Optimization of IKEA’s product delivery process
VerifiedAdded on 2023/03/20
|30
|9113
|94
AI Summary
This report is about optimizing IKEA’s product delivery process to reduce waste and increase business sustainability. It analyzes the current process, identifies problems, proposes solutions, and discusses project risks and resources.
Contribute Materials
Your contribution can guide someone’s learning journey. Share your
documents today.
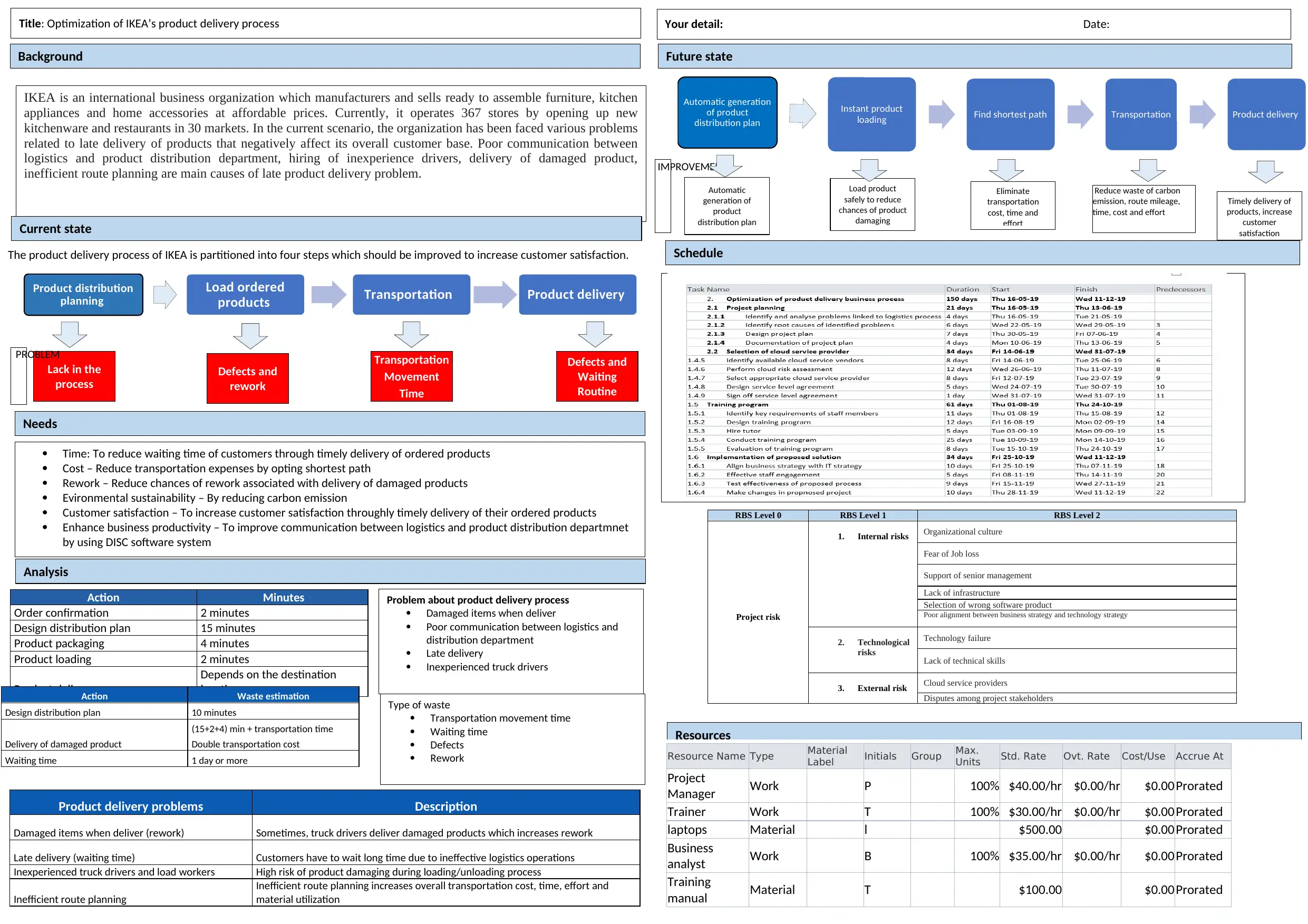
Time: To reduce waiting time of customers through timely delivery of ordered products
Cost – Reduce transportation expenses by opting shortest path
Rework – Reduce chances of rework associated with delivery of damaged products
Evironmental sustainability – By reducing carbon emission
Customer satisfaction – To increase customer satisfaction throughly timely delivery of their ordered products
Enhance business productivity – To improve communication between logistics and product distribution departmnet
by using DISC software system
Background
IKEA is an international business organization which manufacturers and sells ready to assemble furniture, kitchen
appliances and home accessories at affordable prices. Currently, it operates 367 stores by opening up new
kitchenware and restaurants in 30 markets. In the current scenario, the organization has been faced various problems
related to late delivery of products that negatively affect its overall customer base. Poor communication between
logistics and product distribution department, hiring of inexperience drivers, delivery of damaged product,
inefficient route planning are main causes of late product delivery problem.
Your detail: Date:Title: Optimization of IKEA’s product delivery process
Current state
Needs
Analysis
Future state
Schedule
Resources
Resource Name Type Material
Label Initials Group Max.
Units Std. Rate Ovt. Rate Cost/Use Accrue At
Project
Manager Work P 100% $40.00/hr $0.00/hr $0.00 Prorated
Trainer Work T 100% $30.00/hr $0.00/hr $0.00 Prorated
laptops Material l $500.00 $0.00 Prorated
Business
analyst Work B 100% $35.00/hr $0.00/hr $0.00 Prorated
Training
manual Material T $100.00 $0.00 Prorated
Defects and
rework
Transportation
Movement
Time
Defects and
Waiting
Routine
Lack in the
process
Product distribution
planning
Load ordered
products Transportation Product delivery
PROBLEM
The product delivery process of IKEA is partitioned into four steps which should be improved to increase customer satisfaction.
Automatic generation
of product
distribution plan
Instant product
loading Find shortest path Transportation Product delivery
Automatic
generation of
product
distribution plan
Load product
safely to reduce
chances of product
damaging
Eliminate
transportation
cost, time and
effort
Reduce waste of carbon
emission, route mileage,
time, cost and effort
Timely delivery of
products, increase
customer
satisfaction
IMPROVEMENT
Problem about product delivery process
Damaged items when deliver
Poor communication between logistics and
distribution department
Late delivery
Inexperienced truck drivers
Type of waste
Transportation movement time
Waiting time
Defects
Rework
Product delivery problems Description
Damaged items when deliver (rework) Sometimes, truck drivers deliver damaged products which increases rework
Late delivery (waiting time) Customers have to wait long time due to ineffective logistics operations
Inexperienced truck drivers and load workers High risk of product damaging during loading/unloading process
Inefficient route planning
Inefficient route planning increases overall transportation cost, time, effort and
material utilization
RBS Level 0 RBS Level 1 RBS Level 2
Project risk
1. Internal risks Organizational culture
Fear of Job loss
Support of senior management
Lack of infrastructure
Selection of wrong software product
Poor alignment between business strategy and technology strategy
2. Technological
risks
Technology failure
Lack of technical skills
3. External risk Cloud service providers
Disputes among project stakeholders
Action Minutes
Order confirmation 2 minutes
Design distribution plan 15 minutes
Product packaging 4 minutes
Product loading 2 minutes
Product delivery
Depends on the destination
location
Action Waste estimation
Design distribution plan 10 minutes
Delivery of damaged product
(15+2+4) min + transportation time
Double transportation cost
Waiting time 1 day or more
Cost – Reduce transportation expenses by opting shortest path
Rework – Reduce chances of rework associated with delivery of damaged products
Evironmental sustainability – By reducing carbon emission
Customer satisfaction – To increase customer satisfaction throughly timely delivery of their ordered products
Enhance business productivity – To improve communication between logistics and product distribution departmnet
by using DISC software system
Background
IKEA is an international business organization which manufacturers and sells ready to assemble furniture, kitchen
appliances and home accessories at affordable prices. Currently, it operates 367 stores by opening up new
kitchenware and restaurants in 30 markets. In the current scenario, the organization has been faced various problems
related to late delivery of products that negatively affect its overall customer base. Poor communication between
logistics and product distribution department, hiring of inexperience drivers, delivery of damaged product,
inefficient route planning are main causes of late product delivery problem.
Your detail: Date:Title: Optimization of IKEA’s product delivery process
Current state
Needs
Analysis
Future state
Schedule
Resources
Resource Name Type Material
Label Initials Group Max.
Units Std. Rate Ovt. Rate Cost/Use Accrue At
Project
Manager Work P 100% $40.00/hr $0.00/hr $0.00 Prorated
Trainer Work T 100% $30.00/hr $0.00/hr $0.00 Prorated
laptops Material l $500.00 $0.00 Prorated
Business
analyst Work B 100% $35.00/hr $0.00/hr $0.00 Prorated
Training
manual Material T $100.00 $0.00 Prorated
Defects and
rework
Transportation
Movement
Time
Defects and
Waiting
Routine
Lack in the
process
Product distribution
planning
Load ordered
products Transportation Product delivery
PROBLEM
The product delivery process of IKEA is partitioned into four steps which should be improved to increase customer satisfaction.
Automatic generation
of product
distribution plan
Instant product
loading Find shortest path Transportation Product delivery
Automatic
generation of
product
distribution plan
Load product
safely to reduce
chances of product
damaging
Eliminate
transportation
cost, time and
effort
Reduce waste of carbon
emission, route mileage,
time, cost and effort
Timely delivery of
products, increase
customer
satisfaction
IMPROVEMENT
Problem about product delivery process
Damaged items when deliver
Poor communication between logistics and
distribution department
Late delivery
Inexperienced truck drivers
Type of waste
Transportation movement time
Waiting time
Defects
Rework
Product delivery problems Description
Damaged items when deliver (rework) Sometimes, truck drivers deliver damaged products which increases rework
Late delivery (waiting time) Customers have to wait long time due to ineffective logistics operations
Inexperienced truck drivers and load workers High risk of product damaging during loading/unloading process
Inefficient route planning
Inefficient route planning increases overall transportation cost, time, effort and
material utilization
RBS Level 0 RBS Level 1 RBS Level 2
Project risk
1. Internal risks Organizational culture
Fear of Job loss
Support of senior management
Lack of infrastructure
Selection of wrong software product
Poor alignment between business strategy and technology strategy
2. Technological
risks
Technology failure
Lack of technical skills
3. External risk Cloud service providers
Disputes among project stakeholders
Action Minutes
Order confirmation 2 minutes
Design distribution plan 15 minutes
Product packaging 4 minutes
Product loading 2 minutes
Product delivery
Depends on the destination
location
Action Waste estimation
Design distribution plan 10 minutes
Delivery of damaged product
(15+2+4) min + transportation time
Double transportation cost
Waiting time 1 day or more
Secure Best Marks with AI Grader
Need help grading? Try our AI Grader for instant feedback on your assignments.
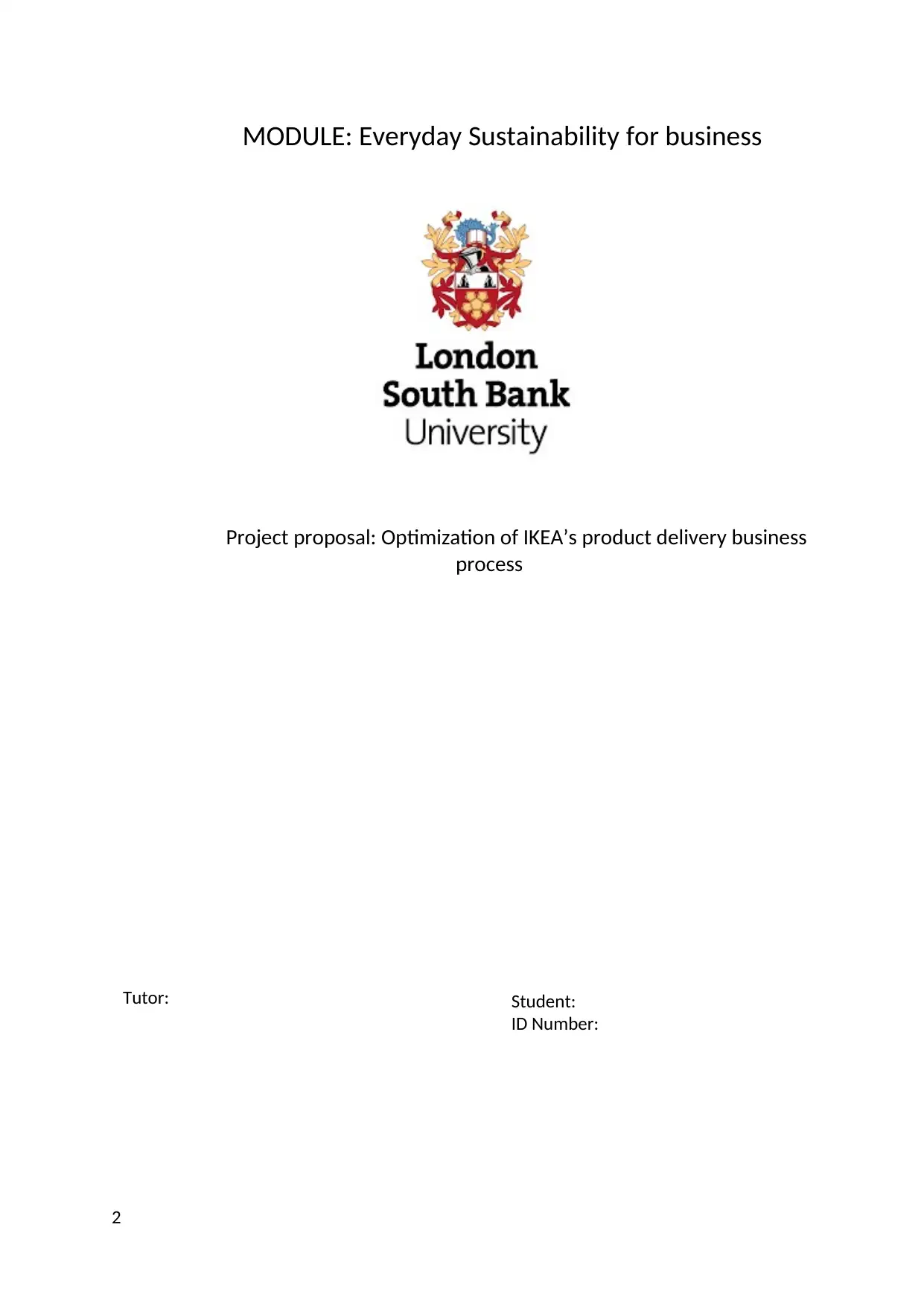
Project proposal: Optimization of IKEA’s product delivery business
process
2
Tutor:
MODULE: Everyday Sustainability for business
Student:
ID Number:
process
2
Tutor:
MODULE: Everyday Sustainability for business
Student:
ID Number:
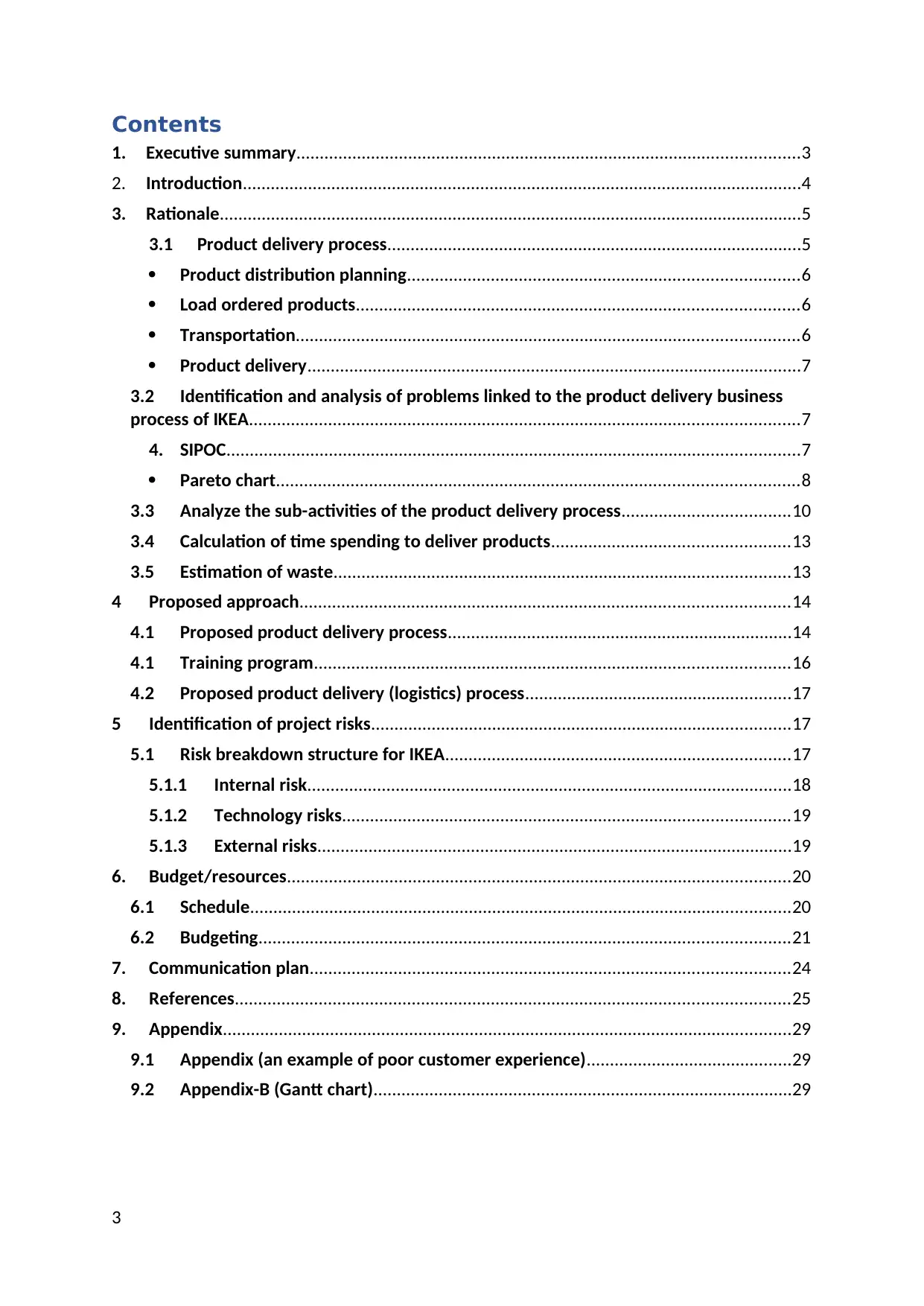
Contents
1. Executive summary............................................................................................................3
2. Introduction........................................................................................................................4
3. Rationale.............................................................................................................................5
3.1 Product delivery process.........................................................................................5
Product distribution planning....................................................................................6
Load ordered products...............................................................................................6
Transportation............................................................................................................6
Product delivery..........................................................................................................7
3.2 Identification and analysis of problems linked to the product delivery business
process of IKEA......................................................................................................................7
4. SIPOC...........................................................................................................................7
Pareto chart................................................................................................................8
3.3 Analyze the sub-activities of the product delivery process....................................10
3.4 Calculation of time spending to deliver products...................................................13
3.5 Estimation of waste..................................................................................................13
4 Proposed approach.........................................................................................................14
4.1 Proposed product delivery process..........................................................................14
4.1 Training program......................................................................................................16
4.2 Proposed product delivery (logistics) process.........................................................17
5 Identification of project risks..........................................................................................17
5.1 Risk breakdown structure for IKEA..........................................................................17
5.1.1 Internal risk........................................................................................................18
5.1.2 Technology risks................................................................................................19
5.1.3 External risks......................................................................................................19
6. Budget/resources............................................................................................................20
6.1 Schedule....................................................................................................................20
6.2 Budgeting..................................................................................................................21
7. Communication plan.......................................................................................................24
8. References.......................................................................................................................25
9. Appendix..........................................................................................................................29
9.1 Appendix (an example of poor customer experience)............................................29
9.2 Appendix-B (Gantt chart)..........................................................................................29
3
1. Executive summary............................................................................................................3
2. Introduction........................................................................................................................4
3. Rationale.............................................................................................................................5
3.1 Product delivery process.........................................................................................5
Product distribution planning....................................................................................6
Load ordered products...............................................................................................6
Transportation............................................................................................................6
Product delivery..........................................................................................................7
3.2 Identification and analysis of problems linked to the product delivery business
process of IKEA......................................................................................................................7
4. SIPOC...........................................................................................................................7
Pareto chart................................................................................................................8
3.3 Analyze the sub-activities of the product delivery process....................................10
3.4 Calculation of time spending to deliver products...................................................13
3.5 Estimation of waste..................................................................................................13
4 Proposed approach.........................................................................................................14
4.1 Proposed product delivery process..........................................................................14
4.1 Training program......................................................................................................16
4.2 Proposed product delivery (logistics) process.........................................................17
5 Identification of project risks..........................................................................................17
5.1 Risk breakdown structure for IKEA..........................................................................17
5.1.1 Internal risk........................................................................................................18
5.1.2 Technology risks................................................................................................19
5.1.3 External risks......................................................................................................19
6. Budget/resources............................................................................................................20
6.1 Schedule....................................................................................................................20
6.2 Budgeting..................................................................................................................21
7. Communication plan.......................................................................................................24
8. References.......................................................................................................................25
9. Appendix..........................................................................................................................29
9.1 Appendix (an example of poor customer experience)............................................29
9.2 Appendix-B (Gantt chart)..........................................................................................29
3
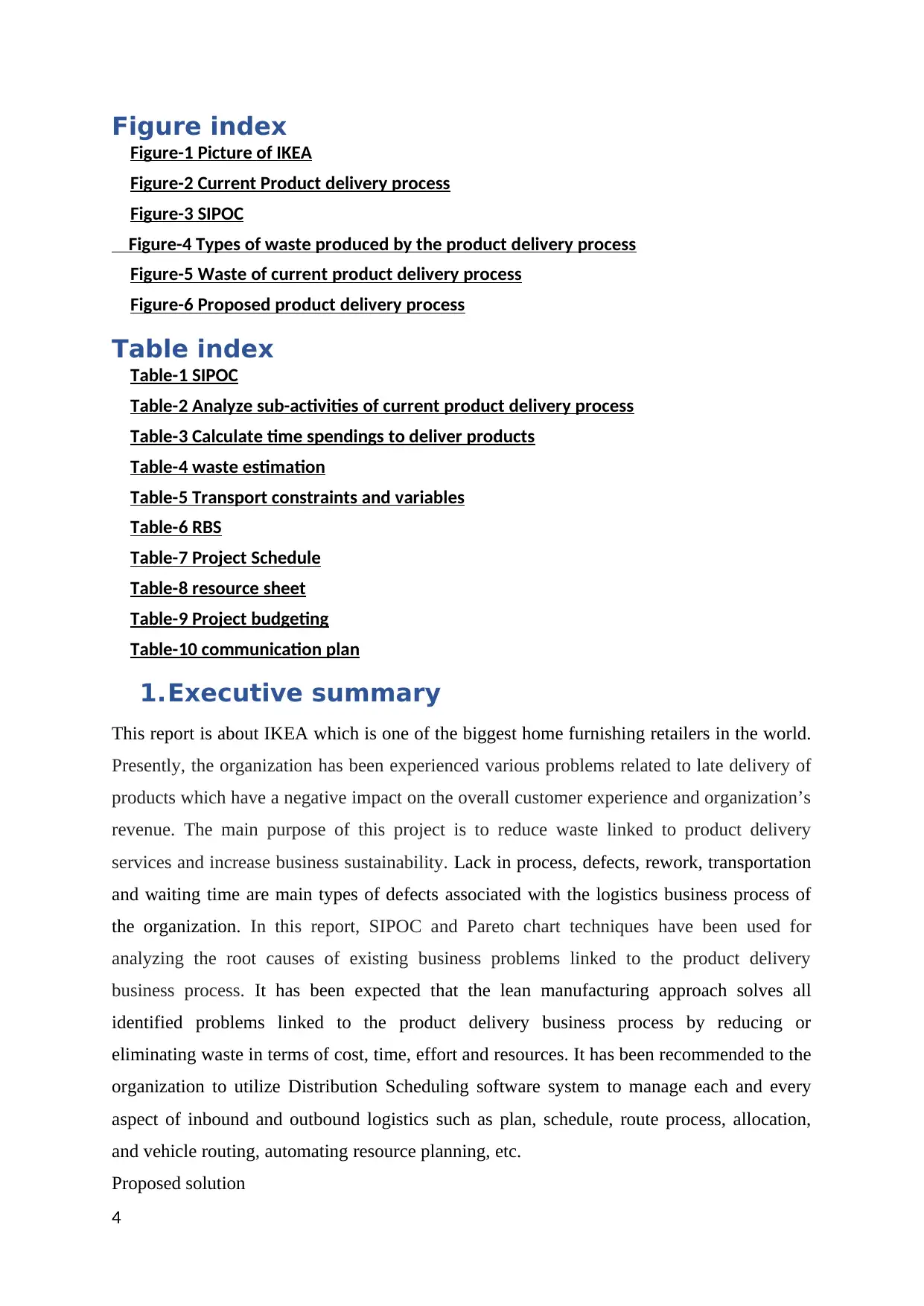
Figure index
Figure-1 Picture of IKEA
Figure-2 Current Product delivery process
Figure-3 SIPOC
Figure-4 Types of waste produced by the product delivery process
Figure-5 Waste of current product delivery process
Figure-6 Proposed product delivery process
Table index
Table-1 SIPOC
Table-2 Analyze sub-activities of current product delivery process
Table-3 Calculate time spendings to deliver products
Table-4 waste estimation
Table-5 Transport constraints and variables
Table-6 RBS
Table-7 Project Schedule
Table-8 resource sheet
Table-9 Project budgeting
Table-10 communication plan
1.Executive summary
This report is about IKEA which is one of the biggest home furnishing retailers in the world.
