Workplace Health & Safety Practices
VerifiedAdded on 2020/04/07
|25
|5234
|164
AI Summary
This assignment delves into the crucial field of Workplace Health and Safety (WHS). It examines various aspects including WHS legislation, codes of practice, risk assessment procedures, and the importance of consultation, cooperation, and coordination in ensuring safe working environments. Students will gain insights into industry standards like AS/NZS 4801 and ISO 45001, along with practical guidance on implementing effective WHS management systems.
Contribute Materials
Your contribution can guide someone’s learning journey. Share your
documents today.
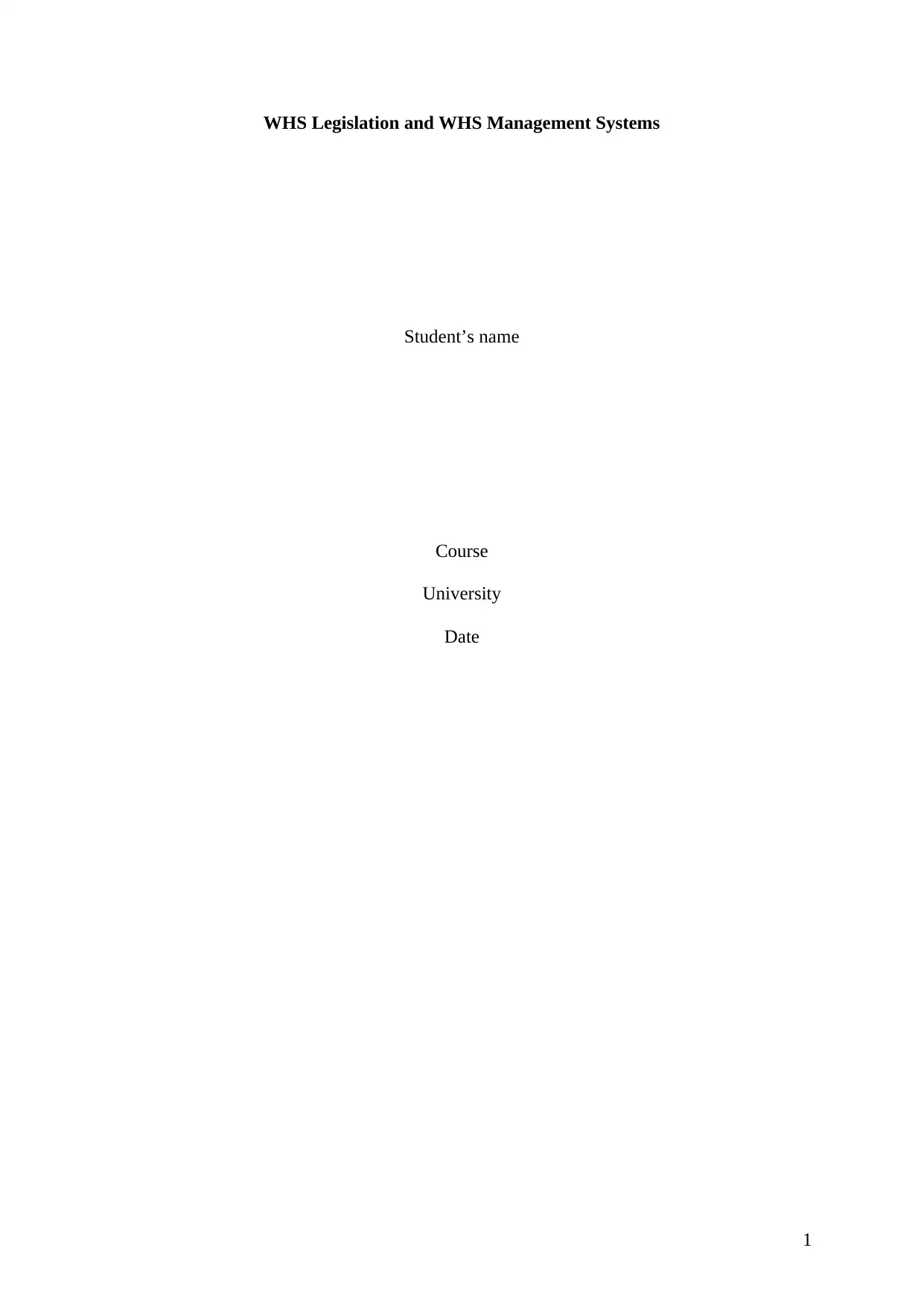
WHS Legislation and WHS Management Systems
Student’s name
Course
University
Date
1
Student’s name
Course
University
Date
1
Secure Best Marks with AI Grader
Need help grading? Try our AI Grader for instant feedback on your assignments.
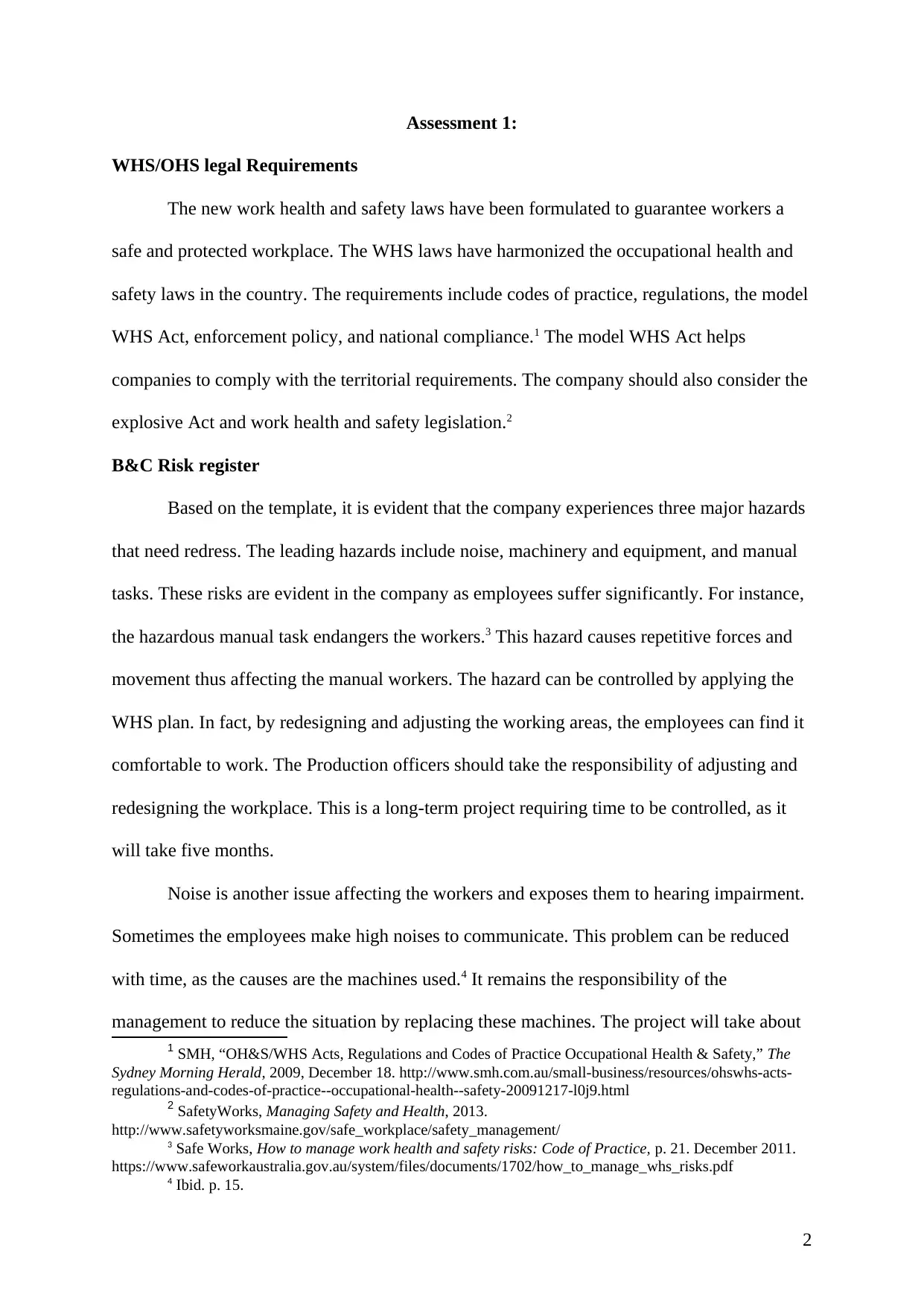
Assessment 1:
WHS/OHS legal Requirements
The new work health and safety laws have been formulated to guarantee workers a
safe and protected workplace. The WHS laws have harmonized the occupational health and
safety laws in the country. The requirements include codes of practice, regulations, the model
WHS Act, enforcement policy, and national compliance.1 The model WHS Act helps
companies to comply with the territorial requirements. The company should also consider the
explosive Act and work health and safety legislation.2
B&C Risk register
Based on the template, it is evident that the company experiences three major hazards
that need redress. The leading hazards include noise, machinery and equipment, and manual
tasks. These risks are evident in the company as employees suffer significantly. For instance,
the hazardous manual task endangers the workers.3 This hazard causes repetitive forces and
movement thus affecting the manual workers. The hazard can be controlled by applying the
WHS plan. In fact, by redesigning and adjusting the working areas, the employees can find it
comfortable to work. The Production officers should take the responsibility of adjusting and
redesigning the workplace. This is a long-term project requiring time to be controlled, as it
will take five months.
Noise is another issue affecting the workers and exposes them to hearing impairment.
Sometimes the employees make high noises to communicate. This problem can be reduced
with time, as the causes are the machines used.4 It remains the responsibility of the
management to reduce the situation by replacing these machines. The project will take about
1 SMH, “OH&S/WHS Acts, Regulations and Codes of Practice Occupational Health & Safety,” The
Sydney Morning Herald, 2009, December 18. http://www.smh.com.au/small-business/resources/ohswhs-acts-
regulations-and-codes-of-practice--occupational-health--safety-20091217-l0j9.html
2 SafetyWorks, Managing Safety and Health, 2013.
http://www.safetyworksmaine.gov/safe_workplace/safety_management/
3 Safe Works, How to manage work health and safety risks: Code of Practice, p. 21. December 2011.
https://www.safeworkaustralia.gov.au/system/files/documents/1702/how_to_manage_whs_risks.pdf
4 Ibid. p. 15.
2
WHS/OHS legal Requirements
The new work health and safety laws have been formulated to guarantee workers a
safe and protected workplace. The WHS laws have harmonized the occupational health and
safety laws in the country. The requirements include codes of practice, regulations, the model
WHS Act, enforcement policy, and national compliance.1 The model WHS Act helps
companies to comply with the territorial requirements. The company should also consider the
explosive Act and work health and safety legislation.2
B&C Risk register
Based on the template, it is evident that the company experiences three major hazards
that need redress. The leading hazards include noise, machinery and equipment, and manual
tasks. These risks are evident in the company as employees suffer significantly. For instance,
the hazardous manual task endangers the workers.3 This hazard causes repetitive forces and
movement thus affecting the manual workers. The hazard can be controlled by applying the
WHS plan. In fact, by redesigning and adjusting the working areas, the employees can find it
comfortable to work. The Production officers should take the responsibility of adjusting and
redesigning the workplace. This is a long-term project requiring time to be controlled, as it
will take five months.
Noise is another issue affecting the workers and exposes them to hearing impairment.
Sometimes the employees make high noises to communicate. This problem can be reduced
with time, as the causes are the machines used.4 It remains the responsibility of the
management to reduce the situation by replacing these machines. The project will take about
1 SMH, “OH&S/WHS Acts, Regulations and Codes of Practice Occupational Health & Safety,” The
Sydney Morning Herald, 2009, December 18. http://www.smh.com.au/small-business/resources/ohswhs-acts-
regulations-and-codes-of-practice--occupational-health--safety-20091217-l0j9.html
2 SafetyWorks, Managing Safety and Health, 2013.
http://www.safetyworksmaine.gov/safe_workplace/safety_management/
3 Safe Works, How to manage work health and safety risks: Code of Practice, p. 21. December 2011.
https://www.safeworkaustralia.gov.au/system/files/documents/1702/how_to_manage_whs_risks.pdf
4 Ibid. p. 15.
2
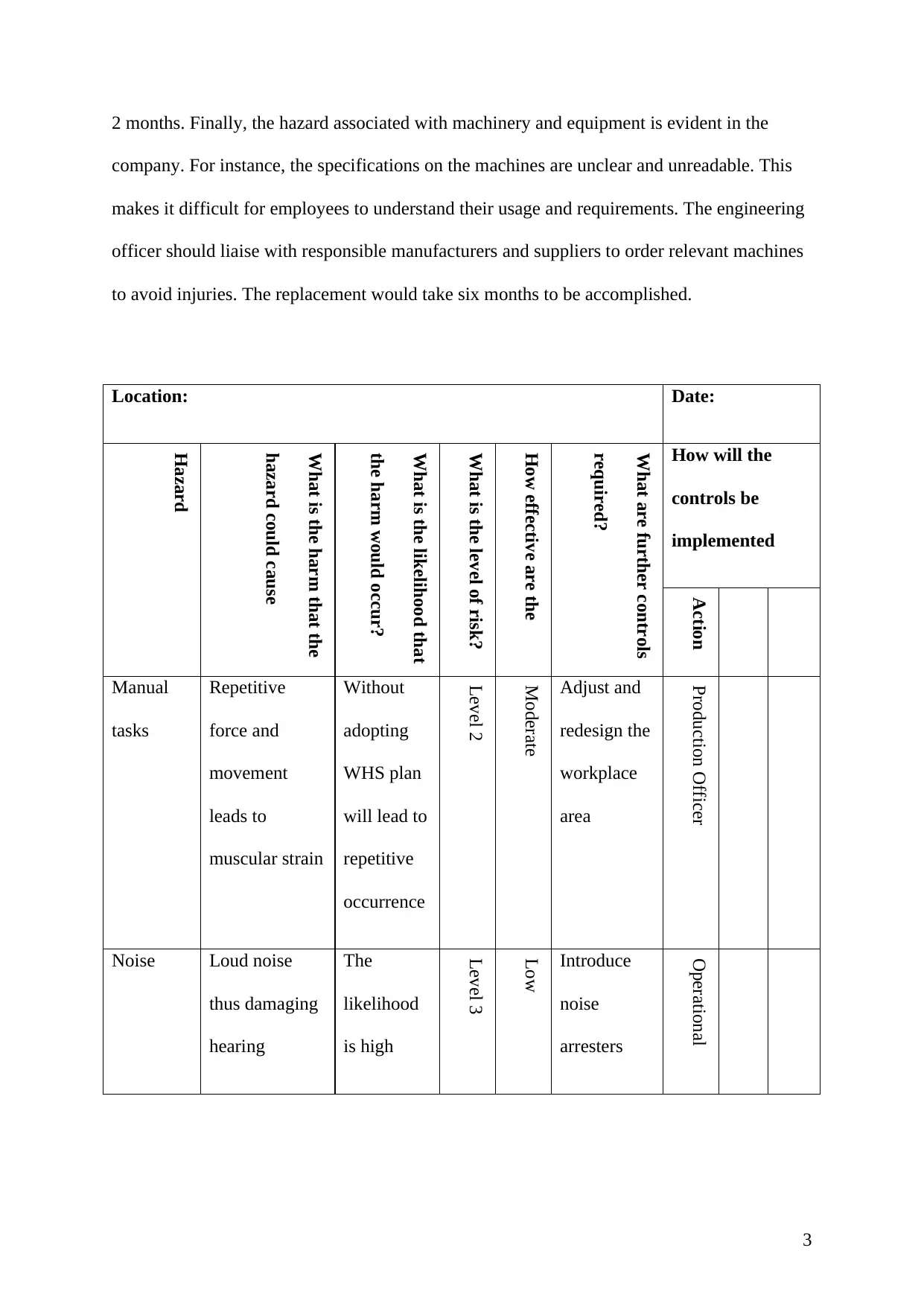
2 months. Finally, the hazard associated with machinery and equipment is evident in the
company. For instance, the specifications on the machines are unclear and unreadable. This
makes it difficult for employees to understand their usage and requirements. The engineering
officer should liaise with responsible manufacturers and suppliers to order relevant machines
to avoid injuries. The replacement would take six months to be accomplished.
Location: Date:
Hazard
What is the harm that the
hazard could cause
What is the likelihood that
the harm would occur?
What is the level of risk?
How effective are the
current controls?
What are further controls
required?
How will the
controls be
implemented
Action
by
Manual
tasks
Repetitive
force and
movement
leads to
muscular strain
Without
adopting
WHS plan
will lead to
repetitive
occurrence
Level 2
Moderate
Adjust and
redesign the
workplace
area
Production Officer
Noise Loud noise
thus damaging
hearing
The
likelihood
is high
Level 3
Low
Introduce
noise
arresters
Operational
officer
3
company. For instance, the specifications on the machines are unclear and unreadable. This
makes it difficult for employees to understand their usage and requirements. The engineering
officer should liaise with responsible manufacturers and suppliers to order relevant machines
to avoid injuries. The replacement would take six months to be accomplished.
Location: Date:
Hazard
What is the harm that the
hazard could cause
What is the likelihood that
the harm would occur?
What is the level of risk?
How effective are the
current controls?
What are further controls
required?
