Thesis Proposal: 3D Printing Revolutionizing Construction Processes
VerifiedAdded on 2020/03/16
|16
|4191
|262
Thesis and Dissertation
AI Summary
This thesis proposal explores the application of 3D printing in the construction industry, examining its potential to revolutionize building processes. The proposal outlines the benefits of 3D printing, including reduced construction time and costs, while also addressing the need for improved printing speed and material optimization. It reviews existing research and case studies, such as the Canal House in Amsterdam and the Winsun company buildings, highlighting various 3D printing techniques like FEM, FDM, and Contour Crafting. The research sets up two hypotheses regarding the impact of printing speed on construction time, quality, and cost, with data analysis planned to confirm their validity. It concludes that the printing speed and material selection must be optimized based on the design and structure requirements. The proposal emphasizes the importance of risk management to ensure project success and quality.
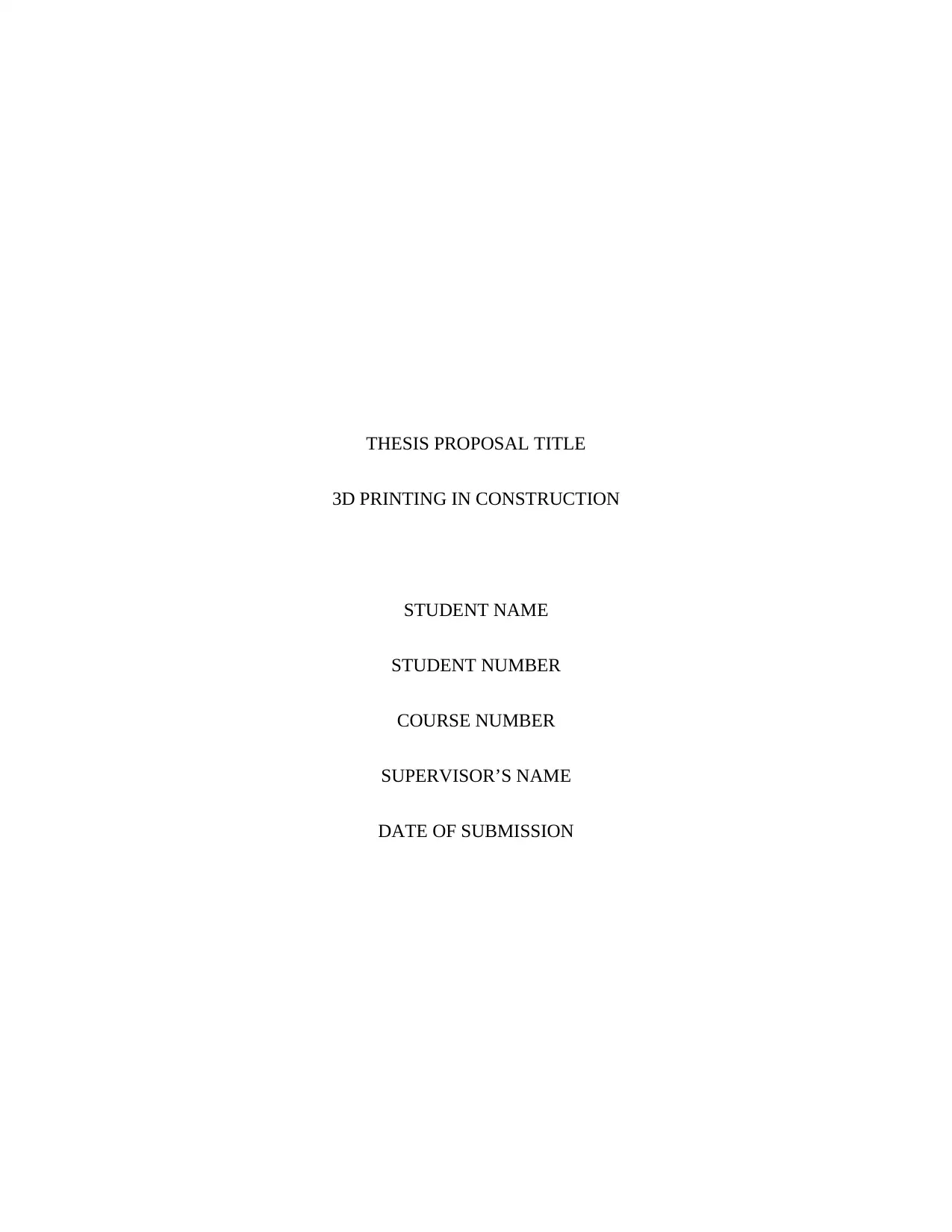
THESIS PROPOSAL TITLE
3D PRINTING IN CONSTRUCTION
STUDENT NAME
STUDENT NUMBER
COURSE NUMBER
SUPERVISOR’S NAME
DATE OF SUBMISSION
3D PRINTING IN CONSTRUCTION
STUDENT NAME
STUDENT NUMBER
COURSE NUMBER
SUPERVISOR’S NAME
DATE OF SUBMISSION
Paraphrase This Document
Need a fresh take? Get an instant paraphrase of this document with our AI Paraphraser
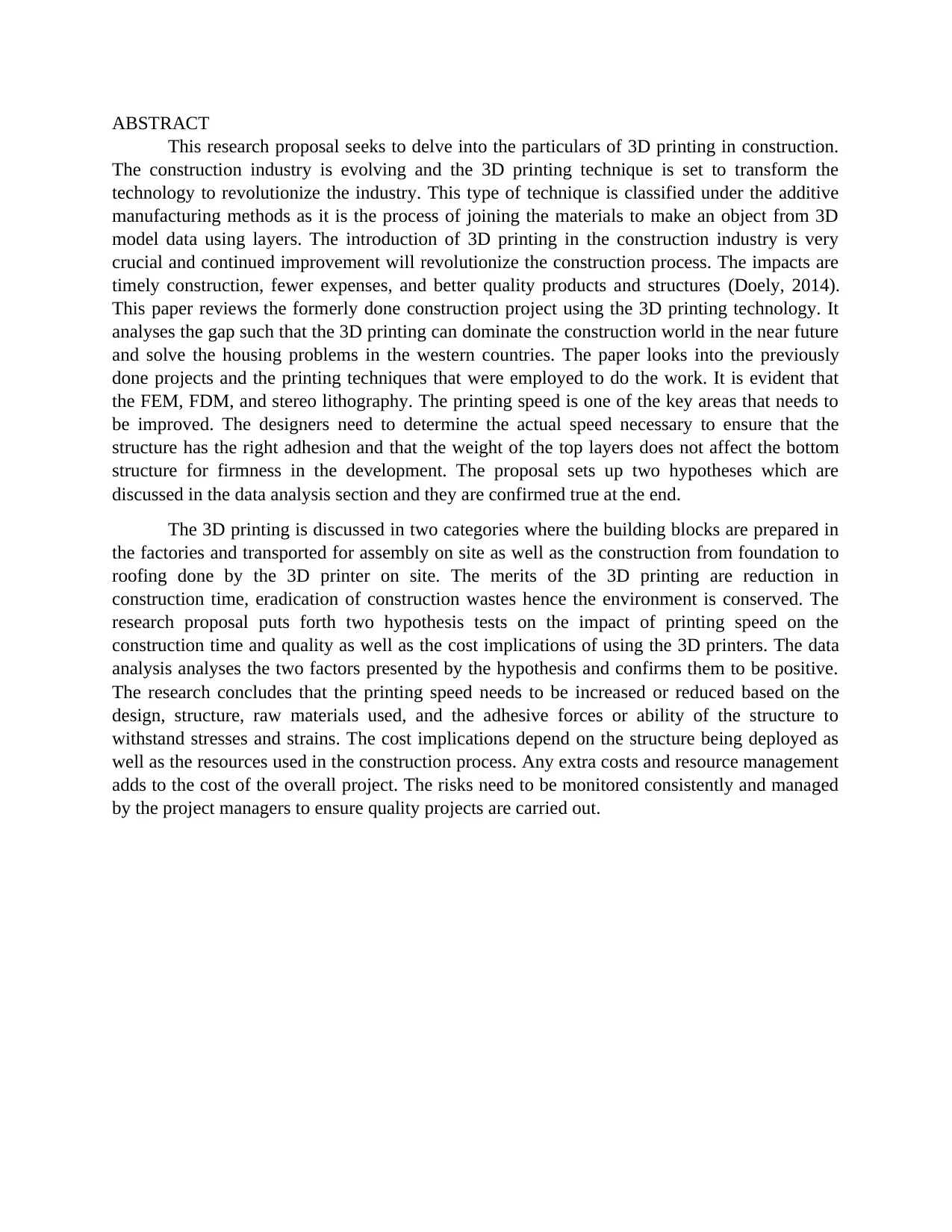
ABSTRACT
This research proposal seeks to delve into the particulars of 3D printing in construction.
The construction industry is evolving and the 3D printing technique is set to transform the
technology to revolutionize the industry. This type of technique is classified under the additive
manufacturing methods as it is the process of joining the materials to make an object from 3D
model data using layers. The introduction of 3D printing in the construction industry is very
crucial and continued improvement will revolutionize the construction process. The impacts are
timely construction, fewer expenses, and better quality products and structures (Doely, 2014).
This paper reviews the formerly done construction project using the 3D printing technology. It
analyses the gap such that the 3D printing can dominate the construction world in the near future
and solve the housing problems in the western countries. The paper looks into the previously
done projects and the printing techniques that were employed to do the work. It is evident that
the FEM, FDM, and stereo lithography. The printing speed is one of the key areas that needs to
be improved. The designers need to determine the actual speed necessary to ensure that the
structure has the right adhesion and that the weight of the top layers does not affect the bottom
structure for firmness in the development. The proposal sets up two hypotheses which are
discussed in the data analysis section and they are confirmed true at the end.
The 3D printing is discussed in two categories where the building blocks are prepared in
the factories and transported for assembly on site as well as the construction from foundation to
roofing done by the 3D printer on site. The merits of the 3D printing are reduction in
construction time, eradication of construction wastes hence the environment is conserved. The
research proposal puts forth two hypothesis tests on the impact of printing speed on the
construction time and quality as well as the cost implications of using the 3D printers. The data
analysis analyses the two factors presented by the hypothesis and confirms them to be positive.
The research concludes that the printing speed needs to be increased or reduced based on the
design, structure, raw materials used, and the adhesive forces or ability of the structure to
withstand stresses and strains. The cost implications depend on the structure being deployed as
well as the resources used in the construction process. Any extra costs and resource management
adds to the cost of the overall project. The risks need to be monitored consistently and managed
by the project managers to ensure quality projects are carried out.
This research proposal seeks to delve into the particulars of 3D printing in construction.
The construction industry is evolving and the 3D printing technique is set to transform the
technology to revolutionize the industry. This type of technique is classified under the additive
manufacturing methods as it is the process of joining the materials to make an object from 3D
model data using layers. The introduction of 3D printing in the construction industry is very
crucial and continued improvement will revolutionize the construction process. The impacts are
timely construction, fewer expenses, and better quality products and structures (Doely, 2014).
This paper reviews the formerly done construction project using the 3D printing technology. It
analyses the gap such that the 3D printing can dominate the construction world in the near future
and solve the housing problems in the western countries. The paper looks into the previously
done projects and the printing techniques that were employed to do the work. It is evident that
the FEM, FDM, and stereo lithography. The printing speed is one of the key areas that needs to
be improved. The designers need to determine the actual speed necessary to ensure that the
structure has the right adhesion and that the weight of the top layers does not affect the bottom
structure for firmness in the development. The proposal sets up two hypotheses which are
discussed in the data analysis section and they are confirmed true at the end.
The 3D printing is discussed in two categories where the building blocks are prepared in
the factories and transported for assembly on site as well as the construction from foundation to
roofing done by the 3D printer on site. The merits of the 3D printing are reduction in
construction time, eradication of construction wastes hence the environment is conserved. The
research proposal puts forth two hypothesis tests on the impact of printing speed on the
construction time and quality as well as the cost implications of using the 3D printers. The data
analysis analyses the two factors presented by the hypothesis and confirms them to be positive.
