Supply Chain and Risk Management Summary 2022
VerifiedAdded on 2022/08/21
|18
|4190
|14
Summary
AI Summary
Contribute Materials
Your contribution can guide someone’s learning journey. Share your
documents today.
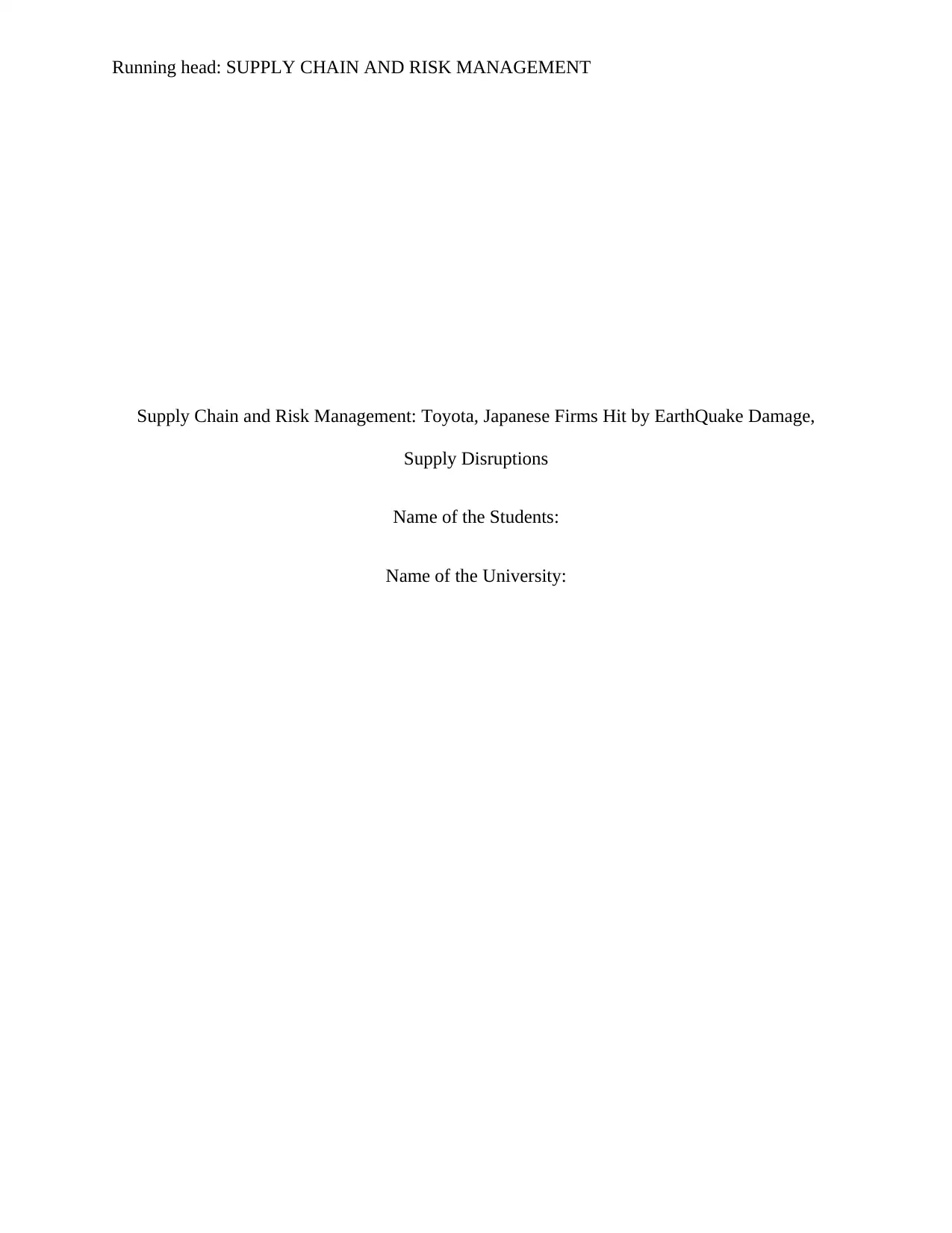
Running head: SUPPLY CHAIN AND RISK MANAGEMENT
Supply Chain and Risk Management: Toyota, Japanese Firms Hit by EarthQuake Damage,
Supply Disruptions
Name of the Students:
Name of the University:
Supply Chain and Risk Management: Toyota, Japanese Firms Hit by EarthQuake Damage,
Supply Disruptions
Name of the Students:
Name of the University:
Secure Best Marks with AI Grader
Need help grading? Try our AI Grader for instant feedback on your assignments.
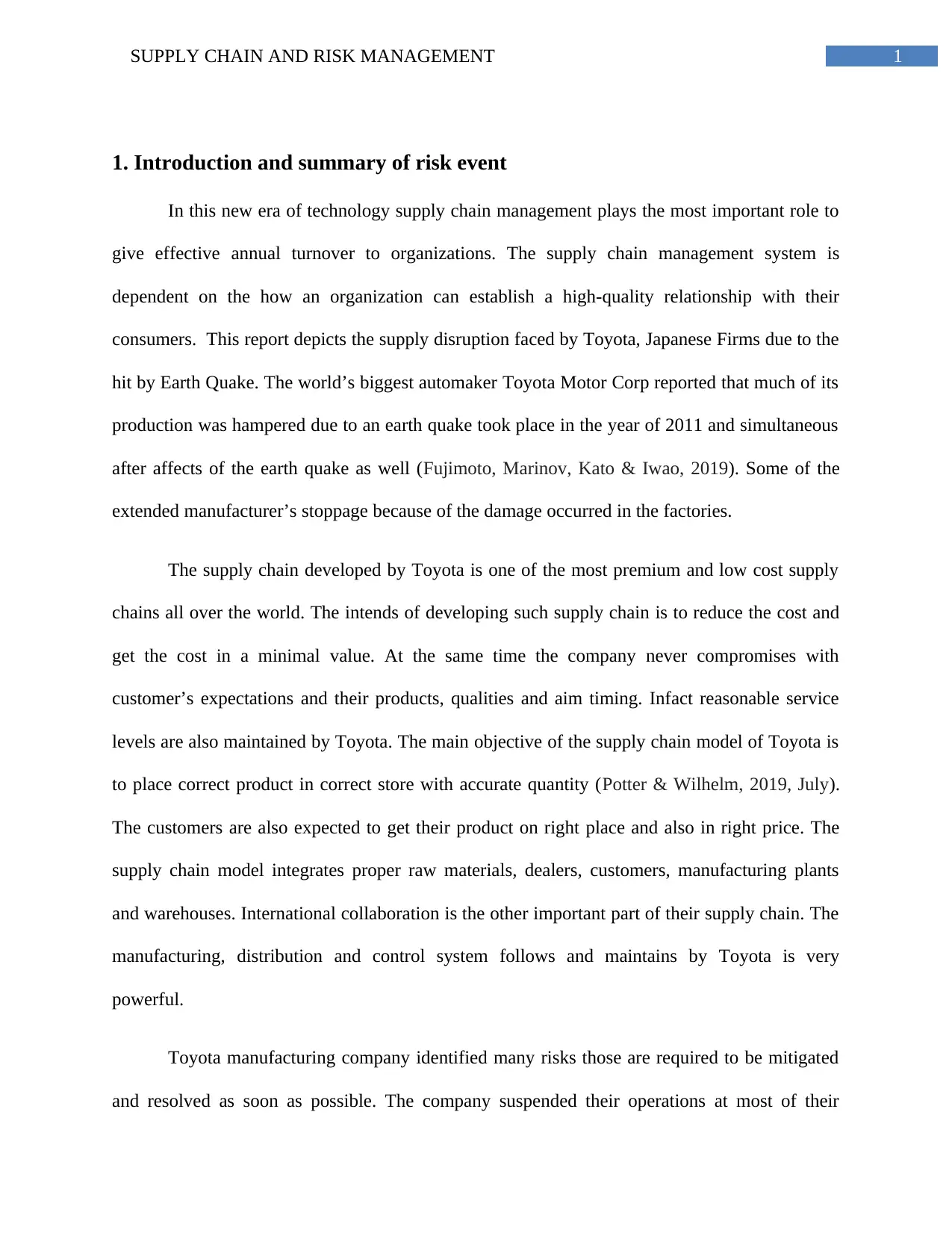
1SUPPLY CHAIN AND RISK MANAGEMENT
1. Introduction and summary of risk event
In this new era of technology supply chain management plays the most important role to
give effective annual turnover to organizations. The supply chain management system is
dependent on the how an organization can establish a high-quality relationship with their
consumers. This report depicts the supply disruption faced by Toyota, Japanese Firms due to the
hit by Earth Quake. The world’s biggest automaker Toyota Motor Corp reported that much of its
production was hampered due to an earth quake took place in the year of 2011 and simultaneous
after affects of the earth quake as well (Fujimoto, Marinov, Kato & Iwao, 2019). Some of the
extended manufacturer’s stoppage because of the damage occurred in the factories.
The supply chain developed by Toyota is one of the most premium and low cost supply
chains all over the world. The intends of developing such supply chain is to reduce the cost and
get the cost in a minimal value. At the same time the company never compromises with
customer’s expectations and their products, qualities and aim timing. Infact reasonable service
levels are also maintained by Toyota. The main objective of the supply chain model of Toyota is
to place correct product in correct store with accurate quantity (Potter & Wilhelm, 2019, July).
The customers are also expected to get their product on right place and also in right price. The
supply chain model integrates proper raw materials, dealers, customers, manufacturing plants
and warehouses. International collaboration is the other important part of their supply chain. The
manufacturing, distribution and control system follows and maintains by Toyota is very
powerful.
Toyota manufacturing company identified many risks those are required to be mitigated
and resolved as soon as possible. The company suspended their operations at most of their
1. Introduction and summary of risk event
In this new era of technology supply chain management plays the most important role to
give effective annual turnover to organizations. The supply chain management system is
dependent on the how an organization can establish a high-quality relationship with their
consumers. This report depicts the supply disruption faced by Toyota, Japanese Firms due to the
hit by Earth Quake. The world’s biggest automaker Toyota Motor Corp reported that much of its
production was hampered due to an earth quake took place in the year of 2011 and simultaneous
after affects of the earth quake as well (Fujimoto, Marinov, Kato & Iwao, 2019). Some of the
extended manufacturer’s stoppage because of the damage occurred in the factories.
The supply chain developed by Toyota is one of the most premium and low cost supply
chains all over the world. The intends of developing such supply chain is to reduce the cost and
get the cost in a minimal value. At the same time the company never compromises with
customer’s expectations and their products, qualities and aim timing. Infact reasonable service
levels are also maintained by Toyota. The main objective of the supply chain model of Toyota is
to place correct product in correct store with accurate quantity (Potter & Wilhelm, 2019, July).
The customers are also expected to get their product on right place and also in right price. The
supply chain model integrates proper raw materials, dealers, customers, manufacturing plants
and warehouses. International collaboration is the other important part of their supply chain. The
manufacturing, distribution and control system follows and maintains by Toyota is very
powerful.
Toyota manufacturing company identified many risks those are required to be mitigated
and resolved as soon as possible. The company suspended their operations at most of their
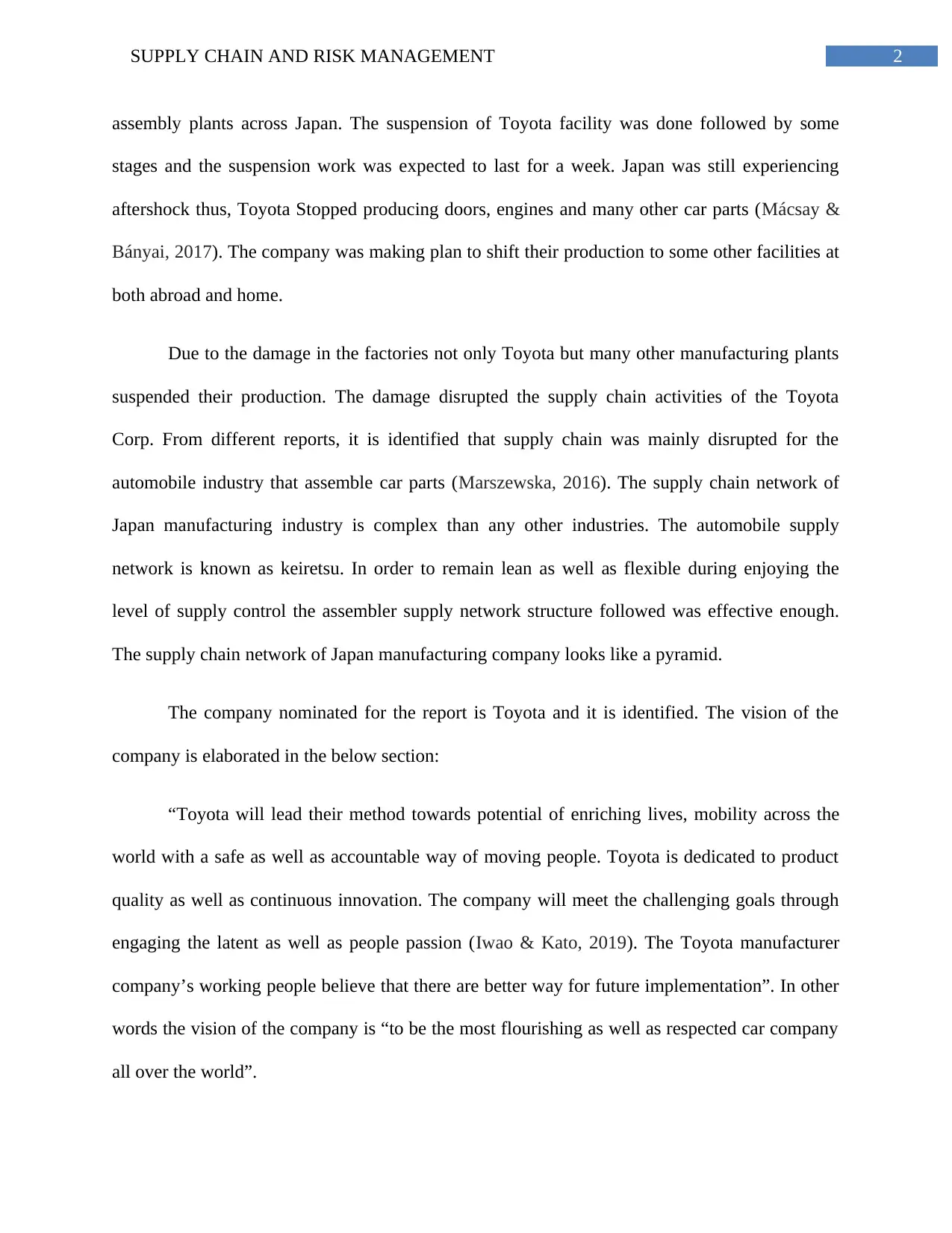
2SUPPLY CHAIN AND RISK MANAGEMENT
assembly plants across Japan. The suspension of Toyota facility was done followed by some
stages and the suspension work was expected to last for a week. Japan was still experiencing
aftershock thus, Toyota Stopped producing doors, engines and many other car parts (Mácsay &
Bányai, 2017). The company was making plan to shift their production to some other facilities at
both abroad and home.