How will the
controls be
implemented
Action
by
Manual
tasks
Repetitive
force and
movement
leads to
muscular strain
Without
adopting
WHS plan
will lead to
repetitive
occurrence
Level 2
Moderate
Adjust and
redesign the
workplace
area
Production Officer
Noise Loud noise
thus damaging
hearing
The
likelihood
is high
Level 3
Low
Introduce
noise
arresters
Operational
officer
3
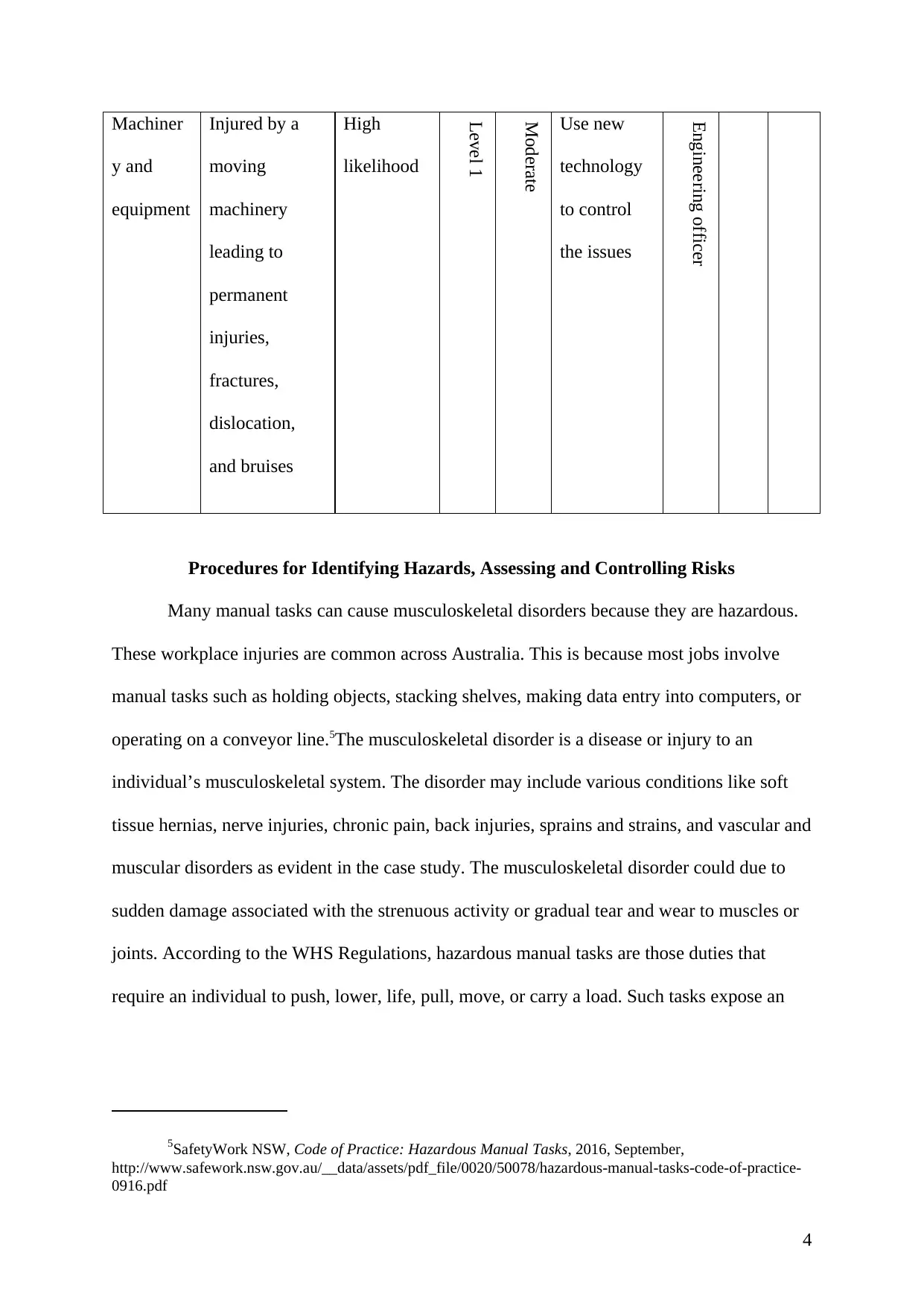
Machiner
y and
equipment
Injured by a
moving
machinery
leading to
permanent
injuries,
fractures,
dislocation,
and bruises
High
likelihood
Level 1
Moderate
Use new
technology
to control
the issues
Engineering officer
Procedures for Identifying Hazards, Assessing and Controlling Risks
Many manual tasks can cause musculoskeletal disorders because they are hazardous.
These workplace injuries are common across Australia. This is because most jobs involve
manual tasks such as holding objects, stacking shelves, making data entry into computers, or
operating on a conveyor line.5The musculoskeletal disorder is a disease or injury to an
individual’s musculoskeletal system. The disorder may include various conditions like soft
tissue hernias, nerve injuries, chronic pain, back injuries, sprains and strains, and vascular and
muscular disorders as evident in the case study. The musculoskeletal disorder could due to
sudden damage associated with the strenuous activity or gradual tear and wear to muscles or
joints. According to the WHS Regulations, hazardous manual tasks are those duties that
require an individual to push, lower, life, pull, move, or carry a load. Such tasks expose an
5SafetyWork NSW, Code of Practice: Hazardous Manual Tasks, 2016, September,
http://www.safework.nsw.gov.au/__data/assets/pdf_file/0020/50078/hazardous-manual-tasks-code-of-practice-
0916.pdf
4
y and
equipment
Injured by a
moving
machinery
leading to
permanent
injuries,
fractures,
dislocation,
and bruises
High
likelihood
Level 1
Moderate
Use new
technology
to control
the issues
Engineering officer
Procedures for Identifying Hazards, Assessing and Controlling Risks
Many manual tasks can cause musculoskeletal disorders because they are hazardous.
These workplace injuries are common across Australia. This is because most jobs involve
manual tasks such as holding objects, stacking shelves, making data entry into computers, or
operating on a conveyor line.5The musculoskeletal disorder is a disease or injury to an
individual’s musculoskeletal system. The disorder may include various conditions like soft
tissue hernias, nerve injuries, chronic pain, back injuries, sprains and strains, and vascular and
muscular disorders as evident in the case study. The musculoskeletal disorder could due to
sudden damage associated with the strenuous activity or gradual tear and wear to muscles or
joints. According to the WHS Regulations, hazardous manual tasks are those duties that
require an individual to push, lower, life, pull, move, or carry a load. Such tasks expose an
5SafetyWork NSW, Code of Practice: Hazardous Manual Tasks, 2016, September,
http://www.safework.nsw.gov.au/__data/assets/pdf_file/0020/50078/hazardous-manual-tasks-code-of-practice-
0916.pdf
4
Secure Best Marks with AI Grader
Need help grading? Try our AI Grader for instant feedback on your assignments.
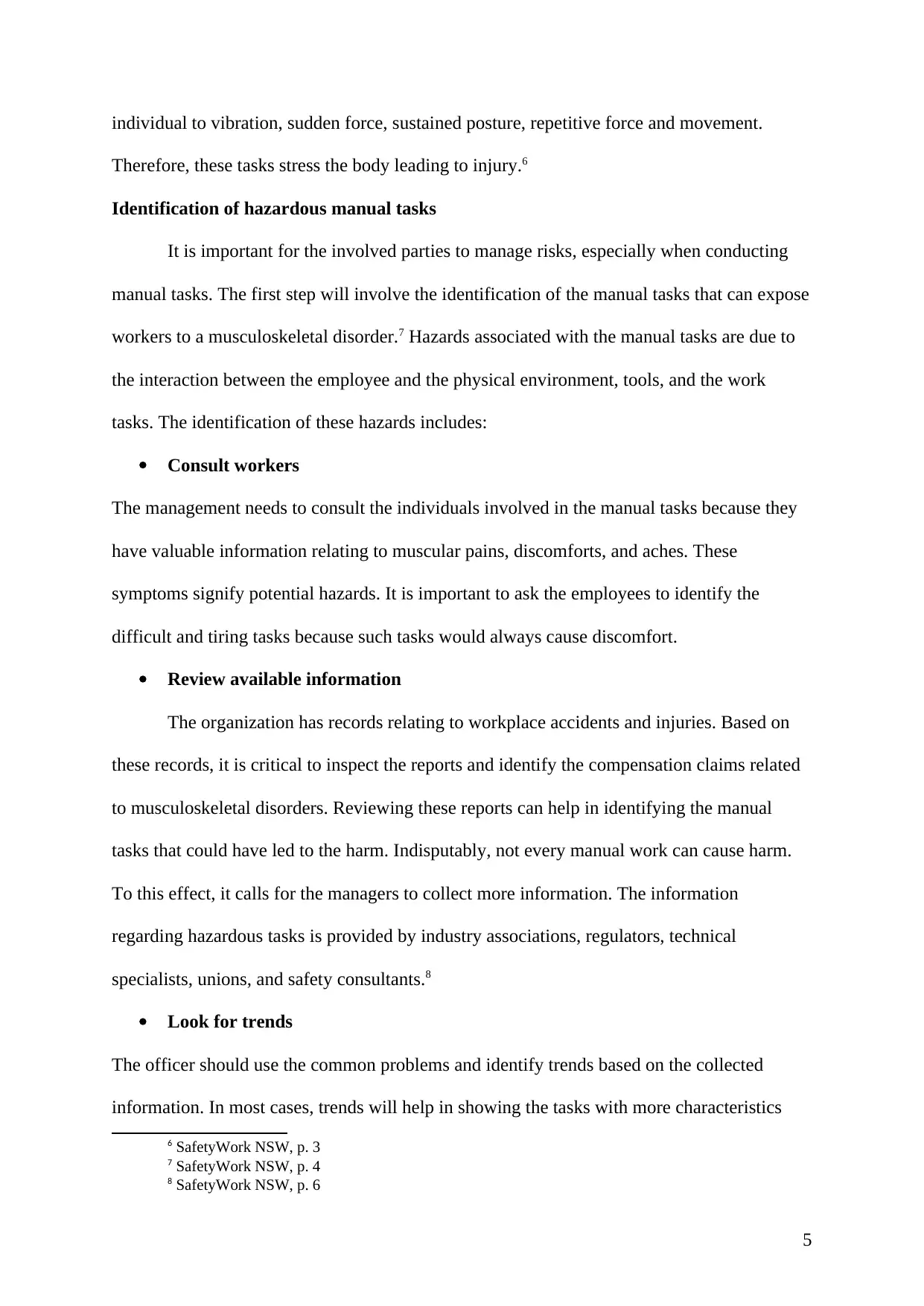
individual to vibration, sudden force, sustained posture, repetitive force and movement.
Therefore, these tasks stress the body leading to injury.6
Identification of hazardous manual tasks
It is important for the involved parties to manage risks, especially when conducting
manual tasks. The first step will involve the identification of the manual tasks that can expose
workers to a musculoskeletal disorder.7 Hazards associated with the manual tasks are due to
the interaction between the employee and the physical environment, tools, and the work
tasks. The identification of these hazards includes:
Consult workers
The management needs to consult the individuals involved in the manual tasks because they
have valuable information relating to muscular pains, discomforts, and aches. These
symptoms signify potential hazards. It is important to ask the employees to identify the
difficult and tiring tasks because such tasks would always cause discomfort.
Review available information
The organization has records relating to workplace accidents and injuries. Based on
these records, it is critical to inspect the reports and identify the compensation claims related
to musculoskeletal disorders. Reviewing these reports can help in identifying the manual
tasks that could have led to the harm. Indisputably, not every manual work can cause harm.
To this effect, it calls for the managers to collect more information. The information
regarding hazardous tasks is provided by industry associations, regulators, technical
specialists, unions, and safety consultants.8
Look for trends
The officer should use the common problems and identify trends based on the collected
information. In most cases, trends will help in showing the tasks with more characteristics
6 SafetyWork NSW, p. 3
7 SafetyWork NSW, p. 4
8 SafetyWork NSW, p. 6
5
Therefore, these tasks stress the body leading to injury.6
Identification of hazardous manual tasks
It is important for the involved parties to manage risks, especially when conducting
manual tasks. The first step will involve the identification of the manual tasks that can expose
workers to a musculoskeletal disorder.7 Hazards associated with the manual tasks are due to
the interaction between the employee and the physical environment, tools, and the work
tasks. The identification of these hazards includes:
Consult workers
The management needs to consult the individuals involved in the manual tasks because they
have valuable information relating to muscular pains, discomforts, and aches. These
symptoms signify potential hazards. It is important to ask the employees to identify the
difficult and tiring tasks because such tasks would always cause discomfort.
Review available information
The organization has records relating to workplace accidents and injuries. Based on
these records, it is critical to inspect the reports and identify the compensation claims related
to musculoskeletal disorders. Reviewing these reports can help in identifying the manual
tasks that could have led to the harm. Indisputably, not every manual work can cause harm.
To this effect, it calls for the managers to collect more information. The information
regarding hazardous tasks is provided by industry associations, regulators, technical
specialists, unions, and safety consultants.8
Look for trends
The officer should use the common problems and identify trends based on the collected
information. In most cases, trends will help in showing the tasks with more characteristics
6 SafetyWork NSW, p. 3
7 SafetyWork NSW, p. 4
8 SafetyWork NSW, p. 6
5
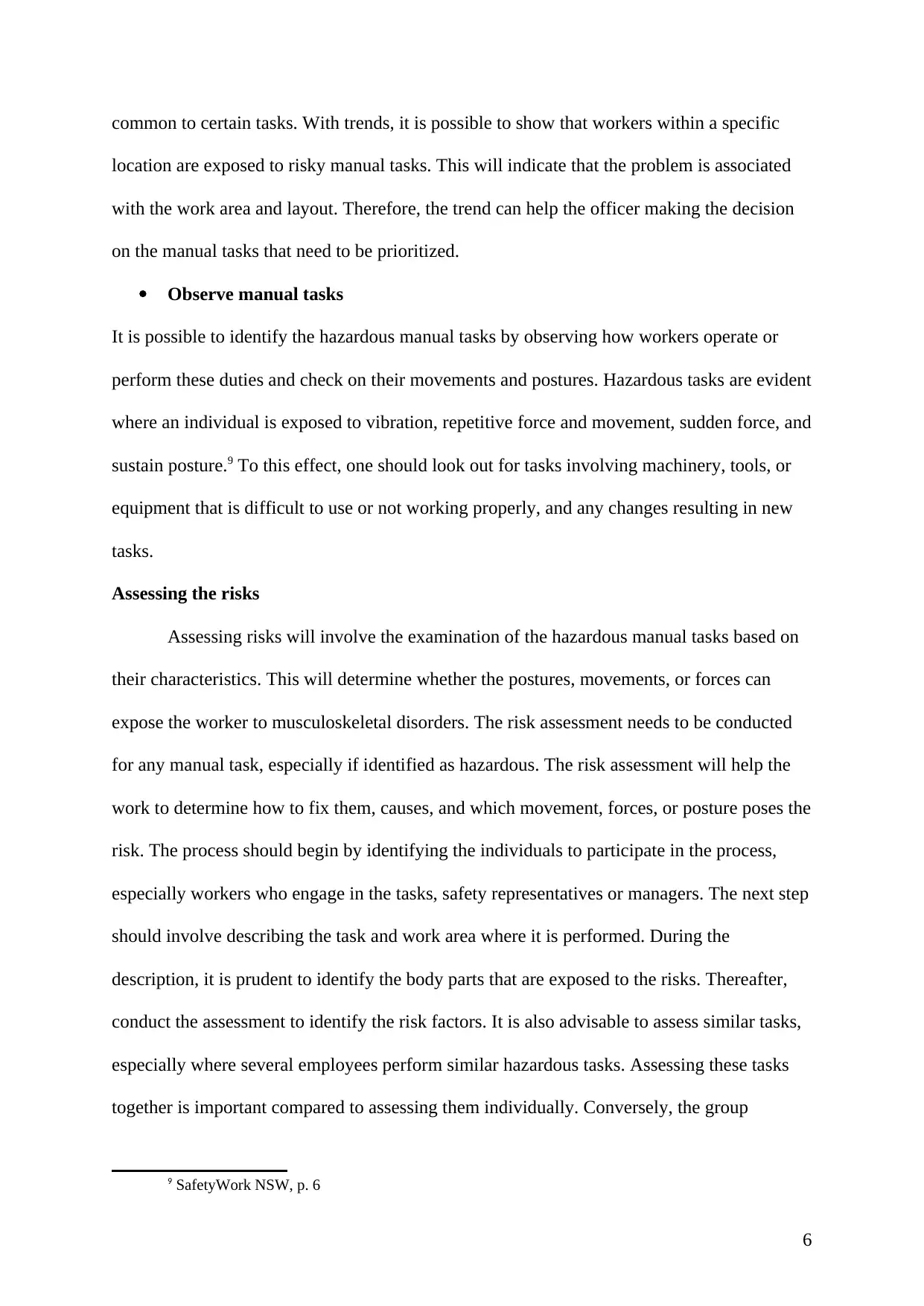
common to certain tasks. With trends, it is possible to show that workers within a specific
location are exposed to risky manual tasks. This will indicate that the problem is associated
with the work area and layout. Therefore, the trend can help the officer making the decision
on the manual tasks that need to be prioritized.
Observe manual tasks
It is possible to identify the hazardous manual tasks by observing how workers operate or
perform these duties and check on their movements and postures. Hazardous tasks are evident
where an individual is exposed to vibration, repetitive force and movement, sudden force, and
sustain posture.9 To this effect, one should look out for tasks involving machinery, tools, or
equipment that is difficult to use or not working properly, and any changes resulting in new
tasks.
Assessing the risks
Assessing risks will involve the examination of the hazardous manual tasks based on
their characteristics. This will determine whether the postures, movements, or forces can
expose the worker to musculoskeletal disorders. The risk assessment needs to be conducted
for any manual task, especially if identified as hazardous. The risk assessment will help the
work to determine how to fix them, causes, and which movement, forces, or posture poses the
risk. The process should begin by identifying the individuals to participate in the process,
especially workers who engage in the tasks, safety representatives or managers. The next step
should involve describing the task and work area where it is performed. During the
description, it is prudent to identify the body parts that are exposed to the risks. Thereafter,
conduct the assessment to identify the risk factors. It is also advisable to assess similar tasks,
especially where several employees perform similar hazardous tasks. Assessing these tasks
together is important compared to assessing them individually. Conversely, the group
9 SafetyWork NSW, p. 6
6
location are exposed to risky manual tasks. This will indicate that the problem is associated
with the work area and layout. Therefore, the trend can help the officer making the decision
on the manual tasks that need to be prioritized.
Observe manual tasks
It is possible to identify the hazardous manual tasks by observing how workers operate or
perform these duties and check on their movements and postures. Hazardous tasks are evident
where an individual is exposed to vibration, repetitive force and movement, sudden force, and
sustain posture.9 To this effect, one should look out for tasks involving machinery, tools, or
equipment that is difficult to use or not working properly, and any changes resulting in new
tasks.
