Comprehensive Report on Thermal Management of EV Battery Packs
VerifiedAdded on 2020/12/29
|15
|4831
|367
Report
AI Summary
This report provides a comprehensive overview of thermal management systems for electric vehicle (EV) battery packs. It begins by exploring the various factors that influence the thermal management needs of EV batteries, including battery composition, cell structure, and the arrangement of modules within a pack. The report then delves into the quantification of key parameters related to currently used thermal management systems, such as temperature and heat attributes, cooling techniques (e.g., forced air, liquid cooling), and heat dissipation and removal methods. The study also analyzes appropriate thermal management solutions for a regular test case, considering factors like cost, performance, safety, and environmental impact. It emphasizes the importance of maintaining optimal battery temperature to ensure longevity, driving range, and overall performance, while also addressing the challenges associated with temperature variations and potential hazards like thermal runaway. The report highlights the trade-offs involved in selecting a thermal management system, considering factors like compactness, compatibility, cost-effectiveness, and the ability to handle climatic variations and hazardous gas emissions. Finally, the report underscores the need for a clear understanding of EV battery thermal behavior, including transient and steady thermal responses and the medium of heat transfer, to design effective thermal management solutions.
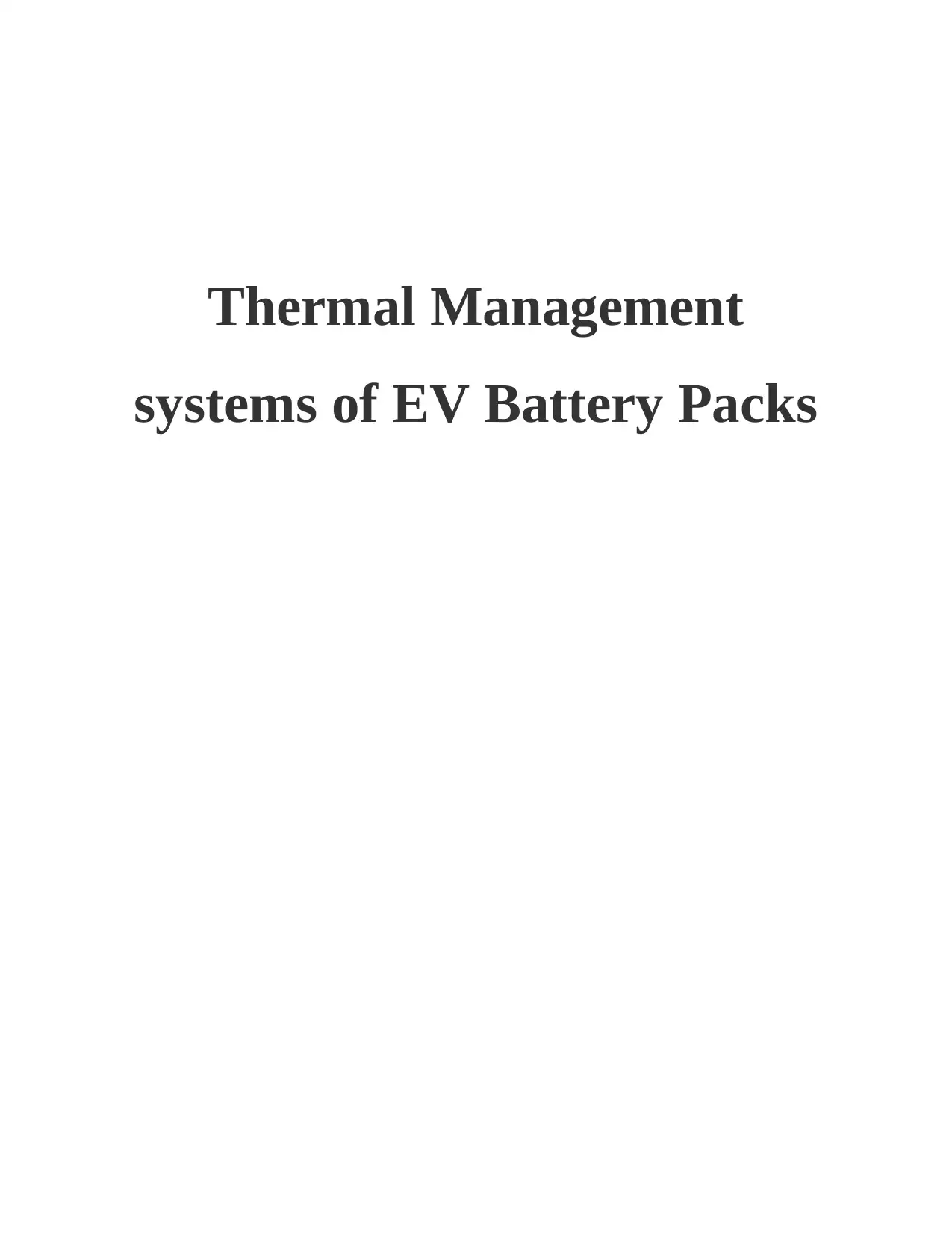
Thermal Management
systems of EV Battery Packs
systems of EV Battery Packs
Paraphrase This Document
Need a fresh take? Get an instant paraphrase of this document with our AI Paraphraser
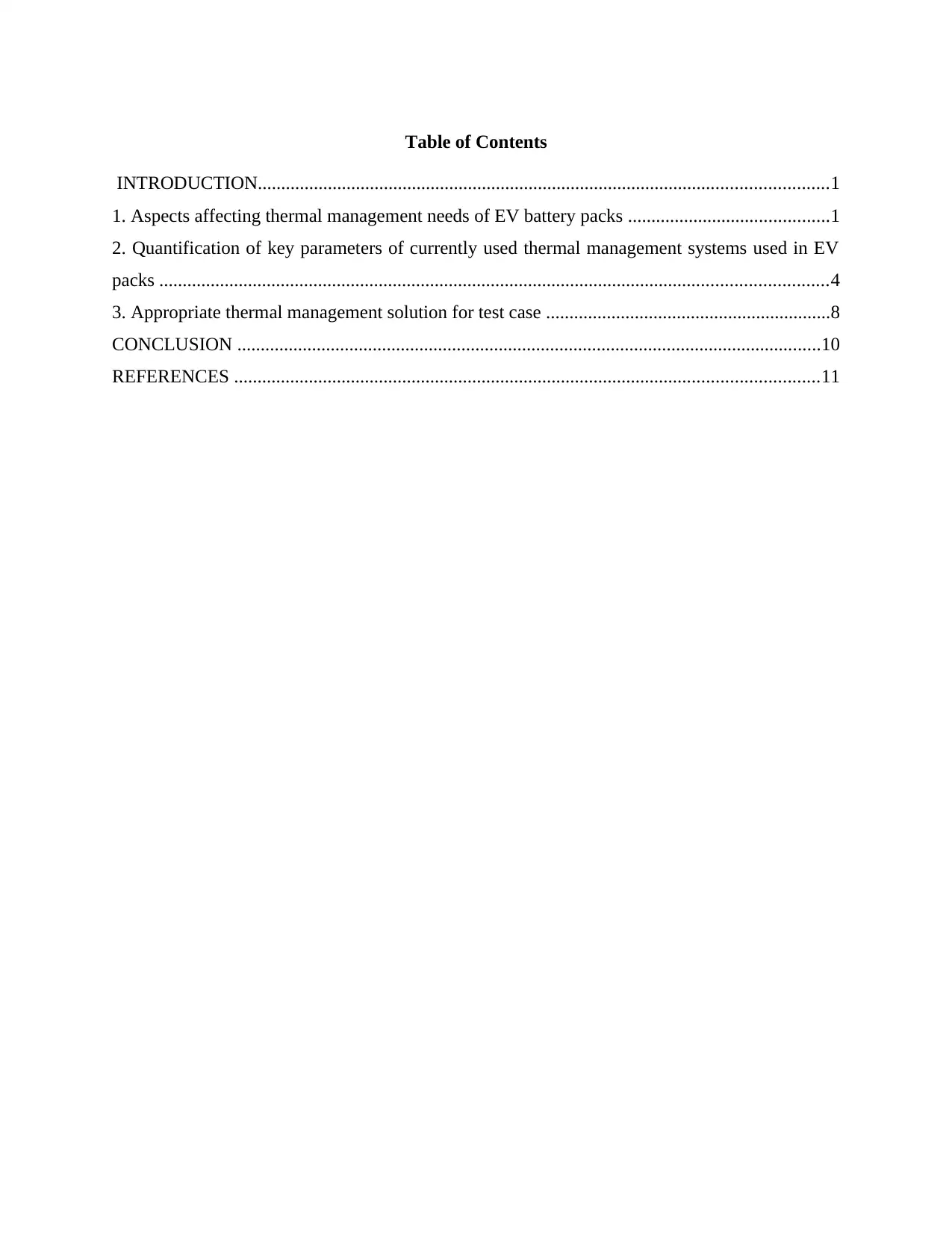
Table of Contents
INTRODUCTION..........................................................................................................................1
1. Aspects affecting thermal management needs of EV battery packs ...........................................1
2. Quantification of key parameters of currently used thermal management systems used in EV
packs ...............................................................................................................................................4
3. Appropriate thermal management solution for test case .............................................................8
CONCLUSION .............................................................................................................................10
REFERENCES .............................................................................................................................11
INTRODUCTION..........................................................................................................................1
1. Aspects affecting thermal management needs of EV battery packs ...........................................1
2. Quantification of key parameters of currently used thermal management systems used in EV
packs ...............................................................................................................................................4
3. Appropriate thermal management solution for test case .............................................................8
CONCLUSION .............................................................................................................................10
REFERENCES .............................................................................................................................11
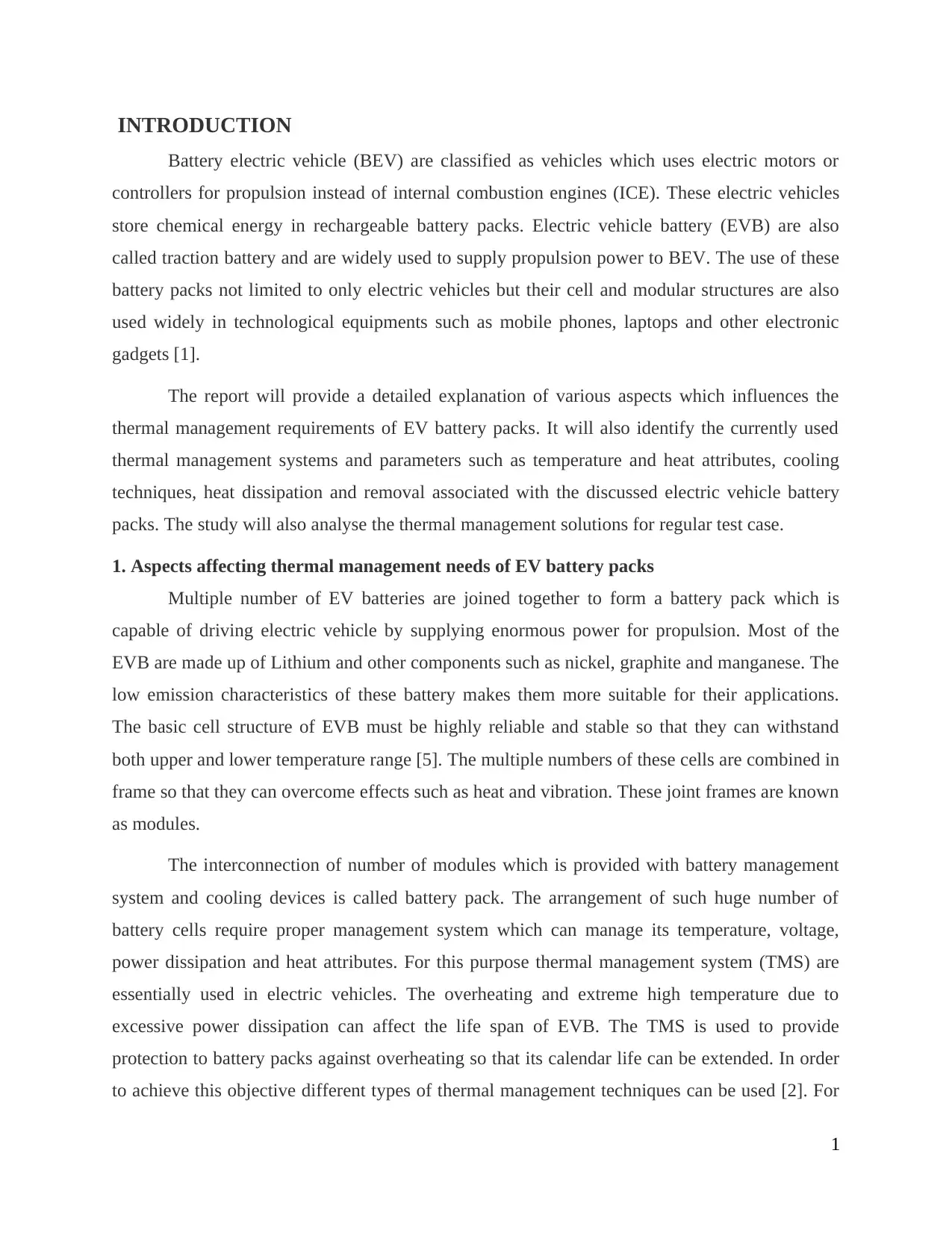
INTRODUCTION
Battery electric vehicle (BEV) are classified as vehicles which uses electric motors or
controllers for propulsion instead of internal combustion engines (ICE). These electric vehicles
store chemical energy in rechargeable battery packs. Electric vehicle battery (EVB) are also
called traction battery and are widely used to supply propulsion power to BEV. The use of these
battery packs not limited to only electric vehicles but their cell and modular structures are also
used widely in technological equipments such as mobile phones, laptops and other electronic
gadgets [1].
The report will provide a detailed explanation of various aspects which influences the
thermal management requirements of EV battery packs. It will also identify the currently used
thermal management systems and parameters such as temperature and heat attributes, cooling
techniques, heat dissipation and removal associated with the discussed electric vehicle battery
