Accounting 2012 Case Study: Wine River Winery Analysis
VerifiedAdded on 2023/06/03
|9
|1094
|277
Case Study
AI Summary
This case study focuses on Wine River Winery, a boutique winery in Adelaide, and its efforts to improve profitability and efficiency. The analysis involves two major cost analysis systems: ABC costing of the Barreling and Maturation Cost Centre and variance analysis of budgeted sales prices and producti...

Accounting 2012
Assignment
Assignment
Paraphrase This Document
Need a fresh take? Get an instant paraphrase of this document with our AI Paraphraser

Executive Summary
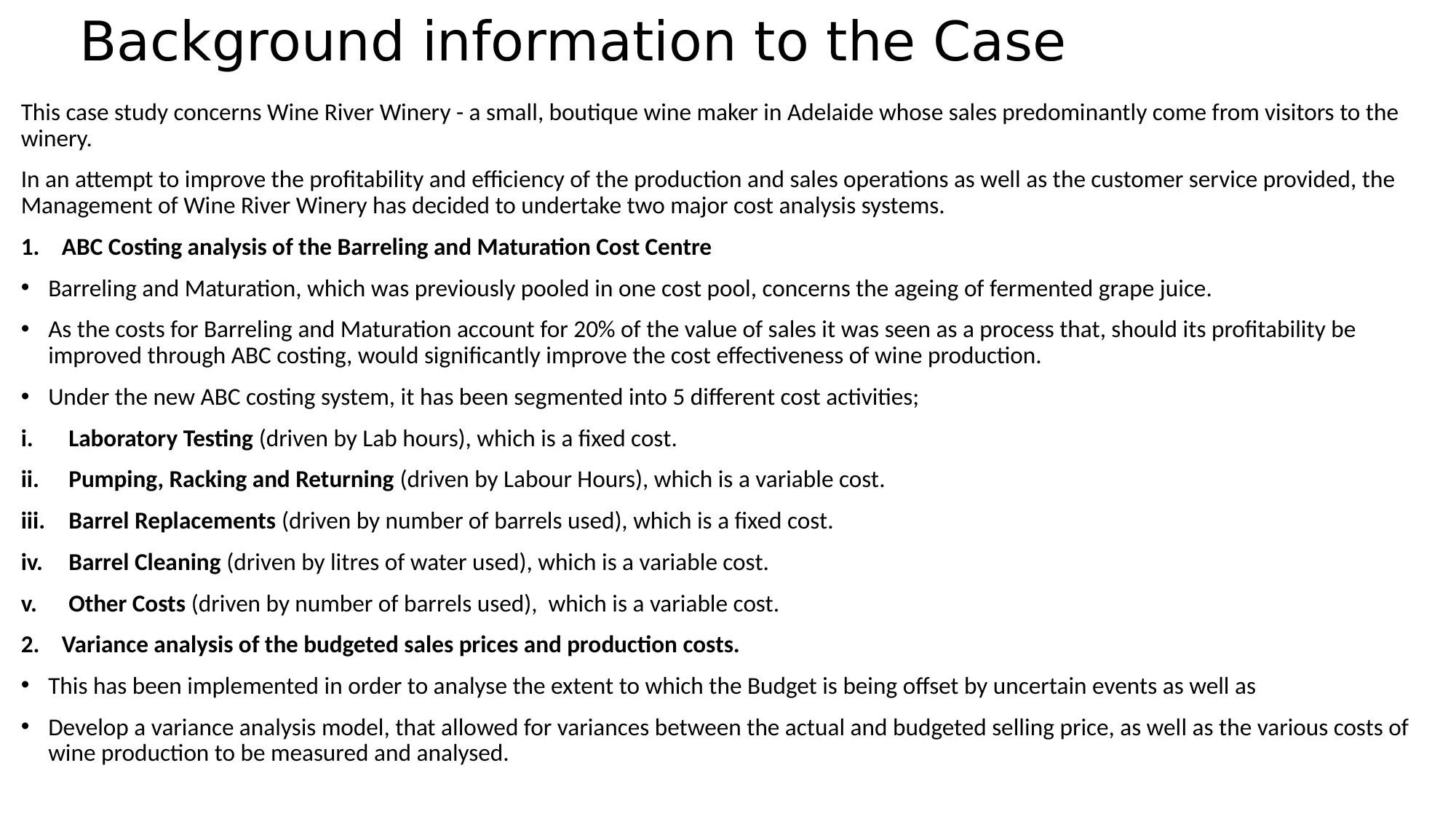
Background information to the Case
This case study concerns Wine River Winery - a small, boutique wine maker in Adelaide whose sales predominantly come from visitors to the
winery.
