Take-Off and Calculations for Proposed Dwelling 15
VerifiedAdded on 2022/11/26
|15
|3276
|420
AI Summary
This task comprises of three class activities: class activity 2 (finishes), class activity 3 (ground floor framing and flooring) and class activity 4 (pitched roof framing and roof trusses). Each of these activities involve writing up the description, which includes take-off and calculations for the proposed single storey dwelling and garage. The calculations include estimating the number of on-site personnel and time required to complete the activities, prices of materials and consumables for the activities, labour rates and plant/equipment requirements for the activities.
Contribute Materials
Your contribution can guide someone’s learning journey. Share your
documents today.
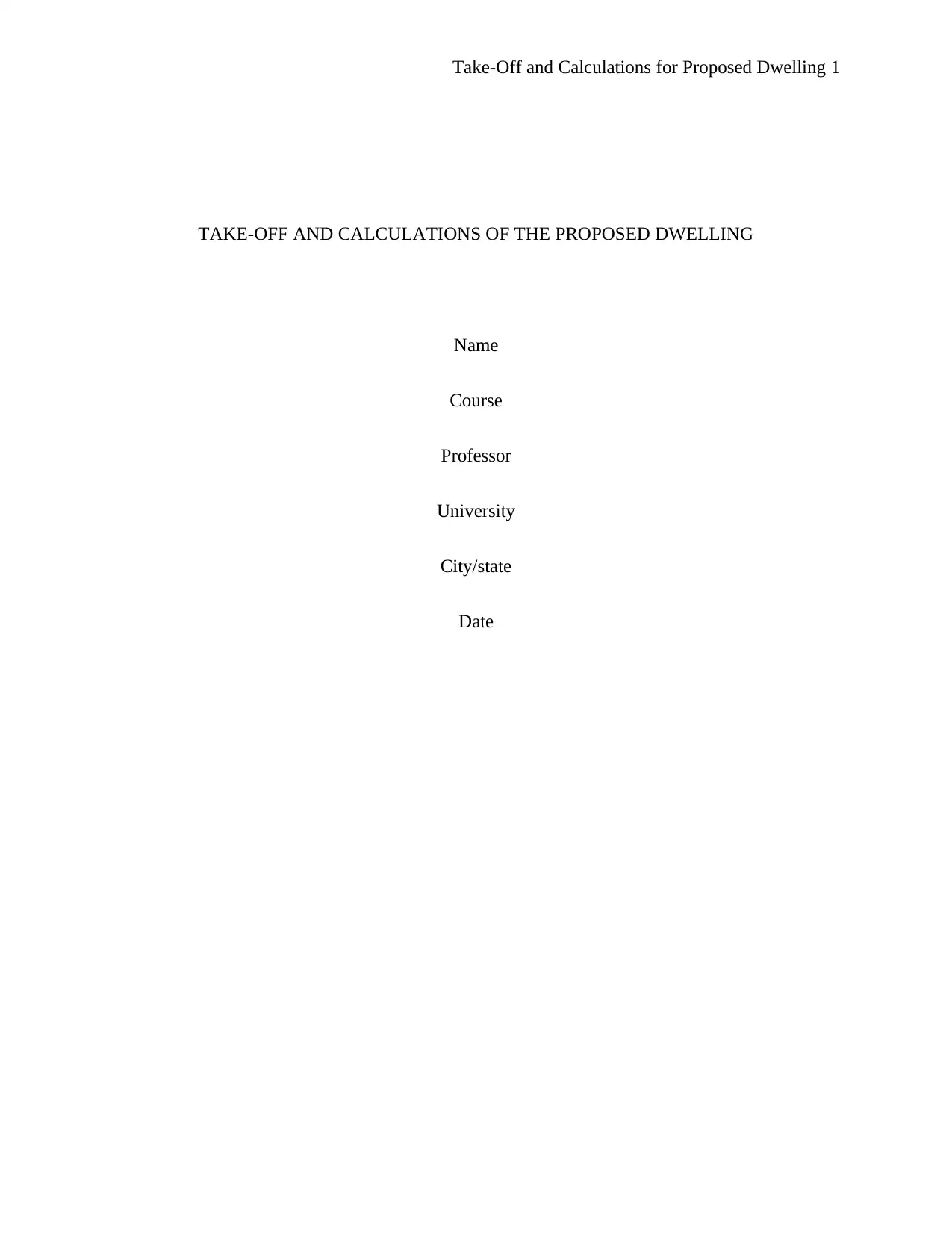
Take-Off and Calculations for Proposed Dwelling 1
TAKE-OFF AND CALCULATIONS OF THE PROPOSED DWELLING
Name
Course
Professor
University
City/state
Date
TAKE-OFF AND CALCULATIONS OF THE PROPOSED DWELLING
Name
Course
Professor
University
City/state
Date
Secure Best Marks with AI Grader
Need help grading? Try our AI Grader for instant feedback on your assignments.
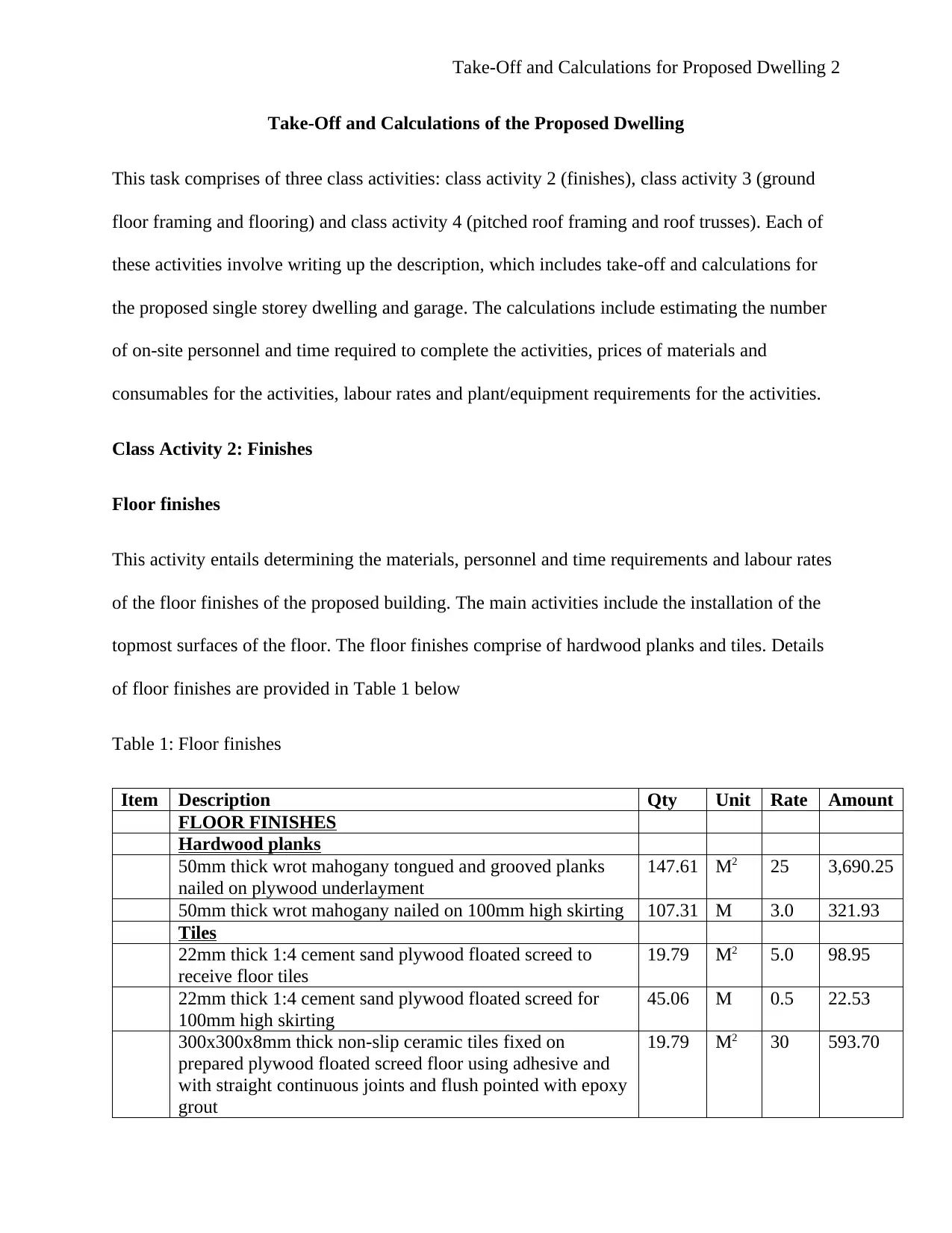
Take-Off and Calculations for Proposed Dwelling 2
Take-Off and Calculations of the Proposed Dwelling
This task comprises of three class activities: class activity 2 (finishes), class activity 3 (ground
floor framing and flooring) and class activity 4 (pitched roof framing and roof trusses). Each of
these activities involve writing up the description, which includes take-off and calculations for
the proposed single storey dwelling and garage. The calculations include estimating the number
of on-site personnel and time required to complete the activities, prices of materials and
consumables for the activities, labour rates and plant/equipment requirements for the activities.
Class Activity 2: Finishes
Floor finishes
This activity entails determining the materials, personnel and time requirements and labour rates
of the floor finishes of the proposed building. The main activities include the installation of the
topmost surfaces of the floor. The floor finishes comprise of hardwood planks and tiles. Details
of floor finishes are provided in Table 1 below
Table 1: Floor finishes
Item Description Qty Unit Rate Amount
FLOOR FINISHES
Hardwood planks
50mm thick wrot mahogany tongued and grooved planks
nailed on plywood underlayment
147.61 M2 25 3,690.25
50mm thick wrot mahogany nailed on 100mm high skirting 107.31 M 3.0 321.93
Tiles
22mm thick 1:4 cement sand plywood floated screed to
receive floor tiles
19.79 M2 5.0 98.95
22mm thick 1:4 cement sand plywood floated screed for
100mm high skirting
45.06 M 0.5 22.53
300x300x8mm thick non-slip ceramic tiles fixed on
prepared plywood floated screed floor using adhesive and
with straight continuous joints and flush pointed with epoxy
grout
19.79 M2 30 593.70
Take-Off and Calculations of the Proposed Dwelling
This task comprises of three class activities: class activity 2 (finishes), class activity 3 (ground
floor framing and flooring) and class activity 4 (pitched roof framing and roof trusses). Each of
these activities involve writing up the description, which includes take-off and calculations for
the proposed single storey dwelling and garage. The calculations include estimating the number
of on-site personnel and time required to complete the activities, prices of materials and
consumables for the activities, labour rates and plant/equipment requirements for the activities.
