Effects of the Japanese Earthquake on Supply Chain Systems
VerifiedAdded on 2023/01/19
|18
|4693
|91
AI Summary
The Japanese earthquake caused damages on the supply chain systems developed by companies. The damages included both transport and communication disruption and loss of physical manufacturing assets and equipment. Therefore, the companies halted operations for a period of time to recover and remodel the supply chain system. The earthquake taught management some valuable lessons on the vulnerabilities present in supply chain systems. Consequently, the management developed and introduced various changes to supply chain such as information systems and the dispersion of supply nodes. The changes allowed the companies to have a higher level of response to future disasters.
Contribute Materials
Your contribution can guide someone’s learning journey. Share your
documents today.
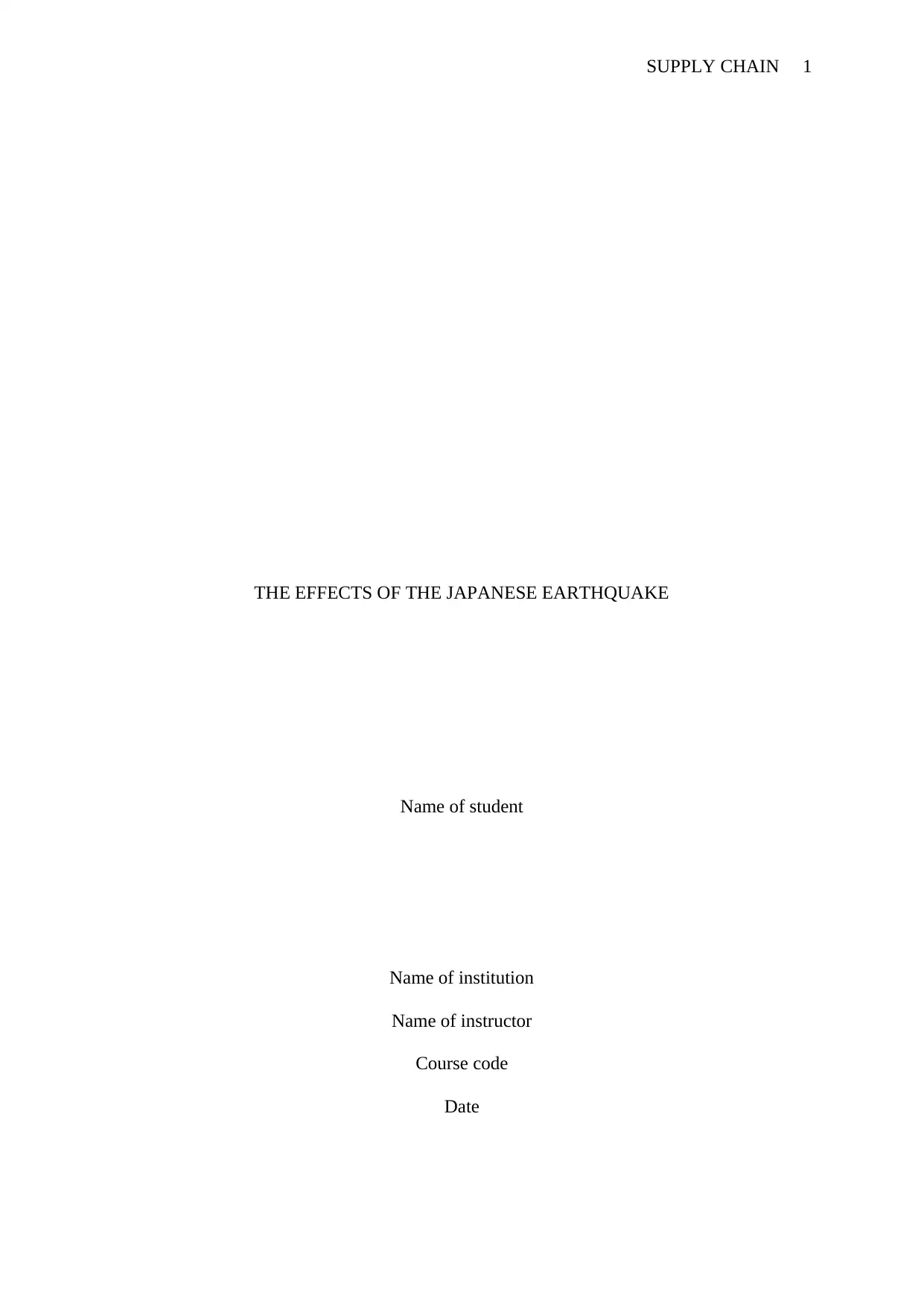
SUPPLY CHAIN 1
THE EFFECTS OF THE JAPANESE EARTHQUAKE
Name of student
Name of institution
Name of instructor
Course code
Date
THE EFFECTS OF THE JAPANESE EARTHQUAKE
Name of student
Name of institution
Name of instructor
Course code
Date
Secure Best Marks with AI Grader
Need help grading? Try our AI Grader for instant feedback on your assignments.
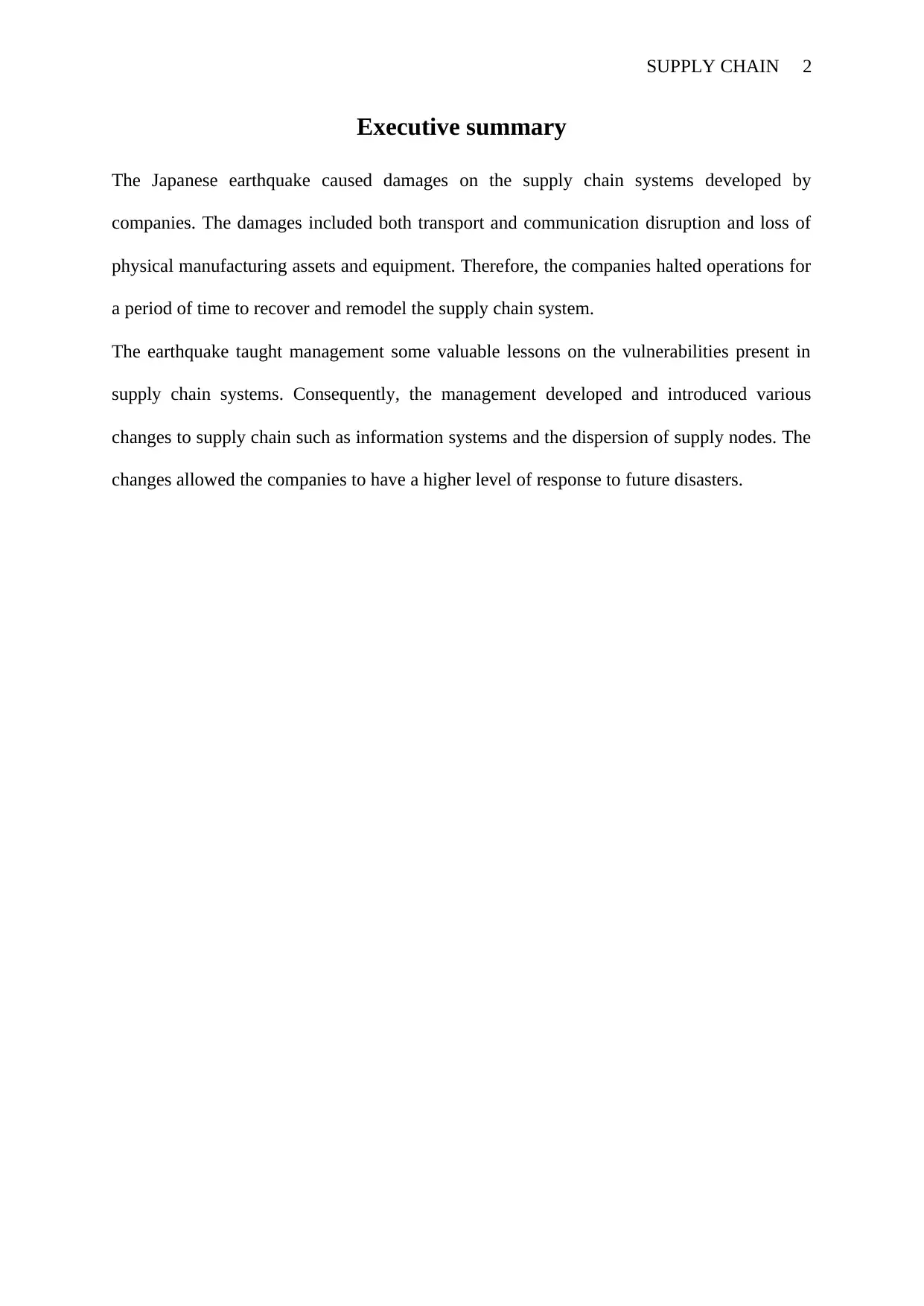
SUPPLY CHAIN 2
Executive summary
The Japanese earthquake caused damages on the supply chain systems developed by
companies. The damages included both transport and communication disruption and loss of
physical manufacturing assets and equipment. Therefore, the companies halted operations for
a period of time to recover and remodel the supply chain system.
The earthquake taught management some valuable lessons on the vulnerabilities present in
supply chain systems. Consequently, the management developed and introduced various
changes to supply chain such as information systems and the dispersion of supply nodes. The
changes allowed the companies to have a higher level of response to future disasters.
Executive summary
The Japanese earthquake caused damages on the supply chain systems developed by
companies. The damages included both transport and communication disruption and loss of
physical manufacturing assets and equipment. Therefore, the companies halted operations for
a period of time to recover and remodel the supply chain system.
The earthquake taught management some valuable lessons on the vulnerabilities present in
supply chain systems. Consequently, the management developed and introduced various
changes to supply chain such as information systems and the dispersion of supply nodes. The
changes allowed the companies to have a higher level of response to future disasters.
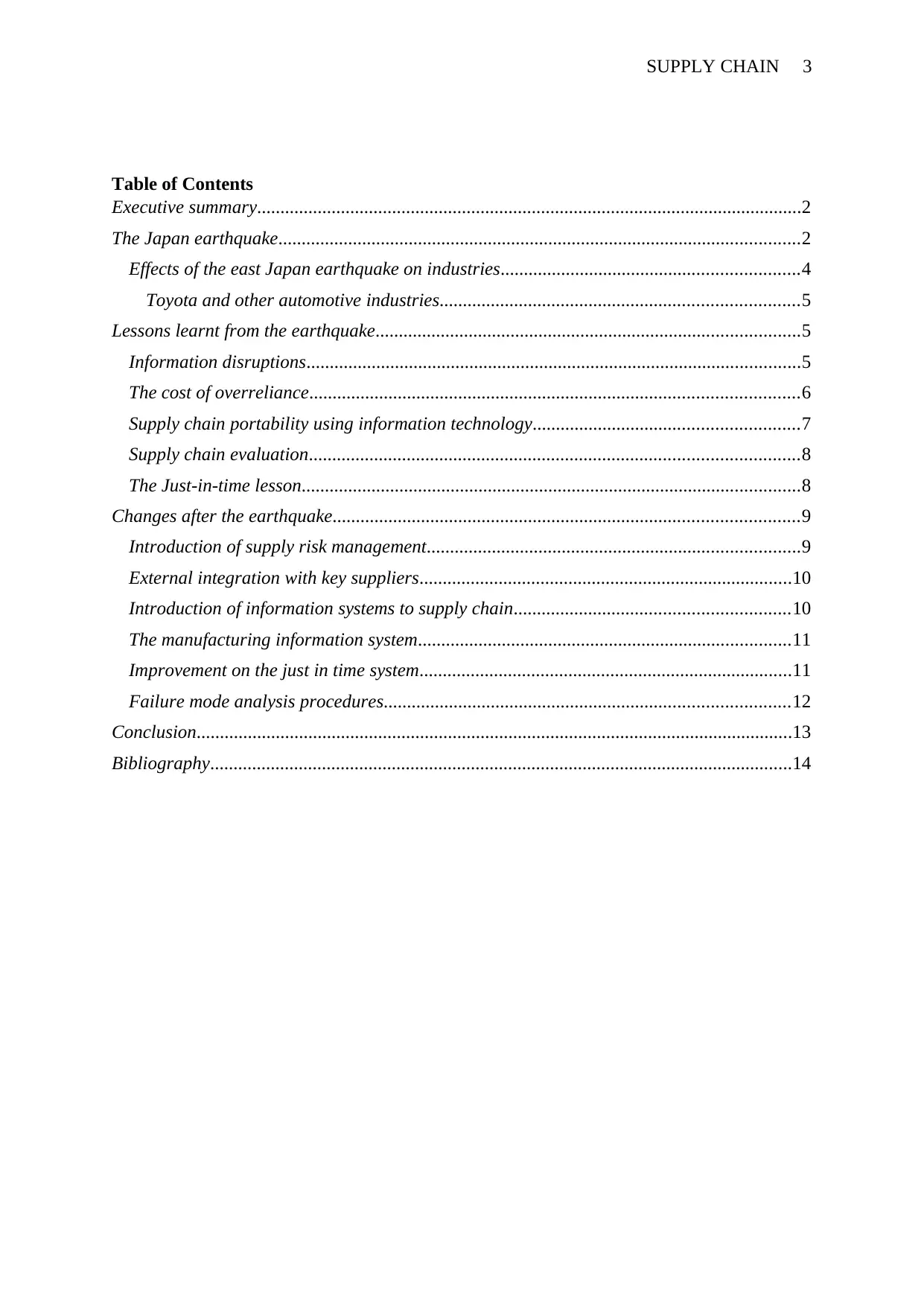
SUPPLY CHAIN 3
Table of Contents
Executive summary.....................................................................................................................2
The Japan earthquake................................................................................................................2
Effects of the east Japan earthquake on industries................................................................4
Toyota and other automotive industries.............................................................................5
Lessons learnt from the earthquake...........................................................................................5
Information disruptions..........................................................................................................5
The cost of overreliance.........................................................................................................6
Supply chain portability using information technology.........................................................7
Supply chain evaluation.........................................................................................................8
The Just-in-time lesson...........................................................................................................8
Changes after the earthquake....................................................................................................9
Introduction of supply risk management................................................................................9
External integration with key suppliers................................................................................10
Introduction of information systems to supply chain...........................................................10
The manufacturing information system................................................................................11
Improvement on the just in time system................................................................................11
Failure mode analysis procedures.......................................................................................12
Conclusion................................................................................................................................13
Bibliography.............................................................................................................................14
Table of Contents
Executive summary.....................................................................................................................2
The Japan earthquake................................................................................................................2
Effects of the east Japan earthquake on industries................................................................4
Toyota and other automotive industries.............................................................................5
Lessons learnt from the earthquake...........................................................................................5
Information disruptions..........................................................................................................5
The cost of overreliance.........................................................................................................6
Supply chain portability using information technology.........................................................7
Supply chain evaluation.........................................................................................................8
The Just-in-time lesson...........................................................................................................8
Changes after the earthquake....................................................................................................9
Introduction of supply risk management................................................................................9
External integration with key suppliers................................................................................10
Introduction of information systems to supply chain...........................................................10
The manufacturing information system................................................................................11
Improvement on the just in time system................................................................................11
Failure mode analysis procedures.......................................................................................12
Conclusion................................................................................................................................13
Bibliography.............................................................................................................................14
