Selection and Management of Subcontractors
VerifiedAdded on  2023/05/29
|32
|7346
|442
AI Summary
This report discusses the selection and management of subcontractors in construction projects. It provides a cost and time analysis of different subcontractors and their exclusions. The report also highlights the critical path of the project.
Contribute Materials
Your contribution can guide someone’s learning journey. Share your
documents today.
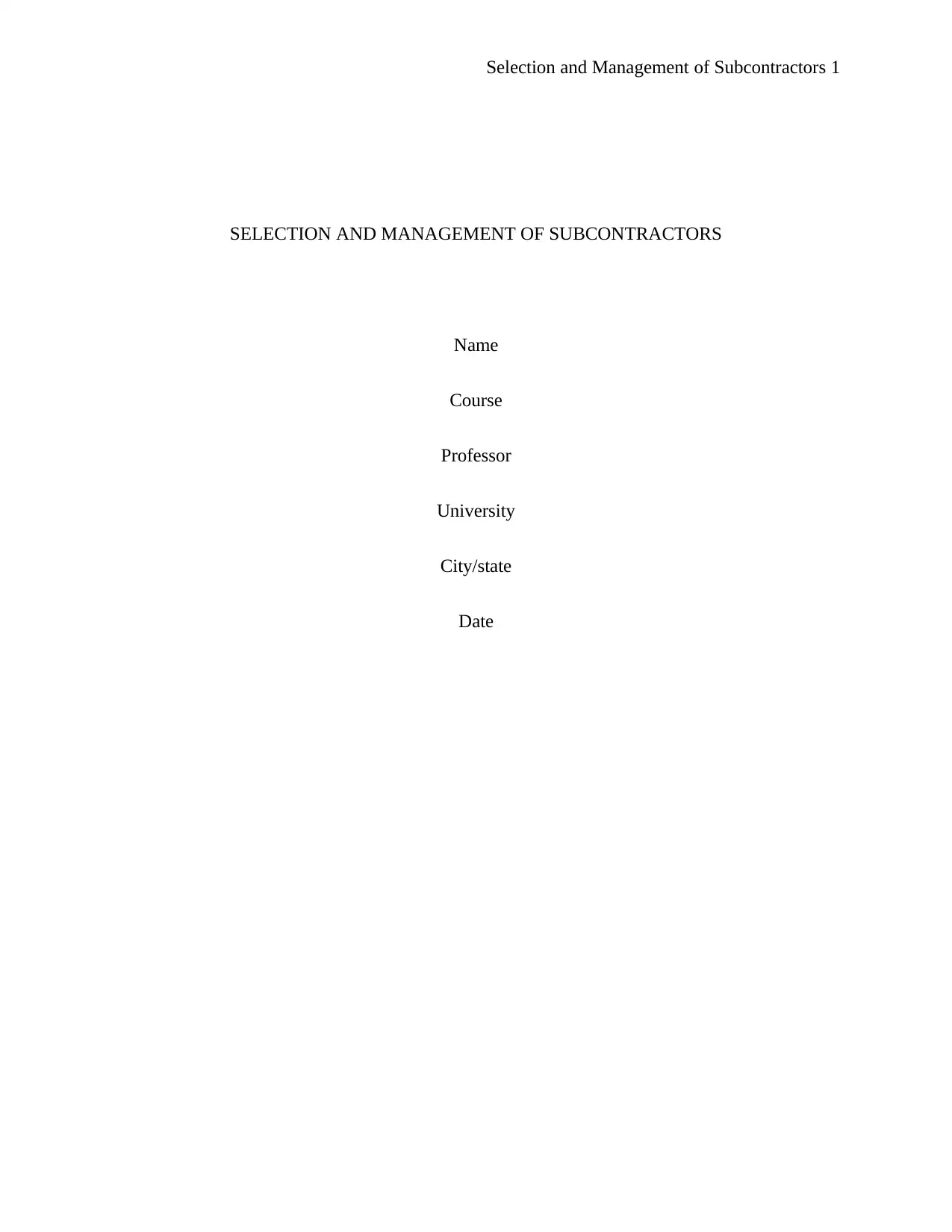
Selection and Management of Subcontractors 1
SELECTION AND MANAGEMENT OF SUBCONTRACTORS
Name
Course
Professor
University
City/state
Date
SELECTION AND MANAGEMENT OF SUBCONTRACTORS
Name
Course
Professor
University
City/state
Date
Secure Best Marks with AI Grader
Need help grading? Try our AI Grader for instant feedback on your assignments.
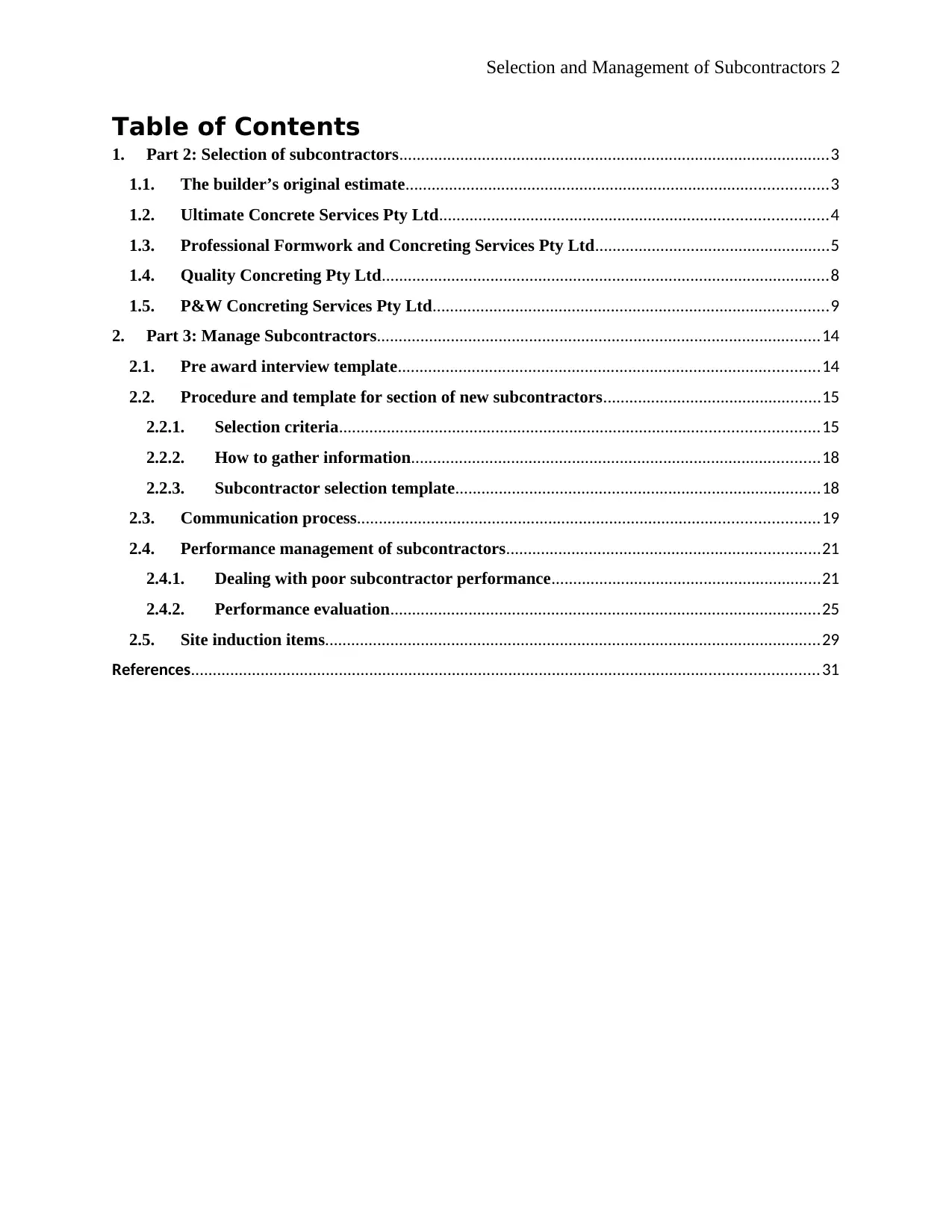
Selection and Management of Subcontractors 2
Table of Contents
1. Part 2: Selection of subcontractors...................................................................................................3
1.1. The builder’s original estimate.................................................................................................3
1.2. Ultimate Concrete Services Pty Ltd.........................................................................................4
1.3. Professional Formwork and Concreting Services Pty Ltd......................................................5
1.4. Quality Concreting Pty Ltd.......................................................................................................8
1.5. P&W Concreting Services Pty Ltd...........................................................................................9
2. Part 3: Manage Subcontractors......................................................................................................14
2.1. Pre award interview template.................................................................................................14
2.2. Procedure and template for section of new subcontractors..................................................15
2.2.1. Selection criteria..............................................................................................................15
2.2.2. How to gather information..............................................................................................18
2.2.3. Subcontractor selection template....................................................................................18
2.3. Communication process..........................................................................................................19
2.4. Performance management of subcontractors........................................................................21
2.4.1. Dealing with poor subcontractor performance..............................................................21
2.4.2. Performance evaluation...................................................................................................25
2.5. Site induction items..................................................................................................................29
References................................................................................................................................................31
Table of Contents
1. Part 2: Selection of subcontractors...................................................................................................3
1.1. The builder’s original estimate.................................................................................................3
1.2. Ultimate Concrete Services Pty Ltd.........................................................................................4
1.3. Professional Formwork and Concreting Services Pty Ltd......................................................5
1.4. Quality Concreting Pty Ltd.......................................................................................................8
1.5. P&W Concreting Services Pty Ltd...........................................................................................9
2. Part 3: Manage Subcontractors......................................................................................................14
2.1. Pre award interview template.................................................................................................14
2.2. Procedure and template for section of new subcontractors..................................................15
2.2.1. Selection criteria..............................................................................................................15
2.2.2. How to gather information..............................................................................................18
2.2.3. Subcontractor selection template....................................................................................18
2.3. Communication process..........................................................................................................19
2.4. Performance management of subcontractors........................................................................21
2.4.1. Dealing with poor subcontractor performance..............................................................21
2.4.2. Performance evaluation...................................................................................................25
2.5. Site induction items..................................................................................................................29
References................................................................................................................................................31
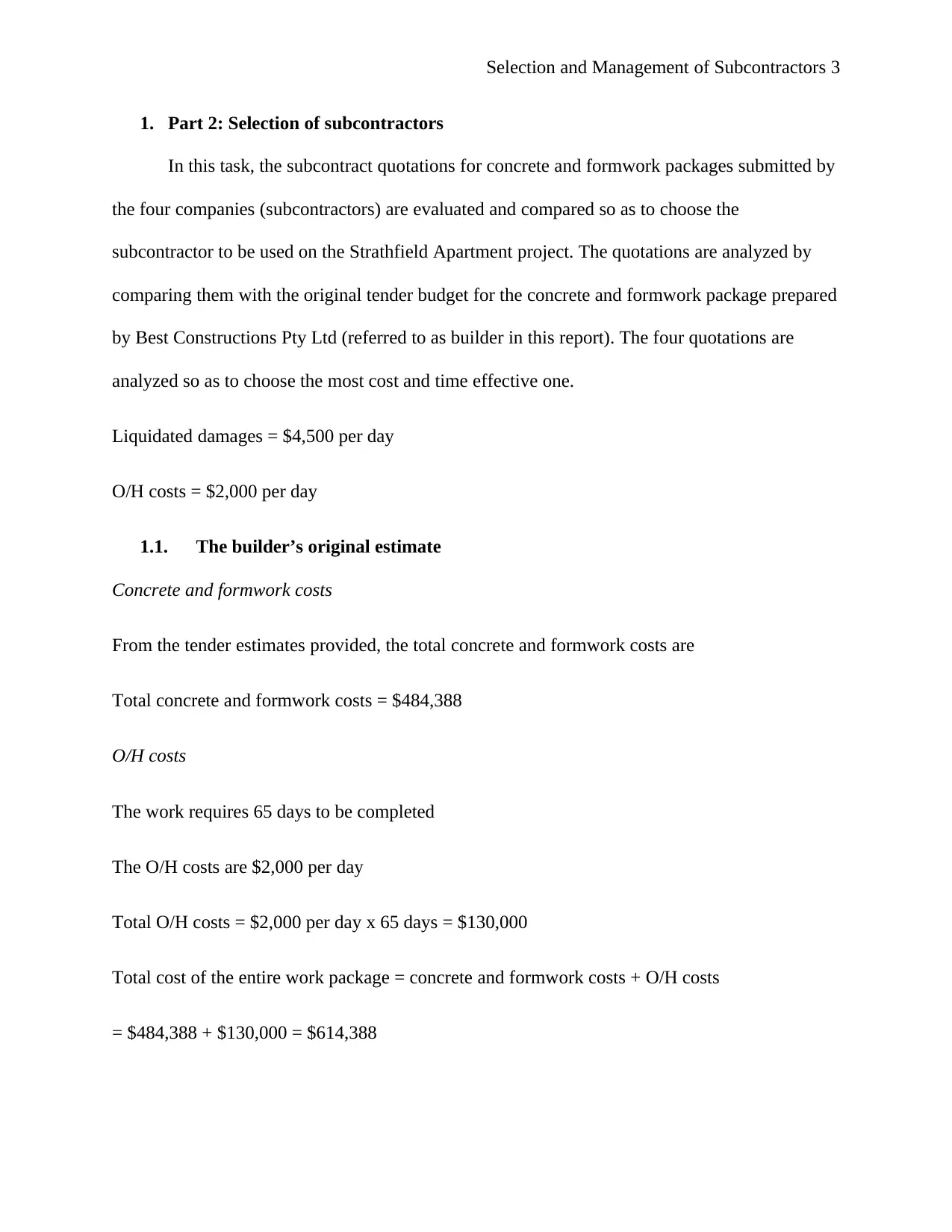
Selection and Management of Subcontractors 3
1. Part 2: Selection of subcontractors
In this task, the subcontract quotations for concrete and formwork packages submitted by
the four companies (subcontractors) are evaluated and compared so as to choose the
subcontractor to be used on the Strathfield Apartment project. The quotations are analyzed by
comparing them with the original tender budget for the concrete and formwork package prepared
by Best Constructions Pty Ltd (referred to as builder in this report). The four quotations are
analyzed so as to choose the most cost and time effective one.
Liquidated damages = $4,500 per day
O/H costs = $2,000 per day
1.1. The builder’s original estimate
Concrete and formwork costs
From the tender estimates provided, the total concrete and formwork costs are
Total concrete and formwork costs = $484,388
O/H costs
The work requires 65 days to be completed
The O/H costs are $2,000 per day
Total O/H costs = $2,000 per day x 65 days = $130,000
Total cost of the entire work package = concrete and formwork costs + O/H costs
= $484,388 + $130,000 = $614,388
1. Part 2: Selection of subcontractors
In this task, the subcontract quotations for concrete and formwork packages submitted by
the four companies (subcontractors) are evaluated and compared so as to choose the
subcontractor to be used on the Strathfield Apartment project. The quotations are analyzed by
comparing them with the original tender budget for the concrete and formwork package prepared
by Best Constructions Pty Ltd (referred to as builder in this report). The four quotations are
analyzed so as to choose the most cost and time effective one.
Liquidated damages = $4,500 per day
O/H costs = $2,000 per day
1.1. The builder’s original estimate
Concrete and formwork costs
From the tender estimates provided, the total concrete and formwork costs are
Total concrete and formwork costs = $484,388
O/H costs
The work requires 65 days to be completed
The O/H costs are $2,000 per day
Total O/H costs = $2,000 per day x 65 days = $130,000
Total cost of the entire work package = concrete and formwork costs + O/H costs
= $484,388 + $130,000 = $614,388
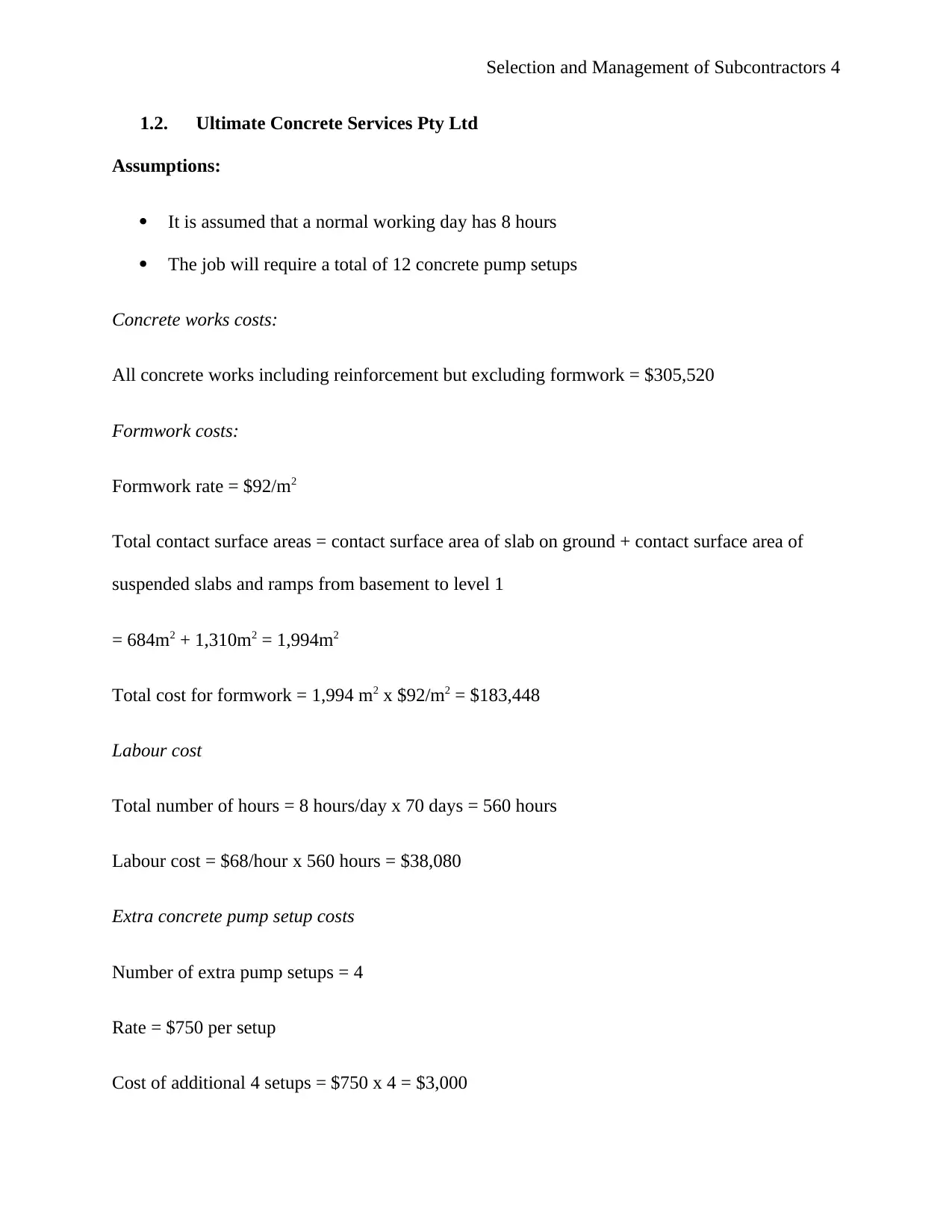
Selection and Management of Subcontractors 4
1.2. Ultimate Concrete Services Pty Ltd
Assumptions:
ď‚· It is assumed that a normal working day has 8 hours
ď‚· The job will require a total of 12 concrete pump setups
Concrete works costs:
All concrete works including reinforcement but excluding formwork = $305,520
Formwork costs:
Formwork rate = $92/m2
Total contact surface areas = contact surface area of slab on ground + contact surface area of
suspended slabs and ramps from basement to level 1
= 684m2 + 1,310m2 = 1,994m2
Total cost for formwork = 1,994 m2 x $92/m2 = $183,448
Labour cost
Total number of hours = 8 hours/day x 70 days = 560 hours
Labour cost = $68/hour x 560 hours = $38,080
Extra concrete pump setup costs
Number of extra pump setups = 4
Rate = $750 per setup
Cost of additional 4 setups = $750 x 4 = $3,000
1.2. Ultimate Concrete Services Pty Ltd
Assumptions:
ď‚· It is assumed that a normal working day has 8 hours
ď‚· The job will require a total of 12 concrete pump setups
Concrete works costs:
All concrete works including reinforcement but excluding formwork = $305,520
Formwork costs:
Formwork rate = $92/m2
Total contact surface areas = contact surface area of slab on ground + contact surface area of
suspended slabs and ramps from basement to level 1
= 684m2 + 1,310m2 = 1,994m2
Total cost for formwork = 1,994 m2 x $92/m2 = $183,448
Labour cost
Total number of hours = 8 hours/day x 70 days = 560 hours
Labour cost = $68/hour x 560 hours = $38,080
Extra concrete pump setup costs
Number of extra pump setups = 4
Rate = $750 per setup
Cost of additional 4 setups = $750 x 4 = $3,000
Secure Best Marks with AI Grader
Need help grading? Try our AI Grader for instant feedback on your assignments.