Due to the damage in the factories not only Toyota but many other manufacturing plants
suspended their production. The damage disrupted the supply chain activities of the Toyota
Corp. From different reports, it is identified that supply chain was mainly disrupted for the
automobile industry that assemble car parts (Marszewska, 2016). The supply chain network of
Japan manufacturing industry is complex than any other industries. The automobile supply
network is known as keiretsu. In order to remain lean as well as flexible during enjoying the
level of supply control the assembler supply network structure followed was effective enough.
The supply chain network of Japan manufacturing company looks like a pyramid.
The company nominated for the report is Toyota and it is identified. The vision of the
company is elaborated in the below section:
“Toyota will lead their method towards potential of enriching lives, mobility across the
world with a safe as well as accountable way of moving people. Toyota is dedicated to product
quality as well as continuous innovation. The company will meet the challenging goals through
engaging the latent as well as people passion (Iwao & Kato, 2019). The Toyota manufacturer
company’s working people believe that there are better way for future implementation”. In other
words the vision of the company is “to be the most flourishing as well as respected car company
all over the world”.
assembly plants across Japan. The suspension of Toyota facility was done followed by some
stages and the suspension work was expected to last for a week. Japan was still experiencing
aftershock thus, Toyota Stopped producing doors, engines and many other car parts (Mácsay &
Bányai, 2017). The company was making plan to shift their production to some other facilities at
both abroad and home.
Due to the damage in the factories not only Toyota but many other manufacturing plants
suspended their production. The damage disrupted the supply chain activities of the Toyota
Corp. From different reports, it is identified that supply chain was mainly disrupted for the
automobile industry that assemble car parts (Marszewska, 2016). The supply chain network of
Japan manufacturing industry is complex than any other industries. The automobile supply
network is known as keiretsu. In order to remain lean as well as flexible during enjoying the
level of supply control the assembler supply network structure followed was effective enough.
The supply chain network of Japan manufacturing company looks like a pyramid.
The company nominated for the report is Toyota and it is identified. The vision of the
company is elaborated in the below section:
“Toyota will lead their method towards potential of enriching lives, mobility across the
world with a safe as well as accountable way of moving people. Toyota is dedicated to product
quality as well as continuous innovation. The company will meet the challenging goals through
engaging the latent as well as people passion (Iwao & Kato, 2019). The Toyota manufacturer
company’s working people believe that there are better way for future implementation”. In other
words the vision of the company is “to be the most flourishing as well as respected car company
all over the world”.
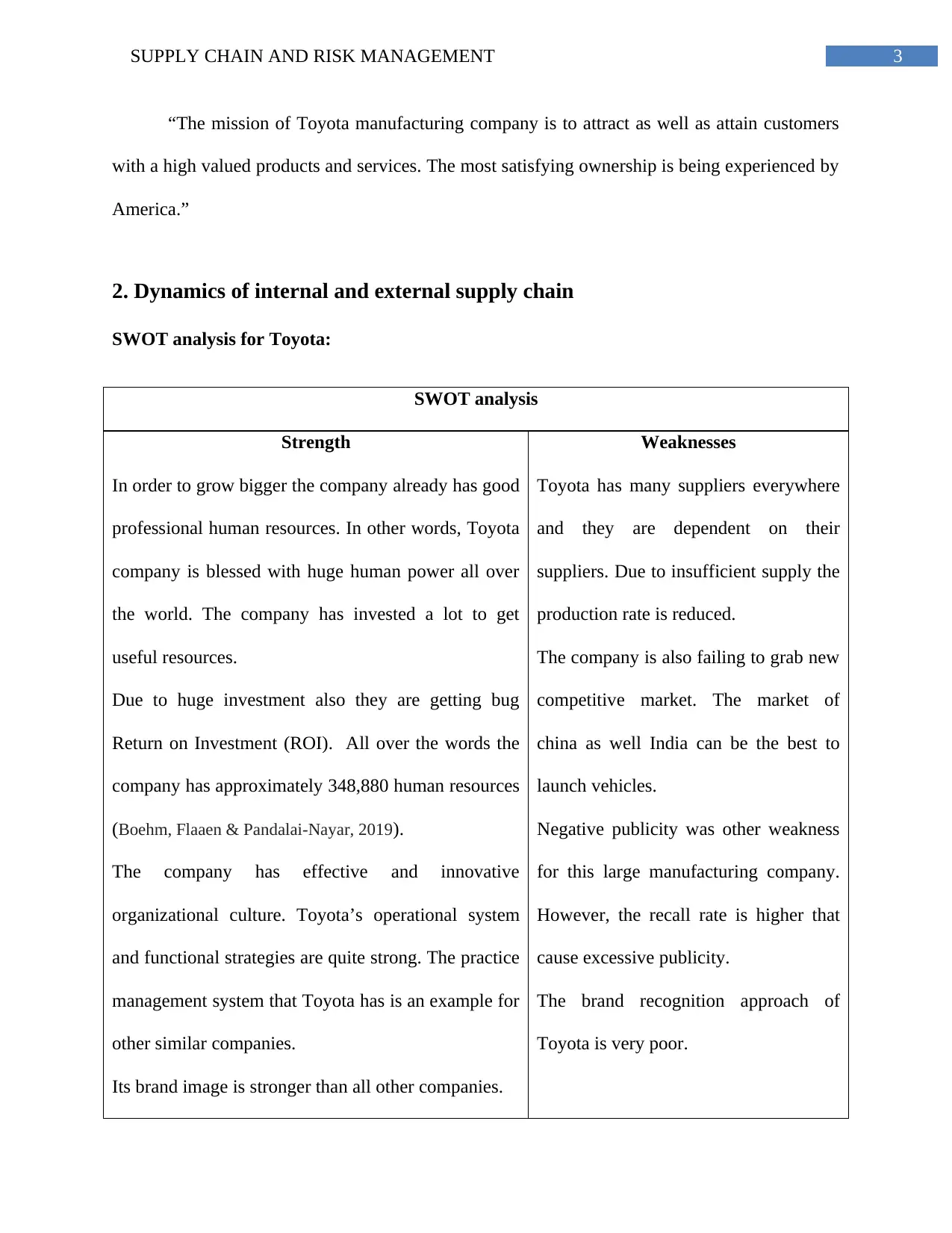
3SUPPLY CHAIN AND RISK MANAGEMENT
“The mission of Toyota manufacturing company is to attract as well as attain customers
with a high valued products and services. The most satisfying ownership is being experienced by
America.”
2. Dynamics of internal and external supply chain
SWOT analysis for Toyota:
SWOT analysis
Strength
In order to grow bigger the company already has good
professional human resources. In other words, Toyota
company is blessed with huge human power all over
the world. The company has invested a lot to get
useful resources.
Due to huge investment also they are getting bug
Return on Investment (ROI). All over the words the
company has approximately 348,880 human resources
(Boehm, Flaaen & Pandalai-Nayar, 2019).
The company has effective and innovative
organizational culture. Toyota’s operational system
and functional strategies are quite strong. The practice
management system that Toyota has is an example for
other similar companies.
Its brand image is stronger than all other companies.
Weaknesses
Toyota has many suppliers everywhere
and they are dependent on their
suppliers. Due to insufficient supply the
production rate is reduced.
The company is also failing to grab new
competitive market. The market of
china as well India can be the best to
launch vehicles.
Negative publicity was other weakness
for this large manufacturing company.
However, the recall rate is higher that
cause excessive publicity.
The brand recognition approach of
Toyota is very poor.
“The mission of Toyota manufacturing company is to attract as well as attain customers
with a high valued products and services. The most satisfying ownership is being experienced by
America.”
2. Dynamics of internal and external supply chain
SWOT analysis for Toyota:
SWOT analysis
Strength
In order to grow bigger the company already has good
professional human resources. In other words, Toyota
company is blessed with huge human power all over
the world. The company has invested a lot to get
useful resources.
Due to huge investment also they are getting bug
Return on Investment (ROI). All over the words the
company has approximately 348,880 human resources
(Boehm, Flaaen & Pandalai-Nayar, 2019).
The company has effective and innovative
organizational culture. Toyota’s operational system
and functional strategies are quite strong. The practice
management system that Toyota has is an example for
other similar companies.
Its brand image is stronger than all other companies.
Weaknesses
Toyota has many suppliers everywhere
and they are dependent on their
suppliers. Due to insufficient supply the
production rate is reduced.
The company is also failing to grab new
competitive market. The market of
china as well India can be the best to
launch vehicles.
Negative publicity was other weakness
for this large manufacturing company.
However, the recall rate is higher that
cause excessive publicity.
The brand recognition approach of
Toyota is very poor.
Secure Best Marks with AI Grader
Need help grading? Try our AI Grader for instant feedback on your assignments.
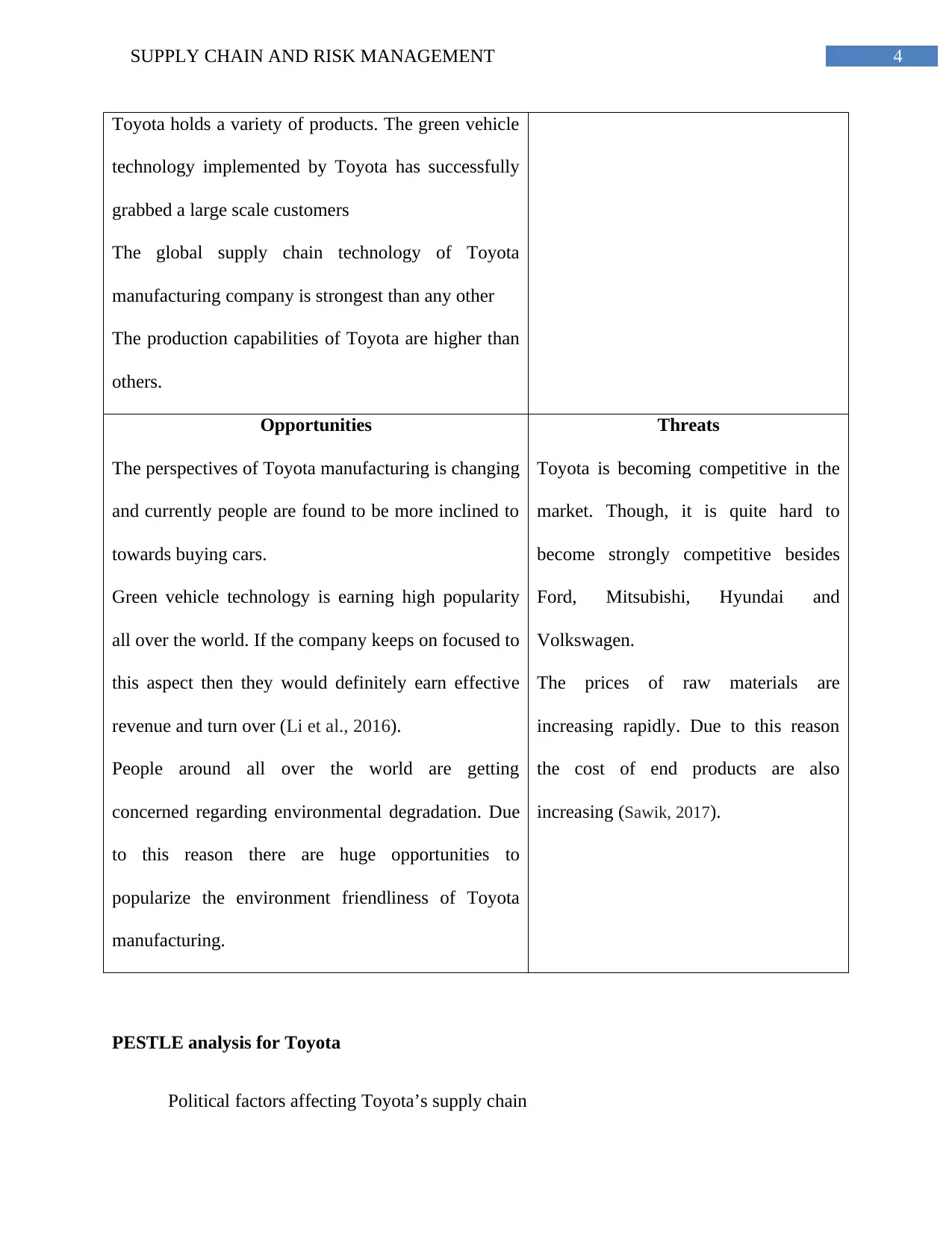
4SUPPLY CHAIN AND RISK MANAGEMENT
Toyota holds a variety of products. The green vehicle
technology implemented by Toyota has successfully
grabbed a large scale customers
The global supply chain technology of Toyota
manufacturing company is strongest than any other
The production capabilities of Toyota are higher than
others.
