A Detailed Fatigue Analysis of 3D Printed Materials Specifically PETG
VerifiedAdded on 2023/04/20
|10
|2354
|331
Literature Review
AI Summary
This literature review explores the fatigue analysis of 3D printed Polyethylene Terephthalate Glycol (PETG) materials, focusing on their mechanical properties and behavior under cyclic loading. It examines the fused deposition modeling (FDM) method and the impact of printing parameters on fatigue strength. The review covers studies on Acrylonitrile Butadiene Styrene (ABS) and Polylactide (PLA) for comparison, highlighting the importance of understanding material qualities in 3D printing. It also discusses fatigue testing methods for 3D printed polymer specimens, concluding that while 3D printed components are suitable for lower-volume, high-design applications, they may not be appropriate for high-power industrial uses due to limitations in mechanical strength and fatigue life. The study emphasizes the need for further research into the mechanical properties of 3D printed materials under active loading conditions to enhance their applicability in various engineering fields.
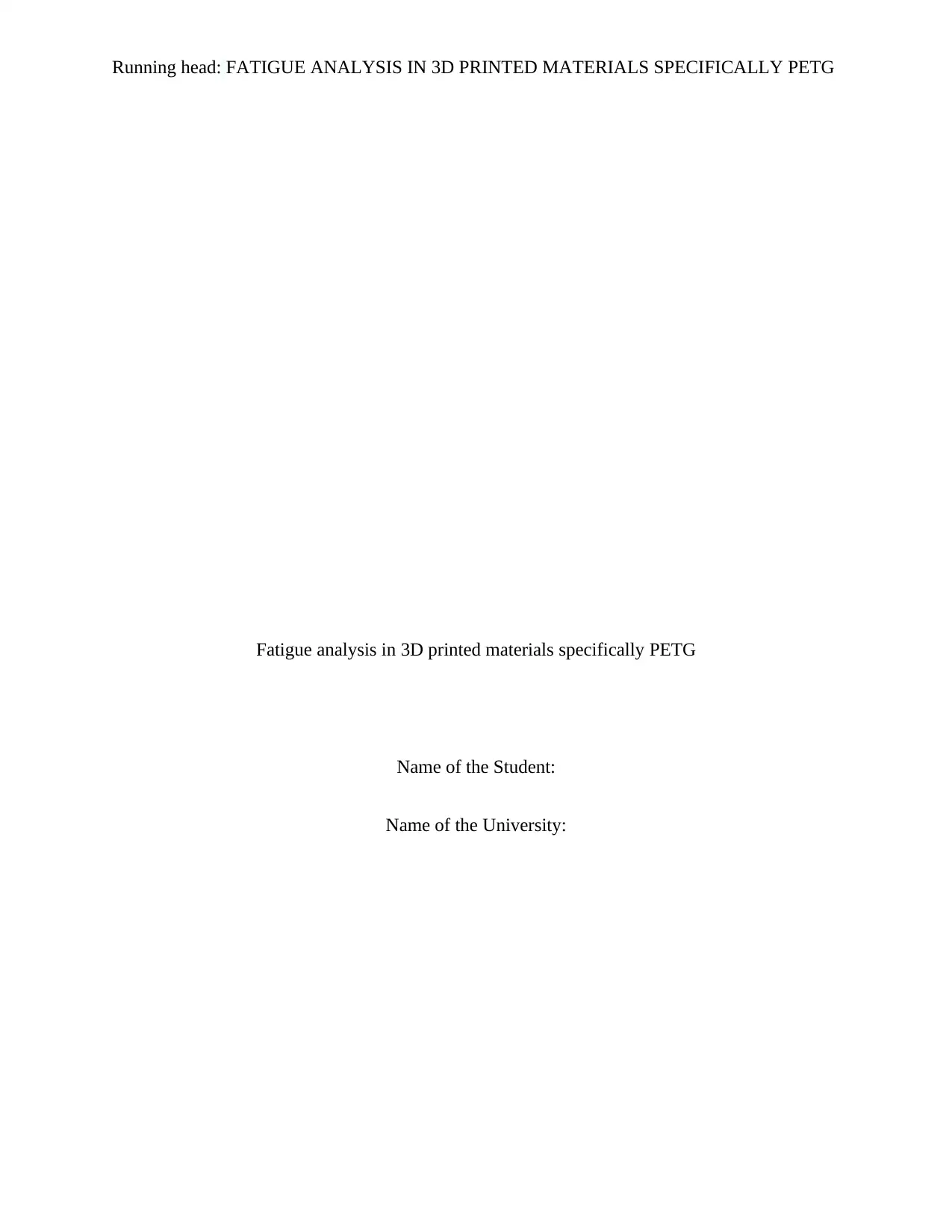
Running head: FATIGUE ANALYSIS IN 3D PRINTED MATERIALS SPECIFICALLY PETG
Fatigue analysis in 3D printed materials specifically PETG
Name of the Student:
Name of the University:
Fatigue analysis in 3D printed materials specifically PETG
Name of the Student:
Name of the University:
Secure Best Marks with AI Grader
Need help grading? Try our AI Grader for instant feedback on your assignments.
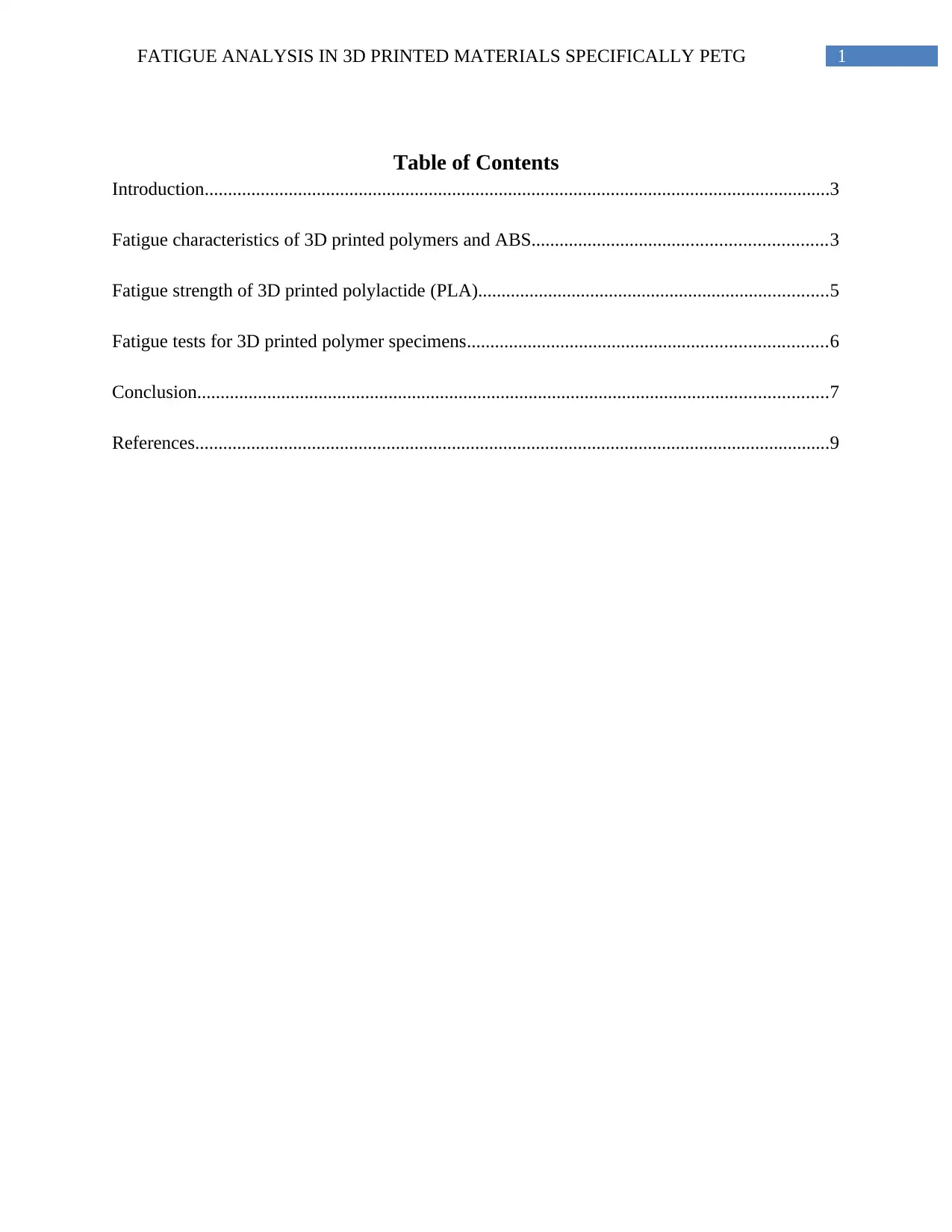
1FATIGUE ANALYSIS IN 3D PRINTED MATERIALS SPECIFICALLY PETG
Table of Contents
Introduction......................................................................................................................................3
Fatigue characteristics of 3D printed polymers and ABS...............................................................3
Fatigue strength of 3D printed polylactide (PLA)...........................................................................5
Fatigue tests for 3D printed polymer specimens.............................................................................6
Conclusion.......................................................................................................................................7
References........................................................................................................................................9
Table of Contents
Introduction......................................................................................................................................3
Fatigue characteristics of 3D printed polymers and ABS...............................................................3
Fatigue strength of 3D printed polylactide (PLA)...........................................................................5
Fatigue tests for 3D printed polymer specimens.............................................................................6
Conclusion.......................................................................................................................................7
