CHEM101 Research Assignment: Sulphuric Acid and Haber Process
VerifiedAdded on 2023/06/04
|8
|1536
|134
Report
AI Summary
This chemistry research report delves into two crucial industrial processes: the contact process for the production of sulphuric acid and the Haber process for the synthesis of ammonia. The report details the stages involved in the contact process, including sulfur dioxide production, its conversion to ...
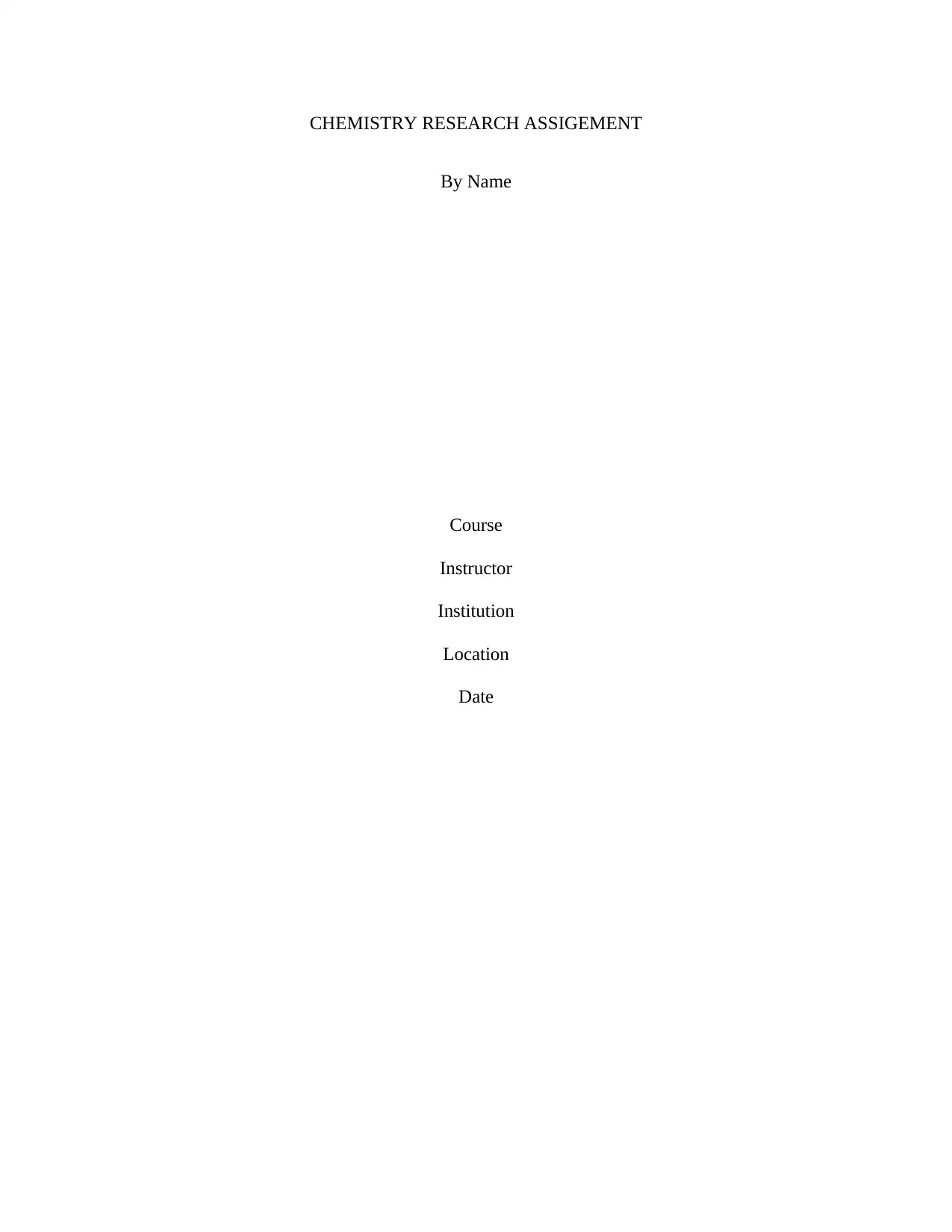
CHEMISTRY RESEARCH ASSIGEMENT
By Name
Course
Instructor
Institution
Location
Date
By Name
Course
Instructor
Institution
Location
Date
Paraphrase This Document
Need a fresh take? Get an instant paraphrase of this document with our AI Paraphraser
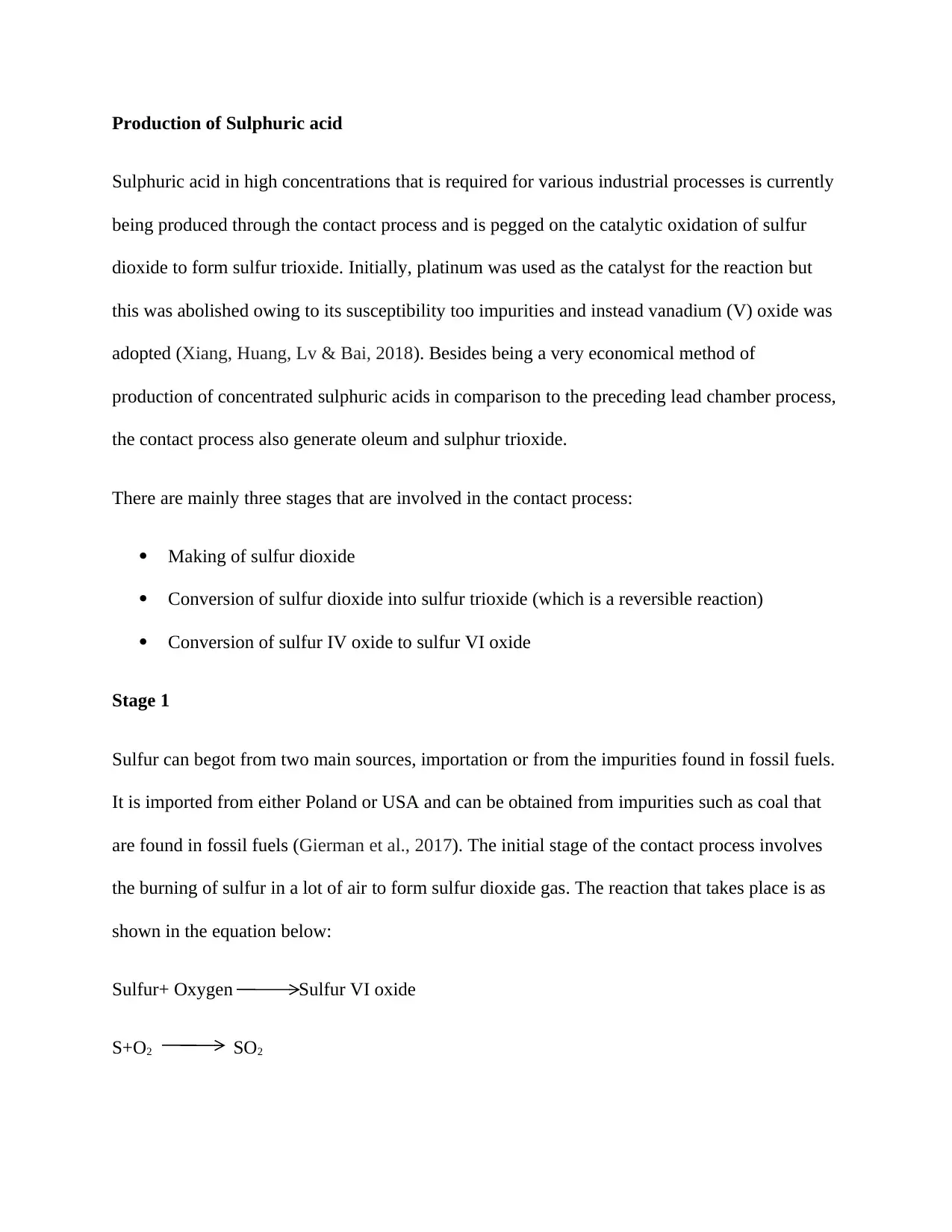
Production of Sulphuric acid
Sulphuric acid in high concentrations that is required for various industrial processes is currently
being produced through the contact process and is pegged on the catalytic oxidation of sulfur
dioxide to form sulfur trioxide. Initially, platinum was used as the catalyst for the reaction but
this was abolished owing to its susceptibility too impurities and instead vanadium (V) oxide was
adopted (Xiang, Huang, Lv & Bai, 2018). Besides being a very economical method of
production of concentrated sulphuric acids in comparison to the preceding lead chamber process,
the contact process also generate oleum and sulphur trioxide.
There are mainly three stages that are involved in the contact process:
Making of sulfur dioxide