Class Activity 2: Finishes
Floor finishes
This activity entails determining the materials, personnel and time requirements and labour rates
of the floor finishes of the proposed building. The main activities include the installation of the
topmost surfaces of the floor. The floor finishes comprise of hardwood planks and tiles. Details
of floor finishes are provided in Table 1 below
Table 1: Floor finishes
Item Description Qty Unit Rate Amount
FLOOR FINISHES
Hardwood planks
50mm thick wrot mahogany tongued and grooved planks
nailed on plywood underlayment
147.61 M2 25 3,690.25
50mm thick wrot mahogany nailed on 100mm high skirting 107.31 M 3.0 321.93
Tiles
22mm thick 1:4 cement sand plywood floated screed to
receive floor tiles
19.79 M2 5.0 98.95
22mm thick 1:4 cement sand plywood floated screed for
100mm high skirting
45.06 M 0.5 22.53
300x300x8mm thick non-slip ceramic tiles fixed on
prepared plywood floated screed floor using adhesive and
with straight continuous joints and flush pointed with epoxy
grout
19.79 M2 30 593.70
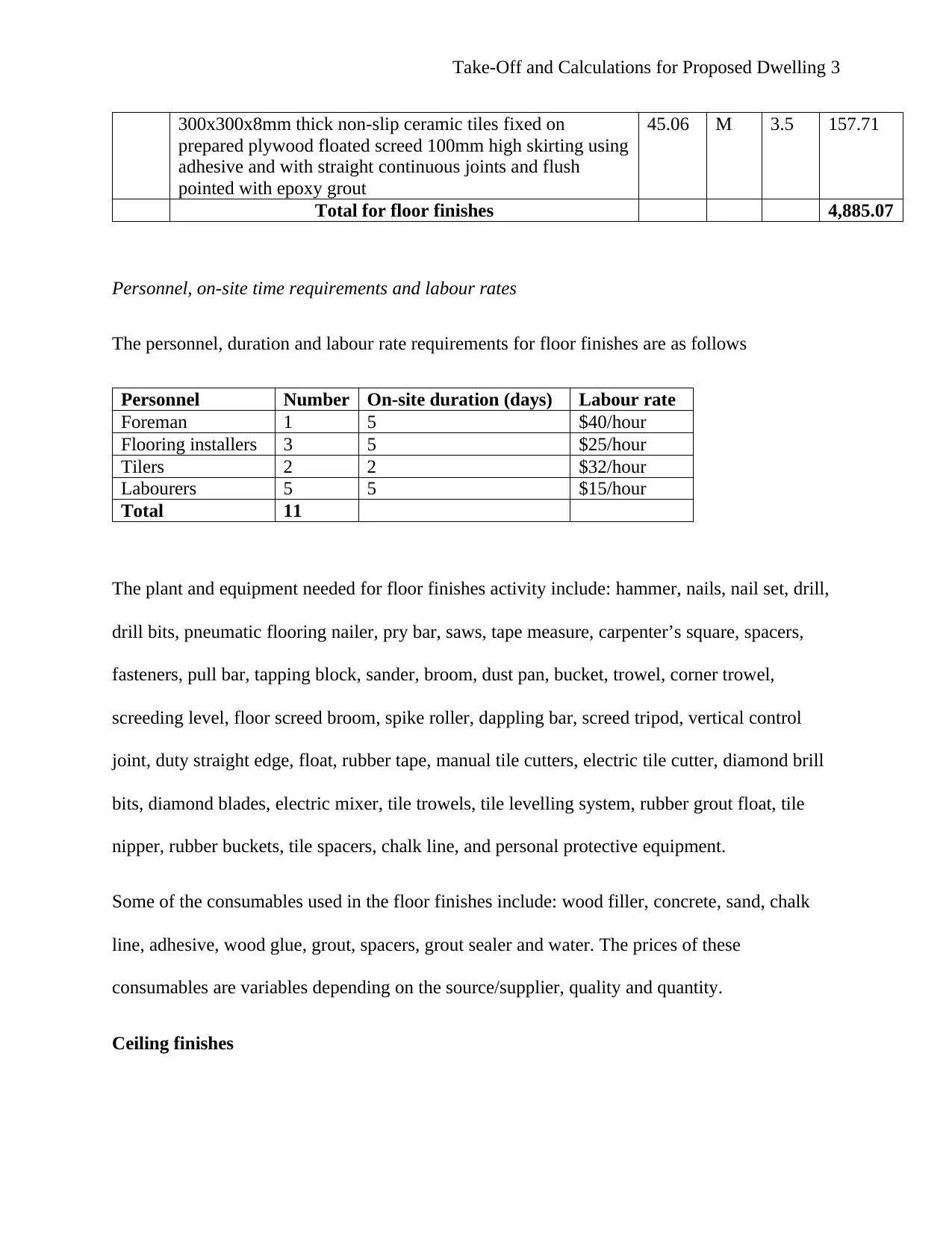
Take-Off and Calculations for Proposed Dwelling 3
300x300x8mm thick non-slip ceramic tiles fixed on
prepared plywood floated screed 100mm high skirting using
adhesive and with straight continuous joints and flush
pointed with epoxy grout
45.06 M 3.5 157.71
Total for floor finishes 4,885.07
Personnel, on-site time requirements and labour rates
The personnel, duration and labour rate requirements for floor finishes are as follows
Personnel Number On-site duration (days) Labour rate
Foreman 1 5 $40/hour
Flooring installers 3 5 $25/hour
Tilers 2 2 $32/hour
Labourers 5 5 $15/hour
Total 11
The plant and equipment needed for floor finishes activity include: hammer, nails, nail set, drill,
drill bits, pneumatic flooring nailer, pry bar, saws, tape measure, carpenter’s square, spacers,
fasteners, pull bar, tapping block, sander, broom, dust pan, bucket, trowel, corner trowel,
screeding level, floor screed broom, spike roller, dappling bar, screed tripod, vertical control
joint, duty straight edge, float, rubber tape, manual tile cutters, electric tile cutter, diamond brill
bits, diamond blades, electric mixer, tile trowels, tile levelling system, rubber grout float, tile
nipper, rubber buckets, tile spacers, chalk line, and personal protective equipment.
Some of the consumables used in the floor finishes include: wood filler, concrete, sand, chalk
line, adhesive, wood glue, grout, spacers, grout sealer and water. The prices of these
consumables are variables depending on the source/supplier, quality and quantity.
Ceiling finishes
300x300x8mm thick non-slip ceramic tiles fixed on
prepared plywood floated screed 100mm high skirting using
adhesive and with straight continuous joints and flush
pointed with epoxy grout
45.06 M 3.5 157.71
Total for floor finishes 4,885.07
Personnel, on-site time requirements and labour rates
The personnel, duration and labour rate requirements for floor finishes are as follows
Personnel Number On-site duration (days) Labour rate
Foreman 1 5 $40/hour
Flooring installers 3 5 $25/hour
Tilers 2 2 $32/hour
Labourers 5 5 $15/hour
Total 11
The plant and equipment needed for floor finishes activity include: hammer, nails, nail set, drill,
drill bits, pneumatic flooring nailer, pry bar, saws, tape measure, carpenter’s square, spacers,
fasteners, pull bar, tapping block, sander, broom, dust pan, bucket, trowel, corner trowel,
screeding level, floor screed broom, spike roller, dappling bar, screed tripod, vertical control
joint, duty straight edge, float, rubber tape, manual tile cutters, electric tile cutter, diamond brill
bits, diamond blades, electric mixer, tile trowels, tile levelling system, rubber grout float, tile
nipper, rubber buckets, tile spacers, chalk line, and personal protective equipment.
Some of the consumables used in the floor finishes include: wood filler, concrete, sand, chalk
line, adhesive, wood glue, grout, spacers, grout sealer and water. The prices of these
consumables are variables depending on the source/supplier, quality and quantity.
Ceiling finishes
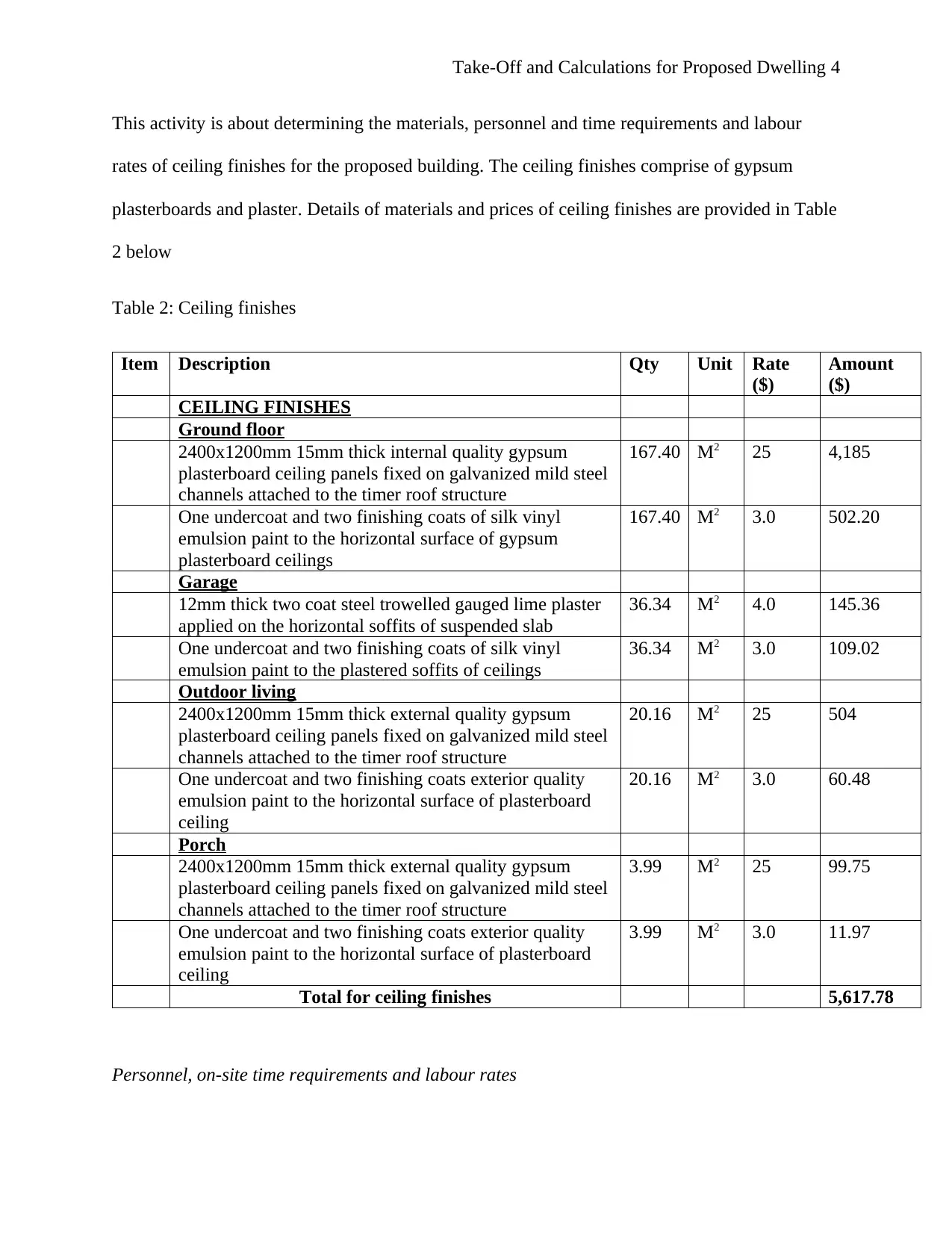
Take-Off and Calculations for Proposed Dwelling 4
This activity is about determining the materials, personnel and time requirements and labour
rates of ceiling finishes for the proposed building. The ceiling finishes comprise of gypsum
plasterboards and plaster. Details of materials and prices of ceiling finishes are provided in Table
2 below
Table 2: Ceiling finishes
Item Description Qty Unit Rate
($)
Amount
($)
CEILING FINISHES
Ground floor
2400x1200mm 15mm thick internal quality gypsum
plasterboard ceiling panels fixed on galvanized mild steel
channels attached to the timer roof structure
167.40 M2 25 4,185
One undercoat and two finishing coats of silk vinyl
emulsion paint to the horizontal surface of gypsum
plasterboard ceilings
167.40 M2 3.0 502.20
Garage
12mm thick two coat steel trowelled gauged lime plaster
applied on the horizontal soffits of suspended slab
36.34 M2 4.0 145.36
One undercoat and two finishing coats of silk vinyl
emulsion paint to the plastered soffits of ceilings
36.34 M2 3.0 109.02
Outdoor living
2400x1200mm 15mm thick external quality gypsum
plasterboard ceiling panels fixed on galvanized mild steel
channels attached to the timer roof structure
20.16 M2 25 504
One undercoat and two finishing coats exterior quality
emulsion paint to the horizontal surface of plasterboard
ceiling
20.16 M2 3.0 60.48
Porch
2400x1200mm 15mm thick external quality gypsum
plasterboard ceiling panels fixed on galvanized mild steel
channels attached to the timer roof structure
3.99 M2 25 99.75
One undercoat and two finishing coats exterior quality
emulsion paint to the horizontal surface of plasterboard
ceiling
3.99 M2 3.0 11.97
Total for ceiling finishes 5,617.78
Personnel, on-site time requirements and labour rates
This activity is about determining the materials, personnel and time requirements and labour
rates of ceiling finishes for the proposed building. The ceiling finishes comprise of gypsum
plasterboards and plaster. Details of materials and prices of ceiling finishes are provided in Table
2 below
Table 2: Ceiling finishes
Item Description Qty Unit Rate
($)
Amount
($)
CEILING FINISHES
Ground floor
2400x1200mm 15mm thick internal quality gypsum
plasterboard ceiling panels fixed on galvanized mild steel
channels attached to the timer roof structure
167.40 M2 25 4,185
One undercoat and two finishing coats of silk vinyl
emulsion paint to the horizontal surface of gypsum
plasterboard ceilings
167.40 M2 3.0 502.20
Garage
12mm thick two coat steel trowelled gauged lime plaster
applied on the horizontal soffits of suspended slab
36.34 M2 4.0 145.36
One undercoat and two finishing coats of silk vinyl
emulsion paint to the plastered soffits of ceilings
36.34 M2 3.0 109.02
Outdoor living
2400x1200mm 15mm thick external quality gypsum
plasterboard ceiling panels fixed on galvanized mild steel
channels attached to the timer roof structure
20.16 M2 25 504
One undercoat and two finishing coats exterior quality
emulsion paint to the horizontal surface of plasterboard
ceiling
20.16 M2 3.0 60.48
Porch
2400x1200mm 15mm thick external quality gypsum
plasterboard ceiling panels fixed on galvanized mild steel
channels attached to the timer roof structure
3.99 M2 25 99.75
One undercoat and two finishing coats exterior quality
emulsion paint to the horizontal surface of plasterboard
ceiling
3.99 M2 3.0 11.97
Total for ceiling finishes 5,617.78
Personnel, on-site time requirements and labour rates
Secure Best Marks with AI Grader
Need help grading? Try our AI Grader for instant feedback on your assignments.
