Analysis of Total Quality Management at Saddle Creek Logistics
VerifiedAdded on 2021/02/22
|6
|2001
|140
Report
AI Summary
This report provides a comprehensive analysis of Total Quality Management (TQM) as implemented by Saddle Creek Logistics. It begins by defining TQM and its significance in organizational advancement, highlighting its precursor role to quality management systems like Lean, ISO, and Six Sigma. The ...
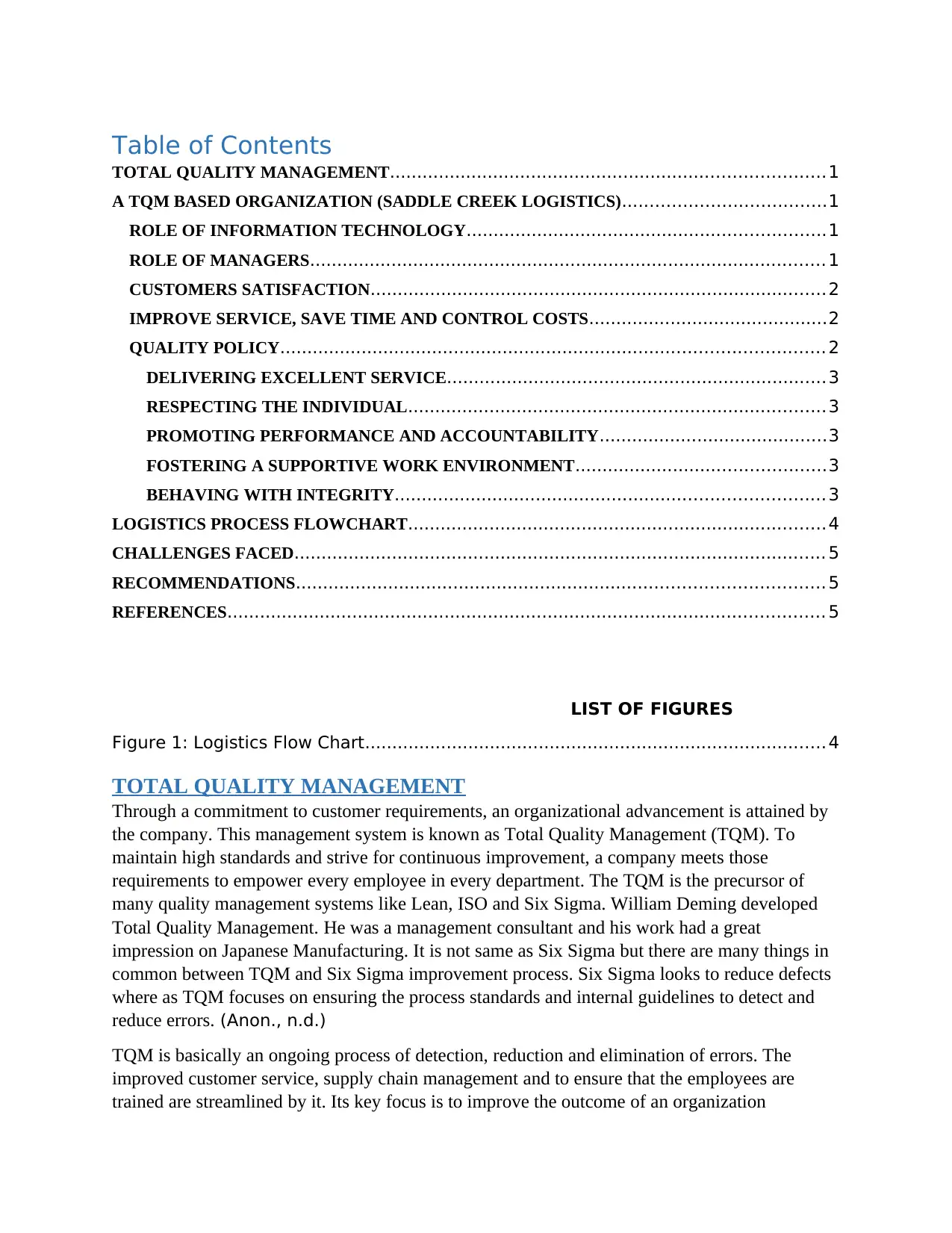
Table of Contents
TOTAL QUALITY MANAGEMENT................................................................................1
A TQM BASED ORGANIZATION (SADDLE CREEK LOGISTICS).....................................1
ROLE OF INFORMATION TECHNOLOGY..................................................................1
ROLE OF MANAGERS............................................................................................... 1
CUSTOMERS SATISFACTION....................................................................................2
IMPROVE SERVICE, SAVE TIME AND CONTROL COSTS............................................2
QUALITY POLICY.................................................................................................... 2
DELIVERING EXCELLENT SERVICE......................................................................3
RESPECTING THE INDIVIDUAL.............................................................................3
PROMOTING PERFORMANCE AND ACCOUNTABILITY..........................................3
FOSTERING A SUPPORTIVE WORK ENVIRONMENT..............................................3
BEHAVING WITH INTEGRITY............................................................................... 3
LOGISTICS PROCESS FLOWCHART.............................................................................4
CHALLENGES FACED.................................................................................................. 5
RECOMMENDATIONS................................................................................................. 5
REFERENCES.............................................................................................................. 5
LIST OF FIGURES
Figure 1: Logistics Flow Chart..................................................................................... 4
TOTAL QUALITY MANAGEMENT
Through a commitment to customer requirements, an organizational advancement is attained by
the company. This management system is known as Total Quality Management (TQM). To
maintain high standards and strive for continuous improvement, a company meets those
requirements to empower every employee in every department. The TQM is the precursor of
many quality management systems like Lean, ISO and Six Sigma. William Deming developed
Total Quality Management. He was a management consultant and his work had a great
impression on Japanese Manufacturing. It is not same as Six Sigma but there are many things in
common between TQM and Six Sigma improvement process. Six Sigma looks to reduce defects
where as TQM focuses on ensuring the process standards and internal guidelines to detect and
reduce errors. (Anon., n.d.)
