Transportation Outsourcing RFQ Report for ABC Company
VerifiedAdded on 2022/10/18
|15
|3663
|10
Report
AI Summary
This report examines the transportation logistics of ABC Company, focusing on the decision to outsource its fleet operations and the subsequent Request for Quotation (RFQ) process. The report begins with an introduction to the importance of transportation management and the role of third-party logi...
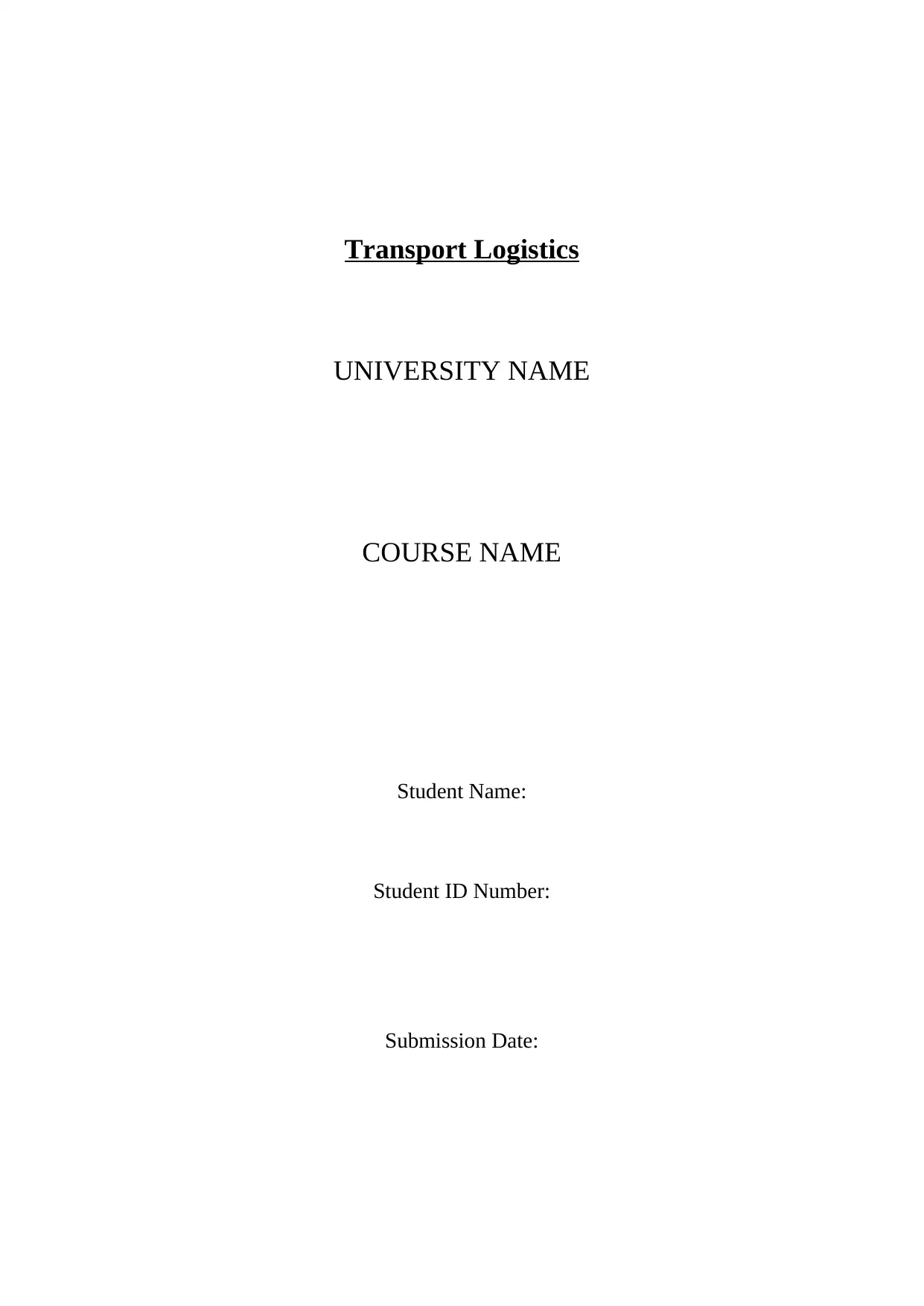
Transport Logistics
UNIVERSITY NAME
COURSE NAME
Student Name:
Student ID Number:
Submission Date:
UNIVERSITY NAME
COURSE NAME
Student Name:
Student ID Number:
Submission Date:
Paraphrase This Document
Need a fresh take? Get an instant paraphrase of this document with our AI Paraphraser
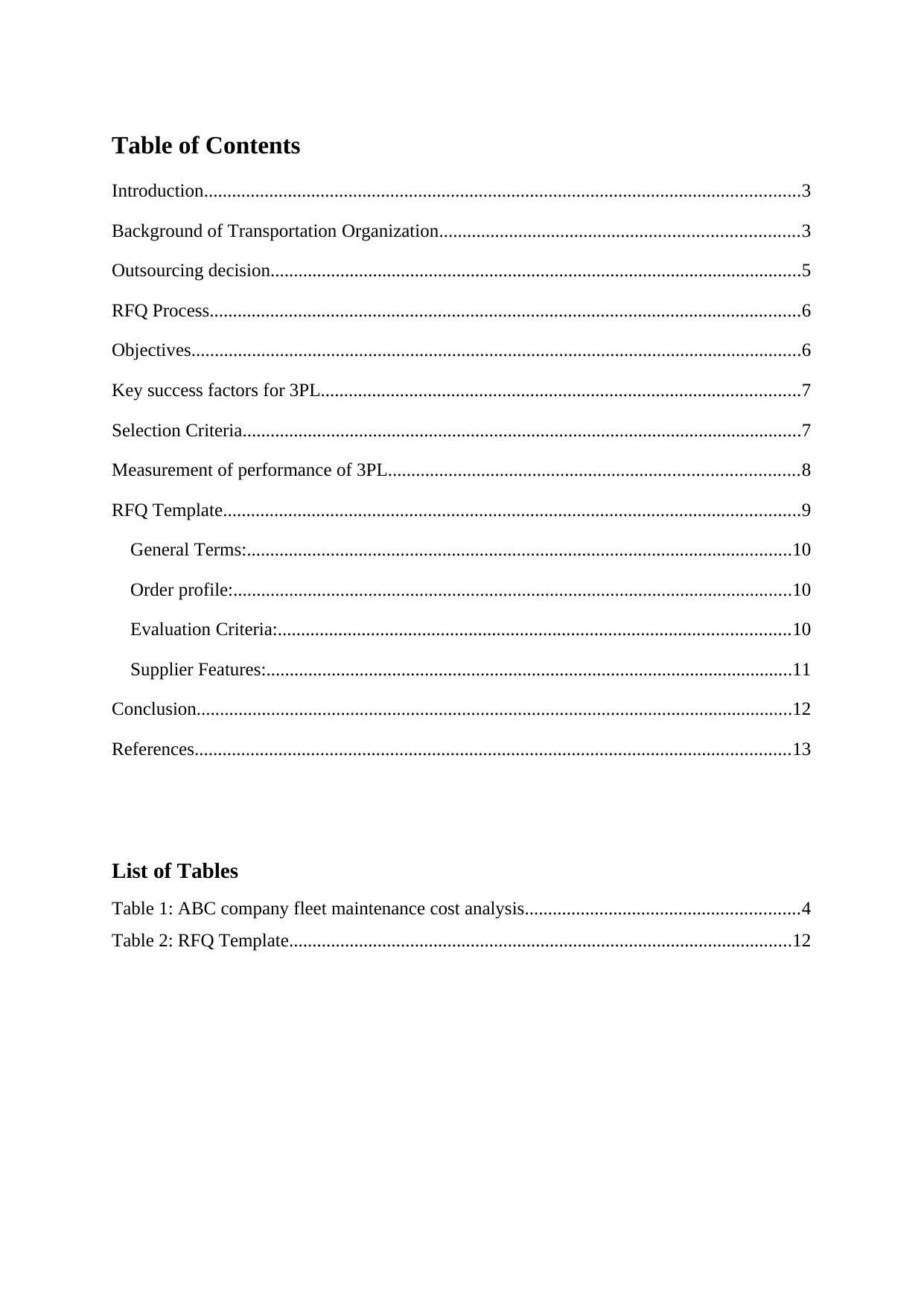
Table of Contents
Introduction................................................................................................................................3
Background of Transportation Organization.............................................................................3
Outsourcing decision..................................................................................................................5
RFQ Process...............................................................................................................................6
Objectives...................................................................................................................................6
Key success factors for 3PL.......................................................................................................7
Selection Criteria........................................................................................................................7
Measurement of performance of 3PL........................................................................................8
RFQ Template............................................................................................................................9
General Terms:.....................................................................................................................10
Order profile:........................................................................................................................10
Evaluation Criteria:..............................................................................................................10
Supplier Features:.................................................................................................................11
Conclusion................................................................................................................................12
References................................................................................................................................13
List of Tables
Table 1: ABC company fleet maintenance cost analysis...........................................................4
Table 2: RFQ Template............................................................................................................12
Introduction................................................................................................................................3
Background of Transportation Organization.............................................................................3
Outsourcing decision..................................................................................................................5
RFQ Process...............................................................................................................................6
Objectives...................................................................................................................................6
Key success factors for 3PL.......................................................................................................7
Selection Criteria........................................................................................................................7
Measurement of performance of 3PL........................................................................................8
RFQ Template............................................................................................................................9
General Terms:.....................................................................................................................10
Order profile:........................................................................................................................10
Evaluation Criteria:..............................................................................................................10
Supplier Features:.................................................................................................................11
Conclusion................................................................................................................................12
References................................................................................................................................13
List of Tables
Table 1: ABC company fleet maintenance cost analysis...........................................................4
Table 2: RFQ Template............................................................................................................12
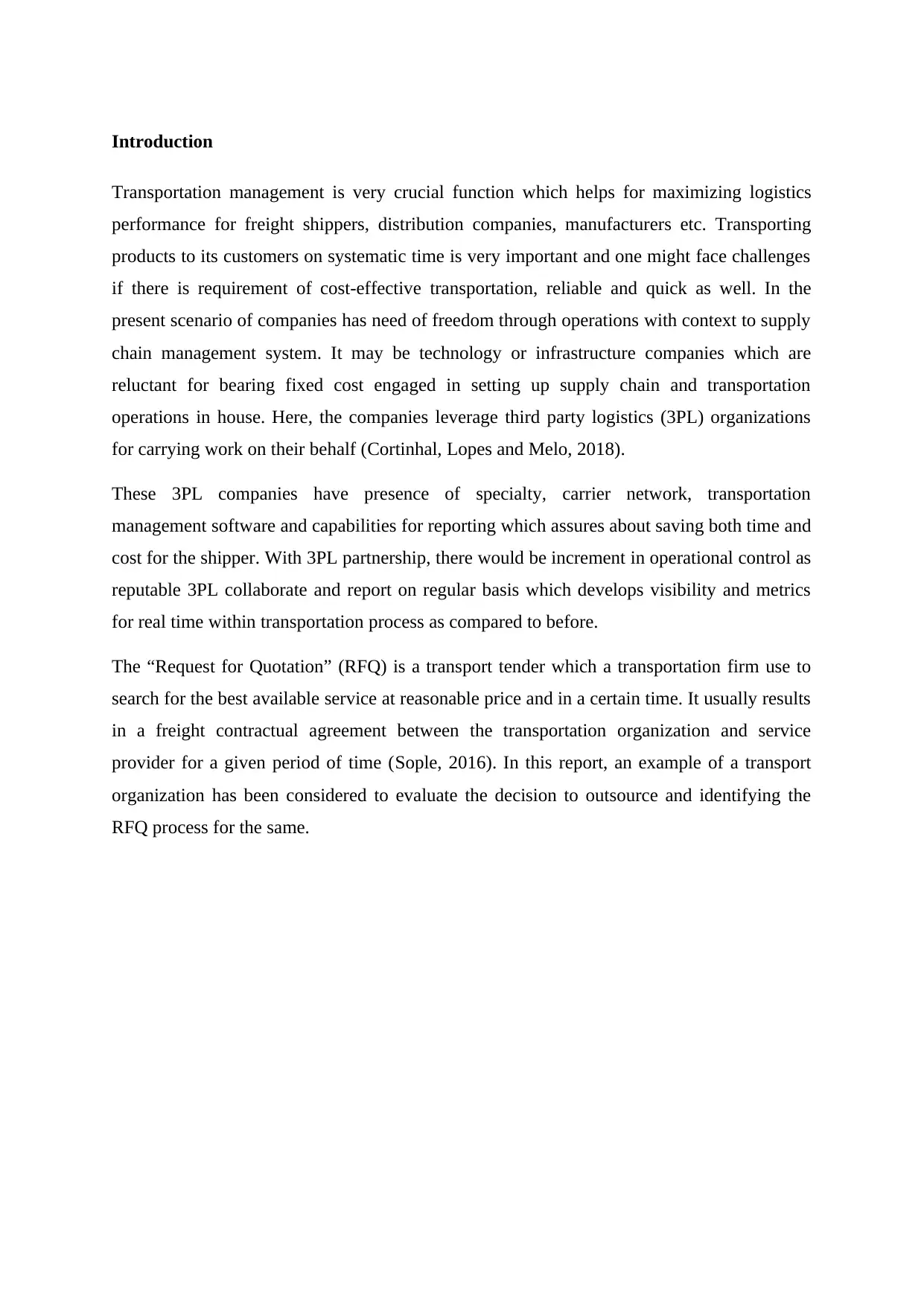
Introduction
Transportation management is very crucial function which helps for maximizing logistics
performance for freight shippers, distribution companies, manufacturers etc. Transporting
products to its customers on systematic time is very important and one might face challenges
if there is requirement of cost-effective transportation, reliable and quick as well. In the
present scenario of companies has need of freedom through operations with context to supply
chain management system. It may be technology or infrastructure companies which are
reluctant for bearing fixed cost engaged in setting up supply chain and transportation
operations in house. Here, the companies leverage third party logistics (3PL) organizations
for carrying work on their behalf (Cortinhal, Lopes and Melo, 2018).
