Thermodynamic Analysis of Pumps: Performance and Analysis Report
VerifiedAdded on 2023/01/23
|8
|1784
|97
Report
AI Summary
This report provides a detailed thermodynamic analysis of pumps, beginning with an introduction to their function and applications across various industries. It explores different pump types, with a focus on centrifugal pumps, and details key components like impellers, pump shafts, and bearings. The r...
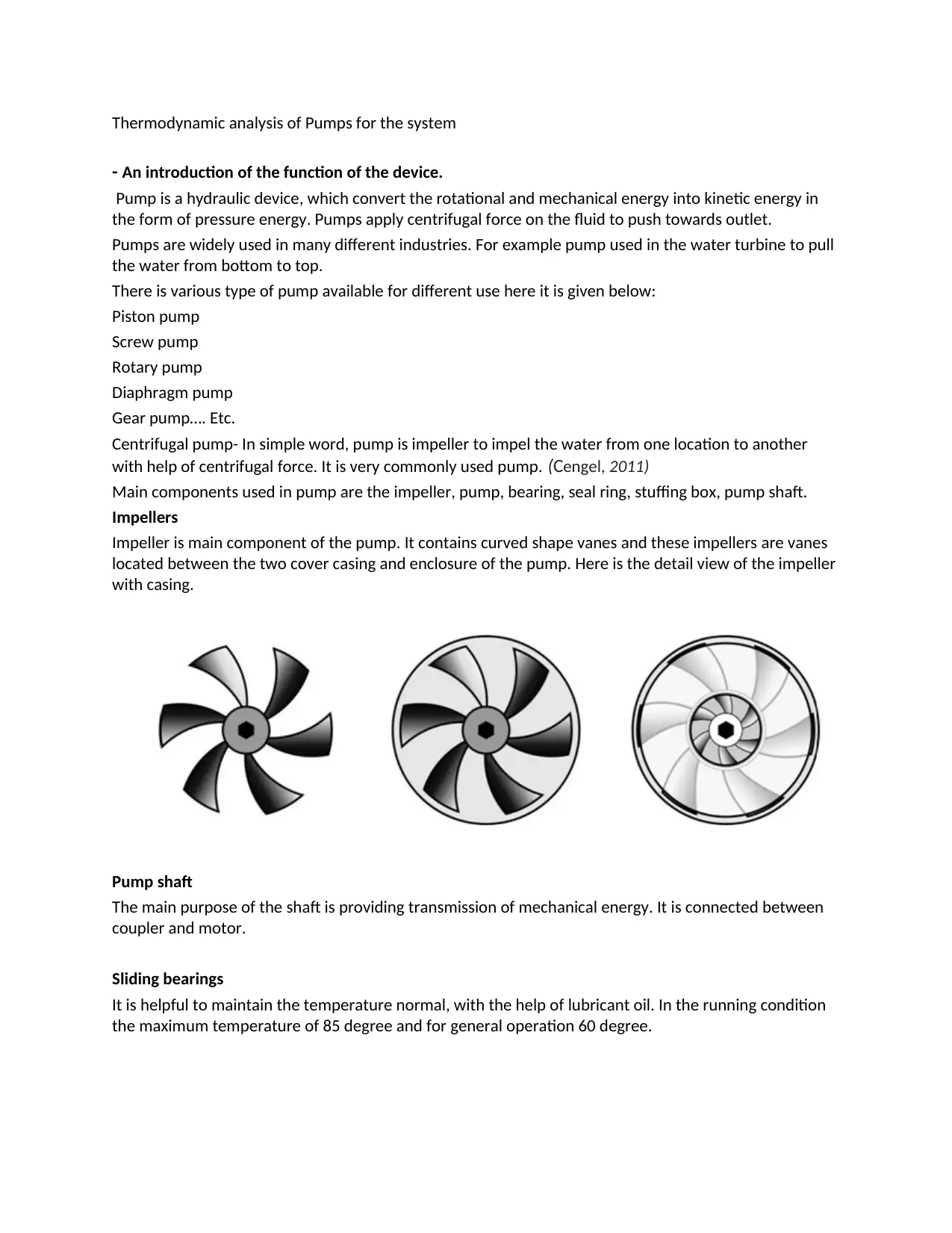
Thermodynamic analysis of Pumps for the system
- An introduction of the function of the device.
Pump is a hydraulic device, which convert the rotational and mechanical energy into kinetic energy in
the form of pressure energy. Pumps apply centrifugal force on the fluid to push towards outlet.
Pumps are widely used in many different industries. For example pump used in the water turbine to pull
the water from bottom to top.
There is various type of pump available for different use here it is given below:
Piston pump
Screw pump
Rotary pump
Diaphragm pump
Gear pump…. Etc.
Centrifugal pump- In simple word, pump is impeller to impel the water from one location to another
with help of centrifugal force. It is very commonly used pump. (Cengel, 2011)
Main components used in pump are the impeller, pump, bearing, seal ring, stuffing box, pump shaft.
Impellers
Impeller is main component of the pump. It contains curved shape vanes and these impellers are vanes
located between the two cover casing and enclosure of the pump. Here is the detail view of the impeller
with casing.
Pump shaft
The main purpose of the shaft is providing transmission of mechanical energy. It is connected between
coupler and motor.
Sliding bearings
It is helpful to maintain the temperature normal, with the help of lubricant oil. In the running condition
the maximum temperature of 85 degree and for general operation 60 degree.
- An introduction of the function of the device.
