Applications of 3D Printing Technology in Geotechnical Studies
VerifiedAdded on 2022/12/27
|13
|3061
|64
Report
AI Summary
This report delves into the applications of 3D printing technology within the field of geotechnical engineering. It highlights the use of 3D printing in creating customizable laboratory testing setups, including the determination of hoop and radial stress fields using tactile pressure sensors, and the measurement of K0 and excess pore water pressure using film-like sensors retrofitted in needle probes. The report further explores the application of 3D printing in constructing a 3D-printed odometer for 1D consolidation tests and in measuring the electrical resistivity anisotropy of unsaturated soil. It also examines the characterization of fabric and musical structures of 2D assemblies of 3D-printed elliptical rods during biaxial shearing. The report discusses the advantages of 3D printing in tunnel model production, such as the ability to generate complex models, overcome labor and time constraints, and minimize artificial errors. Finally, it addresses the prospects and limitations of 3D printing technology in geomechanics and engineering, including material and size constraints, and the need to improve the functionality of 3D printers for producing the internal structures and compositions of rocks.
Contribute Materials
Your contribution can guide someone’s learning journey. Share your
documents today.
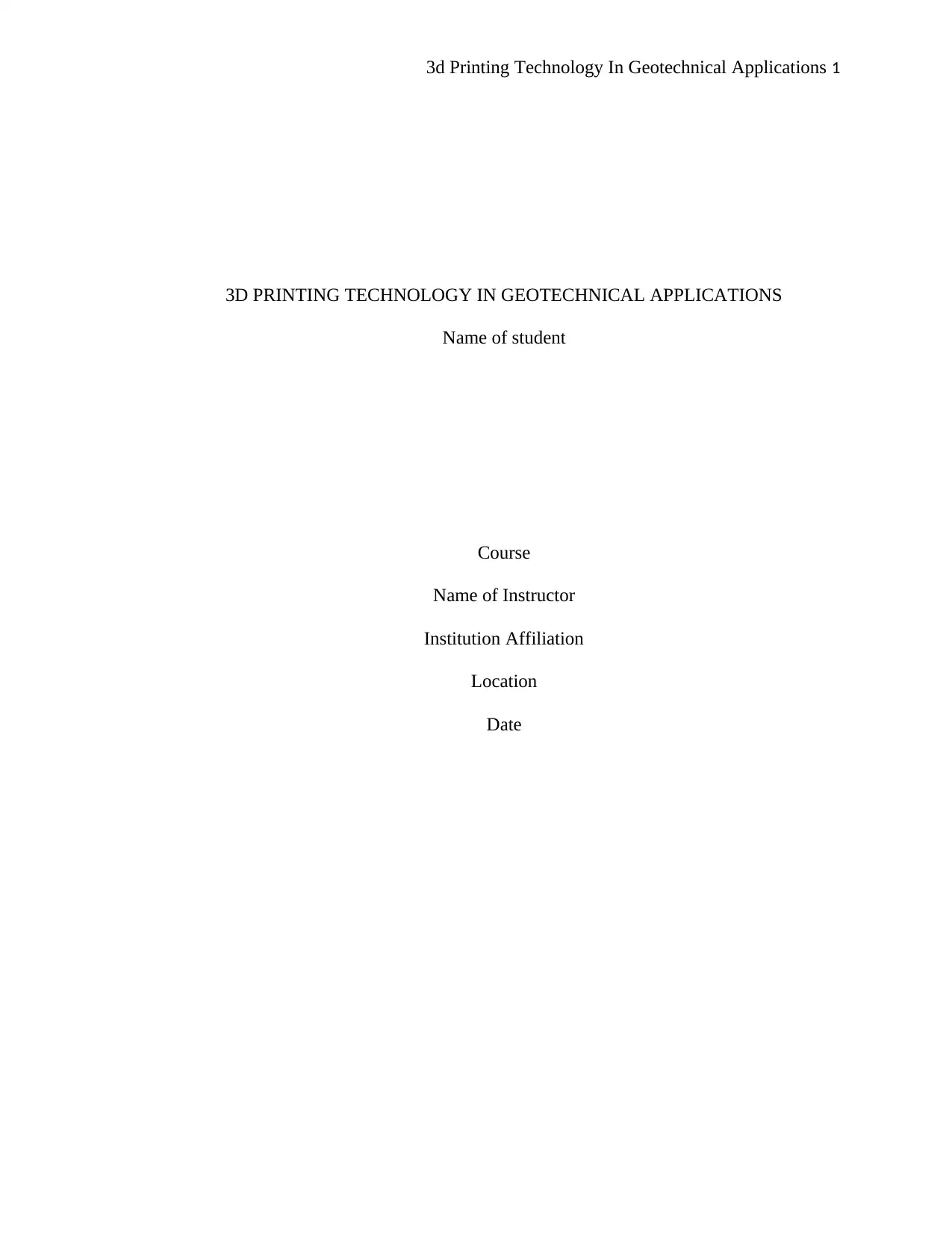
3d Printing Technology In Geotechnical Applications 1
3D PRINTING TECHNOLOGY IN GEOTECHNICAL APPLICATIONS
Name of student
Course
Name of Instructor
Institution Affiliation
Location
Date
3D PRINTING TECHNOLOGY IN GEOTECHNICAL APPLICATIONS
Name of student
Course
Name of Instructor
Institution Affiliation
Location
Date
Secure Best Marks with AI Grader
Need help grading? Try our AI Grader for instant feedback on your assignments.
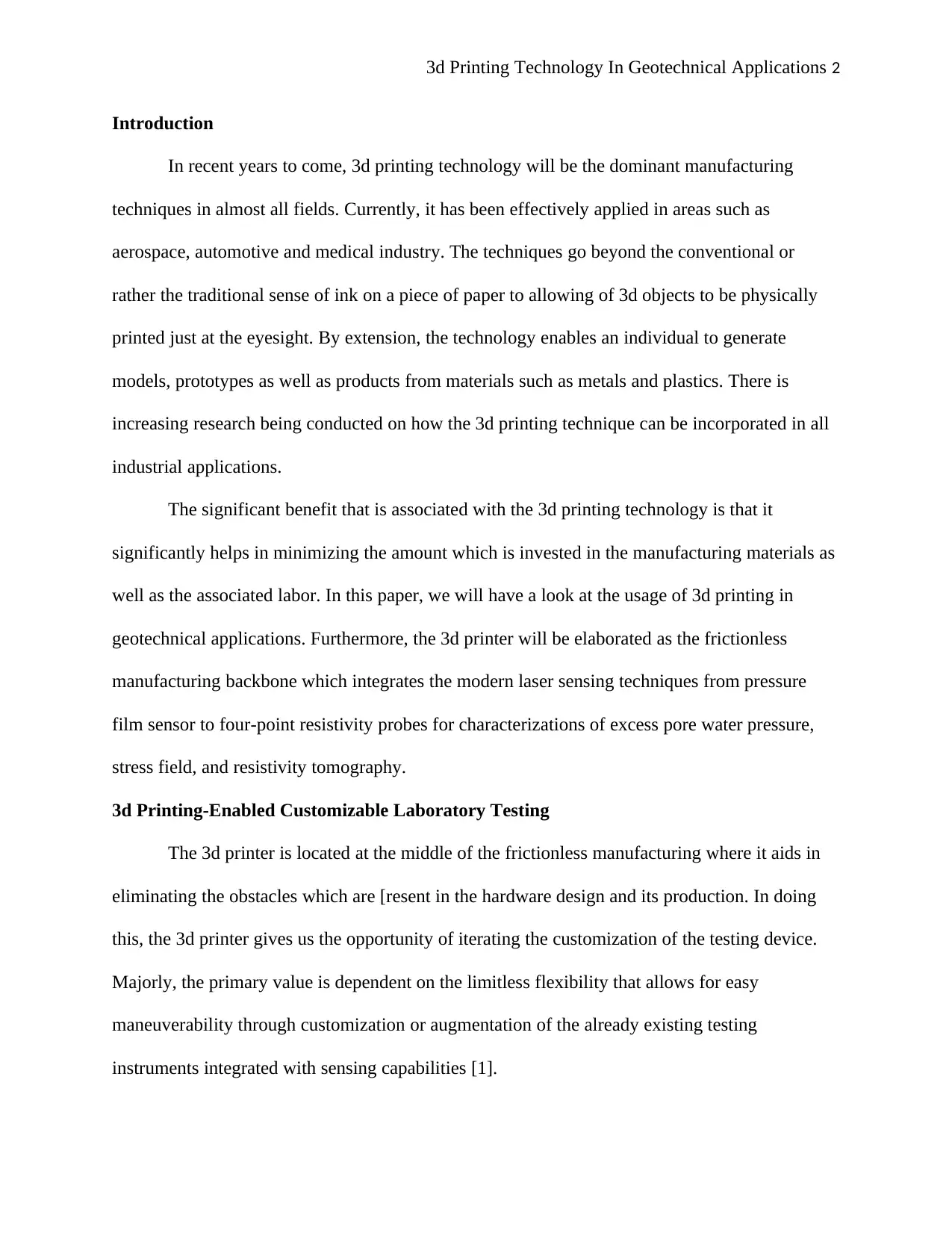
3d Printing Technology In Geotechnical Applications 2
Introduction
In recent years to come, 3d printing technology will be the dominant manufacturing
techniques in almost all fields. Currently, it has been effectively applied in areas such as
aerospace, automotive and medical industry. The techniques go beyond the conventional or
rather the traditional sense of ink on a piece of paper to allowing of 3d objects to be physically
printed just at the eyesight. By extension, the technology enables an individual to generate
models, prototypes as well as products from materials such as metals and plastics. There is
increasing research being conducted on how the 3d printing technique can be incorporated in all
industrial applications.