Assessing the risks
Assessing risks will involve the examination of the hazardous manual tasks based on
their characteristics. This will determine whether the postures, movements, or forces can
expose the worker to musculoskeletal disorders. The risk assessment needs to be conducted
for any manual task, especially if identified as hazardous. The risk assessment will help the
work to determine how to fix them, causes, and which movement, forces, or posture poses the
risk. The process should begin by identifying the individuals to participate in the process,
especially workers who engage in the tasks, safety representatives or managers. The next step
should involve describing the task and work area where it is performed. During the
description, it is prudent to identify the body parts that are exposed to the risks. Thereafter,
conduct the assessment to identify the risk factors. It is also advisable to assess similar tasks,
especially where several employees perform similar hazardous tasks. Assessing these tasks
together is important compared to assessing them individually. Conversely, the group
9 SafetyWork NSW, p. 6
6
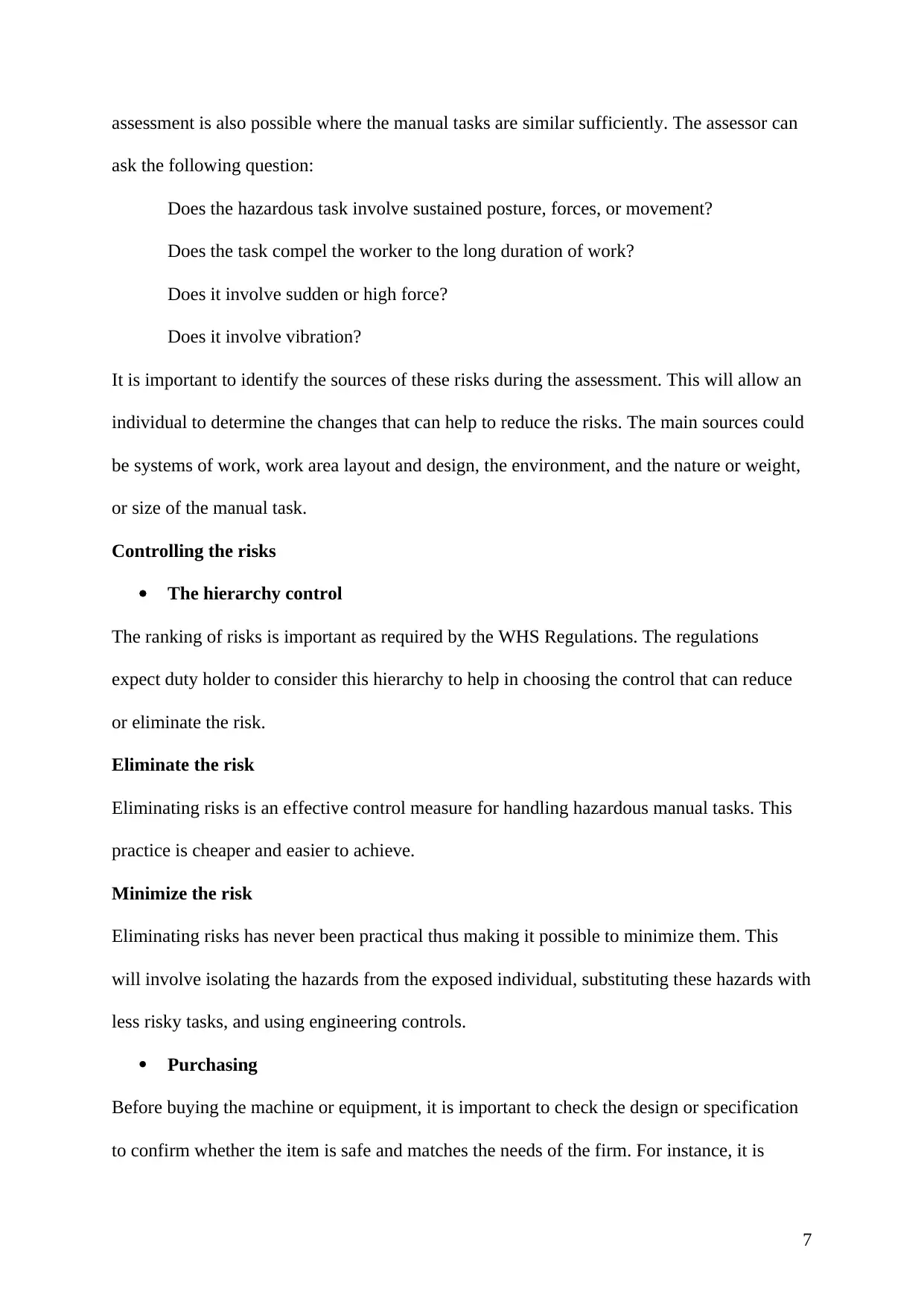
assessment is also possible where the manual tasks are similar sufficiently. The assessor can
ask the following question:
Does the hazardous task involve sustained posture, forces, or movement?
Does the task compel the worker to the long duration of work?
Does it involve sudden or high force?
Does it involve vibration?
It is important to identify the sources of these risks during the assessment. This will allow an
individual to determine the changes that can help to reduce the risks. The main sources could
be systems of work, work area layout and design, the environment, and the nature or weight,
or size of the manual task.
Controlling the risks
The hierarchy control
The ranking of risks is important as required by the WHS Regulations. The regulations
expect duty holder to consider this hierarchy to help in choosing the control that can reduce
or eliminate the risk.
Eliminate the risk
Eliminating risks is an effective control measure for handling hazardous manual tasks. This
practice is cheaper and easier to achieve.
Minimize the risk
Eliminating risks has never been practical thus making it possible to minimize them. This
will involve isolating the hazards from the exposed individual, substituting these hazards with
less risky tasks, and using engineering controls.
Purchasing
Before buying the machine or equipment, it is important to check the design or specification
to confirm whether the item is safe and matches the needs of the firm. For instance, it is
7
ask the following question:
Does the hazardous task involve sustained posture, forces, or movement?
Does the task compel the worker to the long duration of work?
Does it involve sudden or high force?
Does it involve vibration?
It is important to identify the sources of these risks during the assessment. This will allow an
individual to determine the changes that can help to reduce the risks. The main sources could
be systems of work, work area layout and design, the environment, and the nature or weight,
or size of the manual task.
Controlling the risks
The hierarchy control
The ranking of risks is important as required by the WHS Regulations. The regulations
expect duty holder to consider this hierarchy to help in choosing the control that can reduce
or eliminate the risk.
Eliminate the risk
Eliminating risks is an effective control measure for handling hazardous manual tasks. This
practice is cheaper and easier to achieve.
Minimize the risk
Eliminating risks has never been practical thus making it possible to minimize them. This
will involve isolating the hazards from the exposed individual, substituting these hazards with
less risky tasks, and using engineering controls.
Purchasing
Before buying the machine or equipment, it is important to check the design or specification
to confirm whether the item is safe and matches the needs of the firm. For instance, it is
7
Paraphrase This Document
Need a fresh take? Get an instant paraphrase of this document with our AI Paraphraser
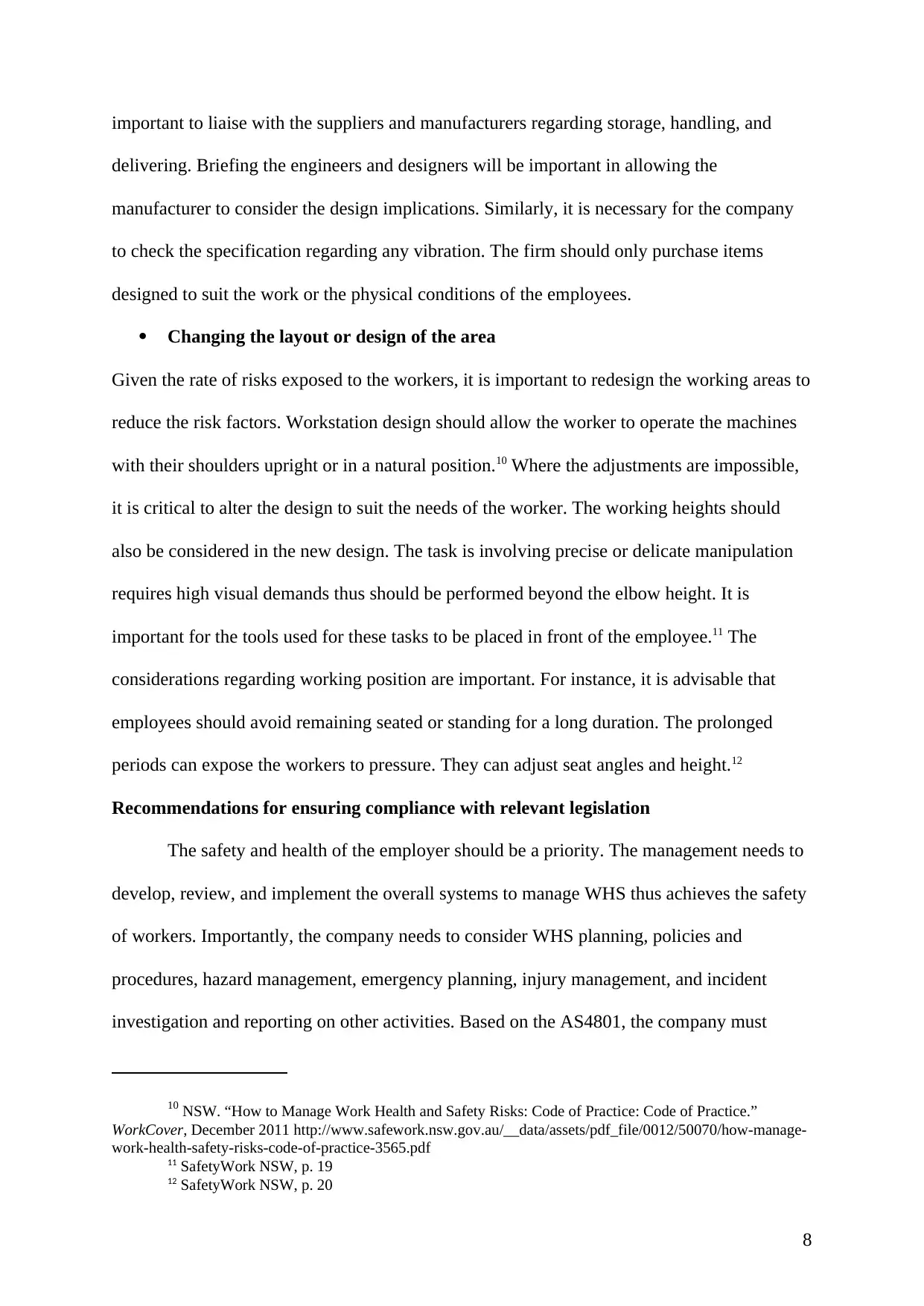
important to liaise with the suppliers and manufacturers regarding storage, handling, and
delivering. Briefing the engineers and designers will be important in allowing the
manufacturer to consider the design implications. Similarly, it is necessary for the company
to check the specification regarding any vibration. The firm should only purchase items
designed to suit the work or the physical conditions of the employees.
Changing the layout or design of the area
Given the rate of risks exposed to the workers, it is important to redesign the working areas to
reduce the risk factors. Workstation design should allow the worker to operate the machines
with their shoulders upright or in a natural position.10 Where the adjustments are impossible,
it is critical to alter the design to suit the needs of the worker. The working heights should
also be considered in the new design. The task is involving precise or delicate manipulation
requires high visual demands thus should be performed beyond the elbow height. It is
important for the tools used for these tasks to be placed in front of the employee.11 The
considerations regarding working position are important. For instance, it is advisable that
employees should avoid remaining seated or standing for a long duration. The prolonged
periods can expose the workers to pressure. They can adjust seat angles and height.12
Recommendations for ensuring compliance with relevant legislation
The safety and health of the employer should be a priority. The management needs to
develop, review, and implement the overall systems to manage WHS thus achieves the safety
of workers. Importantly, the company needs to consider WHS planning, policies and
procedures, hazard management, emergency planning, injury management, and incident
investigation and reporting on other activities. Based on the AS4801, the company must
10 NSW. “How to Manage Work Health and Safety Risks: Code of Practice: Code of Practice.”
WorkCover, December 2011 http://www.safework.nsw.gov.au/__data/assets/pdf_file/0012/50070/how-manage-
work-health-safety-risks-code-of-practice-3565.pdf
11 SafetyWork NSW, p. 19
12 SafetyWork NSW, p. 20
8
delivering. Briefing the engineers and designers will be important in allowing the
manufacturer to consider the design implications. Similarly, it is necessary for the company
to check the specification regarding any vibration. The firm should only purchase items
designed to suit the work or the physical conditions of the employees.
Changing the layout or design of the area
Given the rate of risks exposed to the workers, it is important to redesign the working areas to
reduce the risk factors. Workstation design should allow the worker to operate the machines
with their shoulders upright or in a natural position.10 Where the adjustments are impossible,
it is critical to alter the design to suit the needs of the worker. The working heights should
also be considered in the new design. The task is involving precise or delicate manipulation
requires high visual demands thus should be performed beyond the elbow height. It is
important for the tools used for these tasks to be placed in front of the employee.11 The
considerations regarding working position are important. For instance, it is advisable that
employees should avoid remaining seated or standing for a long duration. The prolonged
periods can expose the workers to pressure. They can adjust seat angles and height.12
Recommendations for ensuring compliance with relevant legislation
The safety and health of the employer should be a priority. The management needs to
develop, review, and implement the overall systems to manage WHS thus achieves the safety
of workers. Importantly, the company needs to consider WHS planning, policies and
procedures, hazard management, emergency planning, injury management, and incident
investigation and reporting on other activities. Based on the AS4801, the company must
10 NSW. “How to Manage Work Health and Safety Risks: Code of Practice: Code of Practice.”
WorkCover, December 2011 http://www.safework.nsw.gov.au/__data/assets/pdf_file/0012/50070/how-manage-
work-health-safety-risks-code-of-practice-3565.pdf
11 SafetyWork NSW, p. 19
12 SafetyWork NSW, p. 20
8
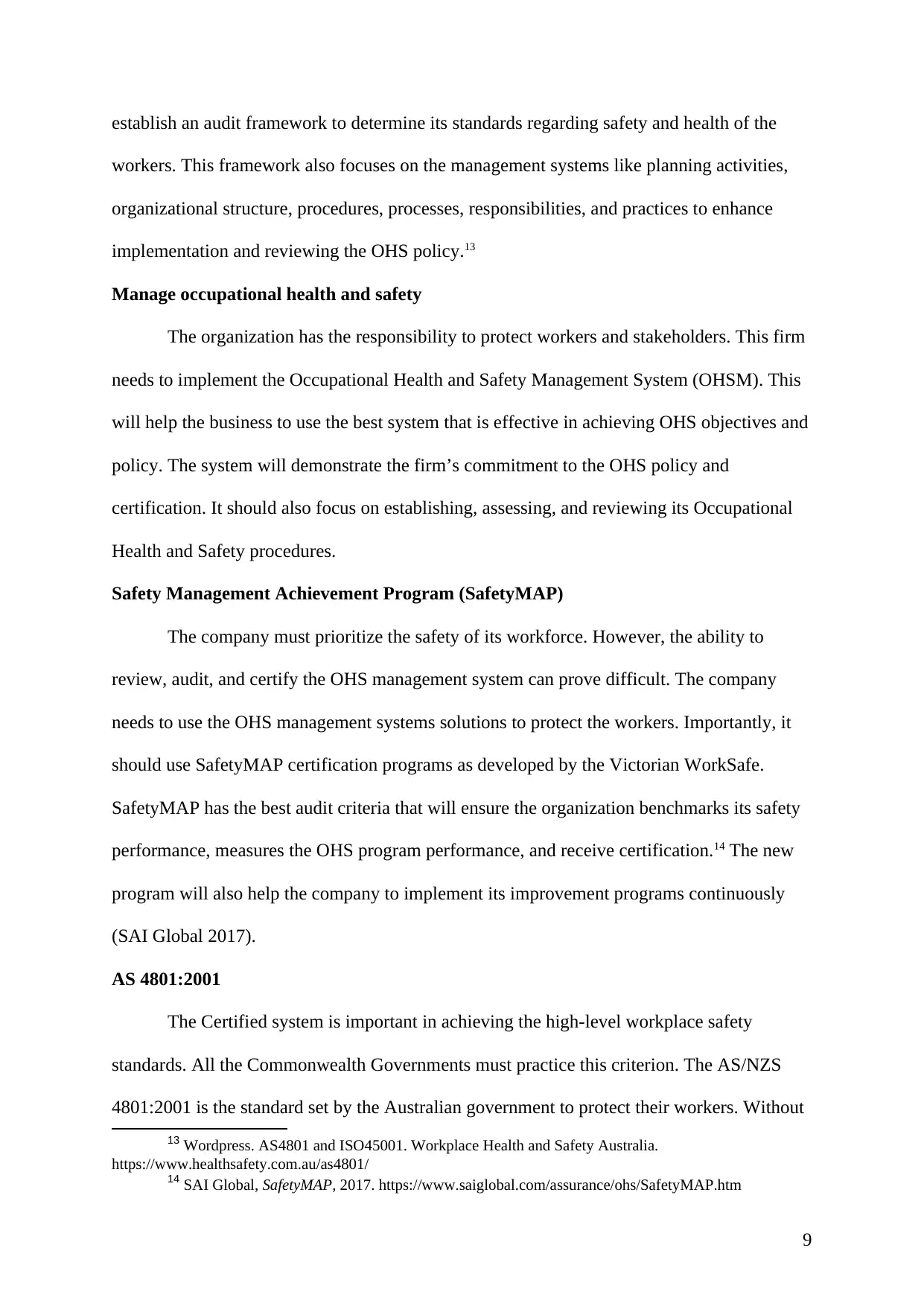
establish an audit framework to determine its standards regarding safety and health of the
workers. This framework also focuses on the management systems like planning activities,
organizational structure, procedures, processes, responsibilities, and practices to enhance
implementation and reviewing the OHS policy.13
Manage occupational health and safety
The organization has the responsibility to protect workers and stakeholders. This firm
needs to implement the Occupational Health and Safety Management System (OHSM). This
will help the business to use the best system that is effective in achieving OHS objectives and
policy. The system will demonstrate the firm’s commitment to the OHS policy and
certification. It should also focus on establishing, assessing, and reviewing its Occupational
Health and Safety procedures.
Safety Management Achievement Program (SafetyMAP)
The company must prioritize the safety of its workforce. However, the ability to
review, audit, and certify the OHS management system can prove difficult. The company
needs to use the OHS management systems solutions to protect the workers. Importantly, it
should use SafetyMAP certification programs as developed by the Victorian WorkSafe.
SafetyMAP has the best audit criteria that will ensure the organization benchmarks its safety
performance, measures the OHS program performance, and receive certification.14 The new
program will also help the company to implement its improvement programs continuously
(SAI Global 2017).
AS 4801:2001
The Certified system is important in achieving the high-level workplace safety
standards. All the Commonwealth Governments must practice this criterion. The AS/NZS
4801:2001 is the standard set by the Australian government to protect their workers. Without
13 Wordpress. AS4801 and ISO45001. Workplace Health and Safety Australia.
https://www.healthsafety.com.au/as4801/
14 SAI Global, SafetyMAP, 2017. https://www.saiglobal.com/assurance/ohs/SafetyMAP.htm
9
workers. This framework also focuses on the management systems like planning activities,
organizational structure, procedures, processes, responsibilities, and practices to enhance
implementation and reviewing the OHS policy.13
Manage occupational health and safety
The organization has the responsibility to protect workers and stakeholders. This firm
needs to implement the Occupational Health and Safety Management System (OHSM). This
will help the business to use the best system that is effective in achieving OHS objectives and
policy. The system will demonstrate the firm’s commitment to the OHS policy and
certification. It should also focus on establishing, assessing, and reviewing its Occupational
Health and Safety procedures.
Safety Management Achievement Program (SafetyMAP)
The company must prioritize the safety of its workforce. However, the ability to
review, audit, and certify the OHS management system can prove difficult. The company
needs to use the OHS management systems solutions to protect the workers. Importantly, it
should use SafetyMAP certification programs as developed by the Victorian WorkSafe.
SafetyMAP has the best audit criteria that will ensure the organization benchmarks its safety
performance, measures the OHS program performance, and receive certification.14 The new
program will also help the company to implement its improvement programs continuously
(SAI Global 2017).