Conversion of sulfur dioxide into sulfur trioxide (which is a reversible reaction)
Conversion of sulfur IV oxide to sulfur VI oxide
Stage 1
Sulfur can begot from two main sources, importation or from the impurities found in fossil fuels.
It is imported from either Poland or USA and can be obtained from impurities such as coal that
are found in fossil fuels (Gierman et al., 2017). The initial stage of the contact process involves
the burning of sulfur in a lot of air to form sulfur dioxide gas. The reaction that takes place is as
shown in the equation below:
Sulfur+ Oxygen Sulfur VI oxide
S+O2 SO2
Sulphuric acid in high concentrations that is required for various industrial processes is currently
being produced through the contact process and is pegged on the catalytic oxidation of sulfur
dioxide to form sulfur trioxide. Initially, platinum was used as the catalyst for the reaction but
this was abolished owing to its susceptibility too impurities and instead vanadium (V) oxide was
adopted (Xiang, Huang, Lv & Bai, 2018). Besides being a very economical method of
production of concentrated sulphuric acids in comparison to the preceding lead chamber process,
the contact process also generate oleum and sulphur trioxide.
There are mainly three stages that are involved in the contact process:
Making of sulfur dioxide
Conversion of sulfur dioxide into sulfur trioxide (which is a reversible reaction)
Conversion of sulfur IV oxide to sulfur VI oxide
Stage 1
Sulfur can begot from two main sources, importation or from the impurities found in fossil fuels.
