Engineering Secondary and Finishing Techniques
Assessment record sheet for Unit 21: Engineering Secondary and Finishing Techniques, Ass't 1: Secondary and Non-Traditional Machining Techniques.
21 Pages5358 Words96 Views
Added on 2023-03-21
About This Document
This document provides an overview of engineering secondary and finishing techniques, including turning, boring, milling, and grinding. It discusses the best practices for different materials and provides insights into non-traditional techniques. The document also explores the assembly process of an aluminium aircraft wing and provides guidance on kinematics applied in secondary machining. Find study material, solved assignments, and essays on engineering secondary and finishing techniques at Desklib.
Engineering Secondary and Finishing Techniques
Assessment record sheet for Unit 21: Engineering Secondary and Finishing Techniques, Ass't 1: Secondary and Non-Traditional Machining Techniques.
Added on 2023-03-21
ShareRelated Documents
UNIT 21: ENGINEERING SECONDARY AND FINISHING TECHNIQUES.
By Name
Course
Instructor
Institution
Location
Date
By Name
Course
Instructor
Institution
Location
Date
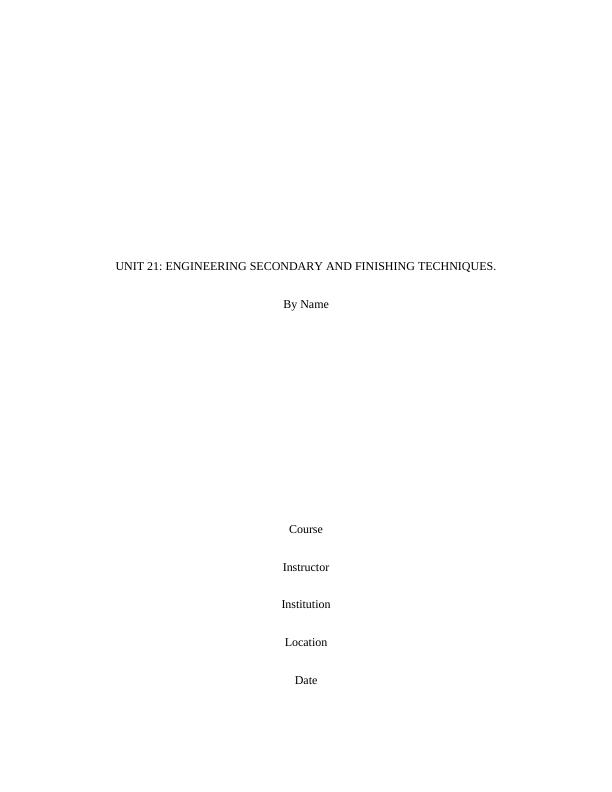
Task 1
Turning Operations
In this this kind of the lathe machine operation, a single turning tool is made to move axially
along the side of the work piece leading to the removal of the material hence formation of
various features like tapers, steps, chamfers and finally contours. Most of these features are
typically machined at very small radial depth of cut as well as multiple passes are made until the
end diameter is reached(Lin et al 2015).
Turning non-ferrous materials (aluminium)
This group of the metals contains soft metals including copper, bronze, metal matrix composite
and finally copper. In turning of this class of metals, the inserts that have positive basic sharp
edges and shape should always be used. The first choice should be given to the PCD and
uncoated grades. For the cases of the aluminium alloys with Si-content beyond 13%, the PCD
should be utilized as the tool life of the cemented carbide grades.
As part of the health and safety factor, aluminium chipping should be used mostly for the
evacuation of chips.
Heat resistant super alloys turning (HRSA)
Super alloys are known to have excellent mechanical strength as well as resistance to creep at
higher temperatures. Such alloys also offer basic resistance to oxidation or corrosion. Due to
these properties, the process of turning will include:
Use of entering angle which is less than 45 degrees
Turning Operations
In this this kind of the lathe machine operation, a single turning tool is made to move axially
along the side of the work piece leading to the removal of the material hence formation of
various features like tapers, steps, chamfers and finally contours. Most of these features are
typically machined at very small radial depth of cut as well as multiple passes are made until the
end diameter is reached(Lin et al 2015).
Turning non-ferrous materials (aluminium)
This group of the metals contains soft metals including copper, bronze, metal matrix composite
and finally copper. In turning of this class of metals, the inserts that have positive basic sharp
edges and shape should always be used. The first choice should be given to the PCD and
uncoated grades. For the cases of the aluminium alloys with Si-content beyond 13%, the PCD
should be utilized as the tool life of the cemented carbide grades.