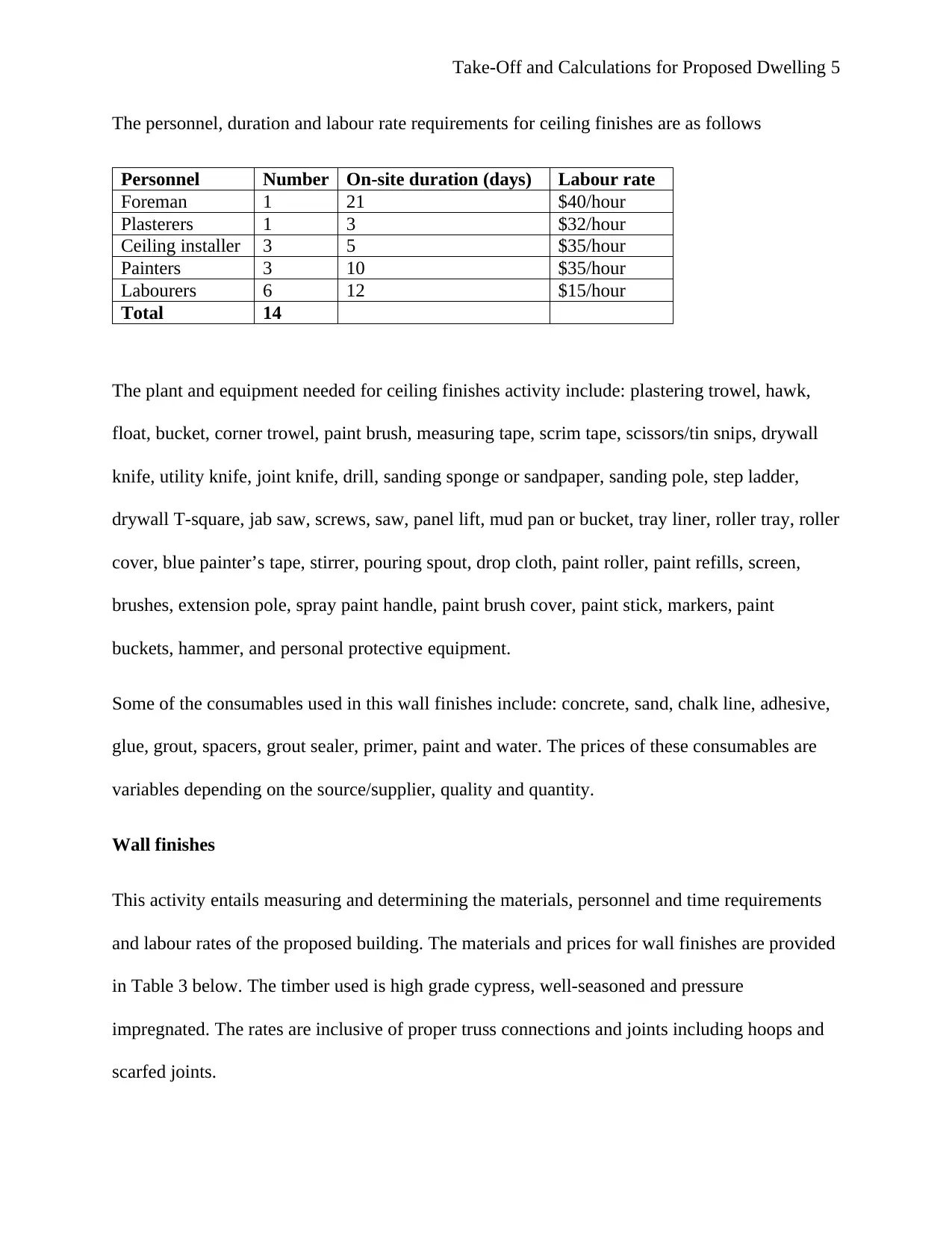
Take-Off and Calculations for Proposed Dwelling 5
The personnel, duration and labour rate requirements for ceiling finishes are as follows
Personnel Number On-site duration (days) Labour rate
Foreman 1 21 $40/hour
Plasterers 1 3 $32/hour
Ceiling installer 3 5 $35/hour
Painters 3 10 $35/hour
Labourers 6 12 $15/hour
Total 14
The plant and equipment needed for ceiling finishes activity include: plastering trowel, hawk,
float, bucket, corner trowel, paint brush, measuring tape, scrim tape, scissors/tin snips, drywall
knife, utility knife, joint knife, drill, sanding sponge or sandpaper, sanding pole, step ladder,
drywall T-square, jab saw, screws, saw, panel lift, mud pan or bucket, tray liner, roller tray, roller
cover, blue painter’s tape, stirrer, pouring spout, drop cloth, paint roller, paint refills, screen,
brushes, extension pole, spray paint handle, paint brush cover, paint stick, markers, paint
buckets, hammer, and personal protective equipment.
Some of the consumables used in this wall finishes include: concrete, sand, chalk line, adhesive,
glue, grout, spacers, grout sealer, primer, paint and water. The prices of these consumables are
variables depending on the source/supplier, quality and quantity.
Wall finishes
This activity entails measuring and determining the materials, personnel and time requirements
and labour rates of the proposed building. The materials and prices for wall finishes are provided
in Table 3 below. The timber used is high grade cypress, well-seasoned and pressure
impregnated. The rates are inclusive of proper truss connections and joints including hoops and
scarfed joints.
The personnel, duration and labour rate requirements for ceiling finishes are as follows
Personnel Number On-site duration (days) Labour rate
Foreman 1 21 $40/hour
Plasterers 1 3 $32/hour
Ceiling installer 3 5 $35/hour
Painters 3 10 $35/hour
Labourers 6 12 $15/hour
Total 14
The plant and equipment needed for ceiling finishes activity include: plastering trowel, hawk,
float, bucket, corner trowel, paint brush, measuring tape, scrim tape, scissors/tin snips, drywall
knife, utility knife, joint knife, drill, sanding sponge or sandpaper, sanding pole, step ladder,
drywall T-square, jab saw, screws, saw, panel lift, mud pan or bucket, tray liner, roller tray, roller
cover, blue painter’s tape, stirrer, pouring spout, drop cloth, paint roller, paint refills, screen,
brushes, extension pole, spray paint handle, paint brush cover, paint stick, markers, paint
buckets, hammer, and personal protective equipment.
Some of the consumables used in this wall finishes include: concrete, sand, chalk line, adhesive,
glue, grout, spacers, grout sealer, primer, paint and water. The prices of these consumables are
variables depending on the source/supplier, quality and quantity.
Wall finishes
This activity entails measuring and determining the materials, personnel and time requirements
and labour rates of the proposed building. The materials and prices for wall finishes are provided
in Table 3 below. The timber used is high grade cypress, well-seasoned and pressure
impregnated. The rates are inclusive of proper truss connections and joints including hoops and
scarfed joints.