Presently, the organization has been experienced various problems related to late delivery of
products which have a negative impact on the overall customer experience and organization’s
revenue. The main purpose of this project is to reduce waste linked to product delivery
services and increase business sustainability. Lack in process, defects, rework, transportation
and waiting time are main types of defects associated with the logistics business process of
the organization. In this report, SIPOC and Pareto chart techniques have been used for
analyzing the root causes of existing business problems linked to the product delivery
business process. It has been expected that the lean manufacturing approach solves all
identified problems linked to the product delivery business process by reducing or
eliminating waste in terms of cost, time, effort and resources. It has been recommended to the
organization to utilize Distribution Scheduling software system to manage each and every
aspect of inbound and outbound logistics such as plan, schedule, route process, allocation,
and vehicle routing, automating resource planning, etc.
Proposed solution
4
Figure-1 Picture of IKEA
Figure-2 Current Product delivery process
Figure-3 SIPOC
Figure-4 Types of waste produced by the product delivery process
Figure-5 Waste of current product delivery process
Figure-6 Proposed product delivery process
Table index
Table-1 SIPOC
Table-2 Analyze sub-activities of current product delivery process
Table-3 Calculate time spendings to deliver products
Table-4 waste estimation
Table-5 Transport constraints and variables
Table-6 RBS
Table-7 Project Schedule
Table-8 resource sheet
Table-9 Project budgeting
Table-10 communication plan
1.Executive summary
This report is about IKEA which is one of the biggest home furnishing retailers in the world.
Presently, the organization has been experienced various problems related to late delivery of
products which have a negative impact on the overall customer experience and organization’s
revenue. The main purpose of this project is to reduce waste linked to product delivery
services and increase business sustainability. Lack in process, defects, rework, transportation
and waiting time are main types of defects associated with the logistics business process of
the organization. In this report, SIPOC and Pareto chart techniques have been used for
analyzing the root causes of existing business problems linked to the product delivery
business process. It has been expected that the lean manufacturing approach solves all
identified problems linked to the product delivery business process by reducing or
eliminating waste in terms of cost, time, effort and resources. It has been recommended to the
organization to utilize Distribution Scheduling software system to manage each and every
aspect of inbound and outbound logistics such as plan, schedule, route process, allocation,
and vehicle routing, automating resource planning, etc.
Proposed solution
4
Secure Best Marks with AI Grader
Need help grading? Try our AI Grader for instant feedback on your assignments.
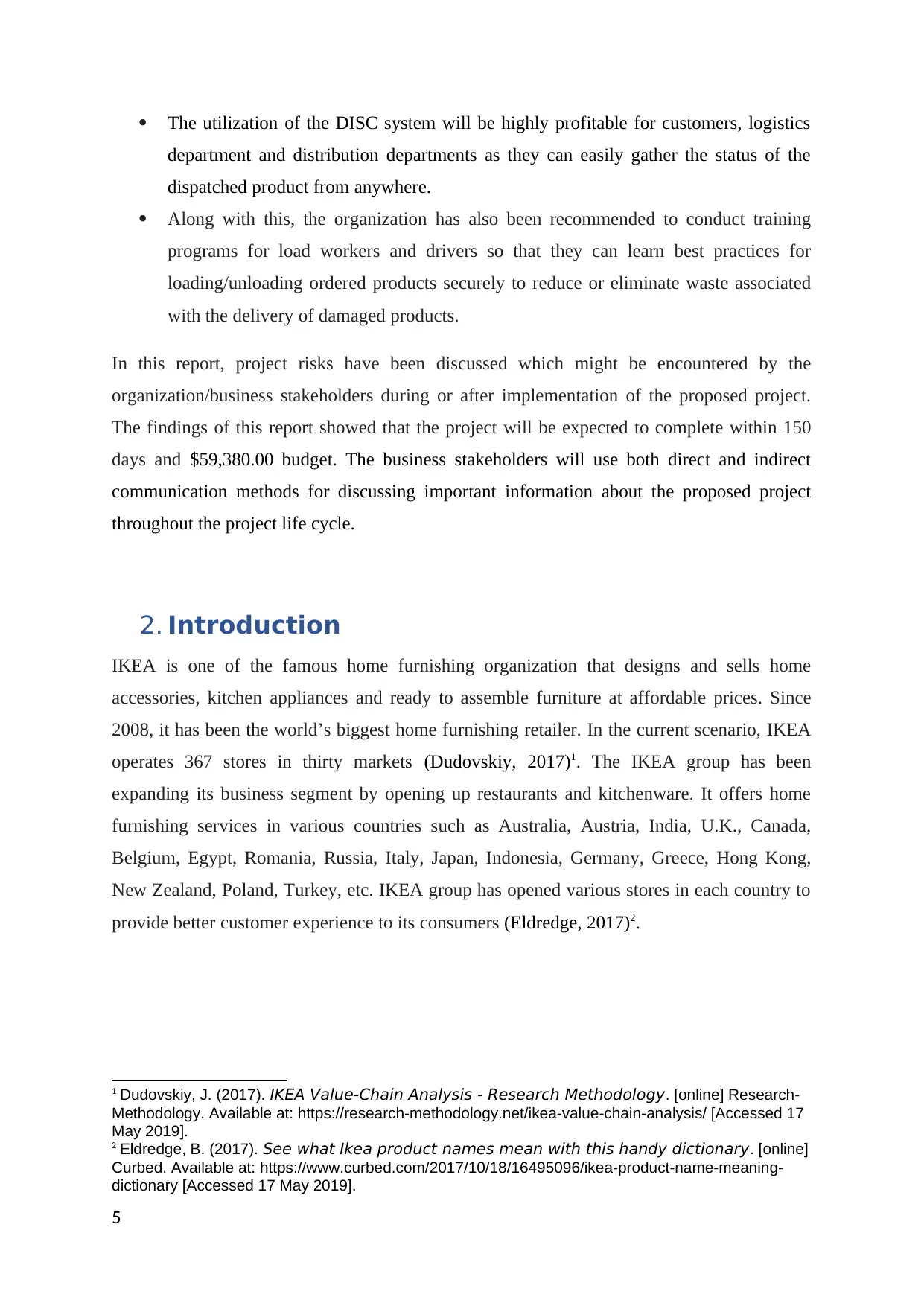
The utilization of the DISC system will be highly profitable for customers, logistics
department and distribution departments as they can easily gather the status of the
dispatched product from anywhere.
Along with this, the organization has also been recommended to conduct training
programs for load workers and drivers so that they can learn best practices for
loading/unloading ordered products securely to reduce or eliminate waste associated
with the delivery of damaged products.
In this report, project risks have been discussed which might be encountered by the
organization/business stakeholders during or after implementation of the proposed project.
The findings of this report showed that the project will be expected to complete within 150
days and $59,380.00 budget. The business stakeholders will use both direct and indirect
communication methods for discussing important information about the proposed project
throughout the project life cycle.
2. Introduction
IKEA is one of the famous home furnishing organization that designs and sells home
accessories, kitchen appliances and ready to assemble furniture at affordable prices. Since
2008, it has been the world’s biggest home furnishing retailer. In the current scenario, IKEA
operates 367 stores in thirty markets (Dudovskiy, 2017)1. The IKEA group has been
expanding its business segment by opening up restaurants and kitchenware. It offers home
furnishing services in various countries such as Australia, Austria, India, U.K., Canada,
Belgium, Egypt, Romania, Russia, Italy, Japan, Indonesia, Germany, Greece, Hong Kong,
New Zealand, Poland, Turkey, etc. IKEA group has opened various stores in each country to
provide better customer experience to its consumers (Eldredge, 2017)2.
1 Dudovskiy, J. (2017). IKEA Value-Chain Analysis - Research Methodology. [online] Research-
Methodology. Available at: https://research-methodology.net/ikea-value-chain-analysis/ [Accessed 17
May 2019].
2 Eldredge, B. (2017). See what Ikea product names mean with this handy dictionary. [online]
Curbed. Available at: https://www.curbed.com/2017/10/18/16495096/ikea-product-name-meaning-
dictionary [Accessed 17 May 2019].
5
department and distribution departments as they can easily gather the status of the
dispatched product from anywhere.
Along with this, the organization has also been recommended to conduct training
programs for load workers and drivers so that they can learn best practices for
loading/unloading ordered products securely to reduce or eliminate waste associated
with the delivery of damaged products.
In this report, project risks have been discussed which might be encountered by the
organization/business stakeholders during or after implementation of the proposed project.
The findings of this report showed that the project will be expected to complete within 150
days and $59,380.00 budget. The business stakeholders will use both direct and indirect
communication methods for discussing important information about the proposed project
throughout the project life cycle.
2. Introduction
IKEA is one of the famous home furnishing organization that designs and sells home
accessories, kitchen appliances and ready to assemble furniture at affordable prices. Since
2008, it has been the world’s biggest home furnishing retailer. In the current scenario, IKEA
operates 367 stores in thirty markets (Dudovskiy, 2017)1. The IKEA group has been
expanding its business segment by opening up restaurants and kitchenware. It offers home
furnishing services in various countries such as Australia, Austria, India, U.K., Canada,
Belgium, Egypt, Romania, Russia, Italy, Japan, Indonesia, Germany, Greece, Hong Kong,
New Zealand, Poland, Turkey, etc. IKEA group has opened various stores in each country to
provide better customer experience to its consumers (Eldredge, 2017)2.
1 Dudovskiy, J. (2017). IKEA Value-Chain Analysis - Research Methodology. [online] Research-
Methodology. Available at: https://research-methodology.net/ikea-value-chain-analysis/ [Accessed 17
May 2019].
2 Eldredge, B. (2017). See what Ikea product names mean with this handy dictionary. [online]
Curbed. Available at: https://www.curbed.com/2017/10/18/16495096/ikea-product-name-meaning-
dictionary [Accessed 17 May 2019].
5
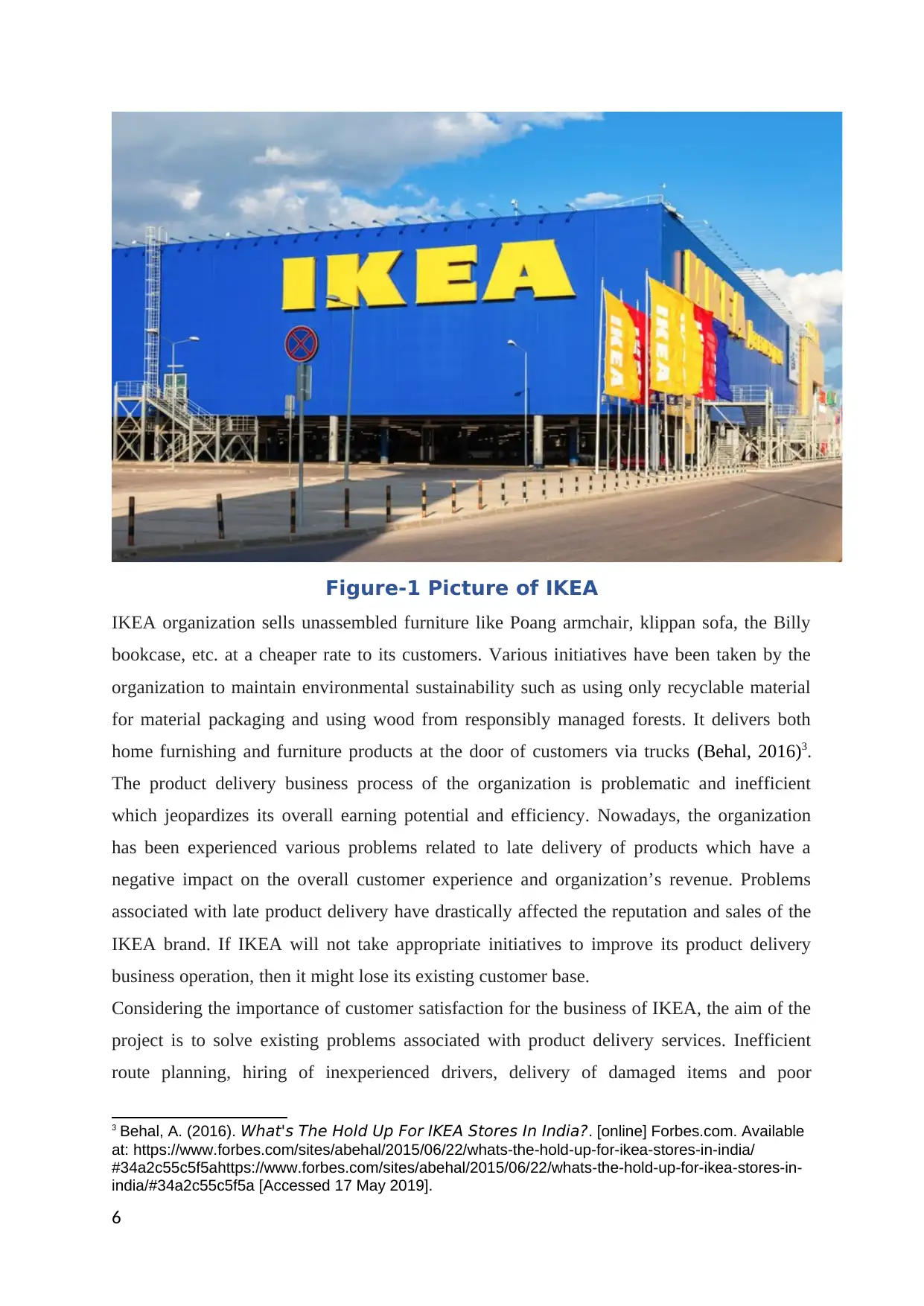
Figure-1 Picture of IKEA
IKEA organization sells unassembled furniture like Poang armchair, klippan sofa, the Billy
bookcase, etc. at a cheaper rate to its customers. Various initiatives have been taken by the
organization to maintain environmental sustainability such as using only recyclable material
for material packaging and using wood from responsibly managed forests. It delivers both
home furnishing and furniture products at the door of customers via trucks (Behal, 2016)3.
The product delivery business process of the organization is problematic and inefficient
which jeopardizes its overall earning potential and efficiency. Nowadays, the organization
has been experienced various problems related to late delivery of products which have a
negative impact on the overall customer experience and organization’s revenue. Problems
associated with late product delivery have drastically affected the reputation and sales of the
IKEA brand. If IKEA will not take appropriate initiatives to improve its product delivery
business operation, then it might lose its existing customer base.
Considering the importance of customer satisfaction for the business of IKEA, the aim of the
project is to solve existing problems associated with product delivery services. Inefficient
route planning, hiring of inexperienced drivers, delivery of damaged items and poor
3 Behal, A. (2016). What's The Hold Up For IKEA Stores In India?. [online] Forbes.com. Available
at: https://www.forbes.com/sites/abehal/2015/06/22/whats-the-hold-up-for-ikea-stores-in-india/
#34a2c55c5f5ahttps://www.forbes.com/sites/abehal/2015/06/22/whats-the-hold-up-for-ikea-stores-in-
india/#34a2c55c5f5a [Accessed 17 May 2019].
6
IKEA organization sells unassembled furniture like Poang armchair, klippan sofa, the Billy
bookcase, etc. at a cheaper rate to its customers. Various initiatives have been taken by the
organization to maintain environmental sustainability such as using only recyclable material
for material packaging and using wood from responsibly managed forests. It delivers both
home furnishing and furniture products at the door of customers via trucks (Behal, 2016)3.
The product delivery business process of the organization is problematic and inefficient
which jeopardizes its overall earning potential and efficiency. Nowadays, the organization
has been experienced various problems related to late delivery of products which have a
negative impact on the overall customer experience and organization’s revenue. Problems
associated with late product delivery have drastically affected the reputation and sales of the
IKEA brand. If IKEA will not take appropriate initiatives to improve its product delivery
business operation, then it might lose its existing customer base.
Considering the importance of customer satisfaction for the business of IKEA, the aim of the
project is to solve existing problems associated with product delivery services. Inefficient
route planning, hiring of inexperienced drivers, delivery of damaged items and poor
3 Behal, A. (2016). What's The Hold Up For IKEA Stores In India?. [online] Forbes.com. Available
at: https://www.forbes.com/sites/abehal/2015/06/22/whats-the-hold-up-for-ikea-stores-in-india/
#34a2c55c5f5ahttps://www.forbes.com/sites/abehal/2015/06/22/whats-the-hold-up-for-ikea-stores-in-
india/#34a2c55c5f5a [Accessed 17 May 2019].
6
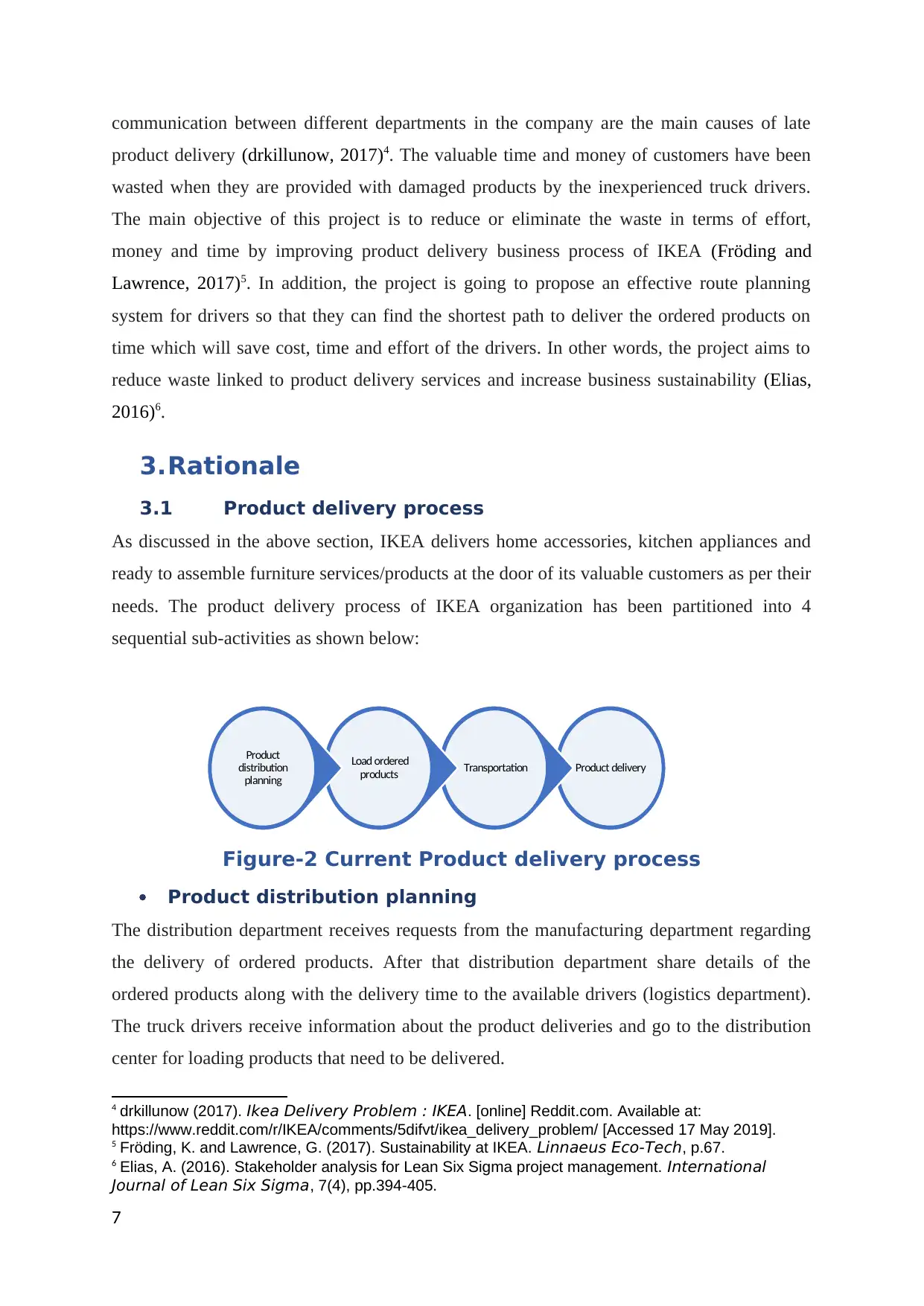
communication between different departments in the company are the main causes of late
product delivery (drkillunow, 2017)4. The valuable time and money of customers have been
wasted when they are provided with damaged products by the inexperienced truck drivers.
The main objective of this project is to reduce or eliminate the waste in terms of effort,
money and time by improving product delivery business process of IKEA (Fröding and
Lawrence, 2017)5. In addition, the project is going to propose an effective route planning
system for drivers so that they can find the shortest path to deliver the ordered products on
time which will save cost, time and effort of the drivers. In other words, the project aims to
reduce waste linked to product delivery services and increase business sustainability (Elias,
2016)6.
3.Rationale
3.1 Product delivery process
As discussed in the above section, IKEA delivers home accessories, kitchen appliances and
ready to assemble furniture services/products at the door of its valuable customers as per their
needs. The product delivery process of IKEA organization has been partitioned into 4
sequential sub-activities as shown below:
Figure-2 Current Product delivery process
Product distribution planning
The distribution department receives requests from the manufacturing department regarding
the delivery of ordered products. After that distribution department share details of the
ordered products along with the delivery time to the available drivers (logistics department).
The truck drivers receive information about the product deliveries and go to the distribution
center for loading products that need to be delivered.
4 drkillunow (2017). Ikea Delivery Problem : IKEA. [online] Reddit.com. Available at:
https://www.reddit.com/r/IKEA/comments/5difvt/ikea_delivery_problem/ [Accessed 17 May 2019].
5 Fröding, K. and Lawrence, G. (2017). Sustainability at IKEA. Linnaeus Eco-Tech, p.67.
6 Elias, A. (2016). Stakeholder analysis for Lean Six Sigma project management. International
Journal of Lean Six Sigma, 7(4), pp.394-405.
7
Product deliveryTransportation
Load ordered
products
Product
distribution
planning
product delivery (drkillunow, 2017)4. The valuable time and money of customers have been
wasted when they are provided with damaged products by the inexperienced truck drivers.
The main objective of this project is to reduce or eliminate the waste in terms of effort,
money and time by improving product delivery business process of IKEA (Fröding and
Lawrence, 2017)5. In addition, the project is going to propose an effective route planning
system for drivers so that they can find the shortest path to deliver the ordered products on
time which will save cost, time and effort of the drivers. In other words, the project aims to
reduce waste linked to product delivery services and increase business sustainability (Elias,
2016)6.
3.Rationale
3.1 Product delivery process
As discussed in the above section, IKEA delivers home accessories, kitchen appliances and
ready to assemble furniture services/products at the door of its valuable customers as per their
needs. The product delivery process of IKEA organization has been partitioned into 4
sequential sub-activities as shown below:
Figure-2 Current Product delivery process
Product distribution planning
The distribution department receives requests from the manufacturing department regarding
the delivery of ordered products. After that distribution department share details of the
ordered products along with the delivery time to the available drivers (logistics department).
The truck drivers receive information about the product deliveries and go to the distribution
center for loading products that need to be delivered.
4 drkillunow (2017). Ikea Delivery Problem : IKEA. [online] Reddit.com. Available at:
https://www.reddit.com/r/IKEA/comments/5difvt/ikea_delivery_problem/ [Accessed 17 May 2019].
5 Fröding, K. and Lawrence, G. (2017). Sustainability at IKEA. Linnaeus Eco-Tech, p.67.
6 Elias, A. (2016). Stakeholder analysis for Lean Six Sigma project management. International
Journal of Lean Six Sigma, 7(4), pp.394-405.
7
Product deliveryTransportation
Load ordered
products
Product
distribution
planning
Paraphrase This Document
Need a fresh take? Get an instant paraphrase of this document with our AI Paraphraser
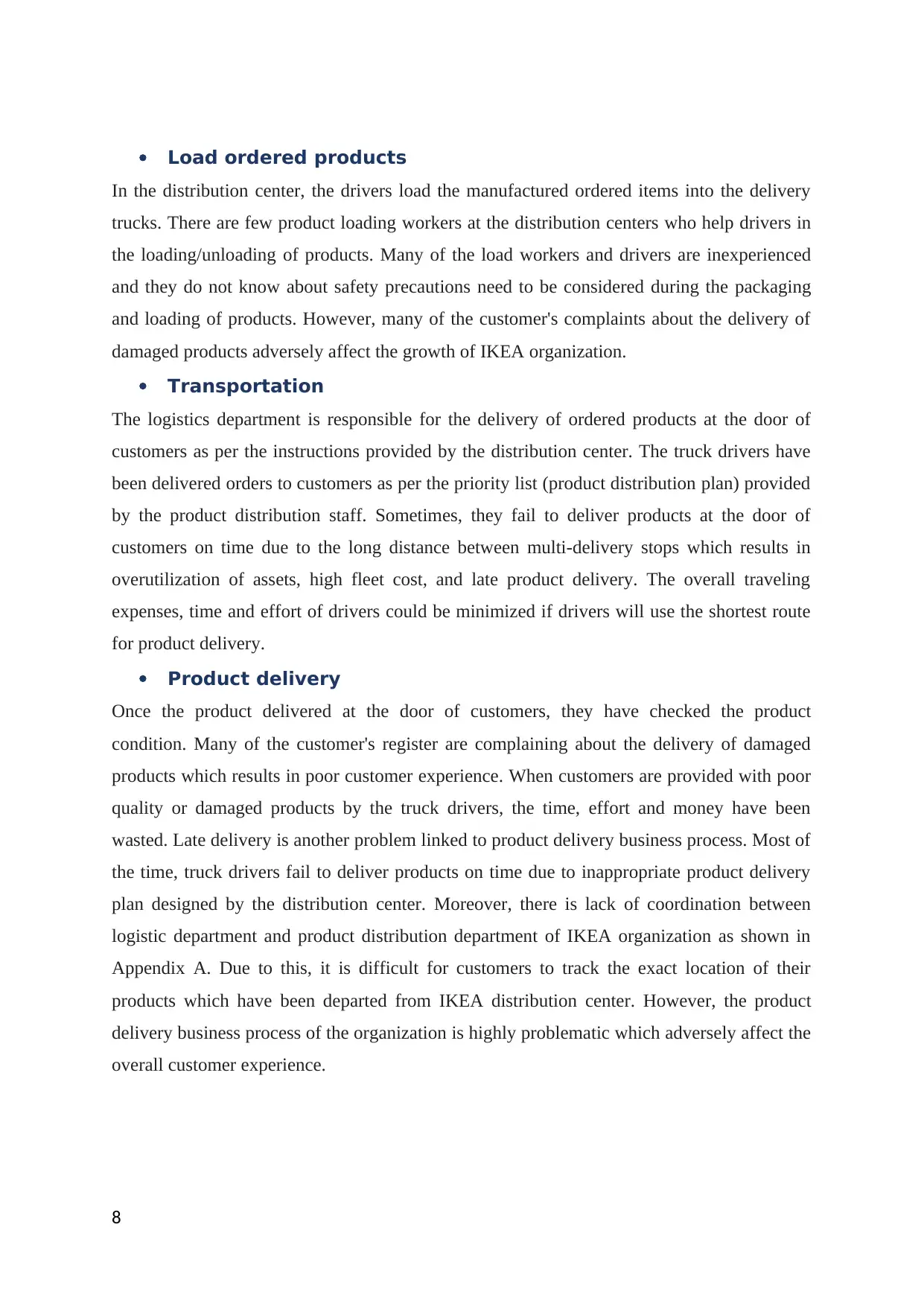
Load ordered products
In the distribution center, the drivers load the manufactured ordered items into the delivery
trucks. There are few product loading workers at the distribution centers who help drivers in
the loading/unloading of products. Many of the load workers and drivers are inexperienced
and they do not know about safety precautions need to be considered during the packaging
and loading of products. However, many of the customer's complaints about the delivery of
damaged products adversely affect the growth of IKEA organization.