In an attempt to improve the profitability and efficiency of the production and sales operations as well as the customer service provided, the
Management of Wine River Winery has decided to undertake two major cost analysis systems.
1. ABC Costing analysis of the Barreling and Maturation Cost Centre
• Barreling and Maturation, which was previously pooled in one cost pool, concerns the ageing of fermented grape juice.
• As the costs for Barreling and Maturation account for 20% of the value of sales it was seen as a process that, should its profitability be
improved through ABC costing, would significantly improve the cost effectiveness of wine production.
• Under the new ABC costing system, it has been segmented into 5 different cost activities;
i. Laboratory Testing (driven by Lab hours), which is a fixed cost.
ii. Pumping, Racking and Returning (driven by Labour Hours), which is a variable cost.
iii. Barrel Replacements (driven by number of barrels used), which is a fixed cost.
iv. Barrel Cleaning (driven by litres of water used), which is a variable cost.
v. Other Costs (driven by number of barrels used), which is a variable cost.
2. Variance analysis of the budgeted sales prices and production costs.
• This has been implemented in order to analyse the extent to which the Budget is being offset by uncertain events as well as
• Develop a variance analysis model, that allowed for variances between the actual and budgeted selling price, as well as the various costs of
wine production to be measured and analysed.
This case study concerns Wine River Winery - a small, boutique wine maker in Adelaide whose sales predominantly come from visitors to the
winery.
In an attempt to improve the profitability and efficiency of the production and sales operations as well as the customer service provided, the
Management of Wine River Winery has decided to undertake two major cost analysis systems.
1. ABC Costing analysis of the Barreling and Maturation Cost Centre
• Barreling and Maturation, which was previously pooled in one cost pool, concerns the ageing of fermented grape juice.
• As the costs for Barreling and Maturation account for 20% of the value of sales it was seen as a process that, should its profitability be
improved through ABC costing, would significantly improve the cost effectiveness of wine production.
• Under the new ABC costing system, it has been segmented into 5 different cost activities;