AS 4801:2001
The Certified system is important in achieving the high-level workplace safety
standards. All the Commonwealth Governments must practice this criterion. The AS/NZS
4801:2001 is the standard set by the Australian government to protect their workers. Without
13 Wordpress. AS4801 and ISO45001. Workplace Health and Safety Australia.
https://www.healthsafety.com.au/as4801/
14 SAI Global, SafetyMAP, 2017. https://www.saiglobal.com/assurance/ohs/SafetyMAP.htm
9
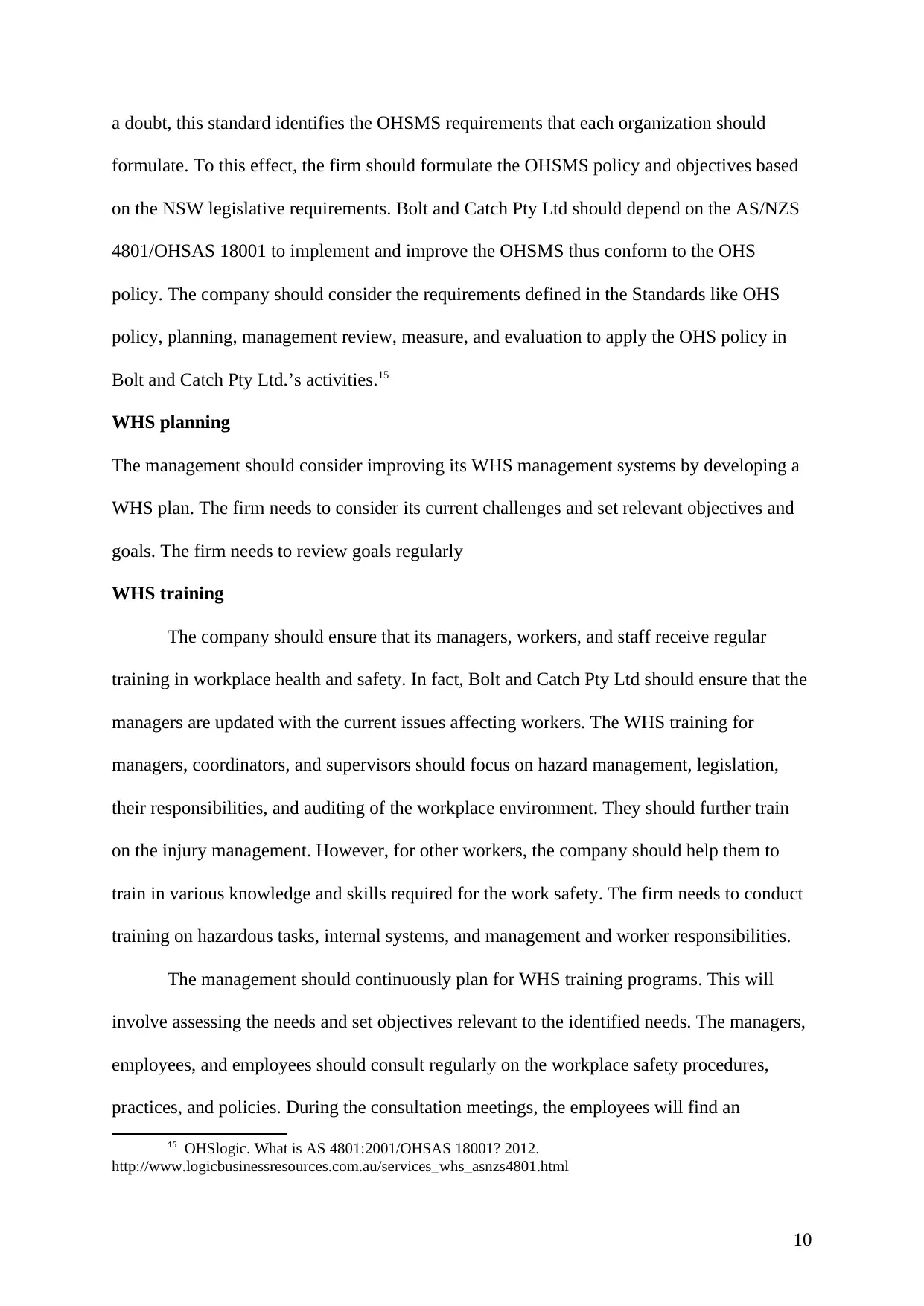
a doubt, this standard identifies the OHSMS requirements that each organization should
formulate. To this effect, the firm should formulate the OHSMS policy and objectives based
on the NSW legislative requirements. Bolt and Catch Pty Ltd should depend on the AS/NZS
4801/OHSAS 18001 to implement and improve the OHSMS thus conform to the OHS
policy. The company should consider the requirements defined in the Standards like OHS
policy, planning, management review, measure, and evaluation to apply the OHS policy in
Bolt and Catch Pty Ltd.’s activities.15
WHS planning
The management should consider improving its WHS management systems by developing a
WHS plan. The firm needs to consider its current challenges and set relevant objectives and
goals. The firm needs to review goals regularly
WHS training
The company should ensure that its managers, workers, and staff receive regular
training in workplace health and safety. In fact, Bolt and Catch Pty Ltd should ensure that the
managers are updated with the current issues affecting workers. The WHS training for
managers, coordinators, and supervisors should focus on hazard management, legislation,
their responsibilities, and auditing of the workplace environment. They should further train
on the injury management. However, for other workers, the company should help them to
train in various knowledge and skills required for the work safety. The firm needs to conduct
training on hazardous tasks, internal systems, and management and worker responsibilities.
The management should continuously plan for WHS training programs. This will
involve assessing the needs and set objectives relevant to the identified needs. The managers,
employees, and employees should consult regularly on the workplace safety procedures,
practices, and policies. During the consultation meetings, the employees will find an
15 OHSlogic. What is AS 4801:2001/OHSAS 18001? 2012.
http://www.logicbusinessresources.com.au/services_whs_asnzs4801.html
10
formulate. To this effect, the firm should formulate the OHSMS policy and objectives based
on the NSW legislative requirements. Bolt and Catch Pty Ltd should depend on the AS/NZS
4801/OHSAS 18001 to implement and improve the OHSMS thus conform to the OHS
policy. The company should consider the requirements defined in the Standards like OHS
policy, planning, management review, measure, and evaluation to apply the OHS policy in
Bolt and Catch Pty Ltd.’s activities.15
WHS planning
The management should consider improving its WHS management systems by developing a
WHS plan. The firm needs to consider its current challenges and set relevant objectives and
goals. The firm needs to review goals regularly
WHS training
The company should ensure that its managers, workers, and staff receive regular
training in workplace health and safety. In fact, Bolt and Catch Pty Ltd should ensure that the
managers are updated with the current issues affecting workers. The WHS training for
managers, coordinators, and supervisors should focus on hazard management, legislation,
their responsibilities, and auditing of the workplace environment. They should further train
on the injury management. However, for other workers, the company should help them to
train in various knowledge and skills required for the work safety. The firm needs to conduct
training on hazardous tasks, internal systems, and management and worker responsibilities.
The management should continuously plan for WHS training programs. This will
involve assessing the needs and set objectives relevant to the identified needs. The managers,
employees, and employees should consult regularly on the workplace safety procedures,
practices, and policies. During the consultation meetings, the employees will find an
15 OHSlogic. What is AS 4801:2001/OHSAS 18001? 2012.
http://www.logicbusinessresources.com.au/services_whs_asnzs4801.html
10
Secure Best Marks with AI Grader
Need help grading? Try our AI Grader for instant feedback on your assignments.
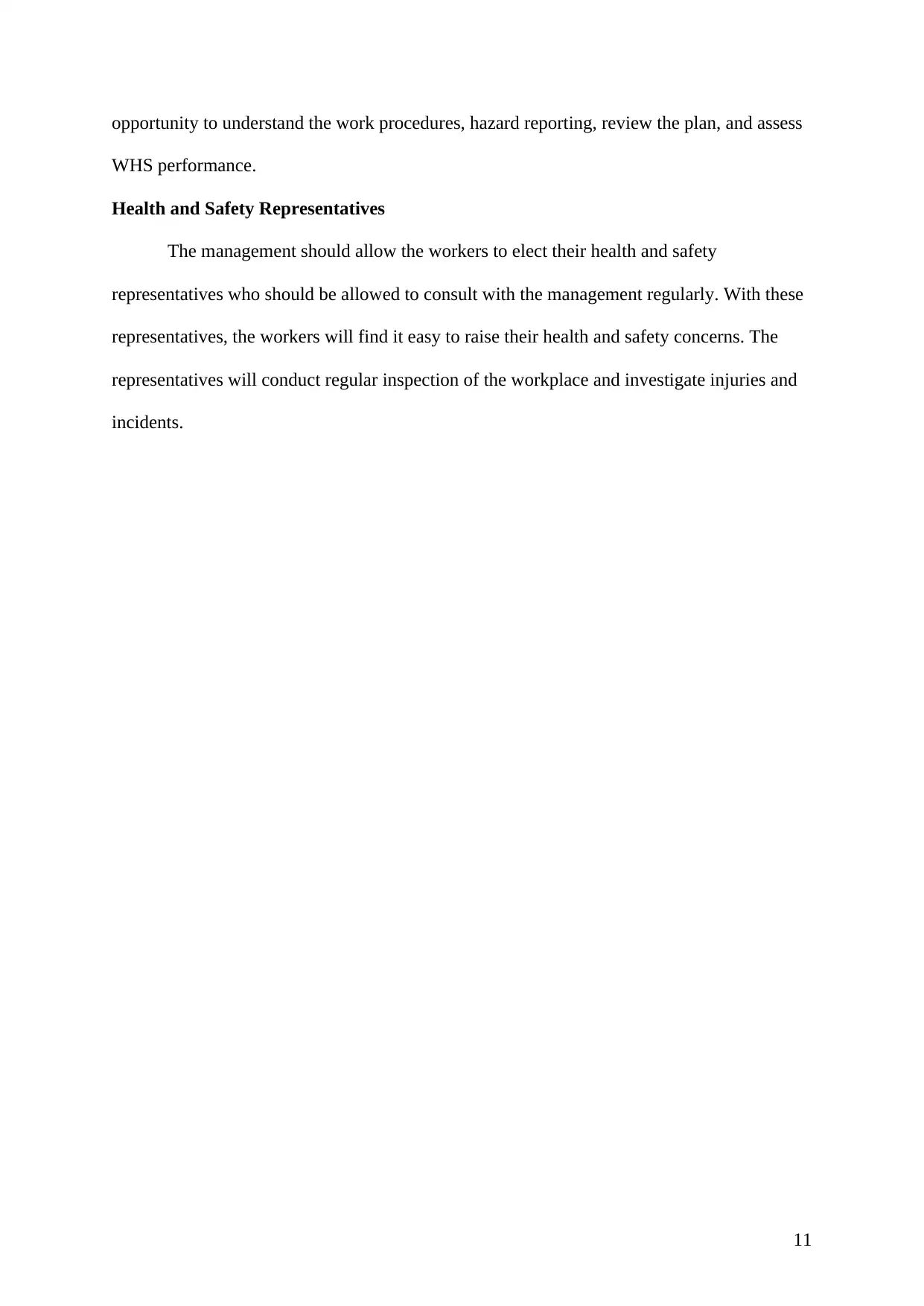
opportunity to understand the work procedures, hazard reporting, review the plan, and assess
WHS performance.
Health and Safety Representatives
The management should allow the workers to elect their health and safety
representatives who should be allowed to consult with the management regularly. With these
representatives, the workers will find it easy to raise their health and safety concerns. The
representatives will conduct regular inspection of the workplace and investigate injuries and
incidents.
11
WHS performance.
Health and Safety Representatives
The management should allow the workers to elect their health and safety
representatives who should be allowed to consult with the management regularly. With these
representatives, the workers will find it easy to raise their health and safety concerns. The
representatives will conduct regular inspection of the workplace and investigate injuries and
incidents.
11
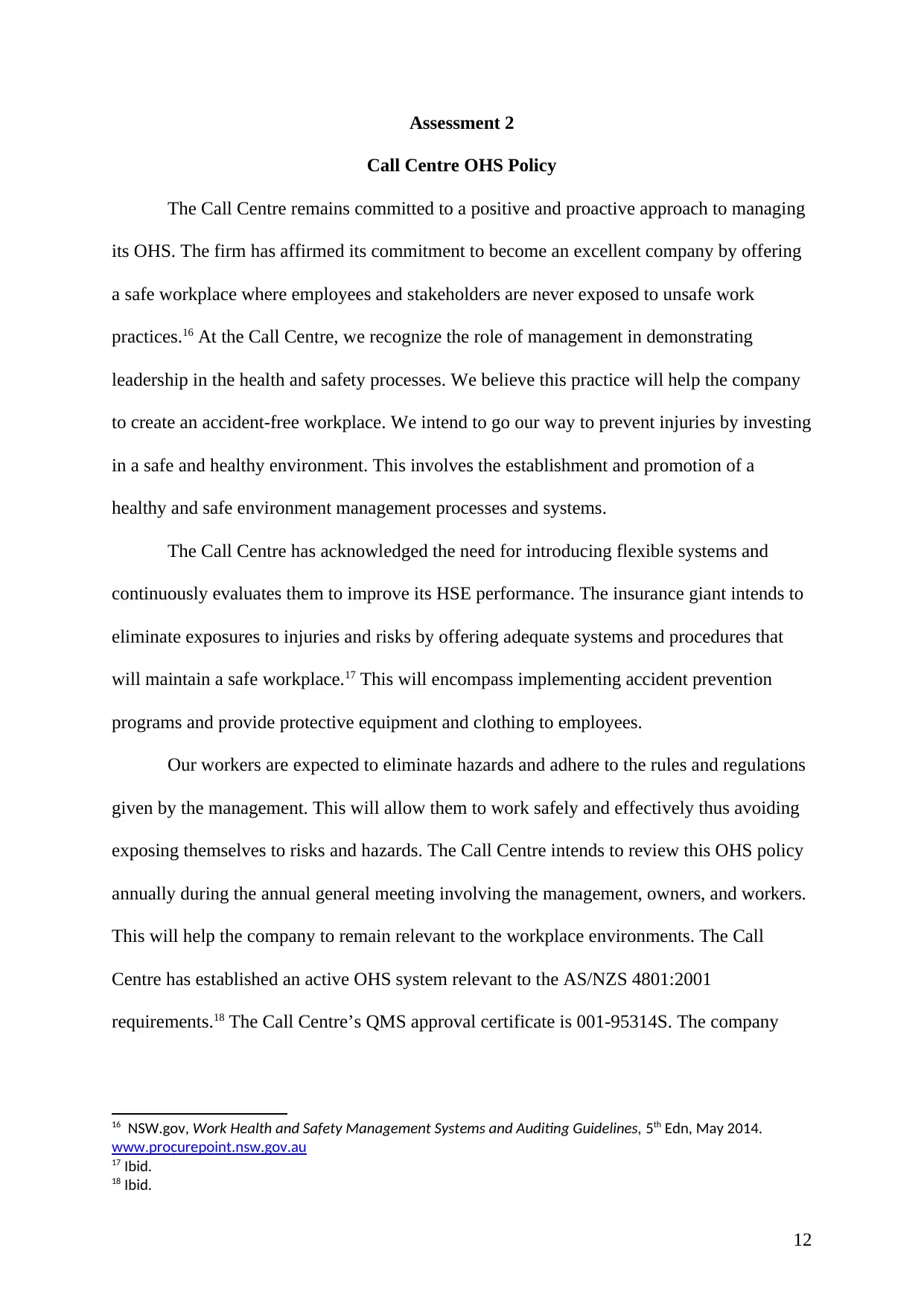
Assessment 2
Call Centre OHS Policy
The Call Centre remains committed to a positive and proactive approach to managing
its OHS. The firm has affirmed its commitment to become an excellent company by offering
a safe workplace where employees and stakeholders are never exposed to unsafe work
practices.16 At the Call Centre, we recognize the role of management in demonstrating
leadership in the health and safety processes. We believe this practice will help the company
to create an accident-free workplace. We intend to go our way to prevent injuries by investing
in a safe and healthy environment. This involves the establishment and promotion of a
healthy and safe environment management processes and systems.
The Call Centre has acknowledged the need for introducing flexible systems and
continuously evaluates them to improve its HSE performance. The insurance giant intends to
eliminate exposures to injuries and risks by offering adequate systems and procedures that
will maintain a safe workplace.17 This will encompass implementing accident prevention
programs and provide protective equipment and clothing to employees.
Our workers are expected to eliminate hazards and adhere to the rules and regulations
given by the management. This will allow them to work safely and effectively thus avoiding
exposing themselves to risks and hazards. The Call Centre intends to review this OHS policy
annually during the annual general meeting involving the management, owners, and workers.
This will help the company to remain relevant to the workplace environments. The Call
Centre has established an active OHS system relevant to the AS/NZS 4801:2001
requirements.18 The Call Centre’s QMS approval certificate is 001-95314S. The company
16 NSW.gov, Work Health and Safety Management Systems and Auditing Guidelines, 5th Edn, May 2014.
www.procurepoint.nsw.gov.au
17 Ibid.
18 Ibid.
12
Call Centre OHS Policy
The Call Centre remains committed to a positive and proactive approach to managing
its OHS. The firm has affirmed its commitment to become an excellent company by offering
a safe workplace where employees and stakeholders are never exposed to unsafe work
practices.16 At the Call Centre, we recognize the role of management in demonstrating
leadership in the health and safety processes. We believe this practice will help the company
to create an accident-free workplace. We intend to go our way to prevent injuries by investing
in a safe and healthy environment. This involves the establishment and promotion of a
healthy and safe environment management processes and systems.
The Call Centre has acknowledged the need for introducing flexible systems and
continuously evaluates them to improve its HSE performance. The insurance giant intends to
eliminate exposures to injuries and risks by offering adequate systems and procedures that
will maintain a safe workplace.17 This will encompass implementing accident prevention
programs and provide protective equipment and clothing to employees.
Our workers are expected to eliminate hazards and adhere to the rules and regulations
given by the management. This will allow them to work safely and effectively thus avoiding
exposing themselves to risks and hazards. The Call Centre intends to review this OHS policy
annually during the annual general meeting involving the management, owners, and workers.