TQM is basically an ongoing process of detection, reduction and elimination of errors. The
improved customer service, supply chain management and to ensure that the employees are
trained are streamlined by it. Its key focus is to improve the outcome of an organization
TOTAL QUALITY MANAGEMENT................................................................................1
A TQM BASED ORGANIZATION (SADDLE CREEK LOGISTICS).....................................1
ROLE OF INFORMATION TECHNOLOGY..................................................................1
ROLE OF MANAGERS............................................................................................... 1
CUSTOMERS SATISFACTION....................................................................................2
IMPROVE SERVICE, SAVE TIME AND CONTROL COSTS............................................2
QUALITY POLICY.................................................................................................... 2
DELIVERING EXCELLENT SERVICE......................................................................3
RESPECTING THE INDIVIDUAL.............................................................................3
PROMOTING PERFORMANCE AND ACCOUNTABILITY..........................................3
FOSTERING A SUPPORTIVE WORK ENVIRONMENT..............................................3
BEHAVING WITH INTEGRITY............................................................................... 3
LOGISTICS PROCESS FLOWCHART.............................................................................4
CHALLENGES FACED.................................................................................................. 5
RECOMMENDATIONS................................................................................................. 5
REFERENCES.............................................................................................................. 5
LIST OF FIGURES
Figure 1: Logistics Flow Chart..................................................................................... 4
TOTAL QUALITY MANAGEMENT
Through a commitment to customer requirements, an organizational advancement is attained by
the company. This management system is known as Total Quality Management (TQM). To
maintain high standards and strive for continuous improvement, a company meets those
requirements to empower every employee in every department. The TQM is the precursor of
many quality management systems like Lean, ISO and Six Sigma. William Deming developed
Total Quality Management. He was a management consultant and his work had a great
impression on Japanese Manufacturing. It is not same as Six Sigma but there are many things in
common between TQM and Six Sigma improvement process. Six Sigma looks to reduce defects
where as TQM focuses on ensuring the process standards and internal guidelines to detect and
reduce errors. (Anon., n.d.)
TQM is basically an ongoing process of detection, reduction and elimination of errors. The
improved customer service, supply chain management and to ensure that the employees are
trained are streamlined by it. Its key focus is to improve the outcome of an organization
Paraphrase This Document
Need a fresh take? Get an instant paraphrase of this document with our AI Paraphraser
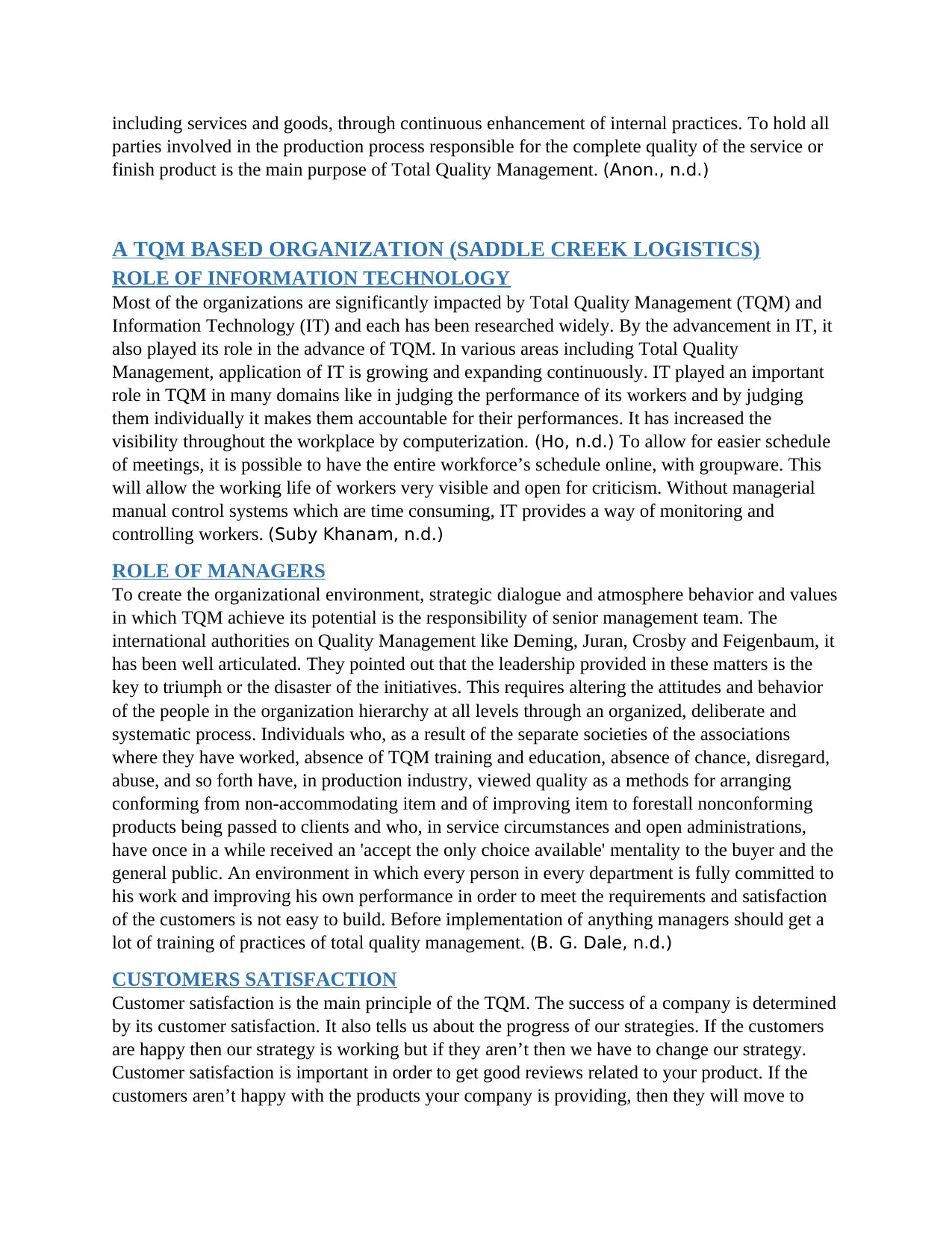
including services and goods, through continuous enhancement of internal practices. To hold all
parties involved in the production process responsible for the complete quality of the service or
finish product is the main purpose of Total Quality Management. (Anon., n.d.)
