Properties and Applications of Maraging Steel
VerifiedAdded on 2021/04/21
|6
|1617
|221
AI Summary
This document provides a detailed analysis of maraging steel, including its machining improvements, properties, and applications. The assignment explains how maraging steel is machined using thin sections and heavy sections, and how it is austenitized and aged to produce fine dispersions of Ni3(X, Y) intermetallic phases. It also discusses the stability of maraging steel and its use in rocket skins, engine parts, and high-wear components.
Contribute Materials
Your contribution can guide someone’s learning journey. Share your
documents today.
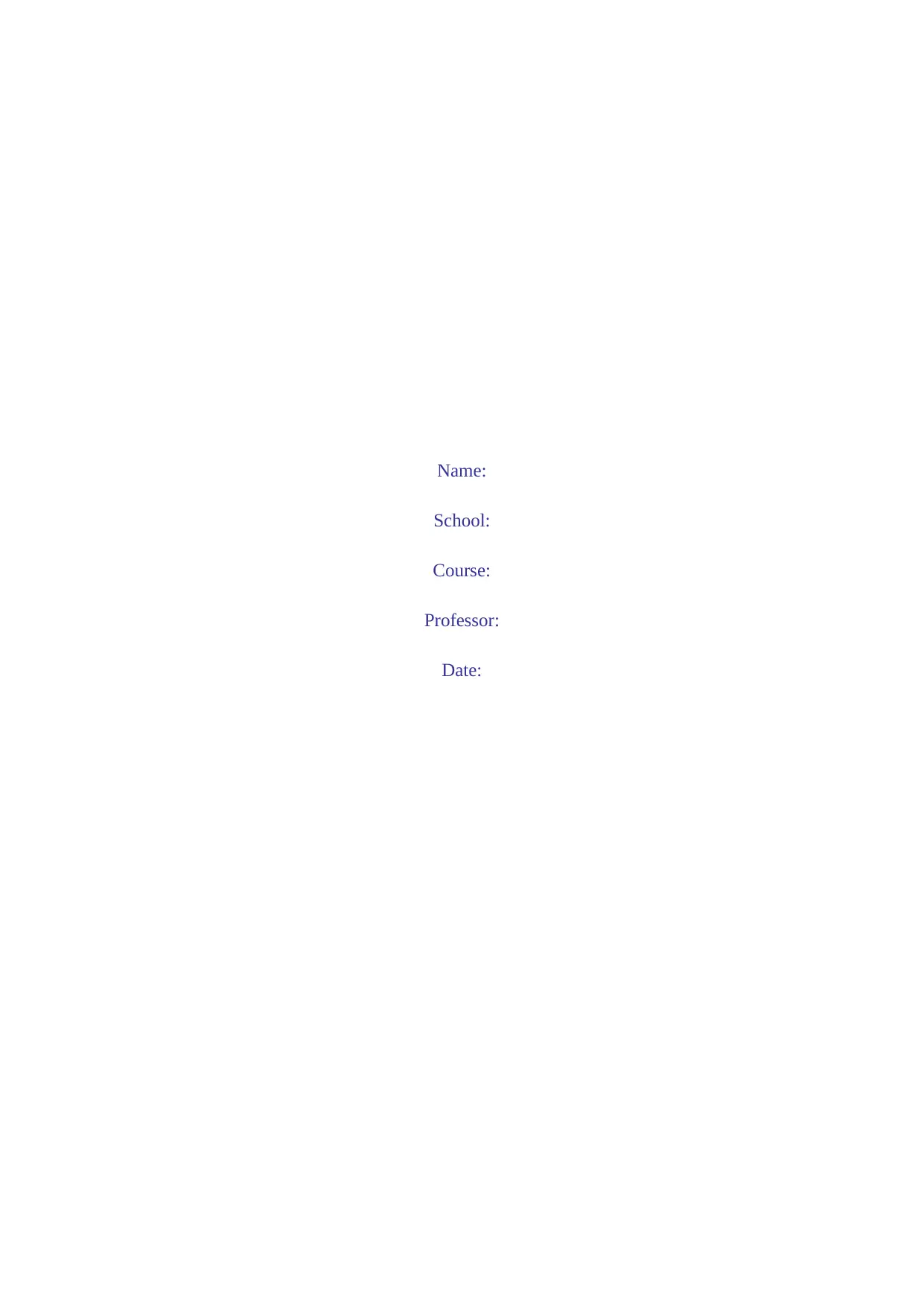
Name:
School:
Course:
Professor:
Date:
School:
Course:
Professor:
Date:
Secure Best Marks with AI Grader
Need help grading? Try our AI Grader for instant feedback on your assignments.
