Cleaning Validation in the Pharmaceutical Industry
VerifiedAdded on 2023/04/10
|11
|2972
|307
AI Summary
Cleaning validation is a crucial process in the pharmaceutical industry to ensure safety, purity, and quality of products. This article discusses the importance and steps involved in cleaning validation, including the selection of cleaning level, method, and sampling method. It also covers the scientific basis for contamination limits and the documentation requirements. By following a systematic approach, pharmaceutical companies can successfully implement cleaning validation programs.
Contribute Materials
Your contribution can guide someone’s learning journey. Share your
documents today.
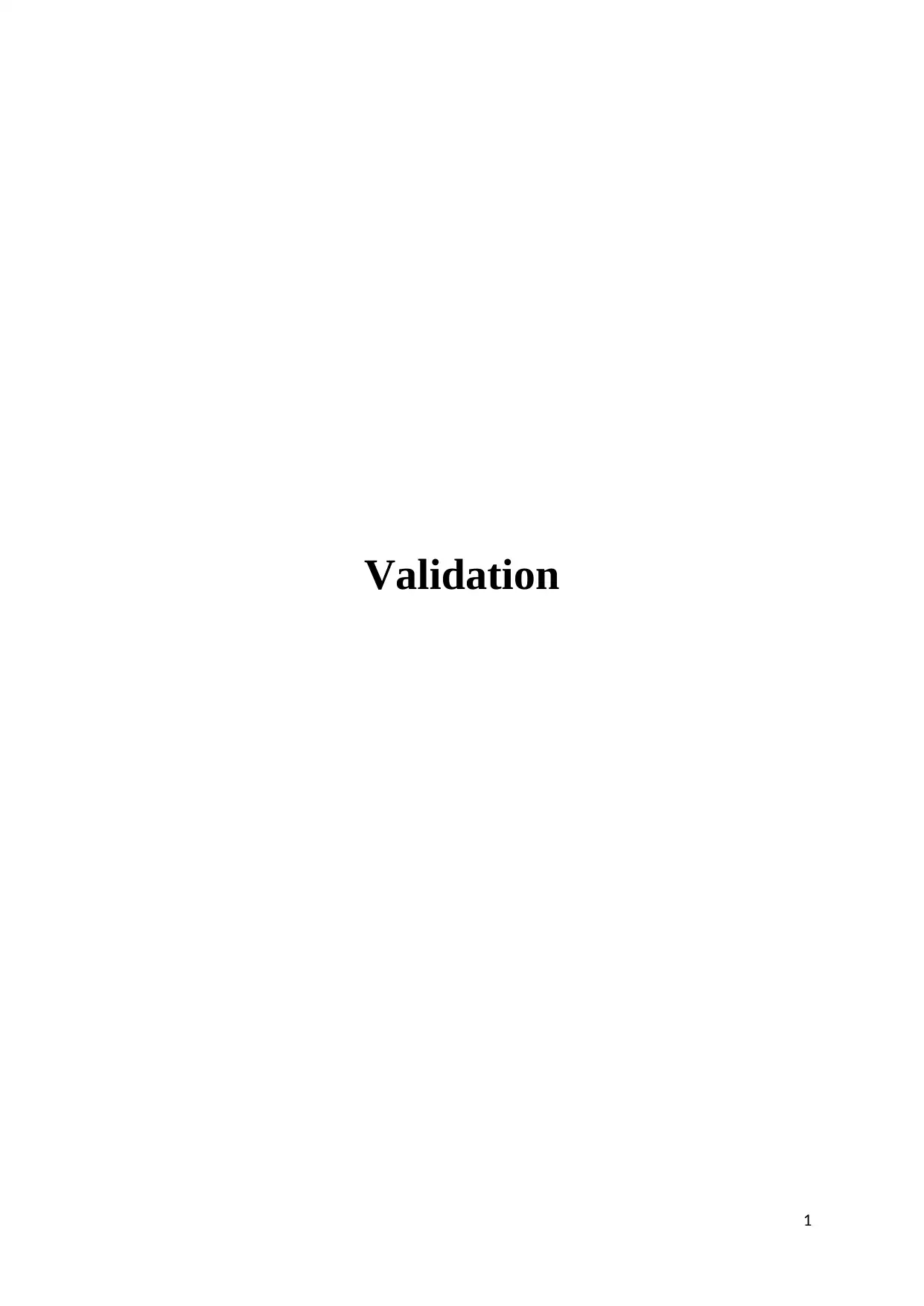
Validation
1
1
Secure Best Marks with AI Grader
Need help grading? Try our AI Grader for instant feedback on your assignments.
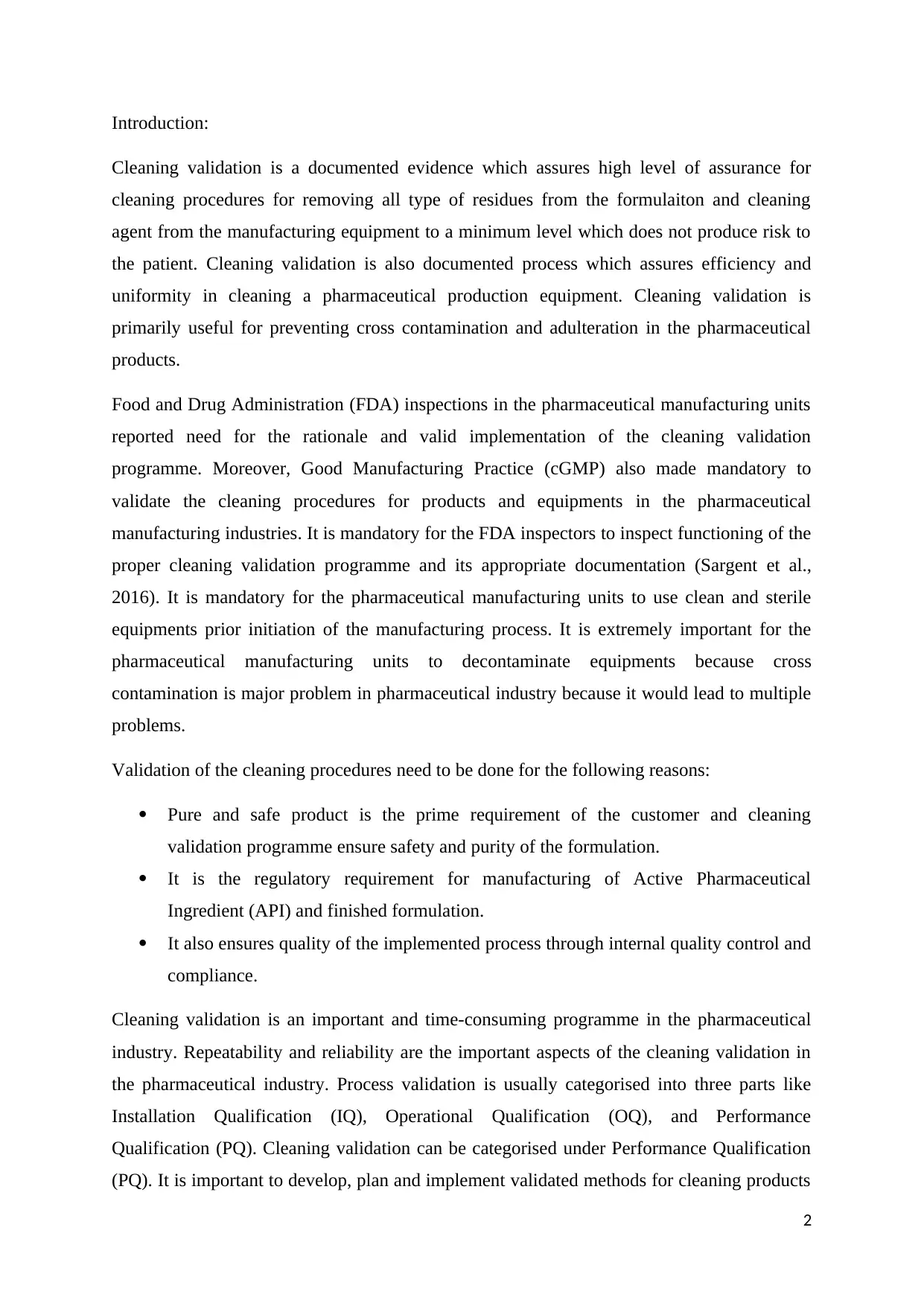
Introduction:
Cleaning validation is a documented evidence which assures high level of assurance for
cleaning procedures for removing all type of residues from the formulaiton and cleaning
agent from the manufacturing equipment to a minimum level which does not produce risk to
the patient. Cleaning validation is also documented process which assures efficiency and
uniformity in cleaning a pharmaceutical production equipment. Cleaning validation is
primarily useful for preventing cross contamination and adulteration in the pharmaceutical
products.
Food and Drug Administration (FDA) inspections in the pharmaceutical manufacturing units
reported need for the rationale and valid implementation of the cleaning validation
programme. Moreover, Good Manufacturing Practice (cGMP) also made mandatory to
validate the cleaning procedures for products and equipments in the pharmaceutical
manufacturing industries. It is mandatory for the FDA inspectors to inspect functioning of the
proper cleaning validation programme and its appropriate documentation (Sargent et al.,
2016). It is mandatory for the pharmaceutical manufacturing units to use clean and sterile
equipments prior initiation of the manufacturing process. It is extremely important for the
pharmaceutical manufacturing units to decontaminate equipments because cross
contamination is major problem in pharmaceutical industry because it would lead to multiple
problems.
Validation of the cleaning procedures need to be done for the following reasons:
Pure and safe product is the prime requirement of the customer and cleaning
validation programme ensure safety and purity of the formulation.