A TQM BASED ORGANIZATION (SADDLE CREEK LOGISTICS)
ROLE OF INFORMATION TECHNOLOGY
Most of the organizations are significantly impacted by Total Quality Management (TQM) and
Information Technology (IT) and each has been researched widely. By the advancement in IT, it
also played its role in the advance of TQM. In various areas including Total Quality
Management, application of IT is growing and expanding continuously. IT played an important
role in TQM in many domains like in judging the performance of its workers and by judging
them individually it makes them accountable for their performances. It has increased the
visibility throughout the workplace by computerization. (Ho, n.d.) To allow for easier schedule
of meetings, it is possible to have the entire workforce’s schedule online, with groupware. This
will allow the working life of workers very visible and open for criticism. Without managerial
manual control systems which are time consuming, IT provides a way of monitoring and
controlling workers. (Suby Khanam, n.d.)
ROLE OF MANAGERS
To create the organizational environment, strategic dialogue and atmosphere behavior and values
in which TQM achieve its potential is the responsibility of senior management team. The
international authorities on Quality Management like Deming, Juran, Crosby and Feigenbaum, it
has been well articulated. They pointed out that the leadership provided in these matters is the
key to triumph or the disaster of the initiatives. This requires altering the attitudes and behavior
of the people in the organization hierarchy at all levels through an organized, deliberate and
systematic process. Individuals who, as a result of the separate societies of the associations
where they have worked, absence of TQM training and education, absence of chance, disregard,
abuse, and so forth have, in production industry, viewed quality as a methods for arranging
conforming from non-accommodating item and of improving item to forestall nonconforming
products being passed to clients and who, in service circumstances and open administrations,
have once in a while received an 'accept the only choice available' mentality to the buyer and the
general public. An environment in which every person in every department is fully committed to
his work and improving his own performance in order to meet the requirements and satisfaction
of the customers is not easy to build. Before implementation of anything managers should get a
lot of training of practices of total quality management. (B. G. Dale, n.d.)
CUSTOMERS SATISFACTION
Customer satisfaction is the main principle of the TQM. The success of a company is determined
by its customer satisfaction. It also tells us about the progress of our strategies. If the customers
are happy then our strategy is working but if they aren’t then we have to change our strategy.
Customer satisfaction is important in order to get good reviews related to your product. If the
customers aren’t happy with the products your company is providing, then they will move to
parties involved in the production process responsible for the complete quality of the service or
finish product is the main purpose of Total Quality Management. (Anon., n.d.)
A TQM BASED ORGANIZATION (SADDLE CREEK LOGISTICS)
ROLE OF INFORMATION TECHNOLOGY
Most of the organizations are significantly impacted by Total Quality Management (TQM) and
Information Technology (IT) and each has been researched widely. By the advancement in IT, it
also played its role in the advance of TQM. In various areas including Total Quality
Management, application of IT is growing and expanding continuously. IT played an important
role in TQM in many domains like in judging the performance of its workers and by judging
them individually it makes them accountable for their performances. It has increased the
visibility throughout the workplace by computerization. (Ho, n.d.) To allow for easier schedule
of meetings, it is possible to have the entire workforce’s schedule online, with groupware. This
will allow the working life of workers very visible and open for criticism. Without managerial
manual control systems which are time consuming, IT provides a way of monitoring and
controlling workers. (Suby Khanam, n.d.)
ROLE OF MANAGERS
To create the organizational environment, strategic dialogue and atmosphere behavior and values
in which TQM achieve its potential is the responsibility of senior management team. The
international authorities on Quality Management like Deming, Juran, Crosby and Feigenbaum, it
has been well articulated. They pointed out that the leadership provided in these matters is the
key to triumph or the disaster of the initiatives. This requires altering the attitudes and behavior
of the people in the organization hierarchy at all levels through an organized, deliberate and
systematic process. Individuals who, as a result of the separate societies of the associations
where they have worked, absence of TQM training and education, absence of chance, disregard,
abuse, and so forth have, in production industry, viewed quality as a methods for arranging
conforming from non-accommodating item and of improving item to forestall nonconforming
products being passed to clients and who, in service circumstances and open administrations,
have once in a while received an 'accept the only choice available' mentality to the buyer and the
general public. An environment in which every person in every department is fully committed to
his work and improving his own performance in order to meet the requirements and satisfaction
of the customers is not easy to build. Before implementation of anything managers should get a
lot of training of practices of total quality management. (B. G. Dale, n.d.)
