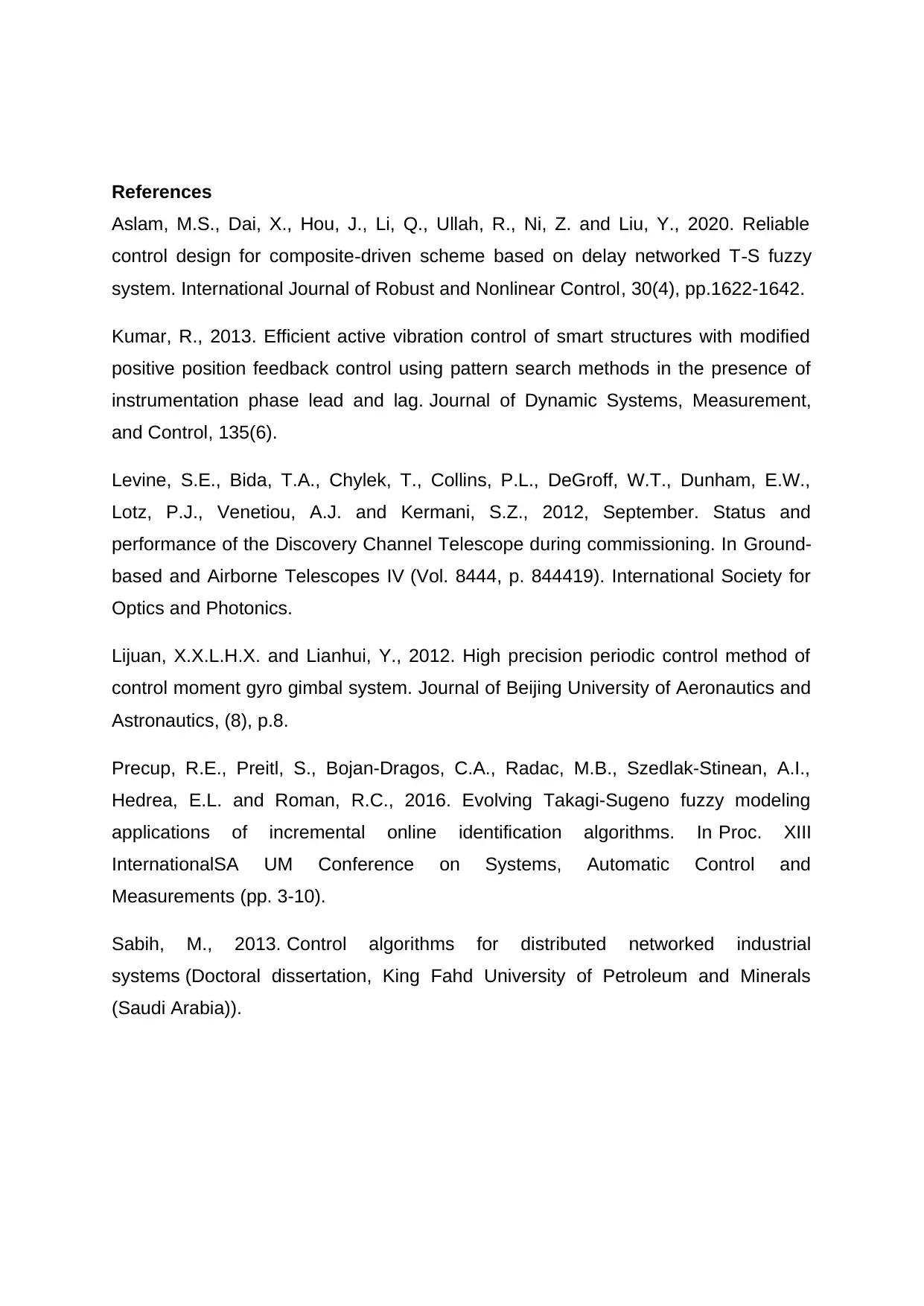
References
Aslam, M.S., Dai, X., Hou, J., Li, Q., Ullah, R., Ni, Z. and Liu, Y., 2020. Reliable
control design for composite‐driven scheme based on delay networked T‐S fuzzy
system. International Journal of Robust and Nonlinear Control, 30(4), pp.1622-1642.
