PROD 1024 Project: Lean Manufacturing and Value Stream Mapping for FEI
VerifiedAdded on 2022/09/10
|14
|2966
|24
Project
AI Summary
This project presents a comprehensive analysis of Farm Equipment International (FEI), focusing on lean manufacturing principles. The assignment begins with a detailed value stream map of the current manufacturing processes, identifying key areas for improvement. It then addresses eight critical ...
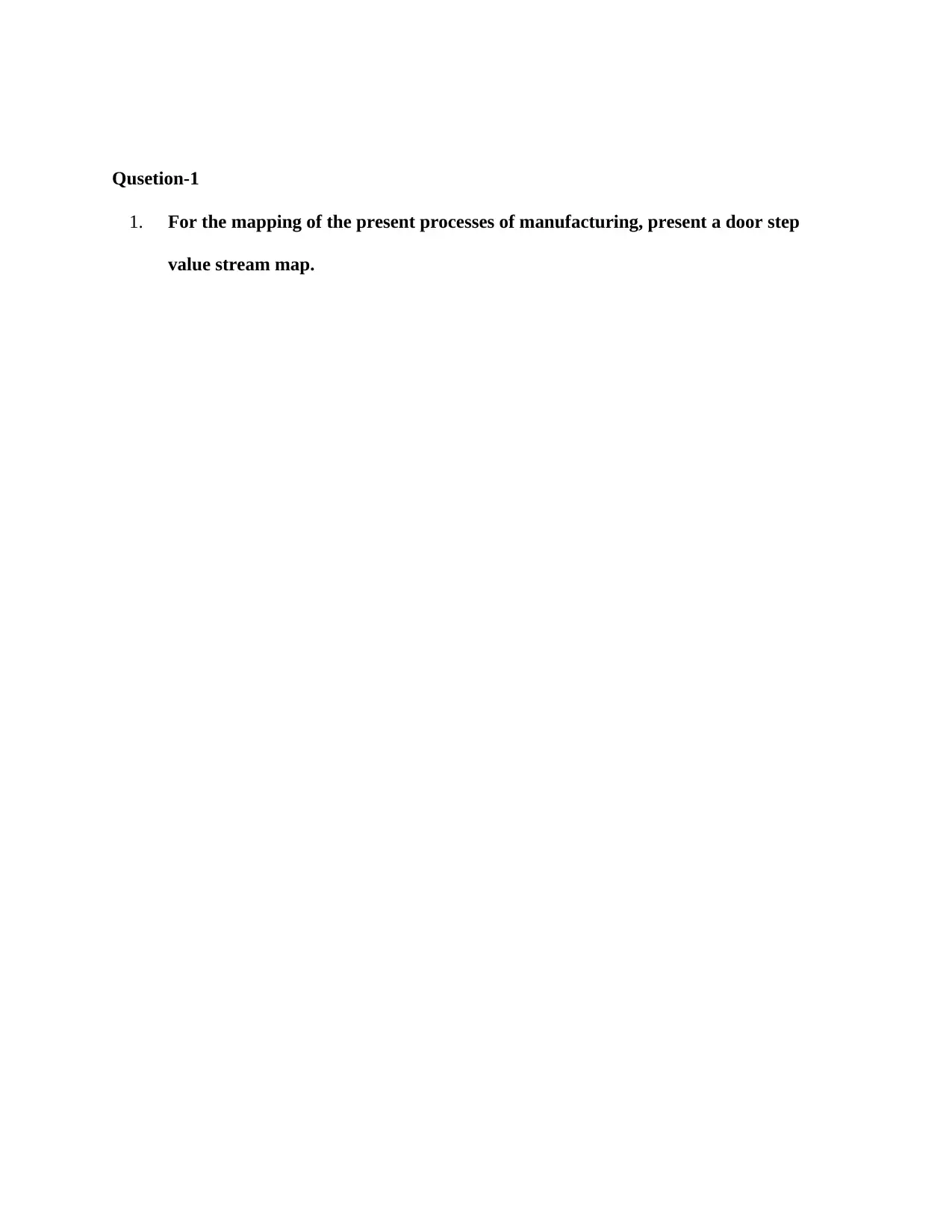
Qusetion-1
1. For the mapping of the present processes of manufacturing, present a door step
value stream map.
1. For the mapping of the present processes of manufacturing, present a door step
value stream map.
Paraphrase This Document
Need a fresh take? Get an instant paraphrase of this document with our AI Paraphraser
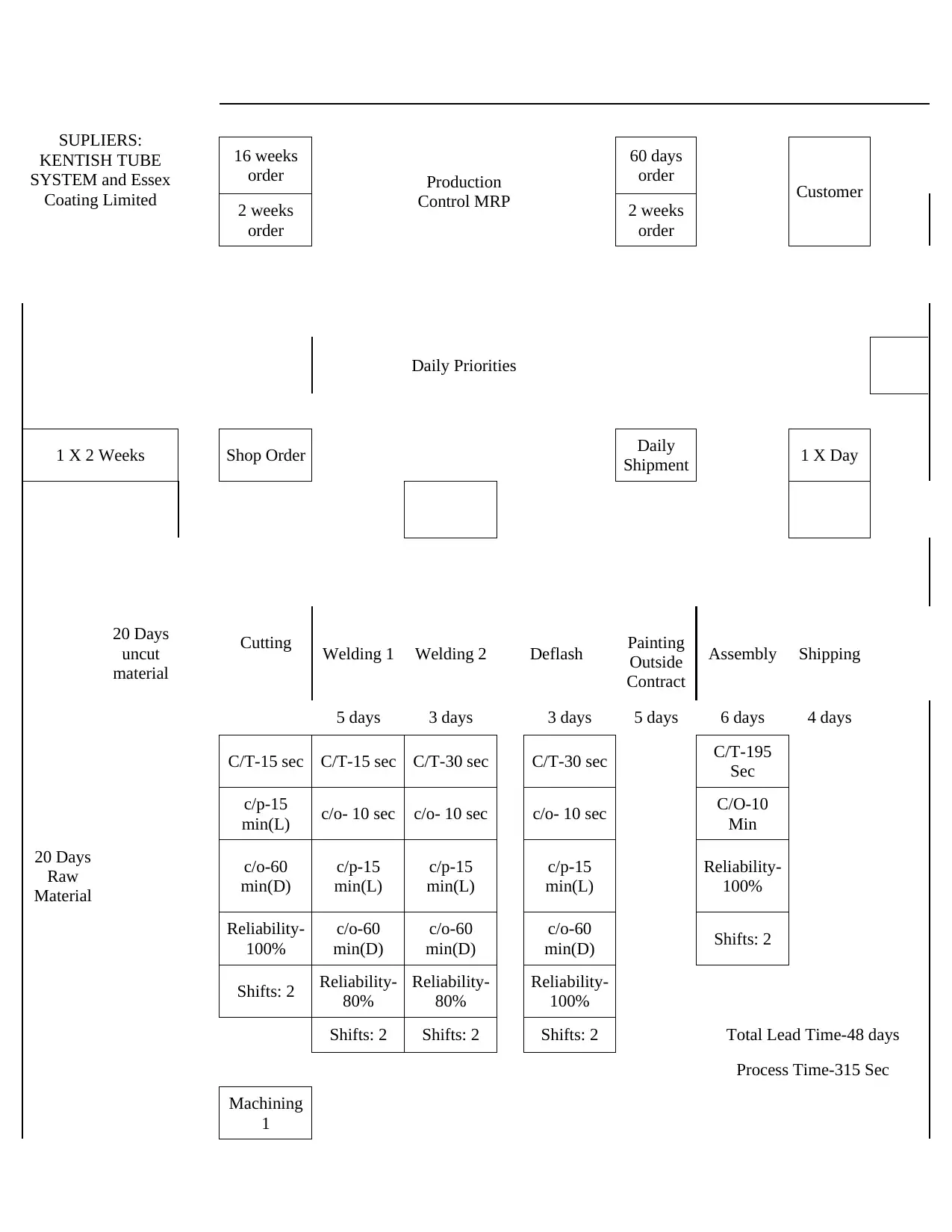
SUPLIERS:
KENTISH TUBE
SYSTEM and Essex
Coating Limited
16 weeks
order Production
Control MRP
60 days
order Customer
2 weeks
order
2 weeks
order
Daily Priorities
1 X 2 Weeks Shop Order Daily
Shipment 1 X Day
20 Days
uncut
material
Cutting Welding 1 Welding 2 Deflash Painting
Outside
Contract
Assembly Shipping
5 days 3 days 3 days 5 days 6 days 4 days
C/T-15 sec C/T-15 sec C/T-30 sec C/T-30 sec C/T-195
Sec
c/p-15
min(L) c/o- 10 sec c/o- 10 sec c/o- 10 sec C/O-10
Min
20 Days
Raw
Material
c/o-60
min(D)
c/p-15
min(L)
c/p-15
min(L)
c/p-15
min(L)
Reliability-
100%
Reliability-
100%
c/o-60
min(D)
c/o-60
min(D)
c/o-60
min(D) Shifts: 2
Shifts: 2 Reliability-
80%
Reliability-
80%
Reliability-
100%
Shifts: 2 Shifts: 2 Shifts: 2 Total Lead Time-48 days
Process Time-315 Sec
Machining
1
KENTISH TUBE
SYSTEM and Essex
Coating Limited
16 weeks
order Production
Control MRP