The research concludes that the printing speed needs to be increased or reduced based on the
design, structure, raw materials used, and the adhesive forces or ability of the structure to
withstand stresses and strains. The cost implications depend on the structure being deployed as
well as the resources used in the construction process. Any extra costs and resource management
adds to the cost of the overall project. The risks need to be monitored consistently and managed
by the project managers to ensure quality projects are carried out.
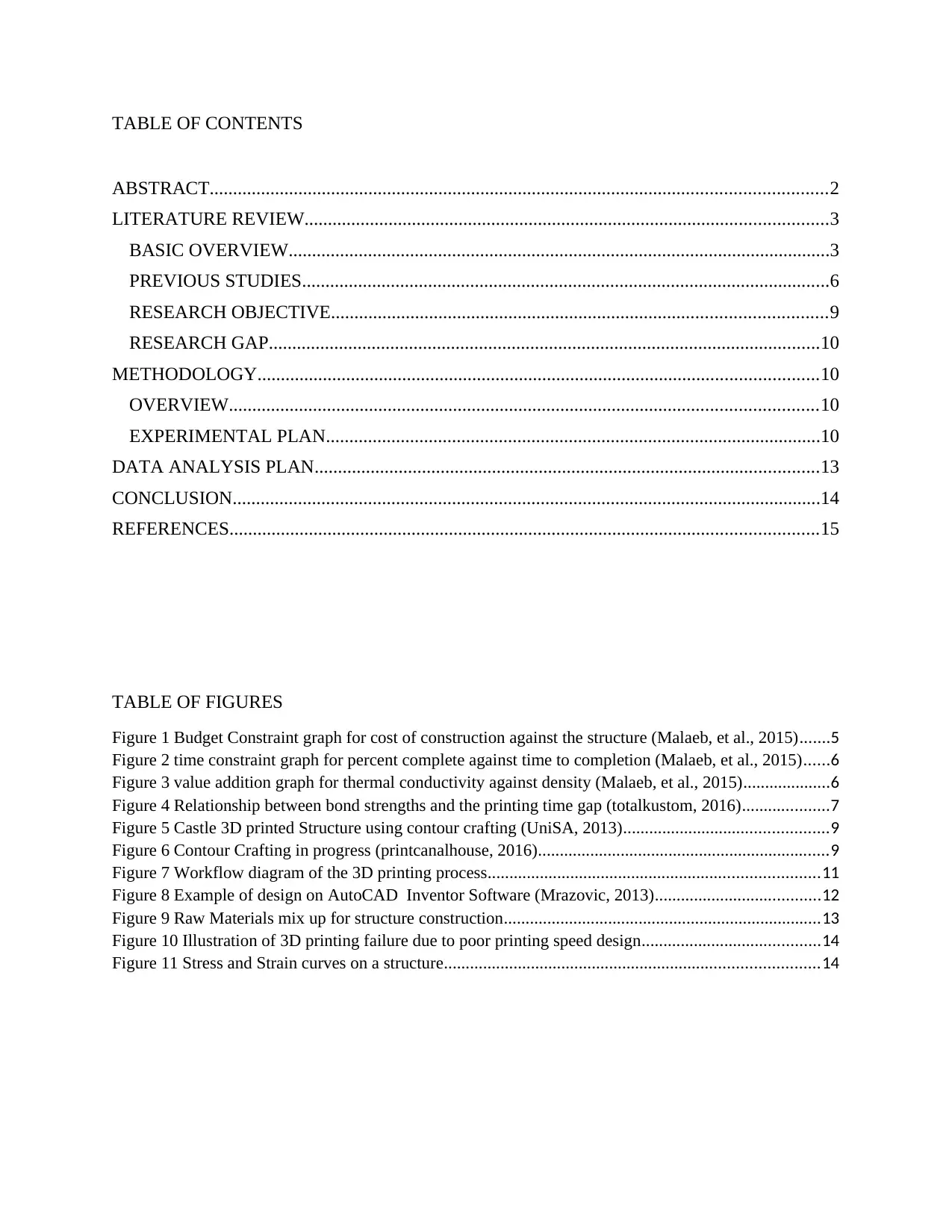
TABLE OF CONTENTS
ABSTRACT....................................................................................................................................2
LITERATURE REVIEW................................................................................................................3
BASIC OVERVIEW....................................................................................................................3
PREVIOUS STUDIES.................................................................................................................6
RESEARCH OBJECTIVE..........................................................................................................9
RESEARCH GAP......................................................................................................................10
METHODOLOGY........................................................................................................................10
OVERVIEW..............................................................................................................................10
EXPERIMENTAL PLAN..........................................................................................................10
DATA ANALYSIS PLAN............................................................................................................13
CONCLUSION..............................................................................................................................14
REFERENCES..............................................................................................................................15
TABLE OF FIGURES
Figure 1 Budget Constraint graph for cost of construction against the structure (Malaeb, et al., 2015).......5
Figure 2 time constraint graph for percent complete against time to completion (Malaeb, et al., 2015)......6
Figure 3 value addition graph for thermal conductivity against density (Malaeb, et al., 2015)....................6
Figure 4 Relationship between bond strengths and the printing time gap (totalkustom, 2016)....................7
Figure 5 Castle 3D printed Structure using contour crafting (UniSA, 2013)...............................................9
Figure 6 Contour Crafting in progress (printcanalhouse, 2016)...................................................................9
Figure 7 Workflow diagram of the 3D printing process............................................................................11
Figure 8 Example of design on AutoCAD Inventor Software (Mrazovic, 2013)......................................12
Figure 9 Raw Materials mix up for structure construction.........................................................................13
Figure 10 Illustration of 3D printing failure due to poor printing speed design.........................................14
Figure 11 Stress and Strain curves on a structure......................................................................................14
ABSTRACT....................................................................................................................................2
LITERATURE REVIEW................................................................................................................3
BASIC OVERVIEW....................................................................................................................3
PREVIOUS STUDIES.................................................................................................................6
RESEARCH OBJECTIVE..........................................................................................................9
RESEARCH GAP......................................................................................................................10
METHODOLOGY........................................................................................................................10
OVERVIEW..............................................................................................................................10
EXPERIMENTAL PLAN..........................................................................................................10
DATA ANALYSIS PLAN............................................................................................................13
CONCLUSION..............................................................................................................................14
REFERENCES..............................................................................................................................15
TABLE OF FIGURES
Figure 1 Budget Constraint graph for cost of construction against the structure (Malaeb, et al., 2015).......5
Figure 2 time constraint graph for percent complete against time to completion (Malaeb, et al., 2015)......6
Figure 3 value addition graph for thermal conductivity against density (Malaeb, et al., 2015)....................6
Figure 4 Relationship between bond strengths and the printing time gap (totalkustom, 2016)....................7
Figure 5 Castle 3D printed Structure using contour crafting (UniSA, 2013)...............................................9
Figure 6 Contour Crafting in progress (printcanalhouse, 2016)...................................................................9
Figure 7 Workflow diagram of the 3D printing process............................................................................11
Figure 8 Example of design on AutoCAD Inventor Software (Mrazovic, 2013)......................................12
Figure 9 Raw Materials mix up for structure construction.........................................................................13
Figure 10 Illustration of 3D printing failure due to poor printing speed design.........................................14
Figure 11 Stress and Strain curves on a structure......................................................................................14
You're viewing a preview
Unlock full access by subscribing today!
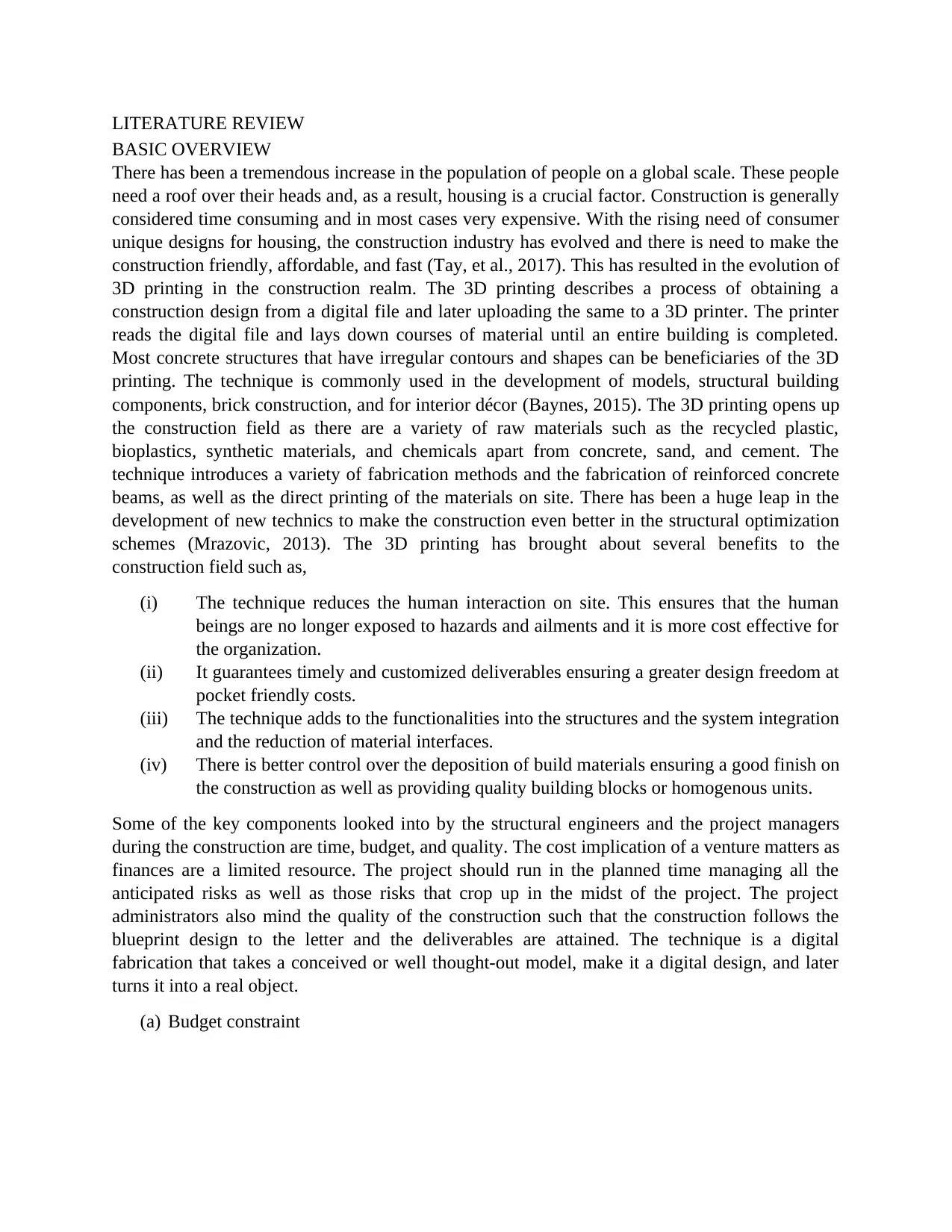
LITERATURE REVIEW
BASIC OVERVIEW
There has been a tremendous increase in the population of people on a global scale. These people
need a roof over their heads and, as a result, housing is a crucial factor. Construction is generally
considered time consuming and in most cases very expensive. With the rising need of consumer
unique designs for housing, the construction industry has evolved and there is need to make the
construction friendly, affordable, and fast (Tay, et al., 2017). This has resulted in the evolution of
3D printing in the construction realm. The 3D printing describes a process of obtaining a
construction design from a digital file and later uploading the same to a 3D printer. The printer
reads the digital file and lays down courses of material until an entire building is completed.
Most concrete structures that have irregular contours and shapes can be beneficiaries of the 3D
printing. The technique is commonly used in the development of models, structural building
components, brick construction, and for interior décor (Baynes, 2015). The 3D printing opens up
the construction field as there are a variety of raw materials such as the recycled plastic,
bioplastics, synthetic materials, and chemicals apart from concrete, sand, and cement. The
technique introduces a variety of fabrication methods and the fabrication of reinforced concrete
beams, as well as the direct printing of the materials on site. There has been a huge leap in the
development of new technics to make the construction even better in the structural optimization
schemes (Mrazovic, 2013). The 3D printing has brought about several benefits to the
construction field such as,
(i) The technique reduces the human interaction on site. This ensures that the human
beings are no longer exposed to hazards and ailments and it is more cost effective for
the organization.
