Addressing Negligence in the Workplace: Lessons from Kenoss
VerifiedAdded on 2019/11/19
|14
|3203
|139
Report
AI Summary
The Kenoss incident highlights the importance of workplace health and safety, particularly when it comes to electrical equipment. The company should have taken steps to ensure that all employees were aware of potential hazards and had a plan in place for preventing accidents. One way to achieve this is by conducting regular training sessions and having a system in place for reporting incidents. Additionally, involving employees in the process of identifying and addressing hazards can help to prevent accidents from occurring in the first place.
Contribute Materials
Your contribution can guide someone’s learning journey. Share your
documents today.
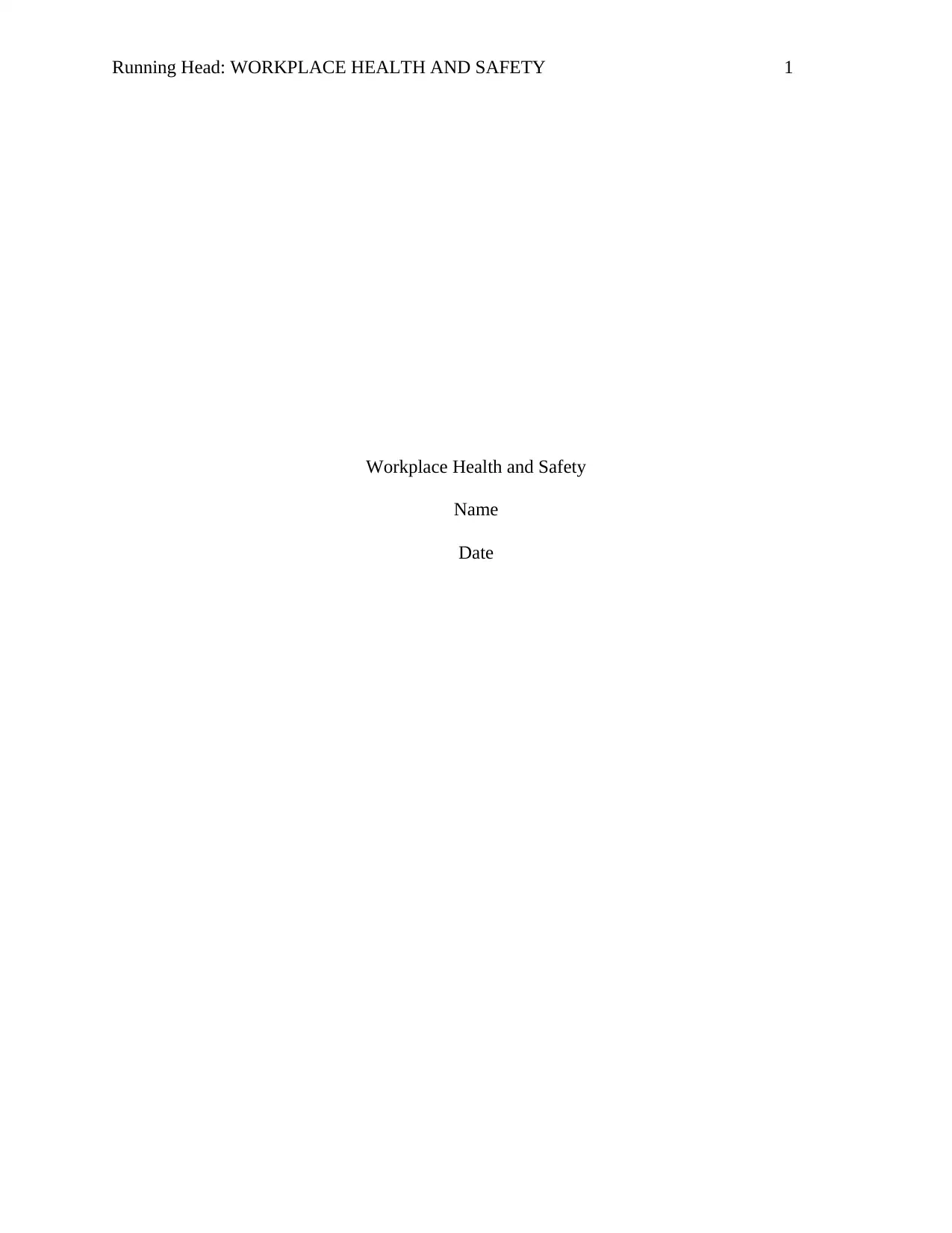
Running Head: WORKPLACE HEALTH AND SAFETY 1
Workplace Health and Safety
Name
Date
Workplace Health and Safety
Name
Date
Secure Best Marks with AI Grader
Need help grading? Try our AI Grader for instant feedback on your assignments.
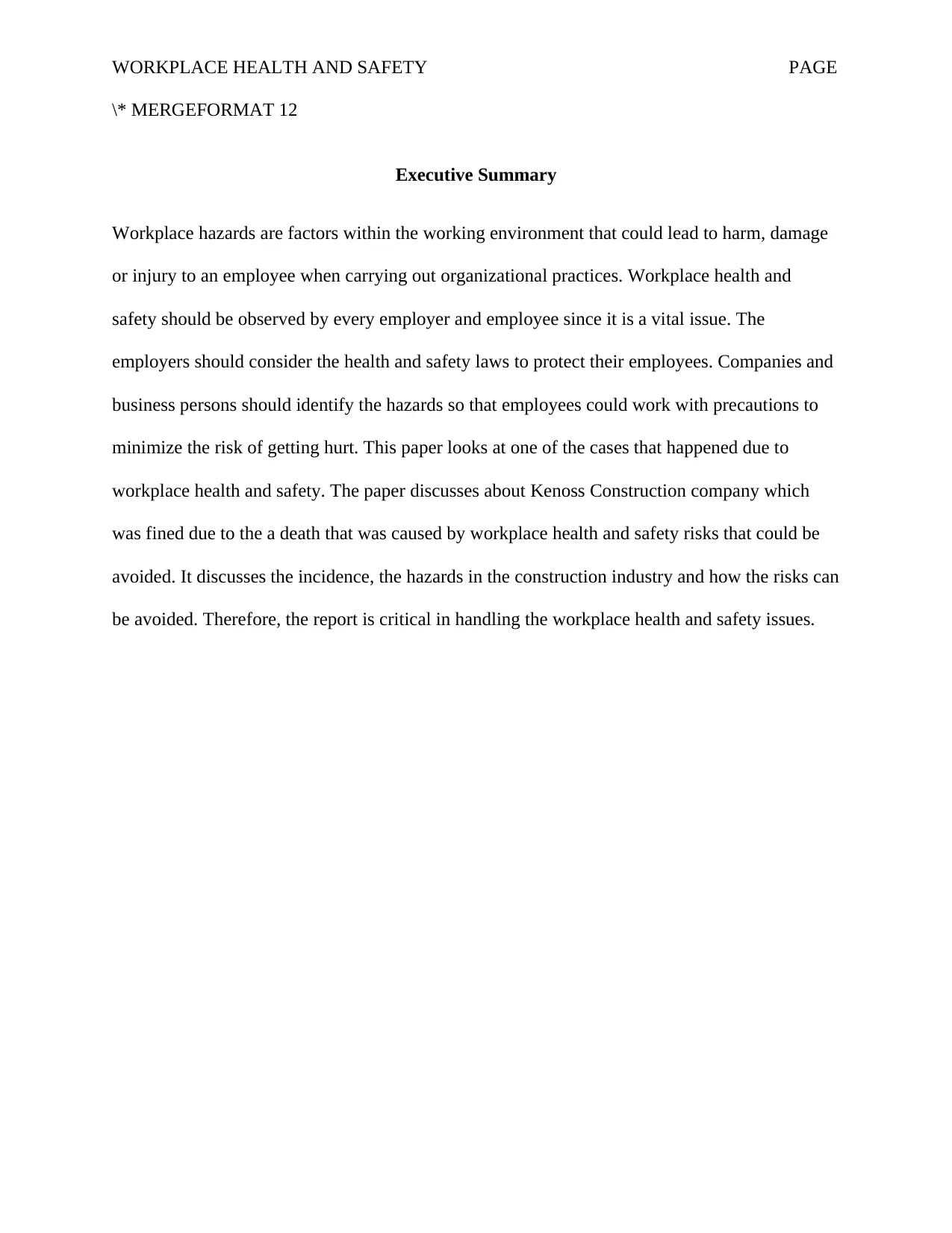
WORKPLACE HEALTH AND SAFETY PAGE
\* MERGEFORMAT 12
Executive Summary
Workplace hazards are factors within the working environment that could lead to harm, damage
or injury to an employee when carrying out organizational practices. Workplace health and
safety should be observed by every employer and employee since it is a vital issue. The
employers should consider the health and safety laws to protect their employees. Companies and
business persons should identify the hazards so that employees could work with precautions to
minimize the risk of getting hurt. This paper looks at one of the cases that happened due to
workplace health and safety. The paper discusses about Kenoss Construction company which
was fined due to the a death that was caused by workplace health and safety risks that could be
avoided. It discusses the incidence, the hazards in the construction industry and how the risks can
be avoided. Therefore, the report is critical in handling the workplace health and safety issues.
\* MERGEFORMAT 12
Executive Summary
Workplace hazards are factors within the working environment that could lead to harm, damage
or injury to an employee when carrying out organizational practices. Workplace health and
safety should be observed by every employer and employee since it is a vital issue. The
employers should consider the health and safety laws to protect their employees. Companies and
business persons should identify the hazards so that employees could work with precautions to
minimize the risk of getting hurt. This paper looks at one of the cases that happened due to
workplace health and safety. The paper discusses about Kenoss Construction company which
was fined due to the a death that was caused by workplace health and safety risks that could be
avoided. It discusses the incidence, the hazards in the construction industry and how the risks can
be avoided. Therefore, the report is critical in handling the workplace health and safety issues.
