Total Quality Management Analysis and Improvement Plan for Toyota
VerifiedAdded on 2020/06/06
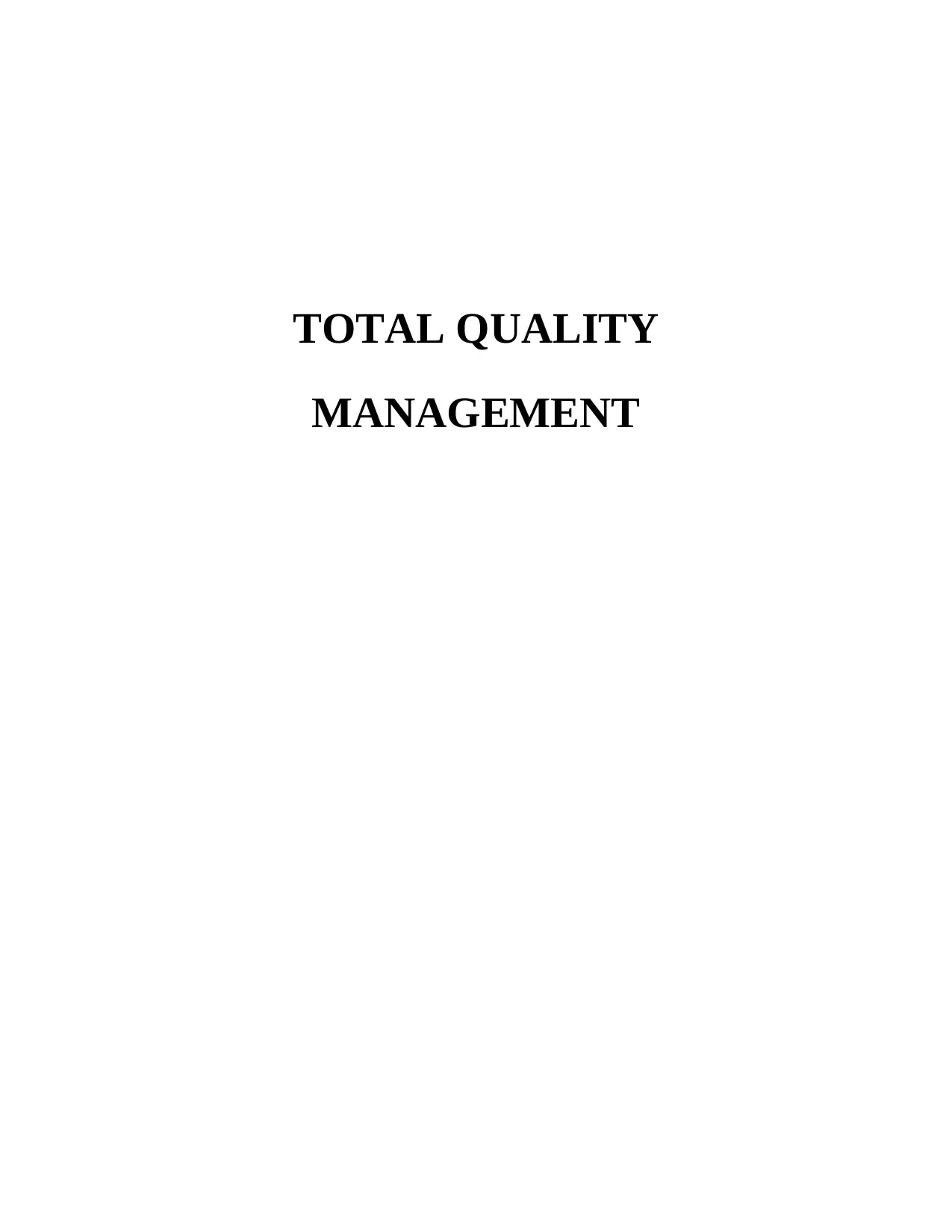
MANAGEMENT
Paraphrase This Document
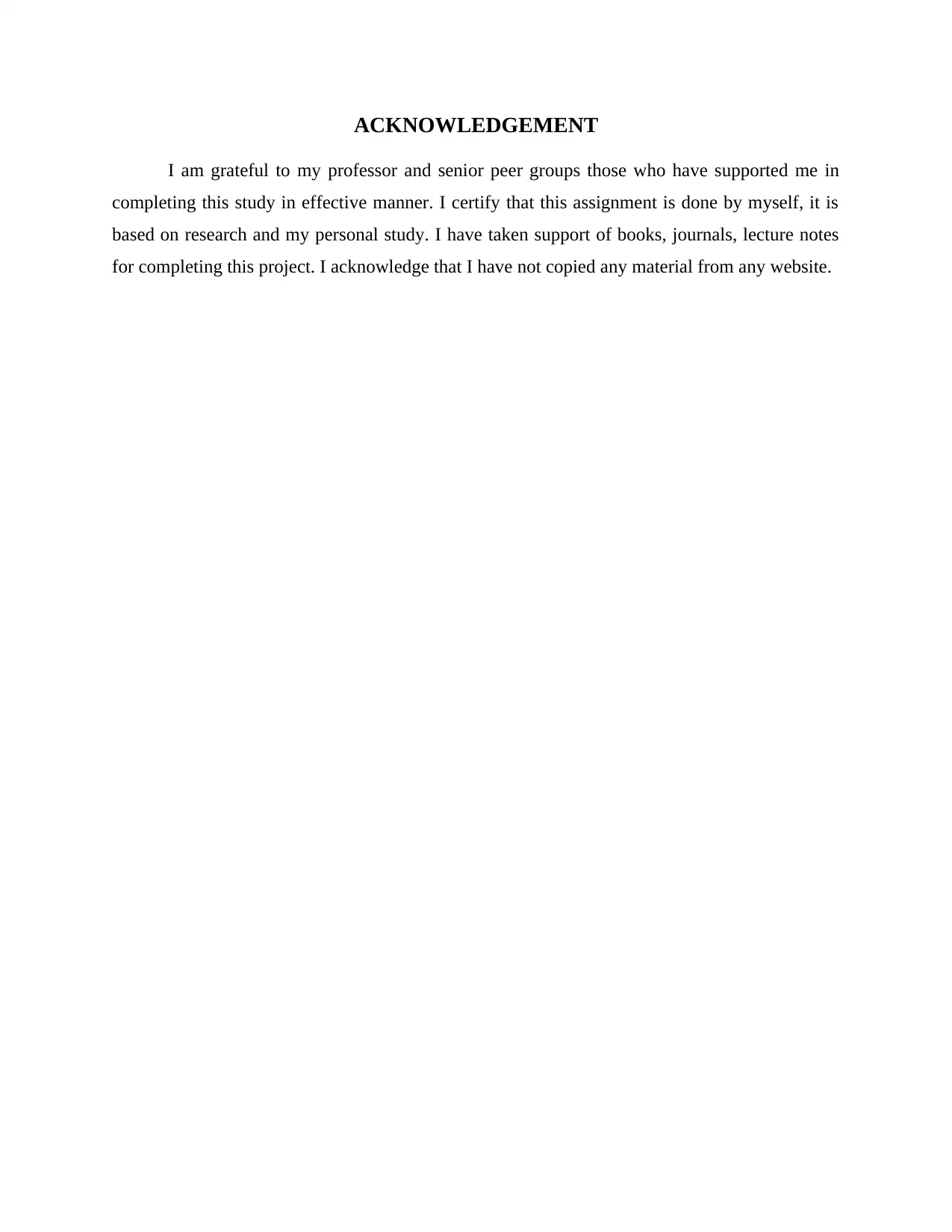
I am grateful to my professor and senior peer groups those who have supported me in
completing this study in effective manner. I certify that this assignment is done by myself, it is
based on research and my personal study. I have taken support of books, journals, lecture notes
for completing this project. I acknowledge that I have not copied any material from any website.
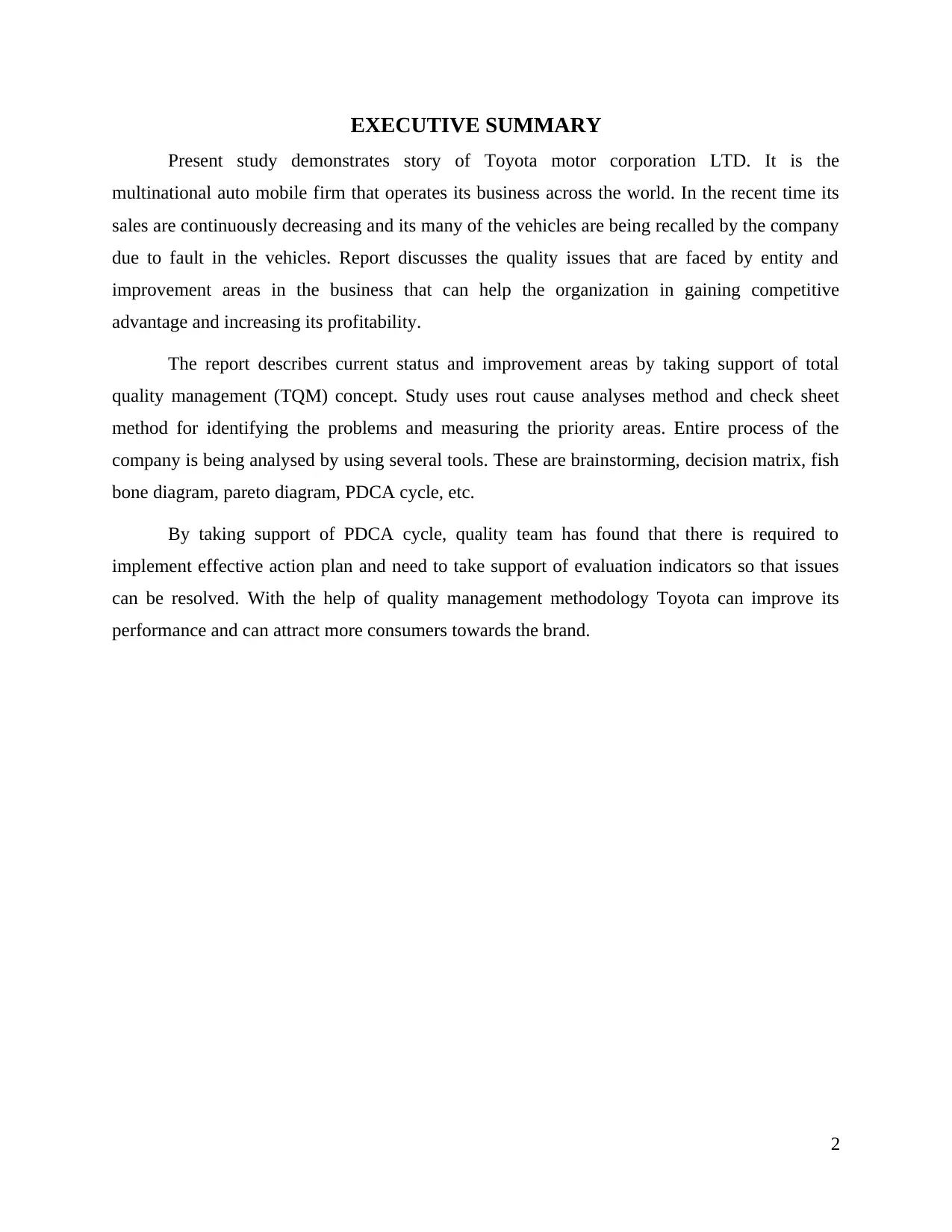
Present study demonstrates story of Toyota motor corporation LTD. It is the
multinational auto mobile firm that operates its business across the world. In the recent time its
sales are continuously decreasing and its many of the vehicles are being recalled by the company
due to fault in the vehicles. Report discusses the quality issues that are faced by entity and
improvement areas in the business that can help the organization in gaining competitive
advantage and increasing its profitability.
The report describes current status and improvement areas by taking support of total
quality management (TQM) concept. Study uses rout cause analyses method and check sheet
method for identifying the problems and measuring the priority areas. Entire process of the
company is being analysed by using several tools. These are brainstorming, decision matrix, fish
bone diagram, pareto diagram, PDCA cycle, etc.
By taking support of PDCA cycle, quality team has found that there is required to
implement effective action plan and need to take support of evaluation indicators so that issues
can be resolved. With the help of quality management methodology Toyota can improve its
performance and can attract more consumers towards the brand.
2
⊘ This is a preview!⊘
Do you want full access?
Subscribe today to unlock all pages.

Trusted by 1+ million students worldwide
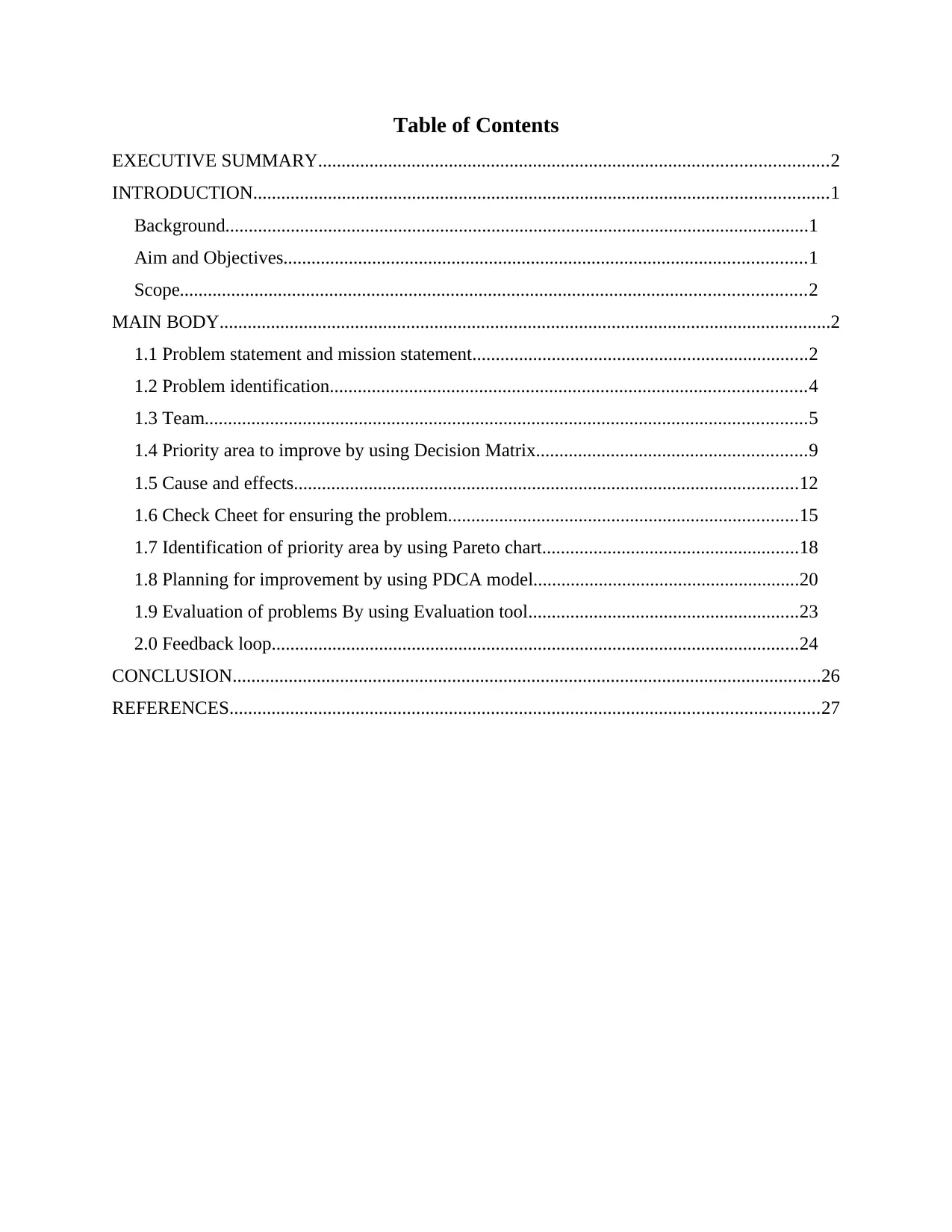
EXECUTIVE SUMMARY.............................................................................................................2
INTRODUCTION...........................................................................................................................1
Background.............................................................................................................................1
Aim and Objectives................................................................................................................1
Scope......................................................................................................................................2
MAIN BODY...................................................................................................................................2
1.1 Problem statement and mission statement........................................................................2
1.2 Problem identification......................................................................................................4
1.3 Team.................................................................................................................................5
1.4 Priority area to improve by using Decision Matrix..........................................................9
1.5 Cause and effects............................................................................................................12
1.6 Check Cheet for ensuring the problem...........................................................................15
1.7 Identification of priority area by using Pareto chart.......................................................18
1.8 Planning for improvement by using PDCA model.........................................................20
1.9 Evaluation of problems By using Evaluation tool..........................................................23
2.0 Feedback loop.................................................................................................................24
CONCLUSION..............................................................................................................................26
REFERENCES..............................................................................................................................27
Paraphrase This Document
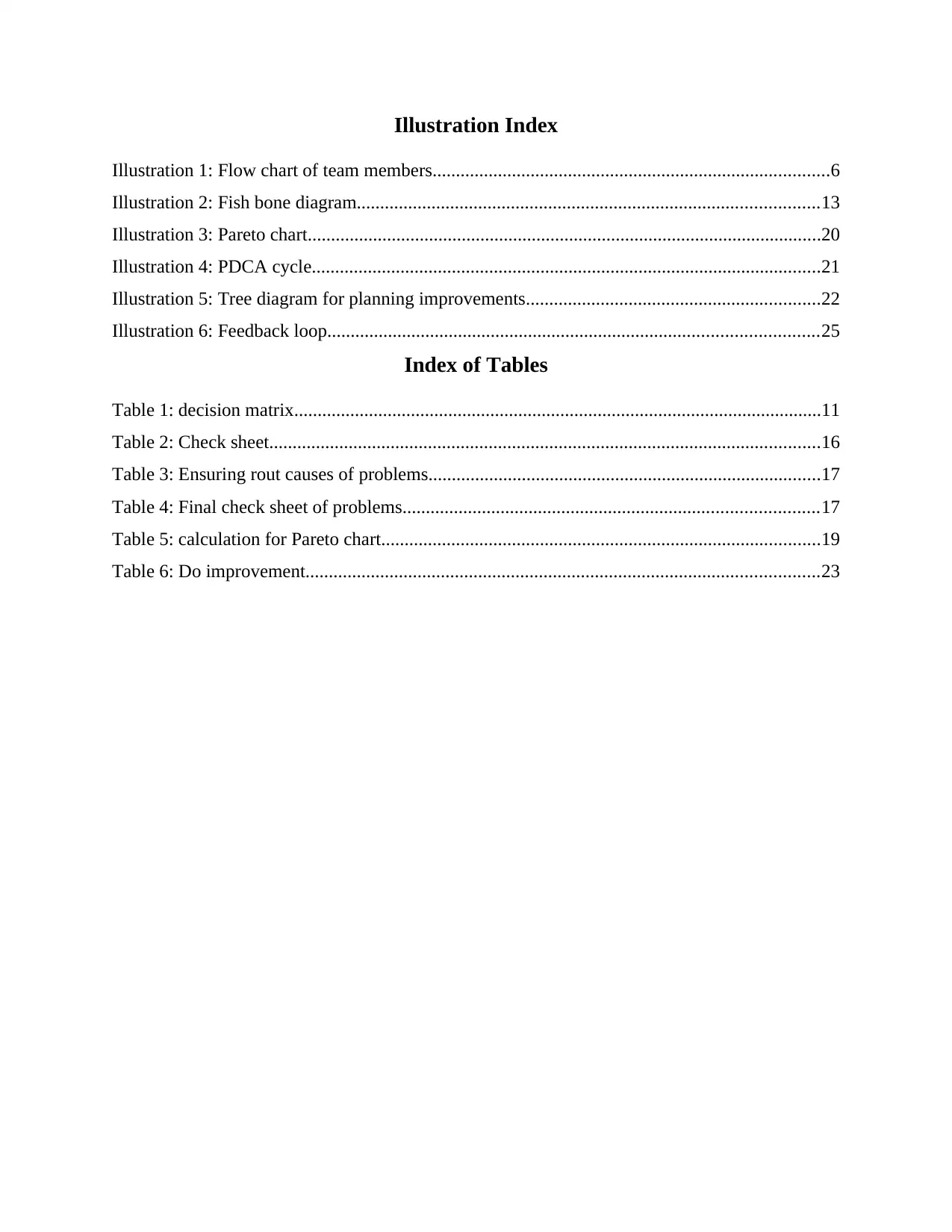
Illustration 1: Flow chart of team members.....................................................................................6
Illustration 2: Fish bone diagram...................................................................................................13
Illustration 3: Pareto chart..............................................................................................................20
Illustration 4: PDCA cycle.............................................................................................................21
Illustration 5: Tree diagram for planning improvements...............................................................22
Illustration 6: Feedback loop.........................................................................................................25
Index of Tables
Table 1: decision matrix.................................................................................................................11
Table 2: Check sheet......................................................................................................................16
Table 3: Ensuring rout causes of problems....................................................................................17
Table 4: Final check sheet of problems.........................................................................................17
Table 5: calculation for Pareto chart..............................................................................................19
Table 6: Do improvement..............................................................................................................23
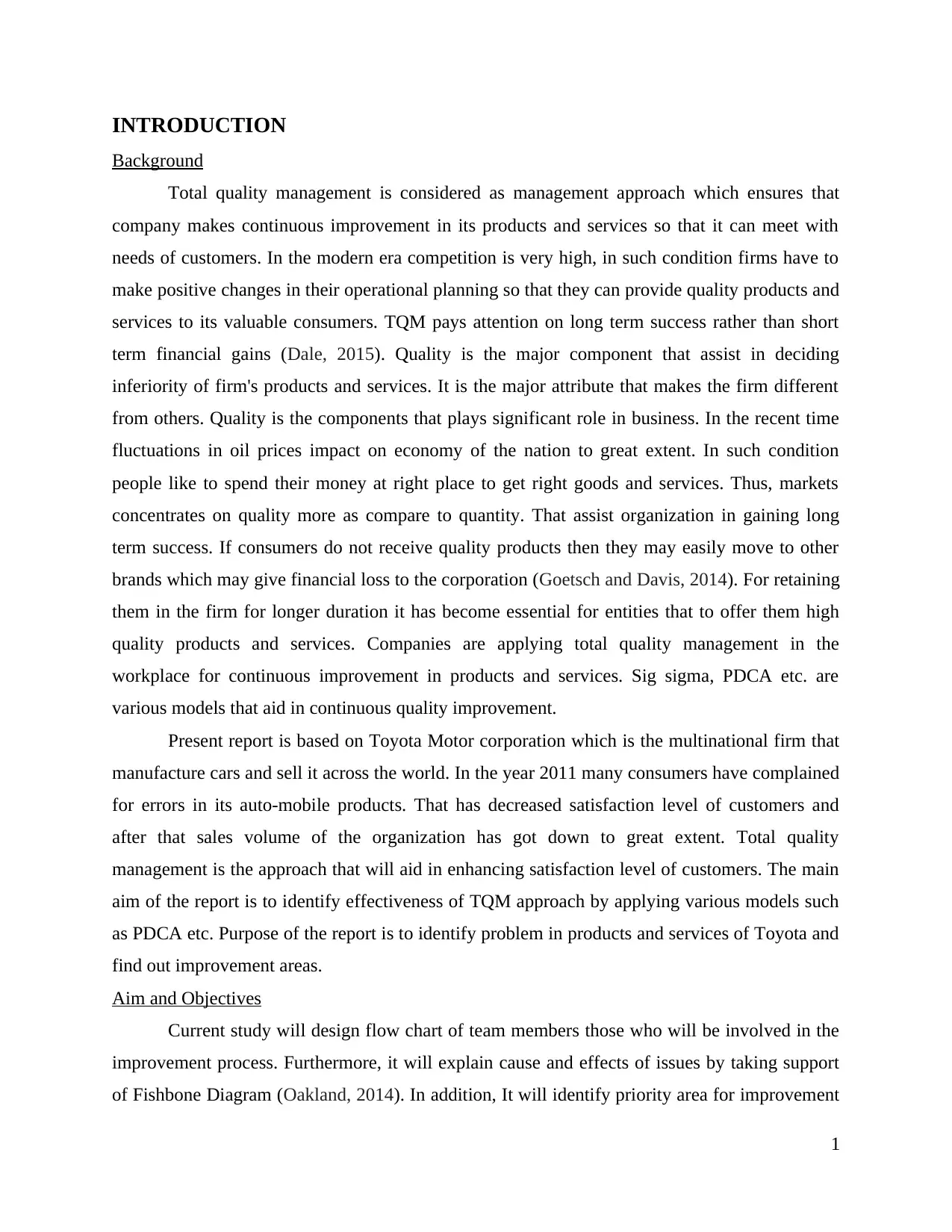
Background
Total quality management is considered as management approach which ensures that
company makes continuous improvement in its products and services so that it can meet with
needs of customers. In the modern era competition is very high, in such condition firms have to
make positive changes in their operational planning so that they can provide quality products and
services to its valuable consumers. TQM pays attention on long term success rather than short
term financial gains (Dale, 2015). Quality is the major component that assist in deciding
inferiority of firm's products and services. It is the major attribute that makes the firm different
from others. Quality is the components that plays significant role in business. In the recent time
fluctuations in oil prices impact on economy of the nation to great extent. In such condition
people like to spend their money at right place to get right goods and services. Thus, markets
