Tittle Engine In Cylinder Pressure Analysis 2022
VerifiedAdded on 2022/09/21
|20
|3236
|19
AI Summary
Contribute Materials
Your contribution can guide someone’s learning journey. Share your
documents today.
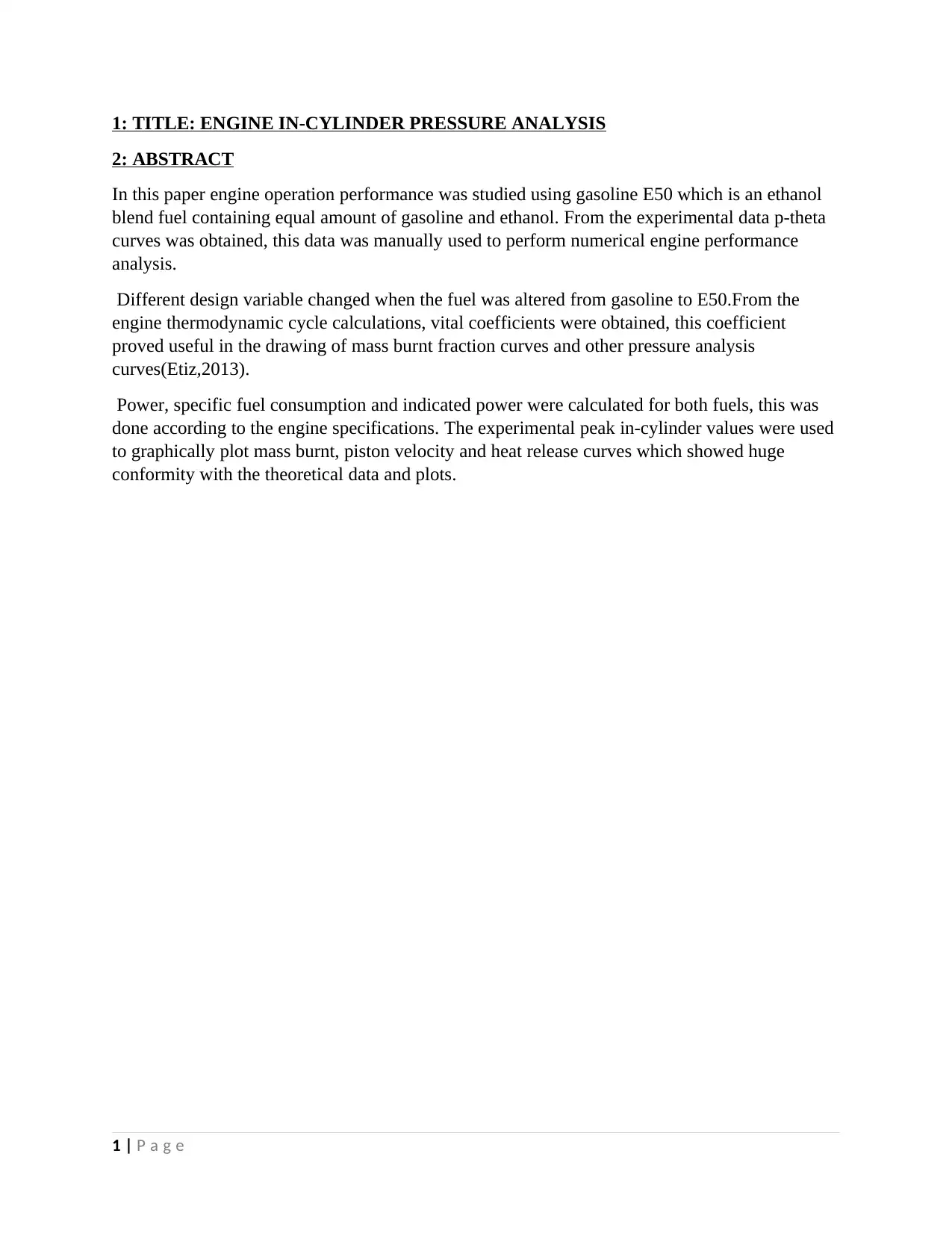
1: TITLE: ENGINE IN-CYLINDER PRESSURE ANALYSIS
2: ABSTRACT
In this paper engine operation performance was studied using gasoline E50 which is an ethanol
blend fuel containing equal amount of gasoline and ethanol. From the experimental data p-theta
curves was obtained, this data was manually used to perform numerical engine performance
analysis.
Different design variable changed when the fuel was altered from gasoline to E50.From the
engine thermodynamic cycle calculations, vital coefficients were obtained, this coefficient
proved useful in the drawing of mass burnt fraction curves and other pressure analysis
curves(Etiz,2013).
Power, specific fuel consumption and indicated power were calculated for both fuels, this was
done according to the engine specifications. The experimental peak in-cylinder values were used
to graphically plot mass burnt, piston velocity and heat release curves which showed huge
conformity with the theoretical data and plots.
1 | P a g e
2: ABSTRACT
In this paper engine operation performance was studied using gasoline E50 which is an ethanol
blend fuel containing equal amount of gasoline and ethanol. From the experimental data p-theta
curves was obtained, this data was manually used to perform numerical engine performance
analysis.
Different design variable changed when the fuel was altered from gasoline to E50.From the
engine thermodynamic cycle calculations, vital coefficients were obtained, this coefficient
proved useful in the drawing of mass burnt fraction curves and other pressure analysis
curves(Etiz,2013).
Power, specific fuel consumption and indicated power were calculated for both fuels, this was
done according to the engine specifications. The experimental peak in-cylinder values were used
to graphically plot mass burnt, piston velocity and heat release curves which showed huge
conformity with the theoretical data and plots.
1 | P a g e
Secure Best Marks with AI Grader
Need help grading? Try our AI Grader for instant feedback on your assignments.
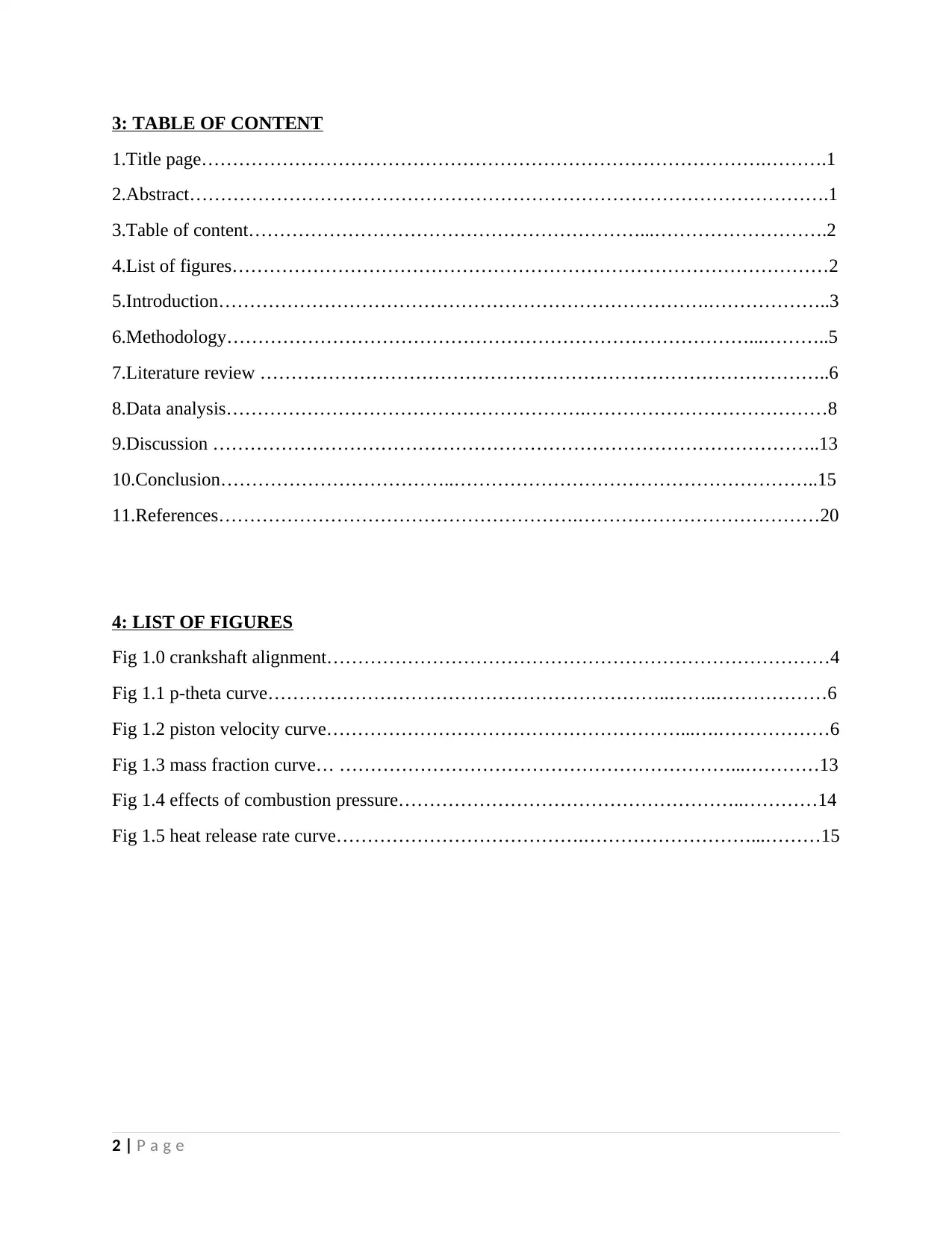
3: TABLE OF CONTENT
1.Title page……………………………………………………………………………….……….1
2.Abstract………………………………………………………………………………………….1
3.Table of content………………………………………………………...……………………….2
4.List of figures……………………………………………………………………………………2
5.Introduction…………………………………………………………………….………………..3
6.Methodology…………………………………………………………………………...………..5
7.Literature review ………………………………………………………………………………..6
8.Data analysis………………………………………………….…………………………………8
9.Discussion ……………………………………………………………………………………..13
10.Conclusion………………………………..…………………………………………………..15
11.References………………………………………………….…………………………………20
4: LIST OF FIGURES
Fig 1.0 crankshaft alignment………………………………………………………………………4
Fig 1.1 p-theta curve………………………………………………………..……..………………6
Fig 1.2 piston velocity curve…………………………………………………...….………………6
Fig 1.3 mass fraction curve… ………………………………………………………...…………13
Fig 1.4 effects of combustion pressure………………………………………………..…………14
Fig 1.5 heat release rate curve………………………………….………………………...………15
2 | P a g e
1.Title page……………………………………………………………………………….……….1
2.Abstract………………………………………………………………………………………….1
3.Table of content………………………………………………………...……………………….2
4.List of figures……………………………………………………………………………………2
5.Introduction…………………………………………………………………….………………..3
6.Methodology…………………………………………………………………………...………..5
7.Literature review ………………………………………………………………………………..6
8.Data analysis………………………………………………….…………………………………8
9.Discussion ……………………………………………………………………………………..13
10.Conclusion………………………………..…………………………………………………..15
11.References………………………………………………….…………………………………20
4: LIST OF FIGURES
Fig 1.0 crankshaft alignment………………………………………………………………………4
Fig 1.1 p-theta curve………………………………………………………..……..………………6
Fig 1.2 piston velocity curve…………………………………………………...….………………6
Fig 1.3 mass fraction curve… ………………………………………………………...…………13
Fig 1.4 effects of combustion pressure………………………………………………..…………14
Fig 1.5 heat release rate curve………………………………….………………………...………15
2 | P a g e
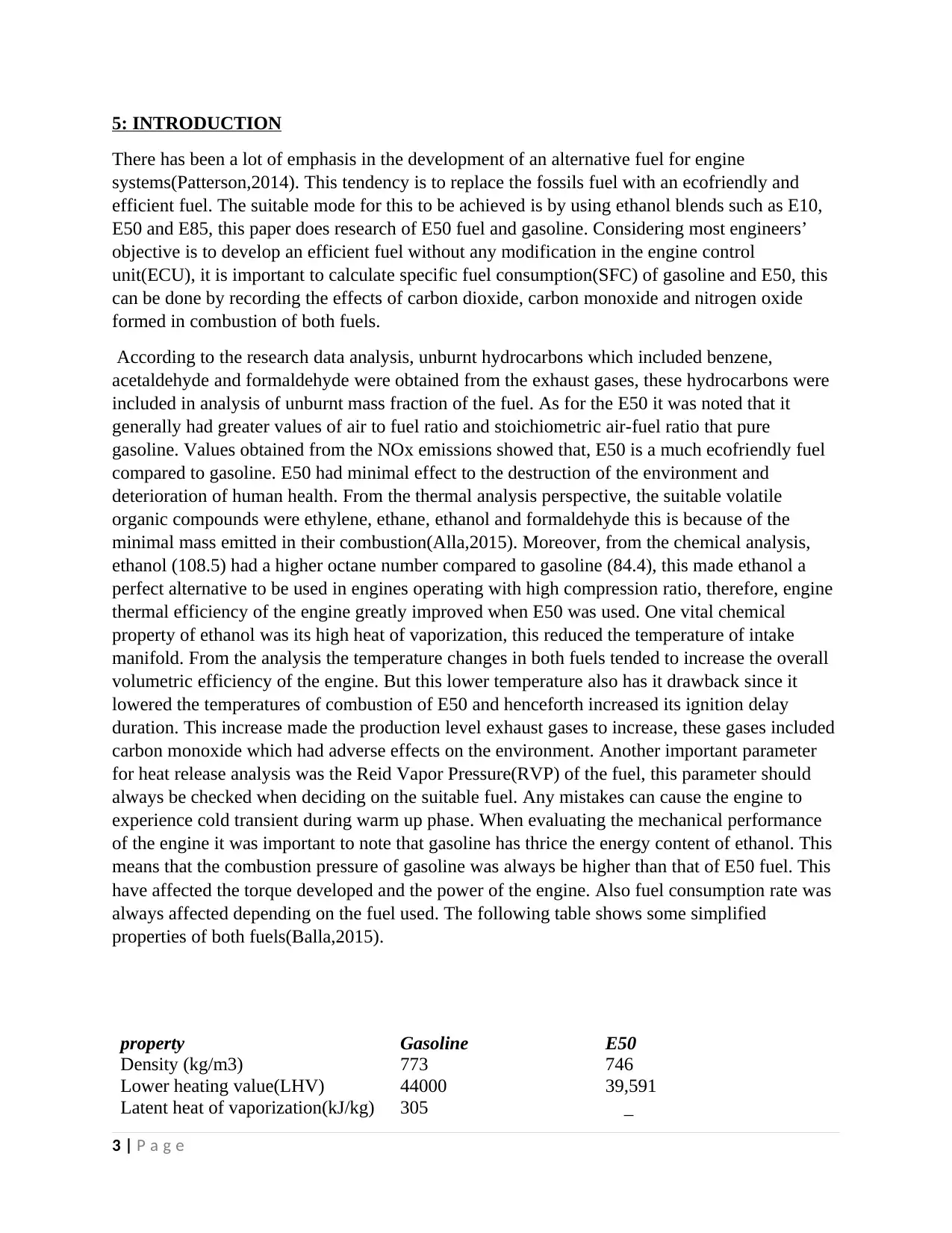
5: INTRODUCTION
There has been a lot of emphasis in the development of an alternative fuel for engine
systems(Patterson,2014). This tendency is to replace the fossils fuel with an ecofriendly and
efficient fuel. The suitable mode for this to be achieved is by using ethanol blends such as E10,
E50 and E85, this paper does research of E50 fuel and gasoline. Considering most engineers’
objective is to develop an efficient fuel without any modification in the engine control
unit(ECU), it is important to calculate specific fuel consumption(SFC) of gasoline and E50, this
can be done by recording the effects of carbon dioxide, carbon monoxide and nitrogen oxide
formed in combustion of both fuels.
