Evaluating the Effectiveness of Activity-Based Costing in Airlines
VerifiedAdded on 2020/05/11
|10
|2451
|265
AI Summary
This analysis explores the implementation of Activity-Based Costing (ABC) in comparison to Traditional Costing methods at GoGo Airlines. The focus is on determining whether ABC can provide a more accurate reflection of costs associated with producing different meal categories—specifically vegan and non-vegan meals. By employing distinct cost drivers, ABC offers a nuanced approach to overhead allocation, thus enabling managers at GoGo Airlines to make more informed decisions regarding pricing and resource utilization. The study concludes that adopting ABC could potentially rectify the misallocations seen in traditional costing systems, resulting in improved operational efficiency and strategic decision-making for airlines like GoGo Airlines.
Contribute Materials
Your contribution can guide someone’s learning journey. Share your
documents today.
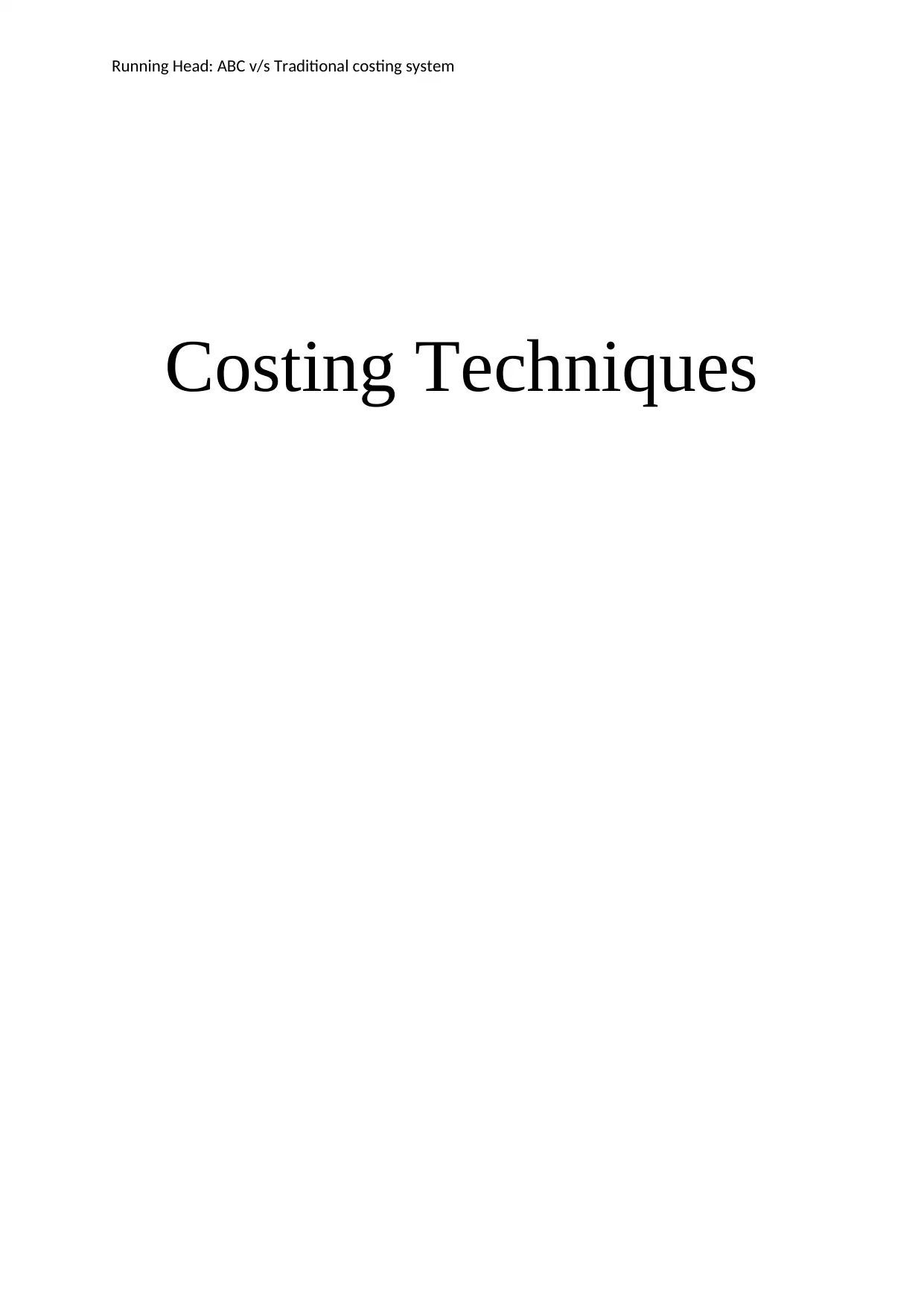
Running Head: ABC v/s Traditional costing system
Costing Techniques
Costing Techniques
Secure Best Marks with AI Grader
Need help grading? Try our AI Grader for instant feedback on your assignments.
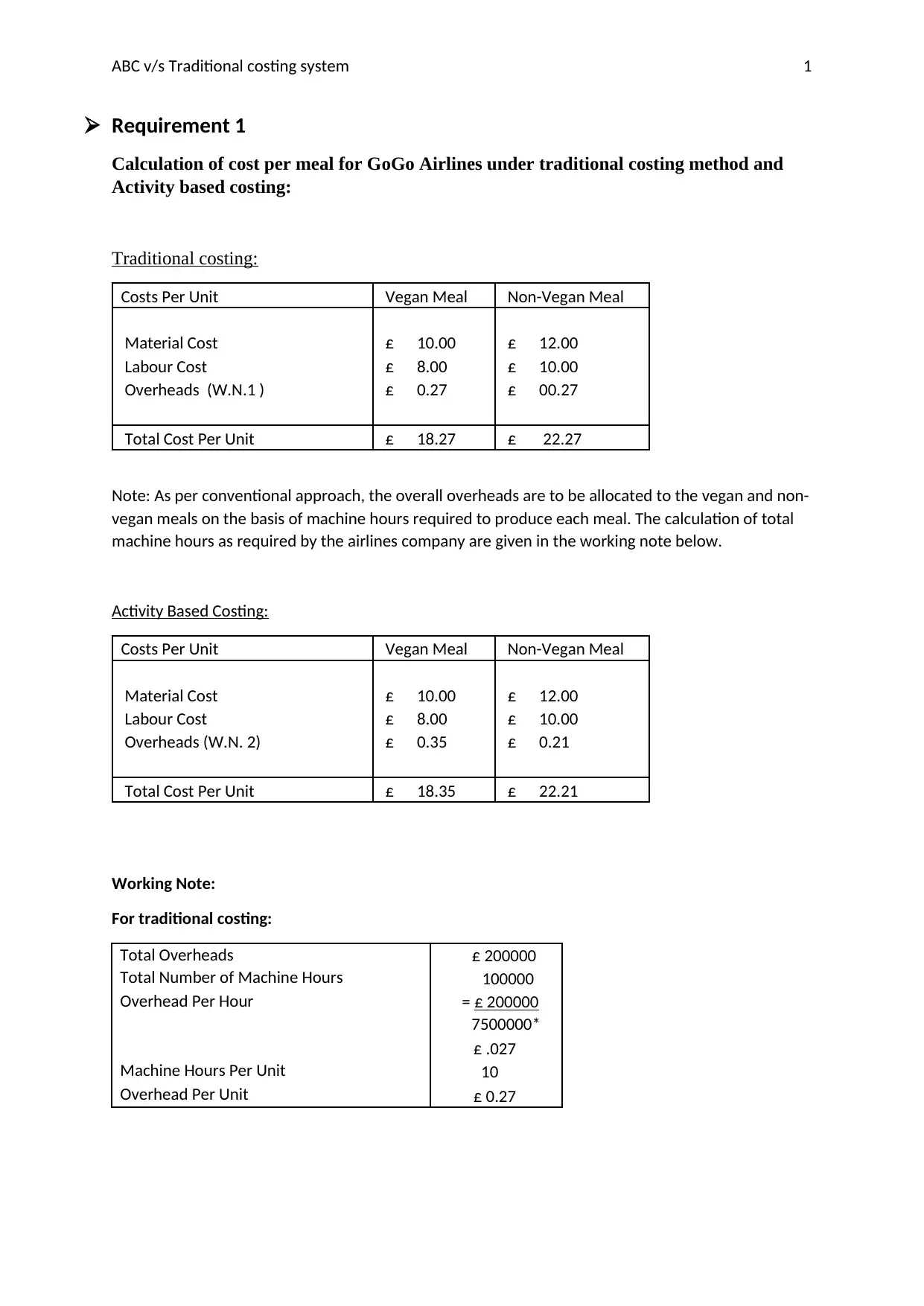
ABC v/s Traditional costing system 1
Requirement 1
Calculation of cost per meal for GoGo Airlines under traditional costing method and
Activity based costing:
Traditional costing:
Costs Per Unit Vegan Meal Non-Vegan Meal
Material Cost £ 10.00 £ 12.00
Labour Cost £ 8.00 £ 10.00
Overheads (W.N.1 ) £ 0.27 £ 00.27
Total Cost Per Unit £ 18.27 £ 22.27
Note: As per conventional approach, the overall overheads are to be allocated to the vegan and non-
vegan meals on the basis of machine hours required to produce each meal. The calculation of total
machine hours as required by the airlines company are given in the working note below.
