Managerial Accounting Report: TDABC for Ansell Tire Company
VerifiedAdded on 2020/05/16
|13
|3230
|280
Report
AI Summary
This report provides a detailed analysis of Time Driven Activity Based Costing (TDABC) within the context of managerial accounting. It begins with an introduction to cost accounting and its importance in manufacturing, followed by a description of the client, Ansell, a tire manufacturing compan...
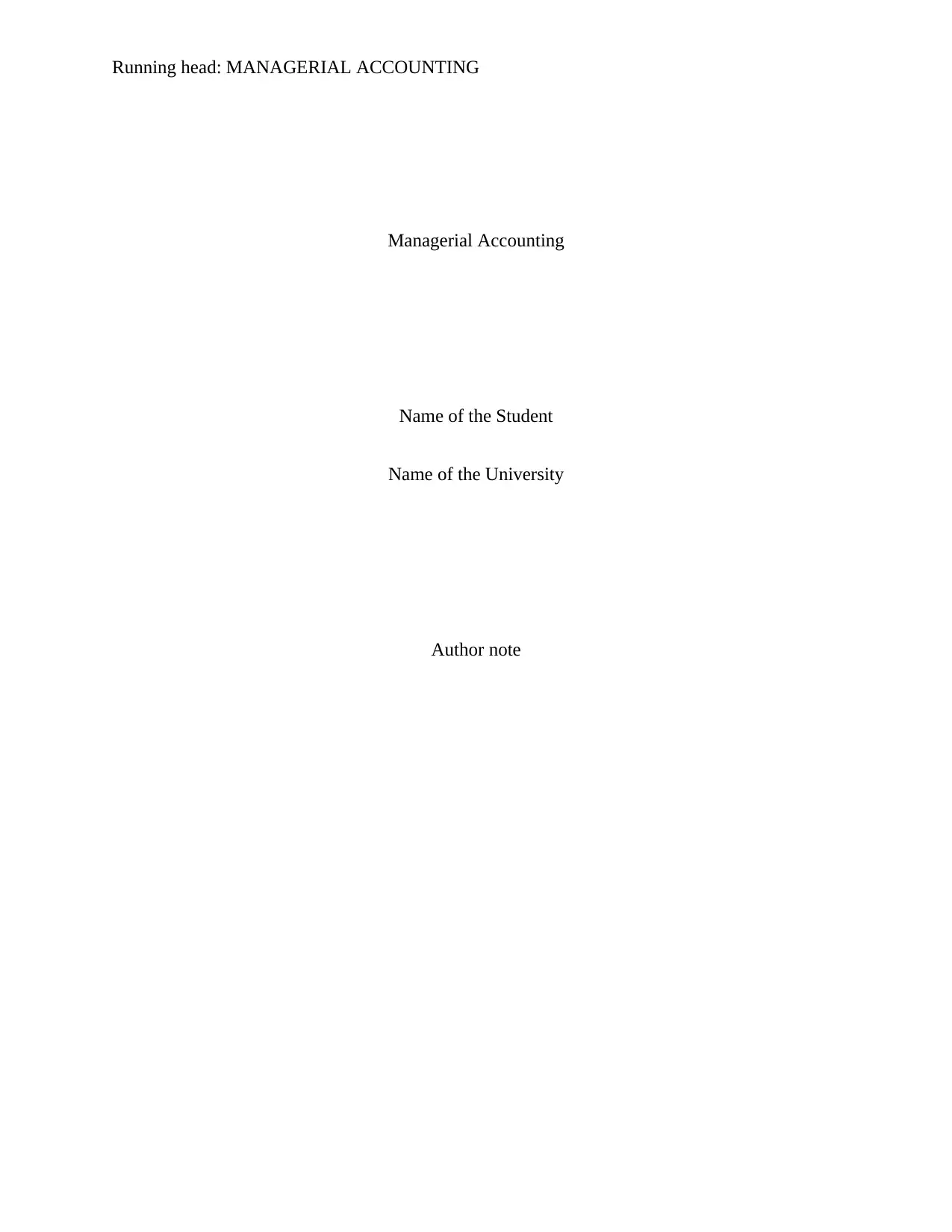
Running head: MANAGERIAL ACCOUNTING
Managerial Accounting
Name of the Student
Name of the University
Author note
Managerial Accounting
Name of the Student
Name of the University
Author note
Paraphrase This Document
Need a fresh take? Get an instant paraphrase of this document with our AI Paraphraser
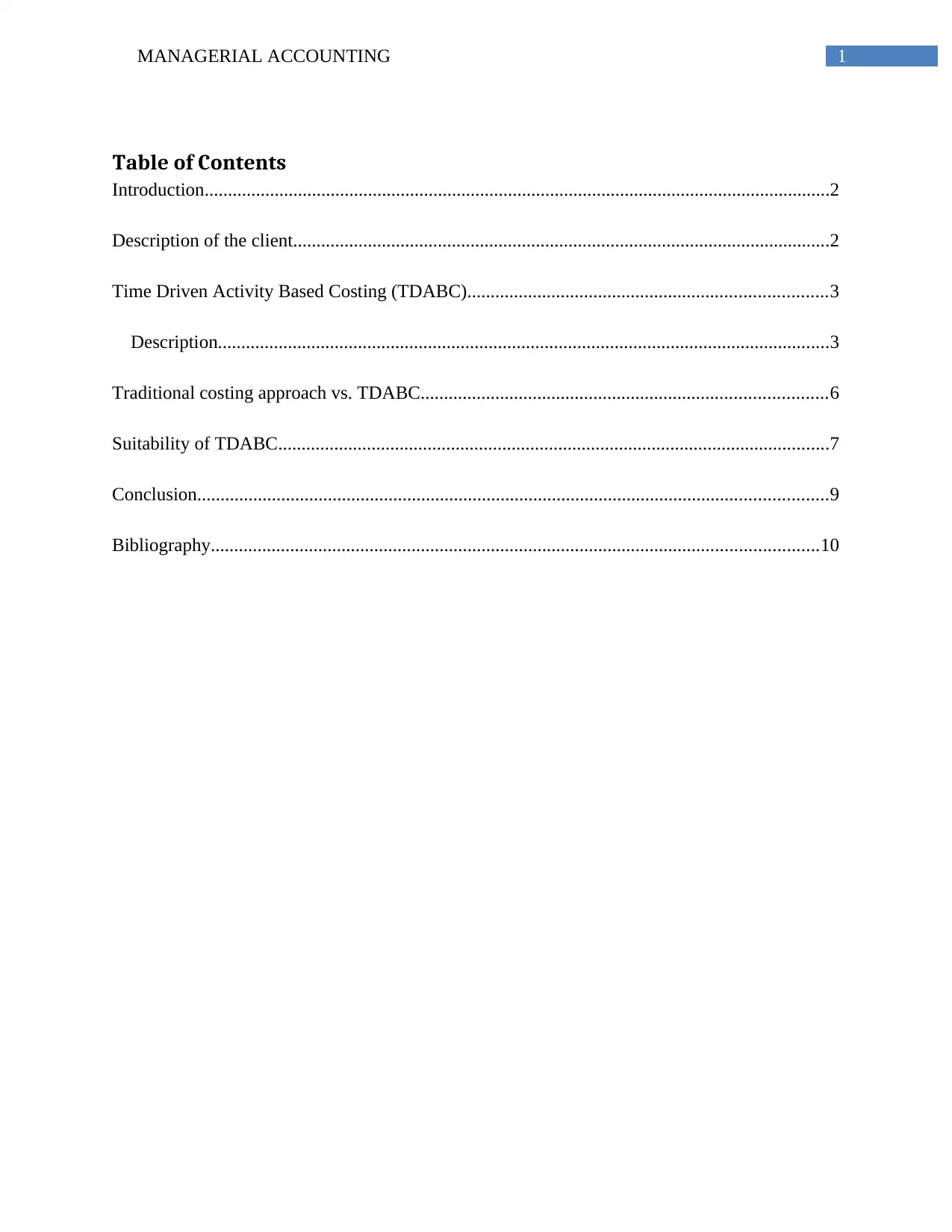
1MANAGERIAL ACCOUNTING
Table of Contents
Introduction......................................................................................................................................2
Description of the client...................................................................................................................2
Time Driven Activity Based Costing (TDABC).............................................................................3
Description...................................................................................................................................3
Traditional costing approach vs. TDABC.......................................................................................6
Suitability of TDABC......................................................................................................................7
Conclusion.......................................................................................................................................9
Bibliography..................................................................................................................................10
Table of Contents
Introduction......................................................................................................................................2
Description of the client...................................................................................................................2
Time Driven Activity Based Costing (TDABC).............................................................................3
Description...................................................................................................................................3
Traditional costing approach vs. TDABC.......................................................................................6
Suitability of TDABC......................................................................................................................7
Conclusion.......................................................................................................................................9
Bibliography..................................................................................................................................10
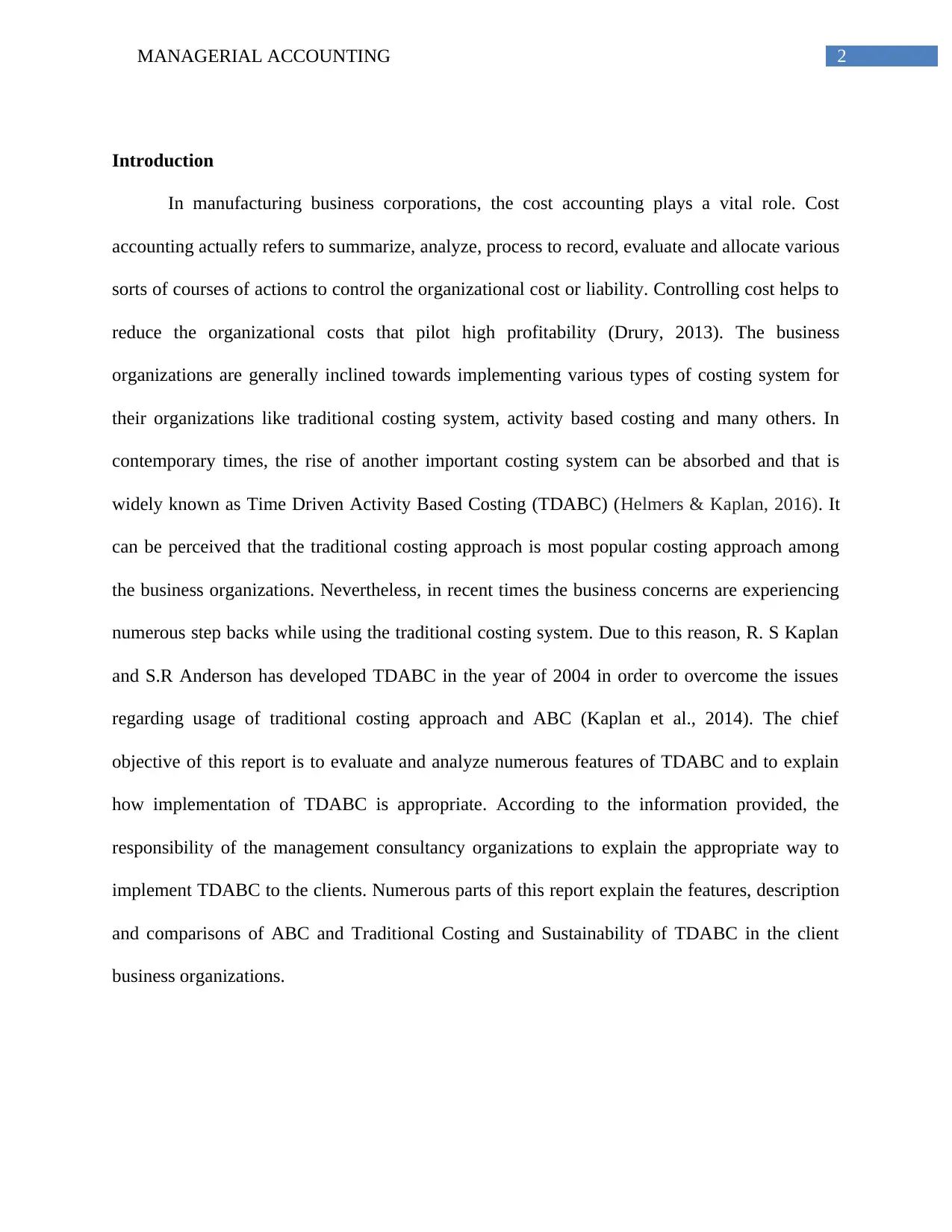
2MANAGERIAL ACCOUNTING
Introduction
In manufacturing business corporations, the cost accounting plays a vital role. Cost
accounting actually refers to summarize, analyze, process to record, evaluate and allocate various
sorts of courses of actions to control the organizational cost or liability. Controlling cost helps to
reduce the organizational costs that pilot high profitability (Drury, 2013). The business
organizations are generally inclined towards implementing various types of costing system for
their organizations like traditional costing system, activity based costing and many others. In
contemporary times, the rise of another important costing system can be absorbed and that is