According to the research data analysis, unburnt hydrocarbons which included benzene,
acetaldehyde and formaldehyde were obtained from the exhaust gases, these hydrocarbons were
included in analysis of unburnt mass fraction of the fuel. As for the E50 it was noted that it
generally had greater values of air to fuel ratio and stoichiometric air-fuel ratio that pure
gasoline. Values obtained from the NOx emissions showed that, E50 is a much ecofriendly fuel
compared to gasoline. E50 had minimal effect to the destruction of the environment and
deterioration of human health. From the thermal analysis perspective, the suitable volatile
organic compounds were ethylene, ethane, ethanol and formaldehyde this is because of the
minimal mass emitted in their combustion(Alla,2015). Moreover, from the chemical analysis,
ethanol (108.5) had a higher octane number compared to gasoline (84.4), this made ethanol a
perfect alternative to be used in engines operating with high compression ratio, therefore, engine
thermal efficiency of the engine greatly improved when E50 was used. One vital chemical
property of ethanol was its high heat of vaporization, this reduced the temperature of intake
manifold. From the analysis the temperature changes in both fuels tended to increase the overall
volumetric efficiency of the engine. But this lower temperature also has it drawback since it
lowered the temperatures of combustion of E50 and henceforth increased its ignition delay
duration. This increase made the production level exhaust gases to increase, these gases included
carbon monoxide which had adverse effects on the environment. Another important parameter
for heat release analysis was the Reid Vapor Pressure(RVP) of the fuel, this parameter should
always be checked when deciding on the suitable fuel. Any mistakes can cause the engine to
experience cold transient during warm up phase. When evaluating the mechanical performance
of the engine it was important to note that gasoline has thrice the energy content of ethanol. This
means that the combustion pressure of gasoline was always be higher than that of E50 fuel. This
have affected the torque developed and the power of the engine. Also fuel consumption rate was
always affected depending on the fuel used. The following table shows some simplified
properties of both fuels(Balla,2015).
property Gasoline E50
Density (kg/m3) 773 746
Lower heating value(LHV) 44000 39,591
Latent heat of vaporization(kJ/kg) 305 _
3 | P a g e
There has been a lot of emphasis in the development of an alternative fuel for engine
systems(Patterson,2014). This tendency is to replace the fossils fuel with an ecofriendly and
efficient fuel. The suitable mode for this to be achieved is by using ethanol blends such as E10,
E50 and E85, this paper does research of E50 fuel and gasoline. Considering most engineers’
objective is to develop an efficient fuel without any modification in the engine control
unit(ECU), it is important to calculate specific fuel consumption(SFC) of gasoline and E50, this
can be done by recording the effects of carbon dioxide, carbon monoxide and nitrogen oxide
formed in combustion of both fuels.
According to the research data analysis, unburnt hydrocarbons which included benzene,
acetaldehyde and formaldehyde were obtained from the exhaust gases, these hydrocarbons were
included in analysis of unburnt mass fraction of the fuel. As for the E50 it was noted that it
generally had greater values of air to fuel ratio and stoichiometric air-fuel ratio that pure
gasoline. Values obtained from the NOx emissions showed that, E50 is a much ecofriendly fuel
compared to gasoline. E50 had minimal effect to the destruction of the environment and
deterioration of human health. From the thermal analysis perspective, the suitable volatile
organic compounds were ethylene, ethane, ethanol and formaldehyde this is because of the
minimal mass emitted in their combustion(Alla,2015). Moreover, from the chemical analysis,
ethanol (108.5) had a higher octane number compared to gasoline (84.4), this made ethanol a
perfect alternative to be used in engines operating with high compression ratio, therefore, engine
thermal efficiency of the engine greatly improved when E50 was used. One vital chemical
property of ethanol was its high heat of vaporization, this reduced the temperature of intake
manifold. From the analysis the temperature changes in both fuels tended to increase the overall
volumetric efficiency of the engine. But this lower temperature also has it drawback since it
lowered the temperatures of combustion of E50 and henceforth increased its ignition delay
duration. This increase made the production level exhaust gases to increase, these gases included
carbon monoxide which had adverse effects on the environment. Another important parameter
for heat release analysis was the Reid Vapor Pressure(RVP) of the fuel, this parameter should
always be checked when deciding on the suitable fuel. Any mistakes can cause the engine to
experience cold transient during warm up phase. When evaluating the mechanical performance
of the engine it was important to note that gasoline has thrice the energy content of ethanol. This
means that the combustion pressure of gasoline was always be higher than that of E50 fuel. This
have affected the torque developed and the power of the engine. Also fuel consumption rate was
always affected depending on the fuel used. The following table shows some simplified
properties of both fuels(Balla,2015).
property Gasoline E50
Density (kg/m3) 773 746
Lower heating value(LHV) 44000 39,591
Latent heat of vaporization(kJ/kg) 305 _
3 | P a g e
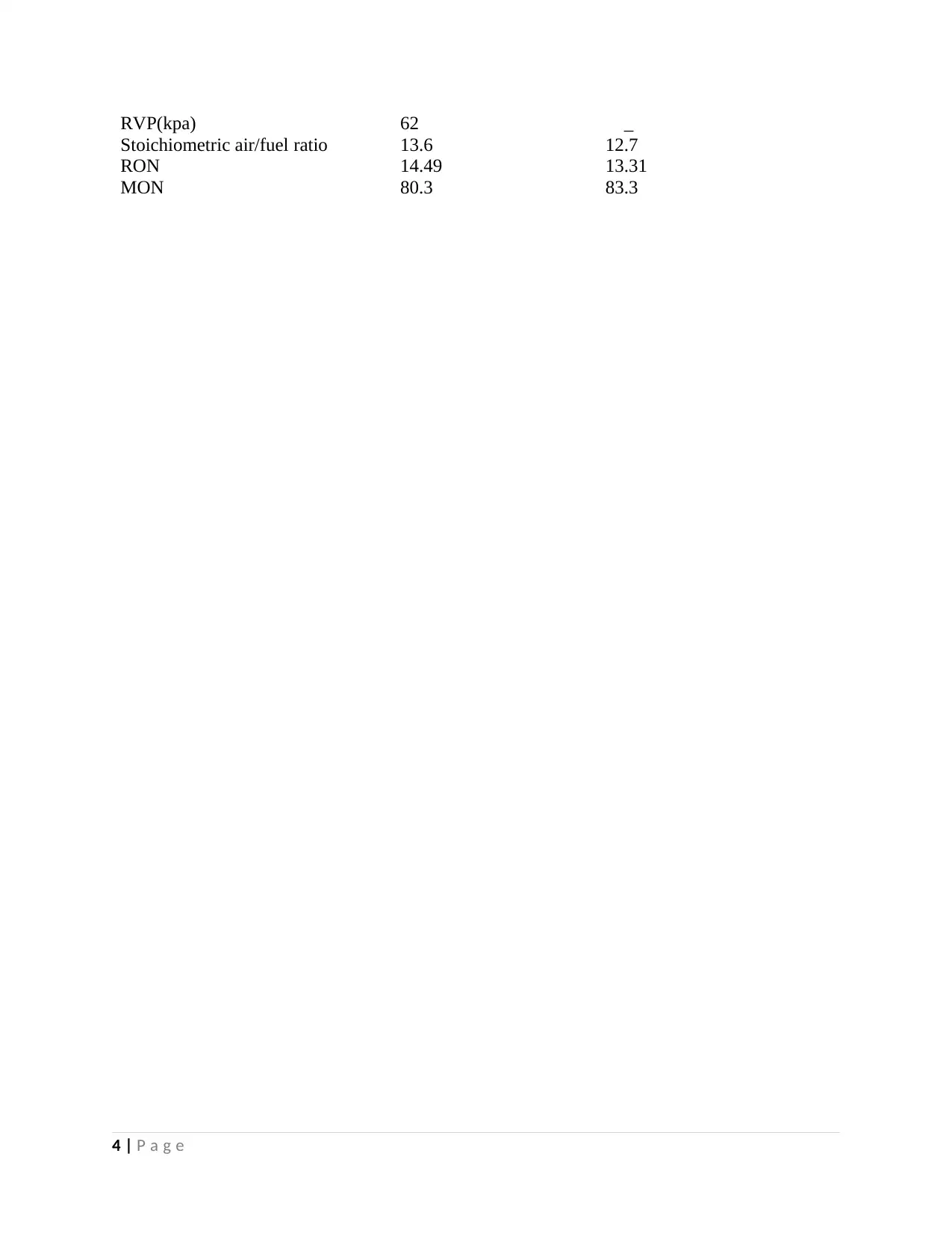
RVP(kpa) 62 _
Stoichiometric air/fuel ratio 13.6 12.7
RON 14.49 13.31
MON 80.3 83.3
4 | P a g e
Stoichiometric air/fuel ratio 13.6 12.7
RON 14.49 13.31
MON 80.3 83.3
4 | P a g e
Secure Best Marks with AI Grader
Need help grading? Try our AI Grader for instant feedback on your assignments.
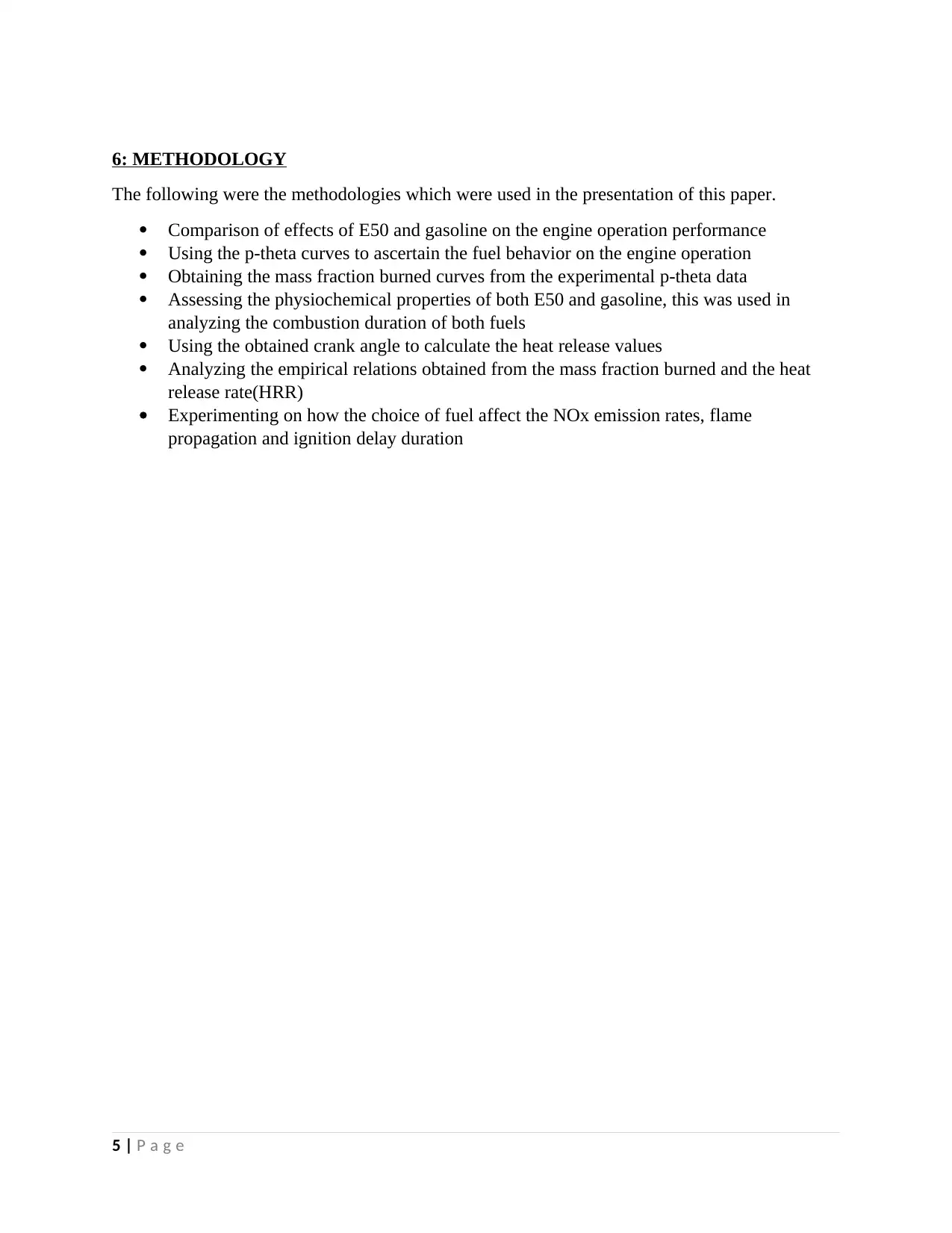
6: METHODOLOGY
The following were the methodologies which were used in the presentation of this paper.
Comparison of effects of E50 and gasoline on the engine operation performance
Using the p-theta curves to ascertain the fuel behavior on the engine operation
Obtaining the mass fraction burned curves from the experimental p-theta data
Assessing the physiochemical properties of both E50 and gasoline, this was used in
analyzing the combustion duration of both fuels
Using the obtained crank angle to calculate the heat release values
Analyzing the empirical relations obtained from the mass fraction burned and the heat
release rate(HRR)
Experimenting on how the choice of fuel affect the NOx emission rates, flame
propagation and ignition delay duration
5 | P a g e
The following were the methodologies which were used in the presentation of this paper.