Activity Based Costing:
Costs Per Unit Vegan Meal Non-Vegan Meal
Material Cost £ 10.00 £ 12.00
Labour Cost £ 8.00 £ 10.00
Overheads (W.N. 2) £ 0.35 £ 0.21
Total Cost Per Unit £ 18.35 £ 22.21
Working Note:
For traditional costing:
Total Overheads £ 200000
Total Number of Machine Hours 100000
Overhead Per Hour = £ 200000
7500000*
£ .027
Machine Hours Per Unit 10
Overhead Per Unit £ 0.27
Requirement 1
Calculation of cost per meal for GoGo Airlines under traditional costing method and
Activity based costing:
Traditional costing:
Costs Per Unit Vegan Meal Non-Vegan Meal
Material Cost £ 10.00 £ 12.00
Labour Cost £ 8.00 £ 10.00
Overheads (W.N.1 ) £ 0.27 £ 00.27
Total Cost Per Unit £ 18.27 £ 22.27
Note: As per conventional approach, the overall overheads are to be allocated to the vegan and non-
vegan meals on the basis of machine hours required to produce each meal. The calculation of total
machine hours as required by the airlines company are given in the working note below.
Activity Based Costing:
Costs Per Unit Vegan Meal Non-Vegan Meal
Material Cost £ 10.00 £ 12.00
Labour Cost £ 8.00 £ 10.00
Overheads (W.N. 2) £ 0.35 £ 0.21
Total Cost Per Unit £ 18.35 £ 22.21
Working Note:
For traditional costing:
Total Overheads £ 200000
Total Number of Machine Hours 100000
Overhead Per Hour = £ 200000
7500000*
£ .027
Machine Hours Per Unit 10
Overhead Per Unit £ 0.27
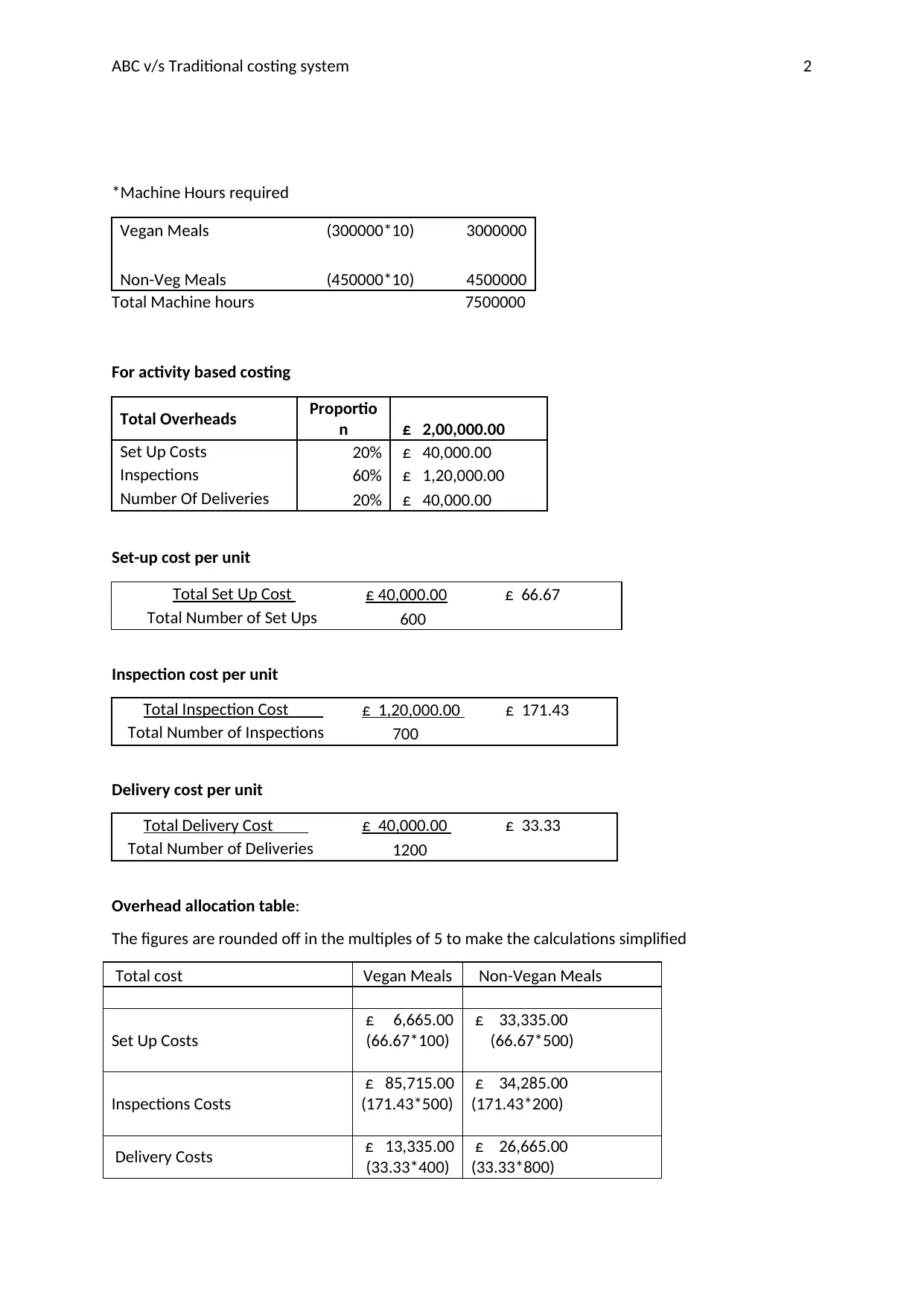
ABC v/s Traditional costing system 2
*Machine Hours required
Vegan Meals (300000*10) 3000000
Non-Veg Meals (450000*10) 4500000
Total Machine hours 7500000
For activity based costing
Total Overheads Proportio
n £ 2,00,000.00
Set Up Costs 20% £ 40,000.00
Inspections 60% £ 1,20,000.00
Number Of Deliveries 20% £ 40,000.00
Set-up cost per unit
Total Set Up Cost £ 40,000.00 £ 66.67
Total Number of Set Ups 600
Inspection cost per unit
Total Inspection Cost £ 1,20,000.00 £ 171.43
Total Number of Inspections 700
Delivery cost per unit
Total Delivery Cost £ 40,000.00 £ 33.33
Total Number of Deliveries 1200
Overhead allocation table:
The figures are rounded off in the multiples of 5 to make the calculations simplified
Total cost Vegan Meals Non-Vegan Meals
Set Up Costs
£ 6,665.00
(66.67*100)
£ 33,335.00
(66.67*500)
Inspections Costs
£ 85,715.00
(171.43*500)
£ 34,285.00
(171.43*200)
Delivery Costs £ 13,335.00
(33.33*400)
£ 26,665.00
(33.33*800)
*Machine Hours required
Vegan Meals (300000*10) 3000000
Non-Veg Meals (450000*10) 4500000
Total Machine hours 7500000
For activity based costing
Total Overheads Proportio
n £ 2,00,000.00
Set Up Costs 20% £ 40,000.00
Inspections 60% £ 1,20,000.00
Number Of Deliveries 20% £ 40,000.00
Set-up cost per unit
Total Set Up Cost £ 40,000.00 £ 66.67
Total Number of Set Ups 600
Inspection cost per unit
Total Inspection Cost £ 1,20,000.00 £ 171.43
Total Number of Inspections 700
Delivery cost per unit
Total Delivery Cost £ 40,000.00 £ 33.33
Total Number of Deliveries 1200
Overhead allocation table:
The figures are rounded off in the multiples of 5 to make the calculations simplified
Total cost Vegan Meals Non-Vegan Meals
Set Up Costs
£ 6,665.00
(66.67*100)
£ 33,335.00
(66.67*500)
Inspections Costs
£ 85,715.00
(171.43*500)
£ 34,285.00
(171.43*200)
Delivery Costs £ 13,335.00
(33.33*400)
£ 26,665.00
(33.33*800)
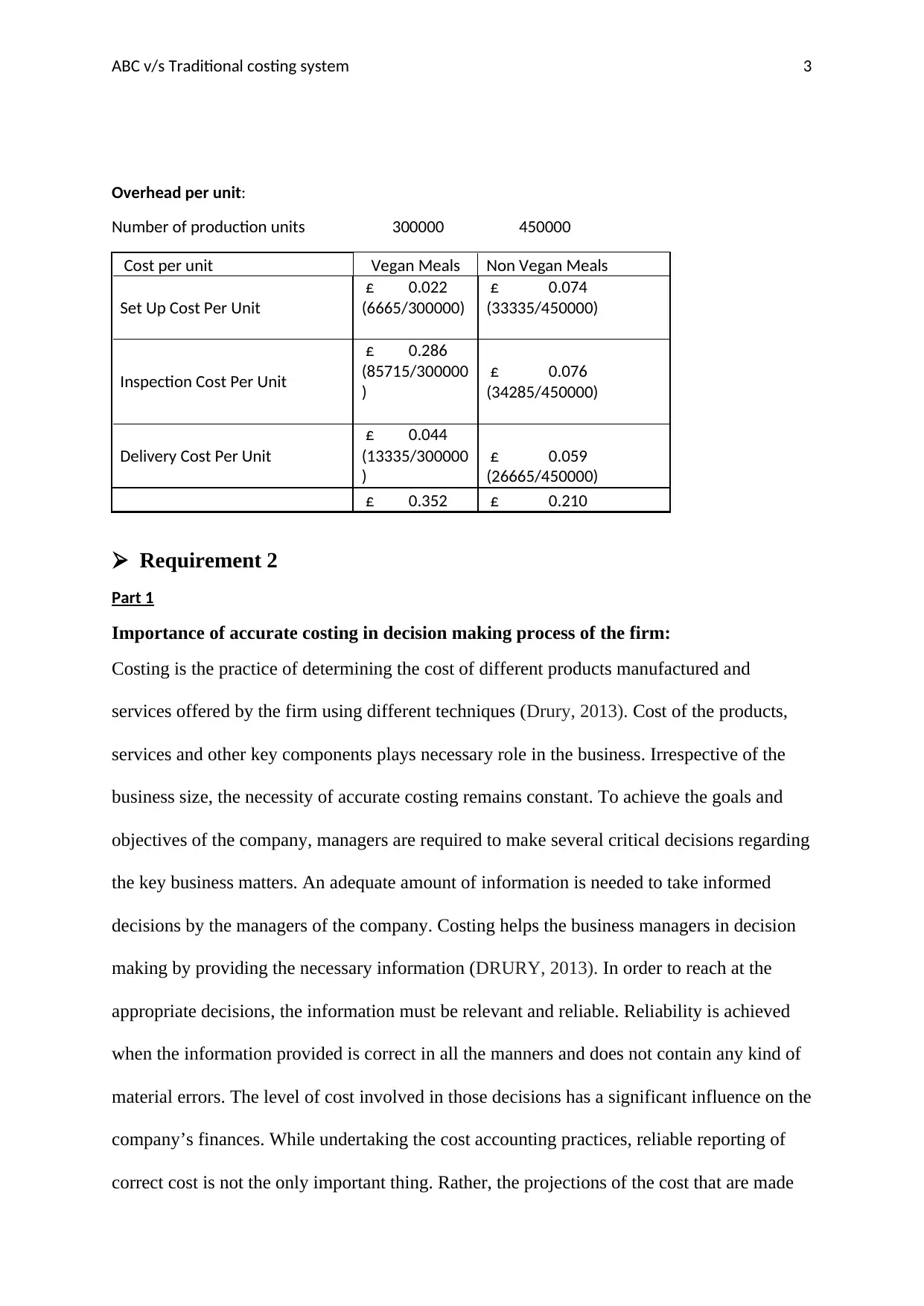
ABC v/s Traditional costing system 3