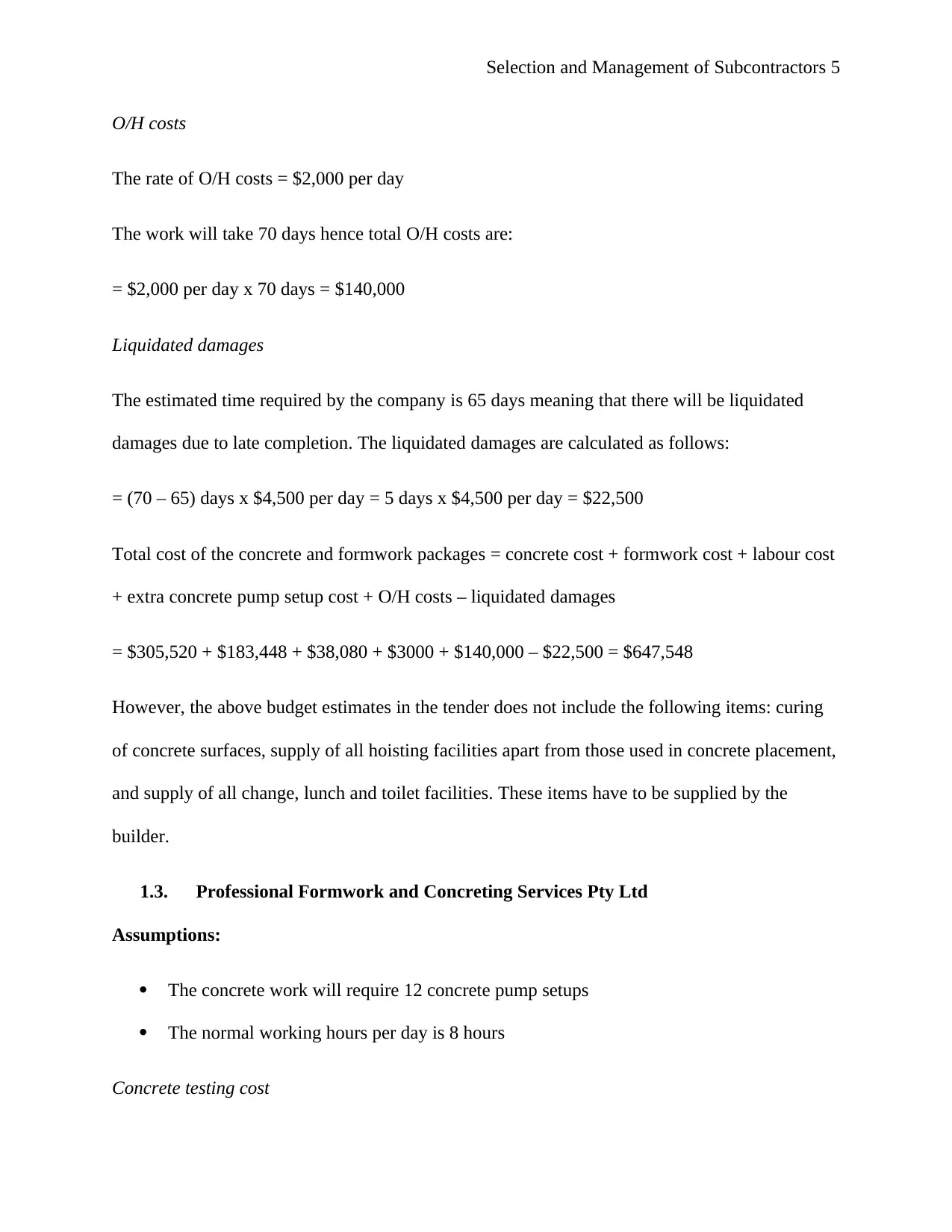
Selection and Management of Subcontractors 5
O/H costs
The rate of O/H costs = $2,000 per day
The work will take 70 days hence total O/H costs are:
= $2,000 per day x 70 days = $140,000
Liquidated damages
The estimated time required by the company is 65 days meaning that there will be liquidated
damages due to late completion. The liquidated damages are calculated as follows:
= (70 – 65) days x $4,500 per day = 5 days x $4,500 per day = $22,500
Total cost of the concrete and formwork packages = concrete cost + formwork cost + labour cost
+ extra concrete pump setup cost + O/H costs – liquidated damages
= $305,520 + $183,448 + $38,080 + $3000 + $140,000 – $22,500 = $647,548
However, the above budget estimates in the tender does not include the following items: curing
of concrete surfaces, supply of all hoisting facilities apart from those used in concrete placement,
and supply of all change, lunch and toilet facilities. These items have to be supplied by the
builder.
1.3. Professional Formwork and Concreting Services Pty Ltd
Assumptions:
ď‚· The concrete work will require 12 concrete pump setups
ď‚· The normal working hours per day is 8 hours
Concrete testing cost
O/H costs
The rate of O/H costs = $2,000 per day
The work will take 70 days hence total O/H costs are:
= $2,000 per day x 70 days = $140,000
Liquidated damages
The estimated time required by the company is 65 days meaning that there will be liquidated
damages due to late completion. The liquidated damages are calculated as follows:
= (70 – 65) days x $4,500 per day = 5 days x $4,500 per day = $22,500
Total cost of the concrete and formwork packages = concrete cost + formwork cost + labour cost
+ extra concrete pump setup cost + O/H costs – liquidated damages
= $305,520 + $183,448 + $38,080 + $3000 + $140,000 – $22,500 = $647,548
However, the above budget estimates in the tender does not include the following items: curing
of concrete surfaces, supply of all hoisting facilities apart from those used in concrete placement,
and supply of all change, lunch and toilet facilities. These items have to be supplied by the
builder.
1.3. Professional Formwork and Concreting Services Pty Ltd
Assumptions:
ď‚· The concrete work will require 12 concrete pump setups
ď‚· The normal working hours per day is 8 hours
Concrete testing cost
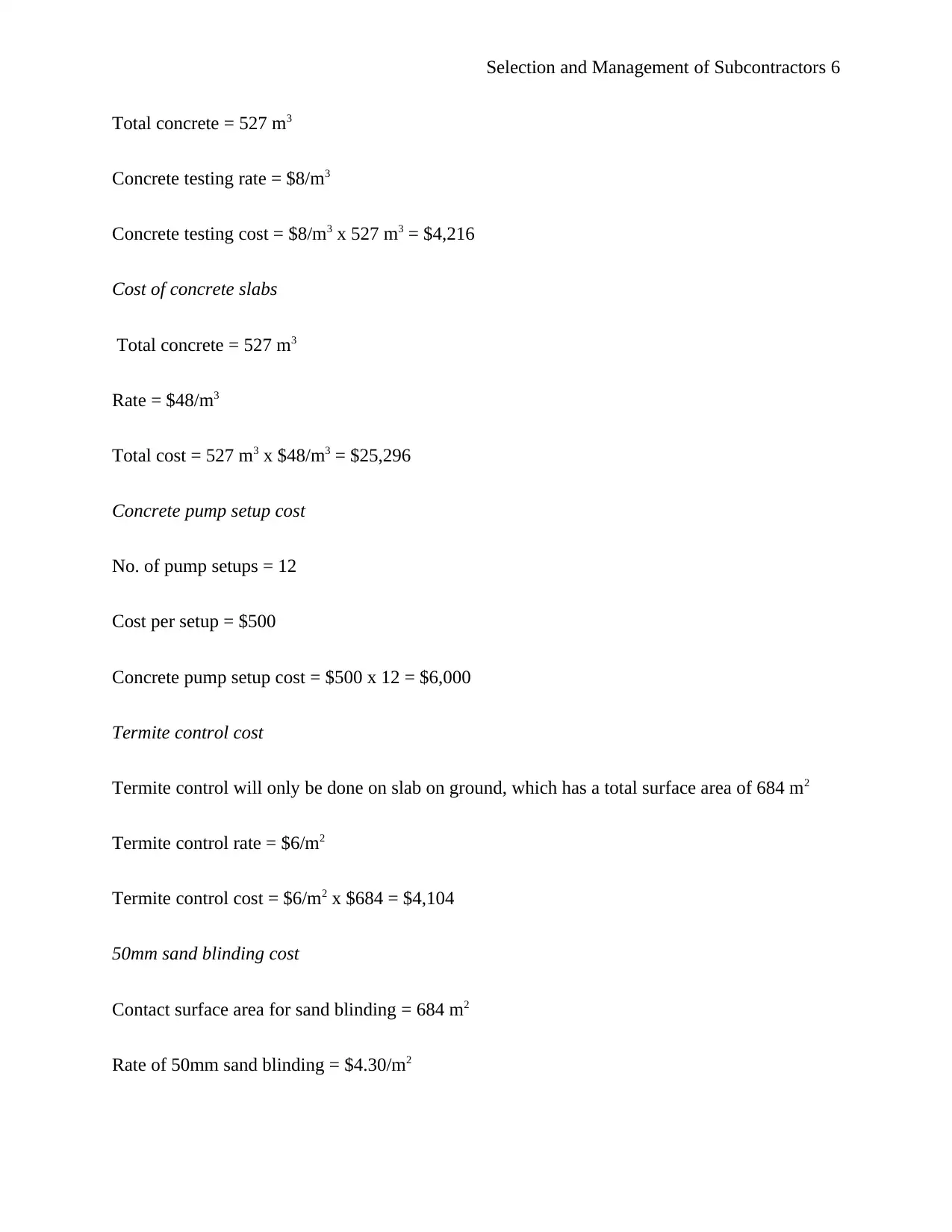
Selection and Management of Subcontractors 6
Total concrete = 527 m3
Concrete testing rate = $8/m3
Concrete testing cost = $8/m3 x 527 m3 = $4,216
Cost of concrete slabs
Total concrete = 527 m3
Rate = $48/m3
Total cost = 527 m3 x $48/m3 = $25,296
Concrete pump setup cost
No. of pump setups = 12
Cost per setup = $500
Concrete pump setup cost = $500 x 12 = $6,000
Termite control cost
Termite control will only be done on slab on ground, which has a total surface area of 684 m2
Termite control rate = $6/m2
Termite control cost = $6/m2 x $684 = $4,104
50mm sand blinding cost
Contact surface area for sand blinding = 684 m2
Rate of 50mm sand blinding = $4.30/m2
Total concrete = 527 m3
Concrete testing rate = $8/m3
Concrete testing cost = $8/m3 x 527 m3 = $4,216
Cost of concrete slabs
Total concrete = 527 m3
Rate = $48/m3
Total cost = 527 m3 x $48/m3 = $25,296
Concrete pump setup cost
No. of pump setups = 12
Cost per setup = $500
Concrete pump setup cost = $500 x 12 = $6,000
Termite control cost
Termite control will only be done on slab on ground, which has a total surface area of 684 m2
Termite control rate = $6/m2
Termite control cost = $6/m2 x $684 = $4,104
50mm sand blinding cost
Contact surface area for sand blinding = 684 m2
Rate of 50mm sand blinding = $4.30/m2
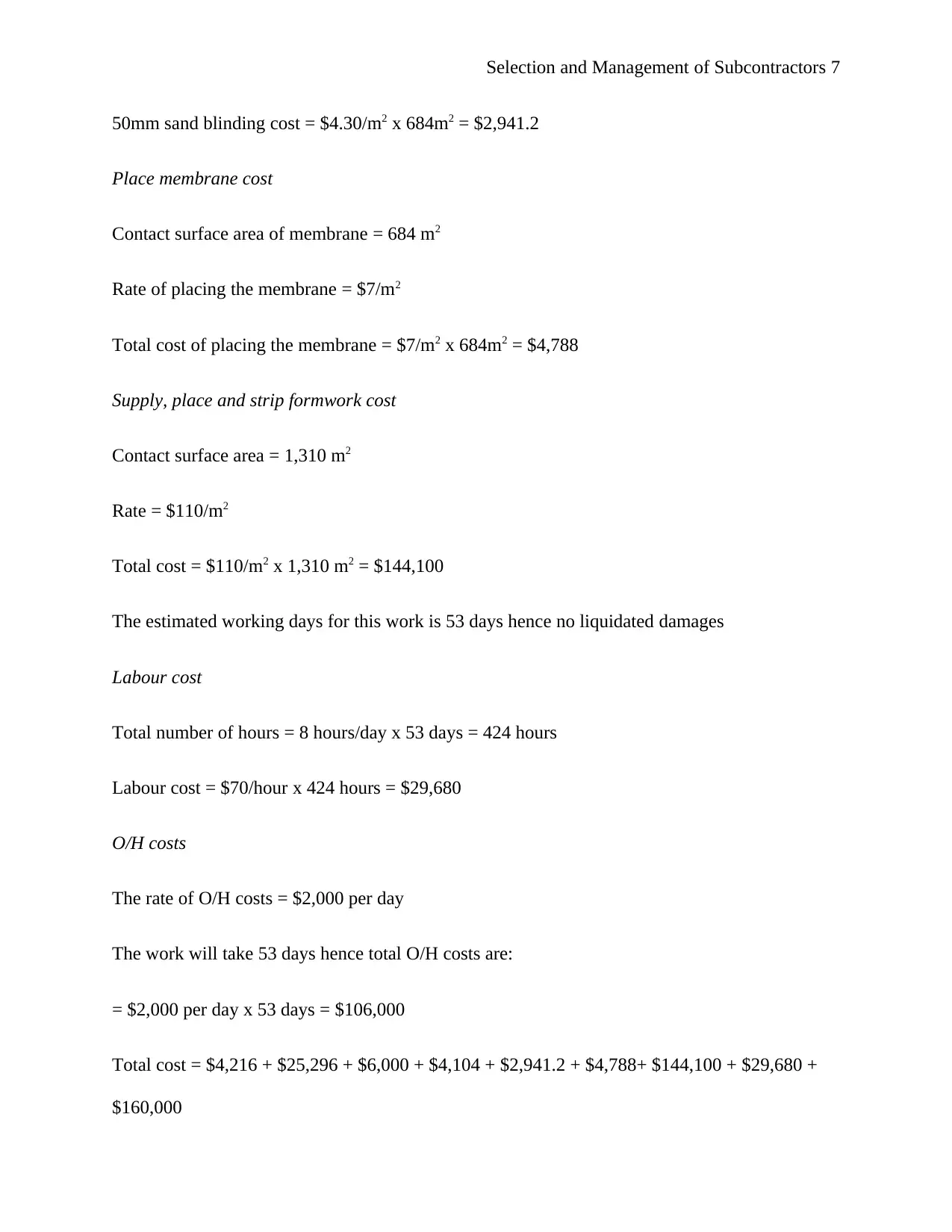
Selection and Management of Subcontractors 7
50mm sand blinding cost = $4.30/m2 x 684m2 = $2,941.2
Place membrane cost
Contact surface area of membrane = 684 m2
Rate of placing the membrane = $7/m2
Total cost of placing the membrane = $7/m2 x 684m2 = $4,788
Supply, place and strip formwork cost
Contact surface area = 1,310 m2
Rate = $110/m2
Total cost = $110/m2 x 1,310 m2 = $144,100
The estimated working days for this work is 53 days hence no liquidated damages
Labour cost
Total number of hours = 8 hours/day x 53 days = 424 hours
Labour cost = $70/hour x 424 hours = $29,680
O/H costs
The rate of O/H costs = $2,000 per day
The work will take 53 days hence total O/H costs are:
= $2,000 per day x 53 days = $106,000
Total cost = $4,216 + $25,296 + $6,000 + $4,104 + $2,941.2 + $4,788+ $144,100 + $29,680 +
$160,000
50mm sand blinding cost = $4.30/m2 x 684m2 = $2,941.2
Place membrane cost
Contact surface area of membrane = 684 m2
Rate of placing the membrane = $7/m2
Total cost of placing the membrane = $7/m2 x 684m2 = $4,788
Supply, place and strip formwork cost
Contact surface area = 1,310 m2
Rate = $110/m2
Total cost = $110/m2 x 1,310 m2 = $144,100
The estimated working days for this work is 53 days hence no liquidated damages
Labour cost
Total number of hours = 8 hours/day x 53 days = 424 hours
Labour cost = $70/hour x 424 hours = $29,680
O/H costs
The rate of O/H costs = $2,000 per day
The work will take 53 days hence total O/H costs are:
= $2,000 per day x 53 days = $106,000
Total cost = $4,216 + $25,296 + $6,000 + $4,104 + $2,941.2 + $4,788+ $144,100 + $29,680 +
$160,000
Paraphrase This Document
Need a fresh take? Get an instant paraphrase of this document with our AI Paraphraser
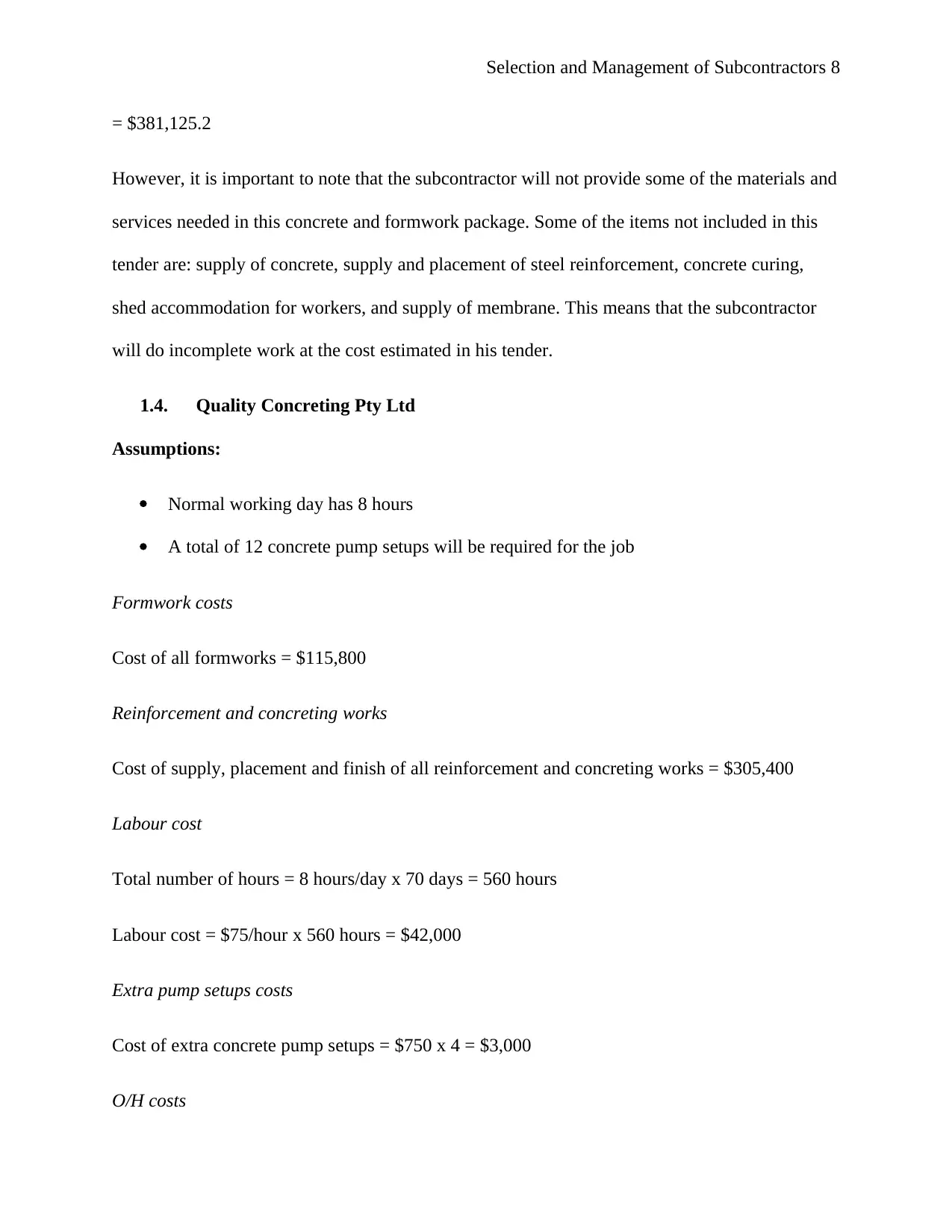
Selection and Management of Subcontractors 8
= $381,125.2
However, it is important to note that the subcontractor will not provide some of the materials and
services needed in this concrete and formwork package. Some of the items not included in this
tender are: supply of concrete, supply and placement of steel reinforcement, concrete curing,
shed accommodation for workers, and supply of membrane. This means that the subcontractor
will do incomplete work at the cost estimated in his tender.
1.4. Quality Concreting Pty Ltd
Assumptions:
ď‚· Normal working day has 8 hours
ď‚· A total of 12 concrete pump setups will be required for the job
Formwork costs
Cost of all formworks = $115,800
Reinforcement and concreting works
Cost of supply, placement and finish of all reinforcement and concreting works = $305,400
Labour cost
Total number of hours = 8 hours/day x 70 days = 560 hours
Labour cost = $75/hour x 560 hours = $42,000
Extra pump setups costs
Cost of extra concrete pump setups = $750 x 4 = $3,000
O/H costs
= $381,125.2
However, it is important to note that the subcontractor will not provide some of the materials and
services needed in this concrete and formwork package. Some of the items not included in this
tender are: supply of concrete, supply and placement of steel reinforcement, concrete curing,
shed accommodation for workers, and supply of membrane. This means that the subcontractor
will do incomplete work at the cost estimated in his tender.
1.4. Quality Concreting Pty Ltd
Assumptions:
ď‚· Normal working day has 8 hours
ď‚· A total of 12 concrete pump setups will be required for the job
Formwork costs
Cost of all formworks = $115,800
Reinforcement and concreting works
Cost of supply, placement and finish of all reinforcement and concreting works = $305,400
Labour cost
Total number of hours = 8 hours/day x 70 days = 560 hours
Labour cost = $75/hour x 560 hours = $42,000
Extra pump setups costs
Cost of extra concrete pump setups = $750 x 4 = $3,000
O/H costs
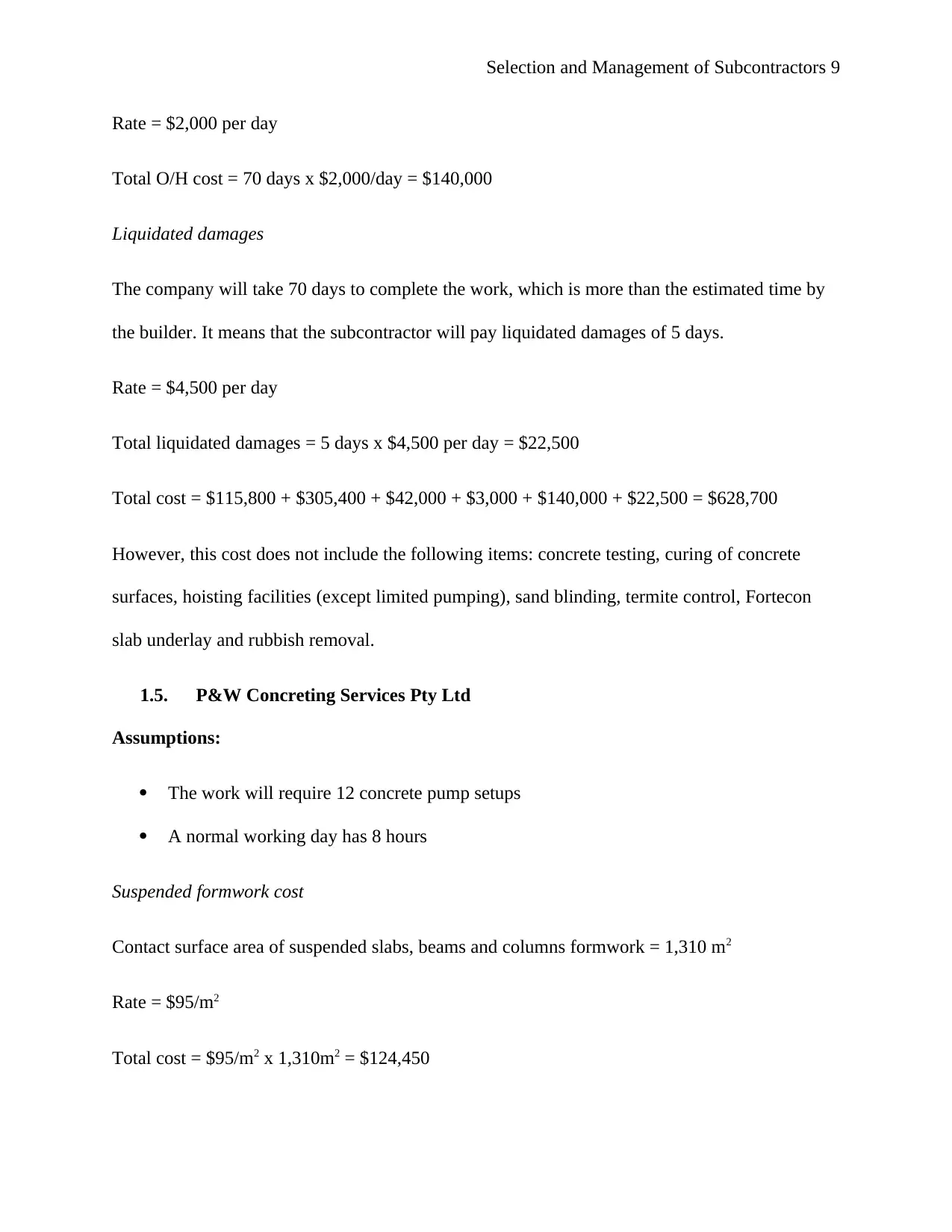
Selection and Management of Subcontractors 9
Rate = $2,000 per day
Total O/H cost = 70 days x $2,000/day = $140,000
Liquidated damages
The company will take 70 days to complete the work, which is more than the estimated time by
the builder. It means that the subcontractor will pay liquidated damages of 5 days.