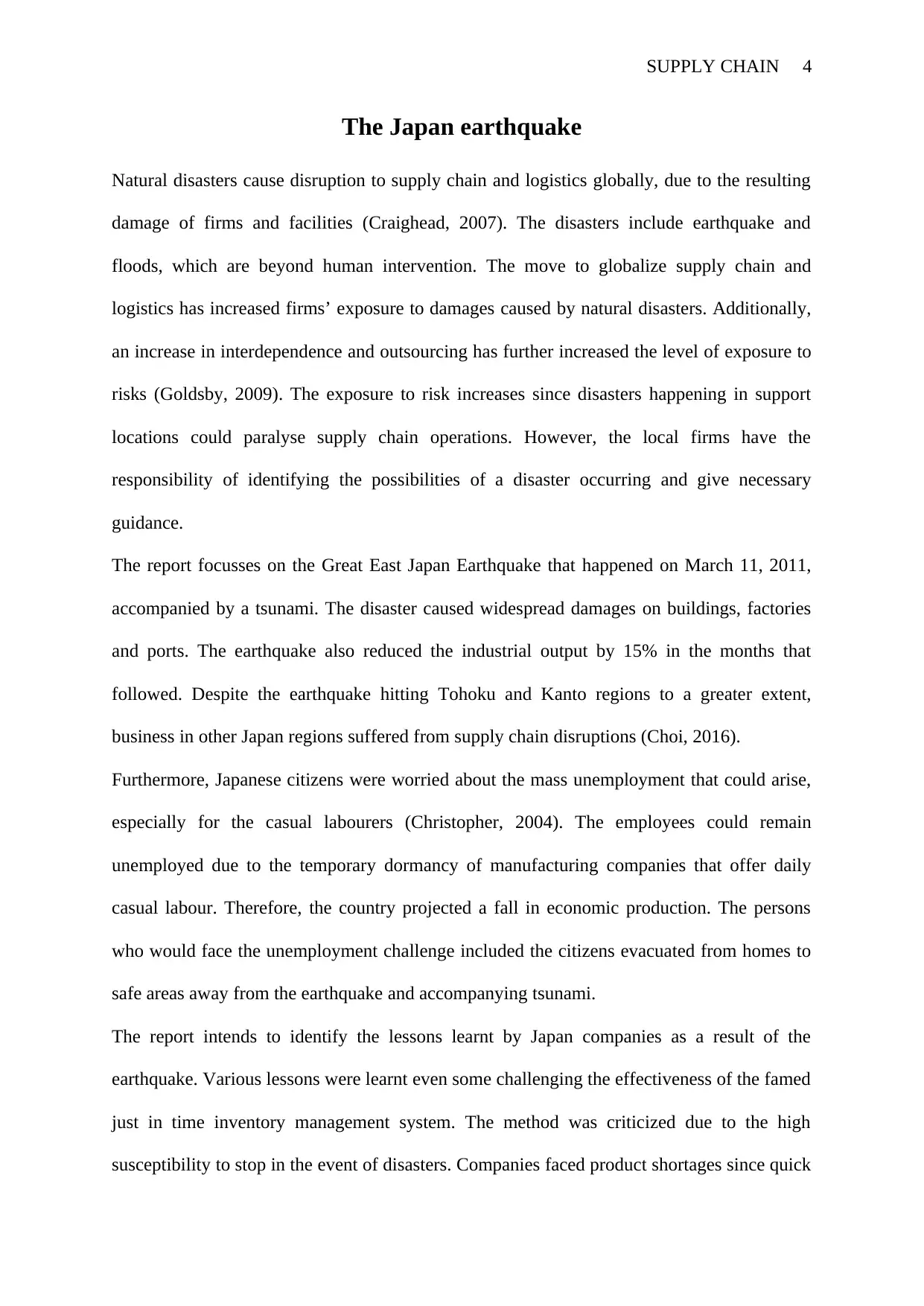
SUPPLY CHAIN 4
The Japan earthquake
Natural disasters cause disruption to supply chain and logistics globally, due to the resulting
damage of firms and facilities (Craighead, 2007). The disasters include earthquake and
floods, which are beyond human intervention. The move to globalize supply chain and
logistics has increased firms’ exposure to damages caused by natural disasters. Additionally,
an increase in interdependence and outsourcing has further increased the level of exposure to
risks (Goldsby, 2009). The exposure to risk increases since disasters happening in support
locations could paralyse supply chain operations. However, the local firms have the
responsibility of identifying the possibilities of a disaster occurring and give necessary
guidance.
The report focusses on the Great East Japan Earthquake that happened on March 11, 2011,
accompanied by a tsunami. The disaster caused widespread damages on buildings, factories
and ports. The earthquake also reduced the industrial output by 15% in the months that
followed. Despite the earthquake hitting Tohoku and Kanto regions to a greater extent,
business in other Japan regions suffered from supply chain disruptions (Choi, 2016).
Furthermore, Japanese citizens were worried about the mass unemployment that could arise,
especially for the casual labourers (Christopher, 2004). The employees could remain
unemployed due to the temporary dormancy of manufacturing companies that offer daily
casual labour. Therefore, the country projected a fall in economic production. The persons
who would face the unemployment challenge included the citizens evacuated from homes to
safe areas away from the earthquake and accompanying tsunami.
The report intends to identify the lessons learnt by Japan companies as a result of the
earthquake. Various lessons were learnt even some challenging the effectiveness of the famed
just in time inventory management system. The method was criticized due to the high
susceptibility to stop in the event of disasters. Companies faced product shortages since quick
The Japan earthquake
Natural disasters cause disruption to supply chain and logistics globally, due to the resulting
damage of firms and facilities (Craighead, 2007). The disasters include earthquake and
floods, which are beyond human intervention. The move to globalize supply chain and
logistics has increased firms’ exposure to damages caused by natural disasters. Additionally,
an increase in interdependence and outsourcing has further increased the level of exposure to
risks (Goldsby, 2009). The exposure to risk increases since disasters happening in support
locations could paralyse supply chain operations. However, the local firms have the
responsibility of identifying the possibilities of a disaster occurring and give necessary
guidance.
The report focusses on the Great East Japan Earthquake that happened on March 11, 2011,
accompanied by a tsunami. The disaster caused widespread damages on buildings, factories
and ports. The earthquake also reduced the industrial output by 15% in the months that
followed. Despite the earthquake hitting Tohoku and Kanto regions to a greater extent,
business in other Japan regions suffered from supply chain disruptions (Choi, 2016).
Furthermore, Japanese citizens were worried about the mass unemployment that could arise,
especially for the casual labourers (Christopher, 2004). The employees could remain
unemployed due to the temporary dormancy of manufacturing companies that offer daily
casual labour. Therefore, the country projected a fall in economic production. The persons
who would face the unemployment challenge included the citizens evacuated from homes to
safe areas away from the earthquake and accompanying tsunami.
The report intends to identify the lessons learnt by Japan companies as a result of the
earthquake. Various lessons were learnt even some challenging the effectiveness of the famed
just in time inventory management system. The method was criticized due to the high
susceptibility to stop in the event of disasters. Companies faced product shortages since quick
Secure Best Marks with AI Grader
Need help grading? Try our AI Grader for instant feedback on your assignments.
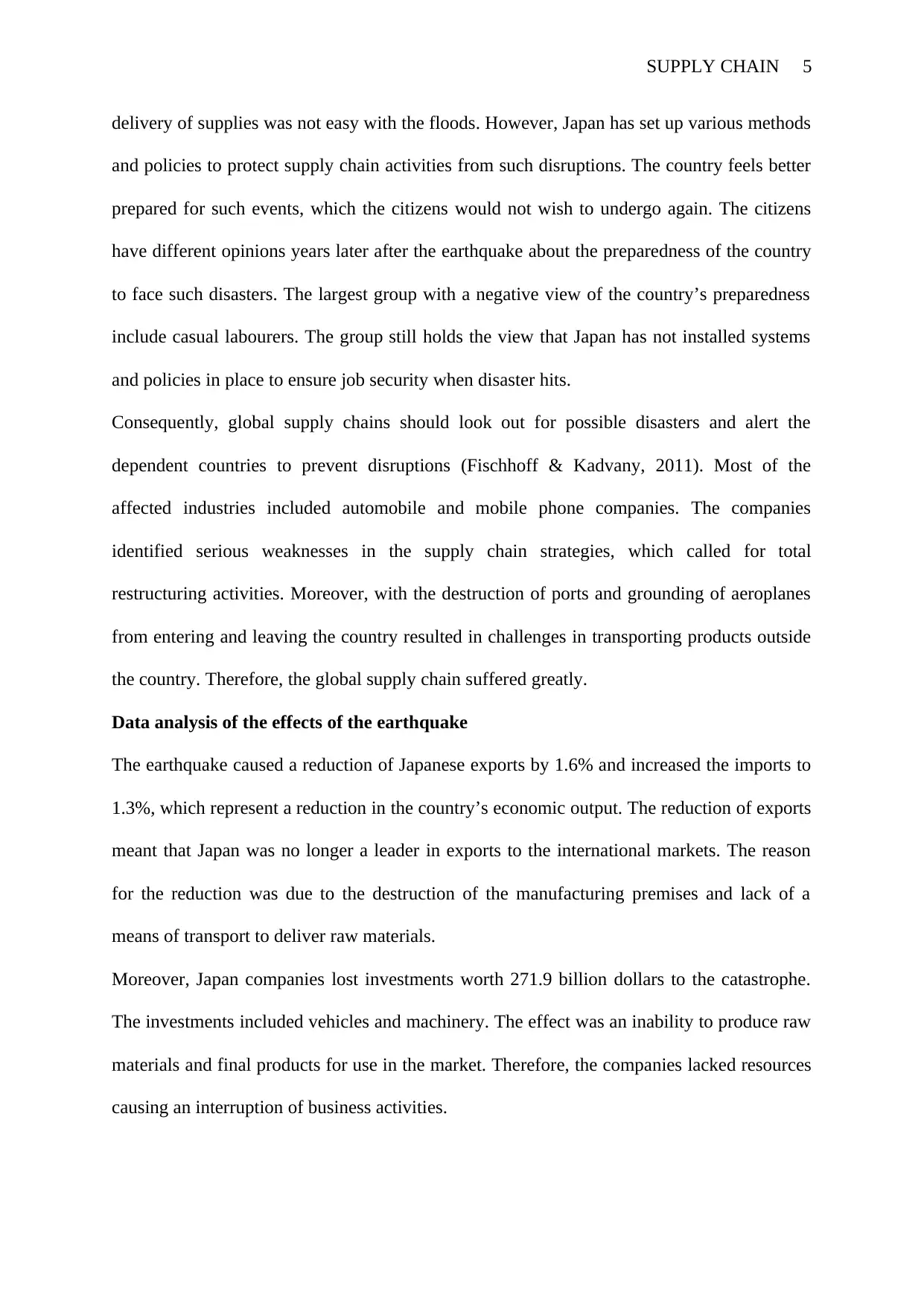
SUPPLY CHAIN 5
delivery of supplies was not easy with the floods. However, Japan has set up various methods
and policies to protect supply chain activities from such disruptions. The country feels better
prepared for such events, which the citizens would not wish to undergo again. The citizens
have different opinions years later after the earthquake about the preparedness of the country
to face such disasters. The largest group with a negative view of the country’s preparedness
include casual labourers. The group still holds the view that Japan has not installed systems
and policies in place to ensure job security when disaster hits.
Consequently, global supply chains should look out for possible disasters and alert the
dependent countries to prevent disruptions (Fischhoff & Kadvany, 2011). Most of the
affected industries included automobile and mobile phone companies. The companies
identified serious weaknesses in the supply chain strategies, which called for total
restructuring activities. Moreover, with the destruction of ports and grounding of aeroplanes
from entering and leaving the country resulted in challenges in transporting products outside
the country. Therefore, the global supply chain suffered greatly.
Data analysis of the effects of the earthquake
The earthquake caused a reduction of Japanese exports by 1.6% and increased the imports to
1.3%, which represent a reduction in the country’s economic output. The reduction of exports
meant that Japan was no longer a leader in exports to the international markets. The reason
for the reduction was due to the destruction of the manufacturing premises and lack of a
means of transport to deliver raw materials.
Moreover, Japan companies lost investments worth 271.9 billion dollars to the catastrophe.
The investments included vehicles and machinery. The effect was an inability to produce raw
materials and final products for use in the market. Therefore, the companies lacked resources
causing an interruption of business activities.
delivery of supplies was not easy with the floods. However, Japan has set up various methods
and policies to protect supply chain activities from such disruptions. The country feels better
prepared for such events, which the citizens would not wish to undergo again. The citizens
have different opinions years later after the earthquake about the preparedness of the country
to face such disasters. The largest group with a negative view of the country’s preparedness
include casual labourers. The group still holds the view that Japan has not installed systems
and policies in place to ensure job security when disaster hits.
Consequently, global supply chains should look out for possible disasters and alert the
dependent countries to prevent disruptions (Fischhoff & Kadvany, 2011). Most of the
affected industries included automobile and mobile phone companies. The companies
identified serious weaknesses in the supply chain strategies, which called for total
restructuring activities. Moreover, with the destruction of ports and grounding of aeroplanes
from entering and leaving the country resulted in challenges in transporting products outside
the country. Therefore, the global supply chain suffered greatly.
