Management of Workplace Hazards: Legal Framework, Hazards and Risks, Risk Evaluation and Management, Control Measures, and Implementation Policies
VerifiedAdded on 2023/06/14
|18
|3886
|112
AI Summary
This article discusses the legal framework for managing workplace hazards, potential hazards and risks in a mechanical workshop, fault tree analysis of events that led to an injury, risk evaluation and management, control measures, and implementation policies to ensure compliance with control measures.
Contribute Materials
Your contribution can guide someone’s learning journey. Share your
documents today.
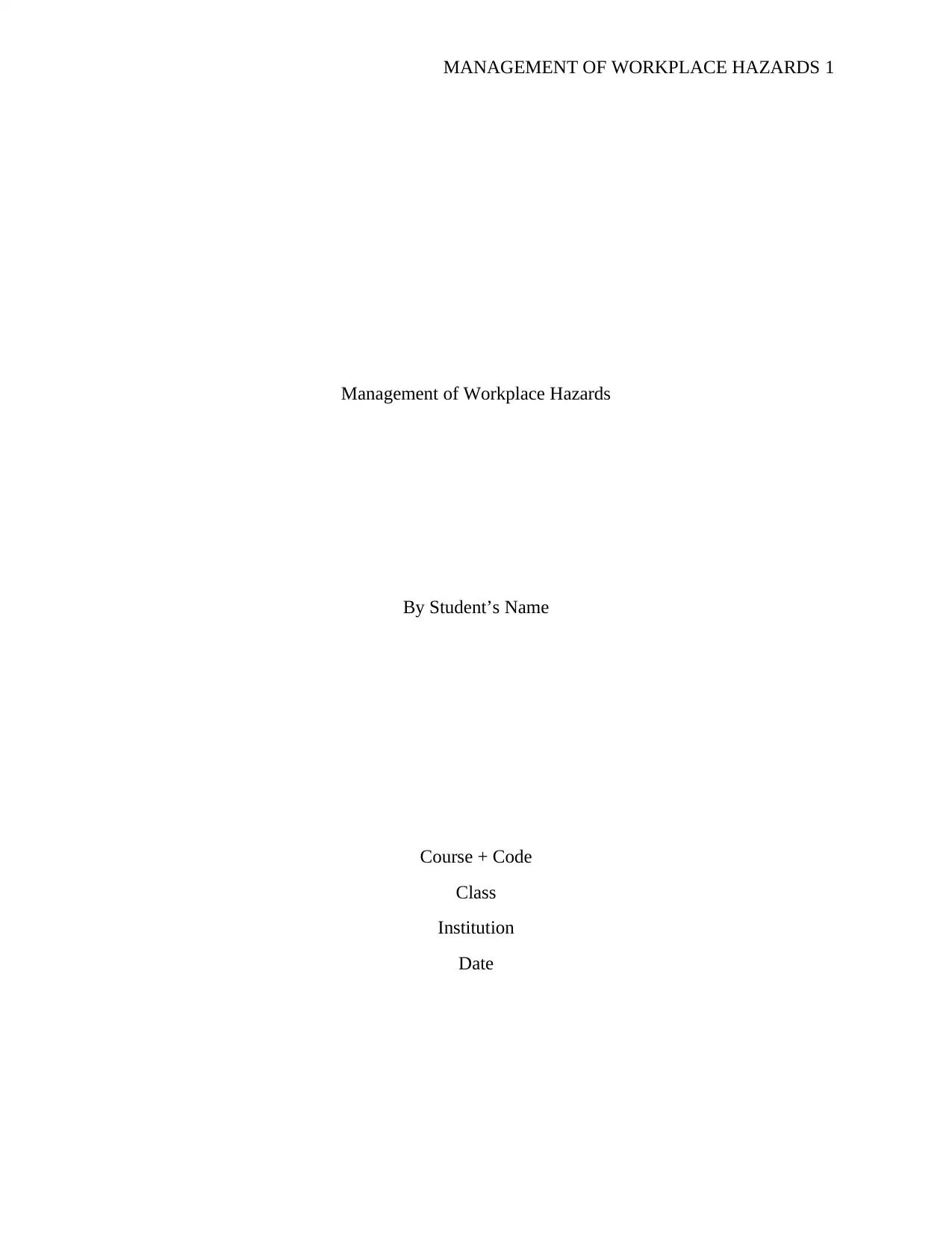
MANAGEMENT OF WORKPLACE HAZARDS 1
Management of Workplace Hazards
By Student’s Name
Course + Code
Class
Institution
Date
Management of Workplace Hazards
By Student’s Name
Course + Code
Class
Institution
Date
Secure Best Marks with AI Grader
Need help grading? Try our AI Grader for instant feedback on your assignments.
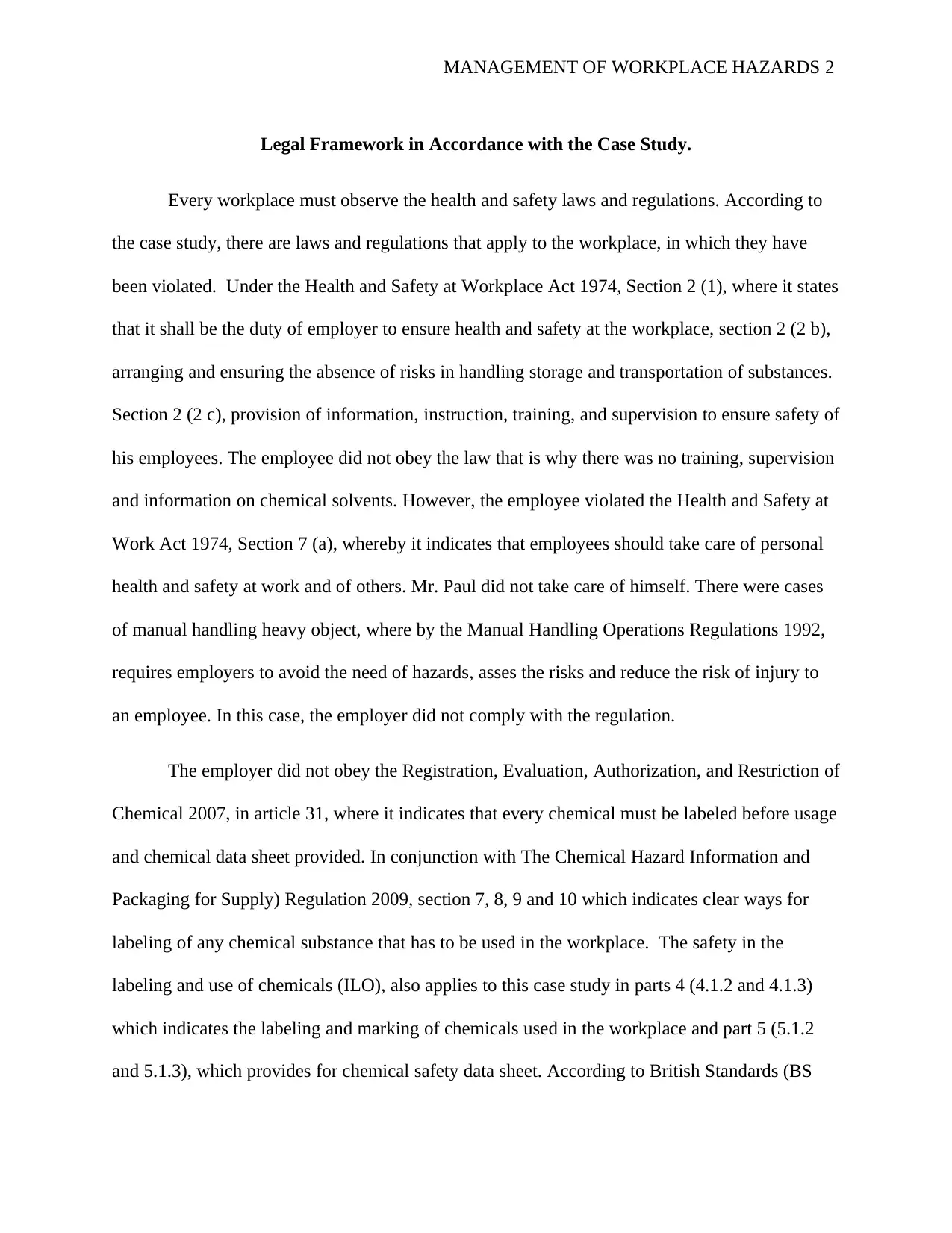
MANAGEMENT OF WORKPLACE HAZARDS 2
Legal Framework in Accordance with the Case Study.
Every workplace must observe the health and safety laws and regulations. According to
the case study, there are laws and regulations that apply to the workplace, in which they have
been violated. Under the Health and Safety at Workplace Act 1974, Section 2 (1), where it states
that it shall be the duty of employer to ensure health and safety at the workplace, section 2 (2 b),
arranging and ensuring the absence of risks in handling storage and transportation of substances.
Section 2 (2 c), provision of information, instruction, training, and supervision to ensure safety of
his employees. The employee did not obey the law that is why there was no training, supervision
and information on chemical solvents. However, the employee violated the Health and Safety at
Work Act 1974, Section 7 (a), whereby it indicates that employees should take care of personal
health and safety at work and of others. Mr. Paul did not take care of himself. There were cases
of manual handling heavy object, where by the Manual Handling Operations Regulations 1992,
requires employers to avoid the need of hazards, asses the risks and reduce the risk of injury to
an employee. In this case, the employer did not comply with the regulation.
The employer did not obey the Registration, Evaluation, Authorization, and Restriction of
Chemical 2007, in article 31, where it indicates that every chemical must be labeled before usage
and chemical data sheet provided. In conjunction with The Chemical Hazard Information and
Packaging for Supply) Regulation 2009, section 7, 8, 9 and 10 which indicates clear ways for
labeling of any chemical substance that has to be used in the workplace. The safety in the
labeling and use of chemicals (ILO), also applies to this case study in parts 4 (4.1.2 and 4.1.3)
which indicates the labeling and marking of chemicals used in the workplace and part 5 (5.1.2
and 5.1.3), which provides for chemical safety data sheet. According to British Standards (BS
Legal Framework in Accordance with the Case Study.
Every workplace must observe the health and safety laws and regulations. According to
the case study, there are laws and regulations that apply to the workplace, in which they have
been violated. Under the Health and Safety at Workplace Act 1974, Section 2 (1), where it states
that it shall be the duty of employer to ensure health and safety at the workplace, section 2 (2 b),
arranging and ensuring the absence of risks in handling storage and transportation of substances.
Section 2 (2 c), provision of information, instruction, training, and supervision to ensure safety of
his employees. The employee did not obey the law that is why there was no training, supervision
and information on chemical solvents. However, the employee violated the Health and Safety at
Work Act 1974, Section 7 (a), whereby it indicates that employees should take care of personal
health and safety at work and of others. Mr. Paul did not take care of himself. There were cases
of manual handling heavy object, where by the Manual Handling Operations Regulations 1992,
requires employers to avoid the need of hazards, asses the risks and reduce the risk of injury to
an employee. In this case, the employer did not comply with the regulation.
