Supply Chain Planning
VerifiedAdded on  2022/11/18
|7
|1251
|134
AI Summary
This document provides solutions to questions related to supply chain planning. It covers topics such as computation of normal time required for production, subcontracting, production planning, and more. The document also includes references and bibliography.
Contribute Materials
Your contribution can guide someone’s learning journey. Share your
documents today.
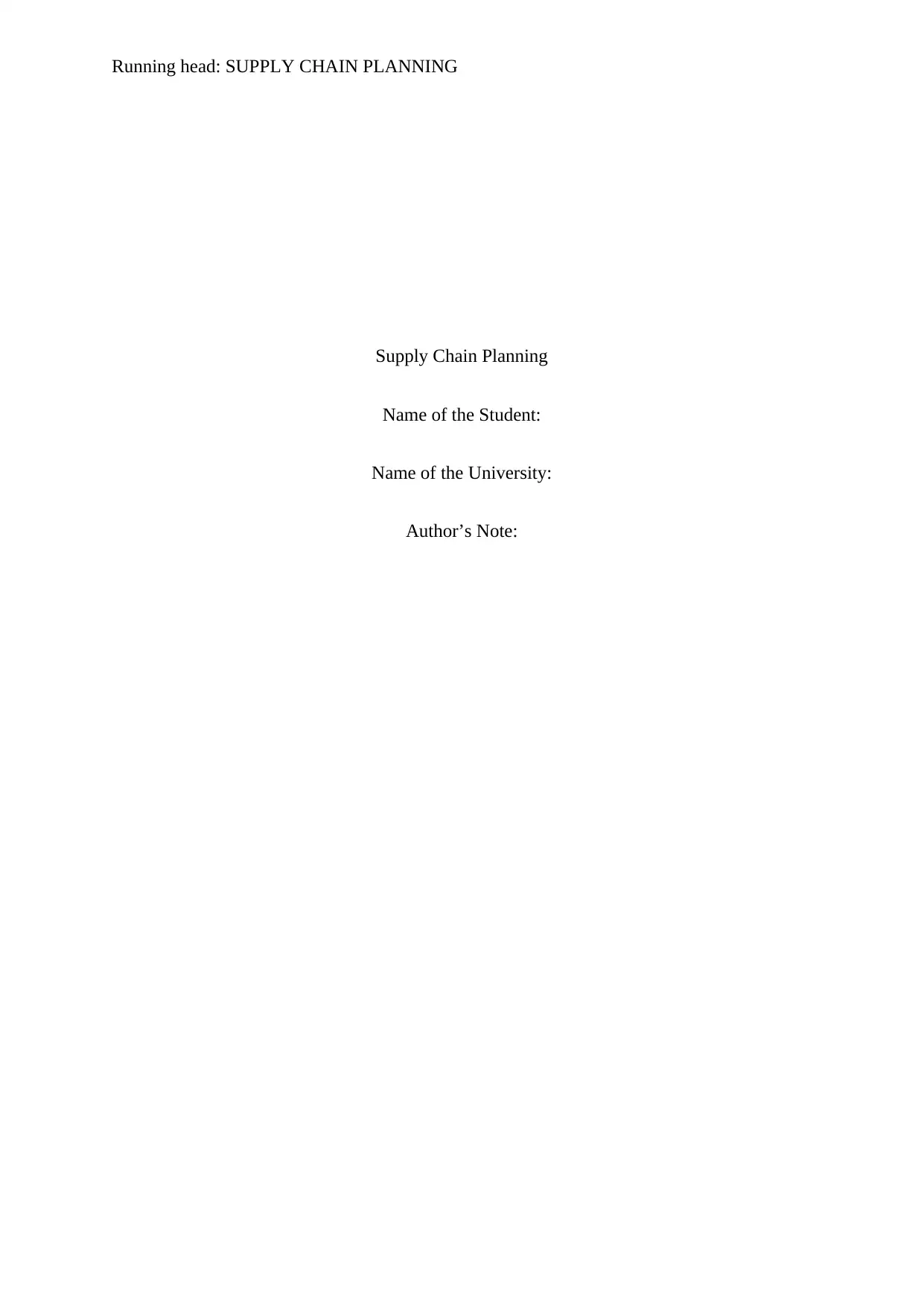
Running head: SUPPLY CHAIN PLANNING
Supply Chain Planning
Name of the Student:
Name of the University:
Author’s Note:
Supply Chain Planning
Name of the Student:
Name of the University:
Author’s Note:
Secure Best Marks with AI Grader
Need help grading? Try our AI Grader for instant feedback on your assignments.