Rate = $4,500 per day
Total liquidated damages = 5 days x $4,500 per day = $22,500
Total cost = $115,800 + $305,400 + $42,000 + $3,000 + $140,000 + $22,500 = $628,700
However, this cost does not include the following items: concrete testing, curing of concrete
surfaces, hoisting facilities (except limited pumping), sand blinding, termite control, Fortecon
slab underlay and rubbish removal.
1.5. P&W Concreting Services Pty Ltd
Assumptions:
ď‚· The work will require 12 concrete pump setups
ď‚· A normal working day has 8 hours
Suspended formwork cost
Contact surface area of suspended slabs, beams and columns formwork = 1,310 m2
Rate = $95/m2
Total cost = $95/m2 x 1,310m2 = $124,450
Rate = $2,000 per day
Total O/H cost = 70 days x $2,000/day = $140,000
Liquidated damages
The company will take 70 days to complete the work, which is more than the estimated time by
the builder. It means that the subcontractor will pay liquidated damages of 5 days.
Rate = $4,500 per day
Total liquidated damages = 5 days x $4,500 per day = $22,500
Total cost = $115,800 + $305,400 + $42,000 + $3,000 + $140,000 + $22,500 = $628,700
However, this cost does not include the following items: concrete testing, curing of concrete
surfaces, hoisting facilities (except limited pumping), sand blinding, termite control, Fortecon
slab underlay and rubbish removal.
1.5. P&W Concreting Services Pty Ltd
Assumptions:
ď‚· The work will require 12 concrete pump setups
ď‚· A normal working day has 8 hours
Suspended formwork cost
Contact surface area of suspended slabs, beams and columns formwork = 1,310 m2
Rate = $95/m2
Total cost = $95/m2 x 1,310m2 = $124,450
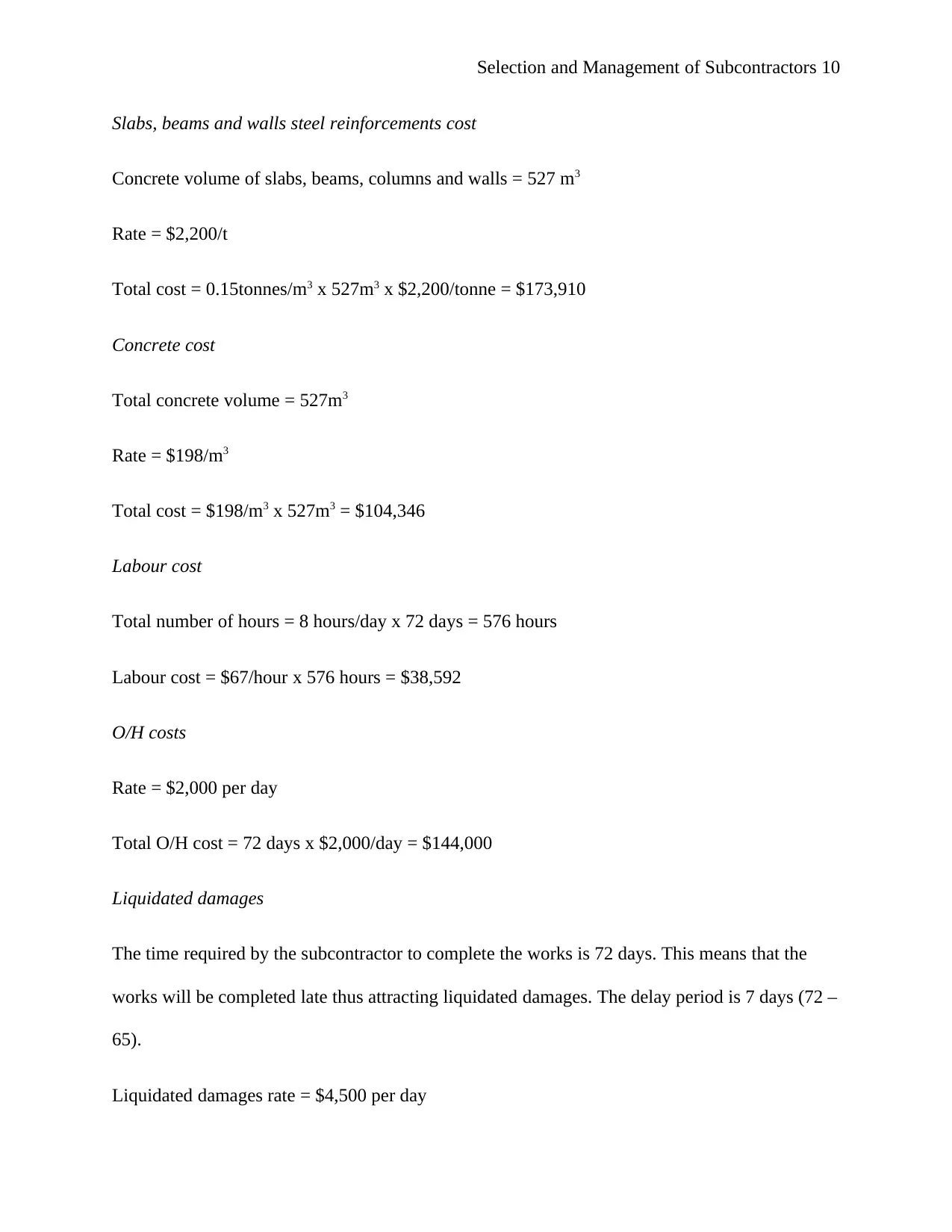
Selection and Management of Subcontractors 10
Slabs, beams and walls steel reinforcements cost
Concrete volume of slabs, beams, columns and walls = 527 m3
Rate = $2,200/t
Total cost = 0.15tonnes/m3 x 527m3 x $2,200/tonne = $173,910
Concrete cost
Total concrete volume = 527m3
Rate = $198/m3
Total cost = $198/m3 x 527m3 = $104,346
Labour cost
Total number of hours = 8 hours/day x 72 days = 576 hours
Labour cost = $67/hour x 576 hours = $38,592
O/H costs
Rate = $2,000 per day
Total O/H cost = 72 days x $2,000/day = $144,000
Liquidated damages
The time required by the subcontractor to complete the works is 72 days. This means that the
works will be completed late thus attracting liquidated damages. The delay period is 7 days (72 –
65).
Liquidated damages rate = $4,500 per day
Slabs, beams and walls steel reinforcements cost
Concrete volume of slabs, beams, columns and walls = 527 m3
Rate = $2,200/t
Total cost = 0.15tonnes/m3 x 527m3 x $2,200/tonne = $173,910
Concrete cost
Total concrete volume = 527m3
Rate = $198/m3
Total cost = $198/m3 x 527m3 = $104,346
Labour cost
Total number of hours = 8 hours/day x 72 days = 576 hours
Labour cost = $67/hour x 576 hours = $38,592
O/H costs
Rate = $2,000 per day
Total O/H cost = 72 days x $2,000/day = $144,000
Liquidated damages
The time required by the subcontractor to complete the works is 72 days. This means that the
works will be completed late thus attracting liquidated damages. The delay period is 7 days (72 –
65).
Liquidated damages rate = $4,500 per day
Secure Best Marks with AI Grader
Need help grading? Try our AI Grader for instant feedback on your assignments.
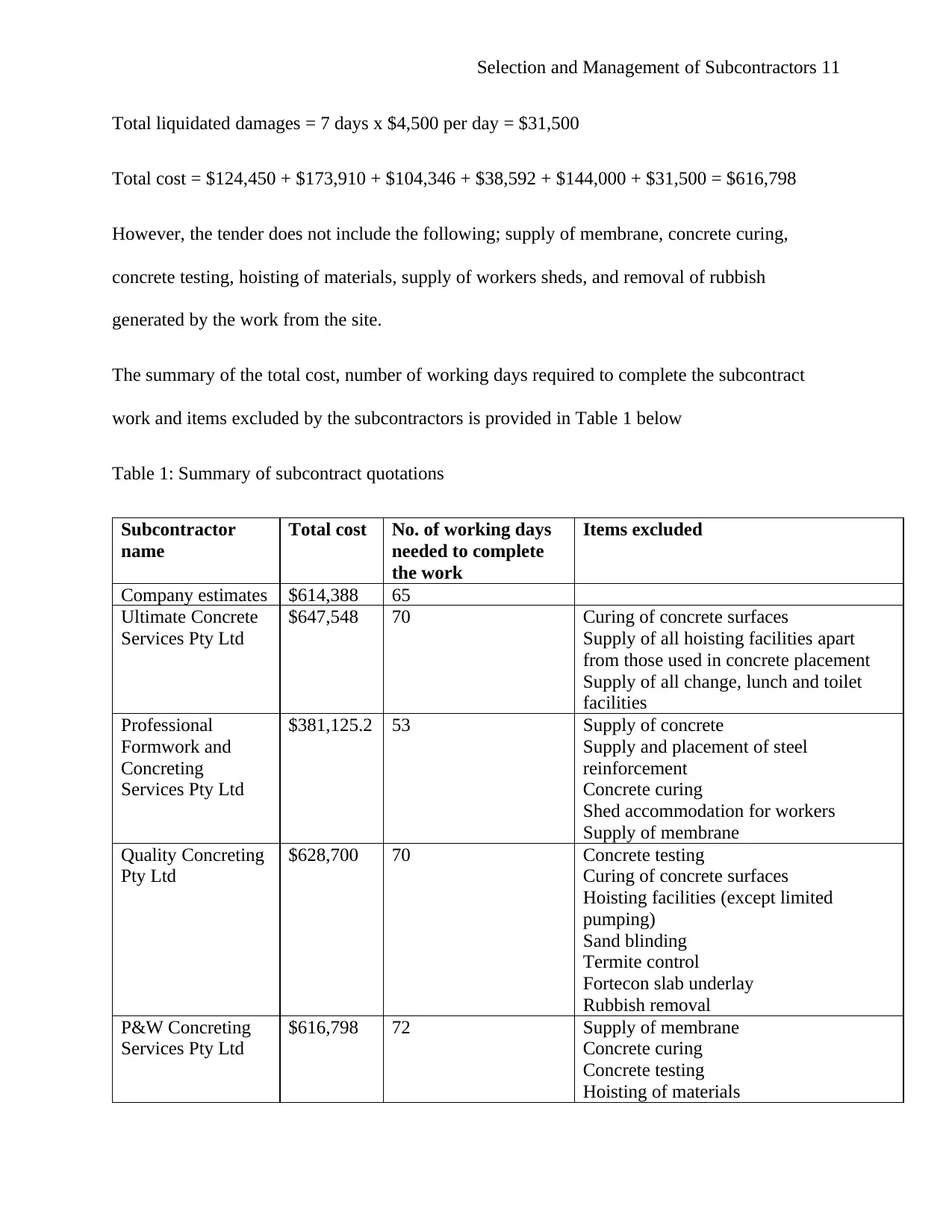
Selection and Management of Subcontractors 11
Total liquidated damages = 7 days x $4,500 per day = $31,500
Total cost = $124,450 + $173,910 + $104,346 + $38,592 + $144,000 + $31,500 = $616,798
However, the tender does not include the following; supply of membrane, concrete curing,
concrete testing, hoisting of materials, supply of workers sheds, and removal of rubbish
generated by the work from the site.
The summary of the total cost, number of working days required to complete the subcontract
work and items excluded by the subcontractors is provided in Table 1 below
Table 1: Summary of subcontract quotations
Subcontractor
name
Total cost No. of working days
needed to complete
the work
Items excluded
Company estimates $614,388 65
Ultimate Concrete
Services Pty Ltd
$647,548 70 Curing of concrete surfaces
Supply of all hoisting facilities apart
from those used in concrete placement
Supply of all change, lunch and toilet
facilities
Professional
Formwork and
Concreting
Services Pty Ltd
$381,125.2 53 Supply of concrete
Supply and placement of steel
reinforcement
Concrete curing
Shed accommodation for workers
Supply of membrane
Quality Concreting
Pty Ltd
$628,700 70 Concrete testing
Curing of concrete surfaces
Hoisting facilities (except limited
pumping)
Sand blinding
Termite control
Fortecon slab underlay
Rubbish removal
P&W Concreting
Services Pty Ltd
$616,798 72 Supply of membrane
Concrete curing
Concrete testing
Hoisting of materials
Total liquidated damages = 7 days x $4,500 per day = $31,500
Total cost = $124,450 + $173,910 + $104,346 + $38,592 + $144,000 + $31,500 = $616,798
However, the tender does not include the following; supply of membrane, concrete curing,
concrete testing, hoisting of materials, supply of workers sheds, and removal of rubbish
generated by the work from the site.
The summary of the total cost, number of working days required to complete the subcontract
work and items excluded by the subcontractors is provided in Table 1 below
Table 1: Summary of subcontract quotations
Subcontractor
name
Total cost No. of working days
needed to complete
the work
Items excluded
Company estimates $614,388 65
Ultimate Concrete
Services Pty Ltd
$647,548 70 Curing of concrete surfaces
Supply of all hoisting facilities apart
from those used in concrete placement
Supply of all change, lunch and toilet
facilities
Professional
Formwork and
Concreting
Services Pty Ltd
$381,125.2 53 Supply of concrete
Supply and placement of steel
reinforcement
Concrete curing
Shed accommodation for workers
Supply of membrane
Quality Concreting
Pty Ltd
$628,700 70 Concrete testing
Curing of concrete surfaces
Hoisting facilities (except limited
pumping)
Sand blinding
Termite control
Fortecon slab underlay
Rubbish removal
P&W Concreting
Services Pty Ltd
$616,798 72 Supply of membrane
Concrete curing
Concrete testing
Hoisting of materials
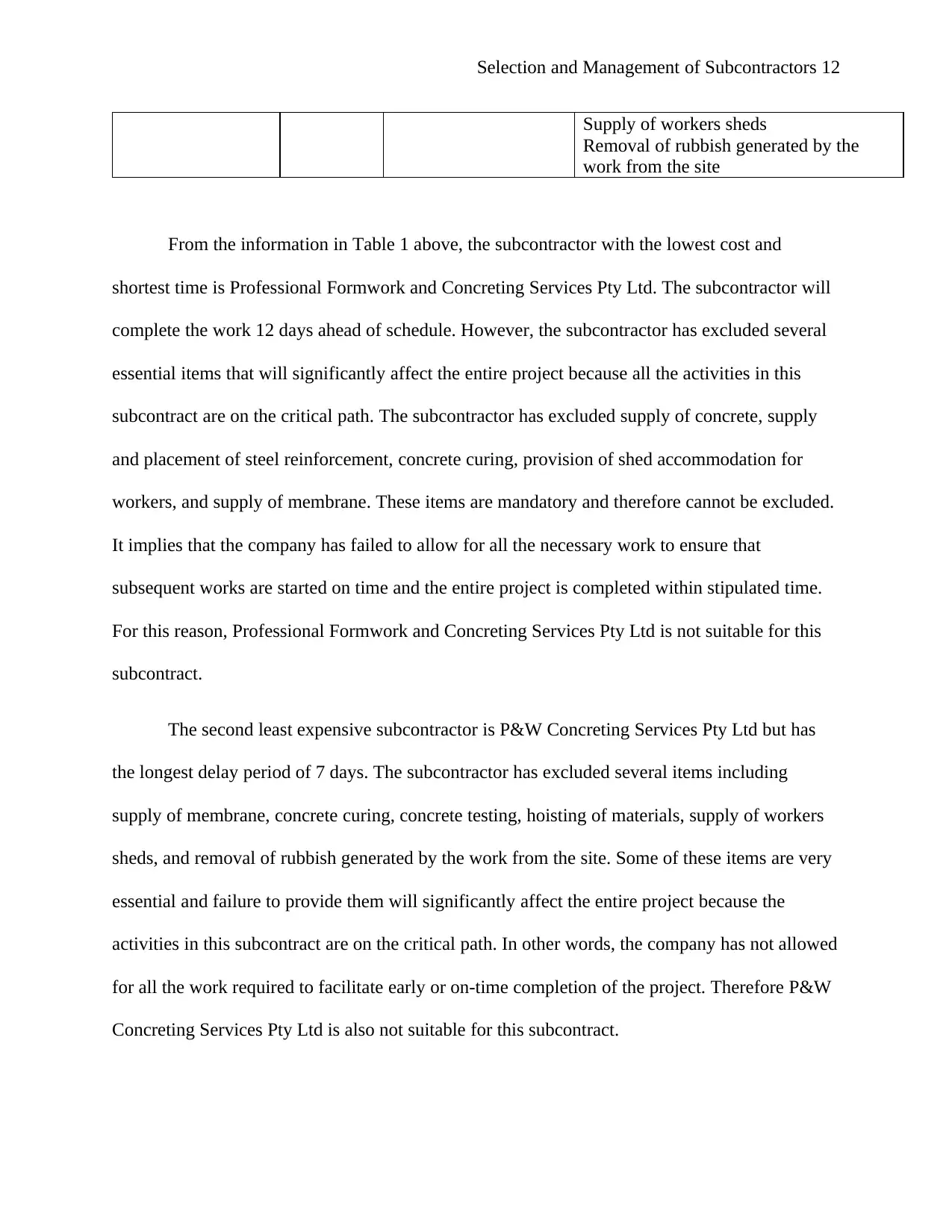
Selection and Management of Subcontractors 12
Supply of workers sheds
Removal of rubbish generated by the
work from the site
From the information in Table 1 above, the subcontractor with the lowest cost and
shortest time is Professional Formwork and Concreting Services Pty Ltd. The subcontractor will
complete the work 12 days ahead of schedule. However, the subcontractor has excluded several
essential items that will significantly affect the entire project because all the activities in this
subcontract are on the critical path. The subcontractor has excluded supply of concrete, supply
and placement of steel reinforcement, concrete curing, provision of shed accommodation for
workers, and supply of membrane. These items are mandatory and therefore cannot be excluded.
It implies that the company has failed to allow for all the necessary work to ensure that
subsequent works are started on time and the entire project is completed within stipulated time.
For this reason, Professional Formwork and Concreting Services Pty Ltd is not suitable for this
subcontract.
The second least expensive subcontractor is P&W Concreting Services Pty Ltd but has
the longest delay period of 7 days. The subcontractor has excluded several items including
supply of membrane, concrete curing, concrete testing, hoisting of materials, supply of workers
sheds, and removal of rubbish generated by the work from the site. Some of these items are very
essential and failure to provide them will significantly affect the entire project because the
activities in this subcontract are on the critical path. In other words, the company has not allowed
for all the work required to facilitate early or on-time completion of the project. Therefore P&W
Concreting Services Pty Ltd is also not suitable for this subcontract.
Supply of workers sheds
Removal of rubbish generated by the
work from the site
From the information in Table 1 above, the subcontractor with the lowest cost and
shortest time is Professional Formwork and Concreting Services Pty Ltd. The subcontractor will
complete the work 12 days ahead of schedule. However, the subcontractor has excluded several
essential items that will significantly affect the entire project because all the activities in this
subcontract are on the critical path. The subcontractor has excluded supply of concrete, supply
and placement of steel reinforcement, concrete curing, provision of shed accommodation for
workers, and supply of membrane. These items are mandatory and therefore cannot be excluded.
It implies that the company has failed to allow for all the necessary work to ensure that
subsequent works are started on time and the entire project is completed within stipulated time.
For this reason, Professional Formwork and Concreting Services Pty Ltd is not suitable for this
subcontract.
The second least expensive subcontractor is P&W Concreting Services Pty Ltd but has
the longest delay period of 7 days. The subcontractor has excluded several items including
supply of membrane, concrete curing, concrete testing, hoisting of materials, supply of workers
sheds, and removal of rubbish generated by the work from the site. Some of these items are very
essential and failure to provide them will significantly affect the entire project because the
activities in this subcontract are on the critical path. In other words, the company has not allowed
for all the work required to facilitate early or on-time completion of the project. Therefore P&W
Concreting Services Pty Ltd is also not suitable for this subcontract.
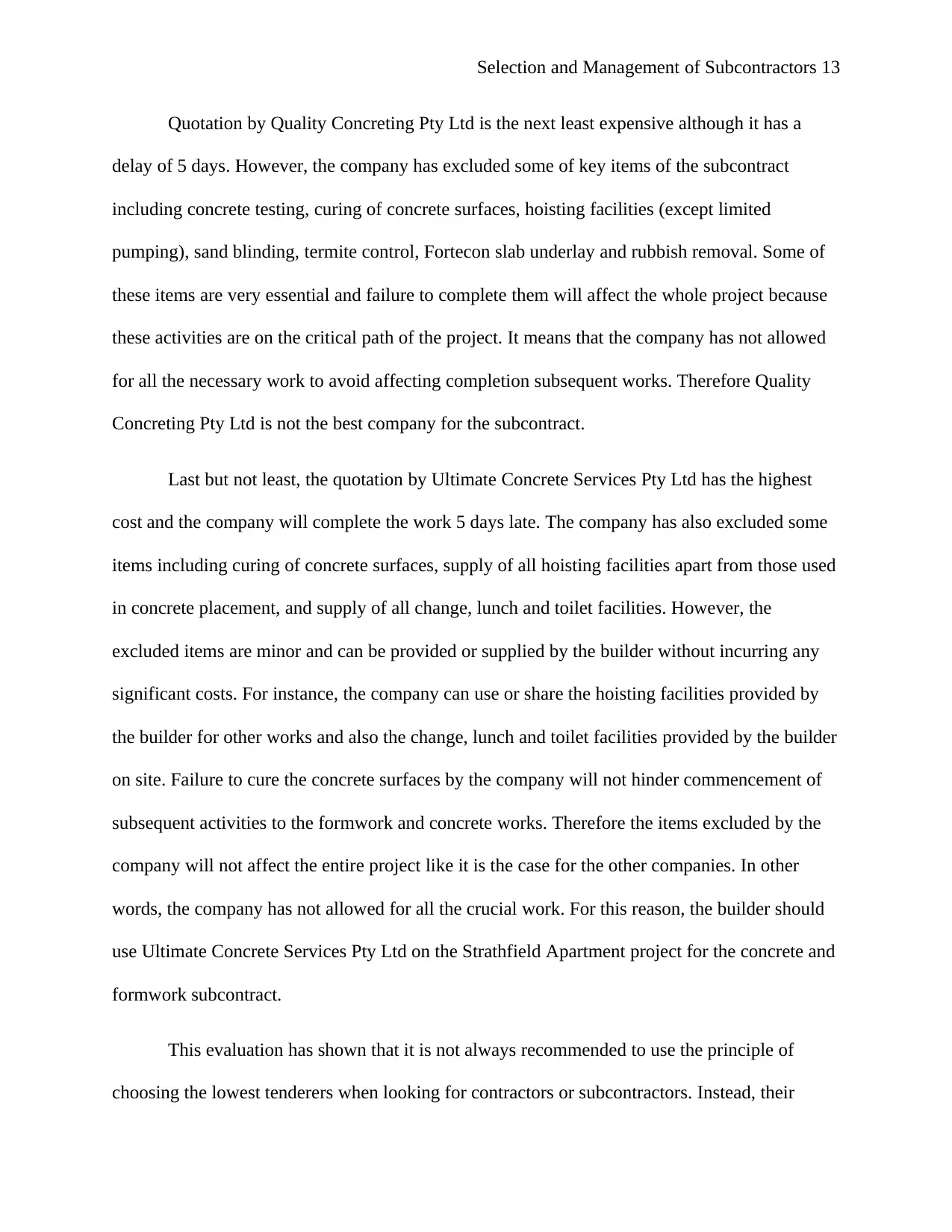
Selection and Management of Subcontractors 13
Quotation by Quality Concreting Pty Ltd is the next least expensive although it has a
delay of 5 days. However, the company has excluded some of key items of the subcontract
including concrete testing, curing of concrete surfaces, hoisting facilities (except limited
pumping), sand blinding, termite control, Fortecon slab underlay and rubbish removal. Some of
these items are very essential and failure to complete them will affect the whole project because
these activities are on the critical path of the project. It means that the company has not allowed
for all the necessary work to avoid affecting completion subsequent works. Therefore Quality
Concreting Pty Ltd is not the best company for the subcontract.