As part of the health and safety factor, aluminium chipping should be used mostly for the
evacuation of chips.
Heat resistant super alloys turning (HRSA)
Super alloys are known to have excellent mechanical strength as well as resistance to creep at
higher temperatures. Such alloys also offer basic resistance to oxidation or corrosion. Due to
these properties, the process of turning will include:
Use of entering angle which is less than 45 degrees
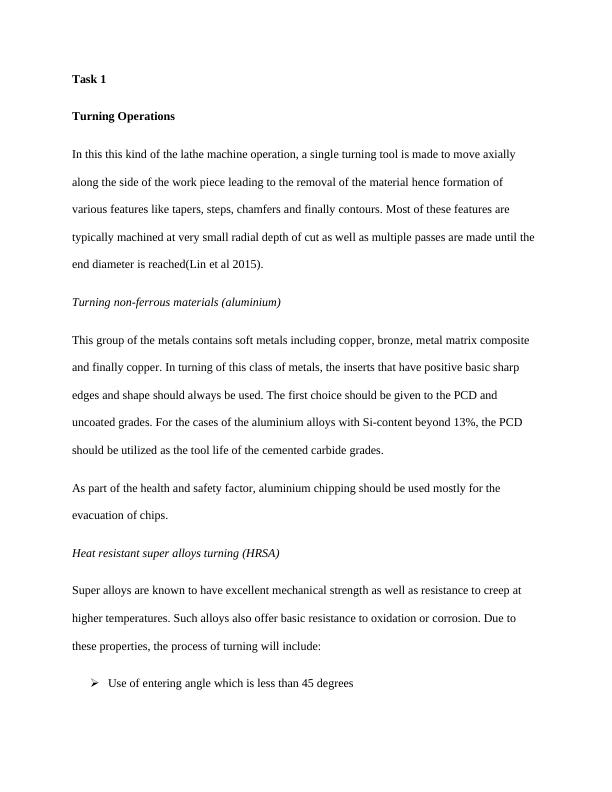
Use of correct relationship between the diameter of the insert as well as the depth of the
cut. In the cases of the ramping or multiple passes, the use of depth of cut that is slightly
above 0.25mm will be recommended.
As part of the health and safety requirement, coolant should be used in order to protect or
prevent the chip evacuation as well as overheating of the cutting tools.
Turning of the Stainless Steels
In the case of the duplex stainless steel, the designations including super complex materials are
used. The higher mechanical strength actually makes this particular compound too difficult to be
machined. This is so common especially when it comes to the generation of heat, chip control
and cutting forces. The feeding angle should be less than 45 degrees to avoid notch wearing.
Coolant should be used to achieve chips control as well as avoid plastic deformation as safety
measure.
Boring Operations
A boring tool will be required to access the work piece axially to cut along the internal surface
leading to the formation of various features. The common features will include tapers, chamfers,
contours as well as steps.
Ferrous materials
In the case of boring of the ferrous material like the low carbon steel, the feed depth should be
relatively small and the feeding angle should also be small. The boring should be performed after
the process of drilling. Coolants should be used in the control of the chips.
Heat resistant super alloys turning (HRSA)
cut. In the cases of the ramping or multiple passes, the use of depth of cut that is slightly
above 0.25mm will be recommended.
As part of the health and safety requirement, coolant should be used in order to protect or
prevent the chip evacuation as well as overheating of the cutting tools.
Turning of the Stainless Steels
In the case of the duplex stainless steel, the designations including super complex materials are
used. The higher mechanical strength actually makes this particular compound too difficult to be
machined. This is so common especially when it comes to the generation of heat, chip control
and cutting forces. The feeding angle should be less than 45 degrees to avoid notch wearing.
Coolant should be used to achieve chips control as well as avoid plastic deformation as safety
measure.
Boring Operations
A boring tool will be required to access the work piece axially to cut along the internal surface
leading to the formation of various features. The common features will include tapers, chamfers,
contours as well as steps.
Ferrous materials
In the case of boring of the ferrous material like the low carbon steel, the feed depth should be
relatively small and the feeding angle should also be small. The boring should be performed after
the process of drilling. Coolants should be used in the control of the chips.