concentrates on quality more as compare to quantity. That assist organization in gaining long
term success. If consumers do not receive quality products then they may easily move to other
brands which may give financial loss to the corporation (Goetsch and Davis, 2014). For retaining
them in the firm for longer duration it has become essential for entities that to offer them high
quality products and services. Companies are applying total quality management in the
workplace for continuous improvement in products and services. Sig sigma, PDCA etc. are
various models that aid in continuous quality improvement.
Present report is based on Toyota Motor corporation which is the multinational firm that
manufacture cars and sell it across the world. In the year 2011 many consumers have complained
for errors in its auto-mobile products. That has decreased satisfaction level of customers and
after that sales volume of the organization has got down to great extent. Total quality
management is the approach that will aid in enhancing satisfaction level of customers. The main
aim of the report is to identify effectiveness of TQM approach by applying various models such
as PDCA etc. Purpose of the report is to identify problem in products and services of Toyota and
find out improvement areas.
Aim and Objectives
Current study will design flow chart of team members those who will be involved in the
improvement process. Furthermore, it will explain cause and effects of issues by taking support
of Fishbone Diagram (Oakland, 2014). In addition, It will identify priority area for improvement
1
⊘ This is a preview!⊘
Do you want full access?
Subscribe today to unlock all pages.

Trusted by 1+ million students worldwide
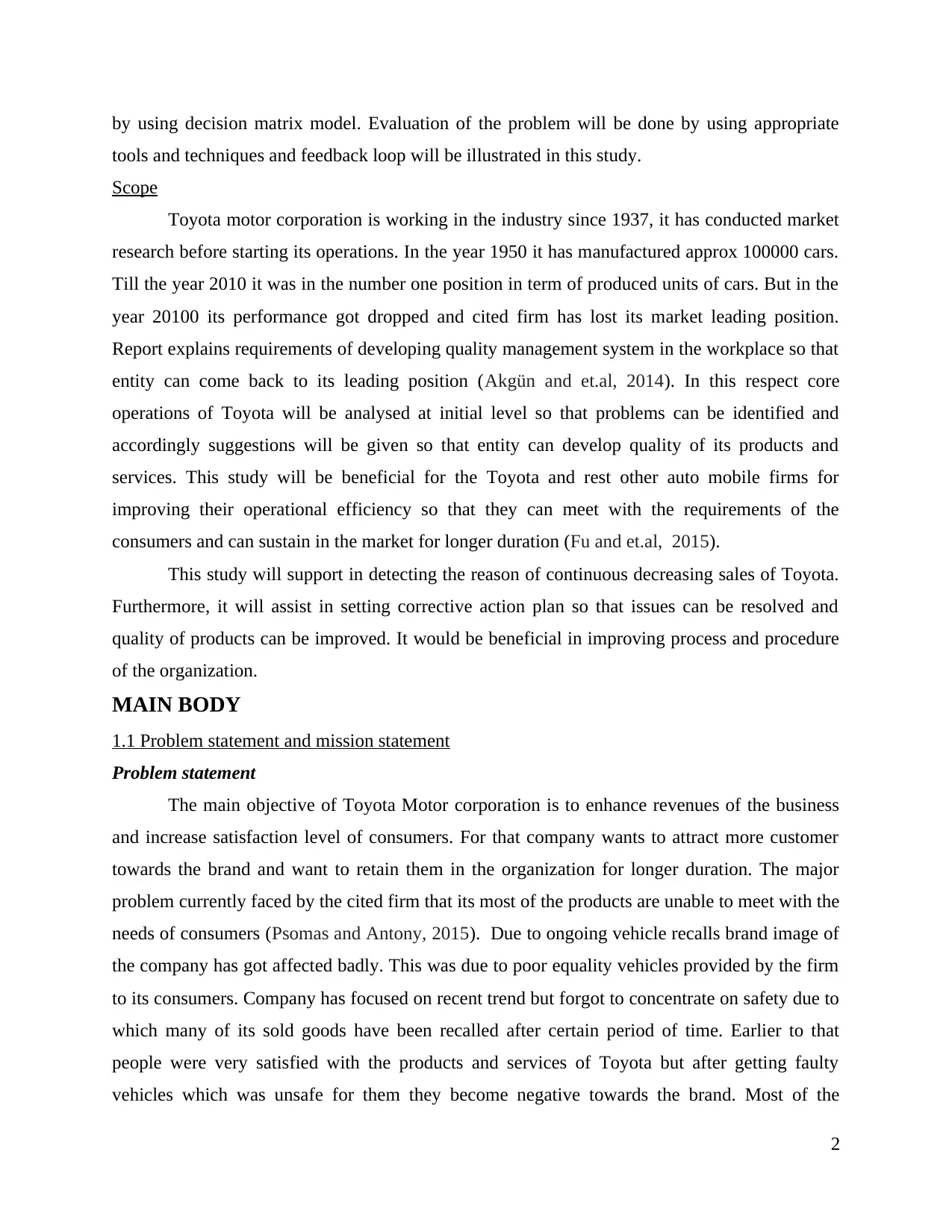
tools and techniques and feedback loop will be illustrated in this study.
Scope
Toyota motor corporation is working in the industry since 1937, it has conducted market
research before starting its operations. In the year 1950 it has manufactured approx 100000 cars.
Till the year 2010 it was in the number one position in term of produced units of cars. But in the
year 20100 its performance got dropped and cited firm has lost its market leading position.
Report explains requirements of developing quality management system in the workplace so that
entity can come back to its leading position (Akgün and et.al, 2014). In this respect core
operations of Toyota will be analysed at initial level so that problems can be identified and
accordingly suggestions will be given so that entity can develop quality of its products and
services. This study will be beneficial for the Toyota and rest other auto mobile firms for
improving their operational efficiency so that they can meet with the requirements of the
consumers and can sustain in the market for longer duration (Fu and et.al, 2015).
This study will support in detecting the reason of continuous decreasing sales of Toyota.
Furthermore, it will assist in setting corrective action plan so that issues can be resolved and
quality of products can be improved. It would be beneficial in improving process and procedure
of the organization.
MAIN BODY
1.1 Problem statement and mission statement
Problem statement
The main objective of Toyota Motor corporation is to enhance revenues of the business
and increase satisfaction level of consumers. For that company wants to attract more customer
towards the brand and want to retain them in the organization for longer duration. The major
problem currently faced by the cited firm that its most of the products are unable to meet with the
needs of consumers (Psomas and Antony, 2015). Due to ongoing vehicle recalls brand image of
the company has got affected badly. This was due to poor equality vehicles provided by the firm
to its consumers. Company has focused on recent trend but forgot to concentrate on safety due to
which many of its sold goods have been recalled after certain period of time. Earlier to that
people were very satisfied with the products and services of Toyota but after getting faulty
vehicles which was unsafe for them they become negative towards the brand. Most of the
2
Paraphrase This Document
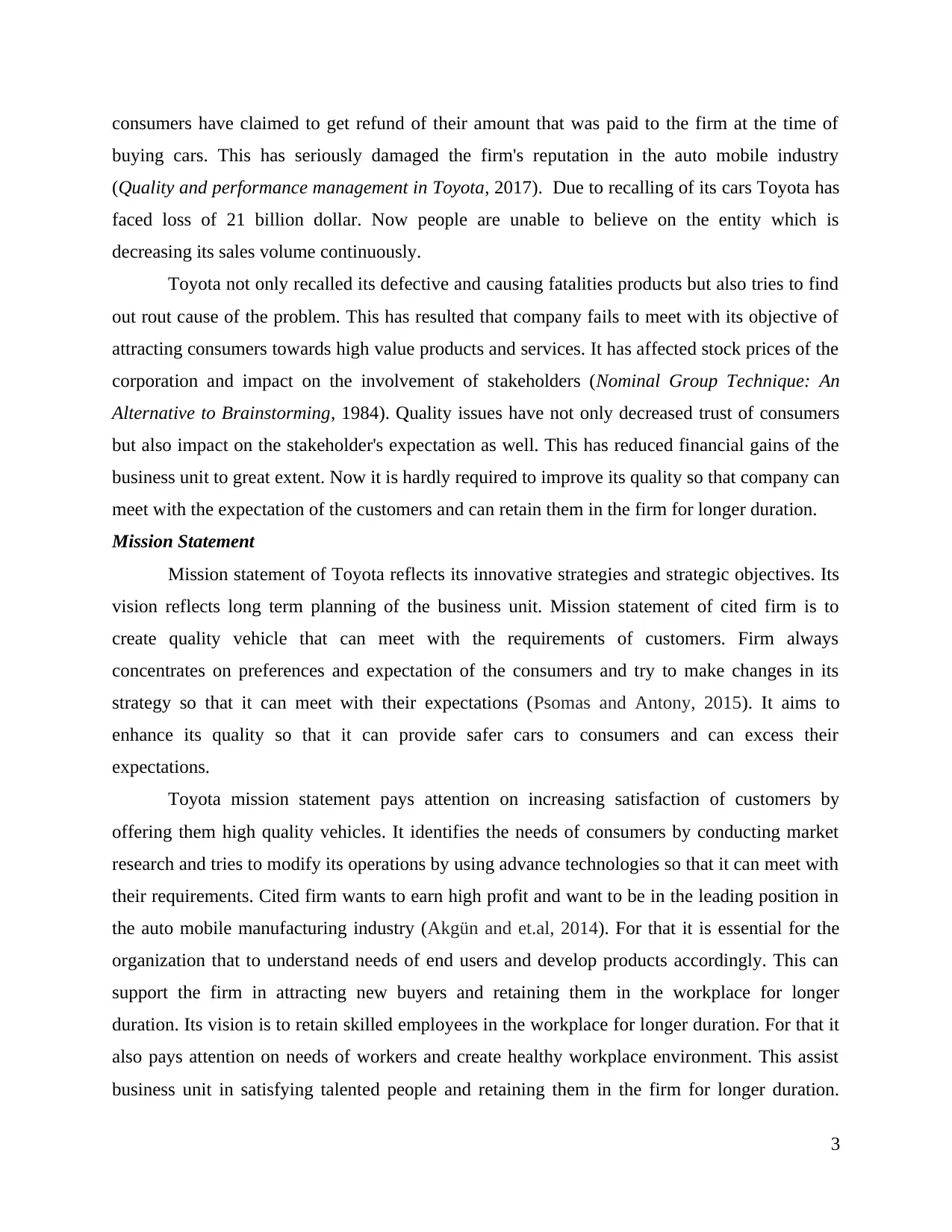
buying cars. This has seriously damaged the firm's reputation in the auto mobile industry
(Quality and performance management in Toyota, 2017). Due to recalling of its cars Toyota has
faced loss of 21 billion dollar. Now people are unable to believe on the entity which is
decreasing its sales volume continuously.
Toyota not only recalled its defective and causing fatalities products but also tries to find
out rout cause of the problem. This has resulted that company fails to meet with its objective of
attracting consumers towards high value products and services. It has affected stock prices of the
corporation and impact on the involvement of stakeholders (Nominal Group Technique: An
Alternative to Brainstorming, 1984). Quality issues have not only decreased trust of consumers
but also impact on the stakeholder's expectation as well. This has reduced financial gains of the
business unit to great extent. Now it is hardly required to improve its quality so that company can
meet with the expectation of the customers and can retain them in the firm for longer duration.
Mission Statement
Mission statement of Toyota reflects its innovative strategies and strategic objectives. Its
vision reflects long term planning of the business unit. Mission statement of cited firm is to
create quality vehicle that can meet with the requirements of customers. Firm always
concentrates on preferences and expectation of the consumers and try to make changes in its
strategy so that it can meet with their expectations (Psomas and Antony, 2015). It aims to
enhance its quality so that it can provide safer cars to consumers and can excess their
expectations.
Toyota mission statement pays attention on increasing satisfaction of customers by
offering them high quality vehicles. It identifies the needs of consumers by conducting market
research and tries to modify its operations by using advance technologies so that it can meet with
their requirements. Cited firm wants to earn high profit and want to be in the leading position in
the auto mobile manufacturing industry (Akgün and et.al, 2014). For that it is essential for the
organization that to understand needs of end users and develop products accordingly. This can
support the firm in attracting new buyers and retaining them in the workplace for longer
duration. Its vision is to retain skilled employees in the workplace for longer duration. For that it
also pays attention on needs of workers and create healthy workplace environment. This assist
business unit in satisfying talented people and retaining them in the firm for longer duration.
3
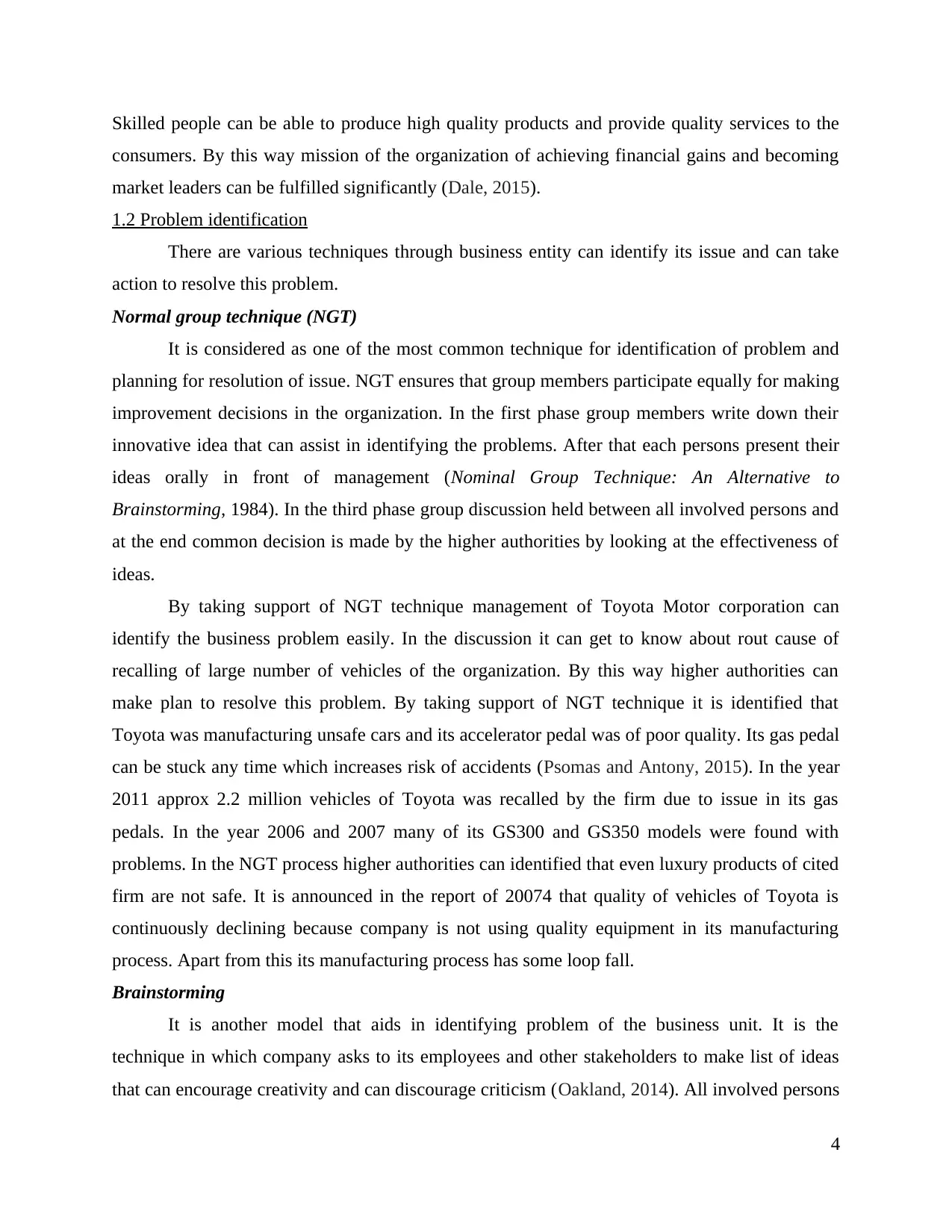
consumers. By this way mission of the organization of achieving financial gains and becoming
market leaders can be fulfilled significantly (Dale, 2015).