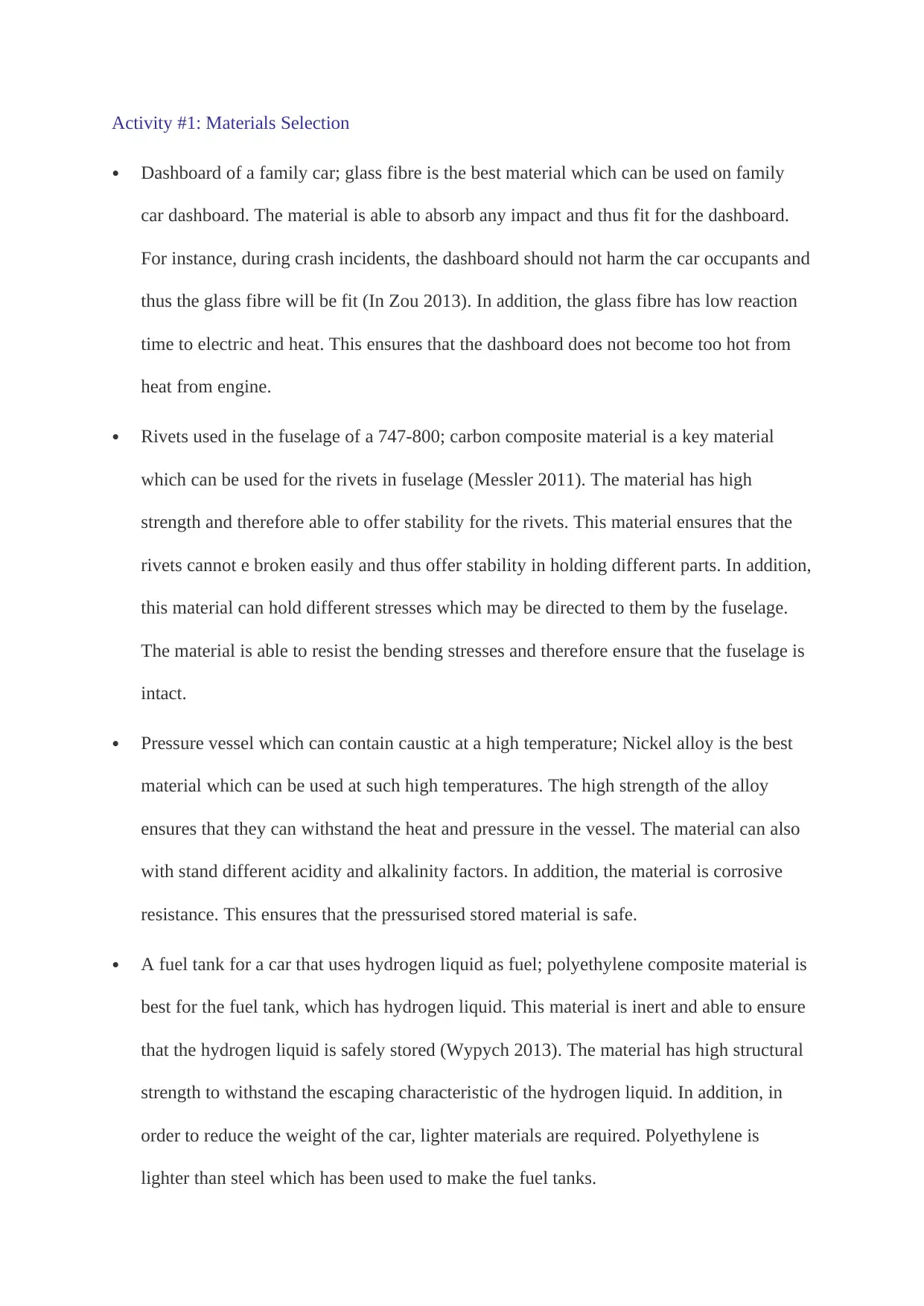
Activity #1: Materials Selection
Dashboard of a family car; glass fibre is the best material which can be used on family
car dashboard. The material is able to absorb any impact and thus fit for the dashboard.
For instance, during crash incidents, the dashboard should not harm the car occupants and
thus the glass fibre will be fit (In Zou 2013). In addition, the glass fibre has low reaction
time to electric and heat. This ensures that the dashboard does not become too hot from
heat from engine.
Rivets used in the fuselage of a 747-800; carbon composite material is a key material
which can be used for the rivets in fuselage (Messler 2011). The material has high
strength and therefore able to offer stability for the rivets. This material ensures that the
rivets cannot e broken easily and thus offer stability in holding different parts. In addition,
this material can hold different stresses which may be directed to them by the fuselage.
The material is able to resist the bending stresses and therefore ensure that the fuselage is
intact.
Pressure vessel which can contain caustic at a high temperature; Nickel alloy is the best
material which can be used at such high temperatures. The high strength of the alloy
ensures that they can withstand the heat and pressure in the vessel. The material can also
with stand different acidity and alkalinity factors. In addition, the material is corrosive
resistance. This ensures that the pressurised stored material is safe.