Data analysis of the effects of the earthquake
The earthquake caused a reduction of Japanese exports by 1.6% and increased the imports to
1.3%, which represent a reduction in the country’s economic output. The reduction of exports
meant that Japan was no longer a leader in exports to the international markets. The reason
for the reduction was due to the destruction of the manufacturing premises and lack of a
means of transport to deliver raw materials.
Moreover, Japan companies lost investments worth 271.9 billion dollars to the catastrophe.
The investments included vehicles and machinery. The effect was an inability to produce raw
materials and final products for use in the market. Therefore, the companies lacked resources
causing an interruption of business activities.
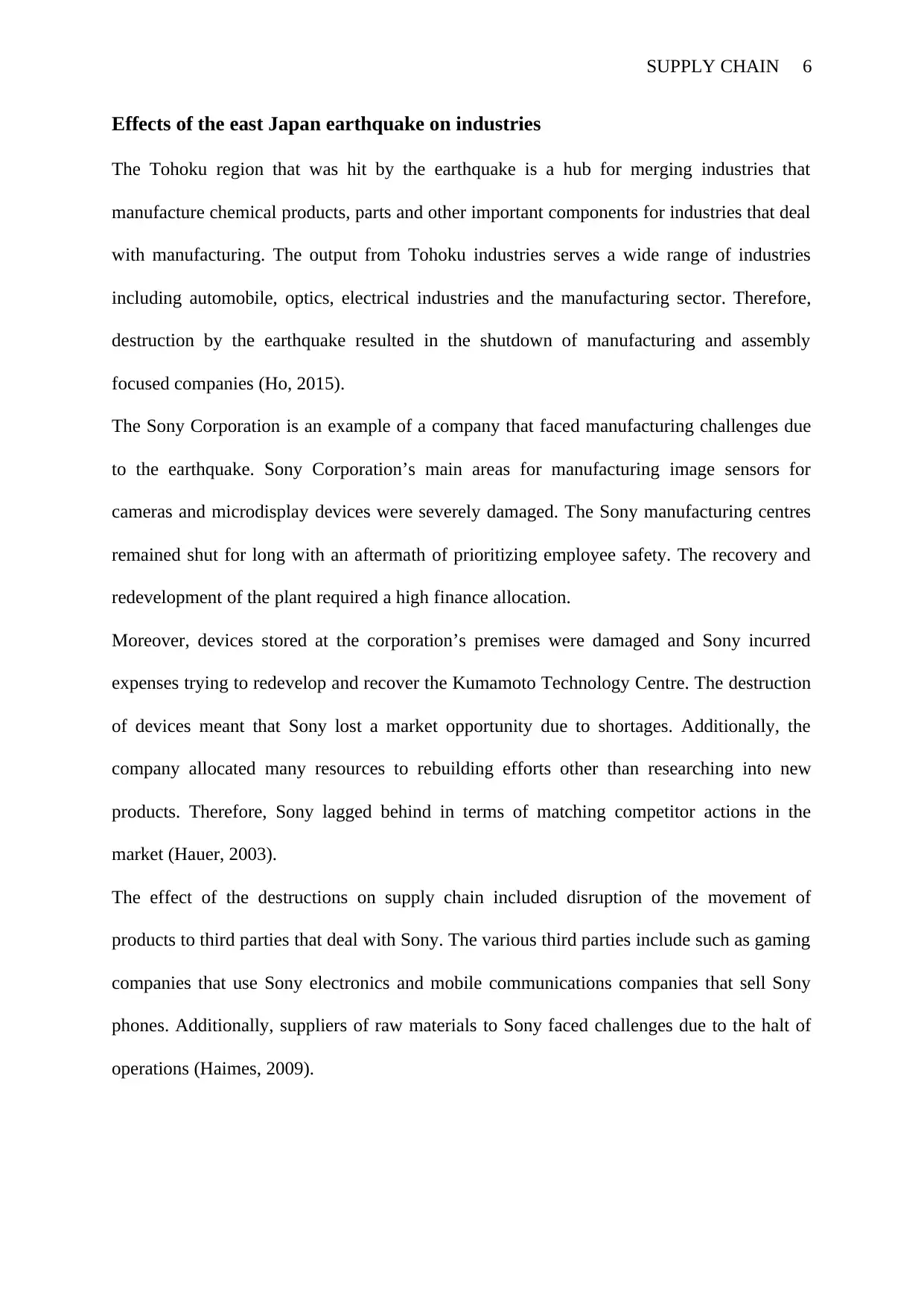
SUPPLY CHAIN 6
Effects of the east Japan earthquake on industries
The Tohoku region that was hit by the earthquake is a hub for merging industries that
manufacture chemical products, parts and other important components for industries that deal
with manufacturing. The output from Tohoku industries serves a wide range of industries
including automobile, optics, electrical industries and the manufacturing sector. Therefore,
destruction by the earthquake resulted in the shutdown of manufacturing and assembly
focused companies (Ho, 2015).
The Sony Corporation is an example of a company that faced manufacturing challenges due
to the earthquake. Sony Corporation’s main areas for manufacturing image sensors for
cameras and microdisplay devices were severely damaged. The Sony manufacturing centres
remained shut for long with an aftermath of prioritizing employee safety. The recovery and
redevelopment of the plant required a high finance allocation.
Moreover, devices stored at the corporation’s premises were damaged and Sony incurred
expenses trying to redevelop and recover the Kumamoto Technology Centre. The destruction
of devices meant that Sony lost a market opportunity due to shortages. Additionally, the
company allocated many resources to rebuilding efforts other than researching into new
products. Therefore, Sony lagged behind in terms of matching competitor actions in the
market (Hauer, 2003).
The effect of the destructions on supply chain included disruption of the movement of
products to third parties that deal with Sony. The various third parties include such as gaming
companies that use Sony electronics and mobile communications companies that sell Sony
phones. Additionally, suppliers of raw materials to Sony faced challenges due to the halt of
operations (Haimes, 2009).
Effects of the east Japan earthquake on industries
The Tohoku region that was hit by the earthquake is a hub for merging industries that
manufacture chemical products, parts and other important components for industries that deal
with manufacturing. The output from Tohoku industries serves a wide range of industries
including automobile, optics, electrical industries and the manufacturing sector. Therefore,
destruction by the earthquake resulted in the shutdown of manufacturing and assembly
focused companies (Ho, 2015).
The Sony Corporation is an example of a company that faced manufacturing challenges due
to the earthquake. Sony Corporation’s main areas for manufacturing image sensors for
cameras and microdisplay devices were severely damaged. The Sony manufacturing centres
remained shut for long with an aftermath of prioritizing employee safety. The recovery and
redevelopment of the plant required a high finance allocation.
Moreover, devices stored at the corporation’s premises were damaged and Sony incurred
expenses trying to redevelop and recover the Kumamoto Technology Centre. The destruction
of devices meant that Sony lost a market opportunity due to shortages. Additionally, the
company allocated many resources to rebuilding efforts other than researching into new
products. Therefore, Sony lagged behind in terms of matching competitor actions in the
market (Hauer, 2003).
The effect of the destructions on supply chain included disruption of the movement of
products to third parties that deal with Sony. The various third parties include such as gaming
companies that use Sony electronics and mobile communications companies that sell Sony
phones. Additionally, suppliers of raw materials to Sony faced challenges due to the halt of
operations (Haimes, 2009).
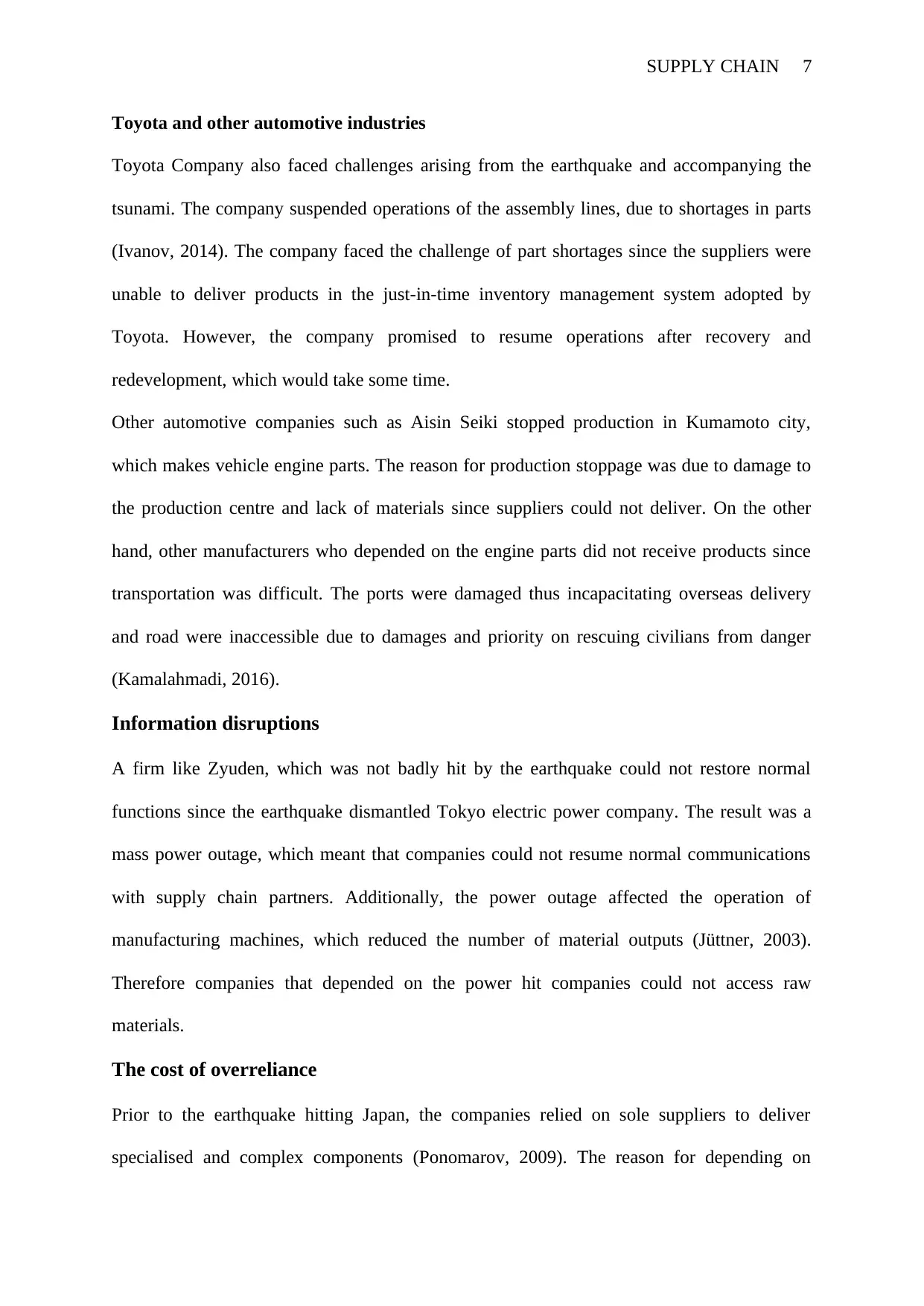
SUPPLY CHAIN 7
Toyota and other automotive industries
Toyota Company also faced challenges arising from the earthquake and accompanying the
tsunami. The company suspended operations of the assembly lines, due to shortages in parts
(Ivanov, 2014). The company faced the challenge of part shortages since the suppliers were
unable to deliver products in the just-in-time inventory management system adopted by
Toyota. However, the company promised to resume operations after recovery and
redevelopment, which would take some time.
Other automotive companies such as Aisin Seiki stopped production in Kumamoto city,
which makes vehicle engine parts. The reason for production stoppage was due to damage to
the production centre and lack of materials since suppliers could not deliver. On the other
hand, other manufacturers who depended on the engine parts did not receive products since
transportation was difficult. The ports were damaged thus incapacitating overseas delivery
and road were inaccessible due to damages and priority on rescuing civilians from danger
(Kamalahmadi, 2016).
Information disruptions
A firm like Zyuden, which was not badly hit by the earthquake could not restore normal
functions since the earthquake dismantled Tokyo electric power company. The result was a
mass power outage, which meant that companies could not resume normal communications
with supply chain partners. Additionally, the power outage affected the operation of
manufacturing machines, which reduced the number of material outputs (Jüttner, 2003).
Therefore companies that depended on the power hit companies could not access raw
materials.
The cost of overreliance
Prior to the earthquake hitting Japan, the companies relied on sole suppliers to deliver
specialised and complex components (Ponomarov, 2009). The reason for depending on
Toyota and other automotive industries
Toyota Company also faced challenges arising from the earthquake and accompanying the
tsunami. The company suspended operations of the assembly lines, due to shortages in parts
(Ivanov, 2014). The company faced the challenge of part shortages since the suppliers were
unable to deliver products in the just-in-time inventory management system adopted by
Toyota. However, the company promised to resume operations after recovery and
redevelopment, which would take some time.
Other automotive companies such as Aisin Seiki stopped production in Kumamoto city,
which makes vehicle engine parts. The reason for production stoppage was due to damage to
the production centre and lack of materials since suppliers could not deliver. On the other
hand, other manufacturers who depended on the engine parts did not receive products since
transportation was difficult. The ports were damaged thus incapacitating overseas delivery
and road were inaccessible due to damages and priority on rescuing civilians from danger
(Kamalahmadi, 2016).
Information disruptions
A firm like Zyuden, which was not badly hit by the earthquake could not restore normal
functions since the earthquake dismantled Tokyo electric power company. The result was a
mass power outage, which meant that companies could not resume normal communications
with supply chain partners. Additionally, the power outage affected the operation of
manufacturing machines, which reduced the number of material outputs (Jüttner, 2003).
Therefore companies that depended on the power hit companies could not access raw
materials.