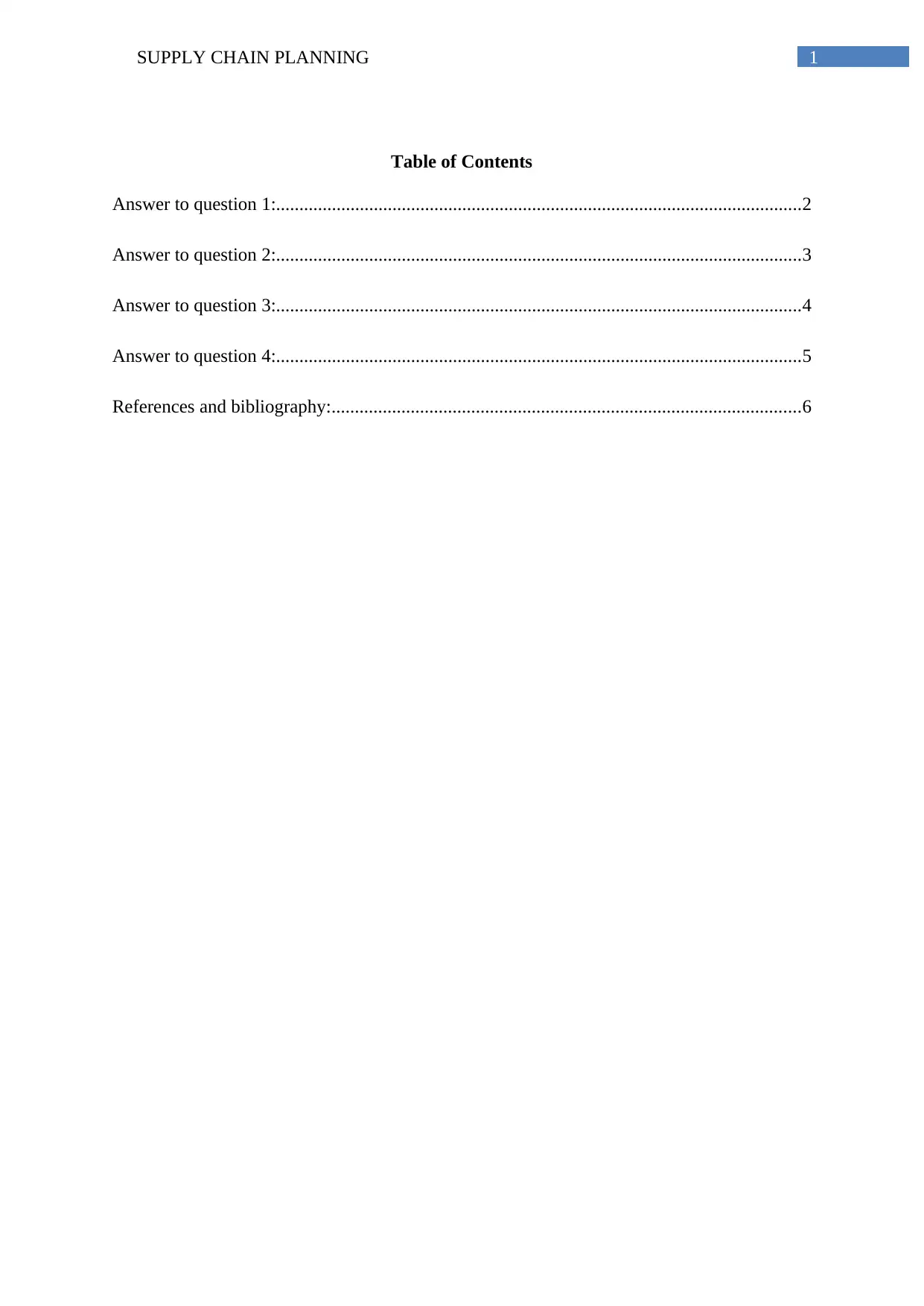
1SUPPLY CHAIN PLANNING
Table of Contents
Answer to question 1:.................................................................................................................2
Answer to question 2:.................................................................................................................3
Answer to question 3:.................................................................................................................4
Answer to question 4:.................................................................................................................5
References and bibliography:.....................................................................................................6
Table of Contents
Answer to question 1:.................................................................................................................2
Answer to question 2:.................................................................................................................3
Answer to question 3:.................................................................................................................4
Answer to question 4:.................................................................................................................5
References and bibliography:.....................................................................................................6
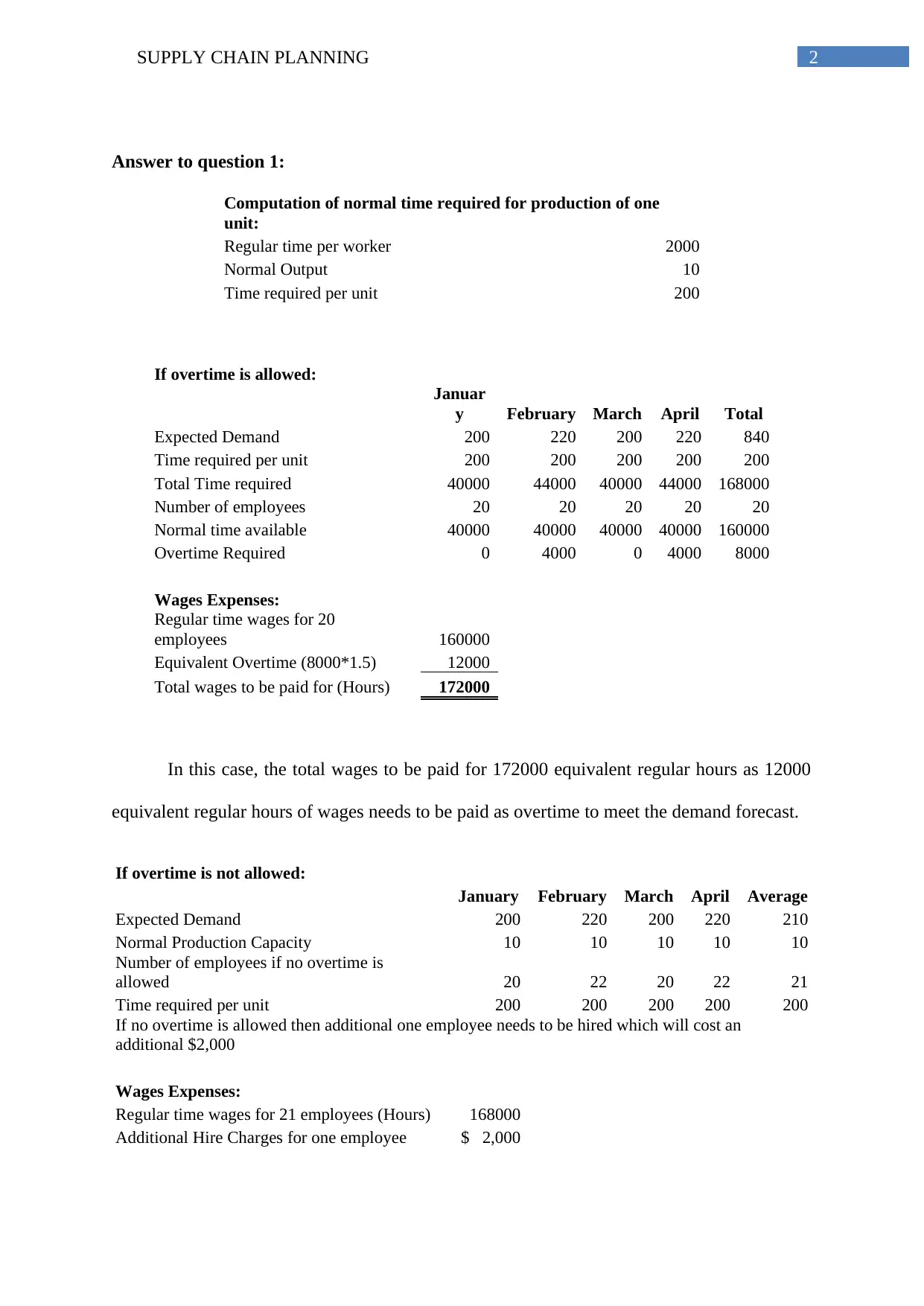
2SUPPLY CHAIN PLANNING
Answer to question 1:
Computation of normal time required for production of one
unit:
Regular time per worker 2000
Normal Output 10
Time required per unit 200
If overtime is allowed:
Januar
y February March April Total
Expected Demand 200 220 200 220 840