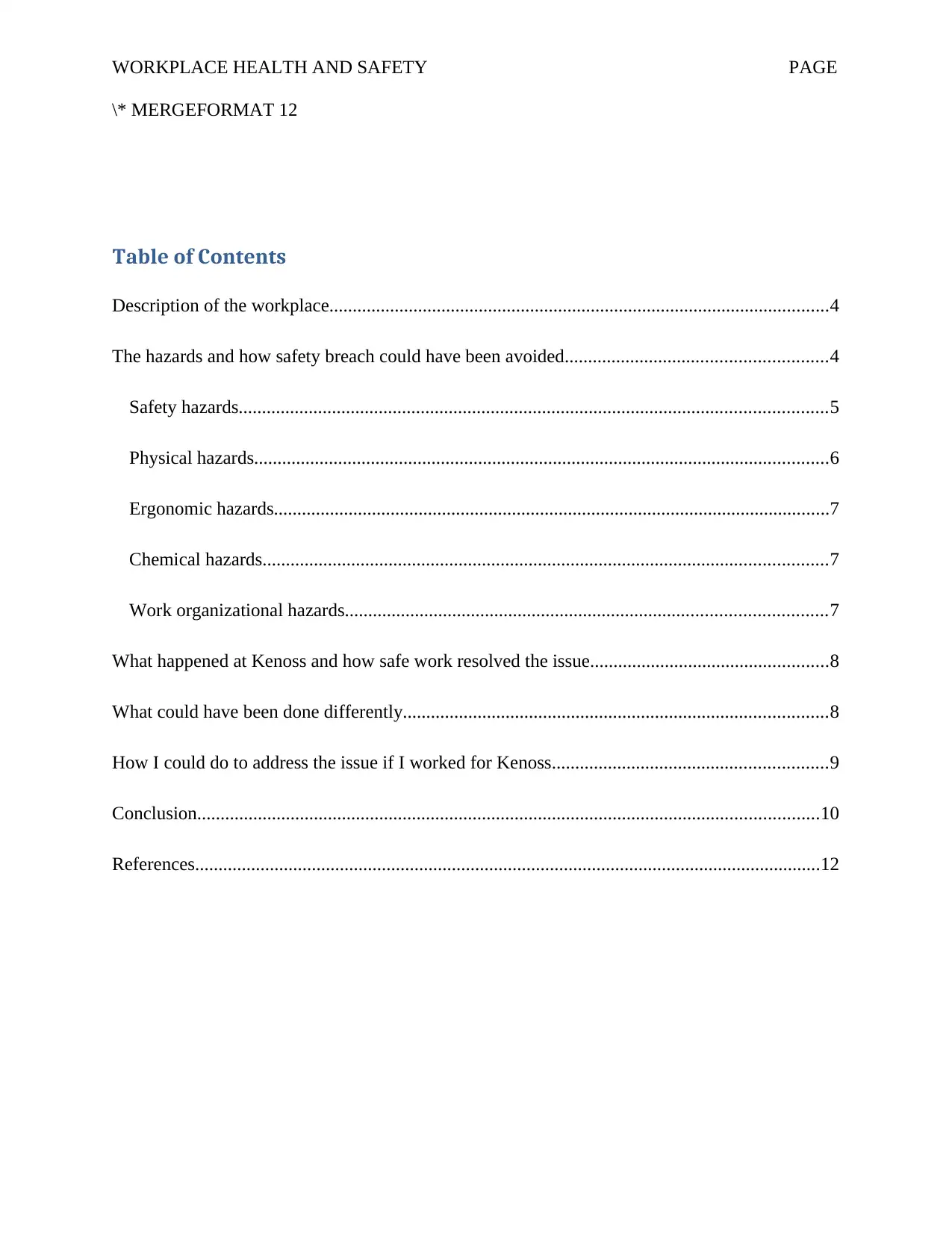
WORKPLACE HEALTH AND SAFETY PAGE
\* MERGEFORMAT 12
Table of Contents
Description of the workplace...........................................................................................................4
The hazards and how safety breach could have been avoided........................................................4
Safety hazards..............................................................................................................................5
Physical hazards...........................................................................................................................6
Ergonomic hazards.......................................................................................................................7
Chemical hazards.........................................................................................................................7
Work organizational hazards.......................................................................................................7
What happened at Kenoss and how safe work resolved the issue...................................................8
What could have been done differently...........................................................................................8
How I could do to address the issue if I worked for Kenoss...........................................................9
Conclusion.....................................................................................................................................10
References......................................................................................................................................12
\* MERGEFORMAT 12
Table of Contents
Description of the workplace...........................................................................................................4
The hazards and how safety breach could have been avoided........................................................4
Safety hazards..............................................................................................................................5
Physical hazards...........................................................................................................................6
Ergonomic hazards.......................................................................................................................7
Chemical hazards.........................................................................................................................7
Work organizational hazards.......................................................................................................7
What happened at Kenoss and how safe work resolved the issue...................................................8
What could have been done differently...........................................................................................8
How I could do to address the issue if I worked for Kenoss...........................................................9
Conclusion.....................................................................................................................................10
References......................................................................................................................................12
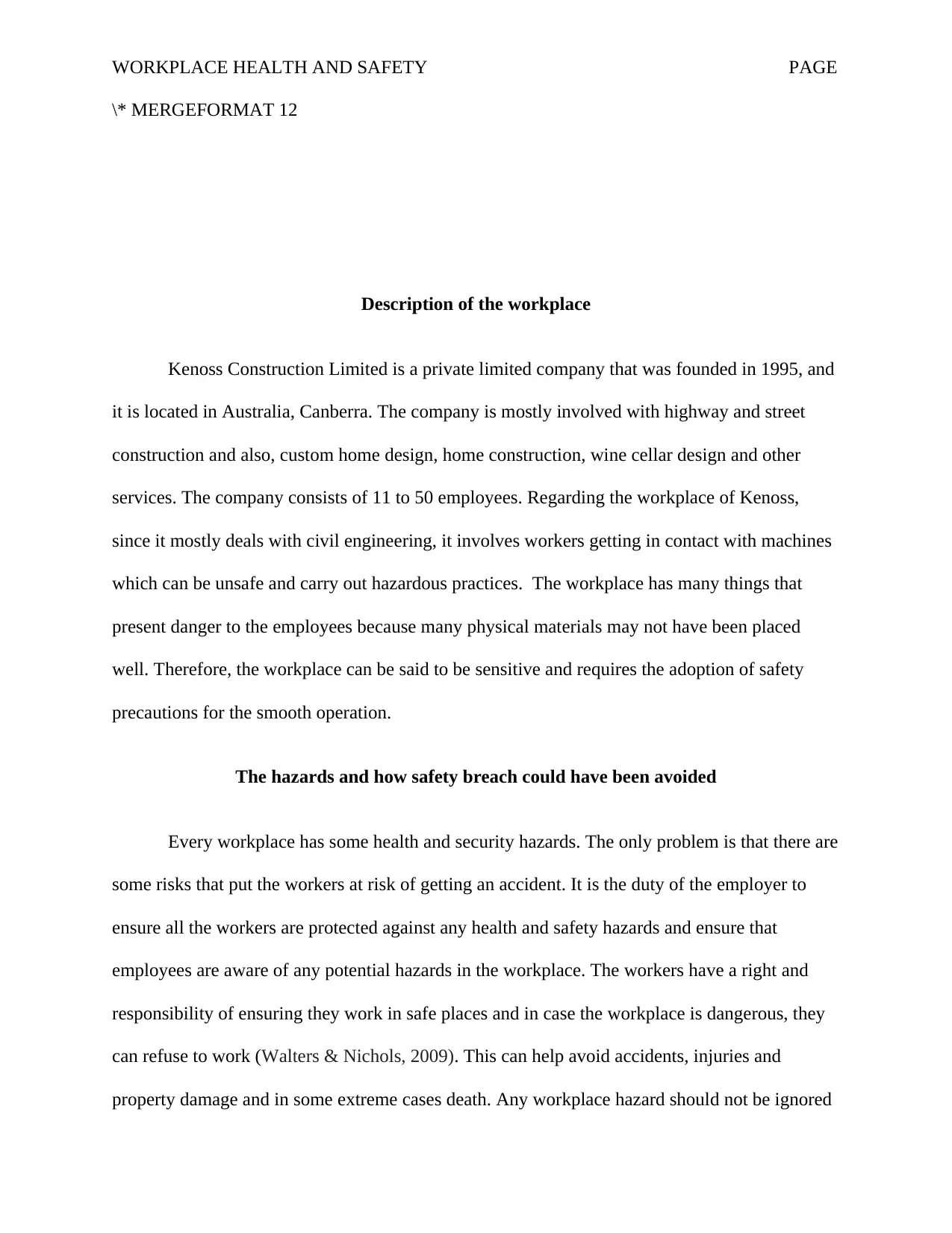
WORKPLACE HEALTH AND SAFETY PAGE
\* MERGEFORMAT 12
Description of the workplace
Kenoss Construction Limited is a private limited company that was founded in 1995, and
it is located in Australia, Canberra. The company is mostly involved with highway and street
construction and also, custom home design, home construction, wine cellar design and other
services. The company consists of 11 to 50 employees. Regarding the workplace of Kenoss,
since it mostly deals with civil engineering, it involves workers getting in contact with machines
which can be unsafe and carry out hazardous practices. The workplace has many things that
present danger to the employees because many physical materials may not have been placed
well. Therefore, the workplace can be said to be sensitive and requires the adoption of safety
precautions for the smooth operation.
The hazards and how safety breach could have been avoided
Every workplace has some health and security hazards. The only problem is that there are
some risks that put the workers at risk of getting an accident. It is the duty of the employer to
ensure all the workers are protected against any health and safety hazards and ensure that
employees are aware of any potential hazards in the workplace. The workers have a right and
responsibility of ensuring they work in safe places and in case the workplace is dangerous, they
can refuse to work (Walters & Nichols, 2009). This can help avoid accidents, injuries and
property damage and in some extreme cases death. Any workplace hazard should not be ignored
\* MERGEFORMAT 12
Description of the workplace
Kenoss Construction Limited is a private limited company that was founded in 1995, and
it is located in Australia, Canberra. The company is mostly involved with highway and street
construction and also, custom home design, home construction, wine cellar design and other
services. The company consists of 11 to 50 employees. Regarding the workplace of Kenoss,
since it mostly deals with civil engineering, it involves workers getting in contact with machines
which can be unsafe and carry out hazardous practices. The workplace has many things that
present danger to the employees because many physical materials may not have been placed
well. Therefore, the workplace can be said to be sensitive and requires the adoption of safety
precautions for the smooth operation.
The hazards and how safety breach could have been avoided
Every workplace has some health and security hazards. The only problem is that there are
some risks that put the workers at risk of getting an accident. It is the duty of the employer to
ensure all the workers are protected against any health and safety hazards and ensure that
employees are aware of any potential hazards in the workplace. The workers have a right and
responsibility of ensuring they work in safe places and in case the workplace is dangerous, they
can refuse to work (Walters & Nichols, 2009). This can help avoid accidents, injuries and
property damage and in some extreme cases death. Any workplace hazard should not be ignored
Secure Best Marks with AI Grader
Need help grading? Try our AI Grader for instant feedback on your assignments.