i. Laboratory Testing (driven by Lab hours), which is a fixed cost.
ii. Pumping, Racking and Returning (driven by Labour Hours), which is a variable cost.
iii. Barrel Replacements (driven by number of barrels used), which is a fixed cost.
iv. Barrel Cleaning (driven by litres of water used), which is a variable cost.
v. Other Costs (driven by number of barrels used), which is a variable cost.
2. Variance analysis of the budgeted sales prices and production costs.
• This has been implemented in order to analyse the extent to which the Budget is being offset by uncertain events as well as
• Develop a variance analysis model, that allowed for variances between the actual and budgeted selling price, as well as the various costs of
wine production to be measured and analysed.
⊘ This is a preview!⊘
Do you want full access?
Subscribe today to unlock all pages.

Trusted by 1+ million students worldwide
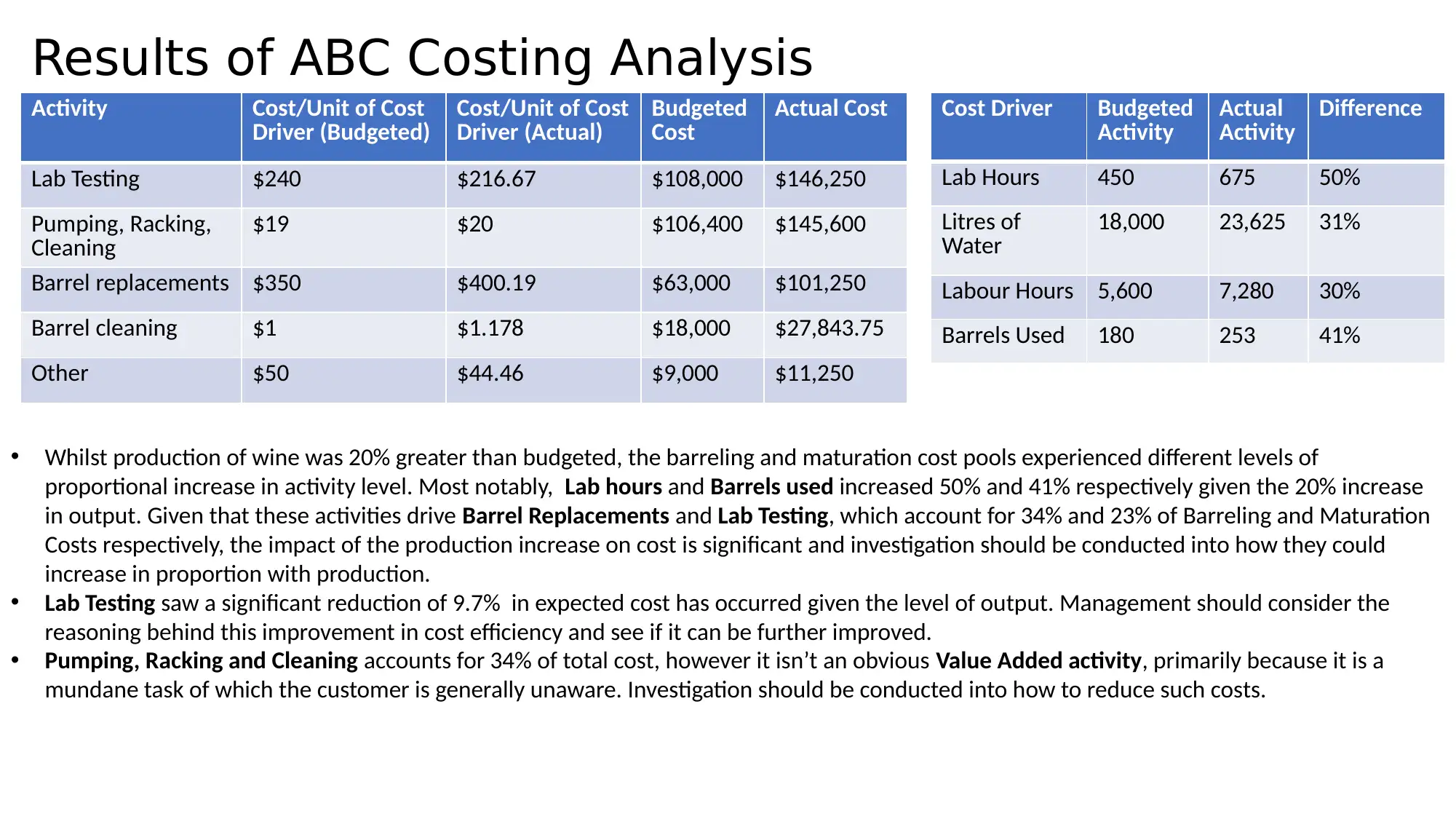
Results of ABC Costing Analysis
Activity Cost/Unit of Cost
Driver (Budgeted)
Cost/Unit of Cost
Driver (Actual)
Budgeted
Cost
Actual Cost
Lab Testing $240 $216.67 $108,000 $146,250
Pumping, Racking,
Cleaning
$19 $20 $106,400 $145,600
Barrel replacements $350 $400.19 $63,000 $101,250
Barrel cleaning $1 $1.178 $18,000 $27,843.75
Other $50 $44.46 $9,000 $11,250
• Whilst production of wine was 20% greater than budgeted, the barreling and maturation cost pools experienced different levels of
proportional increase in activity level. Most notably, Lab hours and Barrels used increased 50% and 41% respectively given the 20% increase
in output. Given that these activities drive Barrel Replacements and Lab Testing, which account for 34% and 23% of Barreling and Maturation
Costs respectively, the impact of the production increase on cost is significant and investigation should be conducted into how they could
increase in proportion with production.
• Lab Testing saw a significant reduction of 9.7% in expected cost has occurred given the level of output. Management should consider the
reasoning behind this improvement in cost efficiency and see if it can be further improved.
• Pumping, Racking and Cleaning accounts for 34% of total cost, however it isn’t an obvious Value Added activity, primarily because it is a
mundane task of which the customer is generally unaware. Investigation should be conducted into how to reduce such costs.