packs. The study will also analyse the thermal management solutions for regular test case.
1. Aspects affecting thermal management needs of EV battery packs
Multiple number of EV batteries are joined together to form a battery pack which is
capable of driving electric vehicle by supplying enormous power for propulsion. Most of the
EVB are made up of Lithium and other components such as nickel, graphite and manganese. The
low emission characteristics of these battery makes them more suitable for their applications.
The basic cell structure of EVB must be highly reliable and stable so that they can withstand
both upper and lower temperature range [5]. The multiple numbers of these cells are combined in
frame so that they can overcome effects such as heat and vibration. These joint frames are known
as modules.
The interconnection of number of modules which is provided with battery management
system and cooling devices is called battery pack. The arrangement of such huge number of
battery cells require proper management system which can manage its temperature, voltage,
power dissipation and heat attributes. For this purpose thermal management system (TMS) are
essentially used in electric vehicles. The overheating and extreme high temperature due to
excessive power dissipation can affect the life span of EVB. The TMS is used to provide
protection to battery packs against overheating so that its calendar life can be extended. In order
to achieve this objective different types of thermal management techniques can be used [2]. For
1
Battery electric vehicle (BEV) are classified as vehicles which uses electric motors or
controllers for propulsion instead of internal combustion engines (ICE). These electric vehicles
store chemical energy in rechargeable battery packs. Electric vehicle battery (EVB) are also
called traction battery and are widely used to supply propulsion power to BEV. The use of these
battery packs not limited to only electric vehicles but their cell and modular structures are also
used widely in technological equipments such as mobile phones, laptops and other electronic
gadgets [1].
The report will provide a detailed explanation of various aspects which influences the
thermal management requirements of EV battery packs. It will also identify the currently used
thermal management systems and parameters such as temperature and heat attributes, cooling
techniques, heat dissipation and removal associated with the discussed electric vehicle battery
packs. The study will also analyse the thermal management solutions for regular test case.
1. Aspects affecting thermal management needs of EV battery packs
Multiple number of EV batteries are joined together to form a battery pack which is
capable of driving electric vehicle by supplying enormous power for propulsion. Most of the
EVB are made up of Lithium and other components such as nickel, graphite and manganese. The
low emission characteristics of these battery makes them more suitable for their applications.
The basic cell structure of EVB must be highly reliable and stable so that they can withstand
both upper and lower temperature range [5]. The multiple numbers of these cells are combined in
frame so that they can overcome effects such as heat and vibration. These joint frames are known
as modules.
The interconnection of number of modules which is provided with battery management
system and cooling devices is called battery pack. The arrangement of such huge number of
battery cells require proper management system which can manage its temperature, voltage,
power dissipation and heat attributes. For this purpose thermal management system (TMS) are
essentially used in electric vehicles. The overheating and extreme high temperature due to
excessive power dissipation can affect the life span of EVB. The TMS is used to provide
protection to battery packs against overheating so that its calendar life can be extended. In order
to achieve this objective different types of thermal management techniques can be used [2]. For
1
⊘ This is a preview!⊘
Do you want full access?
Subscribe today to unlock all pages.

Trusted by 1+ million students worldwide
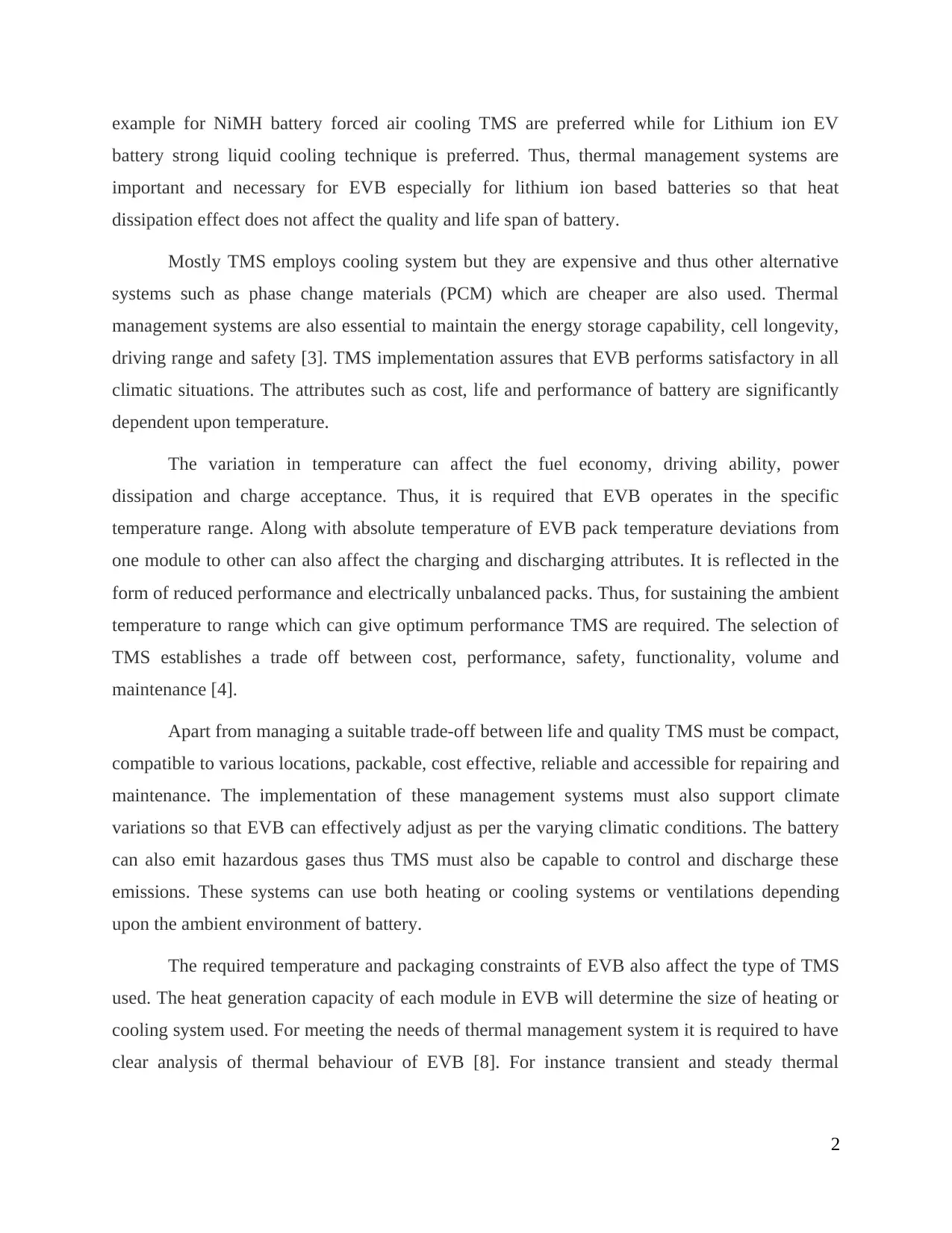
example for NiMH battery forced air cooling TMS are preferred while for Lithium ion EV
battery strong liquid cooling technique is preferred. Thus, thermal management systems are
important and necessary for EVB especially for lithium ion based batteries so that heat
dissipation effect does not affect the quality and life span of battery.
