Subcontractor Selection and Management for Desklib
VerifiedAdded on  2023/06/03
|17
|3878
|346
AI Summary
This article discusses the process of selecting and managing subcontractors for construction projects. It includes budget estimates from different companies, evaluation criteria, pre-award interview questions, communication methods, and more. The article is relevant for students studying construction management or related courses.
Contribute Materials
Your contribution can guide someone’s learning journey. Share your
documents today.
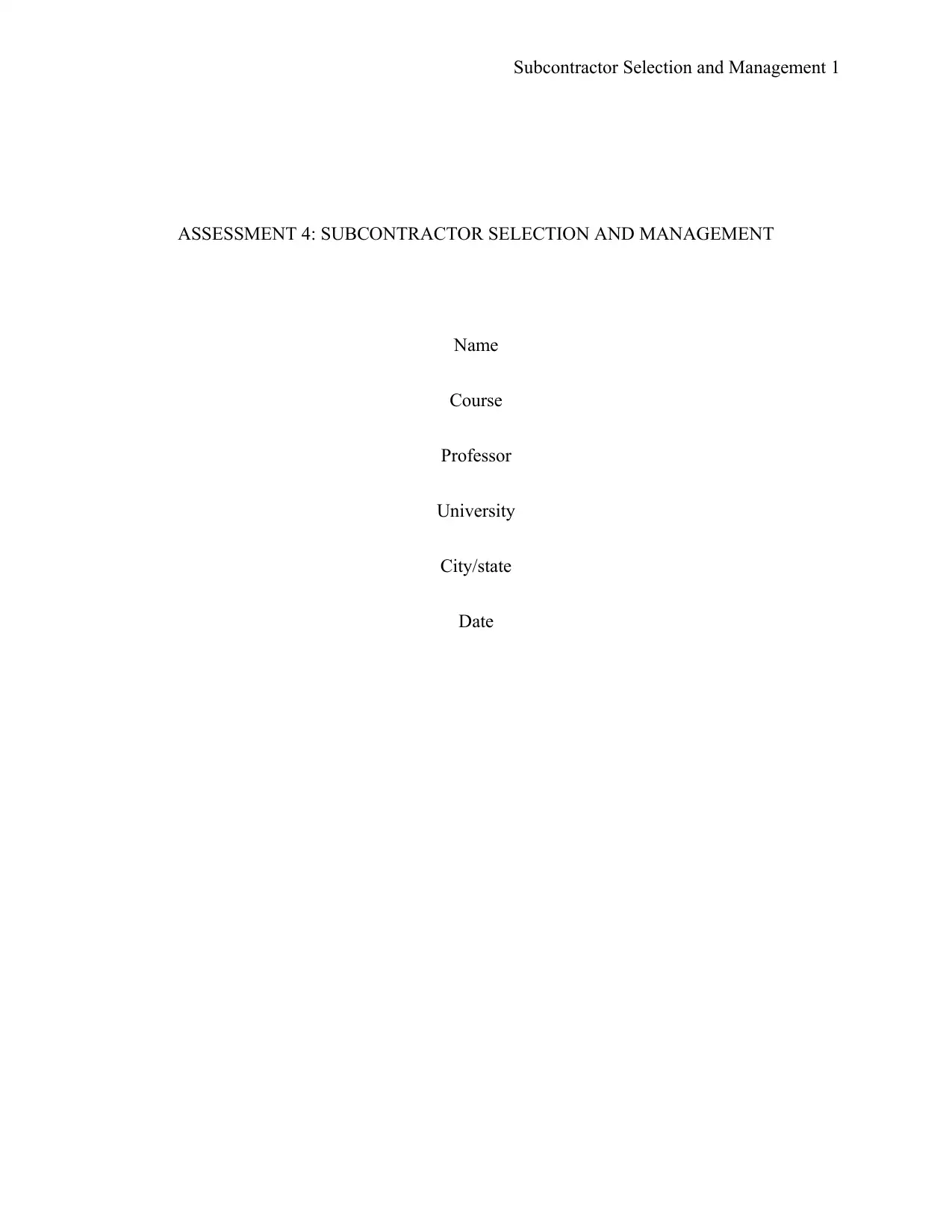
Subcontractor Selection and Management 1
ASSESSMENT 4: SUBCONTRACTOR SELECTION AND MANAGEMENT
Name
Course
Professor
University
City/state
Date
ASSESSMENT 4: SUBCONTRACTOR SELECTION AND MANAGEMENT
Name
Course
Professor
University
City/state
Date
Secure Best Marks with AI Grader
Need help grading? Try our AI Grader for instant feedback on your assignments.
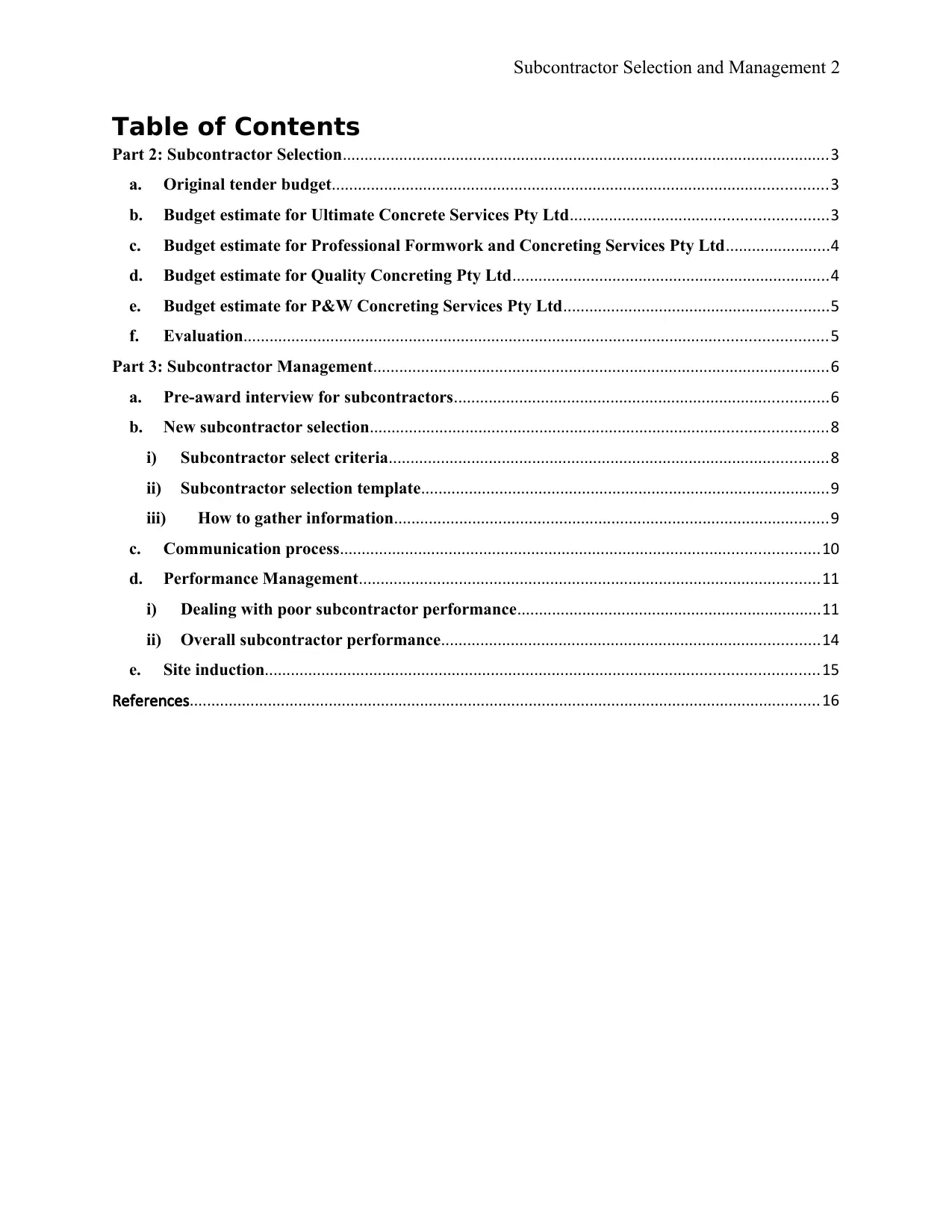
Subcontractor Selection and Management 2
Table of Contents
Part 2: Subcontractor Selection................................................................................................................3
a. Original tender budget..................................................................................................................3
b. Budget estimate for Ultimate Concrete Services Pty Ltd...........................................................3
c. Budget estimate for Professional Formwork and Concreting Services Pty Ltd........................4
d. Budget estimate for Quality Concreting Pty Ltd.........................................................................4
e. Budget estimate for P&W Concreting Services Pty Ltd.............................................................5
f. Evaluation......................................................................................................................................5
Part 3: Subcontractor Management.........................................................................................................6
a. Pre-award interview for subcontractors......................................................................................6
b. New subcontractor selection.........................................................................................................8
i) Subcontractor select criteria.....................................................................................................8
ii) Subcontractor selection template..............................................................................................9
iii) How to gather information....................................................................................................9
c. Communication process..............................................................................................................10
d. Performance Management..........................................................................................................11
i) Dealing with poor subcontractor performance......................................................................11
ii) Overall subcontractor performance.......................................................................................14
e. Site induction...............................................................................................................................15
References.................................................................................................................................................16
Table of Contents
Part 2: Subcontractor Selection................................................................................................................3
a. Original tender budget..................................................................................................................3
b. Budget estimate for Ultimate Concrete Services Pty Ltd...........................................................3
c. Budget estimate for Professional Formwork and Concreting Services Pty Ltd........................4
d. Budget estimate for Quality Concreting Pty Ltd.........................................................................4
e. Budget estimate for P&W Concreting Services Pty Ltd.............................................................5
f. Evaluation......................................................................................................................................5
Part 3: Subcontractor Management.........................................................................................................6
a. Pre-award interview for subcontractors......................................................................................6
b. New subcontractor selection.........................................................................................................8
i) Subcontractor select criteria.....................................................................................................8
ii) Subcontractor selection template..............................................................................................9
iii) How to gather information....................................................................................................9
c. Communication process..............................................................................................................10
d. Performance Management..........................................................................................................11
i) Dealing with poor subcontractor performance......................................................................11
ii) Overall subcontractor performance.......................................................................................14
e. Site induction...............................................................................................................................15
References.................................................................................................................................................16
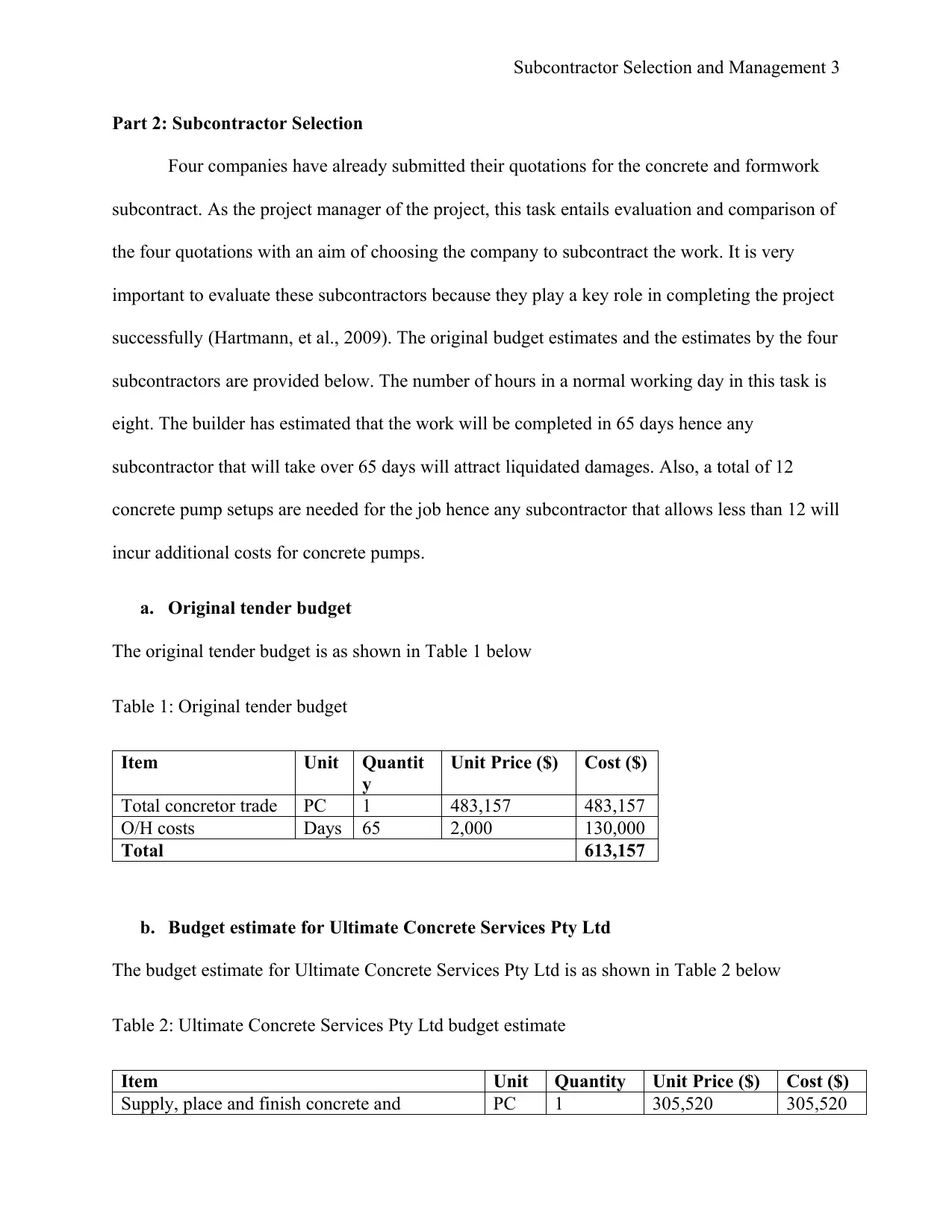
Subcontractor Selection and Management 3
Part 2: Subcontractor Selection
Four companies have already submitted their quotations for the concrete and formwork
subcontract. As the project manager of the project, this task entails evaluation and comparison of
the four quotations with an aim of choosing the company to subcontract the work. It is very
important to evaluate these subcontractors because they play a key role in completing the project
successfully (Hartmann, et al., 2009). The original budget estimates and the estimates by the four
subcontractors are provided below. The number of hours in a normal working day in this task is
eight. The builder has estimated that the work will be completed in 65 days hence any
subcontractor that will take over 65 days will attract liquidated damages. Also, a total of 12
concrete pump setups are needed for the job hence any subcontractor that allows less than 12 will
incur additional costs for concrete pumps.