The employer did not obey the Registration, Evaluation, Authorization, and Restriction of
Chemical 2007, in article 31, where it indicates that every chemical must be labeled before usage
and chemical data sheet provided. In conjunction with The Chemical Hazard Information and
Packaging for Supply) Regulation 2009, section 7, 8, 9 and 10 which indicates clear ways for
labeling of any chemical substance that has to be used in the workplace. The safety in the
labeling and use of chemicals (ILO), also applies to this case study in parts 4 (4.1.2 and 4.1.3)
which indicates the labeling and marking of chemicals used in the workplace and part 5 (5.1.2
and 5.1.3), which provides for chemical safety data sheet. According to British Standards (BS
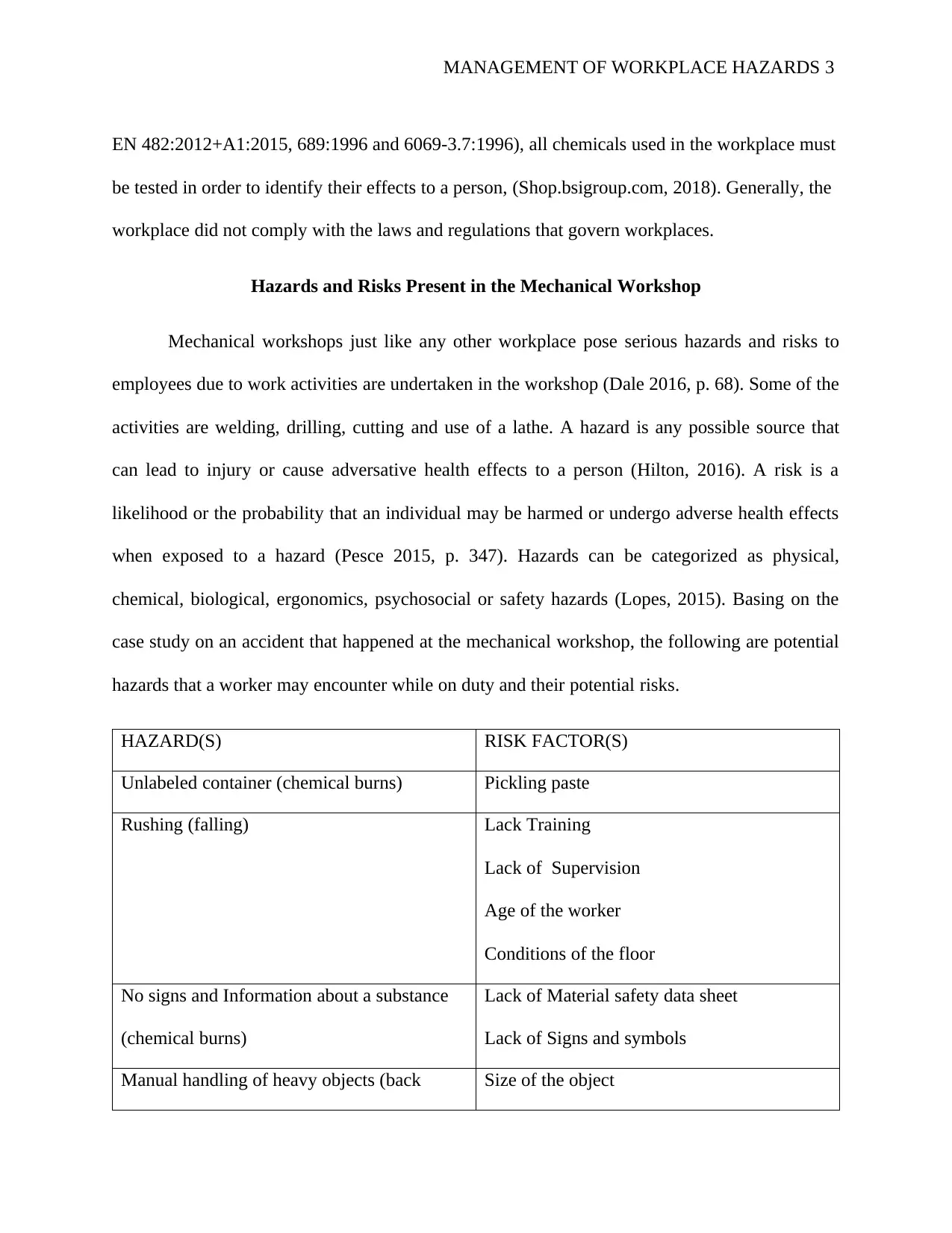
MANAGEMENT OF WORKPLACE HAZARDS 3
EN 482:2012+A1:2015, 689:1996 and 6069-3.7:1996), all chemicals used in the workplace must
be tested in order to identify their effects to a person, (Shop.bsigroup.com, 2018). Generally, the
workplace did not comply with the laws and regulations that govern workplaces.
Hazards and Risks Present in the Mechanical Workshop
Mechanical workshops just like any other workplace pose serious hazards and risks to
employees due to work activities are undertaken in the workshop (Dale 2016, p. 68). Some of the
activities are welding, drilling, cutting and use of a lathe. A hazard is any possible source that
can lead to injury or cause adversative health effects to a person (Hilton, 2016). A risk is a
likelihood or the probability that an individual may be harmed or undergo adverse health effects
when exposed to a hazard (Pesce 2015, p. 347). Hazards can be categorized as physical,
chemical, biological, ergonomics, psychosocial or safety hazards (Lopes, 2015). Basing on the
case study on an accident that happened at the mechanical workshop, the following are potential
hazards that a worker may encounter while on duty and their potential risks.
HAZARD(S) RISK FACTOR(S)
Unlabeled container (chemical burns) Pickling paste
Rushing (falling) Lack Training
Lack of Supervision
Age of the worker
Conditions of the floor
No signs and Information about a substance
(chemical burns)
Lack of Material safety data sheet
Lack of Signs and symbols
Manual handling of heavy objects (back Size of the object
EN 482:2012+A1:2015, 689:1996 and 6069-3.7:1996), all chemicals used in the workplace must
be tested in order to identify their effects to a person, (Shop.bsigroup.com, 2018). Generally, the
workplace did not comply with the laws and regulations that govern workplaces.
Hazards and Risks Present in the Mechanical Workshop
Mechanical workshops just like any other workplace pose serious hazards and risks to
employees due to work activities are undertaken in the workshop (Dale 2016, p. 68). Some of the
activities are welding, drilling, cutting and use of a lathe. A hazard is any possible source that
can lead to injury or cause adversative health effects to a person (Hilton, 2016). A risk is a
likelihood or the probability that an individual may be harmed or undergo adverse health effects
when exposed to a hazard (Pesce 2015, p. 347). Hazards can be categorized as physical,
chemical, biological, ergonomics, psychosocial or safety hazards (Lopes, 2015). Basing on the
case study on an accident that happened at the mechanical workshop, the following are potential
hazards that a worker may encounter while on duty and their potential risks.
HAZARD(S) RISK FACTOR(S)
Unlabeled container (chemical burns) Pickling paste
Rushing (falling) Lack Training
Lack of Supervision
Age of the worker
Conditions of the floor
No signs and Information about a substance
(chemical burns)
Lack of Material safety data sheet
Lack of Signs and symbols
Manual handling of heavy objects (back Size of the object
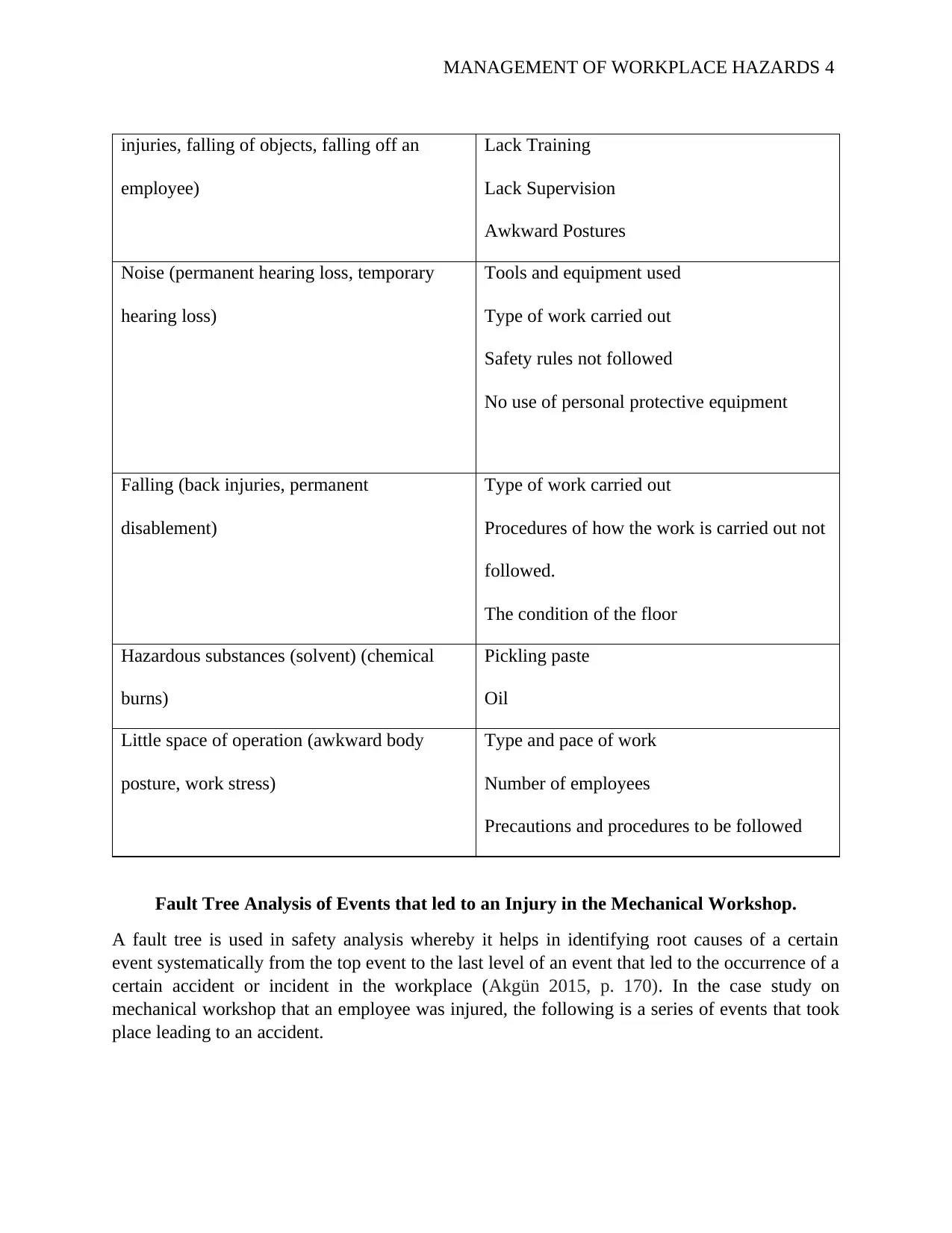
MANAGEMENT OF WORKPLACE HAZARDS 4
injuries, falling of objects, falling off an
employee)
Lack Training
Lack Supervision
Awkward Postures
Noise (permanent hearing loss, temporary
hearing loss)
Tools and equipment used
Type of work carried out
Safety rules not followed
No use of personal protective equipment
Falling (back injuries, permanent
disablement)
Type of work carried out
Procedures of how the work is carried out not
followed.
The condition of the floor
Hazardous substances (solvent) (chemical
burns)
Pickling paste
Oil
Little space of operation (awkward body
posture, work stress)
Type and pace of work
Number of employees
Precautions and procedures to be followed
Fault Tree Analysis of Events that led to an Injury in the Mechanical Workshop.
A fault tree is used in safety analysis whereby it helps in identifying root causes of a certain
event systematically from the top event to the last level of an event that led to the occurrence of a
certain accident or incident in the workplace (Akgün 2015, p. 170). In the case study on
mechanical workshop that an employee was injured, the following is a series of events that took
place leading to an accident.
injuries, falling of objects, falling off an
employee)
Lack Training
Lack Supervision
Awkward Postures
Noise (permanent hearing loss, temporary
hearing loss)
Tools and equipment used
Type of work carried out
Safety rules not followed
No use of personal protective equipment
Falling (back injuries, permanent
disablement)
Type of work carried out
Procedures of how the work is carried out not
followed.
The condition of the floor
Hazardous substances (solvent) (chemical
burns)
Pickling paste
Oil
Little space of operation (awkward body
posture, work stress)
Type and pace of work
Number of employees
Precautions and procedures to be followed
Fault Tree Analysis of Events that led to an Injury in the Mechanical Workshop.
A fault tree is used in safety analysis whereby it helps in identifying root causes of a certain
event systematically from the top event to the last level of an event that led to the occurrence of a
certain accident or incident in the workplace (Akgün 2015, p. 170). In the case study on
mechanical workshop that an employee was injured, the following is a series of events that took
place leading to an accident.
Secure Best Marks with AI Grader
Need help grading? Try our AI Grader for instant feedback on your assignments.