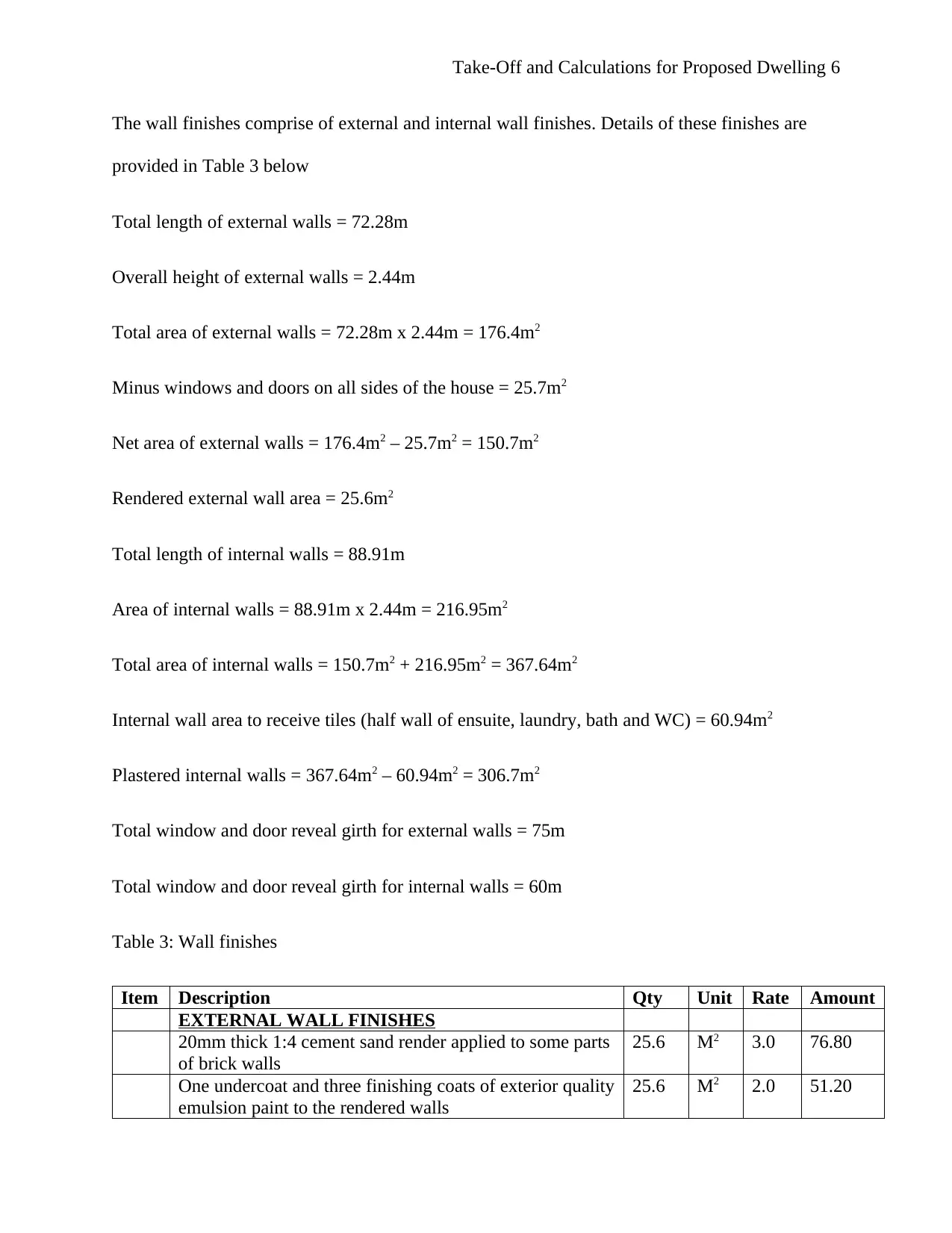
Take-Off and Calculations for Proposed Dwelling 6
The wall finishes comprise of external and internal wall finishes. Details of these finishes are
provided in Table 3 below
Total length of external walls = 72.28m
Overall height of external walls = 2.44m
Total area of external walls = 72.28m x 2.44m = 176.4m2
Minus windows and doors on all sides of the house = 25.7m2
Net area of external walls = 176.4m2 – 25.7m2 = 150.7m2
Rendered external wall area = 25.6m2
Total length of internal walls = 88.91m
Area of internal walls = 88.91m x 2.44m = 216.95m2
Total area of internal walls = 150.7m2 + 216.95m2 = 367.64m2
Internal wall area to receive tiles (half wall of ensuite, laundry, bath and WC) = 60.94m2
Plastered internal walls = 367.64m2 – 60.94m2 = 306.7m2
Total window and door reveal girth for external walls = 75m
Total window and door reveal girth for internal walls = 60m
Table 3: Wall finishes
Item Description Qty Unit Rate Amount
EXTERNAL WALL FINISHES
20mm thick 1:4 cement sand render applied to some parts
of brick walls
25.6 M2 3.0 76.80
One undercoat and three finishing coats of exterior quality
emulsion paint to the rendered walls
25.6 M2 2.0 51.20
The wall finishes comprise of external and internal wall finishes. Details of these finishes are
provided in Table 3 below
Total length of external walls = 72.28m
Overall height of external walls = 2.44m
Total area of external walls = 72.28m x 2.44m = 176.4m2
Minus windows and doors on all sides of the house = 25.7m2
Net area of external walls = 176.4m2 – 25.7m2 = 150.7m2
Rendered external wall area = 25.6m2
Total length of internal walls = 88.91m
Area of internal walls = 88.91m x 2.44m = 216.95m2
Total area of internal walls = 150.7m2 + 216.95m2 = 367.64m2
Internal wall area to receive tiles (half wall of ensuite, laundry, bath and WC) = 60.94m2
Plastered internal walls = 367.64m2 – 60.94m2 = 306.7m2
Total window and door reveal girth for external walls = 75m
Total window and door reveal girth for internal walls = 60m
Table 3: Wall finishes
Item Description Qty Unit Rate Amount
EXTERNAL WALL FINISHES
20mm thick 1:4 cement sand render applied to some parts
of brick walls
25.6 M2 3.0 76.80
One undercoat and three finishing coats of exterior quality
emulsion paint to the rendered walls
25.6 M2 2.0 51.20
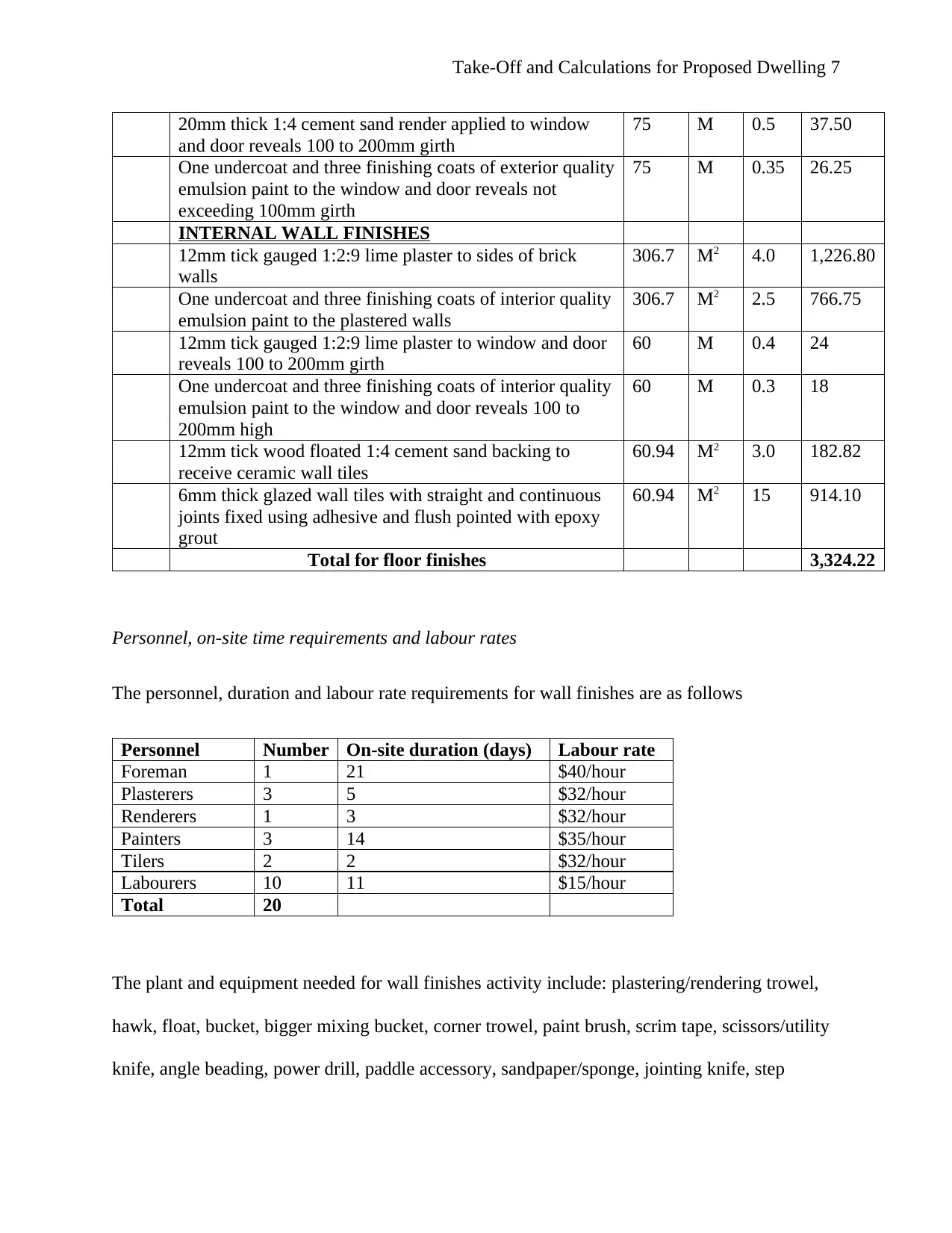
Take-Off and Calculations for Proposed Dwelling 7
20mm thick 1:4 cement sand render applied to window
and door reveals 100 to 200mm girth
75 M 0.5 37.50
One undercoat and three finishing coats of exterior quality
emulsion paint to the window and door reveals not
exceeding 100mm girth
75 M 0.35 26.25
INTERNAL WALL FINISHES
12mm tick gauged 1:2:9 lime plaster to sides of brick
walls
306.7 M2 4.0 1,226.80
One undercoat and three finishing coats of interior quality
emulsion paint to the plastered walls
306.7 M2 2.5 766.75
12mm tick gauged 1:2:9 lime plaster to window and door
reveals 100 to 200mm girth
60 M 0.4 24
One undercoat and three finishing coats of interior quality
emulsion paint to the window and door reveals 100 to
200mm high
60 M 0.3 18
12mm tick wood floated 1:4 cement sand backing to
receive ceramic wall tiles
60.94 M2 3.0 182.82
6mm thick glazed wall tiles with straight and continuous
joints fixed using adhesive and flush pointed with epoxy
grout
60.94 M2 15 914.10
Total for floor finishes 3,324.22
Personnel, on-site time requirements and labour rates
The personnel, duration and labour rate requirements for wall finishes are as follows
Personnel Number On-site duration (days) Labour rate
Foreman 1 21 $40/hour
Plasterers 3 5 $32/hour
Renderers 1 3 $32/hour
Painters 3 14 $35/hour
Tilers 2 2 $32/hour
Labourers 10 11 $15/hour
Total 20
The plant and equipment needed for wall finishes activity include: plastering/rendering trowel,
hawk, float, bucket, bigger mixing bucket, corner trowel, paint brush, scrim tape, scissors/utility
knife, angle beading, power drill, paddle accessory, sandpaper/sponge, jointing knife, step
20mm thick 1:4 cement sand render applied to window
and door reveals 100 to 200mm girth
75 M 0.5 37.50
One undercoat and three finishing coats of exterior quality
emulsion paint to the window and door reveals not
exceeding 100mm girth
75 M 0.35 26.25
INTERNAL WALL FINISHES
12mm tick gauged 1:2:9 lime plaster to sides of brick
walls
306.7 M2 4.0 1,226.80
One undercoat and three finishing coats of interior quality
emulsion paint to the plastered walls
306.7 M2 2.5 766.75
12mm tick gauged 1:2:9 lime plaster to window and door
reveals 100 to 200mm girth
60 M 0.4 24
One undercoat and three finishing coats of interior quality
emulsion paint to the window and door reveals 100 to
200mm high
60 M 0.3 18
12mm tick wood floated 1:4 cement sand backing to
receive ceramic wall tiles
60.94 M2 3.0 182.82
6mm thick glazed wall tiles with straight and continuous
joints fixed using adhesive and flush pointed with epoxy
grout
60.94 M2 15 914.10
Total for floor finishes 3,324.22
Personnel, on-site time requirements and labour rates
The personnel, duration and labour rate requirements for wall finishes are as follows
Personnel Number On-site duration (days) Labour rate
Foreman 1 21 $40/hour
Plasterers 3 5 $32/hour
Renderers 1 3 $32/hour
Painters 3 14 $35/hour
Tilers 2 2 $32/hour
Labourers 10 11 $15/hour
Total 20
The plant and equipment needed for wall finishes activity include: plastering/rendering trowel,
hawk, float, bucket, bigger mixing bucket, corner trowel, paint brush, scrim tape, scissors/utility
knife, angle beading, power drill, paddle accessory, sandpaper/sponge, jointing knife, step
Paraphrase This Document
Need a fresh take? Get an instant paraphrase of this document with our AI Paraphraser
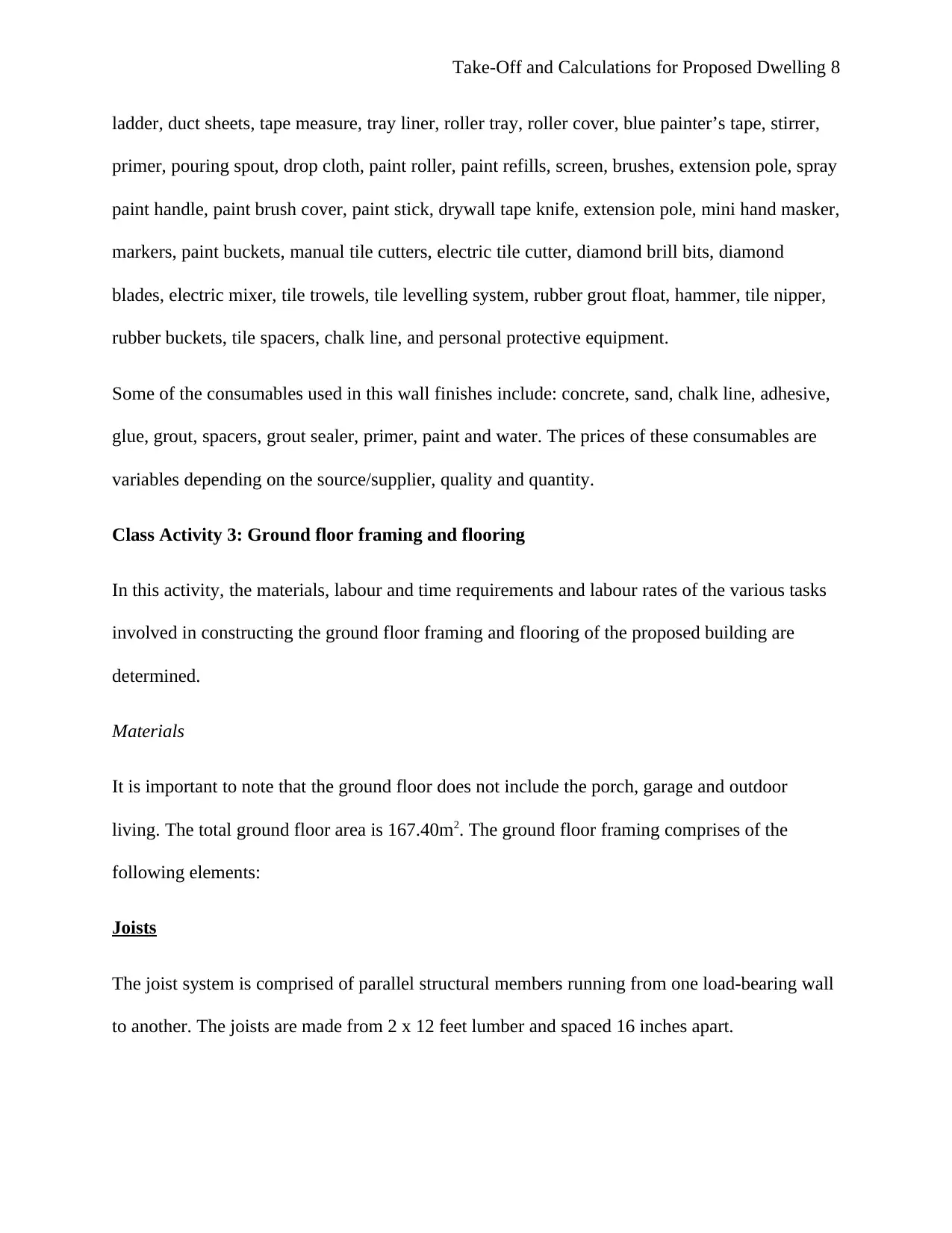
Take-Off and Calculations for Proposed Dwelling 8
ladder, duct sheets, tape measure, tray liner, roller tray, roller cover, blue painter’s tape, stirrer,
primer, pouring spout, drop cloth, paint roller, paint refills, screen, brushes, extension pole, spray
paint handle, paint brush cover, paint stick, drywall tape knife, extension pole, mini hand masker,
markers, paint buckets, manual tile cutters, electric tile cutter, diamond brill bits, diamond
blades, electric mixer, tile trowels, tile levelling system, rubber grout float, hammer, tile nipper,
rubber buckets, tile spacers, chalk line, and personal protective equipment.