It is imported from either Poland or USA and can be obtained from impurities such as coal that
are found in fossil fuels (Gierman et al., 2017). The initial stage of the contact process involves
the burning of sulfur in a lot of air to form sulfur dioxide gas. The reaction that takes place is as
shown in the equation below:
Sulfur+ Oxygen Sulfur VI oxide
S+O2 SO2
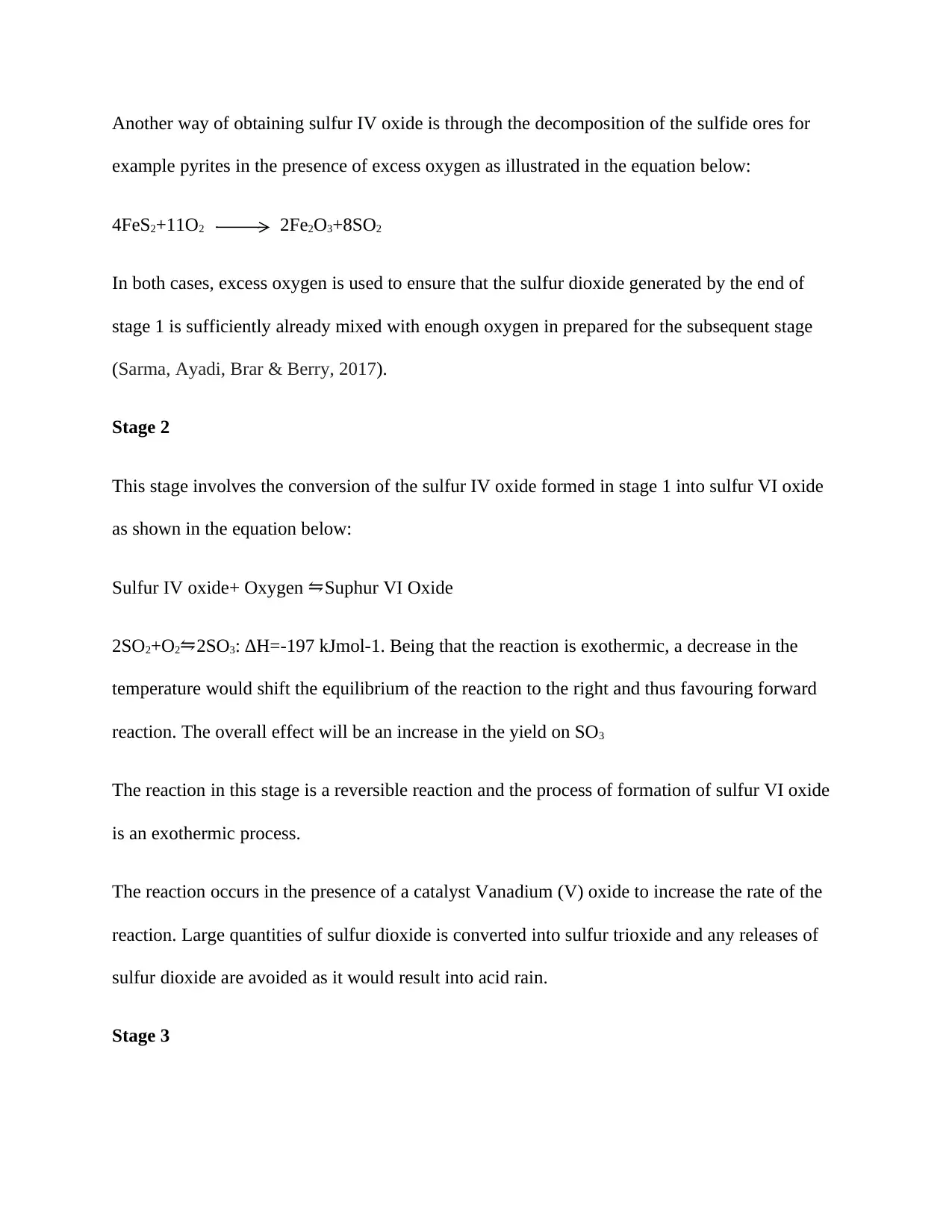
Another way of obtaining sulfur IV oxide is through the decomposition of the sulfide ores for
example pyrites in the presence of excess oxygen as illustrated in the equation below:
4FeS2+11O2 2Fe2O3+8SO2
In both cases, excess oxygen is used to ensure that the sulfur dioxide generated by the end of
stage 1 is sufficiently already mixed with enough oxygen in prepared for the subsequent stage
(Sarma, Ayadi, Brar & Berry, 2017).
Stage 2
This stage involves the conversion of the sulfur IV oxide formed in stage 1 into sulfur VI oxide
as shown in the equation below:
Sulfur IV oxide+ Oxygen ⇋Suphur VI Oxide
2SO2+O2⇋2SO3: ∆H=-197 kJmol-1. Being that the reaction is exothermic, a decrease in the
temperature would shift the equilibrium of the reaction to the right and thus favouring forward
reaction. The overall effect will be an increase in the yield on SO3
The reaction in this stage is a reversible reaction and the process of formation of sulfur VI oxide
is an exothermic process.
The reaction occurs in the presence of a catalyst Vanadium (V) oxide to increase the rate of the
reaction. Large quantities of sulfur dioxide is converted into sulfur trioxide and any releases of
sulfur dioxide are avoided as it would result into acid rain.
Stage 3
example pyrites in the presence of excess oxygen as illustrated in the equation below:
4FeS2+11O2 2Fe2O3+8SO2
In both cases, excess oxygen is used to ensure that the sulfur dioxide generated by the end of
stage 1 is sufficiently already mixed with enough oxygen in prepared for the subsequent stage
(Sarma, Ayadi, Brar & Berry, 2017).
Stage 2
This stage involves the conversion of the sulfur IV oxide formed in stage 1 into sulfur VI oxide
as shown in the equation below:
Sulfur IV oxide+ Oxygen ⇋Suphur VI Oxide
2SO2+O2⇋2SO3: ∆H=-197 kJmol-1. Being that the reaction is exothermic, a decrease in the
temperature would shift the equilibrium of the reaction to the right and thus favouring forward
reaction. The overall effect will be an increase in the yield on SO3
The reaction in this stage is a reversible reaction and the process of formation of sulfur VI oxide
is an exothermic process.
The reaction occurs in the presence of a catalyst Vanadium (V) oxide to increase the rate of the
reaction. Large quantities of sulfur dioxide is converted into sulfur trioxide and any releases of
sulfur dioxide are avoided as it would result into acid rain.
Stage 3
⊘ This is a preview!⊘
Do you want full access?
Subscribe today to unlock all pages.

