Toyota Company Management: Operation, Production System & Strategy
VerifiedAdded on 2023/03/30
|11
|2618
|89
Report
AI Summary
This report examines Toyota Motor Company's operation management, focusing on its production system, lean manufacturing philosophy, and supply chain management. It highlights Toyota's emphasis on efficiency, innovation, and continuous improvement through decentralized structures, teamwork, and employee participation. The analysis covers the Toyota Production System (TPS), Just-in-Time (JIT) inventory management, Total Quality Management (TQM), and the integration of computer application systems like Kanban. The report also explores Toyota's supply chain management strategies, including the development of first and second-tier supplier networks and the Keiretsu system, which have contributed to its competitive advantage in the global automotive market. The study concludes that Toyota's success stems from its ability to minimize waste, reduce costs, and maintain high-quality standards through specialized management techniques and a focus on resource optimization.
Contribute Materials
Your contribution can guide someone’s learning journey. Share your
documents today.
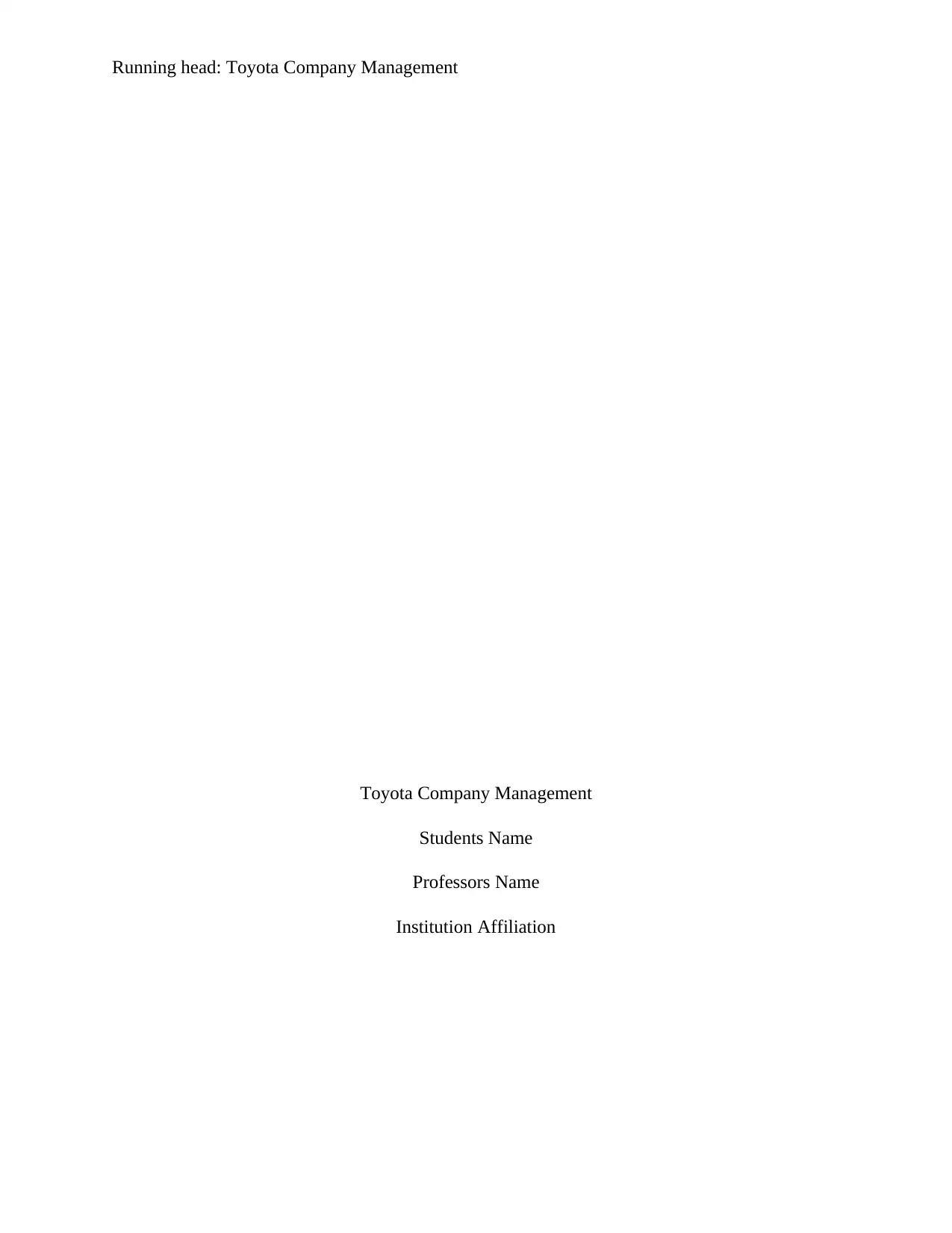
Running head: Toyota Company Management
Toyota Company Management
Students Name
Professors Name
Institution Affiliation
Toyota Company Management
Students Name
Professors Name
Institution Affiliation
Secure Best Marks with AI Grader
Need help grading? Try our AI Grader for instant feedback on your assignments.
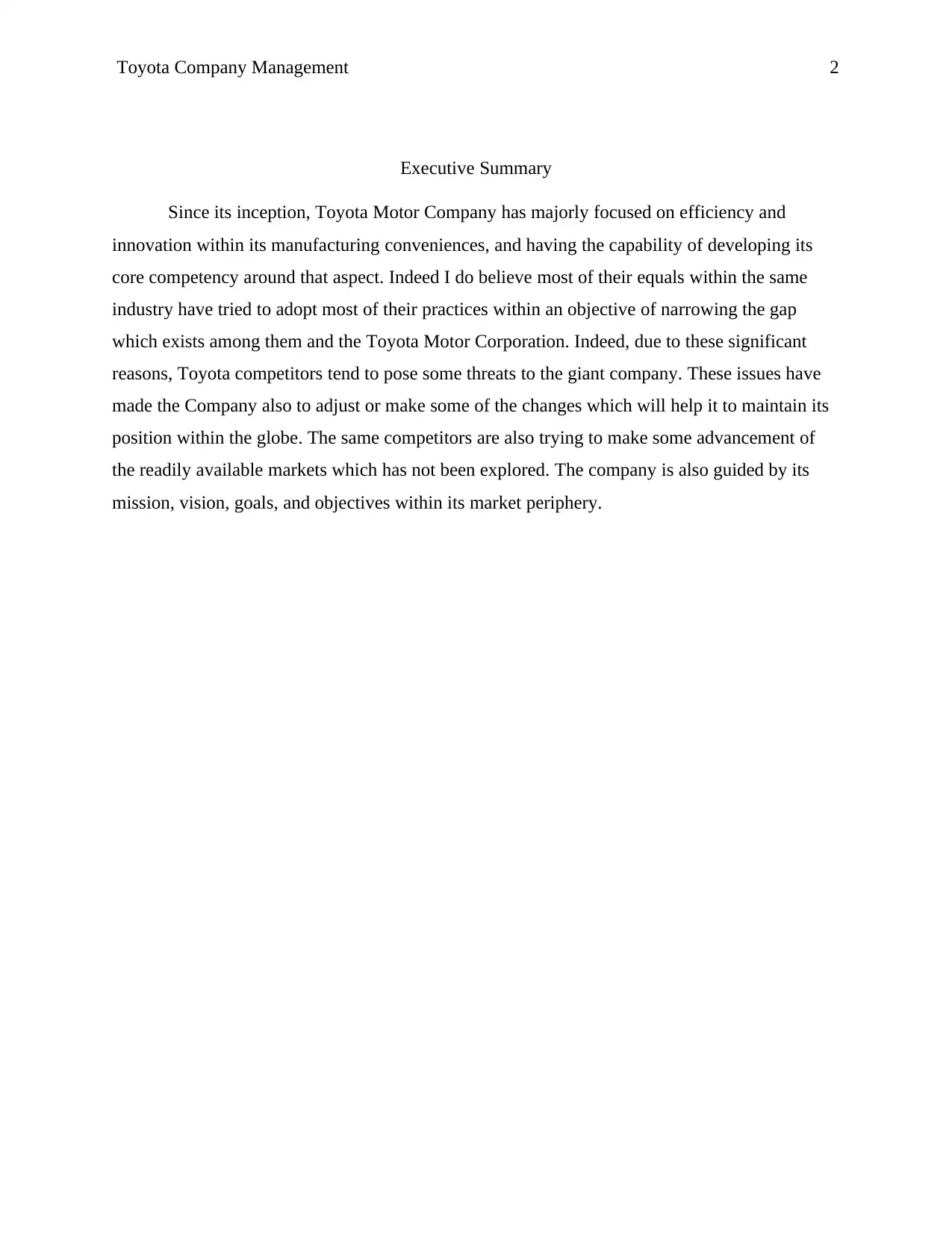
Toyota Company Management 2
Executive Summary
Since its inception, Toyota Motor Company has majorly focused on efficiency and
innovation within its manufacturing conveniences, and having the capability of developing its
core competency around that aspect. Indeed I do believe most of their equals within the same
industry have tried to adopt most of their practices within an objective of narrowing the gap
which exists among them and the Toyota Motor Corporation. Indeed, due to these significant
reasons, Toyota competitors tend to pose some threats to the giant company. These issues have
made the Company also to adjust or make some of the changes which will help it to maintain its
position within the globe. The same competitors are also trying to make some advancement of
the readily available markets which has not been explored. The company is also guided by its
mission, vision, goals, and objectives within its market periphery.