(ii) It guarantees timely and customized deliverables ensuring a greater design freedom at
pocket friendly costs.
(iii) The technique adds to the functionalities into the structures and the system integration
and the reduction of material interfaces.
(iv) There is better control over the deposition of build materials ensuring a good finish on
the construction as well as providing quality building blocks or homogenous units.
Some of the key components looked into by the structural engineers and the project managers
during the construction are time, budget, and quality. The cost implication of a venture matters as
finances are a limited resource. The project should run in the planned time managing all the
anticipated risks as well as those risks that crop up in the midst of the project. The project
administrators also mind the quality of the construction such that the construction follows the
blueprint design to the letter and the deliverables are attained. The technique is a digital
fabrication that takes a conceived or well thought-out model, make it a digital design, and later
turns it into a real object.
(a) Budget constraint
BASIC OVERVIEW
There has been a tremendous increase in the population of people on a global scale. These people
need a roof over their heads and, as a result, housing is a crucial factor. Construction is generally
considered time consuming and in most cases very expensive. With the rising need of consumer
unique designs for housing, the construction industry has evolved and there is need to make the
construction friendly, affordable, and fast (Tay, et al., 2017). This has resulted in the evolution of
3D printing in the construction realm. The 3D printing describes a process of obtaining a
construction design from a digital file and later uploading the same to a 3D printer. The printer
reads the digital file and lays down courses of material until an entire building is completed.
Most concrete structures that have irregular contours and shapes can be beneficiaries of the 3D
printing. The technique is commonly used in the development of models, structural building
components, brick construction, and for interior décor (Baynes, 2015). The 3D printing opens up
the construction field as there are a variety of raw materials such as the recycled plastic,
bioplastics, synthetic materials, and chemicals apart from concrete, sand, and cement. The
technique introduces a variety of fabrication methods and the fabrication of reinforced concrete
beams, as well as the direct printing of the materials on site. There has been a huge leap in the
development of new technics to make the construction even better in the structural optimization
schemes (Mrazovic, 2013). The 3D printing has brought about several benefits to the
construction field such as,
(i) The technique reduces the human interaction on site. This ensures that the human
beings are no longer exposed to hazards and ailments and it is more cost effective for
the organization.
(ii) It guarantees timely and customized deliverables ensuring a greater design freedom at
pocket friendly costs.
(iii) The technique adds to the functionalities into the structures and the system integration
and the reduction of material interfaces.
(iv) There is better control over the deposition of build materials ensuring a good finish on
the construction as well as providing quality building blocks or homogenous units.
Some of the key components looked into by the structural engineers and the project managers
during the construction are time, budget, and quality. The cost implication of a venture matters as
finances are a limited resource. The project should run in the planned time managing all the
anticipated risks as well as those risks that crop up in the midst of the project. The project
administrators also mind the quality of the construction such that the construction follows the
blueprint design to the letter and the deliverables are attained. The technique is a digital
fabrication that takes a conceived or well thought-out model, make it a digital design, and later
turns it into a real object.
(a) Budget constraint
Paraphrase This Document
Need a fresh take? Get an instant paraphrase of this document with our AI Paraphraser
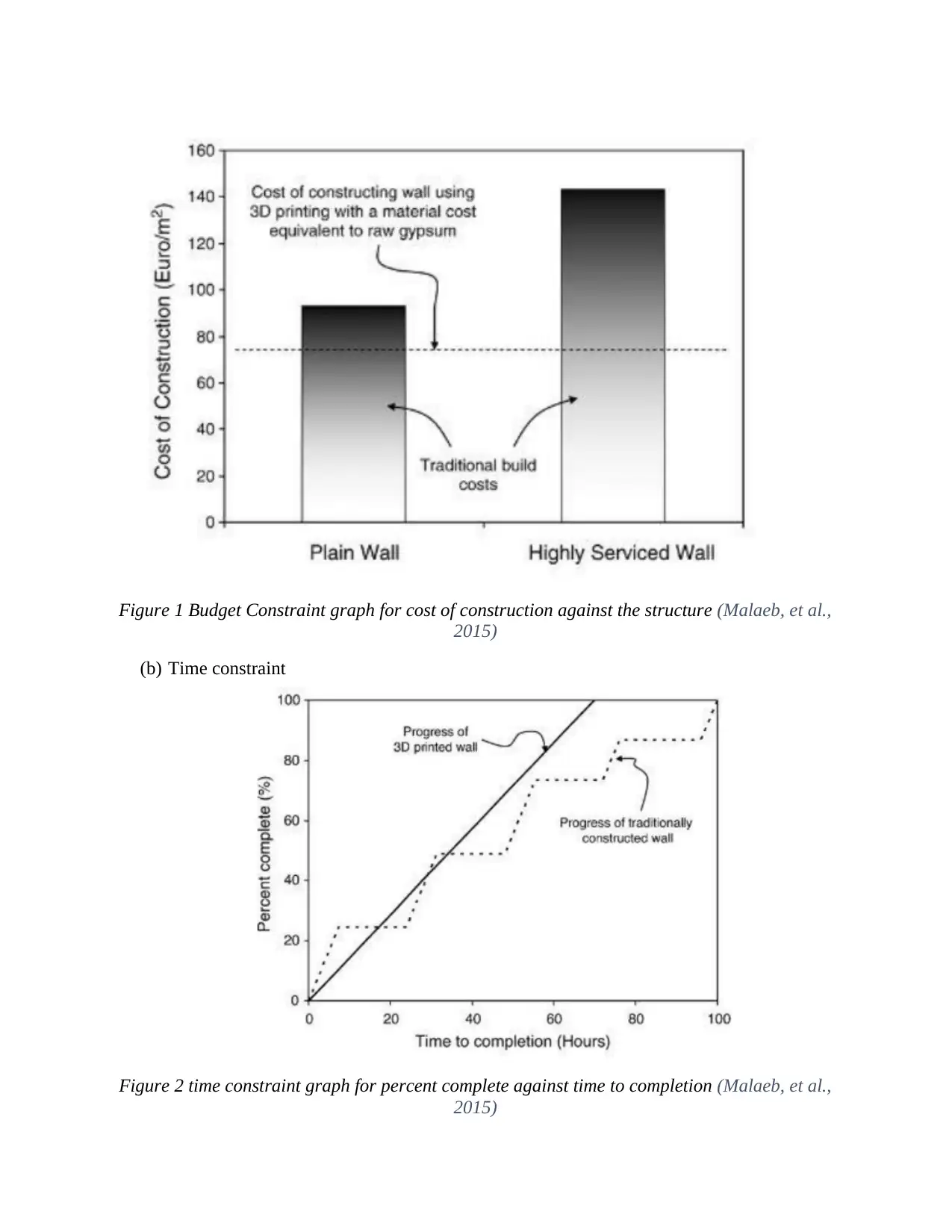
Figure 1 Budget Constraint graph for cost of construction against the structure (Malaeb, et al.,
2015)
(b) Time constraint
Figure 2 time constraint graph for percent complete against time to completion (Malaeb, et al.,
2015)
2015)
(b) Time constraint
Figure 2 time constraint graph for percent complete against time to completion (Malaeb, et al.,
2015)
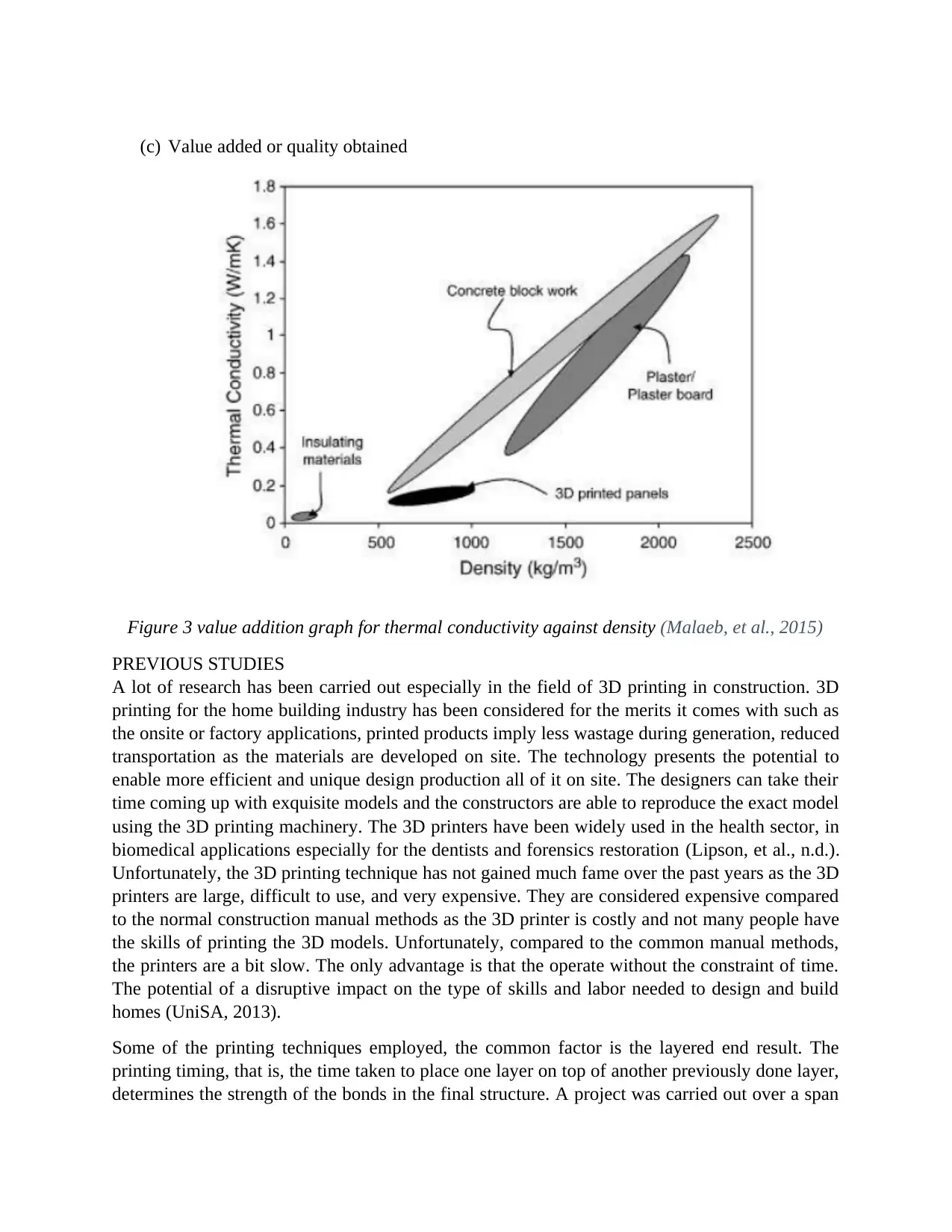
(c) Value added or quality obtained
Figure 3 value addition graph for thermal conductivity against density (Malaeb, et al., 2015)
PREVIOUS STUDIES
A lot of research has been carried out especially in the field of 3D printing in construction. 3D
printing for the home building industry has been considered for the merits it comes with such as
the onsite or factory applications, printed products imply less wastage during generation, reduced
transportation as the materials are developed on site. The technology presents the potential to
enable more efficient and unique design production all of it on site. The designers can take their
time coming up with exquisite models and the constructors are able to reproduce the exact model
using the 3D printing machinery. The 3D printers have been widely used in the health sector, in
biomedical applications especially for the dentists and forensics restoration (Lipson, et al., n.d.).
Unfortunately, the 3D printing technique has not gained much fame over the past years as the 3D
printers are large, difficult to use, and very expensive. They are considered expensive compared
to the normal construction manual methods as the 3D printer is costly and not many people have
the skills of printing the 3D models. Unfortunately, compared to the common manual methods,
the printers are a bit slow. The only advantage is that the operate without the constraint of time.
The potential of a disruptive impact on the type of skills and labor needed to design and build
homes (UniSA, 2013).