60 days
order Customer
2 weeks
order
2 weeks
order
Daily Priorities
1 X 2 Weeks Shop Order Daily
Shipment 1 X Day
20 Days
uncut
material
Cutting Welding 1 Welding 2 Deflash Painting
Outside
Contract
Assembly Shipping
5 days 3 days 3 days 5 days 6 days 4 days
C/T-15 sec C/T-15 sec C/T-30 sec C/T-30 sec C/T-195
Sec
c/p-15
min(L) c/o- 10 sec c/o- 10 sec c/o- 10 sec C/O-10
Min
20 Days
Raw
Material
c/o-60
min(D)
c/p-15
min(L)
c/p-15
min(L)
c/p-15
min(L)
Reliability-
100%
Reliability-
100%
c/o-60
min(D)
c/o-60
min(D)
c/o-60
min(D) Shifts: 2
Shifts: 2 Reliability-
80%
Reliability-
80%
Reliability-
100%
Shifts: 2 Shifts: 2 Shifts: 2 Total Lead Time-48 days
Process Time-315 Sec
Machining
1
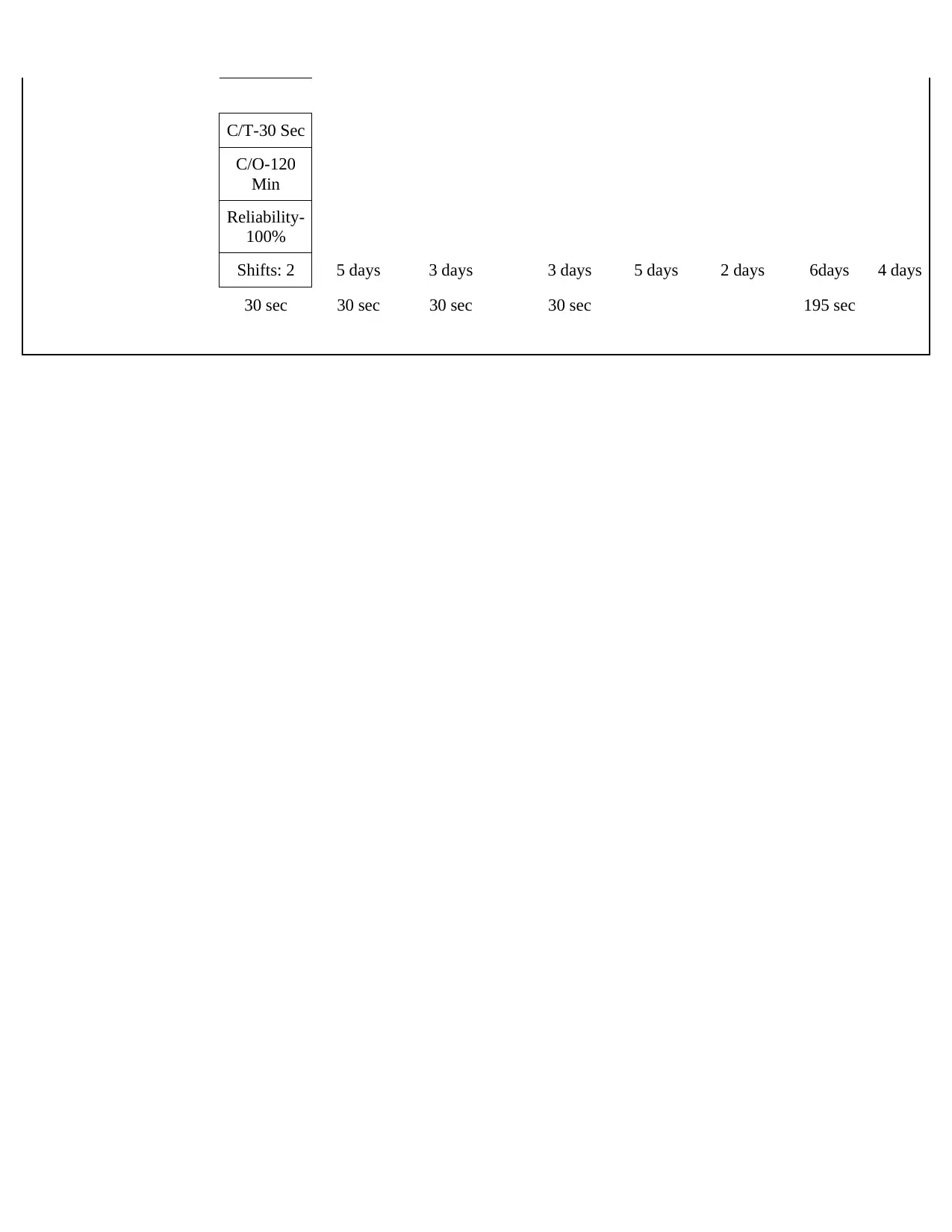
C/T-30 Sec
C/O-120
Min
Reliability-
100%
Shifts: 2 5 days 3 days 3 days 5 days 2 days 6days 4 days
30 sec 30 sec 30 sec 30 sec 195 sec
C/O-120
Min
Reliability-
100%
Shifts: 2 5 days 3 days 3 days 5 days 2 days 6days 4 days
30 sec 30 sec 30 sec 30 sec 195 sec
⊘ This is a preview!⊘
Do you want full access?
Subscribe today to unlock all pages.

Trusted by 1+ million students worldwide
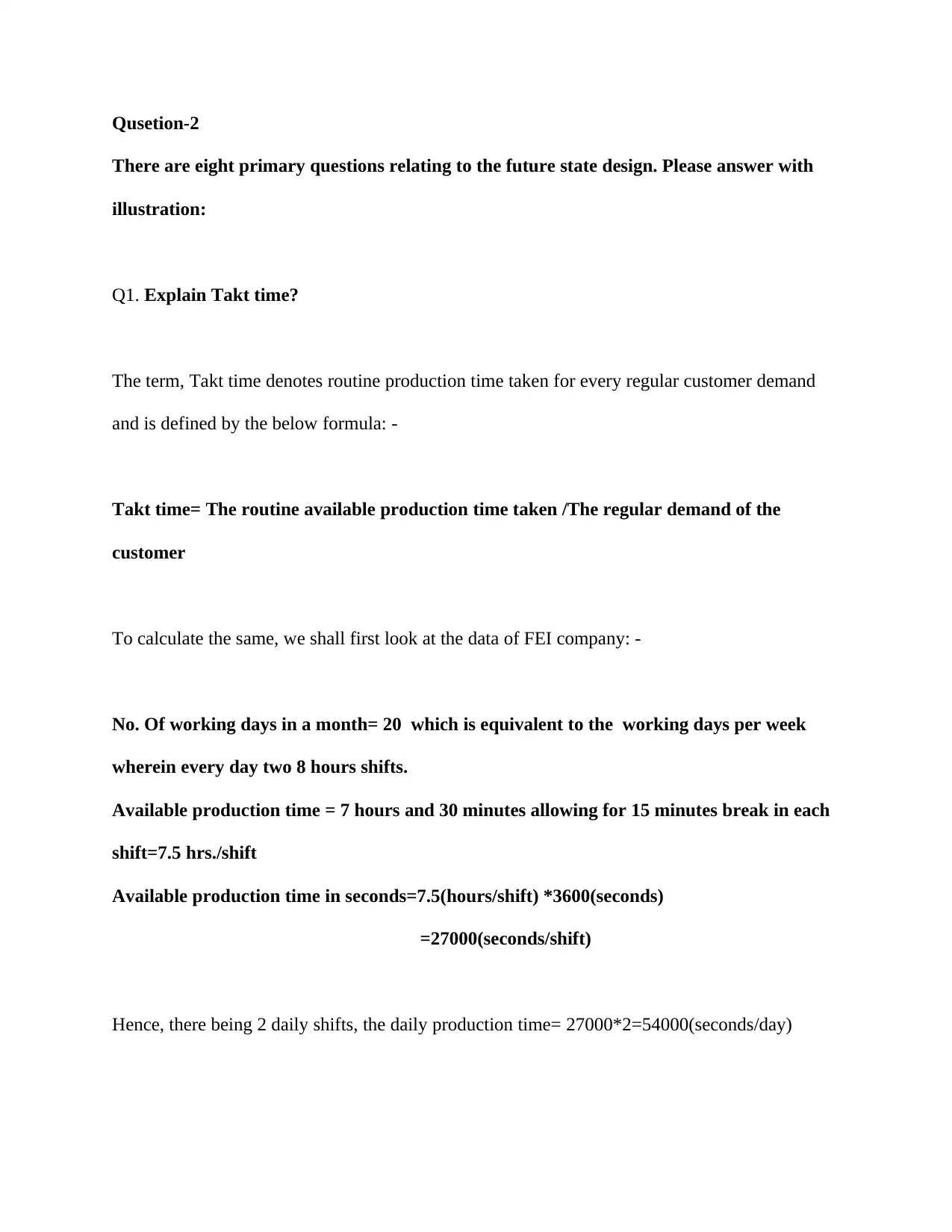
Qusetion-2
There are eight primary questions relating to the future state design. Please answer with
illustration:
Q1. Explain Takt time?
The term, Takt time denotes routine production time taken for every regular customer demand
and is defined by the below formula: -
Takt time= The routine available production time taken /The regular demand of the
customer
To calculate the same, we shall first look at the data of FEI company: -
No. Of working days in a month= 20 which is equivalent to the working days per week
wherein every day two 8 hours shifts.