References........................................................................................................................................9
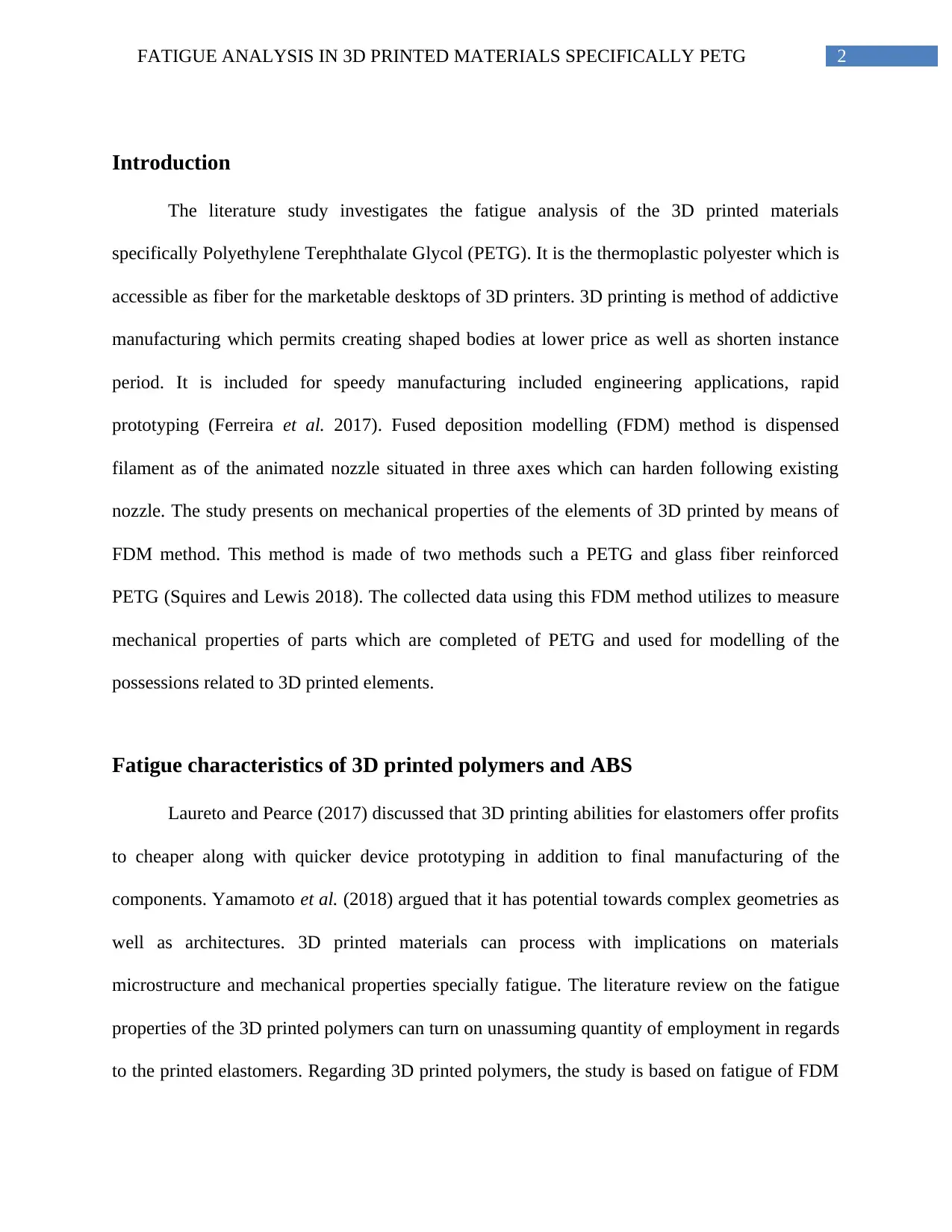
2FATIGUE ANALYSIS IN 3D PRINTED MATERIALS SPECIFICALLY PETG
Introduction
The literature study investigates the fatigue analysis of the 3D printed materials
specifically Polyethylene Terephthalate Glycol (PETG). It is the thermoplastic polyester which is
accessible as fiber for the marketable desktops of 3D printers. 3D printing is method of addictive
manufacturing which permits creating shaped bodies at lower price as well as shorten instance
period. It is included for speedy manufacturing included engineering applications, rapid
prototyping (Ferreira et al. 2017). Fused deposition modelling (FDM) method is dispensed
filament as of the animated nozzle situated in three axes which can harden following existing
nozzle. The study presents on mechanical properties of the elements of 3D printed by means of
FDM method. This method is made of two methods such a PETG and glass fiber reinforced
PETG (Squires and Lewis 2018). The collected data using this FDM method utilizes to measure
mechanical properties of parts which are completed of PETG and used for modelling of the
possessions related to 3D printed elements.
Fatigue characteristics of 3D printed polymers and ABS
Laureto and Pearce (2017) discussed that 3D printing abilities for elastomers offer profits
to cheaper along with quicker device prototyping in addition to final manufacturing of the
components. Yamamoto et al. (2018) argued that it has potential towards complex geometries as
well as architectures. 3D printed materials can process with implications on materials
microstructure and mechanical properties specially fatigue. The literature review on the fatigue
properties of the 3D printed polymers can turn on unassuming quantity of employment in regards
to the printed elastomers. Regarding 3D printed polymers, the study is based on fatigue of FDM
Introduction
The literature study investigates the fatigue analysis of the 3D printed materials
specifically Polyethylene Terephthalate Glycol (PETG). It is the thermoplastic polyester which is
accessible as fiber for the marketable desktops of 3D printers. 3D printing is method of addictive
manufacturing which permits creating shaped bodies at lower price as well as shorten instance
period. It is included for speedy manufacturing included engineering applications, rapid
prototyping (Ferreira et al. 2017). Fused deposition modelling (FDM) method is dispensed
filament as of the animated nozzle situated in three axes which can harden following existing
nozzle. The study presents on mechanical properties of the elements of 3D printed by means of
FDM method. This method is made of two methods such a PETG and glass fiber reinforced
PETG (Squires and Lewis 2018). The collected data using this FDM method utilizes to measure
mechanical properties of parts which are completed of PETG and used for modelling of the
possessions related to 3D printed elements.