Opportunities
The perspectives of Toyota manufacturing is changing
and currently people are found to be more inclined to
towards buying cars.
Green vehicle technology is earning high popularity
all over the world. If the company keeps on focused to
this aspect then they would definitely earn effective
revenue and turn over (Li et al., 2016).
People around all over the world are getting
concerned regarding environmental degradation. Due
to this reason there are huge opportunities to
popularize the environment friendliness of Toyota
manufacturing.
Threats
Toyota is becoming competitive in the
market. Though, it is quite hard to
become strongly competitive besides
Ford, Mitsubishi, Hyundai and
Volkswagen.
The prices of raw materials are
increasing rapidly. Due to this reason
the cost of end products are also
increasing (Sawik, 2017).
PESTLE analysis for Toyota
Political factors affecting Toyota’s supply chain
Toyota holds a variety of products. The green vehicle
technology implemented by Toyota has successfully
grabbed a large scale customers
The global supply chain technology of Toyota
manufacturing company is strongest than any other
The production capabilities of Toyota are higher than
others.
Opportunities
The perspectives of Toyota manufacturing is changing
and currently people are found to be more inclined to
towards buying cars.
Green vehicle technology is earning high popularity
all over the world. If the company keeps on focused to
this aspect then they would definitely earn effective
revenue and turn over (Li et al., 2016).
People around all over the world are getting
concerned regarding environmental degradation. Due
to this reason there are huge opportunities to
popularize the environment friendliness of Toyota
manufacturing.
Threats
Toyota is becoming competitive in the
market. Though, it is quite hard to
become strongly competitive besides
Ford, Mitsubishi, Hyundai and
Volkswagen.
The prices of raw materials are
increasing rapidly. Due to this reason
the cost of end products are also
increasing (Sawik, 2017).
PESTLE analysis for Toyota
Political factors affecting Toyota’s supply chain
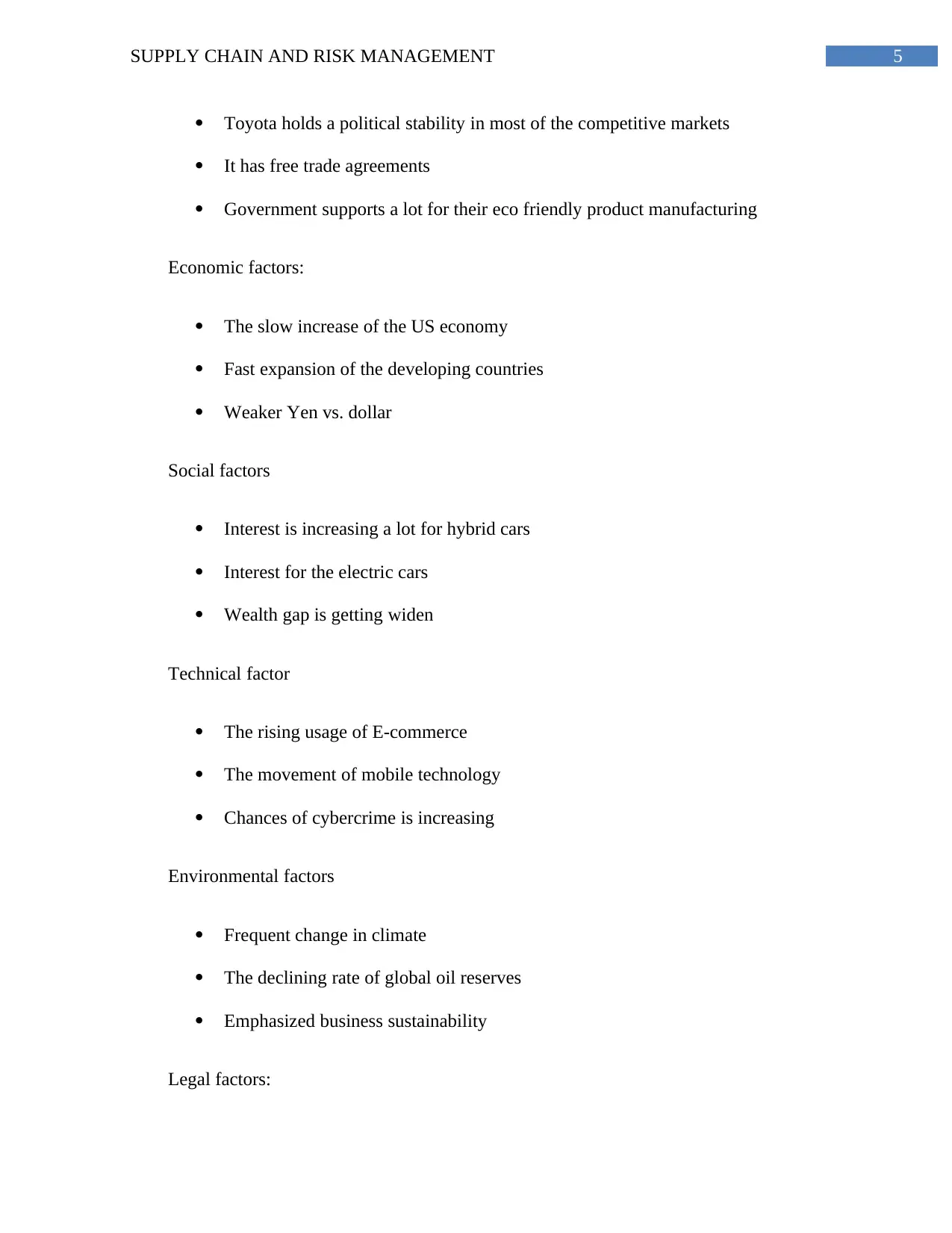
5SUPPLY CHAIN AND RISK MANAGEMENT
Toyota holds a political stability in most of the competitive markets
It has free trade agreements
Government supports a lot for their eco friendly product manufacturing
Economic factors:
The slow increase of the US economy
Fast expansion of the developing countries
Weaker Yen vs. dollar
Social factors
Interest is increasing a lot for hybrid cars
Interest for the electric cars
Wealth gap is getting widen
Technical factor
The rising usage of E-commerce
The movement of mobile technology
Chances of cybercrime is increasing
Environmental factors
Frequent change in climate
The declining rate of global oil reserves
Emphasized business sustainability
Legal factors:
Toyota holds a political stability in most of the competitive markets
It has free trade agreements
Government supports a lot for their eco friendly product manufacturing
Economic factors:
The slow increase of the US economy
Fast expansion of the developing countries
Weaker Yen vs. dollar
Social factors
Interest is increasing a lot for hybrid cars
Interest for the electric cars
Wealth gap is getting widen
Technical factor
The rising usage of E-commerce
The movement of mobile technology
Chances of cybercrime is increasing
Environmental factors
Frequent change in climate
The declining rate of global oil reserves
Emphasized business sustainability
Legal factors:
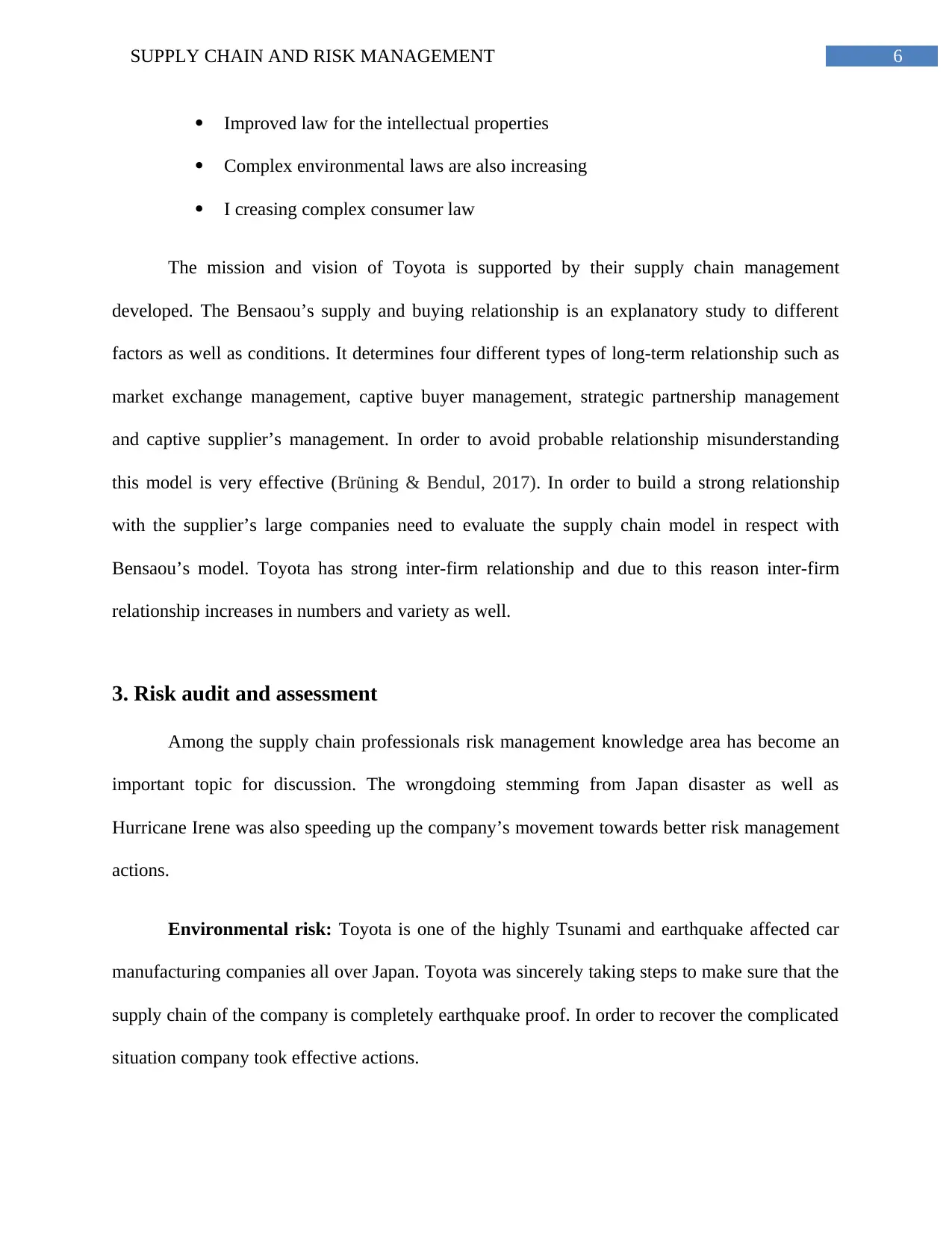
6SUPPLY CHAIN AND RISK MANAGEMENT
Improved law for the intellectual properties
Complex environmental laws are also increasing
I creasing complex consumer law
The mission and vision of Toyota is supported by their supply chain management
developed. The Bensaou’s supply and buying relationship is an explanatory study to different
factors as well as conditions. It determines four different types of long-term relationship such as
market exchange management, captive buyer management, strategic partnership management
and captive supplier’s management. In order to avoid probable relationship misunderstanding
this model is very effective (Brüning & Bendul, 2017). In order to build a strong relationship
with the supplier’s large companies need to evaluate the supply chain model in respect with
Bensaou’s model. Toyota has strong inter-firm relationship and due to this reason inter-firm
relationship increases in numbers and variety as well.
3. Risk audit and assessment
Among the supply chain professionals risk management knowledge area has become an
important topic for discussion. The wrongdoing stemming from Japan disaster as well as
Hurricane Irene was also speeding up the company’s movement towards better risk management
actions.
Environmental risk: Toyota is one of the highly Tsunami and earthquake affected car
manufacturing companies all over Japan. Toyota was sincerely taking steps to make sure that the
supply chain of the company is completely earthquake proof. In order to recover the complicated
situation company took effective actions.
Improved law for the intellectual properties
Complex environmental laws are also increasing
I creasing complex consumer law
The mission and vision of Toyota is supported by their supply chain management
developed. The Bensaou’s supply and buying relationship is an explanatory study to different
factors as well as conditions. It determines four different types of long-term relationship such as
market exchange management, captive buyer management, strategic partnership management
and captive supplier’s management. In order to avoid probable relationship misunderstanding
this model is very effective (Brüning & Bendul, 2017). In order to build a strong relationship
with the supplier’s large companies need to evaluate the supply chain model in respect with
Bensaou’s model. Toyota has strong inter-firm relationship and due to this reason inter-firm
relationship increases in numbers and variety as well.
3. Risk audit and assessment
Among the supply chain professionals risk management knowledge area has become an
important topic for discussion. The wrongdoing stemming from Japan disaster as well as
Hurricane Irene was also speeding up the company’s movement towards better risk management
actions.