Some of the consumables used in this wall finishes include: concrete, sand, chalk line, adhesive,
glue, grout, spacers, grout sealer, primer, paint and water. The prices of these consumables are
variables depending on the source/supplier, quality and quantity.
Class Activity 3: Ground floor framing and flooring
In this activity, the materials, labour and time requirements and labour rates of the various tasks
involved in constructing the ground floor framing and flooring of the proposed building are
determined.
Materials
It is important to note that the ground floor does not include the porch, garage and outdoor
living. The total ground floor area is 167.40m2. The ground floor framing comprises of the
following elements:
Joists
The joist system is comprised of parallel structural members running from one load-bearing wall
to another. The joists are made from 2 x 12 feet lumber and spaced 16 inches apart.
ladder, duct sheets, tape measure, tray liner, roller tray, roller cover, blue painter’s tape, stirrer,
primer, pouring spout, drop cloth, paint roller, paint refills, screen, brushes, extension pole, spray
paint handle, paint brush cover, paint stick, drywall tape knife, extension pole, mini hand masker,
markers, paint buckets, manual tile cutters, electric tile cutter, diamond brill bits, diamond
blades, electric mixer, tile trowels, tile levelling system, rubber grout float, hammer, tile nipper,
rubber buckets, tile spacers, chalk line, and personal protective equipment.
Some of the consumables used in this wall finishes include: concrete, sand, chalk line, adhesive,
glue, grout, spacers, grout sealer, primer, paint and water. The prices of these consumables are
variables depending on the source/supplier, quality and quantity.
Class Activity 3: Ground floor framing and flooring
In this activity, the materials, labour and time requirements and labour rates of the various tasks
involved in constructing the ground floor framing and flooring of the proposed building are
determined.
Materials
It is important to note that the ground floor does not include the porch, garage and outdoor
living. The total ground floor area is 167.40m2. The ground floor framing comprises of the
following elements:
Joists
The joist system is comprised of parallel structural members running from one load-bearing wall
to another. The joists are made from 2 x 12 feet lumber and spaced 16 inches apart.
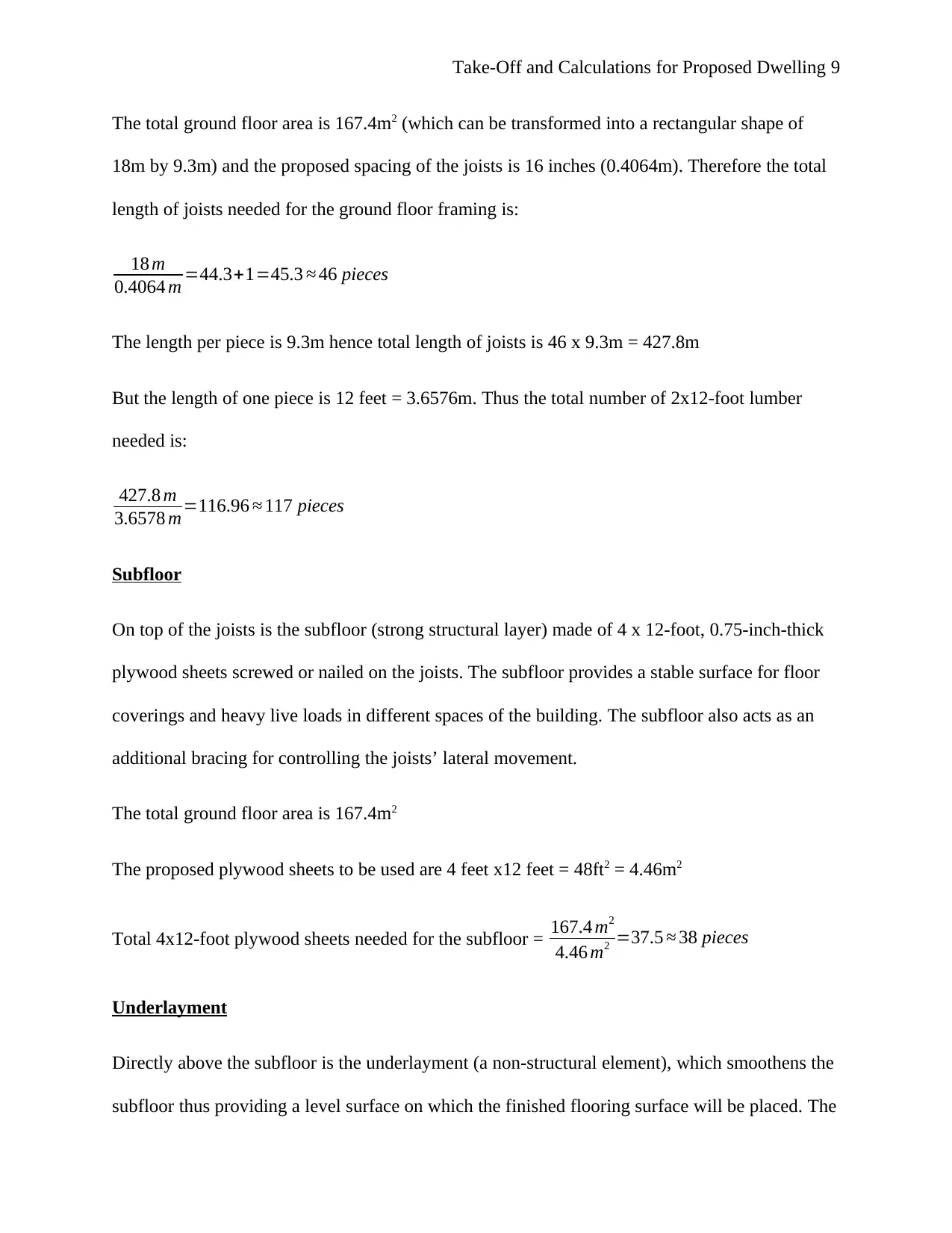
Take-Off and Calculations for Proposed Dwelling 9
The total ground floor area is 167.4m2 (which can be transformed into a rectangular shape of
18m by 9.3m) and the proposed spacing of the joists is 16 inches (0.4064m). Therefore the total
length of joists needed for the ground floor framing is:
18 m
0.4064 m =44.3+1=45.3 ≈ 46 pieces
The length per piece is 9.3m hence total length of joists is 46 x 9.3m = 427.8m
But the length of one piece is 12 feet = 3.6576m. Thus the total number of 2x12-foot lumber
needed is:
427.8 m
3.6578 m=116.96 ≈ 117 pieces
Subfloor
On top of the joists is the subfloor (strong structural layer) made of 4 x 12-foot, 0.75-inch-thick
plywood sheets screwed or nailed on the joists. The subfloor provides a stable surface for floor
coverings and heavy live loads in different spaces of the building. The subfloor also acts as an
additional bracing for controlling the joists’ lateral movement.
The total ground floor area is 167.4m2
The proposed plywood sheets to be used are 4 feet x12 feet = 48ft2 = 4.46m2
Total 4x12-foot plywood sheets needed for the subfloor = 167.4 m2
4.46 m2 =37.5 ≈ 38 pieces
Underlayment
Directly above the subfloor is the underlayment (a non-structural element), which smoothens the
subfloor thus providing a level surface on which the finished flooring surface will be placed. The
The total ground floor area is 167.4m2 (which can be transformed into a rectangular shape of
18m by 9.3m) and the proposed spacing of the joists is 16 inches (0.4064m). Therefore the total
length of joists needed for the ground floor framing is:
18 m
0.4064 m =44.3+1=45.3 ≈ 46 pieces
The length per piece is 9.3m hence total length of joists is 46 x 9.3m = 427.8m
But the length of one piece is 12 feet = 3.6576m. Thus the total number of 2x12-foot lumber
needed is:
427.8 m
3.6578 m=116.96 ≈ 117 pieces
Subfloor
On top of the joists is the subfloor (strong structural layer) made of 4 x 12-foot, 0.75-inch-thick
plywood sheets screwed or nailed on the joists. The subfloor provides a stable surface for floor
coverings and heavy live loads in different spaces of the building. The subfloor also acts as an
additional bracing for controlling the joists’ lateral movement.