Available production time = 7 hours and 30 minutes allowing for 15 minutes break in each
shift=7.5 hrs./shift
Available production time in seconds=7.5(hours/shift) *3600(seconds)
=27000(seconds/shift)
Hence, there being 2 daily shifts, the daily production time= 27000*2=54000(seconds/day)
There are eight primary questions relating to the future state design. Please answer with
illustration:
Q1. Explain Takt time?
The term, Takt time denotes routine production time taken for every regular customer demand
and is defined by the below formula: -
Takt time= The routine available production time taken /The regular demand of the
customer
To calculate the same, we shall first look at the data of FEI company: -
No. Of working days in a month= 20 which is equivalent to the working days per week
wherein every day two 8 hours shifts.
Available production time = 7 hours and 30 minutes allowing for 15 minutes break in each
shift=7.5 hrs./shift
Available production time in seconds=7.5(hours/shift) *3600(seconds)
=27000(seconds/shift)
Hence, there being 2 daily shifts, the daily production time= 27000*2=54000(seconds/day)
Paraphrase This Document
Need a fresh take? Get an instant paraphrase of this document with our AI Paraphraser
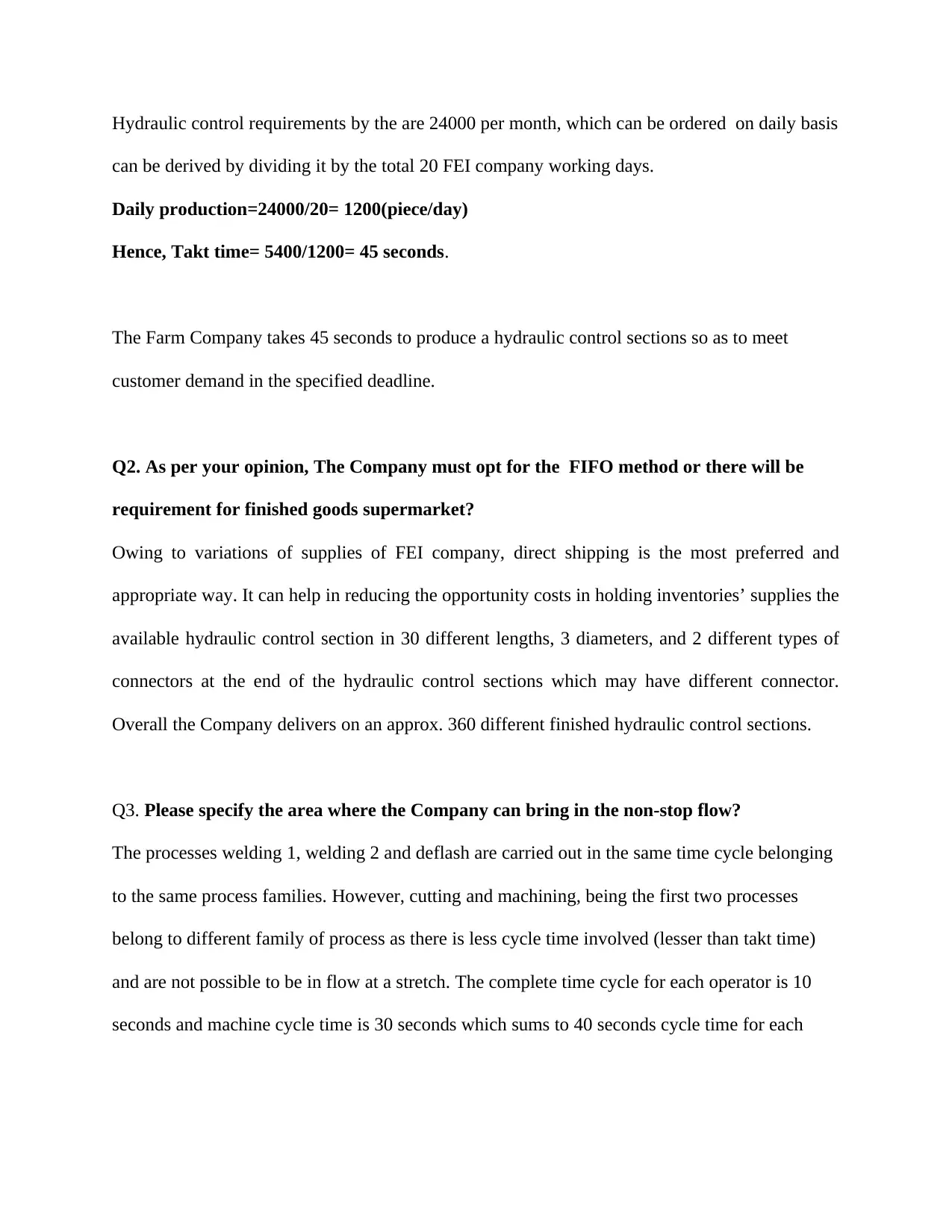
Hydraulic control requirements by the are 24000 per month, which can be ordered on daily basis
can be derived by dividing it by the total 20 FEI company working days.
Daily production=24000/20= 1200(piece/day)
Hence, Takt time= 5400/1200= 45 seconds.
The Farm Company takes 45 seconds to produce a hydraulic control sections so as to meet
customer demand in the specified deadline.
Q2. As per your opinion, The Company must opt for the FIFO method or there will be
requirement for finished goods supermarket?
Owing to variations of supplies of FEI company, direct shipping is the most preferred and
appropriate way. It can help in reducing the opportunity costs in holding inventories’ supplies the
available hydraulic control section in 30 different lengths, 3 diameters, and 2 different types of
connectors at the end of the hydraulic control sections which may have different connector.
Overall the Company delivers on an approx. 360 different finished hydraulic control sections.
Q3. Please specify the area where the Company can bring in the non-stop flow?
The processes welding 1, welding 2 and deflash are carried out in the same time cycle belonging
to the same process families. However, cutting and machining, being the first two processes
belong to different family of process as there is less cycle time involved (lesser than takt time)
and are not possible to be in flow at a stretch. The complete time cycle for each operator is 10
seconds and machine cycle time is 30 seconds which sums to 40 seconds cycle time for each
can be derived by dividing it by the total 20 FEI company working days.
Daily production=24000/20= 1200(piece/day)
Hence, Takt time= 5400/1200= 45 seconds.
The Farm Company takes 45 seconds to produce a hydraulic control sections so as to meet
customer demand in the specified deadline.
Q2. As per your opinion, The Company must opt for the FIFO method or there will be
requirement for finished goods supermarket?
Owing to variations of supplies of FEI company, direct shipping is the most preferred and
appropriate way. It can help in reducing the opportunity costs in holding inventories’ supplies the
available hydraulic control section in 30 different lengths, 3 diameters, and 2 different types of
connectors at the end of the hydraulic control sections which may have different connector.
Overall the Company delivers on an approx. 360 different finished hydraulic control sections.
Q3. Please specify the area where the Company can bring in the non-stop flow?
The processes welding 1, welding 2 and deflash are carried out in the same time cycle belonging
to the same process families. However, cutting and machining, being the first two processes
belong to different family of process as there is less cycle time involved (lesser than takt time)
and are not possible to be in flow at a stretch. The complete time cycle for each operator is 10
seconds and machine cycle time is 30 seconds which sums to 40 seconds cycle time for each
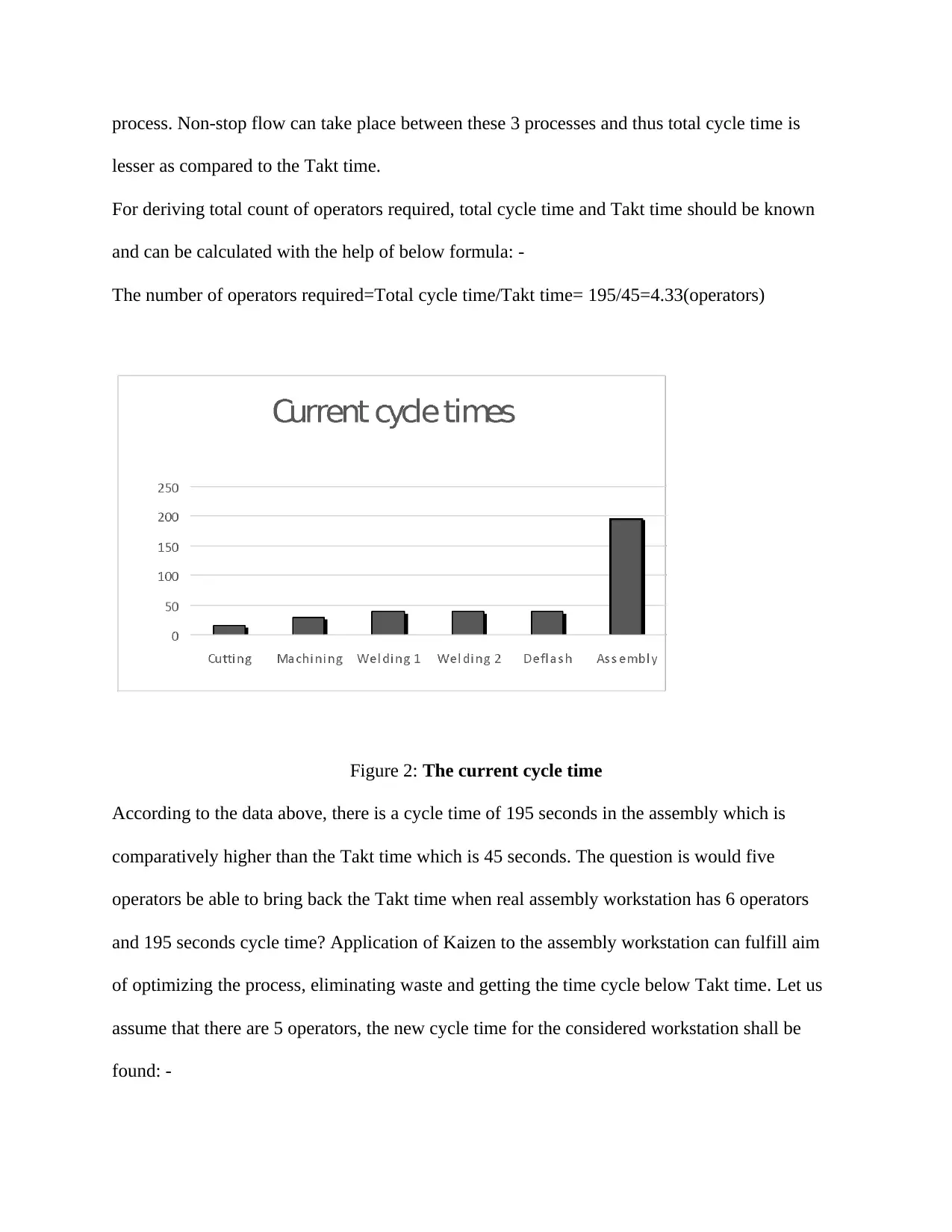
process. Non-stop flow can take place between these 3 processes and thus total cycle time is
lesser as compared to the Takt time.