This will help the company to remain relevant to the workplace environments. The Call
Centre has established an active OHS system relevant to the AS/NZS 4801:2001
requirements.18 The Call Centre’s QMS approval certificate is 001-95314S. The company
16 NSW.gov, Work Health and Safety Management Systems and Auditing Guidelines, 5th Edn, May 2014.
www.procurepoint.nsw.gov.au
17 Ibid.
18 Ibid.
12
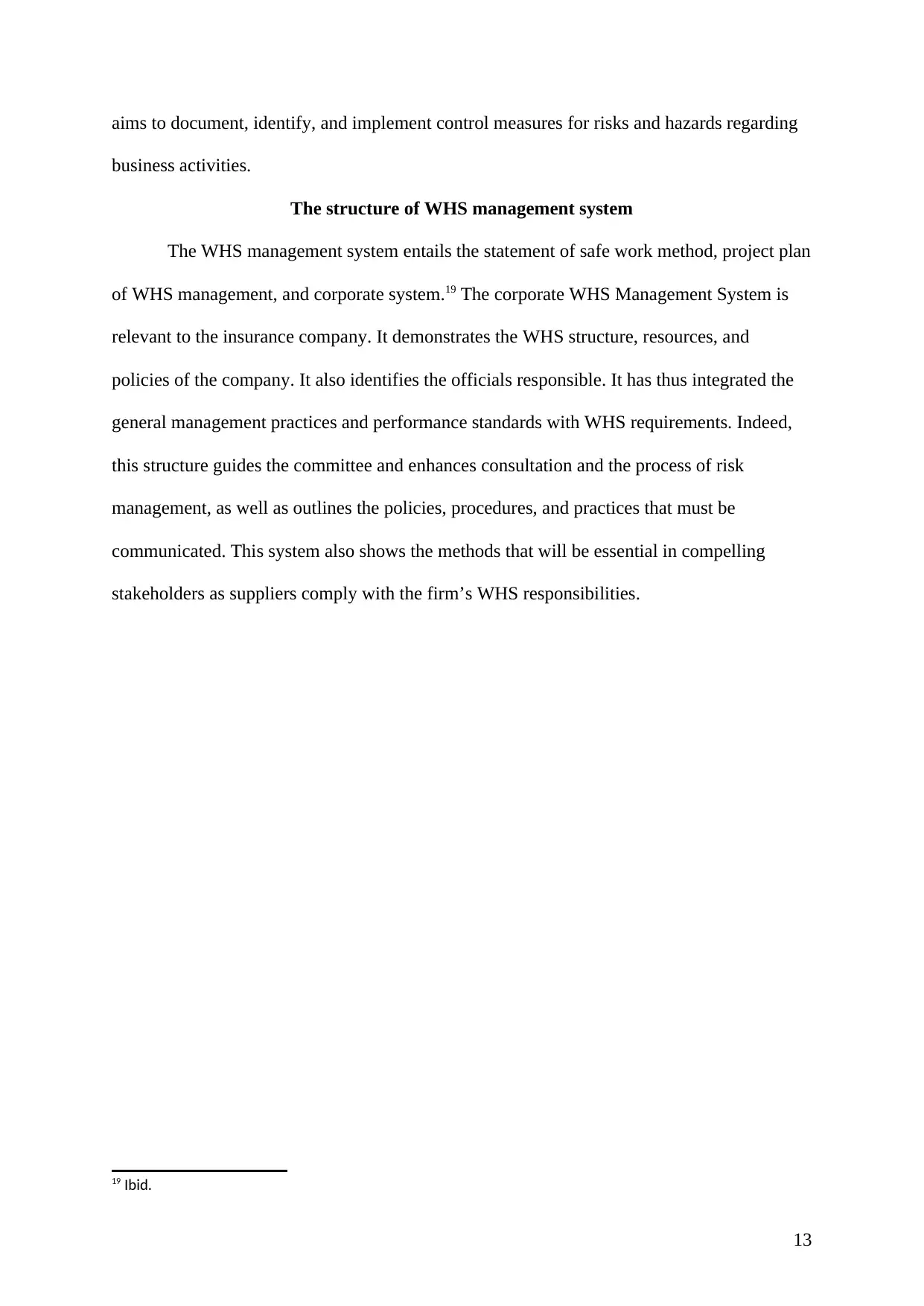
aims to document, identify, and implement control measures for risks and hazards regarding
business activities.
The structure of WHS management system
The WHS management system entails the statement of safe work method, project plan
of WHS management, and corporate system.19 The corporate WHS Management System is
relevant to the insurance company. It demonstrates the WHS structure, resources, and
policies of the company. It also identifies the officials responsible. It has thus integrated the
general management practices and performance standards with WHS requirements. Indeed,
this structure guides the committee and enhances consultation and the process of risk
management, as well as outlines the policies, procedures, and practices that must be
communicated. This system also shows the methods that will be essential in compelling
stakeholders as suppliers comply with the firm’s WHS responsibilities.
19 Ibid.
13
business activities.
The structure of WHS management system
The WHS management system entails the statement of safe work method, project plan
of WHS management, and corporate system.19 The corporate WHS Management System is
relevant to the insurance company. It demonstrates the WHS structure, resources, and
policies of the company. It also identifies the officials responsible. It has thus integrated the
general management practices and performance standards with WHS requirements. Indeed,
this structure guides the committee and enhances consultation and the process of risk
management, as well as outlines the policies, procedures, and practices that must be
communicated. This system also shows the methods that will be essential in compelling
stakeholders as suppliers comply with the firm’s WHS responsibilities.
19 Ibid.
13
Paraphrase This Document
Need a fresh take? Get an instant paraphrase of this document with our AI Paraphraser
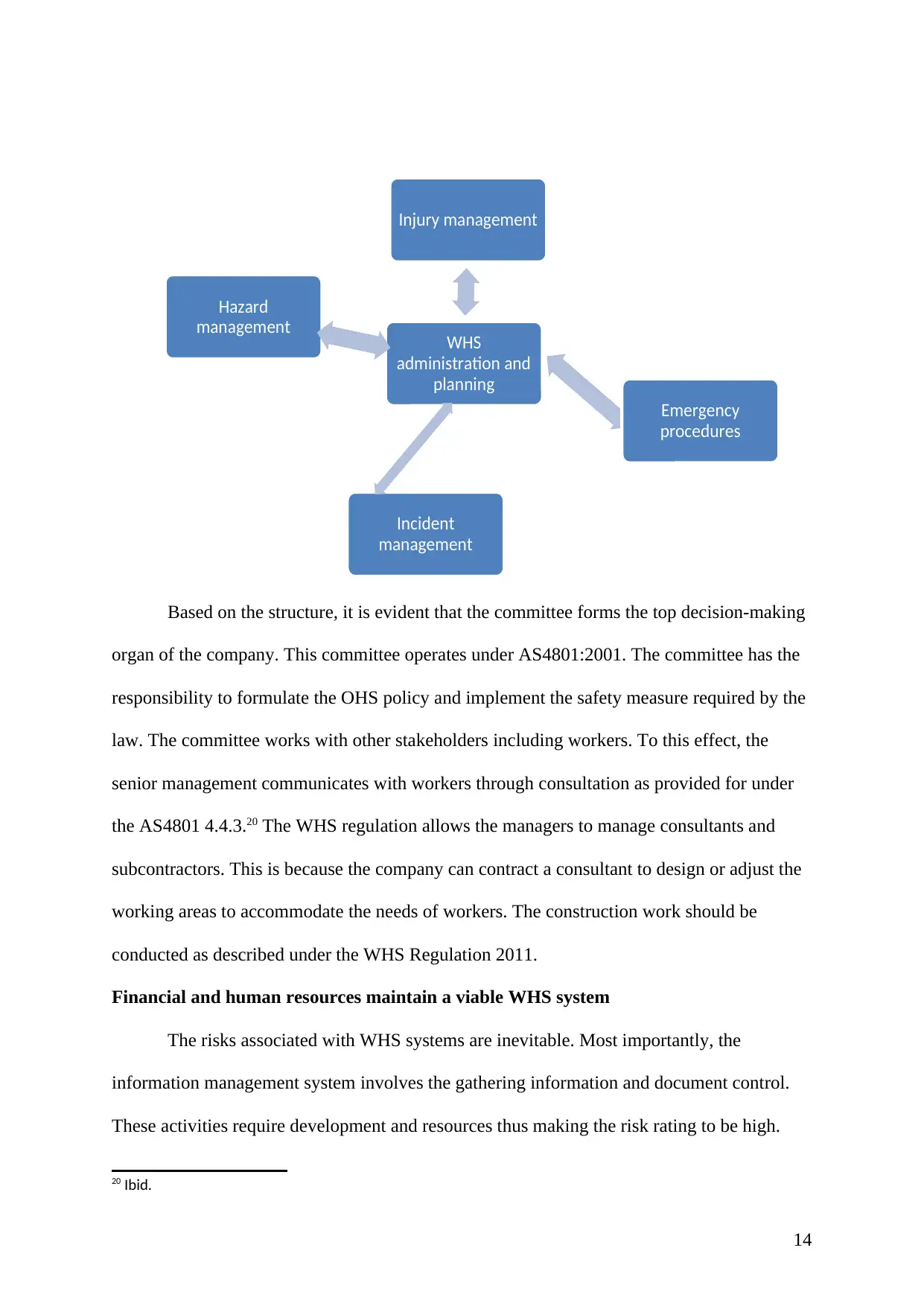
Based on the structure, it is evident that the committee forms the top decision-making
organ of the company. This committee operates under AS4801:2001. The committee has the
responsibility to formulate the OHS policy and implement the safety measure required by the
law. The committee works with other stakeholders including workers. To this effect, the
senior management communicates with workers through consultation as provided for under
the AS4801 4.4.3.20 The WHS regulation allows the managers to manage consultants and
subcontractors. This is because the company can contract a consultant to design or adjust the
working areas to accommodate the needs of workers. The construction work should be
conducted as described under the WHS Regulation 2011.
Financial and human resources maintain a viable WHS system
The risks associated with WHS systems are inevitable. Most importantly, the
information management system involves the gathering information and document control.
These activities require development and resources thus making the risk rating to be high.
20 Ibid.
14
WHS
administration and
planning
Injury management
Emergency
procedures
Incident
management
Hazard
management
organ of the company. This committee operates under AS4801:2001. The committee has the
responsibility to formulate the OHS policy and implement the safety measure required by the
law. The committee works with other stakeholders including workers. To this effect, the
senior management communicates with workers through consultation as provided for under
the AS4801 4.4.3.20 The WHS regulation allows the managers to manage consultants and
subcontractors. This is because the company can contract a consultant to design or adjust the
working areas to accommodate the needs of workers. The construction work should be
conducted as described under the WHS Regulation 2011.
Financial and human resources maintain a viable WHS system
The risks associated with WHS systems are inevitable. Most importantly, the
information management system involves the gathering information and document control.
These activities require development and resources thus making the risk rating to be high.
20 Ibid.
14
WHS
administration and
planning
Injury management
Emergency
procedures
Incident
management
Hazard
management
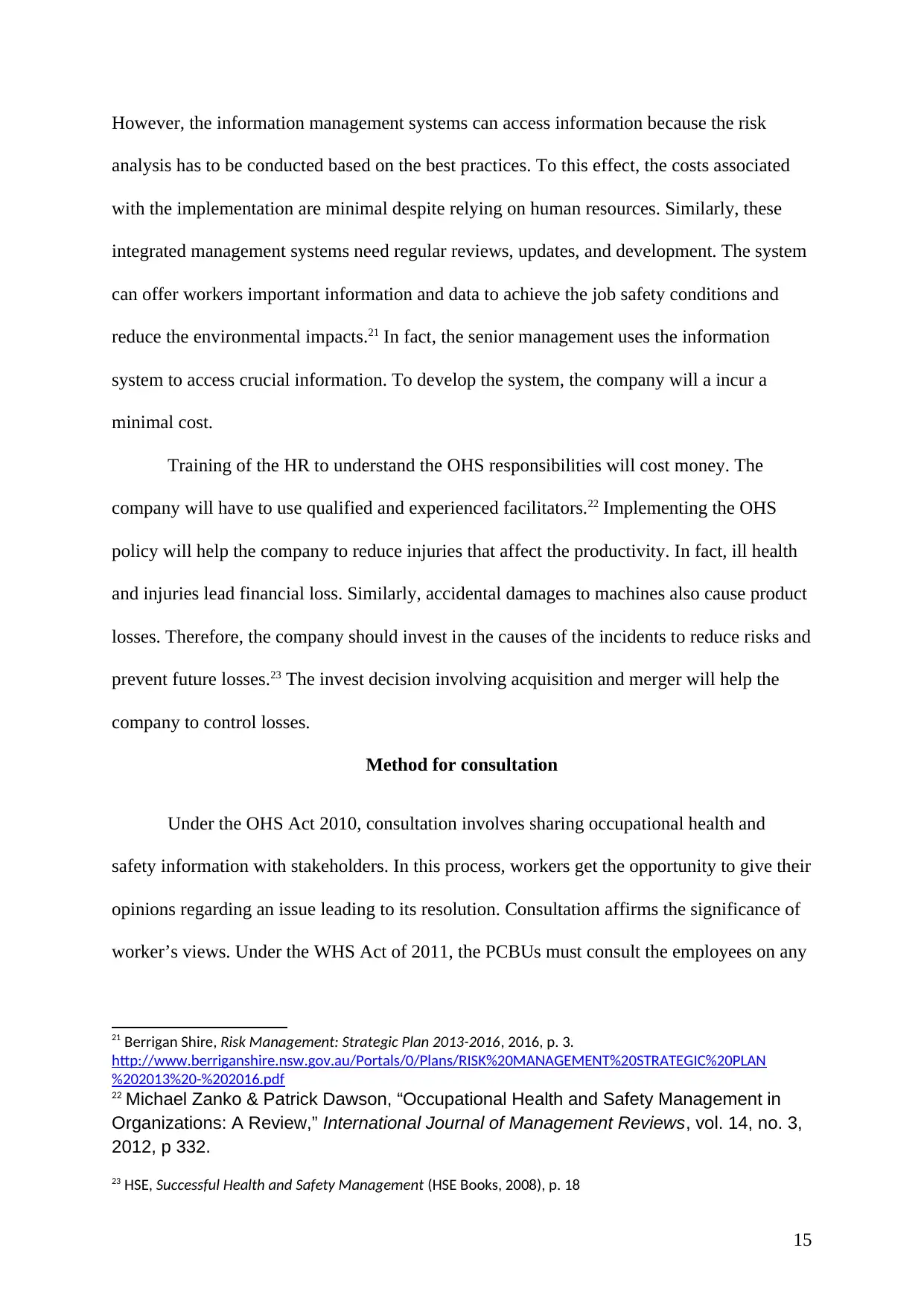
However, the information management systems can access information because the risk
analysis has to be conducted based on the best practices. To this effect, the costs associated
with the implementation are minimal despite relying on human resources. Similarly, these
integrated management systems need regular reviews, updates, and development. The system
can offer workers important information and data to achieve the job safety conditions and
reduce the environmental impacts.21 In fact, the senior management uses the information
system to access crucial information. To develop the system, the company will a incur a
minimal cost.
Training of the HR to understand the OHS responsibilities will cost money. The
company will have to use qualified and experienced facilitators.22 Implementing the OHS
policy will help the company to reduce injuries that affect the productivity. In fact, ill health
and injuries lead financial loss. Similarly, accidental damages to machines also cause product
losses. Therefore, the company should invest in the causes of the incidents to reduce risks and
prevent future losses.23 The invest decision involving acquisition and merger will help the
company to control losses.
Method for consultation
Under the OHS Act 2010, consultation involves sharing occupational health and
safety information with stakeholders. In this process, workers get the opportunity to give their
opinions regarding an issue leading to its resolution. Consultation affirms the significance of
worker’s views. Under the WHS Act of 2011, the PCBUs must consult the employees on any
21 Berrigan Shire, Risk Management: Strategic Plan 2013-2016, 2016, p. 3.
http://www.berriganshire.nsw.gov.au/Portals/0/Plans/RISK%20MANAGEMENT%20STRATEGIC%20PLAN
%202013%20-%202016.pdf
22 Michael Zanko & Patrick Dawson, “Occupational Health and Safety Management in
Organizations: A Review,” International Journal of Management Reviews, vol. 14, no. 3,
2012, p 332.
23 HSE, Successful Health and Safety Management (HSE Books, 2008), p. 18
15
analysis has to be conducted based on the best practices. To this effect, the costs associated
with the implementation are minimal despite relying on human resources. Similarly, these
integrated management systems need regular reviews, updates, and development. The system
can offer workers important information and data to achieve the job safety conditions and
reduce the environmental impacts.21 In fact, the senior management uses the information
system to access crucial information. To develop the system, the company will a incur a
minimal cost.
Training of the HR to understand the OHS responsibilities will cost money. The
company will have to use qualified and experienced facilitators.22 Implementing the OHS
policy will help the company to reduce injuries that affect the productivity. In fact, ill health
and injuries lead financial loss. Similarly, accidental damages to machines also cause product
losses. Therefore, the company should invest in the causes of the incidents to reduce risks and
prevent future losses.23 The invest decision involving acquisition and merger will help the
company to control losses.
Method for consultation
Under the OHS Act 2010, consultation involves sharing occupational health and
safety information with stakeholders. In this process, workers get the opportunity to give their
opinions regarding an issue leading to its resolution. Consultation affirms the significance of
worker’s views. Under the WHS Act of 2011, the PCBUs must consult the employees on any
21 Berrigan Shire, Risk Management: Strategic Plan 2013-2016, 2016, p. 3.
http://www.berriganshire.nsw.gov.au/Portals/0/Plans/RISK%20MANAGEMENT%20STRATEGIC%20PLAN
%202013%20-%202016.pdf
22 Michael Zanko & Patrick Dawson, “Occupational Health and Safety Management in
Organizations: A Review,” International Journal of Management Reviews, vol. 14, no. 3,
2012, p 332.
23 HSE, Successful Health and Safety Management (HSE Books, 2008), p. 18
15
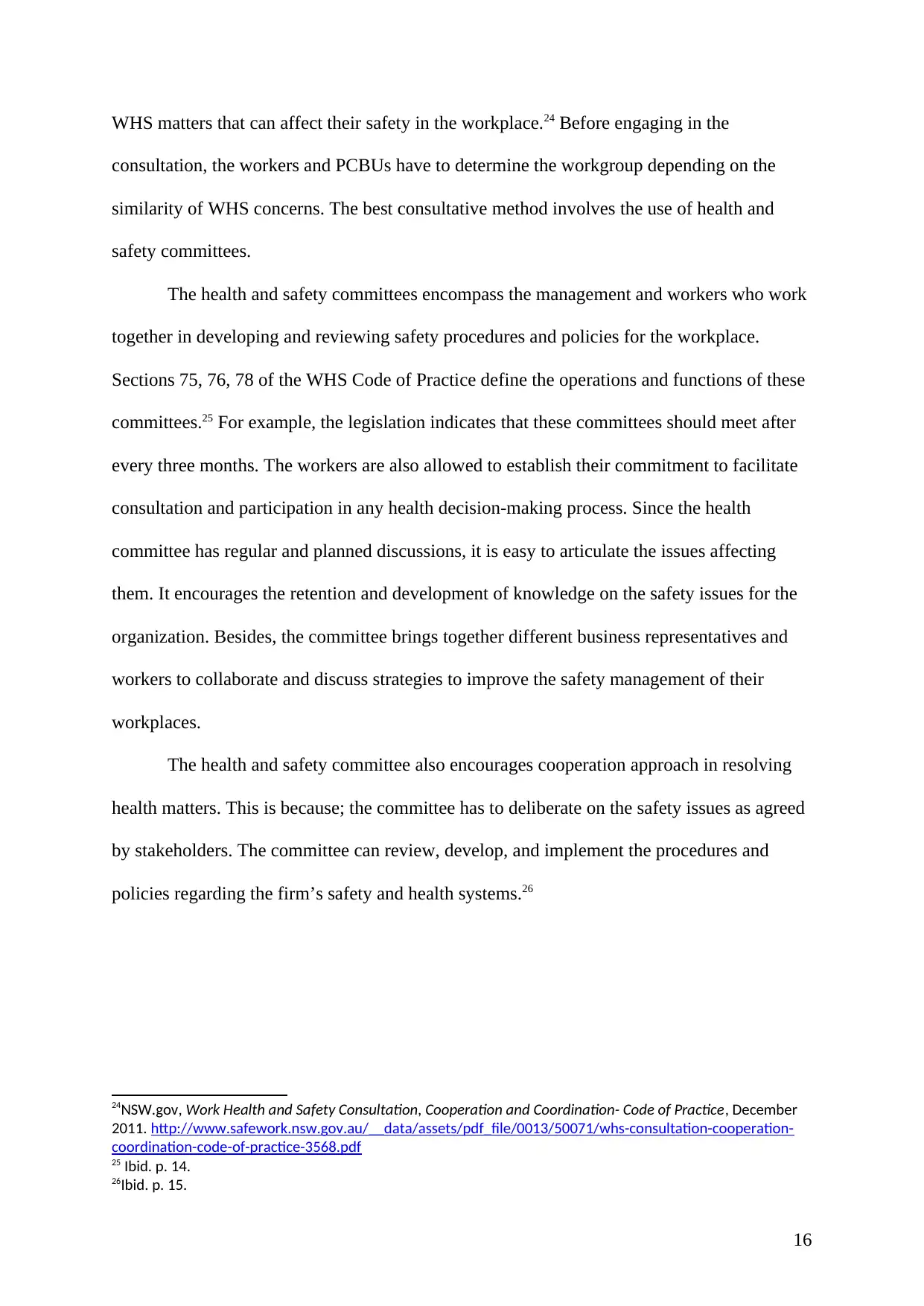
WHS matters that can affect their safety in the workplace.24 Before engaging in the
consultation, the workers and PCBUs have to determine the workgroup depending on the
similarity of WHS concerns. The best consultative method involves the use of health and
safety committees.