Cost Driver Budgeted
Activity
Actual
Activity
Difference
Lab Hours 450 675 50%
Litres of
Water
18,000 23,625 31%
Labour Hours 5,600 7,280 30%
Barrels Used 180 253 41%
Activity Cost/Unit of Cost
Driver (Budgeted)
Cost/Unit of Cost
Driver (Actual)
Budgeted
Cost
Actual Cost
Lab Testing $240 $216.67 $108,000 $146,250
Pumping, Racking,
Cleaning
$19 $20 $106,400 $145,600
Barrel replacements $350 $400.19 $63,000 $101,250
Barrel cleaning $1 $1.178 $18,000 $27,843.75
Other $50 $44.46 $9,000 $11,250
• Whilst production of wine was 20% greater than budgeted, the barreling and maturation cost pools experienced different levels of
proportional increase in activity level. Most notably, Lab hours and Barrels used increased 50% and 41% respectively given the 20% increase
in output. Given that these activities drive Barrel Replacements and Lab Testing, which account for 34% and 23% of Barreling and Maturation
Costs respectively, the impact of the production increase on cost is significant and investigation should be conducted into how they could
increase in proportion with production.
• Lab Testing saw a significant reduction of 9.7% in expected cost has occurred given the level of output. Management should consider the
reasoning behind this improvement in cost efficiency and see if it can be further improved.
• Pumping, Racking and Cleaning accounts for 34% of total cost, however it isn’t an obvious Value Added activity, primarily because it is a
mundane task of which the customer is generally unaware. Investigation should be conducted into how to reduce such costs.
Cost Driver Budgeted
Activity
Actual
Activity
Difference
Lab Hours 450 675 50%
Litres of
Water
18,000 23,625 31%
Labour Hours 5,600 7,280 30%
Barrels Used 180 253 41%
Paraphrase This Document
Need a fresh take? Get an instant paraphrase of this document with our AI Paraphraser

Results of Variance Analysis
Cost Price Variance Efficiency Variance
Direct Materials $24,000 F $90,000 F
Direct Labour $36,400 U $53,200 U
Variable Overheads $40,893.75 U $30,150 U
Fixed Overheads $106,875 U $49,500 F
Direct Materials have been favorably impacted
both in price and efficiency variance.
Direct Materials Price Variance has been
impacted because of a lower price paid of $8.4/kg
than expected. Direct Materials Efficiency
Variance has also been positively impacted as it
only required 0.39 kg of Direct Material to
produce a bottle compared to a budgeted 0.5 kg.
Direct Labour price and efficiency have been
unfavorably impacted. This is because although it
was predicted that each Labour Hour would
produce 2.67 bottles of wine, they in fact only
produced 2.47 bottles of wine. This could be as a
result of an HR issue.
Whilst it was estimated that Variable Overheads would cost
$10.77/Hr they in fact cost $11.89/Hr. Furthermore, although a
20% increase in output was budgeted to result in a 20%
increase in Variable Overheads (bringing it to $361,800),
Variable Overheads increased by 44% which is significantly
more than the production increase. Consequently, both
Variable Overhead Price and Efficiency have been unfavorably
affected. This could be a result of an inefficient system of
production and should be further investigated.
Fixed Overhead Price has been unfavorably affected because
they have increased with production. This could be because the
increased production has required more land thus changing the
relevant range of production.
Cost Price Variance Efficiency Variance
Direct Materials $24,000 F $90,000 F
Direct Labour $36,400 U $53,200 U
Variable Overheads $40,893.75 U $30,150 U
Fixed Overheads $106,875 U $49,500 F
Direct Materials have been favorably impacted
both in price and efficiency variance.
Direct Materials Price Variance has been
impacted because of a lower price paid of $8.4/kg
than expected. Direct Materials Efficiency
Variance has also been positively impacted as it
only required 0.39 kg of Direct Material to
produce a bottle compared to a budgeted 0.5 kg.
Direct Labour price and efficiency have been
unfavorably impacted. This is because although it
was predicted that each Labour Hour would
produce 2.67 bottles of wine, they in fact only
produced 2.47 bottles of wine. This could be as a
result of an HR issue.
Whilst it was estimated that Variable Overheads would cost
$10.77/Hr they in fact cost $11.89/Hr. Furthermore, although a
20% increase in output was budgeted to result in a 20%
increase in Variable Overheads (bringing it to $361,800),
Variable Overheads increased by 44% which is significantly
more than the production increase. Consequently, both
Variable Overhead Price and Efficiency have been unfavorably
affected. This could be a result of an inefficient system of
production and should be further investigated.
Fixed Overhead Price has been unfavorably affected because
they have increased with production. This could be because the
increased production has required more land thus changing the
relevant range of production.
