Sustainability and Operations Management
VerifiedAdded on 2022/09/13
|16
|4268
|10
AI Summary
Contribute Materials
Your contribution can guide someone’s learning journey. Share your
documents today.
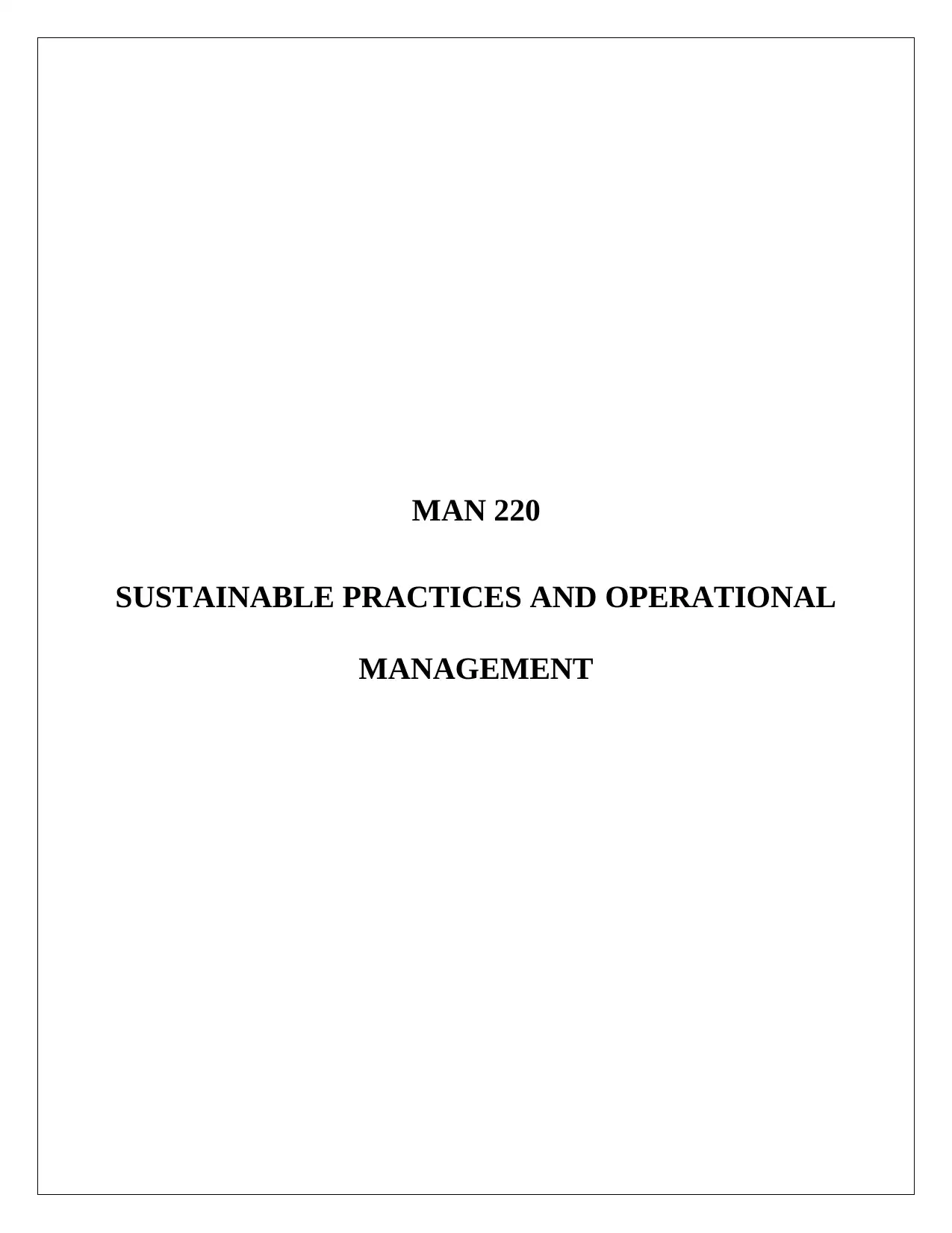
MAN 220
SUSTAINABLE PRACTICES AND OPERATIONAL
MANAGEMENT
SUSTAINABLE PRACTICES AND OPERATIONAL
MANAGEMENT
Secure Best Marks with AI Grader
Need help grading? Try our AI Grader for instant feedback on your assignments.
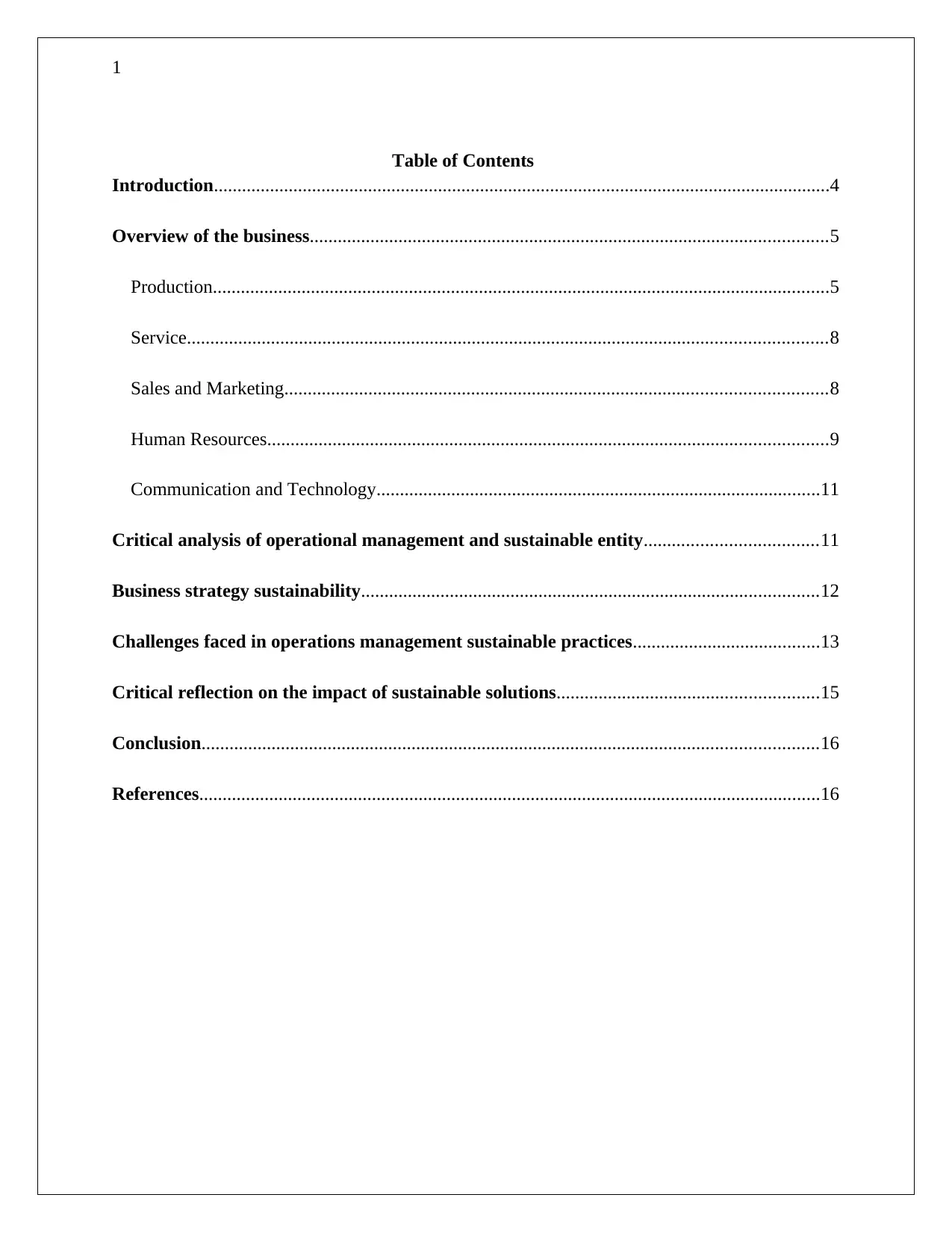
1
Table of Contents
Introduction....................................................................................................................................4
Overview of the business...............................................................................................................5
Production....................................................................................................................................5
Service.........................................................................................................................................8
Sales and Marketing....................................................................................................................8
Human Resources........................................................................................................................9
Communication and Technology...............................................................................................11
Critical analysis of operational management and sustainable entity.....................................11
Business strategy sustainability..................................................................................................12
Challenges faced in operations management sustainable practices........................................13
Critical reflection on the impact of sustainable solutions........................................................15
Conclusion....................................................................................................................................16
References.....................................................................................................................................16
Table of Contents
Introduction....................................................................................................................................4
Overview of the business...............................................................................................................5
Production....................................................................................................................................5
Service.........................................................................................................................................8
Sales and Marketing....................................................................................................................8
Human Resources........................................................................................................................9
Communication and Technology...............................................................................................11
Critical analysis of operational management and sustainable entity.....................................11
Business strategy sustainability..................................................................................................12
Challenges faced in operations management sustainable practices........................................13
Critical reflection on the impact of sustainable solutions........................................................15
Conclusion....................................................................................................................................16
References.....................................................................................................................................16
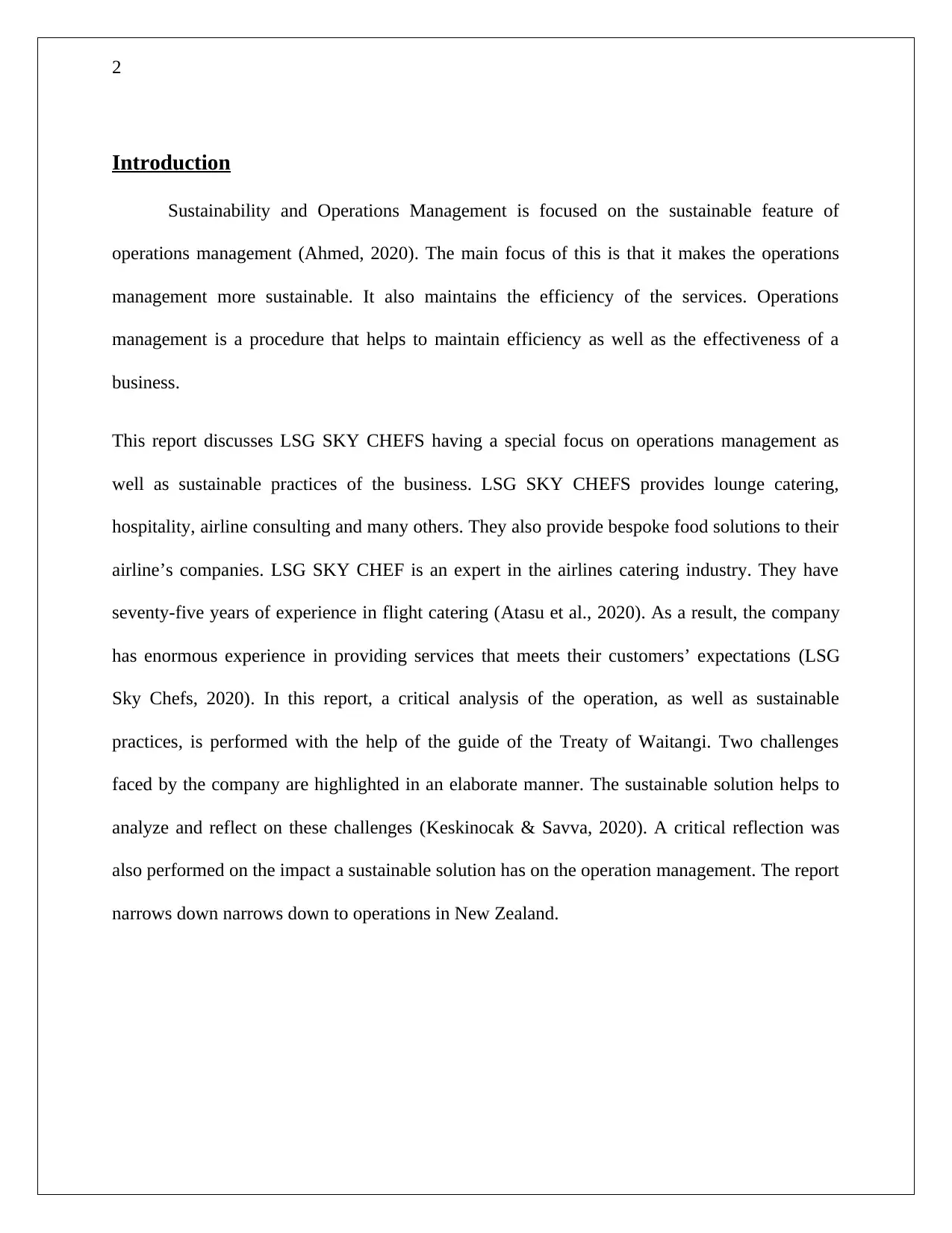
2
Introduction
Sustainability and Operations Management is focused on the sustainable feature of
operations management (Ahmed, 2020). The main focus of this is that it makes the operations
management more sustainable. It also maintains the efficiency of the services. Operations
management is a procedure that helps to maintain efficiency as well as the effectiveness of a
business.