CUSTOMERS SATISFACTION
Customer satisfaction is the main principle of the TQM. The success of a company is determined
by its customer satisfaction. It also tells us about the progress of our strategies. If the customers
are happy then our strategy is working but if they aren’t then we have to change our strategy.
Customer satisfaction is important in order to get good reviews related to your product. If the
customers aren’t happy with the products your company is providing, then they will move to
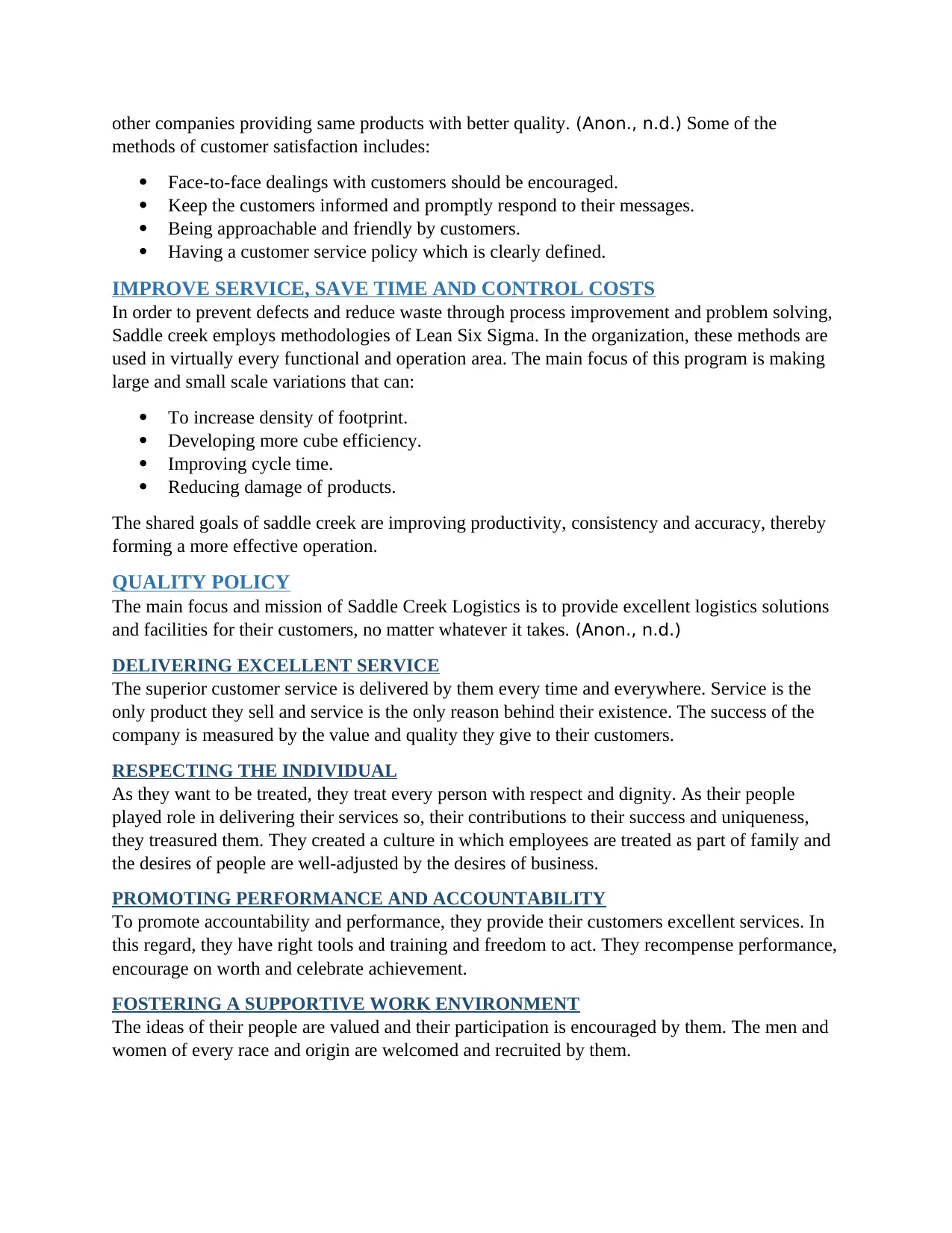
other companies providing same products with better quality. (Anon., n.d.) Some of the
methods of customer satisfaction includes:
Face-to-face dealings with customers should be encouraged.
Keep the customers informed and promptly respond to their messages.
Being approachable and friendly by customers.
Having a customer service policy which is clearly defined.
IMPROVE SERVICE, SAVE TIME AND CONTROL COSTS
In order to prevent defects and reduce waste through process improvement and problem solving,
Saddle creek employs methodologies of Lean Six Sigma. In the organization, these methods are
used in virtually every functional and operation area. The main focus of this program is making
large and small scale variations that can:
To increase density of footprint.
Developing more cube efficiency.
Improving cycle time.
Reducing damage of products.
The shared goals of saddle creek are improving productivity, consistency and accuracy, thereby
forming a more effective operation.
QUALITY POLICY
The main focus and mission of Saddle Creek Logistics is to provide excellent logistics solutions
and facilities for their customers, no matter whatever it takes. (Anon., n.d.)
DELIVERING EXCELLENT SERVICE
The superior customer service is delivered by them every time and everywhere. Service is the
only product they sell and service is the only reason behind their existence. The success of the
company is measured by the value and quality they give to their customers.
RESPECTING THE INDIVIDUAL
As they want to be treated, they treat every person with respect and dignity. As their people
played role in delivering their services so, their contributions to their success and uniqueness,
they treasured them. They created a culture in which employees are treated as part of family and
the desires of people are well-adjusted by the desires of business.