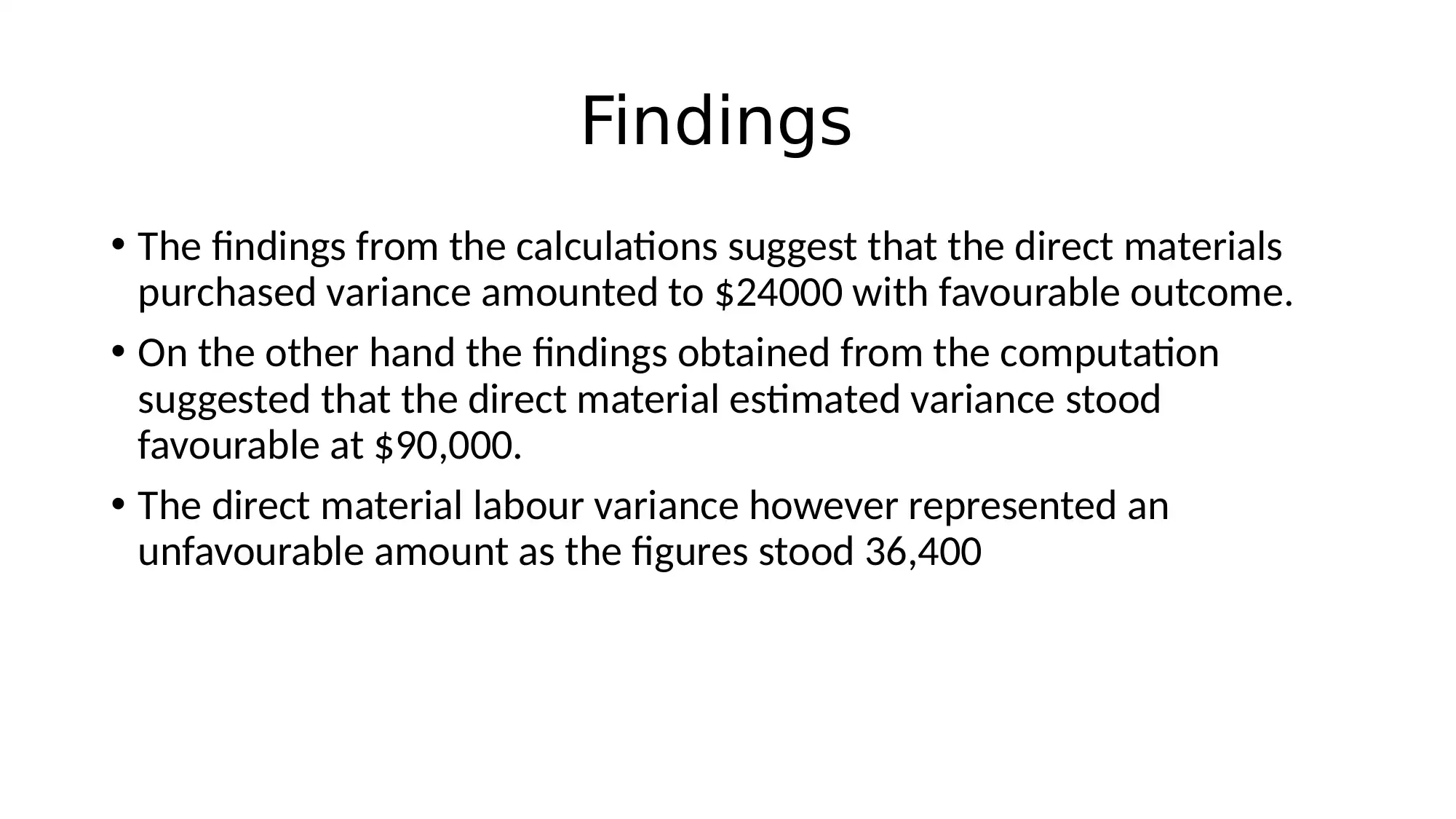
Findings
• The findings from the calculations suggest that the direct materials
purchased variance amounted to $24000 with favourable outcome.
• On the other hand the findings obtained from the computation
suggested that the direct material estimated variance stood
favourable at $90,000.
• The direct material labour variance however represented an
unfavourable amount as the figures stood 36,400
• The findings from the calculations suggest that the direct materials
purchased variance amounted to $24000 with favourable outcome.
• On the other hand the findings obtained from the computation
suggested that the direct material estimated variance stood
favourable at $90,000.
• The direct material labour variance however represented an
unfavourable amount as the figures stood 36,400
⊘ This is a preview!⊘
Do you want full access?
Subscribe today to unlock all pages.