The significant benefit that is associated with the 3d printing technology is that it
significantly helps in minimizing the amount which is invested in the manufacturing materials as
well as the associated labor. In this paper, we will have a look at the usage of 3d printing in
geotechnical applications. Furthermore, the 3d printer will be elaborated as the frictionless
manufacturing backbone which integrates the modern laser sensing techniques from pressure
film sensor to four-point resistivity probes for characterizations of excess pore water pressure,
stress field, and resistivity tomography.
3d Printing-Enabled Customizable Laboratory Testing
The 3d printer is located at the middle of the frictionless manufacturing where it aids in
eliminating the obstacles which are [resent in the hardware design and its production. In doing
this, the 3d printer gives us the opportunity of iterating the customization of the testing device.
Majorly, the primary value is dependent on the limitless flexibility that allows for easy
maneuverability through customization or augmentation of the already existing testing
instruments integrated with sensing capabilities [1].
Introduction
In recent years to come, 3d printing technology will be the dominant manufacturing
techniques in almost all fields. Currently, it has been effectively applied in areas such as
aerospace, automotive and medical industry. The techniques go beyond the conventional or
rather the traditional sense of ink on a piece of paper to allowing of 3d objects to be physically
printed just at the eyesight. By extension, the technology enables an individual to generate
models, prototypes as well as products from materials such as metals and plastics. There is
increasing research being conducted on how the 3d printing technique can be incorporated in all
industrial applications.
The significant benefit that is associated with the 3d printing technology is that it
significantly helps in minimizing the amount which is invested in the manufacturing materials as
well as the associated labor. In this paper, we will have a look at the usage of 3d printing in
geotechnical applications. Furthermore, the 3d printer will be elaborated as the frictionless
manufacturing backbone which integrates the modern laser sensing techniques from pressure
film sensor to four-point resistivity probes for characterizations of excess pore water pressure,
stress field, and resistivity tomography.
3d Printing-Enabled Customizable Laboratory Testing
The 3d printer is located at the middle of the frictionless manufacturing where it aids in
eliminating the obstacles which are [resent in the hardware design and its production. In doing
this, the 3d printer gives us the opportunity of iterating the customization of the testing device.
Majorly, the primary value is dependent on the limitless flexibility that allows for easy
maneuverability through customization or augmentation of the already existing testing
instruments integrated with sensing capabilities [1].

3d Printing Technology In Geotechnical Applications 3
Determination of the hoop and radial stress field of driven pile setup in the sand with the
tactile pressure sensor
Two models of tactile pressure sensors, as well as the i-scan system, is utilized in the
determination of the surrounding soil. The sensor is very flexible and ultrathin in size having a
thickness of 0.3 millimeters. Unlike the traditional sensors, the ultrathin sensors do not result in
an artificial boundary which leads to what is known as soil arching. For the sensing element, the
models are |5027, with a width of 0.2 millimeters, similar to toyoura sand which is as well
applied in the test. These will allow for the distribution of the antiparticle contact forces [2]. A
sensor holder, generated by the use of 3e printer is employed for purposes of enhancing the
coupling between the sensors and the soil, as well as facilitating the installation of the tactile
pressure sensors. In order to fix the position, the sensors are placed in slots having a width of 1
millimeter [15].
After putting in the slots, the holder is gradually removed as the monitoring layer gets
filled with soil. From the pressure sensors measurements, there were insignificant changes in the
tactile pressures difference during the pile set up. Additionally, as time passes by, the regular
contact forces between the soil particles found at the influence zone get uninformed in terms of
magnitude during the pile setup period [3].
Measuring K0 and excess pore water pressure in clay with film-like sensor retrofitted in a
needle probe
For the determination of the ko, a flexi force sensor is employed. The sensor is of model
A201, and also determines the pore water pressure values. The flexi force sensor has a sensing
range beginning from 0 to 111N, an amount that is equal to 0 to 1556kPa. The sensing area has a
diameter of 9.53 millimeter with a thickness of 0.203 millimeters. In order to generate the needle
Determination of the hoop and radial stress field of driven pile setup in the sand with the
tactile pressure sensor
Two models of tactile pressure sensors, as well as the i-scan system, is utilized in the
determination of the surrounding soil. The sensor is very flexible and ultrathin in size having a
thickness of 0.3 millimeters. Unlike the traditional sensors, the ultrathin sensors do not result in
an artificial boundary which leads to what is known as soil arching. For the sensing element, the
models are |5027, with a width of 0.2 millimeters, similar to toyoura sand which is as well
applied in the test. These will allow for the distribution of the antiparticle contact forces [2]. A
sensor holder, generated by the use of 3e printer is employed for purposes of enhancing the
coupling between the sensors and the soil, as well as facilitating the installation of the tactile
pressure sensors. In order to fix the position, the sensors are placed in slots having a width of 1
millimeter [15].
After putting in the slots, the holder is gradually removed as the monitoring layer gets
filled with soil. From the pressure sensors measurements, there were insignificant changes in the
tactile pressures difference during the pile set up. Additionally, as time passes by, the regular
contact forces between the soil particles found at the influence zone get uninformed in terms of
magnitude during the pile setup period [3].
Measuring K0 and excess pore water pressure in clay with film-like sensor retrofitted in a
needle probe
For the determination of the ko, a flexi force sensor is employed. The sensor is of model
A201, and also determines the pore water pressure values. The flexi force sensor has a sensing
range beginning from 0 to 111N, an amount that is equal to 0 to 1556kPa. The sensing area has a
diameter of 9.53 millimeter with a thickness of 0.203 millimeters. In order to generate the needle
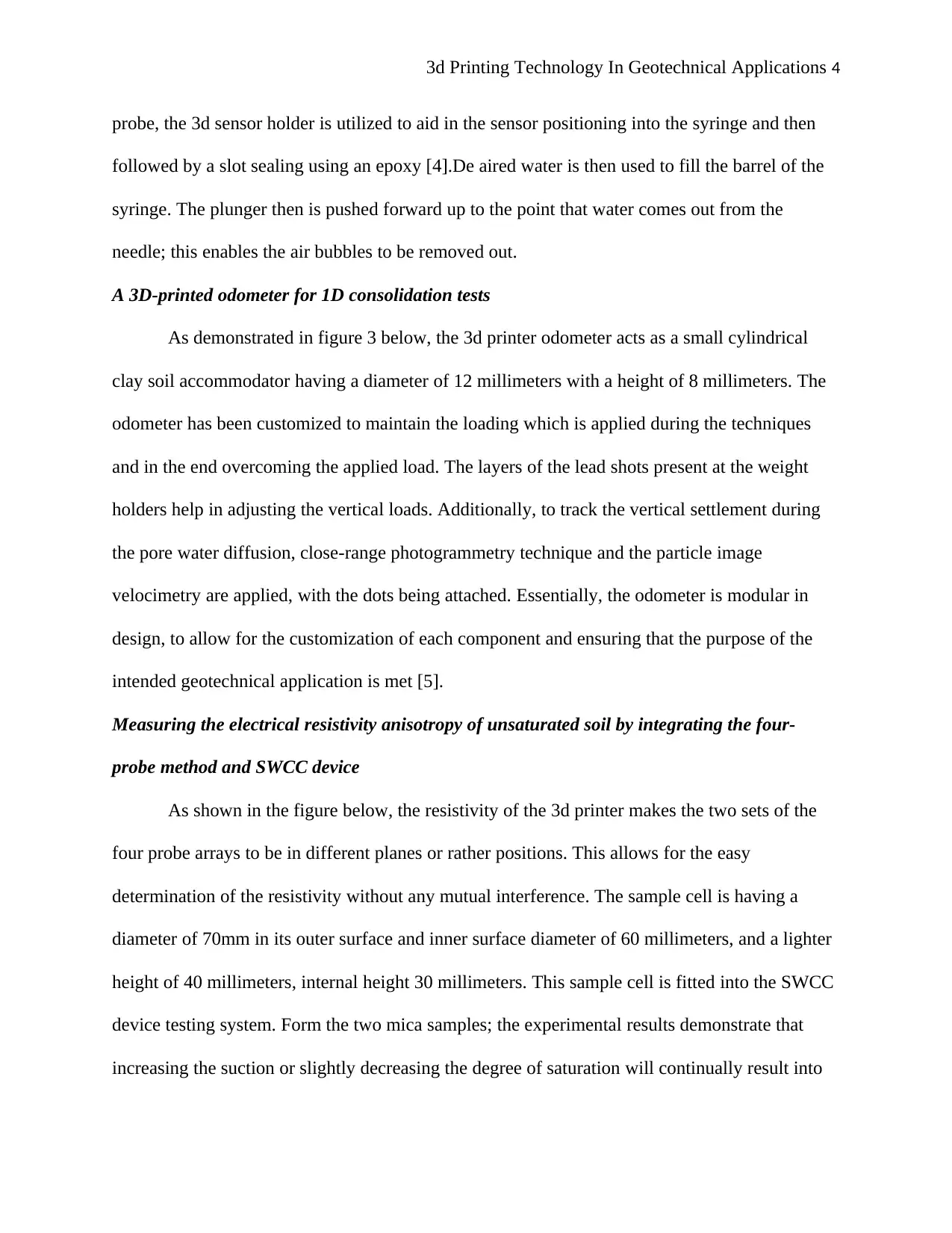
3d Printing Technology In Geotechnical Applications 4
probe, the 3d sensor holder is utilized to aid in the sensor positioning into the syringe and then
followed by a slot sealing using an epoxy [4].De aired water is then used to fill the barrel of the
syringe. The plunger then is pushed forward up to the point that water comes out from the
needle; this enables the air bubbles to be removed out.
