Vibration Analysis of Rotating Machinery Structures
12 Pages2622 Words237 Views
Added on 2021-05-30
Vibration Analysis of Rotating Machinery Structures
Added on 2021-05-30
ShareRelated Documents
Vibration Analysis of Rotating Machinery Structures[Unit name][Professor’s name][Student name][Student number]© May, 2018
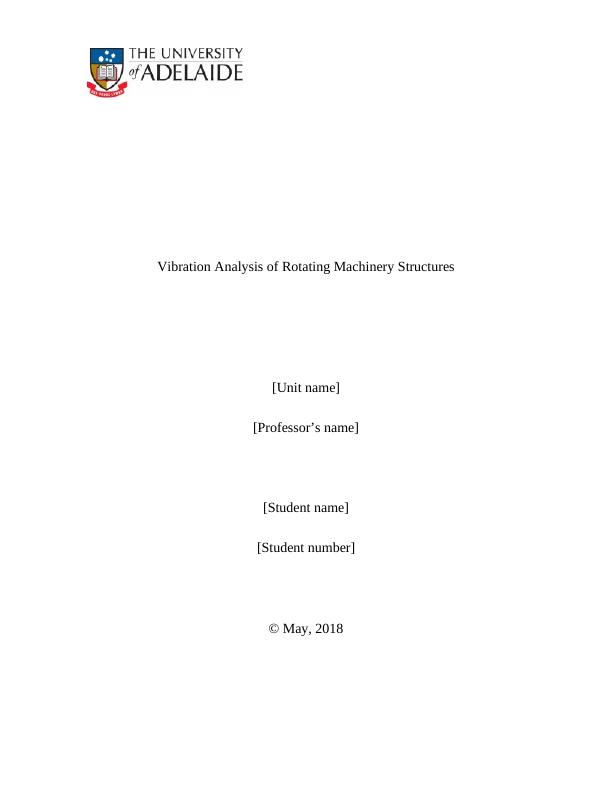
AbstractIn all maintenance engineering activities, vibration analysis forms one of the most prominentapproaches used in machine service to predict the working capacity of a particular machine orcomponent or even determine the service life span of the component. Rotating machines and themachine elements always experience the vibration effect at the start of the operation, whenrunning and also when shut down to a stop of the machinery. Vibration is most prevalent inmachine parts that either undergo pure rotation, pure oscillation or a combination of both motioncriteria thus necessitates the need for an analysis of the extent to which the vibration occur forsafety in design. This technical report therefore aims at giving a clear background and foundationof the vibration of rotating machine elements, the mathematical model inclusive of the dynamicparameters involved, the possible methods used to carry out vibration analysis, the significanceof the analysis and the analytical tools used. The dangers resulting from uncontrolled vibration isalso given citing known examples and their possible causes. Without a full and comprehensivemeasurement of the vibration in an element in all the three possible directions, one cannot knowthe exact contribution of each of the rotating rolls to paper machine vibration. The paper finallyconcludes with the possible areas of application of the vibration system in real world and howresonance cab be avoided in any machine having rotating element.2
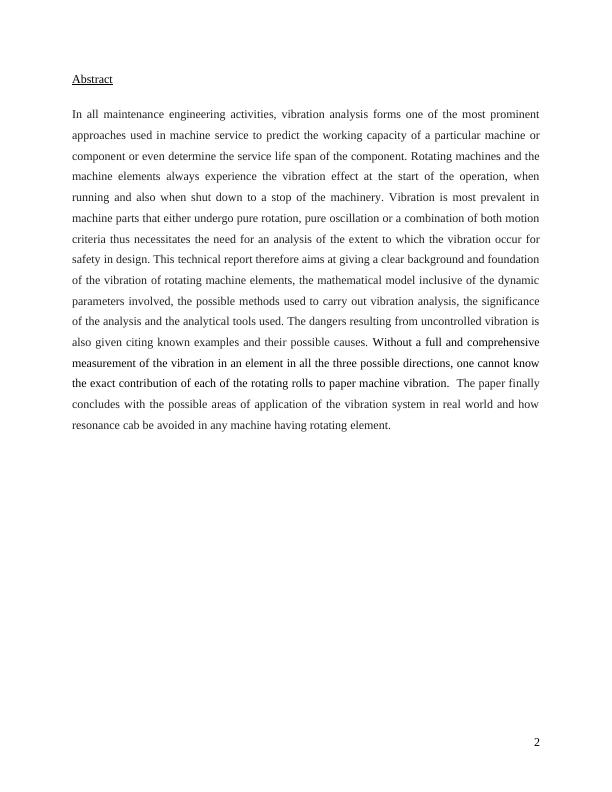
1.0.IntroductionBy definition, vibration is the periodic or random motion of a body in a repetitive manner aboutan equilibrium point. Periodic motion is commonly seen in the pendulum motion while randommotion is seen when a car tire moves in a rough gravel road[ CITATION Gop11 \l 1033 ]. All thesephenomena can either be desirable or undesirable; with machines like oscillating sanders,vibration tumblers used for removing materials and finishing surfaces respectively, a compactormachine, the vibration of a reed in a woodwind instrument, motion of a tuning fork amongothers, considered desirable whereas the vibration experienced in an engine or an electric motorare typically considered undesirable motions since in such cases, energy is normally wastedwhile being converted into distracting sound[ CITATION Gop16 \l 1033 ]. A vibrating body can beconsidered as an elastic element that undergoes a series of continuous conversion of the storedelastic potential energy into kinetic energy and vice versa. Such motion in