Time required per unit 200 200 200 200 200
Total Time required 40000 44000 40000 44000 168000
Number of employees 20 20 20 20 20
Normal time available 40000 40000 40000 40000 160000
Overtime Required 0 4000 0 4000 8000
Wages Expenses:
Regular time wages for 20
employees 160000
Equivalent Overtime (8000*1.5) 12000
Total wages to be paid for (Hours) 172000
In this case, the total wages to be paid for 172000 equivalent regular hours as 12000
equivalent regular hours of wages needs to be paid as overtime to meet the demand forecast.
If overtime is not allowed:
January February March April Average
Expected Demand 200 220 200 220 210
Normal Production Capacity 10 10 10 10 10
Number of employees if no overtime is
allowed 20 22 20 22 21
Time required per unit 200 200 200 200 200
If no overtime is allowed then additional one employee needs to be hired which will cost an
additional $2,000
Wages Expenses:
Regular time wages for 21 employees (Hours) 168000
Additional Hire Charges for one employee $ 2,000
Answer to question 1:
Computation of normal time required for production of one
unit:
Regular time per worker 2000
Normal Output 10
Time required per unit 200
If overtime is allowed:
Januar
y February March April Total
Expected Demand 200 220 200 220 840
Time required per unit 200 200 200 200 200
Total Time required 40000 44000 40000 44000 168000
Number of employees 20 20 20 20 20
Normal time available 40000 40000 40000 40000 160000
Overtime Required 0 4000 0 4000 8000
Wages Expenses:
Regular time wages for 20
employees 160000
Equivalent Overtime (8000*1.5) 12000
Total wages to be paid for (Hours) 172000
In this case, the total wages to be paid for 172000 equivalent regular hours as 12000
equivalent regular hours of wages needs to be paid as overtime to meet the demand forecast.
