Yarra One Project: Structure and Construction Process
VerifiedAdded on 2023/06/03
|13
|3040
|254
AI Summary
This report presents analysis of the structure and construction process/planning of Yarra One, a 27-storey residential apartment tower located at 16-22 Claremont Street in South Yarra, Melbourne, Australia. The building comprises of 256 dwellings that will be built over a total area of 37, 500 square meters. The report covers the structure of the basement, atrium and tower, the construction process, the role of a building surveyor and the conclusion.
Contribute Materials
Your contribution can guide someone’s learning journey. Share your
documents today.

Yarra One Project 1
YARRA ONE PROJECT
Name
Course
Professor
University
City/state
Date
YARRA ONE PROJECT
Name
Course
Professor
University
City/state
Date
Secure Best Marks with AI Grader
Need help grading? Try our AI Grader for instant feedback on your assignments.
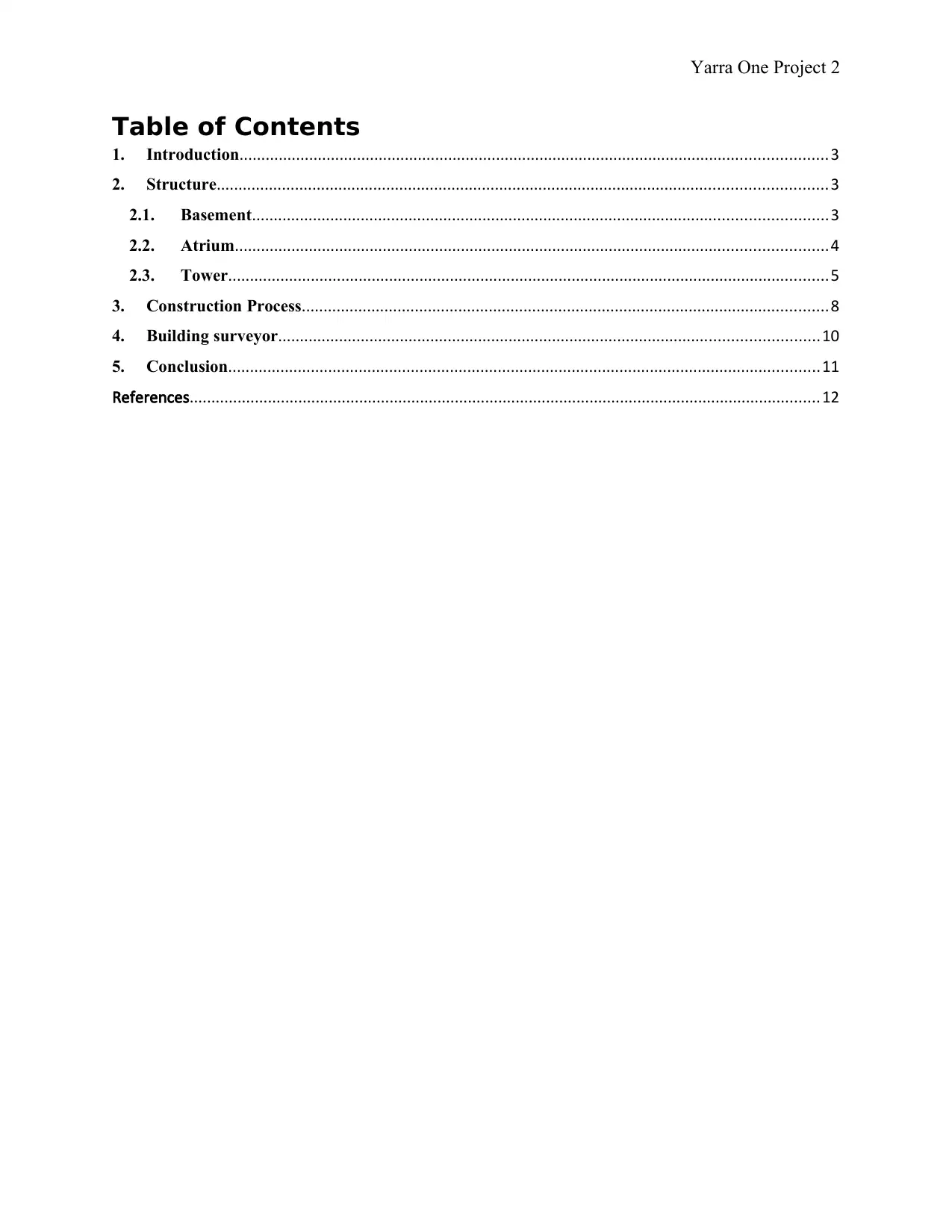
Yarra One Project 2
Table of Contents
1. Introduction.......................................................................................................................................3
2. Structure............................................................................................................................................3
2.1. Basement....................................................................................................................................3
2.2. Atrium........................................................................................................................................4
2.3. Tower..........................................................................................................................................5
3. Construction Process.........................................................................................................................8
4. Building surveyor............................................................................................................................10
5. Conclusion........................................................................................................................................11
References.................................................................................................................................................12
Table of Contents
1. Introduction.......................................................................................................................................3
2. Structure............................................................................................................................................3
2.1. Basement....................................................................................................................................3
2.2. Atrium........................................................................................................................................4
2.3. Tower..........................................................................................................................................5
3. Construction Process.........................................................................................................................8
4. Building surveyor............................................................................................................................10
5. Conclusion........................................................................................................................................11
References.................................................................................................................................................12
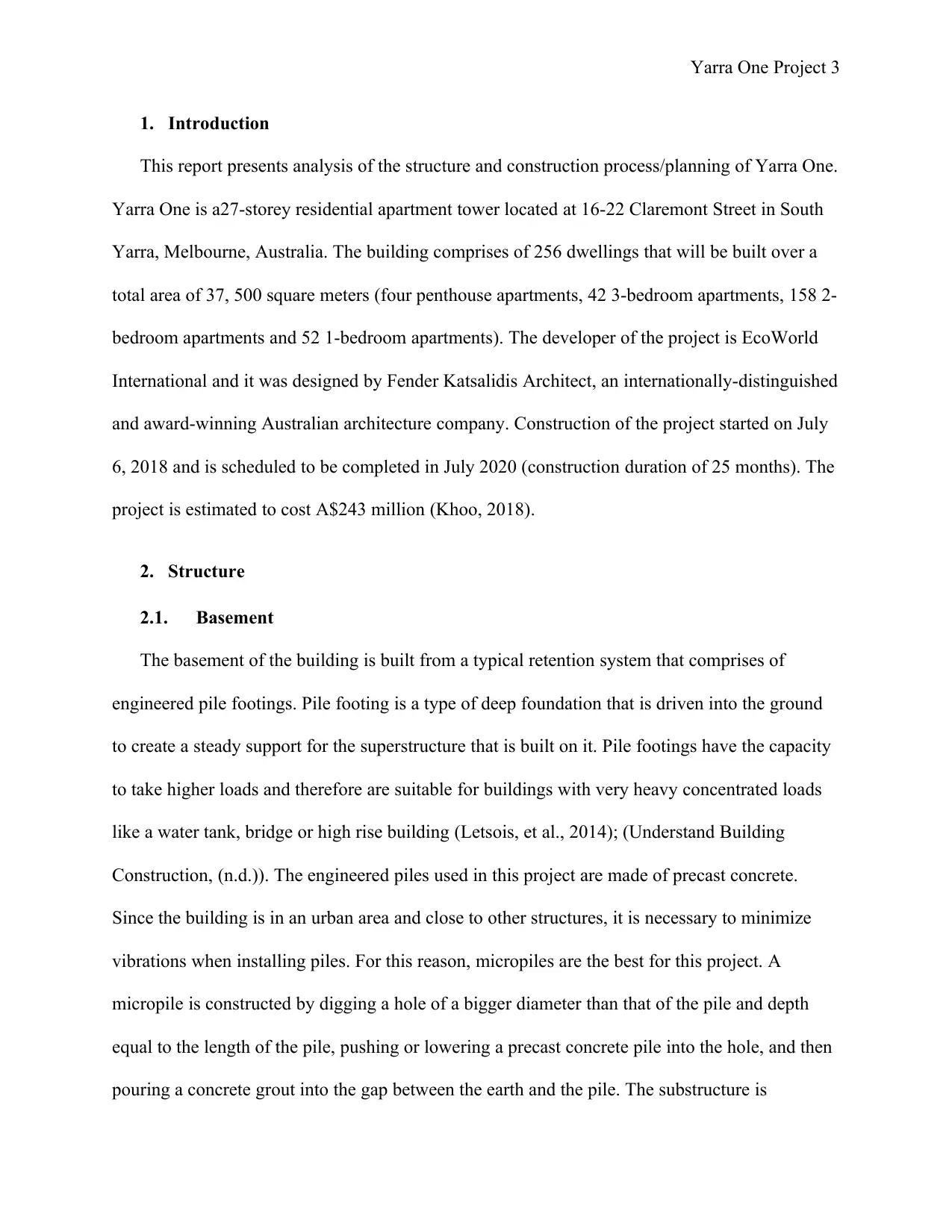
Yarra One Project 3
1. Introduction
This report presents analysis of the structure and construction process/planning of Yarra One.