The health and safety committees encompass the management and workers who work
together in developing and reviewing safety procedures and policies for the workplace.
Sections 75, 76, 78 of the WHS Code of Practice define the operations and functions of these
committees.25 For example, the legislation indicates that these committees should meet after
every three months. The workers are also allowed to establish their commitment to facilitate
consultation and participation in any health decision-making process. Since the health
committee has regular and planned discussions, it is easy to articulate the issues affecting
them. It encourages the retention and development of knowledge on the safety issues for the
organization. Besides, the committee brings together different business representatives and
workers to collaborate and discuss strategies to improve the safety management of their
workplaces.
The health and safety committee also encourages cooperation approach in resolving
health matters. This is because; the committee has to deliberate on the safety issues as agreed
by stakeholders. The committee can review, develop, and implement the procedures and
policies regarding the firm’s safety and health systems.26
24NSW.gov, Work Health and Safety Consultation, Cooperation and Coordination- Code of Practice, December
2011. http://www.safework.nsw.gov.au/__data/assets/pdf_file/0013/50071/whs-consultation-cooperation-
coordination-code-of-practice-3568.pdf
25 Ibid. p. 14.
26Ibid. p. 15.
16
consultation, the workers and PCBUs have to determine the workgroup depending on the
similarity of WHS concerns. The best consultative method involves the use of health and
safety committees.
The health and safety committees encompass the management and workers who work
together in developing and reviewing safety procedures and policies for the workplace.
Sections 75, 76, 78 of the WHS Code of Practice define the operations and functions of these
committees.25 For example, the legislation indicates that these committees should meet after
every three months. The workers are also allowed to establish their commitment to facilitate
consultation and participation in any health decision-making process. Since the health
committee has regular and planned discussions, it is easy to articulate the issues affecting
them. It encourages the retention and development of knowledge on the safety issues for the
organization. Besides, the committee brings together different business representatives and
workers to collaborate and discuss strategies to improve the safety management of their
workplaces.
The health and safety committee also encourages cooperation approach in resolving
health matters. This is because; the committee has to deliberate on the safety issues as agreed
by stakeholders. The committee can review, develop, and implement the procedures and
policies regarding the firm’s safety and health systems.26
24NSW.gov, Work Health and Safety Consultation, Cooperation and Coordination- Code of Practice, December
2011. http://www.safework.nsw.gov.au/__data/assets/pdf_file/0013/50071/whs-consultation-cooperation-
coordination-code-of-practice-3568.pdf
25 Ibid. p. 14.
26Ibid. p. 15.
16
Secure Best Marks with AI Grader
Need help grading? Try our AI Grader for instant feedback on your assignments.
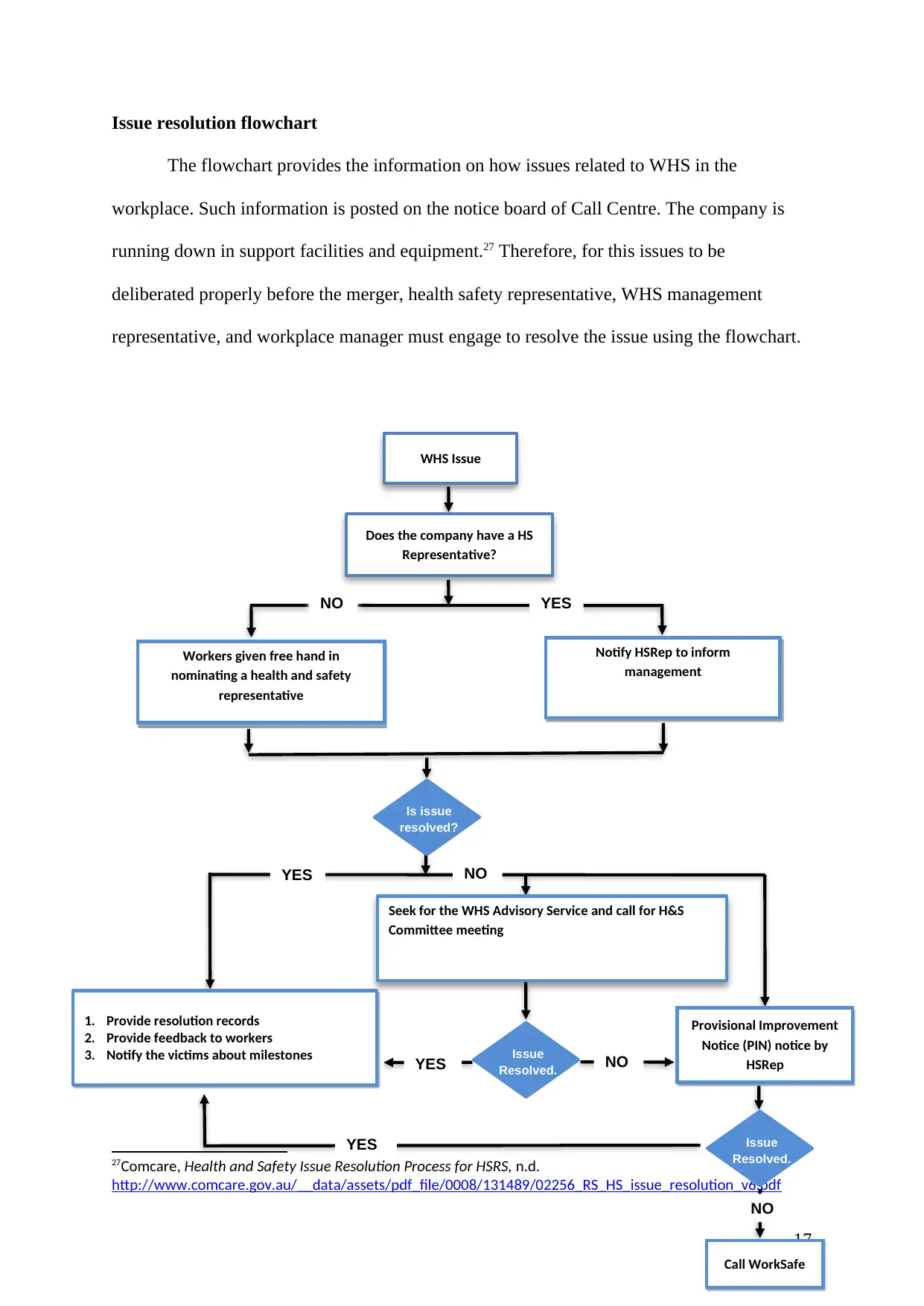
Issue resolution flowchart
The flowchart provides the information on how issues related to WHS in the
workplace. Such information is posted on the notice board of Call Centre. The company is
running down in support facilities and equipment.27 Therefore, for this issues to be
deliberated properly before the merger, health safety representative, WHS management
representative, and workplace manager must engage to resolve the issue using the flowchart.
27Comcare, Health and Safety Issue Resolution Process for HSRS, n.d.
http://www.comcare.gov.au/__data/assets/pdf_file/0008/131489/02256_RS_HS_issue_resolution_v6.pdf
17
YES
YES
YES
YES
NO
NO
NO
WHS Issue
Does the company have a HS
Representative?
Workers given free hand in
nominating a health and safety
representative
Notify HSRep to inform
management
Seek for the WHS Advisory Service and call for H&S
Committee meeting
Provisional Improvement
Notice (PIN) notice by
HSRep
1. Provide resolution records
2. Provide feedback to workers
3. Notify the victims about milestones
Call WorkSafe
Issue
Resolved.
Is issue
resolved?
Issue
Resolved.
NO
The flowchart provides the information on how issues related to WHS in the
workplace. Such information is posted on the notice board of Call Centre. The company is
running down in support facilities and equipment.27 Therefore, for this issues to be
deliberated properly before the merger, health safety representative, WHS management
representative, and workplace manager must engage to resolve the issue using the flowchart.
27Comcare, Health and Safety Issue Resolution Process for HSRS, n.d.
http://www.comcare.gov.au/__data/assets/pdf_file/0008/131489/02256_RS_HS_issue_resolution_v6.pdf
17
YES
YES
YES
YES
NO
NO
NO
WHS Issue
Does the company have a HS
Representative?
Workers given free hand in
nominating a health and safety
representative
Notify HSRep to inform
management
Seek for the WHS Advisory Service and call for H&S
Committee meeting
Provisional Improvement
Notice (PIN) notice by
HSRep
1. Provide resolution records
2. Provide feedback to workers
3. Notify the victims about milestones
Call WorkSafe
Issue
Resolved.
Is issue
resolved?
Issue
Resolved.
NO
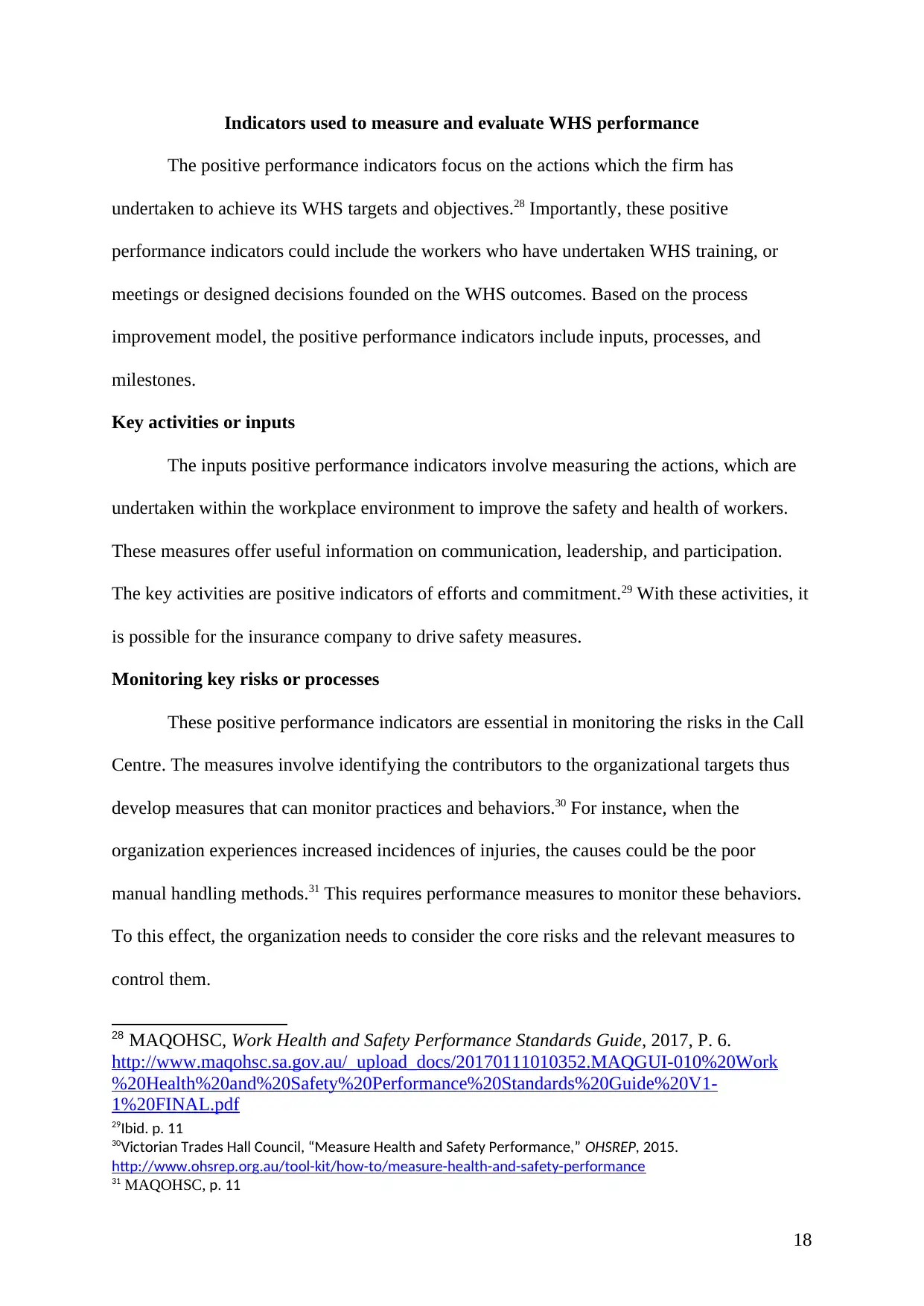
Indicators used to measure and evaluate WHS performance
The positive performance indicators focus on the actions which the firm has
undertaken to achieve its WHS targets and objectives.28 Importantly, these positive
performance indicators could include the workers who have undertaken WHS training, or
meetings or designed decisions founded on the WHS outcomes. Based on the process
improvement model, the positive performance indicators include inputs, processes, and
milestones.
Key activities or inputs
The inputs positive performance indicators involve measuring the actions, which are
undertaken within the workplace environment to improve the safety and health of workers.
These measures offer useful information on communication, leadership, and participation.
The key activities are positive indicators of efforts and commitment.29 With these activities, it
is possible for the insurance company to drive safety measures.
Monitoring key risks or processes
These positive performance indicators are essential in monitoring the risks in the Call
Centre. The measures involve identifying the contributors to the organizational targets thus
develop measures that can monitor practices and behaviors.30 For instance, when the
organization experiences increased incidences of injuries, the causes could be the poor
manual handling methods.31 This requires performance measures to monitor these behaviors.
To this effect, the organization needs to consider the core risks and the relevant measures to
control them.
28 MAQOHSC, Work Health and Safety Performance Standards Guide, 2017, P. 6.
http://www.maqohsc.sa.gov.au/_upload_docs/20170111010352.MAQGUI-010%20Work
%20Health%20and%20Safety%20Performance%20Standards%20Guide%20V1-
1%20FINAL.pdf
29Ibid. p. 11
30Victorian Trades Hall Council, “Measure Health and Safety Performance,” OHSREP, 2015.
http://www.ohsrep.org.au/tool-kit/how-to/measure-health-and-safety-performance
31 MAQOHSC, p. 11
18
The positive performance indicators focus on the actions which the firm has
undertaken to achieve its WHS targets and objectives.28 Importantly, these positive
performance indicators could include the workers who have undertaken WHS training, or
meetings or designed decisions founded on the WHS outcomes. Based on the process
improvement model, the positive performance indicators include inputs, processes, and
milestones.
Key activities or inputs
The inputs positive performance indicators involve measuring the actions, which are
undertaken within the workplace environment to improve the safety and health of workers.
These measures offer useful information on communication, leadership, and participation.
The key activities are positive indicators of efforts and commitment.29 With these activities, it
is possible for the insurance company to drive safety measures.
Monitoring key risks or processes
These positive performance indicators are essential in monitoring the risks in the Call
Centre. The measures involve identifying the contributors to the organizational targets thus
develop measures that can monitor practices and behaviors.30 For instance, when the
organization experiences increased incidences of injuries, the causes could be the poor
manual handling methods.31 This requires performance measures to monitor these behaviors.
To this effect, the organization needs to consider the core risks and the relevant measures to
control them.
28 MAQOHSC, Work Health and Safety Performance Standards Guide, 2017, P. 6.
http://www.maqohsc.sa.gov.au/_upload_docs/20170111010352.MAQGUI-010%20Work
%20Health%20and%20Safety%20Performance%20Standards%20Guide%20V1-
1%20FINAL.pdf
29Ibid. p. 11
30Victorian Trades Hall Council, “Measure Health and Safety Performance,” OHSREP, 2015.
http://www.ohsrep.org.au/tool-kit/how-to/measure-health-and-safety-performance
31 MAQOHSC, p. 11
18
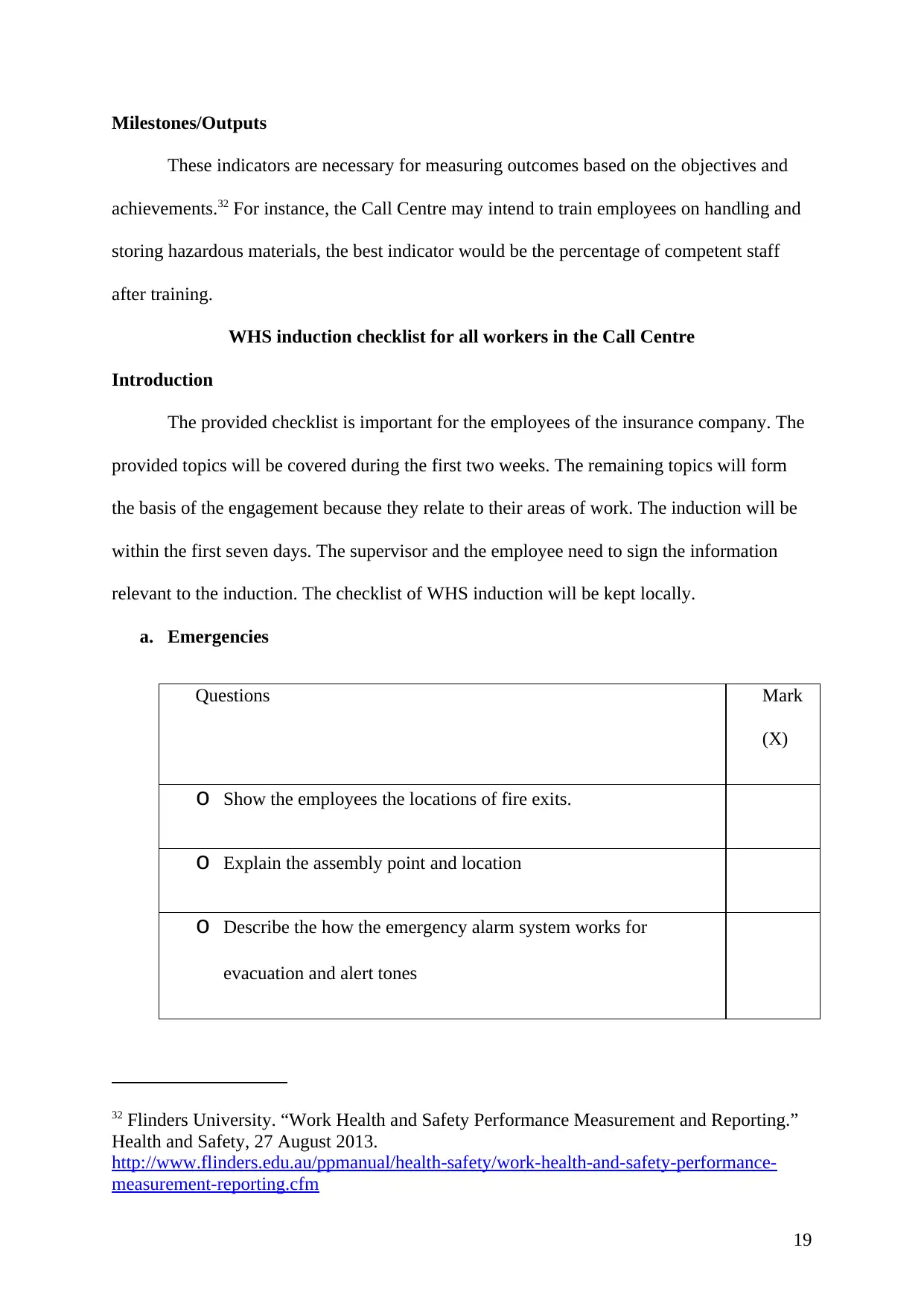
Milestones/Outputs
These indicators are necessary for measuring outcomes based on the objectives and
achievements.32 For instance, the Call Centre may intend to train employees on handling and
storing hazardous materials, the best indicator would be the percentage of competent staff
after training.