If overtime is not allowed:
January February March April Average
Expected Demand 200 220 200 220 210
Normal Production Capacity 10 10 10 10 10
Number of employees if no overtime is
allowed 20 22 20 22 21
Time required per unit 200 200 200 200 200
If no overtime is allowed then additional one employee needs to be hired which will cost an
additional $2,000
Wages Expenses:
Regular time wages for 21 employees (Hours) 168000
Additional Hire Charges for one employee $ 2,000
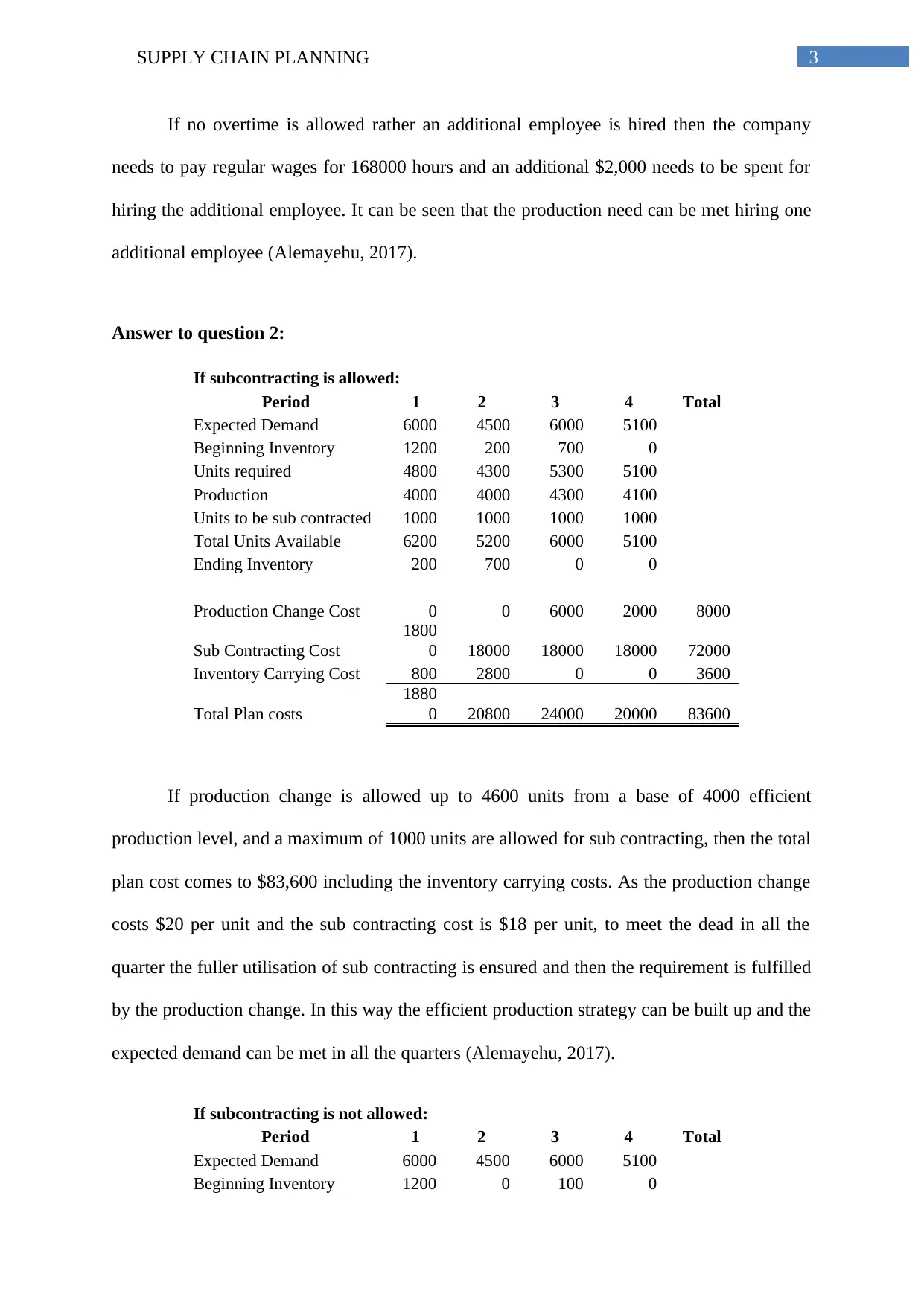
3SUPPLY CHAIN PLANNING
If no overtime is allowed rather an additional employee is hired then the company
needs to pay regular wages for 168000 hours and an additional $2,000 needs to be spent for
hiring the additional employee. It can be seen that the production need can be met hiring one
additional employee (Alemayehu, 2017).
Answer to question 2:
If subcontracting is allowed:
Period 1 2 3 4 Total
Expected Demand 6000 4500 6000 5100
Beginning Inventory 1200 200 700 0
Units required 4800 4300 5300 5100
Production 4000 4000 4300 4100
Units to be sub contracted 1000 1000 1000 1000
Total Units Available 6200 5200 6000 5100
Ending Inventory 200 700 0 0
Production Change Cost 0 0 6000 2000 8000
Sub Contracting Cost
1800
0 18000 18000 18000 72000
Inventory Carrying Cost 800 2800 0 0 3600
Total Plan costs
1880
0 20800 24000 20000 83600
If production change is allowed up to 4600 units from a base of 4000 efficient
production level, and a maximum of 1000 units are allowed for sub contracting, then the total
plan cost comes to $83,600 including the inventory carrying costs. As the production change
costs $20 per unit and the sub contracting cost is $18 per unit, to meet the dead in all the
quarter the fuller utilisation of sub contracting is ensured and then the requirement is fulfilled
by the production change. In this way the efficient production strategy can be built up and the
expected demand can be met in all the quarters (Alemayehu, 2017).
If subcontracting is not allowed:
Period 1 2 3 4 Total
Expected Demand 6000 4500 6000 5100
Beginning Inventory 1200 0 100 0
If no overtime is allowed rather an additional employee is hired then the company
needs to pay regular wages for 168000 hours and an additional $2,000 needs to be spent for
hiring the additional employee. It can be seen that the production need can be met hiring one
additional employee (Alemayehu, 2017).