This report discusses LSG SKY CHEFS having a special focus on operations management as
well as sustainable practices of the business. LSG SKY CHEFS provides lounge catering,
hospitality, airline consulting and many others. They also provide bespoke food solutions to their
airline’s companies. LSG SKY CHEF is an expert in the airlines catering industry. They have
seventy-five years of experience in flight catering (Atasu et al., 2020). As a result, the company
has enormous experience in providing services that meets their customers’ expectations (LSG
Sky Chefs, 2020). In this report, a critical analysis of the operation, as well as sustainable
practices, is performed with the help of the guide of the Treaty of Waitangi. Two challenges
faced by the company are highlighted in an elaborate manner. The sustainable solution helps to
analyze and reflect on these challenges (Keskinocak & Savva, 2020). A critical reflection was
also performed on the impact a sustainable solution has on the operation management. The report
narrows down narrows down to operations in New Zealand.
Introduction
Sustainability and Operations Management is focused on the sustainable feature of
operations management (Ahmed, 2020). The main focus of this is that it makes the operations
management more sustainable. It also maintains the efficiency of the services. Operations
management is a procedure that helps to maintain efficiency as well as the effectiveness of a
business.
This report discusses LSG SKY CHEFS having a special focus on operations management as
well as sustainable practices of the business. LSG SKY CHEFS provides lounge catering,
hospitality, airline consulting and many others. They also provide bespoke food solutions to their
airline’s companies. LSG SKY CHEF is an expert in the airlines catering industry. They have
seventy-five years of experience in flight catering (Atasu et al., 2020). As a result, the company
has enormous experience in providing services that meets their customers’ expectations (LSG
Sky Chefs, 2020). In this report, a critical analysis of the operation, as well as sustainable
practices, is performed with the help of the guide of the Treaty of Waitangi. Two challenges
faced by the company are highlighted in an elaborate manner. The sustainable solution helps to
analyze and reflect on these challenges (Keskinocak & Savva, 2020). A critical reflection was
also performed on the impact a sustainable solution has on the operation management. The report
narrows down narrows down to operations in New Zealand.
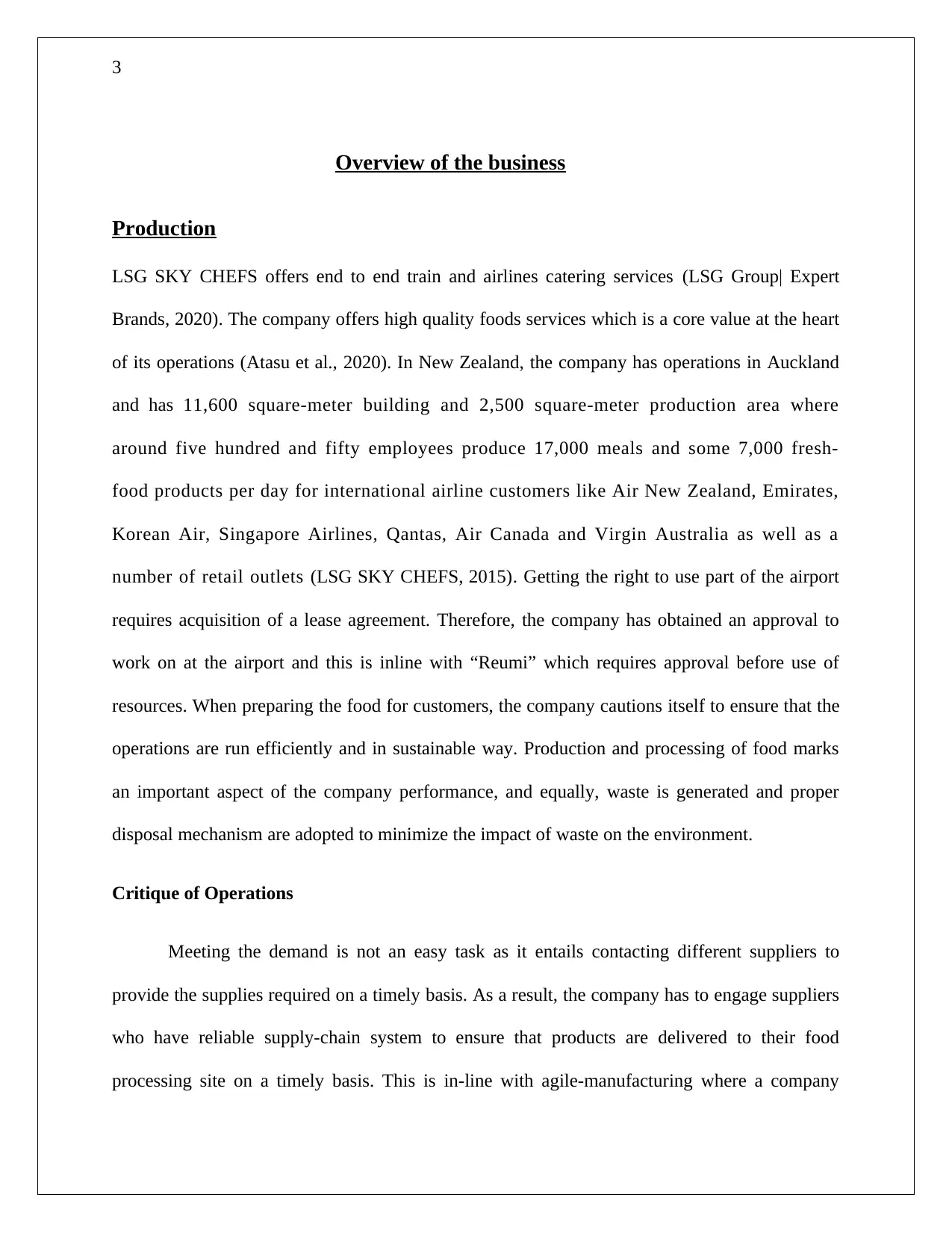
3
Overview of the business
Production
LSG SKY CHEFS offers end to end train and airlines catering services (LSG Group| Expert
Brands, 2020). The company offers high quality foods services which is a core value at the heart
of its operations (Atasu et al., 2020). In New Zealand, the company has operations in Auckland
and has 11,600 square-meter building and 2,500 square-meter production area where
around five hundred and fifty employees produce 17,000 meals and some 7,000 fresh-
food products per day for international airline customers like Air New Zealand, Emirates,
Korean Air, Singapore Airlines, Qantas, Air Canada and Virgin Australia as well as a
number of retail outlets (LSG SKY CHEFS, 2015). Getting the right to use part of the airport
requires acquisition of a lease agreement. Therefore, the company has obtained an approval to
work on at the airport and this is inline with “Reumi” which requires approval before use of
resources. When preparing the food for customers, the company cautions itself to ensure that the
operations are run efficiently and in sustainable way. Production and processing of food marks
an important aspect of the company performance, and equally, waste is generated and proper
disposal mechanism are adopted to minimize the impact of waste on the environment.
Critique of Operations
Meeting the demand is not an easy task as it entails contacting different suppliers to
provide the supplies required on a timely basis. As a result, the company has to engage suppliers
who have reliable supply-chain system to ensure that products are delivered to their food
processing site on a timely basis. This is in-line with agile-manufacturing where a company
Overview of the business
Production
LSG SKY CHEFS offers end to end train and airlines catering services (LSG Group| Expert
Brands, 2020). The company offers high quality foods services which is a core value at the heart
of its operations (Atasu et al., 2020). In New Zealand, the company has operations in Auckland
and has 11,600 square-meter building and 2,500 square-meter production area where
around five hundred and fifty employees produce 17,000 meals and some 7,000 fresh-
food products per day for international airline customers like Air New Zealand, Emirates,
Korean Air, Singapore Airlines, Qantas, Air Canada and Virgin Australia as well as a
number of retail outlets (LSG SKY CHEFS, 2015). Getting the right to use part of the airport
requires acquisition of a lease agreement. Therefore, the company has obtained an approval to
work on at the airport and this is inline with “Reumi” which requires approval before use of
resources. When preparing the food for customers, the company cautions itself to ensure that the
operations are run efficiently and in sustainable way. Production and processing of food marks
an important aspect of the company performance, and equally, waste is generated and proper
disposal mechanism are adopted to minimize the impact of waste on the environment.
Critique of Operations
Meeting the demand is not an easy task as it entails contacting different suppliers to
provide the supplies required on a timely basis. As a result, the company has to engage suppliers
who have reliable supply-chain system to ensure that products are delivered to their food
processing site on a timely basis. This is in-line with agile-manufacturing where a company
Secure Best Marks with AI Grader
Need help grading? Try our AI Grader for instant feedback on your assignments.
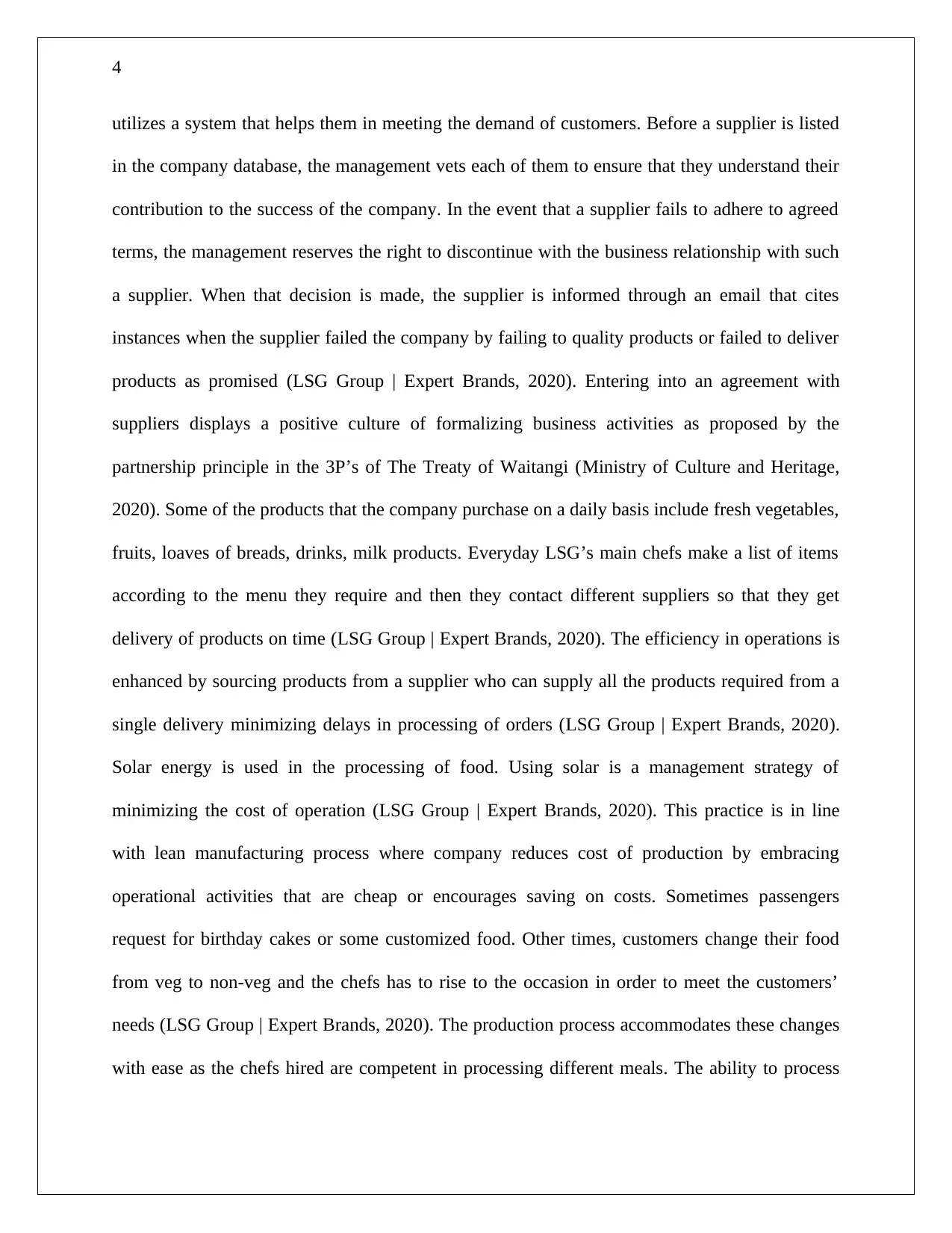
4
utilizes a system that helps them in meeting the demand of customers. Before a supplier is listed
in the company database, the management vets each of them to ensure that they understand their
contribution to the success of the company. In the event that a supplier fails to adhere to agreed
terms, the management reserves the right to discontinue with the business relationship with such
a supplier. When that decision is made, the supplier is informed through an email that cites
instances when the supplier failed the company by failing to quality products or failed to deliver
products as promised (LSG Group | Expert Brands, 2020). Entering into an agreement with
suppliers displays a positive culture of formalizing business activities as proposed by the
partnership principle in the 3P’s of The Treaty of Waitangi (Ministry of Culture and Heritage,
2020). Some of the products that the company purchase on a daily basis include fresh vegetables,
fruits, loaves of breads, drinks, milk products. Everyday LSG’s main chefs make a list of items
according to the menu they require and then they contact different suppliers so that they get
delivery of products on time (LSG Group | Expert Brands, 2020). The efficiency in operations is
enhanced by sourcing products from a supplier who can supply all the products required from a
single delivery minimizing delays in processing of orders (LSG Group | Expert Brands, 2020).