Environmental risk: Toyota is one of the highly Tsunami and earthquake affected car
manufacturing companies all over Japan. Toyota was sincerely taking steps to make sure that the
supply chain of the company is completely earthquake proof. In order to recover the complicated
situation company took effective actions.
Paraphrase This Document
Need a fresh take? Get an instant paraphrase of this document with our AI Paraphraser
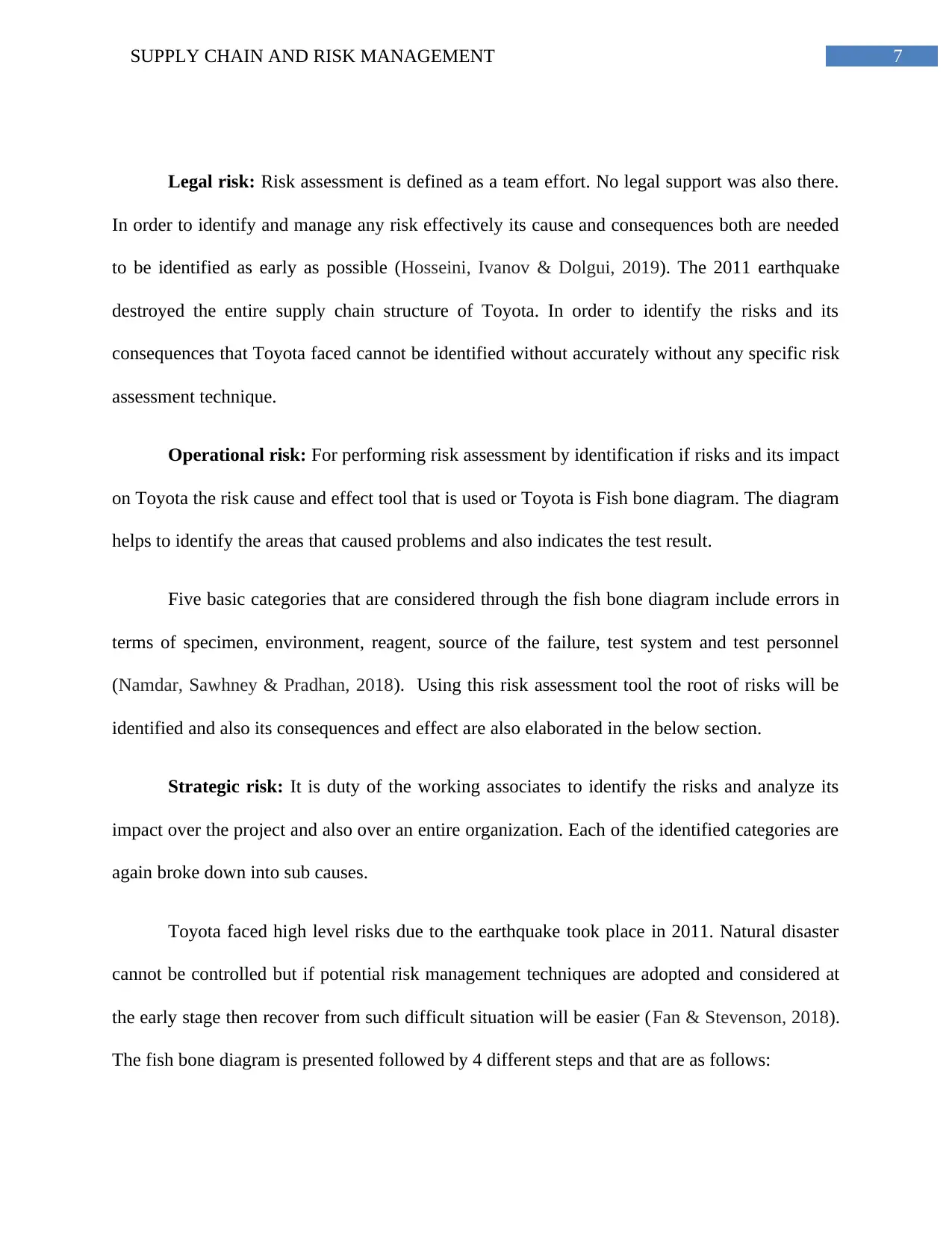
7SUPPLY CHAIN AND RISK MANAGEMENT
Legal risk: Risk assessment is defined as a team effort. No legal support was also there.
In order to identify and manage any risk effectively its cause and consequences both are needed
to be identified as early as possible (Hosseini, Ivanov & Dolgui, 2019). The 2011 earthquake
destroyed the entire supply chain structure of Toyota. In order to identify the risks and its
consequences that Toyota faced cannot be identified without accurately without any specific risk
assessment technique.
Operational risk: For performing risk assessment by identification if risks and its impact
on Toyota the risk cause and effect tool that is used or Toyota is Fish bone diagram. The diagram
helps to identify the areas that caused problems and also indicates the test result.
Five basic categories that are considered through the fish bone diagram include errors in
terms of specimen, environment, reagent, source of the failure, test system and test personnel
(Namdar, Sawhney & Pradhan, 2018). Using this risk assessment tool the root of risks will be
identified and also its consequences and effect are also elaborated in the below section.
Strategic risk: It is duty of the working associates to identify the risks and analyze its
impact over the project and also over an entire organization. Each of the identified categories are
again broke down into sub causes.
Toyota faced high level risks due to the earthquake took place in 2011. Natural disaster
cannot be controlled but if potential risk management techniques are adopted and considered at
the early stage then recover from such difficult situation will be easier (Fan & Stevenson, 2018).
The fish bone diagram is presented followed by 4 different steps and that are as follows:
Legal risk: Risk assessment is defined as a team effort. No legal support was also there.
In order to identify and manage any risk effectively its cause and consequences both are needed
to be identified as early as possible (Hosseini, Ivanov & Dolgui, 2019). The 2011 earthquake
destroyed the entire supply chain structure of Toyota. In order to identify the risks and its
consequences that Toyota faced cannot be identified without accurately without any specific risk
assessment technique.
Operational risk: For performing risk assessment by identification if risks and its impact
on Toyota the risk cause and effect tool that is used or Toyota is Fish bone diagram. The diagram
helps to identify the areas that caused problems and also indicates the test result.
Five basic categories that are considered through the fish bone diagram include errors in
terms of specimen, environment, reagent, source of the failure, test system and test personnel
(Namdar, Sawhney & Pradhan, 2018). Using this risk assessment tool the root of risks will be
identified and also its consequences and effect are also elaborated in the below section.
Strategic risk: It is duty of the working associates to identify the risks and analyze its
impact over the project and also over an entire organization. Each of the identified categories are
again broke down into sub causes.
Toyota faced high level risks due to the earthquake took place in 2011. Natural disaster
cannot be controlled but if potential risk management techniques are adopted and considered at
the early stage then recover from such difficult situation will be easier (Fan & Stevenson, 2018).
The fish bone diagram is presented followed by 4 different steps and that are as follows:
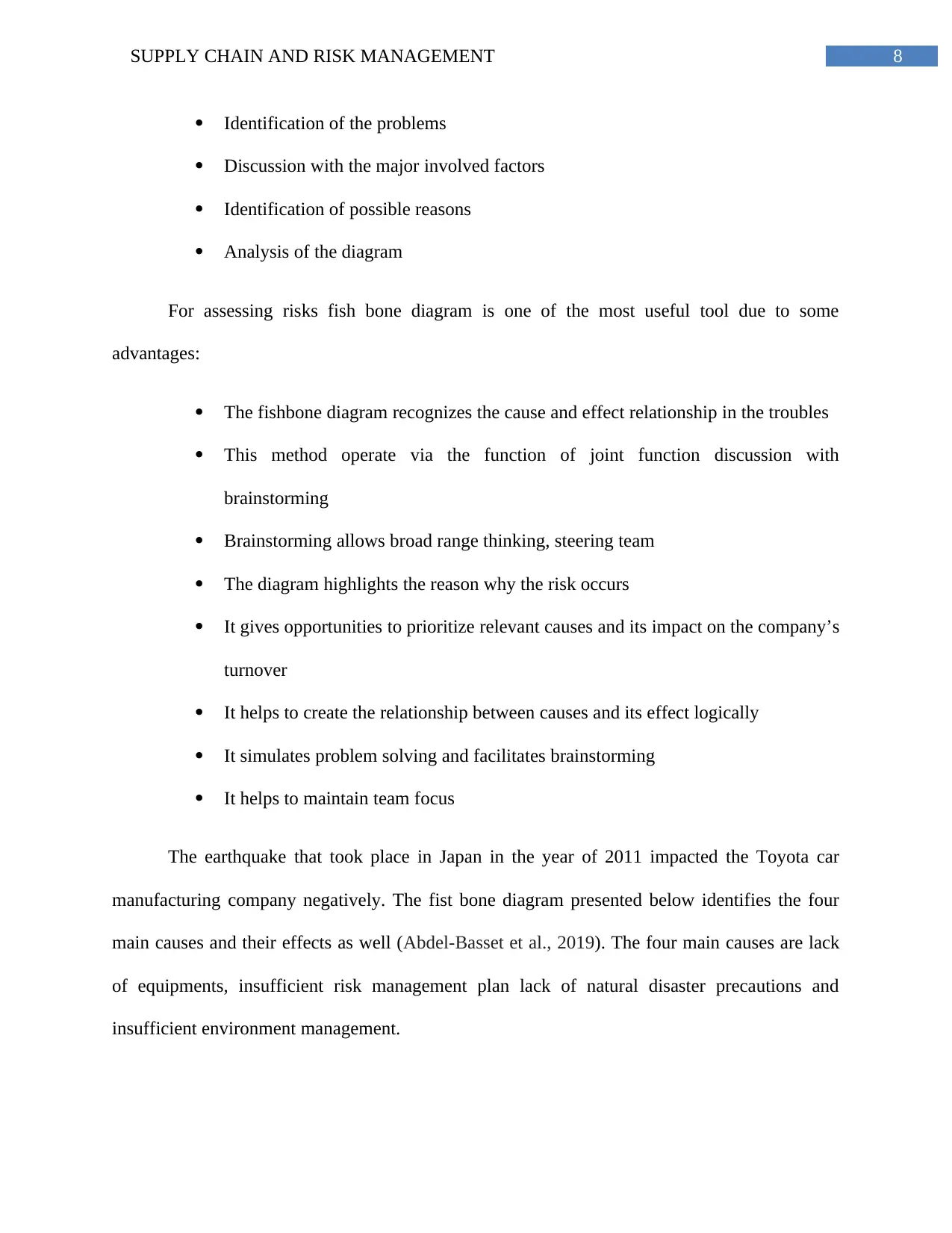
8SUPPLY CHAIN AND RISK MANAGEMENT
Identification of the problems
Discussion with the major involved factors
Identification of possible reasons
Analysis of the diagram
For assessing risks fish bone diagram is one of the most useful tool due to some
advantages:
The fishbone diagram recognizes the cause and effect relationship in the troubles
This method operate via the function of joint function discussion with
brainstorming
Brainstorming allows broad range thinking, steering team
The diagram highlights the reason why the risk occurs
It gives opportunities to prioritize relevant causes and its impact on the company’s
turnover
It helps to create the relationship between causes and its effect logically
It simulates problem solving and facilitates brainstorming
It helps to maintain team focus
The earthquake that took place in Japan in the year of 2011 impacted the Toyota car
manufacturing company negatively. The fist bone diagram presented below identifies the four
main causes and their effects as well (Abdel-Basset et al., 2019). The four main causes are lack
of equipments, insufficient risk management plan lack of natural disaster precautions and
insufficient environment management.
Identification of the problems
Discussion with the major involved factors
Identification of possible reasons
Analysis of the diagram
For assessing risks fish bone diagram is one of the most useful tool due to some
advantages:
The fishbone diagram recognizes the cause and effect relationship in the troubles
This method operate via the function of joint function discussion with
brainstorming
Brainstorming allows broad range thinking, steering team
The diagram highlights the reason why the risk occurs
It gives opportunities to prioritize relevant causes and its impact on the company’s
turnover
It helps to create the relationship between causes and its effect logically
It simulates problem solving and facilitates brainstorming
It helps to maintain team focus
The earthquake that took place in Japan in the year of 2011 impacted the Toyota car
manufacturing company negatively. The fist bone diagram presented below identifies the four
main causes and their effects as well (Abdel-Basset et al., 2019). The four main causes are lack
of equipments, insufficient risk management plan lack of natural disaster precautions and
insufficient environment management.