The cost of overreliance
Prior to the earthquake hitting Japan, the companies relied on sole suppliers to deliver
specialised and complex components (Ponomarov, 2009). The reason for depending on
Paraphrase This Document
Need a fresh take? Get an instant paraphrase of this document with our AI Paraphraser
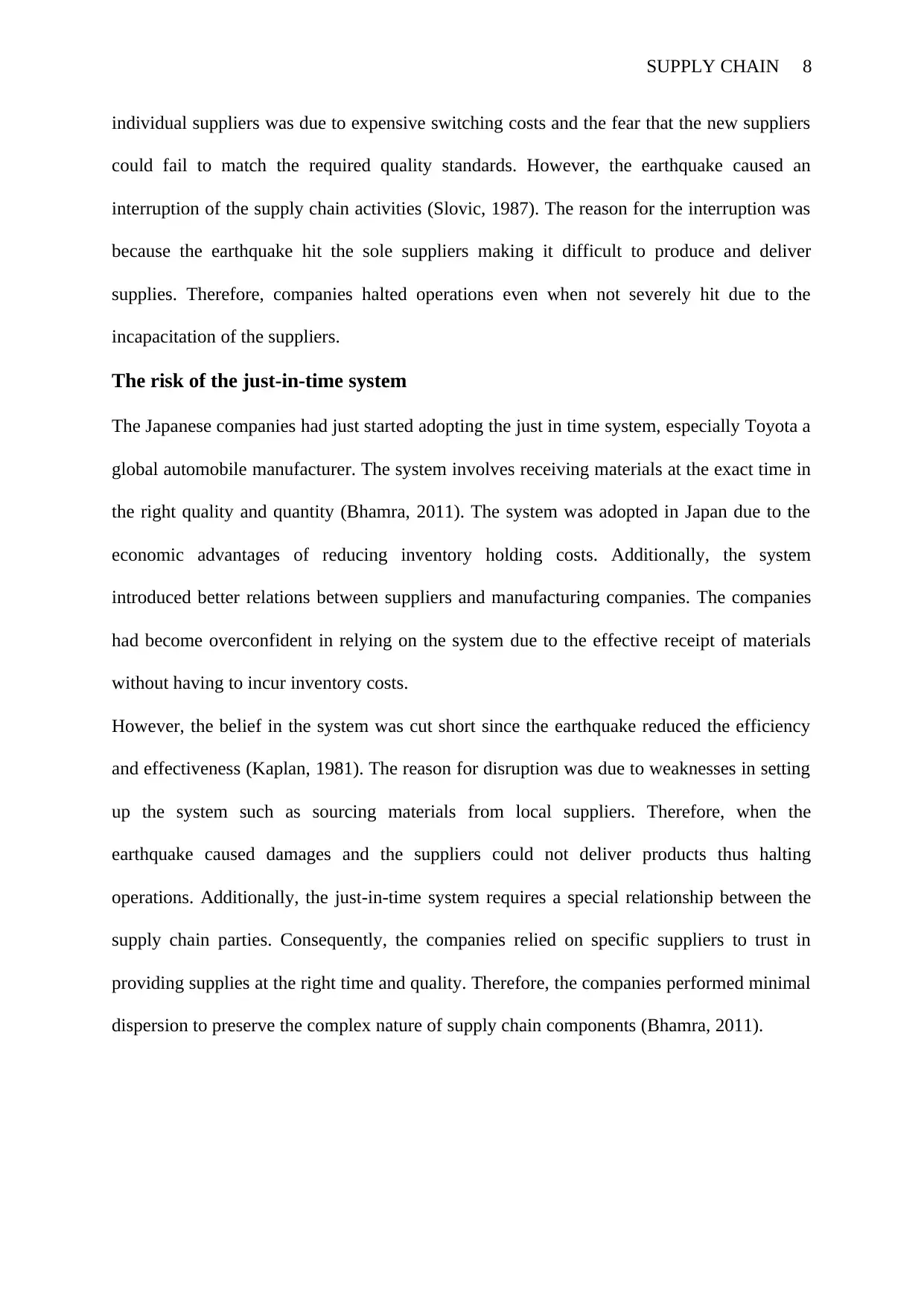
SUPPLY CHAIN 8
individual suppliers was due to expensive switching costs and the fear that the new suppliers
could fail to match the required quality standards. However, the earthquake caused an
interruption of the supply chain activities (Slovic, 1987). The reason for the interruption was
because the earthquake hit the sole suppliers making it difficult to produce and deliver
supplies. Therefore, companies halted operations even when not severely hit due to the
incapacitation of the suppliers.
The risk of the just-in-time system
The Japanese companies had just started adopting the just in time system, especially Toyota a
global automobile manufacturer. The system involves receiving materials at the exact time in
the right quality and quantity (Bhamra, 2011). The system was adopted in Japan due to the
economic advantages of reducing inventory holding costs. Additionally, the system
introduced better relations between suppliers and manufacturing companies. The companies
had become overconfident in relying on the system due to the effective receipt of materials
without having to incur inventory costs.
However, the belief in the system was cut short since the earthquake reduced the efficiency
and effectiveness (Kaplan, 1981). The reason for disruption was due to weaknesses in setting
up the system such as sourcing materials from local suppliers. Therefore, when the
earthquake caused damages and the suppliers could not deliver products thus halting
operations. Additionally, the just-in-time system requires a special relationship between the
supply chain parties. Consequently, the companies relied on specific suppliers to trust in
providing supplies at the right time and quality. Therefore, the companies performed minimal
dispersion to preserve the complex nature of supply chain components (Bhamra, 2011).
individual suppliers was due to expensive switching costs and the fear that the new suppliers
could fail to match the required quality standards. However, the earthquake caused an
interruption of the supply chain activities (Slovic, 1987). The reason for the interruption was
because the earthquake hit the sole suppliers making it difficult to produce and deliver
supplies. Therefore, companies halted operations even when not severely hit due to the
incapacitation of the suppliers.
The risk of the just-in-time system
The Japanese companies had just started adopting the just in time system, especially Toyota a
global automobile manufacturer. The system involves receiving materials at the exact time in
the right quality and quantity (Bhamra, 2011). The system was adopted in Japan due to the
economic advantages of reducing inventory holding costs. Additionally, the system
introduced better relations between suppliers and manufacturing companies. The companies
had become overconfident in relying on the system due to the effective receipt of materials
without having to incur inventory costs.
However, the belief in the system was cut short since the earthquake reduced the efficiency
and effectiveness (Kaplan, 1981). The reason for disruption was due to weaknesses in setting
up the system such as sourcing materials from local suppliers. Therefore, when the
earthquake caused damages and the suppliers could not deliver products thus halting
operations. Additionally, the just-in-time system requires a special relationship between the
supply chain parties. Consequently, the companies relied on specific suppliers to trust in
providing supplies at the right time and quality. Therefore, the companies performed minimal
dispersion to preserve the complex nature of supply chain components (Bhamra, 2011).
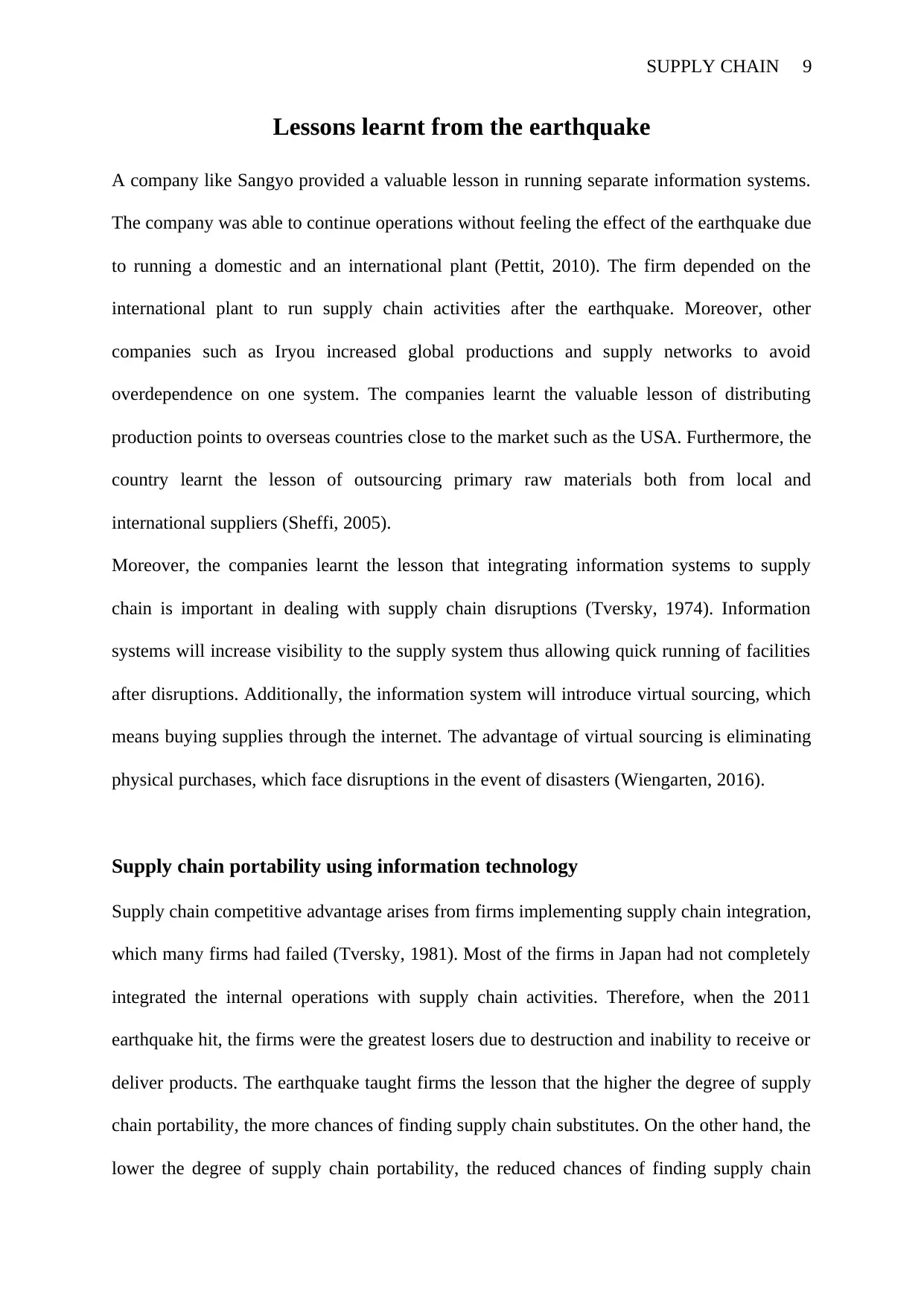
SUPPLY CHAIN 9
Lessons learnt from the earthquake
A company like Sangyo provided a valuable lesson in running separate information systems.
The company was able to continue operations without feeling the effect of the earthquake due
to running a domestic and an international plant (Pettit, 2010). The firm depended on the
international plant to run supply chain activities after the earthquake. Moreover, other
companies such as Iryou increased global productions and supply networks to avoid
overdependence on one system. The companies learnt the valuable lesson of distributing
production points to overseas countries close to the market such as the USA. Furthermore, the
country learnt the lesson of outsourcing primary raw materials both from local and
international suppliers (Sheffi, 2005).
Moreover, the companies learnt the lesson that integrating information systems to supply
chain is important in dealing with supply chain disruptions (Tversky, 1974). Information
systems will increase visibility to the supply system thus allowing quick running of facilities
after disruptions. Additionally, the information system will introduce virtual sourcing, which
means buying supplies through the internet. The advantage of virtual sourcing is eliminating
physical purchases, which face disruptions in the event of disasters (Wiengarten, 2016).
Supply chain portability using information technology
Supply chain competitive advantage arises from firms implementing supply chain integration,
which many firms had failed (Tversky, 1981). Most of the firms in Japan had not completely
integrated the internal operations with supply chain activities. Therefore, when the 2011
earthquake hit, the firms were the greatest losers due to destruction and inability to receive or
deliver products. The earthquake taught firms the lesson that the higher the degree of supply
chain portability, the more chances of finding supply chain substitutes. On the other hand, the
lower the degree of supply chain portability, the reduced chances of finding supply chain
Lessons learnt from the earthquake
A company like Sangyo provided a valuable lesson in running separate information systems.
The company was able to continue operations without feeling the effect of the earthquake due
to running a domestic and an international plant (Pettit, 2010). The firm depended on the
international plant to run supply chain activities after the earthquake. Moreover, other
companies such as Iryou increased global productions and supply networks to avoid
overdependence on one system. The companies learnt the valuable lesson of distributing
production points to overseas countries close to the market such as the USA. Furthermore, the
country learnt the lesson of outsourcing primary raw materials both from local and
international suppliers (Sheffi, 2005).
Moreover, the companies learnt the lesson that integrating information systems to supply
chain is important in dealing with supply chain disruptions (Tversky, 1974). Information
systems will increase visibility to the supply system thus allowing quick running of facilities
after disruptions. Additionally, the information system will introduce virtual sourcing, which
means buying supplies through the internet. The advantage of virtual sourcing is eliminating
physical purchases, which face disruptions in the event of disasters (Wiengarten, 2016).