Solar energy is used in the processing of food. Using solar is a management strategy of
minimizing the cost of operation (LSG Group | Expert Brands, 2020). This practice is in line
with lean manufacturing process where company reduces cost of production by embracing
operational activities that are cheap or encourages saving on costs. Sometimes passengers
request for birthday cakes or some customized food. Other times, customers change their food
from veg to non-veg and the chefs has to rise to the occasion in order to meet the customers’
needs (LSG Group | Expert Brands, 2020). The production process accommodates these changes
with ease as the chefs hired are competent in processing different meals. The ability to process
utilizes a system that helps them in meeting the demand of customers. Before a supplier is listed
in the company database, the management vets each of them to ensure that they understand their
contribution to the success of the company. In the event that a supplier fails to adhere to agreed
terms, the management reserves the right to discontinue with the business relationship with such
a supplier. When that decision is made, the supplier is informed through an email that cites
instances when the supplier failed the company by failing to quality products or failed to deliver
products as promised (LSG Group | Expert Brands, 2020). Entering into an agreement with
suppliers displays a positive culture of formalizing business activities as proposed by the
partnership principle in the 3P’s of The Treaty of Waitangi (Ministry of Culture and Heritage,
2020). Some of the products that the company purchase on a daily basis include fresh vegetables,
fruits, loaves of breads, drinks, milk products. Everyday LSG’s main chefs make a list of items
according to the menu they require and then they contact different suppliers so that they get
delivery of products on time (LSG Group | Expert Brands, 2020). The efficiency in operations is
enhanced by sourcing products from a supplier who can supply all the products required from a
single delivery minimizing delays in processing of orders (LSG Group | Expert Brands, 2020).
Solar energy is used in the processing of food. Using solar is a management strategy of
minimizing the cost of operation (LSG Group | Expert Brands, 2020). This practice is in line
with lean manufacturing process where company reduces cost of production by embracing
operational activities that are cheap or encourages saving on costs. Sometimes passengers
request for birthday cakes or some customized food. Other times, customers change their food
from veg to non-veg and the chefs has to rise to the occasion in order to meet the customers’
needs (LSG Group | Expert Brands, 2020). The production process accommodates these changes
with ease as the chefs hired are competent in processing different meals. The ability to process
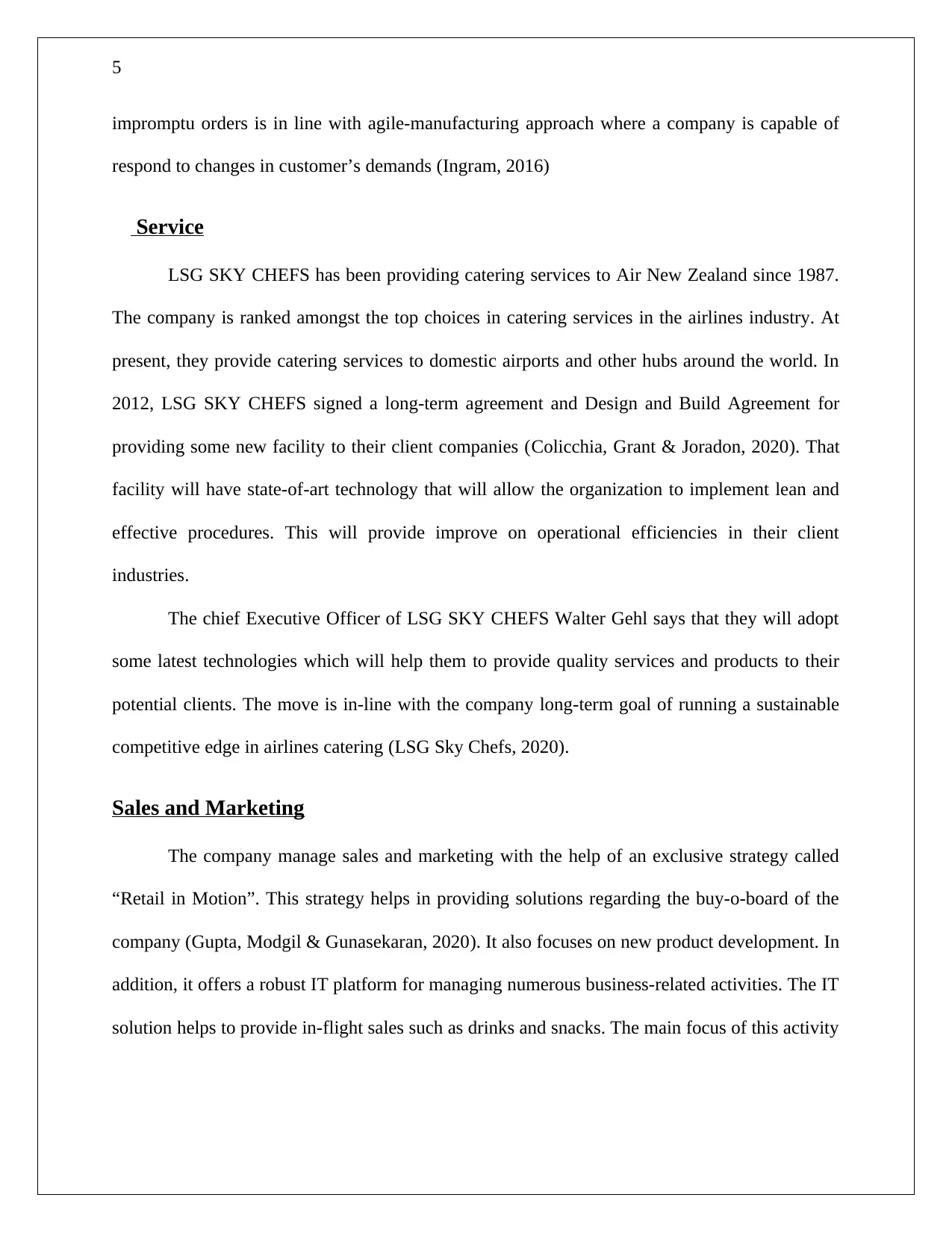
5
impromptu orders is in line with agile-manufacturing approach where a company is capable of
respond to changes in customer’s demands (Ingram, 2016)
Service
LSG SKY CHEFS has been providing catering services to Air New Zealand since 1987.
The company is ranked amongst the top choices in catering services in the airlines industry. At
present, they provide catering services to domestic airports and other hubs around the world. In
2012, LSG SKY CHEFS signed a long-term agreement and Design and Build Agreement for
providing some new facility to their client companies (Colicchia, Grant & Joradon, 2020). That
facility will have state-of-art technology that will allow the organization to implement lean and
effective procedures. This will provide improve on operational efficiencies in their client
industries.
The chief Executive Officer of LSG SKY CHEFS Walter Gehl says that they will adopt
some latest technologies which will help them to provide quality services and products to their
potential clients. The move is in-line with the company long-term goal of running a sustainable
competitive edge in airlines catering (LSG Sky Chefs, 2020).
Sales and Marketing
The company manage sales and marketing with the help of an exclusive strategy called
“Retail in Motion”. This strategy helps in providing solutions regarding the buy-o-board of the
company (Gupta, Modgil & Gunasekaran, 2020). It also focuses on new product development. In
addition, it offers a robust IT platform for managing numerous business-related activities. The IT
solution helps to provide in-flight sales such as drinks and snacks. The main focus of this activity
impromptu orders is in line with agile-manufacturing approach where a company is capable of
respond to changes in customer’s demands (Ingram, 2016)
Service
LSG SKY CHEFS has been providing catering services to Air New Zealand since 1987.
The company is ranked amongst the top choices in catering services in the airlines industry. At
present, they provide catering services to domestic airports and other hubs around the world. In
2012, LSG SKY CHEFS signed a long-term agreement and Design and Build Agreement for
providing some new facility to their client companies (Colicchia, Grant & Joradon, 2020). That
facility will have state-of-art technology that will allow the organization to implement lean and
effective procedures. This will provide improve on operational efficiencies in their client
industries.
The chief Executive Officer of LSG SKY CHEFS Walter Gehl says that they will adopt
some latest technologies which will help them to provide quality services and products to their
potential clients. The move is in-line with the company long-term goal of running a sustainable
competitive edge in airlines catering (LSG Sky Chefs, 2020).
Sales and Marketing
The company manage sales and marketing with the help of an exclusive strategy called
“Retail in Motion”. This strategy helps in providing solutions regarding the buy-o-board of the
company (Gupta, Modgil & Gunasekaran, 2020). It also focuses on new product development. In
addition, it offers a robust IT platform for managing numerous business-related activities. The IT
solution helps to provide in-flight sales such as drinks and snacks. The main focus of this activity
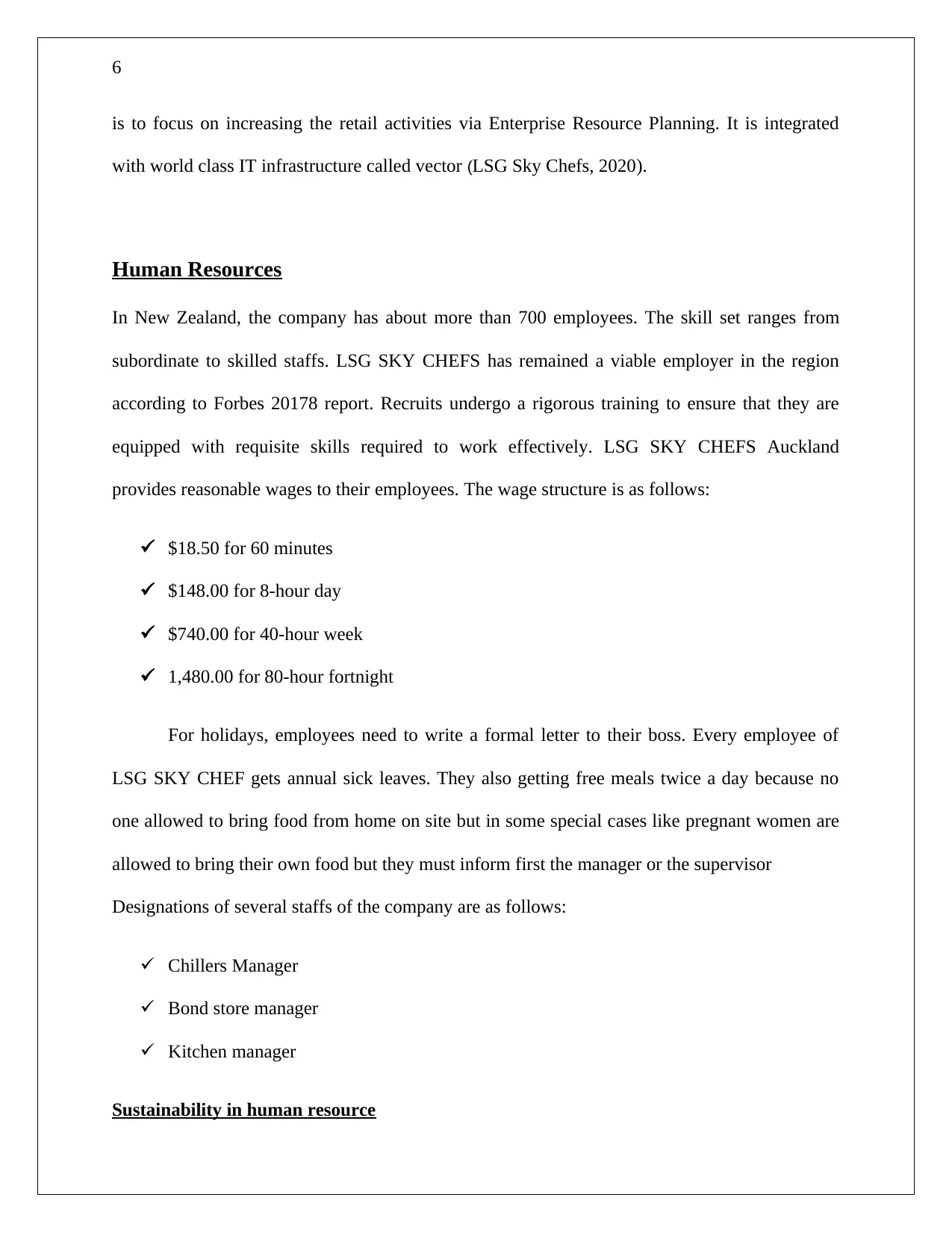
6
is to focus on increasing the retail activities via Enterprise Resource Planning. It is integrated
with world class IT infrastructure called vector (LSG Sky Chefs, 2020).