1.2 Problem identification
There are various techniques through business entity can identify its issue and can take
action to resolve this problem.
Normal group technique (NGT)
It is considered as one of the most common technique for identification of problem and
planning for resolution of issue. NGT ensures that group members participate equally for making
improvement decisions in the organization. In the first phase group members write down their
innovative idea that can assist in identifying the problems. After that each persons present their
ideas orally in front of management (Nominal Group Technique: An Alternative to
Brainstorming, 1984). In the third phase group discussion held between all involved persons and
at the end common decision is made by the higher authorities by looking at the effectiveness of
ideas.
By taking support of NGT technique management of Toyota Motor corporation can
identify the business problem easily. In the discussion it can get to know about rout cause of
recalling of large number of vehicles of the organization. By this way higher authorities can
make plan to resolve this problem. By taking support of NGT technique it is identified that
Toyota was manufacturing unsafe cars and its accelerator pedal was of poor quality. Its gas pedal
can be stuck any time which increases risk of accidents (Psomas and Antony, 2015). In the year
2011 approx 2.2 million vehicles of Toyota was recalled by the firm due to issue in its gas
pedals. In the year 2006 and 2007 many of its GS300 and GS350 models were found with
problems. In the NGT process higher authorities can identified that even luxury products of cited
firm are not safe. It is announced in the report of 20074 that quality of vehicles of Toyota is
continuously declining because company is not using quality equipment in its manufacturing
process. Apart from this its manufacturing process has some loop fall.
Brainstorming
It is another model that aids in identifying problem of the business unit. It is the
technique in which company asks to its employees and other stakeholders to make list of ideas
that can encourage creativity and can discourage criticism (Oakland, 2014). All involved persons
4
⊘ This is a preview!⊘
Do you want full access?
Subscribe today to unlock all pages.

Trusted by 1+ million students worldwide
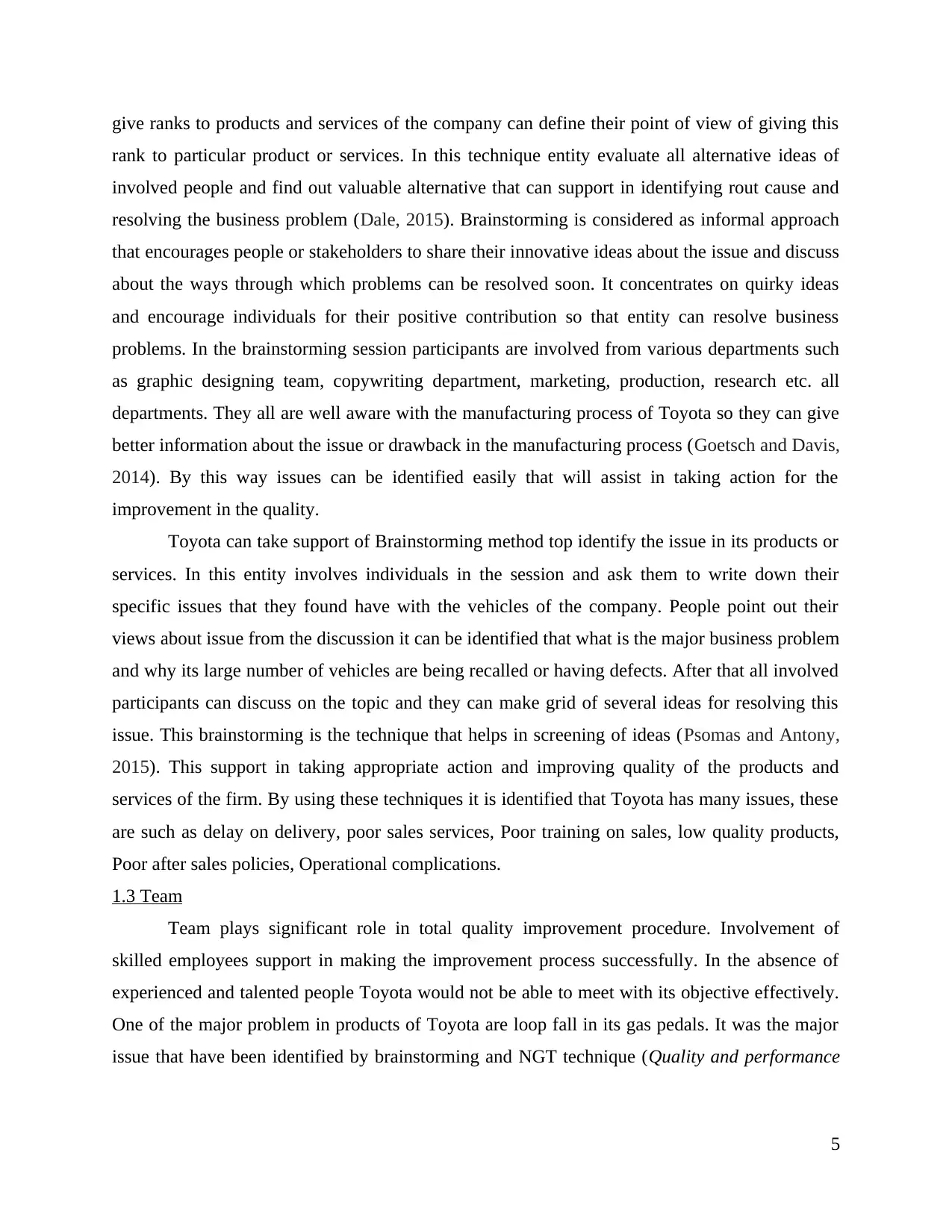
rank to particular product or services. In this technique entity evaluate all alternative ideas of
involved people and find out valuable alternative that can support in identifying rout cause and
resolving the business problem (Dale, 2015). Brainstorming is considered as informal approach
that encourages people or stakeholders to share their innovative ideas about the issue and discuss
about the ways through which problems can be resolved soon. It concentrates on quirky ideas
and encourage individuals for their positive contribution so that entity can resolve business
problems. In the brainstorming session participants are involved from various departments such
as graphic designing team, copywriting department, marketing, production, research etc. all
departments. They all are well aware with the manufacturing process of Toyota so they can give
better information about the issue or drawback in the manufacturing process (Goetsch and Davis,
2014). By this way issues can be identified easily that will assist in taking action for the
improvement in the quality.
Toyota can take support of Brainstorming method top identify the issue in its products or
services. In this entity involves individuals in the session and ask them to write down their
specific issues that they found have with the vehicles of the company. People point out their
views about issue from the discussion it can be identified that what is the major business problem
and why its large number of vehicles are being recalled or having defects. After that all involved
participants can discuss on the topic and they can make grid of several ideas for resolving this
issue. This brainstorming is the technique that helps in screening of ideas (Psomas and Antony,
2015). This support in taking appropriate action and improving quality of the products and
services of the firm. By using these techniques it is identified that Toyota has many issues, these
are such as delay on delivery, poor sales services, Poor training on sales, low quality products,
Poor after sales policies, Operational complications.
1.3 Team
Team plays significant role in total quality improvement procedure. Involvement of
skilled employees support in making the improvement process successfully. In the absence of
experienced and talented people Toyota would not be able to meet with its objective effectively.
One of the major problem in products of Toyota are loop fall in its gas pedals. It was the major
issue that have been identified by brainstorming and NGT technique (Quality and performance
5
Paraphrase This Document
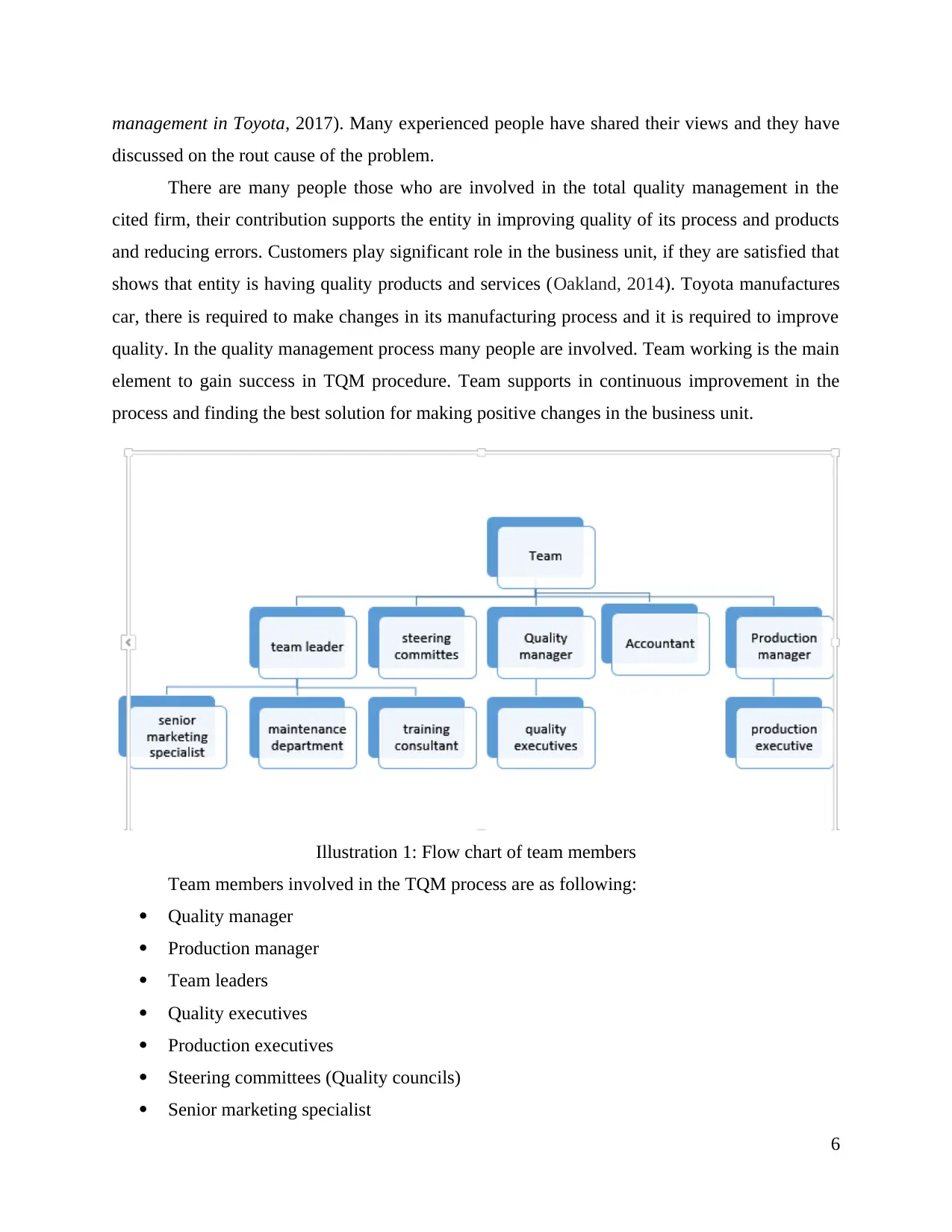
discussed on the rout cause of the problem.
There are many people those who are involved in the total quality management in the
cited firm, their contribution supports the entity in improving quality of its process and products
and reducing errors. Customers play significant role in the business unit, if they are satisfied that
shows that entity is having quality products and services (Oakland, 2014). Toyota manufactures
car, there is required to make changes in its manufacturing process and it is required to improve
quality. In the quality management process many people are involved. Team working is the main
element to gain success in TQM procedure. Team supports in continuous improvement in the
process and finding the best solution for making positive changes in the business unit.
Illustration 1: Flow chart of team members
Team members involved in the TQM process are as following:
Quality manager
Production manager
Team leaders
Quality executives
Production executives
Steering committees (Quality councils)
Senior marketing specialist
6
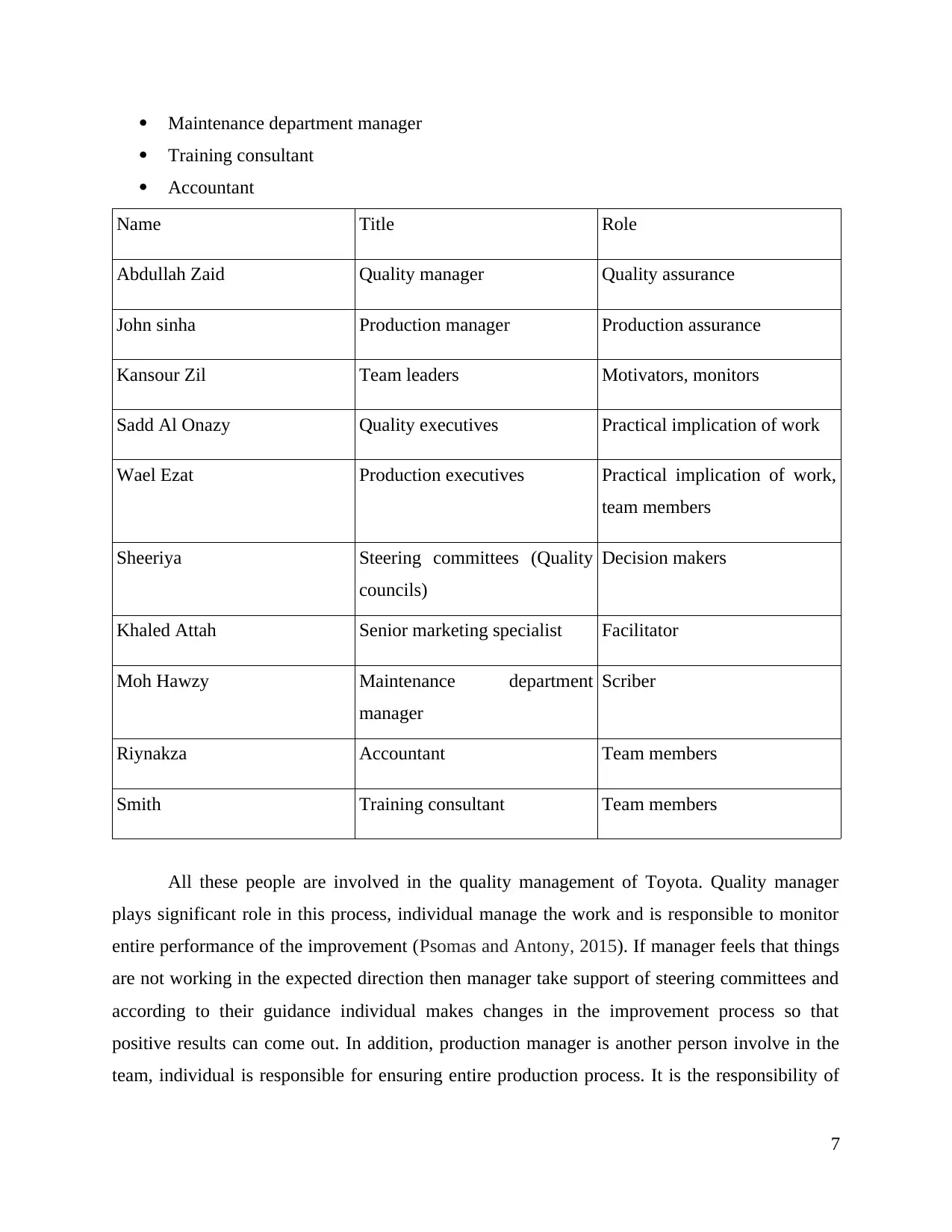
Training consultant
Accountant
Name Title Role
Abdullah Zaid Quality manager Quality assurance
John sinha Production manager Production assurance
Kansour Zil Team leaders Motivators, monitors
Sadd Al Onazy Quality executives Practical implication of work
Wael Ezat Production executives Practical implication of work,
team members
Sheeriya Steering committees (Quality
councils)
Decision makers
Khaled Attah Senior marketing specialist Facilitator
Moh Hawzy Maintenance department
manager
Scriber
Riynakza Accountant Team members
Smith Training consultant Team members
All these people are involved in the quality management of Toyota. Quality manager
plays significant role in this process, individual manage the work and is responsible to monitor
entire performance of the improvement (Psomas and Antony, 2015). If manager feels that things
are not working in the expected direction then manager take support of steering committees and
according to their guidance individual makes changes in the improvement process so that
positive results can come out. In addition, production manager is another person involve in the
team, individual is responsible for ensuring entire production process. It is the responsibility of
7
⊘ This is a preview!⊘
Do you want full access?
Subscribe today to unlock all pages.