Mostly TMS employs cooling system but they are expensive and thus other alternative
systems such as phase change materials (PCM) which are cheaper are also used. Thermal
management systems are also essential to maintain the energy storage capability, cell longevity,
driving range and safety [3]. TMS implementation assures that EVB performs satisfactory in all
climatic situations. The attributes such as cost, life and performance of battery are significantly
dependent upon temperature.
The variation in temperature can affect the fuel economy, driving ability, power
dissipation and charge acceptance. Thus, it is required that EVB operates in the specific
temperature range. Along with absolute temperature of EVB pack temperature deviations from
one module to other can also affect the charging and discharging attributes. It is reflected in the
form of reduced performance and electrically unbalanced packs. Thus, for sustaining the ambient
temperature to range which can give optimum performance TMS are required. The selection of
TMS establishes a trade off between cost, performance, safety, functionality, volume and
maintenance [4].
Apart from managing a suitable trade-off between life and quality TMS must be compact,
compatible to various locations, packable, cost effective, reliable and accessible for repairing and
maintenance. The implementation of these management systems must also support climate
variations so that EVB can effectively adjust as per the varying climatic conditions. The battery
can also emit hazardous gases thus TMS must also be capable to control and discharge these
emissions. These systems can use both heating or cooling systems or ventilations depending
upon the ambient environment of battery.
The required temperature and packaging constraints of EVB also affect the type of TMS
used. The heat generation capacity of each module in EVB will determine the size of heating or
cooling system used. For meeting the needs of thermal management system it is required to have
clear analysis of thermal behaviour of EVB [8]. For instance transient and steady thermal
2
battery strong liquid cooling technique is preferred. Thus, thermal management systems are
important and necessary for EVB especially for lithium ion based batteries so that heat
dissipation effect does not affect the quality and life span of battery.
Mostly TMS employs cooling system but they are expensive and thus other alternative
systems such as phase change materials (PCM) which are cheaper are also used. Thermal
management systems are also essential to maintain the energy storage capability, cell longevity,
driving range and safety [3]. TMS implementation assures that EVB performs satisfactory in all
climatic situations. The attributes such as cost, life and performance of battery are significantly
dependent upon temperature.
The variation in temperature can affect the fuel economy, driving ability, power
dissipation and charge acceptance. Thus, it is required that EVB operates in the specific
temperature range. Along with absolute temperature of EVB pack temperature deviations from
one module to other can also affect the charging and discharging attributes. It is reflected in the
form of reduced performance and electrically unbalanced packs. Thus, for sustaining the ambient
temperature to range which can give optimum performance TMS are required. The selection of
TMS establishes a trade off between cost, performance, safety, functionality, volume and
maintenance [4].
Apart from managing a suitable trade-off between life and quality TMS must be compact,
compatible to various locations, packable, cost effective, reliable and accessible for repairing and
maintenance. The implementation of these management systems must also support climate
variations so that EVB can effectively adjust as per the varying climatic conditions. The battery
can also emit hazardous gases thus TMS must also be capable to control and discharge these
emissions. These systems can use both heating or cooling systems or ventilations depending
upon the ambient environment of battery.
The required temperature and packaging constraints of EVB also affect the type of TMS
used. The heat generation capacity of each module in EVB will determine the size of heating or
cooling system used. For meeting the needs of thermal management system it is required to have
clear analysis of thermal behaviour of EVB [8]. For instance transient and steady thermal
2
Paraphrase This Document
Need a fresh take? Get an instant paraphrase of this document with our AI Paraphraser
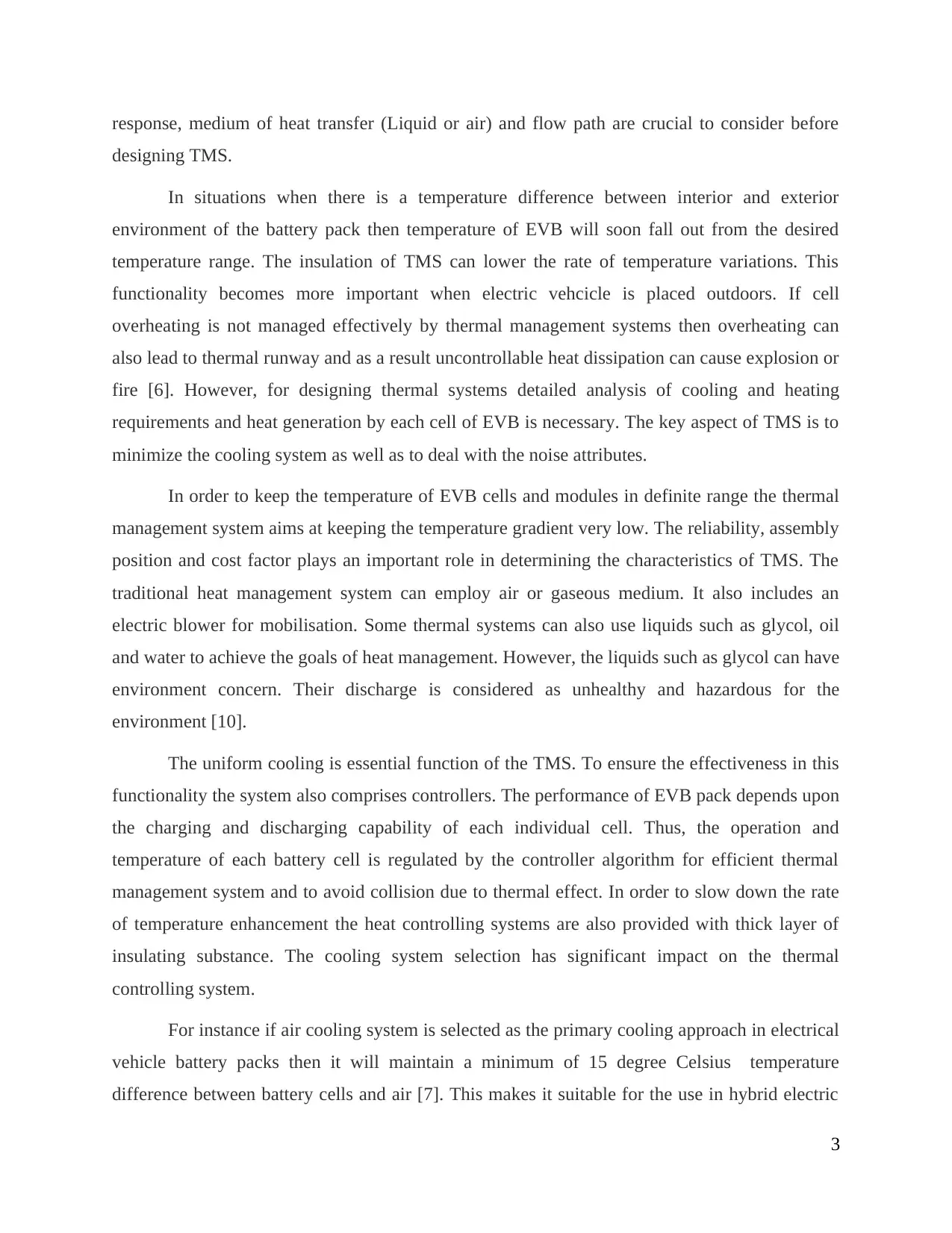
response, medium of heat transfer (Liquid or air) and flow path are crucial to consider before
designing TMS.
In situations when there is a temperature difference between interior and exterior
environment of the battery pack then temperature of EVB will soon fall out from the desired
temperature range. The insulation of TMS can lower the rate of temperature variations. This
functionality becomes more important when electric vehcicle is placed outdoors. If cell
overheating is not managed effectively by thermal management systems then overheating can
also lead to thermal runway and as a result uncontrollable heat dissipation can cause explosion or
fire [6]. However, for designing thermal systems detailed analysis of cooling and heating
requirements and heat generation by each cell of EVB is necessary. The key aspect of TMS is to
minimize the cooling system as well as to deal with the noise attributes.
In order to keep the temperature of EVB cells and modules in definite range the thermal
management system aims at keeping the temperature gradient very low. The reliability, assembly
position and cost factor plays an important role in determining the characteristics of TMS. The
traditional heat management system can employ air or gaseous medium. It also includes an
electric blower for mobilisation. Some thermal systems can also use liquids such as glycol, oil
and water to achieve the goals of heat management. However, the liquids such as glycol can have
environment concern. Their discharge is considered as unhealthy and hazardous for the
environment [10].
The uniform cooling is essential function of the TMS. To ensure the effectiveness in this
functionality the system also comprises controllers. The performance of EVB pack depends upon
the charging and discharging capability of each individual cell. Thus, the operation and
temperature of each battery cell is regulated by the controller algorithm for efficient thermal
management system and to avoid collision due to thermal effect. In order to slow down the rate
of temperature enhancement the heat controlling systems are also provided with thick layer of
insulating substance. The cooling system selection has significant impact on the thermal
controlling system.
For instance if air cooling system is selected as the primary cooling approach in electrical
vehicle battery packs then it will maintain a minimum of 15 degree Celsius temperature
difference between battery cells and air [7]. This makes it suitable for the use in hybrid electric
3
designing TMS.
In situations when there is a temperature difference between interior and exterior
environment of the battery pack then temperature of EVB will soon fall out from the desired
temperature range. The insulation of TMS can lower the rate of temperature variations. This
functionality becomes more important when electric vehcicle is placed outdoors. If cell
overheating is not managed effectively by thermal management systems then overheating can
also lead to thermal runway and as a result uncontrollable heat dissipation can cause explosion or
fire [6]. However, for designing thermal systems detailed analysis of cooling and heating
requirements and heat generation by each cell of EVB is necessary. The key aspect of TMS is to
minimize the cooling system as well as to deal with the noise attributes.