A fuel tank for a car that uses hydrogen liquid as fuel; polyethylene composite material is
best for the fuel tank, which has hydrogen liquid. This material is inert and able to ensure
that the hydrogen liquid is safely stored (Wypych 2013). The material has high structural
strength to withstand the escaping characteristic of the hydrogen liquid. In addition, in
order to reduce the weight of the car, lighter materials are required. Polyethylene is
lighter than steel which has been used to make the fuel tanks.
Dashboard of a family car; glass fibre is the best material which can be used on family
car dashboard. The material is able to absorb any impact and thus fit for the dashboard.
For instance, during crash incidents, the dashboard should not harm the car occupants and
thus the glass fibre will be fit (In Zou 2013). In addition, the glass fibre has low reaction
time to electric and heat. This ensures that the dashboard does not become too hot from
heat from engine.
Rivets used in the fuselage of a 747-800; carbon composite material is a key material
which can be used for the rivets in fuselage (Messler 2011). The material has high
strength and therefore able to offer stability for the rivets. This material ensures that the
rivets cannot e broken easily and thus offer stability in holding different parts. In addition,
this material can hold different stresses which may be directed to them by the fuselage.
The material is able to resist the bending stresses and therefore ensure that the fuselage is
intact.
Pressure vessel which can contain caustic at a high temperature; Nickel alloy is the best
material which can be used at such high temperatures. The high strength of the alloy
ensures that they can withstand the heat and pressure in the vessel. The material can also
with stand different acidity and alkalinity factors. In addition, the material is corrosive
resistance. This ensures that the pressurised stored material is safe.
A fuel tank for a car that uses hydrogen liquid as fuel; polyethylene composite material is
best for the fuel tank, which has hydrogen liquid. This material is inert and able to ensure
that the hydrogen liquid is safely stored (Wypych 2013). The material has high structural
strength to withstand the escaping characteristic of the hydrogen liquid. In addition, in
order to reduce the weight of the car, lighter materials are required. Polyethylene is
lighter than steel which has been used to make the fuel tanks.
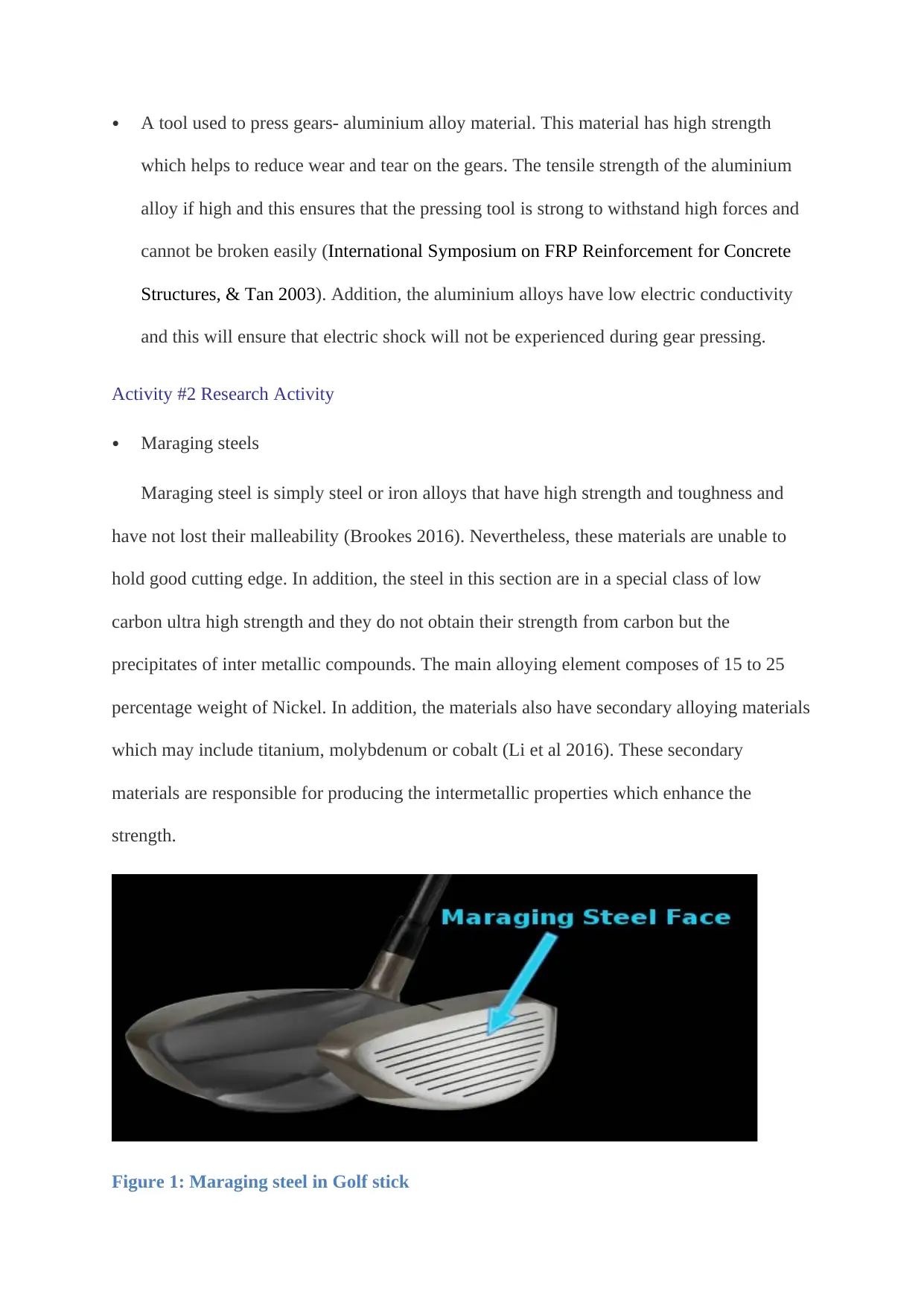
A tool used to press gears- aluminium alloy material. This material has high strength
which helps to reduce wear and tear on the gears. The tensile strength of the aluminium
alloy if high and this ensures that the pressing tool is strong to withstand high forces and
cannot be broken easily (International Symposium on FRP Reinforcement for Concrete
Structures, & Tan 2003). Addition, the aluminium alloys have low electric conductivity
and this will ensure that electric shock will not be experienced during gear pressing.