Last but not least, the quotation by Ultimate Concrete Services Pty Ltd has the highest
cost and the company will complete the work 5 days late. The company has also excluded some
items including curing of concrete surfaces, supply of all hoisting facilities apart from those used
in concrete placement, and supply of all change, lunch and toilet facilities. However, the
excluded items are minor and can be provided or supplied by the builder without incurring any
significant costs. For instance, the company can use or share the hoisting facilities provided by
the builder for other works and also the change, lunch and toilet facilities provided by the builder
on site. Failure to cure the concrete surfaces by the company will not hinder commencement of
subsequent activities to the formwork and concrete works. Therefore the items excluded by the
company will not affect the entire project like it is the case for the other companies. In other
words, the company has not allowed for all the crucial work. For this reason, the builder should
use Ultimate Concrete Services Pty Ltd on the Strathfield Apartment project for the concrete and
formwork subcontract.
This evaluation has shown that it is not always recommended to use the principle of
choosing the lowest tenderers when looking for contractors or subcontractors. Instead, their
Quotation by Quality Concreting Pty Ltd is the next least expensive although it has a
delay of 5 days. However, the company has excluded some of key items of the subcontract
including concrete testing, curing of concrete surfaces, hoisting facilities (except limited
pumping), sand blinding, termite control, Fortecon slab underlay and rubbish removal. Some of
these items are very essential and failure to complete them will affect the whole project because
these activities are on the critical path of the project. It means that the company has not allowed
for all the necessary work to avoid affecting completion subsequent works. Therefore Quality
Concreting Pty Ltd is not the best company for the subcontract.
Last but not least, the quotation by Ultimate Concrete Services Pty Ltd has the highest
cost and the company will complete the work 5 days late. The company has also excluded some
items including curing of concrete surfaces, supply of all hoisting facilities apart from those used
in concrete placement, and supply of all change, lunch and toilet facilities. However, the
excluded items are minor and can be provided or supplied by the builder without incurring any
significant costs. For instance, the company can use or share the hoisting facilities provided by
the builder for other works and also the change, lunch and toilet facilities provided by the builder
on site. Failure to cure the concrete surfaces by the company will not hinder commencement of
subsequent activities to the formwork and concrete works. Therefore the items excluded by the
company will not affect the entire project like it is the case for the other companies. In other
words, the company has not allowed for all the crucial work. For this reason, the builder should
use Ultimate Concrete Services Pty Ltd on the Strathfield Apartment project for the concrete and
formwork subcontract.
This evaluation has shown that it is not always recommended to use the principle of
choosing the lowest tenderers when looking for contractors or subcontractors. Instead, their
Paraphrase This Document
Need a fresh take? Get an instant paraphrase of this document with our AI Paraphraser
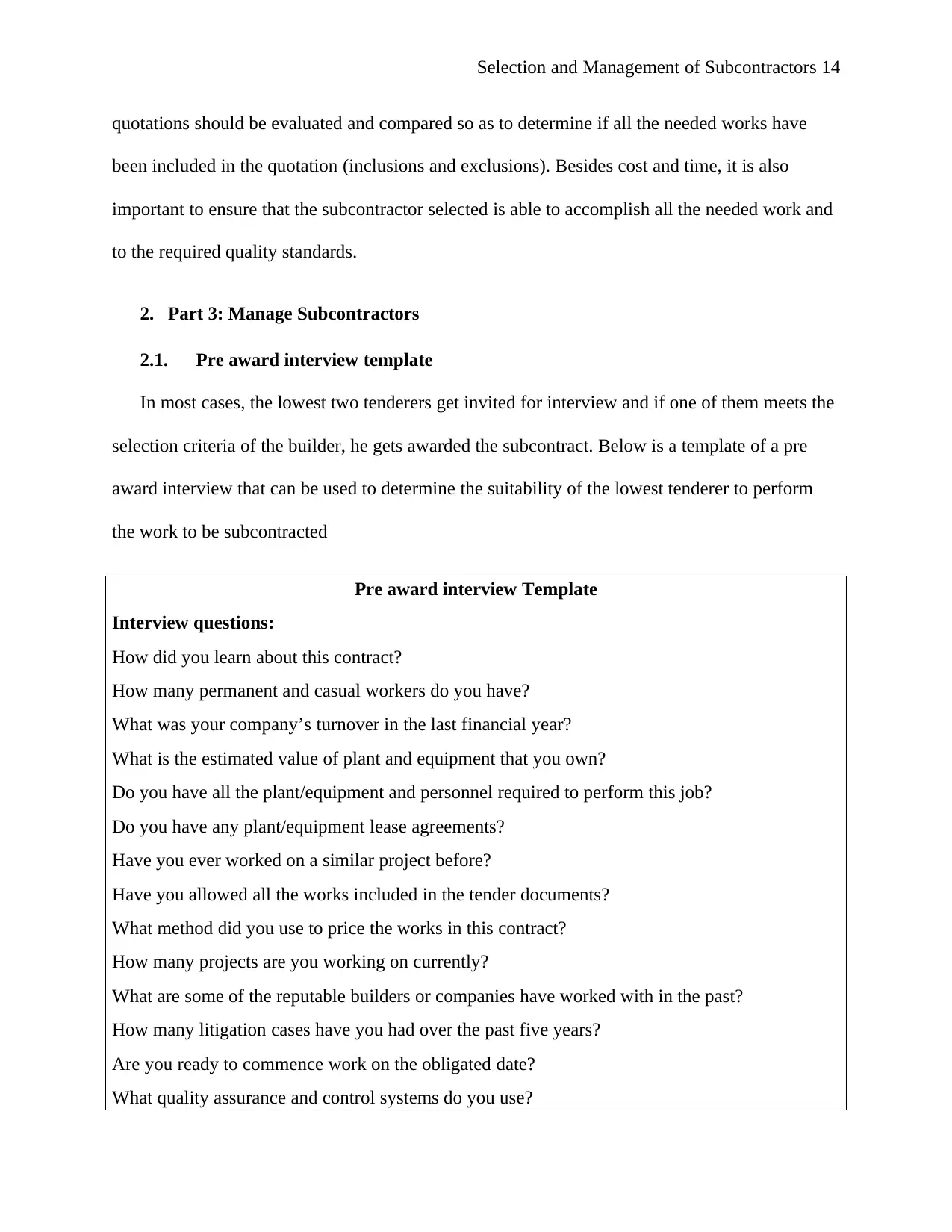
Selection and Management of Subcontractors 14
quotations should be evaluated and compared so as to determine if all the needed works have
been included in the quotation (inclusions and exclusions). Besides cost and time, it is also
important to ensure that the subcontractor selected is able to accomplish all the needed work and
to the required quality standards.
2. Part 3: Manage Subcontractors
2.1. Pre award interview template
In most cases, the lowest two tenderers get invited for interview and if one of them meets the
selection criteria of the builder, he gets awarded the subcontract. Below is a template of a pre
award interview that can be used to determine the suitability of the lowest tenderer to perform
the work to be subcontracted
Pre award interview Template
Interview questions:
How did you learn about this contract?
How many permanent and casual workers do you have?
What was your company’s turnover in the last financial year?
What is the estimated value of plant and equipment that you own?
Do you have all the plant/equipment and personnel required to perform this job?
Do you have any plant/equipment lease agreements?
Have you ever worked on a similar project before?
Have you allowed all the works included in the tender documents?
What method did you use to price the works in this contract?
How many projects are you working on currently?
What are some of the reputable builders or companies have worked with in the past?
How many litigation cases have you had over the past five years?
Are you ready to commence work on the obligated date?
What quality assurance and control systems do you use?
quotations should be evaluated and compared so as to determine if all the needed works have
been included in the quotation (inclusions and exclusions). Besides cost and time, it is also
important to ensure that the subcontractor selected is able to accomplish all the needed work and
to the required quality standards.
2. Part 3: Manage Subcontractors
2.1. Pre award interview template
In most cases, the lowest two tenderers get invited for interview and if one of them meets the
selection criteria of the builder, he gets awarded the subcontract. Below is a template of a pre
award interview that can be used to determine the suitability of the lowest tenderer to perform
the work to be subcontracted
Pre award interview Template
Interview questions:
How did you learn about this contract?
How many permanent and casual workers do you have?
What was your company’s turnover in the last financial year?
What is the estimated value of plant and equipment that you own?
Do you have all the plant/equipment and personnel required to perform this job?
Do you have any plant/equipment lease agreements?
Have you ever worked on a similar project before?
Have you allowed all the works included in the tender documents?
What method did you use to price the works in this contract?
How many projects are you working on currently?
What are some of the reputable builders or companies have worked with in the past?
How many litigation cases have you had over the past five years?
Are you ready to commence work on the obligated date?
What quality assurance and control systems do you use?
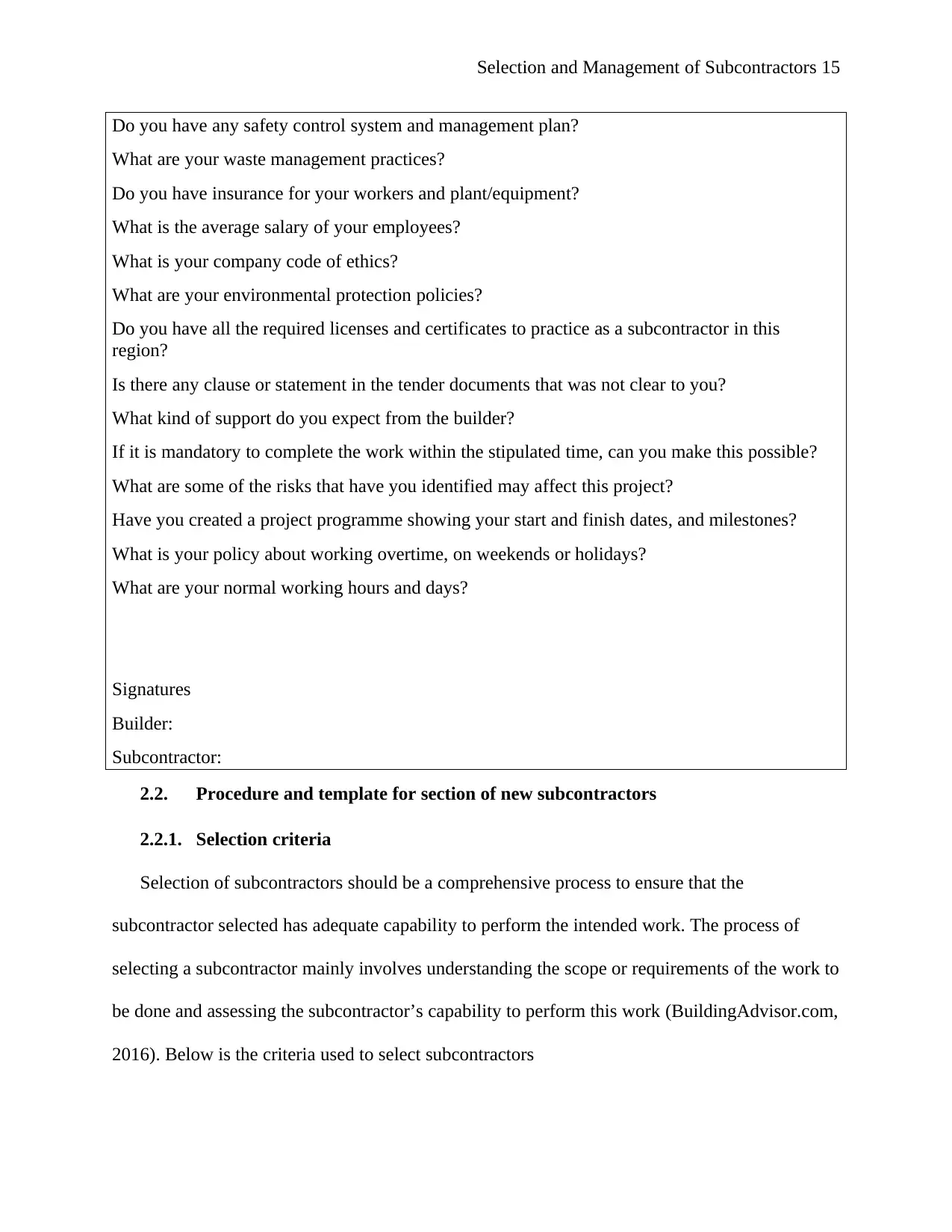
Selection and Management of Subcontractors 15
Do you have any safety control system and management plan?
What are your waste management practices?
Do you have insurance for your workers and plant/equipment?
What is the average salary of your employees?
What is your company code of ethics?
What are your environmental protection policies?
Do you have all the required licenses and certificates to practice as a subcontractor in this
region?
Is there any clause or statement in the tender documents that was not clear to you?
What kind of support do you expect from the builder?
If it is mandatory to complete the work within the stipulated time, can you make this possible?
What are some of the risks that have you identified may affect this project?
Have you created a project programme showing your start and finish dates, and milestones?
What is your policy about working overtime, on weekends or holidays?
What are your normal working hours and days?
Signatures
Builder:
Subcontractor:
2.2. Procedure and template for section of new subcontractors
2.2.1. Selection criteria
Selection of subcontractors should be a comprehensive process to ensure that the
subcontractor selected has adequate capability to perform the intended work. The process of
selecting a subcontractor mainly involves understanding the scope or requirements of the work to
be done and assessing the subcontractor’s capability to perform this work (BuildingAdvisor.com,
2016). Below is the criteria used to select subcontractors
Do you have any safety control system and management plan?
What are your waste management practices?
Do you have insurance for your workers and plant/equipment?
What is the average salary of your employees?
What is your company code of ethics?
What are your environmental protection policies?
Do you have all the required licenses and certificates to practice as a subcontractor in this
region?
Is there any clause or statement in the tender documents that was not clear to you?
What kind of support do you expect from the builder?
If it is mandatory to complete the work within the stipulated time, can you make this possible?
What are some of the risks that have you identified may affect this project?
Have you created a project programme showing your start and finish dates, and milestones?
What is your policy about working overtime, on weekends or holidays?
What are your normal working hours and days?
Signatures
Builder:
Subcontractor:
2.2. Procedure and template for section of new subcontractors
2.2.1. Selection criteria
Selection of subcontractors should be a comprehensive process to ensure that the
subcontractor selected has adequate capability to perform the intended work. The process of
selecting a subcontractor mainly involves understanding the scope or requirements of the work to
be done and assessing the subcontractor’s capability to perform this work (BuildingAdvisor.com,
2016). Below is the criteria used to select subcontractors
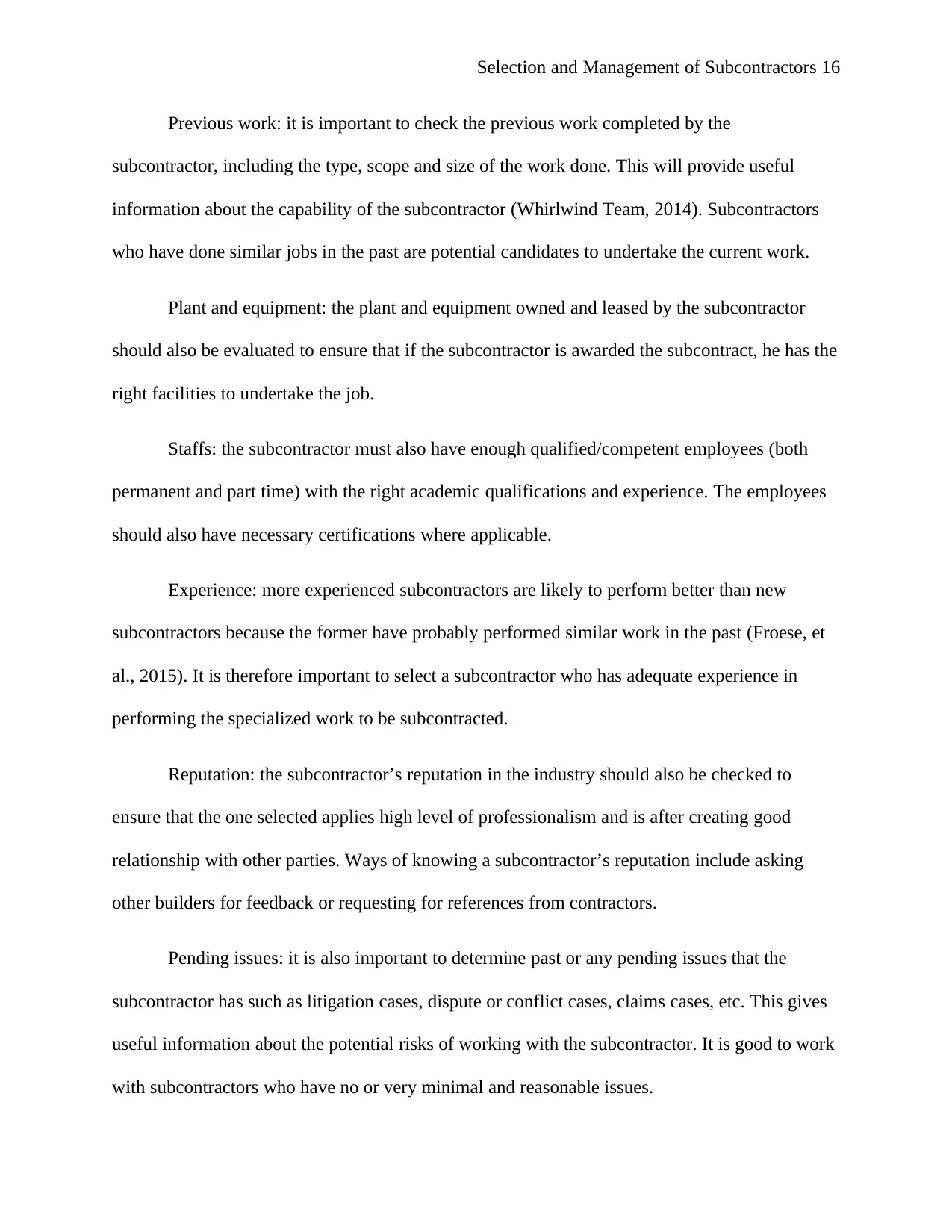
Selection and Management of Subcontractors 16
Previous work: it is important to check the previous work completed by the
subcontractor, including the type, scope and size of the work done. This will provide useful
information about the capability of the subcontractor (Whirlwind Team, 2014). Subcontractors
who have done similar jobs in the past are potential candidates to undertake the current work.
Plant and equipment: the plant and equipment owned and leased by the subcontractor
should also be evaluated to ensure that if the subcontractor is awarded the subcontract, he has the
right facilities to undertake the job.
Staffs: the subcontractor must also have enough qualified/competent employees (both
permanent and part time) with the right academic qualifications and experience. The employees
should also have necessary certifications where applicable.
Experience: more experienced subcontractors are likely to perform better than new
subcontractors because the former have probably performed similar work in the past (Froese, et
al., 2015). It is therefore important to select a subcontractor who has adequate experience in
performing the specialized work to be subcontracted.
Reputation: the subcontractor’s reputation in the industry should also be checked to
ensure that the one selected applies high level of professionalism and is after creating good
relationship with other parties. Ways of knowing a subcontractor’s reputation include asking
other builders for feedback or requesting for references from contractors.
Pending issues: it is also important to determine past or any pending issues that the
subcontractor has such as litigation cases, dispute or conflict cases, claims cases, etc. This gives
useful information about the potential risks of working with the subcontractor. It is good to work
with subcontractors who have no or very minimal and reasonable issues.
Previous work: it is important to check the previous work completed by the
subcontractor, including the type, scope and size of the work done. This will provide useful
information about the capability of the subcontractor (Whirlwind Team, 2014). Subcontractors
who have done similar jobs in the past are potential candidates to undertake the current work.
Plant and equipment: the plant and equipment owned and leased by the subcontractor
should also be evaluated to ensure that if the subcontractor is awarded the subcontract, he has the
right facilities to undertake the job.
Staffs: the subcontractor must also have enough qualified/competent employees (both
permanent and part time) with the right academic qualifications and experience. The employees
should also have necessary certifications where applicable.
Experience: more experienced subcontractors are likely to perform better than new
subcontractors because the former have probably performed similar work in the past (Froese, et
al., 2015). It is therefore important to select a subcontractor who has adequate experience in
performing the specialized work to be subcontracted.
Reputation: the subcontractor’s reputation in the industry should also be checked to
ensure that the one selected applies high level of professionalism and is after creating good
relationship with other parties. Ways of knowing a subcontractor’s reputation include asking
other builders for feedback or requesting for references from contractors.
Pending issues: it is also important to determine past or any pending issues that the
subcontractor has such as litigation cases, dispute or conflict cases, claims cases, etc. This gives
useful information about the potential risks of working with the subcontractor. It is good to work
with subcontractors who have no or very minimal and reasonable issues.
Secure Best Marks with AI Grader
Need help grading? Try our AI Grader for instant feedback on your assignments.