In order to keep the temperature of EVB cells and modules in definite range the thermal
management system aims at keeping the temperature gradient very low. The reliability, assembly
position and cost factor plays an important role in determining the characteristics of TMS. The
traditional heat management system can employ air or gaseous medium. It also includes an
electric blower for mobilisation. Some thermal systems can also use liquids such as glycol, oil
and water to achieve the goals of heat management. However, the liquids such as glycol can have
environment concern. Their discharge is considered as unhealthy and hazardous for the
environment [10].
The uniform cooling is essential function of the TMS. To ensure the effectiveness in this
functionality the system also comprises controllers. The performance of EVB pack depends upon
the charging and discharging capability of each individual cell. Thus, the operation and
temperature of each battery cell is regulated by the controller algorithm for efficient thermal
management system and to avoid collision due to thermal effect. In order to slow down the rate
of temperature enhancement the heat controlling systems are also provided with thick layer of
insulating substance. The cooling system selection has significant impact on the thermal
controlling system.
For instance if air cooling system is selected as the primary cooling approach in electrical
vehicle battery packs then it will maintain a minimum of 15 degree Celsius temperature
difference between battery cells and air [7]. This makes it suitable for the use in hybrid electric
3
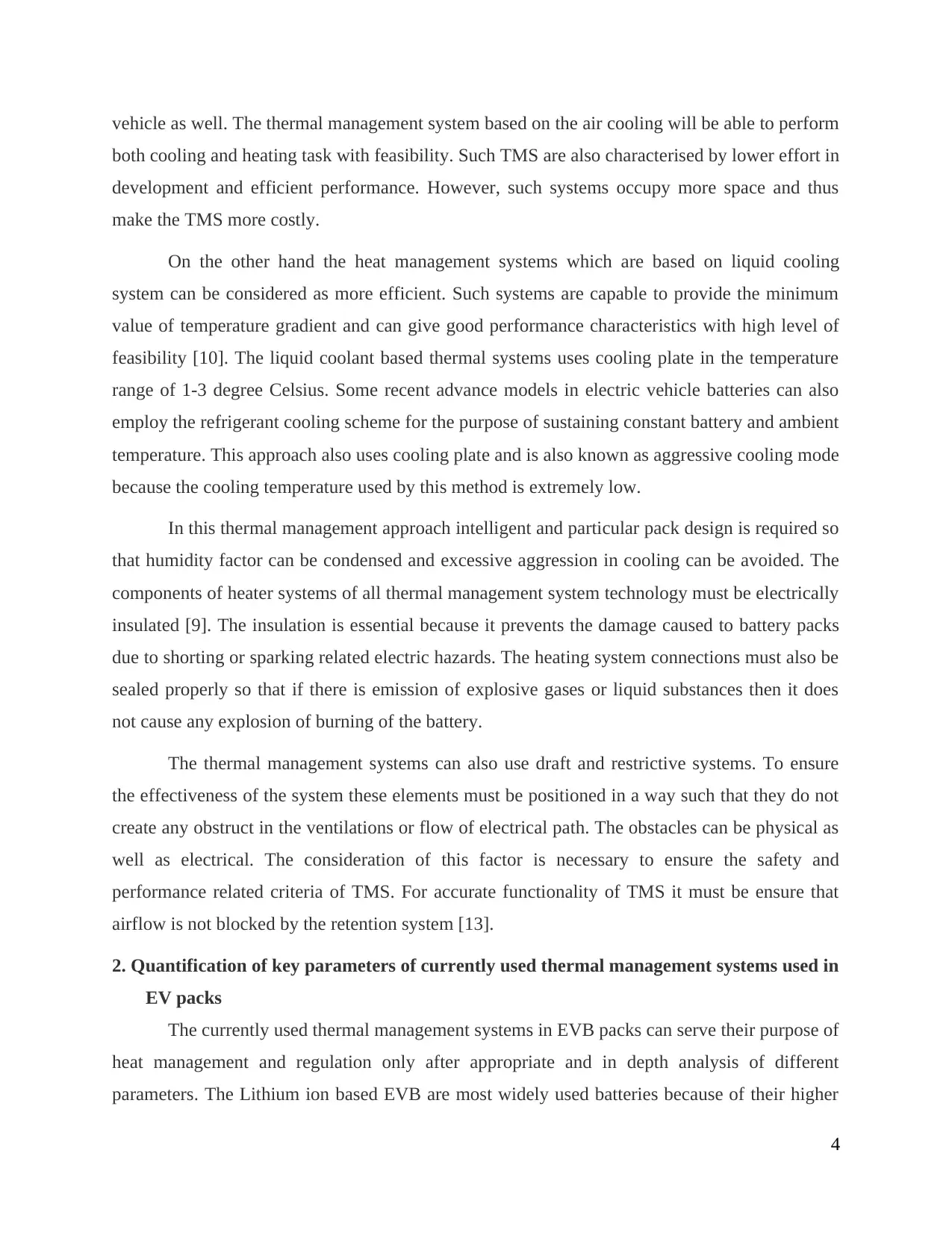
vehicle as well. The thermal management system based on the air cooling will be able to perform
both cooling and heating task with feasibility. Such TMS are also characterised by lower effort in
development and efficient performance. However, such systems occupy more space and thus
make the TMS more costly.
On the other hand the heat management systems which are based on liquid cooling
system can be considered as more efficient. Such systems are capable to provide the minimum
value of temperature gradient and can give good performance characteristics with high level of
feasibility [10]. The liquid coolant based thermal systems uses cooling plate in the temperature
range of 1-3 degree Celsius. Some recent advance models in electric vehicle batteries can also
employ the refrigerant cooling scheme for the purpose of sustaining constant battery and ambient
temperature. This approach also uses cooling plate and is also known as aggressive cooling mode
because the cooling temperature used by this method is extremely low.
In this thermal management approach intelligent and particular pack design is required so
that humidity factor can be condensed and excessive aggression in cooling can be avoided. The
components of heater systems of all thermal management system technology must be electrically
insulated [9]. The insulation is essential because it prevents the damage caused to battery packs
due to shorting or sparking related electric hazards. The heating system connections must also be
sealed properly so that if there is emission of explosive gases or liquid substances then it does
not cause any explosion of burning of the battery.
The thermal management systems can also use draft and restrictive systems. To ensure
the effectiveness of the system these elements must be positioned in a way such that they do not
create any obstruct in the ventilations or flow of electrical path. The obstacles can be physical as
well as electrical. The consideration of this factor is necessary to ensure the safety and
performance related criteria of TMS. For accurate functionality of TMS it must be ensure that
airflow is not blocked by the retention system [13].
2. Quantification of key parameters of currently used thermal management systems used in
EV packs
The currently used thermal management systems in EVB packs can serve their purpose of
heat management and regulation only after appropriate and in depth analysis of different
parameters. The Lithium ion based EVB are most widely used batteries because of their higher
4
both cooling and heating task with feasibility. Such TMS are also characterised by lower effort in
development and efficient performance. However, such systems occupy more space and thus
make the TMS more costly.
On the other hand the heat management systems which are based on liquid cooling
system can be considered as more efficient. Such systems are capable to provide the minimum
value of temperature gradient and can give good performance characteristics with high level of
feasibility [10]. The liquid coolant based thermal systems uses cooling plate in the temperature
range of 1-3 degree Celsius. Some recent advance models in electric vehicle batteries can also
employ the refrigerant cooling scheme for the purpose of sustaining constant battery and ambient
temperature. This approach also uses cooling plate and is also known as aggressive cooling mode
because the cooling temperature used by this method is extremely low.
In this thermal management approach intelligent and particular pack design is required so
that humidity factor can be condensed and excessive aggression in cooling can be avoided. The
components of heater systems of all thermal management system technology must be electrically
insulated [9]. The insulation is essential because it prevents the damage caused to battery packs
due to shorting or sparking related electric hazards. The heating system connections must also be
sealed properly so that if there is emission of explosive gases or liquid substances then it does
not cause any explosion of burning of the battery.
The thermal management systems can also use draft and restrictive systems. To ensure
the effectiveness of the system these elements must be positioned in a way such that they do not
create any obstruct in the ventilations or flow of electrical path. The obstacles can be physical as
well as electrical. The consideration of this factor is necessary to ensure the safety and
performance related criteria of TMS. For accurate functionality of TMS it must be ensure that
airflow is not blocked by the retention system [13].
2. Quantification of key parameters of currently used thermal management systems used in
EV packs
The currently used thermal management systems in EVB packs can serve their purpose of
heat management and regulation only after appropriate and in depth analysis of different
parameters. The Lithium ion based EVB are most widely used batteries because of their higher
4
⊘ This is a preview!⊘
Do you want full access?
Subscribe today to unlock all pages.