Transportation
The logistics department is responsible for the delivery of ordered products at the door of
customers as per the instructions provided by the distribution center. The truck drivers have
been delivered orders to customers as per the priority list (product distribution plan) provided
by the product distribution staff. Sometimes, they fail to deliver products at the door of
customers on time due to the long distance between multi-delivery stops which results in
overutilization of assets, high fleet cost, and late product delivery. The overall traveling
expenses, time and effort of drivers could be minimized if drivers will use the shortest route
for product delivery.
Product delivery
Once the product delivered at the door of customers, they have checked the product
condition. Many of the customer's register are complaining about the delivery of damaged
products which results in poor customer experience. When customers are provided with poor
quality or damaged products by the truck drivers, the time, effort and money have been
wasted. Late delivery is another problem linked to product delivery business process. Most of
the time, truck drivers fail to deliver products on time due to inappropriate product delivery
plan designed by the distribution center. Moreover, there is lack of coordination between
logistic department and product distribution department of IKEA organization as shown in
Appendix A. Due to this, it is difficult for customers to track the exact location of their
products which have been departed from IKEA distribution center. However, the product
delivery business process of the organization is highly problematic which adversely affect the
overall customer experience.
8
In the distribution center, the drivers load the manufactured ordered items into the delivery
trucks. There are few product loading workers at the distribution centers who help drivers in
the loading/unloading of products. Many of the load workers and drivers are inexperienced
and they do not know about safety precautions need to be considered during the packaging
and loading of products. However, many of the customer's complaints about the delivery of
damaged products adversely affect the growth of IKEA organization.
Transportation
The logistics department is responsible for the delivery of ordered products at the door of
customers as per the instructions provided by the distribution center. The truck drivers have
been delivered orders to customers as per the priority list (product distribution plan) provided
by the product distribution staff. Sometimes, they fail to deliver products at the door of
customers on time due to the long distance between multi-delivery stops which results in
overutilization of assets, high fleet cost, and late product delivery. The overall traveling
expenses, time and effort of drivers could be minimized if drivers will use the shortest route
for product delivery.
Product delivery
Once the product delivered at the door of customers, they have checked the product
condition. Many of the customer's register are complaining about the delivery of damaged
products which results in poor customer experience. When customers are provided with poor
quality or damaged products by the truck drivers, the time, effort and money have been
wasted. Late delivery is another problem linked to product delivery business process. Most of
the time, truck drivers fail to deliver products on time due to inappropriate product delivery
plan designed by the distribution center. Moreover, there is lack of coordination between
logistic department and product distribution department of IKEA organization as shown in
Appendix A. Due to this, it is difficult for customers to track the exact location of their
products which have been departed from IKEA distribution center. However, the product
delivery business process of the organization is highly problematic which adversely affect the
overall customer experience.
8
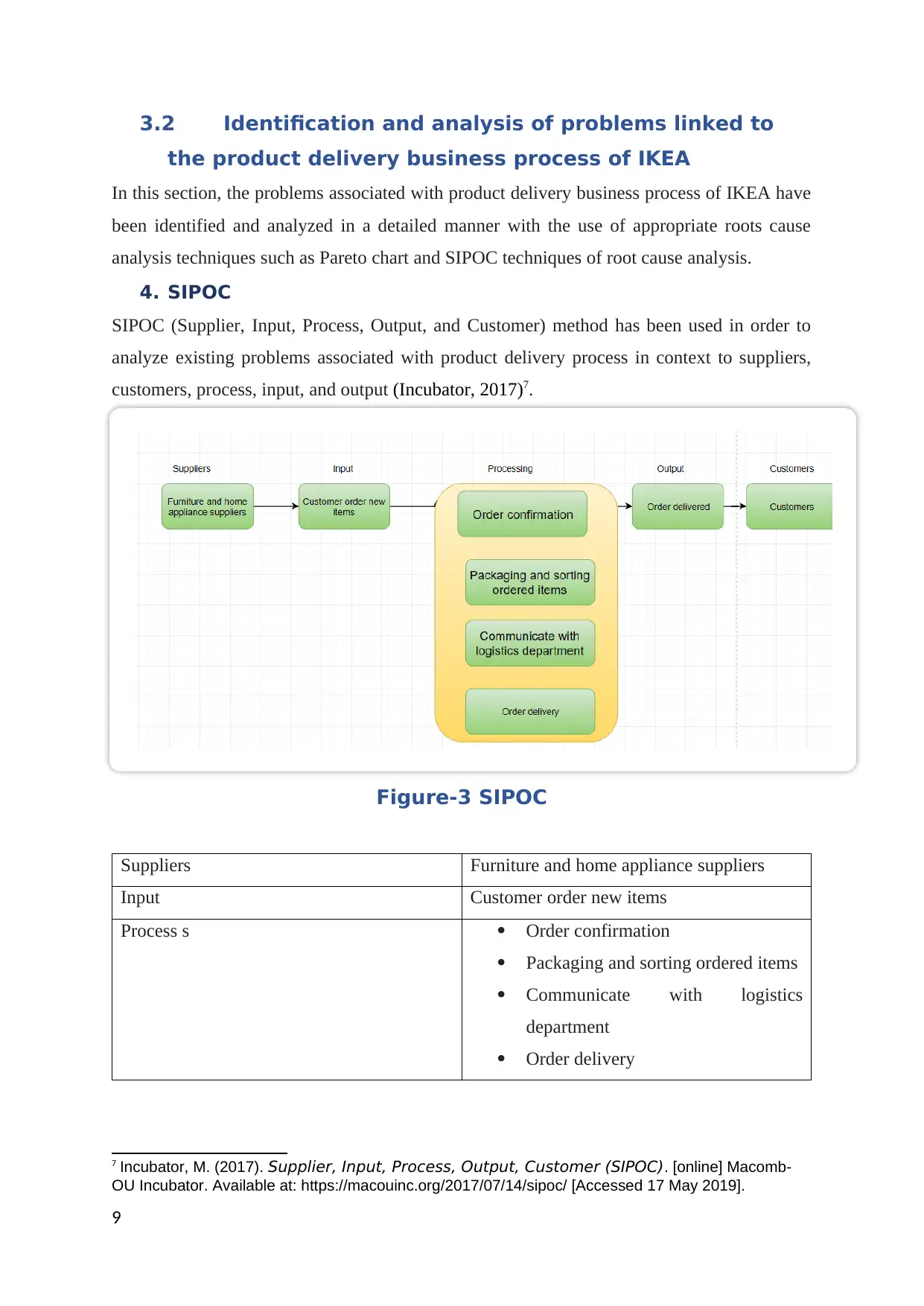
3.2 Identification and analysis of problems linked to
the product delivery business process of IKEA
In this section, the problems associated with product delivery business process of IKEA have
been identified and analyzed in a detailed manner with the use of appropriate roots cause
analysis techniques such as Pareto chart and SIPOC techniques of root cause analysis.
4. SIPOC
SIPOC (Supplier, Input, Process, Output, and Customer) method has been used in order to
analyze existing problems associated with product delivery process in context to suppliers,
customers, process, input, and output (Incubator, 2017)7.
Figure-3 SIPOC
Suppliers Furniture and home appliance suppliers
Input Customer order new items
Process s Order confirmation
Packaging and sorting ordered items
Communicate with logistics
department
Order delivery
7 Incubator, M. (2017). Supplier, Input, Process, Output, Customer (SIPOC). [online] Macomb-
OU Incubator. Available at: https://macouinc.org/2017/07/14/sipoc/ [Accessed 17 May 2019].
9
the product delivery business process of IKEA
In this section, the problems associated with product delivery business process of IKEA have
been identified and analyzed in a detailed manner with the use of appropriate roots cause
analysis techniques such as Pareto chart and SIPOC techniques of root cause analysis.
4. SIPOC
SIPOC (Supplier, Input, Process, Output, and Customer) method has been used in order to
analyze existing problems associated with product delivery process in context to suppliers,
customers, process, input, and output (Incubator, 2017)7.
Figure-3 SIPOC
Suppliers Furniture and home appliance suppliers
Input Customer order new items
Process s Order confirmation
Packaging and sorting ordered items
Communicate with logistics
department
Order delivery
7 Incubator, M. (2017). Supplier, Input, Process, Output, Customer (SIPOC). [online] Macomb-
OU Incubator. Available at: https://macouinc.org/2017/07/14/sipoc/ [Accessed 17 May 2019].
9
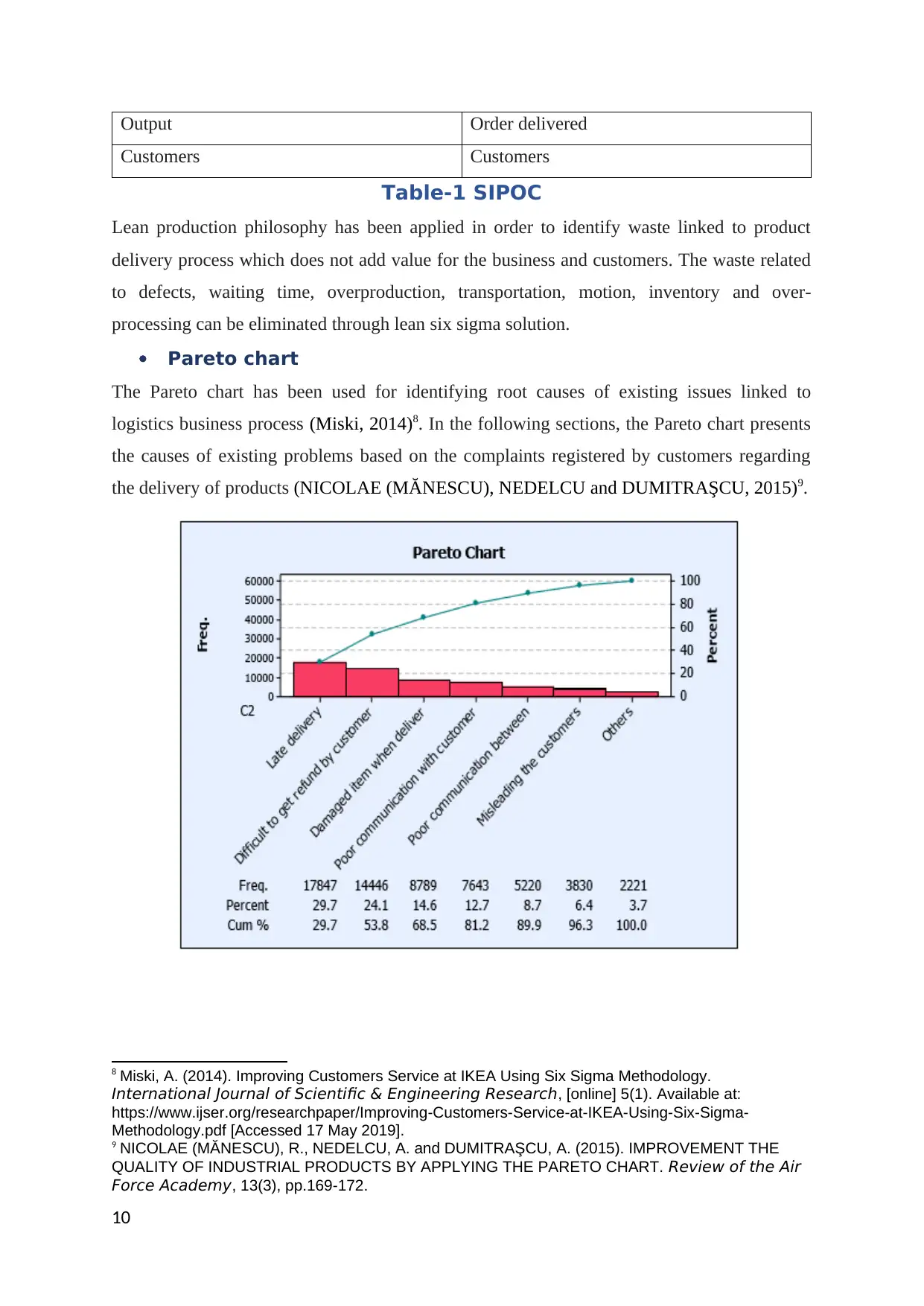
Output Order delivered
Customers Customers
Table-1 SIPOC
Lean production philosophy has been applied in order to identify waste linked to product
delivery process which does not add value for the business and customers. The waste related
to defects, waiting time, overproduction, transportation, motion, inventory and over-
processing can be eliminated through lean six sigma solution.
Pareto chart
The Pareto chart has been used for identifying root causes of existing issues linked to
logistics business process (Miski, 2014)8. In the following sections, the Pareto chart presents
the causes of existing problems based on the complaints registered by customers regarding
the delivery of products (NICOLAE (MĂNESCU), NEDELCU and DUMITRAŞCU, 2015)9.
8 Miski, A. (2014). Improving Customers Service at IKEA Using Six Sigma Methodology.
International Journal of Scientific & Engineering Research, [online] 5(1). Available at:
https://www.ijser.org/researchpaper/Improving-Customers-Service-at-IKEA-Using-Six-Sigma-
Methodology.pdf [Accessed 17 May 2019].
9 NICOLAE (MĂNESCU), R., NEDELCU, A. and DUMITRAŞCU, A. (2015). IMPROVEMENT THE
QUALITY OF INDUSTRIAL PRODUCTS BY APPLYING THE PARETO CHART. Review of the Air
Force Academy, 13(3), pp.169-172.
10
Customers Customers
Table-1 SIPOC
Lean production philosophy has been applied in order to identify waste linked to product
delivery process which does not add value for the business and customers. The waste related
to defects, waiting time, overproduction, transportation, motion, inventory and over-
processing can be eliminated through lean six sigma solution.
Pareto chart
The Pareto chart has been used for identifying root causes of existing issues linked to
logistics business process (Miski, 2014)8. In the following sections, the Pareto chart presents
the causes of existing problems based on the complaints registered by customers regarding
the delivery of products (NICOLAE (MĂNESCU), NEDELCU and DUMITRAŞCU, 2015)9.
8 Miski, A. (2014). Improving Customers Service at IKEA Using Six Sigma Methodology.
International Journal of Scientific & Engineering Research, [online] 5(1). Available at:
https://www.ijser.org/researchpaper/Improving-Customers-Service-at-IKEA-Using-Six-Sigma-
Methodology.pdf [Accessed 17 May 2019].
9 NICOLAE (MĂNESCU), R., NEDELCU, A. and DUMITRAŞCU, A. (2015). IMPROVEMENT THE
QUALITY OF INDUSTRIAL PRODUCTS BY APPLYING THE PARETO CHART. Review of the Air
Force Academy, 13(3), pp.169-172.
10
Secure Best Marks with AI Grader
Need help grading? Try our AI Grader for instant feedback on your assignments.
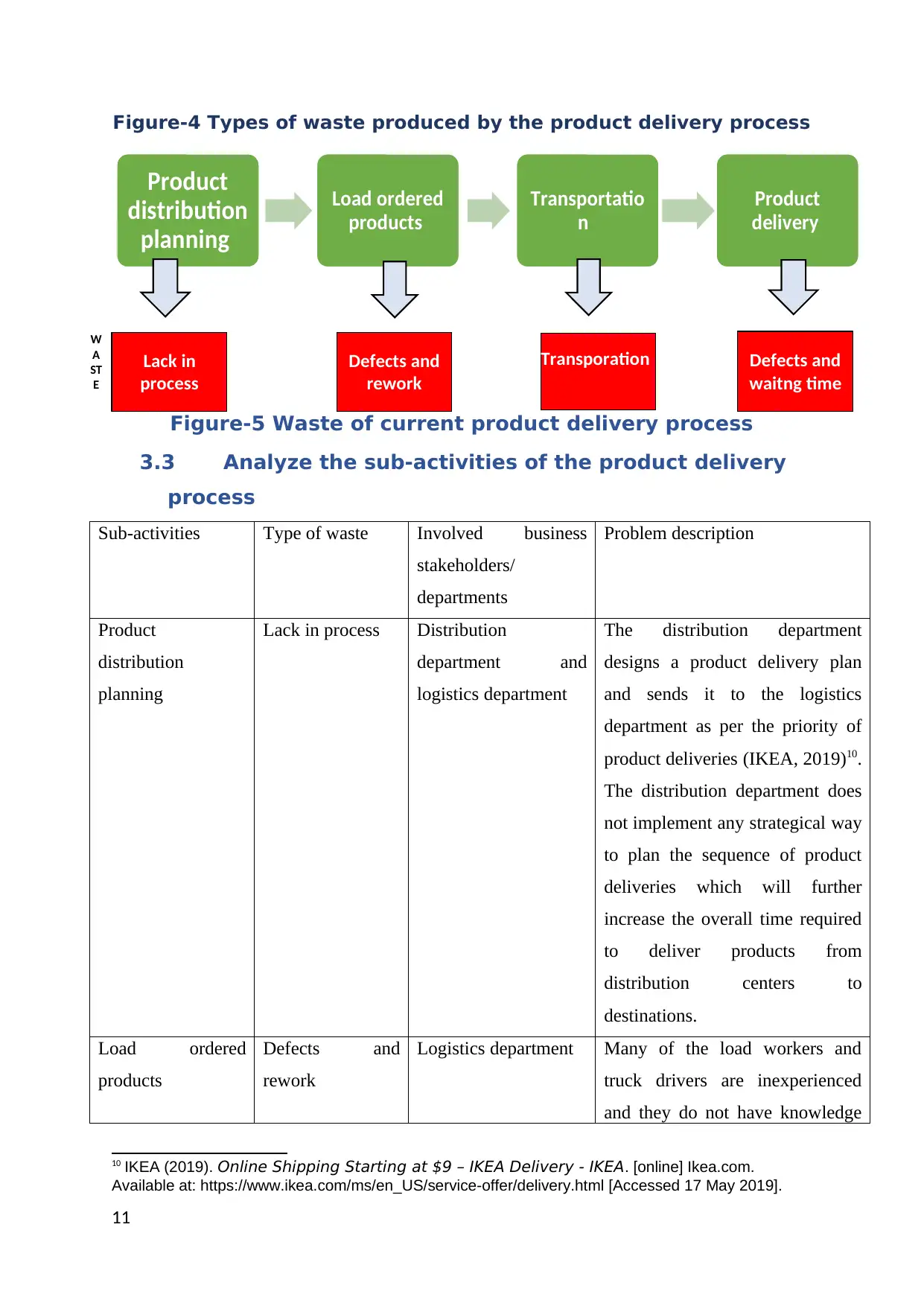
Figure-4 Types of waste produced by the product delivery process
Figure-5 Waste of current product delivery process
3.3 Analyze the sub-activities of the product delivery
process
Sub-activities Type of waste Involved business
stakeholders/
departments
Problem description
Product
distribution
planning
Lack in process Distribution
department and
logistics department
The distribution department
designs a product delivery plan
and sends it to the logistics
department as per the priority of
product deliveries (IKEA, 2019)10.
The distribution department does
not implement any strategical way
to plan the sequence of product
deliveries which will further
increase the overall time required
to deliver products from
distribution centers to
destinations.
Load ordered
products
Defects and
rework
Logistics department Many of the load workers and
truck drivers are inexperienced
and they do not have knowledge
10 IKEA (2019). Online Shipping Starting at $9 – IKEA Delivery - IKEA. [online] Ikea.com.
Available at: https://www.ikea.com/ms/en_US/service-offer/delivery.html [Accessed 17 May 2019].
11
Product
distribution
planning
Load ordered
products
Transportatio
n
Product
delivery
Defects and
rework
Transporation Defects and
waitng time
W
A
ST
E
Lack in
process
Figure-5 Waste of current product delivery process
3.3 Analyze the sub-activities of the product delivery
process
Sub-activities Type of waste Involved business
stakeholders/
departments
Problem description
Product
distribution
planning
Lack in process Distribution
department and
logistics department
The distribution department
designs a product delivery plan
and sends it to the logistics
department as per the priority of
product deliveries (IKEA, 2019)10.
The distribution department does
not implement any strategical way
to plan the sequence of product
deliveries which will further
increase the overall time required
to deliver products from
distribution centers to
destinations.
Load ordered
products
Defects and
rework
Logistics department Many of the load workers and
truck drivers are inexperienced
and they do not have knowledge
10 IKEA (2019). Online Shipping Starting at $9 – IKEA Delivery - IKEA. [online] Ikea.com.
Available at: https://www.ikea.com/ms/en_US/service-offer/delivery.html [Accessed 17 May 2019].
11
Product
distribution
planning
Load ordered
products
Transportatio
n
Product
delivery
Defects and
rework
Transporation Defects and
waitng time
W
A
ST
E
Lack in
process
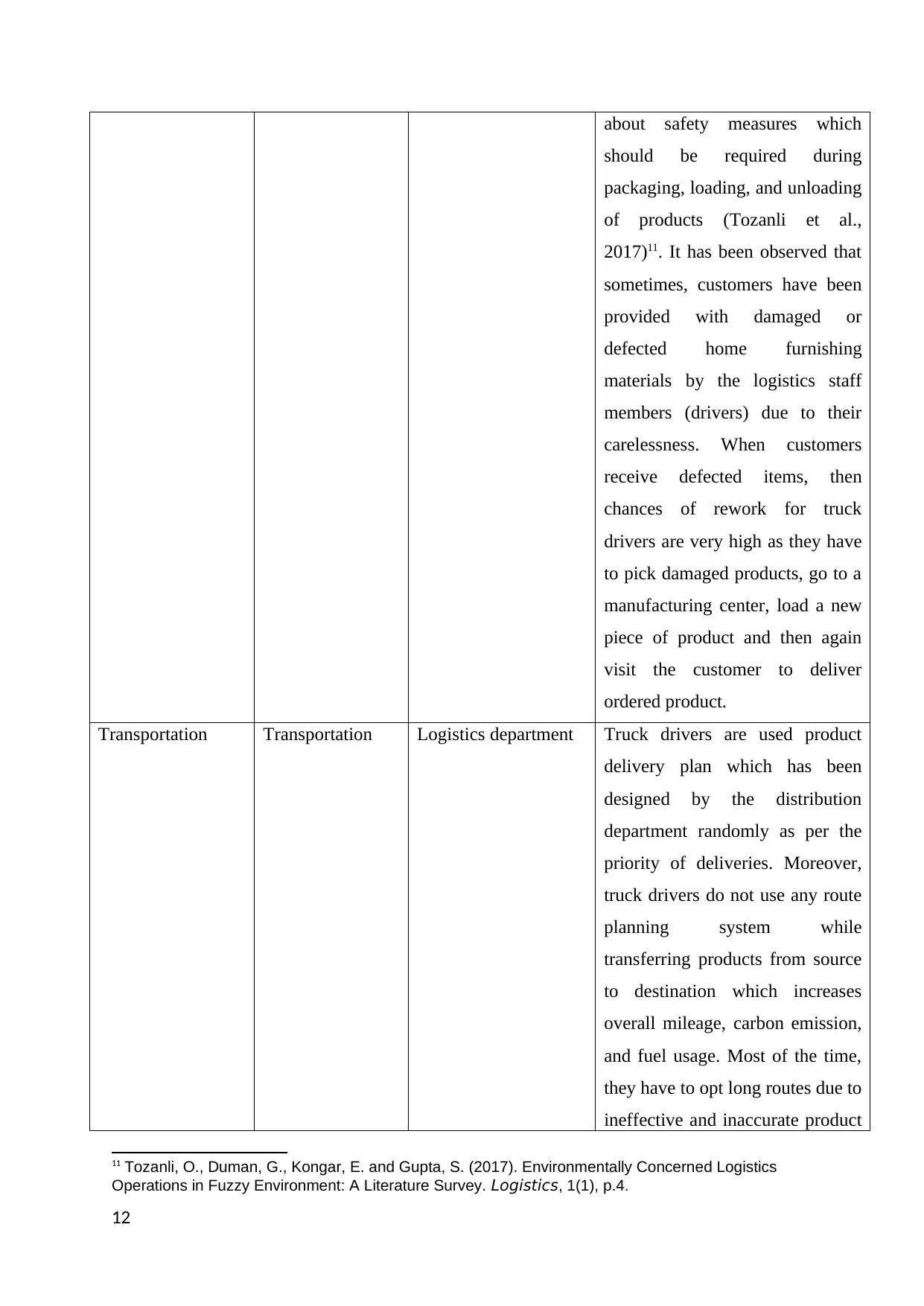
about safety measures which
should be required during
packaging, loading, and unloading
of products (Tozanli et al.,
2017)11. It has been observed that
sometimes, customers have been
provided with damaged or
defected home furnishing
materials by the logistics staff
members (drivers) due to their
carelessness. When customers
receive defected items, then
chances of rework for truck
drivers are very high as they have
to pick damaged products, go to a
manufacturing center, load a new
piece of product and then again
visit the customer to deliver
ordered product.