PROMOTING PERFORMANCE AND ACCOUNTABILITY
To promote accountability and performance, they provide their customers excellent services. In
this regard, they have right tools and training and freedom to act. They recompense performance,
encourage on worth and celebrate achievement.
FOSTERING A SUPPORTIVE WORK ENVIRONMENT
The ideas of their people are valued and their participation is encouraged by them. The men and
women of every race and origin are welcomed and recruited by them.
methods of customer satisfaction includes:
Face-to-face dealings with customers should be encouraged.
Keep the customers informed and promptly respond to their messages.
Being approachable and friendly by customers.
Having a customer service policy which is clearly defined.
IMPROVE SERVICE, SAVE TIME AND CONTROL COSTS
In order to prevent defects and reduce waste through process improvement and problem solving,
Saddle creek employs methodologies of Lean Six Sigma. In the organization, these methods are
used in virtually every functional and operation area. The main focus of this program is making
large and small scale variations that can:
To increase density of footprint.
Developing more cube efficiency.
Improving cycle time.
Reducing damage of products.
The shared goals of saddle creek are improving productivity, consistency and accuracy, thereby
forming a more effective operation.
QUALITY POLICY
The main focus and mission of Saddle Creek Logistics is to provide excellent logistics solutions
and facilities for their customers, no matter whatever it takes. (Anon., n.d.)
DELIVERING EXCELLENT SERVICE
The superior customer service is delivered by them every time and everywhere. Service is the
only product they sell and service is the only reason behind their existence. The success of the
company is measured by the value and quality they give to their customers.
RESPECTING THE INDIVIDUAL
As they want to be treated, they treat every person with respect and dignity. As their people
played role in delivering their services so, their contributions to their success and uniqueness,
they treasured them. They created a culture in which employees are treated as part of family and
the desires of people are well-adjusted by the desires of business.
PROMOTING PERFORMANCE AND ACCOUNTABILITY
To promote accountability and performance, they provide their customers excellent services. In
this regard, they have right tools and training and freedom to act. They recompense performance,
encourage on worth and celebrate achievement.
FOSTERING A SUPPORTIVE WORK ENVIRONMENT
The ideas of their people are valued and their participation is encouraged by them. The men and
women of every race and origin are welcomed and recruited by them.
⊘ This is a preview!⊘
Do you want full access?
Subscribe today to unlock all pages.

Trusted by 1+ million students worldwide
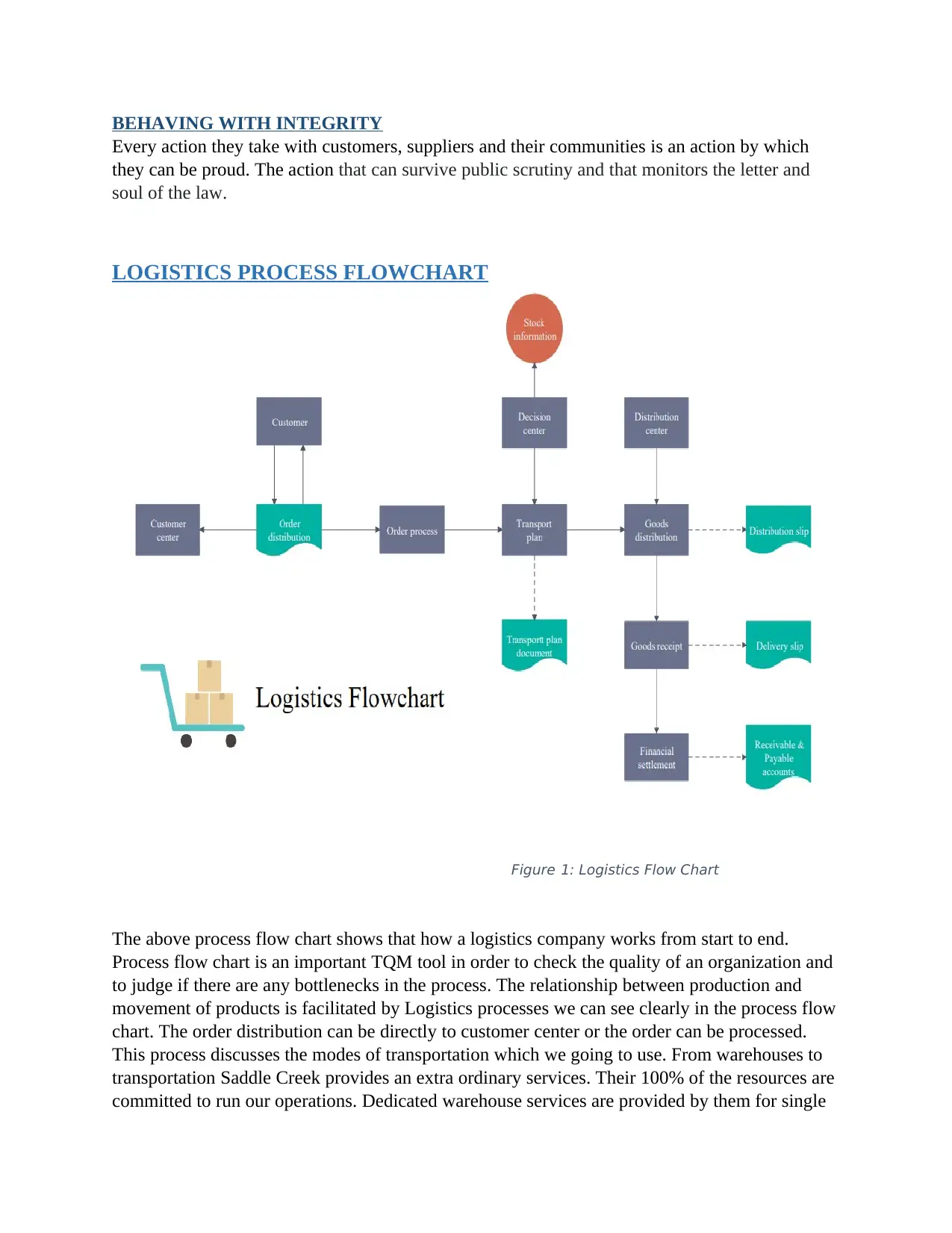
BEHAVING WITH INTEGRITY
Every action they take with customers, suppliers and their communities is an action by which
they can be proud. The action that can survive public scrutiny and that monitors the letter and
soul of the law.