Supply chain portability using information technology
Supply chain competitive advantage arises from firms implementing supply chain integration,
which many firms had failed (Tversky, 1981). Most of the firms in Japan had not completely
integrated the internal operations with supply chain activities. Therefore, when the 2011
earthquake hit, the firms were the greatest losers due to destruction and inability to receive or
deliver products. The earthquake taught firms the lesson that the higher the degree of supply
chain portability, the more chances of finding supply chain substitutes. On the other hand, the
lower the degree of supply chain portability, the reduced chances of finding supply chain
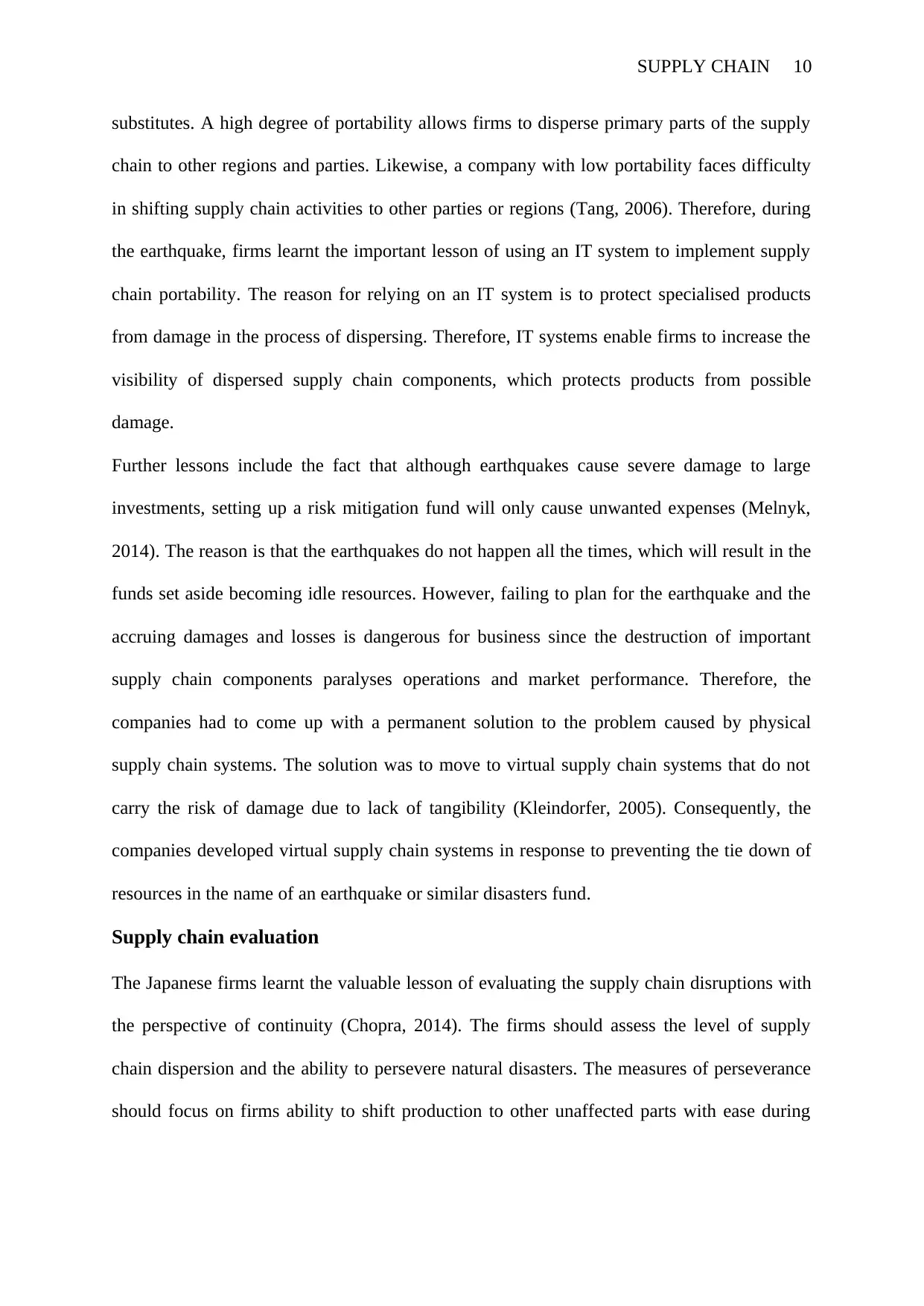
SUPPLY CHAIN 10
substitutes. A high degree of portability allows firms to disperse primary parts of the supply
chain to other regions and parties. Likewise, a company with low portability faces difficulty
in shifting supply chain activities to other parties or regions (Tang, 2006). Therefore, during
the earthquake, firms learnt the important lesson of using an IT system to implement supply
chain portability. The reason for relying on an IT system is to protect specialised products
from damage in the process of dispersing. Therefore, IT systems enable firms to increase the
visibility of dispersed supply chain components, which protects products from possible
damage.
Further lessons include the fact that although earthquakes cause severe damage to large
investments, setting up a risk mitigation fund will only cause unwanted expenses (Melnyk,
2014). The reason is that the earthquakes do not happen all the times, which will result in the
funds set aside becoming idle resources. However, failing to plan for the earthquake and the
accruing damages and losses is dangerous for business since the destruction of important
supply chain components paralyses operations and market performance. Therefore, the
companies had to come up with a permanent solution to the problem caused by physical
supply chain systems. The solution was to move to virtual supply chain systems that do not
carry the risk of damage due to lack of tangibility (Kleindorfer, 2005). Consequently, the
companies developed virtual supply chain systems in response to preventing the tie down of
resources in the name of an earthquake or similar disasters fund.
Supply chain evaluation
The Japanese firms learnt the valuable lesson of evaluating the supply chain disruptions with
the perspective of continuity (Chopra, 2014). The firms should assess the level of supply
chain dispersion and the ability to persevere natural disasters. The measures of perseverance
should focus on firms ability to shift production to other unaffected parts with ease during
substitutes. A high degree of portability allows firms to disperse primary parts of the supply
chain to other regions and parties. Likewise, a company with low portability faces difficulty
in shifting supply chain activities to other parties or regions (Tang, 2006). Therefore, during
the earthquake, firms learnt the important lesson of using an IT system to implement supply
chain portability. The reason for relying on an IT system is to protect specialised products
from damage in the process of dispersing. Therefore, IT systems enable firms to increase the
visibility of dispersed supply chain components, which protects products from possible
damage.
Further lessons include the fact that although earthquakes cause severe damage to large
investments, setting up a risk mitigation fund will only cause unwanted expenses (Melnyk,
2014). The reason is that the earthquakes do not happen all the times, which will result in the
funds set aside becoming idle resources. However, failing to plan for the earthquake and the
accruing damages and losses is dangerous for business since the destruction of important
supply chain components paralyses operations and market performance. Therefore, the
companies had to come up with a permanent solution to the problem caused by physical
supply chain systems. The solution was to move to virtual supply chain systems that do not
carry the risk of damage due to lack of tangibility (Kleindorfer, 2005). Consequently, the
companies developed virtual supply chain systems in response to preventing the tie down of
resources in the name of an earthquake or similar disasters fund.
Supply chain evaluation
The Japanese firms learnt the valuable lesson of evaluating the supply chain disruptions with
the perspective of continuity (Chopra, 2014). The firms should assess the level of supply
chain dispersion and the ability to persevere natural disasters. The measures of perseverance
should focus on firms ability to shift production to other unaffected parts with ease during
Secure Best Marks with AI Grader
Need help grading? Try our AI Grader for instant feedback on your assignments.
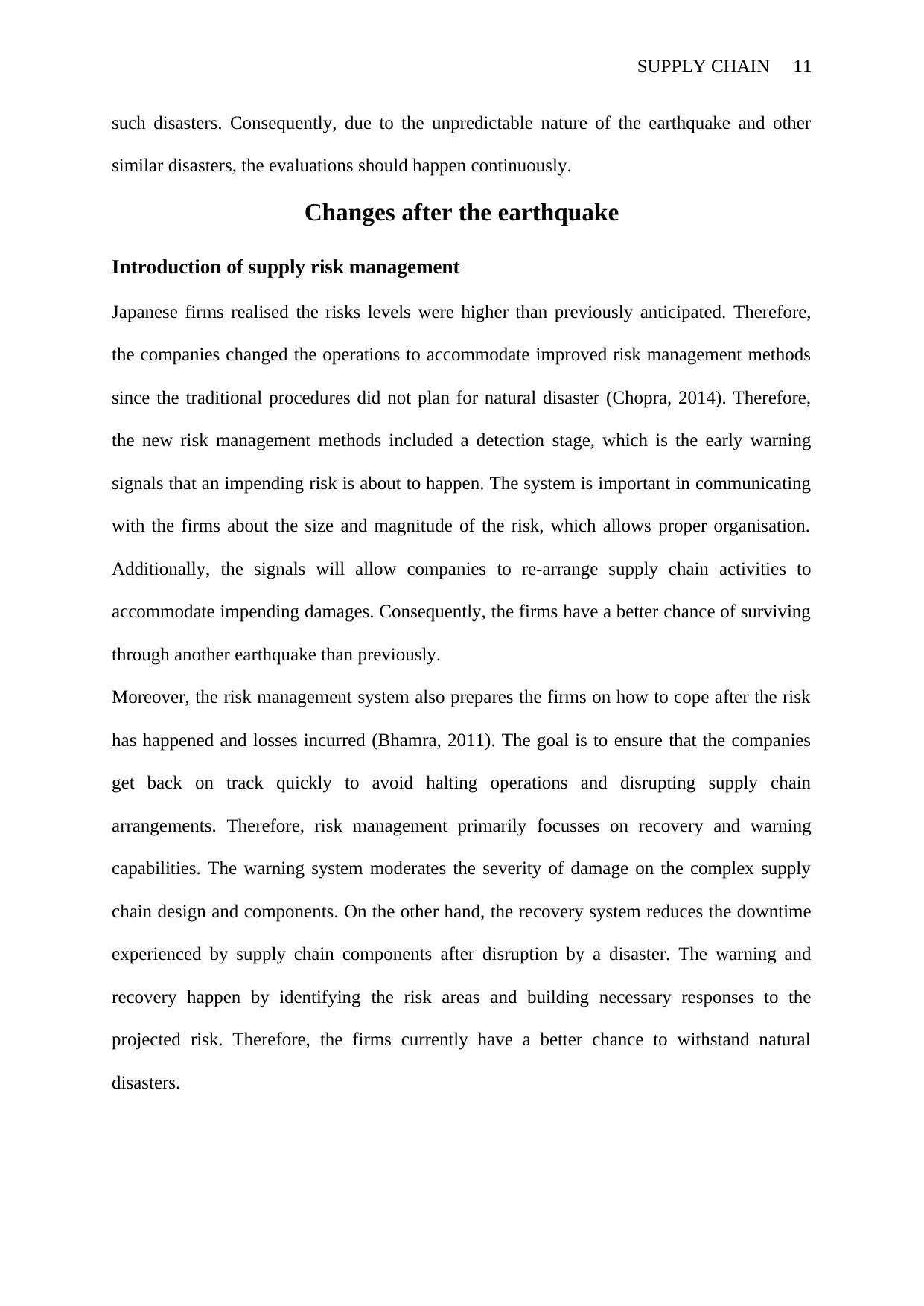
SUPPLY CHAIN 11
such disasters. Consequently, due to the unpredictable nature of the earthquake and other
similar disasters, the evaluations should happen continuously.
Changes after the earthquake
Introduction of supply risk management
Japanese firms realised the risks levels were higher than previously anticipated. Therefore,
the companies changed the operations to accommodate improved risk management methods
since the traditional procedures did not plan for natural disaster (Chopra, 2014). Therefore,
the new risk management methods included a detection stage, which is the early warning
signals that an impending risk is about to happen. The system is important in communicating
with the firms about the size and magnitude of the risk, which allows proper organisation.
Additionally, the signals will allow companies to re-arrange supply chain activities to
accommodate impending damages. Consequently, the firms have a better chance of surviving
through another earthquake than previously.
Moreover, the risk management system also prepares the firms on how to cope after the risk
has happened and losses incurred (Bhamra, 2011). The goal is to ensure that the companies
get back on track quickly to avoid halting operations and disrupting supply chain
arrangements. Therefore, risk management primarily focusses on recovery and warning
capabilities. The warning system moderates the severity of damage on the complex supply
chain design and components. On the other hand, the recovery system reduces the downtime
experienced by supply chain components after disruption by a disaster. The warning and
recovery happen by identifying the risk areas and building necessary responses to the
projected risk. Therefore, the firms currently have a better chance to withstand natural
disasters.
such disasters. Consequently, due to the unpredictable nature of the earthquake and other
similar disasters, the evaluations should happen continuously.
Changes after the earthquake
Introduction of supply risk management
Japanese firms realised the risks levels were higher than previously anticipated. Therefore,
the companies changed the operations to accommodate improved risk management methods
since the traditional procedures did not plan for natural disaster (Chopra, 2014). Therefore,
the new risk management methods included a detection stage, which is the early warning
signals that an impending risk is about to happen. The system is important in communicating
with the firms about the size and magnitude of the risk, which allows proper organisation.
Additionally, the signals will allow companies to re-arrange supply chain activities to
accommodate impending damages. Consequently, the firms have a better chance of surviving
through another earthquake than previously.
Moreover, the risk management system also prepares the firms on how to cope after the risk
has happened and losses incurred (Bhamra, 2011). The goal is to ensure that the companies
get back on track quickly to avoid halting operations and disrupting supply chain
arrangements. Therefore, risk management primarily focusses on recovery and warning
capabilities. The warning system moderates the severity of damage on the complex supply
chain design and components. On the other hand, the recovery system reduces the downtime
experienced by supply chain components after disruption by a disaster. The warning and
recovery happen by identifying the risk areas and building necessary responses to the
projected risk. Therefore, the firms currently have a better chance to withstand natural
disasters.