Yarra One is a27-storey residential apartment tower located at 16-22 Claremont Street in South
Yarra, Melbourne, Australia. The building comprises of 256 dwellings that will be built over a
total area of 37, 500 square meters (four penthouse apartments, 42 3-bedroom apartments, 158 2-
bedroom apartments and 52 1-bedroom apartments). The developer of the project is EcoWorld
International and it was designed by Fender Katsalidis Architect, an internationally-distinguished
and award-winning Australian architecture company. Construction of the project started on July
6, 2018 and is scheduled to be completed in July 2020 (construction duration of 25 months). The
project is estimated to cost A$243 million (Khoo, 2018).
2. Structure
2.1. Basement
The basement of the building is built from a typical retention system that comprises of
engineered pile footings. Pile footing is a type of deep foundation that is driven into the ground
to create a steady support for the superstructure that is built on it. Pile footings have the capacity
to take higher loads and therefore are suitable for buildings with very heavy concentrated loads
like a water tank, bridge or high rise building (Letsois, et al., 2014); (Understand Building
Construction, (n.d.)). The engineered piles used in this project are made of precast concrete.
Since the building is in an urban area and close to other structures, it is necessary to minimize
vibrations when installing piles. For this reason, micropiles are the best for this project. A
micropile is constructed by digging a hole of a bigger diameter than that of the pile and depth
equal to the length of the pile, pushing or lowering a precast concrete pile into the hole, and then
pouring a concrete grout into the gap between the earth and the pile. The substructure is
1. Introduction
This report presents analysis of the structure and construction process/planning of Yarra One.
Yarra One is a27-storey residential apartment tower located at 16-22 Claremont Street in South
Yarra, Melbourne, Australia. The building comprises of 256 dwellings that will be built over a
total area of 37, 500 square meters (four penthouse apartments, 42 3-bedroom apartments, 158 2-
bedroom apartments and 52 1-bedroom apartments). The developer of the project is EcoWorld
International and it was designed by Fender Katsalidis Architect, an internationally-distinguished
and award-winning Australian architecture company. Construction of the project started on July
6, 2018 and is scheduled to be completed in July 2020 (construction duration of 25 months). The
project is estimated to cost A$243 million (Khoo, 2018).
2. Structure
2.1. Basement
The basement of the building is built from a typical retention system that comprises of
engineered pile footings. Pile footing is a type of deep foundation that is driven into the ground
to create a steady support for the superstructure that is built on it. Pile footings have the capacity
to take higher loads and therefore are suitable for buildings with very heavy concentrated loads
like a water tank, bridge or high rise building (Letsois, et al., 2014); (Understand Building
Construction, (n.d.)). The engineered piles used in this project are made of precast concrete.
Since the building is in an urban area and close to other structures, it is necessary to minimize
vibrations when installing piles. For this reason, micropiles are the best for this project. A
micropile is constructed by digging a hole of a bigger diameter than that of the pile and depth
equal to the length of the pile, pushing or lowering a precast concrete pile into the hole, and then
pouring a concrete grout into the gap between the earth and the pile. The substructure is
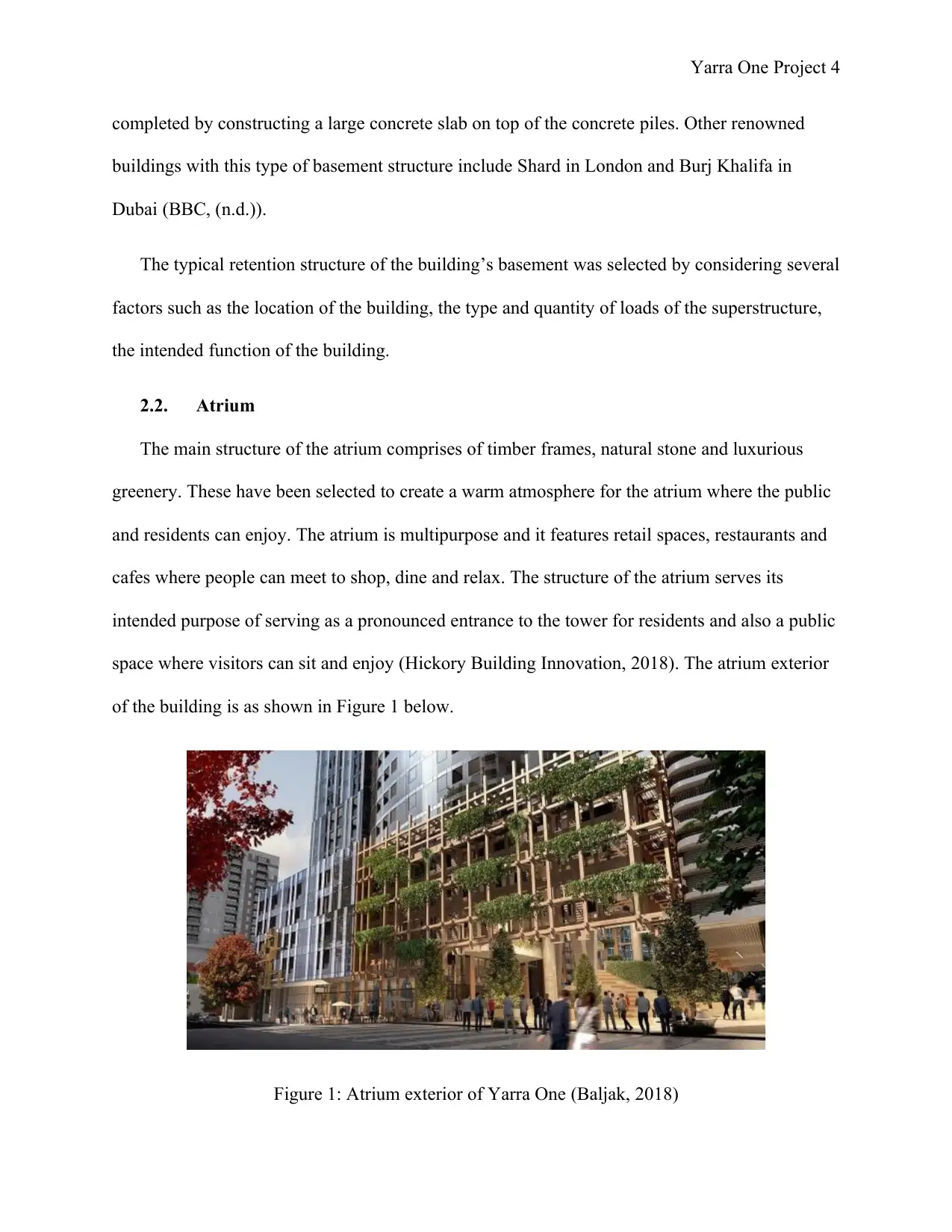
Yarra One Project 4
completed by constructing a large concrete slab on top of the concrete piles. Other renowned
buildings with this type of basement structure include Shard in London and Burj Khalifa in
Dubai (BBC, (n.d.)).
The typical retention structure of the building’s basement was selected by considering several
factors such as the location of the building, the type and quantity of loads of the superstructure,
the intended function of the building.
2.2. Atrium
The main structure of the atrium comprises of timber frames, natural stone and luxurious
greenery. These have been selected to create a warm atmosphere for the atrium where the public
and residents can enjoy. The atrium is multipurpose and it features retail spaces, restaurants and
cafes where people can meet to shop, dine and relax. The structure of the atrium serves its
intended purpose of serving as a pronounced entrance to the tower for residents and also a public
space where visitors can sit and enjoy (Hickory Building Innovation, 2018). The atrium exterior
of the building is as shown in Figure 1 below.
Figure 1: Atrium exterior of Yarra One (Baljak, 2018)
completed by constructing a large concrete slab on top of the concrete piles. Other renowned
buildings with this type of basement structure include Shard in London and Burj Khalifa in
Dubai (BBC, (n.d.)).
The typical retention structure of the building’s basement was selected by considering several
factors such as the location of the building, the type and quantity of loads of the superstructure,
the intended function of the building.
2.2. Atrium
The main structure of the atrium comprises of timber frames, natural stone and luxurious
greenery. These have been selected to create a warm atmosphere for the atrium where the public
and residents can enjoy. The atrium is multipurpose and it features retail spaces, restaurants and
cafes where people can meet to shop, dine and relax. The structure of the atrium serves its
intended purpose of serving as a pronounced entrance to the tower for residents and also a public
space where visitors can sit and enjoy (Hickory Building Innovation, 2018). The atrium exterior
of the building is as shown in Figure 1 below.
Figure 1: Atrium exterior of Yarra One (Baljak, 2018)
Secure Best Marks with AI Grader
Need help grading? Try our AI Grader for instant feedback on your assignments.