LOGISTICS PROCESS FLOWCHART
Figure 1: Logistics Flow Chart
The above process flow chart shows that how a logistics company works from start to end.
Process flow chart is an important TQM tool in order to check the quality of an organization and
to judge if there are any bottlenecks in the process. The relationship between production and
movement of products is facilitated by Logistics processes we can see clearly in the process flow
chart. The order distribution can be directly to customer center or the order can be processed.
This process discusses the modes of transportation which we going to use. From warehouses to
transportation Saddle Creek provides an extra ordinary services. Their 100% of the resources are
committed to run our operations. Dedicated warehouse services are provided by them for single
Every action they take with customers, suppliers and their communities is an action by which
they can be proud. The action that can survive public scrutiny and that monitors the letter and
soul of the law.
LOGISTICS PROCESS FLOWCHART
Figure 1: Logistics Flow Chart
The above process flow chart shows that how a logistics company works from start to end.
Process flow chart is an important TQM tool in order to check the quality of an organization and
to judge if there are any bottlenecks in the process. The relationship between production and
movement of products is facilitated by Logistics processes we can see clearly in the process flow
chart. The order distribution can be directly to customer center or the order can be processed.
This process discusses the modes of transportation which we going to use. From warehouses to
transportation Saddle Creek provides an extra ordinary services. Their 100% of the resources are
committed to run our operations. Dedicated warehouse services are provided by them for single
Paraphrase This Document
Need a fresh take? Get an instant paraphrase of this document with our AI Paraphraser
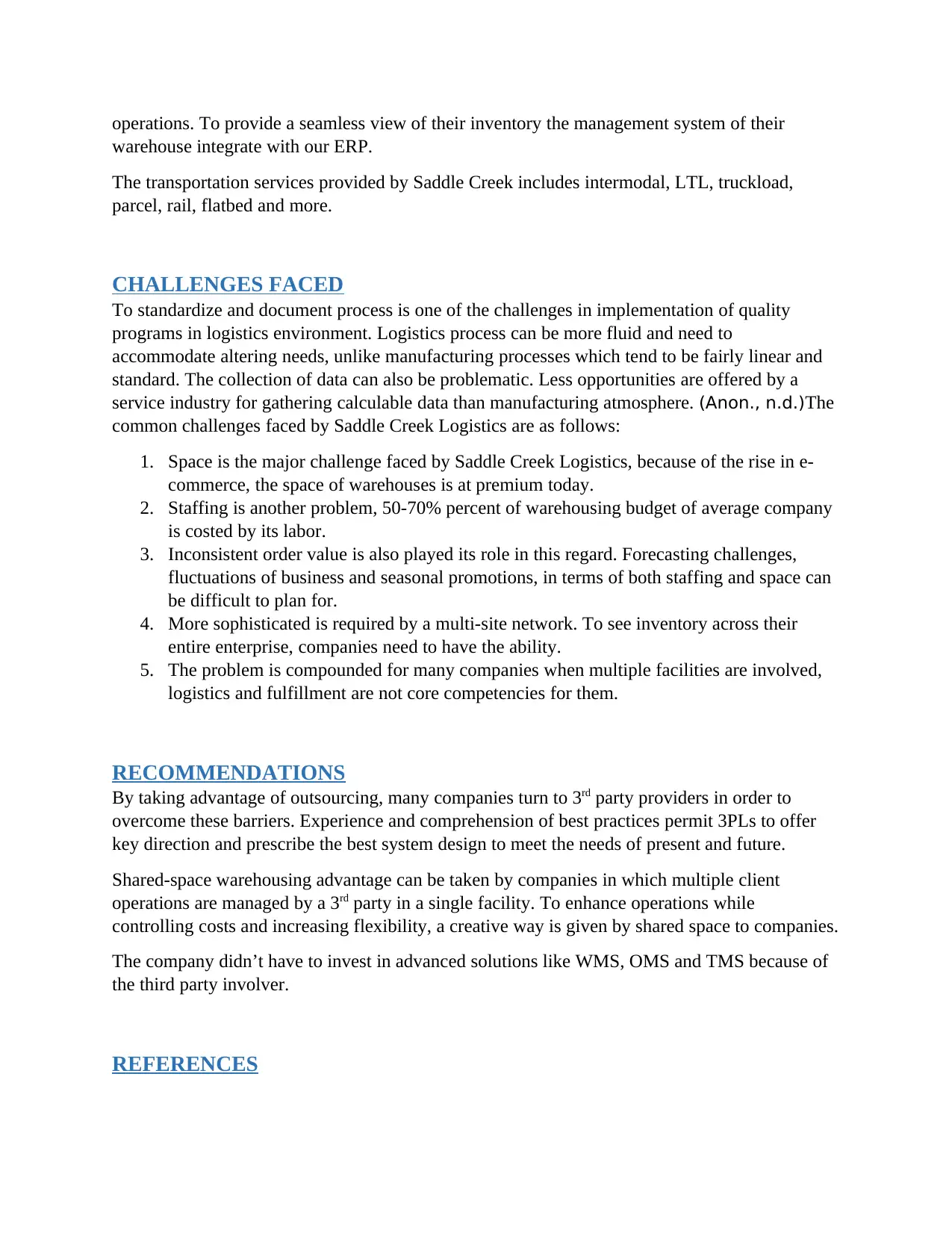
operations. To provide a seamless view of their inventory the management system of their
warehouse integrate with our ERP.