Trusted by 1+ million students worldwide
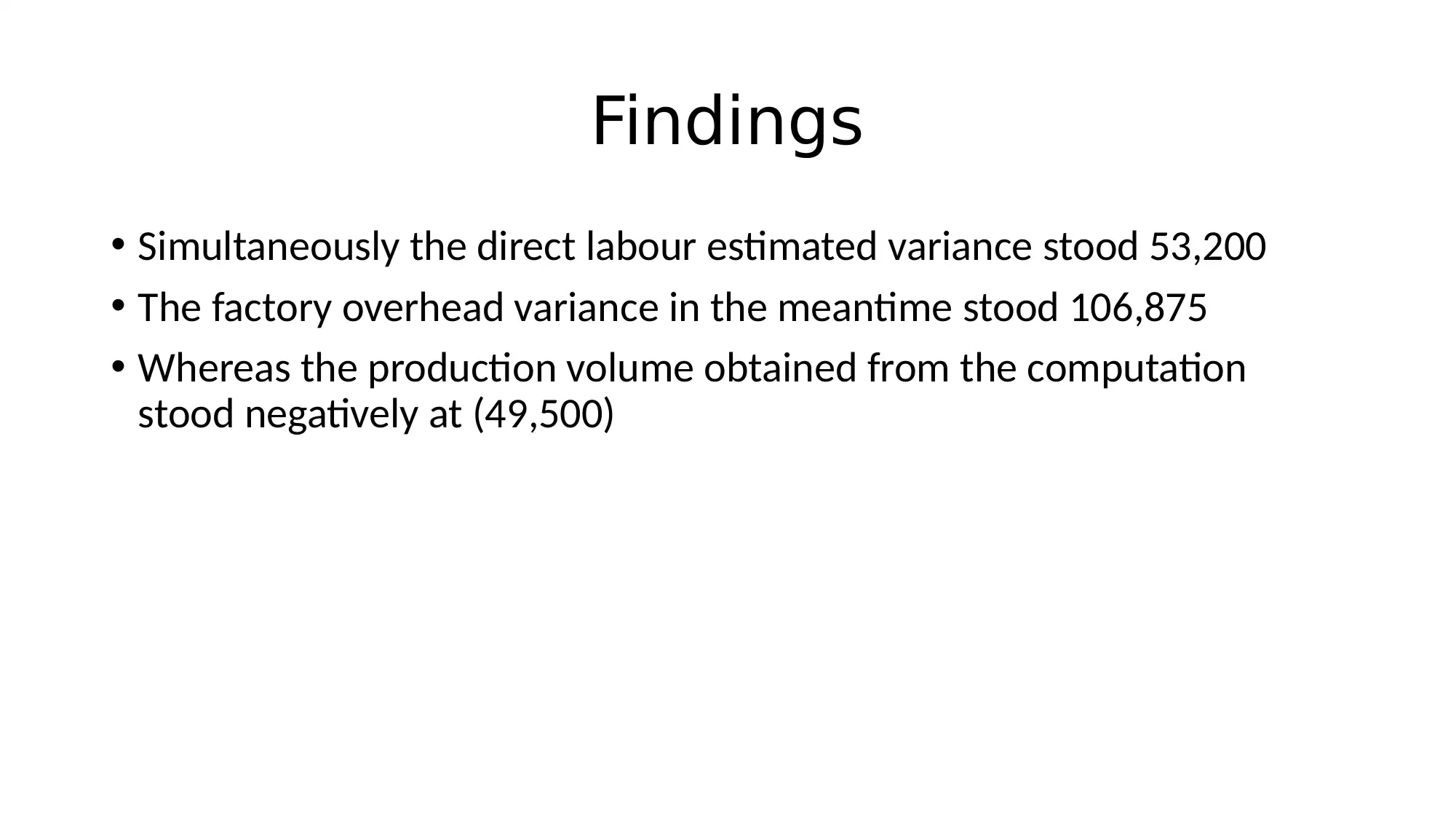
Findings
• Simultaneously the direct labour estimated variance stood 53,200
• The factory overhead variance in the meantime stood 106,875
• Whereas the production volume obtained from the computation
stood negatively at (49,500)
• Simultaneously the direct labour estimated variance stood 53,200
• The factory overhead variance in the meantime stood 106,875
• Whereas the production volume obtained from the computation
stood negatively at (49,500)
Paraphrase This Document
Need a fresh take? Get an instant paraphrase of this document with our AI Paraphraser