Pump is a hydraulic device, which convert the rotational and mechanical energy into kinetic energy in
the form of pressure energy. Pumps apply centrifugal force on the fluid to push towards outlet.
Pumps are widely used in many different industries. For example pump used in the water turbine to pull
the water from bottom to top.
There is various type of pump available for different use here it is given below:
Piston pump
Screw pump
Rotary pump
Diaphragm pump
Gear pump…. Etc.
Centrifugal pump- In simple word, pump is impeller to impel the water from one location to another
with help of centrifugal force. It is very commonly used pump. (Cengel, 2011)
Main components used in pump are the impeller, pump, bearing, seal ring, stuffing box, pump shaft.
Impellers
Impeller is main component of the pump. It contains curved shape vanes and these impellers are vanes
located between the two cover casing and enclosure of the pump. Here is the detail view of the impeller
with casing.
Pump shaft
The main purpose of the shaft is providing transmission of mechanical energy. It is connected between
coupler and motor.
Sliding bearings
It is helpful to maintain the temperature normal, with the help of lubricant oil. In the running condition
the maximum temperature of 85 degree and for general operation 60 degree.
Paraphrase This Document
Need a fresh take? Get an instant paraphrase of this document with our AI Paraphraser
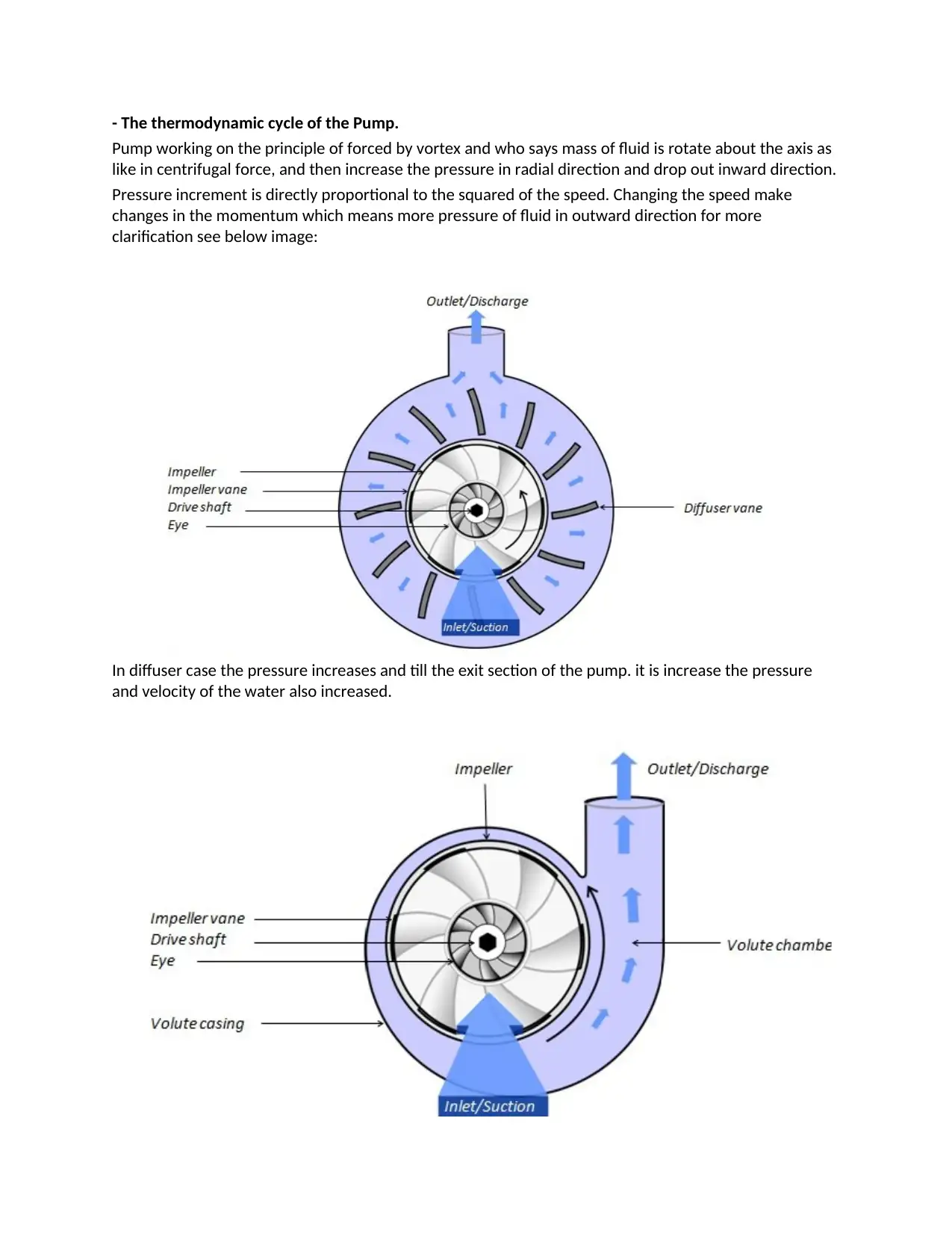
- The thermodynamic cycle of the Pump.
Pump working on the principle of forced by vortex and who says mass of fluid is rotate about the axis as
like in centrifugal force, and then increase the pressure in radial direction and drop out inward direction.
Pressure increment is directly proportional to the squared of the speed. Changing the speed make
changes in the momentum which means more pressure of fluid in outward direction for more
clarification see below image:
In diffuser case the pressure increases and till the exit section of the pump. it is increase the pressure
and velocity of the water also increased.