a. Original tender budget
The original tender budget is as shown in Table 1 below
Table 1: Original tender budget
Item Unit Quantit
y
Unit Price ($) Cost ($)
Total concretor trade PC 1 483,157 483,157
O/H costs Days 65 2,000 130,000
Total 613,157
b. Budget estimate for Ultimate Concrete Services Pty Ltd
The budget estimate for Ultimate Concrete Services Pty Ltd is as shown in Table 2 below
Table 2: Ultimate Concrete Services Pty Ltd budget estimate
Item Unit Quantity Unit Price ($) Cost ($)
Supply, place and finish concrete and PC 1 305,520 305,520
Part 2: Subcontractor Selection
Four companies have already submitted their quotations for the concrete and formwork
subcontract. As the project manager of the project, this task entails evaluation and comparison of
the four quotations with an aim of choosing the company to subcontract the work. It is very
important to evaluate these subcontractors because they play a key role in completing the project
successfully (Hartmann, et al., 2009). The original budget estimates and the estimates by the four
subcontractors are provided below. The number of hours in a normal working day in this task is
eight. The builder has estimated that the work will be completed in 65 days hence any
subcontractor that will take over 65 days will attract liquidated damages. Also, a total of 12
concrete pump setups are needed for the job hence any subcontractor that allows less than 12 will
incur additional costs for concrete pumps.
a. Original tender budget
The original tender budget is as shown in Table 1 below
Table 1: Original tender budget
Item Unit Quantit
y
Unit Price ($) Cost ($)
Total concretor trade PC 1 483,157 483,157
O/H costs Days 65 2,000 130,000
Total 613,157
b. Budget estimate for Ultimate Concrete Services Pty Ltd
The budget estimate for Ultimate Concrete Services Pty Ltd is as shown in Table 2 below
Table 2: Ultimate Concrete Services Pty Ltd budget estimate
Item Unit Quantity Unit Price ($) Cost ($)
Supply, place and finish concrete and PC 1 305,520 305,520
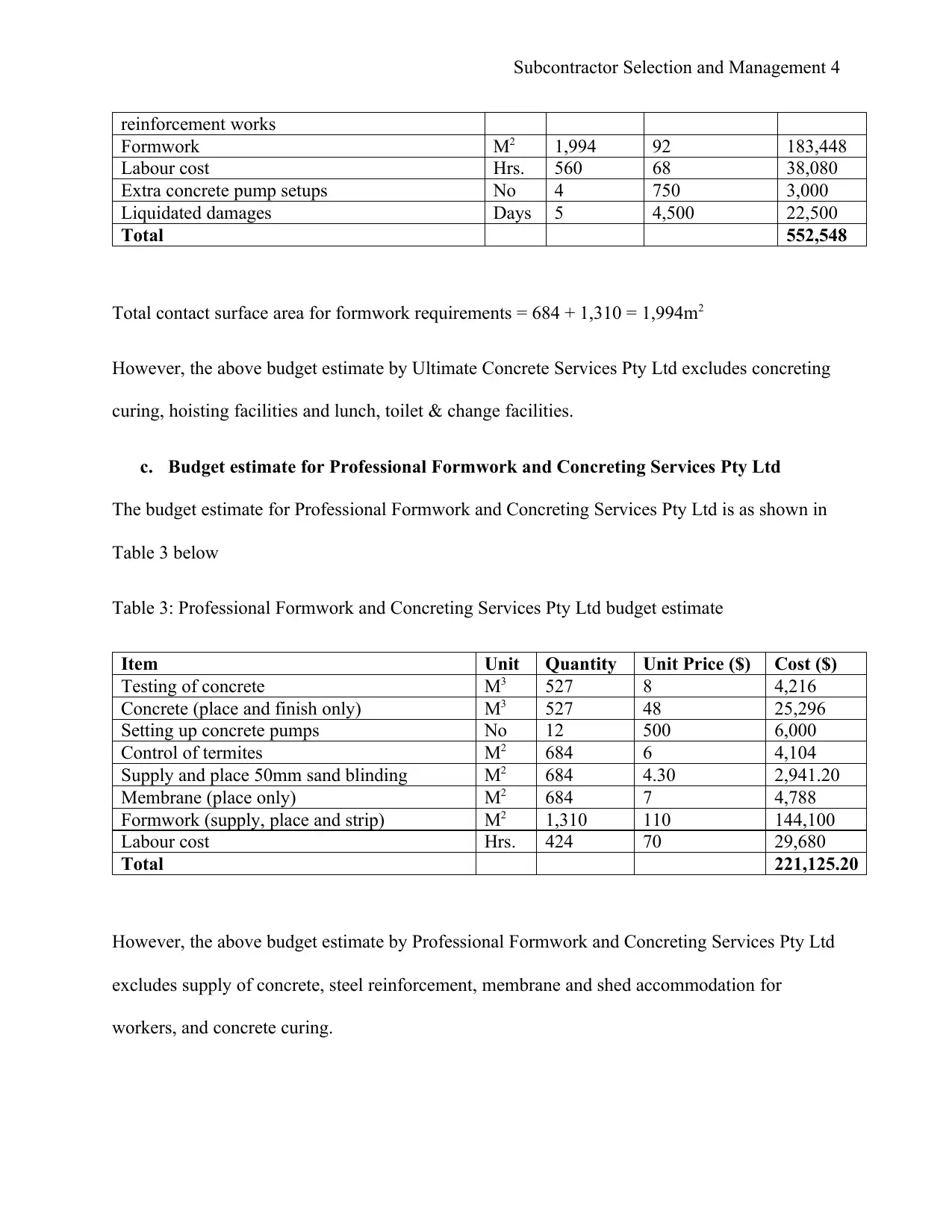
Subcontractor Selection and Management 4
reinforcement works
Formwork M2 1,994 92 183,448
Labour cost Hrs. 560 68 38,080
Extra concrete pump setups No 4 750 3,000
Liquidated damages Days 5 4,500 22,500
Total 552,548
Total contact surface area for formwork requirements = 684 + 1,310 = 1,994m2
However, the above budget estimate by Ultimate Concrete Services Pty Ltd excludes concreting
curing, hoisting facilities and lunch, toilet & change facilities.
c. Budget estimate for Professional Formwork and Concreting Services Pty Ltd
The budget estimate for Professional Formwork and Concreting Services Pty Ltd is as shown in
Table 3 below
Table 3: Professional Formwork and Concreting Services Pty Ltd budget estimate
Item Unit Quantity Unit Price ($) Cost ($)
Testing of concrete M3 527 8 4,216
Concrete (place and finish only) M3 527 48 25,296
Setting up concrete pumps No 12 500 6,000
Control of termites M2 684 6 4,104
Supply and place 50mm sand blinding M2 684 4.30 2,941.20
Membrane (place only) M2 684 7 4,788
Formwork (supply, place and strip) M2 1,310 110 144,100
Labour cost Hrs. 424 70 29,680
Total 221,125.20
However, the above budget estimate by Professional Formwork and Concreting Services Pty Ltd
excludes supply of concrete, steel reinforcement, membrane and shed accommodation for
workers, and concrete curing.
reinforcement works
Formwork M2 1,994 92 183,448
Labour cost Hrs. 560 68 38,080
Extra concrete pump setups No 4 750 3,000
Liquidated damages Days 5 4,500 22,500
Total 552,548
Total contact surface area for formwork requirements = 684 + 1,310 = 1,994m2
However, the above budget estimate by Ultimate Concrete Services Pty Ltd excludes concreting
curing, hoisting facilities and lunch, toilet & change facilities.
c. Budget estimate for Professional Formwork and Concreting Services Pty Ltd
The budget estimate for Professional Formwork and Concreting Services Pty Ltd is as shown in
Table 3 below
Table 3: Professional Formwork and Concreting Services Pty Ltd budget estimate
Item Unit Quantity Unit Price ($) Cost ($)
Testing of concrete M3 527 8 4,216
Concrete (place and finish only) M3 527 48 25,296
Setting up concrete pumps No 12 500 6,000
Control of termites M2 684 6 4,104
Supply and place 50mm sand blinding M2 684 4.30 2,941.20
Membrane (place only) M2 684 7 4,788
Formwork (supply, place and strip) M2 1,310 110 144,100
Labour cost Hrs. 424 70 29,680
Total 221,125.20
However, the above budget estimate by Professional Formwork and Concreting Services Pty Ltd
excludes supply of concrete, steel reinforcement, membrane and shed accommodation for
workers, and concrete curing.
Secure Best Marks with AI Grader
Need help grading? Try our AI Grader for instant feedback on your assignments.