It is the regulatory requirement for manufacturing of Active Pharmaceutical
Ingredient (API) and finished formulation.
It also ensures quality of the implemented process through internal quality control and
compliance.
Cleaning validation is an important and time-consuming programme in the pharmaceutical
industry. Repeatability and reliability are the important aspects of the cleaning validation in
the pharmaceutical industry. Process validation is usually categorised into three parts like
Installation Qualification (IQ), Operational Qualification (OQ), and Performance
Qualification (PQ). Cleaning validation can be categorised under Performance Qualification
(PQ). It is important to develop, plan and implement validated methods for cleaning products
2
Cleaning validation is a documented evidence which assures high level of assurance for
cleaning procedures for removing all type of residues from the formulaiton and cleaning
agent from the manufacturing equipment to a minimum level which does not produce risk to
the patient. Cleaning validation is also documented process which assures efficiency and
uniformity in cleaning a pharmaceutical production equipment. Cleaning validation is
primarily useful for preventing cross contamination and adulteration in the pharmaceutical
products.
Food and Drug Administration (FDA) inspections in the pharmaceutical manufacturing units
reported need for the rationale and valid implementation of the cleaning validation
programme. Moreover, Good Manufacturing Practice (cGMP) also made mandatory to
validate the cleaning procedures for products and equipments in the pharmaceutical
manufacturing industries. It is mandatory for the FDA inspectors to inspect functioning of the
proper cleaning validation programme and its appropriate documentation (Sargent et al.,
2016). It is mandatory for the pharmaceutical manufacturing units to use clean and sterile
equipments prior initiation of the manufacturing process. It is extremely important for the
pharmaceutical manufacturing units to decontaminate equipments because cross
contamination is major problem in pharmaceutical industry because it would lead to multiple
problems.
Validation of the cleaning procedures need to be done for the following reasons:
Pure and safe product is the prime requirement of the customer and cleaning
validation programme ensure safety and purity of the formulation.
It is the regulatory requirement for manufacturing of Active Pharmaceutical
Ingredient (API) and finished formulation.
It also ensures quality of the implemented process through internal quality control and
compliance.
Cleaning validation is an important and time-consuming programme in the pharmaceutical
industry. Repeatability and reliability are the important aspects of the cleaning validation in
the pharmaceutical industry. Process validation is usually categorised into three parts like
Installation Qualification (IQ), Operational Qualification (OQ), and Performance
Qualification (PQ). Cleaning validation can be categorised under Performance Qualification
(PQ). It is important to develop, plan and implement validated methods for cleaning products
2
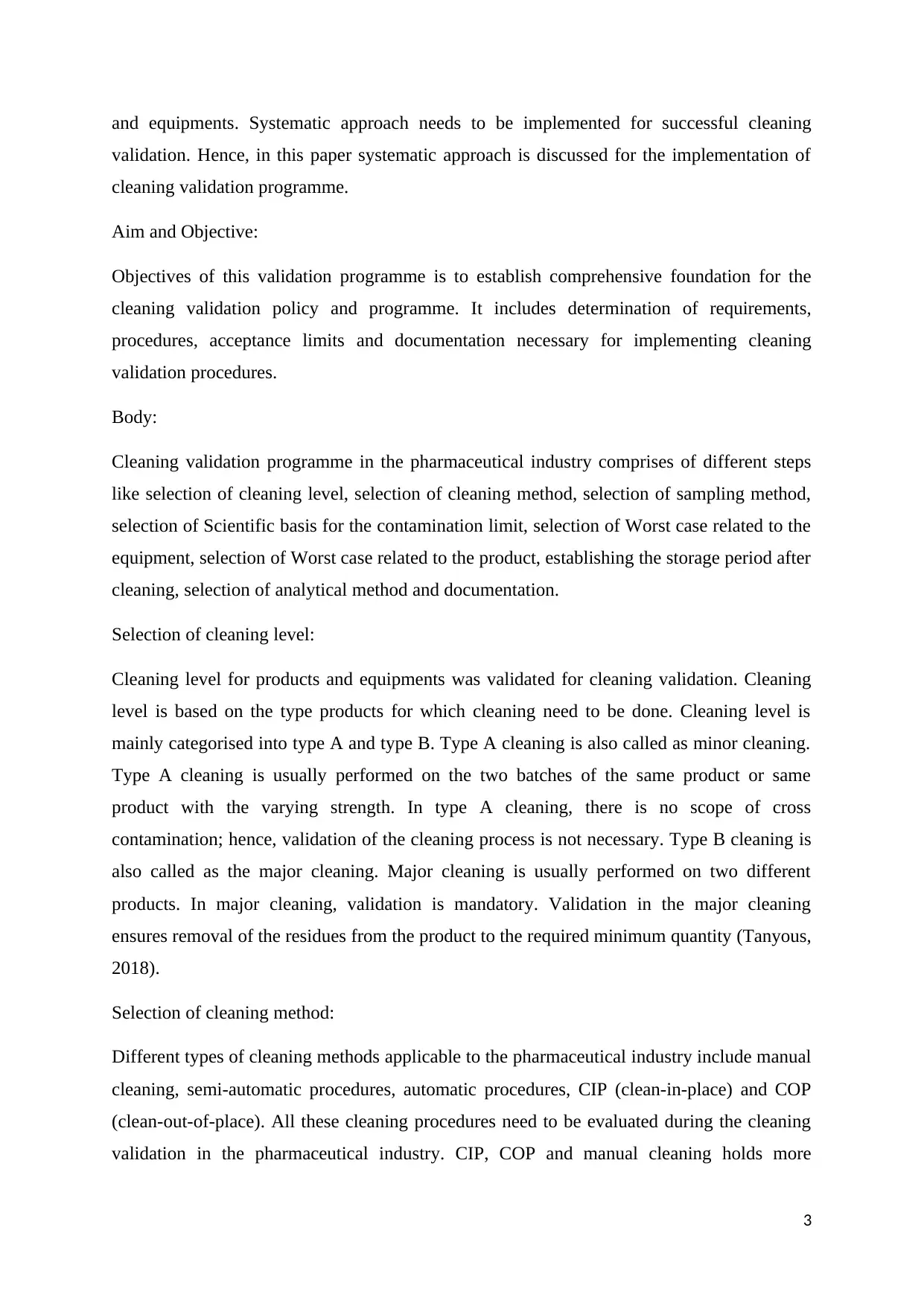
and equipments. Systematic approach needs to be implemented for successful cleaning
validation. Hence, in this paper systematic approach is discussed for the implementation of
cleaning validation programme.
Aim and Objective:
Objectives of this validation programme is to establish comprehensive foundation for the
cleaning validation policy and programme. It includes determination of requirements,
procedures, acceptance limits and documentation necessary for implementing cleaning
validation procedures.
Body:
Cleaning validation programme in the pharmaceutical industry comprises of different steps
like selection of cleaning level, selection of cleaning method, selection of sampling method,
selection of Scientific basis for the contamination limit, selection of Worst case related to the
equipment, selection of Worst case related to the product, establishing the storage period after
cleaning, selection of analytical method and documentation.
Selection of cleaning level:
Cleaning level for products and equipments was validated for cleaning validation. Cleaning
level is based on the type products for which cleaning need to be done. Cleaning level is
mainly categorised into type A and type B. Type A cleaning is also called as minor cleaning.
Type A cleaning is usually performed on the two batches of the same product or same
product with the varying strength. In type A cleaning, there is no scope of cross
contamination; hence, validation of the cleaning process is not necessary. Type B cleaning is
also called as the major cleaning. Major cleaning is usually performed on two different
products. In major cleaning, validation is mandatory. Validation in the major cleaning
ensures removal of the residues from the product to the required minimum quantity (Tanyous,
2018).
Selection of cleaning method:
Different types of cleaning methods applicable to the pharmaceutical industry include manual
cleaning, semi-automatic procedures, automatic procedures, CIP (clean-in-place) and COP
(clean-out-of-place). All these cleaning procedures need to be evaluated during the cleaning
validation in the pharmaceutical industry. CIP, COP and manual cleaning holds more
3
validation. Hence, in this paper systematic approach is discussed for the implementation of
cleaning validation programme.
Aim and Objective:
Objectives of this validation programme is to establish comprehensive foundation for the
cleaning validation policy and programme. It includes determination of requirements,
procedures, acceptance limits and documentation necessary for implementing cleaning
validation procedures.
Body:
Cleaning validation programme in the pharmaceutical industry comprises of different steps
like selection of cleaning level, selection of cleaning method, selection of sampling method,
selection of Scientific basis for the contamination limit, selection of Worst case related to the
equipment, selection of Worst case related to the product, establishing the storage period after
cleaning, selection of analytical method and documentation.
Selection of cleaning level:
Cleaning level for products and equipments was validated for cleaning validation. Cleaning
level is based on the type products for which cleaning need to be done. Cleaning level is
mainly categorised into type A and type B. Type A cleaning is also called as minor cleaning.
Type A cleaning is usually performed on the two batches of the same product or same
product with the varying strength. In type A cleaning, there is no scope of cross
contamination; hence, validation of the cleaning process is not necessary. Type B cleaning is
also called as the major cleaning. Major cleaning is usually performed on two different
products. In major cleaning, validation is mandatory. Validation in the major cleaning
ensures removal of the residues from the product to the required minimum quantity (Tanyous,
2018).