Some of the printing techniques employed, the common factor is the layered end result. The
printing timing, that is, the time taken to place one layer on top of another previously done layer,
determines the strength of the bonds in the final structure. A project was carried out over a span
Figure 3 value addition graph for thermal conductivity against density (Malaeb, et al., 2015)
PREVIOUS STUDIES
A lot of research has been carried out especially in the field of 3D printing in construction. 3D
printing for the home building industry has been considered for the merits it comes with such as
the onsite or factory applications, printed products imply less wastage during generation, reduced
transportation as the materials are developed on site. The technology presents the potential to
enable more efficient and unique design production all of it on site. The designers can take their
time coming up with exquisite models and the constructors are able to reproduce the exact model
using the 3D printing machinery. The 3D printers have been widely used in the health sector, in
biomedical applications especially for the dentists and forensics restoration (Lipson, et al., n.d.).
Unfortunately, the 3D printing technique has not gained much fame over the past years as the 3D
printers are large, difficult to use, and very expensive. They are considered expensive compared
to the normal construction manual methods as the 3D printer is costly and not many people have
the skills of printing the 3D models. Unfortunately, compared to the common manual methods,
the printers are a bit slow. The only advantage is that the operate without the constraint of time.
The potential of a disruptive impact on the type of skills and labor needed to design and build
homes (UniSA, 2013).
Some of the printing techniques employed, the common factor is the layered end result. The
printing timing, that is, the time taken to place one layer on top of another previously done layer,
determines the strength of the bonds in the final structure. A project was carried out over a span
You're viewing a preview
Unlock full access by subscribing today!
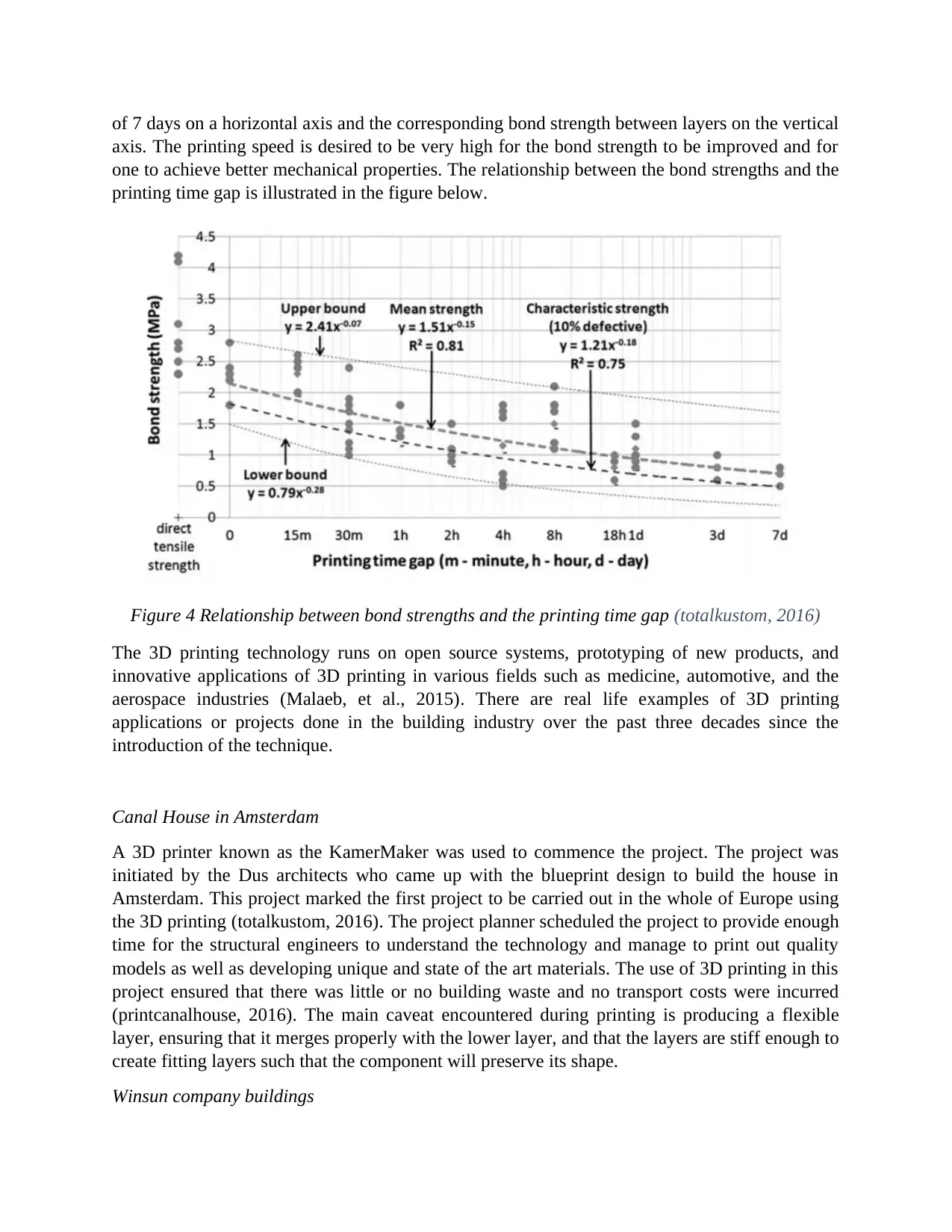
of 7 days on a horizontal axis and the corresponding bond strength between layers on the vertical
axis. The printing speed is desired to be very high for the bond strength to be improved and for
one to achieve better mechanical properties. The relationship between the bond strengths and the
printing time gap is illustrated in the figure below.
Figure 4 Relationship between bond strengths and the printing time gap (totalkustom, 2016)
The 3D printing technology runs on open source systems, prototyping of new products, and
innovative applications of 3D printing in various fields such as medicine, automotive, and the
aerospace industries (Malaeb, et al., 2015). There are real life examples of 3D printing
applications or projects done in the building industry over the past three decades since the
introduction of the technique.
Canal House in Amsterdam
A 3D printer known as the KamerMaker was used to commence the project. The project was
initiated by the Dus architects who came up with the blueprint design to build the house in
Amsterdam. This project marked the first project to be carried out in the whole of Europe using
the 3D printing (totalkustom, 2016). The project planner scheduled the project to provide enough
time for the structural engineers to understand the technology and manage to print out quality
models as well as developing unique and state of the art materials. The use of 3D printing in this
project ensured that there was little or no building waste and no transport costs were incurred
(printcanalhouse, 2016). The main caveat encountered during printing is producing a flexible
layer, ensuring that it merges properly with the lower layer, and that the layers are stiff enough to
create fitting layers such that the component will preserve its shape.
Winsun company buildings
axis. The printing speed is desired to be very high for the bond strength to be improved and for
one to achieve better mechanical properties. The relationship between the bond strengths and the
printing time gap is illustrated in the figure below.
Figure 4 Relationship between bond strengths and the printing time gap (totalkustom, 2016)
The 3D printing technology runs on open source systems, prototyping of new products, and
innovative applications of 3D printing in various fields such as medicine, automotive, and the
aerospace industries (Malaeb, et al., 2015). There are real life examples of 3D printing
applications or projects done in the building industry over the past three decades since the
introduction of the technique.
Canal House in Amsterdam
A 3D printer known as the KamerMaker was used to commence the project. The project was
initiated by the Dus architects who came up with the blueprint design to build the house in
Amsterdam. This project marked the first project to be carried out in the whole of Europe using
the 3D printing (totalkustom, 2016). The project planner scheduled the project to provide enough
time for the structural engineers to understand the technology and manage to print out quality
models as well as developing unique and state of the art materials. The use of 3D printing in this
project ensured that there was little or no building waste and no transport costs were incurred
(printcanalhouse, 2016). The main caveat encountered during printing is producing a flexible
layer, ensuring that it merges properly with the lower layer, and that the layers are stiff enough to
create fitting layers such that the component will preserve its shape.
Winsun company buildings
Paraphrase This Document
Need a fresh take? Get an instant paraphrase of this document with our AI Paraphraser
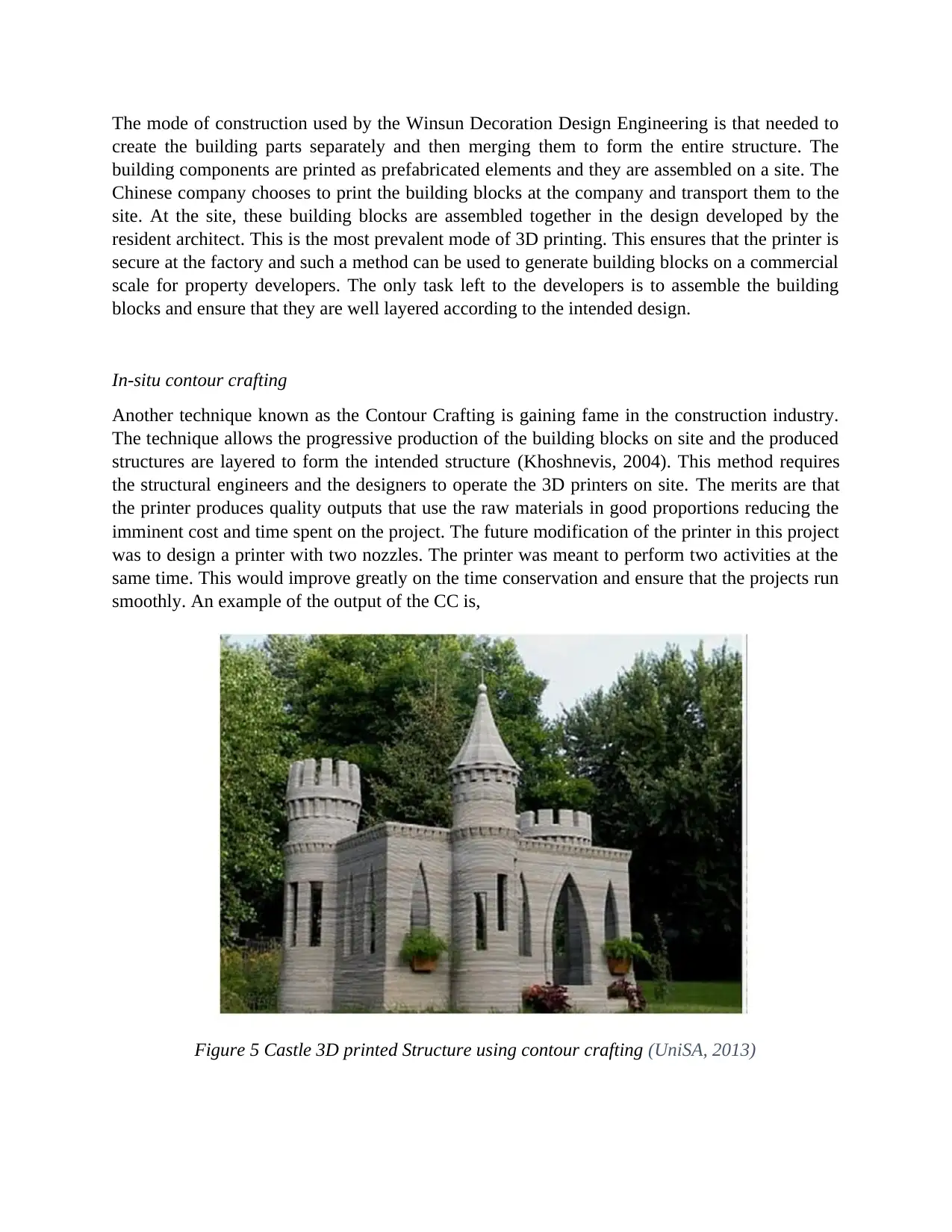
The mode of construction used by the Winsun Decoration Design Engineering is that needed to
create the building parts separately and then merging them to form the entire structure. The
building components are printed as prefabricated elements and they are assembled on a site. The
Chinese company chooses to print the building blocks at the company and transport them to the
site. At the site, these building blocks are assembled together in the design developed by the
resident architect. This is the most prevalent mode of 3D printing. This ensures that the printer is
secure at the factory and such a method can be used to generate building blocks on a commercial
scale for property developers. The only task left to the developers is to assemble the building
blocks and ensure that they are well layered according to the intended design.
In-situ contour crafting
Another technique known as the Contour Crafting is gaining fame in the construction industry.