Fatigue characteristics of 3D printed polymers and ABS
Laureto and Pearce (2017) discussed that 3D printing abilities for elastomers offer profits
to cheaper along with quicker device prototyping in addition to final manufacturing of the
components. Yamamoto et al. (2018) argued that it has potential towards complex geometries as
well as architectures. 3D printed materials can process with implications on materials
microstructure and mechanical properties specially fatigue. The literature review on the fatigue
properties of the 3D printed polymers can turn on unassuming quantity of employment in regards
to the printed elastomers. Regarding 3D printed polymers, the study is based on fatigue of FDM
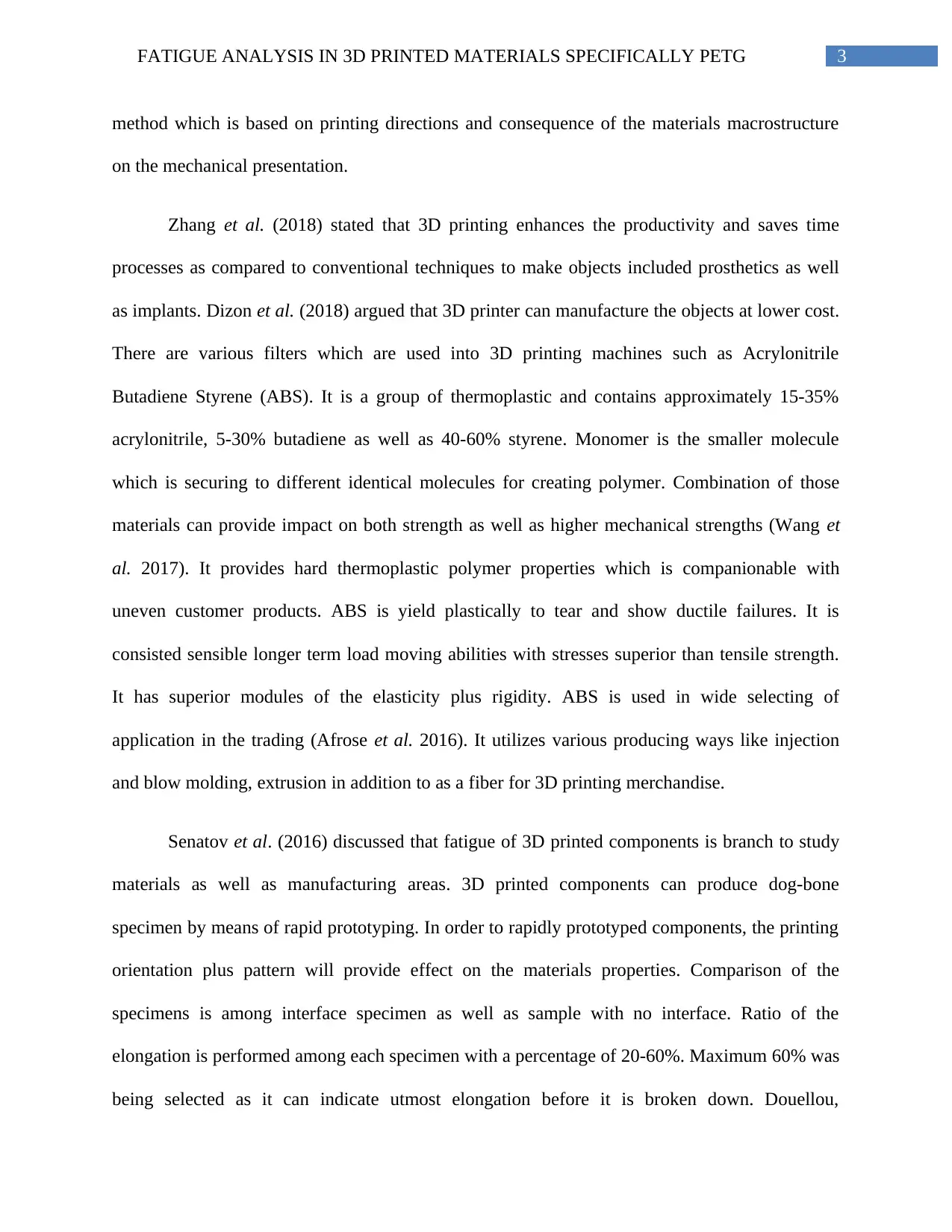
3FATIGUE ANALYSIS IN 3D PRINTED MATERIALS SPECIFICALLY PETG
method which is based on printing directions and consequence of the materials macrostructure
on the mechanical presentation.
Zhang et al. (2018) stated that 3D printing enhances the productivity and saves time
processes as compared to conventional techniques to make objects included prosthetics as well
as implants. Dizon et al. (2018) argued that 3D printer can manufacture the objects at lower cost.
There are various filters which are used into 3D printing machines such as Acrylonitrile
Butadiene Styrene (ABS). It is a group of thermoplastic and contains approximately 15-35%
acrylonitrile, 5-30% butadiene as well as 40-60% styrene. Monomer is the smaller molecule
which is securing to different identical molecules for creating polymer. Combination of those
materials can provide impact on both strength as well as higher mechanical strengths (Wang et
al. 2017). It provides hard thermoplastic polymer properties which is companionable with
uneven customer products. ABS is yield plastically to tear and show ductile failures. It is
consisted sensible longer term load moving abilities with stresses superior than tensile strength.
It has superior modules of the elasticity plus rigidity. ABS is used in wide selecting of
application in the trading (Afrose et al. 2016). It utilizes various producing ways like injection
and blow molding, extrusion in addition to as a fiber for 3D printing merchandise.
Senatov et al. (2016) discussed that fatigue of 3D printed components is branch to study
materials as well as manufacturing areas. 3D printed components can produce dog-bone
specimen by means of rapid prototyping. In order to rapidly prototyped components, the printing
orientation plus pattern will provide effect on the materials properties. Comparison of the
specimens is among interface specimen as well as sample with no interface. Ratio of the
elongation is performed among each specimen with a percentage of 20-60%. Maximum 60% was
being selected as it can indicate utmost elongation before it is broken down. Douellou,
method which is based on printing directions and consequence of the materials macrostructure
on the mechanical presentation.
Zhang et al. (2018) stated that 3D printing enhances the productivity and saves time
processes as compared to conventional techniques to make objects included prosthetics as well
as implants. Dizon et al. (2018) argued that 3D printer can manufacture the objects at lower cost.
There are various filters which are used into 3D printing machines such as Acrylonitrile
Butadiene Styrene (ABS). It is a group of thermoplastic and contains approximately 15-35%
acrylonitrile, 5-30% butadiene as well as 40-60% styrene. Monomer is the smaller molecule
which is securing to different identical molecules for creating polymer. Combination of those
materials can provide impact on both strength as well as higher mechanical strengths (Wang et
al. 2017). It provides hard thermoplastic polymer properties which is companionable with
uneven customer products. ABS is yield plastically to tear and show ductile failures. It is
consisted sensible longer term load moving abilities with stresses superior than tensile strength.
It has superior modules of the elasticity plus rigidity. ABS is used in wide selecting of
application in the trading (Afrose et al. 2016). It utilizes various producing ways like injection
and blow molding, extrusion in addition to as a fiber for 3D printing merchandise.
Senatov et al. (2016) discussed that fatigue of 3D printed components is branch to study
materials as well as manufacturing areas. 3D printed components can produce dog-bone
specimen by means of rapid prototyping. In order to rapidly prototyped components, the printing
orientation plus pattern will provide effect on the materials properties. Comparison of the
specimens is among interface specimen as well as sample with no interface. Ratio of the
elongation is performed among each specimen with a percentage of 20-60%. Maximum 60% was
being selected as it can indicate utmost elongation before it is broken down. Douellou,
Secure Best Marks with AI Grader
Need help grading? Try our AI Grader for instant feedback on your assignments.