Answer to question 2:
If subcontracting is allowed:
Period 1 2 3 4 Total
Expected Demand 6000 4500 6000 5100
Beginning Inventory 1200 200 700 0
Units required 4800 4300 5300 5100
Production 4000 4000 4300 4100
Units to be sub contracted 1000 1000 1000 1000
Total Units Available 6200 5200 6000 5100
Ending Inventory 200 700 0 0
Production Change Cost 0 0 6000 2000 8000
Sub Contracting Cost
1800
0 18000 18000 18000 72000
Inventory Carrying Cost 800 2800 0 0 3600
Total Plan costs
1880
0 20800 24000 20000 83600
If production change is allowed up to 4600 units from a base of 4000 efficient
production level, and a maximum of 1000 units are allowed for sub contracting, then the total
plan cost comes to $83,600 including the inventory carrying costs. As the production change
costs $20 per unit and the sub contracting cost is $18 per unit, to meet the dead in all the
quarter the fuller utilisation of sub contracting is ensured and then the requirement is fulfilled
by the production change. In this way the efficient production strategy can be built up and the
expected demand can be met in all the quarters (Alemayehu, 2017).
If subcontracting is not allowed:
Period 1 2 3 4 Total
Expected Demand 6000 4500 6000 5100
Beginning Inventory 1200 0 100 0
Secure Best Marks with AI Grader
Need help grading? Try our AI Grader for instant feedback on your assignments.
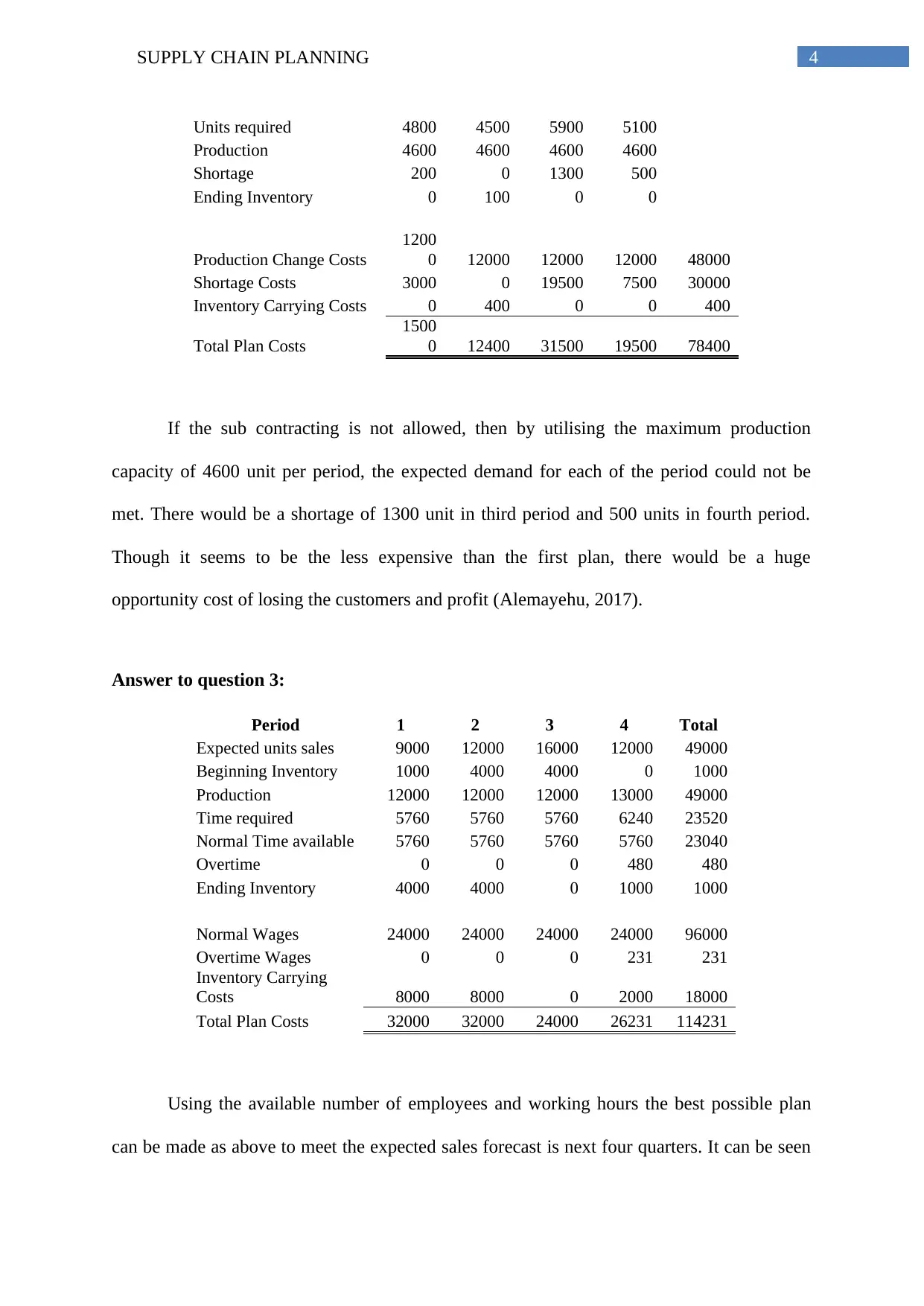
4SUPPLY CHAIN PLANNING
Units required 4800 4500 5900 5100
Production 4600 4600 4600 4600
Shortage 200 0 1300 500
Ending Inventory 0 100 0 0
Production Change Costs
1200
0 12000 12000 12000 48000
Shortage Costs 3000 0 19500 7500 30000
Inventory Carrying Costs 0 400 0 0 400
Total Plan Costs
1500
0 12400 31500 19500 78400
If the sub contracting is not allowed, then by utilising the maximum production
capacity of 4600 unit per period, the expected demand for each of the period could not be
met. There would be a shortage of 1300 unit in third period and 500 units in fourth period.