Transportation Transportation Logistics department Truck drivers are used product
delivery plan which has been
designed by the distribution
department randomly as per the
priority of deliveries. Moreover,
truck drivers do not use any route
planning system while
transferring products from source
to destination which increases
overall mileage, carbon emission,
and fuel usage. Most of the time,
they have to opt long routes due to
ineffective and inaccurate product
11 Tozanli, O., Duman, G., Kongar, E. and Gupta, S. (2017). Environmentally Concerned Logistics
Operations in Fuzzy Environment: A Literature Survey. Logistics, 1(1), p.4.
12
should be required during
packaging, loading, and unloading
of products (Tozanli et al.,
2017)11. It has been observed that
sometimes, customers have been
provided with damaged or
defected home furnishing
materials by the logistics staff
members (drivers) due to their
carelessness. When customers
receive defected items, then
chances of rework for truck
drivers are very high as they have
to pick damaged products, go to a
manufacturing center, load a new
piece of product and then again
visit the customer to deliver
ordered product.
Transportation Transportation Logistics department Truck drivers are used product
delivery plan which has been
designed by the distribution
department randomly as per the
priority of deliveries. Moreover,
truck drivers do not use any route
planning system while
transferring products from source
to destination which increases
overall mileage, carbon emission,
and fuel usage. Most of the time,
they have to opt long routes due to
ineffective and inaccurate product
11 Tozanli, O., Duman, G., Kongar, E. and Gupta, S. (2017). Environmentally Concerned Logistics
Operations in Fuzzy Environment: A Literature Survey. Logistics, 1(1), p.4.
12
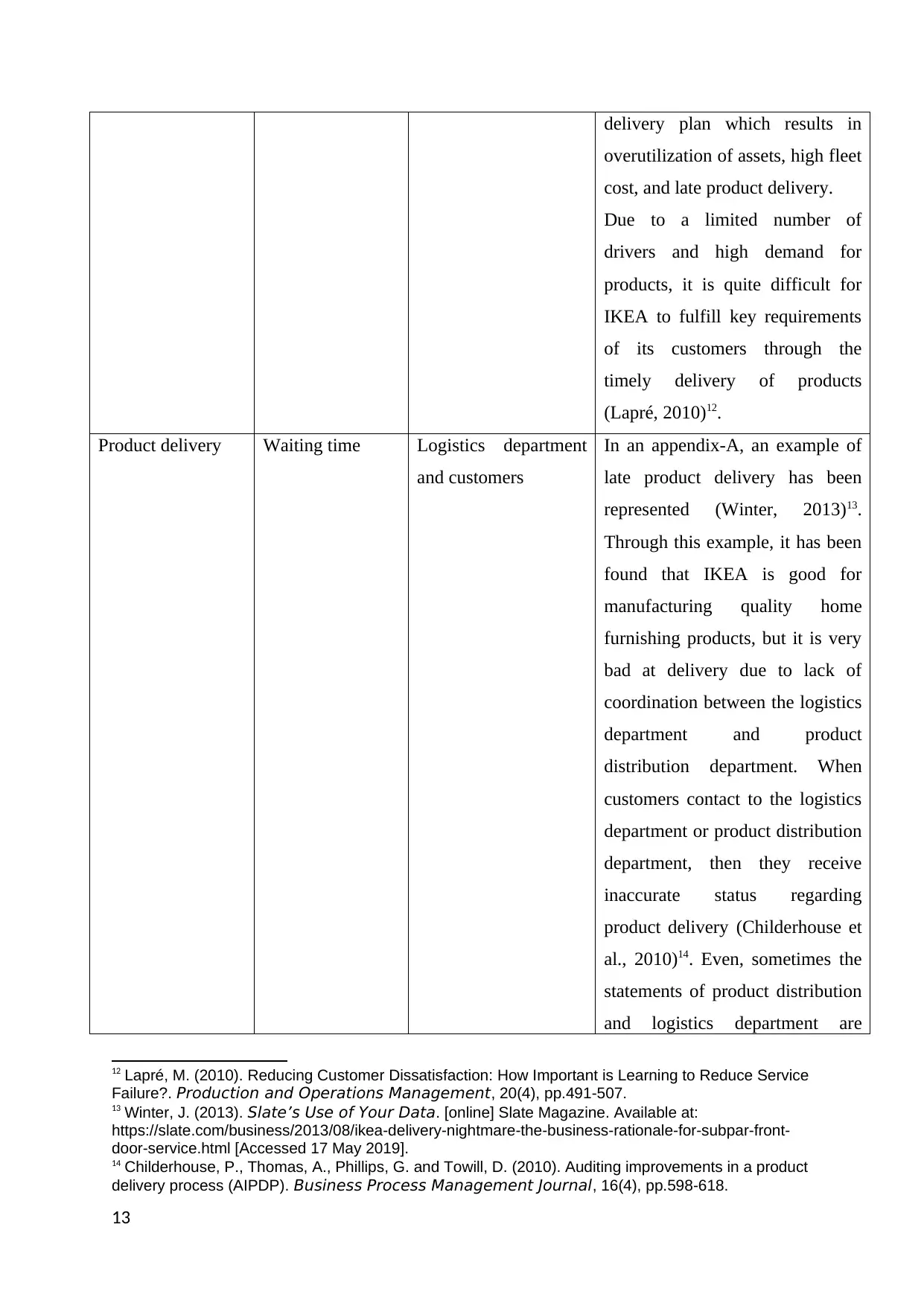
delivery plan which results in
overutilization of assets, high fleet
cost, and late product delivery.
Due to a limited number of
drivers and high demand for
products, it is quite difficult for
IKEA to fulfill key requirements
of its customers through the
timely delivery of products
(Lapré, 2010)12.
Product delivery Waiting time Logistics department
and customers
In an appendix-A, an example of
late product delivery has been
represented (Winter, 2013)13.
Through this example, it has been
found that IKEA is good for
manufacturing quality home
furnishing products, but it is very
bad at delivery due to lack of
coordination between the logistics
department and product
distribution department. When
customers contact to the logistics
department or product distribution
department, then they receive
inaccurate status regarding
product delivery (Childerhouse et
al., 2010)14. Even, sometimes the
statements of product distribution
and logistics department are
12 Lapré, M. (2010). Reducing Customer Dissatisfaction: How Important is Learning to Reduce Service
Failure?. Production and Operations Management, 20(4), pp.491-507.
13 Winter, J. (2013). Slate’s Use of Your Data. [online] Slate Magazine. Available at:
https://slate.com/business/2013/08/ikea-delivery-nightmare-the-business-rationale-for-subpar-front-
door-service.html [Accessed 17 May 2019].
14 Childerhouse, P., Thomas, A., Phillips, G. and Towill, D. (2010). Auditing improvements in a product
delivery process (AIPDP). Business Process Management Journal, 16(4), pp.598-618.
13
overutilization of assets, high fleet
cost, and late product delivery.
Due to a limited number of
drivers and high demand for
products, it is quite difficult for
IKEA to fulfill key requirements
of its customers through the
timely delivery of products
(Lapré, 2010)12.
Product delivery Waiting time Logistics department
and customers
In an appendix-A, an example of
late product delivery has been
represented (Winter, 2013)13.
Through this example, it has been
found that IKEA is good for
manufacturing quality home
furnishing products, but it is very
bad at delivery due to lack of
coordination between the logistics
department and product
distribution department. When
customers contact to the logistics
department or product distribution
department, then they receive
inaccurate status regarding
product delivery (Childerhouse et
al., 2010)14. Even, sometimes the
statements of product distribution
and logistics department are
12 Lapré, M. (2010). Reducing Customer Dissatisfaction: How Important is Learning to Reduce Service
Failure?. Production and Operations Management, 20(4), pp.491-507.
13 Winter, J. (2013). Slate’s Use of Your Data. [online] Slate Magazine. Available at:
https://slate.com/business/2013/08/ikea-delivery-nightmare-the-business-rationale-for-subpar-front-
door-service.html [Accessed 17 May 2019].
14 Childerhouse, P., Thomas, A., Phillips, G. and Towill, D. (2010). Auditing improvements in a product
delivery process (AIPDP). Business Process Management Journal, 16(4), pp.598-618.
13
Paraphrase This Document
Need a fresh take? Get an instant paraphrase of this document with our AI Paraphraser
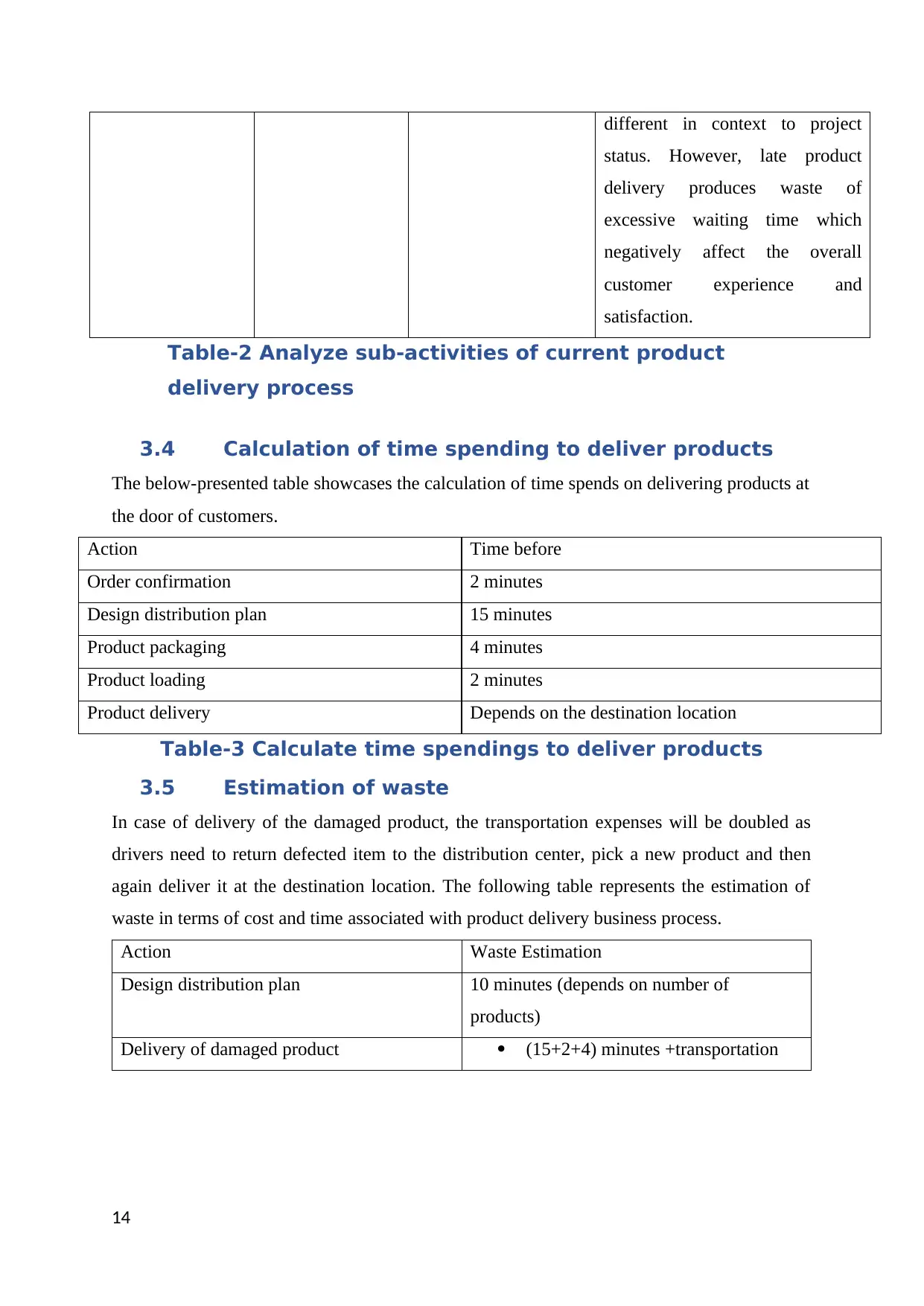
different in context to project
status. However, late product
delivery produces waste of
excessive waiting time which
negatively affect the overall
customer experience and
satisfaction.
Table-2 Analyze sub-activities of current product
delivery process
3.4 Calculation of time spending to deliver products
The below-presented table showcases the calculation of time spends on delivering products at
the door of customers.
Action Time before
Order confirmation 2 minutes
Design distribution plan 15 minutes
Product packaging 4 minutes
Product loading 2 minutes
Product delivery Depends on the destination location
Table-3 Calculate time spendings to deliver products
3.5 Estimation of waste
In case of delivery of the damaged product, the transportation expenses will be doubled as
drivers need to return defected item to the distribution center, pick a new product and then
again deliver it at the destination location. The following table represents the estimation of
waste in terms of cost and time associated with product delivery business process.
Action Waste Estimation
Design distribution plan 10 minutes (depends on number of
products)
Delivery of damaged product (15+2+4) minutes +transportation
14
status. However, late product
delivery produces waste of
excessive waiting time which
negatively affect the overall
customer experience and
satisfaction.
Table-2 Analyze sub-activities of current product
delivery process
3.4 Calculation of time spending to deliver products
The below-presented table showcases the calculation of time spends on delivering products at
the door of customers.
Action Time before
Order confirmation 2 minutes
Design distribution plan 15 minutes
Product packaging 4 minutes
Product loading 2 minutes
Product delivery Depends on the destination location
Table-3 Calculate time spendings to deliver products
3.5 Estimation of waste
In case of delivery of the damaged product, the transportation expenses will be doubled as
drivers need to return defected item to the distribution center, pick a new product and then
again deliver it at the destination location. The following table represents the estimation of
waste in terms of cost and time associated with product delivery business process.
Action Waste Estimation
Design distribution plan 10 minutes (depends on number of
products)
Delivery of damaged product (15+2+4) minutes +transportation
14
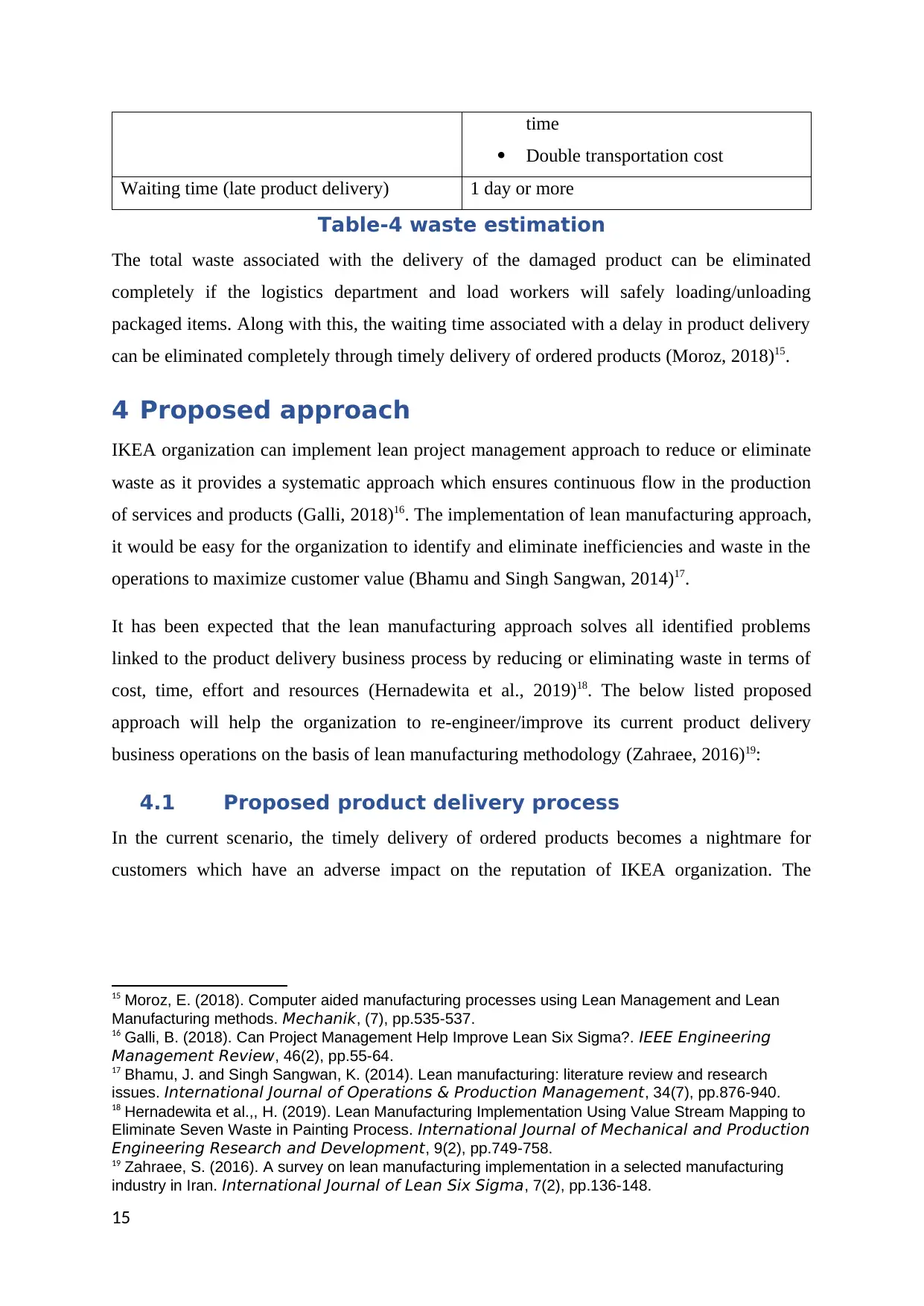
time
Double transportation cost
Waiting time (late product delivery) 1 day or more
Table-4 waste estimation
The total waste associated with the delivery of the damaged product can be eliminated
completely if the logistics department and load workers will safely loading/unloading
packaged items. Along with this, the waiting time associated with a delay in product delivery
can be eliminated completely through timely delivery of ordered products (Moroz, 2018)15.
4 Proposed approach
IKEA organization can implement lean project management approach to reduce or eliminate
waste as it provides a systematic approach which ensures continuous flow in the production
of services and products (Galli, 2018)16. The implementation of lean manufacturing approach,
it would be easy for the organization to identify and eliminate inefficiencies and waste in the
operations to maximize customer value (Bhamu and Singh Sangwan, 2014)17.
It has been expected that the lean manufacturing approach solves all identified problems
linked to the product delivery business process by reducing or eliminating waste in terms of
cost, time, effort and resources (Hernadewita et al., 2019)18. The below listed proposed
approach will help the organization to re-engineer/improve its current product delivery
business operations on the basis of lean manufacturing methodology (Zahraee, 2016)19:
4.1 Proposed product delivery process
In the current scenario, the timely delivery of ordered products becomes a nightmare for
customers which have an adverse impact on the reputation of IKEA organization. The
15 Moroz, E. (2018). Computer aided manufacturing processes using Lean Management and Lean
Manufacturing methods. Mechanik, (7), pp.535-537.
16 Galli, B. (2018). Can Project Management Help Improve Lean Six Sigma?. IEEE Engineering
Management Review, 46(2), pp.55-64.
17 Bhamu, J. and Singh Sangwan, K. (2014). Lean manufacturing: literature review and research
issues. International Journal of Operations & Production Management, 34(7), pp.876-940.
18 Hernadewita et al.,, H. (2019). Lean Manufacturing Implementation Using Value Stream Mapping to
Eliminate Seven Waste in Painting Process. International Journal of Mechanical and Production
Engineering Research and Development, 9(2), pp.749-758.
19 Zahraee, S. (2016). A survey on lean manufacturing implementation in a selected manufacturing
industry in Iran. International Journal of Lean Six Sigma, 7(2), pp.136-148.
15
Double transportation cost
Waiting time (late product delivery) 1 day or more
Table-4 waste estimation
The total waste associated with the delivery of the damaged product can be eliminated
completely if the logistics department and load workers will safely loading/unloading
packaged items. Along with this, the waiting time associated with a delay in product delivery
can be eliminated completely through timely delivery of ordered products (Moroz, 2018)15.
4 Proposed approach
IKEA organization can implement lean project management approach to reduce or eliminate
waste as it provides a systematic approach which ensures continuous flow in the production
of services and products (Galli, 2018)16. The implementation of lean manufacturing approach,
it would be easy for the organization to identify and eliminate inefficiencies and waste in the
operations to maximize customer value (Bhamu and Singh Sangwan, 2014)17.
It has been expected that the lean manufacturing approach solves all identified problems
linked to the product delivery business process by reducing or eliminating waste in terms of
cost, time, effort and resources (Hernadewita et al., 2019)18. The below listed proposed
approach will help the organization to re-engineer/improve its current product delivery
business operations on the basis of lean manufacturing methodology (Zahraee, 2016)19:
4.1 Proposed product delivery process
In the current scenario, the timely delivery of ordered products becomes a nightmare for
customers which have an adverse impact on the reputation of IKEA organization. The
15 Moroz, E. (2018). Computer aided manufacturing processes using Lean Management and Lean
Manufacturing methods. Mechanik, (7), pp.535-537.
16 Galli, B. (2018). Can Project Management Help Improve Lean Six Sigma?. IEEE Engineering
Management Review, 46(2), pp.55-64.
17 Bhamu, J. and Singh Sangwan, K. (2014). Lean manufacturing: literature review and research
issues. International Journal of Operations & Production Management, 34(7), pp.876-940.
18 Hernadewita et al.,, H. (2019). Lean Manufacturing Implementation Using Value Stream Mapping to
Eliminate Seven Waste in Painting Process. International Journal of Mechanical and Production
Engineering Research and Development, 9(2), pp.749-758.
19 Zahraee, S. (2016). A survey on lean manufacturing implementation in a selected manufacturing
industry in Iran. International Journal of Lean Six Sigma, 7(2), pp.136-148.
15
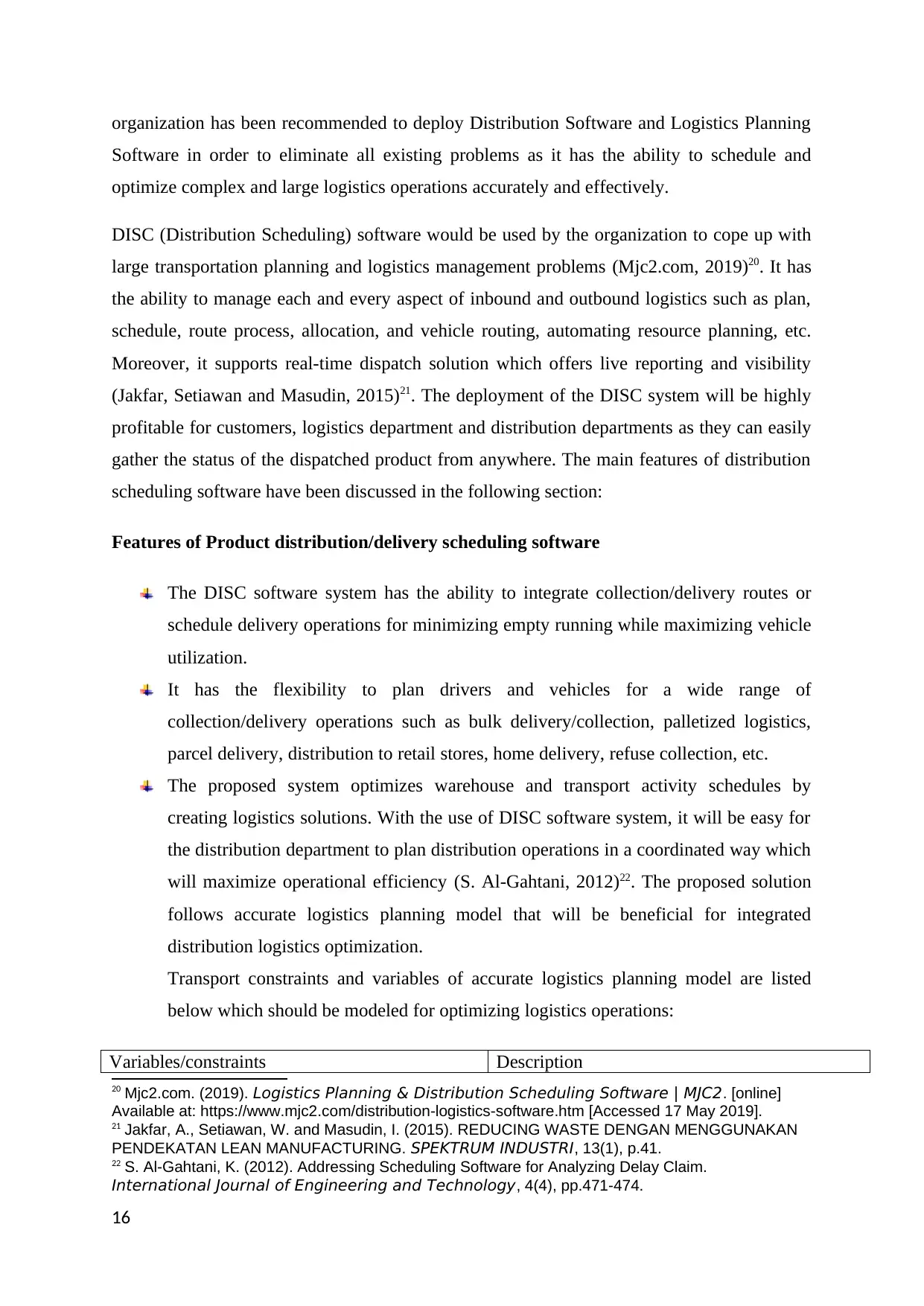
organization has been recommended to deploy Distribution Software and Logistics Planning
Software in order to eliminate all existing problems as it has the ability to schedule and
optimize complex and large logistics operations accurately and effectively.
DISC (Distribution Scheduling) software would be used by the organization to cope up with
large transportation planning and logistics management problems (Mjc2.com, 2019)20. It has
the ability to manage each and every aspect of inbound and outbound logistics such as plan,
schedule, route process, allocation, and vehicle routing, automating resource planning, etc.
Moreover, it supports real-time dispatch solution which offers live reporting and visibility
(Jakfar, Setiawan and Masudin, 2015)21. The deployment of the DISC system will be highly
profitable for customers, logistics department and distribution departments as they can easily
gather the status of the dispatched product from anywhere. The main features of distribution
scheduling software have been discussed in the following section:
Features of Product distribution/delivery scheduling software
The DISC software system has the ability to integrate collection/delivery routes or
schedule delivery operations for minimizing empty running while maximizing vehicle
utilization.