These 3PL companies have presence of specialty, carrier network, transportation
management software and capabilities for reporting which assures about saving both time and
cost for the shipper. With 3PL partnership, there would be increment in operational control as
reputable 3PL collaborate and report on regular basis which develops visibility and metrics
for real time within transportation process as compared to before.
The “Request for Quotation” (RFQ) is a transport tender which a transportation firm use to
search for the best available service at reasonable price and in a certain time. It usually results
in a freight contractual agreement between the transportation organization and service
provider for a given period of time (Sople, 2016). In this report, an example of a transport
organization has been considered to evaluate the decision to outsource and identifying the
RFQ process for the same.
Transportation management is very crucial function which helps for maximizing logistics
performance for freight shippers, distribution companies, manufacturers etc. Transporting
products to its customers on systematic time is very important and one might face challenges
if there is requirement of cost-effective transportation, reliable and quick as well. In the
present scenario of companies has need of freedom through operations with context to supply
chain management system. It may be technology or infrastructure companies which are
reluctant for bearing fixed cost engaged in setting up supply chain and transportation
operations in house. Here, the companies leverage third party logistics (3PL) organizations
for carrying work on their behalf (Cortinhal, Lopes and Melo, 2018).
These 3PL companies have presence of specialty, carrier network, transportation
management software and capabilities for reporting which assures about saving both time and
cost for the shipper. With 3PL partnership, there would be increment in operational control as
reputable 3PL collaborate and report on regular basis which develops visibility and metrics
for real time within transportation process as compared to before.
The “Request for Quotation” (RFQ) is a transport tender which a transportation firm use to
search for the best available service at reasonable price and in a certain time. It usually results
in a freight contractual agreement between the transportation organization and service
provider for a given period of time (Sople, 2016). In this report, an example of a transport
organization has been considered to evaluate the decision to outsource and identifying the
RFQ process for the same.
⊘ This is a preview!⊘
Do you want full access?
Subscribe today to unlock all pages.

Trusted by 1+ million students worldwide
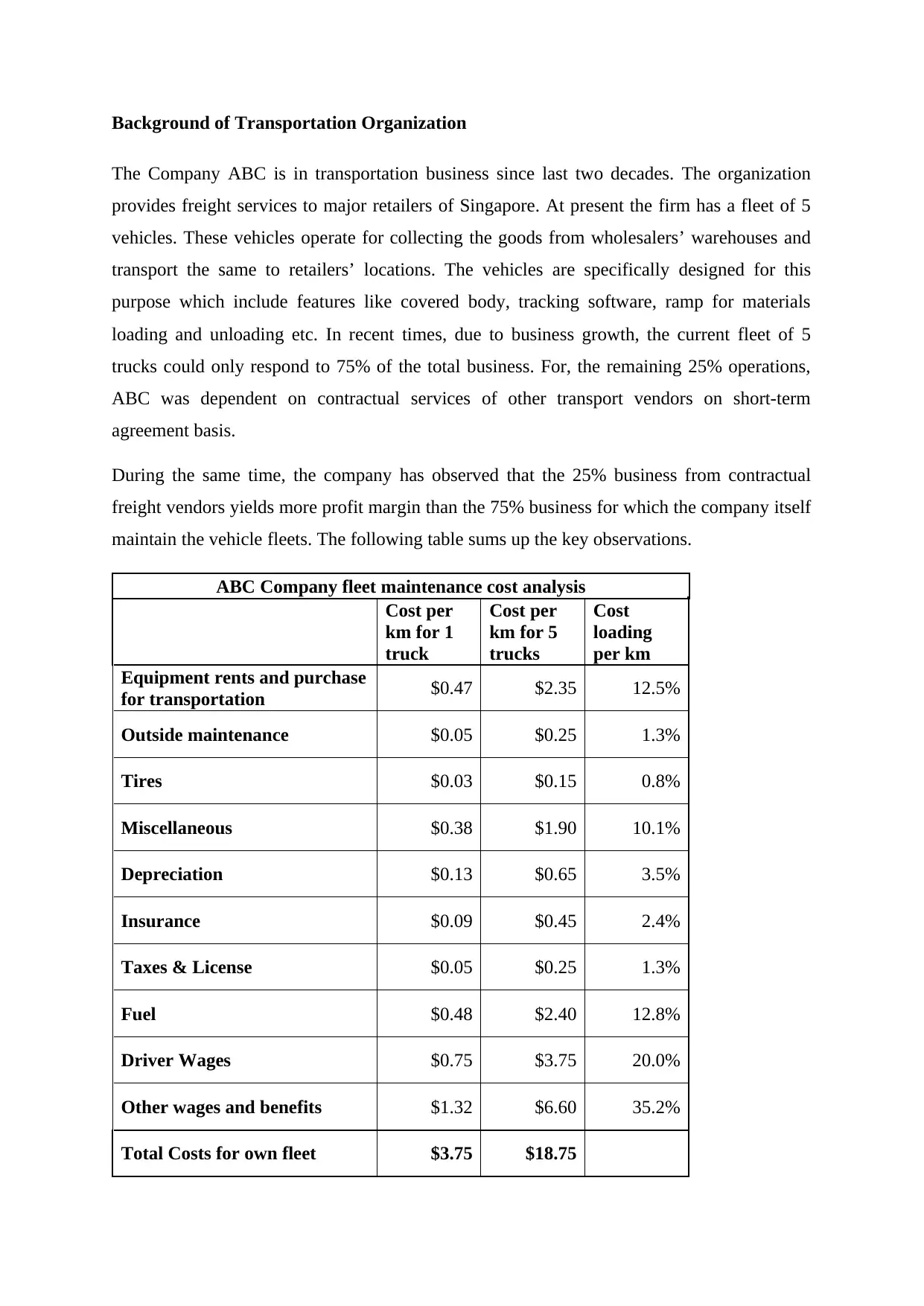
Background of Transportation Organization
The Company ABC is in transportation business since last two decades. The organization
provides freight services to major retailers of Singapore. At present the firm has a fleet of 5
vehicles. These vehicles operate for collecting the goods from wholesalers’ warehouses and
transport the same to retailers’ locations. The vehicles are specifically designed for this
purpose which include features like covered body, tracking software, ramp for materials
loading and unloading etc. In recent times, due to business growth, the current fleet of 5
trucks could only respond to 75% of the total business. For, the remaining 25% operations,
ABC was dependent on contractual services of other transport vendors on short-term
agreement basis.
During the same time, the company has observed that the 25% business from contractual
freight vendors yields more profit margin than the 75% business for which the company itself
maintain the vehicle fleets. The following table sums up the key observations.
ABC Company fleet maintenance cost analysis
Cost per
km for 1
truck
Cost per
km for 5
trucks
Cost
loading
per km
Equipment rents and purchase
for transportation $0.47 $2.35 12.5%
Outside maintenance $0.05 $0.25 1.3%
Tires $0.03 $0.15 0.8%
Miscellaneous $0.38 $1.90 10.1%
Depreciation $0.13 $0.65 3.5%
Insurance $0.09 $0.45 2.4%
Taxes & License $0.05 $0.25 1.3%
Fuel $0.48 $2.40 12.8%
Driver Wages $0.75 $3.75 20.0%
Other wages and benefits $1.32 $6.60 35.2%
Total Costs for own fleet $3.75 $18.75
The Company ABC is in transportation business since last two decades. The organization
provides freight services to major retailers of Singapore. At present the firm has a fleet of 5
vehicles. These vehicles operate for collecting the goods from wholesalers’ warehouses and
transport the same to retailers’ locations. The vehicles are specifically designed for this
purpose which include features like covered body, tracking software, ramp for materials
loading and unloading etc. In recent times, due to business growth, the current fleet of 5
trucks could only respond to 75% of the total business. For, the remaining 25% operations,
ABC was dependent on contractual services of other transport vendors on short-term
agreement basis.
During the same time, the company has observed that the 25% business from contractual
freight vendors yields more profit margin than the 75% business for which the company itself
maintain the vehicle fleets. The following table sums up the key observations.