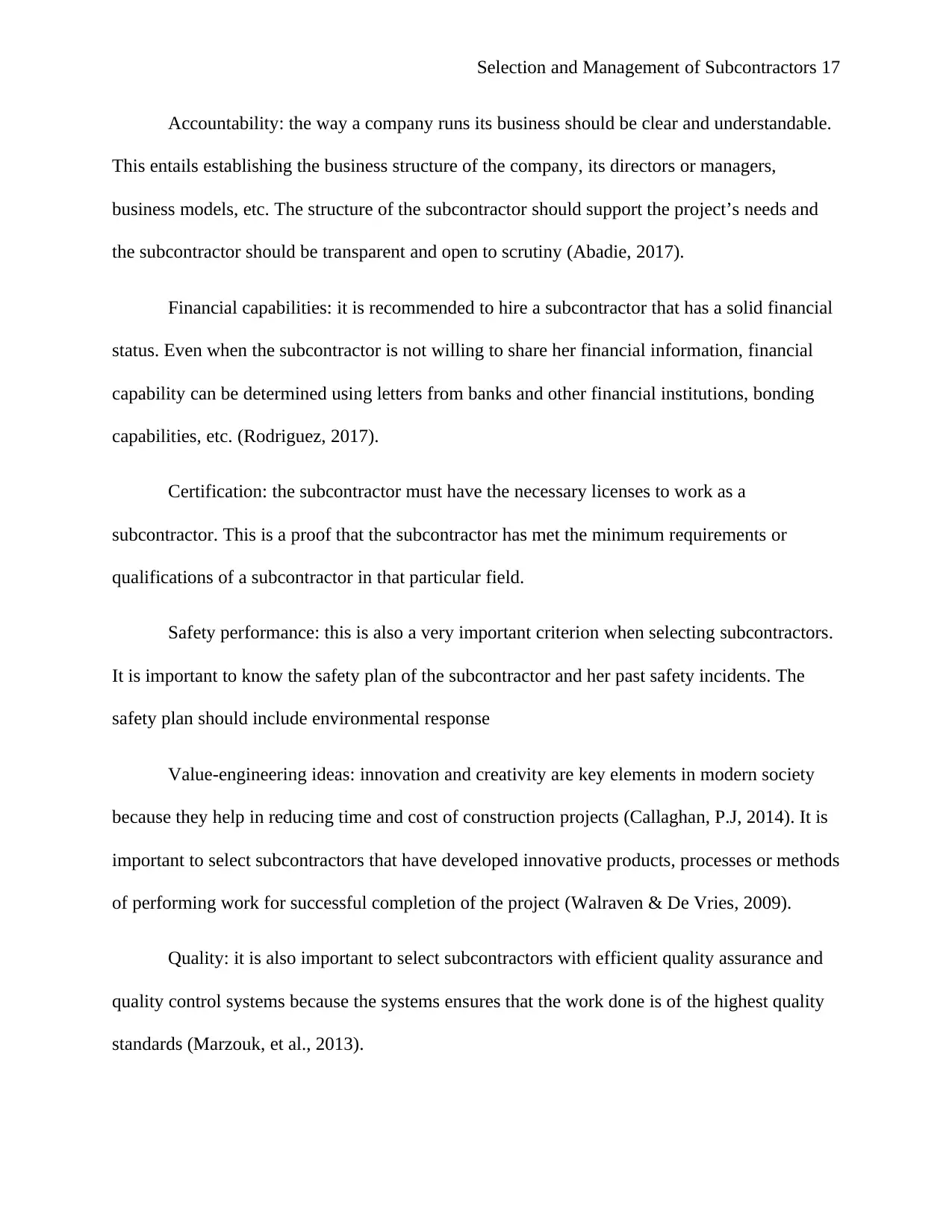
Selection and Management of Subcontractors 17
Accountability: the way a company runs its business should be clear and understandable.
This entails establishing the business structure of the company, its directors or managers,
business models, etc. The structure of the subcontractor should support the project’s needs and
the subcontractor should be transparent and open to scrutiny (Abadie, 2017).
Financial capabilities: it is recommended to hire a subcontractor that has a solid financial
status. Even when the subcontractor is not willing to share her financial information, financial
capability can be determined using letters from banks and other financial institutions, bonding
capabilities, etc. (Rodriguez, 2017).
Certification: the subcontractor must have the necessary licenses to work as a
subcontractor. This is a proof that the subcontractor has met the minimum requirements or
qualifications of a subcontractor in that particular field.
Safety performance: this is also a very important criterion when selecting subcontractors.
It is important to know the safety plan of the subcontractor and her past safety incidents. The
safety plan should include environmental response
Value-engineering ideas: innovation and creativity are key elements in modern society
because they help in reducing time and cost of construction projects (Callaghan, P.J, 2014). It is
important to select subcontractors that have developed innovative products, processes or methods
of performing work for successful completion of the project (Walraven & De Vries, 2009).
Quality: it is also important to select subcontractors with efficient quality assurance and
quality control systems because the systems ensures that the work done is of the highest quality
standards (Marzouk, et al., 2013).
Accountability: the way a company runs its business should be clear and understandable.
This entails establishing the business structure of the company, its directors or managers,
business models, etc. The structure of the subcontractor should support the project’s needs and
the subcontractor should be transparent and open to scrutiny (Abadie, 2017).
Financial capabilities: it is recommended to hire a subcontractor that has a solid financial
status. Even when the subcontractor is not willing to share her financial information, financial
capability can be determined using letters from banks and other financial institutions, bonding
capabilities, etc. (Rodriguez, 2017).
Certification: the subcontractor must have the necessary licenses to work as a
subcontractor. This is a proof that the subcontractor has met the minimum requirements or
qualifications of a subcontractor in that particular field.
Safety performance: this is also a very important criterion when selecting subcontractors.
It is important to know the safety plan of the subcontractor and her past safety incidents. The
safety plan should include environmental response
Value-engineering ideas: innovation and creativity are key elements in modern society
because they help in reducing time and cost of construction projects (Callaghan, P.J, 2014). It is
important to select subcontractors that have developed innovative products, processes or methods
of performing work for successful completion of the project (Walraven & De Vries, 2009).
Quality: it is also important to select subcontractors with efficient quality assurance and
quality control systems because the systems ensures that the work done is of the highest quality
standards (Marzouk, et al., 2013).
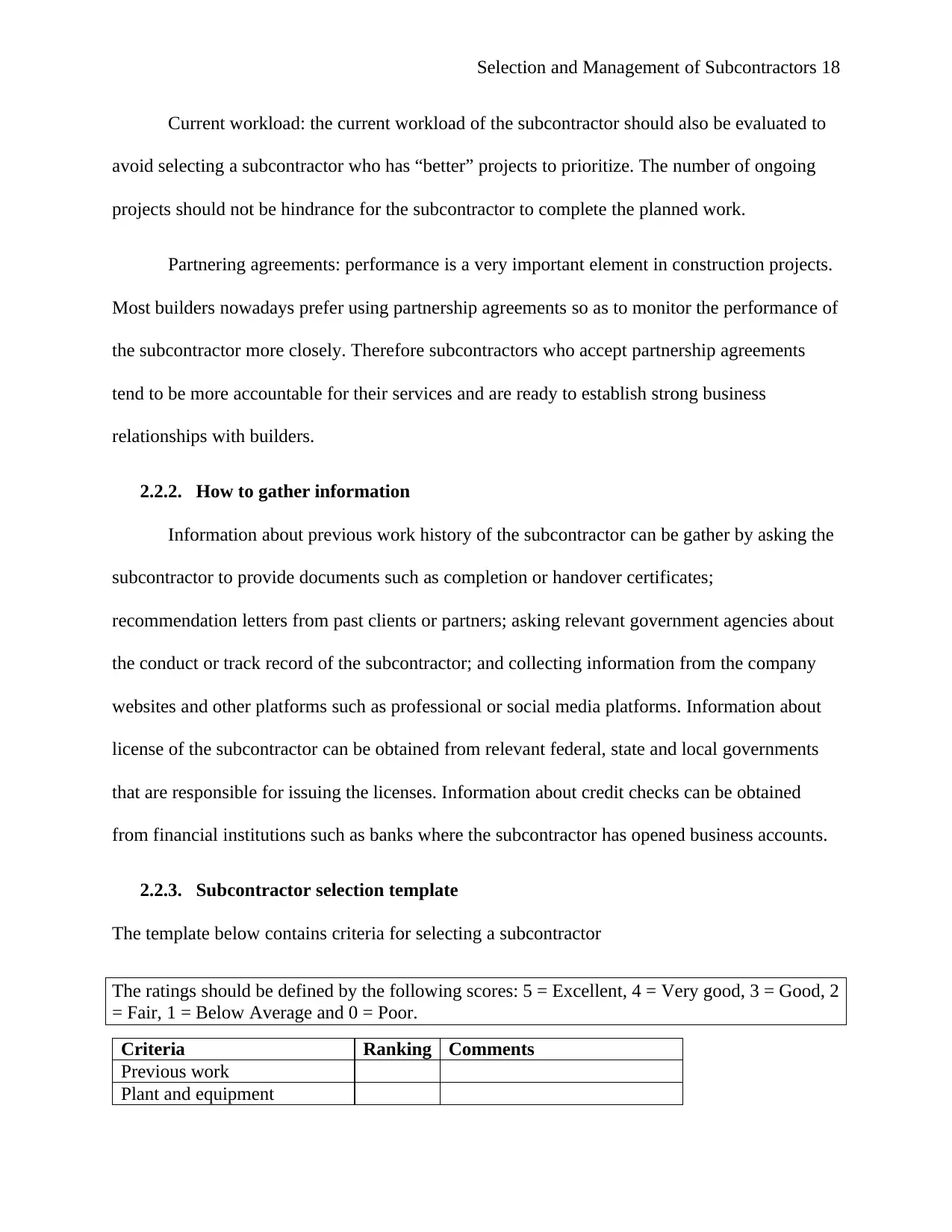
Selection and Management of Subcontractors 18
Current workload: the current workload of the subcontractor should also be evaluated to
avoid selecting a subcontractor who has “better” projects to prioritize. The number of ongoing
projects should not be hindrance for the subcontractor to complete the planned work.
Partnering agreements: performance is a very important element in construction projects.
Most builders nowadays prefer using partnership agreements so as to monitor the performance of
the subcontractor more closely. Therefore subcontractors who accept partnership agreements
tend to be more accountable for their services and are ready to establish strong business
relationships with builders.
2.2.2. How to gather information
Information about previous work history of the subcontractor can be gather by asking the
subcontractor to provide documents such as completion or handover certificates;
recommendation letters from past clients or partners; asking relevant government agencies about
the conduct or track record of the subcontractor; and collecting information from the company
websites and other platforms such as professional or social media platforms. Information about
license of the subcontractor can be obtained from relevant federal, state and local governments
that are responsible for issuing the licenses. Information about credit checks can be obtained
from financial institutions such as banks where the subcontractor has opened business accounts.
2.2.3. Subcontractor selection template
The template below contains criteria for selecting a subcontractor
The ratings should be defined by the following scores: 5 = Excellent, 4 = Very good, 3 = Good, 2
= Fair, 1 = Below Average and 0 = Poor.
Criteria Ranking Comments
Previous work
Plant and equipment
Current workload: the current workload of the subcontractor should also be evaluated to
avoid selecting a subcontractor who has “better” projects to prioritize. The number of ongoing
projects should not be hindrance for the subcontractor to complete the planned work.
Partnering agreements: performance is a very important element in construction projects.
Most builders nowadays prefer using partnership agreements so as to monitor the performance of
the subcontractor more closely. Therefore subcontractors who accept partnership agreements
tend to be more accountable for their services and are ready to establish strong business
relationships with builders.
2.2.2. How to gather information
Information about previous work history of the subcontractor can be gather by asking the
subcontractor to provide documents such as completion or handover certificates;
recommendation letters from past clients or partners; asking relevant government agencies about
the conduct or track record of the subcontractor; and collecting information from the company
websites and other platforms such as professional or social media platforms. Information about
license of the subcontractor can be obtained from relevant federal, state and local governments
that are responsible for issuing the licenses. Information about credit checks can be obtained
from financial institutions such as banks where the subcontractor has opened business accounts.
2.2.3. Subcontractor selection template
The template below contains criteria for selecting a subcontractor
The ratings should be defined by the following scores: 5 = Excellent, 4 = Very good, 3 = Good, 2
= Fair, 1 = Below Average and 0 = Poor.
Criteria Ranking Comments
Previous work
Plant and equipment
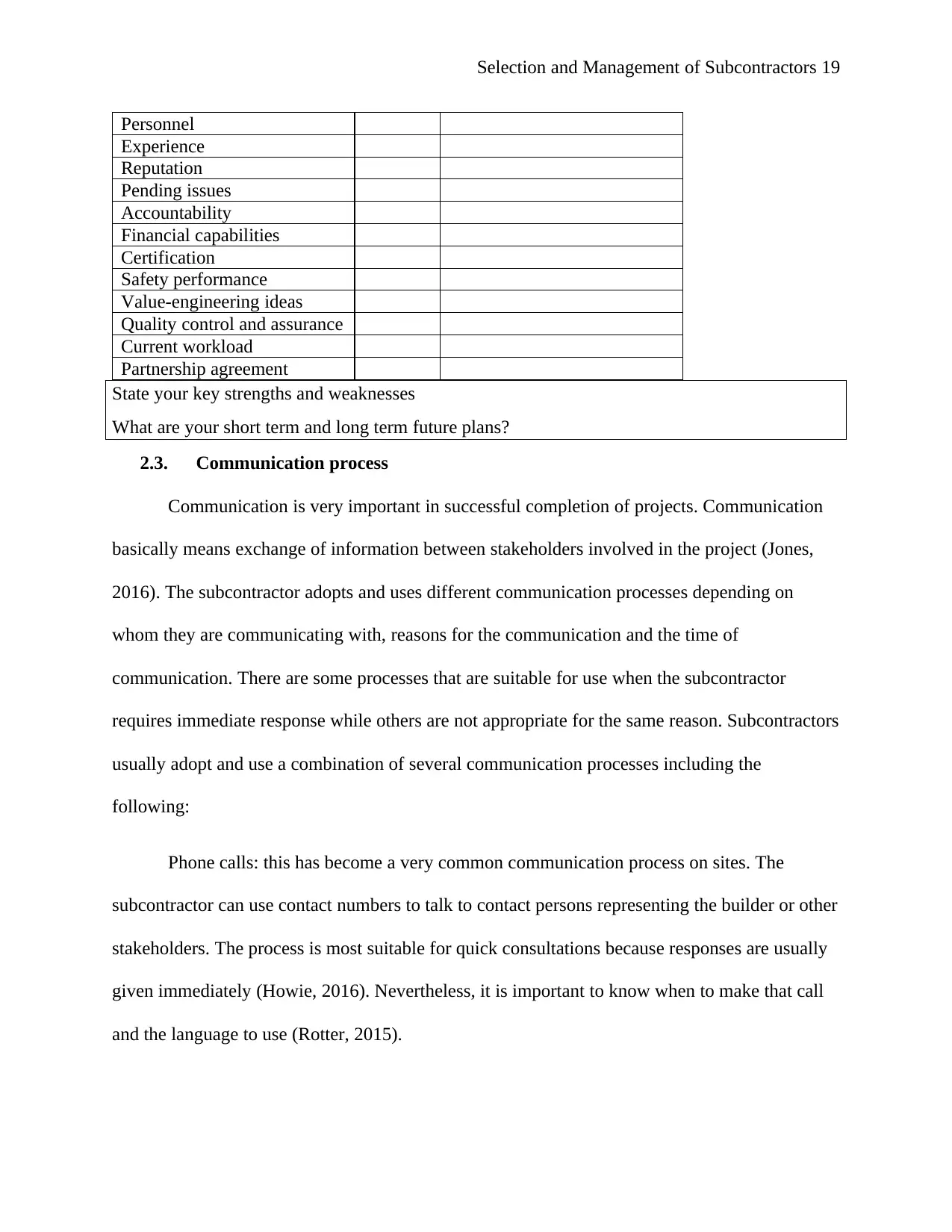
Selection and Management of Subcontractors 19
Personnel
Experience
Reputation
Pending issues
Accountability
Financial capabilities
Certification
Safety performance
Value-engineering ideas
Quality control and assurance
Current workload
Partnership agreement
State your key strengths and weaknesses
What are your short term and long term future plans?
2.3. Communication process
Communication is very important in successful completion of projects. Communication
basically means exchange of information between stakeholders involved in the project (Jones,
2016). The subcontractor adopts and uses different communication processes depending on
whom they are communicating with, reasons for the communication and the time of
communication. There are some processes that are suitable for use when the subcontractor
requires immediate response while others are not appropriate for the same reason. Subcontractors
usually adopt and use a combination of several communication processes including the
following:
Phone calls: this has become a very common communication process on sites. The
subcontractor can use contact numbers to talk to contact persons representing the builder or other
stakeholders. The process is most suitable for quick consultations because responses are usually
given immediately (Howie, 2016). Nevertheless, it is important to know when to make that call
and the language to use (Rotter, 2015).
Personnel
Experience
Reputation
Pending issues
Accountability
Financial capabilities
Certification
Safety performance
Value-engineering ideas
Quality control and assurance
Current workload
Partnership agreement
State your key strengths and weaknesses
What are your short term and long term future plans?
2.3. Communication process
Communication is very important in successful completion of projects. Communication
basically means exchange of information between stakeholders involved in the project (Jones,
2016). The subcontractor adopts and uses different communication processes depending on
whom they are communicating with, reasons for the communication and the time of
communication. There are some processes that are suitable for use when the subcontractor
requires immediate response while others are not appropriate for the same reason. Subcontractors
usually adopt and use a combination of several communication processes including the
following:
Phone calls: this has become a very common communication process on sites. The
subcontractor can use contact numbers to talk to contact persons representing the builder or other
stakeholders. The process is most suitable for quick consultations because responses are usually
given immediately (Howie, 2016). Nevertheless, it is important to know when to make that call
and the language to use (Rotter, 2015).
Paraphrase This Document
Need a fresh take? Get an instant paraphrase of this document with our AI Paraphraser
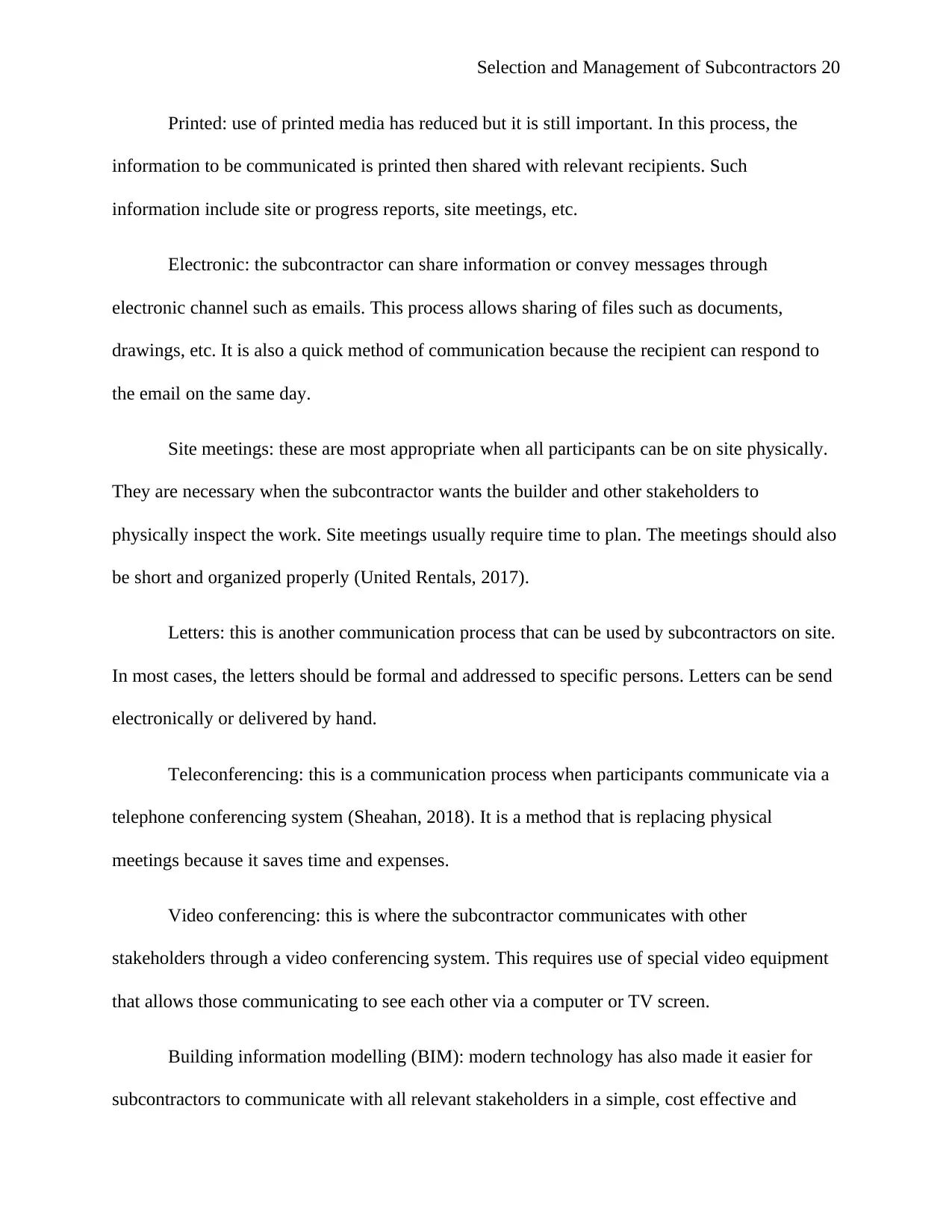
Selection and Management of Subcontractors 20
Printed: use of printed media has reduced but it is still important. In this process, the
information to be communicated is printed then shared with relevant recipients. Such
information include site or progress reports, site meetings, etc.
Electronic: the subcontractor can share information or convey messages through
electronic channel such as emails. This process allows sharing of files such as documents,
drawings, etc. It is also a quick method of communication because the recipient can respond to
the email on the same day.
Site meetings: these are most appropriate when all participants can be on site physically.
They are necessary when the subcontractor wants the builder and other stakeholders to
physically inspect the work. Site meetings usually require time to plan. The meetings should also
be short and organized properly (United Rentals, 2017).
Letters: this is another communication process that can be used by subcontractors on site.
In most cases, the letters should be formal and addressed to specific persons. Letters can be send
electronically or delivered by hand.
Teleconferencing: this is a communication process when participants communicate via a
telephone conferencing system (Sheahan, 2018). It is a method that is replacing physical
meetings because it saves time and expenses.
Video conferencing: this is where the subcontractor communicates with other
stakeholders through a video conferencing system. This requires use of special video equipment
that allows those communicating to see each other via a computer or TV screen.
Building information modelling (BIM): modern technology has also made it easier for
subcontractors to communicate with all relevant stakeholders in a simple, cost effective and
Printed: use of printed media has reduced but it is still important. In this process, the
information to be communicated is printed then shared with relevant recipients. Such
information include site or progress reports, site meetings, etc.