Human Resources
In New Zealand, the company has about more than 700 employees. The skill set ranges from
subordinate to skilled staffs. LSG SKY CHEFS has remained a viable employer in the region
according to Forbes 20178 report. Recruits undergo a rigorous training to ensure that they are
equipped with requisite skills required to work effectively. LSG SKY CHEFS Auckland
provides reasonable wages to their employees. The wage structure is as follows:
$18.50 for 60 minutes
$148.00 for 8-hour day
$740.00 for 40-hour week
1,480.00 for 80-hour fortnight
For holidays, employees need to write a formal letter to their boss. Every employee of
LSG SKY CHEF gets annual sick leaves. They also getting free meals twice a day because no
one allowed to bring food from home on site but in some special cases like pregnant women are
allowed to bring their own food but they must inform first the manager or the supervisor
Designations of several staffs of the company are as follows:
Chillers Manager
Bond store manager
Kitchen manager
Sustainability in human resource
is to focus on increasing the retail activities via Enterprise Resource Planning. It is integrated
with world class IT infrastructure called vector (LSG Sky Chefs, 2020).
Human Resources
In New Zealand, the company has about more than 700 employees. The skill set ranges from
subordinate to skilled staffs. LSG SKY CHEFS has remained a viable employer in the region
according to Forbes 20178 report. Recruits undergo a rigorous training to ensure that they are
equipped with requisite skills required to work effectively. LSG SKY CHEFS Auckland
provides reasonable wages to their employees. The wage structure is as follows:
$18.50 for 60 minutes
$148.00 for 8-hour day
$740.00 for 40-hour week
1,480.00 for 80-hour fortnight
For holidays, employees need to write a formal letter to their boss. Every employee of
LSG SKY CHEF gets annual sick leaves. They also getting free meals twice a day because no
one allowed to bring food from home on site but in some special cases like pregnant women are
allowed to bring their own food but they must inform first the manager or the supervisor
Designations of several staffs of the company are as follows:
Chillers Manager
Bond store manager
Kitchen manager
Sustainability in human resource
Paraphrase This Document
Need a fresh take? Get an instant paraphrase of this document with our AI Paraphraser
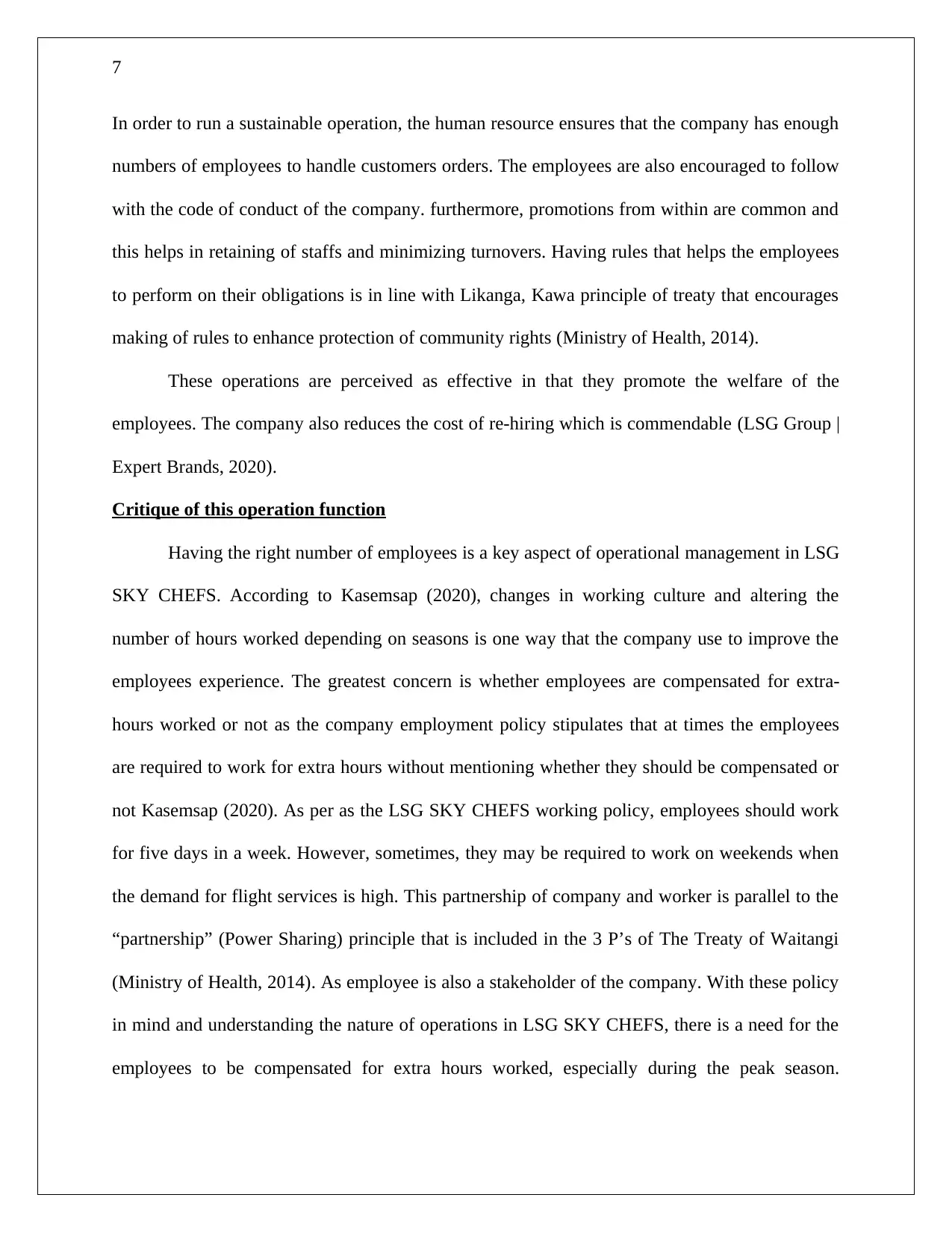
7
In order to run a sustainable operation, the human resource ensures that the company has enough
numbers of employees to handle customers orders. The employees are also encouraged to follow
with the code of conduct of the company. furthermore, promotions from within are common and
this helps in retaining of staffs and minimizing turnovers. Having rules that helps the employees
to perform on their obligations is in line with Likanga, Kawa principle of treaty that encourages
making of rules to enhance protection of community rights (Ministry of Health, 2014).
These operations are perceived as effective in that they promote the welfare of the
employees. The company also reduces the cost of re-hiring which is commendable (LSG Group |
Expert Brands, 2020).
Critique of this operation function
Having the right number of employees is a key aspect of operational management in LSG
SKY CHEFS. According to Kasemsap (2020), changes in working culture and altering the
number of hours worked depending on seasons is one way that the company use to improve the
employees experience. The greatest concern is whether employees are compensated for extra-
hours worked or not as the company employment policy stipulates that at times the employees
are required to work for extra hours without mentioning whether they should be compensated or
not Kasemsap (2020). As per as the LSG SKY CHEFS working policy, employees should work
for five days in a week. However, sometimes, they may be required to work on weekends when
the demand for flight services is high. This partnership of company and worker is parallel to the
“partnership” (Power Sharing) principle that is included in the 3 P’s of The Treaty of Waitangi
(Ministry of Health, 2014). As employee is also a stakeholder of the company. With these policy
in mind and understanding the nature of operations in LSG SKY CHEFS, there is a need for the
employees to be compensated for extra hours worked, especially during the peak season.
In order to run a sustainable operation, the human resource ensures that the company has enough
numbers of employees to handle customers orders. The employees are also encouraged to follow
with the code of conduct of the company. furthermore, promotions from within are common and
this helps in retaining of staffs and minimizing turnovers. Having rules that helps the employees
to perform on their obligations is in line with Likanga, Kawa principle of treaty that encourages
making of rules to enhance protection of community rights (Ministry of Health, 2014).
These operations are perceived as effective in that they promote the welfare of the
employees. The company also reduces the cost of re-hiring which is commendable (LSG Group |
Expert Brands, 2020).
Critique of this operation function
Having the right number of employees is a key aspect of operational management in LSG
SKY CHEFS. According to Kasemsap (2020), changes in working culture and altering the
number of hours worked depending on seasons is one way that the company use to improve the
employees experience. The greatest concern is whether employees are compensated for extra-
hours worked or not as the company employment policy stipulates that at times the employees
are required to work for extra hours without mentioning whether they should be compensated or
not Kasemsap (2020). As per as the LSG SKY CHEFS working policy, employees should work
for five days in a week. However, sometimes, they may be required to work on weekends when
the demand for flight services is high. This partnership of company and worker is parallel to the
“partnership” (Power Sharing) principle that is included in the 3 P’s of The Treaty of Waitangi
(Ministry of Health, 2014). As employee is also a stakeholder of the company. With these policy
in mind and understanding the nature of operations in LSG SKY CHEFS, there is a need for the
employees to be compensated for extra hours worked, especially during the peak season.
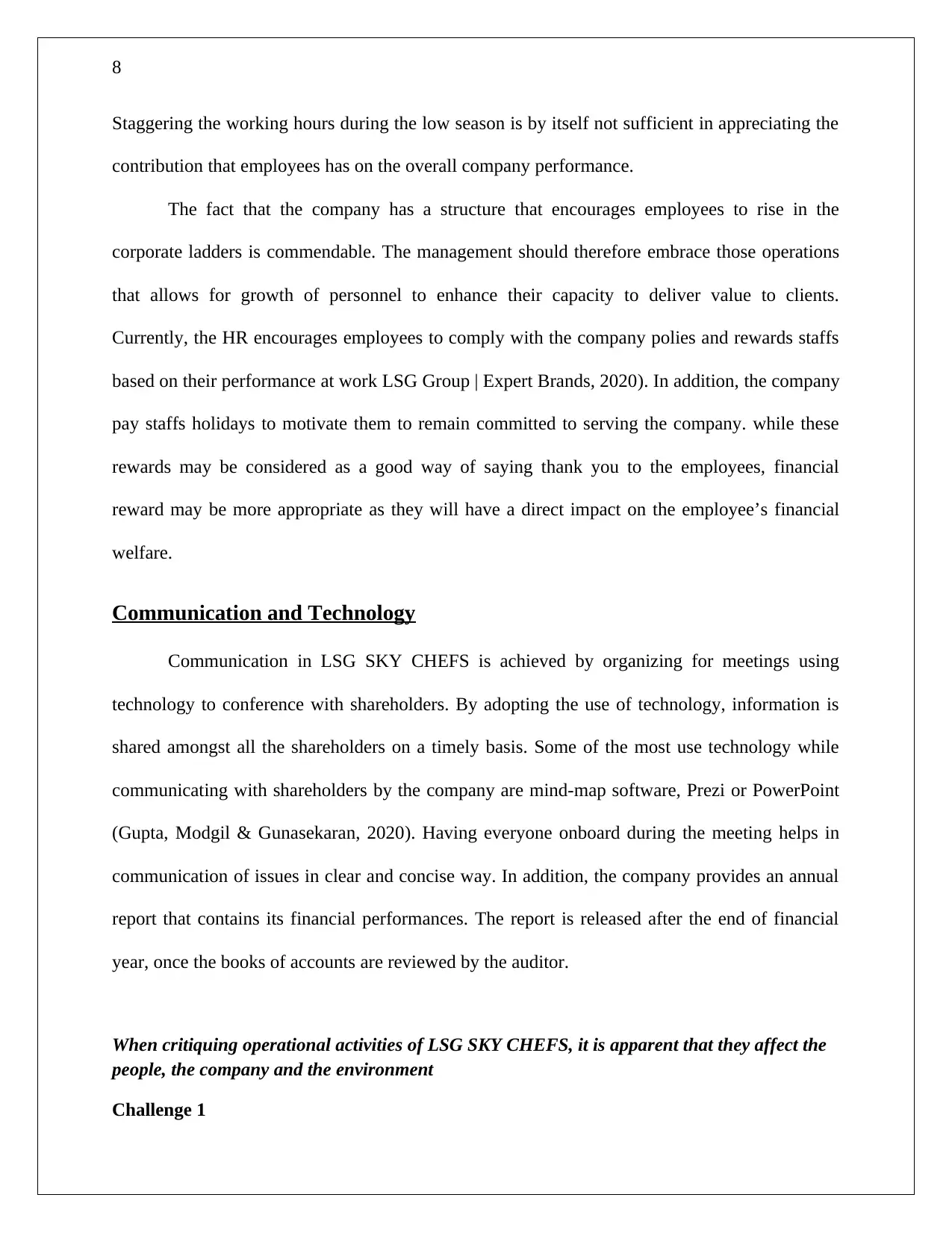
8
Staggering the working hours during the low season is by itself not sufficient in appreciating the
contribution that employees has on the overall company performance.