Trusted by 1+ million students worldwide
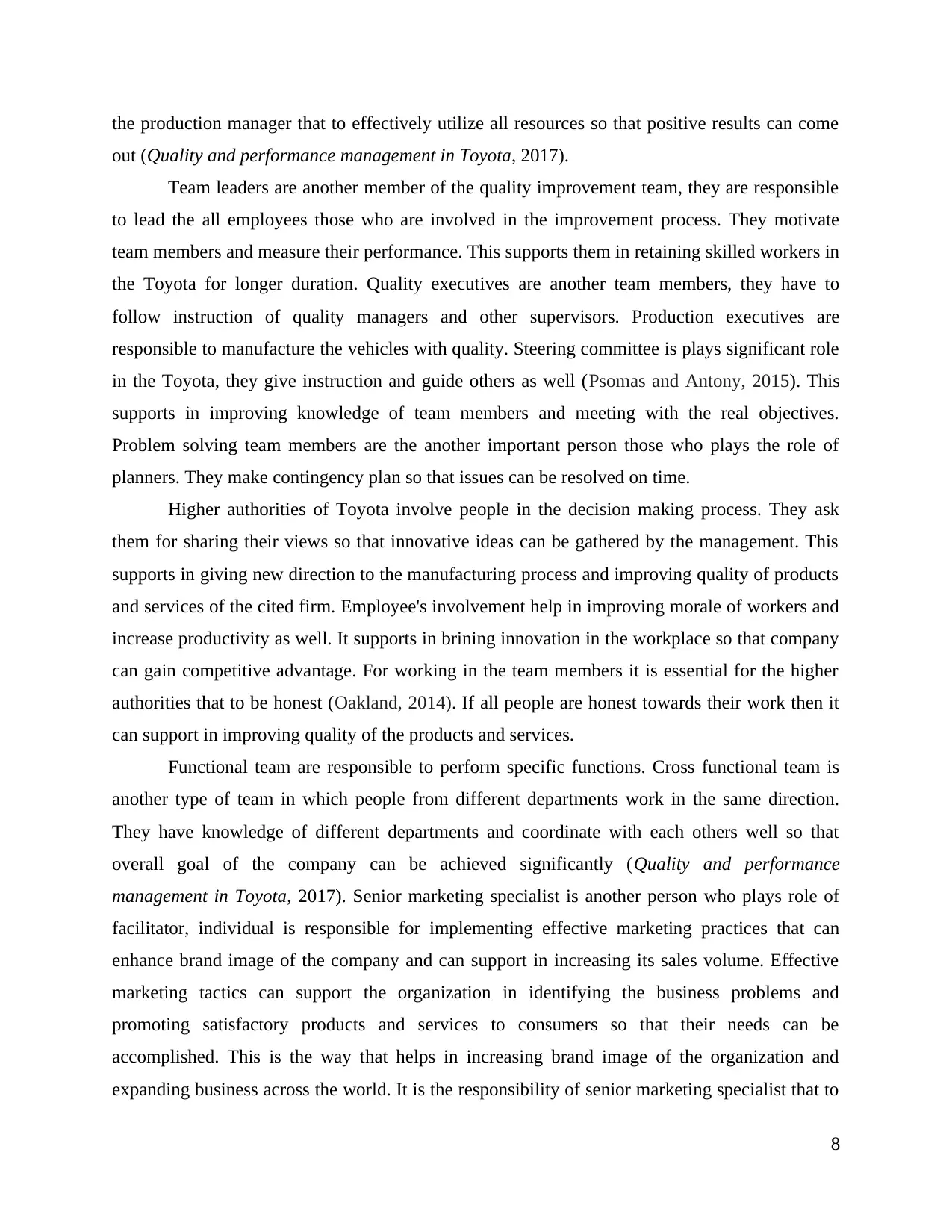
out (Quality and performance management in Toyota, 2017).
Team leaders are another member of the quality improvement team, they are responsible
to lead the all employees those who are involved in the improvement process. They motivate
team members and measure their performance. This supports them in retaining skilled workers in
the Toyota for longer duration. Quality executives are another team members, they have to
follow instruction of quality managers and other supervisors. Production executives are
responsible to manufacture the vehicles with quality. Steering committee is plays significant role
in the Toyota, they give instruction and guide others as well (Psomas and Antony, 2015). This
supports in improving knowledge of team members and meeting with the real objectives.
Problem solving team members are the another important person those who plays the role of
planners. They make contingency plan so that issues can be resolved on time.
Higher authorities of Toyota involve people in the decision making process. They ask
them for sharing their views so that innovative ideas can be gathered by the management. This
supports in giving new direction to the manufacturing process and improving quality of products
and services of the cited firm. Employee's involvement help in improving morale of workers and
increase productivity as well. It supports in brining innovation in the workplace so that company
can gain competitive advantage. For working in the team members it is essential for the higher
authorities that to be honest (Oakland, 2014). If all people are honest towards their work then it
can support in improving quality of the products and services.
Functional team are responsible to perform specific functions. Cross functional team is
another type of team in which people from different departments work in the same direction.
They have knowledge of different departments and coordinate with each others well so that
overall goal of the company can be achieved significantly (Quality and performance
management in Toyota, 2017). Senior marketing specialist is another person who plays role of
facilitator, individual is responsible for implementing effective marketing practices that can
enhance brand image of the company and can support in increasing its sales volume. Effective
marketing tactics can support the organization in identifying the business problems and
promoting satisfactory products and services to consumers so that their needs can be
accomplished. This is the way that helps in increasing brand image of the organization and
expanding business across the world. It is the responsibility of senior marketing specialist that to
8
Paraphrase This Document
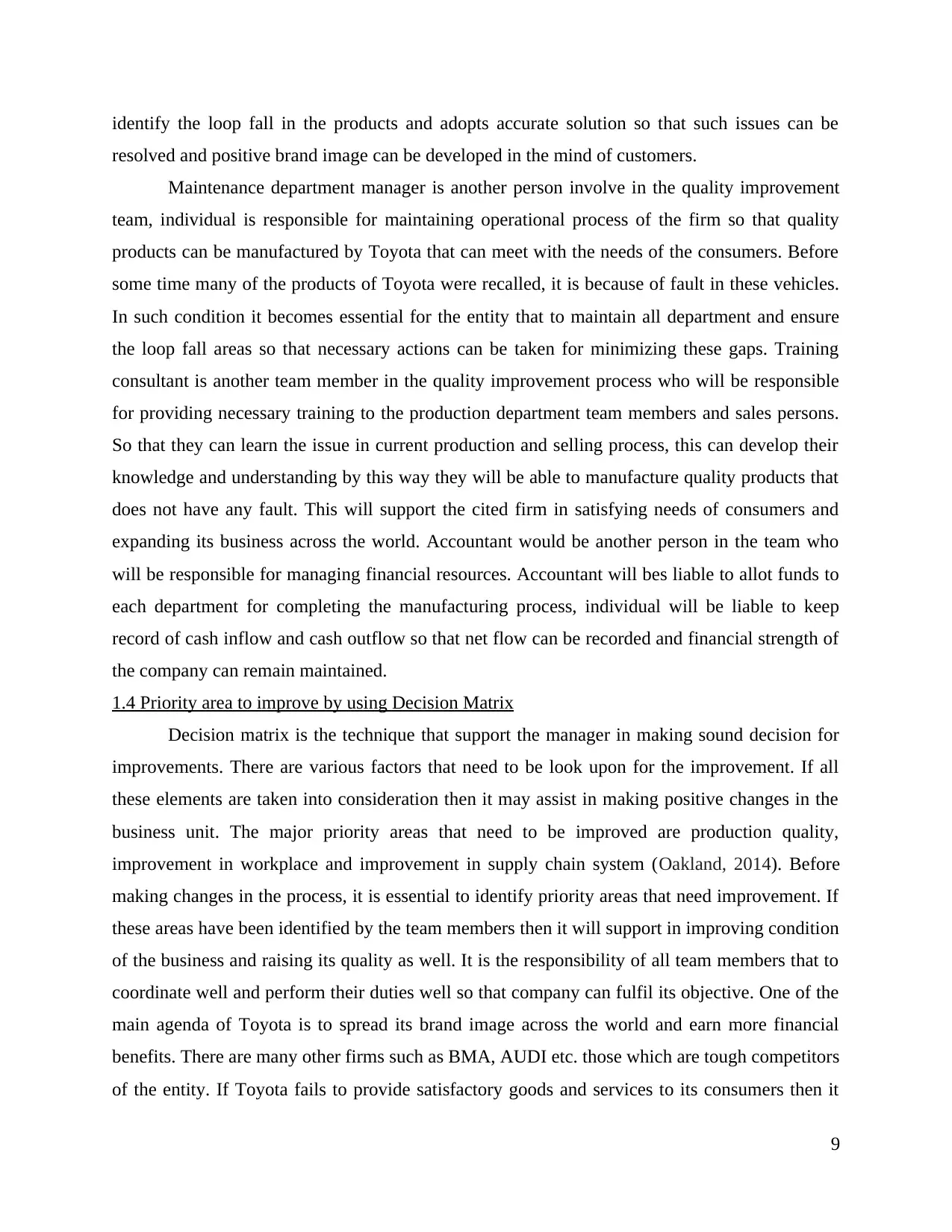
resolved and positive brand image can be developed in the mind of customers.
Maintenance department manager is another person involve in the quality improvement
team, individual is responsible for maintaining operational process of the firm so that quality
products can be manufactured by Toyota that can meet with the needs of the consumers. Before
some time many of the products of Toyota were recalled, it is because of fault in these vehicles.
In such condition it becomes essential for the entity that to maintain all department and ensure
the loop fall areas so that necessary actions can be taken for minimizing these gaps. Training
consultant is another team member in the quality improvement process who will be responsible
for providing necessary training to the production department team members and sales persons.
So that they can learn the issue in current production and selling process, this can develop their
knowledge and understanding by this way they will be able to manufacture quality products that
does not have any fault. This will support the cited firm in satisfying needs of consumers and
expanding its business across the world. Accountant would be another person in the team who
will be responsible for managing financial resources. Accountant will bes liable to allot funds to
each department for completing the manufacturing process, individual will be liable to keep
record of cash inflow and cash outflow so that net flow can be recorded and financial strength of
the company can remain maintained.
1.4 Priority area to improve by using Decision Matrix
Decision matrix is the technique that support the manager in making sound decision for
improvements. There are various factors that need to be look upon for the improvement. If all
these elements are taken into consideration then it may assist in making positive changes in the
business unit. The major priority areas that need to be improved are production quality,
improvement in workplace and improvement in supply chain system (Oakland, 2014). Before
making changes in the process, it is essential to identify priority areas that need improvement. If
these areas have been identified by the team members then it will support in improving condition
of the business and raising its quality as well. It is the responsibility of all team members that to
coordinate well and perform their duties well so that company can fulfil its objective. One of the
main agenda of Toyota is to spread its brand image across the world and earn more financial
benefits. There are many other firms such as BMA, AUDI etc. those which are tough competitors
of the entity. If Toyota fails to provide satisfactory goods and services to its consumers then it
9
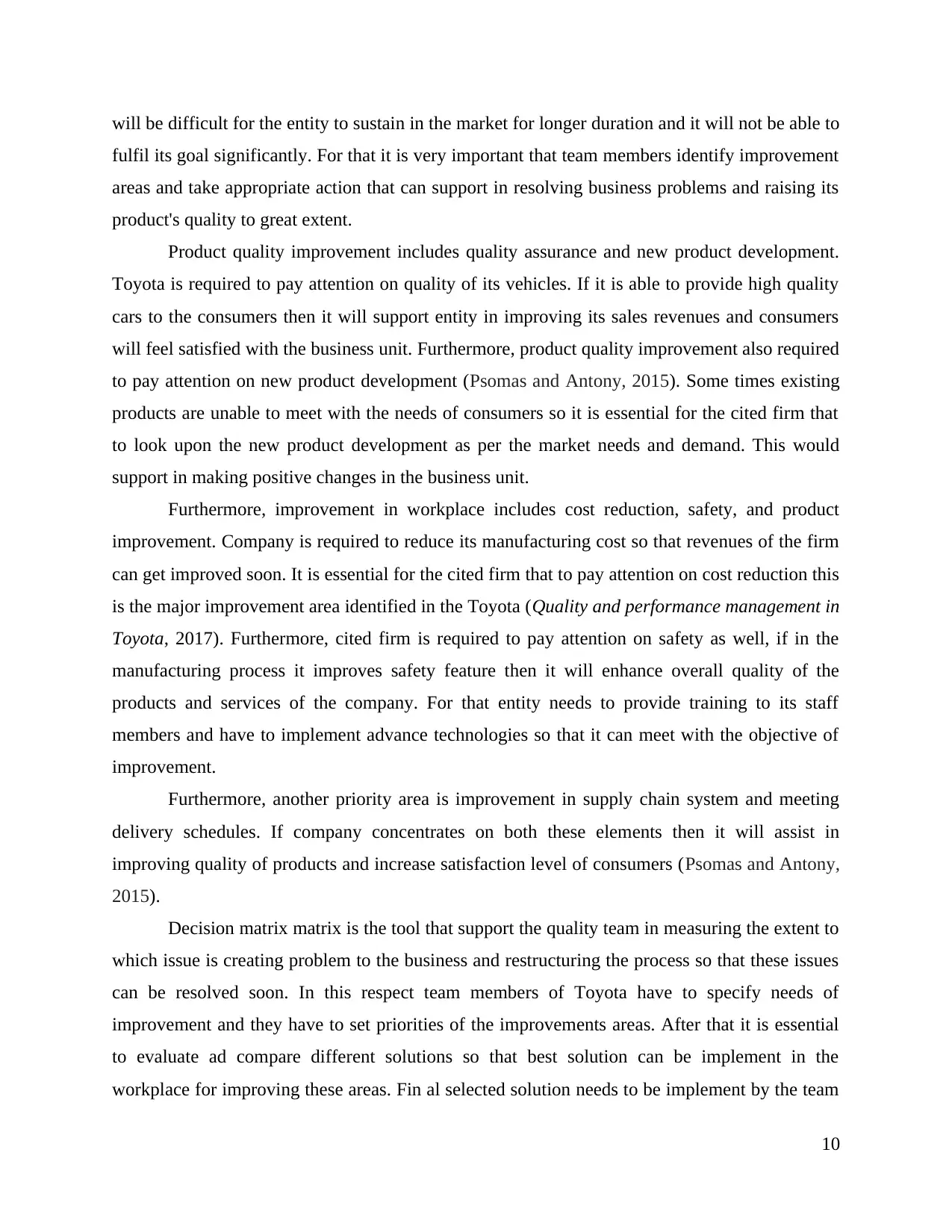
fulfil its goal significantly. For that it is very important that team members identify improvement
areas and take appropriate action that can support in resolving business problems and raising its
product's quality to great extent.
Product quality improvement includes quality assurance and new product development.
Toyota is required to pay attention on quality of its vehicles. If it is able to provide high quality
cars to the consumers then it will support entity in improving its sales revenues and consumers
will feel satisfied with the business unit. Furthermore, product quality improvement also required
to pay attention on new product development (Psomas and Antony, 2015). Some times existing
products are unable to meet with the needs of consumers so it is essential for the cited firm that
to look upon the new product development as per the market needs and demand. This would
support in making positive changes in the business unit.
Furthermore, improvement in workplace includes cost reduction, safety, and product
improvement. Company is required to reduce its manufacturing cost so that revenues of the firm
can get improved soon. It is essential for the cited firm that to pay attention on cost reduction this
is the major improvement area identified in the Toyota (Quality and performance management in
Toyota, 2017). Furthermore, cited firm is required to pay attention on safety as well, if in the
manufacturing process it improves safety feature then it will enhance overall quality of the
products and services of the company. For that entity needs to provide training to its staff
members and have to implement advance technologies so that it can meet with the objective of
improvement.
Furthermore, another priority area is improvement in supply chain system and meeting
delivery schedules. If company concentrates on both these elements then it will assist in
improving quality of products and increase satisfaction level of consumers (Psomas and Antony,
2015).
Decision matrix matrix is the tool that support the quality team in measuring the extent to
which issue is creating problem to the business and restructuring the process so that these issues
can be resolved soon. In this respect team members of Toyota have to specify needs of
improvement and they have to set priorities of the improvements areas. After that it is essential
to evaluate ad compare different solutions so that best solution can be implement in the
workplace for improving these areas. Fin al selected solution needs to be implement by the team
10
⊘ This is a preview!⊘
Do you want full access?
Subscribe today to unlock all pages.

Trusted by 1+ million students worldwide
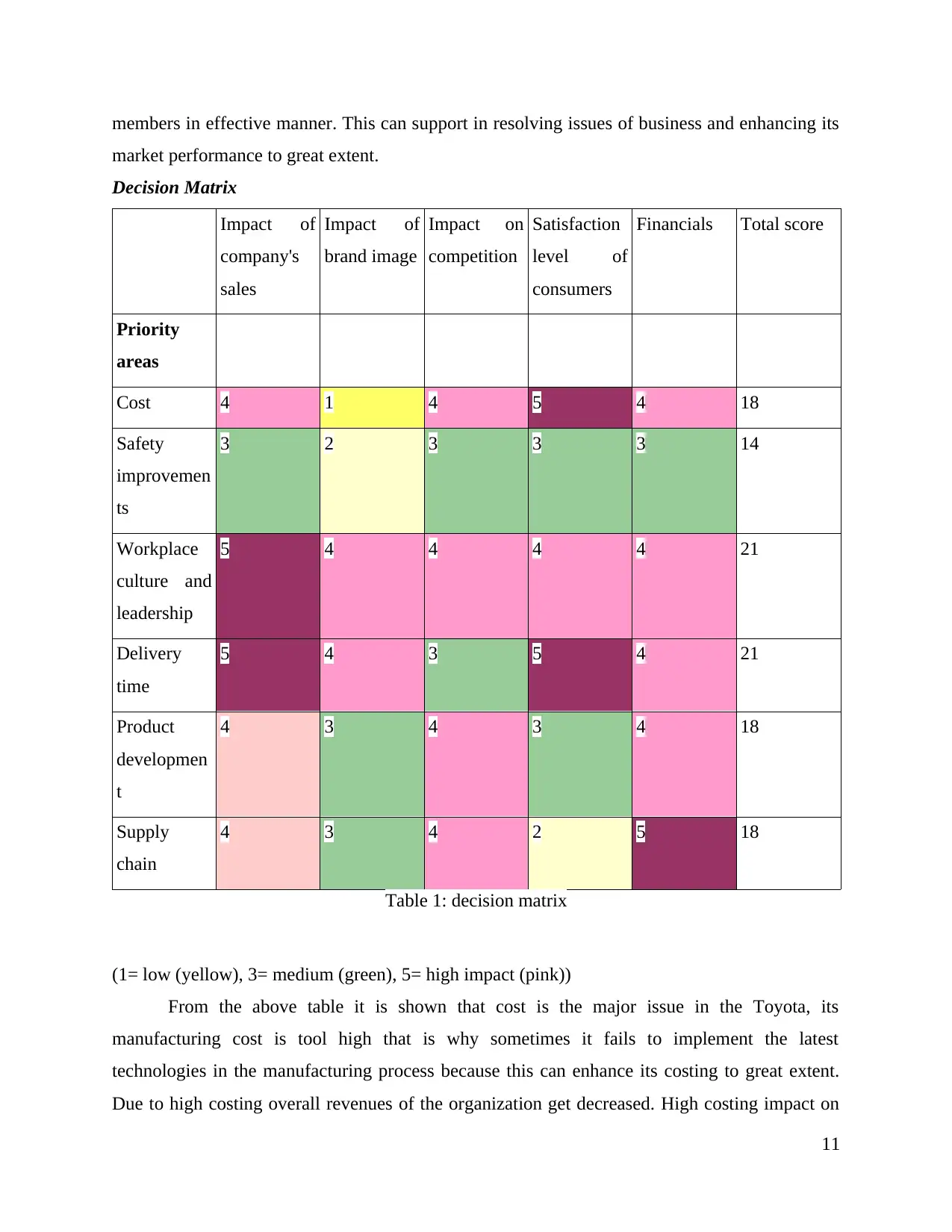
market performance to great extent.
Decision Matrix
Impact of
company's
sales
Impact of
brand image
Impact on
competition
Satisfaction
level of
consumers
Financials Total score
Priority
areas
Cost 4 1 4 5 4 18
Safety
improvemen
ts
3 2 3 3 3 14
Workplace
culture and
leadership
5 4 4 4 4 21
Delivery
time
5 4 3 5 4 21
Product
developmen
t
4 3 4 3 4 18
Supply
chain
4 3 4 2 5 18
Table 1: decision matrix
(1= low (yellow), 3= medium (green), 5= high impact (pink))
From the above table it is shown that cost is the major issue in the Toyota, its
manufacturing cost is tool high that is why sometimes it fails to implement the latest
technologies in the manufacturing process because this can enhance its costing to great extent.