widely known as Time Driven Activity Based Costing (TDABC) (Helmers & Kaplan, 2016). It
can be perceived that the traditional costing approach is most popular costing approach among
the business organizations. Nevertheless, in recent times the business concerns are experiencing
numerous step backs while using the traditional costing system. Due to this reason, R. S Kaplan
and S.R Anderson has developed TDABC in the year of 2004 in order to overcome the issues
regarding usage of traditional costing approach and ABC (Kaplan et al., 2014). The chief
objective of this report is to evaluate and analyze numerous features of TDABC and to explain
how implementation of TDABC is appropriate. According to the information provided, the
responsibility of the management consultancy organizations to explain the appropriate way to
implement TDABC to the clients. Numerous parts of this report explain the features, description
and comparisons of ABC and Traditional Costing and Sustainability of TDABC in the client
business organizations.
Introduction
In manufacturing business corporations, the cost accounting plays a vital role. Cost
accounting actually refers to summarize, analyze, process to record, evaluate and allocate various
sorts of courses of actions to control the organizational cost or liability. Controlling cost helps to
reduce the organizational costs that pilot high profitability (Drury, 2013). The business
organizations are generally inclined towards implementing various types of costing system for
their organizations like traditional costing system, activity based costing and many others. In
contemporary times, the rise of another important costing system can be absorbed and that is
widely known as Time Driven Activity Based Costing (TDABC) (Helmers & Kaplan, 2016). It
can be perceived that the traditional costing approach is most popular costing approach among
the business organizations. Nevertheless, in recent times the business concerns are experiencing
numerous step backs while using the traditional costing system. Due to this reason, R. S Kaplan
and S.R Anderson has developed TDABC in the year of 2004 in order to overcome the issues
regarding usage of traditional costing approach and ABC (Kaplan et al., 2014). The chief
objective of this report is to evaluate and analyze numerous features of TDABC and to explain
how implementation of TDABC is appropriate. According to the information provided, the
responsibility of the management consultancy organizations to explain the appropriate way to
implement TDABC to the clients. Numerous parts of this report explain the features, description
and comparisons of ABC and Traditional Costing and Sustainability of TDABC in the client
business organizations.
⊘ This is a preview!⊘
Do you want full access?
Subscribe today to unlock all pages.

Trusted by 1+ million students worldwide
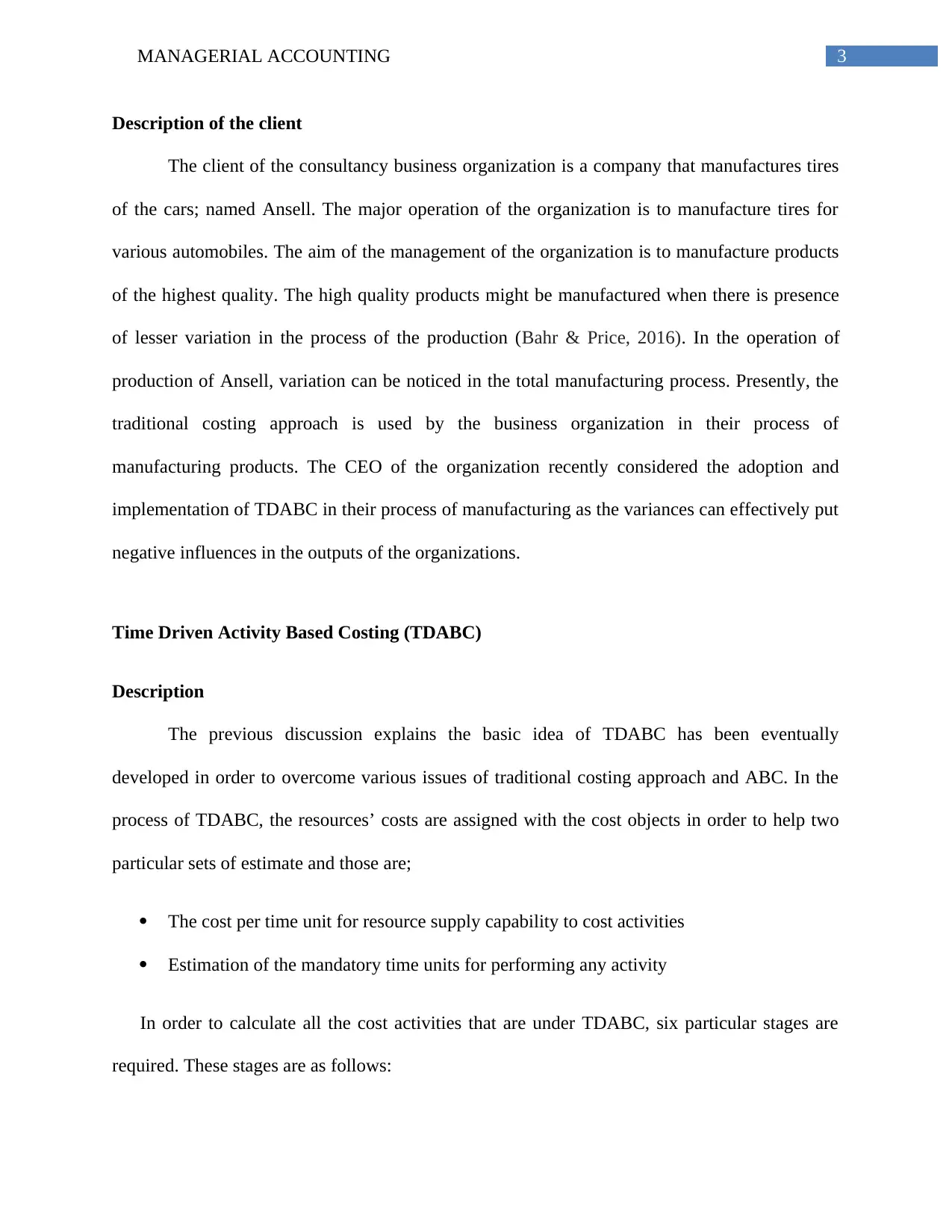
3MANAGERIAL ACCOUNTING
Description of the client
The client of the consultancy business organization is a company that manufactures tires
of the cars; named Ansell. The major operation of the organization is to manufacture tires for
various automobiles. The aim of the management of the organization is to manufacture products
of the highest quality. The high quality products might be manufactured when there is presence
of lesser variation in the process of the production (Bahr & Price, 2016). In the operation of
production of Ansell, variation can be noticed in the total manufacturing process. Presently, the
traditional costing approach is used by the business organization in their process of
manufacturing products. The CEO of the organization recently considered the adoption and
implementation of TDABC in their process of manufacturing as the variances can effectively put
negative influences in the outputs of the organizations.