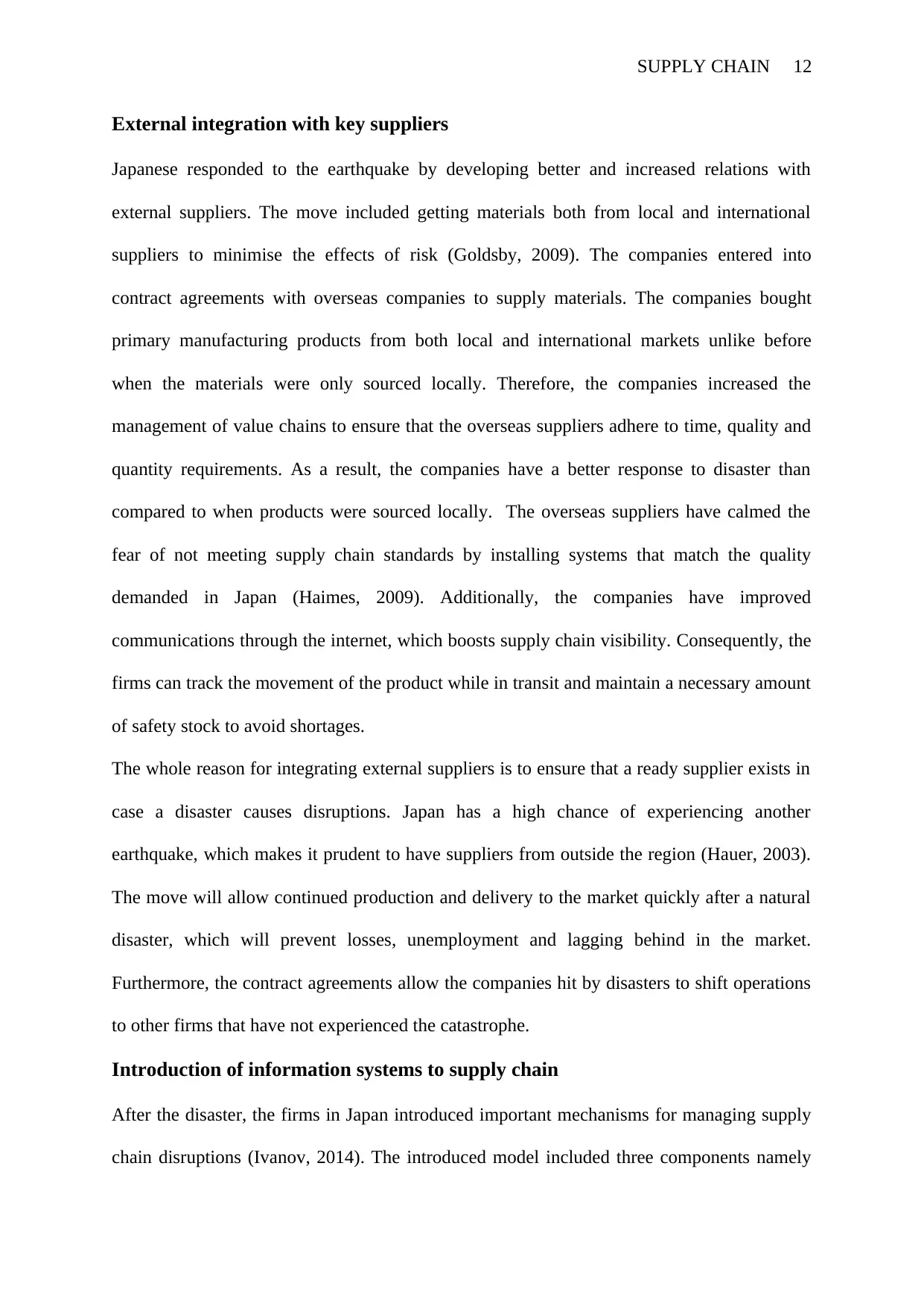
SUPPLY CHAIN 12
External integration with key suppliers
Japanese responded to the earthquake by developing better and increased relations with
external suppliers. The move included getting materials both from local and international
suppliers to minimise the effects of risk (Goldsby, 2009). The companies entered into
contract agreements with overseas companies to supply materials. The companies bought
primary manufacturing products from both local and international markets unlike before
when the materials were only sourced locally. Therefore, the companies increased the
management of value chains to ensure that the overseas suppliers adhere to time, quality and
quantity requirements. As a result, the companies have a better response to disaster than
compared to when products were sourced locally. The overseas suppliers have calmed the
fear of not meeting supply chain standards by installing systems that match the quality
demanded in Japan (Haimes, 2009). Additionally, the companies have improved
communications through the internet, which boosts supply chain visibility. Consequently, the
firms can track the movement of the product while in transit and maintain a necessary amount
of safety stock to avoid shortages.
The whole reason for integrating external suppliers is to ensure that a ready supplier exists in
case a disaster causes disruptions. Japan has a high chance of experiencing another
earthquake, which makes it prudent to have suppliers from outside the region (Hauer, 2003).
The move will allow continued production and delivery to the market quickly after a natural
disaster, which will prevent losses, unemployment and lagging behind in the market.
Furthermore, the contract agreements allow the companies hit by disasters to shift operations
to other firms that have not experienced the catastrophe.
Introduction of information systems to supply chain
After the disaster, the firms in Japan introduced important mechanisms for managing supply
chain disruptions (Ivanov, 2014). The introduced model included three components namely
External integration with key suppliers
Japanese responded to the earthquake by developing better and increased relations with
external suppliers. The move included getting materials both from local and international
suppliers to minimise the effects of risk (Goldsby, 2009). The companies entered into
contract agreements with overseas companies to supply materials. The companies bought
primary manufacturing products from both local and international markets unlike before
when the materials were only sourced locally. Therefore, the companies increased the
management of value chains to ensure that the overseas suppliers adhere to time, quality and
quantity requirements. As a result, the companies have a better response to disaster than
compared to when products were sourced locally. The overseas suppliers have calmed the
fear of not meeting supply chain standards by installing systems that match the quality
demanded in Japan (Haimes, 2009). Additionally, the companies have improved
communications through the internet, which boosts supply chain visibility. Consequently, the
firms can track the movement of the product while in transit and maintain a necessary amount
of safety stock to avoid shortages.
The whole reason for integrating external suppliers is to ensure that a ready supplier exists in
case a disaster causes disruptions. Japan has a high chance of experiencing another
earthquake, which makes it prudent to have suppliers from outside the region (Hauer, 2003).
The move will allow continued production and delivery to the market quickly after a natural
disaster, which will prevent losses, unemployment and lagging behind in the market.
Furthermore, the contract agreements allow the companies hit by disasters to shift operations
to other firms that have not experienced the catastrophe.
Introduction of information systems to supply chain
After the disaster, the firms in Japan introduced important mechanisms for managing supply
chain disruptions (Ivanov, 2014). The introduced model included three components namely
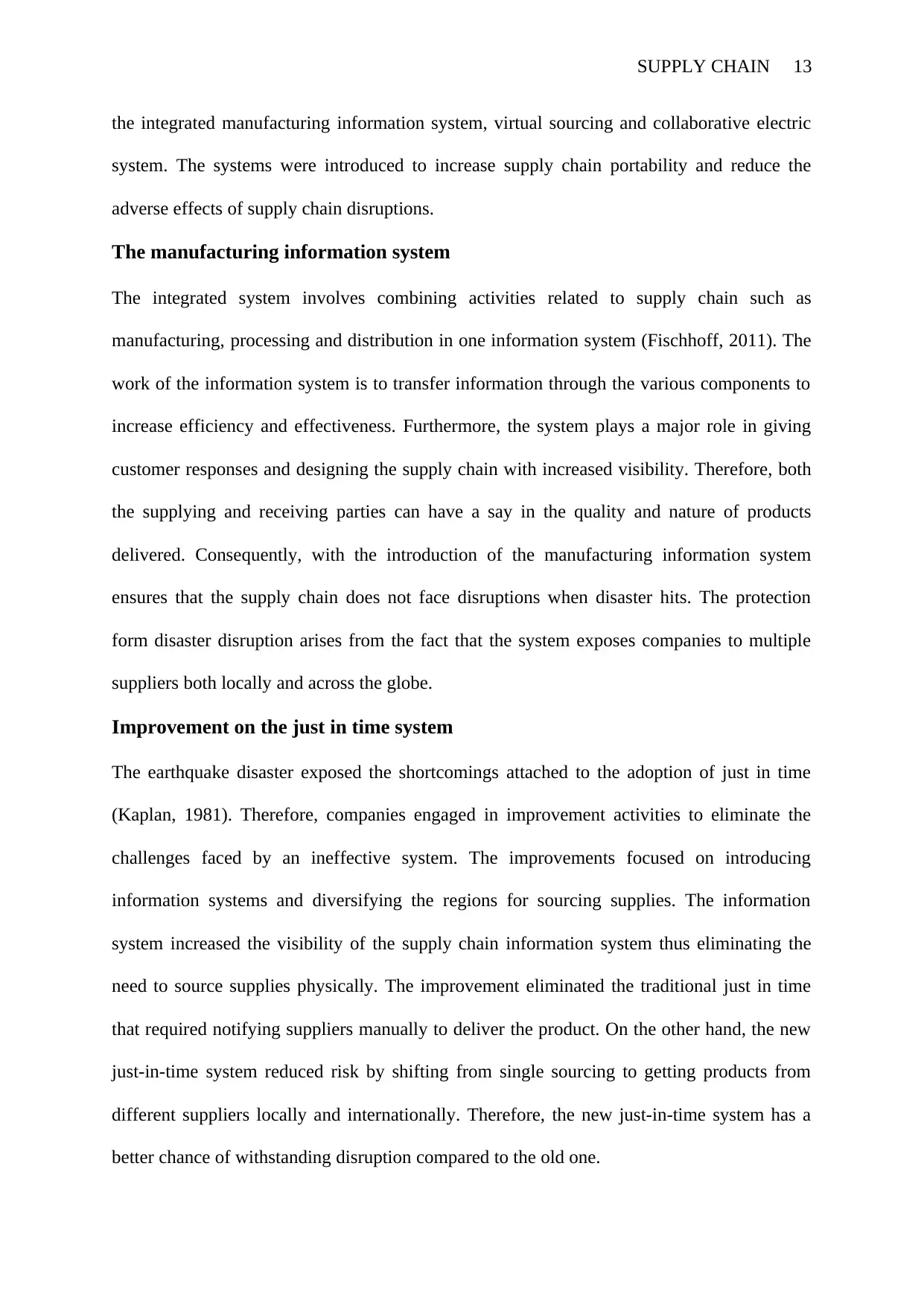
SUPPLY CHAIN 13
the integrated manufacturing information system, virtual sourcing and collaborative electric
system. The systems were introduced to increase supply chain portability and reduce the
adverse effects of supply chain disruptions.
The manufacturing information system
The integrated system involves combining activities related to supply chain such as
manufacturing, processing and distribution in one information system (Fischhoff, 2011). The
work of the information system is to transfer information through the various components to
increase efficiency and effectiveness. Furthermore, the system plays a major role in giving
customer responses and designing the supply chain with increased visibility. Therefore, both
the supplying and receiving parties can have a say in the quality and nature of products
delivered. Consequently, with the introduction of the manufacturing information system
ensures that the supply chain does not face disruptions when disaster hits. The protection
form disaster disruption arises from the fact that the system exposes companies to multiple
suppliers both locally and across the globe.
Improvement on the just in time system
The earthquake disaster exposed the shortcomings attached to the adoption of just in time
(Kaplan, 1981). Therefore, companies engaged in improvement activities to eliminate the
challenges faced by an ineffective system. The improvements focused on introducing
information systems and diversifying the regions for sourcing supplies. The information
system increased the visibility of the supply chain information system thus eliminating the
need to source supplies physically. The improvement eliminated the traditional just in time
that required notifying suppliers manually to deliver the product. On the other hand, the new
just-in-time system reduced risk by shifting from single sourcing to getting products from
different suppliers locally and internationally. Therefore, the new just-in-time system has a
better chance of withstanding disruption compared to the old one.
the integrated manufacturing information system, virtual sourcing and collaborative electric
system. The systems were introduced to increase supply chain portability and reduce the
adverse effects of supply chain disruptions.
The manufacturing information system
The integrated system involves combining activities related to supply chain such as
manufacturing, processing and distribution in one information system (Fischhoff, 2011). The
work of the information system is to transfer information through the various components to
increase efficiency and effectiveness. Furthermore, the system plays a major role in giving
customer responses and designing the supply chain with increased visibility. Therefore, both
the supplying and receiving parties can have a say in the quality and nature of products
delivered. Consequently, with the introduction of the manufacturing information system
ensures that the supply chain does not face disruptions when disaster hits. The protection
form disaster disruption arises from the fact that the system exposes companies to multiple
suppliers both locally and across the globe.
Improvement on the just in time system
The earthquake disaster exposed the shortcomings attached to the adoption of just in time
(Kaplan, 1981). Therefore, companies engaged in improvement activities to eliminate the
challenges faced by an ineffective system. The improvements focused on introducing
information systems and diversifying the regions for sourcing supplies. The information
system increased the visibility of the supply chain information system thus eliminating the
need to source supplies physically. The improvement eliminated the traditional just in time
that required notifying suppliers manually to deliver the product. On the other hand, the new
just-in-time system reduced risk by shifting from single sourcing to getting products from
different suppliers locally and internationally. Therefore, the new just-in-time system has a
better chance of withstanding disruption compared to the old one.
Paraphrase This Document
Need a fresh take? Get an instant paraphrase of this document with our AI Paraphraser
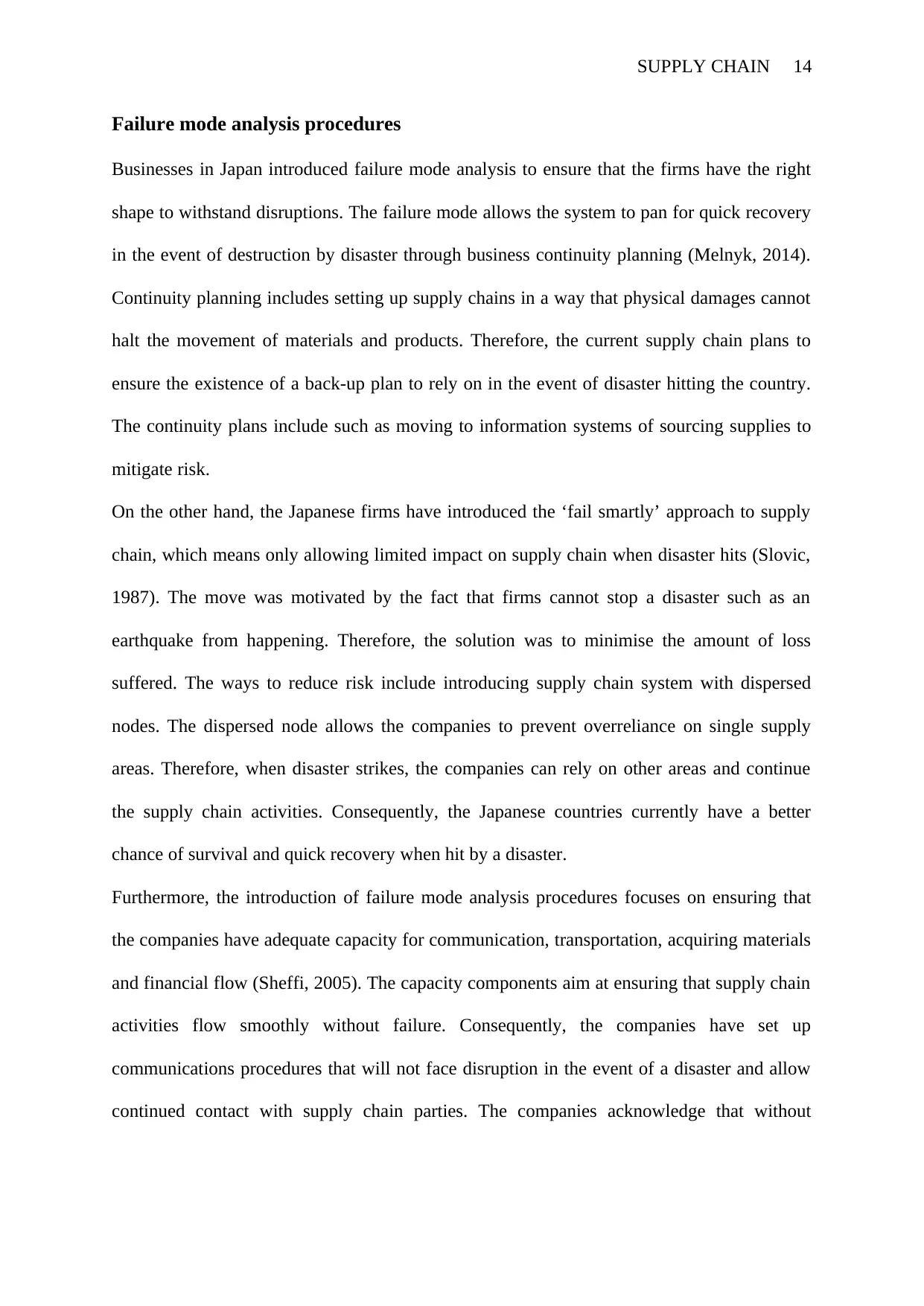
SUPPLY CHAIN 14
Failure mode analysis procedures
Businesses in Japan introduced failure mode analysis to ensure that the firms have the right
shape to withstand disruptions. The failure mode allows the system to pan for quick recovery
in the event of destruction by disaster through business continuity planning (Melnyk, 2014).