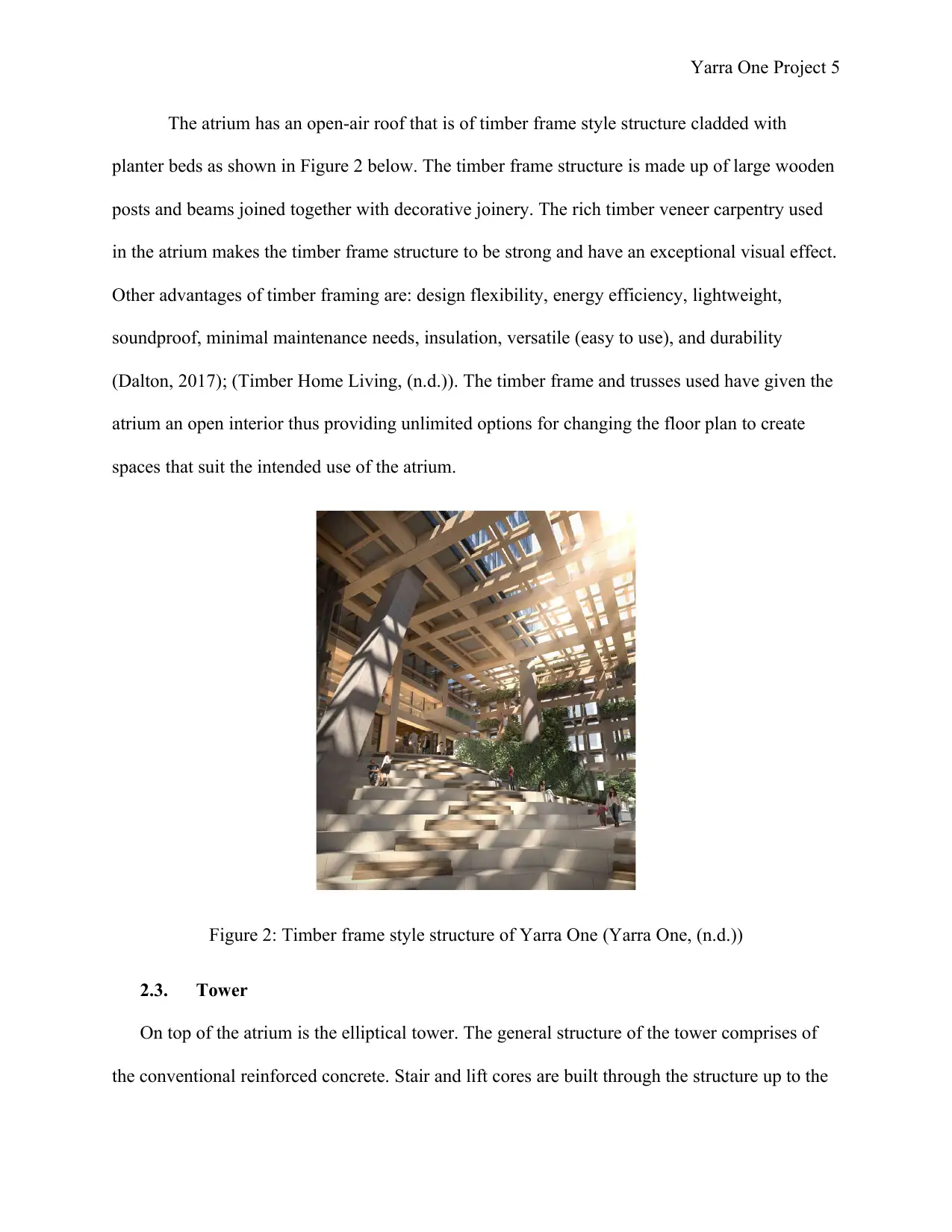
Yarra One Project 5
The atrium has an open-air roof that is of timber frame style structure cladded with
planter beds as shown in Figure 2 below. The timber frame structure is made up of large wooden
posts and beams joined together with decorative joinery. The rich timber veneer carpentry used
in the atrium makes the timber frame structure to be strong and have an exceptional visual effect.
Other advantages of timber framing are: design flexibility, energy efficiency, lightweight,
soundproof, minimal maintenance needs, insulation, versatile (easy to use), and durability
(Dalton, 2017); (Timber Home Living, (n.d.)). The timber frame and trusses used have given the
atrium an open interior thus providing unlimited options for changing the floor plan to create
spaces that suit the intended use of the atrium.
Figure 2: Timber frame style structure of Yarra One (Yarra One, (n.d.))
2.3. Tower
On top of the atrium is the elliptical tower. The general structure of the tower comprises of
the conventional reinforced concrete. Stair and lift cores are built through the structure up to the
The atrium has an open-air roof that is of timber frame style structure cladded with
planter beds as shown in Figure 2 below. The timber frame structure is made up of large wooden
posts and beams joined together with decorative joinery. The rich timber veneer carpentry used
in the atrium makes the timber frame structure to be strong and have an exceptional visual effect.
Other advantages of timber framing are: design flexibility, energy efficiency, lightweight,
soundproof, minimal maintenance needs, insulation, versatile (easy to use), and durability
(Dalton, 2017); (Timber Home Living, (n.d.)). The timber frame and trusses used have given the
atrium an open interior thus providing unlimited options for changing the floor plan to create
spaces that suit the intended use of the atrium.
Figure 2: Timber frame style structure of Yarra One (Yarra One, (n.d.))
2.3. Tower
On top of the atrium is the elliptical tower. The general structure of the tower comprises of
the conventional reinforced concrete. Stair and lift cores are built through the structure up to the
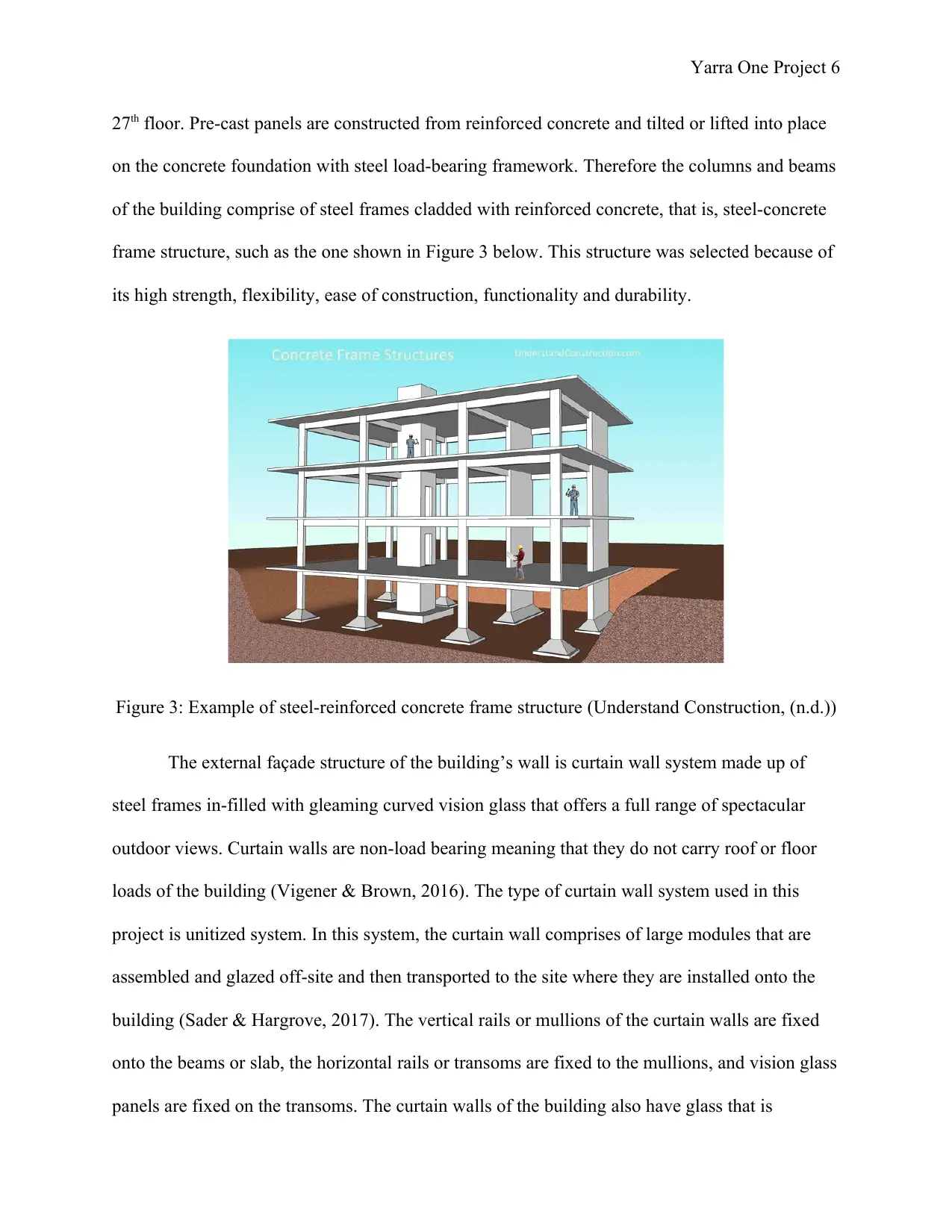
Yarra One Project 6
27th floor. Pre-cast panels are constructed from reinforced concrete and tilted or lifted into place
on the concrete foundation with steel load-bearing framework. Therefore the columns and beams
of the building comprise of steel frames cladded with reinforced concrete, that is, steel-concrete
frame structure, such as the one shown in Figure 3 below. This structure was selected because of
its high strength, flexibility, ease of construction, functionality and durability.