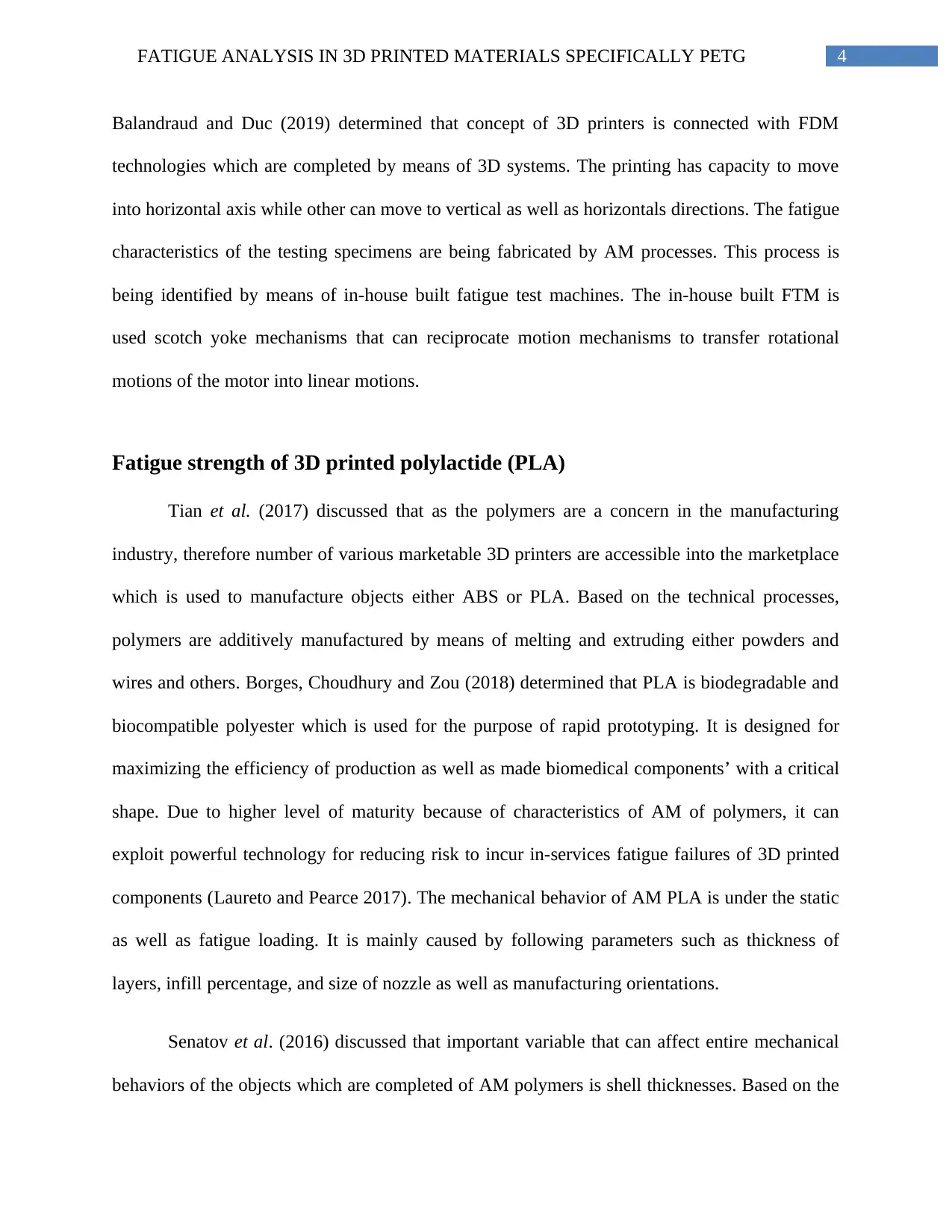
4FATIGUE ANALYSIS IN 3D PRINTED MATERIALS SPECIFICALLY PETG
Balandraud and Duc (2019) determined that concept of 3D printers is connected with FDM
technologies which are completed by means of 3D systems. The printing has capacity to move
into horizontal axis while other can move to vertical as well as horizontals directions. The fatigue
characteristics of the testing specimens are being fabricated by AM processes. This process is
being identified by means of in-house built fatigue test machines. The in-house built FTM is
used scotch yoke mechanisms that can reciprocate motion mechanisms to transfer rotational
motions of the motor into linear motions.
Fatigue strength of 3D printed polylactide (PLA)
Tian et al. (2017) discussed that as the polymers are a concern in the manufacturing
industry, therefore number of various marketable 3D printers are accessible into the marketplace
which is used to manufacture objects either ABS or PLA. Based on the technical processes,
polymers are additively manufactured by means of melting and extruding either powders and
wires and others. Borges, Choudhury and Zou (2018) determined that PLA is biodegradable and
biocompatible polyester which is used for the purpose of rapid prototyping. It is designed for
maximizing the efficiency of production as well as made biomedical components’ with a critical
shape. Due to higher level of maturity because of characteristics of AM of polymers, it can
exploit powerful technology for reducing risk to incur in-services fatigue failures of 3D printed
components (Laureto and Pearce 2017). The mechanical behavior of AM PLA is under the static
as well as fatigue loading. It is mainly caused by following parameters such as thickness of
layers, infill percentage, and size of nozzle as well as manufacturing orientations.
Senatov et al. (2016) discussed that important variable that can affect entire mechanical
behaviors of the objects which are completed of AM polymers is shell thicknesses. Based on the
Balandraud and Duc (2019) determined that concept of 3D printers is connected with FDM
technologies which are completed by means of 3D systems. The printing has capacity to move
into horizontal axis while other can move to vertical as well as horizontals directions. The fatigue
characteristics of the testing specimens are being fabricated by AM processes. This process is
being identified by means of in-house built fatigue test machines. The in-house built FTM is
used scotch yoke mechanisms that can reciprocate motion mechanisms to transfer rotational
motions of the motor into linear motions.
Fatigue strength of 3D printed polylactide (PLA)
Tian et al. (2017) discussed that as the polymers are a concern in the manufacturing
industry, therefore number of various marketable 3D printers are accessible into the marketplace
which is used to manufacture objects either ABS or PLA. Based on the technical processes,
polymers are additively manufactured by means of melting and extruding either powders and
wires and others. Borges, Choudhury and Zou (2018) determined that PLA is biodegradable and
biocompatible polyester which is used for the purpose of rapid prototyping. It is designed for
maximizing the efficiency of production as well as made biomedical components’ with a critical
shape. Due to higher level of maturity because of characteristics of AM of polymers, it can
exploit powerful technology for reducing risk to incur in-services fatigue failures of 3D printed
components (Laureto and Pearce 2017). The mechanical behavior of AM PLA is under the static
as well as fatigue loading. It is mainly caused by following parameters such as thickness of
layers, infill percentage, and size of nozzle as well as manufacturing orientations.