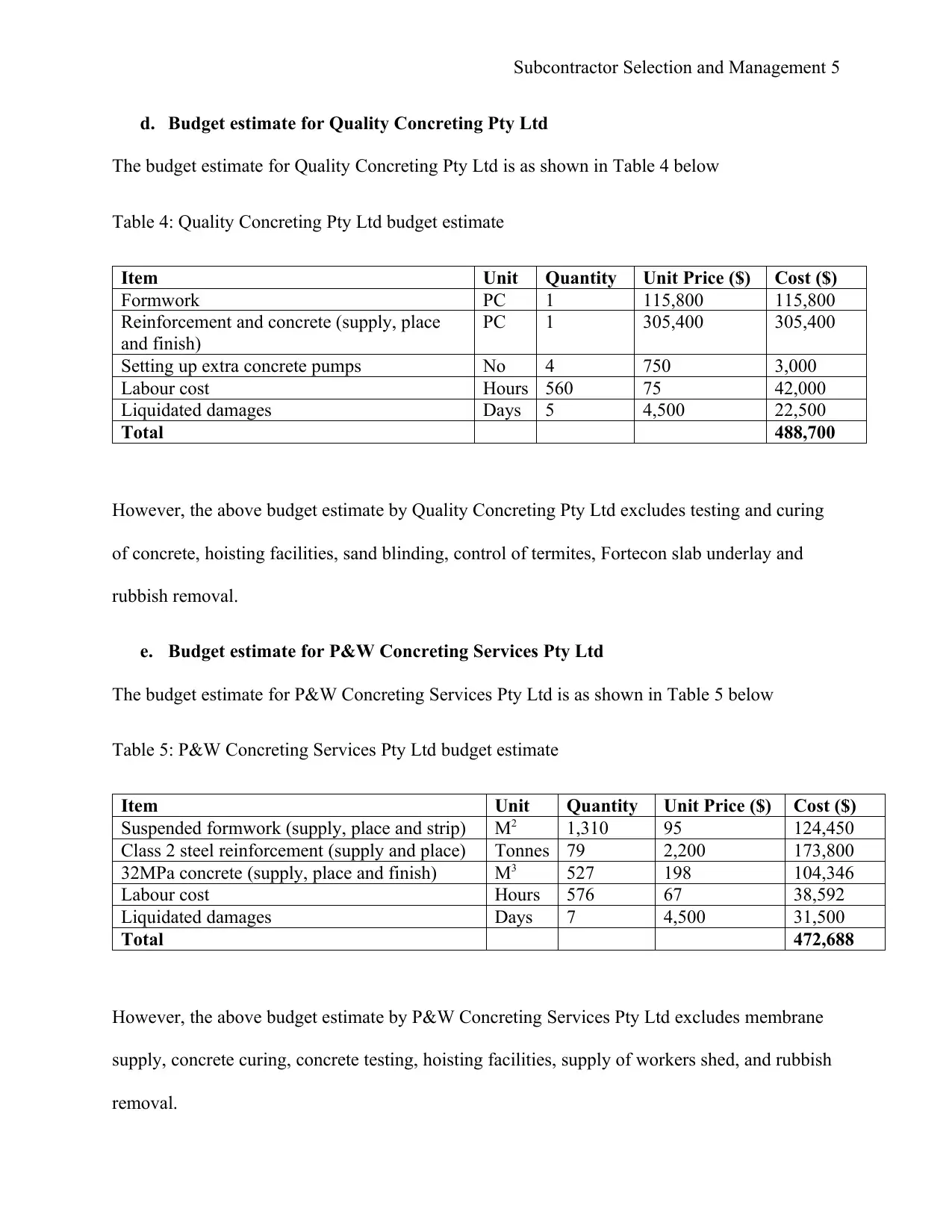
Subcontractor Selection and Management 5
d. Budget estimate for Quality Concreting Pty Ltd
The budget estimate for Quality Concreting Pty Ltd is as shown in Table 4 below
Table 4: Quality Concreting Pty Ltd budget estimate
Item Unit Quantity Unit Price ($) Cost ($)
Formwork PC 1 115,800 115,800
Reinforcement and concrete (supply, place
and finish)
PC 1 305,400 305,400
Setting up extra concrete pumps No 4 750 3,000
Labour cost Hours 560 75 42,000
Liquidated damages Days 5 4,500 22,500
Total 488,700
However, the above budget estimate by Quality Concreting Pty Ltd excludes testing and curing
of concrete, hoisting facilities, sand blinding, control of termites, Fortecon slab underlay and
rubbish removal.
e. Budget estimate for P&W Concreting Services Pty Ltd
The budget estimate for P&W Concreting Services Pty Ltd is as shown in Table 5 below
Table 5: P&W Concreting Services Pty Ltd budget estimate
Item Unit Quantity Unit Price ($) Cost ($)
Suspended formwork (supply, place and strip) M2 1,310 95 124,450
Class 2 steel reinforcement (supply and place) Tonnes 79 2,200 173,800
32MPa concrete (supply, place and finish) M3 527 198 104,346
Labour cost Hours 576 67 38,592
Liquidated damages Days 7 4,500 31,500
Total 472,688
However, the above budget estimate by P&W Concreting Services Pty Ltd excludes membrane
supply, concrete curing, concrete testing, hoisting facilities, supply of workers shed, and rubbish
removal.
d. Budget estimate for Quality Concreting Pty Ltd
The budget estimate for Quality Concreting Pty Ltd is as shown in Table 4 below
Table 4: Quality Concreting Pty Ltd budget estimate
Item Unit Quantity Unit Price ($) Cost ($)
Formwork PC 1 115,800 115,800
Reinforcement and concrete (supply, place
and finish)
PC 1 305,400 305,400
Setting up extra concrete pumps No 4 750 3,000
Labour cost Hours 560 75 42,000
Liquidated damages Days 5 4,500 22,500
Total 488,700
However, the above budget estimate by Quality Concreting Pty Ltd excludes testing and curing
of concrete, hoisting facilities, sand blinding, control of termites, Fortecon slab underlay and
rubbish removal.
e. Budget estimate for P&W Concreting Services Pty Ltd
The budget estimate for P&W Concreting Services Pty Ltd is as shown in Table 5 below
Table 5: P&W Concreting Services Pty Ltd budget estimate
Item Unit Quantity Unit Price ($) Cost ($)
Suspended formwork (supply, place and strip) M2 1,310 95 124,450
Class 2 steel reinforcement (supply and place) Tonnes 79 2,200 173,800
32MPa concrete (supply, place and finish) M3 527 198 104,346
Labour cost Hours 576 67 38,592
Liquidated damages Days 7 4,500 31,500
Total 472,688
However, the above budget estimate by P&W Concreting Services Pty Ltd excludes membrane
supply, concrete curing, concrete testing, hoisting facilities, supply of workers shed, and rubbish
removal.
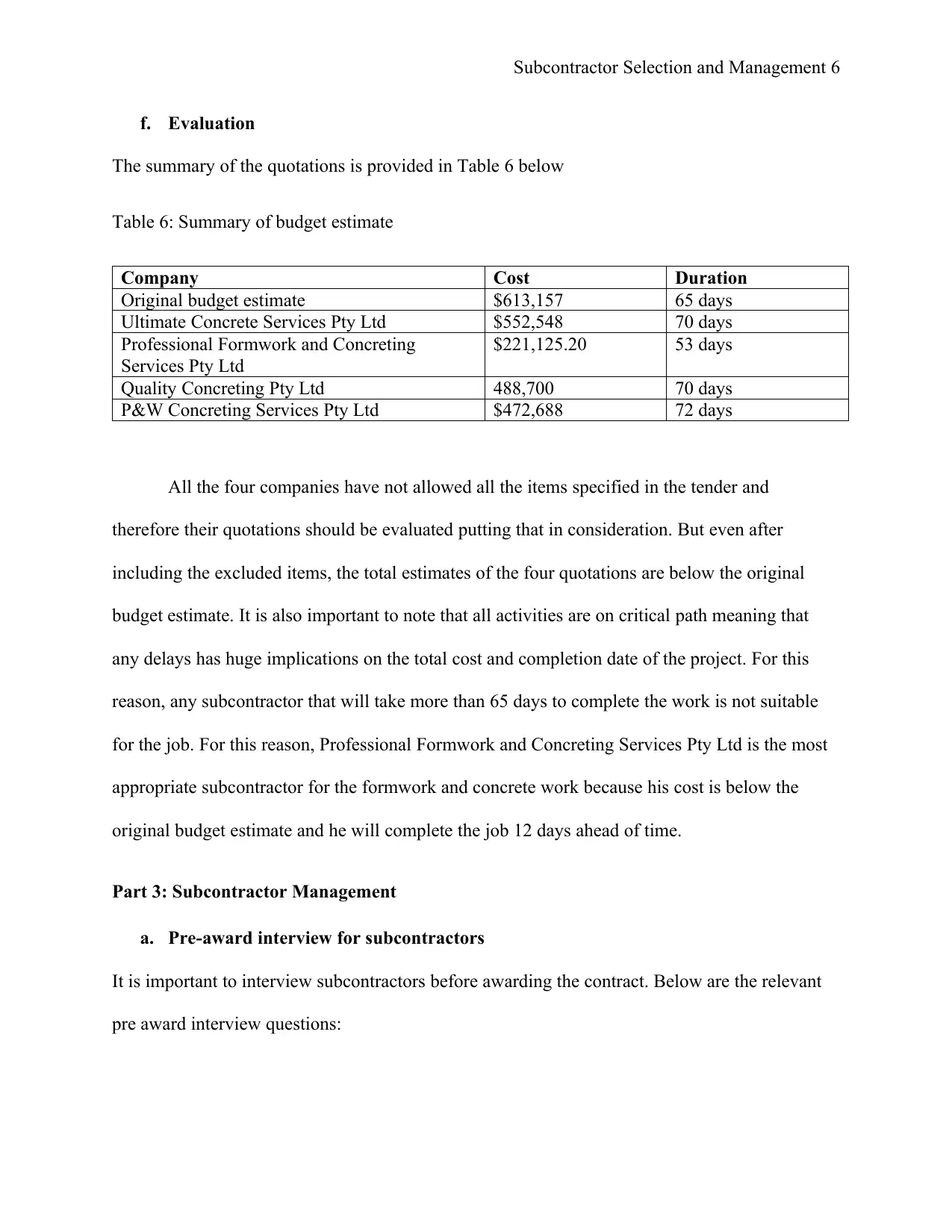
Subcontractor Selection and Management 6
f. Evaluation
The summary of the quotations is provided in Table 6 below
Table 6: Summary of budget estimate
Company Cost Duration
Original budget estimate $613,157 65 days
Ultimate Concrete Services Pty Ltd $552,548 70 days
Professional Formwork and Concreting
Services Pty Ltd
$221,125.20 53 days
Quality Concreting Pty Ltd 488,700 70 days
P&W Concreting Services Pty Ltd $472,688 72 days
All the four companies have not allowed all the items specified in the tender and
therefore their quotations should be evaluated putting that in consideration. But even after
including the excluded items, the total estimates of the four quotations are below the original
budget estimate. It is also important to note that all activities are on critical path meaning that
any delays has huge implications on the total cost and completion date of the project. For this
reason, any subcontractor that will take more than 65 days to complete the work is not suitable
for the job. For this reason, Professional Formwork and Concreting Services Pty Ltd is the most
appropriate subcontractor for the formwork and concrete work because his cost is below the
original budget estimate and he will complete the job 12 days ahead of time.
Part 3: Subcontractor Management
a. Pre-award interview for subcontractors
It is important to interview subcontractors before awarding the contract. Below are the relevant
pre award interview questions:
f. Evaluation
The summary of the quotations is provided in Table 6 below
Table 6: Summary of budget estimate
Company Cost Duration
Original budget estimate $613,157 65 days
Ultimate Concrete Services Pty Ltd $552,548 70 days
Professional Formwork and Concreting
Services Pty Ltd
$221,125.20 53 days
Quality Concreting Pty Ltd 488,700 70 days
P&W Concreting Services Pty Ltd $472,688 72 days
All the four companies have not allowed all the items specified in the tender and
therefore their quotations should be evaluated putting that in consideration. But even after
including the excluded items, the total estimates of the four quotations are below the original
budget estimate. It is also important to note that all activities are on critical path meaning that
any delays has huge implications on the total cost and completion date of the project. For this
reason, any subcontractor that will take more than 65 days to complete the work is not suitable
for the job. For this reason, Professional Formwork and Concreting Services Pty Ltd is the most
appropriate subcontractor for the formwork and concrete work because his cost is below the
original budget estimate and he will complete the job 12 days ahead of time.
Part 3: Subcontractor Management
a. Pre-award interview for subcontractors
It is important to interview subcontractors before awarding the contract. Below are the relevant
pre award interview questions:
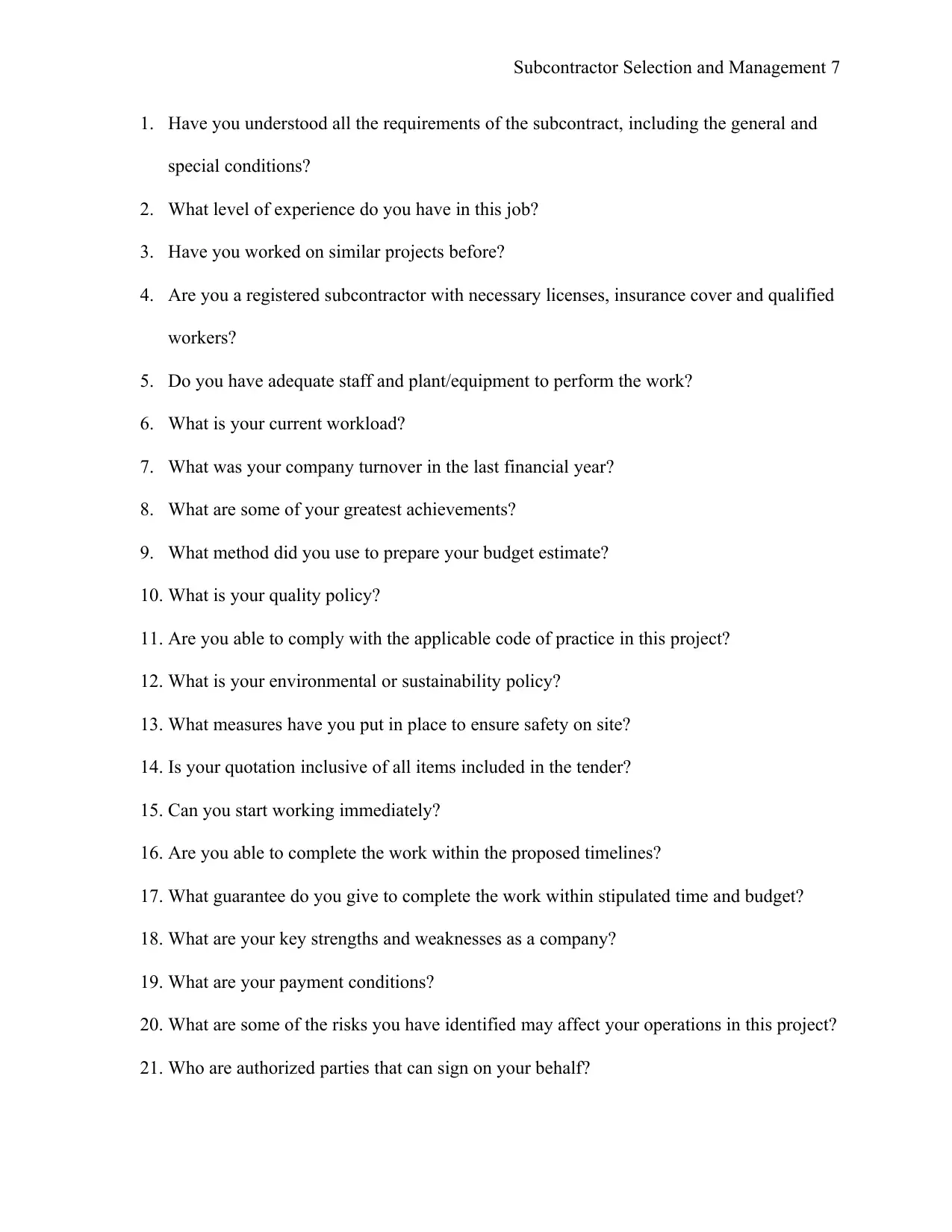
Subcontractor Selection and Management 7
1. Have you understood all the requirements of the subcontract, including the general and
special conditions?