A 3D-printed odometer for 1D consolidation tests
As demonstrated in figure 3 below, the 3d printer odometer acts as a small cylindrical
clay soil accommodator having a diameter of 12 millimeters with a height of 8 millimeters. The
odometer has been customized to maintain the loading which is applied during the techniques
and in the end overcoming the applied load. The layers of the lead shots present at the weight
holders help in adjusting the vertical loads. Additionally, to track the vertical settlement during
the pore water diffusion, close-range photogrammetry technique and the particle image
velocimetry are applied, with the dots being attached. Essentially, the odometer is modular in
design, to allow for the customization of each component and ensuring that the purpose of the
intended geotechnical application is met [5].
Measuring the electrical resistivity anisotropy of unsaturated soil by integrating the four-
probe method and SWCC device
As shown in the figure below, the resistivity of the 3d printer makes the two sets of the
four probe arrays to be in different planes or rather positions. This allows for the easy
determination of the resistivity without any mutual interference. The sample cell is having a
diameter of 70mm in its outer surface and inner surface diameter of 60 millimeters, and a lighter
height of 40 millimeters, internal height 30 millimeters. This sample cell is fitted into the SWCC
device testing system. Form the two mica samples; the experimental results demonstrate that
increasing the suction or slightly decreasing the degree of saturation will continually result into
probe, the 3d sensor holder is utilized to aid in the sensor positioning into the syringe and then
followed by a slot sealing using an epoxy [4].De aired water is then used to fill the barrel of the
syringe. The plunger then is pushed forward up to the point that water comes out from the
needle; this enables the air bubbles to be removed out.
A 3D-printed odometer for 1D consolidation tests
As demonstrated in figure 3 below, the 3d printer odometer acts as a small cylindrical
clay soil accommodator having a diameter of 12 millimeters with a height of 8 millimeters. The
odometer has been customized to maintain the loading which is applied during the techniques
and in the end overcoming the applied load. The layers of the lead shots present at the weight
holders help in adjusting the vertical loads. Additionally, to track the vertical settlement during
the pore water diffusion, close-range photogrammetry technique and the particle image
velocimetry are applied, with the dots being attached. Essentially, the odometer is modular in
design, to allow for the customization of each component and ensuring that the purpose of the
intended geotechnical application is met [5].
Measuring the electrical resistivity anisotropy of unsaturated soil by integrating the four-
probe method and SWCC device
As shown in the figure below, the resistivity of the 3d printer makes the two sets of the
four probe arrays to be in different planes or rather positions. This allows for the easy
determination of the resistivity without any mutual interference. The sample cell is having a
diameter of 70mm in its outer surface and inner surface diameter of 60 millimeters, and a lighter
height of 40 millimeters, internal height 30 millimeters. This sample cell is fitted into the SWCC
device testing system. Form the two mica samples; the experimental results demonstrate that
increasing the suction or slightly decreasing the degree of saturation will continually result into
Secure Best Marks with AI Grader
Need help grading? Try our AI Grader for instant feedback on your assignments.
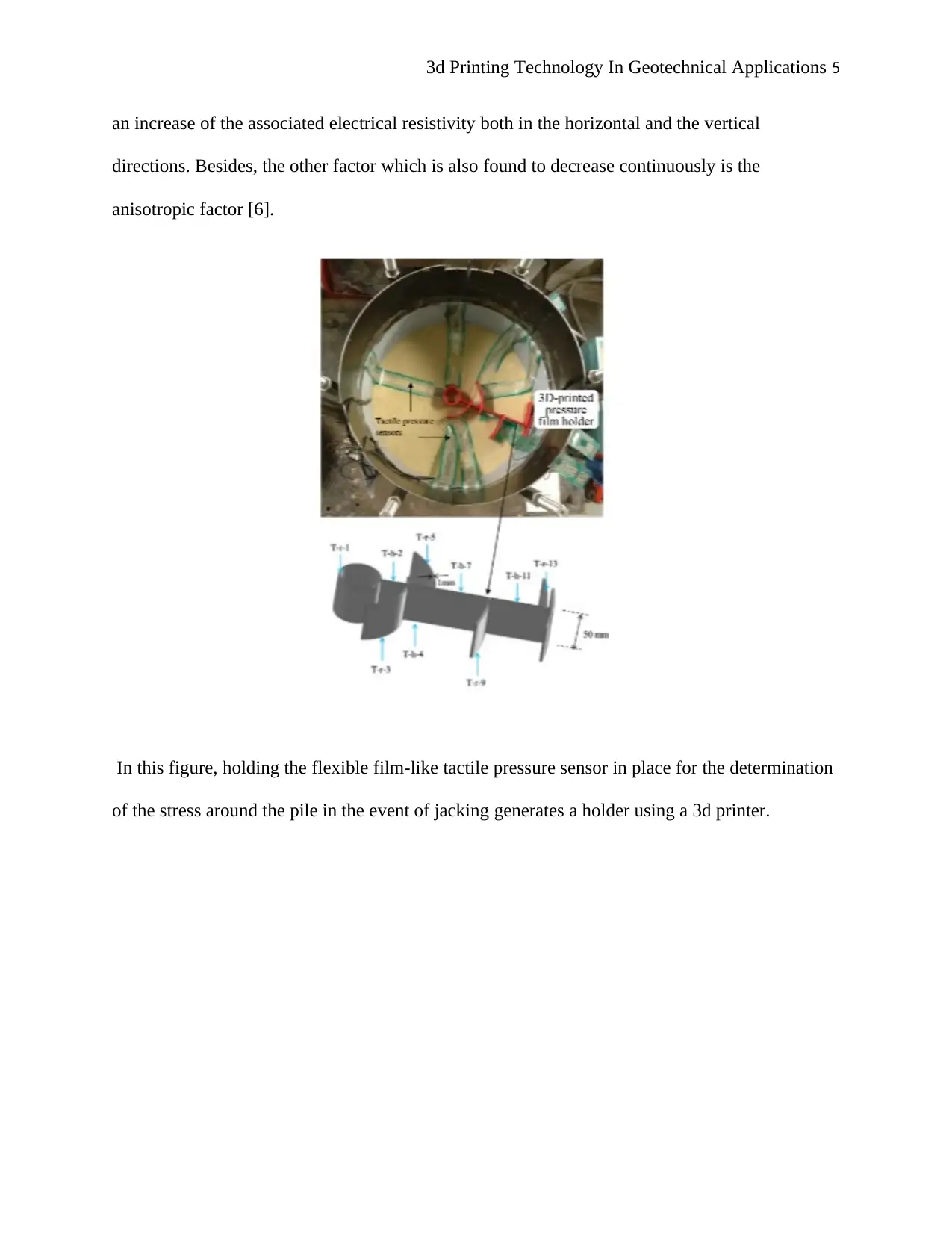
3d Printing Technology In Geotechnical Applications 5
an increase of the associated electrical resistivity both in the horizontal and the vertical
directions. Besides, the other factor which is also found to decrease continuously is the
anisotropic factor [6].
In this figure, holding the flexible film-like tactile pressure sensor in place for the determination
of the stress around the pile in the event of jacking generates a holder using a 3d printer.
an increase of the associated electrical resistivity both in the horizontal and the vertical
directions. Besides, the other factor which is also found to decrease continuously is the
anisotropic factor [6].
In this figure, holding the flexible film-like tactile pressure sensor in place for the determination
of the stress around the pile in the event of jacking generates a holder using a 3d printer.