Executive Summary
Since its inception, Toyota Motor Company has majorly focused on efficiency and
innovation within its manufacturing conveniences, and having the capability of developing its
core competency around that aspect. Indeed I do believe most of their equals within the same
industry have tried to adopt most of their practices within an objective of narrowing the gap
which exists among them and the Toyota Motor Corporation. Indeed, due to these significant
reasons, Toyota competitors tend to pose some threats to the giant company. These issues have
made the Company also to adjust or make some of the changes which will help it to maintain its
position within the globe. The same competitors are also trying to make some advancement of
the readily available markets which has not been explored. The company is also guided by its
mission, vision, goals, and objectives within its market periphery.
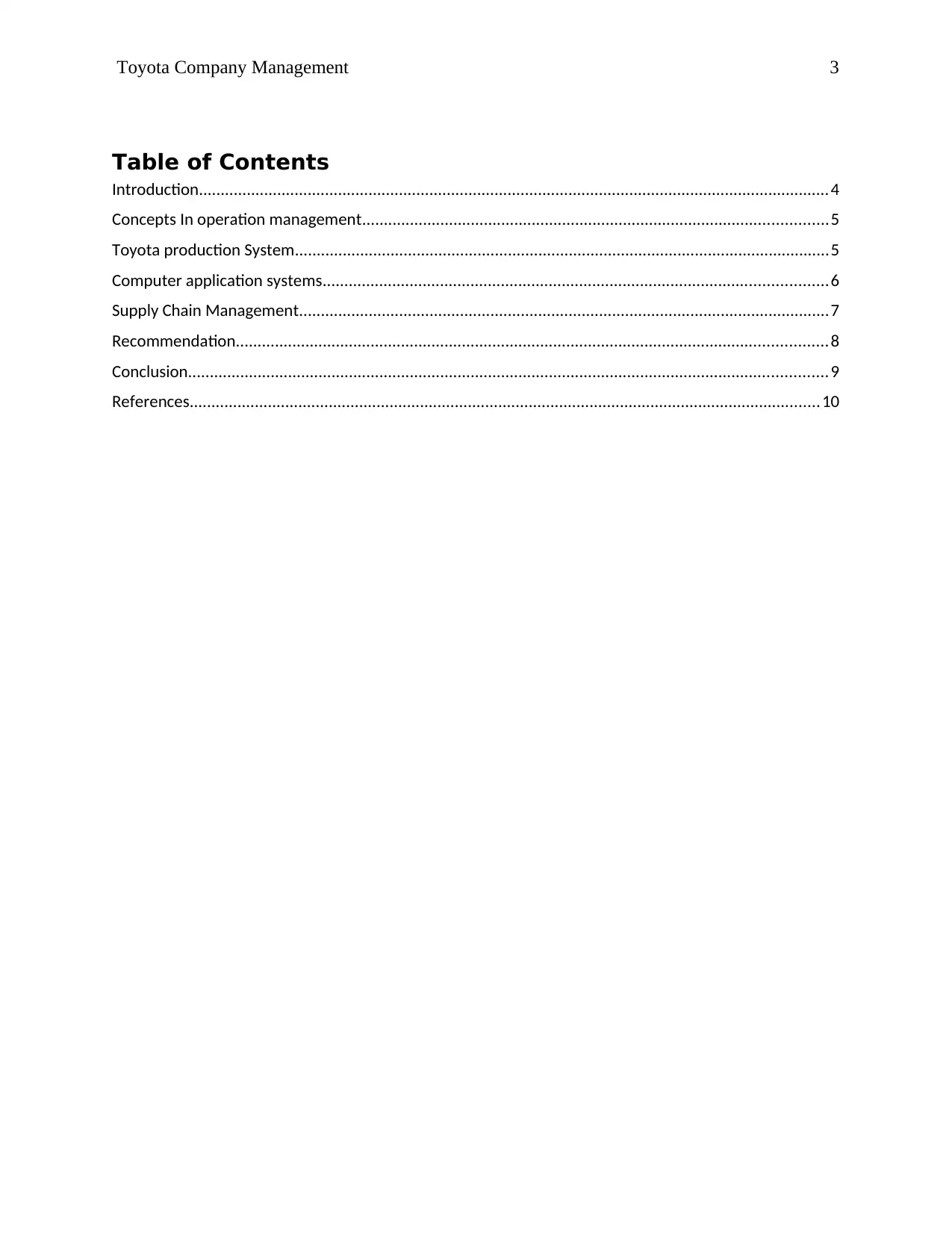
Toyota Company Management 3
Table of Contents
Introduction.................................................................................................................................................4
Concepts In operation management...........................................................................................................5
Toyota production System...........................................................................................................................5
Computer application systems....................................................................................................................6
Supply Chain Management..........................................................................................................................7
Recommendation........................................................................................................................................8
Conclusion...................................................................................................................................................9
References.................................................................................................................................................10
Table of Contents
Introduction.................................................................................................................................................4
Concepts In operation management...........................................................................................................5
Toyota production System...........................................................................................................................5
Computer application systems....................................................................................................................6
Supply Chain Management..........................................................................................................................7
Recommendation........................................................................................................................................8
Conclusion...................................................................................................................................................9
References.................................................................................................................................................10
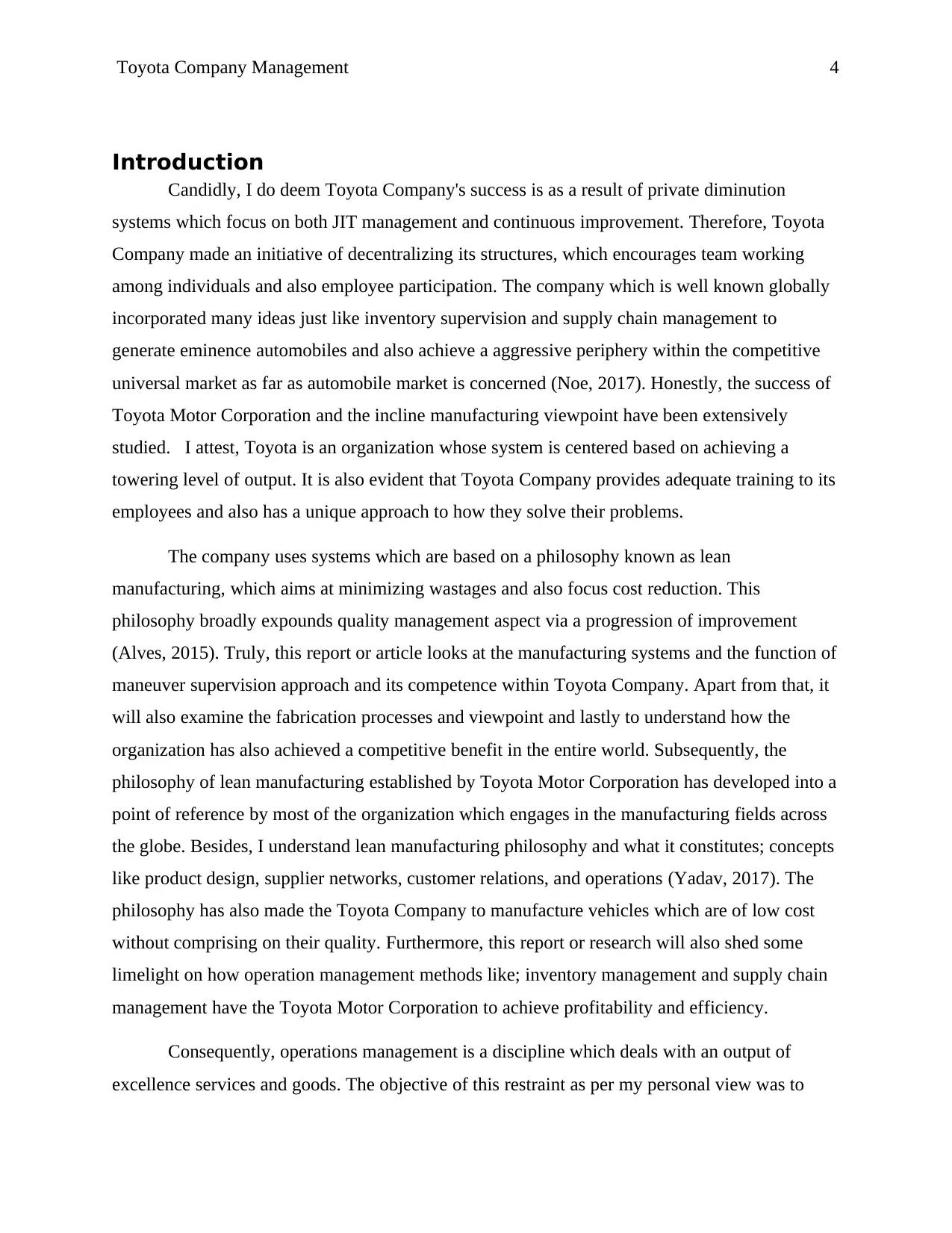
Toyota Company Management 4
Introduction
Candidly, I do deem Toyota Company's success is as a result of private diminution
systems which focus on both JIT management and continuous improvement. Therefore, Toyota
Company made an initiative of decentralizing its structures, which encourages team working
among individuals and also employee participation. The company which is well known globally
incorporated many ideas just like inventory supervision and supply chain management to
generate eminence automobiles and also achieve a aggressive periphery within the competitive
universal market as far as automobile market is concerned (Noe, 2017). Honestly, the success of
Toyota Motor Corporation and the incline manufacturing viewpoint have been extensively
studied. I attest, Toyota is an organization whose system is centered based on achieving a
towering level of output. It is also evident that Toyota Company provides adequate training to its
employees and also has a unique approach to how they solve their problems.