2. What level of experience do you have in this job?
3. Have you worked on similar projects before?
4. Are you a registered subcontractor with necessary licenses, insurance cover and qualified
workers?
5. Do you have adequate staff and plant/equipment to perform the work?
6. What is your current workload?
7. What was your company turnover in the last financial year?
8. What are some of your greatest achievements?
9. What method did you use to prepare your budget estimate?
10. What is your quality policy?
11. Are you able to comply with the applicable code of practice in this project?
12. What is your environmental or sustainability policy?
13. What measures have you put in place to ensure safety on site?
14. Is your quotation inclusive of all items included in the tender?
15. Can you start working immediately?
16. Are you able to complete the work within the proposed timelines?
17. What guarantee do you give to complete the work within stipulated time and budget?
18. What are your key strengths and weaknesses as a company?
19. What are your payment conditions?
20. What are some of the risks you have identified may affect your operations in this project?
21. Who are authorized parties that can sign on your behalf?
1. Have you understood all the requirements of the subcontract, including the general and
special conditions?
2. What level of experience do you have in this job?
3. Have you worked on similar projects before?
4. Are you a registered subcontractor with necessary licenses, insurance cover and qualified
workers?
5. Do you have adequate staff and plant/equipment to perform the work?
6. What is your current workload?
7. What was your company turnover in the last financial year?
8. What are some of your greatest achievements?
9. What method did you use to prepare your budget estimate?
10. What is your quality policy?
11. Are you able to comply with the applicable code of practice in this project?
12. What is your environmental or sustainability policy?
13. What measures have you put in place to ensure safety on site?
14. Is your quotation inclusive of all items included in the tender?
15. Can you start working immediately?
16. Are you able to complete the work within the proposed timelines?
17. What guarantee do you give to complete the work within stipulated time and budget?
18. What are your key strengths and weaknesses as a company?
19. What are your payment conditions?
20. What are some of the risks you have identified may affect your operations in this project?
21. Who are authorized parties that can sign on your behalf?
Paraphrase This Document
Need a fresh take? Get an instant paraphrase of this document with our AI Paraphraser
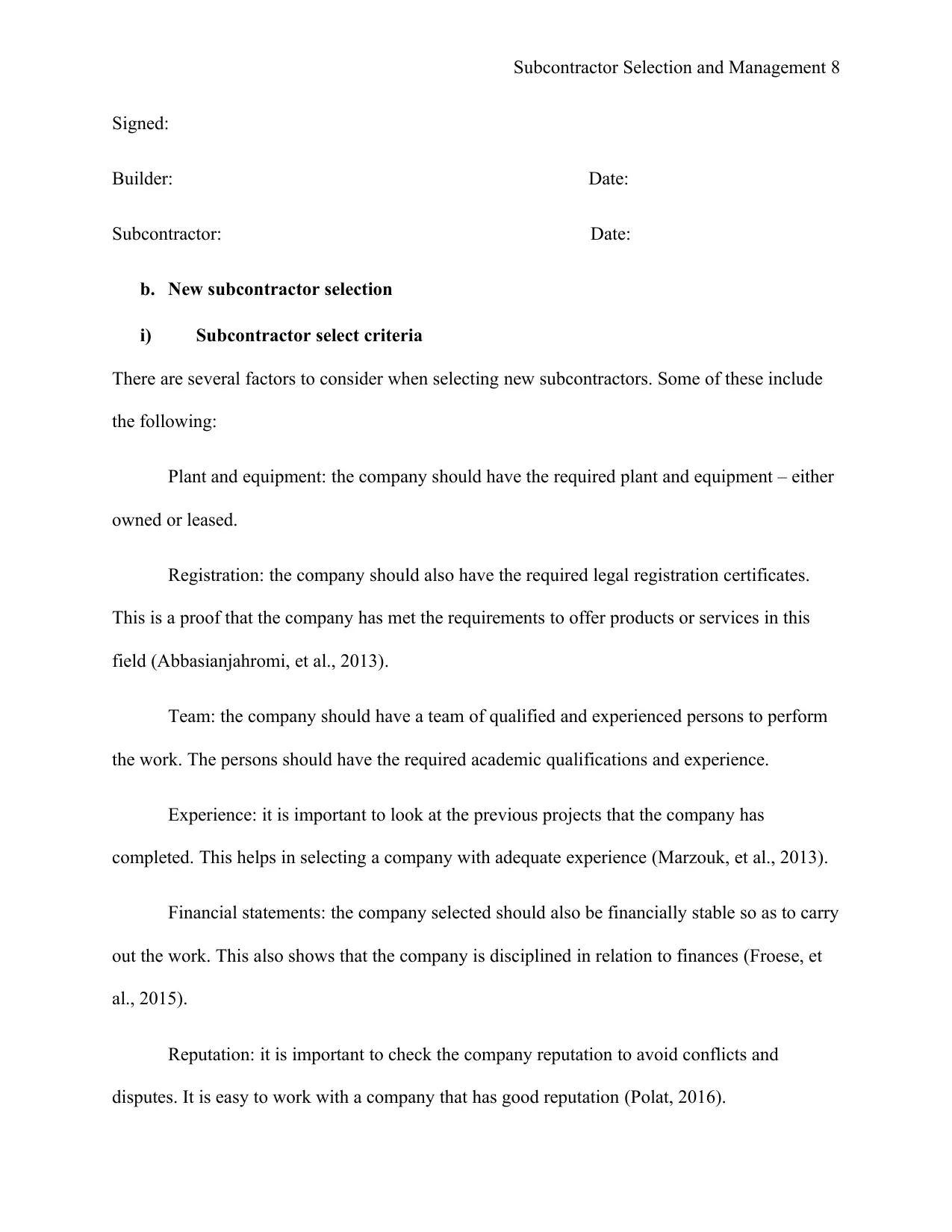
Subcontractor Selection and Management 8
Signed:
Builder: Date:
Subcontractor: Date:
b. New subcontractor selection
i) Subcontractor select criteria
There are several factors to consider when selecting new subcontractors. Some of these include
the following:
Plant and equipment: the company should have the required plant and equipment – either
owned or leased.
Registration: the company should also have the required legal registration certificates.
This is a proof that the company has met the requirements to offer products or services in this
field (Abbasianjahromi, et al., 2013).
Team: the company should have a team of qualified and experienced persons to perform
the work. The persons should have the required academic qualifications and experience.
Experience: it is important to look at the previous projects that the company has
completed. This helps in selecting a company with adequate experience (Marzouk, et al., 2013).
Financial statements: the company selected should also be financially stable so as to carry
out the work. This also shows that the company is disciplined in relation to finances (Froese, et
al., 2015).
Reputation: it is important to check the company reputation to avoid conflicts and
disputes. It is easy to work with a company that has good reputation (Polat, 2016).
Signed:
Builder: Date:
Subcontractor: Date:
b. New subcontractor selection
i) Subcontractor select criteria
There are several factors to consider when selecting new subcontractors. Some of these include
the following:
Plant and equipment: the company should have the required plant and equipment – either
owned or leased.
Registration: the company should also have the required legal registration certificates.
This is a proof that the company has met the requirements to offer products or services in this
field (Abbasianjahromi, et al., 2013).
Team: the company should have a team of qualified and experienced persons to perform
the work. The persons should have the required academic qualifications and experience.
Experience: it is important to look at the previous projects that the company has
completed. This helps in selecting a company with adequate experience (Marzouk, et al., 2013).
Financial statements: the company selected should also be financially stable so as to carry
out the work. This also shows that the company is disciplined in relation to finances (Froese, et
al., 2015).
Reputation: it is important to check the company reputation to avoid conflicts and
disputes. It is easy to work with a company that has good reputation (Polat, 2016).
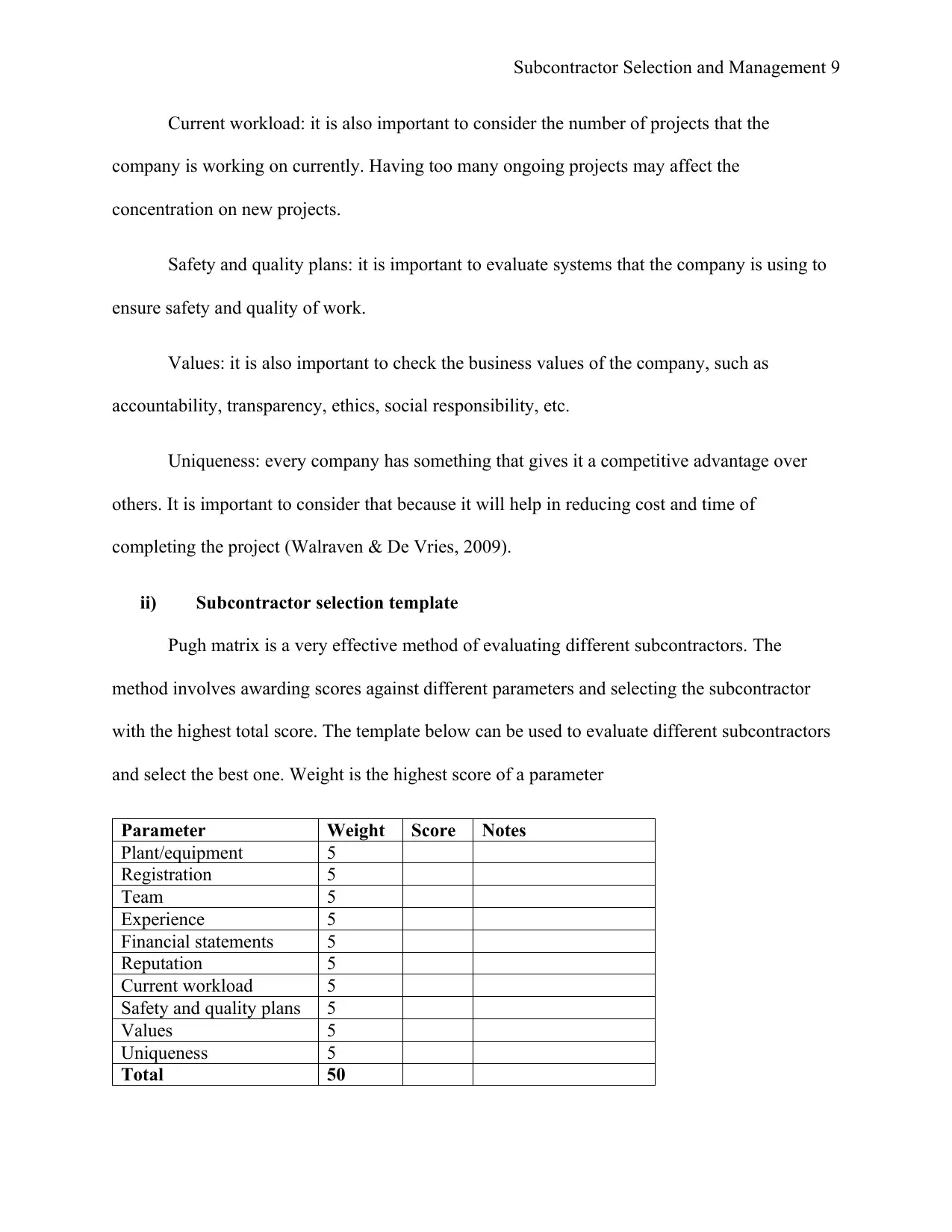
Subcontractor Selection and Management 9
Current workload: it is also important to consider the number of projects that the
company is working on currently. Having too many ongoing projects may affect the
concentration on new projects.