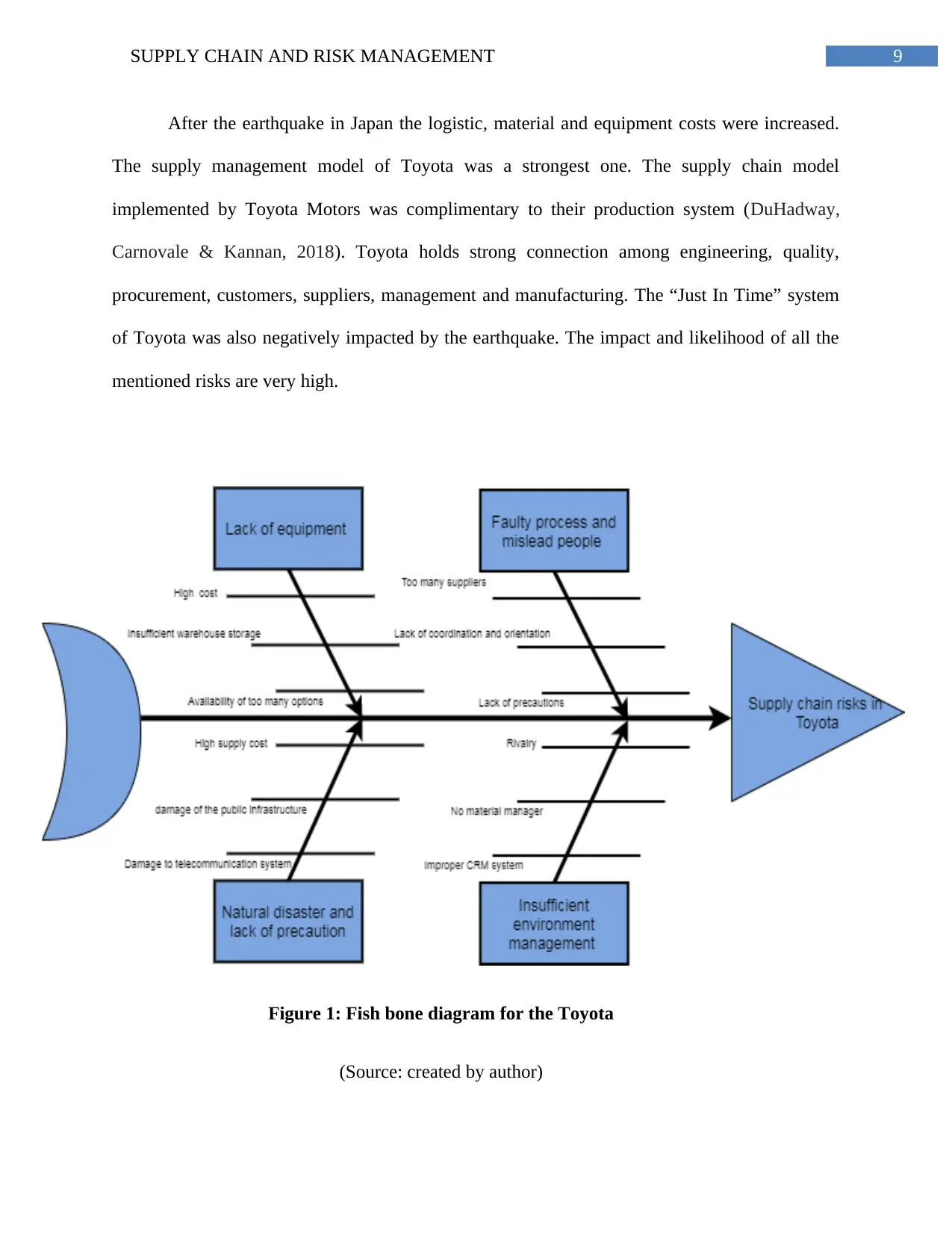
9SUPPLY CHAIN AND RISK MANAGEMENT
After the earthquake in Japan the logistic, material and equipment costs were increased.
The supply management model of Toyota was a strongest one. The supply chain model
implemented by Toyota Motors was complimentary to their production system (DuHadway,
Carnovale & Kannan, 2018). Toyota holds strong connection among engineering, quality,
procurement, customers, suppliers, management and manufacturing. The “Just In Time” system
of Toyota was also negatively impacted by the earthquake. The impact and likelihood of all the
mentioned risks are very high.
Figure 1: Fish bone diagram for the Toyota
(Source: created by author)
After the earthquake in Japan the logistic, material and equipment costs were increased.
The supply management model of Toyota was a strongest one. The supply chain model
implemented by Toyota Motors was complimentary to their production system (DuHadway,
Carnovale & Kannan, 2018). Toyota holds strong connection among engineering, quality,
procurement, customers, suppliers, management and manufacturing. The “Just In Time” system
of Toyota was also negatively impacted by the earthquake. The impact and likelihood of all the
mentioned risks are very high.
Figure 1: Fish bone diagram for the Toyota
(Source: created by author)
Secure Best Marks with AI Grader
Need help grading? Try our AI Grader for instant feedback on your assignments.
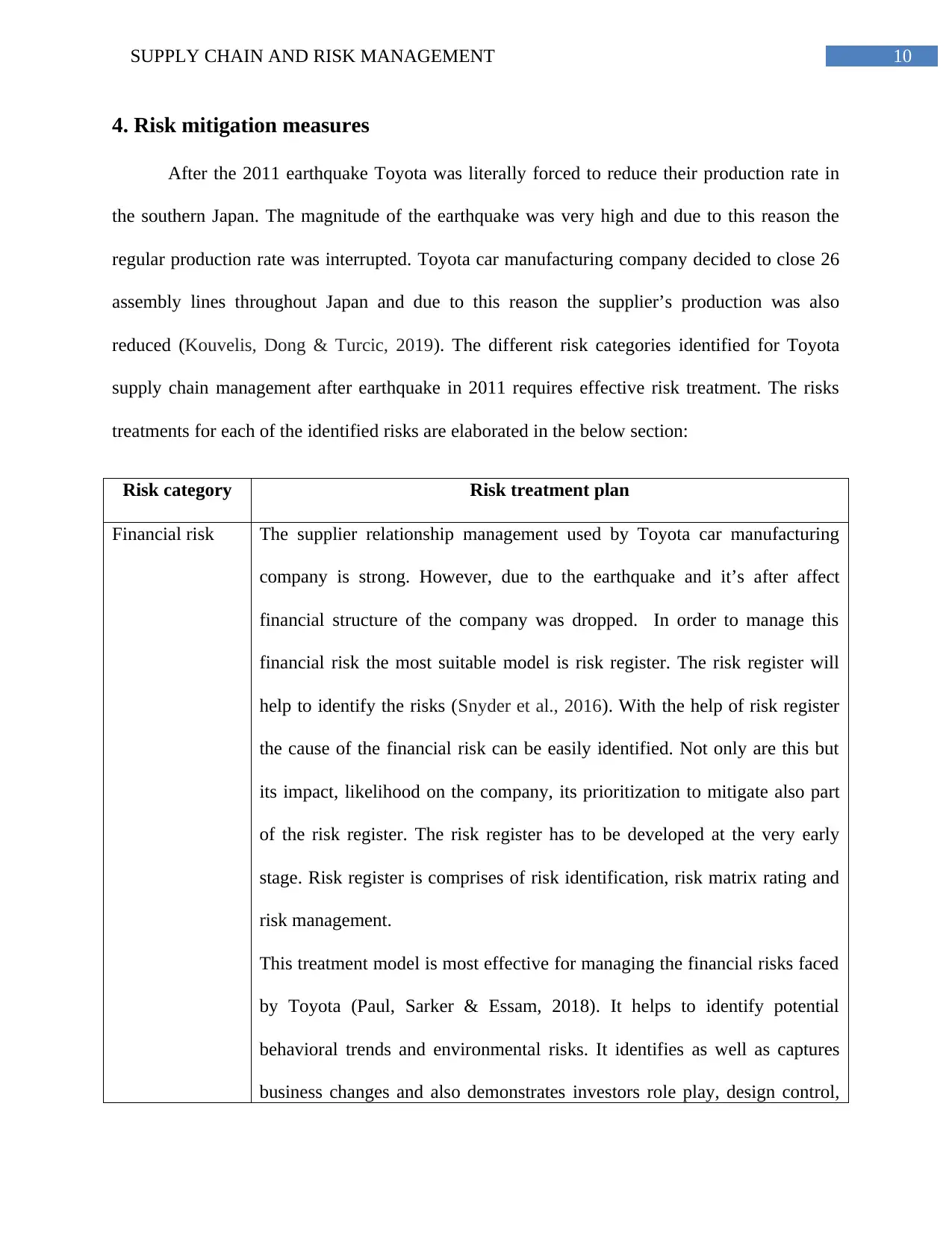
10SUPPLY CHAIN AND RISK MANAGEMENT
4. Risk mitigation measures
After the 2011 earthquake Toyota was literally forced to reduce their production rate in
the southern Japan. The magnitude of the earthquake was very high and due to this reason the
regular production rate was interrupted. Toyota car manufacturing company decided to close 26
assembly lines throughout Japan and due to this reason the supplier’s production was also
reduced (Kouvelis, Dong & Turcic, 2019). The different risk categories identified for Toyota
supply chain management after earthquake in 2011 requires effective risk treatment. The risks
treatments for each of the identified risks are elaborated in the below section:
Risk category Risk treatment plan
Financial risk The supplier relationship management used by Toyota car manufacturing
company is strong. However, due to the earthquake and it’s after affect
financial structure of the company was dropped. In order to manage this
financial risk the most suitable model is risk register. The risk register will
help to identify the risks (Snyder et al., 2016). With the help of risk register
the cause of the financial risk can be easily identified. Not only are this but
its impact, likelihood on the company, its prioritization to mitigate also part
of the risk register. The risk register has to be developed at the very early
stage. Risk register is comprises of risk identification, risk matrix rating and
risk management.
This treatment model is most effective for managing the financial risks faced
by Toyota (Paul, Sarker & Essam, 2018). It helps to identify potential
behavioral trends and environmental risks. It identifies as well as captures
business changes and also demonstrates investors role play, design control,
4. Risk mitigation measures
After the 2011 earthquake Toyota was literally forced to reduce their production rate in
the southern Japan. The magnitude of the earthquake was very high and due to this reason the
regular production rate was interrupted. Toyota car manufacturing company decided to close 26
assembly lines throughout Japan and due to this reason the supplier’s production was also
reduced (Kouvelis, Dong & Turcic, 2019). The different risk categories identified for Toyota
supply chain management after earthquake in 2011 requires effective risk treatment. The risks
treatments for each of the identified risks are elaborated in the below section:
Risk category Risk treatment plan
Financial risk The supplier relationship management used by Toyota car manufacturing
company is strong. However, due to the earthquake and it’s after affect
financial structure of the company was dropped. In order to manage this
financial risk the most suitable model is risk register. The risk register will
help to identify the risks (Snyder et al., 2016). With the help of risk register
the cause of the financial risk can be easily identified. Not only are this but
its impact, likelihood on the company, its prioritization to mitigate also part
of the risk register. The risk register has to be developed at the very early
stage. Risk register is comprises of risk identification, risk matrix rating and
risk management.
This treatment model is most effective for managing the financial risks faced
by Toyota (Paul, Sarker & Essam, 2018). It helps to identify potential
behavioral trends and environmental risks. It identifies as well as captures
business changes and also demonstrates investors role play, design control,
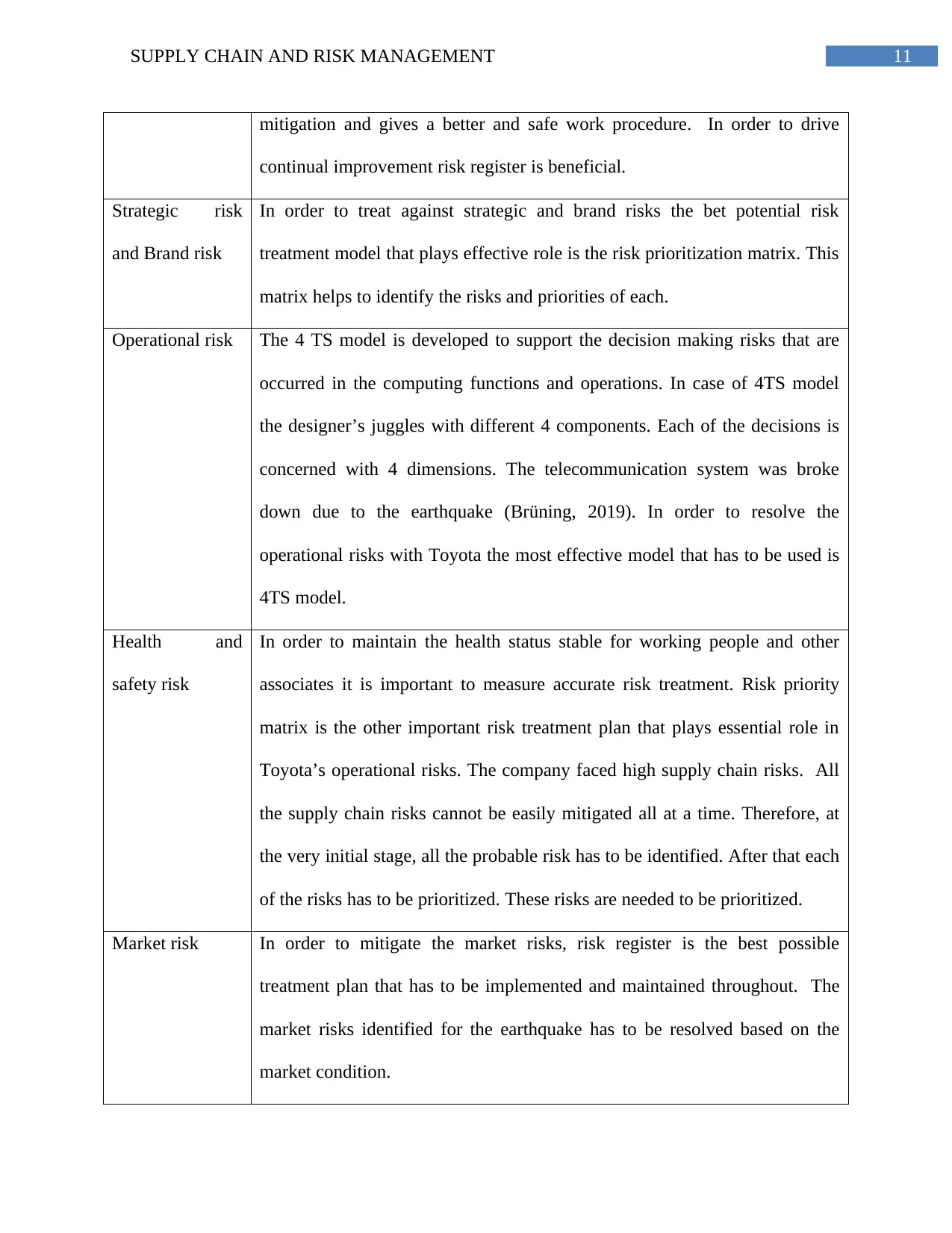
11SUPPLY CHAIN AND RISK MANAGEMENT
mitigation and gives a better and safe work procedure. In order to drive
continual improvement risk register is beneficial.