Due to high costing overall revenues of the organization get decreased. High costing impact on
11
Paraphrase This Document
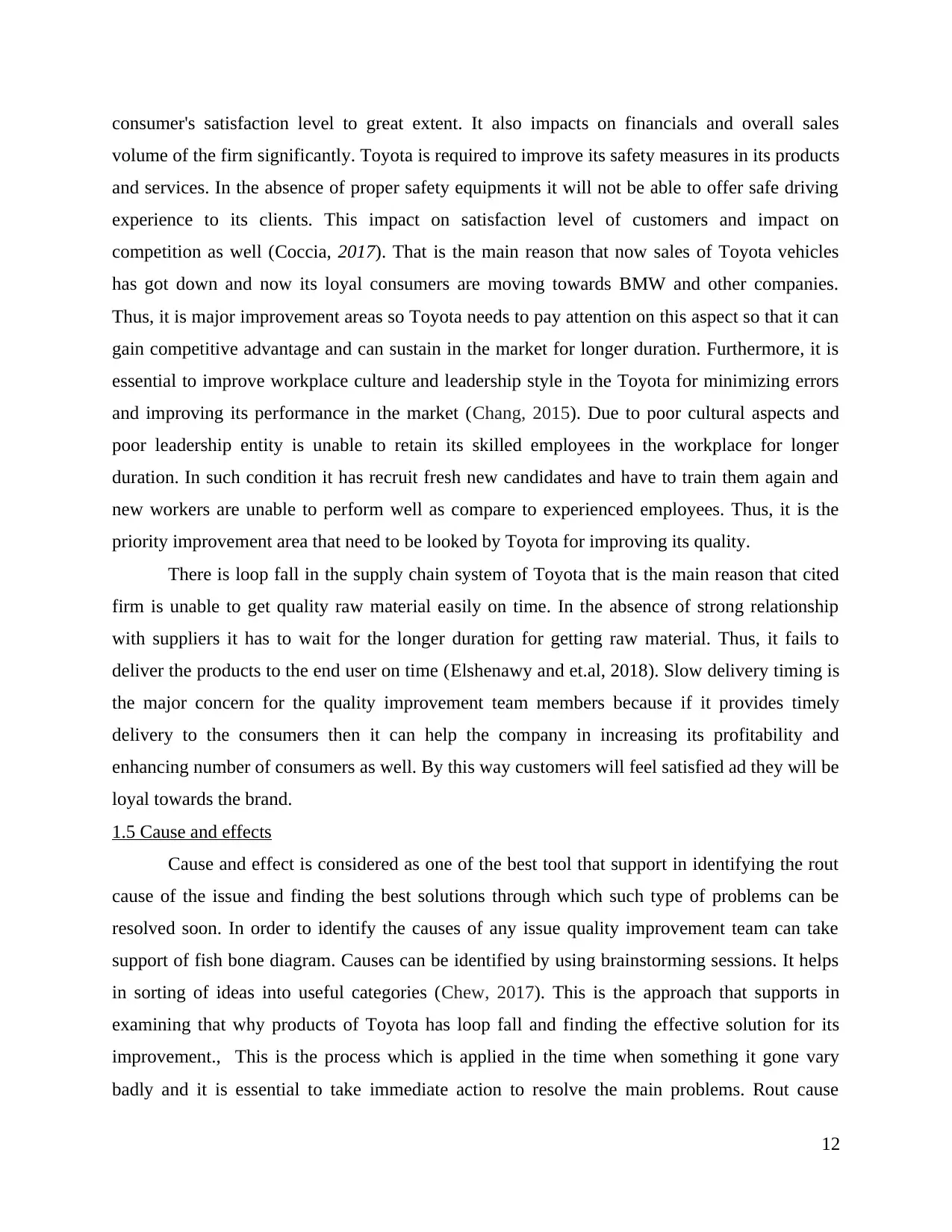
volume of the firm significantly. Toyota is required to improve its safety measures in its products
and services. In the absence of proper safety equipments it will not be able to offer safe driving
experience to its clients. This impact on satisfaction level of customers and impact on
competition as well (Coccia, 2017). That is the main reason that now sales of Toyota vehicles
has got down and now its loyal consumers are moving towards BMW and other companies.
Thus, it is major improvement areas so Toyota needs to pay attention on this aspect so that it can
gain competitive advantage and can sustain in the market for longer duration. Furthermore, it is
essential to improve workplace culture and leadership style in the Toyota for minimizing errors
and improving its performance in the market (Chang, 2015). Due to poor cultural aspects and
poor leadership entity is unable to retain its skilled employees in the workplace for longer
duration. In such condition it has recruit fresh new candidates and have to train them again and
new workers are unable to perform well as compare to experienced employees. Thus, it is the
priority improvement area that need to be looked by Toyota for improving its quality.
There is loop fall in the supply chain system of Toyota that is the main reason that cited
firm is unable to get quality raw material easily on time. In the absence of strong relationship
with suppliers it has to wait for the longer duration for getting raw material. Thus, it fails to
deliver the products to the end user on time (Elshenawy and et.al, 2018). Slow delivery timing is
the major concern for the quality improvement team members because if it provides timely
delivery to the consumers then it can help the company in increasing its profitability and
enhancing number of consumers as well. By this way customers will feel satisfied ad they will be
loyal towards the brand.
1.5 Cause and effects
Cause and effect is considered as one of the best tool that support in identifying the rout
cause of the issue and finding the best solutions through which such type of problems can be
resolved soon. In order to identify the causes of any issue quality improvement team can take
support of fish bone diagram. Causes can be identified by using brainstorming sessions. It helps
in sorting of ideas into useful categories (Chew, 2017). This is the approach that supports in
examining that why products of Toyota has loop fall and finding the effective solution for its
improvement., This is the process which is applied in the time when something it gone vary
badly and it is essential to take immediate action to resolve the main problems. Rout cause
12
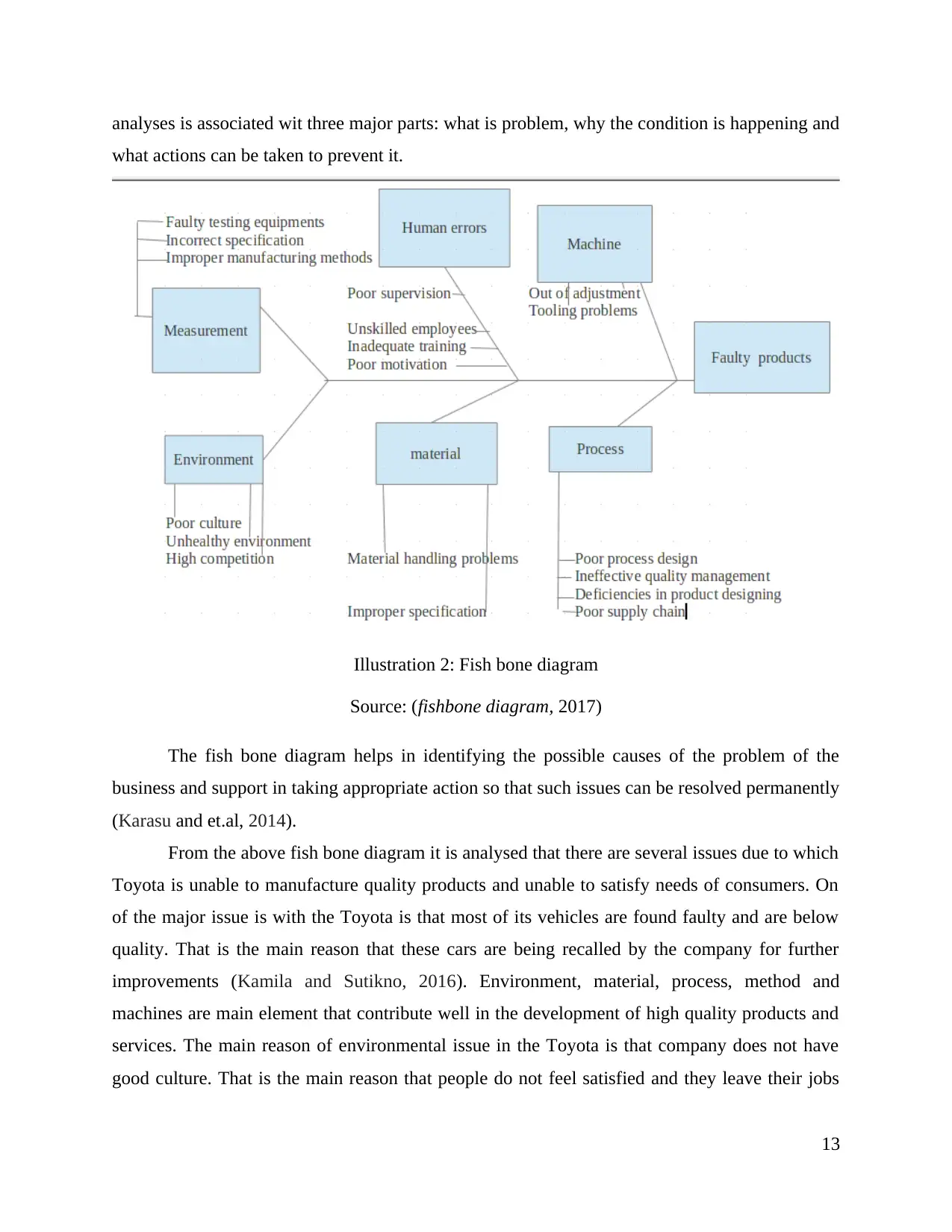
what actions can be taken to prevent it.
Illustration 2: Fish bone diagram
Source: (fishbone diagram, 2017)
The fish bone diagram helps in identifying the possible causes of the problem of the
business and support in taking appropriate action so that such issues can be resolved permanently
(Karasu and et.al, 2014).
From the above fish bone diagram it is analysed that there are several issues due to which
Toyota is unable to manufacture quality products and unable to satisfy needs of consumers. On
of the major issue is with the Toyota is that most of its vehicles are found faulty and are below
quality. That is the main reason that these cars are being recalled by the company for further
improvements (Kamila and Sutikno, 2016). Environment, material, process, method and
machines are main element that contribute well in the development of high quality products and
services. The main reason of environmental issue in the Toyota is that company does not have
good culture. That is the main reason that people do not feel satisfied and they leave their jobs
13
⊘ This is a preview!⊘
Do you want full access?
Subscribe today to unlock all pages.

Trusted by 1+ million students worldwide
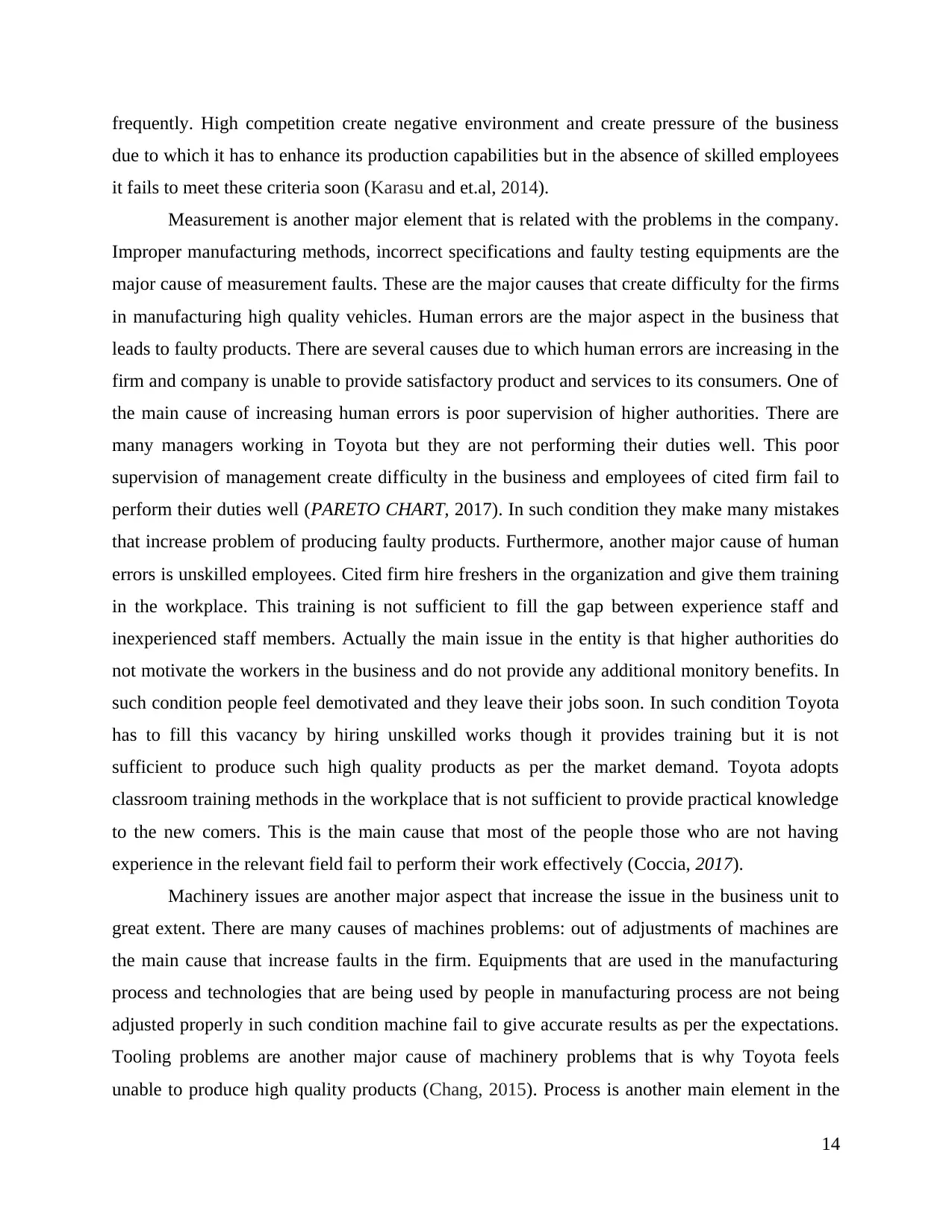
due to which it has to enhance its production capabilities but in the absence of skilled employees
it fails to meet these criteria soon (Karasu and et.al, 2014).
Measurement is another major element that is related with the problems in the company.
Improper manufacturing methods, incorrect specifications and faulty testing equipments are the
major cause of measurement faults. These are the major causes that create difficulty for the firms
in manufacturing high quality vehicles. Human errors are the major aspect in the business that
leads to faulty products. There are several causes due to which human errors are increasing in the
firm and company is unable to provide satisfactory product and services to its consumers. One of
the main cause of increasing human errors is poor supervision of higher authorities. There are
many managers working in Toyota but they are not performing their duties well. This poor
supervision of management create difficulty in the business and employees of cited firm fail to
perform their duties well (PARETO CHART, 2017). In such condition they make many mistakes
that increase problem of producing faulty products. Furthermore, another major cause of human
errors is unskilled employees. Cited firm hire freshers in the organization and give them training
in the workplace. This training is not sufficient to fill the gap between experience staff and
inexperienced staff members. Actually the main issue in the entity is that higher authorities do
not motivate the workers in the business and do not provide any additional monitory benefits. In
such condition people feel demotivated and they leave their jobs soon. In such condition Toyota
has to fill this vacancy by hiring unskilled works though it provides training but it is not
sufficient to produce such high quality products as per the market demand. Toyota adopts
classroom training methods in the workplace that is not sufficient to provide practical knowledge
to the new comers. This is the main cause that most of the people those who are not having
experience in the relevant field fail to perform their work effectively (Coccia, 2017).
Machinery issues are another major aspect that increase the issue in the business unit to
great extent. There are many causes of machines problems: out of adjustments of machines are
the main cause that increase faults in the firm. Equipments that are used in the manufacturing
process and technologies that are being used by people in manufacturing process are not being
adjusted properly in such condition machine fail to give accurate results as per the expectations.
Tooling problems are another major cause of machinery problems that is why Toyota feels
unable to produce high quality products (Chang, 2015). Process is another main element in the
14
Paraphrase This Document
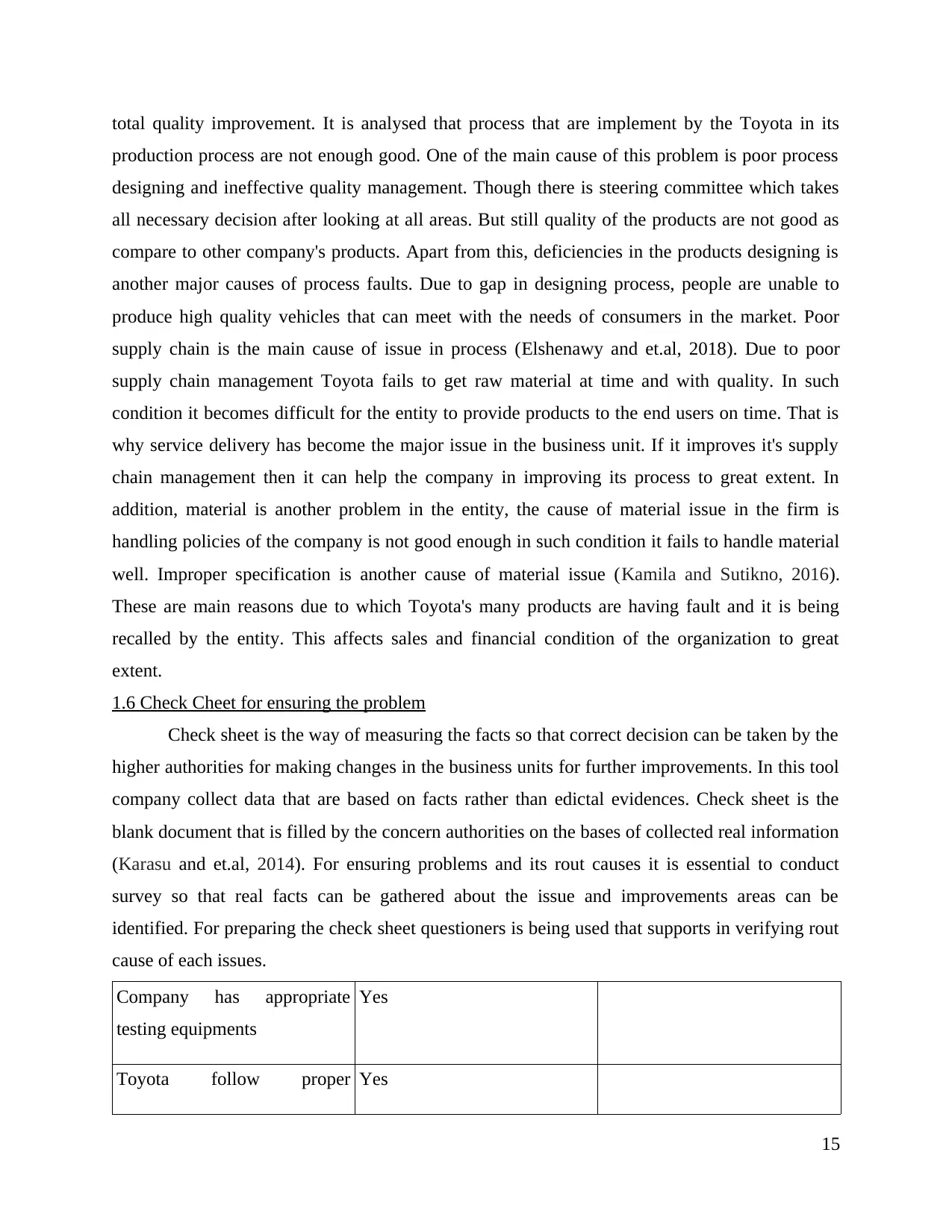
production process are not enough good. One of the main cause of this problem is poor process
designing and ineffective quality management. Though there is steering committee which takes
all necessary decision after looking at all areas. But still quality of the products are not good as
compare to other company's products. Apart from this, deficiencies in the products designing is
another major causes of process faults. Due to gap in designing process, people are unable to
produce high quality vehicles that can meet with the needs of consumers in the market. Poor
supply chain is the main cause of issue in process (Elshenawy and et.al, 2018). Due to poor
supply chain management Toyota fails to get raw material at time and with quality. In such
condition it becomes difficult for the entity to provide products to the end users on time. That is
why service delivery has become the major issue in the business unit. If it improves it's supply
chain management then it can help the company in improving its process to great extent. In
addition, material is another problem in the entity, the cause of material issue in the firm is
handling policies of the company is not good enough in such condition it fails to handle material
well. Improper specification is another cause of material issue (Kamila and Sutikno, 2016).
These are main reasons due to which Toyota's many products are having fault and it is being
recalled by the entity. This affects sales and financial condition of the organization to great
extent.