Senatov et al. (2016) discussed that important variable that can affect entire mechanical
behaviors of the objects which are completed of AM polymers is shell thicknesses. Based on the
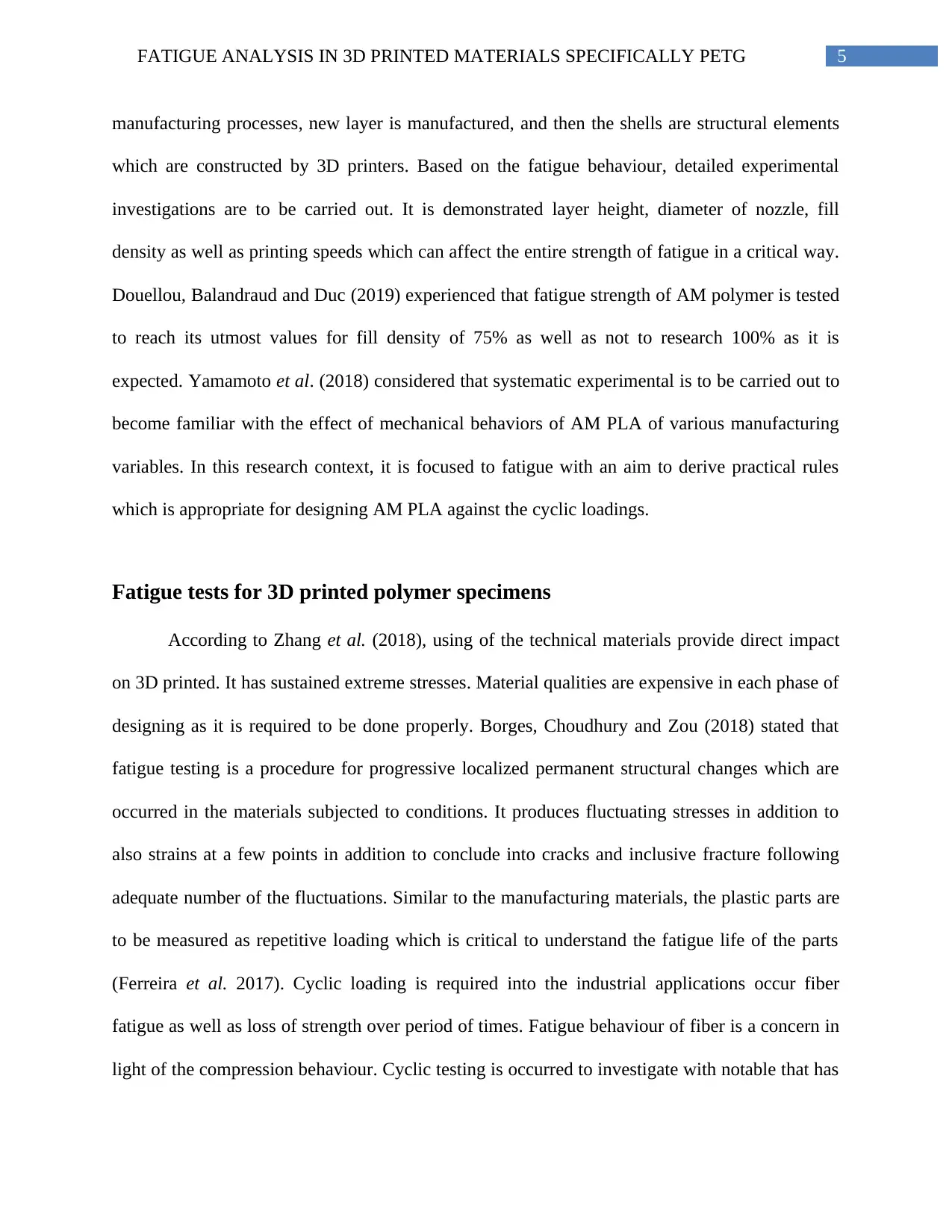
5FATIGUE ANALYSIS IN 3D PRINTED MATERIALS SPECIFICALLY PETG
manufacturing processes, new layer is manufactured, and then the shells are structural elements
which are constructed by 3D printers. Based on the fatigue behaviour, detailed experimental
investigations are to be carried out. It is demonstrated layer height, diameter of nozzle, fill
density as well as printing speeds which can affect the entire strength of fatigue in a critical way.
Douellou, Balandraud and Duc (2019) experienced that fatigue strength of AM polymer is tested
to reach its utmost values for fill density of 75% as well as not to research 100% as it is
expected. Yamamoto et al. (2018) considered that systematic experimental is to be carried out to
become familiar with the effect of mechanical behaviors of AM PLA of various manufacturing
variables. In this research context, it is focused to fatigue with an aim to derive practical rules
which is appropriate for designing AM PLA against the cyclic loadings.
Fatigue tests for 3D printed polymer specimens
According to Zhang et al. (2018), using of the technical materials provide direct impact
on 3D printed. It has sustained extreme stresses. Material qualities are expensive in each phase of
designing as it is required to be done properly. Borges, Choudhury and Zou (2018) stated that
fatigue testing is a procedure for progressive localized permanent structural changes which are
occurred in the materials subjected to conditions. It produces fluctuating stresses in addition to
also strains at a few points in addition to conclude into cracks and inclusive fracture following
adequate number of the fluctuations. Similar to the manufacturing materials, the plastic parts are
to be measured as repetitive loading which is critical to understand the fatigue life of the parts
(Ferreira et al. 2017). Cyclic loading is required into the industrial applications occur fiber
fatigue as well as loss of strength over period of times. Fatigue behaviour of fiber is a concern in
light of the compression behaviour. Cyclic testing is occurred to investigate with notable that has
manufacturing processes, new layer is manufactured, and then the shells are structural elements
which are constructed by 3D printers. Based on the fatigue behaviour, detailed experimental
investigations are to be carried out. It is demonstrated layer height, diameter of nozzle, fill
density as well as printing speeds which can affect the entire strength of fatigue in a critical way.
Douellou, Balandraud and Duc (2019) experienced that fatigue strength of AM polymer is tested
to reach its utmost values for fill density of 75% as well as not to research 100% as it is
expected. Yamamoto et al. (2018) considered that systematic experimental is to be carried out to
become familiar with the effect of mechanical behaviors of AM PLA of various manufacturing
variables. In this research context, it is focused to fatigue with an aim to derive practical rules
which is appropriate for designing AM PLA against the cyclic loadings.