For deriving total count of operators required, total cycle time and Takt time should be known
and can be calculated with the help of below formula: -
The number of operators required=Total cycle time/Takt time= 195/45=4.33(operators)
Figure 2: The current cycle time
According to the data above, there is a cycle time of 195 seconds in the assembly which is
comparatively higher than the Takt time which is 45 seconds. The question is would five
operators be able to bring back the Takt time when real assembly workstation has 6 operators
and 195 seconds cycle time? Application of Kaizen to the assembly workstation can fulfill aim
of optimizing the process, eliminating waste and getting the time cycle below Takt time. Let us
assume that there are 5 operators, the new cycle time for the considered workstation shall be
found: -
lesser as compared to the Takt time.
For deriving total count of operators required, total cycle time and Takt time should be known
and can be calculated with the help of below formula: -
The number of operators required=Total cycle time/Takt time= 195/45=4.33(operators)
Figure 2: The current cycle time
According to the data above, there is a cycle time of 195 seconds in the assembly which is
comparatively higher than the Takt time which is 45 seconds. The question is would five
operators be able to bring back the Takt time when real assembly workstation has 6 operators
and 195 seconds cycle time? Application of Kaizen to the assembly workstation can fulfill aim
of optimizing the process, eliminating waste and getting the time cycle below Takt time. Let us
assume that there are 5 operators, the new cycle time for the considered workstation shall be
found: -
⊘ This is a preview!⊘
Do you want full access?
Subscribe today to unlock all pages.

Trusted by 1+ million students worldwide
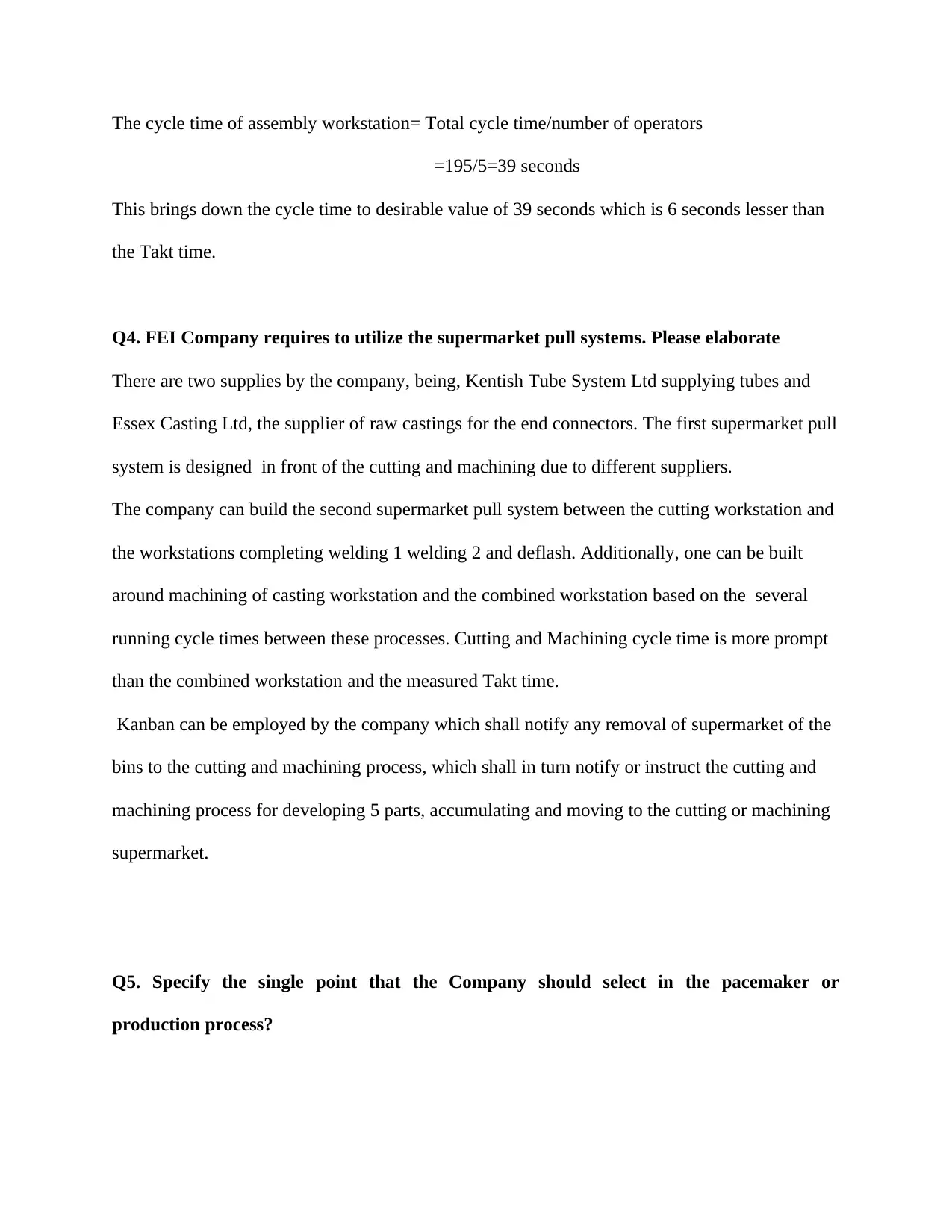
The cycle time of assembly workstation= Total cycle time/number of operators
=195/5=39 seconds
This brings down the cycle time to desirable value of 39 seconds which is 6 seconds lesser than
the Takt time.
Q4. FEI Company requires to utilize the supermarket pull systems. Please elaborate
There are two supplies by the company, being, Kentish Tube System Ltd supplying tubes and
Essex Casting Ltd, the supplier of raw castings for the end connectors. The first supermarket pull
system is designed in front of the cutting and machining due to different suppliers.
The company can build the second supermarket pull system between the cutting workstation and
the workstations completing welding 1 welding 2 and deflash. Additionally, one can be built
around machining of casting workstation and the combined workstation based on the several
running cycle times between these processes. Cutting and Machining cycle time is more prompt
than the combined workstation and the measured Takt time.
Kanban can be employed by the company which shall notify any removal of supermarket of the
bins to the cutting and machining process, which shall in turn notify or instruct the cutting and
machining process for developing 5 parts, accumulating and moving to the cutting or machining
supermarket.
Q5. Specify the single point that the Company should select in the pacemaker or
production process?
=195/5=39 seconds
This brings down the cycle time to desirable value of 39 seconds which is 6 seconds lesser than
the Takt time.
Q4. FEI Company requires to utilize the supermarket pull systems. Please elaborate
There are two supplies by the company, being, Kentish Tube System Ltd supplying tubes and
Essex Casting Ltd, the supplier of raw castings for the end connectors. The first supermarket pull
system is designed in front of the cutting and machining due to different suppliers.
The company can build the second supermarket pull system between the cutting workstation and
the workstations completing welding 1 welding 2 and deflash. Additionally, one can be built
around machining of casting workstation and the combined workstation based on the several
running cycle times between these processes. Cutting and Machining cycle time is more prompt
than the combined workstation and the measured Takt time.
Kanban can be employed by the company which shall notify any removal of supermarket of the
bins to the cutting and machining process, which shall in turn notify or instruct the cutting and
machining process for developing 5 parts, accumulating and moving to the cutting or machining
supermarket.
Q5. Specify the single point that the Company should select in the pacemaker or
production process?