Activity #2 Research Activity
Maraging steels
Maraging steel is simply steel or iron alloys that have high strength and toughness and
have not lost their malleability (Brookes 2016). Nevertheless, these materials are unable to
hold good cutting edge. In addition, the steel in this section are in a special class of low
carbon ultra high strength and they do not obtain their strength from carbon but the
precipitates of inter metallic compounds. The main alloying element composes of 15 to 25
percentage weight of Nickel. In addition, the materials also have secondary alloying materials
which may include titanium, molybdenum or cobalt (Li et al 2016). These secondary
materials are responsible for producing the intermetallic properties which enhance the
strength.
Figure 1: Maraging steel in Golf stick
which helps to reduce wear and tear on the gears. The tensile strength of the aluminium
alloy if high and this ensures that the pressing tool is strong to withstand high forces and
cannot be broken easily (International Symposium on FRP Reinforcement for Concrete
Structures, & Tan 2003). Addition, the aluminium alloys have low electric conductivity
and this will ensure that electric shock will not be experienced during gear pressing.
Activity #2 Research Activity
Maraging steels
Maraging steel is simply steel or iron alloys that have high strength and toughness and
have not lost their malleability (Brookes 2016). Nevertheless, these materials are unable to
hold good cutting edge. In addition, the steel in this section are in a special class of low
carbon ultra high strength and they do not obtain their strength from carbon but the
precipitates of inter metallic compounds. The main alloying element composes of 15 to 25
percentage weight of Nickel. In addition, the materials also have secondary alloying materials
which may include titanium, molybdenum or cobalt (Li et al 2016). These secondary
materials are responsible for producing the intermetallic properties which enhance the
strength.
Figure 1: Maraging steel in Golf stick
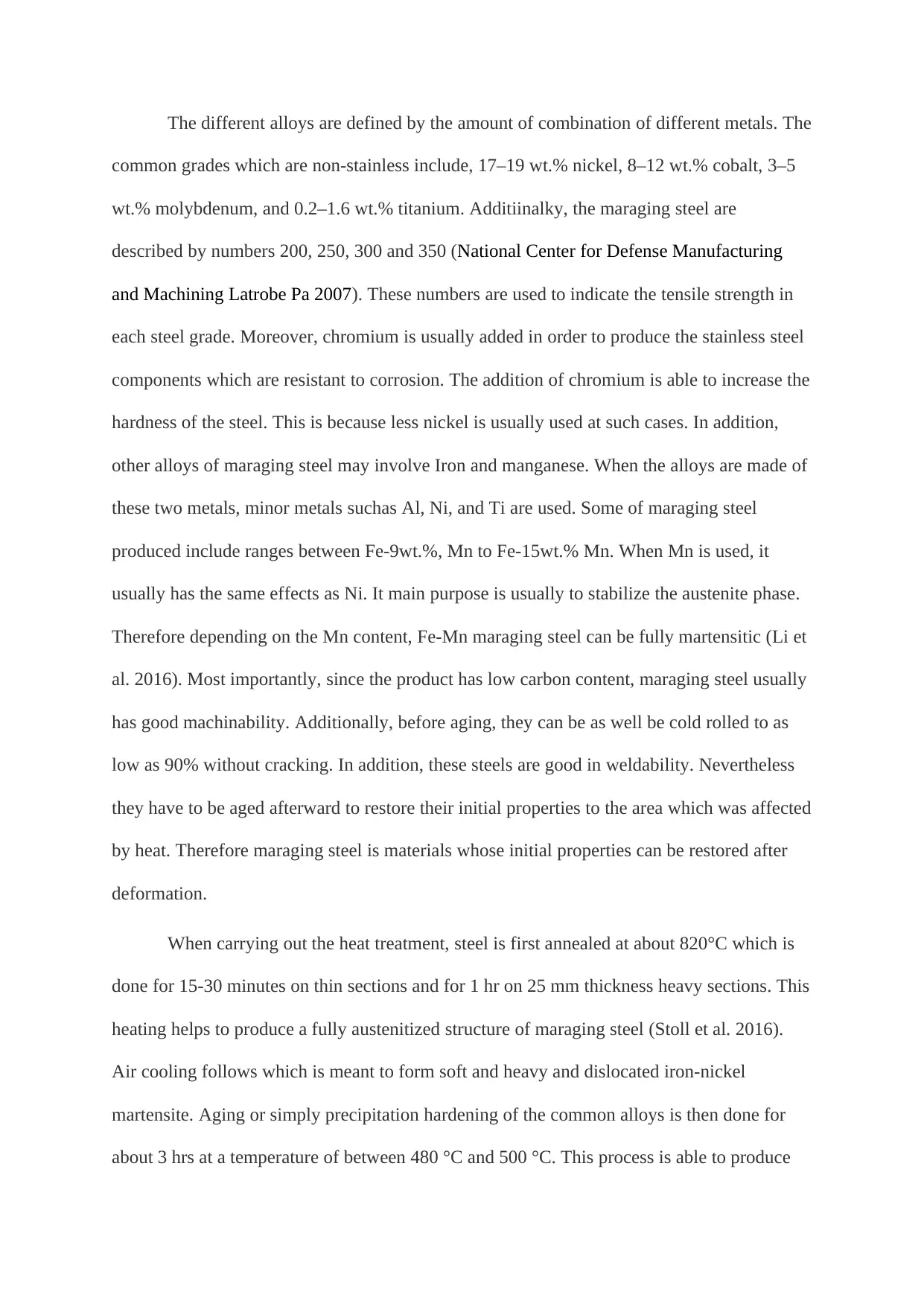
The different alloys are defined by the amount of combination of different metals. The
common grades which are non-stainless include, 17–19 wt.% nickel, 8–12 wt.% cobalt, 3–5
wt.% molybdenum, and 0.2–1.6 wt.% titanium. Additiinalky, the maraging steel are
described by numbers 200, 250, 300 and 350 (National Center for Defense Manufacturing
and Machining Latrobe Pa 2007). These numbers are used to indicate the tensile strength in
each steel grade. Moreover, chromium is usually added in order to produce the stainless steel