Time Driven Activity Based Costing (TDABC)
Description
The previous discussion explains the basic idea of TDABC has been eventually
developed in order to overcome various issues of traditional costing approach and ABC. In the
process of TDABC, the resources’ costs are assigned with the cost objects in order to help two
particular sets of estimate and those are;
The cost per time unit for resource supply capability to cost activities
Estimation of the mandatory time units for performing any activity
In order to calculate all the cost activities that are under TDABC, six particular stages are
required. These stages are as follows:
Description of the client
The client of the consultancy business organization is a company that manufactures tires
of the cars; named Ansell. The major operation of the organization is to manufacture tires for
various automobiles. The aim of the management of the organization is to manufacture products
of the highest quality. The high quality products might be manufactured when there is presence
of lesser variation in the process of the production (Bahr & Price, 2016). In the operation of
production of Ansell, variation can be noticed in the total manufacturing process. Presently, the
traditional costing approach is used by the business organization in their process of
manufacturing products. The CEO of the organization recently considered the adoption and
implementation of TDABC in their process of manufacturing as the variances can effectively put
negative influences in the outputs of the organizations.
Time Driven Activity Based Costing (TDABC)
Description
The previous discussion explains the basic idea of TDABC has been eventually
developed in order to overcome various issues of traditional costing approach and ABC. In the
process of TDABC, the resources’ costs are assigned with the cost objects in order to help two
particular sets of estimate and those are;
The cost per time unit for resource supply capability to cost activities
Estimation of the mandatory time units for performing any activity
In order to calculate all the cost activities that are under TDABC, six particular stages are
required. These stages are as follows:
Paraphrase This Document
Need a fresh take? Get an instant paraphrase of this document with our AI Paraphraser
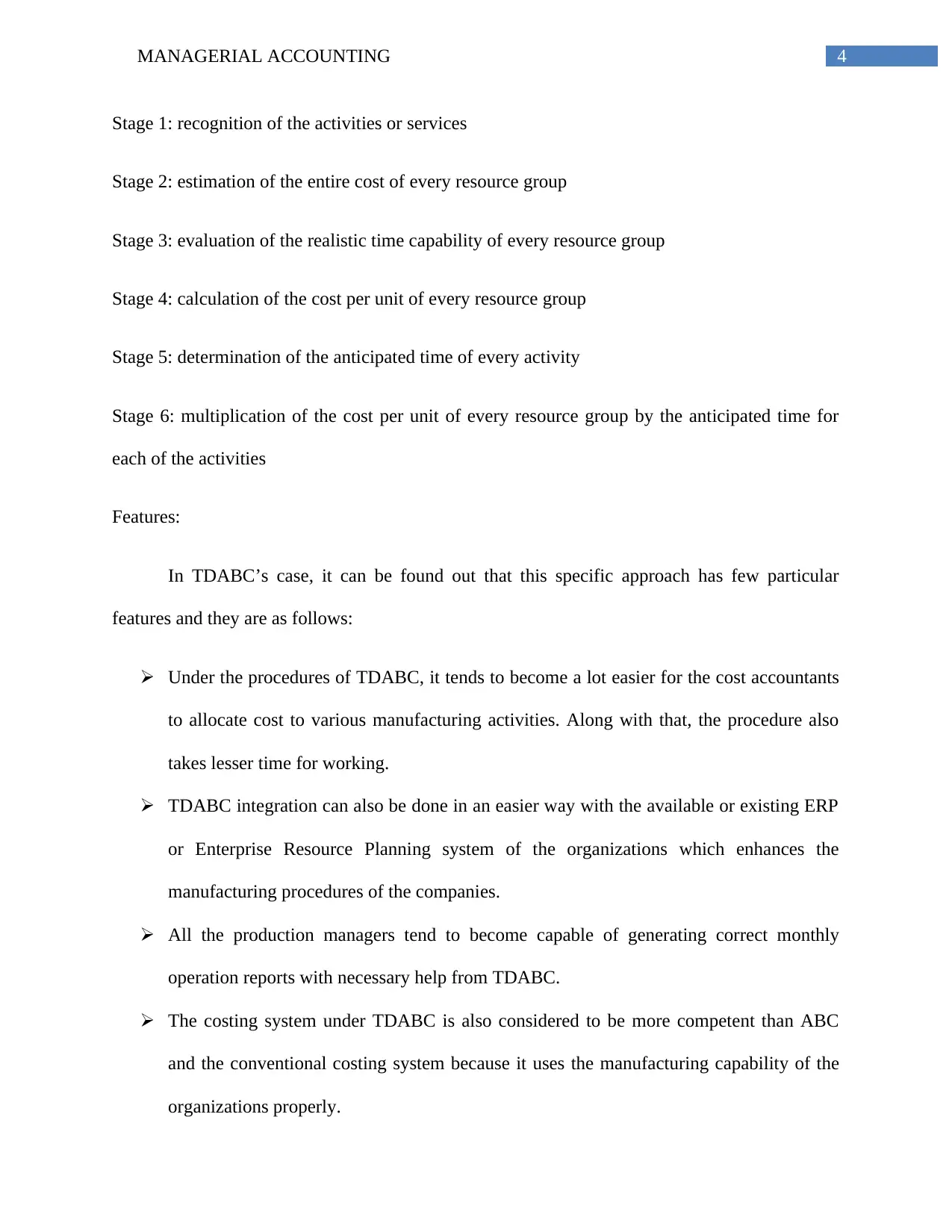
4MANAGERIAL ACCOUNTING
Stage 1: recognition of the activities or services
Stage 2: estimation of the entire cost of every resource group
Stage 3: evaluation of the realistic time capability of every resource group
Stage 4: calculation of the cost per unit of every resource group
Stage 5: determination of the anticipated time of every activity
Stage 6: multiplication of the cost per unit of every resource group by the anticipated time for
each of the activities
Features:
In TDABC’s case, it can be found out that this specific approach has few particular
features and they are as follows:
Under the procedures of TDABC, it tends to become a lot easier for the cost accountants
to allocate cost to various manufacturing activities. Along with that, the procedure also
takes lesser time for working.
TDABC integration can also be done in an easier way with the available or existing ERP
or Enterprise Resource Planning system of the organizations which enhances the
manufacturing procedures of the companies.
All the production managers tend to become capable of generating correct monthly
operation reports with necessary help from TDABC.
The costing system under TDABC is also considered to be more competent than ABC
and the conventional costing system because it uses the manufacturing capability of the
organizations properly.
Stage 1: recognition of the activities or services
Stage 2: estimation of the entire cost of every resource group
Stage 3: evaluation of the realistic time capability of every resource group
Stage 4: calculation of the cost per unit of every resource group
Stage 5: determination of the anticipated time of every activity
Stage 6: multiplication of the cost per unit of every resource group by the anticipated time for
each of the activities
Features:
In TDABC’s case, it can be found out that this specific approach has few particular
features and they are as follows:
Under the procedures of TDABC, it tends to become a lot easier for the cost accountants
to allocate cost to various manufacturing activities. Along with that, the procedure also
takes lesser time for working.
TDABC integration can also be done in an easier way with the available or existing ERP
or Enterprise Resource Planning system of the organizations which enhances the
manufacturing procedures of the companies.
All the production managers tend to become capable of generating correct monthly
operation reports with necessary help from TDABC.
The costing system under TDABC is also considered to be more competent than ABC
and the conventional costing system because it uses the manufacturing capability of the
organizations properly.