Overhead per unit:
Number of production units 300000 450000
Cost per unit Vegan Meals Non Vegan Meals
Set Up Cost Per Unit
£ 0.022
(6665/300000)
£ 0.074
(33335/450000)
Inspection Cost Per Unit
£ 0.286
(85715/300000
)
£ 0.076
(34285/450000)
Delivery Cost Per Unit
£ 0.044
(13335/300000
)
£ 0.059
(26665/450000)
£ 0.352 £ 0.210
Requirement 2
Part 1
Importance of accurate costing in decision making process of the firm:
Costing is the practice of determining the cost of different products manufactured and
services offered by the firm using different techniques (Drury, 2013). Cost of the products,
services and other key components plays necessary role in the business. Irrespective of the
business size, the necessity of accurate costing remains constant. To achieve the goals and
objectives of the company, managers are required to make several critical decisions regarding
the key business matters. An adequate amount of information is needed to take informed
decisions by the managers of the company. Costing helps the business managers in decision
making by providing the necessary information (DRURY, 2013). In order to reach at the
appropriate decisions, the information must be relevant and reliable. Reliability is achieved
when the information provided is correct in all the manners and does not contain any kind of
material errors. The level of cost involved in those decisions has a significant influence on the
company’s finances. While undertaking the cost accounting practices, reliable reporting of
correct cost is not the only important thing. Rather, the projections of the cost that are made
Overhead per unit:
Number of production units 300000 450000
Cost per unit Vegan Meals Non Vegan Meals
Set Up Cost Per Unit
£ 0.022
(6665/300000)
£ 0.074
(33335/450000)
Inspection Cost Per Unit
£ 0.286
(85715/300000
)
£ 0.076
(34285/450000)
Delivery Cost Per Unit
£ 0.044
(13335/300000
)
£ 0.059
(26665/450000)
£ 0.352 £ 0.210
Requirement 2
Part 1
Importance of accurate costing in decision making process of the firm:
Costing is the practice of determining the cost of different products manufactured and
services offered by the firm using different techniques (Drury, 2013). Cost of the products,
services and other key components plays necessary role in the business. Irrespective of the
business size, the necessity of accurate costing remains constant. To achieve the goals and
objectives of the company, managers are required to make several critical decisions regarding
the key business matters. An adequate amount of information is needed to take informed
decisions by the managers of the company. Costing helps the business managers in decision
making by providing the necessary information (DRURY, 2013). In order to reach at the
appropriate decisions, the information must be relevant and reliable. Reliability is achieved
when the information provided is correct in all the manners and does not contain any kind of
material errors. The level of cost involved in those decisions has a significant influence on the
company’s finances. While undertaking the cost accounting practices, reliable reporting of
correct cost is not the only important thing. Rather, the projections of the cost that are made
Secure Best Marks with AI Grader
Need help grading? Try our AI Grader for instant feedback on your assignments.