The transportation services provided by Saddle Creek includes intermodal, LTL, truckload,
parcel, rail, flatbed and more.
CHALLENGES FACED
To standardize and document process is one of the challenges in implementation of quality
programs in logistics environment. Logistics process can be more fluid and need to
accommodate altering needs, unlike manufacturing processes which tend to be fairly linear and
standard. The collection of data can also be problematic. Less opportunities are offered by a
service industry for gathering calculable data than manufacturing atmosphere. (Anon., n.d.)The
common challenges faced by Saddle Creek Logistics are as follows:
1. Space is the major challenge faced by Saddle Creek Logistics, because of the rise in e-
commerce, the space of warehouses is at premium today.
2. Staffing is another problem, 50-70% percent of warehousing budget of average company
is costed by its labor.
3. Inconsistent order value is also played its role in this regard. Forecasting challenges,
fluctuations of business and seasonal promotions, in terms of both staffing and space can
be difficult to plan for.
4. More sophisticated is required by a multi-site network. To see inventory across their
entire enterprise, companies need to have the ability.
5. The problem is compounded for many companies when multiple facilities are involved,
logistics and fulfillment are not core competencies for them.
RECOMMENDATIONS
By taking advantage of outsourcing, many companies turn to 3rd party providers in order to
overcome these barriers. Experience and comprehension of best practices permit 3PLs to offer
key direction and prescribe the best system design to meet the needs of present and future.
Shared-space warehousing advantage can be taken by companies in which multiple client
operations are managed by a 3rd party in a single facility. To enhance operations while
controlling costs and increasing flexibility, a creative way is given by shared space to companies.
The company didn’t have to invest in advanced solutions like WMS, OMS and TMS because of
the third party involver.
REFERENCES
warehouse integrate with our ERP.
The transportation services provided by Saddle Creek includes intermodal, LTL, truckload,
parcel, rail, flatbed and more.
CHALLENGES FACED
To standardize and document process is one of the challenges in implementation of quality
programs in logistics environment. Logistics process can be more fluid and need to
accommodate altering needs, unlike manufacturing processes which tend to be fairly linear and
standard. The collection of data can also be problematic. Less opportunities are offered by a
service industry for gathering calculable data than manufacturing atmosphere. (Anon., n.d.)The
common challenges faced by Saddle Creek Logistics are as follows:
1. Space is the major challenge faced by Saddle Creek Logistics, because of the rise in e-
commerce, the space of warehouses is at premium today.
2. Staffing is another problem, 50-70% percent of warehousing budget of average company
is costed by its labor.
3. Inconsistent order value is also played its role in this regard. Forecasting challenges,
fluctuations of business and seasonal promotions, in terms of both staffing and space can
be difficult to plan for.
4. More sophisticated is required by a multi-site network. To see inventory across their
entire enterprise, companies need to have the ability.
5. The problem is compounded for many companies when multiple facilities are involved,
logistics and fulfillment are not core competencies for them.
RECOMMENDATIONS
By taking advantage of outsourcing, many companies turn to 3rd party providers in order to
overcome these barriers. Experience and comprehension of best practices permit 3PLs to offer
key direction and prescribe the best system design to meet the needs of present and future.
Shared-space warehousing advantage can be taken by companies in which multiple client
operations are managed by a 3rd party in a single facility. To enhance operations while
controlling costs and increasing flexibility, a creative way is given by shared space to companies.
The company didn’t have to invest in advanced solutions like WMS, OMS and TMS because of
the third party involver.