Trusted by 1+ million students worldwide
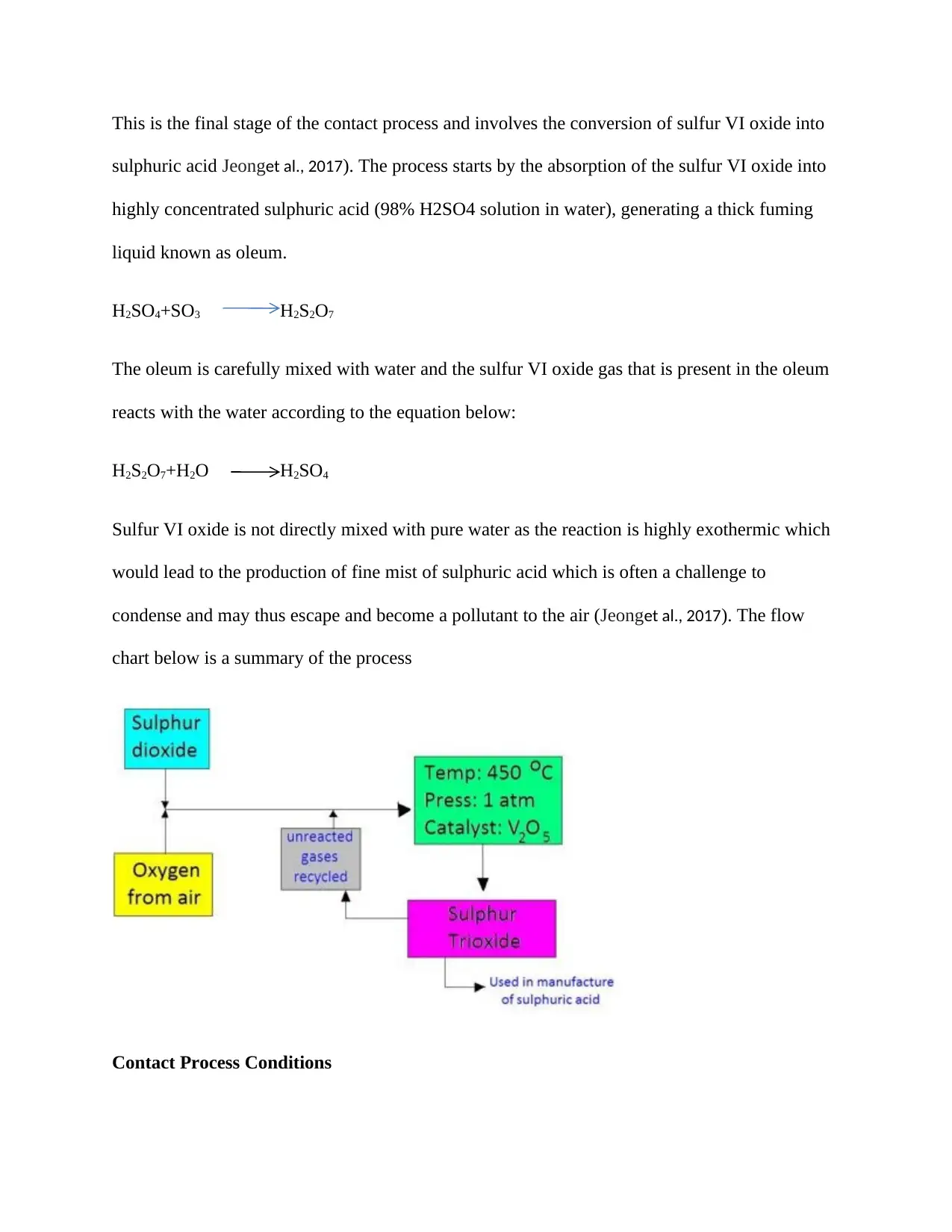
This is the final stage of the contact process and involves the conversion of sulfur VI oxide into
sulphuric acid Jeonget al., 2017). The process starts by the absorption of the sulfur VI oxide into
highly concentrated sulphuric acid (98% H2SO4 solution in water), generating a thick fuming
liquid known as oleum.
H2SO4+SO3 H2S2O7
The oleum is carefully mixed with water and the sulfur VI oxide gas that is present in the oleum
reacts with the water according to the equation below:
H2S2O7+H2O H2SO4
Sulfur VI oxide is not directly mixed with pure water as the reaction is highly exothermic which
would lead to the production of fine mist of sulphuric acid which is often a challenge to
condense and may thus escape and become a pollutant to the air (Jeonget al., 2017). The flow
chart below is a summary of the process
Contact Process Conditions
sulphuric acid Jeonget al., 2017). The process starts by the absorption of the sulfur VI oxide into
highly concentrated sulphuric acid (98% H2SO4 solution in water), generating a thick fuming
liquid known as oleum.
H2SO4+SO3 H2S2O7
The oleum is carefully mixed with water and the sulfur VI oxide gas that is present in the oleum
reacts with the water according to the equation below:
H2S2O7+H2O H2SO4
Sulfur VI oxide is not directly mixed with pure water as the reaction is highly exothermic which
would lead to the production of fine mist of sulphuric acid which is often a challenge to
condense and may thus escape and become a pollutant to the air (Jeonget al., 2017). The flow
chart below is a summary of the process
Contact Process Conditions
Paraphrase This Document
Need a fresh take? Get an instant paraphrase of this document with our AI Paraphraser
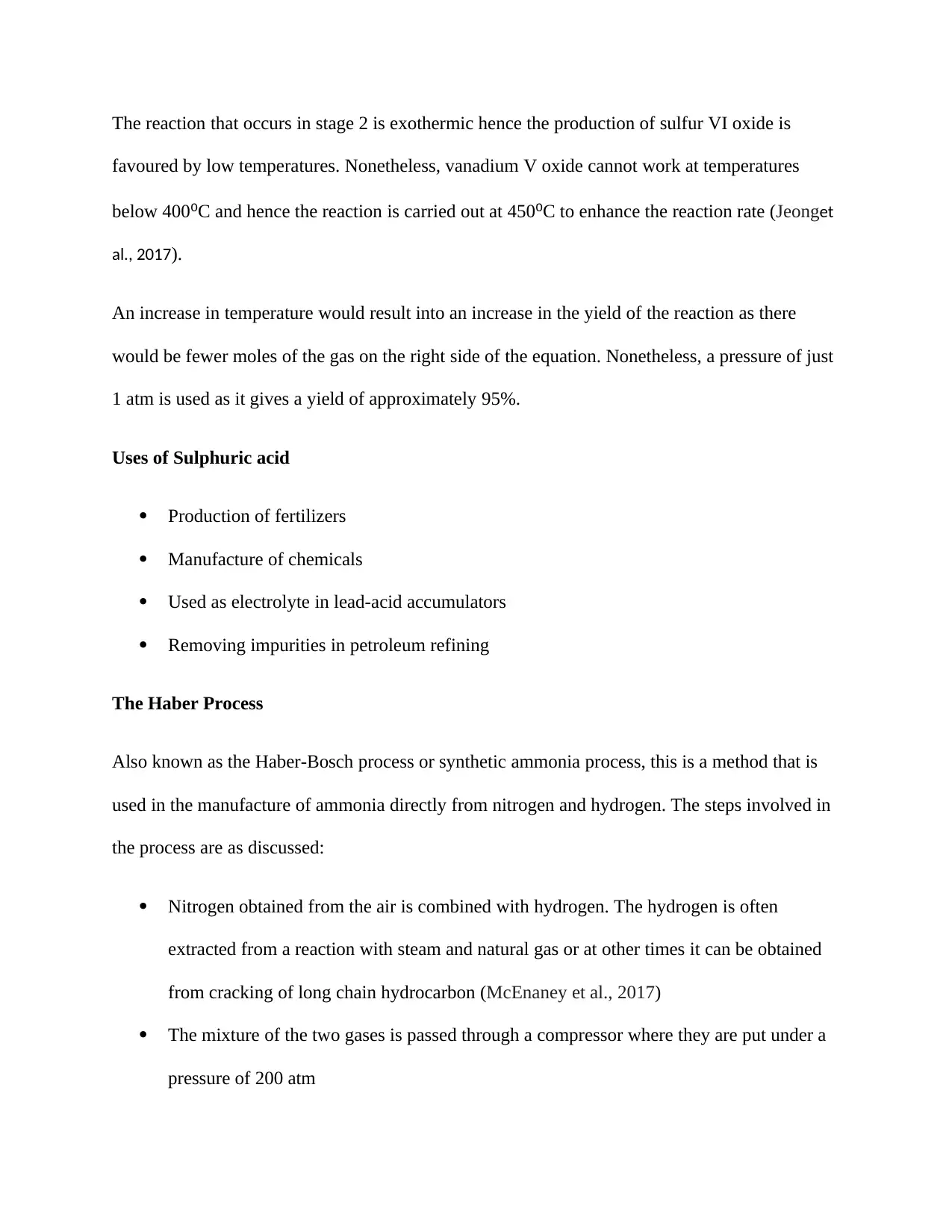
The reaction that occurs in stage 2 is exothermic hence the production of sulfur VI oxide is
favoured by low temperatures. Nonetheless, vanadium V oxide cannot work at temperatures
below 400⁰C and hence the reaction is carried out at 450⁰C to enhance the reaction rate (Jeonget
al., 2017).