Electronic: the subcontractor can share information or convey messages through
electronic channel such as emails. This process allows sharing of files such as documents,
drawings, etc. It is also a quick method of communication because the recipient can respond to
the email on the same day.
Site meetings: these are most appropriate when all participants can be on site physically.
They are necessary when the subcontractor wants the builder and other stakeholders to
physically inspect the work. Site meetings usually require time to plan. The meetings should also
be short and organized properly (United Rentals, 2017).
Letters: this is another communication process that can be used by subcontractors on site.
In most cases, the letters should be formal and addressed to specific persons. Letters can be send
electronically or delivered by hand.
Teleconferencing: this is a communication process when participants communicate via a
telephone conferencing system (Sheahan, 2018). It is a method that is replacing physical
meetings because it saves time and expenses.
Video conferencing: this is where the subcontractor communicates with other
stakeholders through a video conferencing system. This requires use of special video equipment
that allows those communicating to see each other via a computer or TV screen.
Building information modelling (BIM): modern technology has also made it easier for
subcontractors to communicate with all relevant stakeholders in a simple, cost effective and

Selection and Management of Subcontractors 21
timely manner. BIM is a process of sharing information with all parties involved in the project
throughout the project’s lifecycle. BIM involves creating a platform where all necessary
information in shared and accessed by all stakeholders involved in the project.
In general, the communication process used by the subcontractor can be verbal or non-
verbal communication, oral communication (CliffsNotes, (n.d.)), written communication, etc.
2.4. Performance management of subcontractors
2.4.1. Dealing with poor subcontractor performance
2.4.1.1. Steps to follow
Some of the necessary steps when conducting a subcontractor performance interview include
the following: gather relevant information from the contract documents so as to establish areas
where the subcontractor performed poorly; review the documents submitted by the subcontractor
regarding her qualifications and capability of performing the work during tendering; establish the
extent to which the subcontractor performed poorly in each specific area; establish some of the
factors that may have led to subcontractor’s poor performance; identify areas where the
subcontractor failed to avoid poor performance; inform the subcontractor about the planned poor
performance interview; invite the subcontractor to the interview; and then conduct the interview.
Below is an interview template with questions that can be used to conduct a subcontractor poor
performance interview
Poor Performance Interview
Subcontractor Name:
Project Name:
Project No.:
Contract No.:
timely manner. BIM is a process of sharing information with all parties involved in the project
throughout the project’s lifecycle. BIM involves creating a platform where all necessary
information in shared and accessed by all stakeholders involved in the project.
In general, the communication process used by the subcontractor can be verbal or non-
verbal communication, oral communication (CliffsNotes, (n.d.)), written communication, etc.
2.4. Performance management of subcontractors
2.4.1. Dealing with poor subcontractor performance
2.4.1.1. Steps to follow
Some of the necessary steps when conducting a subcontractor performance interview include
the following: gather relevant information from the contract documents so as to establish areas
where the subcontractor performed poorly; review the documents submitted by the subcontractor
regarding her qualifications and capability of performing the work during tendering; establish the
extent to which the subcontractor performed poorly in each specific area; establish some of the
factors that may have led to subcontractor’s poor performance; identify areas where the
subcontractor failed to avoid poor performance; inform the subcontractor about the planned poor
performance interview; invite the subcontractor to the interview; and then conduct the interview.
Below is an interview template with questions that can be used to conduct a subcontractor poor
performance interview
Poor Performance Interview
Subcontractor Name:
Project Name:
Project No.:
Contract No.:
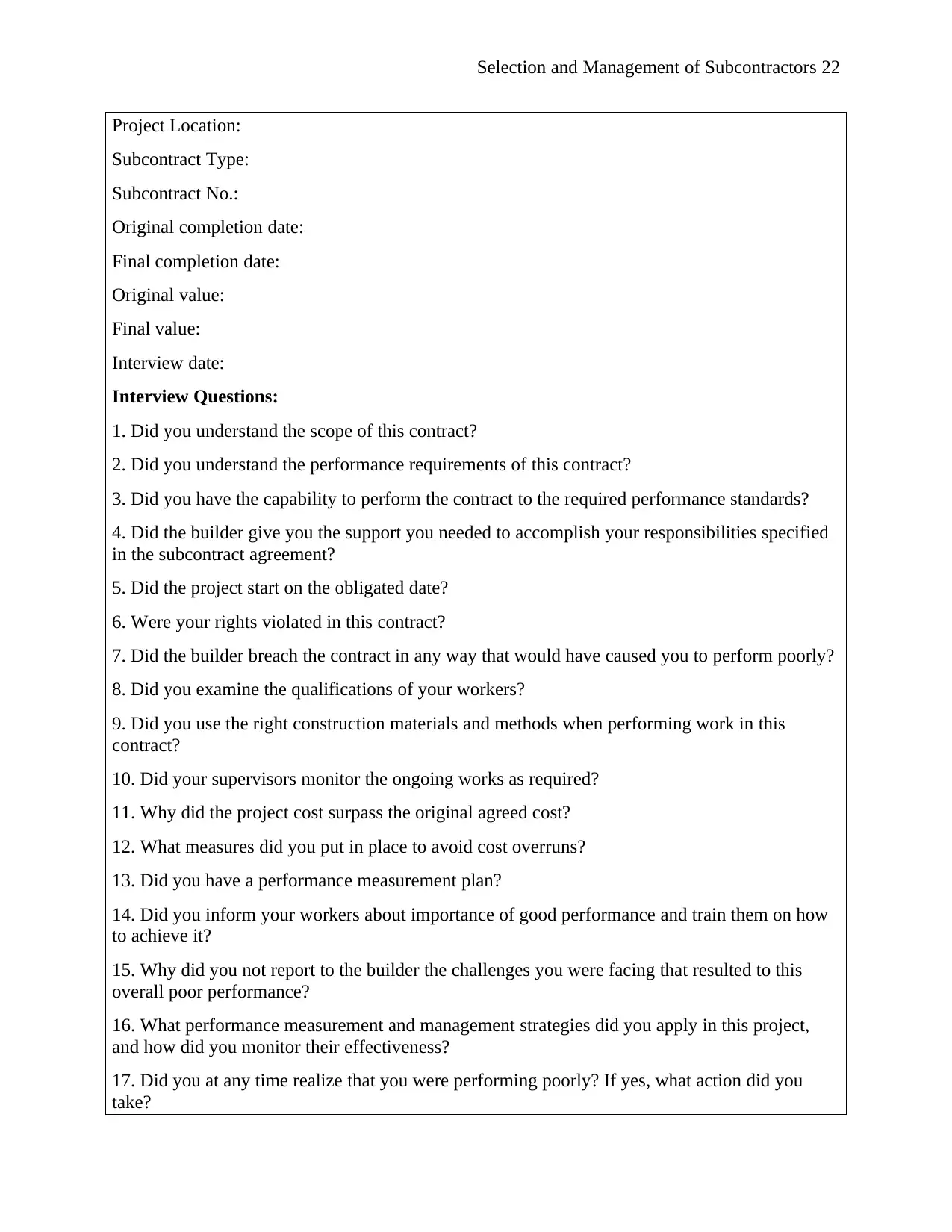
Selection and Management of Subcontractors 22
Project Location:
Subcontract Type:
Subcontract No.:
Original completion date:
Final completion date:
Original value:
Final value:
Interview date:
Interview Questions:
1. Did you understand the scope of this contract?
2. Did you understand the performance requirements of this contract?
3. Did you have the capability to perform the contract to the required performance standards?
4. Did the builder give you the support you needed to accomplish your responsibilities specified
in the subcontract agreement?
5. Did the project start on the obligated date?
6. Were your rights violated in this contract?
7. Did the builder breach the contract in any way that would have caused you to perform poorly?
8. Did you examine the qualifications of your workers?
9. Did you use the right construction materials and methods when performing work in this
contract?
10. Did your supervisors monitor the ongoing works as required?
11. Why did the project cost surpass the original agreed cost?
12. What measures did you put in place to avoid cost overruns?
13. Did you have a performance measurement plan?
14. Did you inform your workers about importance of good performance and train them on how
to achieve it?
15. Why did you not report to the builder the challenges you were facing that resulted to this
overall poor performance?
16. What performance measurement and management strategies did you apply in this project,
and how did you monitor their effectiveness?
17. Did you at any time realize that you were performing poorly? If yes, what action did you
take?
Project Location:
Subcontract Type:
Subcontract No.:
Original completion date:
Final completion date:
Original value:
Final value:
Interview date:
Interview Questions:
1. Did you understand the scope of this contract?
2. Did you understand the performance requirements of this contract?
3. Did you have the capability to perform the contract to the required performance standards?
4. Did the builder give you the support you needed to accomplish your responsibilities specified
in the subcontract agreement?
5. Did the project start on the obligated date?
6. Were your rights violated in this contract?
7. Did the builder breach the contract in any way that would have caused you to perform poorly?
8. Did you examine the qualifications of your workers?
9. Did you use the right construction materials and methods when performing work in this
contract?
10. Did your supervisors monitor the ongoing works as required?
11. Why did the project cost surpass the original agreed cost?
12. What measures did you put in place to avoid cost overruns?
13. Did you have a performance measurement plan?
14. Did you inform your workers about importance of good performance and train them on how
to achieve it?
15. Why did you not report to the builder the challenges you were facing that resulted to this
overall poor performance?
16. What performance measurement and management strategies did you apply in this project,
and how did you monitor their effectiveness?
17. Did you at any time realize that you were performing poorly? If yes, what action did you
take?
Secure Best Marks with AI Grader
Need help grading? Try our AI Grader for instant feedback on your assignments.
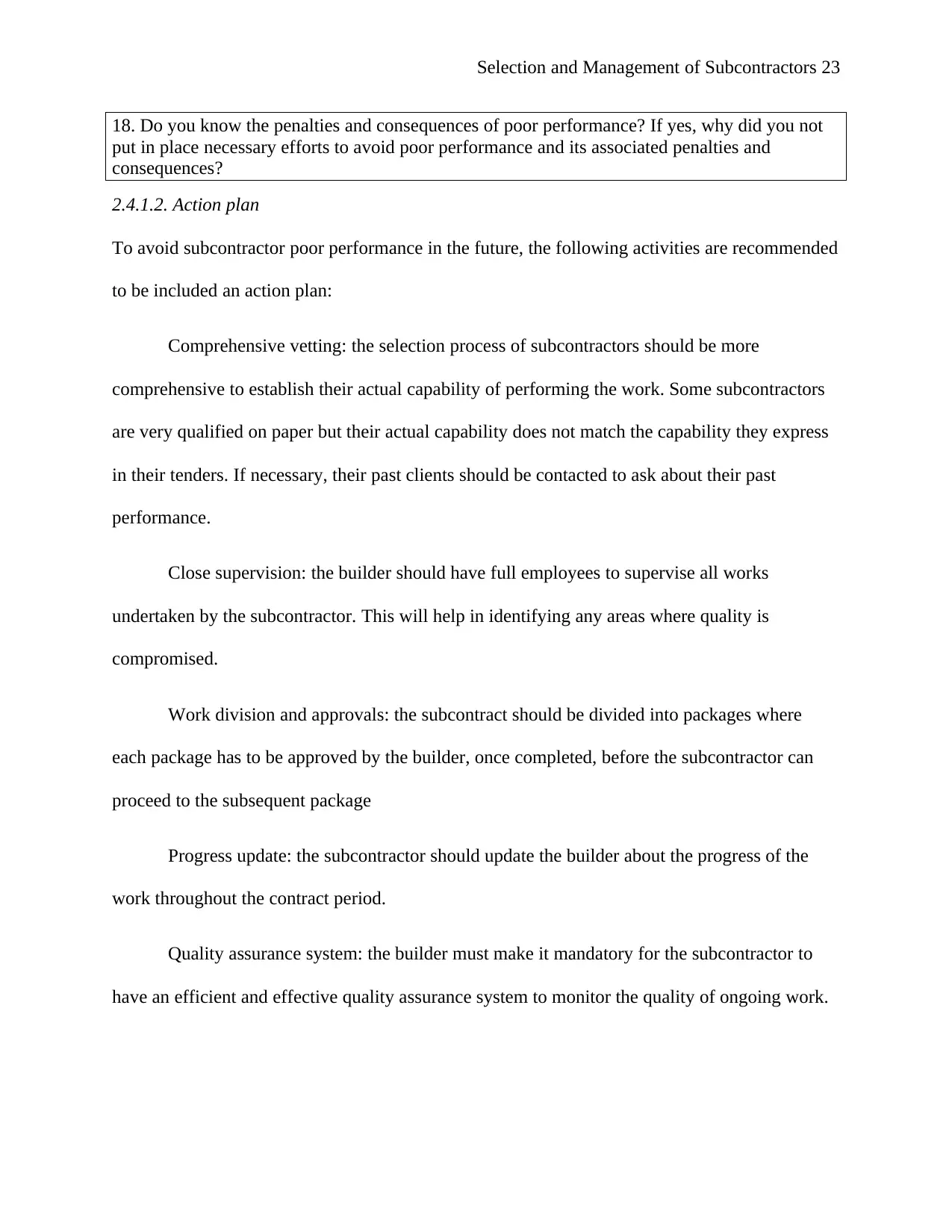
Selection and Management of Subcontractors 23
18. Do you know the penalties and consequences of poor performance? If yes, why did you not
put in place necessary efforts to avoid poor performance and its associated penalties and
consequences?
2.4.1.2. Action plan
To avoid subcontractor poor performance in the future, the following activities are recommended
to be included an action plan:
Comprehensive vetting: the selection process of subcontractors should be more
comprehensive to establish their actual capability of performing the work. Some subcontractors
are very qualified on paper but their actual capability does not match the capability they express
in their tenders. If necessary, their past clients should be contacted to ask about their past
performance.
Close supervision: the builder should have full employees to supervise all works
undertaken by the subcontractor. This will help in identifying any areas where quality is
compromised.
Work division and approvals: the subcontract should be divided into packages where
each package has to be approved by the builder, once completed, before the subcontractor can
proceed to the subsequent package
Progress update: the subcontractor should update the builder about the progress of the
work throughout the contract period.
Quality assurance system: the builder must make it mandatory for the subcontractor to
have an efficient and effective quality assurance system to monitor the quality of ongoing work.
18. Do you know the penalties and consequences of poor performance? If yes, why did you not
put in place necessary efforts to avoid poor performance and its associated penalties and
consequences?
2.4.1.2. Action plan
To avoid subcontractor poor performance in the future, the following activities are recommended
to be included an action plan:
Comprehensive vetting: the selection process of subcontractors should be more
comprehensive to establish their actual capability of performing the work. Some subcontractors
are very qualified on paper but their actual capability does not match the capability they express
in their tenders. If necessary, their past clients should be contacted to ask about their past
performance.
Close supervision: the builder should have full employees to supervise all works
undertaken by the subcontractor. This will help in identifying any areas where quality is
compromised.
Work division and approvals: the subcontract should be divided into packages where
each package has to be approved by the builder, once completed, before the subcontractor can
proceed to the subsequent package
Progress update: the subcontractor should update the builder about the progress of the
work throughout the contract period.
Quality assurance system: the builder must make it mandatory for the subcontractor to
have an efficient and effective quality assurance system to monitor the quality of ongoing work.
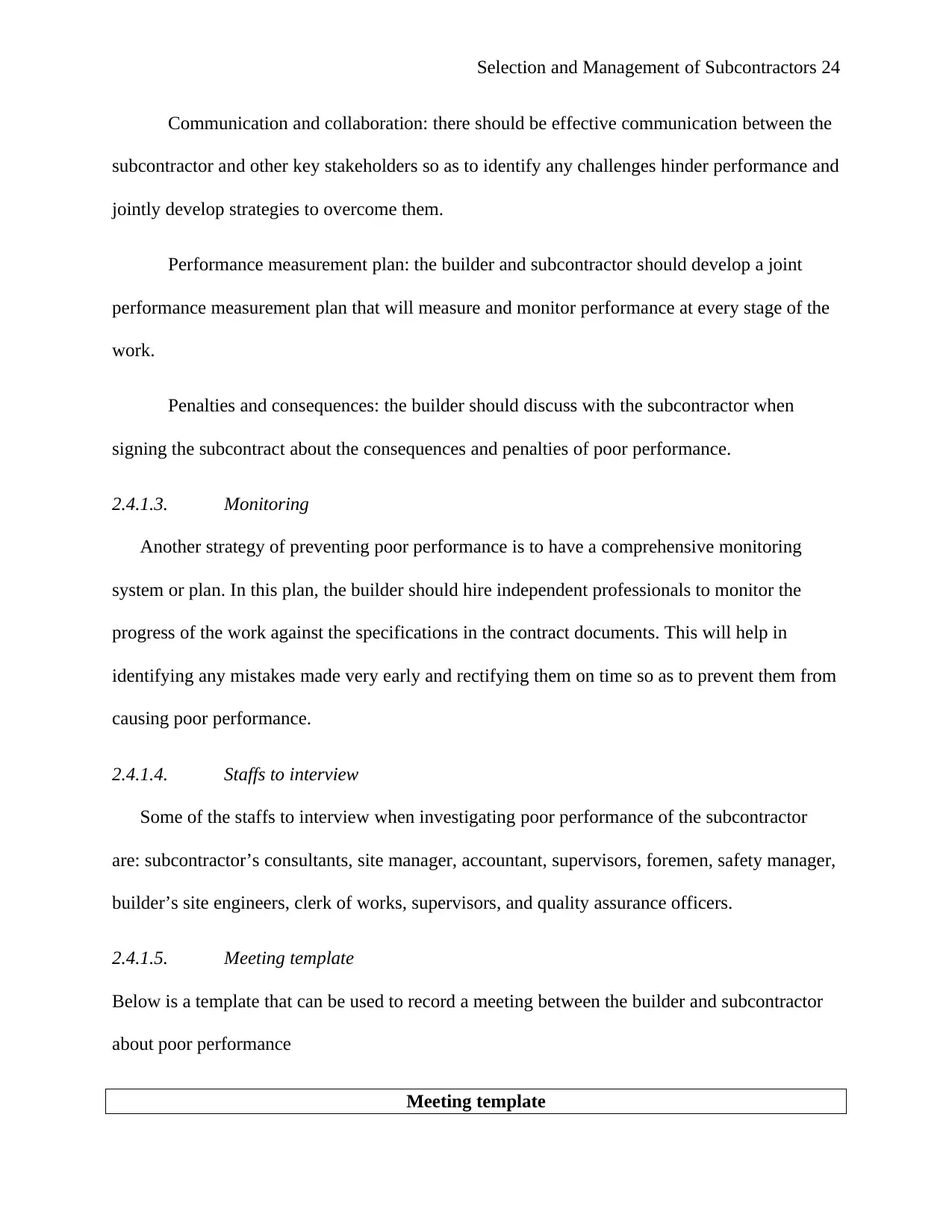
Selection and Management of Subcontractors 24
Communication and collaboration: there should be effective communication between the
subcontractor and other key stakeholders so as to identify any challenges hinder performance and
jointly develop strategies to overcome them.
Performance measurement plan: the builder and subcontractor should develop a joint
performance measurement plan that will measure and monitor performance at every stage of the
work.
Penalties and consequences: the builder should discuss with the subcontractor when
signing the subcontract about the consequences and penalties of poor performance.
2.4.1.3. Monitoring
Another strategy of preventing poor performance is to have a comprehensive monitoring
system or plan. In this plan, the builder should hire independent professionals to monitor the
progress of the work against the specifications in the contract documents. This will help in
identifying any mistakes made very early and rectifying them on time so as to prevent them from
causing poor performance.
2.4.1.4. Staffs to interview
Some of the staffs to interview when investigating poor performance of the subcontractor
are: subcontractor’s consultants, site manager, accountant, supervisors, foremen, safety manager,
builder’s site engineers, clerk of works, supervisors, and quality assurance officers.
2.4.1.5. Meeting template
Below is a template that can be used to record a meeting between the builder and subcontractor
about poor performance
Meeting template
Communication and collaboration: there should be effective communication between the
subcontractor and other key stakeholders so as to identify any challenges hinder performance and
jointly develop strategies to overcome them.
Performance measurement plan: the builder and subcontractor should develop a joint
performance measurement plan that will measure and monitor performance at every stage of the
work.
Penalties and consequences: the builder should discuss with the subcontractor when
signing the subcontract about the consequences and penalties of poor performance.
2.4.1.3. Monitoring
Another strategy of preventing poor performance is to have a comprehensive monitoring
system or plan. In this plan, the builder should hire independent professionals to monitor the
progress of the work against the specifications in the contract documents. This will help in
identifying any mistakes made very early and rectifying them on time so as to prevent them from
causing poor performance.
2.4.1.4. Staffs to interview
Some of the staffs to interview when investigating poor performance of the subcontractor
are: subcontractor’s consultants, site manager, accountant, supervisors, foremen, safety manager,
builder’s site engineers, clerk of works, supervisors, and quality assurance officers.