Comparison of effects of E50 and gasoline on the engine operation performance
Using the p-theta curves to ascertain the fuel behavior on the engine operation
Obtaining the mass fraction burned curves from the experimental p-theta data
Assessing the physiochemical properties of both E50 and gasoline, this was used in
analyzing the combustion duration of both fuels
Using the obtained crank angle to calculate the heat release values
Analyzing the empirical relations obtained from the mass fraction burned and the heat
release rate(HRR)
Experimenting on how the choice of fuel affect the NOx emission rates, flame
propagation and ignition delay duration
5 | P a g e
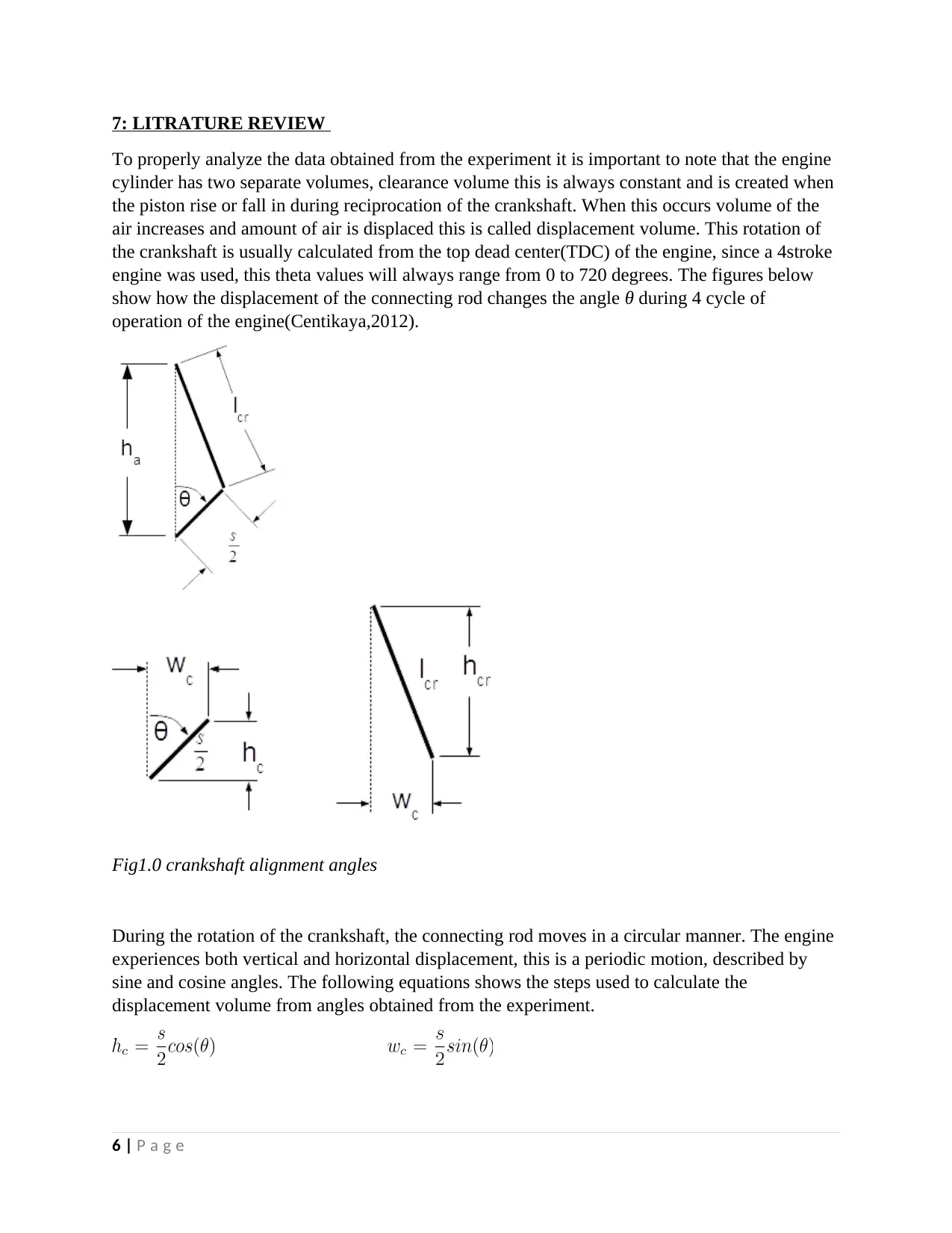
7: LITRATURE REVIEW
To properly analyze the data obtained from the experiment it is important to note that the engine
cylinder has two separate volumes, clearance volume this is always constant and is created when
the piston rise or fall in during reciprocation of the crankshaft. When this occurs volume of the
air increases and amount of air is displaced this is called displacement volume. This rotation of
the crankshaft is usually calculated from the top dead center(TDC) of the engine, since a 4stroke
engine was used, this theta values will always range from 0 to 720 degrees. The figures below
show how the displacement of the connecting rod changes the angle θ during 4 cycle of
operation of the engine(Centikaya,2012).
Fig1.0 crankshaft alignment angles
During the rotation of the crankshaft, the connecting rod moves in a circular manner. The engine
experiences both vertical and horizontal displacement, this is a periodic motion, described by
sine and cosine angles. The following equations shows the steps used to calculate the
displacement volume from angles obtained from the experiment.
6 | P a g e
To properly analyze the data obtained from the experiment it is important to note that the engine
cylinder has two separate volumes, clearance volume this is always constant and is created when
the piston rise or fall in during reciprocation of the crankshaft. When this occurs volume of the
air increases and amount of air is displaced this is called displacement volume. This rotation of
the crankshaft is usually calculated from the top dead center(TDC) of the engine, since a 4stroke
engine was used, this theta values will always range from 0 to 720 degrees. The figures below
show how the displacement of the connecting rod changes the angle θ during 4 cycle of
operation of the engine(Centikaya,2012).
Fig1.0 crankshaft alignment angles
During the rotation of the crankshaft, the connecting rod moves in a circular manner. The engine
experiences both vertical and horizontal displacement, this is a periodic motion, described by
sine and cosine angles. The following equations shows the steps used to calculate the
displacement volume from angles obtained from the experiment.
6 | P a g e
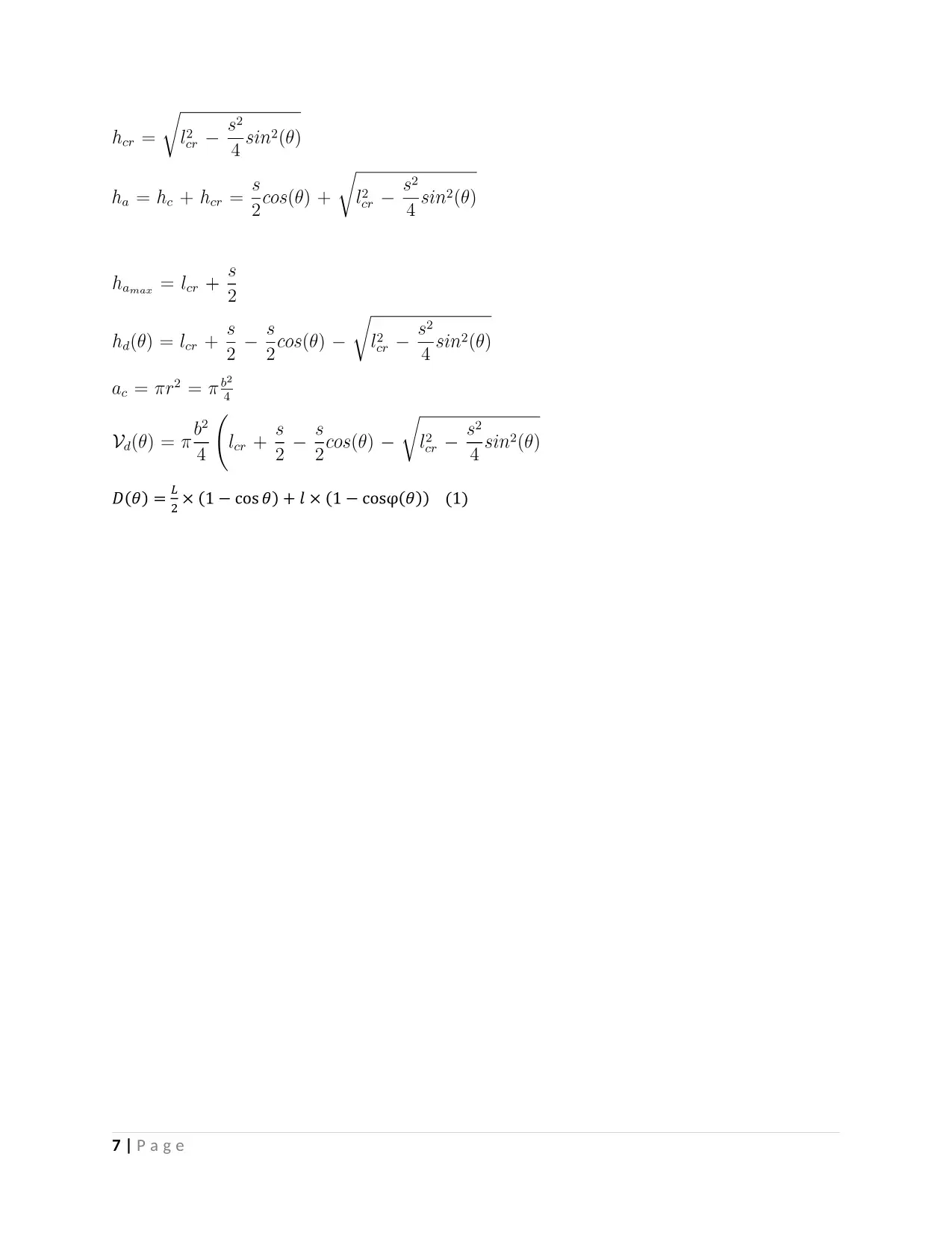
7 | P a g e
Paraphrase This Document
Need a fresh take? Get an instant paraphrase of this document with our AI Paraphraser
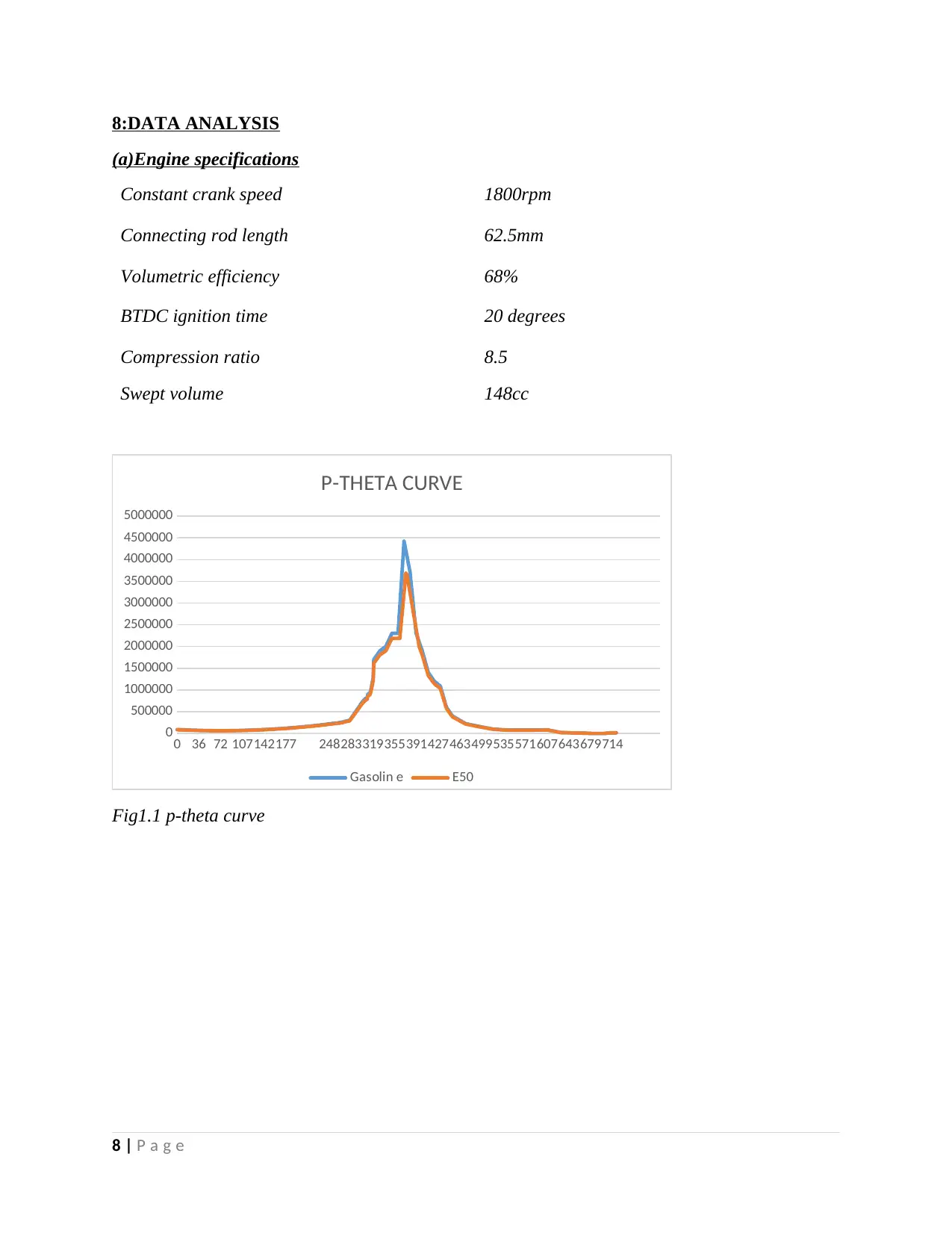
8:DATA ANALYSIS
(a)Engine specifications
Constant crank speed 1800rpm
Connecting rod length 62.5mm
Volumetric efficiency 68%
BTDC ignition time 20 degrees
Compression ratio 8.5
Swept volume 148cc
0 36 72 107142177 248283319355391427463499535571607643679714
0
500000
1000000
1500000
2000000
2500000
3000000
3500000
4000000
4500000
5000000
P-THETA CURVE
Gasolin e E50
Fig1.1 p-theta curve
8 | P a g e
(a)Engine specifications
Constant crank speed 1800rpm
Connecting rod length 62.5mm
Volumetric efficiency 68%
BTDC ignition time 20 degrees
Compression ratio 8.5
Swept volume 148cc
0 36 72 107142177 248283319355391427463499535571607643679714
0
500000
1000000
1500000
2000000
2500000
3000000
3500000
4000000
4500000
5000000
P-THETA CURVE
Gasolin e E50
Fig1.1 p-theta curve
8 | P a g e
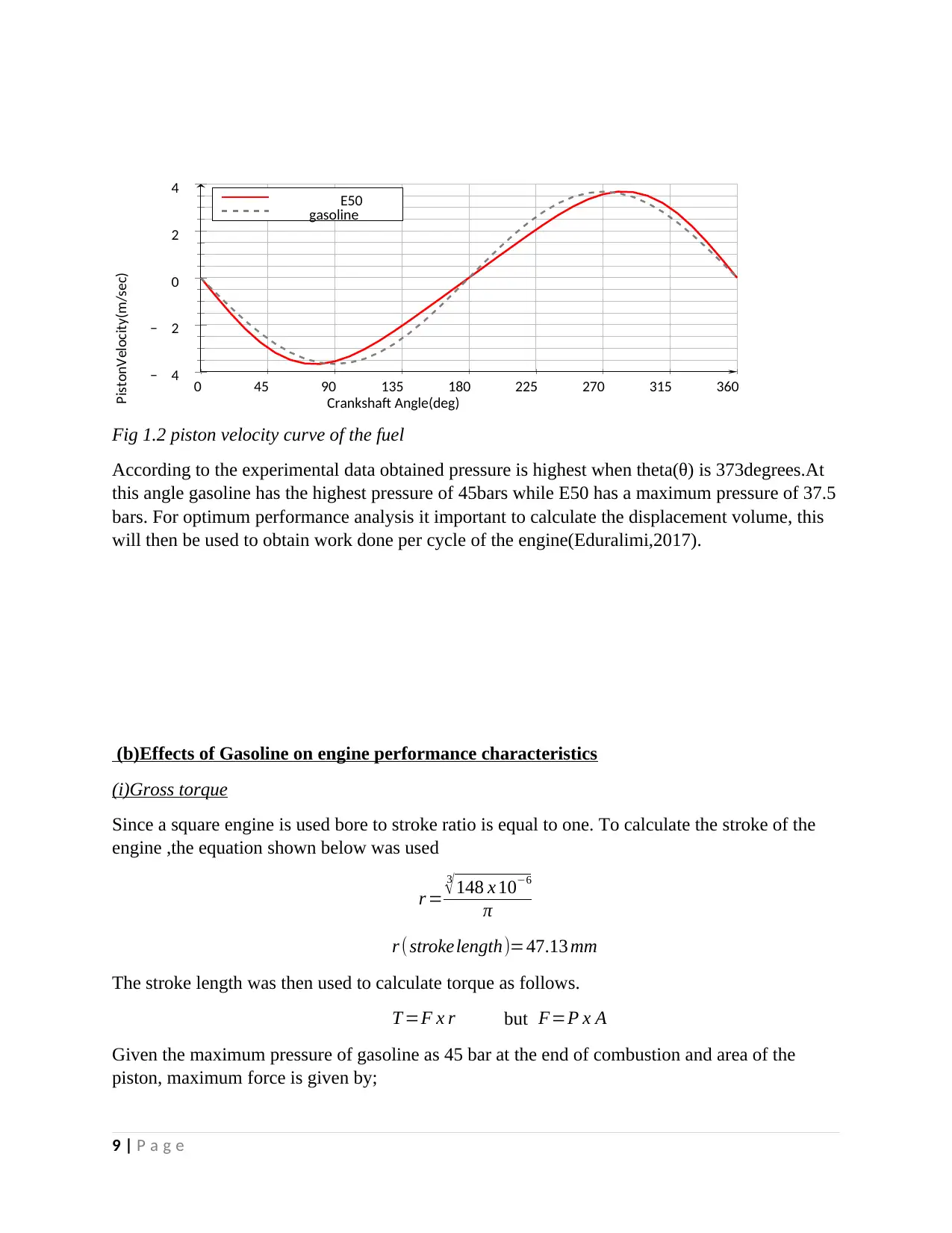
Fig 1.2 piston velocity curve of the fuel
According to the experimental data obtained pressure is highest when theta(θ) is 373degrees.At
this angle gasoline has the highest pressure of 45bars while E50 has a maximum pressure of 37.5
bars. For optimum performance analysis it important to calculate the displacement volume, this
will then be used to obtain work done per cycle of the engine(Eduralimi,2017).