Strategic risk
and Brand risk
In order to treat against strategic and brand risks the bet potential risk
treatment model that plays effective role is the risk prioritization matrix. This
matrix helps to identify the risks and priorities of each.
Operational risk The 4 TS model is developed to support the decision making risks that are
occurred in the computing functions and operations. In case of 4TS model
the designer’s juggles with different 4 components. Each of the decisions is
concerned with 4 dimensions. The telecommunication system was broke
down due to the earthquake (Brüning, 2019). In order to resolve the
operational risks with Toyota the most effective model that has to be used is
4TS model.
Health and
safety risk
In order to maintain the health status stable for working people and other
associates it is important to measure accurate risk treatment. Risk priority
matrix is the other important risk treatment plan that plays essential role in
Toyota’s operational risks. The company faced high supply chain risks. All
the supply chain risks cannot be easily mitigated all at a time. Therefore, at
the very initial stage, all the probable risk has to be identified. After that each
of the risks has to be prioritized. These risks are needed to be prioritized.
Market risk In order to mitigate the market risks, risk register is the best possible
treatment plan that has to be implemented and maintained throughout. The
market risks identified for the earthquake has to be resolved based on the
market condition.
mitigation and gives a better and safe work procedure. In order to drive
continual improvement risk register is beneficial.
Strategic risk
and Brand risk
In order to treat against strategic and brand risks the bet potential risk
treatment model that plays effective role is the risk prioritization matrix. This
matrix helps to identify the risks and priorities of each.
Operational risk The 4 TS model is developed to support the decision making risks that are
occurred in the computing functions and operations. In case of 4TS model
the designer’s juggles with different 4 components. Each of the decisions is
concerned with 4 dimensions. The telecommunication system was broke
down due to the earthquake (Brüning, 2019). In order to resolve the
operational risks with Toyota the most effective model that has to be used is
4TS model.
Health and
safety risk
In order to maintain the health status stable for working people and other
associates it is important to measure accurate risk treatment. Risk priority
matrix is the other important risk treatment plan that plays essential role in
Toyota’s operational risks. The company faced high supply chain risks. All
the supply chain risks cannot be easily mitigated all at a time. Therefore, at
the very initial stage, all the probable risk has to be identified. After that each
of the risks has to be prioritized. These risks are needed to be prioritized.
Market risk In order to mitigate the market risks, risk register is the best possible
treatment plan that has to be implemented and maintained throughout. The
market risks identified for the earthquake has to be resolved based on the
market condition.
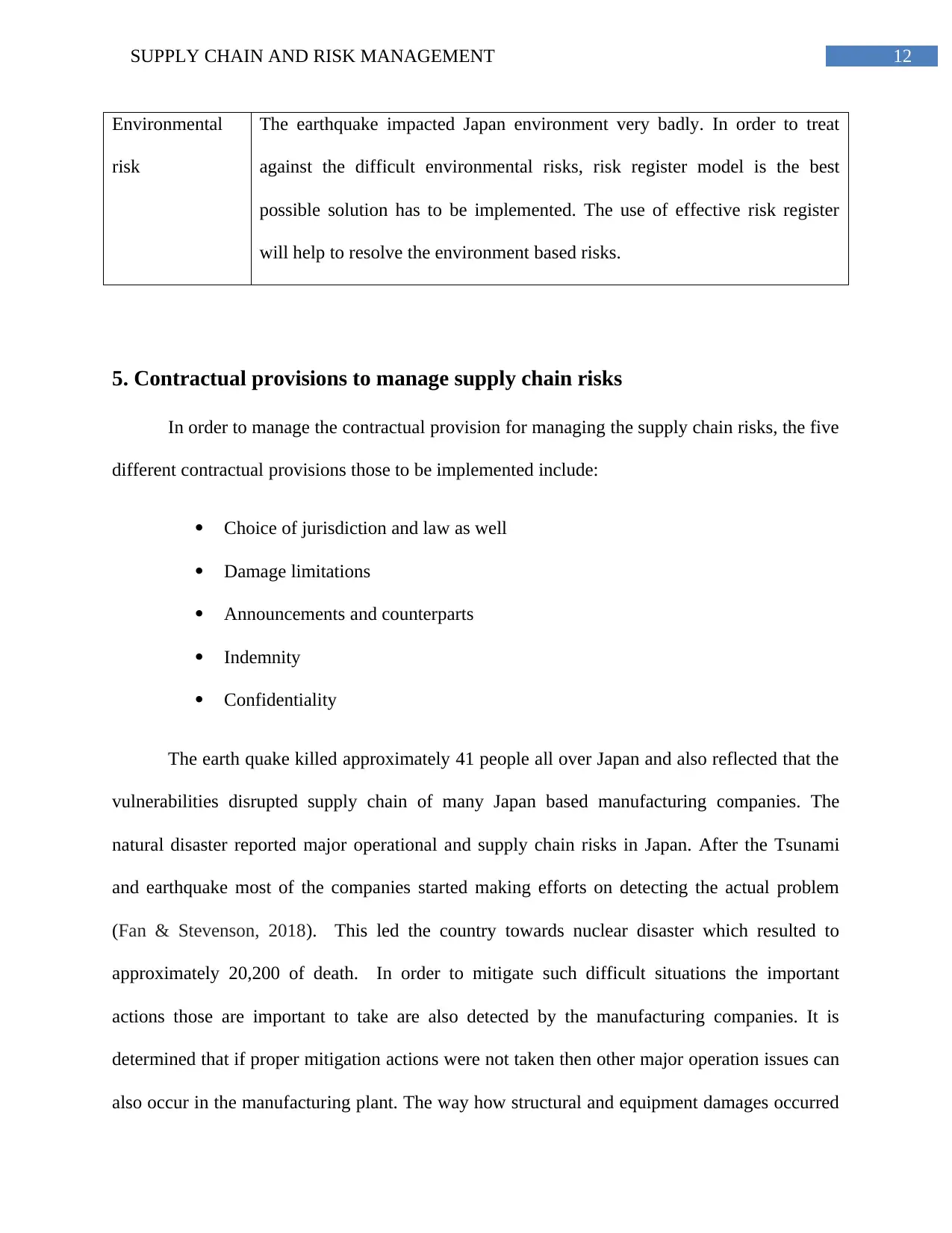
12SUPPLY CHAIN AND RISK MANAGEMENT
Environmental
risk
The earthquake impacted Japan environment very badly. In order to treat
against the difficult environmental risks, risk register model is the best
possible solution has to be implemented. The use of effective risk register
will help to resolve the environment based risks.
5. Contractual provisions to manage supply chain risks
In order to manage the contractual provision for managing the supply chain risks, the five
different contractual provisions those to be implemented include:
Choice of jurisdiction and law as well
Damage limitations
Announcements and counterparts
Indemnity
Confidentiality
The earth quake killed approximately 41 people all over Japan and also reflected that the
vulnerabilities disrupted supply chain of many Japan based manufacturing companies. The
natural disaster reported major operational and supply chain risks in Japan. After the Tsunami
and earthquake most of the companies started making efforts on detecting the actual problem
(Fan & Stevenson, 2018). This led the country towards nuclear disaster which resulted to
approximately 20,200 of death. In order to mitigate such difficult situations the important
actions those are important to take are also detected by the manufacturing companies. It is
determined that if proper mitigation actions were not taken then other major operation issues can
also occur in the manufacturing plant. The way how structural and equipment damages occurred
Environmental
risk
The earthquake impacted Japan environment very badly. In order to treat
against the difficult environmental risks, risk register model is the best
possible solution has to be implemented. The use of effective risk register
will help to resolve the environment based risks.
5. Contractual provisions to manage supply chain risks
In order to manage the contractual provision for managing the supply chain risks, the five
different contractual provisions those to be implemented include:
Choice of jurisdiction and law as well
Damage limitations
Announcements and counterparts
Indemnity
Confidentiality
The earth quake killed approximately 41 people all over Japan and also reflected that the
vulnerabilities disrupted supply chain of many Japan based manufacturing companies. The
natural disaster reported major operational and supply chain risks in Japan. After the Tsunami
and earthquake most of the companies started making efforts on detecting the actual problem
(Fan & Stevenson, 2018). This led the country towards nuclear disaster which resulted to
approximately 20,200 of death. In order to mitigate such difficult situations the important
actions those are important to take are also detected by the manufacturing companies. It is
determined that if proper mitigation actions were not taken then other major operation issues can
also occur in the manufacturing plant. The way how structural and equipment damages occurred
Paraphrase This Document
Need a fresh take? Get an instant paraphrase of this document with our AI Paraphraser
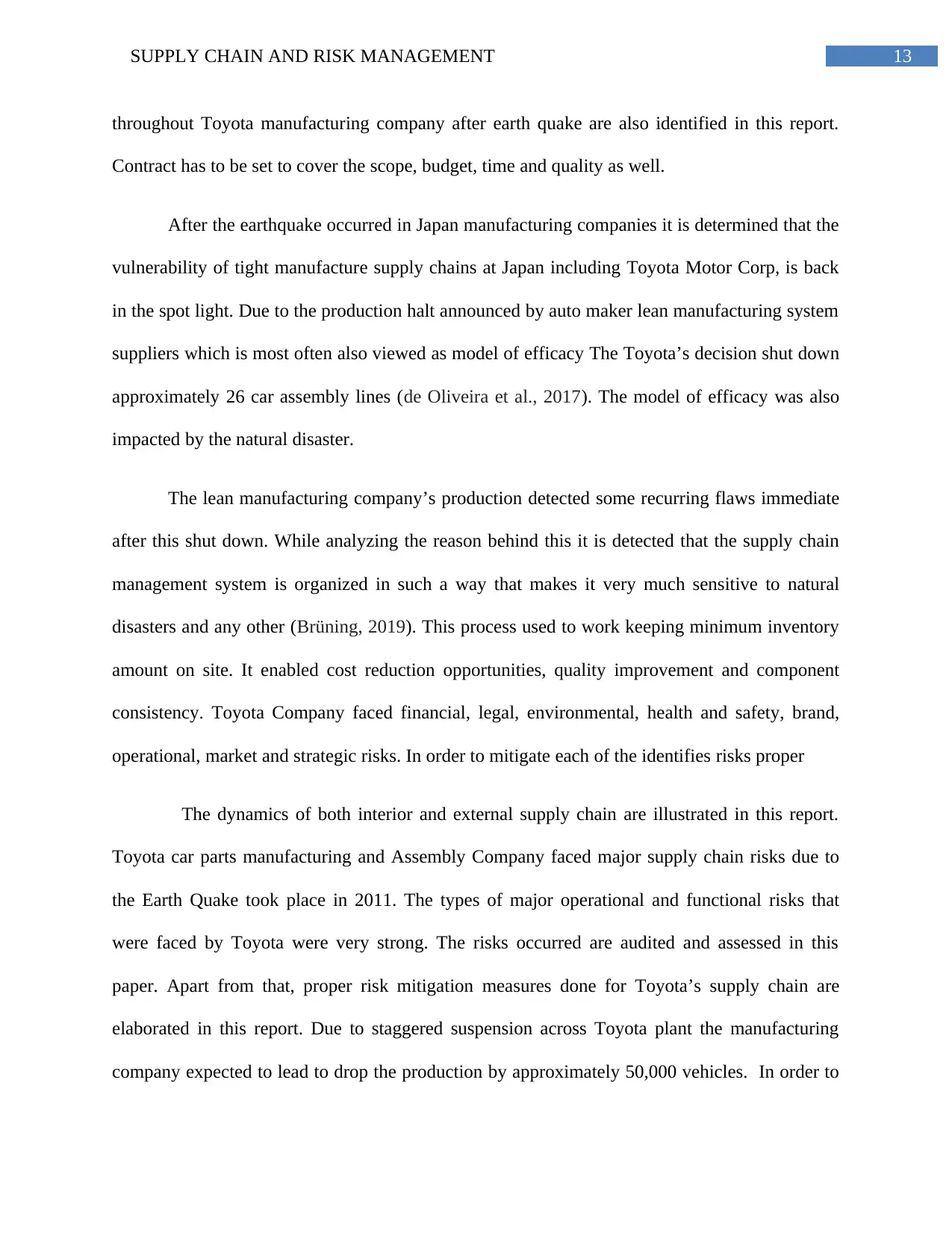
13SUPPLY CHAIN AND RISK MANAGEMENT
throughout Toyota manufacturing company after earth quake are also identified in this report.
Contract has to be set to cover the scope, budget, time and quality as well.
After the earthquake occurred in Japan manufacturing companies it is determined that the
vulnerability of tight manufacture supply chains at Japan including Toyota Motor Corp, is back
in the spot light. Due to the production halt announced by auto maker lean manufacturing system
suppliers which is most often also viewed as model of efficacy The Toyota’s decision shut down
approximately 26 car assembly lines (de Oliveira et al., 2017). The model of efficacy was also
impacted by the natural disaster.