Paraphrase This Document
Need a fresh take? Get an instant paraphrase of this document with our AI Paraphraser
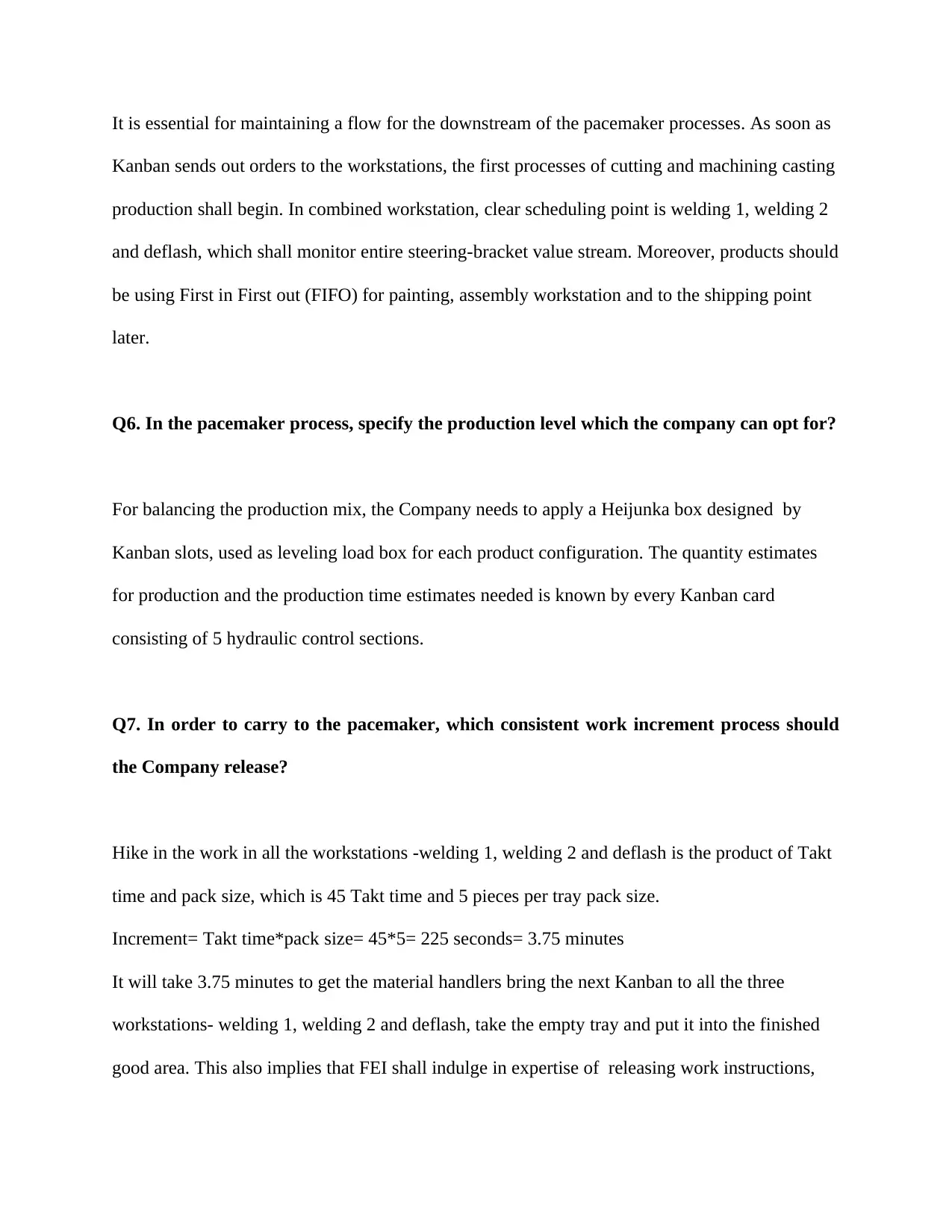
It is essential for maintaining a flow for the downstream of the pacemaker processes. As soon as
Kanban sends out orders to the workstations, the first processes of cutting and machining casting
production shall begin. In combined workstation, clear scheduling point is welding 1, welding 2
and deflash, which shall monitor entire steering-bracket value stream. Moreover, products should
be using First in First out (FIFO) for painting, assembly workstation and to the shipping point
later.
Q6. In the pacemaker process, specify the production level which the company can opt for?
For balancing the production mix, the Company needs to apply a Heijunka box designed by
Kanban slots, used as leveling load box for each product configuration. The quantity estimates
for production and the production time estimates needed is known by every Kanban card
consisting of 5 hydraulic control sections.
Q7. In order to carry to the pacemaker, which consistent work increment process should
the Company release?
Hike in the work in all the workstations -welding 1, welding 2 and deflash is the product of Takt
time and pack size, which is 45 Takt time and 5 pieces per tray pack size.
Increment= Takt time*pack size= 45*5= 225 seconds= 3.75 minutes
It will take 3.75 minutes to get the material handlers bring the next Kanban to all the three
workstations- welding 1, welding 2 and deflash, take the empty tray and put it into the finished
good area. This also implies that FEI shall indulge in expertise of releasing work instructions,
Kanban sends out orders to the workstations, the first processes of cutting and machining casting
production shall begin. In combined workstation, clear scheduling point is welding 1, welding 2
and deflash, which shall monitor entire steering-bracket value stream. Moreover, products should
be using First in First out (FIFO) for painting, assembly workstation and to the shipping point
later.
Q6. In the pacemaker process, specify the production level which the company can opt for?
For balancing the production mix, the Company needs to apply a Heijunka box designed by
Kanban slots, used as leveling load box for each product configuration. The quantity estimates
for production and the production time estimates needed is known by every Kanban card
consisting of 5 hydraulic control sections.
Q7. In order to carry to the pacemaker, which consistent work increment process should
the Company release?
Hike in the work in all the workstations -welding 1, welding 2 and deflash is the product of Takt
time and pack size, which is 45 Takt time and 5 pieces per tray pack size.
Increment= Takt time*pack size= 45*5= 225 seconds= 3.75 minutes
It will take 3.75 minutes to get the material handlers bring the next Kanban to all the three
workstations- welding 1, welding 2 and deflash, take the empty tray and put it into the finished
good area. This also implies that FEI shall indulge in expertise of releasing work instructions,
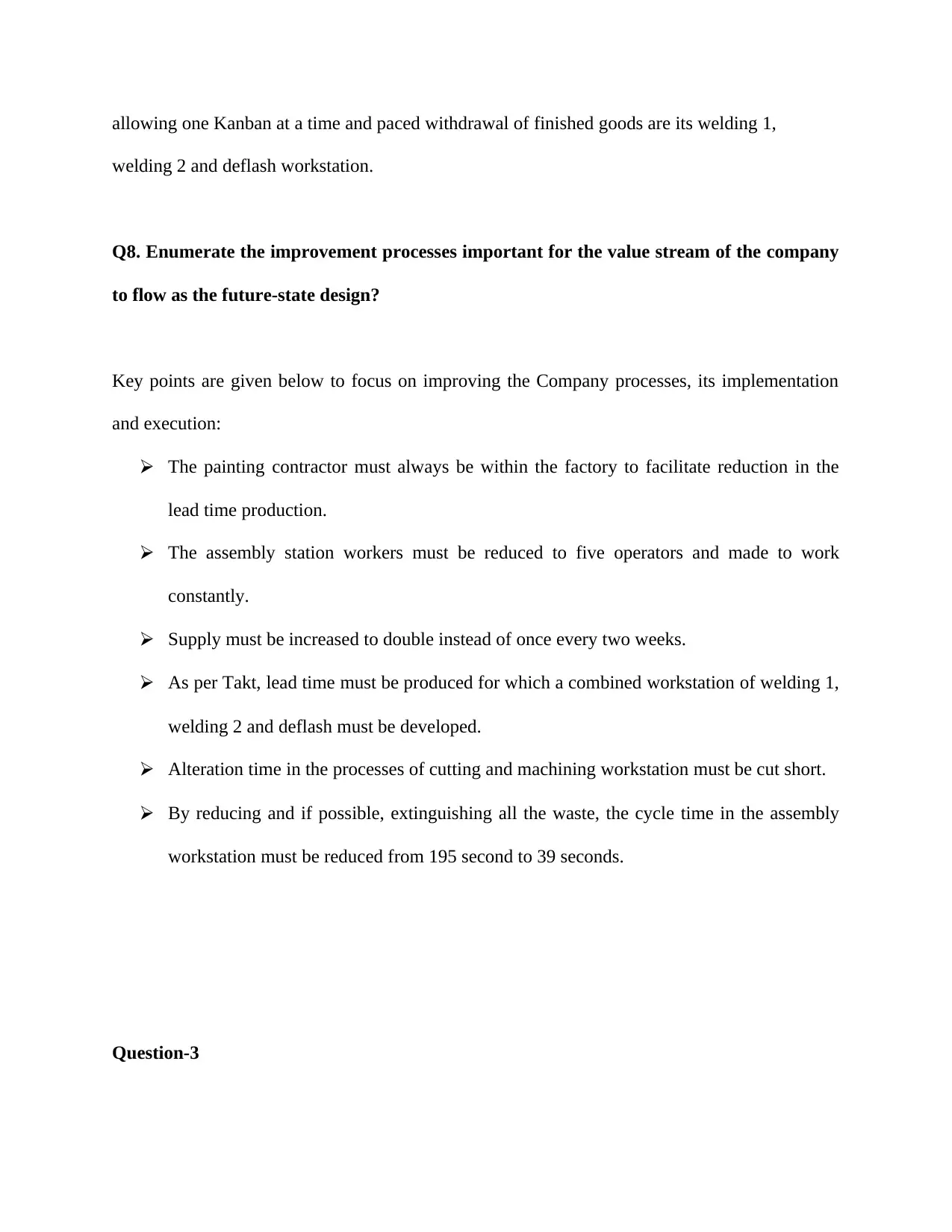
allowing one Kanban at a time and paced withdrawal of finished goods are its welding 1,
welding 2 and deflash workstation.
Q8. Enumerate the improvement processes important for the value stream of the company
to flow as the future-state design?