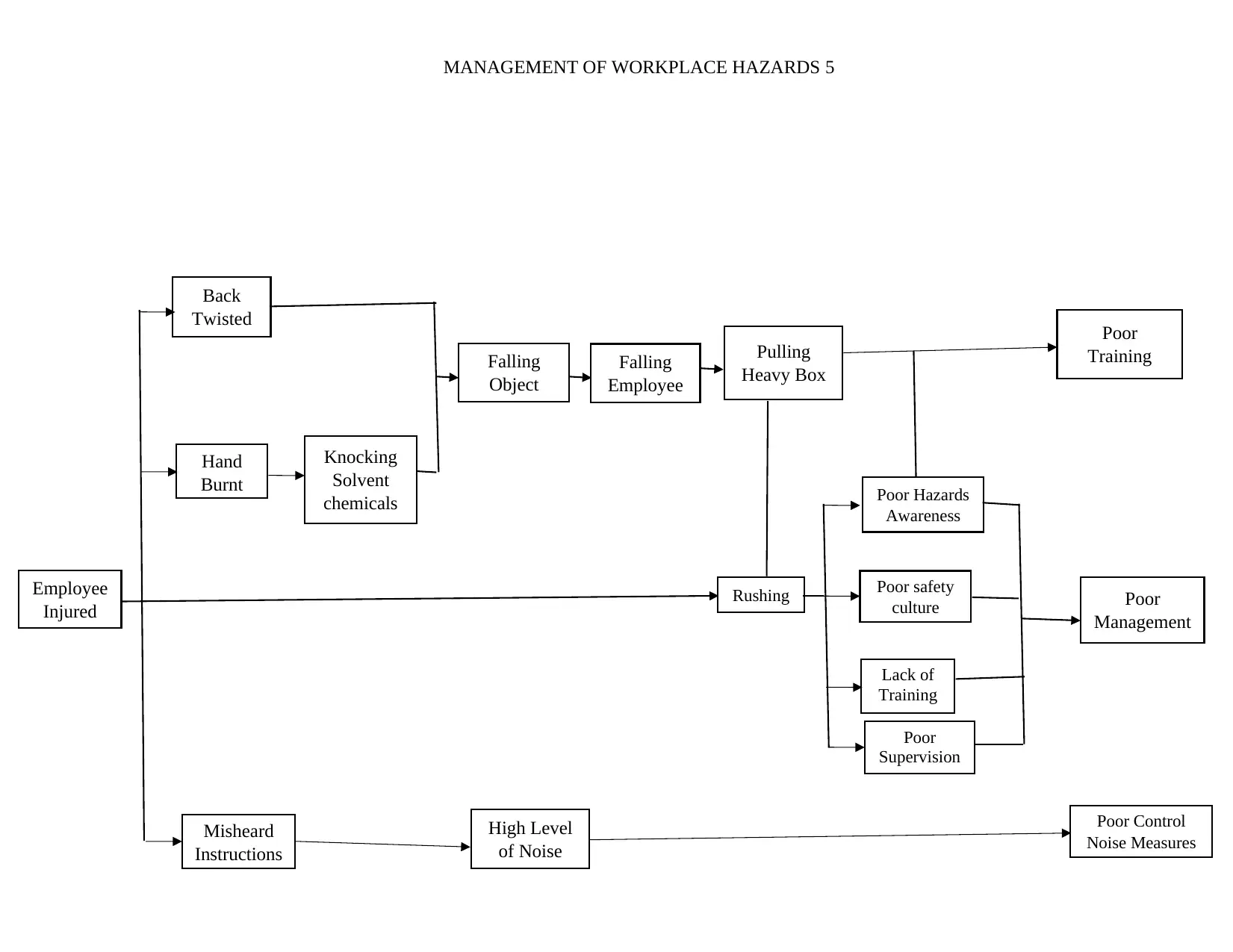
MANAGEMENT OF WORKPLACE HAZARDS 5
Back
Twisted
Rushing
Hand
Burnt
Falling
Object
Falling
Employee
Pulling
Heavy Box
Lack of
Training
Knocking
Solvent
chemicals
Poor Control
Noise Measures
High Level
of Noise
Misheard
Instructions
Employee
Injured
Poor
Training
Poor
Management
Poor
Supervision
Poor Hazards
Awareness
Poor safety
culture
Back
Twisted
Rushing
Hand
Burnt
Falling
Object
Falling
Employee
Pulling
Heavy Box
Lack of
Training
Knocking
Solvent
chemicals
Poor Control
Noise Measures
High Level
of Noise
Misheard
Instructions
Employee
Injured
Poor
Training
Poor
Management
Poor
Supervision
Poor Hazards
Awareness
Poor safety
culture
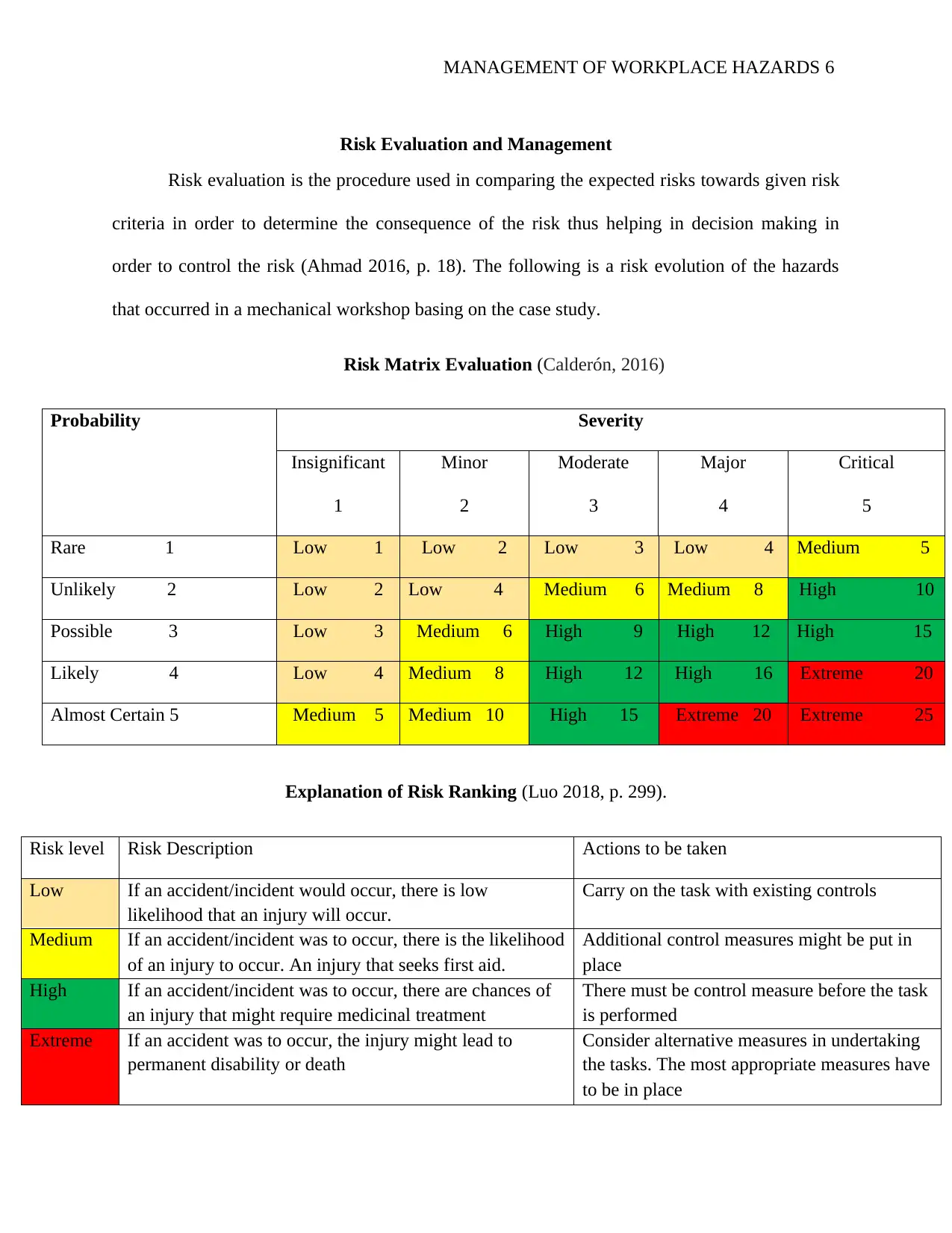
MANAGEMENT OF WORKPLACE HAZARDS 6
Risk Evaluation and Management
Risk evaluation is the procedure used in comparing the expected risks towards given risk
criteria in order to determine the consequence of the risk thus helping in decision making in
order to control the risk (Ahmad 2016, p. 18). The following is a risk evolution of the hazards
that occurred in a mechanical workshop basing on the case study.
Risk Matrix Evaluation (Calderón, 2016)
Probability Severity
Insignificant
1
Minor
2
Moderate
3
Major
4
Critical
5
Rare 1 Low 1 Low 2 Low 3 Low 4 Medium 5
Unlikely 2 Low 2 Low 4 Medium 6 Medium 8 High 10
Possible 3 Low 3 Medium 6 High 9 High 12 High 15
Likely 4 Low 4 Medium 8 High 12 High 16 Extreme 20
Almost Certain 5 Medium 5 Medium 10 High 15 Extreme 20 Extreme 25
Explanation of Risk Ranking (Luo 2018, p. 299).
Risk level Risk Description Actions to be taken
Low If an accident/incident would occur, there is low
likelihood that an injury will occur.
Carry on the task with existing controls
Medium If an accident/incident was to occur, there is the likelihood
of an injury to occur. An injury that seeks first aid.
Additional control measures might be put in
place
High If an accident/incident was to occur, there are chances of
an injury that might require medicinal treatment
There must be control measure before the task
is performed
Extreme If an accident was to occur, the injury might lead to
permanent disability or death
Consider alternative measures in undertaking
the tasks. The most appropriate measures have
to be in place
Risk Evaluation and Management
Risk evaluation is the procedure used in comparing the expected risks towards given risk
criteria in order to determine the consequence of the risk thus helping in decision making in
order to control the risk (Ahmad 2016, p. 18). The following is a risk evolution of the hazards
that occurred in a mechanical workshop basing on the case study.
Risk Matrix Evaluation (Calderón, 2016)
Probability Severity
Insignificant
1
Minor
2
Moderate
3
Major
4
Critical
5
Rare 1 Low 1 Low 2 Low 3 Low 4 Medium 5
Unlikely 2 Low 2 Low 4 Medium 6 Medium 8 High 10
Possible 3 Low 3 Medium 6 High 9 High 12 High 15
Likely 4 Low 4 Medium 8 High 12 High 16 Extreme 20
Almost Certain 5 Medium 5 Medium 10 High 15 Extreme 20 Extreme 25
Explanation of Risk Ranking (Luo 2018, p. 299).
Risk level Risk Description Actions to be taken
Low If an accident/incident would occur, there is low
likelihood that an injury will occur.
Carry on the task with existing controls
Medium If an accident/incident was to occur, there is the likelihood
of an injury to occur. An injury that seeks first aid.
Additional control measures might be put in
place
High If an accident/incident was to occur, there are chances of
an injury that might require medicinal treatment
There must be control measure before the task
is performed
Extreme If an accident was to occur, the injury might lead to
permanent disability or death
Consider alternative measures in undertaking
the tasks. The most appropriate measures have
to be in place
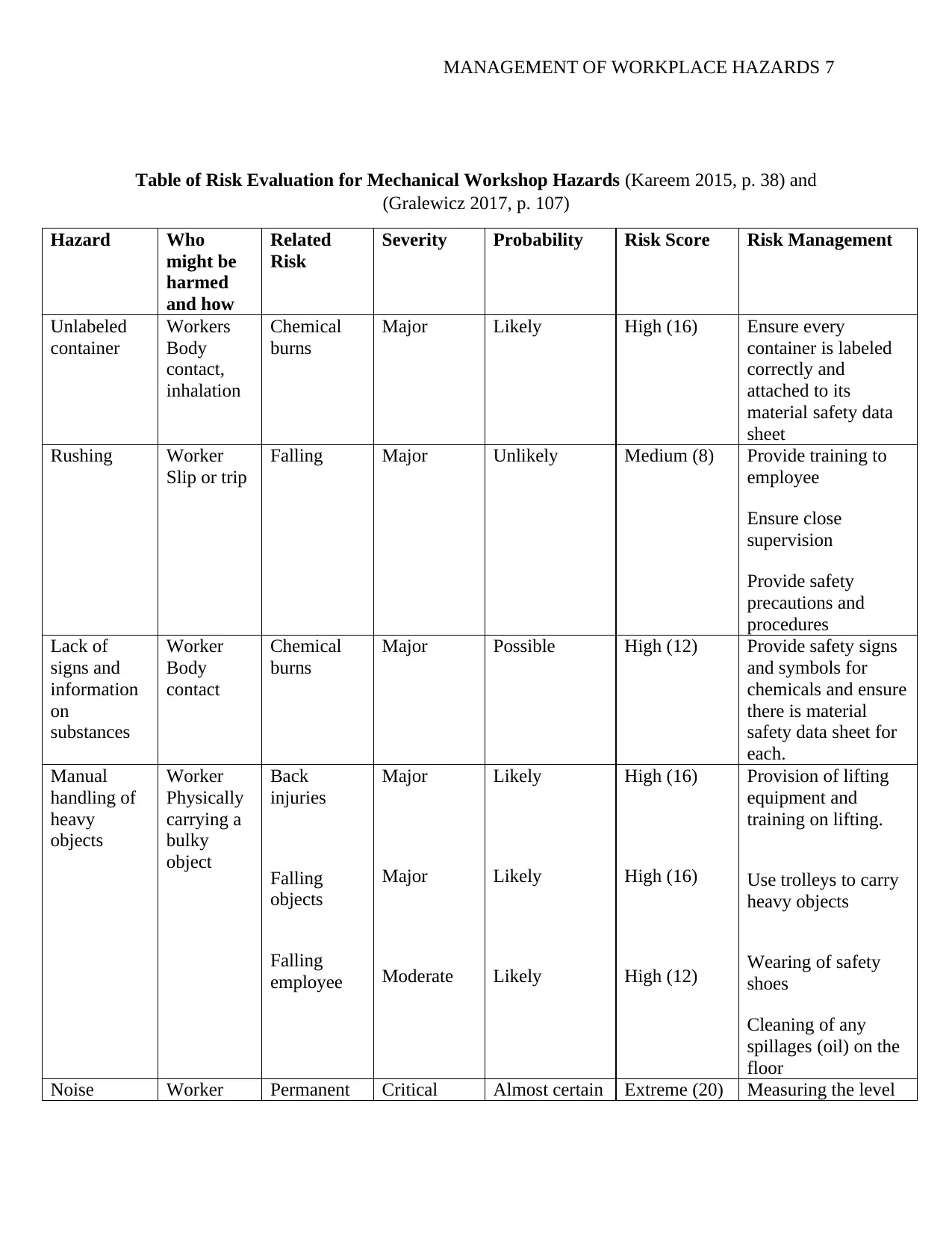
MANAGEMENT OF WORKPLACE HAZARDS 7
Table of Risk Evaluation for Mechanical Workshop Hazards (Kareem 2015, p. 38) and
(Gralewicz 2017, p. 107)
Hazard Who
might be
harmed
and how
Related
Risk
Severity Probability Risk Score Risk Management
Unlabeled
container
Workers
Body
contact,
inhalation
Chemical
burns
Major Likely High (16) Ensure every
container is labeled
correctly and
attached to its
material safety data
sheet
Rushing Worker
Slip or trip
Falling Major Unlikely Medium (8) Provide training to
employee
Ensure close
supervision
Provide safety
precautions and
procedures
Lack of
signs and
information
on
substances
Worker
Body
contact
Chemical
burns
Major Possible High (12) Provide safety signs
and symbols for
chemicals and ensure
there is material
safety data sheet for
each.