ABC v/s Traditional costing system 4
by the management accountant for future must also be accurate (Salawu & Ayoola, 2012).
The accuracy in estimations of cost will help in better planning of business activities which
ultimately contributes to right deployment of business funds at right times. Better decision
making requires reliable data so that any incorrect information may not lead the business to
the heavy loss sufferings. When the information has the direct impact on the decisions of the
manager, accurate costing plays a major role. Moreover, accuracy in cost estimations and
current cost calculations also helps in appropriate price fixation of the products manufactured
by the firm. If the information delivered by the cost management team is not free from all the
material errors it would amount to fixation of unreasonable prices for the products and
services (Schulze, Seuring & Ewering, 2012). If suitable and appropriate prices are not
assigned to the products it could cost the company a loss of profitability due to charging of
less selling prices for its products. Further, if accurate costs for the company’s assets and
investments are not determined by the management accountant it would impair the true
picture of the company’s financial position. Moreover, to determine the gross profits and net
profits, based on which the company’s performance is evaluated, recording of correct cost
related data is quite important. Without assessing the accurate products cost, firm’s profit
cannot be evaluated. If wrong cost data is provided by the management accountant it would
result is under or over estimation of company’s worth (Zimmerman & Yahya-Zadeh, 2011).
In today’s world where the competition between the firms of the same industry is too intense,
high accuracy in cost management is essential in setting the competitive strategies for the
business using the reliable cost information. When a firm needs to evaluate its overall
performance intra-firm and inter firm comparison of various elements of business are needed
to be made and if accurate cost information is not available with the business, performance
analysis is difficult to be undertaken correctly.
Part 2
by the management accountant for future must also be accurate (Salawu & Ayoola, 2012).
The accuracy in estimations of cost will help in better planning of business activities which
ultimately contributes to right deployment of business funds at right times. Better decision
making requires reliable data so that any incorrect information may not lead the business to
the heavy loss sufferings. When the information has the direct impact on the decisions of the
manager, accurate costing plays a major role. Moreover, accuracy in cost estimations and
current cost calculations also helps in appropriate price fixation of the products manufactured
by the firm. If the information delivered by the cost management team is not free from all the
material errors it would amount to fixation of unreasonable prices for the products and
services (Schulze, Seuring & Ewering, 2012). If suitable and appropriate prices are not
assigned to the products it could cost the company a loss of profitability due to charging of
less selling prices for its products. Further, if accurate costs for the company’s assets and
investments are not determined by the management accountant it would impair the true
picture of the company’s financial position. Moreover, to determine the gross profits and net
profits, based on which the company’s performance is evaluated, recording of correct cost
related data is quite important. Without assessing the accurate products cost, firm’s profit
cannot be evaluated. If wrong cost data is provided by the management accountant it would
result is under or over estimation of company’s worth (Zimmerman & Yahya-Zadeh, 2011).
In today’s world where the competition between the firms of the same industry is too intense,
high accuracy in cost management is essential in setting the competitive strategies for the
business using the reliable cost information. When a firm needs to evaluate its overall
performance intra-firm and inter firm comparison of various elements of business are needed
to be made and if accurate cost information is not available with the business, performance
analysis is difficult to be undertaken correctly.
Part 2
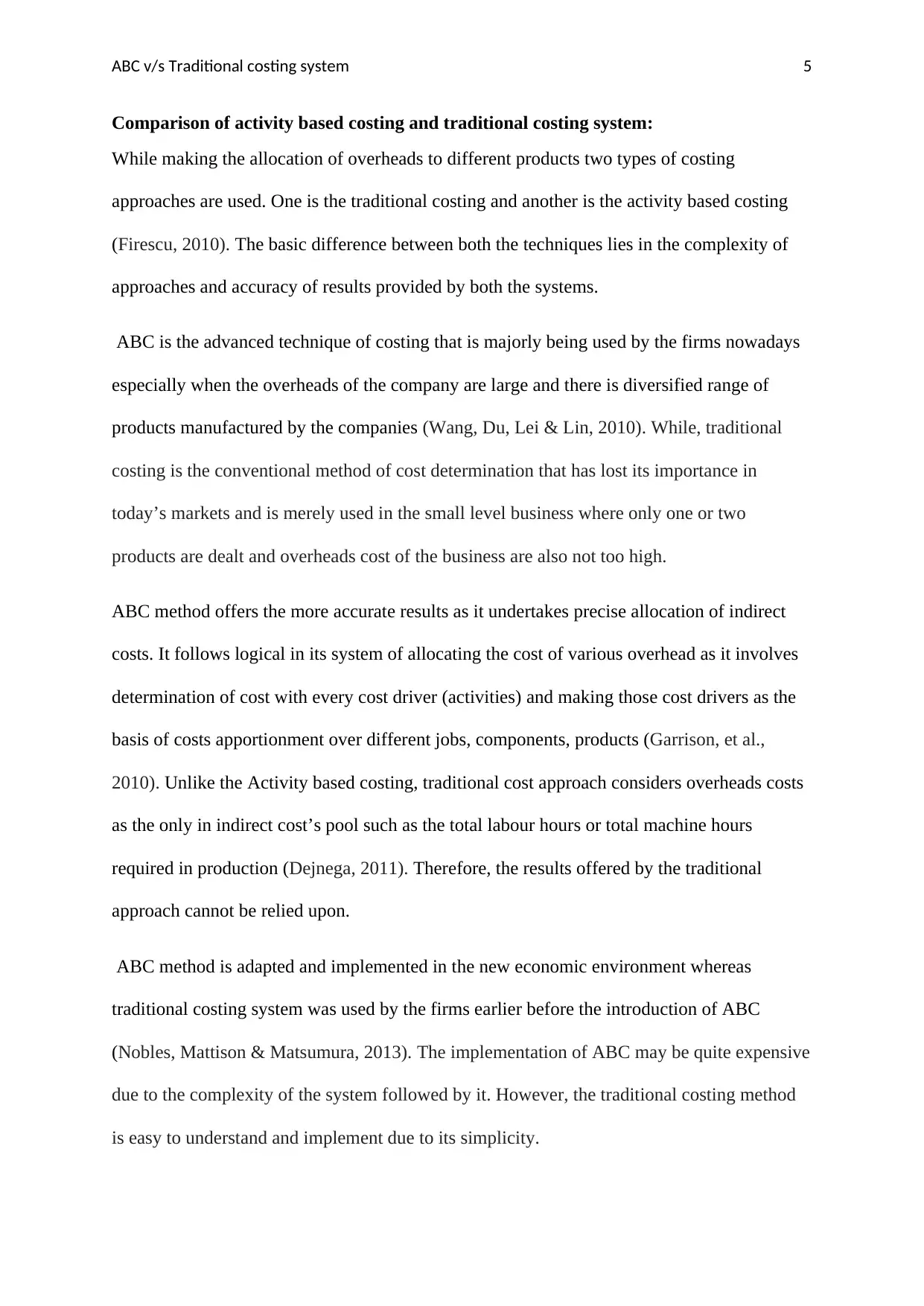
ABC v/s Traditional costing system 5
Comparison of activity based costing and traditional costing system:
While making the allocation of overheads to different products two types of costing
approaches are used. One is the traditional costing and another is the activity based costing
(Firescu, 2010). The basic difference between both the techniques lies in the complexity of
approaches and accuracy of results provided by both the systems.