Safety and quality plans: it is important to evaluate systems that the company is using to
ensure safety and quality of work.
Values: it is also important to check the business values of the company, such as
accountability, transparency, ethics, social responsibility, etc.
Uniqueness: every company has something that gives it a competitive advantage over
others. It is important to consider that because it will help in reducing cost and time of
completing the project (Walraven & De Vries, 2009).
ii) Subcontractor selection template
Pugh matrix is a very effective method of evaluating different subcontractors. The
method involves awarding scores against different parameters and selecting the subcontractor
with the highest total score. The template below can be used to evaluate different subcontractors
and select the best one. Weight is the highest score of a parameter
Parameter Weight Score Notes
Plant/equipment 5
Registration 5
Team 5
Experience 5
Financial statements 5
Reputation 5
Current workload 5
Safety and quality plans 5
Values 5
Uniqueness 5
Total 50
Current workload: it is also important to consider the number of projects that the
company is working on currently. Having too many ongoing projects may affect the
concentration on new projects.
Safety and quality plans: it is important to evaluate systems that the company is using to
ensure safety and quality of work.
Values: it is also important to check the business values of the company, such as
accountability, transparency, ethics, social responsibility, etc.
Uniqueness: every company has something that gives it a competitive advantage over
others. It is important to consider that because it will help in reducing cost and time of
completing the project (Walraven & De Vries, 2009).
ii) Subcontractor selection template
Pugh matrix is a very effective method of evaluating different subcontractors. The
method involves awarding scores against different parameters and selecting the subcontractor
with the highest total score. The template below can be used to evaluate different subcontractors
and select the best one. Weight is the highest score of a parameter
Parameter Weight Score Notes
Plant/equipment 5
Registration 5
Team 5
Experience 5
Financial statements 5
Reputation 5
Current workload 5
Safety and quality plans 5
Values 5
Uniqueness 5
Total 50
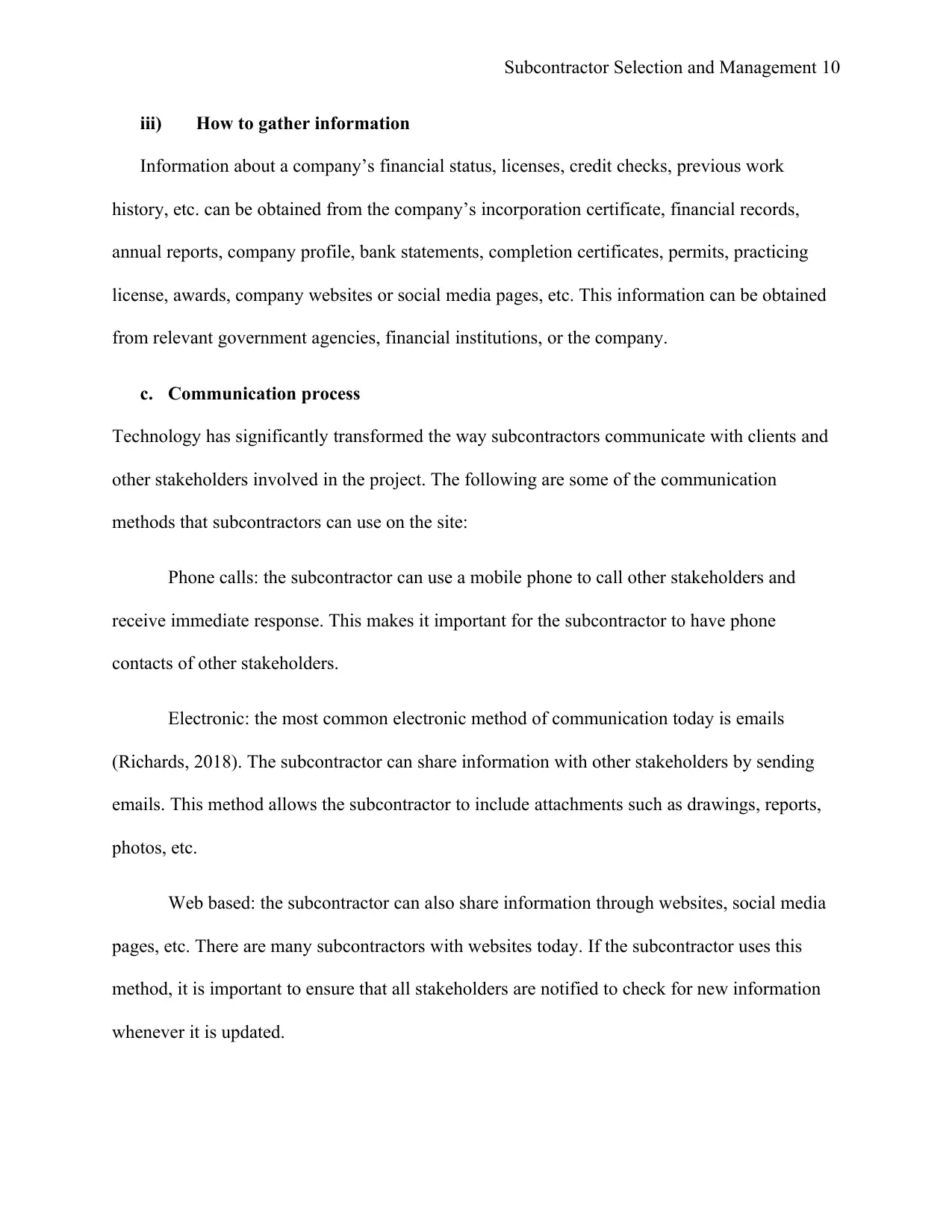
Subcontractor Selection and Management 10
iii) How to gather information
Information about a company’s financial status, licenses, credit checks, previous work
history, etc. can be obtained from the company’s incorporation certificate, financial records,
annual reports, company profile, bank statements, completion certificates, permits, practicing
license, awards, company websites or social media pages, etc. This information can be obtained
from relevant government agencies, financial institutions, or the company.
c. Communication process
Technology has significantly transformed the way subcontractors communicate with clients and
other stakeholders involved in the project. The following are some of the communication
methods that subcontractors can use on the site:
Phone calls: the subcontractor can use a mobile phone to call other stakeholders and
receive immediate response. This makes it important for the subcontractor to have phone
contacts of other stakeholders.
Electronic: the most common electronic method of communication today is emails
(Richards, 2018). The subcontractor can share information with other stakeholders by sending
emails. This method allows the subcontractor to include attachments such as drawings, reports,
photos, etc.
Web based: the subcontractor can also share information through websites, social media
pages, etc. There are many subcontractors with websites today. If the subcontractor uses this
method, it is important to ensure that all stakeholders are notified to check for new information
whenever it is updated.
iii) How to gather information
Information about a company’s financial status, licenses, credit checks, previous work
history, etc. can be obtained from the company’s incorporation certificate, financial records,
annual reports, company profile, bank statements, completion certificates, permits, practicing
license, awards, company websites or social media pages, etc. This information can be obtained
from relevant government agencies, financial institutions, or the company.
c. Communication process
Technology has significantly transformed the way subcontractors communicate with clients and
other stakeholders involved in the project. The following are some of the communication
methods that subcontractors can use on the site:
Phone calls: the subcontractor can use a mobile phone to call other stakeholders and
receive immediate response. This makes it important for the subcontractor to have phone
contacts of other stakeholders.
Electronic: the most common electronic method of communication today is emails
(Richards, 2018). The subcontractor can share information with other stakeholders by sending
emails. This method allows the subcontractor to include attachments such as drawings, reports,
photos, etc.
Web based: the subcontractor can also share information through websites, social media
pages, etc. There are many subcontractors with websites today. If the subcontractor uses this
method, it is important to ensure that all stakeholders are notified to check for new information
whenever it is updated.
Secure Best Marks with AI Grader
Need help grading? Try our AI Grader for instant feedback on your assignments.
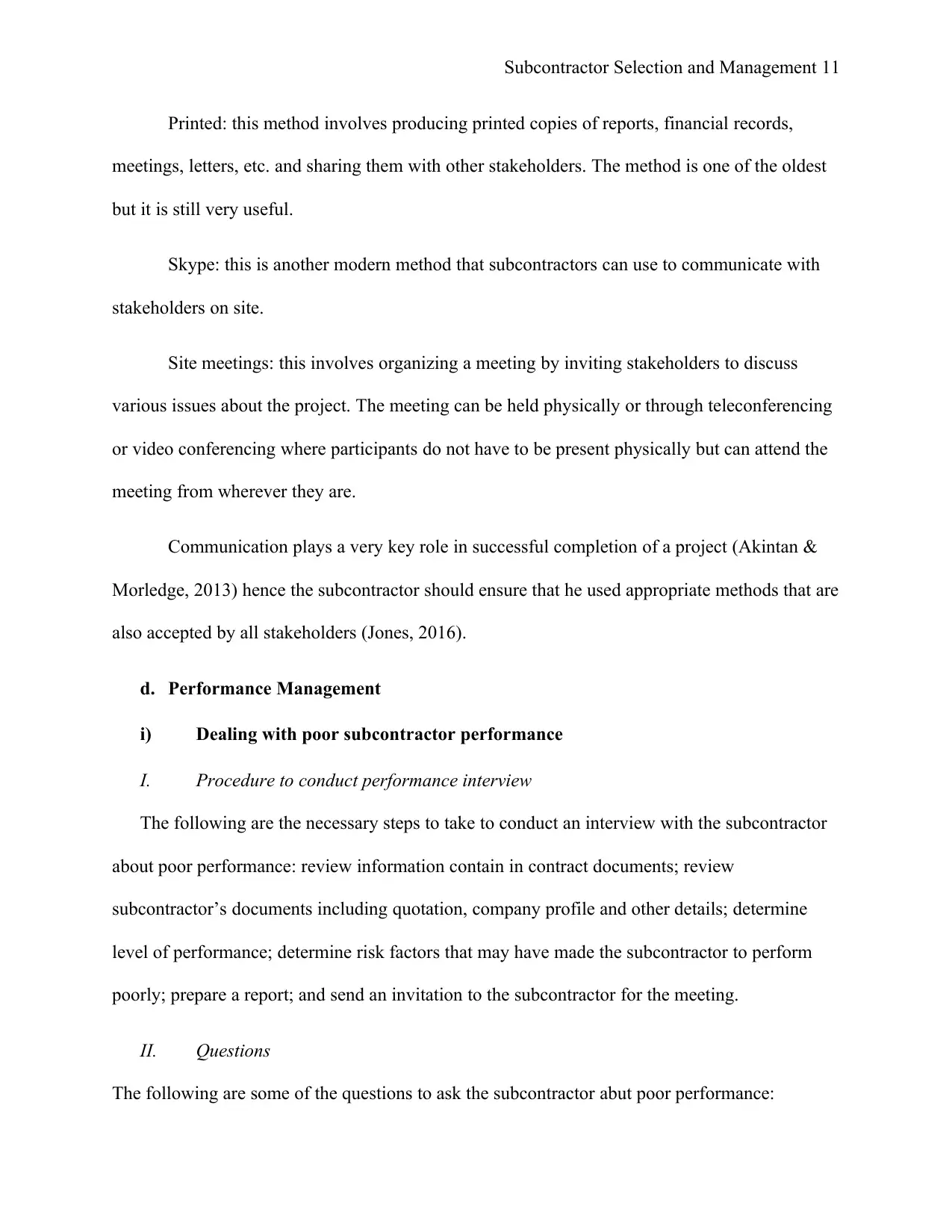
Subcontractor Selection and Management 11
Printed: this method involves producing printed copies of reports, financial records,
meetings, letters, etc. and sharing them with other stakeholders. The method is one of the oldest
but it is still very useful.
Skype: this is another modern method that subcontractors can use to communicate with
stakeholders on site.
Site meetings: this involves organizing a meeting by inviting stakeholders to discuss
various issues about the project. The meeting can be held physically or through teleconferencing
or video conferencing where participants do not have to be present physically but can attend the
meeting from wherever they are.