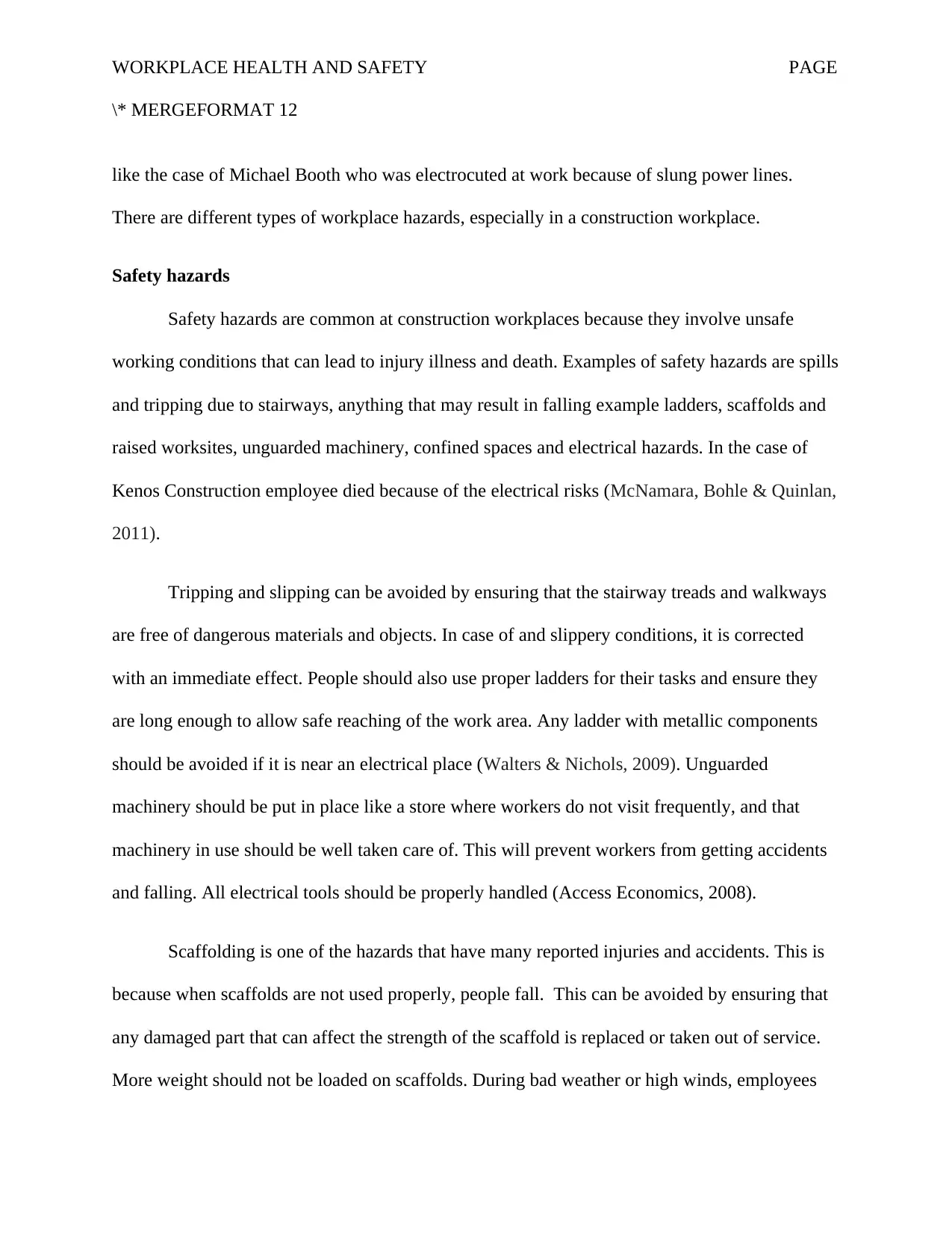
WORKPLACE HEALTH AND SAFETY PAGE
\* MERGEFORMAT 12
like the case of Michael Booth who was electrocuted at work because of slung power lines.
There are different types of workplace hazards, especially in a construction workplace.
Safety hazards
Safety hazards are common at construction workplaces because they involve unsafe
working conditions that can lead to injury illness and death. Examples of safety hazards are spills
and tripping due to stairways, anything that may result in falling example ladders, scaffolds and
raised worksites, unguarded machinery, confined spaces and electrical hazards. In the case of
Kenos Construction employee died because of the electrical risks (McNamara, Bohle & Quinlan,
2011).
Tripping and slipping can be avoided by ensuring that the stairway treads and walkways
are free of dangerous materials and objects. In case of and slippery conditions, it is corrected
with an immediate effect. People should also use proper ladders for their tasks and ensure they
are long enough to allow safe reaching of the work area. Any ladder with metallic components
should be avoided if it is near an electrical place (Walters & Nichols, 2009). Unguarded
machinery should be put in place like a store where workers do not visit frequently, and that
machinery in use should be well taken care of. This will prevent workers from getting accidents
and falling. All electrical tools should be properly handled (Access Economics, 2008).
Scaffolding is one of the hazards that have many reported injuries and accidents. This is
because when scaffolds are not used properly, people fall. This can be avoided by ensuring that
any damaged part that can affect the strength of the scaffold is replaced or taken out of service.
More weight should not be loaded on scaffolds. During bad weather or high winds, employees
\* MERGEFORMAT 12
like the case of Michael Booth who was electrocuted at work because of slung power lines.
There are different types of workplace hazards, especially in a construction workplace.
Safety hazards
Safety hazards are common at construction workplaces because they involve unsafe
working conditions that can lead to injury illness and death. Examples of safety hazards are spills
and tripping due to stairways, anything that may result in falling example ladders, scaffolds and
raised worksites, unguarded machinery, confined spaces and electrical hazards. In the case of
Kenos Construction employee died because of the electrical risks (McNamara, Bohle & Quinlan,
2011).
Tripping and slipping can be avoided by ensuring that the stairway treads and walkways
are free of dangerous materials and objects. In case of and slippery conditions, it is corrected
with an immediate effect. People should also use proper ladders for their tasks and ensure they
are long enough to allow safe reaching of the work area. Any ladder with metallic components
should be avoided if it is near an electrical place (Walters & Nichols, 2009). Unguarded
machinery should be put in place like a store where workers do not visit frequently, and that
machinery in use should be well taken care of. This will prevent workers from getting accidents
and falling. All electrical tools should be properly handled (Access Economics, 2008).
Scaffolding is one of the hazards that have many reported injuries and accidents. This is
because when scaffolds are not used properly, people fall. This can be avoided by ensuring that
any damaged part that can affect the strength of the scaffold is replaced or taken out of service.
More weight should not be loaded on scaffolds. During bad weather or high winds, employees
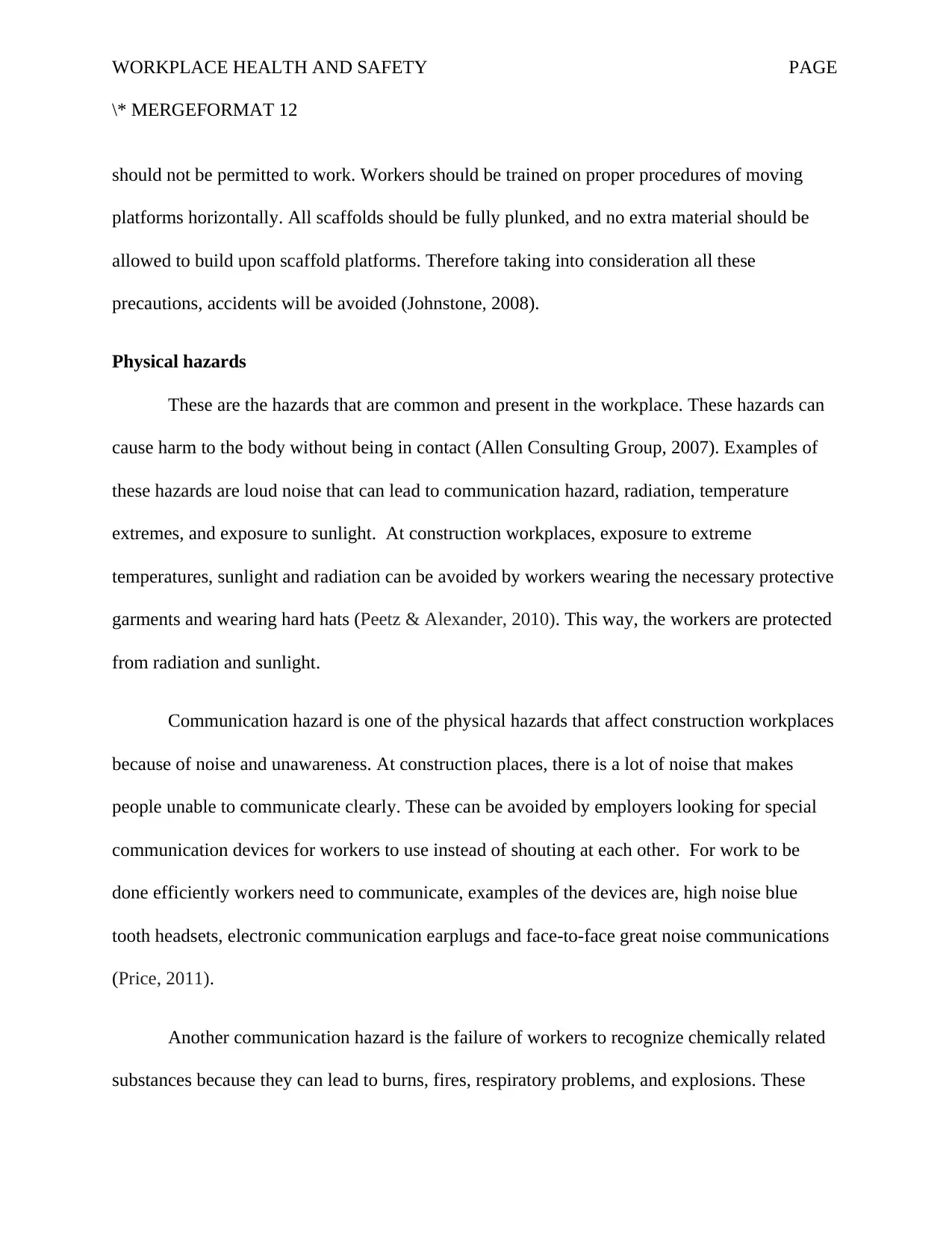
WORKPLACE HEALTH AND SAFETY PAGE
\* MERGEFORMAT 12
should not be permitted to work. Workers should be trained on proper procedures of moving
platforms horizontally. All scaffolds should be fully plunked, and no extra material should be
allowed to build upon scaffold platforms. Therefore taking into consideration all these
precautions, accidents will be avoided (Johnstone, 2008).