Trusted by 1+ million students worldwide
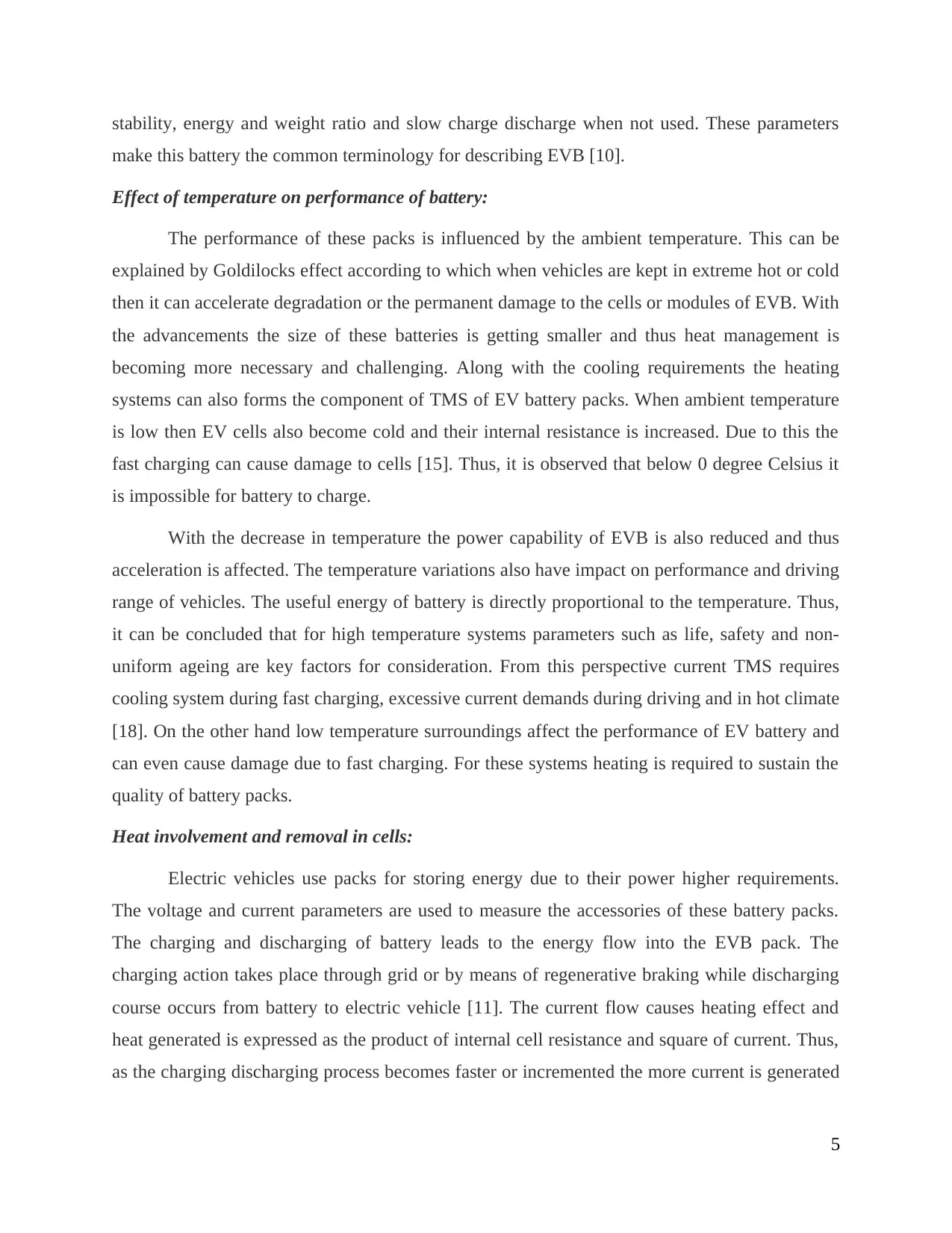
stability, energy and weight ratio and slow charge discharge when not used. These parameters
make this battery the common terminology for describing EVB [10].
Effect of temperature on performance of battery:
The performance of these packs is influenced by the ambient temperature. This can be
explained by Goldilocks effect according to which when vehicles are kept in extreme hot or cold
then it can accelerate degradation or the permanent damage to the cells or modules of EVB. With
the advancements the size of these batteries is getting smaller and thus heat management is
becoming more necessary and challenging. Along with the cooling requirements the heating
systems can also forms the component of TMS of EV battery packs. When ambient temperature
is low then EV cells also become cold and their internal resistance is increased. Due to this the
fast charging can cause damage to cells [15]. Thus, it is observed that below 0 degree Celsius it
is impossible for battery to charge.
With the decrease in temperature the power capability of EVB is also reduced and thus
acceleration is affected. The temperature variations also have impact on performance and driving
range of vehicles. The useful energy of battery is directly proportional to the temperature. Thus,
it can be concluded that for high temperature systems parameters such as life, safety and non-
uniform ageing are key factors for consideration. From this perspective current TMS requires
cooling system during fast charging, excessive current demands during driving and in hot climate
[18]. On the other hand low temperature surroundings affect the performance of EV battery and
can even cause damage due to fast charging. For these systems heating is required to sustain the
quality of battery packs.
Heat involvement and removal in cells:
Electric vehicles use packs for storing energy due to their power higher requirements.
The voltage and current parameters are used to measure the accessories of these battery packs.
The charging and discharging of battery leads to the energy flow into the EVB pack. The
charging action takes place through grid or by means of regenerative braking while discharging
course occurs from battery to electric vehicle [11]. The current flow causes heating effect and
heat generated is expressed as the product of internal cell resistance and square of current. Thus,
as the charging discharging process becomes faster or incremented the more current is generated
5
make this battery the common terminology for describing EVB [10].
Effect of temperature on performance of battery:
The performance of these packs is influenced by the ambient temperature. This can be
explained by Goldilocks effect according to which when vehicles are kept in extreme hot or cold
then it can accelerate degradation or the permanent damage to the cells or modules of EVB. With
the advancements the size of these batteries is getting smaller and thus heat management is
becoming more necessary and challenging. Along with the cooling requirements the heating
systems can also forms the component of TMS of EV battery packs. When ambient temperature
is low then EV cells also become cold and their internal resistance is increased. Due to this the
fast charging can cause damage to cells [15]. Thus, it is observed that below 0 degree Celsius it
is impossible for battery to charge.
With the decrease in temperature the power capability of EVB is also reduced and thus
acceleration is affected. The temperature variations also have impact on performance and driving
range of vehicles. The useful energy of battery is directly proportional to the temperature. Thus,
it can be concluded that for high temperature systems parameters such as life, safety and non-
uniform ageing are key factors for consideration. From this perspective current TMS requires
cooling system during fast charging, excessive current demands during driving and in hot climate
[18]. On the other hand low temperature surroundings affect the performance of EV battery and
can even cause damage due to fast charging. For these systems heating is required to sustain the
quality of battery packs.
Heat involvement and removal in cells:
Electric vehicles use packs for storing energy due to their power higher requirements.
The voltage and current parameters are used to measure the accessories of these battery packs.
The charging and discharging of battery leads to the energy flow into the EVB pack. The
charging action takes place through grid or by means of regenerative braking while discharging
course occurs from battery to electric vehicle [11]. The current flow causes heating effect and
heat generated is expressed as the product of internal cell resistance and square of current. Thus,
as the charging discharging process becomes faster or incremented the more current is generated
5
Paraphrase This Document
Need a fresh take? Get an instant paraphrase of this document with our AI Paraphraser
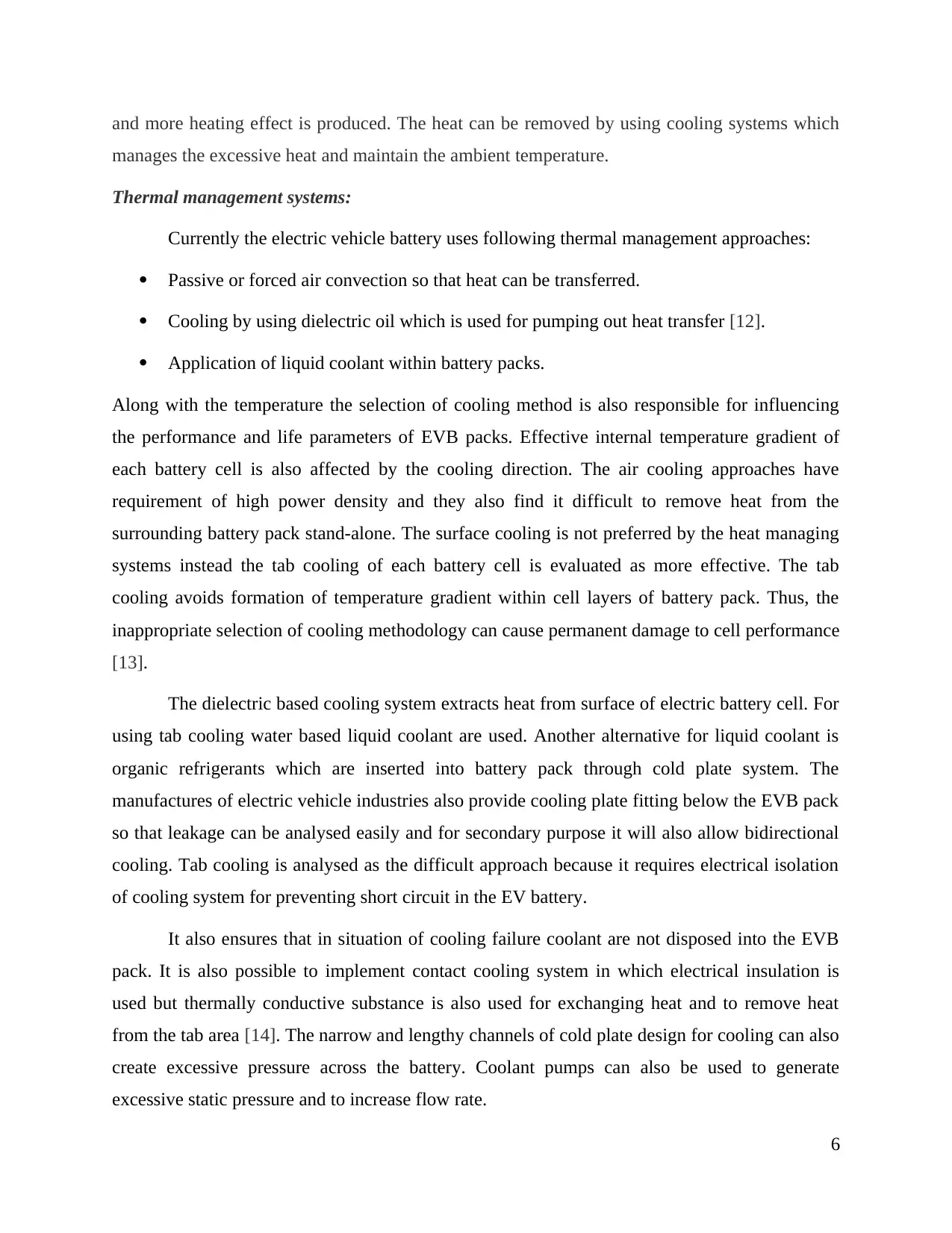
and more heating effect is produced. The heat can be removed by using cooling systems which
manages the excessive heat and maintain the ambient temperature.
Thermal management systems:
Currently the electric vehicle battery uses following thermal management approaches:
Passive or forced air convection so that heat can be transferred.
Cooling by using dielectric oil which is used for pumping out heat transfer [12].
Application of liquid coolant within battery packs.
Along with the temperature the selection of cooling method is also responsible for influencing
the performance and life parameters of EVB packs. Effective internal temperature gradient of
each battery cell is also affected by the cooling direction. The air cooling approaches have
requirement of high power density and they also find it difficult to remove heat from the
surrounding battery pack stand-alone. The surface cooling is not preferred by the heat managing
systems instead the tab cooling of each battery cell is evaluated as more effective. The tab
cooling avoids formation of temperature gradient within cell layers of battery pack. Thus, the
inappropriate selection of cooling methodology can cause permanent damage to cell performance
[13].