The total ground floor area is 167.4m2
The proposed plywood sheets to be used are 4 feet x12 feet = 48ft2 = 4.46m2
Total 4x12-foot plywood sheets needed for the subfloor = 167.4 m2
4.46 m2 =37.5 ≈ 38 pieces
Underlayment
Directly above the subfloor is the underlayment (a non-structural element), which smoothens the
subfloor thus providing a level surface on which the finished flooring surface will be placed. The
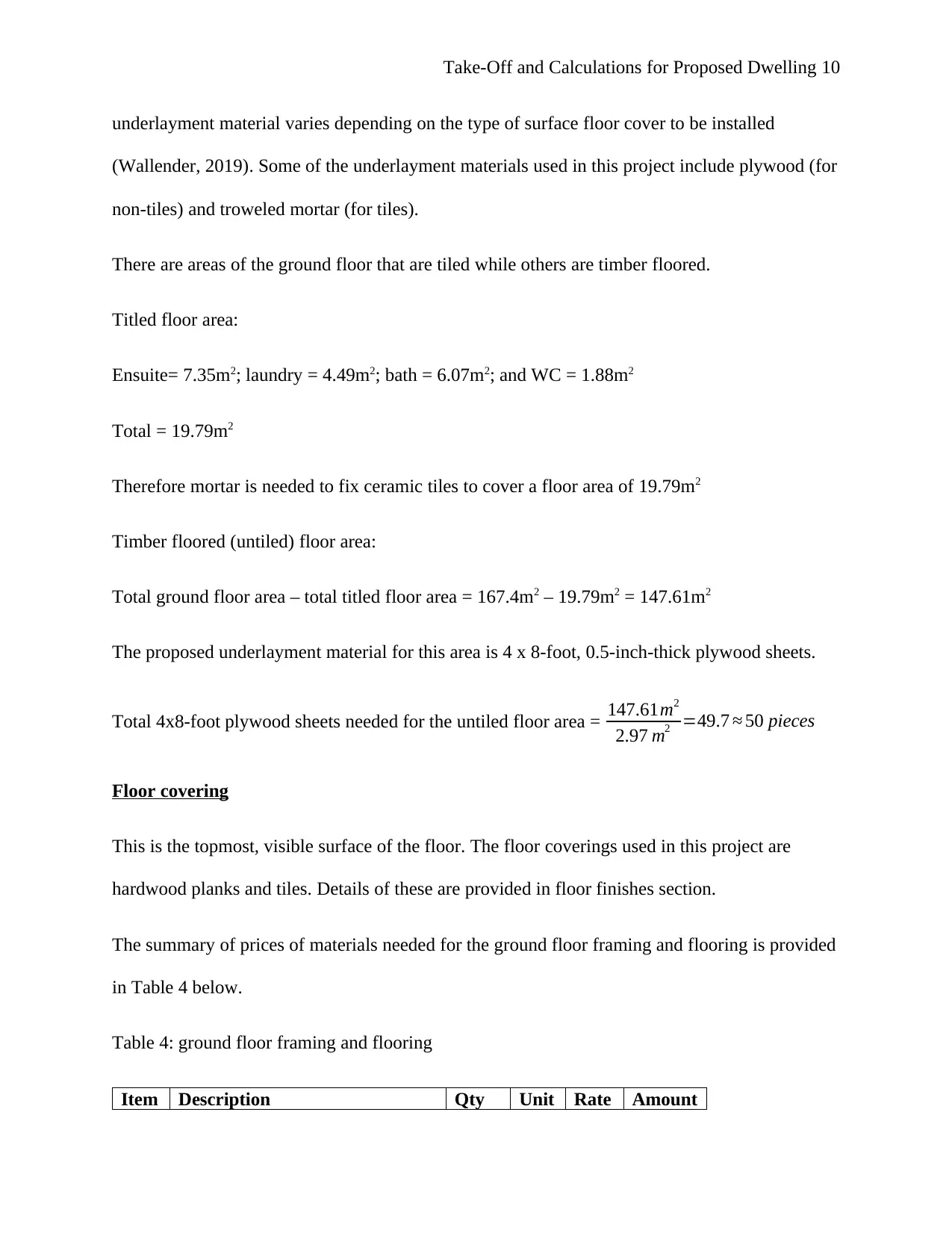
Take-Off and Calculations for Proposed Dwelling 10
underlayment material varies depending on the type of surface floor cover to be installed
(Wallender, 2019). Some of the underlayment materials used in this project include plywood (for
non-tiles) and troweled mortar (for tiles).
There are areas of the ground floor that are tiled while others are timber floored.
Titled floor area:
Ensuite= 7.35m2; laundry = 4.49m2; bath = 6.07m2; and WC = 1.88m2
Total = 19.79m2
Therefore mortar is needed to fix ceramic tiles to cover a floor area of 19.79m2
Timber floored (untiled) floor area:
Total ground floor area – total titled floor area = 167.4m2 – 19.79m2 = 147.61m2
The proposed underlayment material for this area is 4 x 8-foot, 0.5-inch-thick plywood sheets.
Total 4x8-foot plywood sheets needed for the untiled floor area = 147.61m2
2.97 m2 =49.7 ≈ 50 pieces
Floor covering
This is the topmost, visible surface of the floor. The floor coverings used in this project are
hardwood planks and tiles. Details of these are provided in floor finishes section.
The summary of prices of materials needed for the ground floor framing and flooring is provided
in Table 4 below.
Table 4: ground floor framing and flooring
Item Description Qty Unit Rate Amount
underlayment material varies depending on the type of surface floor cover to be installed
(Wallender, 2019). Some of the underlayment materials used in this project include plywood (for
non-tiles) and troweled mortar (for tiles).
There are areas of the ground floor that are tiled while others are timber floored.
Titled floor area:
Ensuite= 7.35m2; laundry = 4.49m2; bath = 6.07m2; and WC = 1.88m2
Total = 19.79m2
Therefore mortar is needed to fix ceramic tiles to cover a floor area of 19.79m2
Timber floored (untiled) floor area:
Total ground floor area – total titled floor area = 167.4m2 – 19.79m2 = 147.61m2
The proposed underlayment material for this area is 4 x 8-foot, 0.5-inch-thick plywood sheets.
Total 4x8-foot plywood sheets needed for the untiled floor area = 147.61m2
2.97 m2 =49.7 ≈ 50 pieces
Floor covering
This is the topmost, visible surface of the floor. The floor coverings used in this project are
hardwood planks and tiles. Details of these are provided in floor finishes section.
The summary of prices of materials needed for the ground floor framing and flooring is provided
in Table 4 below.
Table 4: ground floor framing and flooring
Item Description Qty Unit Rate Amount
Secure Best Marks with AI Grader
Need help grading? Try our AI Grader for instant feedback on your assignments.
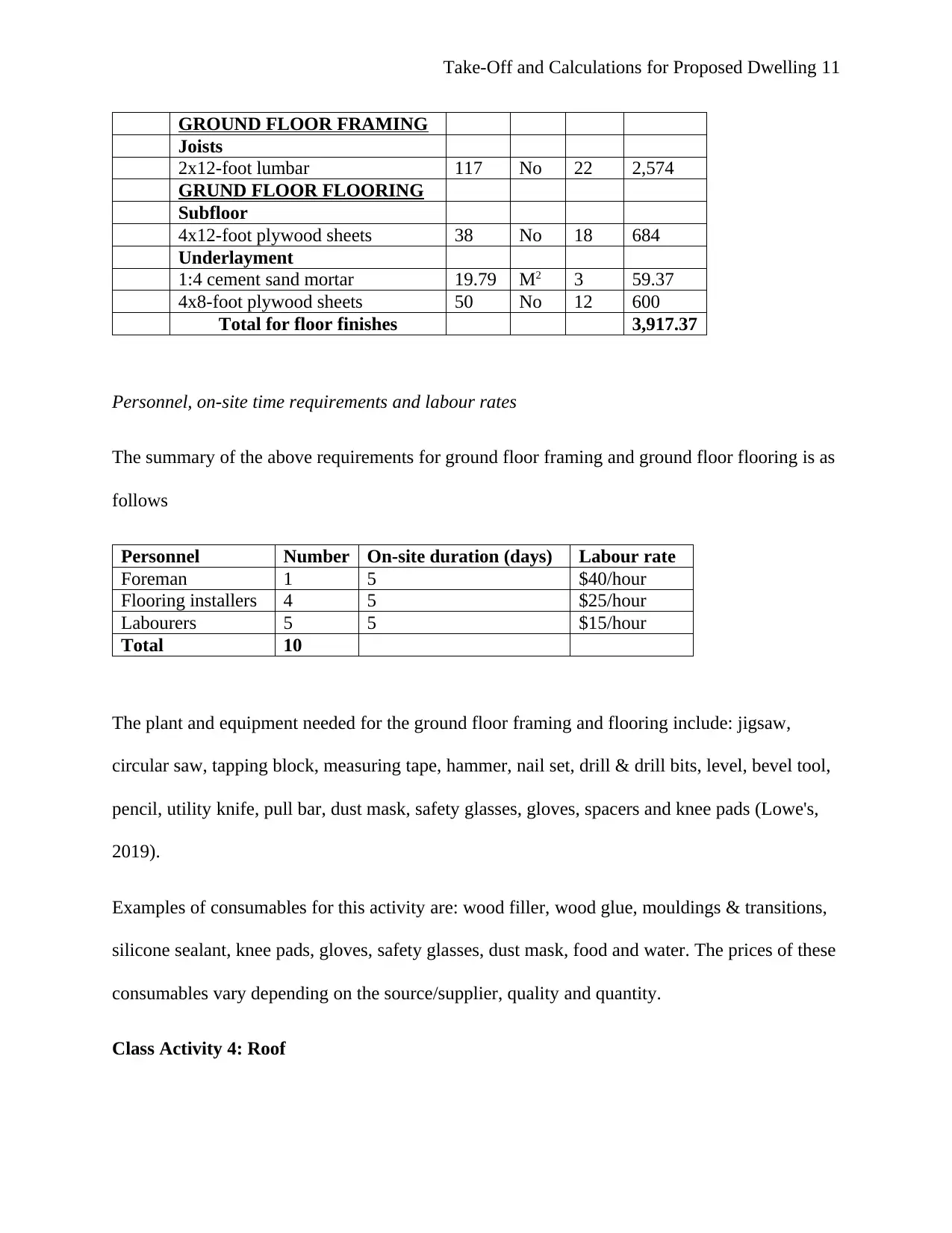
Take-Off and Calculations for Proposed Dwelling 11
GROUND FLOOR FRAMING
Joists
2x12-foot lumbar 117 No 22 2,574
GRUND FLOOR FLOORING
Subfloor
4x12-foot plywood sheets 38 No 18 684
Underlayment
1:4 cement sand mortar 19.79 M2 3 59.37
4x8-foot plywood sheets 50 No 12 600
Total for floor finishes 3,917.37
Personnel, on-site time requirements and labour rates
The summary of the above requirements for ground floor framing and ground floor flooring is as
follows
Personnel Number On-site duration (days) Labour rate
Foreman 1 5 $40/hour
Flooring installers 4 5 $25/hour
Labourers 5 5 $15/hour
Total 10
The plant and equipment needed for the ground floor framing and flooring include: jigsaw,
circular saw, tapping block, measuring tape, hammer, nail set, drill & drill bits, level, bevel tool,
pencil, utility knife, pull bar, dust mask, safety glasses, gloves, spacers and knee pads (Lowe's,
2019).
Examples of consumables for this activity are: wood filler, wood glue, mouldings & transitions,
silicone sealant, knee pads, gloves, safety glasses, dust mask, food and water. The prices of these
consumables vary depending on the source/supplier, quality and quantity.
Class Activity 4: Roof
GROUND FLOOR FRAMING
Joists
2x12-foot lumbar 117 No 22 2,574
GRUND FLOOR FLOORING
Subfloor
4x12-foot plywood sheets 38 No 18 684
Underlayment
1:4 cement sand mortar 19.79 M2 3 59.37
4x8-foot plywood sheets 50 No 12 600
Total for floor finishes 3,917.37
Personnel, on-site time requirements and labour rates
The summary of the above requirements for ground floor framing and ground floor flooring is as
follows
Personnel Number On-site duration (days) Labour rate
Foreman 1 5 $40/hour
Flooring installers 4 5 $25/hour
Labourers 5 5 $15/hour
Total 10
The plant and equipment needed for the ground floor framing and flooring include: jigsaw,
circular saw, tapping block, measuring tape, hammer, nail set, drill & drill bits, level, bevel tool,
pencil, utility knife, pull bar, dust mask, safety glasses, gloves, spacers and knee pads (Lowe's,
2019).