It has the flexibility to plan drivers and vehicles for a wide range of
collection/delivery operations such as bulk delivery/collection, palletized logistics,
parcel delivery, distribution to retail stores, home delivery, refuse collection, etc.
The proposed system optimizes warehouse and transport activity schedules by
creating logistics solutions. With the use of DISC software system, it will be easy for
the distribution department to plan distribution operations in a coordinated way which
will maximize operational efficiency (S. Al-Gahtani, 2012)22. The proposed solution
follows accurate logistics planning model that will be beneficial for integrated
distribution logistics optimization.
Transport constraints and variables of accurate logistics planning model are listed
below which should be modeled for optimizing logistics operations:
Variables/constraints Description
20 Mjc2.com. (2019). Logistics Planning & Distribution Scheduling Software | MJC2. [online]
Available at: https://www.mjc2.com/distribution-logistics-software.htm [Accessed 17 May 2019].
21 Jakfar, A., Setiawan, W. and Masudin, I. (2015). REDUCING WASTE DENGAN MENGGUNAKAN
PENDEKATAN LEAN MANUFACTURING. SPEKTRUM INDUSTRI, 13(1), p.41.
22 S. Al-Gahtani, K. (2012). Addressing Scheduling Software for Analyzing Delay Claim.
International Journal of Engineering and Technology, 4(4), pp.471-474.
16
Software in order to eliminate all existing problems as it has the ability to schedule and
optimize complex and large logistics operations accurately and effectively.
DISC (Distribution Scheduling) software would be used by the organization to cope up with
large transportation planning and logistics management problems (Mjc2.com, 2019)20. It has
the ability to manage each and every aspect of inbound and outbound logistics such as plan,
schedule, route process, allocation, and vehicle routing, automating resource planning, etc.
Moreover, it supports real-time dispatch solution which offers live reporting and visibility
(Jakfar, Setiawan and Masudin, 2015)21. The deployment of the DISC system will be highly
profitable for customers, logistics department and distribution departments as they can easily
gather the status of the dispatched product from anywhere. The main features of distribution
scheduling software have been discussed in the following section:
Features of Product distribution/delivery scheduling software
The DISC software system has the ability to integrate collection/delivery routes or
schedule delivery operations for minimizing empty running while maximizing vehicle
utilization.
It has the flexibility to plan drivers and vehicles for a wide range of
collection/delivery operations such as bulk delivery/collection, palletized logistics,
parcel delivery, distribution to retail stores, home delivery, refuse collection, etc.
The proposed system optimizes warehouse and transport activity schedules by
creating logistics solutions. With the use of DISC software system, it will be easy for
the distribution department to plan distribution operations in a coordinated way which
will maximize operational efficiency (S. Al-Gahtani, 2012)22. The proposed solution
follows accurate logistics planning model that will be beneficial for integrated
distribution logistics optimization.
Transport constraints and variables of accurate logistics planning model are listed
below which should be modeled for optimizing logistics operations:
Variables/constraints Description
20 Mjc2.com. (2019). Logistics Planning & Distribution Scheduling Software | MJC2. [online]
Available at: https://www.mjc2.com/distribution-logistics-software.htm [Accessed 17 May 2019].
21 Jakfar, A., Setiawan, W. and Masudin, I. (2015). REDUCING WASTE DENGAN MENGGUNAKAN
PENDEKATAN LEAN MANUFACTURING. SPEKTRUM INDUSTRI, 13(1), p.41.
22 S. Al-Gahtani, K. (2012). Addressing Scheduling Software for Analyzing Delay Claim.
International Journal of Engineering and Technology, 4(4), pp.471-474.
16
Secure Best Marks with AI Grader
Need help grading? Try our AI Grader for instant feedback on your assignments.
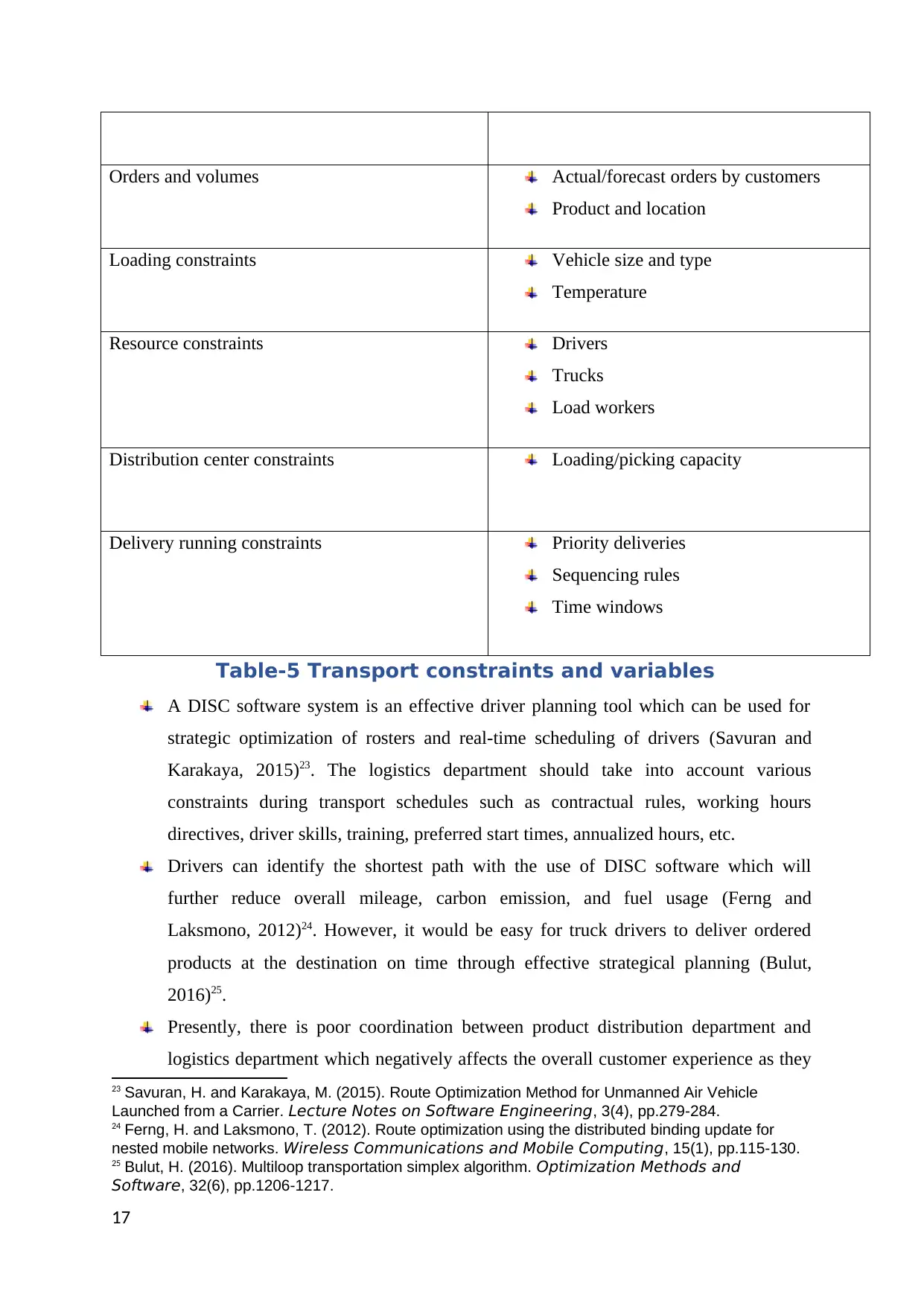
Orders and volumes Actual/forecast orders by customers
Product and location
Loading constraints Vehicle size and type
Temperature
Resource constraints Drivers
Trucks
Load workers
Distribution center constraints Loading/picking capacity
Delivery running constraints Priority deliveries
Sequencing rules
Time windows
Table-5 Transport constraints and variables
A DISC software system is an effective driver planning tool which can be used for
strategic optimization of rosters and real-time scheduling of drivers (Savuran and
Karakaya, 2015)23. The logistics department should take into account various
constraints during transport schedules such as contractual rules, working hours
directives, driver skills, training, preferred start times, annualized hours, etc.
Drivers can identify the shortest path with the use of DISC software which will
further reduce overall mileage, carbon emission, and fuel usage (Ferng and
Laksmono, 2012)24. However, it would be easy for truck drivers to deliver ordered
products at the destination on time through effective strategical planning (Bulut,
2016)25.
Presently, there is poor coordination between product distribution department and
logistics department which negatively affects the overall customer experience as they
23 Savuran, H. and Karakaya, M. (2015). Route Optimization Method for Unmanned Air Vehicle
Launched from a Carrier. Lecture Notes on Software Engineering, 3(4), pp.279-284.
24 Ferng, H. and Laksmono, T. (2012). Route optimization using the distributed binding update for
nested mobile networks. Wireless Communications and Mobile Computing, 15(1), pp.115-130.
25 Bulut, H. (2016). Multiloop transportation simplex algorithm. Optimization Methods and
Software, 32(6), pp.1206-1217.
17
Product and location
Loading constraints Vehicle size and type
Temperature
Resource constraints Drivers
Trucks
Load workers
Distribution center constraints Loading/picking capacity
Delivery running constraints Priority deliveries
Sequencing rules
Time windows
Table-5 Transport constraints and variables
A DISC software system is an effective driver planning tool which can be used for
strategic optimization of rosters and real-time scheduling of drivers (Savuran and
Karakaya, 2015)23. The logistics department should take into account various
constraints during transport schedules such as contractual rules, working hours
directives, driver skills, training, preferred start times, annualized hours, etc.
Drivers can identify the shortest path with the use of DISC software which will
further reduce overall mileage, carbon emission, and fuel usage (Ferng and
Laksmono, 2012)24. However, it would be easy for truck drivers to deliver ordered
products at the destination on time through effective strategical planning (Bulut,
2016)25.
Presently, there is poor coordination between product distribution department and
logistics department which negatively affects the overall customer experience as they
23 Savuran, H. and Karakaya, M. (2015). Route Optimization Method for Unmanned Air Vehicle
Launched from a Carrier. Lecture Notes on Software Engineering, 3(4), pp.279-284.
24 Ferng, H. and Laksmono, T. (2012). Route optimization using the distributed binding update for
nested mobile networks. Wireless Communications and Mobile Computing, 15(1), pp.115-130.
25 Bulut, H. (2016). Multiloop transportation simplex algorithm. Optimization Methods and
Software, 32(6), pp.1206-1217.
17
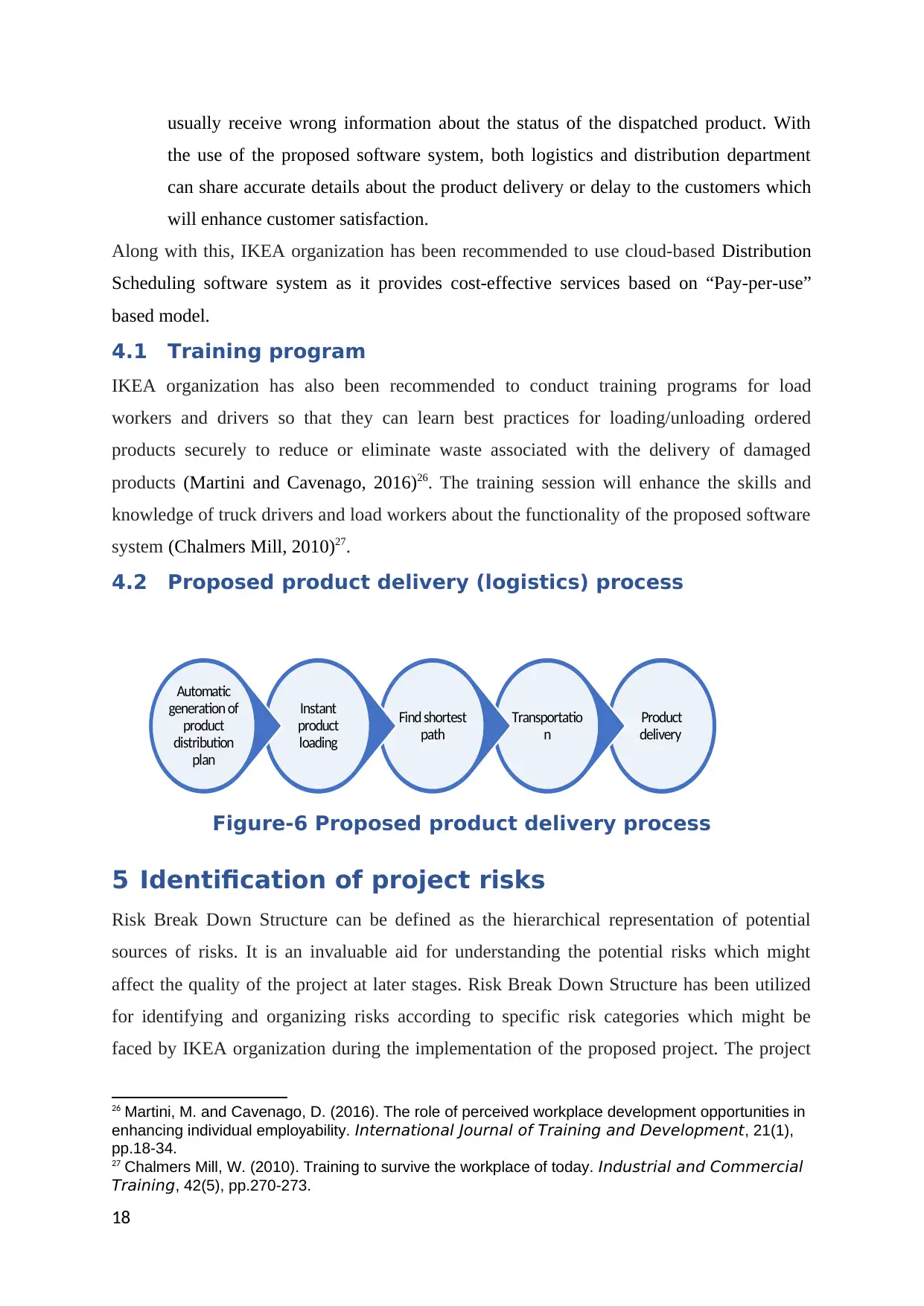
usually receive wrong information about the status of the dispatched product. With
the use of the proposed software system, both logistics and distribution department
can share accurate details about the product delivery or delay to the customers which
will enhance customer satisfaction.
Along with this, IKEA organization has been recommended to use cloud-based Distribution
Scheduling software system as it provides cost-effective services based on “Pay-per-use”
based model.
4.1 Training program
IKEA organization has also been recommended to conduct training programs for load
workers and drivers so that they can learn best practices for loading/unloading ordered
products securely to reduce or eliminate waste associated with the delivery of damaged
products (Martini and Cavenago, 2016)26. The training session will enhance the skills and
knowledge of truck drivers and load workers about the functionality of the proposed software
system (Chalmers Mill, 2010)27.
4.2 Proposed product delivery (logistics) process
Figure-6 Proposed product delivery process
5 Identification of project risks
Risk Break Down Structure can be defined as the hierarchical representation of potential
sources of risks. It is an invaluable aid for understanding the potential risks which might
affect the quality of the project at later stages. Risk Break Down Structure has been utilized
for identifying and organizing risks according to specific risk categories which might be
faced by IKEA organization during the implementation of the proposed project. The project
26 Martini, M. and Cavenago, D. (2016). The role of perceived workplace development opportunities in
enhancing individual employability. International Journal of Training and Development, 21(1),
pp.18-34.
27 Chalmers Mill, W. (2010). Training to survive the workplace of today. Industrial and Commercial
Training, 42(5), pp.270-273.
18
Product
delivery
Transportatio
n
Find shortest
path
Instant
product
loading
Automatic
generation of
product
distribution
plan
the use of the proposed software system, both logistics and distribution department
can share accurate details about the product delivery or delay to the customers which
will enhance customer satisfaction.
Along with this, IKEA organization has been recommended to use cloud-based Distribution
Scheduling software system as it provides cost-effective services based on “Pay-per-use”
based model.
4.1 Training program
IKEA organization has also been recommended to conduct training programs for load
workers and drivers so that they can learn best practices for loading/unloading ordered
products securely to reduce or eliminate waste associated with the delivery of damaged
products (Martini and Cavenago, 2016)26. The training session will enhance the skills and
knowledge of truck drivers and load workers about the functionality of the proposed software
system (Chalmers Mill, 2010)27.
4.2 Proposed product delivery (logistics) process
Figure-6 Proposed product delivery process
5 Identification of project risks
Risk Break Down Structure can be defined as the hierarchical representation of potential
sources of risks. It is an invaluable aid for understanding the potential risks which might
affect the quality of the project at later stages. Risk Break Down Structure has been utilized
for identifying and organizing risks according to specific risk categories which might be
faced by IKEA organization during the implementation of the proposed project. The project
26 Martini, M. and Cavenago, D. (2016). The role of perceived workplace development opportunities in
enhancing individual employability. International Journal of Training and Development, 21(1),
pp.18-34.
27 Chalmers Mill, W. (2010). Training to survive the workplace of today. Industrial and Commercial
Training, 42(5), pp.270-273.
18
Product
delivery
Transportatio
n
Find shortest
path
Instant
product
loading
Automatic
generation of
product
distribution
plan
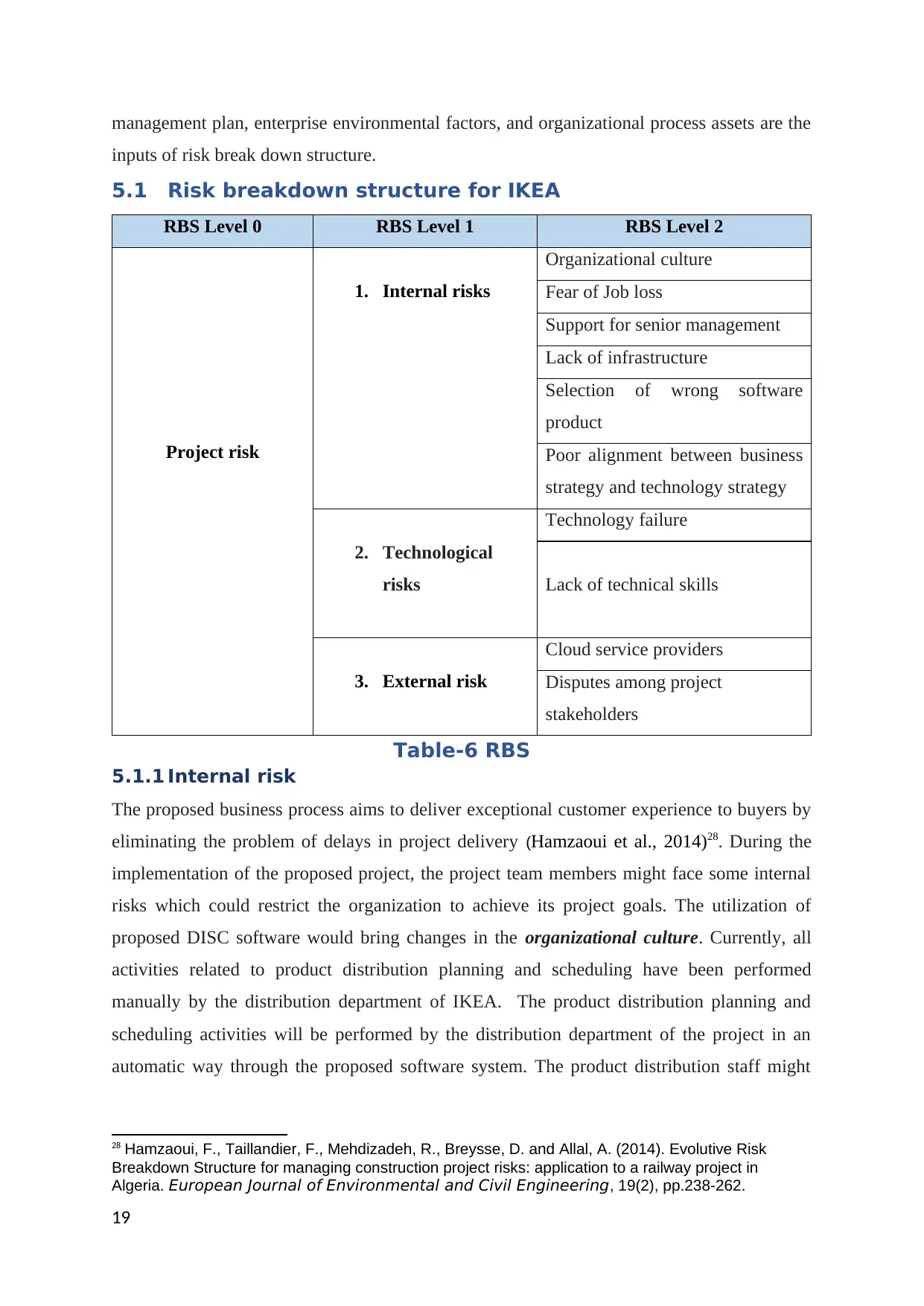
management plan, enterprise environmental factors, and organizational process assets are the
inputs of risk break down structure.
5.1 Risk breakdown structure for IKEA
RBS Level 0 RBS Level 1 RBS Level 2
Project risk
1. Internal risks
Organizational culture
Fear of Job loss
Support for senior management
Lack of infrastructure
Selection of wrong software
product
Poor alignment between business
strategy and technology strategy
2. Technological
risks
Technology failure
Lack of technical skills
3. External risk
Cloud service providers
Disputes among project
stakeholders
Table-6 RBS
5.1.1 Internal risk
The proposed business process aims to deliver exceptional customer experience to buyers by
eliminating the problem of delays in project delivery (Hamzaoui et al., 2014)28. During the
implementation of the proposed project, the project team members might face some internal
risks which could restrict the organization to achieve its project goals. The utilization of
proposed DISC software would bring changes in the organizational culture. Currently, all
activities related to product distribution planning and scheduling have been performed
manually by the distribution department of IKEA. The product distribution planning and
scheduling activities will be performed by the distribution department of the project in an
automatic way through the proposed software system. The product distribution staff might
28 Hamzaoui, F., Taillandier, F., Mehdizadeh, R., Breysse, D. and Allal, A. (2014). Evolutive Risk
Breakdown Structure for managing construction project risks: application to a railway project in
Algeria. European Journal of Environmental and Civil Engineering, 19(2), pp.238-262.
19
inputs of risk break down structure.
5.1 Risk breakdown structure for IKEA
RBS Level 0 RBS Level 1 RBS Level 2
Project risk
1. Internal risks
Organizational culture
Fear of Job loss
Support for senior management
Lack of infrastructure
Selection of wrong software
product
Poor alignment between business
strategy and technology strategy
2. Technological
risks
Technology failure
Lack of technical skills
3. External risk
Cloud service providers
Disputes among project
stakeholders
Table-6 RBS
5.1.1 Internal risk
The proposed business process aims to deliver exceptional customer experience to buyers by
eliminating the problem of delays in project delivery (Hamzaoui et al., 2014)28. During the
implementation of the proposed project, the project team members might face some internal
risks which could restrict the organization to achieve its project goals. The utilization of
proposed DISC software would bring changes in the organizational culture. Currently, all
activities related to product distribution planning and scheduling have been performed
manually by the distribution department of IKEA. The product distribution planning and
scheduling activities will be performed by the distribution department of the project in an
automatic way through the proposed software system. The product distribution staff might
28 Hamzaoui, F., Taillandier, F., Mehdizadeh, R., Breysse, D. and Allal, A. (2014). Evolutive Risk
Breakdown Structure for managing construction project risks: application to a railway project in
Algeria. European Journal of Environmental and Civil Engineering, 19(2), pp.238-262.
19
Paraphrase This Document
Need a fresh take? Get an instant paraphrase of this document with our AI Paraphraser
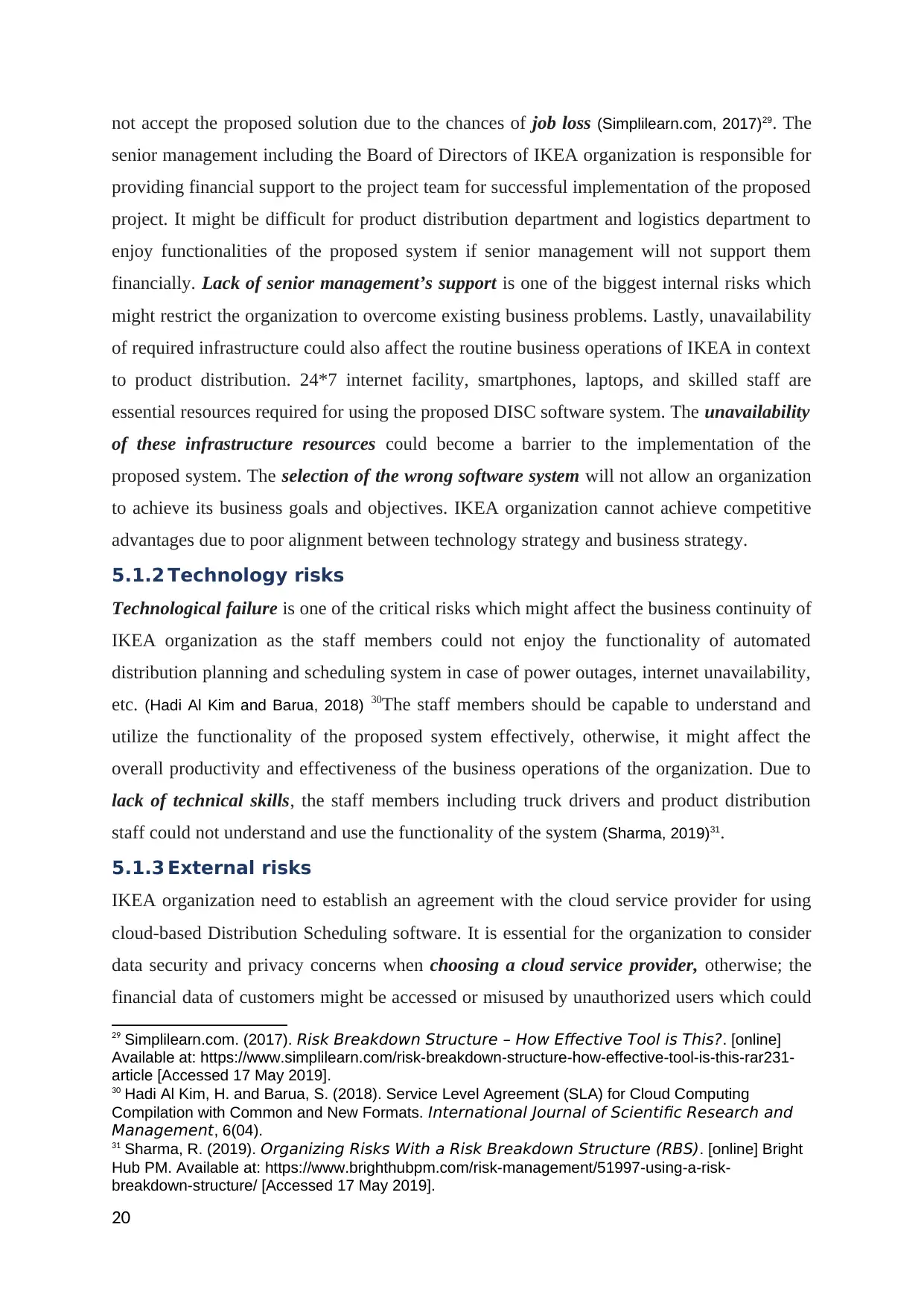
not accept the proposed solution due to the chances of job loss (Simplilearn.com, 2017)29. The
senior management including the Board of Directors of IKEA organization is responsible for
providing financial support to the project team for successful implementation of the proposed
project. It might be difficult for product distribution department and logistics department to
enjoy functionalities of the proposed system if senior management will not support them
financially. Lack of senior management’s support is one of the biggest internal risks which
might restrict the organization to overcome existing business problems. Lastly, unavailability
of required infrastructure could also affect the routine business operations of IKEA in context
to product distribution. 24*7 internet facility, smartphones, laptops, and skilled staff are
essential resources required for using the proposed DISC software system. The unavailability
of these infrastructure resources could become a barrier to the implementation of the
proposed system. The selection of the wrong software system will not allow an organization
to achieve its business goals and objectives. IKEA organization cannot achieve competitive
advantages due to poor alignment between technology strategy and business strategy.