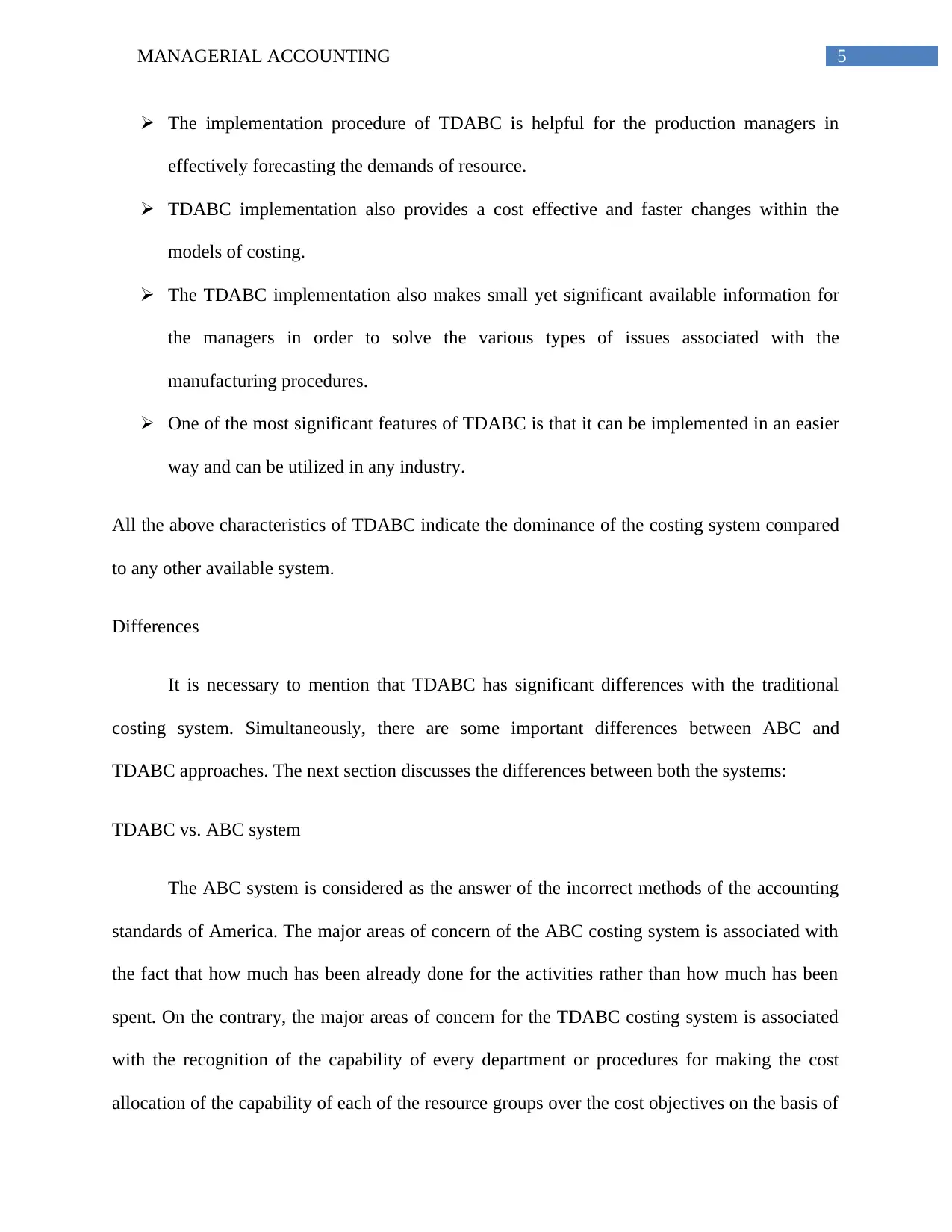
5MANAGERIAL ACCOUNTING
The implementation procedure of TDABC is helpful for the production managers in
effectively forecasting the demands of resource.
TDABC implementation also provides a cost effective and faster changes within the
models of costing.
The TDABC implementation also makes small yet significant available information for
the managers in order to solve the various types of issues associated with the
manufacturing procedures.
One of the most significant features of TDABC is that it can be implemented in an easier
way and can be utilized in any industry.
All the above characteristics of TDABC indicate the dominance of the costing system compared
to any other available system.
Differences
It is necessary to mention that TDABC has significant differences with the traditional
costing system. Simultaneously, there are some important differences between ABC and
TDABC approaches. The next section discusses the differences between both the systems:
TDABC vs. ABC system
The ABC system is considered as the answer of the incorrect methods of the accounting
standards of America. The major areas of concern of the ABC costing system is associated with
the fact that how much has been already done for the activities rather than how much has been
spent. On the contrary, the major areas of concern for the TDABC costing system is associated
with the recognition of the capability of every department or procedures for making the cost
allocation of the capability of each of the resource groups over the cost objectives on the basis of
The implementation procedure of TDABC is helpful for the production managers in
effectively forecasting the demands of resource.
TDABC implementation also provides a cost effective and faster changes within the
models of costing.
The TDABC implementation also makes small yet significant available information for
the managers in order to solve the various types of issues associated with the
manufacturing procedures.
One of the most significant features of TDABC is that it can be implemented in an easier
way and can be utilized in any industry.
All the above characteristics of TDABC indicate the dominance of the costing system compared
to any other available system.
Differences
It is necessary to mention that TDABC has significant differences with the traditional
costing system. Simultaneously, there are some important differences between ABC and
TDABC approaches. The next section discusses the differences between both the systems:
TDABC vs. ABC system
The ABC system is considered as the answer of the incorrect methods of the accounting
standards of America. The major areas of concern of the ABC costing system is associated with
the fact that how much has been already done for the activities rather than how much has been
spent. On the contrary, the major areas of concern for the TDABC costing system is associated
with the recognition of the capability of every department or procedures for making the cost
allocation of the capability of each of the resource groups over the cost objectives on the basis of
⊘ This is a preview!⊘
Do you want full access?
Subscribe today to unlock all pages.

Trusted by 1+ million students worldwide
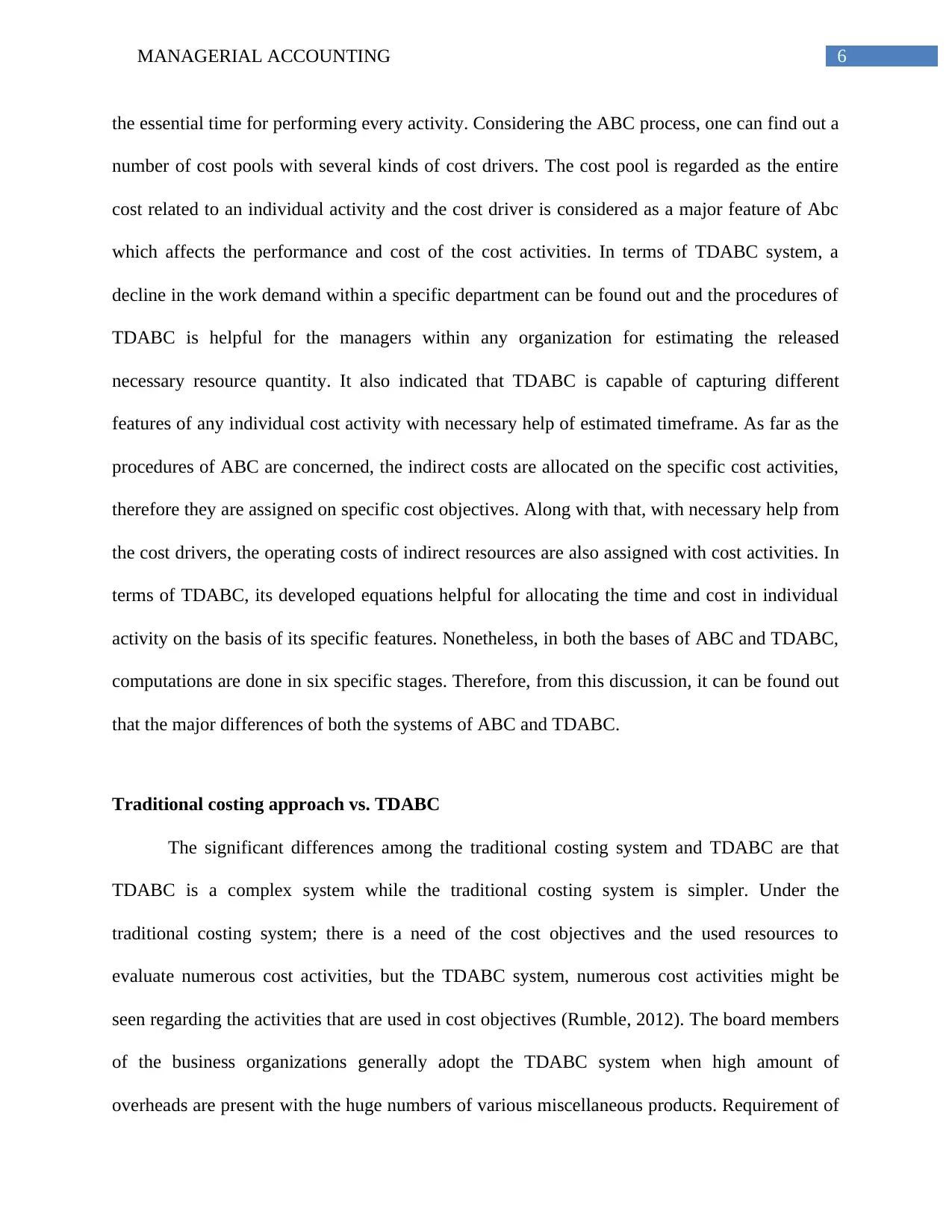
6MANAGERIAL ACCOUNTING
the essential time for performing every activity. Considering the ABC process, one can find out a
number of cost pools with several kinds of cost drivers. The cost pool is regarded as the entire
cost related to an individual activity and the cost driver is considered as a major feature of Abc
which affects the performance and cost of the cost activities. In terms of TDABC system, a
decline in the work demand within a specific department can be found out and the procedures of
TDABC is helpful for the managers within any organization for estimating the released
necessary resource quantity. It also indicated that TDABC is capable of capturing different
features of any individual cost activity with necessary help of estimated timeframe. As far as the
procedures of ABC are concerned, the indirect costs are allocated on the specific cost activities,
therefore they are assigned on specific cost objectives. Along with that, with necessary help from
the cost drivers, the operating costs of indirect resources are also assigned with cost activities. In
terms of TDABC, its developed equations helpful for allocating the time and cost in individual
activity on the basis of its specific features. Nonetheless, in both the bases of ABC and TDABC,
computations are done in six specific stages. Therefore, from this discussion, it can be found out
that the major differences of both the systems of ABC and TDABC.