2.4.1.5. Meeting template
Below is a template that can be used to record a meeting between the builder and subcontractor
about poor performance
Meeting template
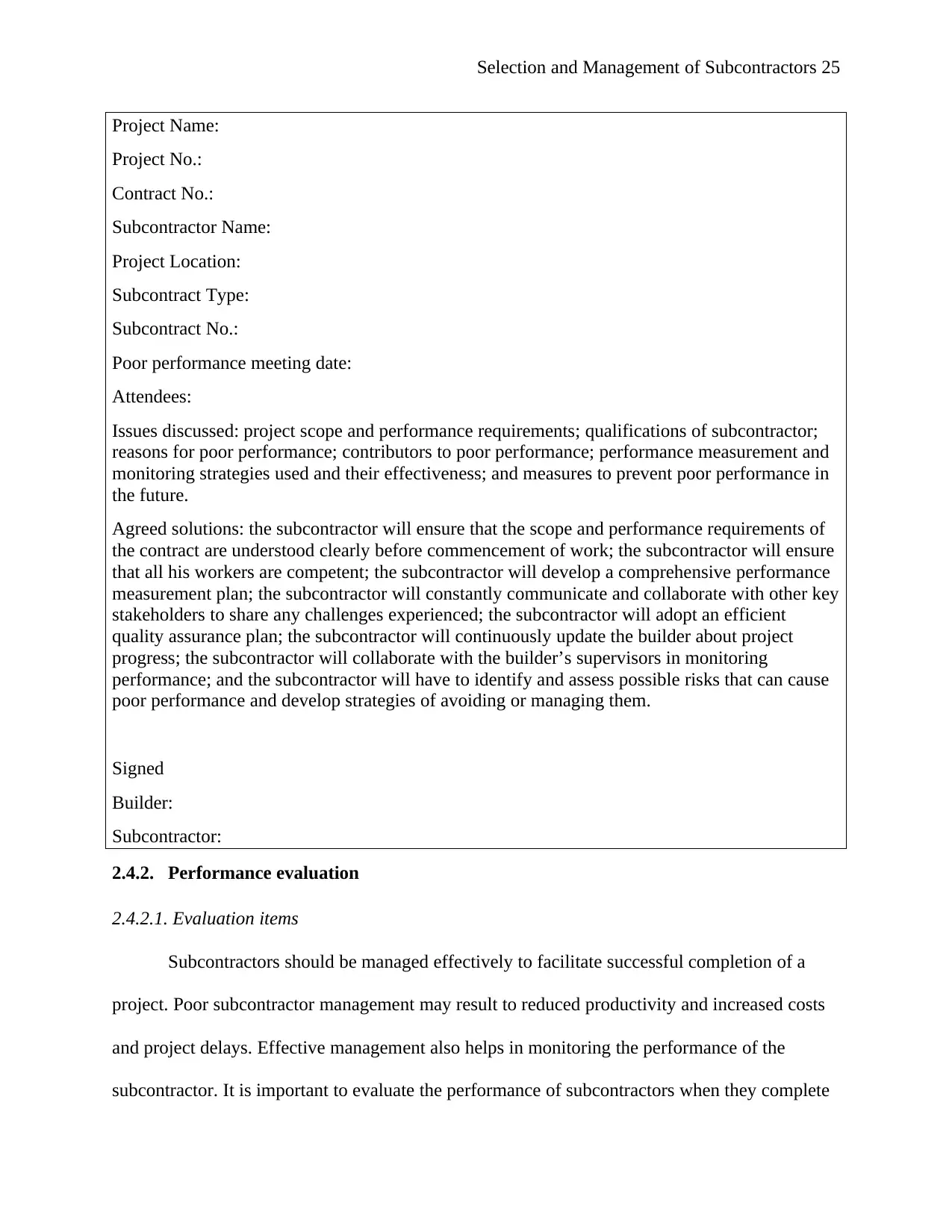
Selection and Management of Subcontractors 25
Project Name:
Project No.:
Contract No.:
Subcontractor Name:
Project Location:
Subcontract Type:
Subcontract No.:
Poor performance meeting date:
Attendees:
Issues discussed: project scope and performance requirements; qualifications of subcontractor;
reasons for poor performance; contributors to poor performance; performance measurement and
monitoring strategies used and their effectiveness; and measures to prevent poor performance in
the future.
Agreed solutions: the subcontractor will ensure that the scope and performance requirements of
the contract are understood clearly before commencement of work; the subcontractor will ensure
that all his workers are competent; the subcontractor will develop a comprehensive performance
measurement plan; the subcontractor will constantly communicate and collaborate with other key
stakeholders to share any challenges experienced; the subcontractor will adopt an efficient
quality assurance plan; the subcontractor will continuously update the builder about project
progress; the subcontractor will collaborate with the builder’s supervisors in monitoring
performance; and the subcontractor will have to identify and assess possible risks that can cause
poor performance and develop strategies of avoiding or managing them.
Signed
Builder:
Subcontractor:
2.4.2. Performance evaluation
2.4.2.1. Evaluation items
Subcontractors should be managed effectively to facilitate successful completion of a
project. Poor subcontractor management may result to reduced productivity and increased costs
and project delays. Effective management also helps in monitoring the performance of the
subcontractor. It is important to evaluate the performance of subcontractors when they complete
Project Name:
Project No.:
Contract No.:
Subcontractor Name:
Project Location:
Subcontract Type:
Subcontract No.:
Poor performance meeting date:
Attendees:
Issues discussed: project scope and performance requirements; qualifications of subcontractor;
reasons for poor performance; contributors to poor performance; performance measurement and
monitoring strategies used and their effectiveness; and measures to prevent poor performance in
the future.
Agreed solutions: the subcontractor will ensure that the scope and performance requirements of
the contract are understood clearly before commencement of work; the subcontractor will ensure
that all his workers are competent; the subcontractor will develop a comprehensive performance
measurement plan; the subcontractor will constantly communicate and collaborate with other key
stakeholders to share any challenges experienced; the subcontractor will adopt an efficient
quality assurance plan; the subcontractor will continuously update the builder about project
progress; the subcontractor will collaborate with the builder’s supervisors in monitoring
performance; and the subcontractor will have to identify and assess possible risks that can cause
poor performance and develop strategies of avoiding or managing them.
Signed
Builder:
Subcontractor:
2.4.2. Performance evaluation
2.4.2.1. Evaluation items
Subcontractors should be managed effectively to facilitate successful completion of a
project. Poor subcontractor management may result to reduced productivity and increased costs
and project delays. Effective management also helps in monitoring the performance of the
subcontractor. It is important to evaluate the performance of subcontractors when they complete
Paraphrase This Document
Need a fresh take? Get an instant paraphrase of this document with our AI Paraphraser
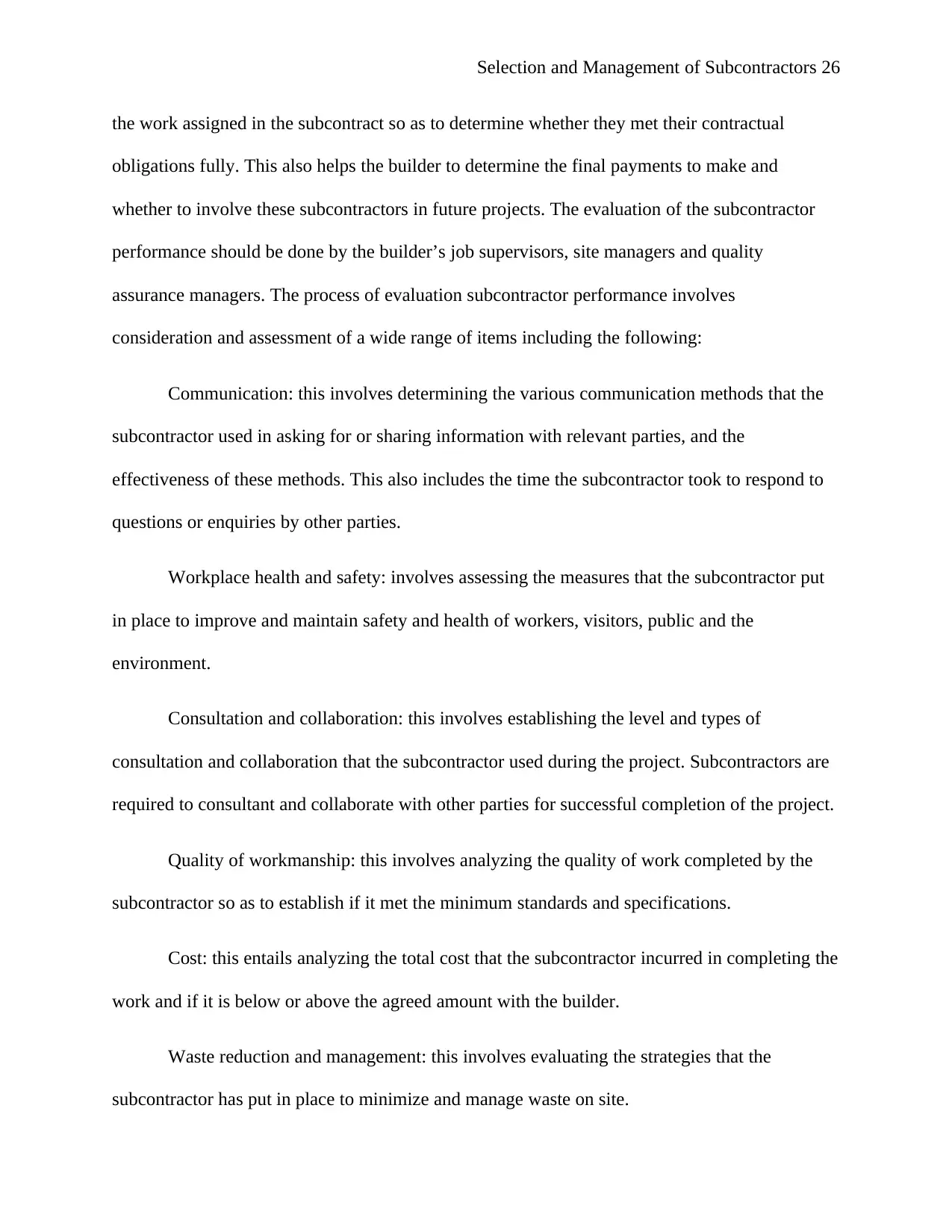
Selection and Management of Subcontractors 26
the work assigned in the subcontract so as to determine whether they met their contractual
obligations fully. This also helps the builder to determine the final payments to make and
whether to involve these subcontractors in future projects. The evaluation of the subcontractor
performance should be done by the builder’s job supervisors, site managers and quality
assurance managers. The process of evaluation subcontractor performance involves
consideration and assessment of a wide range of items including the following:
Communication: this involves determining the various communication methods that the
subcontractor used in asking for or sharing information with relevant parties, and the
effectiveness of these methods. This also includes the time the subcontractor took to respond to
questions or enquiries by other parties.
Workplace health and safety: involves assessing the measures that the subcontractor put
in place to improve and maintain safety and health of workers, visitors, public and the
environment.
Consultation and collaboration: this involves establishing the level and types of
consultation and collaboration that the subcontractor used during the project. Subcontractors are
required to consultant and collaborate with other parties for successful completion of the project.
Quality of workmanship: this involves analyzing the quality of work completed by the
subcontractor so as to establish if it met the minimum standards and specifications.
Cost: this entails analyzing the total cost that the subcontractor incurred in completing the
work and if it is below or above the agreed amount with the builder.
Waste reduction and management: this involves evaluating the strategies that the
subcontractor has put in place to minimize and manage waste on site.
the work assigned in the subcontract so as to determine whether they met their contractual
obligations fully. This also helps the builder to determine the final payments to make and
whether to involve these subcontractors in future projects. The evaluation of the subcontractor
performance should be done by the builder’s job supervisors, site managers and quality
assurance managers. The process of evaluation subcontractor performance involves
consideration and assessment of a wide range of items including the following:
Communication: this involves determining the various communication methods that the
subcontractor used in asking for or sharing information with relevant parties, and the
effectiveness of these methods. This also includes the time the subcontractor took to respond to
questions or enquiries by other parties.
Workplace health and safety: involves assessing the measures that the subcontractor put
in place to improve and maintain safety and health of workers, visitors, public and the
environment.
Consultation and collaboration: this involves establishing the level and types of
consultation and collaboration that the subcontractor used during the project. Subcontractors are
required to consultant and collaborate with other parties for successful completion of the project.
Quality of workmanship: this involves analyzing the quality of work completed by the
subcontractor so as to establish if it met the minimum standards and specifications.
Cost: this entails analyzing the total cost that the subcontractor incurred in completing the
work and if it is below or above the agreed amount with the builder.
Waste reduction and management: this involves evaluating the strategies that the
subcontractor has put in place to minimize and manage waste on site.
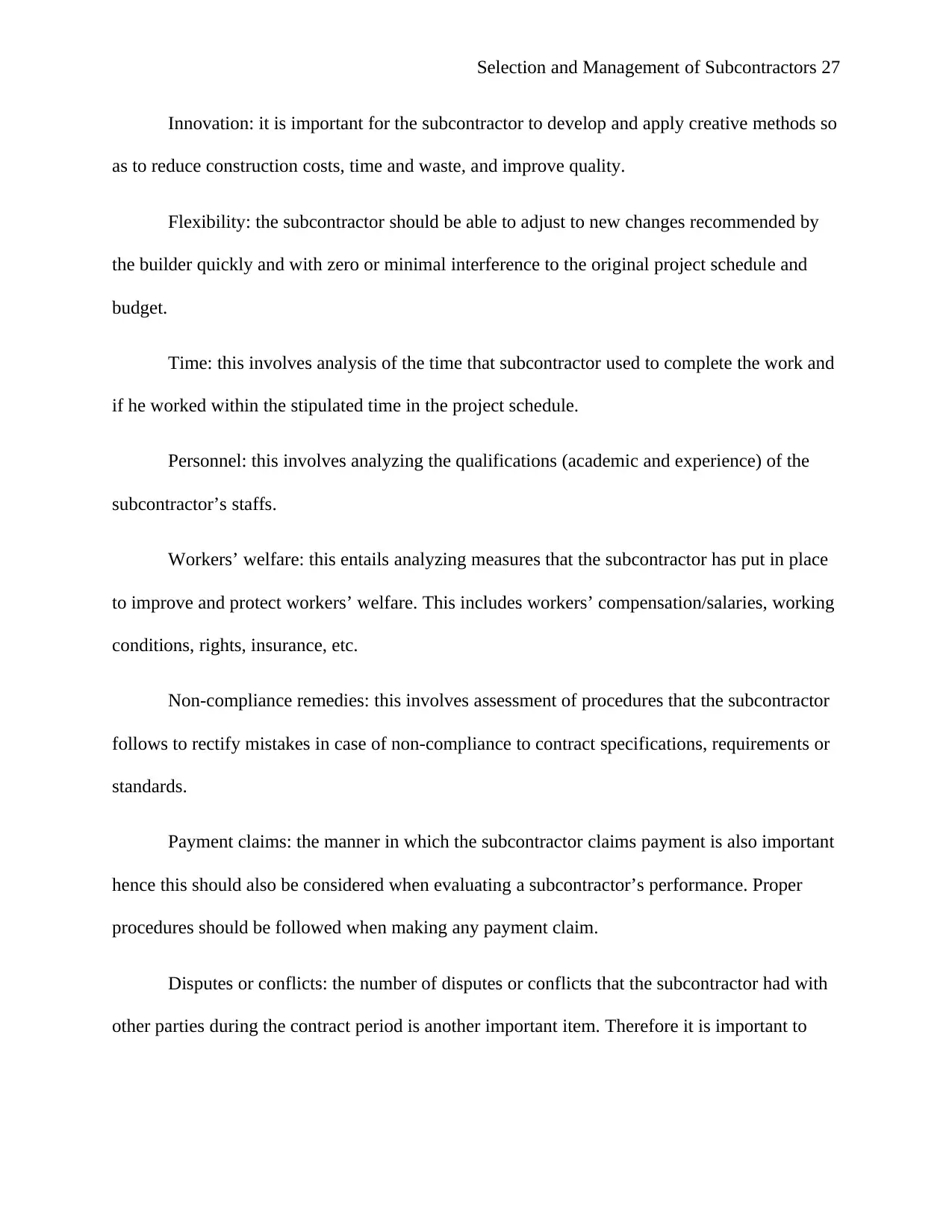
Selection and Management of Subcontractors 27
Innovation: it is important for the subcontractor to develop and apply creative methods so
as to reduce construction costs, time and waste, and improve quality.
Flexibility: the subcontractor should be able to adjust to new changes recommended by
the builder quickly and with zero or minimal interference to the original project schedule and
budget.
Time: this involves analysis of the time that subcontractor used to complete the work and
if he worked within the stipulated time in the project schedule.
Personnel: this involves analyzing the qualifications (academic and experience) of the
subcontractor’s staffs.
Workers’ welfare: this entails analyzing measures that the subcontractor has put in place
to improve and protect workers’ welfare. This includes workers’ compensation/salaries, working
conditions, rights, insurance, etc.
Non-compliance remedies: this involves assessment of procedures that the subcontractor
follows to rectify mistakes in case of non-compliance to contract specifications, requirements or
standards.
Payment claims: the manner in which the subcontractor claims payment is also important
hence this should also be considered when evaluating a subcontractor’s performance. Proper
procedures should be followed when making any payment claim.
Disputes or conflicts: the number of disputes or conflicts that the subcontractor had with
other parties during the contract period is another important item. Therefore it is important to
Innovation: it is important for the subcontractor to develop and apply creative methods so
as to reduce construction costs, time and waste, and improve quality.
Flexibility: the subcontractor should be able to adjust to new changes recommended by
the builder quickly and with zero or minimal interference to the original project schedule and
budget.
Time: this involves analysis of the time that subcontractor used to complete the work and
if he worked within the stipulated time in the project schedule.
Personnel: this involves analyzing the qualifications (academic and experience) of the
subcontractor’s staffs.
Workers’ welfare: this entails analyzing measures that the subcontractor has put in place
to improve and protect workers’ welfare. This includes workers’ compensation/salaries, working
conditions, rights, insurance, etc.
Non-compliance remedies: this involves assessment of procedures that the subcontractor
follows to rectify mistakes in case of non-compliance to contract specifications, requirements or
standards.
Payment claims: the manner in which the subcontractor claims payment is also important
hence this should also be considered when evaluating a subcontractor’s performance. Proper
procedures should be followed when making any payment claim.
Disputes or conflicts: the number of disputes or conflicts that the subcontractor had with
other parties during the contract period is another important item. Therefore it is important to
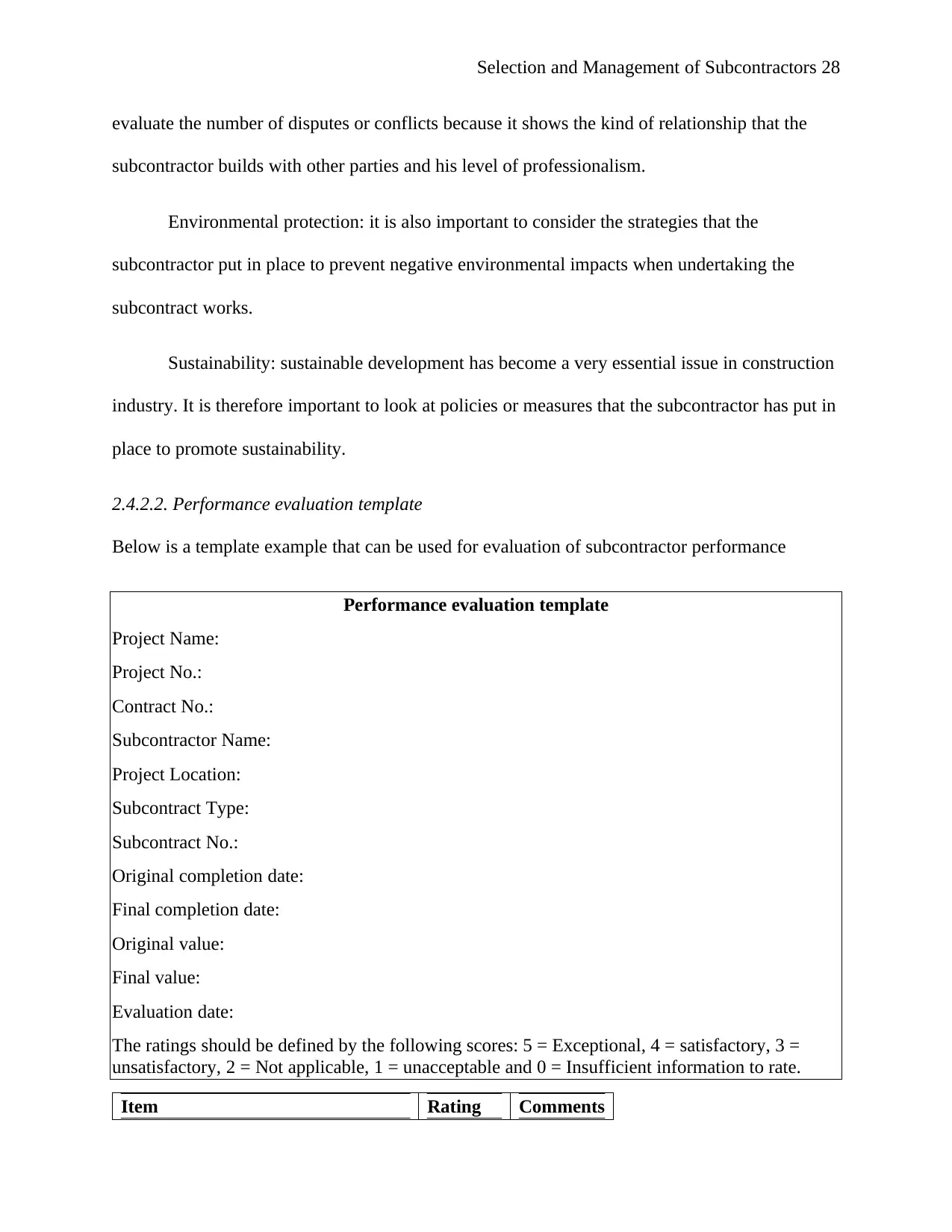
Selection and Management of Subcontractors 28
evaluate the number of disputes or conflicts because it shows the kind of relationship that the
subcontractor builds with other parties and his level of professionalism.
Environmental protection: it is also important to consider the strategies that the
subcontractor put in place to prevent negative environmental impacts when undertaking the
subcontract works.
Sustainability: sustainable development has become a very essential issue in construction
industry. It is therefore important to look at policies or measures that the subcontractor has put in
place to promote sustainability.
2.4.2.2. Performance evaluation template
Below is a template example that can be used for evaluation of subcontractor performance
Performance evaluation template
Project Name:
Project No.:
Contract No.:
Subcontractor Name:
Project Location:
Subcontract Type:
Subcontract No.:
Original completion date:
Final completion date:
Original value:
Final value:
Evaluation date:
The ratings should be defined by the following scores: 5 = Exceptional, 4 = satisfactory, 3 =
unsatisfactory, 2 = Not applicable, 1 = unacceptable and 0 = Insufficient information to rate.
Item Rating Comments
evaluate the number of disputes or conflicts because it shows the kind of relationship that the
subcontractor builds with other parties and his level of professionalism.
Environmental protection: it is also important to consider the strategies that the
subcontractor put in place to prevent negative environmental impacts when undertaking the
subcontract works.
Sustainability: sustainable development has become a very essential issue in construction
industry. It is therefore important to look at policies or measures that the subcontractor has put in
place to promote sustainability.
2.4.2.2. Performance evaluation template
Below is a template example that can be used for evaluation of subcontractor performance
Performance evaluation template
Project Name:
Project No.:
Contract No.:
Subcontractor Name:
Project Location:
Subcontract Type:
Subcontract No.:
Original completion date:
Final completion date:
Original value:
Final value:
Evaluation date:
The ratings should be defined by the following scores: 5 = Exceptional, 4 = satisfactory, 3 =
unsatisfactory, 2 = Not applicable, 1 = unacceptable and 0 = Insufficient information to rate.
Item Rating Comments
Secure Best Marks with AI Grader
Need help grading? Try our AI Grader for instant feedback on your assignments.