The fact that the company has a structure that encourages employees to rise in the
corporate ladders is commendable. The management should therefore embrace those operations
that allows for growth of personnel to enhance their capacity to deliver value to clients.
Currently, the HR encourages employees to comply with the company polies and rewards staffs
based on their performance at work LSG Group | Expert Brands, 2020). In addition, the company
pay staffs holidays to motivate them to remain committed to serving the company. while these
rewards may be considered as a good way of saying thank you to the employees, financial
reward may be more appropriate as they will have a direct impact on the employee’s financial
welfare.
Communication and Technology
Communication in LSG SKY CHEFS is achieved by organizing for meetings using
technology to conference with shareholders. By adopting the use of technology, information is
shared amongst all the shareholders on a timely basis. Some of the most use technology while
communicating with shareholders by the company are mind-map software, Prezi or PowerPoint
(Gupta, Modgil & Gunasekaran, 2020). Having everyone onboard during the meeting helps in
communication of issues in clear and concise way. In addition, the company provides an annual
report that contains its financial performances. The report is released after the end of financial
year, once the books of accounts are reviewed by the auditor.
When critiquing operational activities of LSG SKY CHEFS, it is apparent that they affect the
people, the company and the environment
Challenge 1
Staggering the working hours during the low season is by itself not sufficient in appreciating the
contribution that employees has on the overall company performance.
The fact that the company has a structure that encourages employees to rise in the
corporate ladders is commendable. The management should therefore embrace those operations
that allows for growth of personnel to enhance their capacity to deliver value to clients.
Currently, the HR encourages employees to comply with the company polies and rewards staffs
based on their performance at work LSG Group | Expert Brands, 2020). In addition, the company
pay staffs holidays to motivate them to remain committed to serving the company. while these
rewards may be considered as a good way of saying thank you to the employees, financial
reward may be more appropriate as they will have a direct impact on the employee’s financial
welfare.
Communication and Technology
Communication in LSG SKY CHEFS is achieved by organizing for meetings using
technology to conference with shareholders. By adopting the use of technology, information is
shared amongst all the shareholders on a timely basis. Some of the most use technology while
communicating with shareholders by the company are mind-map software, Prezi or PowerPoint
(Gupta, Modgil & Gunasekaran, 2020). Having everyone onboard during the meeting helps in
communication of issues in clear and concise way. In addition, the company provides an annual
report that contains its financial performances. The report is released after the end of financial
year, once the books of accounts are reviewed by the auditor.
When critiquing operational activities of LSG SKY CHEFS, it is apparent that they affect the
people, the company and the environment
Challenge 1
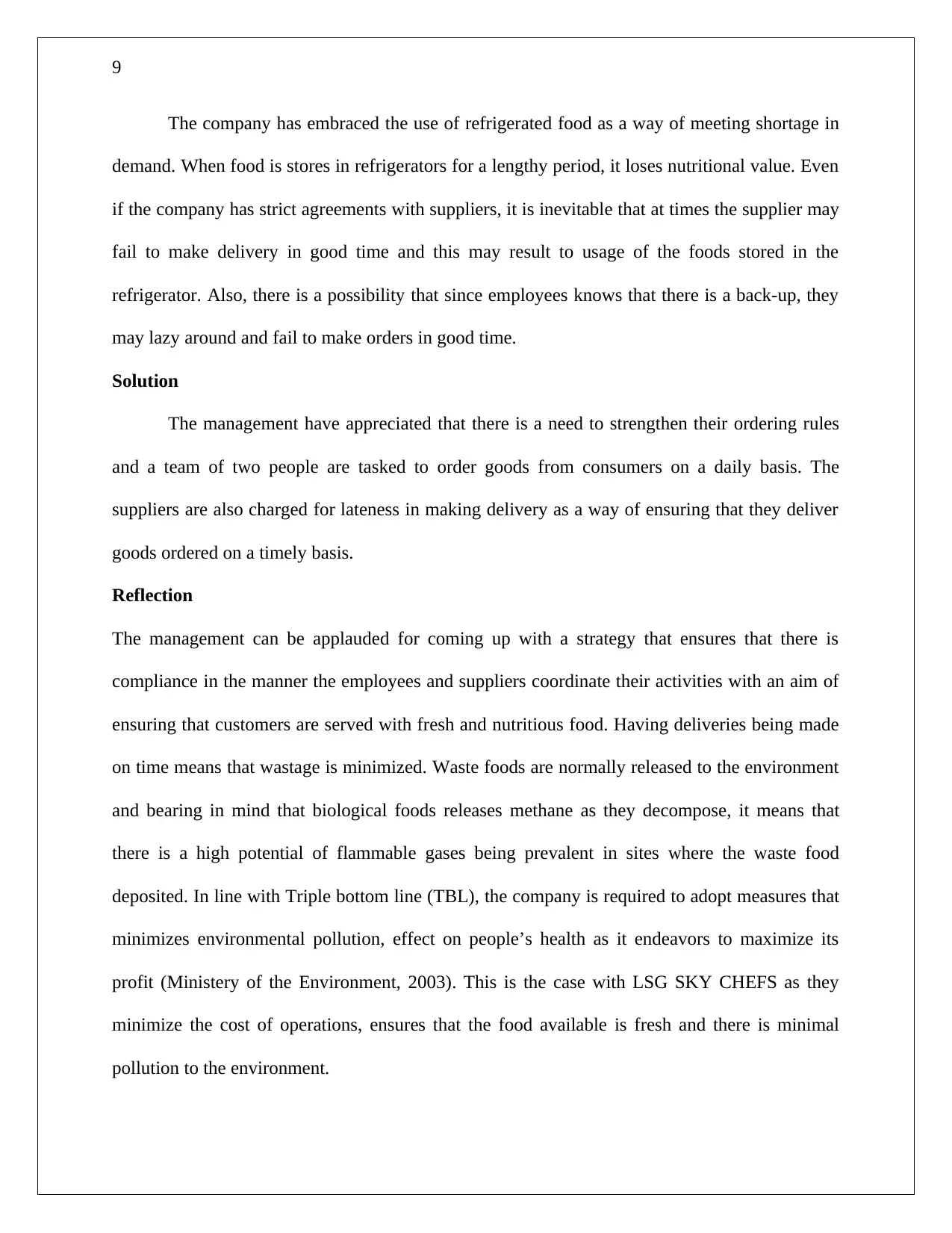
9
The company has embraced the use of refrigerated food as a way of meeting shortage in
demand. When food is stores in refrigerators for a lengthy period, it loses nutritional value. Even
if the company has strict agreements with suppliers, it is inevitable that at times the supplier may
fail to make delivery in good time and this may result to usage of the foods stored in the
refrigerator. Also, there is a possibility that since employees knows that there is a back-up, they
may lazy around and fail to make orders in good time.
Solution
The management have appreciated that there is a need to strengthen their ordering rules
and a team of two people are tasked to order goods from consumers on a daily basis. The
suppliers are also charged for lateness in making delivery as a way of ensuring that they deliver
goods ordered on a timely basis.
Reflection
The management can be applauded for coming up with a strategy that ensures that there is
compliance in the manner the employees and suppliers coordinate their activities with an aim of
ensuring that customers are served with fresh and nutritious food. Having deliveries being made
on time means that wastage is minimized. Waste foods are normally released to the environment
and bearing in mind that biological foods releases methane as they decompose, it means that
there is a high potential of flammable gases being prevalent in sites where the waste food
deposited. In line with Triple bottom line (TBL), the company is required to adopt measures that
minimizes environmental pollution, effect on people’s health as it endeavors to maximize its
profit (Ministery of the Environment, 2003). This is the case with LSG SKY CHEFS as they
minimize the cost of operations, ensures that the food available is fresh and there is minimal
pollution to the environment.
The company has embraced the use of refrigerated food as a way of meeting shortage in
demand. When food is stores in refrigerators for a lengthy period, it loses nutritional value. Even
if the company has strict agreements with suppliers, it is inevitable that at times the supplier may
fail to make delivery in good time and this may result to usage of the foods stored in the
refrigerator. Also, there is a possibility that since employees knows that there is a back-up, they
may lazy around and fail to make orders in good time.
Solution
The management have appreciated that there is a need to strengthen their ordering rules
and a team of two people are tasked to order goods from consumers on a daily basis. The
suppliers are also charged for lateness in making delivery as a way of ensuring that they deliver
goods ordered on a timely basis.
Reflection
The management can be applauded for coming up with a strategy that ensures that there is
compliance in the manner the employees and suppliers coordinate their activities with an aim of
ensuring that customers are served with fresh and nutritious food. Having deliveries being made
on time means that wastage is minimized. Waste foods are normally released to the environment
and bearing in mind that biological foods releases methane as they decompose, it means that
there is a high potential of flammable gases being prevalent in sites where the waste food
deposited. In line with Triple bottom line (TBL), the company is required to adopt measures that
minimizes environmental pollution, effect on people’s health as it endeavors to maximize its
profit (Ministery of the Environment, 2003). This is the case with LSG SKY CHEFS as they
minimize the cost of operations, ensures that the food available is fresh and there is minimal
pollution to the environment.
Secure Best Marks with AI Grader
Need help grading? Try our AI Grader for instant feedback on your assignments.