Continuity planning includes setting up supply chains in a way that physical damages cannot
halt the movement of materials and products. Therefore, the current supply chain plans to
ensure the existence of a back-up plan to rely on in the event of disaster hitting the country.
The continuity plans include such as moving to information systems of sourcing supplies to
mitigate risk.
On the other hand, the Japanese firms have introduced the ‘fail smartly’ approach to supply
chain, which means only allowing limited impact on supply chain when disaster hits (Slovic,
1987). The move was motivated by the fact that firms cannot stop a disaster such as an
earthquake from happening. Therefore, the solution was to minimise the amount of loss
suffered. The ways to reduce risk include introducing supply chain system with dispersed
nodes. The dispersed node allows the companies to prevent overreliance on single supply
areas. Therefore, when disaster strikes, the companies can rely on other areas and continue
the supply chain activities. Consequently, the Japanese countries currently have a better
chance of survival and quick recovery when hit by a disaster.
Furthermore, the introduction of failure mode analysis procedures focuses on ensuring that
the companies have adequate capacity for communication, transportation, acquiring materials
and financial flow (Sheffi, 2005). The capacity components aim at ensuring that supply chain
activities flow smoothly without failure. Consequently, the companies have set up
communications procedures that will not face disruption in the event of a disaster and allow
continued contact with supply chain parties. The companies acknowledge that without
Failure mode analysis procedures
Businesses in Japan introduced failure mode analysis to ensure that the firms have the right
shape to withstand disruptions. The failure mode allows the system to pan for quick recovery
in the event of destruction by disaster through business continuity planning (Melnyk, 2014).
Continuity planning includes setting up supply chains in a way that physical damages cannot
halt the movement of materials and products. Therefore, the current supply chain plans to
ensure the existence of a back-up plan to rely on in the event of disaster hitting the country.
The continuity plans include such as moving to information systems of sourcing supplies to
mitigate risk.
On the other hand, the Japanese firms have introduced the ‘fail smartly’ approach to supply
chain, which means only allowing limited impact on supply chain when disaster hits (Slovic,
1987). The move was motivated by the fact that firms cannot stop a disaster such as an
earthquake from happening. Therefore, the solution was to minimise the amount of loss
suffered. The ways to reduce risk include introducing supply chain system with dispersed
nodes. The dispersed node allows the companies to prevent overreliance on single supply
areas. Therefore, when disaster strikes, the companies can rely on other areas and continue
the supply chain activities. Consequently, the Japanese countries currently have a better
chance of survival and quick recovery when hit by a disaster.
Furthermore, the introduction of failure mode analysis procedures focuses on ensuring that
the companies have adequate capacity for communication, transportation, acquiring materials
and financial flow (Sheffi, 2005). The capacity components aim at ensuring that supply chain
activities flow smoothly without failure. Consequently, the companies have set up
communications procedures that will not face disruption in the event of a disaster and allow
continued contact with supply chain parties. The companies acknowledge that without
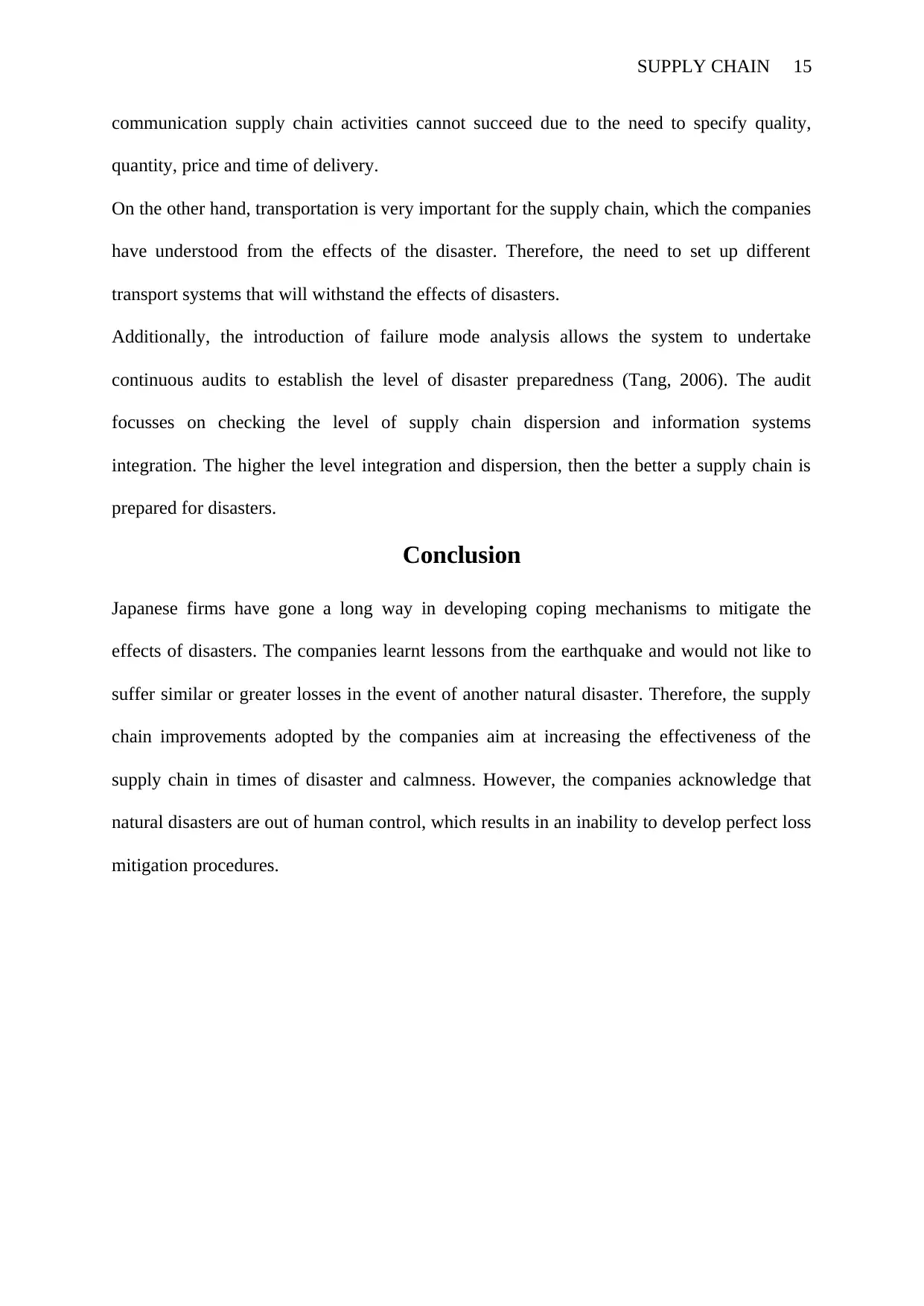
SUPPLY CHAIN 15
communication supply chain activities cannot succeed due to the need to specify quality,
quantity, price and time of delivery.
On the other hand, transportation is very important for the supply chain, which the companies
have understood from the effects of the disaster. Therefore, the need to set up different
transport systems that will withstand the effects of disasters.
Additionally, the introduction of failure mode analysis allows the system to undertake
continuous audits to establish the level of disaster preparedness (Tang, 2006). The audit
focusses on checking the level of supply chain dispersion and information systems
integration. The higher the level integration and dispersion, then the better a supply chain is
prepared for disasters.
Conclusion
Japanese firms have gone a long way in developing coping mechanisms to mitigate the
effects of disasters. The companies learnt lessons from the earthquake and would not like to
suffer similar or greater losses in the event of another natural disaster. Therefore, the supply
chain improvements adopted by the companies aim at increasing the effectiveness of the
supply chain in times of disaster and calmness. However, the companies acknowledge that
natural disasters are out of human control, which results in an inability to develop perfect loss
mitigation procedures.
communication supply chain activities cannot succeed due to the need to specify quality,
quantity, price and time of delivery.
On the other hand, transportation is very important for the supply chain, which the companies
have understood from the effects of the disaster. Therefore, the need to set up different
transport systems that will withstand the effects of disasters.
Additionally, the introduction of failure mode analysis allows the system to undertake
continuous audits to establish the level of disaster preparedness (Tang, 2006). The audit
focusses on checking the level of supply chain dispersion and information systems
integration. The higher the level integration and dispersion, then the better a supply chain is
prepared for disasters.
Conclusion
Japanese firms have gone a long way in developing coping mechanisms to mitigate the
effects of disasters. The companies learnt lessons from the earthquake and would not like to
suffer similar or greater losses in the event of another natural disaster. Therefore, the supply
chain improvements adopted by the companies aim at increasing the effectiveness of the
supply chain in times of disaster and calmness. However, the companies acknowledge that
natural disasters are out of human control, which results in an inability to develop perfect loss
mitigation procedures.
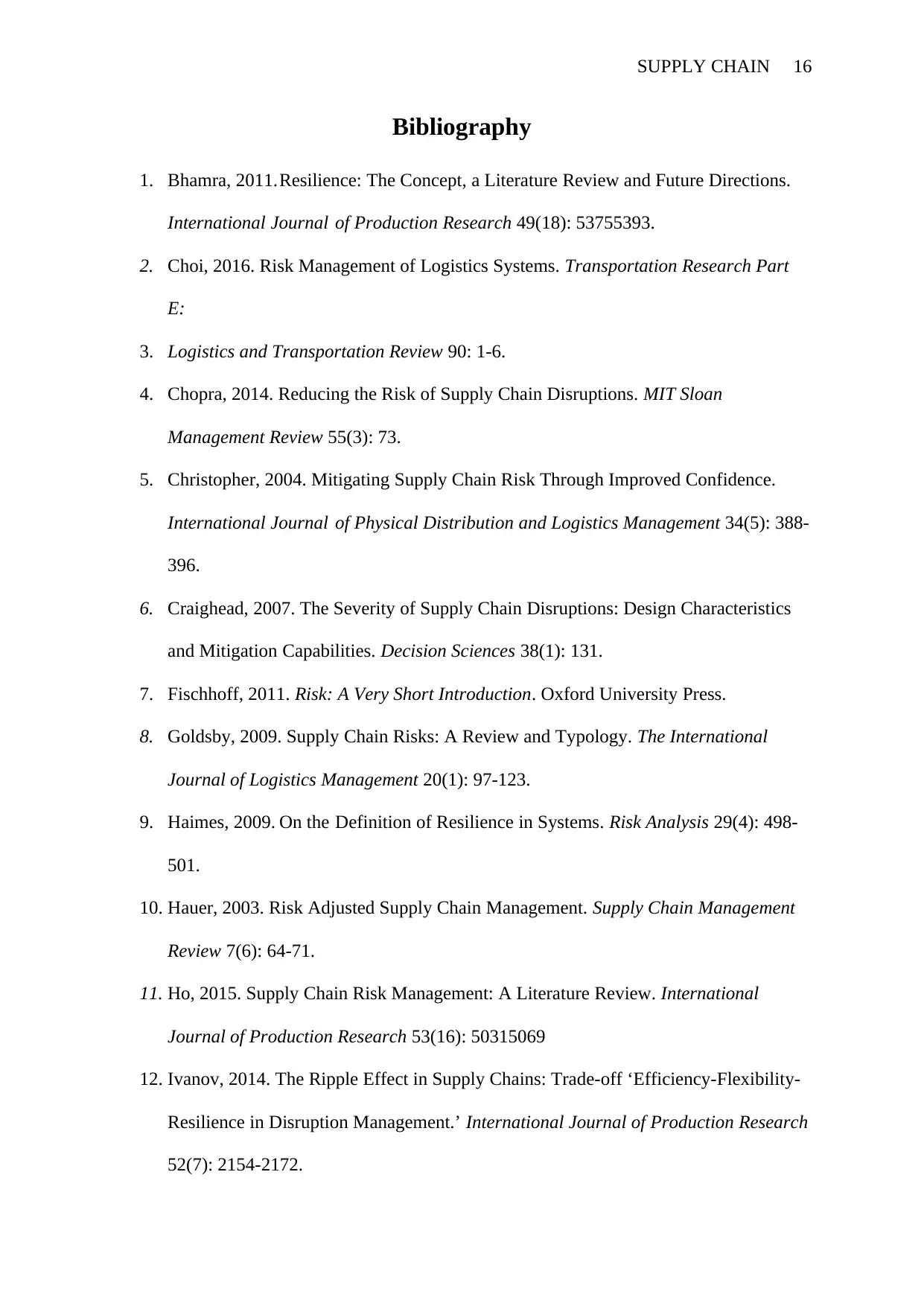
SUPPLY CHAIN 16
Bibliography
1. Bhamra, 2011.Resilience: The Concept, a Literature Review and Future Directions.
International Journal of Production Research 49(18): 53755393.
2. Choi, 2016. Risk Management of Logistics Systems. Transportation Research Part
E:
3. Logistics and Transportation Review 90: 1-6.
4. Chopra, 2014. Reducing the Risk of Supply Chain Disruptions. MIT Sloan
Management Review 55(3): 73.