An increase in temperature would result into an increase in the yield of the reaction as there
would be fewer moles of the gas on the right side of the equation. Nonetheless, a pressure of just
1 atm is used as it gives a yield of approximately 95%.
Uses of Sulphuric acid
Production of fertilizers
Manufacture of chemicals
Used as electrolyte in lead-acid accumulators
Removing impurities in petroleum refining
The Haber Process
Also known as the Haber-Bosch process or synthetic ammonia process, this is a method that is
used in the manufacture of ammonia directly from nitrogen and hydrogen. The steps involved in
the process are as discussed:
Nitrogen obtained from the air is combined with hydrogen. The hydrogen is often
extracted from a reaction with steam and natural gas or at other times it can be obtained
from cracking of long chain hydrocarbon (McEnaney et al., 2017)
The mixture of the two gases is passed through a compressor where they are put under a
pressure of 200 atm
favoured by low temperatures. Nonetheless, vanadium V oxide cannot work at temperatures
below 400⁰C and hence the reaction is carried out at 450⁰C to enhance the reaction rate (Jeonget
al., 2017).
An increase in temperature would result into an increase in the yield of the reaction as there
would be fewer moles of the gas on the right side of the equation. Nonetheless, a pressure of just
1 atm is used as it gives a yield of approximately 95%.
Uses of Sulphuric acid
Production of fertilizers
Manufacture of chemicals
Used as electrolyte in lead-acid accumulators
Removing impurities in petroleum refining
The Haber Process
Also known as the Haber-Bosch process or synthetic ammonia process, this is a method that is
used in the manufacture of ammonia directly from nitrogen and hydrogen. The steps involved in
the process are as discussed:
Nitrogen obtained from the air is combined with hydrogen. The hydrogen is often
extracted from a reaction with steam and natural gas or at other times it can be obtained
from cracking of long chain hydrocarbon (McEnaney et al., 2017)
The mixture of the two gases is passed through a compressor where they are put under a
pressure of 200 atm
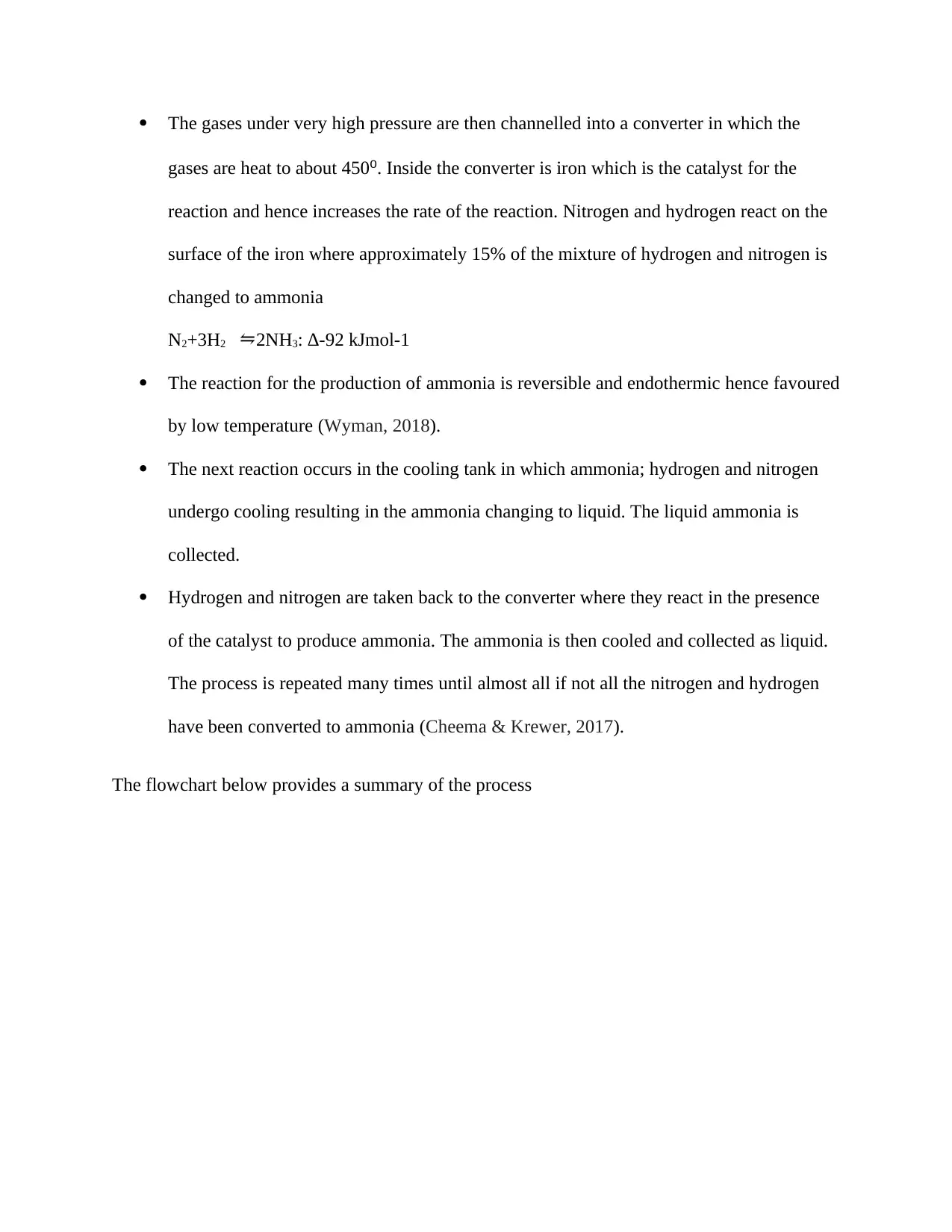