Fatigue tests for 3D printed polymer specimens
According to Zhang et al. (2018), using of the technical materials provide direct impact
on 3D printed. It has sustained extreme stresses. Material qualities are expensive in each phase of
designing as it is required to be done properly. Borges, Choudhury and Zou (2018) stated that
fatigue testing is a procedure for progressive localized permanent structural changes which are
occurred in the materials subjected to conditions. It produces fluctuating stresses in addition to
also strains at a few points in addition to conclude into cracks and inclusive fracture following
adequate number of the fluctuations. Similar to the manufacturing materials, the plastic parts are
to be measured as repetitive loading which is critical to understand the fatigue life of the parts
(Ferreira et al. 2017). Cyclic loading is required into the industrial applications occur fiber
fatigue as well as loss of strength over period of times. Fatigue behaviour of fiber is a concern in
light of the compression behaviour. Cyclic testing is occurred to investigate with notable that has
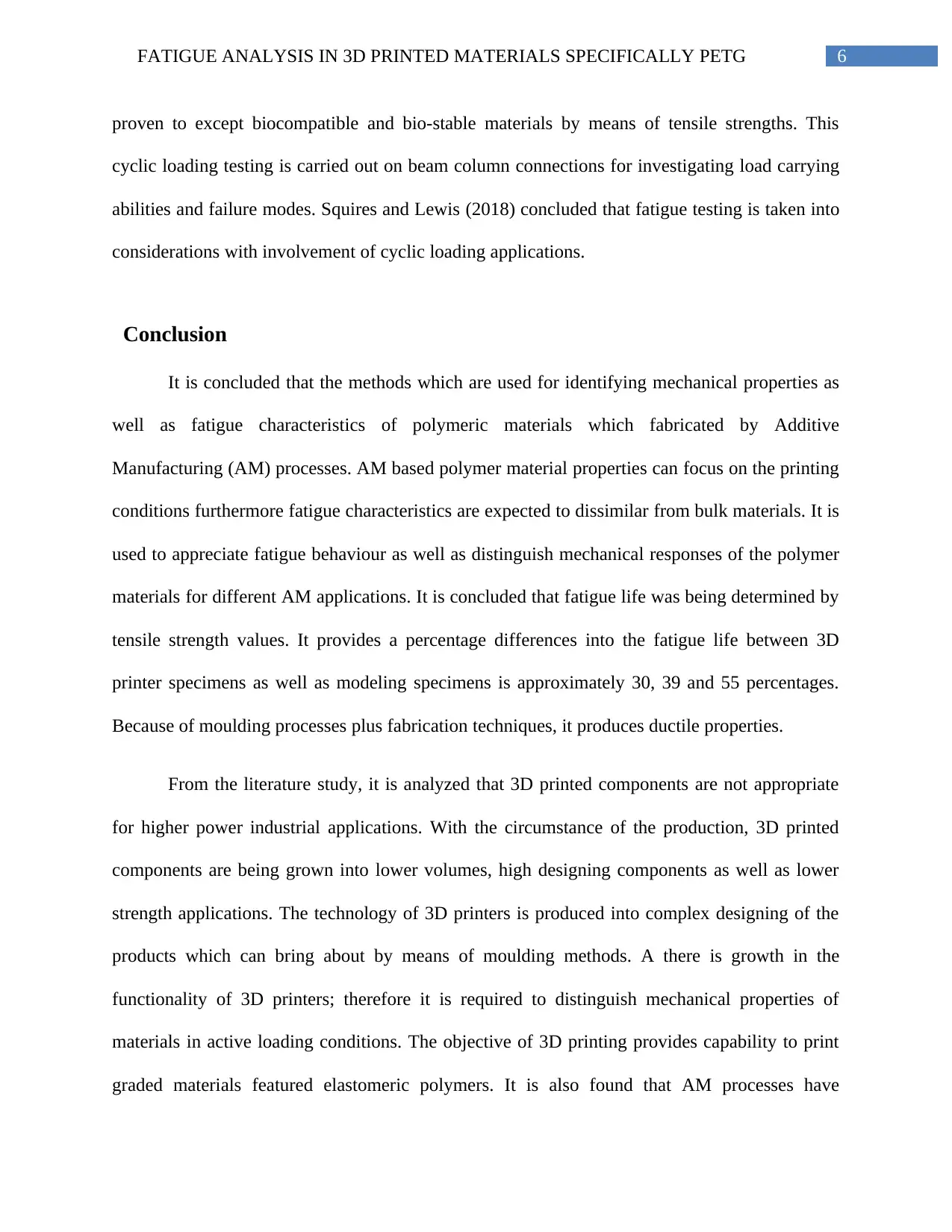
6FATIGUE ANALYSIS IN 3D PRINTED MATERIALS SPECIFICALLY PETG
proven to except biocompatible and bio-stable materials by means of tensile strengths. This
cyclic loading testing is carried out on beam column connections for investigating load carrying
abilities and failure modes. Squires and Lewis (2018) concluded that fatigue testing is taken into
considerations with involvement of cyclic loading applications.
Conclusion
It is concluded that the methods which are used for identifying mechanical properties as
well as fatigue characteristics of polymeric materials which fabricated by Additive
Manufacturing (AM) processes. AM based polymer material properties can focus on the printing
conditions furthermore fatigue characteristics are expected to dissimilar from bulk materials. It is
used to appreciate fatigue behaviour as well as distinguish mechanical responses of the polymer
materials for different AM applications. It is concluded that fatigue life was being determined by
tensile strength values. It provides a percentage differences into the fatigue life between 3D
printer specimens as well as modeling specimens is approximately 30, 39 and 55 percentages.
Because of moulding processes plus fabrication techniques, it produces ductile properties.
From the literature study, it is analyzed that 3D printed components are not appropriate
for higher power industrial applications. With the circumstance of the production, 3D printed
components are being grown into lower volumes, high designing components as well as lower
strength applications. The technology of 3D printers is produced into complex designing of the
products which can bring about by means of moulding methods. A there is growth in the
functionality of 3D printers; therefore it is required to distinguish mechanical properties of
materials in active loading conditions. The objective of 3D printing provides capability to print
graded materials featured elastomeric polymers. It is also found that AM processes have
proven to except biocompatible and bio-stable materials by means of tensile strengths. This
cyclic loading testing is carried out on beam column connections for investigating load carrying
abilities and failure modes. Squires and Lewis (2018) concluded that fatigue testing is taken into
considerations with involvement of cyclic loading applications.
Conclusion
It is concluded that the methods which are used for identifying mechanical properties as
well as fatigue characteristics of polymeric materials which fabricated by Additive
Manufacturing (AM) processes. AM based polymer material properties can focus on the printing
conditions furthermore fatigue characteristics are expected to dissimilar from bulk materials. It is
used to appreciate fatigue behaviour as well as distinguish mechanical responses of the polymer
materials for different AM applications. It is concluded that fatigue life was being determined by
tensile strength values. It provides a percentage differences into the fatigue life between 3D
printer specimens as well as modeling specimens is approximately 30, 39 and 55 percentages.
Because of moulding processes plus fabrication techniques, it produces ductile properties.
From the literature study, it is analyzed that 3D printed components are not appropriate
for higher power industrial applications. With the circumstance of the production, 3D printed
components are being grown into lower volumes, high designing components as well as lower
strength applications. The technology of 3D printers is produced into complex designing of the
products which can bring about by means of moulding methods. A there is growth in the
functionality of 3D printers; therefore it is required to distinguish mechanical properties of
materials in active loading conditions. The objective of 3D printing provides capability to print
graded materials featured elastomeric polymers. It is also found that AM processes have
Paraphrase This Document
Need a fresh take? Get an instant paraphrase of this document with our AI Paraphraser
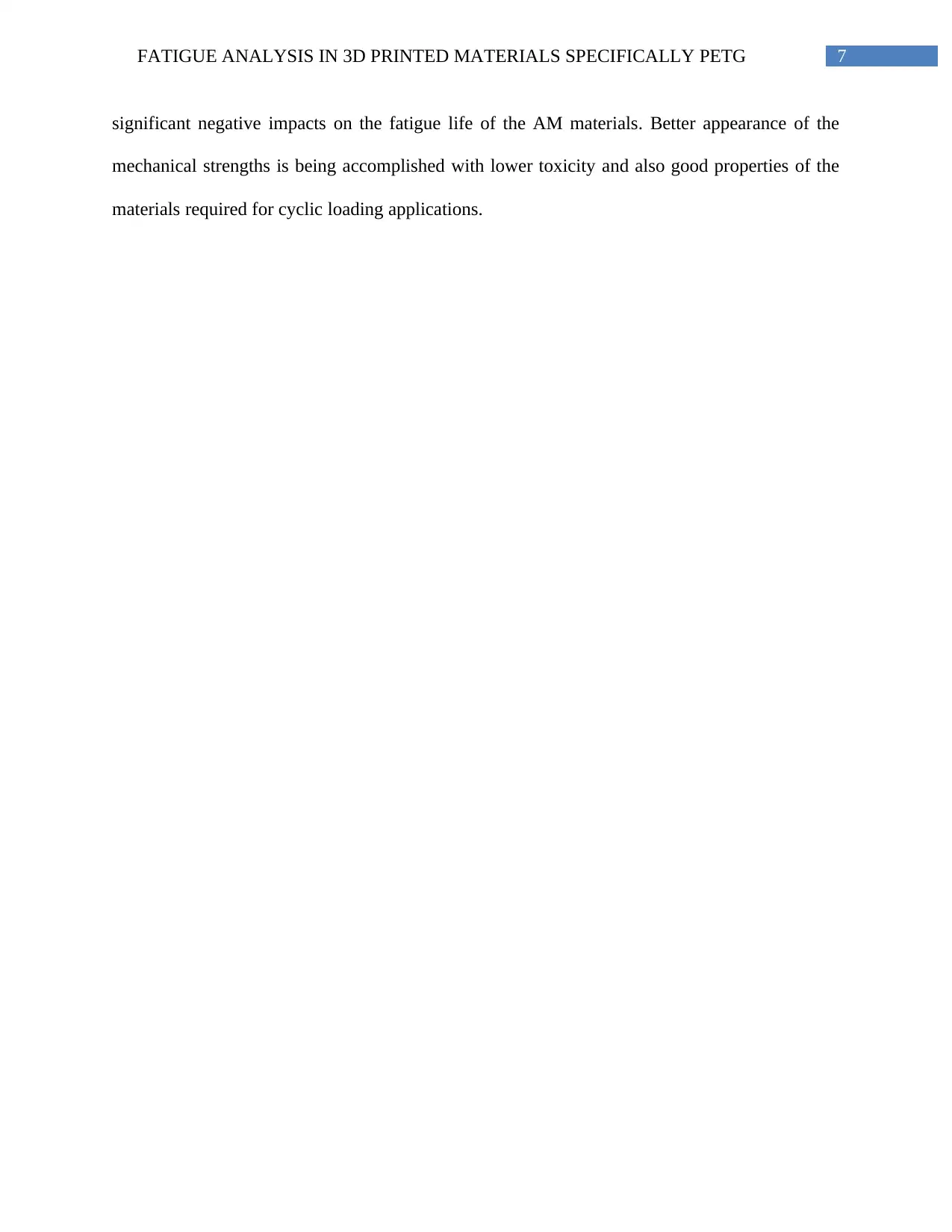
7FATIGUE ANALYSIS IN 3D PRINTED MATERIALS SPECIFICALLY PETG
significant negative impacts on the fatigue life of the AM materials. Better appearance of the
mechanical strengths is being accomplished with lower toxicity and also good properties of the
materials required for cyclic loading applications.