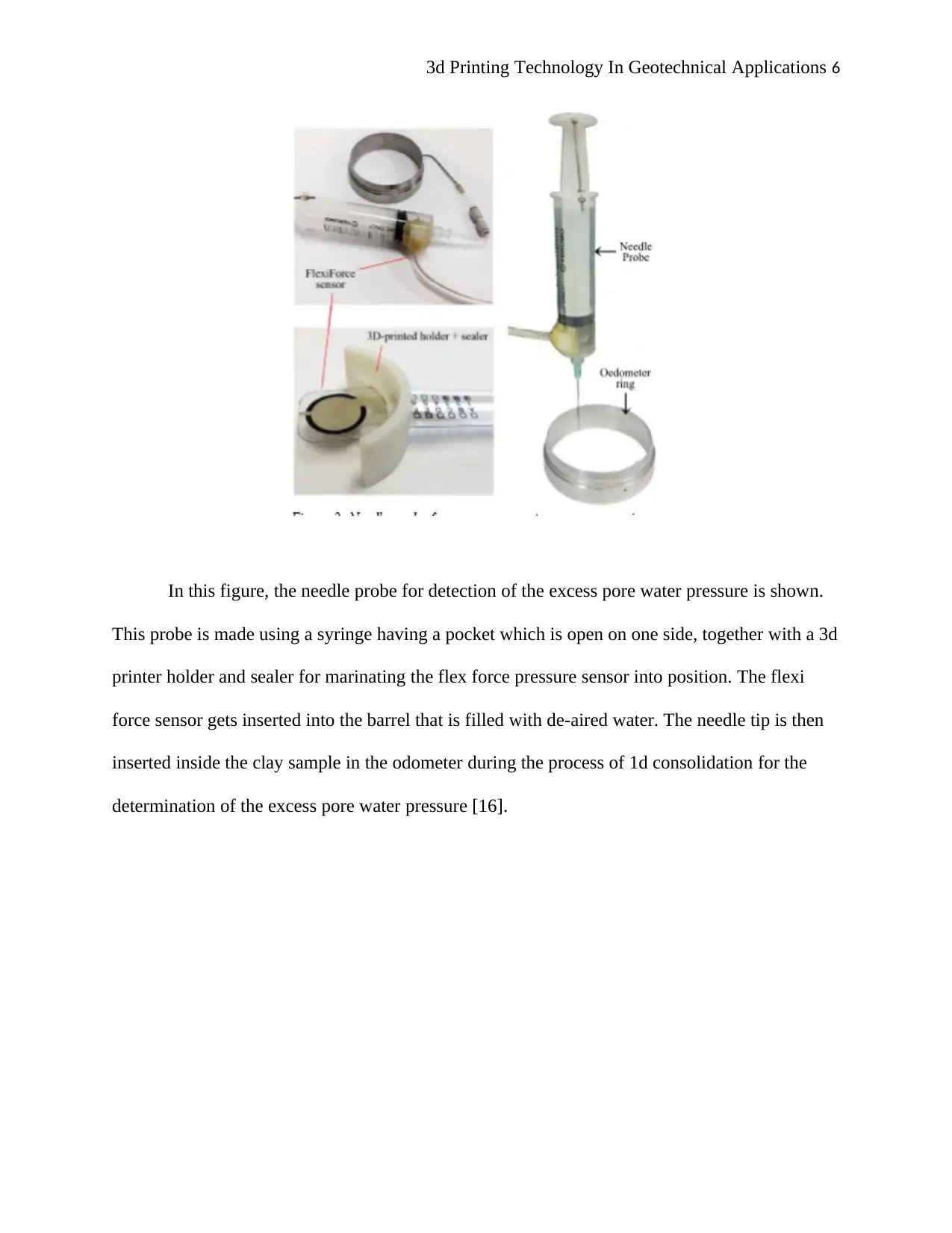
3d Printing Technology In Geotechnical Applications 6
In this figure, the needle probe for detection of the excess pore water pressure is shown.
This probe is made using a syringe having a pocket which is open on one side, together with a 3d
printer holder and sealer for marinating the flex force pressure sensor into position. The flexi
force sensor gets inserted into the barrel that is filled with de-aired water. The needle tip is then
inserted inside the clay sample in the odometer during the process of 1d consolidation for the
determination of the excess pore water pressure [16].
In this figure, the needle probe for detection of the excess pore water pressure is shown.
This probe is made using a syringe having a pocket which is open on one side, together with a 3d
printer holder and sealer for marinating the flex force pressure sensor into position. The flexi
force sensor gets inserted into the barrel that is filled with de-aired water. The needle tip is then
inserted inside the clay sample in the odometer during the process of 1d consolidation for the
determination of the excess pore water pressure [16].
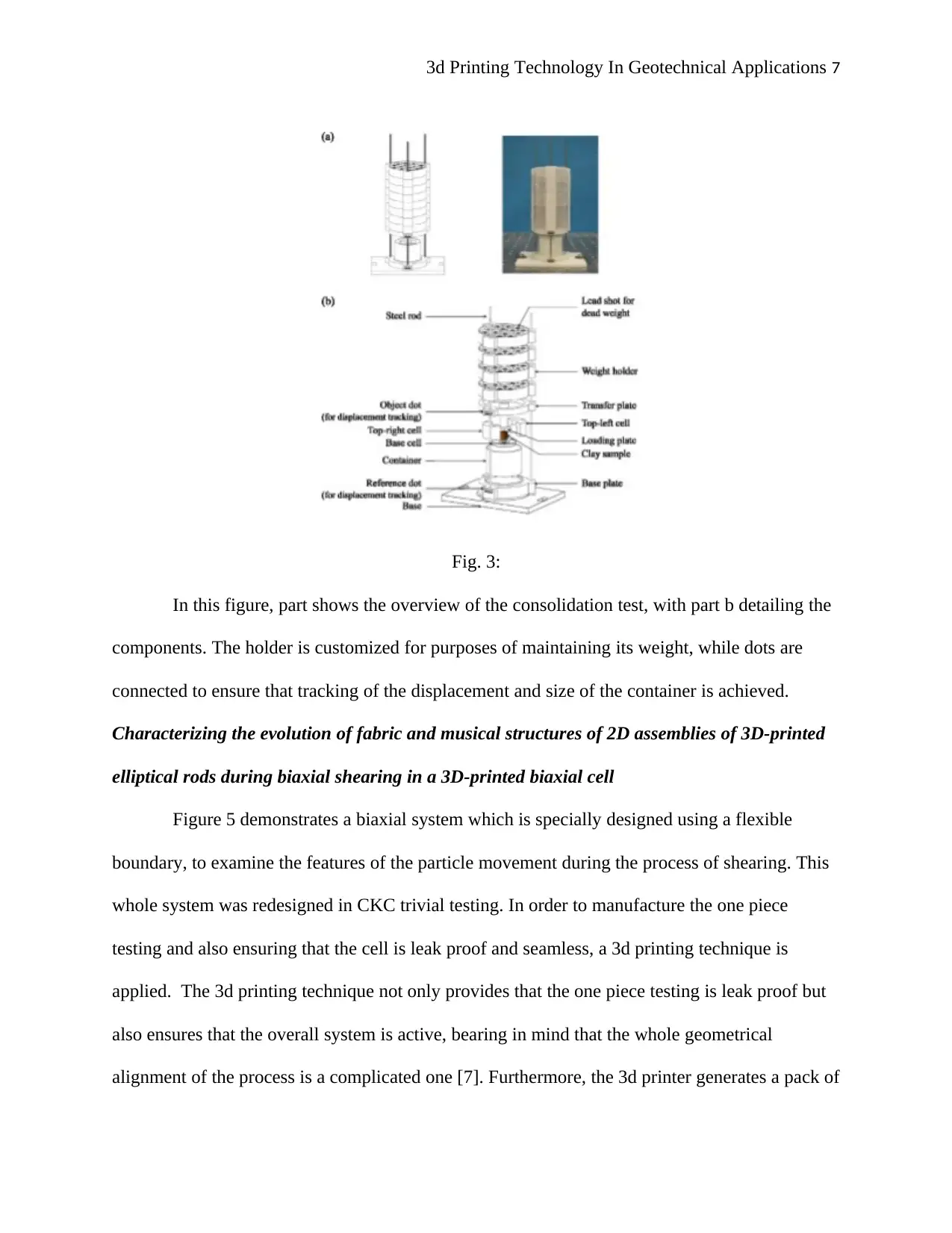
3d Printing Technology In Geotechnical Applications 7
Fig. 3:
In this figure, part shows the overview of the consolidation test, with part b detailing the
components. The holder is customized for purposes of maintaining its weight, while dots are
connected to ensure that tracking of the displacement and size of the container is achieved.