Heat resistant super alloys turning (HRSA)
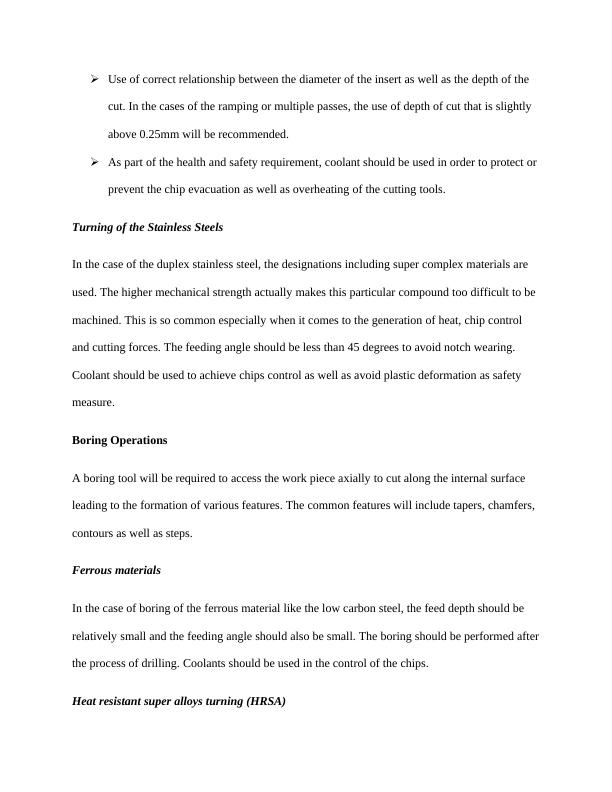
These alloys are known to have excellent mechanical strength as well as resistance to creep at
higher temperatures. Such alloys also offer basic resistance to oxidation or corrosion. The boring
process of these materials should take into account the use of small feed angle as well as depth.
The machining process should be carried out at very low speed to avoid breakage of the
machining tools.
Nonmetallic Materials
The common non- metallic materials that are usually subjected to the boring operation is plastic.
Boring of the plastics can be done while using large angle of feed since they are relatively soft.
Also chances of breaking boring tool are relatively reduced. Coolant should be used to
effectively avoid melting of the plastic materials.
Milling Operations
Nonferrous materials
When milling nonferrous materials, part of the recommendations will include use of the PCD-
tipped inserts that have polished as well as sharp edge for perfect chip breaking. Positive insert
geometrics that have sharp edges are used. The speed will be relatively high to improve the
performance as well as not to affect the tool life. The feeding depth should be at 0.10–0.20 mm
(0.0039–0.0079 inch. When the values are too low, there will be formation of burr. The coolant
of 10% concentration should be used in the control of chips(Ganesan and Mohankumar 2013).
Heat resistant super alloys (HRSA) milling
Considering the hard properties of this particular material, the milling process takes into account
the following recommendations:
higher temperatures. Such alloys also offer basic resistance to oxidation or corrosion. The boring
process of these materials should take into account the use of small feed angle as well as depth.
The machining process should be carried out at very low speed to avoid breakage of the
machining tools.
Nonmetallic Materials
The common non- metallic materials that are usually subjected to the boring operation is plastic.
Boring of the plastics can be done while using large angle of feed since they are relatively soft.
Also chances of breaking boring tool are relatively reduced. Coolant should be used to
effectively avoid melting of the plastic materials.
Milling Operations
Nonferrous materials
When milling nonferrous materials, part of the recommendations will include use of the PCD-
tipped inserts that have polished as well as sharp edge for perfect chip breaking. Positive insert
geometrics that have sharp edges are used. The speed will be relatively high to improve the
performance as well as not to affect the tool life. The feeding depth should be at 0.10–0.20 mm
(0.0039–0.0079 inch. When the values are too low, there will be formation of burr. The coolant
of 10% concentration should be used in the control of chips(Ganesan and Mohankumar 2013).