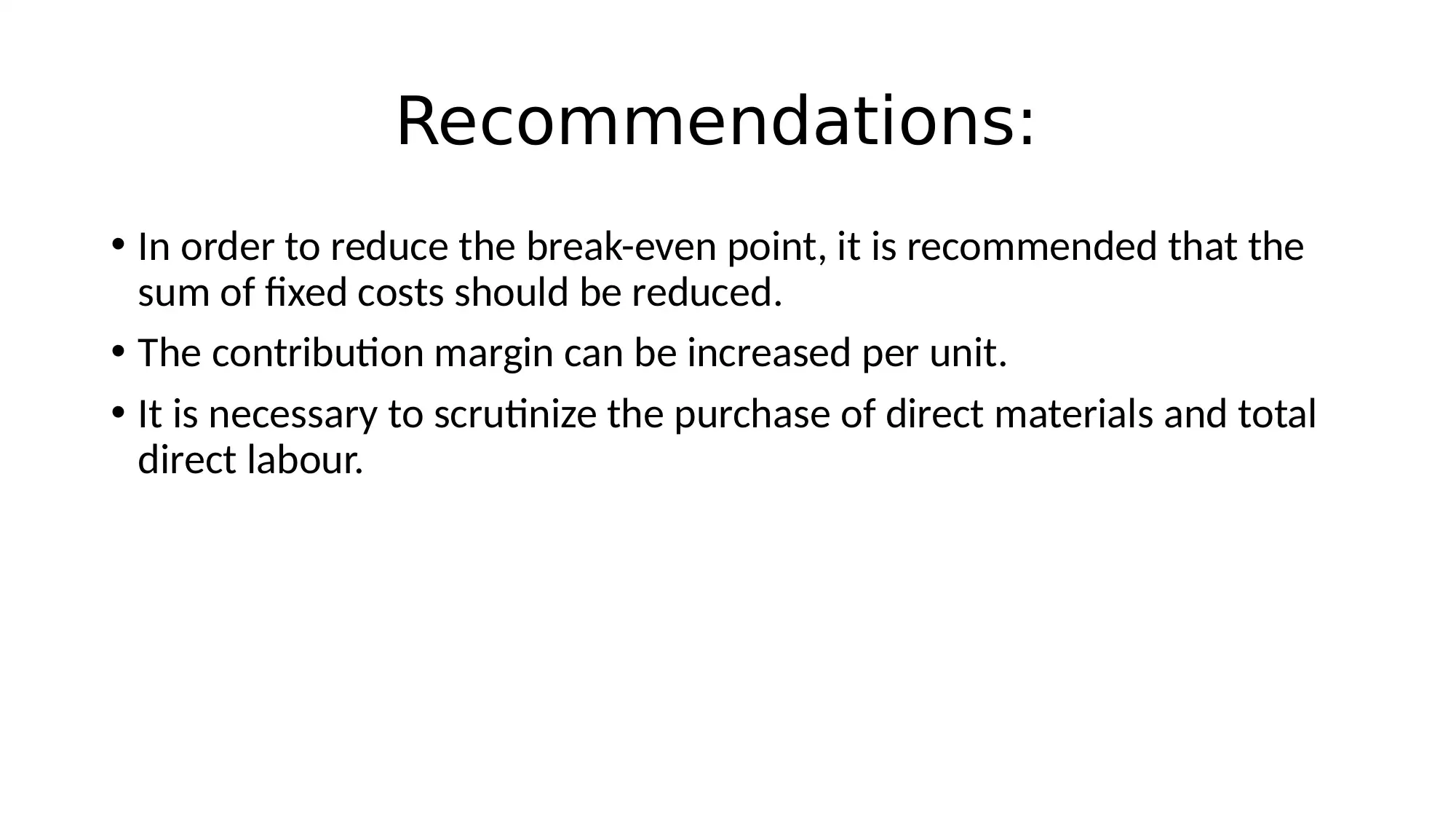
Recommendations:
• In order to reduce the break-even point, it is recommended that the
sum of fixed costs should be reduced.
• The contribution margin can be increased per unit.
• It is necessary to scrutinize the purchase of direct materials and total
direct labour.
• In order to reduce the break-even point, it is recommended that the
sum of fixed costs should be reduced.
• The contribution margin can be increased per unit.
• It is necessary to scrutinize the purchase of direct materials and total
direct labour.