The company uses systems which are based on a philosophy known as lean
manufacturing, which aims at minimizing wastages and also focus cost reduction. This
philosophy broadly expounds quality management aspect via a progression of improvement
(Alves, 2015). Truly, this report or article looks at the manufacturing systems and the function of
maneuver supervision approach and its competence within Toyota Company. Apart from that, it
will also examine the fabrication processes and viewpoint and lastly to understand how the
organization has also achieved a competitive benefit in the entire world. Subsequently, the
philosophy of lean manufacturing established by Toyota Motor Corporation has developed into a
point of reference by most of the organization which engages in the manufacturing fields across
the globe. Besides, I understand lean manufacturing philosophy and what it constitutes; concepts
like product design, supplier networks, customer relations, and operations (Yadav, 2017). The
philosophy has also made the Toyota Company to manufacture vehicles which are of low cost
without comprising on their quality. Furthermore, this report or research will also shed some
limelight on how operation management methods like; inventory management and supply chain
management have the Toyota Motor Corporation to achieve profitability and efficiency.
Consequently, operations management is a discipline which deals with an output of
excellence services and goods. The objective of this restraint as per my personal view was to
Introduction
Candidly, I do deem Toyota Company's success is as a result of private diminution
systems which focus on both JIT management and continuous improvement. Therefore, Toyota
Company made an initiative of decentralizing its structures, which encourages team working
among individuals and also employee participation. The company which is well known globally
incorporated many ideas just like inventory supervision and supply chain management to
generate eminence automobiles and also achieve a aggressive periphery within the competitive
universal market as far as automobile market is concerned (Noe, 2017). Honestly, the success of
Toyota Motor Corporation and the incline manufacturing viewpoint have been extensively
studied. I attest, Toyota is an organization whose system is centered based on achieving a
towering level of output. It is also evident that Toyota Company provides adequate training to its
employees and also has a unique approach to how they solve their problems.
The company uses systems which are based on a philosophy known as lean
manufacturing, which aims at minimizing wastages and also focus cost reduction. This
philosophy broadly expounds quality management aspect via a progression of improvement
(Alves, 2015). Truly, this report or article looks at the manufacturing systems and the function of
maneuver supervision approach and its competence within Toyota Company. Apart from that, it
will also examine the fabrication processes and viewpoint and lastly to understand how the
organization has also achieved a competitive benefit in the entire world. Subsequently, the
philosophy of lean manufacturing established by Toyota Motor Corporation has developed into a
point of reference by most of the organization which engages in the manufacturing fields across
the globe. Besides, I understand lean manufacturing philosophy and what it constitutes; concepts
like product design, supplier networks, customer relations, and operations (Yadav, 2017). The
philosophy has also made the Toyota Company to manufacture vehicles which are of low cost
without comprising on their quality. Furthermore, this report or research will also shed some
limelight on how operation management methods like; inventory management and supply chain
management have the Toyota Motor Corporation to achieve profitability and efficiency.
Consequently, operations management is a discipline which deals with an output of
excellence services and goods. The objective of this restraint as per my personal view was to
Secure Best Marks with AI Grader
Need help grading? Try our AI Grader for instant feedback on your assignments.
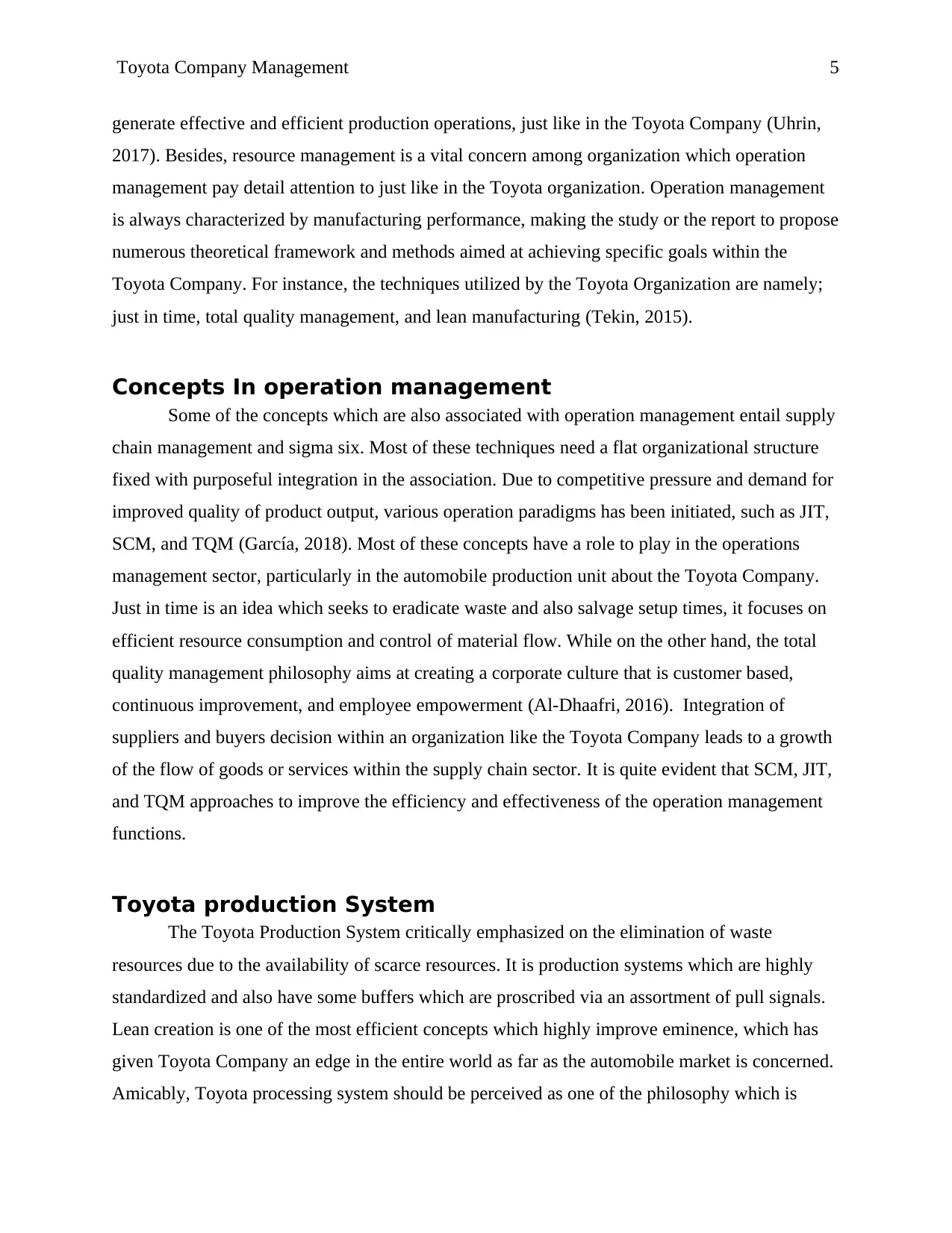
Toyota Company Management 5
generate effective and efficient production operations, just like in the Toyota Company (Uhrin,
2017). Besides, resource management is a vital concern among organization which operation
management pay detail attention to just like in the Toyota organization. Operation management
is always characterized by manufacturing performance, making the study or the report to propose
numerous theoretical framework and methods aimed at achieving specific goals within the
Toyota Company. For instance, the techniques utilized by the Toyota Organization are namely;
just in time, total quality management, and lean manufacturing (Tekin, 2015).