Figure 3: Example of steel-reinforced concrete frame structure (Understand Construction, (n.d.))
The external façade structure of the building’s wall is curtain wall system made up of
steel frames in-filled with gleaming curved vision glass that offers a full range of spectacular
outdoor views. Curtain walls are non-load bearing meaning that they do not carry roof or floor
loads of the building (Vigener & Brown, 2016). The type of curtain wall system used in this
project is unitized system. In this system, the curtain wall comprises of large modules that are
assembled and glazed off-site and then transported to the site where they are installed onto the
building (Sader & Hargrove, 2017). The vertical rails or mullions of the curtain walls are fixed
onto the beams or slab, the horizontal rails or transoms are fixed to the mullions, and vision glass
panels are fixed on the transoms. The curtain walls of the building also have glass that is
27th floor. Pre-cast panels are constructed from reinforced concrete and tilted or lifted into place
on the concrete foundation with steel load-bearing framework. Therefore the columns and beams
of the building comprise of steel frames cladded with reinforced concrete, that is, steel-concrete
frame structure, such as the one shown in Figure 3 below. This structure was selected because of
its high strength, flexibility, ease of construction, functionality and durability.
Figure 3: Example of steel-reinforced concrete frame structure (Understand Construction, (n.d.))
The external façade structure of the building’s wall is curtain wall system made up of
steel frames in-filled with gleaming curved vision glass that offers a full range of spectacular
outdoor views. Curtain walls are non-load bearing meaning that they do not carry roof or floor
loads of the building (Vigener & Brown, 2016). The type of curtain wall system used in this
project is unitized system. In this system, the curtain wall comprises of large modules that are
assembled and glazed off-site and then transported to the site where they are installed onto the
building (Sader & Hargrove, 2017). The vertical rails or mullions of the curtain walls are fixed
onto the beams or slab, the horizontal rails or transoms are fixed to the mullions, and vision glass
panels are fixed on the transoms. The curtain walls of the building also have glass that is
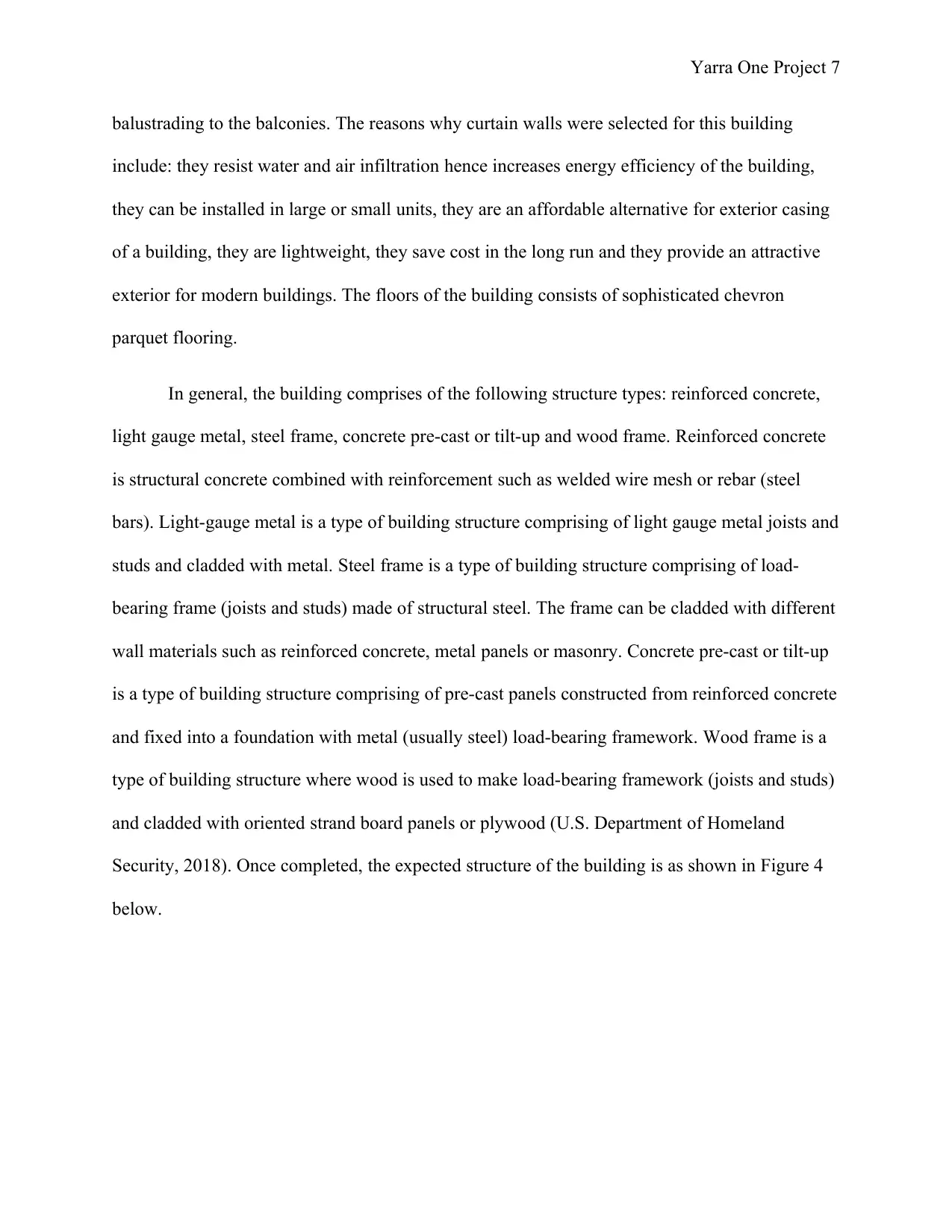
Yarra One Project 7
balustrading to the balconies. The reasons why curtain walls were selected for this building
include: they resist water and air infiltration hence increases energy efficiency of the building,
they can be installed in large or small units, they are an affordable alternative for exterior casing
of a building, they are lightweight, they save cost in the long run and they provide an attractive
exterior for modern buildings. The floors of the building consists of sophisticated chevron
parquet flooring.
In general, the building comprises of the following structure types: reinforced concrete,
light gauge metal, steel frame, concrete pre-cast or tilt-up and wood frame. Reinforced concrete
is structural concrete combined with reinforcement such as welded wire mesh or rebar (steel
bars). Light-gauge metal is a type of building structure comprising of light gauge metal joists and
studs and cladded with metal. Steel frame is a type of building structure comprising of load-
bearing frame (joists and studs) made of structural steel. The frame can be cladded with different
wall materials such as reinforced concrete, metal panels or masonry. Concrete pre-cast or tilt-up
is a type of building structure comprising of pre-cast panels constructed from reinforced concrete
and fixed into a foundation with metal (usually steel) load-bearing framework. Wood frame is a
type of building structure where wood is used to make load-bearing framework (joists and studs)
and cladded with oriented strand board panels or plywood (U.S. Department of Homeland
Security, 2018). Once completed, the expected structure of the building is as shown in Figure 4
below.
balustrading to the balconies. The reasons why curtain walls were selected for this building
include: they resist water and air infiltration hence increases energy efficiency of the building,
they can be installed in large or small units, they are an affordable alternative for exterior casing
of a building, they are lightweight, they save cost in the long run and they provide an attractive
exterior for modern buildings. The floors of the building consists of sophisticated chevron
parquet flooring.
In general, the building comprises of the following structure types: reinforced concrete,
light gauge metal, steel frame, concrete pre-cast or tilt-up and wood frame. Reinforced concrete
is structural concrete combined with reinforcement such as welded wire mesh or rebar (steel
bars). Light-gauge metal is a type of building structure comprising of light gauge metal joists and
studs and cladded with metal. Steel frame is a type of building structure comprising of load-
bearing frame (joists and studs) made of structural steel. The frame can be cladded with different
wall materials such as reinforced concrete, metal panels or masonry. Concrete pre-cast or tilt-up
is a type of building structure comprising of pre-cast panels constructed from reinforced concrete
and fixed into a foundation with metal (usually steel) load-bearing framework. Wood frame is a
type of building structure where wood is used to make load-bearing framework (joists and studs)
and cladded with oriented strand board panels or plywood (U.S. Department of Homeland
Security, 2018). Once completed, the expected structure of the building is as shown in Figure 4
below.