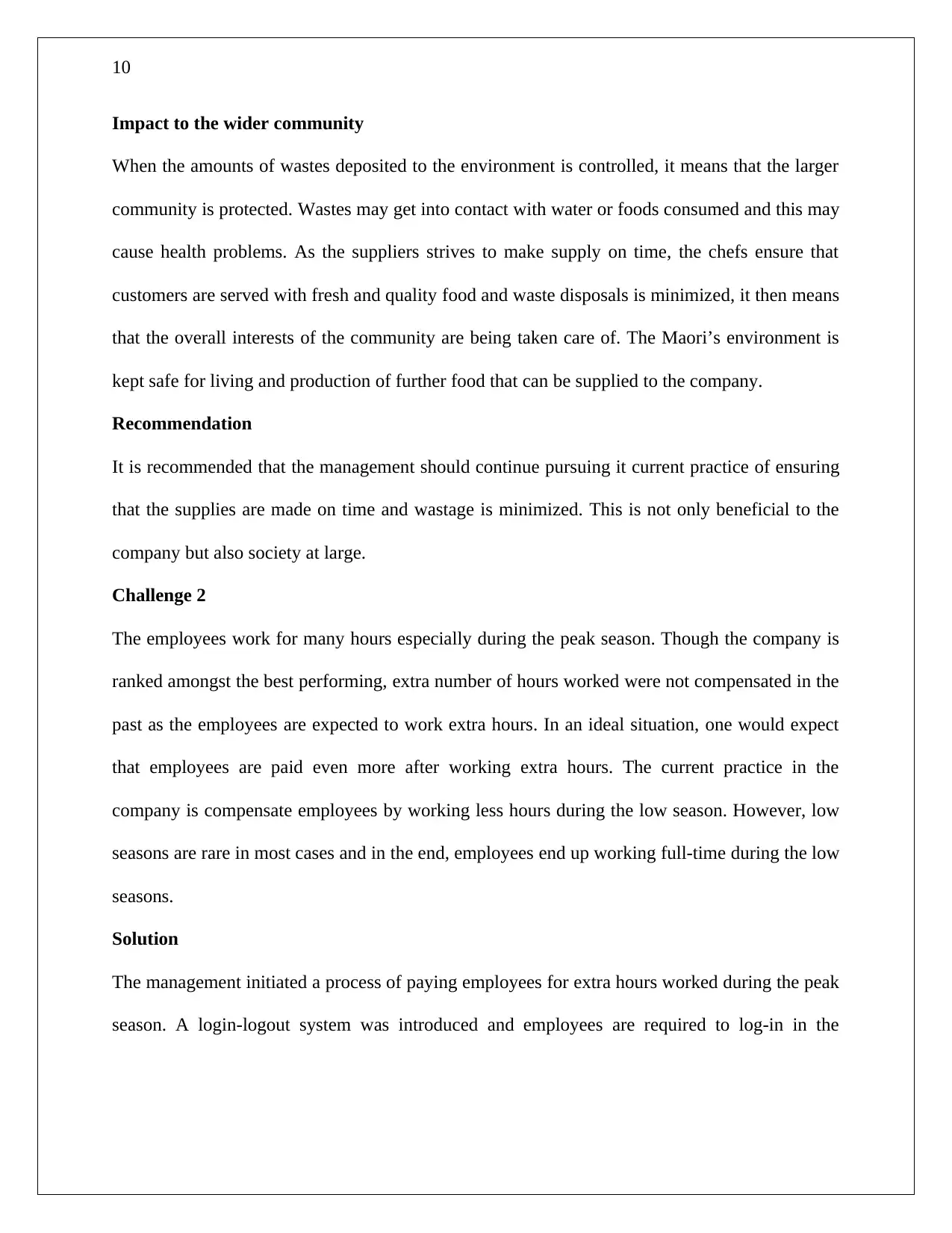
10
Impact to the wider community
When the amounts of wastes deposited to the environment is controlled, it means that the larger
community is protected. Wastes may get into contact with water or foods consumed and this may
cause health problems. As the suppliers strives to make supply on time, the chefs ensure that
customers are served with fresh and quality food and waste disposals is minimized, it then means
that the overall interests of the community are being taken care of. The Maori’s environment is
kept safe for living and production of further food that can be supplied to the company.
Recommendation
It is recommended that the management should continue pursuing it current practice of ensuring
that the supplies are made on time and wastage is minimized. This is not only beneficial to the
company but also society at large.
Challenge 2
The employees work for many hours especially during the peak season. Though the company is
ranked amongst the best performing, extra number of hours worked were not compensated in the
past as the employees are expected to work extra hours. In an ideal situation, one would expect
that employees are paid even more after working extra hours. The current practice in the
company is compensate employees by working less hours during the low season. However, low
seasons are rare in most cases and in the end, employees end up working full-time during the low
seasons.
Solution
The management initiated a process of paying employees for extra hours worked during the peak
season. A login-logout system was introduced and employees are required to log-in in the
Impact to the wider community
When the amounts of wastes deposited to the environment is controlled, it means that the larger
community is protected. Wastes may get into contact with water or foods consumed and this may
cause health problems. As the suppliers strives to make supply on time, the chefs ensure that
customers are served with fresh and quality food and waste disposals is minimized, it then means
that the overall interests of the community are being taken care of. The Maori’s environment is
kept safe for living and production of further food that can be supplied to the company.
Recommendation
It is recommended that the management should continue pursuing it current practice of ensuring
that the supplies are made on time and wastage is minimized. This is not only beneficial to the
company but also society at large.
Challenge 2
The employees work for many hours especially during the peak season. Though the company is
ranked amongst the best performing, extra number of hours worked were not compensated in the
past as the employees are expected to work extra hours. In an ideal situation, one would expect
that employees are paid even more after working extra hours. The current practice in the
company is compensate employees by working less hours during the low season. However, low
seasons are rare in most cases and in the end, employees end up working full-time during the low
seasons.
Solution
The management initiated a process of paying employees for extra hours worked during the peak
season. A login-logout system was introduced and employees are required to log-in in the
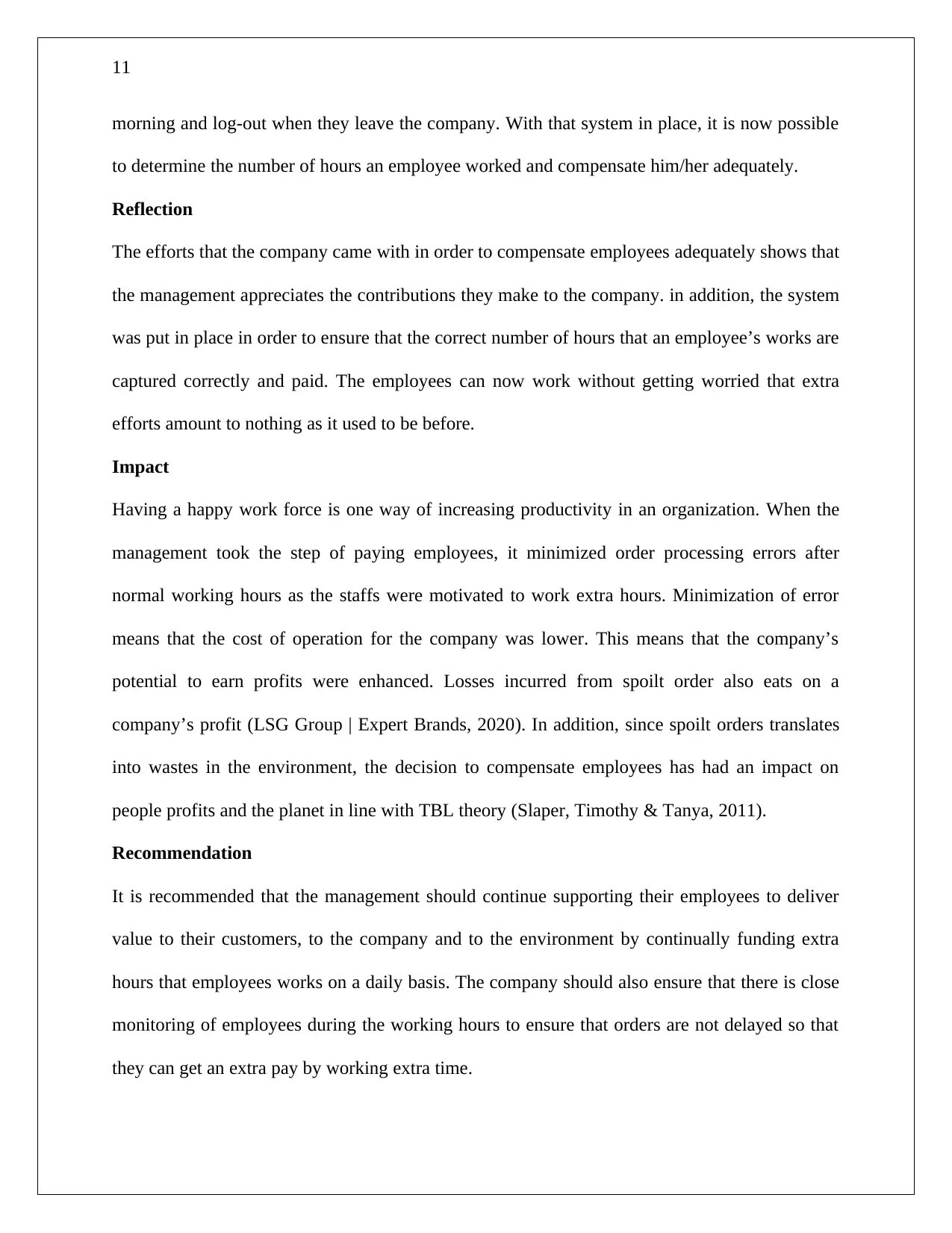
11
morning and log-out when they leave the company. With that system in place, it is now possible
to determine the number of hours an employee worked and compensate him/her adequately.
Reflection
The efforts that the company came with in order to compensate employees adequately shows that
the management appreciates the contributions they make to the company. in addition, the system
was put in place in order to ensure that the correct number of hours that an employee’s works are
captured correctly and paid. The employees can now work without getting worried that extra
efforts amount to nothing as it used to be before.
Impact
Having a happy work force is one way of increasing productivity in an organization. When the
management took the step of paying employees, it minimized order processing errors after
normal working hours as the staffs were motivated to work extra hours. Minimization of error
means that the cost of operation for the company was lower. This means that the company’s
potential to earn profits were enhanced. Losses incurred from spoilt order also eats on a
company’s profit (LSG Group | Expert Brands, 2020). In addition, since spoilt orders translates
into wastes in the environment, the decision to compensate employees has had an impact on
people profits and the planet in line with TBL theory (Slaper, Timothy & Tanya, 2011).
Recommendation
It is recommended that the management should continue supporting their employees to deliver
value to their customers, to the company and to the environment by continually funding extra
hours that employees works on a daily basis. The company should also ensure that there is close
monitoring of employees during the working hours to ensure that orders are not delayed so that
they can get an extra pay by working extra time.
morning and log-out when they leave the company. With that system in place, it is now possible
to determine the number of hours an employee worked and compensate him/her adequately.
Reflection
The efforts that the company came with in order to compensate employees adequately shows that
the management appreciates the contributions they make to the company. in addition, the system
was put in place in order to ensure that the correct number of hours that an employee’s works are
captured correctly and paid. The employees can now work without getting worried that extra
efforts amount to nothing as it used to be before.
Impact
Having a happy work force is one way of increasing productivity in an organization. When the
management took the step of paying employees, it minimized order processing errors after
normal working hours as the staffs were motivated to work extra hours. Minimization of error
means that the cost of operation for the company was lower. This means that the company’s
potential to earn profits were enhanced. Losses incurred from spoilt order also eats on a
company’s profit (LSG Group | Expert Brands, 2020). In addition, since spoilt orders translates
into wastes in the environment, the decision to compensate employees has had an impact on
people profits and the planet in line with TBL theory (Slaper, Timothy & Tanya, 2011).
Recommendation
It is recommended that the management should continue supporting their employees to deliver
value to their customers, to the company and to the environment by continually funding extra
hours that employees works on a daily basis. The company should also ensure that there is close
monitoring of employees during the working hours to ensure that orders are not delayed so that
they can get an extra pay by working extra time.
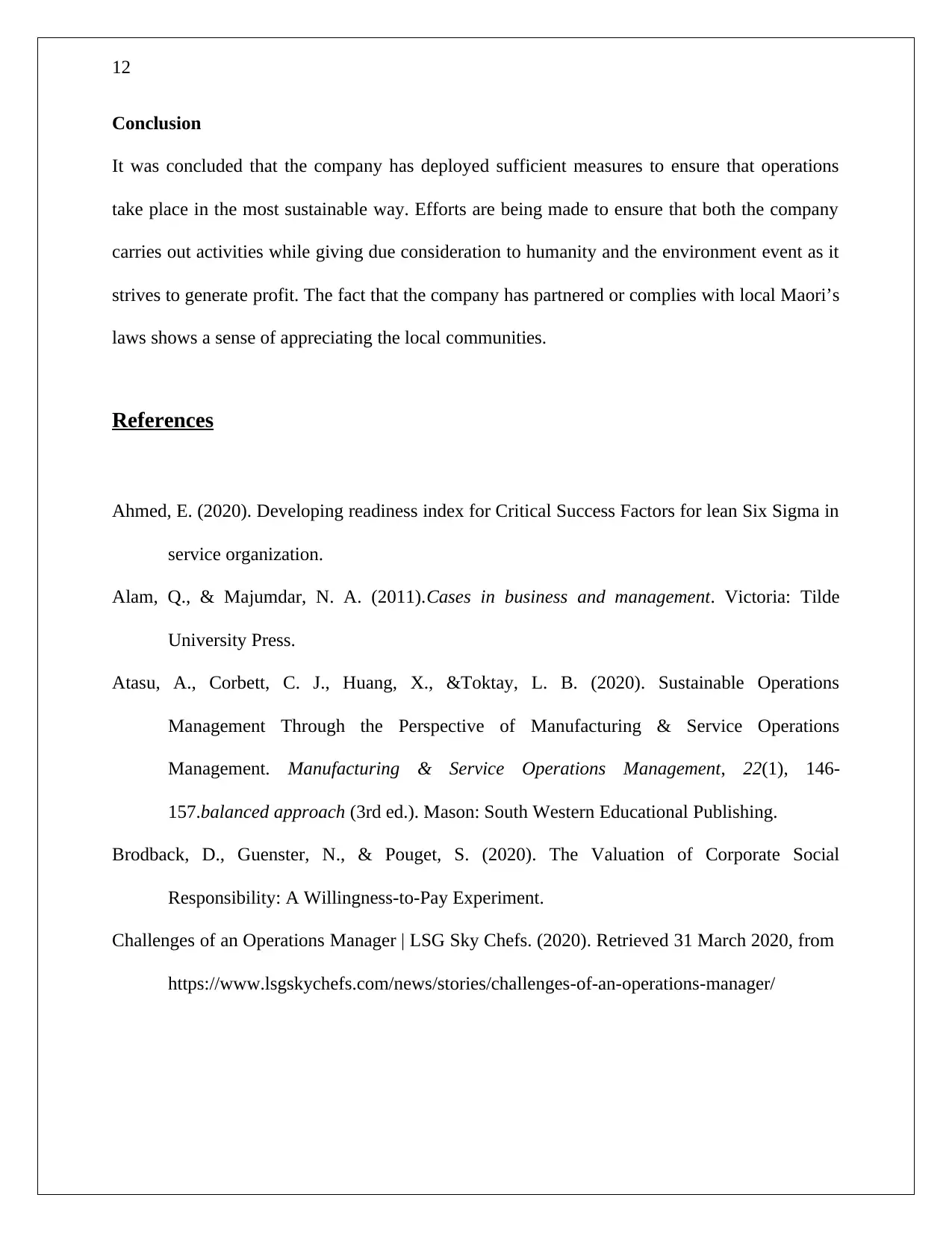
12
Conclusion
It was concluded that the company has deployed sufficient measures to ensure that operations
take place in the most sustainable way. Efforts are being made to ensure that both the company
carries out activities while giving due consideration to humanity and the environment event as it
strives to generate profit. The fact that the company has partnered or complies with local Maori’s
laws shows a sense of appreciating the local communities.