Concepts In operation management
Some of the concepts which are also associated with operation management entail supply
chain management and sigma six. Most of these techniques need a flat organizational structure
fixed with purposeful integration in the association. Due to competitive pressure and demand for
improved quality of product output, various operation paradigms has been initiated, such as JIT,
SCM, and TQM (García, 2018). Most of these concepts have a role to play in the operations
management sector, particularly in the automobile production unit about the Toyota Company.
Just in time is an idea which seeks to eradicate waste and also salvage setup times, it focuses on
efficient resource consumption and control of material flow. While on the other hand, the total
quality management philosophy aims at creating a corporate culture that is customer based,
continuous improvement, and employee empowerment (Al-Dhaafri, 2016). Integration of
suppliers and buyers decision within an organization like the Toyota Company leads to a growth
of the flow of goods or services within the supply chain sector. It is quite evident that SCM, JIT,
and TQM approaches to improve the efficiency and effectiveness of the operation management
functions.
Toyota production System
The Toyota Production System critically emphasized on the elimination of waste
resources due to the availability of scarce resources. It is production systems which are highly
standardized and also have some buffers which are proscribed via an assortment of pull signals.
Lean creation is one of the most efficient concepts which highly improve eminence, which has
given Toyota Company an edge in the entire world as far as the automobile market is concerned.
Amicably, Toyota processing system should be perceived as one of the philosophy which is
generate effective and efficient production operations, just like in the Toyota Company (Uhrin,
2017). Besides, resource management is a vital concern among organization which operation
management pay detail attention to just like in the Toyota organization. Operation management
is always characterized by manufacturing performance, making the study or the report to propose
numerous theoretical framework and methods aimed at achieving specific goals within the
Toyota Company. For instance, the techniques utilized by the Toyota Organization are namely;
just in time, total quality management, and lean manufacturing (Tekin, 2015).
Concepts In operation management
Some of the concepts which are also associated with operation management entail supply
chain management and sigma six. Most of these techniques need a flat organizational structure
fixed with purposeful integration in the association. Due to competitive pressure and demand for
improved quality of product output, various operation paradigms has been initiated, such as JIT,
SCM, and TQM (García, 2018). Most of these concepts have a role to play in the operations
management sector, particularly in the automobile production unit about the Toyota Company.
Just in time is an idea which seeks to eradicate waste and also salvage setup times, it focuses on
efficient resource consumption and control of material flow. While on the other hand, the total
quality management philosophy aims at creating a corporate culture that is customer based,
continuous improvement, and employee empowerment (Al-Dhaafri, 2016). Integration of
suppliers and buyers decision within an organization like the Toyota Company leads to a growth
of the flow of goods or services within the supply chain sector. It is quite evident that SCM, JIT,
and TQM approaches to improve the efficiency and effectiveness of the operation management
functions.
Toyota production System
The Toyota Production System critically emphasized on the elimination of waste
resources due to the availability of scarce resources. It is production systems which are highly
standardized and also have some buffers which are proscribed via an assortment of pull signals.
Lean creation is one of the most efficient concepts which highly improve eminence, which has
given Toyota Company an edge in the entire world as far as the automobile market is concerned.
Amicably, Toyota processing system should be perceived as one of the philosophy which is
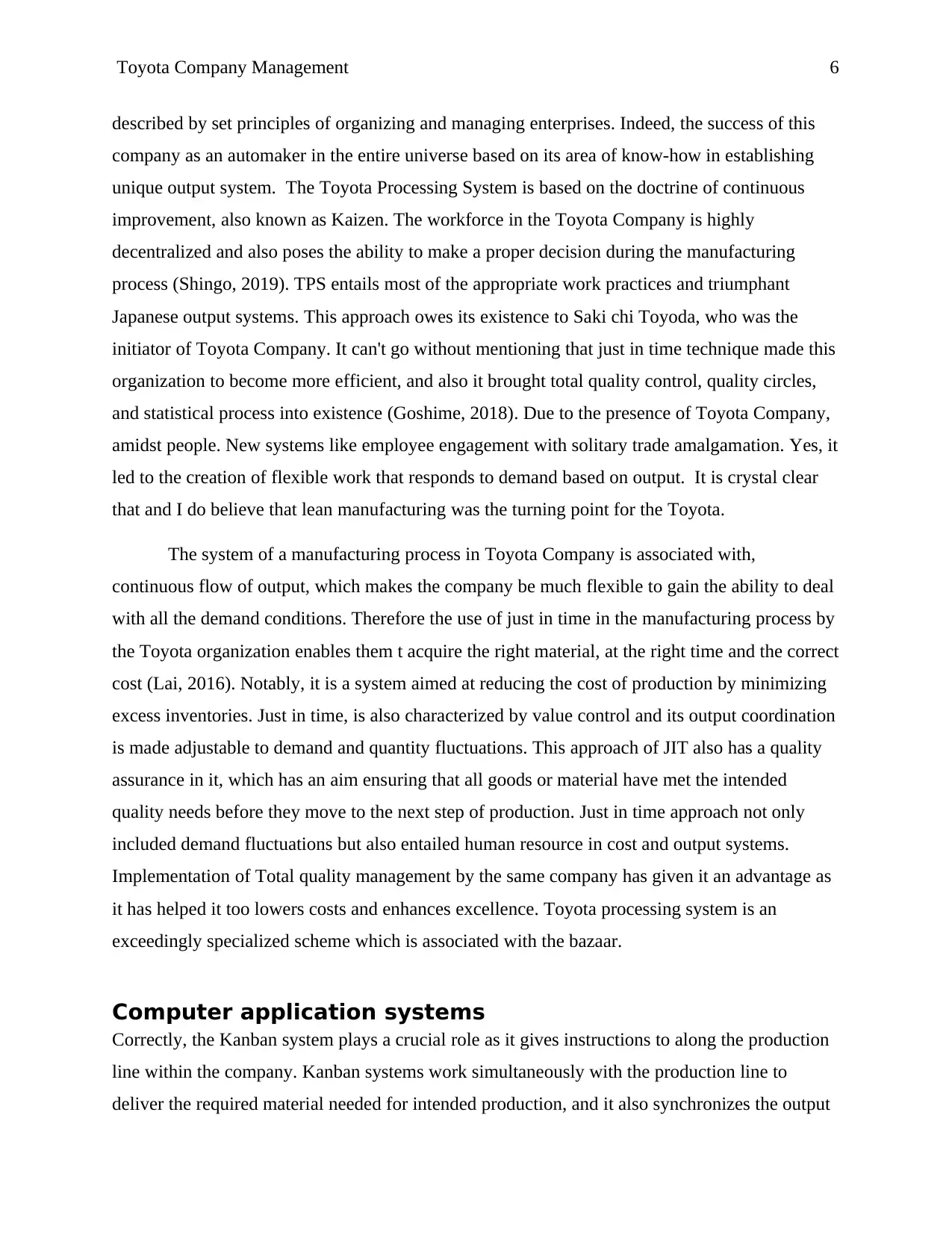
Toyota Company Management 6
described by set principles of organizing and managing enterprises. Indeed, the success of this
company as an automaker in the entire universe based on its area of know-how in establishing
unique output system. The Toyota Processing System is based on the doctrine of continuous
improvement, also known as Kaizen. The workforce in the Toyota Company is highly
decentralized and also poses the ability to make a proper decision during the manufacturing
process (Shingo, 2019). TPS entails most of the appropriate work practices and triumphant
Japanese output systems. This approach owes its existence to Saki chi Toyoda, who was the
initiator of Toyota Company. It can't go without mentioning that just in time technique made this
organization to become more efficient, and also it brought total quality control, quality circles,
and statistical process into existence (Goshime, 2018). Due to the presence of Toyota Company,
amidst people. New systems like employee engagement with solitary trade amalgamation. Yes, it
led to the creation of flexible work that responds to demand based on output. It is crystal clear
that and I do believe that lean manufacturing was the turning point for the Toyota.
The system of a manufacturing process in Toyota Company is associated with,
continuous flow of output, which makes the company be much flexible to gain the ability to deal
with all the demand conditions. Therefore the use of just in time in the manufacturing process by
the Toyota organization enables them t acquire the right material, at the right time and the correct
cost (Lai, 2016). Notably, it is a system aimed at reducing the cost of production by minimizing
excess inventories. Just in time, is also characterized by value control and its output coordination
is made adjustable to demand and quantity fluctuations. This approach of JIT also has a quality
assurance in it, which has an aim ensuring that all goods or material have met the intended
quality needs before they move to the next step of production. Just in time approach not only
included demand fluctuations but also entailed human resource in cost and output systems.
Implementation of Total quality management by the same company has given it an advantage as
it has helped it too lowers costs and enhances excellence. Toyota processing system is an
exceedingly specialized scheme which is associated with the bazaar.