Pump working on the principle of forced by vortex and who says mass of fluid is rotate about the axis as
like in centrifugal force, and then increase the pressure in radial direction and drop out inward direction.
Pressure increment is directly proportional to the squared of the speed. Changing the speed make
changes in the momentum which means more pressure of fluid in outward direction for more
clarification see below image:
In diffuser case the pressure increases and till the exit section of the pump. it is increase the pressure
and velocity of the water also increased.
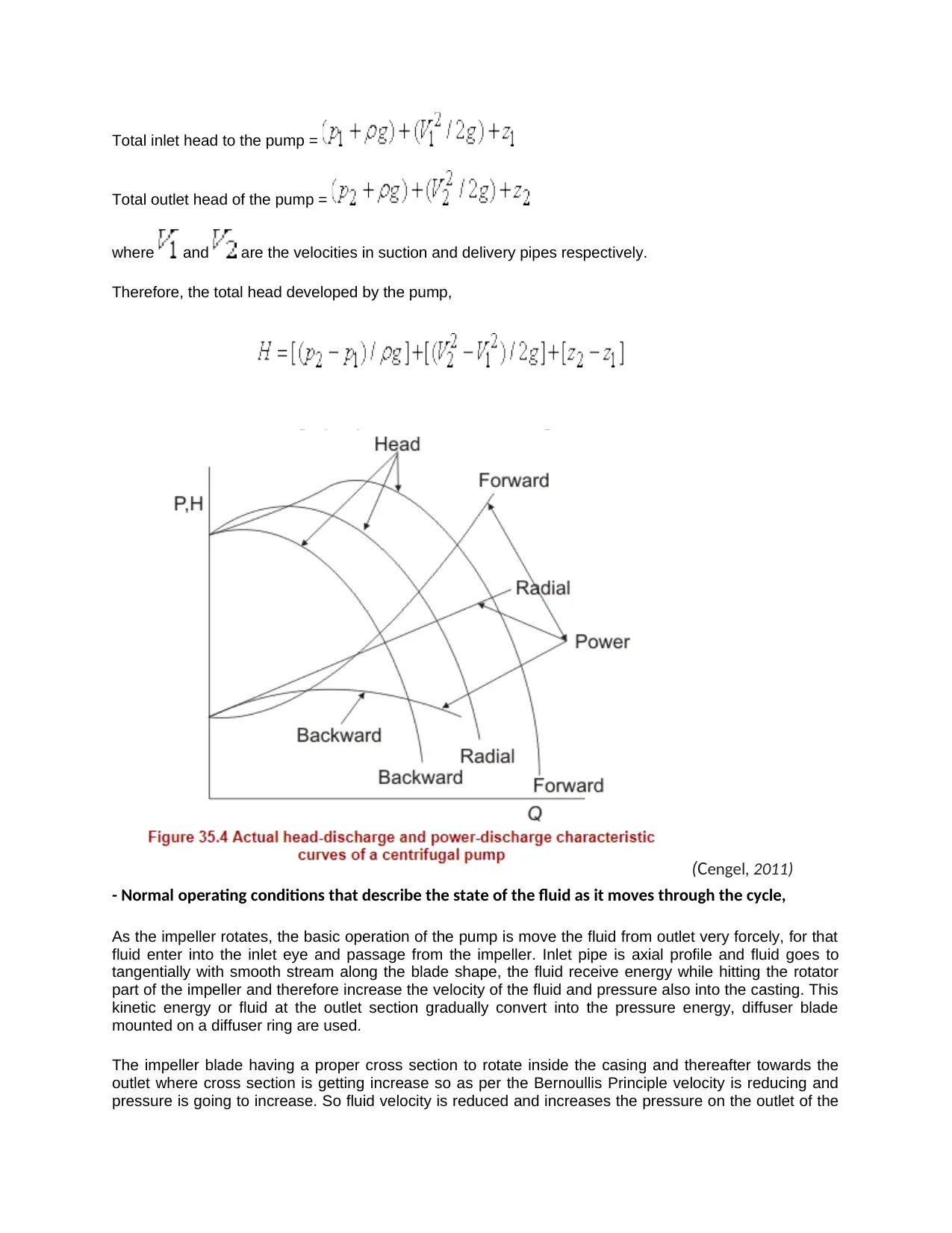
Total inlet head to the pump =
Total outlet head of the pump =
where and are the velocities in suction and delivery pipes respectively.
Therefore, the total head developed by the pump,
(Cengel, 2011)
- Normal operating conditions that describe the state of the fluid as it moves through the cycle,
As the impeller rotates, the basic operation of the pump is move the fluid from outlet very forcely, for that
fluid enter into the inlet eye and passage from the impeller. Inlet pipe is axial profile and fluid goes to
tangentially with smooth stream along the blade shape, the fluid receive energy while hitting the rotator
part of the impeller and therefore increase the velocity of the fluid and pressure also into the casting. This
kinetic energy or fluid at the outlet section gradually convert into the pressure energy, diffuser blade
mounted on a diffuser ring are used.
The impeller blade having a proper cross section to rotate inside the casing and thereafter towards the
outlet where cross section is getting increase so as per the Bernoullis Principle velocity is reducing and
pressure is going to increase. So fluid velocity is reduced and increases the pressure on the outlet of the
Total outlet head of the pump =
where and are the velocities in suction and delivery pipes respectively.