The lean manufacturing company’s production detected some recurring flaws immediate
after this shut down. While analyzing the reason behind this it is detected that the supply chain
management system is organized in such a way that makes it very much sensitive to natural
disasters and any other (Brüning, 2019). This process used to work keeping minimum inventory
amount on site. It enabled cost reduction opportunities, quality improvement and component
consistency. Toyota Company faced financial, legal, environmental, health and safety, brand,
operational, market and strategic risks. In order to mitigate each of the identifies risks proper
The dynamics of both interior and external supply chain are illustrated in this report.
Toyota car parts manufacturing and Assembly Company faced major supply chain risks due to
the Earth Quake took place in 2011. The types of major operational and functional risks that
were faced by Toyota were very strong. The risks occurred are audited and assessed in this
paper. Apart from that, proper risk mitigation measures done for Toyota’s supply chain are
elaborated in this report. Due to staggered suspension across Toyota plant the manufacturing
company expected to lead to drop the production by approximately 50,000 vehicles. In order to
throughout Toyota manufacturing company after earth quake are also identified in this report.
Contract has to be set to cover the scope, budget, time and quality as well.
After the earthquake occurred in Japan manufacturing companies it is determined that the
vulnerability of tight manufacture supply chains at Japan including Toyota Motor Corp, is back
in the spot light. Due to the production halt announced by auto maker lean manufacturing system
suppliers which is most often also viewed as model of efficacy The Toyota’s decision shut down
approximately 26 car assembly lines (de Oliveira et al., 2017). The model of efficacy was also
impacted by the natural disaster.
The lean manufacturing company’s production detected some recurring flaws immediate
after this shut down. While analyzing the reason behind this it is detected that the supply chain
management system is organized in such a way that makes it very much sensitive to natural
disasters and any other (Brüning, 2019). This process used to work keeping minimum inventory
amount on site. It enabled cost reduction opportunities, quality improvement and component
consistency. Toyota Company faced financial, legal, environmental, health and safety, brand,
operational, market and strategic risks. In order to mitigate each of the identifies risks proper
The dynamics of both interior and external supply chain are illustrated in this report.
Toyota car parts manufacturing and Assembly Company faced major supply chain risks due to
the Earth Quake took place in 2011. The types of major operational and functional risks that
were faced by Toyota were very strong. The risks occurred are audited and assessed in this
paper. Apart from that, proper risk mitigation measures done for Toyota’s supply chain are
elaborated in this report. Due to staggered suspension across Toyota plant the manufacturing
company expected to lead to drop the production by approximately 50,000 vehicles. In order to
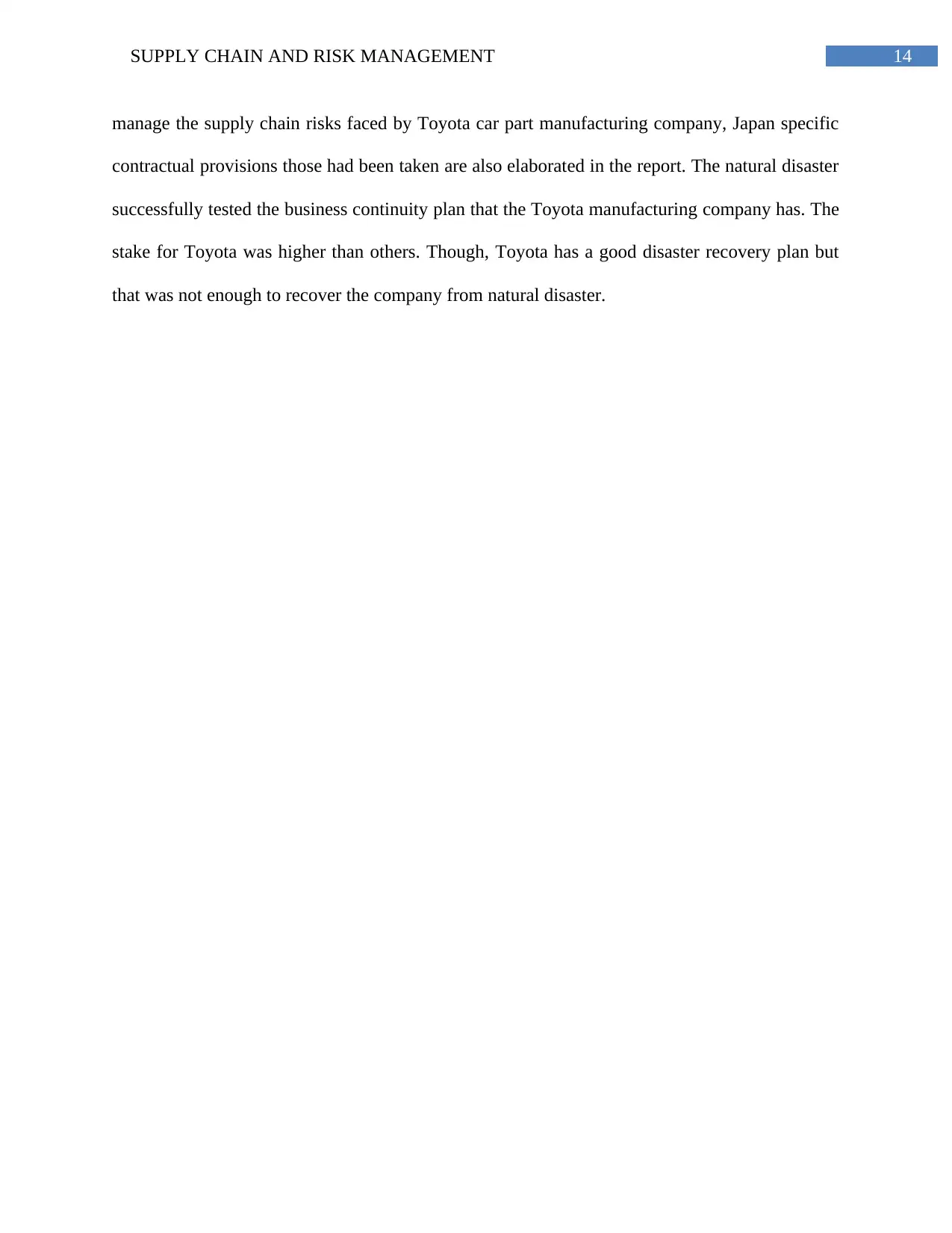
14SUPPLY CHAIN AND RISK MANAGEMENT
manage the supply chain risks faced by Toyota car part manufacturing company, Japan specific
contractual provisions those had been taken are also elaborated in the report. The natural disaster
successfully tested the business continuity plan that the Toyota manufacturing company has. The
stake for Toyota was higher than others. Though, Toyota has a good disaster recovery plan but
that was not enough to recover the company from natural disaster.
manage the supply chain risks faced by Toyota car part manufacturing company, Japan specific
contractual provisions those had been taken are also elaborated in the report. The natural disaster
successfully tested the business continuity plan that the Toyota manufacturing company has. The
stake for Toyota was higher than others. Though, Toyota has a good disaster recovery plan but
that was not enough to recover the company from natural disaster.
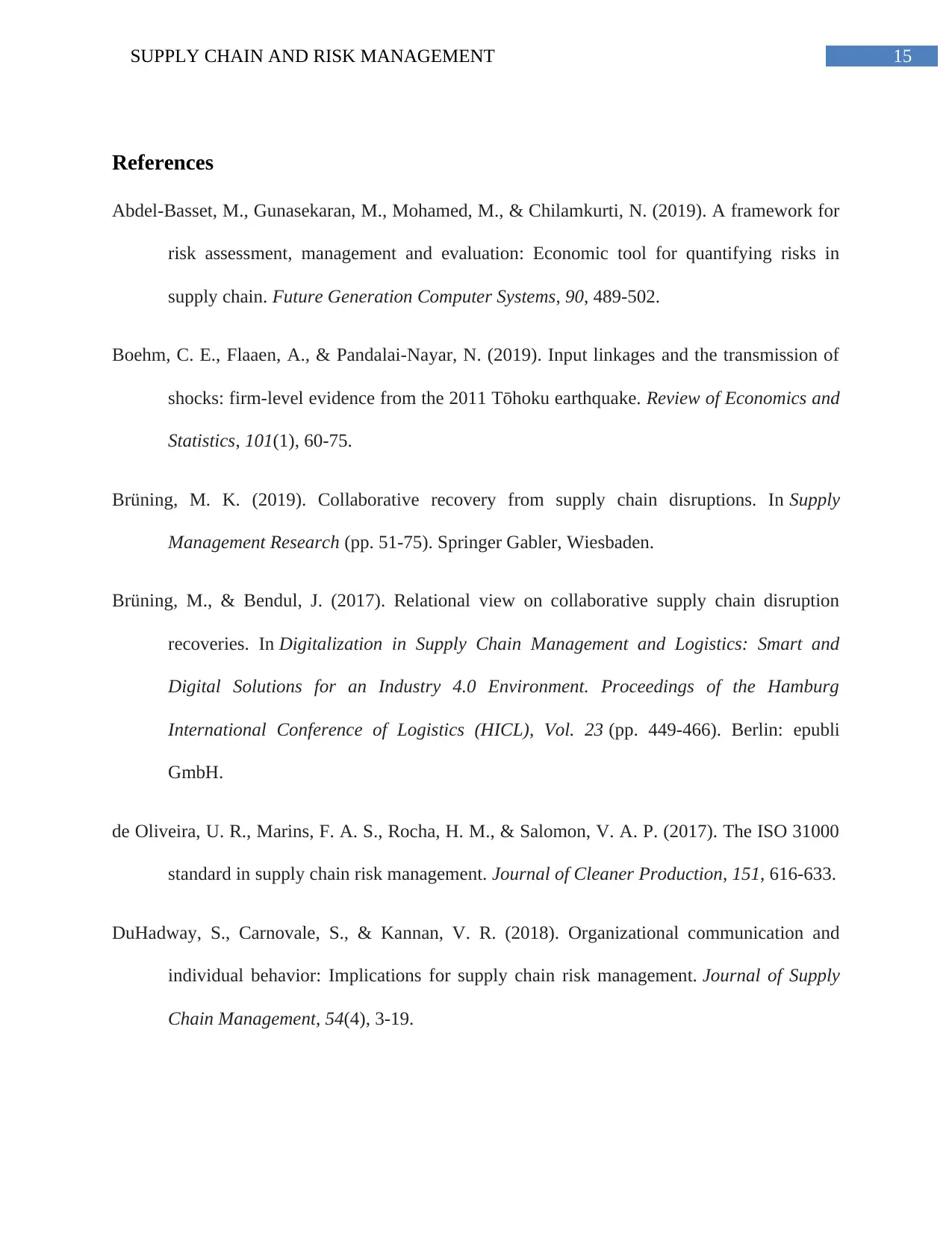
15SUPPLY CHAIN AND RISK MANAGEMENT
References
Abdel-Basset, M., Gunasekaran, M., Mohamed, M., & Chilamkurti, N. (2019). A framework for
risk assessment, management and evaluation: Economic tool for quantifying risks in
supply chain. Future Generation Computer Systems, 90, 489-502.
Boehm, C. E., Flaaen, A., & Pandalai-Nayar, N. (2019). Input linkages and the transmission of
shocks: firm-level evidence from the 2011 Tōhoku earthquake. Review of Economics and
Statistics, 101(1), 60-75.
Brüning, M. K. (2019). Collaborative recovery from supply chain disruptions. In Supply
Management Research (pp. 51-75). Springer Gabler, Wiesbaden.
Brüning, M., & Bendul, J. (2017). Relational view on collaborative supply chain disruption
recoveries. In Digitalization in Supply Chain Management and Logistics: Smart and
Digital Solutions for an Industry 4.0 Environment. Proceedings of the Hamburg
International Conference of Logistics (HICL), Vol. 23 (pp. 449-466). Berlin: epubli
GmbH.
de Oliveira, U. R., Marins, F. A. S., Rocha, H. M., & Salomon, V. A. P. (2017). The ISO 31000
standard in supply chain risk management. Journal of Cleaner Production, 151, 616-633.
DuHadway, S., Carnovale, S., & Kannan, V. R. (2018). Organizational communication and
individual behavior: Implications for supply chain risk management. Journal of Supply
Chain Management, 54(4), 3-19.
References
Abdel-Basset, M., Gunasekaran, M., Mohamed, M., & Chilamkurti, N. (2019). A framework for
risk assessment, management and evaluation: Economic tool for quantifying risks in
supply chain. Future Generation Computer Systems, 90, 489-502.
Boehm, C. E., Flaaen, A., & Pandalai-Nayar, N. (2019). Input linkages and the transmission of
shocks: firm-level evidence from the 2011 Tōhoku earthquake. Review of Economics and
Statistics, 101(1), 60-75.
Brüning, M. K. (2019). Collaborative recovery from supply chain disruptions. In Supply
Management Research (pp. 51-75). Springer Gabler, Wiesbaden.
Brüning, M., & Bendul, J. (2017). Relational view on collaborative supply chain disruption
recoveries. In Digitalization in Supply Chain Management and Logistics: Smart and
Digital Solutions for an Industry 4.0 Environment. Proceedings of the Hamburg
International Conference of Logistics (HICL), Vol. 23 (pp. 449-466). Berlin: epubli
GmbH.
de Oliveira, U. R., Marins, F. A. S., Rocha, H. M., & Salomon, V. A. P. (2017). The ISO 31000
standard in supply chain risk management. Journal of Cleaner Production, 151, 616-633.