Selection of cleaning method:
Different types of cleaning methods applicable to the pharmaceutical industry include manual
cleaning, semi-automatic procedures, automatic procedures, CIP (clean-in-place) and COP
(clean-out-of-place). All these cleaning procedures need to be evaluated during the cleaning
validation in the pharmaceutical industry. CIP, COP and manual cleaning holds more
3
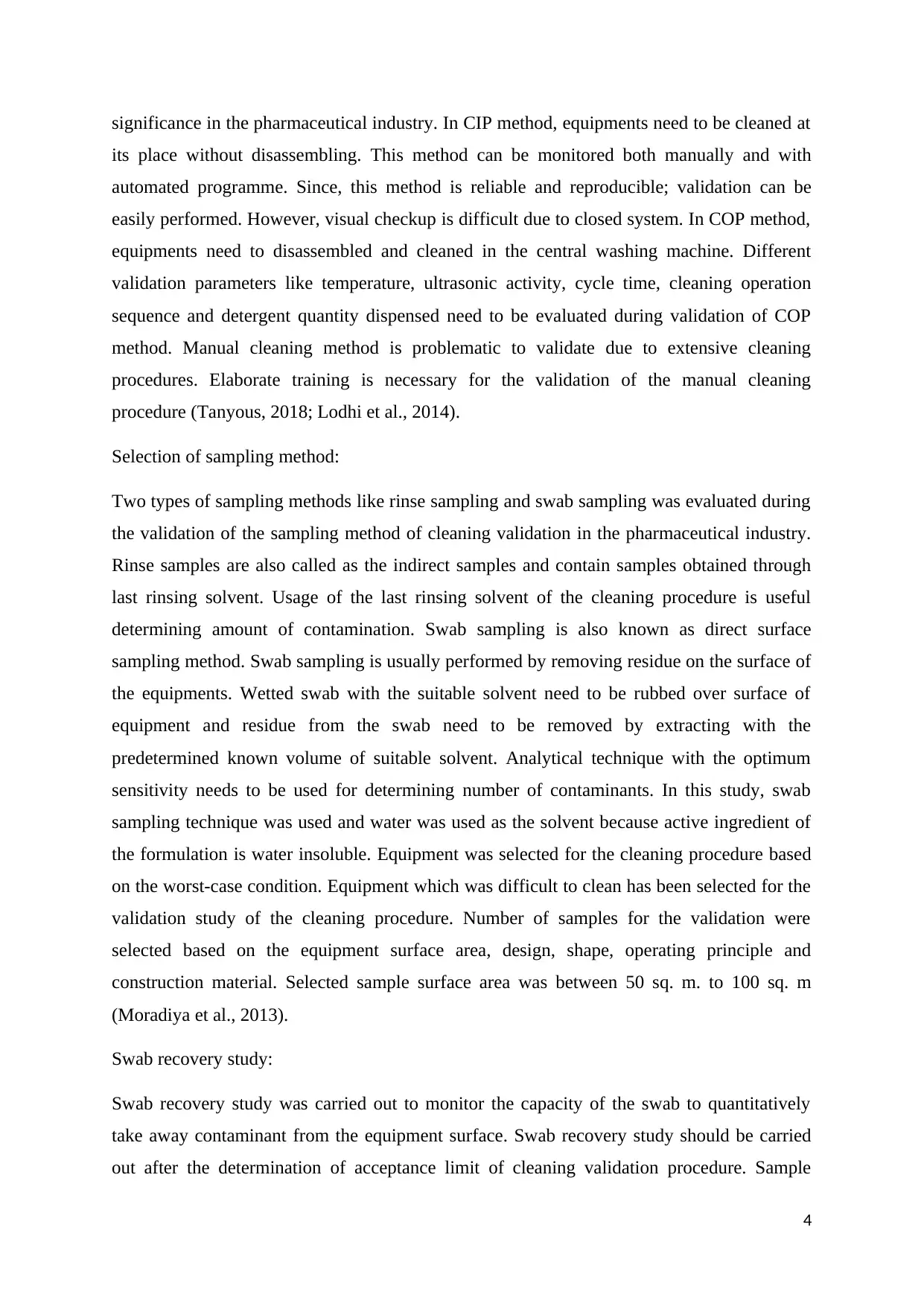
significance in the pharmaceutical industry. In CIP method, equipments need to be cleaned at
its place without disassembling. This method can be monitored both manually and with
automated programme. Since, this method is reliable and reproducible; validation can be
easily performed. However, visual checkup is difficult due to closed system. In COP method,
equipments need to disassembled and cleaned in the central washing machine. Different
validation parameters like temperature, ultrasonic activity, cycle time, cleaning operation
sequence and detergent quantity dispensed need to be evaluated during validation of COP
method. Manual cleaning method is problematic to validate due to extensive cleaning
procedures. Elaborate training is necessary for the validation of the manual cleaning
procedure (Tanyous, 2018; Lodhi et al., 2014).
Selection of sampling method:
Two types of sampling methods like rinse sampling and swab sampling was evaluated during
the validation of the sampling method of cleaning validation in the pharmaceutical industry.
Rinse samples are also called as the indirect samples and contain samples obtained through
last rinsing solvent. Usage of the last rinsing solvent of the cleaning procedure is useful
determining amount of contamination. Swab sampling is also known as direct surface
sampling method. Swab sampling is usually performed by removing residue on the surface of
the equipments. Wetted swab with the suitable solvent need to be rubbed over surface of
equipment and residue from the swab need to be removed by extracting with the
predetermined known volume of suitable solvent. Analytical technique with the optimum
sensitivity needs to be used for determining number of contaminants. In this study, swab
sampling technique was used and water was used as the solvent because active ingredient of
the formulation is water insoluble. Equipment was selected for the cleaning procedure based
on the worst-case condition. Equipment which was difficult to clean has been selected for the
validation study of the cleaning procedure. Number of samples for the validation were
selected based on the equipment surface area, design, shape, operating principle and
construction material. Selected sample surface area was between 50 sq. m. to 100 sq. m
(Moradiya et al., 2013).
Swab recovery study:
Swab recovery study was carried out to monitor the capacity of the swab to quantitatively
take away contaminant from the equipment surface. Swab recovery study should be carried
out after the determination of acceptance limit of cleaning validation procedure. Sample
4
its place without disassembling. This method can be monitored both manually and with
automated programme. Since, this method is reliable and reproducible; validation can be
easily performed. However, visual checkup is difficult due to closed system. In COP method,
equipments need to disassembled and cleaned in the central washing machine. Different
validation parameters like temperature, ultrasonic activity, cycle time, cleaning operation
sequence and detergent quantity dispensed need to be evaluated during validation of COP
method. Manual cleaning method is problematic to validate due to extensive cleaning
procedures. Elaborate training is necessary for the validation of the manual cleaning
procedure (Tanyous, 2018; Lodhi et al., 2014).
Selection of sampling method:
Two types of sampling methods like rinse sampling and swab sampling was evaluated during
the validation of the sampling method of cleaning validation in the pharmaceutical industry.
Rinse samples are also called as the indirect samples and contain samples obtained through
last rinsing solvent. Usage of the last rinsing solvent of the cleaning procedure is useful
determining amount of contamination. Swab sampling is also known as direct surface
sampling method. Swab sampling is usually performed by removing residue on the surface of
the equipments. Wetted swab with the suitable solvent need to be rubbed over surface of
equipment and residue from the swab need to be removed by extracting with the
predetermined known volume of suitable solvent. Analytical technique with the optimum
sensitivity needs to be used for determining number of contaminants. In this study, swab
sampling technique was used and water was used as the solvent because active ingredient of
the formulation is water insoluble. Equipment was selected for the cleaning procedure based
on the worst-case condition. Equipment which was difficult to clean has been selected for the
validation study of the cleaning procedure. Number of samples for the validation were
selected based on the equipment surface area, design, shape, operating principle and
construction material. Selected sample surface area was between 50 sq. m. to 100 sq. m
(Moradiya et al., 2013).
Swab recovery study:
Swab recovery study was carried out to monitor the capacity of the swab to quantitatively
take away contaminant from the equipment surface. Swab recovery study should be carried
out after the determination of acceptance limit of cleaning validation procedure. Sample
4
Secure Best Marks with AI Grader
Need help grading? Try our AI Grader for instant feedback on your assignments.