Computer application systems
Correctly, the Kanban system plays a crucial role as it gives instructions to along the production
line within the company. Kanban systems work simultaneously with the production line to
deliver the required material needed for intended production, and it also synchronizes the output
described by set principles of organizing and managing enterprises. Indeed, the success of this
company as an automaker in the entire universe based on its area of know-how in establishing
unique output system. The Toyota Processing System is based on the doctrine of continuous
improvement, also known as Kaizen. The workforce in the Toyota Company is highly
decentralized and also poses the ability to make a proper decision during the manufacturing
process (Shingo, 2019). TPS entails most of the appropriate work practices and triumphant
Japanese output systems. This approach owes its existence to Saki chi Toyoda, who was the
initiator of Toyota Company. It can't go without mentioning that just in time technique made this
organization to become more efficient, and also it brought total quality control, quality circles,
and statistical process into existence (Goshime, 2018). Due to the presence of Toyota Company,
amidst people. New systems like employee engagement with solitary trade amalgamation. Yes, it
led to the creation of flexible work that responds to demand based on output. It is crystal clear
that and I do believe that lean manufacturing was the turning point for the Toyota.
The system of a manufacturing process in Toyota Company is associated with,
continuous flow of output, which makes the company be much flexible to gain the ability to deal
with all the demand conditions. Therefore the use of just in time in the manufacturing process by
the Toyota organization enables them t acquire the right material, at the right time and the correct
cost (Lai, 2016). Notably, it is a system aimed at reducing the cost of production by minimizing
excess inventories. Just in time, is also characterized by value control and its output coordination
is made adjustable to demand and quantity fluctuations. This approach of JIT also has a quality
assurance in it, which has an aim ensuring that all goods or material have met the intended
quality needs before they move to the next step of production. Just in time approach not only
included demand fluctuations but also entailed human resource in cost and output systems.
Implementation of Total quality management by the same company has given it an advantage as
it has helped it too lowers costs and enhances excellence. Toyota processing system is an
exceedingly specialized scheme which is associated with the bazaar.
Computer application systems
Correctly, the Kanban system plays a crucial role as it gives instructions to along the production
line within the company. Kanban systems work simultaneously with the production line to
deliver the required material needed for intended production, and it also synchronizes the output
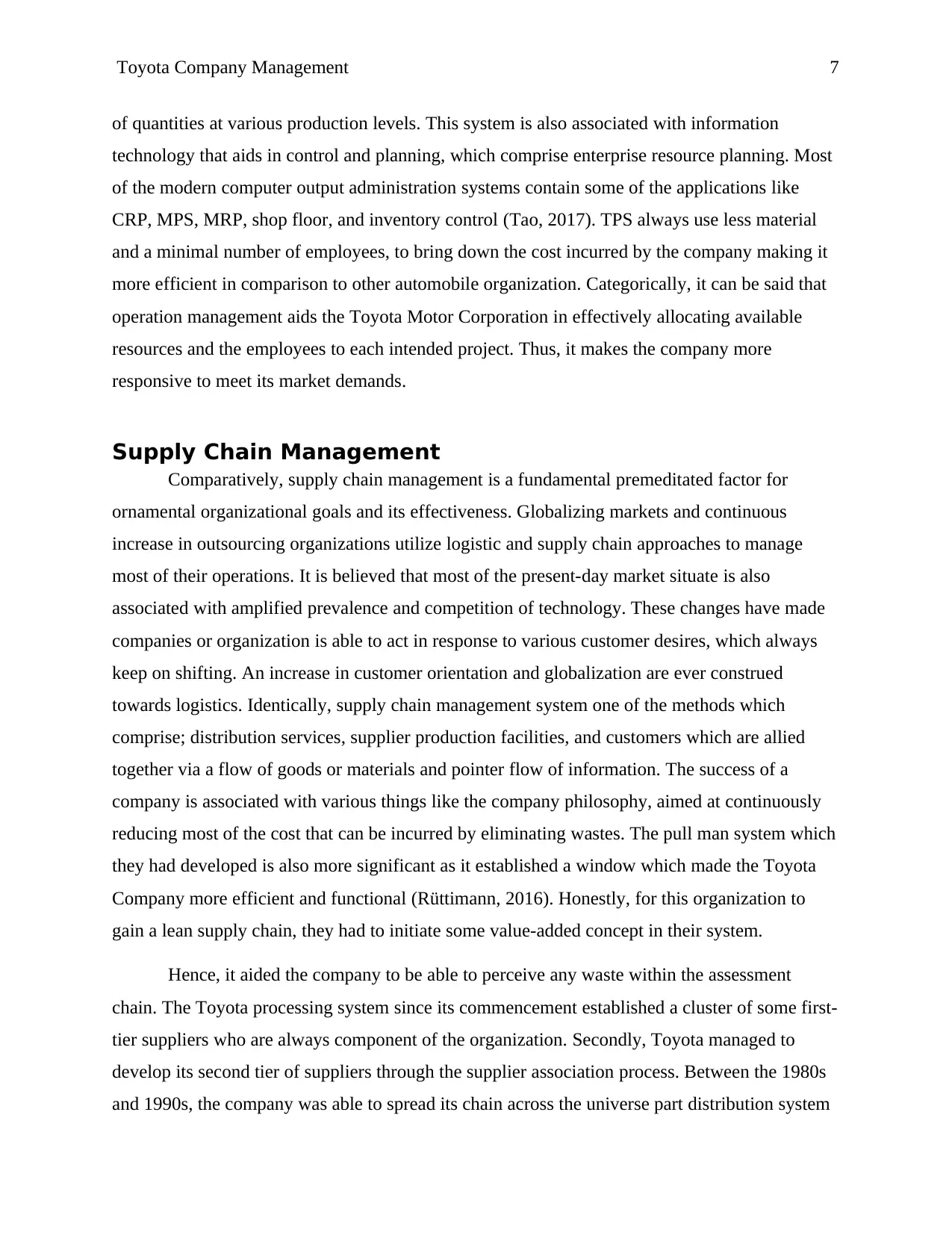
Toyota Company Management 7
of quantities at various production levels. This system is also associated with information
technology that aids in control and planning, which comprise enterprise resource planning. Most
of the modern computer output administration systems contain some of the applications like
CRP, MPS, MRP, shop floor, and inventory control (Tao, 2017). TPS always use less material
and a minimal number of employees, to bring down the cost incurred by the company making it
more efficient in comparison to other automobile organization. Categorically, it can be said that
operation management aids the Toyota Motor Corporation in effectively allocating available
resources and the employees to each intended project. Thus, it makes the company more
responsive to meet its market demands.
Supply Chain Management
Comparatively, supply chain management is a fundamental premeditated factor for
ornamental organizational goals and its effectiveness. Globalizing markets and continuous
increase in outsourcing organizations utilize logistic and supply chain approaches to manage
most of their operations. It is believed that most of the present-day market situate is also
associated with amplified prevalence and competition of technology. These changes have made
companies or organization is able to act in response to various customer desires, which always
keep on shifting. An increase in customer orientation and globalization are ever construed
towards logistics. Identically, supply chain management system one of the methods which
comprise; distribution services, supplier production facilities, and customers which are allied
together via a flow of goods or materials and pointer flow of information. The success of a
company is associated with various things like the company philosophy, aimed at continuously
reducing most of the cost that can be incurred by eliminating wastes. The pull man system which
they had developed is also more significant as it established a window which made the Toyota
Company more efficient and functional (Rüttimann, 2016). Honestly, for this organization to
gain a lean supply chain, they had to initiate some value-added concept in their system.
Hence, it aided the company to be able to perceive any waste within the assessment
chain. The Toyota processing system since its commencement established a cluster of some first-
tier suppliers who are always component of the organization. Secondly, Toyota managed to
develop its second tier of suppliers through the supplier association process. Between the 1980s
and 1990s, the company was able to spread its chain across the universe part distribution system
of quantities at various production levels. This system is also associated with information
technology that aids in control and planning, which comprise enterprise resource planning. Most
of the modern computer output administration systems contain some of the applications like
CRP, MPS, MRP, shop floor, and inventory control (Tao, 2017). TPS always use less material
and a minimal number of employees, to bring down the cost incurred by the company making it
more efficient in comparison to other automobile organization. Categorically, it can be said that
operation management aids the Toyota Motor Corporation in effectively allocating available
resources and the employees to each intended project. Thus, it makes the company more
responsive to meet its market demands.