(b)Effects of Gasoline on engine performance characteristics
(i)Gross torque
Since a square engine is used bore to stroke ratio is equal to one. To calculate the stroke of the
engine ,the equation shown below was used
r =
3
√148 x 10−6
π
r ( strokelength)=47.13 mm
The stroke length was then used to calculate torque as follows.
T =F x r but F=P x A
Given the maximum pressure of gasoline as 45 bar at the end of combustion and area of the
piston, maximum force is given by;
9 | P a g e
0 1801359045 225 270 315 360
− 4
− 2
0
2
4
Crankshaft Angle(deg)
PistonVelocity(m/sec)
E50
gasoline
According to the experimental data obtained pressure is highest when theta(θ) is 373degrees.At
this angle gasoline has the highest pressure of 45bars while E50 has a maximum pressure of 37.5
bars. For optimum performance analysis it important to calculate the displacement volume, this
will then be used to obtain work done per cycle of the engine(Eduralimi,2017).
(b)Effects of Gasoline on engine performance characteristics
(i)Gross torque
Since a square engine is used bore to stroke ratio is equal to one. To calculate the stroke of the
engine ,the equation shown below was used
r =
3
√148 x 10−6
π
r ( strokelength)=47.13 mm
The stroke length was then used to calculate torque as follows.
T =F x r but F=P x A
Given the maximum pressure of gasoline as 45 bar at the end of combustion and area of the
piston, maximum force is given by;
9 | P a g e
0 1801359045 225 270 315 360
− 4
− 2
0
2
4
Crankshaft Angle(deg)
PistonVelocity(m/sec)
E50
gasoline
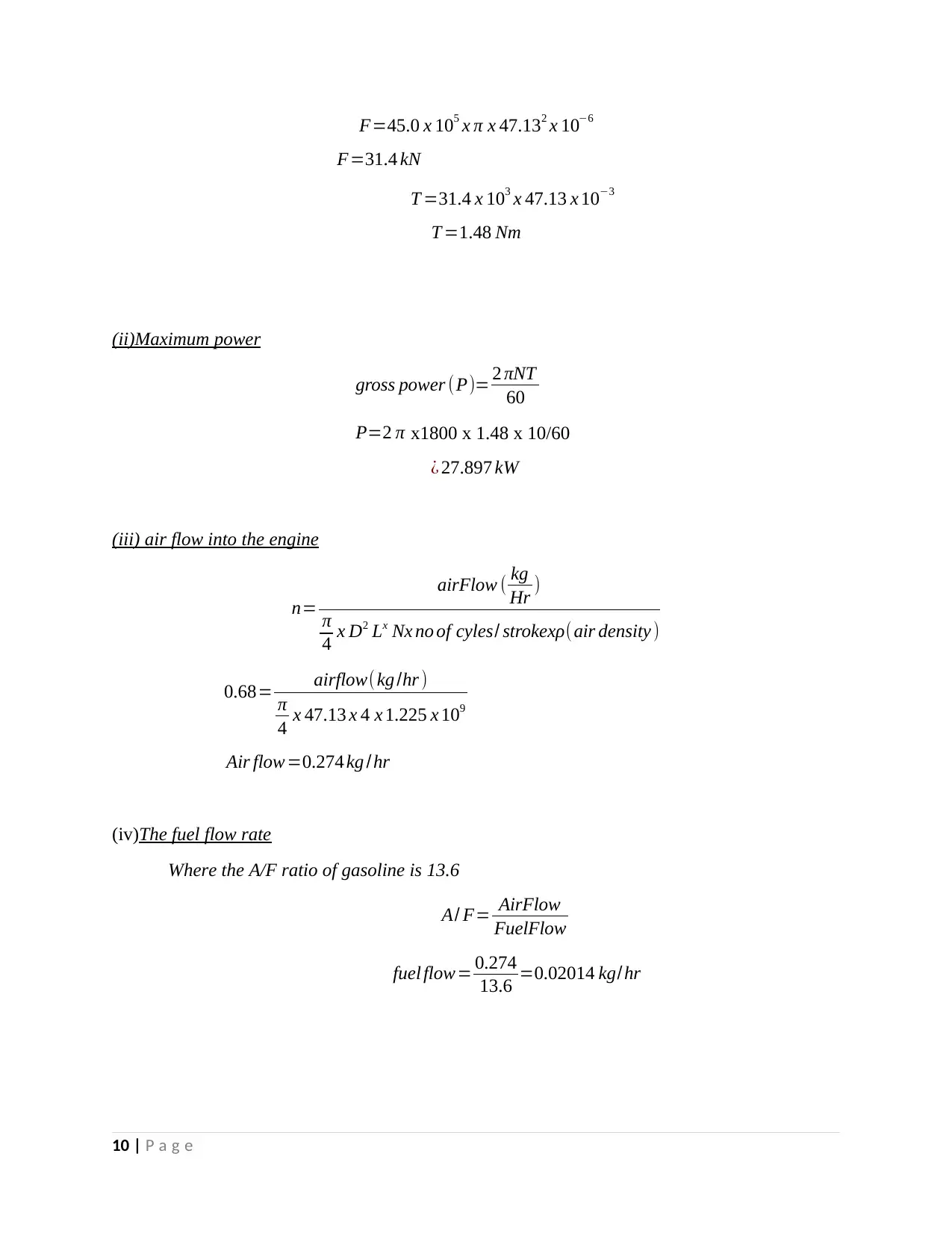
F=45.0 x 105 x π x 47.132 x 10−6
F=31.4 kN
T =31.4 x 103 x 47.13 x 10−3
T =1.48 Nm
(ii)Maximum power
gross power (P)= 2 πNT
60
P=2 π x1800 x 1.48 x 10/60
¿ 27.897 kW
(iii) air flow into the engine
n=
airFlow ( kg
Hr )
π
4 x D2 Lx Nx no of cyles/ strokexρ(air density )
0.68= airflow(kg /hr )
π
4 x 47.13 x 4 x 1.225 x 109
Air flow=0.274 kg /hr
(iv)The fuel flow rate
Where the A/F ratio of gasoline is 13.6
A/ F= AirFlow
FuelFlow
fuel flow= 0.274
13.6 =0.02014 kg/hr
10 | P a g e
F=31.4 kN
T =31.4 x 103 x 47.13 x 10−3
T =1.48 Nm
(ii)Maximum power
gross power (P)= 2 πNT
60
P=2 π x1800 x 1.48 x 10/60
¿ 27.897 kW
(iii) air flow into the engine
n=
airFlow ( kg
Hr )
π
4 x D2 Lx Nx no of cyles/ strokexρ(air density )
0.68= airflow(kg /hr )
π
4 x 47.13 x 4 x 1.225 x 109
Air flow=0.274 kg /hr
(iv)The fuel flow rate
Where the A/F ratio of gasoline is 13.6
A/ F= AirFlow
FuelFlow
fuel flow= 0.274
13.6 =0.02014 kg/hr
10 | P a g e
Secure Best Marks with AI Grader
Need help grading? Try our AI Grader for instant feedback on your assignments.
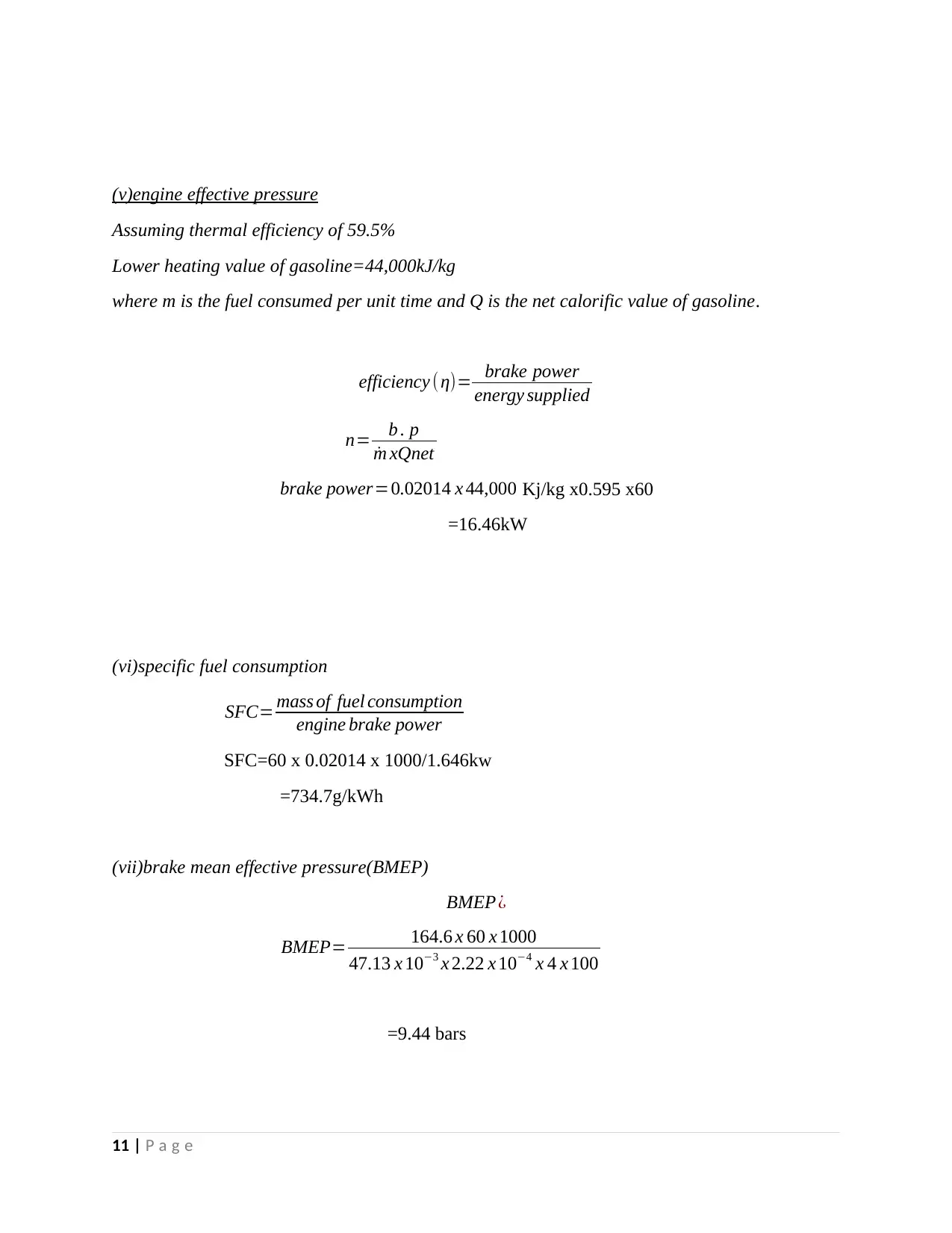
(v)engine effective pressure
Assuming thermal efficiency of 59.5%
Lower heating value of gasoline=44,000kJ/kg
where m is the fuel consumed per unit time and Q is the net calorific value of gasoline.