5.1.2 Technology risks
Technological failure is one of the critical risks which might affect the business continuity of
IKEA organization as the staff members could not enjoy the functionality of automated
distribution planning and scheduling system in case of power outages, internet unavailability,
etc. (Hadi Al Kim and Barua, 2018) 30The staff members should be capable to understand and
utilize the functionality of the proposed system effectively, otherwise, it might affect the
overall productivity and effectiveness of the business operations of the organization. Due to
lack of technical skills, the staff members including truck drivers and product distribution
staff could not understand and use the functionality of the system (Sharma, 2019)31.
5.1.3 External risks
IKEA organization need to establish an agreement with the cloud service provider for using
cloud-based Distribution Scheduling software. It is essential for the organization to consider
data security and privacy concerns when choosing a cloud service provider, otherwise; the
financial data of customers might be accessed or misused by unauthorized users which could
29 Simplilearn.com. (2017). Risk Breakdown Structure – How Effective Tool is This?. [online]
Available at: https://www.simplilearn.com/risk-breakdown-structure-how-effective-tool-is-this-rar231-
article [Accessed 17 May 2019].
30 Hadi Al Kim, H. and Barua, S. (2018). Service Level Agreement (SLA) for Cloud Computing
Compilation with Common and New Formats. International Journal of Scientific Research and
Management, 6(04).
31 Sharma, R. (2019). Organizing Risks With a Risk Breakdown Structure (RBS). [online] Bright
Hub PM. Available at: https://www.brighthubpm.com/risk-management/51997-using-a-risk-
breakdown-structure/ [Accessed 17 May 2019].
20
senior management including the Board of Directors of IKEA organization is responsible for
providing financial support to the project team for successful implementation of the proposed
project. It might be difficult for product distribution department and logistics department to
enjoy functionalities of the proposed system if senior management will not support them
financially. Lack of senior management’s support is one of the biggest internal risks which
might restrict the organization to overcome existing business problems. Lastly, unavailability
of required infrastructure could also affect the routine business operations of IKEA in context
to product distribution. 24*7 internet facility, smartphones, laptops, and skilled staff are
essential resources required for using the proposed DISC software system. The unavailability
of these infrastructure resources could become a barrier to the implementation of the
proposed system. The selection of the wrong software system will not allow an organization
to achieve its business goals and objectives. IKEA organization cannot achieve competitive
advantages due to poor alignment between technology strategy and business strategy.
5.1.2 Technology risks
Technological failure is one of the critical risks which might affect the business continuity of
IKEA organization as the staff members could not enjoy the functionality of automated
distribution planning and scheduling system in case of power outages, internet unavailability,
etc. (Hadi Al Kim and Barua, 2018) 30The staff members should be capable to understand and
utilize the functionality of the proposed system effectively, otherwise, it might affect the
overall productivity and effectiveness of the business operations of the organization. Due to
lack of technical skills, the staff members including truck drivers and product distribution
staff could not understand and use the functionality of the system (Sharma, 2019)31.
5.1.3 External risks
IKEA organization need to establish an agreement with the cloud service provider for using
cloud-based Distribution Scheduling software. It is essential for the organization to consider
data security and privacy concerns when choosing a cloud service provider, otherwise; the
financial data of customers might be accessed or misused by unauthorized users which could
29 Simplilearn.com. (2017). Risk Breakdown Structure – How Effective Tool is This?. [online]
Available at: https://www.simplilearn.com/risk-breakdown-structure-how-effective-tool-is-this-rar231-
article [Accessed 17 May 2019].
30 Hadi Al Kim, H. and Barua, S. (2018). Service Level Agreement (SLA) for Cloud Computing
Compilation with Common and New Formats. International Journal of Scientific Research and
Management, 6(04).
31 Sharma, R. (2019). Organizing Risks With a Risk Breakdown Structure (RBS). [online] Bright
Hub PM. Available at: https://www.brighthubpm.com/risk-management/51997-using-a-risk-
breakdown-structure/ [Accessed 17 May 2019].
20
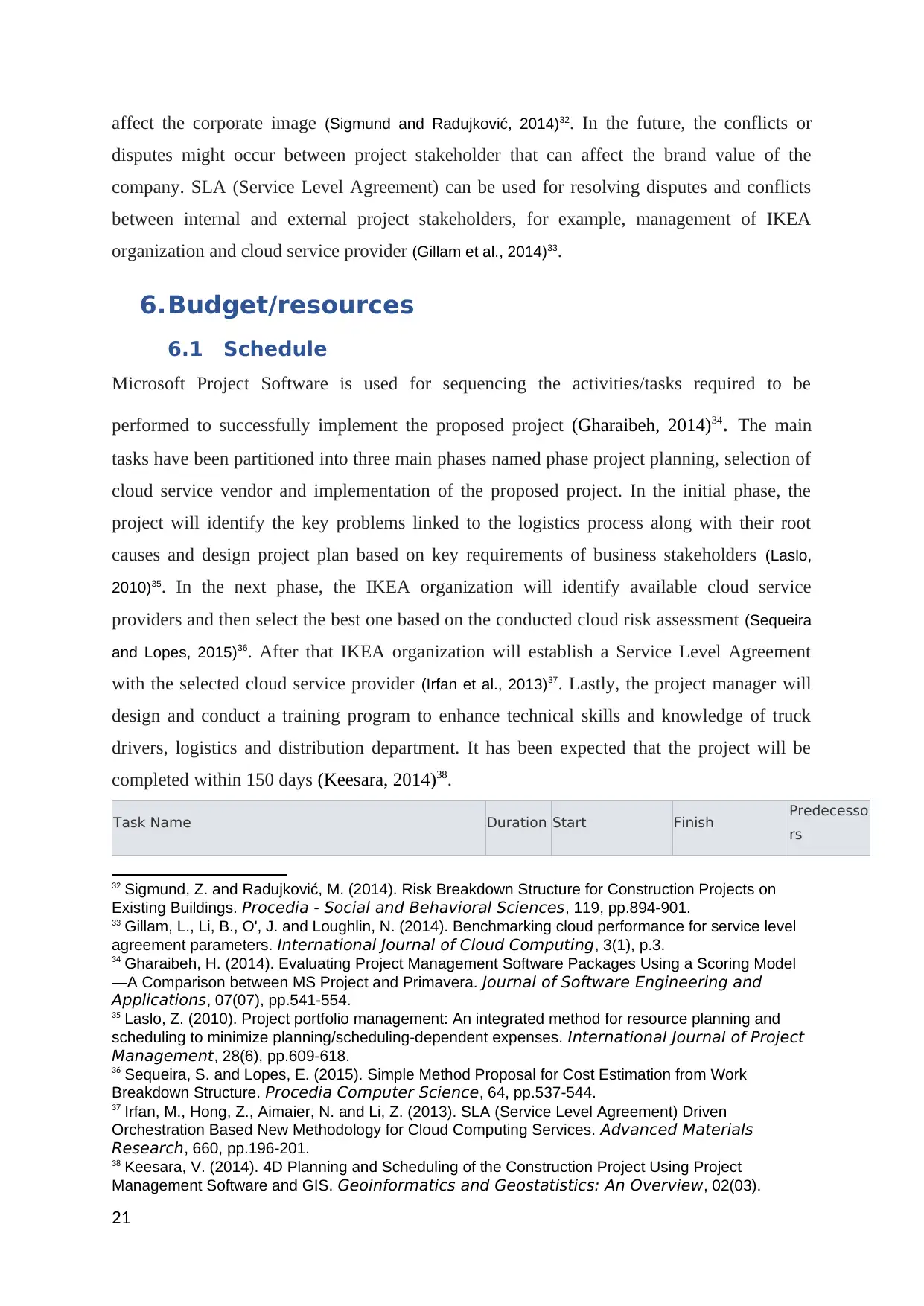
affect the corporate image (Sigmund and Radujković, 2014)32. In the future, the conflicts or
disputes might occur between project stakeholder that can affect the brand value of the
company. SLA (Service Level Agreement) can be used for resolving disputes and conflicts
between internal and external project stakeholders, for example, management of IKEA
organization and cloud service provider (Gillam et al., 2014)33.
6.Budget/resources
6.1 Schedule
Microsoft Project Software is used for sequencing the activities/tasks required to be
performed to successfully implement the proposed project (Gharaibeh, 2014)34. The main
tasks have been partitioned into three main phases named phase project planning, selection of
cloud service vendor and implementation of the proposed project. In the initial phase, the
project will identify the key problems linked to the logistics process along with their root
causes and design project plan based on key requirements of business stakeholders (Laslo,
2010)35. In the next phase, the IKEA organization will identify available cloud service
providers and then select the best one based on the conducted cloud risk assessment (Sequeira
and Lopes, 2015)36. After that IKEA organization will establish a Service Level Agreement
with the selected cloud service provider (Irfan et al., 2013)37. Lastly, the project manager will
design and conduct a training program to enhance technical skills and knowledge of truck
drivers, logistics and distribution department. It has been expected that the project will be
completed within 150 days (Keesara, 2014)38.
Task Name Duration Start Finish Predecesso
rs
32 Sigmund, Z. and Radujković, M. (2014). Risk Breakdown Structure for Construction Projects on
Existing Buildings. Procedia - Social and Behavioral Sciences, 119, pp.894-901.
33 Gillam, L., Li, B., O', J. and Loughlin, N. (2014). Benchmarking cloud performance for service level
agreement parameters. International Journal of Cloud Computing, 3(1), p.3.
34 Gharaibeh, H. (2014). Evaluating Project Management Software Packages Using a Scoring Model
—A Comparison between MS Project and Primavera. Journal of Software Engineering and
Applications, 07(07), pp.541-554.
35 Laslo, Z. (2010). Project portfolio management: An integrated method for resource planning and
scheduling to minimize planning/scheduling-dependent expenses. International Journal of Project
Management, 28(6), pp.609-618.
36 Sequeira, S. and Lopes, E. (2015). Simple Method Proposal for Cost Estimation from Work
Breakdown Structure. Procedia Computer Science, 64, pp.537-544.
37 Irfan, M., Hong, Z., Aimaier, N. and Li, Z. (2013). SLA (Service Level Agreement) Driven
Orchestration Based New Methodology for Cloud Computing Services. Advanced Materials
Research, 660, pp.196-201.
38 Keesara, V. (2014). 4D Planning and Scheduling of the Construction Project Using Project
Management Software and GIS. Geoinformatics and Geostatistics: An Overview, 02(03).
21
disputes might occur between project stakeholder that can affect the brand value of the
company. SLA (Service Level Agreement) can be used for resolving disputes and conflicts
between internal and external project stakeholders, for example, management of IKEA
organization and cloud service provider (Gillam et al., 2014)33.
6.Budget/resources
6.1 Schedule
Microsoft Project Software is used for sequencing the activities/tasks required to be
performed to successfully implement the proposed project (Gharaibeh, 2014)34. The main
tasks have been partitioned into three main phases named phase project planning, selection of
cloud service vendor and implementation of the proposed project. In the initial phase, the
project will identify the key problems linked to the logistics process along with their root
causes and design project plan based on key requirements of business stakeholders (Laslo,
2010)35. In the next phase, the IKEA organization will identify available cloud service
providers and then select the best one based on the conducted cloud risk assessment (Sequeira
and Lopes, 2015)36. After that IKEA organization will establish a Service Level Agreement
with the selected cloud service provider (Irfan et al., 2013)37. Lastly, the project manager will
design and conduct a training program to enhance technical skills and knowledge of truck
drivers, logistics and distribution department. It has been expected that the project will be
completed within 150 days (Keesara, 2014)38.
Task Name Duration Start Finish Predecesso
rs
32 Sigmund, Z. and Radujković, M. (2014). Risk Breakdown Structure for Construction Projects on
Existing Buildings. Procedia - Social and Behavioral Sciences, 119, pp.894-901.
33 Gillam, L., Li, B., O', J. and Loughlin, N. (2014). Benchmarking cloud performance for service level
agreement parameters. International Journal of Cloud Computing, 3(1), p.3.
34 Gharaibeh, H. (2014). Evaluating Project Management Software Packages Using a Scoring Model
—A Comparison between MS Project and Primavera. Journal of Software Engineering and
Applications, 07(07), pp.541-554.
35 Laslo, Z. (2010). Project portfolio management: An integrated method for resource planning and
scheduling to minimize planning/scheduling-dependent expenses. International Journal of Project
Management, 28(6), pp.609-618.
36 Sequeira, S. and Lopes, E. (2015). Simple Method Proposal for Cost Estimation from Work
Breakdown Structure. Procedia Computer Science, 64, pp.537-544.
37 Irfan, M., Hong, Z., Aimaier, N. and Li, Z. (2013). SLA (Service Level Agreement) Driven
Orchestration Based New Methodology for Cloud Computing Services. Advanced Materials
Research, 660, pp.196-201.
38 Keesara, V. (2014). 4D Planning and Scheduling of the Construction Project Using Project
Management Software and GIS. Geoinformatics and Geostatistics: An Overview, 02(03).
21
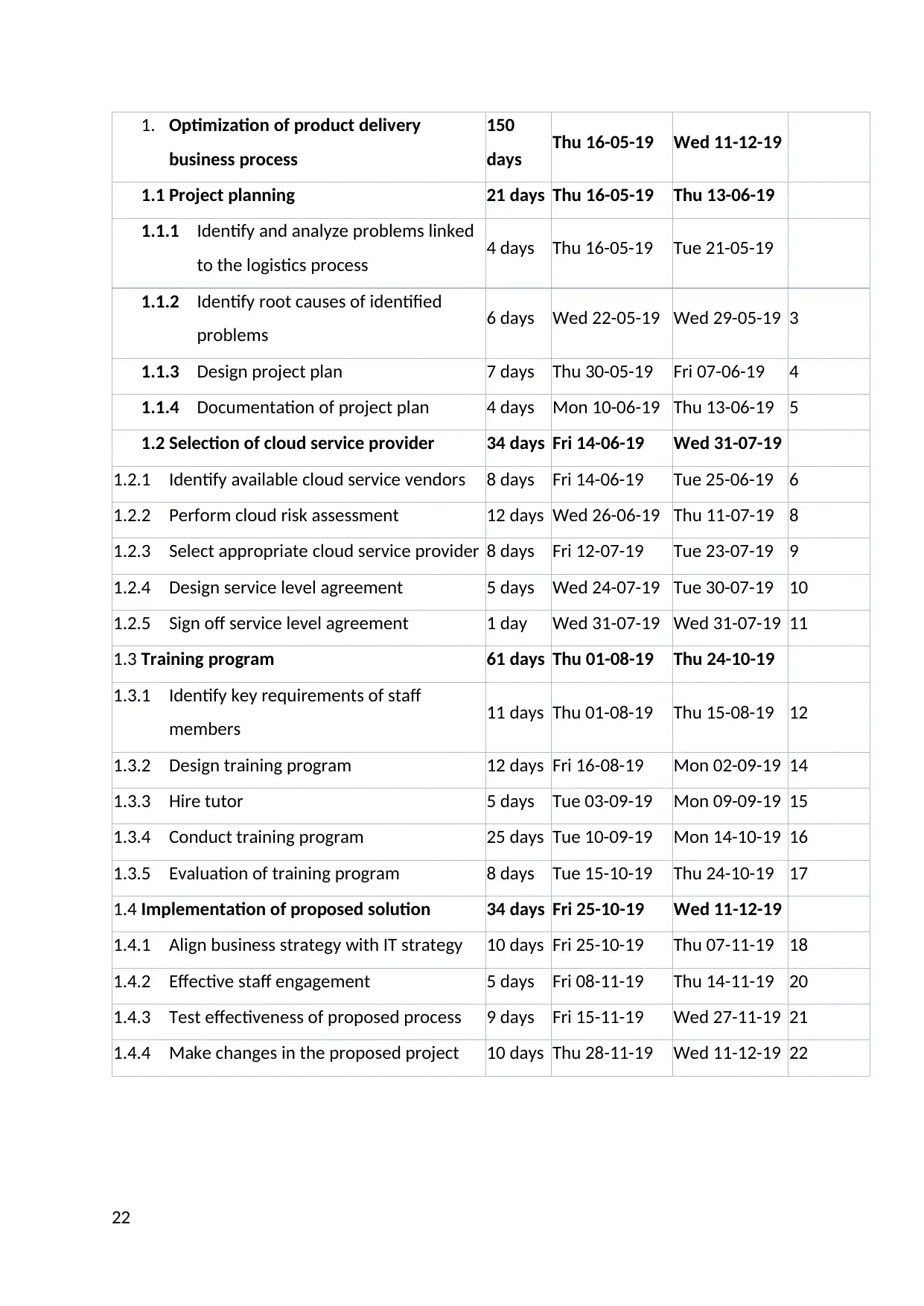
1. Optimization of product delivery
business process
150
days Thu 16-05-19 Wed 11-12-19
1.1 Project planning 21 days Thu 16-05-19 Thu 13-06-19
1.1.1 Identify and analyze problems linked
to the logistics process 4 days Thu 16-05-19 Tue 21-05-19
1.1.2 Identify root causes of identified
problems 6 days Wed 22-05-19 Wed 29-05-19 3
1.1.3 Design project plan 7 days Thu 30-05-19 Fri 07-06-19 4
1.1.4 Documentation of project plan 4 days Mon 10-06-19 Thu 13-06-19 5
1.2 Selection of cloud service provider 34 days Fri 14-06-19 Wed 31-07-19
1.2.1 Identify available cloud service vendors 8 days Fri 14-06-19 Tue 25-06-19 6
1.2.2 Perform cloud risk assessment 12 days Wed 26-06-19 Thu 11-07-19 8
1.2.3 Select appropriate cloud service provider 8 days Fri 12-07-19 Tue 23-07-19 9
1.2.4 Design service level agreement 5 days Wed 24-07-19 Tue 30-07-19 10
1.2.5 Sign off service level agreement 1 day Wed 31-07-19 Wed 31-07-19 11
1.3 Training program 61 days Thu 01-08-19 Thu 24-10-19
1.3.1 Identify key requirements of staff
members 11 days Thu 01-08-19 Thu 15-08-19 12
1.3.2 Design training program 12 days Fri 16-08-19 Mon 02-09-19 14
1.3.3 Hire tutor 5 days Tue 03-09-19 Mon 09-09-19 15
1.3.4 Conduct training program 25 days Tue 10-09-19 Mon 14-10-19 16
1.3.5 Evaluation of training program 8 days Tue 15-10-19 Thu 24-10-19 17
1.4 Implementation of proposed solution 34 days Fri 25-10-19 Wed 11-12-19
1.4.1 Align business strategy with IT strategy 10 days Fri 25-10-19 Thu 07-11-19 18
1.4.2 Effective staff engagement 5 days Fri 08-11-19 Thu 14-11-19 20
1.4.3 Test effectiveness of proposed process 9 days Fri 15-11-19 Wed 27-11-19 21
1.4.4 Make changes in the proposed project 10 days Thu 28-11-19 Wed 11-12-19 22
22
business process
150
days Thu 16-05-19 Wed 11-12-19
1.1 Project planning 21 days Thu 16-05-19 Thu 13-06-19
1.1.1 Identify and analyze problems linked
to the logistics process 4 days Thu 16-05-19 Tue 21-05-19
1.1.2 Identify root causes of identified
problems 6 days Wed 22-05-19 Wed 29-05-19 3
1.1.3 Design project plan 7 days Thu 30-05-19 Fri 07-06-19 4
1.1.4 Documentation of project plan 4 days Mon 10-06-19 Thu 13-06-19 5
1.2 Selection of cloud service provider 34 days Fri 14-06-19 Wed 31-07-19
1.2.1 Identify available cloud service vendors 8 days Fri 14-06-19 Tue 25-06-19 6
1.2.2 Perform cloud risk assessment 12 days Wed 26-06-19 Thu 11-07-19 8
1.2.3 Select appropriate cloud service provider 8 days Fri 12-07-19 Tue 23-07-19 9
1.2.4 Design service level agreement 5 days Wed 24-07-19 Tue 30-07-19 10
1.2.5 Sign off service level agreement 1 day Wed 31-07-19 Wed 31-07-19 11
1.3 Training program 61 days Thu 01-08-19 Thu 24-10-19
1.3.1 Identify key requirements of staff
members 11 days Thu 01-08-19 Thu 15-08-19 12
1.3.2 Design training program 12 days Fri 16-08-19 Mon 02-09-19 14
1.3.3 Hire tutor 5 days Tue 03-09-19 Mon 09-09-19 15
1.3.4 Conduct training program 25 days Tue 10-09-19 Mon 14-10-19 16
1.3.5 Evaluation of training program 8 days Tue 15-10-19 Thu 24-10-19 17
1.4 Implementation of proposed solution 34 days Fri 25-10-19 Wed 11-12-19
1.4.1 Align business strategy with IT strategy 10 days Fri 25-10-19 Thu 07-11-19 18
1.4.2 Effective staff engagement 5 days Fri 08-11-19 Thu 14-11-19 20
1.4.3 Test effectiveness of proposed process 9 days Fri 15-11-19 Wed 27-11-19 21
1.4.4 Make changes in the proposed project 10 days Thu 28-11-19 Wed 11-12-19 22
22
Secure Best Marks with AI Grader
Need help grading? Try our AI Grader for instant feedback on your assignments.
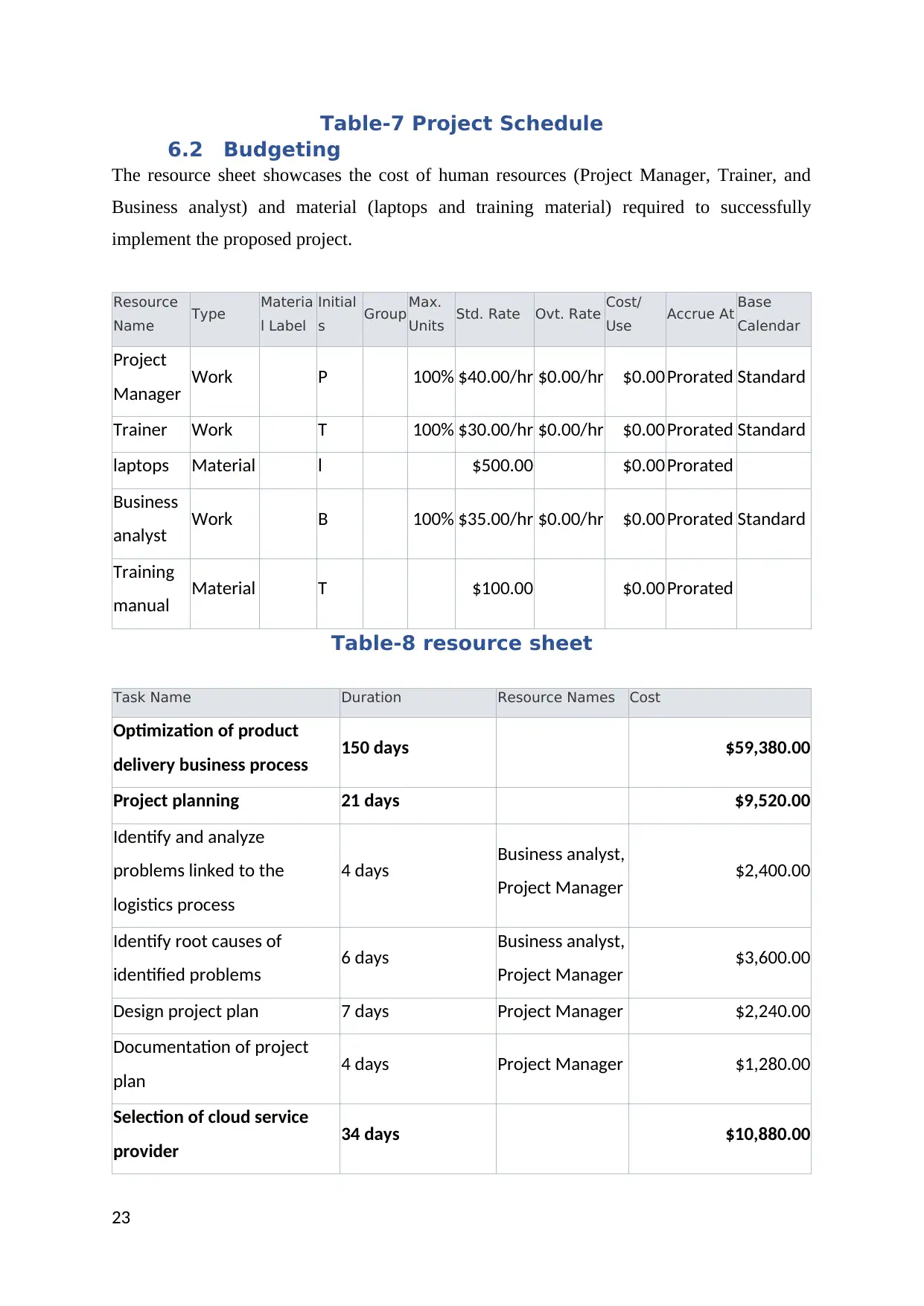
Table-7 Project Schedule
6.2 Budgeting
The resource sheet showcases the cost of human resources (Project Manager, Trainer, and
Business analyst) and material (laptops and training material) required to successfully
implement the proposed project.