The dielectric based cooling system extracts heat from surface of electric battery cell. For
using tab cooling water based liquid coolant are used. Another alternative for liquid coolant is
organic refrigerants which are inserted into battery pack through cold plate system. The
manufactures of electric vehicle industries also provide cooling plate fitting below the EVB pack
so that leakage can be analysed easily and for secondary purpose it will also allow bidirectional
cooling. Tab cooling is analysed as the difficult approach because it requires electrical isolation
of cooling system for preventing short circuit in the EV battery.
It also ensures that in situation of cooling failure coolant are not disposed into the EVB
pack. It is also possible to implement contact cooling system in which electrical insulation is
used but thermally conductive substance is also used for exchanging heat and to remove heat
from the tab area [14]. The narrow and lengthy channels of cold plate design for cooling can also
create excessive pressure across the battery. Coolant pumps can also be used to generate
excessive static pressure and to increase flow rate.
6
manages the excessive heat and maintain the ambient temperature.
Thermal management systems:
Currently the electric vehicle battery uses following thermal management approaches:
Passive or forced air convection so that heat can be transferred.
Cooling by using dielectric oil which is used for pumping out heat transfer [12].
Application of liquid coolant within battery packs.
Along with the temperature the selection of cooling method is also responsible for influencing
the performance and life parameters of EVB packs. Effective internal temperature gradient of
each battery cell is also affected by the cooling direction. The air cooling approaches have
requirement of high power density and they also find it difficult to remove heat from the
surrounding battery pack stand-alone. The surface cooling is not preferred by the heat managing
systems instead the tab cooling of each battery cell is evaluated as more effective. The tab
cooling avoids formation of temperature gradient within cell layers of battery pack. Thus, the
inappropriate selection of cooling methodology can cause permanent damage to cell performance
[13].
The dielectric based cooling system extracts heat from surface of electric battery cell. For
using tab cooling water based liquid coolant are used. Another alternative for liquid coolant is
organic refrigerants which are inserted into battery pack through cold plate system. The
manufactures of electric vehicle industries also provide cooling plate fitting below the EVB pack
so that leakage can be analysed easily and for secondary purpose it will also allow bidirectional
cooling. Tab cooling is analysed as the difficult approach because it requires electrical isolation
of cooling system for preventing short circuit in the EV battery.
It also ensures that in situation of cooling failure coolant are not disposed into the EVB
pack. It is also possible to implement contact cooling system in which electrical insulation is
used but thermally conductive substance is also used for exchanging heat and to remove heat
from the tab area [14]. The narrow and lengthy channels of cold plate design for cooling can also
create excessive pressure across the battery. Coolant pumps can also be used to generate
excessive static pressure and to increase flow rate.
6
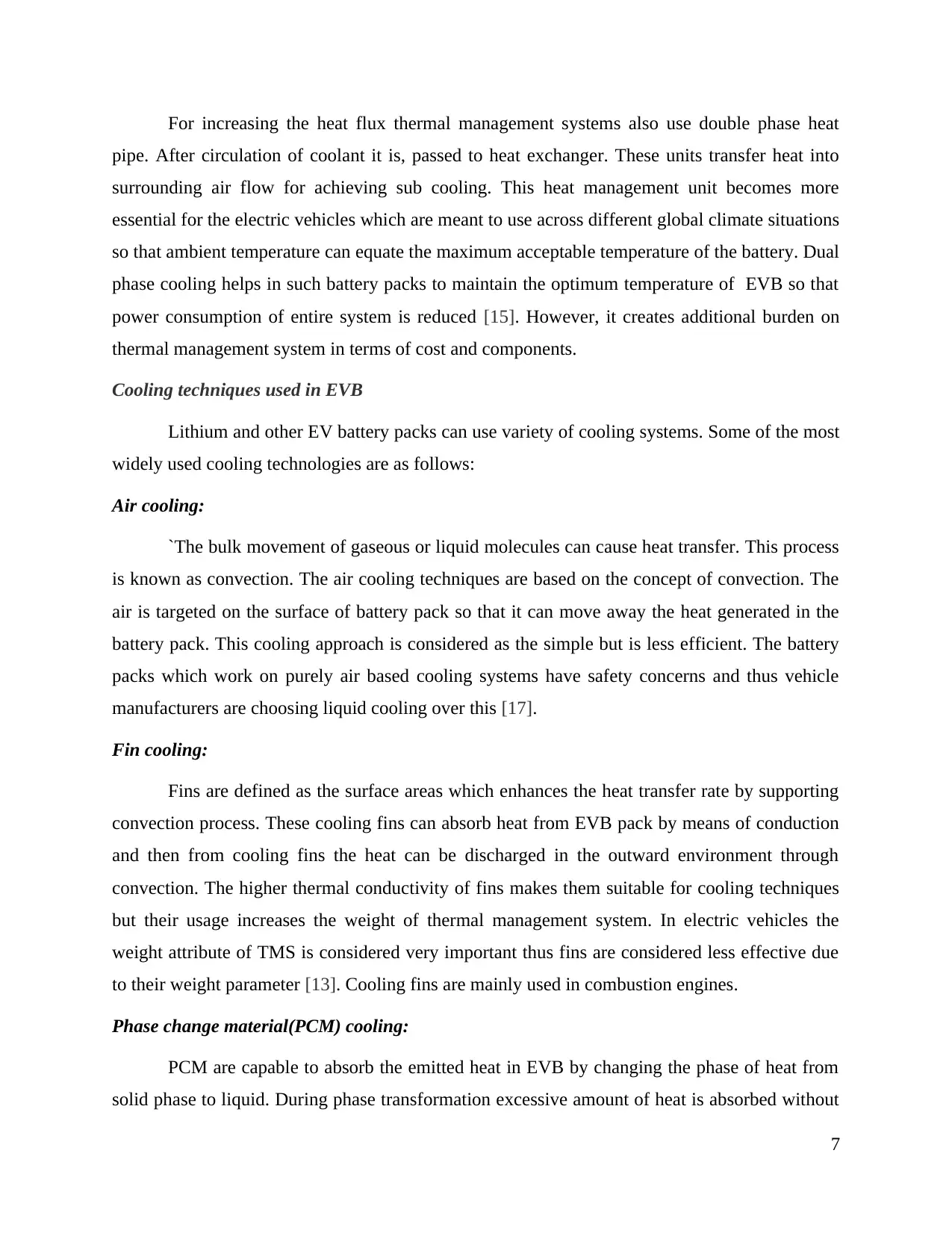
For increasing the heat flux thermal management systems also use double phase heat
pipe. After circulation of coolant it is, passed to heat exchanger. These units transfer heat into
surrounding air flow for achieving sub cooling. This heat management unit becomes more
essential for the electric vehicles which are meant to use across different global climate situations
so that ambient temperature can equate the maximum acceptable temperature of the battery. Dual
phase cooling helps in such battery packs to maintain the optimum temperature of EVB so that
power consumption of entire system is reduced [15]. However, it creates additional burden on
thermal management system in terms of cost and components.
Cooling techniques used in EVB
Lithium and other EV battery packs can use variety of cooling systems. Some of the most
widely used cooling technologies are as follows:
Air cooling:
`The bulk movement of gaseous or liquid molecules can cause heat transfer. This process
is known as convection. The air cooling techniques are based on the concept of convection. The
air is targeted on the surface of battery pack so that it can move away the heat generated in the
battery pack. This cooling approach is considered as the simple but is less efficient. The battery
packs which work on purely air based cooling systems have safety concerns and thus vehicle
manufacturers are choosing liquid cooling over this [17].
Fin cooling:
Fins are defined as the surface areas which enhances the heat transfer rate by supporting
convection process. These cooling fins can absorb heat from EVB pack by means of conduction
and then from cooling fins the heat can be discharged in the outward environment through
convection. The higher thermal conductivity of fins makes them suitable for cooling techniques
but their usage increases the weight of thermal management system. In electric vehicles the
weight attribute of TMS is considered very important thus fins are considered less effective due
to their weight parameter [13]. Cooling fins are mainly used in combustion engines.
Phase change material(PCM) cooling:
PCM are capable to absorb the emitted heat in EVB by changing the phase of heat from
solid phase to liquid. During phase transformation excessive amount of heat is absorbed without
7
pipe. After circulation of coolant it is, passed to heat exchanger. These units transfer heat into
surrounding air flow for achieving sub cooling. This heat management unit becomes more
essential for the electric vehicles which are meant to use across different global climate situations
so that ambient temperature can equate the maximum acceptable temperature of the battery. Dual
phase cooling helps in such battery packs to maintain the optimum temperature of EVB so that
power consumption of entire system is reduced [15]. However, it creates additional burden on
thermal management system in terms of cost and components.
Cooling techniques used in EVB
Lithium and other EV battery packs can use variety of cooling systems. Some of the most
widely used cooling technologies are as follows:
Air cooling:
`The bulk movement of gaseous or liquid molecules can cause heat transfer. This process
is known as convection. The air cooling techniques are based on the concept of convection. The
air is targeted on the surface of battery pack so that it can move away the heat generated in the
battery pack. This cooling approach is considered as the simple but is less efficient. The battery
packs which work on purely air based cooling systems have safety concerns and thus vehicle
manufacturers are choosing liquid cooling over this [17].
Fin cooling:
Fins are defined as the surface areas which enhances the heat transfer rate by supporting
convection process. These cooling fins can absorb heat from EVB pack by means of conduction
and then from cooling fins the heat can be discharged in the outward environment through
convection. The higher thermal conductivity of fins makes them suitable for cooling techniques
but their usage increases the weight of thermal management system. In electric vehicles the
weight attribute of TMS is considered very important thus fins are considered less effective due
to their weight parameter [13]. Cooling fins are mainly used in combustion engines.
Phase change material(PCM) cooling:
PCM are capable to absorb the emitted heat in EVB by changing the phase of heat from
solid phase to liquid. During phase transformation excessive amount of heat is absorbed without
7
⊘ This is a preview!⊘
Do you want full access?
Subscribe today to unlock all pages.