Paraphrase This Document
Need a fresh take? Get an instant paraphrase of this document with our AI Paraphraser
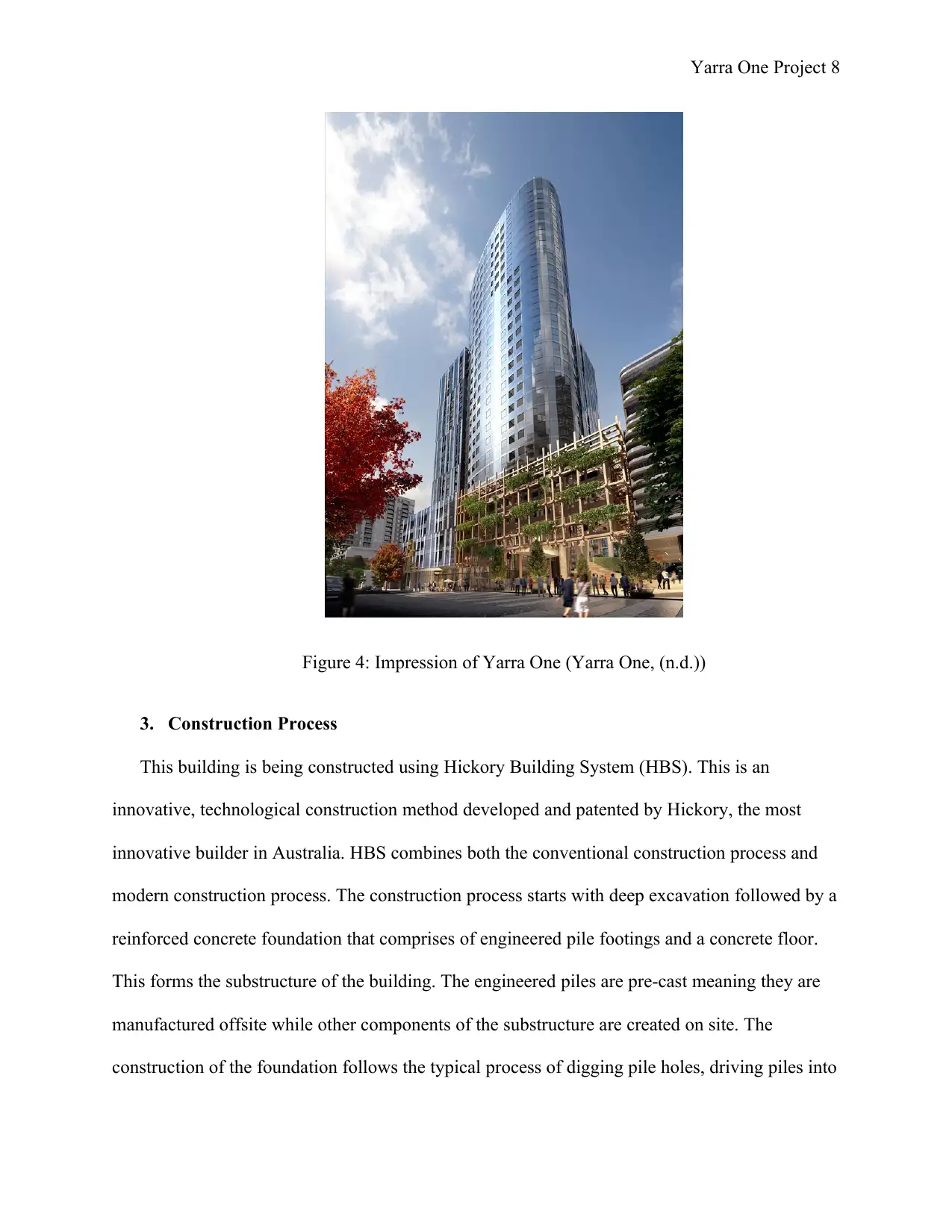
Yarra One Project 8
Figure 4: Impression of Yarra One (Yarra One, (n.d.))
3. Construction Process
This building is being constructed using Hickory Building System (HBS). This is an
innovative, technological construction method developed and patented by Hickory, the most
innovative builder in Australia. HBS combines both the conventional construction process and
modern construction process. The construction process starts with deep excavation followed by a
reinforced concrete foundation that comprises of engineered pile footings and a concrete floor.
This forms the substructure of the building. The engineered piles are pre-cast meaning they are
manufactured offsite while other components of the substructure are created on site. The
construction of the foundation follows the typical process of digging pile holes, driving piles into
Figure 4: Impression of Yarra One (Yarra One, (n.d.))
3. Construction Process
This building is being constructed using Hickory Building System (HBS). This is an
innovative, technological construction method developed and patented by Hickory, the most
innovative builder in Australia. HBS combines both the conventional construction process and
modern construction process. The construction process starts with deep excavation followed by a
reinforced concrete foundation that comprises of engineered pile footings and a concrete floor.
This forms the substructure of the building. The engineered piles are pre-cast meaning they are
manufactured offsite while other components of the substructure are created on site. The
construction of the foundation follows the typical process of digging pile holes, driving piles into
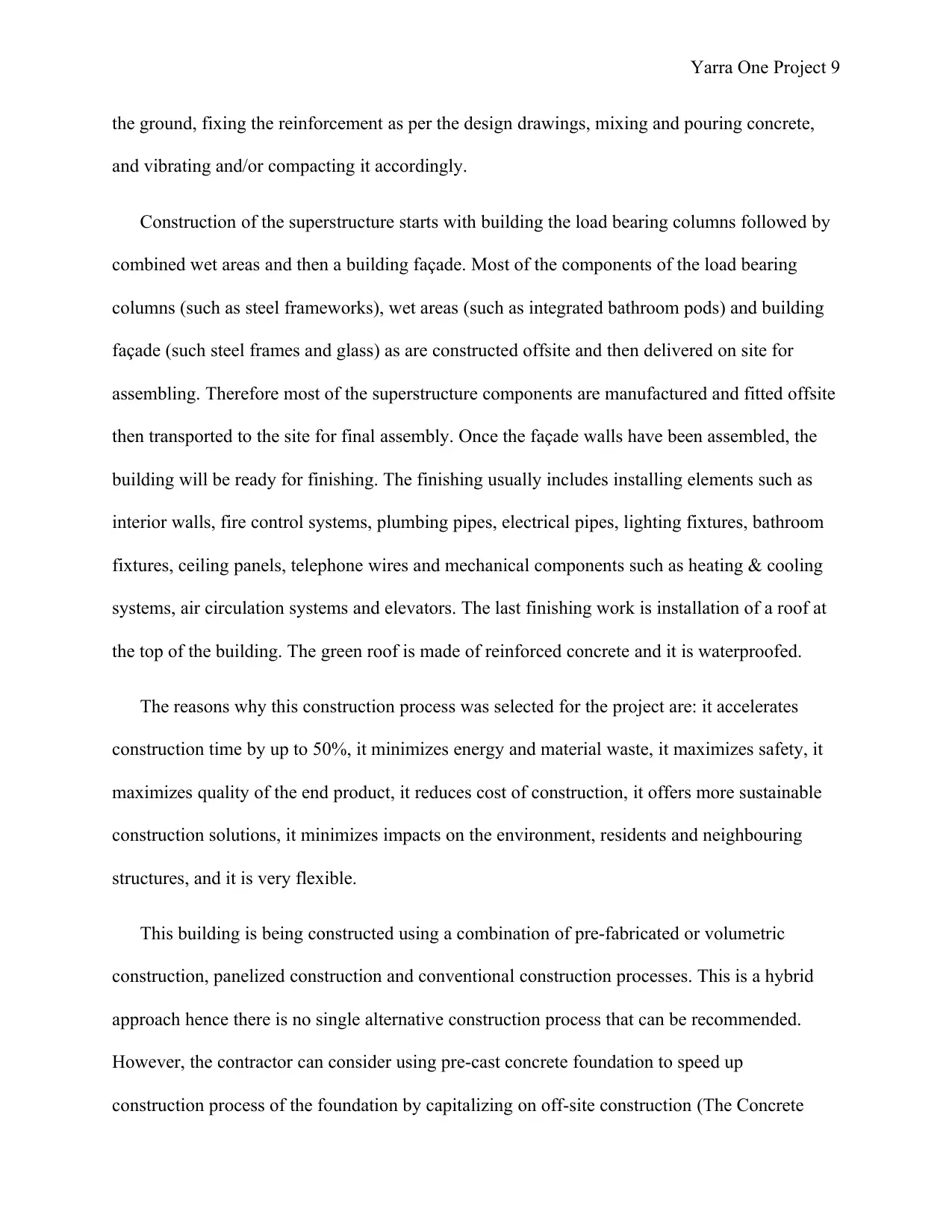
Yarra One Project 9
the ground, fixing the reinforcement as per the design drawings, mixing and pouring concrete,
and vibrating and/or compacting it accordingly.