Traditional costing approach vs. TDABC
The significant differences among the traditional costing system and TDABC are that
TDABC is a complex system while the traditional costing system is simpler. Under the
traditional costing system; there is a need of the cost objectives and the used resources to
evaluate numerous cost activities, but the TDABC system, numerous cost activities might be
seen regarding the activities that are used in cost objectives (Rumble, 2012). The board members
of the business organizations generally adopt the TDABC system when high amount of
overheads are present with the huge numbers of various miscellaneous products. Requirement of
the essential time for performing every activity. Considering the ABC process, one can find out a
number of cost pools with several kinds of cost drivers. The cost pool is regarded as the entire
cost related to an individual activity and the cost driver is considered as a major feature of Abc
which affects the performance and cost of the cost activities. In terms of TDABC system, a
decline in the work demand within a specific department can be found out and the procedures of
TDABC is helpful for the managers within any organization for estimating the released
necessary resource quantity. It also indicated that TDABC is capable of capturing different
features of any individual cost activity with necessary help of estimated timeframe. As far as the
procedures of ABC are concerned, the indirect costs are allocated on the specific cost activities,
therefore they are assigned on specific cost objectives. Along with that, with necessary help from
the cost drivers, the operating costs of indirect resources are also assigned with cost activities. In
terms of TDABC, its developed equations helpful for allocating the time and cost in individual
activity on the basis of its specific features. Nonetheless, in both the bases of ABC and TDABC,
computations are done in six specific stages. Therefore, from this discussion, it can be found out
that the major differences of both the systems of ABC and TDABC.
Traditional costing approach vs. TDABC
The significant differences among the traditional costing system and TDABC are that
TDABC is a complex system while the traditional costing system is simpler. Under the
traditional costing system; there is a need of the cost objectives and the used resources to
evaluate numerous cost activities, but the TDABC system, numerous cost activities might be
seen regarding the activities that are used in cost objectives (Rumble, 2012). The board members
of the business organizations generally adopt the TDABC system when high amount of
overheads are present with the huge numbers of various miscellaneous products. Requirement of
Paraphrase This Document
Need a fresh take? Get an instant paraphrase of this document with our AI Paraphraser
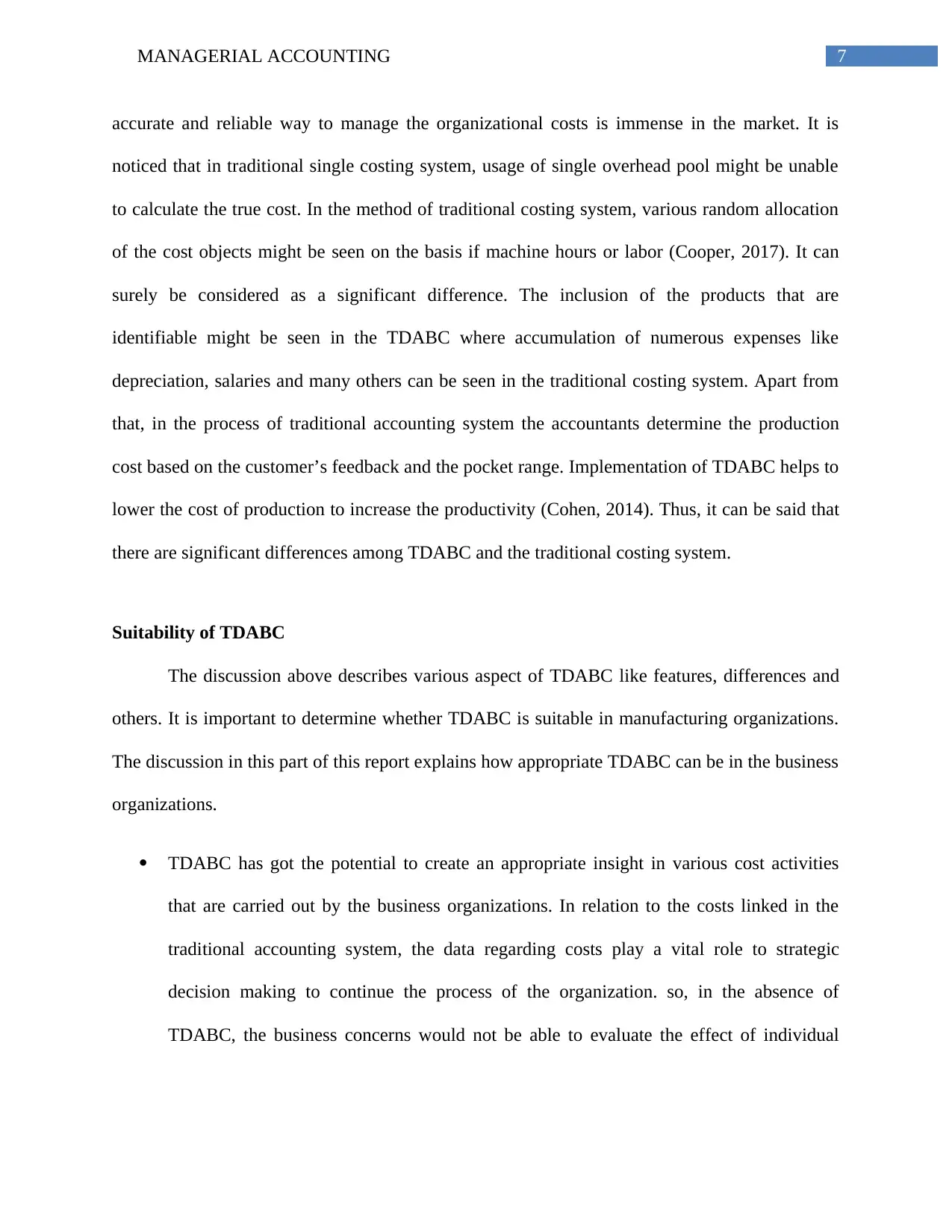
7MANAGERIAL ACCOUNTING
accurate and reliable way to manage the organizational costs is immense in the market. It is
noticed that in traditional single costing system, usage of single overhead pool might be unable
to calculate the true cost. In the method of traditional costing system, various random allocation
of the cost objects might be seen on the basis if machine hours or labor (Cooper, 2017). It can
surely be considered as a significant difference. The inclusion of the products that are
identifiable might be seen in the TDABC where accumulation of numerous expenses like
depreciation, salaries and many others can be seen in the traditional costing system. Apart from
that, in the process of traditional accounting system the accountants determine the production
cost based on the customer’s feedback and the pocket range. Implementation of TDABC helps to
lower the cost of production to increase the productivity (Cohen, 2014). Thus, it can be said that
there are significant differences among TDABC and the traditional costing system.
Suitability of TDABC
The discussion above describes various aspect of TDABC like features, differences and
others. It is important to determine whether TDABC is suitable in manufacturing organizations.
The discussion in this part of this report explains how appropriate TDABC can be in the business
organizations.
TDABC has got the potential to create an appropriate insight in various cost activities
that are carried out by the business organizations. In relation to the costs linked in the
traditional accounting system, the data regarding costs play a vital role to strategic
decision making to continue the process of the organization. so, in the absence of
TDABC, the business concerns would not be able to evaluate the effect of individual
accurate and reliable way to manage the organizational costs is immense in the market. It is
noticed that in traditional single costing system, usage of single overhead pool might be unable
to calculate the true cost. In the method of traditional costing system, various random allocation
of the cost objects might be seen on the basis if machine hours or labor (Cooper, 2017). It can
surely be considered as a significant difference. The inclusion of the products that are
identifiable might be seen in the TDABC where accumulation of numerous expenses like
depreciation, salaries and many others can be seen in the traditional costing system. Apart from
that, in the process of traditional accounting system the accountants determine the production
cost based on the customer’s feedback and the pocket range. Implementation of TDABC helps to
lower the cost of production to increase the productivity (Cohen, 2014). Thus, it can be said that
there are significant differences among TDABC and the traditional costing system.
Suitability of TDABC
The discussion above describes various aspect of TDABC like features, differences and
others. It is important to determine whether TDABC is suitable in manufacturing organizations.
The discussion in this part of this report explains how appropriate TDABC can be in the business
organizations.