Characterizing the evolution of fabric and musical structures of 2D assemblies of 3D-printed
elliptical rods during biaxial shearing in a 3D-printed biaxial cell
Figure 5 demonstrates a biaxial system which is specially designed using a flexible
boundary, to examine the features of the particle movement during the process of shearing. This
whole system was redesigned in CKC trivial testing. In order to manufacture the one piece
testing and also ensuring that the cell is leak proof and seamless, a 3d printing technique is
applied. The 3d printing technique not only provides that the one piece testing is leak proof but
also ensures that the overall system is active, bearing in mind that the whole geometrical
alignment of the process is a complicated one [7]. Furthermore, the 3d printer generates a pack of
Fig. 3:
In this figure, part shows the overview of the consolidation test, with part b detailing the
components. The holder is customized for purposes of maintaining its weight, while dots are
connected to ensure that tracking of the displacement and size of the container is achieved.
Characterizing the evolution of fabric and musical structures of 2D assemblies of 3D-printed
elliptical rods during biaxial shearing in a 3D-printed biaxial cell
Figure 5 demonstrates a biaxial system which is specially designed using a flexible
boundary, to examine the features of the particle movement during the process of shearing. This
whole system was redesigned in CKC trivial testing. In order to manufacture the one piece
testing and also ensuring that the cell is leak proof and seamless, a 3d printing technique is
applied. The 3d printing technique not only provides that the one piece testing is leak proof but
also ensures that the overall system is active, bearing in mind that the whole geometrical
alignment of the process is a complicated one [7]. Furthermore, the 3d printer generates a pack of
Paraphrase This Document
Need a fresh take? Get an instant paraphrase of this document with our AI Paraphraser
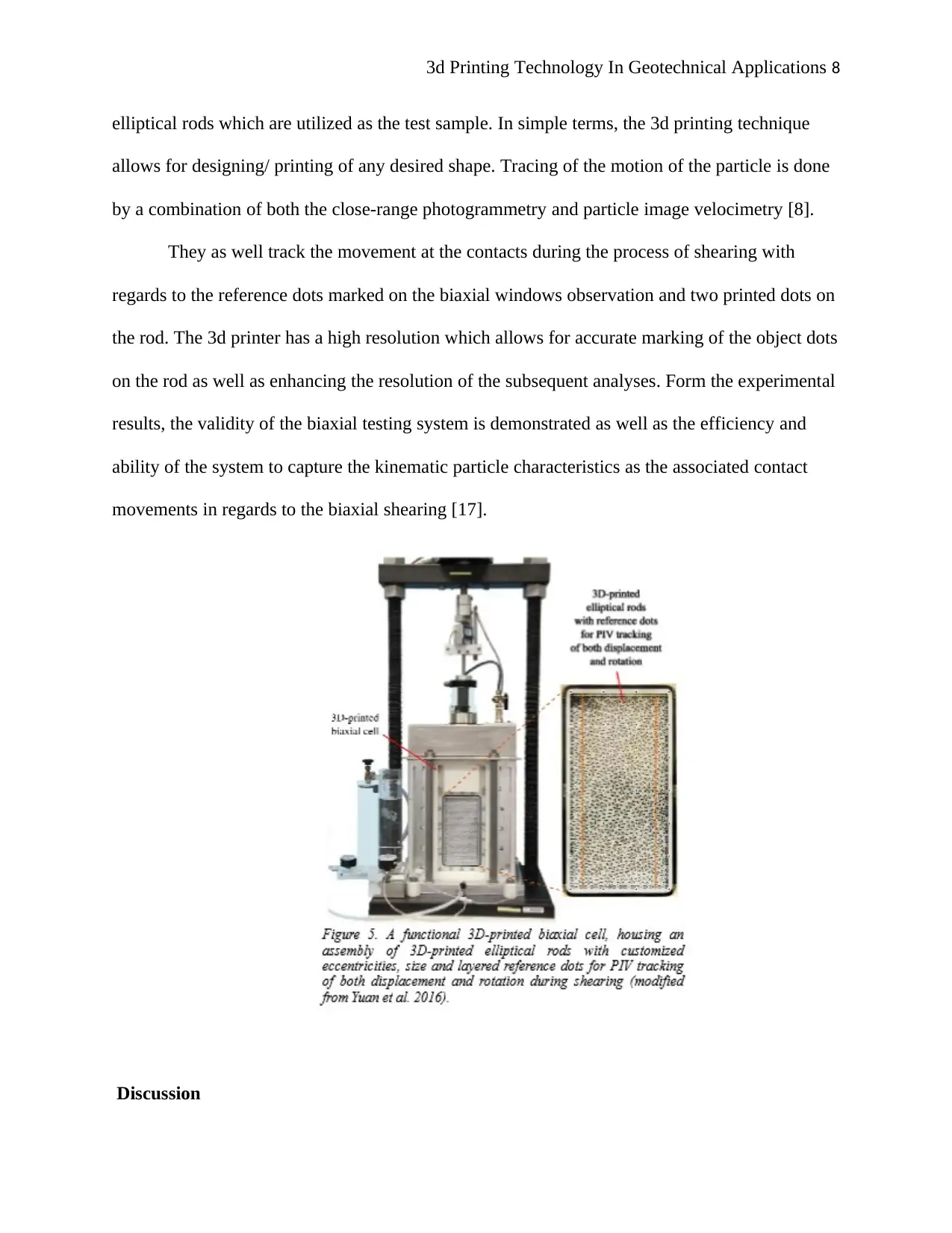
3d Printing Technology In Geotechnical Applications 8
elliptical rods which are utilized as the test sample. In simple terms, the 3d printing technique
allows for designing/ printing of any desired shape. Tracing of the motion of the particle is done
by a combination of both the close-range photogrammetry and particle image velocimetry [8].
They as well track the movement at the contacts during the process of shearing with
regards to the reference dots marked on the biaxial windows observation and two printed dots on
the rod. The 3d printer has a high resolution which allows for accurate marking of the object dots
on the rod as well as enhancing the resolution of the subsequent analyses. Form the experimental
results, the validity of the biaxial testing system is demonstrated as well as the efficiency and
ability of the system to capture the kinematic particle characteristics as the associated contact
movements in regards to the biaxial shearing [17].
Discussion
elliptical rods which are utilized as the test sample. In simple terms, the 3d printing technique
allows for designing/ printing of any desired shape. Tracing of the motion of the particle is done
by a combination of both the close-range photogrammetry and particle image velocimetry [8].
They as well track the movement at the contacts during the process of shearing with
regards to the reference dots marked on the biaxial windows observation and two printed dots on
the rod. The 3d printer has a high resolution which allows for accurate marking of the object dots
on the rod as well as enhancing the resolution of the subsequent analyses. Form the experimental
results, the validity of the biaxial testing system is demonstrated as well as the efficiency and
ability of the system to capture the kinematic particle characteristics as the associated contact
movements in regards to the biaxial shearing [17].
Discussion
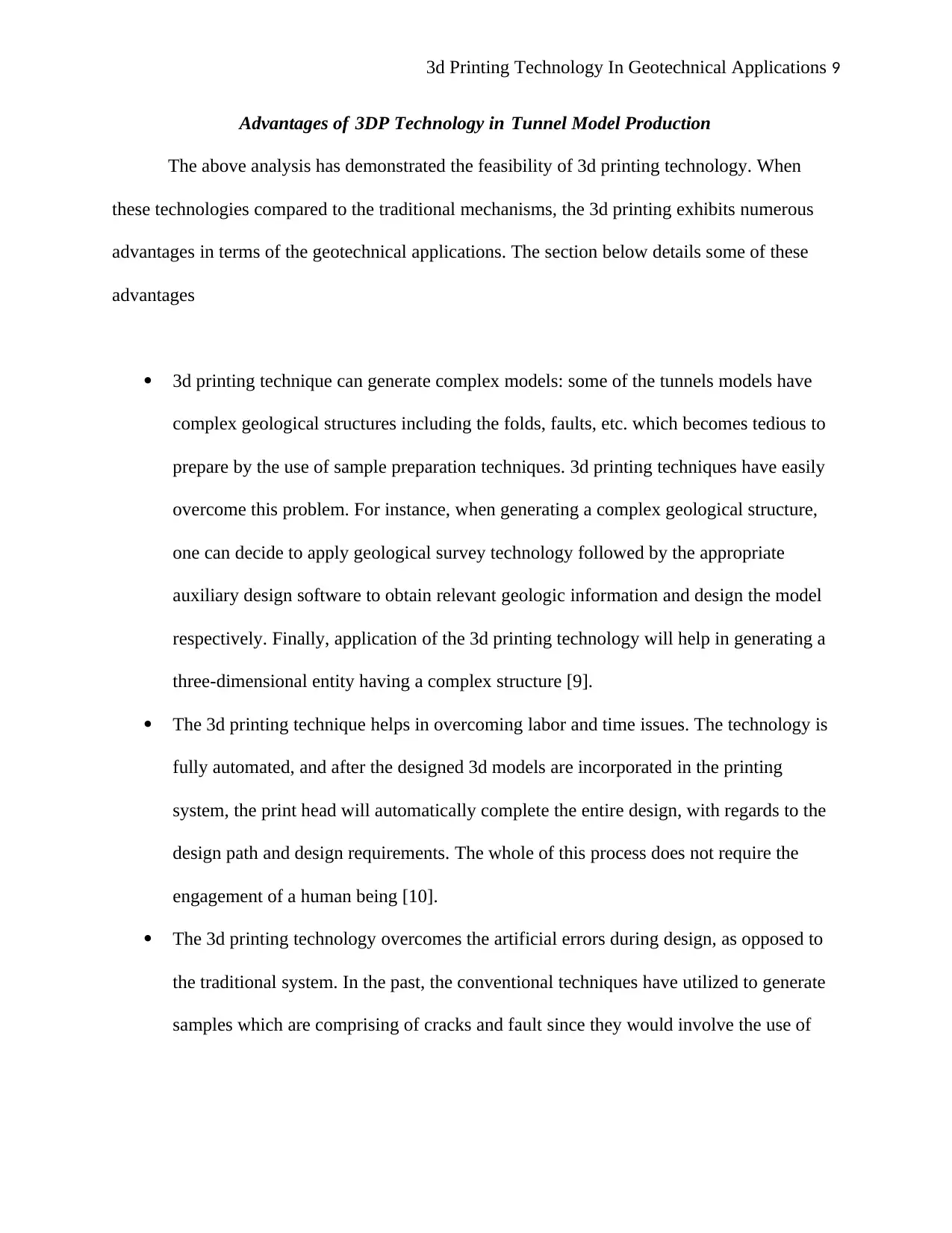
3d Printing Technology In Geotechnical Applications 9
Advantages of 3DP Technology in Tunnel Model Production
The above analysis has demonstrated the feasibility of 3d printing technology. When
these technologies compared to the traditional mechanisms, the 3d printing exhibits numerous
advantages in terms of the geotechnical applications. The section below details some of these
advantages
3d printing technique can generate complex models: some of the tunnels models have
complex geological structures including the folds, faults, etc. which becomes tedious to
prepare by the use of sample preparation techniques. 3d printing techniques have easily
overcome this problem. For instance, when generating a complex geological structure,
one can decide to apply geological survey technology followed by the appropriate
auxiliary design software to obtain relevant geologic information and design the model
respectively. Finally, application of the 3d printing technology will help in generating a
three-dimensional entity having a complex structure [9].