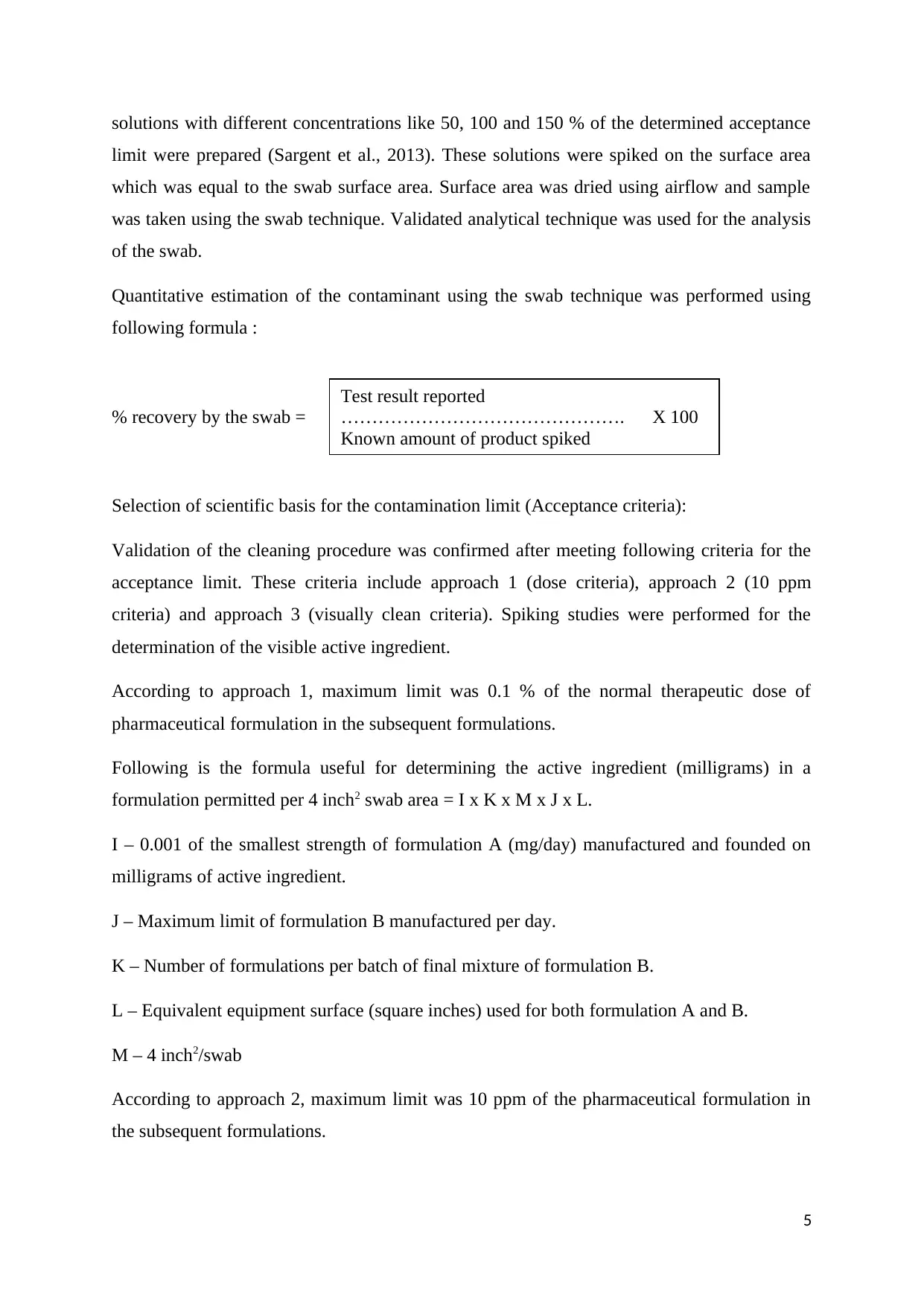
solutions with different concentrations like 50, 100 and 150 % of the determined acceptance
limit were prepared (Sargent et al., 2013). These solutions were spiked on the surface area
which was equal to the swab surface area. Surface area was dried using airflow and sample
was taken using the swab technique. Validated analytical technique was used for the analysis
of the swab.
Quantitative estimation of the contaminant using the swab technique was performed using
following formula :
% recovery by the swab =
Selection of scientific basis for the contamination limit (Acceptance criteria):
Validation of the cleaning procedure was confirmed after meeting following criteria for the
acceptance limit. These criteria include approach 1 (dose criteria), approach 2 (10 ppm
criteria) and approach 3 (visually clean criteria). Spiking studies were performed for the
determination of the visible active ingredient.
According to approach 1, maximum limit was 0.1 % of the normal therapeutic dose of
pharmaceutical formulation in the subsequent formulations.
Following is the formula useful for determining the active ingredient (milligrams) in a
formulation permitted per 4 inch2 swab area = I x K x M x J x L.
I – 0.001 of the smallest strength of formulation A (mg/day) manufactured and founded on
milligrams of active ingredient.
J – Maximum limit of formulation B manufactured per day.
K – Number of formulations per batch of final mixture of formulation B.
L – Equivalent equipment surface (square inches) used for both formulation A and B.
M – 4 inch2/swab
According to approach 2, maximum limit was 10 ppm of the pharmaceutical formulation in
the subsequent formulations.
5
Test result reported
………………………………………. X 100
Known amount of product spiked
limit were prepared (Sargent et al., 2013). These solutions were spiked on the surface area
which was equal to the swab surface area. Surface area was dried using airflow and sample
was taken using the swab technique. Validated analytical technique was used for the analysis
of the swab.
Quantitative estimation of the contaminant using the swab technique was performed using
following formula :
% recovery by the swab =
Selection of scientific basis for the contamination limit (Acceptance criteria):
Validation of the cleaning procedure was confirmed after meeting following criteria for the
acceptance limit. These criteria include approach 1 (dose criteria), approach 2 (10 ppm
criteria) and approach 3 (visually clean criteria). Spiking studies were performed for the
determination of the visible active ingredient.
According to approach 1, maximum limit was 0.1 % of the normal therapeutic dose of
pharmaceutical formulation in the subsequent formulations.
Following is the formula useful for determining the active ingredient (milligrams) in a
formulation permitted per 4 inch2 swab area = I x K x M x J x L.
I – 0.001 of the smallest strength of formulation A (mg/day) manufactured and founded on
milligrams of active ingredient.
J – Maximum limit of formulation B manufactured per day.
K – Number of formulations per batch of final mixture of formulation B.
L – Equivalent equipment surface (square inches) used for both formulation A and B.
M – 4 inch2/swab
According to approach 2, maximum limit was 10 ppm of the pharmaceutical formulation in
the subsequent formulations.
5
Test result reported
………………………………………. X 100
Known amount of product spiked
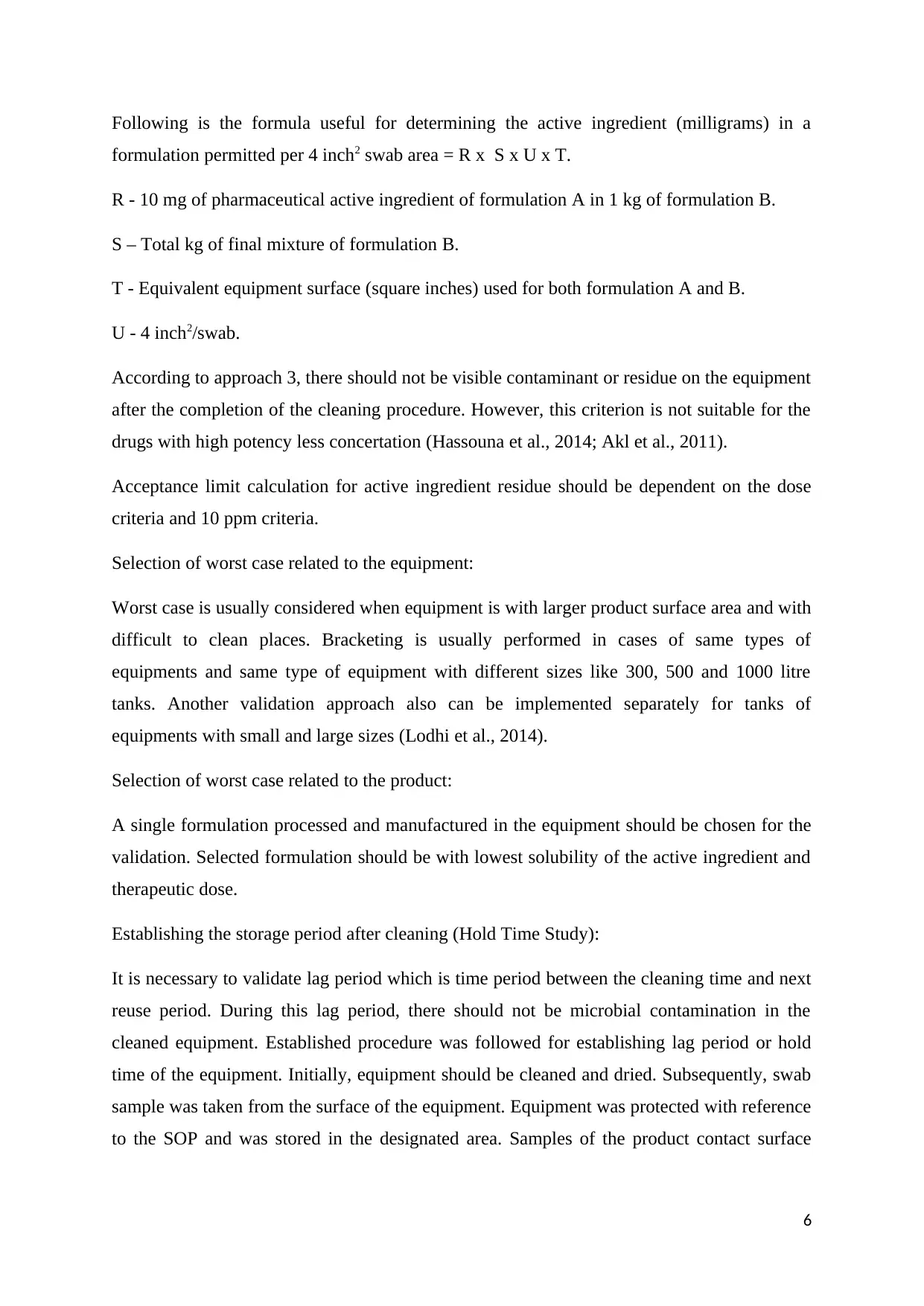
Following is the formula useful for determining the active ingredient (milligrams) in a
formulation permitted per 4 inch2 swab area = R x S x U x T.
R - 10 mg of pharmaceutical active ingredient of formulation A in 1 kg of formulation B.
S – Total kg of final mixture of formulation B.
T - Equivalent equipment surface (square inches) used for both formulation A and B.
U - 4 inch2/swab.
According to approach 3, there should not be visible contaminant or residue on the equipment
after the completion of the cleaning procedure. However, this criterion is not suitable for the
drugs with high potency less concertation (Hassouna et al., 2014; Akl et al., 2011).
Acceptance limit calculation for active ingredient residue should be dependent on the dose
criteria and 10 ppm criteria.
Selection of worst case related to the equipment:
Worst case is usually considered when equipment is with larger product surface area and with
difficult to clean places. Bracketing is usually performed in cases of same types of
equipments and same type of equipment with different sizes like 300, 500 and 1000 litre
tanks. Another validation approach also can be implemented separately for tanks of
equipments with small and large sizes (Lodhi et al., 2014).