TDABC has got the potential to create an appropriate insight in various cost activities
that are carried out by the business organizations. In relation to the costs linked in the
traditional accounting system, the data regarding costs play a vital role to strategic
decision making to continue the process of the organization. so, in the absence of
TDABC, the business concerns would not be able to evaluate the effect of individual
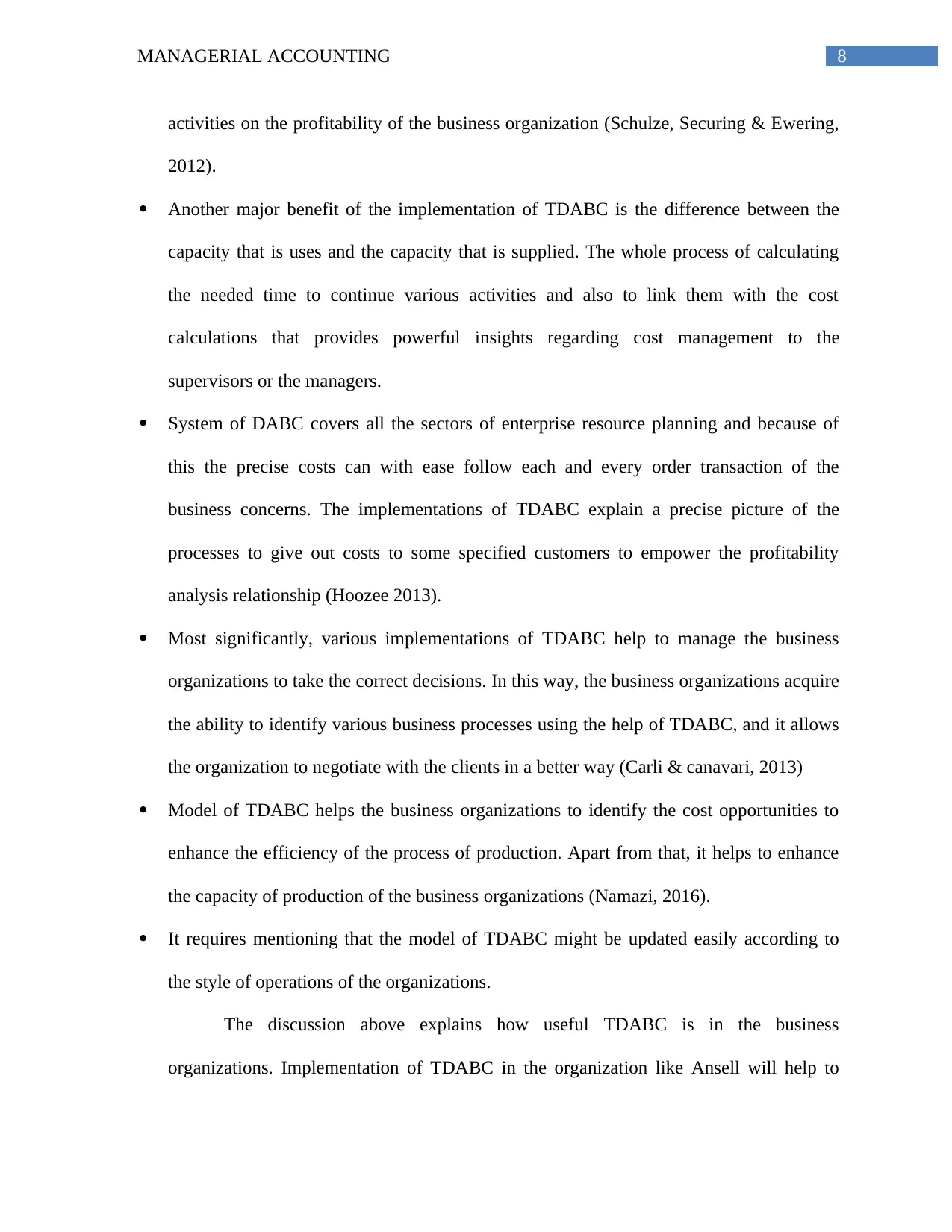
8MANAGERIAL ACCOUNTING
activities on the profitability of the business organization (Schulze, Securing & Ewering,
2012).
Another major benefit of the implementation of TDABC is the difference between the
capacity that is uses and the capacity that is supplied. The whole process of calculating
the needed time to continue various activities and also to link them with the cost
calculations that provides powerful insights regarding cost management to the
supervisors or the managers.
System of DABC covers all the sectors of enterprise resource planning and because of
this the precise costs can with ease follow each and every order transaction of the
business concerns. The implementations of TDABC explain a precise picture of the
processes to give out costs to some specified customers to empower the profitability
analysis relationship (Hoozee 2013).
Most significantly, various implementations of TDABC help to manage the business
organizations to take the correct decisions. In this way, the business organizations acquire
the ability to identify various business processes using the help of TDABC, and it allows
the organization to negotiate with the clients in a better way (Carli & canavari, 2013)
Model of TDABC helps the business organizations to identify the cost opportunities to
enhance the efficiency of the process of production. Apart from that, it helps to enhance
the capacity of production of the business organizations (Namazi, 2016).
It requires mentioning that the model of TDABC might be updated easily according to
the style of operations of the organizations.
The discussion above explains how useful TDABC is in the business
organizations. Implementation of TDABC in the organization like Ansell will help to
activities on the profitability of the business organization (Schulze, Securing & Ewering,
2012).
Another major benefit of the implementation of TDABC is the difference between the
capacity that is uses and the capacity that is supplied. The whole process of calculating
the needed time to continue various activities and also to link them with the cost
calculations that provides powerful insights regarding cost management to the
supervisors or the managers.
System of DABC covers all the sectors of enterprise resource planning and because of
this the precise costs can with ease follow each and every order transaction of the
business concerns. The implementations of TDABC explain a precise picture of the
processes to give out costs to some specified customers to empower the profitability
analysis relationship (Hoozee 2013).
Most significantly, various implementations of TDABC help to manage the business
organizations to take the correct decisions. In this way, the business organizations acquire
the ability to identify various business processes using the help of TDABC, and it allows
the organization to negotiate with the clients in a better way (Carli & canavari, 2013)
Model of TDABC helps the business organizations to identify the cost opportunities to
enhance the efficiency of the process of production. Apart from that, it helps to enhance
the capacity of production of the business organizations (Namazi, 2016).
It requires mentioning that the model of TDABC might be updated easily according to
the style of operations of the organizations.
The discussion above explains how useful TDABC is in the business
organizations. Implementation of TDABC in the organization like Ansell will help to
⊘ This is a preview!⊘
Do you want full access?
Subscribe today to unlock all pages.

Trusted by 1+ million students worldwide

9MANAGERIAL ACCOUNTING
increase the production process’ efficiency (Kaplan et al., 2015). Then the management
of TDABC can acquire appropriate insight regarding the nature of the cost of the
organization; because in integration of TDABC with various other system of the
organization like planning of enterprise recourse and many others. So from the above
mentioned discussion it can be perceived that TDABC will be appropriate for Ansell.
Conclusion
The report explains that TDABC is a new approach for cost accounting in the business
organizations. The aspects of TDABC explain that the new system is easier to assign various cost
activities and it can be integrated with the ERP system. It is seen that TDABC has some basic
differences with the traditional costing system and ABC system as it can be implemented in
diversified organizations with many overheads as well as many products. Apart from that,
TDABC assigns the total costs for the cost activities more accurately than the traditional system
of costing. Finally the report proves the appropriateness of TDABC in Ansell for having various
benefits and above all TDABC helps the business organizations in process of effective decision
making.
increase the production process’ efficiency (Kaplan et al., 2015). Then the management
of TDABC can acquire appropriate insight regarding the nature of the cost of the
organization; because in integration of TDABC with various other system of the
organization like planning of enterprise recourse and many others. So from the above
mentioned discussion it can be perceived that TDABC will be appropriate for Ansell.
Conclusion
The report explains that TDABC is a new approach for cost accounting in the business
organizations. The aspects of TDABC explain that the new system is easier to assign various cost
activities and it can be integrated with the ERP system. It is seen that TDABC has some basic
differences with the traditional costing system and ABC system as it can be implemented in
diversified organizations with many overheads as well as many products. Apart from that,
TDABC assigns the total costs for the cost activities more accurately than the traditional system
of costing. Finally the report proves the appropriateness of TDABC in Ansell for having various
benefits and above all TDABC helps the business organizations in process of effective decision
making.
Paraphrase This Document
Need a fresh take? Get an instant paraphrase of this document with our AI Paraphraser
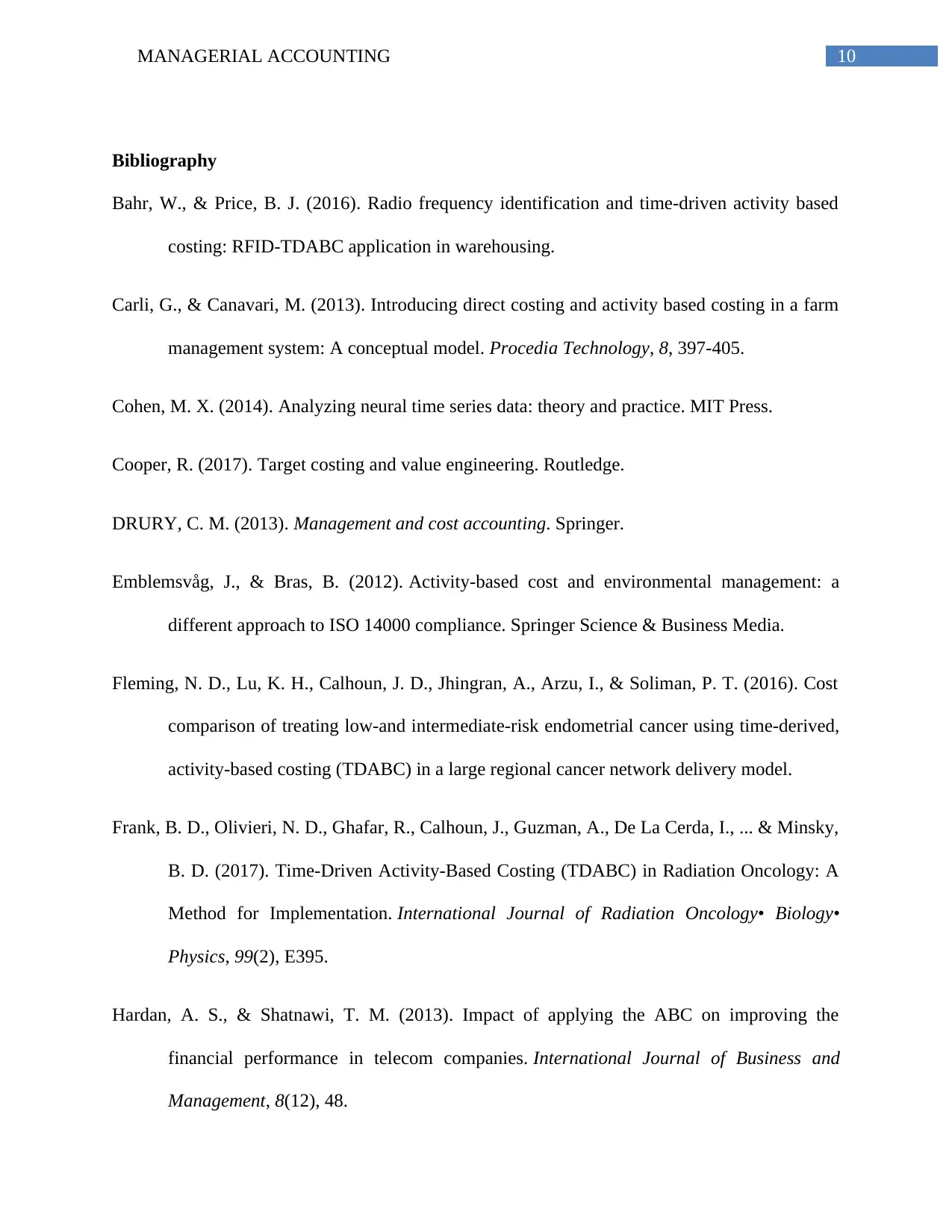
10MANAGERIAL ACCOUNTING
Bibliography
Bahr, W., & Price, B. J. (2016). Radio frequency identification and time-driven activity based
costing: RFID-TDABC application in warehousing.