Physical hazards
These are the hazards that are common and present in the workplace. These hazards can
cause harm to the body without being in contact (Allen Consulting Group, 2007). Examples of
these hazards are loud noise that can lead to communication hazard, radiation, temperature
extremes, and exposure to sunlight. At construction workplaces, exposure to extreme
temperatures, sunlight and radiation can be avoided by workers wearing the necessary protective
garments and wearing hard hats (Peetz & Alexander, 2010). This way, the workers are protected
from radiation and sunlight.
Communication hazard is one of the physical hazards that affect construction workplaces
because of noise and unawareness. At construction places, there is a lot of noise that makes
people unable to communicate clearly. These can be avoided by employers looking for special
communication devices for workers to use instead of shouting at each other. For work to be
done efficiently workers need to communicate, examples of the devices are, high noise blue
tooth headsets, electronic communication earplugs and face-to-face great noise communications
(Price, 2011).
Another communication hazard is the failure of workers to recognize chemically related
substances because they can lead to burns, fires, respiratory problems, and explosions. These
\* MERGEFORMAT 12
should not be permitted to work. Workers should be trained on proper procedures of moving
platforms horizontally. All scaffolds should be fully plunked, and no extra material should be
allowed to build upon scaffold platforms. Therefore taking into consideration all these
precautions, accidents will be avoided (Johnstone, 2008).
Physical hazards
These are the hazards that are common and present in the workplace. These hazards can
cause harm to the body without being in contact (Allen Consulting Group, 2007). Examples of
these hazards are loud noise that can lead to communication hazard, radiation, temperature
extremes, and exposure to sunlight. At construction workplaces, exposure to extreme
temperatures, sunlight and radiation can be avoided by workers wearing the necessary protective
garments and wearing hard hats (Peetz & Alexander, 2010). This way, the workers are protected
from radiation and sunlight.
Communication hazard is one of the physical hazards that affect construction workplaces
because of noise and unawareness. At construction places, there is a lot of noise that makes
people unable to communicate clearly. These can be avoided by employers looking for special
communication devices for workers to use instead of shouting at each other. For work to be
done efficiently workers need to communicate, examples of the devices are, high noise blue
tooth headsets, electronic communication earplugs and face-to-face great noise communications
(Price, 2011).
Another communication hazard is the failure of workers to recognize chemically related
substances because they can lead to burns, fires, respiratory problems, and explosions. These
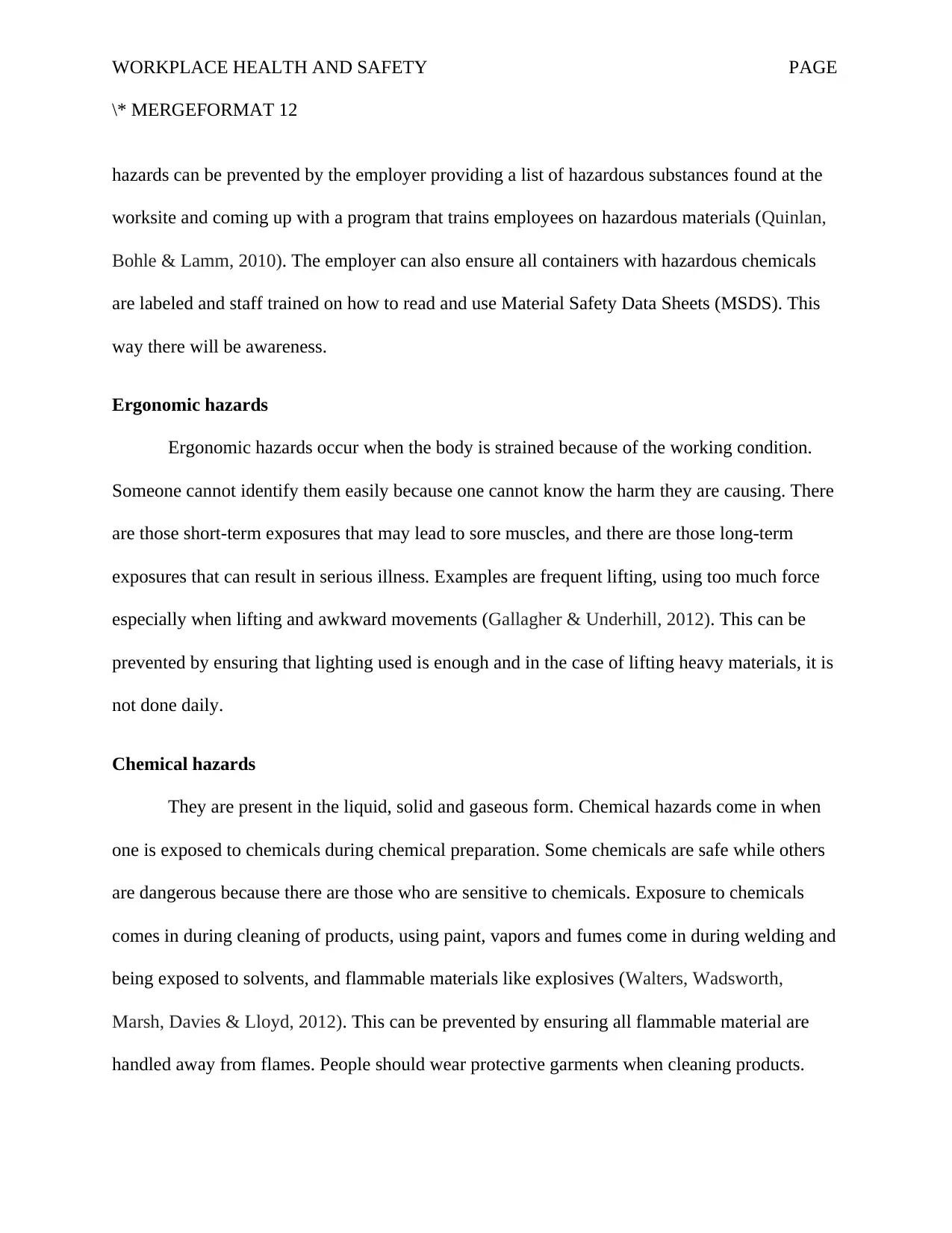
WORKPLACE HEALTH AND SAFETY PAGE
\* MERGEFORMAT 12
hazards can be prevented by the employer providing a list of hazardous substances found at the
worksite and coming up with a program that trains employees on hazardous materials (Quinlan,
Bohle & Lamm, 2010). The employer can also ensure all containers with hazardous chemicals
are labeled and staff trained on how to read and use Material Safety Data Sheets (MSDS). This
way there will be awareness.
Ergonomic hazards
Ergonomic hazards occur when the body is strained because of the working condition.
Someone cannot identify them easily because one cannot know the harm they are causing. There
are those short-term exposures that may lead to sore muscles, and there are those long-term
exposures that can result in serious illness. Examples are frequent lifting, using too much force
especially when lifting and awkward movements (Gallagher & Underhill, 2012). This can be
prevented by ensuring that lighting used is enough and in the case of lifting heavy materials, it is
not done daily.
Chemical hazards
They are present in the liquid, solid and gaseous form. Chemical hazards come in when
one is exposed to chemicals during chemical preparation. Some chemicals are safe while others
are dangerous because there are those who are sensitive to chemicals. Exposure to chemicals
comes in during cleaning of products, using paint, vapors and fumes come in during welding and
being exposed to solvents, and flammable materials like explosives (Walters, Wadsworth,
Marsh, Davies & Lloyd, 2012). This can be prevented by ensuring all flammable material are
handled away from flames. People should wear protective garments when cleaning products.
\* MERGEFORMAT 12
hazards can be prevented by the employer providing a list of hazardous substances found at the
worksite and coming up with a program that trains employees on hazardous materials (Quinlan,
Bohle & Lamm, 2010). The employer can also ensure all containers with hazardous chemicals
are labeled and staff trained on how to read and use Material Safety Data Sheets (MSDS). This
way there will be awareness.
Ergonomic hazards
Ergonomic hazards occur when the body is strained because of the working condition.
Someone cannot identify them easily because one cannot know the harm they are causing. There
are those short-term exposures that may lead to sore muscles, and there are those long-term
exposures that can result in serious illness. Examples are frequent lifting, using too much force
especially when lifting and awkward movements (Gallagher & Underhill, 2012). This can be
prevented by ensuring that lighting used is enough and in the case of lifting heavy materials, it is
not done daily.
Chemical hazards
They are present in the liquid, solid and gaseous form. Chemical hazards come in when
one is exposed to chemicals during chemical preparation. Some chemicals are safe while others
are dangerous because there are those who are sensitive to chemicals. Exposure to chemicals
comes in during cleaning of products, using paint, vapors and fumes come in during welding and
being exposed to solvents, and flammable materials like explosives (Walters, Wadsworth,
Marsh, Davies & Lloyd, 2012). This can be prevented by ensuring all flammable material are
handled away from flames. People should wear protective garments when cleaning products.