ABC Company fleet maintenance cost analysis
Cost per
km for 1
truck
Cost per
km for 5
trucks
Cost
loading
per km
Equipment rents and purchase
for transportation $0.47 $2.35 12.5%
Outside maintenance $0.05 $0.25 1.3%
Tires $0.03 $0.15 0.8%
Miscellaneous $0.38 $1.90 10.1%
Depreciation $0.13 $0.65 3.5%
Insurance $0.09 $0.45 2.4%
Taxes & License $0.05 $0.25 1.3%
Fuel $0.48 $2.40 12.8%
Driver Wages $0.75 $3.75 20.0%
Other wages and benefits $1.32 $6.60 35.2%
Total Costs for own fleet $3.75 $18.75
Paraphrase This Document
Need a fresh take? Get an instant paraphrase of this document with our AI Paraphraser
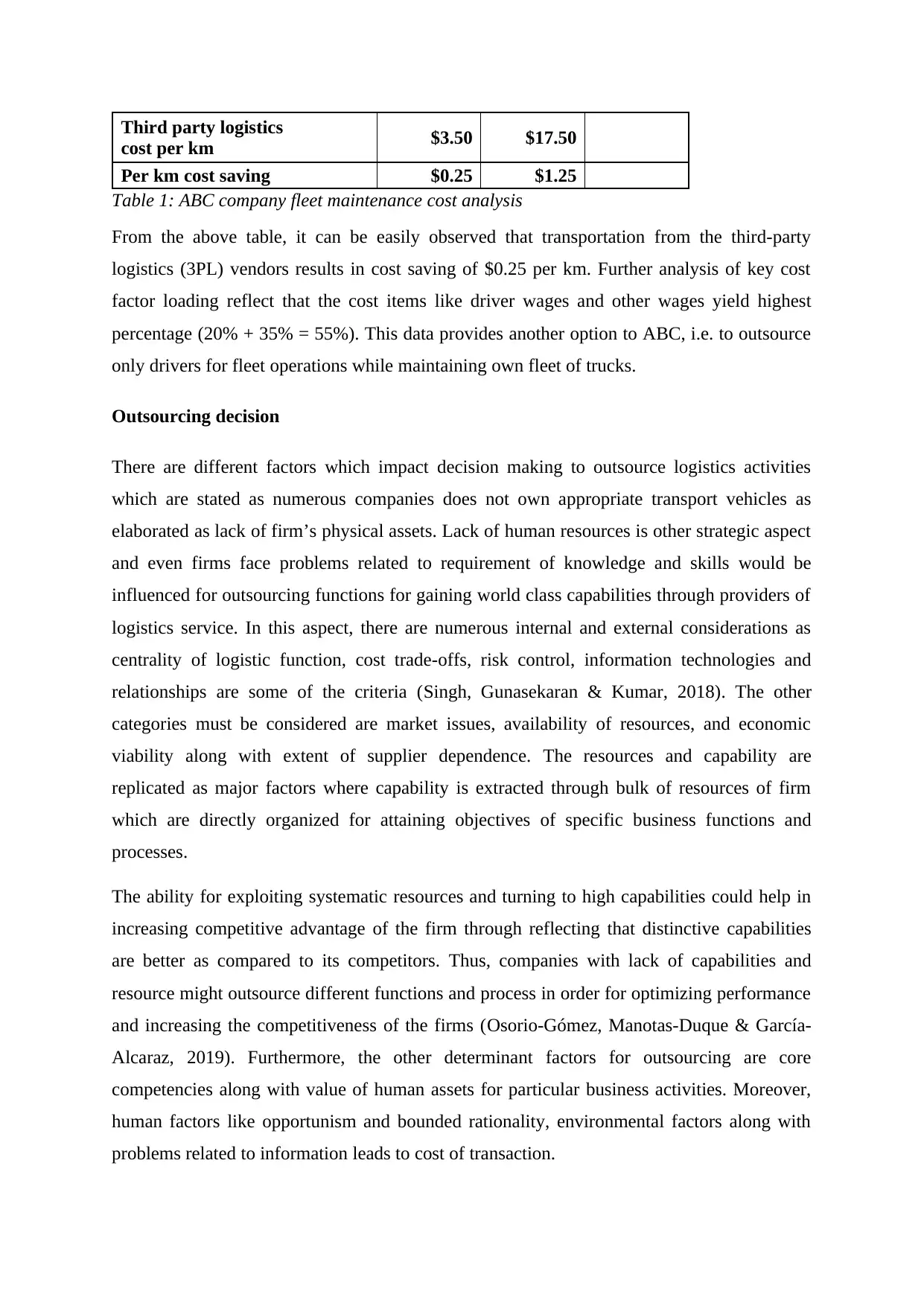
Third party logistics
cost per km $3.50 $17.50
Per km cost saving $0.25 $1.25
Table 1: ABC company fleet maintenance cost analysis
From the above table, it can be easily observed that transportation from the third-party
logistics (3PL) vendors results in cost saving of $0.25 per km. Further analysis of key cost
factor loading reflect that the cost items like driver wages and other wages yield highest
percentage (20% + 35% = 55%). This data provides another option to ABC, i.e. to outsource
only drivers for fleet operations while maintaining own fleet of trucks.
Outsourcing decision
There are different factors which impact decision making to outsource logistics activities
which are stated as numerous companies does not own appropriate transport vehicles as
elaborated as lack of firm’s physical assets. Lack of human resources is other strategic aspect
and even firms face problems related to requirement of knowledge and skills would be
influenced for outsourcing functions for gaining world class capabilities through providers of
logistics service. In this aspect, there are numerous internal and external considerations as
centrality of logistic function, cost trade-offs, risk control, information technologies and
relationships are some of the criteria (Singh, Gunasekaran & Kumar, 2018). The other
categories must be considered are market issues, availability of resources, and economic
viability along with extent of supplier dependence. The resources and capability are
replicated as major factors where capability is extracted through bulk of resources of firm
which are directly organized for attaining objectives of specific business functions and
processes.
The ability for exploiting systematic resources and turning to high capabilities could help in
increasing competitive advantage of the firm through reflecting that distinctive capabilities
are better as compared to its competitors. Thus, companies with lack of capabilities and
resource might outsource different functions and process in order for optimizing performance
and increasing the competitiveness of the firms (Osorio-Gómez, Manotas-Duque & García-
Alcaraz, 2019). Furthermore, the other determinant factors for outsourcing are core
competencies along with value of human assets for particular business activities. Moreover,
human factors like opportunism and bounded rationality, environmental factors along with
problems related to information leads to cost of transaction.
cost per km $3.50 $17.50
Per km cost saving $0.25 $1.25
Table 1: ABC company fleet maintenance cost analysis
From the above table, it can be easily observed that transportation from the third-party
logistics (3PL) vendors results in cost saving of $0.25 per km. Further analysis of key cost
factor loading reflect that the cost items like driver wages and other wages yield highest
percentage (20% + 35% = 55%). This data provides another option to ABC, i.e. to outsource
only drivers for fleet operations while maintaining own fleet of trucks.
Outsourcing decision
There are different factors which impact decision making to outsource logistics activities
which are stated as numerous companies does not own appropriate transport vehicles as
elaborated as lack of firm’s physical assets. Lack of human resources is other strategic aspect
and even firms face problems related to requirement of knowledge and skills would be
influenced for outsourcing functions for gaining world class capabilities through providers of
logistics service. In this aspect, there are numerous internal and external considerations as
centrality of logistic function, cost trade-offs, risk control, information technologies and
relationships are some of the criteria (Singh, Gunasekaran & Kumar, 2018). The other
categories must be considered are market issues, availability of resources, and economic
viability along with extent of supplier dependence. The resources and capability are
replicated as major factors where capability is extracted through bulk of resources of firm
which are directly organized for attaining objectives of specific business functions and
processes.
The ability for exploiting systematic resources and turning to high capabilities could help in
increasing competitive advantage of the firm through reflecting that distinctive capabilities
are better as compared to its competitors. Thus, companies with lack of capabilities and
resource might outsource different functions and process in order for optimizing performance
and increasing the competitiveness of the firms (Osorio-Gómez, Manotas-Duque & García-
Alcaraz, 2019). Furthermore, the other determinant factors for outsourcing are core
competencies along with value of human assets for particular business activities. Moreover,
human factors like opportunism and bounded rationality, environmental factors along with
problems related to information leads to cost of transaction.
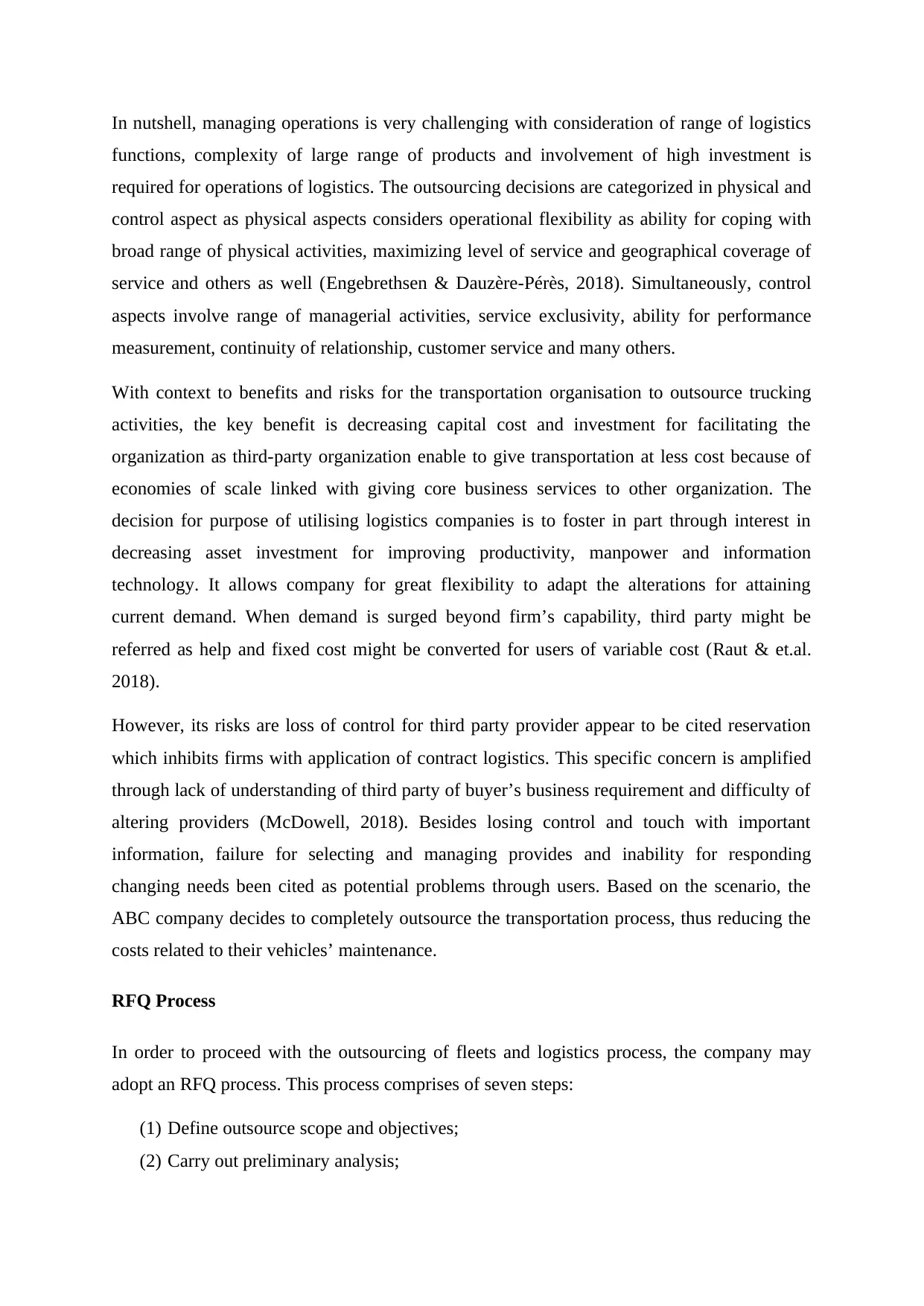
In nutshell, managing operations is very challenging with consideration of range of logistics
functions, complexity of large range of products and involvement of high investment is
required for operations of logistics. The outsourcing decisions are categorized in physical and
control aspect as physical aspects considers operational flexibility as ability for coping with
broad range of physical activities, maximizing level of service and geographical coverage of
service and others as well (Engebrethsen & Dauzère-Pérès, 2018). Simultaneously, control
aspects involve range of managerial activities, service exclusivity, ability for performance
measurement, continuity of relationship, customer service and many others.
With context to benefits and risks for the transportation organisation to outsource trucking
activities, the key benefit is decreasing capital cost and investment for facilitating the
organization as third-party organization enable to give transportation at less cost because of
economies of scale linked with giving core business services to other organization. The
decision for purpose of utilising logistics companies is to foster in part through interest in
decreasing asset investment for improving productivity, manpower and information
technology. It allows company for great flexibility to adapt the alterations for attaining
current demand. When demand is surged beyond firm’s capability, third party might be
referred as help and fixed cost might be converted for users of variable cost (Raut & et.al.