Supply Chain Management
Comparatively, supply chain management is a fundamental premeditated factor for
ornamental organizational goals and its effectiveness. Globalizing markets and continuous
increase in outsourcing organizations utilize logistic and supply chain approaches to manage
most of their operations. It is believed that most of the present-day market situate is also
associated with amplified prevalence and competition of technology. These changes have made
companies or organization is able to act in response to various customer desires, which always
keep on shifting. An increase in customer orientation and globalization are ever construed
towards logistics. Identically, supply chain management system one of the methods which
comprise; distribution services, supplier production facilities, and customers which are allied
together via a flow of goods or materials and pointer flow of information. The success of a
company is associated with various things like the company philosophy, aimed at continuously
reducing most of the cost that can be incurred by eliminating wastes. The pull man system which
they had developed is also more significant as it established a window which made the Toyota
Company more efficient and functional (Rüttimann, 2016). Honestly, for this organization to
gain a lean supply chain, they had to initiate some value-added concept in their system.
Hence, it aided the company to be able to perceive any waste within the assessment
chain. The Toyota processing system since its commencement established a cluster of some first-
tier suppliers who are always component of the organization. Secondly, Toyota managed to
develop its second tier of suppliers through the supplier association process. Between the 1980s
and 1990s, the company was able to spread its chain across the universe part distribution system
Paraphrase This Document
Need a fresh take? Get an instant paraphrase of this document with our AI Paraphraser
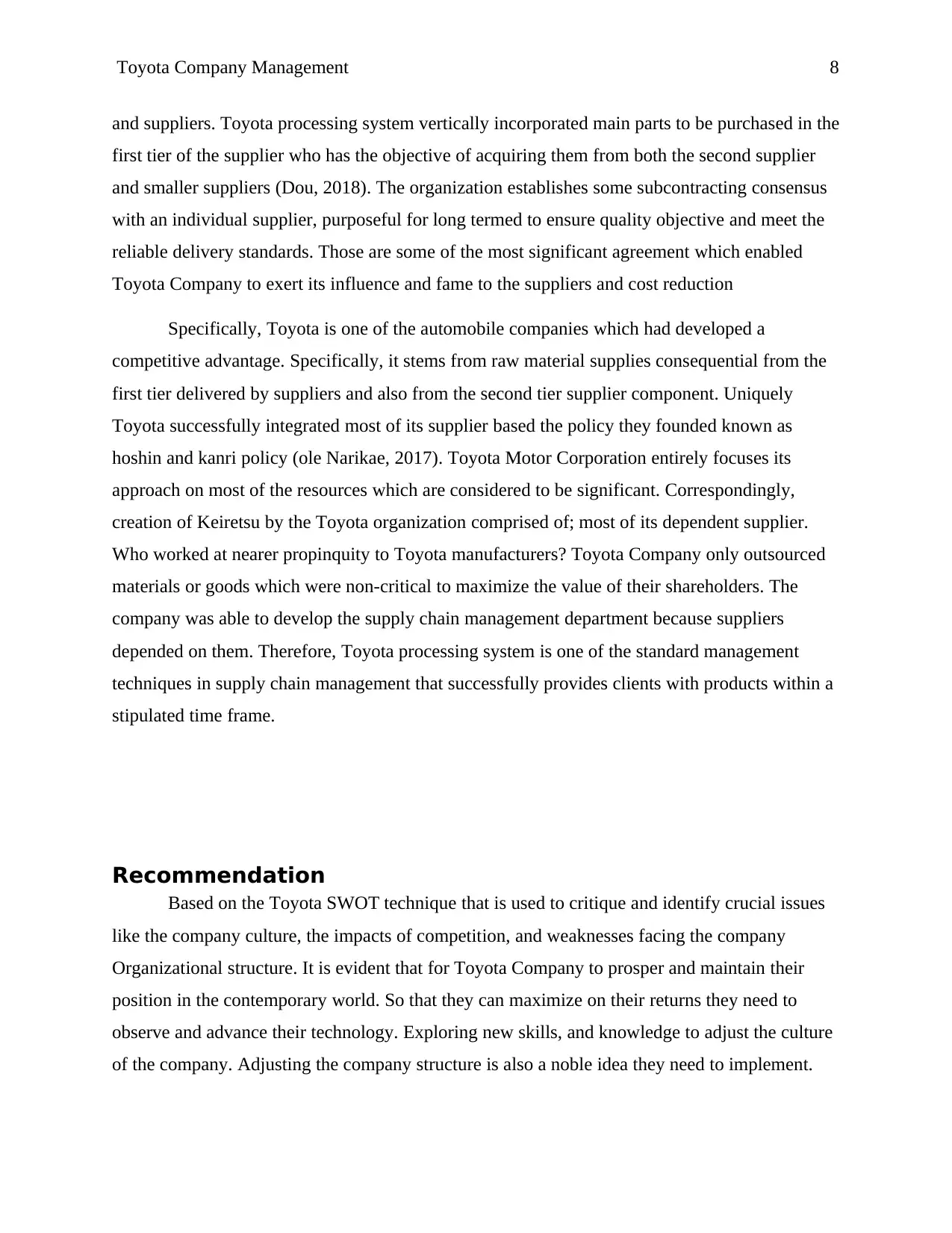
Toyota Company Management 8
and suppliers. Toyota processing system vertically incorporated main parts to be purchased in the
first tier of the supplier who has the objective of acquiring them from both the second supplier
and smaller suppliers (Dou, 2018). The organization establishes some subcontracting consensus
with an individual supplier, purposeful for long termed to ensure quality objective and meet the
reliable delivery standards. Those are some of the most significant agreement which enabled
Toyota Company to exert its influence and fame to the suppliers and cost reduction
Specifically, Toyota is one of the automobile companies which had developed a
competitive advantage. Specifically, it stems from raw material supplies consequential from the
first tier delivered by suppliers and also from the second tier supplier component. Uniquely
Toyota successfully integrated most of its supplier based the policy they founded known as
hoshin and kanri policy (ole Narikae, 2017). Toyota Motor Corporation entirely focuses its
approach on most of the resources which are considered to be significant. Correspondingly,
creation of Keiretsu by the Toyota organization comprised of; most of its dependent supplier.
Who worked at nearer propinquity to Toyota manufacturers? Toyota Company only outsourced
materials or goods which were non-critical to maximize the value of their shareholders. The
company was able to develop the supply chain management department because suppliers
depended on them. Therefore, Toyota processing system is one of the standard management
techniques in supply chain management that successfully provides clients with products within a
stipulated time frame.
Recommendation
Based on the Toyota SWOT technique that is used to critique and identify crucial issues
like the company culture, the impacts of competition, and weaknesses facing the company
Organizational structure. It is evident that for Toyota Company to prosper and maintain their
position in the contemporary world. So that they can maximize on their returns they need to
observe and advance their technology. Exploring new skills, and knowledge to adjust the culture
of the company. Adjusting the company structure is also a noble idea they need to implement.
and suppliers. Toyota processing system vertically incorporated main parts to be purchased in the
first tier of the supplier who has the objective of acquiring them from both the second supplier
and smaller suppliers (Dou, 2018). The organization establishes some subcontracting consensus
with an individual supplier, purposeful for long termed to ensure quality objective and meet the
reliable delivery standards. Those are some of the most significant agreement which enabled
Toyota Company to exert its influence and fame to the suppliers and cost reduction
Specifically, Toyota is one of the automobile companies which had developed a
competitive advantage. Specifically, it stems from raw material supplies consequential from the
first tier delivered by suppliers and also from the second tier supplier component. Uniquely
Toyota successfully integrated most of its supplier based the policy they founded known as
hoshin and kanri policy (ole Narikae, 2017). Toyota Motor Corporation entirely focuses its
approach on most of the resources which are considered to be significant. Correspondingly,
creation of Keiretsu by the Toyota organization comprised of; most of its dependent supplier.
Who worked at nearer propinquity to Toyota manufacturers? Toyota Company only outsourced
materials or goods which were non-critical to maximize the value of their shareholders. The
company was able to develop the supply chain management department because suppliers
depended on them. Therefore, Toyota processing system is one of the standard management
techniques in supply chain management that successfully provides clients with products within a
stipulated time frame.
Recommendation
Based on the Toyota SWOT technique that is used to critique and identify crucial issues
like the company culture, the impacts of competition, and weaknesses facing the company
Organizational structure. It is evident that for Toyota Company to prosper and maintain their
position in the contemporary world. So that they can maximize on their returns they need to
observe and advance their technology. Exploring new skills, and knowledge to adjust the culture
of the company. Adjusting the company structure is also a noble idea they need to implement.