WHS induction checklist for all workers in the Call Centre
Introduction
The provided checklist is important for the employees of the insurance company. The
provided topics will be covered during the first two weeks. The remaining topics will form
the basis of the engagement because they relate to their areas of work. The induction will be
within the first seven days. The supervisor and the employee need to sign the information
relevant to the induction. The checklist of WHS induction will be kept locally.
a. Emergencies
Questions Mark
(X)
o Show the employees the locations of fire exits.
o Explain the assembly point and location
o Describe the how the emergency alarm system works for
evacuation and alert tones
32 Flinders University. “Work Health and Safety Performance Measurement and Reporting.”
Health and Safety, 27 August 2013.
http://www.flinders.edu.au/ppmanual/health-safety/work-health-and-safety-performance-
measurement-reporting.cfm
19
These indicators are necessary for measuring outcomes based on the objectives and
achievements.32 For instance, the Call Centre may intend to train employees on handling and
storing hazardous materials, the best indicator would be the percentage of competent staff
after training.
WHS induction checklist for all workers in the Call Centre
Introduction
The provided checklist is important for the employees of the insurance company. The
provided topics will be covered during the first two weeks. The remaining topics will form
the basis of the engagement because they relate to their areas of work. The induction will be
within the first seven days. The supervisor and the employee need to sign the information
relevant to the induction. The checklist of WHS induction will be kept locally.
a. Emergencies
Questions Mark
(X)
o Show the employees the locations of fire exits.
o Explain the assembly point and location
o Describe the how the emergency alarm system works for
evacuation and alert tones
32 Flinders University. “Work Health and Safety Performance Measurement and Reporting.”
Health and Safety, 27 August 2013.
http://www.flinders.edu.au/ppmanual/health-safety/work-health-and-safety-performance-
measurement-reporting.cfm
19
Paraphrase This Document
Need a fresh take? Get an instant paraphrase of this document with our AI Paraphraser
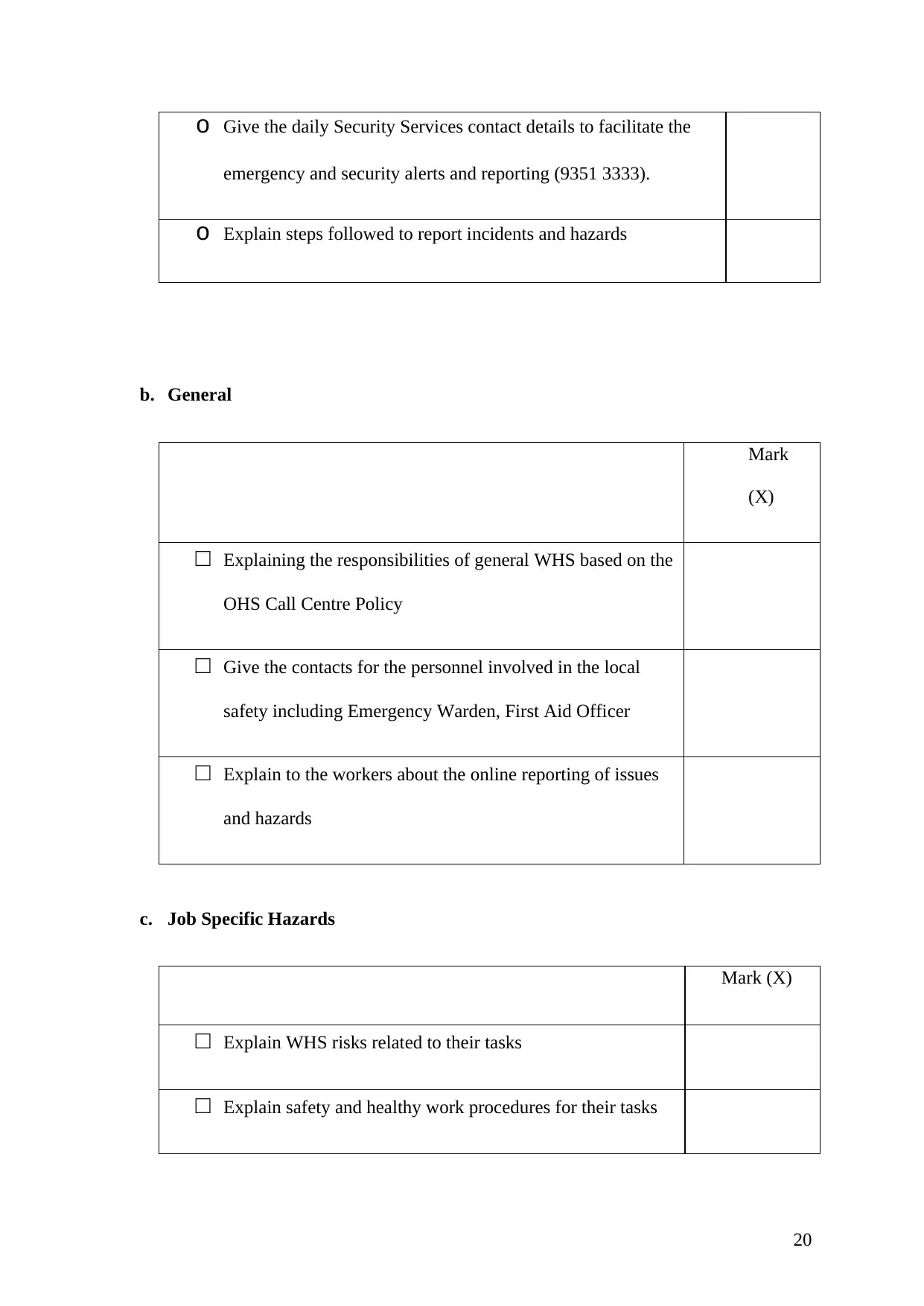
o Give the daily Security Services contact details to facilitate the
emergency and security alerts and reporting (9351 3333).
o Explain steps followed to report incidents and hazards
b. General
Mark
(X)
□ Explaining the responsibilities of general WHS based on the
OHS Call Centre Policy
□ Give the contacts for the personnel involved in the local
safety including Emergency Warden, First Aid Officer
□ Explain to the workers about the online reporting of issues
and hazards
c. Job Specific Hazards
Mark (X)
□ Explain WHS risks related to their tasks
□ Explain safety and healthy work procedures for their tasks
20
emergency and security alerts and reporting (9351 3333).
o Explain steps followed to report incidents and hazards
b. General
Mark
(X)
□ Explaining the responsibilities of general WHS based on the
OHS Call Centre Policy
□ Give the contacts for the personnel involved in the local
safety including Emergency Warden, First Aid Officer
□ Explain to the workers about the online reporting of issues
and hazards
c. Job Specific Hazards
Mark (X)
□ Explain WHS risks related to their tasks
□ Explain safety and healthy work procedures for their tasks
20
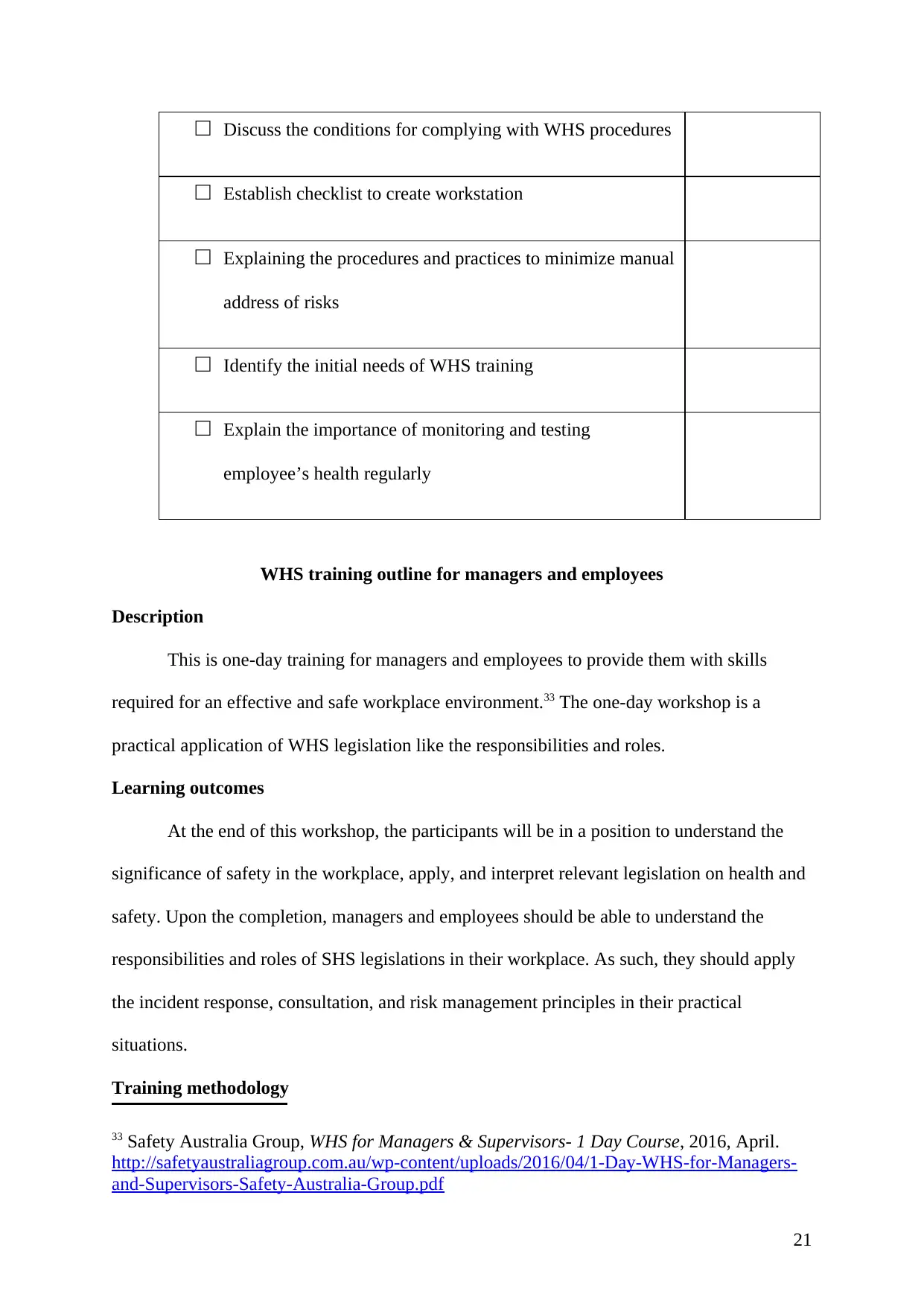
□ Discuss the conditions for complying with WHS procedures
□ Establish checklist to create workstation
□ Explaining the procedures and practices to minimize manual
address of risks
□ Identify the initial needs of WHS training
□ Explain the importance of monitoring and testing
employee’s health regularly
WHS training outline for managers and employees
Description
This is one-day training for managers and employees to provide them with skills
required for an effective and safe workplace environment.33 The one-day workshop is a
practical application of WHS legislation like the responsibilities and roles.
Learning outcomes
At the end of this workshop, the participants will be in a position to understand the
significance of safety in the workplace, apply, and interpret relevant legislation on health and
safety. Upon the completion, managers and employees should be able to understand the
responsibilities and roles of SHS legislations in their workplace. As such, they should apply
the incident response, consultation, and risk management principles in their practical
situations.
Training methodology
33 Safety Australia Group, WHS for Managers & Supervisors- 1 Day Course, 2016, April.
http://safetyaustraliagroup.com.au/wp-content/uploads/2016/04/1-Day-WHS-for-Managers-
and-Supervisors-Safety-Australia-Group.pdf
21
□ Establish checklist to create workstation
□ Explaining the procedures and practices to minimize manual
address of risks
□ Identify the initial needs of WHS training
□ Explain the importance of monitoring and testing
employee’s health regularly
WHS training outline for managers and employees
Description
This is one-day training for managers and employees to provide them with skills
required for an effective and safe workplace environment.33 The one-day workshop is a
practical application of WHS legislation like the responsibilities and roles.
Learning outcomes
At the end of this workshop, the participants will be in a position to understand the
significance of safety in the workplace, apply, and interpret relevant legislation on health and
safety. Upon the completion, managers and employees should be able to understand the
responsibilities and roles of SHS legislations in their workplace. As such, they should apply
the incident response, consultation, and risk management principles in their practical
situations.
Training methodology
33 Safety Australia Group, WHS for Managers & Supervisors- 1 Day Course, 2016, April.
http://safetyaustraliagroup.com.au/wp-content/uploads/2016/04/1-Day-WHS-for-Managers-
and-Supervisors-Safety-Australia-Group.pdf
21
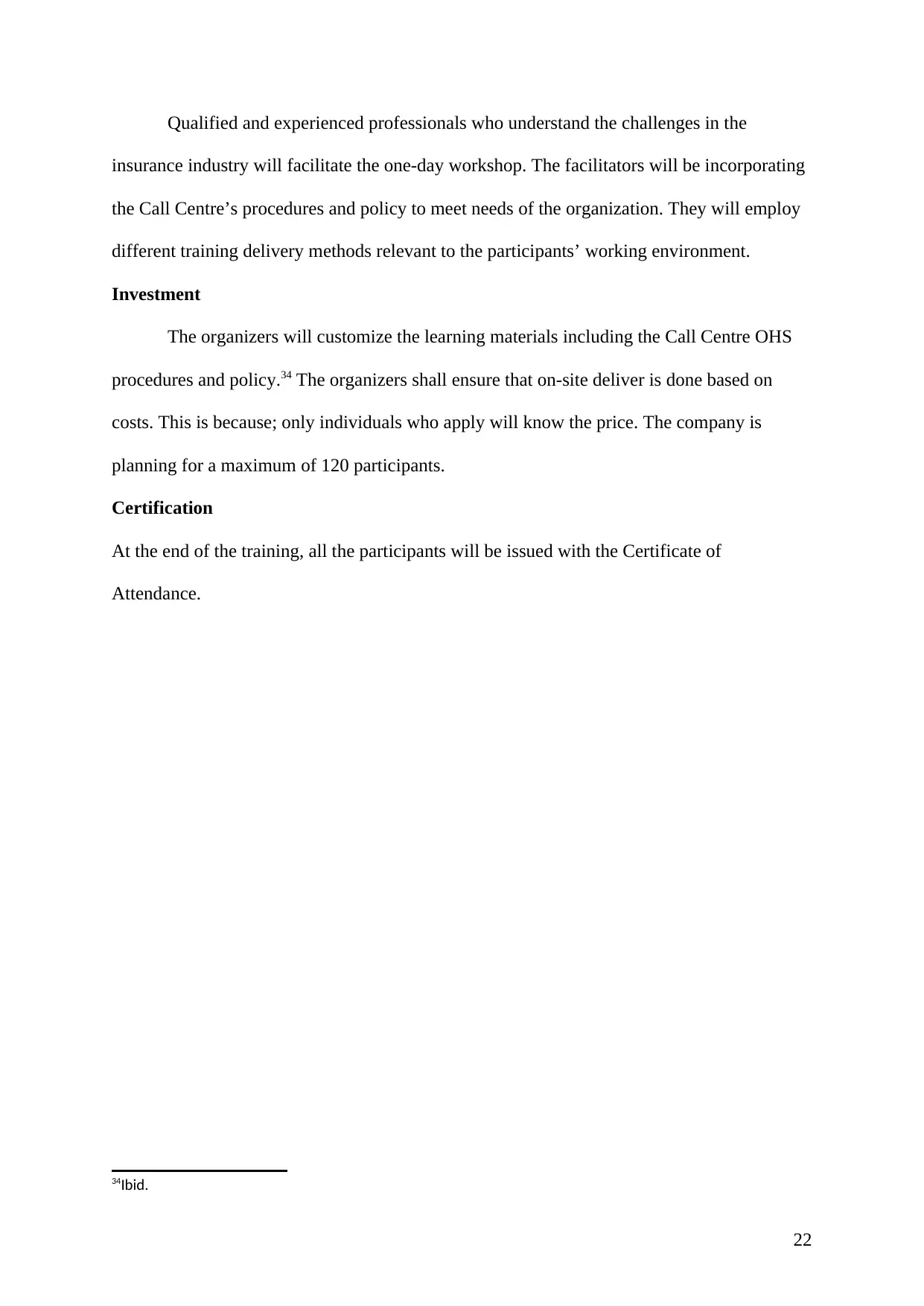
Qualified and experienced professionals who understand the challenges in the
insurance industry will facilitate the one-day workshop. The facilitators will be incorporating
the Call Centre’s procedures and policy to meet needs of the organization. They will employ
different training delivery methods relevant to the participants’ working environment.
Investment
The organizers will customize the learning materials including the Call Centre OHS
procedures and policy.34 The organizers shall ensure that on-site deliver is done based on
costs. This is because; only individuals who apply will know the price. The company is
planning for a maximum of 120 participants.
Certification
At the end of the training, all the participants will be issued with the Certificate of
Attendance.
34Ibid.
22
insurance industry will facilitate the one-day workshop. The facilitators will be incorporating
the Call Centre’s procedures and policy to meet needs of the organization. They will employ
different training delivery methods relevant to the participants’ working environment.
Investment
The organizers will customize the learning materials including the Call Centre OHS
procedures and policy.34 The organizers shall ensure that on-site deliver is done based on
costs. This is because; only individuals who apply will know the price. The company is
planning for a maximum of 120 participants.
Certification
At the end of the training, all the participants will be issued with the Certificate of
Attendance.
34Ibid.
22
Secure Best Marks with AI Grader
Need help grading? Try our AI Grader for instant feedback on your assignments.