2018).
However, its risks are loss of control for third party provider appear to be cited reservation
which inhibits firms with application of contract logistics. This specific concern is amplified
through lack of understanding of third party of buyer’s business requirement and difficulty of
altering providers (McDowell, 2018). Besides losing control and touch with important
information, failure for selecting and managing provides and inability for responding
changing needs been cited as potential problems through users. Based on the scenario, the
ABC company decides to completely outsource the transportation process, thus reducing the
costs related to their vehicles’ maintenance.
RFQ Process
In order to proceed with the outsourcing of fleets and logistics process, the company may
adopt an RFQ process. This process comprises of seven steps:
(1) Define outsource scope and objectives;
(2) Carry out preliminary analysis;
functions, complexity of large range of products and involvement of high investment is
required for operations of logistics. The outsourcing decisions are categorized in physical and
control aspect as physical aspects considers operational flexibility as ability for coping with
broad range of physical activities, maximizing level of service and geographical coverage of
service and others as well (Engebrethsen & Dauzère-Pérès, 2018). Simultaneously, control
aspects involve range of managerial activities, service exclusivity, ability for performance
measurement, continuity of relationship, customer service and many others.
With context to benefits and risks for the transportation organisation to outsource trucking
activities, the key benefit is decreasing capital cost and investment for facilitating the
organization as third-party organization enable to give transportation at less cost because of
economies of scale linked with giving core business services to other organization. The
decision for purpose of utilising logistics companies is to foster in part through interest in
decreasing asset investment for improving productivity, manpower and information
technology. It allows company for great flexibility to adapt the alterations for attaining
current demand. When demand is surged beyond firm’s capability, third party might be
referred as help and fixed cost might be converted for users of variable cost (Raut & et.al.
2018).
However, its risks are loss of control for third party provider appear to be cited reservation
which inhibits firms with application of contract logistics. This specific concern is amplified
through lack of understanding of third party of buyer’s business requirement and difficulty of
altering providers (McDowell, 2018). Besides losing control and touch with important
information, failure for selecting and managing provides and inability for responding
changing needs been cited as potential problems through users. Based on the scenario, the
ABC company decides to completely outsource the transportation process, thus reducing the
costs related to their vehicles’ maintenance.
RFQ Process
In order to proceed with the outsourcing of fleets and logistics process, the company may
adopt an RFQ process. This process comprises of seven steps:
(1) Define outsource scope and objectives;
(2) Carry out preliminary analysis;
⊘ This is a preview!⊘
Do you want full access?
Subscribe today to unlock all pages.

Trusted by 1+ million students worldwide
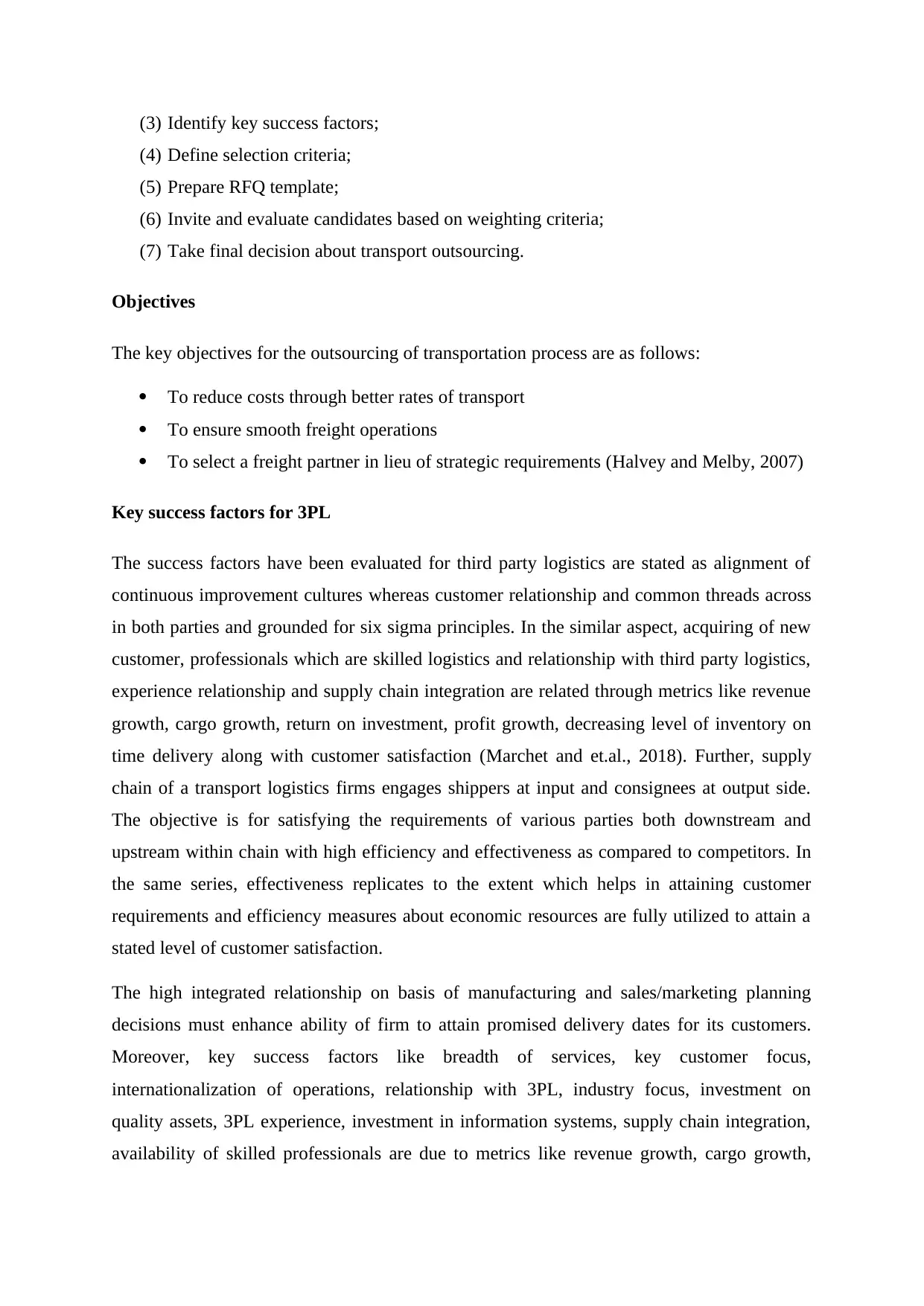
(3) Identify key success factors;
(4) Define selection criteria;
(5) Prepare RFQ template;
(6) Invite and evaluate candidates based on weighting criteria;
(7) Take final decision about transport outsourcing.
Objectives
The key objectives for the outsourcing of transportation process are as follows:
To reduce costs through better rates of transport
To ensure smooth freight operations
To select a freight partner in lieu of strategic requirements (Halvey and Melby, 2007)
Key success factors for 3PL
The success factors have been evaluated for third party logistics are stated as alignment of
continuous improvement cultures whereas customer relationship and common threads across
in both parties and grounded for six sigma principles. In the similar aspect, acquiring of new
customer, professionals which are skilled logistics and relationship with third party logistics,
experience relationship and supply chain integration are related through metrics like revenue
growth, cargo growth, return on investment, profit growth, decreasing level of inventory on
time delivery along with customer satisfaction (Marchet and et.al., 2018). Further, supply
chain of a transport logistics firms engages shippers at input and consignees at output side.
The objective is for satisfying the requirements of various parties both downstream and
upstream within chain with high efficiency and effectiveness as compared to competitors. In
the same series, effectiveness replicates to the extent which helps in attaining customer
requirements and efficiency measures about economic resources are fully utilized to attain a
stated level of customer satisfaction.
The high integrated relationship on basis of manufacturing and sales/marketing planning
decisions must enhance ability of firm to attain promised delivery dates for its customers.
Moreover, key success factors like breadth of services, key customer focus,
internationalization of operations, relationship with 3PL, industry focus, investment on
quality assets, 3PL experience, investment in information systems, supply chain integration,
availability of skilled professionals are due to metrics like revenue growth, cargo growth,
(4) Define selection criteria;
(5) Prepare RFQ template;
(6) Invite and evaluate candidates based on weighting criteria;
(7) Take final decision about transport outsourcing.
Objectives
The key objectives for the outsourcing of transportation process are as follows:
To reduce costs through better rates of transport
To ensure smooth freight operations
To select a freight partner in lieu of strategic requirements (Halvey and Melby, 2007)
Key success factors for 3PL
The success factors have been evaluated for third party logistics are stated as alignment of
continuous improvement cultures whereas customer relationship and common threads across
in both parties and grounded for six sigma principles. In the similar aspect, acquiring of new
customer, professionals which are skilled logistics and relationship with third party logistics,
experience relationship and supply chain integration are related through metrics like revenue
growth, cargo growth, return on investment, profit growth, decreasing level of inventory on
time delivery along with customer satisfaction (Marchet and et.al., 2018). Further, supply
chain of a transport logistics firms engages shippers at input and consignees at output side.
The objective is for satisfying the requirements of various parties both downstream and
upstream within chain with high efficiency and effectiveness as compared to competitors. In
the same series, effectiveness replicates to the extent which helps in attaining customer
requirements and efficiency measures about economic resources are fully utilized to attain a
stated level of customer satisfaction.
The high integrated relationship on basis of manufacturing and sales/marketing planning
decisions must enhance ability of firm to attain promised delivery dates for its customers.
Moreover, key success factors like breadth of services, key customer focus,
internationalization of operations, relationship with 3PL, industry focus, investment on
quality assets, 3PL experience, investment in information systems, supply chain integration,
availability of skilled professionals are due to metrics like revenue growth, cargo growth,
Paraphrase This Document
Need a fresh take? Get an instant paraphrase of this document with our AI Paraphraser
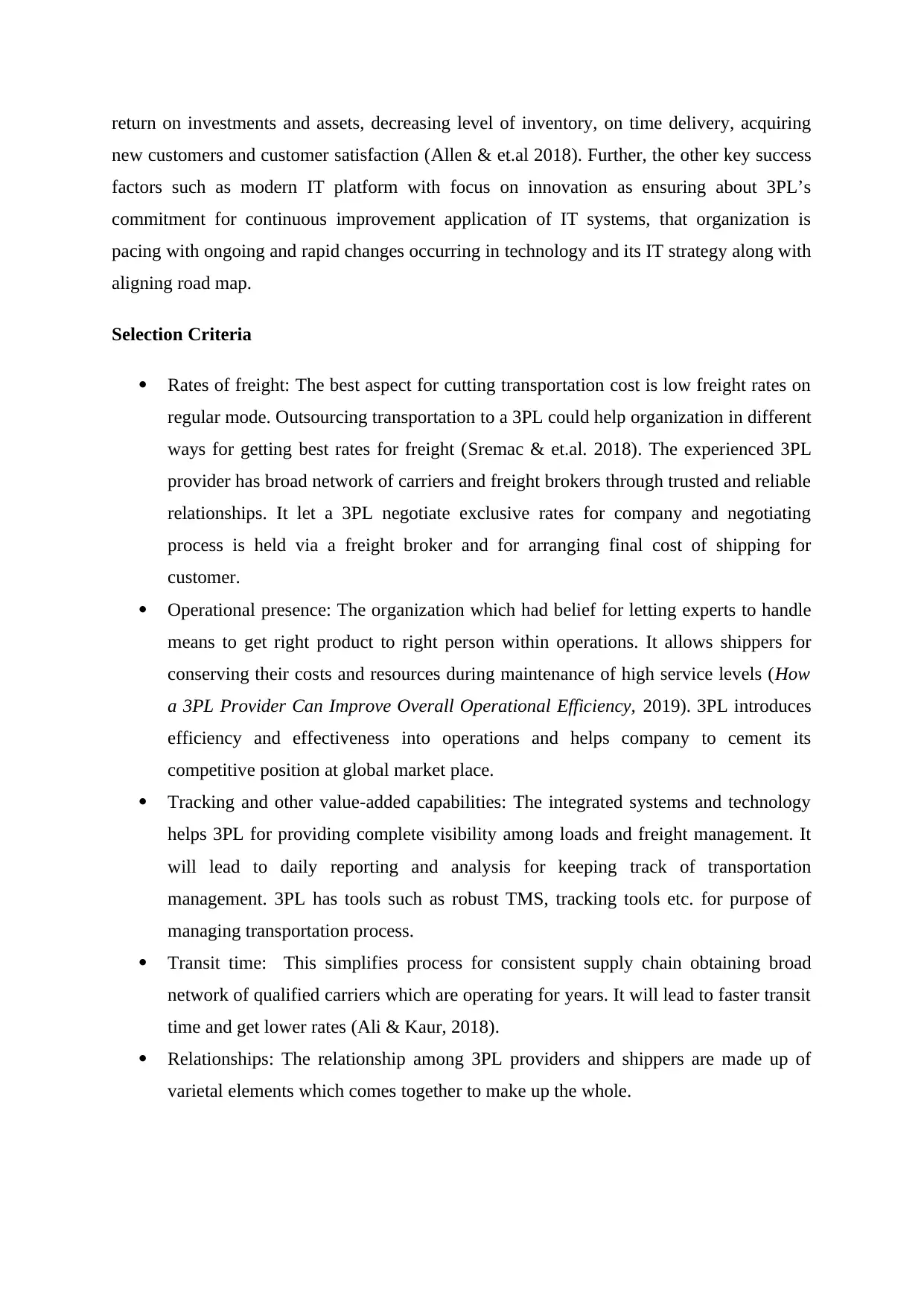
return on investments and assets, decreasing level of inventory, on time delivery, acquiring
new customers and customer satisfaction (Allen & et.al 2018). Further, the other key success
factors such as modern IT platform with focus on innovation as ensuring about 3PL’s
commitment for continuous improvement application of IT systems, that organization is
pacing with ongoing and rapid changes occurring in technology and its IT strategy along with
aligning road map.