Therefore, the total head developed by the pump,
(Cengel, 2011)
- Normal operating conditions that describe the state of the fluid as it moves through the cycle,
As the impeller rotates, the basic operation of the pump is move the fluid from outlet very forcely, for that
fluid enter into the inlet eye and passage from the impeller. Inlet pipe is axial profile and fluid goes to
tangentially with smooth stream along the blade shape, the fluid receive energy while hitting the rotator
part of the impeller and therefore increase the velocity of the fluid and pressure also into the casting. This
kinetic energy or fluid at the outlet section gradually convert into the pressure energy, diffuser blade
mounted on a diffuser ring are used.
The impeller blade having a proper cross section to rotate inside the casing and thereafter towards the
outlet where cross section is getting increase so as per the Bernoullis Principle velocity is reducing and
pressure is going to increase. So fluid velocity is reduced and increases the pressure on the outlet of the
⊘ This is a preview!⊘
Do you want full access?
Subscribe today to unlock all pages.

Trusted by 1+ million students worldwide
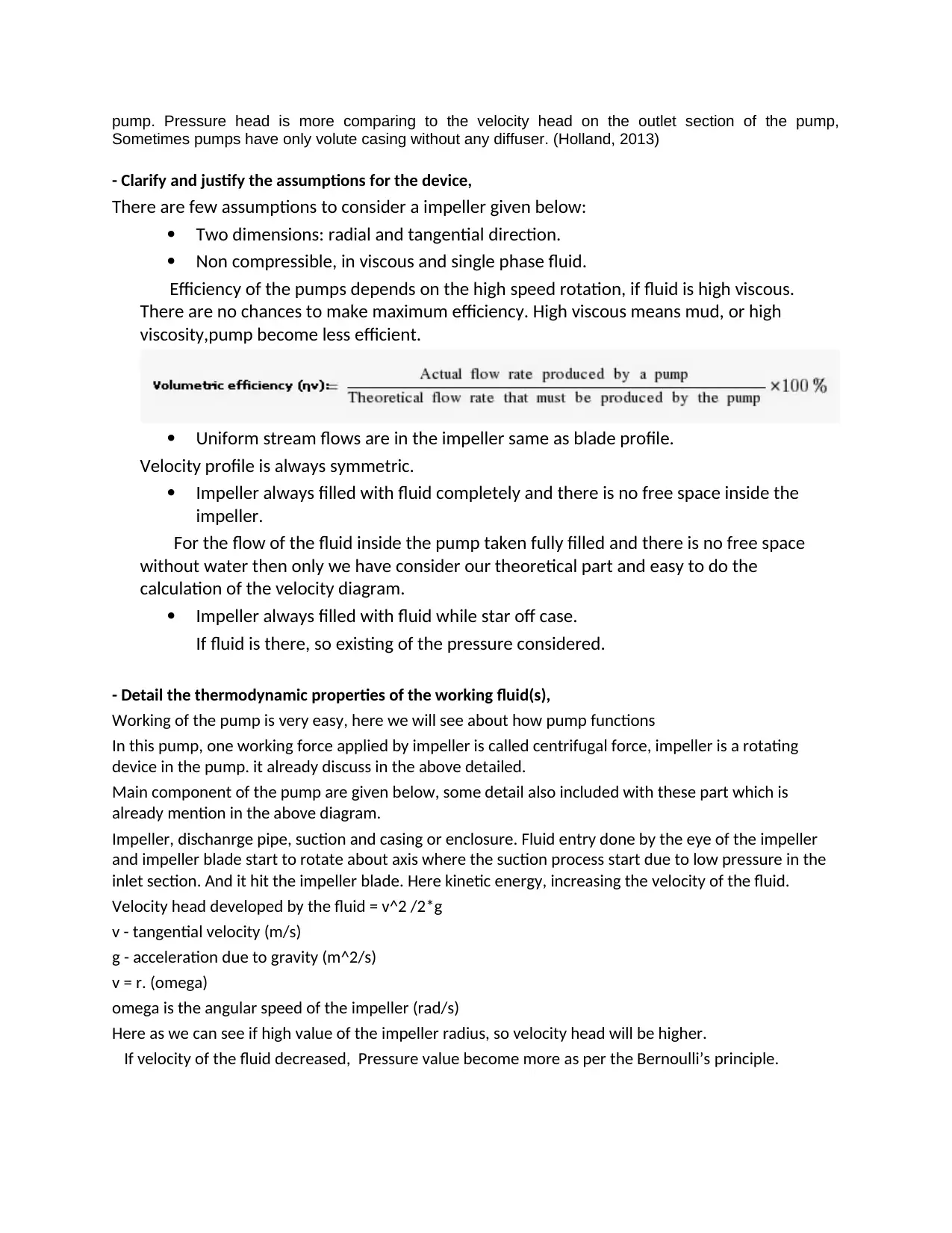
pump. Pressure head is more comparing to the velocity head on the outlet section of the pump,
Sometimes pumps have only volute casing without any diffuser. (Holland, 2013)
- Clarify and justify the assumptions for the device,
There are few assumptions to consider a impeller given below:
Two dimensions: radial and tangential direction.
Non compressible, in viscous and single phase fluid.
Efficiency of the pumps depends on the high speed rotation, if fluid is high viscous.
There are no chances to make maximum efficiency. High viscous means mud, or high
viscosity,pump become less efficient.
Uniform stream flows are in the impeller same as blade profile.
Velocity profile is always symmetric.
Impeller always filled with fluid completely and there is no free space inside the
impeller.