Trusted by 1+ million students worldwide
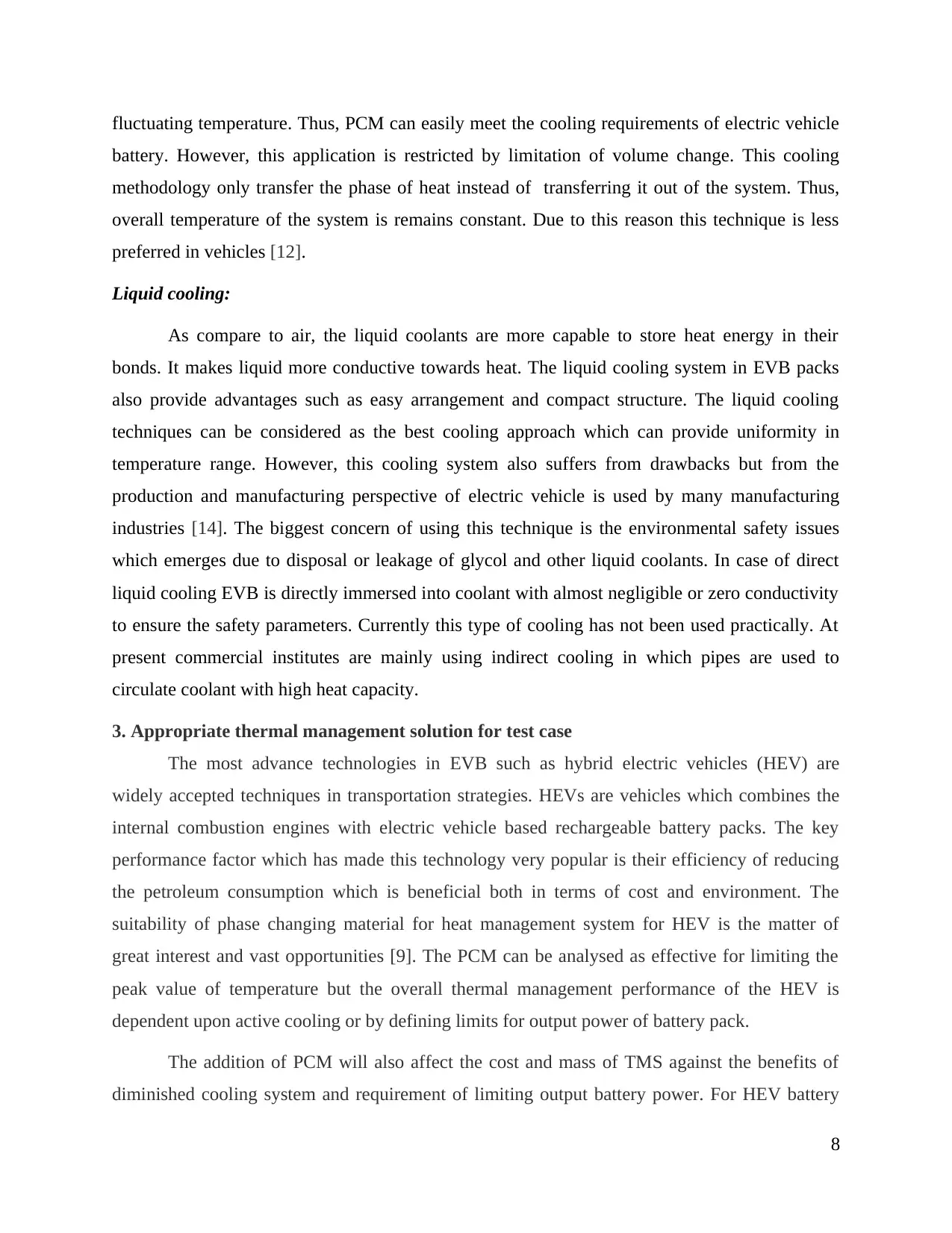
fluctuating temperature. Thus, PCM can easily meet the cooling requirements of electric vehicle
battery. However, this application is restricted by limitation of volume change. This cooling
methodology only transfer the phase of heat instead of transferring it out of the system. Thus,
overall temperature of the system is remains constant. Due to this reason this technique is less
preferred in vehicles [12].
Liquid cooling:
As compare to air, the liquid coolants are more capable to store heat energy in their
bonds. It makes liquid more conductive towards heat. The liquid cooling system in EVB packs
also provide advantages such as easy arrangement and compact structure. The liquid cooling
techniques can be considered as the best cooling approach which can provide uniformity in
temperature range. However, this cooling system also suffers from drawbacks but from the
production and manufacturing perspective of electric vehicle is used by many manufacturing
industries [14]. The biggest concern of using this technique is the environmental safety issues
which emerges due to disposal or leakage of glycol and other liquid coolants. In case of direct
liquid cooling EVB is directly immersed into coolant with almost negligible or zero conductivity
to ensure the safety parameters. Currently this type of cooling has not been used practically. At
present commercial institutes are mainly using indirect cooling in which pipes are used to
circulate coolant with high heat capacity.
3. Appropriate thermal management solution for test case
The most advance technologies in EVB such as hybrid electric vehicles (HEV) are
widely accepted techniques in transportation strategies. HEVs are vehicles which combines the
internal combustion engines with electric vehicle based rechargeable battery packs. The key
performance factor which has made this technology very popular is their efficiency of reducing
the petroleum consumption which is beneficial both in terms of cost and environment. The
suitability of phase changing material for heat management system for HEV is the matter of
great interest and vast opportunities [9]. The PCM can be analysed as effective for limiting the
peak value of temperature but the overall thermal management performance of the HEV is
dependent upon active cooling or by defining limits for output power of battery pack.
The addition of PCM will also affect the cost and mass of TMS against the benefits of
diminished cooling system and requirement of limiting output battery power. For HEV battery
8
battery. However, this application is restricted by limitation of volume change. This cooling
methodology only transfer the phase of heat instead of transferring it out of the system. Thus,
overall temperature of the system is remains constant. Due to this reason this technique is less
preferred in vehicles [12].
Liquid cooling:
As compare to air, the liquid coolants are more capable to store heat energy in their
bonds. It makes liquid more conductive towards heat. The liquid cooling system in EVB packs
also provide advantages such as easy arrangement and compact structure. The liquid cooling
techniques can be considered as the best cooling approach which can provide uniformity in
temperature range. However, this cooling system also suffers from drawbacks but from the
production and manufacturing perspective of electric vehicle is used by many manufacturing
industries [14]. The biggest concern of using this technique is the environmental safety issues
which emerges due to disposal or leakage of glycol and other liquid coolants. In case of direct
liquid cooling EVB is directly immersed into coolant with almost negligible or zero conductivity
to ensure the safety parameters. Currently this type of cooling has not been used practically. At
present commercial institutes are mainly using indirect cooling in which pipes are used to
circulate coolant with high heat capacity.
3. Appropriate thermal management solution for test case
The most advance technologies in EVB such as hybrid electric vehicles (HEV) are
widely accepted techniques in transportation strategies. HEVs are vehicles which combines the
internal combustion engines with electric vehicle based rechargeable battery packs. The key
performance factor which has made this technology very popular is their efficiency of reducing
the petroleum consumption which is beneficial both in terms of cost and environment. The
suitability of phase changing material for heat management system for HEV is the matter of
great interest and vast opportunities [9]. The PCM can be analysed as effective for limiting the
peak value of temperature but the overall thermal management performance of the HEV is
dependent upon active cooling or by defining limits for output power of battery pack.
The addition of PCM will also affect the cost and mass of TMS against the benefits of
diminished cooling system and requirement of limiting output battery power. For HEV battery
8
Paraphrase This Document
Need a fresh take? Get an instant paraphrase of this document with our AI Paraphraser
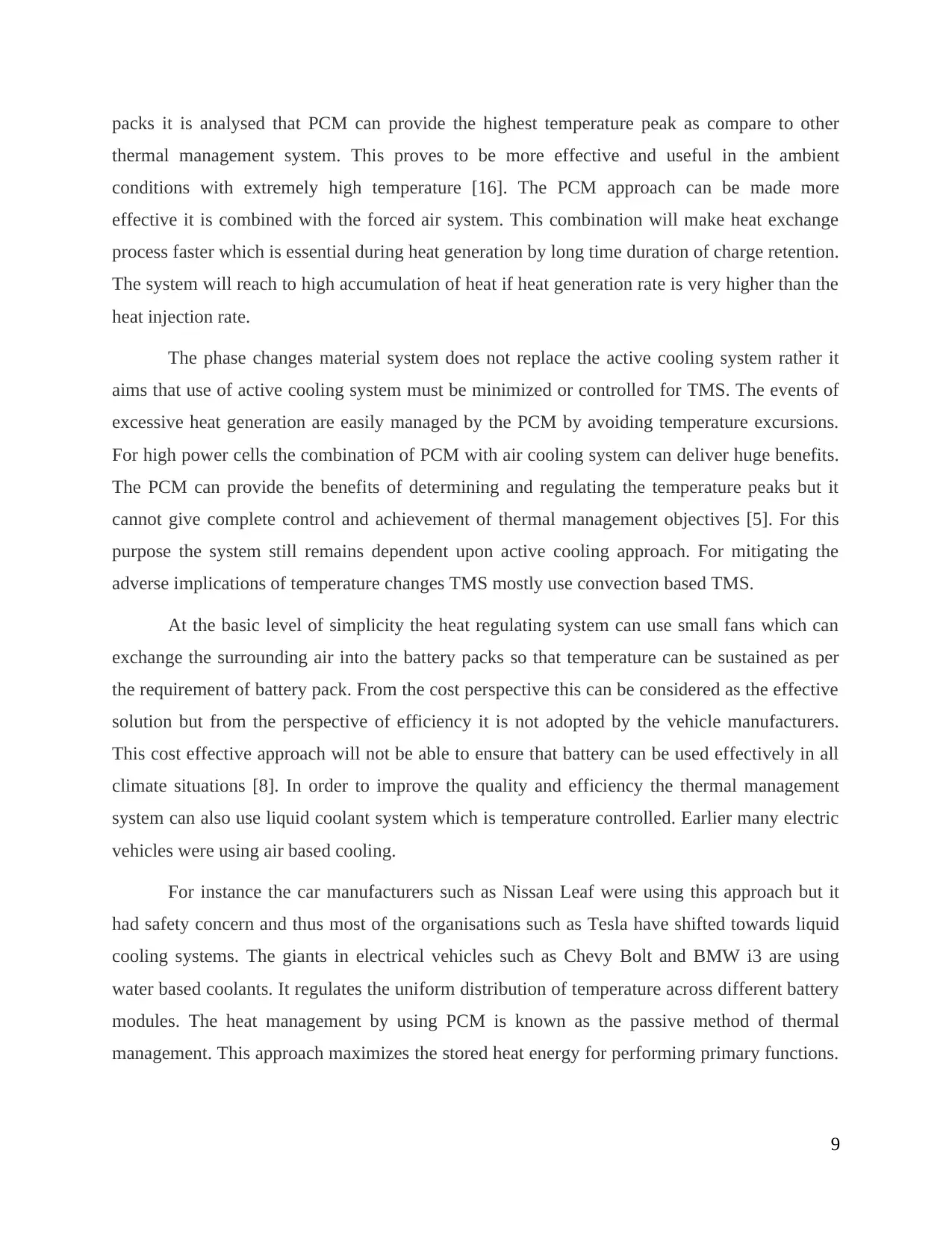
packs it is analysed that PCM can provide the highest temperature peak as compare to other
thermal management system. This proves to be more effective and useful in the ambient
conditions with extremely high temperature [16]. The PCM approach can be made more
effective it is combined with the forced air system. This combination will make heat exchange
process faster which is essential during heat generation by long time duration of charge retention.