References
Ahmed, E. (2020). Developing readiness index for Critical Success Factors for lean Six Sigma in
service organization.
Alam, Q., & Majumdar, N. A. (2011).Cases in business and management. Victoria: Tilde
University Press.
Atasu, A., Corbett, C. J., Huang, X., &Toktay, L. B. (2020). Sustainable Operations
Management Through the Perspective of Manufacturing & Service Operations
Management. Manufacturing & Service Operations Management, 22(1), 146-
157.balanced approach (3rd ed.). Mason: South Western Educational Publishing.
Brodback, D., Guenster, N., & Pouget, S. (2020). The Valuation of Corporate Social
Responsibility: A Willingness-to-Pay Experiment.
Challenges of an Operations Manager | LSG Sky Chefs. (2020). Retrieved 31 March 2020, from
https://www.lsgskychefs.com/news/stories/challenges-of-an-operations-manager/
Conclusion
It was concluded that the company has deployed sufficient measures to ensure that operations
take place in the most sustainable way. Efforts are being made to ensure that both the company
carries out activities while giving due consideration to humanity and the environment event as it
strives to generate profit. The fact that the company has partnered or complies with local Maori’s
laws shows a sense of appreciating the local communities.
References
Ahmed, E. (2020). Developing readiness index for Critical Success Factors for lean Six Sigma in
service organization.
Alam, Q., & Majumdar, N. A. (2011).Cases in business and management. Victoria: Tilde
University Press.
Atasu, A., Corbett, C. J., Huang, X., &Toktay, L. B. (2020). Sustainable Operations
Management Through the Perspective of Manufacturing & Service Operations
Management. Manufacturing & Service Operations Management, 22(1), 146-
157.balanced approach (3rd ed.). Mason: South Western Educational Publishing.
Brodback, D., Guenster, N., & Pouget, S. (2020). The Valuation of Corporate Social
Responsibility: A Willingness-to-Pay Experiment.
Challenges of an Operations Manager | LSG Sky Chefs. (2020). Retrieved 31 March 2020, from
https://www.lsgskychefs.com/news/stories/challenges-of-an-operations-manager/
Paraphrase This Document
Need a fresh take? Get an instant paraphrase of this document with our AI Paraphraser
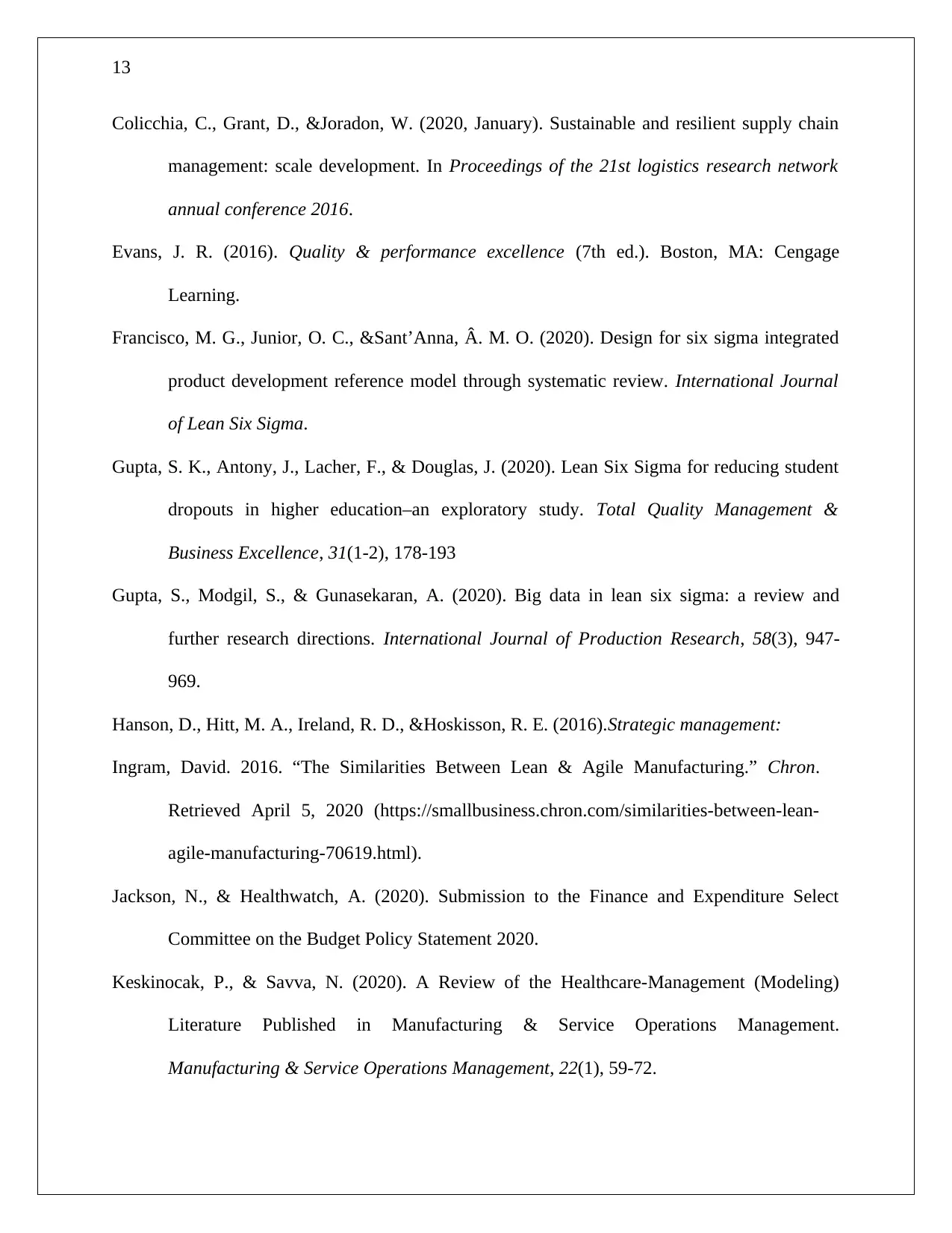
13
Colicchia, C., Grant, D., &Joradon, W. (2020, January). Sustainable and resilient supply chain
management: scale development. In Proceedings of the 21st logistics research network
annual conference 2016.
Evans, J. R. (2016). Quality & performance excellence (7th ed.). Boston, MA: Cengage
Learning.
Francisco, M. G., Junior, O. C., &Sant’Anna, Â. M. O. (2020). Design for six sigma integrated
product development reference model through systematic review. International Journal
of Lean Six Sigma.
Gupta, S. K., Antony, J., Lacher, F., & Douglas, J. (2020). Lean Six Sigma for reducing student
dropouts in higher education–an exploratory study. Total Quality Management &
Business Excellence, 31(1-2), 178-193
Gupta, S., Modgil, S., & Gunasekaran, A. (2020). Big data in lean six sigma: a review and
further research directions. International Journal of Production Research, 58(3), 947-
969.
Hanson, D., Hitt, M. A., Ireland, R. D., &Hoskisson, R. E. (2016).Strategic management:
Ingram, David. 2016. “The Similarities Between Lean & Agile Manufacturing.” Chron.
Retrieved April 5, 2020 (https://smallbusiness.chron.com/similarities-between-lean-
agile-manufacturing-70619.html).
Jackson, N., & Healthwatch, A. (2020). Submission to the Finance and Expenditure Select
Committee on the Budget Policy Statement 2020.
Keskinocak, P., & Savva, N. (2020). A Review of the Healthcare-Management (Modeling)
Literature Published in Manufacturing & Service Operations Management.
Manufacturing & Service Operations Management, 22(1), 59-72.
Colicchia, C., Grant, D., &Joradon, W. (2020, January). Sustainable and resilient supply chain
management: scale development. In Proceedings of the 21st logistics research network
annual conference 2016.
Evans, J. R. (2016). Quality & performance excellence (7th ed.). Boston, MA: Cengage
Learning.
Francisco, M. G., Junior, O. C., &Sant’Anna, Â. M. O. (2020). Design for six sigma integrated
product development reference model through systematic review. International Journal
of Lean Six Sigma.
Gupta, S. K., Antony, J., Lacher, F., & Douglas, J. (2020). Lean Six Sigma for reducing student
dropouts in higher education–an exploratory study. Total Quality Management &
Business Excellence, 31(1-2), 178-193
Gupta, S., Modgil, S., & Gunasekaran, A. (2020). Big data in lean six sigma: a review and
further research directions. International Journal of Production Research, 58(3), 947-
969.
Hanson, D., Hitt, M. A., Ireland, R. D., &Hoskisson, R. E. (2016).Strategic management:
Ingram, David. 2016. “The Similarities Between Lean & Agile Manufacturing.” Chron.
Retrieved April 5, 2020 (https://smallbusiness.chron.com/similarities-between-lean-
agile-manufacturing-70619.html).
Jackson, N., & Healthwatch, A. (2020). Submission to the Finance and Expenditure Select
Committee on the Budget Policy Statement 2020.
Keskinocak, P., & Savva, N. (2020). A Review of the Healthcare-Management (Modeling)
Literature Published in Manufacturing & Service Operations Management.
Manufacturing & Service Operations Management, 22(1), 59-72.