The technique allows the progressive production of the building blocks on site and the produced
structures are layered to form the intended structure (Khoshnevis, 2004). This method requires
the structural engineers and the designers to operate the 3D printers on site. The merits are that
the printer produces quality outputs that use the raw materials in good proportions reducing the
imminent cost and time spent on the project. The future modification of the printer in this project
was to design a printer with two nozzles. The printer was meant to perform two activities at the
same time. This would improve greatly on the time conservation and ensure that the projects run
smoothly. An example of the output of the CC is,
Figure 5 Castle 3D printed Structure using contour crafting (UniSA, 2013)
create the building parts separately and then merging them to form the entire structure. The
building components are printed as prefabricated elements and they are assembled on a site. The
Chinese company chooses to print the building blocks at the company and transport them to the
site. At the site, these building blocks are assembled together in the design developed by the
resident architect. This is the most prevalent mode of 3D printing. This ensures that the printer is
secure at the factory and such a method can be used to generate building blocks on a commercial
scale for property developers. The only task left to the developers is to assemble the building
blocks and ensure that they are well layered according to the intended design.
In-situ contour crafting
Another technique known as the Contour Crafting is gaining fame in the construction industry.
The technique allows the progressive production of the building blocks on site and the produced
structures are layered to form the intended structure (Khoshnevis, 2004). This method requires
the structural engineers and the designers to operate the 3D printers on site. The merits are that
the printer produces quality outputs that use the raw materials in good proportions reducing the
imminent cost and time spent on the project. The future modification of the printer in this project
was to design a printer with two nozzles. The printer was meant to perform two activities at the
same time. This would improve greatly on the time conservation and ensure that the projects run
smoothly. An example of the output of the CC is,
Figure 5 Castle 3D printed Structure using contour crafting (UniSA, 2013)
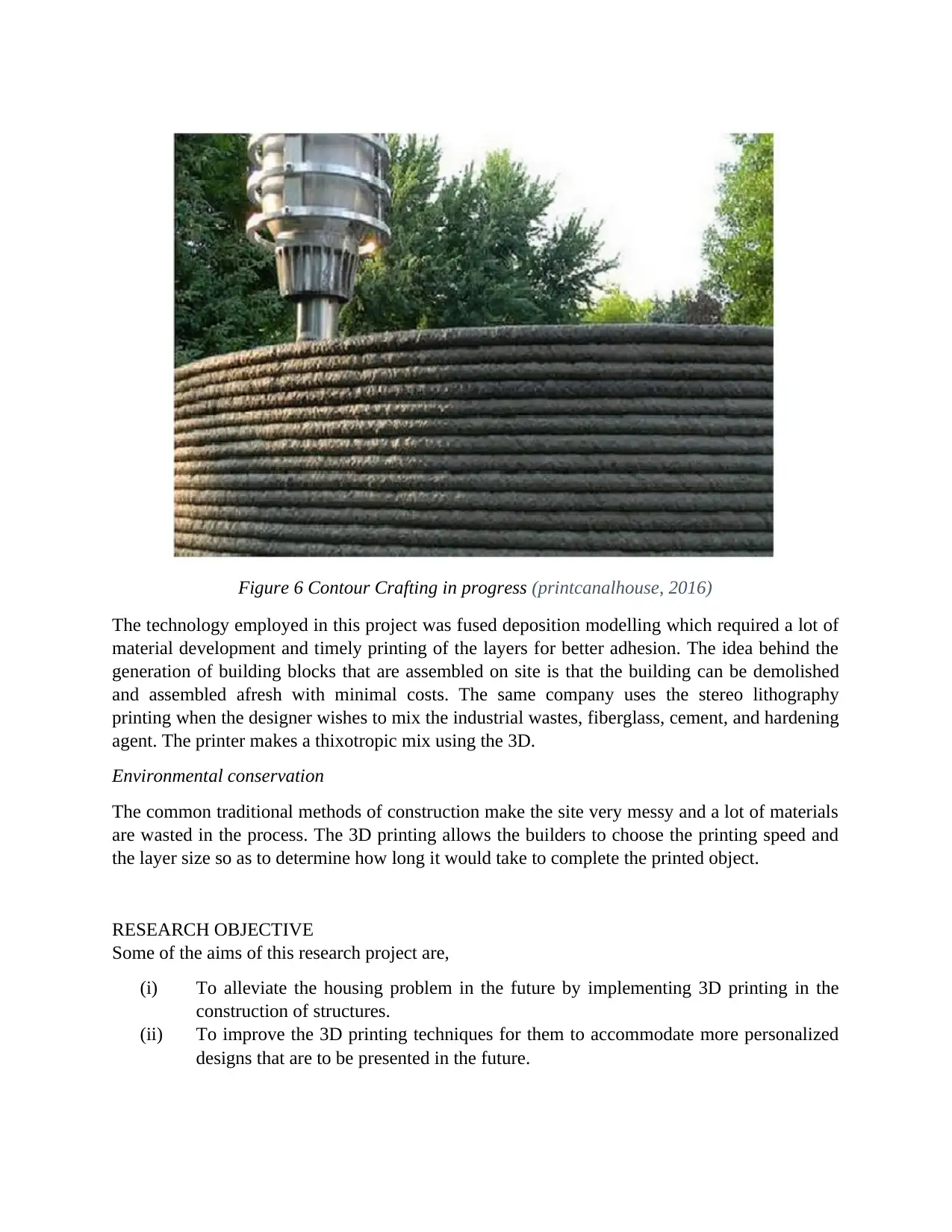
Figure 6 Contour Crafting in progress (printcanalhouse, 2016)
The technology employed in this project was fused deposition modelling which required a lot of
material development and timely printing of the layers for better adhesion. The idea behind the
generation of building blocks that are assembled on site is that the building can be demolished
and assembled afresh with minimal costs. The same company uses the stereo lithography
printing when the designer wishes to mix the industrial wastes, fiberglass, cement, and hardening
agent. The printer makes a thixotropic mix using the 3D.
Environmental conservation
The common traditional methods of construction make the site very messy and a lot of materials
are wasted in the process. The 3D printing allows the builders to choose the printing speed and
the layer size so as to determine how long it would take to complete the printed object.
RESEARCH OBJECTIVE
Some of the aims of this research project are,
(i) To alleviate the housing problem in the future by implementing 3D printing in the
construction of structures.
(ii) To improve the 3D printing techniques for them to accommodate more personalized
designs that are to be presented in the future.
The technology employed in this project was fused deposition modelling which required a lot of
material development and timely printing of the layers for better adhesion. The idea behind the
generation of building blocks that are assembled on site is that the building can be demolished
and assembled afresh with minimal costs. The same company uses the stereo lithography
printing when the designer wishes to mix the industrial wastes, fiberglass, cement, and hardening
agent. The printer makes a thixotropic mix using the 3D.
Environmental conservation
The common traditional methods of construction make the site very messy and a lot of materials
are wasted in the process. The 3D printing allows the builders to choose the printing speed and
the layer size so as to determine how long it would take to complete the printed object.
RESEARCH OBJECTIVE
Some of the aims of this research project are,
(i) To alleviate the housing problem in the future by implementing 3D printing in the
construction of structures.
(ii) To improve the 3D printing techniques for them to accommodate more personalized
designs that are to be presented in the future.
You're viewing a preview
Unlock full access by subscribing today!
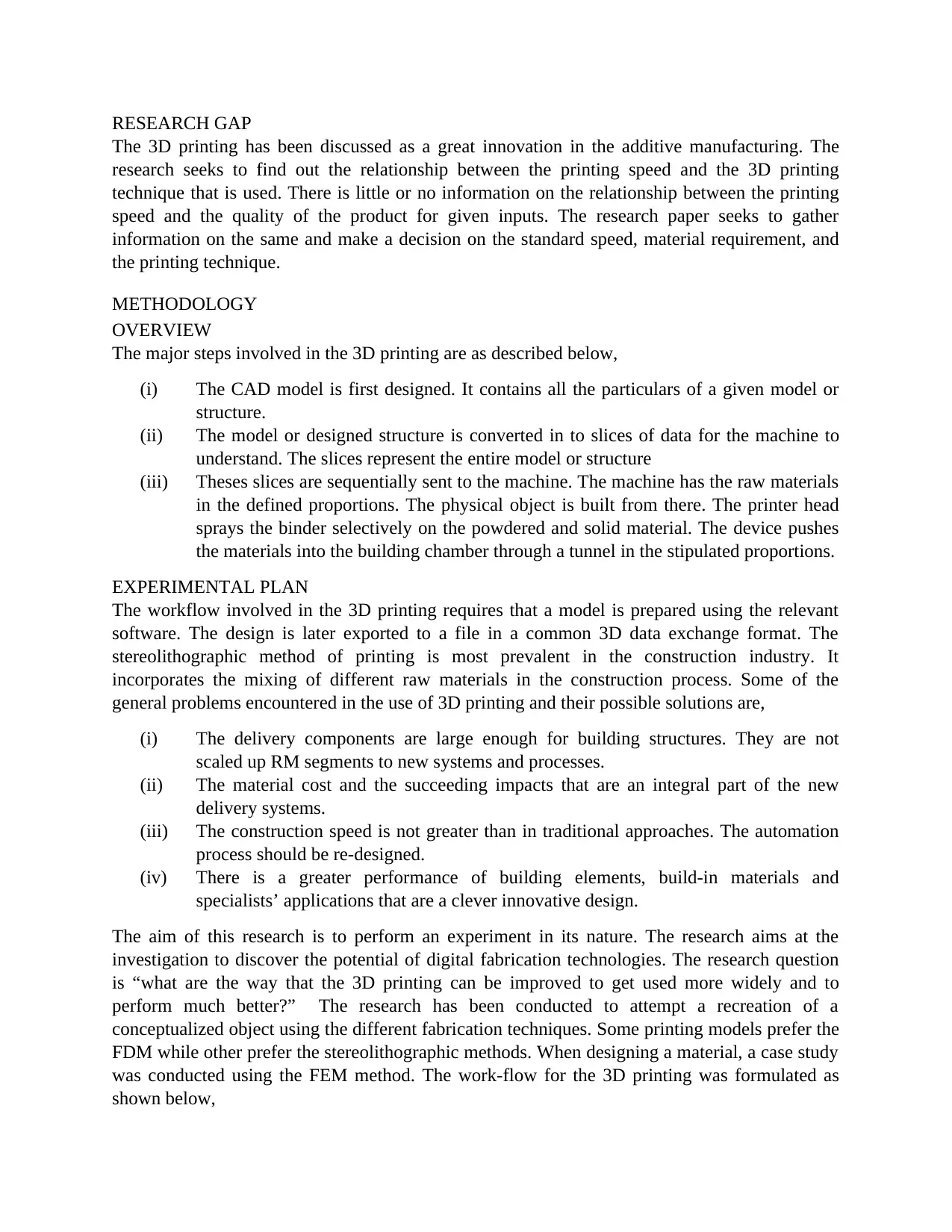
RESEARCH GAP
The 3D printing has been discussed as a great innovation in the additive manufacturing. The
research seeks to find out the relationship between the printing speed and the 3D printing
technique that is used. There is little or no information on the relationship between the printing
speed and the quality of the product for given inputs. The research paper seeks to gather
information on the same and make a decision on the standard speed, material requirement, and
the printing technique.
METHODOLOGY
OVERVIEW
The major steps involved in the 3D printing are as described below,
(i) The CAD model is first designed. It contains all the particulars of a given model or
structure.
(ii) The model or designed structure is converted in to slices of data for the machine to
understand. The slices represent the entire model or structure
(iii) Theses slices are sequentially sent to the machine. The machine has the raw materials
in the defined proportions. The physical object is built from there. The printer head
sprays the binder selectively on the powdered and solid material. The device pushes
the materials into the building chamber through a tunnel in the stipulated proportions.
EXPERIMENTAL PLAN
The workflow involved in the 3D printing requires that a model is prepared using the relevant
software. The design is later exported to a file in a common 3D data exchange format. The
stereolithographic method of printing is most prevalent in the construction industry. It
incorporates the mixing of different raw materials in the construction process. Some of the
general problems encountered in the use of 3D printing and their possible solutions are,
(i) The delivery components are large enough for building structures. They are not
scaled up RM segments to new systems and processes.
(ii) The material cost and the succeeding impacts that are an integral part of the new
delivery systems.
(iii) The construction speed is not greater than in traditional approaches. The automation
process should be re-designed.