The gases under very high pressure are then channelled into a converter in which the
gases are heat to about 450⁰. Inside the converter is iron which is the catalyst for the
reaction and hence increases the rate of the reaction. Nitrogen and hydrogen react on the
surface of the iron where approximately 15% of the mixture of hydrogen and nitrogen is
changed to ammonia
N2+3H2 ⇋2NH3: ∆-92 kJmol-1
The reaction for the production of ammonia is reversible and endothermic hence favoured
by low temperature (Wyman, 2018).
The next reaction occurs in the cooling tank in which ammonia; hydrogen and nitrogen
undergo cooling resulting in the ammonia changing to liquid. The liquid ammonia is
collected.
Hydrogen and nitrogen are taken back to the converter where they react in the presence
of the catalyst to produce ammonia. The ammonia is then cooled and collected as liquid.
The process is repeated many times until almost all if not all the nitrogen and hydrogen
have been converted to ammonia (Cheema & Krewer, 2017).
The flowchart below provides a summary of the process
gases are heat to about 450⁰. Inside the converter is iron which is the catalyst for the
reaction and hence increases the rate of the reaction. Nitrogen and hydrogen react on the
surface of the iron where approximately 15% of the mixture of hydrogen and nitrogen is
changed to ammonia
N2+3H2 ⇋2NH3: ∆-92 kJmol-1
The reaction for the production of ammonia is reversible and endothermic hence favoured
by low temperature (Wyman, 2018).
The next reaction occurs in the cooling tank in which ammonia; hydrogen and nitrogen
undergo cooling resulting in the ammonia changing to liquid. The liquid ammonia is
collected.
Hydrogen and nitrogen are taken back to the converter where they react in the presence
of the catalyst to produce ammonia. The ammonia is then cooled and collected as liquid.
The process is repeated many times until almost all if not all the nitrogen and hydrogen
have been converted to ammonia (Cheema & Krewer, 2017).
The flowchart below provides a summary of the process
⊘ This is a preview!⊘
Do you want full access?
Subscribe today to unlock all pages.