Key points are given below to focus on improving the Company processes, its implementation
and execution:
⮚ The painting contractor must always be within the factory to facilitate reduction in the
lead time production.
⮚ The assembly station workers must be reduced to five operators and made to work
constantly.
⮚ Supply must be increased to double instead of once every two weeks.
⮚ As per Takt, lead time must be produced for which a combined workstation of welding 1,
welding 2 and deflash must be developed.
⮚ Alteration time in the processes of cutting and machining workstation must be cut short.
⮚ By reducing and if possible, extinguishing all the waste, the cycle time in the assembly
workstation must be reduced from 195 second to 39 seconds.
Question-3
welding 2 and deflash workstation.
Q8. Enumerate the improvement processes important for the value stream of the company
to flow as the future-state design?
Key points are given below to focus on improving the Company processes, its implementation
and execution:
⮚ The painting contractor must always be within the factory to facilitate reduction in the
lead time production.
⮚ The assembly station workers must be reduced to five operators and made to work
constantly.
⮚ Supply must be increased to double instead of once every two weeks.
⮚ As per Takt, lead time must be produced for which a combined workstation of welding 1,
welding 2 and deflash must be developed.
⮚ Alteration time in the processes of cutting and machining workstation must be cut short.
⮚ By reducing and if possible, extinguishing all the waste, the cycle time in the assembly
workstation must be reduced from 195 second to 39 seconds.
Question-3
⊘ This is a preview!⊘
Do you want full access?
Subscribe today to unlock all pages.

Trusted by 1+ million students worldwide
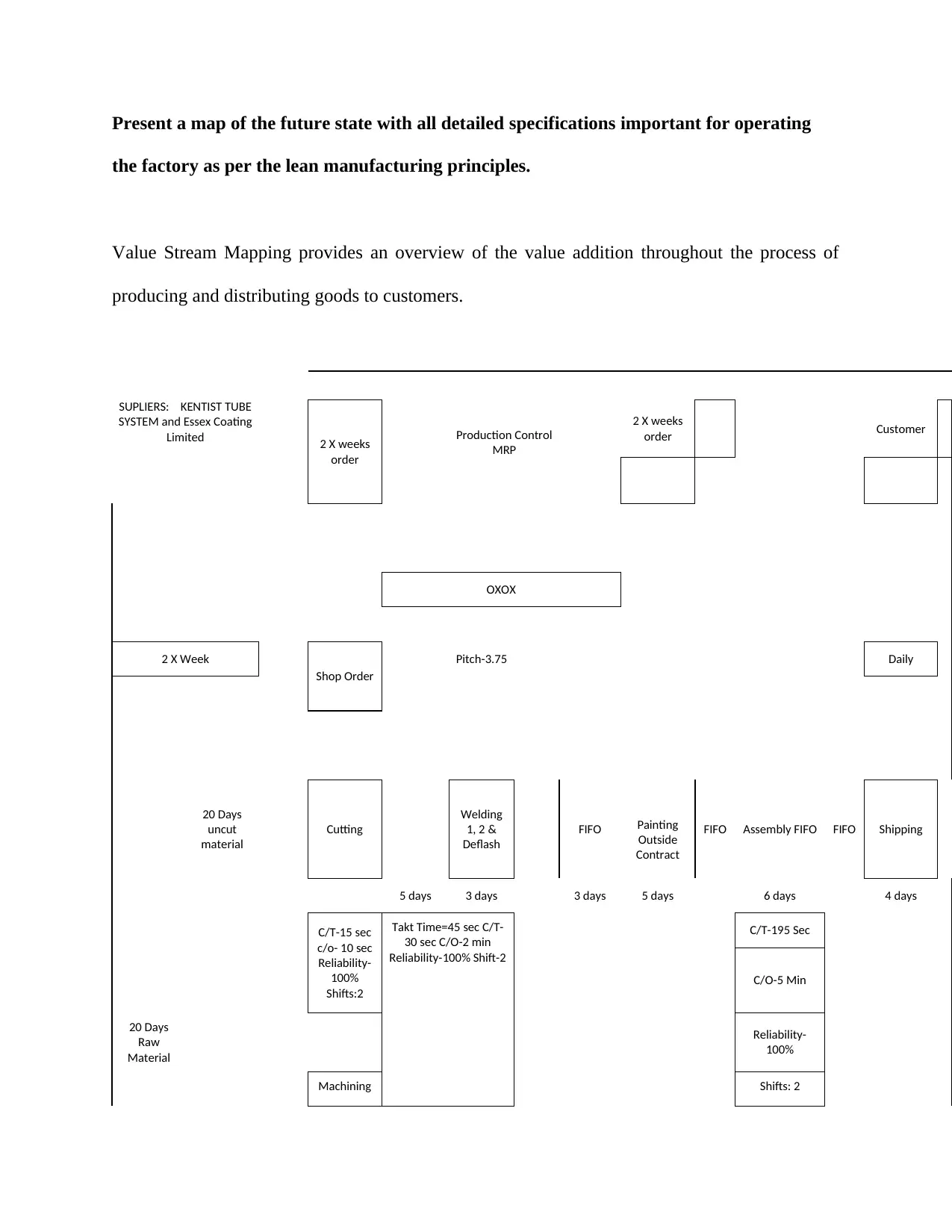
Present a map of the future state with all detailed specifications important for operating
the factory as per the lean manufacturing principles.
Value Stream Mapping provides an overview of the value addition throughout the process of
producing and distributing goods to customers.
SUPLIERS: KENTIST TUBE
SYSTEM and Essex Coating
Limited 2 X weeks
order
Production Control
MRP
2 X weeks
order Customer
OXOX
2 X Week
Shop Order
Pitch-3.75 Daily
20 Days
uncut
material
Cutting
Welding
1, 2 &
Deflash
FIFO Painting
Outside
Contract
FIFO Assembly FIFO FIFO Shipping
5 days 3 days 3 days 5 days 6 days 4 days
C/T-15 sec
c/o- 10 sec
Reliability-
100%
Shifts:2
Takt Time=45 sec C/T-
30 sec C/O-2 min
Reliability-100% Shift-2
C/T-195 Sec
C/O-5 Min
20 Days
Raw
Material
Reliability-
100%
Machining Shifts: 2
the factory as per the lean manufacturing principles.
Value Stream Mapping provides an overview of the value addition throughout the process of
producing and distributing goods to customers.
SUPLIERS: KENTIST TUBE
SYSTEM and Essex Coating
Limited 2 X weeks
order
Production Control
MRP
2 X weeks
order Customer
OXOX
2 X Week
Shop Order
Pitch-3.75 Daily
20 Days
uncut
material
Cutting
Welding
1, 2 &
Deflash
FIFO Painting
Outside
Contract
FIFO Assembly FIFO FIFO Shipping
5 days 3 days 3 days 5 days 6 days 4 days
C/T-15 sec
c/o- 10 sec
Reliability-
100%
Shifts:2
Takt Time=45 sec C/T-
30 sec C/O-2 min
Reliability-100% Shift-2
C/T-195 Sec
C/O-5 Min
20 Days
Raw
Material
Reliability-
100%
Machining Shifts: 2
Paraphrase This Document
Need a fresh take? Get an instant paraphrase of this document with our AI Paraphraser
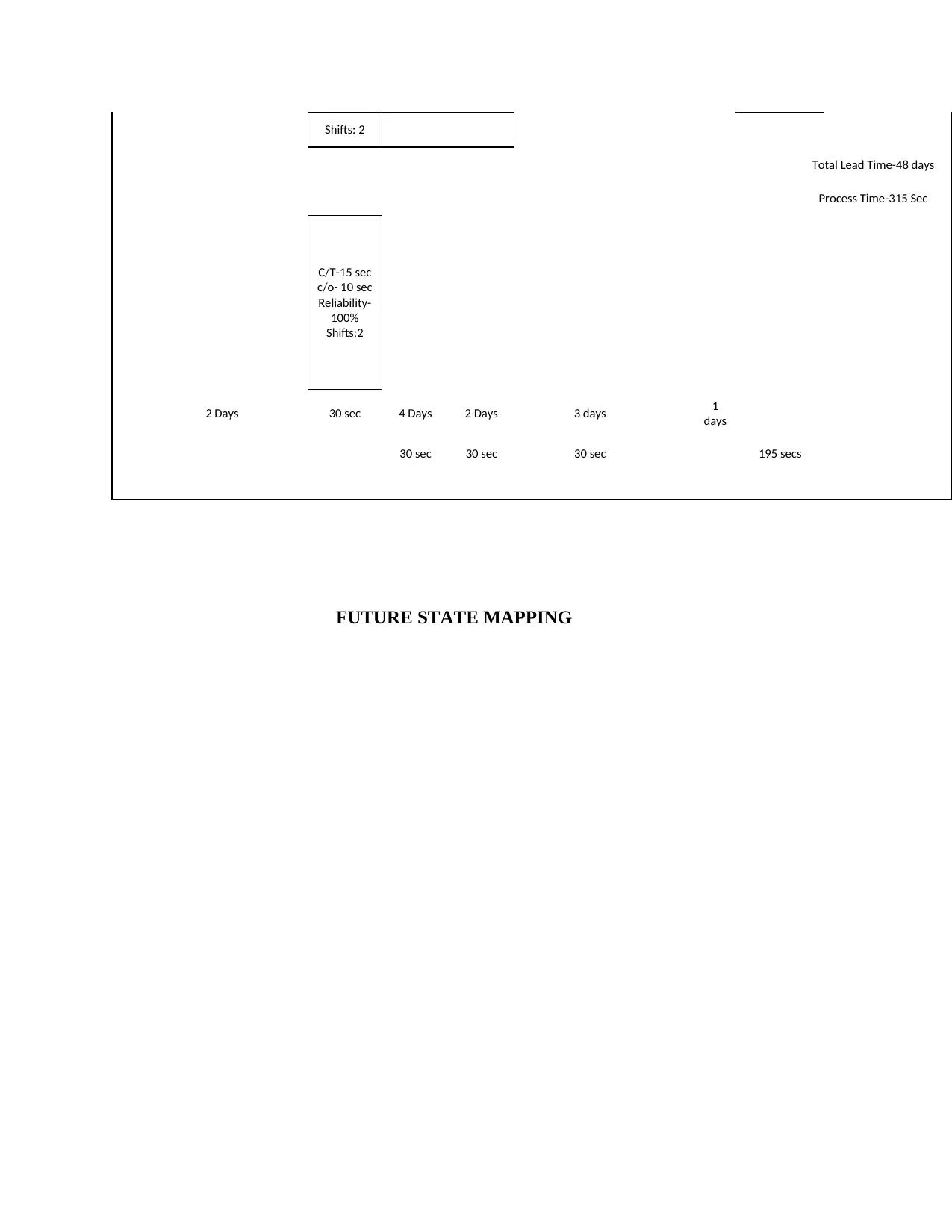
Shifts: 2
Total Lead Time-48 days
Process Time-315 Sec
C/T-15 sec
c/o- 10 sec
Reliability-
100%
Shifts:2
2 Days 30 sec 4 Days 2 Days 3 days 1
days
30 sec 30 sec 30 sec 195 secs
FUTURE STATE MAPPING
Total Lead Time-48 days
Process Time-315 Sec
C/T-15 sec
c/o- 10 sec
Reliability-
100%
Shifts:2
2 Days 30 sec 4 Days 2 Days 3 days 1