1.6 Check Cheet for ensuring the problem
Check sheet is the way of measuring the facts so that correct decision can be taken by the
higher authorities for making changes in the business units for further improvements. In this tool
company collect data that are based on facts rather than edictal evidences. Check sheet is the
blank document that is filled by the concern authorities on the bases of collected real information
(Karasu and et.al, 2014). For ensuring problems and its rout causes it is essential to conduct
survey so that real facts can be gathered about the issue and improvements areas can be
identified. For preparing the check sheet questioners is being used that supports in verifying rout
cause of each issues.
Company has appropriate
testing equipments
Yes
Toyota follow proper Yes
15
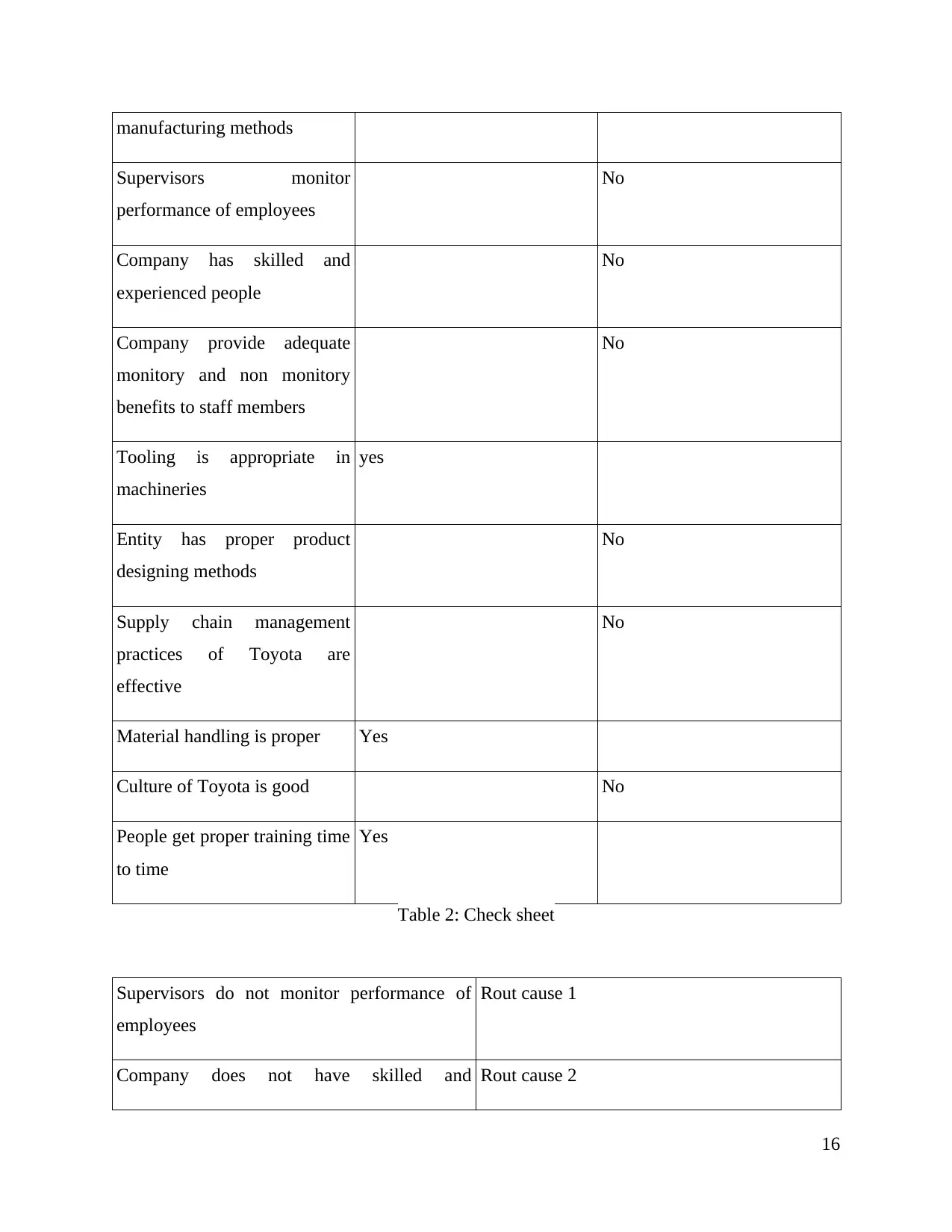
Supervisors monitor
performance of employees
No
Company has skilled and
experienced people
No
Company provide adequate
monitory and non monitory
benefits to staff members
No
Tooling is appropriate in
machineries
yes
Entity has proper product
designing methods
No
Supply chain management
practices of Toyota are
effective
No
Material handling is proper Yes
Culture of Toyota is good No
People get proper training time
to time
Yes
Table 2: Check sheet
Supervisors do not monitor performance of
employees
Rout cause 1
Company does not have skilled and Rout cause 2
16
⊘ This is a preview!⊘
Do you want full access?
Subscribe today to unlock all pages.

Trusted by 1+ million students worldwide
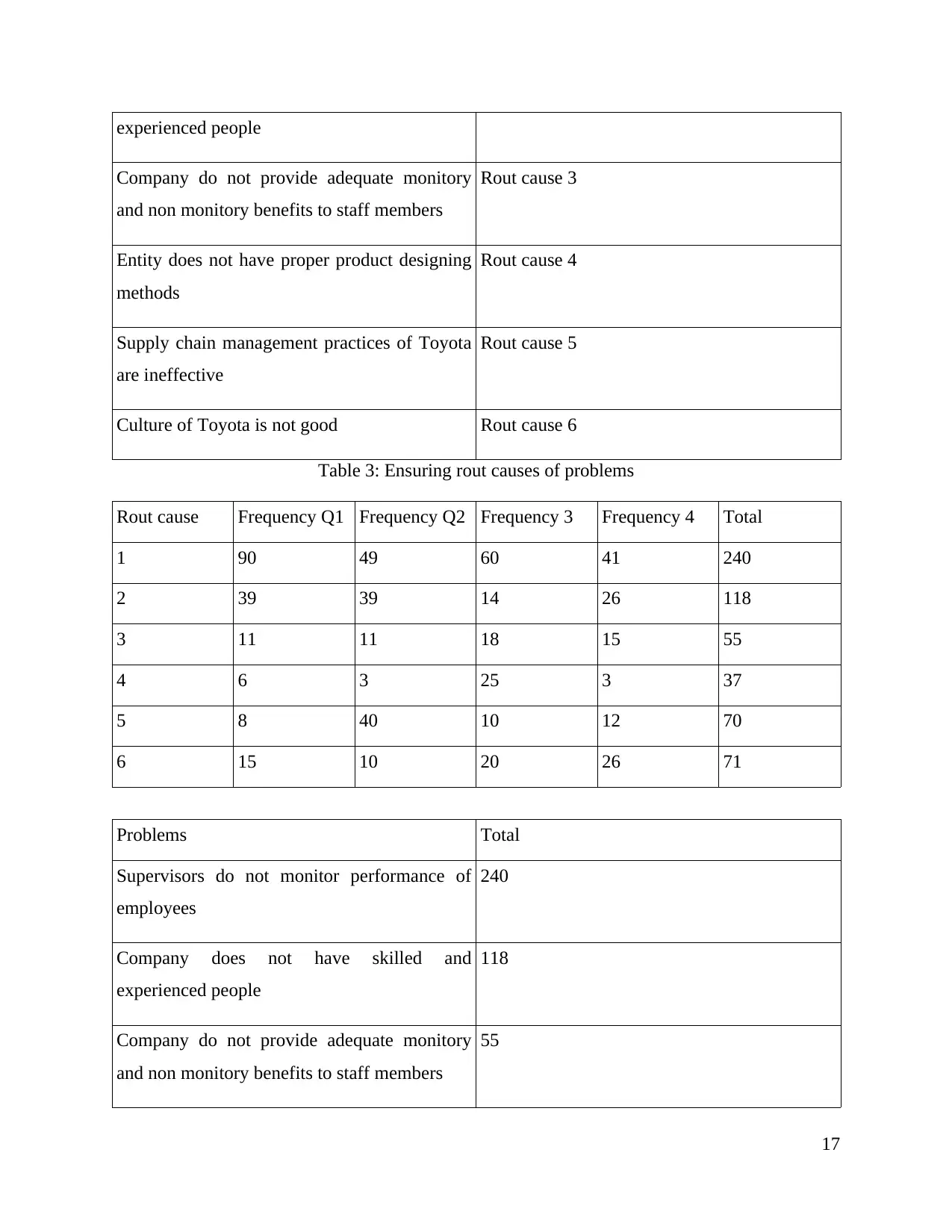
Company do not provide adequate monitory
and non monitory benefits to staff members
Rout cause 3
Entity does not have proper product designing
methods
Rout cause 4
Supply chain management practices of Toyota
are ineffective
Rout cause 5
Culture of Toyota is not good Rout cause 6
Table 3: Ensuring rout causes of problems
Rout cause Frequency Q1 Frequency Q2 Frequency 3 Frequency 4 Total
1 90 49 60 41 240
2 39 39 14 26 118
3 11 11 18 15 55
4 6 3 25 3 37
5 8 40 10 12 70
6 15 10 20 26 71
Problems Total
Supervisors do not monitor performance of
employees
240
Company does not have skilled and
experienced people
118
Company do not provide adequate monitory
and non monitory benefits to staff members
55
17
Paraphrase This Document
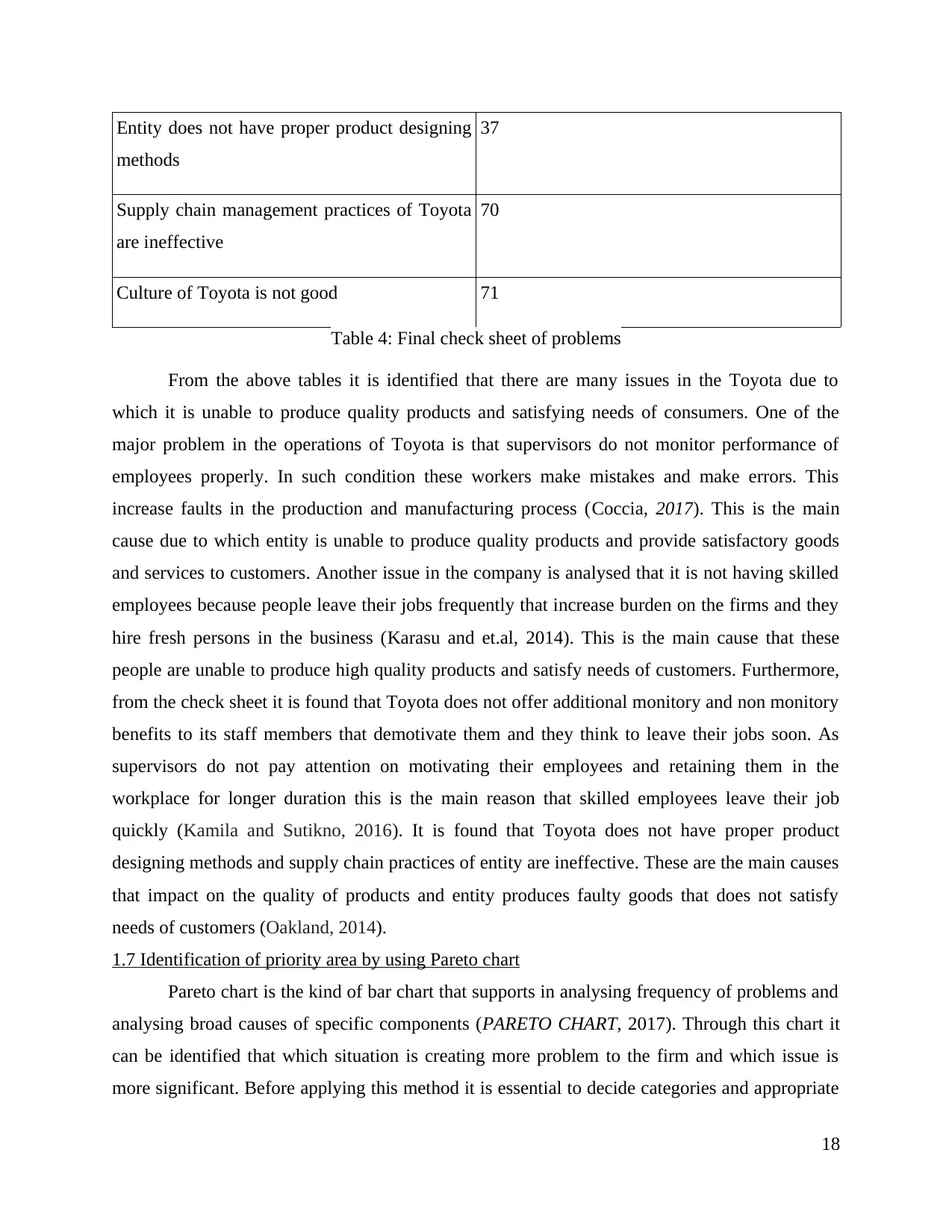
methods
37
Supply chain management practices of Toyota
are ineffective
70
Culture of Toyota is not good 71
Table 4: Final check sheet of problems
From the above tables it is identified that there are many issues in the Toyota due to
which it is unable to produce quality products and satisfying needs of consumers. One of the
major problem in the operations of Toyota is that supervisors do not monitor performance of
employees properly. In such condition these workers make mistakes and make errors. This
increase faults in the production and manufacturing process (Coccia, 2017). This is the main
cause due to which entity is unable to produce quality products and provide satisfactory goods
and services to customers. Another issue in the company is analysed that it is not having skilled
employees because people leave their jobs frequently that increase burden on the firms and they
hire fresh persons in the business (Karasu and et.al, 2014). This is the main cause that these
people are unable to produce high quality products and satisfy needs of customers. Furthermore,
from the check sheet it is found that Toyota does not offer additional monitory and non monitory
benefits to its staff members that demotivate them and they think to leave their jobs soon. As
supervisors do not pay attention on motivating their employees and retaining them in the
workplace for longer duration this is the main reason that skilled employees leave their job
quickly (Kamila and Sutikno, 2016). It is found that Toyota does not have proper product
designing methods and supply chain practices of entity are ineffective. These are the main causes
that impact on the quality of products and entity produces faulty goods that does not satisfy
needs of customers (Oakland, 2014).
1.7 Identification of priority area by using Pareto chart
Pareto chart is the kind of bar chart that supports in analysing frequency of problems and
analysing broad causes of specific components (PARETO CHART, 2017). Through this chart it
can be identified that which situation is creating more problem to the firm and which issue is
more significant. Before applying this method it is essential to decide categories and appropriate
18
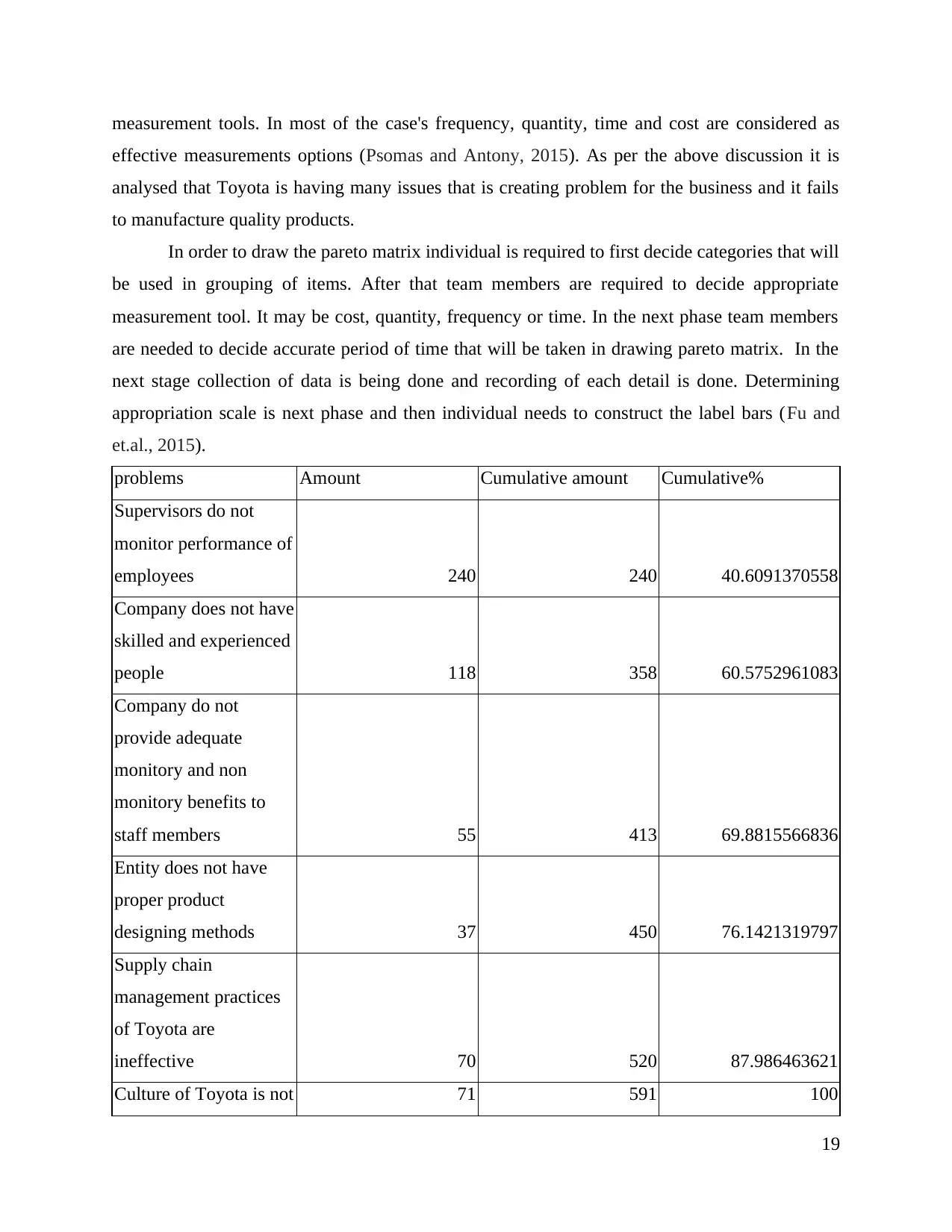
effective measurements options (Psomas and Antony, 2015). As per the above discussion it is
analysed that Toyota is having many issues that is creating problem for the business and it fails
to manufacture quality products.
In order to draw the pareto matrix individual is required to first decide categories that will
be used in grouping of items. After that team members are required to decide appropriate
measurement tool. It may be cost, quantity, frequency or time. In the next phase team members
are needed to decide accurate period of time that will be taken in drawing pareto matrix. In the
next stage collection of data is being done and recording of each detail is done. Determining
appropriation scale is next phase and then individual needs to construct the label bars (Fu and
et.al., 2015).
problems Amount Cumulative amount Cumulative%
Supervisors do not
monitor performance of
employees 240 240 40.6091370558
Company does not have
skilled and experienced
people 118 358 60.5752961083
Company do not
provide adequate
monitory and non
monitory benefits to
staff members 55 413 69.8815566836
Entity does not have
proper product
designing methods 37 450 76.1421319797
Supply chain
management practices
of Toyota are
ineffective 70 520 87.986463621
Culture of Toyota is not 71 591 100
19
⊘ This is a preview!⊘
Do you want full access?
Subscribe today to unlock all pages.