Construction of the superstructure starts with building the load bearing columns followed by
combined wet areas and then a building façade. Most of the components of the load bearing
columns (such as steel frameworks), wet areas (such as integrated bathroom pods) and building
façade (such steel frames and glass) as are constructed offsite and then delivered on site for
assembling. Therefore most of the superstructure components are manufactured and fitted offsite
then transported to the site for final assembly. Once the façade walls have been assembled, the
building will be ready for finishing. The finishing usually includes installing elements such as
interior walls, fire control systems, plumbing pipes, electrical pipes, lighting fixtures, bathroom
fixtures, ceiling panels, telephone wires and mechanical components such as heating & cooling
systems, air circulation systems and elevators. The last finishing work is installation of a roof at
the top of the building. The green roof is made of reinforced concrete and it is waterproofed.
The reasons why this construction process was selected for the project are: it accelerates
construction time by up to 50%, it minimizes energy and material waste, it maximizes safety, it
maximizes quality of the end product, it reduces cost of construction, it offers more sustainable
construction solutions, it minimizes impacts on the environment, residents and neighbouring
structures, and it is very flexible.
This building is being constructed using a combination of pre-fabricated or volumetric
construction, panelized construction and conventional construction processes. This is a hybrid
approach hence there is no single alternative construction process that can be recommended.
However, the contractor can consider using pre-cast concrete foundation to speed up
construction process of the foundation by capitalizing on off-site construction (The Concrete
the ground, fixing the reinforcement as per the design drawings, mixing and pouring concrete,
and vibrating and/or compacting it accordingly.
Construction of the superstructure starts with building the load bearing columns followed by
combined wet areas and then a building façade. Most of the components of the load bearing
columns (such as steel frameworks), wet areas (such as integrated bathroom pods) and building
façade (such steel frames and glass) as are constructed offsite and then delivered on site for
assembling. Therefore most of the superstructure components are manufactured and fitted offsite
then transported to the site for final assembly. Once the façade walls have been assembled, the
building will be ready for finishing. The finishing usually includes installing elements such as
interior walls, fire control systems, plumbing pipes, electrical pipes, lighting fixtures, bathroom
fixtures, ceiling panels, telephone wires and mechanical components such as heating & cooling
systems, air circulation systems and elevators. The last finishing work is installation of a roof at
the top of the building. The green roof is made of reinforced concrete and it is waterproofed.
The reasons why this construction process was selected for the project are: it accelerates
construction time by up to 50%, it minimizes energy and material waste, it maximizes safety, it
maximizes quality of the end product, it reduces cost of construction, it offers more sustainable
construction solutions, it minimizes impacts on the environment, residents and neighbouring
structures, and it is very flexible.
This building is being constructed using a combination of pre-fabricated or volumetric
construction, panelized construction and conventional construction processes. This is a hybrid
approach hence there is no single alternative construction process that can be recommended.
However, the contractor can consider using pre-cast concrete foundation to speed up
construction process of the foundation by capitalizing on off-site construction (The Concrete
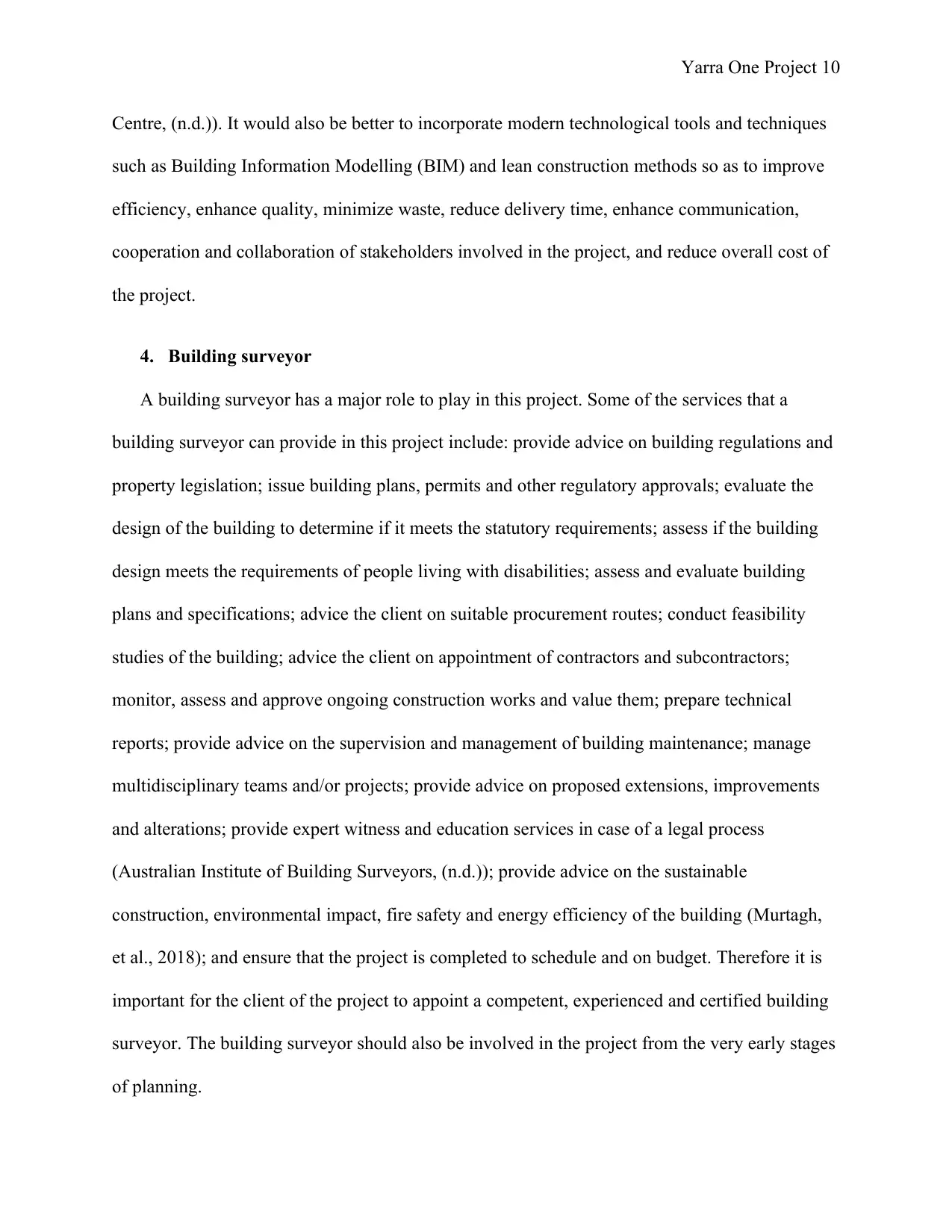
Yarra One Project 10
Centre, (n.d.)). It would also be better to incorporate modern technological tools and techniques
such as Building Information Modelling (BIM) and lean construction methods so as to improve
efficiency, enhance quality, minimize waste, reduce delivery time, enhance communication,
cooperation and collaboration of stakeholders involved in the project, and reduce overall cost of
the project.
4. Building surveyor
A building surveyor has a major role to play in this project. Some of the services that a
building surveyor can provide in this project include: provide advice on building regulations and
property legislation; issue building plans, permits and other regulatory approvals; evaluate the
design of the building to determine if it meets the statutory requirements; assess if the building
design meets the requirements of people living with disabilities; assess and evaluate building
plans and specifications; advice the client on suitable procurement routes; conduct feasibility
studies of the building; advice the client on appointment of contractors and subcontractors;
monitor, assess and approve ongoing construction works and value them; prepare technical
reports; provide advice on the supervision and management of building maintenance; manage
multidisciplinary teams and/or projects; provide advice on proposed extensions, improvements
and alterations; provide expert witness and education services in case of a legal process
(Australian Institute of Building Surveyors, (n.d.)); provide advice on the sustainable
construction, environmental impact, fire safety and energy efficiency of the building (Murtagh,
et al., 2018); and ensure that the project is completed to schedule and on budget. Therefore it is
important for the client of the project to appoint a competent, experienced and certified building
surveyor. The building surveyor should also be involved in the project from the very early stages
of planning.
Centre, (n.d.)). It would also be better to incorporate modern technological tools and techniques
such as Building Information Modelling (BIM) and lean construction methods so as to improve
efficiency, enhance quality, minimize waste, reduce delivery time, enhance communication,
cooperation and collaboration of stakeholders involved in the project, and reduce overall cost of
the project.
4. Building surveyor
A building surveyor has a major role to play in this project. Some of the services that a
building surveyor can provide in this project include: provide advice on building regulations and
property legislation; issue building plans, permits and other regulatory approvals; evaluate the
design of the building to determine if it meets the statutory requirements; assess if the building
design meets the requirements of people living with disabilities; assess and evaluate building
plans and specifications; advice the client on suitable procurement routes; conduct feasibility
studies of the building; advice the client on appointment of contractors and subcontractors;
monitor, assess and approve ongoing construction works and value them; prepare technical
reports; provide advice on the supervision and management of building maintenance; manage
multidisciplinary teams and/or projects; provide advice on proposed extensions, improvements
and alterations; provide expert witness and education services in case of a legal process
(Australian Institute of Building Surveyors, (n.d.)); provide advice on the sustainable
construction, environmental impact, fire safety and energy efficiency of the building (Murtagh,
et al., 2018); and ensure that the project is completed to schedule and on budget. Therefore it is
important for the client of the project to appoint a competent, experienced and certified building
surveyor. The building surveyor should also be involved in the project from the very early stages
of planning.