Paraphrase This Document
Need a fresh take? Get an instant paraphrase of this document with our AI Paraphraser
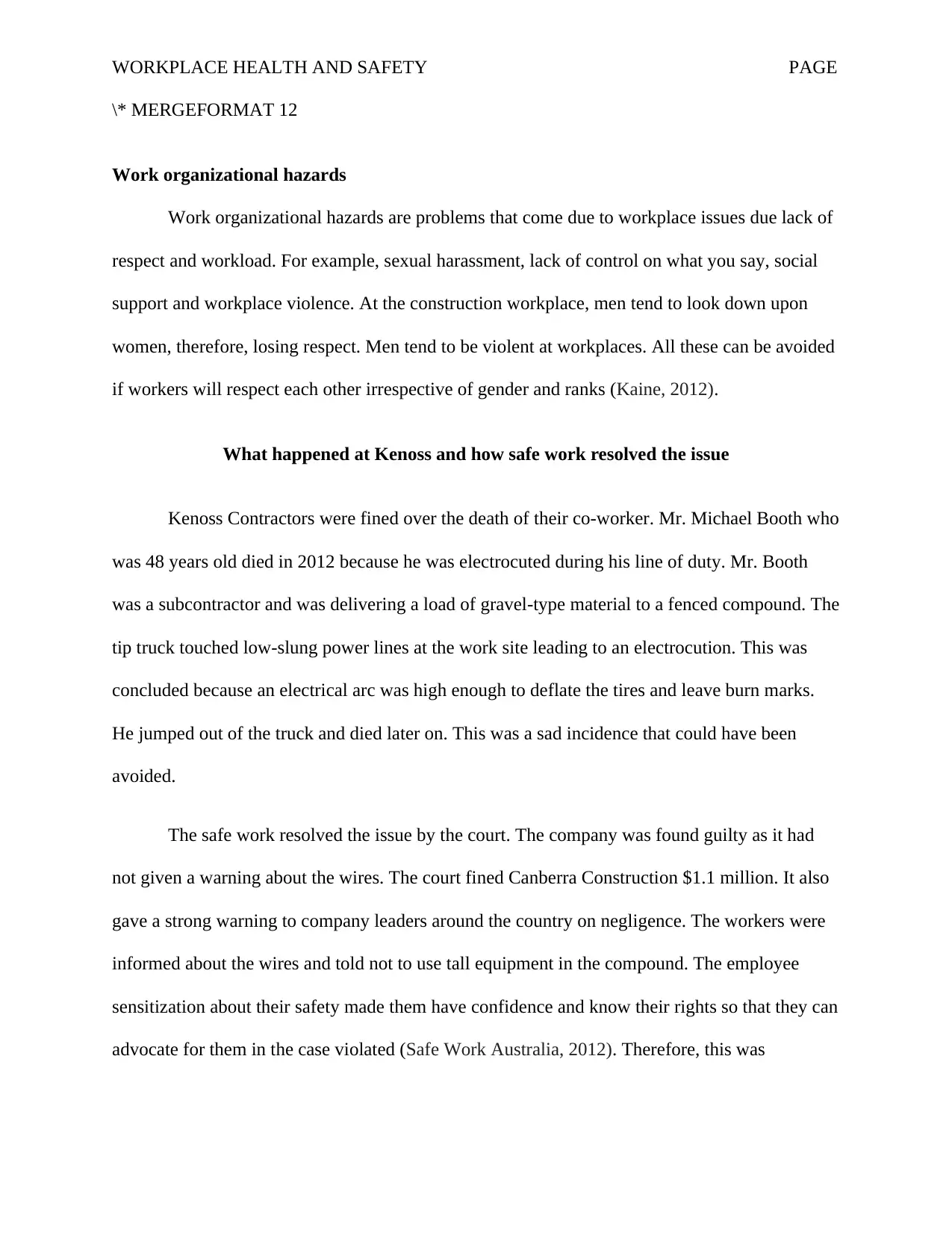
WORKPLACE HEALTH AND SAFETY PAGE
\* MERGEFORMAT 12
Work organizational hazards
Work organizational hazards are problems that come due to workplace issues due lack of
respect and workload. For example, sexual harassment, lack of control on what you say, social
support and workplace violence. At the construction workplace, men tend to look down upon
women, therefore, losing respect. Men tend to be violent at workplaces. All these can be avoided
if workers will respect each other irrespective of gender and ranks (Kaine, 2012).
What happened at Kenoss and how safe work resolved the issue
Kenoss Contractors were fined over the death of their co-worker. Mr. Michael Booth who
was 48 years old died in 2012 because he was electrocuted during his line of duty. Mr. Booth
was a subcontractor and was delivering a load of gravel-type material to a fenced compound. The
tip truck touched low-slung power lines at the work site leading to an electrocution. This was
concluded because an electrical arc was high enough to deflate the tires and leave burn marks.
He jumped out of the truck and died later on. This was a sad incidence that could have been
avoided.
The safe work resolved the issue by the court. The company was found guilty as it had
not given a warning about the wires. The court fined Canberra Construction $1.1 million. It also
gave a strong warning to company leaders around the country on negligence. The workers were
informed about the wires and told not to use tall equipment in the compound. The employee
sensitization about their safety made them have confidence and know their rights so that they can
advocate for them in the case violated (Safe Work Australia, 2012). Therefore, this was
\* MERGEFORMAT 12
Work organizational hazards
Work organizational hazards are problems that come due to workplace issues due lack of
respect and workload. For example, sexual harassment, lack of control on what you say, social
support and workplace violence. At the construction workplace, men tend to look down upon
women, therefore, losing respect. Men tend to be violent at workplaces. All these can be avoided
if workers will respect each other irrespective of gender and ranks (Kaine, 2012).
What happened at Kenoss and how safe work resolved the issue
Kenoss Contractors were fined over the death of their co-worker. Mr. Michael Booth who
was 48 years old died in 2012 because he was electrocuted during his line of duty. Mr. Booth
was a subcontractor and was delivering a load of gravel-type material to a fenced compound. The
tip truck touched low-slung power lines at the work site leading to an electrocution. This was
concluded because an electrical arc was high enough to deflate the tires and leave burn marks.
He jumped out of the truck and died later on. This was a sad incidence that could have been
avoided.
The safe work resolved the issue by the court. The company was found guilty as it had
not given a warning about the wires. The court fined Canberra Construction $1.1 million. It also
gave a strong warning to company leaders around the country on negligence. The workers were
informed about the wires and told not to use tall equipment in the compound. The employee
sensitization about their safety made them have confidence and know their rights so that they can
advocate for them in the case violated (Safe Work Australia, 2012). Therefore, this was
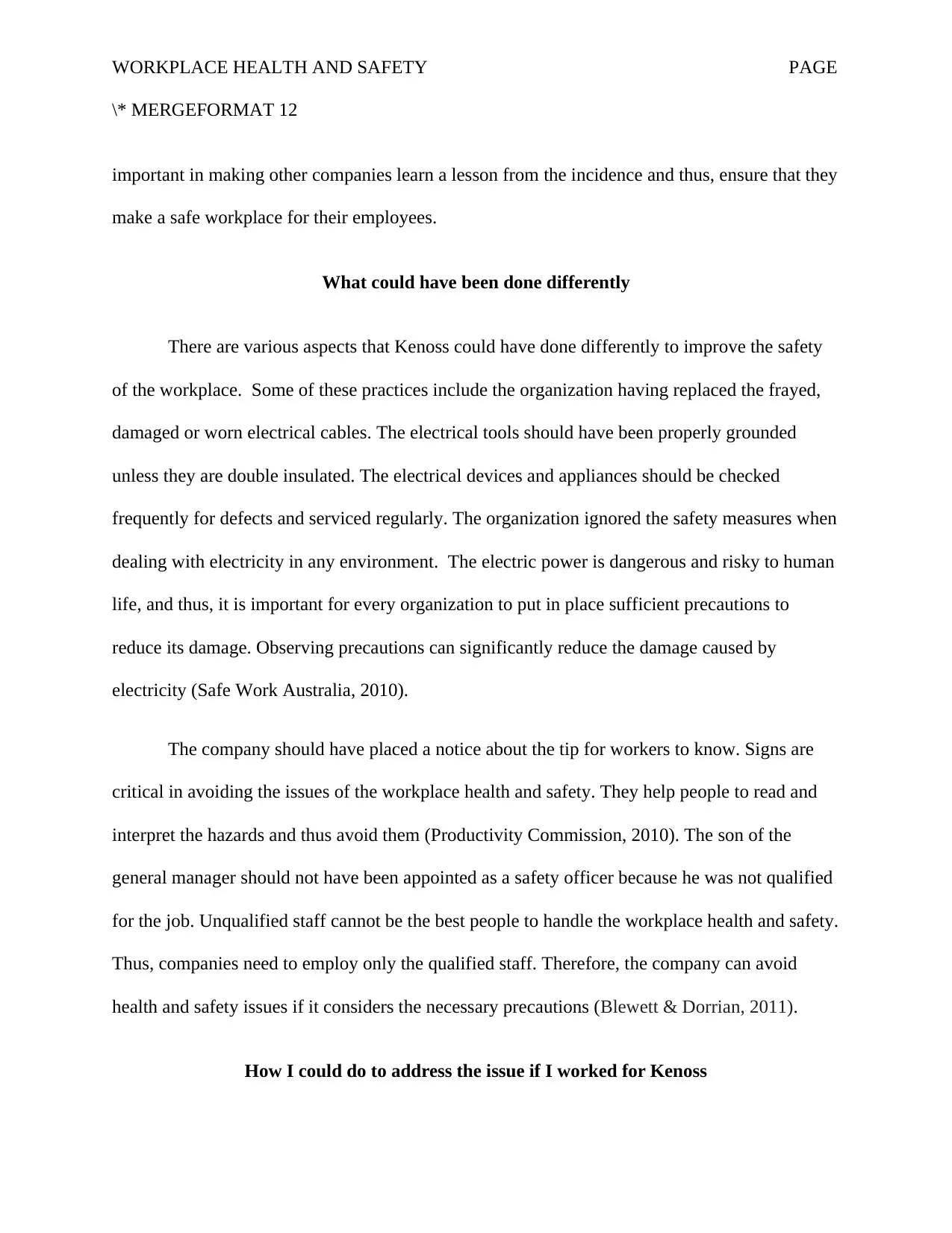
WORKPLACE HEALTH AND SAFETY PAGE
\* MERGEFORMAT 12
important in making other companies learn a lesson from the incidence and thus, ensure that they
make a safe workplace for their employees.
What could have been done differently
There are various aspects that Kenoss could have done differently to improve the safety
of the workplace. Some of these practices include the organization having replaced the frayed,
damaged or worn electrical cables. The electrical tools should have been properly grounded
unless they are double insulated. The electrical devices and appliances should be checked
frequently for defects and serviced regularly. The organization ignored the safety measures when
dealing with electricity in any environment. The electric power is dangerous and risky to human
life, and thus, it is important for every organization to put in place sufficient precautions to
reduce its damage. Observing precautions can significantly reduce the damage caused by
electricity (Safe Work Australia, 2010).
The company should have placed a notice about the tip for workers to know. Signs are
critical in avoiding the issues of the workplace health and safety. They help people to read and
interpret the hazards and thus avoid them (Productivity Commission, 2010). The son of the
general manager should not have been appointed as a safety officer because he was not qualified
for the job. Unqualified staff cannot be the best people to handle the workplace health and safety.
Thus, companies need to employ only the qualified staff. Therefore, the company can avoid
health and safety issues if it considers the necessary precautions (Blewett & Dorrian, 2011).