Selection Criteria
Rates of freight: The best aspect for cutting transportation cost is low freight rates on
regular mode. Outsourcing transportation to a 3PL could help organization in different
ways for getting best rates for freight (Sremac & et.al. 2018). The experienced 3PL
provider has broad network of carriers and freight brokers through trusted and reliable
relationships. It let a 3PL negotiate exclusive rates for company and negotiating
process is held via a freight broker and for arranging final cost of shipping for
customer.
Operational presence: The organization which had belief for letting experts to handle
means to get right product to right person within operations. It allows shippers for
conserving their costs and resources during maintenance of high service levels (How
a 3PL Provider Can Improve Overall Operational Efficiency, 2019). 3PL introduces
efficiency and effectiveness into operations and helps company to cement its
competitive position at global market place.
Tracking and other value-added capabilities: The integrated systems and technology
helps 3PL for providing complete visibility among loads and freight management. It
will lead to daily reporting and analysis for keeping track of transportation
management. 3PL has tools such as robust TMS, tracking tools etc. for purpose of
managing transportation process.
Transit time: This simplifies process for consistent supply chain obtaining broad
network of qualified carriers which are operating for years. It will lead to faster transit
time and get lower rates (Ali & Kaur, 2018).
Relationships: The relationship among 3PL providers and shippers are made up of
varietal elements which comes together to make up the whole.
new customers and customer satisfaction (Allen & et.al 2018). Further, the other key success
factors such as modern IT platform with focus on innovation as ensuring about 3PL’s
commitment for continuous improvement application of IT systems, that organization is
pacing with ongoing and rapid changes occurring in technology and its IT strategy along with
aligning road map.
Selection Criteria
Rates of freight: The best aspect for cutting transportation cost is low freight rates on
regular mode. Outsourcing transportation to a 3PL could help organization in different
ways for getting best rates for freight (Sremac & et.al. 2018). The experienced 3PL
provider has broad network of carriers and freight brokers through trusted and reliable
relationships. It let a 3PL negotiate exclusive rates for company and negotiating
process is held via a freight broker and for arranging final cost of shipping for
customer.
Operational presence: The organization which had belief for letting experts to handle
means to get right product to right person within operations. It allows shippers for
conserving their costs and resources during maintenance of high service levels (How
a 3PL Provider Can Improve Overall Operational Efficiency, 2019). 3PL introduces
efficiency and effectiveness into operations and helps company to cement its
competitive position at global market place.
Tracking and other value-added capabilities: The integrated systems and technology
helps 3PL for providing complete visibility among loads and freight management. It
will lead to daily reporting and analysis for keeping track of transportation
management. 3PL has tools such as robust TMS, tracking tools etc. for purpose of
managing transportation process.
Transit time: This simplifies process for consistent supply chain obtaining broad
network of qualified carriers which are operating for years. It will lead to faster transit
time and get lower rates (Ali & Kaur, 2018).
Relationships: The relationship among 3PL providers and shippers are made up of
varietal elements which comes together to make up the whole.
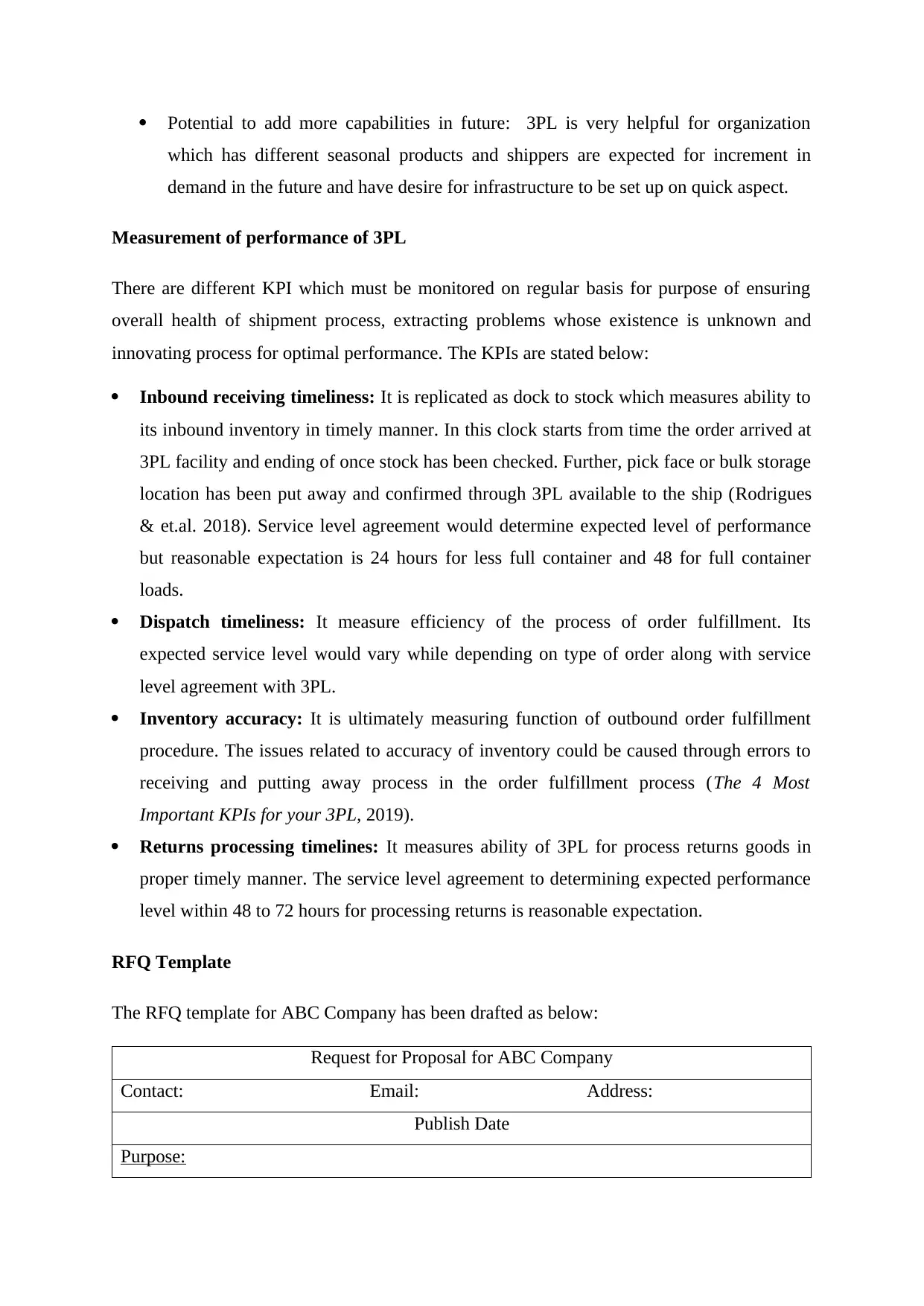
Potential to add more capabilities in future: 3PL is very helpful for organization
which has different seasonal products and shippers are expected for increment in
demand in the future and have desire for infrastructure to be set up on quick aspect.
Measurement of performance of 3PL
There are different KPI which must be monitored on regular basis for purpose of ensuring
overall health of shipment process, extracting problems whose existence is unknown and
innovating process for optimal performance. The KPIs are stated below:
Inbound receiving timeliness: It is replicated as dock to stock which measures ability to
its inbound inventory in timely manner. In this clock starts from time the order arrived at
3PL facility and ending of once stock has been checked. Further, pick face or bulk storage
location has been put away and confirmed through 3PL available to the ship (Rodrigues
& et.al. 2018). Service level agreement would determine expected level of performance
but reasonable expectation is 24 hours for less full container and 48 for full container
loads.
Dispatch timeliness: It measure efficiency of the process of order fulfillment. Its
expected service level would vary while depending on type of order along with service
level agreement with 3PL.
Inventory accuracy: It is ultimately measuring function of outbound order fulfillment
procedure. The issues related to accuracy of inventory could be caused through errors to
receiving and putting away process in the order fulfillment process (The 4 Most
Important KPIs for your 3PL, 2019).
Returns processing timelines: It measures ability of 3PL for process returns goods in
proper timely manner. The service level agreement to determining expected performance
level within 48 to 72 hours for processing returns is reasonable expectation.
RFQ Template
The RFQ template for ABC Company has been drafted as below:
Request for Proposal for ABC Company
Contact: Email: Address:
Publish Date
Purpose:
which has different seasonal products and shippers are expected for increment in
demand in the future and have desire for infrastructure to be set up on quick aspect.
Measurement of performance of 3PL
There are different KPI which must be monitored on regular basis for purpose of ensuring
overall health of shipment process, extracting problems whose existence is unknown and
innovating process for optimal performance. The KPIs are stated below:
Inbound receiving timeliness: It is replicated as dock to stock which measures ability to
its inbound inventory in timely manner. In this clock starts from time the order arrived at
3PL facility and ending of once stock has been checked. Further, pick face or bulk storage
location has been put away and confirmed through 3PL available to the ship (Rodrigues
& et.al. 2018). Service level agreement would determine expected level of performance
but reasonable expectation is 24 hours for less full container and 48 for full container
loads.
Dispatch timeliness: It measure efficiency of the process of order fulfillment. Its
expected service level would vary while depending on type of order along with service
level agreement with 3PL.
Inventory accuracy: It is ultimately measuring function of outbound order fulfillment
procedure. The issues related to accuracy of inventory could be caused through errors to
receiving and putting away process in the order fulfillment process (The 4 Most
Important KPIs for your 3PL, 2019).
Returns processing timelines: It measures ability of 3PL for process returns goods in
proper timely manner. The service level agreement to determining expected performance
level within 48 to 72 hours for processing returns is reasonable expectation.