components which are resistant to corrosion. The addition of chromium is able to increase the
hardness of the steel. This is because less nickel is usually used at such cases. In addition,
other alloys of maraging steel may involve Iron and manganese. When the alloys are made of
these two metals, minor metals suchas Al, Ni, and Ti are used. Some of maraging steel
produced include ranges between Fe-9wt.%, Mn to Fe-15wt.% Mn. When Mn is used, it
usually has the same effects as Ni. It main purpose is usually to stabilize the austenite phase.
Therefore depending on the Mn content, Fe-Mn maraging steel can be fully martensitic (Li et
al. 2016). Most importantly, since the product has low carbon content, maraging steel usually
has good machinability. Additionally, before aging, they can be as well be cold rolled to as
low as 90% without cracking. In addition, these steels are good in weldability. Nevertheless
they have to be aged afterward to restore their initial properties to the area which was affected
by heat. Therefore maraging steel is materials whose initial properties can be restored after
deformation.
When carrying out the heat treatment, steel is first annealed at about 820°C which is
done for 15-30 minutes on thin sections and for 1 hr on 25 mm thickness heavy sections. This
heating helps to produce a fully austenitized structure of maraging steel (Stoll et al. 2016).
Air cooling follows which is meant to form soft and heavy and dislocated iron-nickel
martensite. Aging or simply precipitation hardening of the common alloys is then done for
about 3 hrs at a temperature of between 480 °C and 500 °C. This process is able to produce
common grades which are non-stainless include, 17–19 wt.% nickel, 8–12 wt.% cobalt, 3–5
wt.% molybdenum, and 0.2–1.6 wt.% titanium. Additiinalky, the maraging steel are
described by numbers 200, 250, 300 and 350 (National Center for Defense Manufacturing
and Machining Latrobe Pa 2007). These numbers are used to indicate the tensile strength in
each steel grade. Moreover, chromium is usually added in order to produce the stainless steel
components which are resistant to corrosion. The addition of chromium is able to increase the
hardness of the steel. This is because less nickel is usually used at such cases. In addition,
other alloys of maraging steel may involve Iron and manganese. When the alloys are made of
these two metals, minor metals suchas Al, Ni, and Ti are used. Some of maraging steel
produced include ranges between Fe-9wt.%, Mn to Fe-15wt.% Mn. When Mn is used, it
usually has the same effects as Ni. It main purpose is usually to stabilize the austenite phase.