Communication plays a very key role in successful completion of a project (Akintan &
Morledge, 2013) hence the subcontractor should ensure that he used appropriate methods that are
also accepted by all stakeholders (Jones, 2016).
d. Performance Management
i) Dealing with poor subcontractor performance
I. Procedure to conduct performance interview
The following are the necessary steps to take to conduct an interview with the subcontractor
about poor performance: review information contain in contract documents; review
subcontractor’s documents including quotation, company profile and other details; determine
level of performance; determine risk factors that may have made the subcontractor to perform
poorly; prepare a report; and send an invitation to the subcontractor for the meeting.
II. Questions
The following are some of the questions to ask the subcontractor abut poor performance:
Printed: this method involves producing printed copies of reports, financial records,
meetings, letters, etc. and sharing them with other stakeholders. The method is one of the oldest
but it is still very useful.
Skype: this is another modern method that subcontractors can use to communicate with
stakeholders on site.
Site meetings: this involves organizing a meeting by inviting stakeholders to discuss
various issues about the project. The meeting can be held physically or through teleconferencing
or video conferencing where participants do not have to be present physically but can attend the
meeting from wherever they are.
Communication plays a very key role in successful completion of a project (Akintan &
Morledge, 2013) hence the subcontractor should ensure that he used appropriate methods that are
also accepted by all stakeholders (Jones, 2016).
d. Performance Management
i) Dealing with poor subcontractor performance
I. Procedure to conduct performance interview
The following are the necessary steps to take to conduct an interview with the subcontractor
about poor performance: review information contain in contract documents; review
subcontractor’s documents including quotation, company profile and other details; determine
level of performance; determine risk factors that may have made the subcontractor to perform
poorly; prepare a report; and send an invitation to the subcontractor for the meeting.
II. Questions
The following are some of the questions to ask the subcontractor abut poor performance:
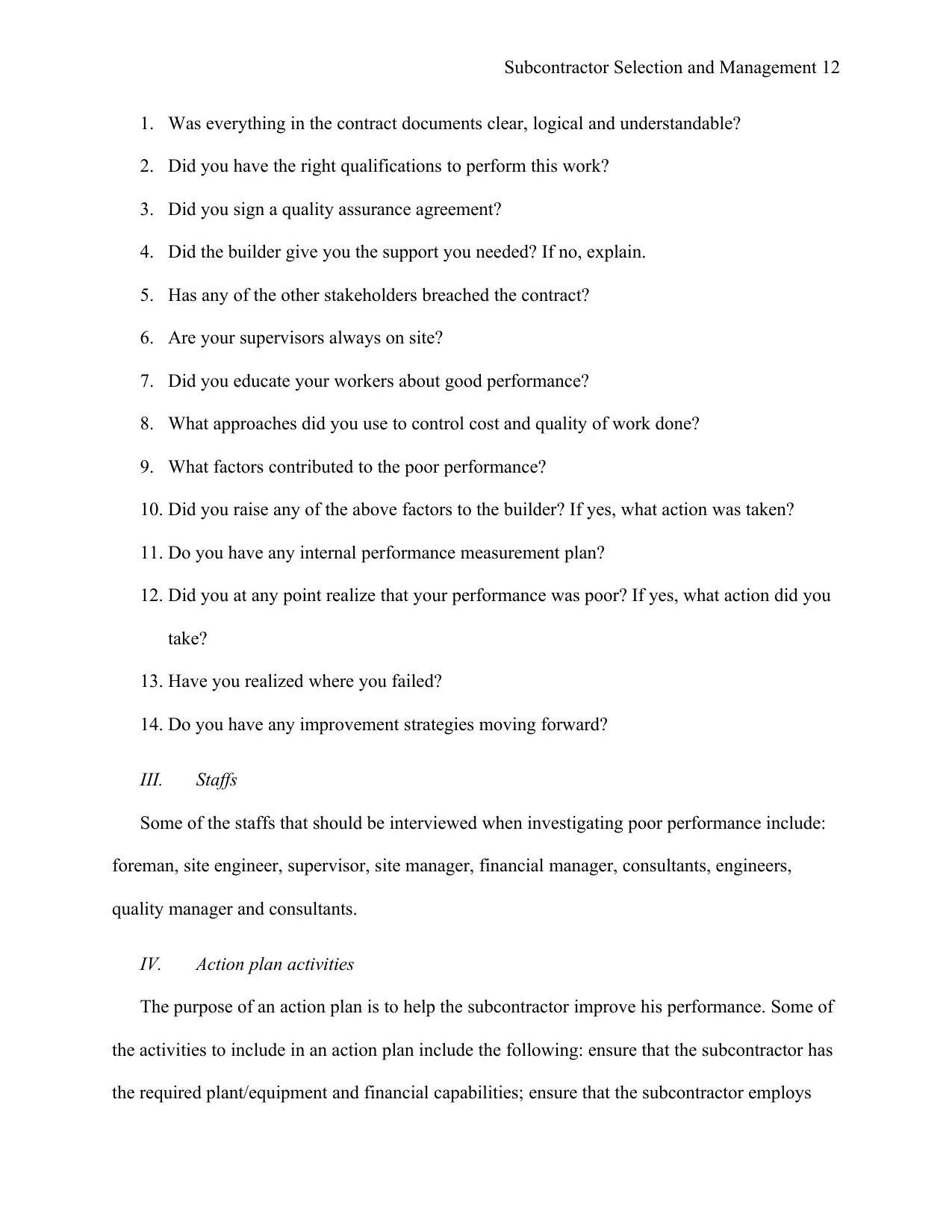
Subcontractor Selection and Management 12
1. Was everything in the contract documents clear, logical and understandable?
2. Did you have the right qualifications to perform this work?
3. Did you sign a quality assurance agreement?
4. Did the builder give you the support you needed? If no, explain.
5. Has any of the other stakeholders breached the contract?
6. Are your supervisors always on site?
7. Did you educate your workers about good performance?
8. What approaches did you use to control cost and quality of work done?
9. What factors contributed to the poor performance?
10. Did you raise any of the above factors to the builder? If yes, what action was taken?
11. Do you have any internal performance measurement plan?
12. Did you at any point realize that your performance was poor? If yes, what action did you
take?
13. Have you realized where you failed?
14. Do you have any improvement strategies moving forward?
III. Staffs
Some of the staffs that should be interviewed when investigating poor performance include:
foreman, site engineer, supervisor, site manager, financial manager, consultants, engineers,
quality manager and consultants.
IV. Action plan activities
The purpose of an action plan is to help the subcontractor improve his performance. Some of
the activities to include in an action plan include the following: ensure that the subcontractor has
the required plant/equipment and financial capabilities; ensure that the subcontractor employs
1. Was everything in the contract documents clear, logical and understandable?
2. Did you have the right qualifications to perform this work?
3. Did you sign a quality assurance agreement?
4. Did the builder give you the support you needed? If no, explain.
5. Has any of the other stakeholders breached the contract?
6. Are your supervisors always on site?
7. Did you educate your workers about good performance?
8. What approaches did you use to control cost and quality of work done?
9. What factors contributed to the poor performance?
10. Did you raise any of the above factors to the builder? If yes, what action was taken?
11. Do you have any internal performance measurement plan?
12. Did you at any point realize that your performance was poor? If yes, what action did you
take?
13. Have you realized where you failed?
14. Do you have any improvement strategies moving forward?
III. Staffs
Some of the staffs that should be interviewed when investigating poor performance include:
foreman, site engineer, supervisor, site manager, financial manager, consultants, engineers,
quality manager and consultants.
IV. Action plan activities
The purpose of an action plan is to help the subcontractor improve his performance. Some of
the activities to include in an action plan include the following: ensure that the subcontractor has
the required plant/equipment and financial capabilities; ensure that the subcontractor employs
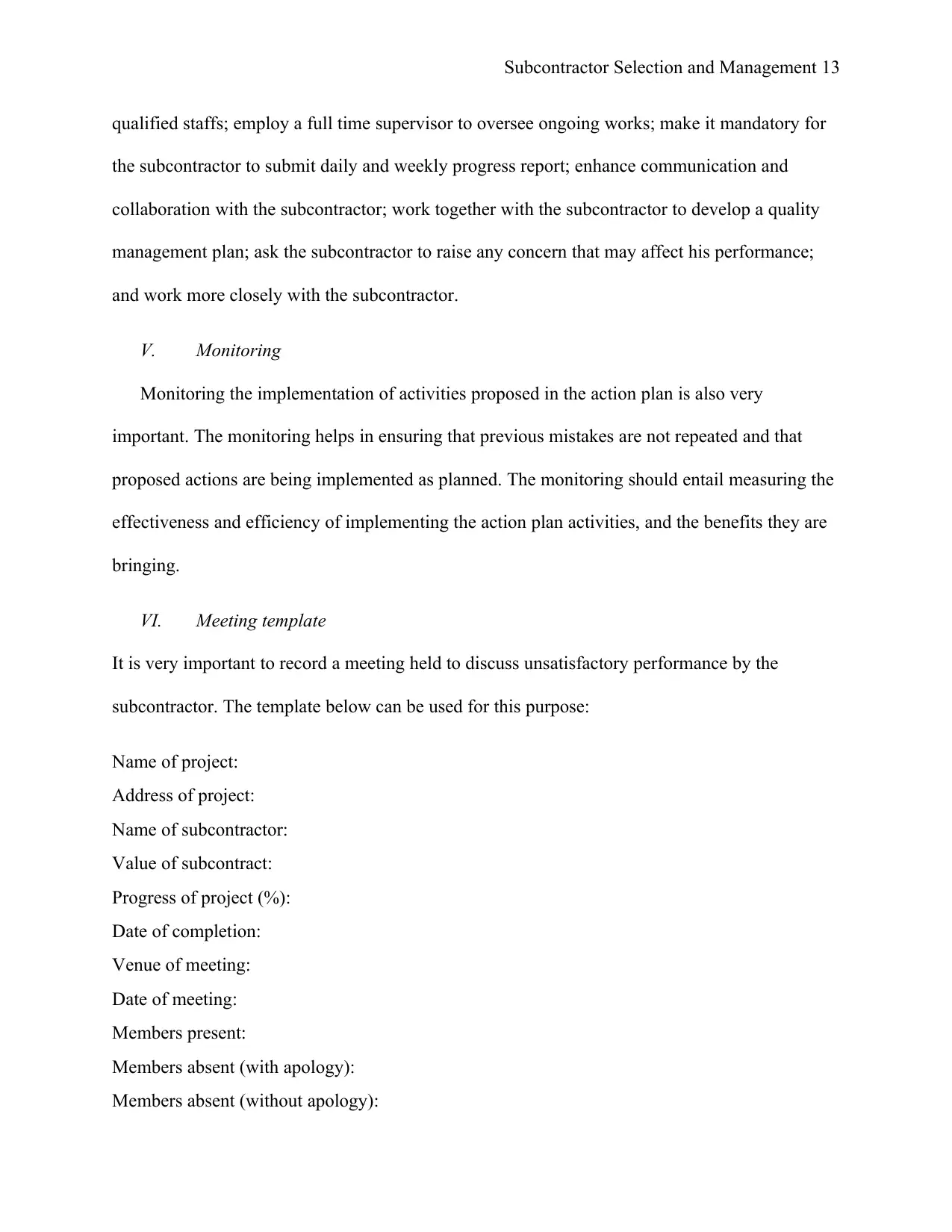
Subcontractor Selection and Management 13
qualified staffs; employ a full time supervisor to oversee ongoing works; make it mandatory for
the subcontractor to submit daily and weekly progress report; enhance communication and
collaboration with the subcontractor; work together with the subcontractor to develop a quality
management plan; ask the subcontractor to raise any concern that may affect his performance;
and work more closely with the subcontractor.
V. Monitoring
Monitoring the implementation of activities proposed in the action plan is also very
important. The monitoring helps in ensuring that previous mistakes are not repeated and that
proposed actions are being implemented as planned. The monitoring should entail measuring the
effectiveness and efficiency of implementing the action plan activities, and the benefits they are
bringing.
VI. Meeting template
It is very important to record a meeting held to discuss unsatisfactory performance by the
subcontractor. The template below can be used for this purpose:
Name of project:
Address of project:
Name of subcontractor:
Value of subcontract:
Progress of project (%):
Date of completion:
Venue of meeting:
Date of meeting:
Members present:
Members absent (with apology):
Members absent (without apology):
qualified staffs; employ a full time supervisor to oversee ongoing works; make it mandatory for
the subcontractor to submit daily and weekly progress report; enhance communication and
collaboration with the subcontractor; work together with the subcontractor to develop a quality
management plan; ask the subcontractor to raise any concern that may affect his performance;
and work more closely with the subcontractor.