Manual
handling of
heavy
objects
Worker
Physically
carrying a
bulky
object
Back
injuries
Falling
objects
Falling
employee
Major
Major
Moderate
Likely
Likely
Likely
High (16)
High (16)
High (12)
Provision of lifting
equipment and
training on lifting.
Use trolleys to carry
heavy objects
Wearing of safety
shoes
Cleaning of any
spillages (oil) on the
floor
Noise Worker Permanent Critical Almost certain Extreme (20) Measuring the level
Table of Risk Evaluation for Mechanical Workshop Hazards (Kareem 2015, p. 38) and
(Gralewicz 2017, p. 107)
Hazard Who
might be
harmed
and how
Related
Risk
Severity Probability Risk Score Risk Management
Unlabeled
container
Workers
Body
contact,
inhalation
Chemical
burns
Major Likely High (16) Ensure every
container is labeled
correctly and
attached to its
material safety data
sheet
Rushing Worker
Slip or trip
Falling Major Unlikely Medium (8) Provide training to
employee
Ensure close
supervision
Provide safety
precautions and
procedures
Lack of
signs and
information
on
substances
Worker
Body
contact
Chemical
burns
Major Possible High (12) Provide safety signs
and symbols for
chemicals and ensure
there is material
safety data sheet for
each.
Manual
handling of
heavy
objects
Worker
Physically
carrying a
bulky
object
Back
injuries
Falling
objects
Falling
employee
Major
Major
Moderate
Likely
Likely
Likely
High (16)
High (16)
High (12)
Provision of lifting
equipment and
training on lifting.
Use trolleys to carry
heavy objects
Wearing of safety
shoes
Cleaning of any
spillages (oil) on the
floor
Noise Worker Permanent Critical Almost certain Extreme (20) Measuring the level
Paraphrase This Document
Need a fresh take? Get an instant paraphrase of this document with our AI Paraphraser

MANAGEMENT OF WORKPLACE HAZARDS 8
Exposed to
high levels
of noise
damaging
eardrum
hearing loss
Temporary
hearing loss
Major
Likely
High (16)
of noise.
Guarding machines
Isolation of noise
generating
equipment
Provision of
appropriate personal
equipment (earmuffs,
ear plugs)
Falling Worker
Slippery
floor
Back
injuries
Permanent
disablement
Major
Critical
Likely
Rare
High (16)
Medium (5)
Cleaning of any
spillages on the floor
Provision of safety
precautions and
procedures on how to
perform a particular
task
Hazardous
substances
(solvent)
Worker
Body
contact
Chemical
burns
Major Likely High (16) Provision of material
safety data sheet for
each chemical
solvent used.
Suitable labeling of
containers used
Proper storage of the
solvent containers
Little space
of operation
Worker
Congestion
Work stress
Awkward
body
posture
Insignificant
Minor
Possible
Unlikely
Low (3)
Low (4)
Provision of
adequate space of
operation to
employees
Control Measures for Hazards and Risks in the Mechanical Workshop
Hazard and risk control is a process of eliminating or minimizing the exposure of hazards
and risk to a worker to an acceptable level (Hilton 2017, p. 24). In order to manage hazards at the
mechanical workshop, the hierarchy of controls has to be observed (Connor 2017, p. 203).
MOST APPROPRIATE Elimination
Substitution
Isolation
Exposed to
high levels
of noise
damaging
eardrum
hearing loss
Temporary
hearing loss
Major
Likely
High (16)
of noise.
Guarding machines
Isolation of noise
generating
equipment
Provision of
appropriate personal
equipment (earmuffs,
ear plugs)
Falling Worker
Slippery
floor
Back
injuries
Permanent
disablement
Major
Critical
Likely
Rare
High (16)
Medium (5)
Cleaning of any
spillages on the floor
Provision of safety
precautions and
procedures on how to
perform a particular
task
Hazardous
substances
(solvent)
Worker
Body
contact
Chemical
burns
Major Likely High (16) Provision of material
safety data sheet for
each chemical
solvent used.
Suitable labeling of
containers used
Proper storage of the
solvent containers
Little space
of operation
Worker
Congestion
Work stress
Awkward
body
posture
Insignificant
Minor
Possible
Unlikely
Low (3)
Low (4)
Provision of
adequate space of
operation to
employees
Control Measures for Hazards and Risks in the Mechanical Workshop
Hazard and risk control is a process of eliminating or minimizing the exposure of hazards
and risk to a worker to an acceptable level (Hilton 2017, p. 24). In order to manage hazards at the
mechanical workshop, the hierarchy of controls has to be observed (Connor 2017, p. 203).
MOST APPROPRIATE Elimination
Substitution
Isolation
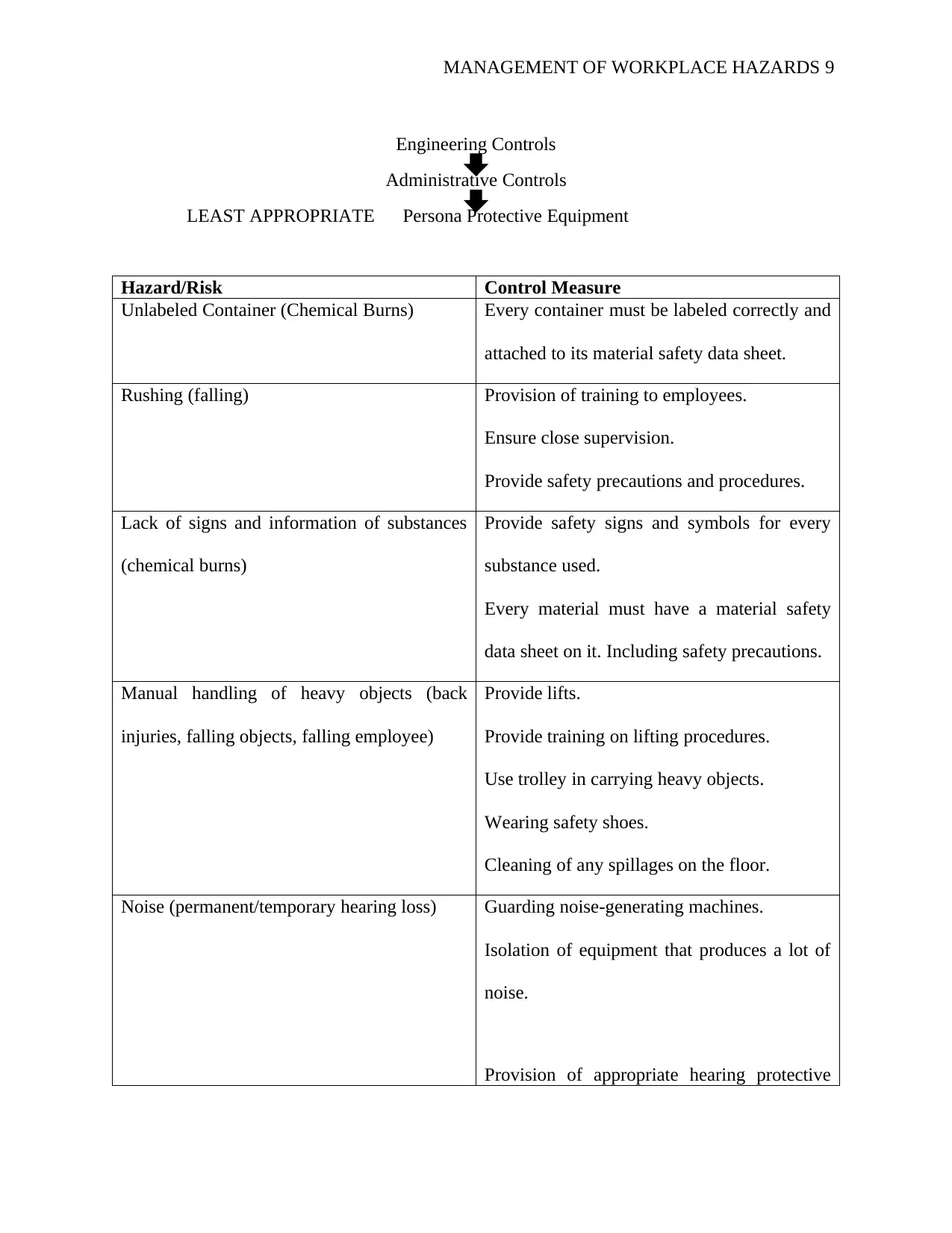
MANAGEMENT OF WORKPLACE HAZARDS 9
Engineering Controls
Administrative Controls
LEAST APPROPRIATE Persona Protective Equipment
Hazard/Risk Control Measure
Unlabeled Container (Chemical Burns) Every container must be labeled correctly and
attached to its material safety data sheet.
Rushing (falling) Provision of training to employees.
Ensure close supervision.
Provide safety precautions and procedures.
Lack of signs and information of substances
(chemical burns)
Provide safety signs and symbols for every
substance used.
Every material must have a material safety
data sheet on it. Including safety precautions.
Manual handling of heavy objects (back
injuries, falling objects, falling employee)
Provide lifts.
Provide training on lifting procedures.
Use trolley in carrying heavy objects.
Wearing safety shoes.
Cleaning of any spillages on the floor.
Noise (permanent/temporary hearing loss) Guarding noise-generating machines.
Isolation of equipment that produces a lot of
noise.
Provision of appropriate hearing protective
Engineering Controls
Administrative Controls
LEAST APPROPRIATE Persona Protective Equipment
Hazard/Risk Control Measure
Unlabeled Container (Chemical Burns) Every container must be labeled correctly and
attached to its material safety data sheet.
Rushing (falling) Provision of training to employees.
Ensure close supervision.
Provide safety precautions and procedures.
Lack of signs and information of substances
(chemical burns)
Provide safety signs and symbols for every
substance used.
Every material must have a material safety
data sheet on it. Including safety precautions.
Manual handling of heavy objects (back
injuries, falling objects, falling employee)
Provide lifts.
Provide training on lifting procedures.
Use trolley in carrying heavy objects.
Wearing safety shoes.
Cleaning of any spillages on the floor.
Noise (permanent/temporary hearing loss) Guarding noise-generating machines.
Isolation of equipment that produces a lot of
noise.