Though it seems to be the less expensive than the first plan, there would be a huge
opportunity cost of losing the customers and profit (Alemayehu, 2017).
Answer to question 3:
Period 1 2 3 4 Total
Expected units sales 9000 12000 16000 12000 49000
Beginning Inventory 1000 4000 4000 0 1000
Production 12000 12000 12000 13000 49000
Time required 5760 5760 5760 6240 23520
Normal Time available 5760 5760 5760 5760 23040
Overtime 0 0 0 480 480
Ending Inventory 4000 4000 0 1000 1000
Normal Wages 24000 24000 24000 24000 96000
Overtime Wages 0 0 0 231 231
Inventory Carrying
Costs 8000 8000 0 2000 18000
Total Plan Costs 32000 32000 24000 26231 114231
Using the available number of employees and working hours the best possible plan
can be made as above to meet the expected sales forecast is next four quarters. It can be seen
Units required 4800 4500 5900 5100
Production 4600 4600 4600 4600
Shortage 200 0 1300 500
Ending Inventory 0 100 0 0
Production Change Costs
1200
0 12000 12000 12000 48000
Shortage Costs 3000 0 19500 7500 30000
Inventory Carrying Costs 0 400 0 0 400
Total Plan Costs
1500
0 12400 31500 19500 78400
If the sub contracting is not allowed, then by utilising the maximum production
capacity of 4600 unit per period, the expected demand for each of the period could not be
met. There would be a shortage of 1300 unit in third period and 500 units in fourth period.
Though it seems to be the less expensive than the first plan, there would be a huge
opportunity cost of losing the customers and profit (Alemayehu, 2017).
Answer to question 3:
Period 1 2 3 4 Total
Expected units sales 9000 12000 16000 12000 49000
Beginning Inventory 1000 4000 4000 0 1000
Production 12000 12000 12000 13000 49000
Time required 5760 5760 5760 6240 23520
Normal Time available 5760 5760 5760 5760 23040
Overtime 0 0 0 480 480
Ending Inventory 4000 4000 0 1000 1000
Normal Wages 24000 24000 24000 24000 96000
Overtime Wages 0 0 0 231 231
Inventory Carrying
Costs 8000 8000 0 2000 18000
Total Plan Costs 32000 32000 24000 26231 114231
Using the available number of employees and working hours the best possible plan
can be made as above to meet the expected sales forecast is next four quarters. It can be seen