V. Monitoring
Monitoring the implementation of activities proposed in the action plan is also very
important. The monitoring helps in ensuring that previous mistakes are not repeated and that
proposed actions are being implemented as planned. The monitoring should entail measuring the
effectiveness and efficiency of implementing the action plan activities, and the benefits they are
bringing.
VI. Meeting template
It is very important to record a meeting held to discuss unsatisfactory performance by the
subcontractor. The template below can be used for this purpose:
Name of project:
Address of project:
Name of subcontractor:
Value of subcontract:
Progress of project (%):
Date of completion:
Venue of meeting:
Date of meeting:
Members present:
Members absent (with apology):
Members absent (without apology):
Paraphrase This Document
Need a fresh take? Get an instant paraphrase of this document with our AI Paraphraser
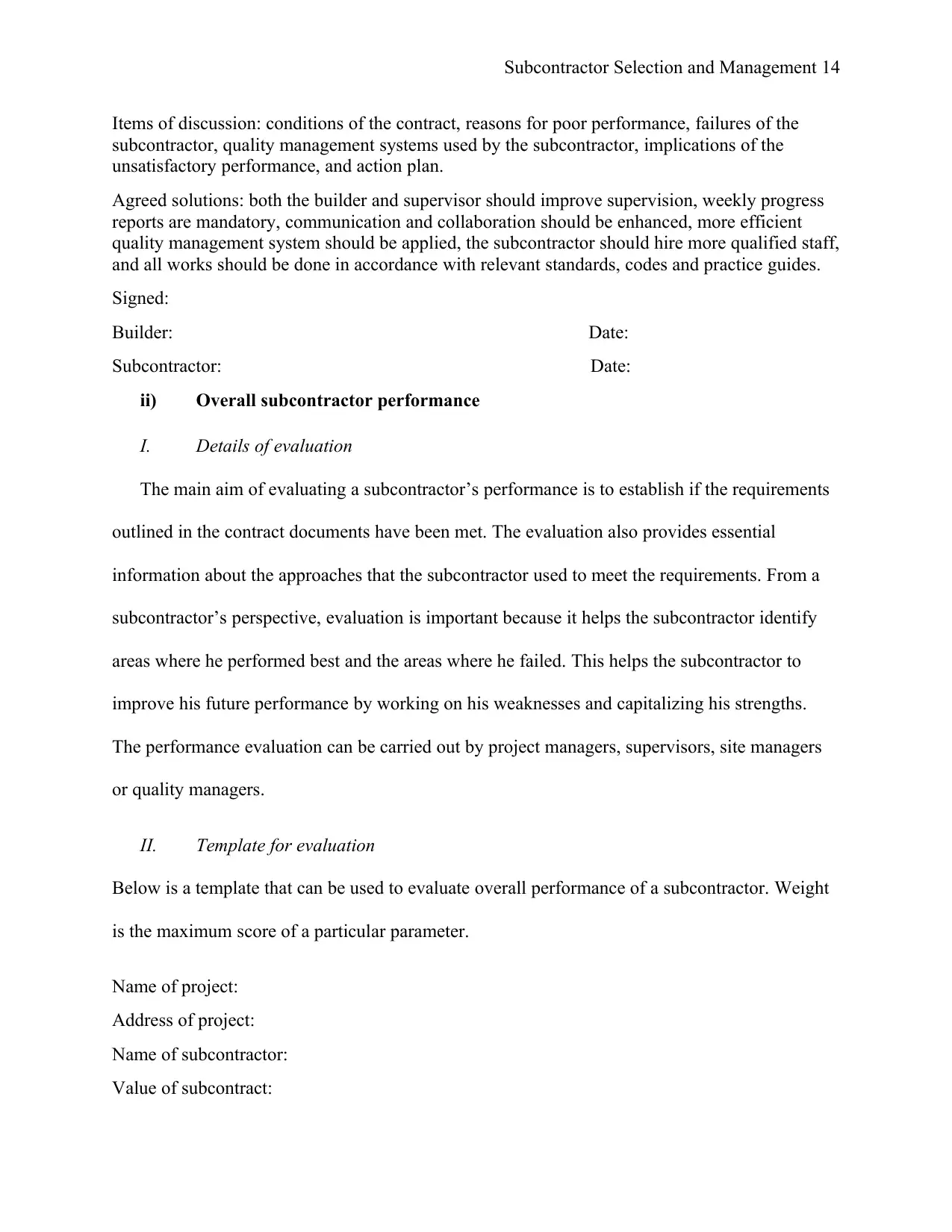
Subcontractor Selection and Management 14
Items of discussion: conditions of the contract, reasons for poor performance, failures of the
subcontractor, quality management systems used by the subcontractor, implications of the
unsatisfactory performance, and action plan.
Agreed solutions: both the builder and supervisor should improve supervision, weekly progress
reports are mandatory, communication and collaboration should be enhanced, more efficient
quality management system should be applied, the subcontractor should hire more qualified staff,
and all works should be done in accordance with relevant standards, codes and practice guides.
Signed:
Builder: Date:
Subcontractor: Date:
ii) Overall subcontractor performance
I. Details of evaluation
The main aim of evaluating a subcontractor’s performance is to establish if the requirements
outlined in the contract documents have been met. The evaluation also provides essential
information about the approaches that the subcontractor used to meet the requirements. From a
subcontractor’s perspective, evaluation is important because it helps the subcontractor identify
areas where he performed best and the areas where he failed. This helps the subcontractor to
improve his future performance by working on his weaknesses and capitalizing his strengths.
The performance evaluation can be carried out by project managers, supervisors, site managers
or quality managers.
II. Template for evaluation
Below is a template that can be used to evaluate overall performance of a subcontractor. Weight
is the maximum score of a particular parameter.
Name of project:
Address of project:
Name of subcontractor:
Value of subcontract:
Items of discussion: conditions of the contract, reasons for poor performance, failures of the
subcontractor, quality management systems used by the subcontractor, implications of the
unsatisfactory performance, and action plan.
Agreed solutions: both the builder and supervisor should improve supervision, weekly progress
reports are mandatory, communication and collaboration should be enhanced, more efficient
quality management system should be applied, the subcontractor should hire more qualified staff,
and all works should be done in accordance with relevant standards, codes and practice guides.
Signed:
Builder: Date:
Subcontractor: Date:
ii) Overall subcontractor performance
I. Details of evaluation
The main aim of evaluating a subcontractor’s performance is to establish if the requirements
outlined in the contract documents have been met. The evaluation also provides essential
information about the approaches that the subcontractor used to meet the requirements. From a
subcontractor’s perspective, evaluation is important because it helps the subcontractor identify
areas where he performed best and the areas where he failed. This helps the subcontractor to
improve his future performance by working on his weaknesses and capitalizing his strengths.
The performance evaluation can be carried out by project managers, supervisors, site managers
or quality managers.
II. Template for evaluation
Below is a template that can be used to evaluate overall performance of a subcontractor. Weight
is the maximum score of a particular parameter.
Name of project:
Address of project:
Name of subcontractor:
Value of subcontract:
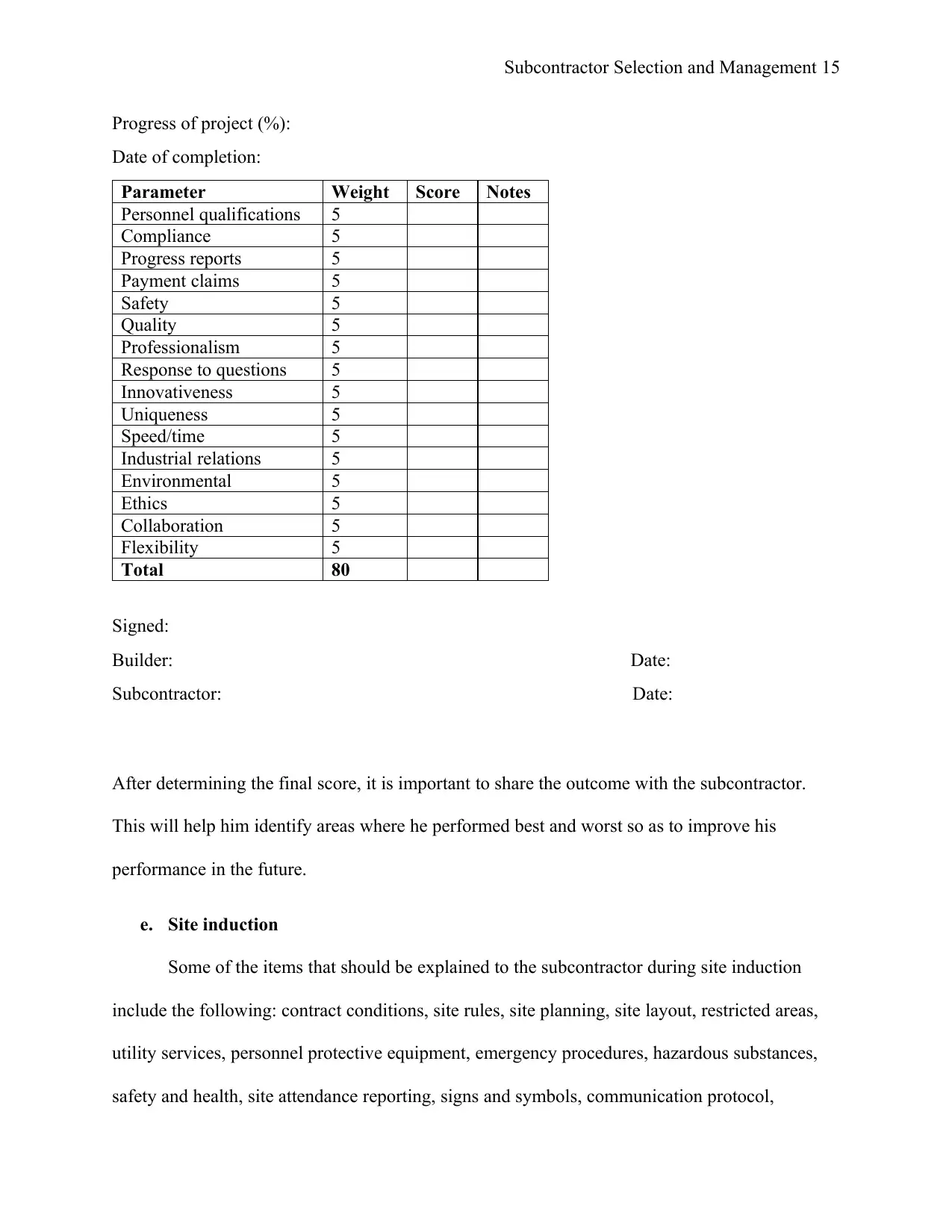
Subcontractor Selection and Management 15
Progress of project (%):
Date of completion:
Parameter Weight Score Notes
Personnel qualifications 5
Compliance 5
Progress reports 5
Payment claims 5
Safety 5
Quality 5
Professionalism 5
Response to questions 5
Innovativeness 5
Uniqueness 5
Speed/time 5
Industrial relations 5
Environmental 5
Ethics 5
Collaboration 5
Flexibility 5
Total 80
Signed:
Builder: Date:
Subcontractor: Date:
After determining the final score, it is important to share the outcome with the subcontractor.
This will help him identify areas where he performed best and worst so as to improve his
performance in the future.
e. Site induction
Some of the items that should be explained to the subcontractor during site induction
include the following: contract conditions, site rules, site planning, site layout, restricted areas,
utility services, personnel protective equipment, emergency procedures, hazardous substances,
safety and health, site attendance reporting, signs and symbols, communication protocol,
Progress of project (%):
Date of completion:
Parameter Weight Score Notes
Personnel qualifications 5
Compliance 5
Progress reports 5
Payment claims 5
Safety 5
Quality 5
Professionalism 5
Response to questions 5
Innovativeness 5
Uniqueness 5
Speed/time 5
Industrial relations 5
Environmental 5
Ethics 5
Collaboration 5
Flexibility 5
Total 80
Signed:
Builder: Date:
Subcontractor: Date:
After determining the final score, it is important to share the outcome with the subcontractor.