Provision of appropriate hearing protective
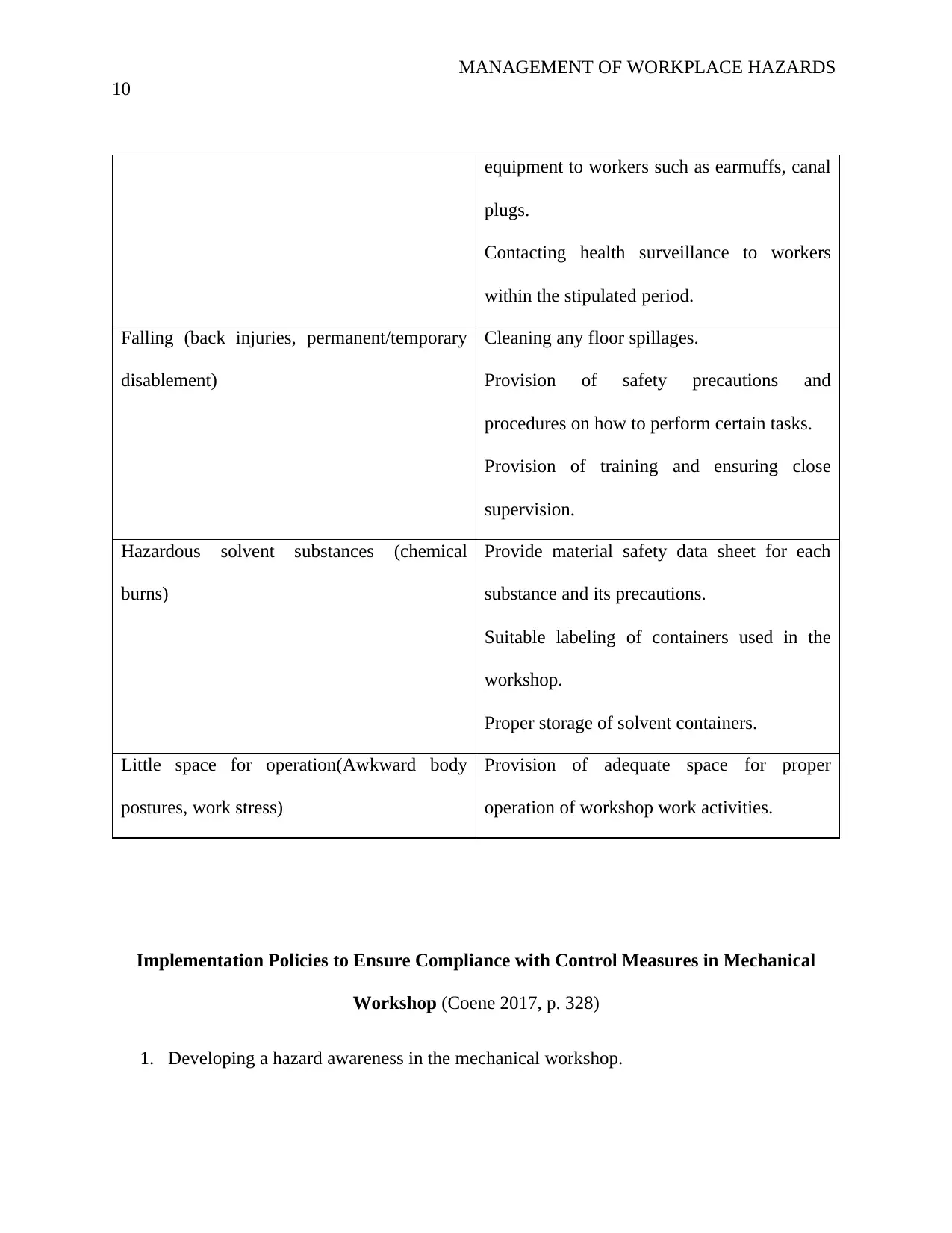
MANAGEMENT OF WORKPLACE HAZARDS
10
equipment to workers such as earmuffs, canal
plugs.
Contacting health surveillance to workers
within the stipulated period.
Falling (back injuries, permanent/temporary
disablement)
Cleaning any floor spillages.
Provision of safety precautions and
procedures on how to perform certain tasks.
Provision of training and ensuring close
supervision.
Hazardous solvent substances (chemical
burns)
Provide material safety data sheet for each
substance and its precautions.
Suitable labeling of containers used in the
workshop.
Proper storage of solvent containers.
Little space for operation(Awkward body
postures, work stress)
Provision of adequate space for proper
operation of workshop work activities.
Implementation Policies to Ensure Compliance with Control Measures in Mechanical
Workshop (Coene 2017, p. 328)
1. Developing a hazard awareness in the mechanical workshop.
10
equipment to workers such as earmuffs, canal
plugs.
Contacting health surveillance to workers
within the stipulated period.
Falling (back injuries, permanent/temporary
disablement)
Cleaning any floor spillages.
Provision of safety precautions and
procedures on how to perform certain tasks.
Provision of training and ensuring close
supervision.
Hazardous solvent substances (chemical
burns)
Provide material safety data sheet for each
substance and its precautions.
Suitable labeling of containers used in the
workshop.
Proper storage of solvent containers.
Little space for operation(Awkward body
postures, work stress)
Provision of adequate space for proper
operation of workshop work activities.
Implementation Policies to Ensure Compliance with Control Measures in Mechanical
Workshop (Coene 2017, p. 328)
1. Developing a hazard awareness in the mechanical workshop.
Secure Best Marks with AI Grader
Need help grading? Try our AI Grader for instant feedback on your assignments.

MANAGEMENT OF WORKPLACE HAZARDS
11
Action: Safety Officer certified in training.
Timing: Before the commencement of next activities in the workshop, henceforth.
2. Ensure adequate space provision to enhance work activities in the workshop and avoid
congestion.
Action: Construction Designing Engineer
Timing: Before the next workshop design
3. Provide first aid boxes in the mechanical workshop.
Action: Manager.
Timing: Before work activities commence.
4. Ensure there is close supervision of employees.
Action: Supervisor.
Timing: In the next work activities carried out.
5. Ensure adequate training for employees.
Action: Training Safety Officer.
Timing: Before the next activities in the workshop, and continuously after a stipulated period.
6. Examine the feasibility of installation of noise measuring equipment.
Action: Safety Engineer.
11
Action: Safety Officer certified in training.
Timing: Before the commencement of next activities in the workshop, henceforth.
2. Ensure adequate space provision to enhance work activities in the workshop and avoid
congestion.
Action: Construction Designing Engineer
Timing: Before the next workshop design
3. Provide first aid boxes in the mechanical workshop.
Action: Manager.
Timing: Before work activities commence.
4. Ensure there is close supervision of employees.
Action: Supervisor.
Timing: In the next work activities carried out.
5. Ensure adequate training for employees.
Action: Training Safety Officer.
Timing: Before the next activities in the workshop, and continuously after a stipulated period.
6. Examine the feasibility of installation of noise measuring equipment.
Action: Safety Engineer.
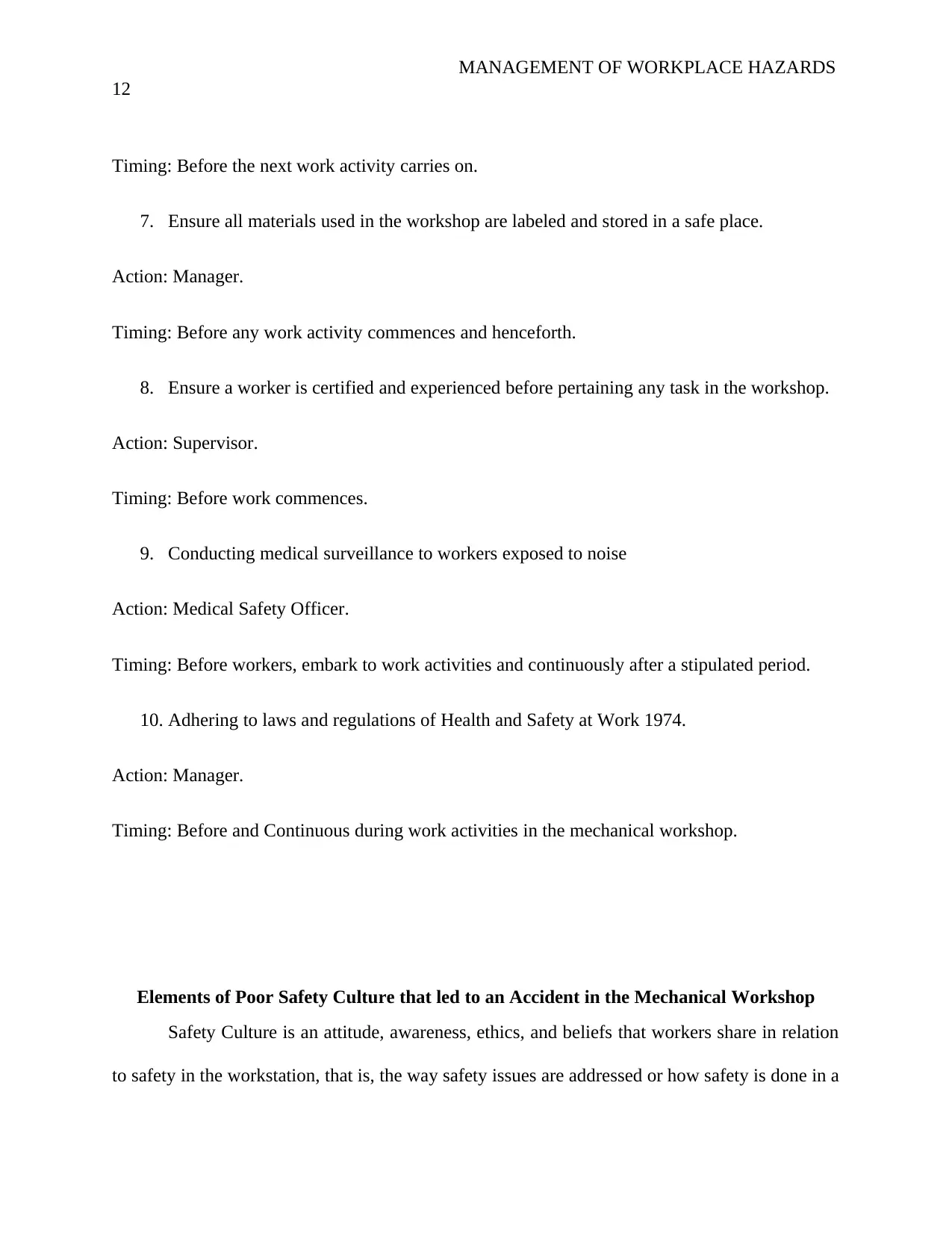
MANAGEMENT OF WORKPLACE HAZARDS
12
Timing: Before the next work activity carries on.
7. Ensure all materials used in the workshop are labeled and stored in a safe place.
Action: Manager.
Timing: Before any work activity commences and henceforth.
8. Ensure a worker is certified and experienced before pertaining any task in the workshop.
Action: Supervisor.
Timing: Before work commences.
9. Conducting medical surveillance to workers exposed to noise
Action: Medical Safety Officer.
Timing: Before workers, embark to work activities and continuously after a stipulated period.
10. Adhering to laws and regulations of Health and Safety at Work 1974.
Action: Manager.
Timing: Before and Continuous during work activities in the mechanical workshop.
Elements of Poor Safety Culture that led to an Accident in the Mechanical Workshop
Safety Culture is an attitude, awareness, ethics, and beliefs that workers share in relation
to safety in the workstation, that is, the way safety issues are addressed or how safety is done in a
12
Timing: Before the next work activity carries on.
7. Ensure all materials used in the workshop are labeled and stored in a safe place.
Action: Manager.
Timing: Before any work activity commences and henceforth.
8. Ensure a worker is certified and experienced before pertaining any task in the workshop.
Action: Supervisor.
Timing: Before work commences.
9. Conducting medical surveillance to workers exposed to noise
Action: Medical Safety Officer.
Timing: Before workers, embark to work activities and continuously after a stipulated period.
10. Adhering to laws and regulations of Health and Safety at Work 1974.
Action: Manager.
Timing: Before and Continuous during work activities in the mechanical workshop.