Kumar, R., 2013. Efficient active vibration control of smart structures with modified
positive position feedback control using pattern search methods in the presence of
instrumentation phase lead and lag. Journal of Dynamic Systems, Measurement,
and Control, 135(6).
Levine, S.E., Bida, T.A., Chylek, T., Collins, P.L., DeGroff, W.T., Dunham, E.W.,
Lotz, P.J., Venetiou, A.J. and Kermani, S.Z., 2012, September. Status and
performance of the Discovery Channel Telescope during commissioning. In Ground-
based and Airborne Telescopes IV (Vol. 8444, p. 844419). International Society for
Optics and Photonics.
Lijuan, X.X.L.H.X. and Lianhui, Y., 2012. High precision periodic control method of
control moment gyro gimbal system. Journal of Beijing University of Aeronautics and
Astronautics, (8), p.8.
Precup, R.E., Preitl, S., Bojan-Dragos, C.A., Radac, M.B., Szedlak-Stinean, A.I.,
Hedrea, E.L. and Roman, R.C., 2016. Evolving Takagi-Sugeno fuzzy modeling
applications of incremental online identification algorithms. In Proc. XIII
InternationalSA UM Conference on Systems, Automatic Control and
Measurements (pp. 3-10).
Sabih, M., 2013. Control algorithms for distributed networked industrial
systems (Doctoral dissertation, King Fahd University of Petroleum and Minerals
(Saudi Arabia)).
Aslam, M.S., Dai, X., Hou, J., Li, Q., Ullah, R., Ni, Z. and Liu, Y., 2020. Reliable
control design for composite‐driven scheme based on delay networked T‐S fuzzy
system. International Journal of Robust and Nonlinear Control, 30(4), pp.1622-1642.
Kumar, R., 2013. Efficient active vibration control of smart structures with modified
positive position feedback control using pattern search methods in the presence of
instrumentation phase lead and lag. Journal of Dynamic Systems, Measurement,
and Control, 135(6).
Levine, S.E., Bida, T.A., Chylek, T., Collins, P.L., DeGroff, W.T., Dunham, E.W.,
Lotz, P.J., Venetiou, A.J. and Kermani, S.Z., 2012, September. Status and
performance of the Discovery Channel Telescope during commissioning. In Ground-
based and Airborne Telescopes IV (Vol. 8444, p. 844419). International Society for
Optics and Photonics.
Lijuan, X.X.L.H.X. and Lianhui, Y., 2012. High precision periodic control method of
control moment gyro gimbal system. Journal of Beijing University of Aeronautics and
Astronautics, (8), p.8.
Precup, R.E., Preitl, S., Bojan-Dragos, C.A., Radac, M.B., Szedlak-Stinean, A.I.,
Hedrea, E.L. and Roman, R.C., 2016. Evolving Takagi-Sugeno fuzzy modeling
applications of incremental online identification algorithms. In Proc. XIII
InternationalSA UM Conference on Systems, Automatic Control and
Measurements (pp. 3-10).
Sabih, M., 2013. Control algorithms for distributed networked industrial
systems (Doctoral dissertation, King Fahd University of Petroleum and Minerals
(Saudi Arabia)).
1 out of 8
Related Documents
![[object Object]](/_next/image/?url=%2F_next%2Fstatic%2Fmedia%2Flogo.6d15ce61.png&w=640&q=75)
Your All-in-One AI-Powered Toolkit for Academic Success.
+13062052269
info@desklib.com
Available 24*7 on WhatsApp / Email
Unlock your academic potential
© 2024 | Zucol Services PVT LTD | All rights reserved.