Examples of consumables for this activity are: wood filler, wood glue, mouldings & transitions,
silicone sealant, knee pads, gloves, safety glasses, dust mask, food and water. The prices of these
consumables vary depending on the source/supplier, quality and quantity.
Class Activity 4: Roof
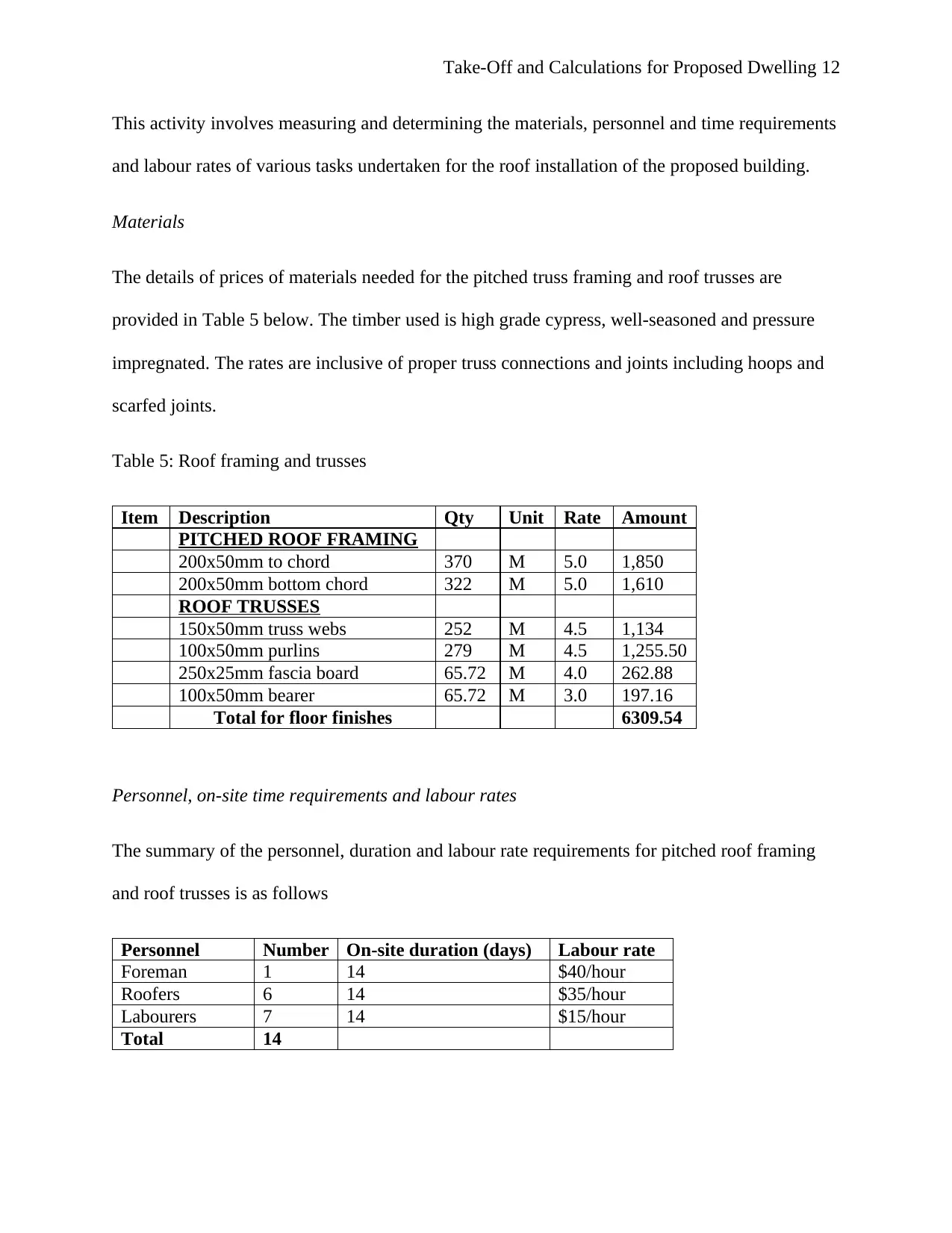
Take-Off and Calculations for Proposed Dwelling 12
This activity involves measuring and determining the materials, personnel and time requirements
and labour rates of various tasks undertaken for the roof installation of the proposed building.
Materials
The details of prices of materials needed for the pitched truss framing and roof trusses are
provided in Table 5 below. The timber used is high grade cypress, well-seasoned and pressure
impregnated. The rates are inclusive of proper truss connections and joints including hoops and
scarfed joints.
Table 5: Roof framing and trusses
Item Description Qty Unit Rate Amount
PITCHED ROOF FRAMING
200x50mm to chord 370 M 5.0 1,850
200x50mm bottom chord 322 M 5.0 1,610
ROOF TRUSSES
150x50mm truss webs 252 M 4.5 1,134
100x50mm purlins 279 M 4.5 1,255.50
250x25mm fascia board 65.72 M 4.0 262.88
100x50mm bearer 65.72 M 3.0 197.16
Total for floor finishes 6309.54
Personnel, on-site time requirements and labour rates
The summary of the personnel, duration and labour rate requirements for pitched roof framing
and roof trusses is as follows
Personnel Number On-site duration (days) Labour rate
Foreman 1 14 $40/hour
Roofers 6 14 $35/hour
Labourers 7 14 $15/hour
Total 14
This activity involves measuring and determining the materials, personnel and time requirements
and labour rates of various tasks undertaken for the roof installation of the proposed building.
Materials
The details of prices of materials needed for the pitched truss framing and roof trusses are
provided in Table 5 below. The timber used is high grade cypress, well-seasoned and pressure
impregnated. The rates are inclusive of proper truss connections and joints including hoops and
scarfed joints.
Table 5: Roof framing and trusses
Item Description Qty Unit Rate Amount
PITCHED ROOF FRAMING
200x50mm to chord 370 M 5.0 1,850
200x50mm bottom chord 322 M 5.0 1,610
ROOF TRUSSES
150x50mm truss webs 252 M 4.5 1,134
100x50mm purlins 279 M 4.5 1,255.50
250x25mm fascia board 65.72 M 4.0 262.88
100x50mm bearer 65.72 M 3.0 197.16
Total for floor finishes 6309.54
Personnel, on-site time requirements and labour rates
The summary of the personnel, duration and labour rate requirements for pitched roof framing
and roof trusses is as follows
Personnel Number On-site duration (days) Labour rate
Foreman 1 14 $40/hour
Roofers 6 14 $35/hour
Labourers 7 14 $15/hour
Total 14
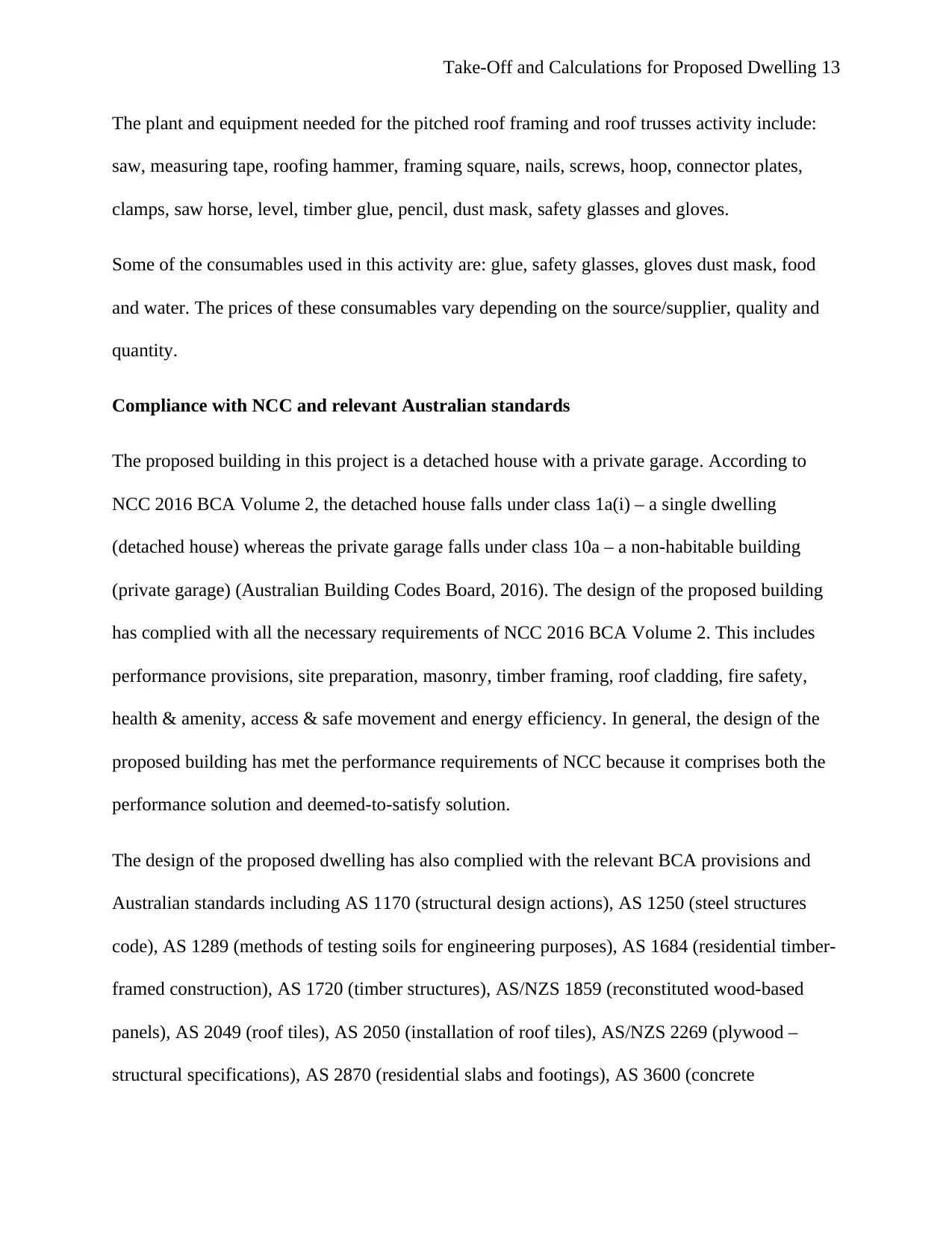
Take-Off and Calculations for Proposed Dwelling 13
The plant and equipment needed for the pitched roof framing and roof trusses activity include:
saw, measuring tape, roofing hammer, framing square, nails, screws, hoop, connector plates,
clamps, saw horse, level, timber glue, pencil, dust mask, safety glasses and gloves.
Some of the consumables used in this activity are: glue, safety glasses, gloves dust mask, food
and water. The prices of these consumables vary depending on the source/supplier, quality and
quantity.
Compliance with NCC and relevant Australian standards
The proposed building in this project is a detached house with a private garage. According to
NCC 2016 BCA Volume 2, the detached house falls under class 1a(i) – a single dwelling
(detached house) whereas the private garage falls under class 10a – a non-habitable building
(private garage) (Australian Building Codes Board, 2016). The design of the proposed building
has complied with all the necessary requirements of NCC 2016 BCA Volume 2. This includes
performance provisions, site preparation, masonry, timber framing, roof cladding, fire safety,
health & amenity, access & safe movement and energy efficiency. In general, the design of the
proposed building has met the performance requirements of NCC because it comprises both the
performance solution and deemed-to-satisfy solution.