Elements of Poor Safety Culture that led to an Accident in the Mechanical Workshop
Safety Culture is an attitude, awareness, ethics, and beliefs that workers share in relation
to safety in the workstation, that is, the way safety issues are addressed or how safety is done in a
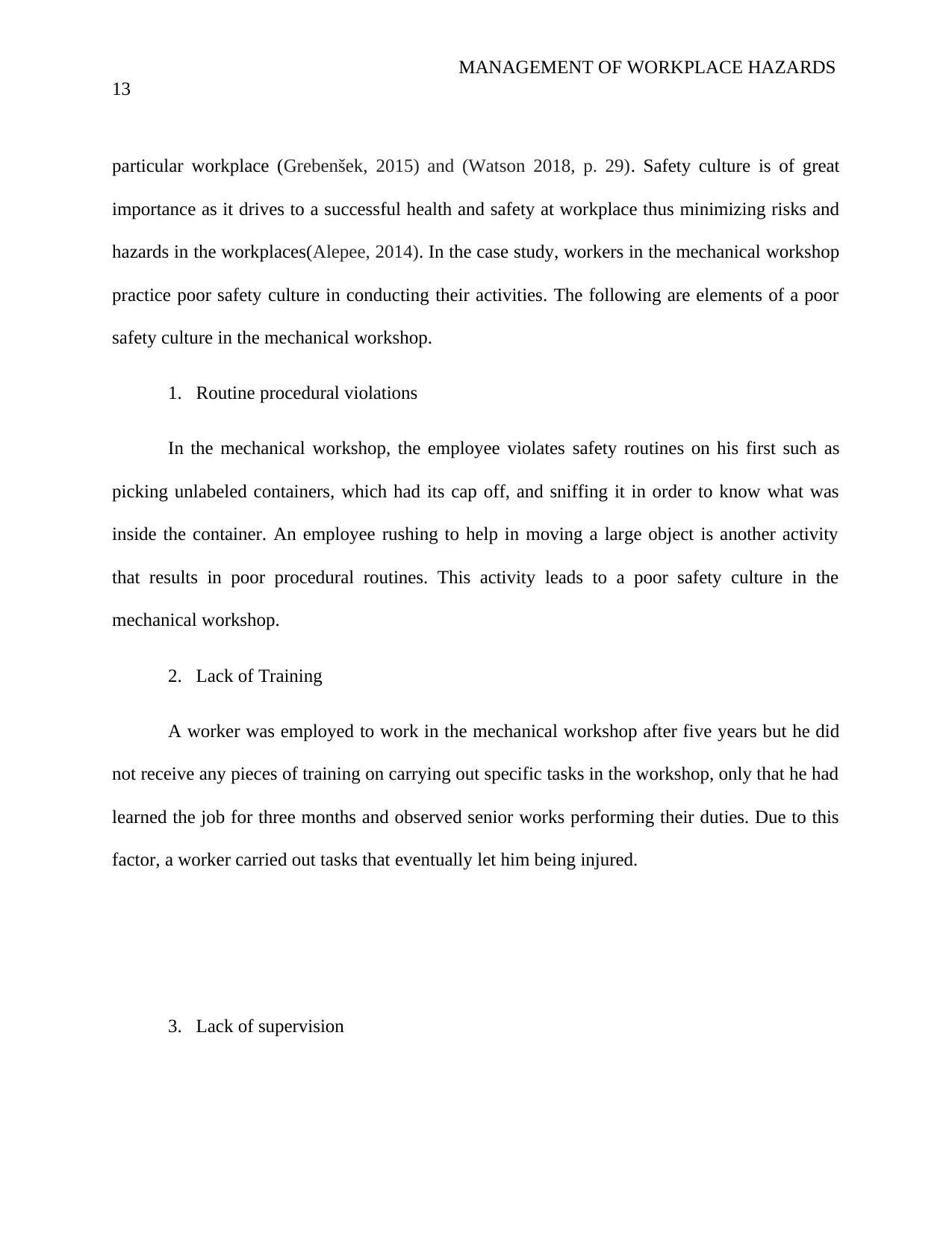
MANAGEMENT OF WORKPLACE HAZARDS
13
particular workplace (Grebenšek, 2015) and (Watson 2018, p. 29). Safety culture is of great
importance as it drives to a successful health and safety at workplace thus minimizing risks and
hazards in the workplaces(Alepee, 2014). In the case study, workers in the mechanical workshop
practice poor safety culture in conducting their activities. The following are elements of a poor
safety culture in the mechanical workshop.
1. Routine procedural violations
In the mechanical workshop, the employee violates safety routines on his first such as
picking unlabeled containers, which had its cap off, and sniffing it in order to know what was
inside the container. An employee rushing to help in moving a large object is another activity
that results in poor procedural routines. This activity leads to a poor safety culture in the
mechanical workshop.
2. Lack of Training
A worker was employed to work in the mechanical workshop after five years but he did
not receive any pieces of training on carrying out specific tasks in the workshop, only that he had
learned the job for three months and observed senior works performing their duties. Due to this
factor, a worker carried out tasks that eventually let him being injured.
3. Lack of supervision
13
particular workplace (Grebenšek, 2015) and (Watson 2018, p. 29). Safety culture is of great
importance as it drives to a successful health and safety at workplace thus minimizing risks and
hazards in the workplaces(Alepee, 2014). In the case study, workers in the mechanical workshop
practice poor safety culture in conducting their activities. The following are elements of a poor
safety culture in the mechanical workshop.
1. Routine procedural violations
In the mechanical workshop, the employee violates safety routines on his first such as
picking unlabeled containers, which had its cap off, and sniffing it in order to know what was
inside the container. An employee rushing to help in moving a large object is another activity
that results in poor procedural routines. This activity leads to a poor safety culture in the
mechanical workshop.
2. Lack of Training
A worker was employed to work in the mechanical workshop after five years but he did
not receive any pieces of training on carrying out specific tasks in the workshop, only that he had
learned the job for three months and observed senior works performing their duties. Due to this
factor, a worker carried out tasks that eventually let him being injured.
3. Lack of supervision
Paraphrase This Document
Need a fresh take? Get an instant paraphrase of this document with our AI Paraphraser
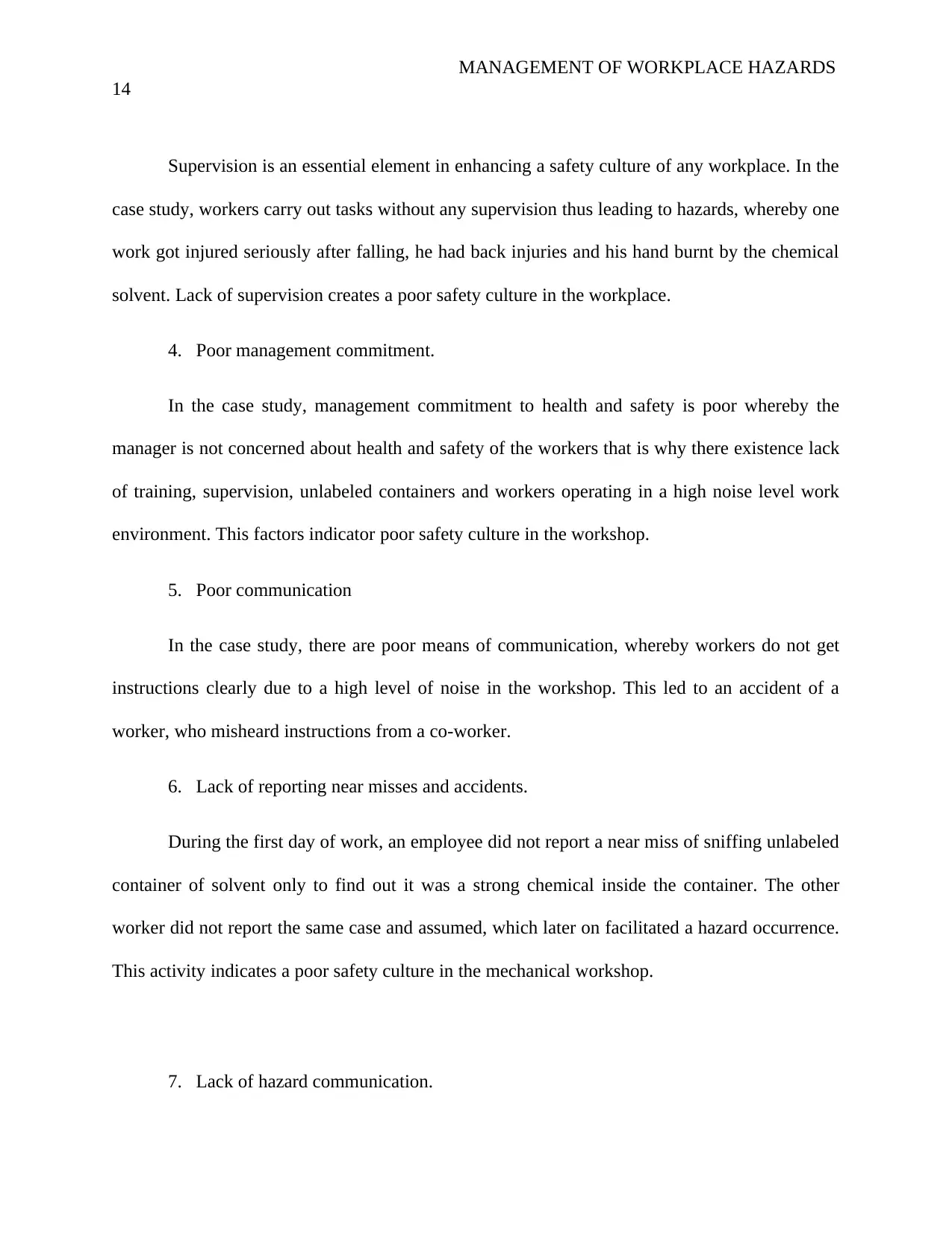
MANAGEMENT OF WORKPLACE HAZARDS
14
Supervision is an essential element in enhancing a safety culture of any workplace. In the
case study, workers carry out tasks without any supervision thus leading to hazards, whereby one
work got injured seriously after falling, he had back injuries and his hand burnt by the chemical
solvent. Lack of supervision creates a poor safety culture in the workplace.
4. Poor management commitment.
In the case study, management commitment to health and safety is poor whereby the
manager is not concerned about health and safety of the workers that is why there existence lack
of training, supervision, unlabeled containers and workers operating in a high noise level work
environment. This factors indicator poor safety culture in the workshop.
5. Poor communication
In the case study, there are poor means of communication, whereby workers do not get
instructions clearly due to a high level of noise in the workshop. This led to an accident of a
worker, who misheard instructions from a co-worker.
6. Lack of reporting near misses and accidents.
During the first day of work, an employee did not report a near miss of sniffing unlabeled
container of solvent only to find out it was a strong chemical inside the container. The other
worker did not report the same case and assumed, which later on facilitated a hazard occurrence.
This activity indicates a poor safety culture in the mechanical workshop.
7. Lack of hazard communication.
14
Supervision is an essential element in enhancing a safety culture of any workplace. In the
case study, workers carry out tasks without any supervision thus leading to hazards, whereby one
work got injured seriously after falling, he had back injuries and his hand burnt by the chemical
solvent. Lack of supervision creates a poor safety culture in the workplace.
4. Poor management commitment.
In the case study, management commitment to health and safety is poor whereby the
manager is not concerned about health and safety of the workers that is why there existence lack
of training, supervision, unlabeled containers and workers operating in a high noise level work
environment. This factors indicator poor safety culture in the workshop.
5. Poor communication
In the case study, there are poor means of communication, whereby workers do not get
instructions clearly due to a high level of noise in the workshop. This led to an accident of a
worker, who misheard instructions from a co-worker.
6. Lack of reporting near misses and accidents.
During the first day of work, an employee did not report a near miss of sniffing unlabeled
container of solvent only to find out it was a strong chemical inside the container. The other
worker did not report the same case and assumed, which later on facilitated a hazard occurrence.
This activity indicates a poor safety culture in the mechanical workshop.