Trusted by 1+ million students worldwide
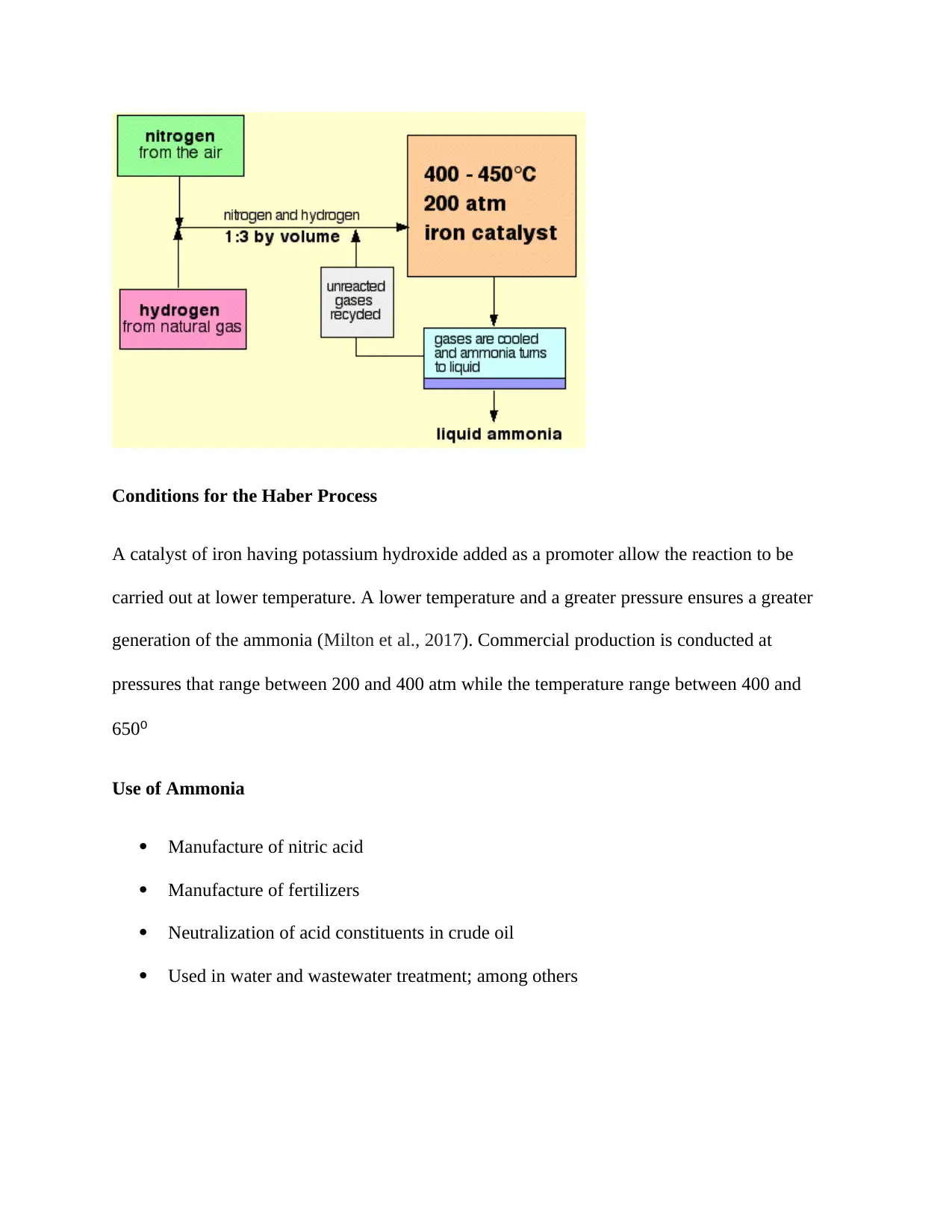
Conditions for the Haber Process
A catalyst of iron having potassium hydroxide added as a promoter allow the reaction to be
carried out at lower temperature. A lower temperature and a greater pressure ensures a greater
generation of the ammonia (Milton et al., 2017). Commercial production is conducted at
pressures that range between 200 and 400 atm while the temperature range between 400 and
650⁰
Use of Ammonia
Manufacture of nitric acid
Manufacture of fertilizers
Neutralization of acid constituents in crude oil
Used in water and wastewater treatment; among others
A catalyst of iron having potassium hydroxide added as a promoter allow the reaction to be
carried out at lower temperature. A lower temperature and a greater pressure ensures a greater
generation of the ammonia (Milton et al., 2017). Commercial production is conducted at
pressures that range between 200 and 400 atm while the temperature range between 400 and
650⁰
Use of Ammonia
Manufacture of nitric acid
Manufacture of fertilizers
Neutralization of acid constituents in crude oil
Used in water and wastewater treatment; among others
Paraphrase This Document
Need a fresh take? Get an instant paraphrase of this document with our AI Paraphraser
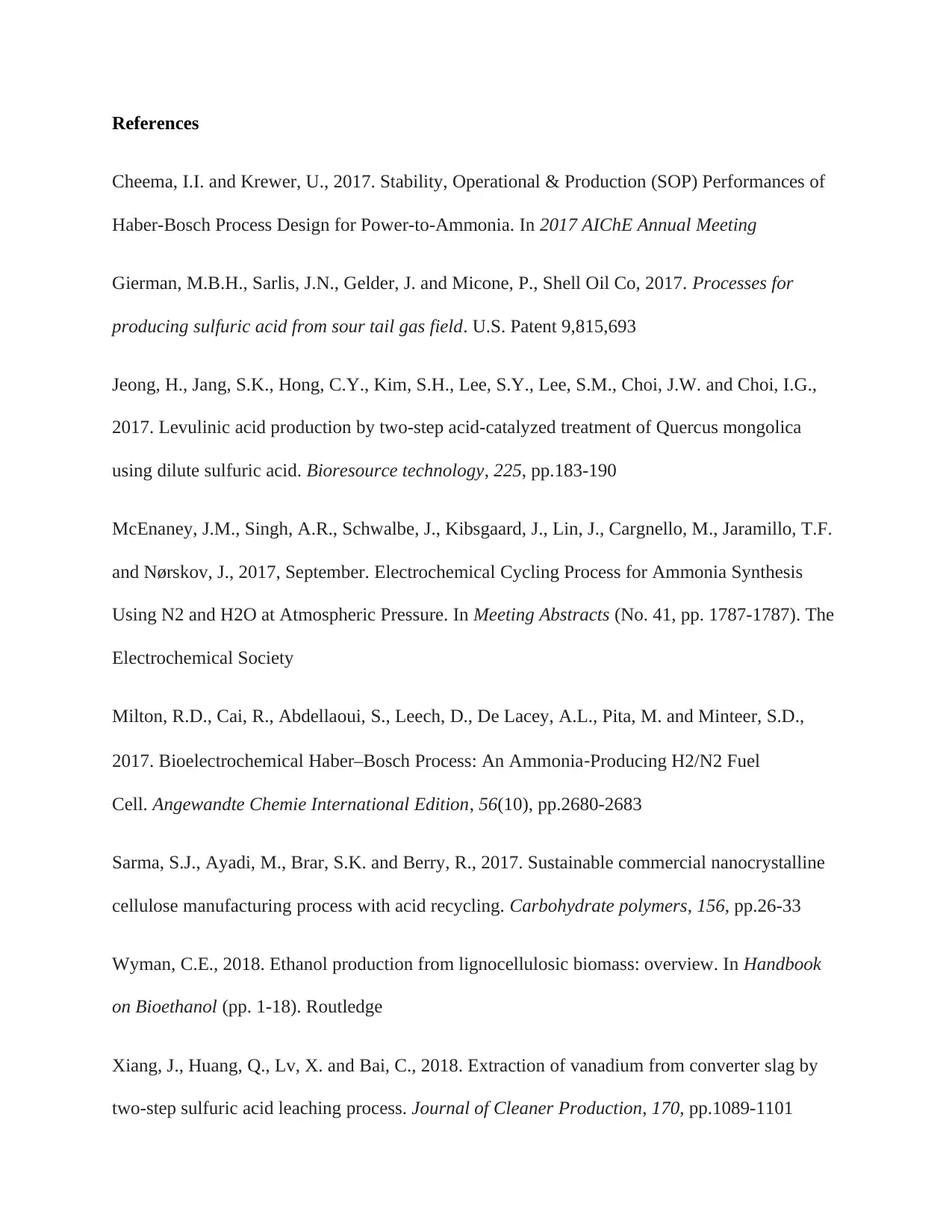
References
Cheema, I.I. and Krewer, U., 2017. Stability, Operational & Production (SOP) Performances of
Haber-Bosch Process Design for Power-to-Ammonia. In 2017 AIChE Annual Meeting
Gierman, M.B.H., Sarlis, J.N., Gelder, J. and Micone, P., Shell Oil Co, 2017. Processes for
producing sulfuric acid from sour tail gas field. U.S. Patent 9,815,693
Jeong, H., Jang, S.K., Hong, C.Y., Kim, S.H., Lee, S.Y., Lee, S.M., Choi, J.W. and Choi, I.G.,
2017. Levulinic acid production by two-step acid-catalyzed treatment of Quercus mongolica
using dilute sulfuric acid. Bioresource technology, 225, pp.183-190
McEnaney, J.M., Singh, A.R., Schwalbe, J., Kibsgaard, J., Lin, J., Cargnello, M., Jaramillo, T.F.
and Nørskov, J., 2017, September. Electrochemical Cycling Process for Ammonia Synthesis
Using N2 and H2O at Atmospheric Pressure. In Meeting Abstracts (No. 41, pp. 1787-1787). The
Electrochemical Society
Milton, R.D., Cai, R., Abdellaoui, S., Leech, D., De Lacey, A.L., Pita, M. and Minteer, S.D.,
2017. Bioelectrochemical Haber–Bosch Process: An Ammonia‐Producing H2/N2 Fuel