The design of the proposed dwelling has also complied with the relevant BCA provisions and
Australian standards including AS 1170 (structural design actions), AS 1250 (steel structures
code), AS 1289 (methods of testing soils for engineering purposes), AS 1684 (residential timber-
framed construction), AS 1720 (timber structures), AS/NZS 1859 (reconstituted wood-based
panels), AS 2049 (roof tiles), AS 2050 (installation of roof tiles), AS/NZS 2269 (plywood –
structural specifications), AS 2870 (residential slabs and footings), AS 3600 (concrete
The plant and equipment needed for the pitched roof framing and roof trusses activity include:
saw, measuring tape, roofing hammer, framing square, nails, screws, hoop, connector plates,
clamps, saw horse, level, timber glue, pencil, dust mask, safety glasses and gloves.
Some of the consumables used in this activity are: glue, safety glasses, gloves dust mask, food
and water. The prices of these consumables vary depending on the source/supplier, quality and
quantity.
Compliance with NCC and relevant Australian standards
The proposed building in this project is a detached house with a private garage. According to
NCC 2016 BCA Volume 2, the detached house falls under class 1a(i) – a single dwelling
(detached house) whereas the private garage falls under class 10a – a non-habitable building
(private garage) (Australian Building Codes Board, 2016). The design of the proposed building
has complied with all the necessary requirements of NCC 2016 BCA Volume 2. This includes
performance provisions, site preparation, masonry, timber framing, roof cladding, fire safety,
health & amenity, access & safe movement and energy efficiency. In general, the design of the
proposed building has met the performance requirements of NCC because it comprises both the
performance solution and deemed-to-satisfy solution.
The design of the proposed dwelling has also complied with the relevant BCA provisions and
Australian standards including AS 1170 (structural design actions), AS 1250 (steel structures
code), AS 1289 (methods of testing soils for engineering purposes), AS 1684 (residential timber-
framed construction), AS 1720 (timber structures), AS/NZS 1859 (reconstituted wood-based
panels), AS 2049 (roof tiles), AS 2050 (installation of roof tiles), AS/NZS 2269 (plywood –
structural specifications), AS 2870 (residential slabs and footings), AS 3600 (concrete
Paraphrase This Document
Need a fresh take? Get an instant paraphrase of this document with our AI Paraphraser
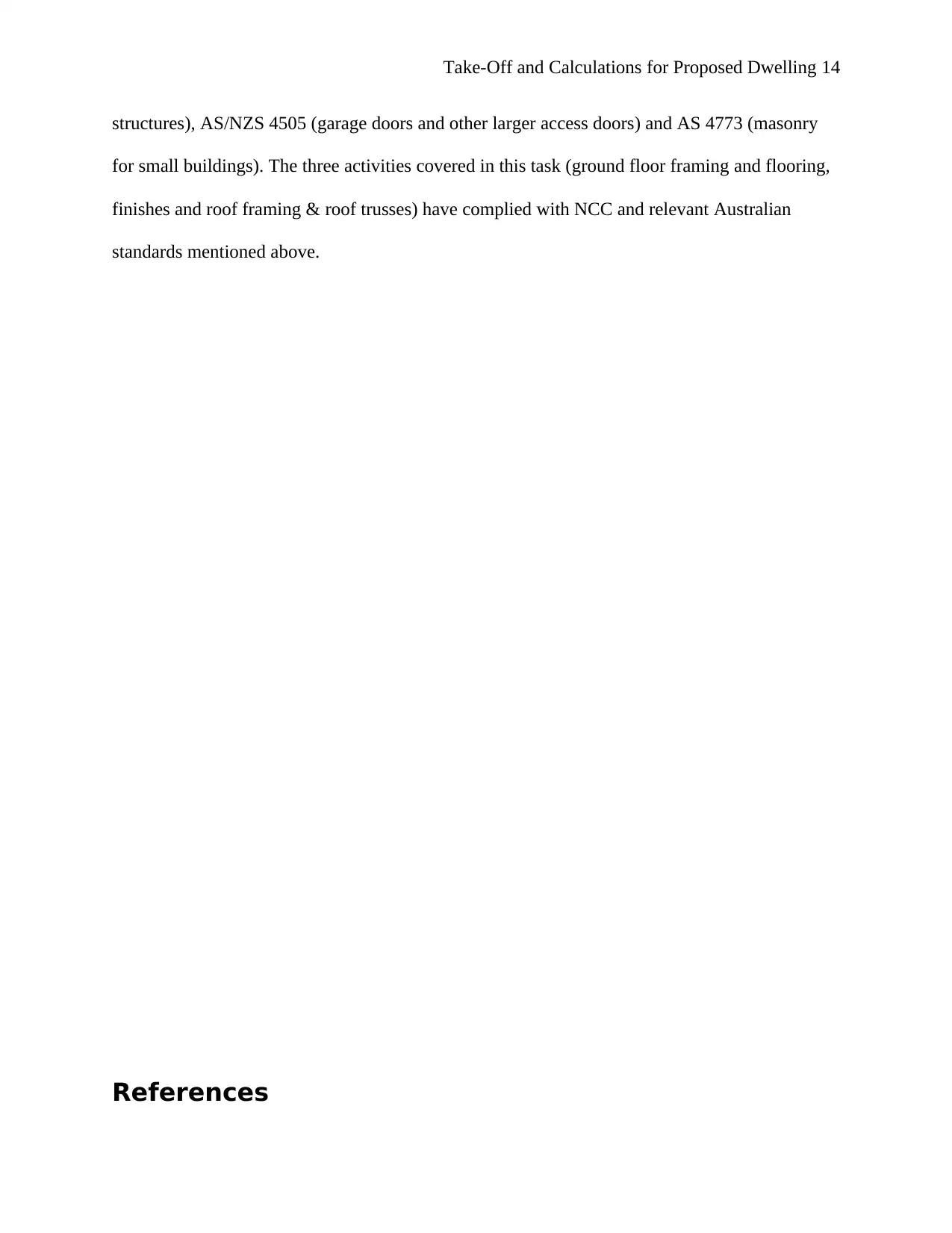
Take-Off and Calculations for Proposed Dwelling 14
structures), AS/NZS 4505 (garage doors and other larger access doors) and AS 4773 (masonry
for small buildings). The three activities covered in this task (ground floor framing and flooring,
finishes and roof framing & roof trusses) have complied with NCC and relevant Australian
standards mentioned above.
References
structures), AS/NZS 4505 (garage doors and other larger access doors) and AS 4773 (masonry
for small buildings). The three activities covered in this task (ground floor framing and flooring,
finishes and roof framing & roof trusses) have complied with NCC and relevant Australian
standards mentioned above.
References
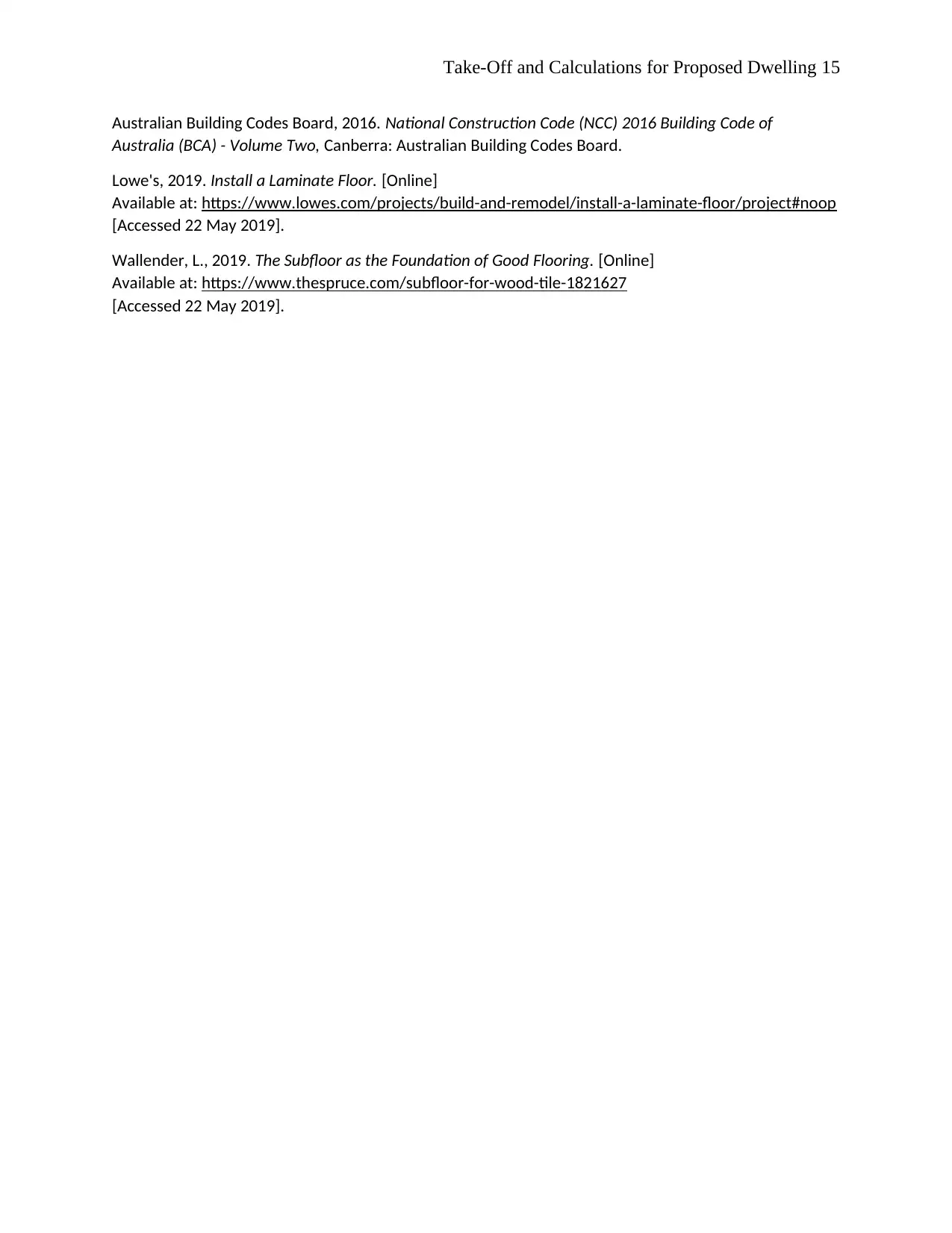
Take-Off and Calculations for Proposed Dwelling 15
Australian Building Codes Board, 2016. National Construction Code (NCC) 2016 Building Code of
Australia (BCA) - Volume Two, Canberra: Australian Building Codes Board.
Lowe's, 2019. Install a Laminate Floor. [Online]
Available at: https://www.lowes.com/projects/build-and-remodel/install-a-laminate-floor/project#noop
[Accessed 22 May 2019].
Wallender, L., 2019. The Subfloor as the Foundation of Good Flooring. [Online]
Available at: https://www.thespruce.com/subfloor-for-wood-tile-1821627
[Accessed 22 May 2019].
Australian Building Codes Board, 2016. National Construction Code (NCC) 2016 Building Code of
Australia (BCA) - Volume Two, Canberra: Australian Building Codes Board.
Lowe's, 2019. Install a Laminate Floor. [Online]
Available at: https://www.lowes.com/projects/build-and-remodel/install-a-laminate-floor/project#noop
[Accessed 22 May 2019].
Wallender, L., 2019. The Subfloor as the Foundation of Good Flooring. [Online]
Available at: https://www.thespruce.com/subfloor-for-wood-tile-1821627
[Accessed 22 May 2019].
1 out of 15

Your All-in-One AI-Powered Toolkit for Academic Success.
+13062052269
info@desklib.com
Available 24*7 on WhatsApp / Email
Unlock your academic potential
© 2024 | Zucol Services PVT LTD | All rights reserved.