RFQ Template
The RFQ template for ABC Company has been drafted as below:
Request for Proposal for ABC Company
Contact: Email: Address:
Publish Date
Purpose:
⊘ This is a preview!⊘
Do you want full access?
Subscribe today to unlock all pages.

Trusted by 1+ million students worldwide
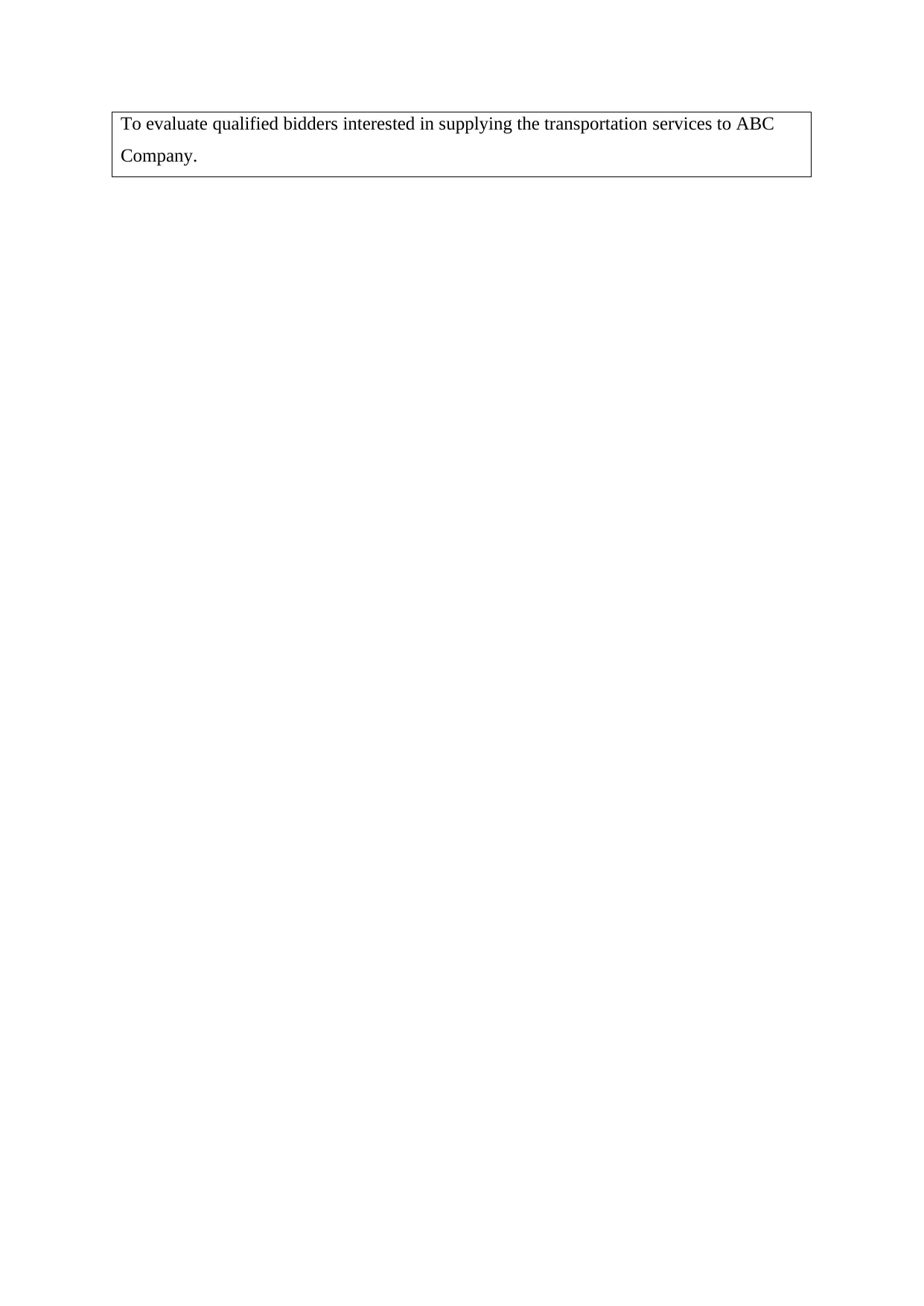
To evaluate qualified bidders interested in supplying the transportation services to ABC
Company.
Company.
Paraphrase This Document
Need a fresh take? Get an instant paraphrase of this document with our AI Paraphraser
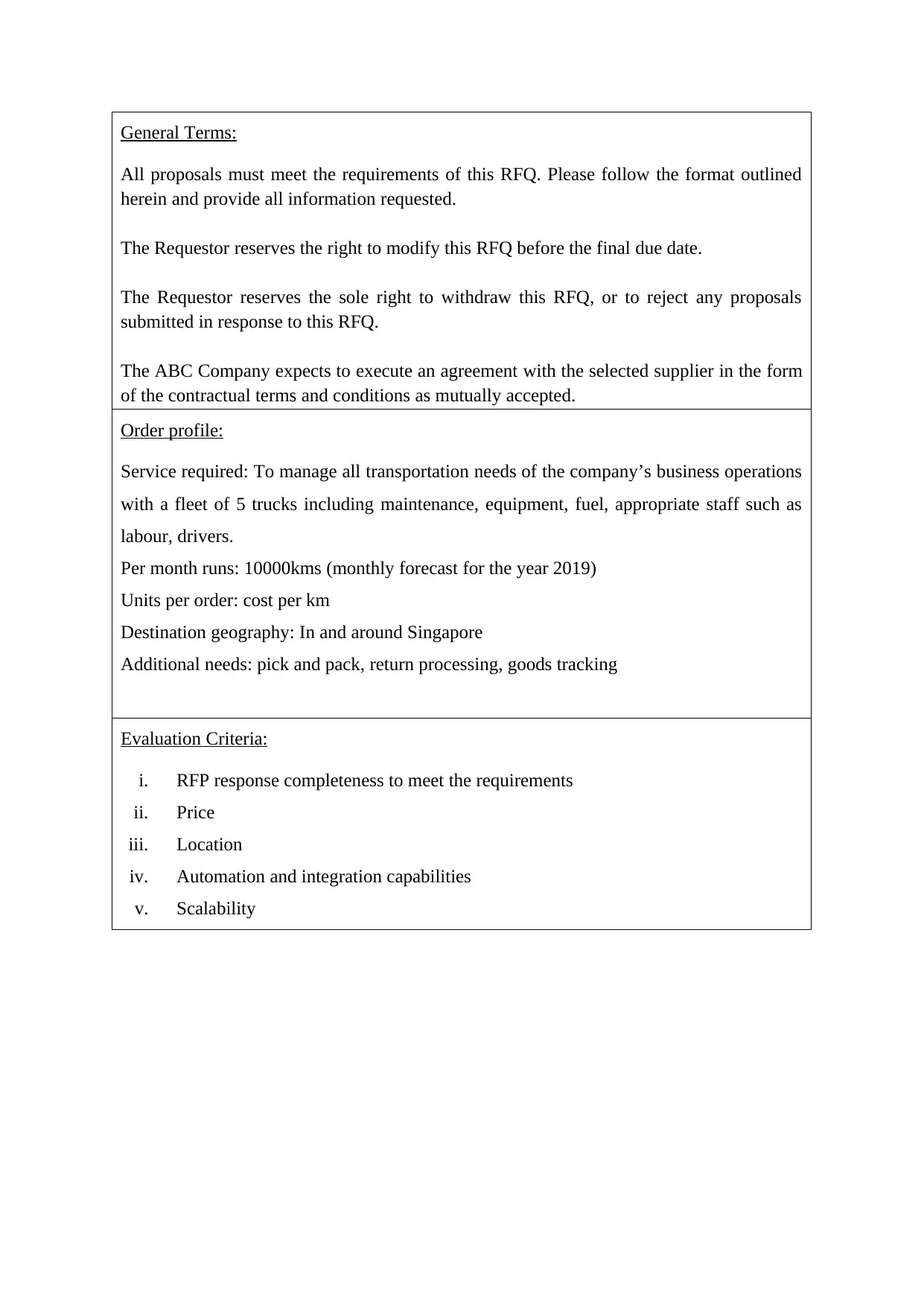
General Terms:
All proposals must meet the requirements of this RFQ. Please follow the format outlined
herein and provide all information requested.
The Requestor reserves the right to modify this RFQ before the final due date.
The Requestor reserves the sole right to withdraw this RFQ, or to reject any proposals
submitted in response to this RFQ.
The ABC Company expects to execute an agreement with the selected supplier in the form
of the contractual terms and conditions as mutually accepted.
Order profile:
Service required: To manage all transportation needs of the company’s business operations
with a fleet of 5 trucks including maintenance, equipment, fuel, appropriate staff such as
labour, drivers.
Per month runs: 10000kms (monthly forecast for the year 2019)
Units per order: cost per km
Destination geography: In and around Singapore
Additional needs: pick and pack, return processing, goods tracking
Evaluation Criteria:
i. RFP response completeness to meet the requirements
ii. Price
iii. Location
iv. Automation and integration capabilities
v. Scalability
All proposals must meet the requirements of this RFQ. Please follow the format outlined
herein and provide all information requested.
The Requestor reserves the right to modify this RFQ before the final due date.
The Requestor reserves the sole right to withdraw this RFQ, or to reject any proposals
submitted in response to this RFQ.
The ABC Company expects to execute an agreement with the selected supplier in the form
of the contractual terms and conditions as mutually accepted.
Order profile:
Service required: To manage all transportation needs of the company’s business operations
with a fleet of 5 trucks including maintenance, equipment, fuel, appropriate staff such as
labour, drivers.
Per month runs: 10000kms (monthly forecast for the year 2019)
Units per order: cost per km
Destination geography: In and around Singapore
Additional needs: pick and pack, return processing, goods tracking
Evaluation Criteria:
i. RFP response completeness to meet the requirements
ii. Price
iii. Location
iv. Automation and integration capabilities
v. Scalability
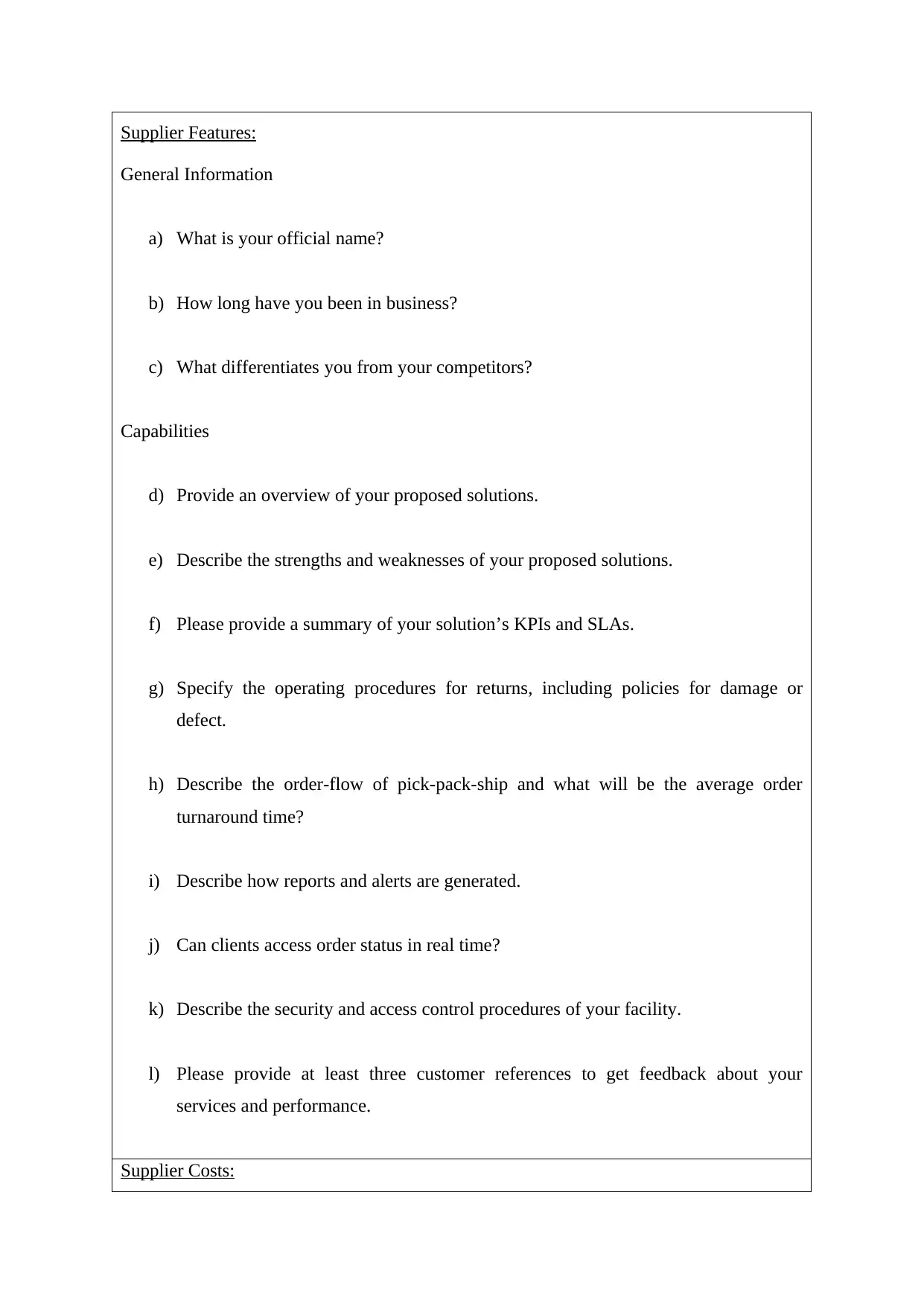
Supplier Features:
General Information
a) What is your official name?