Therefore depending on the Mn content, Fe-Mn maraging steel can be fully martensitic (Li et
al. 2016). Most importantly, since the product has low carbon content, maraging steel usually
has good machinability. Additionally, before aging, they can be as well be cold rolled to as
low as 90% without cracking. In addition, these steels are good in weldability. Nevertheless
they have to be aged afterward to restore their initial properties to the area which was affected
by heat. Therefore maraging steel is materials whose initial properties can be restored after
deformation.
When carrying out the heat treatment, steel is first annealed at about 820°C which is
done for 15-30 minutes on thin sections and for 1 hr on 25 mm thickness heavy sections. This
heating helps to produce a fully austenitized structure of maraging steel (Stoll et al. 2016).
Air cooling follows which is meant to form soft and heavy and dislocated iron-nickel
martensite. Aging or simply precipitation hardening of the common alloys is then done for
about 3 hrs at a temperature of between 480 °C and 500 °C. This process is able to produce
Secure Best Marks with AI Grader
Need help grading? Try our AI Grader for instant feedback on your assignments.
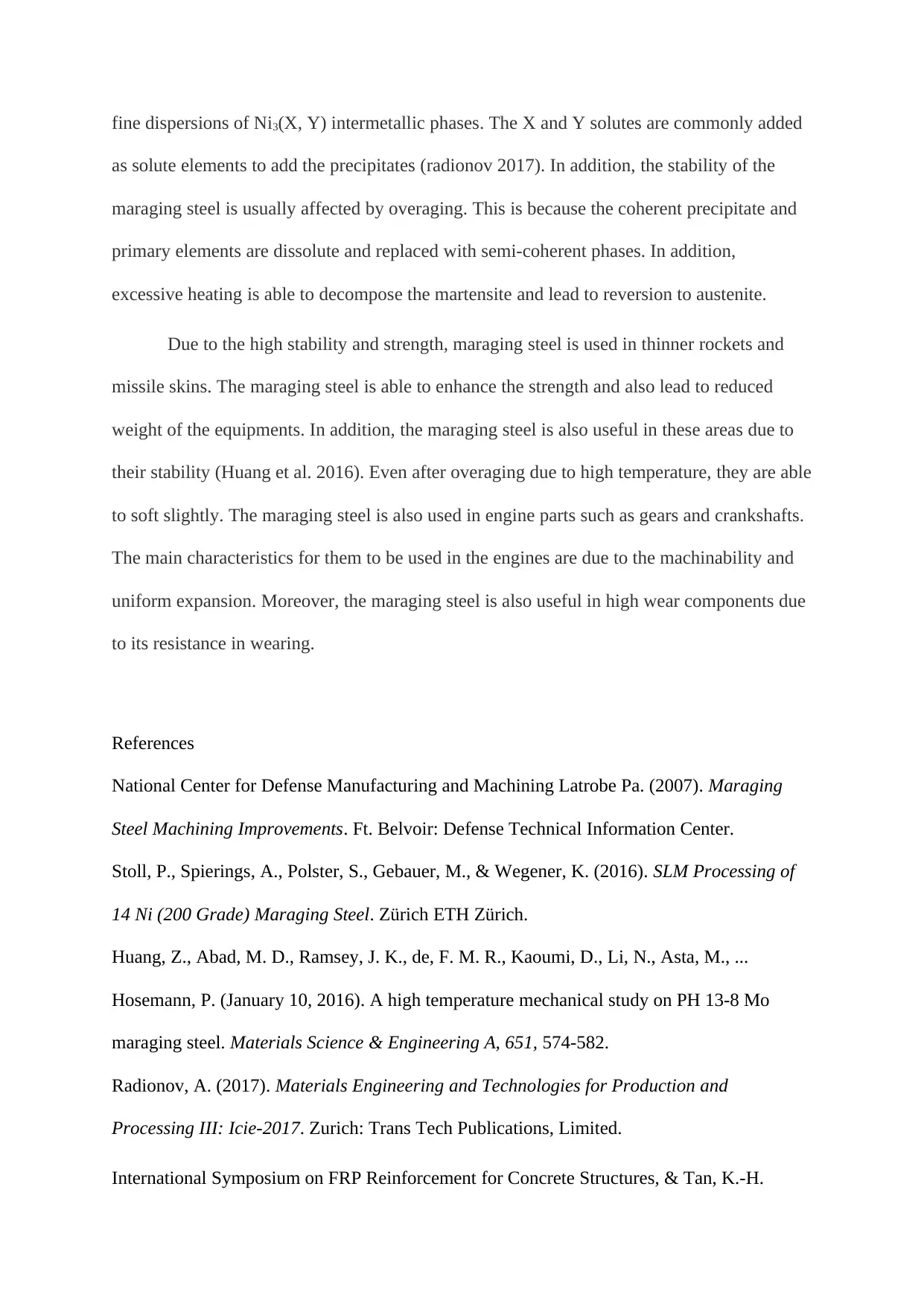
fine dispersions of Ni3(X, Y) intermetallic phases. The X and Y solutes are commonly added
as solute elements to add the precipitates (radionov 2017). In addition, the stability of the
maraging steel is usually affected by overaging. This is because the coherent precipitate and
primary elements are dissolute and replaced with semi-coherent phases. In addition,
excessive heating is able to decompose the martensite and lead to reversion to austenite.