(iv) There is a greater performance of building elements, build-in materials and
specialists’ applications that are a clever innovative design.
The aim of this research is to perform an experiment in its nature. The research aims at the
investigation to discover the potential of digital fabrication technologies. The research question
is “what are the way that the 3D printing can be improved to get used more widely and to
perform much better?” The research has been conducted to attempt a recreation of a
conceptualized object using the different fabrication techniques. Some printing models prefer the
FDM while other prefer the stereolithographic methods. When designing a material, a case study
was conducted using the FEM method. The work-flow for the 3D printing was formulated as
shown below,
The 3D printing has been discussed as a great innovation in the additive manufacturing. The
research seeks to find out the relationship between the printing speed and the 3D printing
technique that is used. There is little or no information on the relationship between the printing
speed and the quality of the product for given inputs. The research paper seeks to gather
information on the same and make a decision on the standard speed, material requirement, and
the printing technique.
METHODOLOGY
OVERVIEW
The major steps involved in the 3D printing are as described below,
(i) The CAD model is first designed. It contains all the particulars of a given model or
structure.
(ii) The model or designed structure is converted in to slices of data for the machine to
understand. The slices represent the entire model or structure
(iii) Theses slices are sequentially sent to the machine. The machine has the raw materials
in the defined proportions. The physical object is built from there. The printer head
sprays the binder selectively on the powdered and solid material. The device pushes
the materials into the building chamber through a tunnel in the stipulated proportions.
EXPERIMENTAL PLAN
The workflow involved in the 3D printing requires that a model is prepared using the relevant
software. The design is later exported to a file in a common 3D data exchange format. The
stereolithographic method of printing is most prevalent in the construction industry. It
incorporates the mixing of different raw materials in the construction process. Some of the
general problems encountered in the use of 3D printing and their possible solutions are,
(i) The delivery components are large enough for building structures. They are not
scaled up RM segments to new systems and processes.
(ii) The material cost and the succeeding impacts that are an integral part of the new
delivery systems.
(iii) The construction speed is not greater than in traditional approaches. The automation
process should be re-designed.
(iv) There is a greater performance of building elements, build-in materials and
specialists’ applications that are a clever innovative design.
The aim of this research is to perform an experiment in its nature. The research aims at the
investigation to discover the potential of digital fabrication technologies. The research question
is “what are the way that the 3D printing can be improved to get used more widely and to
perform much better?” The research has been conducted to attempt a recreation of a
conceptualized object using the different fabrication techniques. Some printing models prefer the
FDM while other prefer the stereolithographic methods. When designing a material, a case study
was conducted using the FEM method. The work-flow for the 3D printing was formulated as
shown below,
Paraphrase This Document
Need a fresh take? Get an instant paraphrase of this document with our AI Paraphraser
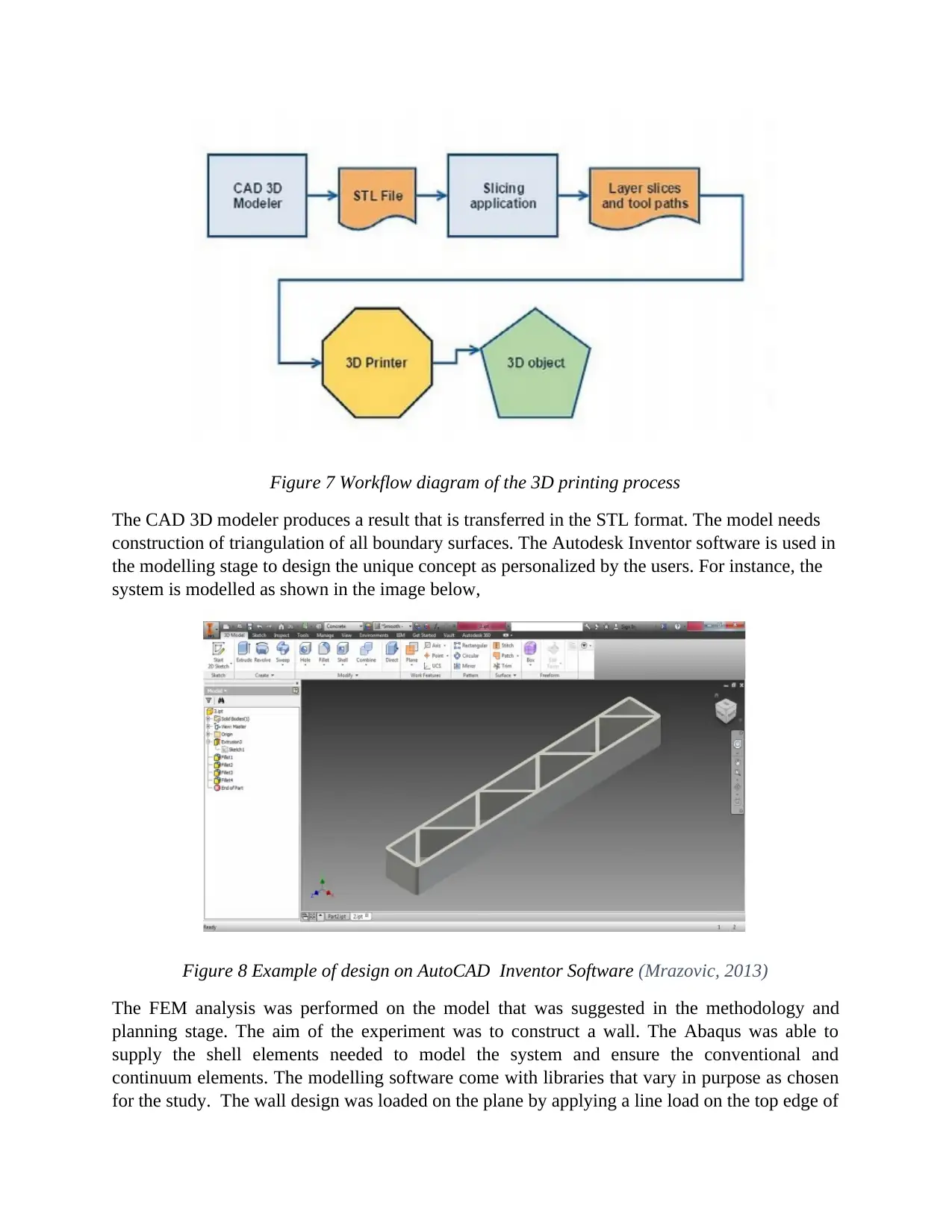
Figure 7 Workflow diagram of the 3D printing process
The CAD 3D modeler produces a result that is transferred in the STL format. The model needs
construction of triangulation of all boundary surfaces. The Autodesk Inventor software is used in
the modelling stage to design the unique concept as personalized by the users. For instance, the
system is modelled as shown in the image below,
Figure 8 Example of design on AutoCAD Inventor Software (Mrazovic, 2013)
The FEM analysis was performed on the model that was suggested in the methodology and
planning stage. The aim of the experiment was to construct a wall. The Abaqus was able to
supply the shell elements needed to model the system and ensure the conventional and
continuum elements. The modelling software come with libraries that vary in purpose as chosen
for the study. The wall design was loaded on the plane by applying a line load on the top edge of
The CAD 3D modeler produces a result that is transferred in the STL format. The model needs
construction of triangulation of all boundary surfaces. The Autodesk Inventor software is used in
the modelling stage to design the unique concept as personalized by the users. For instance, the
system is modelled as shown in the image below,
Figure 8 Example of design on AutoCAD Inventor Software (Mrazovic, 2013)
The FEM analysis was performed on the model that was suggested in the methodology and
planning stage. The aim of the experiment was to construct a wall. The Abaqus was able to
supply the shell elements needed to model the system and ensure the conventional and
continuum elements. The modelling software come with libraries that vary in purpose as chosen
for the study. The wall design was loaded on the plane by applying a line load on the top edge of
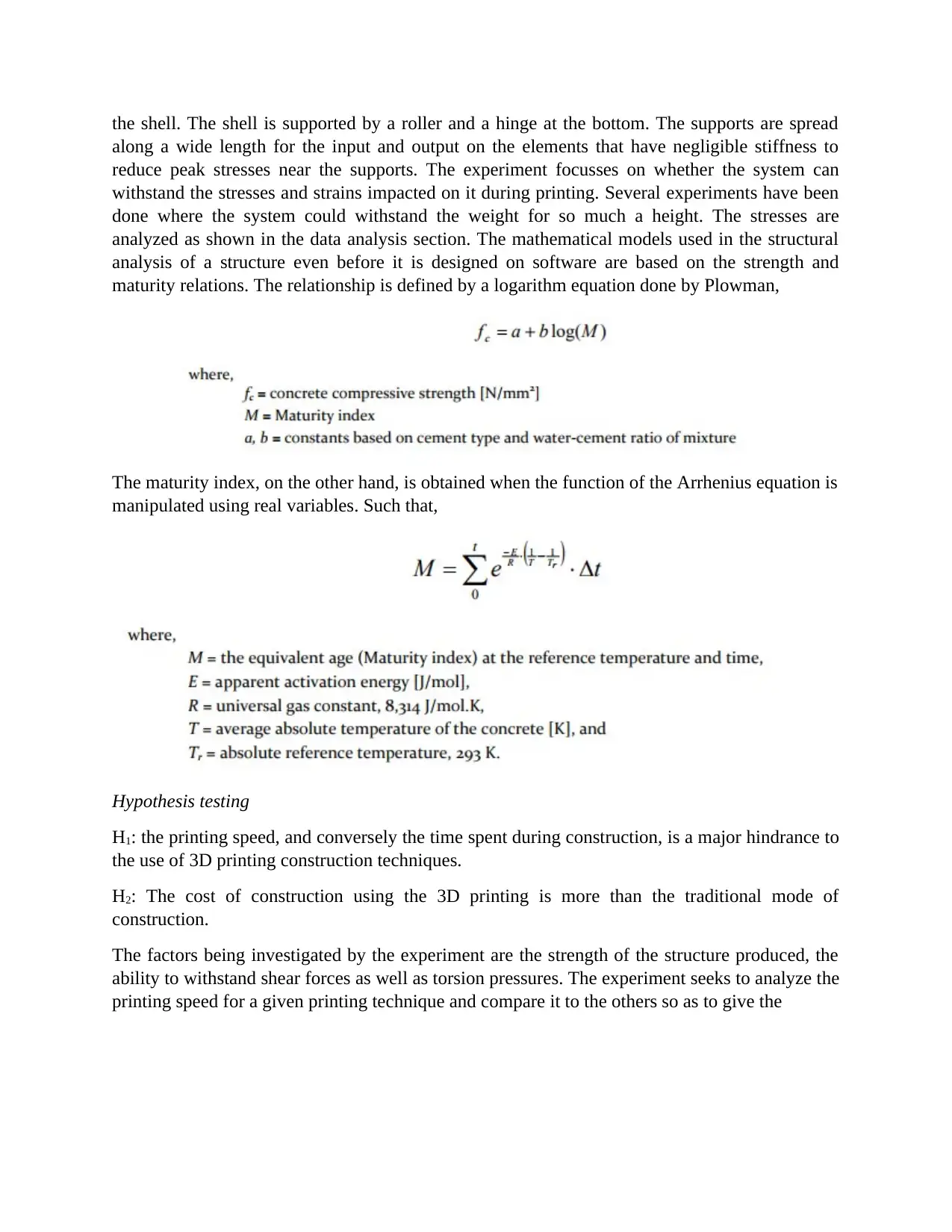
the shell. The shell is supported by a roller and a hinge at the bottom. The supports are spread
along a wide length for the input and output on the elements that have negligible stiffness to
reduce peak stresses near the supports. The experiment focusses on whether the system can
withstand the stresses and strains impacted on it during printing. Several experiments have been
done where the system could withstand the weight for so much a height. The stresses are
analyzed as shown in the data analysis section. The mathematical models used in the structural
analysis of a structure even before it is designed on software are based on the strength and
maturity relations. The relationship is defined by a logarithm equation done by Plowman,
The maturity index, on the other hand, is obtained when the function of the Arrhenius equation is
manipulated using real variables. Such that,
Hypothesis testing
H1: the printing speed, and conversely the time spent during construction, is a major hindrance to
the use of 3D printing construction techniques.