ABC is the advanced technique of costing that is majorly being used by the firms nowadays
especially when the overheads of the company are large and there is diversified range of
products manufactured by the companies (Wang, Du, Lei & Lin, 2010). While, traditional
costing is the conventional method of cost determination that has lost its importance in
today’s markets and is merely used in the small level business where only one or two
products are dealt and overheads cost of the business are also not too high.
ABC method offers the more accurate results as it undertakes precise allocation of indirect
costs. It follows logical in its system of allocating the cost of various overhead as it involves
determination of cost with every cost driver (activities) and making those cost drivers as the
basis of costs apportionment over different jobs, components, products (Garrison, et al.,
2010). Unlike the Activity based costing, traditional cost approach considers overheads costs
as the only in indirect cost’s pool such as the total labour hours or total machine hours
required in production (Dejnega, 2011). Therefore, the results offered by the traditional
approach cannot be relied upon.
ABC method is adapted and implemented in the new economic environment whereas
traditional costing system was used by the firms earlier before the introduction of ABC
(Nobles, Mattison & Matsumura, 2013). The implementation of ABC may be quite expensive
due to the complexity of the system followed by it. However, the traditional costing method
is easy to understand and implement due to its simplicity.
Comparison of activity based costing and traditional costing system:
While making the allocation of overheads to different products two types of costing
approaches are used. One is the traditional costing and another is the activity based costing
(Firescu, 2010). The basic difference between both the techniques lies in the complexity of
approaches and accuracy of results provided by both the systems.
ABC is the advanced technique of costing that is majorly being used by the firms nowadays
especially when the overheads of the company are large and there is diversified range of
products manufactured by the companies (Wang, Du, Lei & Lin, 2010). While, traditional
costing is the conventional method of cost determination that has lost its importance in
today’s markets and is merely used in the small level business where only one or two
products are dealt and overheads cost of the business are also not too high.
ABC method offers the more accurate results as it undertakes precise allocation of indirect
costs. It follows logical in its system of allocating the cost of various overhead as it involves
determination of cost with every cost driver (activities) and making those cost drivers as the
basis of costs apportionment over different jobs, components, products (Garrison, et al.,
2010). Unlike the Activity based costing, traditional cost approach considers overheads costs
as the only in indirect cost’s pool such as the total labour hours or total machine hours
required in production (Dejnega, 2011). Therefore, the results offered by the traditional
approach cannot be relied upon.
ABC method is adapted and implemented in the new economic environment whereas
traditional costing system was used by the firms earlier before the introduction of ABC
(Nobles, Mattison & Matsumura, 2013). The implementation of ABC may be quite expensive
due to the complexity of the system followed by it. However, the traditional costing method
is easy to understand and implement due to its simplicity.
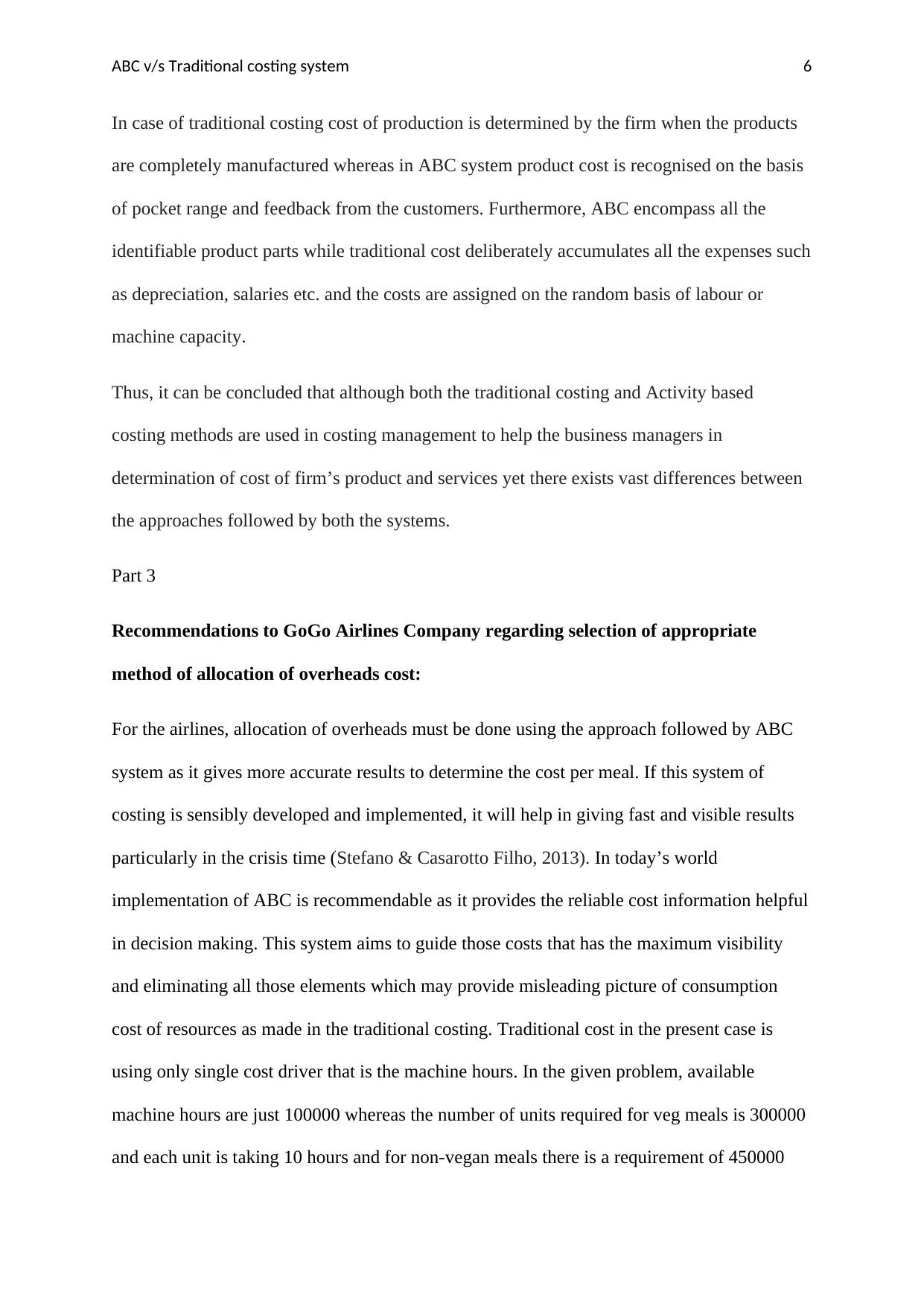
ABC v/s Traditional costing system 6
In case of traditional costing cost of production is determined by the firm when the products
are completely manufactured whereas in ABC system product cost is recognised on the basis
of pocket range and feedback from the customers. Furthermore, ABC encompass all the
identifiable product parts while traditional cost deliberately accumulates all the expenses such
as depreciation, salaries etc. and the costs are assigned on the random basis of labour or
machine capacity.