7. Lack of hazard communication.
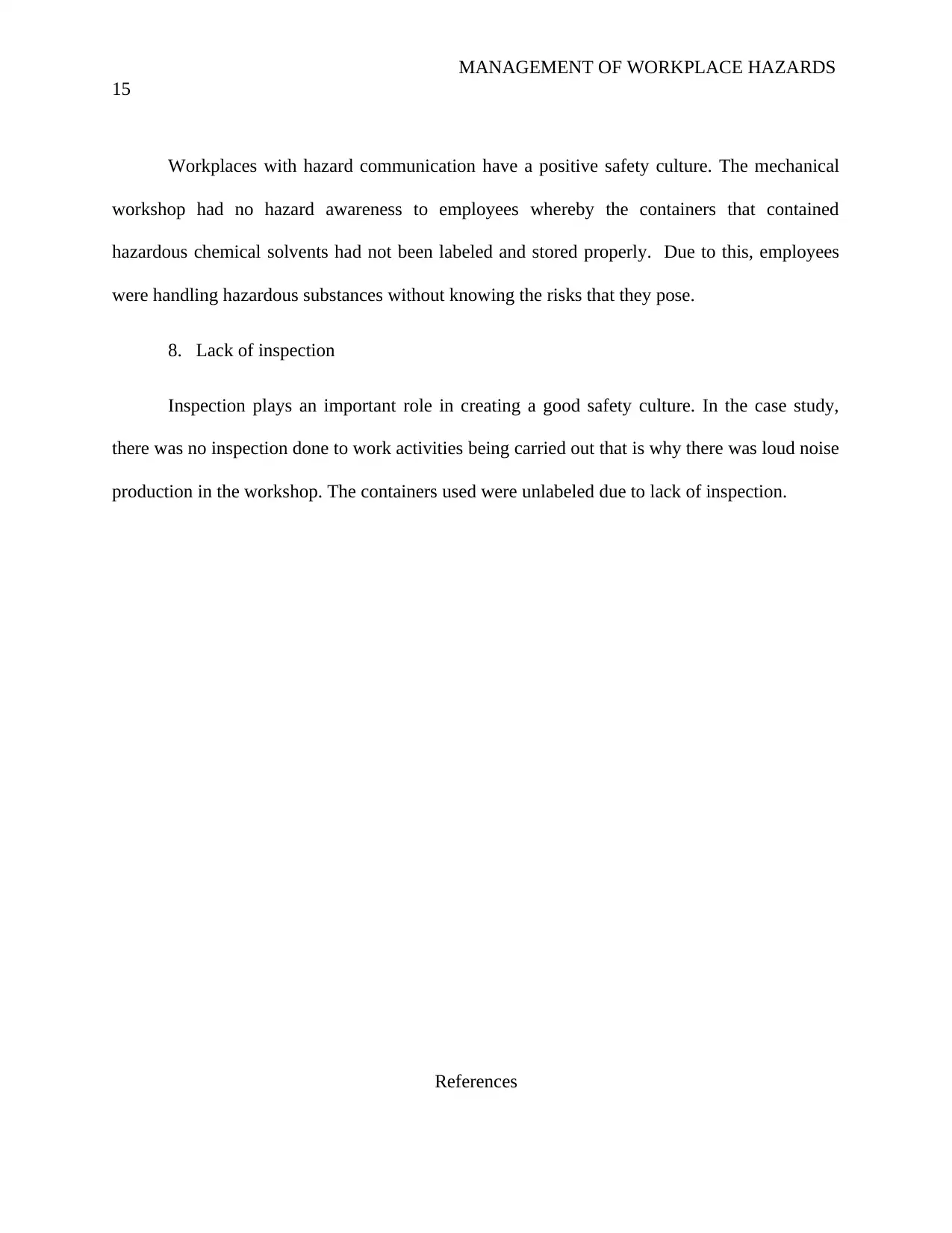
MANAGEMENT OF WORKPLACE HAZARDS
15
Workplaces with hazard communication have a positive safety culture. The mechanical
workshop had no hazard awareness to employees whereby the containers that contained
hazardous chemical solvents had not been labeled and stored properly. Due to this, employees
were handling hazardous substances without knowing the risks that they pose.
8. Lack of inspection
Inspection plays an important role in creating a good safety culture. In the case study,
there was no inspection done to work activities being carried out that is why there was loud noise
production in the workshop. The containers used were unlabeled due to lack of inspection.
References
15
Workplaces with hazard communication have a positive safety culture. The mechanical
workshop had no hazard awareness to employees whereby the containers that contained
hazardous chemical solvents had not been labeled and stored properly. Due to this, employees
were handling hazardous substances without knowing the risks that they pose.
8. Lack of inspection
Inspection plays an important role in creating a good safety culture. In the case study,
there was no inspection done to work activities being carried out that is why there was loud noise
production in the workshop. The containers used were unlabeled due to lack of inspection.
References
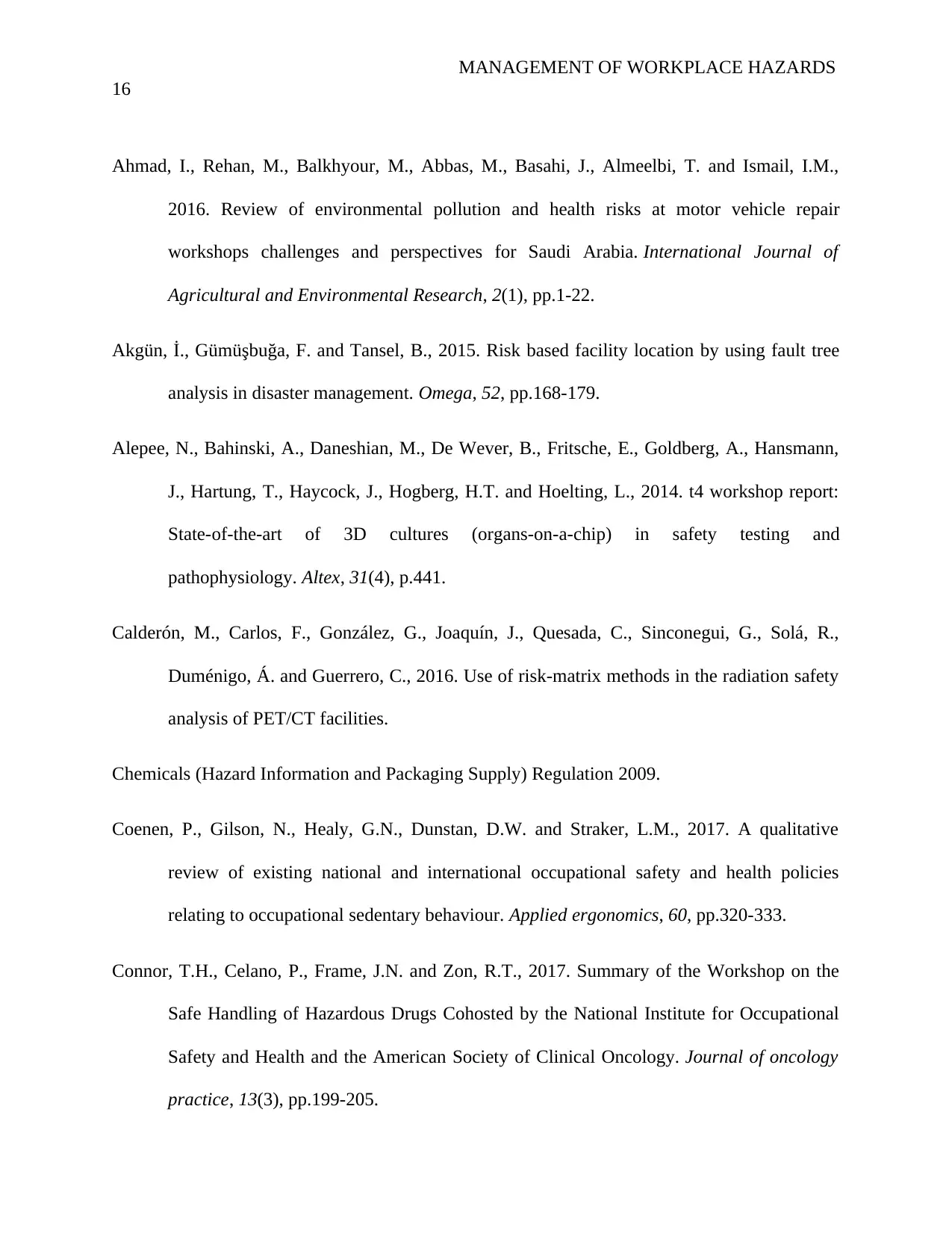
MANAGEMENT OF WORKPLACE HAZARDS
16
Ahmad, I., Rehan, M., Balkhyour, M., Abbas, M., Basahi, J., Almeelbi, T. and Ismail, I.M.,
2016. Review of environmental pollution and health risks at motor vehicle repair
workshops challenges and perspectives for Saudi Arabia. International Journal of
Agricultural and Environmental Research, 2(1), pp.1-22.
Akgün, İ., Gümüşbuğa, F. and Tansel, B., 2015. Risk based facility location by using fault tree
analysis in disaster management. Omega, 52, pp.168-179.
Alepee, N., Bahinski, A., Daneshian, M., De Wever, B., Fritsche, E., Goldberg, A., Hansmann,
J., Hartung, T., Haycock, J., Hogberg, H.T. and Hoelting, L., 2014. t4 workshop report:
State-of-the-art of 3D cultures (organs-on-a-chip) in safety testing and
pathophysiology. Altex, 31(4), p.441.
Calderón, M., Carlos, F., González, G., Joaquín, J., Quesada, C., Sinconegui, G., Solá, R.,
Duménigo, Á. and Guerrero, C., 2016. Use of risk-matrix methods in the radiation safety
analysis of PET/CT facilities.
Chemicals (Hazard Information and Packaging Supply) Regulation 2009.
Coenen, P., Gilson, N., Healy, G.N., Dunstan, D.W. and Straker, L.M., 2017. A qualitative
review of existing national and international occupational safety and health policies
relating to occupational sedentary behaviour. Applied ergonomics, 60, pp.320-333.
Connor, T.H., Celano, P., Frame, J.N. and Zon, R.T., 2017. Summary of the Workshop on the
Safe Handling of Hazardous Drugs Cohosted by the National Institute for Occupational
Safety and Health and the American Society of Clinical Oncology. Journal of oncology
practice, 13(3), pp.199-205.
16
Ahmad, I., Rehan, M., Balkhyour, M., Abbas, M., Basahi, J., Almeelbi, T. and Ismail, I.M.,
2016. Review of environmental pollution and health risks at motor vehicle repair
workshops challenges and perspectives for Saudi Arabia. International Journal of
Agricultural and Environmental Research, 2(1), pp.1-22.
Akgün, İ., Gümüşbuğa, F. and Tansel, B., 2015. Risk based facility location by using fault tree
analysis in disaster management. Omega, 52, pp.168-179.
Alepee, N., Bahinski, A., Daneshian, M., De Wever, B., Fritsche, E., Goldberg, A., Hansmann,
J., Hartung, T., Haycock, J., Hogberg, H.T. and Hoelting, L., 2014. t4 workshop report:
State-of-the-art of 3D cultures (organs-on-a-chip) in safety testing and
pathophysiology. Altex, 31(4), p.441.
Calderón, M., Carlos, F., González, G., Joaquín, J., Quesada, C., Sinconegui, G., Solá, R.,
Duménigo, Á. and Guerrero, C., 2016. Use of risk-matrix methods in the radiation safety
analysis of PET/CT facilities.
Chemicals (Hazard Information and Packaging Supply) Regulation 2009.
Coenen, P., Gilson, N., Healy, G.N., Dunstan, D.W. and Straker, L.M., 2017. A qualitative
review of existing national and international occupational safety and health policies
relating to occupational sedentary behaviour. Applied ergonomics, 60, pp.320-333.
Connor, T.H., Celano, P., Frame, J.N. and Zon, R.T., 2017. Summary of the Workshop on the
Safe Handling of Hazardous Drugs Cohosted by the National Institute for Occupational
Safety and Health and the American Society of Clinical Oncology. Journal of oncology
practice, 13(3), pp.199-205.
Secure Best Marks with AI Grader
Need help grading? Try our AI Grader for instant feedback on your assignments.