REFERENCES
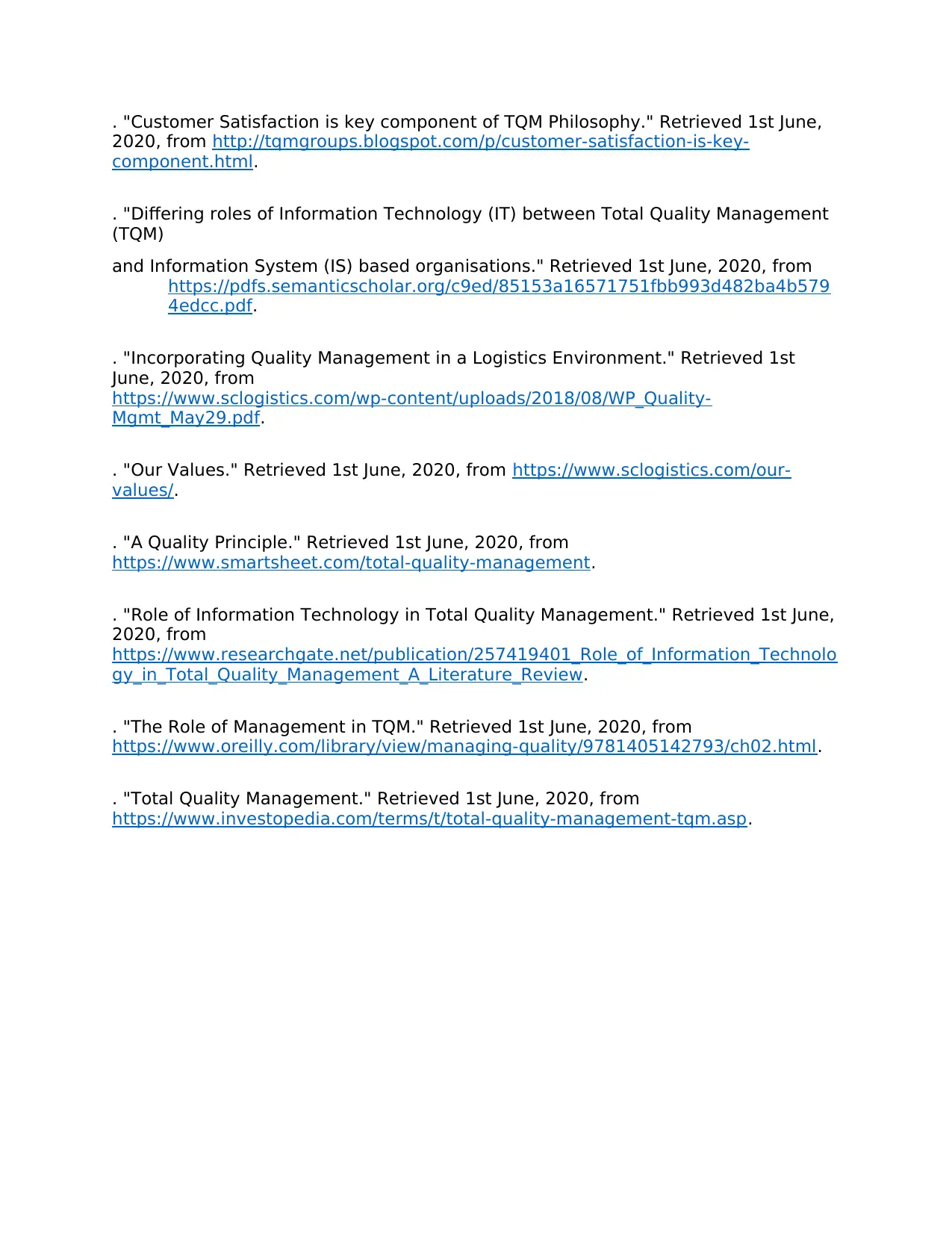
. "Customer Satisfaction is key component of TQM Philosophy." Retrieved 1st June,
2020, from http://tqmgroups.blogspot.com/p/customer-satisfaction-is-key-
component.html.
. "Differing roles of Information Technology (IT) between Total Quality Management
(TQM)
and Information System (IS) based organisations." Retrieved 1st June, 2020, from
https://pdfs.semanticscholar.org/c9ed/85153a16571751fbb993d482ba4b579
4edcc.pdf.
. "Incorporating Quality Management in a Logistics Environment." Retrieved 1st
June, 2020, from
https://www.sclogistics.com/wp-content/uploads/2018/08/WP_Quality-
Mgmt_May29.pdf.
. "Our Values." Retrieved 1st June, 2020, from https://www.sclogistics.com/our-
values/.
. "A Quality Principle." Retrieved 1st June, 2020, from
https://www.smartsheet.com/total-quality-management.
. "Role of Information Technology in Total Quality Management." Retrieved 1st June,
2020, from
https://www.researchgate.net/publication/257419401_Role_of_Information_Technolo
gy_in_Total_Quality_Management_A_Literature_Review.
. "The Role of Management in TQM." Retrieved 1st June, 2020, from
https://www.oreilly.com/library/view/managing-quality/9781405142793/ch02.html.
. "Total Quality Management." Retrieved 1st June, 2020, from
https://www.investopedia.com/terms/t/total-quality-management-tqm.asp.
2020, from http://tqmgroups.blogspot.com/p/customer-satisfaction-is-key-
component.html.
. "Differing roles of Information Technology (IT) between Total Quality Management
(TQM)
and Information System (IS) based organisations." Retrieved 1st June, 2020, from
https://pdfs.semanticscholar.org/c9ed/85153a16571751fbb993d482ba4b579
4edcc.pdf.
. "Incorporating Quality Management in a Logistics Environment." Retrieved 1st
June, 2020, from
https://www.sclogistics.com/wp-content/uploads/2018/08/WP_Quality-
Mgmt_May29.pdf.
. "Our Values." Retrieved 1st June, 2020, from https://www.sclogistics.com/our-
values/.
. "A Quality Principle." Retrieved 1st June, 2020, from
https://www.smartsheet.com/total-quality-management.
. "Role of Information Technology in Total Quality Management." Retrieved 1st June,
2020, from
https://www.researchgate.net/publication/257419401_Role_of_Information_Technolo
gy_in_Total_Quality_Management_A_Literature_Review.
. "The Role of Management in TQM." Retrieved 1st June, 2020, from
https://www.oreilly.com/library/view/managing-quality/9781405142793/ch02.html.
. "Total Quality Management." Retrieved 1st June, 2020, from
https://www.investopedia.com/terms/t/total-quality-management-tqm.asp.
⊘ This is a preview!⊘
Do you want full access?
Subscribe today to unlock all pages.

Trusted by 1+ million students worldwide
1 out of 6
Related Documents

Your All-in-One AI-Powered Toolkit for Academic Success.
+13062052269
info@desklib.com
Available 24*7 on WhatsApp / Email
Unlock your academic potential
© 2024 | Zucol Services PVT LTD | All rights reserved.