H2: The cost of construction using the 3D printing is more than the traditional mode of
construction.
The factors being investigated by the experiment are the strength of the structure produced, the
ability to withstand shear forces as well as torsion pressures. The experiment seeks to analyze the
printing speed for a given printing technique and compare it to the others so as to give the
along a wide length for the input and output on the elements that have negligible stiffness to
reduce peak stresses near the supports. The experiment focusses on whether the system can
withstand the stresses and strains impacted on it during printing. Several experiments have been
done where the system could withstand the weight for so much a height. The stresses are
analyzed as shown in the data analysis section. The mathematical models used in the structural
analysis of a structure even before it is designed on software are based on the strength and
maturity relations. The relationship is defined by a logarithm equation done by Plowman,
The maturity index, on the other hand, is obtained when the function of the Arrhenius equation is
manipulated using real variables. Such that,
Hypothesis testing
H1: the printing speed, and conversely the time spent during construction, is a major hindrance to
the use of 3D printing construction techniques.
H2: The cost of construction using the 3D printing is more than the traditional mode of
construction.
The factors being investigated by the experiment are the strength of the structure produced, the
ability to withstand shear forces as well as torsion pressures. The experiment seeks to analyze the
printing speed for a given printing technique and compare it to the others so as to give the
You're viewing a preview
Unlock full access by subscribing today!
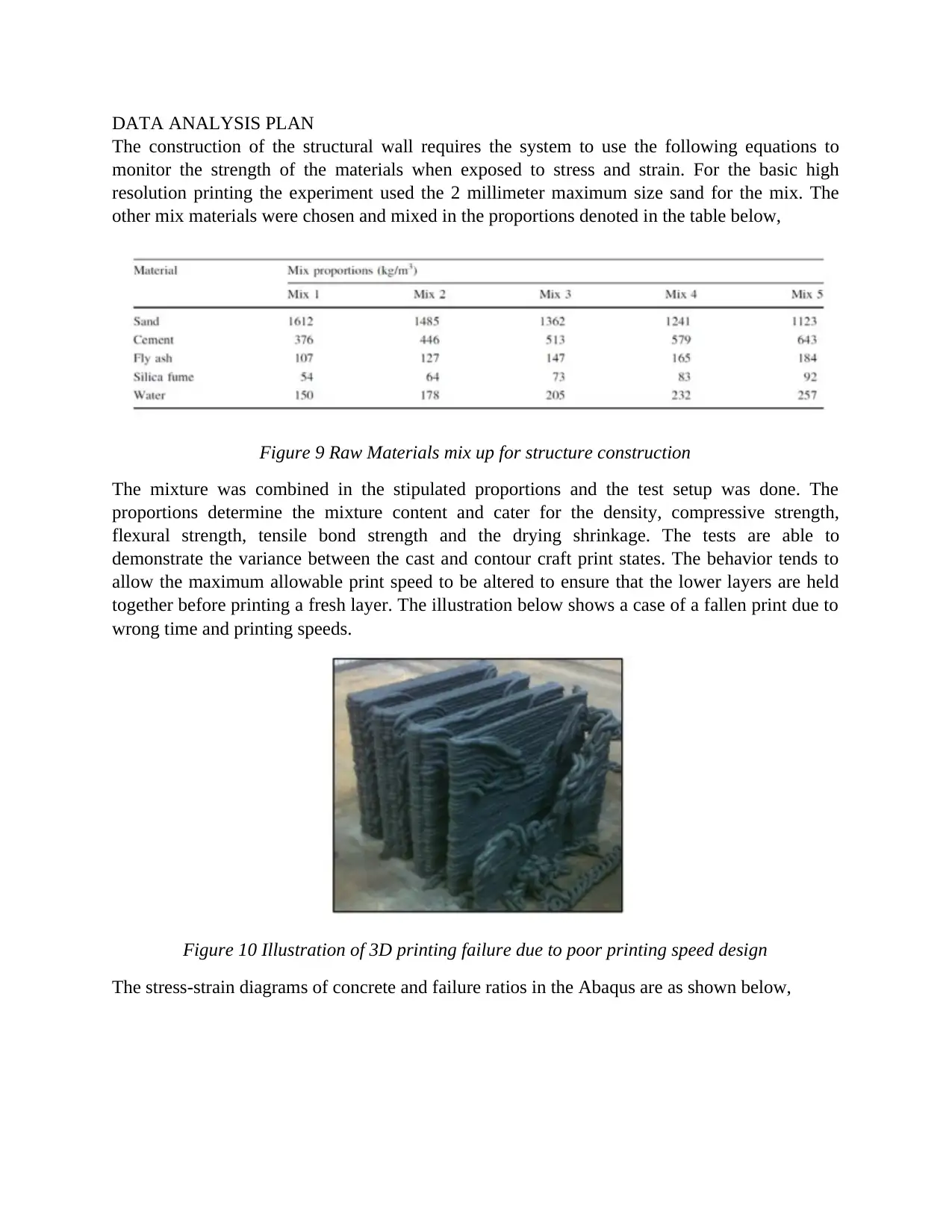
DATA ANALYSIS PLAN
The construction of the structural wall requires the system to use the following equations to
monitor the strength of the materials when exposed to stress and strain. For the basic high
resolution printing the experiment used the 2 millimeter maximum size sand for the mix. The
other mix materials were chosen and mixed in the proportions denoted in the table below,
Figure 9 Raw Materials mix up for structure construction
The mixture was combined in the stipulated proportions and the test setup was done. The
proportions determine the mixture content and cater for the density, compressive strength,
flexural strength, tensile bond strength and the drying shrinkage. The tests are able to
demonstrate the variance between the cast and contour craft print states. The behavior tends to
allow the maximum allowable print speed to be altered to ensure that the lower layers are held
together before printing a fresh layer. The illustration below shows a case of a fallen print due to
wrong time and printing speeds.
Figure 10 Illustration of 3D printing failure due to poor printing speed design
The stress-strain diagrams of concrete and failure ratios in the Abaqus are as shown below,
The construction of the structural wall requires the system to use the following equations to
monitor the strength of the materials when exposed to stress and strain. For the basic high
resolution printing the experiment used the 2 millimeter maximum size sand for the mix. The
other mix materials were chosen and mixed in the proportions denoted in the table below,
Figure 9 Raw Materials mix up for structure construction
The mixture was combined in the stipulated proportions and the test setup was done. The
proportions determine the mixture content and cater for the density, compressive strength,
flexural strength, tensile bond strength and the drying shrinkage. The tests are able to
demonstrate the variance between the cast and contour craft print states. The behavior tends to
allow the maximum allowable print speed to be altered to ensure that the lower layers are held
together before printing a fresh layer. The illustration below shows a case of a fallen print due to
wrong time and printing speeds.
Figure 10 Illustration of 3D printing failure due to poor printing speed design
The stress-strain diagrams of concrete and failure ratios in the Abaqus are as shown below,
Paraphrase This Document
Need a fresh take? Get an instant paraphrase of this document with our AI Paraphraser
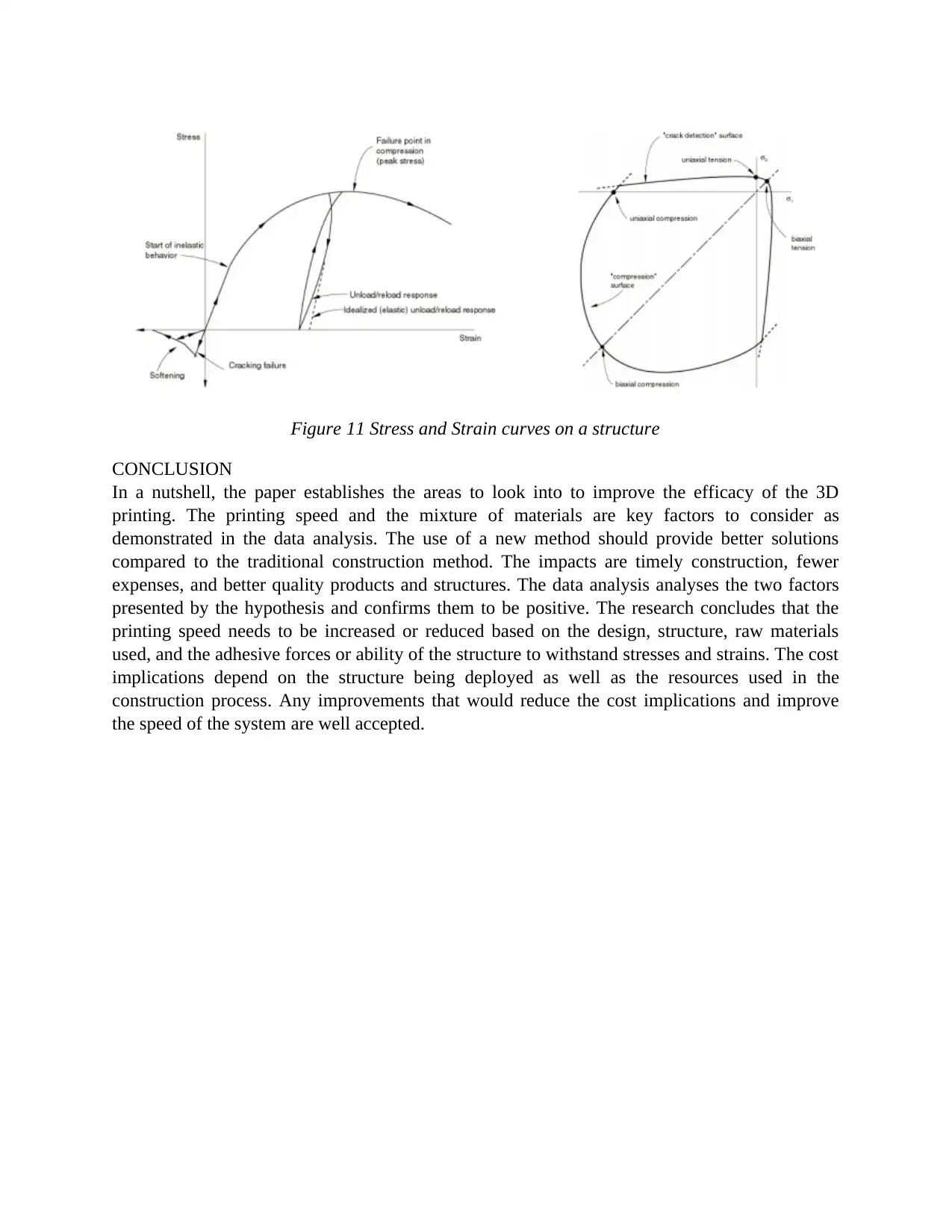
Figure 11 Stress and Strain curves on a structure
CONCLUSION
In a nutshell, the paper establishes the areas to look into to improve the efficacy of the 3D
printing. The printing speed and the mixture of materials are key factors to consider as
demonstrated in the data analysis. The use of a new method should provide better solutions
compared to the traditional construction method. The impacts are timely construction, fewer
expenses, and better quality products and structures. The data analysis analyses the two factors
presented by the hypothesis and confirms them to be positive. The research concludes that the
printing speed needs to be increased or reduced based on the design, structure, raw materials
used, and the adhesive forces or ability of the structure to withstand stresses and strains. The cost
implications depend on the structure being deployed as well as the resources used in the
construction process. Any improvements that would reduce the cost implications and improve
the speed of the system are well accepted.
CONCLUSION
In a nutshell, the paper establishes the areas to look into to improve the efficacy of the 3D
printing. The printing speed and the mixture of materials are key factors to consider as
demonstrated in the data analysis. The use of a new method should provide better solutions
compared to the traditional construction method. The impacts are timely construction, fewer
expenses, and better quality products and structures. The data analysis analyses the two factors
presented by the hypothesis and confirms them to be positive. The research concludes that the
printing speed needs to be increased or reduced based on the design, structure, raw materials
used, and the adhesive forces or ability of the structure to withstand stresses and strains. The cost
implications depend on the structure being deployed as well as the resources used in the
construction process. Any improvements that would reduce the cost implications and improve
the speed of the system are well accepted.