b) How long have you been in business?
c) What differentiates you from your competitors?
Capabilities
d) Provide an overview of your proposed solutions.
e) Describe the strengths and weaknesses of your proposed solutions.
f) Please provide a summary of your solution’s KPIs and SLAs.
g) Specify the operating procedures for returns, including policies for damage or
defect.
h) Describe the order-flow of pick-pack-ship and what will be the average order
turnaround time?
i) Describe how reports and alerts are generated.
j) Can clients access order status in real time?
k) Describe the security and access control procedures of your facility.
l) Please provide at least three customer references to get feedback about your
services and performance.
Supplier Costs:
General Information
a) What is your official name?
b) How long have you been in business?
c) What differentiates you from your competitors?
Capabilities
d) Provide an overview of your proposed solutions.
e) Describe the strengths and weaknesses of your proposed solutions.
f) Please provide a summary of your solution’s KPIs and SLAs.
g) Specify the operating procedures for returns, including policies for damage or
defect.
h) Describe the order-flow of pick-pack-ship and what will be the average order
turnaround time?
i) Describe how reports and alerts are generated.
j) Can clients access order status in real time?
k) Describe the security and access control procedures of your facility.
l) Please provide at least three customer references to get feedback about your
services and performance.
Supplier Costs:
⊘ This is a preview!⊘
Do you want full access?
Subscribe today to unlock all pages.

Trusted by 1+ million students worldwide
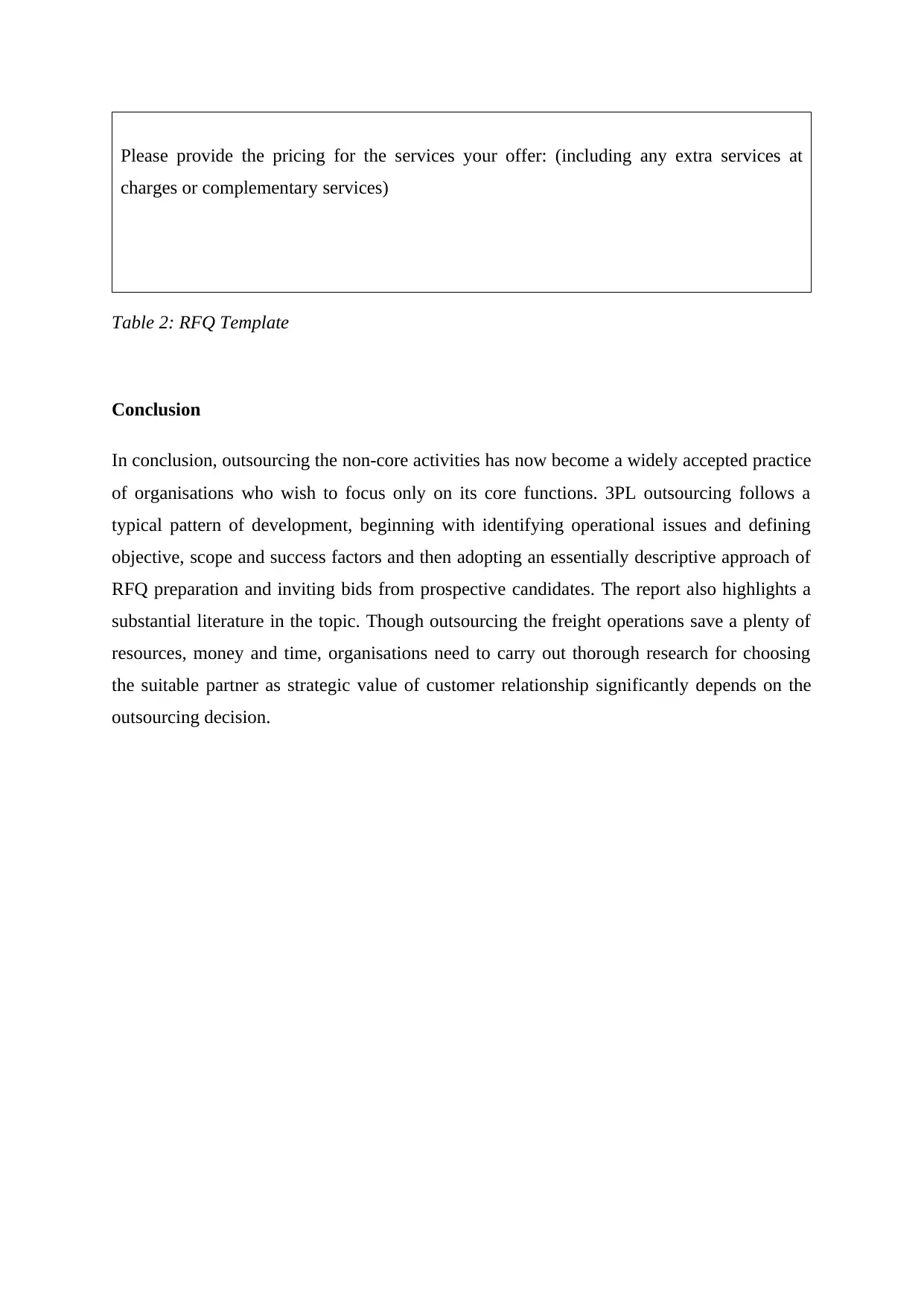
Please provide the pricing for the services your offer: (including any extra services at
charges or complementary services)
Table 2: RFQ Template
Conclusion
In conclusion, outsourcing the non-core activities has now become a widely accepted practice
of organisations who wish to focus only on its core functions. 3PL outsourcing follows a
typical pattern of development, beginning with identifying operational issues and defining
objective, scope and success factors and then adopting an essentially descriptive approach of
RFQ preparation and inviting bids from prospective candidates. The report also highlights a
substantial literature in the topic. Though outsourcing the freight operations save a plenty of
resources, money and time, organisations need to carry out thorough research for choosing
the suitable partner as strategic value of customer relationship significantly depends on the
outsourcing decision.
charges or complementary services)
Table 2: RFQ Template
Conclusion
In conclusion, outsourcing the non-core activities has now become a widely accepted practice
of organisations who wish to focus only on its core functions. 3PL outsourcing follows a
typical pattern of development, beginning with identifying operational issues and defining
objective, scope and success factors and then adopting an essentially descriptive approach of
RFQ preparation and inviting bids from prospective candidates. The report also highlights a
substantial literature in the topic. Though outsourcing the freight operations save a plenty of
resources, money and time, organisations need to carry out thorough research for choosing
the suitable partner as strategic value of customer relationship significantly depends on the
outsourcing decision.
Paraphrase This Document
Need a fresh take? Get an instant paraphrase of this document with our AI Paraphraser
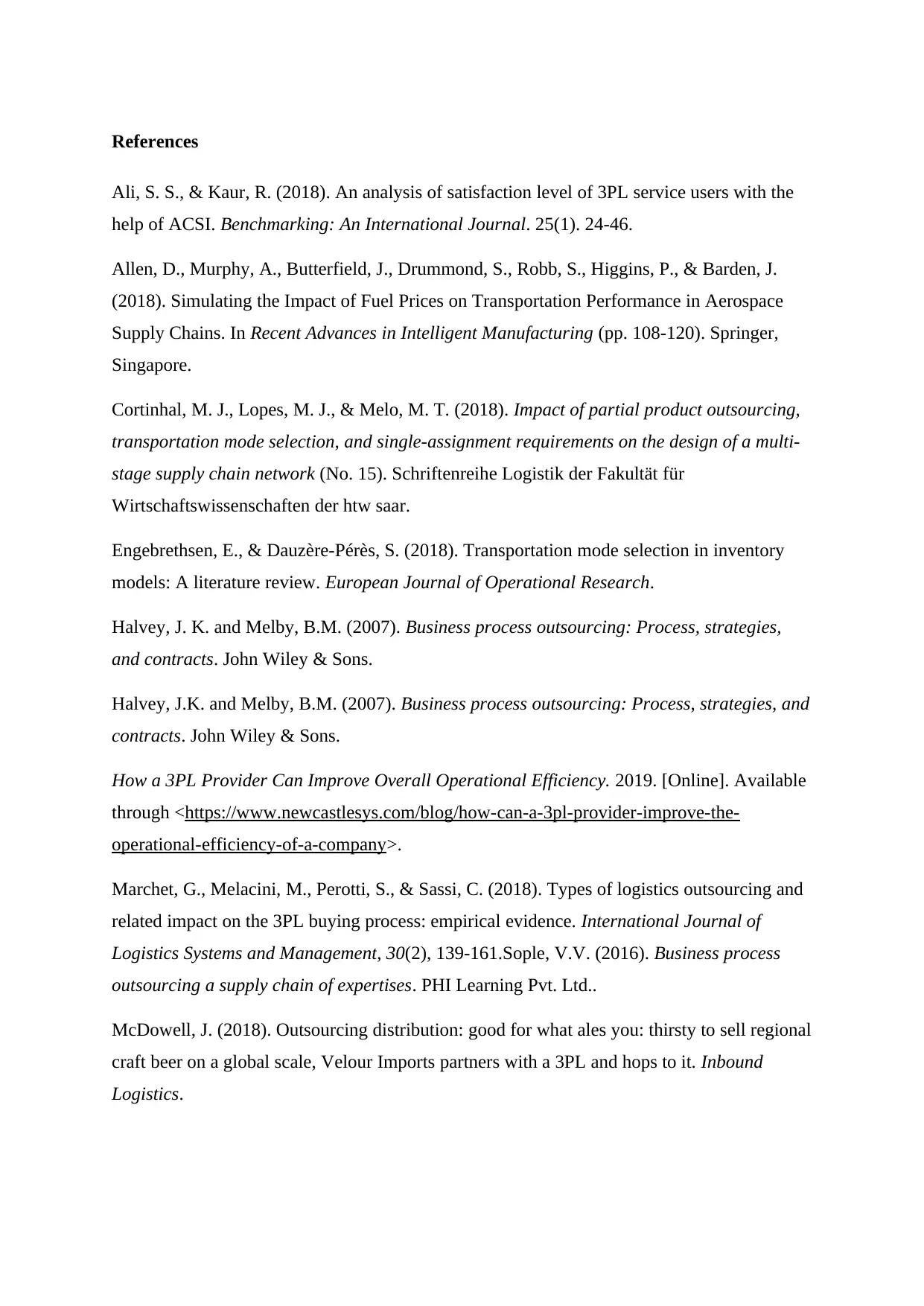
References
Ali, S. S., & Kaur, R. (2018). An analysis of satisfaction level of 3PL service users with the
help of ACSI. Benchmarking: An International Journal. 25(1). 24-46.