significant negative impacts on the fatigue life of the AM materials. Better appearance of the
mechanical strengths is being accomplished with lower toxicity and also good properties of the
materials required for cyclic loading applications.
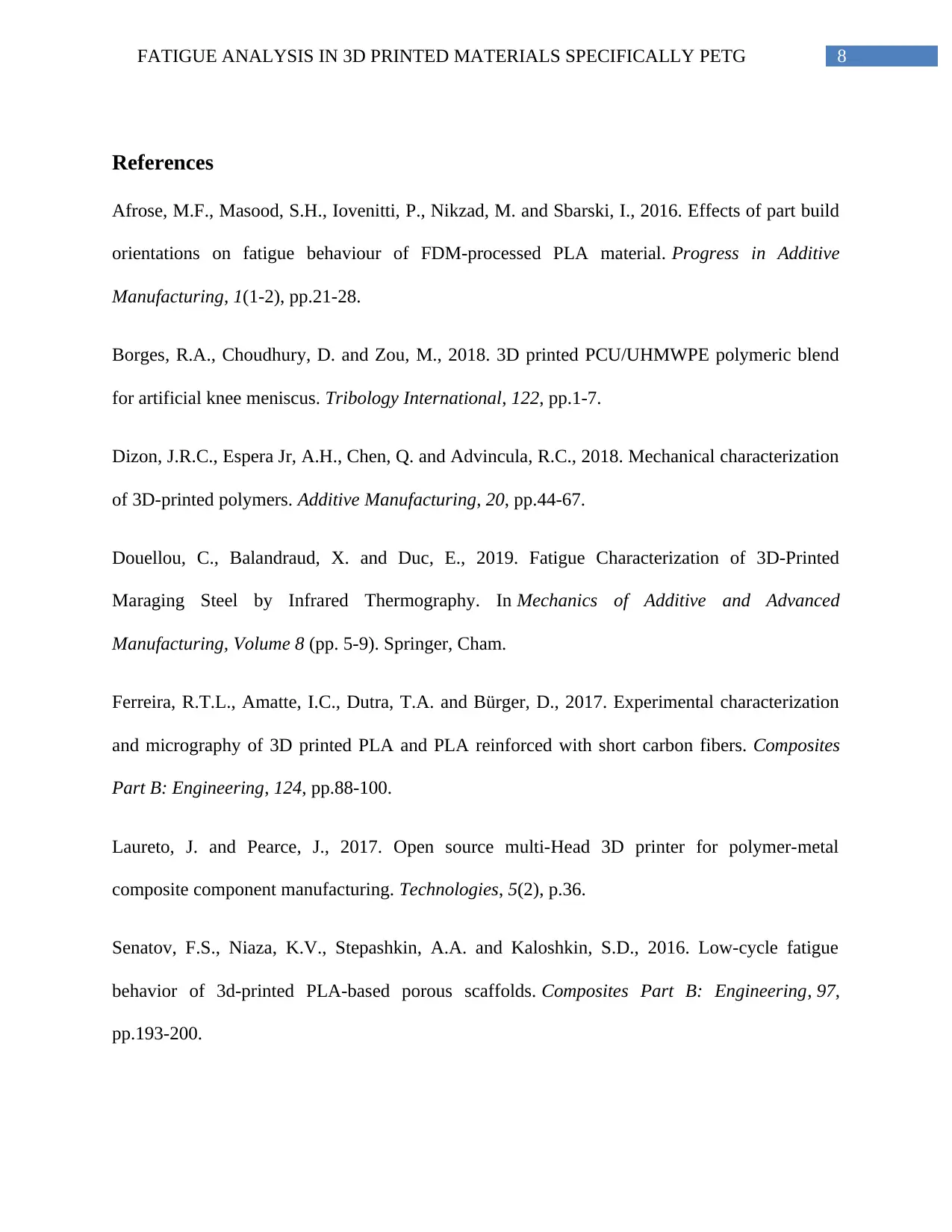
8FATIGUE ANALYSIS IN 3D PRINTED MATERIALS SPECIFICALLY PETG
References
Afrose, M.F., Masood, S.H., Iovenitti, P., Nikzad, M. and Sbarski, I., 2016. Effects of part build
orientations on fatigue behaviour of FDM-processed PLA material. Progress in Additive
Manufacturing, 1(1-2), pp.21-28.
Borges, R.A., Choudhury, D. and Zou, M., 2018. 3D printed PCU/UHMWPE polymeric blend
for artificial knee meniscus. Tribology International, 122, pp.1-7.
Dizon, J.R.C., Espera Jr, A.H., Chen, Q. and Advincula, R.C., 2018. Mechanical characterization
of 3D-printed polymers. Additive Manufacturing, 20, pp.44-67.
Douellou, C., Balandraud, X. and Duc, E., 2019. Fatigue Characterization of 3D-Printed
Maraging Steel by Infrared Thermography. In Mechanics of Additive and Advanced
Manufacturing, Volume 8 (pp. 5-9). Springer, Cham.
Ferreira, R.T.L., Amatte, I.C., Dutra, T.A. and Bürger, D., 2017. Experimental characterization
and micrography of 3D printed PLA and PLA reinforced with short carbon fibers. Composites
Part B: Engineering, 124, pp.88-100.
Laureto, J. and Pearce, J., 2017. Open source multi-Head 3D printer for polymer-metal
composite component manufacturing. Technologies, 5(2), p.36.
Senatov, F.S., Niaza, K.V., Stepashkin, A.A. and Kaloshkin, S.D., 2016. Low-cycle fatigue
behavior of 3d-printed PLA-based porous scaffolds. Composites Part B: Engineering, 97,
pp.193-200.
References
Afrose, M.F., Masood, S.H., Iovenitti, P., Nikzad, M. and Sbarski, I., 2016. Effects of part build
orientations on fatigue behaviour of FDM-processed PLA material. Progress in Additive
Manufacturing, 1(1-2), pp.21-28.
Borges, R.A., Choudhury, D. and Zou, M., 2018. 3D printed PCU/UHMWPE polymeric blend
for artificial knee meniscus. Tribology International, 122, pp.1-7.
Dizon, J.R.C., Espera Jr, A.H., Chen, Q. and Advincula, R.C., 2018. Mechanical characterization
of 3D-printed polymers. Additive Manufacturing, 20, pp.44-67.