For the flow of the fluid inside the pump taken fully filled and there is no free space
without water then only we have consider our theoretical part and easy to do the
calculation of the velocity diagram.
Impeller always filled with fluid while star off case.
If fluid is there, so existing of the pressure considered.
- Detail the thermodynamic properties of the working fluid(s),
Working of the pump is very easy, here we will see about how pump functions
In this pump, one working force applied by impeller is called centrifugal force, impeller is a rotating
device in the pump. it already discuss in the above detailed.
Main component of the pump are given below, some detail also included with these part which is
already mention in the above diagram.
Impeller, dischanrge pipe, suction and casing or enclosure. Fluid entry done by the eye of the impeller
and impeller blade start to rotate about axis where the suction process start due to low pressure in the
inlet section. And it hit the impeller blade. Here kinetic energy, increasing the velocity of the fluid.
Velocity head developed by the fluid = v^2 /2*g
v - tangential velocity (m/s)
g - acceleration due to gravity (m^2/s)
v = r. (omega)
omega is the angular speed of the impeller (rad/s)
Here as we can see if high value of the impeller radius, so velocity head will be higher.
If velocity of the fluid decreased, Pressure value become more as per the Bernoulli’s principle.
Sometimes pumps have only volute casing without any diffuser. (Holland, 2013)
- Clarify and justify the assumptions for the device,
There are few assumptions to consider a impeller given below:
Two dimensions: radial and tangential direction.
Non compressible, in viscous and single phase fluid.
Efficiency of the pumps depends on the high speed rotation, if fluid is high viscous.
There are no chances to make maximum efficiency. High viscous means mud, or high
viscosity,pump become less efficient.
Uniform stream flows are in the impeller same as blade profile.
Velocity profile is always symmetric.
Impeller always filled with fluid completely and there is no free space inside the
impeller.
For the flow of the fluid inside the pump taken fully filled and there is no free space
without water then only we have consider our theoretical part and easy to do the
calculation of the velocity diagram.
Impeller always filled with fluid while star off case.
If fluid is there, so existing of the pressure considered.
- Detail the thermodynamic properties of the working fluid(s),
Working of the pump is very easy, here we will see about how pump functions
In this pump, one working force applied by impeller is called centrifugal force, impeller is a rotating
device in the pump. it already discuss in the above detailed.
Main component of the pump are given below, some detail also included with these part which is
already mention in the above diagram.
Impeller, dischanrge pipe, suction and casing or enclosure. Fluid entry done by the eye of the impeller
and impeller blade start to rotate about axis where the suction process start due to low pressure in the
inlet section. And it hit the impeller blade. Here kinetic energy, increasing the velocity of the fluid.
Velocity head developed by the fluid = v^2 /2*g
v - tangential velocity (m/s)
g - acceleration due to gravity (m^2/s)
v = r. (omega)
omega is the angular speed of the impeller (rad/s)
Here as we can see if high value of the impeller radius, so velocity head will be higher.
If velocity of the fluid decreased, Pressure value become more as per the Bernoulli’s principle.
Paraphrase This Document
Need a fresh take? Get an instant paraphrase of this document with our AI Paraphraser

(Nag P.K.,
2010)
In this above chart they explained the velocity diagram on the blade profile of the impeller. Where Cm1 is
the inlet section and Cm2 is outlet area of the impeller cutting section. There are Known 3 operational
parameters used in the reference:
1. pump blade geometry, Angle, b
2. rotational speed, Tangential velocity, U