The 3d printing technique helps in overcoming labor and time issues. The technology is
fully automated, and after the designed 3d models are incorporated in the printing
system, the print head will automatically complete the entire design, with regards to the
design path and design requirements. The whole of this process does not require the
engagement of a human being [10].
The 3d printing technology overcomes the artificial errors during design, as opposed to
the traditional system. In the past, the conventional techniques have utilized to generate
samples which are comprising of cracks and fault since they would involve the use of
Advantages of 3DP Technology in Tunnel Model Production
The above analysis has demonstrated the feasibility of 3d printing technology. When
these technologies compared to the traditional mechanisms, the 3d printing exhibits numerous
advantages in terms of the geotechnical applications. The section below details some of these
advantages
3d printing technique can generate complex models: some of the tunnels models have
complex geological structures including the folds, faults, etc. which becomes tedious to
prepare by the use of sample preparation techniques. 3d printing techniques have easily
overcome this problem. For instance, when generating a complex geological structure,
one can decide to apply geological survey technology followed by the appropriate
auxiliary design software to obtain relevant geologic information and design the model
respectively. Finally, application of the 3d printing technology will help in generating a
three-dimensional entity having a complex structure [9].
The 3d printing technique helps in overcoming labor and time issues. The technology is
fully automated, and after the designed 3d models are incorporated in the printing
system, the print head will automatically complete the entire design, with regards to the
design path and design requirements. The whole of this process does not require the
engagement of a human being [10].
The 3d printing technology overcomes the artificial errors during design, as opposed to
the traditional system. In the past, the conventional techniques have utilized to generate
samples which are comprising of cracks and fault since they would involve the use of
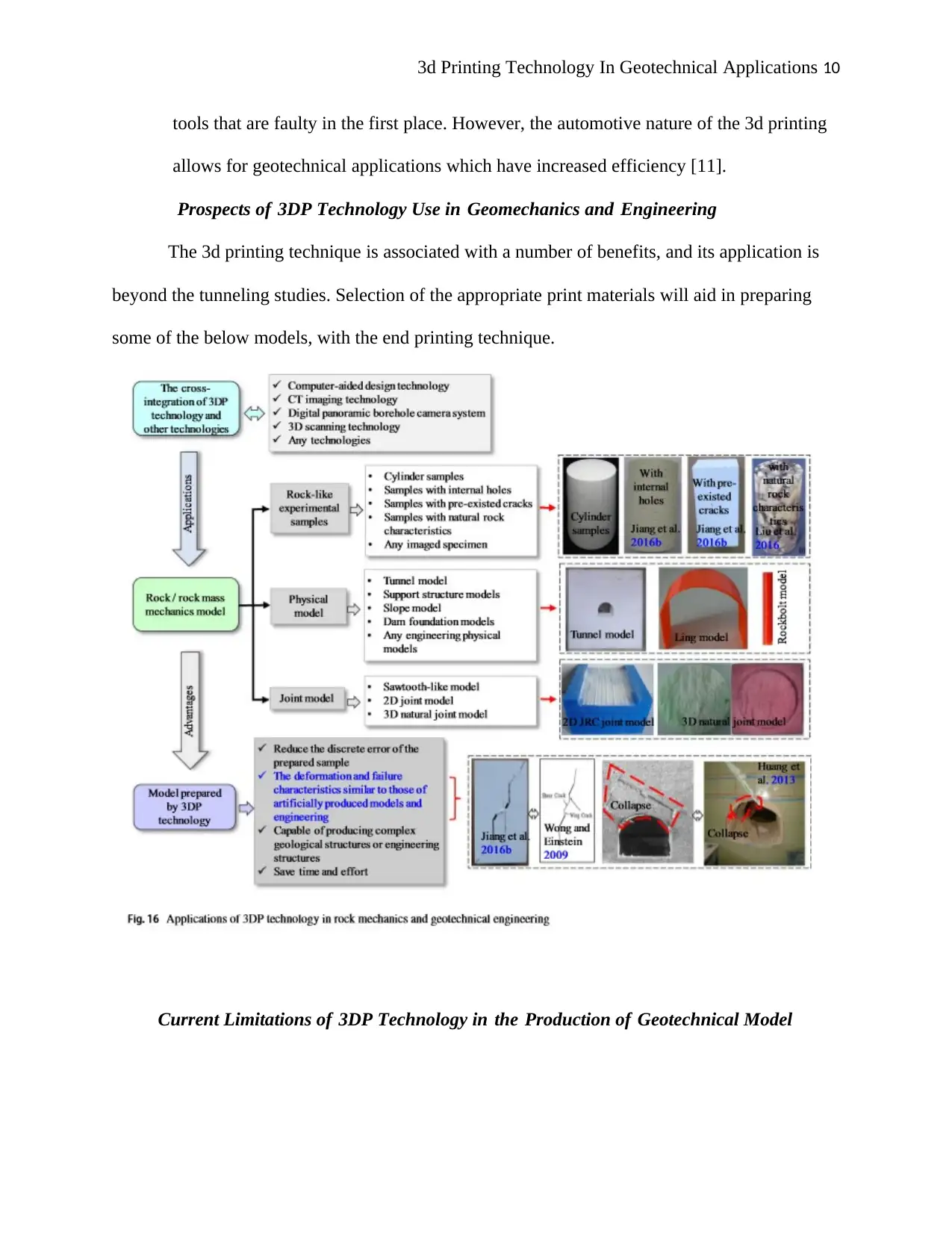
3d Printing Technology In Geotechnical Applications 10
tools that are faulty in the first place. However, the automotive nature of the 3d printing
allows for geotechnical applications which have increased efficiency [11].
Prospects of 3DP Technology Use in Geomechanics and Engineering
The 3d printing technique is associated with a number of benefits, and its application is
beyond the tunneling studies. Selection of the appropriate print materials will aid in preparing
some of the below models, with the end printing technique.
Current Limitations of 3DP Technology in the Production of Geotechnical Model
tools that are faulty in the first place. However, the automotive nature of the 3d printing
allows for geotechnical applications which have increased efficiency [11].
Prospects of 3DP Technology Use in Geomechanics and Engineering
The 3d printing technique is associated with a number of benefits, and its application is
beyond the tunneling studies. Selection of the appropriate print materials will aid in preparing
some of the below models, with the end printing technique.
Current Limitations of 3DP Technology in the Production of Geotechnical Model
Secure Best Marks with AI Grader
Need help grading? Try our AI Grader for instant feedback on your assignments.