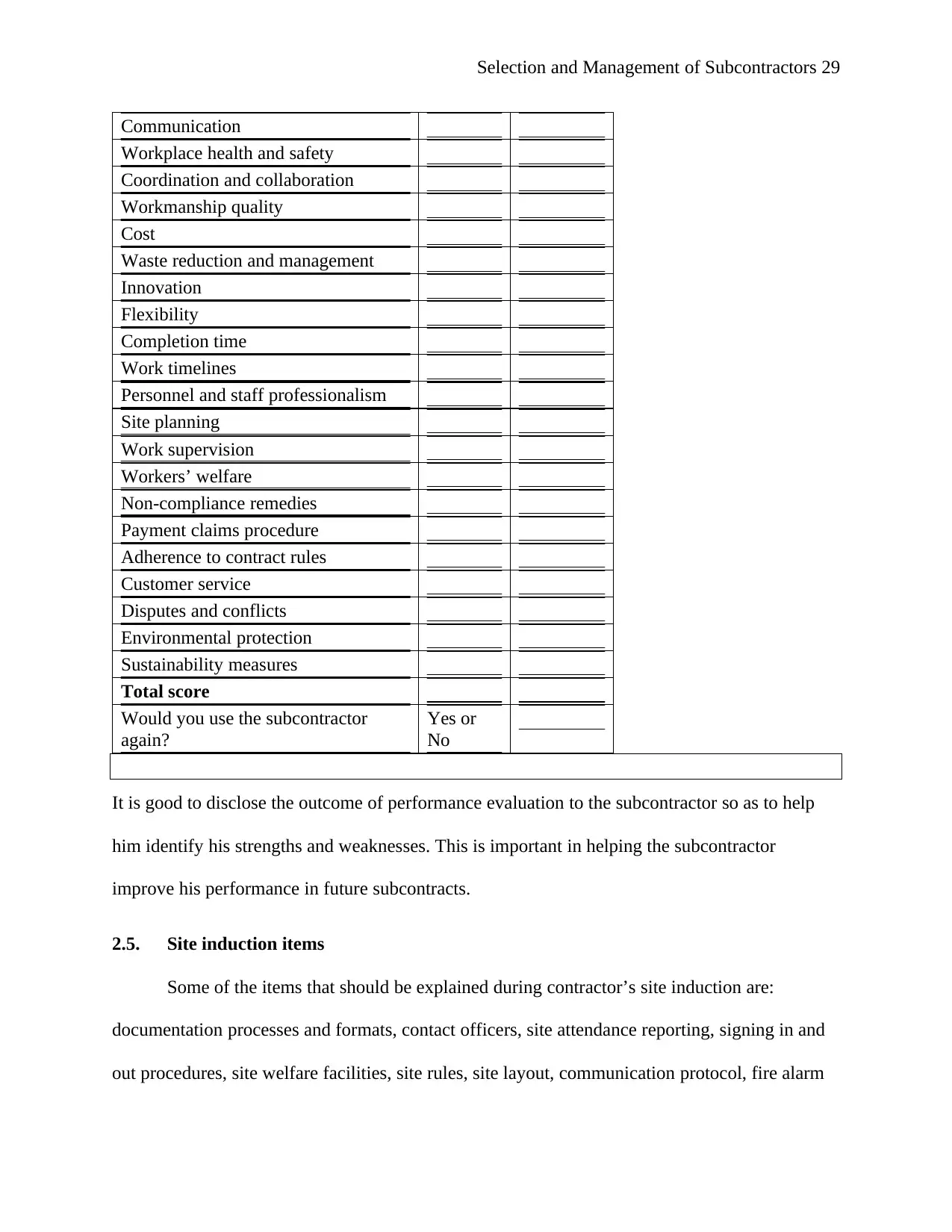
Selection and Management of Subcontractors 29
Communication
Workplace health and safety
Coordination and collaboration
Workmanship quality
Cost
Waste reduction and management
Innovation
Flexibility
Completion time
Work timelines
Personnel and staff professionalism
Site planning
Work supervision
Workers’ welfare
Non-compliance remedies
Payment claims procedure
Adherence to contract rules
Customer service
Disputes and conflicts
Environmental protection
Sustainability measures
Total score
Would you use the subcontractor
again?
Yes or
No
It is good to disclose the outcome of performance evaluation to the subcontractor so as to help
him identify his strengths and weaknesses. This is important in helping the subcontractor
improve his performance in future subcontracts.
2.5. Site induction items
Some of the items that should be explained during contractor’s site induction are:
documentation processes and formats, contact officers, site attendance reporting, signing in and
out procedures, site welfare facilities, site rules, site layout, communication protocol, fire alarm
Communication
Workplace health and safety
Coordination and collaboration
Workmanship quality
Cost
Waste reduction and management
Innovation
Flexibility
Completion time
Work timelines
Personnel and staff professionalism
Site planning
Work supervision
Workers’ welfare
Non-compliance remedies
Payment claims procedure
Adherence to contract rules
Customer service
Disputes and conflicts
Environmental protection
Sustainability measures
Total score
Would you use the subcontractor
again?
Yes or
No
It is good to disclose the outcome of performance evaluation to the subcontractor so as to help
him identify his strengths and weaknesses. This is important in helping the subcontractor
improve his performance in future subcontracts.
2.5. Site induction items
Some of the items that should be explained during contractor’s site induction are:
documentation processes and formats, contact officers, site attendance reporting, signing in and
out procedures, site welfare facilities, site rules, site layout, communication protocol, fire alarm
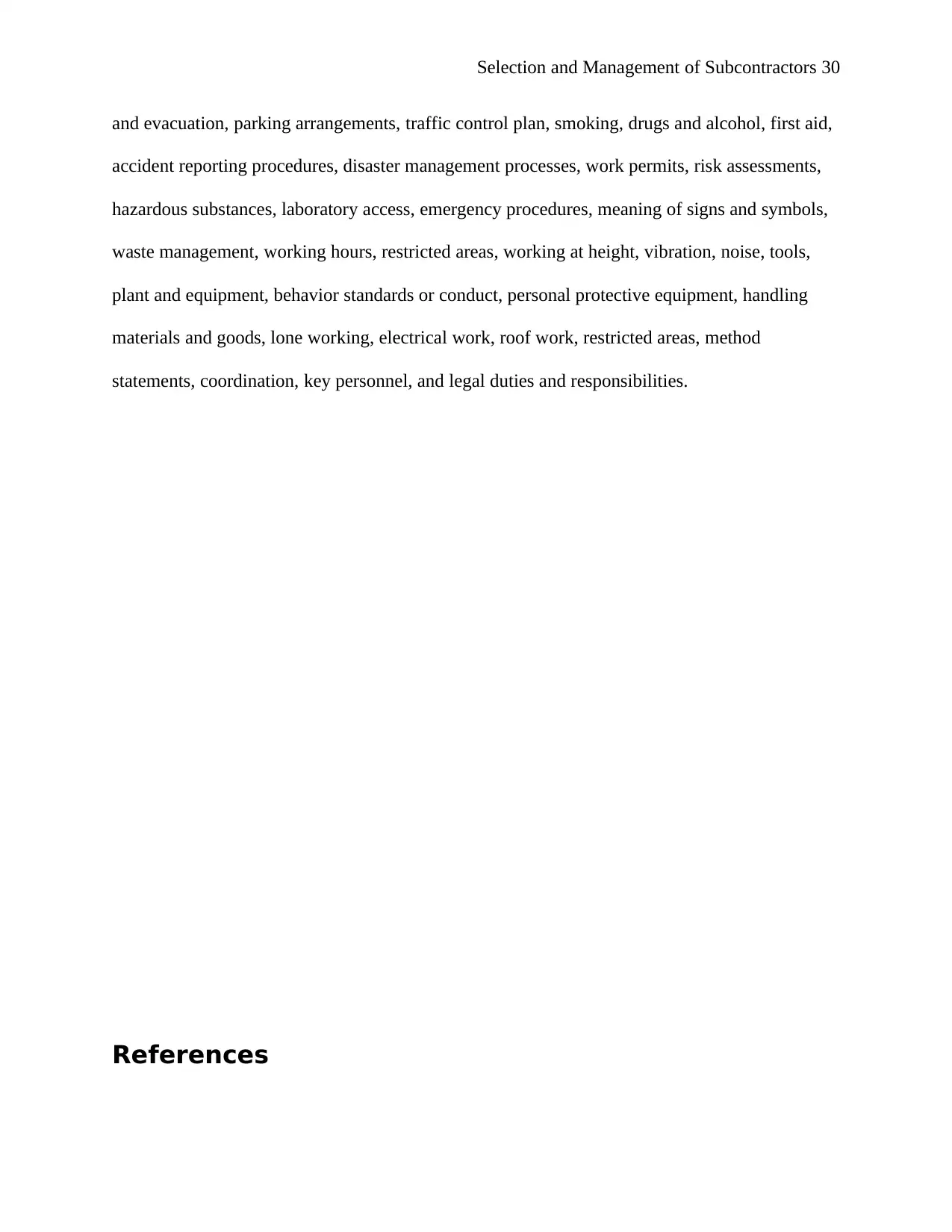
Selection and Management of Subcontractors 30
and evacuation, parking arrangements, traffic control plan, smoking, drugs and alcohol, first aid,
accident reporting procedures, disaster management processes, work permits, risk assessments,
hazardous substances, laboratory access, emergency procedures, meaning of signs and symbols,
waste management, working hours, restricted areas, working at height, vibration, noise, tools,
plant and equipment, behavior standards or conduct, personal protective equipment, handling
materials and goods, lone working, electrical work, roof work, restricted areas, method
statements, coordination, key personnel, and legal duties and responsibilities.
References
and evacuation, parking arrangements, traffic control plan, smoking, drugs and alcohol, first aid,
accident reporting procedures, disaster management processes, work permits, risk assessments,
hazardous substances, laboratory access, emergency procedures, meaning of signs and symbols,
waste management, working hours, restricted areas, working at height, vibration, noise, tools,
plant and equipment, behavior standards or conduct, personal protective equipment, handling
materials and goods, lone working, electrical work, roof work, restricted areas, method
statements, coordination, key personnel, and legal duties and responsibilities.
References
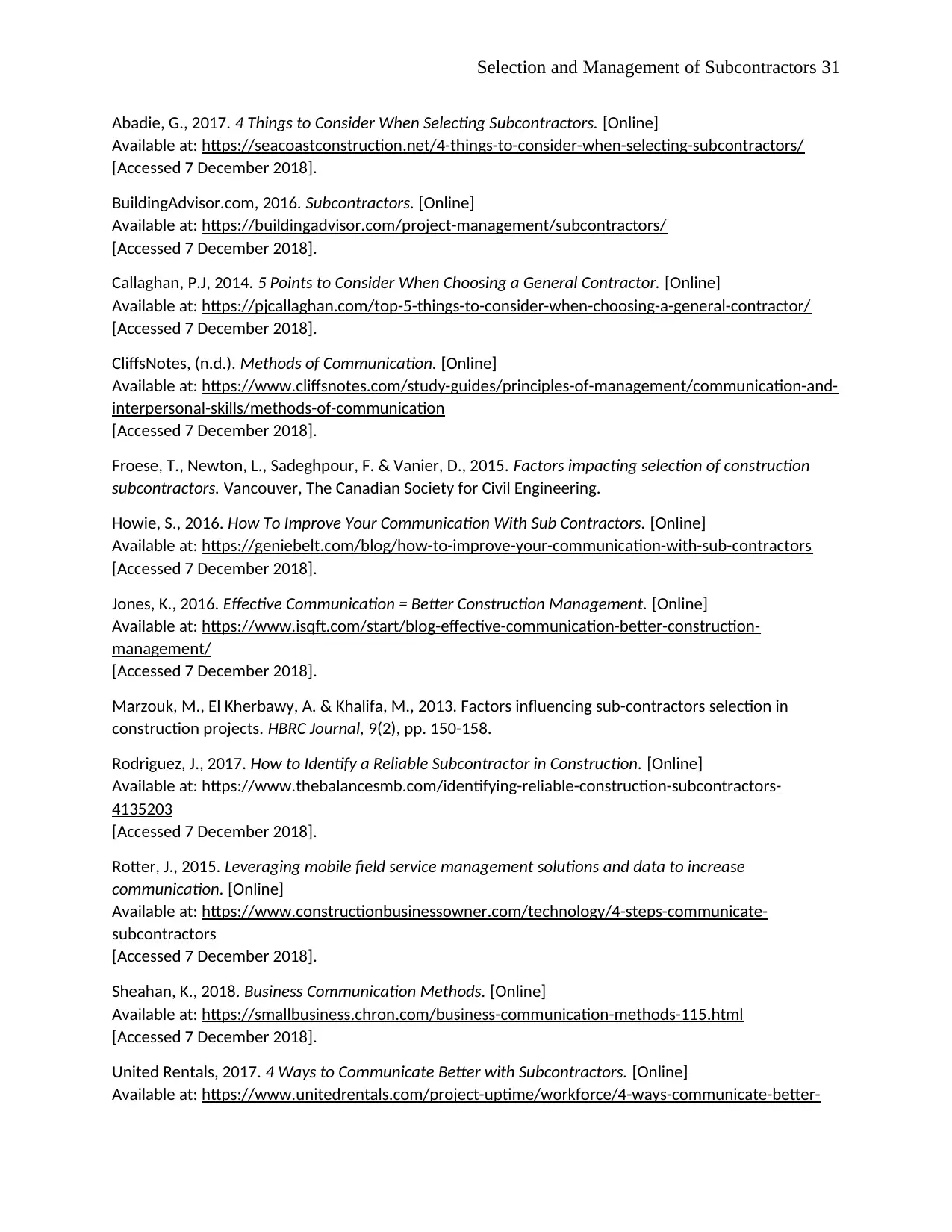
Selection and Management of Subcontractors 31
Abadie, G., 2017. 4 Things to Consider When Selecting Subcontractors. [Online]
Available at: https://seacoastconstruction.net/4-things-to-consider-when-selecting-subcontractors/
[Accessed 7 December 2018].
BuildingAdvisor.com, 2016. Subcontractors. [Online]
Available at: https://buildingadvisor.com/project-management/subcontractors/
[Accessed 7 December 2018].
Callaghan, P.J, 2014. 5 Points to Consider When Choosing a General Contractor. [Online]
Available at: https://pjcallaghan.com/top-5-things-to-consider-when-choosing-a-general-contractor/
[Accessed 7 December 2018].
CliffsNotes, (n.d.). Methods of Communication. [Online]
Available at: https://www.cliffsnotes.com/study-guides/principles-of-management/communication-and-
interpersonal-skills/methods-of-communication
[Accessed 7 December 2018].
Froese, T., Newton, L., Sadeghpour, F. & Vanier, D., 2015. Factors impacting selection of construction
subcontractors. Vancouver, The Canadian Society for Civil Engineering.
Howie, S., 2016. How To Improve Your Communication With Sub Contractors. [Online]
Available at: https://geniebelt.com/blog/how-to-improve-your-communication-with-sub-contractors
[Accessed 7 December 2018].
Jones, K., 2016. Effective Communication = Better Construction Management. [Online]
Available at: https://www.isqft.com/start/blog-effective-communication-better-construction-
management/
[Accessed 7 December 2018].
Marzouk, M., El Kherbawy, A. & Khalifa, M., 2013. Factors influencing sub-contractors selection in
construction projects. HBRC Journal, 9(2), pp. 150-158.
Rodriguez, J., 2017. How to Identify a Reliable Subcontractor in Construction. [Online]
Available at: https://www.thebalancesmb.com/identifying-reliable-construction-subcontractors-
4135203
[Accessed 7 December 2018].
Rotter, J., 2015. Leveraging mobile field service management solutions and data to increase
communication. [Online]
Available at: https://www.constructionbusinessowner.com/technology/4-steps-communicate-
subcontractors
[Accessed 7 December 2018].
Sheahan, K., 2018. Business Communication Methods. [Online]
Available at: https://smallbusiness.chron.com/business-communication-methods-115.html
[Accessed 7 December 2018].
United Rentals, 2017. 4 Ways to Communicate Better with Subcontractors. [Online]
Available at: https://www.unitedrentals.com/project-uptime/workforce/4-ways-communicate-better-
Abadie, G., 2017. 4 Things to Consider When Selecting Subcontractors. [Online]
Available at: https://seacoastconstruction.net/4-things-to-consider-when-selecting-subcontractors/
[Accessed 7 December 2018].
BuildingAdvisor.com, 2016. Subcontractors. [Online]
Available at: https://buildingadvisor.com/project-management/subcontractors/
[Accessed 7 December 2018].
Callaghan, P.J, 2014. 5 Points to Consider When Choosing a General Contractor. [Online]
Available at: https://pjcallaghan.com/top-5-things-to-consider-when-choosing-a-general-contractor/
[Accessed 7 December 2018].
CliffsNotes, (n.d.). Methods of Communication. [Online]
Available at: https://www.cliffsnotes.com/study-guides/principles-of-management/communication-and-
interpersonal-skills/methods-of-communication
[Accessed 7 December 2018].
Froese, T., Newton, L., Sadeghpour, F. & Vanier, D., 2015. Factors impacting selection of construction
subcontractors. Vancouver, The Canadian Society for Civil Engineering.
Howie, S., 2016. How To Improve Your Communication With Sub Contractors. [Online]
Available at: https://geniebelt.com/blog/how-to-improve-your-communication-with-sub-contractors
[Accessed 7 December 2018].
Jones, K., 2016. Effective Communication = Better Construction Management. [Online]
Available at: https://www.isqft.com/start/blog-effective-communication-better-construction-
management/
[Accessed 7 December 2018].
Marzouk, M., El Kherbawy, A. & Khalifa, M., 2013. Factors influencing sub-contractors selection in
construction projects. HBRC Journal, 9(2), pp. 150-158.
Rodriguez, J., 2017. How to Identify a Reliable Subcontractor in Construction. [Online]
Available at: https://www.thebalancesmb.com/identifying-reliable-construction-subcontractors-
4135203
[Accessed 7 December 2018].
Rotter, J., 2015. Leveraging mobile field service management solutions and data to increase
communication. [Online]
Available at: https://www.constructionbusinessowner.com/technology/4-steps-communicate-
subcontractors
[Accessed 7 December 2018].
Sheahan, K., 2018. Business Communication Methods. [Online]
Available at: https://smallbusiness.chron.com/business-communication-methods-115.html
[Accessed 7 December 2018].
United Rentals, 2017. 4 Ways to Communicate Better with Subcontractors. [Online]
Available at: https://www.unitedrentals.com/project-uptime/workforce/4-ways-communicate-better-
Paraphrase This Document
Need a fresh take? Get an instant paraphrase of this document with our AI Paraphraser
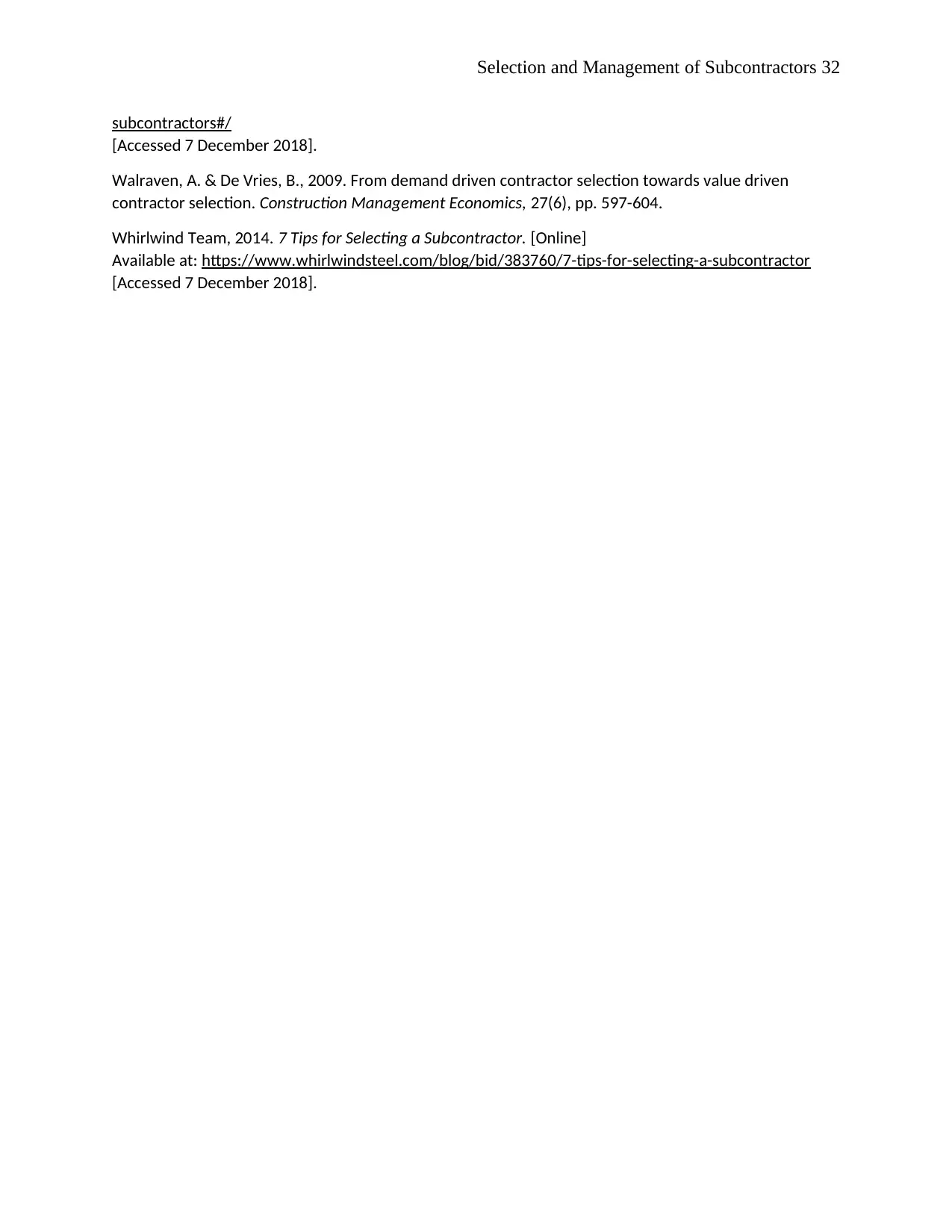
Selection and Management of Subcontractors 32
subcontractors#/
[Accessed 7 December 2018].
Walraven, A. & De Vries, B., 2009. From demand driven contractor selection towards value driven
contractor selection. Construction Management Economics, 27(6), pp. 597-604.
Whirlwind Team, 2014. 7 Tips for Selecting a Subcontractor. [Online]
Available at: https://www.whirlwindsteel.com/blog/bid/383760/7-tips-for-selecting-a-subcontractor
[Accessed 7 December 2018].
subcontractors#/
[Accessed 7 December 2018].
Walraven, A. & De Vries, B., 2009. From demand driven contractor selection towards value driven
contractor selection. Construction Management Economics, 27(6), pp. 597-604.
Whirlwind Team, 2014. 7 Tips for Selecting a Subcontractor. [Online]
Available at: https://www.whirlwindsteel.com/blog/bid/383760/7-tips-for-selecting-a-subcontractor
[Accessed 7 December 2018].
1 out of 32
![[object Object]](/_next/image/?url=%2F_next%2Fstatic%2Fmedia%2Flogo.6d15ce61.png&w=640&q=75)
Your All-in-One AI-Powered Toolkit for Academic Success.
 +13062052269
info@desklib.com
Available 24*7 on WhatsApp / Email
Unlock your academic potential
© 2024  |  Zucol Services PVT LTD  |  All rights reserved.