Cell. Angewandte Chemie International Edition, 56(10), pp.2680-2683
Sarma, S.J., Ayadi, M., Brar, S.K. and Berry, R., 2017. Sustainable commercial nanocrystalline
cellulose manufacturing process with acid recycling. Carbohydrate polymers, 156, pp.26-33
Wyman, C.E., 2018. Ethanol production from lignocellulosic biomass: overview. In Handbook
on Bioethanol (pp. 1-18). Routledge
Xiang, J., Huang, Q., Lv, X. and Bai, C., 2018. Extraction of vanadium from converter slag by
two-step sulfuric acid leaching process. Journal of Cleaner Production, 170, pp.1089-1101
Cheema, I.I. and Krewer, U., 2017. Stability, Operational & Production (SOP) Performances of
Haber-Bosch Process Design for Power-to-Ammonia. In 2017 AIChE Annual Meeting
Gierman, M.B.H., Sarlis, J.N., Gelder, J. and Micone, P., Shell Oil Co, 2017. Processes for
producing sulfuric acid from sour tail gas field. U.S. Patent 9,815,693
Jeong, H., Jang, S.K., Hong, C.Y., Kim, S.H., Lee, S.Y., Lee, S.M., Choi, J.W. and Choi, I.G.,
2017. Levulinic acid production by two-step acid-catalyzed treatment of Quercus mongolica
using dilute sulfuric acid. Bioresource technology, 225, pp.183-190
McEnaney, J.M., Singh, A.R., Schwalbe, J., Kibsgaard, J., Lin, J., Cargnello, M., Jaramillo, T.F.
and Nørskov, J., 2017, September. Electrochemical Cycling Process for Ammonia Synthesis
Using N2 and H2O at Atmospheric Pressure. In Meeting Abstracts (No. 41, pp. 1787-1787). The
Electrochemical Society
Milton, R.D., Cai, R., Abdellaoui, S., Leech, D., De Lacey, A.L., Pita, M. and Minteer, S.D.,
2017. Bioelectrochemical Haber–Bosch Process: An Ammonia‐Producing H2/N2 Fuel
Cell. Angewandte Chemie International Edition, 56(10), pp.2680-2683
Sarma, S.J., Ayadi, M., Brar, S.K. and Berry, R., 2017. Sustainable commercial nanocrystalline
cellulose manufacturing process with acid recycling. Carbohydrate polymers, 156, pp.26-33
Wyman, C.E., 2018. Ethanol production from lignocellulosic biomass: overview. In Handbook
on Bioethanol (pp. 1-18). Routledge
Xiang, J., Huang, Q., Lv, X. and Bai, C., 2018. Extraction of vanadium from converter slag by
two-step sulfuric acid leaching process. Journal of Cleaner Production, 170, pp.1089-1101
1 out of 8

Your All-in-One AI-Powered Toolkit for Academic Success.
+13062052269
info@desklib.com
Available 24*7 on WhatsApp / Email
Unlock your academic potential
© 2024 | Zucol Services PVT LTD | All rights reserved.