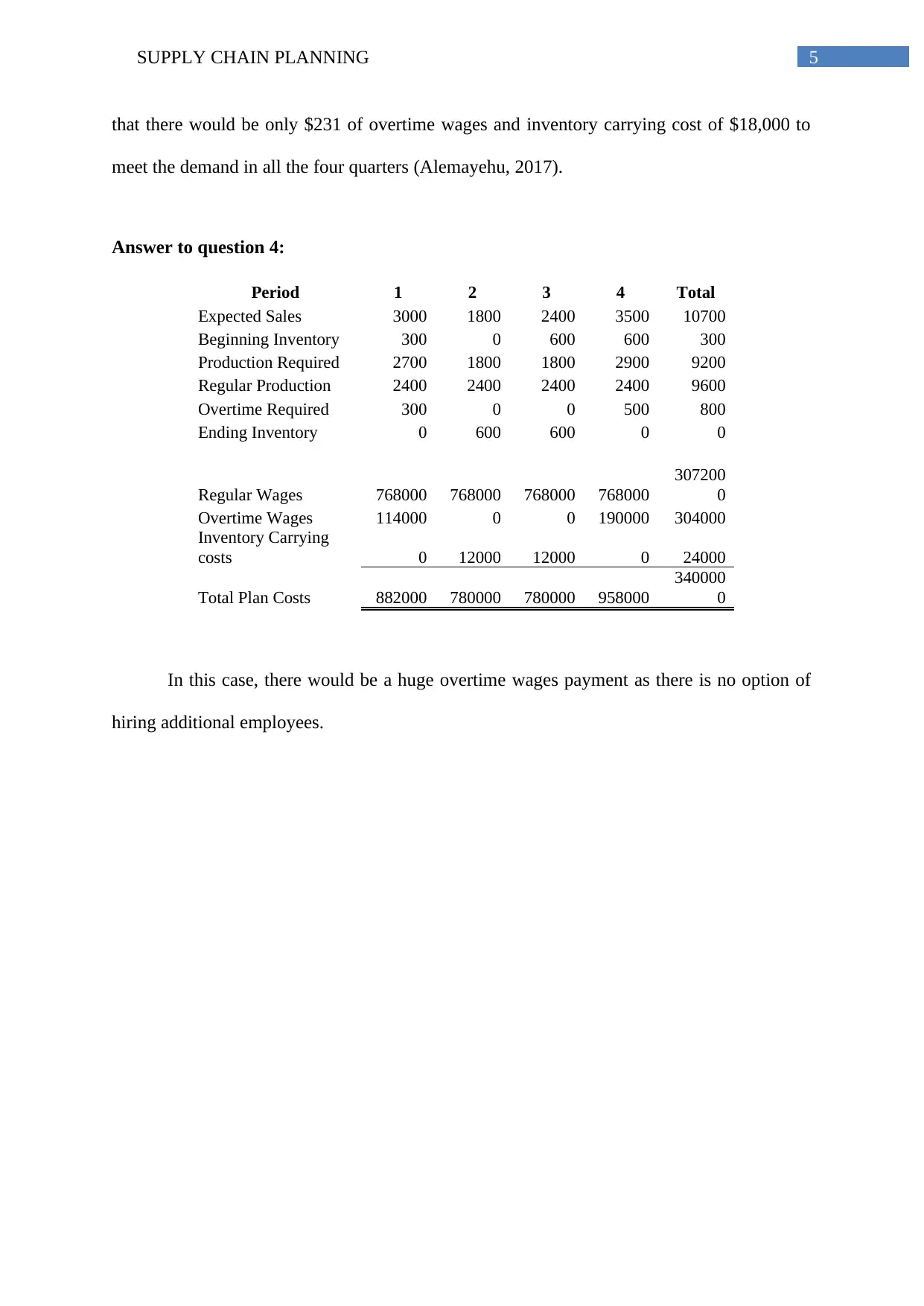
5SUPPLY CHAIN PLANNING
that there would be only $231 of overtime wages and inventory carrying cost of $18,000 to
meet the demand in all the four quarters (Alemayehu, 2017).
Answer to question 4:
Period 1 2 3 4 Total
Expected Sales 3000 1800 2400 3500 10700
Beginning Inventory 300 0 600 600 300
Production Required 2700 1800 1800 2900 9200
Regular Production 2400 2400 2400 2400 9600
Overtime Required 300 0 0 500 800
Ending Inventory 0 600 600 0 0
Regular Wages 768000 768000 768000 768000
307200
0
Overtime Wages 114000 0 0 190000 304000
Inventory Carrying
costs 0 12000 12000 0 24000
Total Plan Costs 882000 780000 780000 958000
340000
0
In this case, there would be a huge overtime wages payment as there is no option of
hiring additional employees.
that there would be only $231 of overtime wages and inventory carrying cost of $18,000 to
meet the demand in all the four quarters (Alemayehu, 2017).
Answer to question 4:
Period 1 2 3 4 Total
Expected Sales 3000 1800 2400 3500 10700
Beginning Inventory 300 0 600 600 300
Production Required 2700 1800 1800 2900 9200
Regular Production 2400 2400 2400 2400 9600
Overtime Required 300 0 0 500 800
Ending Inventory 0 600 600 0 0
Regular Wages 768000 768000 768000 768000
307200
0
Overtime Wages 114000 0 0 190000 304000
Inventory Carrying
costs 0 12000 12000 0 24000
Total Plan Costs 882000 780000 780000 958000
340000
0
In this case, there would be a huge overtime wages payment as there is no option of
hiring additional employees.
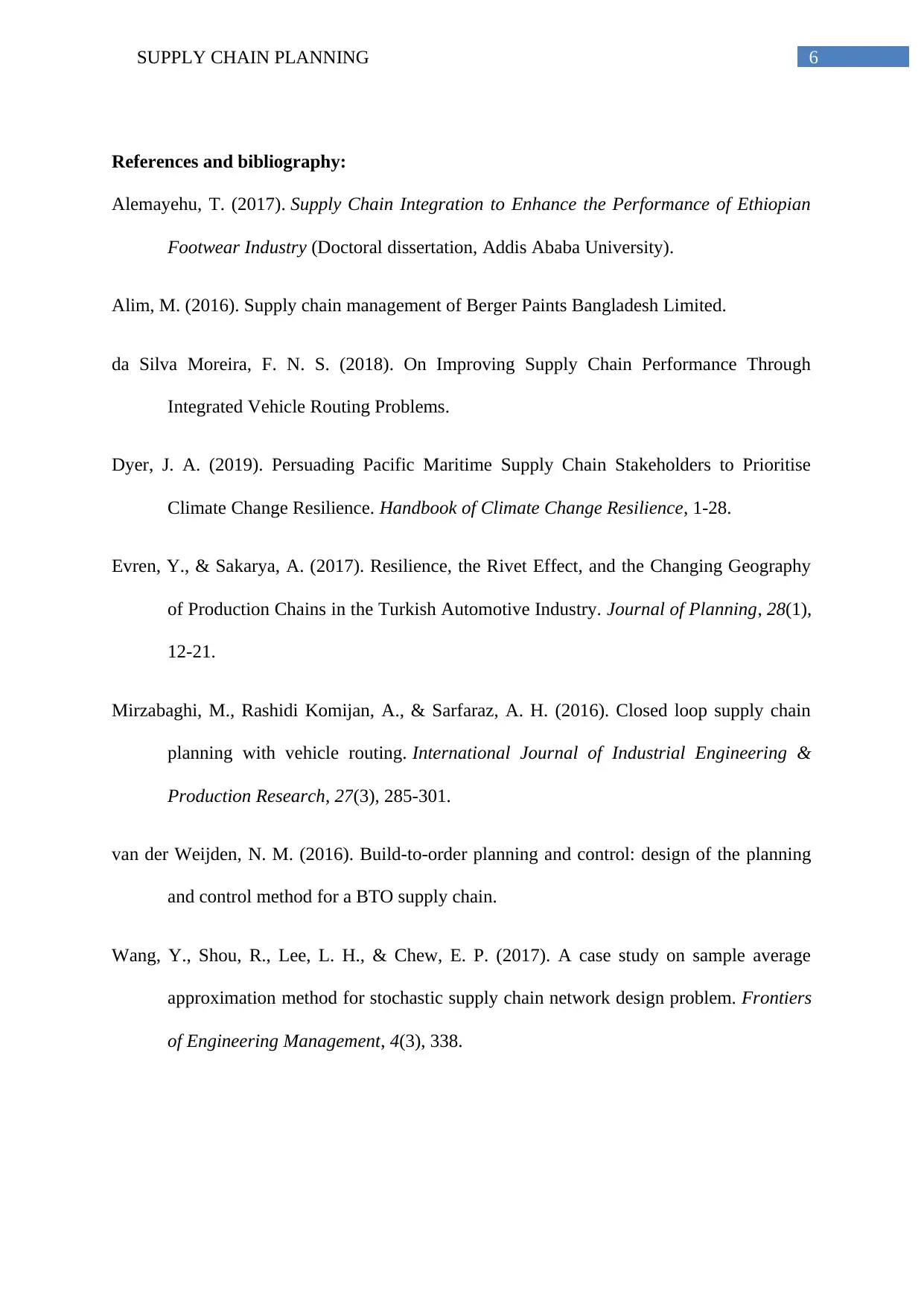
6SUPPLY CHAIN PLANNING
References and bibliography:
Alemayehu, T. (2017). Supply Chain Integration to Enhance the Performance of Ethiopian
Footwear Industry (Doctoral dissertation, Addis Ababa University).
Alim, M. (2016). Supply chain management of Berger Paints Bangladesh Limited.
da Silva Moreira, F. N. S. (2018). On Improving Supply Chain Performance Through
Integrated Vehicle Routing Problems.
Dyer, J. A. (2019). Persuading Pacific Maritime Supply Chain Stakeholders to Prioritise
Climate Change Resilience. Handbook of Climate Change Resilience, 1-28.
Evren, Y., & Sakarya, A. (2017). Resilience, the Rivet Effect, and the Changing Geography