efficiency (η)= brake power
energy supplied
n= b . p
˙m xQnet
brake power=0.02014 x 44,000 Kj/kg x0.595 x60
=16.46kW
(vi)specific fuel consumption
SFC= mass of fuel consumption
engine brake power
SFC=60 x 0.02014 x 1000/1.646kw
=734.7g/kWh
(vii)brake mean effective pressure(BMEP)
BMEP¿
BMEP= 164.6 x 60 x 1000
47.13 x 10−3 x 2.22 x 10−4 x 4 x 100
=9.44 bars
11 | P a g e
Assuming thermal efficiency of 59.5%
Lower heating value of gasoline=44,000kJ/kg
where m is the fuel consumed per unit time and Q is the net calorific value of gasoline.
efficiency (η)= brake power
energy supplied
n= b . p
˙m xQnet
brake power=0.02014 x 44,000 Kj/kg x0.595 x60
=16.46kW
(vi)specific fuel consumption
SFC= mass of fuel consumption
engine brake power
SFC=60 x 0.02014 x 1000/1.646kw
=734.7g/kWh
(vii)brake mean effective pressure(BMEP)
BMEP¿
BMEP= 164.6 x 60 x 1000
47.13 x 10−3 x 2.22 x 10−4 x 4 x 100
=9.44 bars
11 | P a g e
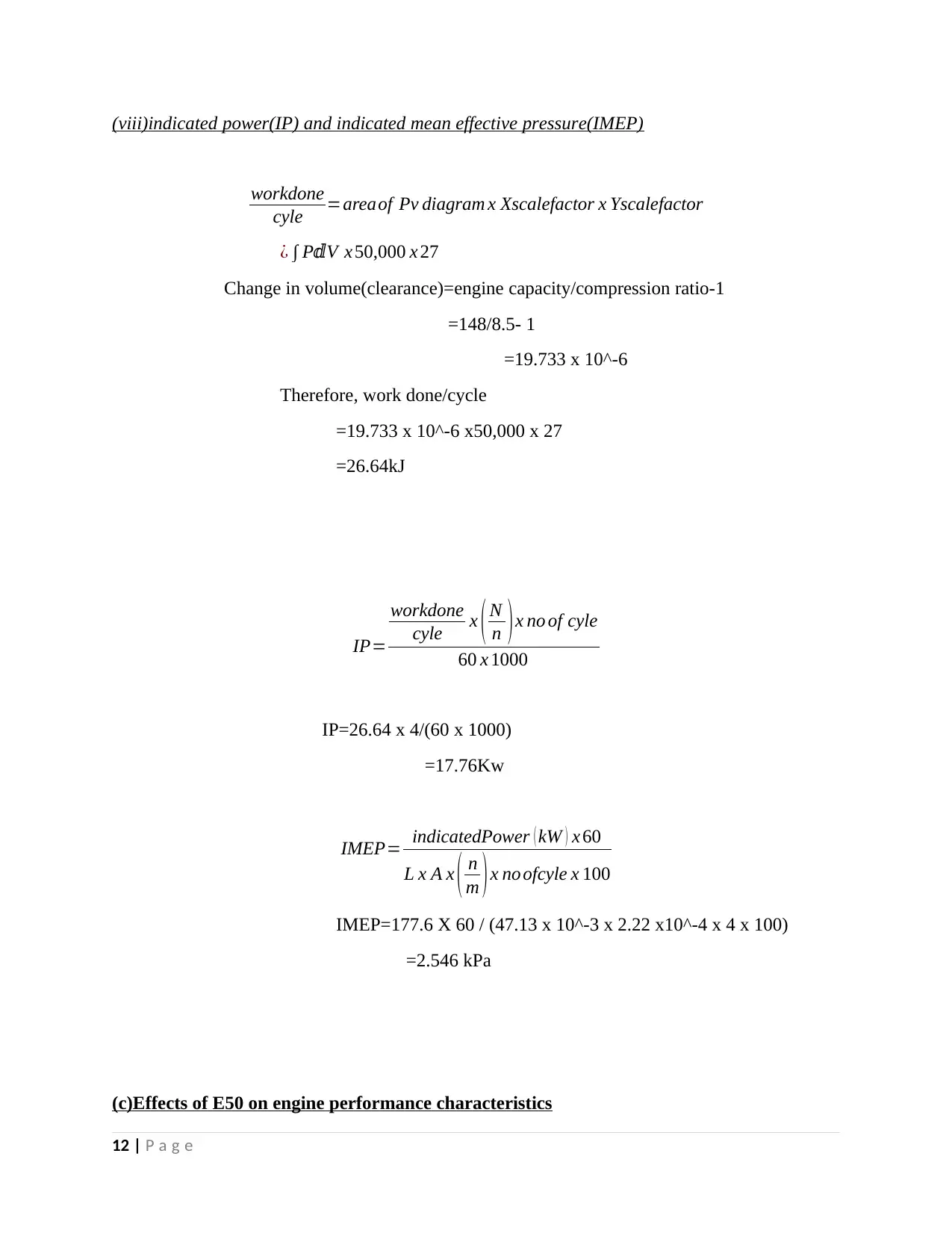
(viii)indicated power(IP) and indicated mean effective pressure(IMEP)
workdone
cyle =areaof Pv diagram x Xscalefactor x Yscalefactor
¿ ∫ P Vⅆ x 50,000 x 27
Change in volume(clearance)=engine capacity/compression ratio-1
=148/8.5- 1
=19.733 x 10^-6
Therefore, work done/cycle
=19.733 x 10^-6 x50,000 x 27
=26.64kJ
IP=
workdone
cyle x ( N
n )x no of cyle
60 x 1000
IP=26.64 x 4/(60 x 1000)
=17.76Kw
IMEP= indicatedPower ( kW ) x 60
L x A x ( n
m )x no ofcyle x 100
IMEP=177.6 X 60 / (47.13 x 10^-3 x 2.22 x10^-4 x 4 x 100)
=2.546 kPa
(c)Effects of E50 on engine performance characteristics
12 | P a g e
workdone
cyle =areaof Pv diagram x Xscalefactor x Yscalefactor
¿ ∫ P Vⅆ x 50,000 x 27
Change in volume(clearance)=engine capacity/compression ratio-1
=148/8.5- 1
=19.733 x 10^-6
Therefore, work done/cycle
=19.733 x 10^-6 x50,000 x 27
=26.64kJ
IP=
workdone
cyle x ( N
n )x no of cyle
60 x 1000
IP=26.64 x 4/(60 x 1000)
=17.76Kw
IMEP= indicatedPower ( kW ) x 60
L x A x ( n
m )x no ofcyle x 100
IMEP=177.6 X 60 / (47.13 x 10^-3 x 2.22 x10^-4 x 4 x 100)
=2.546 kPa
(c)Effects of E50 on engine performance characteristics
12 | P a g e
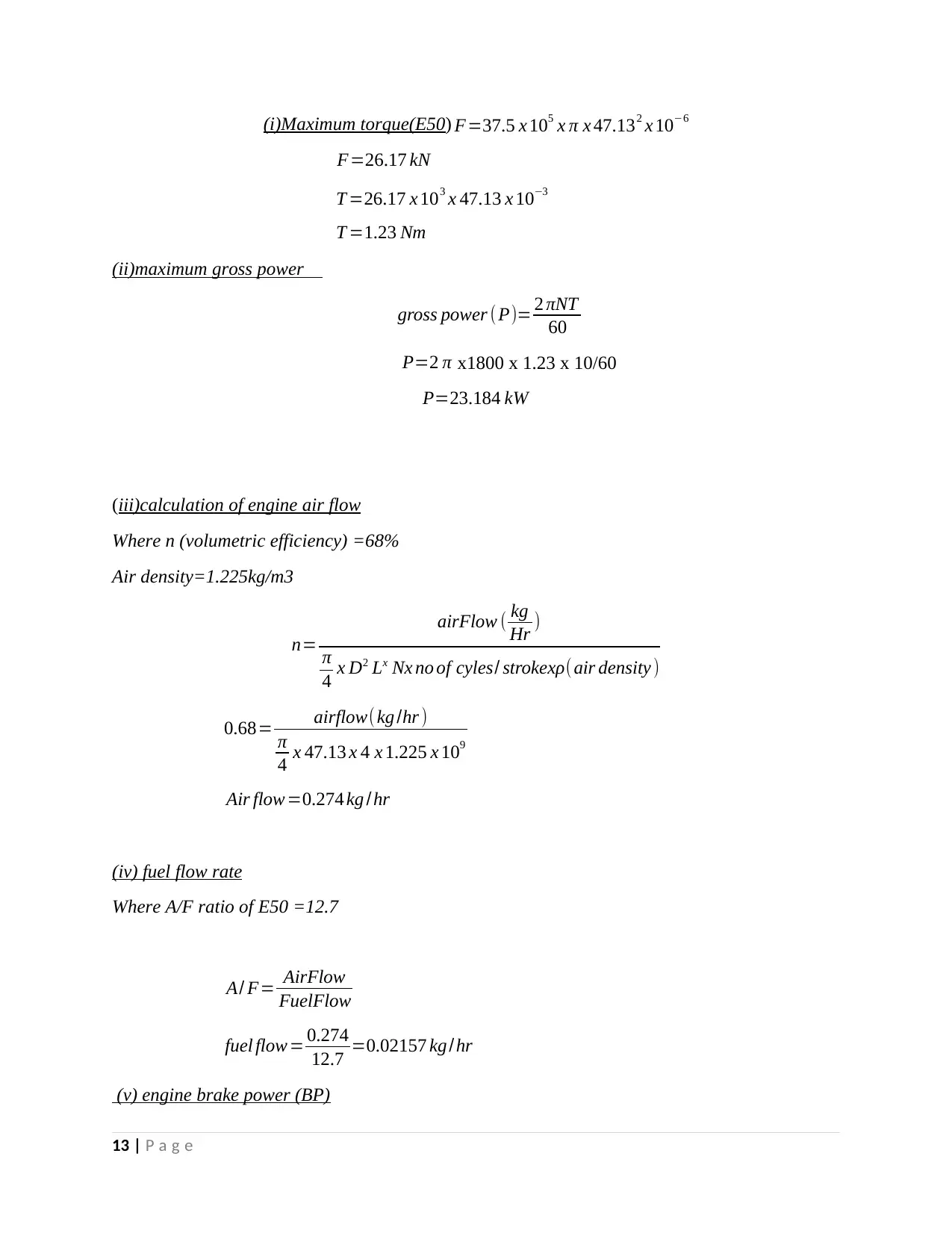
(i)Maximum torque(E50) F=37.5 x 105 x π x 47.132 x 10−6
F=26.17 kN
T =26.17 x 103 x 47.13 x 10−3
T =1.23 Nm
(ii)maximum gross power
gross power (P)= 2 πNT
60
P=2 π x1800 x 1.23 x 10/60
P=23.184 kW
(iii)calculation of engine air flow
Where n (volumetric efficiency) =68%
Air density=1.225kg/m3
n=
airFlow ( kg
Hr )
π
4 x D2 Lx Nx no of cyles/ strokexρ(air density )
0.68= airflow(kg /hr )
π
4 x 47.13 x 4 x 1.225 x 109
Air flow=0.274 kg /hr
(iv) fuel flow rate
Where A/F ratio of E50 =12.7
A/ F= AirFlow
FuelFlow
fuel flow= 0.274
12.7 =0.02157 kg /hr
(v) engine brake power (BP)
13 | P a g e
F=26.17 kN
T =26.17 x 103 x 47.13 x 10−3
T =1.23 Nm
(ii)maximum gross power
gross power (P)= 2 πNT
60
P=2 π x1800 x 1.23 x 10/60
P=23.184 kW
(iii)calculation of engine air flow
Where n (volumetric efficiency) =68%
Air density=1.225kg/m3
n=
airFlow ( kg
Hr )
π
4 x D2 Lx Nx no of cyles/ strokexρ(air density )
0.68= airflow(kg /hr )
π
4 x 47.13 x 4 x 1.225 x 109
Air flow=0.274 kg /hr
(iv) fuel flow rate
Where A/F ratio of E50 =12.7
A/ F= AirFlow
FuelFlow
fuel flow= 0.274
12.7 =0.02157 kg /hr
(v) engine brake power (BP)
13 | P a g e
Paraphrase This Document
Need a fresh take? Get an instant paraphrase of this document with our AI Paraphraser
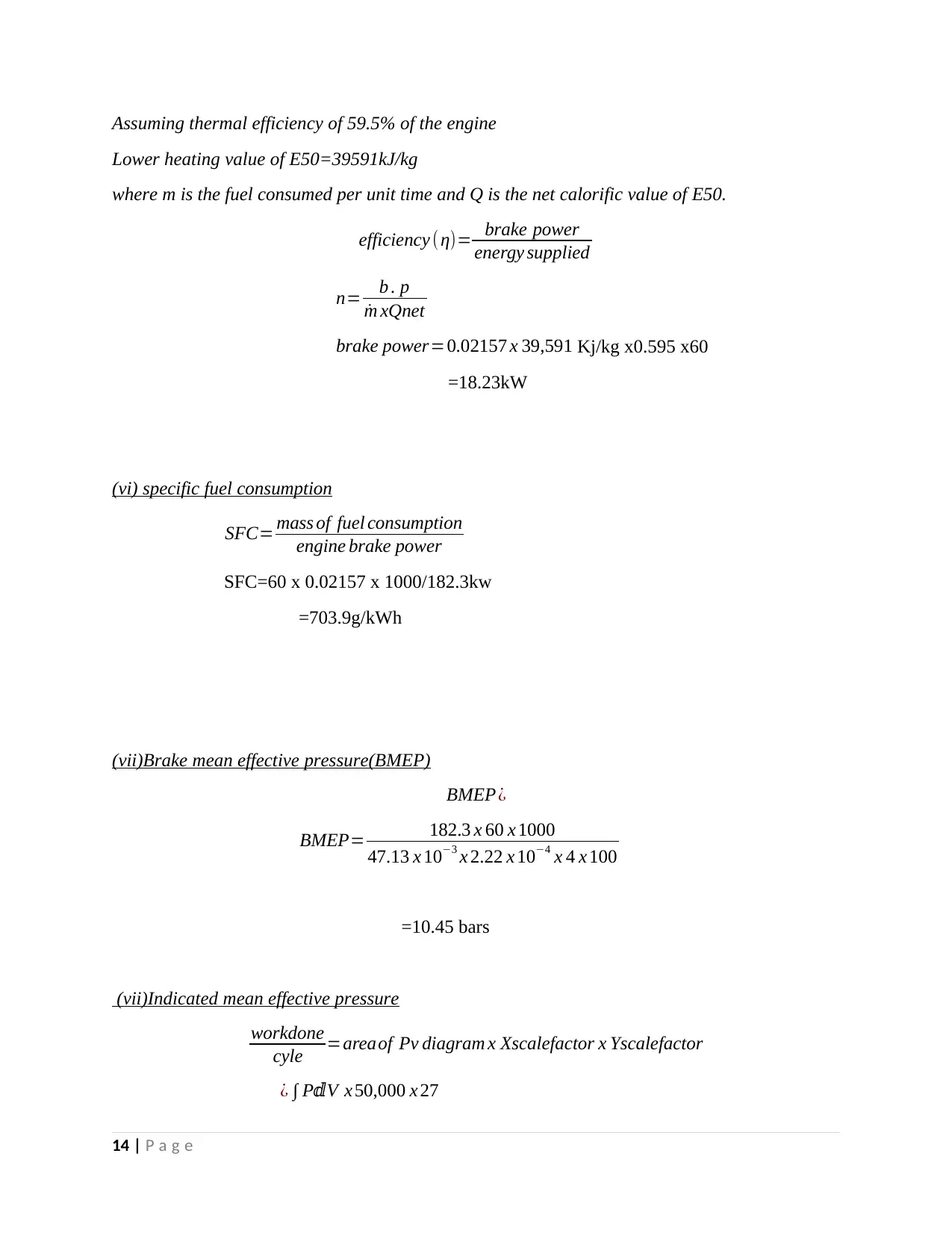
Assuming thermal efficiency of 59.5% of the engine
Lower heating value of E50=39591kJ/kg
where m is the fuel consumed per unit time and Q is the net calorific value of E50.