Resource
Name Type Materia
l Label
Initial
s Group Max.
Units Std. Rate Ovt. Rate Cost/
Use Accrue At Base
Calendar
Project
Manager Work P 100% $40.00/hr $0.00/hr $0.00 Prorated Standard
Trainer Work T 100% $30.00/hr $0.00/hr $0.00 Prorated Standard
laptops Material l $500.00 $0.00 Prorated
Business
analyst Work B 100% $35.00/hr $0.00/hr $0.00 Prorated Standard
Training
manual Material T $100.00 $0.00 Prorated
Table-8 resource sheet
Task Name Duration Resource Names Cost
Optimization of product
delivery business process 150 days $59,380.00
Project planning 21 days $9,520.00
Identify and analyze
problems linked to the
logistics process
4 days Business analyst,
Project Manager $2,400.00
Identify root causes of
identified problems 6 days Business analyst,
Project Manager $3,600.00
Design project plan 7 days Project Manager $2,240.00
Documentation of project
plan 4 days Project Manager $1,280.00
Selection of cloud service
provider 34 days $10,880.00
23
6.2 Budgeting
The resource sheet showcases the cost of human resources (Project Manager, Trainer, and
Business analyst) and material (laptops and training material) required to successfully
implement the proposed project.
Resource
Name Type Materia
l Label
Initial
s Group Max.
Units Std. Rate Ovt. Rate Cost/
Use Accrue At Base
Calendar
Project
Manager Work P 100% $40.00/hr $0.00/hr $0.00 Prorated Standard
Trainer Work T 100% $30.00/hr $0.00/hr $0.00 Prorated Standard
laptops Material l $500.00 $0.00 Prorated
Business
analyst Work B 100% $35.00/hr $0.00/hr $0.00 Prorated Standard
Training
manual Material T $100.00 $0.00 Prorated
Table-8 resource sheet
Task Name Duration Resource Names Cost
Optimization of product
delivery business process 150 days $59,380.00
Project planning 21 days $9,520.00
Identify and analyze
problems linked to the
logistics process
4 days Business analyst,
Project Manager $2,400.00
Identify root causes of
identified problems 6 days Business analyst,
Project Manager $3,600.00
Design project plan 7 days Project Manager $2,240.00
Documentation of project
plan 4 days Project Manager $1,280.00
Selection of cloud service
provider 34 days $10,880.00
23
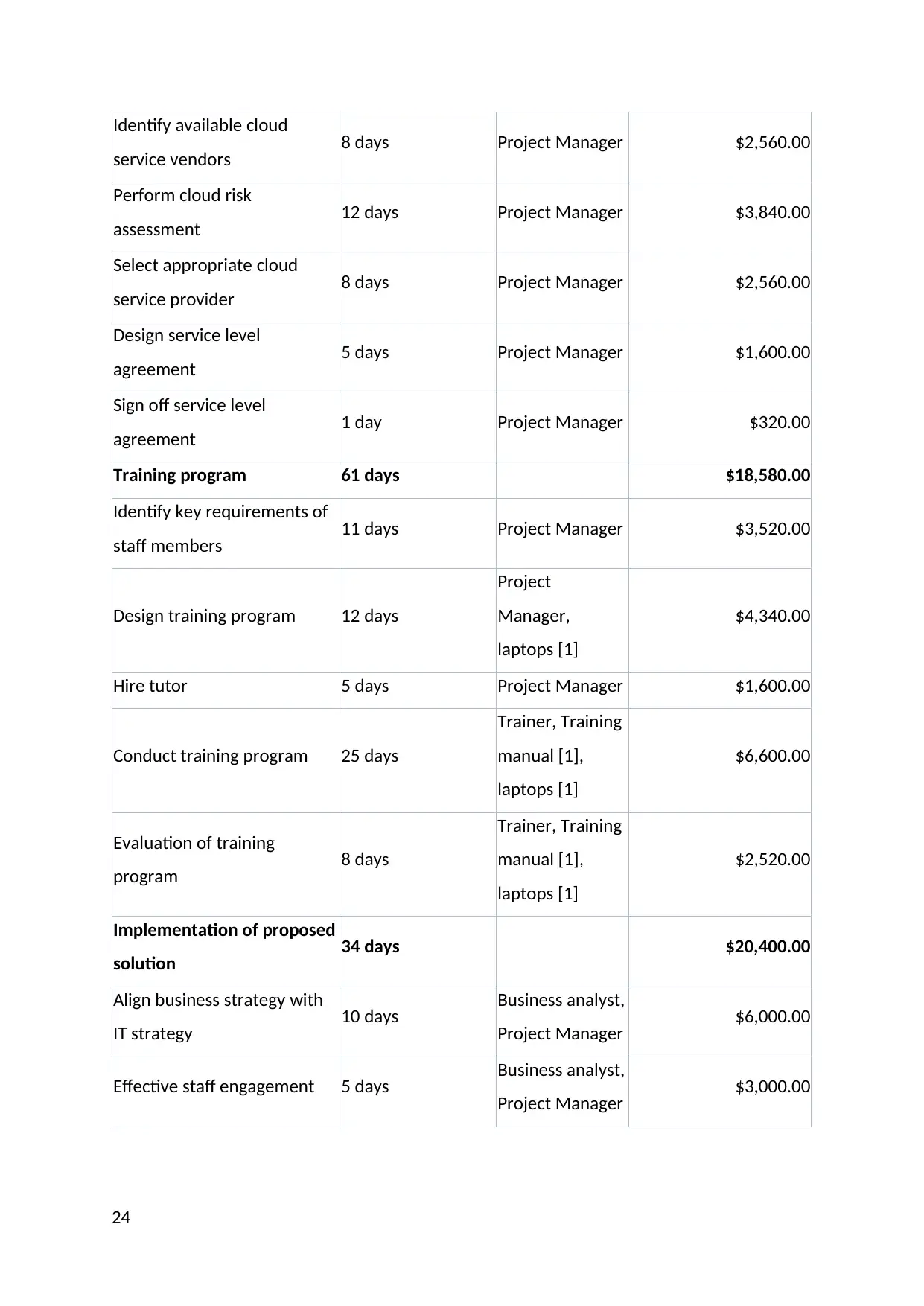
Identify available cloud
service vendors 8 days Project Manager $2,560.00
Perform cloud risk
assessment 12 days Project Manager $3,840.00
Select appropriate cloud
service provider 8 days Project Manager $2,560.00
Design service level
agreement 5 days Project Manager $1,600.00
Sign off service level
agreement 1 day Project Manager $320.00
Training program 61 days $18,580.00
Identify key requirements of
staff members 11 days Project Manager $3,520.00
Design training program 12 days
Project
Manager,
laptops [1]
$4,340.00
Hire tutor 5 days Project Manager $1,600.00
Conduct training program 25 days
Trainer, Training
manual [1],
laptops [1]
$6,600.00
Evaluation of training
program 8 days
Trainer, Training
manual [1],
laptops [1]
$2,520.00
Implementation of proposed
solution 34 days $20,400.00
Align business strategy with
IT strategy 10 days Business analyst,
Project Manager $6,000.00
Effective staff engagement 5 days Business analyst,
Project Manager $3,000.00
24
service vendors 8 days Project Manager $2,560.00
Perform cloud risk
assessment 12 days Project Manager $3,840.00
Select appropriate cloud
service provider 8 days Project Manager $2,560.00
Design service level
agreement 5 days Project Manager $1,600.00
Sign off service level
agreement 1 day Project Manager $320.00
Training program 61 days $18,580.00
Identify key requirements of
staff members 11 days Project Manager $3,520.00
Design training program 12 days
Project
Manager,
laptops [1]
$4,340.00
Hire tutor 5 days Project Manager $1,600.00
Conduct training program 25 days
Trainer, Training
manual [1],
laptops [1]
$6,600.00
Evaluation of training
program 8 days
Trainer, Training
manual [1],
laptops [1]
$2,520.00
Implementation of proposed
solution 34 days $20,400.00
Align business strategy with
IT strategy 10 days Business analyst,
Project Manager $6,000.00
Effective staff engagement 5 days Business analyst,
Project Manager $3,000.00
24
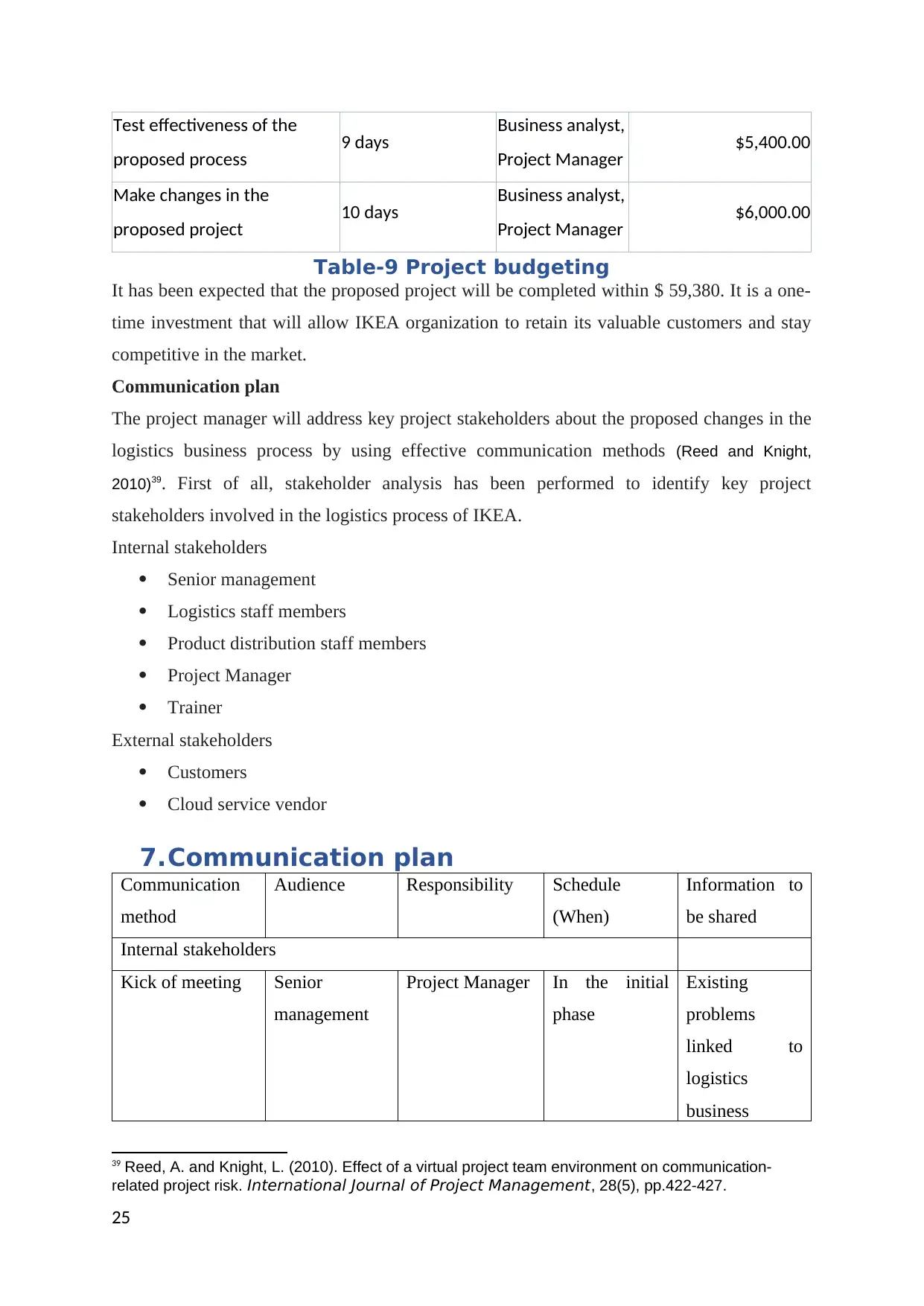
Test effectiveness of the
proposed process 9 days Business analyst,
Project Manager $5,400.00
Make changes in the
proposed project 10 days Business analyst,
Project Manager $6,000.00
Table-9 Project budgeting
It has been expected that the proposed project will be completed within $ 59,380. It is a one-
time investment that will allow IKEA organization to retain its valuable customers and stay
competitive in the market.
Communication plan
The project manager will address key project stakeholders about the proposed changes in the
logistics business process by using effective communication methods (Reed and Knight,
2010)39. First of all, stakeholder analysis has been performed to identify key project
stakeholders involved in the logistics process of IKEA.
Internal stakeholders
Senior management
Logistics staff members
Product distribution staff members
Project Manager
Trainer
External stakeholders
Customers
Cloud service vendor
7.Communication plan
Communication
method
Audience Responsibility Schedule
(When)
Information to
be shared
Internal stakeholders
Kick of meeting Senior
management
Project Manager In the initial
phase
Existing
problems
linked to
logistics
business
39 Reed, A. and Knight, L. (2010). Effect of a virtual project team environment on communication-
related project risk. International Journal of Project Management, 28(5), pp.422-427.
25
proposed process 9 days Business analyst,
Project Manager $5,400.00
Make changes in the
proposed project 10 days Business analyst,
Project Manager $6,000.00
Table-9 Project budgeting
It has been expected that the proposed project will be completed within $ 59,380. It is a one-
time investment that will allow IKEA organization to retain its valuable customers and stay
competitive in the market.
Communication plan
The project manager will address key project stakeholders about the proposed changes in the
logistics business process by using effective communication methods (Reed and Knight,
2010)39. First of all, stakeholder analysis has been performed to identify key project
stakeholders involved in the logistics process of IKEA.
Internal stakeholders
Senior management
Logistics staff members
Product distribution staff members
Project Manager
Trainer
External stakeholders
Customers
Cloud service vendor
7.Communication plan
Communication
method
Audience Responsibility Schedule
(When)
Information to
be shared
Internal stakeholders
Kick of meeting Senior
management
Project Manager In the initial
phase
Existing
problems
linked to
logistics
business
39 Reed, A. and Knight, L. (2010). Effect of a virtual project team environment on communication-
related project risk. International Journal of Project Management, 28(5), pp.422-427.
25
Paraphrase This Document
Need a fresh take? Get an instant paraphrase of this document with our AI Paraphraser
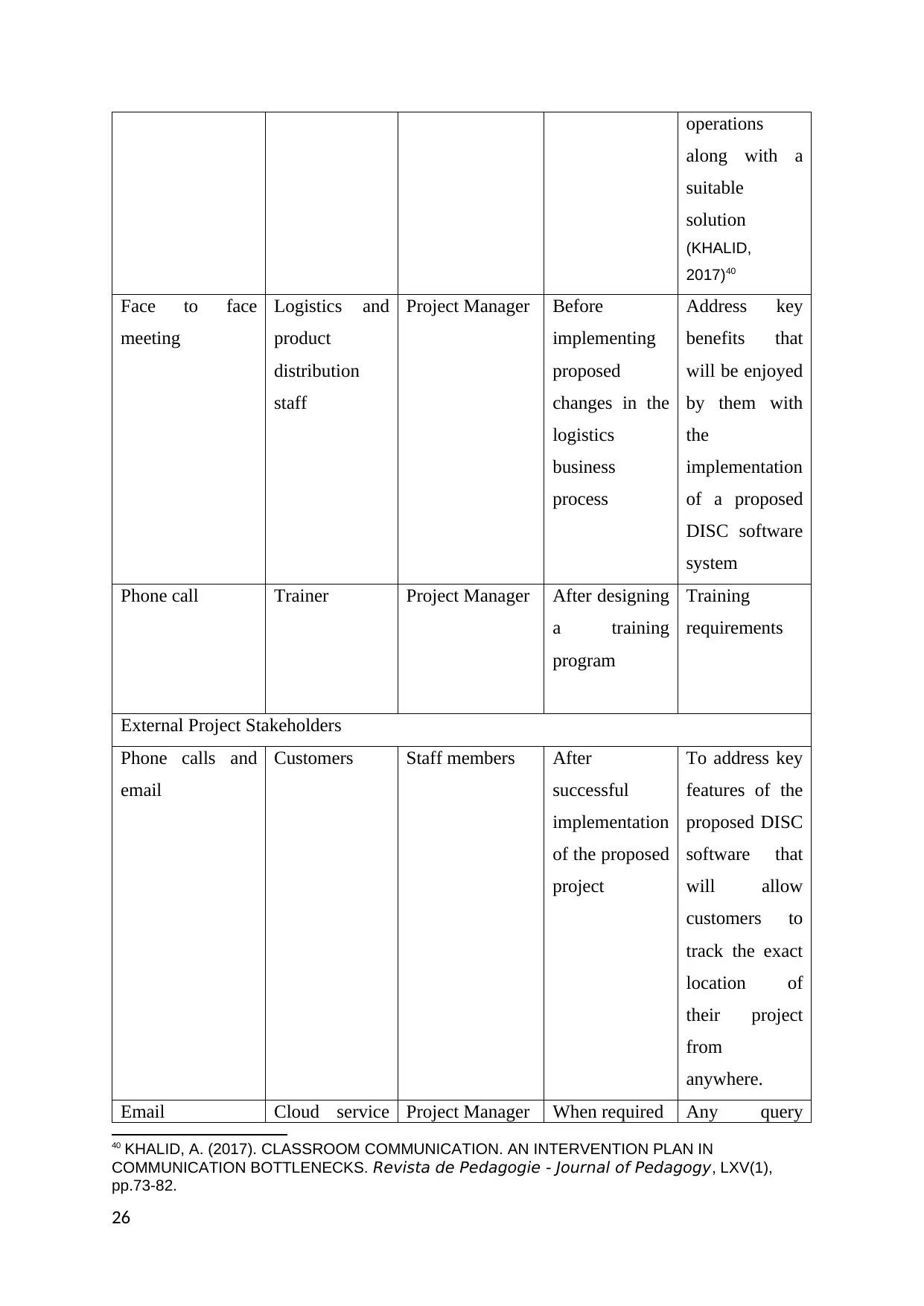
operations
along with a
suitable
solution
(KHALID,
2017)40
Face to face
meeting
Logistics and
product
distribution
staff
Project Manager Before
implementing
proposed
changes in the
logistics
business
process
Address key
benefits that
will be enjoyed
by them with
the
implementation
of a proposed
DISC software
system
Phone call Trainer Project Manager After designing
a training
program
Training
requirements
External Project Stakeholders
Phone calls and
email
Customers Staff members After
successful
implementation
of the proposed
project
To address key
features of the
proposed DISC
software that
will allow
customers to
track the exact
location of
their project
from
anywhere.
Email Cloud service Project Manager When required Any query
40 KHALID, A. (2017). CLASSROOM COMMUNICATION. AN INTERVENTION PLAN IN
COMMUNICATION BOTTLENECKS. Revista de Pedagogie - Journal of Pedagogy, LXV(1),
pp.73-82.
26
along with a
suitable
solution
(KHALID,
2017)40
Face to face
meeting
Logistics and
product
distribution
staff
Project Manager Before
implementing
proposed
changes in the
logistics
business
process
Address key
benefits that
will be enjoyed
by them with
the
implementation
of a proposed
DISC software
system
Phone call Trainer Project Manager After designing
a training
program
Training
requirements
External Project Stakeholders
Phone calls and
Customers Staff members After
successful
implementation
of the proposed
project
To address key
features of the
proposed DISC
software that
will allow
customers to
track the exact
location of
their project
from
anywhere.
Email Cloud service Project Manager When required Any query
40 KHALID, A. (2017). CLASSROOM COMMUNICATION. AN INTERVENTION PLAN IN
COMMUNICATION BOTTLENECKS. Revista de Pedagogie - Journal of Pedagogy, LXV(1),
pp.73-82.
26
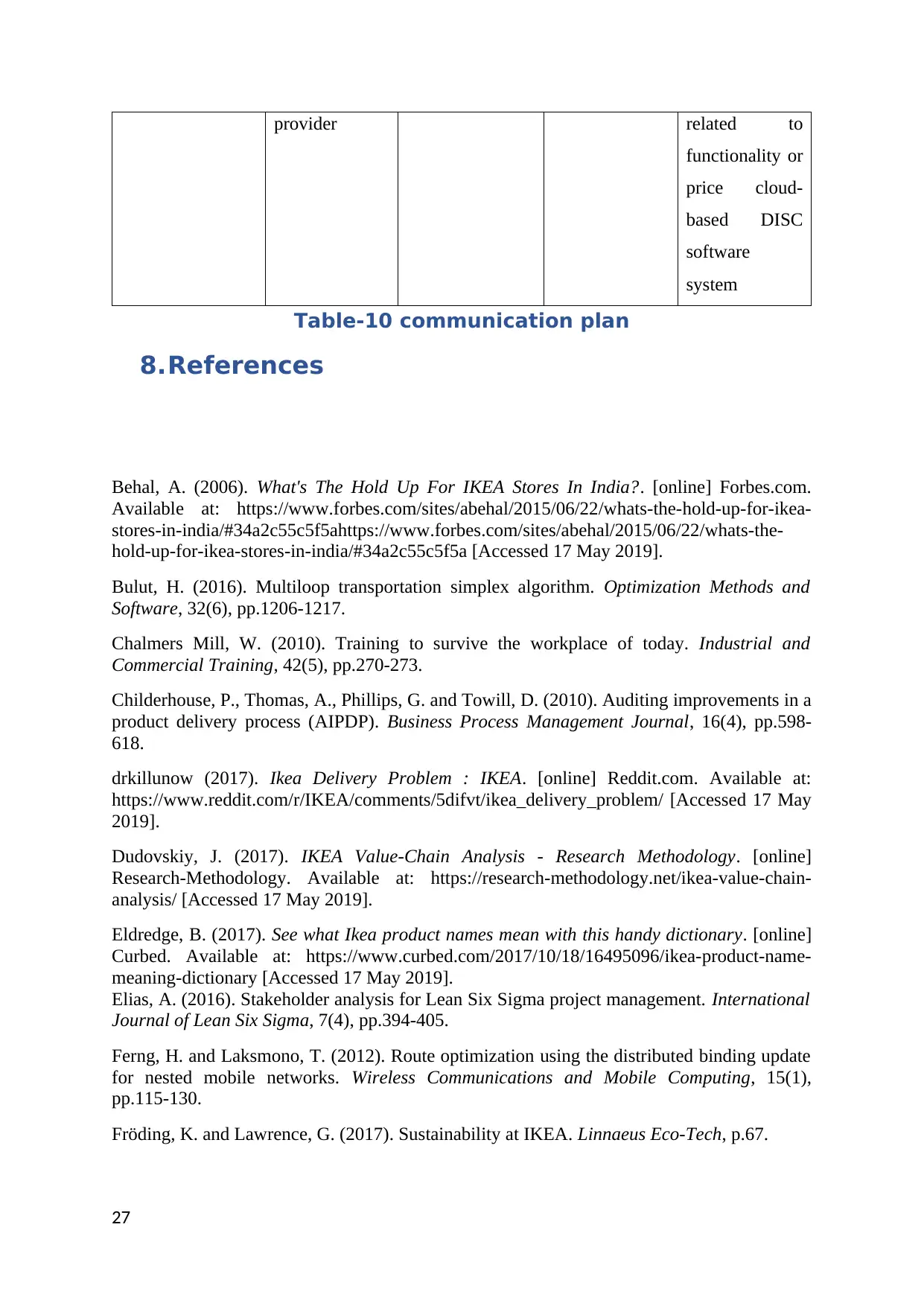
provider related to
functionality or
price cloud-
based DISC
software
system
Table-10 communication plan
8.References
Behal, A. (2006). What's The Hold Up For IKEA Stores In India?. [online] Forbes.com.
Available at: https://www.forbes.com/sites/abehal/2015/06/22/whats-the-hold-up-for-ikea-
stores-in-india/#34a2c55c5f5ahttps://www.forbes.com/sites/abehal/2015/06/22/whats-the-
hold-up-for-ikea-stores-in-india/#34a2c55c5f5a [Accessed 17 May 2019].
Bulut, H. (2016). Multiloop transportation simplex algorithm. Optimization Methods and
Software, 32(6), pp.1206-1217.
Chalmers Mill, W. (2010). Training to survive the workplace of today. Industrial and
Commercial Training, 42(5), pp.270-273.
Childerhouse, P., Thomas, A., Phillips, G. and Towill, D. (2010). Auditing improvements in a
product delivery process (AIPDP). Business Process Management Journal, 16(4), pp.598-
618.
drkillunow (2017). Ikea Delivery Problem : IKEA. [online] Reddit.com. Available at:
https://www.reddit.com/r/IKEA/comments/5difvt/ikea_delivery_problem/ [Accessed 17 May
2019].
Dudovskiy, J. (2017). IKEA Value-Chain Analysis - Research Methodology. [online]
Research-Methodology. Available at: https://research-methodology.net/ikea-value-chain-
analysis/ [Accessed 17 May 2019].
Eldredge, B. (2017). See what Ikea product names mean with this handy dictionary. [online]
Curbed. Available at: https://www.curbed.com/2017/10/18/16495096/ikea-product-name-
meaning-dictionary [Accessed 17 May 2019].
Elias, A. (2016). Stakeholder analysis for Lean Six Sigma project management. International
Journal of Lean Six Sigma, 7(4), pp.394-405.
Ferng, H. and Laksmono, T. (2012). Route optimization using the distributed binding update
for nested mobile networks. Wireless Communications and Mobile Computing, 15(1),
pp.115-130.