Due to the high stability and strength, maraging steel is used in thinner rockets and
missile skins. The maraging steel is able to enhance the strength and also lead to reduced
weight of the equipments. In addition, the maraging steel is also useful in these areas due to
their stability (Huang et al. 2016). Even after overaging due to high temperature, they are able
to soft slightly. The maraging steel is also used in engine parts such as gears and crankshafts.
The main characteristics for them to be used in the engines are due to the machinability and
uniform expansion. Moreover, the maraging steel is also useful in high wear components due
to its resistance in wearing.
References
National Center for Defense Manufacturing and Machining Latrobe Pa. (2007). Maraging
Steel Machining Improvements. Ft. Belvoir: Defense Technical Information Center.
Stoll, P., Spierings, A., Polster, S., Gebauer, M., & Wegener, K. (2016). SLM Processing of
14 Ni (200 Grade) Maraging Steel. Zürich ETH Zürich.
Huang, Z., Abad, M. D., Ramsey, J. K., de, F. M. R., Kaoumi, D., Li, N., Asta, M., ...
Hosemann, P. (January 10, 2016). A high temperature mechanical study on PH 13-8 Mo
maraging steel. Materials Science & Engineering A, 651, 574-582.
Radionov, A. (2017). Materials Engineering and Technologies for Production and
Processing III: Icie-2017. Zurich: Trans Tech Publications, Limited.
International Symposium on FRP Reinforcement for Concrete Structures, & Tan, K.-H.
as solute elements to add the precipitates (radionov 2017). In addition, the stability of the
maraging steel is usually affected by overaging. This is because the coherent precipitate and
primary elements are dissolute and replaced with semi-coherent phases. In addition,
excessive heating is able to decompose the martensite and lead to reversion to austenite.
Due to the high stability and strength, maraging steel is used in thinner rockets and
missile skins. The maraging steel is able to enhance the strength and also lead to reduced
weight of the equipments. In addition, the maraging steel is also useful in these areas due to
their stability (Huang et al. 2016). Even after overaging due to high temperature, they are able
to soft slightly. The maraging steel is also used in engine parts such as gears and crankshafts.
The main characteristics for them to be used in the engines are due to the machinability and
uniform expansion. Moreover, the maraging steel is also useful in high wear components due
to its resistance in wearing.
References
National Center for Defense Manufacturing and Machining Latrobe Pa. (2007). Maraging
Steel Machining Improvements. Ft. Belvoir: Defense Technical Information Center.
Stoll, P., Spierings, A., Polster, S., Gebauer, M., & Wegener, K. (2016). SLM Processing of
14 Ni (200 Grade) Maraging Steel. Zürich ETH Zürich.
Huang, Z., Abad, M. D., Ramsey, J. K., de, F. M. R., Kaoumi, D., Li, N., Asta, M., ...
Hosemann, P. (January 10, 2016). A high temperature mechanical study on PH 13-8 Mo
maraging steel. Materials Science & Engineering A, 651, 574-582.
Radionov, A. (2017). Materials Engineering and Technologies for Production and
Processing III: Icie-2017. Zurich: Trans Tech Publications, Limited.
International Symposium on FRP Reinforcement for Concrete Structures, & Tan, K.-H.