days
30 sec 30 sec 30 sec 195 secs
FUTURE STATE MAPPING
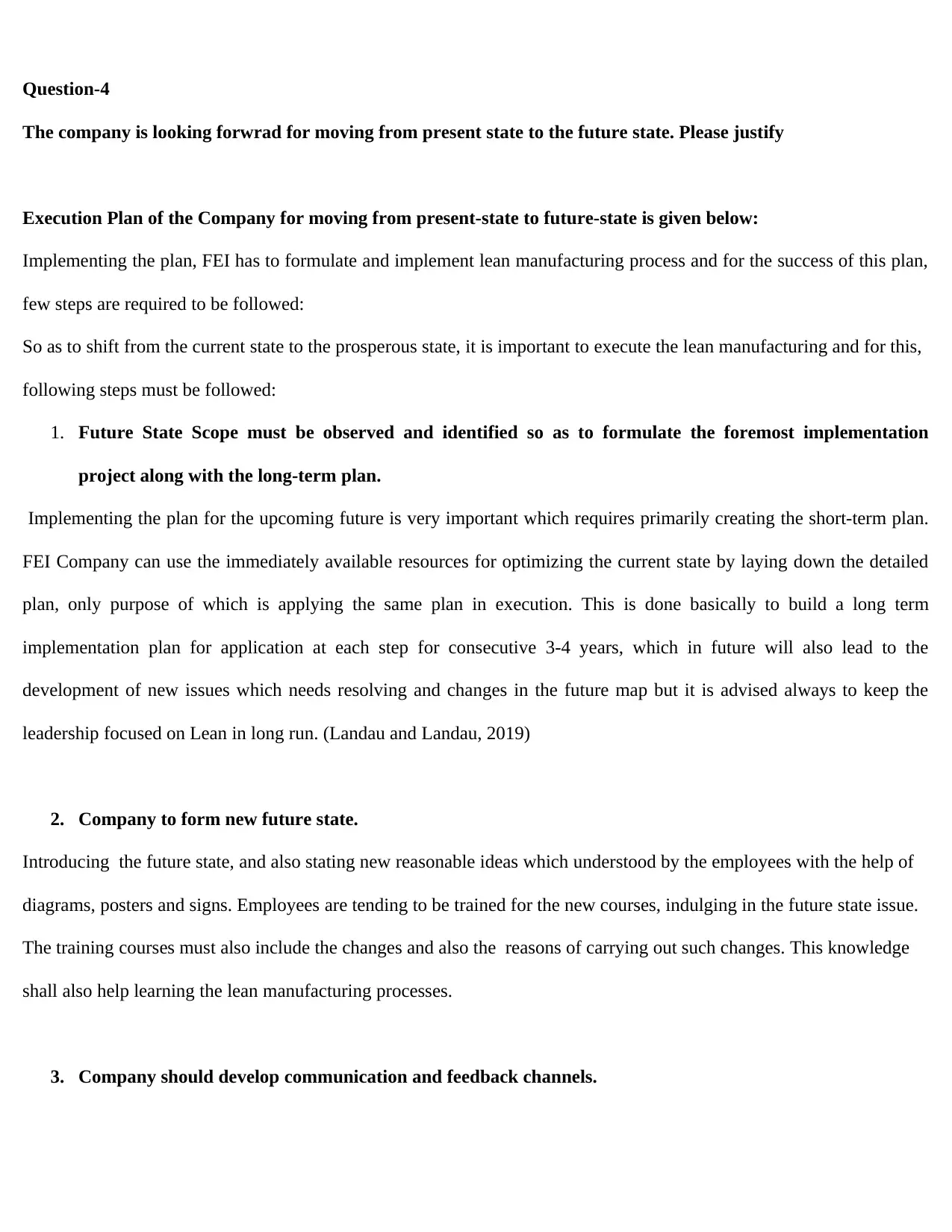
Question-4
The company is looking forwrad for moving from present state to the future state. Please justify
Execution Plan of the Company for moving from present-state to future-state is given below:
Implementing the plan, FEI has to formulate and implement lean manufacturing process and for the success of this plan,
few steps are required to be followed:
So as to shift from the current state to the prosperous state, it is important to execute the lean manufacturing and for this,
following steps must be followed:
1. Future State Scope must be observed and identified so as to formulate the foremost implementation
project along with the long-term plan.
Implementing the plan for the upcoming future is very important which requires primarily creating the short-term plan.
FEI Company can use the immediately available resources for optimizing the current state by laying down the detailed
plan, only purpose of which is applying the same plan in execution. This is done basically to build a long term
implementation plan for application at each step for consecutive 3-4 years, which in future will also lead to the
development of new issues which needs resolving and changes in the future map but it is advised always to keep the
leadership focused on Lean in long run. (Landau and Landau, 2019)
2. Company to form new future state.
Introducing the future state, and also stating new reasonable ideas which understood by the employees with the help of
diagrams, posters and signs. Employees are tending to be trained for the new courses, indulging in the future state issue.
The training courses must also include the changes and also the reasons of carrying out such changes. This knowledge
shall also help learning the lean manufacturing processes.
3. Company should develop communication and feedback channels.
The company is looking forwrad for moving from present state to the future state. Please justify
Execution Plan of the Company for moving from present-state to future-state is given below:
Implementing the plan, FEI has to formulate and implement lean manufacturing process and for the success of this plan,
few steps are required to be followed:
So as to shift from the current state to the prosperous state, it is important to execute the lean manufacturing and for this,
following steps must be followed:
1. Future State Scope must be observed and identified so as to formulate the foremost implementation
project along with the long-term plan.
Implementing the plan for the upcoming future is very important which requires primarily creating the short-term plan.
FEI Company can use the immediately available resources for optimizing the current state by laying down the detailed
plan, only purpose of which is applying the same plan in execution. This is done basically to build a long term
implementation plan for application at each step for consecutive 3-4 years, which in future will also lead to the
development of new issues which needs resolving and changes in the future map but it is advised always to keep the
leadership focused on Lean in long run. (Landau and Landau, 2019)
2. Company to form new future state.
Introducing the future state, and also stating new reasonable ideas which understood by the employees with the help of
diagrams, posters and signs. Employees are tending to be trained for the new courses, indulging in the future state issue.
The training courses must also include the changes and also the reasons of carrying out such changes. This knowledge
shall also help learning the lean manufacturing processes.
3. Company should develop communication and feedback channels.
⊘ This is a preview!⊘
Do you want full access?
Subscribe today to unlock all pages.