Trusted by 1+ million students worldwide

Total 591
Table 5: calculation for Pareto chart
From the above Pareto chart it is analysed that there are two major priority areas that
need to be looked upon by the quality team. One of the main issue in the Toyota is that
supervisors do not monitor performance of employees. This is the major area to work op because
if supervisor monitor working performance of each person well then it will help in identifying
their mistakes and providing them training accordingly so that such type of mistakes can not be
repeated in the future (PARETO CHART. 2017). Thus, it is the priority area and Toyota needs to
improve this aspect soon. If manager monitor each employee performance then it may help in
providing satisfactory products and services to the consumers. Second priority area is that
company does not have skilled employees in the workplace. The main reason of this problem is
that it is not offering additional monitory and non monitory benefits to its workers thus, they feel
demotivated. In such condition skilled and experienced people leave their jobs soon. That is why
entity losses its skilled workers those who have great experienced in this field. These are priority
areas that are essential to be looked on by the higher authorities. By resolving these issues
20
Illustration 3: Pareto chart
Paraphrase This Document
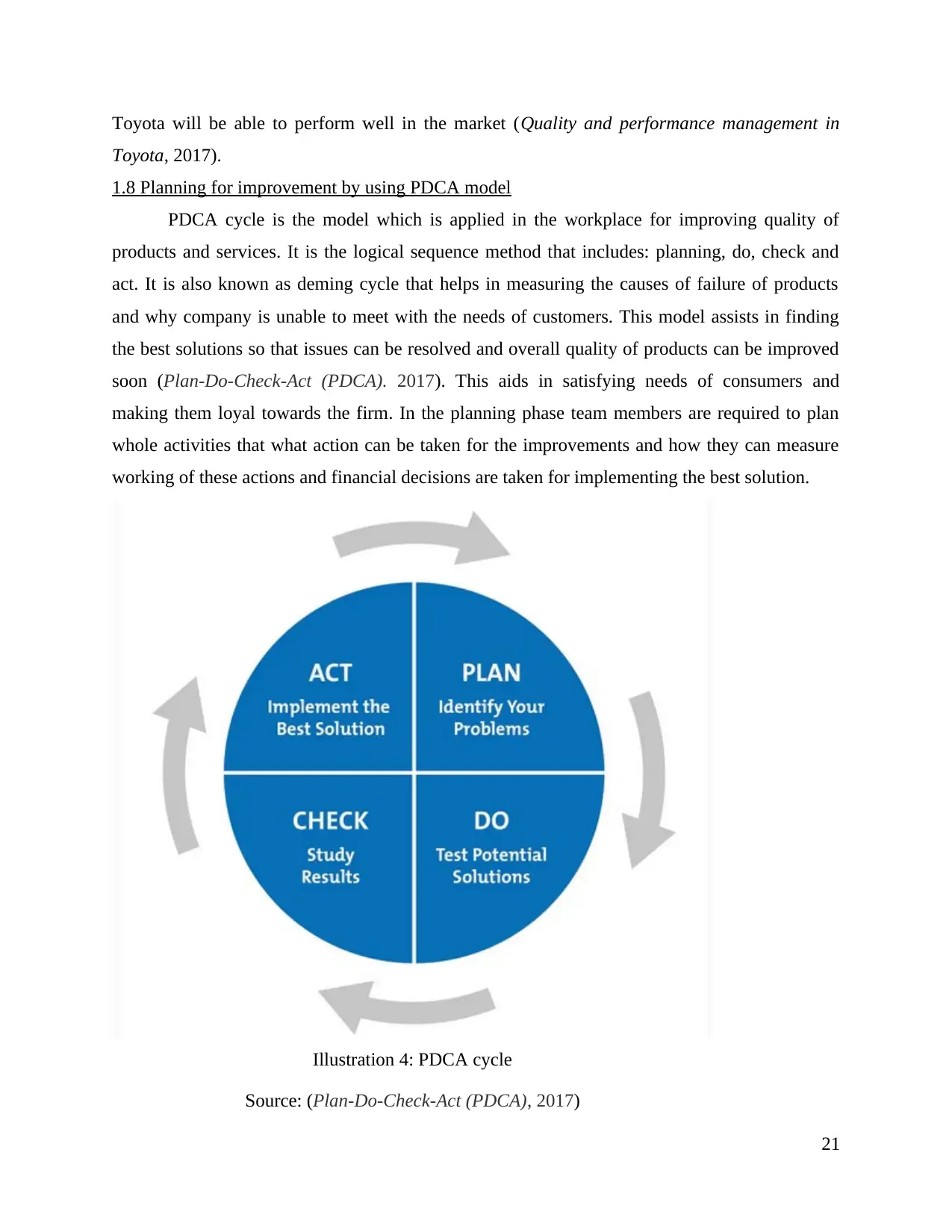
Toyota, 2017).
1.8 Planning for improvement by using PDCA model
PDCA cycle is the model which is applied in the workplace for improving quality of
products and services. It is the logical sequence method that includes: planning, do, check and
act. It is also known as deming cycle that helps in measuring the causes of failure of products
and why company is unable to meet with the needs of customers. This model assists in finding
the best solutions so that issues can be resolved and overall quality of products can be improved
soon (Plan-Do-Check-Act (PDCA). 2017). This aids in satisfying needs of consumers and
making them loyal towards the firm. In the planning phase team members are required to plan
whole activities that what action can be taken for the improvements and how they can measure
working of these actions and financial decisions are taken for implementing the best solution.
Illustration 4: PDCA cycle
Source: (Plan-Do-Check-Act (PDCA), 2017)
21
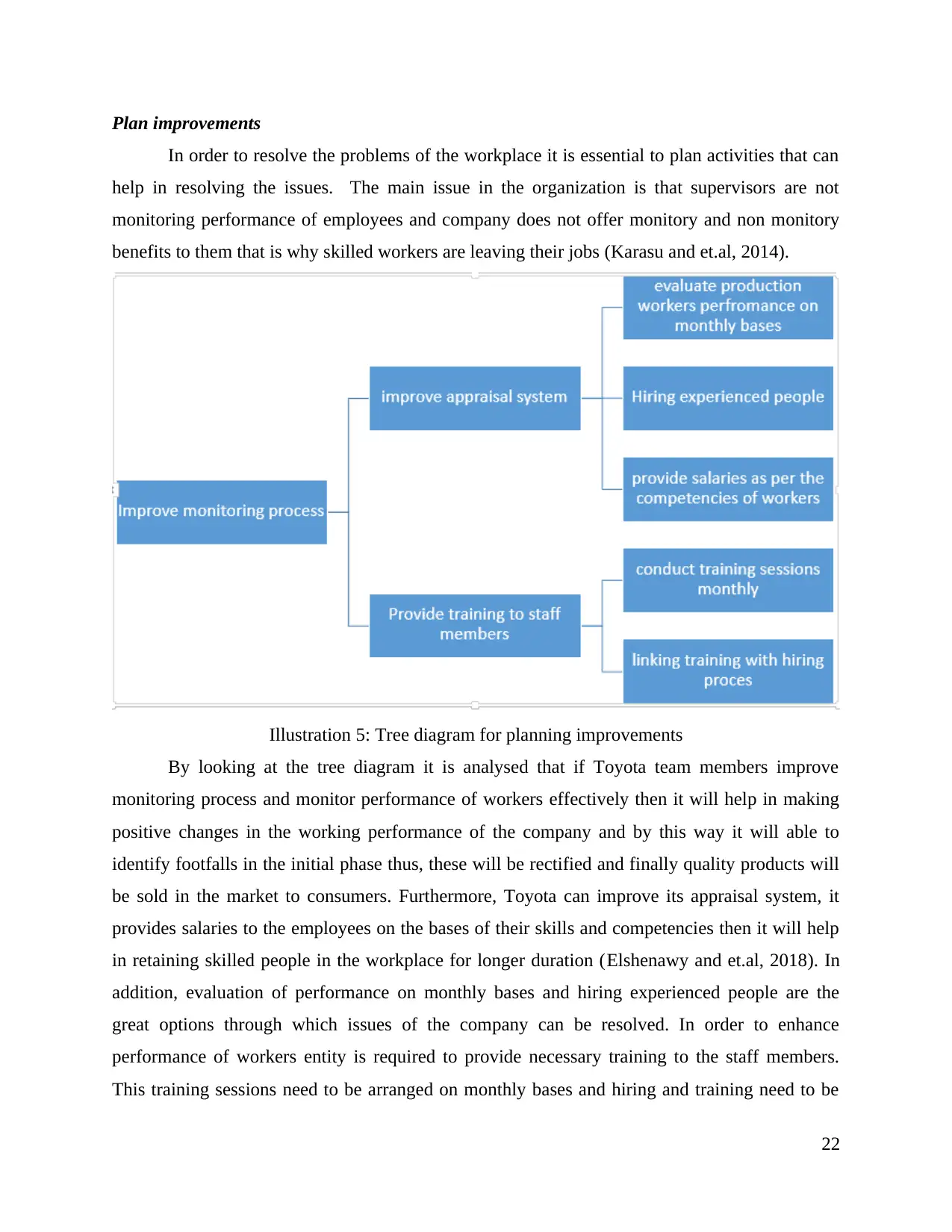
In order to resolve the problems of the workplace it is essential to plan activities that can
help in resolving the issues. The main issue in the organization is that supervisors are not
monitoring performance of employees and company does not offer monitory and non monitory
benefits to them that is why skilled workers are leaving their jobs (Karasu and et.al, 2014).
Illustration 5: Tree diagram for planning improvements
By looking at the tree diagram it is analysed that if Toyota team members improve
monitoring process and monitor performance of workers effectively then it will help in making
positive changes in the working performance of the company and by this way it will able to
identify footfalls in the initial phase thus, these will be rectified and finally quality products will
be sold in the market to consumers. Furthermore, Toyota can improve its appraisal system, it
provides salaries to the employees on the bases of their skills and competencies then it will help
in retaining skilled people in the workplace for longer duration (Elshenawy and et.al, 2018). In
addition, evaluation of performance on monthly bases and hiring experienced people are the
great options through which issues of the company can be resolved. In order to enhance
performance of workers entity is required to provide necessary training to the staff members.
This training sessions need to be arranged on monthly bases and hiring and training need to be
22
⊘ This is a preview!⊘
Do you want full access?
Subscribe today to unlock all pages.

Trusted by 1+ million students worldwide
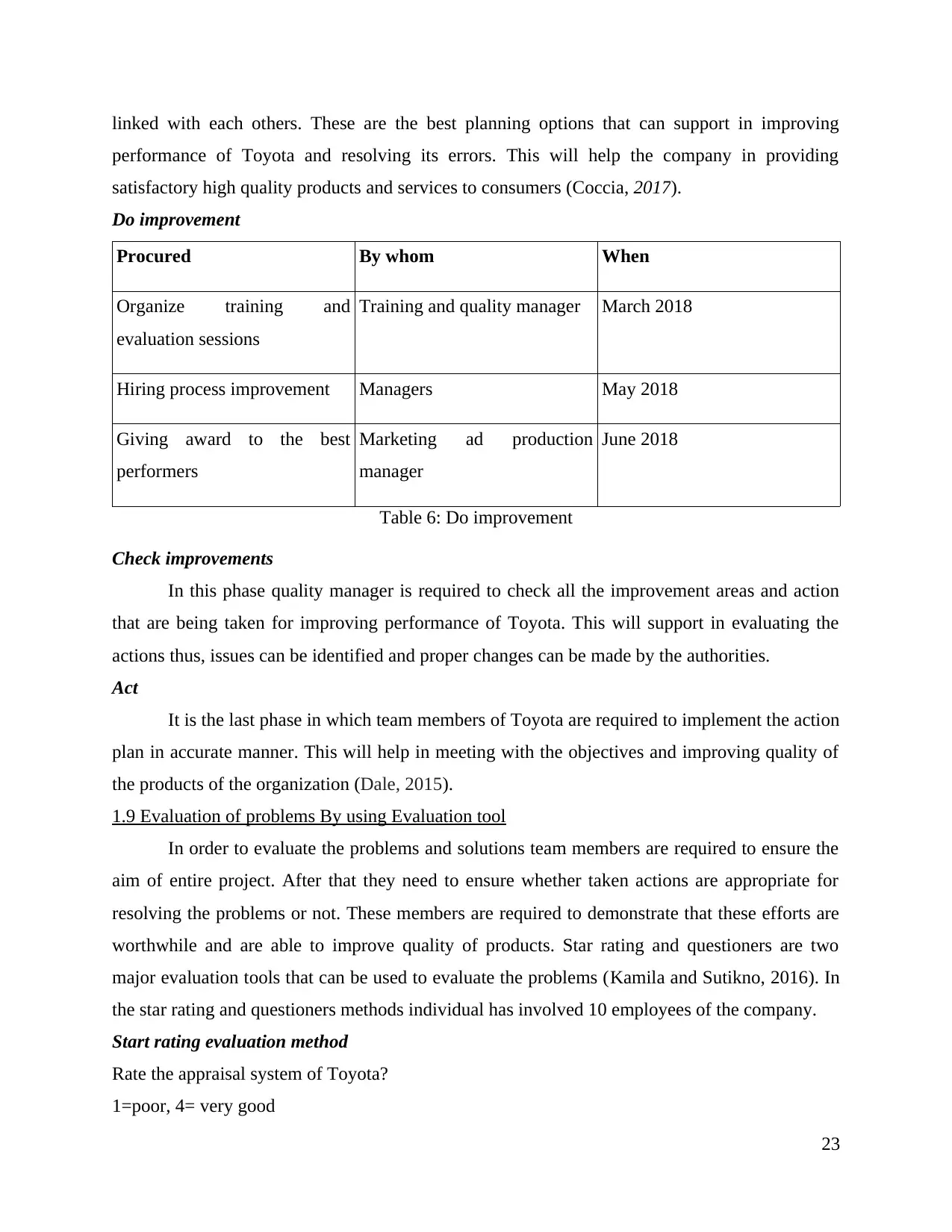
performance of Toyota and resolving its errors. This will help the company in providing
satisfactory high quality products and services to consumers (Coccia, 2017).
Do improvement
Procured By whom When
Organize training and
evaluation sessions
Training and quality manager March 2018
Hiring process improvement Managers May 2018
Giving award to the best
performers
Marketing ad production
manager
June 2018
Table 6: Do improvement
Check improvements
In this phase quality manager is required to check all the improvement areas and action
that are being taken for improving performance of Toyota. This will support in evaluating the
actions thus, issues can be identified and proper changes can be made by the authorities.
Act
It is the last phase in which team members of Toyota are required to implement the action
plan in accurate manner. This will help in meeting with the objectives and improving quality of
the products of the organization (Dale, 2015).
1.9 Evaluation of problems By using Evaluation tool
In order to evaluate the problems and solutions team members are required to ensure the
aim of entire project. After that they need to ensure whether taken actions are appropriate for
resolving the problems or not. These members are required to demonstrate that these efforts are
worthwhile and are able to improve quality of products. Star rating and questioners are two
major evaluation tools that can be used to evaluate the problems (Kamila and Sutikno, 2016). In
the star rating and questioners methods individual has involved 10 employees of the company.
Start rating evaluation method
Rate the appraisal system of Toyota?
1=poor, 4= very good
23
Paraphrase This Document
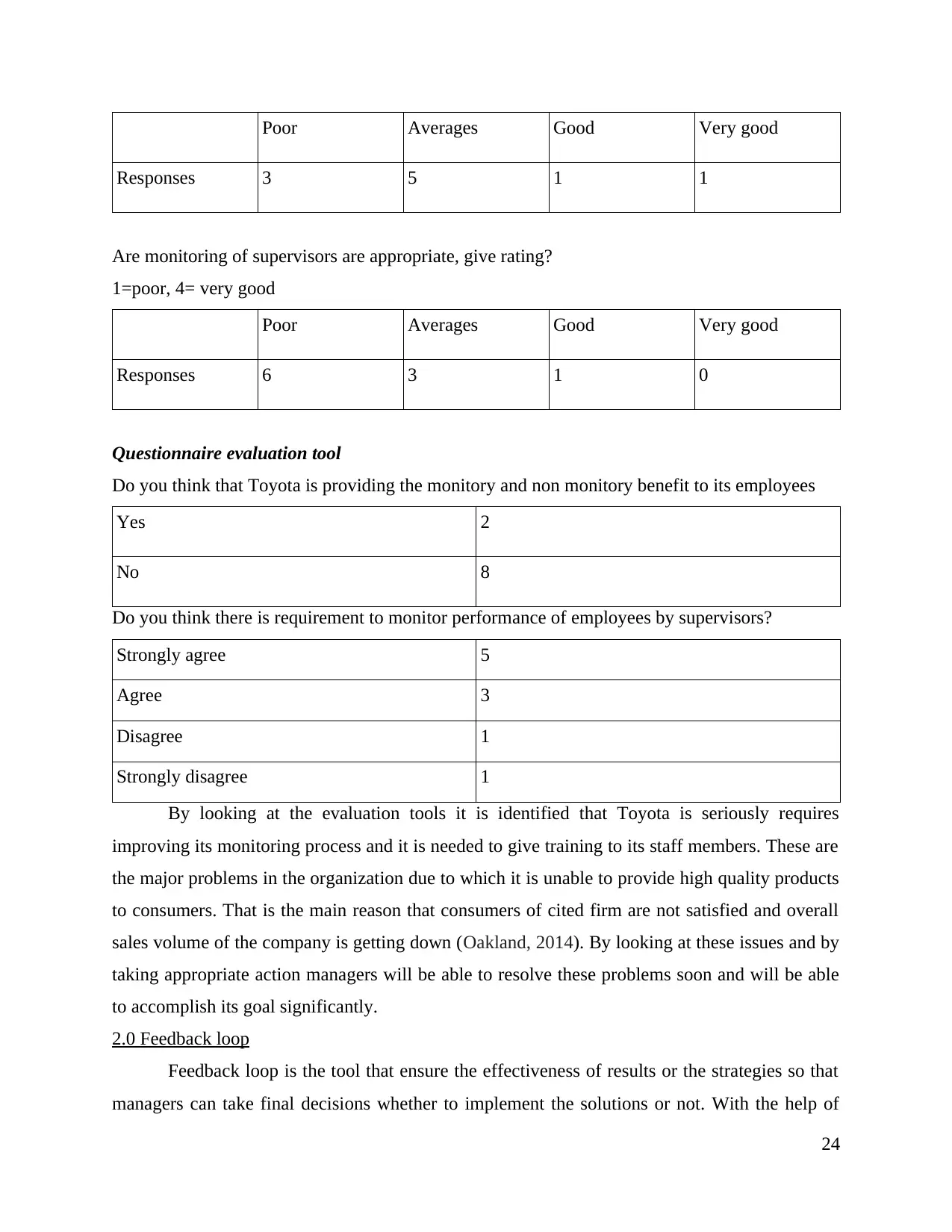
Responses 3 5 1 1
Are monitoring of supervisors are appropriate, give rating?
1=poor, 4= very good
Poor Averages Good Very good
Responses 6 3 1 0
Questionnaire evaluation tool
Do you think that Toyota is providing the monitory and non monitory benefit to its employees
Yes 2
No 8
Do you think there is requirement to monitor performance of employees by supervisors?
Strongly agree 5
Agree 3
Disagree 1
Strongly disagree 1
By looking at the evaluation tools it is identified that Toyota is seriously requires
improving its monitoring process and it is needed to give training to its staff members. These are
the major problems in the organization due to which it is unable to provide high quality products
to consumers. That is the main reason that consumers of cited firm are not satisfied and overall
sales volume of the company is getting down (Oakland, 2014). By looking at these issues and by
taking appropriate action managers will be able to resolve these problems soon and will be able
to accomplish its goal significantly.