Secure Best Marks with AI Grader
Need help grading? Try our AI Grader for instant feedback on your assignments.
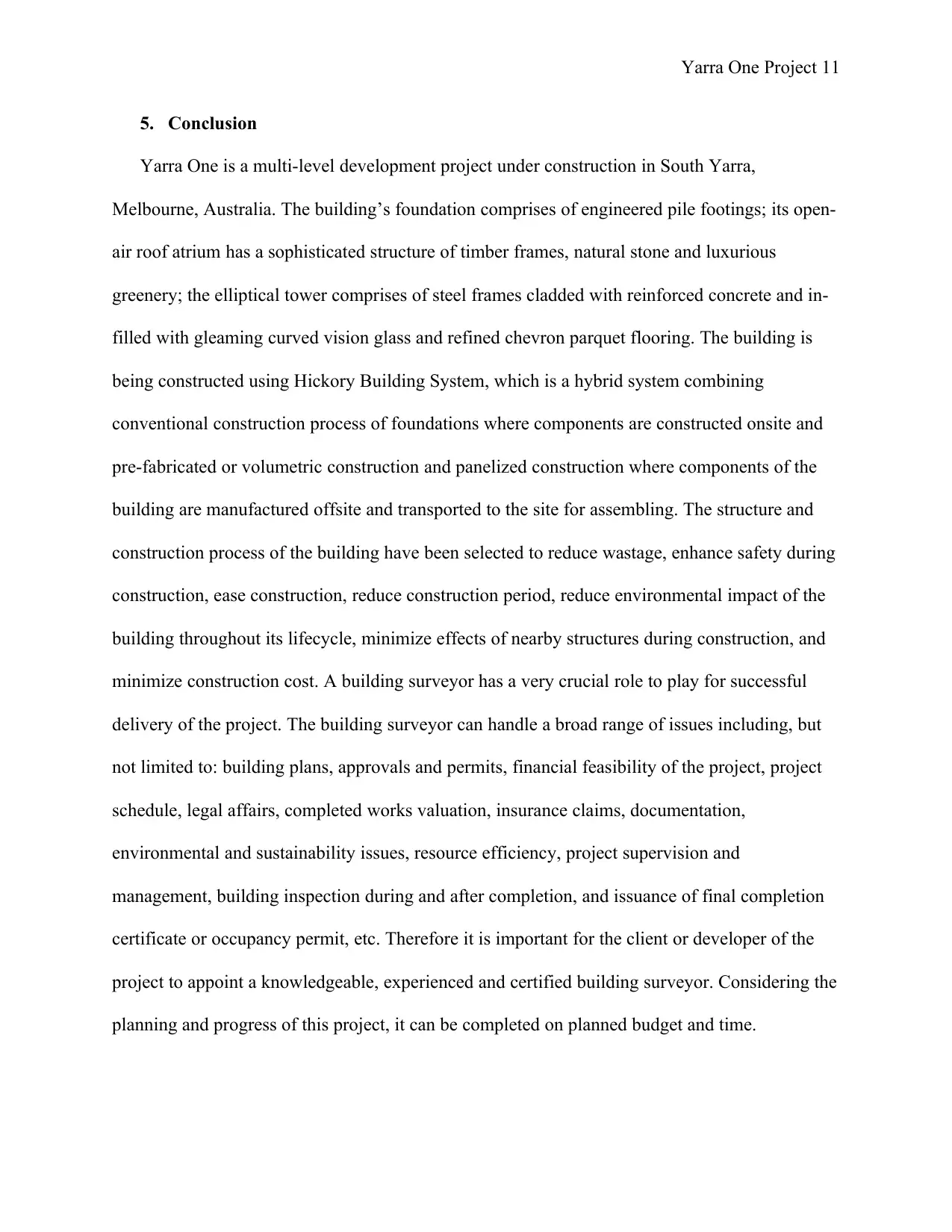
Yarra One Project 11
5. Conclusion
Yarra One is a multi-level development project under construction in South Yarra,
Melbourne, Australia. The building’s foundation comprises of engineered pile footings; its open-
air roof atrium has a sophisticated structure of timber frames, natural stone and luxurious
greenery; the elliptical tower comprises of steel frames cladded with reinforced concrete and in-
filled with gleaming curved vision glass and refined chevron parquet flooring. The building is
being constructed using Hickory Building System, which is a hybrid system combining
conventional construction process of foundations where components are constructed onsite and
pre-fabricated or volumetric construction and panelized construction where components of the
building are manufactured offsite and transported to the site for assembling. The structure and
construction process of the building have been selected to reduce wastage, enhance safety during
construction, ease construction, reduce construction period, reduce environmental impact of the
building throughout its lifecycle, minimize effects of nearby structures during construction, and
minimize construction cost. A building surveyor has a very crucial role to play for successful
delivery of the project. The building surveyor can handle a broad range of issues including, but
not limited to: building plans, approvals and permits, financial feasibility of the project, project
schedule, legal affairs, completed works valuation, insurance claims, documentation,
environmental and sustainability issues, resource efficiency, project supervision and
management, building inspection during and after completion, and issuance of final completion
certificate or occupancy permit, etc. Therefore it is important for the client or developer of the
project to appoint a knowledgeable, experienced and certified building surveyor. Considering the
planning and progress of this project, it can be completed on planned budget and time.
5. Conclusion
Yarra One is a multi-level development project under construction in South Yarra,
Melbourne, Australia. The building’s foundation comprises of engineered pile footings; its open-
air roof atrium has a sophisticated structure of timber frames, natural stone and luxurious
greenery; the elliptical tower comprises of steel frames cladded with reinforced concrete and in-
filled with gleaming curved vision glass and refined chevron parquet flooring. The building is
being constructed using Hickory Building System, which is a hybrid system combining
conventional construction process of foundations where components are constructed onsite and
pre-fabricated or volumetric construction and panelized construction where components of the
building are manufactured offsite and transported to the site for assembling. The structure and
construction process of the building have been selected to reduce wastage, enhance safety during
construction, ease construction, reduce construction period, reduce environmental impact of the
building throughout its lifecycle, minimize effects of nearby structures during construction, and
minimize construction cost. A building surveyor has a very crucial role to play for successful
delivery of the project. The building surveyor can handle a broad range of issues including, but
not limited to: building plans, approvals and permits, financial feasibility of the project, project
schedule, legal affairs, completed works valuation, insurance claims, documentation,
environmental and sustainability issues, resource efficiency, project supervision and
management, building inspection during and after completion, and issuance of final completion
certificate or occupancy permit, etc. Therefore it is important for the client or developer of the
project to appoint a knowledgeable, experienced and certified building surveyor. Considering the
planning and progress of this project, it can be completed on planned budget and time.
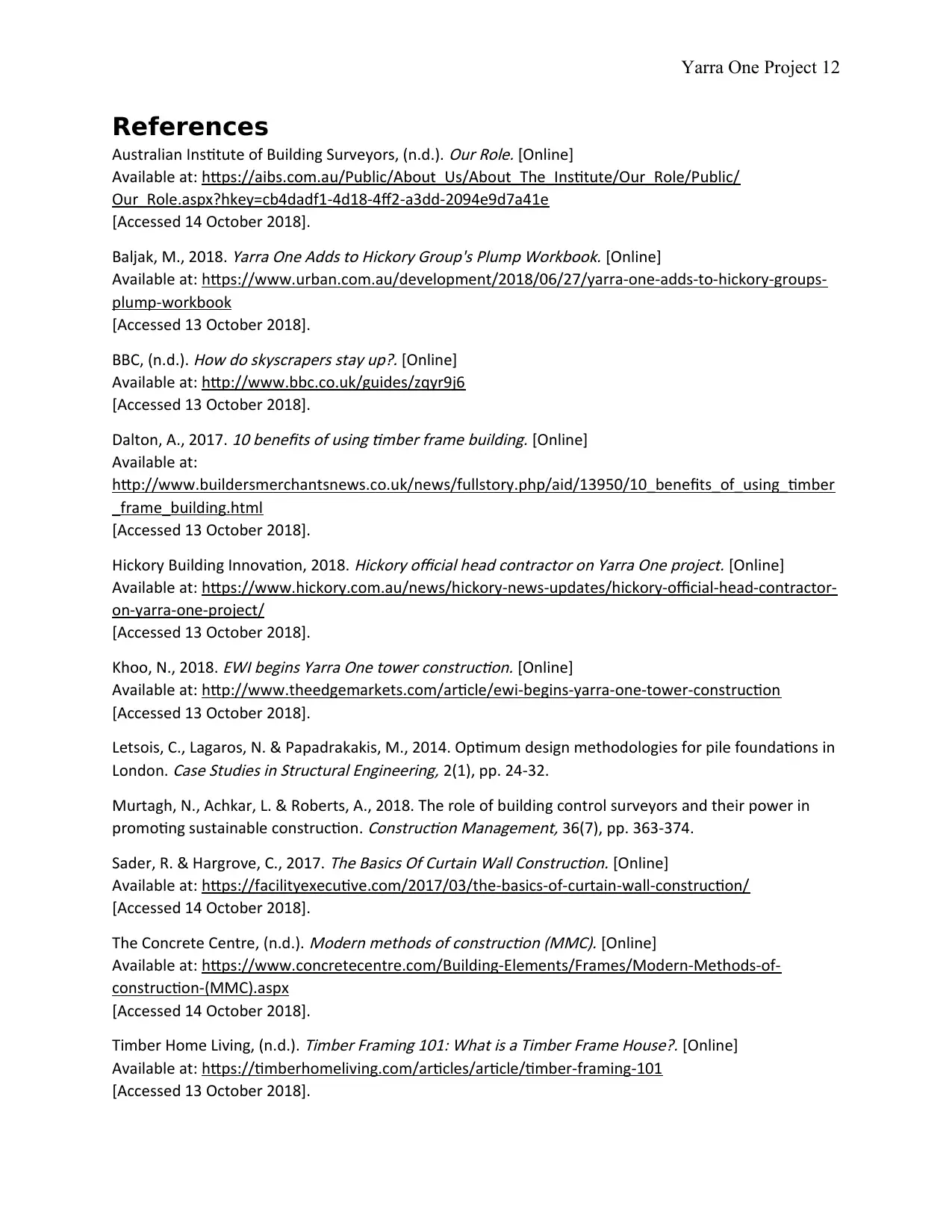
Yarra One Project 12
References
Australian Institute of Building Surveyors, (n.d.).