Trusted by 1+ million students worldwide
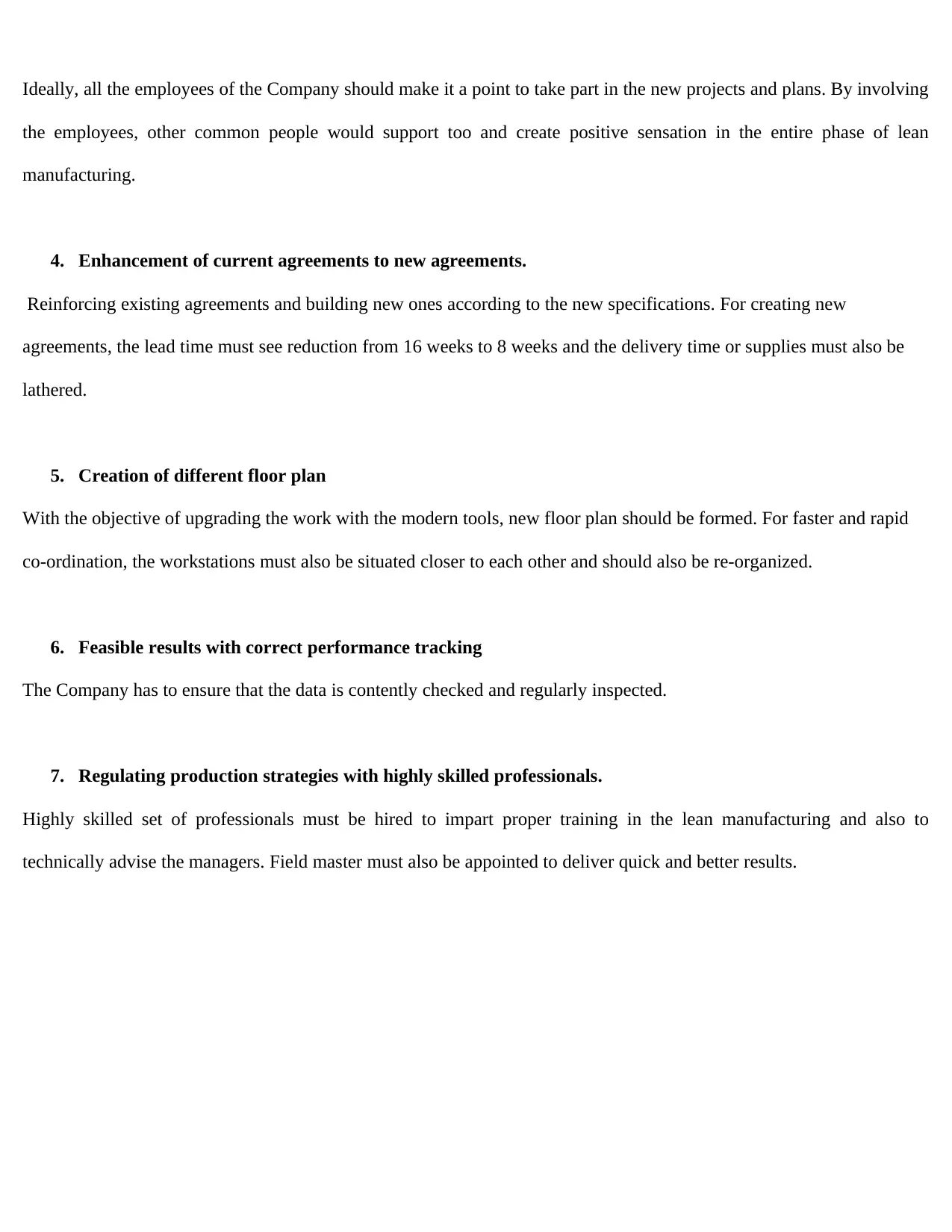
Ideally, all the employees of the Company should make it a point to take part in the new projects and plans. By involving
the employees, other common people would support too and create positive sensation in the entire phase of lean
manufacturing.
4. Enhancement of current agreements to new agreements.
Reinforcing existing agreements and building new ones according to the new specifications. For creating new
agreements, the lead time must see reduction from 16 weeks to 8 weeks and the delivery time or supplies must also be
lathered.
5. Creation of different floor plan
With the objective of upgrading the work with the modern tools, new floor plan should be formed. For faster and rapid
co-ordination, the workstations must also be situated closer to each other and should also be re-organized.
6. Feasible results with correct performance tracking
The Company has to ensure that the data is contently checked and regularly inspected.
7. Regulating production strategies with highly skilled professionals.
Highly skilled set of professionals must be hired to impart proper training in the lean manufacturing and also to
technically advise the managers. Field master must also be appointed to deliver quick and better results.
the employees, other common people would support too and create positive sensation in the entire phase of lean
manufacturing.
4. Enhancement of current agreements to new agreements.
Reinforcing existing agreements and building new ones according to the new specifications. For creating new
agreements, the lead time must see reduction from 16 weeks to 8 weeks and the delivery time or supplies must also be
lathered.
5. Creation of different floor plan
With the objective of upgrading the work with the modern tools, new floor plan should be formed. For faster and rapid
co-ordination, the workstations must also be situated closer to each other and should also be re-organized.
6. Feasible results with correct performance tracking
The Company has to ensure that the data is contently checked and regularly inspected.
7. Regulating production strategies with highly skilled professionals.
Highly skilled set of professionals must be hired to impart proper training in the lean manufacturing and also to
technically advise the managers. Field master must also be appointed to deliver quick and better results.
Paraphrase This Document
Need a fresh take? Get an instant paraphrase of this document with our AI Paraphraser
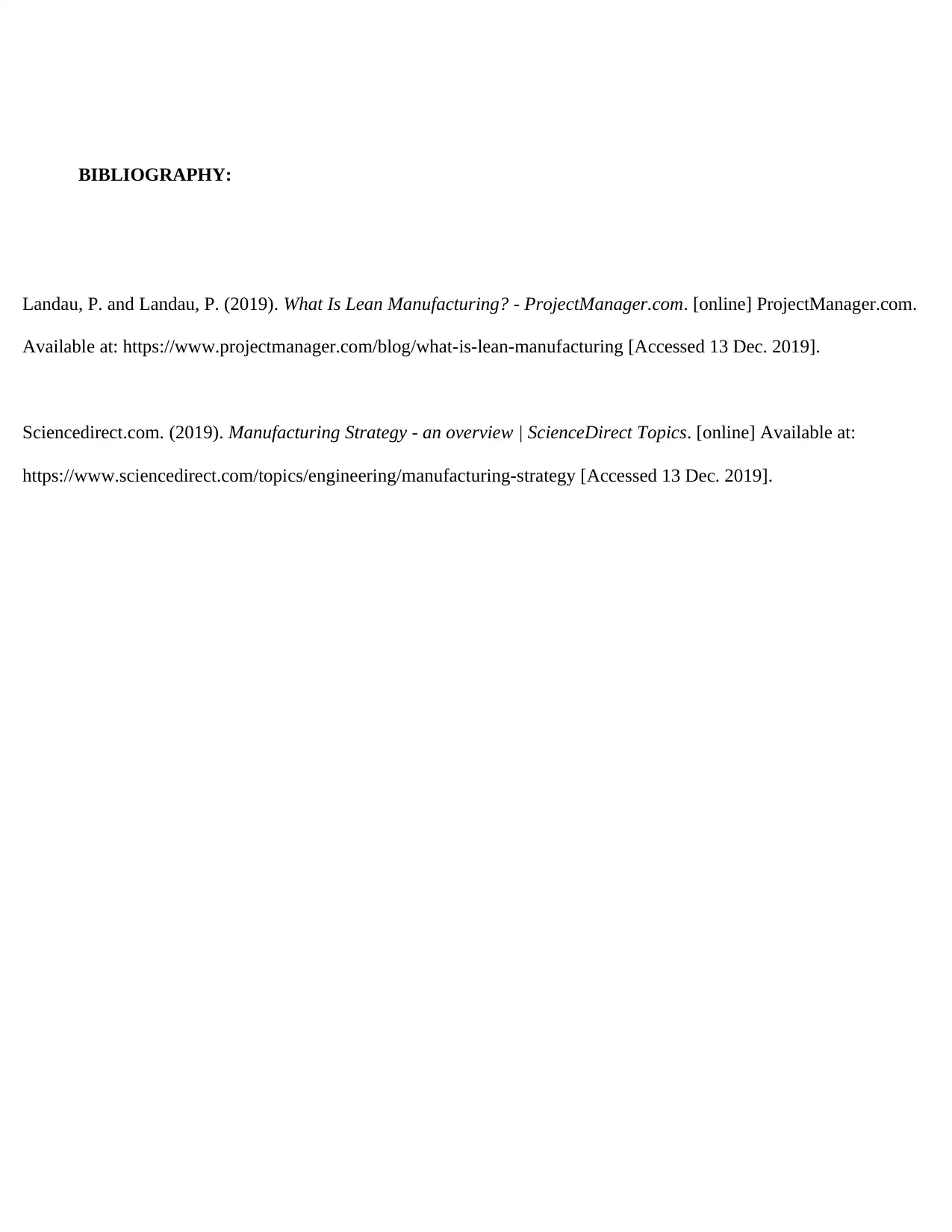
BIBLIOGRAPHY:
Landau, P. and Landau, P. (2019). What Is Lean Manufacturing? - ProjectManager.com. [online] ProjectManager.com.
Available at: https://www.projectmanager.com/blog/what-is-lean-manufacturing [Accessed 13 Dec. 2019].
Sciencedirect.com. (2019). Manufacturing Strategy - an overview | ScienceDirect Topics. [online] Available at:
https://www.sciencedirect.com/topics/engineering/manufacturing-strategy [Accessed 13 Dec. 2019].
Landau, P. and Landau, P. (2019). What Is Lean Manufacturing? - ProjectManager.com. [online] ProjectManager.com.
Available at: https://www.projectmanager.com/blog/what-is-lean-manufacturing [Accessed 13 Dec. 2019].
Sciencedirect.com. (2019). Manufacturing Strategy - an overview | ScienceDirect Topics. [online] Available at:
https://www.sciencedirect.com/topics/engineering/manufacturing-strategy [Accessed 13 Dec. 2019].
1 out of 14
Related Documents

Your All-in-One AI-Powered Toolkit for Academic Success.
+13062052269
info@desklib.com
Available 24*7 on WhatsApp / Email
Unlock your academic potential
© 2024 | Zucol Services PVT LTD | All rights reserved.