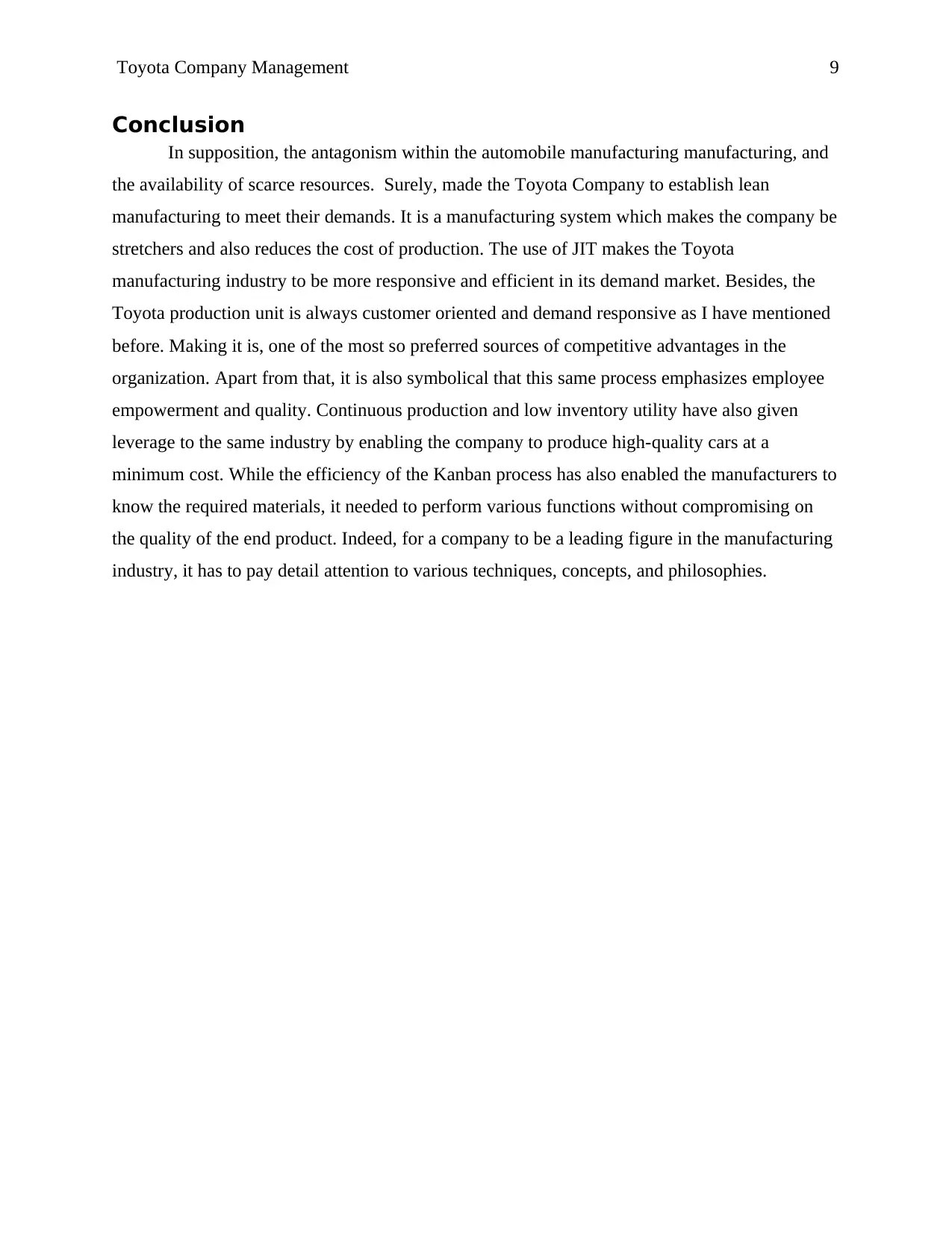
Toyota Company Management 9
Conclusion
In supposition, the antagonism within the automobile manufacturing manufacturing, and
the availability of scarce resources. Surely, made the Toyota Company to establish lean
manufacturing to meet their demands. It is a manufacturing system which makes the company be
stretchers and also reduces the cost of production. The use of JIT makes the Toyota
manufacturing industry to be more responsive and efficient in its demand market. Besides, the
Toyota production unit is always customer oriented and demand responsive as I have mentioned
before. Making it is, one of the most so preferred sources of competitive advantages in the
organization. Apart from that, it is also symbolical that this same process emphasizes employee
empowerment and quality. Continuous production and low inventory utility have also given
leverage to the same industry by enabling the company to produce high-quality cars at a
minimum cost. While the efficiency of the Kanban process has also enabled the manufacturers to
know the required materials, it needed to perform various functions without compromising on
the quality of the end product. Indeed, for a company to be a leading figure in the manufacturing
industry, it has to pay detail attention to various techniques, concepts, and philosophies.
Conclusion
In supposition, the antagonism within the automobile manufacturing manufacturing, and
the availability of scarce resources. Surely, made the Toyota Company to establish lean
manufacturing to meet their demands. It is a manufacturing system which makes the company be
stretchers and also reduces the cost of production. The use of JIT makes the Toyota
manufacturing industry to be more responsive and efficient in its demand market. Besides, the
Toyota production unit is always customer oriented and demand responsive as I have mentioned
before. Making it is, one of the most so preferred sources of competitive advantages in the
organization. Apart from that, it is also symbolical that this same process emphasizes employee
empowerment and quality. Continuous production and low inventory utility have also given
leverage to the same industry by enabling the company to produce high-quality cars at a
minimum cost. While the efficiency of the Kanban process has also enabled the manufacturers to
know the required materials, it needed to perform various functions without compromising on
the quality of the end product. Indeed, for a company to be a leading figure in the manufacturing
industry, it has to pay detail attention to various techniques, concepts, and philosophies.
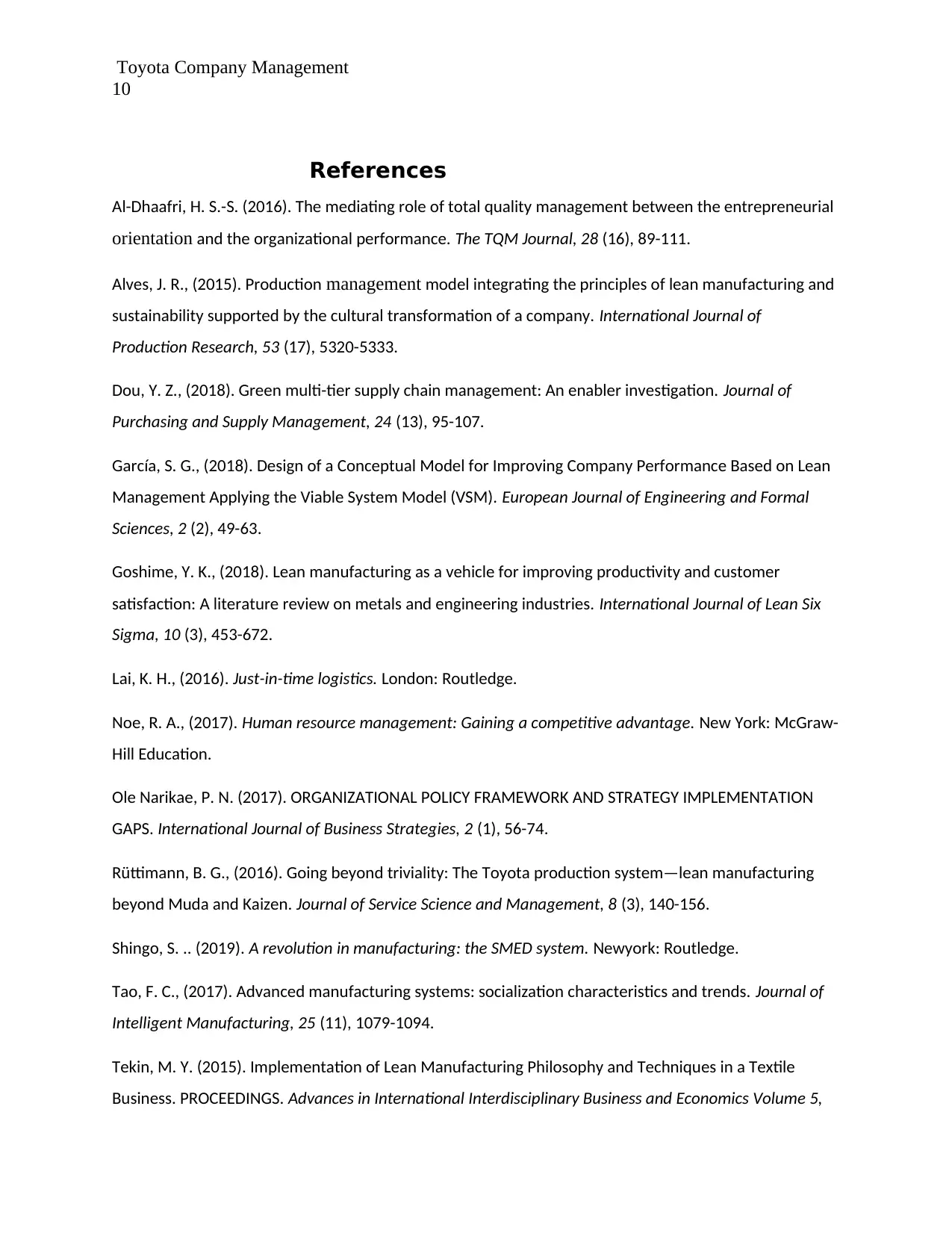
Toyota Company Management
10
References
Al-Dhaafri, H. S.-S. (2016). The mediating role of total quality management between the entrepreneurial
orientation and the organizational performance. The TQM Journal, 28 (16), 89-111.