The system will reach to high accumulation of heat if heat generation rate is very higher than the
heat injection rate.
The phase changes material system does not replace the active cooling system rather it
aims that use of active cooling system must be minimized or controlled for TMS. The events of
excessive heat generation are easily managed by the PCM by avoiding temperature excursions.
For high power cells the combination of PCM with air cooling system can deliver huge benefits.
The PCM can provide the benefits of determining and regulating the temperature peaks but it
cannot give complete control and achievement of thermal management objectives [5]. For this
purpose the system still remains dependent upon active cooling approach. For mitigating the
adverse implications of temperature changes TMS mostly use convection based TMS.
At the basic level of simplicity the heat regulating system can use small fans which can
exchange the surrounding air into the battery packs so that temperature can be sustained as per
the requirement of battery pack. From the cost perspective this can be considered as the effective
solution but from the perspective of efficiency it is not adopted by the vehicle manufacturers.
This cost effective approach will not be able to ensure that battery can be used effectively in all
climate situations [8]. In order to improve the quality and efficiency the thermal management
system can also use liquid coolant system which is temperature controlled. Earlier many electric
vehicles were using air based cooling.
For instance the car manufacturers such as Nissan Leaf were using this approach but it
had safety concern and thus most of the organisations such as Tesla have shifted towards liquid
cooling systems. The giants in electrical vehicles such as Chevy Bolt and BMW i3 are using
water based coolants. It regulates the uniform distribution of temperature across different battery
modules. The heat management by using PCM is known as the passive method of thermal
management. This approach maximizes the stored heat energy for performing primary functions.
9
thermal management system. This proves to be more effective and useful in the ambient
conditions with extremely high temperature [16]. The PCM approach can be made more
effective it is combined with the forced air system. This combination will make heat exchange
process faster which is essential during heat generation by long time duration of charge retention.
The system will reach to high accumulation of heat if heat generation rate is very higher than the
heat injection rate.
The phase changes material system does not replace the active cooling system rather it
aims that use of active cooling system must be minimized or controlled for TMS. The events of
excessive heat generation are easily managed by the PCM by avoiding temperature excursions.
For high power cells the combination of PCM with air cooling system can deliver huge benefits.
The PCM can provide the benefits of determining and regulating the temperature peaks but it
cannot give complete control and achievement of thermal management objectives [5]. For this
purpose the system still remains dependent upon active cooling approach. For mitigating the
adverse implications of temperature changes TMS mostly use convection based TMS.
At the basic level of simplicity the heat regulating system can use small fans which can
exchange the surrounding air into the battery packs so that temperature can be sustained as per
the requirement of battery pack. From the cost perspective this can be considered as the effective
solution but from the perspective of efficiency it is not adopted by the vehicle manufacturers.
This cost effective approach will not be able to ensure that battery can be used effectively in all
climate situations [8]. In order to improve the quality and efficiency the thermal management
system can also use liquid coolant system which is temperature controlled. Earlier many electric
vehicles were using air based cooling.
For instance the car manufacturers such as Nissan Leaf were using this approach but it
had safety concern and thus most of the organisations such as Tesla have shifted towards liquid
cooling systems. The giants in electrical vehicles such as Chevy Bolt and BMW i3 are using
water based coolants. It regulates the uniform distribution of temperature across different battery
modules. The heat management by using PCM is known as the passive method of thermal
management. This approach maximizes the stored heat energy for performing primary functions.
9
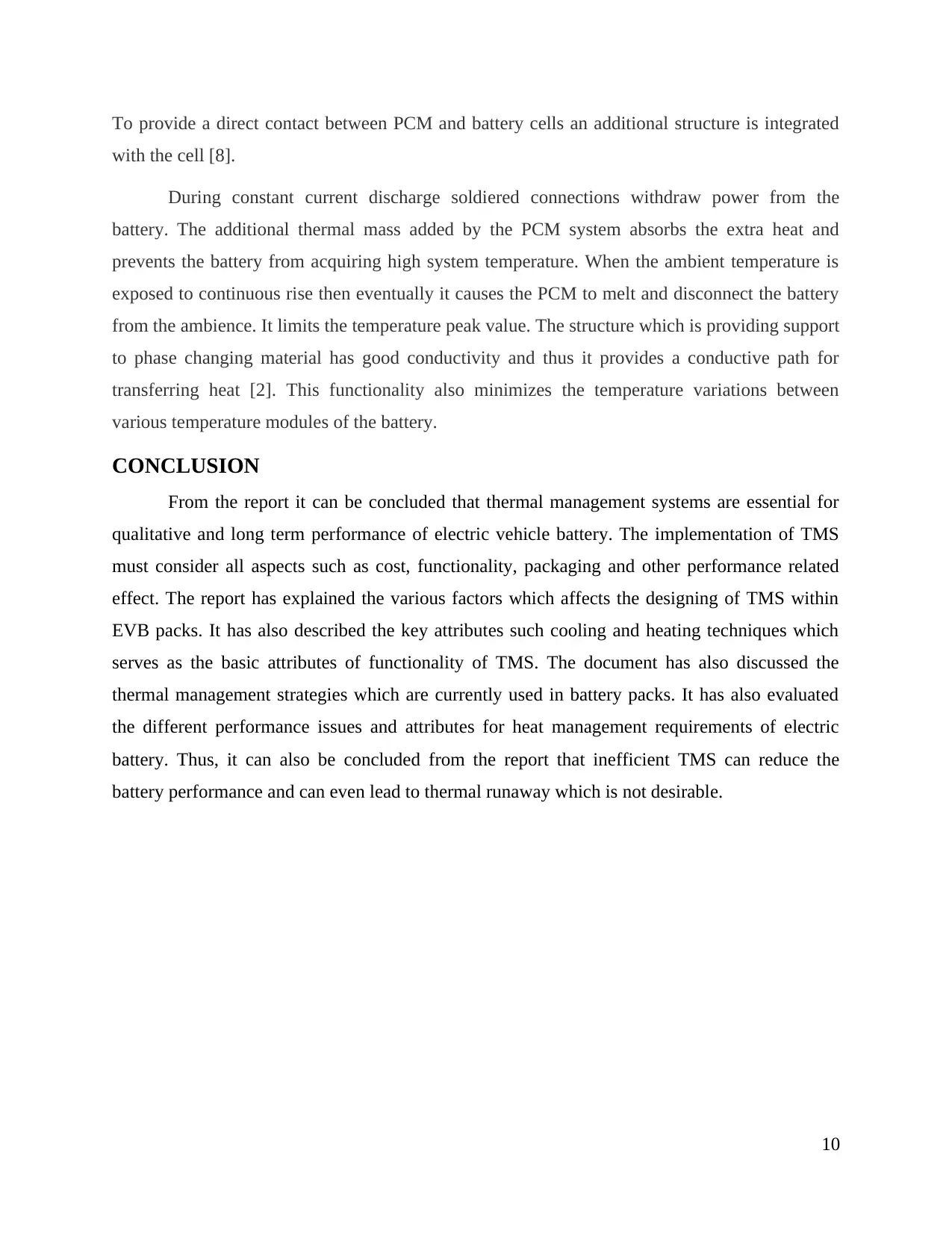
To provide a direct contact between PCM and battery cells an additional structure is integrated
with the cell [8].
During constant current discharge soldiered connections withdraw power from the
battery. The additional thermal mass added by the PCM system absorbs the extra heat and
prevents the battery from acquiring high system temperature. When the ambient temperature is
exposed to continuous rise then eventually it causes the PCM to melt and disconnect the battery
from the ambience. It limits the temperature peak value. The structure which is providing support
to phase changing material has good conductivity and thus it provides a conductive path for
transferring heat [2]. This functionality also minimizes the temperature variations between
various temperature modules of the battery.
CONCLUSION
From the report it can be concluded that thermal management systems are essential for
qualitative and long term performance of electric vehicle battery. The implementation of TMS
must consider all aspects such as cost, functionality, packaging and other performance related
effect. The report has explained the various factors which affects the designing of TMS within
EVB packs. It has also described the key attributes such cooling and heating techniques which
serves as the basic attributes of functionality of TMS. The document has also discussed the
thermal management strategies which are currently used in battery packs. It has also evaluated
the different performance issues and attributes for heat management requirements of electric
battery. Thus, it can also be concluded from the report that inefficient TMS can reduce the
battery performance and can even lead to thermal runaway which is not desirable.
10
with the cell [8].
During constant current discharge soldiered connections withdraw power from the
battery. The additional thermal mass added by the PCM system absorbs the extra heat and
prevents the battery from acquiring high system temperature. When the ambient temperature is
exposed to continuous rise then eventually it causes the PCM to melt and disconnect the battery
from the ambience. It limits the temperature peak value. The structure which is providing support
to phase changing material has good conductivity and thus it provides a conductive path for
transferring heat [2]. This functionality also minimizes the temperature variations between
various temperature modules of the battery.
CONCLUSION
From the report it can be concluded that thermal management systems are essential for
qualitative and long term performance of electric vehicle battery. The implementation of TMS
must consider all aspects such as cost, functionality, packaging and other performance related
effect. The report has explained the various factors which affects the designing of TMS within
EVB packs. It has also described the key attributes such cooling and heating techniques which
serves as the basic attributes of functionality of TMS. The document has also discussed the
thermal management strategies which are currently used in battery packs. It has also evaluated
the different performance issues and attributes for heat management requirements of electric
battery. Thus, it can also be concluded from the report that inefficient TMS can reduce the
battery performance and can even lead to thermal runaway which is not desirable.
10
⊘ This is a preview!⊘
Do you want full access?
Subscribe today to unlock all pages.

Trusted by 1+ million students worldwide
1 out of 15