Heat resistant super alloys (HRSA) milling
Considering the hard properties of this particular material, the milling process takes into account
the following recommendations:
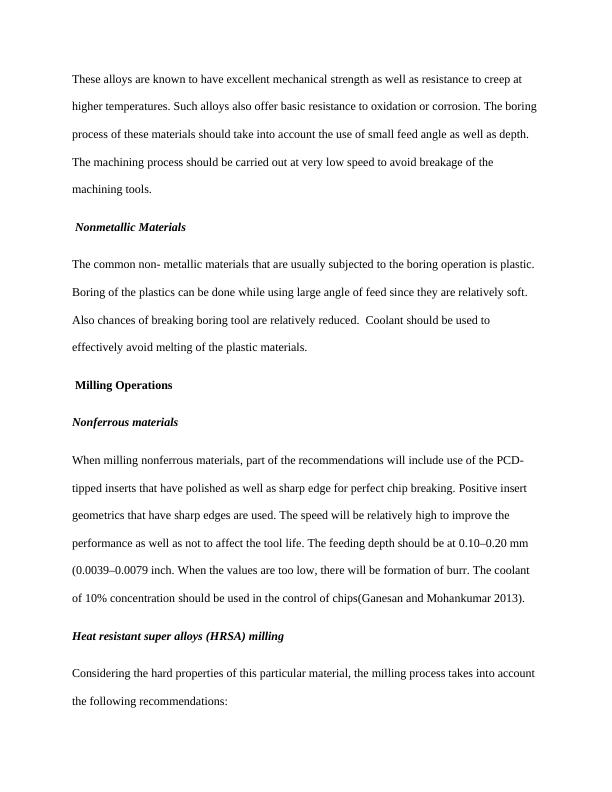
Use of cutters which are round inserts whenever possible so as to increase the effect of
chip thinning
The entering angle for the depth below 5mm to be less than 45 degrees
Use of positive cutting edge geometry
Increased number of the cutting teeth.
Milling of Hardened steel
It will be recommended that positive inserts geometries to be used especially those with sharp
edges. This assist in the reduction of the forces of cutting. In this case there should be no use of
the fluid that is it should be run dry. The strategy of machining should include use of extra close
pitch center of the cutter.
Grinding Operations
Non-metallic materials
Grinding of these compounds will require particle size reduction. In order to achieve such
reductions in the size, different machines can be used depending on the materials size that is
required finally. Considering that relatively low force is requirement, grit size ranges will be
used effectively. The fraction that is needed will be recovered as the final product before it is
returned to the grinding machine as oversized. Multideck screeners are therefore used as part of
the safety requirement.
Stainless steel grinding
This process is usually achieved by the use of the impact mill. This is actually a set of hammers
that are rotating with the breaker blades attached to them. This kind of the grinding process is
chip thinning
The entering angle for the depth below 5mm to be less than 45 degrees
Use of positive cutting edge geometry
Increased number of the cutting teeth.
Milling of Hardened steel
It will be recommended that positive inserts geometries to be used especially those with sharp
edges. This assist in the reduction of the forces of cutting. In this case there should be no use of
the fluid that is it should be run dry. The strategy of machining should include use of extra close
pitch center of the cutter.
Grinding Operations
Non-metallic materials
Grinding of these compounds will require particle size reduction. In order to achieve such
reductions in the size, different machines can be used depending on the materials size that is
required finally. Considering that relatively low force is requirement, grit size ranges will be
used effectively. The fraction that is needed will be recovered as the final product before it is
returned to the grinding machine as oversized. Multideck screeners are therefore used as part of
the safety requirement.
Stainless steel grinding
This process is usually achieved by the use of the impact mill. This is actually a set of hammers
that are rotating with the breaker blades attached to them. This kind of the grinding process is
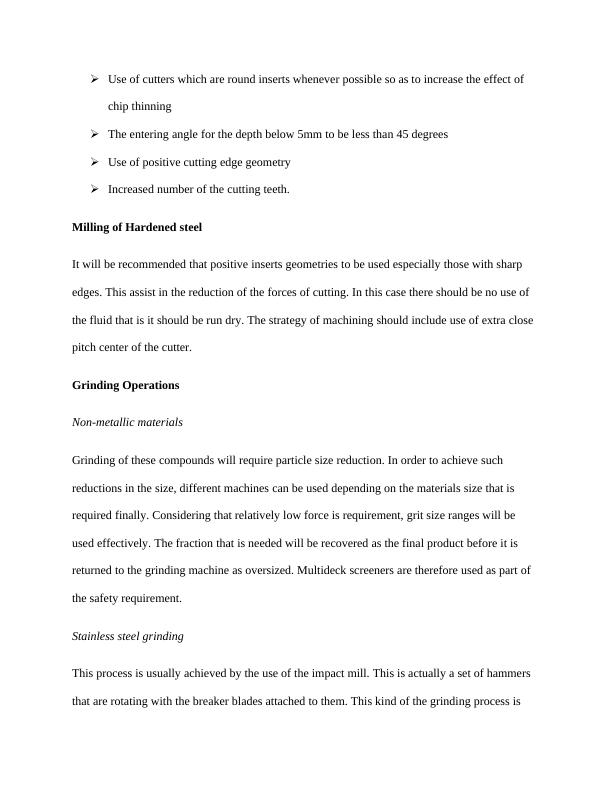
associated with the wearing of the hammers and therefore continuous replacement of the
hammers will be recommended. The casing should be made of very strong material to ensure that
particles that may cause harm are completely blocked from escaping.