Alves, J. R., (2015). Production management model integrating the principles of lean manufacturing and
sustainability supported by the cultural transformation of a company. International Journal of
Production Research, 53 (17), 5320-5333.
Dou, Y. Z., (2018). Green multi-tier supply chain management: An enabler investigation. Journal of
Purchasing and Supply Management, 24 (13), 95-107.
García, S. G., (2018). Design of a Conceptual Model for Improving Company Performance Based on Lean
Management Applying the Viable System Model (VSM). European Journal of Engineering and Formal
Sciences, 2 (2), 49-63.
Goshime, Y. K., (2018). Lean manufacturing as a vehicle for improving productivity and customer
satisfaction: A literature review on metals and engineering industries. International Journal of Lean Six
Sigma, 10 (3), 453-672.
Lai, K. H., (2016). Just-in-time logistics. London: Routledge.
Noe, R. A., (2017). Human resource management: Gaining a competitive advantage. New York: McGraw-
Hill Education.
Ole Narikae, P. N. (2017). ORGANIZATIONAL POLICY FRAMEWORK AND STRATEGY IMPLEMENTATION
GAPS. International Journal of Business Strategies, 2 (1), 56-74.
Rüttimann, B. G., (2016). Going beyond triviality: The Toyota production system—lean manufacturing
beyond Muda and Kaizen. Journal of Service Science and Management, 8 (3), 140-156.
Shingo, S. .. (2019). A revolution in manufacturing: the SMED system. Newyork: Routledge.
Tao, F. C., (2017). Advanced manufacturing systems: socialization characteristics and trends. Journal of
Intelligent Manufacturing, 25 (11), 1079-1094.
Tekin, M. Y. (2015). Implementation of Lean Manufacturing Philosophy and Techniques in a Textile
Business. PROCEEDINGS. Advances in International Interdisciplinary Business and Economics Volume 5,
10
References
Al-Dhaafri, H. S.-S. (2016). The mediating role of total quality management between the entrepreneurial
orientation and the organizational performance. The TQM Journal, 28 (16), 89-111.
Alves, J. R., (2015). Production management model integrating the principles of lean manufacturing and
sustainability supported by the cultural transformation of a company. International Journal of
Production Research, 53 (17), 5320-5333.
Dou, Y. Z., (2018). Green multi-tier supply chain management: An enabler investigation. Journal of
Purchasing and Supply Management, 24 (13), 95-107.
García, S. G., (2018). Design of a Conceptual Model for Improving Company Performance Based on Lean
Management Applying the Viable System Model (VSM). European Journal of Engineering and Formal
Sciences, 2 (2), 49-63.
Goshime, Y. K., (2018). Lean manufacturing as a vehicle for improving productivity and customer
satisfaction: A literature review on metals and engineering industries. International Journal of Lean Six
Sigma, 10 (3), 453-672.
Lai, K. H., (2016). Just-in-time logistics. London: Routledge.
Noe, R. A., (2017). Human resource management: Gaining a competitive advantage. New York: McGraw-
Hill Education.
Ole Narikae, P. N. (2017). ORGANIZATIONAL POLICY FRAMEWORK AND STRATEGY IMPLEMENTATION
GAPS. International Journal of Business Strategies, 2 (1), 56-74.
Rüttimann, B. G., (2016). Going beyond triviality: The Toyota production system—lean manufacturing
beyond Muda and Kaizen. Journal of Service Science and Management, 8 (3), 140-156.
Shingo, S. .. (2019). A revolution in manufacturing: the SMED system. Newyork: Routledge.
Tao, F. C., (2017). Advanced manufacturing systems: socialization characteristics and trends. Journal of
Intelligent Manufacturing, 25 (11), 1079-1094.
Tekin, M. Y. (2015). Implementation of Lean Manufacturing Philosophy and Techniques in a Textile
Business. PROCEEDINGS. Advances in International Interdisciplinary Business and Economics Volume 5,
Secure Best Marks with AI Grader
Need help grading? Try our AI Grader for instant feedback on your assignments.
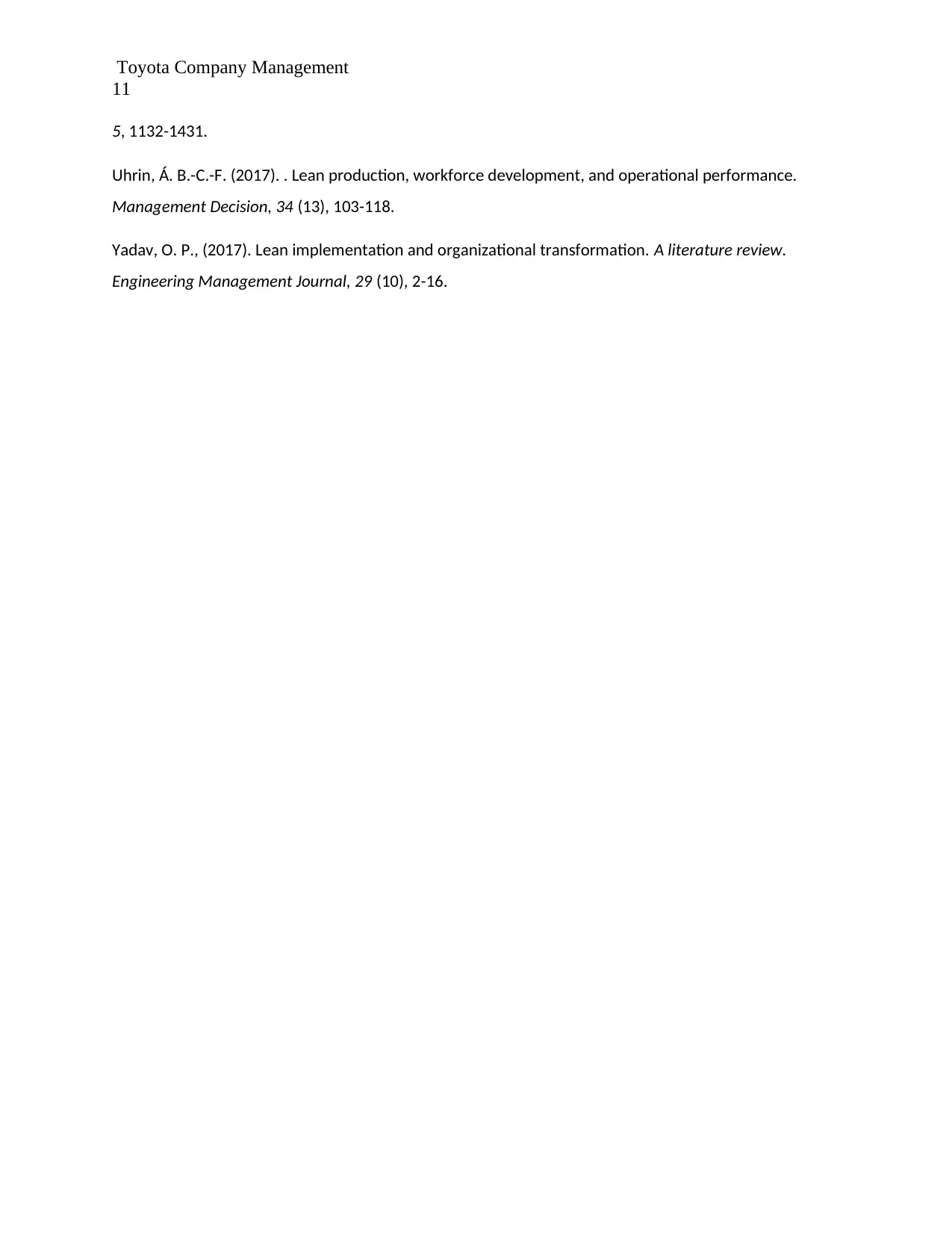
Toyota Company Management
11
5, 1132-1431.
Uhrin, Á. B.-C.-F. (2017). . Lean production, workforce development, and operational performance.
Management Decision, 34 (13), 103-118.
Yadav, O. P., (2017). Lean implementation and organizational transformation. A literature review.
Engineering Management Journal, 29 (10), 2-16.
11
5, 1132-1431.
Uhrin, Á. B.-C.-F. (2017). . Lean production, workforce development, and operational performance.
Management Decision, 34 (13), 103-118.
Yadav, O. P., (2017). Lean implementation and organizational transformation. A literature review.
Engineering Management Journal, 29 (10), 2-16.
1 out of 11
Related Documents

Your All-in-One AI-Powered Toolkit for Academic Success.
+13062052269
info@desklib.com
Available 24*7 on WhatsApp / Email
Unlock your academic potential
© 2024 | Zucol Services PVT LTD | All rights reserved.