Selection of worst case related to the product:
A single formulation processed and manufactured in the equipment should be chosen for the
validation. Selected formulation should be with lowest solubility of the active ingredient and
therapeutic dose.
Establishing the storage period after cleaning (Hold Time Study):
It is necessary to validate lag period which is time period between the cleaning time and next
reuse period. During this lag period, there should not be microbial contamination in the
cleaned equipment. Established procedure was followed for establishing lag period or hold
time of the equipment. Initially, equipment should be cleaned and dried. Subsequently, swab
sample was taken from the surface of the equipment. Equipment was protected with reference
to the SOP and was stored in the designated area. Samples of the product contact surface
6
formulation permitted per 4 inch2 swab area = R x S x U x T.
R - 10 mg of pharmaceutical active ingredient of formulation A in 1 kg of formulation B.
S – Total kg of final mixture of formulation B.
T - Equivalent equipment surface (square inches) used for both formulation A and B.
U - 4 inch2/swab.
According to approach 3, there should not be visible contaminant or residue on the equipment
after the completion of the cleaning procedure. However, this criterion is not suitable for the
drugs with high potency less concertation (Hassouna et al., 2014; Akl et al., 2011).
Acceptance limit calculation for active ingredient residue should be dependent on the dose
criteria and 10 ppm criteria.
Selection of worst case related to the equipment:
Worst case is usually considered when equipment is with larger product surface area and with
difficult to clean places. Bracketing is usually performed in cases of same types of
equipments and same type of equipment with different sizes like 300, 500 and 1000 litre
tanks. Another validation approach also can be implemented separately for tanks of
equipments with small and large sizes (Lodhi et al., 2014).
Selection of worst case related to the product:
A single formulation processed and manufactured in the equipment should be chosen for the
validation. Selected formulation should be with lowest solubility of the active ingredient and
therapeutic dose.
Establishing the storage period after cleaning (Hold Time Study):
It is necessary to validate lag period which is time period between the cleaning time and next
reuse period. During this lag period, there should not be microbial contamination in the
cleaned equipment. Established procedure was followed for establishing lag period or hold
time of the equipment. Initially, equipment should be cleaned and dried. Subsequently, swab
sample was taken from the surface of the equipment. Equipment was protected with reference
to the SOP and was stored in the designated area. Samples of the product contact surface
6
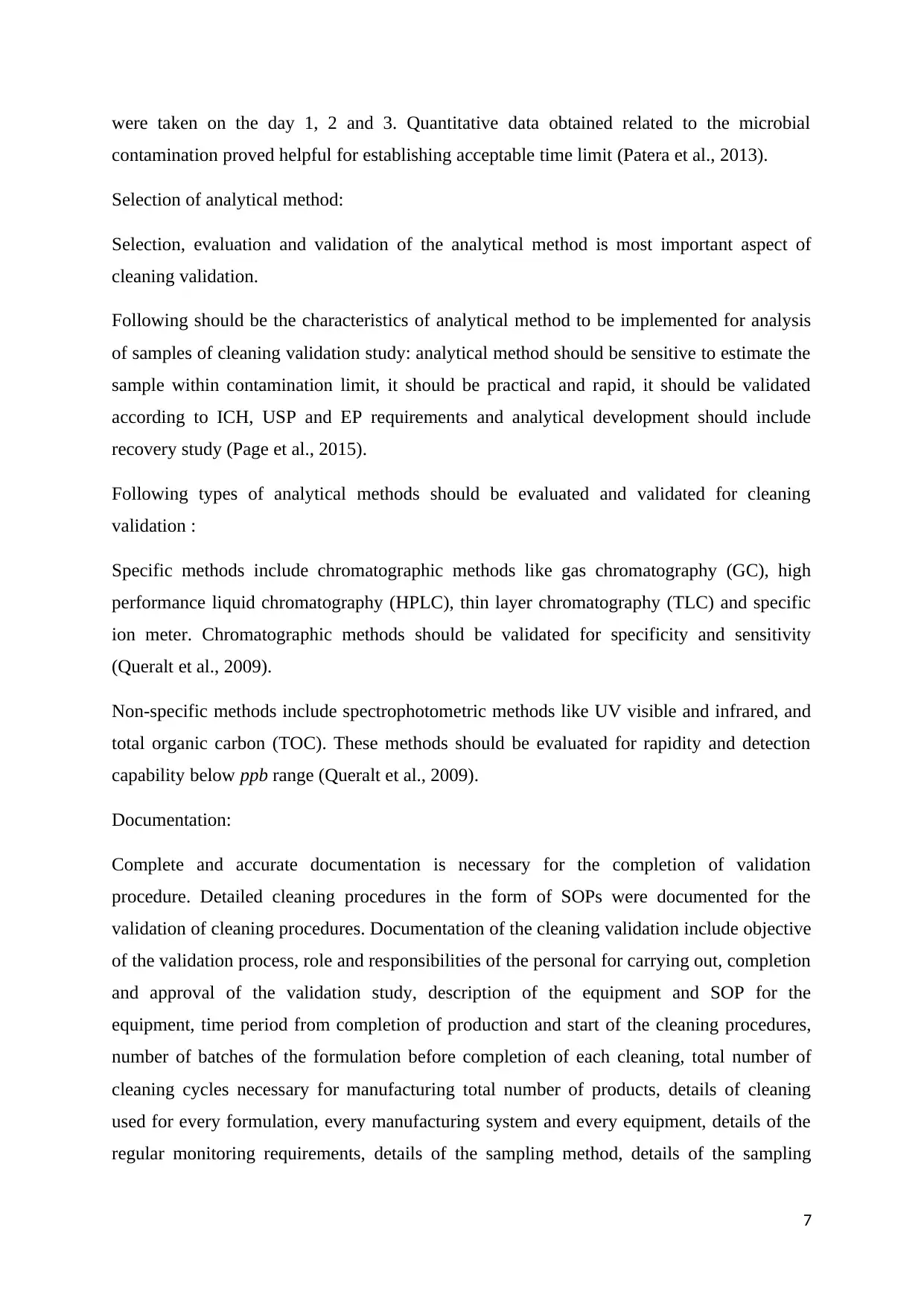
were taken on the day 1, 2 and 3. Quantitative data obtained related to the microbial
contamination proved helpful for establishing acceptable time limit (Patera et al., 2013).
Selection of analytical method:
Selection, evaluation and validation of the analytical method is most important aspect of
cleaning validation.
Following should be the characteristics of analytical method to be implemented for analysis
of samples of cleaning validation study: analytical method should be sensitive to estimate the
sample within contamination limit, it should be practical and rapid, it should be validated
according to ICH, USP and EP requirements and analytical development should include
recovery study (Page et al., 2015).
Following types of analytical methods should be evaluated and validated for cleaning
validation :
Specific methods include chromatographic methods like gas chromatography (GC), high
performance liquid chromatography (HPLC), thin layer chromatography (TLC) and specific
ion meter. Chromatographic methods should be validated for specificity and sensitivity
(Queralt et al., 2009).
Non-specific methods include spectrophotometric methods like UV visible and infrared, and
total organic carbon (TOC). These methods should be evaluated for rapidity and detection
capability below ppb range (Queralt et al., 2009).
Documentation:
Complete and accurate documentation is necessary for the completion of validation
procedure. Detailed cleaning procedures in the form of SOPs were documented for the
validation of cleaning procedures. Documentation of the cleaning validation include objective
of the validation process, role and responsibilities of the personal for carrying out, completion
and approval of the validation study, description of the equipment and SOP for the
equipment, time period from completion of production and start of the cleaning procedures,
number of batches of the formulation before completion of each cleaning, total number of
cleaning cycles necessary for manufacturing total number of products, details of cleaning
used for every formulation, every manufacturing system and every equipment, details of the
regular monitoring requirements, details of the sampling method, details of the sampling
7
contamination proved helpful for establishing acceptable time limit (Patera et al., 2013).
Selection of analytical method:
Selection, evaluation and validation of the analytical method is most important aspect of
cleaning validation.
Following should be the characteristics of analytical method to be implemented for analysis
of samples of cleaning validation study: analytical method should be sensitive to estimate the
sample within contamination limit, it should be practical and rapid, it should be validated
according to ICH, USP and EP requirements and analytical development should include
recovery study (Page et al., 2015).
Following types of analytical methods should be evaluated and validated for cleaning
validation :
Specific methods include chromatographic methods like gas chromatography (GC), high
performance liquid chromatography (HPLC), thin layer chromatography (TLC) and specific
ion meter. Chromatographic methods should be validated for specificity and sensitivity
(Queralt et al., 2009).
Non-specific methods include spectrophotometric methods like UV visible and infrared, and
total organic carbon (TOC). These methods should be evaluated for rapidity and detection
capability below ppb range (Queralt et al., 2009).