Allen, D., Murphy, A., Butterfield, J., Drummond, S., Robb, S., Higgins, P., & Barden, J.
(2018). Simulating the Impact of Fuel Prices on Transportation Performance in Aerospace
Supply Chains. In Recent Advances in Intelligent Manufacturing (pp. 108-120). Springer,
Singapore.
Cortinhal, M. J., Lopes, M. J., & Melo, M. T. (2018). Impact of partial product outsourcing,
transportation mode selection, and single-assignment requirements on the design of a multi-
stage supply chain network (No. 15). Schriftenreihe Logistik der Fakultät für
Wirtschaftswissenschaften der htw saar.
Engebrethsen, E., & Dauzère-Pérès, S. (2018). Transportation mode selection in inventory
models: A literature review. European Journal of Operational Research.
Halvey, J. K. and Melby, B.M. (2007). Business process outsourcing: Process, strategies,
and contracts. John Wiley & Sons.
Halvey, J.K. and Melby, B.M. (2007). Business process outsourcing: Process, strategies, and
contracts. John Wiley & Sons.
How a 3PL Provider Can Improve Overall Operational Efficiency. 2019. [Online]. Available
through <https://www.newcastlesys.com/blog/how-can-a-3pl-provider-improve-the-
operational-efficiency-of-a-company>.
Marchet, G., Melacini, M., Perotti, S., & Sassi, C. (2018). Types of logistics outsourcing and
related impact on the 3PL buying process: empirical evidence. International Journal of
Logistics Systems and Management, 30(2), 139-161.Sople, V.V. (2016). Business process
outsourcing a supply chain of expertises. PHI Learning Pvt. Ltd..
McDowell, J. (2018). Outsourcing distribution: good for what ales you: thirsty to sell regional
craft beer on a global scale, Velour Imports partners with a 3PL and hops to it. Inbound
Logistics.
Ali, S. S., & Kaur, R. (2018). An analysis of satisfaction level of 3PL service users with the
help of ACSI. Benchmarking: An International Journal. 25(1). 24-46.
Allen, D., Murphy, A., Butterfield, J., Drummond, S., Robb, S., Higgins, P., & Barden, J.
(2018). Simulating the Impact of Fuel Prices on Transportation Performance in Aerospace
Supply Chains. In Recent Advances in Intelligent Manufacturing (pp. 108-120). Springer,
Singapore.
Cortinhal, M. J., Lopes, M. J., & Melo, M. T. (2018). Impact of partial product outsourcing,
transportation mode selection, and single-assignment requirements on the design of a multi-
stage supply chain network (No. 15). Schriftenreihe Logistik der Fakultät für
Wirtschaftswissenschaften der htw saar.
Engebrethsen, E., & Dauzère-Pérès, S. (2018). Transportation mode selection in inventory
models: A literature review. European Journal of Operational Research.
Halvey, J. K. and Melby, B.M. (2007). Business process outsourcing: Process, strategies,
and contracts. John Wiley & Sons.
Halvey, J.K. and Melby, B.M. (2007). Business process outsourcing: Process, strategies, and
contracts. John Wiley & Sons.
How a 3PL Provider Can Improve Overall Operational Efficiency. 2019. [Online]. Available
through <https://www.newcastlesys.com/blog/how-can-a-3pl-provider-improve-the-
operational-efficiency-of-a-company>.
Marchet, G., Melacini, M., Perotti, S., & Sassi, C. (2018). Types of logistics outsourcing and
related impact on the 3PL buying process: empirical evidence. International Journal of
Logistics Systems and Management, 30(2), 139-161.Sople, V.V. (2016). Business process
outsourcing a supply chain of expertises. PHI Learning Pvt. Ltd..
McDowell, J. (2018). Outsourcing distribution: good for what ales you: thirsty to sell regional
craft beer on a global scale, Velour Imports partners with a 3PL and hops to it. Inbound
Logistics.
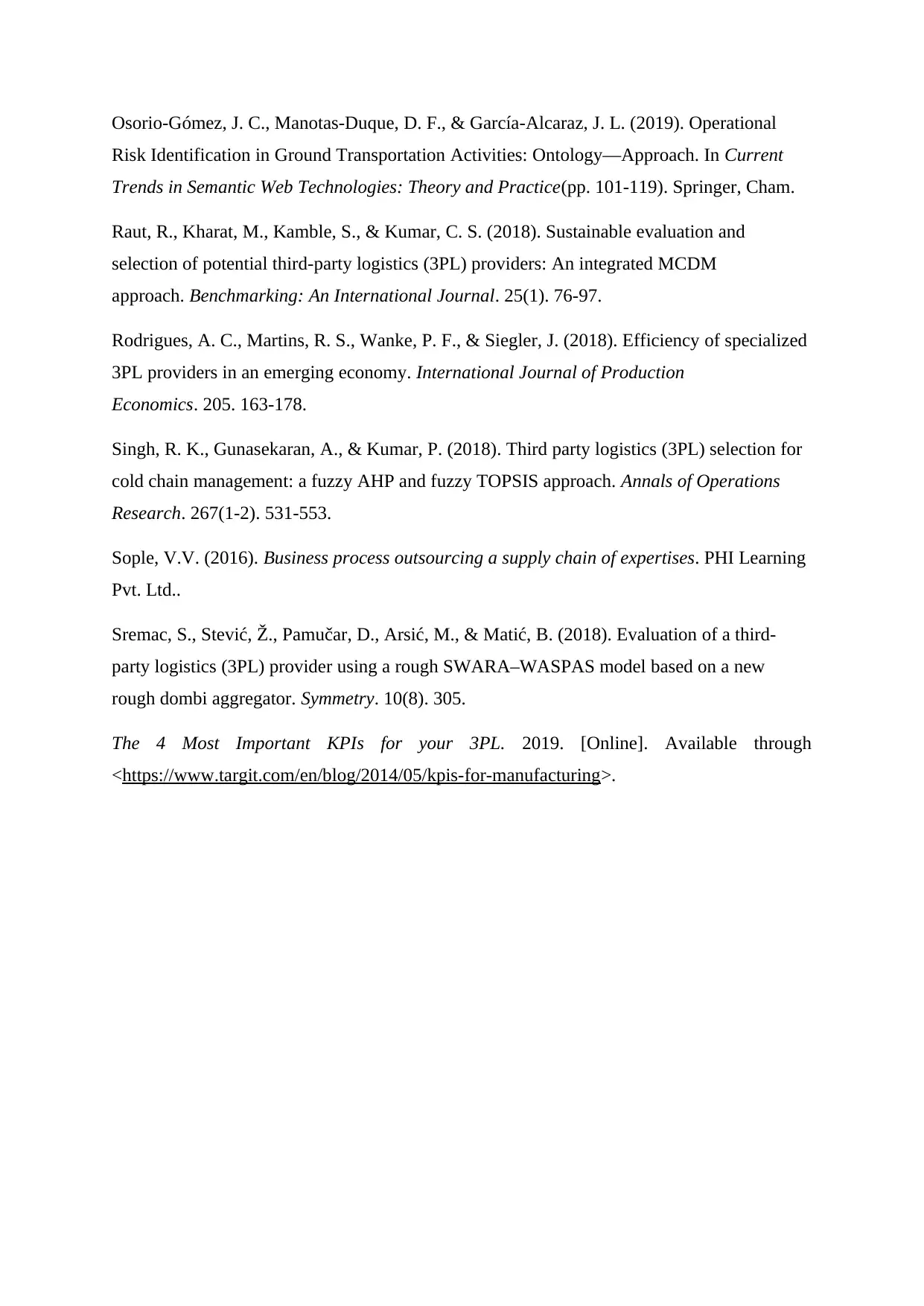
Osorio-Gómez, J. C., Manotas-Duque, D. F., & García-Alcaraz, J. L. (2019). Operational
Risk Identification in Ground Transportation Activities: Ontology—Approach. In Current
Trends in Semantic Web Technologies: Theory and Practice(pp. 101-119). Springer, Cham.
Raut, R., Kharat, M., Kamble, S., & Kumar, C. S. (2018). Sustainable evaluation and
selection of potential third-party logistics (3PL) providers: An integrated MCDM
approach. Benchmarking: An International Journal. 25(1). 76-97.
Rodrigues, A. C., Martins, R. S., Wanke, P. F., & Siegler, J. (2018). Efficiency of specialized
3PL providers in an emerging economy. International Journal of Production
Economics. 205. 163-178.
Singh, R. K., Gunasekaran, A., & Kumar, P. (2018). Third party logistics (3PL) selection for
cold chain management: a fuzzy AHP and fuzzy TOPSIS approach. Annals of Operations
Research. 267(1-2). 531-553.
Sople, V.V. (2016). Business process outsourcing a supply chain of expertises. PHI Learning
Pvt. Ltd..
Sremac, S., Stević, Ž., Pamučar, D., Arsić, M., & Matić, B. (2018). Evaluation of a third-
party logistics (3PL) provider using a rough SWARA–WASPAS model based on a new
rough dombi aggregator. Symmetry. 10(8). 305.
The 4 Most Important KPIs for your 3PL. 2019. [Online]. Available through
<https://www.targit.com/en/blog/2014/05/kpis-for-manufacturing>.
Risk Identification in Ground Transportation Activities: Ontology—Approach. In Current
Trends in Semantic Web Technologies: Theory and Practice(pp. 101-119). Springer, Cham.
Raut, R., Kharat, M., Kamble, S., & Kumar, C. S. (2018). Sustainable evaluation and
selection of potential third-party logistics (3PL) providers: An integrated MCDM
approach. Benchmarking: An International Journal. 25(1). 76-97.
Rodrigues, A. C., Martins, R. S., Wanke, P. F., & Siegler, J. (2018). Efficiency of specialized
3PL providers in an emerging economy. International Journal of Production
Economics. 205. 163-178.
Singh, R. K., Gunasekaran, A., & Kumar, P. (2018). Third party logistics (3PL) selection for
cold chain management: a fuzzy AHP and fuzzy TOPSIS approach. Annals of Operations
Research. 267(1-2). 531-553.
Sople, V.V. (2016). Business process outsourcing a supply chain of expertises. PHI Learning
Pvt. Ltd..
Sremac, S., Stević, Ž., Pamučar, D., Arsić, M., & Matić, B. (2018). Evaluation of a third-
party logistics (3PL) provider using a rough SWARA–WASPAS model based on a new
rough dombi aggregator. Symmetry. 10(8). 305.
The 4 Most Important KPIs for your 3PL. 2019. [Online]. Available through
<https://www.targit.com/en/blog/2014/05/kpis-for-manufacturing>.
⊘ This is a preview!⊘
Do you want full access?
Subscribe today to unlock all pages.

Trusted by 1+ million students worldwide
1 out of 15

Your All-in-One AI-Powered Toolkit for Academic Success.
+13062052269
info@desklib.com
Available 24*7 on WhatsApp / Email
Unlock your academic potential
© 2024 | Zucol Services PVT LTD | All rights reserved.