Carli, G., & Canavari, M. (2013). Introducing direct costing and activity based costing in a farm
management system: A conceptual model. Procedia Technology, 8, 397-405.
Cohen, M. X. (2014). Analyzing neural time series data: theory and practice. MIT Press.
Cooper, R. (2017). Target costing and value engineering. Routledge.
DRURY, C. M. (2013). Management and cost accounting. Springer.
Emblemsvåg, J., & Bras, B. (2012). Activity-based cost and environmental management: a
different approach to ISO 14000 compliance. Springer Science & Business Media.
Fleming, N. D., Lu, K. H., Calhoun, J. D., Jhingran, A., Arzu, I., & Soliman, P. T. (2016). Cost
comparison of treating low-and intermediate-risk endometrial cancer using time-derived,
activity-based costing (TDABC) in a large regional cancer network delivery model.
Frank, B. D., Olivieri, N. D., Ghafar, R., Calhoun, J., Guzman, A., De La Cerda, I., ... & Minsky,
B. D. (2017). Time-Driven Activity-Based Costing (TDABC) in Radiation Oncology: A
Method for Implementation. International Journal of Radiation Oncology• Biology•
Physics, 99(2), E395.
Hardan, A. S., & Shatnawi, T. M. (2013). Impact of applying the ABC on improving the
financial performance in telecom companies. International Journal of Business and
Management, 8(12), 48.
Bibliography
Bahr, W., & Price, B. J. (2016). Radio frequency identification and time-driven activity based
costing: RFID-TDABC application in warehousing.
Carli, G., & Canavari, M. (2013). Introducing direct costing and activity based costing in a farm
management system: A conceptual model. Procedia Technology, 8, 397-405.
Cohen, M. X. (2014). Analyzing neural time series data: theory and practice. MIT Press.
Cooper, R. (2017). Target costing and value engineering. Routledge.
DRURY, C. M. (2013). Management and cost accounting. Springer.
Emblemsvåg, J., & Bras, B. (2012). Activity-based cost and environmental management: a
different approach to ISO 14000 compliance. Springer Science & Business Media.
Fleming, N. D., Lu, K. H., Calhoun, J. D., Jhingran, A., Arzu, I., & Soliman, P. T. (2016). Cost
comparison of treating low-and intermediate-risk endometrial cancer using time-derived,
activity-based costing (TDABC) in a large regional cancer network delivery model.
Frank, B. D., Olivieri, N. D., Ghafar, R., Calhoun, J., Guzman, A., De La Cerda, I., ... & Minsky,
B. D. (2017). Time-Driven Activity-Based Costing (TDABC) in Radiation Oncology: A
Method for Implementation. International Journal of Radiation Oncology• Biology•
Physics, 99(2), E395.
Hardan, A. S., & Shatnawi, T. M. (2013). Impact of applying the ABC on improving the
financial performance in telecom companies. International Journal of Business and
Management, 8(12), 48.
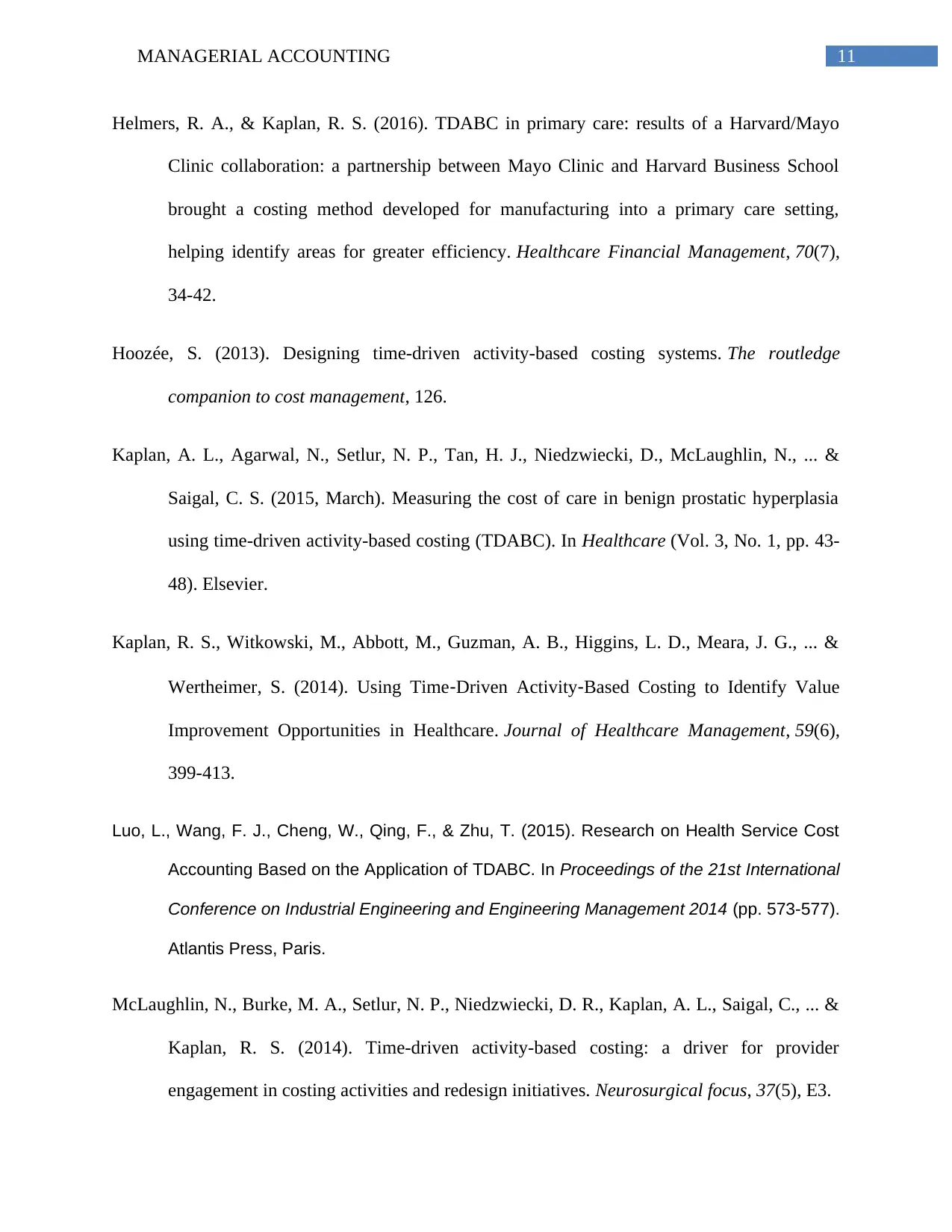
11MANAGERIAL ACCOUNTING
Helmers, R. A., & Kaplan, R. S. (2016). TDABC in primary care: results of a Harvard/Mayo
Clinic collaboration: a partnership between Mayo Clinic and Harvard Business School
brought a costing method developed for manufacturing into a primary care setting,
helping identify areas for greater efficiency. Healthcare Financial Management, 70(7),
34-42.
Hoozée, S. (2013). Designing time-driven activity-based costing systems. The routledge
companion to cost management, 126.
Kaplan, A. L., Agarwal, N., Setlur, N. P., Tan, H. J., Niedzwiecki, D., McLaughlin, N., ... &
Saigal, C. S. (2015, March). Measuring the cost of care in benign prostatic hyperplasia
using time-driven activity-based costing (TDABC). In Healthcare (Vol. 3, No. 1, pp. 43-
48). Elsevier.
Kaplan, R. S., Witkowski, M., Abbott, M., Guzman, A. B., Higgins, L. D., Meara, J. G., ... &
Wertheimer, S. (2014). Using Time‐Driven Activity‐Based Costing to Identify Value
Improvement Opportunities in Healthcare. Journal of Healthcare Management, 59(6),
399-413.