Thus, it can be concluded that although both the traditional costing and Activity based
costing methods are used in costing management to help the business managers in
determination of cost of firm’s product and services yet there exists vast differences between
the approaches followed by both the systems.
Part 3
Recommendations to GoGo Airlines Company regarding selection of appropriate
method of allocation of overheads cost:
For the airlines, allocation of overheads must be done using the approach followed by ABC
system as it gives more accurate results to determine the cost per meal. If this system of
costing is sensibly developed and implemented, it will help in giving fast and visible results
particularly in the crisis time (Stefano & Casarotto Filho, 2013). In today’s world
implementation of ABC is recommendable as it provides the reliable cost information helpful
in decision making. This system aims to guide those costs that has the maximum visibility
and eliminating all those elements which may provide misleading picture of consumption
cost of resources as made in the traditional costing. Traditional cost in the present case is
using only single cost driver that is the machine hours. In the given problem, available
machine hours are just 100000 whereas the number of units required for veg meals is 300000
and each unit is taking 10 hours and for non-vegan meals there is a requirement of 450000
In case of traditional costing cost of production is determined by the firm when the products
are completely manufactured whereas in ABC system product cost is recognised on the basis
of pocket range and feedback from the customers. Furthermore, ABC encompass all the
identifiable product parts while traditional cost deliberately accumulates all the expenses such
as depreciation, salaries etc. and the costs are assigned on the random basis of labour or
machine capacity.
Thus, it can be concluded that although both the traditional costing and Activity based
costing methods are used in costing management to help the business managers in
determination of cost of firm’s product and services yet there exists vast differences between
the approaches followed by both the systems.
Part 3
Recommendations to GoGo Airlines Company regarding selection of appropriate
method of allocation of overheads cost:
For the airlines, allocation of overheads must be done using the approach followed by ABC
system as it gives more accurate results to determine the cost per meal. If this system of
costing is sensibly developed and implemented, it will help in giving fast and visible results
particularly in the crisis time (Stefano & Casarotto Filho, 2013). In today’s world
implementation of ABC is recommendable as it provides the reliable cost information helpful
in decision making. This system aims to guide those costs that has the maximum visibility
and eliminating all those elements which may provide misleading picture of consumption
cost of resources as made in the traditional costing. Traditional cost in the present case is
using only single cost driver that is the machine hours. In the given problem, available
machine hours are just 100000 whereas the number of units required for veg meals is 300000
and each unit is taking 10 hours and for non-vegan meals there is a requirement of 450000
Paraphrase This Document
Need a fresh take? Get an instant paraphrase of this document with our AI Paraphraser
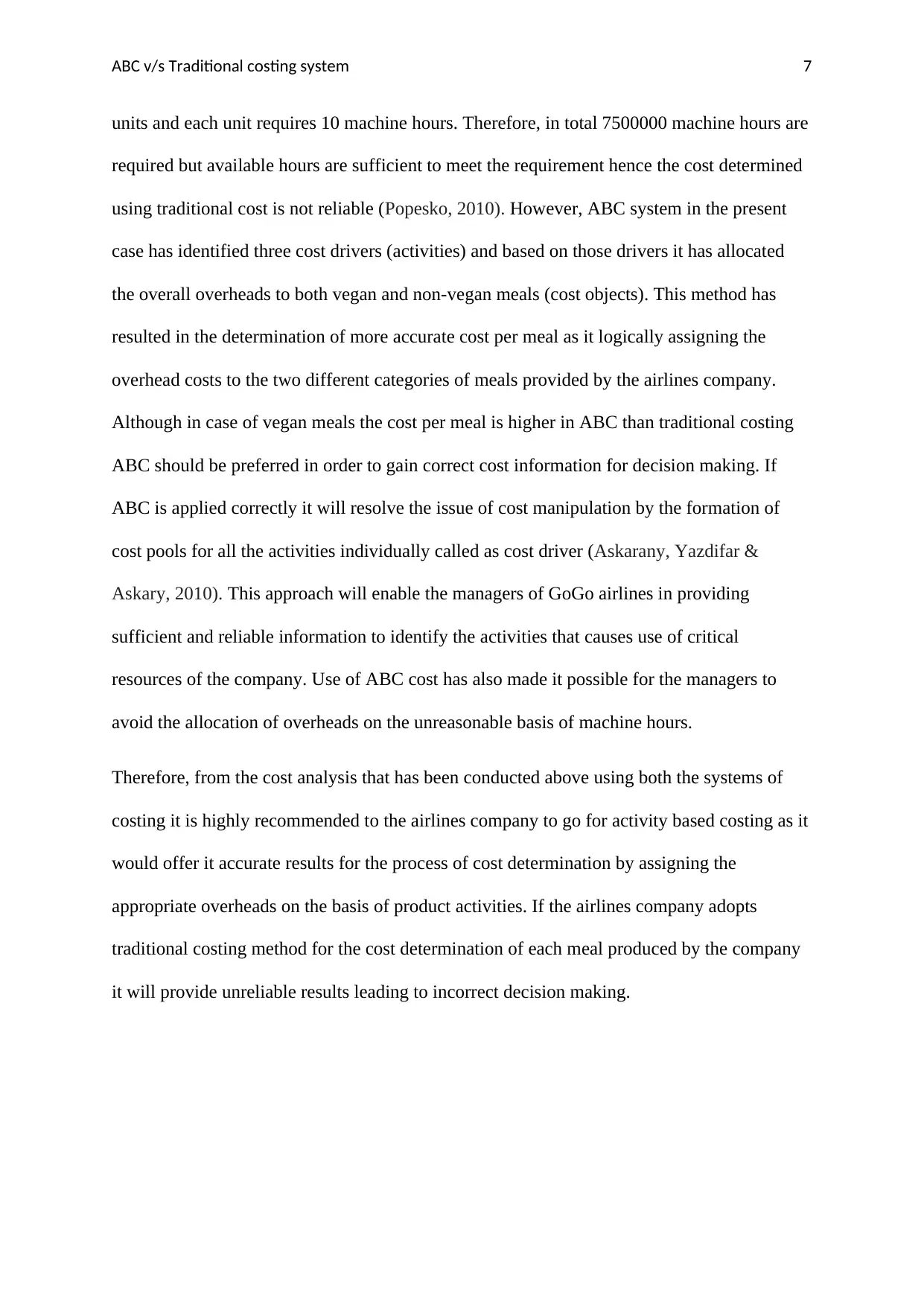
ABC v/s Traditional costing system 7
units and each unit requires 10 machine hours. Therefore, in total 7500000 machine hours are
required but available hours are sufficient to meet the requirement hence the cost determined
using traditional cost is not reliable (Popesko, 2010). However, ABC system in the present
case has identified three cost drivers (activities) and based on those drivers it has allocated
the overall overheads to both vegan and non-vegan meals (cost objects). This method has
resulted in the determination of more accurate cost per meal as it logically assigning the
overhead costs to the two different categories of meals provided by the airlines company.