2.0 Feedback loop
Feedback loop is the tool that ensure the effectiveness of results or the strategies so that
managers can take final decisions whether to implement the solutions or not. With the help of
24
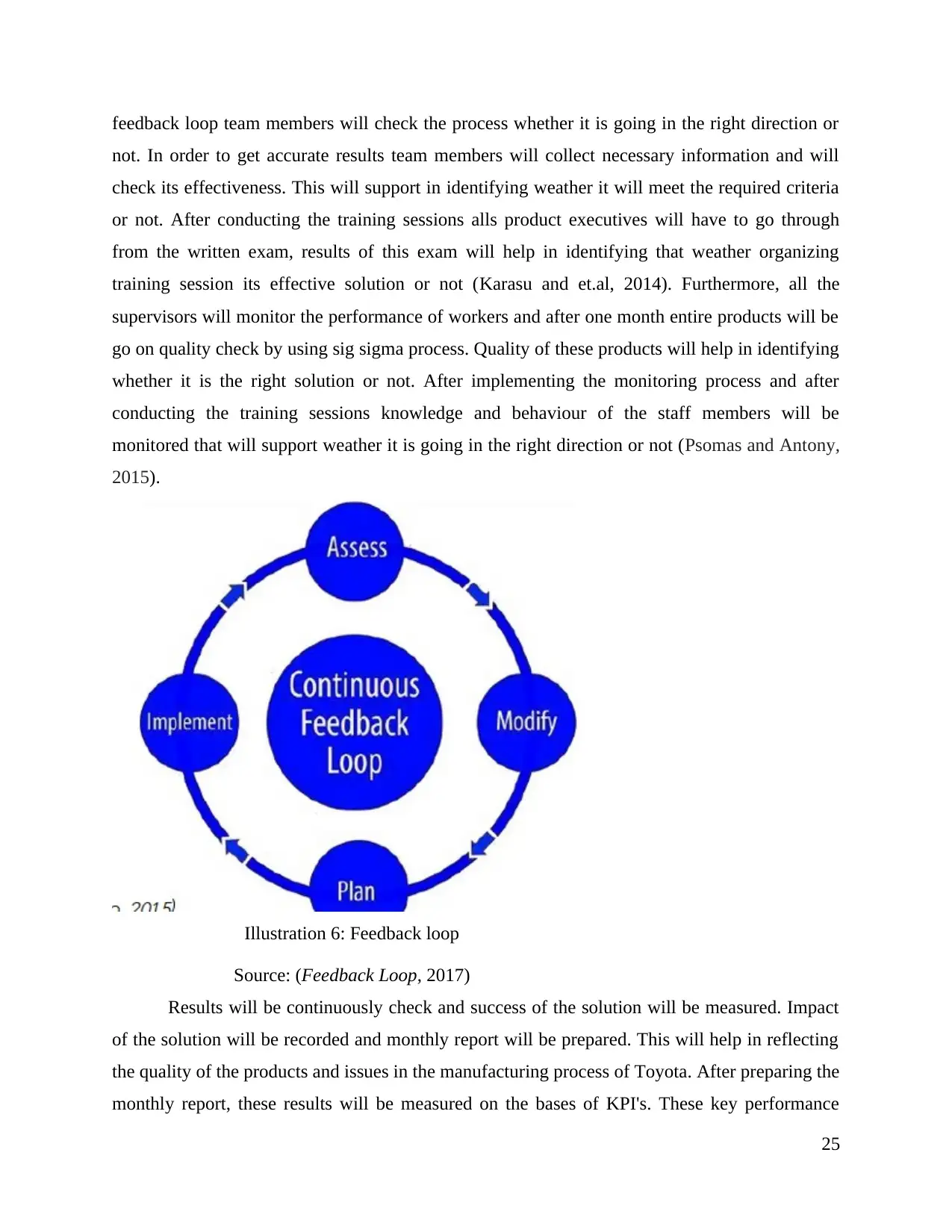
not. In order to get accurate results team members will collect necessary information and will
check its effectiveness. This will support in identifying weather it will meet the required criteria
or not. After conducting the training sessions alls product executives will have to go through
from the written exam, results of this exam will help in identifying that weather organizing
training session its effective solution or not (Karasu and et.al, 2014). Furthermore, all the
supervisors will monitor the performance of workers and after one month entire products will be
go on quality check by using sig sigma process. Quality of these products will help in identifying
whether it is the right solution or not. After implementing the monitoring process and after
conducting the training sessions knowledge and behaviour of the staff members will be
monitored that will support weather it is going in the right direction or not (Psomas and Antony,
2015).
Illustration 6: Feedback loop
Source: (Feedback Loop, 2017)
Results will be continuously check and success of the solution will be measured. Impact
of the solution will be recorded and monthly report will be prepared. This will help in reflecting
the quality of the products and issues in the manufacturing process of Toyota. After preparing the
monthly report, these results will be measured on the bases of KPI's. These key performance
25
⊘ This is a preview!⊘
Do you want full access?
Subscribe today to unlock all pages.

Trusted by 1+ million students worldwide
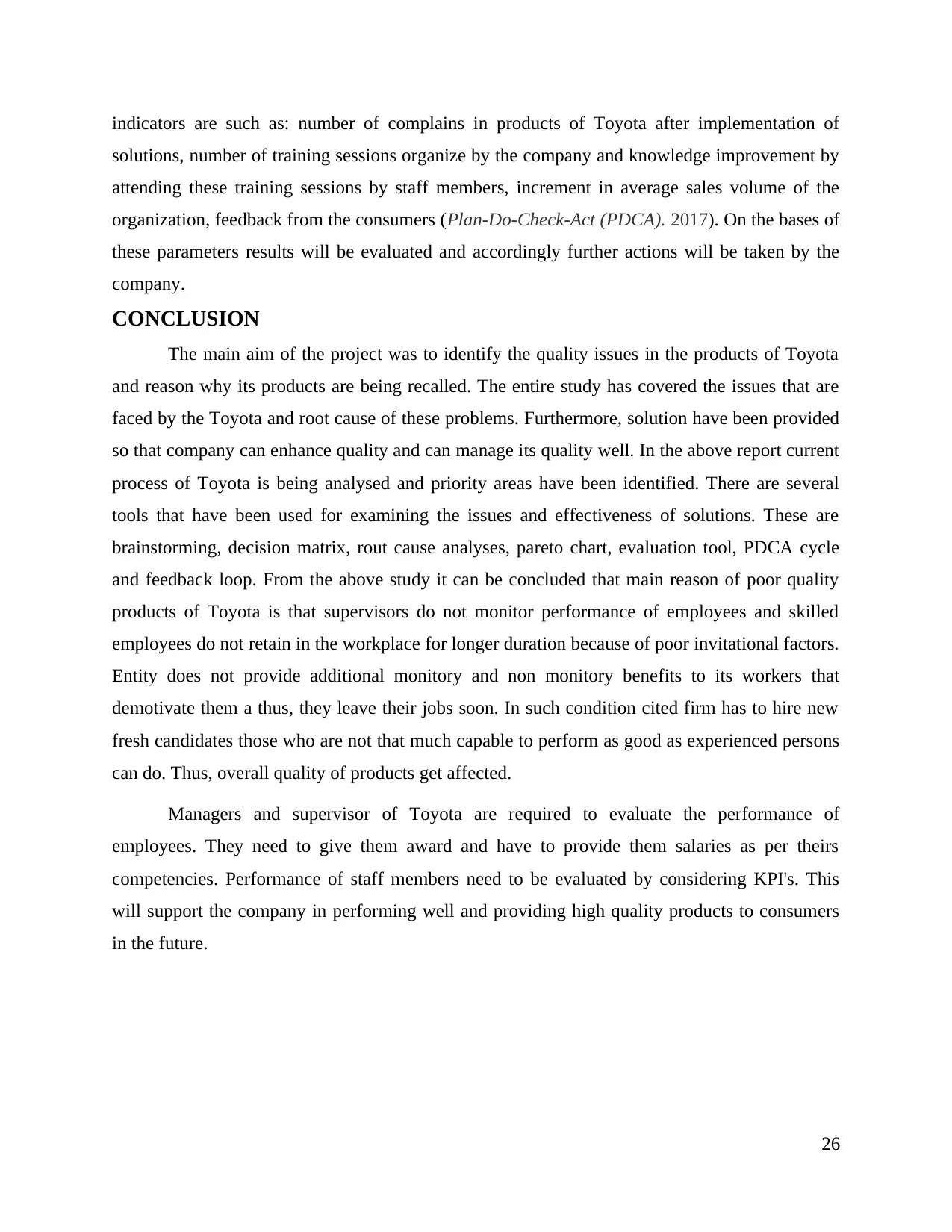
solutions, number of training sessions organize by the company and knowledge improvement by
attending these training sessions by staff members, increment in average sales volume of the
organization, feedback from the consumers (Plan-Do-Check-Act (PDCA). 2017). On the bases of
these parameters results will be evaluated and accordingly further actions will be taken by the
company.
CONCLUSION
The main aim of the project was to identify the quality issues in the products of Toyota
and reason why its products are being recalled. The entire study has covered the issues that are
faced by the Toyota and root cause of these problems. Furthermore, solution have been provided
so that company can enhance quality and can manage its quality well. In the above report current
process of Toyota is being analysed and priority areas have been identified. There are several
tools that have been used for examining the issues and effectiveness of solutions. These are
brainstorming, decision matrix, rout cause analyses, pareto chart, evaluation tool, PDCA cycle
and feedback loop. From the above study it can be concluded that main reason of poor quality
products of Toyota is that supervisors do not monitor performance of employees and skilled
employees do not retain in the workplace for longer duration because of poor invitational factors.
Entity does not provide additional monitory and non monitory benefits to its workers that
demotivate them a thus, they leave their jobs soon. In such condition cited firm has to hire new
fresh candidates those who are not that much capable to perform as good as experienced persons
can do. Thus, overall quality of products get affected.
Managers and supervisor of Toyota are required to evaluate the performance of
employees. They need to give them award and have to provide them salaries as per theirs
competencies. Performance of staff members need to be evaluated by considering KPI's. This
will support the company in performing well and providing high quality products to consumers
in the future.
26
Paraphrase This Document
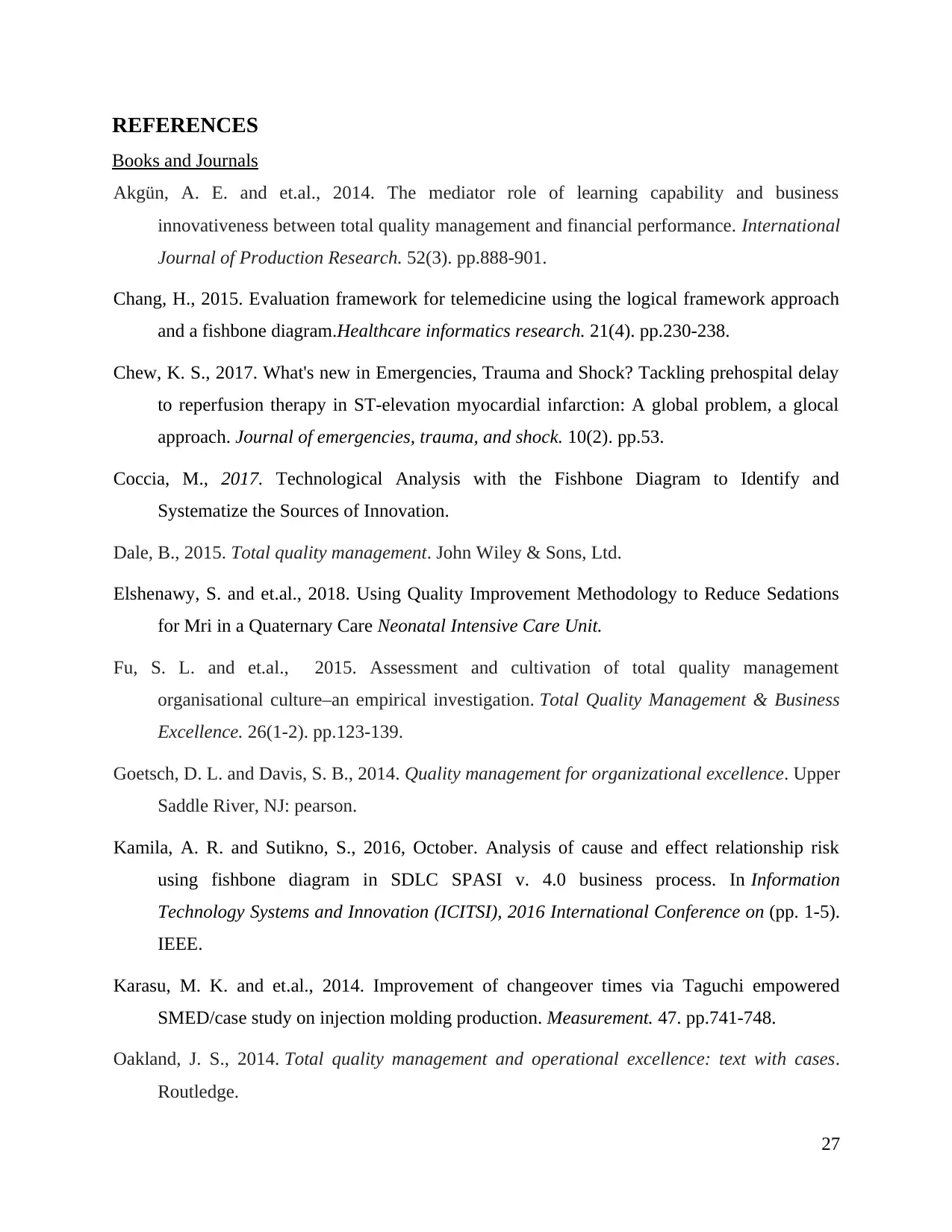
Books and Journals
Akgün, A. E. and et.al., 2014. The mediator role of learning capability and business
innovativeness between total quality management and financial performance. International
Journal of Production Research. 52(3). pp.888-901.
Chang, H., 2015. Evaluation framework for telemedicine using the logical framework approach
and a fishbone diagram.Healthcare informatics research. 21(4). pp.230-238.
Chew, K. S., 2017. What's new in Emergencies, Trauma and Shock? Tackling prehospital delay
to reperfusion therapy in ST-elevation myocardial infarction: A global problem, a glocal
approach. Journal of emergencies, trauma, and shock. 10(2). pp.53.
Coccia, M., 2017. Technological Analysis with the Fishbone Diagram to Identify and
Systematize the Sources of Innovation.
Dale, B., 2015. Total quality management. John Wiley & Sons, Ltd.
Elshenawy, S. and et.al., 2018. Using Quality Improvement Methodology to Reduce Sedations
for Mri in a Quaternary Care Neonatal Intensive Care Unit.
Fu, S. L. and et.al., 2015. Assessment and cultivation of total quality management
organisational culture–an empirical investigation. Total Quality Management & Business
Excellence. 26(1-2). pp.123-139.
Goetsch, D. L. and Davis, S. B., 2014. Quality management for organizational excellence. Upper
Saddle River, NJ: pearson.
Kamila, A. R. and Sutikno, S., 2016, October. Analysis of cause and effect relationship risk
using fishbone diagram in SDLC SPASI v. 4.0 business process. In Information
Technology Systems and Innovation (ICITSI), 2016 International Conference on (pp. 1-5).
IEEE.
Karasu, M. K. and et.al., 2014. Improvement of changeover times via Taguchi empowered
SMED/case study on injection molding production. Measurement. 47. pp.741-748.
Oakland, J. S., 2014. Total quality management and operational excellence: text with cases.
Routledge.
27
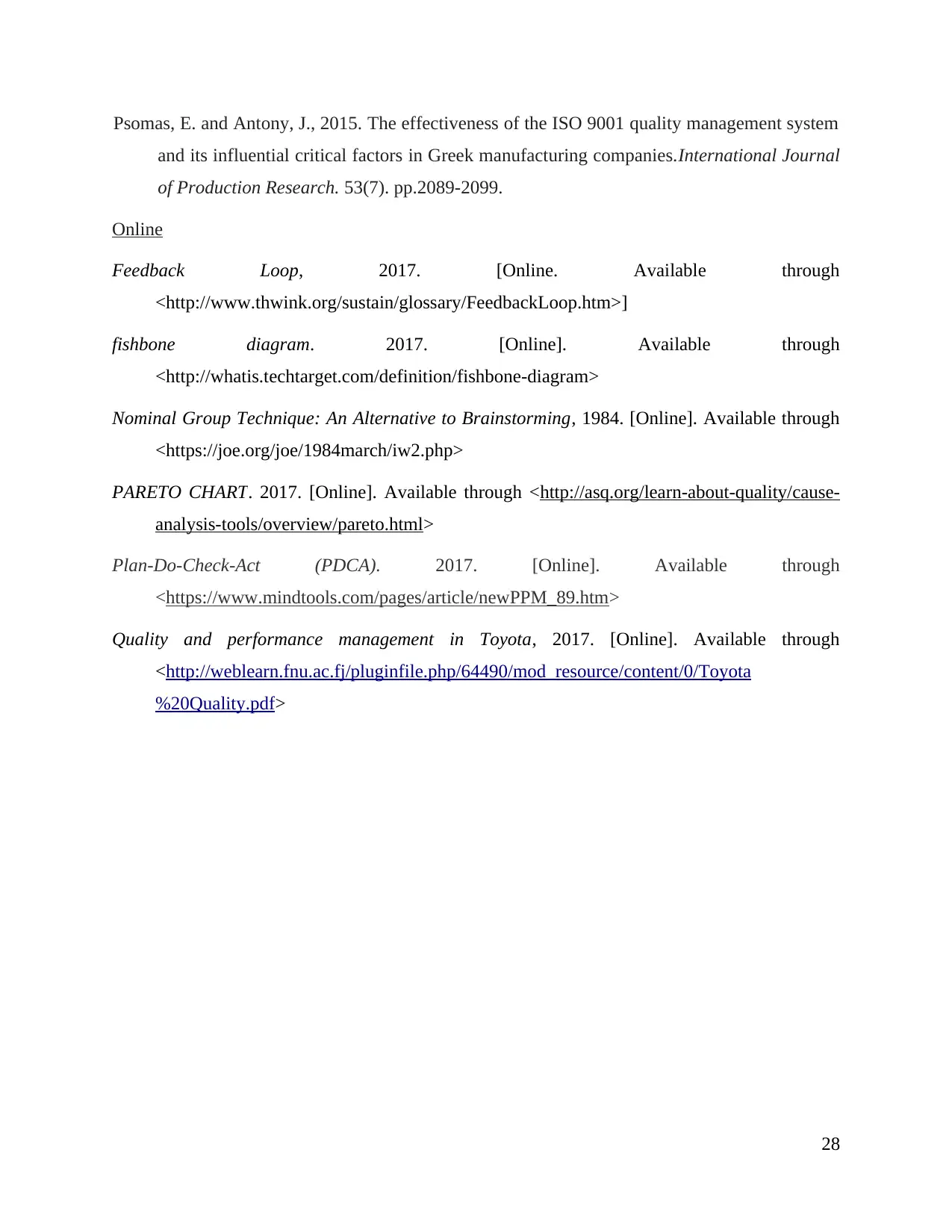
and its influential critical factors in Greek manufacturing companies.International Journal
of Production Research. 53(7). pp.2089-2099.
Online
Feedback Loop, 2017. [Online. Available through
<http://www.thwink.org/sustain/glossary/FeedbackLoop.htm>]
fishbone diagram. 2017. [Online]. Available through
<http://whatis.techtarget.com/definition/fishbone-diagram>
Nominal Group Technique: An Alternative to Brainstorming, 1984. [Online]. Available through
<https://joe.org/joe/1984march/iw2.php>
PARETO CHART. 2017. [Online]. Available through <http://asq.org/learn-about-quality/cause-
analysis-tools/overview/pareto.html>
Plan-Do-Check-Act (PDCA). 2017. [Online]. Available through
<https://www.mindtools.com/pages/article/newPPM_89.htm>
Quality and performance management in Toyota, 2017. [Online]. Available through
<http://weblearn.fnu.ac.fj/pluginfile.php/64490/mod_resource/content/0/Toyota
%20Quality.pdf>
28
⊘ This is a preview!⊘
Do you want full access?
Subscribe today to unlock all pages.

Trusted by 1+ million students worldwide

Your All-in-One AI-Powered Toolkit for Academic Success.
+13062052269
info@desklib.com
Available 24*7 on WhatsApp / Email
© 2024 | Zucol Services PVT LTD | All rights reserved.