Luo, L., Wang, F. J., Cheng, W., Qing, F., & Zhu, T. (2015). Research on Health Service Cost
Accounting Based on the Application of TDABC. In Proceedings of the 21st International
Conference on Industrial Engineering and Engineering Management 2014 (pp. 573-577).
Atlantis Press, Paris.
McLaughlin, N., Burke, M. A., Setlur, N. P., Niedzwiecki, D. R., Kaplan, A. L., Saigal, C., ... &
Kaplan, R. S. (2014). Time-driven activity-based costing: a driver for provider
engagement in costing activities and redesign initiatives. Neurosurgical focus, 37(5), E3.
Helmers, R. A., & Kaplan, R. S. (2016). TDABC in primary care: results of a Harvard/Mayo
Clinic collaboration: a partnership between Mayo Clinic and Harvard Business School
brought a costing method developed for manufacturing into a primary care setting,
helping identify areas for greater efficiency. Healthcare Financial Management, 70(7),
34-42.
Hoozée, S. (2013). Designing time-driven activity-based costing systems. The routledge
companion to cost management, 126.
Kaplan, A. L., Agarwal, N., Setlur, N. P., Tan, H. J., Niedzwiecki, D., McLaughlin, N., ... &
Saigal, C. S. (2015, March). Measuring the cost of care in benign prostatic hyperplasia
using time-driven activity-based costing (TDABC). In Healthcare (Vol. 3, No. 1, pp. 43-
48). Elsevier.
Kaplan, R. S., Witkowski, M., Abbott, M., Guzman, A. B., Higgins, L. D., Meara, J. G., ... &
Wertheimer, S. (2014). Using Time‐Driven Activity‐Based Costing to Identify Value
Improvement Opportunities in Healthcare. Journal of Healthcare Management, 59(6),
399-413.
Luo, L., Wang, F. J., Cheng, W., Qing, F., & Zhu, T. (2015). Research on Health Service Cost
Accounting Based on the Application of TDABC. In Proceedings of the 21st International
Conference on Industrial Engineering and Engineering Management 2014 (pp. 573-577).
Atlantis Press, Paris.
McLaughlin, N., Burke, M. A., Setlur, N. P., Niedzwiecki, D. R., Kaplan, A. L., Saigal, C., ... &
Kaplan, R. S. (2014). Time-driven activity-based costing: a driver for provider
engagement in costing activities and redesign initiatives. Neurosurgical focus, 37(5), E3.
⊘ This is a preview!⊘
Do you want full access?
Subscribe today to unlock all pages.

Trusted by 1+ million students worldwide
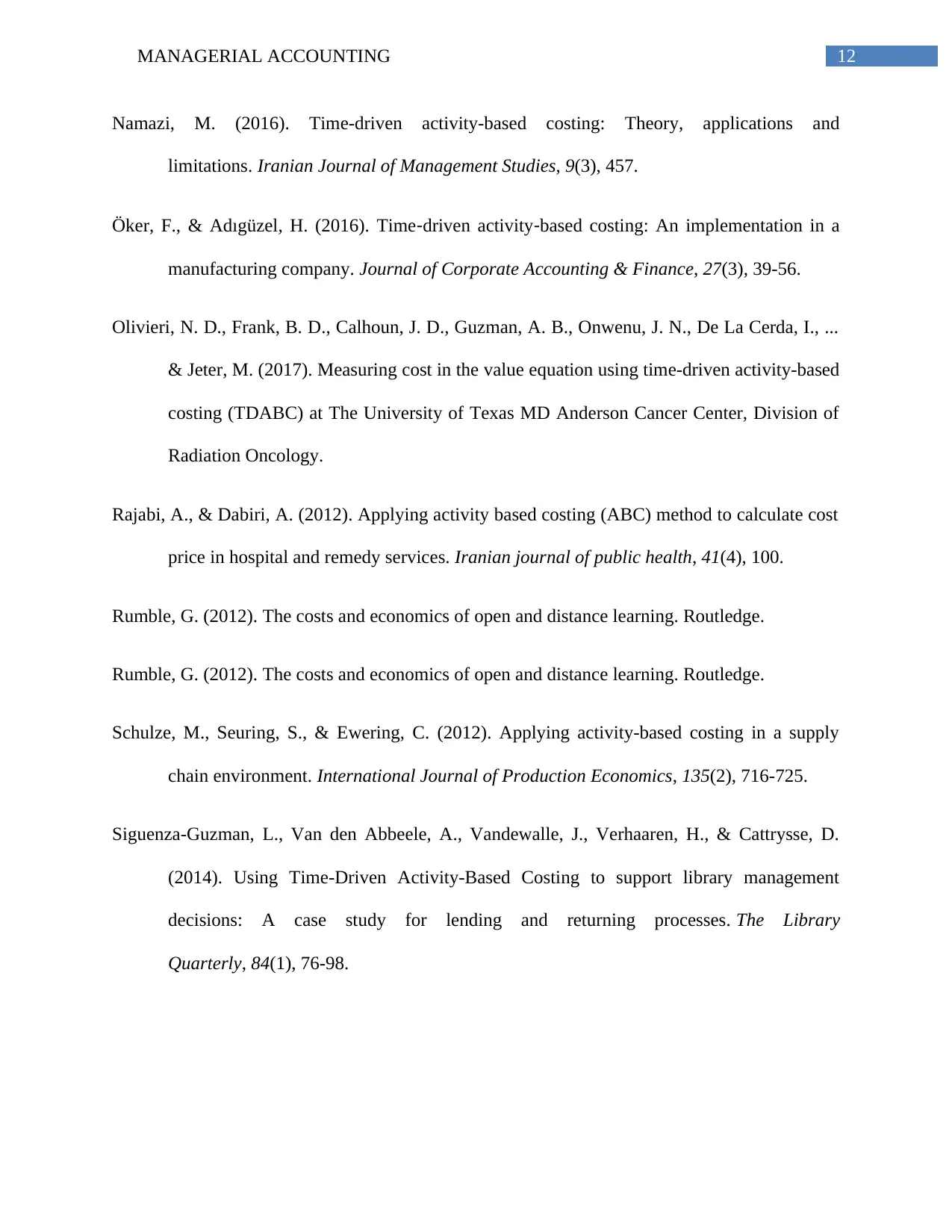
12MANAGERIAL ACCOUNTING
Namazi, M. (2016). Time-driven activity-based costing: Theory, applications and
limitations. Iranian Journal of Management Studies, 9(3), 457.
Öker, F., & Adıgüzel, H. (2016). Time‐driven activity‐based costing: An implementation in a
manufacturing company. Journal of Corporate Accounting & Finance, 27(3), 39-56.
Olivieri, N. D., Frank, B. D., Calhoun, J. D., Guzman, A. B., Onwenu, J. N., De La Cerda, I., ...
& Jeter, M. (2017). Measuring cost in the value equation using time-driven activity-based
costing (TDABC) at The University of Texas MD Anderson Cancer Center, Division of
Radiation Oncology.
Rajabi, A., & Dabiri, A. (2012). Applying activity based costing (ABC) method to calculate cost
price in hospital and remedy services. Iranian journal of public health, 41(4), 100.
Rumble, G. (2012). The costs and economics of open and distance learning. Routledge.
Rumble, G. (2012). The costs and economics of open and distance learning. Routledge.
Schulze, M., Seuring, S., & Ewering, C. (2012). Applying activity-based costing in a supply
chain environment. International Journal of Production Economics, 135(2), 716-725.
Siguenza-Guzman, L., Van den Abbeele, A., Vandewalle, J., Verhaaren, H., & Cattrysse, D.
(2014). Using Time-Driven Activity-Based Costing to support library management
decisions: A case study for lending and returning processes. The Library
Quarterly, 84(1), 76-98.
Namazi, M. (2016). Time-driven activity-based costing: Theory, applications and
limitations. Iranian Journal of Management Studies, 9(3), 457.
Öker, F., & Adıgüzel, H. (2016). Time‐driven activity‐based costing: An implementation in a
manufacturing company. Journal of Corporate Accounting & Finance, 27(3), 39-56.
Olivieri, N. D., Frank, B. D., Calhoun, J. D., Guzman, A. B., Onwenu, J. N., De La Cerda, I., ...
& Jeter, M. (2017). Measuring cost in the value equation using time-driven activity-based
costing (TDABC) at The University of Texas MD Anderson Cancer Center, Division of
Radiation Oncology.
Rajabi, A., & Dabiri, A. (2012). Applying activity based costing (ABC) method to calculate cost
price in hospital and remedy services. Iranian journal of public health, 41(4), 100.
Rumble, G. (2012). The costs and economics of open and distance learning. Routledge.
Rumble, G. (2012). The costs and economics of open and distance learning. Routledge.
Schulze, M., Seuring, S., & Ewering, C. (2012). Applying activity-based costing in a supply
chain environment. International Journal of Production Economics, 135(2), 716-725.
Siguenza-Guzman, L., Van den Abbeele, A., Vandewalle, J., Verhaaren, H., & Cattrysse, D.
(2014). Using Time-Driven Activity-Based Costing to support library management
decisions: A case study for lending and returning processes. The Library
Quarterly, 84(1), 76-98.
1 out of 13
Related Documents

Your All-in-One AI-Powered Toolkit for Academic Success.
+13062052269
info@desklib.com
Available 24*7 on WhatsApp / Email
Unlock your academic potential
© 2024 | Zucol Services PVT LTD | All rights reserved.