Douellou, C., Balandraud, X. and Duc, E., 2019. Fatigue Characterization of 3D-Printed
Maraging Steel by Infrared Thermography. In Mechanics of Additive and Advanced
Manufacturing, Volume 8 (pp. 5-9). Springer, Cham.
Ferreira, R.T.L., Amatte, I.C., Dutra, T.A. and Bürger, D., 2017. Experimental characterization
and micrography of 3D printed PLA and PLA reinforced with short carbon fibers. Composites
Part B: Engineering, 124, pp.88-100.
Laureto, J. and Pearce, J., 2017. Open source multi-Head 3D printer for polymer-metal
composite component manufacturing. Technologies, 5(2), p.36.
Senatov, F.S., Niaza, K.V., Stepashkin, A.A. and Kaloshkin, S.D., 2016. Low-cycle fatigue
behavior of 3d-printed PLA-based porous scaffolds. Composites Part B: Engineering, 97,
pp.193-200.
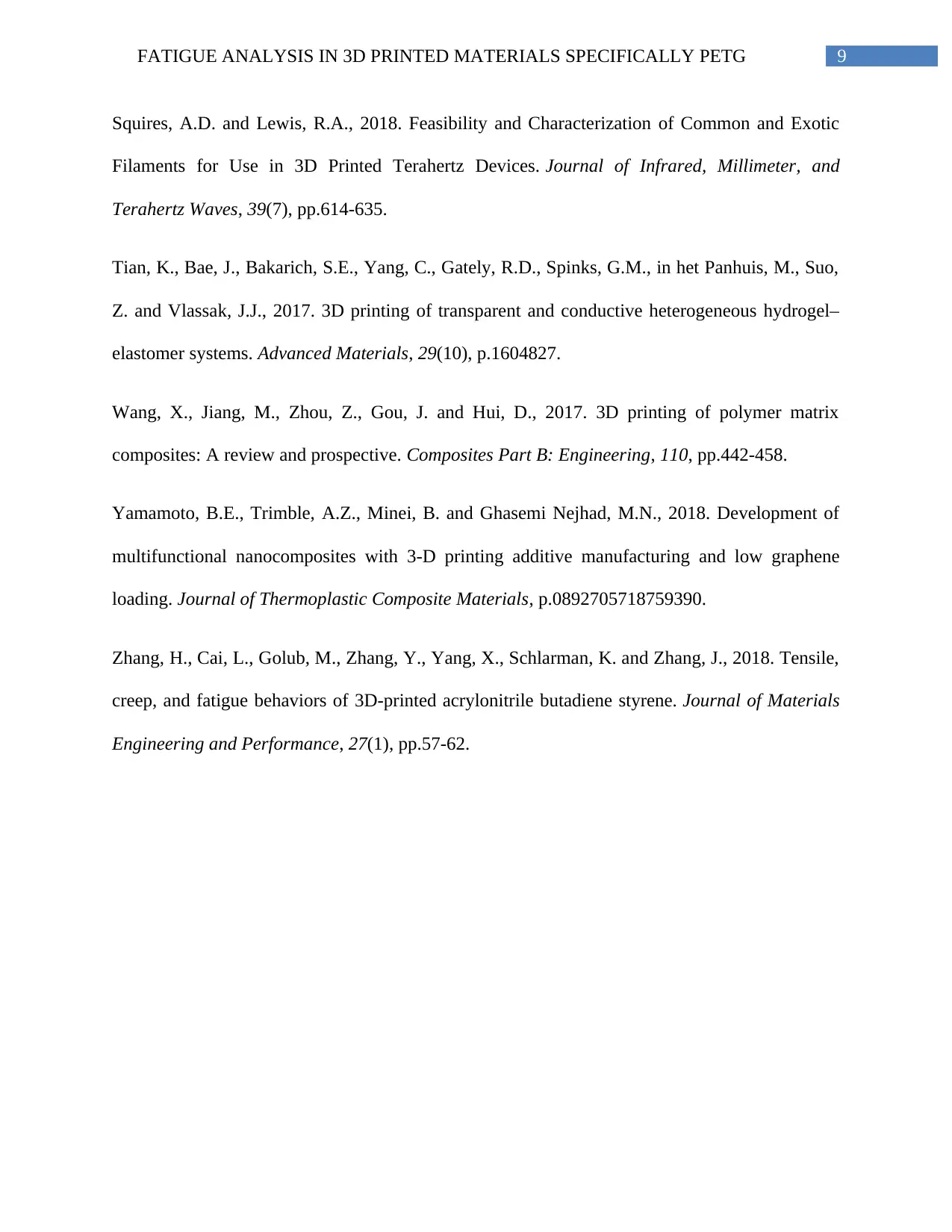
9FATIGUE ANALYSIS IN 3D PRINTED MATERIALS SPECIFICALLY PETG
Squires, A.D. and Lewis, R.A., 2018. Feasibility and Characterization of Common and Exotic
Filaments for Use in 3D Printed Terahertz Devices. Journal of Infrared, Millimeter, and
Terahertz Waves, 39(7), pp.614-635.
Tian, K., Bae, J., Bakarich, S.E., Yang, C., Gately, R.D., Spinks, G.M., in het Panhuis, M., Suo,
Z. and Vlassak, J.J., 2017. 3D printing of transparent and conductive heterogeneous hydrogel–
elastomer systems. Advanced Materials, 29(10), p.1604827.
Wang, X., Jiang, M., Zhou, Z., Gou, J. and Hui, D., 2017. 3D printing of polymer matrix
composites: A review and prospective. Composites Part B: Engineering, 110, pp.442-458.
Yamamoto, B.E., Trimble, A.Z., Minei, B. and Ghasemi Nejhad, M.N., 2018. Development of
multifunctional nanocomposites with 3-D printing additive manufacturing and low graphene
loading. Journal of Thermoplastic Composite Materials, p.0892705718759390.
Zhang, H., Cai, L., Golub, M., Zhang, Y., Yang, X., Schlarman, K. and Zhang, J., 2018. Tensile,
creep, and fatigue behaviors of 3D-printed acrylonitrile butadiene styrene. Journal of Materials
Engineering and Performance, 27(1), pp.57-62.
Squires, A.D. and Lewis, R.A., 2018. Feasibility and Characterization of Common and Exotic
Filaments for Use in 3D Printed Terahertz Devices. Journal of Infrared, Millimeter, and
Terahertz Waves, 39(7), pp.614-635.
Tian, K., Bae, J., Bakarich, S.E., Yang, C., Gately, R.D., Spinks, G.M., in het Panhuis, M., Suo,
Z. and Vlassak, J.J., 2017. 3D printing of transparent and conductive heterogeneous hydrogel–
elastomer systems. Advanced Materials, 29(10), p.1604827.
Wang, X., Jiang, M., Zhou, Z., Gou, J. and Hui, D., 2017. 3D printing of polymer matrix
composites: A review and prospective. Composites Part B: Engineering, 110, pp.442-458.
Yamamoto, B.E., Trimble, A.Z., Minei, B. and Ghasemi Nejhad, M.N., 2018. Development of
multifunctional nanocomposites with 3-D printing additive manufacturing and low graphene
loading. Journal of Thermoplastic Composite Materials, p.0892705718759390.
Zhang, H., Cai, L., Golub, M., Zhang, Y., Yang, X., Schlarman, K. and Zhang, J., 2018. Tensile,
creep, and fatigue behaviors of 3D-printed acrylonitrile butadiene styrene. Journal of Materials
Engineering and Performance, 27(1), pp.57-62.
1 out of 10

Your All-in-One AI-Powered Toolkit for Academic Success.
+13062052269
info@desklib.com
Available 24*7 on WhatsApp / Email
Unlock your academic potential
© 2024 | Zucol Services PVT LTD | All rights reserved.