3. flow rate. Radial velocity, vr (about impeller) (Nag P.K., 2010)
- Identify the relevant ‘actual’ performance characteristics at the inlet(s) and outlet(s) of the
equipment from the system schematic document,
If we consider impeller is fully filled and both entry and exit are closed, and rotation of impeller about
the axis, need circulation on that place, but flow will oppose the rotation of the impeller, in this case
velocity will be less or reduce at the outlet section but in inlet it will be higher. (Donald T., 2009)
(Donald T., 2009)
Exit Velocity
Triangle
Entrance Velocity
Triangle
Theoretical
diagram
Diagram with
recirculation
2010)
In this above chart they explained the velocity diagram on the blade profile of the impeller. Where Cm1 is
the inlet section and Cm2 is outlet area of the impeller cutting section. There are Known 3 operational
parameters used in the reference:
1. pump blade geometry, Angle, b
2. rotational speed, Tangential velocity, U
3. flow rate. Radial velocity, vr (about impeller) (Nag P.K., 2010)
- Identify the relevant ‘actual’ performance characteristics at the inlet(s) and outlet(s) of the
equipment from the system schematic document,
If we consider impeller is fully filled and both entry and exit are closed, and rotation of impeller about
the axis, need circulation on that place, but flow will oppose the rotation of the impeller, in this case
velocity will be less or reduce at the outlet section but in inlet it will be higher. (Donald T., 2009)
(Donald T., 2009)
Exit Velocity
Triangle
Entrance Velocity
Triangle
Theoretical
diagram
Diagram with
recirculation
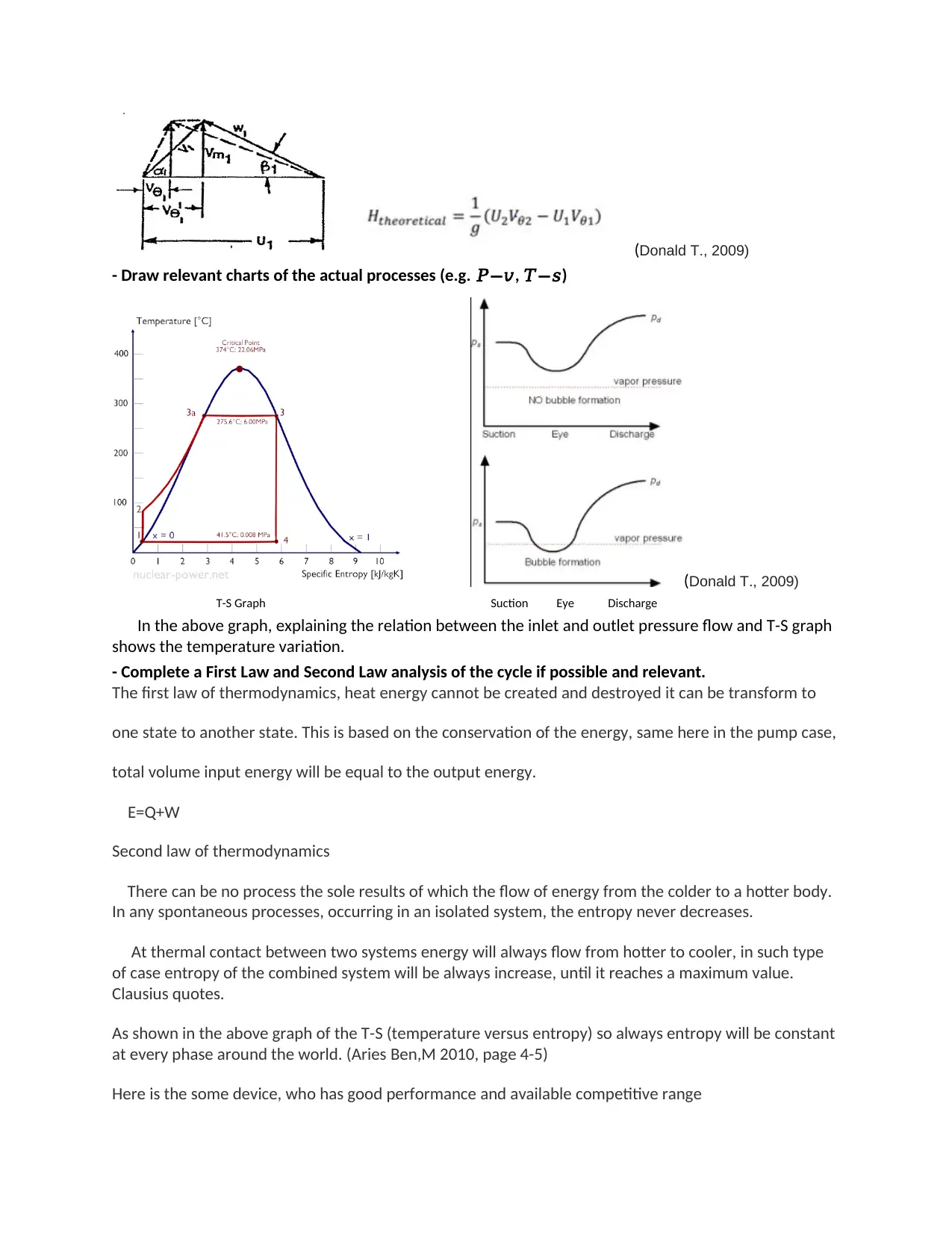
(Donald T., 2009)
- Draw relevant charts of the actual processes (e.g. 𝑃−𝑣, 𝑇−𝑠)
(Donald T., 2009)
T-S Graph Suction Eye Discharge
In the above graph, explaining the relation between the inlet and outlet pressure flow and T-S graph
shows the temperature variation.
- Complete a First Law and Second Law analysis of the cycle if possible and relevant.
The first law of thermodynamics, heat energy cannot be created and destroyed it can be transform to
one state to another state. This is based on the conservation of the energy, same here in the pump case,
total volume input energy will be equal to the output energy.
E=Q+W
Second law of thermodynamics
There can be no process the sole results of which the flow of energy from the colder to a hotter body.
In any spontaneous processes, occurring in an isolated system, the entropy never decreases.
At thermal contact between two systems energy will always flow from hotter to cooler, in such type
of case entropy of the combined system will be always increase, until it reaches a maximum value.
Clausius quotes.
As shown in the above graph of the T-S (temperature versus entropy) so always entropy will be constant
at every phase around the world. (Aries Ben,M 2010, page 4-5)
Here is the some device, who has good performance and available competitive range
- Draw relevant charts of the actual processes (e.g. 𝑃−𝑣, 𝑇−𝑠)
(Donald T., 2009)
T-S Graph Suction Eye Discharge
In the above graph, explaining the relation between the inlet and outlet pressure flow and T-S graph
shows the temperature variation.
- Complete a First Law and Second Law analysis of the cycle if possible and relevant.
The first law of thermodynamics, heat energy cannot be created and destroyed it can be transform to
one state to another state. This is based on the conservation of the energy, same here in the pump case,
total volume input energy will be equal to the output energy.
E=Q+W
Second law of thermodynamics
There can be no process the sole results of which the flow of energy from the colder to a hotter body.
In any spontaneous processes, occurring in an isolated system, the entropy never decreases.
At thermal contact between two systems energy will always flow from hotter to cooler, in such type
of case entropy of the combined system will be always increase, until it reaches a maximum value.
Clausius quotes.