This will help him identify areas where he performed best and worst so as to improve his
performance in the future.
e. Site induction
Some of the items that should be explained to the subcontractor during site induction
include the following: contract conditions, site rules, site planning, site layout, restricted areas,
utility services, personnel protective equipment, emergency procedures, hazardous substances,
safety and health, site attendance reporting, signs and symbols, communication protocol,
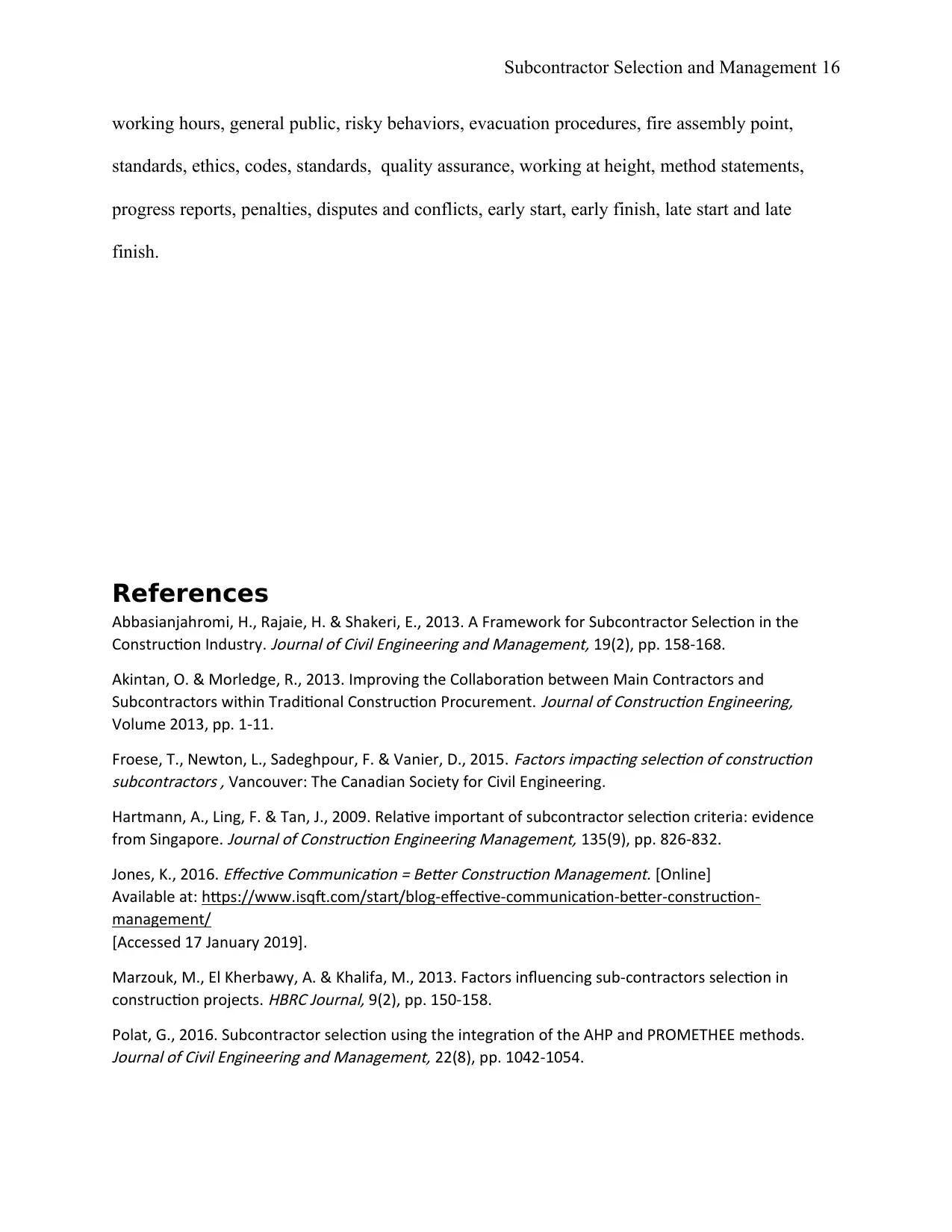
Subcontractor Selection and Management 16
working hours, general public, risky behaviors, evacuation procedures, fire assembly point,
standards, ethics, codes, standards, quality assurance, working at height, method statements,
progress reports, penalties, disputes and conflicts, early start, early finish, late start and late
finish.
References
Abbasianjahromi, H., Rajaie, H. & Shakeri, E., 2013. A Framework for Subcontractor Selection in the
Construction Industry.
Journal of Civil Engineering and Management, 19(2), pp. 158-168.
Akintan, O. & Morledge, R., 2013. Improving the Collaboration between Main Contractors and
Subcontractors within Traditional Construction Procurement.
Journal of Construction Engineering,
Volume 2013, pp. 1-11.
Froese, T., Newton, L., Sadeghpour, F. & Vanier, D., 2015.
Factors impacting selection of construction
subcontractors , Vancouver: The Canadian Society for Civil Engineering.
Hartmann, A., Ling, F. & Tan, J., 2009. Relative important of subcontractor selection criteria: evidence
from Singapore.
Journal of Construction Engineering Management, 135(9), pp. 826-832.
Jones, K., 2016.
Effective Communication = Better Construction Management. [Online]
Available at: https://www.isqft.com/start/blog-effective-communication-better-construction-
management/
[Accessed 17 January 2019].
Marzouk, M., El Kherbawy, A. & Khalifa, M., 2013. Factors influencing sub-contractors selection in
construction projects.
HBRC Journal, 9(2), pp. 150-158.
Polat, G., 2016. Subcontractor selection using the integration of the AHP and PROMETHEE methods.Journal of Civil Engineering and Management, 22(8), pp. 1042-1054.
working hours, general public, risky behaviors, evacuation procedures, fire assembly point,
standards, ethics, codes, standards, quality assurance, working at height, method statements,
progress reports, penalties, disputes and conflicts, early start, early finish, late start and late
finish.
References
Abbasianjahromi, H., Rajaie, H. & Shakeri, E., 2013. A Framework for Subcontractor Selection in the
Construction Industry.
Journal of Civil Engineering and Management, 19(2), pp. 158-168.
Akintan, O. & Morledge, R., 2013. Improving the Collaboration between Main Contractors and
Subcontractors within Traditional Construction Procurement.
Journal of Construction Engineering,
Volume 2013, pp. 1-11.
Froese, T., Newton, L., Sadeghpour, F. & Vanier, D., 2015.
Factors impacting selection of construction
subcontractors , Vancouver: The Canadian Society for Civil Engineering.
Hartmann, A., Ling, F. & Tan, J., 2009. Relative important of subcontractor selection criteria: evidence
from Singapore.
Journal of Construction Engineering Management, 135(9), pp. 826-832.
Jones, K., 2016.
Effective Communication = Better Construction Management. [Online]
Available at: https://www.isqft.com/start/blog-effective-communication-better-construction-
management/
[Accessed 17 January 2019].
Marzouk, M., El Kherbawy, A. & Khalifa, M., 2013. Factors influencing sub-contractors selection in
construction projects.
HBRC Journal, 9(2), pp. 150-158.
Polat, G., 2016. Subcontractor selection using the integration of the AHP and PROMETHEE methods.Journal of Civil Engineering and Management, 22(8), pp. 1042-1054.
Secure Best Marks with AI Grader
Need help grading? Try our AI Grader for instant feedback on your assignments.
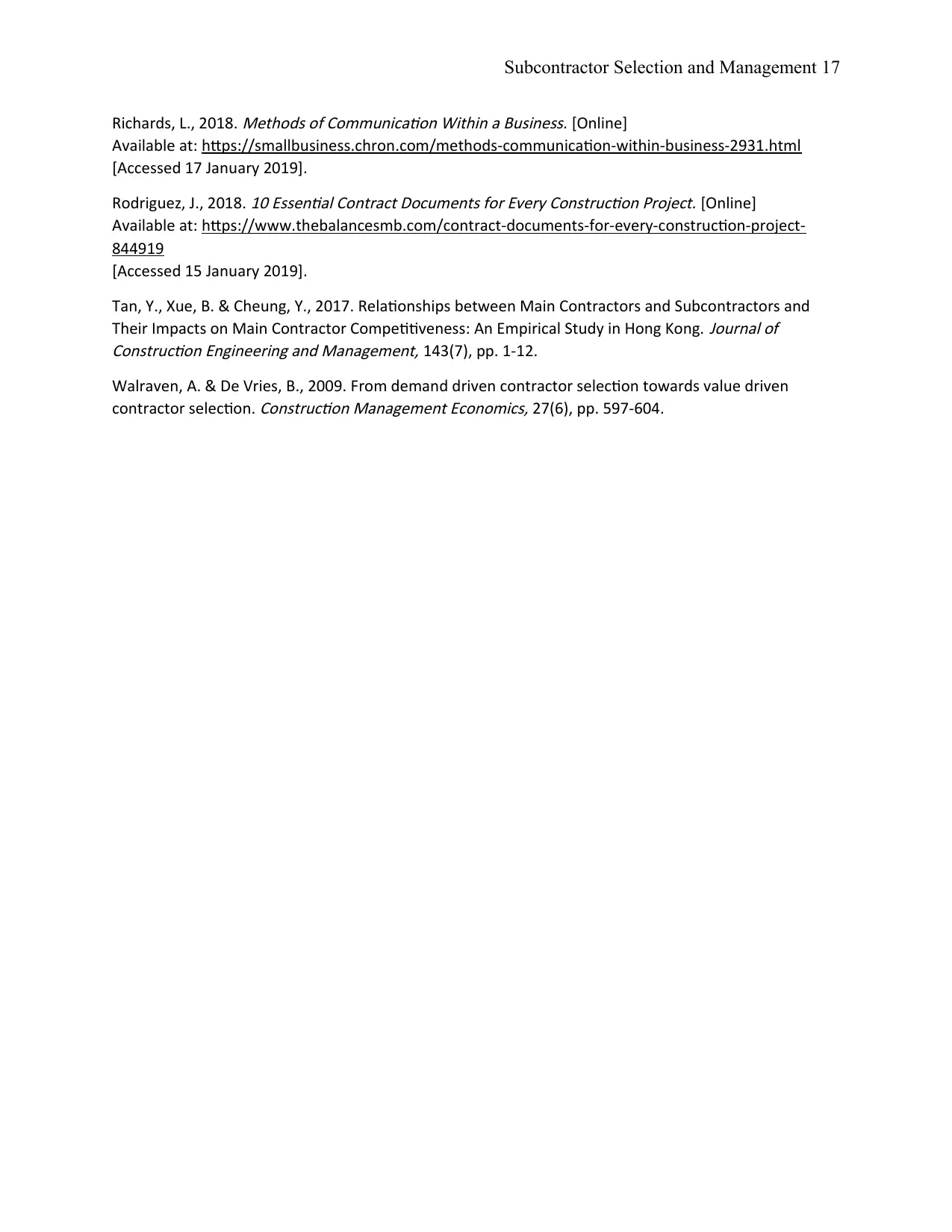
Subcontractor Selection and Management 17
Richards, L., 2018.
Methods of Communication Within a Business. [Online]
Available at: https://smallbusiness.chron.com/methods-communication-within-business-2931.html
[Accessed 17 January 2019].
Rodriguez, J., 2018.
10 Essential Contract Documents for Every Construction Project. [Online]
Available at: https://www.thebalancesmb.com/contract-documents-for-every-construction-project-
844919
[Accessed 15 January 2019].
Tan, Y., Xue, B. & Cheung, Y., 2017. Relationships between Main Contractors and Subcontractors and
Their Impacts on Main Contractor Competitiveness: An Empirical Study in Hong Kong.
Journal of
Construction Engineering and Management, 143(7), pp. 1-12.
Walraven, A. & De Vries, B., 2009. From demand driven contractor selection towards value driven
contractor selection.
Construction Management Economics, 27(6), pp. 597-604.
Richards, L., 2018.
Methods of Communication Within a Business. [Online]
Available at: https://smallbusiness.chron.com/methods-communication-within-business-2931.html
[Accessed 17 January 2019].
Rodriguez, J., 2018.
10 Essential Contract Documents for Every Construction Project. [Online]
Available at: https://www.thebalancesmb.com/contract-documents-for-every-construction-project-
844919
[Accessed 15 January 2019].
Tan, Y., Xue, B. & Cheung, Y., 2017. Relationships between Main Contractors and Subcontractors and
Their Impacts on Main Contractor Competitiveness: An Empirical Study in Hong Kong.
Journal of
Construction Engineering and Management, 143(7), pp. 1-12.
Walraven, A. & De Vries, B., 2009. From demand driven contractor selection towards value driven
contractor selection.
Construction Management Economics, 27(6), pp. 597-604.
1 out of 17
Related Documents
![[object Object]](/_next/image/?url=%2F_next%2Fstatic%2Fmedia%2Flogo.6d15ce61.png&w=640&q=75)
Your All-in-One AI-Powered Toolkit for Academic Success.
 +13062052269
info@desklib.com
Available 24*7 on WhatsApp / Email
Unlock your academic potential
© 2024  |  Zucol Services PVT LTD  |  All rights reserved.