any machine elementmay lead to excess wear in the joint bearings, presence of cracks within the elements, looseningof fasteners, machine failures of the mechanical parts, increased interval of costly maintenanceof the machines, electronic malfunction due to cracked soldered joints, and a general short circuitwithin the system.Figure1: Basic parts of a vibrating systemWhenever vibration occurs four elements are usually involved that determine the characteristicsof the vibration i.e. the spring effect or elasticity which stores the potential energy; the mass ofthe component or its corresponding inertia that stores the kinetic form of energy; a dampermaterial which ensures that energy is gradually lost and finally an exciting force, such asimbalance or misalignment of the structure. Examples of common vibrating machine elements3
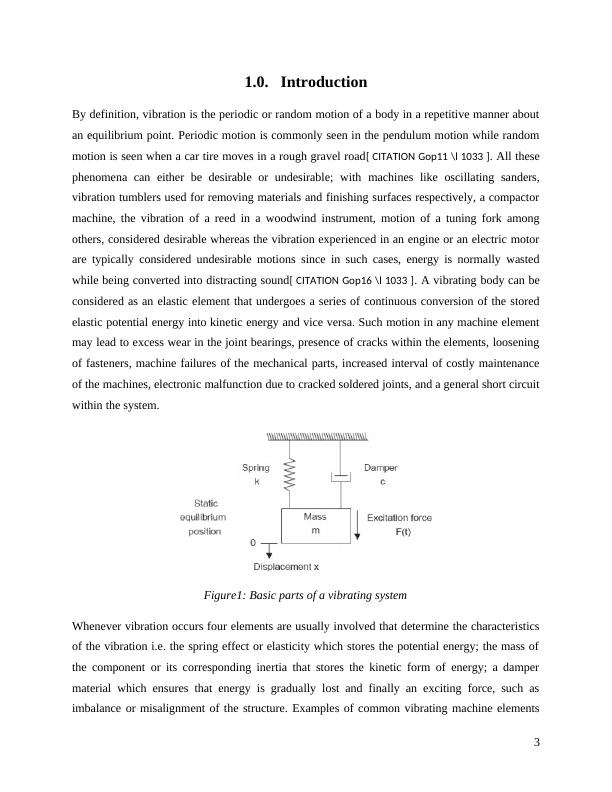
include the connecting rod and crank shaft of an I.C. engine, the vehicle wheel axles, a train’srail wheels, the power shaft of a machine lathe and rotating gears or pulleys. 2.0.Literature ReviewA full analysis of all vibrating systems can be defined by the number of degrees of freedom(dof), which is the lowest number of coordinates that are independent from one another, requiredfor a complete determination of the position of all the system components at any time instance.Thus a simple oscillating pendulum falls under the single-degree-of-freedom vibration systemsince its motion can be fully defined in terms of the displacement angle θ,whereas a cranksystem represent a two-degree-of-freedom system with the crank angle φand the piston’s lineardisplacement xas the required parameters to fully define the position of all the parts making upthe system[ CITATION Mut17 \l 1033 ]. From the dof, mathematical models can thus be developedwhich are then solved numerically or through computational software like MATLAB orLabView to predict the motion and also the maxim possible amplitude of vibration thuspredicting its use.2.1.Types of Vibration There exist two common categories of vibration in machines i.e.:a)Free and forced vibrationFree vibration occurs when the system is left alone to vibrate, when given an initialdisturbance on its own, thus the motion is therefore maintained by elastic restoring forcesor gravitational forces. A forced vibration is a type whereby an external force (oftenrepetitive in nature) acts upon the vibrating system e.g. in an international combustionengine[ CITATION Pet10 \l 1033 ]. Resonance occur when the externally applied force has afrequency whose magnitude and phase coincides with that of the system’s naturalfrequency.4
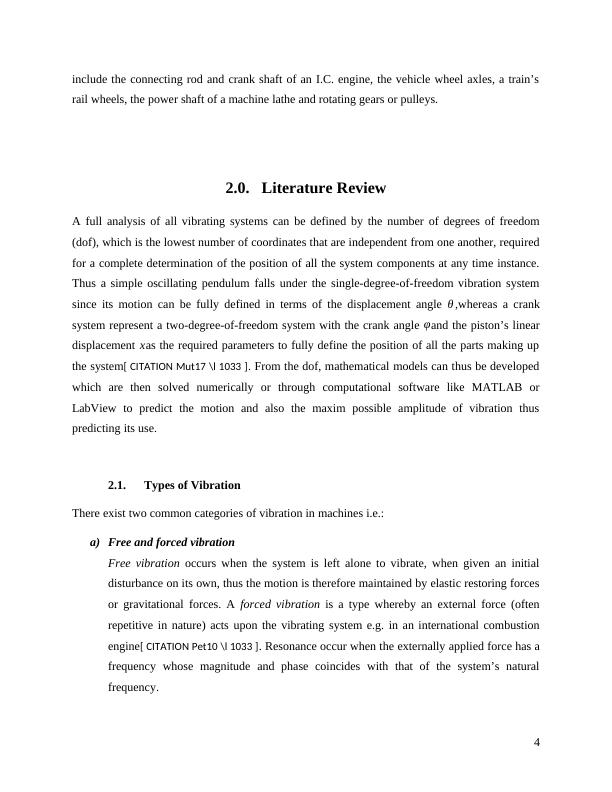
End of preview
Want to access all the pages? Upload your documents or become a member.
Related Documents
Advanced Maintenance Techniques: Oil Analysis, Vibration Analysis, Thermography, TPM, RCM, and ISO 55000lg...
|19
|3219
|323