As shown in the above graph of the T-S (temperature versus entropy) so always entropy will be constant
at every phase around the world. (Aries Ben,M 2010, page 4-5)
Here is the some device, who has good performance and available competitive range
⊘ This is a preview!⊘
Do you want full access?
Subscribe today to unlock all pages.

Trusted by 1+ million students worldwide
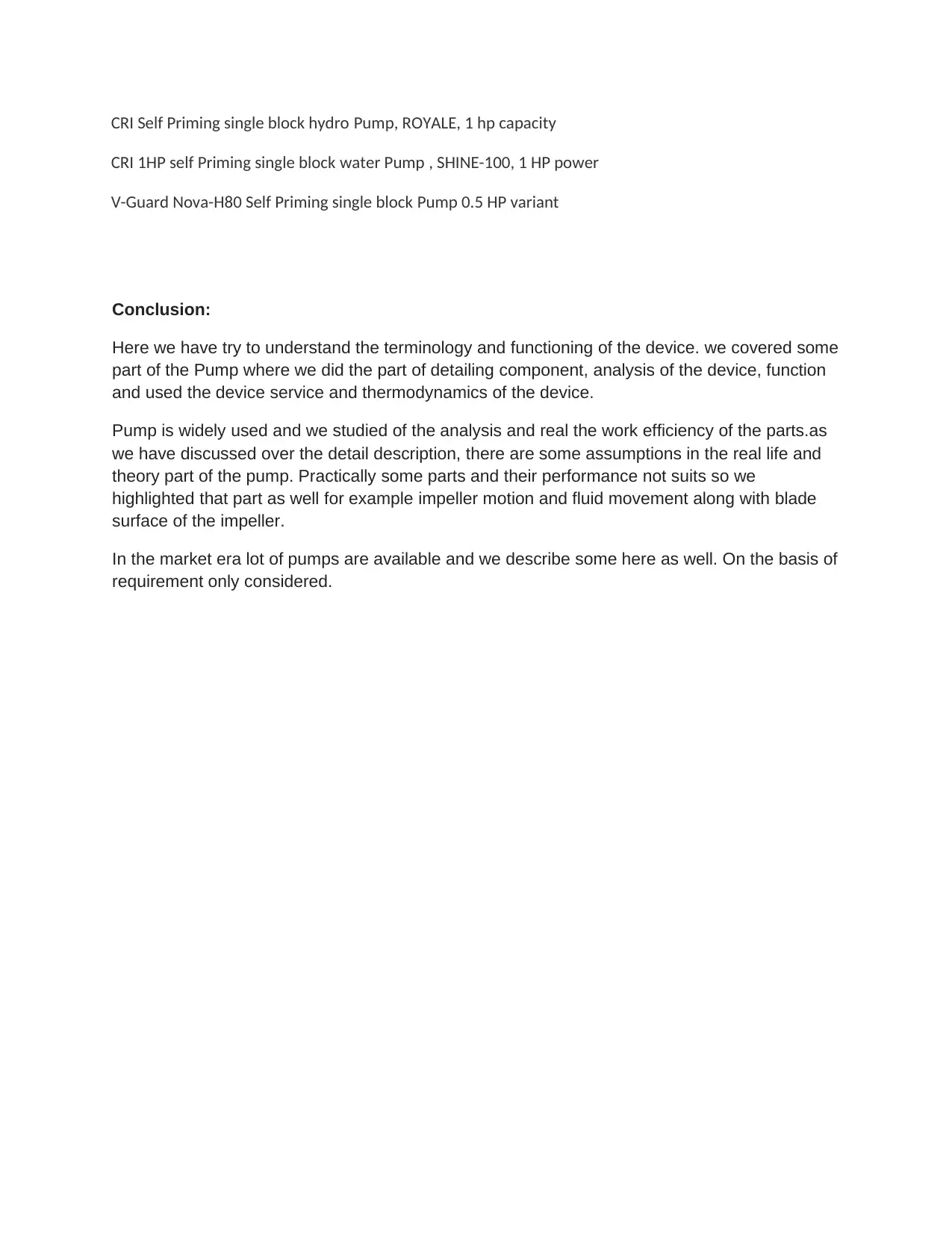
CRI Self Priming single block hydro Pump, ROYALE, 1 hp capacity
CRI 1HP self Priming single block water Pump , SHINE-100, 1 HP power
V-Guard Nova-H80 Self Priming single block Pump 0.5 HP variant
Conclusion:
Here we have try to understand the terminology and functioning of the device. we covered some
part of the Pump where we did the part of detailing component, analysis of the device, function
and used the device service and thermodynamics of the device.
Pump is widely used and we studied of the analysis and real the work efficiency of the parts.as
we have discussed over the detail description, there are some assumptions in the real life and
theory part of the pump. Practically some parts and their performance not suits so we
highlighted that part as well for example impeller motion and fluid movement along with blade
surface of the impeller.
In the market era lot of pumps are available and we describe some here as well. On the basis of
requirement only considered.
CRI 1HP self Priming single block water Pump , SHINE-100, 1 HP power
V-Guard Nova-H80 Self Priming single block Pump 0.5 HP variant
Conclusion:
Here we have try to understand the terminology and functioning of the device. we covered some
part of the Pump where we did the part of detailing component, analysis of the device, function
and used the device service and thermodynamics of the device.
Pump is widely used and we studied of the analysis and real the work efficiency of the parts.as
we have discussed over the detail description, there are some assumptions in the real life and
theory part of the pump. Practically some parts and their performance not suits so we
highlighted that part as well for example impeller motion and fluid movement along with blade
surface of the impeller.