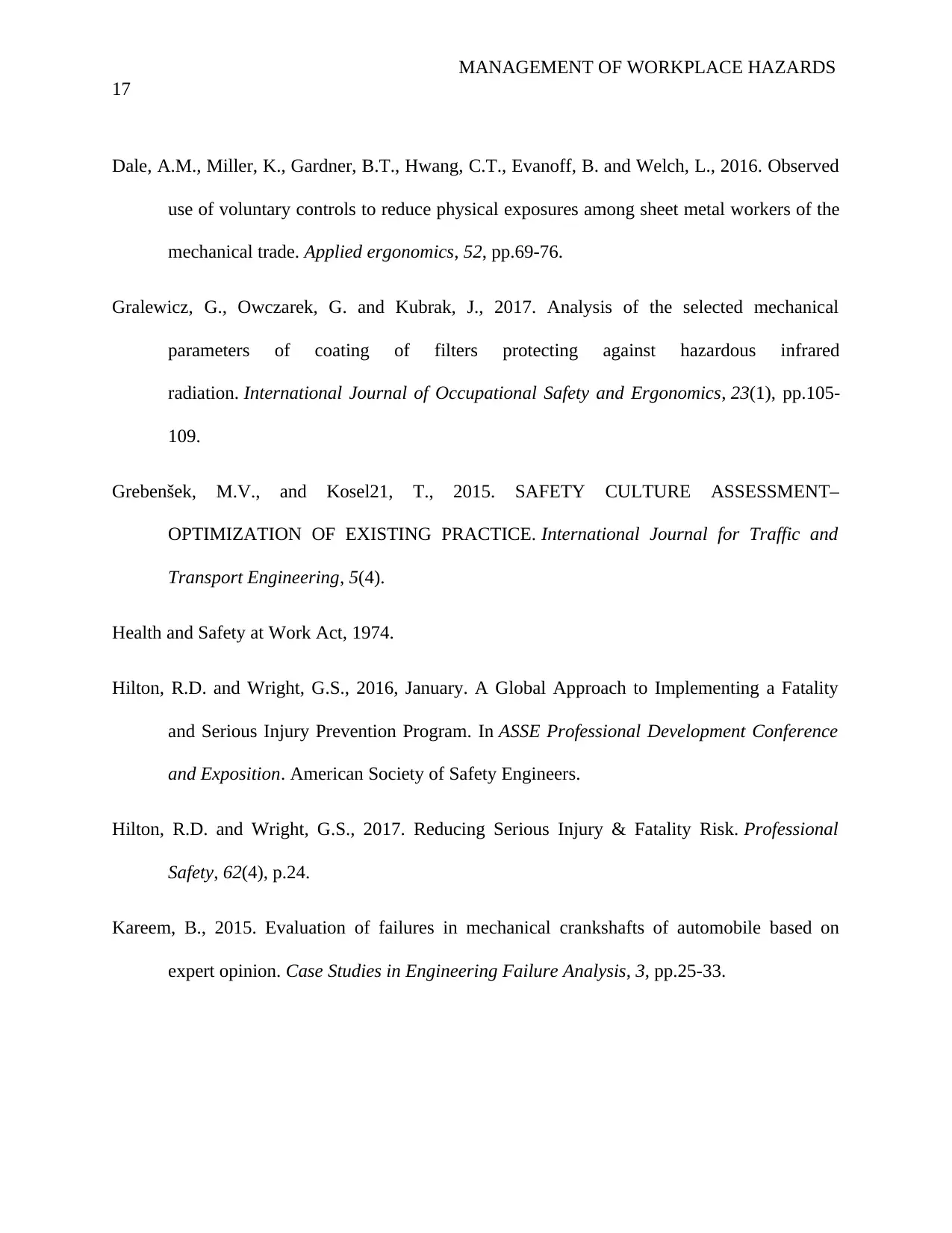
MANAGEMENT OF WORKPLACE HAZARDS
17
Dale, A.M., Miller, K., Gardner, B.T., Hwang, C.T., Evanoff, B. and Welch, L., 2016. Observed
use of voluntary controls to reduce physical exposures among sheet metal workers of the
mechanical trade. Applied ergonomics, 52, pp.69-76.
Gralewicz, G., Owczarek, G. and Kubrak, J., 2017. Analysis of the selected mechanical
parameters of coating of filters protecting against hazardous infrared
radiation. International Journal of Occupational Safety and Ergonomics, 23(1), pp.105-
109.
Grebenšek, M.V., and Kosel21, T., 2015. SAFETY CULTURE ASSESSMENT–
OPTIMIZATION OF EXISTING PRACTICE. International Journal for Traffic and
Transport Engineering, 5(4).
Health and Safety at Work Act, 1974.
Hilton, R.D. and Wright, G.S., 2016, January. A Global Approach to Implementing a Fatality
and Serious Injury Prevention Program. In ASSE Professional Development Conference
and Exposition. American Society of Safety Engineers.
Hilton, R.D. and Wright, G.S., 2017. Reducing Serious Injury & Fatality Risk. Professional
Safety, 62(4), p.24.
Kareem, B., 2015. Evaluation of failures in mechanical crankshafts of automobile based on
expert opinion. Case Studies in Engineering Failure Analysis, 3, pp.25-33.
17
Dale, A.M., Miller, K., Gardner, B.T., Hwang, C.T., Evanoff, B. and Welch, L., 2016. Observed
use of voluntary controls to reduce physical exposures among sheet metal workers of the
mechanical trade. Applied ergonomics, 52, pp.69-76.
Gralewicz, G., Owczarek, G. and Kubrak, J., 2017. Analysis of the selected mechanical
parameters of coating of filters protecting against hazardous infrared
radiation. International Journal of Occupational Safety and Ergonomics, 23(1), pp.105-
109.
Grebenšek, M.V., and Kosel21, T., 2015. SAFETY CULTURE ASSESSMENT–
OPTIMIZATION OF EXISTING PRACTICE. International Journal for Traffic and
Transport Engineering, 5(4).
Health and Safety at Work Act, 1974.
Hilton, R.D. and Wright, G.S., 2016, January. A Global Approach to Implementing a Fatality
and Serious Injury Prevention Program. In ASSE Professional Development Conference
and Exposition. American Society of Safety Engineers.
Hilton, R.D. and Wright, G.S., 2017. Reducing Serious Injury & Fatality Risk. Professional
Safety, 62(4), p.24.
Kareem, B., 2015. Evaluation of failures in mechanical crankshafts of automobile based on
expert opinion. Case Studies in Engineering Failure Analysis, 3, pp.25-33.
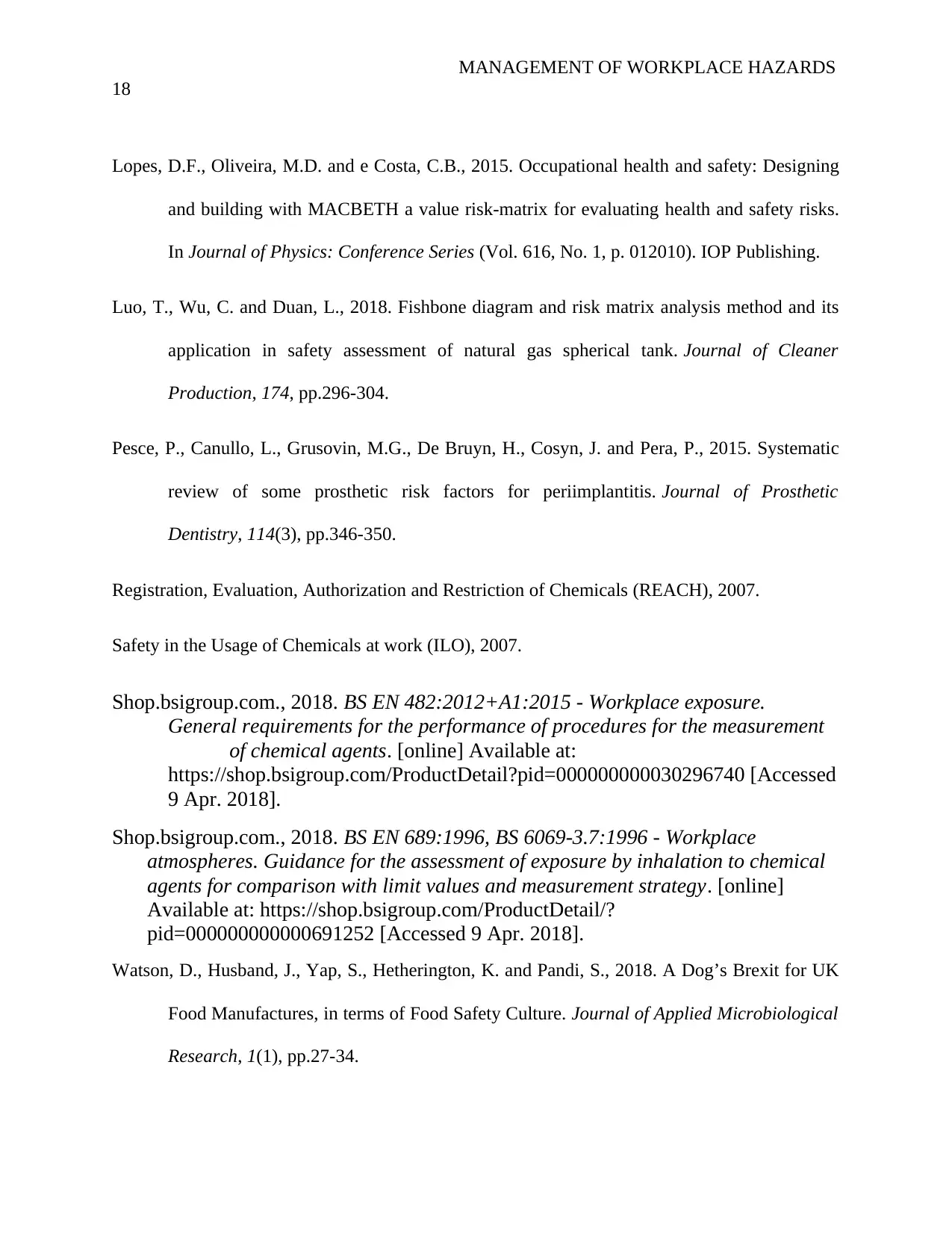
MANAGEMENT OF WORKPLACE HAZARDS
18
Lopes, D.F., Oliveira, M.D. and e Costa, C.B., 2015. Occupational health and safety: Designing
and building with MACBETH a value risk-matrix for evaluating health and safety risks.
In Journal of Physics: Conference Series (Vol. 616, No. 1, p. 012010). IOP Publishing.
Luo, T., Wu, C. and Duan, L., 2018. Fishbone diagram and risk matrix analysis method and its
application in safety assessment of natural gas spherical tank. Journal of Cleaner
Production, 174, pp.296-304.
Pesce, P., Canullo, L., Grusovin, M.G., De Bruyn, H., Cosyn, J. and Pera, P., 2015. Systematic
review of some prosthetic risk factors for periimplantitis. Journal of Prosthetic
Dentistry, 114(3), pp.346-350.
Registration, Evaluation, Authorization and Restriction of Chemicals (REACH), 2007.
Safety in the Usage of Chemicals at work (ILO), 2007.
Shop.bsigroup.com., 2018. BS EN 482:2012+A1:2015 - Workplace exposure.
General requirements for the performance of procedures for the measurement
of chemical agents. [online] Available at:
https://shop.bsigroup.com/ProductDetail?pid=000000000030296740 [Accessed
9 Apr. 2018].
Shop.bsigroup.com., 2018. BS EN 689:1996, BS 6069-3.7:1996 - Workplace
atmospheres. Guidance for the assessment of exposure by inhalation to chemical
agents for comparison with limit values and measurement strategy. [online]
Available at: https://shop.bsigroup.com/ProductDetail/?
pid=000000000000691252 [Accessed 9 Apr. 2018].
Watson, D., Husband, J., Yap, S., Hetherington, K. and Pandi, S., 2018. A Dog’s Brexit for UK
Food Manufactures, in terms of Food Safety Culture. Journal of Applied Microbiological
Research, 1(1), pp.27-34.
18
Lopes, D.F., Oliveira, M.D. and e Costa, C.B., 2015. Occupational health and safety: Designing
and building with MACBETH a value risk-matrix for evaluating health and safety risks.
In Journal of Physics: Conference Series (Vol. 616, No. 1, p. 012010). IOP Publishing.
Luo, T., Wu, C. and Duan, L., 2018. Fishbone diagram and risk matrix analysis method and its
application in safety assessment of natural gas spherical tank. Journal of Cleaner
Production, 174, pp.296-304.
Pesce, P., Canullo, L., Grusovin, M.G., De Bruyn, H., Cosyn, J. and Pera, P., 2015. Systematic
review of some prosthetic risk factors for periimplantitis. Journal of Prosthetic
Dentistry, 114(3), pp.346-350.
Registration, Evaluation, Authorization and Restriction of Chemicals (REACH), 2007.
Safety in the Usage of Chemicals at work (ILO), 2007.
Shop.bsigroup.com., 2018. BS EN 482:2012+A1:2015 - Workplace exposure.
General requirements for the performance of procedures for the measurement
of chemical agents. [online] Available at:
https://shop.bsigroup.com/ProductDetail?pid=000000000030296740 [Accessed
9 Apr. 2018].
Shop.bsigroup.com., 2018. BS EN 689:1996, BS 6069-3.7:1996 - Workplace
atmospheres. Guidance for the assessment of exposure by inhalation to chemical
agents for comparison with limit values and measurement strategy. [online]
Available at: https://shop.bsigroup.com/ProductDetail/?
pid=000000000000691252 [Accessed 9 Apr. 2018].
Watson, D., Husband, J., Yap, S., Hetherington, K. and Pandi, S., 2018. A Dog’s Brexit for UK
Food Manufactures, in terms of Food Safety Culture. Journal of Applied Microbiological
Research, 1(1), pp.27-34.
1 out of 18
Related Documents
![[object Object]](/_next/image/?url=%2F_next%2Fstatic%2Fmedia%2Flogo.6d15ce61.png&w=640&q=75)
Your All-in-One AI-Powered Toolkit for Academic Success.
+13062052269
info@desklib.com
Available 24*7 on WhatsApp / Email
Unlock your academic potential
© 2024 | Zucol Services PVT LTD | All rights reserved.