How I could do to address the issue if I worked for Kenoss
\* MERGEFORMAT 12
important in making other companies learn a lesson from the incidence and thus, ensure that they
make a safe workplace for their employees.
What could have been done differently
There are various aspects that Kenoss could have done differently to improve the safety
of the workplace. Some of these practices include the organization having replaced the frayed,
damaged or worn electrical cables. The electrical tools should have been properly grounded
unless they are double insulated. The electrical devices and appliances should be checked
frequently for defects and serviced regularly. The organization ignored the safety measures when
dealing with electricity in any environment. The electric power is dangerous and risky to human
life, and thus, it is important for every organization to put in place sufficient precautions to
reduce its damage. Observing precautions can significantly reduce the damage caused by
electricity (Safe Work Australia, 2010).
The company should have placed a notice about the tip for workers to know. Signs are
critical in avoiding the issues of the workplace health and safety. They help people to read and
interpret the hazards and thus avoid them (Productivity Commission, 2010). The son of the
general manager should not have been appointed as a safety officer because he was not qualified
for the job. Unqualified staff cannot be the best people to handle the workplace health and safety.
Thus, companies need to employ only the qualified staff. Therefore, the company can avoid
health and safety issues if it considers the necessary precautions (Blewett & Dorrian, 2011).
How I could do to address the issue if I worked for Kenoss
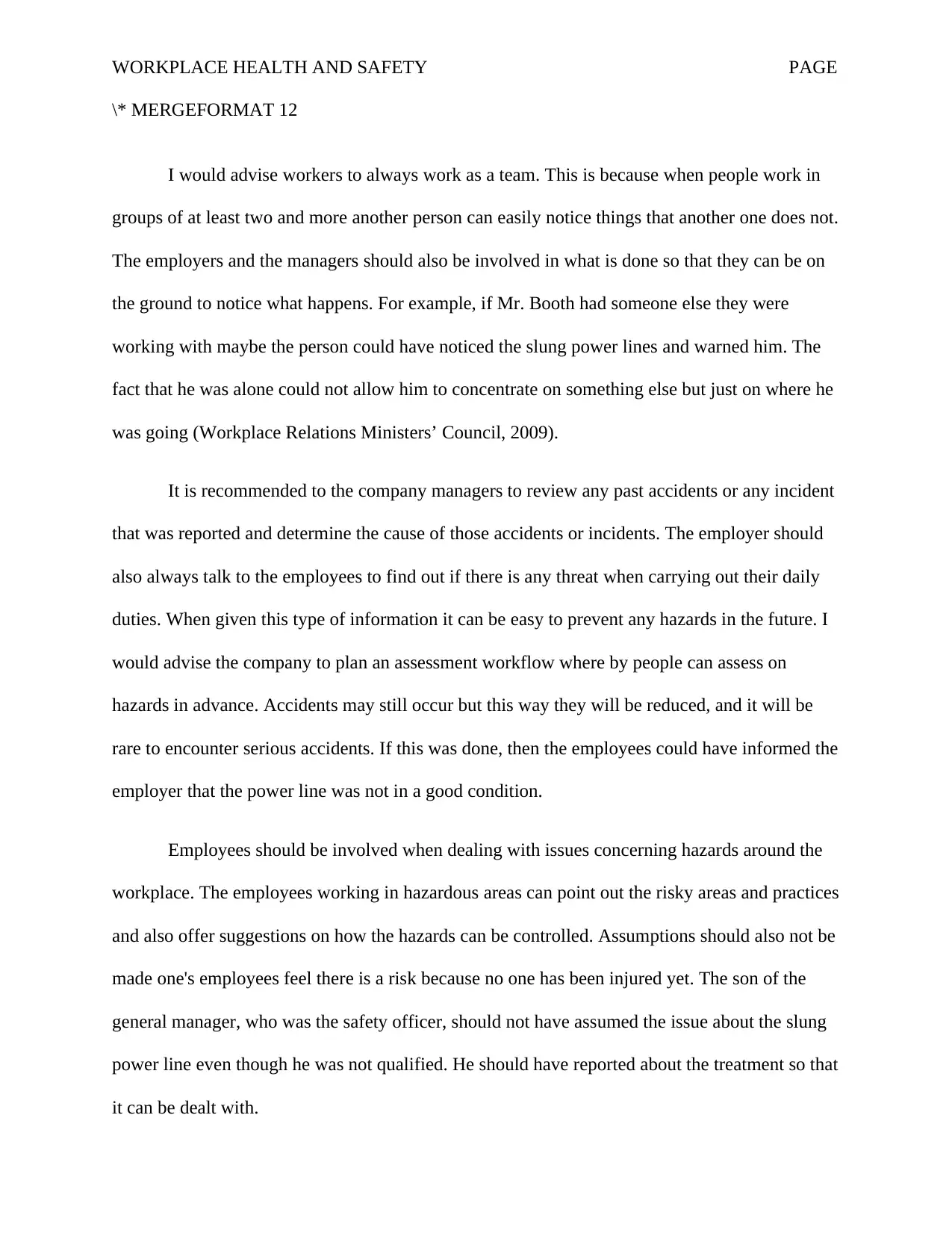
WORKPLACE HEALTH AND SAFETY PAGE
\* MERGEFORMAT 12
I would advise workers to always work as a team. This is because when people work in
groups of at least two and more another person can easily notice things that another one does not.
The employers and the managers should also be involved in what is done so that they can be on
the ground to notice what happens. For example, if Mr. Booth had someone else they were
working with maybe the person could have noticed the slung power lines and warned him. The
fact that he was alone could not allow him to concentrate on something else but just on where he
was going (Workplace Relations Ministers’ Council, 2009).
It is recommended to the company managers to review any past accidents or any incident
that was reported and determine the cause of those accidents or incidents. The employer should
also always talk to the employees to find out if there is any threat when carrying out their daily
duties. When given this type of information it can be easy to prevent any hazards in the future. I
would advise the company to plan an assessment workflow where by people can assess on
hazards in advance. Accidents may still occur but this way they will be reduced, and it will be
rare to encounter serious accidents. If this was done, then the employees could have informed the
employer that the power line was not in a good condition.
Employees should be involved when dealing with issues concerning hazards around the
workplace. The employees working in hazardous areas can point out the risky areas and practices
and also offer suggestions on how the hazards can be controlled. Assumptions should also not be
made one's employees feel there is a risk because no one has been injured yet. The son of the
general manager, who was the safety officer, should not have assumed the issue about the slung
power line even though he was not qualified. He should have reported about the treatment so that
it can be dealt with.
\* MERGEFORMAT 12
I would advise workers to always work as a team. This is because when people work in
groups of at least two and more another person can easily notice things that another one does not.
The employers and the managers should also be involved in what is done so that they can be on
the ground to notice what happens. For example, if Mr. Booth had someone else they were
working with maybe the person could have noticed the slung power lines and warned him. The
fact that he was alone could not allow him to concentrate on something else but just on where he
was going (Workplace Relations Ministers’ Council, 2009).
It is recommended to the company managers to review any past accidents or any incident
that was reported and determine the cause of those accidents or incidents. The employer should
also always talk to the employees to find out if there is any threat when carrying out their daily
duties. When given this type of information it can be easy to prevent any hazards in the future. I
would advise the company to plan an assessment workflow where by people can assess on
hazards in advance. Accidents may still occur but this way they will be reduced, and it will be
rare to encounter serious accidents. If this was done, then the employees could have informed the
employer that the power line was not in a good condition.
Employees should be involved when dealing with issues concerning hazards around the
workplace. The employees working in hazardous areas can point out the risky areas and practices
and also offer suggestions on how the hazards can be controlled. Assumptions should also not be
made one's employees feel there is a risk because no one has been injured yet. The son of the
general manager, who was the safety officer, should not have assumed the issue about the slung
power line even though he was not qualified. He should have reported about the treatment so that
it can be dealt with.
Secure Best Marks with AI Grader
Need help grading? Try our AI Grader for instant feedback on your assignments.
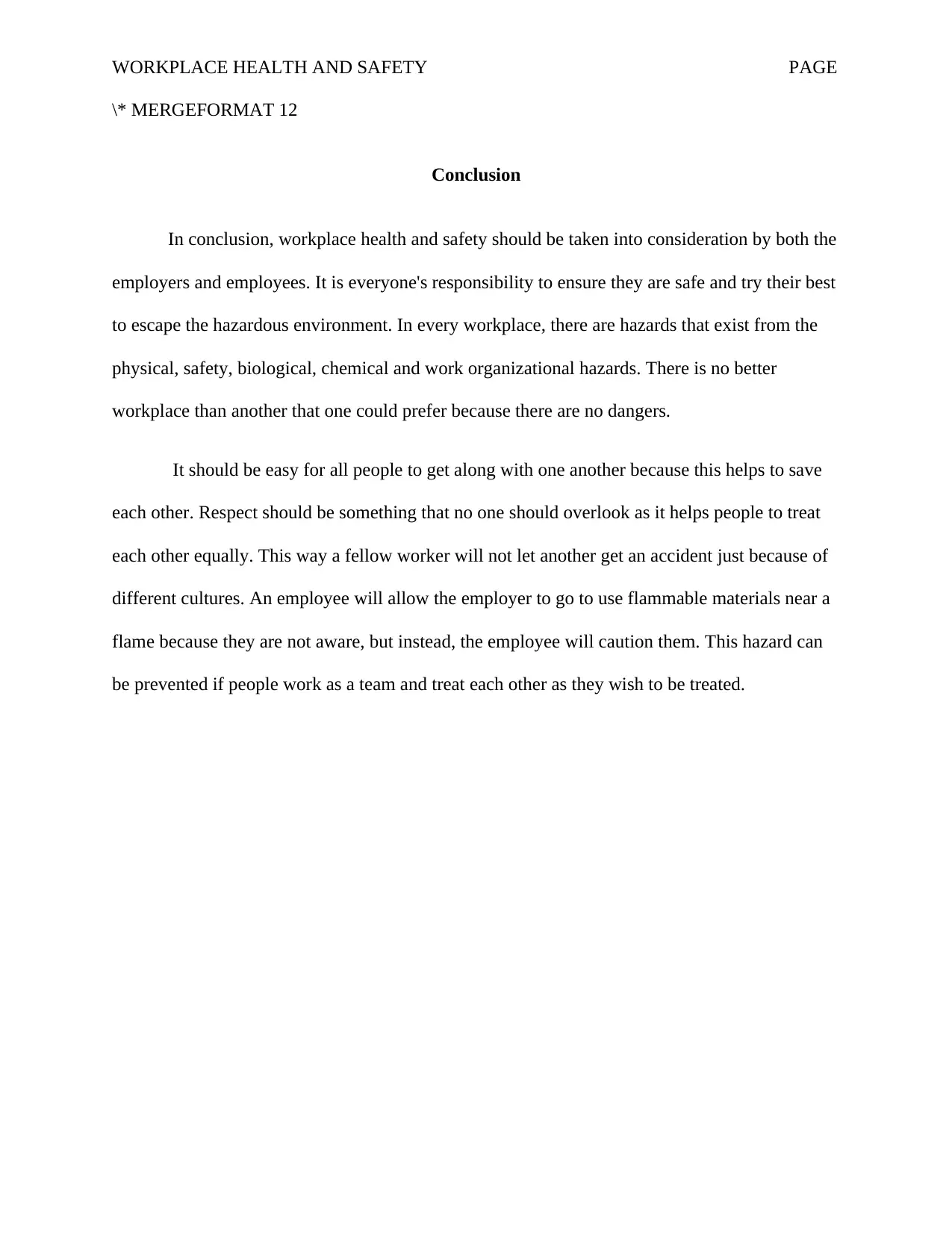
WORKPLACE HEALTH AND SAFETY PAGE
\* MERGEFORMAT 12
Conclusion
In conclusion, workplace health and safety should be taken into consideration by both the
employers and employees. It is everyone's responsibility to ensure they are safe and try their best
to escape the hazardous environment. In every workplace, there are hazards that exist from the
physical, safety, biological, chemical and work organizational hazards. There is no better
workplace than another that one could prefer because there are no dangers.