5. Christopher, 2004. Mitigating Supply Chain Risk Through Improved Confidence.
International Journal of Physical Distribution and Logistics Management 34(5): 388-
396.
6. Craighead, 2007. The Severity of Supply Chain Disruptions: Design Characteristics
and Mitigation Capabilities. Decision Sciences 38(1): 131.
7. Fischhoff, 2011. Risk: A Very Short Introduction. Oxford University Press.
8. Goldsby, 2009. Supply Chain Risks: A Review and Typology. The International
Journal of Logistics Management 20(1): 97-123.
9. Haimes, 2009. On the Definition of Resilience in Systems. Risk Analysis 29(4): 498-
501.
10. Hauer, 2003. Risk Adjusted Supply Chain Management. Supply Chain Management
Review 7(6): 64-71.
11. Ho, 2015. Supply Chain Risk Management: A Literature Review. International
Journal of Production Research 53(16): 50315069
12. Ivanov, 2014. The Ripple Effect in Supply Chains: Trade-off ‘Efficiency-Flexibility-
Resilience in Disruption Management.’ International Journal of Production Research
52(7): 2154-2172.
Bibliography
1. Bhamra, 2011.Resilience: The Concept, a Literature Review and Future Directions.
International Journal of Production Research 49(18): 53755393.
2. Choi, 2016. Risk Management of Logistics Systems. Transportation Research Part
E:
3. Logistics and Transportation Review 90: 1-6.
4. Chopra, 2014. Reducing the Risk of Supply Chain Disruptions. MIT Sloan
Management Review 55(3): 73.
5. Christopher, 2004. Mitigating Supply Chain Risk Through Improved Confidence.
International Journal of Physical Distribution and Logistics Management 34(5): 388-
396.
6. Craighead, 2007. The Severity of Supply Chain Disruptions: Design Characteristics
and Mitigation Capabilities. Decision Sciences 38(1): 131.
7. Fischhoff, 2011. Risk: A Very Short Introduction. Oxford University Press.
8. Goldsby, 2009. Supply Chain Risks: A Review and Typology. The International
Journal of Logistics Management 20(1): 97-123.
9. Haimes, 2009. On the Definition of Resilience in Systems. Risk Analysis 29(4): 498-
501.
10. Hauer, 2003. Risk Adjusted Supply Chain Management. Supply Chain Management
Review 7(6): 64-71.
11. Ho, 2015. Supply Chain Risk Management: A Literature Review. International
Journal of Production Research 53(16): 50315069
12. Ivanov, 2014. The Ripple Effect in Supply Chains: Trade-off ‘Efficiency-Flexibility-
Resilience in Disruption Management.’ International Journal of Production Research
52(7): 2154-2172.
Secure Best Marks with AI Grader
Need help grading? Try our AI Grader for instant feedback on your assignments.
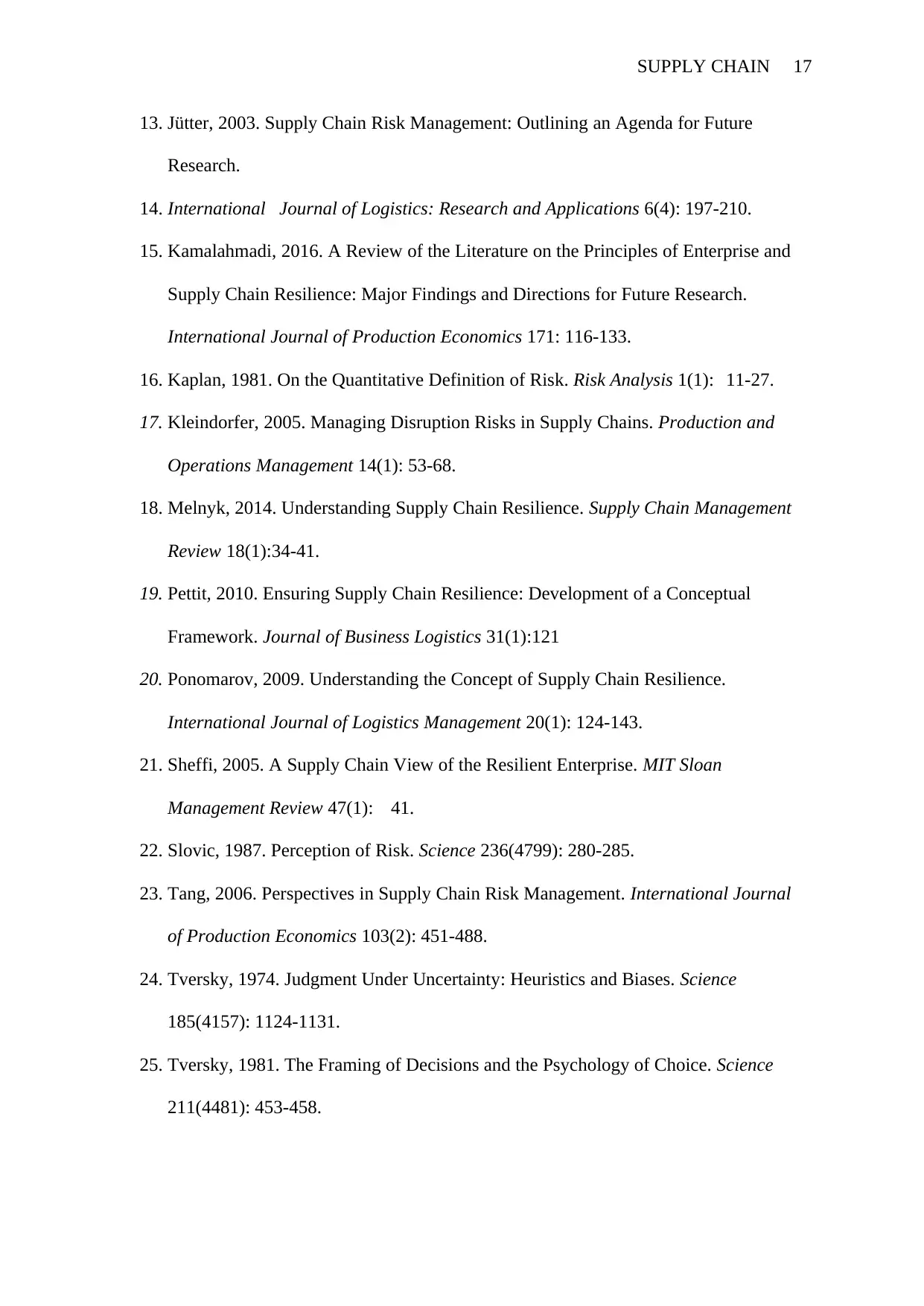
SUPPLY CHAIN 17
13. Jütter, 2003. Supply Chain Risk Management: Outlining an Agenda for Future
Research.
14. International Journal of Logistics: Research and Applications 6(4): 197-210.
15. Kamalahmadi, 2016. A Review of the Literature on the Principles of Enterprise and
Supply Chain Resilience: Major Findings and Directions for Future Research.
International Journal of Production Economics 171: 116-133.
16. Kaplan, 1981. On the Quantitative Definition of Risk. Risk Analysis 1(1): 11-27.
17. Kleindorfer, 2005. Managing Disruption Risks in Supply Chains. Production and
Operations Management 14(1): 53-68.
18. Melnyk, 2014. Understanding Supply Chain Resilience. Supply Chain Management
Review 18(1):34-41.
19. Pettit, 2010. Ensuring Supply Chain Resilience: Development of a Conceptual
Framework. Journal of Business Logistics 31(1):121
20. Ponomarov, 2009. Understanding the Concept of Supply Chain Resilience.
International Journal of Logistics Management 20(1): 124-143.
21. Sheffi, 2005. A Supply Chain View of the Resilient Enterprise. MIT Sloan
Management Review 47(1): 41.
22. Slovic, 1987. Perception of Risk. Science 236(4799): 280-285.
23. Tang, 2006. Perspectives in Supply Chain Risk Management. International Journal
of Production Economics 103(2): 451-488.
24. Tversky, 1974. Judgment Under Uncertainty: Heuristics and Biases. Science
185(4157): 1124-1131.
25. Tversky, 1981. The Framing of Decisions and the Psychology of Choice. Science
211(4481): 453-458.
13. Jütter, 2003. Supply Chain Risk Management: Outlining an Agenda for Future
Research.
14. International Journal of Logistics: Research and Applications 6(4): 197-210.
15. Kamalahmadi, 2016. A Review of the Literature on the Principles of Enterprise and
Supply Chain Resilience: Major Findings and Directions for Future Research.
International Journal of Production Economics 171: 116-133.
16. Kaplan, 1981. On the Quantitative Definition of Risk. Risk Analysis 1(1): 11-27.
17. Kleindorfer, 2005. Managing Disruption Risks in Supply Chains. Production and
Operations Management 14(1): 53-68.
18. Melnyk, 2014. Understanding Supply Chain Resilience. Supply Chain Management
Review 18(1):34-41.
19. Pettit, 2010. Ensuring Supply Chain Resilience: Development of a Conceptual
Framework. Journal of Business Logistics 31(1):121
20. Ponomarov, 2009. Understanding the Concept of Supply Chain Resilience.
International Journal of Logistics Management 20(1): 124-143.
21. Sheffi, 2005. A Supply Chain View of the Resilient Enterprise. MIT Sloan
Management Review 47(1): 41.
22. Slovic, 1987. Perception of Risk. Science 236(4799): 280-285.
23. Tang, 2006. Perspectives in Supply Chain Risk Management. International Journal
of Production Economics 103(2): 451-488.
24. Tversky, 1974. Judgment Under Uncertainty: Heuristics and Biases. Science
185(4157): 1124-1131.
25. Tversky, 1981. The Framing of Decisions and the Psychology of Choice. Science
211(4481): 453-458.
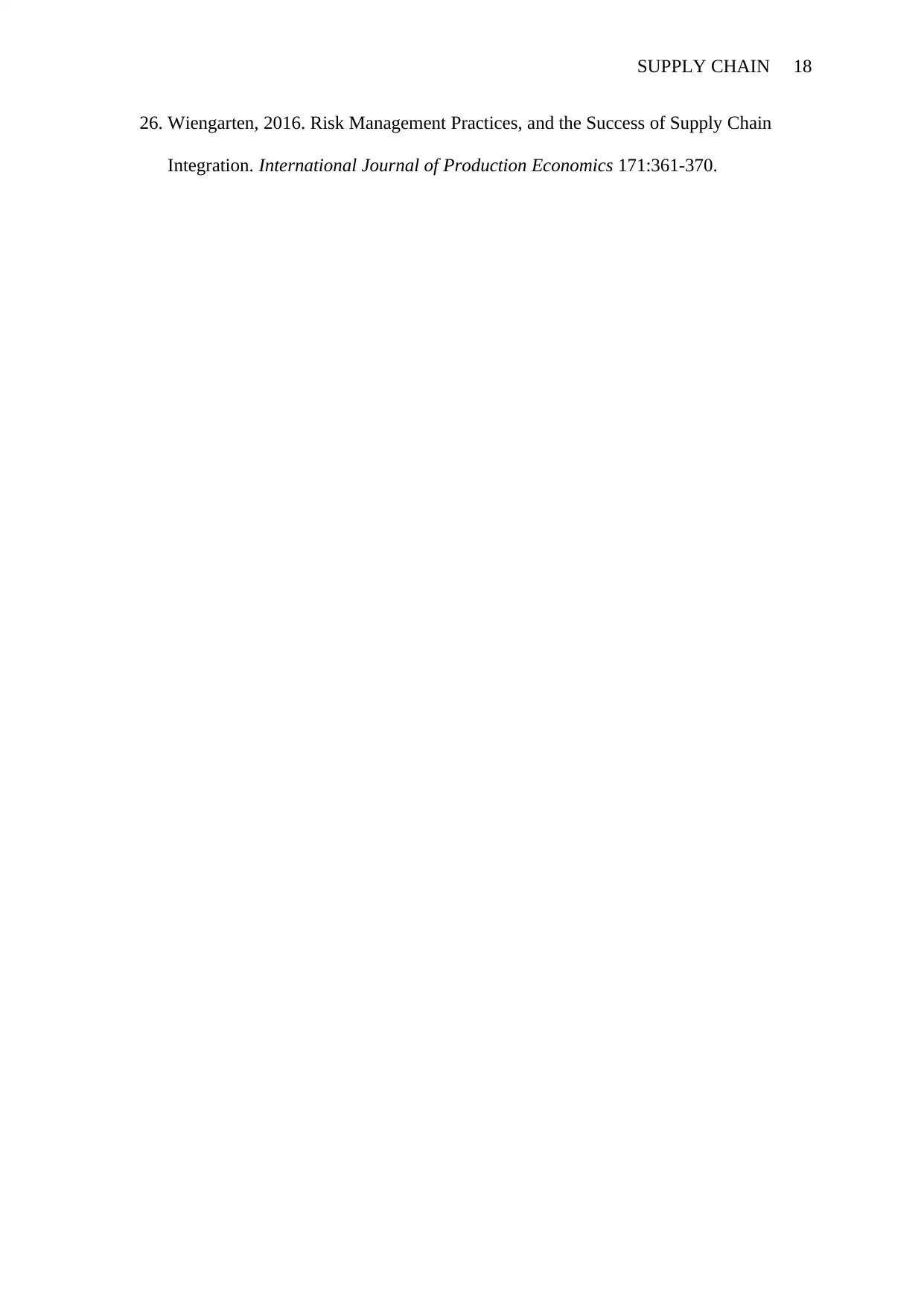
SUPPLY CHAIN 18
26. Wiengarten, 2016. Risk Management Practices, and the Success of Supply Chain
Integration. International Journal of Production Economics 171:361-370.
26. Wiengarten, 2016. Risk Management Practices, and the Success of Supply Chain
Integration. International Journal of Production Economics 171:361-370.
1 out of 18
![[object Object]](/_next/image/?url=%2F_next%2Fstatic%2Fmedia%2Flogo.6d15ce61.png&w=640&q=75)
Your All-in-One AI-Powered Toolkit for Academic Success.
+13062052269
info@desklib.com
Available 24*7 on WhatsApp / Email
Unlock your academic potential
© 2024 | Zucol Services PVT LTD | All rights reserved.