efficiency (η)= brake power
energy supplied
n= b . p
˙m xQnet
brake power=0.02157 x 39,591 Kj/kg x0.595 x60
=18.23kW
(vi) specific fuel consumption
SFC= mass of fuel consumption
engine brake power
SFC=60 x 0.02157 x 1000/182.3kw
=703.9g/kWh
(vii)Brake mean effective pressure(BMEP)
BMEP¿
BMEP= 182.3 x 60 x 1000
47.13 x 10−3 x 2.22 x 10−4 x 4 x 100
=10.45 bars
(vii)Indicated mean effective pressure
workdone
cyle =areaof Pv diagram x Xscalefactor x Yscalefactor
¿ ∫ P Vⅆ x 50,000 x 27
14 | P a g e
Lower heating value of E50=39591kJ/kg
where m is the fuel consumed per unit time and Q is the net calorific value of E50.
efficiency (η)= brake power
energy supplied
n= b . p
˙m xQnet
brake power=0.02157 x 39,591 Kj/kg x0.595 x60
=18.23kW
(vi) specific fuel consumption
SFC= mass of fuel consumption
engine brake power
SFC=60 x 0.02157 x 1000/182.3kw
=703.9g/kWh
(vii)Brake mean effective pressure(BMEP)
BMEP¿
BMEP= 182.3 x 60 x 1000
47.13 x 10−3 x 2.22 x 10−4 x 4 x 100
=10.45 bars
(vii)Indicated mean effective pressure
workdone
cyle =areaof Pv diagram x Xscalefactor x Yscalefactor
¿ ∫ P Vⅆ x 50,000 x 27
14 | P a g e
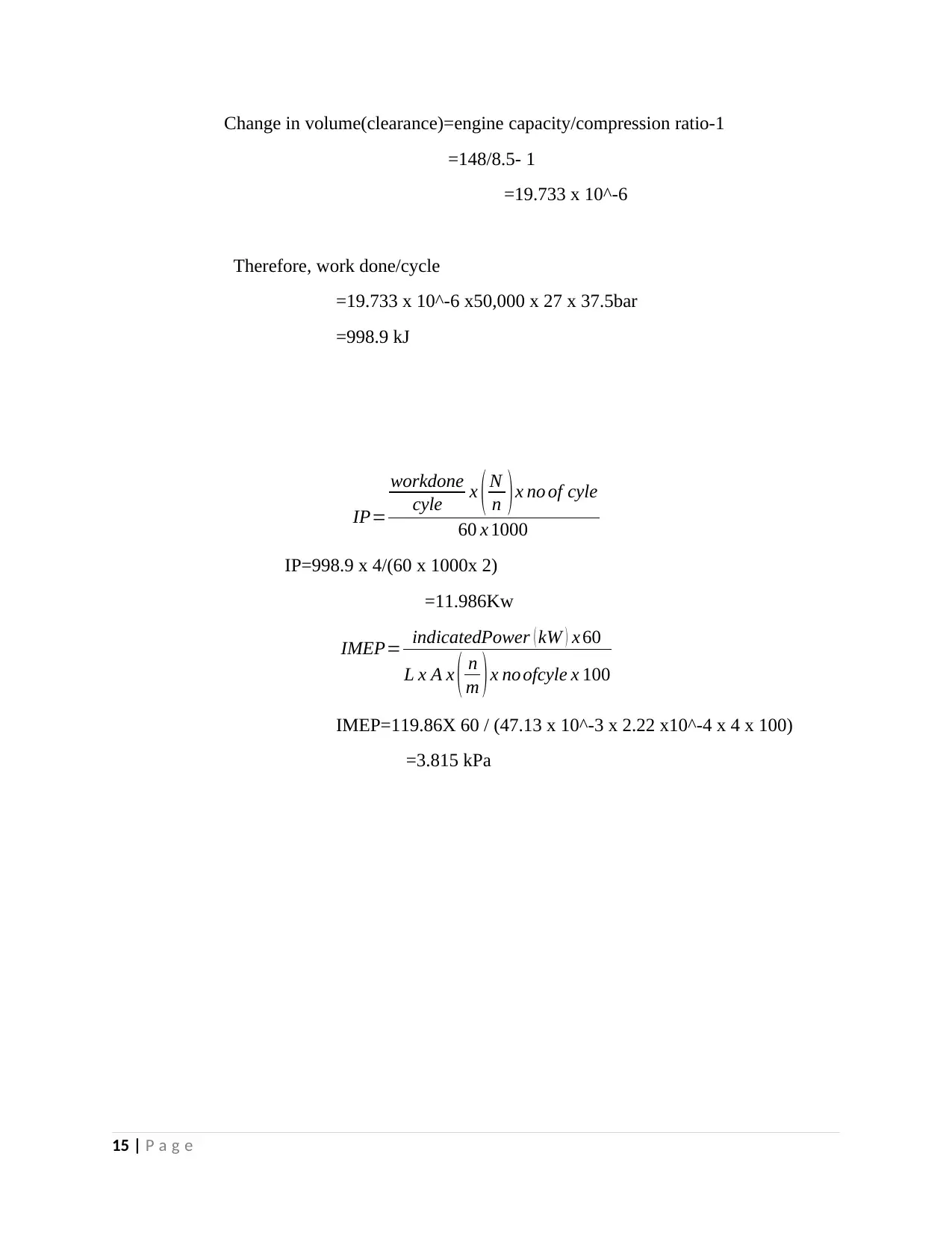
Change in volume(clearance)=engine capacity/compression ratio-1
=148/8.5- 1
=19.733 x 10^-6
Therefore, work done/cycle
=19.733 x 10^-6 x50,000 x 27 x 37.5bar
=998.9 kJ
IP=
workdone
cyle x ( N
n )x no of cyle
60 x 1000
IP=998.9 x 4/(60 x 1000x 2)
=11.986Kw
IMEP= indicatedPower ( kW ) x 60
L x A x ( n
m ) x no ofcyle x 100
IMEP=119.86X 60 / (47.13 x 10^-3 x 2.22 x10^-4 x 4 x 100)
=3.815 kPa
15 | P a g e
=148/8.5- 1
=19.733 x 10^-6
Therefore, work done/cycle
=19.733 x 10^-6 x50,000 x 27 x 37.5bar
=998.9 kJ
IP=
workdone
cyle x ( N
n )x no of cyle
60 x 1000
IP=998.9 x 4/(60 x 1000x 2)
=11.986Kw
IMEP= indicatedPower ( kW ) x 60
L x A x ( n
m ) x no ofcyle x 100
IMEP=119.86X 60 / (47.13 x 10^-3 x 2.22 x10^-4 x 4 x 100)
=3.815 kPa
15 | P a g e
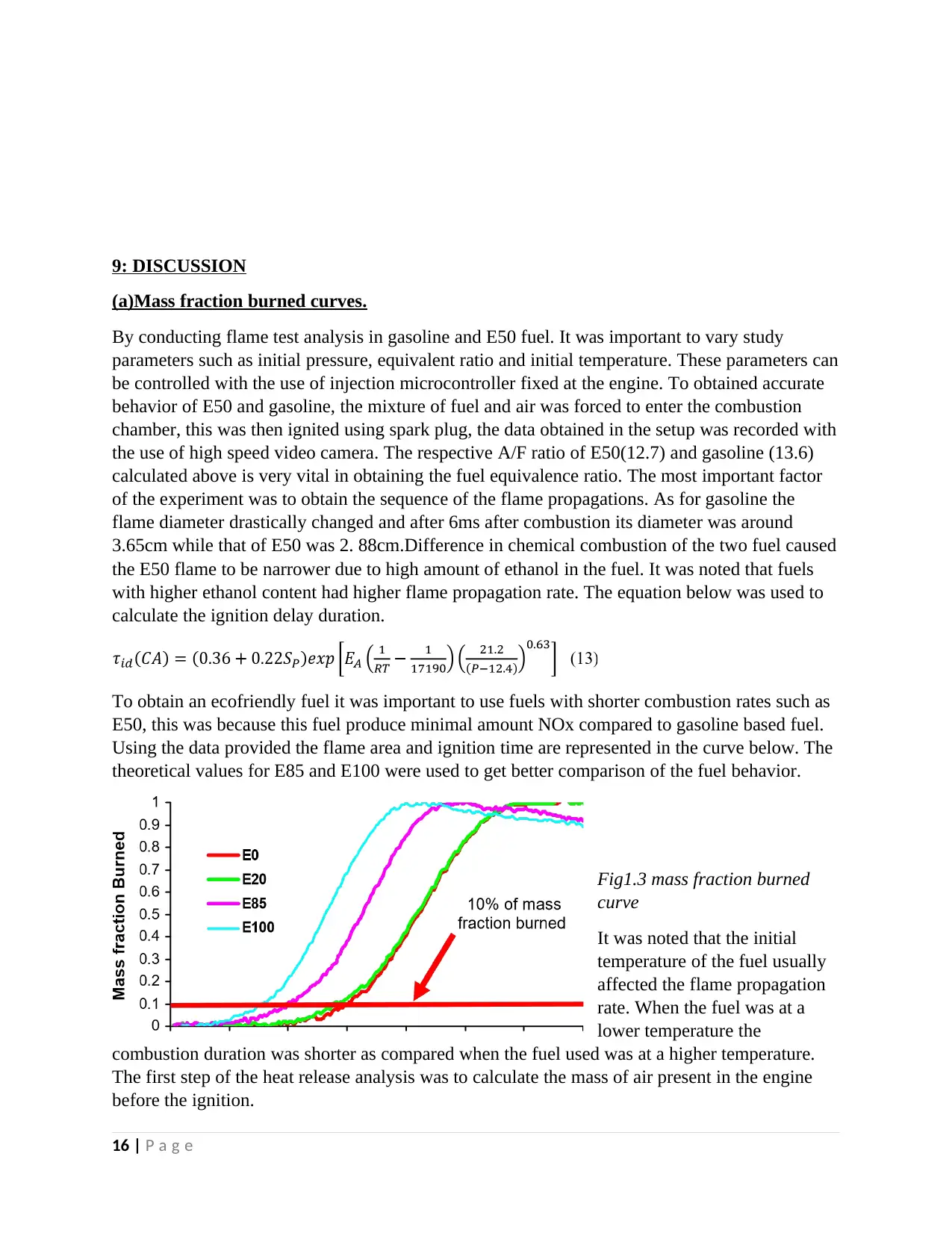
9: DISCUSSION
(a)Mass fraction burned curves.
By conducting flame test analysis in gasoline and E50 fuel. It was important to vary study
parameters such as initial pressure, equivalent ratio and initial temperature. These parameters can
be controlled with the use of injection microcontroller fixed at the engine. To obtained accurate
behavior of E50 and gasoline, the mixture of fuel and air was forced to enter the combustion
chamber, this was then ignited using spark plug, the data obtained in the setup was recorded with
the use of high speed video camera. The respective A/F ratio of E50(12.7) and gasoline (13.6)
calculated above is very vital in obtaining the fuel equivalence ratio. The most important factor
of the experiment was to obtain the sequence of the flame propagations. As for gasoline the
flame diameter drastically changed and after 6ms after combustion its diameter was around
3.65cm while that of E50 was 2. 88cm.Difference in chemical combustion of the two fuel caused
the E50 flame to be narrower due to high amount of ethanol in the fuel. It was noted that fuels
with higher ethanol content had higher flame propagation rate. The equation below was used to
calculate the ignition delay duration.
To obtain an ecofriendly fuel it was important to use fuels with shorter combustion rates such as
E50, this was because this fuel produce minimal amount NOx compared to gasoline based fuel.
Using the data provided the flame area and ignition time are represented in the curve below. The
theoretical values for E85 and E100 were used to get better comparison of the fuel behavior.
Fig1.3 mass fraction burned
curve
It was noted that the initial
temperature of the fuel usually
affected the flame propagation
rate. When the fuel was at a
lower temperature the
combustion duration was shorter as compared when the fuel used was at a higher temperature.
The first step of the heat release analysis was to calculate the mass of air present in the engine
before the ignition.
16 | P a g e
(a)Mass fraction burned curves.
By conducting flame test analysis in gasoline and E50 fuel. It was important to vary study
parameters such as initial pressure, equivalent ratio and initial temperature. These parameters can
be controlled with the use of injection microcontroller fixed at the engine. To obtained accurate
behavior of E50 and gasoline, the mixture of fuel and air was forced to enter the combustion
chamber, this was then ignited using spark plug, the data obtained in the setup was recorded with
the use of high speed video camera. The respective A/F ratio of E50(12.7) and gasoline (13.6)
calculated above is very vital in obtaining the fuel equivalence ratio. The most important factor
of the experiment was to obtain the sequence of the flame propagations. As for gasoline the
flame diameter drastically changed and after 6ms after combustion its diameter was around
3.65cm while that of E50 was 2. 88cm.Difference in chemical combustion of the two fuel caused
the E50 flame to be narrower due to high amount of ethanol in the fuel. It was noted that fuels
with higher ethanol content had higher flame propagation rate. The equation below was used to
calculate the ignition delay duration.