Special Alloy Grinding
These kinds of the materials are known to be very hard. In order to achieve effective mechanisms
of grinding, roll crashers can be used. A roll crasher is made up of set of opposed rolls which
spins in the opposite direction. This process is associated with the low wear properties as well as
low speed. This gives very nice reductions in the size while dealing with the allowable clearance.
The feeding should be done bits to avoid damage to the machine as well as harm to the operator.
The casing should be properly secured to avoid harm to the operator.
Press Work Machine
Nonmetallic materials blanking
Non –ferrous materials like aluminium can be taken through fine blanking. This is actually a
form of shearing that produces parts with the clearance that is relatively tighter at the sheared
edge. The obtained edge which is relatively smooth is the result of special tooling that effectively
holds the material during the operation of shearing. This allows the activities of holding tight
tolerance thereby eliminating secondary operations of manufacturing like deburring.
Cutting operations on plastics
The cutting of the materials including plastics will involve the use of the cutting tools that are
effectively capable of performing the same operation. The machining process thus targets the
hammers will be recommended. The casing should be made of very strong material to ensure that
particles that may cause harm are completely blocked from escaping.
Special Alloy Grinding
These kinds of the materials are known to be very hard. In order to achieve effective mechanisms
of grinding, roll crashers can be used. A roll crasher is made up of set of opposed rolls which
spins in the opposite direction. This process is associated with the low wear properties as well as
low speed. This gives very nice reductions in the size while dealing with the allowable clearance.
The feeding should be done bits to avoid damage to the machine as well as harm to the operator.
The casing should be properly secured to avoid harm to the operator.
Press Work Machine
Nonmetallic materials blanking
Non –ferrous materials like aluminium can be taken through fine blanking. This is actually a
form of shearing that produces parts with the clearance that is relatively tighter at the sheared
edge. The obtained edge which is relatively smooth is the result of special tooling that effectively
holds the material during the operation of shearing. This allows the activities of holding tight
tolerance thereby eliminating secondary operations of manufacturing like deburring.
Cutting operations on plastics
The cutting of the materials including plastics will involve the use of the cutting tools that are
effectively capable of performing the same operation. The machining process thus targets the
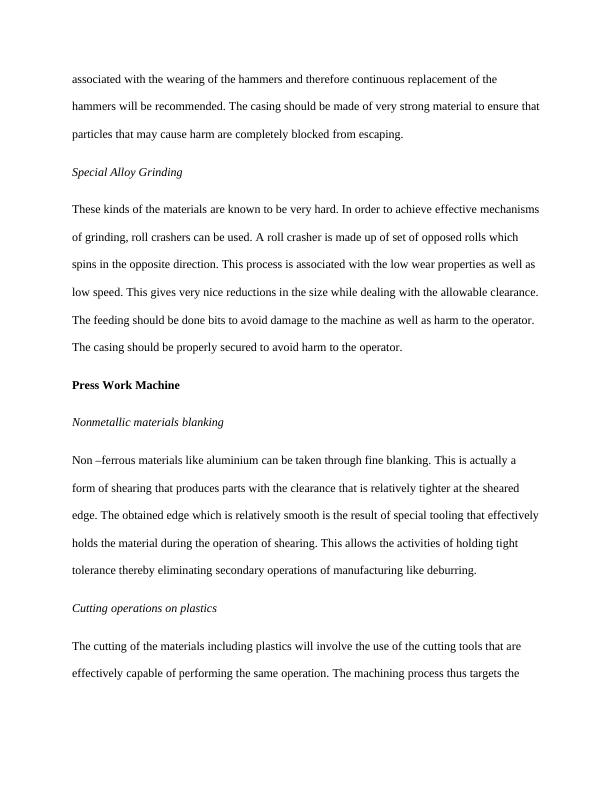
End of preview
Want to access all the pages? Upload your documents or become a member.