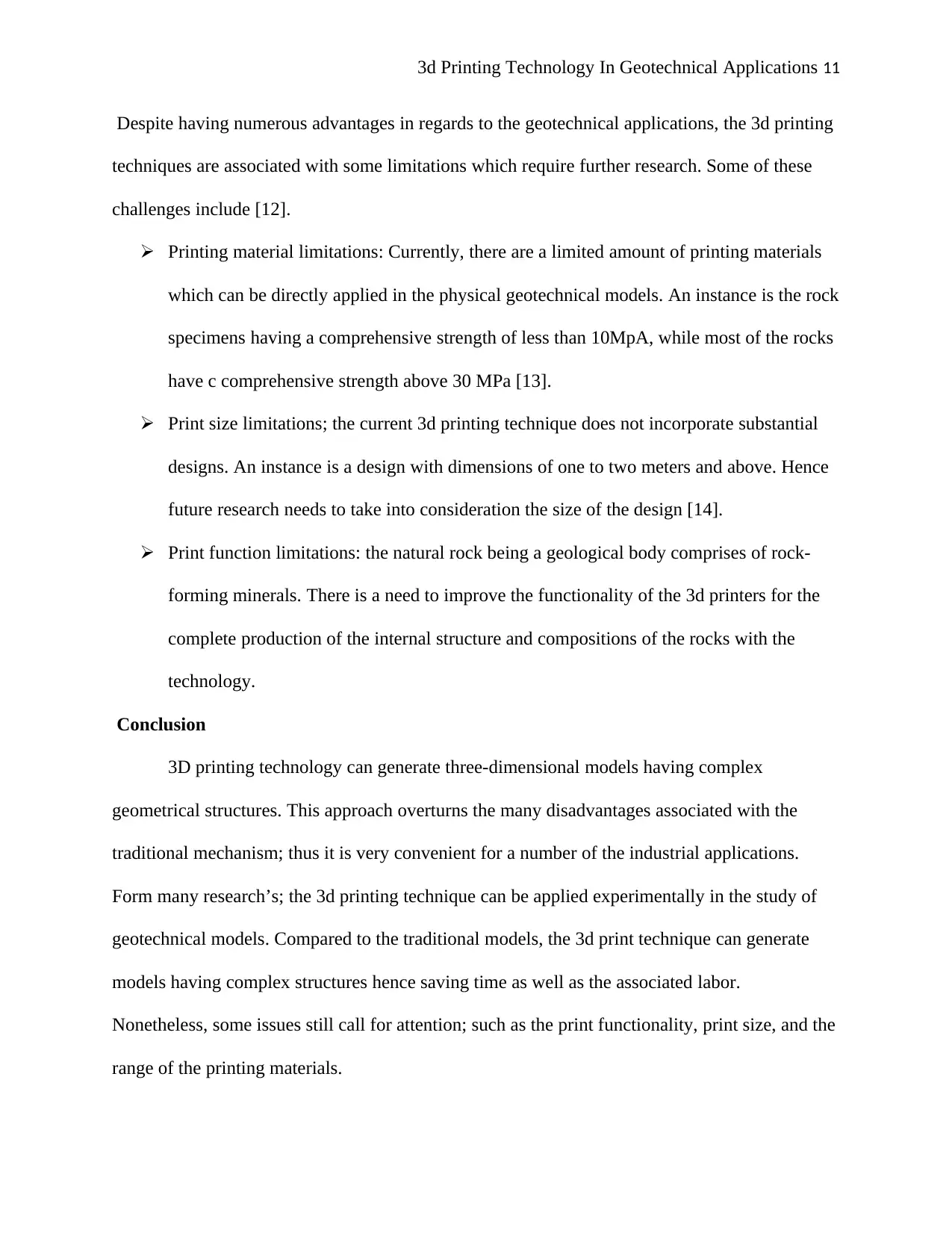
3d Printing Technology In Geotechnical Applications 11
Despite having numerous advantages in regards to the geotechnical applications, the 3d printing
techniques are associated with some limitations which require further research. Some of these
challenges include [12].
Printing material limitations: Currently, there are a limited amount of printing materials
which can be directly applied in the physical geotechnical models. An instance is the rock
specimens having a comprehensive strength of less than 10MpA, while most of the rocks
have c comprehensive strength above 30 MPa [13].
Print size limitations; the current 3d printing technique does not incorporate substantial
designs. An instance is a design with dimensions of one to two meters and above. Hence
future research needs to take into consideration the size of the design [14].
Print function limitations: the natural rock being a geological body comprises of rock-
forming minerals. There is a need to improve the functionality of the 3d printers for the
complete production of the internal structure and compositions of the rocks with the
technology.
Conclusion
3D printing technology can generate three-dimensional models having complex
geometrical structures. This approach overturns the many disadvantages associated with the
traditional mechanism; thus it is very convenient for a number of the industrial applications.
Form many research’s; the 3d printing technique can be applied experimentally in the study of
geotechnical models. Compared to the traditional models, the 3d print technique can generate
models having complex structures hence saving time as well as the associated labor.
Nonetheless, some issues still call for attention; such as the print functionality, print size, and the
range of the printing materials.
Despite having numerous advantages in regards to the geotechnical applications, the 3d printing
techniques are associated with some limitations which require further research. Some of these
challenges include [12].
Printing material limitations: Currently, there are a limited amount of printing materials
which can be directly applied in the physical geotechnical models. An instance is the rock
specimens having a comprehensive strength of less than 10MpA, while most of the rocks
have c comprehensive strength above 30 MPa [13].
Print size limitations; the current 3d printing technique does not incorporate substantial
designs. An instance is a design with dimensions of one to two meters and above. Hence
future research needs to take into consideration the size of the design [14].
Print function limitations: the natural rock being a geological body comprises of rock-
forming minerals. There is a need to improve the functionality of the 3d printers for the
complete production of the internal structure and compositions of the rocks with the
technology.
Conclusion
3D printing technology can generate three-dimensional models having complex
geometrical structures. This approach overturns the many disadvantages associated with the
traditional mechanism; thus it is very convenient for a number of the industrial applications.
Form many research’s; the 3d printing technique can be applied experimentally in the study of
geotechnical models. Compared to the traditional models, the 3d print technique can generate
models having complex structures hence saving time as well as the associated labor.
Nonetheless, some issues still call for attention; such as the print functionality, print size, and the
range of the printing materials.

3d Printing Technology In Geotechnical Applications 12
References
[1] Choi, W., Woo, J.H., Jeon, J.B. and Yoon, S.S., 2015. Measurement of Structural Properties of
PLA Filament as a Supplier of 3D Printer. Journal of The Korean Society of Agricultural
Engineers, 57(6), pp.141-152.
[2] Geliga, E.A. and Ismail, D.S.A., 2010. Geotechnical properties of fly ash and its application on
soft soil stabilization. Journal of Civil Engineering, Science and Technology, 1(2), pp.1-6.
[3] Hanaor, A.H., Gan, Y., Revay, M., Airey, D.W. and Einav, I., 2016. 3D printable geomaterials.
Géotechnique, 66(4), pp.323-332.
[4] Henke K, Treml S (2013) Wood based bulk material in 3D printing processes for applications in
construction. Eur J Wood Wood Prod 71(1):139–141
[5] Huang D, Huang RQ, Zhang YX (2009) Analysis on influence of fault location and strength on
deformation and stress distribution of surrounding rocks of large underground openings. J Civ
Archit Environ Eng 31(2):68–73
[6] Huang F, Zhu H, Xu Q, Cai Y, Zhuang X (2013) The effect of weak interlayer on the failure
pattern of rock mass around tunnel–Scaled model tests and numerical analysis. Tunn Undergr
Space Technol 35(4):207–218
[7] Ishutov, S., Hasiuk, F.J., Harding, C. and Gray, J.N., 2015. 3D printing sandstone porosity
models. Interpretation, 3(3), pp.SX49-SX61.
[8] Jiang Q, Feng XT, Hatzor YH, Hao XJ, Li SJ (2014) Mechanical anisotropy of columnar jointed
basalts: an example from the Baihetan hydropower station, China. Eng Geol 175:35–45
[9] Jiang, Q., Feng, X., Song, L., Gong, Y., Zheng, H. and Cui, J., 2016. Modeling rock specimens
through 3D printing: Tentative experiments and prospects. Acta Mechanica Sinica, 32(1),
pp.101-111.
References
[1] Choi, W., Woo, J.H., Jeon, J.B. and Yoon, S.S., 2015. Measurement of Structural Properties of
PLA Filament as a Supplier of 3D Printer. Journal of The Korean Society of Agricultural
Engineers, 57(6), pp.141-152.
[2] Geliga, E.A. and Ismail, D.S.A., 2010. Geotechnical properties of fly ash and its application on
soft soil stabilization. Journal of Civil Engineering, Science and Technology, 1(2), pp.1-6.
[3] Hanaor, A.H., Gan, Y., Revay, M., Airey, D.W. and Einav, I., 2016. 3D printable geomaterials.
Géotechnique, 66(4), pp.323-332.