In the market era lot of pumps are available and we describe some here as well. On the basis of
requirement only considered.
Paraphrase This Document
Need a fresh take? Get an instant paraphrase of this document with our AI Paraphraser
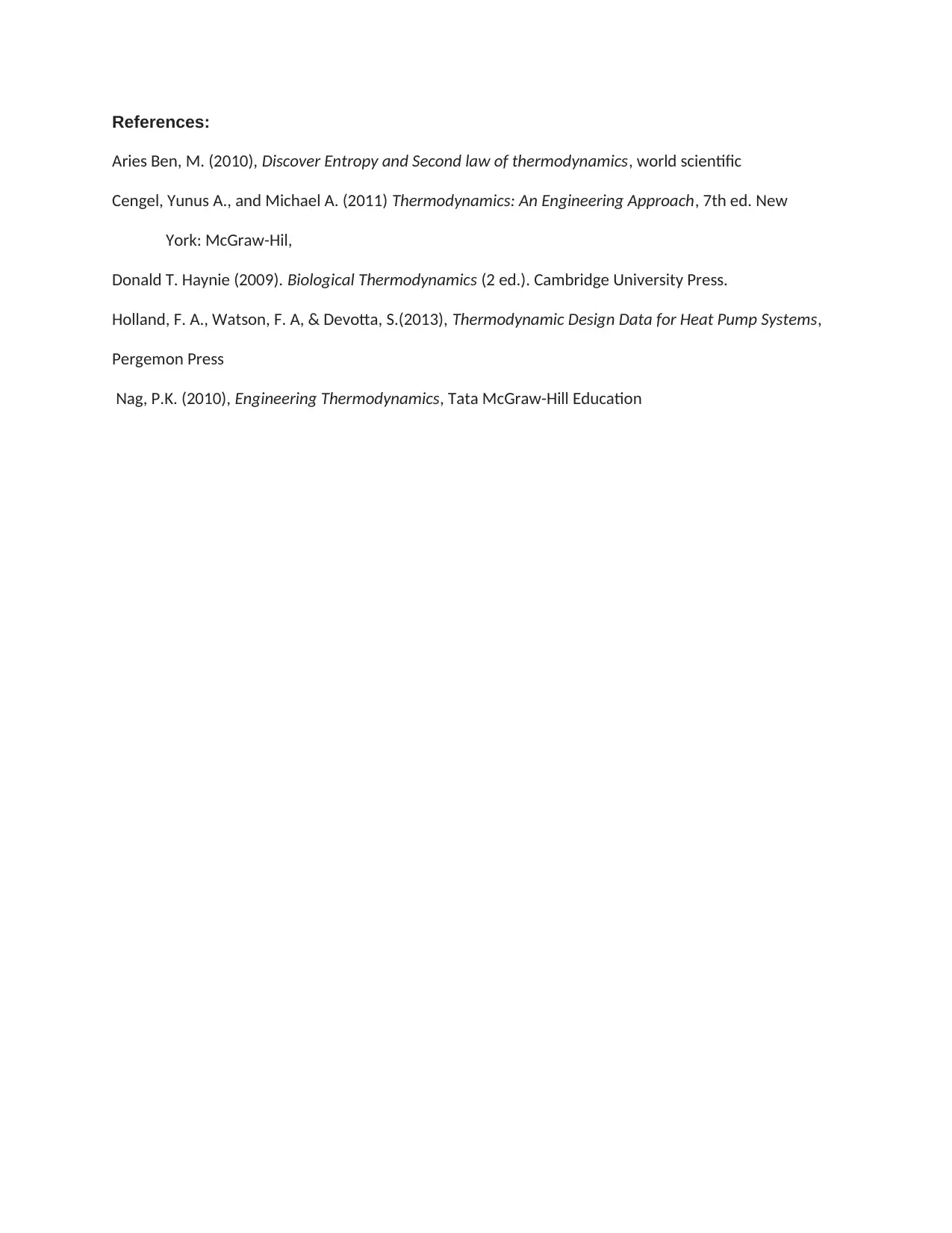
References:
Aries Ben, M. (2010), Discover Entropy and Second law of thermodynamics, world scientific
Cengel, Yunus A., and Michael A. (2011) Thermodynamics: An Engineering Approach, 7th ed. New
York: McGraw-Hil,
Donald T. Haynie (2009). Biological Thermodynamics (2 ed.). Cambridge University Press.
Holland, F. A., Watson, F. A, & Devotta, S.(2013), Thermodynamic Design Data for Heat Pump Systems,
Pergemon Press
Nag, P.K. (2010), Engineering Thermodynamics, Tata McGraw-Hill Education
Aries Ben, M. (2010), Discover Entropy and Second law of thermodynamics, world scientific
Cengel, Yunus A., and Michael A. (2011) Thermodynamics: An Engineering Approach, 7th ed. New
York: McGraw-Hil,
Donald T. Haynie (2009). Biological Thermodynamics (2 ed.). Cambridge University Press.
Holland, F. A., Watson, F. A, & Devotta, S.(2013), Thermodynamic Design Data for Heat Pump Systems,
Pergemon Press
Nag, P.K. (2010), Engineering Thermodynamics, Tata McGraw-Hill Education
1 out of 8
Related Documents

Your All-in-One AI-Powered Toolkit for Academic Success.
+13062052269
info@desklib.com
Available 24*7 on WhatsApp / Email
Unlock your academic potential
© 2024 | Zucol Services PVT LTD | All rights reserved.