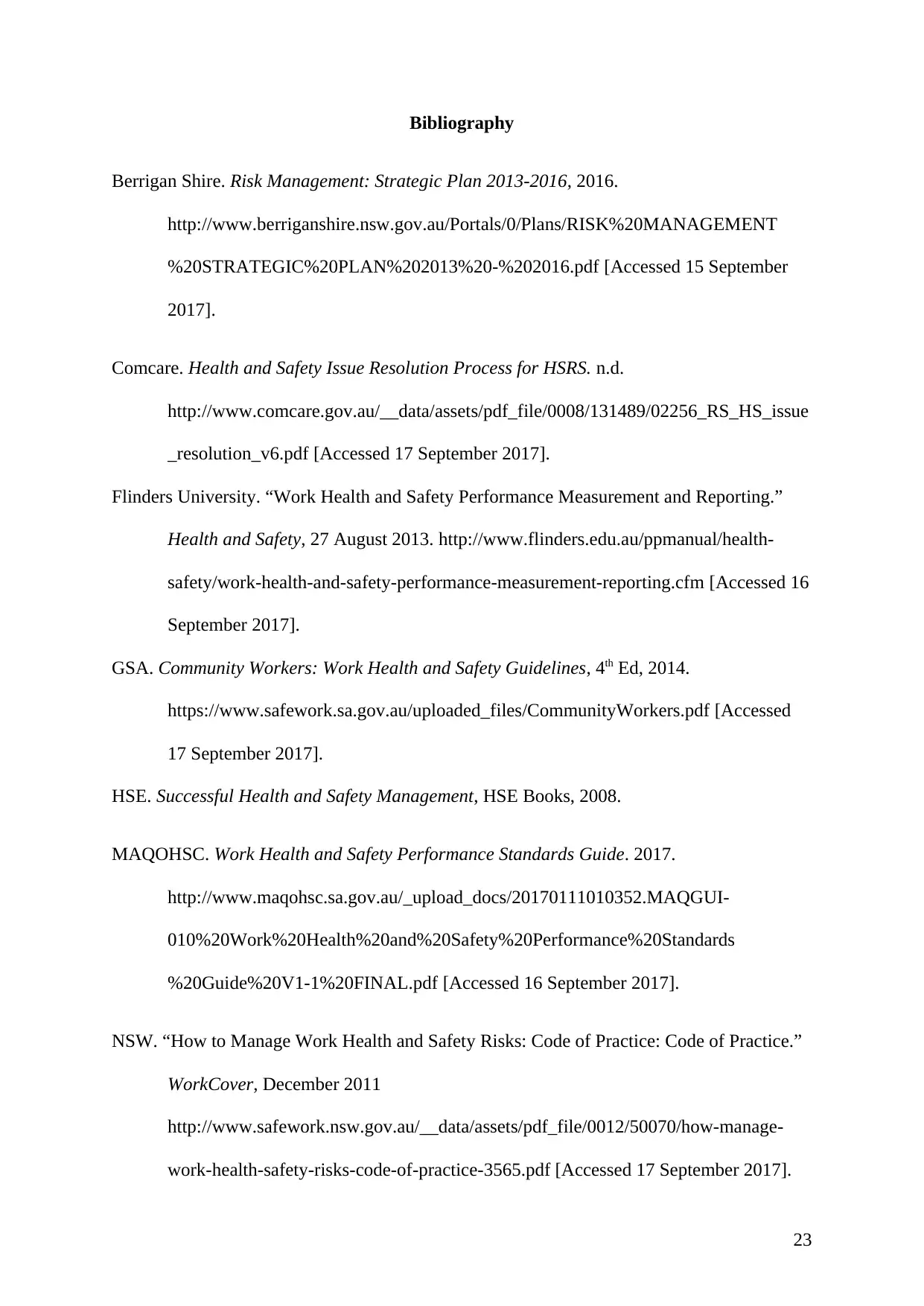
Bibliography
Berrigan Shire. Risk Management: Strategic Plan 2013-2016, 2016.
http://www.berriganshire.nsw.gov.au/Portals/0/Plans/RISK%20MANAGEMENT
%20STRATEGIC%20PLAN%202013%20-%202016.pdf [Accessed 15 September
2017].
Comcare. Health and Safety Issue Resolution Process for HSRS. n.d.
http://www.comcare.gov.au/__data/assets/pdf_file/0008/131489/02256_RS_HS_issue
_resolution_v6.pdf [Accessed 17 September 2017].
Flinders University. “Work Health and Safety Performance Measurement and Reporting.”
Health and Safety, 27 August 2013. http://www.flinders.edu.au/ppmanual/health-
safety/work-health-and-safety-performance-measurement-reporting.cfm [Accessed 16
September 2017].
GSA. Community Workers: Work Health and Safety Guidelines, 4th Ed, 2014.
https://www.safework.sa.gov.au/uploaded_files/CommunityWorkers.pdf [Accessed
17 September 2017].
HSE. Successful Health and Safety Management, HSE Books, 2008.
MAQOHSC. Work Health and Safety Performance Standards Guide. 2017.
http://www.maqohsc.sa.gov.au/_upload_docs/20170111010352.MAQGUI-
010%20Work%20Health%20and%20Safety%20Performance%20Standards
%20Guide%20V1-1%20FINAL.pdf [Accessed 16 September 2017].
NSW. “How to Manage Work Health and Safety Risks: Code of Practice: Code of Practice.”
WorkCover, December 2011
http://www.safework.nsw.gov.au/__data/assets/pdf_file/0012/50070/how-manage-
work-health-safety-risks-code-of-practice-3565.pdf [Accessed 17 September 2017].
23
Berrigan Shire. Risk Management: Strategic Plan 2013-2016, 2016.
http://www.berriganshire.nsw.gov.au/Portals/0/Plans/RISK%20MANAGEMENT
%20STRATEGIC%20PLAN%202013%20-%202016.pdf [Accessed 15 September
2017].
Comcare. Health and Safety Issue Resolution Process for HSRS. n.d.
http://www.comcare.gov.au/__data/assets/pdf_file/0008/131489/02256_RS_HS_issue
_resolution_v6.pdf [Accessed 17 September 2017].
Flinders University. “Work Health and Safety Performance Measurement and Reporting.”
Health and Safety, 27 August 2013. http://www.flinders.edu.au/ppmanual/health-
safety/work-health-and-safety-performance-measurement-reporting.cfm [Accessed 16
September 2017].
GSA. Community Workers: Work Health and Safety Guidelines, 4th Ed, 2014.
https://www.safework.sa.gov.au/uploaded_files/CommunityWorkers.pdf [Accessed
17 September 2017].
HSE. Successful Health and Safety Management, HSE Books, 2008.
MAQOHSC. Work Health and Safety Performance Standards Guide. 2017.
http://www.maqohsc.sa.gov.au/_upload_docs/20170111010352.MAQGUI-
010%20Work%20Health%20and%20Safety%20Performance%20Standards
%20Guide%20V1-1%20FINAL.pdf [Accessed 16 September 2017].
NSW. “How to Manage Work Health and Safety Risks: Code of Practice: Code of Practice.”
WorkCover, December 2011
http://www.safework.nsw.gov.au/__data/assets/pdf_file/0012/50070/how-manage-
work-health-safety-risks-code-of-practice-3565.pdf [Accessed 17 September 2017].
23
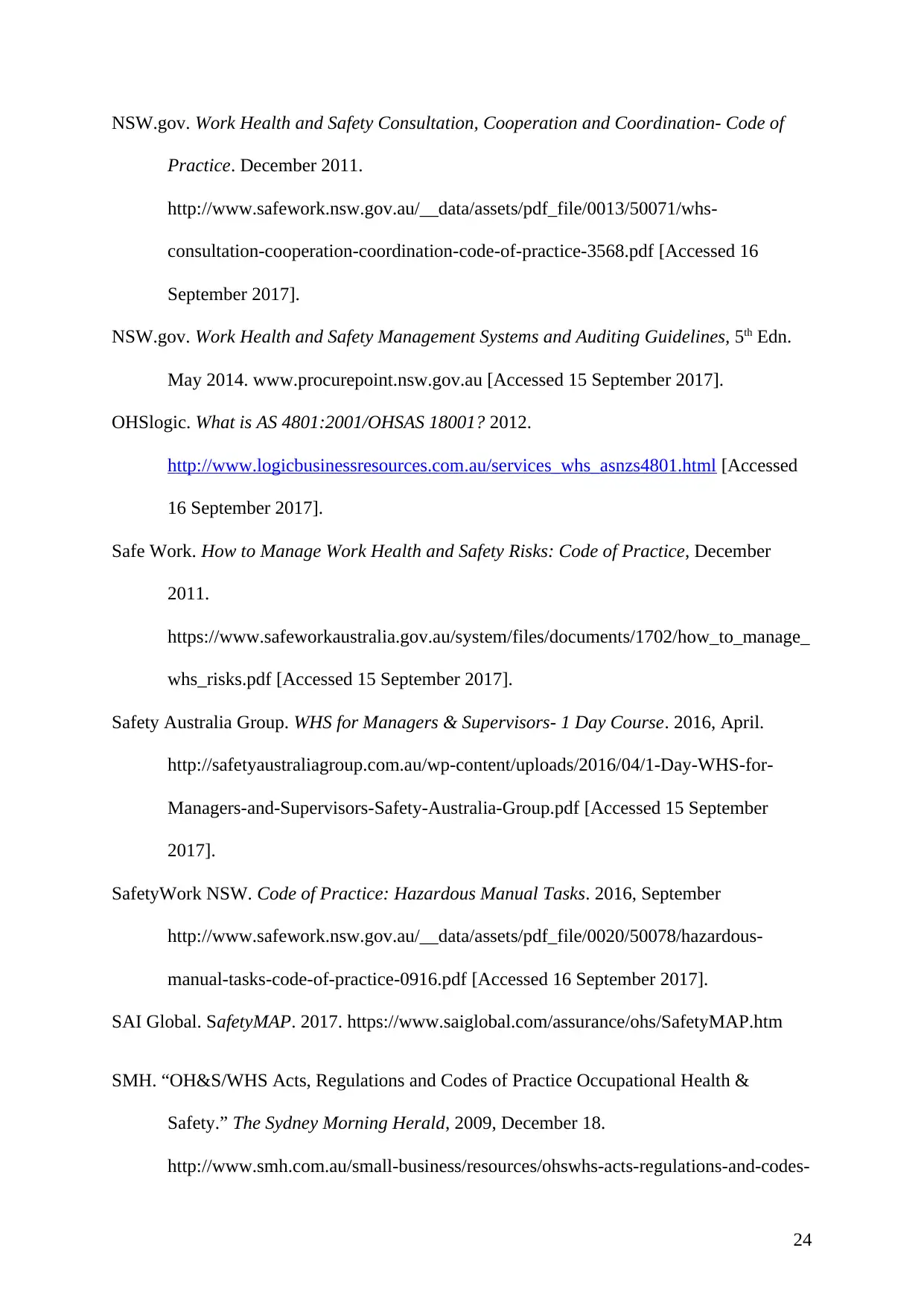
NSW.gov. Work Health and Safety Consultation, Cooperation and Coordination- Code of
Practice. December 2011.
http://www.safework.nsw.gov.au/__data/assets/pdf_file/0013/50071/whs-
consultation-cooperation-coordination-code-of-practice-3568.pdf [Accessed 16
September 2017].
NSW.gov. Work Health and Safety Management Systems and Auditing Guidelines, 5th Edn.
May 2014. www.procurepoint.nsw.gov.au [Accessed 15 September 2017].
OHSlogic. What is AS 4801:2001/OHSAS 18001? 2012.
http://www.logicbusinessresources.com.au/services_whs_asnzs4801.html [Accessed
16 September 2017].
Safe Work. How to Manage Work Health and Safety Risks: Code of Practice, December
2011.
https://www.safeworkaustralia.gov.au/system/files/documents/1702/how_to_manage_
whs_risks.pdf [Accessed 15 September 2017].
Safety Australia Group. WHS for Managers & Supervisors- 1 Day Course. 2016, April.
http://safetyaustraliagroup.com.au/wp-content/uploads/2016/04/1-Day-WHS-for-
Managers-and-Supervisors-Safety-Australia-Group.pdf [Accessed 15 September
2017].
SafetyWork NSW. Code of Practice: Hazardous Manual Tasks. 2016, September
http://www.safework.nsw.gov.au/__data/assets/pdf_file/0020/50078/hazardous-
manual-tasks-code-of-practice-0916.pdf [Accessed 16 September 2017].
SAI Global. SafetyMAP. 2017. https://www.saiglobal.com/assurance/ohs/SafetyMAP.htm
SMH. “OH&S/WHS Acts, Regulations and Codes of Practice Occupational Health &
Safety.” The Sydney Morning Herald, 2009, December 18.
http://www.smh.com.au/small-business/resources/ohswhs-acts-regulations-and-codes-
24
Practice. December 2011.
http://www.safework.nsw.gov.au/__data/assets/pdf_file/0013/50071/whs-
consultation-cooperation-coordination-code-of-practice-3568.pdf [Accessed 16
September 2017].
NSW.gov. Work Health and Safety Management Systems and Auditing Guidelines, 5th Edn.
May 2014. www.procurepoint.nsw.gov.au [Accessed 15 September 2017].
OHSlogic. What is AS 4801:2001/OHSAS 18001? 2012.
http://www.logicbusinessresources.com.au/services_whs_asnzs4801.html [Accessed
16 September 2017].
Safe Work. How to Manage Work Health and Safety Risks: Code of Practice, December
2011.
https://www.safeworkaustralia.gov.au/system/files/documents/1702/how_to_manage_
whs_risks.pdf [Accessed 15 September 2017].
Safety Australia Group. WHS for Managers & Supervisors- 1 Day Course. 2016, April.
http://safetyaustraliagroup.com.au/wp-content/uploads/2016/04/1-Day-WHS-for-
Managers-and-Supervisors-Safety-Australia-Group.pdf [Accessed 15 September
2017].
SafetyWork NSW. Code of Practice: Hazardous Manual Tasks. 2016, September
http://www.safework.nsw.gov.au/__data/assets/pdf_file/0020/50078/hazardous-
manual-tasks-code-of-practice-0916.pdf [Accessed 16 September 2017].
SAI Global. SafetyMAP. 2017. https://www.saiglobal.com/assurance/ohs/SafetyMAP.htm
SMH. “OH&S/WHS Acts, Regulations and Codes of Practice Occupational Health &
Safety.” The Sydney Morning Herald, 2009, December 18.
http://www.smh.com.au/small-business/resources/ohswhs-acts-regulations-and-codes-
24
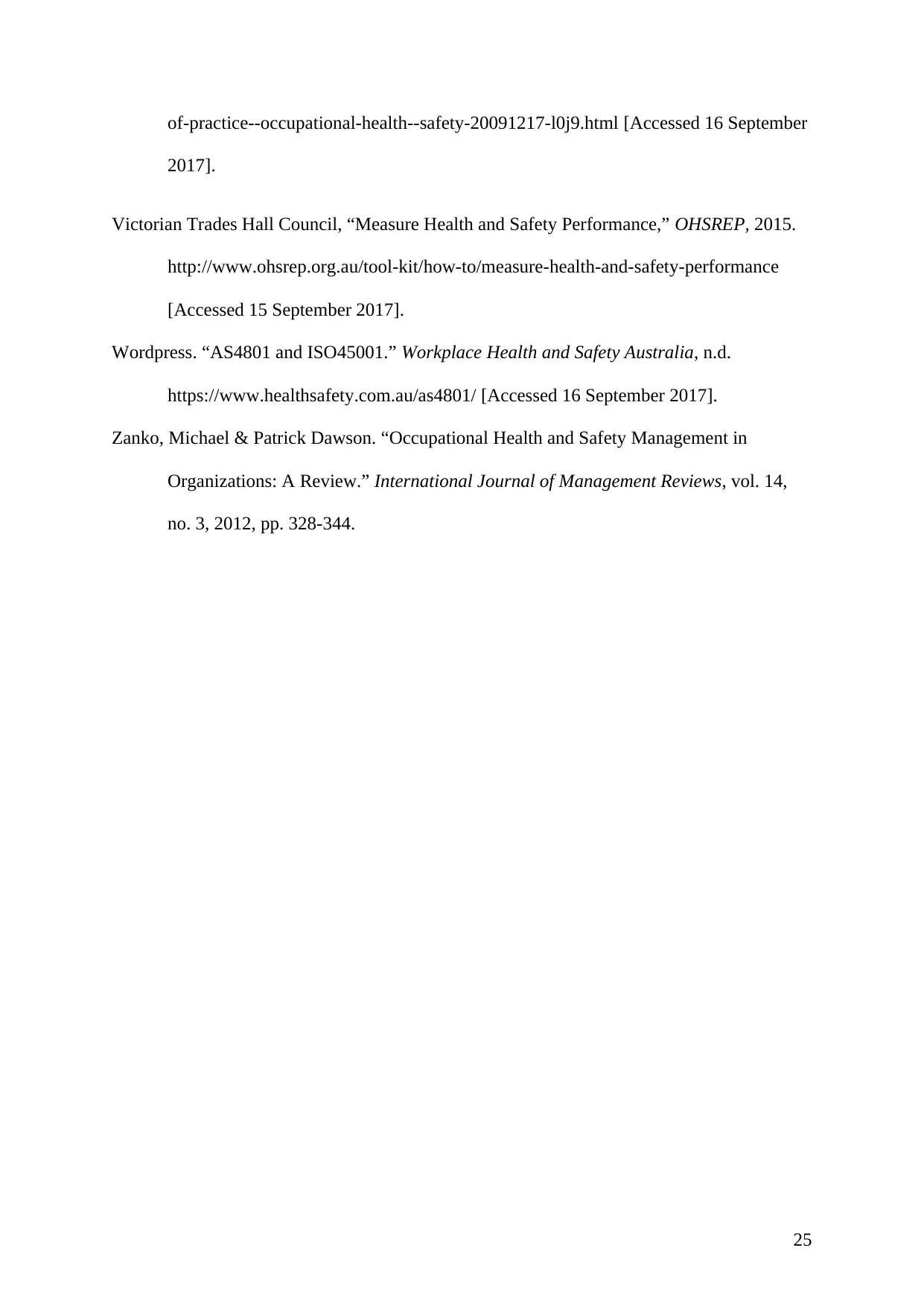
of-practice--occupational-health--safety-20091217-l0j9.html [Accessed 16 September
2017].
Victorian Trades Hall Council, “Measure Health and Safety Performance,” OHSREP, 2015.
http://www.ohsrep.org.au/tool-kit/how-to/measure-health-and-safety-performance
[Accessed 15 September 2017].
Wordpress. “AS4801 and ISO45001.” Workplace Health and Safety Australia, n.d.
https://www.healthsafety.com.au/as4801/ [Accessed 16 September 2017].
Zanko, Michael & Patrick Dawson. “Occupational Health and Safety Management in
Organizations: A Review.” International Journal of Management Reviews, vol. 14,
no. 3, 2012, pp. 328-344.
25
2017].
Victorian Trades Hall Council, “Measure Health and Safety Performance,” OHSREP, 2015.
http://www.ohsrep.org.au/tool-kit/how-to/measure-health-and-safety-performance
[Accessed 15 September 2017].
Wordpress. “AS4801 and ISO45001.” Workplace Health and Safety Australia, n.d.
https://www.healthsafety.com.au/as4801/ [Accessed 16 September 2017].
Zanko, Michael & Patrick Dawson. “Occupational Health and Safety Management in
Organizations: A Review.” International Journal of Management Reviews, vol. 14,
no. 3, 2012, pp. 328-344.
25
1 out of 25
Related Documents
![[object Object]](/_next/image/?url=%2F_next%2Fstatic%2Fmedia%2Flogo.6d15ce61.png&w=640&q=75)
Your All-in-One AI-Powered Toolkit for Academic Success.
+13062052269
info@desklib.com
Available 24*7 on WhatsApp / Email
Unlock your academic potential
© 2024 | Zucol Services PVT LTD | All rights reserved.