Documentation:
Complete and accurate documentation is necessary for the completion of validation
procedure. Detailed cleaning procedures in the form of SOPs were documented for the
validation of cleaning procedures. Documentation of the cleaning validation include objective
of the validation process, role and responsibilities of the personal for carrying out, completion
and approval of the validation study, description of the equipment and SOP for the
equipment, time period from completion of production and start of the cleaning procedures,
number of batches of the formulation before completion of each cleaning, total number of
cleaning cycles necessary for manufacturing total number of products, details of cleaning
used for every formulation, every manufacturing system and every equipment, details of the
regular monitoring requirements, details of the sampling method, details of the sampling
7
Paraphrase This Document
Need a fresh take? Get an instant paraphrase of this document with our AI Paraphraser
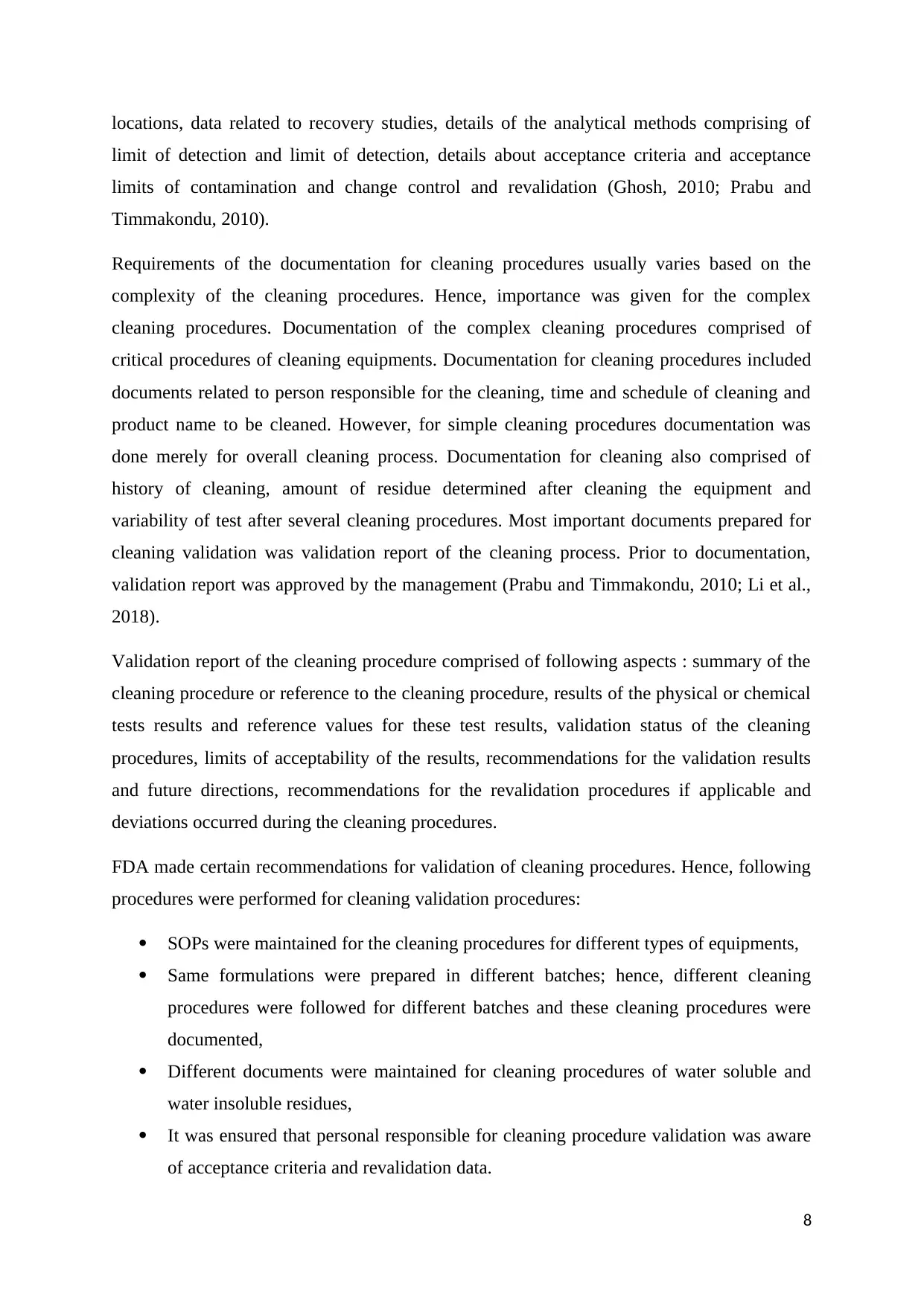
locations, data related to recovery studies, details of the analytical methods comprising of
limit of detection and limit of detection, details about acceptance criteria and acceptance
limits of contamination and change control and revalidation (Ghosh, 2010; Prabu and
Timmakondu, 2010).
Requirements of the documentation for cleaning procedures usually varies based on the
complexity of the cleaning procedures. Hence, importance was given for the complex
cleaning procedures. Documentation of the complex cleaning procedures comprised of
critical procedures of cleaning equipments. Documentation for cleaning procedures included
documents related to person responsible for the cleaning, time and schedule of cleaning and
product name to be cleaned. However, for simple cleaning procedures documentation was
done merely for overall cleaning process. Documentation for cleaning also comprised of
history of cleaning, amount of residue determined after cleaning the equipment and
variability of test after several cleaning procedures. Most important documents prepared for
cleaning validation was validation report of the cleaning process. Prior to documentation,
validation report was approved by the management (Prabu and Timmakondu, 2010; Li et al.,
2018).
Validation report of the cleaning procedure comprised of following aspects : summary of the
cleaning procedure or reference to the cleaning procedure, results of the physical or chemical
tests results and reference values for these test results, validation status of the cleaning
procedures, limits of acceptability of the results, recommendations for the validation results
and future directions, recommendations for the revalidation procedures if applicable and
deviations occurred during the cleaning procedures.
FDA made certain recommendations for validation of cleaning procedures. Hence, following
procedures were performed for cleaning validation procedures:
SOPs were maintained for the cleaning procedures for different types of equipments,
Same formulations were prepared in different batches; hence, different cleaning
procedures were followed for different batches and these cleaning procedures were
documented,
Different documents were maintained for cleaning procedures of water soluble and
water insoluble residues,
It was ensured that personal responsible for cleaning procedure validation was aware
of acceptance criteria and revalidation data.
8
limit of detection and limit of detection, details about acceptance criteria and acceptance
limits of contamination and change control and revalidation (Ghosh, 2010; Prabu and
Timmakondu, 2010).
Requirements of the documentation for cleaning procedures usually varies based on the
complexity of the cleaning procedures. Hence, importance was given for the complex
cleaning procedures. Documentation of the complex cleaning procedures comprised of
critical procedures of cleaning equipments. Documentation for cleaning procedures included
documents related to person responsible for the cleaning, time and schedule of cleaning and
product name to be cleaned. However, for simple cleaning procedures documentation was
done merely for overall cleaning process. Documentation for cleaning also comprised of
history of cleaning, amount of residue determined after cleaning the equipment and
variability of test after several cleaning procedures. Most important documents prepared for
cleaning validation was validation report of the cleaning process. Prior to documentation,
validation report was approved by the management (Prabu and Timmakondu, 2010; Li et al.,
2018).
Validation report of the cleaning procedure comprised of following aspects : summary of the
cleaning procedure or reference to the cleaning procedure, results of the physical or chemical
tests results and reference values for these test results, validation status of the cleaning
procedures, limits of acceptability of the results, recommendations for the validation results
and future directions, recommendations for the revalidation procedures if applicable and
deviations occurred during the cleaning procedures.
FDA made certain recommendations for validation of cleaning procedures. Hence, following
procedures were performed for cleaning validation procedures:
SOPs were maintained for the cleaning procedures for different types of equipments,
Same formulations were prepared in different batches; hence, different cleaning
procedures were followed for different batches and these cleaning procedures were
documented,
Different documents were maintained for cleaning procedures of water soluble and
water insoluble residues,
It was ensured that personal responsible for cleaning procedure validation was aware
of acceptance criteria and revalidation data.
8
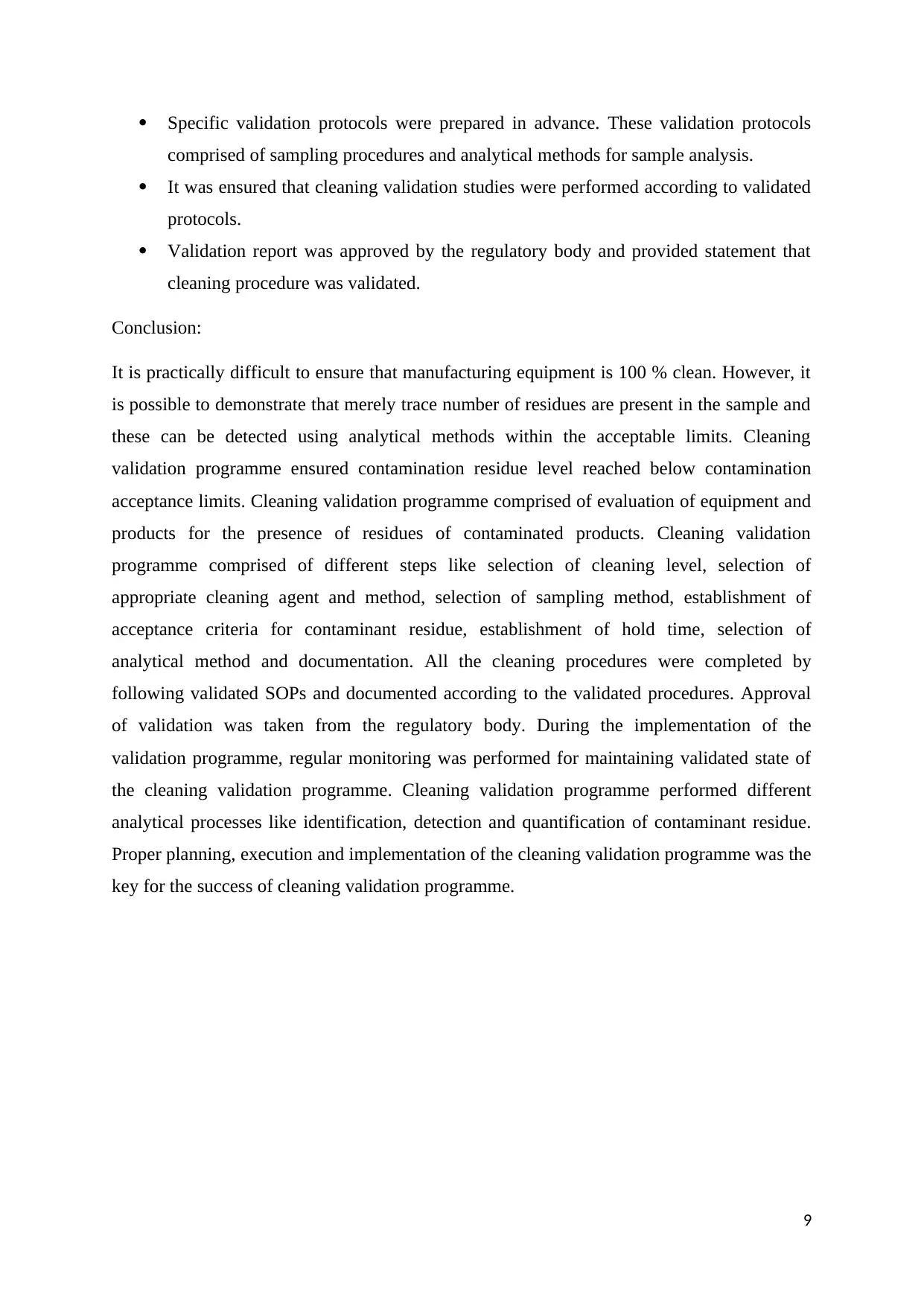
Specific validation protocols were prepared in advance. These validation protocols
comprised of sampling procedures and analytical methods for sample analysis.