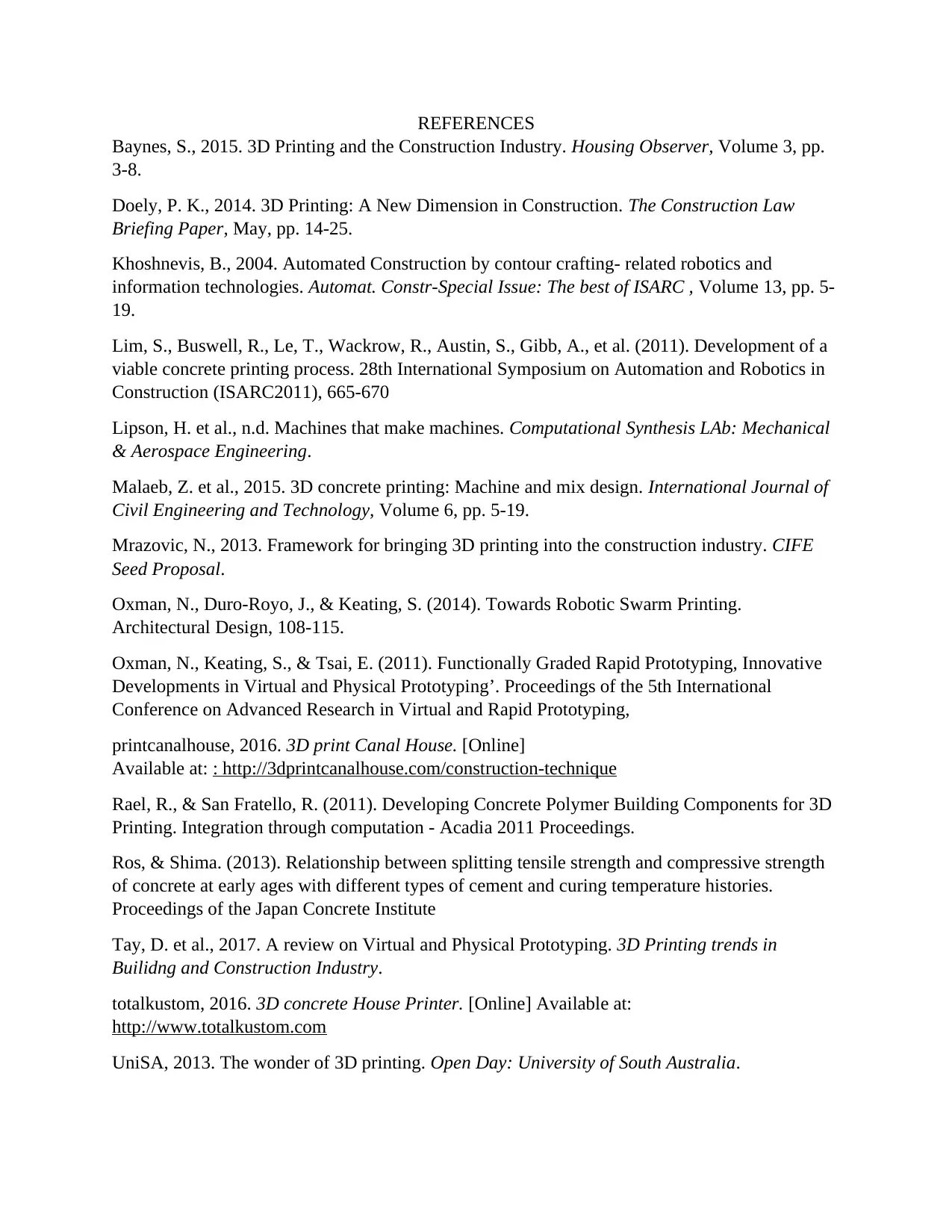
REFERENCES
Baynes, S., 2015. 3D Printing and the Construction Industry. Housing Observer, Volume 3, pp.
3-8.
Doely, P. K., 2014. 3D Printing: A New Dimension in Construction. The Construction Law
Briefing Paper, May, pp. 14-25.
Khoshnevis, B., 2004. Automated Construction by contour crafting- related robotics and
information technologies. Automat. Constr-Special Issue: The best of ISARC , Volume 13, pp. 5-
19.
Lim, S., Buswell, R., Le, T., Wackrow, R., Austin, S., Gibb, A., et al. (2011). Development of a
viable concrete printing process. 28th International Symposium on Automation and Robotics in
Construction (ISARC2011), 665-670
Lipson, H. et al., n.d. Machines that make machines. Computational Synthesis LAb: Mechanical
& Aerospace Engineering.
Malaeb, Z. et al., 2015. 3D concrete printing: Machine and mix design. International Journal of
Civil Engineering and Technology, Volume 6, pp. 5-19.
Mrazovic, N., 2013. Framework for bringing 3D printing into the construction industry. CIFE
Seed Proposal.
Oxman, N., Duro-Royo, J., & Keating, S. (2014). Towards Robotic Swarm Printing.
Architectural Design, 108-115.
Oxman, N., Keating, S., & Tsai, E. (2011). Functionally Graded Rapid Prototyping, Innovative
Developments in Virtual and Physical Prototyping’. Proceedings of the 5th International
Conference on Advanced Research in Virtual and Rapid Prototyping,
printcanalhouse, 2016. 3D print Canal House. [Online]
Available at: : http://3dprintcanalhouse.com/construction-technique
Rael, R., & San Fratello, R. (2011). Developing Concrete Polymer Building Components for 3D
Printing. Integration through computation - Acadia 2011 Proceedings.
Ros, & Shima. (2013). Relationship between splitting tensile strength and compressive strength
of concrete at early ages with different types of cement and curing temperature histories.
Proceedings of the Japan Concrete Institute
Tay, D. et al., 2017. A review on Virtual and Physical Prototyping. 3D Printing trends in
Builidng and Construction Industry.
totalkustom, 2016. 3D concrete House Printer. [Online] Available at:
http://www.totalkustom.com
UniSA, 2013. The wonder of 3D printing. Open Day: University of South Australia.
Baynes, S., 2015. 3D Printing and the Construction Industry. Housing Observer, Volume 3, pp.
3-8.
Doely, P. K., 2014. 3D Printing: A New Dimension in Construction. The Construction Law
Briefing Paper, May, pp. 14-25.
Khoshnevis, B., 2004. Automated Construction by contour crafting- related robotics and
information technologies. Automat. Constr-Special Issue: The best of ISARC , Volume 13, pp. 5-
19.
Lim, S., Buswell, R., Le, T., Wackrow, R., Austin, S., Gibb, A., et al. (2011). Development of a
viable concrete printing process. 28th International Symposium on Automation and Robotics in
Construction (ISARC2011), 665-670
Lipson, H. et al., n.d. Machines that make machines. Computational Synthesis LAb: Mechanical
& Aerospace Engineering.
Malaeb, Z. et al., 2015. 3D concrete printing: Machine and mix design. International Journal of
Civil Engineering and Technology, Volume 6, pp. 5-19.
Mrazovic, N., 2013. Framework for bringing 3D printing into the construction industry. CIFE
Seed Proposal.
Oxman, N., Duro-Royo, J., & Keating, S. (2014). Towards Robotic Swarm Printing.
Architectural Design, 108-115.
Oxman, N., Keating, S., & Tsai, E. (2011). Functionally Graded Rapid Prototyping, Innovative
Developments in Virtual and Physical Prototyping’. Proceedings of the 5th International
Conference on Advanced Research in Virtual and Rapid Prototyping,
printcanalhouse, 2016. 3D print Canal House. [Online]
Available at: : http://3dprintcanalhouse.com/construction-technique
Rael, R., & San Fratello, R. (2011). Developing Concrete Polymer Building Components for 3D
Printing. Integration through computation - Acadia 2011 Proceedings.
Ros, & Shima. (2013). Relationship between splitting tensile strength and compressive strength
of concrete at early ages with different types of cement and curing temperature histories.
Proceedings of the Japan Concrete Institute
Tay, D. et al., 2017. A review on Virtual and Physical Prototyping. 3D Printing trends in
Builidng and Construction Industry.
totalkustom, 2016. 3D concrete House Printer. [Online] Available at:
http://www.totalkustom.com
UniSA, 2013. The wonder of 3D printing. Open Day: University of South Australia.
You're viewing a preview
Unlock full access by subscribing today!
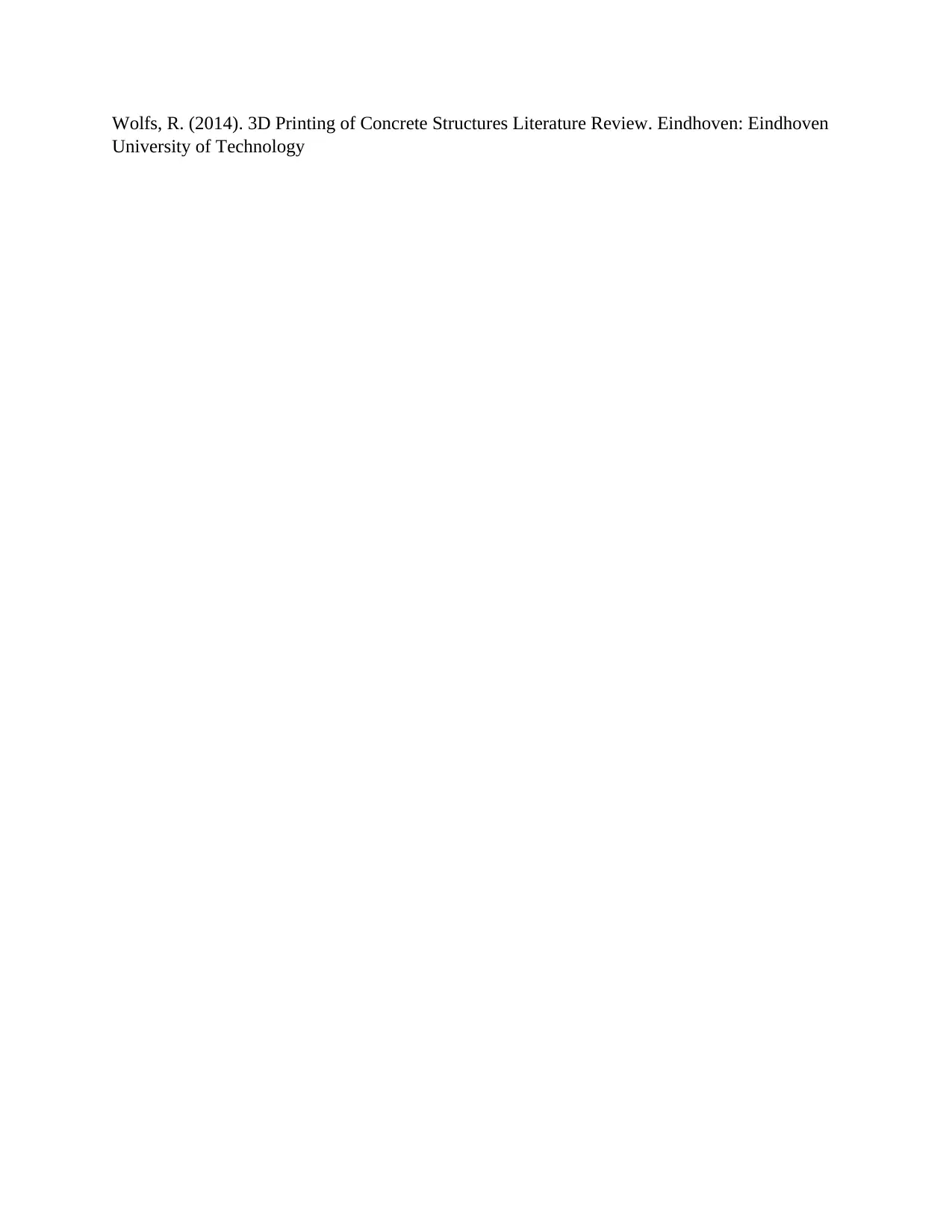
Wolfs, R. (2014). 3D Printing of Concrete Structures Literature Review. Eindhoven: Eindhoven
University of Technology
University of Technology
1 out of 16

Your All-in-One AI-Powered Toolkit for Academic Success.
+13062052269
info@desklib.com
Available 24*7 on WhatsApp / Email
Unlock your academic potential
© 2024 | Zucol Services PVT LTD | All rights reserved.