To obtain an ecofriendly fuel it was important to use fuels with shorter combustion rates such as
E50, this was because this fuel produce minimal amount NOx compared to gasoline based fuel.
Using the data provided the flame area and ignition time are represented in the curve below. The
theoretical values for E85 and E100 were used to get better comparison of the fuel behavior.
Fig1.3 mass fraction burned
curve
It was noted that the initial
temperature of the fuel usually
affected the flame propagation
rate. When the fuel was at a
lower temperature the
combustion duration was shorter as compared when the fuel used was at a higher temperature.
The first step of the heat release analysis was to calculate the mass of air present in the engine
before the ignition.
16 | P a g e
Secure Best Marks with AI Grader
Need help grading? Try our AI Grader for instant feedback on your assignments.
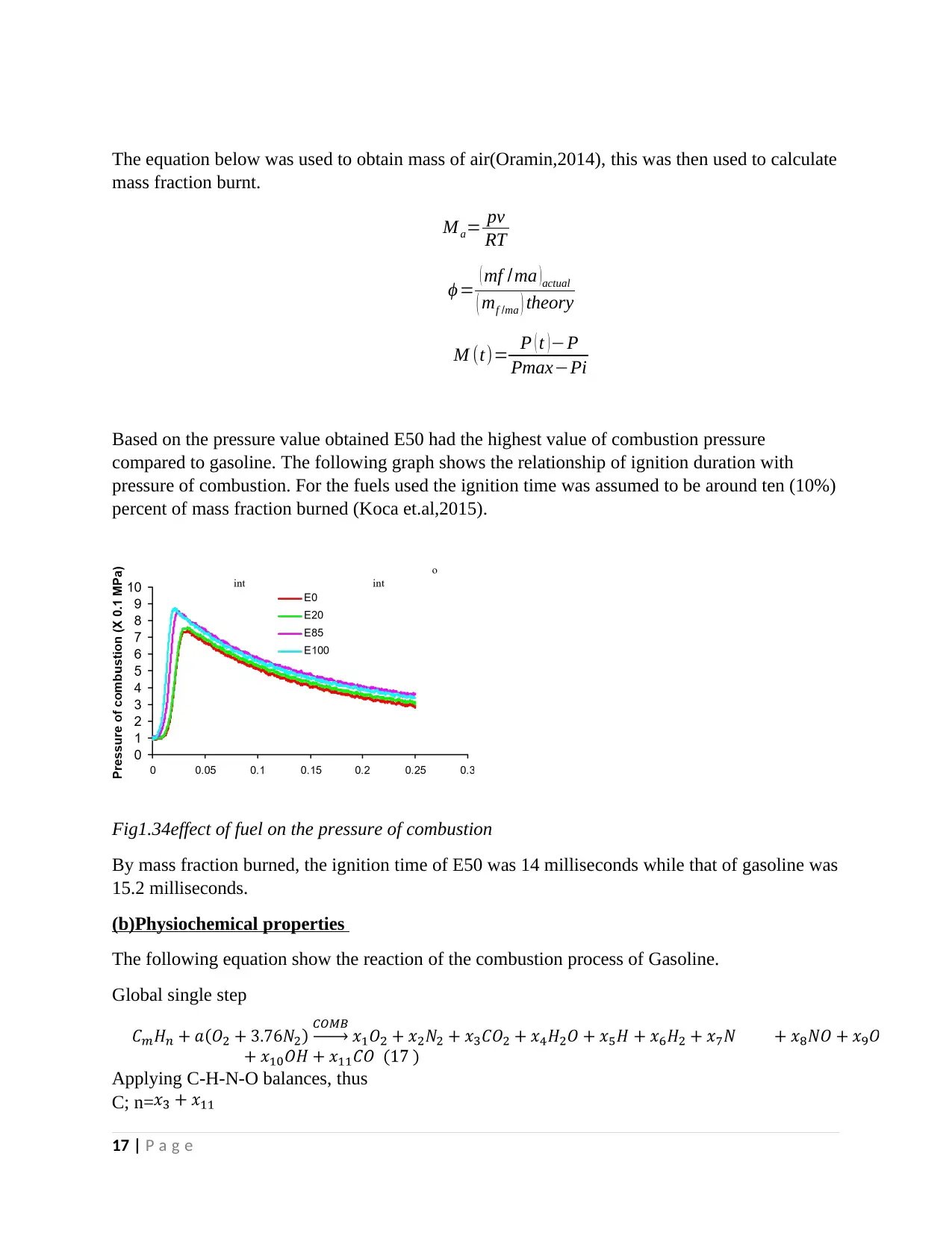
The equation below was used to obtain mass of air(Oramin,2014), this was then used to calculate
mass fraction burnt.
M a= pv
RT
ϕ = ( mf /ma )actual
( mf /ma ) theory
M (t)= P ( t )−P
Pmax−Pi
Based on the pressure value obtained E50 had the highest value of combustion pressure
compared to gasoline. The following graph shows the relationship of ignition duration with
pressure of combustion. For the fuels used the ignition time was assumed to be around ten (10%)
percent of mass fraction burned (Koca et.al,2015).
Fig1.34effect of fuel on the pressure of combustion
By mass fraction burned, the ignition time of E50 was 14 milliseconds while that of gasoline was
15.2 milliseconds.
(b)Physiochemical properties
The following equation show the reaction of the combustion process of Gasoline.
Global single step
Applying C-H-N-O balances, thus
C; n=
17 | P a g e
mass fraction burnt.
M a= pv
RT
ϕ = ( mf /ma )actual
( mf /ma ) theory
M (t)= P ( t )−P
Pmax−Pi
Based on the pressure value obtained E50 had the highest value of combustion pressure
compared to gasoline. The following graph shows the relationship of ignition duration with
pressure of combustion. For the fuels used the ignition time was assumed to be around ten (10%)
percent of mass fraction burned (Koca et.al,2015).
Fig1.34effect of fuel on the pressure of combustion
By mass fraction burned, the ignition time of E50 was 14 milliseconds while that of gasoline was
15.2 milliseconds.
(b)Physiochemical properties
The following equation show the reaction of the combustion process of Gasoline.
Global single step
Applying C-H-N-O balances, thus
C; n=
17 | P a g e
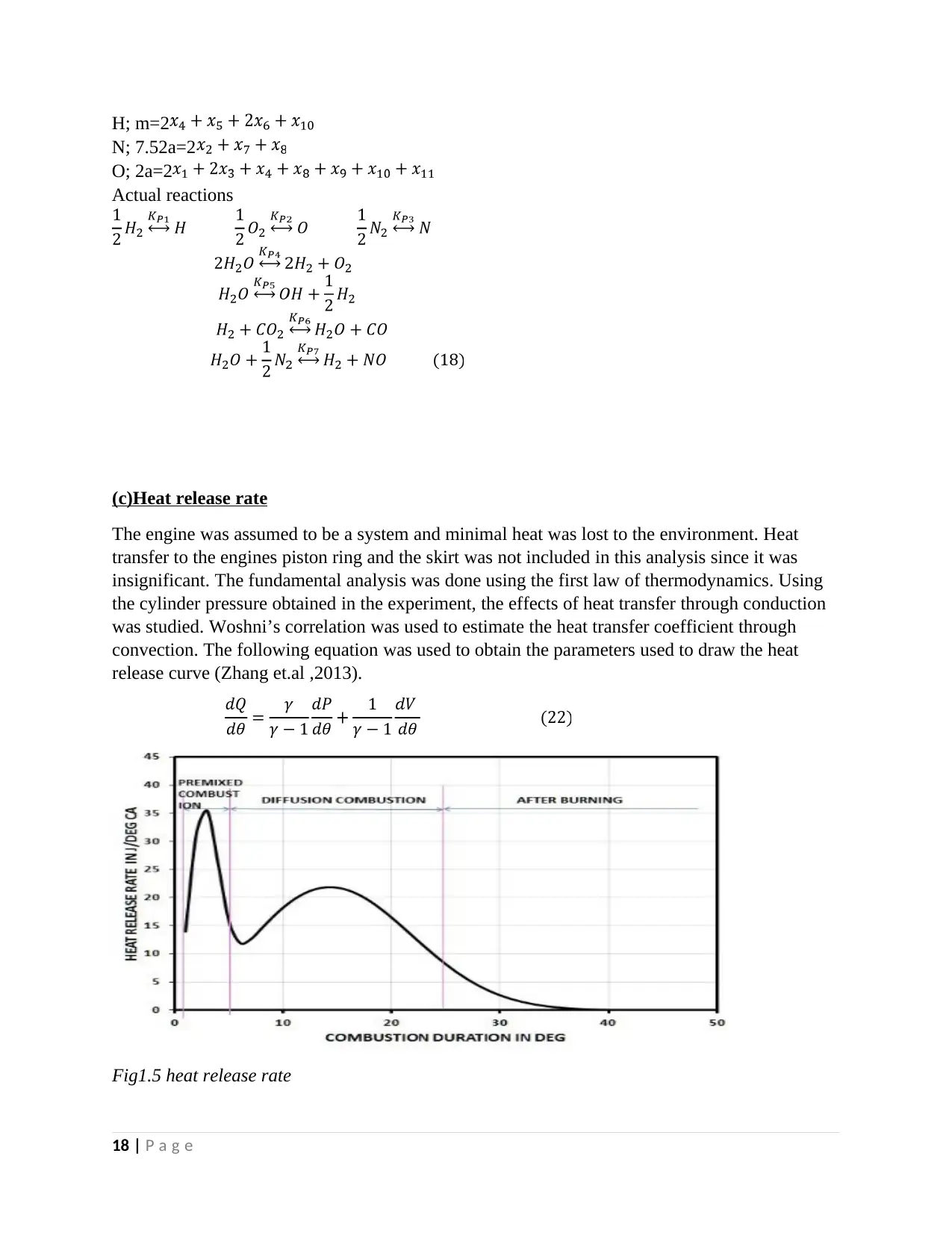
H; m=2
N; 7.52a=2
O; 2a=2
Actual reactions
(c)Heat release rate
The engine was assumed to be a system and minimal heat was lost to the environment. Heat
transfer to the engines piston ring and the skirt was not included in this analysis since it was
insignificant. The fundamental analysis was done using the first law of thermodynamics. Using
the cylinder pressure obtained in the experiment, the effects of heat transfer through conduction
was studied. Woshni’s correlation was used to estimate the heat transfer coefficient through
convection. The following equation was used to obtain the parameters used to draw the heat
release curve (Zhang et.al ,2013).
Fig1.5 heat release rate
18 | P a g e
N; 7.52a=2
O; 2a=2
Actual reactions
(c)Heat release rate
The engine was assumed to be a system and minimal heat was lost to the environment. Heat
transfer to the engines piston ring and the skirt was not included in this analysis since it was
insignificant. The fundamental analysis was done using the first law of thermodynamics. Using
the cylinder pressure obtained in the experiment, the effects of heat transfer through conduction
was studied. Woshni’s correlation was used to estimate the heat transfer coefficient through
convection. The following equation was used to obtain the parameters used to draw the heat
release curve (Zhang et.al ,2013).
Fig1.5 heat release rate
18 | P a g e
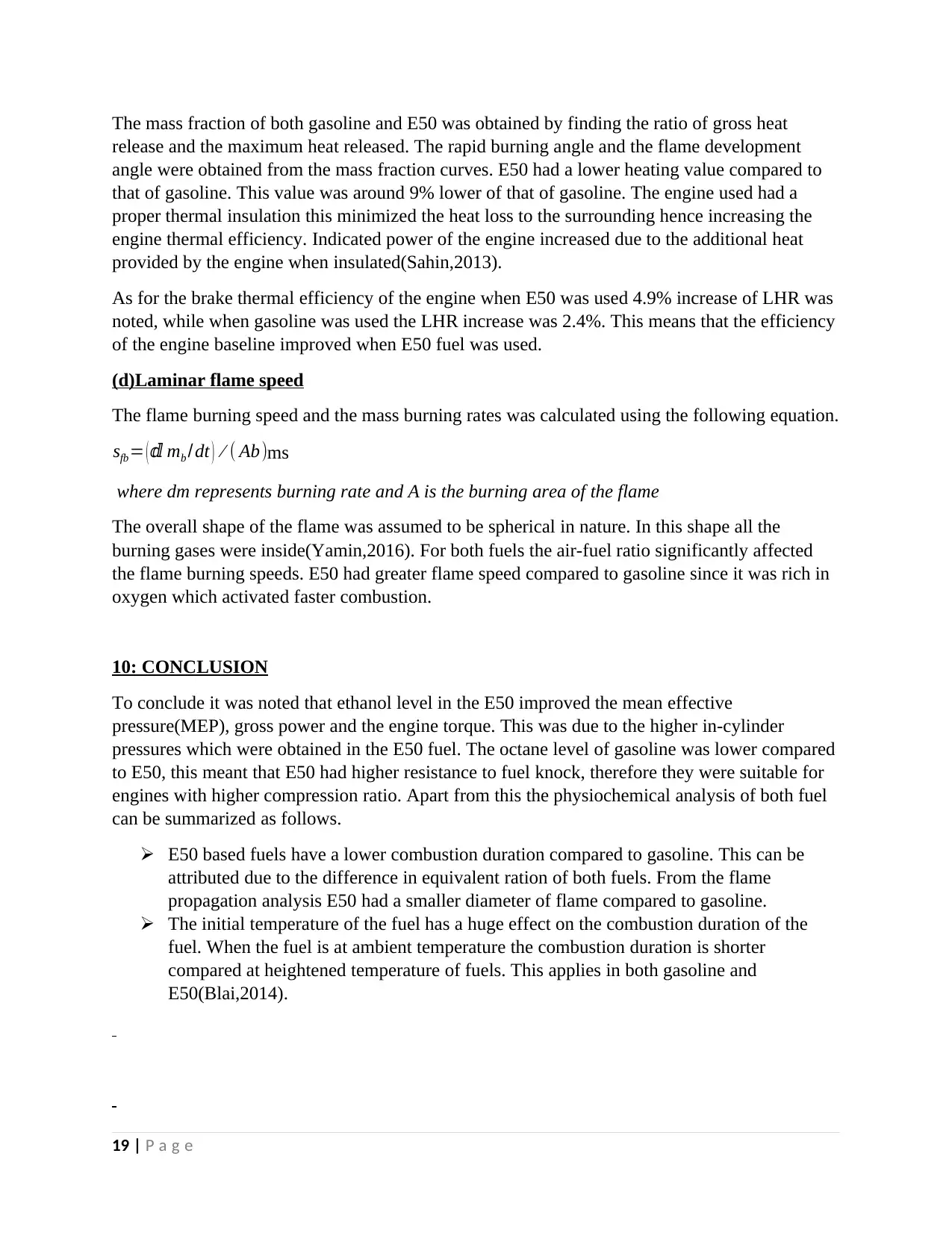
The mass fraction of both gasoline and E50 was obtained by finding the ratio of gross heat
release and the maximum heat released. The rapid burning angle and the flame development
angle were obtained from the mass fraction curves. E50 had a lower heating value compared to
that of gasoline. This value was around 9% lower of that of gasoline. The engine used had a
proper thermal insulation this minimized the heat loss to the surrounding hence increasing the
engine thermal efficiency. Indicated power of the engine increased due to the additional heat
provided by the engine when insulated(Sahin,2013).