It was ensured that cleaning validation studies were performed according to validated
protocols.
Validation report was approved by the regulatory body and provided statement that
cleaning procedure was validated.
Conclusion:
It is practically difficult to ensure that manufacturing equipment is 100 % clean. However, it
is possible to demonstrate that merely trace number of residues are present in the sample and
these can be detected using analytical methods within the acceptable limits. Cleaning
validation programme ensured contamination residue level reached below contamination
acceptance limits. Cleaning validation programme comprised of evaluation of equipment and
products for the presence of residues of contaminated products. Cleaning validation
programme comprised of different steps like selection of cleaning level, selection of
appropriate cleaning agent and method, selection of sampling method, establishment of
acceptance criteria for contaminant residue, establishment of hold time, selection of
analytical method and documentation. All the cleaning procedures were completed by
following validated SOPs and documented according to the validated procedures. Approval
of validation was taken from the regulatory body. During the implementation of the
validation programme, regular monitoring was performed for maintaining validated state of
the cleaning validation programme. Cleaning validation programme performed different
analytical processes like identification, detection and quantification of contaminant residue.
Proper planning, execution and implementation of the cleaning validation programme was the
key for the success of cleaning validation programme.
9
comprised of sampling procedures and analytical methods for sample analysis.
It was ensured that cleaning validation studies were performed according to validated
protocols.
Validation report was approved by the regulatory body and provided statement that
cleaning procedure was validated.
Conclusion:
It is practically difficult to ensure that manufacturing equipment is 100 % clean. However, it
is possible to demonstrate that merely trace number of residues are present in the sample and
these can be detected using analytical methods within the acceptable limits. Cleaning
validation programme ensured contamination residue level reached below contamination
acceptance limits. Cleaning validation programme comprised of evaluation of equipment and
products for the presence of residues of contaminated products. Cleaning validation
programme comprised of different steps like selection of cleaning level, selection of
appropriate cleaning agent and method, selection of sampling method, establishment of
acceptance criteria for contaminant residue, establishment of hold time, selection of
analytical method and documentation. All the cleaning procedures were completed by
following validated SOPs and documented according to the validated procedures. Approval
of validation was taken from the regulatory body. During the implementation of the
validation programme, regular monitoring was performed for maintaining validated state of
the cleaning validation programme. Cleaning validation programme performed different
analytical processes like identification, detection and quantification of contaminant residue.
Proper planning, execution and implementation of the cleaning validation programme was the
key for the success of cleaning validation programme.
9
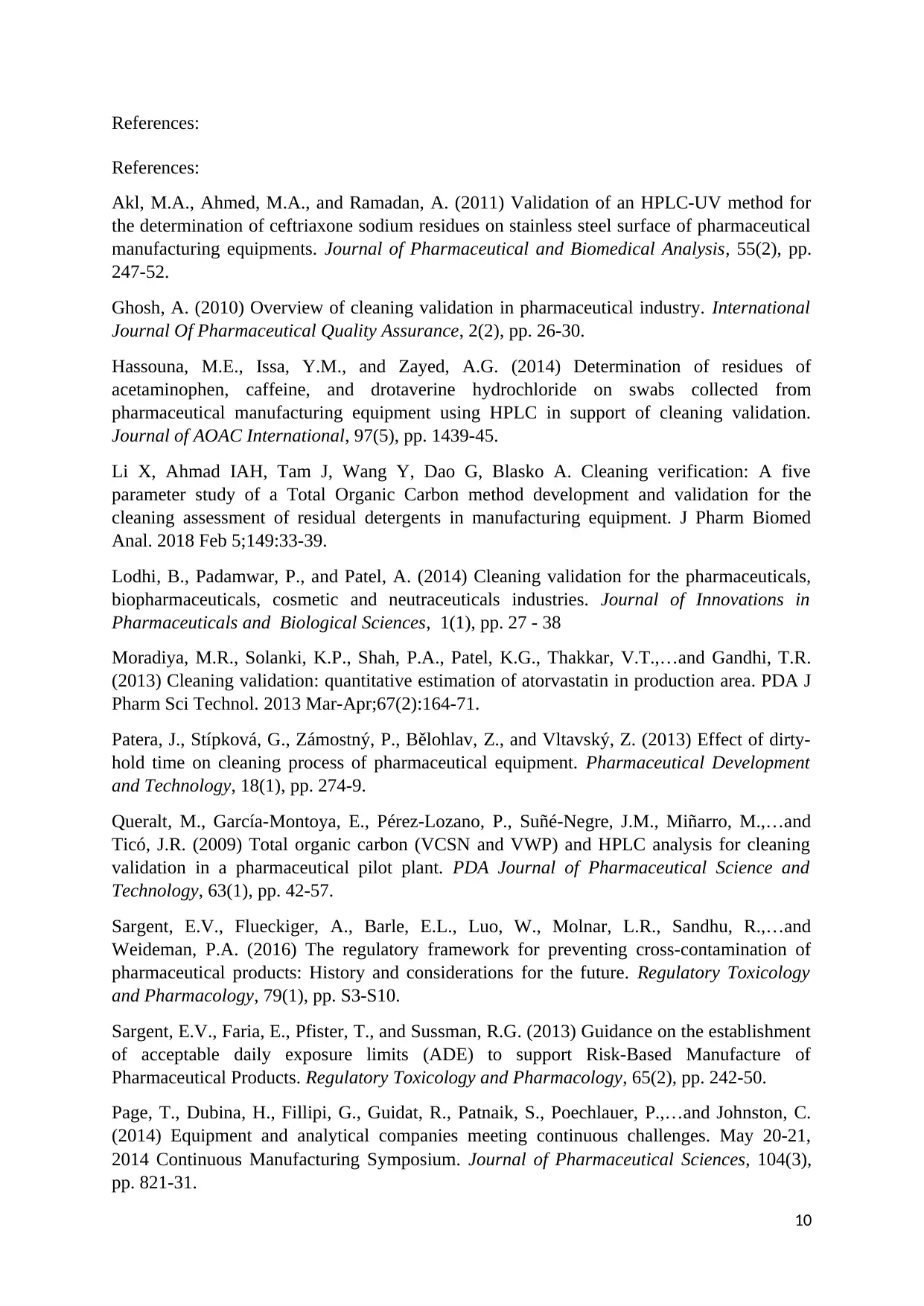
References:
References:
Akl, M.A., Ahmed, M.A., and Ramadan, A. (2011) Validation of an HPLC-UV method for
the determination of ceftriaxone sodium residues on stainless steel surface of pharmaceutical
manufacturing equipments. Journal of Pharmaceutical and Biomedical Analysis, 55(2), pp.
247-52.
Ghosh, A. (2010) Overview of cleaning validation in pharmaceutical industry. International
Journal Of Pharmaceutical Quality Assurance, 2(2), pp. 26-30.
Hassouna, M.E., Issa, Y.M., and Zayed, A.G. (2014) Determination of residues of
acetaminophen, caffeine, and drotaverine hydrochloride on swabs collected from
pharmaceutical manufacturing equipment using HPLC in support of cleaning validation.
Journal of AOAC International, 97(5), pp. 1439-45.
Li X, Ahmad IAH, Tam J, Wang Y, Dao G, Blasko A. Cleaning verification: A five
parameter study of a Total Organic Carbon method development and validation for the
cleaning assessment of residual detergents in manufacturing equipment. J Pharm Biomed
Anal. 2018 Feb 5;149:33-39.
Lodhi, B., Padamwar, P., and Patel, A. (2014) Cleaning validation for the pharmaceuticals,
biopharmaceuticals, cosmetic and neutraceuticals industries. Journal of Innovations in
Pharmaceuticals and Biological Sciences, 1(1), pp. 27 - 38
Moradiya, M.R., Solanki, K.P., Shah, P.A., Patel, K.G., Thakkar, V.T.,…and Gandhi, T.R.
(2013) Cleaning validation: quantitative estimation of atorvastatin in production area. PDA J
Pharm Sci Technol. 2013 Mar-Apr;67(2):164-71.
Patera, J., Stípková, G., Zámostný, P., Bělohlav, Z., and Vltavský, Z. (2013) Effect of dirty-
hold time on cleaning process of pharmaceutical equipment. Pharmaceutical Development
and Technology, 18(1), pp. 274-9.