[4] Henke K, Treml S (2013) Wood based bulk material in 3D printing processes for applications in
construction. Eur J Wood Wood Prod 71(1):139–141
[5] Huang D, Huang RQ, Zhang YX (2009) Analysis on influence of fault location and strength on
deformation and stress distribution of surrounding rocks of large underground openings. J Civ
Archit Environ Eng 31(2):68–73
[6] Huang F, Zhu H, Xu Q, Cai Y, Zhuang X (2013) The effect of weak interlayer on the failure
pattern of rock mass around tunnel–Scaled model tests and numerical analysis. Tunn Undergr
Space Technol 35(4):207–218
[7] Ishutov, S., Hasiuk, F.J., Harding, C. and Gray, J.N., 2015. 3D printing sandstone porosity
models. Interpretation, 3(3), pp.SX49-SX61.
[8] Jiang Q, Feng XT, Hatzor YH, Hao XJ, Li SJ (2014) Mechanical anisotropy of columnar jointed
basalts: an example from the Baihetan hydropower station, China. Eng Geol 175:35–45
[9] Jiang, Q., Feng, X., Song, L., Gong, Y., Zheng, H. and Cui, J., 2016. Modeling rock specimens
through 3D printing: Tentative experiments and prospects. Acta Mechanica Sinica, 32(1),
pp.101-111.
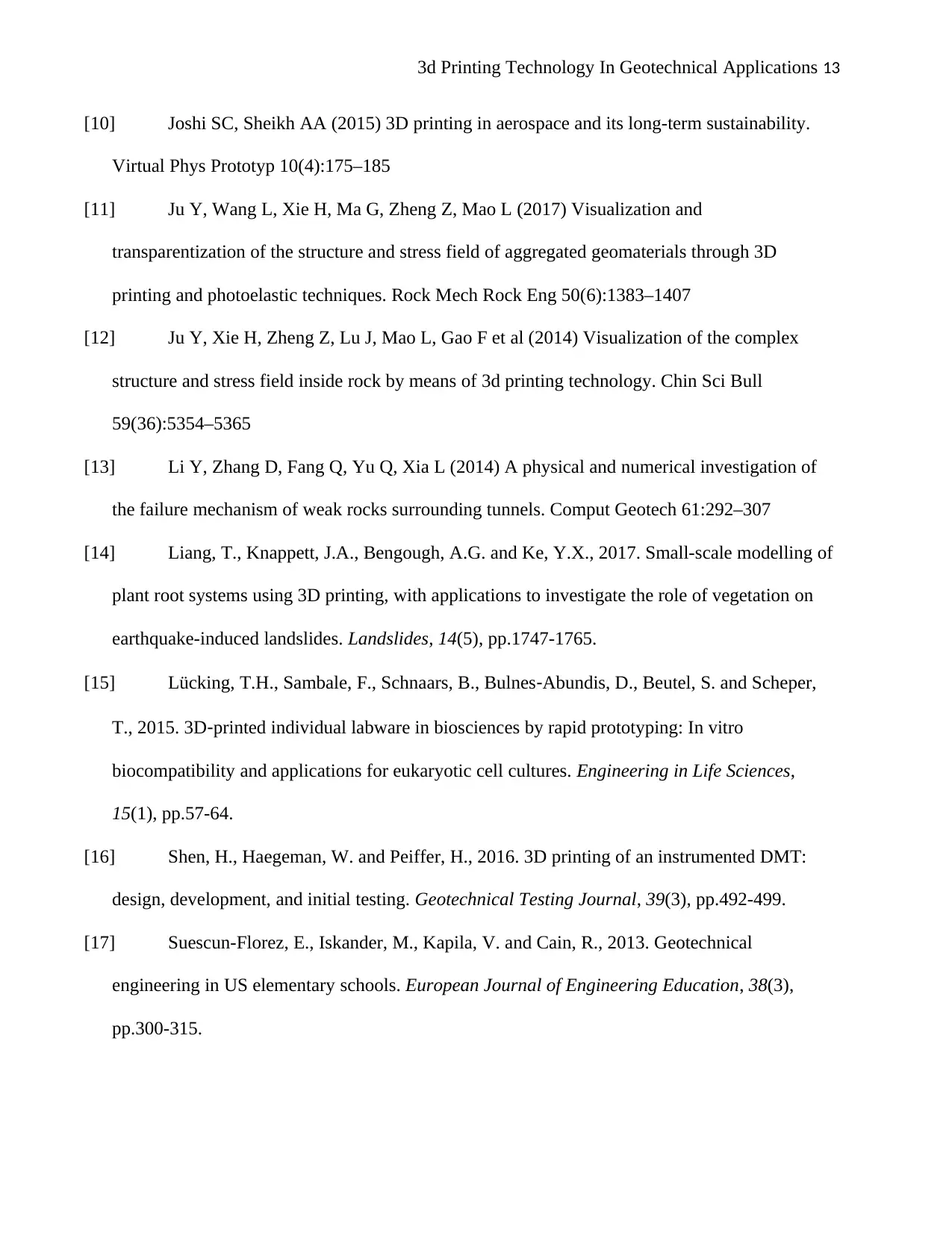
3d Printing Technology In Geotechnical Applications 13
[10] Joshi SC, Sheikh AA (2015) 3D printing in aerospace and its long-term sustainability.
Virtual Phys Prototyp 10(4):175–185
[11] Ju Y, Wang L, Xie H, Ma G, Zheng Z, Mao L (2017) Visualization and
transparentization of the structure and stress field of aggregated geomaterials through 3D
printing and photoelastic techniques. Rock Mech Rock Eng 50(6):1383–1407
[12] Ju Y, Xie H, Zheng Z, Lu J, Mao L, Gao F et al (2014) Visualization of the complex
structure and stress field inside rock by means of 3d printing technology. Chin Sci Bull
59(36):5354–5365
[13] Li Y, Zhang D, Fang Q, Yu Q, Xia L (2014) A physical and numerical investigation of
the failure mechanism of weak rocks surrounding tunnels. Comput Geotech 61:292–307
[14] Liang, T., Knappett, J.A., Bengough, A.G. and Ke, Y.X., 2017. Small-scale modelling of
plant root systems using 3D printing, with applications to investigate the role of vegetation on
earthquake-induced landslides. Landslides, 14(5), pp.1747-1765.
[15] Lücking, T.H., Sambale, F., Schnaars, B., Bulnes‐Abundis, D., Beutel, S. and Scheper,
T., 2015. 3D‐printed individual labware in biosciences by rapid prototyping: In vitro
biocompatibility and applications for eukaryotic cell cultures. Engineering in Life Sciences,
15(1), pp.57-64.
[16] Shen, H., Haegeman, W. and Peiffer, H., 2016. 3D printing of an instrumented DMT:
design, development, and initial testing. Geotechnical Testing Journal, 39(3), pp.492-499.
[17] Suescun-Florez, E., Iskander, M., Kapila, V. and Cain, R., 2013. Geotechnical
engineering in US elementary schools. European Journal of Engineering Education, 38(3),
pp.300-315.
[10] Joshi SC, Sheikh AA (2015) 3D printing in aerospace and its long-term sustainability.
Virtual Phys Prototyp 10(4):175–185
[11] Ju Y, Wang L, Xie H, Ma G, Zheng Z, Mao L (2017) Visualization and
transparentization of the structure and stress field of aggregated geomaterials through 3D
printing and photoelastic techniques. Rock Mech Rock Eng 50(6):1383–1407
[12] Ju Y, Xie H, Zheng Z, Lu J, Mao L, Gao F et al (2014) Visualization of the complex
structure and stress field inside rock by means of 3d printing technology. Chin Sci Bull
59(36):5354–5365
[13] Li Y, Zhang D, Fang Q, Yu Q, Xia L (2014) A physical and numerical investigation of
the failure mechanism of weak rocks surrounding tunnels. Comput Geotech 61:292–307
[14] Liang, T., Knappett, J.A., Bengough, A.G. and Ke, Y.X., 2017. Small-scale modelling of
plant root systems using 3D printing, with applications to investigate the role of vegetation on
earthquake-induced landslides. Landslides, 14(5), pp.1747-1765.
[15] Lücking, T.H., Sambale, F., Schnaars, B., Bulnes‐Abundis, D., Beutel, S. and Scheper,
T., 2015. 3D‐printed individual labware in biosciences by rapid prototyping: In vitro
biocompatibility and applications for eukaryotic cell cultures. Engineering in Life Sciences,
15(1), pp.57-64.
[16] Shen, H., Haegeman, W. and Peiffer, H., 2016. 3D printing of an instrumented DMT:
design, development, and initial testing. Geotechnical Testing Journal, 39(3), pp.492-499.
[17] Suescun-Florez, E., Iskander, M., Kapila, V. and Cain, R., 2013. Geotechnical
engineering in US elementary schools. European Journal of Engineering Education, 38(3),
pp.300-315.
1 out of 13

Your All-in-One AI-Powered Toolkit for Academic Success.
+13062052269
info@desklib.com
Available 24*7 on WhatsApp / Email
Unlock your academic potential
© 2024 | Zucol Services PVT LTD | All rights reserved.