Although in case of vegan meals the cost per meal is higher in ABC than traditional costing
ABC should be preferred in order to gain correct cost information for decision making. If
ABC is applied correctly it will resolve the issue of cost manipulation by the formation of
cost pools for all the activities individually called as cost driver (Askarany, Yazdifar &
Askary, 2010). This approach will enable the managers of GoGo airlines in providing
sufficient and reliable information to identify the activities that causes use of critical
resources of the company. Use of ABC cost has also made it possible for the managers to
avoid the allocation of overheads on the unreasonable basis of machine hours.
Therefore, from the cost analysis that has been conducted above using both the systems of
costing it is highly recommended to the airlines company to go for activity based costing as it
would offer it accurate results for the process of cost determination by assigning the
appropriate overheads on the basis of product activities. If the airlines company adopts
traditional costing method for the cost determination of each meal produced by the company
it will provide unreliable results leading to incorrect decision making.
units and each unit requires 10 machine hours. Therefore, in total 7500000 machine hours are
required but available hours are sufficient to meet the requirement hence the cost determined
using traditional cost is not reliable (Popesko, 2010). However, ABC system in the present
case has identified three cost drivers (activities) and based on those drivers it has allocated
the overall overheads to both vegan and non-vegan meals (cost objects). This method has
resulted in the determination of more accurate cost per meal as it logically assigning the
overhead costs to the two different categories of meals provided by the airlines company.
Although in case of vegan meals the cost per meal is higher in ABC than traditional costing
ABC should be preferred in order to gain correct cost information for decision making. If
ABC is applied correctly it will resolve the issue of cost manipulation by the formation of
cost pools for all the activities individually called as cost driver (Askarany, Yazdifar &
Askary, 2010). This approach will enable the managers of GoGo airlines in providing
sufficient and reliable information to identify the activities that causes use of critical
resources of the company. Use of ABC cost has also made it possible for the managers to
avoid the allocation of overheads on the unreasonable basis of machine hours.
Therefore, from the cost analysis that has been conducted above using both the systems of
costing it is highly recommended to the airlines company to go for activity based costing as it
would offer it accurate results for the process of cost determination by assigning the
appropriate overheads on the basis of product activities. If the airlines company adopts
traditional costing method for the cost determination of each meal produced by the company
it will provide unreliable results leading to incorrect decision making.
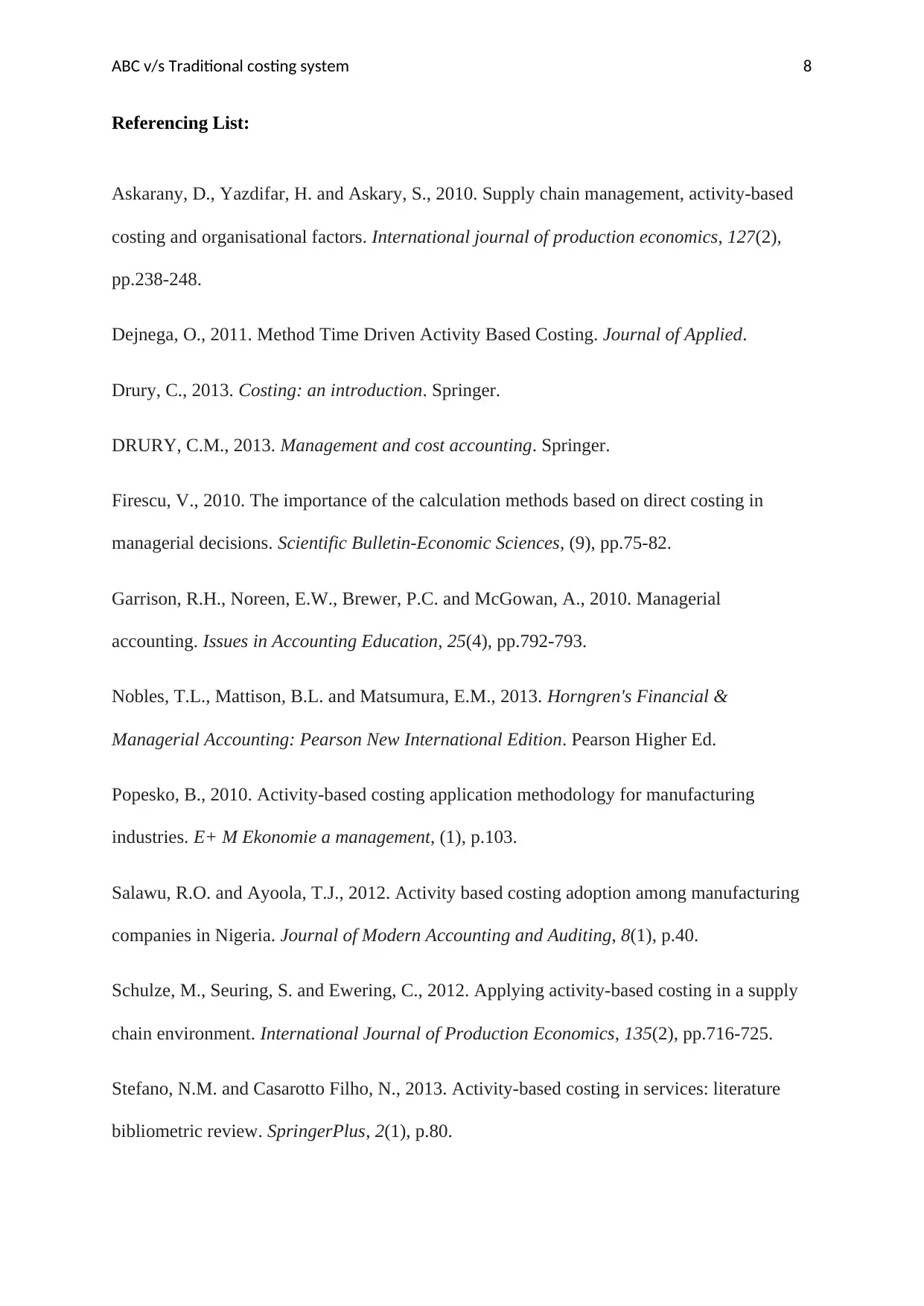
ABC v/s Traditional costing system 8
Referencing List:
Askarany, D., Yazdifar, H. and Askary, S., 2010. Supply chain management, activity-based
costing and organisational factors. International journal of production economics, 127(2),
pp.238-248.
Dejnega, O., 2011. Method Time Driven Activity Based Costing. Journal of Applied.
Drury, C., 2013. Costing: an introduction. Springer.
DRURY, C.M., 2013. Management and cost accounting. Springer.
Firescu, V., 2010. The importance of the calculation methods based on direct costing in
managerial decisions. Scientific Bulletin-Economic Sciences, (9), pp.75-82.
Garrison, R.H., Noreen, E.W., Brewer, P.C. and McGowan, A., 2010. Managerial
accounting. Issues in Accounting Education, 25(4), pp.792-793.
Nobles, T.L., Mattison, B.L. and Matsumura, E.M., 2013. Horngren's Financial &
Managerial Accounting: Pearson New International Edition. Pearson Higher Ed.