Queralt, M., García-Montoya, E., Pérez-Lozano, P., Suñé-Negre, J.M., Miñarro, M.,…and
Ticó, J.R. (2009) Total organic carbon (VCSN and VWP) and HPLC analysis for cleaning
validation in a pharmaceutical pilot plant. PDA Journal of Pharmaceutical Science and
Technology, 63(1), pp. 42-57.
Sargent, E.V., Flueckiger, A., Barle, E.L., Luo, W., Molnar, L.R., Sandhu, R.,…and
Weideman, P.A. (2016) The regulatory framework for preventing cross-contamination of
pharmaceutical products: History and considerations for the future. Regulatory Toxicology
and Pharmacology, 79(1), pp. S3-S10.
Sargent, E.V., Faria, E., Pfister, T., and Sussman, R.G. (2013) Guidance on the establishment
of acceptable daily exposure limits (ADE) to support Risk-Based Manufacture of
Pharmaceutical Products. Regulatory Toxicology and Pharmacology, 65(2), pp. 242-50.
Page, T., Dubina, H., Fillipi, G., Guidat, R., Patnaik, S., Poechlauer, P.,…and Johnston, C.
(2014) Equipment and analytical companies meeting continuous challenges. May 20-21,
2014 Continuous Manufacturing Symposium. Journal of Pharmaceutical Sciences, 104(3),
pp. 821-31.
10
References:
Akl, M.A., Ahmed, M.A., and Ramadan, A. (2011) Validation of an HPLC-UV method for
the determination of ceftriaxone sodium residues on stainless steel surface of pharmaceutical
manufacturing equipments. Journal of Pharmaceutical and Biomedical Analysis, 55(2), pp.
247-52.
Ghosh, A. (2010) Overview of cleaning validation in pharmaceutical industry. International
Journal Of Pharmaceutical Quality Assurance, 2(2), pp. 26-30.
Hassouna, M.E., Issa, Y.M., and Zayed, A.G. (2014) Determination of residues of
acetaminophen, caffeine, and drotaverine hydrochloride on swabs collected from
pharmaceutical manufacturing equipment using HPLC in support of cleaning validation.
Journal of AOAC International, 97(5), pp. 1439-45.
Li X, Ahmad IAH, Tam J, Wang Y, Dao G, Blasko A. Cleaning verification: A five
parameter study of a Total Organic Carbon method development and validation for the
cleaning assessment of residual detergents in manufacturing equipment. J Pharm Biomed
Anal. 2018 Feb 5;149:33-39.
Lodhi, B., Padamwar, P., and Patel, A. (2014) Cleaning validation for the pharmaceuticals,
biopharmaceuticals, cosmetic and neutraceuticals industries. Journal of Innovations in
Pharmaceuticals and Biological Sciences, 1(1), pp. 27 - 38
Moradiya, M.R., Solanki, K.P., Shah, P.A., Patel, K.G., Thakkar, V.T.,…and Gandhi, T.R.
(2013) Cleaning validation: quantitative estimation of atorvastatin in production area. PDA J
Pharm Sci Technol. 2013 Mar-Apr;67(2):164-71.
Patera, J., Stípková, G., Zámostný, P., Bělohlav, Z., and Vltavský, Z. (2013) Effect of dirty-
hold time on cleaning process of pharmaceutical equipment. Pharmaceutical Development
and Technology, 18(1), pp. 274-9.
Queralt, M., García-Montoya, E., Pérez-Lozano, P., Suñé-Negre, J.M., Miñarro, M.,…and
Ticó, J.R. (2009) Total organic carbon (VCSN and VWP) and HPLC analysis for cleaning
validation in a pharmaceutical pilot plant. PDA Journal of Pharmaceutical Science and
Technology, 63(1), pp. 42-57.
Sargent, E.V., Flueckiger, A., Barle, E.L., Luo, W., Molnar, L.R., Sandhu, R.,…and
Weideman, P.A. (2016) The regulatory framework for preventing cross-contamination of
pharmaceutical products: History and considerations for the future. Regulatory Toxicology
and Pharmacology, 79(1), pp. S3-S10.
Sargent, E.V., Faria, E., Pfister, T., and Sussman, R.G. (2013) Guidance on the establishment
of acceptable daily exposure limits (ADE) to support Risk-Based Manufacture of
Pharmaceutical Products. Regulatory Toxicology and Pharmacology, 65(2), pp. 242-50.
Page, T., Dubina, H., Fillipi, G., Guidat, R., Patnaik, S., Poechlauer, P.,…and Johnston, C.
(2014) Equipment and analytical companies meeting continuous challenges. May 20-21,
2014 Continuous Manufacturing Symposium. Journal of Pharmaceutical Sciences, 104(3),
pp. 821-31.
10
Secure Best Marks with AI Grader
Need help grading? Try our AI Grader for instant feedback on your assignments.
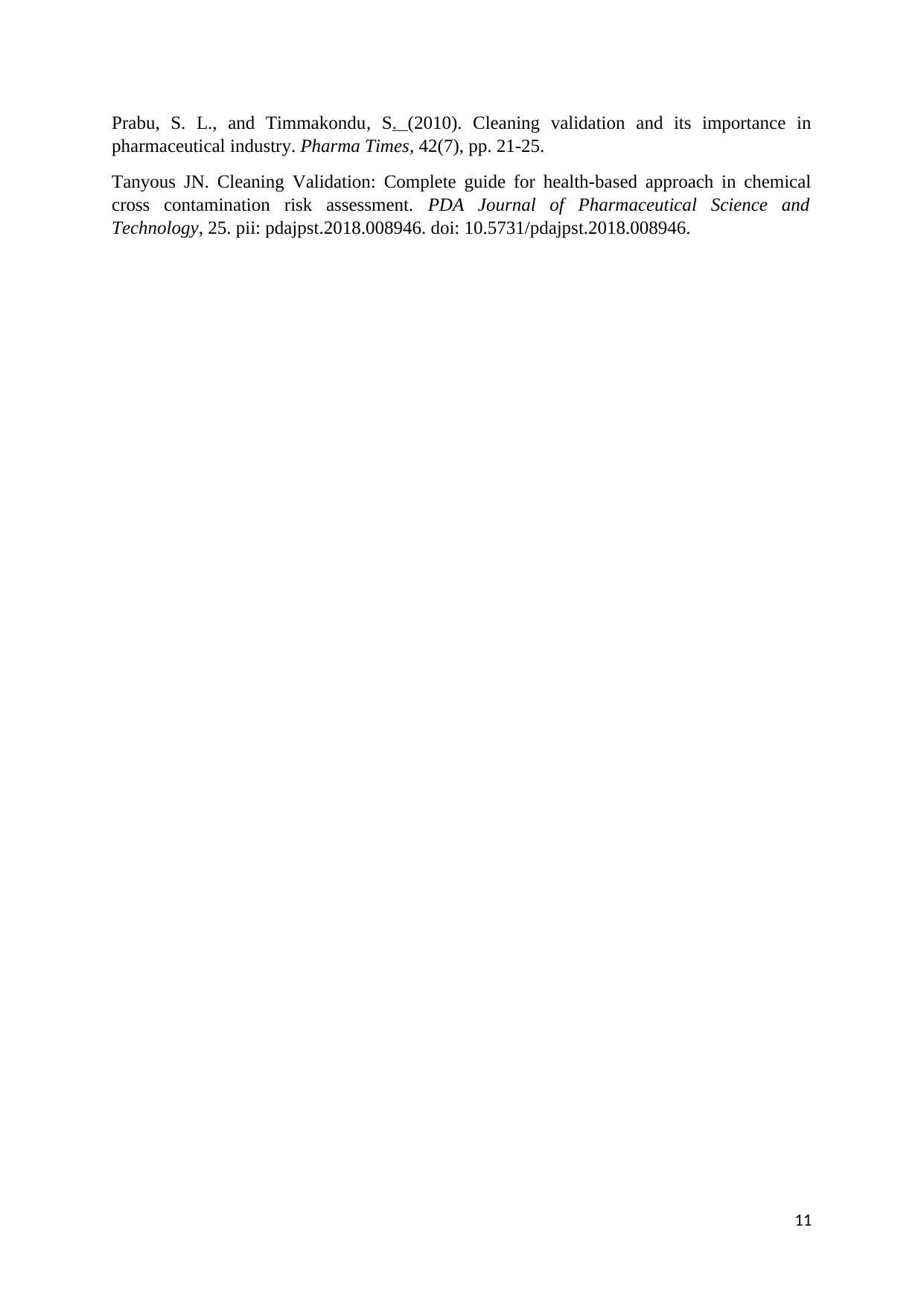
Prabu, S. L., and Timmakondu, S. (2010). Cleaning validation and its importance in
pharmaceutical industry. Pharma Times, 42(7), pp. 21-25.
Tanyous JN. Cleaning Validation: Complete guide for health-based approach in chemical
cross contamination risk assessment. PDA Journal of Pharmaceutical Science and
Technology, 25. pii: pdajpst.2018.008946. doi: 10.5731/pdajpst.2018.008946.
11
pharmaceutical industry. Pharma Times, 42(7), pp. 21-25.
Tanyous JN. Cleaning Validation: Complete guide for health-based approach in chemical
cross contamination risk assessment. PDA Journal of Pharmaceutical Science and
Technology, 25. pii: pdajpst.2018.008946. doi: 10.5731/pdajpst.2018.008946.
11
1 out of 11
![[object Object]](/_next/image/?url=%2F_next%2Fstatic%2Fmedia%2Flogo.6d15ce61.png&w=640&q=75)
Your All-in-One AI-Powered Toolkit for Academic Success.
+13062052269
info@desklib.com
Available 24*7 on WhatsApp / Email
Unlock your academic potential
© 2024 | Zucol Services PVT LTD | All rights reserved.