DuHadway, S., Carnovale, S., & Kannan, V. R. (2018). Organizational communication and
individual behavior: Implications for supply chain risk management. Journal of Supply
Chain Management, 54(4), 3-19.
Secure Best Marks with AI Grader
Need help grading? Try our AI Grader for instant feedback on your assignments.
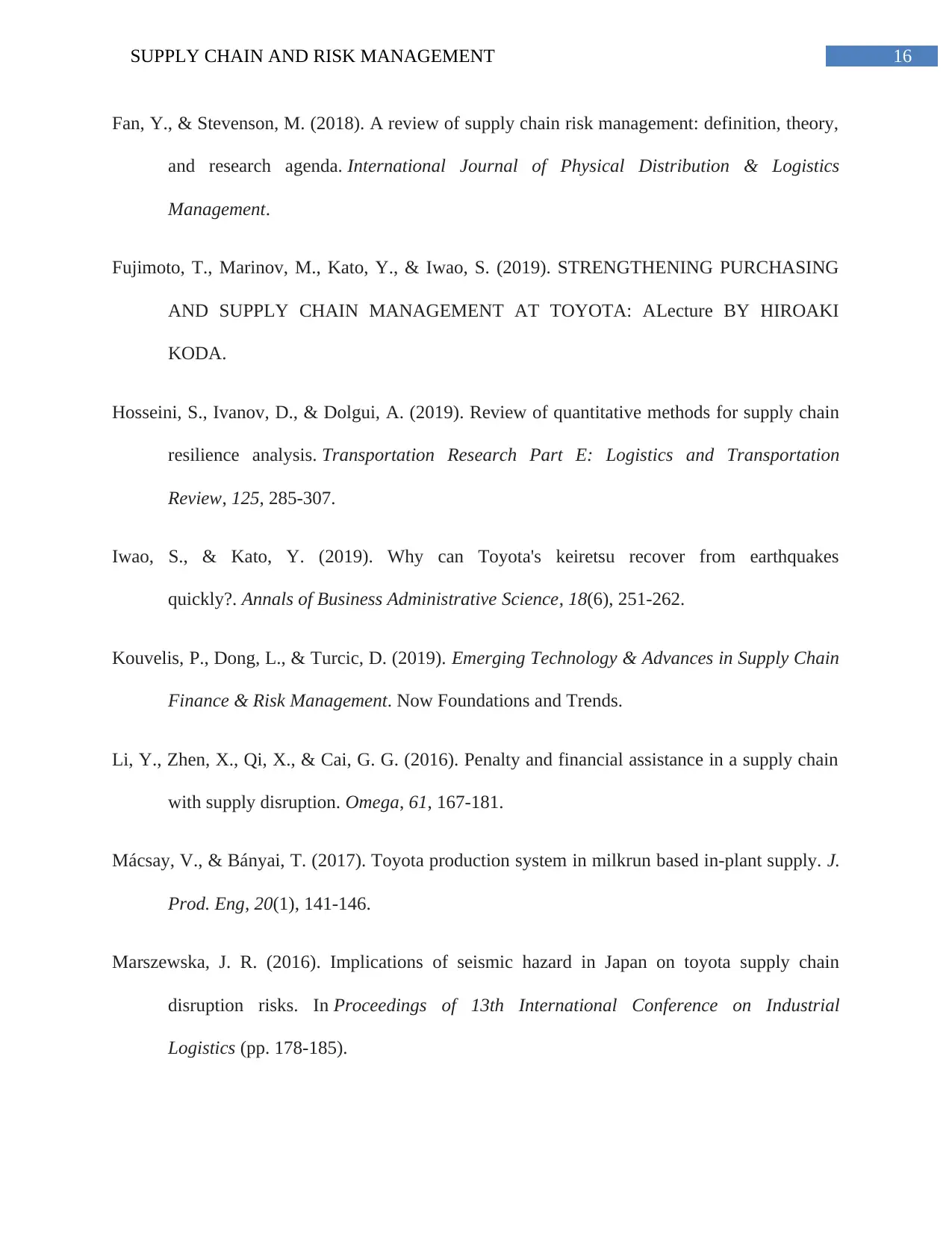
16SUPPLY CHAIN AND RISK MANAGEMENT
Fan, Y., & Stevenson, M. (2018). A review of supply chain risk management: definition, theory,
and research agenda. International Journal of Physical Distribution & Logistics
Management.
Fujimoto, T., Marinov, M., Kato, Y., & Iwao, S. (2019). STRENGTHENING PURCHASING
AND SUPPLY CHAIN MANAGEMENT AT TOYOTA: ALecture BY HIROAKI
KODA.
Hosseini, S., Ivanov, D., & Dolgui, A. (2019). Review of quantitative methods for supply chain
resilience analysis. Transportation Research Part E: Logistics and Transportation
Review, 125, 285-307.
Iwao, S., & Kato, Y. (2019). Why can Toyota's keiretsu recover from earthquakes
quickly?. Annals of Business Administrative Science, 18(6), 251-262.
Kouvelis, P., Dong, L., & Turcic, D. (2019). Emerging Technology & Advances in Supply Chain
Finance & Risk Management. Now Foundations and Trends.
Li, Y., Zhen, X., Qi, X., & Cai, G. G. (2016). Penalty and financial assistance in a supply chain
with supply disruption. Omega, 61, 167-181.
Mácsay, V., & Bányai, T. (2017). Toyota production system in milkrun based in-plant supply. J.
Prod. Eng, 20(1), 141-146.
Marszewska, J. R. (2016). Implications of seismic hazard in Japan on toyota supply chain
disruption risks. In Proceedings of 13th International Conference on Industrial
Logistics (pp. 178-185).
Fan, Y., & Stevenson, M. (2018). A review of supply chain risk management: definition, theory,
and research agenda. International Journal of Physical Distribution & Logistics
Management.
Fujimoto, T., Marinov, M., Kato, Y., & Iwao, S. (2019). STRENGTHENING PURCHASING
AND SUPPLY CHAIN MANAGEMENT AT TOYOTA: ALecture BY HIROAKI
KODA.
Hosseini, S., Ivanov, D., & Dolgui, A. (2019). Review of quantitative methods for supply chain
resilience analysis. Transportation Research Part E: Logistics and Transportation
Review, 125, 285-307.
Iwao, S., & Kato, Y. (2019). Why can Toyota's keiretsu recover from earthquakes
quickly?. Annals of Business Administrative Science, 18(6), 251-262.
Kouvelis, P., Dong, L., & Turcic, D. (2019). Emerging Technology & Advances in Supply Chain
Finance & Risk Management. Now Foundations and Trends.
Li, Y., Zhen, X., Qi, X., & Cai, G. G. (2016). Penalty and financial assistance in a supply chain
with supply disruption. Omega, 61, 167-181.
Mácsay, V., & Bányai, T. (2017). Toyota production system in milkrun based in-plant supply. J.
Prod. Eng, 20(1), 141-146.
Marszewska, J. R. (2016). Implications of seismic hazard in Japan on toyota supply chain
disruption risks. In Proceedings of 13th International Conference on Industrial
Logistics (pp. 178-185).
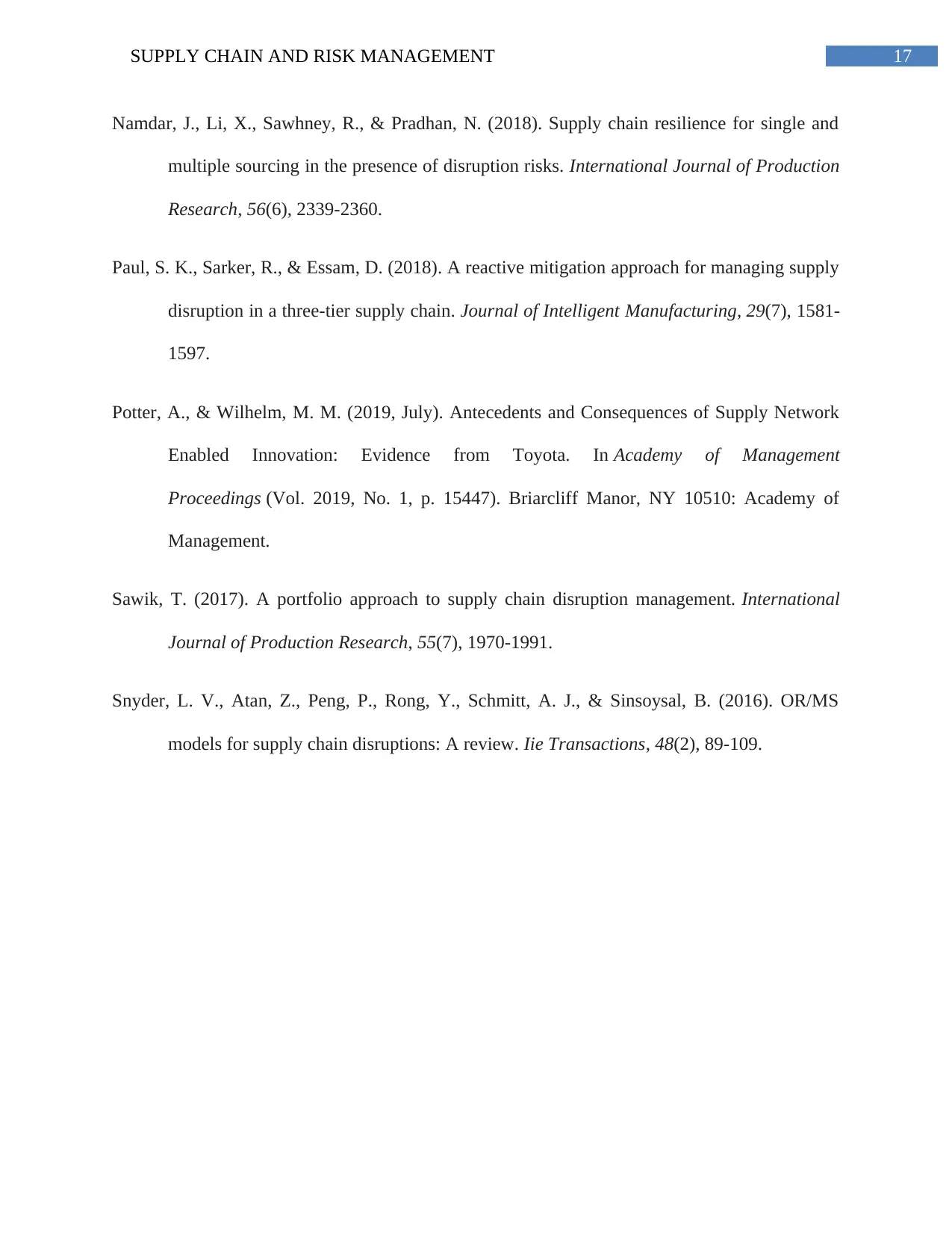
17SUPPLY CHAIN AND RISK MANAGEMENT
Namdar, J., Li, X., Sawhney, R., & Pradhan, N. (2018). Supply chain resilience for single and
multiple sourcing in the presence of disruption risks. International Journal of Production
Research, 56(6), 2339-2360.
Paul, S. K., Sarker, R., & Essam, D. (2018). A reactive mitigation approach for managing supply
disruption in a three-tier supply chain. Journal of Intelligent Manufacturing, 29(7), 1581-
1597.
Potter, A., & Wilhelm, M. M. (2019, July). Antecedents and Consequences of Supply Network
Enabled Innovation: Evidence from Toyota. In Academy of Management
Proceedings (Vol. 2019, No. 1, p. 15447). Briarcliff Manor, NY 10510: Academy of
Management.
Sawik, T. (2017). A portfolio approach to supply chain disruption management. International
Journal of Production Research, 55(7), 1970-1991.
Snyder, L. V., Atan, Z., Peng, P., Rong, Y., Schmitt, A. J., & Sinsoysal, B. (2016). OR/MS
models for supply chain disruptions: A review. Iie Transactions, 48(2), 89-109.
Namdar, J., Li, X., Sawhney, R., & Pradhan, N. (2018). Supply chain resilience for single and
multiple sourcing in the presence of disruption risks. International Journal of Production
Research, 56(6), 2339-2360.
Paul, S. K., Sarker, R., & Essam, D. (2018). A reactive mitigation approach for managing supply
disruption in a three-tier supply chain. Journal of Intelligent Manufacturing, 29(7), 1581-
1597.
Potter, A., & Wilhelm, M. M. (2019, July). Antecedents and Consequences of Supply Network
Enabled Innovation: Evidence from Toyota. In Academy of Management
Proceedings (Vol. 2019, No. 1, p. 15447). Briarcliff Manor, NY 10510: Academy of
Management.
Sawik, T. (2017). A portfolio approach to supply chain disruption management. International
Journal of Production Research, 55(7), 1970-1991.
Snyder, L. V., Atan, Z., Peng, P., Rong, Y., Schmitt, A. J., & Sinsoysal, B. (2016). OR/MS
models for supply chain disruptions: A review. Iie Transactions, 48(2), 89-109.
1 out of 18
Related Documents
![[object Object]](/_next/image/?url=%2F_next%2Fstatic%2Fmedia%2Flogo.6d15ce61.png&w=640&q=75)
Your All-in-One AI-Powered Toolkit for Academic Success.
+13062052269
info@desklib.com
Available 24*7 on WhatsApp / Email
Unlock your academic potential
© 2024 | Zucol Services PVT LTD | All rights reserved.