It should be easy for all people to get along with one another because this helps to save
each other. Respect should be something that no one should overlook as it helps people to treat
each other equally. This way a fellow worker will not let another get an accident just because of
different cultures. An employee will allow the employer to go to use flammable materials near a
flame because they are not aware, but instead, the employee will caution them. This hazard can
be prevented if people work as a team and treat each other as they wish to be treated.
\* MERGEFORMAT 12
Conclusion
In conclusion, workplace health and safety should be taken into consideration by both the
employers and employees. It is everyone's responsibility to ensure they are safe and try their best
to escape the hazardous environment. In every workplace, there are hazards that exist from the
physical, safety, biological, chemical and work organizational hazards. There is no better
workplace than another that one could prefer because there are no dangers.
It should be easy for all people to get along with one another because this helps to save
each other. Respect should be something that no one should overlook as it helps people to treat
each other equally. This way a fellow worker will not let another get an accident just because of
different cultures. An employee will allow the employer to go to use flammable materials near a
flame because they are not aware, but instead, the employee will caution them. This hazard can
be prevented if people work as a team and treat each other as they wish to be treated.
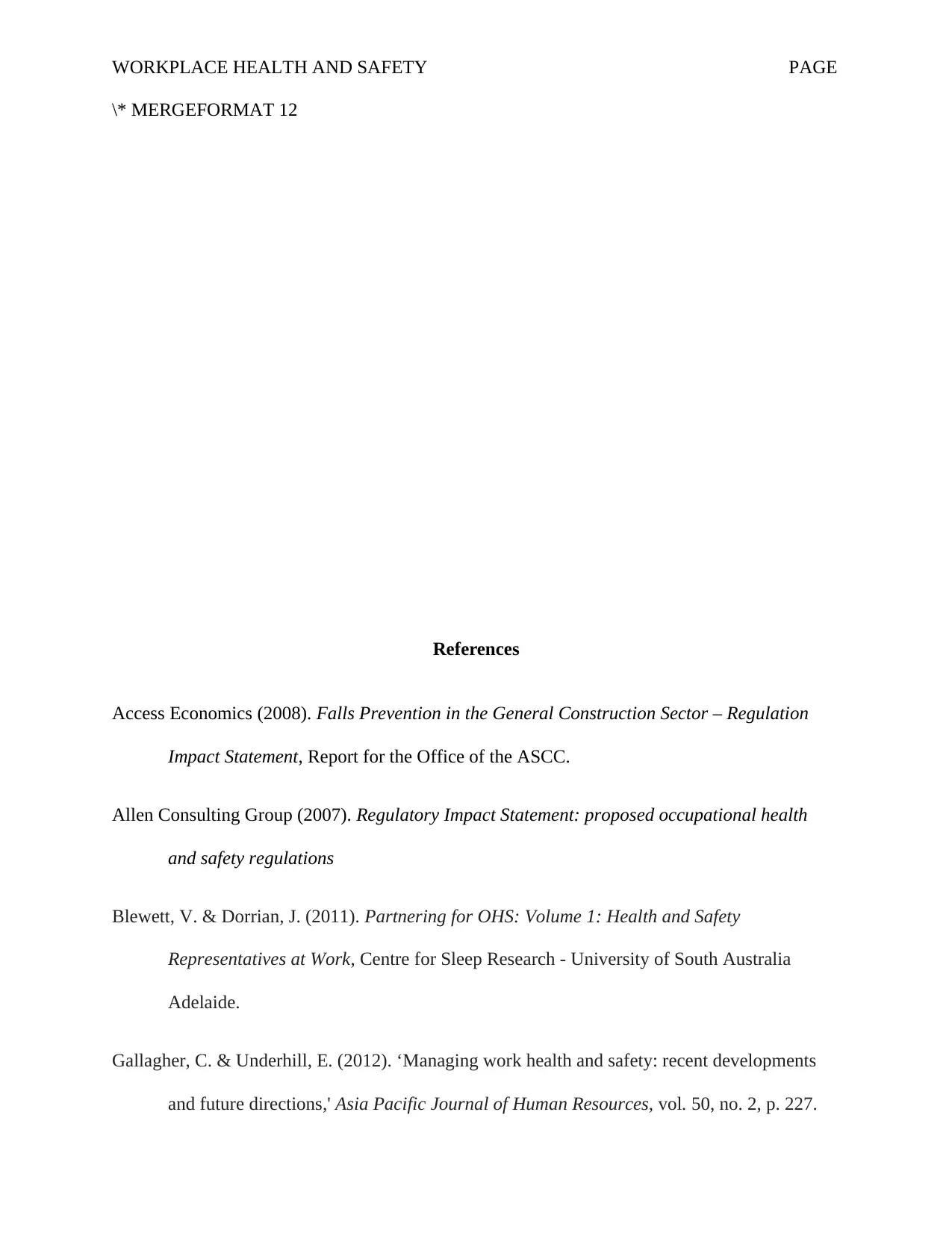
WORKPLACE HEALTH AND SAFETY PAGE
\* MERGEFORMAT 12
References
Access Economics (2008). Falls Prevention in the General Construction Sector – Regulation
Impact Statement, Report for the Office of the ASCC.
Allen Consulting Group (2007). Regulatory Impact Statement: proposed occupational health
and safety regulations
Blewett, V. & Dorrian, J. (2011). Partnering for OHS: Volume 1: Health and Safety
Representatives at Work, Centre for Sleep Research - University of South Australia
Adelaide.
Gallagher, C. & Underhill, E. (2012). ‘Managing work health and safety: recent developments
and future directions,' Asia Pacific Journal of Human Resources, vol. 50, no. 2, p. 227.
\* MERGEFORMAT 12
References
Access Economics (2008). Falls Prevention in the General Construction Sector – Regulation
Impact Statement, Report for the Office of the ASCC.
Allen Consulting Group (2007). Regulatory Impact Statement: proposed occupational health
and safety regulations
Blewett, V. & Dorrian, J. (2011). Partnering for OHS: Volume 1: Health and Safety
Representatives at Work, Centre for Sleep Research - University of South Australia
Adelaide.
Gallagher, C. & Underhill, E. (2012). ‘Managing work health and safety: recent developments
and future directions,' Asia Pacific Journal of Human Resources, vol. 50, no. 2, p. 227.
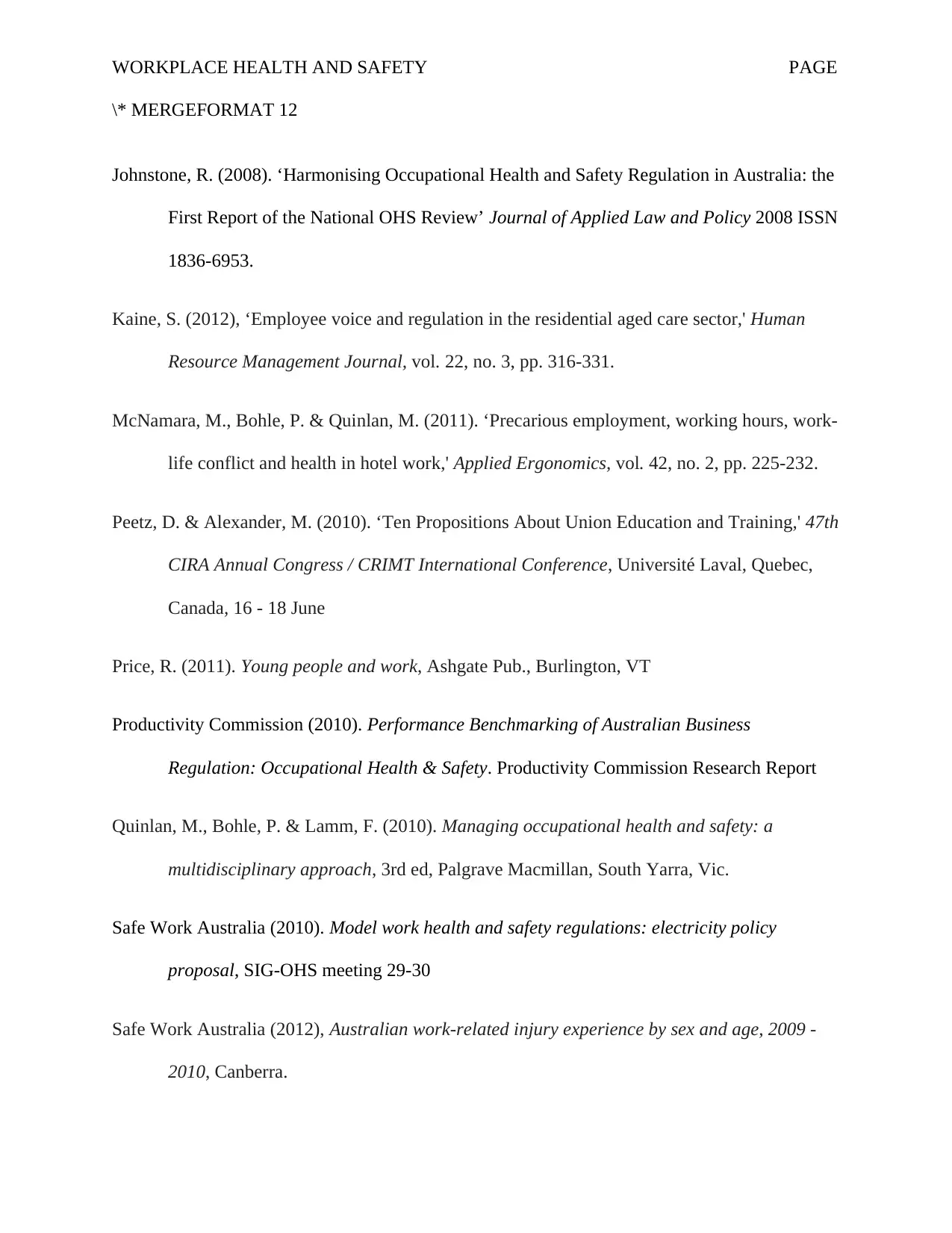
WORKPLACE HEALTH AND SAFETY PAGE
\* MERGEFORMAT 12
Johnstone, R. (2008). ‘Harmonising Occupational Health and Safety Regulation in Australia: the
First Report of the National OHS Review’ Journal of Applied Law and Policy 2008 ISSN
1836-6953.