As for the brake thermal efficiency of the engine when E50 was used 4.9% increase of LHR was
noted, while when gasoline was used the LHR increase was 2.4%. This means that the efficiency
of the engine baseline improved when E50 fuel was used.
(d)Laminar flame speed
The flame burning speed and the mass burning rates was calculated using the following equation.
sfb= ( ⅆ mb /dt ) ∕ ( Ab)ms
where dm represents burning rate and A is the burning area of the flame
The overall shape of the flame was assumed to be spherical in nature. In this shape all the
burning gases were inside(Yamin,2016). For both fuels the air-fuel ratio significantly affected
the flame burning speeds. E50 had greater flame speed compared to gasoline since it was rich in
oxygen which activated faster combustion.
10: CONCLUSION
To conclude it was noted that ethanol level in the E50 improved the mean effective
pressure(MEP), gross power and the engine torque. This was due to the higher in-cylinder
pressures which were obtained in the E50 fuel. The octane level of gasoline was lower compared
to E50, this meant that E50 had higher resistance to fuel knock, therefore they were suitable for
engines with higher compression ratio. Apart from this the physiochemical analysis of both fuel
can be summarized as follows.
E50 based fuels have a lower combustion duration compared to gasoline. This can be
attributed due to the difference in equivalent ration of both fuels. From the flame
propagation analysis E50 had a smaller diameter of flame compared to gasoline.
The initial temperature of the fuel has a huge effect on the combustion duration of the
fuel. When the fuel is at ambient temperature the combustion duration is shorter
compared at heightened temperature of fuels. This applies in both gasoline and
E50(Blai,2014).
19 | P a g e
release and the maximum heat released. The rapid burning angle and the flame development
angle were obtained from the mass fraction curves. E50 had a lower heating value compared to
that of gasoline. This value was around 9% lower of that of gasoline. The engine used had a
proper thermal insulation this minimized the heat loss to the surrounding hence increasing the
engine thermal efficiency. Indicated power of the engine increased due to the additional heat
provided by the engine when insulated(Sahin,2013).
As for the brake thermal efficiency of the engine when E50 was used 4.9% increase of LHR was
noted, while when gasoline was used the LHR increase was 2.4%. This means that the efficiency
of the engine baseline improved when E50 fuel was used.
(d)Laminar flame speed
The flame burning speed and the mass burning rates was calculated using the following equation.
sfb= ( ⅆ mb /dt ) ∕ ( Ab)ms
where dm represents burning rate and A is the burning area of the flame
The overall shape of the flame was assumed to be spherical in nature. In this shape all the
burning gases were inside(Yamin,2016). For both fuels the air-fuel ratio significantly affected
the flame burning speeds. E50 had greater flame speed compared to gasoline since it was rich in
oxygen which activated faster combustion.
10: CONCLUSION
To conclude it was noted that ethanol level in the E50 improved the mean effective
pressure(MEP), gross power and the engine torque. This was due to the higher in-cylinder
pressures which were obtained in the E50 fuel. The octane level of gasoline was lower compared
to E50, this meant that E50 had higher resistance to fuel knock, therefore they were suitable for
engines with higher compression ratio. Apart from this the physiochemical analysis of both fuel
can be summarized as follows.
E50 based fuels have a lower combustion duration compared to gasoline. This can be
attributed due to the difference in equivalent ration of both fuels. From the flame
propagation analysis E50 had a smaller diameter of flame compared to gasoline.
The initial temperature of the fuel has a huge effect on the combustion duration of the
fuel. When the fuel is at ambient temperature the combustion duration is shorter
compared at heightened temperature of fuels. This applies in both gasoline and
E50(Blai,2014).
19 | P a g e
Paraphrase This Document
Need a fresh take? Get an instant paraphrase of this document with our AI Paraphraser
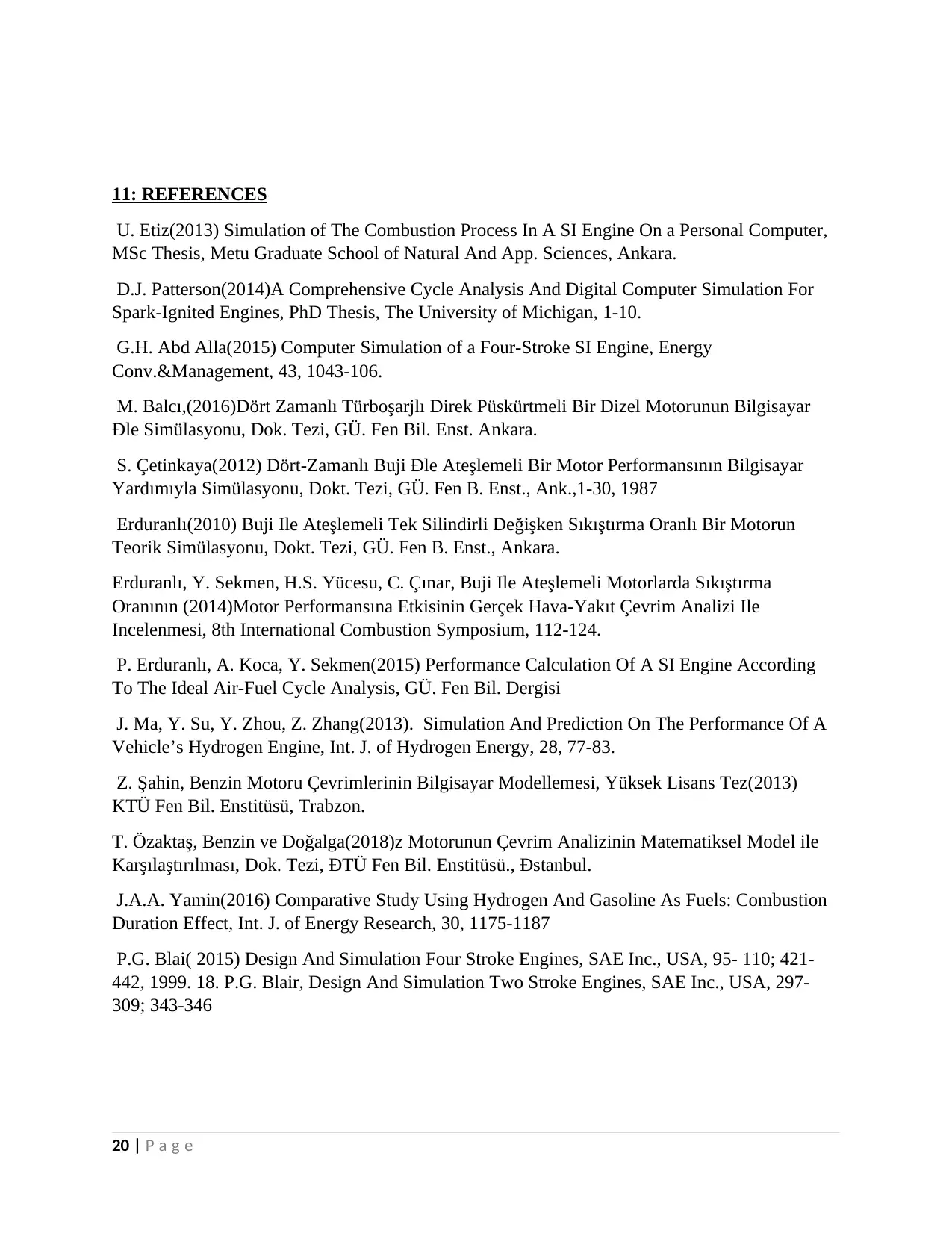
11: REFERENCES
U. Etiz(2013) Simulation of The Combustion Process In A SI Engine On a Personal Computer,
MSc Thesis, Metu Graduate School of Natural And App. Sciences, Ankara.
D.J. Patterson(2014)A Comprehensive Cycle Analysis And Digital Computer Simulation For
Spark-Ignited Engines, PhD Thesis, The University of Michigan, 1-10.
G.H. Abd Alla(2015) Computer Simulation of a Four-Stroke SI Engine, Energy
Conv.&Management, 43, 1043-106.
M. Balcı,(2016)Dört Zamanlı Türboşarjlı Direk Püskürtmeli Bir Dizel Motorunun Bilgisayar
Đle Simülasyonu, Dok. Tezi, GÜ. Fen Bil. Enst. Ankara.
S. Çetinkaya(2012) Dört-Zamanlı Buji Đle Ateşlemeli Bir Motor Performansının Bilgisayar
Yardımıyla Simülasyonu, Dokt. Tezi, GÜ. Fen B. Enst., Ank.,1-30, 1987
Erduranlı(2010) Buji Ile Ateşlemeli Tek Silindirli Değişken Sıkıştırma Oranlı Bir Motorun
Teorik Simülasyonu, Dokt. Tezi, GÜ. Fen B. Enst., Ankara.
Erduranlı, Y. Sekmen, H.S. Yücesu, C. Çınar, Buji Ile Ateşlemeli Motorlarda Sıkıştırma
Oranının (2014)Motor Performansına Etkisinin Gerçek Hava-Yakıt Çevrim Analizi Ile
Incelenmesi, 8th International Combustion Symposium, 112-124.
P. Erduranlı, A. Koca, Y. Sekmen(2015) Performance Calculation Of A SI Engine According
To The Ideal Air-Fuel Cycle Analysis, GÜ. Fen Bil. Dergisi
J. Ma, Y. Su, Y. Zhou, Z. Zhang(2013). Simulation And Prediction On The Performance Of A
Vehicle’s Hydrogen Engine, Int. J. of Hydrogen Energy, 28, 77-83.
Z. Şahin, Benzin Motoru Çevrimlerinin Bilgisayar Modellemesi, Yüksek Lisans Tez(2013)
KTÜ Fen Bil. Enstitüsü, Trabzon.
T. Özaktaş, Benzin ve Doğalga(2018)z Motorunun Çevrim Analizinin Matematiksel Model ile
Karşılaştırılması, Dok. Tezi, ĐTÜ Fen Bil. Enstitüsü., Đstanbul.
J.A.A. Yamin(2016) Comparative Study Using Hydrogen And Gasoline As Fuels: Combustion
Duration Effect, Int. J. of Energy Research, 30, 1175-1187
P.G. Blai( 2015) Design And Simulation Four Stroke Engines, SAE Inc., USA, 95- 110; 421-
442, 1999. 18. P.G. Blair, Design And Simulation Two Stroke Engines, SAE Inc., USA, 297-
309; 343-346
20 | P a g e
U. Etiz(2013) Simulation of The Combustion Process In A SI Engine On a Personal Computer,
MSc Thesis, Metu Graduate School of Natural And App. Sciences, Ankara.
D.J. Patterson(2014)A Comprehensive Cycle Analysis And Digital Computer Simulation For
Spark-Ignited Engines, PhD Thesis, The University of Michigan, 1-10.
G.H. Abd Alla(2015) Computer Simulation of a Four-Stroke SI Engine, Energy
Conv.&Management, 43, 1043-106.
M. Balcı,(2016)Dört Zamanlı Türboşarjlı Direk Püskürtmeli Bir Dizel Motorunun Bilgisayar
Đle Simülasyonu, Dok. Tezi, GÜ. Fen Bil. Enst. Ankara.
S. Çetinkaya(2012) Dört-Zamanlı Buji Đle Ateşlemeli Bir Motor Performansının Bilgisayar
Yardımıyla Simülasyonu, Dokt. Tezi, GÜ. Fen B. Enst., Ank.,1-30, 1987
Erduranlı(2010) Buji Ile Ateşlemeli Tek Silindirli Değişken Sıkıştırma Oranlı Bir Motorun
Teorik Simülasyonu, Dokt. Tezi, GÜ. Fen B. Enst., Ankara.
Erduranlı, Y. Sekmen, H.S. Yücesu, C. Çınar, Buji Ile Ateşlemeli Motorlarda Sıkıştırma
Oranının (2014)Motor Performansına Etkisinin Gerçek Hava-Yakıt Çevrim Analizi Ile
Incelenmesi, 8th International Combustion Symposium, 112-124.
P. Erduranlı, A. Koca, Y. Sekmen(2015) Performance Calculation Of A SI Engine According
To The Ideal Air-Fuel Cycle Analysis, GÜ. Fen Bil. Dergisi
J. Ma, Y. Su, Y. Zhou, Z. Zhang(2013). Simulation And Prediction On The Performance Of A
Vehicle’s Hydrogen Engine, Int. J. of Hydrogen Energy, 28, 77-83.
Z. Şahin, Benzin Motoru Çevrimlerinin Bilgisayar Modellemesi, Yüksek Lisans Tez(2013)
KTÜ Fen Bil. Enstitüsü, Trabzon.
T. Özaktaş, Benzin ve Doğalga(2018)z Motorunun Çevrim Analizinin Matematiksel Model ile
Karşılaştırılması, Dok. Tezi, ĐTÜ Fen Bil. Enstitüsü., Đstanbul.
J.A.A. Yamin(2016) Comparative Study Using Hydrogen And Gasoline As Fuels: Combustion
Duration Effect, Int. J. of Energy Research, 30, 1175-1187
P.G. Blai( 2015) Design And Simulation Four Stroke Engines, SAE Inc., USA, 95- 110; 421-
442, 1999. 18. P.G. Blair, Design And Simulation Two Stroke Engines, SAE Inc., USA, 297-
309; 343-346
20 | P a g e
1 out of 20
![[object Object]](/_next/image/?url=%2F_next%2Fstatic%2Fmedia%2Flogo.6d15ce61.png&w=640&q=75)
Your All-in-One AI-Powered Toolkit for Academic Success.
+13062052269
info@desklib.com
Available 24*7 on WhatsApp / Email
Unlock your academic potential
© 2024 | Zucol Services PVT LTD | All rights reserved.