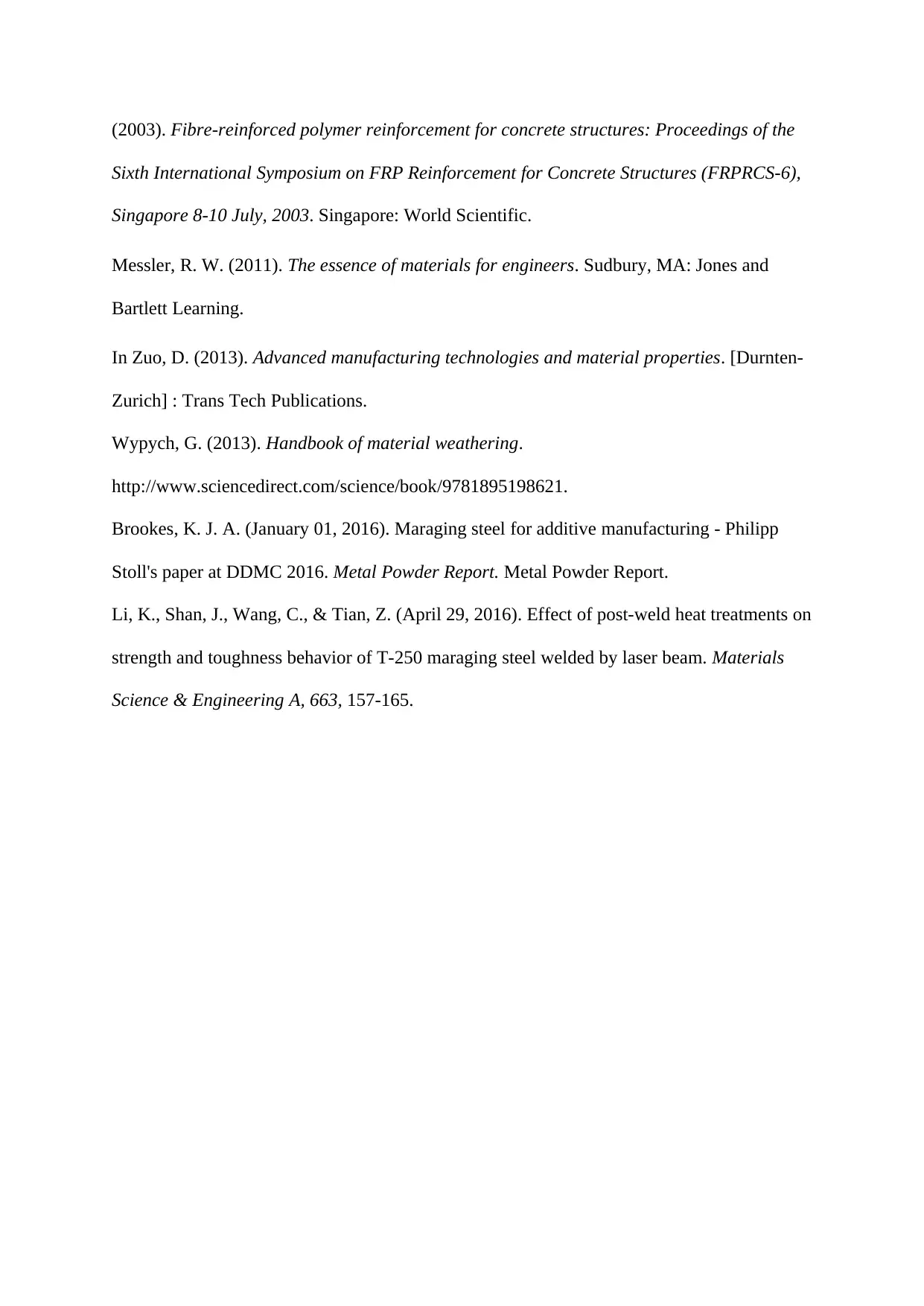
(2003). Fibre-reinforced polymer reinforcement for concrete structures: Proceedings of the
Sixth International Symposium on FRP Reinforcement for Concrete Structures (FRPRCS-6),
Singapore 8-10 July, 2003. Singapore: World Scientific.
Messler, R. W. (2011). The essence of materials for engineers. Sudbury, MA: Jones and
Bartlett Learning.
In Zuo, D. (2013). Advanced manufacturing technologies and material properties. [Durnten-
Zurich] : Trans Tech Publications.
Wypych, G. (2013). Handbook of material weathering.
http://www.sciencedirect.com/science/book/9781895198621.
Brookes, K. J. A. (January 01, 2016). Maraging steel for additive manufacturing - Philipp
Stoll's paper at DDMC 2016. Metal Powder Report. Metal Powder Report.
Li, K., Shan, J., Wang, C., & Tian, Z. (April 29, 2016). Effect of post-weld heat treatments on
strength and toughness behavior of T-250 maraging steel welded by laser beam. Materials
Science & Engineering A, 663, 157-165.
Sixth International Symposium on FRP Reinforcement for Concrete Structures (FRPRCS-6),
Singapore 8-10 July, 2003. Singapore: World Scientific.
Messler, R. W. (2011). The essence of materials for engineers. Sudbury, MA: Jones and
Bartlett Learning.
In Zuo, D. (2013). Advanced manufacturing technologies and material properties. [Durnten-
Zurich] : Trans Tech Publications.
Wypych, G. (2013). Handbook of material weathering.
http://www.sciencedirect.com/science/book/9781895198621.
Brookes, K. J. A. (January 01, 2016). Maraging steel for additive manufacturing - Philipp
Stoll's paper at DDMC 2016. Metal Powder Report. Metal Powder Report.
Li, K., Shan, J., Wang, C., & Tian, Z. (April 29, 2016). Effect of post-weld heat treatments on
strength and toughness behavior of T-250 maraging steel welded by laser beam. Materials
Science & Engineering A, 663, 157-165.
1 out of 6
Related Documents
![[object Object]](/_next/image/?url=%2F_next%2Fstatic%2Fmedia%2Flogo.6d15ce61.png&w=640&q=75)
Your All-in-One AI-Powered Toolkit for Academic Success.
+13062052269
info@desklib.com
Available 24*7 on WhatsApp / Email
Unlock your academic potential
© 2024 | Zucol Services PVT LTD | All rights reserved.