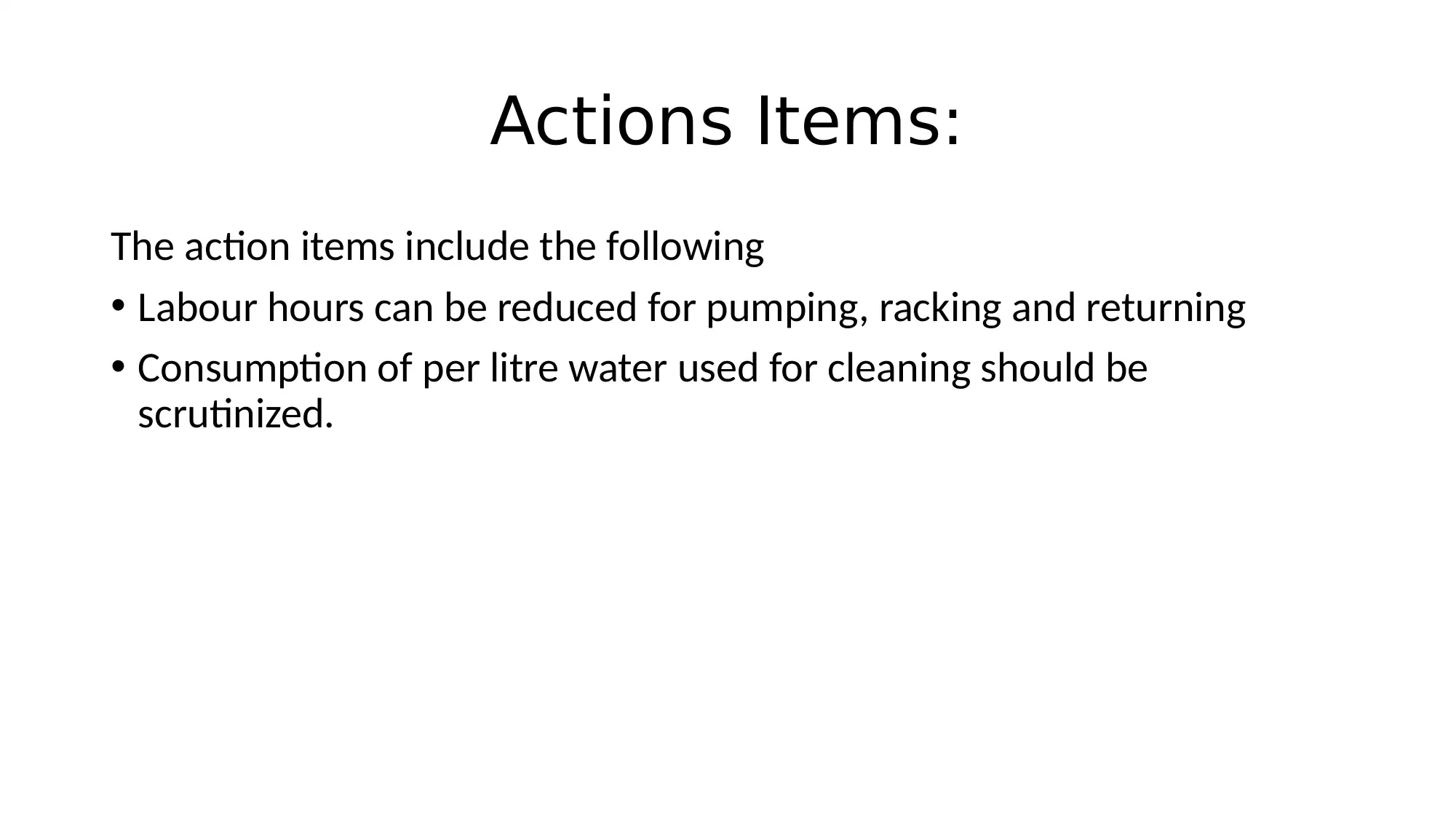
Actions Items:
The action items include the following
• Labour hours can be reduced for pumping, racking and returning
• Consumption of per litre water used for cleaning should be
scrutinized.
The action items include the following
• Labour hours can be reduced for pumping, racking and returning
• Consumption of per litre water used for cleaning should be
scrutinized.
⊘ This is a preview!⊘
Do you want full access?
Subscribe today to unlock all pages.

Trusted by 1+ million students worldwide
1 out of 9

Your All-in-One AI-Powered Toolkit for Academic Success.
+13062052269
info@desklib.com
Available 24*7 on WhatsApp / Email
Unlock your academic potential
© 2024 | Zucol Services PVT LTD | All rights reserved.