Our Role. [Online]
Available at: https://aibs.com.au/Public/About_Us/About_The_Institute/Our_Role/Public/
Our_Role.aspx?hkey=cb4dadf1-4d18-4ff2-a3dd-2094e9d7a41e
[Accessed 14 October 2018].
Baljak, M., 2018.
Yarra One Adds to Hickory Group's Plump Workbook. [Online]
Available at: https://www.urban.com.au/development/2018/06/27/yarra-one-adds-to-hickory-groups-
plump-workbook
[Accessed 13 October 2018].
BBC, (n.d.).
How do skyscrapers stay up?. [Online]
Available at: http://www.bbc.co.uk/guides/zqyr9j6
[Accessed 13 October 2018].
Dalton, A., 2017.
10 benefits of using timber frame building. [Online]
Available at:
http://www.buildersmerchantsnews.co.uk/news/fullstory.php/aid/13950/10_benefits_of_using_timber
_frame_building.html
[Accessed 13 October 2018].
Hickory Building Innovation, 2018.
Hickory official head contractor on Yarra One project. [Online]
Available at: https://www.hickory.com.au/news/hickory-news-updates/hickory-official-head-contractor-
on-yarra-one-project/
[Accessed 13 October 2018].
Khoo, N., 2018.
EWI begins Yarra One tower construction. [Online]
Available at: http://www.theedgemarkets.com/article/ewi-begins-yarra-one-tower-construction
[Accessed 13 October 2018].
Letsois, C., Lagaros, N. & Papadrakakis, M., 2014. Optimum design methodologies for pile foundations in
London.
Case Studies in Structural Engineering, 2(1), pp. 24-32.
Murtagh, N., Achkar, L. & Roberts, A., 2018. The role of building control surveyors and their power in
promoting sustainable construction.
Construction Management, 36(7), pp. 363-374.
Sader, R. & Hargrove, C., 2017.
The Basics Of Curtain Wall Construction. [Online]
Available at: https://facilityexecutive.com/2017/03/the-basics-of-curtain-wall-construction/
[Accessed 14 October 2018].
The Concrete Centre, (n.d.).
Modern methods of construction (MMC). [Online]
Available at: https://www.concretecentre.com/Building-Elements/Frames/Modern-Methods-of-
construction-(MMC).aspx
[Accessed 14 October 2018].
Timber Home Living, (n.d.).
Timber Framing 101: What is a Timber Frame House?. [Online]
Available at: https://timberhomeliving.com/articles/article/timber-framing-101
[Accessed 13 October 2018].
References
Australian Institute of Building Surveyors, (n.d.).
Our Role. [Online]
Available at: https://aibs.com.au/Public/About_Us/About_The_Institute/Our_Role/Public/
Our_Role.aspx?hkey=cb4dadf1-4d18-4ff2-a3dd-2094e9d7a41e
[Accessed 14 October 2018].
Baljak, M., 2018.
Yarra One Adds to Hickory Group's Plump Workbook. [Online]
Available at: https://www.urban.com.au/development/2018/06/27/yarra-one-adds-to-hickory-groups-
plump-workbook
[Accessed 13 October 2018].
BBC, (n.d.).
How do skyscrapers stay up?. [Online]
Available at: http://www.bbc.co.uk/guides/zqyr9j6
[Accessed 13 October 2018].
Dalton, A., 2017.
10 benefits of using timber frame building. [Online]
Available at:
http://www.buildersmerchantsnews.co.uk/news/fullstory.php/aid/13950/10_benefits_of_using_timber
_frame_building.html
[Accessed 13 October 2018].
Hickory Building Innovation, 2018.
Hickory official head contractor on Yarra One project. [Online]
Available at: https://www.hickory.com.au/news/hickory-news-updates/hickory-official-head-contractor-
on-yarra-one-project/
[Accessed 13 October 2018].
Khoo, N., 2018.
EWI begins Yarra One tower construction. [Online]
Available at: http://www.theedgemarkets.com/article/ewi-begins-yarra-one-tower-construction
[Accessed 13 October 2018].
Letsois, C., Lagaros, N. & Papadrakakis, M., 2014. Optimum design methodologies for pile foundations in
London.
Case Studies in Structural Engineering, 2(1), pp. 24-32.
Murtagh, N., Achkar, L. & Roberts, A., 2018. The role of building control surveyors and their power in
promoting sustainable construction.
Construction Management, 36(7), pp. 363-374.
Sader, R. & Hargrove, C., 2017.
The Basics Of Curtain Wall Construction. [Online]
Available at: https://facilityexecutive.com/2017/03/the-basics-of-curtain-wall-construction/
[Accessed 14 October 2018].
The Concrete Centre, (n.d.).
Modern methods of construction (MMC). [Online]
Available at: https://www.concretecentre.com/Building-Elements/Frames/Modern-Methods-of-
construction-(MMC).aspx
[Accessed 14 October 2018].
Timber Home Living, (n.d.).
Timber Framing 101: What is a Timber Frame House?. [Online]
Available at: https://timberhomeliving.com/articles/article/timber-framing-101
[Accessed 13 October 2018].

Yarra One Project 13
U.S. Department of Homeland Security, 2018.
Structure Type Definitions. [Online]
Available at: https://www.fema.gov/structure-type-definitions
[Accessed 13 October 2018].
Understand Building Construction, (n.d.).
Pile Foundations. [Online]
Available at: http://www.understandconstruction.com/pile-foundations.html
[Accessed 13 October 2018].
Understand Construction, (n.d.).
Concrete Frame Structures. [Online]
Available at: http://www.understandconstruction.com/concrete-frame-structures.html
[Accessed 14 October 2018].
Vigener, N. & Brown, M., 2016.
Curtain Walls. [Online]
Available at: https://www.wbdg.org/guides-specifications/building-envelope-design-guide/fenestration-
systems/curtain-walls
[Accessed 13 October 2018].
Yarra One, (n.d.).
Design. [Online]
Available at: https://yarraone.com.au/design
[Accessed 13 October 2018].
U.S. Department of Homeland Security, 2018.
Structure Type Definitions. [Online]
Available at: https://www.fema.gov/structure-type-definitions
[Accessed 13 October 2018].
Understand Building Construction, (n.d.).
Pile Foundations. [Online]
Available at: http://www.understandconstruction.com/pile-foundations.html
[Accessed 13 October 2018].
Understand Construction, (n.d.).
Concrete Frame Structures. [Online]
Available at: http://www.understandconstruction.com/concrete-frame-structures.html
[Accessed 14 October 2018].
Vigener, N. & Brown, M., 2016.
Curtain Walls. [Online]
Available at: https://www.wbdg.org/guides-specifications/building-envelope-design-guide/fenestration-
systems/curtain-walls
[Accessed 13 October 2018].
Yarra One, (n.d.).
Design. [Online]
Available at: https://yarraone.com.au/design
[Accessed 13 October 2018].
1 out of 13
![[object Object]](/_next/image/?url=%2F_next%2Fstatic%2Fmedia%2Flogo.6d15ce61.png&w=640&q=75)
Your All-in-One AI-Powered Toolkit for Academic Success.
+13062052269
info@desklib.com
Available 24*7 on WhatsApp / Email
Unlock your academic potential
© 2024 | Zucol Services PVT LTD | All rights reserved.