Popesko, B., 2010. Activity-based costing application methodology for manufacturing
industries. E+ M Ekonomie a management, (1), p.103.
Salawu, R.O. and Ayoola, T.J., 2012. Activity based costing adoption among manufacturing
companies in Nigeria. Journal of Modern Accounting and Auditing, 8(1), p.40.
Schulze, M., Seuring, S. and Ewering, C., 2012. Applying activity-based costing in a supply
chain environment. International Journal of Production Economics, 135(2), pp.716-725.
Stefano, N.M. and Casarotto Filho, N., 2013. Activity-based costing in services: literature
bibliometric review. SpringerPlus, 2(1), p.80.
Referencing List:
Askarany, D., Yazdifar, H. and Askary, S., 2010. Supply chain management, activity-based
costing and organisational factors. International journal of production economics, 127(2),
pp.238-248.
Dejnega, O., 2011. Method Time Driven Activity Based Costing. Journal of Applied.
Drury, C., 2013. Costing: an introduction. Springer.
DRURY, C.M., 2013. Management and cost accounting. Springer.
Firescu, V., 2010. The importance of the calculation methods based on direct costing in
managerial decisions. Scientific Bulletin-Economic Sciences, (9), pp.75-82.
Garrison, R.H., Noreen, E.W., Brewer, P.C. and McGowan, A., 2010. Managerial
accounting. Issues in Accounting Education, 25(4), pp.792-793.
Nobles, T.L., Mattison, B.L. and Matsumura, E.M., 2013. Horngren's Financial &
Managerial Accounting: Pearson New International Edition. Pearson Higher Ed.
Popesko, B., 2010. Activity-based costing application methodology for manufacturing
industries. E+ M Ekonomie a management, (1), p.103.
Salawu, R.O. and Ayoola, T.J., 2012. Activity based costing adoption among manufacturing
companies in Nigeria. Journal of Modern Accounting and Auditing, 8(1), p.40.
Schulze, M., Seuring, S. and Ewering, C., 2012. Applying activity-based costing in a supply
chain environment. International Journal of Production Economics, 135(2), pp.716-725.
Stefano, N.M. and Casarotto Filho, N., 2013. Activity-based costing in services: literature
bibliometric review. SpringerPlus, 2(1), p.80.
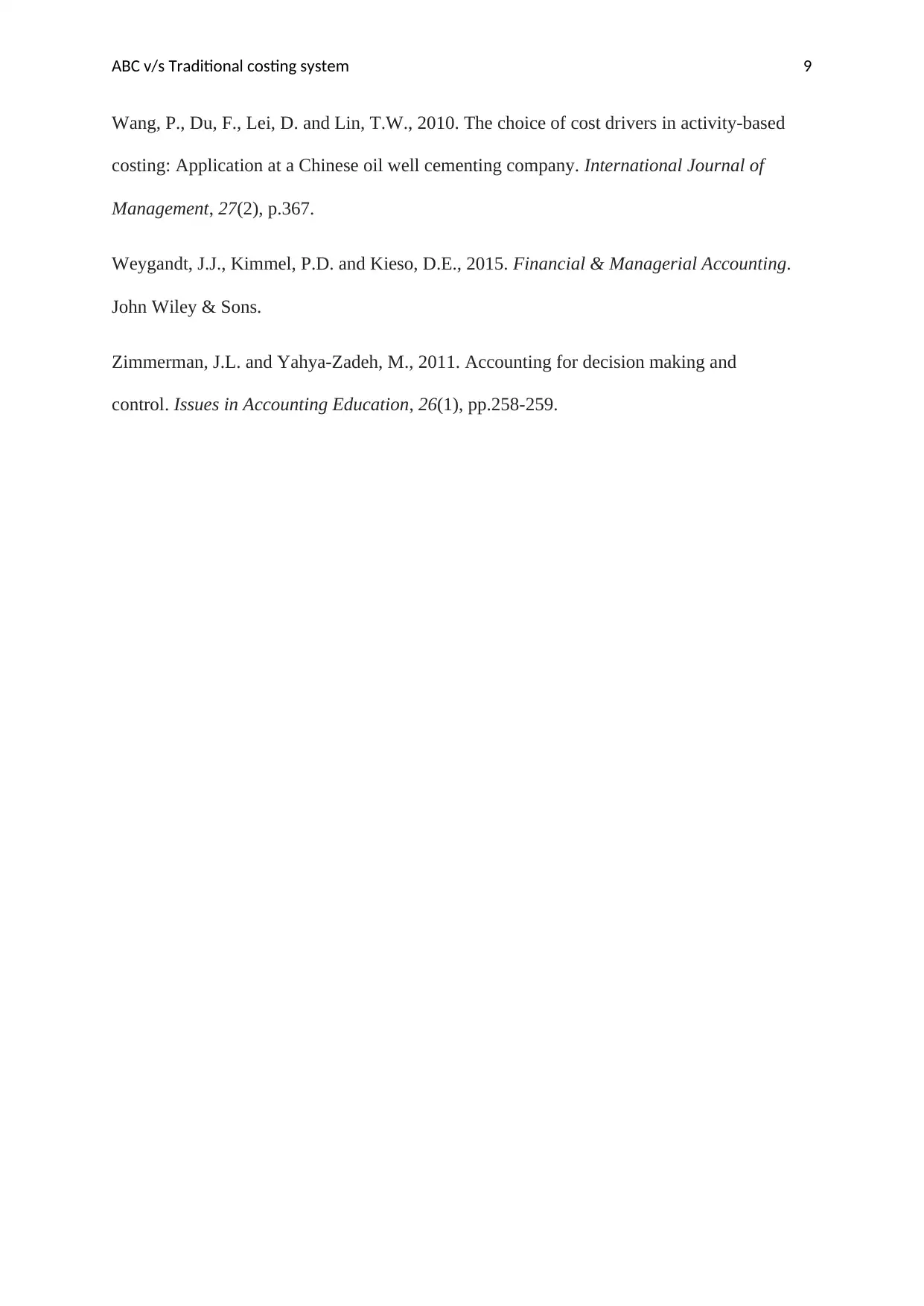
ABC v/s Traditional costing system 9
Wang, P., Du, F., Lei, D. and Lin, T.W., 2010. The choice of cost drivers in activity-based
costing: Application at a Chinese oil well cementing company. International Journal of
Management, 27(2), p.367.
Weygandt, J.J., Kimmel, P.D. and Kieso, D.E., 2015. Financial & Managerial Accounting.
John Wiley & Sons.
Zimmerman, J.L. and Yahya-Zadeh, M., 2011. Accounting for decision making and
control. Issues in Accounting Education, 26(1), pp.258-259.
Wang, P., Du, F., Lei, D. and Lin, T.W., 2010. The choice of cost drivers in activity-based
costing: Application at a Chinese oil well cementing company. International Journal of
Management, 27(2), p.367.
Weygandt, J.J., Kimmel, P.D. and Kieso, D.E., 2015. Financial & Managerial Accounting.
John Wiley & Sons.
Zimmerman, J.L. and Yahya-Zadeh, M., 2011. Accounting for decision making and
control. Issues in Accounting Education, 26(1), pp.258-259.
1 out of 10

Your All-in-One AI-Powered Toolkit for Academic Success.
+13062052269
info@desklib.com
Available 24*7 on WhatsApp / Email
Unlock your academic potential
© 2024 | Zucol Services PVT LTD | All rights reserved.