Fröding, K. and Lawrence, G. (2017). Sustainability at IKEA. Linnaeus Eco-Tech, p.67.
27
functionality or
price cloud-
based DISC
software
system
Table-10 communication plan
8.References
Behal, A. (2006). What's The Hold Up For IKEA Stores In India?. [online] Forbes.com.
Available at: https://www.forbes.com/sites/abehal/2015/06/22/whats-the-hold-up-for-ikea-
stores-in-india/#34a2c55c5f5ahttps://www.forbes.com/sites/abehal/2015/06/22/whats-the-
hold-up-for-ikea-stores-in-india/#34a2c55c5f5a [Accessed 17 May 2019].
Bulut, H. (2016). Multiloop transportation simplex algorithm. Optimization Methods and
Software, 32(6), pp.1206-1217.
Chalmers Mill, W. (2010). Training to survive the workplace of today. Industrial and
Commercial Training, 42(5), pp.270-273.
Childerhouse, P., Thomas, A., Phillips, G. and Towill, D. (2010). Auditing improvements in a
product delivery process (AIPDP). Business Process Management Journal, 16(4), pp.598-
618.
drkillunow (2017). Ikea Delivery Problem : IKEA. [online] Reddit.com. Available at:
https://www.reddit.com/r/IKEA/comments/5difvt/ikea_delivery_problem/ [Accessed 17 May
2019].
Dudovskiy, J. (2017). IKEA Value-Chain Analysis - Research Methodology. [online]
Research-Methodology. Available at: https://research-methodology.net/ikea-value-chain-
analysis/ [Accessed 17 May 2019].
Eldredge, B. (2017). See what Ikea product names mean with this handy dictionary. [online]
Curbed. Available at: https://www.curbed.com/2017/10/18/16495096/ikea-product-name-
meaning-dictionary [Accessed 17 May 2019].
Elias, A. (2016). Stakeholder analysis for Lean Six Sigma project management. International
Journal of Lean Six Sigma, 7(4), pp.394-405.
Ferng, H. and Laksmono, T. (2012). Route optimization using the distributed binding update
for nested mobile networks. Wireless Communications and Mobile Computing, 15(1),
pp.115-130.
Fröding, K. and Lawrence, G. (2017). Sustainability at IKEA. Linnaeus Eco-Tech, p.67.
27
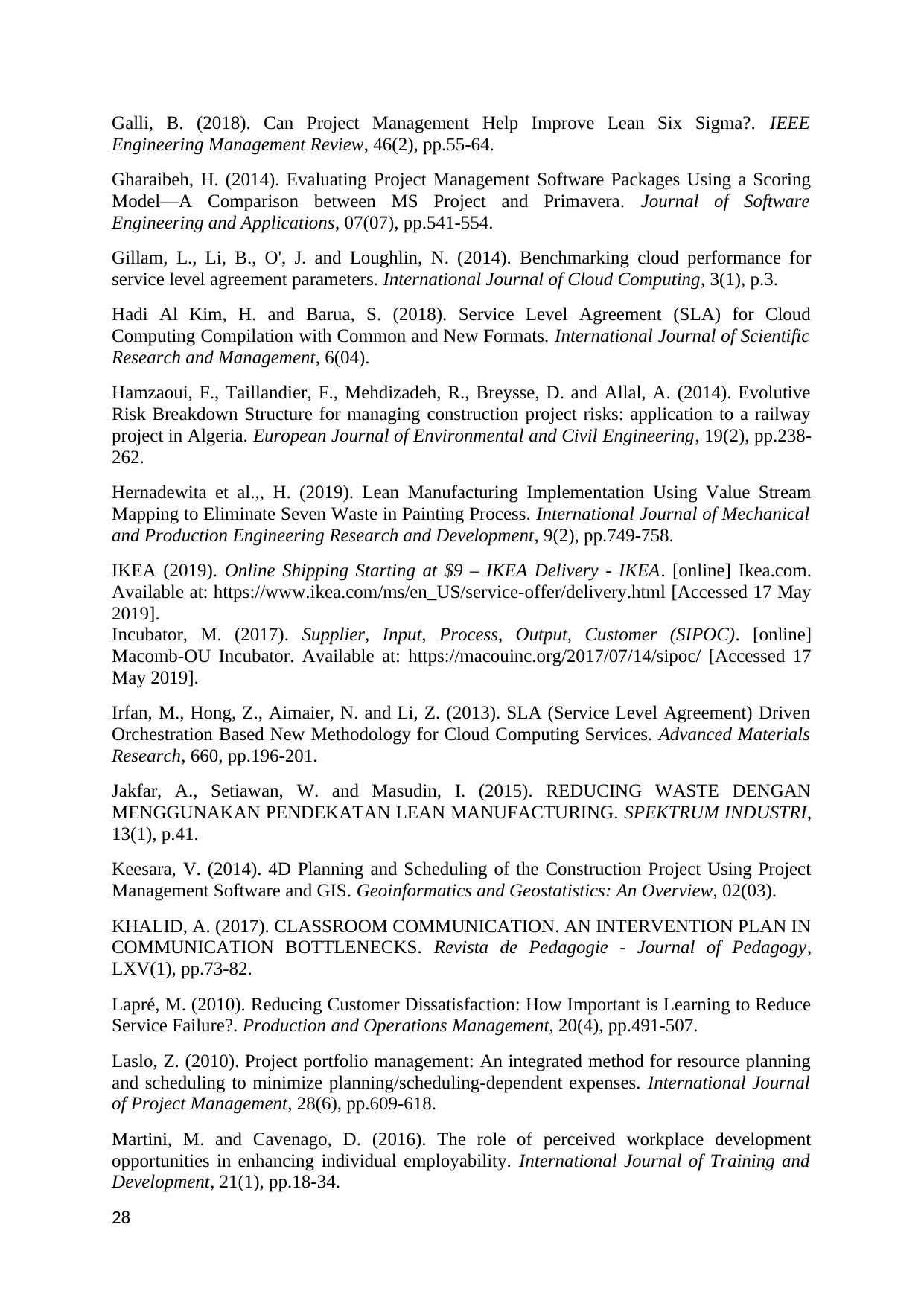
Galli, B. (2018). Can Project Management Help Improve Lean Six Sigma?. IEEE
Engineering Management Review, 46(2), pp.55-64.
Gharaibeh, H. (2014). Evaluating Project Management Software Packages Using a Scoring
Model—A Comparison between MS Project and Primavera. Journal of Software
Engineering and Applications, 07(07), pp.541-554.
Gillam, L., Li, B., O', J. and Loughlin, N. (2014). Benchmarking cloud performance for
service level agreement parameters. International Journal of Cloud Computing, 3(1), p.3.
Hadi Al Kim, H. and Barua, S. (2018). Service Level Agreement (SLA) for Cloud
Computing Compilation with Common and New Formats. International Journal of Scientific
Research and Management, 6(04).
Hamzaoui, F., Taillandier, F., Mehdizadeh, R., Breysse, D. and Allal, A. (2014). Evolutive
Risk Breakdown Structure for managing construction project risks: application to a railway
project in Algeria. European Journal of Environmental and Civil Engineering, 19(2), pp.238-
262.
Hernadewita et al.,, H. (2019). Lean Manufacturing Implementation Using Value Stream
Mapping to Eliminate Seven Waste in Painting Process. International Journal of Mechanical
and Production Engineering Research and Development, 9(2), pp.749-758.
IKEA (2019). Online Shipping Starting at $9 – IKEA Delivery - IKEA. [online] Ikea.com.
Available at: https://www.ikea.com/ms/en_US/service-offer/delivery.html [Accessed 17 May
2019].
Incubator, M. (2017). Supplier, Input, Process, Output, Customer (SIPOC). [online]
Macomb-OU Incubator. Available at: https://macouinc.org/2017/07/14/sipoc/ [Accessed 17
May 2019].
Irfan, M., Hong, Z., Aimaier, N. and Li, Z. (2013). SLA (Service Level Agreement) Driven
Orchestration Based New Methodology for Cloud Computing Services. Advanced Materials
Research, 660, pp.196-201.
Jakfar, A., Setiawan, W. and Masudin, I. (2015). REDUCING WASTE DENGAN
MENGGUNAKAN PENDEKATAN LEAN MANUFACTURING. SPEKTRUM INDUSTRI,
13(1), p.41.
Keesara, V. (2014). 4D Planning and Scheduling of the Construction Project Using Project
Management Software and GIS. Geoinformatics and Geostatistics: An Overview, 02(03).
KHALID, A. (2017). CLASSROOM COMMUNICATION. AN INTERVENTION PLAN IN
COMMUNICATION BOTTLENECKS. Revista de Pedagogie - Journal of Pedagogy,
LXV(1), pp.73-82.
Lapré, M. (2010). Reducing Customer Dissatisfaction: How Important is Learning to Reduce
Service Failure?. Production and Operations Management, 20(4), pp.491-507.
Laslo, Z. (2010). Project portfolio management: An integrated method for resource planning
and scheduling to minimize planning/scheduling-dependent expenses. International Journal
of Project Management, 28(6), pp.609-618.
Martini, M. and Cavenago, D. (2016). The role of perceived workplace development
opportunities in enhancing individual employability. International Journal of Training and
Development, 21(1), pp.18-34.
28
Engineering Management Review, 46(2), pp.55-64.
Gharaibeh, H. (2014). Evaluating Project Management Software Packages Using a Scoring
Model—A Comparison between MS Project and Primavera. Journal of Software
Engineering and Applications, 07(07), pp.541-554.
Gillam, L., Li, B., O', J. and Loughlin, N. (2014). Benchmarking cloud performance for
service level agreement parameters. International Journal of Cloud Computing, 3(1), p.3.
Hadi Al Kim, H. and Barua, S. (2018). Service Level Agreement (SLA) for Cloud
Computing Compilation with Common and New Formats. International Journal of Scientific
Research and Management, 6(04).
Hamzaoui, F., Taillandier, F., Mehdizadeh, R., Breysse, D. and Allal, A. (2014). Evolutive
Risk Breakdown Structure for managing construction project risks: application to a railway
project in Algeria. European Journal of Environmental and Civil Engineering, 19(2), pp.238-
262.
Hernadewita et al.,, H. (2019). Lean Manufacturing Implementation Using Value Stream
Mapping to Eliminate Seven Waste in Painting Process. International Journal of Mechanical
and Production Engineering Research and Development, 9(2), pp.749-758.
IKEA (2019). Online Shipping Starting at $9 – IKEA Delivery - IKEA. [online] Ikea.com.
Available at: https://www.ikea.com/ms/en_US/service-offer/delivery.html [Accessed 17 May
2019].
Incubator, M. (2017). Supplier, Input, Process, Output, Customer (SIPOC). [online]
Macomb-OU Incubator. Available at: https://macouinc.org/2017/07/14/sipoc/ [Accessed 17
May 2019].
Irfan, M., Hong, Z., Aimaier, N. and Li, Z. (2013). SLA (Service Level Agreement) Driven
Orchestration Based New Methodology for Cloud Computing Services. Advanced Materials
Research, 660, pp.196-201.
Jakfar, A., Setiawan, W. and Masudin, I. (2015). REDUCING WASTE DENGAN
MENGGUNAKAN PENDEKATAN LEAN MANUFACTURING. SPEKTRUM INDUSTRI,
13(1), p.41.
Keesara, V. (2014). 4D Planning and Scheduling of the Construction Project Using Project
Management Software and GIS. Geoinformatics and Geostatistics: An Overview, 02(03).
KHALID, A. (2017). CLASSROOM COMMUNICATION. AN INTERVENTION PLAN IN
COMMUNICATION BOTTLENECKS. Revista de Pedagogie - Journal of Pedagogy,
LXV(1), pp.73-82.
Lapré, M. (2010). Reducing Customer Dissatisfaction: How Important is Learning to Reduce
Service Failure?. Production and Operations Management, 20(4), pp.491-507.
Laslo, Z. (2010). Project portfolio management: An integrated method for resource planning
and scheduling to minimize planning/scheduling-dependent expenses. International Journal
of Project Management, 28(6), pp.609-618.
Martini, M. and Cavenago, D. (2016). The role of perceived workplace development
opportunities in enhancing individual employability. International Journal of Training and
Development, 21(1), pp.18-34.
28
Secure Best Marks with AI Grader
Need help grading? Try our AI Grader for instant feedback on your assignments.
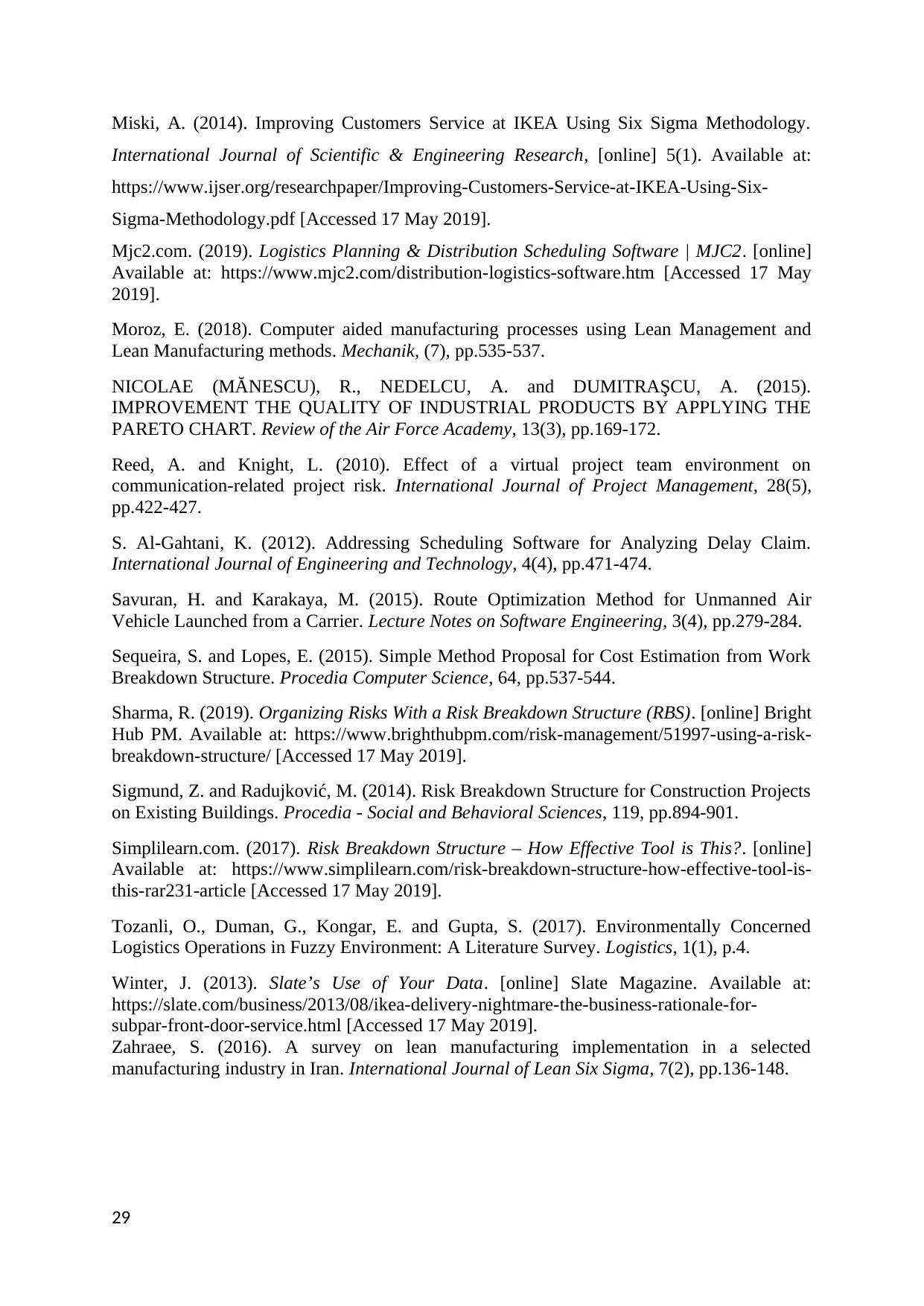
Miski, A. (2014). Improving Customers Service at IKEA Using Six Sigma Methodology.
International Journal of Scientific & Engineering Research, [online] 5(1). Available at:
https://www.ijser.org/researchpaper/Improving-Customers-Service-at-IKEA-Using-Six-
Sigma-Methodology.pdf [Accessed 17 May 2019].
Mjc2.com. (2019). Logistics Planning & Distribution Scheduling Software | MJC2. [online]
Available at: https://www.mjc2.com/distribution-logistics-software.htm [Accessed 17 May
2019].
Moroz, E. (2018). Computer aided manufacturing processes using Lean Management and
Lean Manufacturing methods. Mechanik, (7), pp.535-537.
NICOLAE (MĂNESCU), R., NEDELCU, A. and DUMITRAŞCU, A. (2015).
IMPROVEMENT THE QUALITY OF INDUSTRIAL PRODUCTS BY APPLYING THE
PARETO CHART. Review of the Air Force Academy, 13(3), pp.169-172.
Reed, A. and Knight, L. (2010). Effect of a virtual project team environment on
communication-related project risk. International Journal of Project Management, 28(5),
pp.422-427.
S. Al-Gahtani, K. (2012). Addressing Scheduling Software for Analyzing Delay Claim.
International Journal of Engineering and Technology, 4(4), pp.471-474.
Savuran, H. and Karakaya, M. (2015). Route Optimization Method for Unmanned Air
Vehicle Launched from a Carrier. Lecture Notes on Software Engineering, 3(4), pp.279-284.
Sequeira, S. and Lopes, E. (2015). Simple Method Proposal for Cost Estimation from Work
Breakdown Structure. Procedia Computer Science, 64, pp.537-544.
Sharma, R. (2019). Organizing Risks With a Risk Breakdown Structure (RBS). [online] Bright
Hub PM. Available at: https://www.brighthubpm.com/risk-management/51997-using-a-risk-
breakdown-structure/ [Accessed 17 May 2019].
Sigmund, Z. and Radujković, M. (2014). Risk Breakdown Structure for Construction Projects
on Existing Buildings. Procedia - Social and Behavioral Sciences, 119, pp.894-901.
Simplilearn.com. (2017). Risk Breakdown Structure – How Effective Tool is This?. [online]
Available at: https://www.simplilearn.com/risk-breakdown-structure-how-effective-tool-is-
this-rar231-article [Accessed 17 May 2019].
Tozanli, O., Duman, G., Kongar, E. and Gupta, S. (2017). Environmentally Concerned
Logistics Operations in Fuzzy Environment: A Literature Survey. Logistics, 1(1), p.4.
Winter, J. (2013). Slate’s Use of Your Data. [online] Slate Magazine. Available at:
https://slate.com/business/2013/08/ikea-delivery-nightmare-the-business-rationale-for-
subpar-front-door-service.html [Accessed 17 May 2019].
Zahraee, S. (2016). A survey on lean manufacturing implementation in a selected
manufacturing industry in Iran. International Journal of Lean Six Sigma, 7(2), pp.136-148.
29
International Journal of Scientific & Engineering Research, [online] 5(1). Available at:
https://www.ijser.org/researchpaper/Improving-Customers-Service-at-IKEA-Using-Six-
Sigma-Methodology.pdf [Accessed 17 May 2019].
Mjc2.com. (2019). Logistics Planning & Distribution Scheduling Software | MJC2. [online]
Available at: https://www.mjc2.com/distribution-logistics-software.htm [Accessed 17 May
2019].
Moroz, E. (2018). Computer aided manufacturing processes using Lean Management and
Lean Manufacturing methods. Mechanik, (7), pp.535-537.
NICOLAE (MĂNESCU), R., NEDELCU, A. and DUMITRAŞCU, A. (2015).
IMPROVEMENT THE QUALITY OF INDUSTRIAL PRODUCTS BY APPLYING THE
PARETO CHART. Review of the Air Force Academy, 13(3), pp.169-172.
Reed, A. and Knight, L. (2010). Effect of a virtual project team environment on
communication-related project risk. International Journal of Project Management, 28(5),
pp.422-427.
S. Al-Gahtani, K. (2012). Addressing Scheduling Software for Analyzing Delay Claim.
International Journal of Engineering and Technology, 4(4), pp.471-474.
Savuran, H. and Karakaya, M. (2015). Route Optimization Method for Unmanned Air
Vehicle Launched from a Carrier. Lecture Notes on Software Engineering, 3(4), pp.279-284.
Sequeira, S. and Lopes, E. (2015). Simple Method Proposal for Cost Estimation from Work
Breakdown Structure. Procedia Computer Science, 64, pp.537-544.
Sharma, R. (2019). Organizing Risks With a Risk Breakdown Structure (RBS). [online] Bright
Hub PM. Available at: https://www.brighthubpm.com/risk-management/51997-using-a-risk-
breakdown-structure/ [Accessed 17 May 2019].
Sigmund, Z. and Radujković, M. (2014). Risk Breakdown Structure for Construction Projects
on Existing Buildings. Procedia - Social and Behavioral Sciences, 119, pp.894-901.
Simplilearn.com. (2017). Risk Breakdown Structure – How Effective Tool is This?. [online]
Available at: https://www.simplilearn.com/risk-breakdown-structure-how-effective-tool-is-
this-rar231-article [Accessed 17 May 2019].
Tozanli, O., Duman, G., Kongar, E. and Gupta, S. (2017). Environmentally Concerned
Logistics Operations in Fuzzy Environment: A Literature Survey. Logistics, 1(1), p.4.
Winter, J. (2013). Slate’s Use of Your Data. [online] Slate Magazine. Available at:
https://slate.com/business/2013/08/ikea-delivery-nightmare-the-business-rationale-for-
subpar-front-door-service.html [Accessed 17 May 2019].
Zahraee, S. (2016). A survey on lean manufacturing implementation in a selected
manufacturing industry in Iran. International Journal of Lean Six Sigma, 7(2), pp.136-148.
29
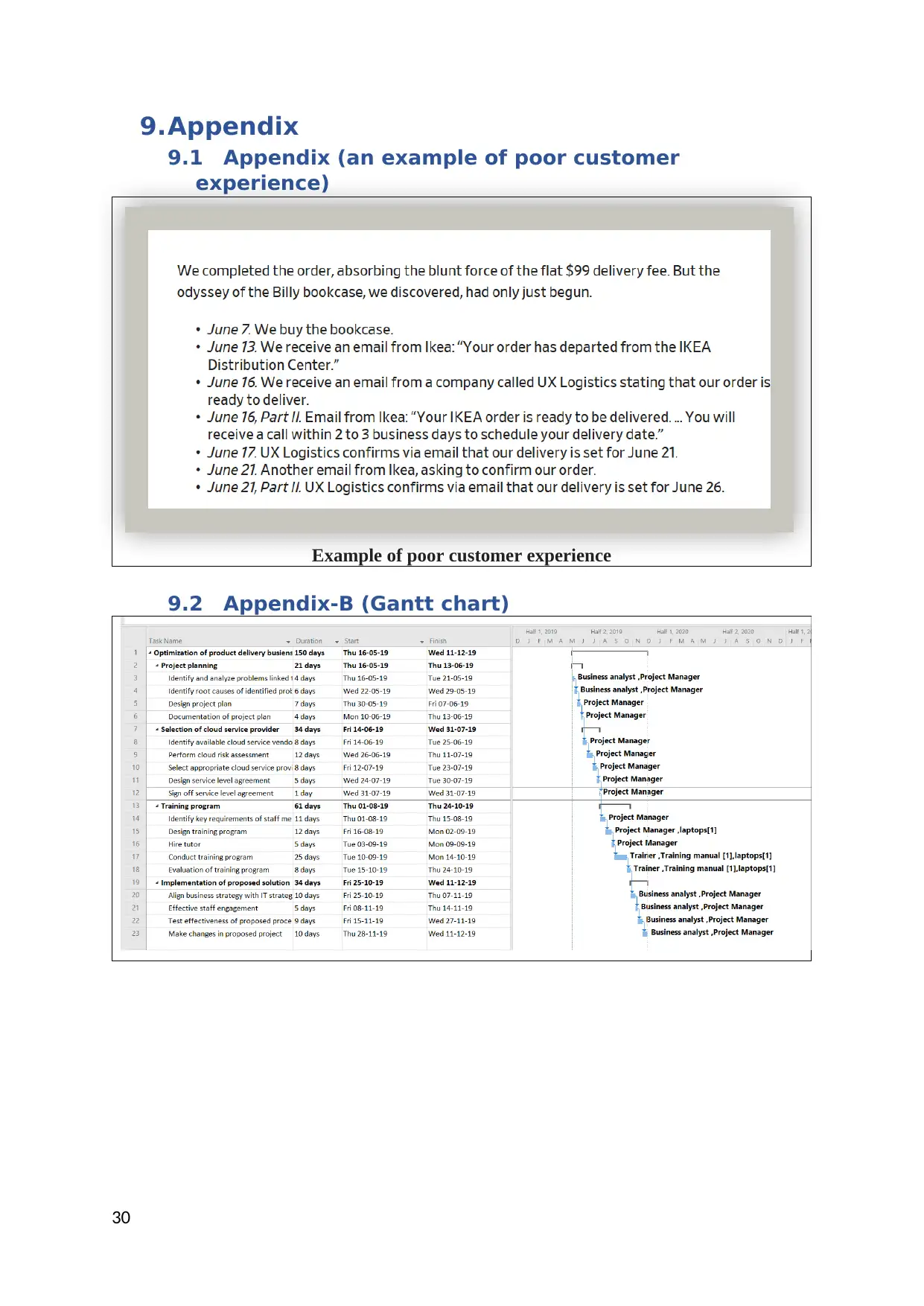
9.Appendix
9.1 Appendix (an example of poor customer
experience)
Example of poor customer experience
9.2 Appendix-B (Gantt chart)
30
9.1 Appendix (an example of poor customer
experience)
Example of poor customer experience
9.2 Appendix-B (Gantt chart)
30
1 out of 30
Related Documents
![[object Object]](/_next/image/?url=%2F_next%2Fstatic%2Fmedia%2Flogo.6d15ce61.png&w=640&q=75)
Your All-in-One AI-Powered Toolkit for Academic Success.
+13062052269
info@desklib.com
Available 24*7 on WhatsApp / Email
Unlock your academic potential
© 2024 | Zucol Services PVT LTD | All rights reserved.