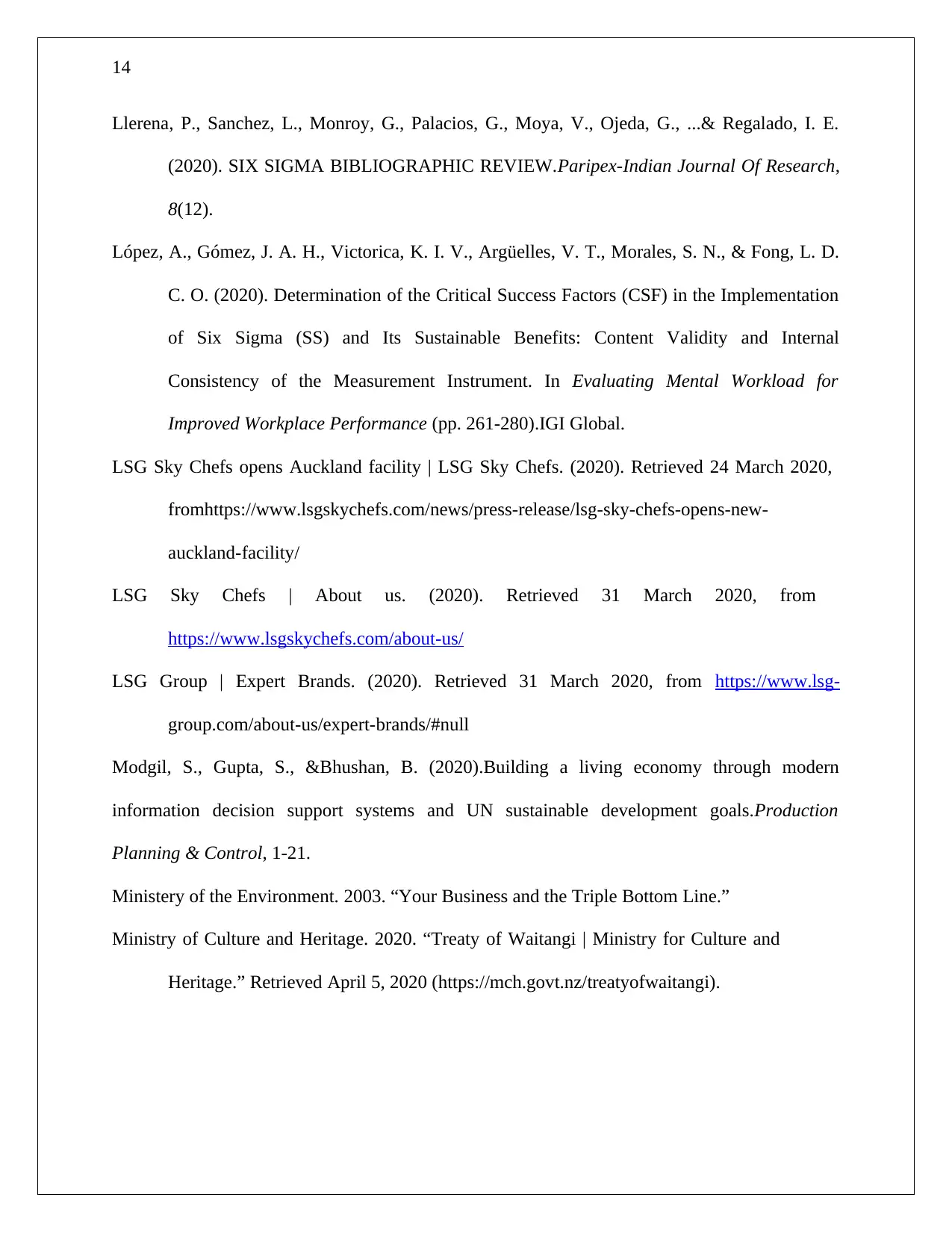
14
Llerena, P., Sanchez, L., Monroy, G., Palacios, G., Moya, V., Ojeda, G., ...& Regalado, I. E.
(2020). SIX SIGMA BIBLIOGRAPHIC REVIEW.Paripex-Indian Journal Of Research,
8(12).
López, A., Gómez, J. A. H., Victorica, K. I. V., Argüelles, V. T., Morales, S. N., & Fong, L. D.
C. O. (2020). Determination of the Critical Success Factors (CSF) in the Implementation
of Six Sigma (SS) and Its Sustainable Benefits: Content Validity and Internal
Consistency of the Measurement Instrument. In Evaluating Mental Workload for
Improved Workplace Performance (pp. 261-280).IGI Global.
LSG Sky Chefs opens Auckland facility | LSG Sky Chefs. (2020). Retrieved 24 March 2020,
fromhttps://www.lsgskychefs.com/news/press-release/lsg-sky-chefs-opens-new-
auckland-facility/
LSG Sky Chefs | About us. (2020). Retrieved 31 March 2020, from
https://www.lsgskychefs.com/about-us/
LSG Group | Expert Brands. (2020). Retrieved 31 March 2020, from https://www.lsg-
group.com/about-us/expert-brands/#null
Modgil, S., Gupta, S., &Bhushan, B. (2020).Building a living economy through modern
information decision support systems and UN sustainable development goals.Production
Planning & Control, 1-21.
Ministery of the Environment. 2003. “Your Business and the Triple Bottom Line.”
Ministry of Culture and Heritage. 2020. “Treaty of Waitangi | Ministry for Culture and
Heritage.” Retrieved April 5, 2020 (https://mch.govt.nz/treatyofwaitangi).
Llerena, P., Sanchez, L., Monroy, G., Palacios, G., Moya, V., Ojeda, G., ...& Regalado, I. E.
(2020). SIX SIGMA BIBLIOGRAPHIC REVIEW.Paripex-Indian Journal Of Research,
8(12).
López, A., Gómez, J. A. H., Victorica, K. I. V., Argüelles, V. T., Morales, S. N., & Fong, L. D.
C. O. (2020). Determination of the Critical Success Factors (CSF) in the Implementation
of Six Sigma (SS) and Its Sustainable Benefits: Content Validity and Internal
Consistency of the Measurement Instrument. In Evaluating Mental Workload for
Improved Workplace Performance (pp. 261-280).IGI Global.
LSG Sky Chefs opens Auckland facility | LSG Sky Chefs. (2020). Retrieved 24 March 2020,
fromhttps://www.lsgskychefs.com/news/press-release/lsg-sky-chefs-opens-new-
auckland-facility/
LSG Sky Chefs | About us. (2020). Retrieved 31 March 2020, from
https://www.lsgskychefs.com/about-us/
LSG Group | Expert Brands. (2020). Retrieved 31 March 2020, from https://www.lsg-
group.com/about-us/expert-brands/#null
Modgil, S., Gupta, S., &Bhushan, B. (2020).Building a living economy through modern
information decision support systems and UN sustainable development goals.Production
Planning & Control, 1-21.
Ministery of the Environment. 2003. “Your Business and the Triple Bottom Line.”
Ministry of Culture and Heritage. 2020. “Treaty of Waitangi | Ministry for Culture and
Heritage.” Retrieved April 5, 2020 (https://mch.govt.nz/treatyofwaitangi).
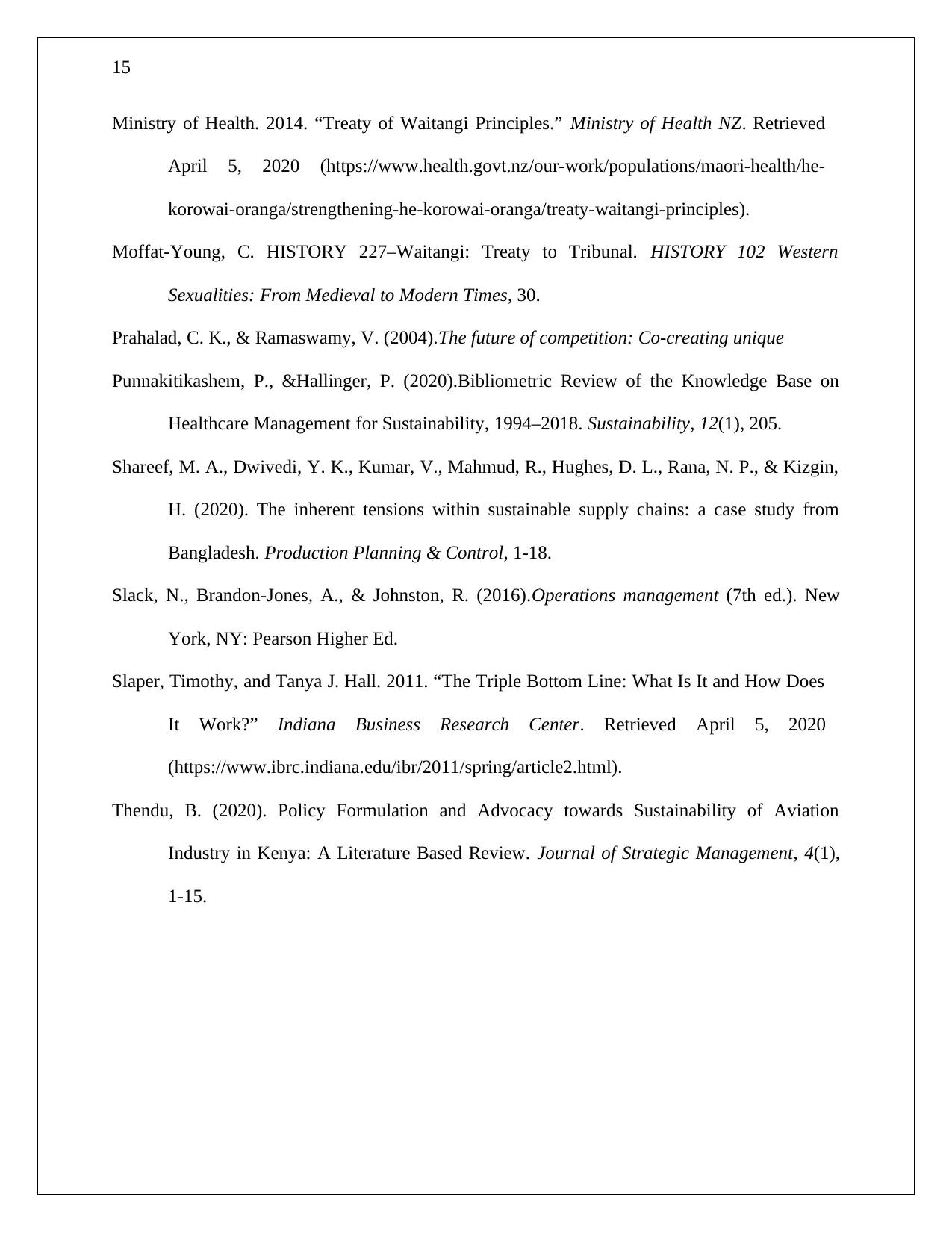
15
Ministry of Health. 2014. “Treaty of Waitangi Principles.” Ministry of Health NZ. Retrieved
April 5, 2020 (https://www.health.govt.nz/our-work/populations/maori-health/he-
korowai-oranga/strengthening-he-korowai-oranga/treaty-waitangi-principles).
Moffat-Young, C. HISTORY 227–Waitangi: Treaty to Tribunal. HISTORY 102 Western
Sexualities: From Medieval to Modern Times, 30.
Prahalad, C. K., & Ramaswamy, V. (2004).The future of competition: Co-creating unique
Punnakitikashem, P., &Hallinger, P. (2020).Bibliometric Review of the Knowledge Base on
Healthcare Management for Sustainability, 1994–2018. Sustainability, 12(1), 205.
Shareef, M. A., Dwivedi, Y. K., Kumar, V., Mahmud, R., Hughes, D. L., Rana, N. P., & Kizgin,
H. (2020). The inherent tensions within sustainable supply chains: a case study from
Bangladesh. Production Planning & Control, 1-18.
Slack, N., Brandon-Jones, A., & Johnston, R. (2016).Operations management (7th ed.). New
York, NY: Pearson Higher Ed.
Slaper, Timothy, and Tanya J. Hall. 2011. “The Triple Bottom Line: What Is It and How Does
It Work?” Indiana Business Research Center. Retrieved April 5, 2020
(https://www.ibrc.indiana.edu/ibr/2011/spring/article2.html).
Thendu, B. (2020). Policy Formulation and Advocacy towards Sustainability of Aviation
Industry in Kenya: A Literature Based Review. Journal of Strategic Management, 4(1),
1-15.
Ministry of Health. 2014. “Treaty of Waitangi Principles.” Ministry of Health NZ. Retrieved
April 5, 2020 (https://www.health.govt.nz/our-work/populations/maori-health/he-
korowai-oranga/strengthening-he-korowai-oranga/treaty-waitangi-principles).
Moffat-Young, C. HISTORY 227–Waitangi: Treaty to Tribunal. HISTORY 102 Western
Sexualities: From Medieval to Modern Times, 30.
Prahalad, C. K., & Ramaswamy, V. (2004).The future of competition: Co-creating unique
Punnakitikashem, P., &Hallinger, P. (2020).Bibliometric Review of the Knowledge Base on
Healthcare Management for Sustainability, 1994–2018. Sustainability, 12(1), 205.
Shareef, M. A., Dwivedi, Y. K., Kumar, V., Mahmud, R., Hughes, D. L., Rana, N. P., & Kizgin,
H. (2020). The inherent tensions within sustainable supply chains: a case study from
Bangladesh. Production Planning & Control, 1-18.
Slack, N., Brandon-Jones, A., & Johnston, R. (2016).Operations management (7th ed.). New
York, NY: Pearson Higher Ed.
Slaper, Timothy, and Tanya J. Hall. 2011. “The Triple Bottom Line: What Is It and How Does
It Work?” Indiana Business Research Center. Retrieved April 5, 2020
(https://www.ibrc.indiana.edu/ibr/2011/spring/article2.html).
Thendu, B. (2020). Policy Formulation and Advocacy towards Sustainability of Aviation
Industry in Kenya: A Literature Based Review. Journal of Strategic Management, 4(1),
1-15.
1 out of 16
![[object Object]](/_next/image/?url=%2F_next%2Fstatic%2Fmedia%2Flogo.6d15ce61.png&w=640&q=75)
Your All-in-One AI-Powered Toolkit for Academic Success.
+13062052269
info@desklib.com
Available 24*7 on WhatsApp / Email
Unlock your academic potential
© 2024 | Zucol Services PVT LTD | All rights reserved.