Kaine, S. (2012), ‘Employee voice and regulation in the residential aged care sector,' Human
Resource Management Journal, vol. 22, no. 3, pp. 316-331.
McNamara, M., Bohle, P. & Quinlan, M. (2011). ‘Precarious employment, working hours, work-
life conflict and health in hotel work,' Applied Ergonomics, vol. 42, no. 2, pp. 225-232.
Peetz, D. & Alexander, M. (2010). ‘Ten Propositions About Union Education and Training,' 47th
CIRA Annual Congress / CRIMT International Conference, Université Laval, Quebec,
Canada, 16 - 18 June
Price, R. (2011). Young people and work, Ashgate Pub., Burlington, VT
Productivity Commission (2010). Performance Benchmarking of Australian Business
Regulation: Occupational Health & Safety. Productivity Commission Research Report
Quinlan, M., Bohle, P. & Lamm, F. (2010). Managing occupational health and safety: a
multidisciplinary approach, 3rd ed, Palgrave Macmillan, South Yarra, Vic.
Safe Work Australia (2010). Model work health and safety regulations: electricity policy
proposal, SIG-OHS meeting 29-30
Safe Work Australia (2012), Australian work-related injury experience by sex and age, 2009 -
2010, Canberra.
\* MERGEFORMAT 12
Johnstone, R. (2008). ‘Harmonising Occupational Health and Safety Regulation in Australia: the
First Report of the National OHS Review’ Journal of Applied Law and Policy 2008 ISSN
1836-6953.
Kaine, S. (2012), ‘Employee voice and regulation in the residential aged care sector,' Human
Resource Management Journal, vol. 22, no. 3, pp. 316-331.
McNamara, M., Bohle, P. & Quinlan, M. (2011). ‘Precarious employment, working hours, work-
life conflict and health in hotel work,' Applied Ergonomics, vol. 42, no. 2, pp. 225-232.
Peetz, D. & Alexander, M. (2010). ‘Ten Propositions About Union Education and Training,' 47th
CIRA Annual Congress / CRIMT International Conference, Université Laval, Quebec,
Canada, 16 - 18 June
Price, R. (2011). Young people and work, Ashgate Pub., Burlington, VT
Productivity Commission (2010). Performance Benchmarking of Australian Business
Regulation: Occupational Health & Safety. Productivity Commission Research Report
Quinlan, M., Bohle, P. & Lamm, F. (2010). Managing occupational health and safety: a
multidisciplinary approach, 3rd ed, Palgrave Macmillan, South Yarra, Vic.
Safe Work Australia (2010). Model work health and safety regulations: electricity policy
proposal, SIG-OHS meeting 29-30
Safe Work Australia (2012), Australian work-related injury experience by sex and age, 2009 -
2010, Canberra.
Paraphrase This Document
Need a fresh take? Get an instant paraphrase of this document with our AI Paraphraser
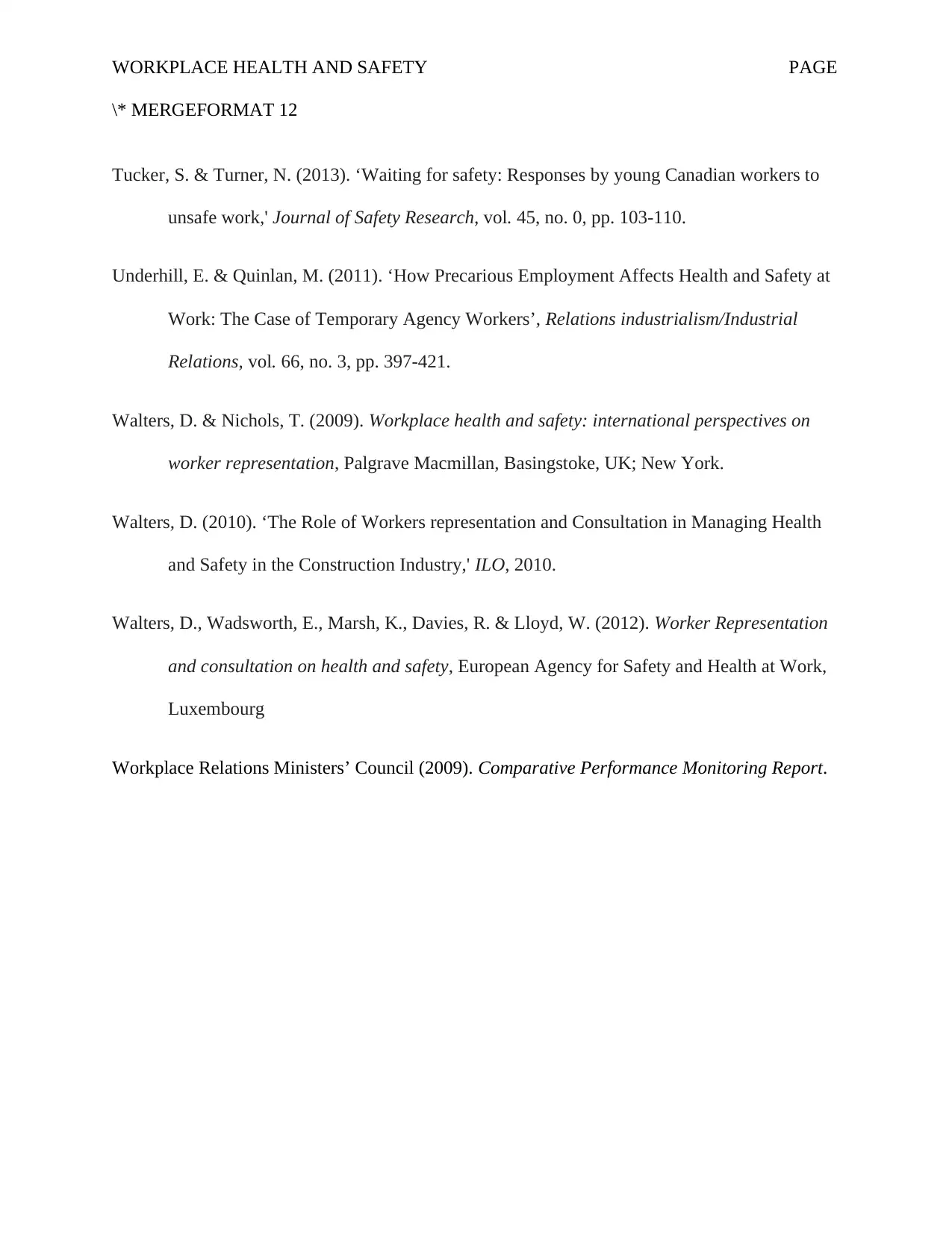
WORKPLACE HEALTH AND SAFETY PAGE
\* MERGEFORMAT 12
Tucker, S. & Turner, N. (2013). ‘Waiting for safety: Responses by young Canadian workers to
unsafe work,' Journal of Safety Research, vol. 45, no. 0, pp. 103-110.
Underhill, E. & Quinlan, M. (2011). ‘How Precarious Employment Affects Health and Safety at
Work: The Case of Temporary Agency Workers’, Relations industrialism/Industrial
Relations, vol. 66, no. 3, pp. 397-421.
Walters, D. & Nichols, T. (2009). Workplace health and safety: international perspectives on
worker representation, Palgrave Macmillan, Basingstoke, UK; New York.
Walters, D. (2010). ‘The Role of Workers representation and Consultation in Managing Health
and Safety in the Construction Industry,' ILO, 2010.
Walters, D., Wadsworth, E., Marsh, K., Davies, R. & Lloyd, W. (2012). Worker Representation
and consultation on health and safety, European Agency for Safety and Health at Work,
Luxembourg
Workplace Relations Ministers’ Council (2009). Comparative Performance Monitoring Report.
\* MERGEFORMAT 12
Tucker, S. & Turner, N. (2013). ‘Waiting for safety: Responses by young Canadian workers to
unsafe work,' Journal of Safety Research, vol. 45, no. 0, pp. 103-110.
Underhill, E. & Quinlan, M. (2011). ‘How Precarious Employment Affects Health and Safety at
Work: The Case of Temporary Agency Workers’, Relations industrialism/Industrial
Relations, vol. 66, no. 3, pp. 397-421.
Walters, D. & Nichols, T. (2009). Workplace health and safety: international perspectives on
worker representation, Palgrave Macmillan, Basingstoke, UK; New York.
Walters, D. (2010). ‘The Role of Workers representation and Consultation in Managing Health
and Safety in the Construction Industry,' ILO, 2010.
Walters, D., Wadsworth, E., Marsh, K., Davies, R. & Lloyd, W. (2012). Worker Representation
and consultation on health and safety, European Agency for Safety and Health at Work,
Luxembourg
Workplace Relations Ministers’ Council (2009). Comparative Performance Monitoring Report.
1 out of 14
Related Documents
![[object Object]](/_next/image/?url=%2F_next%2Fstatic%2Fmedia%2Flogo.6d15ce61.png&w=640&q=75)
Your All-in-One AI-Powered Toolkit for Academic Success.
+13062052269
info@desklib.com
Available 24*7 on WhatsApp / Email
Unlock your academic potential
© 2024 | Zucol Services PVT LTD | All rights reserved.