of Production Chains in the Turkish Automotive Industry. Journal of Planning, 28(1),
12-21.
Mirzabaghi, M., Rashidi Komijan, A., & Sarfaraz, A. H. (2016). Closed loop supply chain
planning with vehicle routing. International Journal of Industrial Engineering &
Production Research, 27(3), 285-301.
van der Weijden, N. M. (2016). Build-to-order planning and control: design of the planning
and control method for a BTO supply chain.
Wang, Y., Shou, R., Lee, L. H., & Chew, E. P. (2017). A case study on sample average
approximation method for stochastic supply chain network design problem. Frontiers
of Engineering Management, 4(3), 338.
References and bibliography:
Alemayehu, T. (2017). Supply Chain Integration to Enhance the Performance of Ethiopian
Footwear Industry (Doctoral dissertation, Addis Ababa University).
Alim, M. (2016). Supply chain management of Berger Paints Bangladesh Limited.
da Silva Moreira, F. N. S. (2018). On Improving Supply Chain Performance Through
Integrated Vehicle Routing Problems.
Dyer, J. A. (2019). Persuading Pacific Maritime Supply Chain Stakeholders to Prioritise
Climate Change Resilience. Handbook of Climate Change Resilience, 1-28.
Evren, Y., & Sakarya, A. (2017). Resilience, the Rivet Effect, and the Changing Geography
of Production Chains in the Turkish Automotive Industry. Journal of Planning, 28(1),
12-21.
Mirzabaghi, M., Rashidi Komijan, A., & Sarfaraz, A. H. (2016). Closed loop supply chain
planning with vehicle routing. International Journal of Industrial Engineering &
Production Research, 27(3), 285-301.
van der Weijden, N. M. (2016). Build-to-order planning and control: design of the planning
and control method for a BTO supply chain.
Wang, Y., Shou, R., Lee, L. H., & Chew, E. P. (2017). A case study on sample average
approximation method for stochastic supply chain network design problem. Frontiers
of Engineering Management, 4(3), 338.
1 out of 7
![[object Object]](/_next/image/?url=%2F_next%2Fstatic%2Fmedia%2Flogo.6d15ce61.png&w=640&q=75)
Your All-in-One AI-Powered Toolkit for Academic Success.
 +13062052269
info@desklib.com
Available 24*7 on WhatsApp / Email
Unlock your academic potential
© 2024  |  Zucol Services PVT LTD  |  All rights reserved.